Сверла, зенкеры, развертки.
Для обработки отверстий на токарных станках применяют сверла, зенкеры и развертки, которые выбирают исходя из вида заготовки, требуемой точности размеров и шероховатости обработанной поверхности.
Сверла предназначены для сверления сквозных или глухих отверстий в сплошном материале, а так же для увеличения диаметра ранее просверленных отверстий (рассверливание), а так же для надсверливания.
По конструкции режущей части сверла разделяются на спиральные, или точнее, сверла с винтовыми канавками, сверла с прямыми канавками, сверла для глубоких отверстий (ружейные и пушечные), универсальные и др.
Спиральные сверла применяют для сверления сравнительно неглубоких отверстий, глубина которых не превышает шести диаметров сверла. Οʜᴎ изготавливаются из углеродистой стали У10А и У12А, легированной стали 9ХС, быстрорежущей стали Р9 и Р18, а так же оснащаются пластинками из твердого сплава.
Для увеличения диаметра предварительно просверленных отверстий, а так же для дальнейшей обработки отверстий в отливках, поковках и штамповках широко применяют инструмент, называемый зенкером.
Зенкер подобно сверлу закрепляют в коническом отверстии пиноли задней бабки, подают его вручную, вращая маховичок задней бабки. При этом можно механизировать подачу, в случае если закрепить зенкер в специальном приспособлении.
Учитывая зависимость отдиаметра обрабатываемых отверстий применяют различные конструкции зенкеров. Для малых отверстий (12 –35 мм) применяют трезубые зенкеры с коническим хвостовиком. Для больших отверстий зенкера изготовляют насадными с четырьмя зубьями. Их насаживают на оправки из углеродистой стали.
Сверла из быстрорежущей стали обеспечивают обработку отверстий по 4—5-му классу, точности и по 3—4-му классу шероховатости. Сверла с пластинками из твердых сплавов, работающие на более высоких скоростях, резания обеспечивают обработку отверстий по 3—4-му классу точности и 4—5-му классу шероховатости. Для получения более точных отверстий (3—-4-й класс точности, 6-й класс шероховатости) применяют зенкерование.
Процесс зенкерования осуществляется зенкером (рис. 10), который служит для дальнейшей обработки отверстий, полученных после литья, штамповки или сверления. Эта обработка отверстия должна быть либо окончательной, либо промежуточной ( получистовой ) перед развертыванием, дающие еще более точные отверстия(с 3 по 1 класс точности, 7-9 класс шероховатости).
Фрезы.
Теоретические сведения. Фрезы классифицируют по характеру выполняемой работы, по конструкции, и креплению зубьев относительно оси фрезы и другими признаками. Основные типы фрез показаны на рис. 12, 13. Цилиндрические фрезы применяют для обработки открытых плоскостей. Торцевые фрезы имеют зубья на цилиндрической и торцевой поверхностях. Эти фрезы применяют для обработки уступов, пазов, лысок, многогранных и других боковых поверхностях на прямоугольных и кривых заготовках. Дисковые фрезы бывают одно,- двух- трехсторонними. Режущие кромки трехсторонней дисковой фрезы расположены на обоих торцах и на цилиндрической части, могут располагаться параллельно оси фрезы или под некоторым углом к ней.
Двухсторонняя дисковая фреза имеет режущие кромки на одном торце и на цилиндрической части, односторонняя дисковая фреза имеет режущие кромки только на цилиндрической части. Прорезные и отрезные фрезы применяют для фрезерования узких пазов (шлицы винтов и др.) и отрезки (разрезания) заготовок.
Концевые фрезы применяют для обработки плоскостей, уступов, пазов. Οʜᴎ имеют режущие кромки на цилиндрической части и на торце. Основное отличие от торцевых фрез в том что концевые более вытянутые, а у торцевые наоборот D > H (сплюснутые).
Угловые фрезы применяют для обработки поверхностей, расположенных под некоторым углом друг другу.
Рис. 9. Части и элементы спирального сверла.
Рис. 10. Основные части зенкеров
а – цельный с конусным хвостовиком, б – насадной цельный
Рис. 11. Основные части развертки.
Рис. 12. Фасонные фрезы: а — с выпуклым профилем;
б — с вогнутым профилем; в — угловые
Рис. 13. Виды фрезерования и основные типы фрез:
а — цилиндрические; б — торцовые; в и г — дисковые;
д — прорезные и отрезные; е и ж — концевые
Фасонные фрезы применяют для обработки сложно- фасонных поверхностей: профиль фасонной фрезы должен соответствовать профилю обрабатываемой детали.
а)
б)
в)
Рис.14 Зуборезный инструмент: а- дисковая модульная фреза;
б- пальцевая модульная фреза; в- червячная модульная фреза
Зенкер чем отличается от сверла
Зенкеры, зенковки, цековки, развертки. Слесарное дело |
Зенкеры (рис. 3.34, а) предназначены для обработки отверстий в заготовках, полученных отливкой, штамповкой или предварительным сверлением. В отличие от сверла зенкер имеет большее число режущих кромок (три или четыре), что обеспечивает получение поверхностей с более высокими показателями точности и шероховатости.
По конструкции зенкеры бывают насадные и цельные и могут иметь различное направление угла спирали (правое, левое, прямое). Зенкеры изготавливают из быстрорежущей стали или оснащают пластинами из твердого сплава марок ВК6, ВК8, BKbM, ВК8В, Т5К10, Т15К6. Пластины из твердого сплава закрепляются в зенкере при помощи пайки или клинового крепление, что позволяет многократно использовать корпус зенкера.
В качестве режущей части насадных зенкеров используются многогранные твердосплавные пластины. Крепление таких пластин в корпусе насадного зенкера осуществляют механическим путем (рис. 3.35). Режущие пластины 1 закрепляются в корпусе 2 при помощи тяги 3, что позволяет производить замену пластин непосредственно на станке. Для этого достаточно сместить тягу 3, повернуть пластину следующей гранью или заменить ее на новую, снова закрепить тягу и продолжать работу. Возможность оснащения таких зенкеров пластинами из различных инструментальных материалов позволяет существенно расширить технологические возможности и производительность при зенкеровании.
Геометрические параметры режущей части зенкеров (см. рис. 3.34, б) выбираются в зависимости от условий обработки: главный угол в плане ф = 30… 60 передний угол у = 3… 30 ° для зенкеров из быстрорежущей стали,для зенкеров, оснащенных пластинами твердого сплава, этот угол составляет от 5 до -5°; задний угол а на главных режущих кромках составляет 8… 15 Выбор конструкции зенкера и материала рабочей части в значительной степени зависит от обрабатываемого материала и параметров обрабатываемого отверстия:
• зенкеры из быстрорежущей стали, имеющие три-четыре зуба и диаметр от 10 до 40 мм, применяются для обработки отверстий в заготовках из конструкционной стали;
• зенкеры, оснащенные пластинами из твердого сплава, имеющие три-четыре зуба и номинальный диаметр от 14 до 50 мм, используются при обработке отверстий в заготовках из труднообрабатываемых и закаленных сталей;
• зенкеры с насадными головками из быстрорежущей стали номинальным диаметром от 32 до 80 мм предназначены для обработки отверстий в заготовках из конструкционной стали;
• перовые зенкеры служат для обработки глухих отверстий в заготовках из чугуна и цветных металлов;
• для обработки глухих отверстий диаметром от 15 до 25 мм применяется специальный зенкер, у которого в корпусе выполнено специальное отверстие для подачи СОЖ в зону резания (рис. 3.36).
Изнашивание зенкеров (рис. 3.37) происходит по задним поверхностям, где образуются площадки с задним углом, равным нулю, и шириной h5; по передним поверхностям с образованием лунки; по ленточке с образованием поперечных проточин на длине Лл; по уголкам с образованием конических или цилиндрических участков hy. В качестве критерия износа зенкеров при обработке заготовок из стали принят износ зенкера по уголкам, равный 1,2… 1,5 мм, а при обработке заготовок из чугуна — 0,8… 1,5 мм. Затачивание и перетачивание изношенных зенкеров осуществляется, как правило, на специальном оборудовании в заточных цехах.
Зенковки и цековки
Зенковки и цековки (рис. 3.38) для обработки опорных поверхностей под крепежные винты в отличие от зенкеров имеют режущие зубья на торце и направляющие цапфы, которые обеспечивают нужное направление зенковок и цековок в процессе обработки. Цапфа вводится в предварительно просверленное отверстие, при этом оси отверстия и образованного зенковкой углубления совпадают.
Зенковки для обработки конических углублений с углами 60, 90 и 120° (рис. 3.38, в, г) такие», изготавливают и с цилиндрическим, и с коническим хвостовиком. Зенковки с цилиндрическим хвостовиком изготавливают диаметром 8; 10; 12; 16; 20; 25 мм, а с коническим хвостовиком — диаметром 16; 20; 25; 31,5; 40; 50; 63 и 80 мм.
Для подрезания торцев приливов и бобышек в литых корпусных деталях применяются одно- и двухсторонние пековки (рис. 3.38, д, е) из быстрорежущей стали или оснащенные пластинами твердого сплава. Они крепятся на специальных оправках с помощью байонетного замка. Выпускаются цековки диаметром 25; 32; 40; 50; ЬЗ; 80 и 10С мм.
Развертки
Развертки (рис. 3.39) изготовляются цельными и насадными с коническим и цилиндрическим хвостовиком, оснащаются вставными ножами, впаянными пластинами из твердого сплава либо изготовляются из быстрорежущей стали. Развертки в отличие от сверла и зенкера имеют большее количество режущих кромок, что позволяет при обработке снимать слой материала небольшой толщины, составляющий десятые и даже сотые доли миллиметра. Припуски на развертывание выбираются по таблицам в зависимости от диаметра обрабатываемого отверстия Различают развертки для ручного и машинного развертывания, цилиндрические и конические. Развертки для ручного развертывания на конце цилиндрического хвостовика имеют квадратную часть, на которую устанавливают вороток для вращения развертки в обрабатываемом отверстии.
Конструктивно развертка для ручного развертывания состоит из рабочей части, хвостовика и шейки. Рабочая часть конуса включает в себя режущую часть (заборный конус и направляющий конус, который обеспечивает центрирование развертки в отверстии) и калибрующую часть, обеспечивающую получение отверстия с заданной точностью и шероховатостью обработанной поверхности.
Режущая часть заборного конуса развертки имеет угол при вершине 2ф. Для обработки вязких металлов этот угол составляет 12… 15°, а для обработки хрупких и твердых материалов — от 3 до 5°.
Твердосплавные развертки имеют угол при вершине 30… 45 Направляющий конус рабочей части развертки расположен под углом 45 э к ее оси. Задний угол а на режущей части составляет от 6 до 15°, на калибрующей части этот угол обычно равен нулю, а передний угол у — 0… 15 . Для хрупких материалов передний угол равен нулю, а для твердосплавных разверток он составляет от 0 до -5°. Ручные развертки используют, как правило, при обработке отверстий диаметром от 3 до 50 мм в материала;, невысокой твердости (конструкционные стали, цветные металлы). Конические развертки (рис. 3.40) применяются для развертывания конических отверстий и, как правило, работают в комплекте из двух трех штук.
Машинные развертки бывают цилиндрическими и коническими, насадными и цельными. Цельные машинные развертки предназначены для обработки отверстий диаметром от 3 до 100 мм, а для развертывания отверстий диаметром от 25 до 300 мм используются насадные развертки. И цельные (рис. 3.41, а, б), и насадные (рис. 3.41, в, г) развертки изготавливают из быстрорежущей стали или оснащают пластинами из твердого сплава. Конструкция и материал машинной развертки выбирается в зависимости от характера выполняемых работ, материала обрабатываемой заготовки и требований, предъявляемых к качеству обработанной поверхности.
dlja-mashinostroitelja.info
Чем отличается зенкование от зенкерования – объясняем простым языком
После завершения сверления металлической детали возникает необходимость сделать сложные геометрические углубления внутри детали для последующей установки в них различных крепежных элементов – болтов, винтов, заклепок. Для этого, а также при необходимости качественно обработать поверхность и снять фаски внутри детали берем зенковку. Данный инструмент может быть различной формы. Ее можно подбирать, ориентируясь на конечный результат. На сегодняшний день различают конические, цилиндрические или торцевые (плоские) зенковки. Последние иногда носят названия цековки, а зенкование отверстий, как технологический процесс, может называться цекованием.
Работа зенковки
Зенковки цилиндрического типа необходимы для получения отверстий соответствующей формы в просверленных гнездах для последующей установки в них болтов и винтов различного типа. Зенковка имеет две части – рабочую поверхность и хвостовик, а также специальный направляющий пояс (цапфу), который необходим, чтобы обеспечивать контроль соосности инструмента в процессе работы над поверхностью металлической детали.
Конические зенковки имеют аналогичную составляющую, которая включает в себя хвостовик и рабочую часть с поясами, они обеспечивают соосность при работе.
Такие зенковки, как правило, используют при создании отверстий в виде конуса внутри детали, снятия фасок и для углублений под болты, различные плоские шайбы или упорные кольца. Наибольшее распространение получили зенковки с конусным углом в 90 или 120 градусов. Торцевые или плоские цековки применяются преимущественно для зачистки и обработки металлических углублений для установки крепежных элементов. Все зенковки различаются между собой диаметром, углом и режимами работы. Зенкование, как и зенкерование, осуществляется на сверлильных, агрегатных, фрезерных и токарно-фрезерных станках.
Зенкерование – это процесс расширения и обработки просверленных металлических отверстий штампованного или литого типа, который позволяет придать им строгую геометрическую форму. Зенкерование отверстий является промежуточным процессом, который чаще всего нужен после сверления и до металлического развертывания. С помощью качественного оборудования и инструмента можно добиться получения геометрических отверстий четвертого, а иногда и пятого класса точности. Инструмент для зенкерования называется зенкером.
Зенкер по металлу
Зенкеры бывают нескольких типов и различаются по количеству зубьев (трех- или четырехперые), а по конструкции могут быть цельными, вставными или насадными. От обычного сверла зенкеры отличаются увеличенной перемычкой, которая соединяет режущие кромки, срезанным углом, а также наличием большего количества режущих зубьев-кромок. Они позволяют обеспечить устойчивость инструмента в процессе работы и максимально точную соосность зенкера и обрабатываемого отверстия.
Зенкерование
Применение зенкеров определенного типа напрямую зависит от диаметра отверстия в обрабатываемой заготовке. Так, для отверстий, диаметр которых менее 12 мм, нужны цельные зенкеры, для отверстий свыше 20 мм – зенкеры вставного типа (со вставными ножами). При необходимости получить более точные и сложные поверхности используются комбинированные типы, в которых может быть до восьми режущих кромок, при этом зенкеры сборного типа могут дополнительно комбинироваться со сверлами, развертками и другими инструментами.
Развертывание отверстий – это сложный технологический процесс чистовой обработки металлических отверстий на фрезерном оборудовании, который выполняется после процессов сверления и зенкерования. С помощью развертывания удается добиться высокого класса точности. Оно производится на ручных и автоматизированных сверлильных или токарно-фрезерных станках с ЧПУ или с ручным управлением. Инструмент, который применяется при развертывании, называется развертка.
По типу обработку развертки могут быть ручными или механическими (машинными), а по форме – конусообразными или цилиндрическими. Инструмент состоит из трех частей с калибрующей частью и режущими кромками, которые равномерно или неравномерно распределяются по окружности. Как правило, развертки используются комплектом по три штуки, это необходимо для выполнения поочередно черновой, получистовой и чистовой обработки. В таком случае удается добиться максимального эффекта при обработке поверхности.
При развертывании также широко применяется комбинированный тип инструмента, в который входит зенкер, зенковка, развертка, сверло и другие элементы. Комбинация инструментов позволяет существенно сократить время на получение отверстие нужной формы, класса точности и шероховатости. Сверление, как и зенкерование, и развертывание, можно называть схожими технологическими процессами в определенных режимах работы. Они выполняются на схожих видах ручного и механического оборудования.
tutmet.ru
Чем отличается зенкование от зенкерования
Зенкерование и зенкование представляют собой технологические операции, предназначенные для обработки отверстий. Несмотря на схожесть названий, данные операции отличаются по своему назначению и применяемому технологическому инструменту. Зенкерование и зенкование представляют собой различные операции по обработке отверстий. Зенкерование предназначено для улучшения качества поверхности отверстий, выполненных методами сверления, литья или обработки давлением. В отличие от зенкерования, зенкованием получают углубления в отверстиях под потайные крепежные элементы. Инструментом для операций зенкерования служат зенкеры, а для зенкования – конические и цилиндрические зенковки.
Назначение и особенности зенкерования
Назначением зенкерования является улучшение точности и шероховатости отверстий. Данная операция относится к этапу получистовой обработки и располагается в технологическом процессе между сверлением и развертыванием.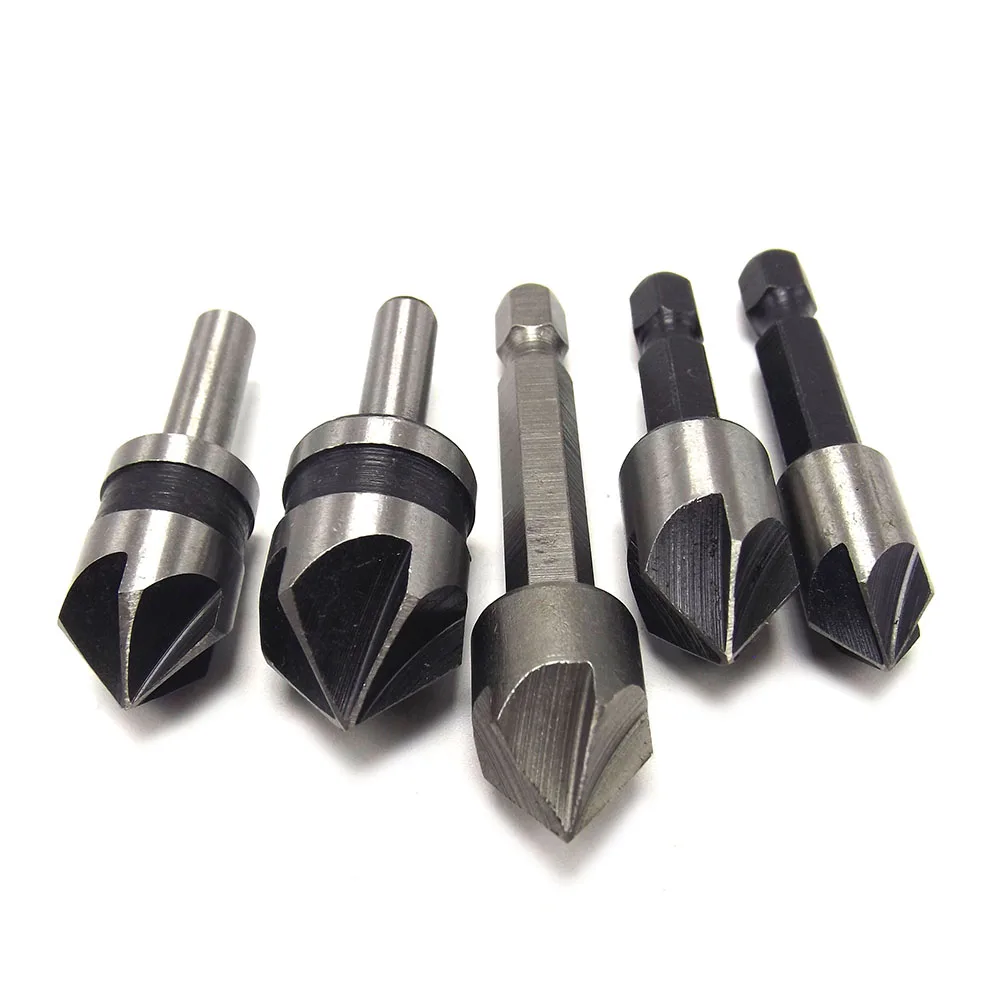
Назначение и особенности зенкования
Зенкование предназначено для получения на торцах отверстий гнезд для потайного размещения головок крепежных элементов. Данные углубления, которые могут иметь цилиндрическую либо коническую форму, обрабатываются соответственно коническими или цилиндрическими зенковками.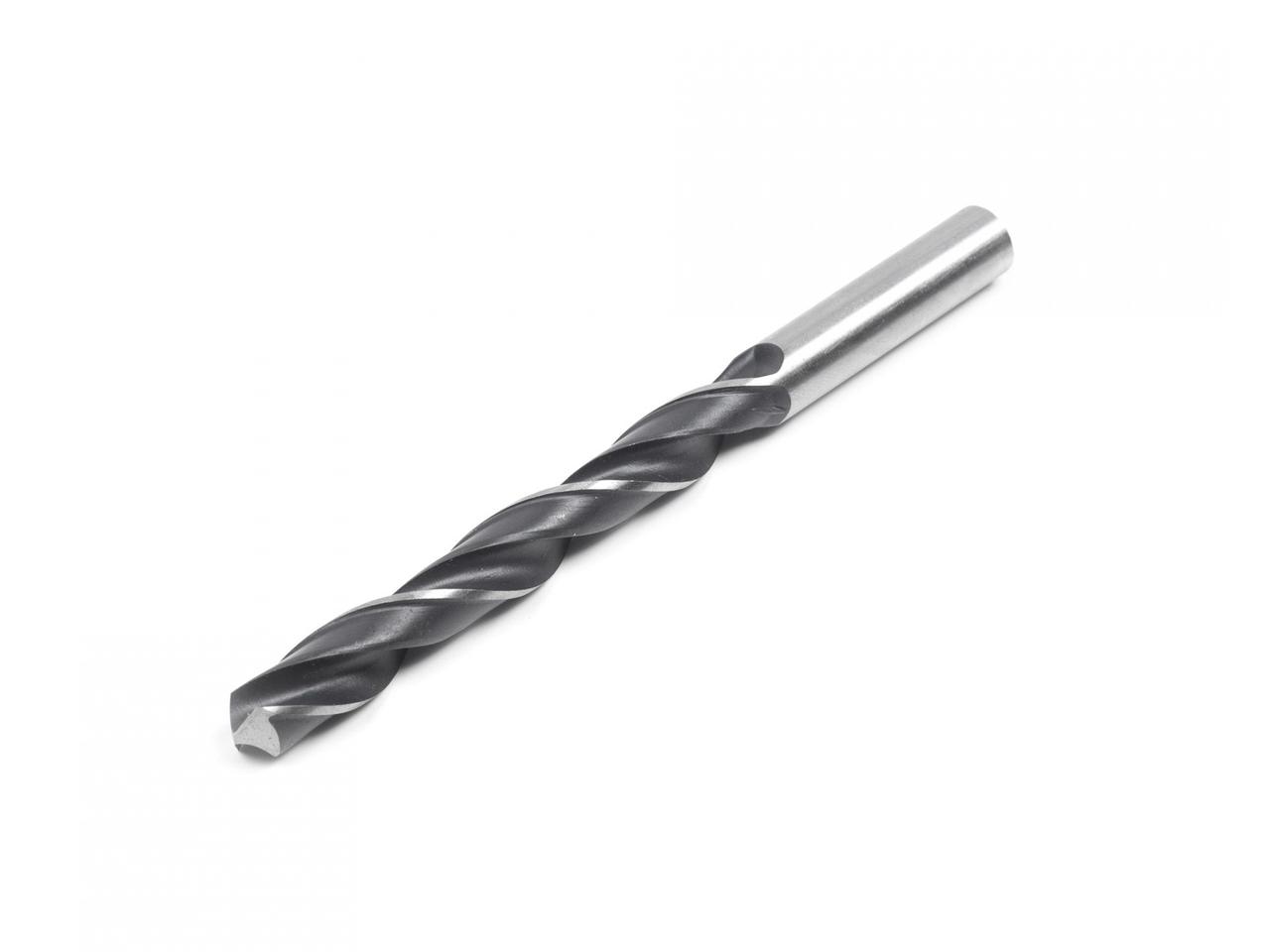
Геометрия цилиндрической зенковки напоминает зенкер, а рабочая часть конической зенковки вместо спиральных режущих кромок имеет зубчатые. В конструкции цилиндрической зенковки должен быть предусмотрен направляющий поясок. Конические зенковки также применяются для зачистки острых кромок и снятия фасок.
Оборудование
Операции зенкерования и зенкования выполняются на том же технологическом оборудовании, что и сверление. Таким оборудованием может выступать сверлильный станок или универсальный обрабатывающий центр. Также существует возможность зенкования и зенкерования с использованием токарного станка. Выполнять данные операции с помощью ручного инструмента не рекомендуется в связи с невозможностью обеспечения необходимой точности его позиционирования.
Чем отличается зенкование от зенкерованияwww.kakprosto.ru
Зенкерование и развертывание отверстий
Операции механической обработки заготовок на токарных станках редко становятся финальными в технологическом процессе. Создание отверстий – это основной этап в получении необходимой формы детали. Но за ним, как правило, следует этап доработки. Отчасти это мероприятия чистовой коррекции, но иногда применяются и методы базового изменения параметров выполненного реза. К таким операциям относят зенкование и развертывание отверстий, в результате чего оператор получает оптимальную по характеристикам заготовку. Во-первых, подготовленное углубление обретает необходимые размеры, а во-вторых, его кромки и поверхности очищаются от лишних заусенцев и стружки.
Какие задачи решает зенкерование?
К процедуре зенкерования допускаются отверстия разного происхождения. Это могут быть литые, штампованные или просверленные ниши, над которыми в дальнейшем будет работать мастер по зенкерованию. В чем же заключается суть данной операции? У нее могут быть две цели. Как минимум будет обеспечена зачистка поверхностей отверстия. Это особенно важно в тех случаях, если предварительно выполняется грубое сверление и развертывание отверстий, кромки которых нуждаются в доработке. В зависимости от качества формирования отверстия может применяться получистовое или чистовое зенкерование. В результате меняется и степень сглаживания рабочих поверхностей. Еще более ответственна задача калибровки. В этом случае мастер не ограничивается зачисткой и корректирует параметры отверстия, например глубину и толщину. Потребность в таких действиях возникает, если изначально полученное отверстие не подходит по размерам к целевой шпильке, винту или другой крепежной детали. После зенкерования как раз выполняется нарезка резьбы в соответствии с размерами метиза.
Что представляет собой зенкер?
Это режущий инструмент, конструкция которого формируется функциональной обрабатывающей частью и хвостовиком-державкой. Внешне некоторые виды зенкера напоминают сверла, но они гораздо прочнее. И еще более важная разница заключается в наличии как минимум трех режущих кромок, обеспечивающих более эффективный съем лишней массы металла. Кстати, этим отличается и развертывание отверстий, для которого иногда требуется интенсивная ликвидация стружки с целью достижения более точной формы заготовки. Но у зенкера несколько режущих кромок также выступают в некотором роде стабилизатором инструмента. Этот аспект гарантирует обеспечение равномерности обработки кромок, что сказывается на точности выполнения операции. Впрочем, качество результата будет зависеть и от того, насколько правильно был выбран тип инструмента.
Разновидности зенкеров
Простейшие конические модели зенковок состоят из резчика и хвостовика. Угол конуса в рабочей части может варьироваться от 30 до 120 °. Более сложной вариацией инструмента является резчик с торцевыми зубцами. Количество зубьев в среднем составляет от 4 до 8. Соответственно, чем точнее требуется зенкерование, тем меньше должна быть поверхность резчика. Также существуют цилиндрические устройства, в которых предусмотрена направляющая цапфа. Она входит в формируемые отверстия, обеспечивая, таким образом, совпадение образованного цилиндрического углубления и оси отверстия. Это универсальная техника, при которой сверление, зенкерование и развертывание отверстий производятся инструментом единой формации. В итоге упрощается цикл формирования отверстия и повышается качество очистки прилегающих поверхностей. Почти все модели зенкеров изготавливаются из инструментальных легированных и углеродистых сталей.
Техника выполнения зенкерования
Обычно зенкерование выполняется на сверлильных станках. Так же как и сверла, зенкеры устанавливаются в соответствующих патронах или зажимных механизмах. Далее выходные части отверстий обрабатываются коническими зенковками. По этой технике формируются конусные углубления, подходящие для головок заклепок и потайных винтов. Углубления для болтов производятся таким же образом, но уже цилиндрическими зенковками. Данным инструментом также выполняют подрезку торцов, выборку углов и выступов. И зенкерование, и развертывание отверстий на станке контролируются оператором. В современных моделях пневматических и электрических станков допускается возможность обработки в полуавтоматическом и автоматическом режимах. Станки с программным управлением могут использовать аналогичные настройки обработки зенкерами для серийного обслуживания деталей.
Назначение операции развертывания
Операция развертывания во многом схожа с зенкерованием. Она также рассчитана на формирование оптимальных по размерам отверстий с возможностью коррекции формы. Но если зенкеры подготавливают отверстия для последующего использования заклепок и болтов, то развертывание позволяет получать точные калиброванные ниши для валов, плунжерных деталей и подшипников. Также развертывание отверстий позволяет минимизировать трение в обрабатываемой зоне и обеспечивать высокую плотность контакта между элементами. Эти задачи достигаются за счет сокращения шероховатости поверхностей отверстия.
Инструмент для развертывания
Развертки также представляют собой инструмент, напоминающий сверла. Рабочая часть в данном случае обеспечивается расположенными по окружности стержня зубьями. Помимо этого, существуют вспомогательные функциональные части резчика. Это заборная, калибрующая и цилиндрическая части. Непосредственную резку производит направляющий конус, края которого снимают припуск металла, но в то же время предохраняют вершину режущей кромки от забоин. И здесь можно выделить отдельные конструктивные части, различающие данную методику и зенкование. Зенкерование и развертывание отверстий сходятся в операциях резки, однако калибрующая часть развертки также выполняет функции направления и отвода стружки. Для этого предназначены специальные канавки, делающие инструмент более самостоятельным.
Машинные и ручные развертки
Развертывание может выполняться ручным и машинным способом, то есть на тех же станках. Инструмент, применяемый для ручных операций, отличается удлиненной рабочей частью. Диаметр обратного конуса в данном случае варьируется от 0,06 до 0,1 мм в среднем. Для сравнения, станочные развертки имеют толщину конуса от 0,05 до 0,3 мм. С помощью ручного развертывания можно получать отверстия диаметром от 3 до 60 мм. При этом степень точности будет невелика. Машинный инструмент ориентируется под определенные типоразмеры, зачастую по спецзаказам. Например, развертывание отверстий в деталях для строительных конструкций может выполняться в соответствии с техническими данными по конкретному проекту. К преимуществам такого способа относят высокую точность резки, качественную зачистку и отсутствие деформационного эффекта.
Выполнение развертывания
Машинное развертывание выполняется по тем же принципам, что и зенкование. Инструмент фиксируется в патроне, а затем направляется в обрабатываемую зону станком. Единственным отличием являются более высокие требования к охлаждению рабочей оснастки в процессе работы и смазке отверстий. В качестве смазывающего состава используют минеральное масло, скипидар и синтетические эмульсии. Иначе выполняется ручная обработка отверстий. Развертывание такого типа предполагает изначальную фиксацию заготовки в тисках. Далее в отверстие вставляется наконечник развертки и путем кручения воротка достигается результат. Причем вращать инструмент можно только в одном направлении – до формирования необходимых параметров изделия.
Заключение
Механическая обработка металлов постепенно уступает место технологичным лазерным и термическим методам. Также конкуренцию традиционным способам резки составляет гидроабразивная техника, отличающаяся высокой скоростью раскроя и точностью. Что на этом фоне могут предложить в качестве преимуществ зенковка, а также развертывание отверстий? В первую очередь это возможность ручной обработки без применения сложного оборудования в виде станков. Кроме того, в отличие от гидроабразивов и термических аппаратов, данные технологии не требуют подключения дополнительных расходных материалов. Поэтому можно говорить о преимуществах экономического, организационного и эргономического характера. Но качеством обработки и темпами производственного процесса, конечно, придется пожертвовать.
fb.ru
Зенкеры и зенковки – по дереву, зенкеры по металлу, твердосплавные
Сверлильный и резьбонарезной инструмент по металлуПроцесс зенкования, или обработка просверленных отверстий в деталях и изделиях под головки винтов, болтов, осуществляется при помощи зенковок. Зенковки делятся по форме режущей части на несколько видов:
- цилиндрические,
- конические,
- торцовые (их еще называют цековками).
- простые,
- снабженные или нет предохранительным конусом,
- с конусным хвостовиком.
Зенкер – это режущий инструмент, снабженный несколькими лезвиями и использующийся в целях улучшения качества поверхности, увеличения диаметра отверстий цилиндрической или конической формы, повышения точности. Предназначается для получистовой обработки перед операцией развертывания или реже окончательной обработки отверстий в пределах 4-5 класса точности, обработки гнезд, имеющих плоское дно, под головки болтов или винтов.
Развертка используется при необходимости произвести окончательную обработку отверстий, достигая шероховатости поверхности от 7 до 9 класса и точности в пределах 6-9 квалитетов. Такое высокое качество обработки возможно благодаря особой конструкции развертки, предполагающей большое количество режущих кромок (до 14 штук), и снятию в процессе работы малого припуска. Зенкер отличается от развертки тем, что снабжен меньшим числом кромок, имеет другую заточку и используется, по большей части, для формирования отверстий с невысокой точностью.
Вы можете купить зенкеры, развертки и зенковки по металлу отечественного и импортного производства. Уточнить наличие товара можно, позвонив по бесплатному телефону 8-800-100-39-81.
Сверлильный и резьбонарезной инструмент по металлу и Зенкеры и зенковки, зенкер по металлу Зенкер конический по металлу.Процесс зенкования, или обработка просверленных отверстий в деталях и изделиях под головки винтов, болтов, осуществляется при помощи зенковок. Зенковки делятся по форме режущей части на несколько видов:
- цилиндрические,
- конические,
- торцовые (их еще называют цековками).
- простые,
- снабженные или нет предохранительным конусом,
- с конусным хвостовиком.
Зенкер – это режущий инструмент, снабженный несколькими лезвиями и использующийся в целях улучшения качества поверхности, увеличения диаметра отверстий цилиндрической или конической формы, повышения точности. Предназначается для получистовой обработки перед операцией развертывания или реже окончательной обработки отверстий в пределах 4-5 класса точности, обработки гнезд, имеющих плоское дно, под головки болтов или винтов.
Развертка используется при необходимости произвести окончательную обработку отверстий, достигая шероховатости поверхности от 7 до 9 класса и точности в пределах 6-9 квалитетов. Такое высокое качество обработки возможно благодаря особой конструкции развертки, предполагающей большое количество режущих кромок (до 14 штук), и снятию в процессе работы малого припуска. Зенкер отличается от развертки тем, что снабжен меньшим числом кромок, имеет другую заточку и используется, по большей части, для формирования отверстий с невысокой точностью.
Вы можете купить зенкеры, развертки и зенковки по металлу отечественного и импортного производства. Уточнить наличие товара можно, позвонив по бесплатному телефону 8-800-100-39-81.
Сверлильный и резьбонарезной инструмент по металлу и Зенкеры и зенковки, зенкер по металлу Зенкер конический по металлу, купить зенкер по дереву, зенкер по металлу 30 мм.Металлорежущий инструмент
Зенкер — металлорежущий инструмент для обработки уже готовых отверстий.
Зенкером можно обработать отверстие чище, чем сверлом, поскольку у зенкера больше режущих кромок. Обычно у зенкера три или четыре винтовых канавок, и, следовательно, столько же режущих кромок.
Конусный зенкер, называемый зенковкой, служит для углубления входных частей отверстий для потайных головок винтов.
Для подготовки отверстия под цилиндрическую или полукруглую головку винта пользуются цилиндрическим зенкером с направляющей.
Так же как и сверла, зенкеры изготавливают с цилиндрическими или конусными хвостовиками.
Метчик — инструмент, с помощью которого нарезают резьбу в отверстиях. Метчик по сути является винтом, в котором проделаны продольные канавки. Эти канавки формируют режущие кромки.
Обычно, чтобы облегчить нарезание резьбы вручную, используют комплект метчиков. Комплект состоит из чернового, среднего и чистового метчиков.
Первым используют черновой метчик, которым снимают черновую стружку и нарезают грубую резьбу. Используют затем средний и чистовой метчики. Именно чистовой метчик окончательно калибрует резьбу.
Каждый метчик промаркирован размером резьбы. Кроме того, на хвостовике каждого метчика присутствует одна, две или три круговых отметки, по которым определяют какой: черновой, средний или чистовой метчик используется.
При нарезании резьбы вручную метчик вращают воротком. Начиная работу, нужно установить метчик соосно нарезаемому отверстию. В противном случае резьба пойдет косо или метчик сломается.
Обычно нарезая резьбу вручную, метчик поворачивают на один оборот вперед, затем делают ¼ оборота обратно и т.д. В результате снимаемая стружка дробится.
Для того, чтобы получить более чистую резьбу и облегчить работу, метчик необходимо смачивать: эмульсионным раствором – при нарезании отверстий в мягкой стали или латуни, олифой – при резке твердой стали, керосином – при резке алюминия.
Ножовочное полотно — режущий инструмент для разрезания вручную металла.
Ножовочное полотно это стальная полоса с прорезанными на ее кромке треугольными зубьями, с шагом (расстоянием между зубьями) 0,8мм — 1,6мм. При изготовлении ножовочного полотна зубья разводят так, чтобы толщина полотна была меньше на 0,25мм — 0,5мм, чем ширина пропила. Для увеличения твердости и уменьшения износа зубьев ножовочное полотно подвергается термической обработке.
Для работы по резке металла ножовочным полотном используют ножовочный станок. Затупившиеся в процессе работы полотна заменяют. Иногда, для увеличения срока службы ножовочного полотна зубья наносят на него с двух сторон.
Плашка резьбовая — инструмент, с помощью которого нарезают резьбу на болтах, винтах, шпильках и других цилиндрических деталях.
Раздвижная (призматическая) плашка служит для нарезания резьбы клуппом. Она состоит из двух пластин, имеющих полукруглые резьбовые вырезы.
Режущие кромки в круглой плашке (лерке) образованы в отверстиях с вырезами. На плоской поверхности плашки обозначен размер нарезаемой резьбы. Прорезь, сделанная в плашке позволяет в небольших пределах менять диаметр резьбы. В новой плашке вырез отсутствует, а есть только надрез. Для того, чтобы плашку сделать регулируемой, необходимо ее прорезать тонким шлифовальным кругом.
Для вращения плашки используется вороток. Одним из винтов, входящим в прорезь плашки можно несколько расширить диаметр резьбы, а двумя другими сжать ее с боков, тем самым уменьшить диаметр.
Развёртка — инструмент, который применяют для точной окончательной обработки отверстий.
В состав развертки входят режущая (заборная) часть, калибрующая часть, шейка и хвостовик. У развертки хвостовик может быть цилиндрическим с квадратом на конце для работы вручную, или коническим, для зажима в шпиндель станка. Для вращения развертки вручную используют вороток.
Для хранения разверток, предохраняя от забоин режущие кромки, используют деревянный ящик, разделенный картонками на отсеки.
Сверло — режущий инструмент, с помощью которого получают отверстия в металле и других материалах.
Спиральные сверла имеют две винтовые канавки, прорезанные на рабочей части сверла. Стружка, которая образуется при сверлении, выходит по винтовым канавкам. На кромках винтовых канавок расположены узкие направляющие ленточки.
Центральная осевая сплошная часть сверла носит название сердцевины и служит для повышения прочности сверла. Толщина сердцевины увеличивается в направлении хвостовика. Хвостовик не имеет винтовых канавок и служит для закрепления сверла на сверлильном станке.
Хвостовики у сверел бывают конусными или цилиндрическими. Сверло с конусным хвостовиком вставляют в шпиндель станка. Когда выбивают сверло из шпинделя, в лапку конусного хвостовика упираются клином. Сверла, у которых цилиндрический хвостовик устанавливают в патронах.
Обычные сверла изготовляют из литой стали, о чем можно судить в момент заточки по виду искр, возникающих при заточке: искры литой стали имеют светло-желтый цвет. Сверла из быстрорежущей стали имеют более высокую стойкость и обладают хорошим сопротивлением нагреву в процессе сверления. Искры быстрорежущей стали имеют оранжевый цвет.
Концевые части двух спиральных перьев, закрученных вокруг сердцевины, подвергаются заточке так, чтобы режущие кромки образовали угол, равный 120°. В данном случае образуется пара режущих кромок, с перемычкой между ними. Длина режущих кромок должна быть одинакова, в противном случае диаметр просверленного отверстия будет больше диаметра сверла. Задний угол сверла, предотвращающий трение задней поверхности сверла, принимают равным 12—15°.
В больших мастерских имеются станки для заточки сверл. Однако чаще всего — в небольших мастерских сверла затачивают вручную. Требуется определенный навык, чтобы правильно затачивать сверло. Точность заточки может быть определена лишь с помощью контрольного калибра.
При заточке необходимо установить сверло под углом к плоскости круга и его периферии и поворачивать его относительно оси, одновременно перемещая налево хвостовик сверла.
Начинающие рабочие производят заточку без выполнения этих движений, в результате задняя поверхность получается плоской, но угол при вершине, образованный режущими кромками будет правильным.Далее по мере накопления опыта они могут выполнять заточку с вращением и перемещением сверла, что позволит получить коническую заднюю поверхность. Пересечение этих двух задних конических поверхностей образует центральную кромку, наклоненную к каждой режущей кромке под углом 130°.
У сверла заточенного правильно, работают две режущие кромки и стружка выходит по обеим спиральным канавкам. У сверла заточенного неправильно, работает только одна режущая кромка, и стружка выходит лишь по одной спиральной канавке.
Скажите “спасибо” автору.
ГОСТ 10079-71 | Развертки конические с коническим хвостовиком под конусы Морзе. Конструкция и размеры |
ГОСТ 10080-71 | Развертки конические с коническим хвостовиком под метрические конусы.![]() |
ГОСТ 10081-84 | Развертки машинные конические конусностью 1:50. Основные размеры |
ГОСТ 10082-71 | Развертки машинные конические конусностью 1:30 с коническим хвостовиком. Основные размеры |
ГОСТ 10083-81 | Развертки конические. Технические условия |
ГОСТ 10902-77 | Сверла спиральные с цилиндрическим хвостовиком. Средняя серия. Основные размеры |
ГОСТ 10903-77 | Сверла спиральные с коническим хвостовиком. Основные размеры |
ГОСТ 11172-70 | Развертки машинные с удлиненной рабочей частью. Конструкция и размеры |
ГОСТ 11173-76 | Развертки с припуском под доводку.![]() |
ГОСТ 11176-71 | Развертки сборные насадные с привернутыми ножами, оснащенными пластинами из твердого сплава. Конструкция и размеры |
ГОСТ 11177-84 | Развертки ручные конические конусностью 1:50 с цилиндрическим хвостовиком. Основные размеры |
ГОСТ 11179-71 | Развертки конические. Конусность 1:10. Конструкция и размеры |
ГОСТ 11180-71 | Развертки конические. Конусность 1:7. Конструкция и размеры |
ГОСТ 11181-71 | Развертки конические под укороченные конусы Морзе. Конструкция и размеры |
ГОСТ 11182-71 | Развертки конические с цилиндрическим хвостовиком под конусы Морзе. Конструкция и размеры |
ГОСТ 11183-71 | Развертки конические с цилиндрическим хвостовиком под метрические конусы.![]() |
ГОСТ 11184-84 | Развертки ручные конические конусностью 1:30 с цилиндрическим хвостовиком. Основные размеры |
ГОСТ 12121-77 | Сверла спиральные длинные с коническим хвостовиком. Основные размеры |
ГОСТ 12122-77 | Сверла спиральные с коротким цилиндрическим хвостовиком. Длинная серия. Основные размеры |
ГОСТ 12489-71 | Зенкеры цельные. Конструкция и размеры |
ГОСТ 12509-75 | Зенкеры, оснащенные твердосплавными пластинами. Технические условия |
ГОСТ 1336-77 | Фрезы резьбовые гребенчатые. Технические условия |
ГОСТ 13779-77 | Развертки цилиндрические.![]() |
ГОСТ 14952-75 | Сверла центровочные комбинированные. Технические условия |
ГОСТ 14953-80 | Зенковки конические. Технические условия |
ГОСТ 1523-81 | Развертки цилиндрические. Технические условия |
ГОСТ 1604-71 | Метчики гаечные. Конструкция |
ГОСТ 16602-80 | Ножи рифленые из быстрорежущей стали для сборных разверток. Основные размеры |
ГОСТ 16603-80 | Клинья для сборных машинных разверток со вставными ножами из быстрорежущей стали. Основные размеры |
ГОСТ 1672-80 | Развертки машинные цельные. Типы, параметры и размеры |
ГОСТ 1677-75 | Зенкеры цельные и со вставными ножами из быстрорежущей стали.![]() |
ГОСТ 16806-71 | Ножи привертываемые, оснащенные пластинами из твердого сплава, для сборных насадных разверток. Конструкция и размеры |
ГОСТ 16858-71 | Ножи из быстрорежущей стали для насадных зенкеров. Конструкция и размеры |
ГОСТ 16859-71 | Клинья для зенкеров со вставными ножами. Конструкция и размеры |
ГОСТ 17012-71 | Сверла твердосплавные. Типы и основные размеры |
ГОСТ 17013-71 | Сверла кольцевые твердосплавные. Основные размеры |
ГОСТ 17014-71 | Коронки долотчатые твердосплавные. Основные размеры |
ГОСТ 17015-71 | Коронки крестовые с центральной опережающей вставкой твердосплавные.![]() |
ГОСТ 17016-71 | Буры долотчатые твердосплавные. Типы и основные размеры |
ГОСТ 17017-71 | Инструмент твердосплавный для образования отверстий в строительных материалах. Технические требования |
ГОСТ 17273-71 | Сверла спиральные цельные твердосплавные укороченные. Конструкция и размеры |
ГОСТ 17274-71 | Сверла спиральные цельные твердосплавные. Короткая серия. Конструкция и размеры |
ГОСТ 17275-71 | Сверла спиральные цельные твердосплавные. Средняя серия. Конструкция и размеры |
ГОСТ 17276-71 | Сверла спиральные цельные твердосплавные с коническим хвостовиком. Конструкция и размеры |
ГОСТ 17277-71 | Сверла спиральные цельные твердосплавные.![]() |
ГОСТ 18121-72 | Развертки котельные машинные. Размеры |
ГОСТ 19267-73 | Развертки машинные цилиндрические с цилиндрическим хвостовиком для обработки деталей из легких сплавов. Конструкция и размеры |
ГОСТ 19268-73 | Развертки машинные цилиндрические с коническим хвостовиком для обработки деталей из легких сплавов. Конструкция и размеры |
ГОСТ 19269-73 | Развертки машинные цилиндрические твердосплавные с цилиндрическим хвостовиком для обработки деталей из легких сплавов. Конструкция и размеры |
ГОСТ 19272-73 | Развертки машинные цилиндрические для обработки деталей из легких сплавов. Допуски на диаметр |
ГОСТ 19543-74 | Сверла спиральные с цилиндрическим хвостовиком для обработки легких сплавов.![]() |
ГОСТ 19544-74 | Сверла спиральные с цилиндрическим хвостовиком для обработки легких сплавов. Длинная серия. Конструкция |
ГОСТ 19545-74 | Сверла спиральные левые с цилиндрическим хвостовиком для обработки легких сплавов. Конструкция |
ГОСТ 19546-74 | Сверла спиральные с коническим хвостовиком для обработки легких сплавов. Конструкция |
ГОСТ 19547-74 | Сверла спиральные удлиненные с коническим хвостовиком для обработки легких сплавов. Конструкция |
ГОСТ 19548-88 | Сверла спиральные для обработки легких сплавов. Технические условия |
ГОСТ 2034-80 | Сверла спиральные. Технические условия |
ГОСТ 20388-74 | Развертки машинные насадные цельные прямозубые для обработки деталей из легких сплавов.![]() |
ГОСТ 20389-74 | Развертки машинные насадные цельные с винтовыми канавками для обработки деталей из легких сплавов. Конструкция и размеры |
ГОСТ 20390-74 | Развертки машинные насадные цельные с торцовыми зубьями для обработки деталей из легких сплавов. Конструкция и размеры |
ГОСТ 20392-74 | Развертки машинные насадные со вставными ножами из быстрорежущей стали для обработки деталей из легких сплавов. Конструкция и размеры |
ГОСТ 20686-75 | Сверла комбинированные твердосплавные для печатных плат. Технические условия |
ГОСТ 20694-75 | Сверла спиральные с цилиндрическим хвостовиком для труднообрабатываемых материалов. Короткая серия. Конструкцияи размеры |
ГОСТ 20695-75 | Сверла спиральные с цилиндрическим хвостовиком для труднообрабатываемых материалов.![]() |
ГОСТ 20696-75 | Сверла спиральные с коническим хвостовиком для труднообрабатываемых материалов. Короткая серия. Конструкция и размеры |
ГОСТ 20697-75 | Сверла спиральные с коническим хвостовиком для труднообрабатываемых материалов. Средняя серия. Конструкция и размеры |
ГОСТ 20698-75 | Сверла спиральные для обработки труднообрабатываемых материалов. Технические условия |
ГОСТ 2092-77 | Сверла спиральные удлиненные с коническим хвостовиком. Основные размеры |
ГОСТ 21527-76 | Развертки машинные насадные со вставными ножами, оснащенными твердосплавными пластинами для обработки деталей из нержавеющих и жаропрочных сталей и сплавов. Конструкция и размеры |
ГОСТ 21540-76 | Зенкеры, оснащенные твердосплавными пластинами, для обработки деталей из нержавеющих и жаропрочных сталей и сплавов.![]() |
ГОСТ 21541-76 | Зенкеры со вставными ножами, оснащенные твердосплавными пластинами, для обработки деталей из нержавеющих и жаропрочных сталей и сплавов. Конструкция и размеры |
ГОСТ 21542-76 | Зенкеры, оснащенные твердосплавными пластинами, для обработки деталей из нержавеющих и жаропрочных сталей и сплавов. Технические условия |
ГОСТ 21543-76 | Зенкеры цельные твердосплавные с цилиндрическим хвостовиком для обработки деталей из нержавеющих и жаропрочных сталей и сплавов. Конструкция и размеры |
ГОСТ 21544-76 | Зенкеры цельные твердосплавные с коническим хвостовиком для обработки деталей из нержавеющих и жаропрочных сталей и сплавов. Конструкция и размеры |
ГОСТ 21545-76 | Зенкеры цельные, твердосплавные для обработки деталей из нержавеющих и жаропрочных сталей и сплавов.![]() |
ГОСТ 21579-76 | Зенкеры с цилиндрическим хвостовиком для обработки деталей из легких сплавов. Конструкция и размеры |
ГОСТ 21580-76 | Зенкеры торцовые с цилиндрическим хвостовиком для обработки деталей из легких сплавов. Конструкция и размеры |
ГОСТ 21581-76 | Зенкеры с коническим хвостовиком для обработки деталей из легких сплавов. Конструкция и размеры |
ГОСТ 21582-76 | Зенкеры торцовые с коническим хвостовиком для обработки деталей из легких сплавов. Конструкция и размеры |
ГОСТ 21583-76 | Зенкеры с коническим хвостовиком, оснащенные твердосплавными пластинами, для обработки деталей из легких сплавов. Конструкция и размеры |
ГОСТ 21584-76 | Зенкеры насадные для обработки деталей из легких сплавов.![]() |
ГОСТ 21585-76 | Зенкеры насадные, оснащенные твердосплавными пластинами, для обработки деталей из легких сплавов. Конструкция и размеры |
ГОСТ 21586-76 | Зенкеры для обработки отверстий диаметром от 3 до 80 мм в деталях из легких сплавов. Допуски на диаметр |
ГОСТ 2255-71 | Зенкеры насадные со вставными ножами из быстрорежущей стали. Конструкция и размеры |
ГОСТ 22735-77 | Сверла спиральные с цилиндрическим хвостовиком, оснащенные пластинами из твердого сплава. Основные размеры |
ГОСТ 22736-77 | Сверла спиральные с коническим хвостовиком, оснащенные пластинами из твердого сплава. Основные размеры |
ГОСТ 25526-82 | Пластины сменные режущие из быстрорежущей стали для сборных перовых сверл.![]() |
ГОСТ 27724-88 | Сверла с механическим креплением сменных многогранных пластин. Технические условия |
ГОСТ 28319-89 | Сверла спиральные ступенчатые для отверстий под винты с цилиндрической головкой. Основные размеры |
ГОСТ 28320-89 | Сверла спиральные ступенчатые для отверстий под метрическую резьбу. Основные размеры |
ГОСТ 28321-89 | Развертки машинные, оснащенные твердосплавными напаиваемыми пластинами. Типы, параметры и размеры |
ГОСТ 28706-90 | Хвостовики цилиндрические с лыской для сверл. Размеры |
ГОСТ 29240-91 | Развертки. Термины, определения и типы |
ГОСТ 3231-71 | Зенкеры, оснащенные твердосплавными пластинами.![]() |
ГОСТ 3509-71 | Развертки ручные разжимные. Конструкция и размеры |
ГОСТ 4010-77 | Сверла спиральные с цилиндрическим хвостовиком. Короткая серия. Основные размеры |
ГОСТ 5735-81 | Развертки машинные, оснащенные пластинами твердого сплава. Технические условия |
ГОСТ 5756-81 | Сверла спиральные с твердосплавными пластинами. Технические условия |
ГОСТ 6226-71 | Развертки машинные конические конусностью 1:16 с коническим хвостовиком. Основные размеры |
ГОСТ 7722-77 | Развертки ручные цилиндрические. Конструкция и размеры |
ГОСТ 8034-76 | Сверла спиральные малоразмерные диаметром от 0,1 до 1,5 мм с утолщенным цилиндрическим хвостовиком.![]() |
ГОСТ 883-80 | Развертки машинные со вставными ножами из быстрорежущей стали. Типы и основные размеры |
ГОСТ 885-77 | Сверла спиральные. Диаметры |
ГОСТ 886-77 | Сверла спиральные с цилиндрическим хвостовиком. Длинная серия. Основные размеры |
ГОСТ Р 50427-92 | Сверла спиральные. Термины, определения и типы |
ГОСТ Р 52966-2008 | Сверла спиральные ступенчатые для отверстий под метрическую резьбу. Основные размеры |
Сверлильный инструмент во Владимире ✔ Изготовление деталей из металла по чертежам заказчика
Сверла.
Сверло – осевой режущий инструмент для обработки отверстий в сплошном материале и увеличения диаметра имеющегося отверстия.
По конструкции сверла классифицируют:
Спиральные сверла используются для обработки отверстий диаметром от 0,25 до 80 мм, обеспечивают точность, соответствующую 11…12 квалитету, и шероховатость Rz =40…160 мкм.; Сверла с коническим хвостовиком диаметром от 6 мм и с цилиндрическим диаметром от 8 мм изготавливаются сварными. Хвостовики сварных сверл делают из стали 45 или 40Х. Рабочая часть быстрорежущих сверл должна иметь твердость HRC 62—64, а лапки у сверл с коническим хвостовиком — HRC 30—45.Спиральные сверла изготавливают из быстрорежущей стали, но могут быть и твердосплавными. Сверла диаметром от 1,8 до 5,2 мм изготовляются монолитными из твердых сплавов марок ВК6 и ВК8М, а диаметром свыше 6 мм оснащаются пластинками твердого сплава, Для корпусов твердосплавных сверл используют сталь марок 40Х и 45Х.
Кольцевые сверла представляет собой трубу, на одном конце которой располагаются режущие элементы. Зубья режущей части имеют различную заточку для того, чтобы обеспечить разделение стружки по ширине. Трапецевидный зуб срезает среднюю часть, плоский нож срезает боковые части.
СОЖ подается под давлением по наружной поверхности трубы и отводится со стружкой через внутреннюю ее полость. Направление сверла и гидравлическое уплотнение обеспечивает втулка;
Глубоким считается сверление отверстий на глубину, превышающую диаметр сверла в 5 и более раз.
Глубокое сверление производится, как правило, при вращающейся заготовке, реже при вращении инструмента и заготовки вместе.
При сверлении глубоких отверстий возникают проблемы:
-затруднен отвод стружки;
-затруднен отвод тепла, необходимо обеспечить подвод СОЖ в зону резания;
-требуется обеспечить более точное направление сверла в процессе работы.
Сверла для глубокого сверления можно разделить на две группы:
Многокромочные сверла с поперечной кромкой, имеющие две главные режущие кромки.
Их преимущество – высокая производительность.
Недостаток – наличие поперечной кромки, вследствие чего появляются вибрации в работе, снижается качество обработки. Возможен увод сверла с оси детали, не обеспечивается прямолинейность оси.
Однокромочные сверла или сверла одностороннего резания;
-Предназначены для сверления центровых отверстий;
-Изготовляют двухсторонними;
-Относятся к комбинированным инструментам, т.к. одновременно применяются для обработки:
— сверления и зенкования;
— сверления и развертывания;
— сверления и нарезания резьбы.
Для получения конических поверхностей, прилегающих к основному отверстию и расположенных концентрично с ним, осуществ¬ляется инструментами, называемыми зенковками. Для обработки отверстий под конические головки винтов и заклепок, а также для центрования деталей применяют коническиезенковки. Наибольшее распространение получили конические зенковки с угла конуса при вершине 30, 60, 90 и 120°.
Зенкеры.
Зенкеры предназначены для повышения точности формы отверстий, полученных сверлением, отливкой, ковкой или штамповкой; обеспечивают точность, соответствующую 9…10 квалитету, и шероховатость Ra =6,3 мкм. Зенкеры изготовляют двух видов: для обработки цилиндрических отверстий и для обработки ступенчатых, фасонных и комбинированных отверстий.лезвия у зенкеров расположены на забор¬ном конусе под углом <р (угол в плане). При обработке стали угол в плане <р = 60°, а чугуна <р=45 — 60°. У зенкеров с пластинками из твердых сплавов угол в плане ф=60 — 75°.
Задний угол главного лезвия принимается равным 8 -10°.
-хвостовые с цилиндрическим или коническим хвостовиком;
-насадные с коническим посадочным отверстием (конусность 1:30) и торцовой шпонкой пря предохранения от проворачивания в работе,
-цельные,
-сборные.
Основные отличия зенкеров от сверл: отсутствие поперечной кромки; большее число режущих кромок (3…6)Развертка.
Развертывание выполняют для получения точных отверстий после сверления, зенкерования или растачивания. Достигается точность, соответствующая 6…9 квалитету, и шероховатость Ra = 0,32…1,25 мкм.
Высокая точность и качество поверхности при развертывании обеспечиваются малыми припусками (0,05…0,25 мм для чистовых и 0,15…0,5 мм для черновых) и срезанием весьма тонких стружек, благодаря наличию у разверток сравнительно большого числа зубьев (6…14) и малого угла ?.
Хвостовые и насадные;
цилиндрические и конические;
ручные и машинные;
быстрорежущие и твердосплавные;
цельные и сборные.
В централизованном порядке развертки выпускаются в доведенном виде для обработки отверстий с
допусками по К6, Js6, Н6, G6, N7, М7, К7, Js7, Н7, G7, F8, Е8, Н8, F9, D9, Н9, Н10, h21, Р7 и Е9 и с припуском под доводку №1-6
Зная отклонения и допуски на развертки, можно легко выбрать инструмент нужного размера. При отсут-ствии такового берется развертка, размер которой близок к заданному, и путем шлифования или доводки обрабатывается до требуемого размера.
По техническим требованиям в ка¬честве режущей части разверток должны применяться пластинки из твердого сплава марки ВК6, ВК6М, Т15К6, ВК8. Корпуса разверток изготовляют из стали 40Х, а корпуса ножей — из стали 40Х, У7 или У8.
Развертки конические с цилиндрическим хвостовиком по техническим требованиям выполня¬ются из стали 9ХС. Развертки диа¬метром больше 13 мм должны быть сварными. Ручная разжимная развертка имеет на корпусе прорезанные вдоль зубьев шлицы. В корпусе имеется коническое отверстие, куда помещается шарик. Перемещение шарика винтом в осевом направлении вызывает деформацию корпуса и увеличение диаметра развертки. Диапазон регулирования 0,16…0,5 мм в зависимости от диаметра развертки. У ручной раздвижной развертки в корпусе выфрезерованы конусные пазы, в которые вставлены ножы.
Конические развертки применяются для превращения цилиндрического отверстия в коническое или для калибрования цилиндрического отверстия.
Конические развертки для конусов Морзе работают в комплекте из трех или двух штук:
Обдирочная развертка снимает значительный припуск. Для облегчения работы режущую кромку делают ступенчатой. На конической образующей поверхности нарезают затылованный винтовой зуб. Направление резьбы совпадает с направлением резания. Эта развертка превращает цилиндрическое отверстие в ступенчатое.
Промежуточная развертка имеет стружкоразделительные канавки в виде конической прямоугольной резьбы, по направлению противоположной обдирочной развертке. Шаг резьбы Р = 1,5…3 мм в зависимости от номера обрабатываемого конуса. Зубья незатылованные, с ленточкой f =1…2 мм
Чистовая развертка имеет прямые зубья по всей длине. Ленточка минимальна (0,05 мм). Шаг зубьев равномерный.
Источник: Космачев И. Г. Название: Слесарь-инструментальщик. Издательство: Лениздат, Ленинград Год: 1973
StimZet
StimZet (Чехия) – один из крупнейших европейских производителей режущего инструмента для обработки отверстий. Производственная программа фирмы включает в себя преимущественно сверла, зенкеры, развертки, зенковки и специальные инструменты марки “STIMZET”, изготовленные из самой высококачественной быстрорежущей стали HSS и HSSCo. Высокое и постоянное качество продукции обусловлено более чем 160-летней историей производства свёрл, разверток, зенкеров.
Традиция изготовления инструментов для сверления и путь к нынешнему успеху торговой марки “STIMZET” начался в 1937 году с бывшей фирмы “Збройовка Всетин”. Результатом объединения многолетнего опыта с использованием современных технологий и постоянным внедрением инноваций стало высокое качество инструментов “STIMZET” и соответствующее доверие наших клиентов.
В настоящее время компания является одним из крупнейших европейских производителей. Она добилась этого положения в первую очередь благодаря своей ориентации на клиента, а также благодаря выгодным ценам на инструменты при сохранении их отличного качества. Помимо стандартной продукции, фирма StimZet также выпускает специальные инструменты по чертежам в соответствии с требованиями заказчика.
Геометрия инструмента и качество его покрытия, позволяет изготавливать высококачественный и износостойкий режущий инструмент. Покрытие защищает инструмент таким образом, что даже после многократного использования эффективность и качество его работы остается неизменным.
Обычно используемые покрытия:
– TiN (нитрид титана) – является одним из наиболее используемых покрытий. Высокая твердость 85 НРС, покрытие золотого цвета. Срок службы инструмента в 5 раз больше, благодаря этому покрытию. За счет своих свойств покрытие Tin (нитрид титана) широко используют в медицинском направлении и пищевой промышленности. Преимуществом TiN является хорошое высокое качество и сцепление.
– TiAlN (титан алюминий нитрид) – обладает высокой твердостью при высоких температурах. Покрытие фиолетово-черного цвета. Микротвердость HV3300. Термостойкость до 900’ С. Подходит для высокоскоростной обработки. Можно использовать без смазочно-охлаждающей жидкости.
Преимущества покрытий для сверления:
– Пресекает удерживание стружки при обработке предмета (особенно при работе с мягкими материалами)
– является препятствием образования нароста на кромке инструмента
– уменьшает трения инструмента
– пресекает возможность возникновения холодных швов
– увеличивает скорость резания на 40 – 60 %
– повышает стойкость инструмента на 400 – 600 %
– увеличивает производительность, качество и надежность при работе
Продукция:
Сверла Конический Хвостовик
· Средняя серия
· Длинная серия
Сверла Цилиндрический Хвостовик
· Ступенчатые
· Короткая серия
· Средняя серия
· Длинная серия
· Сверхдлинная серия
Центровочные сверла
Развертки
· Машинные
· Насадные
· Ручные
· Державки
Зенкера
Зенковки и цековки
Компания СКБ-4 готова оказать услуги по поставке продукции
StimZet
Осуществляя заказ оборудования через нашу компанию, вы получаете:
– гарантии своевременной доставки товаров в самые сжатые сроки по приемлемым ценам;
– Индивидуальный подход к каждому клиенту.
– Четкое соблюдение всех пунктов договора.
– И многое другое.
Сэкономьте свои деньги и время, сделайте заказ прямо сейчас!
Развертки от HMT для увеличения отверстий меньшего диаметра
Заводские развертки от Holemaker Technology: продолжайте работу, когда размер соединения недостаточен.
Наш ассортимент конических разверток разработан для стальных конструкций и мостов, где требуется расширение или повторное выравнивание отверстий. Доступны диаметры от 8 до 39 мм.
Этот тип развертки имеет коническую секцию для увеличения отверстия, а затем параллельную секцию для получения точного размера отверстия. Этот тип расширителя также может называться автомобильным или мостовым расширителем.
Диапазон заводских разверток
Развертка ImpactaMag 14-39 мм (готовый размер)
Развертка ImpactaMag ™ HSS – это уникальная развертка двойного назначения для увеличения и выравнивания отверстий в металлах и твердых материалах.
Специально разработанная геометрия резания позволяет использовать инструмент в ударном гайковерте или магнитной дрели. При использовании в ударном гайковерте он закрепляется в специальном адаптере, что означает, что инструментом легче управлять, применять правильную скорость подачи и извлекать из готового отверстия, что увеличивает срок службы инструмента.Эта развертка также подходит для стандартной оправки для магнитного сверла с хвостовиком Weldon 19,05 мм (3/4 дюйма).
Развертка VersaDrive 8-26 мм (готовый размер)
Развертки VersaDrive®– это идеальный инструмент для выравнивания и увеличения отверстий для слесарей и монтажников, позволяющий поддерживать работу при смещении отверстия или неправильном размере для крепления.
Обладая специально разработанной геометрией резания с 6 зубьями и титановым покрытием, развертки VersaDrive® полностью рассчитаны на ударную нагрузку и работают быстрее всего при использовании с ударным гайковертом, обеспечивая максимальную производительность резания практически без отдачи электроинструмента.
Доступны развертки ImpactaCut 14 и 39 мм (готовый размер)
Ударная развертка HMT ImpactaCut ™ разработана для выравнивания и увеличения существующих отверстий в конструкционной стали, конструкциях мостов, судостроении и другой тяжелой промышленности. У них есть специальный шестигранный хвостовик для использования с аккумуляторными, электрическими или пневматическими гайковертами.
Некоторые размеры этого продукта больше не выпускаются – заказы на размеры снятых с производства будут обновлены до эквивалентной развертки ImpactaMag или VersaDrive® плюс соответствующий адаптер.
Reamer Drill – обзор
19.3.1 Пример: реконструкция сустава с помощью роботов
Относительная жесткость кости и отличный контраст, доступные на рентгеновских и компьютерных изображениях, делают ортопедические процедуры, особенно операции по замене суставов, естественными для медицинских роботов и около 20% всех медицинских роботов, опрошенных в 2005 г. , были предназначены для таких приложений [166]. Два автора этой главы (Тейлор, Казанзидес) были разработчиками одной из первых роботизированных систем для ортопедии (Robodoc [167,168]), поэтому для нас естественно использовать ее в качестве примера при обсуждении хирургических приложений CAD / CAM.Ранее в Вашингтонском университете [169] проводились исследования с использованием робота для полной замены коленного сустава, а впоследствии ряд других групп также разработали системы для аналогичных приложений (например, [170–174]).
Robodoc (Think Surgical, Fremont, CA) был первоначально разработан для операции по тотальному эндопротезированию тазобедренного сустава (THR) [175,176], а позже был применен для тотального эндопротезирования коленного сустава (TKR) [177]. Операция THR [178] включает подготовку удлиненной полости в бедренной кости (бедренной кости) и округлой полости в вертлужной впадине (тазобедренной впадине) для размещения двух компонентов протеза бедра: бедренной ножки и вертлужной впадины [179]. Ежегодно в США выполняется более 300 000 процедур [180]. Точное размещение компонентов относительно костей пациента очень важно для достижения хорошего результата. Кроме того, в случае имплантатов без цемента кость должна иметь такую форму, чтобы обеспечить плотное прилегание между имплантатом и костью, чтобы способствовать врастанию кости в пористое покрытие на имплантате.
При традиционной операции THR предоперационное планирование выполняется путем наложения шаблонов (контуров) и проведения измерений на двумерных рентгеновских снимках.Доступны шаблоны с разным коэффициентом увеличения, что позволяет свести к минимуму ошибки, связанные с увеличением рентгеновских лучей. Обычно планирование ограничивается определением приблизительного диапазона размеров имплантата и приблизительного желаемого положения имплантата относительно кости. Во время операции кость препарируется с помощью ручных разверток (сверл) и протяжек, чтобы подготовить желаемые полости. Правильное выполнение требует значительного опыта и «хирургического чутья», особенно при подготовке бедренной полости. В этом случае хирург обычно начинает с расширителя и протяжки, соответствующих наименьшему размеру имплантата. Если полость кажется «рыхлой» (т.е. недостаточный контакт с твердой кортикальной костью), хирург переключается на следующий больший размер, пока не почувствует, что имеется достаточный, но не чрезмерный кортикальный контакт. Если хирург выберет слишком большой протез, бедро может сломаться либо во время подготовки полости, либо во время установки протеза. Это одно из наиболее частых интраоперационных осложнений, связанных с THR.Точно так же, хотя хирург может спланировать любое желаемое положение протеза, фактическое положение определяется в основном анатомическими ограничениями, поскольку портативные инструменты имеют тенденцию следовать по пути наименьшего сопротивления.
Лабораторные испытания [181] показали, что традиционный метод препарирования полости по своей сути неточен. Образовавшиеся полости были чрезвычайно неровными, с большими промежутками между имплантатом и костью. Кроме того, точное совмещение полости относительно кости было крайне неопределенным, поскольку внутренняя поверхность кости могла отклонять путь протяжки.Эти соображения побудили наших коллег-хирургов (доктора Пол и Баргар) предложить использовать робота для подготовки полости имплантата, и в конце 1980-х они обратились в IBM, чтобы посмотреть, можно ли построить такую систему. Доктор Пол был ветеринарным хирургом, и наша команда в IBM разработала прототип системы [168, 181, 182], который мог выполнять этап подготовки кости при замене тазобедренного сустава у его пациентов-ветеринаров. Впоследствии эта система была коммерчески разработана для хирургии бедра и колена у людей под названием «Robodoc» компанией Integrated Surgical Systems [175, 177 183] и теперь является продуктом Think Surgical (Фремонт, Калифорния).
Процедура Robodoc состоит из двух фаз: фазы предоперационного планирования (ORTHODOC) и фазы интраоперации (ROBODOC). Входные данные ORTHODOC состоят из компьютерной томографии анатомии пациента, геометрии протеза, предоставленной производителями, и клинических решений, принимаемых хирургом. Хирург планирует процедуру, выбирая протез из базы данных и размещая его на КТ-изображении. ORTHODOC отображает три ортогональных вида (т. Е. Ортогональные срезы) данных, а также трехмерную модель (см. Рис.19.15). Каждый сустав пятиосевого хирургического робота (рис. 19.16A и B) содержит два оптических датчика положения для дублирования обратной связи по положению. Система включает в себя устанавливаемый на запястье шестиосевой датчик силы, который отслеживает силы, приложенные к инструменту. Эта информация о силе позволяет реализовать такие функции, как ручное ведение, тактильный поиск, проверка безопасности и адаптивная скорость подачи резца. Robodoc выполняет предоперационный план, обрабатывая указанную полость протеза в бедренной кости. Это требует, чтобы кость была жестко прикреплена к роботу.Монитор движения кости используется в качестве датчика безопасности для обнаружения движения кости относительно робота. Кроме того, точное размещение полости требует совмещения анатомии пациента в предоперационном плане (то есть костей на компьютерной томографии) и анатомии реального пациента.
Предоперационный план указывается в координатах изображения (КТ), тогда как интраоперационная локализация пациента может быть получена в координатах робота, поэтому регистрация подразумевает нахождение преобразования между изображением и координатами робота.
Рисунок 19.15. Типичный вид экрана системы планирования ORTHODOC CT для ортопедического робота Robodoc.
Изображение любезно предоставлено Think Surgical, Фремонт, Калифорния. Рисунок 19.16. Клинически применяемые роботы для ортопедической хирургии. (A, B) Система Robodoc для бесцементной тотальной операции по замене тазобедренного и коленного суставов обрабатывает кость в соответствии с формой имплантата, выбранной хирургом, в соответствии с дооперационным планом, основанным на изображениях КТ пациента [168,319]. (C) В системе Mako Rio [170] используется совместное руководство рукой с «активными ограничениями», полученными на основе формы имплантата для тотальной операции по замене коленного сустава.(D) Робот Excelsius GPS [212] позиционирует сверло в хирургии позвоночника.
Первоначально Robodoc использовал метод регистрации «на основе штифта», который требовал имплантации титановых костных винтов (штифтов) в бедренную кость перед компьютерной томографией. Регистрация была достигнута путем определения по крайней мере трех контрольных точек на штырях, а затем их идентификации в системах координат CT и робота.Поскольку штифты выполнены из титана, программное обеспечение ORTHODOC может легко найти их в данных компьютерной томографии, используя методы обработки изображений. Роботизированная система идентифицировала физические штифты посредством тактильного поиска, используя обратную связь от своего датчика силы, установленного на запястье [168]. Первоначально Robodoc использовал три регистрационных штифта, причем центры головок штифтов служили тремя опорными точками, но вскоре после этого перешел на двухштырьковый метод, при котором третья опорная точка была получена путем создания «виртуального штифта» на основе центра. и ось дистального штифта.В этом случае потребовался более длинный дистальный штифт, чтобы обеспечить точное определение оси штифта в данных CT.
Хотя регистрация на основе штифтов надежна, она включает в себя дополнительную (незначительную) операцию по имплантации штифтов перед компьютерной томографией, а также была источником послеоперационной боли в коленях для многих пациентов. Это послужило стимулом для разработки системы «без штифта» [184], в которой в качестве реперных точек используются анатомические элементы вместо металлических штифтов. Регистрация выполняется с использованием метода, аналогичного методу повторной ближайшей точки, описанному в Разделе 19.2.2, с использованием положений точек на поверхности кости, измеренных небольшой рукой для оцифровки.
После начала резки Robodoc визуально отображает процесс резки на мониторе компьютера. Когда робот фрезерует полость, на мониторе отображаются данные компьютерной томографии, наложенные на модель полости протеза. Завершенная часть полости отображается одним цветом, а оставшаяся часть – другим. Это похоже на визуализацию, предоставляемую большинством навигационных систем. Во время резки управляющее программное обеспечение непрерывно контролирует датчик силы и регулирует скорость подачи резца на основе измеренной силы и параметров, специфичных для конструкции протеза и режущего инструмента [185].Это позволяет роботу адаптироваться к анатомии пациента за счет замедления в областях твердой кортикальной кости и ускорения в других областях.
Система Robodoc также применялась для тотального эндопротезирования коленного сустава [177] и ревизионной операции по замене тазобедренного сустава [183]. При замене коленного сустава [186] бедренная и большеберцовая поверхности поврежденного коленного сустава заменяются искусственными компонентами. Ежегодно в США выполняется более 700 000 процедур [187]. Традиционно поверхности костей обрабатывались с помощью ручных пил с направляющими для резки, прикрепленными к костям, чтобы обеспечить правильный угол между разрезами. Точность ручного размещения направляющих и ограничения рабочего процесса являются важными соображениями, и был предложен ряд альтернативных подходов, включая роботов и компьютерные навигационные системы. На рис. 19.16A и B показано интраоперационное использование Robodoc в процедуре TKR.
Альтернативный подход к препарированию кости сочетает ручное управление хирургическим роботом, держащим режущий инструмент, с виртуальными приспособлениями (см. 19.4.6), чтобы ограничить движение робота так, чтобы резак удалял только ту кость, которая должна быть удалена. .Этот подход был применен к хирургии колена с использованием системы Acrobot [170] и в настоящее время используется системой Mako Rio (Stryker, Kalamazoo, Mi.) [188] для хирургии колена и бедра [189,190]. На рис. 19.16C показано использование системы Mako для направления костной пилы.
Другой подход к удалению кости, который в настоящее время используется в системе Navio (Smith and Nephew, Andover, Mass.), Использует ручное роботизированное режущее устройство, которое отключает или защищает режущий инструмент, когда он выходит за пределы разрешенного объема резки [37]. Еще один подход использует хирургическую навигацию для помощи ручной хирургической пилы [191] или (альтернативно) использует робота для позиционирования направляющей пилы [192].
При подготовке кости к протезу, независимо от того, обрабатывается ли кость автоматически активным роботом, совместно обрабатывается хирургом и полуактивным роботом или обрабатывается хирургом с помощью направляющей для инструмента, установленной роботом, очень важно, чтобы резка должна выполняться в правильном положении и в правильной ориентации. Точность регистрации имеет решающее значение.Кроме того, любой из этих роботов должен иметь систему безопасности, чтобы гарантировать, что отказы датчиков не приведут к неправильному позиционированию режущего инструмента или направляющей инструмента.
Правильное развертывание | Разработка режущего инструмента
Соответствующие сценарии применения расширителя при чистовой обработке отверстий.
Предоставлено Комет оф Америка
Режущие кольца Komet имеют регулируемый диапазон диаметров и могут быть точно отрегулированы с помощью специальных держателей врезных колец. По словам компании, это компенсирует износ, обеспечивая правильную настройку на точный размер отверстия.
При обработке отверстия точно по размеру развертка часто является лучшим выбором для машиниста. Обычно его нельзя использовать для правки отверстий, и он может удалить только ограниченное количество материала, но при правильном выполнении развертывание может быть быстрым и высокоточным процессом.
Однако правильное развертывание требует хорошей подготовки. Важные факторы включают оставление точного количества припуска после бурения; зная, когда следует развернуть дважды, использовать многофункциональную развертку или полностью использовать другой инструмент; и определение правильной развертки для работы.Что касается последнего, доступно множество различных стилей разверток, включая регулируемые, зажимные и спиральные развертки, и во многих случаях специальный инструмент является лучшим инструментом для работы.
По словам Райана Бистербуша, руководителя группы конструкторских разработок производителя инструментов Komet of America Inc. , Шаумбург, штат Иллинойс, при развертывании наиболее важным является подготовка отверстия. Это связано с тем, что развертка увеличивает просверленное отверстие до размера за счет удаления небольшого количества запаса и не исправляет дырку.«Развертка следует за отверстием», – сказал он, но отметил, что развертка помогает немного улучшить прямолинейность, если инструмент имеет режущую способность спереди.
Предоставлено Alvord-Polk
Набор зажимных разверток от Alvord-Polk, включая (вверху) развертку с прямым хвостовиком и прямой канавкой; (вверху посередине) инструмент с коническим хвостовиком, правый, со спиральной канавкой; и (вверху внизу) развертка с прямым хвостовиком и правой спиральной канавкой с покрытием из нитрида титана.
Джош Линберг, президент поставщика инструментов Monster Tool Co., Виста, Калифорния, согласился с тем, что перед развертыванием необходимо отверстие «хорошего качества». Например, он отметил, что при расширении отверстия диаметром 0,240 дюйма расширителем 0,250 дюйма отверстие не будет выпрямляться, если оно сужается на 0,005 дюйма или более.
Если форма или расположение отверстия нуждаются в корректировке, Уилл Нестор, инженер по продажам приложений / проектов из Феникс-Сити, штат Алабама, для производителя инструментов Mapal Inc., Порт-Гурон, штат Мичиган, рекомендует растачивание.«Но развертывание обычно дает вам более короткое время цикла, чем растачивание», – сказал он, добавив, что развертка чаще применяется для достижения нужного размера отверстия, чем для получения чистой поверхности.
Качество поверхности, достигаемое при расширении, обычно зависит от материала заготовки. По словам Бистербуша, диапазон для чугуна составляет от 50 до 80 среднеквадратичных значений и от 30 до 60 среднеквадратичных значений для сталей, а развертка PCD может обеспечить чистоту обработки алюминия до 8 среднеквадратичных значений.
Иногда отверстие просверливается перед расширением, но это не обязательно. «Любое отверстие, которое соответствует минимально необходимому количеству материала для развернутого размера, не требует другой подготовки перед расширением», – сказал Линберг. «Если готовое отверстие имеет чрезвычайно жесткий допуск, а станок, используемый для создания отверстия, не обладает достаточной точностью или жесткостью, просверленное отверстие помогает поддерживать развертку в соответствии с осью отверстия, помогая станку поддерживать прямое отверстие. . »
Существенные проблемы
Количество припуска, остающегося для развёртывания, зависит от качества и диаметра отверстия.Как отметил Линберг, после сверления для развертывания должно оставаться от 0,010 до 0,015 дюйма, за исключением небольших диаметров, таких как 1⁄32 дюйма, которые должны содержать от 0,003 до 0,006 дюйма материала для развертывания. «Плохо просверленное отверстие. может потребоваться немного больше материала, чтобы развертка могла «очистить» стенки отверстия », – сказал он.
Компания Nestor предоставила общий диапазон DOC от 0,0039 “до 0,0098” для разверток Mapal с направляющими прокладками и до 0,0394 “DOC для разверток с фиксированной пайкой из PCD, в зависимости от материала заготовки.«Что касается алюминиевых компонентов двигателя, мы смогли удалить до 1 мм с каждой стороны отверстия», – сказал он, добавив, что больший DOC возможен для расширителя с геометрией режущей кромки, встроенной в режущую кромку.
Согласно Bysterbusch, помимо алюминия, запас магния обычно больше, чем для стали, чугуна, титана и суперсплавов на основе никеля. Если при развертывании последних материалов стружка слишком толстая, в стружку попадает слишком много тепла, что делает ее пластичной и трудной для разрушения, что создает проблему удаления стружки.«Лучше удалять как можно меньше».
Другие предоставляют больший диапазон размеров отверстий. Кевин Моррисон, главный инженер по оснастке компании Alvord-Polk Inc., указал, что производитель твердотельных разверток с несколькими зубьями из Миллерсбурга, штат Пенсильвания, рекомендует от 0,003 до 0,006 дюйма для расширения отверстий диаметром до 3⁄32 дюйма, 0,008 “до 0,010” для отверстий размером более 3⁄32 “до to”, от 0,012 “до 0,015” для от “до ½”, от 0,017 “до 0,020” для ½ “до 1”, от 0,020 “до 0,025” для 1 “до 2 “и 0. От 030 до 0,035 для отверстий размером более 2 дюймов. «Это скользящая шкала, – сказал он. – Она даже не работает в процентах».
Моррисон добавил, что диапазон составляет от 0,002 до 0,004 дюйма для ручной развертки. «Это все, для чего предназначено человеческое тело», – сказал он. «У нас нет механического преимущества, чтобы забирать больше материала».
Хотя некоторые не считают упрочнение материала серьезной проблемой при развертывании, Нестор отметил, что это может создать проблемы. Желательно использовать легкий DOC, например, при развертке титана.Легкий DOC сохраняет стружку тонкой для облегчения ее удаления при обработке, например, отверстия малого диаметра. «Обрабатываемость играет большую роль в том, как вы будете разворачивать», – сказал он.
Размер отверстия
Когда после бурения остается слишком много материала для развертывания, конечные пользователи имеют возможность развернуть дважды. Линберг из Monster Tool предлагает сначала установить развертку меньшего размера, а затем развертку необходимого размера. «Сверление с целью вскрытия отверстия обычно приводит к отказу сверла из-за неравномерного и неравномерного напряжения вдоль режущей кромки сверла, и не рекомендуется», – сказал он.Линберг добавил, что врезное фрезерование также возможно при наличии концевой фрезы подходящего размера.
Кроме того, ступенчатая развертка с диаметром для черновой и чистовой обработки может помочь. «Это зависит от материала», – сказал Бистербуш. «Как только вы перейдете к более прочным сталям, мы должны более подробно изучить их применение».
Нестор отметил, что другим вариантом является применение инструмента для чистового растачивания. Инструмент для чистового растачивания имеет не менее трех направляющих пластин и способен выдерживать значительно больший DOC, чем развертка.Он добавил, что корректировки местоположения отверстия можно также выполнить с помощью инструмента для чистового растачивания со временем цикла, сравнимым с разверткой с направляющей.
Объем детали также определяет приемлемое решение. «Вы должны помнить, что заказчик всегда хочет сократить время цикла», – сказал Донато Пиньо, специалист по продукции компании Komet. «Обычно он использует инструмент для черновой обработки и инструмент для чистовой обработки».
Моррисон из компании Alvord-Polk предположил, что корончатое сверло, представляющее собой нечто среднее между расширителем и сверлом, может решить проблему, когда необходимо удалить значительно больше материала, чем рекомендуется.Корончатое сверло предназначено для удаления большого количества материала из отверстия, но само по себе оно не создает отверстия. «Бывают случаи, когда корончатое сверло обеспечивает достаточную обработку поверхности, и конечные пользователи используют ее для чистовой обработки отверстия», – сказал он.
Рекомендации по использованию инструмента
При указании развертки размер – это единственная особенность, о которой нужно заботиться конечному пользователю, если только он не расширяет необычно глубокое отверстие, для которого требуется дополнительная длина инструмента, для чего, по словам Линберга, требуется особый размер. «Правильно изготовленная развертка будет выполнять свою работу независимо от обрабатываемого материала».
Предоставлено Monster Tool
Размер – единственное, что нужно учитывать конечному пользователю при выборе развертки, согласно Monster Tool.
Хотя Бистербуш отметил, что «полноценные специальные предложения» составляют около 40% продаж разверток Komet, стандартные моноблочные стандарты компании являются «полуспециальными». Это связано с тем, что стандартные заготовки шлифуются по размеру для удовлетворения требований конкретного клиента после того, как компания получает заказ.Стандартный диапазон составляет от 6 мм до 110 мм, но специальные охватывают более широкий спектр. «Мы разворачиваем все от 1,5 мм до более 300 мм», – сказал он.
Согласно Mapal’s Nestor, допуск на размер играет важную роль при выборе стиля развертки. Хотя фиксированный инструмент подходит для большего диапазона допусков, «каждый раз, когда у вас есть допуск ± 5 мкм или более жесткий на ваш диаметр, – сказал он, – вам понадобится регулируемая развертка».
Нестор добавил, что патронные развертки могут применяться в сверлильном станке, токарном станке для инструментальных цехов или даже в фрезерном станке Бриджпорт, но развертки с направляющими и другие высокопроизводительные развертки требуют станка с механической подачей для обеспечения постоянной точности.Достаточная подача охлаждающей жидкости также требуется для высокопроизводительного развёртывания. «Обычно растворимые масла и полусинтетики работают лучше, но мы добились успеха с синтетической охлаждающей жидкостью для инструментов с направляющими, – сказал он.
Обрывы отверстий, таких как шпоночная канавка или поперечное отверстие, также диктуют требования к инструменту для развертывания. Когда такая особенность присутствует, Моррисон Alvord-Polk рекомендует развертку со спиральной канавкой, чтобы спираль перекрывала зазор при вращении развертки, а инструмент постоянно поддерживался.«Если у вас прямая флейта, каждый раз, когда зуб касается, он ловит и колотит, как будто это никого не касается», – сказал он.
Независимо от области применения развертки, некоторые обслуживают только настоящую развертку, которая справится с этой задачей должным образом. «Опасно говорить, что вы просто хотите использовать сверло с высоким качеством развёртывания», – сказал Пиньо из Komet. «Вы никогда не получите такого же результата». CTE
Об авторе: Алан Рихтер, редактор журнала Cutting Tool Engineering, присоединился к изданию в 2000 году.Свяжитесь с ним по телефону (847) 714-0175 или [email protected].
Предоставлено Комет оф Америка
Срок службы инструмента увеличился с 1200 отверстий до 50 000 отверстий, когда Magna Powertrain USA перешла с твердосплавной развертки на развертку Monomax Solid с металлокерамическими наконечниками Dihart от Komet of America при чистовой обработке небольшого отверстия на концах рычагов привода из стали 8620.
Развёртывание как свисток Расширение отверстий в стали 8620 с твердостью 217 HB не обязательно является сложным процессом, если только вы не делаете около полумиллиона таких отверстий в год и не должны обеспечивать жесткие допуски, короткое время цикла и низкую стоимость инструмента на каждую деталь. Magna Powertrain USA Inc., Манси, штат Индиана, оказалась в такой ситуации, когда производила рычаги привода и нуждалась в расширении отверстия диаметром 0,388 дюйма на глубину 0,393 дюйма на горизонтальном обрабатывающем центре OKK HP500S.
Дэвид Бокселл, инженер-технолог компании Magna, производителя компонентов для раздаточных коробок и трансмиссий, знает, что самая дешевая развертка не может быть способом достижения самой низкой стоимости отверстия. «Я могу купить развертку по цене от 35 до 40 долларов на полке, но я получу только несколько сотен деталей, поэтому моя цена за единицу довольно высока», – сказал он.
Первоначально Magna применяла стандартные развертки с твердосплавными напайками и обрабатывала около 1200 деталей до износа инструмента. Затем компания переключилась на специальные твердосплавные развертки, но с ограниченным успехом. «Они были очень дорогими и слишком быстро изнашивались», – сказал Бокселл.
Чтобы обеспечить требуемый размер чистового отверстия от 0,3952 “до 0,3948”, Magna просверливает отверстие в сплошном материале и оставляет около 0,013 дюйма заготовки для развертывания. Затем отверстия расширяются на размер больше, чтобы они сжимались до указанного размера при термообработке.После термообработки никаких дополнительных операций не требуется.
Раньше Boxell производила другую линейку продуктов, и во время разговора с другим специалистом по металлообработке узнала, как развертка Dihart, производимая Komet of America Inc., помогла сократить время изготовления детали с нескольких дней до 1 дня при выдержке 0,0002. “прямолинейность в 4” -толщинных отверстиях. Не будучи полностью убежденным, Boxell пригласил продавца и дистрибьютора Komet Haggard & Stocking, Индианаполис, для тестирования развертки Dihart со стороны Magna.«Он был прав в деньгах», – сказал Бокселл. «Развертки сделали именно то, что он сказал». Magna начала их использовать.
Позже Boxell поговорил с инженером-технологом Джоном Хершбергером, который отвечал за рычаги привода, и предложил ему также попробовать развертку Komet. «Ему это понравилось, и он сразу начал им пользоваться», – сказал Бокселл. «Потом я унаследовал эту работу, и теперь у меня целая клетка».
Развертка Dihart 525.91.4030 Monomax Solid с металлокерамическими наконечниками имеет геометрию, позволяющую выталкивать стружку вперед.Работая со скоростью шпинделя около 1800 об / мин, предыдущим разверткам требовалось от 3 до 4 секунд для обработки отверстия, в то время как время резания для нового инструмента составляет 0,14 секунды на отверстие при работе при 4385 об / мин, скорости резания 453 sfm и 157 -IPM скорость подачи. Развертки с металлокерамическими наконечниками имеют охлаждающую жидкость через инструмент, в то время как компания применила охлаждающую жидкость заливкой для твердосплавных.
В дополнение к жесткому допуску по размеру развертка Monomax обеспечивает чистоту поверхности 0,6 мкм Rz, когда по спецификации требуется чистовая обработка только 1.99 мкм Rz. «Когда мы закончим, финиш будет выглядеть чистым», – сказал Бокселл. “Это просто как свисток”.
Срок службы инструмента также значительно увеличился: с 1200 отверстий на развертку до 30 000–50 000 штук без потери размера от 4 мкм до 5 мкм. Бокселл отметил, что он мог бы применить сверло большего размера и увеличить срок службы расширителя, оставив всего 0,008 дюйма запаса для развертывания, «но у меня на складе так много других сверл, что, вероятно, не стоит покупать 200 или 300 сверл, когда развертка работает так хорошо.”
Хотя цена на новые специальные развертки является стандартной и по-прежнему стоит около 400 долларов каждая, стоимость инструмента на одну деталь снизилась с 0,018 до 0,009 доллара. По словам Бокселла, предполагаемая годовая экономия составляет 85 000 долларов без учета времени цикла и увеличения времени безотказной работы шпинделя. Кроме того, Magna обеспечивает дополнительную экономию за счет того, что использованные развертки Komet с повторными наконечниками составляют примерно треть стоимости новых. Согласно Komet, он может повторно насадить инструмент три или четыре раза. «Мы купили около 20 таких разверток и использовали только четыре за последние 4 месяца», – сказал Бокселл, добавив, что расчетное ежегодное использование инструмента сократилось с 1000 до 13 инструментов. «Когда готовые инструменты готовы, значит, готово».
—A. Рихтер
Участники
Alvord-Polk Inc.
www.reamers.com
(800) 441-2751
Komet of America Inc.
www.komet.com
(847) 923-8400
Magna Powertrain USA Inc.
(765) 245-9750
www.magnapowertrain.com
Mapal Inc.
www.mapal.us
(810) 364-8020
Monster Tool Co.
www.monstertool.com
(888) КАРБИД
YG-1 Tool Co.
(800) 765-8665
www.yg1usa.com
Предоставлено YG-1 Tool
Хонингованная кромка на Dream Drill YG-1 Tool помогает укрепить кромку, поля помогают достичь требований к допуску и чистоте поверхности, а угол наклона спирали, наряду с шириной канавки, улучшает контроль стружки и удаление стружки.
Мечтаю не расширять
При выполнении отверстий выполнение требований к размеру и чистоте поверхности развертки с помощью всего одного инструмента может повысить производительность и снизить затраты. Хотя производители инструментов давно продвигают различные сверла для устранения развёртывания, YG-1 Tool Co., Вернон-Хиллз, штат Иллинойс, заявляет, что их Dream Drill также выполняет центрирование и позиционное растачивание.
Сверло, покрытое нитридом титана-алюминия, может достигать допуска на расширенное отверстие M7 согласно YG-1 (см. Таблицу). Твердосплавные сверла со сквозной подачей охлаждающей жидкости доступны от 0,039 до 0,787 дюйма, а сверла I Dream со сменными пластинами со сквозной подачей охлаждающей жидкости доступны от 0,4724 дюйма до 1.250 дюймов. Также доступны сверла без отверстий для СОЖ.
YG-1 предлагает две конструкции для обработки материалов с твердостью до 50 HRC: стандартная для стали, чугуна и аналогичных сплавов и Inox для нержавеющей стали и более мягких, более пластичных сплавов. «Небольшие кудри – всегда цель, – сказал Аль Зайтун, менеджер по продажам и маркетингу YG-1.
Производитель инструмента сообщает, что утонение S-образной формы острия стенки Dream Drill снижает осевую осевую нагрузку и стабилизирует острие для получения точных отверстий, а угол при вершине 140 ° немного увеличивает поперечное сечение стружки, что помогает разрушать стружку.
Зайтун отметил, что скорость проходки Dream Drill в три-пять раз выше, чем у обычного сверла, а подача от 20 до 30 дюймов в минуту не редкость при сверлении отверстия диаметром 0,250 дюйма в низколегированной стали.
«Как правило, чем выше скорость, тем более пластичным становится материал, поэтому уменьшается усилие, необходимое для сверления, – сказал он, – а размер отверстий для охлаждающей жидкости рассчитан на максимальное давление и объем, чтобы уменьшить тепловые проблемы».
Согласно Зайтуну, Dream Drill подходит для замены от 50 до 70 процентов развертываний при сверлении твердой заготовки.К ним относятся приложения, в которых требования к чистоте поверхности указаны «как развернутые» и сверло может обеспечить допуск по размеру.
—A. Рихтер
Таблица: Допуски диаметра сверла
Stabil Drill Fleet – развертки
развертки
развертки Stabil Drill для тяжелых условий эксплуатации обеспечивают высококачественную разработку скважин как для прямого, так и для наклонно-направленного бурения.

Развертки – это скважинные режущие инструменты, используемые для увеличения и сглаживания выносов, исправления кривых отверстий, восстановления отверстий с недостаточным калибром или исправления неровностей отверстий, которые могут вызвать осложнения или задержку для бурильной колонны.Эти инструменты предназначены для работы в любых условиях бурения, они спроектированы и обработаны с высокой точностью на собственном предприятии.
Поскольку наши инструменты спроектированы, изготовлены, испытаны и сертифицированы на предприятиях Stabil Drill, у нас есть больший контроль над общим качеством и надежностью. Фактически, каждая из наших разверток подлежит одним из самых строгих мер по обеспечению качества и контролю качества в отрасли.
Развертки Stabil Drill также разработаны для быстрого и легкого обслуживания – с резцами, которые можно заменить на буровой.Мы даже предлагаем комбинированный расширитель / стабилизатор, который помогает оптимизировать управление направлением. Подробную информацию о продукте можно получить у представителя Stabil Drill.
Наши роликовые развертки помогают поддерживать оптимальный диаметр ствола скважины во время буровых работ, а также оказывают стабилизирующее действие на долото во время работы. Роликовые расширители служат для снижения крутящего момента в скважине во время работы по сравнению с развертыванием только стабилизатора. Доступны в 3- или 6-точечной конфигурации и в различных вариантах в зависимости от формации.
Эксцентриковые развертки Последняя инновация Stabil Drill, наша эксцентриковая развертка Smoothbore ™ помогает быстрее достигать заданной глубины. Его спиральная конструкция обеспечивает полный проход за один оборот, увеличивая скорость проходки таким образом, чтобы сократить расходы на бурение до двух дней и 100 000 долларов США. Благодаря номинальной скорости инструмента 240 футов в час или выше и твердосплавным кнопкам, защищающим режущую структуру, Smoothbore быстро доставит вас в нужное русло.
Развертка Phantom PDC – это решение для изгибов, выступов и режущих пластов при горизонтальном бурении.Этот расширитель с восемью лопастями, созданный для исключения срабатывания очистителя, очищает ствол скважины во время обратного развертывания или путем вытягивания до вершины кривой, а затем вращения вперед до достижения общей глубины.
Сопоставление пилотного долота и расширителя: скважинные данные в реальном времени позволяют дифференцировать совместимость гибридного бурового долота с концентрическим расширителем в глубоководных районах Мексиканского залива Применение | Конференция и выставка SPE / IADC по бурению
В глубоководных скважинах обычно используются концентрические расширительные устройства в компоновке низа бурильной колонны (КНБК) для снижения эквивалентной плотности циркуляции (ECD). В применениях в Мексиканском заливе (GOM) часто используются концентрические расширители, которые размещаются на расстоянии примерно 100–150 футов за пилотным долотом для решения проблемы оценки пласта и других эксплуатационных ограничений. Такое расстояние между буровым долотом и концентрическим расширителем создает проблемы синхронизации долота и расширителя, особенно при бурении пластов с переслаивающимися пластами, когда долото может пробурить более мягкий пласт, в то время как расширитель помещается в более твердый пласт, или наоборот. Эта ситуация вызывает колебания сжимающей нагрузки на долоте и расширителе.Повреждение режущего элемента часто происходит в результате перегрузки, что приводит к преждевременному и дорогостоящему отключению. Во многих случаях пилотное долото или расширитель могут быть лишены оптимальной сжимающей нагрузки для разрезания пласта, что приводит к более низким, чем ожидалось, скоростям проникновения. Неадекватные и непостоянные сжимающие нагрузки на долото или расширитель часто вызывают неустойчивые вибрации.
Усилия по решению проблемы согласования бит-расширитель продолжаются в отрасли, и управление агрессивностью пилотного долота и расширителя часто используется в качестве потенциального решения.Хотя программы моделирования широко используются в процессе планирования скважин, в отрасли по-прежнему существует недостаток конкретных руководящих принципов.
Гибридные долота, сочетающие в себе режущие элементы из компакта из поликристаллического алмаза (PDC) и режущих кромок из карбида вольфрама (TCI), широко и успешно используются в GOM. Эти долота обеспечивают более высокую эффективность бурения благодаря двойным режущим элементам и сбалансированной агрессивности. Результаты 18⅛ дюйм. Использование гибридного бурового долота с концентрическим расширителем дало обнадеживающие результаты и предложило потенциальное решение проблемы синхронизации долота и расширителя.
Используя скважинные данные в реальном времени, в этой статье оценивается и сравнивается распределение нагрузки на долото и расширитель, механика бурения PDC и гибридных долот, а также дается ценная аналитическая информация об успешном применении гибридных долот для решения проблемы синхронизации долота и расширителя.
Буровой инструмент Продукты | Drill-N-Ream
Drill-N-Ream ™
Техническое резюме
Drill-N-Ream ™ – это последняя инновация, добавленная к нашему ассортименту продукции.Технология подготовки ствола скважины необходима для того, чтобы операторы нефтегазовой отрасли могли достичь технические ограничения сегодняшних проблем бурения. Drill-N-Ream может эффективно сократить / исключить обратное рассверливание или развертывание как в двигателях, так и в приложениях RSS. Сделайте это предпочтительным выбором для решения проблемы качества ствола скважины.
Drilling Tools International является авторизованным дистрибьютором Drill-N-Ream в Северной Америке и Канаде.Более подробную информацию о Drill-N-Ream можно найти на Superior Сайт “Буровые изделия”.
Преимущества
- Повышение качества отверстий
- Уменьшить крутящий момент и сопротивление
- Уменьшение нагрузки на крюк
- Уменьшить залипание / проскальзывание
- Преимущества бурения
- Увеличить перенос веса на бит
- Повышение скорости проникновения
- Минимизация отказов забойного двигателя
- Увеличить срок службы долота
- Более эффективный перепад давления
- Уменьшение вибрации в скважине
- Нижняя MSE
- Сократить время поездки
- Эффективность обсадной трубы
- Улучшение согласованности установки обсадной трубы
- Повышение срока службы и усталости обсадной колонны
- Повысить качество цементирования
Запатентованные функции
Противоположные эксцентриковые развертки PDC централизуют и стабилизируют силы резания |
Эксцентриковая конструкция, позволяющая увеличить отклонение ствола скважины до 1/4 дюйма по сравнению с размером долота |
Прогрессивные лопасти постепенно срезают пласт с минимальным крутящим моментом |
Рельеф профиля эффективно втягивает зону резания PDC в пласт |
Алмазные купола защищают обсадную колонну и режущую структуру PDC во время спусков и разбуривания |
Патенты США 8,752,649 | 8,813,877 | 8,851,205 | 9 163 460
Технические характеристики
Размер инструмента (ID) | 1 1/2 дюйма – 3 3/4 дюйма |
Размер инструмента (OD) | 4 3/4 дюйма – 14 3/4 дюйма |
Длина | 8 футов – 10 футов |
Масса | 350 – 1200 фунтов |
Подключения | любой |
Максимальное усилие | Зависимая от резьбы |
* Инструменты можно настроить для каждого приложения
** Стандартный размер инструмента = 1/16 дюйма по сравнению с размером бит
Дополнительная информация
Развертка и сверло Техническая информация и процедуры
* Процедуры выбора развертки и сверла
Посмотреть версию для печати этой страницы Выбор правильного диаметра развертки не так прост, как можно было бы подумать.Выбор правильного размера сверла также важен, так как это продлит срок службы развертки и обеспечит правильный размер и качество обработки. Чтобы выбрать правильную развертку Yankee и размер сверла для вашего применения, необходимо выполнить 3 шага:
1) Определите правильный диаметр развертки Янки на основе общего допуска отверстия и обрабатываемости вашего материала.
2) Рассчитайте правильный диаметр отверстия, необходимый перед расширением,
3) Выберите правильный диаметр сверла, чтобы проделать это отверстие.
Пример следует за каждым шагом.
Шаг № 1:
Для расчета правильного диаметра развертки Янки на основе обрабатываемости материала, который будет разворачиваться, вычтите припуски в следующей таблице из максимального размера готового отверстия:
Например: Если размер готового отверстия составляет 0,5000 с допуском -,0005 +,0000, а материал – нержавеющая сталь 302 (с рейтингом обрабатываемости 50), диаграмма показывает, что вычитаемый диапазон равен. 0004-.0005.
.5000 -.0004 = .4996
.5000 -.0005 = .4995
Следовательно, лучший размер развертки Yankee – .4995
Обрабатываемость | Рейтинг | |
---|---|---|
Доп. | 30 или меньше или больше 100 | 31-100 |
.0005 ″ | .0003-.0004 | .0004-.0005 |
.0010 | .0004-.0006 | .0006-.0008 |
.0015 | .0005-.0008 | .0008-.0010 |
.0020 | .0006-.0010 | .0010-.0014 |
.0030 | .0009-.0020 | .0009-.0020 |
.0040 | .0012-.0026 | .0012-.0026 |
.0050 | .0014-.0032 | .0014-.0032 |
.0060 | .0017-.0038 | .0017-.0038 |
.0070 | .0019-.0044 | .0019-.0044 |
.0080 | .0022-.0050 | .0022-.0050 |
.0090 | .0024-.0056 | .0024-.0056 |
.0100 | .0027-.0062 | .0027-.0062 |
Шаг # 2:
На основе развертки Yankee, выбранной на шаге 1, в следующей таблице показано количество материала, которое должно быть удалено расширителем (оставление рекомендуемого количества обеспечит наилучшую отделку и допуск):
На том же примере (размер готового отверстия.5000 с допуском -,0005 +,0000, и материал – нержавеющая сталь 302 (рейтинг обрабатываемости 50): диаграмма показывает, что сумма, которую нужно вычесть из размера развертки Yankee, составляет 0,007-0,015.
4995 -,015 = 0,4845
4995 -,007 = 0,4925
Следовательно, наилучший размер отверстия перед развертыванием находится между 0,4845 и 0,4925
Обрабатываемость | Рейтинг | |
---|---|---|
Диапазон диаметров | 30 или меньше | 31 и выше |
.0000-.0625 | .006-.010 | .003-.005 |
.0626-.1250 | .006-.010 | .004-.007 |
.1251-.2500 | .006-.010 | .005-.010 |
. 2501-.5000 | .012-.020 | .007-.015 |
. 5001-1,0000 | .012-.020 | .010-.020 |
Шаг № 3:
На основании диаметра отверстия перед рассверливанием, выбранного на этапе № 2, в следующей таблице показан припуск на размер, который следует вычесть из размера отверстия, чтобы получить правильный размер сверла:
На том же примере (размер отверстия перед рассверливанием находится между.4845 и .4925, а материал – нержавеющая сталь 302 (который имеет рейтинг обрабатываемости 50): диаграмма показывает, что сумма, которую нужно вычесть из размера развертки Yankee, составляет 0,0048.
4845 -.0048 = .4797
4925 -.0048 = .4877
Следовательно, лучший практический размер сверла – 31/64 (.4844), потому что он находится между .4797 и .4877 Напомним: в этом примере вы должны использовать сверло 31/64 и развертку Yankee .4995.
Обрабатываемость | Рейтинг | |
---|---|---|
Диапазон диаметров | 30 или меньше или больше 100 | 31-100 |
.0000-.0625 | .0005 | .0015 |
.0626-.1250 | .0006 | .0028 |
.1251-.1875 | .0008 | .0036 |
. 1876-.2500 | .0008 | .0042 |
. 2501-.5000 | .0010 | ,0048 |
.5001-.7500 | .0012 | .0052 |
. 7501-1.0000 | .0020 | .0065 |
Обратите внимание: Вся информация, содержащаяся на этих страницах, является точной, насколько нам известно. Материалы и условия могут различаться, вызывая различия, которые мы не можем контролировать. Поэтому мы не можем нести ответственность за вашу конкретную ситуацию.
.