инженер поможет – 5 правил сверления глубоких отверстий
Современный подход раскрывает потенциал новейших сверл со сменными режущими частями для обработки глубоких отверстий с ЧПУ.
1. Предварительная настройка процесса сверления
Чем глубже отверстие, тем длиннее сверло. Чем длиннее сверло (чем больше расстояние между острием инструмента и шпинделем), тем больше степень влияния биения на результаты. В некоторых операциях с глубокими отверстиями малейшее колебание может привести к преждевременному износу инструмента и нарушить как прямолинейность, так и чистоту поверхности.
Тем не менее, необходимость тщательной настройки не освобождает от необходимости тратить непомерное количество времени на определение и корректировку биения при каждом изменении инструмента или пластины.
В частности, в современной производственной среде нет места для лазания по рабочим зонам для установки индикаторов или для удержания кусочков бумаги на месте для прикосновений инструмента. Скорее всего, сборка инструментов в автономном режиме с устройством предварительной настройки сэкономит значительное количество времени при любой операции глубокого бурения.
В современной производственной среде нет места ни для работы оператора в рабочей зоне, ни для установки индикаторов, ни для удержания кусочков бумаги в месте соприкосновения инструмента и детали.
На объекте одного клиента в начале каждой смены в инструментальном магазине устанавливаются три сверла «Stealth» со сменным пластинами Allied Machine. Этот процесс занимает менее 10 минут. Установка трех инструментов на линии обработки может занять до 30 минут, что составляет 90 минут потерянного времени в течение трех смен. В производственной среде, работающей круглосуточно и без выходных, это составляет почти 2200 часов в год (показатель, не учитывающий простои станков при смене инструмента). Предварительная настройка, вероятно, составляет 5% от стоимости этих потерянных часов.
Это сверло имеет регулируемый штифт, который перемещает пластину в радиальном направлении, чтобы уменьшить набор допусков, общий для всех сверл со сменным наконечником. В результате этого для набора номера больше не требуется разбирать и чистить сборку инструмента, регулировать смещения, добавлять прокладки в револьверные головки или полагаться на опытных машинистов, которые пытаются найти неортодоксальное решение.
2. Влияние СОЖ при сверлении
Формирование стружки является единственным способом оценить производительность сверла во время обработки. Формы изогнутой формы (то есть «шестерки» и «девятки») идеальны, в то время как более длинные и жесткие стружки отводят тепло из зоны резания менее эффективно. Цвет тоже имеет значение. Когда зона резания перегревается, стружка постепенно становится серой, черной и синей. Обесцвеченные стружки могут указывать на необходимость уменьшения нагрева путем замедления оборотов шпинделя, в то время как вязкие стружки могут указывать на необходимость увеличения скорости подачи до точки, в которой обрабатываемый материал ломается, а не отслаивается.
Одним из наиболее недооцененных факторов в любом процессе обработки, даже после сверления, является охлаждающая жидкость. Учитывая значительное влияние охлаждающей жидкости на то, как образуется стружка, регулировка концентрации и потока охлаждающей жидкости также может помочь решить проблемы с оптимизацией работы сверла в зоне резания.
Водорастворимые охлаждающие жидкости являются наиболее распространенными, поскольку они хорошо отводят тепло. Тем не менее, полусинтетические или полностью масляные составы могут быть лучшим выбором для улучшения смазывающей способности и обеспечения коротких сегментированных стружек. Хотя инструменты могут изнашиваться быстрее и параметры резания должны быть менее агрессивными, чем при использовании охлаждающей жидкости на водной основе, покрытие пластины, которое повышает термостойкость, может помочь компенсировать это.
Одним из не подлежащих обсуждению факторов является использование сквозных отверстий для подачи СОЖ. Станки также должны обеспечивать достаточное давление охлаждающей жидкости. Небольшие сверла требуют значительно большего давления для удаления стружки, потому что они должны работать при более высоких оборотах, чтобы достичь той же скорости поверхности, чем и у более больших диаметров инструментов. Чем больше давление, тем быстрее стружка выходит из отверстия и тем быстрее вы можете вращать сверло.
3. Проблемы с циклами
Периодическое изменение подачи инструмента во время обработки не требуется для обеспечения удаления стружки из отверстия, также как и частое вынимание сверла из отверстия для его очистки от стружки. Уменьшение циклов резания приводит к улучшению качества обработанной поверхности, поэтому необходимо уменьшить.
4. Сверла с самоцентрированием
Другой устаревшей практикой является использование точечного сверла под углом 90 градусов с меньшим диаметром для пилотного отверстия. Отверстие меньшего диаметра, просверленное немного смещено от центра, легче исправить, чем большее, в то время как острый угол помогает сверлу быстро и легко проникнуть в деталь. Однако большинство станков с ЧПУ позиционируются достаточно точно, чтобы диаметр контрольного сверла соответствовал диаметру основного сверла.
Фактически, большинство сменных сверлильных наконечников имеют самоцентрирующиеся наконечники с точечным углом менее 90 градусов. В результате пластина может воздействовать на большой диаметр отверстия до точки самоцентрирования. Использование одного и того же диаметра пластины и точечного угла гарантирует, что более длинное сверло будет идеально входить там, где остановлено центровочное сверление.
5. Осторожность – добродетель
При сверлении глубоких отверстий наращивание до полной скорости и подач может создать проблемы безопасности и поставить под угрозу работу.Таким образом, многие из стандартных рекомендаций по универсальным сверлам T-A можно обобщить в одной фразе: осторожно подходите к пилотному отверстию.
Приближение к уже существующему отверстию осторожно помогает избежать образования рубцов или повреждений. Это позволяет полям сверла взаимодействовать с материалом до того, как вы наберете скорость. Отверстие начинает действовать как втулка, которая удерживает сверло в центре и обеспечивает качество деталей.
engcrafts.com
Сверла для глубокого сверления отверстий:спиральные,ружейные
Особенности углубленной сверловки
Метод глубокого сверления используется во время резания отверстий, которые имеют глубину 5хD и более. Данный метод позволяет обработать материал с наибольшей точностью, а также оптимальной прямолинейностью, благодаря нему обеспечивается хорошее качество поверхности. Это достаточно сложная и трудоемкая операция. Главным условием обработки режущим инструментом методом глубокого сверления является охлаждение под давлением.
Особенность данного метода – необходимость определения правильного направления во время начала процесса резания. Это направление проходит через специальную кондукторную втулку либо же в заранее подготовленное просверленное пилотное отверстие.
Главная трудность – нельзя свободно вращать режущий инструмент при глубоком сверлении на полных оборотах вне самой детали. А также при увеличении длины сверла для глубокого сверления создаются неблагоприятные условия образования стружки, которую трудно отводить и извлекать из отверстия во время процесса. Поэтому очень важно соблюдать увод сверла при глубоком сверлении.
Виды сверл для углубленной сверловки
Сверла для глубокого сверления бывают нескольких видов:
- Спиральная конструкция, которая имеет отверстие для подвода жидкости в зону резания.
- Ружейное устройство, которое имеет припаянные твердосплавные пластинки.
- Ружейное устройство, которое имеет цельную твердосплавную рабочую часть.
- Ружейная установка с твердосплавной пластинкой и промежуточной режущей пластинкой.
- Шпиндельные (перовые) приборы, которые используются для обработки отверстий в шпинделях станков.
- Пушечные устройства.
Спиральные инструменты – это стандартные спиральные сверла, которые имеют удлиненную рабочую часть. Они изготавливаются из таких материалов, как быстрорежущая часть и твердый сплав. Первые имеют наружный подвод СОЖ, а вторые – внутренний подвод СОЖ. Сверление ними реализуется посредством глубокого сверления, когда инструмент удаляется из отверстия, для того чтобы вывести стружку, и без этого процесса. Их производительность в 8 раз выше, чем у ружейных.
фото:спиральные длинные сверла по металлу
Ружейные и пушечные – это однорезцовые режущие инструменты, которые используются для того, чтобы получить глубокие отверстия малого диаметра и большого (от 0,5 мм до 100 мм). СОЖ подводится через корпус прибора, стружка выводится через канавку в корпусе конструкции. Ружейная установка обеспечивает лучшее направление режущей части, рабочая часть делается конической по направлению от режущей кромки к стержню.
фото:ружейные сверла по металлу
Пушечный прибор имеет твердосплавную режущую часть, стебель из закаленной стали и хвостовик из улучшенной стали.
Также существуют двустороннего резания (эжекторные и шнековые) и одностороннего резания конструкции (ружейные и пушечные) по их назначению. И третий вид – это кольцевые или трепанирующие головки.
Подбор сверла для глубокой сверловки
Сверла для глубокого сверления имеют определенные критерии выбора. Чаще всего применяются спиральные, а также перовые режущие инструменты.
На критерии выбора влияет наличие определенного специального оборудования, системы подготовки и подачи СОЖ, а также системы защиты от разбрызгивания. Применять сверла для глубокого сверления необходимо исключительно на станках глубокого сверления.
Выбирая конструкцию, необходимо определяться с нужным диаметром, общей длиной отверстия, типом хвостовика и обрабатываемым материалом. Также обращать внимание на скорость подачи.
Общие рекомендации:
- Если вы собираетесь сверлить отверстие, которое имеет длину больше, чем 40d, то стоит одновременно использовать два сверла, имеющие диаметр 10х400 мм и 9,95х800 мм.
- Если глубина 40d, то конструкция должна иметь левое направление вращения, для того чтобы она смогла зайти в пилотное отверстие.
- В случае, когда материал имеет длинную стружку, выбирайте прибор, который имеет полированные стружечные канавки.
- Когда вы обрабатываете алюминиевый сплав, применяйте однолезвийные конструкции, имеющие заточку угла при вершине 180 градусов.
Технология процесса
Подача СОЖ должна быть под давлением до 10 МПа. Объем охлаждающей жидкости – 20-120 л/мин. Данный показатель зависит от диаметра обрабатывающей конструкции. Точность обработки по диаметру – 7-9 квалитетов. Параметр шероховатости – 2,5-1,25 мкм. Возможное отклонение отверстия не больше, чем на 0,5 мм на каждом метре длины.
фото:глубокое сверление детали
Этапы работы:
- Необходимо изготовить пилотное отверстие с допуском Н8.
- Подвести инструмент в заданное положение на небольшом режиме.
- Частота вращения должна быть 200 об/мин, подача 500 мм/мин.
- Включить подачу СОЖ и частоту вращения.
- Непрерывно сверлить до полной глубины, не отводя инструмент.
- Если вы используете устройство, которое имеет очень большое соотношение длины к диаметру, то необходимо достигать глубины 25 мм с уменьшенным режимом резания. 75% от оптимальной скорости резания.
- Отключить подачу СОЖ, когда достигнете необходимой глубины.
- Ускоренно произвести отвод и остановить шпиндель.
Также существует способ сверления глубокого сквозного отверстия и способ обработки глубоких отверстий. Последний предполагает установку технологической бобышки на заготовке, ось которой располагается на одинаковом расстоянии от торца заготовки.
Компания «Тула Лифт» – производитель лифтов, которая предлагает своим клиентам большой ассортимент подъемно-транспортного оборудования. Очень низкие цены!
www.metalstanki.com.ua
Глубокое сверление в металле – способы, инструменты, виды сверл
Сверление – процесс образования механическим путем отверстий посредством вращающихся механизмов. Отверстия подразделяют на обычные до 10 см и глубокие более 10 см. По способу сверления различают:- • кольцевое, позволяет высверлить плоскость в металлической детали, с погружным стержнем по центру, которое затем вынимается;
- • сплошное, при котором весь спиливаемый материал превращает в стружку.
Особенности углубленной сверловки
Сверловкой углубленного характера принято считать углубление, диаметр которого в 5 раз превышает диаметр самого сверла. Способы сверления:
- • с зафиксированным сверлом, когда осуществляется продольная подача на вращающуюся заготовку;
- • с зафиксированной заготовкой;
- • комбинированный метод, когда происходит одновременное вращение детали самого режущего инструмента.
Какие сверла применяют для глубокого сверления
Обработка металлических изделий проводится спиральными, ружейными и эжекторными сверлами. Структура спиральных сверл предполагает наличие винтовых отверстий, по которым поступает охлаждающая жидкость. Инструмент используют в высококачественной обработке деталей, глубина – более 3 диаметров. Ружейные выполнены из стали, а на конце расположены твердосплавные пластины. Диаметр 8-30 мм, длинна до 1700 мм. Сверло не только режет по принципу пера, но и дополнительно устраняет всевозможные шероховатости поверхности. Эжекторные с конусообразной насадкой, предназначены для высокоскоростных отверстий диаметром до 20 мм.
p-z-o.ru
сверла для глубоких отверстий
ПФО
Сверла для обработки глубоких отверстий
Глубокое сверление – это обработка отверстий с большим отношением диаметра к глубине.
При глубоком сверлении условия работы сверла резко ухудшаются – затрудняется отвод стружки, охлаждение режущей части, уменьшается жесткость сверла.
Основные трудности при сверлении глубоких отверстий заключаются:
в сложных условиях подвода СОЖ в зону резания и отвода стружки;
в уводе осей отверстий;
в погрешностях размера и формы отверстий в радиальном и продольном сечениях.
К сверлам для обработки глубоких отверстий относятся:
сверла с подводом СОЖ
Пушечные сверла
Ружейные сверла
.Перовые.
Сверла с подводом СОЖ
Наиболее совершенным методом является подача жидкости через отверстия, проходящие внутри перьев сверла. Инструментальными заводами выпускается ряд конструкций спиральных сверл с отверстиями для подвода СОЖ (рис.1), проходящими через хвостовик сверла или через радиальные отверстия.
Такие сверла изготовляются из специального проката с винтовыми отверстиями, из заготовок, полученных радиальной ковкой, прокатом заготовок с использованием твердых наполнителей, прокатом трубчатых заготовок, литьем.
Для подвода СОЖ в зону резания твердосплавная рабочая часть имеет отверстия круглой или овальной (для увеличения объема пропускаемой жидкости) формы. Трубчатый корпус с канавкой, образованной пластической деформацией, изготовляется из сталей марок 40Х или 35ХГСА.
Внутренняя полость корпуса имеет серпообразную форму, образованную при деформации; используется она для подвода СОЖ к рабочей части и сопряжения с отверстиями в рабочей части.
Сверла этого типа обладают не только повышенным ресурсом работы из-за большей длины по сравнению со сверлами, но и повышенным расходом твердого сплава.
(Рис.1)
Пушечные сверла.
Рабочая часть пушечного сверла представляет собой полукруглый стержень, плоская поверхность которого является передней поверхностью (рис. 2, а). На торце стержня создается режущая кромка, перпендикулярно оси сверла. Задняя торцевая плоскость сверла затачивается под углом а = 10 … 20°.
Для лучшего направления сверло имеет цилиндрическую опорную поверхность, на которой срезаются лыски под углом 30—45° и делается обратный конус порядка 0,03—0,05 мм на 100 мм длины рабочей части. В результате этого уменьшается трение сверла о стенки обрабатываемого отверстия. Пушечное сверло работает в тяжелых условиях, имеет неблагоприятную геометрию передней поверхности, не обеспечивает непрерывного процесса резания, так как для удаления стружки приходится периодически выводить сверло из отверстия.
Ружейные сверла.
Ружейные сверла (рис. 2, б) в отличие от пушечных имеют внутренний канал для подвода СОЖ и прямую (иногда винтовую) канавку для наружного отвода пульпы (смесь стружки и СОЖ). Они применяются для сверления отверстий глубиной (5…100)d и диаметром 1…30мм. Первоначально ружейные сверла использовали для сверления стволов огнестрельного оружия. В настоящее время ружейные сверла получили широкое распространение во всех отраслях машиностроения, главным образом для сверления глубоких отверстий на специальных станках в условиях крупносерийного и массового производств. Благодаря оснащению твердым сплавом и внутренней подаче СОЖ они обеспечивают высокую производительность при сверлении отверстий с минимальным уводом оси при высокой точности (H8…H9) и низкой шероховатости поверхности отверстий (Ra 0,32…1,25).
Рис. 2. Сверла для глубокого сверления
а – пушечное сверло; б – ружейное сверло
Перовые сверла.
Цельные перовые сверла (рис. 3, а) изготавливают из прутка путем ковки или фрезерования режущей части в форме пластины, которая затачивается на конус под углом 2φ =118°. При этом образуются две главные и две вспомогательные режущие кромки. Заточкой двух плоских задних поверхностей создается задний угол α = 10…12°. При пересечении этих поверхностей образуется поперечная режущая кромка (перемычка). Если передние поверхности плоские, то передние углы на главных режущих кромках имеют отрицательные значения, что нежелательно из-за возрастания силовой нагрузки на сверло и появления вибраций.
Конструкция на рис. (3, б) применяется для сверления неглубоких ступенчатых отверстий на станках-автоматах; позволяет сократить число операций и, следовательно, инструментов. Вторая конструкция (рис. 3, в) представляет собой сборное перовое сверло с режущей сменной пластиной, закрепляемой в стержне любой длины. Рис. 3. Перовые сверла:
а – цельное; б – для сверления ступенчатых отверстий;
в – сборное, с внутренним напорным охлаждением
Достоинствами перовых сверл являются простота конструкции, а также возможность изготовления их любого диаметра и длины даже в условиях ремонтных мастерских.
К недостаткам перовых сверл можно отнести:
затрудненные условия отвода стружки;
склонность к вибрациям из-за малой жесткости режущей части;
небольшой запас на переточку;
низкую производительность процесса сверления из-за малых значений подачи и в связи с необходимостью периодического вывода сверла из отверстия для освобождения от стружки.
studfile.net
Глубокое сверление, станки для глубокого сверления, инструменты для глубокого сверления, операция глубокого сверления, Кольцевые сверла, трепанирование, ружейные сверла, эжекторная система, STS
Главная страница » Глубокое сверление
Глубокое сверление
Традиционно глубоким отверстием считается отверстие, у которого соотношение его длины к диаметру превышает 5, т.е. L/D>5. На обычных станках и обрабатывающих центрах возможно сверление подобных отверстий, но для этого необходимо применять различные дополнительные меры, задавать длинному и не жёсткому сверлу направление, и так обеспечивать жёсткость системы. Для этого возможно применение кондукторных втулок, предварительное сверление пилотного отверстия и т.д.
Но когда длина отверстия превышает диаметр в 10 раз, т.е. L/D>10, его необходимо обрабатывать методом глубокого сверления на специальном оборудовании и специальными сверлами.
Это достаточно специфическая операция, но имеющая широкое применение в различных отраслях, особенно в таких, как нефтегазовой, аэрокосмической, металлургической промышленности.
Основными сложностями глубокого сверления являются увод сверла, непрямолинейность оси, получаемого отверстия, разностенность, некруглость отверстия, сложность вывода стружки, и доставки СОЖ в зону резания и т.д.
В глубоком сверлении необходимо обеспечить дробление стружки, чтобы она не пакетировалась и не портила обрабатываемую поверхность.
Инструменты для глубокого сверления
Для глубокого сверления применяются специальные сверла, выделяют 3 типа таких сверл или систем сверления. У данных систем существенно отличается организация подвода СОЖ.
1. Эжекторная система (двуштанговая)
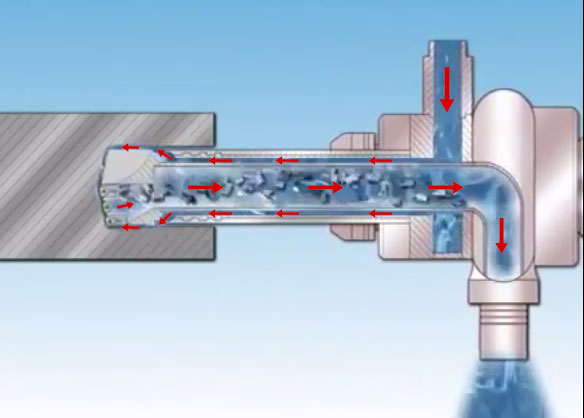
В этой системе используется две штанги одна внутренняя и одна внешняя, т.е. труба в трубе, на конце эти две штанги присоединены к сверлильной головке. СОЖ подается между двумя штангами и движется она внутри корпуса сверла. Вымывание стружки происходит через отверстие внутренней штанги.
В такой системе требуется меньшее давление СОЖ, чем в STS системе. Эжекторная система может применяться на универсальных станках и в основном применяется для средних партий.
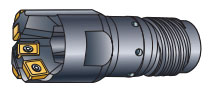
2. Система STS (одноштанговая)
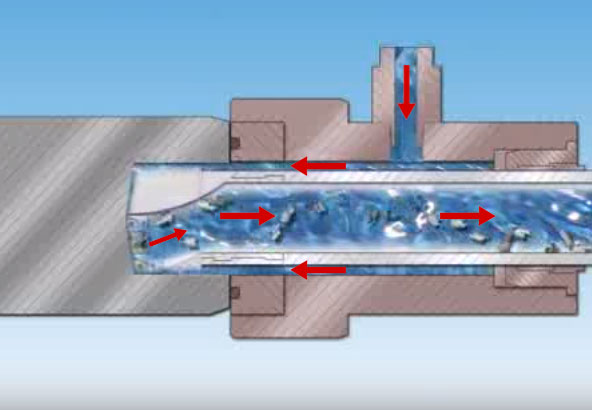
В данной системе применяется одна штанга, а СОЖ поступает через устройство подачи СОЖ, плотно прилегающего через уплотнение к торцу заготовки. СОЖ поступает под высоким давлением между штангой и заготовкой. Вымывание стружки осуществляется также через внутреннее отверстие штанги, как и в системе эжекторного сверления.
Это первый выбор для высокопроизводительной обработки и крупносерийного производства
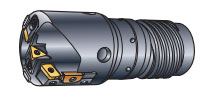
3. Система сверления ружейными сверлами

Ружейные (или пушечные) сверла имеют внутренний подвод СОЖ через отверстие в сверле, а вымывание стружки и удаление СОЖ происходит через наружную V-образную стружечную канавку в сверле.
Ружейные сверла могут применяться на обрабатывающих центрах, необходимым условием является наличие достаточного давления внутренней подачи СОЖ.
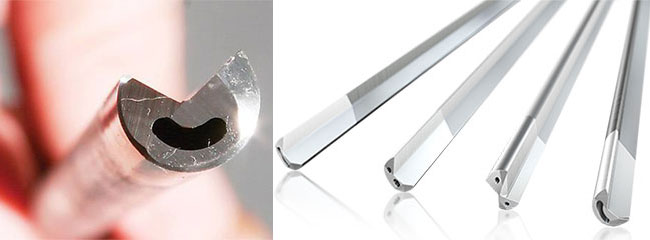
Кольцевые сверла, трепанирование
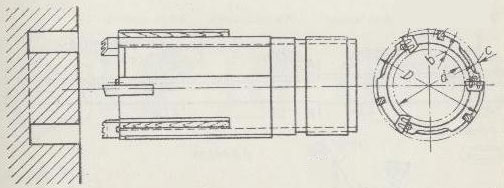
Для обработки глубоких отверстий, имеющих диаметр отверстия больше 80 мм используют кольцевые сверла, сверление такими сверлами еще называют трепанированием, здесь в стружку переводится только кольцевая полость, а в центре остается стержень. Данный тип сверления более прогрессивный, в будущем он может вытеснять сплошное сверление даже при меньших диаметрах отверстий.
Производительность глубокого сверления
Глубокое сверление, особенно скоростное, в большинстве случаев превосходит по производительности и качеству все другие технологические способы обработки отверстий.
Если взять даже простые спиральные сверла, которые успешно применяются только для неглубоких отверстий (L/DСтанки для глубокого сверления
Существуют различные компоновки станков для глубокого сверления, преобладающая часть создана для обработки отверстий в цилиндрических заготовках, которым придается вращение, а инструмент перемещается с заданной подачей, т.е. по принципу токарного типа, это обеспечивает высокую точность и производительность обработки. Но возможно обрабатывать только отверстия соосные оси заготовки.
Существуют компоновки, где вращение передается и заготовке в противоположном направлении сверла, и самому сверлу, этот вариант достигает лучших показателей точности и производительности.
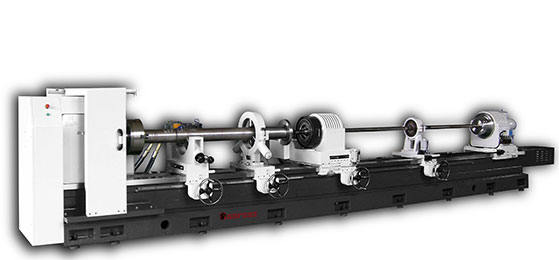
Также применяют многошпиндельные станки глубокого сверления.
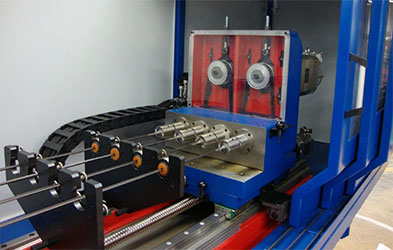
Станки могут быть как одно, так и двухсторонними, т.е. для сверления заготовки с одной или с нескольких сторон.
Для обработки тяжелых заготовок или сверления эксцентричных отверстий используют станки, где вращение задается только инструменту.
Станки глубокого сверления выполняются как горизонтального типа, так и вертикального. Хотя вертикальный тип может сверлить заготовки сравнительно небольшой длинны имеет некоторые преимущества. Так инструмент в вертикальной компоновке не подвергается изгибающим усилиям от собственного веса.
Существуют станки глубокого сверления вертлюжного типа, здесь заготовка устанавливается в полый шпиндель называемого вертлюг, в силу того, что его нельзя сильно вращать, применение в основном получил в деталях, которым нельзя задавать большие крутящие моменты. Принцип схож со станками токарного типа.
Станки для глубокого сверления могут иметь самые различные компоновки, они относятся к группе специальных станков. Также они могут выполнять и операции растачивания отверстия.
Станки занимают большое пространство в цехе, требуют особого внимания к сбору и охлаждению СОЖ, обеспечению высокого давления СОЖ, сбору стружки и т.д. Необходимо учитывать, что в случае неисправности такой станок трудно заменить каким-либо другим, надо быть предусмотрительным и принять меры по этому поводу заранее, возможно приобретение второго подобного станка, заручиться гарантийной поддержкой производителя или поставщика станка, а также проведение каких-либо других мероприятий.
Заключение
Операция глубокого сверления проводится на больших и довольно дорогостоящих заготовках, ее качественное исполнение и стабильность получения результатов имеет огромное значение для различных предприятий. Выбор и внедрение такого станка важный и необходимый момент для многих предприятий.
Главными критериями инвестирования в такой станок являются множество факторов — это конечно же срок окупаемости, повышение производительности и качества продукции, расширение производственных возможностей, повышение статуса и авторитета предприятия, увеличение экономической эффективности производства и, как следствие, увеличение прибыли.
Похожие записи:
vys-tech.ru
Сверление глубоких отверстий твердосплавным сверлом малого диаметра
Твердосплавное сверло маленького диаметра имеет очень маленький объём стружечных канавок, который не оставляет достаточно много свободного пространства для вывода по нему металлической стружки из зоны резания. Дополнительное полирование стружечных канавок при изготовлении твердосплавного сверла может помочь решить эту проблему. Процесс глубокого сверления создаёт отверстия, у которых большая величина отношения глубины отверстия к его диаметру. В то время как стандартные операции по сверлению редко сверлят отверстия, которые не более глубоки, чем пять диаметров (5xD), при глубоком сверлении — это отверстия, длина которых может достигать 10xD и даже больше. Поэтому требуется
специальной конфигурации и применять особые методы сверления. Что делает сверление глубоких маленьких отверстий проблемой? Как и в любом глубоком сверлении, удаление металлической стружки всегда является проблемой. Нужно полагаться на правильную конфигурацию стружечной винтовой канавки, чтобы она могла эффективно эвакуировать металлическую стружку вверх из отверстия. У твердосплавного сверла малого диаметра объём стружечных канавок очень маленький, которого не всегда достаточно, чтобы надёжно выводить металлическую стружку из зоны резания и пропускать СОЖ к вершине режущей кромки. Твердосплавное сверло является предпочтительным выбором в этом применении? Материал твёрдый сплав намного более твёрдый, имеет лучшие характеристики по изнашиванию и более жёсткий, чем быстрорежущая сталь (HSS). Таким образом, первоначально это всегда – лучший выбор. Однако, это также более дорого, и в случае поломки твердосплавного сверла, его извлечение из детали может быть очень затруднено. В зависимости от применения и конкретного обрабатываемого материала, иногда и сверло из HSS может быть лучшим выбором. Конструкция твердосплавного сверла для глубоких отверстий отличается от стандартного твердосплавного сверла. Они оба имеют те же главные компоненты — вершину, режущую кромки и тело с хвостовиком. Но небольшие изменения внесены в их конфигурацию из-за большой величины соотношения длины к диаметру. У короткого твердосплавного сверла нет необходимости в глубоких стружечных канавках, в то время как, у твердосплавного сверла для глубоких отверстий должен быть значительный объём стружечных винтовых канавок, и они должны быть более глубокие, чтобы позволить по ним свободно выводить металлическую стружку наверх из зоны резания. Кроме того, эта область стружечных канавок должна полироваться, что также помогает эвакуации металлической стружки.
Какие типы материалов можно обрабатывать таким твердосплавным сверлом? Обычно твердосплавные свёрла для глубоких отверстий сконструированы для обработки различных типов материалов, это означает, что все эти типы материалов будут обработаны с одинаковым успехом. Но в определённых случаях, конечно, их конфигурация может адаптироваться под обработку данного конкретного материала. Например, у твердосплавного сверла для обработки алюминия должно быть большое пространство винтовой стружечной канавки, чтобы разместить более объёмную металлическую стружку, в то время, как у твердосплавного сверла для обработки нержавеющей стали должна быть специальная геометрия режущей кромки, делающая его вершину более острой. Чтобы добиться максимальной стойкости твердосплавного сверла и высокой производительности процесса сверления, нужно купить твердосплавное сверло, специально предназначенное только для того материала, который нужно обрабатывать. Почему на твердосплавном сверле есть покрытие? Материалы, используемые в качестве покрытий, обычно обладают более высокой твёрдостью и прочностью, чем основа тела твердосплавного сверла. Эти свойства препятствуют тому, чтобы режущие кромки быстро ломались или скалывались в процессе изнашивания. Однако, поверхность твердосплавного сверла с нанесённым покрытием также может быть и немного более грубой и шероховатой по сравнению с полированной твердосплавной поверхностью. Твердосплавное сверло с покрытием только на вершине, где именно и происходит процесс резания, может быть более выгодным. Остаток твердосплавного тела полируется и оставляется без покрытия, чтобы улучшить эвакуацию металлической стружки из зоны резания. Если она достаточно вовремя не удаляется из отверстия, то может произойти её уплотнение, её повторное резание и, возможно, даже поломка твердосплавного сверла. Периодический вывод твердосплавного сверла из отверстия делается в тех случаях, когда металлическая стружка образовывается быстрее, чем она удаляется из зоны резания. Поэтому временная остановка рабочей подачи или периодический вывод твердосплавного сверла из отверстия просто позволяют быстрее удалить металлическую стружку прежде, чем успеет появиться новая. Поскольку величина отношения глубины отверстия к диаметру бывает чрезвычайно большой (достигает даже 50xD и больше), то правильный выбор значения рабочей подачи и скорости резания также крайне важен, как и правильное образование металлической стружки и её удаление без повреждения самого твердосплавного сверла и поверхности просверливаемого отверстия на выходе. Периодический вывод твердосплавного сверла из отверстия, как правило, делается, что позволить металлической стружке эвакуироваться из отверстия, прежде чем процесс сверления будет продолжен, и будет образовываться новая стружка. Однако, улучшенная конструкция твердосплавного сверла, усовершенствованные технологии его производства и более качественные сырьевые материалы позволяют формироваться более тяжёлой и более толстой металлической стружке. Управлять эвакуацией из зоны резания именно такой стружки более легко, чем тонкой, длинной и волокнистой. Результирующий эффект – сокращение по времени или полное устранение вывода твердосплавного сверла в процессе сверления. Высокое давление смазочно-охлаждающей жидкости (СОЖ), проведённой через внутренние каналы к режущей вершине, помогает быстро вывести металлическую стружку из зоны резания, избавляя от необходимости периодического вывода твердосплавного сверла из отверстия, поэтому для такого метода сверления не рекомендуется использовать твердосплавное сверло с каналами для внутреннего подвода СОЖ. СОЖ играет важную роль в процессе глубокого сверления, потому что выполняет несколько функций. Самой очевидной функцией является помощь в охлаждении режущих кромок твердосплавного сверла и материала заготовки. В точке контакта между ними в процессе трения механической обработки появляется чрезвычайно высокая температура, которая очень вредна и для режущих кромок и для качества поверхности обрабатываемого отверстия. Погружение вершины твердосплавного сверла в жидкость, специально предназначенную, чтобы это тепло рассеять, помогает увеличить его стойкость и препятствует его преждевременной поломке. Некоторые виды СОЖ также разработаны для увеличенного эффекта смазывания. Подача более смазывающей СОЖ помогает быстрее металлической стружке выводиться по спиральным стружечным канавкам твердосплавного сверла. Наконец, объем и давление СОЖ, выталкивающейся из просверливаемого отверстия, физически уносят металлическую стружку и помогают её более быстрой эвакуации из зоны резания. Единственным недостатком использования каналов для внутреннего подвода СОЖ является ослабление тела твердосплавного сверла и, соответственно, уменьшение его жёсткости. Каждый раз, когда нужно сделать любое глубокое отверстие, то операторам станков крайне рекомендуется использовать твердосплавное сверо с каналами для внутреннего подвода СОЖ. Для этого используется металлорежущее оборудование, которое может прокачивать поток СОЖ под высоким давлением через шпиндель и зажимную шпиндельную оснастку, а далее – через внутренние каналы твердосплавного сверла, выводя её на дне просверливаемого отверстия прямо в зоне резания. В итоге, этот поток СОЖ прокачивается по одному пути – только в направлении из отверстия. Если будет использоваться наружный подвод потока СОЖ, то, мало того, что более трудно доставить СОЖ к снованию отверстия, где и происходит сам процесс резания, то и этот поток СОЖ будет идти в противоположном выводу металлической стружки направлению. Объём СОЖ тоже является важным фактором. Этот фактор заключается в двух параметрах – величине давления СОЖ на металлорежущем станке и размере отверстий в твердосплавном сверле. Идеальное соотношение этих параметров должно просчитываться ещё на стадии проектирования, чтобы осторожно соблюдать баланс при использовании самых больших каналов для подвода СОЖ в твердосплавном сверле, в то же время, всё ещё поддерживая достаточную жёсткость и целостность его тела. Какое соотношение между скоростью резания и стойкостью? Скорость резания обычно определяется через величину частоты вращения шпинделя RPM (об./мин.) и диаметра самого твердосплавного сверла (мм). Дополнительно существует величина подачи твердосплавного сверла в заготовку (мм/мин, мм/зуб или мм/об.). Если скорость резания будет выше, чем рекомендуется для сверления данного конкретного материала, то твердосплавное сверло очень быстро износится или сгорит. Повышенная скорость резания создаёт значительное увеличение выделения тепла в зоне резания, которое приводит к скорому разрушению режущих кромок твердосплавного сверла. Кроме того, сверление на слишком низкой скорости резания создаёт тот же самый отрицательный эффект, как и на слишком высокой, потому что вместо процесса нормально резания происходит процесс повышенного трения, таким образом, эти два режима являются не самыми экономичными способами использовать твердосплавное сверло. Производители современных твердосплавных свёрл при разработке их новых конфигураций, как правило, стараются сделать так, чтобы заставить их работать быстрее (на более высоких режимах резания). Если скорость резания и, соответственно, производительность процесса сверления не будут максимальными, то металлообрабатывающие производства будут не полностью использовать то, за что они платят, т.е.будет снижаться экономический эффект. Какое отношение между величиной подачи и стойкостью твердосплавного сверла? Величина подачи в соединении вместе с частотой вращения шпинделя, определяет нагрузку на твердосплавное сверло или, по существу, толщину срезаемой стружки. Более массивная металлическая стружка забирает с собой больше тепла из зоны резания. Если это тепло не отводится вместе со срезаемой стружкой, то оно уходит или в тело твердосплавного сверла, или в обрабатываемую заготовку. По этой причине подача твердосплавного сверла слишком медленно или создание стружки, которая является слишком тонкой, будет отрицательно влиять на весь процесс сверления, неэффективно справляясь с удалением тепла. Более тонкой металлической стружкой также более трудно управлять, потому что она более гибкая. Более толстую стружку легче сформировать в завитую форму или даже сломать на чуть меньший удобный размер. Конечно, это всё должно быть урегулировано с мощностью, требуемой для процесса сверления конкретной величины диаметра. Получение слишком большой металлической стружки приводит к потреблению большей мощности оборудования и создаёт более высокие силы резания, которые также могут сломать режущие кромки твердосплавного сверла или вызвать нежелательные вибрации в процессе сверления.Дополнительную техническую информацию можно прочитать в разделе “Статьи”.
www.met-instrument.ru
Сверление
Сверление часто выполняется на поздней стадии производственного процесса, когда себестоимость детали уже достигла определенного уровня за счёт предыдущих операций. Эта операция, на первый взгляд простая, на самом деле отличается высокой сложностью и может привести к серьёзным последствиям в случае неправильного функционирования или перегрузки инструмента.
Важные условия для сверления отверстия
1. Отверстие
Три самых важных параметра при сверлении отверстия:
- Диаметр отверстия
- Глубина отверстия
- Качество отверстия
Тип отверстия и требования к точности определяют выбор инструмента. На процесс сверления влияют такие факторы, как вход и выход инструмента в наклонную или криволинейную поверхность, а также наличие пересекающихся отверстий.
Типы отверстий
Сквозное

Глухое

Фаска

Ступень

Вход

Выход

Пересечение


- Отверстия под болтовые соединения
- Отверстия с винтовой резьбой
- Отверстия с цековкой
- Высокоточные отверстия (для соединений с натягом)
- Отверстия для труб (теплообменники)
- Отверстия, образующие каналы
- Балансировочные отверстия
- Глубокие отверстия/отверстия для СОЖ
2. Деталь

После анализа параметров самого отверстия обратите внимание на материал заготовки, форму детали и количество отверстий.
Материал заготовки
- Обеспечивает ли материал хорошее стружкодробление? Длинно- или короткостружечный материал?
- Обрабатываемость?
- Твёрдость материала?
- Легирующие элементы?
Форма детали
- Симметрична ли деталь относительно отверстия, то есть можно ли обрабатывать отверстие с помощью невращающегося сверла?
- Обладает ли деталь достаточной стабильностью или имеет элементы, которые могут вызывать вибрацию?
- Можно ли надёжно закрепить деталь? Какие вопросы относительно стабильности необходимо учитывать?
- Необходим ли удлинитель инструмента? Должны ли использоваться большие вылеты?
Количество
Размер партии деталей также влияет на выбор сверла.
- Большая партия – используйте оптимизированное сверло (возможно, с индивидуальными параметрами).
- Небольшая партия – используйте универсальные свёрла
3. Станок

Важно понимать принципы безопасного и производительного сверления отверстий на конкретном станке. Параметры станка влияют на выбор:
- Типа операции
- Типа используемого держателя и/или патрона
Обязательно учитывайте следующее:
- Стабильность станка в целом и шпинделя в частности
- Достаточна ли частота вращения шпинделя (об/мин) для обработки малых диаметров?
- Подвод СОЖ. Достаточен ли объём СОЖ для обработки больших диаметров?
- Достаточно ли давление СОЖ для обработки малых диаметров?
- Закрепление заготовки. Достаточно ли оно жёсткое?
- Горизонтальный или вертикальный шпиндель? Горизонтальный шпиндель обеспечивает более эффективную эвакуацию стружки
- Мощность и крутящий момент. Достаточна ли мощность для обработки больших диаметров? Если нет, можно ли использовать трепанирующее сверло или лучше применить фрезерование методом винтовой интерполяции?
- Достаточно ли места в инструментальном магазине? В этом случае подходящим решением может стать сверло со ступенью и фаской.
Инструментальная оснастка



На производительность влияют не только сплав и геометрия, но и инструментальная оснастка и возможность надёжно и точно закрепить инструмент. Всегда используйте максимально короткое сверло и вылет.
Рассмотрите вариант с модульной инструментальной системой, предназначенной для всех операций, включая все методы обработки отверстий. Благодаря этой системе одни и те же режущие инструменты и держатели могут использоваться для различных видов обработки и различных станков. Это позволяет стандартизировать процесс обработки, применяя единую инструментальную систему для всего цеха.
Биение инструмента
Для успешного сверления отверстий крайне важно минимальное биение инструмента. Максимальное биение не должно превышать 20 микрон. Отсутствие биения является гарантией следующего:
- Высокая точность и прямолинейность отверстия
- Хорошее качество обработанной поверхности
- Стабильно высокая стойкость инструмента

Выбор метода обработки
Обработка отверстия – стратегии
Решение с одним инструментом- Ступенчатые отверстия/зенкованные отверстия
- Тип сверла 4/5

Преимущества
+ Инженерные решения
+ Самый быстрый метод
Недостатки
– Меньшая гибкость Решение с двумя инструментами

Преимущества
+ Стандартные инструменты
+ Относительная универсальность
Недостатки
– Два инструмента
– Необходимость в двух позициях инструмента
– Увеличенная длительность цикла обработки
Ступень и фаска – стратегия обработки одним сверлом

Тип сверла 1
Стандартное

Тип сверла 2
2 диаметра (пилотный диаметр + диаметр корпуса)
Отверстие и фаска. Без обработки ступени.

Тип сверла 4
2 диаметра (пилотный диаметр + диаметр корпуса)
Пилотное отверстие, фаска и ступень

Тип сверла 5
3 диаметра (пилотный + ступень + диаметр корпуса)
Пилотное отверстие, ступень и фаска. Без обработки 2 ступени.

Тип сверла 6
3 диаметра (пилотный + диаметр корпуса)
Пилотное отверстие, ступень, фаска и 2 ступень
www.sandvik.coromant.com