Токарная группа станков, Реферат
В XIV веке был изобретен ножной привод, в XVIII русский ученый Андрей Нартов изобрел токарно-винторезный станок с механизированным суппортом и сменными зубчатыми колесами.
Особенно бурный период развития пришелся на промышленную революцию конца XIX века – станок менял источники привода, приобретал всё большие размеры, усложнялся.
Сейчас его основной источник энергии – электричество. Наиболее современная версия станка появилась в 1950-х годах, когда для управления обработкой начали применять числовое программное управление (ЧПУ) и сервомеханизмы.
Токарный станок часто называют «матерью всех станков», потому что с его помощью впервые стали создавать и другие станки.
Основные узлы
Стол
. На нём находится планшайба, на которой крепится заготовка. Две стойки . Стойки соединяются порталом. По двум стойкам перемещается траверса. На траверсе находится два суппорта. Правый суппорт – револьверный суппорт. Он состоит из продольной каретки и ползуна (перемещающегося вертикально).
На ползуне расположена револьверная головка. В отверстия револьверной головки устанавливается державки с инструментом. Револьверный суппорт используется при подрезании торцов при сверлении отверстий, иногда для обработки наружных поверхностей. Второй суппорт называется расточным суппортом. Он состоит из продольной каретки, на которой устанавливается поворотная часть, на которой есть ползун, на который устанавливается резцедержатель. Расточной суппорт используется при растачивании отверстий, прорезания внутренних канавок и при обработке конических поверхностей. На правой стойке расположен боковой суппорт. Он состоит из продольной каретки, ползуна и резцедержателя. Он предназначен для обработки наружных поверхностей.
Характерным размером токарно-карусельных станков является диаметр планшайбы. В зависимости от этого размера бывают 1 и 2х стоечные станки Одностоечные станки выпускаются с диаметром планшайбы d ≤2000мм Двухстоечные станки выпускаются с диаметром свыше 2000 мм
Движения в станке:
Главное движение, Движение подачи, Вспомогательное движение, Лоботокарный станок
1. 2. Токарно-револьверный станок
33 стр., 16044 слов
Проектирование технологического процесса механической обработки …
… «Технология машиностроения». Целью курсовой работы является закрепление, углублении и обобщение знаний, полученных на предыдущих этапах изучения предмета, и приобретение практических навыков решения различных технологических задач подготовки производства деталей машин …
Токарно-револьверный станок применяется для обработки штучных заготовок или деталей из калиброванного прутка.
На станке производятся следующие виды токарной обработки: обточка, расточка, подрезка, проточка и расточка канавок, сверление, зенкерование, развертывание, фасонное точение, обработка резьб метчиками, плашками и резцами.
Название револьверный происходит от способа закрепления режущих инструментов в барабане. Многие станки подобного рода могут работать в полуавтоматическом режиме. «Программой» является набор кулачков и концевых упоров, осуществляющих в нужные моменты остановку, выбор направления, смену инструмента и другие действия.
Токарно-револьверные станки применяют в серийном производстве для изготовления деталей сложной конфигурации из прутков или штучных заготовок. В зависимости от этого станки делятся на прутковые и патронные
1.3. Автомат продольного точения
Автоматы продольного точения используют при изготовленя мелких серийных деталей из холоднотянутого, калиброванного прутка, фасонного профиля и свернутой в бунт проволоки.
Автомат может выполнять точение различных материалов — от меди до легированых сталей.
Преимущественно автоматы продольного точения применяются в крупном и массовом производстве, но могут быть также использованы в серийном производстве при проектировании и изготовлении необходимой оснастки для выпуска специальных групп деталей с максимально возможным использованием одного и того же комплекта кулачков, зажимных и подающих цанг, державок и инструментов.
Устройство токарного автомата с неподвижной шпиндельной бабкой: На верхней плоскости станины закреплена шпиндельная бабка. На её передней плоскости имеется платик для установки специальных приспособлений. На задней плоскости бабки имеется качающийся упор, а на верхней — вертикальный суппорт. На верхней плоскости станины находятся также приводы приспособлений, привод шпинделя, либо револьверной головки, приводы поперечных суппортов. Токарный автомат с подвижной шпиндельной бабкой называется автоматом «Швейцарского типа — Swiss type»
Управление автоматом происходит через систему кулачков и распределительных валов, смонтированных в станине автомата. Также возможна установка систем ЧПУ с приводами подач и приводного инструмента.
Различают одношпиндельные и револьверные автоматы продольного точения. В отличие от одношпиндельных, револьверные автоматы могу выполнять одновременно несколько различных операций точения для различных деталей, зафиксированных в револьверном шпинделе автомата
1.4. Многошпиндельный токарный автомат
Автоматы предназначены для токарной обработки сложных и точных деталей из калиброванного холоднотянутого прутка круглого, шестигранного и квадратного сечения или из труб в условиях серийного производства.
На них можно выполнять: черновое и фасонное обтачивание, подрезку, сверление, растачивание, зенкерование, развёртывание, резьбонарезание, отрезку, накатывание резьбы.
Достаточная мощность привода и жёсткость конструкции обеспечивают высокую производительность. Некоторые модели могут одновременно выполнять более одной операции, что серьёзно повышает производительность таких станков.
5 стр., 2025 слов
Контрольная работа: Токарные станки и комплексы
… токарных автоматов с ЧПУ и многоцелевых станков Для токарной обработки деталей … карусельные станки с ЧПУ мод.1А525МФЗ и 1А532ЛМФЗ предназначены для токарной обработки … токарной обработки в патроне деталей сложной конфигурации. На нем выполняют … точение торца с постоянной скоростью резания; сверление, растачивание, зенкерование, развертывание, фрезерование, нарезание резьбы резцом и метчиком при работе …
2. Станки с ЧПУ
Развитие вычислительной техники привело к созданию станков с программным управлением. В СССР выпускалось большое количество типов станков с ЧПУ -16А20 (Красный пролетарий, Москва), 16Б16 (Куйбышев), ЛА155 (Ленинград) и др. Станки с ЧПУ заняли нишу между универсальными и агрегатными станками при производстве большой номенклатуры продукции (обеспечивается библиотекой программ обработки) относительно небольшими партиями (десятки- сотни штук).
Малое время переналадки и высокая повторяемость обработки на станках с ЧПУ позволили резко увеличить выход годных деталей при многооперационной обработке. Базовыми системами ЧПУ в СССР были НЦ-31 и 2Р22 (токарная группа) и 2С42 и 2Р32 (фрезерная группа).
3. Интересный факт
Самый большой токарный станок (длина 38,4 м, вес 416,2 т) построен западногерманской в 1973 г. по заказу Комиссии по электроснабжению из Рошервилля (ЮАР).
Он способен обрабатывать детали весом 300 т. Диаметр его поворотного основания — 5 м [1] .
Примечания
Данный реферат составлен на основе .
Примеры похожих учебных работ
Компоновка гибкой производственной системы для обработки деталей
… имеют следующие уровни: гибкая автоматизированная линия (ГАЛ) гибкий автоматизированный участок или гибкий производственный комплекс (ГАУ или ГПК) гибкий автоматизированный цех (ГАЦ). Гибкая автоматизированная линия — гибкая производственная система, …
Технологический процесс обработки детали «Ось»
… машиностроении широко внедряются станки с ЧПУ. Применение такого оборудования позволяет сократить: слесарно-доводочные работы; … технологического процесса обработки детали «Ось»; разработка мероприятий по дальнейшему увеличению экономии основных …
«Методики и технологии обработки деталей на станках с ЧПУ»…………….65 4.5. Разработка …
… операции – это отношение сумм всех технологических операций, осуществляемых на протяжении месяца к числу рабочих мест.[4] На первом этапе проектирования, … Цель дипломного проекта является проектирование технологического процесса механической обработки …
Обработка деталей на сверлильных и расточных станках
… о технологической точности, достигаемой при обработке отверстий 44 вин. Различают следующие способы и виды сверления [7,стр. 333-335]: 1. Сверление по разметке (для одиночных отверстий) По разметке сверлятся одиночные отверстия …
Проектирование технологического процесса механической обработки детали типа вал
… 1 Исходная информация для разработки курсового проекта Целью данного курсового проекта является закрепление знаний по предмету «Технология Машиностроения» и разработка технологического процесса производства детали типа вал с полным обоснованием …
История развития токарных станков
История относит изобретение токарного станка к 650 гг. до н. э. Станок представлял собой два соосно установленных центра, между которыми зажималась заготовка из дерева, кости или рога. Раб или подмастерье вращал заготовку (один или несколько оборотов в одну сторону, затем в другую). Мастер держал резец в руках и, прижимая его в нужном месте к заготовке, снимал стружку, придавая заготовке требуемую форму.
Позднее для приведения заготовки в движение применяли лук со слабо натянутой (провисающей) тетивой. Тетиву оборачивали вокруг цилиндрической части заготовки так, чтобы она образовала петлю вокруг заготовки. При движении лука то в одну, то в другую сторону, аналогично движению пилы при распиливании бревна, заготовка делала несколько оборотов вокруг своей оси сначала в одну, а затем в другую сторону.
В XIV — XV веках были распространены токарные станки с ножным приводом. Ножной привод состоял из очепа — упругой жерди, консольно закрепленной над станком. К концу жерди крепилась бечевка, которая была обернута на один оборот вокруг заготовки и нижним концом крепилась к педали. При нажатии на педаль бечевка натягивалась, заставляя заготовку сделать один — два оборота, а жердь — согнуться. При отпускании педали жердь выпрямлялась, тянула вверх бечевку и заготовка делала те же обороты в другую сторону.
Примерно к 1430 г. вместо очепа стали применять механизм, включающий педаль, шатун и кривошип, получив, таким образом, привод, аналогичный распространенному в XX веке ножному приводу швейной машинки. С этого времени заготовка на токарном станке получила вместо колебательного движения вращение в одну сторону в течение всего процесса точения.
В 1500 г. токарный станок уже имел стальные центры и люнет, который мог быть укреплен в любом месте между центрами.
На таких станках обрабатывали довольно сложные детали, представляющие собой тела вращения, — вплоть до шара. Но привод существовавших тогда станков был слишком маломощным для обработки металла, а усилия руки, держащей резец, недостаточными, чтобы снимать большую стружку с заготовки. В результате обработка металла оказывалась малоэффективной. необходимо было заменить руку рабочего специальным механизмом, а мускульную силу, приводящую станок в движение, более мощным двигателем.
Появление водяного колеса привело к повышению производительности труда, оказав при этом мощное революционизирующее действие на развитие техники. А с середины XIV в. водяные приводы стали распространяться в металлообработке.
В середине XVI Жак Бессон (умер в 1569 г.) — изобрел токарный станк для нарезки цилиндрических и конических винтов.
В начале XVIII века Андрей Константинович Нартов (1693-1756), механик Петра первого, изобретает оригинальный токарно-копировальный и винторезный станок с механизированным суппортом и набором сменных зубчатых колес. Чтобы по-настоящему понять мировое значение этих изобретений, вернемся к эволюции токарного станка.
В XVII в. появились токарные станки, в которых обрабатываемое изделие приводилось в движение уже не мускульной силой токаря, а с помощью водяного колеса, но резец, как и раньше держал в руке токарь. В начале XVIII в. токарные станки все чаще использовали для резания металлов, а не дерева, и поэтому проблема жесткого крепления резца и перемещения его вдоль обрабатываемой поверхности стола весьма актуальной. И вот впервые проблема самоходного суппорта была успешно решена в копировальном станке А.К.Нартова в 1712 г.
К идее механизированного передвижения резца изобретатели шли долго. Впервые эта проблема особенно остро встала при решении таких технических задач, как нарезание резьбы, нанесение сложных узоров на предметы роскоши, изготовление зубчатых колес и т.д. Для получения резьбы на валу, например, сначала производили разметку, для чего на вал навивали бумажную ленту нужной ширины, по краям которой наносили контур будущей резьбы. После разметки резьбу опиливали напильником вручную. Не говоря уже о трудоемкости такого процесса, получить удовлетворительное качество резьбы таким способом весьма трудно. А Нартов не только решил задачу механизации этой операции, но в 1718-1729 гг. сам усовершенствовал схему. Копировальный палец и суппорт приводились в движение одним ходовым винтом, но с разным шагом нарезки под резцом и под копиром. Таким образом было обеспечено автоматическое перемещение суппорта вдоль оси обрабатываемой заготовки. Правда, поперечной подачи еще не было, вместо нее было введено качание системы «копир-заготовка». Поэтому работы над созданием суппорта продолжались. Свой суппорт создали, в частности, тульские механики Алексей Сурнин и Павел Захава. Более совершенную конструкцию суппорта, близкую к современной, создал английский станкостроитель Модсли, но А.К. Нартов остается первым, кто нашел путь к решению этой задачи.
Вообще нарезка винтов долго оставалась сложной технической задачей, поскольку требовала высокой точности и мастерства. Механики давно задумывались над тем, как упростить эту операцию. Еще в 1701 году в труде Ш. Плюме описывался способ нарезки винтов с помощью примитивного суппорта. Для этого к заготовке припаивали отрезок винта в качестве хвостовика. Шаг напаиваемого винда должен был быть равен шагу того винта, который нужно было нарезать на заготовке. Затем заготовку устанавливали в простейших разъемных деревянных бабках; передняя бабка поддерживала тело заготовки, а в заднюю вставлялся припаянный винт. При вращении винта деревянное гнездо задней бабки сминалось по форме винта и служило гайкой, вследствие чего вся заготовка перемещалась в сторону передней бабки. Подача на оборот была такова, что позволяла неподвижному резцу резать винт с требуемым шагом. Подобного же рода приспособление было на токарно-винторезном станке 1785 года, который был непосредственным предшественником станка Модсли. Здесь нарезка резьбы, служившая образцом для изготавливаемого винта, наносилась непосредственно на шпиндель, удерживавший заготовку и приводивший ее во вращение. (Шпинделем называют вращающийся вал токарного станка с устройством для зажима обрабатываемой детали.) Это давало возможность делать нарезку на винтах машинным способом: рабочий приводил во вращение заготовку, которая за счет резьбы шпинделя, точно так же как и в приспособлении Плюме, начинала поступательно перемещаться относительно неподвижного резца, который рабочий держал на палке.
Таким образом ни изделии получалась резьба, точно соответствующая резьбе шпинделя. Впрочем, точность и прямолинейность обработки зависели здесь исключительно от силы и твердости руки рабочего, направлявшего инструмент. В этом заключалось большое неудобство. Кроме того, резьба на шпинделе была всего 8-10 мм, что позволяло нарезать только очень короткие винты.
Вторая половина XVIII в. в станкостроении ознаменовалась резким увеличением сферы применения металлорежущих станков и поисками удовлетворительной схемы универсального токарного станка, который мог бы использоваться в различных целях.
В 1751 г. Ж. Вокансон во Франции построил станок, который по своим техническим данным уже походил на универсальный. Он был выполнен из металла, имел мощную станину, два металлических центра, две направляющие V-образной формы, медный суппорт, обеспечивающий механизированное перемещение инструмента в продольном и поперечном направлениях. В то же время в этом станке отсутствовала система зажима заготовки в патроне, хотя это устройство существовало в других конструкциях станков. Здесь предусматривалось крепление заготовки только в центрах. Расстояние между центрами можно было менять в пределах 10 см. Поэтому обрабатывать на станке Вокансона можно было лишь детали примерно одинаковой длины.
В 1778 г. англичанин Д. Рамедон разработал два типа станков для нарезания резьб. В одном станке вдоль вращаемой заготовки по параллельным направляющим передвигался алмазный режущий инструмент, скорость перемещения которого задавалась вращением эталонного винта. Сменные шестерни позволяли получать резьбы с разным шагом. Второй станок давал возможность изготавливать резьбу с различным шагом на детали большей длины, чем длина эталона. Резец продвигался вдоль заготовки с помощью струны, накручивавшейся на центральную шпонку.
В 1795 г. французский механик Сено изготовил специализированный токарный станок для нарезки винтов. Конструктор предусмотрел сменные шестерни, большой ходовой винт, простой механизированный суппорт. Станок был лишен каких-либо украшений, которыми любили украшать свои изделия мастера прежде.
Накопленный опыт позволил к концу XVIII века создать универсальный токарный станок, ставший основой машиностроения. Его автором стал Генри Модсли. В 1794 г. он создал конструкцию суппорта, довольно несовершенную. В 1798 г., основав собственную мастерскую по производству станков, он значительно улучшил суппорт, что позволило создать вариант универсального токарного станка. В 1800 г. Модсли усовершенствовал этот станок, а затем создал и третий вариант, содержавший все элементы, которые имеют токарно-винторезные станки сегодня. При этом существенно то, что Модсли понял необходимость унификации некоторых видов деталей и первым стал внедрять стандартизацию резьб на винтах и гайках. Он начал выпускать наборы метчиков и плашек для нарезки резьб.
Одним из учеников и продолжателей дела Модсли был Р. Робертс. Он улучшил токарный станок тем, что расположил ходовой винт перед станиной, добавил зубчатый перебор, ручки управления вынес на переднюю панель станка, что сделало более удобным управление станком. Этот станок работал до 1909 г.
Другой бывший сотрудник Модсли — Д.Клемент создал лоботокарный станок для обработки деталей большого диаметра. Он учел, что при постоянной скорости вращения детали и постоянной скорости подачи по мере движения резца от периферии к центру скорость резания будет падать, и создал систему увеличения скорости.
В 1835 г. Д.Витворт изобрел автоматическую подачу в поперечном направлении, которая была связана с механизмом продольной подачи. Этим было завершено принципиальное совершенствование токарного оборудования.
Следующий этап — автоматизация токарных станков. Здесь пальма первенства принадлежала американцам. В США развитие техники обработки металлов началось позднее, чем в Европе. Американские станки первой половины XIХ в. значительно уступали станкам Модсли.
Во второй половине XIХ в. качество американских станков было уже достаточно высоким. Станки выпускались серийно, причем вводилась полная взаимозаменяемость деталей и блоков, выпускаемых одной фирмой. При поломке детали достаточно было выписать с завода аналогичную и заменить сломанную деталь на целую без всякой подгонки.
Во второй половине XIХ в. были введены элементы, обеспечивающие полную механизацию обработки — блок автоматической подачи по обеим координатам, совершенную систему крепления резца и детали. Режимы резания и подач изменялись быстро и без значительных усилий. В токарных станках имелись элементы автоматики — автоматический останов станка при достижении определенного размера, система автоматического регулирования скорости лобового точения и т.д.
Однако основным достижением американского станкостроения было не развитие традиционного токарного станка, а создание его модификации — револьверного станка. В связи с необходимостью изготовления нового стрелкового оружия (револьверов) С.Фитч в 1845 г. разработал и построил револьверный станок с восемью режущими инструментами в револьверной головке. Быстрота смены инструмента резко повысила производительность станка при изготовлении серийной продукции. Это был серьезный шаг к созданию станков-автоматов.
В деревообработке первые станки-автоматы уже появились: в 1842 г. такой автомат построил К.Випиль, а в 1846 г. Т.Слоан.
Первый универсальный токарный автомат изобрел в 1873 г. Хр.Спенсер.
Физические и механические свойства алмаза
и кубического нитрида бора (эльбора)
Вещество | Удельный вес, , т/м3 | Теплопроводность, , Вт/(мּ ˚С) | Твердость, HВ, ГПа | Относительная режущая способность |
Алмаз Кубический нитрид бора | 3,51 3,48 | 137,9–146,3 41,86 | 100–120 80–100 | 0,58–0,64 – |
Материалы,
указанные в табл.
Контрольные вопросы и задания
1. Каковы физико-механические свойства инструментальных материалов, определяющие их режущую способность?
2. Приведите классификацию инструментальных материалов.
3. Охарактеризуйте инструментальные и быстрорежущие стали.
4. Каковы состав и назначение твердых сплавов для режущих инструментов?
4. ОБРАБОТКА МЕТАЛЛОВ НА ТОКАРНЫХ СТАНКАХ
4.1. Устройство токарного станка
Точение
– технологический способ обработки
резанием наружных и внутренних
цилиндрических и конических, а также
плоских торцовых поверхностей тел
вращения. Точение ведется токарными
резцами как на универсальных, так и на
специальных металлорежущих станках, в
том числе с числовым программным
управлением, а также на карусельных и
револьверных станках, токарных
полуавтоматах, автоматах и автоматических
линиях.
По своему технологическому назначению точение разделяется на предварительное, межоперационное формообразующее, чистовое формообразующее и окончательное формообразующее.
При выборе и назначении рабочих режимов резания при точении необходимо учитывать характерную особенность этого вида обработки, которая заключается в том, что режущий инструмент имеет всего лишь одно главное лезвие, причем активная длина главного лезвия ограничена шириной b срезаемого слоя. На протяжении всего периода стойкости единственное лезвие резца режет металл, находясь в состоянии большой динамической и температурной напряженности.
Около половины всего станочного парка машиностроительных заводов составляют станки токарной группы.
По
назначению, конструкции, количеству
инструмента, степени механизации и
другим признакам токарные станки делятся
на следующие типы: 1) однорезцовые; 2)
многорезцовые; 3) револьверные; 4)
карусельные; 5) автоматы и полуавтоматы,
6) специализированные и др.
Каждый тип токарных станков имеет несколько моделей, например, выпускают однорезцовые токарно-винторезные станки, токарно-револьверные, многорезцовые полуавтоматы, однорезцовые автоматы.
Станки токарно-револьверной группы в зависимости от назначения подразделяются на токарно-винторезные (в том числе для особых точных работ), револьверные, карусельные, фасонно-токарные, лобовые и др. Особыми видами токарных станков являются многорезцовые станки, одно- и многошпиндельные токарные полуавтоматы и автоматы [6].
Токарно-винторезные станки широко применяют в индивидуальном и серийном производстве, а также для ремонтных и инструментальных работ. На этих станках обрабатывают заготовки разнообразной формы. Токарно-винторезные станки различны по размерам – от настольных, предназначенных для изготовления деталей приборов, до тяжелых, используемых при обработке крупных заготовок.
На
рис. 16 показан токарно-винторезный
станок модели 1К62, конструкция которого
создана в результате модернизации
токарного станка модели 1А62.
Рис. 16. Схема токарно-винторезного станка 1К62: 1 – рукоятка переключения скорости передач; 2 – рукоятка включения шпинделя; 3 – привод; 4 – передняя бабка; |
Модернизации
подверглась как кинематика станка, так
и конструкция его отдельных узлов и
механизмов.
На станине 21 смонтирована передняя бабка
4, в которой расположен механизм коробки скоростей, служащий для изменения чисел оборотов шпинделя. Передняя бабка соединена с приводом 3, непосредственно передающим вращение от электродвигателя к первичному валу коробки скоростей.Число ступеней скорости шпинделя увеличено при модернизации от 21 до 23 без добавления зубчатых колес в коробке скоростей. Пределы чисел оборотов составляют 12,5–2000 об/мин. Изменение чисел оборотов осуществляется рукоятками 5 и 8, а включение и выключение станка, а также реверсирование шпинделя – рукояткой 13.
Коробка скоростей снабжена реверсирующей передачей, необходимой для нарезания правой и левой резьб, а также передачей для увеличения передаточного отношения цепи подач в 2 раза. Звено увеличения шага управляется рукояткой 7, а реверсирующая и повышающая передачи – рукояткой 6.
В пиноли задней бабки 16 установлен съемный задний центр
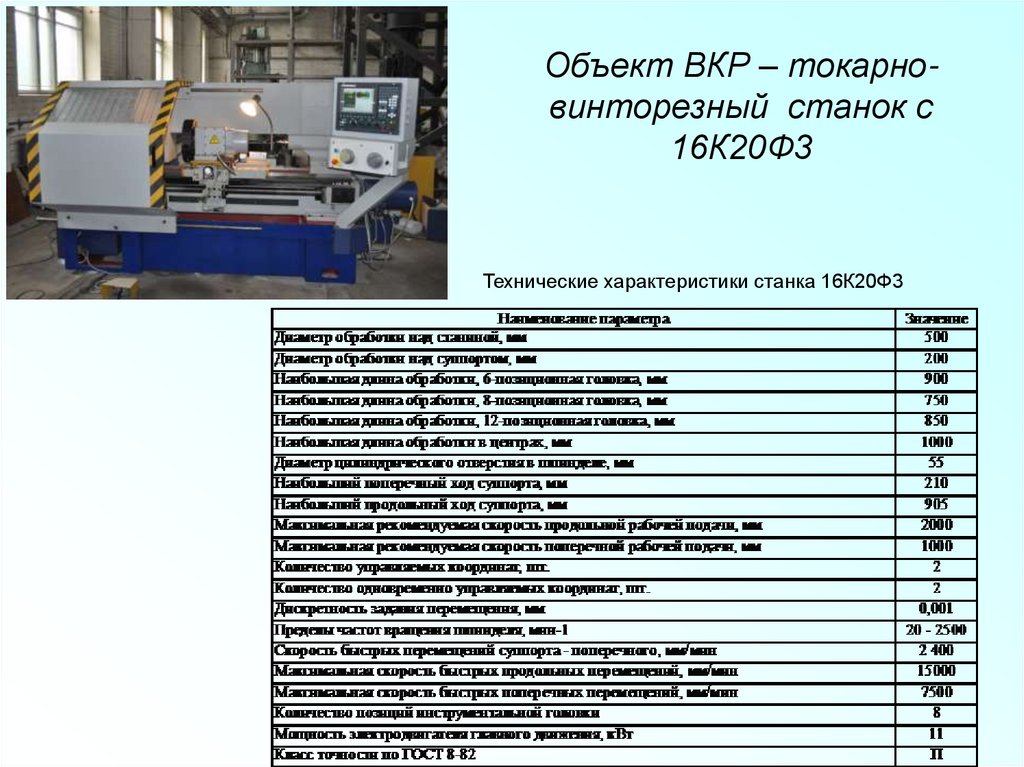
Резцы, используемые для обработки, закрепляются в резцедержателе 11, находящемся на суппорте 10; другие виды инструментов (сверла, зенкеры, развертки и пр.), часто применяемые на токарных станках, устанавливают в отверстие пиноли задней бабки 16 после удаления съемного центра.
Суппорт 10, соединенный с фартуком
20, перемещается по направляющим станины станка посредством ходового винта 17 (при нарезании резьбы) или ходового вала 18 (при точении). При
продольном движении суппорта обтачиваются
поверхности тел вращения. При поперечном
движении суппорта производятся подрезка
торцов заготовки, протачивание канавок
и т. п.
Суппорт перемещается автоматически механизмом подачи. От шпинделя станка через сменные зубчатые колеса и коробку подач 22 приводится во вращение ходовой винт 17 или ходовой вал 18, передающие движение суппорту станка. Коробка подач имеет две основные кинематические цепи: одну для нарезания метрических и модульных резьб, вторую для нарезания дюймовых и питчевых резьб.
Для получения заданной подачи по ходовому валику можно пользоваться как первой, так и второй цепью. Все переключения коробки подач осуществляют рукоятками
В фартуке станка имеются четыре кулачковые муфты, которые служат для включения и реверсирования продольной и поперечной подач. Маточную гайку замыкают рукояткой 12, в реверсировании подачи – рукояткой 14.
Для
быстрого перемещения суппорта применяют
электродвигатель ускоренного хода.
Кнопка 19 предназначена для пуска и остановки главного привода.
Основными узлами токарно-винторезного станка являются (см. рис. 16): станина, передняя бабка, задняя бабка, коробка подач с ходовым винтом и ходовым валиком, фартук с механизмами подачи, суппорт и электропривод. Кроме этих узлов станок имеет масляный электронасос для смазки механизмов передней бабки, плунжерный насос для смазки механизмов фартука и суппорта, насос для подачи охлаждающей жидкости и кнопочное или рычажное управление для пуска и остановки. Включение, выключение и реверсирование электродвигателя производится посредством реверсивного магнитного пускателя. Торможение шпинделя осуществляется противотоком.
Главное
движение и движение подачи производятся
при помощи соответствующих приводов –
совокупности механизмов, передающих
движение от его источника (электродвигателя)
к тому или иному механизму станка
(шпинделю, суппорту и т. д.). Токарный
станок имеет два привода: главного
движения и движения подачи.
Привод главного движения (рис. 17) состоит из электродвигателя 1, ременной передачи 2, коробки скоростей 3 и шпинделя 4. При помощи этого привода через передачу, состоящую из ведущего шкива электродвигателя, приводного ремня и ведомого шкива трансмиссионного вала
У некоторых современных токарно-винторезных станков коробка скоростей из передней (шпиндельной) бабки вынесена в переднюю тумбу, а в средней части передней бабки помещен приводной шкив, обычно монтируемый на двух шарикоподшипниках, разгружая шпиндель от консольного натяжения приводного ремня.
Существуют
два типа коробок скоростей: со ступенчатым
и с бесступенчатым регулированием чисел
оборотов шпинделя. В первом случае
получают максимальное, минимальное и
ряд промежуточных чисел оборотов в 1
мин, во втором – любое плавно изменяемое
число оборотов, что дает возможность
подбирать наивыгоднейшие скорости
резания в зависимости от диаметра
обрабатываемой заготовки, получать
требуемую чистоту поверхности изделия
без снижения производительности станка.
Рис. 17. Схема привода главного движения токарного станка с шестеренчатой коробкой скоростей: 1 – электродвигатель; 2 – ременная передача; 3 – коробка скоростей; 4 – шпиндель; 5 – шпонка |
В
токарных станках со ступенчатым
регулированием чисел оборотов шпинделя
применяются шестеренчатые коробки
скоростей (см. рис. 17)
или ступенчатые шкивы. Привод главного
движения с шестеренчатой коробкой
скоростей компактнее других типов
приводов. От электромотора через ременную
передачу движение сообщается валу I–I,
на котором расположен подвижный блок
из трех зубчатых колес z1, z2 и z3.
Подвижный блок, находящийся на скользящей
шпонке 5,
при помощи рукояти А перемещается вдоль вала I–I и поочередно сцепляется с зубчатыми
колесами z4, z5 и z6,
неподвижно закрепленными на втулке Б.
Втулка свободно размещена на шпинделе II–II токарного станка. Зубчатые колеса z9 и z10,
насаженные на шпиндель II–II,
находятся в постоянном зацеплении с
колесами z7и z8 перебора III–III шестеренчатой коробки. При включении
кулачковой муфты В влево перебор III–III выключается, и шпиндель в зависимости
от положения подвижного зубчатого блока
получает три значения чисел оборотов
– n1, n2 и n3.
Привод движения подачи служит для передачи движения от шпинделя ко второму исполнительному органу токарного станка – суппорту, т. е. для преобразования вращательного движения в поступательное, а также для выбора заданной величины подачи и изменения ее направления. При помощи привода движения подачи можно обеспечить заданную величину подачи не только при точении, но и при нарезании резьбы в широком диапазоне.
Движение привода подачи обычно заимствуется от конечного звена привода главного движения – шпинделя. В этом случае зубчатое колесо реверсивного механизма насаживается либо на шпиндель, либо на промежуточный вал, связанный со шпинделем посредством отдельной зубчатой передачи. Иногда источником движения привода подачи является отдельный электродвигатель.
Привод
движения подачи токарного станка
(рис. 18) состоит из реверсивного
механизма 1,
гитары 2 сменных зубчатых колес, коробки подач 3 с ходовым винтом 4 и валиком 5,
фартука 6.
Рис. 18. Схема привода движения подачи токарного станка: 1 – реверсивный механизм; 2 – гитара; 3 – коробка передач; 4 – ходовой винт; 5 – валик; 6 – фартук |
Реверсивный механизм предназначен для изменения направления вращения ходового винта или ходового валика, что обеспечивает перемещение суппорта с резцом справа налево или слева направо.
Конструктивно реверсивный механизм может состоять из систем:
1) четырех цилиндрических зубчатых колес с последовательным сцеплением так называемого транзеля с цилиндрическими зубчатыми колесами;
2) цилиндрических зубчатых колес с параллельным сцеплением и перемещающимся на скользящей шпонке блоком зубчатых колес;
3) цилиндрических зубчатых колес с параллельным сцеплением и кулачковой муфтой;
4)
конических зубчатых колес с кулачковой
муфтой и др.
Под гитарой привода подачи токарного станка понимают механизм, состояший из набора сменных зубчатых колес и особого устройства, называемого собственно гитарой. Гитара служит для настройки привода подачи станка на различные числа оборотов, подачу при точении деталей, шаг при нарезании резьбы, а также осуществляет передачу движения от трензеля к коробке подач или ходовому винту.
В токарных станках используют три способа установки сменных зубчатых колес гитары: однопарную, двухпарную и трехпарную.
Для эффективной работы токарного станка соответствующими рас-четами установлен нормальный ряд чисел зубьев и минимальные ком-плекты сменных зубчатых колес.
Коробка подач, расположенная с передней стороны станка под бабкой, позволяет путем переключения рычагов быстро изменять величину подачи при выполнении на станке чисто токарных или резьбонарезных работ.
В
токарных станках чаще всего применяют
коробки подач с накидной шестерней и с
вытяжной (плавающей) шпонкой.
Фартук прикреплен к нижней части каретки суппорта. Заключенные в фартук механизмы подачи служат для преобразования вращательного движения, получаемого от ходового винта или ходового валика, в поступательное движение (подачу) суппорта, на котором закреплен резец. В фартуке имеется система червячных и зубчатых передач.
Червячная и зубчатая передачи механизмов фартука постоянны, их составные части несменяемы; поэтому различная подача может быть задана только изменением скорости вращения ходового винта или ходового валика, получающих движение от коробки подач.
Суппорт предназначен для закрепления резца и сообщения ему продольной или поперечной подачи.
Основанием суппорта служат нижние (продольные) салазки, скользящие по направляющим станины токарного станка (см. рис. 16).
Продольную
механическую подачу суппорта осуществляют
включением соответствующей рукоятки,
расположенной на фартуке; подачу суппорта
вручную производят при помощи вращения
маховика, размещенного на фартуке. Укрепленный на суппорте резец будет
при этом перемещаться параллельно оси
шпинделя.
Для поперечной подачи суппорта вручную вращают рукоятку, при этом поперечные салазки суппорта перемещаются перпендикулярно оси шпинделя, скользя по направляющим нижних салазок. На поперечных салазках закрепляется поворотная часть суппорта с верхними салазками и резцедержателем. При необходимости верхние салазки могут быть повернуты на нужный угол.
Задняя бабка токарного станка (см. рис. 16) поддерживает в центрах обрабатываемые детали значительной длины (L > 4D), а также служит для закрепления режущего инструмента – сверл, зенкеров, разверток. Состоит она из чугунного корпуса, установленного на скользящей плите. Эту плиту вместе с корпусом можно передвигать по направляющим станины. В зависимости от длины обрабатываемой детали задняя бабка устанавливается на станине в нужном месте.
Верхняя
часть корпуса задней бабки имеет
отверстие, куда вставляют пуcтотелый
шпиндель – пиноль с закрепленным в ней
задним центром станка, которые могут
перемещаться в продольном направлении
при помощи винта с рукояткой. Закрепление
пиноли в определенном положении
производится рукояткой.
При обтачивании конических заготовок корпус задней бабки токарного станка может быть смещен относительно основания в поперечном направлении посредством специального болта.
При скоростном резании в пиноль вставляют вращающийся центр.
Кинематическая схема токарного станка. Кинематической схемой токарного станка называется условное изображение всех его движущихся (кинематических) цепей в их взаимной связи.
В токарном станке имеются две кинематические цепи: электродвигатель–шпиндель (цепь главного движения), шпиндель–суппорт (цепи подач). Последняя цепь изображается в двух вариантах – для продольной (при нарезании резьбы и точении) и поперечной подач резца.
Каждая
кинематическая цепь токарного станка
состоит из ряда кинематических пар
зубчатых колес или шкивов. Последовательность
соединения кинематических пар зубчатых
колес или шкивов в цепи изображается
обычно цифрами, указывающими число
зубьев в зубчатых колесах или диаметры
шкивов, мм. Запись ведется в строчку следующим
образом: для элементов кинематических
пар, закрепленных на одном валу, – через
тире, для элементов кинематических пар,
закрепленных на различных валах, –
через знак деления.
На рис. 19 приведена упрощенная кинематическая схема токарно-винторезного станка модели 1Е61МТ. Проследим по данной схеме кинематическую цепь электродвигатель–шпиндель. Эта цепь связывает вал двигателя (диаметр шкива d1) через клиноременную передачу со шкивом d2 вала I коробки скоростей токарного станка, где находится шлицевой вал II с соответствующим набором цилиндрических шестеренок с шестью ступенями чисел оборотов. Далее вал II со шкивом d3 через клиноременную передачу связан с валом III со шкивом d4 и валом IV перебора с зубчатыми шестернями 1:2, 3:4 или же, минуя перебор, непосредственно с валом III (шпинделем). Структурная формула рассматриваемой кинематической цепи сокращенно выражается следующим образом, об/мин:
,
где nшп – число оборотов шпинделя в 1 мин; nэд – число оборотов электродвигателя в 1
мин; iк. с–
переменное передаточное число коробки
скоростей; iп–
переменное
передаточное число перебора; – коэффициент скольжения ременных передач
(обычно принимают равным 0,98).
Токарно-винторезный станок 1Е61МТ имеет 12 чисел оборотов шпинделя (от 35 до 1600 об/мин).
Таким же способом можно установить кинематическую цепь суппорта при продольной и поперечной подачах, а также при нарезании резьбы.
Продольное и поперечное перемещение суппорта при обтачивании производится механически при помощи ходового валика XI через механизмы коробки подач и фартука или при помощи ходового винта 5 и разъемной гайки 6.
Ручное
продольное перемещение суппорта
осуществляется маховиком а через шестерни 7:8–9.
Поперечное перемещение суппорта от
руки осуществляется через винт 10 и гайку 11 при помощи рукоятки б (см. рис. 19).
Рис. 19. Кинематическая схема токарно-винторезного станка модели 1Е61МТ |
Коробка подач получает движение через шестерни 12:13 и 13:14 (механизм передней бабки) и сменные шестерни А, Б, В и Г на гитаре.
Для нарезания точных резьб ходовой винт 5 соединяют напрямую с валом VI посредством муфты в и вала X.
Через
ходовой валик XI суппорт получает механические продольные
подачи от 0,04 до 6 мм
на 1 оборот шпинделя через шестерни 15:16,
червячную пару 17:18,
шестерни 19:20–21:8,
реечную шестерню 9 и рейку 22 и поперечные подачи от 0,012 до 1,87 мм на 1
оборот шпинделя через зацепление
шестерен 20:23,
винт 10 и гайку 11.
Изменение направления движения суппорта достигается переключением трензельной шестерни 14 и при помощи рукоятки г.
Перемещение верхних салазок производится от руки винтом 24 и гайкой 25 при помощи рукоятки д.
Продольное перемещение пиноли задней бабки осуществляется от руки через винт 26 и гайку 27 при помощи рукоятки е.
Анализируя кинематическую схему токарного станка в целом и ее кинематические цепи, можно подобрать необходимую структурную формулу настройки станка для выполнения конкретной задачи. Полученные таким образом обобщенные данные записывают в таблицу настройки станка и вывешивают на металлической дощечке вблизи рабочего места токаря.
Свойства токарного станка
| |||||||||||||||||||||||||||||||||||||||||||||||
| |||||||||||||||||||||||||||||||||||||||||||||||
Предыдущий Следующий | |||||||||||||||||||||||||||||||||||||||||||||||
| |||||||||||||||||||||||||||||||||||||||||||||||
Токарный станок для грунта, триммер, экструдер | Группа управления
Токарный станок для грунта, триммер, экструдер | Группа элементов управленияГлавная > Сталь > Испытания стали и арматуры > Подготовка проб > Токарный станок для грунта, триммер, экструдер
- Описаниеиконка стрелка вправо
- Продуктызначок стрелка вправо
- Технические характеристикизначок стрелка вправо
- Значок со стрелкой вправо
Технические характеристики
icon arrow-downОписание
Этот прибор используется для приготовления цилиндрических образцов грунта любого размера:
– Функция токарного станка: от диам. 35×70 мм до диам. 100×220 мм
– Функция обрезки и выдавливания образца: от диам. 35×70 мм до диам. 50×100 мм-
Устройство, которое можно использовать как триммер или пробоотборник, состоит из:
- Вращающееся круглое основание с направляющей, куда помещается образец;
- Стержень с вертикальной резьбой, приводимый в действие маховичком, предназначенный для регулирования высоты образца по вертикали и удержания его в нужном положении во время обрезки;
- Два вертикальных боковых стержня, которые используются в качестве направляющих для торцовочной пилы;
- Регулируемый стержень, прикрепленный к градуированному слайду, который используется для проверки и установки диаметра образца почвы
- Адаптер для вытачивания образца (100, 70 мм) при токарной обработке
- Адаптер для вытачивания образца (50, 38, 35 мм) при токарной обработке
- Адаптер для обрезки (35-38 мм) и выдавливания (50 мм) образца
- Адаптер для обрезки (50 мм)
Для уменьшения образцов требуется открытая проволочная пила. См. принадлежности, модель 16-D1689.
Изделия
Код
Описание
Шт.
Технические характеристики
- Функция токарного станка: от диам.35×70 мм до диам. 100×200 мм
- Функция обрезки и выдавливания образцов: от диам. 35×70 мм до диам. 50×100 мм
- Регулируемый вертикальный дневной свет: до 240 мм
- Горизонтальный дневной свет: 155 мм
- Габаритные размеры: 220x300x450 мм
- Приблизительный вес: 15 кг
Аксессуары и запасные части
Код
Описание
Единицы
Сопутствующие товары
Пробоотборник почвы, резак и экструдер
Используется для экструдирования и подготовки образцов почвы.
Почвенный экструдер с ручным управлением
Используется для выдавливания пробоотборной трубки, образцов Marshall, Proctor и CBR.