Основы литья пластмасс под давлением Heatle
Независимо от того, являетесь ли вы новичком в области переработки полимеров, пытаетесь создать свой следующий проект или являетесь инженером, чтобы полностью понять процесс литья под давлением, вы должны сначала понять основы того, как все это работает. В этой статье мы попытаемся сделать описание процесса литья как можно более простым, чтобы помочь вам узнать все, что входит в формование пластиковых деталей.
Что такое литье под давлением?
Литье под давлением – наиболее распространенный производственный процесс для изготовления пластмассовых деталей. Процесс включает в себя проектирование продукта, оснастку пресс-формы, а затем производство гранул пластикового полимера и использование давления для их впрыскивания в пресс-форму.
Процесс литья пластмасс под давлением
Чтобы сделать его максимально простым и понятным, мы разделили процесс литья пластмасс под давлением на 3 части:
- Инженерное проектирование продукта
- Проектирование и разработка пресс-форм
- Производственный процесс
Инженерное проектирование продукта
Когда дело доходит до производства детали, изготовленной методом литья под давлением, конструкция детали является абсолютно важной. Вы должны убедиться, что деталь разработана с учетом процесса литья под давлением.
Некоторые важные элементы конструкции продукта включают:
- Однородная толщина стенок во избежание вмятин и пустот
- Углы уклона, чтобы деталь могла эффективно вытолкнуть изделие из формы
- Определение выбора материала на этапе проектирования критически важно для обеспечения соответствия эксплуатационным характеристикам, поскольку каждый материал имеет разную усадку, плавление и скорость потока, изменение материала может привести к ухудшению характеристик деталей или выходу за пределы допуска.
Другой аспект конструкции продукта, который часто упускается из виду, – это допуск детали для литья под давлением. Есть много причин, по которым допуски на детали, полученные литьем под давлением, шире, чем у металла, например, степень усадки не является однородным процентом (они являются средними), расположение инструмента (закрытие против фиксированных размеров), толщина стенки, место впрыска, давление и поток материала – все это играет жизненно важную роль для многократного повторения. Кто угодно может сделать хорошую деталь один раз, но то, кто может сделать 100 000 или 1 000 000 единиц с возможностью повторения, – вот что важно в производстве.
Проектирование и разработка пресс-форм
Качество детали начинается с качественной пресс-формы. Распространенная ошибка, которую мы все совершаем при покупке нового компонента, полученного литьем под давлением, – это попытаться сократить углы, чтобы снизить затраты на пресс-форму. Если инструмент построен неправильно, у вас могут возникнуть проблемы с качеством в будущем, это может занять 1 месяц, 6 месяцев или 2 года.
Чтобы предотвратить дефекты и соответствовать определенным требованиям к качеству, вы и ваш инструментальный мастер должны работать вместе, чтобы разработать форму, которая будет правильно изготавливать детали, которые вам нужны. Это сложная задача, поскольку конструкция пресс-формы иногда требует изменения конструкции детали.
Инструменты обычно изготавливаются из закаленной инструментальной стали или алюминия, в зависимости от того, что вам нужно. Алюминиевый инструмент обычно используется для создания прототипов или когда требуется небольшое количество деталей. Сталь – более дорогой материал, но, как правило, самый долговечный из двух вариантов. Производители, которым требуется более 10 000 деталей, почти всегда будут использовать стальную форму.
Элементы конструкции пресс-формы:
- Расположение литника / желоба: это один из наиболее важных факторов, которые следует учитывать на этапе заполнения процесса закачки.
- Линии охлаждающей жидкости: неправильное размещение или недостаточное количество охлаждающих линий приводит к увеличению продолжительности цикла и короблению
- Термоусадка: Усадка обычно составляет от 0,4 – 2% и должны быть приняты во внимание проектировщиком пресс – формы. Точная величина усадки зависит от нескольких факторов, включая материал, условия процесса и расположение затвора.
- Допуски деталей: допуски и требования к рабочим характеристикам критически важно определить перед запуском.
Недостатки литья под давлением:
- Высокие затраты на оборудование: Стоимость пресс-формы зависит от количества необходимых деталей (сколько полостей потребуется), сложности детали и размера детали. В то время как инструменты для изготовления прототипов с одной полостью могут стоить от 3000 до 10000 долларов, в автомобильной промышленности инструменты для литья под давлением могут варьироваться от 10000 до 100000 долларов и более. Это очень сложные инструменты, которые изготавливаются из больших блоков закаленной стали и долго изготавливаются вручную.
- Длительное время выполнения: как и стоимость пресс-формы, время выполнения заказа зависит от сложности детали, ее размера и требований к полости. Большинству компаний также требуются прототипы перед окончательным утверждением серийных изделий, что лишь увеличивает время окончательного выполнения заказа. Как правило, вы увидите, что простая форма может быть готова к использованию через 2–4 недели, а сложный инструмент может занять примерно 6–10 недель.
- Трудность изменения: поскольку пресс-формы сделаны из стали или алюминия, внести изменения может быть довольно сложно. Если вы хотите немного увеличить размер детали, вы всегда можете увеличить полость, отрезав металл. Но если вы хотите сделать деталь меньше, вам нужно уменьшить размер полости пресс-формы, что потребует добавления в нее стали или алюминия. Это сложный процесс, и иногда вам придется начинать заново и отказываться от исходной формы. Вот почему очень важно сначала использовать прототип пресс-формы.
Производственный процесс
Чтобы сделать процесс производства максимально простым, мы разбили его на 5 этапов. Каждый этап важен и играет жизненно важную роль в проектировании деталей и пресс-форм. 5 этапов производственного процесса литья пластмасс под давлением включают в себя:
-
1 – Стадия наполнения / плавления: процесс литья под давлением начинается с заполнения бункера пластиковыми гранулами, которые подаются в цилиндр шнека литьевой машины. Кольцевые нагреватели помогают расплавить гранулы, но на самом деле в большей степени пластик плавится из-за его уплотнения коническим винтом шнека. Это потому, что гранулы «трутся» друг о друга, выделяя чистое тепло. К концу гранулы переходят в расплавленное состояние.
-
2 – Этап впрыска / упаковки: Затем винт проталкивает расплавленный пластик в полость формы, где он принимает форму и начинает этап охлаждения.
Этот этап важен, потому что при недостаточном давлении полость не будет заполнена полностью, что приведет к проблемам с качеством
-
3 – Стадия охлаждения: Линии охлаждающей жидкости, обычно заполненные водой, проходят через форму для поддержания температуры формы, что помогает быстрее охладить деталь. Это очень важно, поскольку фаза охлаждения является наиболее трудоемкой стадией цикла литья под давлением из-за изоляционных свойств пластика. Когда пластик охлаждается и затвердевает, он дает усадку (так называемая «усадка пресс-формы»). Усадка обычно составляет от 0,4 до 2% и должна быть принята во внимание разработчиком пресс-формы. В зависимости от используемого материала вам может потребоваться охладить форму или нагреть форму с помощью патронных нагревателей или горячего масла.
-
4 – Этап выталкивания: после охлаждения форма открывается, и пластиковая часть выталкивается встроенными в нее выталкивающими штифтами.
Если вы посмотрите на большинство пластиковых деталей, лежащих у вас в доме, скорее всего, вы сможете найти следы от выталкивающих штифтов. Затем форма снова закроется, чтобы повторить процесс.
-
5 – Стадия после выталкивания: одна из последних стадий этого процесса – когда оператор станка должен отломать литник, направляющую или заслонку от формованной детали, скручивая или отрезая их вручную, в зависимости от конструкции пресс-формы. Система горячеканальной пресс-формы со спиральными и гибкими нагревателями фактически исключает наличие желобов и литника, что также устраняет отходы. К сожалению, горячеканальная система делает пресс-форму более дорогой.
Заключение
Литье пластмасс под давлением за прошедшие годы значительно улучшилось, и это фантастический способ крупномасштабного производства компонентов с минимальными трудозатратами. Хотя это кажется относительно простым процессом плавления пластиковых гранул и впрыска в полость формы, существует так много критических элементов конструкции, инструментов и производственного процесса, которые потребуют от вас работы, а также от литьевого формовщика, который знает, как удовлетворить ваши потребности и особые требования.
Мы производим кольцевые и плоские нагревательные элементы для цилиндров термопластавтоматов, а также спиральные, патронные и гибкие ТЭНы для пресс-форм. По всем вопросам обращайтесь к нам по электронной почте или просто звоните по телефону прямо сейчас.
Основные методы литья пластмасс под давлением » Термопластавтоматы бренда «CMT»
В литье пластмасс под давлением используют два основных метода – инжекционный и интрузионный. Все остальные по сути представляют собой их развития и вариации с целью получения лучшего качества деталей сложной конфигурации, многослойных и многоцветных изделий.
Инжекционный метод
Название ведёт начало от латинского слова inject, что означает впрыснуть. При формовке пластическая масса впрыскивается в литейную форму и там застывает. Во время затвердевания для получения необходимой прочности литой продукции надо обязательно поддерживать определённое сжатие. Для обеспечения этого требования процесс должен проходить быстро, чтобы успели заполниться все уголки полости до начала застывания смеси. Это обязательное условие достижения качественного формования. Таким способом получают детали с различной толщиной стенок и мелким рельефом поверхности.
При изготовлении крупногабаритных отливок с тонкими стенками вязкость расплава может препятствовать его нормальному растеканию с требуемым для обеспечения качества давлением. В этом случае рекомендуется применять подачу смеси в полость одновременно с нескольких точек – через разные литники. Иногда для этого могут быть задействованы несколько инъекционных установок.
Это увеличивает стоимость оборудования и оправдано в крупносерийном и массовом производстве. Например, изготовление пластиковых панелей салона в автомобилестроении.
Составляющие впрыскиваются в пресс-форму из так называемого материального цилиндра (ЛМ), усилие создаётся поршнем. Объём изначально рассчитывается так, чтобы расплав без остатка заполнил полость и литниковую систему.
Инжекционно- газовое литье
Это разновидность отличается тем, что впрыск разделён на два этапа. После ввода первой порции состава в формователь через специальное сопло подаётся комбинация газов под давлением. Она раздувает жидкую пластмассу, прижимая её к внутренней поверхности. Получается деталь с пустотой внутри. Далее газ удаляется и на его место вводится дополнительная порция ингредиентов.
В некоторых случаях освободившееся пространство может не заполняться. Так изготавливаются различные ёмкости. Следует отличать выдувные изделия, полученные из предварительно инжектированной смеси, от раздува нагретых пресс-форм.
Двойная инжекция позволяет получать особо качественный продукт комбинированной структуры. Для её реализации требуется сложное оборудование и тщательная проработка технологического процесса. Помимо приобретения такого термопластавтомата, в России есть возможность аренды ТПА с возможностью литья с газом.
Инжекционно-прессовый
Ещё одна вариация, отличающаяся процедурой формования. Первоначально в составную пресс-форму инжектируется разогретый пластичный компонент. Затем части штампа сжимаются, сдавливая массу и распределяя её по всему пространству.
Вариант применяется для случаев, когда качественному заполнению крайних участков полости препятствует падение напора инжекции. Например, деталь имеет тонкие стенки большой ширины, вязкость расплава препятствует нормальному растеканию.
Для этого способа необходима разработка конструкции пресса, допускающей дополнительное сжатие введённого состава после смыкания частей штампа.
Соинжекционное литье
Метод основан на подаче жидких пластических составляющих из нескольких инжекционных машин. В отличие от многолитниковой системы здесь впрыск разных смесей производится через одну точку. В зависимости от поставленных задач можно получать отливки с различными характеристиками. Для реализации требуется сложное оборудование с комбинированием инжекторных головок.
Способ совместного инъектирования можно разделить на подвиды:
* Многослойное. Разновидность заключается во впрыскивании в зону будущего изделия нескольких различных спецсмесей из двух или более инъекционных машин. Существуют многочисленные варианты сочетаний сырья. Это могу быть различающиеся, как по цвету, так и по прочим свойствам пластмассы. Например, наружные слои выполняются из прочных высококачественных полимеров, а внутренние – из более мягкой пластической массы, пенополистирола (пенопласта) или более дешёвого вторичного сырья.
Конкретные ингредиенты и цвет определяются требованиями, предъявляемыми к готовой продукции.
* Сэндвич-литьё. Этот подвид отличается тем, что виден только наружный слой пластика. Техпроцесс производится в 3 стадии. Сначала в штамповочное пространство впрыскивается состав No 1. Затем внутрь первого инжектируется No 2. В конце снова добавляется порция первоначальной пластических компонентов. Она закрывает вход, через который вводился вторая составляющая и окончательно запечатывает его, формируя наружный слой.
Технология также позволяет получать детали из нескольких видов сырья, преследуя цели от достижения специальных механических характеристик до утилизации продуктов вторичной переработки полимеров.
Интрузионный
Название восходит к латинскому слову intrusio – вталкивать, вдавливать. В основе техпроцесса лежит разогрев и расплавление пластмассовых гранул в шнековом механизме, сопровождающийся перемешиванием и гомогенизацией в случае использования разных компонентов. Затем жидкий расплав предварительно вводится в полость пресс-формы и далее, создаётся и выдерживается давление, в процессе которого подаётся дополнительное количество до полного заполнения объёма.
На входе в пресс состав соприкасается со стенками, охлаждается и начинает застывать. Поэтому технология применяется преимущественно для изготовления отливок без сложных, тонких элементов.
Интрузионная технология применяется самостоятельно или в комбинации с инжекционной.
Литье в многокомпонентные формы
Методика предполагает раздельное формование двух и более элементов, входящих в структуру изделия и последующее их соединение в единое целое.
Для реализации необходимы специальные штампы, состоящие из нескольких формовочных узлов. Кроме того конструкция должна позволять после предварительной заливки перемещать их спрессовывать друг с другом.
Технология отличается от частично сходных по конечному результату многослойного и сэндвич-литья тем, что формовка составных частей производится одновременно. А после его окончания они перемещаются для последующего соединения в единое целое.
В процессе участвуют одновременно несколько установок, подающих расплав. Допускается изготовление одних элементов инжекцией, других – интрузией.
Такие термопластавтоматы производит тайваньский производитель JONWAI.
Ротационное литье
Технология представляет собой разновидностью заливки пластмасс в многокомпонентные формы. Основное различие заключается в том, что формование происходит не одновременно, а последовательно.
Первоначальный объём образуют корпус пресс-форма и вставка. После заполнения, вставной элемент извлекается, и пластичный состав впрыскивается в оставшуюся часть. Если изделие состоит не из двух, а их трёх и более частей, технологический переход повторяется соответствующее количество раз.
После каждого этапа подключается следующая литейная установка (производится ротирование). Соответственно процесс занимает много времени и требует большого количества оборудования.
Так же, как и отливка в многокомпонентные формы ротационное допускает комбинирование методов инжекции и интрузии.
{“type”:”sr”}
Технологии литья под давлением в Rosenberger Group
Время для файлов cookie и настроек
Этот веб-сайт использует файлы cookie, которые необходимы для его работы, для проведения статистического анализа, чтобы вы могли делиться контентом в социальных сетях или показывать вам рекламу, соответствующую вашим интересам. В зависимости от активированного уровня вы принимаете предыдущие уровни, нажимая соответствующую кнопку. Нажимая «Подтвердить выбор» или «Выбрать и подтвердить все», вы также даете свое согласие в соответствии со ст. 49Пара. 1 п. 1 лит. GDPR для обработки ваших данных соответствующими службами в США.
Политика конфиденциальности и изменение настроекПодробная информация
Литье под давлением – это процесс, который в основном используется при переработке пластмасс.
В этом процессе соответствующий материал сжижается и впрыскивается в форму под давлением. Hörl Kunststofftechnik GmbH & Co. KG, входящая в состав Rosenberger Group с 2010 года, специализируется на производстве инновационных и высокоточных литьевых пластмассовых деталей неизменно высокого качества. Полностью автоматизированное производство малых и микродеталей, изготовленных методом литья под давлением из инженерных пластмасс, осуществляется на объединенном в цифровую сеть производственном блоке с централизованным управлением и контролем. Самостоятельная стратегия нулевого брака демонстрирует четко структурированную систему управления качеством компании в сочетании с обширными ноу-хау.
Что такое технология литья под давлением?
Желаемый конечный продукт создается путем плавления пластиковых гранул термореактивных или термопластичных полимеров с последующим впрыскиванием под давлением в форму и последующим охлаждением. Основным преимуществом технологии литья под давлением, помимо высокой точности и объема производства, является способность воспроизводить сложные формы и геометрические формы .
Производство осуществляется с максимальной точностью, поэтому нет необходимости в постобработке заготовок. Благодаря технологии литья под давлением требования клиентов могут быть максимально удовлетворены, поскольку выбор доступных пластиков очень широк. Постоянное развитие новых пластиков приводит к постоянно расширяющемуся диапазону применения этой технологии.
Щелкните здесь, чтобы просмотреть пояснительное видео
Производство
Когда дело доходит до производства, технология литья под давлением в Rosenberger Group полностью автоматизирована.
Инновационные разработки в отношении Индустрия 4.0 гарантируют высочайшие стандарты качества : Главная компьютерная система контролирует и контролирует все производственные процессы; информация об отклонениях от производственных параметров передается в режиме реального времени. Это обеспечивает стабильные процессы и стратегию нулевой ошибки.
Соответственно, Rosenberger Group поддерживает самые современные процессы, которые обеспечивают точную, полностью автоматизированную сборку высококачественных отдельных компонентов в готовую продукцию. Нет никаких ограничений для требований клиентов, от микролитья под давлением до крупных компонентов . Hörl Kunststofftechnik является компетентным технологическим партнером, использующим самое современное оборудование, способное реализовать даже самые сложные производственные требования с максимальной эффективностью.
Защита окружающей среды
Успех с ответственностью: в роли международной промышленной компании Rosenberger Group признает свою ответственность за защиту окружающей среды.
Рециркуляция и энергоэффективность являются решающими факторами в области литья под давлением. Таким образом, процессы непрерывного совершенствования и эффективные системы мониторинга процессов служат для экономии ресурсов и обеспечения устойчивости. Кроме того, отопление в Hörl осуществляется за счет энергии систем рекуперации тепла, а охлаждение и кондиционирование воздуха — за счет родниковой воды. До 30% необходимой электроэнергии вырабатывается собственной фотоэлектрической системой компании. Любые образующиеся пластиковые отходы перерабатываются и используются повторно (повторное гранулирование).
Технология литья под давлением в Hörl в цифрах
Общая площадь 13 000 м² включает производственные площади и склады для технологии литья под давлением
5 – 6 миллионов компонентов производится в среднем в день
1300 тонн пластикового гранулята 9 литье под давлением 9 литье под давлением 9 литье в год
3 ежегодно
3 машины в повседневном использовании 265 сотрудников , 42 ученика и 3 студента-двойника, ответственных за процессы литья под давлением
Станьте частью компетентной команды и специалистом по перспективным технологиям.
Здесь вы можете найти дополнительную информацию о своей карьере в Hörl.
6 типов технологии литья под давлением
От достижений, которые помогали отрасли более 40 лет, до последних передовых инноваций, существует ряд интересных технологий литья пластмасс под давлением, которые можно использовать для создания вашего прототипа. в производство.
Ниже приведены шесть технологий, которые помогают современным компаниям, занимающимся литьем под давлением, производить детали быстрее и качественнее. Чем больше вы знаете, тем больше вы будете готовы запросить такую технологию, когда придет время выбирать партнера по литью под давлением!
1. Тонкостенное литье
Тонкостенное литье — это технология литья под давлением, которая позволяет получить пластиковую деталь с очень тонкой стенкой. Он часто используется в испытательных приборах, электронике, сосудах, трубках и других корпусах. Производителям литья пластмасс под давлением, занимающимся тонкостенным литьем, приходится детально учитывать каждый аспект конструкции детали, конструкции пресс-формы и обработки, чтобы гарантировать, что геометрия тонкой стенки будет сохраняться без проблем с качеством.
Здесь, в Micron, мы используем сложную систему технического зрения для проверки каждой готовой детали, чтобы убедиться в отсутствии трещин.
2. Литье под давлением с помощью газа
Проблема с любой толстой пластиковой деталью, полученной методом литья под давлением, заключается в том, что она может деформироваться при охлаждении. Литье под давлением с помощью газа помогает решить эту проблему путем подачи газа в форму для литья под давлением, заполненную пластиковым материалом. Это позволяет пластику снаружи формы сохранять гладкий и законченный вид, в то время как внутренняя часть остается пористой или полой. Это не только предотвращает деформацию детали на этапе охлаждения, но и снижает стоимость детали (поскольку вы используете меньше материала).
3. Литье металла под давлением
Литье под давлением можно производить не только из пластика, но и из металла. Эта новая технология значительно дороже, чем литье пластмасс под давлением, и обычно используется для узкой ниши на рынке.
Рынок сотовых телефонов, например, иногда использует литье металла под давлением для защиты сотовой электроники от радио или микроволн.
4. Литье жидкого силикона под давлением
Большая часть литья пластмасс под давлением термореактивная , что означает, что холодный материал впрыскивается в очень горячую форму для создания детали. Этот процесс отверждает деталь, поэтому ее нельзя будет снова расплавить. Но если вам нужна деталь, способная выдерживать очень высокие температуры или химические вещества — как это может быть с некоторыми медицинскими устройствами или автомобильными деталями — вам может понадобиться литье под давлением из термопласта , в котором часто используется жидкий силикон.
5. 3D-печать
3D-печать — известная технология литья под давлением из-за роли, которую она играет в создании прототипа литой детали. Здесь, в Micron, мы создаем прототип детали клиента, напечатанный на 3D-принтере, прежде чем мы передадим дизайн в производство.
Это позволяет нам обсуждать потенциальные улучшения более подробно, чем мы могли бы, например, при просмотре онлайн-рендеринга. Также стоит отметить, что 3D-печать можно использовать для печати реальных форм для литья под давлением из пластика или металла. В настоящее время доступная технология 3D-печати не позволяет нам печатать с узкими допусками деталей, необходимыми для литьевой формы, но мы полагаем, что это возможно в будущем.
6. Уникальные составы материалов
Хотя это не «технология» литья пластмасс под давлением в традиционном смысле, использование уникальных составов материалов расширяет возможности литья. Компании, занимающиеся литьем под давлением, могут, например, использовать углеродный или минеральный наполнитель, вспенивающий агент и смазывающую добавку для придания детали определенных свойств. Например, здесь, в Micron, мы использовали 40% углеродистый АБС (акрилонитрилбутадиенстирол) для достижения определенной степени электропроводности пластикового штифта или датчика.
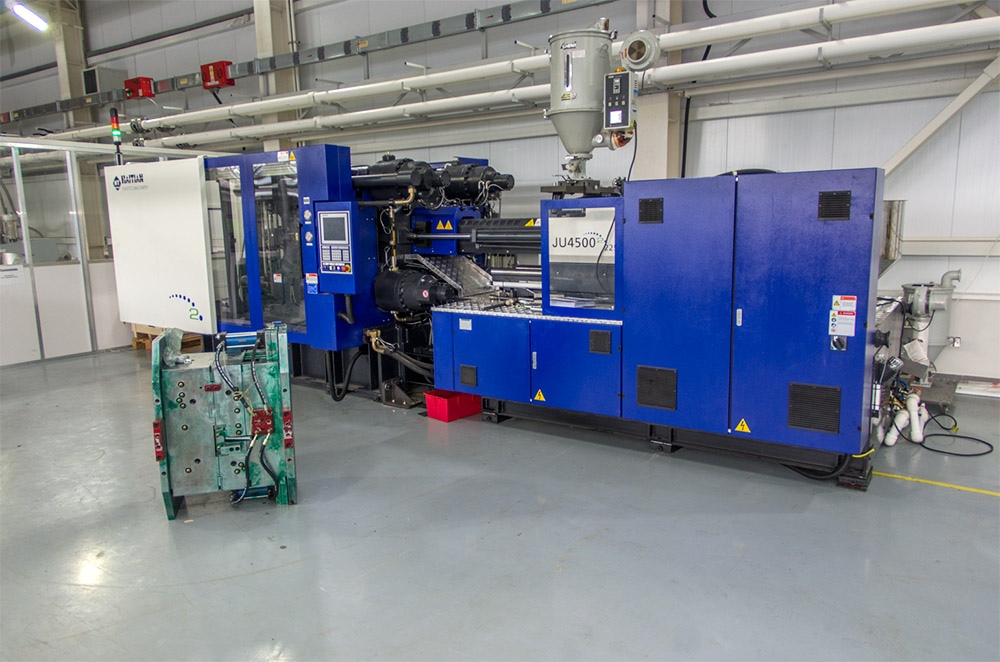
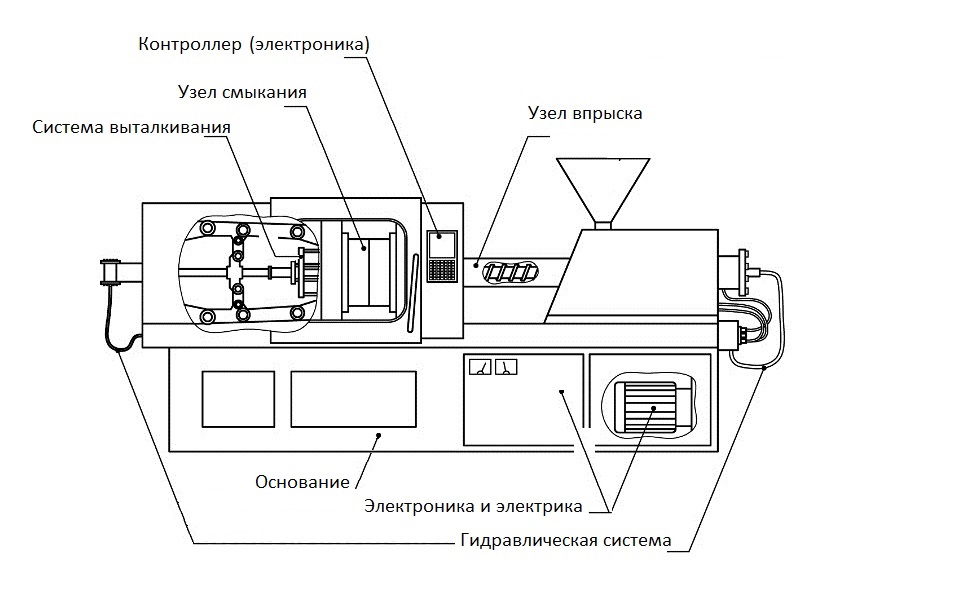
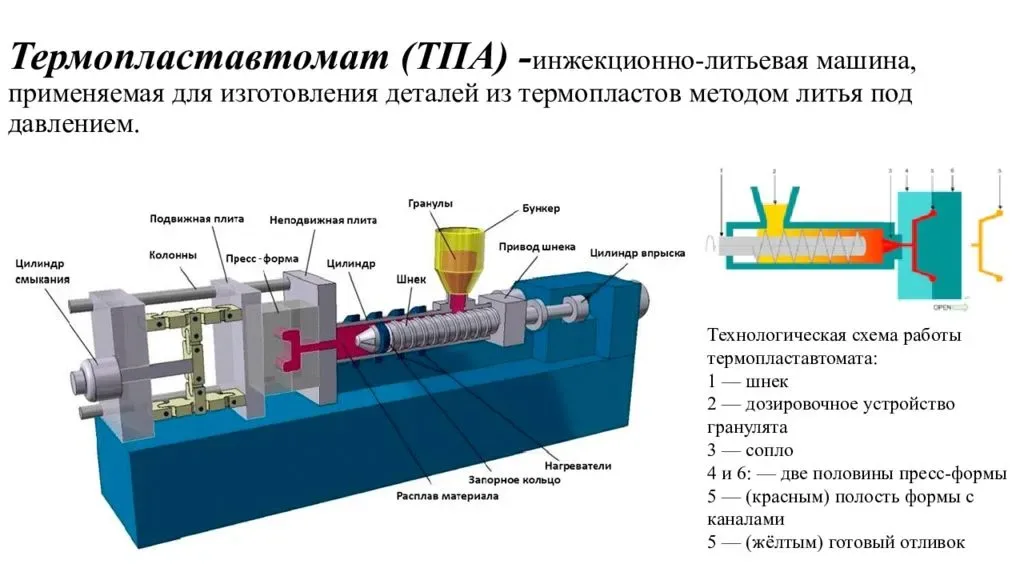

