Резцы для токарной обработки металлов обновлено 02.05.2020 — MULTICUT
Качество и производительность обработки на токарно-винторезных станках зависит от того, соответствует ли режущий инструмент обрабатываемой заготовке. Для точения дерева, пластиков, металлов используются разные виды резцов. Опасность неправильного выбора состоит в высокой вероятности порчи резца, деформации ходовых винтов, поломки шпинделя. Токарные резцы по металлу различаются размерами, формой, твердостью режущей кромки и другими параметрами. Чтобы выбрать правильный инструмент и режим обработки, необходимо хорошо ориентироваться в его классификации.
Конструкция резца
Все токарные резцы состоят двух конструктивных элементов:
- державки с прямоугольным или квадратным сечением, которая служит для фиксации в резцедержателе;
- головки – рабочей части, состоящей из нескольких режущих кромок.
По форме державки резцы могут быть:
- прямыми;
- изогнутыми;
- отогнутыми;
- оттянутыми.
По способу изготовления они бывают:
- Монолитными (цельными).
- Напайными.
- С механическим креплением сменных пластин.
Рабочая часть формируется несколькими плоскостями и режущими кромками, форма которых зависит от назначения инструмента. Большинство резцов изготавливается в левом и правом исполнениях и выбираются в соответствии с направлением подачи.
Классификация резцов
Мы разберем основные признаки, по которым классифицируют токарные резцы по металлу для станков с ручным управлением, полуавтоматов и автоматов с ЧПУ.
Материал рабочей части
Головки резцов для токарных станков по металлу изготавливают из материалов с высокой твердостью и устойчивостью к износу.
Инструментальные быстрорежущие стали
Основной легирующий элемент в таких сплавах – вольфрам (Р9, Р18). Некоторые марки быстрорежущих сталей содержат также молибден (Р6М5) и кобальт (Р6М5К5). Из этих сравнительно недорогих сплавов изготавливаются преимущественно монолитные резцы. Их используют для обработки заготовок из рядовых незакаленных сталей, цветных материалов и их сплавов.
Один из существенных недостатков быстрорежущих сталей – снижение твердости при нагреве свыше 200 °C. Резцы быстро теряют свои свойства при обработке на высоких скоростях вращения шпинделя и подачах, при недостаточной подаче СОЖ.
Твердые сплавы
Основу всех твердых сплавов составляют карбиды. В качестве связки используется кобальт. Из-за высокой цены твердые сплавы производятся преимущественно в виде пластин, которые припаиваются или закрепляются механическим способом на головках резцов. Существуют также монолитные твердосплавные инструменты (центровки, сверла) небольшого размера.
Твердые сплавы получают путем спекания и горячего прессования. Они имеют высокую твердость (86 – 92 HRA) и красностойкость (до 1150 °С), поэтому используются для изготовления деталей из труднообрабатываемых материалов: чугунных отливок, нержавеющих, жаропрочных, титансодержащих и закаленных сталей. По химическому составу твердые сплавы разделяют на следующие группы:
- Вольфрамокобальтовые (ВК3, ВК6, ВК8).
- Титановольфрамокотальтовые (Т15К6, Т5К10).
- Титанотанталовольфрамокобальтовые (ТТ7К12, ТТ20К9).
Из-за высокой стоимости вольфрама были созданы безвольфрамовые твердые сплавы на основе карбидов и цианидов титана. Твердосплавные пластины с износостойкими покрытиями выпускаются как отдельная группа материалов и имеют буквенную маркировку ВП.
Большинство зарубежных производителей твердых сплавов использует собственную маркировку. Чаще всего она не содержит сведений о составе материала и покрытия, поскольку эта информация считается коммерческой тайной. Вместо этого производители дают наглядные рекомендации по применению.
Твердые сплавы имеют ряд ограничений и недостатков в сравнении с быстрорежущими сталями: они нетехнологичны и имеют низкую ударную вязкость (склонны к образованию трещин при ударах). Для заточки токарных резцов по металлу с твердосплавными напайками используется специализированный абразивный инструмент (преимущественно алмазный).
Качество обработки
Некоторые источники предлагают делить резцы на черновые, получистовые и чистовые. В действительности качество обработки (шероховатость поверхности) зависит не только от конструктивных особенностей режущего инструмента, но также от качества его заточки и режима обработки – подачи на оборот и припуска. Поэтому один и тот же резец может использоваться как для обдирочных, так и для финишных токарных операций.
Виды резцов по выполняемым операциям
Токарно-винторезные станки способны выполнять множество видов обработки и с помощь них получают детали разных форм. В зависимости от назначения (выполняемой операции) резцы для них делят на несколько типов:
- Проходные служат для обработки наружных поверхностей цилиндрической и конической форм, формирования фасок. Подача выполняется параллельно оси заготовки.
- Подрезные используются для торцевания деталей. Резец подается перпендикулярно к оси заготовки.
- Проходные упорные резцы выполняют все перечисленные выше операции. Их широко применяют при изготовлении ступенчатых валов.
- Расточные резцы служат для обработки внутренних цилиндрических и конических поверхностей. Одна из особенностей их конструкции – массивная державка. От жесткости этого элемента зависит размерная точность.
- Резьбовые (наружные и внутренние) резцы служат для нарезания метрической и трубной резьбы. Их углы заточки составляют 60° и 55° соответственно. Для упорной и трапецеидальной резьбы используются специализированные фасонные резцы.
- Отрезные используются для отрезания заготовок.
- Прорезные (канавочные) резцы служат для протачивания наружных и внутренних канавок (для выхода шлифовального круга, для установки стопорных колец и т. д.)
- Фасонные – разнообразные по форме узкоспециализированные инструменты для создания профильных поверхностей.
- Резцы для контурного точения. Этот вид инструмента появился сравнительно недавно и используется преимущественно на станках с ЧПУ для чистовой обработки сложных поверхностей. Такие резцы снабжены пластинами ромбовидной формы, имеют острый угол заточки и рассчитаны на работу с небольшими припусками (до 2 мм).
Особенности твердосплавных пластин с механическим креплением
Резцы с механическим креплением пластин в настоящее время считаются наиболее востребованными для токарной обработки. Они обладают широким спектром технологических преимуществ в сравнении с напайными инструментами. Сменные пластины имеют высококачественную заводскую заточку и несколько режущих кромок. При износе одной из них пластину устанавливают в другое положение. Это позволяет сэкономить большое количество станочного времени. Державки и пластины унифицированы и стандартизированы, но не взаимозаменяемы. Современные твердые сплавы, из которых изготовлен инструмент, состоят из мелкодисперсных карбидов, поэтому отличаются повышенной ударной вязкостью и износостойкостью.
Запросить дополнительную информацию по выбору режущего инструмента для станков с ЧПУ вы может у консультантов компании Multicut по телефону или в онлайн-чате.
Выбор резцов для токарных станков по металлу
Мастера уже давно работающие с данным инструментом прекрасно осведомлены обо всех его разновидностях и функциональных возможностях. Новичкам, конечно же, придется потратить несколько больше времени на то, чтобы детально разобраться в разновидностях токарных резцов.
Конструкционные особенности инструмента для токарных работ
Любой резец обязательно оснащен двумя конструкционными компонентами:
- рабочая головка, чтобы обрабатывать металлическую деталь;
- державка, закрепляющая всю конструкцию на станочном оборудовании.
Для создания головки потребовалось разработать несколько плоскостей. Помимо этого, конструкция данной детали представлена и режущими кромками. Они заточены под определенным углом. Делается это с учетом таких параметров — вида обработки, специфических свойств того материала, из которого изготовлена деталь.
Вариантов исполнения державки — два. Мастера могут воспользоваться инструментами, представленными в таких поперечных сечениях — прямоугольных, квадратных. Известно несколько модификаций токарного инструментария исходя из его конструкционных особенностей:
- инструменты прямого исполнения, отличающие тем, что главные рабочие элементы расположены на одной осевой направляющей. Иногда они расположены и на двух, однако важно соблюсти параллельность последних;
- инструменты изогнутой конфигурации, в данном случае речь идет об изогнутой державке;
- отогнутые модели характеризуются тем, что имеется некоторый отгиб головки изделия относительно осевой направляющей державки;
- у оттянутых модификаций ширина головки уступает по аналогичному показателю державке. Правда, их осевые направляющие идентичны, либо смещены относительно друг друга.
Подразделение на категории токарных резцов
Весь инструментарий сертифицирован, создан по стандартам. Он может быть представлен цельным инструментом. Производство подобных изделий основано на использовании легированной стали, несколько реже — инструментальной. Однако последние практически не используются.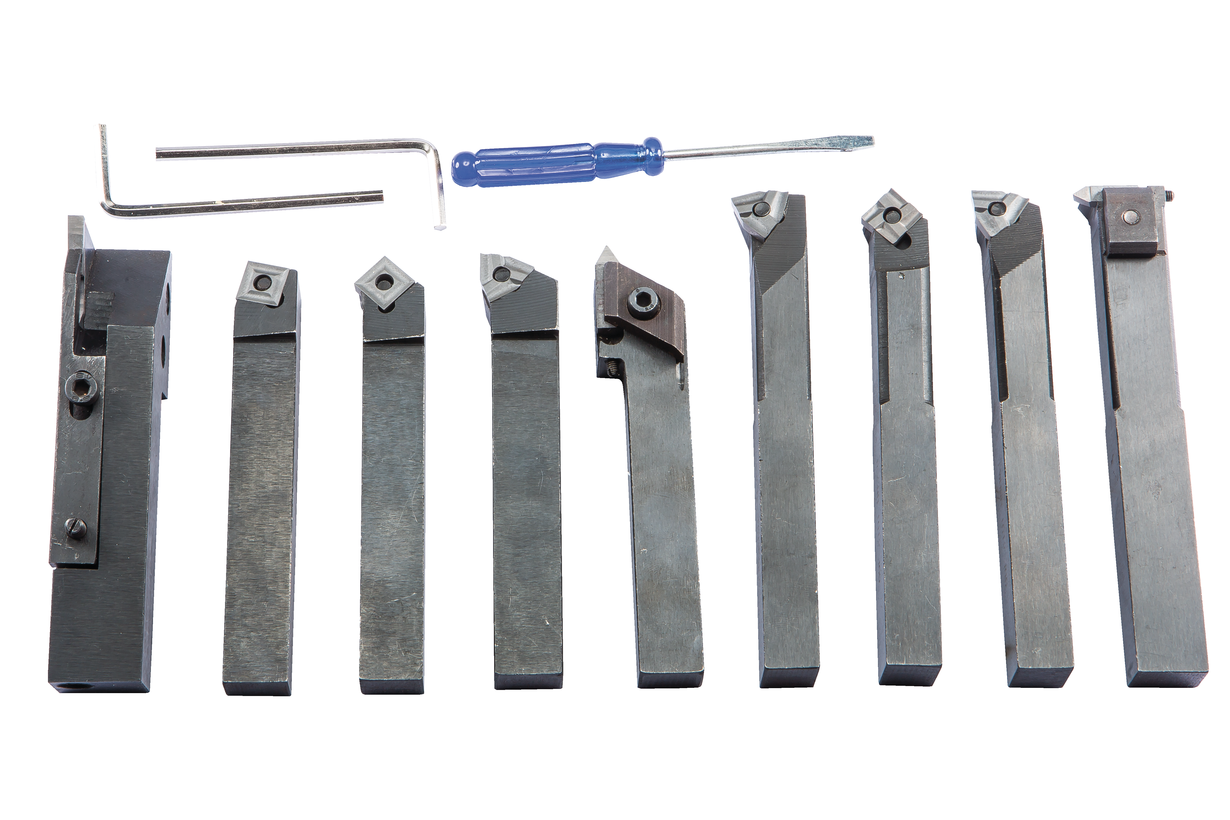
Еще одна интересная модификация — на изделие напаивается твердосплавный металл в виде пластины. Такие резцы особенно популярны, наиболее известны и востребованы. Но еще существует инструмент, пластины которого также представлены твердосплавным элементом, но являются съемными. К его рабочей зоне они прикреплены винтами. Но в рабочем процессе данный вид инструмента практически не задействуется.
Работать инструментом реально в разных направлениях. Решающую роль играет то, как необходимо совершить подающее движение. Поэтому инструмент классифицируется на такие разновидности — правого и левого типа. Первые наиболее распространены. Определить такой инструмент достаточно просто — по режущей кромке. Она должна находиться в той же стороне, что и большой палец в отогнутом положении, если на инструменте лежит правая рука. Точно также определяется и изделие левого типа.
Мастера выбирают необходимый инструмент для проведения определенного вида токарных работ. Следовательно, инструмент можно разделить на определенные виды и по этому показателю:
- обработка металлических изделий на чистовую;
- резцы для первичной обработки, черновой;
- изделия, необходимые для осуществления получистовой работы;
- модели, благодаря которым специалисты выполняют высокотехнологические операции.
Каждый инструмент наделен особенными свойствами, возможностями и отлично подходит для реализации специфических целей. Классификация инструментальных изделий для работы на токарном станочном оборудовании достаточно обширна. Например, известны еще и такие модели — проходные резцы. Они представлены несколькими модификациями. Прямые инструменты нужны, чтобы работать с изделиями цилиндрической формы, обрабатывать их внешнюю поверхность. Державки как прямоугольные, так и квадратные. Отогнутые модели актуальны в отделочном процессе торцевой зоны заготовочного материала. И, наконец, упорно отогнутые резцы, которыми работают с заготовками цилиндрической формы.
Помимо проходных резцов, специалисты пользуются и подрезными отогнутыми изделиями, которые между собой внешне несколько похожи. Однако последние отличаются формой пластины, которая режет заготовку. У них она треугольная. Резцы данного типа служат для того, чтобы работать с деталями в направлении, которое перпендикулярное оси их вращения.
Отрезные модификации очень распространены для работы с металлическими изделиями, чтобы отрезать их под углом девяносто градусов. Но можно использовать инструмент и с другой целью, например, прорезать канавки той глубины, которая требуется, на поверхности металлоизделия. Эта модель имеет специфическое конструкционное исполнение — тонкая ножка с напайной твердосплавной пластиной.
Что же касается наружной резьбы, то она обычно выполняется благодаря резьбонарезному инструменту. Если наружную поверхность заготовочной детали необходимо «украсить» резьбой, то именно этот резец воплотит в реальность поставленную задачу.
Перейти к списку статей >>Резец для токарного станка по металлу. Виды и заточка резцов для токарного станка по металлу
Условно любой резец для токарного станка по металлу представлен двумя элементами: головкой и державкой.
Головка — это исполняющая часть, состоящая из ряда плоскостей и режущих кромок с определенным углом. В зависимости от требуемого вида заточки резцу задается определенный угол.
Державка отвечает за фиксацию резца в держателе токарного устройства. Она имеет квадратную или же прямоугольную форму. Существует ряд стандартных размеров сечений каждой формы.
Разновидности конструкции
Существуют следующие виды резцов для токарного станка по металлу:
- Прямые. Державка и головка расположены на одной или параллельных осях.
- Изогнутые. Державка имеет согнутую форму при взгляде на нее сбоку.
- Отогнутые. Головка изогнута к державке при взгляде сверху.
- Оттянутые. Ширина державки больше, чем у головки.
Головка располагается на одной оси с державкой или же смещена по отношению к ней.
Если опираться на общеизвестную классификацию устройств в соответствии с ГОСТ, то они подразделяются на следующие виды:
- Обладающие режущей кромкой на основе легированной стали. Инструмент монолитный. Он может быть изготовлен из инструментального вида стали. В настоящее время к его использованию прибегают крайне редко.
- Начиненные напайками из твердых сплавов. Кромка-пластина припаяна к головке. Это наиболее часто встречаемый вид.
- Пластины из твердых сплавов, фиксируемые посредством механического способа. Режущая пластина закреплена на головке при помощи винтов и прижимов. За основу сменных резцов берутся металл и металлокерамика. Это самый редкий вид.
Классификация по направлению подающего движения
- Левая модель подается слева при взятии в левую руку. Главная рабочая кромка расположена над большим пальцем.
- Правая модель, соответственно, подается справа. Главная рабочая кромка находится под большим пальцем. В практике она встречается чаще.
Способы установки приспосбления
Резец для токарного станка по металлу может различаться по способу установки относительно поверхности для обработки:
- Радиальный вид. При обрабатывании резец принимает прямой угол к оси заготовки для обработки. Такой способ широко применим в промышленных предприятиях. Резец имеет унифицированную конструкцию крепления на станках. Он также обладает более удобным выбором геометрических положений режущей части.
- Тангенциальные. При обрабатывании резец располагается к оси заготовки под углом, отличным от прямого. Обладает более сложным способом крепления и применяется на токарных приспособлениях, позволяющих производить обработку высокой чистоты.
Различие по методу обработки
Резцы можно подразделить и по способу обработки:
- чистовой;
- черновой;
- получистовой;
- для работ, производимых с особой тонкостью.
На неровность обрабатываемой детали оказывает влияние радиус закругленности верхушки приспособления. Гладкая поверхность достигается при использовании резца, заточенного под большим радиусом.
Виды токарных резцов
Резец для токарного станка по металлу имеет множество видов. Самыми распространенными являются:
- Проходной. Он создает контуры детали при вращении, а также обеспечивает обточку, подрезку при подаче в поперечном и продольном направлении.
- Расточной вид создает разнообразные пазы, углубления и отверстия. Может выполнить сквозные отверстия.
- Подрезная модель применятся лишь для поперечного направления подачи для обточки деталей, обладающих ступенчатой формой и торцевых.
- Отрезной. Его подача осуществляется в поперечном направлении по отношению к оси вращения. Он производит пазы и канавки вокруг детали, применяется для отделения готового изделия.
- Резьбовой. Нарезает резьбу любого вида на деталях с любой формой сечения. Этот вид может быть изогнутым, прямым или же круглым.
- Фасонный. Он производит обточку детали сложной конструкции, может вынуть различные фаски изнутри и снаружи.
Набор резцов для токарного станка по металлу можно приобрести в специализированных магазинах или же заказать через Интернет.
Основа резцов
Материалы, из которых изготавливаются приспособления, подразделяются на три категории:
- Первая предназначена для режущих приспособлений, используемых при низкой скорости. Это инструментальные или же углеродистые металлы с показателем твердости закаливания 60-64. При повышении температуры резца для токарного инструмента выше 200-240 градусов качество его резки заметно снижается, поэтому на практике их применяют нечасто. К этой группе можно отнести приспособления на основе хромовольфрама, хромокремния и легированной стали с уровнем стойкости к температуре до 300 градусов.
- Вторая категория резцов применятся при высоком уровне вращения головки токарного станка.
Основу таких устройств составляет сталь с высокой категорией нарезания Р12 Р9 или Р9К5Ф2. После закалки материал твердеет до показателя 62-65 и сохраняет все свои свойства при температуре 650 градусов. Не подлежит протирке длительное время.
- Третью категорию составляют резцы на основе металлокерамики. Это твердосплавные приспособления, которые функционируют при высокой скорости станка и выдерживают температуру нагревания до 1000 градусов. Чугунные и некоторые детали из цветных сплавов точат устройствами на основе вольфрамокобальта (ВК6 для чистового и получистового исполнения, ВК8 для первичного обрабатывания). Сталь обтачивается твердым сплавом титановольфрамокобальтом Т15К6. При этом производится чистая обработка.
Приспособления для настольных токарных станков
Резцы для настольного токарного станка по металлу обладают малым сечением 8 х 8 и 10 х 10 мм. Они применяются для обрабатывания деталей малых размеров.
Резцы в форме сменных пластин
Резец для токарного станка по металлу категории Т5 К10 используется для первичной и прерывистой обточки. На основе кубического нитрида бора делаются сменные пластины для обрабатывания металлов, отличающихся особой твердостью, в том числе и чугуна. Цветные металлы обтачиваются посредством поликристаллического алмаза.
Пластины могут быть сменными. Они вставляются в державку. Некоторые модели содержат стружколомы, отлично дробящие стружку при невысокой подаче и поверхностной обточке. Такого рода пластины применяются при высокочистовой резке нержавейки и других видов стали.
Затачивание резцов
Любые виды резцов, помимо сменных пластин, время от времени подлежат затачиванию. Заточка резцов для токарного станка по металлу обеспечивает достижение требуемых величин углов и формы. В промышленных условиях она осуществляется на специализированных агрегатах.
Процесс этот в домашних условиях можно произвести посредством химических реактивов и кругов для шлифовки. Ручная заточка по уровню качества уступает промышленной. Главное здесь — правильная подборка шлифовального круга.
Для затачивания резцов из твердых сплавов берется круг из зеленого карборунда. Токарные резцы из углеродистых материалов затачивают кругами из корунда.
Затачивание рекомендовано выполнять при посредстве охлаждения (равномерная подача холодной воды на место контакта круга с обрабатываемым резцом). Можно осуществлять и сухую заточку, но после этого деталь не следует опускать в холодную воду, так как она может треснуть.
Стандартная схема процесса затачивания
В первую очередь обработке подлежит основная задняя грань, затем задняя вспомогательная и только потом передняя часть. В самом конце процесса обрабатывается вершина приспособления (радиус закругления). Затачиваемый резец следует постоянно передвигать на поверхности круга для шлифовки и слегка прижимать к образиву.
Обязательная составляющая процесса — это доводка резца, а точнее режущих граней (участков возле кромки, ширина которых достигает 4 мм).
Устройства из твердых сплавов затачивают при помощи оселков из меди, которые смазываются специальным составом в виде пасты или же смесью керосина и карбида бора.
Остальные виды резцов затачивают оселком с низким видом абразивности, смоченным машинным маслом или керосином.
Изготовление самодельных резцов
Можно изготовить и самодельные резцы для токарного станка по металлу. За основу таких устройств берутся ненужные сломанные сверла.
Центровки на основе сверл не ломаются. В особенности они подходят токарным станкам старой модификации. Они подлежат многократной переточке. Срок их службы достигает 30 лет.
Самодельные резцы для мини токарного станка по металлу изготавливаются из сегмента пилы Геллера. Он нарезается отрезным диском.
Как осуществить правильный выбор резца?
Выбирая резец, необходимо принять во внимание ряд рекомендаций.
Определите, с какого рода металлом вам предстоит работать, какие операции по обрабатыванию вы намечаете и какой степени нагрузку при этом испытает резец.
Решите, что является главным — точность соблюдения геометрии изделия или уровень обработки его поверхности. В зависимости от этого подбирается резец в соответствии с классифицирующими признаками и геометрическими пропорциями.
Обозначьте для себя, насколько является важным соблюдение условия износостойкости приспособления и как долго она должна оставаться неизменной.
Как заточить резцы для токарного станка по металлу
как правильно затачивать своими руками, видео
Заточка токарных резцов по металлу имеет большое значение в технологическом процессе. Каждый мастер должен знать нюансы этого процесса, которые зависят от материала резца, а также его предназначения.
Правильно проведенная операция помогает значительно продлить срок службы оборудования.
В каких случаях она необходима?
В процессе эксплуатации происходит трение стружки о рабочую поверхность инструмента. За счет повышения температуры в процессе работы происходит износ детали. Если не проводить заточку, то значительно снижается полноценный срок службы детали и всего оборудования.
В документации указана допустимые параметры износа резца. Если эти параметры превышены – инструмент использовать нельзя. Его необходимо заточить по передней и задней поверхности.
Допустимая величина износа отличается в зависимости от условий работы и колеблется в пределах 0.3-2 мм.
Инструменты и приспособления
В зависимости от сплава, твердости, угла затачивания и других технологических деталей, необходимо подобрать инструмент для заточки резцов. У каждого приспособления есть свои преимущества и недостатки.
Мусаты
Действенный инструмент, который представляет собой металлический стержень с рубчиком. Обработка ведется при помощи рукоятки.
Точильные бруски
Еще один вариант ручной обработки. Для заточки резцов при помощи точильных брусков потребуется сноровка, которая приобретается лишь с опытом. Резец необходимо приложить к детали и провести по ней от 10 раз.
Механические точилки
Автоматизированный способ заточки. Для начала нужно выставить входные параметры и в зависимости от них активно действовать инструментом.
Электрические точилки или заточный станок
Это наиболее универсальный и простой метод заточный станок удобно использовать, внешне он напоминает металлический брус с отверстиями разных размеров.
Наждачный, алмазный круг
Широко применяется алмазный круг, поскольку он обеспечивает высокую чистоту режущих поверхностей. Также с применением алмазных кругов увеличивается ресурс работы заточных резцов – количество возможных переточек возрастает на 20-30%.
Как правильно затачивать?
Заточку нужно производить в зависимости от износа и конструкции резца. Процесс можно проводить по передней, задней или обоим поверхностям. Для стандартных резцов следует выбрать заточку по всем режущим поверхностям. Если износ небольшой, то достаточно восстановить геометрию только задней поверхности.
Для многорезцовых станков заточка оснастки проводится по задней поверхности, а фасонных – по передней.
Выбираем способ в зависимости от вида режущего инструмента
Вид резца определяется количеством поверхностей, а также шириной лезвия и его формой. В соответствии с этими параметрами и следует выбирать способ заточки и его технологические особенности.
Вид резца, как и способ его заточки выбирает мастер в зависимости от работ, которые ему необходимо провести на токарном станке.
Плоские прямые
Основное предназначение данных резцов – обработка поверхности. Также с их помощью создают небольшие отверстия, выемки и пазы в готовых изделиях. Ширина лезвия у плоских прямых резцов колеблется в пределах 4-40 мм.
Угол заточки 25-40°.
Сам процесс заточки имеет упрощенную схему. Достаточно выровнять повреждённый при использовании торец. Обработка происходит аккуратной заточкой, без пресыщения на области. В последнюю очередь выставляется ручка.
Косые прямые
Заточка этих резцов происходит по следующей схеме:
- Выбрать нужные параметры ширины в пределах 4-40 мм.
- Подобрать подходящую для работы резца ширину.
- Срезать один угол до соотношения 70-75°.
- Провести заточку под углом в 25°.
Необходимо проверять с определенной регулярностью расположение кромки. Это требуется для контроля, чтобы резец лежал ровно с обоих поверхностей. Если кромка содержит изъяны, то такого эффекта добиться не получится.
Отрезные
Это специальные модели, необходимые для образования углового резца. Заточка этого инструментария производится только с одной стороны. Отрезные резцы применяются для черновой отделки изделий по металлу или дереву в зависимости от вида токарного станка. Алгоритм заточки:
- Вырезать угол торца под углом не больше 45°.
- Произвести заточку до 40°. Также заточка не должна быть меньше 30°, так как инструментарий становится неэффективным в работе.
Длину мастер может выбрать сам в зависимости от требуемого варианта для конкретной работы.
Полукруглые плоские
Этот резец необходим, чтобы делать выемки в готовых изделиях круглыми. Но при этом сфера применения резца более широкая, например, он используется для обеспечения обработки после проведения черновой работы.
Алгоритм заточки:
- Обточка с использованием необходимых материалов.
- Примерка торца, чтобы он четко подходил по форме.
- Проведение заточки в параметрах от 20 до 45 градусов.
Если мастер на токарном станке собирается делать декоративные вариации выемок, то ему понадобится несколько различных полукруглых плоских резцов.
Желобчатые
Это самые необычные виды резцов, в первую очередь из-за своей формы в виде желоба. Ширина инструмента не превышает 3 см на изношенном каркасе для начала необходимо обработать торец до 10 см, чтобы получить полукруг. Заточить нижнюю часть, которая расположена на выпуклой поверхности до 40 градусов.
Рассчитываем углы затачивания: типы и характеристики
Если неправильно выбрать угол затачивания в результате вся процедура будет неэффективной. При длительной неправильной заточке легко повредить резец и тогда придется приобретать новый инструмент. У резцов существует несколько типов углов: вспомогательные, в проекции, в плане, главные. Каждый из углов имеет свои особенные характеристики.
Главные углы
Все на резце 2 главных угла: передний и задний. Передний определяет качество работы и сколько в итоге получится стружки. Если угол заточки выбран неправильно, то будет возникать значительная деформация изделия. В итоге это приводит к увеличению амплитуды колебаний и отрицательному воздействию на держатель.
Вспомогательные углы
Эти углы расположены на вспомогательной площадке. Главный вспомогательный угол находится между направлением и режущей кромкой. Есть еще и второй вспомогательный угол, который образован отрезком прямой, идущей через вершину плана, и пересекается в площади кромки.
Углы в плане
Углы находятся в трех местах. Главный угол в плане – возле проекции и главной линии. Вспомогательный угол – продолжает проекцию по направлению рабочего процесса. Угол у вершины – у плоскости с пересечением основной. Первые два угла не могут иметь показатели ниже нуля, а с третьим это вполне возможно.
Способы измерения углов режущего инструмента
Измерения проводятся с помощью простого угломера. Угломер стандартный состоит из основания, непосредственно сектора изменений, шаблона и винта для фиксации. Схема измерений:
- Размещение на основании.
- Соприкосновение кромки и плоскости.
- Направить деталь параллельно кромке.
- Проложить шаблон к площадке.
Показатели измеряются при помощи специальной линейки, но есть и нониус, который помогает провести более точные измерения.
Подробные схемы и инструкции, как это сделать своими руками
Мастер должен знать полный технологический процесс, чтобы правильно производить заточку инструмента своими руками.
Технологический процесс
Технологический процесс включает в себя несколько основных моментов:
- Заднюю поверхность обрабатывают под углом равным заднему углу державки.
- На втором этапе происходит обработка самой режущей поверхности.
- Угол заточки должен быть на пару градусов больше, чем задний угол резания на пару градусов.
- Уже на третьем этапе формируется задний угол.
После доводки следует шлифовка, как финальный этап заточки.
Проведение доводки
Доводку следует проводить по выбранной методике. Основные моменты:
- резцы не погружают в воду, поскольку они могут сломаться;
- при доводке обязательно подавать воду для охлаждения;
- сначала обрабатывают заднюю грань, затем главную и вспомогательную.
Шлифовка
Шлифовку проводят с использованием наждачного круга. Оптимальный вариант – мелкозернистая модель.
Техника безопасности
Каждый мастер, работающий на токарном станке, должен уметь проводить заточку резцов своими руками. Важно только соблюдать правила техники безопасности. Для этого необходимо использовать защитное оборудование для лица. Прикасаться к станку, резцу разрешено только после полного остывания.
Заточка резцов для станка – один из наиболее важных технологических процессов, который должен уметь выполнять любой квалифицированный токарь. Детали процесса зависят от вида резца, выполняемых работ и степени износа.
Заточка бит для токарных станков из быстрорежущей стали
Каковы типичные углы наклона и зазора (спуска) для коронок из быстрорежущей стали?
См. Рисунок A – 1 и таблицу A – 1.
Рисунок A – 1. Номенклатура инструментальных долот.
Материал | Боковой зазор | Передний просвет | Боковые | Задний |
Алюминий | 12 | 8 | 16 | 35 |
Латунь | 10 | 8 | от 5 до 24 | 0 |
бронза | 10 | 8 | от 5 до 24 | 0 |
Чугун | 10 | 8 | 12 | 5 |
Медь | 12 | 10 | 20 | 16 |
Машинная сталь | 10–12 | 8 | 12–18 | 8–15 |
Инструментальная сталь | 10 | 8 | 12 | 8 |
Нержавеющая сталь | 10 | 8 | 15–20 | 8 |
Таблица A – 1.Свободный и передний углы в градусах для обычных металлов.
Какова процедура заточки токарных инструментов общего назначения из быстрорежущей стали?
Начните с правки шлифовального круга. Затем найдите типичные углы для материала заготовки, а затем выполните шаги, показанные на Рисунке A – 2. Часто окунайте инструмент в охлаждающую жидкость, чтобы не допустить перегрева и отжига. Любое изменение цвета биты указывает на то, что она больше не затвердевает. Если это произойдет, подумайте о том, чтобы начать заново с самого начала.Углы резцов не являются критичными, и большинство инструментов будут резать материал удовлетворительно, только менее эффективно.
Рисунок A – 2. Этапы заточки резцов из быстрорежущей стали.
.Фреза для токарного станка по металлу. Виды и заточка инструмента для токарного станка по металлу
Условно любой инструмент для токарного станка по металлу представлен двумя элементами: головкой и держателем.
Головка – это исполнительская часть, состоящая из ряда плоскостей и режущих кромок с определенным углом. В зависимости от требуемого типа заточки резцу дается определенный угол.
Держатель отвечает за фиксацию инструмента в держателе токарного станка. Имеет квадратную или прямоугольную форму.Для каждой формы существует ряд стандартных размеров сечения.
Типы конструкции
Резцы для токарного станка по металлу бывают следующих типов:
- Прямые. Держатель и головка расположены на одной или параллельных осях.
- Изогнутая. При взгляде сбоку держатель имеет изогнутую форму.
- Отклонено. Если смотреть сверху, голова наклонена к держателю.
- Обращается. Ширина держателя больше, чем у головы.Головка расположена на одной оси с держателем или смещена относительно нее.
Если опираться на общеизвестную классификацию устройств по ГОСТу, то они делятся на следующие типы:
- Имеющие режущую кромку на основе легированной стали. Инструмент монолитный. Может быть изготовлен из инструментальной стали. В настоящее время его использование крайне редко.
- Наплавленные твердыми сплавами. Кромка припаяна к голове. Это самый распространенный вид.
- Пластины из твердых сплавов, закрепленные механическим способом. Режущая пластина крепится к головке винтами и струбцинами.
Металл и металлокерамика используются в качестве основы для сменных резцов. Это самый редкий вид.
Классификация по направлению поступательного движения
- Левая модель подается влево, когда берется в левую руку. Основная рабочая кромка расположена над большим пальцем.
- Правая модель соответственно питается справа. Основная рабочая кромка находится под большим пальцем.На практике это происходит чаще.
Способы настройки приспособлений
Инструмент для токарного станка по металлу можно отличить по способу установки относительно обрабатываемой поверхности:
- Радиальный вид. При обработке резец принимает прямой угол к поверхности ось заготовки для обработки. Этот метод широко применяется на промышленных предприятиях. Фреза имеет унифицированную конструкцию крепления на станках. Также имеется более удобный выбор геометрического положения режущей части.
- Тангенциальный. При обработке фреза располагается к оси заготовки под углом, отличным от прямой линии. Он имеет более сложный способ крепления и используется на токарных станках, допускающих высокую степень чистоты обработки.
Разница в обработке
Резцы также можно подразделить по способу обработки:
- чистовая;
- черновая;
- полудрагоценные;
- Для особо тонких работ.
На шероховатость детали влияет радиус кривизны верхней части устройства. Гладкая поверхность достигается за счет использования инструмента, заточенного под большой радиус.
Типы токарных инструментов
Инструмент для токарной обработки металла имеет много типов. Наиболее распространены:
- Walk-through. Создает контуры детали при вращении, а также обеспечивает точение, обрезку при подаче в поперечном и продольном направлениях.
- При растачивании можно увидеть множество канавок, канавок и отверстий.Можно проделывать сквозные отверстия.
- Подрезная модель применяется только для поперечного направления подачи для токарных деталей ступенчатой формы и торца.
- Раскрой. Подача его осуществляется в поперечном направлении относительно оси вращения. Он производит бороздки и бороздки вокруг детали, используемые для разделения готового продукта.
- Резьбовой. Резьба любого вида на деталях с любой формой сечения. Этот вид может быть изогнутым, прямым или круглым.
- Фасонный.Изготавливает токарные детали сложной конструкции, позволяет снимать различные фаски изнутри и снаружи.
Набор инструмента для токарного станка по металлу можно приобрести в специализированных магазинах или заказать через Интернет.
Основа резцов
Материалы, из которых изготовлены устройства, делятся на три категории:
- Первая предназначена для режущих устройств, используемых на малой скорости. Это инструментальные или углеродистые металлы с индексом твердости 60-64.Когда температура инструмента для токарного инструмента поднимается выше 200-240 градусов, качество его резки заметно снижается, поэтому на практике они используются нечасто. В эту группу входят устройства на основе хромовольфрама, хромо-кремниевой и легированной стали с уровнем устойчивости к температурам до 300 градусов.
- Резцы второй категории используются на высоком уровне вращения головки токарного станка. Основа таких устройств – сталь высокой категории резания П12 П9 или П9К5Ф2. После застывания материал затвердевает до значения 62-65 и сохраняет все свои свойства при температуре 650 градусов.Не тереть долго.
- Третья категория – фрезы на основе цемента. Это устройства с твердосплавными напайками, которые работают на высоких оборотах станка и выдерживают температуру нагрева до 1000 градусов. Заточка чугуна и некоторых деталей из цветных сплавов осуществляется с помощью приспособлений на основе вольфрамокобальта (ВК6 для чистового и полуфабрикатного исполнения, ВК8 для первичной обработки). Сталь шлифуется твердым сплавом титан-летучего кобальта Т15К6. В этом случае проводится чистая обработка.
Принадлежности для настольных токарных станков
Резцы для настольных токарных станков по металлу имеют малое сечение 8 x 8 и 10 x 10 мм. Их используют для обработки мелких деталей.
Резцы в виде сменных пластин
Режущий инструмент для токарного станка по металлу категории Т5 К10 предназначен для первичного и прерывистого точения. На основе кубического нитрида бора изготавливаются сменные пластины для обработки металлов, отличающихся особой твердостью, в том числе чугуна.Цветные металлы шлифуются поликристаллическим алмазом.
Пластины сменные. Они вставляются в держатель. Некоторые модели содержат стружколомы, отличное измельчение стружки с низкой подачей и заточкой поверхности. Такие пластины используются для высокоточной резки нержавеющей стали и других марок стали.
Заточка резцов
Любые фрезы, кроме сменных пластин, время от времени, оттачивать. Заточка резцов на токарном станке по металлу обеспечивает получение необходимых углов и форм.В промышленных условиях выполняется на специализированных агрегатах.
Этот процесс можно выполнять в домашних условиях с помощью химических реагентов и шлифовальных кругов. Ручная заточка по качеству уступает промышленной заточке. Здесь главное – правильный подбор шлифовального круга.
.ТОКАРНО-ТОКАРНЫЕ ИНСТРУМЕНТЫ – Скачать PDF бесплатно
ХОНИТИРОВАНИЕ ДУБЛИКАТОРНЫХ ФРЕЗОВ
Положите плоскую поверхность фрезы или сверла на плоскую верхнюю поверхность хона, так чтобы остальная часть фрезы выступала за край. Потрите резаком или коронкой вверх и вниз по хону (Рисунок 24-44).Обязательно держите
Дополнительная информацияИзготовление часовых колес и шестерен
Изготовление часовых колес и зубчатых фрез При изготовлении часов своими руками или при ремонте иногда требуется резак нестандартного размера. Иногда требуется только одна шестерня, и это не оправдывает стоимость коммерческого
. Дополнительная информацияЗаточка компаньона
Resharpening Companion 10950 Правильные углы, изображения и пошаговые инструкции Инструмент Resharpening Companion предназначен для использования в качестве руководства и краткого справочника, который поможет вам увеличить резкость. Он не предназначен для замены
Основы притирки и полировки
Основы притирки и полировки Приложения Лабораторный отчет 54 Притирка и полировка 1.0: Введение Притирка и полировка – это процесс точного удаления материала с заготовки (или образца)
Дополнительная информацияИнструмент и шлифовальный станок Bonelle
Инструмент Bonelle и шлифовальный станок для фрез. Шлифовальный станок был построен примерно в 1987 году и выставлен на 89-й выставке модельного машиностроения, где был награжден бронзовой медалью (см. ME Vol164 № 3868, стр. 273).Впоследствии
Дополнительная информацияСОВЕТЫ ПО СВАРКЕ TIG от Тома Белла
(Этот документ состоит из двух частей: сначала общая сварка TIG, а затем одна, посвященная алюминию.) СОВЕТЫ ПО СВАРКЕ TIG от Тома Белла 1. Чем больше стержень, тем легче его подавать. Используйте стержни большего диаметра (3/32
Дополнительная информацияГлава 9: Заточка инструментов
Глава 9: Заточка инструментов За последние несколько лет в пародонтологическом лечении произошел ряд интересных изменений.Однако краеугольным камнем пародонтологического лечения остается механический
. Дополнительная информацияУстройство для резки прямоугольников Speed-Mat
Резак для прямоугольных матов Speed-Mat 1 Плинтус с сотовым покрытием. 2 Удерживать левую. 14 3 Нижний прижим. 4 4 Правило левого / правого. 8 5 8 5 Указатель линейки влево / вправо. 1 6 Правило сверху / снизу. 7 Указатель верхней / нижней линейки.
Дополнительная информацияИНСТРУКЦИЯ ДЛЯ ПЕЧИ PEPSI CAN
Gear PEPSI CAN STOVE INSTRUCTIONS [ПРИМЕЧАНИЕ: теперь доступны обновленные инструкции.В новой печи меньше шансов развить утечки пламени, а топливно-воздушная смесь улучшена. Инструкция по приготовлению кольца для тушения
Дополнительная информацияБЛОК ОБРЕЗКИ / АЛМАЗНЫЙ СТАНОК TST.13
БЛОК ОБРЕЗКИ / АЛМАЗНЫЙ СТАНОК TST.13 СПРАВОЧНИК, отн. 02.15 БЛОК ОБРЕЗКИ / АЛМАЗНЫЙ СТАНОК TST.13 REL. 02.15 АНГЛИЙСКИЙ ЯЗЫК 1 ОПИСАНИЕ МАШИНЫ TST.13 был разработан и построен для обработки метакрилата.
Проекты детской мебели
Это отрывок из книги Джеффа Миллера «Проекты детской мебели», авторское право 2002 г., издательство Taunton Press www.taunton.com ДЕТИ-РОКЕРЫ ВСЕГДА В ДВИЖЕНИИ. Получить их даже
непросто. Дополнительная информацияКОМПАКТНЫЙ ЭЛИТНЫЙ РЕЗАК ДЛЯ МАТОВ
ИНСТРУКЦИЯ ПО ЭКСПЛУАТАЦИИ МОДЕЛИ 350-1 КОМПАКТНЫЙ ЭЛИТНЫЙ РЕЗАК ДЛЯ МАТОВ ИНСТРУКЦИЯ И РУКОВОДСТВО ПО ЭКСПЛУАТАЦИИ Система резки матов 32 дюймов (81 см) с косыми и прямыми резаками, производственными ограничителями и 20-дюймовым (51 см) бруском.
Дополнительная информацияРУКОВОДСТВО ПО ЭКСПЛУАТАЦИИ СТАНКОМЕЛЬЧАТОГО СТАНКА 8 ”
8 “РУКОВОДСТВО ПОЛЬЗОВАТЕЛЯ СТАНКОМОЛИКОВОЙ СТАНКИ ПРЕДУПРЕЖДЕНИЕ: внимательно прочтите и усвойте все ИНСТРУКЦИИ перед работой.Несоблюдение правил техники безопасности и других основных мер предосторожности может привести к серьезным личным
Дополнительная информацияВведение в ДЖИГЫ И СВЕТИЛЬНИКИ
Введение в ПРИСОЕДИНЕНИЯ И ПРИСПОСОБЛЕНИЯ Введение Успешное выполнение любого массового производства зависит от взаимозаменяемости, которая облегчает сборку и снижает стоимость единицы продукции. Серийное производство
Дополнительная информацияБУКЛЕТ ПО РЕМОНТУ НОЖЕЙ
БУКЛЕТ С ИНСТРУКЦИЯМИ ПО РЕМОНТУ ЛЕЗВИЯ Содержание Раздел I: Раздел II: Раздел III: Раздел IV: Раздел V: Раздел VI: Снятие лезвия Обратитесь к этому разделу, если вам необходимо снять лезвие с вала весла.
Дополнительная информацияЛИДЕР В ТЕХНОЛОГИИ РЕЗКИ
ЛИДЕР В ТЕХНОЛОГИИ РЕЗКИ БОЛЕЕ 2 ЛЕТ ПРИЧИНЫ, ПОЧЕМУ TRONEX ЯВЛЯЕТСЯ ЛУЧШИМ В МИРЕ 1 2 ПРЕВОСХОДНАЯ ПРОИЗВОДИТЕЛЬНОСТЬ РЕЗКИ Сотни тысяч разрезов до затупления. Вырезать сотни тысяч
Дополнительная информацияУрок 6: Измерение деревьев
Обзор и введение Урок 6: Измерение деревьев В Уроке 4 и Уроке 5 вы узнали, как создать фиксированный или изменяемый график. После того, как ваш участок создан, и ваши деревья подсчитаны, теперь
S&W Race Cars and Components, Inc.
S&W Race Cars and Components, Inc. 11 Mennonite Church Road Spring City, PA 19475 ТЕХНИКА И ИНФОРМАЦИЯ: 610-948-7303 ЗАКАЗЫ: 1-800-523-3353 ОФИСНЫЙ ФАКС: 610-948-7342 EZ INFO FAX 610-792- 1234 ВНИМАНИЕ !!! –
Дополнительная информацияПреобразование хромированного бампера MGB
Инструкции по установке переделки хромированного бампера MGB на 1974 1 / 2-1980 MGB Этот комплект требует резки, сварки и покраски.Рекомендуется профессиональная установка. Примечание: каждый корпус MGB немного отличается
Дополнительная информацияОсновы сегментированной токарной обработки клепок
Основы сегментированной токарной обработки нотоносца Джима Роджерса Версия 1.2 Февраль 2005 г. JL Rodgers, Incorporated 36 Briar Drive Martinez, CA 94553 9925) 229-5773 Основы сегментированной токарной обработки нотоносца
Дополнительная информацияКраткое руководство по шлифовке полов
Краткое руководство по шлифовке полов Подготовка / зачистка полов Выравнивающие полы Восстановление полов Шлифовка и полировка натурального камня Шлифовка и полировка бетона Шлифование дерева HTC – Professional Floor Systems Руководство по инструментам Бетон
Дополнительная информацияПромышленные ножи и лезвия
Промышленные ножи и лезвия Hyde Tools производит специальные инструменты, которые профессионалы во многих областях используют для быстрой и точной работы.Есть универсальные ножи и ручные ножи для паркета
. Дополнительная информациядля ручных станков
UC RIVERSIDE МЕХАНИЧЕСКИЙ МАГАЗИН СТАНДАРТНЫЕ ПРОЦЕДУРЫ ЭКСПЛУАТАЦИИ СТАНКОВ ДЛЯ РУЧНЫХ СТАНКОВ РЕДАКТИРОВАНИЕ: V5 ДАТА: 11-28-2011 СОДЕРЖАНИЕ ТЕМА (И) РАЗДЕЛА СТРАНИЦА Основные возможности
Дополнительная информация74 Глава 5.5.5 Очистка CO 2
74 Глава 5 5.5 Очистка CO 2 Метод CO 2 включает распыление CO 2 снега на оптическую поверхность. Снег производится с помощью специальной насадки (рис. 5.7), которая расширяет газ или жидкость через отверстие.
Целая рука
Упражнения Ходьба и переворот 5 Вращение дубинки Вращайте карандаш, вокруг и между пальцами, как будто это дубинка.10 Проведите пальцами по карандашу (ваш указательный палец будет похож на червяка, поднимающегося на
Дополнительная информацияДумайте о точности, думайте о HSS REAMING
Думайте о точности, думайте о HSS РАЗВЕРТЫВАНИЕ ОБЩИЕ ИНСТРУМЕНТЫ ДЛЯ РАЗВЕРТЫВАНИЯ 2 Увеличьте масштаб развертки 3 Какая HSS обеспечивает максимальную эффективность? 4 Покрытия для наилучших характеристик 5 Словарь 6 Выберите правильный дизайн 7 Типы фаски
Дополнительная информацияАвтор: Уолтер Галан
Замена передней панели ipad 2 GSM Замените переднюю панель вашего ipad 2 GSM.Автор: Вальтер Галан ВВЕДЕНИЕ Примечание: это полное руководство по замене простой передней панели. Если у вас Front
Дополнительная информацияТокарный фрезерный станок
Токарно-фрезерная насадка L C. MASON Путем умелого складывания холоднокатаной плоской заготовки вместе, Т-образные пазы и салазки для этой токарной фрезерной насадки сделаны без дорогостоящего оборудования. Фактически всего два инструмента,
Дополнительная информацияАкриловый экструдированный лист (FF)
Техническая информация Экструдированный лист АКРИЛИТА (FF) №2 Резка дисковыми пилами В этом кратком описании приведены рекомендации по: Эксплуатации оборудования Устранение неисправностей Оборудование Акрилитовый лист обычно режется с накладными расходами
Дополнительная информацияТехническая информация
нарезание резьбы Техническая информация Руководство по поиску и устранению неисправностей 115 СТРЕЛКА НЕ ЗАПУСКАЕТСЯ Глубина программы: Размер сверла метчика: Резкость метчика: ход сжатия может использовать всю глубину программы.Проверьте размер сверла для метчика.
Руководство по сварке MIG для новичков
Руководство по сварке MIG для новичков Названия сварки MIG Сварка MIG, или MIG, является аббревиатурой от слова «сварка металла в инертном газе». MIG – широко используемый и общепринятый сленговый термин, который был уместен, когда процесс
Дополнительная информацияРисование от руки. Разделы
3 секции эскиза от руки 3.1 Почему эскизы от руки? 3.2 Основы создания эскизов от руки 3.3 Основы создания эскизов от руки 3.4 Расширенные эскизы от руки Ключевые термины Цели Объяснить, почему создание эскизов от руки
Дополнительная информацияИНСТРУКЦИИ ДЛЯ МАСТЕРА КАСТЕРА 10/1/91
ПРИНАДЛЕЖНОСТИ МАШИНЫ A. Перегородка дефлектора литника, которая должна быть подвешена к существующей перегородке, чтобы помочь отделить литники от пуль. B. Деревянная поворотная ручка для установки после распаковки.Вкрутите деревянную ручку в
Дополнительная информация .видов режущих инструментов, используемых при обработке
Обрабатывающие режущие инструменты превращают куски металла в надежные прецизионные детали, от внутренностей автомобиля до деталей самолета. Обрабатывающий режущий инструмент варьируется от оборудования для грубой резки, такого как отрезная пила или шлифовальный станок, до программируемых, ориентированных на производство станков, таких как металлообрабатывающий завод. Узнайте о различных типах режущих инструментов, используемых машинистами, чтобы украсить свой магазин базовыми инструментами для хобби или тяжелым оборудованием для промышленных проектов.
Токарный станок
Если вы когда-нибудь задумывались, как повернуть лестничные столбы, то вам подойдет токарный станок. Токарный станок механика работает как дровяной стол, но дает мощность и точность для фрезерования металла. Установите материал с каждого конца на токарный станок, затем поверните токарный станок и прижмите режущие кромки к материалу, когда он вращается. Вы также можете вручную прижать режущие кромки к материалу или запрограммировать и управлять резом через компьютерные данные.
Сверлильный пресс
Сверлильный станок сверлит прецизионные отверстия, разворачивает отверстия и нарезает резьбу.Сверлильный станок оснащен рычагом, который подвешивает сверло на стационарном основании. Поместите материал в основание, затем активируйте сверло и опустите его через материал. Дрель прижимной нижний на неподвижной оси; они режут точно вверх и вниз.
Фрезерный станок
Станок, известный также как металлообрабатывающий завод; Фрезерные станки – это различные станки для резки и формовки металла, которые могут быть специально построены, коммерчески доступны или запатентованы. Программируемые фрезерные станки, которые выполняют множество операций резания на различных осях, называются станками с ЧПУ.Большинство фрезерных станков оснащены мобильными вращающимися режущими инструментами, которые протыкают, разрезают и формируют деталь из неподвижного материала.
Шлифовальный станок
Ручной электроинструмент, вращающий абразивные или заостренные диски для шлифования, придания формы и резки материалов. Портативность шлифовального станка позволяет выполнять резку и формовку на участках, недоступных для стационарных режущих инструментов.
Рубильная пила
Рубильная пила – это стационарный инструмент для черновой резки, который можно использовать для резки материалов по длине.Разделочная пила оснащена вращающимся абразивным или заостренным лезвием, подвешенным к рычагу над неподвижным основанием. При опускании лезвие режет материал, лежащий на основании, рубящим движением.
Сварщики
Сварочные инструменты используют сверхгорячее концентрированное пламя для резки материала. Пламя сварщика может расплавлять твердые и толстые материалы без физического сопротивления. Однако это обычно приводит к грубым или грязным краям.
Ручные вращающиеся инструменты
Насадки вращающихся инструментов, называемые битами, используются для резьбы, резки, развертывания и удаления заусенцев.Ручные вращающиеся инструменты обычно весят меньше фунта и, поскольку их насадки имеют небольшие размеры, их можно использовать для выполнения мелких или точных работ вручную.
Если у вас есть обучение или опыт, вы сможете самостоятельно обращаться с некоторыми режущими инструментами. Но если вы все еще новичок в этой профессии, лучше всего обратиться в компанию, занимающуюся механической обработкой в Сан-Хосе. Таким образом, вы можете быть уверены в качестве и точности резки деталей вашего хобби или машин.
Высокоскоростные токарные станкипротив твердосплавных – снова
Эта тема была задушена до смерти, но несколько лет назад продажа, объявленная в каталоге Enco, побудила провести несколько экспериментов с инструментами из быстрорежущей стали и твердосплавными пластинами.Этот пост предназначен для HSM и посвящен тому, что хорошо работает на небольших токарных станках, которые обычно можно найти в домашнем магазине. Вот материалы, которые были оценены, и их стоимость:- Бланк из быстрорежущей стали 1/4 M2, отшлифованный вручную по 1,10 долл. США за штуку (Enco 383-5316, производитель: Interstate) с заводским держателем в 4-позиционной стойке, инструмент всегда по центру (без регулировочных шайб)
- Державки 5/8 для пластин, набор из 5 предметов 35,00 долл. США (Enco TG250-1402) с 3/8 I.C. твердосплавные пластины, 10 по 3 доллара за штуку (Enco TG340-1014, производитель: Interstate).Державки были изменены таким образом, что фрезы всегда находятся по центру (без прокладок).
(Обратите внимание, что сменные державки + фрезы можно приобрести по более низкой цене у других дистрибьюторов.)
Вот пять различных державок; есть правый и левый инструмент для обработки уступа, правый и левый угловой «черновой» инструмент (идентичный первым двум, за исключением того, что режущая поверхность ориентирована под углом 30 градусов) и «своего рода» резьбонарезной инструмент (не не имеет достаточного бокового рельефа, чтобы нарезать крупную резьбу).
Мое первое впечатление заключалось в том, что некоторые из этих державок могут не понадобиться, в зависимости от стойки токарного станка. Слегка повернув стойку инструмента, два инструмента для поворота под прямым углом («под прямым углом» в том смысле, что они обычно расположены под углом девяноста градусов к оси поворота) могут выполнять те же операции, которые предназначены для выполнения двух угловых державок.
Резцедержатель “резьбонарезной” также может быть заменен другими в комплекте – одна и та же пластина используется для всех державок (угол 60 градусов).Единственная причина для предпочтения любого из инструментов (кроме правого или левого) – это удобство, такое как близость / натяжение к / с патроном или задней бабкой.
Державки, предназначенные для “заплечика”, могут не пригодиться для HSM, если глубина резания невелика. Большинство небольших токарных станков не любят делать такой рез (режущая кромка параллельно уступу) без жалоб: типичное явление – чрезмерное вибрирование и следы от инструмента. Чтобы выполнить операцию запрессовки без дребезга, скорость вращения шпинделя должна быть ЗАМЕДЛЕНА, что иногда сводит на нет цель твердосплавного инструмента по сокращению времени обточки.
Однако есть альтернатива для небольших токарных станков. Можно повернуть с желаемой скоростью / подачей почти до заплечика, а затем выключить двигатель, оставив подачу включенной (это также способ, которым я подхожу к некоторым работам с одноточечной резьбой на небольшом токарном станке).
После того, как шпиндель заведен, шпиндель / заготовку можно вращать вручную, пока не будет достигнут размер заплечика – в этот момент отключите подачу и продолжайте вращать шпиндель вручную, пока не будет получена чистая поверхность без вибрации. .Обычно это занимает всего один или два хода.
Более традиционный метод – вероятно, тот, который использует большинство из нас – это повернуть диаметр к уступу с помощью фрезы, расположенной под углом (так, чтобы поверхность была слегка вогнутой), без учета вибрации. Затем вытащите режущий инструмент (с поперечным суппортом), повернув его к уступу на размер без следов вибрации и перпендикулярно оси токарного станка.
Я не использую резцедержатель QC на моем меньшем токарном станке; они снижают жесткость на малых токарных станках , IMO.Заказанные мною державки нужно было модифицировать, чтобы они подходили к моей 4-ходовой части, чтобы пластины находились точно на центральной линии шпинделя (я не использую прокладки). Я намеренно купил больший набор, чтобы можно было подогнать их под свой токарный станок.
Чтобы режущая кромка держалась близко к краю четырехходового резцедержателя, а не свешивалась слишком сильно, мне нужно было удалить 1,50 дюйма из длины хвостовика. Чтобы разместить режущий инструмент на центральной линии шпинделя, необходимо было удалить около 0,060 с нижней части державок.
Ни одна из этих модификаций не создала бы проблемы, если бы державки были изготовлены из (типичного) полутвердого материала, такого как 4140. Но, к моему удивлению (и радости), державки были ЗАВЕРШЕННЫМИ – я не ожидал этого от скромно- ценовой набор. Обычно можно отколоть лишнюю длину абразивным отрезным кругом в шлифовальном станке, но мой шурин позаимствовал мой компрессор примерно на месяц назад для проекта автоматического восстановления (примечание для себя: когда компрессор возвращается, удалите колеса и выбросьте их, чтобы не брать взаймы в будущем).
Я установил абразивный отрезной круг в обрезной фрезер и вырезал хвостовик держателя. Державка была помещена в тиски фрезы (перевернутой, на параллели), а толщина уменьшена до размера в вертикальной фрезере. (Эту операцию можно было бы выполнить в три раза быстрее и с лучшими результатами на горизонтальном стане, но на момент написания статьи у меня не было твердосплавного инструмента для этого станка.)
Скорость шпинделя фрезы составляла 3200 об / мин, и в цангу была установлена твердосплавная концевая фреза с 4 зубьями 1/4 дюйма. С державкой, прочно зажатой в тисках фрезы, смещение всех салазок было сведено к минимуму за счет затягивания / фиксации фиксаторов клинка. Половину лишнего материала удалили за три продольных прохода со скоростью около двух дюймов в минуту. Более мелкая подача удаляла остаток материала (четыре прохода со скоростью около одного дюйма в минуту).
Тонкая подача была необходима, чтобы избежать напряжения на конце хрупкой концевой фрезы. Как мы знаем, вертикальный фрезерный станок не является жестким станком, поэтому необходимо проявлять осторожность… даже при вытаскивании фрезы из разреза все еще может быть достаточный изгиб, чтобы сколоть режущую кромку, если используется быстрая подача.Вот урезанный держатель со вставкой, установленный в четырехходовой стойке для инструментов; обратите внимание на опору под углом стойки инструмента:
Вы также можете просмотреть эти сообщения:
http://www.hobby-machinist.com/threads/sharpening-cutting-tools.32987/
http://www.hobby-machinist.com/thre … ting-tools-on-small-токарные станки. 32266 / # post-273258
Мы знаем, что есть две основные причины, по которым твердосплавные режущие инструменты предпочитают быстрорежущую сталь:
- Воспользуйтесь преимуществами более высокого шпинделя скорости (в три раза быстрее, чем HSS).
- Способность обрабатывать материал, который слишком твердый для инструмента из быстрорежущей стали (как в приведенном выше примере, где закаленные хвостовики державок можно было подобрать только твердосплавным резцом, шлифовальной машиной или электроэрозионным электроэрозионным инструментом).
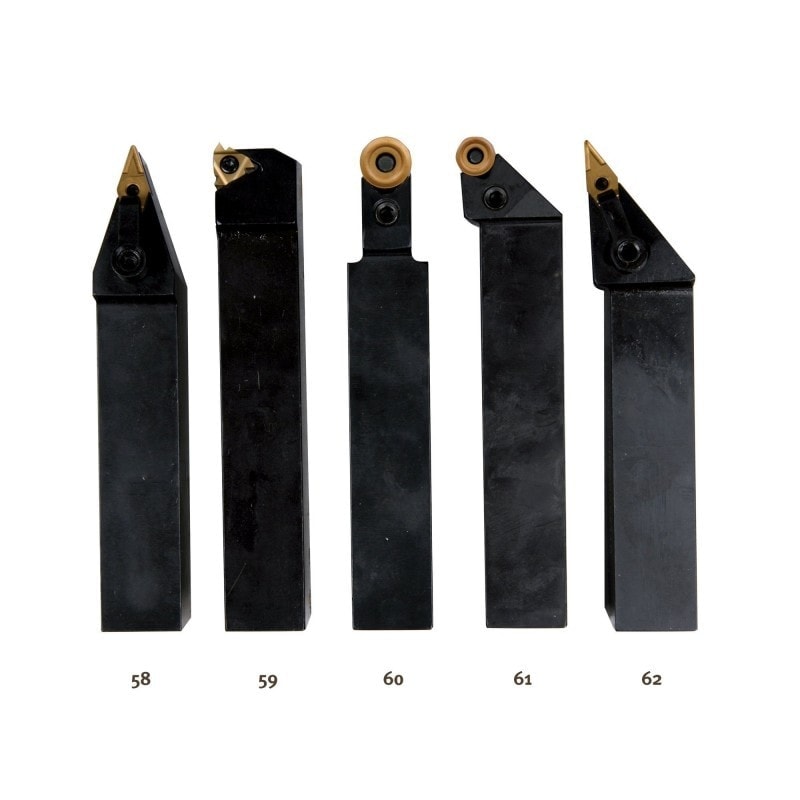
Я не так хорошо знаком с современной твердосплавной оснасткой, но практическое правило, которое я использовал для установки скорости, составляет около 300 SFPM – по сравнению с примерно 100 SFPM для HSS. Это примерно соответствует скорости шпинделя (в об / мин) 1200 / диаметр, где диаметр – это диаметр заготовки (для токарных станков) или диаметр фрезы (для фрез и инструментов для резки по всему периметру) в дюймах.
Мы могли бы оценить практичность использования твердого сплава, рассмотрев заготовку СРЕДНЕГО диаметра (та, которая удовлетворяет 75% наших потребностей).В моем случае это, вероятно, будет около 0,5 дюйма в диаметре. Используя мое эмпирическое правило, это означает, что скорость шпинделя составляет 2400 об / мин. Мой небольшой токарный станок старый, а максимальная скорость шпинделя составляет около 2200 об / мин. Это достаточно высокий уровень, так что карбид, очевидно, пригодится для повышения производительности в моем случае.
Для тех из вас, кто регулярно обрабатывает деталей меньшего размера , ваш токарный станок может не иметь достаточно высоких оборотов шпинделя, чтобы сделать твердый сплав хорошим выбором – вам нужно будет иметь возможность вращать до 4800 оборотов в минуту, чтобы в полной мере использовать твердосплавные инструменты для поворот 0.Например, заготовки диаметром 25 мм.
Вот примерная оценка среднего диаметра стальной заготовки, которая может эффективно использоваться с твердым сплавом на основе максимальной частоты вращения вашего токарного станка:
- Если максимальная частота вращения шпинделя составляет 1200 об / мин, наименьший диаметр, при котором можно эффективно использовать карбид, будет около одного дюйма
- Если максимальная частота вращения шпинделя составляет 2400 об / мин, наименьший диаметр, при котором можно эффективно использовать твердый сплав, составляет около 0,5 дюйма.
- Если ваша максимальная частота вращения шпинделя составляет 3600 об / мин, наименьший диаметр, при котором можно эффективно использовать твердый сплав, составляет около 0.
3 дюйма
Хотя твердосплавные режущие инструменты очень твердые, они не очень острые. Из-за хрупкости материала бессмысленно пытаться получить лезвие бритвы (даже если возможно), которое будет скалываться при первом контакте с заготовкой.
Это означает, что трудно добиться жестких допусков и чистовой обработки тонких заготовок из-за отклонения заготовки (из-за давления инструмента) и “хлыста”, вызванного увеличением числа оборотов шпинделя. Однако это может и не быть проблемой, если вы не боитесь глубины резания.
Жесткий малый токарный станок может обрабатывать низкоуглеродистую сталь с глубиной резания (DOC) 0,250 острым инструментом с тонкой подачей. Вывод: снимите материал за один проход, если возможно, верно? Компромисс – прогиб (заготовка становится конической).Это может не быть проблемой для многих приложений – конечно, в зависимости от конуса.
И это то, что мы собираемся исследовать в этой очень краткой оценке. Все эксперименты будут проводиться на моей маленькой «Компактной восьмерке». Эта машина очень жесткая, потому что отношение длины направляющих к ширине направляющих невелико (около 5: 1), он довольно тяжелый, а четырехходовой инструментальный стержень имеет хорошую опору. Станок, вероятно, более жесткий, чем средний 12-дюймовый азиатский токарный станок с резцедержателем QC.Это старое фото машины:
Я купил подержанный токарный станок более тридцати лет назад, и в то время он казался дорогим, но на нем можно было производить точные детали в разумные сроки. Токарный станок обычно удаляет кубический дюйм мягкой стали в минуту с помощью острого инструмента из быстрорежущей стали, и мы скоро узнаем, как он работает с твердосплавными пластинами.
Хотя токарный станок, кажется, установлен на хрупкой конструкции, основание было подставкой для 100-галлонного аквариума (содержащего около 600 фунтов воды).Стенд был дополнительно усилен за счет приварки опор канала под верхом и приварки распорок из черной трубы ко всем опорам. (Токарный станок 8 x 18 весит около 450 фунтов.)
Простые тесты, которые я разработал для сравнения практического качества режущей кромки, не включают в себя эзотерические измерения углов или исследование режущих кромок под микроскопом – даже срок службы инструмента. Обычно они не подходят для гаражных машинистов, LOL, как я.
Я просто собираюсь сравнить пластину с достаточно острой фрезой из быстрорежущей стали, сделав легкий рез (что трудно сделать с твердосплавными инструментами, когда требуется точность), используя оба типа инструментов на длине стального кабелепровода 3/4. без поддержки конца.Я сделал одно небольшое изменение в инструменте HSS: я сделал небольшой радиус на кончике так, чтобы он приближался по форме к кончику вставки. Если бы я этого не сделал, сравнение качества поверхности было бы бесполезным.
Ожидается, что материал будет отклоняться от режущей кромки, поскольку длина неподдерживаемого кабелепровода будет установлена на три дюйма. Я использовал инструмент из быстрорежущей стали при 415 об / мин, а твердосплавную пластину – при 1330 об / мин. Они консервативны для соответствующих материалов инструмента, но я ограничен доступными комбинациями шкивов на моем самом маленьком токарном станке.После выполнения одного прохода при DOC около 0,035 и скорости подачи 0,005 ipr была измерена величина сужения от конца до конца, как показатель отклонения (и, следовательно, остроты инструмента).
Инструмент из быстрорежущей стали 1/4 отклоняется на 0,00055 радиальных дюймов, чистота поверхности оценивается примерно в 32 микродюйма
Инструмент 3/8 I.C. Твердосплавная пластина отклонена на 0,00155 радиальных дюймов, качество поверхности оценивается от 32 до 63 микродюймов
Никаких сюрпризов: HSS обеспечила меньший прогиб и более качественную поверхность, как и следовало ожидать, в то время как твердосплавная пластина удаляла такое же количество материала примерно в три раза быстрее при трехкратном увеличении прогиба. Несомненно, чистовую обработку твердосплавной пластины можно было бы улучшить, отточив наконечник алмазным напильником, но это могло бы произойти за счет увеличения стойкости инструмента.
(Интересно, что измерение диаметров трубопровода было непростым делом из-за тонкой толщины стенки, остающейся после поворота. Небольшая сила, создаваемая крутящим моментом микрометрового наконечника, была достаточной для небольшого отклонения стенки трубопровода, поэтому использовался метод «годен / не годен».)
Следующий тест, также связанный с резкостью кромок, предложит относительное количество энергии, необходимое для удаления одного и того же объема материала с одинаковых стержней с помощью различных инструментов.Давайте задумаемся об этом… простые тесты измеряют потребление тока электродвигателем токарного станка как показатель проделанной работы.
Я, конечно, мог бы это сделать, но результаты могут оказаться бесполезными – сопротивление обмотки двигателя будет меняться по мере нагрева, поэтому потребление тока также изменится, если только двигатель не охладится в течение длительного периода времени. Моя цель состояла в том, чтобы провести тесты за тридцать минут, а затем потратить тридцать минут на запись результатов (кстати, я потерпел неудачу).
Я решил использовать методы, аналогичные методам Ньютона и других первых экспериментаторов, работающих с мощностью и энергией, путем измерения количества тепла, производимого режущим инструментом. Я провел инфракрасные измерения температуры деталей до и после удаления фиксированного количества материала обоими типами режущих инструментов. Предполагается, что повышение температуры дает хорошее представление об объеме работы, выполняемой каждым инструментом.
Испытуемая заготовка представляет собой CRS диаметром 3/4, длина реза составляет 2 дюйма с использованием тех же скоростей шпинделя, которые указаны выше при токарной обработке стального канала.Один проход 0,100 DOC и 0,005 ipr был сделан для каждого инструмента, и разница в температуре была отмечена сразу после выполнения резки. Это был первый тест, в котором были проблемы, которые будут описаны ниже. Вот фотография инструмента из быстрорежущей стали 1/4, который готовится к повороту стержня 3/4:
Измерения температуры и прогиба при первом испытании не дали смысла. Инструмент из быстрорежущей стали плавно резал без СОЖ, в то время как твердосплавная пластина мгновенно вызывала ужасный стук (помните, что заготовка не поддерживается на конце) и требовала СОЖ для всего резания; нет смысла измерять повышение температуры.
Дребезжание снова указывало на отсутствие острого края на твердосплавной пластине – заготовка имела тенденцию отклоняться и создавать вибрацию, которая требовала применения охлаждающей жидкости, чтобы «успокоиться». FWIW съем материала составил 0,42 куб. Дюйма / мин для фрезы из быстрорежущей стали и 1,36 куб. Дюйма / мин для твердосплавной пластины.
Я просверлил две тестовые заготовки так, чтобы они могли опираться на заднюю бабку, и повторил два теста, за исключением использования 0,050 DOC без изменения скорости вращения шпинделя для соответствия меньшим диаметрам (напомним, что образцы для испытаний были уменьшены с.От 750 до 0,550 диаметра). Ни на одной из деталей не использовалась охлаждающая жидкость, и при поддерживаемой работе не было никаких вибраций.
Чистота поверхности была похожа на чистоту поверхности, о которой сообщалось на двух кусках кабелепровода, повернутых ранее. То есть, HSS давала немного более гладкую поверхность, чем твердосплавная пластина, и то и другое было приемлемым для требования к чистоте 63 микродюймов.
Повышение температуры детали с использованием инструмента из быстрорежущей стали составило 16 градусов Цельсия, в то время как температура детали, обработанной твердосплавной пластиной, поднялась на 32 градуса.Можно сделать (довольно разумное) предположение, что для удаления того же количества материала твердосплавной пластиной требовалось примерно вдвое больше мощности.
Для приложений HSM это может не иметь смысла с экономической точки зрения (стоимость электроэнергии обычно не имеет значения). Но это предполагает дополнительную нагрузку на вашу машину из-за необходимости работать вдвое тяжелее для достижения того же результата. Опять же, это неудивительно, это было общеизвестно на протяжении десятилетий.
Было интересно сравнить твердосплавные пластины с твердосплавными инструментами с квадратным припоем 3/8 дюйма, которые я обычно использую.Пластины кажутся более острыми (в зависимости от качества поверхности), хотя это может происходить за счет увеличения стойкости инструмента. Однако с тремя режущими поверхностями на каждой пластине я бы ожидал, что пластина прослужит столько же, сколько твердосплавный инструмент (при условии, что ни одна из них не была заточена в течение срока службы). Первоначальные затраты на инструмент между пластиной и твердосплавной фрезой примерно равны.
Что касается качества резки, стоимости и износа на токарном станке, HSS выигрывает, если только заготовку не слишком сложно резать без использования твердого сплава или если не учитывать время.Прогиб заготовки при использовании твердого сплава почти в три раза больше, чем при использовании HSS, в то время как скорость вращения может быть в три раза выше, ЕСЛИ ваш токарный станок может выдерживать более высокие обороты. Чаще всего это не относится к токарным станкам с углом поворота более 10 дюймов, поэтому преимущество в производительности может быть потеряно для работы с малым диаметром.
Я не вижу причин менять свою давнюю привычку черновой обработки твердым сплавом, если необходимо удалить большое количество металла (кубические дюймы), и чистовой токарной обработки с использованием быстрорежущей стали.Однако столкновение могло бы быть другим делом. Я определенно могу использовать эти пластины для обработки больших заготовок, когда я не хочу беспокоиться о замене ремней при изменении диаметра резания. Мне кажется, что эти пластины производят не в три раза больше, а примерно в 1-1 / 2 или вдвое большую эффективность.
Когда необходимо удалить менее одного кубического дюйма материала, нет особых причин отдавать предпочтение твердому сплаву перед HSS, учитывая преимущества последнего в отношении отделки поверхности и чистовой обработки. Как и при каждой новой работе, целесообразно иметь набор инструментов, способных справиться с 95% материалов и операций, с которыми, вероятно, придется столкнуться. Я не мог работать только на HSS. Точно так же я не мог работать только с твердосплавными пластинами, будь то пластинки или припой.
Это, вероятно, то, как мой 4-ходовой резцедержатель (на моем самом маленьком токарном станке) какое-то время будет выглядеть: 1/4 HSS в держателе, 3/8 I.C. твердосплавная пластина в державке, отрезной инструмент из быстрорежущей стали 3/32 x 1/2 в державке и одна станция для заготовок для любых деталей…
Обратите внимание, что этот тест был ОЧЕНЬ ограниченным по объему, основанным только на одной конфигурации и твердосплавном материале.У меня нет текущих знаний о твердосплавных инструментах, поэтому вполне может быть лучший выбор, чем набор инструментов и вставки, которые я купил.
Глава 5: Методы и станки токарной обработки | Применение режущего инструмента
Базовый токарный станок для двигателей, один из наиболее широко используемых станков, очень универсален при использовании опытным машинистом. Однако это не особенно эффективно, когда нужно как можно быстрее обрабатывать множество идентичных деталей. Еще в 1850 году предпринимались попытки разработать варианты токарного станка для двигателя, которым мог управлять относительно неквалифицированный человек для массового производства обработанных деталей.Режущие инструменты были предварительно настроены или «настроены» опытным механиком, и обычно несколько режущих инструментов работали одновременно, что сокращало время, затрачиваемое на обработку каждой детали. Это все еще основная концепция, на которой базируются токарные станки массового производства.
Токарно-револьверный станок и автоматический винторезный станок в их различных формах были разработаны и усовершенствованы с целью более быстрого и точного производства обрабатываемых деталей с меньшими затратами. На большинстве станков этого типа мощность, доступная на шпинделе, была значительно увеличена, чтобы использовать преимущества лучшего материала режущего инструмента.Механическая сила, в электрической, гидравлической или пневматической форме, заменила человеческую мускульную силу для таких функций, как подача инструментов, управление зажимными патронами или цангами и подача прутка в машину.
Токарные станки и компоненты для токарных станков
Из множества стандартных и специальных типов токарных станков, которые были построены, наиболее важным, универсальным и широко признанным является токарный станок для двигателей. Стандартный токарный станок для двигателей не является высокопроизводительным станком, но его можно легко приспособить для выполнения множества отдельных или краткосрочных работ.Также возможно модифицировать базовую машину для многих приложений более высокого уровня производства. Современный токарный станок для двигателей обеспечивает широкий диапазон скоростей и подач, что позволяет оптимизировать настройки практически для любой операции. Были усовершенствованы конструкции передней бабки, чтобы обеспечить большую прочность и жесткость. Это позволяет использовать двигатели с высокой мощностью, так что тяжелые резания твердосплавными инструментами становятся практичными. Чтобы использовать эту высокую мощность без потери точности, новые токарные станки включают в себя более тяжелые станины, более широкие закаленные направляющие и каретки с более глубоким сечением.
Передняя бабка: Передняя бабка – это сторона с приводом, и она всегда находится слева от оператора. Он содержит шестерни переключения скорости и вращающийся приводной шпиндель, к которому прикреплен любой из нескольких типов держателей заготовок. Центр шпинделя полый, так что через него можно пропускать длинные стержни для обработки.
Задняя бабка: Задняя бабка не вращается, но на закаленных способах ее можно перемещать влево или вправо, чтобы приспособиться к длине работы. Его также можно смещать для резки малоугловых конусов.
Каретка: Каретка может перемещаться влево или вправо с помощью маховика или механической подачи. Это обеспечивает движение по оси Z. Во время этого хода выполняются токарные пропилы.
Фартук: Фартук, прикрепленный к передней части каретки, удерживает большинство рычагов управления. К ним относятся рычаги, которые включают и реверсируют подачу в продольном (ось Z) или поперечном (ось X) направлении, а также рычаг, который включает в себя резьбонарезные шестерни.
Поперечный суппорт: Поперечный суппорт установлен на каретке и может перемещаться внутрь и наружу (ось X) перпендикулярно движению каретки. Это деталь, которая перемещается, когда торцевые разрезы выполняются с механической подачей, или в любой момент разрез должен выполняться «под прямым углом» к оси Z. Это или компаунд также используется для установки глубины резания при точении. Поперечный суппорт можно перемещать с помощью маховика или механической подачи. .
Составная опора: Составная опора, сокращенно составная, устанавливается на каретке.Его можно задвигать и выдвигать с помощью маховика для облицовки или для настройки глубины резания. Его также можно поворачивать на 360 градусов и подавать с помощью маховика под любым углом. Компаунд не имеет механической подачи, но всегда движется продольно с поперечными суппортами и кареткой.
Резцедержатель: Резцедержатель установлен на составной опоре. Это может быть любая из нескольких разновидностей, но в простейшей форме это просто цилиндр с прорезями, который можно перемещать влево или вправо в Т-образном пазу в соединении и зажимать на месте.Его также можно поворачивать, чтобы резец попадал на работу под любым углом, который лучше всего подходит для работы.
Станина: Станина токарного станка является его основой. Он должен быть достаточно жестким, чтобы противостоять прогибу в любом направлении под нагрузкой. Станина изготавливается из чугуна или стальной сварной конструкции в форме коробки или двутавровой балки и поддерживается на ножках, шкафу или скамейке.
Способы: Способы токарного станка – это плоские или V-образные поверхности, по которым каретка и задняя бабка перемещаются влево и вправо.У каждого есть своя пара отдельных путей, часто одна плоская поверхность для устойчивости и одна V-образная направляющая для направления по идеально прямой линии. Эти дорожки закалены, зачищены или отшлифованы до жестких допусков. Основная точность передвижения каретки зависит от способов.
Размер: Размер токарного станка задается двумя или тремя размерами:
• Заготовка самого большого диаметра, которая очищает станину токарного станка. Центр – это центр шпинделя передней бабки.
• Иногда также указывается заготовка наибольшего диаметра, которая будет очищать поперечный суппорт.
• Самая длинная заготовка, которую можно удерживать по центру между передней и задней бабками.
Токарно-револьверный станок
Стандартный токарный станок для двигателей универсален, но не является высокопроизводительным. Когда производственные требования высоки, необходимо использовать больше автоматических токарных станков. Токарно-револьверный станок представляет собой первый шаг от токарного станка для двигателей к высокопроизводительным токарным станкам. Токарно-револьверный станок аналогичен токарному станку для двигателей, за исключением того, что револьверные головки заменяют заднюю бабку и составной узел резцедержателя.Эти машины обладают специальными характеристиками, которые позволяют адаптировать их к производственному процессу. «Мастерство рабочего» заложено в этих машинах, что позволяет неопытным операторам воспроизводить идентичные детали. В отличие от этого, токарный станок для двигателей требует квалифицированного оператора и требует больше времени для производства деталей с одинаковыми размерами.
Основной характеристикой токарных станков с револьверной головкой является то, что инструменты для последовательных операций настроены для использования в правильной последовательности. Хотя для правильной настройки и регулировки инструментов требуются навыки, после того, как они будут правильными, для работы с револьверным токарным станком потребуется меньше навыков.Многие детали могут быть изготовлены до того, как потребуется регулировка. Эти станки обычно используются для малых и средних производственных циклов, когда токарный станок для двигателей работает слишком медленно, но желаемая дополнительная производительность не требует специального станка.
Квадратные и шестигранные револьверные головки: Квадратная револьверная головка установлена на верхней части поперечных суппортов и способна удерживать четыре инструмента. Если требуется несколько различных инструментов, они устанавливаются последовательно и могут быть быстро проиндексированы и заблокированы в правильном рабочем положении.Чтобы можно было дублировать пропилы, салазки снабжены упорами или механизмами подачи. Точно так же продольное положение всей сборки можно контролировать с помощью упоров с левой стороны фартука. Разрезы можно выполнять с помощью квадратной револьверной головки и инструментов, установленных на шестигранной револьверной головке одновременно.
Отличительной особенностью является револьверная головка вместо задней бабки. Эта револьверная головка, установленная либо на выдвижном цилиндре, либо на седле, либо на задней части конструкции, вмещает от 4 до 18 инструментальных позиций.Инструменты предварительно настроены для различных операций. Инструменты устанавливаются в надлежащей последовательности на различных поверхностях револьверной головки, так что, когда револьверная головка индексируется между операциями обработки, соответствующие инструменты входят в нужное положение. Для каждого инструмента есть стопорный винт или электрический / электронный преобразователь, который контролирует расстояние, на которое инструмент будет подавать и резать. По достижении этого расстояния рычаг автоматического отключения останавливает дальнейшее движение инструмента, отключая приводную муфту.
Подобно токарному станку для двигателя, современный токарно-револьверный станок обеспечивает высокую скорость вращения шпинделя, широкий диапазон скорости и подачи, высокую мощность и большую жесткость.Станок работает на верхнем пределе своего диапазона скоростей больше, чем токарный станок для двигателей, отчасти потому, что инструменты, размещенные в револьверной головке, часто работают с заготовками небольшого диаметра, но также потому, что оператор больше заботится о производстве.
Горизонтально-револьверные станки:
Горизонтальные токарно-револьверные станки бывают двух основных типов и известны как поршневые и седельные. Револьверно-токарный станок ползунного типа имеет револьверную головку, установленную на суппорте или ползуне, который перемещается вперед и назад на суппорте, закрепленном на станине токарного станка.Седельный токарно-револьверный станок имеет револьверную головку, установленную непосредственно на суппорте, который перемещается вперед и назад вместе с револьверной головкой.
Вертикальные револьверные станки:
Вертикальный токарно-револьверный станок напоминает вертикально-расточной станок, но имеет характерное расположение револьверной головки для удержания инструментов. Он состоит из вращающегося патрона или стола в горизонтальном положении с револьверной головкой, установленной сверху на поперечной направляющей. Кроме того, имеется по крайней мере одна боковая головка с квадратной револьверной головкой для удерживания инструментов.У всех инструментов, установленных на револьверной головке или боковой головке, установлены соответствующие упоры, так что длина резов может быть одинаковой в последовательных циклах обработки. По сути, это то же самое, что револьверный токарный станок, стоящий на конце передней бабки, и он имеет все функции, необходимые для производства дублирующих деталей. Этот станок был разработан для облегчения монтажа, удержания и обработки тяжелых деталей большого диаметра. На таких станках выполняются только зажимные работы.
Вертикальный токарно-револьверный станок, показанный ниже, снабжен двумя режущими головками: поворотной главной револьверной головкой и боковой головкой.Револьверная головка и боковые головки работают так же, как шестигранные и квадратные револьверные головки на горизонтальном токарном станке. Чтобы обеспечить резку под углом, как цилиндр, так и револьверная головка могут поворачиваться на 30 градусов вправо или влево от центра.
Станок может быть снабжен системой управления, которая позволяет автоматически управлять каждой головкой, включая скорость и направление подачи, изменение подачи шпинделя, индексацию револьверной головки, запуск и остановку. После того, как цикл операций задан и инструменты правильно отрегулированы, оператору нужно только загрузить, разгрузить и запустить машину.Производительность увеличена по сравнению с машинами с ручным управлением, потому что они работают почти непрерывно и меняют одну операцию на другую без колебаний или усталости. За счет сокращения времени обработки и автоматического выполнения цикла оператор может обслуживать несколько машин.
Револьверно-токарный станок обычно имеет патрон с кулачками для удержания заготовки; однако цанговый патрон может быть более подходящим при производстве деталей из пруткового материала. Токарный станок, оснащенный цанговым патроном и револьверной головкой, называется винторезным, но на самом деле это специальный револьверный токарный станок.Особенности винтовых станков направлены в первую очередь на сокращение времени простоя обрабатываемых деталей, тем самым повышая производительность.
Преимущества револьверных станков
Разница между токарными станками для двигателей и револьверными станками заключается в том, что токарно-револьверные станки адаптированы для серийного производства, тогда как токарные станки для двигателей используются в основном для выполнения различных работ, в инструментальном цехе или для однооперационных работ.
Автоматизированное оборудование
Существуют токарные станки, которые позволяют автоматически зажимать, индексировать, подавать, изменять скорость вращения шпинделя и выполнять другую работу, которую должен выполнять оператор на токарном станке с двигателем.Эти токарные автоматы представляют собой усовершенствованный вариант токарно-револьверных станков и особенно подходят для длительных серийных производств.
Автоматические токарные станки могут быть одно- и многошпиндельными. Как правило, одношпиндельные станки обеспечивают токарную обработку заготовки, которая удерживается в цанге или зажимается на передней бабке. Многошпиндельные токарные автоматы обычно предоставляют средства для индексации заготовки к инструментам, установленным на различных шпинделях. Эти инструменты могут включать сверла, зенковки, расточные оправки и другие вращающиеся фрезы.Как одно-, так и многошпиндельная автоматика может быть выполнена как с вертикальным, так и с горизонтальным выравниванием шпинделя.
Что касается процессов обработки на автоматическом токарном станке, то основными соображениями являются высокие скорости, необходимые для хорошей производительности, экономичность процесса резания и уравновешивание скоростей на различных этапах операции для получения желаемой скорости обработки. износ на каждом режущем инструменте.
Одношпиндельные автоматические станки
Большинство одношпиндельных токарных автоматов предназначены для обработки деталей, находящихся между двумя центрами.Однако некоторые держат заготовку в патроне, цанге или специально разработанном приспособлении. Большинство из них имеют горизонтальные шпиндели. Обычный одношпиндельный токарный автомат состоит из шести основных компонентов: основания, станины и направляющих; передняя бабка; рабочий шпиндель; передний инструментальный суппорт; задняя салазка инструмента.
Инструмент: Можно использовать любой из нескольких доступных держателей заготовок, которые подходят для конкретного применения, включая патроны, приводы планшайбы, цанги и специально разработанные приспособления. Патроны, если они используются, должны приводиться в действие силовым приводом, чтобы избежать потери времени на ручной приведение в действие патронов.
обычно имеют прорези для установки и зажимы для удержания отдельных режущих инструментов в нужных местах. Собранные державки, в свою очередь, фиксируются шпонками и зажимаются в определенном месте на передних и задних суппортах.
Области применения: Осевые и трансмиссионные валы, заготовки шестерен, приводы насосов и шестерни – все они особенно хорошо подходят для обработки на одношпиндельных токарных автоматах. Фактически, практически любая обрабатываемая металлическая деталь, допускающая размер, которую можно зажимать, закреплять или перемещать между центрами, является потенциальным кандидатом для этого станка.Одношпиндельные токарные автоматы выполняют операции токарной обработки, торцевания, снятия фасок, обработки канавок и формовки, и обычно используются для обработки деталей с умеренной производительностью.
Одношпиндельные автоматические винторезные машины
Автоматические винтовые машины – это современные разработки более ранних машин, единственной функцией которых было производство винтов. Современные станки не только сохраняют возможности нарезания резьбы, но и способны выполнять все токарные операции. Эти станки производят широкий спектр деталей из пруткового материала, подаваемого через полый рабочий шпиндель.Некоторые машины приспособлены для производства деталей из катушек.
Одношпиндельные автоматические винторезные станки имеют горизонтальные полые шпиндели, совмещенные с трубками подачи материала. Большинство из них имеют кулачковое управление, но версии без бруса, иногда с ЧПУ или ЧПУ, более гибкие и быстро настраиваются, что делает их более подходящими для более коротких производственных циклов. Машины доступны в нескольких размерах и состоят из шести основных компонентов: основания, передней бабки, полого рабочего шпинделя, передних суппортов, задних суппортов и револьверной головки.
Скорость подачи и движение салазок инструмента контролируются кулачками или гидравликой. Скорость шпинделя изменяется в соответствии с диаметром заготовки / материалом с помощью сменных шестерен в основании станка. Пруток автоматически подается к упору поворота или к упору револьверной головки после того, как каждая деталь завершена и отрезана. Цанга автоматически разблокируется при продвижении запаса.
Оснастка: Круглые, квадратные, шестигранные и другие цанги стандартной формы доступны в размерах, соответствующих размерам промышленных прутков.Специальные предложения также сделаны по индивидуальному заказу.
Применения: Одношпиндельные автоматические винторезные станки используются для производства чрезвычайно широкого спектра мелких деталей, включая валы, штифты, ручки, винты, болты и т. Д., Из любого обрабатываемого металла. Можно фрезеровать плоские поверхности и пазы, а также просверливать поперечные отверстия. Один оператор может управлять несколькими станками, количество которых зависит от частоты, необходимой для перезарядки прутка и регулировки или смены инструментов.
Многошпиндельные автоматические прутковые и патронные станки
Обычные многошпиндельные автоматические прутковые и зажимные станки имеют два основных преимущества по сравнению с одношпиндельными автоматами, оба из которых сокращают время, необходимое для изготовления детали:
- Многошпиндельный станок выполняет работу на каждой из своих рабочих станций одновременно; также возможно выполнить разные операции над деталью в каждой позиции за одно и то же время.
- Максимальное время, необходимое для выполнения одной детали, – это время, необходимое для самого длинного реза, плюс время индексации, и в некоторых случаях самый длинный отрез может быть разбит на части. Например, просверленное отверстие, которое является самым длинным вырезом определенной детали, может быть выполнено в трех или более положениях.
Размеры деталей и сложность конструкции одинаково хорошо подходят для многошпиндельных или одношпиндельных станков. Более короткое время переналадки дает преимущество одношпиндельным станкам для коротких производственных циклов, но более короткое время обработки на единицу многошпиндельного станка делает его более экономичным для больших серий.
Многошпиндельные вертикальные автоматические патронные станки
Многошпиндельные вертикальные автоматические патронные станки производятся несколькими производителями станков в различных размерах и моделях, от четырех до восьми шпинделей. Один производитель поставляет 16-шпиндельный станок, то есть на самом деле двойной шпиндель для каждой позиции 8-шпиндельного станка.
Эти машины занимают меньше места на полу, чем эквивалентные горизонтальные модели, и более гибки в применении.Однако они не принимают пруток. Некоторые другие преимущества заключаются в том, что их удобно загружать, эксплуатировать, настраивать или менять инструменты.
Токарные станки с компьютерным управлением
В самых современных токарных станках движение и управление станком и его компонентами осуществляется с помощью числового программного управления (ЧПУ). Эти токарные станки обычно оснащены одной или несколькими револьверными головками. Каждая револьверная головка оснащена множеством инструментов и выполняет несколько операций на разных поверхностях заготовки.
Эти машины высоко автоматизированы, операции повторяются, и они поддерживают желаемую точность. Они подходят для малых и средних объемов производства.
Джордж Шнайдер, младший CMfgE, является автором Cutting Tool Applications, справочника по материалам, принципам и конструкциям станков. Он является почетным профессором инженерных технологий Технологического университета Лоуренса и бывшим председателем Детройтского отделения Общества инженеров-технологов.
Все, что вам нужно знать – сделать из металла
Алюминий – незаменимый продукт в любом механическом цехе. Это один из самых обрабатываемых металлов, поэтому его можно обрабатывать быстро и эффективно.
Вот почему это сложно. Поскольку все режут его, обработка алюминия представляет собой действительно конкурентное место. Особенно это касается производственной обработки.
В этой статье я поделюсь всем, что вам нужно знать, чтобы сразу приступить к делу, чтобы вы могли получить несколько хороших рабочих мест и справиться с ними как профессионал.
Почему алюминий может быть сложной задачей?
Для начала давайте разберемся, с чем вы боретесь.
Если вы делаете скобу для фермера Джо, на самом деле не имеет значения, насколько эффективно вы удаляете материал. Но если вы делаете 10 000 скобок в неделю для Hustler Joe, вам нужно делать хорошую работу.
Основная проблема при эффективной обработке алюминия – просто добиться максимальной производительности съема материала, не взорвав что-либо.
Алюминий может расплавиться и пригореть к инструменту при слишком сильном нагреве.Таким образом, даже если он режет как масло, это ненадолго, если алюминий прилипнет к инструменту, и вы в конечном итоге будете выполнять сварку трением с перемешиванием вместо механической обработки.
Помимо сведения к минимуму трения, болтовня может быть просто чудовищной, когда вы толкаете машину. Это особенно проблематично, когда вы пытаетесь обработать машинкой чистые на вид карманы.
Ладно, хватит нытье. Давайте разберемся, как его можно убить на полу.
Различные виды алюминия
Не все марки алюминия обладают одинаковой обрабатываемостью.Некоторые режут, как сон, другие настолько липкие, что забитые сломанные инструменты превращаются в кошмар. Главное здесь – понять, с чем вы работаете.
Вот список некоторых распространенных типов алюминия и некоторые примечания по обрабатываемости:
2011 | Самое сливочное масло. Это самая обрабатываемая из всех марок алюминия.![]() |
2024 | У него отличное соотношение прочности и веса, поэтому вы увидите его там, где он находится под напряжением. Он отлично обрабатывает, но есть одна вещь, на которую нужно обратить внимание: он может сколоть в конце тяжелого резания, когда инструмент выйдет из строя. Примером возможной проблемной области является прорезание пазов полного диаметра. Возможно, вам придется настроить траектории инструмента, чтобы смягчить выходы, чтобы предотвратить это. Чипсы в целом получаются симпатичные, не слишком тягучие (но все относительно). Еще одна вещь, на которую следует обратить внимание, – это коррозия. Коррозия 2024 на самом деле очень плохая, поэтому будьте осторожны, не оставляйте ее в жидкой охлаждающей жидкости или в барабане деталей. Нет смысла в отличной отделке, если она вся покрыта коррозией. В целом, тем не менее, это отличный материал для работы. Лучше всего резать его в состоянии T351 или отжигать. |
5052 | Это действительно мягкий материал, который обычно используется для формования. Обычно вы получаете это в виде листа. Вы также можете найти его в морских приложениях, поскольку он обладает отличной коррозионной стойкостью.Это не ужасно, но нужно следить за липкостью. Это может быстро засорить инструмент. Убедитесь, что ваши инструменты острые как бритва для этого материала и у вас хорошая смазка, иначе ваша поверхность будет повреждена, и вы рискуете взорвать свой инструмент. Держите инструмент острым, и у вас не будет проблем с получением яркого зеркального блеска. |
6061 | Это общая скоба для обработки. Это отличный материал, который нужно вырезать. Это, наверное, самая обычная вещь, которую вы найдете в механической мастерской.Вы все равно должны быть осторожны с выходом материала из очень тяжелых разрезов; есть небольшой риск сколов.![]() Чем тверже этот материал, тем легче его обрабатывать. T4 идеально подходит для обработки, но T6 занимает второе место. По сравнению с алюминием 2011 года показатели обрабатываемости этих сплавов составляют 90% и 80% соответственно. |
6063 | Это действительно похоже на 6061 по функциям, но чаще встречается в экструзиях. Однако он не такой жесткий. Это делает обработку 6063 немного сложнее; он мягче и тягучей. При резке алюминиевых профилей используйте действительно острые инструменты, хорошую смазку и следите за удалением стружки. |
7075 | Это чрезвычайно популярно в конструктивных элементах, таких как лонжероны крыльев самолетов и рамы велосипедов. Это действительно жесткий алюминий. Машина довольно хорошо обрабатывается; не так хорошо, как 6061, но не так плохо, как 5052. Однако получить яркую отделку на этом материале непросто; у вас больше шансов получить что-то более гладкое, но тускло-серое. |
Здесь следует помнить, что из всех марок алюминия хорошо поддается механической обработке.Единственный раз, когда вы заметите разницу между этими оценками, – это когда вы действительно толкаете свой тренажер. Если вы занимаетесь мелкосерийным производством, вряд ли вы что-нибудь заметите.
Стоит отметить заметную разницу между литым и кованым алюминием. Отливка всегда более липкая, поэтому держите инструменты острыми и действуйте осторожно.
Основные проблемы, с которыми вы столкнетесь, связаны с трением и нагревом. В следующем разделе мы рассмотрим, как решать эти проблемы, чтобы вы могли более точно настроить свой процесс.
Режущие инструменты для алюминия
Ни при каких обстоятельствах нельзя использовать универсальный резак для алюминия. Технически это работает, но алюминий полностью отличается от стали.
Черт возьми нет. Черт возьми, да. Вот несколько аспектов выбора инструмента, которые помогут вам максимально использовать возможности вашего станка.
Материал режущего инструмента
Карбид.
Надеюсь, для вас это не проблема. Даже в неэффективных областях применения твердый сплав будет превосходить быстрорежущую сталь по стоимости как по стоимости инструмента в течение срока службы, так и по качеству поверхности.
Тем не менее, есть несколько полезных сведений о карбиде, которые помогут вам подобрать идеальный инструмент для работы.
По сути, нам просто нужно понять, чего мы хотим от инструмента. Алюминий режет мягко, что означает, что инструмент не подвергается сильным ударам во время резки.
Главное, чтобы лезвие оставалось острым как бритва. По этой причине для характеристик материала мы предпочли бы твердость твердости.
На это свойство влияют два основных фактора: размер зерна карбида и соотношение связующего.
Изображение фрезерованного алюминия для визуального облегченияЧто касается размера зерна, то большее зерно дает более твердый материал, тогда как меньшее зерно дает более ударопрочный и прочный материал. Что касается алюминия, мы хотим сохранить эту остроту кромок, поэтому нам нужен небольшой размер зерна для максимального удержания кромки.
Другой фактор – соотношение связующего. Для твердосплавных режущих инструментов в качестве связки используется кобальт. Он может иметь содержание кобальта от 2% до 20%. Поскольку кобальт мягче, чем зерна карбида, больше кобальта означает более прочный инструмент, меньшее количество кобальта означает более твердый инструмент.
Итак, мы просто ищем твердосплавные фрезы с большим размером зерна и низким содержанием кобальта.
Флейты
3 канавки – идеальное место для твердосплавных концевых фрез в 98% случаев. Удаление стружки – это игра для алюминия, а 3 канавки обеспечивают идеальный баланс прочности инструмента и зазора от стружки.
2 канавки могут быть жизнеспособным вариантом, когда силы резания ниже, а зазоры от стружки имеют большее значение. Это также может быть способом уменьшить силы резания для легких, ненадежных разрезов.Одна из областей, где это имеет смысл, – это когда у вас есть очень длинный инструмент, подверженный вибрации. 2 канавки слегка режут, поэтому это может помочь вам справиться с вибрацией.
В конце концов, 3 флейты являются отраслевым стандартом. Для более крупных инструментов, таких как ракушечные мельницы, это количество желобков зависит от диаметра. Ключевым моментом здесь является наличие большого зазора для стружки, чтобы ничего не забивалось. Никому не нужен инструмент от запора на 700 IPM.
Угол винтовой линии
Вот баланс, который мы пытаемся достичь: меньший угол наклона спирали уменьшит тепло, поскольку режется меньше времени.Более высокая спираль обеспечивает более плавное резание, дает отличную отделку поверхности, но выделяет больше тепла.
Если ваш инструмент нагревается, алюминий приваривается к нему, и игра окончена. Это происходит менее чем за секунду; все, что вы слышите, это стремительный рост нагрузки на шпиндель и щелчков !
Итак, вот твердое практическое правило, которое работало у меня годами:
Для черновой обработки лучше всего подходит более низкий угол наклона спирали около 35 градусов. Благодаря этому инструмент остается прохладным, и никто не заботится о чистоте поверхности при черновой обработке.
Для чистовой обработки больший угол спирали 45 градусов – это настоящая рок-звезда. Конечно, он выделяет больше тепла, но кого это волнует при чистовой чистовой обработке с высокой подачей? Гладкая резка оставляет красивую и аккуратную поверхность.
Для того, что подходит как для черновой, так и для чистовой обработки, используйте угол спирали 40 градусов.
Черновая обработка: угол наклона спирали 35 градусов
Чистовая обработка: угол наклона спирали 45 градусов
Многоцелевой: угол наклона спирали 40 градусов
Полезные функции
Помимо этих основ, есть еще несколько вещей, которые могут дать вам дополнительное преимущество.
Одна вещь, в которой я добился большого успеха, – это отполированные инструменты. Когда режущие канавки гладко отполированы, алюминий плавно скользит по ним. Так как трение очень мало, срок службы инструмента зашкаливает, и вы можете работать с ним быстрее.
Это действительно полезно, если вы выполняете высокопроизводительное фрезерование алюминия.
Также стоит упомянуть покрытие инструмента. В общем, лучше использовать инструменты без покрытия. Вы не добьетесь хороших результатов от специальных покрытий, а более «стандартные» покрытия для инструментов принесут больше вреда, чем пользы.
Вот краткий список хороших и плохих покрытий для резки алюминия:
AlTiN | Ужасная идея №1. Это покрытие для стали, а не для алюминия. Поверхность инструмента с таким покрытием не особо гладкая, и в ней есть алюминий! Это означает, что материал, который вы режете, будет иметь тенденцию привариваться к покрытию, что приведет к ужасной отделке поверхности и, вероятно, взорвет ваш инструмент. Нехорошо. |
TiN | Ужасная идея №2.Не так плохо, как AlTiN, но и не намного лучше. |
ZrN | Хорошая идея №1. У него сверхнизкий коэффициент трения, поэтому он помогает отводить стружку и сохранять все в холодном состоянии. |
TiB2 | Хорошая идея №2. Многие парни предпочитают это ZrN. Он имеет низкое сродство к алюминию, а это означает, что он сразу соскальзывает. |
Хорошо, если честно, я не нашел покрытий, которые сильно повлияли бы на алюминий.По крайней мере, не так, как со сталью. Я предпочитаю просто полированную концевую фрезу или пластину без покрытия. Я предпочитаю поиграть с покрытиями, когда продавец предложит мне бесплатные инструменты для экспериментов. Вставьте сюда хитрый смешок.
Подачи и скорости
Многие люди просто используют 1000 SFM для расчета своих оборотов в минуту. Если вы сделаете это, вы действительно не станете быстрее всех.
Если честно, обычно это то, что рекомендуется для большинства фрез. 1000-1500 SFM – это нормальная скорость для работы вашего шпинделя.Однако с помощью гармонического тестирования вы можете увеличить скорость в 3 раза. Подробнее об этом позже.
Скорость подачи – это то, от чего отказываются многие ребята. Если вы используете концевую фрезу 1/2 дюйма с расходом всего 0,003 дюйма на зуб, вы просто теряете время. Для производства вы хотите протолкнуть его как минимум на 1% диаметра фрезы на зуб. Это означает, что на концевую фрезу 1/2 дюйма необходимо подавать не менее 0,005 дюйма на зуб. При стабильной настройке и коротком инструменте вы можете даже удвоить это количество.
Единственное исключение – когда вы работаете с небольшими инструментами, например, 1/8 дюйма или меньше.Очистка от стружки может стать проблемой, а это означает, что вам придется снизить скорость для более тонкой стружки.
Даже при точении вам нужно очень сильно подавать, чтобы стружка разбилась. В противном случае конвейер для стружки всегда будет заблокирован.В конце концов, мощность шпинделя и частота вращения должны быть основными факторами, замедляющими процесс черновой обработки алюминия на большинстве станков для деталей среднего размера.
Балансировка и гармоники
Это действительно то, что отличает мальчиков от мужчин на алюминиевой фабрике.Алюминий можно резать на очень высоких скоростях, но ваши инструменты должны быть в состоянии справиться с этим.
Вообще говоря, все, что превышает 10 000 об / мин, должно быть хорошо сбалансировано. Вы найдете рейтинги баланса прямо на ваших инструментах, поэтому подбирайте их соответствующим образом.
Это само собой разумеется, но если вы ударите инструменты в станок, они перестанут быть сбалансированными. Также имейте в виду, что весь инструментальный узел необходимо сбалансировать. Если у вас есть цанговый патрон ER, рассчитанный на 20 000 об / мин, но вы устанавливаете расточную головку, этот рейтинг цанги ничего не значит.
Это также верно, когда речь идет об определении точности фрезы. Многие ребята полностью игнорируют это, но у твердосплавных концевых фрез действительно есть рейтинг посадки хвостовика. Это может иметь большое значение для некоторых типов державок, например гидравлических. Более плотная и точная посадка будет означать лучший баланс, большую стойкость инструмента и более длительный срок службы шпинделя.
Помимо балансировочных инструментов, которые не повредят ваш шпиндель при высоких оборотах, тестирование гармоник действительно является огромным преимуществом при обработке алюминия.Поскольку алюминий очень маслянистый, его можно резать с очень большой скоростью.
Тестирование гармоникпоможет вам найти эти резонансные частоты инструментов и позволит определить оптимальную скорость и подачу. Если частота среза выключена, инструмент начнет вибрировать, как струна скрипки, и у вас будут все причины вернуться домой пораньше.
Найти оптимальные места для частоты вращения инструмента по сравнению с числом оборотов в минуту – большое дело. Это может повысить вашу частоту вращения с 7000 до 22000 об / мин при соответствующей скорости подачи.
Если вы попытаетесь сделать это без системы тестирования, вы гарантированно разнесете свои инструменты на миллион острых маленьких кусочков из безумных гармоник, которые вы получаете, когда немного не в себе.
В одном цехе, где я работал, тестирование метчиков позволило нам запустить наши концевые фрезы 3/4 ″ с шагом 10 ″ со скоростью около 22 тыс. Об / мин и 700 дюймов в минуту. Иногда мы могли пойти быстрее. Попробуйте сделать это без тестирования гармоник. Попробуй.
Эти системы недешевы, и вам, очевидно, понадобится мельница, способная справиться с такой высокой производительностью. Однако, когда у вас есть такая возможность, вы будете намного впереди обычных конкурентов в механических цехах.
Стратегии обработки алюминия
Для большинства применений при фрезеровании алюминия я добился наибольшего успеха со старомодной агрессией для получения хорошего расхода материала. Такие вещи, как фрезерование на кожухе, в большинстве случаев являются пустой тратой времени, за исключением случаев, когда вы работаете с очень маленькими фрезами с узкой геометрией.
Основная причина этого заключается в том, что станки часто не могут справиться с чрезвычайно высокими ускорениями и замедлениями, необходимыми для реального использования преимущества утонения стружки при фрезеровании отслаивания.Вы не можете заставить стол весом 1000 фунтов работать ни копейки при 1200 IPM.
Хорошо, может, десять центов – плохое выражение. Даймы огромные. Но вы поняли.
Использование традиционных параметров, таких как полная ширина и глубина реза 1 / 2xD, обычно лучше работает в реальной жизни при резке алюминия.
Общие операции по обработке алюминия
Вот список обычных вещей, которые вы собираетесь делать с алюминием, а также несколько полезных советов.
Облицовка
Если вы собираетесь использовать ракушечную фрезу, определенно выбирайте сверхагрессивный передний угол и полированные пластины.Ваш финиш будет потрясающим, и вы действительно сможете увеличить обороты.
Карманы
Это то, что многие ребята делают неправильно. Если вы перешагнете половину диаметра фрезы и наполовину вниз, вы сделаете ошибку по двум причинам:
- Резак может обработать больше. Идти почти на всю ширину. Мой выбор – 95% плоского резака. Причина в том, что резак все равно будет зарываться в углы. Это означает, что вам придется замедлить подачу, чтобы инструмент не взорвался по углам.Если вы перейдете на 100%, вы можете получить бумажные пластины между траекториями инструмента из-за отклонения резца и материала.
- Шаг 50% ужасен для гармоник, когда черновая обработка выполняется с приличной скоростью. Удар инструмента, входящего в заготовку, происходит в худшем из возможных мест, ударяясь каждым зубом. Даже подъем инструмента до 65% приведет к заметному снижению вибрации.
Другой совет – использовать фрезу, диаметр которой немного меньше внутреннего радиуса кармана.Если вы используете концевую фрезу 1/2 дюйма для вырезания карманов на 1/4 дюйма рад, у вас будет тенденция выдолбить углы с дребезжанием, когда инструмент меняет направление. На высоких скоростях инструменты не меняют направление мгновенно, что означает, что инструмент снимает давление резания. Это то, что вызывает эти щебечущие звуки.
Обычно я спрашиваю, могу ли я изменить размер этих рад до 0,265 дюйма для чистых углов. Это уменьшает контакт инструмента с геометрией детали. Машина также способна справиться с этим закругленным поворотом на более высоких скоростях.Просто представьте машину на гоночной трассе. В крутом повороте машина замедляется. Если радиус больше, машине не нужно снижать скорость.
Это довольно хорошо устранит то щебетание в углах, которое делает ваши детали некрасивыми.
Прорези
Для очень глубоких пазов мне подходят два варианта: либо трохоидальное фрезерование, чтобы уменьшить отклонение фрезы и вибрацию, либо концевую фрезу с короткими канавками.
Лично я предпочитаю короткие канавки, так как инструмент значительно прочнее, и вы не получаете лишних движений, когда инструмент движется вперед и назад.Глубокие прорези – одно из тех приложений, где часто бывает целесообразно использовать специализированный инструмент.
Для мелкой прорези пазов (4xD и ниже) особых соображений не требуется. Просто дай.
Бурение
Использование. Острый. Сверла.
Твердосплавные сверла – не всегда ответ; На самом деле нет никакого смысла запускать дорогостоящее твердосплавное сверло, если у вас нет числа оборотов шпинделя или объема производства, чтобы это оправдать.
Вообще говоря, просто используйте сверло с разделительной точкой 135 градусов, и все будет в порядке.Если на кончике сверла есть перепонка, значит, вы подвергаете резку лишнему нагреву.
Нарезание резьбы
Метчики общего назначения технически работают, но метчики, специально предназначенные для алюминия, намного надежнее. У них гораздо более агрессивный передний угол, что означает более чистый срез и меньшее нагревание.
Также не будьте слабаком с RPM. Если вы никогда не превышаете 200 об / мин на своих машинах, вы просто теряете время.
Конечно, некоторые станки просто старые и изношенные, и люфт слишком велик, чтобы резать быстрее.На самом деле, вы все равно не будете конкурентоспособны на этих машинах.
Дело в том, что работать с алюминием легко, не тратьте на это время.
Как добиться превосходного качества обработки поверхности алюминия
Высокие обороты. Это не секрет. Проверните его.
Использование инструмента для чистовой обработки с острой бритвой, высокой спиралью и очень агрессивными углами наклона также поможет вам получить супер-блестящую поверхность.
Стоит упомянуть одну вещь: вы не хотите тратить свое время на то, чтобы сделать деталь красивее, чем она должна быть.Иногда вы просто хотите порадовать покупателя и произвести на него впечатление, но помните, что есть разница между блестящим и высоким Ra.
Это действительно стоит того, чтобы произвести расчеты чистоты поверхности, чтобы вы могли определить максимальную скорость подачи для чистовых пропилов. Обычно я делаю математические вычисления, а затем откладываю их примерно на 10% на всякий случай. Если вы переступите через эту границу, в половине случаев вы ошибетесь.
Смазочно-охлаждающая жидкость
Никогда не режьте алюминий насухо. Ребята, которые делают это на YouTube, делают это только для того, чтобы вы могли видеть, что происходит.В реальной жизни (и за кадром) резаки взрываются, когда они забиваются из расплавленного алюминия, накапливающегося на краю.
Многие компании скажут вам, что тип СОЖ имеет огромное значение для таких вещей, как стойкость инструмента и качество обработки поверхности. Имеет ли это?
Что-то вроде, но ничего особенного.
На самом деле, единственный раз, когда я действительно заметил заметную разницу, это когда все остальные факторы были точно установлены в .
Вот порядок действий для того, как я подхожу к совершенствованию процесса:
- Параметры резания – шаг / ступень, скорость подачи, число оборотов в минуту, траектория инструмента
- Геометрия режущего инструмента – подходит для алюминия и тип операции (черновая, чистовая и т. Д.) – угол винтовой линии, сорт твердого сплава, количество канавок и т. Д.
- Покрытия резца / отделка
- Охлаждающая жидкость
Ладно, ну вот и все.Конечно, резка алюминия позволит вам научиться гораздо большему, но это статья, а не электронная книга.
В конечном счете, если вы действительно хотите добиться успеха с алюминием, вам придется поэкспериментировать самостоятельно. Работайте со своими представителями по инструментам, чтобы придумать отличные решения для улучшения ваших процессов.
Если вас интересуют дополнительные советы по обработке, вот несколько статей, которые я действительно рекомендую вам взглянуть:
Что такое высокоскоростная обработка и как это сделать
Обработка квадрата внутри углов: победите кошмар! (советы по созданию отличных углов для фрезерования)
Руководство для механика по трохоидальному и лущильному фрезерованию
5 распространенных типов станков с ЧПУ
Исправлено 11 марта 2019 г.
Станки с числовым программным управлением (ЧПУ) становятся все более популярными в инструментальной промышленности и в последние годы приобрели популярность у некоторых любителей.Станки с ЧПУ полагаются на компьютеры, а не на людей для выполнения задач. Эти машины, хотя и становятся все более популярными во всем мире, в основном используются в автомобильной и технической отраслях. Используя приводы, приводы, коммутационные платы и программное обеспечение, станки с ЧПУ могут создавать множество продуктов.
Существуют различные типы станков с ЧПУ, в том числе:
- Фрезерный станок – Фрезерный станок с ЧПУ может резать и гравировать дерево, металл или пластик и является очень распространенным типом станков с ЧПУ.Пользователь не манипулирует роутером, только вводит информацию в компьютер. Если вы заказываете вырубку из этих материалов, скорее всего, для ее изготовления использовался маршрутизатор.
- Plasma – Плазменные резаки с ЧПУ используются для резки металла и дерева (двухмерные) и не требуют такой большой мощности, как фрезерный станок с ЧПУ. В этих машинах используется плазменный резак для проникновения в дерево или листовой металл.
- Laser – Станки лазерной резки с ЧПУ работают так же, как и плазменные резаки с ЧПУ, но вместо этого для резки дерева или металла используется лазер.Лазеры также можно использовать для резки пластика.
- 3D-принтер – 3D-принтеры используют технологию ЧПУ и работают с использованием той же технологии, что и лазеры с ЧПУ, но используют экструдер для медленного нанесения пластика последовательным движением до тех пор, пока желаемый продукт не будет готов.
- Pick and Place – Pick and Place Станки с ЧПУ состоят из нескольких сопел, которые захватывают электрические компоненты электронного оборудования и помещают их в желаемое место. Они очень часто используются при изготовлении сотовых телефонов, компьютеров, планшетов и т. Д.
Универсальность этих инструментов позволяет быстрее выполнять желаемую задачу. Они также обеспечивают точность работы и более стабильное производство в целом.
При поиске оборудования с ЧПУ лучше всего иметь дело с проверенными профессионалами, которые знакомы со всеми типами оборудования с ЧПУ и найдут необходимое время, чтобы обсудить ваши уникальные потребности в обработке. Эксперты Tramar Industries уже более десяти лет поставляют высококачественную продукцию с ЧПУ предприятиям и любителям.Компания Tramar Industries, гордая членством в Национальной ассоциации дилеров машинного оборудования, является очевидным выбором для станков с ЧПУ всех типов. Если вам нужен станок с ЧПУ, свяжитесь с Tramar Industries сегодня!
Эта статья написана Sierra Harbin.
% PDF-1.7 % 310 0 объект > эндобдж xref 310 92 0000000016 00000 н. 0000003031 00000 н. 0000003219 00000 н. 0000003930 00000 н. 0000004044 00000 н. 0000028319 00000 п. 0000050259 00000 п. 0000072699 00000 п. 0000095602 00000 п. 0000118326 00000 н. 0000118440 00000 н. 0000142471 00000 н. 0000142508 00000 н. 0000142944 00000 н. 0000143057 00000 н. 0000143173 00000 п. 0000143478 00000 н. 0000143575 00000 н. 0000143946 00000 н. 0000144414 00000 н. 0000144560 00000 н. 0000144657 00000 н. 0000144803 00000 н. 0000144949 00000 н. 0000145068 00000 н. 0000145184 00000 н. 0000167325 00000 н. 0000167677 00000 н. 0000189532 00000 н. 0000189762 00000 н. 00001
00000 н.
0000213632 00000 н.
0000214019 00000 н.
0000215390 00000 н.
0000215465 00000 н.
0000215852 00000 н.
0000218876 00000 н.
0000221525 00000 н.
0000221556 00000 н.
0000221631 00000 н.
0000227469 00000 н.
0000227762 00000 н.
0000227828 00000 н.
0000227944 00000 н.
0000229030 00000 н.
0000229334 00000 н.
0000229678 00000 н.
0000264973 00000 п.
0000265012 00000 н.
0000295324 00000 н.
0000295363 00000 п.
0000334283 00000 н.
0000334322 00000 н.
0000334709 00000 н.
0000335096 00000 н.
0000335326 00000 н.
0000335472 00000 н.
0000335618 00000 п.
0000335692 00000 н.
0000335766 00000 н.
0000335840 00000 н.
0000337061 00000 н.
0000337527 00000 н.
0000338007 00000 н.
0000338081 00000 н.
0000338155 00000 н.
0000338229 00000 н.
0000339532 00000 н.
0000340036 00000 н.
0000340513 00000 н.
0000340587 00000 н.
0000340661 00000 н.
0000340735 00000 н. 0000342723 00000 н.
0000343206 00000 н.
0000343688 00000 п.
0000343762 00000 н.
0000345747 00000 н.
0000345822 00000 н.
0000360730 00000 н.
0000376607 00000 н.
0000376970 00000 н.
0000377045 00000 н.
0000377864 00000 н.
0000377912 00000 н.
0000392820 00000 н.
0000394594 00000 н.
0000394960 00000 н.
0000395035 00000 н.
0000395148 00000 н.
0000395426 00000 н.
0000002136 00000 п.
трейлер
] / Назад 916778 >>
startxref
0
%% EOF
401 0 объект
> поток
h ތ SWLQNQo) / R
֑ 8 @> aWQ! 1 “bQV4 & h 3} 99
Различные типы фрез, используемых в процессе обработки
Типы фрез
Вам интересно узнать о типах фрез? Что ж, эта статья даст вам информацию обо всех фрезах.Так чего же ты ждешь? Давайте начнем.
Давайте начнем с того, что узнаем, что такое фрезерование? Фрезерование – это процесс резки, при котором мы используем резак для удаления материала с поверхности металла или заготовки. Этот резак, который мы используем, имеет несколько вращающихся режущих поверхностей. Фрезы играют важную роль в процессе фрезерования и используются на нескольких фрезерных станках. Фрезы бывают разных размеров и форм.
Ниже приведены типы фрез, которые мы используем в различных фрезерных станках:
- Концевая фреза для черновой обработки
- Слябовый стан
- Концевая фреза
- Полый стан
- Фреза шаровая
- Эвольвентная зуборезка
- Фреза торцевая
- Нож для ершей по дереву
- Фрезы для резьбовых фрез
- Мухорезка
- Фреза для скольжения и торца
- Зуборез
- Фреза
Чтобы узнать больше о каждом резаке, продолжайте читать …………..
Также читают:
1. Концевая фреза для черновой обработки Этот тип фрезы используется, когда вам нужно удалить большее количество материала с заготовки. Используя концевые фрезы для черновой обработки, мы получаем черновую чистовую обработку поверхности. Концевые фрезы для черновой обработки также известны как фрезы «риппа». Они более выгодны с коммерческой точки зрения и используются в различных промышленных приложениях.
В основном слябовые фрезы используются для обработки поверхностей как большой, так и широкой формы.Слябовые станы изготавливаются из быстрорежущей стали. Слябовые станы в основном используются в процессах группового фрезерования.
3. Концевая фрезаЭти фрезы имеют режущие зубья с обеих сторон. Мы больше используем концевые фрезы в процессах вертикального фрезерования. Для создания концевых фрез используют быстрорежущую сталь или твердый сплав. Быстрорежущая сталь также называется HS или HSS. Быстрорежущая сталь не теряет твердости при повышении температуры.Следовательно, из-за большей твердости для изготовления концевых фрез используется быстрорежущая сталь. Концевые фрезы в основном используются для врезания, копировального фрезерования, торцевого фрезерования и т. Д. Торцевые фрезы и т. Д. – это различные фрезы, которые используются в термине концевые фрезы.
4. Полая мельницаИх также называют полыми фрезами. Они похожи на трубу с более толстыми стенками. На внутренних поверхностях вы найдете режущие зубья полых фрез. В винтовых станках используются полые фрезы.
5. Фреза с шаровой мельницейШариковые фрезы также известны как фрезы со сферическим концом. Вас можно легко идентифицировать как шаровые ножи, так как их конец имеет полусферическую форму. Шаровые фрезы используются для уменьшения концентрации напряжений и также известны как шаровые концевые фрезы. Всякий раз, когда возникает необходимость вырезать трехмерные формы, можно использовать шаровые фрезы, чтобы идеально вырезать эти трехмерные формы.
6. Эвольвентная зуборезка Он состоит из множества фрез и имеет угол прижатия 14. 5º. Имеет большое количество зубов. Некоторые из зубов могут быть половинного размера и, следовательно, они не считаются фрезами.
Также читают:
7. Торцевая фрезаОн состоит из режущих зубьев, имеющихся на его сторонах. Он состоит из твердого сплава и всегда режет горизонтально. Ее также называют пластиной из твердого сплава со сменными пластинами. Он имеет корпус, который можно заменить на твердосплавные наконечники. Эти твердосплавные вставки имеют золотой цвет. Эти наконечники можно обменять, и, таким образом, всякий раз, когда один из наконечников повреждается, вы можете заменить его на новый.
8. Нож для обрезки деревянных ершейИсточник изображения
Этот резак широко используется в приложениях, связанных с ключами Вудраффа.
9. Резьбовая фрезаФрезы для фрезерования резьбы – это еще один вид фрез, который чаще всего используется в различных отраслях промышленности. Он работает так же, как и концевая фреза. Он удаляет материал из заготовки, двигаясь по спирали по металлической поверхности. Его легко идентифицировать по спиральному движению, которым он обладает.Это очень дорогое удовольствие.
10. МухорезСамое лучшее в мухорезках – это то, что они намного дешевле. В мухорезке присутствуют некоторые невращающиеся резцы. Фрезы с двумя невращающимися фрезами называются двойными фрезами или фрезами. Мыши очень эффективны и облегчают процесс резки.
11. Фреза для скольжения и торцаЭти фрезы самые ранние и были открыты в 1800 году.Они были самыми известными фрезами в период с 1810 по 1880 год. Этот тип фрезы доступен в различных размерах и формах. Вы найдете режущие зубы на его периферии и по бокам. Боковой и торцевой резак делает одностороннюю резку простым и эффективным процессом.
12. ЗуборезИсточник изображения
Это специальные фрезы, которые используются для создания различных типов шестерен.