Токарная обработка цилиндрических поверхностей – в Москве
Процесс обточки
Токарная обработка цилиндрических поверхностей, для целей уменьшения погрешностей при размещении относительно заданной оси отверстий, заключается в точном соблюдении последовательности производственных действий:
– на первом этапе обрабатываемый элемент подвергается центрированию, направляющему к подаче следующих инструментов;
– на следующем этапе осуществляется сверление;
– далее производится расточка, которая требуется для устранения осевого смещения;
– контроль промышленным штангенциркулем размеров углубления;
– производится процесс развертки для доведения до требуемых геометрических и точных параметров формы отверстия изделия.
Установка резца
Прежде чем на токарном станке будет проводиться обработка цилиндрической поверхности, необходимо установить резец. Перед началом установки опорные поверхности держатели подвергаются тщательной очистке. Одним из главных правил при установке резца является то, что его вершина должна обязательно находиться по уровню оси центров токарного станка. Установка выше этой линии приведет к быстрому износу и нагреву, а ниже – к выталкиванию при набегании деталей из центров. Максимальную точность при установке придаст регулировка резца по высоте (при этом необходимо подстилать не более 3-х подкладок).
Правила пользования лимбами
Лимб представляет собой плоскую шайбу или кольцо, на внешнюю часть которого на равном расстоянии друг от друга нанесены риски. Градуировка может быть в градусах, миллиметрах и прочих метрических величинах. При эксплуатации лимба требуется учитывать, имеется ли люфт и его величина в передачах движения суппорта. При выполнении отсчетов размеров маховичок ручной подачи можно плавно поворачивать, причем только в одну сторону. Если имеет место ошибка и лимб повернут на большее количество делений, чем необходимо, маховичок на величину чуть больше люфта поворачивается в обратную сторону, и лимб доводится до необходимого деления.
Обточка ступенчатой поверхности
Во время обрабатывания ступенчатых поверхностей необходимо соблюдать рациональную последовательность обточки (обеспечивается при наименьшей суммарной длине рабочих ходов резца) и постоянное продольное положение заготовок на станке (позволяет значительно сократить время на замер длины и пробный отсчет). Для этого уступ подвергаемой обработке заготовки или ее левый торец требуется поджать к уступам прямых или обратных кулачков, или к уступу небольшой выточки и к регулируемому шпиндельному упору. Токарный станок рекомендуется настроить по поперечным и продольным упорам для повышения производительности обработки.
Выбор режима резания
Одной из ключевых задач технологической подготовки производственного процесса при проведении токарных работ является выбор оптимального режима резания. В своей работе любой профильный специалист руководствуется такими показателями, как:
– скорость вращения шпинделя, где внимание обращается на вид обрабатываемого материала;

Токарная обработка цилиндрических поверхностей
Цилиндрические поверхности обрабатывают при продольном перемещении продольного суппорта или верхнего суппорта. Внешние цилиндрические поверхности обрабатывают обычно проходными резцами, а внутренние расточными.
Приспособления для закрепления заготовок выбирают в зависимости от их формы и размеров. Заготовку типа вал зависимости от отношения ее длины к диаметру рекомендуется закреплять так:
при l / d <4 – в патроне;
при 4 ³ l / d <10 – в центрах;
при l / d> 10 … 12 – в центрах по дополнительной опорой заготовки на кулачки движимого или недвижимого люнета.
2.2 Обработка конических поверхностей
Конические поверхности на токарном станке могут быть обработаны одним из следующих методов:
– Резцом с наклонно расположенной режущей кромкой;
– С помощью поворота верхней каретки суппорта (верхнего суппорта)
– Смещением задней бабки;
– С помощью копировальной линейки.
Резцом с наклонно расположенной режущей кромкой обрабатывают внешние 1 и 2 внутренних конические поверхности (рис. 38, а), длина которых не превышает 20 … 25 мм.
С помощью поворота верхнего суппорта обрабатывают наружные и внутренние конические поверхности, длина которых не превышает длины хода верхнего суппорта. Направляющие верхнего суппорта устанавливают под углом j (6, рис. 38, г) к оси вращения заготовки, равный половине угла при вершине обрабатываемого конуса. Подача резца производится вручную.
Методом смещения корпуса задней бабки обрабатывают только внешние конические поверхности, у которых длина образующей сравнительно большая, а угол при вершине конуса не превышает 10 … 12о. Заготовку в этом случае закрепляют в центрах, а корпус задней бабки смещают в поперечном направлении на величину h (рис. 38, в):
h = L × sin j,
где L – длина заготовки, мм;
j – половина угла при вершине конуса.
С помощью копировальной линейки можно обрабатывать внешние и внутренние конические поверхности большой длины, угол при вершине в которых не превышает 25 °.
На рис. 38, г показано строение одной из конструкций конусной линейки.
Основой конусной линейки служит кронштейн 5, прикрепленный болтами к продольным полозьев суппорта; в кронштейне имеются продольные направляющие в виде ласточкиного хвоста для основы линейки 7. В основу линейки ввернут стержень 8, который другим концом входит в отверстие кронштейна 10 и закрепляется в нем болтом 9.
Кронштейн 10 с помощью болтов 11 закрепляют на станине станка. На верхней плоскости основания линейки установлена конусная линейка 1, в которой сделана прямоугольный паз 6. В пазу находится ползунок 2, с которым с помощью болта 4 соединена тяга 3, второй конец тяги винтами соединен с поперечными салазками суппорта.
При использовании конусной линейкой поперечные салазки отделяют от винта поперечной подачи, для чего обычно винт поперечной подачи вынимают из суппорта. Конусную линейку устанавливают по одной из шкал, нанесенных на концах основы линейки, на угол j, равный половине угла при вершине конуса, обрабатывается, и закрепляют болтами. При продольном автоматическом или ручном перемещении суппорта ползунок 2 и резец перемещаются параллельно образующей обрабатываемого конуса. Необходимую глубину резания устанавливают ручным перемещением верхнего суппорта.
Загрузка…
Точение цилиндрических поверхностей
Механическая обработка цилиндрических поверхностей
Наша компания оказывает широкий спектр токарных услуг. У нас работают профессиональные токари, которые грамотно подходят к поставленной перед ними задаче. Любой заказ можно реализовать с высоким качеством обработки металла, ведь мы используем самое современное оборудование.
Прайс – токарные цены
Точение цилиндрических поверхностей, гладких и ступенчатых производится по лучшим ценам. При выполнении работ наши специалисты руководствуются чертежом заказчика, либо предлагают консультационные услуги для реализации пожеланий клиента. Мы гарантируем, что обработка металла будет произведена вовремя, а деталь прослужит долго.
О ТОКАРНОЙ УСЛУГЕ
Обработка металлических поверхностей осуществляется с помощью специальных фрез, благодаря которым изделие приобретает нужную геометрическую форму (коническую, сферическую, цилиндрическую). Подобные детали нужны для вращающихся конструкций. Наше оборудование позволяет работать с различными видами металла, начиная от меди и стали, заканчивая материалами с высокой прочностью, такими как титан.
Технология резания предполагает движение двух частей – заготовки и самого резца, снимающего лишний слой с металла. Также деталь подлежит токарной обработке, сверлению и любой другой процедуре, которую необходимо произвести для ее подготовки. Качество обработки зависит от типа фрезы, а так как для обработки мы используем новые станки, то в точности работы можно не сомневаться.
Автоматизация обработки заготовок позволяет минимизировать неточности по вине человеческого фактора, а также увеличить скорость выполнения заказа. Это значит, что ваши детали будут изготовлены в короткие сроки, даже если вы заказываете большую партию.
ПРЕИМУЩЕСТВА УСЛУГИ
Услуга обработки металлических изделий имеет сразу несколько преимуществ:
- позволяет создать деталь по индивидуальному чертежу даже из высокопрочного металла;
- гарантируется высокая точность при обработке, а также высокая скорость изготовления;
- детали изготавливаются без брака, благодаря использованию токарных станков с новейшим программным обеспечением;
- обработанная деталь будет иметь чистую, гладкую поверхность без дефектов.
Оборудование с ЧПУ и мастерство наших специалистов с большим опытом работы позволяет воплотить все вышеперечисленные преимущества обработки.
ПОЧЕМУ НУЖНО СВЯЗАТЬСЯ С НАМИ?
Есть как минимум пять причин, по которым наши клиенты высоко оценивают наш уровень обслуживания.
- У нас работают профессиональные специалисты, которые изготавливают детали с фантастической точностью параметров.
- Новейшее оборудование позволяет создавать заготовки любой сложности.
- Стоимость услуг зависит от сложности заказа и вида обработки, однако наши цены вполне конкурентоспособны и удовлетворят большинство клиентов.
- Мы готовы предложить весь спектр услуг по работе с металлом.
- Консультируем и выполняем заказы в короткие сроки.
Перед тем, как отдать детали заказчику, наши мастера всегда проверяют их на наличие брака, поэтому брак полностью исключен. Мы дорожим репутацией компании, поэтому всегда добиваемся высокого качества цилиндрических поверхностей.
- Пред.
- Следующий
Исследования применения скользящего выглаживания для улучшения качества поверхности наружных цилиндрических поверхностей
Исследования применения скользящего выглаживания для улучшения качества поверхности наружных цилиндрических поверхностей·Содержание ·Общие 90 104 | Обследования Использование скользящего выглаживания для улучшения качества поверхности наружных цилиндрических поверхностейД-р Дьюла Варга, профессор Иллес Дудас, 9 лет0082 Факультет технологии производства, Университет Мишкольца,H – 3515 Мишкольц – Едьетемварош, Венгрия Контакт |
1. Введение
- Качество обработанной поверхности становится все более и более важным для удовлетворения растущих требований к производительности и надежности. В обеспечении качества продукции машиностроения важную роль играют так называемые «процессы окончательной отделки».
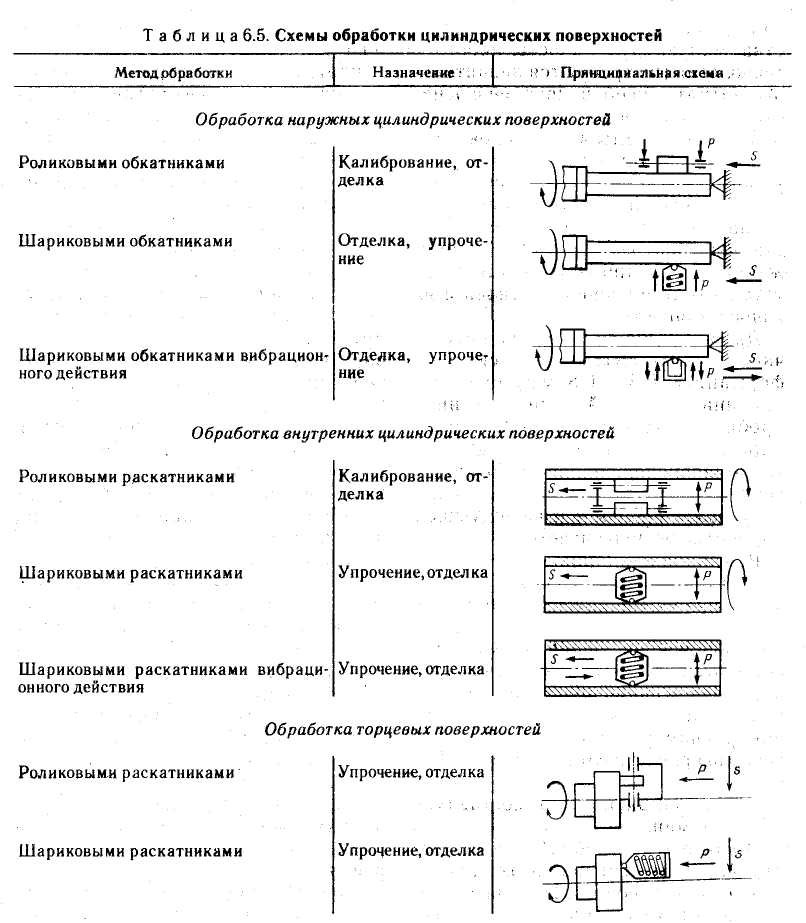
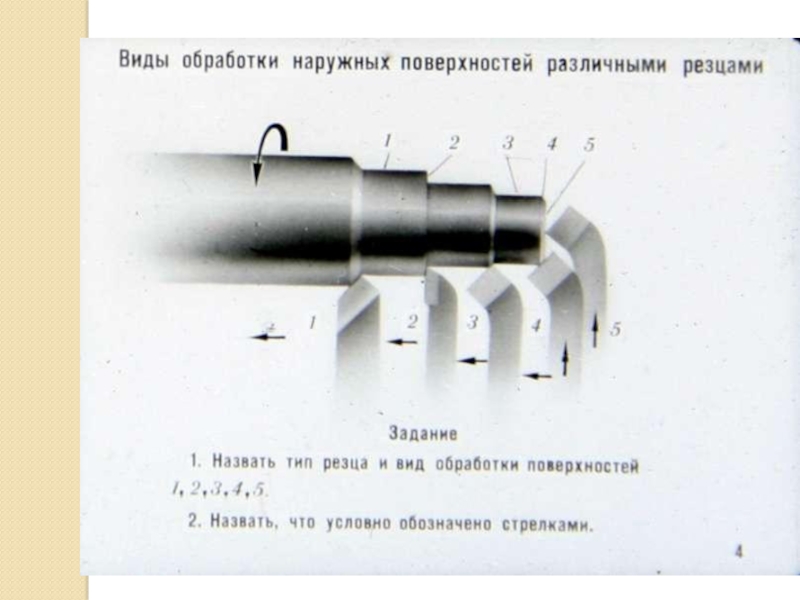
- Главной особенностью всех применяемых методов скользящего выглаживания является то, что в зоне контакта между рабочей частью инструмента и обрабатываемой поверхностью всегда происходит скольжение. Из-за действия давления – находящегося между контактирующими поверхностями – и скольжения характеристики шероховатости ранее изготовленной (точеной, шлифованной и т.п.) поверхности изменяются (уменьшаются) вследствие упруго- пластик деформация поверхностного слоя.
Размер микрогеометрических неровностей зависит, прежде всего, от силы прижатия инструмента F и параметров изготовления, то есть подачи f v и скорости выглаживания v v . В другой литературе [3] рассматривается влияние радиуса R инструмента на шероховатость поверхности.
Современные токарные обрабатывающие центры с ЧПУ способны обеспечить класс точности 6 th

Значение силы полировки, необходимой для полировки, можно отрегулировать по калиброванной шкале. Программирование и управление полировкой очень похоже на чистовую токарную обработку.
- Целью обслуживания поршневого пальца методом полировки скольжением является повышение эксплуатационной надежности и снижение затрат. Метод может быть использован в штучном производстве в ремонтных мастерских – там, где нет высокоточных прецизионных станков, но есть шлифовальный станок, токарно-центральный станок, шлифовальный инструмент. Эта ремонтная деятельность может быть выполнена легко и точно.
- сила полировки:
- подача полировки:
- скорость полировки:
- твердость закаленных пистолетных пальцев:
- Размер шлифованных пистолетных пальцев:
- среднее арифметическое отклонение (R a ) и максимальная высота профиля (R max ) профиля шлифуемой поверхности:
- угол регулировки инструмента:
- Эффект скорости скольжения зависит от значения силы полировки. В случае небольшого значения усилия выглаживания (например, F=125 Н) увеличение скорости приводит к улучшению значения R max . Увеличение значения силы выглаживания (например, до F=150 Н) при использовании большего значения скорости заготовки, r Rmax Коэффициент уменьшится.
- Уменьшение подачи увеличивает значение отношения r Rmax , поэтому значение R max будет меньше.
Другой целью было создание эмпирических формул. С их помощью можно заранее рассчитать влияние силы выглаживания и технологических параметров на шероховатость поверхности.
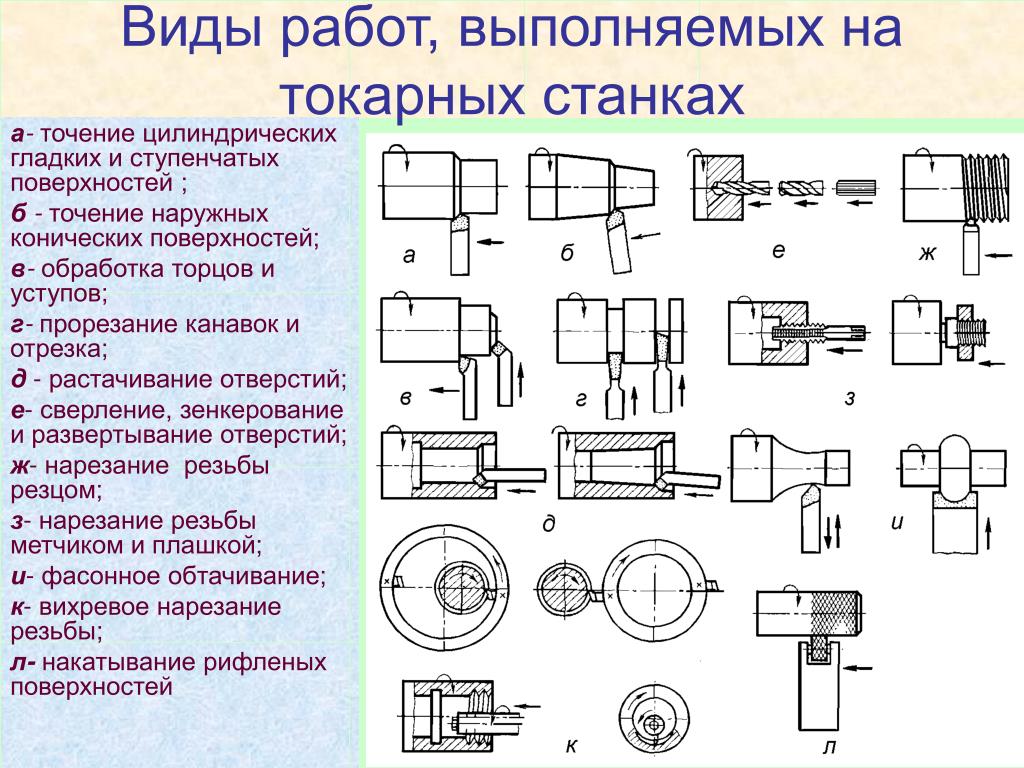
3. 1. Корректировка параметров и экспериментального фона
Подготовительное изготовление изношенных поршневых пальцев было шлифованием, а плавная шлифовка скольжения производилась на токарно-центровом станке типа Е400/1000. Зажим заготовки производился согласно рис. 1.б. Сила выглаживания обеспечивалась калиброванным выглаживающим инструментом с пружиной, зажатой в резцедержателе.
Входные данные:
F vmin = 125 Н, | F vmax = 150 Н, | |
f vmin = 0,0203 мм/об, | f vmax = 0,05 мм/об, | |
v vмин = 60 м/мин, | v vmax = 83 м/мин.![]() |
HRC @ 55, | |
Æ24,9 x 100 мм, | |
a @0°. |
При выглаживании инструмент проходил однократно по поверхности с использованием интенсивного объема масляных охлаждающих жидкостей (смазок). Исследуемые – измеренные характеристики – выходные данные – представляли собой после воронения средние значения R a,v и R max,v шероховатости поверхности вороненых поверхностей.
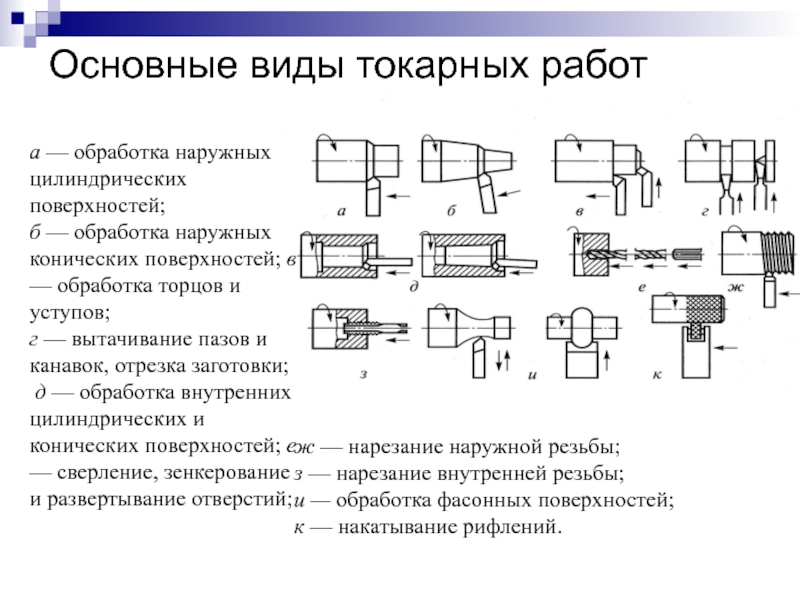
Эти размеры были измерены в 8 различных местах на периферии поршневых пальцев, и были рассчитаны средние значения:
Шероховатость поверхности после шлифовки | Скорректированные параметры | Измеренные значения шероховатости поверхности после полировки | ||||
R max,g | R a,g | f v | v v 9 0104 | Ф в | R max,v | R а.в |
мм | мм/брод | м/мин | Н | мм | ||
2,66 | 0,33 | 0,0203 | 60 | | 1,03 | 0,112 |
3,32 | 0,33 | 0,0500 | | 125 | 1,92 | 0,260 |
3,39 | 0,37 | 0,0203 | 83 | | 0,70 | 0,096 |
3,32 | 0,37 | 0,0500 | | | 1,40 | 0,180 |
2,79 | 0,37 | 0,0203 | 60 | | 0,75 | 0,100 |
3,89 | 0,42 | 0,0500 | | 150 | 1,18 | 0,160 |
3,53 | 0,43 | 0,0203 | 83 | | 0,97 | 0,130 |
2,95 | 0,34 | 0,0500 | | | 1,20 | 0,150 |
Таблица 1: |
Помимо измерений, упомянутых выше, мы также измерили ошибку круглости. Измерения проводились с помощью пассаметра, трехмерной измерительной машины, пертометра и талирунда (для измерения погрешности круглости).
3.2 Изучение микрогеометрических особенностей
Выбор входных параметров, приведение их в правильный порядок с помощью факторного планирования эксперимента может осуществляться активно [4]. Выходные параметры R max.v и R a.v .
Мы записываем эмпирические функции для этих параметров в качестве функции отклика следующим образом:
(1) | |
(2) |
Применяя этапы метода к этому конкретному случаю, константы C vm и C va , a м , г м , д м , а а , г a , d a были определены показатели степени. Константы и показатели R max,v можно найти следующим образом:
формула (1) |
С вм = е 218,152 |
а м = (11,5073 – 0,2899 ln v v – 1,9766 ln F v ) |
г м = – (41,9107 – 8,2493 ln F v ) |
д м = – 42,7924 |
Эти формулы несколько усложнены, но описывают результаты полировки. Однако, если принять во внимание, что величина шероховатости поверхности не была одинаковой, то, может быть, можно принять эти расчеты с оговорками.
Замечание: константы и показатели R a,v легко вычисляются, однако мы их здесь не публикуем.
Мы можем больше сказать об улучшении качества поверхности, если будем рассматривать только улучшение/разницу между шероховатостью поверхности до и после полировки. Итак, введите следующие внутренние параметры:
(3) | |
(4) |
Эффект воронения наилучший при расчетном значении R max,D и R а, д – максимальные. Для улучшения шероховатости мы можем создать новые формулы:
(5) | |
(6) |
Применяя факторный план эксперимента для расчетных значений из таблицы 1, константа и показатели степени формулы (5) следующие:
формула (5) |
С р м = е -230,5053 |
а р м = 0,4515 |
г р m = (52,8366 – 10,6419 ln F v ) |
д р м = 46,34 |
Замечание: эти формулы (1), (2), (5), (6), справедливые только для интервалов, можно найти в табл.

Улучшения максимальной высоты профиля (R max ) поверхности можно увидеть на рис. 1.
Рис. 1: Гладкое шлифование наружных цилиндрических поверхностей на производственном центре (а) и на токарном станке. Заготовка (1), инструмент для полировки (2), вставка для полировки (3), активный элемент наконечника (A). |
Поскольку влияние различных параметров можно увидеть явно, поэтому следует только одно замечание. Замечания к рис. 1.
Рис. 2. Характеристика относительной характеристики шероховатости поверхности r Rmax в зависимости от технологических параметров f v , v v и силы выглаживания F v |
- Зная применяемые технологические параметры (f v , v v ) и прикладываемое усилие выглаживания, кроме того, значения характеристик шероховатости поверхности (R max,g , R a,g ) шлифованной внешней цилиндрической поверхности перед полировкой, улучшение R max или R a можно планировать при заданном R-радиусе рабочего органа и заданном материале, подлежащем полировке.
