Режимы резания при фрезеровании | Фрезерование металла
Расчет режимов фрезерования заключается в определении скорости резания, частоты вращения фрезы, и выбора подачи. При фрезеровании различают два основных движения: вращение фрезы вокруг своей оси – главное движение и перемещение заготовки относительно фрезы – движение подачи. Скорость вращения фрезы называют скоростью резания, а скорость перемещения детали – подачей. Скорость резания при фрезеровании – это длина пути (в м), которую проходит за 1 мин наиболее удаленная от оси вращения точка главной режущей кромки.
Скорость резания легко определить, зная диаметр фрезы и частоту ее вращения (число оборотов в минуту). За один оборот фрезы режущая кромка зуба пройдет путь, равный длине окружности, имеющей диаметр D:
l = πD, где l – путь режущей кромки за один оборот фрезы.
Длина пути
Длина пути, пройденная кромкой зуба фрезы в единицу времени,
L = ln = πDn, где n – частота вращения, об/мин.
Скорость резания
Принято обозначать диаметр фрезы в миллиметрах, а скорость резания в метрах в минуту (м/мин), поэтому написанную выше формулу можно записать в виде:
Частота вращения фрезы
В производственных условиях часто требуется определить необходимую частоту вращения фрезы для получения заданной скорости, резания. В этом случае используют формулу:
Подача при фрезеровании
При фрезеровании различают подачу на зуб, на оборот и минутную подачу. Подачей на зуб Sz называют расстояние, на которое перемещается заготовка (или фреза) за время поворота фрезы на один шаг, т. е. на угол между двумя соседними зубьями. Подачей на оборот S0 называют расстояние, на которое перемещается обрабатываемая деталь (или фреза) за время одного полного оборота фрезы:
S0 = Sz Z
Минутная подача
Минутной подачей Sм называют расстояние, на которое перемещается заготовка (или фреза) в процессе резания за 1 мин. Минутная подача измеряется в мм/мин:
Sм = S0n, или Sм = Sz Zn
Определение времени фрезерования детали
Зная минутную подачу, легко подсчитать время, необходимое для фрезерования детали. Для этого достаточно разделить длину обработки (т. е. путь, который должна пройти заготовка по отношению к фрезе) на минутную подачу. Таким образом, по величине минутной подачи удобно судить о производительности обработки. Глубиной резания t называют расстояние (в мм) между обрабатываемой и обработанной поверхностями, измеренное перпендикулярно обработанной поверхности, или толщину слоя металла, снимаемого за один проход фрезы.
Скорость резания, подача и глубина резания являются элементами режима резания. При наладке станка устанавливают глубину резания, подачу и скорость резания, исходя из возможностей “режущего инструмента, способа фрезерования обрабатываемого материала и особенностей обработки. Чем большее количество металла в единицу времени фреза снимает с заготовки, тем выше будет производительность фрезерования. Естественно, что производительность фрезерования при прочих равных условиях будет повышаться с увеличением глубины резания, подачи или скорости резания.
Похожие материалы
www.metalcutting.ru
Подача – это… Что такое Подача?
ПОДАЧА — ПОДАЧА, подачи, жен. Действие по гл. подать во всех знач., кроме 2. Подача пара в котел. Подача корпуса влево. Талантливая подача образа автором. У этого игрока хорошая подача мяча. Подача поезда к перрону. Подача жалобы. Подача первой… … Толковый словарь Ушакова
Подача — Подача удар в некоторых играх с мячом (теннис, пинг понг, волейбол), начинающий розыгрыш очка. Подача проводится по специальным правилам, часто заметно отличающимся от требований к последующим ударам. В теннисе, особенно мужском, игроки… … Википедия
подача — 1. Порция одноврем. загружаемых в шахтную печь рудных материалов, флюсов и тв. топлива с определ. соотношением компонентов. 2. Операция перемещения заготовки в одном из направлений (продольном, поперечном, или др.) в промежутках между единичными… … Справочник технического переводчика
подача — См … Словарь синонимов
подача — ПОДАЧА, и, ПОДАЧКА, и, ж. 1. Подача документов на выезд из страны. 2. Рекомендации, «замолвленное словечко». С чьей подачи его взяли? Ректорская подача то! Быть в подаче подать документы на выезд из страны и находиться в ожидании официального… … Словарь русского арго
ПОДАЧА — один из основных параметров режима резания, относительное перемещение режущего инструмента или обрабатываемой на станке заготовки. Различают подачу непрерывную прямолинейную (напр., на токарных станках), прерывистую прямолинейную (напр., на… … Большой Энциклопедический словарь
ПОДАЧА — ПОДАЧА, и, жен. 1. см. подать. 2. В спортивных играх: удар, к рым мяч (шайба, волан) вводятся в игру или направляются партнёру. Удачная п. Забить мяч с подачи нападающего. • С подачи кого, в знач. предлога с род. (разг.) начиная с (о том, кто… … Толковый словарь Ожегова
ПОДАЧА — доставка боезапаса из погребов к орудиям. Самойлов К. И. Морской словарь. М. Л.: Государственное Военно морское Издательство НКВМФ Союза ССР, 1941 … Морской словарь
ПОДАЧА — перемещение режущего инструмента или заготовки за один оборот или рабочий ход заготовки либо инструмента; может быть ручной или автоматической (по заданной программе или копиру). В зависимости от направления П. инструмента по отношению к… … Большая политехническая энциклопедия
подача — 3.5 подача: Объем газа, входящий в компрессор с определенными параметрами, сжатого и доставленного при определенном давлении на выходе. Примечание Подача компрессора не включает газ, который вытекает из компрессора в процессе сжатия, а также… … Словарь-справочник терминов нормативно-технической документации
подача — сущ., ж., употр. сравн. часто Морфология: (нет) чего? подачи, чему? подаче, (вижу) что? подачу, чем? подачей, о чём? о подаче; мн. что? подачи, (нет) чего? подач, чему? подачам, (вижу) что? подачи, чем? подачами, о чём? о подачах 1. Подачей… … Толковый словарь Дмитриева
dic.academic.ru
Элементы режима резания. Основные понятия
Режимом резания называется совокупность элементов, определяющих условия протекания процесса резания.
К элементам режима резания относятся – глубина резания, подача, период стойкости режущего инструмента, скорость резания, частота вращения шпинделя
, сила и мощность резания.При проектировании технологических процессов механической обработки или режущих инструментов возникает необходимость в определении и назначении элементов режима резания. Отечественная практика механической обработки накопила огромный нормативно – справочный материал, с помощью которого можно назначить любой режим резания для любого вида механической обработки. Однако, табличный метод назначения режимов резания является весьма громоздким, так как требует анализа большого количества справочной информации. Более того, все режимные параметры взаимосвязаны и при изменении хотя бы одного из них автоматически изменяются и другие, что еще более усложняет процесс назначения режимов резания.
Аналитический (расчетный) метод определения режима резания менее трудоёмок и более предпочтителен при учебном проектировании технологических процессов механической обработки резанием. Он сводится к определению, по эмпирическим формулам, скорости, сил и мощности резания по выбранным значениям глубины резания и подачи.
Для проведения расчетов необходимо иметь паспортные данные выбранного станка, а именно – значения подач и частот вращения шпинделя, мощности электродвигателя главного движения. При отсутствии паспортных данных расчет выполняется приблизительно, в проделах тех подач и частот вращения шпинделя, которые указаны в справочной литературе.
Выбор режущего инструмента
Его следует начинать с анализа шероховатости поверхностей детали, которая задана на чертеже. В зависимости от параметра шероховатости выбирается метод обработки данной поверхности, которому соответствует свой специфический режущий инструмент. В табл. 1 приведена зависимость шероховатости поверхности от различных методов обработки.
Немаловажное значение для расчета режимов резания имеет выбор материала инструмента. При его выборе следует руководствоваться рекомендациями табл. 2. Для тонких (отделочных) методов обработки материалов с высокими скоростями резания (свыше 500 м/мин) рекомендуется применение сверхтвердых инструментальных материалов.
Наиболее распространенными среди них являются материалы, полученные на основе кубического нитрида бора.
Выбор и назначение глубины резания
Рис. 1.Схема к определению глубины резания при точении
Глубиной резания называется расстояние между обрабатываемой и обработанной поверхностями, измеренное по нормали к последней.
При черновых методах обработки назначают по возможности максимальную глубину резанияt, равную всему припуску или большей части его. При чистовом резании припуск срезается за два прохода и более. На каждом следующем проходе следует назначать меньшую глубину резания, чем на предшествующем. Глубину последнего прохода назначают в зависимости от требований точности и шероховатости обработанной поверхности.
В данной работе рекомендуются следующие глубины резания t
черновая обработка t >2;
получистовая и чистовая обработка t = 2,0 – 0,5;
отделочная обработка (3,2 мкм і Ra > 0,8 мкм) t = 0,5 – 0,1.
При сверлении глубина резания t=0,5·D, при рассверливании, зенкеровании и развертывании t=0,5·(D-d) мм, где
D – диаметр осевого инструмента,
d – диаметр предварительно полученного отверстия, мм.
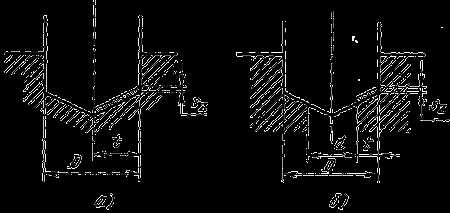
Рис. 2.Схемы для определения глубины резания при сверлении (а) и рассверливании (б) отверстий.
При отрезании, точении канавок и фасонном точении глубина резания приравнивается длине лезвия резца (см. рис. 3).
Рис. 3. Схема к определению глубины резания при отрезании
Выбор величины подачи
Подачей называется путь, пройденный какой-либо точкой режущей кромки инструмента, относительно заготовки, за один оборот заготовки (режущего инструмента), либо за один двойной ход режущего инструмента.
Различают подачу на один зуб Sz, подачу на один оборот S и подачу минутную Sм, мм/мин, которые находятся в следующей зависимости:
(1)
где: – частота вращения режущего инструмента, мин-1;
– число зубьев режущего инструмента.
При черновой обработке выбирают максимально возможную подачу, исходя из жесткости и прочности системы, мощности привода станка, периода стойкости режущего инструмента и других ограничивающих факторов. При чистовой обработке – в зависимости от требуемого параметра шероховатости обработанной поверхности.
При черновом точении выполняется вариантный расчёт режимов резания для нескольких значений подач в диапазоне, ограниченном чистовой (табл. 3) и максимальной подачей, допустимой прочностью режущей пластины (табл. 4).
При обработке отверстий осевым режущим инструментом выбирают рекомендуемую подачу, допустимую по прочности инструмента (табл.5).
Исходной величиной подачи при фрезеровании является подача Sz – на зуб. Рекомендуемые подачи для чистового фрезерования приведены в табл. 6.
В учебных целях рекомендуется значения подач выбирать из наиболее распространённого диапазона: 0,05- 0,5 мм/об.
Меньшие значения назначать для чистовой обработки, большие – для черновой.
Выбор значения периода стойкости
Периодом стойкости (стойкостью) режущего инструмента называется время его непрерывной работы между двумя смежными переточками.
Выбор значения периода стойкости режущего инструмента рекомендуется сделать из следующего ряда:
15;30;45;60;90;120 мин.
Меньшие значения периода стойкости следует назначать для мелких инструментов.
Расчёт режимов резания при сверлении, рассверливании, зенкеровании и развёртывании
Расчёт режимов резания при резьбонарезании
Расчёт режима резания при шлифовании
Расчёт режимов резания при строгании и долблении
Расчёт режимов резания при фрезеровании
osntm.ru
Скорость резания и подача при токарной обработке
И снова здравствуйте! Сегодня тема моего поста главные движения при токарной обработке такие как скорость резания и подача. Эти две составляющие режимов резания являются основополагающие при токарной обработке металла и других материалов.
Скорость резания и подача при токарной обработке.
Главное движение или скорость резания.
Если мы посмотрим на рисунок который приведен выше то увидим, что главное движение при токарной обработке тел вращения на токарном станке совершает именно заготовка. Она может вращаться как по часовой стрелке так и против. В основном как видим вращение направленно на резец, так как это обеспечивает срезание поверхностного слоя с заготовки и образования стружки.
Вращение заготовке придает шпиндель токарного станка и диапазон оборотов шпинделя (n) достаточно большой и может регулироваться в зависимости от диаметра детали ее материала и применяемого режущего инструмента. При точении в основном это токарные резцы различных видов и назначения.
Скорость резания при токарной обработке рассчитывается по формуле:
где
V — это само главное движение именуемое скорость резани.
П — это постоянная константа которая равняется 3,14
D — диаметр обрабатываемой детали (заготовки).
n — число оборотов шпинделя станка и зажатой в нем детали.
Движение подачи при токарной обработке.
Про движение подачи вы наверное уже поняли. ДА это перемещение режущего инструмента который закреплен в резцедержателе (для данного эскиза). Крепление резцов может быть и другим, но об этом позже 🙂 . Для осуществления подачи на токарном станке используется специальная кинематическая схема шестерен. Если это простое точение то тут не важна синхронизация вращения обрабатываемой заготовки и режущего инструмента, но если вы решите нарезать резьбу то тут все будет по другому. Об этом поговорим в следующих статьях. Если не хотите пропустить их то подписывайтесь на обновления моего блога.
Формулы для расчета движения подачи на токарном станке выглядит по разному,ведь это может быть как подача на оборот так и минутная подача.
Подача на оборот — это расстояние которое проходит режущий инструмент в нашем случае резец за один оборот обрабатываемой детали. В зависимости от вида обработки определение может быть другим. Например при фрезеровании — это расстояние на которое перемещается заготовка относительно фрезы за один ее оборот.
Минутная подача — это расстояние которое проходит резец за одну минуту (что и логично из названия).
Скорость резания и подача. Заключение.
И так можно подвести итог. Сегодня мы с вами узнали про главные движения при токарной обработке такие как скорость резания и подача. Я не ставлю своей целью загрузить вас массой формул и тягомотных определений их вы можете найти в различных книгах про машиностроение и резание металлов, я хочу вам разъяснить основные понятия человеческим и понятным языком. Думаю у нас все получится 🙂 .
На сегодня все. До скорой встречи друзья!
С вами был Андрей!
mextexnologii.ru
Скорость резания и подача | Мир сварки
Скорость резания и подача
Скоростью резания называется путь, пройденный в 1 мин точкой на обрабатываемой поверхности по отношению к режущей кромке инструмента, или скорость главного движения, выраженная в м/мин.
При точении, сверлении, фрезеровании и других операциях, выполняемых на станках с вращательным главным движением, скорость резания определяется по формуле
1) |
При строгании, протягивании и других операциях, выполняемых на станках с прямолинейным главным движением,
где
d | — | диаметр заготовки или инструмента в мм; |
n | — | число оборотов шпинделя в минуту; |
L | — | длина хода в мм; |
Tр | — | время рабочего хода в мин. |
При шлифовании скорость резания измеряется в м/с определяется по формуле
где
D | — | диаметр шлифовального круга в мм; |
n | — | число оборотов шлифовального круга в минуту. |
Из уравнения (1) число оборотов шпинделя станка определяется по зависимости
Станки должны обрабатывать значительный диапазон диаметров заготовок или на них может быть применен большой диапазон диаметров инструмента при различных значениях скорости резания.
Следовательно, наименьшее и наибольшее числа оборотов шпинделя устанавливаются такими:
где
nmin и nmax | — | предельные числа оборотов шпиндели в минуту; |
vmin и vmax | — | предельные скорости резания в м/мин. |
Одновременно на станках применяются и различные подачи S (инструмента или стола). Подачей называется путь перемещения инструмента за время одного оборота заготовки или инструмента на токарных, сверлильных станках. На фрезерных станках подачей называется перемещение заготовки, отнесенное к одному обороту фрезы, к величине поворота фрезы на 1 зуб, или в единицу времени, и обозначается: Smin – минутная подача (мм/мин), Sn – подача при повороте фрезы на 1 оборот; Sz – подача при повороте фрезы на 1 зуб. На шлифовальных станках применяется минутная подача стола с заготовкой или минутная подача шлифовального круга. Максимальные (Smax) и минимальные (Smin) величины подач устанавливаются по режимам резания.
ЛИТЕРАТУРА
- Металлорежущие станки инструментального производства / Д.А. Локтев. Машиностроение. 1967. – 327 с.
weldworld.ru
Дайте определение глубины резания, подачи и скорости резания в единицах измерения. Правила выбора этих элементов.
Билет 1
Дайте определение глубины резания, подачи и скорости резания в единицах измерения. Правила выбора этих элементов.
Глубина резания t измеряется в мм- определяется толщиной снимаемого слоя металла, измеренной по перпендикуляру к обработанной поверхности металла, за один рабочий ход инструмента относительно обрабатываемой поверхности.
Подача S измеряется в мм / об называют путь, пройденный режущей кромкой инструмента относительно вращающейся заготовки в направлении движения подачи за один оборот заготовки. Подача может быть продольной , если инструмент перемещается параллельно оси .
Скорость резания U (м/с или м/мин) называют путь режущей кромки инструмента, относительно обрабатываемой заготовки в направлении главного движения за единицу времени.
Для обработки детали необходимо установить наиболее рациональные режимы резания, т.е. скорость резания, подачу и глубину резания. Глубину резания определяют припуском на обработку, который выгодно удалять за один рабочих ход. Для уменьшения влияния сил резания иногда разделяют припуск на несколько рабочих ходов. 60%- при черновой обработке,20-30%- при получистовой обработке и 10-20 %- при чистовой обработке.
Глубина резания для черновой обработке=3-5 мм, для получистовой=2-3 мм
Для чистовой от0,5-1 мм.
Подача, ограниченная силами, действующими в процессе резания, которые могут привести к поломке режущего инструмента станка. Целесообразно работать с максимально возможной подачей. Обычно подачу назначают по таблице справочника, составленной на основе специальных исследований. После выбора подачи из справочника ,ее корректируют по кинематическим данным станка. При этом выбирают ближайшую меньшую подачу. Для черновой обработки подача= от 0,3 до 1,5 мм/об. Для чистовой обработки от 0,1 до 0,4 мм / об. При одинаковой площади поперечного сечения среза нагрузка на резец меньше, при работе с меньшей подачи и большей глубиной резания, а нагрузках на станок по мощности, наоборот меньше при работе с большей подачей и меньшей глубиной резания. Скорость резания зависит от конкретных условий обработки, которые влияют на стойкость (время работы от переточки до переточки ) инструмента.
Чем больше скорость резания при работе инструмента при одной и той же скорости, тем выше его режущие свойства, тем более он производительность . на допустимую скорость резания влияют: стойкость инструмента, физико-механические свойства обрабатываемого материала, подача и глубина резания, геометрические элементы режущей части инструмента, размеры его сечения державки резца. С,О,Ж, допустимый износ инструмента, температура в зоне резания. С большей скоростью резания обрабатывают автоматные стали, цветные и легкие сплавы. Например, скорость резания алюминия в 5,6 раз больше, чем скорость обработки углеродистой конструкционной стали. Для достижения большей производительности резания выгоднее работать с большими сечениями среза. За счет уменьшения скорости резания. Например, при увеличении подачи в 2 раза (с 0,3-0,6 мм/об) скорость резания необходимо уменьшить на 20-25 %, а при увеличении в 2 раза глубина резания , скорость резания необходимо уменьшить на10-15 % на практике скорость резания увеличивают после того, как достигнуты предельные значения глубины резания и подачи.
Контроль заточки фрез.
– проверка геометрических параметров режущей части фрезы
– шаблон
– Биение фрезы (индикатор часового типа)
– класс шероховатости (по образцам)
– контроль качества заточки производят с помощью линзы во избежание трещин зазубрин и забоин. Параметры углов(альфа и сигма) определяют угломером.
Контроль фрез после заточки
При контроле фрез после заточки проверяют геометрические параметры режущей части фрезы, биение фрезы и класс шероховатости заточенных или доведенных поверхностей. Для контроля геометрических параметров фрез применяют ряд приборов.
Основное требование, предъявляемое к этим приборам, — простота в эксплуатации и возможность пользования ими непосредственно на рабочем месте.
Контроль биения зубьев фрез осуществляется с помощью индикатора в тех приспособлениях, где они затачиваются в центровых бабках или в специальных приспособлениях.
Фрезы, у которых посадочным местом является отверстие, при контроле устанавливают на горизонтальной или вертикальной оправке. Фрезы с цилиндрическим или коническим хвостовиком при контроле устанавливают либо в направляющей призме, либо в приборе для контроля биения рабочей части концевых инструментов. Биение проверяют по цилиндрической поверхности зубьев, по торцовым зубьям, по угловым кромкам и по опорному торцу. Проверку биения фрезы производят после установки ее на оправку или на шпиндель фрезерного станка.
Проверку качества заточки или доводки производят внешним осмотром с помощью лупы. Режущие кромки фрез должны быть острыми, без зазубрин и выбоин. Наличие трещин на пластинках твердого сплава определяют, пользуясь лупой, смачивая пластины керосином или обдувая их песком. В этом случае при наличии трещин выступает керосин.
Билет 2
1. Правила заточки резцов и других инструментов с пластинами твердых сплавов. Как производится доводка резцов на алмазных кругах.
Заточка резцов производится из твердого сплава часто затачивают по всем режущим поверхностям. В ряде случаев при незначительном износе резцов по передней поверхности их затачивают только по задней поверхности.
При заточке твердосплавных резцов предварительно обрабатывают задние поверхности стержня под углом, на 2-3 0 большем, чем угол заточки на пластине твердого сплава.
Затем затачивают по передней, затем по главной и вспомогательной задней поверхностям. У твердосплавных сверл сначала затачивают пластину, а затем корпус сверла оснащенной пластинами твердого сплава не должно быть заусенцев и мест выкрашивания режущих кромок. При заточке резца на мелкозернистом круге на режущей кромке его остаются неровности, которые интенсивно изнашивают резец. Поэтому после заточки резец доводят на алмазном круге, скорость вращения круга до 25 м/с. резец доводят по главной, задней и передней поверхностям на фаске 1,5-4 мм. Вспомогательную заднюю поверхность резца не обрабатывают .
2. Расскажите о способах крепления и выверки деталей сложной формы.
На примере установки детали для обработки конической поверхности.
Крепление трехкулачковым патроном. Наружные и внутренние конусы длиной до 15 мм.
Разрабатывают резцом, главную режущую кромку которого устанавливают под требуемым углом к оси конуса, осуществляя при этом продольную и поперечную передачу. Этот способ применяют в том случае, когда обрабатываемая деталь жесткая, угол наклона конуса большой, а точности угла конуса, шероховатостей образующей не предъявляют высоких требований. Получение конической поверхности поворотом верхнего суппорта, определяет угол поворота верхнего суппорта по формуле:
|
По таблице тангенсов углов становить величину угла уклона конуса α.
Повернуть верхнюю поворотную часть суппорта на требуемый угол уклона конуса, когда вершина конуса обращена к задней бабке. Если конус детали обращен в сторону задней бабки, то верхнюю часть суппорта повернуть от себя на величину угла уклона конуса α и наоборот.
Настройка по образцу.
3. Обработка отверстий
Метод получения отверстия является сверление. Движение резания при сверлении вращательное, движение подачи поступательное. Перед началом работы проверяют совпадение вершин переднего и заднего центров станка. Заготовку устанавливают в патрон и проверяют , чтобы ее биение (эксцентричность) относительно оси вращения не превышала припуска, снимаемого при наружном обтачивании.
Проверяют также биение торца заготовки , в которой будет обрабатываться отверстие, и выверяют заготовку по торцу. Перпендикулярность торца к оси вращение можно обеспечивать подрезной , при этом в центре заготовки можно выполнить углубление для нужного направления сверла. Для обработки штучных заготовок устанавливают трехкулачковый патрон и производят расточку сырых кулачков, а для обработки детали из кружка зажимную цанту и соответствующие размеру кружка вкладыш падающую цанту и направляющую втулку. Сверла с коническими хвостовиками устанавливают непосредственно в конусное отверстие киноли задней бабки. Если размеры конусов не совпадают, то сверла устанавливают посредством переходных втулок. Для крепления переходных втулок. Для крепления сверл с цилиндрическими хвостовиками диаметром до 16 мм применяют сверлильные кулачковые патроны, которые устанавливаются в пиноле задней бабки. Сверло закрепляется кулачками, которые могут сводится и разводиться.
Перед сверлением отверстий заднюю бабку перемещают по станине н таком расстоянии от обрабатываемой поверхности заготовки, чтобы сверление можно было производить на требуемую глубину при минимальном выдвижении пиноли из корпуса задней бабки обрабатываемого материала, вида обрабатываемого отверстия (сквозное, ступенчатое, глухое) диаметра отверстия и заданной прочности. Отверстие , обработанное зенкером, получается более точным, чем обработанное сверлом. Зенкер имеет три или более режущих кромки , он прочнее сверла, стружка тоньше , а подача в 2,5-3 раза больше, чем при сверлении. Для уменьшения увода зенкера от оси, отверстия предварительно растачивают резцом до диаметра, равного диаметру зенкера на глубину, примерно равную половине рабочей части зенкера.
Рассверливание – применяют для получения более точной и качественной поверхности отверстия, развертка имеет больше режущих кромок, чем зенкер, поэтому при развершивании уменьшается сечение стружки и повышается точность отверстия диаметром до 10 мм развешивающей после сверления. Отверстия большего диаметра перед развершиванием обрабатывают , а торец подрезают . припуск под развершиванием равен 0,15-0,5 мм- для черновых разверток,0,05-0,25 для чистовых . Для высокого качества обработки изделия производят за одну установку на станине.
Подача при рассверливании стальных деталей равна 0,5-2 мм/ об, чугуна 1-4 мм/ об. Скорость резания при развертывании 6-16 м/мин. Чем больше диаметр отверстия, тем меньше скорость резания при одинаковой подаче, при увеличении подачи скорость резания снижают .
Растачивание- производится , если диаметр отверстия нельзя обработать зенкером или сверлом на данном станке, а также , если отверстие имеет неравномерный припуск или непрямолинейную образующую.
У токарных расточных стержневых резцов консольная часть выполняется круглой, а стержень для крепления квадратный(12х12; 16Х16, 20Х20;25х25).
Для этих резцов наименьший диаметр отверстия равен 30-60 мм. Для повышения виброустойчивости режущей кромки резцов выполняет по оси стержня и крепят в специальных державках. Расточный резец имеет меньшее сечение державки и большей вылет, чем резец для наружного точения, что вызывает отжим резца и способствует возникновению вибрации, поэтому при растачивании снижают скорость резания. При черновом растачивании стали глубина резания стали достигает 3 мм, продольная подача 0,08 –0,2 мм/об скорость резания 25 м/мин для быстрорежущих резцов50-10 м/мин для твердосплавных резцов. При чистовом растачивании стали, глубина резания не превышает 1 мм, продольная подача 0,05-0,1 мм/об скорость резания 40-80 м/мин для быстрорежущих резцов и 150-200 м/мин для твердосплавных резцов.
Билет 3
1. Обработка наружных цилиндрических поверхностей.
Для наружного продольного чернового точения применяют проходные резцы.
Резцы для чернового точения работают обычно с более высокими скоростями резания и снимают стружку большего сечения, чем резцы для чистового точения.
Проходные резцы бывают прямые, отогнутые. По направлению подачи различают резцы левые и правые. Правые резцы применяют для обработки наружных поверхностей при продольной подаче справа налево, левые при продольной подаче слева направо.
Прямые переходные твердосплавные резцы изготавливаются с главным углом 450, 600, 750.
Билет 4
Требования безопасности при зачистке деталей.
Требования безопасности при зачистки деталей:
Деталь для зачистки устанавливается в тиски;
Запрещается удалять заусенцы руками;
Запрещается пользоваться неисправным инструментом;
Запрещается зачищать деталь при вращении фрезы.
Билет 4
1. Какие вы знаете методы и средства (включая оптико- механические приборы) для контроля расстояния между осями отверстий, расположенных в одной плоскости. И заданных в полярной системы координат.
Какой разрез называют сложным. Как подразделяются сложные разрезы? Покажите условные обозначения отклонения от пересечения осей.
Ответ:
Сложные разрезы бывают: ломанный разрез и ступенчатый разрез
Разрез – это условное изображение предмета, мысленно рассеченного одной или несколькими плоскостями. На разрезе показывают только то, что находится в секущей плоскости и что расположено за ней.
Ломанный разрез-выполнен на чертежах посредством двух пересекающихся плоскостей, из которых одна в большинстве случаев параллельно плоскости проекции.
Ступенчатый разрез- это разрез, образованный двумя и более параллельными секущимися плоскостями.
Сложнымназывают разрез при двух секущихся и более параллельными плоскостями.
Сложным называют разрез при двух секущихся и более.
отклонение от прямолинейности
2. Правила пользования спецодеждой и защитными средствами.
При работе на токарных станках необходимо пользоваться спецодеждой с застегнутыми рукавами. Пуговицы должны быть застегнутыми на куртке. Надет головной убор и обязательное наличие очков. Токарю запрещается работать в шапочках, сандалиях, босоножках.
3. Какие вы знаете способы обработки фасонных поверхностей и применением копировальных устройств.
Ответ :
– Обычными резцами (Без копира с комбинированием продольной и поперечной ручных подач.) Этот способ приемлем при небольшом количестве обрабатываемых заготовок.
– Фасонными резцами для обработки деталей не большой длины (до 50 мм)
– Обычными резцами при помощи приспособления с круговой подачей поводковых устройств. Этот способ применяют для средних размеров.
– Специальными (кольцеобразными или подобными им) режущим инструментами для сферических поверхностей.
– Обычными резцами при помощи копировальных средств. Он допускает использование нормальных резцов для обточки поверхностей разной длины и конфигурации. В некоторых случаях роль копира выполняет первая образцовая деталь.
Возможно также применение гидрокопировальных суппортов.
Билет 5
1. Обработка канавок и торцевых поверхностей.
Торцы и уступы обрабатывают подрезным, проходным отогнутым или проходным упорным резцами. Подрезной торцовый резец предназначен для обработки наружных торцовых поверхностей. При подрезании торца подача резца осуществляется перпендикулярно оси обрабатываемой детали. Подрезные резцы изготавливают с пластинами из быстрорежущих сталей и твердых сплавов. Главный задний угол 10-15 0 передний угол выбирают в зависимости от обрабатываемого материала. Узкие канавки обрабатываются прорезными резцами. Бывают прямые и отогнутые, правые и левые.
Чаще применяются прорезные резцы правые прямые или левые отогнутые. Канавочные резцы с режущей кромкой . заготовки отрезают отрезными резцами.
2. Обработка конических поверхностей. Коническая поверхность характеризуется меньшим α конуса и большим D диаметром и расстоянием (между плоскостями , в которых расположены окружности с диаметрами D и d) α- угол наклона корпуса, 2α- угол нониуса.
При обработке валов часто встречается переходы между обрабатываемыми поверхностями, которые имеют коническую форму. Если длина конуса не превышает 50 мм, то его обрабатывают широким резцом. При этом режущая кромка резца должна быть установлена относительно оси центров на угол, соответствующий углу наклона нониуса на обработанной детали. Резцу сообщают подачу в поперечном или продольном направлении. Чтобы уменьшить искажение образующей конической поверхности и отклонение угла наклона нониуса, режущую кромку резца устанавливают по оси вращения детали. Конические поверхности с большими уклонами можно обрабатывать при повернутых верхних салазках суппорта с резцедержателем на угол, равный углу наклона обрабатываемого конуса. Конические поверхности большей длины с углом наклона 8-10 0 можно обрабатывать при смещении заднего центра. Величину смещения задней бабки – определяют по шкале, нанесенной на торце опорной плиты со стороны маховика и риски на торце корпуса задней бабки.
Конические поверхности с углом 0-12 0 обрабатывают с использованием копирных устройств.
Для получения конического отверстия в сплошном материале предварительно (сверлят, зенкеруют, растачивают), а за тем окончательно (развертывают , растачивают) сначала сверлят отверстие на 0,5-1,0 мм меньшего диаметра, затем черновой разверткой, имеющую форму уступов, вторая получистовая развертка снимает неровности , тренья чистовая имеет сплошные режущие кромки по всей длине и калибрует отверстие.
Заточка инструмента
На машиностроительных предприятиях инструмент, как правило , затачивают централизованно. Для ручной заточки применяют точильно- шлифовальные станции.
Например, станок модели 3 Б633, состоящий из шлифовальной головки и станины. В шлифовальную головку встроен двухскоростной электродвигатель. На выходящих концах вала ротора крепятся шлифовальные круги, которые закрываются кожухами с защитными экранами. Подразделяются на 3 группы: малые станки с кругом диаметром 100-175 мм для заточки мелкого инструмента. Средние станки диаметром круга 200-350 мм для заточки основных резцов. Крупные станки, диаметр круга 400 мм и более для шлифования деталей и обдирочно- зачистных работ. Резцы в зависимости от их конструкции и характера изнашивания затачивают по передней, задней или по обеим поверхностям стандартные резцы с пластинками из твердого сплава или быстрорежущей стали наиболее часто затачивают по всем режущим поверхностям. При заточке на станке резец устанавливают на поворотный столик или подручник вручную прижимают обрабатываемую поверхность к шлифовальному кругу. При заточке резца по задним поверхностям столик или подручник поворачивают на заданный задний угол и закрепляют в непосредственной близости к кругу. Резец устанавливают на столике или подручнике так, чтобы режущая кромка располагалась параллельно рабочей поверхности круга. Переднюю поверхность резца чаще всего затачивают боковой поверхностью круга, при этом резец устанавливают на подручнике боковой поверхности. Резцы из быстрорежущей стали затачивают сначала по передней, затем по главной и вспомогательной задней поверхностям. При заточке твердосплавных резцов применяют такой же порядок операции, но предварительно обрабатывают задние поверхности стержня под углом на 2-3 0 больше, чем угол заточки на пластине твердого сплава.
Резец в резцедержателе устанавливают по высоте оси центров станка. Для этого резцедержатель подводят к центру задней бабки, вершину головки резца устанавливают так, чтобы вылет резца не превышал 1-1,5 высоты его державки, определяют взаимное положение вершины головки резца и центра станка и совмещают их по высоте введением подкладок под державки резца. Подкладки должны иметь параллельные и хорошо обработанные поверхности, не должны по длине и ширине выходить за опорные поверхности резцедержателя. Число подкладок должно быть не более двух.
Билет 6
1. Чем вызвана необходимость балансировки вращающихся деталей. приведите примеры статической балансировки.
Детали проходят могут иметь различную шероховатость поверхности . Обозначение шероховатости поверхности располагают на линиях видимого контура изображения, на выносных линиях, а также на вспомогательных линиях типа выносных, и, как правило, вблизи от размеров.
Для обозначения шероховатости поверхности, когда указывается класс (или класс и разряд)..
Например, ▼3▼6б
▼3(▼)
Для обозначения поверхностей, у которых может быть допущена шероховатость, превышающая 320 мк (т.е. грубее , чем для 1 кл)над знаком может быть указана допустимая высота неровностей в мк,
Например, 500√,500√
Билет 7
Расскажите о приемах установки и выверки эксцентричных деталей. С точными размерами между главной осью и осями эксцентричных поверхностей. Какие контрольно – измерительные инструменты применяются при этом.
Пример, заготовка эксцентрического вала.
При обработке эксцентрических деталей обычно указывается величина расстояния между главной осью деталей и осью эксцентричной поверхности.
1) Разместить и померить центры на главной оси ОО и оси эксцентрической поверхности О1О1
У заготовки эксцентрического вала с подрезанными торцами покрыть мелом торцевые поверхности и положить заготовку на призму, расположенную на разметочной плите.
Установить на плите штангенрейсмус так, чтобы его измерительная поверхность с рамкой касалось наружной поверхности заготовки вала. Опустить измерительную поверхность штангенрейсмуса с рамкой на ½ диаметра заготовки и провести на торцах горизонтальные линии установились точно в вертикальное положение. На торцах заготовки провести вторые горизонтальные линии той же высоты.
Пересечение двух проведенных линий образует на торцах центры оси О1О1 эксцентричной поверхности.
Очистить раму с измерительной поверхностью штангенрейсмуса точно на 5мм , т.е. на величину эксцентриситета, и провести на торцах третью линию, пересечение которой с вертикальной линией теперь образует на торцах центры главной оси ОО основной поверхности вала. С помощью корнера и молотка накернить центры осей ОО О1О1 с двух сторон.
2) Совершить центровые отверстия осей ОО и О1О1
Заготовку с накерненными центрами поочередно подставлять к заднему центру и , вращая маховичок задней бабки, подавать на вращающееся центровое комбинированное сверло до образования центровых отверстий соответствующих размеров. Таким же образом сделать центровые отверстия на другом торце.
3) Установить заготовку вала в центры центровыми отверстиями от ОО1 обточить поверхность В и надрезать торец поверхности Б. При обработке массивного эксцентричного вала с большим эксцентриситетом устанавливать на план-шайбу груз (противовес) для предупреждения вибрации вала и элитности обтачиваемых поверхностей. Для удобства обработки поверхностей В и Б применить проходной упорный резец. В таком же порядке обработать другую сторону заготовки А.
4) Установить заготовку вала в центрах отверстиями оси О1О1 и обточить эксцентричную поверхность Б.
При обтачивании эксцентрической поверхности Б ранее установленный груз заменить другим, в зависимости от величины эксцентричной поверхности Б и эксцентриситета.
Применяемые при этом контрольно – измерительные приборы: штангенциркуль, микрометр, центровая оправа.
2. Какой предел измерения должен иметь штангенциркуль, чтобы измерить размер 145±1 мм.
Ответ: Штангенциркуль с пределом измерения 0-150 мм.
Как подразделяются разрезы в зависимости от направления секущих плоскостей. Как записать условным обозначением следующий пласт: не перпендикулярность оси отверстия Б относительно поверхности А не более 1 мм (допуск зависит).
Ответ: В зависимости от положения секущей плоскости проекций различают :
– Вертикальные- это фронтальный разрез, если секущая плоскость параллельна фронтальной плоскости проекции
– Горизонтальные,
– Наклонные.
Билет 8
Билет 9
Билет 1
Дайте определение глубины резания, подачи и скорости резания в единицах измерения. Правила выбора этих элементов.
Глубина резания t измеряется в мм- определяется толщиной снимаемого слоя металла, измеренной по перпендикуляру к обработанной поверхности металла, за один рабочий ход инструмента относительно обрабатываемой поверхности.
Подача S измеряется в мм / об называют путь, пройденный режущей кромкой инструмента относительно вращающейся заготовки в направлении движения подачи за один оборот заготовки. Подача может быть продольной , если инструмент перемещается параллельно оси .
Скорость резания U (м/с или м/мин) называют путь режущей кромки инструмента, относительно обрабатываемой заготовки в направлении главного движения за единицу времени.
Для обработки детали необходимо установить наиболее рациональные режимы резания, т.е. скорость резания, подачу и глубину резания. Глубину резания определяют припуском на обработку, который выгодно удалять за один рабочих ход. Для уменьшения влияния сил резания иногда разделяют припуск на несколько рабочих ходов. 60%- при черновой обработке,20-30%- при получистовой обработке и 10-20 %- при чистовой обработке.
Глубина резания для черновой обработке=3-5 мм, для получистовой=2-3 мм
Для чистовой от0,5-1 мм.
Подача, ограниченная силами, действующими в процессе резания, которые могут привести к поломке режущего инструмента станка. Целесообразно работать с максимально возможной подачей. Обычно подачу назначают по таблице справочника, составленной на основе специальных исследований. После выбора подачи из справочника ,ее корректируют по кинематическим данным станка. При этом выбирают ближайшую меньшую подачу. Для черновой обработки подача= от 0,3 до 1,5 мм/об. Для чистовой обработки от 0,1 до 0,4 мм / об. При одинаковой площади поперечного сечения среза нагрузка на резец меньше, при работе с меньшей подачи и большей глубиной резания, а нагрузках на станок по мощности, наоборот меньше при работе с большей подачей и меньшей глубиной резания. Скорость резания зависит от конкретных условий обработки, которые влияют на стойкость (время работы от переточки до переточки ) инструмента.
Чем больше скорость резания при работе инструмента при одной и той же скорости, тем выше его режущие свойства, тем более он производительность . на допустимую скорость резания влияют: стойкость инструмента, физико-механические свойства обрабатываемого материала, подача и глубина резания, геометрические элементы режущей части инструмента, размеры его сечения державки резца. С,О,Ж, допустимый износ инструмента, температура в зоне резания. С большей скоростью резания обрабатывают автоматные стали, цветные и легкие сплавы. Например, скорость резания алюминия в 5,6 раз больше, чем скорость обработки углеродистой конструкционной стали. Для достижения большей производительности резания выгоднее работать с большими сечениями среза. За счет уменьшения скорости резания. Например, при увеличении подачи в 2 раза (с 0,3-0,6 мм/об) скорость резания необходимо уменьшить на 20-25 %, а при увеличении в 2 раза глубина резания , скорость резания необходимо уменьшить на10-15 % на практике скорость резания увеличивают после того, как достигнуты предельные значения глубины резания и подачи.
cyberpedia.su
Измерение – подача – Большая Энциклопедия Нефти и Газа, статья, страница 1
Измерение – подача
Cтраница 1
Измерение подачи в случае испытании насосов и вентиляторов удобно производить при помощи диафрагмы, вмонтированной в напорный или всасывающий трубопровод. [2]
Измерение подачи объемным способом с помощью мерного бака является наиболее точным. [4]
Измерение подачи мощных центробежных и особенно осевых насосов в натурных условиях может оказаться весьма затруднительным. Точность устанавливаемых на насосных станциях эксплуатационных расходомеров бывает, как правило, недостаточной, особенно для кави-тационных испытаний. Кроме того, предпочтительно не пользоваться этими расходомерами, так как в натурные испытания входит проверка правильности их тарировки и надежности работы. Высокие подачи насосов, большие габаритные размеры их проточной части и конструктивные особенности крупных насосных станций исключают возможность применения объемного или весового способов. [5]
Измерение подачи перемещаемой среды ( воздуха, газа) удобнее всего осуществлять комбинированными приемниками давления ( см. рис. 8.22) [140] или напорными трубками Прандтля, устанавливая их на прямом участке всасывающего короба или за нагнетательным патрубком вентилятора, но обязательно до воздушного подогревателя. Сечение для измерения подачи перемещаемой среды на прямом участке ограниченной длины должно находиться не на середине этого участка, а ближе к его концу в направлении движения среды, так как возмущения в начале участка в значительно большей степени влияют на поле скоростей. [6]
Измерение подачи погружных насосов производится при помощи измерительных диафрагм или мерных баков. Диафрагмы изготавливаются из прочных и коррозионно-стойких материалов. Диаметр диафрагмы рассчитывается исходя из заданной максимальной подачи насосов. Конструкция узла диафрагмы и способ его крепления должны при необходимости обеспечивать возможность периодического осмотра и замену диафрагмы. Исключительно важно обеспечить прямой угол между цилиндрическим отверстием и передней торцовой плоскостью диафрагмы. Смещение оси диафрагмы относительно оси трубопровода не должно превышать 0 6 мм для трубопроводов диаметром в пределах 200 – 500 мм. [7]
Для измерения подачи необходимо отсутствие между точкой замера и насосом подвода и отвода жидкости; герметичность всасывающего трубопровода, постоянство температур перекачиваемой жидкости, а следовательно, и соответствующая вязкость. Подачу измеряют при помощи описанных ниже приборов. [8]
Для измерения подачи разработаны различные устройства. Наиболее широкое применение в практике нашел индукционный расходомер РГР-7, принцип действия которого основан на законе электромагнитной индукции. [10]
Однако измерение подачи как воздуха, так и газа производится по их объему, а не по массе, что обеспечивало бы более точное стехиометри-ческое соотношение реагентов. [11]
Допускается измерение подачи и давления другими средствами, обеспечивающими достаточную точность. [12]
Для измерения подачи насосов используются мерные баки, диафрагмы, насадки, водомеры. Способ измерения подачи выбирается в каждом отдельном случае в зависимости от местных условий и величины подачи. Так например, в случае небольших расходов измерение при помощи мерного блока, как дающее наиболее точные результаты, следует предпочесть всем остальным. [13]
Для измерения подачи насоса используют сужающие устройства ( сопла, диафрагмы), мерный бак, водослив, трубку Пито ( в зависимости от условий испытания и размера насоса), а для измерения давления – манометры и вакуумметры. [14]
Для измерения подачи насосов используют диафрагмы, сопла, трубы Вентури. Перепад давления в этих приборах измеряется жидкостными манометрами. При протекании жидкости через суженное отверстие получается местное увеличение скорости потока и связанное с ним понижение давления, при этом часть потенциальной энергии жидкости переходит в кинетическую. [15]
Страницы: 1 2 3 4
www.ngpedia.ru