Вакуумная формовка пластика, особенности технологии
Вакуумной формовкой называется процесс производства серийных или единичных изделий из листовых полимерных материалов путем придания им формы матрицы под воздействием температуры и вакуума. В процессе производства изделия лист пластика нагревается до температуры размягчения и плотно облегает поверхность матрицы за счет создания отрицательного давления.
В серийном промышленном производстве для вакуумного формования изделий применяется современное высокотехнологичное оборудование, осуществляющее процессы разогрева сырья и откачки воздуха в режиме постоянно действующего конвейера.
В качестве сырьевых заготовок могут использоваться практически все полимеры, обладающие свойствами термопластов (полипропилен, полиэтилен, поливинилхлорид, поликарбонат и другие).
Методом вакуумной формовки выпускаются пластиковые изделия для всех направлений и сфер деятельности, в том числе:
- для авиационной, автомобильной и судостроительной отраслей промышленности;
- для производства упаковочной тары и емкостей всех видов;
- для нужд пищевого производства, химической промышленности, медицины;
- для производства бытовой техники, приборов и оборудования;
- для нужд строительства и дизайна.
Технология производства
Особенностью метода вакуумной формовки является возможность протекания производственного процесса с невысоким отрицательным давлением. Такие процессы не требуют наличия мощного оборудования, высокопрочных матричных форм и значительных расходов энергоносителей. Вследствие этого производство считается экономным, а готовые изделия имеют низкую себестоимость.
Широкие возможности для применения автоматизированных производственных процессов позволяют наладить непрерывный цикл изготовления продукции самого различного назначения. Немаловажную роль играет и то, что для формовки используются готовые листовые материалы, не требующие глубокой переработки сырья.
Стандартный метод вакуумной формовки состоит из нескольких этапов, включающих в себя:
- фиксацию заготовки на матрице;
- нагрев полимерного листа;
- предварительное растяжение листа;
- откачку воздуха из матрицы и вдавливание заготовки;
- охлаждение материала;
- извлечение изделия из матрицы;
- окончательную доработку изделия.
Для того чтобы понять, что представляет собой вакуумная формовка пластика, необходимо подробно рассмотреть все стадии производственного процесса.
Фиксация заготовки
Листы полимера крепятся к матрице при помощи зажимной рамы. Фиксирующие элементы должны обеспечивать прижимное усилие, достаточное для удержания листов толщиною до 6 мм. При автоматизированной подаче заготовок на формовку работа подвижных элементов прижимной рамы должна исключать возможность повреждения готового изделия.
Нагрев заготовки
Общая площадь поверхности заготовки делится на несколько зон, каждая из которых нагревается отдельным элементом, а температура нагрева контролируется при помощи специальных пирометров. Данные о температуре обрабатываются компьютерной системой для своевременной корректировки разницы нагрева различных участков заготовки.
До окончания процесса нагрева лист полимера должен сохранять свое первоначальное положение. Провисание пластика фиксируется фотоэлектрическим сканером, после чего система дает команду, и в аппарат подается воздух для корректировки формы заготовки. Благодаря этому исключается возможность разрыва материала.
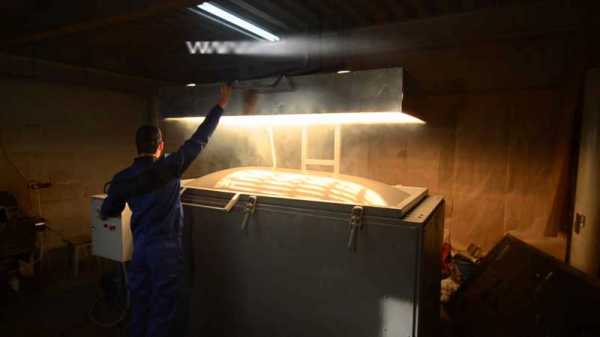
Предварительное растяжение листа
В некоторых случаях в процесс производства включают предварительное растяжение материала, называемое также раздувом. Растяжение выполняется после достижения пластиком рабочей температуры формовки и служит для выравнивания толщины заготовки. Процесс раздува необходим при формовании заготовок на глубоких матрицах со сложной геометрией поверхности.
Откачка воздуха и вдавливание заготовки
После предварительного нагрева и растяжения закрепленной заготовки из аппарата для формовки производится откачка воздуха вакуумным насосом. При снижении давления внутри аппарата полимерный материал, достигший состояния пластичности, начинает облегать форму матрицы.
В зависимости от требований, предъявляемых к конечному продукту, технология вакуумной формовки, может совмещаться с технологией штампования при помощи пуансона. В этом случае помимо откачки воздуха на заготовку сверху воздействует специальная конструкция, профиль которой повторяет поверхность матрицы.
Комбинацией этих методов можно добиться максимальной точности заданных форм деталей, а также обеспечить равномерное распределение полимерного материала по поверхности матрицы, полностью исключив образование складок и участков с различной толщиной.
Охлаждение изделия и извлечение из матрицы
Во избежание повреждения детали при извлечении из матрицы необходимо дождаться полного остывания материала. Если применяемое для процесса вакуумная формовка пластика оборудование оснащено системами воздушного охлаждения, время остывания изделий может быть сокращено на 20-30%.
Для изготовления наиболее ответственных деталей вакуумные матрицы оснащаются системами управления температурными процессами.
Наличие таких систем позволяет добиваться равномерного охлаждения изделия, что способствует повышению его эксплуатационных качеств. Извлечение остывшей детали из матрицы происходит под воздействием создаваемого внутри давления.
Окончательная обработка
Изделие, извлеченное из матрицы необходимо отделить по контуру от излишков полимерного материала. Сформованная деталь может являться полуфабрикатом для дальнейшего сборочного производства. Для этого изделие может разрезаться, в нем могут высверливаться отверстия для крепежных элементов и делаться пропилы для вставок.
Для окончательной обработки материала могут использоваться:
- механический обрезной пресс;
- ленточная пила вертикального или горизонтального типа;
- станок строгально-шлифовальный;
- фрезерный станок;
- сверлильный станок;
- ручной механический и электроинструмент.
polimerinfo.com
Вакуумная формовка. Оборудование для вакуумной формовки пластиков и пленок
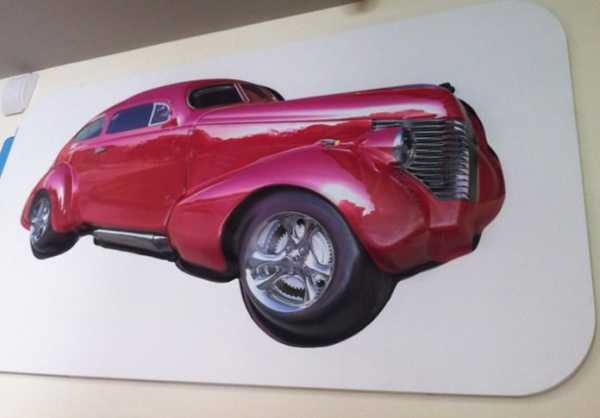
Навигация:
- Вакуумная формовка пластиков
- Вакуумно-пленочная формовка
- Формы для вакуумной формовки
- Метод вакуумной формовки
- Станок для вакуумной формовки пластика
Вакуумная формовка является технологией формирования изделий при помощи горячего вакуума. Такой вид производства осуществляется при помощи пластичных материалов, которые под воздействием горячего вакуума или низкого давления способны менять свою форму. Такой способ изготовления изделий в большинстве случаев применяется в серийном производстве пластиковых изделий крупных размеров, но не исключено применение при единичных изготовлениях пластмассовых форм.
Вариант вакуумной формовки
Принцип работы вакуумной формовки заключается в размещении листового пластика под или над заготовкой, и при помощи нагревания под действием вакуума пластик повторяет форму требуемой заготовки в точности до миллиметра. Все виды заготовок именуются как матрица, которая является основой для любой формы будущего изделия.
Основные привилегии использования метода вакуумной формовки:
- Имеется возможность использовать пластик, толщина которого в зависимости от характеристик нужного изделия составляет од 0, 04 до 7 мм, а что касаемо конечных габаритов изделия, то они могут достигать 5 м в диаметре;
- Готовое изделие от матрицы можно отделять вручную;
- Низкая цена заготовки;
- Относительно маленькая цена на обустройство системы вакуумной формовки.
Для формирования готового изделия применяется достаточно обширный ряд материалов: пластик, прозрачный либо цветной акрил, полистирол, ПВХ, поликарбонат и так далее. Негативным фактором при изготовлении таких изделий является то, что осуществить создание заготовки, один из углов которой будет меньше 90 градусов невозможно.
Вакуумная формовка пластиков
- Оргстекло. Этот материал является полиметилметакрилатным пластиком либо акрилом, и в своей стандартной форме он полностью прозрачный, но при необходимости его цвет можно изменить при помощи добавления красителей любых оттенков. Прежде чем использовать такой вид материала, его необходимо тщательно высушить, так как он предрасположен к интенсивному впитыванию влаги из окружающей среды. Из недостатков использования данного сырья, можно отметить, что в процессе формирования необходимого изделия, затрачивается большое количество электричества, но это с лихвой компенсируется долговечностью готового продукта, который применяется в рекламных стендах, в изготовлении объемных цифр и букв, и прочих деталей продукции для рекламных кампаний.
- Пластик ABS. Этот материал свободно поддаётся вакуумной формовке и отличается изумительными качествами выдерживания ударных нагрузок. Благодаря этому, основное предназначение при использовании данного материала является изготовление спортивного инвентаря. В дополнение можно подчеркнуть, что ABS пластик способен выдерживать нагрев до 90 градусов в процессе его формовки.
Вакуумная формовка пластиков
Вакуумно-пленочная формовка
Одним из разновидностей формовочного материала является плёнка ПЭТ, которая очень просто и технологически удобна в процессе вакуумной формовки. Такой материал не требует заблаговременной просушки, обладает низким внутренним напряжением, имеет пониженную теплоемкость, что многократно экономит затраты на использование электроэнергии в процессе формовки деталей из вакуумной пленки. Таким образом, характеристики изготовленных элементов способствуют широкому применению в рекламной и осветительной сфере.
Вакуумно-пленочная формовка
Формы для вакуумной формовки
Существует два типа материала для создания форм, которые используются в процессе вакуумной формовки:
- Формы из МДФ
Наиболее простым, недорогим и быстрым вариантом для изготовления форм, является фрезеровка МДФ плит при помощи ЧПУ. С таких плит набирается нужная толщина и в соответствии с 3D моделью, которая запрограммирована в ЧПУ, выполняется фрезеровка необходимой формы. После окончательной фрезеровки детали, её высушивают и обрабатывают специальным раствором, и в заключение поверхность обрабатывается шлифовочным материалом, после чего, её уже можно использовать для вакуумной формовки. В зависимости от сложности формы матрицы или иными словами болванки, разница количества циклов отличается при использовании. Таким образом, если форма имеет округлые края и невысокие выступы, то количество использования может достигать до 500 раз. Но если конструкция состоит из острых углов и высоких выступов, то её стойкость значительно сокращается, появится необходимость в реставрации болванки. Но реставрация в большинстве случаев является довольно дешевым процессом, за счет низкой цены на материалы для повторного изготовления.
- Формы из стеклопластика
Такой материал можно использовать большее количество раз, нежели МДФ. Технология производства такой матрицы состоит в том, что предварительно необходимо иметь полую заготовку, в которую заливается полимерная смола, армированная стеклотканью. Данная процедура занимает значительный отрезок времени, но с лихвой окупается за счёт многократного использования формы в дальнейшем. В дополнение, если необходимо за один цикл изготовить, к примеру, 10 одинаковых изделий при помощи вакуумной формировки, то использование стеклопластика гораздо удешевляет размножение болванок в отличие от МДФ форм.
Метод вакуумной формовки
Чтобы создать изделия при помощи вакуумной формовки, в первую очередь необходимо приобрести соответствующий вакуум-формовочный станок. Касательно материалов, которые необходимы для создания изделий, то их тип зависит от сферы деятельности предприятия и дальнейшей области применения готовых изделий. Главным требованием, которое предъявляется сырью для производства, это одинаковая толщина всех листов для единой серии деталей.
Процедуру формовки при помощи вакуума можно разделить на 2 ступени:
- Изготовление болванки;
- Вакуумное формирование по матрице из подобранного материала.
Касательно изготовления матрицы нужно отметить, что этот процесс отнимает довольно мало средств, так как основным материалом для изготовления болванок является МДФ или стеклопластик. Существуют и другие типы материалов, такие как дюраль алюминий, всевозможные смолы и так далее, но их применение целесообразно только на производствах, где изготовления формовочных изделий основана на постоянном серийном цикле.
Сама формовка начинается с того, что к матричной рамке станка крепится сырьевой лист, который кстати необходимо тщательно очистить от всякого рода пыли и загрязнений, так как в противном случае эти компоненты станут единым целым с готовым изделием. В середине расположен элемент матрицы либо серия болванок, при множественном изготовлении за один цикл. Для вакуумного формирования над рамкой с материалом находится разогретая панель, которую необходимо опустить на формируемый лист, чтобы установленный материал разогрелся до нужной температуры и принял форму матрицы.
Станок для вакуумной формовки пластика
Предлагаемая к независимому производству установка станка предполагает из себя конструкцию с недвижимой матрицей с прикрепленной модификацией, к которой перемещается рамочка, в которую прижимается сырье с целью формовки, в верхней части конструкции находится нагреватель. Вакуум формируется вакуумнасосом, что и формирует разряжение. В последствии нагрева пластмассы, вводится вакуум и совершается непосредственно само изготовление. Как только лишь сырье получил установленную фигуру, вакуум выключается и допускается доставать лист с отделанной фигурой. За один раз допускается формовать с 1-го вплоть до нескольких 10-ов продуктов – всё зависит от масштабов рабочего стола станка и объемов модификации. Остаётся прибавить, что средний период цикла формовки забирает от 40 вплоть до 120 сек. – всё находится в зависимости от толщины материала и сложности самого продукта.
Станок для вакуумной формовки пластика
pv-system.ru
Вакуумная формовка для изготовления деталей
Вакуумная формовка – это специальная технология, применяющаяся при производстве различных изделий из пластика путем влияния вакуумного воздействия или давления воздуха. В последнее время, с увеличением требований к производимым изделиям, изготовление вакуумной формовкой приобрело большую популярность, в связи с тем, что данный способ позволяет реализовать различные идеи и создать разнообразные объемные пластиковые изделия, которые могут иметь простой рельеф, так и отличаться достаточно сложными рельефными поверхностями. Данная методика активно используется при производстве изделий в больших объемах, но нередко ее применяют и с целью изготовления единичного тиража. Для реализации формовки используют специальное оборудование для вакуумной формовки – вакуум-формовочные машины.
Навигация:
- Вакуумная формовка пластиков
- Вакуумные насосы для формовки
- Станки для вакуумной формовки
- Формы для вакуумной формовки
Одним из наиболее важных преимуществ считается то, что возможности данной технологии позволяют заказчику полностью определять каким в итоге получится изделие, здесь все характеристики, такие как форма, цветовая гамма, материал, определяются и регулируются заказчиков, учитываются пожелания и в результате доступно получить индивидуальный продукт, полностью соответствующий задумке и идее. Можно выделить основные этапы, выполняемые в процессе изготовления.
- Изготавливается матрица
- Проводится формирование из необходимых материалов.
- Этап реализации вакуумной формовки.
Наиболее часто применяемые материалы для вакуумной формовки это абс-пластик, акрил, полистирол. Толщина таких материалов может составлять до 6 миллиметров. Матрицы для вакуумной формовки производятся из разнообразных материалов, все зависит от того, какие требования предъявляются к итоговому продукту. Здесь заказчиком подбирается подходящая стоимость, которая зависит от требуемых размеров, типа поверхности и других параметров.
К процессу по изготовлению матрицы необходимо подходить крайне ответственно, ведь именно от этого зависит то, насколько правильно и качественно будет выполнено изготавливаемое изделие. При изготовлении учитываются все требования и условия, от которых зависит получение задуманного результата. Для более детального восприятия конечного продукта предоставляются эскизы и чертежи.
Вакуумная формовка пластиков
Вакуумная формовка пластиков представляет собой своеобразный процесс вытяжки, при этом листовой материал, который располагается над матрицей или под ней подвергается нагреванию и как следствие размягчается, за счет чего принимает необходимые очертания прессоформы, из-за образования между материалом и прессоформой вакуумной прослойки. Вакуумная формовка пластика отличается огромным количеством преимуществ. Так, например, допустимо использование оборудование по приемлемой цене благодаря тому, что изготовление производится с использованием низкого давления. Производство изделий экономически выгодно не зависимо от их размеров, так как матрицы изготавливаются из доступных материалов и такое изготовление занимает небольшое количество времени. Если предполагается автоматизированное производство в условиях непрерывного производства, то применяются более сложные подходы к изготовлению прессформы. Вакуумная формовка производится из специальных пластиковых листов, что позволяет значительно упростить процесс, а также допускает возможность срезать излишки с готовых изделий и переработав, использовать их повторно. Данная технология имеет свои преимущества и недостатки. К преимуществам можно отнести следующие:
- Возможность выбирать различную толщину материала для изготовления, получаемые элементы могут иметь всевозможные толщины и достигают иногда до нескольких метров.
- Доступность создания матрицы.
- Небольшие временные затраты на изготовление прессоформы.
- Технология позволяет изготавливать различные тиражи изделий.
Однако, данная технология имеет и свои недостатки, ним относятся такие:
- Стоимость одной единицы продукции выходит достаточно высокая.
- После выполнения вытяжки пластика могут образовываться различные толщины на стенках изделия.
- Габаритные размеры изделия могут быть созданы с погрешностью.
Вакуумные насосы для формовки
Вакуумные насосы для формовки это качественное оборудование, которое применяется для данной технологии производства. Вакуумные насосы используются с целью откачивания воздуха после процедуры нагревания и этапа растяжения обрабатываемой заготовки. Под действием снижения давления разогретый материал становится пластичным и принимает требуемую форму матрицы.
Станки для вакуумной формовки
Станки для вакуумной формовки предназначены для формовки специально предназначенных для таких операций материалов, например, полистирол, пвх, акрил, пластик, характеризующиеся разнообразными толщинами. Заготовка подвергается нагреванию до необходимой температуры и достижения требуемой пластичности материала. Так, поле, предназначенное для формования, может быть разделен на несколько участков, каждый из которых производит нагрев заготовки до разных температур для более удобного в автоматизированного процесса изготовления и формовки. Практически все процессы формовки производятся в автоматизированном режиме.
Оборудование для вакуумной формовки предназначено для возможности производства разнообразных индивидуальных изделий, а также массового производства пластиковых продукций, методом перенимания контурной формы с матрицы (прессоформы) на готовую единицу продукции. Станок для вакуумной формовки предназначен для работы такими материалами как пластиковые листы или же специализированные пленки термопластичных полимерных материалов, например, поликарбоната, полистирола, абс-пластика или же схожих по составу материалов. В работе станков могут использоваться листы с толщиной до 12 миллиметров.
Данная технология и оборудование предоставляет возможность получать высокое качество изготавливаемой продукции при достаточно небольших экономических затратах, а также позволяет за небольшие временные промежутки получать нужные партии продукции. Такие характеристики и преимущества обуславливают высокую популярность применения на производстве технологии вакуумной формовки изделий их пластика и сходных материалов.
Формы для вакуумной формовки
Для возможности получения необходимых объемных заготовок используют специальное оборудование – формовочные машины, благодаря которым подобные заготовки можно изготовить из всевозможных видов пластика. Первоначально, прежде чем преступить к изготовлению элемента, необходимо провести обязательные расчеты и создать чертежи по которым и буду проводиться работы по созданию индивидуальных матриц для формовки, являющихся основополагающей составляющей изготавливаемого изделия, а также форм для формовки.
Производятся такие формы вакуумные несколькими этапами, следующими в точной последовательности друг за другом. Данный процесс достаточно кропотливый и технологически сложный, в связи с чем, требует от мастера высокой концентрации внимания, а также специальные знания и соответствующая подготовка. При соблюдении всех необходимых условий, требований и правил, в результате создается форма для формовки достаточно высокого качества.
Предварительным этапом подготовки к созданию модели является точный анализ технического задания и пожеланий заказчика, для более достоверной реализации изначальной задумки, разрабатывается модель формы. Кроме обязательных эскизов и чертежей также может быть выполнена визуализация путем создания соответствующей компьютерной модели. На современной этапе развития технологий и высокого уровня квалификации мастеров, занимающихся данными задачами, возможно реализовать даже самую смелую идею и изготовить деталь абсолютно любо сложности, точно соответствующей начальным требованиям.
Таким образом, благодаря своим широким возможностям выполнения самых сложных задач, данная технологическая операция широко применяется в производственных сферах и пользуется большой популярностью.
generic-lasix.ru
Вакуумная формовка
Широко распространено производство отливок в разовых песчаных формах. Этот способ применяется для изготовления из различных сплавов отливок широкого диапазона размеров и конфигураций. Технологический процесс литья в песчаные формы состоит из ряда последовательных операций: подготовка материалов, приготовление формовочных и стержневых смесей, изготовление форм и стержней, установка стержней и сборка форм, плавка металла, и заливка его в формы, охлаждение металла и выбивка готовой отливки, очистка отливки, термообработки и отделки.
Материалы, применяемые для изготовления разовых литейных форм и стержней делятся на исходные формовочные материалы и на формовочные смеси; их масса равна в среднем 5-6 тонн на 1 тонну годных отливок. При изготовлении формовочной смеси используют отработанную формовочную смесь, выбитую из опок, свежие песчано- глинистые материалы, добавки, улучшающие свойства смеси, воду. Приготовление смеси производят в определенной последовательности на смесеприготовительном оборудовании: ситах, сушилах, дробилках, мельницах, магнитных сепараторах, смесителях и т. п.
Формы и стержни изготавливают на специальном формовочном оборудовании. Насыпанная в опоки смесь уплотняется встряхиванием, прессованием или совместно тем и другим способом. Крупные формы заполняют с помощью пескометов. Формы в опоках подвергаются тепловой сушке в литейных сушилах.
После заливки форм жидким металлом и его отвердения отливки обычно выбивают из форм на вибрационных решетках. Полученные отливки поступают в очистное отделение, в котором отделяют пригоревшую смесь, элементы литниковой системы, зачищают остатки литников. Крупные отливки очищают гидравлическим способом в специальных камерах.
Самым многооперационным процессом производства отливок является формовка, реализация которой требует применение большого количества по массе и номенклатуры исходных материалов, а также задействования парка специализированного оборудования.
Особенностью вакуумной формовки является использование только кварцевого песка, пленки и вакуумного насоса. Сущность способа вакуумной формовки и последовательность операций иллюстрируется схемой, представленной на рисунке 1. Модельная плита 1 с закрепленной на ней моделью 2 монтируется на вакуумируемой камере 3, полость которой соединена сквозными каналами с поверхностью плиты и модели (рис. 1 а)
Полимерную пленку 4 толщиной 0,05-0,10 мм в течение нескольких секунд нагревают электрическим нагревателем 5 до перевода пленки в пластическое состояние (рис. 1 б).
Пленку накладывают сверху на модель (рис. 1 в), а полость камеры 3 подключают к вакуумному насосу. При этом пленка плотно облегает поверхность модельной плиты и модели, точно воспроизводя её контур.
На модельную плиту устанавливают опоку 6, которая через вытяжную камеру соединена с трубопроводом 7 и коллектором 8 (рис. 1 г). В опоку засыпают сухой мелкозернистый песок без связующего и предварительно уплотняют песок легкой вибрацией (рис. 1 д).
Далее отформовывают литниковую чашу, удаляют избыток песка из полуформы, накладывают на её поверхность полимерную пленку (без предварительного её нагрева) и уплотняют формовочный материал отсосом воздуха (вакуумированием формовочного материала) (рис. 1 е).
После вакуумирования полуформа приобретает необходимую прочность. Полуформу отключают от вакуумной системы и отделяют от модельной плиты (рис. 1 ж).
Вторую полуформу изготовляют аналогично, затем собирают из них форму. После сборки формы можно выполнять заливку. В процессе сборки формы, заливки металла и затвердевания отливки опоки подключены к вакуумному насосу (рис. 3.1 з). Как только температура отливки достигает значения, необходимого для сохранения её прочности, насос отключают, а песок, удаляемый из опок, через охладительное и пылеулавливающее устройство поступает в бункер (рис. 3.1 и).
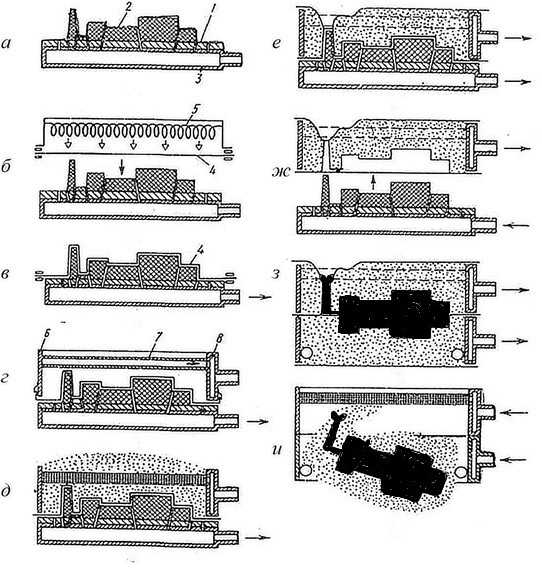
Рисунок 1 – Последовательность операций при вакуумной формовке
При заливке пленка испаряется либо сгорает под влиянием заливаемого металла. Под воздействием вакуума продукты деструкции пленки проникают в форму и вместе с частицами песка образуют тонкую оболочку, которая упрочняет граничный слой формы. Это наряду с противопригарным покрытием обеспечивает получение отливок с низкой шероховатостью поверхности, что не требует дополнительных затрат на финишные операции очистки отливок.
Достоинства и недостатки вакуумной формовки
По сравнению с литьем в химически твердеющие или сырые песчаные формы при вакуумной формовке требуется практически в 2 раза меньше рабочих, а оборудование в 2 раза дешевле, чем оборудование для изготовления химически твердеющих форм.
Практически отпадает смесеприготовление, так как подготовка формовочного материала сводится лишь к просеиванию, охлаждению и регенерации использованного песка. Это резко сокращает затраты, связанные с использованием приготовительного оборудования. Значительный экономический эффект достигается за счет отсутствия в формовочном материале связующего вещества.
Производительность труда при формовке повышается в 2-5 раз. Так, цикл изготовления вакуумной формовкой двух полуформ размерами 1200×1400×250 мм составляет 10 мин. Цикл изготовления этих же форм по традиционной технологии составляет 40-60 мин.
По сравнению с встряхиванием и подпрессовкой вакуумная формовка обеспечивает равномерно высокую твердость, в результате разброс размеров уменьшается в среднем в два раза.
Полимерная пленка между моделью и песчаной формой обеспечивает снижение сопротивления трению, что позволяет извлекать модели с нулевым уклоном.
Высокая размерная точность отливок достигается путем использования отсортированного формовочного песка, отсутствием износа модельной оснастки, высокой равномерной степенью уплотнения песка, отсутствием литейных уклонов, отсутствием изменения размеров формы из-за улетучивающихся добавок формовочного материала.
В результате этого обеспечивается постоянство массы отливок больших размеров и сложной геометрической формы. Кроме того, обеспечивается высокая степень воспроизводимости при серийном производстве, от партии к партии не наблюдается каких-либо различий.
Способ вакуумной формовки можно использовать для получения отливок практически из любых сплавов, при любом уровне серийности, без каких-либо ограничений в отношении толщины стенок отливки. Однако имеются ограничения по сложности, высоте и конфигурации отливок.
Вакуумная формовка перспективна для получения отливок из сплавов, склонных к трещинообразованию при высокой температуре, поскольку этот способ позволяет регулировать прочность формы после образования на отливке твердой корки.
Область применения вакуумной формовки в отношении размеров отливаемых заготовок ограничивается практически только размерами опоки и мощностью вакуумного насоса.
Полученная вакуумной формовкой отливка массой 1000 кг размером 2020×405 мм заняла первое место на съезде литейщиков США в 2005 г. Отливка предназначена для гусеничного транспортера НАСА. Это стало заслуженным признанием способа вакуумной формовки и доверия к нему производителей литых деталей.
Просмотров: 81
extxe.com
Вакуумная формовка – сфера применения вакуумной формовки. Особенности вакуумной формовки пластиков.
Вакуумная формовка – это процесс, главная задача которого заключается в процессе создания силиконовых и пластиковых изделий. Процесс вакуумной формовки пластиков напрямую зависит от оборудования, которое будет при этом использоваться. Вакуумная формовка пластика — это процесс, который позволяет извлечь из данного материала все сторонние примеси, которые отрицательным образом на него влияют.
Еще одной распространенной категорий данного процесса, является вакуумно пленочная формовка. Данный процесс отличается от предыдущих, еще и наличием специальной пленки, которая позволяет обрести изделию еще большую степень прочности и надежности в процессе эксплуатации.
Цена вакуумной формовки пластика на данный момент выглядит не столь привлекательно, из-за чего далеко не каждый человек может себе позволить проделывать подобные процессы. Благо, на огромном рынке вакуумных технологий можно найти и недорогие станки вакуумной формовки, с помощью которых подобный процесс можно проделать и самостоятельно.
На самом деле, наибольшую роль в данном процессе играет оборудование для вакуумной формовки. Если оно будет достаточно качественным и мощным, то вы с легкостью сможете быстро произвести процесс формовки. Если же его мощность не будет столь высокой, то данный процесс может немного и затянуться.
Пластик для вакуумной формовки, купить можно в любом магазине вакуумного оборудования. Благо, подобных магазинов на данный момент достаточно много, а это значит, что пользователь может выбрать как более дорогостоящий, так и вполне бюджетный пластик для вакуумной формовки.
Не менее актуальными в подобных процессах являются и формы для вакуумной формовки, без которых проделать подобную процедуру практически невозможно. Именно поэтому, ни в коем случае на забывайте об этом, и обращайте на подобные моменты особое внимание.
Применение вакуумной формовки
Не трудно догадаться, что столь огромный функционал данного процесса, позволяет задействовать подобный процесс в самых разных направлениях. Одним из них можно назвать вакуумную формовку пластика, где многое зависит от оборудования, которое при этом используется.
Не менее популярной сферой применения, является вакуумная формовка стеклопластика, которая в плане технологии является более запутанной. Сам метод вакуумной формовки стеклопластика вместил в себе несколько этапов, каждый из которых должен проделываться в точности с тем, как все указано в инструкции.
В ином же случае, вакуумная формовка, несмотря на все оборудование, не сможет производиться с максимальной эффективностью. Еще одним важным аспектом, на который стоит обращать свое внимание, является изготовление матрицы для вакуумной формовки. Роль матрицы в этом процессе максимально велика. Сама матрица, обретает таковую форму, которую на финальной стадии должно иметь обрабатываемое изделие.
Еще одним важным элементом является насос для вакуумной формовки, без которого достичь нужного уровня вакуума практически невозможно. Технология вакуумной формовки, во многом зависит от менее крупных деталей, что собственно и говорит о высокой степени взаимосвязанности каждого элемента в системе.
Если же говорить о менее распространенных видах формовки, то сюда можно отнеси формовку поликарбоната. Данный процесс является уже более сложным, из-за чего далеко не все готовы производить подобную процедуру.
Вакуумная формовка пластиков
Вакуумная формовка пластиков – это процесс, от которого зависит не только качество изготовляемых изделий, а еще и возможность их дальнейшего использования в других направлениях.
Важно осознавать тот факт, что провести данный процесс без наличия требуемого оборудования попросту невозможно. Цена оборудования для вакуумной формовки пластика на данный момент далеко не самая вменяемая. А это значит, что придется искать все подходящие материалы для вакуумной формовки, которые смогут помочь в проделывании подобного процесса.
Вакуумная формовка акрила – это один из наиболее необычных методов вакуумной формовки. Столь необычное покрытие, делает изделие по-настоящему надежным и что немаловажно, позволяет обрести товарный вид. Не менее эффективной является и вакуумно пленочная формовка, технология которой заключается в накладывании специальной защитной поверхности на изготавливаемый материал.
В любом из направлений, процесс вакуумной формовки показывает себя исключительно с положительной стороны. Это можно даже понять по вакуумной формовке полистирола, что способно проделать далеко не каждое устройство. Данный метод вакуумной формовки является более трудоемким, но не менее эффективным.
tkm71.ru
Как произвести вакуумную формовку в домашних условиях
Перевел SaorY для mozgochiny.ru
Приветствую, мозгочины! Как и многие самодельщики, я всегда мечтал иметь у себя дома свой собственный аппарат вакуумной формовки. О реализации этой мозгомечты и пойдет речь в этом руководстве.
Несмотря на то, что в мастерской я чувствую себя как дома, в реальности собственной мастерской дома у меня. Поэтому я искал способ создать своими руками с помощью подручных инструментов аппарат для вакуумного формования, который можно использовать в домашних условиях. Найденное мной решение этой мозгозадачи не требует труднодоступных материалов и электроинструментов, поэтому подходит для самодельщиков не имеющих доступа к профессиональному электрооборудованию и специализированным мастерским, чтобы создать подобный вакуумный аппарат.
Нам потребуется (по минимуму):
— этюдник художника или ящик-органайзер — 2шт.
— дрель и сверла
— силиконовый герметик
— столярный клей
— зажимы или стопка книг в качестве пресса
— круглый напильник
— защитный экран на для пластиковых окон (по размерам вашего этюдника или ящика)
— металлические уголки для рамки — 8шт.
— ножовка по металлу
— уплотнитель на клеевой основе (той же ширины, что и профиль защитного экрана)
— большие канцелярские зажимы — 4шт.
— пылесос со шлангом
— линейка и карандаш
Дополнительно (но не обязательно):
— белый уксус
— бумажные полотенца
— монтировка, молоток или прочная плоская отвертка
— кольцевая пила или бита Форстнера (диаметром со шлаг пылесоса)
— стусло
— замазка
Для самого процесса формования необходимы:
— термопластик для формовки (например 0.03-й стирол)
— плита с духовкой
— кухонные варежки или прихватки
— алюминиевая фольга
— тальк
Шаг 1: Короб основания
От другого проекта у меня остался этюдник, и, как оказалось, из него легко сделать основание для мозгоподелки без необходимости собирать его из брусков и досок. Но те, у кого имеются и условия, и оборудование могут собрать основание с нуля и сразу перейти к Шагу 8: Создание рамки.
Шаг 2: Удаление перегородок
Ящики-органайзеры как правило имеют секционные перегородки. И их первым делом необходимо аккуратно удалить — в идеале просто вытаскиваем, если они снимаются, а если же они приклеены, то пропитываем бумажные полотенца уксусом, прикладываем их к клеевым швам и оставляем на ночь.
Уксус размягчает клей и, следовательно, ослабляет клеевое соединение, поэтому перегородки возможно сразу поддадутся, или же их придется поддеть монтировкой или плоской отверткой. Может быть даже придется выдержать их в уксусе еще раз.
Так как это уксусное «волшебство» требует времени, то планируйте этот мозгошаг заранее.
Шаг 3: Высверливание отверстий
На внешней стороне одного из ящиков расчерчиваем сетку, размеры которой должны соответствовать вашей крепежной рамке. Шаг сетки в 10мм вполне функционален.
Для данного шага нужно заранее определиться каких размеров будет ваша крепежная рамка, которая удерживает лист термопластика. По площади она должна соответствовать площади ящика основания, либо быть чуть меньше.
Итак, расчерчиваем сетку и в пересечении линий высверливаем отверстия сверлом небольшого диаметра, я использовал сверло 2.4мм.
Шаг 4: Герметизация внутренних стыков
Для герметичности основания поделки все стыки изнутри промазываем герметиком, при этом следуем инструкциям производителя и в соответствии с ними даем ему время на высыхание.
Шаг 5: Склеивание ящиков
По верхнему периметру ящиков наносим столярный клей и прикладываем их друг к другу для склеивания. Зажимаем и оставляем для высыхания как минимум на час. Если зажимов у вас нет, то ставим на конструкцию из ящиков стопку тяжелых книг, чтобы тем самым создать давление необходимое для склеивания.
Шаг 6: Высверливание отверстия для шланга пылесоса
Измеряем диаметр шланга вашего пылесоса и на одной из боковых сторон, по середине, размечаем окружность того же диаметра.
Далее сверлом Форстнера или кольцевой пилой высверливаем намеченное отверстие. Если же подобных мозгоприспособлений у вас нет, то по всей площади этого отверстия насверлите мелких отверстий, срежьте получившиеся перемычки с помощью небольшой стамески, и дремелем с шлифовальной насадкой или круглым напильником сровняйте неровности окружности. Во время этой процедуры примеряйте шланг и продолжайте шлифовать до его плотного прилегания.
Шаг 7: Герметизация шва по внешнему краю
По шву склеивающему два ящика мозгооснования накладываем слой герметика.
Шаг 8: Создание рамки
Из защитного экрана для пластиковых окон делаем рамку в которой будет крепиться лист термопластика.
Шаг 9: Удаление сетки защитного экрана
Профиль защитного экрана это две защелкивающиеся половинки, между которыми располагается сетка. С небольшими усилиями раскрываем эти мозгополовинки и отделяем их друг от друга, далее вынимаем защитную сетку, она должна легко податься.
Шаг 10: Нарезка профиля по размеру
Разбираем защитный экран по частям, профиль должен легко выниматься из скрепляющих его уголков.
Добытый таким образом алюминиевый профиль нарезаем по размерам рамки, которая, кстати, должна быть одинаковой по размерам с основанием, либо чуть меньше его. При резке для получения ровного среза используйте стусло и ножовку по металлу.
Далее собираем обе половинки крепежной рамки, используем для этого металлические уголки, а не пластиковые, которыми скреплялся защитный экран.
Шаг 11: Наклеивание уплотнителя
На одну из половинок рамки наклеиваем по ее периметру уплотнитель, при этом необходимо убедиться, что он охватывает весь мозгоконтур и создает герметичное соединение.
Шаг 12: Поделка в действии!
Эта самая интересная часть процесса.
Шаг 13: Подготовка к формованию
1. Обрезка листа термопластика по размеру:
Для формования я выбрал 0.03-й стирол, который можно легко приобрести, он также легко режется (даже обычными ножницами) и шлифуется. Обрезаем лист по размеру вашей рамки.
2. Подготовка духовки:
Из духовки вынимаем все решетки, кроме одной. Дно духовки устилаем фольгой, фольгой также обертываем два кирпича или небольших кухонных горшочка, и устанавливаем их на решетку духовки, они послужат опорой для рамки с пластиком, которая должна располагаться на несколько сантиметров ниже нагревателя. На открытую дверку духовки расстилаем фольгу и поверх нее ставим основание мозгоподелки.
3. Подсоединение пылесоса:
Рядом с духовкой, в пределах досягаемости шланга, ставим пылесос и вставляем его шланг в отверстие сбоку основания. Для дополнительной герметичности обмазываем соединение замазкой.
4. Крепление листа в рамке:
Между половинками рамки помещаем обрезанный лист и скрепляем все канцелярскими зажимами, и лучше чтобы их желобки располагались за уплотнителем. Затем рамку устанавливаем на кирпичи в духовку, при этом уплотнитель должен располагаться снизу, по другую сторону от нагревателя, а мозгопластик может свободно провисать.
5. Установка молда:
По центру основания устанавливаем то, что будет шаблоном для формования. Этот шаблон полезно сверху присыпать тальком, чтобы в последствие было проще отделить пластик.
6. Безопасность:
Поблизости с духовкой кладем кухонные рукавицы или прихватки, и убеждаемся, что достаем до кнопки включения пылесоса. Суть в том, чтобы быстро вынуть рамку из духовки, поместить её по центру основания поверх молда, включить пылесос и открыть окно, так как пластик немного чадит.
Примечание: пользуйтесь данной поделкой ТОЛЬКО при достаточной вентиляции, надевайте респиратор, духовку устилайте фольгой, а после окончания всего процесса очищайте духовку. Если у вас возникают какие-либо вопросы по нагреванию пластика в домашних условиях, то осуществляйте формование только если вы осознаете все риски. Часто весь этот процесс производить не рекомендуется.
7. Нагревание пластика:
Включаем нагрев, если температура вашего нагревателя регулируется, то оптимальная температура 193 градуса Цельсия, пр которой минимально количества дыма и испарений.
8. Разогрев до провисания пластика:
На данной стадии тщательно наблюдаем за пластиком, а потом действуем очень быстро. Сначала пластик будет слегка колебаться от нагревания, затем он снова станет ровным, а уже потом начнет провисать. После этого включаем пылесос и надеваем рукавицы (или берем прихватки). Суть в том, чтобы позволить пластику провиснуть более чем на половину высоты вашего молда.
Шаг 14: Окончание процесса формования
Когда пластик будет достаточно разогрет, осторожно берем рамку, аккуратно вынимаем её и быстро помещаем по центру мозгооснования поверх молда, при уплотнитель должен соприкасаться с поверхностью основания, а пылесос быть включенным . К самому пластику не прикасаемся вообще! Если герметичность не нарушена пластик сразу же примет нужную форму, после этого через несколько секунд выключаем пылесос. Пару минут даем рамке и пластику на остывание, а потом вынимаем пластик из рамки и отставляем его в сторону.
Пользуйтесь, НО СОБЛЮДАЙТЕ БЕЗОПАСНОСТЬ! Как вы могли заметить, данный проект рассчитан больше на взрослых, опытных мозгосамодельщиков, детям он не рекомендуется.
На этом все, надеюсь было полезно!
(A-z Source)
ПОДЕЛИТЕСЬ С ДРУЗЬЯМИ!
About SaorY
mozgochiny.ru
Технологии, методы, сфера применения вакуумной формовки
Вакуумная формовка
Вакуумная формовка представляет собой технологию, которая позволяет получать объемные изделия из различных пластиков. Как правило представляет собой серийную формовку листовых пластиков, из которых благодаря высоким температурам и отрицательному давлению получаются р…
Краткое описание технологии вакуумной формовки пластика
Процесс изготовления изделия способом вакуумной формовки можно разбить на два основных этапа. Сначала изготавливают оснастку – матрицу, на которой будет непосредственно происходить процесс вакуумного формования пластика. В зависимости от требований к …
Методы формования листовых пластиков
Формование изделий из листовых материалов может производиться за счет создания вакуума по двум схемам: негативной и позитивной. В негативной схеме формование изделия происходит в матрицу под действием вакуума на разогретую заготовку.
Принцип работы термовакуум-формовочной машины
Вакуумное формование производится на вакуум-формовочном оборудовании (ТВФМ). Сам процесс формования включает в себя несколько этапов:
Сферы применения термовакуум-формовочного оборудования
Автомобильная промышленность: бампера, капот, крылья, пороги, спойлера, детали внутреннего интерьера. Навесное оборудование автомобилей(Тюнинг): бампера, спойлера, детали автокресел, накладки на: бампера, пороги, двери, ручки, зеркала, стекло, капот, крылья; Сув…
Термовакуумная формовка полистирола, пвх, пэт
Спектр материалов, применяемых для вакуумной формовки достаточно широк. Основное требование к материалам в термовакуумной формовке – равная толщина листа пластика. Часто применяемые в формовании материалами служат листы, изготовленные из АБС пластика, ПЭТ,…
Технологический процесс вакуум-формовочных изделий
Вакуумное формование считается основным методом обработки пластика. Такой технологический процесс обладает рядом преимуществ. Рассмотрим подробнее о том как происходит процесс вакуумной формовки Сам процесс, начиная закладкой листа и заканчивая готовым и…
vacforming.ru