Модернизация шпиндельного узла для повышения точности станка Текст научной статьи по специальности «Механика и машиностроение»
УДК 621.9.06
Модернизация шпиндельного узла для повышения точности станка
© С.Н. Бриченков, И. Д. Соколова КФ МГТУ им. Н.Э. Баумана, Калуга, 248000, Россия
Рассмотрено одно из решений проблемы повышения точности обработки изделий на металлорежущем станке. Выявлены пути повышения точности центрирования шпиндельного узла вертикально-фрезерного станка в различных конструктивных исполнениях: введена промежуточная опора, заменены подшипники в опорах шпиндельного узла. Для предложенных вариантов выполнены проверочные расчеты на жесткость. Выявлена конструктивная схема, обеспечивающая наибольшую точность обработки.
Ключевые слова: шпиндель, точность, жесткость.
Шпиндельный узел является одним из основных узлов, во многом определяющих точностные параметры станка и производительность обработки. К нему предъявляют высокие требования по точности вращения, виброустойчивости, быстроходности, а также несущей способности шпиндельных опор, их долговечности и допустимому нагреву. Поэтому, когда возникает проблема повышения точности обработки на металлорежущем станке, самым эффективным путем ее решения является модернизация или замена шпиндельного узла и его опор.
В данной работе рассмотрены различные варианты модернизации шпиндельного узла вертикально-фрезерного станка с ЧПУ 65А90ПМФ4. Для расчета шпиндельного узла на точность воспользуемся методикой, предложенной в работе [1].
Сначала рассчитаем силу резания, которая будет общая для всех исполнений рассматриваемого шпиндельного узла.
Исходные данные: станок вертикально-фрезерный с ЧПУ 65А90ПМФ4, торцевая фреза диаметром Б = 160 мм, со сменными пластинами из твердого сплава ВК8, заготовка — плита 1500 х 850 х 700 мм из стали 12Х18Н9Т (ств = 610 МПа).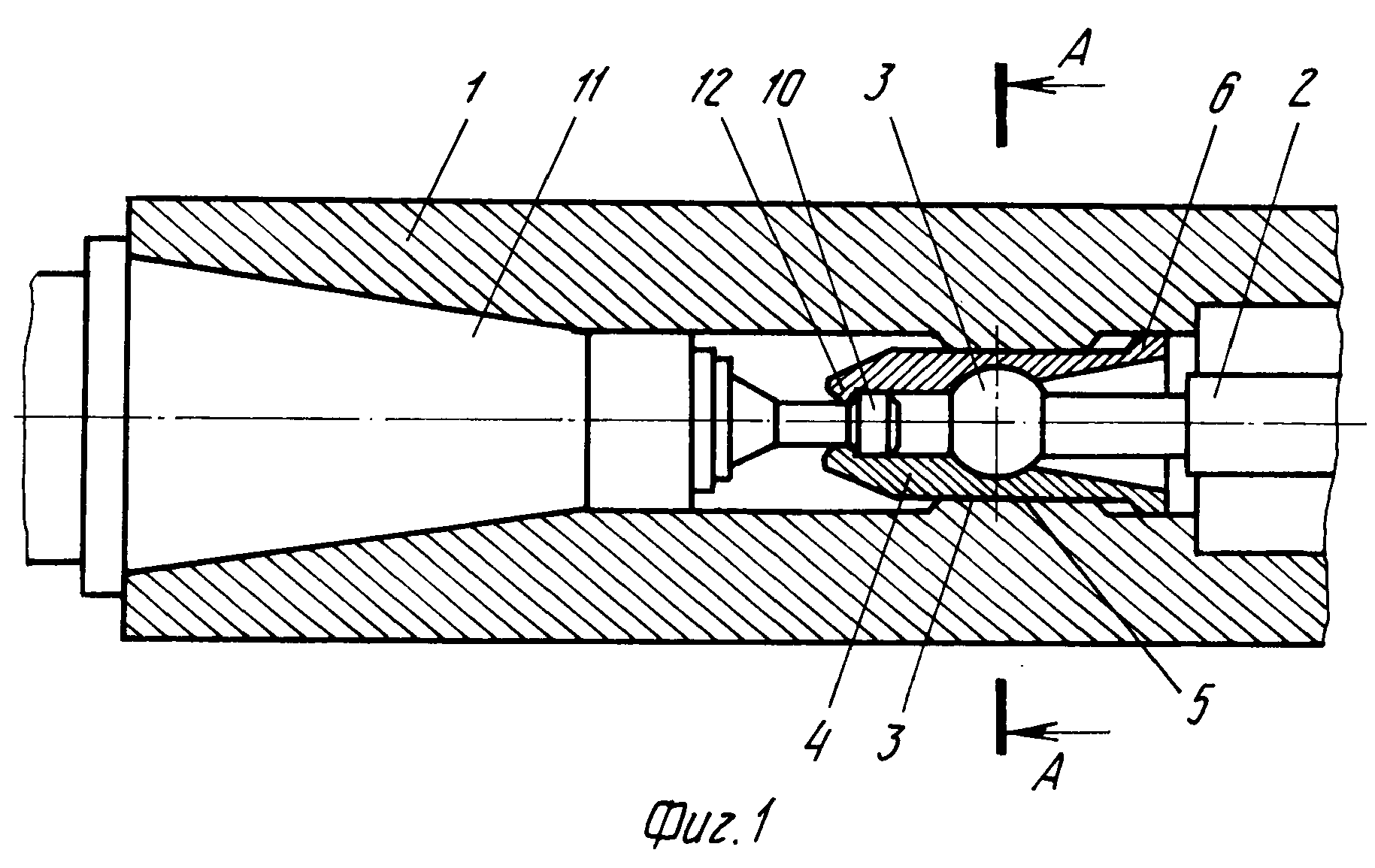
где , q, т, х, у, и, р — коэффициенты, Cv = 108; q = 0,2; т = 0,32; х = 0,06; у = 0,3; и = 0,2; р = 0; Т — период стойкости фрезы,
Т = 180 мин; B — ширина фрезерования, B = = -160 = 128 мм;
1,25 1,25
z — число зубьев фрезы, z = 7; Kv — поправочный коэффициент на скорость резания,
Kv = KmvKnvKuv, (2)
1,35
J
750 610
= 0,8|-| = 0,908; Km = 0,9; Km = 1.
где Кт, = Кг Тогда
Кч = 0,908 • 0,9 • 1 = 0,8172. -СЛ5″8 • 128′ •7 = 10048,4Н.
1601,15 • 640
Мощность резания вычисляем по формуле [2]
N = (5)
1020•60
или с учетом найденных значений скорости резания и составляющей силы резания
N =
10 048,4 • 32,08 1020•60
= 5,3 кВт.
На рис. 1 показано направление действия силы Р. Согласно [3], угол Р = 30°. Тогда значение равнодействующей силы резания
Рг 10 048,4
РР =
8Ш Р 8Ш30°
= 20 096,8 Н. (6)
Рис. 1. Направление действия направляющей сил резания
Рассчитаем шпиндельный узел в исходном исполнении, показанном на рис. 2, а [4]. Следует отметить, что на данном рисунке, как и на всех последующих, шпиндельный узел показан условно, а линейные размеры указаны приближенно.
450
_в|_
с — 190
а = 450
6= 140
б
Рис. 2. Конструкция (а) и расчетная схема (б) шпиндельного узла базовой модели станка (исполнение 1)
В шпиндельном узле исполнения 1 в качестве задней опоры используется двухрядный роликовый радиальный подшипник 3182122 класса точности 4, а в качестве передней — двухрядный роликовый радиальный подшипник 3182124 класса точности 2 и радиально-упорный шариковый двухрядный подшипник 178824 класса точности 4 [5].
Расчетная схема приведена на рис. 2, б. Шпиндельные опоры на схеме показаны подробно для наглядного изображения подшипников в опорах. На схеме имеются следующие обозначения: А — передняя опора; В — задняя опора; ЯА, ЯВ — реакция, возникающая в передней и задней опоре соответственно; Рр — равнодействующая силы резания.
В передней опоре два подшипника расположены один относительно другого на незначительном расстоянии, поэтому расчет ведем как для одного двухрядного роликового радиального подшипника с большой шириной наружного кольца.
Согласно [6], назначаем предварительный натяг e = —3 мкм. Радиальная податливость 5г0 = 3,75 мкм; относительный предваритель-е —3
5 г 0 3,75
или натяг в подшипнике, Р = 0,5. Вычисляем радиальную податливость в контакте наиболее нагруженного тела качения с дорожкой качения в подшипнике с предварительным натягом:
5; = р5г0 = 0,5 • 3,75 = 1,875 мкм.
Определяем радиальную податливость в контакте колец с посадочной поверхностью вала и корпуса:
5„ = АР?к
лБВ1
(7)
где Рг — главная составляющая сил резания, Рг = 10 048,4 Н; Б — наружный диаметр подшипника, Б = 180 мм; В1 — ширина наружного кольца подшипника, В1 = 120 мм; й — посадочный диаметр подшипника, й = 120 мм.
Подставив данные значения в формулу (7), получим
5 Г =
4 -10 048,4 • 0,05
с
120
1 +-1 = 0,0494 мкм. = 5221,6 -103 Н/мм.
5Г 1,9244
В задней опоре расположен один подшипник, поэтому расчет ведем без упрощений. Назначаем предварительный натяг е = —3 мкм. Радиальная податливость 5Г0 = 3,75 мкм; относительный предвари-
е —3
тельный натяг -=-= —0,8 мкм; коэффициент, учитывающий
5 г 0 3,75
зазор или натяг в подшипнике, Р = 0,5. Вычисляем радиальную податливость в контакте наиболее нагруженного тела качения с дорожкой качения в подшипнике с предварительным натягом:
5; =р5;0 = 0,5 • 3,75 = 1,875 мкм.
Радиальную податливость в контакте колец с посадочной поверхностью вала и корпуса рассчитываем по формуле (7) с подстановкой следующих данных: Б = 170 мм; й = 110 мм; к = 0,1; В = 45 мм. В результате получаем
„ 4-10048,4 • 0,05
5; =
1 + — | = 0,1378 мкм. 170)3,14-170 • 45 Общая радиальная податливость
5; =5; +5Г = 1,875 + 0,1378 = 2,0128 мкм. Отсюда жесткость задней опоры
/В = Р= = 4992,25-103 Н/мм.
5; 2,0128
По условию наибольшей точности шпиндельного узла должно
выполняться условие /а > /В. Поскольку 5221,6 -10 Н/мм >
> 4 992,25 -10 Н/мм, условие выполняется.
Рассчитаем теперь прогиб шпинделя, возникающий под действием равнодействующей силы резания Рр:
\2
(а + Ь) + Ь2 + Ь2(а + Ь) /а а2 /Ва2 3Е1
(8)
где а, Ь — размеры с расчетной схемы; Е — модуль упругости,
Е = 2 -105 МПа. -‘- =-*-‘- = 89,956 -105 мм4, (9)
64 64
где Бшп — наружный диаметр шпинделя, Бшп = 120 мм; йшп — внутренний диаметр шпинделя, й шп = 110 мм.
Подставляем полученные значения в формулу (8) и вычисляем прогиб шпинделя:
у1 = _20096,8
(450 +140)2 1402
5 221,6 • 103 • 4502 4 992,25 • 103 • 4502
1402(450+140) 3• 2-105 • 89,956• 105
= _0,05 мм.
Суммарный прогиб шпинделя у = у1 = 0,05 мм.
Допустимый прогиб шпинделя
удоп = (0,0001. 89,956 •Ю5
Максимально допустимый угол поворота переднего конца шпинделя 0доп = 0,001 рад. Для нормальной работы шпинделя должно выполняться условие 0доп > 0. В связи с тем, что 0,001 рад > > 0,00019 рад, это условие выполняется.
Поскольку все проверки успешно пройдены, можно утверждать, что принимаемые значения коэффициентов и величин верны.
По аналогичной методике рассчитаем жесткости других исполнений шпиндельного узла для выбора оптимального варианта.
На рис. 3, а показан шпиндельный узел исполнения 2, в котором по сравнению с узлом исполнения 1 заменена задняя опора, добавлена промежуточная опора и убран подшипник из передней опоры. В результате в передней опоре имеем двухрядный роликовый радиальный с короткими цилиндрическими роликами подшипник 3182124 класса точности 2, в промежуточной опоре — роликовый радиальный сферический двухрядный подшипник 4053722 класса точности 4, а в задней опоре — роликовый радиальный двухрядный с короткими цилиндрическими роликами подшипник 3282122 класса точности 4.
Расчетная схема данного трехопорного шпиндельного узла показана на рис. 3, б.
500
Яр
в!
Яг
с!
_а1
140
а2 = 300
= 200
Ъ = 100
Рис. 3. Конструкция (а) и расчетная схема (б) шпиндельного узла
(исполнение 2)
Определим жесткости подшипников аналогично их расчету для конструктивного исполнения 1:
jA = 6 168,45-103 Н/мм, ^ = 4467,94-103 Н/мм,
^ = 4 163,59-103 Н/мм. + аа2а\ (3Е1)
300 – 300
500 -100
6 1 68,45 -103 4 1 63,59 -103
100 -2003- 300 6-2-105 -89,956-105
3002
5002
2002
500 -2002-3002
6 168,45 -103 4 163,59-103 4 467,94 -103 3-2 -105 -89,956-105
= 2,4 -10-5.
(13)
Тогда суммарный прогиб шпинделя
у = у = -20 096,8 =
л-5
300(300 – (2,4 -10^) – 300) +100 – (100 – (2,4-10-5) – 500) +
6 1 68,45-103 – 2002
4 163,59-103 -2002
100 – (2 -100 – 500 + 200 – 300 – (2,4-10-5))
+
6-2-10 -89,956-10э = -0,027 мм.
На рис. 4, а показан шпиндельный узел исполнения 3. В нем по сравнению со шпиндельным узлом исполнения 1 заменен задний подшипник и добавлен еще один подшипник в заднюю опору. В результате в передней опоре имеем двухрядный роликовый радиальный с короткими цилиндрическими роликами подшипник 3182124 класса точности 2 и радиально-упорный шариковый двухрядный подшипник 178824 класса точности 4, в задней опоре — роликовый радиальный двухрядный с короткими цилиндрическими роликами подшипник 3282122 класса точности 4 и роликовый радиальный сферический двухрядный подшипник 4053722 класса точности 4. Расчетная схема шпиндельного узла исполнения 3 показана на рис. 4, б.
400
оа СЗР
■ СЮ. 5р
□□ □□
в А
А с =190 \7. а = 400 N Ъ= 140
б
Рис. 4. Конструкция (а) и расчетная схема (б) шпиндельного узла
(исполнение 3)
Рассчитаем жесткости подшипников аналогично их расчету для конструктивного исполнения 1:
jA = 5 221,6 -103 Н/мм; ув = 5134,6-103 Н/мм.
Прогиб шпинделя в этом случае
у = -0,047 мм.
На рис. 5, а показан шпиндельный узел исполнения 4, где по сравнению с узлом исполнения 1 заменен один передний подшипник. В результате в передней опоре имеем двухрядный роликовый радиальный с короткими цилиндрическими роликами подшипник 3182124 класса точности 2 и роликовый радиальный сферический двухрядный подшипник 4053722 класса точности 4, а в задней опоре — роликовый радиальный двухрядный с короткими цилиндрическими роликами подшипник 3282122 класса точности 4. Расчетная схема шпиндельного узла исполнения 4 показана на рис. 5, б.
450
Яр
в!
с — 190
а = 450
Ь= 140
б
Рис. 5. Констукция (а) и расчетная схема (б) шпиндельного узла
(исполнение 4)
Жесткости подшипников для этого исполнения уА = 5266,54 • 103 Н/мм,
ув = 4992,25 • 103 Н/мм,
а прогиб шпинделя
у = -0,05 мм.
Таким образом, анализ полученных расчетных значений прогибов шпинделей разных исполнений позволяет сделать вывод о том, что шпиндельный узел исполнения 2 дает наибольший положительный эффект от модернизации — прогиб уменьшается на 46 %.
ЛИТЕРАТУРА
[1] ГОСТ 9726-89. Станки фрезерные вертикальные с крестовым столом. Терминология. Размеры. Нормы точности и жесткости. Введен 1991-01-01. Москва, Изд-во стандартов, 1989, 40 с.
[2] Перель Л.Я., Филатов А.А. Подшипники качения: Расчет, проектирование и обслуживание опор. Москва, Машиностроение, 1992, 606 с.
[3] Справочник технолога-машиностроителя. Дальский А.М., Косилова А.Г., Мещеряков Р.К., Суслова А.Г., ред. Москва, Машиностроение-1, 2003, 944 с.
[4] 65А90ПМФ4-11. Станок вертикально-фрезерный с крестовым столом [Электронный ресурс]. МашИнформ.ру технические характеристики металлообрабатывающего оборудования. URL: http://mashinform.ru/ frezernye-stanki/65/65a90pmf4-11.shtml.
[5] Чернянский П.М. Проектирование и ремонт шпиндельных узлов. Москва, НИЦ ИНФРА-М, 2014, 272 с.
[6] Шестернинов А.В. Конструирование шпиндельных узлов металлорежущих станков. Ульяновск, УлГТУ, 2006, 96 с.
Статья поступила в редакцию 05.06.2014
Ссылку на эту статью просим оформлять следующим образом:
Бриченков С.Н., Соколова И.Д. Модернизация шпиндельного узла для повышения точности станка. Инженерный журнал: наука и инновации, 2014, вып. 10. URL: http://engjournal.ru/catalog/machin/hidden/1288.html
Бриченков Сергей Николаевич родился в 1991 г. Студент кафедры «Инструментальная техника и технологии» КФ МГТУ им. Н.Э. Баумана. Область научных интересов: повышение точности шпиндельных узлов станков. e-mail: [email protected]
Соколова Ирина Дмитриевна родилась в 1963 г, окончила КФ МВТУ им. Н.Э. Баумана в 1986 г. Канд. техн. наук, доцент кафедры «Инструментальная техника и технологии» КФ МГТУ им. Н.Э. Баумана. Область научных интересов: повышение точности шпиндельных узлов станков. e-mail: [email protected]
Upgrade of spindle assembly to increase accuracy of the machine
© S.N. Brichenkov, I.D. Sokolova Kaluga Branch of Bauman Moscow State Technical University, Kaluga, 248000, Russia
The article considers one of the problem solutions of increasing processing accuracy of the products on metal-cutting machines. Spindle unit is one of the basic elements that determines the accuracy and productivity of the processing. The ways to improve the centering accuracy of different designs of vertical milling machine spindle unit were identified. We reviewed double-seat design of base model spindle, and introduced intermediate support in one design, in other versions replacement of bearings in a spindle unit support was carried out. We made checking calculations of rigidity for all design versions. To this purpose we made calculations of the spindle deflection caused by the resultant of cutting forces for various design versions. In order to determine the resultant cutting forces the modes ofprocessing of heat-resistant steel were calculated. In the result of the study we identified structural scheme that ensured the highest precision processing.
Keywords: spindle, accuracy, rigidity. REFERENCES
[1] GOST 9726-89. Stanki fresernye verticalnye s krestovym stolom. Tekhnologiya. Razmery. Normy tochnosti i zhestkosti [Milling machines with vertical cross table. Terminology. Dimensions. Standards of accuracy and rigidity]. Moscow, Standards Publ., 1989, 40 p.
[2] Perel L.Ya., Filatov A.A. Rolling bearings: Calculation, design and maintenance of bearings. Moscow, Mashinostroenie Publ., 1992, 606 p.
[3] Dalsky A.M., Kosilova A.G., Meshcheryakov R.K. Suslov A.G., eds. Spravochnik tekhnologa-mashinostroitelya [Handbook for technologist- mechanician]. In 2 volumes. Moscow, Mashinostroenie-1 Publ., 2003, 944 p.
[4] 65A90PMF4-11. Stanok verticalno-frezernyi s krestovym stolom [Vertical milling machine with cross table]. MashInform.ru. Available at: http://mashinform.ru/ frezernye-stanki/65/65a90pmf4-11.shtml.
[5] Chernyansky P. M. Proektirovanie i remont shpindelnykh uzlov [Design and repair of spindles]. Moscow, INFRA-M Publ., 2014, 272 p.
[6] Shesterninov A.V. Konstruirovanie shpindelnykh uzlov metallorezhu-schikh stankov [Construction of machine tool spindles]. Ulyanovsk: UlSTU, 2006, 96 p.
Brichenkov S.N. (b. 1991) is a 5th year student of the Instrumental Equipment and Technologies Department of Kaluga Branch of Bauman Moscow State Technical University. e-mail: [email protected]
Sokolova I.D. (b. 1963) graduated from Kaluga Branch of Bauman Moscow Higher Technical School in 1986. Ph.D., Assoc. Professor of the Instrumental Equipment and Technologies Department of Kaluga Branch of Bauman Moscow State Technical University. Research interests: increasing accuracy of machine spindle units. e-mail: [email protected]
Шпиндели станков
Шпиндели станков нормальной и повышенной точности изготовляют из легированных сталей 50Х, 40ХГТР, 40ХФА, цементируемых сталей 18ХТ, 20Х, а станков высокой и особо высокой точности из сталей 40ХФА, 18ХГТ, 12ХНЗА.

Предельные отклонения шеек шпинделя под подшипники качения (в порядке ужесточения условий работы) js5, k5, m5, а шеек под патрон – js5. Класс точности применяемых для шпиндельного узла подшипников качения зависит от точности станка. В таблице приведена эта зависимость для токарных станков.
Возможные дефекты и способы ремонта шпинделей.
При износе шеек до 0,01-0,02 мм производят притирку на токарном станке сначала смесью наждачного порошка и масла, а затем доводочной пастой с керосином. При износе шеек более 0,02 мм производят:1) шлифование с последующей доводкой под ремонтный размер (при возможности изменения размера отверстия сопрягаемой со шпинделем детали).

2) при условии сохранения размера отверстия – восстановление шеек, изношенных до 0,05 мм, хромированием с последующим шлифованием, а изношенных более 0,05 мм – металлизацией или вибродуговой наплавкой с последующим обтачиванием и шлифованием;
3) при значительном износе – протачивание шейки и напрессовка или установка на клею ремонтной втулки с последующим ее протачиванием и шлифованием.
Связь точности токарной обработки и точности шпиндельного узла станка.
некруглость, мкм | 5 | 3 | 2 | 1,2 | 0,7 |
шероховатость поверхности Ra, мкм | 2,0 | 1,0 | 0,8 | 0,63 | 0,3 |
Подшипник качения d<80 мм – класс точности | 4-5 | 4 | 2-4 | 2 | Св.![]() |
шпинделя | 1,3 | 0,8 | 0,5 | 0,3 | 0,2 |
корпуса | 2,5 | 1,3 | 1,0 | 0,6 | 0,4 |
Шпиндельный узел в сборе – радиальное биение оси вращения шпинделя, мкм | 4,0 | 2,3 | 1,6 | 0,9 | 0,5 |
При небольших износах конического отверстия шпинделя, рисках и забоинах на его поверхности производят шлифование на внутришлифовальном станке или не снимая шпинделя со станка с помощью специального приспособления.

При износе или повреждении резьбы производят наплавку или металлизацию с последующим нарезанием резьбы, реже перенарезают резьбу на меньший диаметр.
Отремонтированные шпиндели должны отвечать следующим требованиям:
1. Отклонение от цилиндричности шеек под подшипники не должно превышать 10 % допуска на диаметр шейки для шпинделей станков точности А и С, 25 % допуска – при точности станков П и В и 50 % допуска – при точности Н.
2. При проверке правильности геометрической формы конусных поверхностей шпинделя с помощью конусного калибра длина неокрашенных мест не должна превышать 5 мм по окружности и 20 % длины образующей вдоль нее; нанесенные на калибр через 90° четыре продольные риски должны равномерно растираться, нестертые места не должны быть более 3 мм.
3. При проверке размера конусного отверстия торец шпинделя должен находиться в пределах двух рисок на конусном калибре.
4. При протачивании и перешлифовке основных поверхностей шпинделя допускается уменьшение диаметра в пределах 5%, а уменьшение диаметра резьбы – до следующего меньшего стандартного размера.
5. Увеличение размеров шпоночного паза недопустимо.
6. Вращение шпинделя от руки должно происходить без люфта и заедания.
7. После сборки шпиндельного узла проверяется параллельность или перпендикулярность оси шпинделя к поверхности стола или направляющих. Допустимые погрешности расположения поверхностей шпинделя приведены в таблице.
Нормы точности шпинделей металлорежущих станков
Радиальное биение центрирующей поверхности шпинделя: | ||||
1. Токарные станки с наибольшим диаметром обработки, мм: | ||||
до 250 | 8 | 5 | 3 | – |
от 250 до 800 | 10 | 7 | 5 | – |
2.![]() | 10 | 6 | – | – |
3. Круглошлифовальные станки при диаметре изделия, мм: | ||||
до 100 | – | 4 | 2,5 | 1,5 |
от 100 до 200 | – | 5 | 3 | 2 |
Осевое биение шпинделя: | ||||
1.![]() | ||||
до 400 | 8 | 5 | 3 | – |
от 400 до 800 | 10 | 7 | 5 | – |
2. Фрезерные станки с шириной стола до 500 мм | 10 | 6 | – | – |
3.![]() | ||||
до 200 | – | 4 | 2,5 | 1,5 |
от 200 до 400 | – | 5 | 3 | 2 |
Торцовое биение базовой поверхности шпинделя (опорного буртика): | ||||
1. Токарные станки с наибольшим диаметром обработки, мм: | ||||
до 400 | 16 | 10 | 7 | – |
от 400 до 800 | 20 | 12 | 7 | – |
2.![]() | 20 | 12 | – | – |
3. Круглошлифовальные станки при диаметре изделия, мм: | ||||
до 200 | – | 6 | 4 | 2,5 |
200-400 | – | 8 | 5 | – |
Радиальное биение конического отверстия шпинделя (у торца): | ||||
1.![]() | ||||
до 400 | 10 | 7 | 5 | |
400-800 | 12 | 5 | 5 | |
2. Фрезерные станки с шириной стола до 500 мм | 10 | 6 | – | – |
3. Круглошлифовальные станки при диаметре изделия, мм: | ||||
до 100 | – | 4 | 2,5 | 1,5 |
100-200 | – | 5 | 3 | 2 |
Смотрите также:
Шпиндельные узлы станков по металлу
Статическая жесткость шпиндельного узла определяется по радиальному и осевому смещениям конца шпинделя под действием прилагаемых к шпинделю сил. При этом суммарное смещение складывается из собственной деформации шпинделя и деформации его опор.
Жесткость и нагрузочную способность шпиндельных узлов станков с ЧПУ увеличивают, не только создавая более рациональные конструкции, но и применяя в качестве опор шпинделей новые подшипники качения. Например, для восприятия радиальных нагрузок шпинделями в современных станках применяют двухрядные роликовые подшипники с регулированием величины радиального зазора. Для восприятия осевых нагрузок, действующих на шпиндель, применяют прецизионные двухрядные упорно-радиальные шарикоподшипники с углом контакта 60° (сер. 178800). Их устанавливают рядом с двухрядным роликовым подшипником с цилиндрическими роликами в передней опоре шпинделя. Параметр быстроходности у них в 2–2,5 раза больше, чем у обычных упорных шарикоподшипников.
Наиболее характерными показателями динамического качества шпиндельных узлов станков являются частота собственных колебаний, амплитудно-частотные характеристики, форма колебаний на собственной частоте. Часто виброустойчивость станков на 40–50% определяется шпиндельным узлом.
Причинами вибраций могут быть дисбаланс вращающихся деталей (зубчатые колеса, шкивы, втулки и др.), прерывистый характер резания, переменная жесткость опор шпинделя и др.
Нагрев опор шпинделя приводит к изменению предварительного натяга в подшипниках, что в свою очередь влияет на снижение работоспособность шпиндельного узла, а также к смещению конца шпинделя с заготовкой или с инструментом из-за температурных деформаций.
Энергетические потери в шпиндельном узле характеризуются моментом трения и мощностью холостого хода и учитываются при выборе опор шпинделя и назначении мощности приводного электродвигателя (особенно для скоростных шпинделей).
Как видно из указанного выше, многие характеристики шпиндельных узлов станков по металлу определяют тип опор шпинделя и их конструктивное исполнение.
На рис. 1 схематично показаны основные виды опор шпинделей. Наибольшее применение в ШУ станков с ЧПУ получили опоры с подшипниками качения.
В отдельных станках при специфических требованиях к точности, быстроходности, демпфированию, снижению потерь на трение применяются также опоры с подшипниками скольжения с жидкой смазкой (гидростатические и гидродинамические), с подшипниками с газовой смазкой (рис. 1, г), а в последнее время и с активными магнитными подшипниками шпиндельного узла (рис. 1, д).
Диагностика и ремонт шпинделей фрезерных станков с ЧПУ
Выполняем профессиональный ремонт и восстановление шпинделей для фрезерных, токарных и сверлильных станков с ЧПУ
Осуществляем ремонт и восстановление высокоскоростных шпинделей всех известных брендов, в том числе европейского (HSD, Giordano Colombo, ELTE) и китайского (GDZ, HQD, GMT) производства, а также шпинделей с автоматической сменой инструмента. У нас действует обширная складская программа, в рамках которой существует возможность оперативного поиска и поставки запчастей и комплектующих.
Ремонт шпинделя:
- фрезерного станка
- токарного станка
- сверлильного станка
Почему стоит заказать ремонт шпинделя у нас?
Диагностика в сжатые сроки
Всего пара дней понадобится, чтобы выполнить полную диагностику и найти точные причины неисправности.
Любая сложность
Выполняем ремонт любой степени сложности
Комплектующие в наличии
Все запчасти и комплектующие в наличии на складе
Керамические подшипники
Как правило, при ремонте используем более надёжные и долговечные керамические подшипники
Модернизация
Увеличение ресурса, увеличение точностных и скоростных характеристик
Специалисты с опытом
Наши мастера имеют большой опыт ремонта и диагностики
Этапы процесса восстановления шпиндельных узлов:
- Общий визуальный осмотр;
- Входной контроль и тестирование;
- Проверка двигателя и электрики;
- Контроль привода;
- Разборка шпинделя;
- Проверка системы фиксации инструмента;
- Проверка подшипников;
- Определение неисправностей;
- Проверка системы охлаждения;
- Проверка системы смазки;
- Проверка герметичности;
- Проверка герметичности;
- Проверка посадочных мест подшипников;
- Проверка вала и посадочного места инструмента;
- Определение ремонтопригодности;
- Балансировка вращающихся компонентов;
- Сборка шпиндельного узла с новыми подшипниками;
- Регулировка датчика положения;
- Контроль биения шпиндельного узла;
- Контроль зазора;
- Обкатка шпиндельного узла;
- Проверка дисбаланса и уровня вибрации;
Как мы работаем
Выполняем диагностику
Производим ремонт
Отправляем шпиндель Вам
Наш сервисный центр укомплектован современным оборудованием. Работы производятся квалифицированными специалистами
Мы выполняем ремонт высокоскоростных шпинделей, включая их гарантийное и постгарантийное обслуживание. Наши специалисты производут профессиональный ремонт и восстановят работоспособность высокоскоростных шпинделей любого типа и предназначения: деревообработка, металлообработка, камнеобработка, стеклообработка и др. Мы выполняем ремонт шпинделей всех производителей: Omlat, HSD, Umbra Group, Hiteco (SCM GROUP), Colombo, Kessler, ELTE, Perske, DMG MORI, IBAG, SKF, GMN, SIEMENS и др.
Какие работы мы выполняем
Профилактика шпинделя
Проверим работу Шпинделя на всех рабочих режимах, корректность срабатывания датчиков, усилия зажима, состояния конуса и системы охлаждения, виброскорости, радиального, осевого биения и т. д.
Восстановление работы зажимного устройства
Полностью разберём систему зажима, очистим от загрязнений, заменим смазку. По результатам осмотра отполируем тяги, заменим тарельчатые пружины и т.д.
Перемотка обмоток электродвигателя
При перегорании или повреждении обмотки статора выполним полную перемотку электродвигателя
Замена подшипника, балансировка ротора
Заменим подшипники новыми, керамическими (опционально). Произведём балансировку ротора и обкатку.
Замена датчиков шпинделя
Произведём диагностику датчиков и настроим их правильное положение
Прочие и дополнительные услуги
При необходимости выполним шлифовку и хромирование поверхностей, отремонтируем контур охлаждения, систему зажима инструмента. Также выполним настройку шпинделя под ваши требования, например, увеличим число оборотов и т.п.
Телефоны для связи:
8-800-55-15-301
(звонок бесплатный)
+7-918-019-00-09
+7-960-482-88-66
+7-988-386-87-55
Ремонт шпинделей ЧПУ станков – фрезерных, токарных, сверлильных по низким ценам
Возможные поломки шпинделя
Шпиндель – это один из основных элементов станка, испытывающий большие нагрузки. От него зависит качество и точность изготавливаемых деталей. Самыми частыми причинами сбоев в работе шпинделя являются повреждения резьбы цангового зажима, его корпуса, поломки подшипников, которые сопровождаются возникновением шума, хруста. Шпиндель может износиться при длительной эксплуатации, потерять форму, изменить размеры. Это касается шеек подшипников, посадочных мест под зубчатые колеса, всех вращающихся элементов. В большинстве случаев проблемы решаются ремонтом поврежденных деталей, который должен проводить специалист.
Этапы ремонта
При возникновении неполадок в функционировании шпинделя его в первую очередь. Проверяется работа двигателя и состояние электропривода. Затем шпиндель разбирают и оценивают подшипники с системой фиксации. После этого проверяют систему охлаждения, наличие смазки, посадочные места. Вал тестируется на герметичность. Потом проводится балансировка вращающихся деталей. При необходимости устанавливаются новые подшипники. Узел собирается, проводится контроль датчиков и всех зазоров. Шпиндель монтируется на станок и тестируется на степень вибрации и дисбаланс. Все работы осуществляются с помощью специального оборудования, позволяющего создавать надежные крепления. Время ремонта зависит от его сложности и подобранного способа. Шпиндели можно восстанавливать неоднократно. Изготовление новых узлов обходится намного дороже.
Особенности ремонта
При ремонте шпинделей важно точно сохранить размеры поверхностей всех его элементов. Иначе придется переделывать всю технологическую оснастку станка. Для восстановления узла подбирается самый рациональный метод. Это может быть механическая обработка, нанесение гальванического покрытия, монтаж деталей, компенсирующих износ. Механическая обработка помогает восстановить геометрию поверхностей и представляет собой заточку, шлифование и притирку. Она может использоваться при наплавке, хромировании деталей. Шпиндель сначала подготавливают. Не подверженные износу поверхности используются в качестве основы для центрирования. На них устанавливаются специальные пробки после того, как отверстия на концах узла зачищаются от царапин. Пробки имеют резьбу и должны ставиться очень точно. Это определяет качество ремонта.
Ремонт шпинделей для станков
Вид ремонта шпинделей зависит от типа повреждений. При сильном износе шеек проводят их шлифование и притирку до нужных размеров. На поверхность деталей наносится хромированное покрытие. Если на шейки устанавливаются подшипники с жесткой посадкой, можно использовать электролитический метод ремонта. Шейки для скользящих подшипников восстанавливаются с помощью приклеивания вставок. Для этого с поверхности узла стачивают тонкий слой металла. Если сильный износ наблюдается на конусном отверстии, его сначала растачивают, а затем вклеивают втулку. В этом случае шпиндель можно не убирать со станка. Если присутствует деформация или изгиб узла, его лучше заменить. Ремонт в данном случае нецелесообразен.
Шпиндели ремонт – Энциклопедия по машиностроению XXL
Ремонт шпинделя.
При ремонте направляющих корпуса шпиндельной бабки восстанавливают параллельность поверхностей 3 и 4 к оси шпинделя, а поверхности 7 п 8 располагают перпендикулярно оси шпинделя. Ремонт указанных поверхностей осуществляют путем механической обработки и шабрением. [c.192]
Ремонт шпинделя. Ремонт шпинделя (рис. П5, а) в основном включает операции по восстановлению шеек под подшипники и конусного отверстия. [c.234]
Ремонт шпинделя. Ремонт шпинделя (рис. 8.11, а) в основном включают операции по восстановлению шеек под подшипники и конусного отверстия. При незначительном износе шейки шпинделя [c.173]
Как было указано выше, одним из важных факторов, влияющих на точность приспособления, является зазор между шпинделем и втулкой, который по мере износа непрерывно увеличивается. Это требует восстановительного ремонта с заменой или хромированием изношенных деталей. Такого недостатка лишены шпиндели с конической посадочной поверхностью.
[c.78]
В ремонтно-механическом цехе организован централизованный ремонт станков со сдачей их по нормам точности, установленным государственными стандартами для новых станков. Срок службы отремонтированных станков выше, чем новых, так как их станины, зубчатые колеса и шпиндели подвергаются поверхностной закалке и шлифовке. Во всех механических цехах построены хорошо оборудованные заточные отделения, организована централизованная заточка инструмента на электроалмазных станках с доставкой его на рабочие места. [c.237]
Капитальный ремонт предназначен для восстановления ресурса арматуры и включает в себя объем работ стоимостью до 75% стоимости нового изделия. Арматура демонтируется с трубопровода и направляется на ремонтный участок или ремонтный цех предприятия или на предприятие централизованного ремонта арматуры. При капитальном ремонте производится разборка изделия, очистка и дефектация всех деталей, замена деталей, вышедших из строя, вновь изготовленными, запасными или восстановленными. Детали обычно восстанавливаются наплавкой металла на изношенные поверхности или электролитическим хромированием изношенных поверхностей. Уплотнительные поверхности из металла обрабатываются и притираются. Уплотнительные кольца из резины или фторопласта в вентилях заменяются новыми. Верхнее уплотнение шпиндель—крышка для отключения сальниковой камеры приводится в работоспособное состояние. Набивка сальника и прокладки заменяются новыми. Крепежные детали, имеющие дефекты, также заменяются новыми. После окончания всех работ по очистке, ремонту, замене и восстановлению деталей арматура собирается, испытывается на прочность, плотность металла и герметичность соединений. Объем и характер проведенного ремонта записывают в формуляр изделия
[c.266]
В процессе ремонта отбраковывается значительная часть крепежных деталей в связи с коррозией и повреждениями резьбы. Отбракованные детали заменяются новыми. В ряде случаев, при отсутствии запасных, крепежные детали изготовляются силами ремонтного цеха или завода. Возможны случаи, когда возникает необходимость в изготовлении новых шпинделей, штоков и ходовых гаек (резьбовых втулок). Крепежные резьбы выполняются с полем допуска 8д для болтов и 7Н для гаек по ГОСТ 6093—70. Трапецеидальная резьба для шпинделей и штоков выполняется по классу ЗХ, а для резьбовых втулок (ходовых гаек) по классу 3 по ГОСТ 9562—75.
[c.283]
На многих типах металлорежущих станков в подшипниковой промышленности до недавнего времени применялись для опор шпинделей подшипники скольжения с баббитовой заливкой вкладышей. Эти подшипники не выдерживали температурного режима, обусловленного интенсификацией скоростей резания и подач. Эта проблема теперь решена путем замены подшипников скольжения подшипниками качения. Группа экспериментальных станков прошла длительные испытания, которые показали целесообразность и эффективность такой модернизации.

На другом конце рычага на шпильках смонтирован противовес, уравновешивающий рычаг с грузовой подвеской и шпинделем. Положение противовеса относительно оси вращения рычага можно регулировать, но только при капитальных ремонтах прибора, т. е. после полной его разборки. [c.255]
Производительность модулей при серийном выпуске увеличивают повышением концентрации операций обработки. Она достигается установкой нескольких станков, обрабатывающих деталь с нескольких сторон (крупные детали), применением многошпиндельных насадок, закрепляемых на шпинделе станка или на револьверных головках, причем обработка крупных деталей с разных сторон выполняется с помощью нескольких револьверных головок. Таким образом, развитие ГАП в серийном производстве идет так же, как развивалась автоматизация в массовом производстве,— по пути увеличения концентрации операций. В условиях ГАП особенно необходимо строить обрабатывающие центры из агрегатированных узлов, позволяющих осуществлять их перекомпоновку в случаях резкого изменения профиля заказов, и заменять узлы на запасные для последующего ремонта вне производственного участка. Наблюдается тенденция применения в переналаживаемых агрегатных станках числового программного управления, что значительно уменьшает время их переналадки. Таким образом, агрегатирование основного и вспомогательного (загрузочных поворотных столов, делительных столов для спутников и шпиндельных насадок, накопителей-транспортеров, поворотных механизмов для инструмента, кантователей, транспортных самоходных тележек, роботизированных тележек, манипуляторов и роботов) оборудования создает хорошую базу для разработки унифицированных методов и средств диагностирования типовых агрегатных сборочных единиц.
[c.131]
С увеличением размеров станка возрастает его стоимость, необходимая площадь и расходы по обслуживанию и ремонту. В связи с этим при выборе станка нужно стремиться проектировать обработку деталей на станках меньших размеров. При работе на карусельных станках часто бывает необходимо увеличивать размеры станка, так как вес обрабатываемой детали превышает допустимую грузоподъемность имеющегося оборудования. Большинство карусельных станков для повышения грузоподъемности и улучшения условий работы направляющих имеют под шпинделем подпятник, воспринимающий часть нагрузок. Иногда подпятники регулируются вручную с помощью червячного или резьбового устройства. Однако из-за неудобства обслуживания такой регулировкой пользуются очень редко. [c.342]
Подлежащую ремонту арматуру разбирают, промывают, сушат и осматривают для выявления дефектов и определения объема работ. Характерными работами при ремонте арматуры являются притирка уплотнительных поверхностей, устранение повреждений шпинделя и корпуса, замена сальниковой набивки.
[c.442]
Ремонт шпинделя и сальника. Покрытый нагаром, ржавчиной или имеющий задиры поверхности шпиндель не обеспечивает плотности сальника даже при высококачественной набивке. Очистку шпинделя производят, соблюдая осторожность, с тем чтобы не повредить полированную поверхность. С этой целью порошок окиси хрома разводят в чистом машинном масле до консистенции сметаны и наносят его на кусок чистого войлока, которым очищают нагар или ржавчину с поверхности шпинделя. [c.447]
Станок Завод-изготовитель или фирма Модель Наибольшее расстояние от торца шпинделя до нижней кромки суппорта в мм Категории сложности ремонта [c.173]
Станок Завод-изготовитель или фирма Модель Наибольший диаметр шпинделя в мм Категории сложности ремонта [c.175]
Мелкий ремонт или замена крепежных элементов ножевых валов, пильных валов и шпинделей.
[c.204]
Ремонт ножевых валов, пильных валов и шпинделей. [c.205]
Ремонт станины фрезерного станка сводится в основном к восстановлению прямолинейности, параллельности и точности расположения направляющих по отношению к оси отверстия под шпиндель. Ремонт напра вляющих станины часто производят путем их шабрения. [c.103]
Овалыюсть обработанной поверхности Биение шпинделя Ремонт станка [c.197]
Запас точности (работоспособности) целесообразно характеризовать коэффициентом запаса точности К-,-, равным отношению допускаемой погрешности детали, соединения или машины в конце срока их эксплуатации к погрешности новой детали, составных частей или машииы. Так, если радиальное биение шпинделя нового шлифовального станка равно 0,005 мм, а допускаемое биение в конце срока эксплуатации (до ремонта) станка данного класса точности составляет 0,01 мм, то = 0,01/0,005 = 2. [c.27]
На этой ступени развития оборудования функции управления процессом и контроля за его ходом по-прежнему выполняет рабочий. Он включает машину, изменяет скорости ее рабочих органов (шпинделя, ползуна), включает вспомогательные перемещения узлов. Рабочий также контролирует ход технологического процесса и при необходимости вмешивается в него, подналаживает инструмент или механизмы, регулирует или заменяет инструмент и т. п. При значительном износе отдельных механизмов машину отправляют в ремонт.
[c.460]
Длительность ремонтного цикла оборудования линий определяется сроком службы рабочих поверхностей базовых деталей арегатов и сборочных единиц (направляющих станин, столов, салазок, посадочных мест опор шпинделей шпиндельных бабок и др.), поскольку восстановление базовых деталей осуществляется при капитальном ремонте агрегатов. [c.294]
Основные коррозионные повреждения штоков происходят на стадии транспортировки и хранения арматуры, т.е. до начала ее эксплуатации. Процесс коррозии начинается сразу после заводской гидроопрессовки арматуры, когда в сальниковую камеру попадает техническая недеаэрированиая вода, содержащая значительное количество хлор-ионов. В процессе же эксплуатации заметная коррозия возникает во время ремонта оборудования (стояночная коррозия). Многолетние статистические данные свидетельствуют о том, что от 20 до 80% установленной арматуры уже имеет перед пуском энергоустановок пораженные коррозией штоки и шпиндели, требующие замены.
[c.55]
Твердое никелирование можно применять для упрочнения и восстановления коленчатых валов, шпинделей металлорежущих станков, поршневых пальцев, гильз цилиндров, поршней гидравлических машин, направляющих втулок и т. п., а также при ремонте наподвижных посадок и деталей приборов. При восстановлении шпинделей металлорежущих станков, шеек коленчатых валов, гильз цилиндров осаждается слой твердого никеля толщиной 0,75—1,25 мм, [c.334]
Механизмы подачи, зажима п упора материала 5 Значительное увеличение нагрузок на привод ири разжиме и зажиме материала во всех шпинделях (иики и Неиравпльная регулировка зажимных устройств всех шпинделей (большая величина тяговых усилий) повышенный размер закрепляемого материала повышенный износ детален зажимных устройств износ ролика рычага механизма зажима или кривых зажима Отрегулировать зажимные устройства всех шпинделей в соответствии с техническими условиями заменить прутки произвести ремонт или замену изношенных деталей зажимных устройств произвести ремонт или замену ролика и кривых зажима
[c. 45]
С подачей шпиндельной головки, одно- н двухшпиндельные Непосредственно на столе или в приспособлении по одной ил 1 по две детали В расточной однорезцовой головке или двух-трёхрез-цовой державке в шпинделе м I. Вращение II, Вертикальная подача шпиндельной головки ремонте Блоки и гильзы цилиндров, шатуны н поршни в массовом производстве (двухшпиндельные сганки) [c.33]
Параллельная задвижка с выдвижным шн ИНД ел ем (рис. 3-36) состоит из корпуса, крышки, маховика, двух дисков с клином шпинделя с левой нарезкой. Такие задвижки. изготовляются из чугуна на условное давлание 10 кгс1см Задвижки, предназначенные для воды и для насыщенного пара с температурой до 225° С, снабжаются бронзовыми уплотнительными кольцами. Чтобы закрыть задвижку, вращают маховик вправо, при ЭТОМ вращается запрессованная в его ступицу гайка, которая сообщает шпинделю поступательное движение. Диски, укрепленные в нижнем конце шпинделя, онуокаются до упора клина в дно корпуса. Задвижки этого типа работают вполне надежно, ремонт их несложен. К недостаткам их следует отнести поломки грундбуксы. Уход за параллельными задвижками заключается главным образом в наблюдении за сальником и в смазке резьбы шпинделя.
[c.147]
Капитальный ремонт и испытание после ремонта горизонтального сверлильно-фрезерного станка со шпинделем диаметром 250—300 мм, карусельного станка с планшайбой диаметром 40С0—6000 мм, зуборезного станка с наибольп1им диаметром изделия 5000 мм. и с наибольшим модулем свыше 30, токарного станка с высотой центров 1500 Мм и расстоянием между центрами 20 м, строгального станка с ходом стола 12 м, паро-гидравлического пресса 10 ОСО т. [c.117]
Капитальный ремонт и испытание после ремонта горизонтального сверлильно-фрезерного (расточного) станка со шпинделем диаметром 80мм, зуборезного станка с наибольшим нарезаемым модулем 30, карусельного станка с планшайбой диаметром 2С00 мм, токарно-винторезного станка с высотой центров 8С0 — 1300 мм и длиной станины 12 м, строгального станка с ходом стола 6 м, парового молота с весом падающих частей 5 т, паро-гидравлического пресса 2000/л, кромкострогального станка с длиной станины до 10 Л , паро-воздушных штамповочных молотов с весом падающих частей 2000 кГ, мостового электрического крана грузоподъемностью 75 т.
[c.117]
Неточности станков, устранение которых требует перешабривания направляющих или замены крупных деталей (шпинделей, штосселей, борштанг и т. п.), устраняют при ближайшем плановом ремонте, если они не влияют на качество изготовляемых изделий, если же выявленные отклонения от норм точности агрегата влияют на качество изготовляемых изделий, то их устраняет механик цеха в сроки, устанавливаемые начальником ОТК или начальником цеха. Оплату таких работ производят по нарядам. [c.126]
Ремонт шпинделя шлифование шеек под ио.дшипыики, эачисттеа или шлифование г. ест под инструмент и под приспособления, замена или пришабривание подшипников. [c.150]
I де А — длина стола в мм г — количество шпинделей С = 1,5 (харакгерн.зует сложность ремонта механизма нояачн) а = 1,0 для нормального исполнения а. = 1,25 при механической подаче или кареткой ( = 1,1 для копировально-фрезерных станков. [c.208]
Неисправности шпинделя и способы их устранения (список проблем и решений).

Ниже приведён список наиболее часто встречающихся неисправностей, возникающих в процессе эксплуатации шпинделей в течение срока их службы. Основные неисправности шпинделя следующие:
- повышенное радиальное биение
- необходимость замены смазки в подшипниках
- износ подшипников с необходимостью их замены
- неправильное расположение подшипников
- межвитковое замыкание
- пробой обмоток
- перегрузка по току
В этот список также можно включить следующие неисправности:
По каждой проблеме приведены признаки неисправности и типовые решения.
Повышенное радиальное биение
Радиальное биение проявляется в понижении точности обработки фрезой поверхности детали. Проверку величины радиального биения проводят специальными индикаторами.
Причин повышенного радиально биения может быть несколько:
- изогнутость рабочего вала (может возникнуть вследствие удара при обработке фрезерованием) – исправляется правкой вала шпинделя
- недостаточная затяжка подшипников, зазоры – исправляется регулировкой подшипников, подтяжкой гайки затяжки подшипников шпинделя
- износ подшипников – неисправность устраняется заменой подшипников
- износ посадочных шеек подшипников на валу – способ устранения состоит в восстановлении вала шпинделя
Диагностика причины повышенного биения должна проводиться опытными специалистами.
Необходимость замены смазки в подшипниках
Если шпиндель работал в условиях повышенной загрязнённости, в подшипники могли попасть пыль и грязь. Также пыль может образовываться вследствие работы шпинделя в нештатных режимах и интенсивном износе посадочных гнёзд на валу.
Неисправность проявляется в повышенном температурном режиме подшипников, а также другими признаками, например шум в верхнем подшипнике (для диагностики необходим осмотр опытного специалиста).
Устраняется снятием подшипников, промывкой их с последующей заменой смазки. Смазка для подшипников должна использоваться качественная, рассчитанная на длительный срок службы и высокие скорости вращения подшипников.
Износ подшипников с необходимостью их замены
Подшипники при работе шпинделя могут изнашиваться в интенсивном режиме, если нарушены какие-либо из условий их нормальной работы. Об износе подшипников может свидетельствовать, например, шум в верхнем подшипнике. Факторами ускоренного износа подшипников могут быть:
- неправильная установка подшипников на валу шпинделя
- загрязнение смазки подшипников (когда смазка после загрязнения не была своевременно заменена)
- повышенные нагрузки при обработке (повышенные подачи, не предусмотренные условиями эксплуатации фрезерного станка)
- общий износ шпинделя
Замена подшипников в шпинделе – на первый взгляд несложная операция, однако требующая высокой точности при запрессовке и контроля правильности установки подшипников. Рекомендуется проводить замену подшипников в условиях сервисной мастерской.
Неправильное расположение подшипников
При самостоятельной замене радиально-упорных подшипников в шпинделе они были неправильно установлены – не той стороной, с перекосами и т.д. Неисправность проявляется следующими признаками – повышенное биение на валу, чрезмерный нагрев подшипников, повышенный шум в верхнем подшипнике и т. д.
Устранение неисправности – правильная установка подшипников. Может потребоваться не только правильная установка, но и замена подшипников на новые.
Межвитковое замыкание
Межвитковое замыкание проявляется, как правило, сообщением инвертора об ошибке (перегрузка по току). На холостом ходу шпиндель может вращаться нормально, достигать номинальной скорости, но под нагрузкой инвертор будет его аварийно останавливать.
Одна из причин межвиткового замыкания – превышение номинальных режимов эксплуатации шпинделя, в этом случае, подаваемый инвертором ток может значительно превысить номинальный ток шпинделя, что приведет к повреждению лака на обмотках и, соответственно, межвитковому замыканию.
Конечно, если на инвертор настроен правильно и у него правильно выставлены параметры перегрузок, такого не произойдет. Наша компания может поставить вам заранее настроенные инверторы с корректными настройками, защищающими Ваше оборудование.
Исправление – перемотка обмоток (при экономической целесообразности подобного ремонта шпинделя), либо замена обмоток шпинделя на новые.
Пробой обмоток
Короткое замыкание обмоток шпинделя на корпус. Для выявления точного места неисправности необходима диагностика специалиста. Исправление – по результатам диагностики.
Перегрузка по току
Перегрузка по току может возникать, если шпиндель при вращении получает слишком большой тормозящий момент. Например, при заклинивании или затруднённом вращении подшипников шпиндель не в состоянии разогнаться и набрать обороты, вследствие чего происходит перегрузка по току и на дисплее отображается ошибка E004 – «перегрузка по току во время разгона ротора шпинделя».
Существует также ошибка E006 – «перегрузка по току после разгона шпинделя». Отличается тем, что происходит не во время разгона, а после. Причина ошибки та же – чрезмерная нагрузка на ротор шпинделя.
Исправление – по результатам диагностики. Например, если причиной было затруднённое вращение подшипников – замена смазки подшипников либо замена подшипников на новые.
Ремонт шпинделя
При выходе из строя какого-либо узла шпинделя может потребоваться его замена. Диагностика определяет, какой из узлов шпинделя неисправен. Замену лучше проводить в условиях сервисной мастерской.
Восстановление шпинделя
При общем сильном износе шпинделя не всегда возможно провести его восстановление. Эта операция стоит редко дешевле покупки нового шпинделя и осуществляется квалифицированными специалистами, с согласованием сметы расходов. После восстановления шпиндель такую же получает гарантию, как и новый шпиндель.
Цель нашей компании – обеспечить бесперебойную работу фрезеровочного оборудования. У нас всегда есть в наличии как готовые шпиндели и привода, так и аксессуары к ним.
Заказать услугу ремонта шпинделя можно позвонив по телефону 8 (499) 653-52-64 Квалифицированная консультация гарантируется. А также вы можете у нас со склада купить шпиндель.
Мы работаем для того, чтобы ваше оборудование работало без сбоев! Компания CNC Motors.
Ремонт шпинделя и восстановление шпинделя
Ремонт промышленных шпинделей
Наш сервисный центр по ремонту шпинделей предлагает ремонт, восстановление, восстановление, восстановление и переделку шпинделей, используемых в автомобильной, аэрокосмической, авиационной, военной, инструментальной, станкостроительной, деревообрабатывающей, пластмассовой, каменной, мраморной, гранитной, стекольной и керамической промышленности. В спектр услуг по ремонту входит:
- Услуги по ремонту прецизионных шпинделей, ремонт прецизионных шпинделей, услуги по восстановлению прецизионных шпинделей, ремонт шпинделей с ЧПУ, ремонт фрезерных шпинделей, услуги по ремонту шпинделей, услуги по ремонту шпинделей, ремонт шпинделей станков, восстановление шпинделей всех стилей, типов и размеров, включая картридж, блок, с ременным приводом, моторизованные, высокочастотные электрошпиндели, высокочастотные двигатели шпинделя и высокоскоростные двигатели шпинделя
- Наши услуги по ремонту шпинделей включают в себя: каталогизацию фотографий в исходном состоянии и всех деталей после разборки и очистки, осмотр всех деталей и измерение критических поверхностей с помощью электронного контроля, доработку конуса, шлифование конуса, ремонт дышла, ремонт и замену зажимной цанги, посадочное место подшипника.
доработка, доработка отверстия корпуса, твердое хромирование и шлифование, шлифование проставок, ремонт двигателя, перемотка двигателя, балансировка всех вращающихся частей, смазка подшипников, повторная сборка, приработка, проверка вибрации, проверка температуры, проверка биения и окончательная балансировка с такими принадлежностями, как установленный шкив и резцедержатель
Процесс ремонта шпинделя
Процесс ремонта шпинделя состоит из осмотра, анализа, ремонта, балансировки, сборки и тестирования вашего шпинделя.Контроль качества встроен в каждый этап ремонта, и каждый этап выполняется на современном ремонтно-производственном предприятии. Если ваш шпиндель вышел из строя, лучший способ вернуться к производительности – это своевременный и качественный ремонт на нашем предприятии. Мы восстановим весь шпиндель или частичный шпиндель только из нескольких компонентов. Мы можем производить новые компоненты.
- Технический персонал проверяет все шпиндели, поступающие в ремонт.
Каждый блок входит в систему, и открывается рабочее задание. Этот отчет следует за шпинделем процесса ремонта, подробно описывая все необходимые и выполненные работы.Перед разборкой каждый блок проходит визуальный осмотр на предмет внешних повреждений, которые могли привести к отказу.
- Техники осторожно разбирают каждый блок, обращая особое внимание на признаки загрязнения, отсутствия масла, неправильного использования или других признаков неисправности. Каждый компонент полируется для удаления ржавчины или поврежденных выступов. Каждый компонент промывают растворителем и сушат на воздухе. Все это происходит в специально отведенном для этого месте, поэтому контроль качества будет поддерживаться.
- В зоне проверки обученные техники осматривают и анализируют каждый компонент.Затем с помощью современных методов анализа каждый критический компонент проверяется на размер, биение, выравнивание и параллельность. После тщательного осмотра составляется письменный отчет о возможных основных причинах отказа устройства и методах предотвращения отказов.
- Практически любой компонент может быть обработан, переработан или изготовлен новый в нашем полностью оборудованном и современном механическом цехе. Опытные машинисты восстановят или воспроизведут любую необходимую деталь. Эти внутренние возможности обеспечивают контроль качества и своевременный возврат к производительности.
- Полностью модернизированная шлифовальная площадка с климат-контролем, оснащенная новыми современными шлифовальными станками с ЧПУ, управляемыми квалифицированными машинистами, способна шлифовать внешний и внутренний диаметр, а также внутреннюю и внешнюю конусность до ППИ 0,000025 ″ или менее. Возможность шлифования центральных отверстий, поверхностей, вращения и кондуктора с допусками до 0,000010 ″ дополняет собственные возможности компании по обеспечению контроля качества.
- Несбалансированные компоненты серьезно уменьшат срок службы подшипников и вызовут плохую отделку вашего продукта.Для устранения проблемы дисбаланса необходимо удалить компонент или увеличить его вес.
Правильная балансировка шпинделя улучшает производительность и продлевает срок службы подшипников, а также улучшает контроль качества всех работ. При использовании новейшего высокотехнологичного балансировочного оборудования с компьютерным управлением процесс балансировки шпинделя выполняется сначала на всех отдельных вращающихся компонентах, а затем на собранном узле.
- Обученные специалисты по сборке тщательно собирают шпиндели в специально отведенном чистом помещении.Шпиндели собираются с использованием всех новых подшипников, с правильными и отфильтрованными смазочными материалами. Наша команда специалистов по сборке имеет более чем вековой практический опыт в ремонте шпинделей. Они прошли обучение на всех этапах обработки, расточки, шлифования, кондукторного шлифования, токарной обработки и обработки с ЧПУ.
- Во время обкатки каждый шпиндель постепенно доводится до рабочей скорости в специально отведенной чистой зоне тестирования. Каждый шпиндель тестируется для проверки скорости, вибрации, температуры и критического биения.Все критические рабочие параметры контролируются, чтобы гарантировать, что шпиндели работают в соответствии с исходными спецификациями или превосходят их.
- Строгие стандарты контроля качества соблюдаются даже в процессе отгрузки. Если требуется краска, тщательно наносится соответствующий цвет. Шпиндели обернуты инертным материалом и покрыты пеной. Для дополнительной защиты во время обратного хода шпинделя используются высокопрочные картонные коробки. Шпиндели весом 125 фунтов. или более отправляются в деревянных ящиках, изготовленных по индивидуальному заказу.
Типы ремонтируемых шпинделей
Мы ремонтируем, перестраиваем, перестраиваем, ремонтируем, переделываем и заменяем:
- Шарикоподшипник, роликоподшипник, гидростатический подшипник и шпиндели гидродинамического подшипника
- Внутреннее шлифование и внутреннее шлифование, внешнее шлифование и внешнее шлифование, круглое шлифование, бесцентровые шлифовальные шпиндели
- Высокочастотные двигатели шпинделя, высокочастотные электрошпиндели, шпиндели с ЧПУ, высокоскоростные двигатели шпинделя и двигатели шпинделя с ЧПУ
- Плоскошлифовальный станок с ЧПУ, инструмент и фрезерный станок с ЧПУ, формовочное шлифование, шпиндели шлифовального станка с медленным ходом
- Шлифовальная головка, рабочая головка, правка, правочные шпиндели
- Автоматическая смена инструмента, фрезерование через шпиндель с подачей СОЖ с конусом Морзе, конусом HSK, конусом DIN, конусом Big Plus, конусом Capto
- Сверлильные шпиндели с ЧПУ, чистовая расточка, токарные шпиндели с ЧПУ, фрезерные шпиндели с ЧПУ
- Высокоскоростной фрезерный станок, двигатели шпинделя фрезерного станка с ЧПУ, формовочные шпиндели, формирователь, высокоскоростной электрошпиндель
- Гравировальные шпиндели, шпиндели для сверления печатных плат
Смета на ремонт шпинделя
Если вашего шпинделя нет в списке, мы можем его отремонтировать .
Для приблизительной оценки стоимости ремонта шпинделя щелкните [email protected] или Свяжитесь с нами в верхнем или нижнем колонтитуле и предоставьте информацию о своем шпинделе! Или позвоните по телефону 519-671-3911 .
Список отремонтированных марок шпинделей
Щелкните свой бренд, чтобы проверить отремонтированные модели
- ABB
- ABL
- ABL Hitachi
- ABTech
- Accretech
- Acer
- Акролок
- Продвинутая машина
- ADT
- Aetna
- Агафон
- Акира Сэйки
- Альберти Херарди
- Алекс-Тех
- Альфинг Кесслер
- Альфред
- Амада
- Амера Сейки
- AMS
- Анаяк
- Анка
- Андерсон
- Антралюкс
- Аоно Гикен
- Арес-Сейки
- Арго Сейки
- Артер
- Асахи
- Asa Tech
- ASC
- ASV
- Атлас
- Атрамп
- Ауэрбах
- Эйвон
- Awea
- Axa
- Axisco
- Axxiom
- Отель типа «постель и завтрак»
- Баччи
- Пансионат
- Барбер-Колман
- Барнс
- Баумюллер
- Бавеллони
- Байер
- Behr
- Бенц
- Berger Ag
- Berg Spanntechnik
- Бертье
- Bertoni & Cotti
- Стажер
- Biesse
- Большой Кайзер
- Биматех
- Бирмингем
- Блейк
- Бланшар
- Блом
- Бломбах
- Boart Longyear
- Берингер
- Boneham
- Boneham & Turner
- Bostomatic
- Боуэн
- Боярин Шульц
- Brembana
- Бретонский
- Бриджпорт
- Brio
- Брат
- Браун и Шарп
- Брайант
- BSI
- Буффоли
- Буркард Вебер
- Буллард
- Bumotec
- Busellato
- BWF
- Камау
- Кэмпбелл
- Canon
- Кантон
- Капитальное строительство
- Кардинал
- Карлтон
- Карвер
- CEC
- Cells Tec
- Челощи
- Cencorp
- Шевалье
- Хирон
- Тюо-Сэйки
- Черчилль
- Цинциннати
- Цинциннати Ламбе
- Цинциннати Милакрон
- Цинциннати Unova
- Cincom
- Cinex
- Гражданин
- Заявление
- Клеерман
- Кливленд
- CMS
- Coborn
- Кобурн
- Колчестер
- Колгар
- Колибри
- Colmatic
- Коломбо
- Колониальный инструмент
- Комау
- Расчесывание
- Combitec
- Comec
- Compumill
- Корреанаяк
- Ковель
- Cross Huller
- Кубические машины
- Циклон
- Cytec
- ЦАП
- Daewoo
- Дайдо
- Да Лих
- Дайя Сэйки
- Дайничи
- Даниэли
- Данкаерт
- Данобат
- Датрон
- Дирборн
- Deckel
- Демер
- Дензо
- Надежный
- DeVlieg
- Diebold
- Дидесхайм
- Дискотека
- Дикси
- DMG-Mori
- DMH
- DoAll
- Doosan
- Доррис
- Дрейк
- Комод
- Дроп и Рейн
- DRR
- Технология DS
- Duall
- Дюмор
- Данхэм
- Dürr
- Динамическая скорость
- Dynamotion
- Dynomax
- Эберхард Бауэр
- Ecoka
- EFC
- Эгуро
- Eitzenberger
- Экстром Карлсон
- ELB
- Эльдорадо
- Элит
- Эллиотт
- Элмо
- Элокс
- Elte
- Emag
- Emco
- Эммеги
- Engis
- Эншу
- ESEC
- Etxetar
- Эверит
- ЕвроШпиндель
- Евро шпиндель
- Евротек
- Ewag
- Excel
- Ex-Cell-O
- Ex-Cell-O Ягненок
- Excellon
- Фадаль
- Faemat
- FAG
- Сокол
- Фальва
- Рободрель Fanuc
- Щуп
- Фелкер
- Стипендиаты
- Femco
- Фемина
- Фидиа
- Финли
- Первая
- Fischer AG
- Fischer Precise
- Flow International
- FM Еврошпиндель
- FMN
- Fom Industrie
- Forest-Liné
- Фортуна
- Fortune Виктор Фосдик
- Нападающий
- FPT
- Фрауэнталь
- Франц Кесслер
- Fuji Seiki
- Фукуда
- FWS
- Галлмейер и Ливингстон
- G&L
- GAF
- Гамфиор
- Гарднер
- GAT
- Гербер
- Гиддингс и Льюис
- Гильдемейстер
- Гилман
- Джордано Коломбо
- Глисон
- GMN
- GMS
- Гомия
- Гортон
- Гризетти
- Гроб
- Гросите
- Гюринг
- Хаас
- H&D
- Хамай
- Хамал
- Повесить
- Хардиндж
- Хариг
- Харил
- Харвилл
- Хаузер
- Исцеление
- Хитуэй
- Heckert
- Хейан
- Heimatec
- Хайнц Фиге
- Хеллер
- Хембург
- Hemple
- Хендрикс
- Хеннингер
- Герберт Линднер
- Гербольд
- Hermle
- Хертлен
- Hessapp
- Heyligenstaedt
- Хиллер
- Химмель
- Hitachi
- Hitachi Seiki
- HNK
- Holzma
- Homag
- Homma
- Хоркос
- Хортон
- Howa
- HSD
- Хаффман
- Халлер Хилле
- Hurco
- Hwacheon
- Hybco
- Гидромат
- Hyundai
- Ибаг
- Ибармия Инноватек
- IBC
- Icore
- Ихира
- Икегай
- IMC
- Имес
- МВФ
- IMP
- Impco
- IMT
- Incor
- Индекс
- Инке Косоку Кикай
- Intermac
- Индрамат
- Ингерсолл
- Инвинсибл
- Ионный
- Ингерсолл
- ITW Рансбург
- Ивата
- J&L
- Ягер
- Джет
- Джонфорд
- Joisten & Kettenbaum
- Шутка
- Джонс и Ламсон
- Джонс и Шипман
- Jtekt
- Juaristi
- Юнг
- Юнгнер
- Чону
- Као Мин
- Каратов
- Касифудзи
- Каспер
- Касуга
- Kaswin
- К О Ли
- K&S
- Келленбергер
- Келлер
- Кент
- Кентурн
- Kenward
- Кесслер
- Кеттерер
- Киа
- Кикинда
- Киндт Коллинз
- Кингсбери
- Кира
- Китагава
- Китако
- Китамура
- Кива
- KLKJ
- тыс. Тонн
- Колб
- Komatsu NTC
- Комет
- Комо
- Кондиа
- Койо
- Кптек
- Крюгер
- Куглер
- Куммер
- Кураки
- Лагун
- Баранина
- Landis
- Ласаль
- Лаццати
- Леблон Макино
- Выщелачивание
- Leadwell
- Лянь Фэн
- Lidk Ping
- Лима
- Linco
- LMT
- Подшипники LoadPoint
- Loewe
- LOH
- Луи Эллис
- Maag
- Магерле
- Mag-IAS
- Magnix
- Махо
- Майер
- Макино
- Makino Seiki
- Мальтех
- Манурхин
- Манделли
- Манекс
- Мао Лин
- Маркип
- Гражданин Марубени – Cincom
- Masco
- Масса 5
- Мастер-машина
- Матрица
- Мацуура
- Мэттисон
- Maus
- Маут
- Макс Равилер
- Maxxis
- Mazak
- МакДоно
- Мехатроник
- Mectron
- Мейден
- Метоса
- Мейрат
- Могучая комета
- Микрон
- Микроса
- Милпорт
- Milltronics
- Minganti
- Митсубиси
- Мицубоши Когио
- Мицуи
- Mitsui Seiki
- Мияно
- Mizoguchi
- MFM
- ММК
- Modig
- Монарх
- Monoset
- Мур
- Морбиделли
- Мори-Сай
- Мори Сэйки
- Мотч
- Мотокубо
- Перемещение
- Мюльбаур
- Мультикам
- МВт Hydralink
- Майфорд
- MYL
- Начи
- Накамура
- Накамура Томе
- Наканиши
- Naxos
- Neo
- Newall
- Новая Британия
- Ниагара
- Никко
- Николс
- Николя Корреа
- Нигата
- Найлс
- Ниппи
- Nippon
- Подшипник Nippon
- Нисида
- Nishijimax
- Ниссин
- Номура
- Nordson
- Normac
- Нортон
- NSK
- НСП
- НТК
- Обатаке
- Оберг
- Эрликон
- Отори
- Окамото
- ОКК
- Окума
- Окума Хау
- Оливер
- Олофссон
- Олимпия
- О-М
- OMC
- OMG
- Омлат
- Онсруд
- Ооя
- Орион
- Овербек
- Паатц
- Пама
- Пэнгборн
- Паркер Маджестик
- Парпас
- PBA
- ПБС
- Peron Скорость
- Перске
- Пиат
- PiboMulti
- Пьетро Карнаги
- Питтлер Кесслер
- Pluritec
- PMC
- Поин
- Папа
- Порта
- Портер
- Posa
- Posalux
- Пратт Уитни
- Precise
- Пума
- Quantum
- Quaser
- Рамбауди
- Рансбург
- Рыжая
- Рекерт
- Рейд
- Рейден
- Райнекер
- Рено
- Республика Лагун
- Жесткий
- Риветт
- R O
- Роквелл
- Року Року
- Ролломатик
- RO.MA.
- Роми
- Росс
- Routech
- Дуб Королевский
- Инструменты Royal Precision
- Рудель
- Раш
- Sacem
- Саимп
- Sajo
- Сакадзаки
- То же
- Samsung
- Savway
- Шарманн
- Шаудт
- Schiess
- Шмоль
- Шнеебергер
- Шунк
- Шусслер
- Schutte
- SCHÜTTE
- SCM
- Seco
- Seiko
- Seiko Seiki
- Sempuco
- Sencorp
- Водопад Сенека
- Senjo Seiki
- Setco
- SFJ
- Шань Жун
- Шарноа
- Sharp
- Шеффилд
- Шигия
- Шинко
- Синкс
- Шино
- Сидзуока
- Shoda
- Сиарто
- Sicar
- Сига
- Сигма
- Симплекс
- Синтекс
- SIP
- Sirmec
- Сьогрен Сагино
- SKF
- SLF
- Smec
- SMG
- Смит Рено
- SMS
- СНК
- Содик
- Сомекс
- Сопко
- Соралуче
- Spindel-und-Lagerungstechnik-Fraureuth
- Спиндер
- Spintec
- SPL Шпиндель
- Спрингфилд
- Stama
- Станко
- Старраг
- StarragHeckert
- Стейнель
- Наклейка
- Stoffel
- Страусак
- Studer
- Сугино
- Зунер
- Саммит
- Sunmax
- Sunstrand
- Инструмент Sun
- Sunwoo
- Supermax
- Supertec
- Швейцарский токарный станок
- Синхрон
- TAC
- Тафт Пирс
- Таймак-Зпс
- Тайцзинь
- Тайсэй
- Такамаз Кикаи Когё
- Такисава
- Такуми
- Танабэ
- Телец
- TDM
- Technica
- Техно
- Текна
- Темп
- Tenco
- Themac
- Тета
- Томпсон
- Тор
- Тонгтай Сэйки
- Топпер
- Top-Turn
- Торнос
- Toshiba
- ТОС Гостивар
- TOS Varnsdorf
- Тояма
- Тойо Когио
- Тойода
- Тойо Когио
- Toyo Seiki
- Траминер
- Трауб
- Дерево
- Truflute
- ТСК
- Чудин
- TS Точность
- Цудакома
- Цугами
- Учинэ
- Угинт
- Улам
- Ультра-Поворот
- Умбра
- Унисон
- Уцуномия
- UVA
- Ван Норман
- VDF Берингер
- Vero
- Виктор
- Виктор Тайчжун
- Гадюка
- Воллмер
- Вумар
- Вулканайр
- Вадкин
- Вагнер
- Вайда
- Вальдрих Кобург
- Уолтер
- Палата
- Wardell
- Warner & Swasey
- Васино
- Вебстер и Беннет
- Wedalco
- Вайс
- Вайссер
- Веле
- Вендт
- Westwind
- Виллабратор
- Wia
- Белый Sundstrand
- Уитнон
- Викман Шеффилд
- Виллемин
- Вит-о-Матик
- WMW
- Вудс
- Вудтроник
- Ячио
- ЯМ
- Ямаге
- Ямагути
- Ямасаки Гикен
- Ямашина
- Ямасита
- Ямадзаки
- Ян
- Ясда
- Яскава
- Ясунага
- YCI
- YCM
- YMT
- YSP
- Ю Хунг
- Загар
- Заер
- Циммерманн
- ЗПС
- Загрязнение (охлаждающая жидкость, шлифовальный песок, алюминиевая или стальная стружка)
- Неисправность смазки
- Случайный контакт с деталью или приспособлением (авария)
- Чрезмерная вибрация (неуравновешенный шпиндель или держатель инструмента)
- Низкое усилие дышла в фрезерных шпинделях, позволяющее высвободиться из держателя инструмента во время работы.
Смета на ремонт шпинделя
Если вашего шпинделя нет в списке, мы можем его отремонтировать .
Для приблизительной оценки стоимости ремонта шпинделя щелкните [email protected] или Свяжитесь с нами в верхнем или нижнем колонтитуле и предоставьте информацию о своем шпинделе! Или позвоните по телефону 519-671-3911 .
Часто задаваемые вопросы
Сколько стоит ремонт шпинделя и доставка?
Срок поставки зависит от состояния шпинделя. Он может варьироваться от нескольких дней до нескольких недель.Первоначальный осмотр занимает от 2 до 5 рабочих дней, и вскоре после этого будет доступна разумная оценка времени и стоимости.
Каковы наиболее частые причины выхода из строя шпинделя?
Какие типы шпинделей мы ремонтируем?
Мы ремонтируем практически все шпиндели подшипников качения – шпиндели шариковых или роликовых подшипников, а также шпиндели гидростатических, гидродинамических и пневматических подшипников. Для – Списка марок шпинделей щелкните здесь.
Можно ли модернизировать шпиндели?
Практически во всех случаях да. Мы можем доработать ваш шпиндель, чтобы он работал быстрее, работал холоднее, повышал жесткость, сопротивлялся загрязнению с помощью дополнительной продувки воздухом или уплотнений и т. Д.
Какой класс подшипников шпинделя мы используем?
Прецизионные подшипники ABEC 7 и ABEC 9 равного или лучшего качества, чем оригинал. Мы также используем прецизионные керамические гибридные подшипники в соответствии с требованиями применения.
Что делать, если в моем шпинделе отсутствуют или повреждены детали?
У нас есть опыт и оборудование для производства недостающих или поврежденных деталей. Мы также производим сменные шпиндели.
Смета на ремонт шпинделя
Для приблизительной сметы ремонта шпинделя щелкните haviland @ Precisionspindleinc.com или Свяжитесь с нами в верхнем или нижнем колонтитуле и предоставьте информацию о своем шпинделе! Или позвоните по телефону 519-671-3911 .
Шпиндельные узлы станков | Запрос PDF
Для проведения точных испытаний производительности при высокоскоростной работе и долгосрочных испытаний стабильной надежности моторизованного шпинделя представлен стенд для проверки надежности (RTR), который может моделировать силу резания в реальном процессе обработки. Во-первых, разумный прототип, объединяющий устройства динамической нагрузки и устройства нагрузки крутящим моментом, разработан и создан на основе анализа нагрузки шпинделя, а также разработана полная и явная стратегия управления испытанием нагрузки на надежность.Во-вторых, анализируются эффекты перекоса муфты диафрагмы, вызванные сборкой, и проводятся эксперименты для проверки орбиты оси моторизованного шпинделя. Результаты экспериментов показывают, что по орбите оси можно определить возникновение несоосности, что обеспечивает своевременную корректировку несоосности и точное испытание характеристик при работе на высоких скоростях. Наконец, в механическую структуру электрогидравлической сервоприводной системы нагружения (EHSLS) добавлен демпфер, а сравнение карт Боде до и после оптимизации анализируется по критерию Найквиста.После оптимизации коэффициент усиления и запас по фазе на диаграмме Боде составляют 12,9 дБ и 57,2 °, соответственно, которые находятся в пределах стабильного диапазона и подтверждают улучшение возможности долгосрочных испытаний надежности моторизованного шпинделя. Представленный RTR может моделировать реальную силу резания и обеспечивает эффективный подход к загрузке, чтобы гарантировать точность и стабильность испытаний моторизованного шпинделя. 1. Введение Как один из ключевых функциональных компонентов станков с ЧПУ [1–4], надежность шпинделей станков имеет прямое влияние на надежность всей системы станков, поэтому очень важно исследовать надежность моторизованных станков. шпиндель [5].Для фундаментальных исследований надежности требуются данные о характеристиках и неисправностях, которые являются основой для последующей работы, такой как моделирование и анализ надежности [6–8], диагностика неисправностей и прогноз оставшегося срока службы [9]. Данные о характеристиках и неисправностях могут быть получены как из записей о неисправностях в полевых условиях в мастерской [10], так и с испытательных стендов в лаборатории [11, 12]. Данные, собранные непосредственно в мастерской, заслуживают доверия и идеально подходят для анализа надежности с развитием больших данных и сенсорных технологий [13], но это требует значительных затрат времени и материалов.Для сравнения: стенд для испытания надежности (RTR), моделирующий силы резания для моторизованного шпинделя в реальном процессе обработки, более удобен и экологически безопасен для сбора данных в условиях моделирования, которые близки к реальным рабочим условиям [14–16] . Моторизованный шпиндель обычно испытывает силы резания в процессе обработки; следовательно, загрузочное устройство должно иметь способность прикладывать динамическую силу к движущемуся шпинделю. В последние годы специалисты провели множество исследований динамической нагрузки моторизованного шпинделя для испытаний производительности и сбора данных о неисправностях [17, 18].Мацубара и др. [19, 20] предложили магнитное нагружающее устройство для обеспечения нагрузки в виде синусоидальной развертки на моторизованный шпиндель и исследовали характеристики жесткости высокоскоростного шпинделя в состоянии нагрузки. Ван и др. [21] разработали бесконтактное электромагнитное нагружающее устройство для обеспечения желаемого возбуждения и измерения динамических характеристик шпиндельной системы при различных условиях вращения. Цю и Лю [22, 23] реализовали моделирование силы резания для моторизованного шпинделя с помощью электромагнитных сил и проанализировали влияющие факторы, чтобы подтвердить эффективность метода бесконтактной электромагнитной нагрузки.Ли и др. [24] предложил метод магнитореологической жидкости для испытаний на динамическую нагрузку, чтобы эффективно прогнозировать срок службы высокоскоростного моторизованного шпинделя и оценивать прецизионную сохраняющую способность. Feng et al. [25] разработали устройство бесконтактной загрузки воздушной пленки с 5 степенями свободы для проверки статической жесткости моторизованного шпинделя при высокоскоростном вращении, которое образует воздушную пленку статического давления между загрузчиком воздушной пленки и испытанным шпинделем. Однако из-за проблемы нагрева электромагнита объекты, которые будут нагружены в этих исследованиях, в основном сосредоточены на измерении динамических характеристик и характеристик жесткости, что не может удовлетворить потребности в долговременной эксплуатации высокоскоростного моторизованного шпинделя. тестовое задание.Кроме того, принцип настолько сложен, что необходимо точно прикладывать нагрузку, а размер устройства для бесконтактной нагрузки, ограниченного воздушным зазором, слишком велик. Для разработки комплексного испытательного стенда с динамической нагрузочной способностью, который может одновременно удовлетворять требованиям испытания производительности и испытания долгосрочной надежности моторизованного шпинделя, проводится ряд исследований, рассматривающих другие методы нагружения. Guo et al. В [26, 27] представлено многоосевое загрузочное устройство (MLD) для моделирования условий нагрузки действующей системы подачи станка в реальном процессе обработки.Hu et al. [28] разработали испытательный стенд на надежность на основе силового динамометра и пьезоэлектрического нагружающего устройства для проведения динамических нагрузочных испытаний моторизованного шпинделя. Ограничение перемещением пьезокерамики затрудняет выполнение вращательной характеристики высокоскоростного моторизованного шпинделя. Chen [29] и Meng et al. [30] модифицировали динамометр, чтобы сделать нагрузку между тягами точной в эксперименте на высокоскоростном шпинделе. Jin et al. [31] разработали новый метод нагружения крутящим моментом, основанный на стратегии прямого управления крутящим моментом для двойных моторизованных шпинделей, чтобы применить фактические статические и динамические крутящие силы, и проверили точность предложенной системы динамометра.Можно видеть, что некоторые исследователи приложили усилия для создания комплексного испытательного стенда, например, крутящего момента, связанного с муфтой, и силовой нагрузки, передаваемой механизмом. Однако все ранее упомянутые исследования страдают некоторыми ограничениями, и о повышении его способности к высокоскоростным и долгосрочным испытаниям сообщалось редко. Поэтому, всесторонне учитывая функциональные требования, RTR, который может оказывать как динамическую силовую нагрузку, так и крутящую нагрузку, спроектирован и установлен с полной и явной стратегией управления.Чтобы улучшить возможность проведения точных испытаний производительности на высокой скорости, были проанализированы эффекты перекоса муфты диафрагмы, и были проведены эксперименты для выявления возникновения перекоса. Для повышения стабильности испытаний на долговременную надежность в механическую структуру EHSLS добавлен демпфер, а эффективность проверяется по критерию Найквиста. Остальная часть этого документа организована следующим образом: Раздел 2 описывает прототип и состав RTR.В разделе 3 устанавливается модель мембранной муфты с 3 степенями свободы и анализируются эффекты перекоса. Механическая структура EHSLS оптимизирована критерием Найквиста в разделе 4, а выводы сделаны в разделе 5. 2. Конструкция заряжающего устройства и состав РТР. Функция динамической силовой нагрузки и нагрузки крутящим моментом интегрирована в RTR, и схематическая конструкция показана на рисунке 1. Кроме того, для обеспечения точности и удобства нагрузки устройство радиальной и осевой нагрузки применяется отдельно к механизму, а крутящая нагрузка связана с работающим шпинделем через муфту.
Прецизионная обработка в мире микронов
Насколько мал микрон и почему мы работаем в таком маленьком масштабе?
Точность определяется как качество, состояние или факт точности и точности. Но насколько точно «точно»? Все зависит от приложения. Не существует четко определенного диапазона допуска для заготовки, которая считалась бы «высокоточной», но в нашей линии по ремонту шпинделей мы часто сталкиваемся со спецификациями, требующими допуска +/- 2 мкм .
Микрон (мкм) или микрометр – это одна миллионная метра или 1/25 400 дюйма. Это примерно 0,00004 дюйма. Для сравнения, в общей терминологии обработки, «thou» относится к тысячным долям дюйма или 0,001 дюйма, что равно 25,4 мкм.
Итак, насколько мал микрон? Микрон – это общепринятая единица измерения длин волн инфракрасного излучения, а также размеров клеток и бактерий. Вот несколько примеров относительных размеров частиц обычных материалов:
Нажмите, чтобы увидеть разрезаемую сталь под микроскопом- Человеческий волос: 50-100 мкм
- Пылевой клещ: 3-10 мкм
- Споры грибов: 0.5–7 мкм
- Песок на пляже: 100-2000 мкм
- Игольное ушко: 1230 мкм
- Эритроциты: 6-8 мкм
- Паутина: 2-3 мкм
- Зрение человека: 40 мкм
(видно невооруженным глазом)
Почему мы работаем с допуском на микронном уровне?
Наши клиенты представляют широкий спектр отраслей, и они используют машины для производства компонентов, которые будут использоваться в аэрокосмической, оборонной и медицинской сферах, поэтому их машины должны обеспечивать стабильное производство высокоточных деталей.
Точность станка в значительной степени зависит от исправности станка , шпиндель , который должен работать в соответствии со спецификациями производителя. Продолжение использования с течением времени или повреждение после поломки станка потребует восстановления шпинделя. Когда мы получаем шпиндель для восстановления, мы измеряем все критические размеры и применяем процесс шлифования / хромирования / чистовой шлифовки, чтобы вернуть размеры в соответствие со спецификациями OEM. Наш собственный шлифовальный цех может выдерживать микронный допуск, гарантируя, что ваш восстановленный шпиндель будет работать как новый.
Если ваш шпиндель выходит из строя, обратитесь к специалистам Northland Tool, где мы живем в мире микрон. Щелкните здесь, чтобы отправить нам свой шпиндель сегодня.
Новые шпинделипомогают мировому производителю добиться повышения производительности
ОБРАБОТКА МЕТАЛЛА – ЭТО ВСЕ ЗАДАЧИ О высокой точности, производительности и повторяемости. Эти и многие другие требования учитываются на этапе проектирования оборудования. Благодаря систематическому процессу модернизации, AMD & E смогла добиться значительного повышения производительности существующего горизонтального обрабатывающего центра с ЧПУ.Модернизированный станок позволил мировому поставщику тяжелого вращающегося оборудования достичь более высокой производительности без значительных капитальных вложений в совершенно новый станок.
Challenge
BOURN & KOCH, INC. В РОКФОРД, ИЛЛИНОИС, разрабатывает и производит новые станки, включая токарные, шлифовальные и зубофрезерные станки. Компания также ремонтирует машины и поставляет компоненты для устаревших станков своих клиентов. Один из основных клиентов Bourn & Koch искал замену двух шпиндельных узлов на станке Ingersoll Mastercenter на узлы, лучше соответствующие текущим производственным требованиям заказчика.Заказчик – производитель промышленного вращающегося оборудования Dresser-Rand из Хьюстона, штат Техас, – использует этот горизонтальный обрабатывающий центр с ЧПУ для обработки корпусов компрессоров и семейства массивных отливок для паровых турбин.
«Accelerated сотрудничала с нами по ряду проектов, – сказал Роб Мюллер, менеджер по обслуживанию Bourn & Koch. «На сегодняшний день это был самый сложный проект. Объединив опыт нашего конструкторского отдела с оборудованием для изготовления зубчатых колес и опыт команды Accelerated с прецизионными станками, мы смогли разработать эффективное решение.”
Совершенно новый дизайн
ТЕКУЩИЙ ПРОЦЕСС ПРОИЗВОДСТВА обрабатываемых деталей Dresser-Rand требует больших усилий и времени. По мере развития потребностей производителя в механической обработке оригинальные шпиндельные узлы оказались недостаточными с точки зрения допустимого крутящего момента и предъявляемых к ним конструктивных требований. Время простоя, вызванное низкой жесткостью шпинделя и высокой вибрацией, повлияло на дальнейшие производственные процессы.
«Dresser-Rand хотела новую прочную конструкцию шпинделя с другими передаточными числами для достижения необходимой мощности и крутящего момента», – сказал Мюллер.«Конструкция шпинделя должна учитывать требуемую мощность, скорость, крутящий момент, систему инструментов, точность и срок службы. Стоимость также оказывает значительное влияние на окончательную конструкцию шпинделя ».
Bourn & Koch оценила существующие конструкции шпинделей в качестве отправной точки для процесса проектирования. Для достижения надлежащей поверхностной скорости предлагаемым шпиндельным узлам требовалось передаточное число 5: 1, чтобы выдавать 50 л.с. при 300 об / мин, но оставаться в строго ограниченном пространстве шириной 400 мм, высотой 800 мм и глубиной 450 мм.
«Исходя из нашего концептуального дизайна, Accelerated предоставила законченный дизайн шпинделя», – сказал Мюллер.«Каждая деталь, включая инженерные расчеты, исследования нагрузок на шпиндель и строгие геометрические допуски для посадки и чистовой обработки прецизионных деталей, была рассмотрена и учтена. Они проделали исключительную работу по проверке и перепроверке первоначальных расчетов и соответствия нашим техническим спецификациям, чертежам, структуре условных обозначений и структуре номеров деталей ».
Новые конструкции компонентов и сборок сравнивались с предыдущими конструкциями для обеспечения приемлемой рентабельности инвестиций.
Повышенная производительность
ОСОБЕННОСТИ MASTERCENTER ОБЕСПЕЧИВАЕТ ВЗАИМОЗАМЕНЯЕМЫЕ шпиндельные узлы, которые выполняют полный спектр функций резания на заготовках из чугуна и стальных сплавов. Диаметр заготовок Dresser-Rand составляет от 1 до 3,5 метров. Плоские части могут быть длиной до 5 метров. Состоящие из вращающейся секции, секции удержания инструмента и секции поддержки шпинделя, шпиндельные узлы Mastercenter присоединяются непосредственно к безредукторному приводному валу в системе привода шпинделя.Система привода шпинделя обеспечивает охлаждающую жидкость, гидравлические, электрические и управляющие услуги для шпиндельного узла.
Для каждого шпиндельного узла требуется уникальная конфигурация и зубчатая передача, соответствующие конкретным материалам, инструментам и операциям резания. Для двух новых узлов станок должен глубоко проникать в узкие пазы и делать резки под прямым углом в нижней части детали. Высокая жесткость шпинделя, минимальная вибрация при вращении и низкие тепловые искажения обеспечивают тяжелую резку и удовлетворительную чистовую обработку и шлифование.
Проектирование конструкций, анализ зубчатых колес и проектирование приводов были выполнены для оптимизации системы.Оригинальные шпиндели – в данном случае прямой и прямоугольный варианты – были разработаны для удержания традиционных торцевых фрез и меньших режущих инструментов диаметром от 4 до 12 дюймов. При передаточном числе 1: 1 оригинальные шпиндельные узлы передавали 50 л.с. при выходной скорости 1500 об / мин. Переход на более крупные инструменты для прорезания пазов (до 38 дюймов в диаметре) начал вызывать проблемы с производительностью.
Для поддержания той же скорости резания, что и мелкие инструменты, более крупные долбежные инструменты должны работать с более низкой скоростью вращения. Однако эта более низкая скорость вращения выходила за рамки оптимального рабочего окна для приводного двигателя, что ограничивает возможность выполнения станком более легких резов.
Сокращенное обслуживание
ОДИН ПОБОЧНЫЙ ПРОДУКТ НИЗКОЙ СКОРОСТИ ВРАЩЕНИЯ – это высокая вибрация в зубчатой передаче шпиндельного узла. Высокий уровень вибрации не только сокращает срок службы шпинделя и снижает постоянную точность обработки, но также вызывает сильный износ торцовых шпонок шпинделя.В результате Dresser-Rand была вынуждена ремонтировать оригинальные шпиндельные узлы каждые четыре года. Поскольку соотношение 5: 1 в новых шпиндельных узлах увеличивает входную скорость в пять раз, уровни вибрации в зубчатой передаче значительно ниже, что приводит к менее частому техническому обслуживанию.
Precision first
AMD & E РАЗРАБОТАЛА ШПИНДЕЛЬНЫЕ УЗЛЫ для стабильной работы с минимальными изменениями предварительного натяга подшипников и центровки шестерен во время работы. Особое внимание было уделено динамическому балансу каждого вращающегося компонента.Точная динамическая балансировка и стабильная работа шпинделя во всем диапазоне частот вращения шпинделя повышает достижимую точность и прецизионность, продлевает срок службы инструмента и позволяет создавать прекрасную поверхность.
Подгонка и отделка
СРЕДИ САМЫХ БОЛЬШИХ ЗАДАЧ для команды Accelerated было определение оптимальной подгонки и отделки примерно 80 деталей (для каждого шпинделя), которые должны были быть получены от семи поставщиков.
Тщательный процесс детального проектирования (включая GD&T и анализ допусков), а также строгий и повторяющийся процесс проверки обеспечили надлежащую подгонку и отделку.
«Как и при любом проектировании и последующем процессе сборки, было очень важно, чтобы каждая деталь соответствовала правильно», – заявила команда Accelerated. «В некоторых случаях детали были точно подогнаны друг к другу, чтобы все было упаковано в корпус. Некоторые из деталей были старыми деталями Ingersoll, которые мы в основном модернизировали, чтобы обновить информацию о деталях. Мы должны были очень точно подходить к материалам и термообработке и очень точно применять все геометрические допуски ».
Более глубокий вылет
ХОТЯ КОНСТРУКЦИЯ ШПИНДЕЛЯ делала упор на более высокую производительность, более высокий крутящий момент и меньшее техническое обслуживание, инженеры быстро поняли, что новая конструкция может предложить еще больше улучшений производительности.Увеличение расстояния от монтажной поверхности до средней линии резца позволяет машине проникать глубже во внутренние полости корпуса турбины и выполнять более глубокие пропилы.
Текущая поддержка
ПОСЛЕДУЮЩАЯ ИНЖЕНЕРНАЯ ПОДДЕРЖКА Bourn & Koch на протяжении всего процесса производства и сборки была критически важна для успеха этого проекта. Bourn & Koch производила детали на своем заводе в Рокфорде и заключила контракты с другими производителями на определенные компоненты. Команда Accelerated подготовила полную книгу подробных производственных чертежей со спецификацией материалов, идентификацией материалов и требованиями к обработке.Компоновки сборки для каждого шпинделя содержали инструкции по сборке деталей на цеху сборки.
«Использование инженерных решений Accelerated в нашей компании облегчило нашу жизнь», – сказал Мюллер. «Они всегда были доступны по телефону или лично, либо на нашем предприятии, либо по дороге к конечному потребителю. Каждый этап проектирования и инженерии был хорошо проинформирован, чтобы избежать возможных задержек. Accelerated позволила реализовать проект в соответствии с графиком и в рамках затрат ».
Один шпиндель, два шпинделя, три шпинделя, еще?
По-видимому, существует бесконечное количество вариантов оснащения фрезерных и токарных станков, включая токарно-фрезерные и токарно-фрезерные станки.Но один из основных способов различать станки – это подсчет шпинделей.
Токарный станок Index MS одновременно обрабатывает шесть независимых шпинделей (здесь показаны три). Шпиндели вращаются в барабане, поэтому каждая станция атакует деталь по очереди, создавая сложные формы за секунды. (Предоставлено Index Corp.)На токарных станках первичный шпиндель удерживает деталь, и обычно их бывает больше одного. На мельницах шпиндель удерживает режущий инструмент, а у большинства станков есть только один. Какие компромиссы привели к этому выбору, и меняются ли они?
Когда дело доходит до токарных станков, вероятно, есть только три ситуации, в которых конфигурация с одним шпинделем является правильным выбором.Первый простой: детали, которые можно собрать с одного конца. Но, по словам Филиппа Джадта, инженера по приложениям компании Absolute Machine Tools Inc., Лорейн, штат Огайо, проблема в том, что таких деталей не так много. Таким образом, эти станки становятся трудоемкими, если пользователи вынуждены повторно зажимать детали, требующие механической обработки с обеих сторон. Это указывает на вторую причину покупки одношпиндельного станка: бюджет.
Токарные шпиндели и экономия
Джадт сказал, что он обычно находит одношпиндельные токарные станки в небольших магазинах.«Они выполняют опцию 10 партии, а затем помещают ее в другую машину, которая выполняет опцию 20. Может быть, это идет на другой машине, которая выполняет опцию 30 и так далее». Но, добавил он, разница в цене между одношпиндельным и многошпиндельным токарными станками «больше не так велика, особенно с учетом затрат на рабочую силу».
В конце концов, простое добавление вспомогательного шпинделя дает возможность обрабатывать все шесть сторон детали, не обращаясь с ней. (Контршпиндель захватывает деталь перед обрезкой и удерживает ее для последующей обработки.) И если детали требуют поперечного сверления или других неповоротных сложностей, аргумент в пользу более новых многофункциональных токарных станков становится убедительным.
Как выразился Джадт: «Мои двухшпиндельные станки стоят намного меньше, чем два, три или четыре одношпиндельных станка и вертикальный обрабатывающий центр». Это сравнение не является несправедливым, потому что двухшпиндель LICO, о котором он упоминает, не просто имеет вспомогательный шпиндель, который удерживает деталь для обработки «другого конца». Он также оснащен тремя или четырьмя независимо программируемыми поперечными суппортами, установленными вокруг главного шпинделя, и револьверной головкой с приводными инструментами для бокового сверления и фрезерования.
«У вас может быть пять независимо задействованных инструментов, когда деталь удерживается в основном шпинделе, а затем отрезать ее и переместить на вспомогательный шпиндель, а затем задействовать по одному инструменту за раз», – пояснил Джадт. Это ускоряет работу со сложными деталями.
Станок Okuma MULTUS оснащен настоящим фрезерным шпинделем на шарнирной оси B для полной пятиосевой обработки. Револьверная станция может использоваться как задняя бабка, как показано здесь. (Предоставлено Okuma America Corp.)Общая тенденция в производстве – отделка деталей за одну настройку и минимальное обслуживание, нежно называемое «одно-и-готово».«Стремление к массовой кастомизации – ключевая причина, – заметил Дэвид Фишер, специалист по токарным изделиям в Okuma America Corp., Шарлотта, Северная Каролина». «Номера деталей, которые использовались десятилетием, теперь действуют в лучшем случае на год», – сказал он. «Происходят постоянные изменения конструкции и постоянные обновления. Поэтому все больше и больше клиентов хотят адаптировать машины ». В результате, по словам Фишера, растет популярность токарных станков с вспомогательным шпинделем, револьверными головками по оси Y, а также многоцелевых станков, таких как Okuma MULTUS.
Фишер сказал, что несколько лет назад общее практическое правило диктовало многофункциональный токарный станок только в том случае, если фрезерование ограничивалось примерно 20 процентами общего времени обработки.Теперь револьверные головки токарных станков обеспечивают гораздо большую мощность и крутящий момент для приводного инструмента, так что сочетание фрезерования и токарной обработки 50-50 является разумным. На таких станках, как MULTUS или Index G220, деталь также может быть призматической, при этом обрезка является единственной операцией токарной обработки. Это потому, что эти станки оснащены «настоящим» фрезерным шпинделем на шарнирно-сочлененной головке (ось B) для полной пятиосевой способности.
По словам Рафаэля Энгеля, менеджера по разработке приложений для Index Corp., Ноблсвилл, Индиана, зубчатые передачи и держатели, необходимые для привода нескольких инструментов в револьверной головке, приводят к более низким скоростям и меньшему крутящему моменту, чем у сравнительно компактных мотор-шпинделей.Index G220 может похвастаться фрезерным шпинделем с осью B с интерфейсом HSK 63, который обеспечивает мощность до 17 кВт и крутящий момент 90 Нм при скорости вращения до 12 000 об / мин. (Опция HSK 40 рассчитана на 11 кВт, 30 Нм и 18 000 об / мин.) Сравните это с приводным инструментом в револьверной головке, который максимален на 6 кВт, 18 Нм и 7200 об / мин. Эти многоцелевые станки также имеют большие инструментальные магазины для автоматической смены инструмента.
Фишер хорошо выразился, когда сказал, что «токарный станок и обрабатывающий центр не принесут больших жертв» на токарно-фрезерном станке, таком как MULTUS или G220.Фактически, с учетом скорости съема материала шпинделей оси B и скорости и эффективности подачи прутка многофункциональный токарный станок часто является лучшим решением для многих мелких фрезерованных деталей.
Насколько он должен быть маленьким? Index G220 имеет диаметр стержня 90 мм, больший G420 – до 120 мм, а Okuma MULTUS – до 4 дюймов (101,6 мм). При необходимости эти станки также могут выполнять токарную обработку и фрезеровку более крупных деталей, которые не загружаются через устройство подачи прутков. Фишер также указал, что револьверная головка имеет больше ограничений по размеру и проблем с помехами, чем шарнирно-сочлененная фрезерная головка.
Index называет свой вспомогательный шпиндель «противошпинделем», чтобы подчеркнуть тот факт, что оба шпинделя имеют одинаковый крутящий момент, мощность и размер. «Вспомогательные шпиндели обычно немного слабее основного», – сказал Энгель. Index также называет свои двухшпиндельные станки «одношпиндельными» станками, поскольку они предлагают другой подход к многошпиндельным станкам. Он не предлагает по-настоящему одношпиндельный станок в США
.Джадт сказал, что команда Absolute относится к мультишпинделю LICO как к винторезному станку с ЧПУ, что, вероятно, помогает объяснить его возможности старожилам из нас.Наконец, Fischer из Okuma сказал, что зубофрезерование и зубофрезерование теперь можно выполнять как на его токарных станках револьверного типа, так и на MULTUS.
Программное обеспечение CAD / CAM помогает определить, какая конфигурация шпинделя наиболее эффективна, и помогает предотвратить столкновения. (Предоставлено компанией Methods Machine Tools)«Зубообрабатывающее нарезание обычно выполняется на другом станке, и его часто отправляют для обработки в другое место», – заметил он. «При отправке запчастей легко потерять контроль над производственным графиком, и это может быстро превратиться в кошмар.Имея такую возможность на машине, мы сохраняем контроль ».
Токарная обработка большого объема
Третья ситуация, в которой одношпиндельный токарный станок может быть лучшим, – это обработка больших объемов деталей. В таком случае специальный набор относительно недорогих одношпиндельных станков, каждый из которых оптимизирован для определенной операции, мог бы сбалансировать ситуацию, чтобы время цикла соответствовало. Например, две машины, выполняющие 30-секундную операцию 1, плюс третья машина, выполняющая 15-секундную операцию 2. Точно так же операции фрезерования могут выполняться отдельными станками, а затем роботы могут передавать детали между всеми устройствами.Фактически, это будет означать одновременную работу трех, четырех или более шпинделей.
Однако, утверждал Фишер, при таком подходе необходимо учитывать стоимость инструмента. «Для каждой машины необходимо приспособление, которое может включать поворотные столы для фрезерных операций», – заметил он. А если конструкция детали изменится, возможно, все это придется изменить, увеличив расход.
Напротив, для многофункционального токарного станка потребуется всего два набора кулачков, и даже они могут не измениться при изменении конструкции.Кроме того, автоматизация в этом подходе так же проста, как использование устройства подачи прутка и перемещение руки главного шпинделя от детали к вспомогательному шпинделю.
Index предлагает уникальную альтернативу для деталей большого объема: токарные станки серии MS с шестью или восемью (в зависимости от модели) независимыми шпинделями оси Z во вращающемся барабане, а также одним или двумя контршпинделями, которые в данном контексте они называют «Синхронные шпиндели». Моментный двигатель вращает шпиндельный барабан из одного положения в другое за 0,4 секунды (каждые 60 ° для шести шпинделя и каждые 45 ° для восьмишпинделя), где он точно фиксируется на месте с помощью муфты Хирта.Два независимых поперечных суппорта оси X обслуживают каждый шпиндель, каждый с фиксированным или приводным инструментом.
В общем, цех будет выполнять одну и ту же операцию в каждом положении шпинделя и перемещать шпиндель к следующему набору инструментов для другой операции и так далее, пока не будет завершена передняя сторона. Затем синхронный шпиндель захватил бы деталь, инструмент в этом положении шпинделя отрубил бы ее, а затем станок выполнял бы конечную работу.
В большинстве конфигураций шпиндели синхронизатора могут поворачиваться, обеспечивая возможность применения до шести инструментов на тыльной стороне детали.Также есть возможность добавить поворотную ось Y к поперечным салазкам осей X / Z. Система управления может интерполировать это движение вместе с вращением шпинделя (ось C) и линейным движением X для получения линейного движения Y к плоскостям станка и другим функциям.
Энгель объяснил, что балансировка объема работы для каждой позиции шпинделя является ключевым моментом для увеличения производительности. «Если одно положение шпинделя занимает 30 секунд, а все остальные положения шпинделя – три секунды, время цикла для этой детали составляет 30 секунд.Цель состоит в том, чтобы иметь одинаковое время цикла для каждой позиции шпинделя. Это возможно только теоретически, но мы часто укладываемся в пределах нескольких процентов ».
Новый UNISIG B850 отличается современными концепциями зубчатых колес и силовой передачи и обладает мощностью 166 л.с. как в головке, так и в головке инструмента для глубокого сверления никелевых сплавов и углеродистой стали. (Предоставлено UNISIG)Фактически, среднее время полного цикла обработки сложных деталей в этой установке составляет всего от 3,5 до 40 секунд. Для относительно простых деталей станки с двумя синхронными шпинделями могут удвоить производительность следующим образом: выполнить первую операцию с деталями 1 и 2 в положениях шпинделя 1 и 2, затем вторую операцию в положениях шпинделя 3 и 4 и так далее.И наоборот, если деталь слишком сложна для выполнения на одной машине, обычно подают пруток на первую машину, а затем робот загружает частично готовые детали, выходящие из этой машины, во вторую машину. Хотя время переналадки любой из этих конфигураций довольно короткое, с учетом их стоимости экономическое обоснование зависит от потребности в высокой производительности.
CAD / CAM инструмент Vital
Engel от Index настоятельно рекомендует использовать пакет CAD / CAM для предотвращения столкновений и оптимизации резки.
CAD / CAM также может быть полезен при выборе правильной конфигурации станка, – сказал Серджио Тондато, менеджер по продукции линии Накамура-Томе из компании Methods Machine Tools Inc., Садбери, Массачусетс. «Мы регулярно моделируем работу детали на разных станках и сравниваем время цикла. Например, какова производительность двухшпиндельной или одинарной револьверной головки? Двойная башня? Три башни? И так далее. Требуемый объем детали и такие соображения, как принадлежность к семейству аналогичных деталей, помогают выбрать лучшую машину.”
Однако Тондато сказал, что постпроцессор в большинстве пакетов CAM не так точен в отношении времени цикла, поэтому Methods сотрудничает с CAMplete в этой области. Помимо точной проверки времени цикла, программное обеспечение CAMplete также выполняет проверку столкновений и упрощает изменение конфигурации инструмента. Компания Methods настолько увлечена своими преимуществами, что включает в себя токарную фрезу CAMplete TurnMill со всеми ее токарными станками с несколькими револьверными головками Nakamura-Tome, что является эксклюзивной разработкой для компании Methods. CAMplete только что выпустил TurnMill V9, в котором есть улучшенные возможности 3D-просмотра, улучшения моделирования и обновленная поддержка постобработки.
Многошпиндельное фрезерование
Для крупных деталей и большинства отливок и поковок лучше всего подходят обрабатывающие центры. И, как мы уже говорили вначале, подавляющее большинство этих станков имеет только один шпиндель. Как объяснил Фишер из Index, «для обработки нескольких инструментов на фрезе вы обычно используете многосверловую головку от такой компании, как Zagar. Станок загружал эту головку, чтобы просверлить круг под болт с шестью отверстиями, а затем заменял ее на обычную оправку для инструмента ».
Горизонтальный станок PCI METEOR имеет два полностью независимых шпинделя и может обрабатывать две разные детали одновременно, что на 30 процентов меньше, чем у двух одношпиндельных станков.Так почему же растет интерес к горизонтальным многошпиндельным обрабатывающим центрам? Почему их предлагают несколько поставщиков высоких технологий? В этот список входят SW North America, New Hudson, Mich., И PCI-SCEMM, который распространяется в Северной Америке компанией Absolute Machine Tools.
Согласно расчетам SW, двухшпиндель потребляет на 36 процентов меньше электроэнергии, чем одношпиндель, при той же мощности, а четырехшпиндель потребляет на 52 процента меньше. Но президент и руководитель службы безопасности Джим Кэмпбелл сказал, что это даже не отображается в электронной таблице покупателя в США.S. В США большим преимуществом многошпинделя является максимизация производительности при заданной площади пола. SW считает, что сдвоенный шпиндель занимает на 33 процента меньше места, чем одношпиндель, при той же производительности, в то время как четырехшпиндель занимает на 66 процентов меньше. Кэмпбелл сказал, что для обработки алюминия двухшпиндельный станок компании обычно заменяет три одношпиндельных станка «из-за конструкции наших приспособлений и устройств смены инструмента, а также всех перемещений, которые станок может выполнять одновременно. Так что для парня, у которого есть работа, но нет места на полу и он не может найти людей, это идеальная ситуация.”
Макс Поле, менеджер по работе с ключевыми клиентами PCI-SCEMM, добавил, что его двухшпиндельный станок стоит на 30 процентов меньше, чем два одношпиндельных станка. Так что цифры убедительны с нескольких точек зрения.
Мультишпиндели являются центральным элементом фирменного стиля SW, и Кэмпбелл сказал, что на данный момент компания продает только одношпиндели для больших батарейных отсеков, новый рынок для всех. «Благодаря линейным приводам этот станок будет производить намного больше, чем обычный одношпиндельный станок», – добавил Кэмпбелл.«И эти детали требуют большого количества перемещений, что проще для одношпинделя, чем для двухшпинделя».
Он также отметил, что, хотя рынок США не решался выйти за рамки двухшпинделя, «в этом году мы продаем много четырехшпинделя. Теперь, когда все больше людей видят, на что способен двухшпиндель, некоторые приходят к выводу, что они могут удвоить свою производительность с помощью четырехшпинделя ».
SW производит многошпиндельные HMC, такие как этот твин W02. (Предоставлено SW)Устойчивость к многошпиндельным обрабатывающим центрам обусловлена, по крайней мере, частично, опасениями по поводу настройки и тем фактом, что при большем количестве шпинделей, естественно, будет прикладываться большее усилие к рабочему столу и приспособлениям, чем при традиционной обработке.Последнее решается с помощью продуманной конструкции машины, и Кэмпбелл сказал, что предполагаемая сложность настройки – это «скорее воспринимаемая проблема, чем реальная проблема. И даже если на это уйдет немного времени, к тому времени, когда станки будут работать, они уже будут производить больше, чем на одношпиндельном ».
В большинстве случаев эти многошпиндельные фрезы используют все шпиндели для выполнения одной и той же операции с несколькими деталями одновременно. Точно так же, пояснил Поле, «шпиндели обычно устанавливаются на одной каретке с одной независимой осью, которой обычно является Z.Но как на таком станке обработать две очень точные детали, если невозможно ввести точную компенсацию с обеих сторон? »
Для PCI ответ заключался в том, чтобы сделать каждый шпиндель независимым по осям X, Y и Z. Это обеспечило точную компенсацию и высокую точность на каждом шпинделе, а также возможность каждого шпинделя одновременно обрабатывать разные области одной и той же детали. Примеры применения сдвоенных шпинделей к одной и той же детали включают обработку правой и левой стороны больших деталей шасси, таких как поворотные кулаки, и обработку большого поддона для аккумуляторной батареи, что, по словам Пола, привело к сокращению времени цикла почти на 40 процентов по сравнению с одиночным шпинделем. шпиндельное решение.
Благодаря концепции PCI «две машины в одной» можно обрабатывать совершенно разные детали одновременно. Полет сказал, что клиенты начинают двигаться к этому инновационному решению, и PCI уже продала линейку двухшпиндельных станков, в которых корпус коробки передач изготавливается на одном шпинделе, а другой шпиндель обрабатывает корпус сцепления.
БОКОВАЯ ШИНА: Легкое бурение глубоких скважин
Независимо от мощности токарного станка или обрабатывающего центра, сверление глубоких отверстий может быть чрезвычайно сложной задачей, настолько сложной, что UNISIG, Menomonee Falls, Wis., имеет надежные машины для построения бизнеса специально для этого приложения. Генеральный директор Энтони Феттиг сказал, что большая часть бизнеса его компании сосредоточена на станках, которые просверливают отверстия с отношением длины к диаметру от 20: 1 до 200: 1, но они могут быть подходящими и для меньших соотношений, если допускаются допуски на диаметр отверстия и прямолинейность. , и отделка поверхности плотные.
Еще один фактор, как выразился Феттиг, – это «терпимость к разочарованию». При ручном сверлении на обрабатывающем центре обычно ломаются сверла, или вырезаются отверстия слишком большого размера, или они довольно сильно смещаются, и вы действительно не знаете, почему.Так что надежность процесса и требуемое качество ствола побуждают некоторых людей к глубокому бурению. Наши станки предназначены для процесса глубокого бурения и, как правило, позволяют делать отверстия гораздо более высокого качества. И они будут делать это каждый раз, тысячи раз подряд. Машина вмешается, если в процессе что-то пойдет не так ».
UNISIG достигает этого с помощью комбинации специализированных конфигураций станка, специализированного инструментария и, конечно же, ноу-хау в области применения.Ключевым методом обработки отверстий большего диаметра (20-200 мм) является использование инструментов BTA. (BTA – это аббревиатура от Boring and Trepanning Association.) С помощью оснастки BTA станок продувает охлаждающую жидкость под высоким давлением вокруг внешней части инструмента, и стружка проходит через центр инструмента и обратно через бурильную трубу и шпиндель станка. Этот подход в пять-семь раз быстрее, чем gundrilling, но требует большей мощности.
UNISIG также справляется с глубокими скважинами с использованием нескольких шпинделей, когда это необходимо.Феттиг сказал, что UNISIG спрашивает клиентов об ожидаемых объемах и геометрии деталей, а затем пытается «сбалансировать общую эффективность и удобство переналадки и использования оборудования».
Феттиг выделил три общие категории применения: «Очень сложные детали с большим количеством отверстий в одной и той же детали, и в этом случае вы проектируете станок так, чтобы на детали было задействовано как можно больше шпинделей, чтобы максимально использовать ее». Примером может служить теплообменник с 5000 отверстиями.
«Другой крайностью будут идентичные, простые детали, которым просто нужно много одного и того же шпинделя, выполняющего одно и то же», – сказал он.Примером могут служить идентичные трансмиссионные валы, каждый из которых требует просверливания 14-миллиметрового отверстия в центре. В этом случае UNISIG может использовать четыре шпинделя для обработки четырех деталей в каждом цикле.
Третий случай, золотая середина, по словам Феттига, довольно распространен, когда требуются последовательные операции в одной и той же части. Например, трансмиссионный вал со ступенчатым отверстием (фактически два глубоких отверстия, концентричные друг другу). В этом случае Fettig может порекомендовать двухшпиндельный станок с независимой подачей, при котором каждый шпиндель последовательно ударяет по детали, или двухшпиндель, на котором деталь перемещается от шпинделя к шпинделю.Феттиг добавил, что несколько лет назад UNISIG обычно поставляла шестишпиндельные станки, но сегодня наблюдается тенденция размещать робота между несколькими двухшпиндельными станками с использованием более производительных инструментов.
«Это обеспечивает большую гибкость и очень высокую степень использования шпинделя, потому что время переналадки на двухшпиндельном станке очень короткое, и станки могут реконфигурироваться для работы с заготовками различной длины и диаметра», – сказал он. «И робот достаточно быстр, чтобы не отставать от двухшпиндельного станка.”
быстрых времен для машинных шпинделей
Новая технология шпинделя вращается быстрее, служит дольше и становится умнее.
Система iSpeed5 от NSK – это электрический шпиндель с полной заменой инструмента, который может превращать станки с ЧПУ в высокоскоростные обрабатывающие центры.Приводные шпиндели – это техническое ядро станка, обеспечивающее вращение режущих инструментов, которые формируют нашу продукцию и наш мир. Присоединение одного к пятиосевому механизму создает усовершенствованный станок с ЧПУ.Присоединение шпинделя к роботу с шарнирно-сочлененной рукой создает прецизионный сверлильный станок. Прикрепите улучшенный к существующей машине, и новые приложения оживают. Во всем спектре использования клиентам нужны шпиндели с большей прочностью, скоростью и умом для выполнения операций без отключения света.
Возможности творческого использования шпинделей ограничиваются только тем, насколько быстрыми, долговечными и умными становятся современные шпиндели.
Малый инструмент Требуемая скорость, точность
По словам Грега Ноттоли, старшего менеджера по продукции в NSK America Corp., требования клиентов начинаются с повышенной скорости и точности., Хоффман Эстейтс, Иллинойс. Одна из специализаций NSK – производство шпинделей с электрическим и пневматическим приводом для микроинструментов. Микроинструменты – это любой круглый инструмент для фрезерования или сверления диаметром от 1/8 дюйма (3,18 мм) до 0,001 дюйма (0,025 мм). «Инструмент малого диаметра – это, по сути, мокрая лапша, которую очень легко сломать. При токарной обработке сверла или фрезы, чем меньше диаметр инструмента, тем быстрее он должен вращаться, чтобы быть эффективным », – сказал Ноттоли, сохраняя при этом жесткость для точности. Многие станки с ЧПУ делают просто точную токарную обработку стандартных инструментов со скоростью от 8000 до 15000 об / мин.По словам Ноттоли, микроинструментам часто требуется скорость до 42 000 об / мин. «Использование микроинструмента со шпинделем на 8000 об / мин не является оптимальным, потому что вы неправильно откачиваете стружку, не получаете нужную съемку поверхности и просто ломаете инструменты. Вот где мы заполняем пробел на этом специализированном рынке », – сказал он.
По словам Ноттоли, шпиндели, доступные от NSK, могут быть установлены на любой станок с существующим державкой, например CAT 40, 50 или BT. «Это позволяет конечному пользователю получить эти более высокие скорости», – сказал он, добавив, что это настоящие шпиндели, а не устройства умножения скорости, которые преобразуют скорость существующего шпинделя в более высокие обороты.По его словам, множитель скорости – это «коробка с шестернями». Хотя он может обеспечить необходимую скорость и точность с минимальными потерями мощности для стандартных инструментов, он также вызывает вибрацию и нагрев. Это проблемы для микрообработки, где точность указывается в субмикронах.
«У нас есть шпиндели для токарных центров и шлифовальных станков или специально построенные роботизированные станки», – сказал Ноттоли. «Если это обрабатывающий центр, наш шпиндель входит в шпиндель станка [пространство] и обеспечивает собственное вращение.«Обрабатывающий центр обеспечивает позиционирование оси, шпиндель NSK – мощность.
Хотя у пневматики и электричества есть свои применения, Ноттоли также отметил преимущества электрического. «Лучшая отдача будет от электричества. Наши электродвигатели представляют собой бесщеточные двигатели постоянного тока с замкнутым контуром управления. С нашим контроллером, когда скорость устанавливается на тысячу об / мин, он поддерживает шпиндель на этой скорости после включения режущего инструмента. «Не так с пневматическим шпинделем для навесного оборудования, поскольку, как только он входит в контакт с деталью, скорость вращения обычно падает», – пояснил он.«Мы можем попробовать контролировать это с помощью регулятора. Но на самом деле нет активной обратной связи, чтобы это контролировать ».
Новейший электрический шпиндель от NSK, iSpeed5, может развивать скорость до 80 000 об / мин с максимальной выходной мощностью 350 Вт. Это полностью заменяемая система, состоящая из мотор-шпинделя, стопорного блока, реле давления воздуха и блока управления. Питание, охлаждающий воздух и управляющие сигналы поступают на шпиндель, когда он соединен с электромеханическим стопорным блоком, который прикреплен к шпинделю станка.Керамические подшипники обеспечивают эти высокие обороты.
Точность, универсальность и контроль
Уильям Гиллкрист, национальный менеджер по продукции и менеджер по приложениям компании MC Machinery Systems, Inc., Элк-Гроув, штат Иллинойс, согласился с тем, что для новых шпинделей важны большая скорость и мощность, а также подчеркнул точность. «В приложениях с высокой точностью вы должны убедиться, что инструмент вращается идеально, поэтому технологии подшипников важны», – сказал он. «Биение и минимизация роста шпинделя с использованием высокотехнологичных подшипников имеют решающее значение», – сказал он.Это означает, что керамические или воздушные подшипники, когда об / мин достигают более 20 000 об / мин. Не менее важен и более длительный срок службы шпинделя. Шпиндель может быть самым дорогим компонентом станка, и обращение с ним как с расходным материалом влияет на чистую прибыль.
Согласно MC Machinery, системы, которые контролируют тепловое расширение в радиальном или осевом направлении, имеют решающее значение.Но не вся новая шпиндельная технология обеспечивает высокие скорости, малое биение и низкий уровень вибрации при меньших размерах подшипников и долгом сроке службы. По-прежнему необходимы шпиндели, обеспечивающие высокий крутящий момент и высокую скорость съема металла при более низких оборотах в минуту.Это создает значительную нагрузку на подшипники и компоненты. В идеале один шпиндель должен обеспечивать как высокий крутящий момент / низкие обороты, так и низкий крутящий момент / высокие обороты. «То, что мы наблюдаем, – это более совершенные шпиндели с большим крутящим моментом и скоростью, обеспечивающие крутящий момент на более низких скоростях, но все же способные достигать более высоких оборотов, значительно превышающих 30 000. Высокий крутящий момент в сочетании с максимальной скоростью в долговечном шпинделе – это то, чего хочет большинство людей », – сказал Гиллкрист. Он также предлагает практичный совет – именно высокий крутящий момент ограничивает срок службы шпинделя.
Еще один важный фактор, который необходимо компенсировать, – это тепловое расширение.Контроль радиального биения важен, но также важен рост шпинделя в осевом направлении. «Одна из главных вещей, которые мы видим в машинах, которые мы продаем, – это способность контролировать любой рост шпинделя или адаптироваться к нему», – объяснил Гиллкрист. «Если я пытаюсь удерживать на пресс-форме очень тугую глубину Z, мой шпиндель не может колебаться». Его ответ – сбор данных и компенсация с помощью средств управления машиной.
Двумя наиболее распространенными методами корректировки роста шпинделя являются алгоритмический метод, предполагающий математическое вычисление роста шпинделя по температуре и времени по кривым, полученным в лаборатории, и метод прямого определения зазора, согласно Gillcrist.
Прямой метод становится все более практичным благодаря усовершенствованию датчиков. «У нас есть обнаружение зазоров в реальном времени на некоторых машинах, которые могут регулировать [положение] в реальном времени, если есть какой-либо рост или изменение, если инструмент изнашивается или когда инструмент вообще не задействован. Стиль алгоритма кажется не таким благоприятным [сегодня]. Но у нас также есть производитель, который использует и то, и другое в пятиосевой среде, чтобы они могли фиксировать все, что касается прогнозов температуры / времени и фактического зазора », – сказал Гиллкрист.
Умные шпиндели, Умное сверление
Есть несколько причин, по которым данные становятся настолько важными, от процессов обработки с обратной связью до подачи данных в пул данных умного предприятия. Но для того, чтобы это было полезно, данные должны быть переданы. «Связь важна для развития технологии шпинделей», – сказал Макс Поле, менеджер по развитию бизнеса в Северной Америке компании PCI-SCEMM, которая базируется в Сент-Этьене, Франция и Мейсон, Огайо, и является партнером Absolute Machine Tools, Лорейн, Огайо. .«Я думаю, что все пытаются сделать станок более интеллектуальным и автономным, собирая данные очень близко к режущему инструменту и детали, которую он режет».
Новый электрошпиндель от PCI-SCEMM, доступный в Северной Америке от Absolute Machines Tools, объединяет датчики и приводы для контроля процессов резания и настройки параметров для оптимизации срока службы инструмента и качества заготовки.PCI-SCEMM теперь предлагает свой электрошпиндель, или e-SPINDLE, чтобы предоставить эти возможности производителям станков. Он доступен в Северной Америке от Absolute Machine Tools.По словам Пола, система e-SPINDLE объединяет датчики на режущих инструментах или державках, а не на шпинделе. «Таким образом, датчики расположены близко к зоне вырубки или назначенной зоне измерения, что обеспечивает сбор и обработку высококачественных данных», – сказал он. Существует гибкость: если используются стандартные инструменты, шпиндель будет действовать как стандартный, неподключенный шпиндель. Можно использовать практически любой тип датчика, например акселерометр, датчик усилия, термопару или устройства генерации движения, такие как пьезоэлектрический привод, электрический привод или тепловой привод.
Какие датчики наиболее полезны для конечных пользователей? По словам Поле, вибрация, крутящий момент и – при сверлении или фрезеровании отверстий – датчики, измеряющие диаметр отверстия. «Измерение вибрации – это то, с чего мы начали, и это очень мощный инструмент; есть много эффектов, которые можно измерить и контролировать с помощью вибрации », – сказал он. При измерении базовой модели вибрации с контролируемым процессом любое отклонение от этой целевой вибрации приводит к проблемам. Если контакт между деталью и инструментом неправильный, если инструмент сломан, разбалансирован или дребезжит, шаблон вибрации предупредит контроллер о необходимости регулировки или, в худшем случае, остановит процесс и предупредит оператора.
«Второй по распространенности датчик – это крутящий момент», – сказал Поле. Изменения крутящего момента снова предоставляют полезную информацию о сбоях в процессе. При резких изменениях рисунка можно обнаружить дребезжание или поломку инструмента, а также ожидаемые изменения материала. «Кроме того, сочетание крутящего момента с вибрацией дает более глубокое понимание процесса в реальном времени», – сказал он. Он отметил, что это полезно при сверлении отверстий для соединения разнородных материалов, таких как алюминий и пластмассы, армированные углеродным волокном (CFRP), распространенные в аэрокосмической отрасли.Система управления достаточно умна, чтобы регулировать сверло при резке от алюминия до углепластика и алюминия в штабелированных материалах.
Третий наиболее распространенный датчик, как отметил Полет, измеряет диаметры в процессе. Компания использует лазерный датчик, который непрерывно измеряет, когда режущие инструменты находятся внутри отверстия цилиндра, и отправляет контроллеру данные о фактическом диаметре в данный момент. «Измеряя диаметр в процессе обработки, вы можете отрегулировать этот процесс и узнать, сколько материала нужно удалить, или как скомпенсировать шпиндель», – пояснил Поле.«Это обеспечивает точное сверление и фрезерование с точностью до микрон».
Okuma производит шпиндели, которые входят в ее станки, такие как показанный здесь в одном из обрабатывающих центров с ЧПУ компании.Лучшие станки, лучшие шпиндели
Уэйд Андерсон, менеджер по продажам компании Okuma Americas Corp., Шарлотт, Северная Каролина, также отметил потребность в еще более высоких характеристиках машины, надежности и времени безотказной работы. Okuma производит не только станки, но и шпиндели, которые в них входят.«В связи с тенденцией к [повышению] производительности, я вижу, что число оборотов и мощность увеличиваются, что также означает более высокий крутящий момент», – сказал Андерсон. «Это было не так давно, когда я использовал станки с двигателями шпинделя мощностью 10 л.с. (7,46 кВт). Теперь у нас есть станки с двигателями шпинделя мощностью 30, 40, 60 и даже 75 л.с. ” Это соответствует диапазону от 22 до 56 кВт. Дело не только в том, что шпиндели становятся лучше. Эти улучшения сопровождаются улучшением станков и инструментальной техники. Вместе это позволяет производителям точно резать все более сложные материалы.
Больше мощности от шпинделя – это хорошо. Тепло, которое он выделяет, плохое. «Одним из самых больших теплогенераторов любого станка является двигатель шпинделя. Обычно это один из самых мощных двигателей станков, – пояснил Андерсон.
Как Окума контролирует эту жару? «Мы уделяем много времени и внимания тепловой динамике машины и измерениям в реальном времени», – сказал он. «Мы измеряем температуру шпинделя и с помощью теплового картографирования можем корректировать кинематику станка по мере необходимости.Мы называем эту систему TAS (термоактивный стабилизатор), и в сочетании с нашими запатентованными технологиями охлаждения шпинделя она дает нам инструменты, необходимые для [создания] одной из наиболее термически стабильных платформ станков ».
Как насчет надежности и безотказной работы машины? Андерсон предупредил, что, хотя время цикла для номинальной работы хорошо рассчитывать, следует сосредоточиться на эффективности всего процесса, особенно при выявлении и устранении непредвиденных простоев. «Если я смогу сделать деталь очень быстро, я могу сломать станок и преждевременно разорвать шпиндель», – сказал он.Помните, что приложения с высоким крутящим моментом могут создавать ситуации, которые могут повлиять на срок службы шпинделя. «Если вдруг станок выходит из строя из-за того, что он или шпиндель повреждены, это будет стоить мне намного больше, чем сокращение времени цикла».
Однако слишком медленный цикл также стоит денег. Как лучше всего оптимизировать время цикла? Это требует данных, знаний и суждений. Okuma предлагает возможность оптимизировать процесс резки металла с помощью данных, полученных с датчиков, в сочетании со знаниями и оценками искусственного интеллекта (ИИ).По словам Андерсона, определение базового процесса для новой машины с точки зрения фундаментальных измерений, таких как вибрация, мощность и крутящий момент (создание отпечатка пальца), является хорошей идеей. По отпечатку пальца контроллер может определить, когда процесс отклоняется от базовой линии.
В результате машинисты могут выполнять быстрый цикл с большей уверенностью в том, что машина отправит сигнал тревоги, когда достигнет красной черты, и автоматически вмешается, чтобы предотвратить катастрофические простои. Оптимизация процессов и снижение затрат.«Прогнозирование отказа до того, как он произойдет, поднимает планку вашего производственного процесса», – сказал он.
Токарные станки и приводная оснастка в современном мире
Производители все чаще запрашивают живые инструменты для своих токарных станков, которые включают датчики для мониторинга данных, а также несколько шпинделей, как показано здесь.Это может показаться нелогичным, но умение поворачивать инструмент может быть важным при токарных операциях. Токарные станки, по определению, поворачивают заготовку и используют статический инструмент для вырезания цилиндрических элементов в заготовке.Однако, чтобы просверлить отверстия или нарезать плоские поверхности на простом токарном станке, машинист должен снять деталь с токарного станка и переустановить ее на фрезерном станке с ЧПУ.
«Живые инструменты используют привод револьверной головки станка», – сказал Пребен Хансен, президент Platinum Tooling, Prospect Heights, штат Иллинойс. В станках, оснащенных приводными инструментами, заготовка останавливается, включается режущий инструмент, который вращается, и просверливаются отверстия или фрезеруются плоские поверхности. «Они приводятся в движение револьверной головкой станка, которую можно назвать шпинделем. Представьте, что мы предлагаем, как трансмиссию, набор шестерен, который использует двигатель в револьверной головке токарного станка для вращения рабочего инструмента.«Эти живые инструменты могут настраивать передаточное число, увеличивая или уменьшая, в зависимости от того, требуется ли приложению скорость в зависимости от крутящего момента. Platinum Tooling предлагает живые инструменты от Heimatec.
О чем просят клиенты? «Скорость – самая важная характеристика. Они хотят быстрее поворачивать свои инструменты », – сказал Хансен. Скорость – это деньги, и это имеет смысл, но это еще не все, что им нужно. «Не менее важным становится наличие живых инструментов с датчиками, позволяющих использовать данные для мониторинга. Это огромная проблема, которую нужно решить прямо сейчас.«Существует потребность в шпинделях для динамического инструмента, который контролирует время работы, скорость, влажность и температуру. «Нагрев вреден для подшипников, поэтому мониторинг и контроль температуры означает, что подшипники и шпиндели прослужат дольше», – сказал Хансен. «Влажность тоже плохо сказывается на устройстве. Датчик влажности может подать сигнал тревоги, чтобы немедленно отключить его и избежать каких-либо катастрофических сбоев ».
Какова конечная цель этих сенсорных систем? «Более быстрая работа, мониторинг операций резания в реальном времени и, в конечном итоге, операции отключения света», – сказал он.
Хирургия сердца | Производство режущего инструмента
Ремонт шпинделя – сердца станка – более экономичен, чем покупка нового, но производители деталей должны понимать этот процесс.
Однажды вы замечаете следы дребезжания на деталях, изготовленных на станке, который раньше не доставлял вам проблем. Ничего не изменилось, кроме, возможно, состояния шпинделя.
Множественные подсказки указывают на то, что шпиндель нуждается в ремонте или восстановлении, включая чрезмерный шум, вибрацию, потерю допуска детали, шероховатость поверхности, тепловыделение и показания спектрального анализа, которые указывают на повреждение или разрушение подшипников.
Обычно проблема со шпинделем сначала проявляется в заготовке, отмечает Митчелл Кирби, вице-президент по производству Riten Industries Inc. «Вы обнаружите, что не получаете ту отделку, которую получали раньше», – сказал он. Здание суда Вашингтона, штат Огайо, производитель торцевых приводов, а также рабочих и мертвых центров, также ремонтирует Heald Red Head и другие шлифовальные шпиндели шкивного типа со скоростью вращения менее 10 000 об / мин.
Повод для беспокойства
Причин «нездорового» веретена столь же многочисленны, как и признаков того, что что-то не так.По данным GMN Paul Müller Industrie GmbH & Co. KG, немецкого производителя шпинделей для станков, столкновение или авария являются причиной 60 процентов повреждений шпинделей, за которыми следуют износ на 11 процентов, утечки на 9 процентов и проблемы со смазкой. на 7 процентов, с другими причинами, составляющими оставшиеся 13 процентов.
Предоставлено Службой прецизионных шпинделей
Шпиндель станка перед ремонтом (вверху) и после ремонта шпинделя.
По словам Дуга Кранца, вице-президента по продажам и маркетингу компании Fischer Precise USA Inc., Расин, Висконсин, поломка станка – это субъективное понятие, и его трудно определить, не засвидетельствовав его. Компания производит шпиндели трех основных брендов – Fischer, Precise. и Fortuna – и ремонтирует эти шпиндели и шпиндели других производителей. «Возможно, вы заметите признаки перегрузки, но фактор номер один, способствующий ремонту шпинделей, – это вибрация во время операции резания», – сказал он.«Это особенно актуально при обработке больших сложных деталей с большим количеством узких углов, которые часто производятся на больших станках с применением режущих инструментов с большим вылетом», – добавил Кранц.
Fischer Precise предлагает систему мониторинга SmartVision, которая позволяет клиентам отслеживать вибрацию и рабочее состояние своих шпинделей во время выполнения программ обработки деталей. «Тогда мы сможем определить некоторые из этих участков с высокой вибрацией и лучше согласовать стратегии резания и помочь им лучше удерживать шпиндель в детали с меньшей вибрацией», – сказал Кранц.
Загрязнение шпинделя и перегрузка – вторая и третья по частоте причины, соответственно, согласно Кранцу. «Вы можете назвать перегрузку аварией, но шпиндель не обязательно нуждается в ремонте после простого удара о станину станка», – сказал он. «Шпиндели устойчивы к некоторым ударам».
По словам Кирби, износ – основная причина, по которой пользователь отправляет Riten шлифовальный шпиндель ID для ремонта. «Подшипниковый узел – это вращающийся элемент», – пояснил он. «Вы запускаете его достаточно долго и интенсивно, со временем подшипники начинают изнашиваться, и их нужно менять.”
В отличие от других типов шпинделей станков, шлифовальный шпиндель внутреннего диаметра является очень специфическим продуктом и, в некотором смысле, взаимозаменяемым аксессуаром, подчеркнул Кирби. Такой шпиндель заметно отличается от подшипникового узла в задней бабке, который является неотъемлемой частью станка, будь то вертикальный токарный центр, токарный станок, шлифовальный станок или другой тип станка. «У меня есть несколько шлифовальных шпинделей для некоторых моих станков, – сказал он. «Это шлифовальные машины ID, которые поддерживают автономный шлифовальный шпиндель.С другой стороны, шлифовальный станок OD может иметь живую или мертвую заднюю бабку. «В случае задней бабки, это все еще вращающийся подшипниковый узел, но он не является взаимозаменяемым», – добавил Кирби.
Являясь высокотехнологичной механической системой, шпиндель состоит из множества компонентов, любой из которых может быть поврежден. GMN заявила, что список включает, в порядке абсолютной частоты, дефект подшипника, неплотный проход вращения, неисправный датчик угла поворота, сломанную или изогнутую тягу, неисправный датчик зажима и неисправный датчик температуры.И список продолжается.
К вашим услугам
Какой бы ни была причина, неисправный шпиндель не вылечит сам себя. По словам Дэвида Маршика, совладельца (вместе с Уильямом Фоя) компании Precision Spindle Service Co. Inc., Ферндейл, Мичиган, которая ремонтирует шпиндели со скоростью до 124 000 об / мин, лучше использовать специалиста, когда требуется ремонт. Магазин основан в 1946 году.
В то время как производитель деталей может иметь персонал для аварийного ремонта шпинделя, очень немногие могут обеспечить полный ремонт, сказал он.«Неважно, горизонтальный это, вертикальный, шлифовальный или фрезерный станок. Все, что есть в производстве сверхточных шарикоподшипников, мы ремонтируем ».
Маршик добавил, что десять лет назад ремонт шпинделя на дому был более распространен, в первую очередь у крупных производителей. Однако поддерживать эту способность дорого, потому что специалисты по ремонту должны работать в чистой комнате, в идеале с контролируемой температурой и атмосферой, и даже волосы и промышленный дым могут повредить шпиндельный узел.«Ремонтный бизнес процветает, потому что они ограничили или урезали эти программы», – сказал он.
«Чистота от начала до конца, безусловно, является главным приоритетом», – соглашается Кранц из Fischer Precise. «Говоря о допусках и чистоте, мы живем в мире микрон, а 3 мкм – это большой размер в нашем мире, поэтому даже самые мелкие частицы могут вызвать проблемы при сборке шпинделя».
Кранц оценивает, что покупка оборудования, необходимого для надлежащего анализа, тестирования, поиска и устранения неисправностей, балансировки и поддержки услуг по ремонту высокоскоростных шпинделей картриджного типа, обойдется примерно в 1 миллион долларов.Хотя Fischer Precise выполняет полный ремонт шпинделя на своем предприятии, он отметил, что у компании есть два представителя на местах, которые выполняют частичный ремонт на объекте клиента, например, ремонтируют неисправный энкодер, неисправный датчик или сломанный узел зажима инструмента HSK. Ремонт в полевых условиях может сэкономить клиентам значительное количество времени и денег. Он добавил, что хотя загрязнение является проблемой при выполнении ремонта на месте, технический специалист может успешно завершить работу с должной осторожностью и вниманием к деталям.
Иногда внутренний ремонт отправляется в специализированную ремонтную мастерскую. Например, попытка ремонта клиентом обнаруживается, когда поставщик услуг по ремонту проверяет вал и видит, что гнезда подшипников изношены и не имеют надлежащей посадки, пояснил Кирби из Riten, отметив, что плечи, с которыми выступы подшипников упираются, должны быть перпендикулярными. в пределах 0,0001 дюйма. «Если подшипник трется о дорожку качения, где он действительно движется, или сам вал изгибается, – сказал он, – тогда эти выступы выходят из квадрата и нуждаются в доработке.”
Подшипники источника
Наличие надежных источников подшипников, которые не используются повторно при восстановлении шпинделя, также имеет решающее значение для компаний, занимающихся ремонтом шпинделей. Не всегда легко найти даже в лучшие времена, доступность подшипников стала особенно сложной во время Великой рецессии, когда производители подшипников ограничили запасы для контроля затрат, но улучшились вместе с экономией, отметил Маршик из Precision Spindle Service. Однако «это все еще занимает некоторое время, и вам нужно много разных источников», – сказал он.
«Поставка высокоточных подшипников имеет первостепенное значение», – сказал Кранц. «Если у вас его нет в наличии или нет в наличии, вы не сможете обслуживать клиентов в те сроки, которых они заслуживают, а для некоторых подшипников время выполнения заказа может растянуться до 6-8 месяцев».
Он добавил, что Fischer Precise должна прогнозировать спрос, поддерживать и инвестировать в собственные запасы подшипников. «У нас есть подшипники на сумму около 2 миллионов долларов, которые хранятся в том, что мы называем« хранилищем »на нашем складе, просто для поддержки нашей собственной линейки продуктов», – сказал Кранц.«У нас есть такой огромный набор [подшипников] для нашего продукта, что мы можем обслуживать и продукт сторонних производителей – любой другой шпиндель». Если какой-либо подшипник отсутствует на складе, у компании есть представительства в Европе и Азии, из которых она может извлечь.
Предоставлено Riten Industries
A до (вверху) и после фото шлифовального шпинделя внутреннего диаметра, отремонтированного в Riten Industries.
После замены подшипников шпиндель необходимо отбалансировать, чтобы обеспечить достаточный срок службы подшипников. «Когда подшипниковый узел выходит из равновесия, он хочет вибрировать, и вы видите дребезжание в заготовке», – сказал Кирби из Riten.«Вы также добавляете дополнительную нагрузку на подшипниковый узел, поэтому подшипники быстро изнашиваются из-за дисбаланса узла. Это становится более важным по мере увеличения числа оборотов в минуту ».
Помимо установки новых подшипников и балансировки, полный ремонт шпинделя в Precision Spindle Service может включать разборку шпинделя, восстановление отверстий конуса и корпуса, восстановление и повторное хромирование вала, а также работы с гидравликой и электроникой, отметил Маршик из Precision Spindle Service. . По его словам, для восстановления компонентов шпинделя посредством токарной обработки, фрезерования и шлифования у компании есть «полнопрофильный» механический цех.«Мы ремонтируем любой вид отказа. Нормальный срок выполнения составляет 3 недели ».
Кранц объяснил, что у Fischer Precise есть определенный процесс при ремонте шпинделя и начинается с получения как можно большего количества информации от клиента, если нет необходимости четко определять тип отказа или обслуживание. В целях поиска и устранения неисправностей компания просит включить в шпиндель любые инструменты в случае возникновения проблем. «Мы начинаем снаружи внутрь, – сказал он. «У нас есть несколько входных проверок и 54-точечный осмотр при разборке агрегата.Когда мы разбираем шпиндель, мы проверяем все системы, включая охлаждение, подшипники, опоры подшипников, корпус, состояние смазки и подачу, вал, ротор и зажим ».
Типичное время выполнения заказа для сложного ремонта шпинделя составляет от 4 до 6 недель, но, по словам Кранца, компания может выполнить ремонт за 1-2 недели, работая сверхурочно и в выходные дни, в зависимости от потребностей клиента. По его словам, замена шпинделя на новый занимает от 18 до 20 недель. Отремонтированный шпиндель также стоит меньше, при этом, как правило, на 50 процентов или меньше, чем стоимость нового шпинделя, что дает значительную экономию для высокопроизводительного шпинделя, который может стоить 75 000 долларов и более, добавил он.
Вопросы технического обслуживания
Возраст может диктовать экономическую целесообразность ремонта шпинделя. Маршик из Precision Spindle Service сказал, что обычно более экономически целесообразно заменить шпиндель, которому более 20 лет, но если новый шпиндель недоступен, замена станка стоит значительно дороже. «Иногда заказчик говорит:« Эй, это отличная машина, и я брошу на нее деньги, просто оставлю ее работать еще 7–10 лет ».
Маршик добавил, что конечные пользователи также обращают внимание на восстановление шпинделей, когда сроки поставки новых машин длительные, а доступность ограничена.
Предоставлено Службой прецизионных шпинделей
Отдел шлифовки и обработкиPrecision Spindle Service восстанавливает компоненты шпинделя в процессе восстановления.
Как и в случае с любым другим обрабатывающим оборудованием, пользователи могут максимально продлить срок службы шпинделя при надлежащем обслуживании. Однако техническое обслуживание в первую очередь требует заботы о периферийных компонентах шпинделя и рабочем состоянии, включая смазку подшипников, охлаждающую жидкость, а также давление и поток воздуха. Кранц из Fischer Precise отмечает, что если в шпинделе есть охладитель для контроля температуры, он также должен поддерживаться в рабочем состоянии.
«Вы мало что можете сделать с самим шпинделем, пока он находится в станке, так сказать,« сменить масло »», – сказал он. «Вы следите за тем, чтобы все вокруг было в наилучшем состоянии, потому что шпиндель действительно является сердцем станка. Если о системе шпинделя позаботиться, шпиндель прослужит тысячи и тысячи часов ».
Когда дело доходит до шлифовальных шпинделей, Кирби из Riten согласился с тем, что конечным пользователям не рекомендуется открывать их для выполнения какого-либо обслуживания, поскольку они смазываются на заводе на весь срок службы подшипникового узла.Таким образом, техническое обслуживание означает минимизацию проникновения охлаждающей жидкости и загрязняющих веществ в шпиндель и поддержание его в чистоте.
Поскольку шарикоподшипник вращается очень много часов, шпиндель станка является скоропортящимся предметом и в конечном итоге потребует ремонта, независимо от того, насколько хорошо он обслуживается. Когда это происходит, Маршик рекомендует искать поставщика услуг по ремонту шпинделей, а не специализированную мастерскую, которая выполняет все работы по ремонту станков. «Репутация, вероятно, является самым важным фактором», – сказал он.CTE
Предоставлено Jakob Antriebstechnik
Механические компоненты системы безопасности мотор-шпинделя Jakob обеспечивают контролируемое и обратимое отсоединение главного шпинделя от конструкции станка при столкновении.
Система безопасности шпинделя при аварийной посадке
Авария станка, особенно при быстром движении со скоростью 60 м / мин. или быстрее, может повредить шпиндель, что потребует дорогостоящего ремонта. Во время большинства аварий активация аварийной остановки вручную выполняется слишком медленно, чтобы предотвратить повреждение.Даже при упреждающем предотвращении столкновений с помощью программирования CAD / CAM и методов реактивного уменьшения повреждений, таких как электронные датчики и механические предохранительные муфты, аварии все равно происходят.
Для защиты шпинделя от повреждений при столкновении компания Jakob Antriebstechnik GmbH, Кляйнвалльштадт, Германия, представила систему безопасности мотор-шпинделя (MS 3 ), которая немедленно отключает передачу мощности на стыке между шпиндельной бабкой станка и мотор-шпинделем во время столкновения. .Таким образом, по заявлению компании, чувствительные к ударам компоненты шпинделя защищены от пиковых ударных нагрузок при столкновении.
Кроме того, отсоединение шпинделя от конструкции станка снижает жесткость станка, уменьшая силу столкновения. Чтобы избежать потери производительности машины, это снижение жесткости не происходит до тех пор, пока не будет превышен критический порог усилия.
Роликовые подшипникиособенно подвержены повреждениям при авариях. Из-за небольших площадей контакта между внутренней и внешней дорожками качения и телом качения максимально допустимое контактное давление может быть превышено во время столкновений.Это приводит к пластической деформации в зоне контакта колец с телами качения (бринеллинг), а также разрушению тел качения.
MS 3 также защищает валы, зажимные системы, преобразователь и вращающуюся подачу.
Конструкция системы с двумя фланцами включает встроенные магниты для обеспечения высоких удерживающих сил и жесткости, добавили в компании. Помимо амортизации ударов шпинделя, пружинные и демпфирующие элементы автоматически возвращают в исходное положение фланцевую систему.
Когда датчики системы безопасности обнаруживают столкновение, ЧПУ немедленно останавливает все движения оси. Сразу после этого станок движется назад по пути возврата на основе сохраненной программы ЧПУ. Затем станок останавливается при аварийной остановке и ждет, пока оператор не проверит наличие повреждений режущего инструмента, шпинделя и заготовки. Только после того, как оператор выполнил проверки и обеспечен зазор вручную, система управления позволяет станку возобновить резку или повторить первоначальную операцию обработки.
Якоб установил MS 3 на станке от MAG IAS LLC, Хеврон, штат Кентукки, на испытательном предприятии в Германии, и производитель станков рассматривает возможность предложения его в качестве опции на нескольких моделях, отметил руководитель MAG. Специалист по технологиям Дуг Уоттс. По его словам, поскольку диаметр шпинделя двигателя увеличивается при внедрении системы безопасности, MAG потребуется изменить конструктивный элемент станка, на котором установлен шпиндель.
Помимо защиты шпинделя от повреждений из-за ошибок программирования и ошибок вмешательства человека, система безопасности шпинделя предотвращает финансовые потери из-за простоя станка на ремонт или замену шпинделя, отметил Уоттс.
Поскольку человек, вызвавший аварию, не хочет признавать свою вину, поставщику станков сложно определить точную причину поломки, отметил Уоттс. «Во многих случаях поставщик заменяет шпиндель бесплатно, потому что не может доказать, что кто-то повредил станок», – сказал он. «Если мы сможем предотвратить нанесение ущерба, в долгосрочной перспективе это сэкономит нам деньги и сделает наших клиентов более удовлетворенными».
ГАМ, г. Проспект, Иллинойс., является североамериканским дистрибьютором системы безопасности шпинделя, а также поставщиком редукторов, сервомуфтов, линейных монтажных комплектов и средств автоматизации.
– Якоб Антрибстник и А. Рихтер
Контрольные признаки выхода из строя шарикоподшипника
Шарикоподшипники играют центральную роль в узле шпинделя, поддерживая вал шпинделя и обеспечивая жесткость. «Против них работает вибрация», – сказал Боб Коул, техник по ремонту шпинделей компании Barden Corp., в видео под названием «Ремонт шпинделя: учебник по оптимизации производительности шпинделя». Компания из Данбери, штат Коннектикут, производит прецизионные шарикоподшипники для множества применений.
В видео, доступном для просмотра на веб-сайте Бардена, Коул описывает 12 видов отказа шарикоподшипников и их контрольные признаки в шпинделях станков.
- Чрезмерная нагрузка вызывает сильное выкрашивание дорожек качения.
- Перегрев, который может привести к отказу, вызывает изменение цвета подшипников в сине-черный или серебристо-золотой цвет.
- Неисправность смазки также может привести к обесцвечиванию подшипников.
- Ложное бринеллирование, которое является результатом чрезмерной внешней вибрации, когда подшипник не находится в движении, оставляет крошечные эллиптические следы износа на внутреннем и внешнем кольцах шпинделя с равномерными интервалами в осевом направлении.
- Истинное бринеллирование возникает, когда нагрузки превышают пределы упругости материала подшипника, что приводит к более выраженным вмятинам в кольцах.
- Выкрашивание или трещины на рабочей поверхности подшипника возникают в результате нормального усталостного разрушения.
- Полосы по окружности шариковых подшипников указывают на обратную нагрузку, а радиально-упорные подшипники в станках воспринимают нагрузки только в одном направлении.
- Неровные вмятины или материал, застрявший в дорожках качения в результате загрязнения.
- Красные или коричневые пятна на кольцах указывают на проблему коррозии.
- Несоосность подшипника является причиной, если внутреннее кольцо имеет широкий ход шара, а внешнее кольцо – непараллельный путь шара.
- Неплотная посадка между корпусом и наружным кольцом вызывает образование задиров или изменение цвета внешнего кольца.
- Напротив, слишком тугая посадка приводит к сильному износу в глубине дорожки шара в нижней части дорожек качения.
Авторы
The Barden Corp.
(203) 744-2211
www.bardenbearings.com
Fischer Precise USA Inc.