Навивка пружины на токарном станке: способы, видео
Это техпроцесс, в ходе которого проволока или лента подвергается обработке. В результате чего получаются навивка пружин различной формы: цилиндрической, конической, фасонной или плоской. Основным методом производства считается холодный способ. Навивка пружины выполняется на токарном станке, для этого используется специальное приспособление, вручную или с применением автомата. Производство подобных изделий, возможно и горячим методом, диаметр используемой проволоки от 10 мм. Выбор варианта навивки пружины зависит от размера и типа металла.
Холодный способ изготовления
Технология навивки пружин на токарных станках в России считается более предпочтительной. Обусловлено тем, что горячий способ требует серьезных затрат связанных с приобретением дорогостоящего дополнительного оборудования. Холодный метод имеет ограничения по диаметру проволоки, он не превышает 16 мм. Оснастка для этого техпроцесса состоит из оправок, приспособленных для направления металлической нити на вращающейся катушке.
Вид зависит от формы пружины (цилиндрической, бочкообразной или конической). Приспособление для натяжения и направления проволоки представлено в виде двух вращающихся роликов. Причём верхний имеет винт, который позволяет регулировать натяг и направление. При холодной завивке пружин берется металл с необходимыми качествами, из него делают нужную деталь. В конце проводят термообработку с целью избавления от внутренних напряжений.
Сама технология выглядит так. Стальную проволоку подают через планку, установленную на суппорте оборудования, а конец фиксируется зажимом на оправке. Роликовое приспособление выполняет натяг металлической нити, который важен при изготовлении изделия. После включения станка, начинается намотка пружины, при этом скорость в зависимости от диаметра, используемого материла, находится в пределах 10 – 40 м/мин. Количество витков подсчитывается визуально или счетчиком. По окончании поделка подлежит мехобработке.
Это может быть технология торцовки для пружин сжатия абразивными кругами на специальных автоматах или на промышленных точилах. На изделиях другого профиля технологические концы подлежат обрубке или обрезке, используя специальное приспособление и соответствующий инструмент. Готовый продукт подвергается термообработке в электрических печах.
Технология термической обработки деталей зависит от материала. Для одних марок сталей отпуск и закалка, для других, в том числе и для бронзы – низкотемпературный отпуск, после которого поделки приобретают пружинящие свойства.
Готовую продукцию проверяют и испытывают на соответствие технологическим параметрам (растяжение, сжатие, изгиб, кручение). При необходимости или с согласия заказчика выполняется дополнительная обработка (гальваническое, лакокрасочное или другое покрытие).
Горячий метод изготовления
Навивки пружин на токарных станках таким методом доступны для изготовления изделий из пруткового материала диаметром 10 мм и более. Технологический процесс при этом состоит из ряда этапов:
- обрезка и последующий нагрев;
- оттяжка и вальцовка концов;
- повторный нагрев;
- навивка из нагретого материала;
- отрубаются концы заготовки;
- разводка и правка изделия, последующая термообработка;
- заточка и шлифовка торцов, защита от коррозии, контроль размеров и испытания (прочность, износостойкость и т. п.).
Нагрев заготовки выполняется в короткое время, при этом должно выполниться обязательное условие – равномерный по всему объему прогрев. Для горячей навивки требуется инструмент и оснастка (оправка, молотки, клещи, клинья и т. д.). Все перечисленное навивщику нужно иметь под рукой при выполнении работ по изготовлению пружин. Оправка нужна для навивки пружин на токарных станках, а с помощью клина крепится заготовка на ней. Клещи имеют форму губок обеспечивающих удержание, установку и поворот детали.
В процессе работы нужно руководствоваться технологическими инструкциями, которые обеспечат получение качественных изделий. С целью снижения отходов при изготовлении коротких изделий на оправку укладывается длинная спираль, т. е. делается заготовка на несколько деталей. Процесс навивки пружин на токарных станках большого размера включает практически те же этапы операции, что применяют для средних и мелких заготовок.
Особенности процесса завивки
Полученные после навивки пружины при эксплуатации, находятся в режиме многочисленных повторяющихся нагрузок. Поэтому они должны иметь высокие характеристики по упругости, в процессе работы выдерживать большое количество повторных загрузок без осадки и поломок. Первое означает, что пружины после нагрузки должны быстро восстанавливать заложенную форму и размеры. Практика показывает, что долговечность продукта, изготовленного на станке, напрямую зависит от качества и чистоты обработки проволоки. На поверхности пружин не должны быть царапины, волосовины, риски и другие дефекты, т. к. они приводят к резкому снижению эксплуатационных качеств изделия.
Важным моментом для навивки пружин считается использование оправок (приспособлений), они предупреждают коробление в момент закалки и при отпуске. Даже если деталь покоробилась при закалке, исправить ситуацию можно насадив ее перед процедурой отпуска на оправку. У пружин большого размера дефект, полученный при закалке трудно исправить, т. к. в этом случае затруднена фиксация на оправке. Чтобы этого не случалось нужно термообработку заготовки проводить уже на ней.
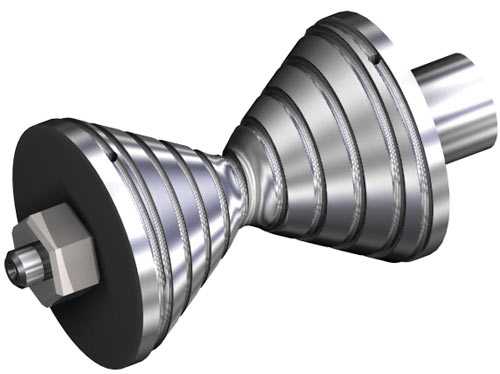
Приспособление для навивки пружин на токарном станке
При любом из двух способов навивки пружин на токарных станках должны обеспечиваться следующие параметры:
- внутренний, средний или наружный диаметр продукта;
- общие и рабочие витки, их число;
- высота и шаг пружины с учетом последующей обработки.
Если вы нашли ошибку, пожалуйста, выделите фрагмент текста и нажмите Ctrl+Enter.
stankiexpert.ru
Холодная навивка пружин – Пружины
Холодная навивка пружин
Категория:
Пружины
Холодная навивка пружин
Холодная навивка применяется при изготовлении средних и мелких винтовых пружин.
После навивки пружины, изготовленные из сортов стали (ГОСТ 2052—53), подвергают полной термической обработке, т. е. закалке и отпуску, а при изготовлении из высокоуглеродистой патентированной проволоки — только отпуску.
Технология изготовления пружин холодной навивки отличается от технологии горячей навивки главным образом отсутствием операций оттяжки концов заготовок и нагрева их перед навивкой. Изготовляют пружины холодной навивки обычно из проволоки, смотанной в мотки с наружным диаметром от 100 мм и более в зависимости от диаметра проволоки.
В технологический процесс холодной навивки пружин входят следующие операции:
при изготовлении средних винтовых пружин:
1) навивка пружин;
2) правка пружин;
3) заточка и шлифование торцов пружин;
5) предварительное обжатие или растяжение пружин;
6) испытание пружин и проверка размеров; при изготовлении мелких винтовых пружин:
1) навивка пружин;
2) обрубка излишне навитых крайних витков и удаление заусенцев;
3) термическая обработка пружин;
4) обжатие на специальной оправке до соприкосновения витков;
5) заточка торцов пружин;
6) правка пружин;
7) испытание пружин и проверка размеров;
8) нанесение антикоррозионных покрытий;
9) проверка качества защитного покрытия;
10) испытание пружин и проверка размеров.
При изготовлении пружин холодной навивкой применяются ручные приборы, станки токарного типа и пружинонавивальные автоматы.
Ручная навивка
Ручная навивка применяется при изготовлении мелких винтовых пружин из высокоуглеродистой патентированной проволоки диаметром от 0,2 мм и более. Проволока наматывается на оправку, закрепленную в патроне ручного прибора, имеющую прорезь для закрепления проволоки. Оправки бывают двух типов: гладкие и с винтовой нарезкой.
Качество пружин при ручной навивке зависит от направления проволоки, от ручного натяга и вообще от опытности рабочего. Кроме того, ручной навивке присуща весьма низкая производительность труда.
Рис. 1. Ручной прибор для навивки пружин
Поэтому ручная навивка может применяться только в индивидуальном производстве или при изготовлении небольшой опытной партии изделий.
Навивка на станках
Винтовые пружины могут изготовляться на токарных станках обычного типа или на специально приспособленных токарных станках; при этом проволока навивается на оправки. Оправка одним концом закрепляется в патроне, сидящем на шпинделе станка, другим — упирается в центр задней бабки. Проволока пропускается через продольный суппорт станка и закрепляется на оправке.
При изготовлении пружин, работающих на сжатие, на токарных станках величина шага пружины достигается применением гитары и ходового винта, с которым соединяется продольный суппорт станка.
При применении специально приспособленных токарных станков на их станине вместо задней бабки устанавливается специальное приспособление, служащее для укрепления оправки и заправки проволоки при навивке, а за передней бабкой станка укрепляется копирный винт с квадратной нарезкой для навивки пружин на заданный шаг. При изготовлении пружин, работающих на сжатие, шаг навиваемой пружины должен соответствовать выбранному шагу копирного винта. При навивке таких пружин с прижатыми крайними витками часть резьбы копирного винта запаивается пластинками в тех местах, где витки пружины должны быть навиты вплотную.
Запаивание пластинками производится с учетом плавного перехода от наружного диаметра нарезки копирного винта к внутренней нарезке.
При отсутствии оборудования, обеспечивающего навивку пружин с заданным шагом, на станках можно навивать пружины с плотно прижатыми друг к другу витками. В этом случае после навивки пружины разводятся на шаг вручную разводным зубилом, при этом разводку производят таким образом, чтобы крайние витки пружины остались прижатыми. Разводятся пружины на несколько большую свободную высоту, чем требуется чертежом, с учетом ее осадки при дальнейшем обжатии и испытаниях.
При навивке на станке длинной пружины ее рубят вручную или на прессе на отдельные пружины с заданной свободной высотой.
Подбор оправок. Наиболее трудоемким процессом при навивке пружин на ручных приборах и токарных станках является подбор оправок, т. е. определение диаметра оправки.
Оправки могут быть подобраны на основе простейших экспериментальных формул или теоретического расчета. При расчете оправок необходимо принимать во внимание основные моменты, характерные для пружин:
1) после навивки пружина увеличивается в диаметре вследствие упругих деформаций проволоки;
Поэтому на практике диаметр оправки обычно определяется опытной навивкой пружин.
Изложенное выше подтверждается результатами обмера пружин А, В, С, которые были навиты на оправки, диаметры которых больше полученных при расчете. При этом навитые пружины удовлетворяют заданным требованиям по внутреннему диаметру пружин. Размеры оправок зависят исключительно от механических свойств проволоки и не зависят от конструктивных требований пружин.
Зная только и определив диаметр оправки по рекомендуемой нами эмпирической формуле путем регулирования натяжения проволоки при навивке пружин, на выбранную оправку можно навить пружины в соответствии с заданными требованиями.
Необходимо отметить, что на изготовление качественных пружин кроме диаметра оправки существенное влияние оказывают направление и натяжение проволоки, с которым навивается пружина. При навивке пружин на станках натяжение проволоки осуществляется зажатием в суппорте или в специальном приспособлении, а при ручной навивке — пальцами руки. Направление и величина натяжения проволоки устанавливается после определения диаметра оправки опытной навивкой пружин.
Выбор шага навивки и числа витков. Навитые пружины после предварительного обжатия до соприкосновения витков и после испытания на прессах с целью определения рабочих нагрузок обычно имеют некоторую осадку и уменьшаются по свободной высоте.
Выше было указано, что остаточная деформация пружин, получающаяся после первого их обжатия, зависит от характеристического модуля и от напряжения при кручении.
При достаточно обоснованном выборе модуля сдвига и допускаемого напряжения при кручении пружины
имеют незначительную остаточную деформацию. Наоборот, если основные механические характеристики были выбраны произвольно, без достаточного обоснования, то пружины будут иметь большую остаточную деформацию и их навивка будет затруднительна. Представленные на рис. 2 пружины в результате остаточных деформаций имеют разную свободную высоту после навивки и после первого обжатия до соприкосновения витков.
Навивка таких вытянутых пружин для обеспечения заданной техническими условиями свободной высоты также весьма затруднительна и сопровождается большим процентом брака. Обеспечение заданной свободной высоты путем изготовления сильно вытянутых пружин еще не гарантирует соблюдения технических условий по рабочим нагрузкам: такие пружины дают дополнительную остаточную деформацию при испытании на грузовых приборах и обычно оказываются слабыми, т. е. имеющими осадку под рабочей нагрузкой больше заданной.
Пружины С и D с напряжениями при кручении в пределах допускаемых имеют незначительную остаточную деформацию, и их навивка не вызывает особых затруднений. При испытании таких пружин на грузовых приборах обычно удовлетворяются требования технических условий по рабочим нагрузкам на заданной высоте. Отсюда вытекают и требования, предъявляемые при выборе шага навивки и чисел витков.
Рис. 2. Пружины после навивки и испытания:
1 — после навивки; 2—после первого обжатия; 3 — после испытания
При изготовлении пружин с напряжениями при кручении выше допускаемых выбор шага навивки и чисел витков для обеспечения требований технических условий достигается многочисленными опытными навивками, зависящими от искусства мастера и обычно сопровождающимися большим процентом брака. При изготовлении пружин с напряжением при кручении в допускаемых пределах шаг навивки и числа витков могут быть выбраны теоретическим расчетом либо опытной навивкой.
Ввиду сложности теоретического расчета шаг навивки и число витков обычно устанавливаются опытным путем. Практически шаг навивки выбирается примерно на 5—8% больше или равным заданному шагу пружины, а число витков — немного больше количества витков, заданных техническими условиями, так как пружина после снятия с оправки раскручивается.
Навивка на пружинонавивальных автоматах
Навивка пружин на токарных станках является примитивным способом изготовления, связанным с последующими весьма трудоемкими ручными операциями:
1) заправкой проволоки в станок для каждой изготовляемой пружины в отдельности;
2) отрезкой навитой пружины от мотка проволоки;
3) разрезкой на отдельные пружины при навивке длинных пружин;
4) разводкой навитой пружины на заданный шаг при навивке вплотную;
5) подбором оправок по заданному внутреннему диаметру пружины и т. д.
Навивка пружин на специальных универсальных пружинонавивальных автоматах, получивших широкое распространение, наиболее рентабельна и высокопроизводительна.
Все перечисленные ручные операции отпадают при применении пружинонавивальных автоматов. Заправка проволоки в автомат производится только один раз при установке нового мотка, а все другие операции: подача проволоки в автомат, сматывание проволоки с мотка, навивка пружины, фиксация заданного шага пружины, прекращение подачи проволоки и отрезка навитой пружины — совершаются автоматически. Рабочий только наблюдает за работой автомата и может обслуживать одновременно несколько автоматов.
На автоматах можно изготовлять пружины любой формы (цилиндрической, конической, бочкообразной и др.) из проволоки любых профилей (размером oт 0,2 до 12 мм) правой и левой навивки и в полном соответствии шага с заданным чертежом.
Автоматы для холодной навивки пружин бывают двух основных типов: секторные и муфтные с прерывистой автоматической подачей проволоки.
Автоматы секторного типа. Они изготовляют пружины с более точной свободной высотой, но максимальную длину заготовки ограничивают до 2 м, т. е. обеспечивают навивку только коротких пружин с повышенной точностью изготовления.
Автоматы муфтного типа. Эти автоматы не обеспечивают навивку пружин с повышенной точностью по свободной высоте, но допускают максимальную длину заготовки до 18 м.
При навивке пружин на автоматах необходимо учитывать, что наружный диаметр пружины должен быть не меньше пятикратного диаметра проволоки, так как в противном случае в деталях автомата при навивке пружин будут возникать большие внутренние напряжения.
Технологический процесс навивки пружин на автоматах включает следующие операции:
1) надевание мотка проволоки на барабан автомата; при этом моток проволоки должен быть расположен таким образом, чтобы положение нити проволоки было на одной линии в процессе навивки;
2) заправка конца проволоки в подающий механизм автомата;
3) настройка узла навивки автомата;
4) навивка 5—10 шт. пружин;
5) выключение автомата;
6) проверка навитых пружин в соответствии с требованиями чертежа;
7) при удовлетворительных результатах проверки пружин продолжение навивки пружин на автомате.
Пружинонавивальный автомат типа «Вафиос». Представленный на рис. 19 автомат относится к типу «Вафиос» УФМ-4. На нем можно навивать пружины, работающие на сжатие и растяжение, различной конфигурации с наружным диаметром 30—160 мм с прижатыми и неприжатыми крайними витками, правой и левой навивки из проволоки 0 6—12 мм. Производительность автомата 5—60 пружин в минуту в зависимости от длины заготовки.
Основные механизмы автомата: правильный, подачи, навивальный, шаговый, отрезной.
Правильный механизм служит для выпрямления проволоки, обычно поступающей в пружинный цех в мотках различных наружных диаметров в зависимости от диаметров проволоки.
Механизм для выпрямления проволоки состоит из нескольких пар правящих роликов с канавками, через которые проволока пропускается в автомат. Верхние правящие ролики могут перемещаться в вертикальной плоскости; при заправке проволоки в автомат они несколько поднимаются и между ними и нижними роликами заправляется проволока. Степень зажатия проволоки между верхними и нижними правящими роликами устанавливается в зависимости от кривизны проволоки. Обычно проволока небольших сечений имеет большую кривизну; в этом случае правящие ролики устанавливаются с такой степенью зажатия, чтобы проволока слегка перегибалась между ними, или же применяется большое количество правящих роликов, располагаемых не только в вертикальной, но и в горизонтальной плоскостях. При применении проволоки, не требующей выпрямления, правильный механизм из работы автомата выключается.
Механизм подачи служит для транспортирования проволоки к навивальному механизму и состоит из двух пар подающих роликов и двух направляющих пластинок с продольными канавками для проволоки.
Подающие ролики имеют комбинированные канавки в соответствии с размером и формой сечения навиваемой проволоки. Размер проволоки обычно указывается на роликах и на направляющих пластинках. Подающие ролики имеют несколько калиброванных канавок для различных размеров проволоки. При закреплении роликов на автомате канавки, через которые пропускается проволока, располагаются ближе к стенке автомата. От степени зажатия проволоки между подающими роликами зависит подача проволоки в автомат к навивальному механизму.
Направляющие пластинки служат для направления проволоки от подающих роликов к навивальному механизму. Для того чтобы во время навивки пружин направляющие пластинки не разбалтывались и не сдвигались после заправки проволоки в имеющиеся прорези направляющих пластинок, их плотно прижимают планками при помощи болтов.
Планки применяют двух размеров в зависимости от диаметра изготовляемых пружин. При навивке пружин большого диаметра применяется короткая планка, а при изготовлении пружин небольшого диаметра — длинная. Эти планки предохраняют проволоку также от искривления.
У описываемых автоматов имеются две направляющие пластинки: одна расположена между подающими роликами, другая — за этими роликами, ближе к навивальному механизму. Устанавливается направляющая пластинка за подающими роликами так, чтобы скошенная грань ее канавки находилась против верхнего отрезного резца, а расстояние между направляющей пластинкой и нижним ножевым шипом было равно 0,5 мм.
После установки направляющих пластинок и плотного зажатия проволоки между подающими роликами они приводятся во вращение и подают проволоку к навивальному механизму. Подача проволоки регулируется кинематической связью подающих роликов с диском подачи, установленном на распределительном валу автомата. Диск подачи состоит из трех кулачков: два кулачка включают и выключают механизм подачи проволоки, а третий предназначен для одновременного включения отрезного механизма. Скорость распределительного вала устанавливается в зависимости от длины изготовляемой пружины при помощи коробки скоростей.
Рис. 3. Пружинонавивальный автомат типа «Вафиос»
Навивальный механизм служит непосредственно для изготовления пружин и состоит из двух навивальных штифтов, вставленных в специальные патроны—штифтодержатели, кинематически связанные между собой и фигурными кулачками, сидящими на распределительном валу автомата.
Навивальные штифты изготовлены из незакаленной стали и имеют канавки в соответствии с размерами перерабатываемой проволоки. Канавки навивальных штифтов выбираются в соответствии с размером проволоки. При отсутствии навивальных штифтов требуемого размера применяются штифты ближайшего большего размера. На каждом навивальном штифте указана длина в миллиметрах, на которую он должен выходить из патрона штифтодержателя. При износе навивальные штифты протачиваются и обрабатываются напильником.
Наладка автомата на требуемый диаметр изготовляемой пружины производится передвижением навивальных штифтов при помощи маховика. Установка пружины на диаметр осуществляется посредством передвижения первого навивального штифта, встречаемого проволокой при выходе ее из направляющей. Второй навивальный штифт устанавливается по шаблону и располагается под углом 45° к горизонтальной оси, проходящей через центр круга пружины. Оба навивальных штифта связаны между собой зубчатыми муфтами, сцепляющимися с шестернями, и их взаимное перемещение осуществляется при помощи изогнутого рычага, один конец которого скреплен со штифтодержателем, а другой — при помощи ролика скользит по фигурному эксцентриковому диску, сидящему на распределительном валу автомата.
Эксцентриковые диски сменные и выбираются в зависимости от формы изготовляемой пружины (цилиндрическая, конусная, бочкообразная и т. д.)
При переналадке автомата с изготовления пружин правой навивки на левую навивальный механизм демонтируется и вновь устанавливается в нижнем положении с поворотом в противоположное направление на 180°.
Шаговый механизм применяется при навивке пружин, работающих на сжатие с крайними прижатыми витками. При помощи этого механизма достигается заданная техническими условиями величина шага пружины. Шаговый механизм состоит из двух шаговых штифтов: верхнего и нижнего, заточенных наподобие язычков. Верхний шаговый штифт предназначен для пружин правой навивки, а нижний — для пружин левой навивки. Шаговые штифты применяются в зависимости от характера изготовляемой пружины и не должны работать одновременно.
При наладке автомата шаговые штифты устанавливаются на заданный шаг; при этом шаг навивки так же, как и при изготовлении пружин на токарных станках, выбирается с учетом уменьшения свободной высоты пружины при дальнейших обжатиях и испытаниях. Шаговый штифт располагается между витками пружины, внутри ее и перпендикулярно ее оси и приводится в движение после образования первого крайнего витка пружины. Шаговый штифт исчезает незадолго до образования последнего витка пружины и возвращается в исходное положение во время навивки последнего крайнего витка пружины. Шаговые штифты при помощи рычагов кинематически связаны с шаговым эксцентриком, состоящим из отдельных секторов различных профилей и сидящим на распределительном валу автомата.
Величина заданного техническими условиями шага пружины и прижатие крайних ее витков достигаются подбором кривой отдельных секторов шагового эксцентрика.
Отрезной механизм предназначен для принудительной отрезки навитой пружины от мотка проволоки и состоит из верхнего отрезного резца и нижнего отрезного шипа, которые находятся вне пружины во время ее навивки.
Пружины отрезаются автоматическим включением отрезного механизма. При этом сначала немного выдвигается вперед в направлении оси пружины отрезной шип, а затем опускается отрезной верхний резец. Отрезной шип имеет закругленную форму, обращенную к навивальным штифтам, и выбирается в зависимости от внутреннего диаметра навиваемой пружины. Устанавливается он в вертикальном направлении так, чтобы отрезаемый виток пружины слегка прилегал к нему. Во избежание упора конца первого витка пружины в шаговой штифт пружину отрезают при крайнем навитом витке следующей пружины.
Автомат снабжен двумя отрезными резцами — коротким и длинным. Короткий резец применяется при отрезке пружин большого диаметра, длинный — при отрезке пружин малого диаметра.
Одновременно с включением отрезного механизма происходит остановка подающих роликов, осуществляемая кулачками, сидящими на распределительном валу и кинематически связанными с отрезным валом. В момент отрезки навитой пружины подача проволоки автоматически прекращается.
Наладка автомата осуществляется путем точной фиксации заданного чертежом числа витков пружины, что достигается автоматической остановкой роликов, подающих проволоку, с одновременной отрезкой изготовленной пружины.
Число витков пружины связано с длиной заготовки пружины, которая либо указывается в рабочем чертеже пружины, либо подсчитывается по формуле. Следовательно, чтобы навить на автомате пружину с требуемым числом витков, достаточно при его наладке точно фиксировать длину заготовки пружины. Для этого к автомату прилагается таблица, в которой указываются скорость хода распределительного вала и длина заготовки пружины, соответствующая определенному номеру положения рукоятки коробки скоростей автомата при повороте отрезного механизма относительно распределительного вала на угол от 1 до 360° с интервалами через 10°.
Если точного числа требуемой длины заготовки пружины в таблице не имеется, то поступают следующим образом. Пусть заданная чертежом длина заготовки пружины равна 1875 мм. По таблице находим ближайшую большую длину заготовки, которая для данного случая равна 2403 мм при скорости хода распределительного вала равной 6. Далее по таблице находим, что скорости хода 6 при 260° соответствует длина заготовки пружины 1838 мм, а при 270° — длина 1908 мм. Значит, требуемая длина заготовки 1875 мм находится между табличными величинами 1908 и 1838 мм. Разность между заданной длиной заготовки 1875 мм и ближайшей, определенной по таблице, 1838 мм будет равна: 1875 — 1838 = 37 мм.
Определив положение кулачка в градусах на распределительном валу автомата и скорость хода последнего, устанавливают рукоятку коробки скоростей соответственно найденным величинам. Переключение скоростей необходимо производить при остановленном автомате посредством маховика ручного привода во избежание возможных поломок передаточных шестерен коробки скоростей.
Наивыгоднейшая наладка автомата достигается при наибольшем градусе установки кулачка подачи проволоки на распределительном валу, так как при этом положении время между остановкой подающих проволоку роликов и их последующим включением будет минимальным.
После установки отрезного механизма и включения выбранной передачи устанавливают навивальный и шаговый механизмы, руководствуясь следующим.
1. При навивке пружин, работающих на растяжение (со всеми прижатыми витками), шаговый механизм не применяется.
2. При навивке пружин, работающих на сжатие без прижатых крайних витков, необходимый шаг пружины устанавливают путем соответствующего регулирования навивальных штифтов без применения шагового механизма.
3. При навивке фасонных и конических пружин на распределительном валу автомата монтируется фасонный кулачок требуемого профиля, который кинематически связывается при помощи рычагов с навивальными штифтами. Можно навивать пружины любой конфигурации путем соответствующего изменения профиля кулачка. Обычно фасонные кулачки прилагаются к автомату и на них указываются род пружин, длина проволоки и нулевые положения. Правильная установка фасонного кулачка на распределительном валу достигается при совпадении нулевого положения с серединой ролика рычага навивального механизма, в начале ввода проволоки. Маховик навивального механизма, которым регулируются навивальные штифты, выключается, так как в противном случае навивальные штифты не смогут перемещаться посредством фасонного кулачка и при пуске автомата неизбежна будет поломка деталей. При изготовлении конических пружин их навивка начинается с малого диаметра.
4. Шаговый механизм монтируется при навивке пружин с прижатыми крайними витками.
После установки сменных деталей всех механизмов автомата производится заправка проволоки. Моток проволоки располагается на барабане на расстоянии 1—1,5 м от автомата. Один конец проволоки пропускается через правящие и подающие ролики в открытую направляющую пластинку.
Конец проволоки, предварительно загнутый, заправляется в канавки навивального штифта, установленного на большой диаметр, вручную или при помощи специального инструмента в зависимости от ее размера. После этого подающие ролики прижимаются друг к другу для создания необходимого натяга и укрепляются, а навивальные штифты продвигают внутрь до тех пор, пока не упрутся в загнутый конец проволоки. Затем загнутый конец проволоки продвигается за навивальные штифты вращением маховика ручного привода автомата. Далее навивальные штифты устанавливаются по штангенциркулю на заданный диаметр пружины, и их положение регулируется винтами штифто-держателей. Конструкция штифтодержателей гарантирует установку диаметра пружины с точностью до 0,01 мм. После этого закрепляют винты и гайки сменных деталей и, вращая вручную маховик ручного привода, изготовляют несколько пружин для проверки правильности наладки автомата. Убедившись в правильности наладки автомата и в том, что навитые пружины удовлетворяют требованиям чертежа, направляющие пластинки закрывают планками и плотно закрепляют болтами; еще раз проверяют крепление всех установленных деталей, после чего приступают к навивке пружин.
Автомат включается поворотом рукоятки, связанной с тягой, останавливается нажатием на педаль 9 ножного рычага; при этом собачка рычага освобождает тягу и пружиной оттягивается назад.
Смазка автомата применяется для предохранения подающих роликов и штифтов автомата от преждевременного износа. Проволока подается в автомат смазанной тонким слоем жира, что достигается путем обертывания проволоки перед правящими роликами ветошью, пропитанной обычным машинным маслом.
Пружинонавивальный автомат типа «Слипер и Хартлей». Автомат типа «Слипер и Хартлей» служит для изготовления пружин, работающих на сжатие и растяжение, из проволоки диаметром от 0,3 до 1,5 мм. В пределах этих размеров проволоки могут быть изготовлены пружины правой и левой навивки с прижатыми и неприжатыми крайними витками и различной формы: цилиндрической, конической, бочкообразной и т. д.
Отличительной особенностью этого автомата является отсутствие у него правильного аппарата, вследствие чего проволока непосредственно от мотка, устанавливаемого на специальной стойке около автомата, поступает в подающий механизм.
Производительность автомата типа «Слипер иХартлей» зависит от числа оборотов распределительного вала, которые можно изменять по своему усмотрению, включая соответствующие сменные шестерни редуктора.
Автомат типа «Слипер и Хартлей» имеет следующие основные механизмы: подающий, навивальный, шаговый, отрезной.
Подающий механизм состоит из двух пар роликов и направляющих: крайней, средней и конечной. Ролики, крайняя и средняя направляющие изготовляются из стали с последующей закалкой и отпуском с тремя ручьями для разных размеров проволоки. Конечная направляющая имеет два ручья и изготовляется также из стали с последующей термообработкой. Направляющие служат для проводки проволоки от подающих роликов к навивальному механизму.
Проволока заправляется непосредственно от мотка (установленного на стойке около автомата) в ручей крайней направляющей и зажимается между первой парой роликов при помощи маховичка. Затем поворотом штурвала ручной подачи в направлении, обратном движению часовой стрелки, проволока пропускается через ручьи средней направляющей и второй пары роликов. Затем по проволоке на инструментальной державке устанавливается конечная направляющая, окончательные размеры которой, зависящие от шага навиваемой пружины и от диаметра перерабатываемой проволоки, придаются путем заточки в процессе наладки станка. После заправки проволоки в ручьи направляющих их во избежание разбалтывания и сдвига во время навивки пружины прижимают при помощи болтов планками.
Рис. 4. Пружинонавивальный автомат типа «Слипер и Хартлей»
После установки направляющих и зажатия проволоки между подающими роликами с достаточным трением для автоматической подачи проволоки к навивальному механизму ролики приводят во вращение.
Рис. 5. Механизмы подачи и навивки автомата типа «Слипер и Хартлей»
Подача проволоки регулируется кинематической связью подающих роликов с кулисной шестерней распределительного вала автомата через кулисный механизм.
Навивальный механизм состоит из оправки, укрепляемой посредством инструментальной державки, и одного навивального штифта, вставленного в специальный патрон. Оправка и навивальный штифт изготовлены из закаленной стали твердостью HRC 60—64.
Оправка имеет срезанную плоскость, необходимую для свободного прохода начального витка пружины. Окончательные размеры и угол наклона срезанной плоскости оправки, как зависящие от диаметра проволоки и пружины, подгоняются заточкой при наладке автомата. Диаметр оправки должен быть немного меньше внутреннего диаметра навиваемой пружины.
Навивальные штифты имеют ручьи, соответствующие диаметрам перерабатываемой проволоки. Окончательные размеры и форма придаются навивальному штифту заточкой при наладке автомата в зависимости от шага пружины и диаметра проволоки и с учетом свободного прохода соседнего витка навиваемой пружины. Навивальный штифт имеет автоматическое поступательное перемещение от распределительного вала, с которым кинематически связан тягой и системой рычагов.
При навивке пружин цилиндрической формы наладка навивального механизма на требуемый диаметр изготовляемой пружины заключается в соответствующей установке навивального штифта при помощи регулирования упора.
Конические и фигурные пружины навиваются при помощи специальных кулачков, устанавливаемых на распределительном валу автомата. В этом случае навивальный штифт устанавливается в соответствующее положение для получения требуемого диаметра пружины перемещением тяги, соединяющей навивальный штифт с распределительным валом и регулированием упора.
Шаговый механизм состоит из шагового штифта с укрепленной на нем шаговой пластинкой и служит для образования шага пружины.
Шаговая пластинка изготовлена со срезанной плоскостью и закруглением, размеры и форма которых также подгоняются при наладке автомата заточкой в зависимости от диаметра, шага и направления спирали изготовляемой пружины и от диаметра перерабатываемой проволоки.
Шаговый механизм при помощи тяги и системы рычагов кинематически связан с распределительным валом автомата, на котором установлены шаговые шестерни. Ход шагового штифта в зависимости от изменения величины рабочей части подъема кулачка, сидящего на распределительном валу, осуществляется вращением маховичка, связанного через тягу и систему рычагов с роликом, скользящим по шаговому кулачку. Изменяя положение ролика по отношению к работающей части кулачка, тем самым изменяем величину хода шагового штифта.
Шаговый механизм регулируется после установки навивального механизма на заданный диаметр пружины вращением маховичка 2 и перемещением ползунка, находящегося внутри автомата. При этом достигается совпадение моментов выхода конца проволоки из оправки с выдвинутым положением шагового штифта.
Отрезной механизм служит для автоматической отрезки изготовленной пружины от мотка проволоки и представляет собой отрезной резец 13, устанавливаемый в специальной державке таким образом, чтобы его режущее ребро проходило над срезанной плоскостью оправки. Ширина режущей кромки резца изготовляется равной диаметру проволоки во избежание отрезки пружины на соседнем следующем ее витке.
Включение отрезного механизма осуществляется при помощи кулачка, сидящего на распределительном валу автомата, и происходит одновременно с остановкой роликов, подающих проволоку.
Наладка автомата производится в зависимости от формы, диаметра и шага пружины и от диаметра проволоки.
Перед наладкой автомата по формуле или по чертежу определяют длину проволоки, необходимую для изготовления одной пружины, и затем по прилагаемой к автомату таблице находят величину эксцентриситета в кулисном механизме, посредством которого движение передается к подающим роликам. Положение эксцентриситета в соответствии с определенной его величиной устанавливается перемещением ползунка вдоль оси кулисной шестерни. Длина проволоки, подаваемой на одну пружину, определяется углом качания кулисы за один цикл.
Навивальный штифт и комплект подающих роликов с направляющими, за исключением конечной направляющей, выбираются и устанавливаются в зависимости от диаметра перерабатываемой проволоки. При установке инструментальной державки руководствуются характером спирали изготовляемой пружины.
При навивке пружины с правой спиралью инструментальная державка устанавливается отверстием с резьбой, служащим для укрепления конечной направляющей, выше ее центра, а отрезной резец монтируется в нижней резцовой державке. При навивке пружин с левой спиралью инструментальная державка укрепляется отверстием с резьбой для конечной направляющей ниже ее центра, а резец устанавливается в верхней резцовой державке.
На распределительном валу монтируются кулачки, управляющие работой навивального, шагового и отрезного механизмов. При навивке конических и фигурных пружин на распределительном валу монтируются кулачки соответствующего профиля.
После установки инструментальной державки в ней укрепляется оправка и монтируется резец в резцовой державке. Оправка монтируется так, чтобы выступала только срезанная ее плоскость, а режущее ребро резца проходило над срезанной частью оправки.
После монтажа навивального и отрезного механизмов проволока заправляется в ручьи крайних направляющих, прижимается с достаточным трением между первой парой подающих роликов и пропускается через ручьи остальных направляющих и второй пары роликов вручную путем поворота штурвала до тех пор, пока конец проволоки не выйдет с обратной стороны направляющей на 30—40 мм. Затем устанавливаются конечная направляющая и планка по проволоке на инструментальной державке. Резец отводится в сторону и в инструментальной державке укрепляется шаговый штифт так, чтобы его внешняя грань касалась внутренней стороны первого витка пружины. Проволока, пропущенная через подающие ролики и направляющие, загибается и пропускается по ручью навивального штифта и вокруг оправки, затем путем поворота штурвала вручную отрезается конец проволоки.
После установки деталей всех механизмов производится настройка вначале навивального механизма на диаметр изготовляемой пружины, а затем шагового механизма путем соответствующего регулирования. Для проверки правильности наладки автомата изготовляют несколько пружин вручную. Установив, что навитые пружины удовлетворяют требованиям чертежа, производят массовую навивку пружин.
Включение и остановка автомата осуществляются кнопочной станцией, расположенной на его передней стенке, или рубильником.
Смазка деталей механизмов автомата производится через индивидуальные постоянные масленки, наполняемые маслом. Смазка же подшипников и шестерен редуктора осуществляется с помощью масляной ванны, расположенной в его корпусе. Масло заливается через отверстие в крышке, выпускается — через отверстие в нижней части корпуса редуктора.
Контроль работы автоматов. Работа автоматов со временем нарушается, вследствие чего изготовляемые пружины могут оказаться негодными. Разброс автомата типа «Слипер и Хартлей», перерабатывающего пружинную проволоку диаметром от 0,3 до 1,5 мм по свободной высоте пружин, как показывает опыт, составляет 3—4%. Поэтому необходимо периодически проверять качество изготовляемых автоматом пружин и в случае образования брака регулировать механизмы.
При массовом изготовлении на автоматах мелких винтовых пружин через каждую сотню навитых пружин проверяют качество двух-трех штук.
Если пружины удовлетворяют всем требованиям чертежа, то это свидетельствует о правильной наладке и работе автомата. При получении неудовлетворительных результатов проверки пружин необходимо проверить наладку автомата.
Реклама:
Читать далее:
Операции при навивке пружин
Статьи по теме:
pereosnastka.ru
Навивка пружин на автоматах :: Книги по металлургии
3.МЕТОДЫ ИСПЫТАНИЯ ПРУЖИННОЙ ПРОВОЛОКИ
Значительная часть дефектов пружин возникает из-за плохого качества пружинной проволоки. Наиболее распространены следующие дефекты:
недопустимый разброс геометрических параметров при навивке вследствие неравномерности механических свойств проволоки по длине и при спутанной проволоке в бунте;
отклонение контрольной нагрузки от номинального значения вследствие несоответствия диаметра проволоки требованиям чертежа;
поломка проволоки при навивке или пружин при испытании из-за недостаточных пластических свойств проволоки, ее внутренних дефектов;
поверхностные дефекты витков, переходящие с проволоки на пружину и снижающие ее динамическую прочность;
значительная остаточная деформация пружины при контроле силовой характеристики и упругих свойств из-за пониженной прочности проволоки и большого обезуглероженного слоя и др.
В большинстве случаев такие дефекты неисправимы, поэтому проволоку перед навивкой следует подвергать контролю и испытаниям различных видов.
Измерение диаметра проволоки и контроль овальности необходимо выполнять измерительным прибором соответствующей точности в двух-трех местах по длине бунта (катушки). Овальность проволоки не должна превышать половины допуска по диаметру.
Поверхность проволоки осматривают невооруженным глазом, с применением лупы пятикратного увеличения, с зачисткой поверхности проволоки в сомнительных местах. Проволока должна иметь гладкую поверхность без трещин, плен, закатов, раковин и ржавчины. На поверхности проволоки допускаются следы волочения в виде рисок, а также омеднение и другие покрытия, применяемые в процессе волочения. Глубина допускаемых рисок не должна превышать половины допуска по диаметру. Глубина обезуглероживающего слоя определяется по ГОСТ 1763—68 и не должна превышать 1% фактического диаметра с каждой стороны. Наиболее распространенный метод определения глубины обезуглероженного слоя — металлографический. Образцы для изготовления шлифов вырезают поперек проволоки механическим способом, не вызывающим изменений в структуре металла. Травление шлифа, выполняемое в 2— 4% -ном растворе азотной или никриновой кислоты в этиловом спирте, должно гарантировать четкое выявление структурных составляющих. Общую глубину обезуглероженного слоя, включающего зоны полного (чистый феррит) и частичного (переходная структура) обезуглероживания, определяют под микроскопом. Измерять следует в месте наибольшей для данного образца глубины.
Микроструктура закаленной и отпущенной проволоки по ГОСТ 1071—67 должна состоят из сорбита или тростосорбита. Наличие в структуре игольчатой ориентировки и участков структурно-свободного феррита не допускается.
Для определения механических характеристик и проверки технологических свойств проводят четыре вида испытаний проволоки: на растяжение по ГОСТ 10446—63, на скручивание по ГОСТ 1545—63, на перегиб по ГОСТ 1579—63, на навивание по ГОСТ 10447—63.
Для неупрочненной проволоки необходимо также измерение твердости по ГОСТ 9012—59 и ГОСТ 9013—59.
Испытание упрочненной проволоки на растяжение является наиболее распространенным, его выполняют на образцах с расчетной длиной 100—200 мм на разрывной машине, максимальная нагрузка которой не превышает пятикратного разрывного усилия проволоки. Характеристика разрывной машины должна соответствовать ГОСТ 7855—74. Полная длина образца должна включать участки для закрепления в зажимах. Тонкая пружинная проволока, обладающая высокой прочностью, часто обрывается в универсальных зажимах, поэтому для ее испытаний применяют специальные зажимы (рис. 12), состоящие из двух пар щечек (гладких и с насечкой). Перед испытанием замеряют начальный диаметр проволоки do, в процессе испытания определяют максимальную силу при разрыве Ртах- Если разрушение произошло в зажимах разрывной машины, то испытание считают недействительным и повторяют его на другом образце. Предел прочности при растяжении определяют как отношение нагрузки к начальной площади поперечного сечения:
После испытаний измеряют минимальный диаметр шейки du и определяют относительное сужение ψ — отношение уменьшения площади поперечного сечения в месте разрыва к начальной площади:
Поскольку модуль упрочнения нагартованной, а также закаленной проволоки сравнительно мал и локализация деформации происходит без заметных остаточных удлинений проволоки, то относительное удлинение при разрыве не проверяют. Полученные при испытании пределы прочности должны соответствовать техническим требованиям. При испытании на разрыв с узлом, применяемым для тонкой проволоки вместо испытаний на перегиб, разрывающее усилие должно составлять не менее 50% разрывающего усилия той же проволоки при испытании ее без узла. Для определения предела пропорциональности и условного предела текучести применяют тензометры с ценой деления шкалы 0,002 мм. Метод определения механических характеристик при растяжении регламентирован ГОСТ 1497—73.
• При испытании проволоки на скручивание выявляются пластические свойства металла. Один из захватов прибора для испытания на кручение должен вращаться, не перемещаясь вдоль осевой линии, другой должен иметь только продольное перемещение для нагружения осевой силой, не превышающей 2% разрывного усилия Ртах- Образец должен быть зажат в захватах так, чтобы в процессе испытания он не проворачивался. Скручивание образца должно проводиться до его разрушения без остановки, с равномерной частотой вращения, не превышающей: 90 об/мин для проволоки диаметром d< 1,5 мм, 60 об/мин для 1,5-3,0 мм, 30 об/мин для r = 3 мм и более.
Расчетную длину образца устанавливают равной 100 d, но не менее 50 мм и не более 500 мм.
Испытание считается недействительным и должно быть повторено на другом образце, если разрушение его произошло в захватах машины или вблизи захватов (на расстоянии менее 5 мм) и образец при этом не выдержал число скручиваний, установленное стандартом или техническими условиями на проволоку. В соответствии с требованиями стандартов и технических условий может проводиться испытание на скручивание с переменой направления кручения.
При испытании на перегиб образец зажимают в губках тисков и с помощью рычага и поводка подвергают знакопеременному изгибу на ±90° через валики. Диаметры валиков, параметры прибора и его конструкция приведены в ГОСТ 1579—63. Последний перегиб, на котором произошло разрушение образца, в расчет не принимают.
При испытании проволоки на навивание используют оборудование, обеспечивающее возможность закрепления и вращение стержня необходимого диаметра с равномерной частотой вращения, не превышающей 60 об/мин. Проволока для пружин ответственного назначения по ГОСТ 1071—67 диаметром <4 мм не должна расслаиваться и ломаться при навивке пяти витков на стержень, равный диаметру проволоки. Проволока по ГОСТ 9389—75 по требованию потребителя не должна ломаться или растрескиваться после навивки пяти витков вокруг стержня, диаметр которого равен тройному диаметру испытуемой проволоки — для проволоки диаметром d>6 мм, двойному диаметру испытуемой проволоки — для d = 4,0—6,0 мм, диаметру испытуемой проволоки—для d<4,0 мм.
4. КОНТРОЛЬ ПРУЖИН
Контроль и испытание пружин является заключительной, операцией их изготовления. Объем испытаний и их виды должны быть указаны в чертеже или технических условиях. Основные требования к готовым цилиндрическим пружинам сжатия и растяжения регламентированы ГОСТ 16118—70.
Наиболее распространенными видами контроля и испытаний пружин холодной навивки являются следующие: наружный осмотр, дефектоскопия; контроль геометрических параметров силовой характеристики и упругих свойств при обычной и повышенной температурах; заневоливание; динамические испытания.
На практике применяют и другие виды контроля и испытаний пружин, например монтажные испытания, испытания коррозионной стойкости пружин после гальванического покрытия контроль интенсивности наклепа при дробеметной обработке (технологический), контроль химического состава материала структуры, глубины обезуглероженного слоя и др.
Предъявленные к приемке пружины подвергают визуальному контролю снаружи, иногда с применением лупы пятикратного увеличения. На поверхности витков не допускаются трещины, волосовины, раковины, расслоения, закаты, ржавчина, а также местная скрученность. Допускаются без зачистки мелкие забоины, морщины, отдельные царапины и риски, а также следы от навивочных оправок и роликов, если они распространены не глубже, чем наполовину поля допуска на диаметр проволоки. В сомнительных случаях глубину дефектов определяют контрольной пологой зачисткой.
Для выявления дефектов (трещин, расслоений) ответственных пружин применяют метод магнитной дефектоскопии. Намагниченные пружины погружают в суспензию магнитного порошка в масле. Благодаря резкому изменению характера магнитного поля в местах нарушения сплошности металла магнитный порошок оседает вдоль трещин в виде черных линий и пятен. Контроль методом дефектоскопии оговаривается в чертеже пружины. Наружный осмотр проводят до и после контрольных испытаний.
Геометрические параметры пружин проверяют как универсальным измерительным инструментом (штангенциркуль, микрометр, угломер), так и специальными калибрами, применяемыми в серийном и массовом производстве. При использовании универсального инструмента наружный диаметр пружины измеряют не менее чем в трех местах во взаимно перпендикулярных направлениях. При контроле калибрами пружина должна свободно проходить через проходную гильзу-калибр, длина рабочей части которой должна быть не меньше утроенного шага пружины. Если пружина предназначена для эксплуатации в ограниченном пространстве, то ее наружный диаметр следует проверять в предельно сжатом состоянии с помощью гильзы. Длина гильзы должна быть на 10% меньше длины сжатой пружины. Пружину при контроле помещают внутрь гильзы и сжимают до соприкосновения витков, при этом необходимо, чтобы гильза свободно перемещалась вдоль пружины. Если в чертеже указан контроль внутреннего диаметра пружины, то проходной контрольный стержень-калибр должен проходить через полость не- нагруженной пружины. Одновременное задание размеров с отклонениями на внутренний и наружный диаметры не допускается. При единичном и мелкосерийном производстве обычно установочным диаметром назначают наружный.
При холодной називке на автоматах наблюдается отклонение пружины от цилиндрической формы, связанное с изменением шага навивки (поджатые торцы и др.). В зависимости от индекса и схемы навивки (сжатие + изгиб, растяжение + изгиб) появляется бочкообразность или корсетность пружины, так как при изменении угла подъема винтовой линии изменяется кривизна и упругая отдача после разгрузки. Кроме того, при без- оправочной навивке (сжатие + изгиб) в моменты реза и начала подачи происходит отклонение от окружности первого витка (преимущественно в сторону увеличения диаметра) вследствие разновидности трения скольжения и трения покоя и от действия усилия реза и усилия внедрения шагового клина. Поэтому при холодной навивке пружин сжатия на автоматах (крупносерийное производство) наиболее удобный способ технологического контроля диаметра при навивке — назначение предельных отклонений на внутренний диаметр и указание максимально допустимого наружного диаметра пружины в свободном состоянии. В этом случае для технологического контроля пружины применяют совмещенные калибры, состоящие из проходного и непроходного стержней-калибров и проходной гильзы.
Проходной стержень-калибр выполняют по высоте равным длине пружины в свободном состоянии, а выступ на торце равен допуску по длине. Высота непроходного стержня-калибра и гильзы должна быть больше половины длины пружины. Калибр окончательного контроля изготовляют для размеров, указанных в чертеже, от технологического он отличается на величину изменения геометрических параметров пружины после отпуска, шлифования торцов и других технологических операций.
У пружин растяжения установочным диаметром является наружный. Полный допуск (поле допуска) диаметра пружин в зависимости от индекса пружины и группы точности выбирают по ГОСТ 16118—70. Точность по геометрическим параметрам: пружин из проволоки d< 1,4 мм, а также пружин, подвергающихся технологической осадке и упрочнению дробью, должна быть не выше II группы.
Длину пружины контролируют с помощью универсального инструмента или при измерении силовых параметров на динамометрических весах.
ТЕХНОЛОГИЯ НАВИВКИ. КОНСТРУКЦИЯ АВТОМАТОВ
1. СПОСОБЫ НАВИВКИ ПРУЖИН
Все существующие методы навивки винтовых пружин можно разделить на две принципиально различные схемы: навивка на оправку по схеме растяжение+изгиб и навивка с помощью подающих роликов на упорные штифты по схеме сжатие+изгиб. Если при навивке по схеме сжатие +изгиб установлен один упорный штифт и необходима оправка для перегиба через нее (или через кромку направляющей планки), то схема докритическая, если же установлены два упорных штифта и перегиб через оправку не требуется, то схема закритическая. Большая часть современных пружинонавивочных автоматов работает по схеме сжатие + изгиб, наиболее применяемые из них двухштифтовые автоматы.
На рис. 37 представлена классификация схем холодной навивки винтовых пружин.
Навивка на вращающуюся оправку — наиболее простой способ, его применяют в единичном и мелкосерийном производстве при ручной навивке на приспособлениях, при механизированной навивке, например с помощью токарного станка. В серийном и массовом производстве применяют специализированные автоматы с вращающейся оправкой (шенкельного типа). На рис. 38, а показана схема навивки пружины на вращающуюся оправку с разводом витков. Развод витков может быть осуществлен или смещением вращающейся справки вдоль оси, или соответствующим смещением направляющей втулки. При навивке пружин без развода витков направляющая втулка приспособления для натяжения проволоки может быть расположена на значительном расстоянии или смещена вдоль оправки с шагом, равным диаметру проволоки. Навивка с отгибом проволоки заключается в том, что проволока подается к оправке под углом 90° — а, причем отгиб происходите сторону навитой части пружины. При такой навивке витки плотно прилегают друг к другу с межвитковым давлением.
Если при навивке на оправку обеспечить скручивание проволоки в направлении к навитой части пружины (рис. 38, б), то в полученной пружине возникает межвитковое давление (предварительная нагрузка). Большее межвитковое давление получается при навивке с отгибом и обкаткой роликом (рис. 38, в). Навиваемая проволока проходит под углом 90° — а к оправке в пазу направляющей колодки 5, по винтовой линии предварительной навивки огибает уже навитую часть пружины 1 и с помощью ролика 2 прижимается к оправке 4 между навитой частью и упором 3.
markmet.ru
Навивка пружин на токарном станке
Навивка пружины на токарном станке
Это техпроцесс, в ходе которого проволока или лента подвергается обработке. В результате чего получаются навивка пружин различной формы: цилиндрической, конической, фасонной или плоской. Основным методом производства считается холодный способ. Навивка пружины выполняется на токарном станке, для этого используется специальное приспособление, вручную или с применением автомата. Производство подобных изделий, возможно и горячим методом, диаметр используемой проволоки от 10 мм. Выбор варианта навивки пружины зависит от размера и типа металла.
Холодный способ изготовления
Технология навивки пружин на токарных станках в России считается более предпочтительной. Обусловлено тем, что горячий способ требует серьезных затрат связанных с приобретением дорогостоящего дополнительного оборудования. Холодный метод имеет ограничения по диаметру проволоки, он не превышает 16 мм. Оснастка для этого техпроцесса состоит из оправок, приспособленных для направления металлической нити на вращающейся катушке.
Вид зависит от формы пружины (цилиндрической, бочкообразной или конической). Приспособление для натяжения и направления проволоки представлено в виде двух вращающихся роликов. Причём верхний имеет винт, который позволяет регулировать натяг и направление. При холодной завивке пружин берется металл с необходимыми качествами, из него делают нужную деталь. В конце проводят термообработку с целью избавления от внутренних напряжений.
Сама технология выглядит так. Стальную проволоку подают через планку, установленную на суппорте оборудования, а конец фиксируется зажимом на оправке. Роликовое приспособление выполняет натяг металлической нити, который важен при изготовлении изделия. После включения станка, начинается намотка пружины, при этом скорость в зависимости от диаметра, используемого материла, находится в пределах 10 – 40 м/мин. Количество витков подсчитывается визуально или счетчиком. По окончании поделка подлежит мехобработке.
Это может быть технология торцовки для пружин сжатия абразивными кругами на специальных автоматах или на промышленных точилах. На изделиях другого профиля технологические концы подлежат обрубке или обрезке, используя специальное приспособление и соответствующий инструмент. Готовый продукт подвергается термообработке в электрических печах.
Технология термической обработки деталей зависит от материала. Для одних марок сталей отпуск и закалка, для других, в том числе и для бронзы – низкотемпературный отпуск, после которого поделки приобретают пружинящие свойства.
Готовую продукцию проверяют и испытывают на соответствие технологическим параметрам (растяжение, сжатие, изгиб, кручение). При необходимости или с согласия заказчика выполняется дополнительная обработка (гальваническое, лакокрасочное или другое покрытие).
Горячий метод изготовления
Навивки пружин на токарных станках таким методом доступны для изготовления изделий из пруткового материала диаметром 10 мм и более. Технологический процесс при этом состоит из ряда этапов:
- обрезка и последующий нагрев;
- оттяжка и вальцовка концов;
- повторный нагрев;
- навивка из нагретого материала;
- отрубаются концы заготовки;
- разводка и правка изделия, последующая термообработка;
- заточка и шлифовка торцов, защита от коррозии, контроль размеров и испытания (прочность, износостойкость и т. п.).
Нагрев заготовки выполняется в короткое время, при этом должно выполниться обязательное условие – равномерный по всему объему прогрев. Для горячей навивки требуется инструмент и оснастка (оправка, молотки, клещи, клинья и т. д.). Все перечисленное навивщику нужно иметь под рукой при выполнении работ по изготовлению пружин. Оправка нужна для навивки пружин на токарных станках, а с помощью клина крепится заготовка на ней. Клещи имеют форму губок обеспечивающих удержание, установку и поворот детали.
В процессе работы нужно руководствоваться технологическими инструкциями, которые обеспечат получение качественных изделий. С целью снижения отходов при изготовлении коротких изделий на оправку укладывается длинная спираль, т. е. делается заготовка на несколько деталей. Процесс навивки пружин на токарных станках большого размера включает практически те же этапы операции, что применяют для средних и мелких заготовок.
Полученные после навивки пружины при эксплуатации, находятся в режиме многочисленных повторяющихся нагрузок. Поэтому они должны иметь высокие характеристики по упругости, в процессе работы выдерживать большое количество повторных загрузок без осадки и поломок. Первое означает, что пружины после нагрузки должны быстро восстанавливать заложенную форму и размеры. Практика показывает, что долговечность продукта, изготовленного на станке, напрямую зависит от качества и чистоты обработки проволоки. На поверхности пружин не должны быть царапины, волосовины, риски и другие дефекты, т. к. они приводят к резкому снижению эксплуатационных качеств изделия.
Важным моментом для навивки пружин считается использование оправок (приспособлений), они предупреждают коробление в момент закалки и при отпуске. Даже если деталь покоробилась при закалке, исправить ситуацию можно насадив ее перед процедурой отпуска на оправку. У пружин большого размера дефект, полученный при закалке трудно исправить, т. к. в этом случае затруднена фиксация на оправке. Чтобы этого не случалось нужно термообработку заготовки проводить уже на ней.
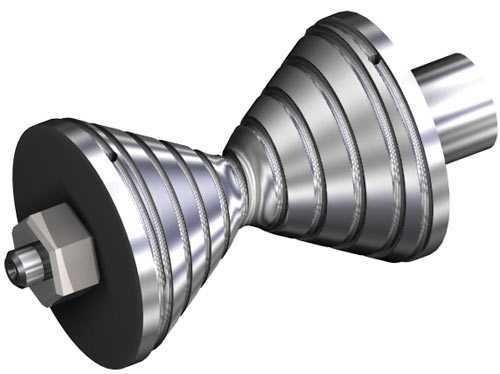
Приспособление для навивки пружин на токарном станке
При любом из двух способов навивки пружин на токарных станках должны обеспечиваться следующие параметры:
- внутренний, средний или наружный диаметр продукта;
- общие и рабочие витки, их число;
- высота и шаг пружины с учетом последующей обработки.
Если вы нашли ошибку, пожалуйста, выделите фрагмент текста и нажмите Ctrl+Enter.
stankiexpert.ru
ПРУЖИНУ — НА ТОКАРНОМ?
Да, на любом токарном станке с полым шпинделем можно навить пружину диаметром до 12 мм из проволоки толщиной от 0,1 до 2 мм. Более того — любой длины. Все это обеспечивается несложным приспособлением, внедренным участниками НТТМ на Ленинградском ордена Трудового Красного Знамени заводе подъемно-транспортного оборудования имени С. М. Кирова. В отличие от подобных устройств здесь узел подачи проволоки благодаря остроумному решению доступен для самостоятельного изготовления даже в сельских мастерских.
Основная деталь приспособления — труба с продольным пазом. Она крепится в задней бабке станка или в кронштейне, установленном на станине, оборудованной передней бабкой и снабженной двигателем.
В продольный паз трубы-направляющей вставлен челнок со втулкой, диаметр которой чуть меньше внутреннего диаметра трубы. Это позволяет челноку свободно перемещаться вдоль паза. Сквозь челнок под углом к осевой его втулки пропущена подающая трубка, через которую и пропускается проволока. А навивается она на стержень-оправку, проходящую внутри трубы через втулку челнока. В зависимости от желаемого диаметра изготовляемой п
i-perf.ru
Холодная навивка пружины
Пружина подвески – ее предназначение
Пружина подвески представляет собой специальную конструктивную механическую часть автомобиля. Основная ее функция – аккумулирование поступающей кинетической энергии.
Именно пружина выступает, как гарантия дорожного просвета автомобиля (клиренса), который установлен автопроизводителем, при нагрузках различной интенсивности. Назначение данной детали – удержание массы автомобиля и максимально возможное сглаживание негативного воздействия существующих дорожных условий (покрытия).
Именно на пружину возлагаются функции обеспечения безопасности во время поездки и комфортной езды. Хорошая, качественная пружина способна значительно уменьшить силу толчков и вибрации, поступающих в салон и кузов транспортного средства. Также, данная деталь, создает оптимальные условия для удержания контакта шин и дороги.
Еще одна немаловажная функция пружин подвески – сведение к минимуму приседания авто при начале движения и клевка во время остановки (торможения). Помимо этого пружина дает возможность увеличить срок эксплуатации такого важного механизма, как амортизатор, а также и многих других конструктивных элементов подвески, в том числе и шин.
К чему приводит износ пружины
Функциональность пружины – очень важна и не только для подвески, но и для всего автомобиля в целом. Износ пружины отрицательно и в высокой степени влияет на безопасность транспортного средства. Поврежденные пружины способствуют увеличению тормозного пути, быстрому износу резины и созданию более сложных условий для управления авто. Пружины необходимо менять, когда они проседают, на них имеются повреждения или они ломаются. Замена пружин возвращает автомобилю его клиренс, позволяет поддерживать хорошее сцепление с дорожным покрытием, увеличивает срок эксплуатации амортизатора и способствует значительному повышению показателей управляемости транспортного средства.
Метод холодной навивки пружин
Изготовление витых пружин может осуществляться различными способами, один из которых – холодная навивка. Холодные пружины навивают на пружинонавивочных автоматах или специальных станках. Технология холодной навивки предусматривает обязательный предварительный визуальный осмотр проволоки, для определения ее состояния. Также следует рихтовать или править проволоку для возможного выявления наличия расслоений. Пренебрежение данными требованиями, зачастую приводит к изготовлению некачественных пружин, которые раньше установленного срока выходят из строя.
Холодная навивка пружин осуществляется по определенной последовательности, этапы которой зависят от диаметра (максимальный диаметр 16мм) используемой проволоки и требуемого размера детали. Иногда, холодная навивка пружин осуществляется вручную на приспособлении, оснащенном ручным приводом, что может отразиться на ее качестве. Это связано с тем, что натяжение проволоки и направление ее во время навивки на оправку может быть выполнено ненадлежащим образом, в случаях несоответствующей квалификации рабочего, задействованного в процессе производства. Так как ручная навивка совершенно непроизводительна, на сегодняшний день она применяется только в процессе изготовления мелких серий деталей или при их единичном выпуске.
Для изготовления больших партий пружин, целесообразно использовать специальные станки и автоматические устройства, которые характеризуются высокой производительностью.
К чему приводят недостатки метода
Сегодня, огромное количество мировых производителей, осуществляющих серийный выпуск пружин, изготавливают их методом холодной навивки. Эта технология довольно распространена, но, несмотря на это, она имеет ряд существенных недостатков. Это связано с тем, что большинство даже самых известных компаний после навивки, не проводят отпуск (термическую обработку) деталей, что необходимо для устранения напряжения внутри пружины, которое всегда образуется во время ее изготовления. Не уделяя внимания этому моменту, расчет пружины осуществляется по сопромату, что и сказывается на качестве изготовленной детали.
Изготовление пружины на автоматических устройствах – довольно быстрый процесс и он составляет всего несколько секунд. Такой способ производства, изначально предусматривает определенные технические характеристики будущей детали. Для увеличения жесткости каждой пружины, производитель может увеличить шаг ее витка, что создает условия для последующего просаживания данной пружины во время эксплуатации. Просадка пружины обусловлена шагом витка, который при любых условиях, занимает свое установленное изначальное расстояние, а имеющиеся твердость прутка и внутренний диаметр детали могут не соответствовать данным условиям. Более твердые прутки при навивке в таком случае имеют склонность к ломкости.
При холодной навивке пружин, когда увеличивается ее высота, создаются определенные условия для увеличения (в прямо пропорциональном отношении) нагрузки на амортизатор. Это, в свою очередь может создать впечатление, что амортизатор попросту не работает. Для устранения данной неисправности, как правило, устанавливаются более тугие амортизаторы с целью увеличения временного промежутка хода рычага до отбойника или хода моста. Тугой амортизатор (двусторонний) в процессе эксплуатации, берет на себя некоторую часть работы холоднокатаной пружины, а это совершенно недопустимо, хотя и способствует устранению возможности пробоин подвески. Двусторонний амортизатор целесообразно эксплуатировать при удовлетворительных дорожных условиях – во время езды по асфальтированной поверхности. Но, к сожалению, российские дороги далеки от совершенства, поэтому холоднокатаные пружины в большинстве случаев не могут обеспечить полноценное выполнение функций подвески.
Также, к недостаткам пружин, которые изготовлены холоднокатаным методом, можно отнести их показатели сопротивления нагрузки, которые близки к линейным (торсионным).
Вышеперечисленные недостатки сказываются на характеристиках пружин, что и влияет на долговечность их эксплуатации. Стоит остановиться более подробно на тех причинах, которые способствуют выходу из строя пружин.
Самой распространенной причиной износа пружин подвески считается усталость металла. Это понятие обозначает разновидность износа, которая возникает на фоне вибраций и нагрузок. Усталость металла накапливается постепенно, в результате чего деталь деформируется наличием все большего количеством повреждений, которые в определенный момент становятся причиной окончательного разрушения пружины.
Повреждения поверхности и коррозия – причины, способствующие преждевременному износу пружин и выходу их из строя. Также, пружины слабеют в связи с ударами камней, нарушением геометрических показателей, повышенных нагрузках, полном сжатии, постоянными перегрузками. Далеко не все современные дорожные покрытия дают возможность эксплуатировать автомобиль в оптимальных условиях. Именно поэтому, большому количеству владельцев транспортных средств знакомы различные проблемы с подвеской. Многие из них, в свою очередь, спровоцированы именно выходом из строя или повреждением пружин, которые изготовлены холоднокатаным способом. Некачественные пружины, которые быстро выходят из строя, создают условия для различных нарушений работы подвески и увеличения жесткости.
Некоторые последствия износа пружин могут быть довольно опасны. Так, например, изношенная пружина в некоторых случаях приводит к нарушению управляемости транспортным средством и во время езды авто уводит в одну сторону. Такая неисправность, как угловые колебания рулевого колеса – также может являться следствием изношенных, сломанных или поврежденных пружин. Колебания возникают самопроизвольно, и автомобиль теряет свою устойчивость. Это может привести к полной потере управляемости транспортным средством.
Частые пробои подвески – результат поломки или износа пружин. Пробои являются одним из основных признаков просадки пружины, наряду с ухудшением плавности хода автомобиля, перекосом его задней и передней частей и заметная разница по высоте. Холоднокатаная пружина – одна из причин частых пробоин на дороге, которые происходят даже во время преодоления незначительных препятствий, таких как небольшая яма, лежачие полицейские и.т.п. Это происходит в связи со свойством холоднокатаной пружины быстро терять высоту, что создает условия для передачи даже малейших ударов в кузов или салон автомобиля, так как в момент преодоления препятствия, подвеска упирается в демпферные резинки.
На основании вышесказанного можно сделать вывод, что во время езды по дорогам России, подвеска с холоднокатаными пружинами, дает возможность почувствовать множество недостатков ее недоработки. Это может привести, как к незначительным поломкам, так и к ситуациям на дороге, которые могут быть опасны. Качество российских дорог на сегодняшний день далеко от идеала, в связи с чем, каждый владелец автомобиля вынужден прибегать к частому ремонту автомобиля и искать способы устранения возможных поломок, появляющихся из-за дорожных условий. Нельзя не согласиться, что российское бездорожье в гораздо большей степени, чем западное, приводит к износу холоднокатаные пружины и способствует их преждевременному выходу из строя. И не всегда владелец автомобиля ограничивается только лишь заменой пружин. В большом количестве случаев, наряду с их заменой, приходится сталкиваться и с ремонтом подвески, что еще более трудоемко и затратно.
www.vlad-springs.com
Навивка пружин – Гибка и правка металла
Навивка пружин
Категория:
Гибка и правка металла
Навивка пружин
Пружиной называют пластинку или спираль, способную под действием определенной силы изменять свое первоначальное положение и восстанавливать его после прекращения действия этой силы. По форме пружины разделяются на цилиндрические, конические и спиральные, а по роду работы — на пружины, работающие на сжатие, растяжение и скручивание. На рис. 1 показаны наиболее часто встречающиеся пружины — цилиндрическая, коническая и специальная.
Рис. 1. Пружины: а — цилиндрическая, работающая на сжатие, б — коническая, работающая на растяжение, в — специальная пружина, работающая на скручивание, d— диаметр проволоки, Ден~ внутренний диаметр пружины, Д —наружный диаметр пружины, 1 — шаг пружины
Цилиндрическая пружина замеряется двояко: по внутреннему диаметру, если она должна быть посажена на шток или стержень (внутренний диаметр пружины необходимо также знать при подборе диаметра оправки для навивки пружины), и по наружному диаметру, если пружина должна быть заключена в трубу или в какое-либо отверстие. Наружный диаметр пружины равен внутреннему диаметру плюс два диаметра проволоки, из которой сделана пружина.
Средний диаметр пружины практически не измеряется; он служит лишь для производства технических расчетов.
У пружины различают шаг и длину.
Шагом называется расстояние между средними (осевыми) линиями двух витков, измеренное по оси пружины, или, иначе, расстояние между началом и концом одного витка при свободном положении пружины.
Пружины небольшого диаметра навивают в тисках на^цилин-дрической оправке. Диаметр оправки должен быть меньше внутреннего диаметра пружины, так как пружина после снятия ее с оправки немного расходится, т. е. увеличивается в диаметре. На конце оправки сверлят отверстие диаметром на 0,1—0,2 мм больше диаметра проволоки, из которой навивается пружина. Конец пружинной проволоки заправляют в отверстие и в холодном или нагретом состоянии загибают проволоку под углом, чтобы она при навивке не соскочила с оправки. Оправку со вставленной в ее отверстие проволокой зажимают в тисках между деревянными, свинцовыми или медными нагубниками (зажим должен быть такой силы, чтобы оправка могла туго вращаться в нагубниках) и, придерживая левой рукой проволоку, начинают правой рукой вращать оправку при помощи рукоятки.
Рис. 2. Навивка пружины: а — в тисках при помощи ручных тисочков или с помощью изогну» того стержня, б — на токарном станке, в — на сверлильном станке
Закончив навивку пружины, откусывают конец проволоки кусачками или отламывают его, сделав предварительно надрез трехгранным личным напильником или надфилем. Затем отрезают противоположный конец проволоки, вставленный в оправку.
Если полученная пружина по длине рассчитана на то, чтобы из нее сделать несколько отрезков (несколько пружин), то ее разрубают на части соответственно требуемым размерам. Делают это вручную зубилом при помощи приспособления (рис. 3) или на реечном прессе.
У нажимных (работающих на сжатие) пружин концы прижимают к телу пружины и, кроме того, затачивают. Обработка концов пружин показана на рис. 4,а,б. Чтобы прижать конец пружины, ее последний виток нагревают пламенем газовой горелки или паяльной лампы. При этом пламя пропускают через направляющую трубку и виток пружины вставляют в трубку так, как показано на рис. 1, е. Как только виток нагреется до красного каления, его вынимают из трубки и быстро прижимают пружину к какой-либо плоской поверхности. После обжатия концы затачивают на шлифовальных кругах. Сначала делается грубая обдирка, а затем окончательная заточка, у пружин, работающих на растяжение, концам придают форму полукольца или кольца. Сначала полукольцо или кольцо отгибают на 60 или 90й, потом его отводят в центр.
Рис. 4. Обработка концов пружины: а — концы не обработаны, б — концы обработаны, прижаты и заточены, в — нагрев конца пружины в трубе перед обработкой, г — концы пружины, заделанные в виде полукольца, д — концы пружины, заделанные в виде коль, ца, е — отводка кольца и окончательная обработка его в приспособлении
Реклама:
Читать далее:
Брак при правке и гибке металла и правила безопасной работы
Статьи по теме:
Главная → Справочник → Статьи → Блог → Форум
pereosnastka.ru
Пружина – холодная навивка – Большая Энциклопедия Нефти и Газа, статья, страница 1
Пружина – холодная навивка
Cтраница 1
Пружины холодной навивки, изготовленные из холоднотянутой проволоки диаметром до 7 мм, только отпускают. Отпуск пружины из проволоки диаметром больше 1 мм производят в печах при температуре 400 – 420 С с выдержкой 5 – 10 мин. [2]
Большинство пружин холодной навивки изготовляют из проволоки, прошедшей термическую обработку до навивки, и после навивки пружину подвергают только отпуску. Все пружины горячей навивки и наиболее ответственные пружины холодной навивки, в частности, из большинства легированных сталей, подвергают закалке в навитом состоянии. Благодаря этому происходит укрупнение зерна, и проволока при окончательном волочении получает большой наклеп и упрочняется. [3]
Большинство пружин холодной навивки изготовляют из проволоки, прошедшей термическую обработку до навивки, и после навивкп пружину подвергают только отпуску. Все пружины горячей навивки и наиболее ответственные пружины холодной навивки, в частности, из большинства легированных сталей, подвергают закалке в навитом состоянии. Благодаря этому происходит укрупнение зерна, и проволока при окончательном волочении получает большой наклеп и упрочняется. [4]
При выборе шага пружины холодной навивки должна быть учтена возможность получения такого шага на автомате. [5]
Примеры технологии термической обработки пружин: светлая закалка пружин холодной навивки из проволоки диаметром до 6 мм из стали 60С2А i 1 ]; нагрев пружин под закалку в электродной соляной ванне ( NaCl) до 820; закалка в щелочной ванне ( 63 % КОН и 37 % NaOH) при 270 в течение 20 мин. [6]
Пружины холодной навивки, изготовленные из холоднотянутой проволоки диаметром до 7 мм, подвергаются только отпуску, пружины из проволоки больших диаметров подвергаются закалке с последующим отпуском. [8]
Осаживание опорных витков производят разными приемами. У пружин холодной навивки опорные витки осаживают после навивки вручную или в приспособлениях, состоящих из оправки со спиральной нарезкой, с шагом, равным шагу рабочих витков, ввертываемой в центральную часть пружины так. [10]
После навивкп такие пружины подвергают тщательной термообработке. Для изготовления пружин холодной навивки из предварительно подготовленного материала, подвергаемых после навивки только отпуску, обычно используется углеродистая проволока. Легированные пружинные стали применяют главным образом для пружин, подвергаемых термообработке в готовом виде. Исключение составляют кремпевольф-рамовая и хромованадиевая стали, которые в виде предварительно подготовленного холоднокатаного материала используются для изготовления ответственных ( клаианных) пружин. [11]
Последующая термическая обработка этих пружин ( закалка и отпуск) производится аналогично обработке крупногабаритных пружин горячей навивки. Помещенные в таблице последние четыре марки стали для изготовления пружин холодной навивки не применяются. [13]
Страницы: 1
www.ngpedia.ru