ТЕХНОЛОГИИ ОБМАНА: СВАРОЧНЫЕ АППАРАТЫ MMA
Статья бренд-менеджера ТМ BestWeld Шкляревского Ю.
ТЕХНОЛОГИИ ОБМАНА: СВАРОЧНЫЕ АППАРАТЫ MMA
Сварка штучным электродом на просторах бывшего СССР имеет традиционное отечественное название – Ручная Дуговая Сварка, или сокращенно РДС. В западном мире и среди соотечественников, приступивших к освоению этой технологии не так давно, распространено англоязычное название MMA (от Manual Metal Arc – в буквальном переводе «ручная дуговая сварка металлов»). Речь идет абсолютно об одном и том же процессе.
Китайская промышленная революция сделала сварочное оборудование доступным для сотен миллионов людей с точки зрения цены. А применение инверторных технологий резко снизило уровень требований к уровню подготовки сварщика и к мощности источника электропитания. В итоге со второй половины нулевых годов мировой рынок инструмента потряс настоящий бум сварочного оборудования. В первую очередь, MMA: не менее 9 из 10 аппаратов, приобретаемых в розницу в нашей стране, относятся именно к ручной дуговой сварке штучным электродом.
НЕОДИНАКОВЫЙ ОДИНАКОВЫЙ СВАРОЧНЫЙ ТОК: ОДИН ВАРИТ, ДРУГОЙ НЕТ
Одной из немногих характеристик сварочного аппарата, в которых потребители разбираются хорошо (или думают, что разбираются), является диапазон сварочного тока. Причем главной является именно верхняя граница диапазона. Даже не искушенному в электрических процессах человеку понятно, что чем больше сила тока, выдаваемая аппаратом, тем лучше. По крайней мере, тем легче будет идти сварочный процесс.
Зерно разумного в таком предположении есть, но в целом оно ошибочно. Любой продавец в магазине сварочного оборудования пояснит, что чем выше сила максимального тока, тем больше диаметр электрода, который можно использовать с данным аппаратом. Подбор типа и диаметра электрода зависит от многих параметров, но непрофессиональным сварщикам обычно рекомендуют электроды АНО-21 или МР-3 из расчета диаметра «1 к 1»: чтобы диаметр электрода приблизительно был равен толщине свариваемого металла. Отсюда и выбор аппарата по току: ориентировочно 40-50А сварочного тока на 1 мм диаметра электрода. Еще раз, обе эти «методики» расчета – и диаметра электрода, и тока, требуемого для работы им – очень неточные. Зато просты и доступны для человека с ограниченным опытом или вообще без него. Именно ими, а не справочными таблицами, пользуется большинство обученных продавцов в профильных магазинах.
И вот покупатель определился с решением: будет варить электродом до 4,0 мм включительно. Значит, аппарат нужен, чтобы выдавал 160-200А сварочного тока. В магазин пришли 2 соседа по дачам. Один берет «по-минимуму» – аппарат на 160А. Второй с запасом – на 200А. Благо, разница в цене незначительна. Производитель первого заявляет, что аппарат справится с электродом до 4,0 мм, второго – до 5,0 мм.
Оба покупателя остаются довольными до того момента, пока решают попробовать свои аппараты в деле на электродах 4,0 мм. И вот тут вдруг обнаруживается удивительный сюрприз: поочередно подключаемые к одному и тому же источнику питания, аппарат с пределом в 160А 4,0-мм электрод «тянет». А аппарат с заявленным пределом в 200А 4,0-мм электрод поджигает, но дугу вести не дает – сразу обрывает. Про 5,0-мм электрод и говорить нечего. Расстроенный покупатель идет в сервисный центр, где его аппарат ставят на стенд и наглядно демонстрируют, что тот выдает даже больше заявленных 200А. Может, все 250А. Так что к аппарату претензий быть не может, и проблемы нужно искать где-то еще: в источнике электропитания, используемых электродах или вообще в том месте, откуда руки растут. Как же такое возможно???
Точно так же, как при игре в наперстки или обмене валюты с рук. Хотя иногда у поставщика оборудования нет заведомого умысла обмануть покупателя. Возможно, выдача менее мощного оборудования за более мощное происходит вследствие элементарной безграмотности. Но нередко, если верить менеджерам китайских заводов, это прямое указание российских (а также украинских, азиатских, ближневосточных, африканских и многих других) импортеров.
Оптимальный режим работы при сварке штучным электродом подразумевает ведение электрода на расстоянии от поверхности свариваемого металла, приблизительно равном диаметру электрода. (Точно выдерживать это расстояние, конечно, невозможно, но с опытом получается неплохо). Для поддержания дуги, т.е. перетекания электрического тока, требуется электрическое напряжение. И не какое-нибудь, а строго определенное. Рабочее сварочное напряжение регламентируется отечественными и международными стандартами. Оно должно составлять:
Uсв=20+0,04*Iсв,
где Iсв – сварочный ток.
Несложно подсчитать, что для тока 160А сварочное напряжение должно составлять 26,4В, а для тока 200А – 28В. Практически на любом сварочном аппарате ММА можно обнаружить табличку, обычно отпечатанную прямо на корпусе, где обязательно указаны эти два показателя – сварочного тока (I2) и сварочного напряжения (U2).
Именно тот максимальный ток, для которого сварочный аппарат способен обеспечить предписываемое стандартом сварочное напряжение, и является его фактическим максимальным током. Иначе этот показатель называют максимальным номинальным током сварочного аппарата, или просто номинальным током аппарата. Так что, если ваш аппарат «не тянет» электрод, проверить нужно не только выдаваемый им сварочный ток, но и выдаваемое при этом сварочное напряжение.
Если последнее недотягивает до положенного по стандарту уровня пару вольт, аппарат расчетным электродом варить будет. Электрод придется вести ближе к свариваемому металлу, т.е. поддерживать более короткую дугу. Это неудобно и чревато непроизвольным «чирканьем». Но все-таки для опытного сварщика не смертельно – шов положить получится, хотя и не без мучений. При сварочном напряжении ниже 20 Вольт вести 3-4 мм электродом дугу не удастся в принципе.
«Зачем же так делать аппараты?» – наивный вопрос. Чтобы сэкономить на комплектующих. Чаще всего с умыслом привлечь покупателя, выдавая менее мощный аппарат за более мощный. Ведь величина номинального тока сварочного аппарата всецело зависит от источника питания и его собственной мощности. А собственная мощность определяется мощностью основных компонентов самого аппарата: высокочастотного трансформатора, конденсаторов, транзисторов, реле. Естественно, чем мощнее компонент, тем дороже.
Если мощности источника питания недостаточно для обеспечения выходной мощности аппарата (произведение сварочного тока на сварочное напряжение), то, конечно, даже самая добросовестная комплектация аппарата ситуацию не спасет. Однако если в аппарат вставлены компоненты, не способные обеспечить заявленную мощность на выходе, то тут уж возможности источника питания ни при чем. Хоть к гидроэлектростанции подключай, а повысить мощность на выходе не удастся.
НЕОДИНАКОВЫЙ ОДИНАКОВЫЙ СВАРОЧНЫЙ ТОК-2, ИЛИ ВОЛЬТ-АМПЕРНАЯ ХАРАКТЕРИСТИКА (ВАХ)
Сложновато? Если нет, то об этом же еще более сложно, зато наглядно. Я имею ввиду вольт-амперные характеристики аппаратов, а если точнее, параметров выдаваемой ими сварочной дуги (это не одно и тоже, но для простоты понимания будем считать, что одно).
Режим обеспечения аппаратом сварочного тока и соответствующего сварочного напряжения обеспечивается только в определенном диапазоне выдаваемого сварочного тока. Этот диапазон называется рабочим диапазоном сварочного тока аппарата – на рис. соответствует отрезку «B». В пределах этого диапазона сварочное напряжение с изменением сварочного тока изменяется незначительно – по упомянутой выше формуле 20+0,04*Iсв. Получается, что разница между сварочными токами 160А и 200А составляет 40 ампер. В то же время разница между сварочными напряжениями, соответствующими этим токам, – всего 1,6 вольта.
А что лежит в диапазоне ниже минимальной и выше максимальной границ сварочного тока?
На токах ниже минимальной границы рабочего диапазона (отрезок «A» на диаграммах ВАХ выше) сварочное напряжение значительно превышает требуемое стандартом. Однако этот участок соответствует очень важному этапу сварочного процесса – поджигу сварочной дуги. Чем выше напряжение до момента возникновения дуги, тем легче ее поджиг. (Ниже вопрос уровня напряжения холостого хода разъясню подробнее). С поджигом дуги напряжение снижается до рабочего.
Гораздо интереснее поведение сварочной дуги различных аппаратов за пределами верхней границы диапазона рабочих токов (на диаграмме выше отрезок «С»). Потому как ведут себя разные аппараты по-разному. Одни аппараты за пределами верхней границы рабочего диапазона удерживают сварочный ток на уровне, близком к уровню верхней границы. О таких аппаратах говорят, что вольт-амперная характеристика у них крутопадающая, или «штыковая» (левая диаграмма). У других аппаратов по достижении предела рабочего диапазона ток продолжает расти, но сварочное напряжение падает. Чем выше ток, тем ниже сварочное напряжение. О таких аппаратах говорят, что вольт-амперная характеристика у них полого падающая (правая диаграмма).
Падающий отрезок ВАХ начинается с номинального тока аппарата. Эта точка на диаграмме соответствует достижению максимума мощности аппарата. Дальнейшее увеличение сварочного тока может достигаться только за счет одновременного снижения сварочного напряжения. Кульминацией роста тока аппарата является момент «втыкания» электрода в свариваемый металл. Т.е. короткое замыкание электрода на свариваемый метал. При прямом контакте сопротивление минимально, и ток достигает максимума.
Получается, что аппараты со «штыковой» ВАХ имеют максимальный сварочный ток, близкий к току короткого замыкания. При «втыкании» электрода в листовой металл такой аппарат его не прожжет, если только ток подобран правильно. Аппараты с полого падающей ВАХ имеют «значительный запас по току», т.е. способны выдавать ток, существенно превышающий номинальный. При этом уровень напряжения, естественно, обратно пропорционален току. Такие аппараты при «втыкании» электрода в листовой металл вполне прожечь его могут, даже если ток сварки был подобран правильно, – ведь при «втыкании» сила тока резко возрастет. Все зависит, конечно, от толщины металла и величины тока на режимах, близких к короткому замыканию.
Если посмотреть на проблему с мошенничеством на мощности аппаратов с точки зрения вольт-амперных характеристик, получается, что недобросовестные (реже неграмотные) производители и импортеры конструируют аппараты с полого падающей характеристикой, выдавая их нерабочий диапазон токов за рабочий. Т.е. выдавая менее мощные аппараты, рассчитанные на меньшие номинальные сварочные токи, но с полого падающей характеристикой, за более мощные аппараты, рассчитанные на большие сварочные токи.
На приводимом выше изображении двух ВАХ, схематически выполненном автором в «детском» редакторе Paint Brush без претензий на какую-либо точность, тем не менее, видно, что штыковая ВАХ слева принадлежит более мощному аппарату, чем полого падающая ВАХ справа. Номинальный сварочный ток у аппарата с ВАХ, приведенной слева, выше. Но ток короткого замыкания у полого падающей ВАХ справа значительно выше. Такая картина соответствует описанному в начале примеру, когда аппарат на 160А способен варить электродом 4,0 мм, а аппарат «на 200А» нет.
ФОКУС-ПОКУС: «АВТОМАТИЧЕСКАЯ» ФУНКЦИЯ ФОРСИРОВАНИЯ ДУГИ ARC-FORCE
Применение электроники позволяет делать оборудование «умным». Инженеры научили сварочные инверторы предугадывать некоторые типовые проблемы сварщика в процессе работы и помогать, компенсируя ошибки человека. Так аппараты, оборудованные функцией Arc Force, отслеживают увеличение длины дуги и на непродолжительное время (доли секунды) форсируют (т.е. увеличивают) подаваемый ток. Если рука просто дернулась, а не специально отводится с целью прерывания шва, такая помощь аппарата удержит дугу, позволив быстро вернуть руку в правильное положение и продолжить шов. Если же рука в отведенное время не вернулась в нормальное положение, это с высокой вероятностью указывает на то, что сварщик отвел руку не случайно. Ток отключается. Очень полезная функция, настоящее достижение научно-технического прогресса! Это понимают практически все производители и импортеры. Поэтому практически все рекламируют данную функцию на своих инверторных аппаратах. В том числе те, на чьих аппаратах ее нет. А таких большинство.
Признаком наличия функции форсирования дуги Arc-Force на аппарате является ручка, регулирующая силу набрасываемого при срабатывании Arc-Force тока. Если же на панели управления в гордом одиночестве красуется лишь ручка регулировки силы тока, с высокой вероятностью никакой функции форсирования дуги в аппарате не предусмотрено. Зато аппарат имеет пологую ВАХ, обеспечивающую при укороченной дуге ток заметно выше номинального. Т.е. на стенде он может продемонстрировать «дополнительный» ток сверх заявленного номинального. Но удержать дугу этот ток никак не поможет. Еще раз см. случай выше с аппаратом на 200А.
Кстати, помните, что даже аппараты с действительно присутствующей функцией Arc Force не способны форсировать сварочный ток, если Вы и так работаете на его пределе. На языке действий это означает, что если ваш аппарат рассчитан на номинальный ток 160А, а в режиме срабатывания Arc Force набрасывает до 20А, при срабатывании функции в режиме 120А, аппарат форсирует ток до 140А. Но в режиме работы на предельном токе 160А набрасывать ему уже нечего – в таком режиме вся мощность аппарата уже задействована. Поэтому, если продавец Вас уверяет, что «это аппарат на 160А, но с включенным режимом форсажа – все 180», это очень маловероятно. Зачем производителю оставлять не реализованной мощность аппарата «про запас» для функции Arc Force? Непозволительная роскошь – ведь эту мощность можно задействовать не для краткосрочных набрасываний тока, а постоянного использования. Т.е. для увеличения верхней границы диапазона рабочего тока.
НЕ ДРЕВНИЕ, НО МИФЫ: ОБ ЭНЕРГЕТИЧЕСКОЙ ЭФФЕКТИВНОСТИ
Важный вывод из изложенного выше: при одной и той же силе сварочного тока уровень сопутствующего ему сварочного напряжения у всех сварочных аппаратов должен быть одинаковым. Он определяется отечественными государственными и международными стандартами, которые, кстати, полностью совпадают. Соответственно, мощность на выходе всех сварочных аппаратов при одинаковом сварочном токе тоже должна быть одинакова:
Pвых=Iсвар*Uсвар,
Где Pвых – мощность на выходе аппарата, Iсвар – выдаваемый аппаратом сварочный ток, Uсвар – сварочное напряжение, соответствующее сварочному току по ГОСТ (=20+0,04*Iсвар). Например, выходная мощность при сварочном токе 160А у любого аппарата должна быть:
Pвых=160А*(20+0,04*160)=4,24кВт
Ну это на выходе – понятно, у всех должно быть одинаково. А на входе? Это же важный вопрос: какова должна быть мощность электрического источника, чтобы к нему можно было подключить сварочник? Полная потребляемая от источника мощность сварочных аппаратов конечно, может отличаться. Но чтобы понять, в каких пределах и насколько, предлагаю разобраться, от чего она зависит.
Мощность на выходе сварочного аппарата – это только часть мощности, поступающей на него из розетки или от генератора. В процессе работы электрические компоненты греются и отдают тепло в окружающую среду. Отношение мощности на выходе к непосредственно потребленной мощности на входе называется коэффициентом полезного действия, или сокращенно КПД. Для современных инверторных аппаратов этот показатель обычно лежит в пределах от 80% до 90%. Для расчетов можно брать 85%.
Итого, инверторный сварочный аппарат с номинальным током 160А с КПД 85% потребляет активную мощность, равную:
Pакт=Pвых/КПД
Пример расчета потребляемой активной мощности аппарата для сварочного тока 160А:
Pактив=160А*(20+0,04*160)/0,85=4,97кВт
Но это еще не все. Сварочный аппарат относится к типу приборов, преобразующих в выходную мощность и потери на КПД не всю электроэнергию, потребляемую от источника. Часть этой энергии он возвращает в сеть, не потребив. Возвращенная часть мощности называется реактивной мощностью. Специфика данной статьи не позволяет подробно разложить графики синусоиды тока и напряжения переменного тока, проходящего через сварочный аппарат, и продемонстрировать, откуда берется реактивная составляющая мощности, что такое «сдвиг по фазе» (он же «коэффициент мощности») и как его рассчитать. Вам придется поверить мне на слово, что чтобы получить полную мощность источника питания, требуемую для аппарата, активную мощность придется разделить на тот самый коэффициент мощности, иначе называемый «косинус фи» или еще «косинус угла сдвига по фазе». Опять-таки, Вам придется поверить мне на слово, что для большинства «приличных» современных сварочных инверторов он лежит в пределах 0,8-0,9. Для удобства я беру ту же усредненную цифру, что и для КПД – 0,85. Итого:
Pполн=Pактив/Кмощности
Пример расчета потребляемой полной мощности аппарата для сварочного тока 160А:
Pполн=(160А*(20+0,04*160)/0,85)/0,85=5,85кВА
Обратите внимание, что полная мощность измеряется в Вольт-Амперах (ВА), а не в Ваттах (Вт). Для приборов, преобразующих 100% потребляемой электроэнергии в тепло, показатели в ВА и Вт будут равны. Но не для сварочного аппарата. Рекомендую Вам пользоваться упрощенной формулой, выведенной выше:
Pполн= Iсвар*Uсвар /0,85/0,85
Зачем пользоваться? Чтобы сразу определить, не вводит ли Вас продавец или производитель в заблуждение. Да и Вам полезно знать, выдержит ли ваш источник электроэнергии подключение сварочного аппарата.
Например, продавец нахваливает Вам аппарат на 160А номинального тока, заявляя, что у него суперэффективное энергопотребление и что с его помощью Вы сможете варить электродом 3,2 мм от обычной бытовой 16-амперной розетки, которая, кстати, рассчитана не более чем на 3,5кВА (16А*220В=3,52кВА).
Какой ток потребуется для ведения работ электродом 3,2 мм? Ну даже из расчета 40А на 1 мм диаметра:
Iсвар=40Ах3,2мм=128А
Какое сварочное напряжение должен обеспечивать аппарат при токе 128А?
Uсвар=20+0,04*128А=25,12В
Теперь осталось подставить полученные значения сварочного тока и соответствующего ему сварочного напряжения в формулу полной мощности:
Pполн= Iсвар*Uсвар /0,85/0,85
Pполн= 128А*25,12В/0,85/0,85=4450ВА=4,45кВа
Продавец вводит в заблуждение. Даже если предлагаемый аппарат и потянет электрод 3,2 мм током 128А, ему нужен для этого источник минимум 4,45кВА. Подключение к розетке 16А в случае продолжительной работы может вызвать перегрев самой розетки или проводки. Хотя, скорее всего, выбьет пробки.
С минимальным уровнем энергопотребления понятно. А можно ли рассчитать максимальный уровень мощности источника, который может потребоваться аппарату?
Увы, нет. Все приведенные выше формулы позволяют произвести расчеты для оптимального режима сварки, при котором длина дуги приблизительно равна диаметру электрода. Формулы для расчета сварочного напряжения в зависимости от длины дуги тоже существуют. Но вот предсказать поведение аппарата при растягивании дуги только на взгляд нельзя.
На большинстве современных сварочных инверторов растянуть дугу сильно длиннее диаметра электрода не удастся. Компоненты аппарата рассчитаны по мощности впритык.
Хороший аппарат (почти всегда со штыковой вольт-амперной характеристикой) иногда небольшой запас по мощности имеет. При растягивании дуги потребляемая мощность такого аппарата начинает расти. Чтобы не перегружать источник питания, такие аппараты оборудованы функцией ограничения потребляемой мощности. Как только входной ток превышает определенный уровень, срабатывает схема ограничения, и сварочный ток на выходе сбрасывается.
Редко, но попадаются представители китайской промышленности, обладающие значительным запасом по мощности и не оборудованные ограничителем мощности. В частности, автор испытывал аппарат на номинальный ток 200А, который удерживал растягиваемую сварочную дугу вплоть до потребляемой мощности 13кВА (вместо расчетных 7,75кВА). Поэтому при работе от генератора или других источников, где перегрузка может вызвать повреждение источника или другие нежелательные последствия, аппарат сначала нужно проверить на способность ограничивать потребляемую мощность. На веру не стоит воспринимать ни подозрительно низкие показатели энергопотребления, ни даже вполне высокие.
ХОРОШО, ЧТО «.. ВАРИТ ОТ 100В!». НО НАСКОЛЬКО ХОРОШО?
Занижение нижнего порога напряжения источника питания распространено не столь широко, как завышение номинального тока. Этот параметр очевиден для любого потребителя, и его легко проверить. Скорее, имеет место умолчание второй части правды: какой номинальный ток аппарат выдает при пониженном входном напряжении.
Проблема пониженного напряжения, к сожалению, в нашей огромной стране распространена очень широко – производственные и распределительные мощности не успевают за ростом энергопотребления, особенно индивидуального. Первый признак перегрузки – напряжение пониженного уровня: если с источника электропитания отбирать больше зарядов, чем он способен воспроизводить, плотность зарядов на источнике снижается, напряжение падает.
При уровне входного напряжения ниже расчетного, снижается потребляемая, а с ней и выходная мощность сварочного аппарата. Соответственно, существенно снижается его номинальный ток.
Существует 2 принципиальных пути инженерного решения проблемы пониженного напряжения источника питания. Первый: изменение схемы и параметров штатных компонентов аппарата. В первую очередь, коэффициента трансформации высокочастотного трансформатора.
Второй способ – добавление блока корректировки входного питания. Наибольшее распространение получила установка т.н. блоков PFC (Power Factor Correction – в буквальном переводе «корректировки фактора мощности»).
Оба способа требуют дополнительных затрат, особенно установка на входе блока PFC, стоимость которого может составлять более половины сварочного инвертора на 160 ампер без такого блока. Поэтому на аппаратах с номинальным током менее 160 ампер блоки PFC устанавливаются редко. Зато использование блоков корректировки входного питания позволяет работать от более низкого напряжения, чем обычно позволяет добиться изменение параметров штатных узлов.
Если Вы приобретаете аппарат, который планируете эксплуатировать в условиях заведомо пониженного напряжения, недостаточно сравнить уровень ожидаемого напряжения питания с заявленным минимальным порогом напряжения питания аппарата. Нужно разобраться, какой ток будет при вашем входном напряжении выдавать аппарат. Иначе может получиться, что аппарат от обещанного пониженного уровня работает, вот только сварочный ток выдает бесполезно малый.
ПВ, ОН ЖЕ ПН ИЛИ РАБОЧИЙ ЦИКЛ – ВСЕ СОГЛАСНО СТАНДАРТОВ. РАЗНЫХ СТАНДАРТОВ.
Сварочный аппарат работает с очень высокими токами, вызывающими нагрев силовых элементов. Поэтому одна из главных задач разработчиков сварочного аппарата – обеспечение эффективного охлаждения. Силовые транзисторы размещаются на объемных алюминиевых «постаментах» – радиаторах, имеющих ребристую поверхность, обеспечивающую максимально возможную площадь отдачи тепла. Мощный вентилятор (иногда 2 или 3 шт) обеспечивает непрерывный обдув с целью охлаждения, Несмотря на это, практически в любом аппарате при работе на токах выше определенного происходит перегрев, срабатывает термическая защита и аппарат на время отключается. Вентилятор продолжает дуть, компоненты аппарата, включая защиту, охлаждаются и снова готовы к работе. Это не аварийная ситуация, а нормальный рабочий режим аппарата.
Отношение времени, которое аппарат в течение контрольного периода выдает заданный ток, к этому самому контрольному периоду, называется рабочим циклом аппарата или, иначе, полезным временем (ПВ). Еще иногда – продолжительностью нагрузки (ПН).
ПВ указывается в %. Обычно указывается сварочный ток, на котором аппарат имеет данный показатель ПВ. Например, «120А-90%» означает, что при работе током 120А данный аппарат может выдавать ток 90% времени, и только 10% остывать. Естественно, чем ближе ток к номиналу аппарата, тем быстрее аппарат греется. Т.е. тем ниже показатель ПВ. Если ПВ указан без упоминания силы тока, значит, данный ПВ соответствует режиму номинального тока аппарата. Так показатель ПВ «30%» для аппарата с диапазоном сварочного тока 10-160А означает, что при рабочем токе 160А данный аппарат будет варить 30% времени, а 70% остывать.
Вроде бы все понятно. Но… Существуют различные методики измерения ПВ. И в отличие от единых для всего мира стандартов соответствия сварочного тока и сварочного напряжения дуги, методики измерения ПВ отличаются принципиально. Один и тот же аппарат по разным методикам получит совершенно разный процент ПВ!
Знакомьтесь: самые распространенные методики измерения ПВ сварочного аппарата – европейская, китайская и советская.
Европейская. Подразумеваются условия испытаний, описанные в европейском стандарте EN60974-1. При температуре окружающей среды 40С аппарат включают на заданный сварочный ток и засекают, сколько он непрерывно проработает до первого отключения. Полученный результат относят к 10-минутному отрезку времени. Если за эти 10 минут термозащита так и не сработала (и аппарат при этом не сгорел), значит, рабочий цикл аппарата на этом токе равен 100%.
Методика фирмы Telwin. Ее же в наши дни можно с полным правом назвать китайской. Итальянский концерн Telwin оказал колоссальное влияние на развитие китайских производителей. Его аппараты MMA, MIG-MAG и контактной сварки были прародителями значительной части китайской продукции. И еще сегодня в Поднебесной на неисчислимых производственных линиях можно отыскать братиков-близнецов аппаратов TELWIN. Кроме схем аппаратов, в Китае по достоинству оценили и предложенную итальянским производителем методику измерения ПВ аппаратов. При температуре 20С аппарат не просто нагружают сварочным током, но жгут реальные электроды. При этом учитывается не непрерывное время работы до первого отключения, а суммарное рабочее время сварки за 10 минут. Естественно, показатель ПВ по методике TELWIN получается значительно (до 2 раз) выше, чем при следовании методике EN60974-1. Сама компания TELWIN при указании ПВ по своей методике уточняет это, добавляя «Telwin» после процентного показателя. Замеряющие ПВ по ее методике китайские производители таких подробностей не указывают.
Российская, она же советская. ГОСТ претерпел ряд редакций, в частности – ГОСТ Р МЭК 60974-1-2004. Условием отечественной методики является обязательное доведение аппарата до режима срабатывания защиты перед началом измерений. Т.е. сначала вводят в режим интенсивной эксплуатации, и только потом производят замеры. Для аппаратов ручной дуговой сварки отечественная методика предусматривает измерения в течение 5 минут, а не 10.
Характерно, что ГОСТ Р МЭК 60974-1-2004 в обязательном порядке относится лишь к сварочному оборудованию промышленного и профессионального назначения и – цитирую – «Стандарт не распространяется на источники питания для ручной дуговой сварки с ограниченным режимом эксплуатации, которые проектируются преимущественно для эксплуатации непрофессионалами». Вероятно, именно этим обстоятельством объясняется не только слабая распространенность отечественной методики, но и свобода трактовки показателя ПВ производителями и импортерами.
И все-таки, какой цикл работы можно считать подходящим? По оценкам специалистов, опубликованных в открытых источниках, реальный цикл работы сварщика ручной дуговой сварки не превышает 20%. Причем эти 20% времени не являются непрерывным отрезком. Более 80% времени уходит на перемещения, контроль уложенного шва, сбив шлака, замену электрода и др. Так что даже ПВ 30%, замеренного по китайской методике, практически любому сварщику при не очень жаркой погоде будет достаточно – простаивать в ожидании охлаждения аппарата не придется. Если же данный показатель критичен, то лучше не сверять показатель ПВ аппаратов разных марок, а купить аппарат, рассчитанный на более высокий номинальный ток. У него ПВ на том же токе будет точно выше.
А пока ценники реальных и виртуальных магазинов пестрят различными впечатляющими показателями ПВ. И чинные продавцы объясняют неопытным покупателям преимущества больших циферок над маленькими.
НАПРЯЖЕНИЕ ХОЛОСТОГО ХОДА И ФУНКЦИЯ HOT START – ЗВУЧИТ КРАСИВО
Чем выше напряжение, тем легче поджечь дугу. Поэтому напряжение на кончике электрода до возгорания дуги кратно выше, чем при горящей дуге (в большинстве случаев от 1,8 до 2,5 раз). Но слишком высокое напряжение опасно для жизни и здоровья человека. Поэтому выше 80-85В напряжение холостого хода, иначе называемое напряжением без нагрузки, не делают. (В своей книге «Сварочный инвертор – это просто» В.Негуляев утверждает, что до 95В; Ф.Кобелев в своей книге «Как сделать сварочные аппараты своими руками» ссылается на ГОСТ95-77Е и его требование – не более 80В; ГОСТ 12.2.007.8-75 предусматривает предел в 80В для аппаратов переменного тока и 100В постоянного). Впрочем, автору не известны электроды для сварки черных металлов, которые для поджига требовали бы больше 60В. Одновременно автор не слышал об инверторных аппаратах, у которых заявленное напряжение холостого хода было бы ниже 63В.
Чтобы сделать процесс поджига дуги еще легче, изобрели функцию «горячего поджига дуги» – Hot Start. По своей сути она обратна функции Arc Force. Arc Force кратковременно набрасывает ток при опасности разрыва дуги. Hot Start кратковременно набрасывает ток при попытке разжечь дугу.
Как и Arc Force, Hot Start «прыгнуть выше крыши» не может. Для аппарата с номинальным током 160A Hot Start не увеличит ток до 180А. Как показывают тестирования аппаратов, у большинства аппаратов с заявленной функцией HOT START по факту она отсутствует. Вместо нее имеет место повышенный ток при замыкании электрода на метал. И чем более пологая ВАХ, тем больший ток «накидывает» заявленная, но в действительности не существующая на таком аппарате функция HOT START. Помочь разжечь дугу такой дополнительный ток вряд ли может – сварочное напряжение не выдерживается.
На практике заметить разницу напряжения холостого хода в 70 и 80 вольт «по ощущениям» сможет не каждый эксперт, не говоря о новичке. Равно как и набрасывание незначительного тока, если только электроды не дефектные и не отсыревшие, или напряжение холостого хода 60В и ниже.
ЛЮБОЙ КАПРИЗ ЗА ВАШИ ДЕНЬГИ И ЛЮБОЙ СЮРПРИЗ ВМЕСТО НИХ
Я перечислил лишь самые распространенные случаи «экономии» за счет характеристик продаваемого оборудования, встречаемые у некоторых торговых марок федерального масштаба. Еще цена может отличаться в зависимости от марки комплектующих. На характеристиках это обычно не отражается. Более того, нельзя однозначно утверждать, что из 2 аппаратов обязательно надежнее и дольше прослужит именно тот, на котором стоят более высококлассные (и дорогие) комплектующие. Хотя если взять статистику на 2 000 аппаратов, такое, скорее всего, утверждать будет можно.
Цифровые аппараты обычно стоят дороже, чем аналоговые на тот же ток. Цифровой сварочный аппарат – это аппарат с микропроцессорным управлением. Они могут общаться с пользователем посредством дисплея. Аналоговый аппарат – тоже электронный. Но обработка сигналов в нем происходит на уровне взаимного влияния электрических параметров компонентов друг на друга. Является ли цифровой аппарат гарантией более качественного сварочного процесса? Вовсе нет. Лучше купить аналоговый инвертор, выдающий заявленные характеристики, чем цифровой, вводящий в заблуждение. Хотя стремящиеся к экономии производители редко усложняют свои модели с завышенными характеристиками. Их первейшая задача – экономия. Электронный дисплей, кстати, – не признак микропроцессорного управления. Более того, амперметр можно настроить так, что он будет показывать на дисплее не тот ток, который в действительности выдает аппарат.
В Китае более 3000 заводов, выпускающих сварочные аппараты MMA. При такой конкуренции и отсутствии прямой связи с рынками, где их продукция продается, многие заводы концентрируются на самом очевидном направлении повышения конкурентоспособности – на цене. Иногда сами, иногда их толкают на это заказчики – импортеры из других стран.
Выдача менее мощных аппаратов за более мощные – самая распространенная, но не самая вопиющая форма такой «экономии». Автору доводилось лицезреть аппарат, где вентиляторы охлаждения питались от тоненькой проволочки, накрученной в виде еще одной вторичной обмотки на сердечник высокочастотного трансформатора изделия. Экономия, надо полагать, значительная. Но жить такому аппарату недолго, даже если у него превосходно функционирующая термозащита. А купившему его потребителю – мучаться. Потому что цикл работы у такого аппарата, пока он не сгорит, будет выдающийся. Как только сработает термозащита и аппарат отключится, вместе с ним отключится и вентилятор. Ждать охлаждения аппарата придется в несколько раз дольше, чем при наличии полноценного блока питания вентилятора.
СОВЕТ АВТОРА
Мы живем в век товарного изобилия. Чем дальше, тем выбор больше, а свободного времени, чтобы в нем разбираться, меньше. Рекомендую Вам выбирать тех профессионалов, которым доверяете, и пользоваться их услугами.
Конечно, если разница между товарами непонятна, почему бы не выбрать подешевле? Но Вы наверняка стремитесь попасть к конкретному зубному врачу или автомеханику, которых знаете давно и убедились в их компетенции и порядочности. Такой подход разумен и в отношении подбора оборудования, в котором у Вас нет времени разбираться. Доверьте эту работу достойному магазину и торговым маркам производителей, которые этого заслуживают.
Обман является обманом, если его осознает и признает таковым обманутый. Покупатель, которого убедили в магазине, что для сварки электродом 3,2 мм ему «как раз подойдет» аппарат на сварочный ток 200 ампер, который, к тому же, предлагается приблизительно в одну цену с 160-амперными аппаратами конкурентов, может быть вполне доволен и счастлив. Но часто покупателю все же предлагают переплатить за характеристики, которыми предлагаемый аппарат не обладает.
Как бы там ни было, выбор всегда за покупателем.
КРАТКАЯ ИНСТРУКЦИЯ ПО ПОДБОРУ СВАРОЧНОГО ИНВЕРТОРА
А. Подбор аппарата по мощности.
1. Определить тип работ – тип свариваемого черного металла, его толщина, объем работ.
2. Исходя из предыдущего пункта, выбрать расходник – электроды. Назначения по типам стали указаны на упаковке. Для бытовых работ в большинстве случаев подходят самые распространенные – АНО-21 и МР3. Для профессиональных задач – УОНИ. Диаметр выбирается по толщине свариваемого металла. Упрощенно: 1 мм свариваемого металла = 1 мм диаметра электрода.
3. Подбор аппарата по току. На 1 мм диаметра электрода – 40-50А сварочного тока. Получается, для сварки электродом 3,2 мм при нормальном (не пониженном) напряжении в сети питания нужен аппарат на ток 128-160А.
Б. Подбор аппарата по источнику питания
4. Важнейшими характеристиками источника электропитания, влияющими на подбор сварочного аппарата являются уровень напряжения и мощность источника электропитания.
5. Исходя из уровня напряжения, подобрать аппарат. Большинство аппаратов заявляют требование к источнику напряжения не ниже 185 вольт. Но даже те, которые заявлены для работы от пониженного напряжения, выдают при пониженном напряжении более низкий максимальный сварочный ток. Т.е. снижение входного напряжения приводит к уменьшению диапазона рабочего тока. Если планируете работать он пониженного напряжения, нужно знать, какой номинальный сварочный ток выдает конкретный аппарат при конкретном пониженном напряжении. Если источник имеет пониженное напряжение, но высокую мощность, лучше всего взять значительно более мощный аппарат.
6. Определить минимально требуемую мощность источника питания для работы на определенном токе можно по формуле:
P=Iсв*(20+0,04* Iсв)/*0,85/0,85
Однако помните, что эта мощность может оказаться выше при растягивании дуги. Особенно это важно помнить при работе от генератора. Резкое повышение уровня потребляемой мощности может вывести генератор из строя.
Сварочные аппараты можно подключать к традиционным генераторам достаточной мощности. Большинство инверторных генераторов, даже достаточной мощности, не рассчитаны на работу со сварочными инверторами. Так как в инверторных генераторах для увеличения стартовой мощности используются конденсаторные блоки, не переносящие сколько-нибудь длительную продолжительную нагрузку.
Обычная бытовая 16-амперная розетка 220В рассчитана на продолжительное подключение мощности не более 3,5кВА. А значит, может выдержать сварку током не выше:
3500ВА= Iсв*(20+0,04* Iсв)/*0,85/0,85, откуда = Iсв=104А
Поэтому для сварки электродом 3,2 мм и толще, подключать аппарат нужно либо к силовой розетке, в том числе на генераторе, либо напрямую к электрощитку. При подключении к силовой розетке (обычно на 32А) вилка на 16А с аппарата демонтируется. На ее место ставится силовая вилка.
7. Подбор аппарата по интенсивности работы
ПВ (оно же ПН) в 30% даже по методике компании Telwin для непрофессионального сварщика достаточно. Если же производительность является ключевым требованием, лучше не сравнивать показатели ПВ, которые замерены по разным методикам и потому вводят в заблуждение, а выбрать аппарат большей мощности, т.е. с большим номинальным током. У него ПВ на том же токе будет точно выше, чем у однотипного меньшей мощности.
8. Дополнительные функции
Чем больше дополнительных функций, тем на начальном этапе лучше.
Функция против залипания электрода Anti-Stick. Автоматически определяет режим короткого замыкания (т.е когда электрод «прилип» к свариваемому металлу) и отслеживает его продолжительность. Если в течение контрольного времени (долей секунды) режим не меняется, сбрасывает ток, «отпуская» электрод. Очень полезная функция для начинающих сварщиков. На отдельных дорогих аппаратах можно регулировать контрольное время срабатывания Anti-Stick. К настоящему моменту наличие данной функции на сварочном инверторе является почти стандартом индустрии. Однако на некоторых дешевых аппаратах неизвестных производителей может не срабатывать или даже отсутствовать вовсе. Визуально определить наличие или отсутствие функции нельзя.
Функция форсирования дуги Arc-Force.
Облегчает процесс сварки неопытному сварщику, у которого дергается рука. На предельном токе в большинстве аппаратов не действует. Фактически присутствует только на аппаратах, где на панели есть отдельная ручка регулирования силы набрасываемого тока. «Автоматическая» функция Arc-Force в большинстве случаев – обман, при котором за «набрасываемый ток» выдается участок вольт-амперной характеристики вне рабочего диапазона сварочного тока, где аппарат не может обеспечить достаточное для нормальной работы сварочное напряжение. Удержать дугу такое увеличение тока никак не может.
Функция горячего поджига Hot-Start.
Облегчает разжигание сварочной дуги набрасыванием тока в момент поджига. При напряжении холостого хода свыше 65В и нормальных электродах не требуется. По факту в большинстве аппаратов, где заявлена, отсутствует. Признаком наличия является отдельная ручка, позволяющая регулировать силу набрасываемого тока. Даже в тех аппаратах, где действительно есть, на предельном сварочном токе не действует. Аналогично функции Arc-Force, за наличие функции Hot-Start часто выдают увеличивающийся при коротком замыкании ток, относящийся к участку вольт-амперной характеристики вне рабочего диапазона сварочного тока. У аппаратов с полого падающей ВАХ ток короткого замыкания может существенно превышать номинальный сварочный ток. Но удержать дугу после чиркания электродом такая «автоматическая функция» не поможет – сварочное напряжение будет ниже положенного.
9. Комплектация. Что обычно входит в базовую комплектацию бытового сварочного инвертора?
* Провода электрододержателя и клеммы массы (а вот в комплектацию профессиональных аппаратов они обычно не входят).
* Маска-щиток, она же щиток сварщика. Маской это назвать нельзя. Это простенький светофильтр, годящийся разве что на проверку аппарата разовым поджигом дуги. Для нормальной работы нужна маска с автоматическим затемнением, т.н. «Хамелеон». Иногда такая маска идет в одном комплекте с аппаратом. Но помните, что маски сварщика профессионального уровня, обеспечивающие максимальную защиту глаз, никогда не кладут в комплекты. И в продаже отдельно они далеко не самые дешевые.
* Щетка-молоточек. Простой, но очень полезный аксессуар, востребованный в работе. Если его в комплекте нет, нужно приобрести.
* Ремень для переноски. Актуальный аксессуар для тех, кому требуется перемещаться с аппаратом по стройке и другим обширным участкам работ, в т.ч. вверх-вниз по лестницам.
* Пластиковый кейс. Не только удобен для хранения и перевозки, но и защищает аппарат от пыли, к которой инверторная техника весьма чувствительна.
Общая тенденция: чем аппарат профессиональнее, тем проще комплектация.
10. Работа на морозе. Отдельные электронные компоненты управления не выносят отрицательных температур. Их аналоги с возможностью функционирования стоят несколько дороже. Поэтому большинство инверторных аппаратов в стандартной комплектации могут работать только от 0 градусов и выше. Если такой аппарат вынести из тепла и активно эксплуатировать, не давая ему остыть, работать он будет. А вот при промерзании просто не включится. Поэтому если планируется эксплуатация при постоянной отрицательной температуре, аппарат нужно выбрать с соответствующим температурным диапазоном.
Электрод ОК 46.00 (2 мм; 2 кг) ESAB СВ000009933 – цена, отзывы, характеристики, 1 видео, фото
Электрод ОК 46.00 ESAB СВ000009933 предназначен для сварки методом MMA углеродистых конструкционных и судовых сталей. Сварка ведется во всех пространственных положениях. Работы следует проводить на постоянном токе обратной полярности и переменным током. Наплавленный металл образует ровный и высококачественный шов. Электрод широко применяется при сварке листов с гальваническим покрытием. Не чувствителен к ржавчине и поверхностным загрязнениям.
Параметры:
- Предел текучести — 400 МПа;
- Предел прочности — 510 МПа;
- Относительное удлинение — 28%;
- Ударная вязкость при 0°C — 70 Дж/см2;
- Ударная вязкость при -20°C — 35 Дж/см2.
Химический состав наплавленного металла:
- C: 0.08%;
- Mn: 0.4%;
- Si: 0.3%.
- Тип Э46
- Диаметр, мм 2.0
- Марка электрода ОК 46.00
- Свариваемый материал углеродистые стали
- Покрытие рутил-целлюлозное
- Длина, мм 300
- Вес, кг 2
Этот товар из подборок
Параметры упакованного товара
Единица товара: Штука
Вес, кг: 2,03
Длина, мм: 315
Ширина, мм: 74
Высота, мм: 29
Произведено
- Швеция — родина бренда
- Россия — страна производства*
- Информация о производителе
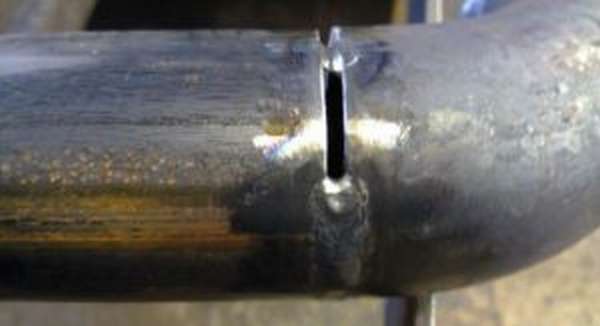
Указанная информация не является публичной офертой
На данный момент для этого товара нет расходных материаловСварка тонкого металла электродом – правильная техника
Изобретение сварочного аппарата значительно упростило процесс соединения металлических предметов. При работах с тонкими заготовками, новички могут испытывать определенные трудности.
Сварка тонкого металла электродом должна выполняться с применением сварочных аппаратов, которые
позволяют осуществить данную операцию без деформации и прогорания тонкого листа.
Технология сварки
Чтобы не произошло прогорания металла, сварка должна осуществляться как можно быстрее. Электрод проводится один раз вдоль шва, без задержек. Чтобы без проблем сварить тонкий металлический лист, необходимо, насколько это возможно, снизить рабочий ток.
Инверторный аппарат, который используется для этой цели, должен иметь плавную регулировку выходной мощности. Чтобы не возникло проблем с запалом дуги, применяются устройства, которые имеют напряжение холостого хода не менее 70 В.
При выполнении работ следует обращать внимание на геометрию тонкого листа, которая может изменяться во время сильного нагрева. Для надежного соединения встык, необходимо зачистить кромки материала от ржавчины. Следует, также выровнять заготовки, если в этом есть необходимость и закрепить. Только чистый и ровный металлический лист, позволит получить требуемое качество свариваемых поверхностей.
Когда подготовительные работы будут окончены, свариваемые изделия прихватывают через каждые 7 — 10 см, и только затем уже производят окончательное соединение материала.
Видео:
Если нужно сделать соединение двух тонких листов внахлёст, то такой вариант сварки, позволяет использовать больший ток, при этом значительно снижаются негативные проявления высокой температуры на свариваемые поверхности. Вероятность прожога материала снижается в несколько раз, а изменение геометрии практически не наблюдается.
Чтобы минимизировать влияние высокой температуры, на соединяемый встык или внахлёст металл, под него следует подложить листовую медь. Этот материал отлично отводит излишки тепла от свариваемой поверхности, тем самым предотвращая появления коробления и других негативных проявлений температурного расширения свариваемых поверхностей. Иногда, с этой же целью используется проволока, которая укладывается в месте стыка двух металлов.
Видео:
https://www.youtube.com/watch?v=P2CzIuF_VhQ
Работа инвертором
Сварка тонкого металла инвертором, позволяет выполнить эту операцию с применением обратной полярности. В этом случае ” — ” подключается к свариваемому металлу, а «+» к держателю электродов.
Такая техника сварки электродом позволяет минимизировать вероятность деформации и прогорания металлического изделия. При обратной полярности электрод нагревается значительно сильнее, чем соединяемый металл, поэтому удаётся выполнить работу по соединению, максимально эффективно.
Для получения качественного шва, необходимо использовать тонкие электроды диаметром не более 2 мм. Следует использовать изделия, которые обладают высоким коэффициентом расплавления. Это качество позволяет осуществлять сварку тонких конструкций при малом токе, что положительно отразится на качестве сварного шва.
Сварка тонких листов инвертором должна осуществлять плавным движением электрода. Чтобы не прожечь изделие и чтобы шов получился ровным необходимо располагать электрод в пределах 45 — 90 градусов к свариваемой поверхности. Соединение лучше выполнять углом вперед.
От качества используемых электродов зависит уровень соединения. Электроды для сварки тонкого металла инвертором должны быть хорошего качества и, желательно, импортного производства.
Видео: показываются простые приемы в нахлест и стык.
Достоинства сварки тонких заготовок инвертором
Этот способ позволяет выполнить качественное соединение тонкого металла. Если сварочные работы осуществляются профессионалом, то не происходит температурной деформации и изделие будет иметь эстетичный внешний вид. Постоянным током варить тонкие изделия можно меньшим током, поэтому вероятность прогорания, значительно сокращается.
Микропроцессорное управление такого устройства позволяет устранить «ямы» и сбои напряжения, генерируя на выходе идеальный ток, который подходит для проведения сварочных работ.
Единственным недостатком использования инвертора, является нестабильная работа при низкой температуре воздуха. Даже качественные приборы при минусовой температуре дают сбой.
Особенности сварки тонкой оцинковки
Если необходимо сварить оцинкованную сталь, то потребуется полностью очистить от слоя цинка кромки соединяемого металла. Слой цинка можно удалить с помощью шлифовальной машинки или вручную.
Можно выжечь кромки металла с помощью сварки, но в этом случае необходимо соблюдать осторожность. Пары цинка очень ядовиты и при их вдыхании способны вызвать сильное отравление организма. Работы необходимо выполнять только при правильно организованной вытяжке, или варить изделие на улице.
Видео:
Заключение
Мы разобрали, как варить тонкий металл инвертором. Главное правильно подготовить заготовки, сделать отвод излишков температуры, подобрать электроды, выставить ток и можно приступать к работе.
Во время соединения, необходимо тщательно следить за качеством шва, вовремя отрывать на мгновение электрод, чтобы не произошло прожога, пользоваться теплоотводящими пластинами или проволокой. Только практика поможет в освоение процесса.
Сварка нержавейки (нержавеющей стали) штучным электродом с применением инвертора (РДС метод)
Нержавеющая сталь уже более ста лет исправно служит человечеству, застрагивая все сферы жизни каждого из нас. Из этого материала создают болты, крепежи, баки, арматуру, консервные банки, инструменты и многое другое. А для того, чтобы изготовить или починить необходимые детали, чаще всего применяется ручная дуговая сварка нержавейки электродом при помощи инвертора. Об особенностях метода, достоинствах и недочетах, а также «сюрпризах», которые могут ожидать новичков, в ходе ММА сварки подробно читайте в нашей статье.
Содержание
Что представляет собой метод сварки нержавеющей стали электродом с применением РДС инвертора?
РДС нержавейки электродом – процесс, при котором расплавляющееся в ходе плавления стержня покрытие электрода создает газошлаковую защиту. Эта корка из шлаков, изолирующая зону дуги и сварочную ванну от окружающего воздуха (кислород, содержащийся в воздухе, стремительно окисляет расплавленный металл и значительно уменьшает качество сварки). Сварное соединение возникает благодаря расплавленному металлу детали и металлу электродного стержня (и металлу из покрытия электрода). В международной практике кратко подобную технологию именуют сваркой ММА (Manual Metal Arc).
Где чаще всего применяется метод РДС сварки?
Применять сварку нержавеющей стали инвертором можно во всех пространственных положениях, но качественные вертикальные швы проложить сможет не каждый опытный сварщик.
- Ручная дуговая сварка покрытыми электродами рационально применяется для коротких швов, в мелкосерийном производстве деталей. На монтаже металлоконструкций использование данной технологии сварки рекомендовано при небольшом объеме работ.
- РДС нержавейки покрытыми электродами нашла применение для осуществления прихваток при сборке конструкций под сварку и при необходимости исправления дефектов на небольших участках шва.
- Подобным методом может производиться и наплавка.
Вывод: Таким образом, ММА сварка чаще применяется при небольших объемах производств и в личных бытовых целях, к методу прибегают для сварки труб, металлоконструкций, емкостей или баков из нержавейки и других изделий на дачах, в гаражах и т. д.
Плюсы и минусы метода
Если сравнивать с другими способами сваривания, такими как сварка ТИГ, сварка в защитных газах плавящимся электродом МИГ/МАГ, сварка под флюсом, ручная сварка нержавейки ММА имеет следующие преимущества:
- оборудование для сварки этим методом является простым, недорогим и по большей части компактным;
- РДС используется для сваривания большинства черных и цветных металлов и различных сплавов практически любой толщины;
- не нужно использовать дополнительную флюсовую или газовую защиту;
- этот способ сварки подходит для труднодоступных областей из-за небольших габаритов отдельных моделей сварочных инверторов;
К недочетам этого метода относятся:
- необходимость избавления от шлака после создания шва;
- по причине того, что сварочный ток постоянно протекает по всей длине электрода, необходимо ограничивать максимально допустимый ток из-за проблемы перегрева электрода и разрушения покрытия;
- медленная скорость сварки.
Вывод: Преимуществ метода не много, но все они заключаются в простоте ММА сварки и ее универсальности, которая делает технологию такой популярной.
Как варить нержавейку инвертором в бытовых условиях и возможно ли это?
Многие интересуются, можно ли варить нержавейку инвертором в домашних условиях, и на что стоит обращать особое внимание.
- Перед тем как приступать к сварке изделий из нержавейки, требуется тщательно обработать и подготовить поверхности к дальнейшей работе. Процесс предварительной обработки является идентичным тому, который проводится с низкоуглеродистыми сталями:
- очищается поверхность изделия от загрязнений,
- кромки и поверхность обрабатываются растворителем (бензином или ацетоном), подобная обработка даст возможность избавиться от жира, наличие которого ведет к ухудшению стабильности дуги,
- свариваемая поверхность обрабатывается средством от налипания брызг.
Отличие состоит в том, что сварной стык должен обладать зазором, способным обеспечить оптимальную усадку.
- Нержавейку сваривают на токе обратной полярности. При осуществлении работ нужно стараться меньше проплавлять шов.
- Большие по диаметру электроды, как правило, не применяются. Необходимость их использования появляется лишь при сварке толстых поверхностей. Подобрать электрод для металлов разных толщин, в том числе и тонколистовой стали, можно, воспользовавшись таблицей 1, представленной ниже. Не правильно выбранный электрод станет причиной плохой герметичности шва, в нем будут образовываться микротрещины, раковины и поры. Они получаются из-за вскипания металла.
- При варке нержавейки ток должен быть на 20% ниже, чем для варки низколегированных сталей. Для инвертора, применяемого в быту и частном строительстве, хватит диапазона 60-160 А. Плавная регулировка даст возможность точнее подобрать ток сварки и улучшить качество шва. Оптимальные значения сварочного тока имеются в таблице 1 и обусловлены толщиной свариваемого материала.
- После образования шва нужно выполнить процедуру охлаждения для сохранения устойчивости высоколегированной стали к воздействию коррозийных процессов.
Охлаждение осуществляется с использованием медных прокладок. В случае с аустенитной сталью возможно охлаждение с использованием воды.
Вывод: Таким образом, сварка нержавеющей стали требует от исполнителя определенного опыта и навыков, а также знаний соотношения толщины металла, значений силы тока и диаметра электрода. Сразу рассчитывать новичку на идеальный результат не приходится.
Что нужно для того, чтобы сваривать нержавейку инвертором?
Для самостоятельной сварки нержавейки инвертором вам понадобится следующее:
Необходимыми составляющими являются зажимы типа «крокодил» для заземления, электрододержатели, а также силовой и кабель для заземления. Иногда эти компоненты идут сразу в комплекте с инвертором, но чаще всего их приходиться докупать. Оптимальная длина кабелей должна быть не менее 2-х метров.
Многие спрашивают, какими электродами варить нержавейку. Важным условием для того, чтобы процесс сварки удался, является выбор оптимального соотношения толщины металла и используемого электрода.
Таблица 1.
Толщина свариваемого металла, мм | 1-3 | 3-4 | 4-5 | 5-6 | 6-8 | 8-10 | 12-15 | 15-18 |
Рекомендованные значения сварочного тока, А | 20-60 | 50-90 | 60-100 | 80-120 | 110-150 | 140-180 | 180-220 | 220-260 |
Диаметр сварочного электрода, мм | 1,0-1,5 | 1,6-2,0 | 2,0-2,4 | 2,5-3,1 | 3,2-3,9 | 4,0-4,9 | 5,0-5,9 | 6,0 и более |
Какие типы металлов (стали) можно сваривать с нержавейкой инвертором и особенности сварки таких металлов?
Ручная дуговая сварка нержавейки инвертором представляет собой универсальный технологический процесс, используемый для сваривания цветных и черных металлов и различных сплавов любой толщины (от 1 мм до 100 мм), но, как правило, диапазон толщин колеблется в границах от 3 до 20 мм.
При определенных условиях работы конструкции, а также при использовании электродов конкретных марок, можно сваривать разные группы нержавеющих сталей: жаропрочные, коррозионно-стойкие и жаростойкие стали. Значения для наиболее часто свариваемой нержавейки – аустенитных сталей представлены в таблице.
Таблица 2.
Марка стали | Условия работы | Марка электрода | Тип электрода | Содержание α фазы (%) и структура шва | |
Жаропрочные стали | |||||
Х25Н38ВТ ХН75МБТЮ |
Высокая температура | ЭА-981-15 | Э-09Х15Н25М6Г2Ф | Аустенитная | |
20Х20Х14С2 20Х25Н20С2 30Х18Н25С2 |
Температуры до 900-1100°С Температура до 1050°С; жаростойкость и жаропрочность | ОЗЛ ОЗЛ-9-1 |
Э-12Х24Н14С2 Э-28Х24Н16Г6 |
3-10 % Аустенитно- карбидная | |
Коррозионно-стойкие стали | |||||
08Х18Н10 | Агрессивные среды; стойкость к межкристаллитной коррозии | ЦЛ-11 | Э-04Х20Н9 | 2,5-7,0 | |
12Х18Н10Т 08Х22Н6Т |
Температура до 600оС; жидкие среды; стойкость к межкристаллитной коррозии | Л38М |
Э 07Х20Н9 Э-08Х19Н10Г2Б Э-02Х10Н9Б |
3-5 | |
10Х17НИМ2Т 08Х18Н19Б 08Х21Н6М2Т |
Температура до 700 °С; стойкость к межкристаллитной коррозии | СЛ-28 |
Э-08Х19Н10Г2МБ Э-09Х19Н10Г2М2Б |
4-5 | |
10Х17Н13МЗТ | Стойкость к межкристаллитной коррозии | НЖ-13 | Э-09Х19НЮГ2М2Б | 4-8 | |
Жаростойкие стали | |||||
20Х20Х14С2 20Х25Н20С2 30Х18Н25С2 |
Температуры до 900-1100°С Температура до 1050°С; жаростойкость и жаропрочность |
ОЗЛ ОЗЛ-9-1 |
Э-12Х24Н14С2 Э-28Х24Н16Г6 |
3-10 % Аустенитно- карбидная | |
Х25Н38ВТ ХН75МБТЮ |
Высокая температура | ЭА-981-15 | Э-09Х15Н25М6Г2Ф | Аустенитная | |
Какие электроды для сварки нержавейки необходимо использовать?
Для ручной дуговой сварки нержавеющей стали различают два основных типа электродов.
- с основным покрытием (СЭЗ ЗИО-8 d4,0, СЭЗ ЦТ-15 d5,0, ESAB FILARC 88S d3,2) которые применяются лишь на постоянном токе на обратной полярности («+» на электроде), где основным покрытием наиболее часто выступают карбонаты кальция и магния;
- с рутиловым покрытием (Lincoln Electric Omnia 46 D3,0, Межгосметиз Omnia 46 d3,0, ESAB OK 46.00 d3,0) в основном из двуокиси титана, которые используются, если требуется сваривать на переменном токе и постоянном токе обратной полярности. Они обеспечивают стабильность горения дуги и уменьшают количество брызг при сварке.
Ответ на вопрос, какими электродами варить нержавейку, зависит от того, какой именно вид стали необходимо сваривать. В таблице 2 приведены оптимальные марки электродов в зависимости от типа и марки свариваемого металла.
Какие модели сварочных аппаратов лучше всего подойдут для сварки нержавейки?
Выбирая инвертор для РДС, необходимо учесть следующие моменты:
- Рабочий диапазон температур (поскольку некоторые модели не способны функционировать при низких температурах в условиях открытого воздуха).
- Мощность и сила сварочного тока агрегата. Для применения в быту достаточно инвертора, который выдает на выходе 180А. Более 200А выдают уже более профессиональные сварочники.
- Возможные отклонения не менее ± 20% напряжения сети от номинального параметра без вреда качеству сварки.
Также важно наличие дополнительных функций, самые популярные из них: Hotstart, Arcforce, Antistick
На нашем сайте представлены современные сварочники известных производителей, успешно зарекомендовавших себя на рынке сварочного оборудования. В зависимости от требуемого напряжения можно выбрать:
- модели сварочных инверторов для РДС (MMA-сварки) под напряжение сети в 220В,
- модели сварочных инверторов для РДС (MMA-сварки) под напряжение сети в 380В.
В ассортименте Тиберис представлены бюджетные агрегаты, применимые для работы в домашних условиях.
- Для напряжения 220В Сварог PRO ARC 160 (Z211S) , Сварог PRO ARC 180, Сварог TECH ARC 205B (Z203), ПАТОН ВДИ-200P.
- Для работы под напряжением сети 380В это такие инверторы как Сварог ARC 315 (R14), BRIMA ARC 250 (380В).
И сложные многофункциональные установки премиум класса для профессиональной сварки.
- Для напряжения 220В это EWM Pico 162, Lincoln Electric Invertec 170S, KEMPPI Minarc 150.
- Для работы под напряжением 380В это Lincoln Electric Invertec 270-SX, EWM Pico 220 CEL Puls, Kemppi Minarc 220.
Вывод: Выбор определенной модели сварочного инвертора зависит от имеющейся рабочей задачи, условий работы и финансовых возможностей исполнителя. В Тиберис вы без труда подберете тот аппарат, который устроит по всем параметрам.
Особенности сварки нержавейки электродом при помощи ручной дуговой сварки
Каждый, кто не сталкивался с таким способом сварки, спрашивает, как варить нержавейку электродом. Принцип сваривания нержавейки электросваркой состоит в том, что возбуждение дуги происходит между электродом и плоскостью свариваемого изделия.
- К свариваемой поверхности необходимо прикрепить кабель массы (-), который выходит из сварочного аппарата.
- Второй кабель (+) с электродом нужно приблизить к свариваемой поверхности, вследствие чего, образуется сварочная дуга.
- Для надежности процесса стоит помнить, что оптимальное расстояние между кончиком электрода (который необходимо так же правильно выбрать в соответствии с толщиной металла) и свариваемым элементом находится в пределах от 2 до 6 мм. За счет влияния высоких температур происходит проплавление металла, а затем заполняется образуемая во время воздействия дуги на поверхность свариваемого металла канавка.
- Электрод в ходе сваривания должен находиться под правильным углом. Это обеспечит контроль над сварочным процессом. Угол наклона должен составлять приблизительно 80 градусов. Наклон должен осуществляться к дуге. Дуга возникает из-за того, что электрод касается поверхности свариваемого металла или же за счет ударов со средней силой по свариваемой поверхности.
- Силу тока тоже подбирать нужно правильно. Несоответствие этой величины толщине металла не приведут к положительному результату. При слабой силе тока электрод будет постоянно затухать, и процесс сварки окажется не эффективным. При излишне высокой силе тока металл будет прожигаться. Рекомендуемые значения этого параметра приведены в таблице 1.
Вывод: Процесс ММА сварки не особенно сложен, хотя и требует определенной внимательности от исполнителя.
Обработка нержавейки после сварки инвертором
После сварки нержавейку необходимо обработать. Игнорирование подобных манипуляций способно привести к отрицательным последствиям: возникновению коррозии и снижению качества изделия.
Технология обработки изделий из нержавейки после ММА сварки включает:
- механическую зачистку сварного шва, такая операция улучшает внешний вид изделия и выполняется жесткими щетками из стали;
- пескоструйную обработку, после которой шов смотрится еще более эстетично;
- шлифование, позволяющее добиться однородности и гладкости поверхности шва.
Для шлифовки сварного шва после сварки нержавейки применяются абразивные материалы на основе циркония, оксида алюминия или керамического искусственного минерала. Средства, в состав которых входит корунд, использовать не рекомендуется, поскольку он способствует возникновению коррозии.
Но все подобные мероприятия являются лишь предварительной обработкой изделия, так как влияют только на внешний вид детали. Для надежной защиты места сварки от разрушения, необходимо прибегнуть к пассивации и травлению.
Пассивацией называют нанесение на место сварки специального вещества, под влиянием которого на металлической поверхности появляется защитная пленка из оксида хрома.
Травление представляет собой обработку места сварки химически активными средствами (специальными жидкостями либо кислотами). Кислоты разрушают окалину, которая способна вызвать возникновение ржавчины.
Только после осуществления химической обработки зона сварки надежно противостоит коррозийным процессам.
Смотрите также:
Сварка вертикальных швов
Темы: Технология сварки, Сварные соединения, Сварные швы, Ручная дуговая сварка.
Сварка одиночных валиков снизу вверх.
Сварка вертикальных швов ведется только на короткой дуге. Сварочный ток в основном минимальный или средний, позволяющий вести непрерывную сварку без отрыва дуги, без подтеков металла шва. Угол наклона электрода к вертикальной плоскости составляет 80°-90°, что способствует более прямому воздействию сварочной дуги на изделие и создает легкость в управлении сварочным процессом (рис. 1). При сварке электродом под углом 45°-60° (рис. 2) искусственно создается «козырек» (неравномерное расплавление покрытия), что мешает управлению сварочным процессом. Обязательно манипулирование электродом на ширину валика в 2-4 диаметра электрода с покрытием.
Другие страницы по теме Сварка вертикальных швов:
Рис.1. Правильный угол наклона. | Рис.2. Правильный угол наклона. |
При сварке вертикальных швов рекомендуется применять два метода манипулирования – «лестница» и «дугой вперед», что позволит выполнить швы нормальной формы (рис. 3).
Рисунок 3.
По мере наполнения сварочной ванны электродным металлом необходимо с каждым переходом из точки 1 в положение 2 и обратно в положение 3 производить подъем, задерживаясь в местах перехода. Задержка по времени должна быть такой, чтобы заполнить кратер электродным металлом и плавно вернуться на противоположную сторону не позднее, чем закристаллизуется там металл шва. Это способствует формированию «нормального» валика без подрезов и с плавным переходом к основному металлу и минимальным перепадам между чешуйками. Поэтому очень важен момент перехода. Ушел раньше – получил подрез и «выпуклый» валик. Передержал – наплыв и грубая чешуйка.
Многие сварщики при сварке вертикальных швов применяют манипулирование электродом «дугой назад», что приводит к чрезмерной выпуклости шва. Это объясняется тем, что большая часть жидкого металла шва стекает в центр сварочной ванны, т.к. в центре шва более высокая температура, чем на краях валика. Методом «дугой назад», спускаясь к центру, увеличиваем количество жидкого металла в центре валика. Такой метод при сварке вертикальных швов исключить.
Сварка корневого валика (рис. 4).
Рисунок 4. | Рисунок 5. |
В зависимости от толщины металла, притупления кромок, величины зазора, рекомендуется применять три способа сварки корневого валика:
1. Сварка «треугольником» (рис. 5) позволяет получить хорошее проплавление при малом зазоре (2 мм и меньше) и максимальном притуплении кромки (от 1 до 2 мм).

2. Сварка «елочкой» (рис. 6) при притуплении кромок и зазоре от 2 до 3 мм позволяет получить хорошее проплавление. Сечение валика средней полноты (меньше, чем при сварке «треугольником») дает возможность сформировать «нормальный» валик. Техника сварки вертикальных швов следующая: от зазора по одной из кромок (как бы прижавшись электродом к кромке) спуститься по ней, подавая электрод на себя на небольшое расстояние 5-7 мм, затем с небольшим постоянным подъемом и .подачей электрода от себя вернуться в зазор; проплавить притупление (при необходимости сделать задержку) и спуститься по другой стороне, выполняя те же движения, не допуская подтеков, подрезов, наблюдая за формированием валика и поддерживая точку «а» выше линии «б». Диаметр электрода 3 мм. Сварочный ток для V-образной разделки – 60…90 А, для X-образной разделки – 90…100 А.
Рисунок 6.
Сварка вертикальных швов
“ёлочкой” :
3. Сварка вертикальных швов методом «лестница» (рис. 7) применяется при максимальном зазоре более 2 мм и минимальном притуплении кромок (или без притупления), что обеспечивает хорошее проплавление, формирование обратного валика. Переход от кромки к кромке производится по прямой с постоянным минимальным подъемом. Сварка ведется короткой дугой, но без опирания на «козырек» покрытия. Задержка на кромках – максимальная, переход – более быстрый, но плавный; сечение валика малое («легкий» валик). Диаметр электрода 3 мм. Сварочный ток минимальный 80 А ± 5 А – для V-образной разделки кромок и средний 90-100 А для Х-образной. Сварочный процесс вести непрерывно (исключение – замена электрода и сварка тонкого металла).
Рисунок 7.
Большое значение для качества сварного шва имеет зажигание дуги. Начало зажигания дуги рекомендуется производить в нижней части застывшего кратера, сбоку или в центре шва, где есть доступ к выборке (рис. 8). Первый проход (из положения 1 в положение 2) следует производить быстро.Это необходимо для выполнения более «плоского» валика, что позволяет стекать шлаку вниз и избежать зашлаковки при возвращении между первым и вторым проходом, поскольку дуга еще не стабилизировалась, а ванна не набрала определенную температуру. При возвращении через место зажигания (положение 3) следует сделать короткую задержку для проплавления начала сварки, и только после стабильного зажигания дуги и разогрева ванны, не допуская затекания шлака в зазор, необходимо перейти центром электрода в зазор (в положение 4). В точке 4 обязательно сделать задержку. Дуга короткая, горит в основном с обратной стороны разделки, оплавляя застывший шлак с обратной стороны и металлическую перемычку, что позволяет сформировать обратный валик без «ямочек» на месте стыковки электродов. Как только дуга начнет в основном гореть с лицевой стороны и жидкий металл выйдет на лицевую сторону разделки, необходим спуститься электродом по одной из кромок (или по центру шва, в зависимости от расположения шлака) и, сгоняя дугой жидкий шлак, пройти по предыдущему проходу.
Рисунок 8.
При корневом валике малого сечения (сварка «лестницей») после первого прохода по краю кратера необходимо (не допуская зашлаковки в зазоре) сразу перемещать электрод в точку 4 (в зазор).
Второй корневой валик.
Второй корневой валик с обратной стороны при Х-образной разделке выполняется электродом диаметром 3 мм на среднем или максимально токе 100-110A. Повышенный сварочный ток необходим для хорошего проплавления обратной стороны корня шва. Предварительно нужно произвести зачистку от шлака, а при необходимости – механическую выборку.
В зависимости от полноты первого или второго корневого валика сварку третьего производить со следующей манипуляцией:
а) когда корневой валик легкий (малого сечения) – вариант 2 или 3 – манипулирование производить «лестницей», проплавляя корневой вали и кромки по краям, при этом обязательно центром дуги (электрода) при манипулировании доходить до края предыдущего валика и произвести задержку;
Рисунок 9.
б) когда корневой валик полный (вариант 1), кроме манипулирования электродом для формирования «нормального» или «вогнутого» второго последующего третьего валиков, помогает в процессе сварки разворот электрода к проплавляемой стенке (плоскости). Это достигается разворотом кисти руки. На рис. 9 показано, в какой момент удобней производит изменение угла электрода. В положении 1 дуга горит на плоскости «а» предыдущем валике, центр дуги направлен на край валика. Электрод расположен приблизительно параллельно плоскости «б».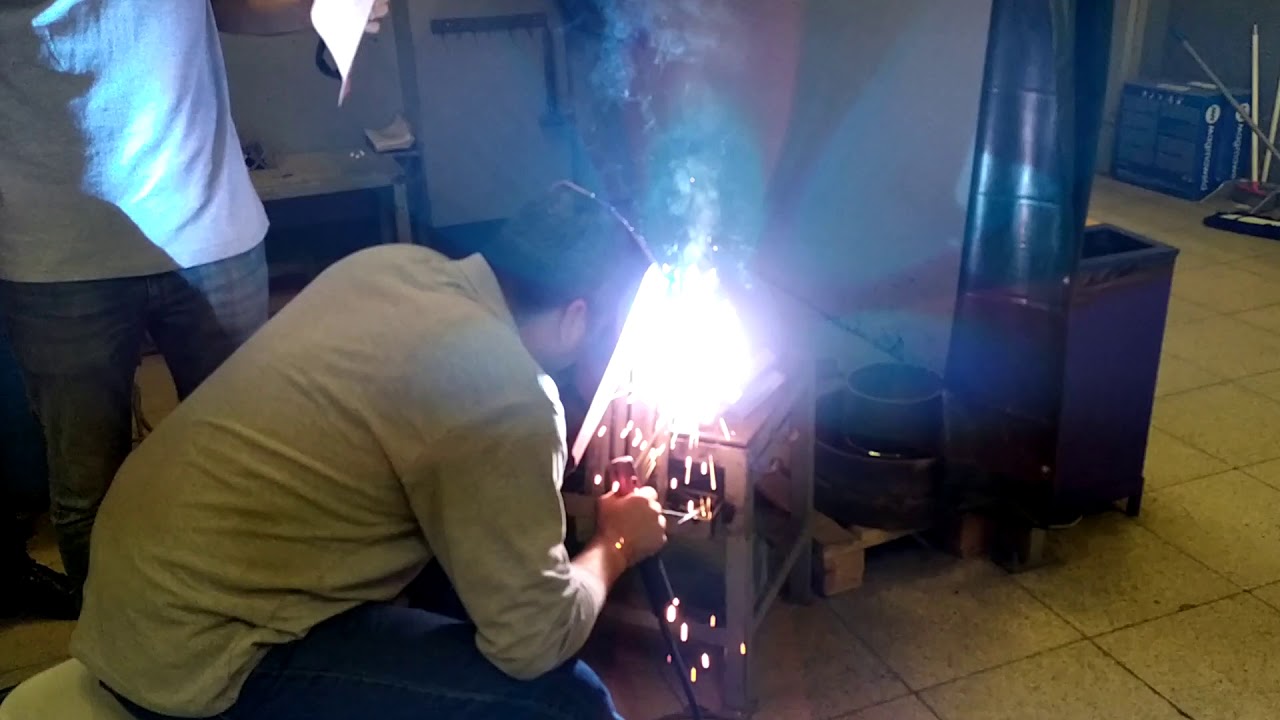

Многослойная и многопроходная сварка вертикальных швов.
При сварке больших толщин применяется многослойная, многопроходная сварка (рис. 10). После корневого валика второй и третий слой варятся электродом диаметром 3 мм или 4 мм (в зависимости от толщины основного металла и от ширины предыдущего валика) в один проход, при этом каждый валик должен быть «вогнутый» или «нормальный», что позволяет добиться качественной сварки последующих валиков. В следующих слоях, при переходе на два, три и более проходов, валики выполняются с небольшим усилением электродом диаметром 4 мм. Между предпоследним валиком каждого слоя и кромкой разделки необходимо оставлять расстояние не менее диаметра электрода с покрытием.
Предпоследний слой не должен выходить за пределы разделки. Рекомендуется оставлять незаполненную разделку от 0,5 мм до 2 мм, что позволяет легче сформировать качественный лицевой слой.
Рисунок 10. | Рисунок 11. |
Ширина лицевого слоя.
Ширина лицевого слоя равняется ширине разделки плюс половина диаметра электрода с каждой стороны (рис. 11). Рекомендуется применять манипулирование электродом «лестницей» или «дугой вперед».
- < Видео уроки сварки
- Возбуждение сварочной дуги >
7 лучших сварочных электродов — Рейтинг 2020 года (Топ 7)
Обзор лучших электродов для ручной сварки углеродистых и коррозионно-стойких сталей составлен при использовании публикаций журналов «Сварка и диагностика», «Металлургический бюллетень» и других специализированных источников. В статье обобщены интернет-отзывы профессиональных сварщиков о продукции разных производителей.
Критерии отбора
К сожалению, российские электроды проигрывают многим зарубежным аналогам по большинству параметров. Однако «прорывы» в этой области уже наметились. Российская электродная продукция, выпускаемая на немногочисленных пока совместных предприятиях, по стабильности качества уже не уступает многим маститым брендам. Начали «подтягиваться» к ним и некоторые заводы отечественной подчиненности. Однако в случаях, когда требуется уверенно обеспечить высокое качество шва, профессионалы по-прежнему предпочитают использовать более дорогие, но и более качественные электроды зарубежного производства. Для сварочных инверторов подходят электроды любого типа, для сварочных аппаратов переменного тока подходят не все типы.
При выборе лучших электродов для обзора мы руководствовались следующими критериями:
- объемы производства;
- качество продукции;
- попадание производителя в обзоры по электродной промышленности;
- отзывы профессионалов.
Для корректности сравнения цен мы включили в обзор только самый часто применяемые электроды диаметром 3 мм.
Основным параметром любого сварочного электрода, определяющим большинство его свойств – от легкости розжига до качества шва – является состав его обмазки. Наиболее распространенными сегодня являются следующие виды обмазок:
- Рутиловые электроды (и электроды со смешанной обмазкой на этой основе – рутилово-целлюлозные и так далее) стали одними из самых популярных благодаря легкости розжига, в том числе и повторного, сниженной (в разумных пределах) чувствительности к отсыреванию. Они могут использоваться и на переменном, и на постоянном токе во всех направлениях шва, но при выборе рутилового электрода нужно быть внимательным – можно купить как хороший электрод, так и загрязняющий шов огромным количеством шлаковых язв, пригодный разве что для прихваток.
- Электроды с основным покрытием чаще всего используются при сварке постоянным током в особо ответственных местах. При горении обмазки в большом количестве выделяется углекислый газ, надежно защищающий сварочную ванну от воздействия кислорода. Сам шов получается более пластичным, чем при сварке распространенными типами рутиловых электродов. Обратная сторона медали – это повышенная чувствительность к влажности и затрудненный розжиг: варить такими электродами заметно труднее.
Рейтинг лучших электродов для сварки
Правильный выбор электрода требует учитывать многие факторы. К примеру, при необходимости сварить сталь с высоким содержанием углерода многие сварщики посоветуют Вам электроды УОНИ – но не факт, что в неопытных руках из получится что-то хорошее. Вместе с тем более удобные в работе электроды наподобие ОЗС-12 позволят получить более качественный результат – но только до того момента, когда Вы не освоите сварку более сложными в работе типами электродов.
Нужно учитывать и условия хранения: держать в гараже большинство типов электродов с основным покрытием значит обречь себя на постоянный и длительный прожиг обмазки перед сваркой, которая сама может занимать буквально несколько минут, и рутиловые электроды в таком случае будут более предпочтительными, особенно типы с самой низкой температурой прокалки (ESAB OK 46.00, Omnia 46).
Машина контактной сварки МТР-14073-750с, 14кА, вылет 750 мм – цена, описание и характеристики
Диапазон толщин свариваемых деталей, мм: | |
– листовая сталь (оптимальные режимы сварки): | 0,2 – 1,2 |
– листовая сталь (мягкий, многоимпульсный режимы): | до 1,5+1,5 |
– проволока, арматура (оптимальные режимы сварки): | 2 – 5 |
– проволока, арматура (мягкий, многоимпульсный режимы): | до 6 |
– алюминий и его сплавы: | 0,2 – 1,2 |
Максимальная производительность, сварок в мин: | 280 |
Продолжительность включения, %: | 6 – 20 |
Вылет электродов, мм: | 750 |
Диапазон сварочных токов, кА: | 5,6 – 14 |
Номинальный сварочный ток, кА: | 10 |
Число ступеней регулирования сварочного тока: | 4 |
Напряжение сети, В: | 3 х 380 |
Максимальная потребляемая мощность в импульсе, кВА: | 68,4 |
Потребляемый ток в момент сварочного импульса, А: | 60 – 180 |
Выходное напряжение холостого хода, В: | 4,1 – 5,5 |
Максимальный рабочий ход верхнего электрода, мм: | 45 |
Номинальное усилие сжатия электродов, кг: | 80 – 140 |
Привод сжатия электродов: | электромагнитный |
Охлаждение: | жидкостное, автономное, скрытое |
Охлаждающая жидкость: | вода, смесь воды с тосолом |
Количество охлаждающей жидкости: | 4,5 л. |
Габаритные размеры, м: | |
длина | 1,33 |
ширина | 0,42 |
высота | 1,22 |
Сухая масса, кг: | 188 |
– положение, движение и техника стержня
Дуговая сварка требует определенных усилий, и это очень чувствителен к положению работы. Это хорошая идея, чтобы все было легко Для начала укладываем бусинки на квартиру. Швы прикроем позже.
Следующая установка является хорошей отправной точкой для этого урока:
- Работа: Низкоуглеродистая сталь 6мм. Дуговая сварка более устойчива к
слегка ржавый металл и прокатная окалина по сравнению с другими процессами электросварки,
но рекомендуется перед сваркой очистить самые худшие участки шлифовальной машиной.
- Стержни: 3,2 мм 6013 стержней. ИСПОЛЬЗУЙТЕ УДИЛИЩА ХОРОШЕГО КАЧЕСТВА! Форум участник, пытающийся учиться с помощью стержней из магазина DIY, имел ужасные проблемы, пока кто-то прислал ему несколько удочек фирменных знаков, чтобы доказать свою точку зрения. Также стержни 3,2 мм легче учиться со стержнями более 2,5 мм.
- Ампер: 110 Ампер. (если вы хотите использовать стержни 2,5 мм, уменьшите ток примерно до 80 ампер – ток определяется больше стержнем размер, чем толщина листа).
- Полярность: DCEP (стержень положительный, заземляющий отрицательный – это противоположная полярности, используемой в TIG). Используйте кондиционер, если это все, что у вас есть.
Это то, что мы использовали на следующих нескольких страницах. Вы можете сравнить свои
практиковаться с нашими усилиями, в частности с ошибкой
руководство по поиску на следующей странице. Не все сварщики правильно откалибровали
усилители, поэтому вам, возможно, придется отрегулировать свои, чтобы избежать неисправностей.
Угол штанги (угол упора)
Для сварки на плоскости (как на фото) стержень должен быть под углом. От 10 до 20 градусов от вертикали и тянуть в направлении стрелки.Угол стержня предотвращает налет шлака на стержень (сварка шлак может вызвать включения в сварном шве).
На фотографии стержень изогнут у электрододержателя до установите держатель под более удобным углом.
Можно поддерживать верхнюю часть электрода свободной рукой и это улучшает контроль над электродом. Поражение электрическим током не проблема, но будьте осторожны, чтобы убрать руку с огня перед электрод становится слишком коротким.
Длина дуги
Длина дуги – это расстояние между электродом и сварочной ванной.
Он должен быть примерно таким же, как диаметр стержня.
Это далеко не так просто, как кажется!
На фото видно, как электрод заглубляется внутрь флюса. покрытие на штанге. Сварочная ванна также будет скрыта расплавленным шлаком.
Для достижения правильной длины дуги с помощью стержней 3,2 мм расстояние между флюсовое покрытие на стержне и флюс поверх сварного шва могут быть менее 1 мм.
О длине дуги обычно судят по звуку и видимому свету. от дуги.
На видео длина дуги варьируется от правильной, слишком длинной и слишком коротко. Меняются как интенсивность света, так и звук сварного шва. резко с длиной дуги.
Дуга должна быть короткой и скрывать большую часть света от сварку без проталкивания прутка в шлаковую ванну. Хорошая короткая дуга длина приведет к постоянному резкому потрескивающему звуку.
Внешний вид завершенного сварного шва даст дополнительные подсказки – см. фото сварных швов с неправильной длиной дуги на дефектах
страница.
Сохранение угла подъема и длины дуги
Стержень становится короче по мере сварки, и это требует сознательного усилие для уменьшения длины дуги по мере того, как стержень становится короче.Избыток длина дуги может привести к нестабильной дуге, перегреву и подрезке и это, вероятно, самая распространенная ошибка новичков.
Угол стержня также должен быть сохранен по всей длине сварка. Требуется небольшая практика, чтобы избежать уменьшения угла опережения. в процессе сварки, так как это может привести к включению шлака и даже вызвать остановку дуги. Самый простой способ сохранить угол наклона стержня – сфокусировать Обратите внимание на перемещение держателя стержня, а не стержня в процессе сварки.
На видео видно, как расходуется стержень диаметром 2,5 мм при движении по кругу
200 мм в длину.
Сварочное движение
Для большинства дуговой сварки стержень перемещается по прямой линии, образуя “стрингер”. Можно использовать небольшое количество плетения, чтобы контролировать скорость и направление.
На видео дуга запускается простым нажатием. Удочка быстро становится короче по мере продвижения сварного шва, а движение, которое можно увидеть, является постоянным коррекция для поддержания короткой длины дуги.
Обратите внимание, что угол штанги также сохраняется. Чтобы поддерживать длина дуги и угол наклона стержня, особенно если вы переходите на дуговую сварку от другого процесса сварки.
Шлак
Не смотрите внимательно на горячий сварной шов – кусочки шлака постоянно отслаиваются
сварной шов, поскольку он остывает, и их очень больно снимать после
они обожгли себе глаз.Защита глаз тоже хороший
Идея при скалывании шлака, так как он хрупкий и может лететь на значительное расстояние.
Шлак, покрывающий сварной шов, должен достаточно легко удаляться, хотя это действительно зависит от типа и качества удилищ (мы использовали хорошие качество 6013 удочек вот так было легко).
Практика делает колодки
Другие позиции пойдут к сожалению плохо, пока вы не усовершенствовались укладка бус.Хороший способ попрактиковаться – приварить площадку к пластине толщиной 6 мм.
Тщательно очистите пластину, затем уложите первый сварной шов по прямой линии. у края тарелки. Удалите шлак и сразу сделайте второй шов сбоку от первого, достаточно близко, чтобы два сварных шва слились вместе без зазора. Повторение несколько раз должно привести к образованию сварных швов. с плоским верхом. Если вам сложно удерживать прямую линию, то рисуйте линия мелом может помочь.
Поверните подушку на 90 градусов и сварите следующий слой подушки.
При обучении в колледже подушечка будет разрезана для проверки на включения в сварном шве. Практика помогает развить последовательность, сохранение прямой линии шва и хорошая подготовка к более толстым металл, в котором соединение часто образуется из множества сварных швов. Техника также используется для наплавки и наращивания изношенного материала.
Сварочные электроды
При отказе от навыков, необходимых для выполнения подводной мокрой сварки, вы должны изменить фундаментальный подход к тому, как выполняется сварка. Преимущества включают; нет необходимости в особых конфигурациях швов и всей соответствующей подготовке.
Нет необходимости даже в обычном угловом или стыковом соединении. Нет необходимости очищать зону стыка или откалывать шлак перед нанесением дополнительных проходов, фактически нет необходимости в дополнительных проходах, так как процесс является однократным i.е. один электрод обеспечивает один полный точечный / электрозаклепочный шов.
За счет исключения фактических навыков сварки из операции водолазу-сварщику нет необходимости контролировать такие параметры, как скорость движения, углы электродов, длину дуги и т. Д., Как это связано с обычными навыками сварки. Нет необходимости даже в хорошей видимости, поскольку дайверу не нужно видеть или контролировать дугу в общепринятом смысле этого слова. Даже в условиях плохой видимости постоянно производятся высококачественные сварные швы.
Как всего этого достичь?
Используя нашу новую систему управления (как показано на рисунке), подключенную к сварочному аппарату, он управляет процессом сварки.Процесс будет пронизывать два материала, требуемых для соединения, а затем через блок управления токи, необходимые для протыкания и последующего заполнения отверстия, приводят к образованию точечной / электрозащитной сварки, которая проникает в оба набора материалов в достаточной степени для образования прочного соединения. , по принципу похожий на заклепку. Преимущества включают в себя отсутствие необходимости в особых конфигурациях швов и всей необходимой подготовки.
Размер и частоту сварных швов можно определить по следующей формуле.
| ||||
|
Обычно предполагается, что прочность на сдвиг составляет 4/5 от предела прочности на растяжение для большинства сталей.Электрод имеет предел прочности на разрыв 650 Н / мм2 и, следовательно, обеспечивает сопротивление сдвигу ок. 520 Н / мм2. Таким образом, сварной шов диаметром 10,0 мм обеспечивает максимальную нагрузочную способность 40840 Н на точку (40,84 кН).
Система управления, которая находится над водой, контролирует три вещи:
Пиковый ток
Низкий ток
Время
Оператор устанавливает их в соответствии с набором рекомендаций, рассчитанных для толщины материала.
Первое значение тока позволяет электроду непосредственно протыкать материал, создавая отверстие, через которое материалы могут соединяться вместе. Во время этой операции водолазу или роботу нужно только приложить давление, достаточное для проталкивания электрода через соединяемые материалы. Абсолютно никаких сварочных навыков не требуется. После завершения первого цикла сварки и достижения глубины проплавления автоматически инициируется второй ток, который затем позволяет электроду заполнить это отверстие, тем самым создавая точечный / электрозаклепной шов, пронизывающий оба участка материала; Таким образом создается самородок / точечная сварка. Система может соединять материалы общей толщиной до 32 мм (1 1/4 дюйма).
Хотя этот процесс не является полностью автоматическим, поскольку, в конце концов, процесс все еще представляет собой «ручную металлическую дугу», тем не менее, навыки, необходимые водолазу для выполнения сварного шва, были удалены, как и многие традиционные приготовления и факторы окружающей среды, которые обычно оказывают такое влияние на сварку под водой. Если этого было недостаточно, качество окончательного сварного шва также улучшается, поскольку большая часть сварного шва ограничивается сквозной толщиной материала, такие факторы, как эрозия, коррозия, не вызывают беспокойства.Зона термического влияния (HAZ) меньше, общая твердость сварного шва ниже, а вероятность возникновения дефектов сварного шва сведена к минимуму.
Загрузите брошюру Hammerhead в формате PDF здесь
Крепежная сварка гаек и шпилек
Сварка выступом крепежных деталей, в том числе фланцевых гаек и резьбовых шпилек, к горячештампованной стали с бором и упрочненной прессованной сталью, где присутствует покрытие AlSi.

Приваривание фланцевых гаек и резьбовых шпилек может быть затруднено.Крепеж часто бывает значительно мягче штамповки 1500 МПа. При таком большом изменении твердости выступы в креплении разрушатся до того, как будет выполнен хороший сварной шов. Конечным результатом обычно являются испаренные выступы и увеличенное время сварки в целях ковки материалов, а не их сварки. Кроме того, когда используется этот тип процесса сварки, конечный результат – слабый, непостоянный крутящий момент и значения выталкивания, а также большая зона термического влияния (HAZ).
Кроме того, другой проблемой является стабильность основного материала из-за внутренней обработки.Наблюдаемые воздействия могут включать температуру печи, время цикла нагрева, расход воды, температуру воды и время закалки.
Сварка выступающих элементов крепежа Задача:
- Крепежные детали, включая фланцевые гайки и резьбовые шпильки, чрезвычайно мягкие по сравнению с основным материалом.
- На материалах горячей штамповки в печи образуется покрытие AlSi.
- Резистивные качества покрытия AlSi могут быть неодинаковыми по всей детали и от партии к партии.
- Более длительное время сварки при более низком сварочном токе (как это обычно требуется в схемах сварки выступами) затрудняет подачу достаточного количества тепла к основному материалу, часто испаряя выступы без сварки.
- Равномерная сварка выступами затруднена для большинства процессов, и даже для многих аппаратов для сварки конденсаторным разрядом, которые могут быть неправильно спроектированы для процесса сварки выступами.
Раствор для выступающей сварки крепежа:
В результате сварка крепежных деталей с использованием конденсаторных сварочных аппаратов от компании Weld Systems Integrators (WSI) – ваше решение. Сварка сопротивлением конденсаторным разрядом (иногда называемая емкостным разрядом) накапливает энергию для чрезвычайно быстрого выделения энергии с большими пиковыми токами.Больше энергии на формирование сварного шва и меньше на нагрев окружающего материала. Зона термического влияния сварного шва, в которой были изменены свойства металла, меньше, что сводит к минимуму изменения в металлургии детали.
Статьи и новости о сварке крепежных изделий
Интеграторы систем контактной сварки
Компания Weld Systems Integrators имеет более 10 лет проверенных результатов в областях, связанных с трудностями при сварке, такими как крепежные детали для сварки выступом для горячештампованного бора, упрочненной стали, сверхтвердого алюминия, сплавов нержавеющей стали и новейших материалов поколения III! Сварочные аппаратыWSI с конденсаторным разрядом могут обеспечить хорошие сварочные швы закаленных под давлением сталей в 100% случаев.
СВЯЗАТЬСЯ с интеграторами сварочных систем или ЗАПРОСИТЬ ЦЕНУ для получения дополнительной информации о наших вариантах оборудования для проекционной сварки. Чтобы поговорить с членом команды WSI, позвоните нам по телефону 844-WSI-WELD или + 1-216-475-5629.
Электроды для сварочной проволоки
ERN сварочный стержень сплав 9011 Электроды для дуплексной стали 904L N08904 ERNiCrMo-3 90MO-3 90MO-3 90MO-3 90MO-3 90MO-8 90MO-3 90MO-3 90MO-90 провод для AL- 6XN N08367 сплав 9011 Сплав Inoj1 9011 Электроды никелевый сплав 9011 .2 электрода сварочного стержня Электроды Никелевый сплав Сварочная проволока Монель 400 Электрод Сварочный электрод N0118 Инконель Сварочная проволока из инконеля Никель хромированный сплав 9012 33 Распространенные методы сварки нержавеющей стали
Процесс сварки нержавеющей стали зависит от толщины и отделки материала, а также от использования готового продукта. Хотя существует множество методов сварки нержавеющей стали, есть три, которые наиболее часто используются сварщиками в Соединенных Штатах. К этим методам сварки нержавеющей стали относятся сварка TIG, контактная сварка и сварка MIG.
Это сварка TIG, контактная сварка и сварка MIG. Продолжайте читать, чтобы узнать больше о каждом.
1. Сварка TIG или дуговая сварка вольфрамовым электродом
Предлагая высокое качество, универсальность и долговечность, TIG является наиболее часто используемым процессом сварки нержавеющей стали.Этот процесс сварки обеспечивает низкое тепловложение, что делает его идеальным для обработки тонких материалов. Газ аргон часто смешивают с другими газами, в зависимости от потребностей конкретного проекта, включая гелий, водород и азот. Чтобы предотвратить окисление и повысить устойчивость к коррозии, можно использовать процесс односторонней сварки, создавая инертную газовую защиту между внутренними и внешними сварными швами.
2. Контактная или точечная сварка
Контактная или «точечная» сварка, как ее часто называют, является одним из самых экономичных видов сварки. Оборудование для контактной сварки (RW) невероятно универсально, что означает, что его можно использовать как в небольших, так и в крупных проектах.
RW использует электрический ток для нагрева истертых металлических кромок и их склейки. Этот тип сварки исключительно эффективен для металла с низкой температурой плавления, поскольку его можно адаптировать для предотвращения деформации металла.
3. Сварка МИГ или газовая сварка металлов переменным током
СваркаMIG – это полуавтоматический процесс, который при правильном выполнении обеспечивает прочное соединение двух частей нержавеющей стали.В этом процессе используется защитный газ, богатый аргоном, и сплошной проволочный электрод.
Сварка MIG популярна, потому что позволяет сварщику использовать импульсный источник тока, который может упростить сварку труднодоступных мест на сложных проектах из нержавеющей стали. Смеси других газов, в том числе с гелием, кислородом и углекислым газом, часто используются для стабилизации дуги и улучшения качества сварного шва.
Какой метод сварки нержавеющей стали лучше всего?
Выбор правильного метода сварки нержавеющей стали на самом деле зависит от того, какие качества вы ищете.Если вам нужен более доступный сварной шов, то лучше всего подойдет точечная сварка. Но если материал, с которым мы работаем, тонкий, то лучшим выбором может быть сварка TIG или газовая вольфрамовая дуга.
В All-Type Welding and Fabrication, Inc. наша команда экспертов по сварке оценит материалы, возможности и стиль отделки, которые вы хотите использовать для каждого проекта, чтобы определить, какой метод сварки будет наиболее эффективным для данной задачи.
Благодаря обширным знаниям в области сварки и многолетнему опыту работы компания ATWF может выбрать и реализовать для вас лучший метод сварки нержавеющей стали.Свяжитесь с нами сегодня, чтобы получить расценки, узнать больше о нашем процессе и получить все ответы, которые вы ищете.
Сварка – SteelConstruction.info
Сварка – это основной вид деятельности на заводе-изготовителе, которым занимаются квалифицированные специалисты, работающие в системе управления качеством сварки под контролем ответственного координатора сварки. Он используется для подготовки стыков к подключению в магазине и на месте, а также для крепления других приспособлений и фурнитуры.На заводе-изготовителе для различных видов деятельности используются разные методы сварки.
По сути, в процессе сварки используется электрическая дуга для выработки тепла для плавления основного материала в соединении. Отдельный присадочный материал, поставляемый в качестве расходуемого электрода, также плавится и соединяется с основным материалом, образуя расплавленную сварочную ванну. По мере того, как сварка продолжается вдоль соединения, сварочная ванна затвердевает, сплавляя основной металл и металл сварного шва. Для заполнения стыка или нарастания сварного шва до проектного размера может потребоваться несколько проходов или проходов.
Сварка
(Изображение любезно предоставлено William Haley Engineering Ltd.)
[вверх] Принципы дуговой сварки металлом
Терминология зоны сварки
Сварка – это сложное взаимодействие физических и химических наук. Правильное определение металлургических требований и разумное практическое применение являются предпосылкой успешной сварки плавлением.
В процессе дуговой сварки металлическим электродом используется электрическая дуга для выработки тепла для плавления основного материала в соединении. Отдельный присадочный материал, поставляемый в качестве расходуемого электрода, также плавится и соединяется с основным материалом, образуя расплавленную сварочную ванну. Сварочная ванна подвержена атмосферному загрязнению и, следовательно, нуждается в защите во время критической фазы замерзания жидкости и твердого тела. Защита достигается либо за счет использования защитного газа, путем покрытия бассейна инертным шлаком, либо за счет комбинации обоих действий.
В процессах с защитой от газа поступает газ из удаленного источника, который подается в сварочную дугу через горелку или горелку. Газ окружает дугу и эффективно исключает атмосферу. Точный контроль необходим для поддержания подачи газа с подходящей скоростью потока, так как слишком большое количество может вызвать турбулентность и засасывать воздух, а может быть настолько же вредным, насколько и слишком маленьким.
В некоторых процессах используется флюс, который плавится в дуге для образования шлакового покрытия, которое, в свою очередь, покрывает сварочную ванну и защищает ее во время замерзания.Шлак также затвердевает и самораспускается или легко удаляется легким сколом. Действие плавления флюса также создает газовый экран для защиты.
По мере продвижения сварки вдоль стыка сварочная ванна затвердевает, сплавляя основной металл и металл шва. Для заполнения стыка или нарастания сварного шва до проектного размера может потребоваться несколько проходов или проходов.
Тепло от сварки вызывает металлургические изменения в основном материале, непосредственно примыкающем к границе или линии плавления.Эта область изменения известна как зона термического влияния (HAZ). Общая терминология, используемая в области сварного шва, показана справа вверху.
Сварочные операции требуют надлежащего технологического контроля со стороны компетентных сварщиков, чтобы гарантировать достижение проектных характеристик, минимизировать риск дефектных соединений, вызванных низким качеством сварки, и предотвратить образование склонных к образованию трещин микроструктур в ЗТВ.
[вверх] Виды сварных соединений
Большинство конструкционных сварных соединений выполняется на заводе-изготовителе и описывается как стыковые или угловые швы.Сварка на месте также возможна, и руководство по вопросам сварки на месте доступно в GN 7.01.
[вверху] Стыковые швы
Макрос клиновидного стыкового шва
(Изображение любезно предоставлено Mabey Bridge Ltd.)
Стыковые сварные швы обычно представляют собой стыковые соединения в прокатных профилях или стыковые соединения листов на стенках и фланцах, чтобы приспособиться к изменению толщины или восполнить доступный материал по длине.Положения этих стыковых швов допускаются при проектировании, хотя ограничения доступности материалов или схема монтажа могут потребовать согласования различных или дополнительных сварных швов. Тройники, приваренные встык, могут потребоваться, если при поперечных соединениях возникают значительные нагрузки или усталость.
Стыковые швы – это сварные швы с полным или частичным проплавлением, выполняемые между материалами со скошенными или скошенными кромками. Стыковые швы с полным проплавлением предназначены для передачи всей прочности сечения.Как правило, эти соединения можно сваривать с одной стороны, но по мере увеличения толщины материала желательна сварка с обеих сторон, чтобы уравновесить эффекты деформации, с операцией обратной строжки и / или шлифования в процессе для обеспечения целостности корень шва. Односторонние стыковые сварные швы с подкладными полосами из керамической или прочной стали обычно используются для соединения больших площадей пластин (например, стальных пластин настила) и там, где есть закрытые коробчатые секции, трубы или элементы жесткости, доступ к которым для сварки возможен только с одного сторона.Расчетная толщина горловины определяет глубину проплавления, необходимую для швов с частичным проплавлением. Обратите внимание, что соображения усталости могут ограничивать использование сварных швов с частичным проплавлением, особенно на мостах. Руководство по подготовке к сварке доступно в GN 5.01.
Необходимо приложить все усилия, чтобы избежать стыковой сварки приспособлений из-за затрат, связанных с подготовкой, временем сварки, более высоким уровнем квалификации сварщика и более строгими и трудоемкими требованиями к испытаниям. Кроме того, стыковые швы имеют тенденцию иметь большие объемы наплавленного металла шва; это увеличивает эффект усадки сварного шва и приводит к более высокому уровню остаточного напряжения в соединении.Чтобы уравновесить усадку и распределить остаточное напряжение, минимизируя таким образом деформацию, необходима тщательная последовательность сварочных операций.
Иногда бывает необходимо обработать стыковые сварные швы заподлицо по причинам усталости, или для улучшения дренажа стальных балок, устойчивых к атмосферным воздействиям, или для улучшения режима испытаний. Следует избегать зачистки заподлицо только по эстетическим соображениям, потому что трудно обработать поверхность, чтобы она соответствовала смежной поверхности после прокатки, и результат часто более визуально заметен, чем исходный сварной шов. Кроме того, шлифование представляет собой дополнительную опасность для здоровья и безопасности, которую следует избегать по возможности. Правка стыковых сварных швов до гладкой поверхности обычно не требуется для строительных стальных конструкций, поскольку обычно они не подвержены усталости.
- Пример обработанного стыкового шва с гладкой поверхностью и сливными пластинами
(изображения любезно предоставлены Mabey Bridge Ltd.)
[вверх] Угловые швы
Макрос однократного углового сварного шва
(Изображение любезно предоставлено Mabey Bridge Ltd.)
В большинстве сварных соединений в зданиях и мостах используются угловые сварные швы, обычно в форме тройника. Обычно они включают в себя концевую пластину, ребро жесткости, подшипниковые и распорные соединения с прокатными секциями или плоскими балками, а также соединения стенки с фланцами на самих пластинчатых балках. Их относительно просто подготовить, сварить и испытать в обычных конфигурациях, при этом главным соображением является сборка стыков.
В S275 полная прочность сталей также развивается в угловых сварных швах и сварных швах с частичным проплавлением с вышележащими угловыми швами при условии, что такие сварные швы симметричны, выполнены с использованием правильных расходных материалов и сумма сварных швов равна толщине элемента, который сварные швы стыкуются.
Размеры сварных швов должны быть подробно описаны на чертежах проекта вместе с любыми специальными требованиями классификации усталости. BS EN ISO 22553 [1] предписывает правила использования символов для детализации сварных соединений на чертежах.
Обращает на себя внимание тот факт, что в традиционной британской практике для определения размера углового сварного шва обычно используется длина ветви, но это не универсально: в европейской практике используется толщина горловины, а в BS EN 1993-1-8 [2] дает требования относительно размера горла, а не длины ноги. Проектировщик должен следить за тем, чтобы было ясно, какой размер указан, и что все стороны должны знать, что было указано.
[вверх] Процессы
Важными факторами, которые подрядчик по изготовлению металлоконструкций следует учитывать при выборе процесса сварки, являются способность выполнить проектные требования и, с точки зрения производительности, скорость наплавки, которая может быть достигнута, а также рабочий цикл или эффективность процесса. (Эффективность – это отношение фактического времени сварки или дуги к общему времени, в течение которого сварщик или оператор занят выполнением сварочного задания.Общее время включает настройку оборудования, чистку и проверку выполненного шва.)
Ниже описаны четыре основных процесса сварки, которые регулярно используются при производстве стальных конструкций в Великобритании. Номера процессов определены в BS EN ISO 4063 [3] . Разновидности этих процессов были разработаны с учетом практики и оборудования отдельных производителей, и другие процессы также имеют место для конкретных приложений, но выходят за рамки данной статьи.
[вверх] Металлоактивная газовая сварка (MAG), процесс 135
Сварка MAG
(Изображение любезно предоставлено Kiernan Structural Steel Ltd.)
MAG-сварка сплошным проволочным электродом – это наиболее широко используемый процесс с ручным управлением для заводских производственных работ; иногда это называют полуавтоматической сваркой или сваркой CO 2 . Сплошной проволочный электрод из сплошной проволоки пропускается через устройство подачи проволоки к «пистолету», который обычно удерживается и управляется оператором. Питание подается от источника выпрямителя или инвертора по соединительным кабелям к устройству подачи проволоки и кабелю горелки; электрическое подключение к проводу осуществляется через контактный наконечник на конце пистолета.Дуга защищена защитным газом, который направляется в зону сварного шва через кожух или сопло, окружающее контактный наконечник. Защитные газы обычно представляют собой смесь аргона, диоксида углерода и, возможно, кислорода или гелия.
Хорошая производительность наплавки и рабочий цикл можно ожидать от процесса, который также можно механизировать с помощью простых моторизованных кареток. Газовая защита может быть сдута сквозняками, что может вызвать пористость и возможные вредные металлургические изменения в металле шва.Таким образом, этот процесс лучше подходит для заводского производства, хотя он используется на месте, где могут быть предусмотрены эффективные укрытия. Он также более эффективен в плоском и горизонтальном положениях; Сварные швы в других положениях наплавляются с более низкими параметрами напряжения и силы тока и более подвержены дефектам плавления.
Металлоактивная газовая сварка (МАГ), процесс 135
Металлоактивная газовая сварка (MAG), процесс 135
MAG-сварка электродом с флюсовой сердцевиной, процесс 136 представляет собой разновидность, в которой используется то же оборудование, что и MAG-сварка, за исключением того, что плавящийся проволочный электрод имеет форму трубки малого диаметра, заполненной флюсом.Преимущество использования этих проволок состоит в том, что можно использовать более высокие скорости наплавки, особенно при сварке в вертикальном положении (между двумя вертикальными поверхностями) или в верхнем положении. Наличие тонкого шлака помогает преодолевать силу тяжести и позволяет наносить сварные швы в местах с относительно высокими током и напряжением, тем самым уменьшая возможность дефектов плавления. Добавки флюса также влияют на химию сварного шва и, таким образом, улучшают механические свойства соединения.
[вверху] Ручная дуговая сварка металлом (MMA), процесс 111
Этот процесс остается наиболее универсальным из всех сварочных процессов, но его использование в современной мастерской ограничено.Трансформаторы переменного тока, выпрямители постоянного тока или инверторы подают электроэнергию по кабелю на электрододержатель или клещи. Проволочный электрод с флюсовым покрытием (или «стержень») вставляется в держатель, и сварочная дуга возникает на конце электрода, когда он ударяется о заготовку. На острие электрода плавится, образуя ванну расплава, которая сплавляется с основным материалом, образуя сварной шов. Флюс также плавится, образуя защитный шлак и создавая газовую защиту, предотвращающую загрязнение сварочной ванны по мере ее затвердевания.Добавки флюса и сердечник электрода используются для влияния на химический состав и механические свойства сварного шва.
Обычно используются электроды с основным покрытием, контролируемым водородом. Эти электроды необходимо хранить и обращаться с ними в соответствии с рекомендациями производителя расходных материалов, чтобы сохранить их низкие водородные характеристики. Это достигается либо путем использования сушильных шкафов и подогреваемых колчанов для хранения и обработки продукта, либо путем приобретения электродов в герметичных упаковках, специально разработанных для поддержания низкого уровня водорода.
Недостатками процесса являются относительно низкая скорость осаждения и высокий уровень отходов, связанных с непригодными для использования концевыми штырями электродов. Тем не менее, он остается основным процессом для сварки на стройплощадке и для труднодоступных мест, где громоздкое оборудование не подходит.
Ручная дуговая сварка металлом (MMA), процесс 111
Ручная дуговая сварка металлом (MMA), процесс 111
[вверх] Дуговая сварка под флюсом (SAW), процесс 121
Оперативная сварка под флюсом
(Изображение любезно предоставлено Mabey Bridge Ltd.)
Это, вероятно, наиболее широко используемый процесс для сварки угловых швов перемычки между стенкой и фланцем и стыковых стыковых швов толстых листов для получения отрезков фланца и стенки. В процессе процесса непрерывная проволока подается через контактный наконечник, где она обеспечивает электрический контакт с мощностью от выпрямителя, в зону сварки, где она изгибается и образует ванну расплава. Сварочная ванна заполняется флюсом, подаваемым из бункера. Флюс, непосредственно покрывающий расплавленную сварочную ванну, плавится, образуя шлак и защищая сварной шов во время затвердевания; избыточный флюс собирается и повторно используется.По мере охлаждения шва шлак замерзает и отслаивается, оставляя высококачественные профильные швы.
Этот процесс по своей природе более безопасен, чем другие процессы, поскольку дуга полностью покрывается во время сварки, отсюда и термин дуга под флюсом. Это также означает, что требования к личной защите меньше. Высокая производительность наплавки – особенность процесса, поскольку он обычно механизируется на портальных мостах, тракторах или другом специализированном оборудовании. Это позволяет контролировать параметры и дает рекомендации по точному размещению сварных швов.
Сварка под флюсом (SAW), процесс 121
Сварка под флюсом (SAW), процесс 121
[вверху] Приварка шпилек методом вытяжной дуги, способ 783
Композитные мосты требуют приваривания соединителей со срезными шпильками к верхнему фланцу пластинчатых или коробчатых балок и в других местах, где требуется композитное воздействие стали на бетон, например.грамм. на интегральных абатментах. В зданиях композитные балки требуют приваривания соединителей срезных шпилек к элементам либо непосредственно к верхнему фланцу, либо чаще через постоянный настил из оцинкованной стали на композитных полах, где верхний фланец балки остается неокрашенным.
Сварка шпильки на балке моста
(Изображение любезно предоставлено Mabey Bridge Ltd.)Приварка сквозных шпилек
(Изображение любезно предоставлено Structural Metal Decks Ltd.)
Метод приварки шпилек известен как процесс с натянутой дугой, и требуется специальное оборудование в виде мощного выпрямителя и специального пистолета. Шпильки загружаются в пистолет, и при электрическом контакте с изделием концевые дуги сгибаются и плавятся. Продолжительность дуги рассчитывается таким образом, чтобы между концом шпильки и основным материалом установилось расплавленное состояние. В нужный момент пистолет погружает шпильку в сварочную ванну.Керамическая манжета окружает шпильку для защиты и поддержки сварочной ванны, стабилизации дуги и формовки смещенной сварочной ванны для формирования сварной манжеты. Когда сварной шов затвердевает, наконечник отслаивается. У удовлетворительных сварных швов обычно есть правильная, яркая и чистая втулка, полностью окружающая шпильку.
Приварка шпилек методом вытяжной дуги 783
[вверху] Спецификации процедуры сварки
Чертежи детализируют конструктивную форму, выбор материала и указывают сварные соединения.Подрядчик по изготовлению металлоконструкций выбирает методы сварки каждой конфигурации стыка, обеспечивающие требуемые характеристики. Прочность, вязкость разрушения, пластичность и усталость – важные металлургические и механические свойства, которые необходимо учитывать. Тип соединения, положение сварки, производительность и требования к ресурсам влияют на выбор подходящего процесса сварки.
Выбранный метод представлен в спецификации процедуры сварки (WPS), в которой подробно описана информация, необходимая для инструктирования и руководства сварщиками, чтобы обеспечить повторяемость характеристик для каждой конфигурации соединения.Пример формата WPS показан в Приложении А стандарта BS EN ISO 15609-1 [4] . Подрядчики по изготовлению металлоконструкций могут иметь свой собственный корпоративный шаблон, но все они включают важную информацию, позволяющую передать сварщику надлежащие инструкции.
Необходимо подкрепить WPS свидетельством удовлетворительных испытаний процедуры в виде протокола аттестации процедуры сварки (WPQR), подготовленного в соответствии с BS EN ISO 15614-1 [5] . Введение этого стандарта гласит, что испытания процедуры сварки, проведенные в соответствии с прежними национальными стандартами и спецификациями, не аннулируются при условии их технической эквивалентности; Для этого могут потребоваться дополнительные тесты.Основные подрядчики по изготовлению металлоконструкций в Великобритании прошли предварительную квалификацию сварочных работ, позволяющих производить удовлетворительные сварные швы в большинстве конфигураций стыков, которые могут встретиться в производстве стальных конструкций и мостов.
В случаях, когда данные предыдущих испытаний не имеют отношения к делу, необходимо провести испытание процедуры сварки, чтобы установить и подтвердить пригодность предлагаемого WPS.
Руководство по стандартным техническим условиям сварки для стальных конструкций доступно в публикации BCSA No.58/18.
[вверх] Процедура испытаний
BS EN ISO 15614-1 [5] описывает условия проведения испытаний процедуры сварки и пределы действия в пределах квалификационных диапазонов, указанных в стандарте. Координатор сварки составляет предварительную спецификацию процедуры сварки (pWPS), которая является первоначальным предложением для проведения испытания процедуры. Для каждой конфигурации стыка, будь то стыковой или угловой сварной шов, учитывается марка и толщина материала, а также ожидаемые допуски посадки, которые могут быть достигнуты на практике.Выбор процесса определяется методом сборки, положением сварки и тем, является ли механизация жизнеспособным предложением для повышения производительности и обеспечения постоянного качества сварки. Размеры подготовки швов зависят от выбора процесса, любых ограничений доступа и толщины материала.
Расходные материалы выбираются из соображений совместимости с марками материалов и достижения указанных механических свойств, в первую очередь с точки зрения прочности и вязкости. Для сталей марок S355 и выше используются водородо-регулируемые изделия.
Риск водородного растрескивания, пластинчатого разрыва, растрескивания при затвердевании или любой другой потенциальной проблемы оценивается не только с целью проведения испытания, но также для предполагаемого применения процедуры сварки в проекте. Соответствующие меры, такие как предварительный или последующий нагрев, включены в pWPS.
Контроль искажений обеспечивается правильной последовательностью сварки. При необходимости вводятся обратная строжка и / или обратное шлифование для достижения целостности корневого шва.
Приведены диапазоны сварочного напряжения, тока и скорости, чтобы определить оптимальные условия сварки.
Допустимые диапазоны групп материалов, толщины и типа соединения в пределах спецификации тщательно рассматриваются, чтобы максимально использовать pWPS. Подготавливаются испытательные пластины достаточного размера для извлечения образцов для механических испытаний, включая образцы для любых дополнительных испытаний, указанных или необходимых для повышения применимости процедуры.
Пластины и pWPS передаются сварщику; испытание проводится в присутствии эксперта (обычно из независимого проверяющего органа), и ведется запись фактических параметров сварки вместе с любыми необходимыми изменениями процедуры.
Завершенные испытания передаются независимому эксперту для визуального осмотра и неразрушающего контроля в соответствии с таблицей 1 Стандарта. Удовлетворительные испытательные пластины затем отправляются на разрушающий контроль, опять же в соответствии с таблицей 1. Неразрушающие методы контроля обычно включают ультразвуковой контроль для объемного контроля и контроль магнитных частиц для выявления дефектов поверхности.
Пример испытательного образца процедуры сварки
(Изображение любезно предоставлено Mabey Bridge Ltd.)
Существует ряд дополнительных стандартов, детализирующих подготовку, обработку и испытания всех типов образцов для разрушающих испытаний. Обычно специализированные лаборатории организуют подготовку образцов для испытаний и проводят фактические механические испытания и составление отчетов. Типичные образцы для стыкового сварного шва пластины включают испытания на поперечное растяжение, испытания на поперечный изгиб, испытания на удар и образец для макроэкспертизы, на котором проводится испытание на твердость.Для испытаний на удар минимальные требования к поглощению энергии и температура испытания обычно такие же, как и для основного материала в соединении. Целесообразно проверить все сварочные процедуры до предела возможного применения, чтобы избежать повторения подобных испытаний в будущем.
Завершенные результаты испытаний заносятся в квалификационную запись процедуры сварки (WPQR), утверждаемую экзаменатором. Типичный формат показан в Приложении B стандарта BS EN ISO 15614-1 [5] .
Существует дополнительное общее требование, касающееся испытаний процедуры сварки, согласно которому, если грунтовки краски должны быть нанесены на работу до изготовления, они должны наноситься на образец материала, используемого для испытаний. На практике требуется тщательный контроль толщины краски, чтобы избежать дефектов сварки.
BS EN ISO 14555 [6] описывает метод испытаний для соединителей с резьбой, приваренных дуговой сваркой. Стандарт включает требования к испытаниям, необходимым для подтверждения целостности сварных швов шпилек, а также устанавливает требования к производственным испытаниям для контроля приваривания шпилек в процессе.Допускается также квалификация, основанная на предыдущем опыте, и большинство подрядчиков по производству стальных конструкций могут предоставить доказательства, подтверждающие это.
Дополнительное руководство по испытаниям процедуры сварки доступно в GN 4.02.
[вверх] Водородный крекинг
Растрескивание может привести к хрупкому разрушению соединения с потенциально катастрофическими результатами. Водородное (или холодное) растрескивание может происходить в области основного металла, прилегающей к границе плавления сварного шва, известной как зона термического влияния (HAZ).Разрушение металла сварного шва также может быть вызвано определенными условиями. Механизмы, вызывающие отказ, сложны и подробно описаны в специальных текстах.
Рекомендуемые методы предотвращения растрескивания водородом / HAZ описаны в BS EN 1011-2 [7] , приложение C. Эти методы определяют уровень предварительного нагрева для изменения скорости охлаждения, что дает время водороду для миграции на поверхность. и ускользнуть (особенно если поддерживается в виде пост-нагрева после завершения соединения) вместо того, чтобы оставаться в жестких, напряженных зонах.Предварительный нагрев не препятствует образованию микроструктур, подверженных образованию трещин; он просто снижает один из факторов, водород, так что растрескивания не происходит. Предварительный нагрев также снижает термический шок.
Подкладки предварительного нагрева
(Изображение предоставлено Mabey Bridge Ltd.)
Одним из параметров, необходимых для расчета предварительного нагрева, является подвод тепла. Заметным изменением в стандарте является отказ от термина «энергия дуги» в пользу тепловложения для описания энергии, вводимой в сварной шов на единицу длины прогона.Расчет подводимого тепла основан на сварочном напряжении, токе и скорости движения и включает коэффициент теплового КПД; формула подробно описана в BS EN 1011-1 [8] .
Высокая устойчивость и повышенные значения углеродного эквивалента, связанные с более толстыми листами и более высокими марками стали, могут потребовать более строгого контроля процедур. Опытные подрядчики по изготовлению металлоконструкций могут выполнить эту дополнительную операцию и соответственно учесть ее.
BS EN 1011-2 [7] подтверждает, что наиболее эффективной гарантией предотвращения водородного растрескивания является снижение поступления водорода в металл шва из сварочных материалов.Процессы с изначально низким водородным потенциалом эффективны как часть стратегии, так же как и принятие строгих процедур хранения и обращения с водородными электродами. Данные и рекомендации поставщиков расходных материалов служат руководством для обеспечения минимально возможных уровней водорода для типа продукта, выбранного в процедуре.
Дополнительные информативные приложения к стандарту BS EN 1011-2 [7] описывают влияние условий сварки на ударную вязкость и твердость в зоне термического влияния и дают полезные советы по предотвращению растрескивания при затвердевании и разрыва пластин.
Дополнительное руководство по крекингу водородом / HAZ доступно в GN 6.04.
[вверх] Квалификация сварщика
Квалифицированный сварщик
(Изображение любезно предоставлено Mabey Bridge Ltd.)
BS EN 1090-2 [9] требует, чтобы сварщики имели квалификацию в соответствии с BS EN ISO 9606-1 [10] . Этот стандарт предписывает испытания для аттестации сварщиков в зависимости от процесса, расходных материалов, типа соединения, положения сварки и материала.Сварщики, прошедшие успешные испытания процедуры, автоматически получают одобрение в пределах квалификационных диапазонов, указанных в стандарте. Операторы сварки должны быть аттестованы в соответствии с BS EN ISO 14732 [11] , когда сварка полностью механизирована или автоматическая. В этом стандарте особое внимание уделяется проверке способности оператора настраивать и регулировать оборудование до и во время сварки.
Квалификация сварщика ограничена по времени и требует подтверждения действительности в зависимости от продолжительности работы, участия в работе соответствующего технического характера и удовлетворительной работы.Продление квалификации сварщика зависит от записанных подтверждающих свидетельств, демонстрирующих продолжающуюся удовлетворительную работу в пределах исходного диапазона испытаний, и доказательства должны включать либо объемные разрушающие испытания, либо разрушающие испытания. Успех всех сварочных операций зависит от персонала, имеющего соответствующее обучение и регулярного контроля компетентности посредством инспекций и испытаний.
[наверх] Контроль и испытания
BS EN 1090-2 [9] устанавливает объем проверки до, во время и после сварки и дает критерии приемки, связанные с классом исполнения.Большинство испытаний неразрушающие; Разрушающие испытания проводятся только на отводных плитах.
[вверх] Неразрушающий контроль
Магнитный контроль частиц (MPI) сварного шва
(Изображение любезно предоставлено Mabey Bridge Ltd.)
Неразрушающий контроль проводится в соответствии с принципами BS EN ISO 17635 [12] . Для стальных конструкций основными методами являются визуальный контроль после сварки (см. GN 6.06), магнитопорошковый контроль (обычно сокращенно MPI или MT) для поверхностного контроля сварных швов (см. GN 6.02) и ультразвуковой контроль (UT) для подповерхностного контроля сварных швов (см. GN 6.03). Радиографические испытания также упоминаются в BS EN 1090-2 [9] . Радиография требует строгого контроля здоровья и безопасности; это относительно медленно и требует специального оборудования. Использование этого метода для стальных конструкций уменьшилось по сравнению с более безопасным и портативным оборудованием, используемым в UT.Безопасные запретные зоны необходимы на производстве и на месте во время рентгенографии. Однако рентгенографию можно использовать для уточнения природы, размеров или степени множественных внутренних дефектов, обнаруженных ультразвуком.
Технические специалисты с признанной подготовкой и квалификацией в соответствии с BS EN ISO 9712 [13] требуются для всех методов неразрушающего контроля.
BS EN 1090-2 [9] требует, чтобы все сварные швы подвергались визуальному контролю по всей их длине.С практической точки зрения сварные швы следует визуально осматривать сразу после сварки, чтобы гарантировать своевременное устранение очевидных дефектов поверхности.
Дальнейшие требования к неразрушающему контролю основаны на эксплуатационных методах и требуют более строгого исследования первых пяти соединений новых технических требований к процедуре сварки, чтобы установить, что процедура способна производить сварные швы соответствующего качества при внедрении в производство. Затем указываются дополнительные неразрушающие испытания, основанные на типах соединений, а не на конкретных критических соединениях.Цель состоит в том, чтобы опробовать различные сварные швы в зависимости от типа соединения, марки материала, сварочного оборудования и работы сварщиков и, таким образом, поддерживать общий мониторинг производительности.
Если указано частичное или процентное обследование, руководство по выбору продолжительности испытания дано в BS EN ISO 17635 [12] ; При обнаружении недопустимых разрывов площадь исследования соответственно увеличивается.
BS EN 1090-2 [9] также включает в таблицу минимальное время выдержки перед дополнительным неразрушающим контролем в зависимости от размера сварного шва, подводимой теплоты и марки материала.
Признавая, что там, где требования к усталостной прочности более обременительны и требуется более строгая проверка, BS EN 1090-2 [9] действительно предусматривает спецификацию выполнения проекта для определения конкретных соединений для более высокого уровня проверки вместе с объемом и метод тестирования.
Для класса EXC3 критерием приемлемости дефектов сварного шва является уровень качества B стандарта BS EN ISO 5817 [14] . Там, где необходимо достичь повышенного уровня качества для удовлетворения конкретных требований к усталостной прочности, BS EN 1090-2 [9] дает дополнительные критерии приемлемости с точки зрения категории деталей в BS EN 1993-1-9 [15] для расположения сварного шва.
Как правило, дополнительные критерии приемки практически не достижимы при обычном производстве. Стандартные испытания процедуры сварки и квалификационные испытания сварщиков не оцениваются по требованиям этого уровня. Если необходимо достичь такого уровня качества, требования должны быть сосредоточены на соответствующих деталях соединения, чтобы подрядчик имел возможность подготовить спецификации процедуры сварки, квалифицировать сварщиков и разработать соответствующие методы контроля и испытаний.
Неразрушающий контроль
[вверх] Разрушающий контроль
В стандарте BS EN 1090-2 [9] нет требований о проведении разрушающих испытаний поперечных соединений на растянутых фланцах. Тем не менее, объем для определения конкретных соединений для проверки позволит в спецификации проекта испытать, например, образцы от «стекающих» пластин, прикрепленных к встроенным стыковым сварным швам. Дополнительно производственные испытания могут быть указаны для: марок стали выше S460; угловые швы, в которых используются характеристики глубокого проплавления сварочного процесса; для мостовидных ортотропных настилов, где требуется макросъемка для проверки проплавления сварного шва; и на соединениях ребер жесткости с соединительными пластинами.
[вверх] Производственные испытания приварки шпилек
Испытание на изгиб приварной шпильки
(Изображение любезно предоставлено Mabey Bridge Ltd.)
Сварные шпильки для соединителей, работающих на сдвиг, исследуются и испытываются в соответствии с BS EN ISO 14555 [6] . В стандарте подчеркивается необходимость контроля процесса до, во время и после сварки. Предпроизводственные испытания используются для подтверждения процедуры сварки и, в зависимости от области применения, включают испытания на изгиб, испытания на растяжение, испытания на крутящий момент, макросъемку и радиографическое обследование.
Производственные испытания сварных швов также необходимы для приварки шпилек с дугой протяжки. Они должны выполняться производителем до начала сварочных работ на конструкции или группе аналогичных конструкций и / или после определенного количества сварных швов. Каждое испытание должно состоять как минимум из 10 сварных шпилек и быть испытано / оценено в соответствии с требованиями BS EN ISO 14555 [6] . Количество необходимых тестов должно быть указано в спецификации контракта.
[вверх] Качество сварки
Влияние дефектов на характеристики сварных соединений зависит от приложенной нагрузки и свойств материала.Эффект также может зависеть от точного расположения и ориентации дефекта, а также от таких факторов, как рабочая среда и температура. Основное влияние дефектов сварного шва на эксплуатационные характеристики стальных конструкций заключается в повышении риска разрушения из-за усталости или хрупкого разрушения.
Типы дефектов сварки можно разделить на одну из нескольких общих рубрик:
- Трещины.
- Плоские дефекты, кроме трещин, например непробиваемость, отсутствие плавления.
- Включения шлака.
- Пористость, поры.
- Поднутрения или дефекты профиля.
Трещины или плоские дефекты, проникающие через поверхность, потенциально являются наиболее серьезными. Включения вкрапленного шлака и пористость вряд ли станут причиной разрушения, если только они не будут чрезмерными. Подрезание обычно не является серьезной проблемой, если не существуют значительные растягивающие напряжения поперек стыка.
Путем выбора класса исполнения в BS EN 1090-2 [9] устанавливаются критерии приемки, за пределами которых дефект считается дефектом.
Если дефекты обнаружены в результате осмотра и испытаний во время производства, вероятно, потребуется обработка после сварки (см. GN 5.02) или другие меры по исправлению положения, хотя во многих случаях конкретный дефект может быть оценен на основе концепции « пригодность для цели ». Такое принятие зависит от фактических уровней напряжения и значимости усталости на месте. Это вопрос для быстрой консультации между подрядчиком по изготовлению металлоконструкций и проектировщиком, поскольку, если это приемлемо, можно избежать дорогостоящего ремонта (и возможности появления дополнительных дефектов или искажений).
Руководство по контролю качества сварных швов и контролю сварных швов доступно в BCSA № 54/12 и GN 6.01.
[вверх] Список литературы
- ↑ BS EN ISO 22553: 2019, Сварка и родственные процессы. Символическое изображение на чертежах. Сварные соединения. BSI.
- ↑ BS EN 1993-1-8: 2005, Еврокод 3. Проектирование стальных конструкций. Дизайн стыков, BSI
- ↑ BS EN ISO 4063: 2010, Сварка и родственные процессы. Номенклатура процессов и ссылочные номера, BSI
- ↑ BS EN ISO 15609-1: 2019, Технические требования и аттестация процедур сварки металлических материалов.Спецификация процедуры сварки. Дуговая сварка, BSI
- ↑ 5,0 5,1 5,2 BS EN ISO 15614-1: 2017 + A1: 2019, Технические требования и квалификация процедур сварки металлических материалов. Проверка процедуры сварки. Дуговая и газовая сварка сталей и дуговая сварка никеля и никелевых сплавов, BSI
- ↑ 6,0 6,1 6,2 BS EN ISO 14555: 2017, Сварка. Дуговая сварка металлических материалов, BSI
- ↑ 7.0 7,1 7,2 BS EN 1011-2: 2001, Сварка. Рекомендации по сварке металлических материалов. Дуговая сварка ферритных сталей, BSI
- ↑ BS EN 1011-1: 2009, Сварка. Рекомендации по сварке металлических материалов. Общее руководство по дуговой сварке, BSI
- ↑ 9,0 9,1 9,2 9,3 9,4 9,5 9,6 9,7 9,8 BS EN 1090-2: 2018, Изготовление металлоконструкций и алюминиевых конструкций.Технические требования к стальным конструкциям, BSI
- ↑ BS EN ISO 9606-1: 2017 Квалификационные испытания сварщиков. Сварка плавлением. Стали, BSI
- ↑ BS EN ISO 14732: 2013. Сварочный персонал. Квалификационные испытания сварщиков и наладчиков механизированной и автоматической сварки металлических материалов BSI
- ↑ 12,0 12,1 BS EN ISO 17635: 2016, Неразрушающий контроль сварных швов. Общие правила для металлических материалов, BSI
- ↑ BS EN ISO 9712: 2012.Неразрушающий контроль. Квалификация и сертификация персонала по неразрушающему контролю, BSI
- ↑ BS EN ISO 5817: 2014, Сварка. Соединения, сваренные плавлением стали, никеля, титана и их сплавов (за исключением лучевой сварки). Уровни качества для выявления недостатков, BSI
- ↑ BS EN 1993-1-9: 2005, Еврокод 3. Проектирование стальных конструкций. Усталость, BSI
[вверх] Ресурсы
- Стальные здания, 2003 г. (Публикация № 35/03), BCSA
- Стальные мосты: практический подход к проектированию для эффективного изготовления и строительства, 2010 г. (Публикация №51/10), BCSA
- Национальные технические условия на стальные конструкции (7-е издание), 2020 г. (Публикация № 62/20), BCSA
- Типовые спецификации процедуры сварки металлоконструкций – Второе издание, 2018 г. (Публикация № 58/18), BCSA
- Высокопрочные стали для применения в конструкциях: Руководство по производству и сварке, 2020 г. (Публикация № 62/20), BCSA
- Руководство по контролю сварных швов металлоконструкций, 2012 г. (Публикация № 54/12), BCSA
- Хенди, К.Р.; Айлс, округ Колумбия (2015) Steel Bridge Group: Рекомендации по передовой практике в строительстве стальных мостов (6-й выпуск). (P185). SCI
[вверх] Дополнительная литература
- Руководство разработчика стальных конструкций (7-е издание), 2011 г., глава 26 – Сварные швы и проектирование для сварки, Институт стальных конструкций.
[вверху] См. Также
Электроды для контактной точечной сварки: описание переменных
Принято считать, что материалы электродов с высокой проводимостью (классы 1 и согласно системе ISO 5182) идеально подходят для сварки деталей с низкой проводимостью.И наоборот, для металлов с высокой проводимостью требуются электроды с более низкой проводимостью, такие как электроды из тугоплавкого металла, называемые электродами класса 3 в соответствии с ISO 5182.
Например, широко доступные электроды из меди / хрома и меди / хрома / циркония отлично работают с низкоуглеродистыми сталями и высокопрочными сталями. Для точечной сварки этого семейства черных металлов используются различные стратегии упрочнения меди для достижения необходимой твердости материала. (Примечательно, что для высокоуглеродистых нержавеющих сталей по-прежнему рекомендуются сплавы меди, однако процесс контактной сварки регулируется для обеспечения более высокого усилия и меньшего тока, которые требуются.) В качестве альтернативы при сварке меди лучше всего работают металлы с низкой проводимостью, такие как семейство тугоплавких металлических электродов, включая электроды из чистого вольфрама, молибдена и вольфрама / меди, а также некоторые другие варианты.
При контактной точечной сварке металлов с низкой проводимостью нагревается материал заготовки, а не сварочный электрод. Медь идеальна тем, что пропускает ток и тепло к заготовке. С другой стороны, когда вы свариваете металл с высокой проводимостью, обрабатываемая деталь позволяет теплу рассеиваться, действуя подобно радиатору.В этом случае вам понадобится электрод, который может удерживать тепло, особенно в наконечнике, и быть достаточно жестким при высоких температурах, чтобы сохранять положение, обеспечивающее максимальный контакт между электродом и заготовкой.
Несмотря на эти принципы, ни один электродный материал не может быть лучшим во всех сферах применения. Например, электроды из тугоплавкого металла часто ошибочно, но с некоторыми достоинствами воспринимаются как трескающиеся или расслаивающиеся на наконечнике из-за термоциклирования. Несмотря на то, что это верно, если выбрана точечная сварка действительно неподходящих металлов с высоким удельным сопротивлением, существуют стратегии для устранения отслоения наконечника, и в тех случаях, когда это удается, преимущества огнеупора, заключающиеся в выживании сильноточного и повторяющегося цикла, делают их незаменимыми.
Проблемы с электродами с высокой проводимостью могут быть обнаружены в сплавах с дисперсионной твердостью, таких как хром-медь (CrCu). Было обнаружено, что во время использования повторяющиеся циклы нагрева вызывают дальнейшую диффузию выделений в медную матрицу, что приводит к увеличению твердости электрода и, в конечном итоге, к снижению электропроводности. Однако этим металлургическим преобразованием во время использования можно управлять, и преимущества классов 1 и 2 остаются убедительными для правильных свариваемых металлов.
Чтобы узнать больше о переменных, влияющих на выбор подходящих электродов для контактной точечной сварки, загрузите нашу бесплатную техническую документацию по материалам электродов для контактной сварки: выбор подходящего для вашего приложения.
. SUS316 ПРОВОЛОЧНАЯ СЕТКА № 10 ДИАМ.![]() | Электроды сварочной проволоки из никелевого сплава N06600 | ER385 1,6 Проволока ER385 2,4 мм для сварки | ||||||||||||
N04400 | Никелевый сплав Электроды сварочного стержня Hastelloy C22 | Сварочные электроды ENiCu-7 для Monel 400 N04400 | ||||||||||||
ERNiCrCoMo-1 Сварочная проволока для сплава Incoloy 800H N0117 | Сварочные электроды ENiCrCoMo-1 для Incoloy 800H N08810 | |||||||||||||
Сварочная проволока ERNiCrCoMo-1 для Incoloy 800 N08800 | Super Duplex Steel S32750 Сварочные электроды N088 1CO118 | |||||||||||||
Сварочная проволока ERNiCrMo-3 для Incoloy 825 N08825 | Super Duplex Steel Электроды сварочного стержня 2507 | Сварочные электроды ENiCrMo-3 для Incoloy 825 N08825 | ||||||||||||
ERNiCrMo-3 Сварочная проволока для сварочной проволоки Inconel | Сварочная проволока Duplex | Сварочные электроды ENiCrMo-3 для Inconel 625 N06625 | ||||||||||||
Сварочная проволока ERNiCr-3 для Inconel 600 N06600 | Super Duplex Steel N08904 Сварочные электроды электроды для сварочных прутьев Inconel 625 N06625 | EN | EN | |||||||||||
Сварочная проволока ERNiCrMo-10 для Hastelloy C22 | Электроды сварочных стержней из супердуплексной стали 904L | Сварочные электроды ENiCrMo-10 для сварки Hastelloy C22 | ||||||||||||
MO | S31254 Электроды сварочной проволоки | Сварочные электроды ENiCrMo-4 для Hastelloy C276 | ||||||||||||
Сварочная проволока ER2594 для дуплексной стали 2507 S32750 | Электроды сварочного стержня 254SMO | Электроды сварочного стержня ER2594 9011 S | Сварочные электроды | Сварочные электроды для дуплексной стали для дуплексной стали 2205 | N08020 электроды сварочного стержня | сварочные электроды E2209 для дуплексной стали 2205 | ||||||||
ER385 сварочная проволока для дуплексной стали 904L N08904 | ||||||||||||||
Сварочная проволока ERNiCrMo-3 для сплава 20 N08020 | Электроды сварочного стержня из сплава 926 | ENiCrMo-3 Сварочные электроды для дуплексной стали | ||||||||||||
N08926 Электроды сварочного стержня | Сварочные электроды ENiCrMo-3 для сплава 20 N08020 | |||||||||||||
Никелевый сплав N04400 Электроды сварочного стержня | 1 | .![]() | Сварочные электроды ENiCrMo-3 для AL-6XN N08367 | |||||||||||
Электроды для сварочных стержней из никелевого сплава Монель 400 | Электроды для сварочных стержней из никеля 201 | Электроды для сварки ENiCr 1.45 | ||||||||||||
Электроды из никелевого сплава N08801 | Электроды для сварочных стержней из никеля 200 | Сварочная проволока ERNiCrMo-3 для дуплексной стали 254SMO S31254 | ||||||||||||
Сварочная проволока ERNi-1 для никеля 201 | ||||||||||||||
Электроды сварочного стержня из никелевого сплава Incoloy 800 | Электроды сварочного стержня из титана Gr.1 | ERTi-2 сварочная проволока для титана Gr. .2 | ||||||||||||
Электроды сварочного стержня из никелевого сплава N08800 | Сварочная проволока из никелевого сплава N04400 | Сварочная проволока ERTi-1 для титана Gr.![]() | ||||||||||||
Никелевый сплав Инконель | Электроды сварочной проволоки | |||||||||||||
Электроды сварочной проволоки из никелевого сплава N08825 | Никелевый сплав N08801 Сварочная проволока | Вольфрамовый электрод | ||||||||||||
Никелевый сплав Инколой 80 Сварочная проволока 0H | 304 Проволока из нержавеющей стали | |||||||||||||
Электроды сварочного стержня из никелевого сплава Инконель 625 | Сварочная проволока из никелевого сплава Incoloy 800 | Проволока из нержавеющей стали AISI 316 | TIG 321 сварочная проволока из нержавеющей стали | |||||||||||
ER316L Сварочная проволока из нержавеющей стали для сварки TIG | ||||||||||||||
Titanium Gr.![]() | Сварочная проволока из никелевого сплава N08800 | E308 E309L Сварочная проволока из нержавеющей стали | ||||||||||||
ENiCrCoMo-1 3.2 Сварочные электроды 4,0 мм | Никелевый сплав | |||||||||||||
Сварочные электроды 254SFER | Сварочная проволока из никелевого сплава N08825 | Сварочная проволока S31254 | ||||||||||||
Сварочная проволока ERNiCrMo-3 для 1.4529 N08926 | Сварочная проволока из никелевого сплава N06625 | Сварочная проволока 254SMO | ||||||||||||
Сварочные электроды 253MA | Никелевый сплав Инконель 625 Сварочная проволока | EN | Сварочные электроды 4,0 мм | Сварочная проволока из никелевого сплава N06600 | Сварочная проволока из сплава 20 | |||||||||
ENiCu-7 3.![]() | Сварочная проволока из никелевого сплава Inconel 600 | Сварочная проволока из сплава 926 | ||||||||||||
E2594 2,5 3,2 Сварочные электроды 4,0 мм | Никелевый сплав Hastelloy C22 Сварочная проволока | Сварочная проволока | проволока | |||||||||||
E2209 3.2 Сварочные электроды 4,0 мм | Сварочная проволока из никелевого сплава Hastelloy C276 | 1.4529 сварочная проволока | ||||||||||||
ENiCrMo-10 3.2 Сварочные электроды 4,0 мм | Сварочная проволока Super Duplex из стали S32750 | Никель 201 сварочная проволока | ||||||||||||
ENiCrMo-4 2,4 3,28 4,0 мм | электроды | Сварочная проволока из супердуплексной стали 2507 | Сварочная проволока для никеля 200 | |||||||||||
E385 3.2 Сварочные электроды 4,0 мм | Сварочная проволока из дуплексной стали 2205 | Титан Gr.![]() | ||||||||||||
ENiCrMo-3 3.2 Сварочные электроды 4,0 мм | Сварочная проволока Super Duplex из стали N08904 | ERNiCu-7 Сварочная проволока 2,4 мм | ||||||||||||
ERNiCrMo-3 сварочная проволока 9011 90 мм | Super Duplex Steel Сварочная проволока 904L | ER2594 Сварочная проволока 2,4 мм | ||||||||||||
Сварочная проволока ERTi-1 2,4 мм | ERNiCrMo-10 Сварочная проволока 2,4 мм | ER2209 1.6 Сварочная проволока 2,4 мм | ||||||||||||
Сварочная проволока 253MA | ERNiCrMo-4 1.0 1,2 Сварочная проволока 1,6 мм | нитиноловая проволока | ||||||||||||
ERNiCrCoMo-1 Сварочная проволока | ERNiCrCoMo-1 | Сварочная проволока 2,4 мм | Молибденовая проволока | |||||||||||
ERNiCr-3 Сварочная проволока 2,4 мм | вольфрамовые электроды | Нихромовая проволока | ||||||||||||
Cr20Ni Хромовый сплав | Cr20Ni Проволока | Проволока из хромоникелевого сплава Cr30Ni70 | ||||||||||||
Проволока из хромоникелевого сплава Cr15Ni60 | Проволока из хромоникелевого сплава Cr20Ni35 | Cr20Ni30 Никель-хромовый сплав 9011 9011 9011 9011 9011 9011 9011 9011 9011 9011 9011 9011 9011 9011 9011 9011 9011 |