точка сварки – это… Что такое точка сварки?
ГОСТ Р ИСО 857-1-2009: Сварка и родственные процессы. Словарь. Часть 1. Процессы сварки металлов. Термины и определения — Терминология ГОСТ Р ИСО 857 1 2009: Сварка и родственные процессы. Словарь. Часть 1. Процессы сварки металлов. Термины и определения оригинал документа: 6.4 автоматическая сварка: Сварка, при которой все операции механизированы (см. таблицу 1).… … Словарь-справочник терминов нормативно-технической документации
ГОСТ Р 55139-2012: Совместимость технических средств электромагнитная. Оборудование для контактной сварки. Часть 2. Требования и методы испытаний — Терминология ГОСТ Р 55139 2012: Совместимость технических средств электромагнитная. Оборудование для контактной сварки. Часть 2. Требования и методы испытаний оригинал документа: 3.6 порт (port): Граница между оборудованием и внешней… … Словарь-справочник терминов нормативно-технической документации
ГОСТ Р 51526-2012: Совместимость технических средств электромагнитная.
источник — 3.18 источник (source): Объект или деятельность с потенциальными последствиями. Примечание Применительно к безопасности источник представляет собой опасность (см. ИСО/МЭК Руководство 51). [ИСО/МЭК Руководство 73:2002, пункт 3.1.5] Источник … Словарь-справочник терминов нормативно-технической документации
порт — 3.32 порт (port): Конечная точка соединения. Примечание В контексте Интернет протокола порт представляет собой конечную точку логического канала TCP или UDP соединения. Протоколы приложений на основе TCP или UDP обычно имеют назначенные по… … Словарь-справочник терминов нормативно-технической документации
условия — (см. раздел 1) d) Может ли машина представлять опасности при создании или потреблении определенных материалов? Нет Источник: ГОСТ Р МЭК 60204 1 2007: Безопасность машин. Электрооборудование машин и механизмов. Часть 1. Общие требования … Словарь-справочник терминов нормативно-технической документации
ГОСТ 2601-84: Сварка металлов. Термины и определения основных понятий — Терминология ГОСТ 2601 84: Сварка металлов. Термины и определения основных понятий оригинал документа: 47. Cвapкa трением Сварка с применением давления, при которой нагрев осуществляется трением, вызванным относительным перемещением свариваемых… … Словарь-справочник терминов нормативно-технической документации
Китайская Национальная Нефтегазовая корпорация — (CNPC) Китайская Национальная Нефтегазовая корпорация это одна из крупнейших нефтегазовых компаний мира Китайская Национальная Нефтегазовая корпорация занимается добычей нефти и газа, нефтехимическим производством, продажей нефтепродуктов,… … Энциклопедия инвестора
зона — 3. 11 зона: Пространство, содержащее логически сгруппированные элементы данных в МСП. Примечание Для МСП определяются семь зон. Источник: ГОСТ Р 52535.1 2006: Карты идентификационные. Машиносчитываемые дорожные документы. Часть 1. Машин … Словарь-справочник терминов нормативно-технической документации
СВАРКА — общее название более 50 разных технологических процессов создания неразъемного соединения металлических деталей. Один из старейших способов сварки, в настоящее время редко применяемый, кузнечная сварка, при которой соединение деталей… … Энциклопедия Кольера
температура — 3.1 температура: Средняя кинетическая энергия частиц среды, обусловленная их разнонаправленным движением в среде, находящейся в состоянии термодинамического равновесия. Источник: ГОСТ Р ЕН 306 2011: Теплообменники. Измерения и точность измерений… … Словарь-справочник терминов нормативно-технической документации
Как имитировать точечную сварку?
Имитация точек контактной сварки может потребоваться для восстановления заводского вида отремонтированной области кузова автомобиля. На кузове есть места, где невозможно подступиться контактной сваркой даже при её наличии. Для имитации точек сварки могут потребоваться разные инструменты и методы, в зависимости от доступа к месту, где должны быть точки контактной сварки. В этой небольшой статье описаны несколько разных способов имитации точек сварки. Точки лучше расположить на немного разном расстоянии и с небольшим смещением, как это бывает с завода.
Имитация ластиком карандаша
- Нужно распылить 2–3 слоя наполняющего грунта, потом использовать ластик на карандаше и прикоснуться им, чтобы имитировать точки контактной сварки. Нажмите и поверните карандаш пока грунт всё ещё мокрый.
- Другой вариант – наклеить на ластик карандаша шлифовальную бумагу круглой формы, с абразивом P180 или P240. Такой ластик можно будет использовать на просохшем грунте или на затвердевшей шпаклёвке перед грунтованием.
Нужно прислонить ластик с наклеенной шлиф.бумагой и вращать вокруг своей оси, сначала в одну, потом в другую сторону.
Имитация точек сварки выбиванием стержнем определённого размера
Метод заключался в том, чтобы использовать стержень того же диаметра, что и точка сварки. Пара ударов по нему молотком оставляет небольшой круглый отпечаток, напоминающий точку от контактной сварки. Нужно сделать это в местах, где нет шпаклёвки или зачищенных сварных швов.
Имитация точек сварки гревером со специальной насадкой
Используйте гревер с насадкой для заточки цепной пилы (5.5 мм – 5.6 мм D455 ). Это сделать не просто и насадка может легко соскальзывать. Нужно держать инструмент двумя руками. Можно сначала наклонить насадку, сделать один край точки, потом другой, а потом шлифовать, удерживая насадку в плоском состоянии.
Изготовление специального устройства для имитации точек контактной сварки
- Можно использовать плоскогубцы с фиксатором (vise grip). На один конец нужно приварить выступ (к примеру, кончик от болта) и доработать его, чтобы он был по размеру как сварная точка. На другом конце нужно приварить гайку большего размера, чтобы контролировать прижим на обратной стороне панели, на которой будет имитироваться точка сварки. Сожмите зажим, затяните его туго, потом повертите его влево, вправо. Он обеспечит хорошую имитацию точки сварки. Поэкспериментируйте, им можно контролировать глубину точки.
- Другое устройство можно изготовить из маленькой струбцины (продаётся под названием: струбцина монтажная, балочный зажим). Она предназначена для монтажа трубопроводов, вентиляционных каналов, спринклерных установок и других элементов на стальных несущих балках без сверления и сварки.
Можно также приспособить съёмник шаровых опор подходящей конфигурации. Измените болт до нужного размера точечного сварного шва, а с другой стороны просверлите полость нужного диаметра.
Печатать статью
Ещё интересные статьи:
Настройка tig сварки – от А до Я + Полезные советы
Ранее мы рассказывали о том, как подобрать электрод, газ и другие расходные материалы. В этой статье продолжим рассматривать сварочный процесс, а точнее работу с аргонодуговым аппаратом tig. Для удобства сразу же выделим вопросы, которые будут затронуты в данном материале:-
Как подготовить tig горелку к работе?
-
Как настроить сварочный аппарат?
-
Как начать аргонодуговую сварку?
-
Как правильно вести сварочную горелку?
Для наглядности используем конкретные модели и заготовки. Сваривать будем нержавеющую сталь, а в качестве tig-аппарата выступит надежный и простой в управлении аппарат FUBAG INTIG 200 DC Pulse. Помимо основных функций оборудование обладает функцией импульсной сварки.
Что касается расходных материалов, то в приведенном примере используется баллон с аргоном, электроды WL 20 (для постоянного тока) и присадочный пруток.
Подготовка аргонодугового аппарата к работе
Все комплектующие под рукой. Собираем все воедино:
-
Устанавливаем редуктор на баллон с газом
-
Подключаем газовый шланг к редуктору
-
Подключаем байонетный разъем горелки к минусовому разъему
-
Подключаем кабель управления к пяти-пиновому разъему на лицевой панели
-
Последним подключаем кабель массы к плюсовому разъему
Аппарат практически готов к работе, теперь переходим к сборке tig горелки:
1. Первым устанавливаем цангодержатель
2. Аккуратно вставляем в него цангу
3. Прикручиваем хвостовик (не до конца)
4. Устанавливаем керамическое сопло
5. Вставляем вольфрамовый электрод
6. Настраиваем вылет электрода
7. Хорошенько затягиваем хвостовик.
Как только все выполнено, выставляем расход газа в зависимости от места проведения и диаметра сопла. Для сопла с диаметром 10 мм вполне подойдет расход газа равный 10 л/мин.
Внимание! Помимо самого аппарата и горелки, подготовка требуется и заготовкам. Очистив их от ржавчины, оксидной пленки и других загрязнений, вы позаботитесь о качестве сварки. Для обезжиривания можно воспользоваться ацетоном, уайт-спирпитом или другим растворителем. Присадочный пруток также зачищается наждачкой и обезжиривается.
![]()
Настройка tig аппарата от А до Я
Практически все металлы свариваются на прямой полярности (на электроде минус). Исключением является лишь сварка алюминия и его сплавов. Ярким примером сплава может могут стать медные сплавы со значительным содержанием алюминия. Для них обязательным является использование переменного тока.
Итак, настраиваем FUBAG INTIG 200 DC Pulse:
-
На панели управления выставляем метод сварки – TIG.
-
Устанавливаем предпродувку газа на 0,5 сек.
-
Настраиваем ток поджига – 25% от рабочего тока (А).
-
Фиксируем время нарастания до рабочего тока – 0,2-1,0 сек.
-
Устанавливаем ток сварки (А) (см. Таблицу ниже)
-
Выставляем время до тока заварки кратера (спада в секундах)
-
Выбираем значение тока заварки кратера в амперах
-
Последним параметром станет время продувки газа после сварки (сек)
Параметры, которые относятся к заварке кратера, подбираются в зависимости от толщины металла.
В данной таблице даны общие рекомендации по подбору сварочного тока для наиболее используемых металлов и толщин. Это поможет вам сориентироваться при подготовке к началу работы.
Таблица. Настройка аргонодугового аппарата в зависимости от вида металла и толщины
Вид металла |
Толщина металла, мм |
Род тока |
Сила тока¸А |
Стальные сплавы |
1,0 |
DC |
20 – 30 |
1,5 |
DC |
40 – 60 |
|
2,0 |
DC |
70 -90 |
|
3,0 |
DC |
100 – 120 |
|
4, 0 |
DC |
120 – 140 |
|
Алюминий |
1-2 |
AC |
20 – 60 |
4-6 |
AC |
120-180 |
|
6-10 |
AC |
220-230 |
|
11-15 |
AC |
280-360 |
Почему следить за силой тока важнее, чем за остальными параметрами? Во время TIG сварки можно прожечь заготовку, выставив слишком сильный ток. Низкое значение не позволит расплавить металл, что сведет все попытки сварить деталь на нет.
Правильный запуск и сварка TIG-горелкой
Параметры выставлены и пора начинать. У владельцев данной модели сварочного аппарата есть целых два варианта:
-
Использовать контактный поджиг
-
Прибегнуть к функции высокочастотного поджига
Последний предотвратит прожиг металла в случае неправильно выставленных параметров во время настройки аппарата аргонодуговой сварки. Он убережет металл от вольфрамовых включений и позволит самостоятельно контролировать расстояние до детали с момента начала работы.
И теперь самое главное – как же правильно вести горелку? Большинство опытных сварщиков проводят сварку справа налево. Во время процесса без присадочного материала электрод стоит расположить практически перпендикулярно свариваемой поверхности. Если присадочный материал присутствует, то достаточно удерживать небольшой угол (15-20 градусов).
Процесс сварки завершается заваркой кратера. Заварка кратера – финальный участок сварочного шва длиной, высота которого уменьшается до нуля. С точки зрения качества сварного соединения, необходимо исключить образования кратера в финальной части шва. Для этого в аппарате предусматривается режим плавного уменьшения тока.Внимание! Чтобы металл шва не окислялся, надо следить, чтобы конец присадочного прутка постоянно находился в зоне защитного газа.
Для наглядности всего вышеописанного специалисты подготовили специальный видеоролик:
Получите 10 самых читаемых статей + подарок!
*
Подписаться
сварка вольфрамовым электродом в среде защитного газа в нефтегазовой промышленности
На морских платформах для транспортировки сырых и переработанных нефти и газа применяются входные и выходные трубопроводы. Эти трубопроводы подвергаются воздействию значительных внешних сил во время прокладки и эксплуатации (высокое давление и/или температура, химическое воздействие перекачиваемой среды изнутри, давление воды и воздействие течений снаружи), и поэтому должны выдерживать сильные механические напряжения. Они должны поглощать высокие динамические нагрузки, обладать стойкостью к коррозии.
Соединение труб осуществляется вручную либо при помощи механизированных либо автоматизированных сварочных систем. Особенно важным этапом является сварка корневого слоя щва, поскольку отклонение от допустимого тепловложения может значительно уменьшить стойкость металла к коррозии. В любом случае, если оборудование для механизированной сварки недоступно, корневой и верхний слои шва могут быть выполнены ручной сваркой вольфрамовым электродом в среде защитного газа с добавлением заполняющего материала. Необходимо подчеркнуть, что данный процесс обладает теми же недостатками: низкая производительнось, значительная зависимость от опыта и навыков работы сварщика, недостаточноая воспроизводимость, ограниченный контроль качества и др. При помощи механизированного либо автоматизированного сварочного оборудования можно выполнить любое количество сварных швов, причем каждый из них будет соответствовать самым строгим требованиям по качеству (так называемый подход «нулевых рисков/нулевых дефектов». Результаты работы больше не зависят от навыков сварщика, которому поручена эксплуатация оборудования.
Механизированная либо автоматическая сварка вольфрамовым электродом в среде защитного газа означает, что сам процесс, а также весь комплекс связанных с ним параметров оптимизируется и заранее утверждается. Результаты работы окончательно документируются посредством сварочных инструкций, соответствующие программы реализуются в сварочных аппаратах, применяемых на заводах и на объектах. Для работы с автоматизированным оборудованием больше не требуются навыки ручной сварки, поэтому профессиональные операторы заменяют ручных сварщиков.
Для проекта Shah Deniz 2 подряжчику потребовалось сварить большое количество 16-дюймовых труб CRA, а также фланцев и колен. Несущие трубы с толщиной стенок 41,9 мм были изготовлены из стали API 5L X65, имели внутреннюю плакирову ERNICrMo-3 толщиной 3,0 мм. На заводе-изготовителе трубы (длиной 12 м каждая) объединялись в секции по 24 м. Исходя из имевшегося в наличии оборудования (как это обычно бывает при необходимости выполнять кольцевые швы), для сварки корневого и верхнего слоев применялся ручной сварочный аппарат для сварки вольфрамовым электродом в среде защитного газа (в положении 5G), а для сварки заполняющих слоев – дуговая сварка под флюсом (SMAW). Тем не менее, в процессе утверждения обнаружилось, что заполняющие слои не соответствуют всем техническим требованиям. Проблемы были вызваны зонами начала и окончания сварочного прохода, а также недостаточным проплавлением и потребностью в ремонтных работах. Более того, высокое тепловложение, характерное для SMAW, помешало добиться требуемых свойств металла сварного шва, включая вязкость и предел прочности.
Нем не менее, чтобы не сорвать сроки поставки, руководитель проекта принял решение перейти на механизированную сварку вольфрамовым электродом в среде защитного газа с подачей горячей проволоки. Для этого была заказан соответствующий сварочный аппарат (с вращением трубы 1G). Поскольку трубы уже были разделаны под ручную сварку (угол 30°), корневой и верхний слои по-прежнему выполнялись вручную.
Роботы для сварки
Аналоговое/Цифровое управление
Аналоговое управление: система управления сварочным аппаратом позволяет зажигать дугу, регулировать ток, напряжение, подачу газаДанный протокол соответствует большинству аналоговых интерфейсов сварочных аппаратов, предназначенных для внешнего управления посредством аналоговых сигналов.
Цифровое управление: система управления может контролировать ток, напряжение, подачу проволоки, газа, параметры поджига дуги, заварки кратера, осуществлять поиск сварного соединения посредством контура обратной связи. Простое подключение и устойчивость к помехам. Цифровой интерфейс подходит для управление сварочным оборудованием компаний MEGMEET/AOTAI.Скорость сварки и регулировка скорости
Скорость сварочного процесса: в инструкции движения робота задавайте скорость движения в процессе сварки, выбирая линейную скорость (мм/с) или номинальную скорость во время движений перемещения (%)
Ручная подача проволоки
Интерфейс робота обладает кнопками ручной подачи проволоки, что упрощает процедуру ее заправки и процесс программирования.
На пульте робота расположена кнопка подачи газа, что дает возможность легко осуществить контроль его наличия.
Регулирование подачи газа
Регулирование подачи газа с помощью интервалов позволяет осуществлятьпредварительную подачу газа перед и продолжение подачи газа после окончания процесса сварки. Подача газа перед началом сварки облегчает запуск дуги и снижает разбрызгивание. Подача газа после позволяет защитить сварочную ванну во время ее охлаждения.
Режим симуляции сварки
На пульте обучения есть кнопка режима отладки сварки, которую можно использовать для проверки программы или сварки выборочных швов. После активации функции движениявыполняются в соответствии с фактической сварочной траекторией, но не зажигается дуга, не подается проволока и защитный газ. Скорость совпадает с фактическим процессом сварки.
Контроль сварочной дуги
При обрыве дуги во время процесса сварки, система остановит робота и выдаст сигнал об ошибке.
Сохранение точки обрыва дуги
Если в процессе сварки происходит обрыв дуги, робот запомнит данную точку, после проверки оператором причин обрыва и их устранения робот запустит программу с той же строки, и продолжит процесс сварки с того же места. Точка разрыва дуги будет удалена после сброса программы или возобновления процесса сварки.
Мониторинг сварочного процесса
Мониторинг в режиме реального времени может отображать: ток, напряжение, время сварки, время выполнения программы.Это удобно для анализа и оптимизации программы.
Функция защиты горелки от столкновений
Роботы CRP оснащены функцией защиты сварочной горелки от столкновений с деталью и элементами оснастки. Это помогает сохранить ее целостность и геометрию, а так же предотвратить повреждение самого манипулятора. Для реализации данной функции блок сварочной горелки оснащен подвижным шарниром и датчиками его положения. При отклонении шарнира от нормального положения, происходит исчезновение соответствующего программного сигнала, что приводит к остановке робота.
Поиск заготовки датчиком оптического слежения
Поиск сварного соединения возможно осуществлять посредством датчика оптического слежения за швом. Поиск осуществляется посредством лазерного луча, который сканирует текущее положение соединения. Робот сравнивает текущее положение с записанным положением эталонного шва.
При обнаружении отклонений в позициях, робот соответствующим образом корректирует сварочную траекторию.
Поиск касанием (интегральный поиск)
Поиск положения заготовки касанием осуществляется, используя сварочный контур в качестве инструмента. На робота заведен соответствующий цифровой сигнал, свидетельствующий о замыкании данного контура. Сварочный аппарат подает напряжение на положительный электрод сварочной горелки (проволоку). В момент касания сварочной проволокой заготовки (отрицательного электрода), робот получает соответствующий сигнал.
На практике процесс поиска осуществляется следующим образом. Сначала происходит настройка данной функции путем калибровки на эталонном изделии. Робот производит ощупывание детали и при ее касании записывает положение ее опорных точек (настройка эталонной детали производится единожды). Далее, происходит установка последующих заготовок, перед процессом сварки каждой из них производится ощупывание и запись текущих координат опорных точек. Далее происходит сравнение текущих положений с эталонными, вычисляется разница в координатах и в управляющую программу вносится соответствующий сдвиг. Корректировка положений может производиться как в одной, так и в нескольких плоскостях (1D, 2D, 3D, 2D +, 3D +).
Сварочные режимы
Легкая настройка параметров, связанных со сваркой: сварочный ток и напряжение, ток и напряжение поджига дуги и заварки кратера, время предварительной продувки газом и время продувки газом по окончанию сварки задаются посредством сварочных таблиц.
Гибкая система изменения параметров сварки
Сварочные инструкции поддерживают корректировку сварочного тока и напряжения непосредственно в сварочной программе. Это позволяет удобно регулировать сварочные параметры прямо в процессе написания программ.
Функция возврата проволоки
Когда данная функция активирована, при переходе между сварочными швам (холостые перемещения) робот будет автоматически уменьшать вылет сварочной проволоки. Это происходит для предотвращения возможности столкновения проволоки с деталями и оснасткой, что препятствует смещению деталей и предотвращает загиб кончика проволоки.
Функция горячего старта
(предварительная подача проволоки)
В обычном режиме поджиг дуги производится следующим образом. Сначала происходит позиционирование робота в начальной точке сварки, затем начинается предварительная подача газа и подача проволоки. Дуга зажигается в момент касания проволоки свариваемой детали. За счет того, что подача проволоки в момент запуска сварки происходит достаточно медленно, мы имеем значительную временную паузу между позиционированием робота и поджигом дуги. Когда функция горячего старта активна, робот начинает подачу проволоки для поджига дуги заранее, в точке подхода к месту сварки. Это позволяет сделать поджиг в точке старта сварки практически мгновенным и значительно сократить общее время цикла сварки изделия.
Функция повторного поджига дуги
Данная функция предназначена для повторного поджига дуги, если она по каким либо причинам погасла. Если данная функция активна, то при прерывании дуги робот возвращается на некоторое расстояние назад по сварочной траектории, производит поджиг дуги заново и продолжает выполнение программы.
Линейная синхронизация (интерполяция)
Опция линейной синхронизации позволяет роботу совершать синхронные (согласованные) движения совместно с внешними линейными осями, направление которых должно соответствовать направлениям осей Х, Y, Z абсолютной системы координат робота. Данная опция позволяет роботу совершать линейные перемещения не отрываясь от своего производственного процесса. Это к примеру позволяет роботу с помощью трека производить сварку протяженных соединений сложной геометрии без отрыва горелки на всей протяженности сварного шва.
Круговая синхронизация (интерполяция)
Круговая синхронизация позволяет роботу согласовывать свои движения с движениями внешних дополнительных осей вращения. Робот способен совершать синхронные движения совместно с позиционером, имеющим одну или более осей вращения. Это позволяет роботу выполнять полный охват даже очень больших деталей с возможностью выбора для себя наиболее удобной точки подхода и положения сварного соединения в пространстве. Данная технология позволяет совершать операции, где требуется выполнить сплошной шов на изделии со сложной геометрией без перепозиционирования робота в процессе сварки.
Z-образные колебания
Z-образные колебания: при включении данной функции сварочная горелка робота совершает Z-образные колебания во время сварочного процесса. Направление колебаний перпендикулярно направлению движения сварочной горелки.
Кольцевые колебания
Дуговые колебания: если активировать данную функцию, то во время сварочного процесса горелка робота будет совершать круговые колебания. .
Функция плавной коррекции сварочных параметров
Функция плавной коррекции сварочных параметров может использоваться для сварки сложных изделий, где требуется плавное изменение параметров непосредственно по ходу сварочного процесса. Во время выполнения сварного шва можно использовать плавное изменение тока и напряжения на заданное значение. Необходимо лишь задать исходные параметры тока и напряжения в желаемой точке начала плавной регулировки параметров и установить конечные значения в нужной точке. Процесс изменения параметров является линейным.
Функция мгновенной коррекции сварочных параметров
Функция мгновенной коррекции сварочных параметров может использоваться для сварки сложных изделий, где требуется мгновенное изменение тока и напряжения непосредственно во врем сварочного процесса. Необходимо лишь задать новые сварочные параметры в требуемой точке и во время сварочного процесса именно в этом месте произойдет мгновенное изменение тока и напряжения.
Чешуйчатый шов/Прерывистый шов
Функция чешуйчатого шва представляет собой технологию сварки точками. Функция легка в применении, задается лишь время установки прихватки и шаг. Функция прерывистого шва позволяет выполнить такой шов задав лишь траекторию, длину стежка и шаг.
Слежение за сварочной дугой по току
Данная функция поможет компенсировать позиционные отклонения сварного соединения в пространстве. Если сварочное соединение имеет зазор или разделку и сварочный шов выполняется с колебаниями, данная функция идеально подойдет. С помощью дополнительного датчика робот осуществляет контроль тока во время сварочного процесса. Фиксируя наименьшие и наибольшие значения по ходу траектории робот определяет центр разделки и кромки сварного соединения и корректирует запрограммированную траекторию движения относительно реального положения детали.
Оптическое слежение за швом
Для работоспособности данной функции манипулятор оснащается дополнительным датчиком оптического слежения за сварочным швом. Данный датчик позволяет как предварительно производить поиск сварных соединения, так и осуществлять онлайн корректировку траектории непосредственно во врем сварки. Слежение осуществляется за счет проецирования лазерного луча на сварное соединение. На основе заданных параметров (зазор, разделка, вид соединения) система определяет реальное положение шва и корректирует сварочную траекторию.
Функция многопроходной сварки
Используя функцию многопроходной сварки необходимо всего лишь один раз обучить робота сварочной траектории, а затем с помощью инструкции скорректировать скорость и сварочные параметры для требуемого количества проходов. Это значительно сокращает время программирования и уменьшает его сложность.
Слежение с фиксированной точкой
Функция оптического слежения с фиксированной точкой предназначена для сварки протяженных кольцевых или линейных швов. Для работоспособности данной функции необходима внешняя ось. Движение по ходу сварочной траектории осуществляется за счет вращение позиционера или движения робота по линейной оси. Сам робот при этом остается практически неподвижным и совершает минимальные перемещения для компенсации смещения реального сварного шва от запрограммированного. Определение положения сварного соединения осуществляется за счет датчика оптического слежения.
Не удается найти страницу | Autodesk Knowledge Network
(* {{l10n_strings.REQUIRED_FIELD}})
{{l10n_strings.CREATE_NEW_COLLECTION}}*
{{l10n_strings.ADD_COLLECTION_DESCRIPTION}}
{{l10n_strings.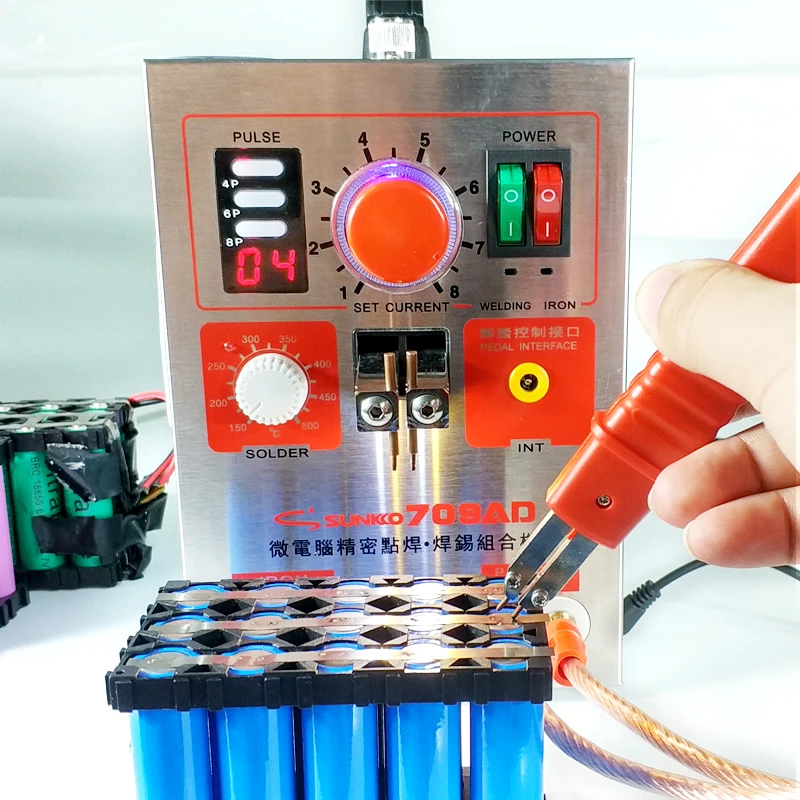
{{l10n_strings.DRAG_TEXT_HELP}}
{{l10n_strings.LANGUAGE}} {{$select.selected.display}}{{article.content_lang.display}}
{{l10n_strings.
{{l10n_strings.AUTHOR_TOOLTIP_TEXT}}
{{$select.selected.display}} {{l10n_strings.CREATE_AND_ADD_TO_COLLECTION_MODAL_BUTTON}} {{l10n_strings.CREATE_A_COLLECTION_ERROR}}Расстояния между центрами точек при сварке
С помощью точечной сварки удобно соединять вкрест арматуру железобетона. На нормальных точечных машинах возможна сварка стержней, расположенных под углом друг к другу или параллельно.
Детали, предназначенные для сварки на точечных машинах, должны удовлетворять ряду требований в отношении конструктивного оформления и размещения точек на соединяемых участках. При этом необходимо, чтобы было возможно; 1) выполнять сварку на машинах, оснащенных нормальными электродами; 2) выполнять сварку без введения больших участков стальных деталей в сварочный контур машины; 3) сваривать точки в любой последовательности.
Нормальные электроды имеют хорошее водяное охлаждение, ввиду чего они длительное время сохраняют правильные размеры контактной поверхности. Введение в сварочный контур больших участков стальных деталей приводит к сильному снижению сварочного тока, в результате чего могут быть непровары. Сварка точек в любой последовательности позволяет облегчить борьбу с деформациями детали в процессе сварки и последующего охлаждения.
Размещать сварочные точки на узле или детали необходимо с учетом шунтирования тока, которое зависит от расстояния между точками, толщины и материала свариваемых деталей. В табл. 108 приведены минимальные значения расстояния между центрами точек при сварке низкоуглеродистой, нержавеющей стали и алюминиевых сплавов.
Таблица 108.Минимальные расстояния между центрами точек при сварке низкоуглеродистой и нержавеющей стали и алюминиевых сплавов.
Толщина одной заготовки в мм | Расстояние между центрами точек в мм | |||
низкоуглеродистая сталь | нержавеющая сталь 18—8, две заготовки | алюминиевые сплавы, две заготовки | ||
две заготовки | три заготовки | |||
0,5 | 10 | 15 | 7,5 | 10 |
1 | 15 | 20 | 15 | 11 |
1,5 | 20 | 25 | 25 | 13 |
2 | 25 | 30 | 30 | 16 |
2,5 | 28 | 35 | 35 | 18 |
3 | 30 | 40 | 45 | 25 |
Существенное влияние на прочность соединения при точечной сварке имеет подготовка поверхности заготовок, изготовление их и сборка. Вопросы подготовки поверхности сводятся, главным образом, к очистке от загрязнений и разобраны вышел Изготовление и сборка заготовок должны обеспечить достаточную точность и плотное прилегание поверхностей в местах сварки. Этого необходимо добиваться, так как при наличии зазоров между свариваемыми поверхностями часто невозможно достичь хорошего контакта в месте сварки, в результате чего будут непровары, а следовательно, и брак деталей.
Помимо этого, наличие зазоров приводит к появлению в местах сварки глубоких вмятин.
Справочник– Условия сварки Справочник
– Условия сварки 1 Продолжение на следующей странице … Условия сварки В этом разделе более подробно рассматривается собственно сварка низкоуглеродистых мягких сталей, нержавеющих сталей, алюминиевые сплавы и медные сплавы. Это цель этого раздела установить рекомендуемые общие сварочные процедуры и условия для каждый материал. В таблицы условий сварки должны служить только отправной точкой при начале новые приложения.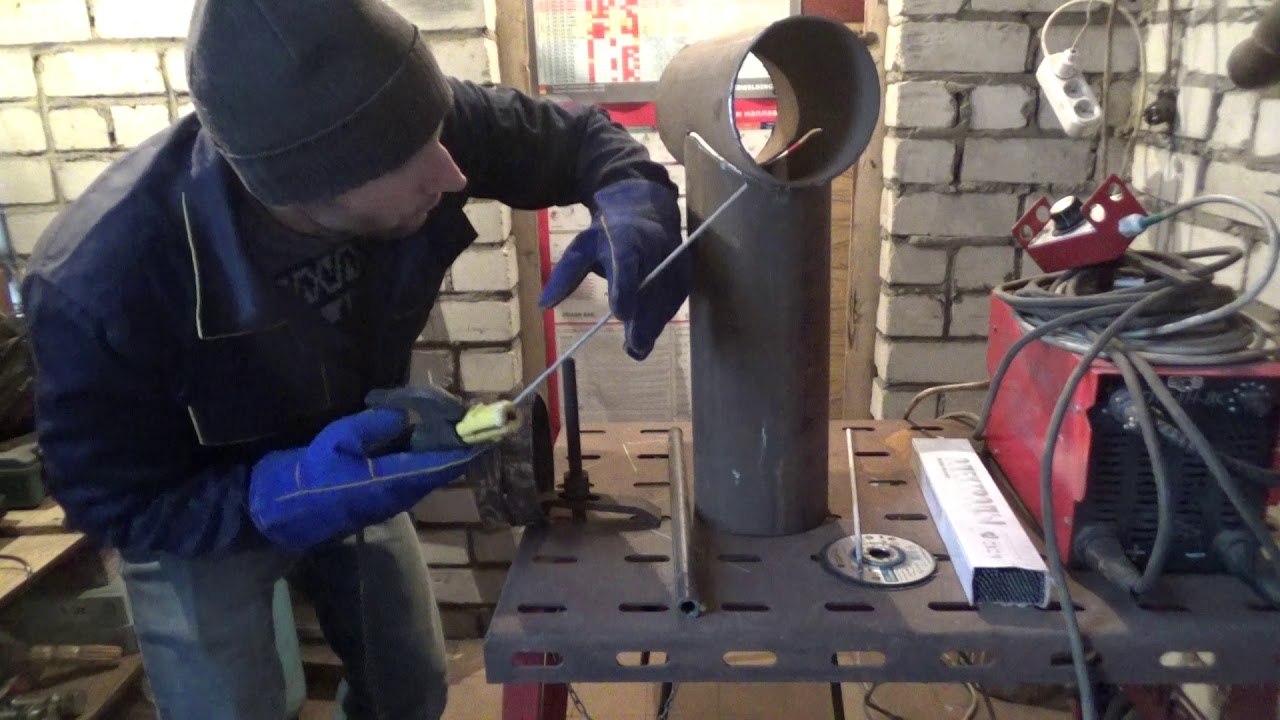
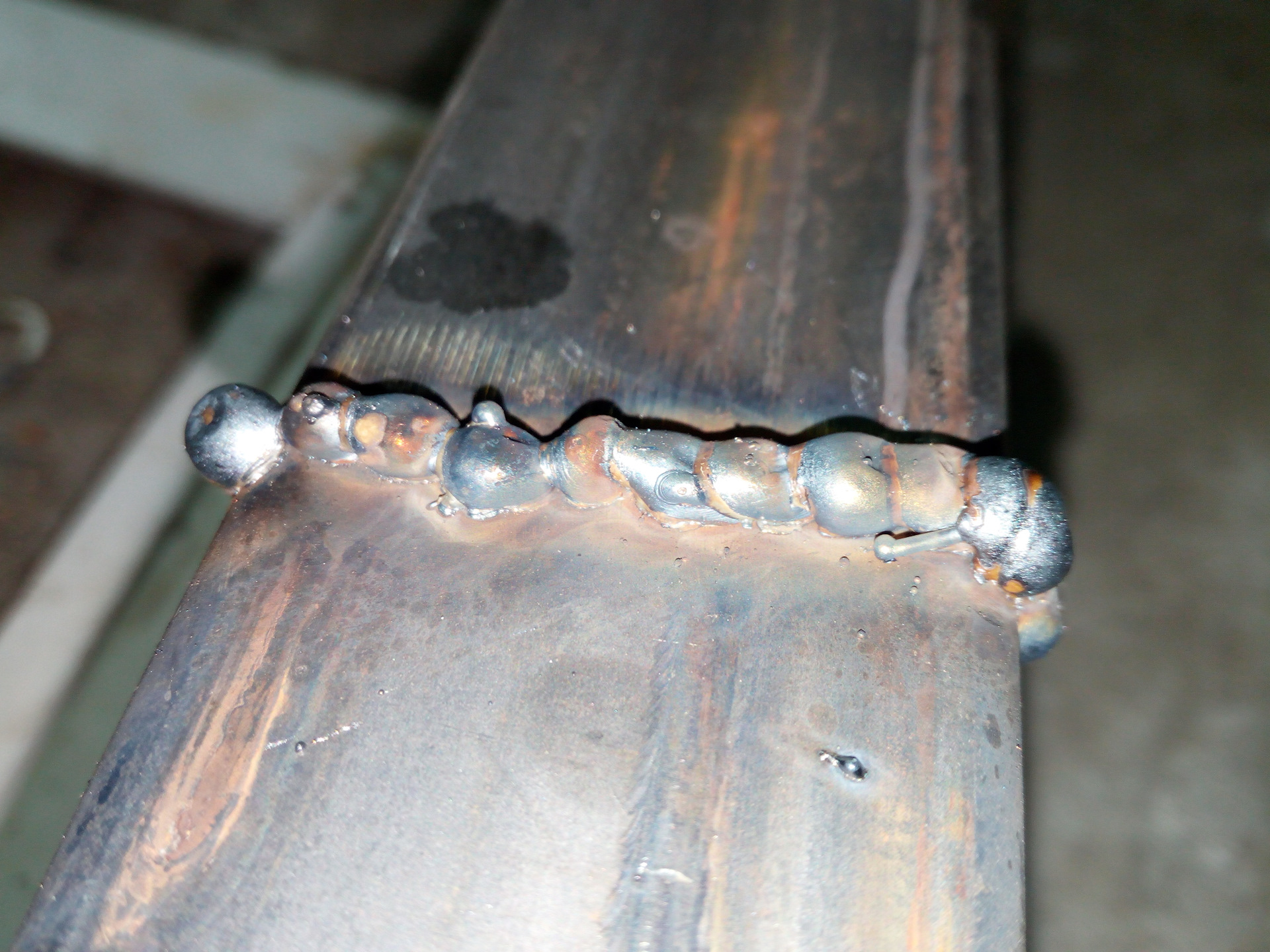
Соединение металлов: пайка против сварки
Соединение металлов: пайка против сварки
Существует несколько методов соединения металлов, включая сварку, пайку и пайку. В чем разница между сваркой и пайкой? В чем разница между пайкой и пайкой? Давайте рассмотрим различия и сравнительные преимущества, а также общие области применения. Это обсуждение углубит ваше понимание соединения металлов и поможет вам определить оптимальный подход для вашего приложения.
Как работает пайка
Паяное соединение выполняется совершенно иначе, чем сварное соединение. Первая большая разница заключается в температуре – пайка не плавит основные металлы.Это означает, что температуры пайки неизменно ниже, чем точки плавления основных металлов. Температуры пайки также значительно ниже, чем температуры сварки тех же основных металлов, при этом требуется меньше энергии.
Если пайка не расплавляет недрагоценные металлы, как она соединяется с ними? Он работает, создавая металлургическую связь между присадочным металлом и поверхностями двух соединяемых металлов. Принцип, по которому присадочный металл протягивается через соединение для создания этой связи, – это капиллярное действие. При пайке вы широко применяете тепло к основным металлам. Затем присадочный металл контактирует с нагретыми деталями. Он мгновенно плавится под действием тепла в основных металлах и полностью протягивается капиллярным действием через соединение. Так делается пайка.
Применяется для пайки в электронике / электротехнике, авиакосмической, автомобильной, климатической / холодильной технике, строительстве и т. Д. Примеры варьируются от систем кондиционирования воздуха для автомобилей до высокочувствительных лопастей реактивных турбин, вспомогательных компонентов и ювелирных изделий.Пайка дает значительное преимущество в областях, где требуется соединение разнородных основных металлов, включая медь и сталь, а также неметаллов, таких как карбид вольфрама, оксид алюминия, графит и алмаз.
Сравнительные преимущества. Во-первых, паяное соединение – это прочное соединение. Правильно выполненное паяное соединение (например, сварное соединение) во многих случаях будет таким же прочным или прочным, как соединяемые металлы. Во-вторых, соединение выполняется при относительно низких температурах, в диапазоне от примерно 1150 ° F до 1600 ° F (от 620 ° C до 870 ° C).
Наиболее важно то, что неблагородные металлы никогда не плавятся. Поскольку основные металлы не плавятся, они обычно могут сохранять большую часть своих физических свойств. Такая целостность основного металла характерна для всех паяных соединений, включая соединения как тонкого, так и толстого сечения. Кроме того, более низкий нагрев сводит к минимуму опасность деформации или коробления металла. Учтите также, что более низкие температуры требуют меньше тепла – значительный фактор экономии.
Еще одним важным преимуществом пайки является легкость соединения разнородных металлов с использованием флюса или сплавов с порошковой сердцевиной и покрытием.Если вам не нужно плавить основные металлы, чтобы соединить их, не имеет значения, имеют ли они сильно различающиеся точки плавления. Вы можете паять сталь с медью так же легко, как сталь со сталью. Сварка – это другая история, потому что вы должны расплавить основные металлы, чтобы сплавить их. Это означает, что если вы пытаетесь сварить медь (точка плавления 1981 ° F / 1083 ° C) со сталью (точка плавления 2500 ° F / 1370 ° C), вы должны использовать довольно сложные и дорогие методы сварки. Полная простота соединения разнородных металлов с помощью обычных процедур пайки означает, что вы можете выбрать любые металлы, которые лучше всего подходят для функции сборки, зная, что у вас не возникнет проблем с их соединением, независимо от того, насколько сильно они различаются по температурам плавления.
Кроме того, паяное соединение имеет приятный внешний вид. Здесь проводится дневное и ночное сравнение крошечной аккуратной кромки паяного шва и толстого неровного валика сварного шва. Эта характеристика особенно важна для соединений на потребительских товарах, где внешний вид имеет решающее значение. Паяное соединение почти всегда можно использовать «как есть», без каких-либо чистовых операций – еще одна экономия средств.
Пайка предлагает еще одно существенное преимущество перед сваркой, так как операторы обычно приобретают навыки пайки быстрее, чем навыки сварки.Причина кроется во внутренней разнице между двумя процессами. Линейный сварной шов необходимо отслеживать с точной синхронизацией подачи тепла и наплавки присадочного металла. Паяное соединение, с другой стороны, имеет тенденцию «создавать себя» за счет капиллярного действия. Фактически, значительная часть навыков, связанных с пайкой, основана на проектировании и проектировании соединения. Сравнительная скорость обучения высококвалифицированных операторов является важным фактором затрат.
Наконец, пайку относительно легко автоматизировать.Характеристики процесса пайки – широкий диапазон нагрева и простота размещения присадочного металла – помогают устранить потенциальные проблемы. Существует множество способов автоматического нагрева стыка, множество форм припоя и множество способов их нанесения, так что операцию пайки можно легко автоматизировать практически для любого уровня производства.
Как работает сварка
Сварка соединяет металлы путем их плавления и сплавления, обычно с добавлением присадочного металла.Соединения получаются прочными – обычно такими же прочными, как соединяемые металлы, или даже прочнее. Чтобы сплавить металлы, вы прикладываете концентрированное тепло непосредственно к месту соединения. Это тепло должно иметь высокую температуру, чтобы расплавить основные металлы (соединяемые металлы) и присадочные металлы. Следовательно, температуры сварки начинаются с точки плавления основных металлов.
Сварка обычно подходит для соединения больших сборок, у которых обе металлические секции относительно толстые (0,5 дюйма / 12,7 мм) и соединены в одной точке.Поскольку валик сварного шва имеет неправильную форму, он обычно не используется в изделиях, требующих косметических швов. Области применения включают транспорт, строительство, производство и ремонтные мастерские. Примерами являются роботизированные сборки плюс изготовление сосудов под давлением, мостов, строительных конструкций, самолетов, железнодорожных вагонов и путей, трубопроводов и многого другого.
Сравнительные преимущества . Поскольку сварочное тепло очень интенсивное, оно обычно локализовано и точечно; нецелесообразно наносить его равномерно на большой площади.Этот четко очерченный аспект имеет свои преимущества. Например, если вы хотите соединить две небольшие полосы металла в одной точке, практичным будет метод контактной сварки сопротивлением. Это быстрый и экономичный способ изготовления сотен и тысяч прочных неразъемных соединений.
Однако, если соединение является линейным, а не точечным, возникают проблемы. Местный нагрев при сварке может стать недостатком. Например, если вы хотите сварить встык два куска металла, вы начинаете со скоса краев металлических деталей, чтобы оставить место для сварочного присадочного металла.Затем вы свариваете, сначала нагревая один конец области соединения до температуры плавления, затем медленно перемещая тепло вдоль линии соединения, нанося присадочный металл синхронно с нагревом. Это типичная обычная сварочная операция. Правильно выполненный сварной шов не менее прочен, чем соединяемые металлы.
Однако у этого метода сварки линейных стыков есть недостатки. Соединения выполняются при высоких температурах – достаточно высоких, чтобы плавить как основные металлы, так и присадочный металл.Эти высокие температуры могут вызвать проблемы, в том числе возможные деформации и коробление основных металлов или напряжения в области сварного шва. Эти опасности минимальны, когда соединяемые металлы имеют большую толщину, но они могут стать проблемой, когда основные металлы представляют собой тонкие секции. Кроме того, высокие температуры обходятся дорого, поскольку тепло – это энергия, а энергия стоит денег. Чем больше тепла вам нужно, чтобы сделать стык, тем больше будет затрат на производство стыка.
Теперь рассмотрим автоматизированный процесс сварки.Что происходит, когда вы присоединяетесь не к одной сборке, а к сотням или тысячам сборок? Сварка по своей природе создает проблемы для автоматизации. Соединение контактной сваркой, выполненное в одной точке, относительно легко автоматизировать. Однако, как только точка становится линией – линейным соединением – снова необходимо провести линию. Эту операцию отслеживания можно автоматизировать, перемещая линию стыка, например, мимо нагревательной станции и автоматически подавая присадочную проволоку с больших катушек. Однако это сложная и требовательная установка, которая оправдана только в том случае, если у вас есть большие партии идентичных деталей.
Имейте в виду, что методы сварки постоянно совершенствуются. Сварку на производстве можно производить электронным пучком, разрядом конденсатора, трением и другими методами. Эти сложные процессы обычно требуют специального и дорогостоящего оборудования, а также сложных и трудоемких настроек. Подумайте, подходят ли они для более коротких производственных циклов, изменения конфигурации сборки или типичных повседневных требований к соединению металлов.
Выбор правильного процесса соединения металлов
Если вам нужны долговечные и прочные соединения, вы, вероятно, сузите круг вопросов, касающихся соединения металлов, до сварки, а не пайки. При сварке и пайке используются термические и присадочные металлы. И то, и другое может быть выполнено на производственной основе. Однако на этом сходство заканчивается. Они работают по-разному, поэтому помните, что нужно учитывать при пайке и сварке:
- Размер в сборе
- Толщина профилей основного металла
- Точечные или линейные соединения
- Металл присоединяется
- Необходимое количество окончательной сборки
Другие варианты? Механически скрепленные соединения (резьбовые, стержневые или заклепочные) обычно не сравнятся с паяными по прочности, устойчивости к ударам и вибрации или герметичности.Адгезионное соединение и пайка обеспечат прочное соединение, но, как правило, ни одно из них не может обеспечить прочность паяного соединения – такую же или большую, чем у самих основных металлов. Они также, как правило, не могут производить соединения, устойчивые к температурам выше 200 ° F (93 ° C). Когда вам нужны постоянные, прочные соединения металла с металлом, пайка является сильным конкурентом.
Общие сведения о контактных наконечниках для сварки MIG
Контактные наконечники для сварки – это очень неправильно понимаемые компоненты в установке горелки MIG.Выбор правильного контактного наконечника для вашего сварочного применения и понимание того, как поддерживать его наилучшую производительность, столь же важны, как и все остальное, необходимое для получения качественного сварного шва.
Использование слишком большого или слишком маленького контактного наконечника может вызвать такие проблемы, как микродуговое искрение, перегрев, трение и заклинивание проволоки – все это может привести к возгоранию проволоки.
Как контактные советы влияют на затраты на сварку
Контактные наконечники – один из наиболее часто заменяемых компонентов сварочного пистолета MIG.Контактный наконечник отвечает за направление провода и передачу тока от проводящей трубки – иногда называемой «лебединая шея» или «гусиная шея» – через присадочную проволоку и, в конечном итоге, к заготовке. Его критически важные функции включают текущую передачу и наведение на провод.
Являясь одним из наиболее часто заменяемых компонентов пистолета MIG, он также является одним из самых дорогих компонентов пистолета MIG в год. Считайте, что для смены контактного наконечника требуется около 10 минут. Если вашему сварщику платят 30 долларов в час и ему приходится менять контактный наконечник пять раз в день, пока вы работаете в две смены, вы теряете более 13000 долларов в год на работе на этой сварочной станции, поскольку меняете контактный наконечник чаще, чем вам нужно. до, и это даже без учета стоимости контактного наконечника.
Простая замена пяти контактных наконечников в день на две смены приведет к экономии более 7500 долларов в год на одной сварочной станции. И значительная часть этих затрат может быть реализована за счет простого использования материала контактного наконечника, который соответствует вашим параметрам сварки и процессу и имеет надежное качество. Использование качественных контактных насадок для сварки продлит срок службы и позволит сократить расходы на контактные насадки в долгосрочной перспективе.
Хотя обычно вы хотите доверять контактным наконечникам для сварки от вашего OEM-производителя, модернизированные контактные наконечники от известных производителей сварочного оборудования также могут оказаться для вас экономичным вариантом, когда дело доходит до уменьшения частоты замены контактных наконечников, если ваш OEM-производитель не получает Вы нуждаетесь в результатах.
Размер контактного наконечника имеет значение
Размер контактного наконечника определяет, какой размер проволоки можно использовать, и количество присадочного материала, которое будет распределяться во время сварки. Когда контактный наконечник начинает изнашиваться, сквозное отверстие удлиняется и теряет электропроводность, что сильно влияет на способность пистолета передавать ток сварочной проволоке. Кроме того, центральная точка инструмента (TCP) начинает колебаться, когда проволока танцует внутри теперь уже слишком большого наконечника. Эти условия приводят к плохому зажиганию дуги, меньшему провару и снижению качества сварки.
Размеры сварочных контактных наконечников варьируются от 0,024 дюйма до 0,094 дюйма с точки зрения размера проволоки, которую они могут направлять. Вообще говоря, чем больше проволока, тем выше параметры и тем выше скорость наплавки. Настоятельно рекомендуется согласовать размер контактного наконечника с размером проволоки для сварочного пистолета MIG.
Точно так же резьба контактного наконечника бывает разных размеров от M6 до M12. Эти размеры полностью зависят от размера держателя контактного наконечника, но размер резьбы напрямую зависит от номинала пистолета MIG.Вы не увидите, например, пистолета MIG на 500 ампер с контактным наконечником M6. Точно так же вы не увидите пистолет MIG на 200 А с контактным наконечником M10, потому что он не нужен.
Выбор правильного контактного наконечника для вашего сварочного применения и понимание того, как поддерживать его наилучшую производительность, так же важны, как и выбор всех других компонентов и параметров, необходимых для получения качественного сварного шва.
Обычные типы сварочных контактных наконечников
При сварке чаще всего используются четыре типа контактных наконечников (а также один для лазерной сварки), и у каждого из них есть свои плюсы и минусы:
# 1: Стандартный контактный наконечник для медной сварки (E-Cu)Стандартный медный контактный наконечник для сварки имеет относительно высокую скорость передачи тока при электрической проводимости более 55 См / м * и используется в основном в ручных сварочных устройствах.
Хотя стандартная медь обеспечивает самую высокую проводимость из всех стандартных сплавов, она более подвержена механическому износу, чем другие материалы. Как сырье, медь по своей природе относительно мягкая, что означает, что она облегчает передачу тока, но это также означает, что материал имеет более низкую температуру плавления. При повышении температуры наконечник из E-Cu становится мягче, чем проволока, проходящая через него. По мере размягчения меди проволока изнашивается и деформирует внутренний диаметр наконечника. Это препятствует правильному контакту проволоки с наконечником, что снижает проводимость и приводит к проблемам с зажиганием дуги, возгоранию и плохим сварным швам.
Наконечник из E-Cu обычно является наиболее доступным по цене, поэтому, как правило, приемлемым компромиссом является его частая замена, когда точное наведение на проволоку не является критичным.
# 2: Контактный наконечник для сварки медь-хром-цирконий (CuCrZr)Контактный наконечник для сварки медь-хром-цирконий обычно используется в автоматизированных и роботизированных сварочных процессах, где требуется точное TCP или центральная точка инструмента и возникают высокие рабочие циклы.Хотя наблюдается некоторое снижение электропроводности по сравнению со стандартным медным наконечником (50 См / м), этого достаточно для большинства стальных применений.
Однако, поскольку сплав CuCrZr размягчается при гораздо более высокой температуре, он имеет более длительный срок службы, чем стандартные медные наконечники. Вообще говоря, наконечник сохраняет свою форму примерно до 932 градусов по Фаренгейту по сравнению с 500 градусами для E-Cu. Следовательно, материал с более высокой плотностью снижает скорость износа и увеличивает рабочие характеристики и производительность наконечника.
Для процессов подачи горячей проволоки в оптике для лазерной сварки необходимо использовать сварочные наконечники из медно-хромо-циркониевого сплава, поскольку они способны выдерживать процессы подачи горячей проволоки.
# 3: Посеребренный сварочный контактный наконечникЗа прошедшие годы технический прогресс в области контактных наконечников показал, что серебряное покрытие внутренней и внешней поверхности контактных наконечников еще больше улучшает их общие характеристики.
Когда контактный наконечник начинает изнашиваться, сквозное отверстие удлиняется и теряет электропроводность, что сильно влияет на способность пистолета передавать ток сварочной проволоке.
Серебро обладает большей проводимостью, чем медь (62,1 См / м), что снижает образование микродуги, продлевает срок службы контактного наконечника, улучшает зажигание дуги и обеспечивает стабильное качество сварки. Серебро примерно на 17 процентов плотнее меди и имеет более высокую температуру плавления. Блестящая поверхность серебра помогает отражать тепло. В результате брызги не так легко прилипают к наконечнику, и он не так быстро изнашивается. Фактически, срок службы посеребренного контактного наконечника может быть в девять раз больше, чем срок службы стандартного прецизионного медного наконечника.
Благодаря значительному усовершенствованию материала, посеребренный контактный наконечник может стоить на 50 процентов дороже, чем стандартный наконечник из CuCrZr без покрытия. Сварщики, которые предпочитают использовать посеребренный контактный наконечник, обычно делают это по одной причине – меньше времени на сварку. Чем больше сварочный робот сваривает, тем выше производительность. Посеребренные наконечники, учитывая общую долговечность, передачу тока и качество материала, являются отличным выбором для автоматической и роботизированной сварки.
# 4: Посеребренный контактный наконечник из CuCrZr для тяжелых условий эксплуатации Используя процесс, называемый дисперсионным упрочнением, который в основном сохраняет свойства металла от диспергирования при повышенной температуре, сварочные наконечники с покрытием из серебра для тяжелых условий эксплуатации могут служить даже дольше, чем указанные выше наконечники с покрытием из серебра.
Эта марка контактного наконечника имеет значение твердости 180 и не будет изнашиваться, пока температура контактного наконечника не достигнет 1472 градусов F (800 градусов C)! Из-за своей проводимости он также будет испытывать гораздо меньшее прилипание брызг, чем медь или медь без покрытия, хром-цирконий.
Сверхмощные посеребренные контактные наконечники для сварки всегда изготавливаются с использованием контактных наконечников из CuCrZr в качестве основы, поскольку они сочетают в себе лучшее упрочнение меди, хрома, циркония и превосходной проводимости серебра.Это дает в целом лучший профиль электропроводности, но при этом остается более твердым. Они дороже, чем стандартные посеребренные сварочные контактные наконечники, но имеют низкую стоимость владения при правильном применении – как правило, в роботизированных процессах с большим током.
# 5: Контактный наконечник из нержавеющей стали X8CrNi18-9 Контактные наконечники из нержавеющей стали действительно используются только в лазерной оптике. Нержавеющая сталь хороша для процессов подачи холодной проволоки.
Стальные контактные наконечники для сварки имеют очень низкую электропроводность, но обладают хорошей износостойкостью.Нержавеющая сталь в качестве материала также тверже меди, поэтому отверстие контактного наконечника обычно меньше изнашивается.
Контактные наконечники из нержавеющей стали рекомендуется использовать при использовании медной проволоки в лазерно-оптических процессах. Если вы используете алюминий, лучше обратить внимание на медь или медь, хром, цирконий, потому что этот профиль контактного наконечника часто слишком жесткий для профиля из мягкой алюминиевой проволоки.
Сварочные контактные насадки: нарисованные и просверленные
Помимо материала контакта, который вы используете, и не менее важно при выборе горелки для сварки MIG или при смене производителя контактных наконечников, прежде всего важно, как были изготовлены ваши сварочные контактные наконечники.
Есть два способа изготовления сварочных контактных наконечников. Самый распространенный способ – использовать оправку и вытягивать медь в форме наконечника, а затем давать ей остыть. Просверленный контактный наконечник добавляет дополнительный шаг в этот процесс изготовления контактного наконечника и просверливает отверстие с помощью высокоскоростного холодного сверла после вытягивания меди или легированного металла. Этот процесс создает более гладкую поверхность отверстия внутри внутреннего диаметра контактного наконечника и устраняет большинство проблем, с которыми сварщики часто сталкиваются со своими контактными наконечниками.
Различие между волочением и просверливанием действительно сводится к гладкости внутреннего диаметра контактного наконечника. Это критически важная функция для увеличения срока службы сварочного контактного наконечника. Из-за того, что наконечники изготавливаются с использованием процесса вытяжки, внутри внутреннего диаметра гораздо больше выступов, потому что по мере охлаждения медь не оседает плавно по внутреннему диаметру.
Когда вы используете перфорированный сварочный контактный наконечник, все эти высокие точки устраняются, и вы получаете гораздо более гладкую поверхность внутреннего диаметра и более жесткие допуски.И из-за этого ваши контактные советы действуют намного дольше. В этих высотных точках, пока вы свариваете, проволока будет контактировать с этими высотными точками. Эта сварка при высоких температурах является особенностью, которая создает множество проблем, вызывающих выход из строя контактных наконечников, таких как возгорание, микродуговое искрение или приготовление на одной стороне. И это часто является причиной того, что контактные наконечники одного производителя выходят из строя быстрее, чем другие.
Можно разумно ожидать, что ваш сварочный контактный наконечник прослужит в два-три раза дольше, если не больше, в результате использования перфорированного контактного наконечника, а не вытянутого.
После того, как вы подберете контактный наконечник для вашего сварочного применения, вы можете сделать несколько вещей, чтобы получить от него максимум пользы и случайно не создать проблемы, которые могут снизить срок его службы или эффективность.
Эта запись в блоге изначально была опубликована в The Fabricator и с тех пор обновлялась несколько раз для большей детализации.
Что такое точечная сварка (и насколько это важно)?
Точечная сварка – одна из самых первых сварочных процедур.Он используется в большом количестве предприятий, но особенно для сварки автомобильных кузовов из листовой стали.
Так что же такое точечная сварка? Точечная сварка считается одним из наиболее эффективных сварочных процессов и обычно используется для соединения двух или более металлических листов в один. Чтобы сделать это возможным, сварщик должен приложить не только огромное давление и тепло, но и электрический ток через листы, чтобы устранить сопротивление и заставить их плавиться.
Этот метод используется в нескольких отраслях, о которых мы поговорим в конце, но он особенно важен для сварки листов низкоуглеродистой стали для кузовов автомобилей.Размер и форма сварных швов зависят от размера используемых электродов, которые, в свою очередь, зависят от толщины основного металла и квалификации сварщика.
Как работает точечная сварка
Лучший способ понять, как работает точечная сварка, – это выполнить входящие в нее шаги. Вот краткий обзор:
Шаг 1 – заготовки и металлические листы выровнены
Сначала заготовки или металлические листы точно выстраиваются в линию. Это важный шаг, потому что после того, как листы будут сварены, пути назад уже не будет.Если они не выровнены правильно, сварной шов будет неправильным, и этот шаг придется повторить с новыми листами.
Этап 2 – прессование электрода
На следующем этапе выбираются подходящие электроды для сварки двух деталей вместе. Вместо электродов сопротивления из чистой меди используются чисто тугоплавкие из-за их способности удерживать тепло и противостоять окислению. Он также содержит фракции молибдена (МО), температура плавления которого достаточно высока, чтобы предотвратить расслоение.
Этап 3 – ток проходит через электроды
После того, как электроды помещены в нужное положение, ножная педаль используется для генерирования тока высокого напряжения, который течет через стержни в заготовки. Прижатие электродов к металлическим листам с соответствующим давлением имеет жизненно важное значение, когда речь идет о качественных сварных швах.
Тепло, необходимое для плавления металла, генерируется за счет сопротивления основного металла и ограничивается точкой, где встречаются электрод и область сварного шва.Ток отключается на стадии выдержки, пока поддерживается давление, и самородку дают остыть.
Время, в течение которого ток проходит через детали, и тип используемого тока зависят от толщины и типа материала, с которым вы работаете. После точного соединения листов электроды снимаются и перемещаются в следующей точке сварки.
Материалы, подходящие для точечной сварки
Для точечной сварки можно использовать несколько типов материалов, помимо металлических материалов; это также включает проволочную сетку.Сталь предпочтительнее, особенно в автомобильной промышленности, потому что она имеет высокое электрическое сопротивление и не так прочен в качестве проводника, как другие материалы.
Точно так же низкоуглеродистая сталь используется чаще, чем сталь с высоким содержанием углерода из-за ее устойчивости к трещинам. Сварные швы из нержавеющей стали также считаются менее твердыми, чем сварные швы из низкоуглеродистой стали и смешанной стали, но никелевые сплавы и титан также являются популярным выбором.
Напротив, точечная сварка металлов, таких как алюминий и гальванизированная сталь, может быть затруднена, поскольку для образования сварного шва в обоих случаях требуется более высокий уровень электрического тока.Однако даже самый лучший материал может быть трудно сваривать, если он не соответствующей толщины.
Как правило, толщина листов должна быть не менее 3 мм. И оба должны быть одинакового размера для достижения оптимальных результатов. С другой стороны, если листы имеют разные размеры, для получения качественного сварного шва следует поддерживать соотношение 3: 1.
Параметры точечной сварки
Как один из наиболее широко используемых вариантов процесса контактной сварки, точечная сварка зависит от нескольких параметров, каждый из которых имеет свои применения и преимущества. К ним относятся:
Сила электрода
Под силой электрода мы понимаем энергию, которая требуется для соединения металлических листов, которые должны быть сплавлены. Чем сильнее сила, тем больше тепла выделяется, поэтому инженеры должны быть осторожны, чтобы не ухудшить качество сварного шва.
Для увеличения усилия также необходимо увеличить сварочный ток. Однако, если его повернуть слишком высоко, разбрызгивание между листами и электродом также будет большим. Результат? Электроды прилипнут к листам и, возможно, испортятся.
Кроме того, если давление будет слишком высоким, вы в конечном итоге создадите небольшой точечный сварной шов по мере прохождения тока, а тепло, создаваемое листами и электродами, будет распространяться по большей площади, тем самым уменьшая проплавление сварного шва.
Время сжатия
Время сжатия относится к периоду между первоначальным приложением силы электрода к заготовкам и первым приложением тока. Этот параметр, также известный как запрограммированное время сжатия, стабилизирует наконечник перед текущим приложением. Если этот шаг пропустить, это может привести к преждевременному износу электрода, выбросу на поверхности раздела и возникновению дуги.
Если продолжительность обжатия будет увеличена, это может дать вам качественный сварной шов, но это может стоить вам рабочих операций, поскольку будет производить меньше сварных деталей за смену. Точно так же более короткое время сжатия может привести к нестабильному качеству и удалению металла.
Обычно время сжатия должно быть запрограммировано в источнике питания таким образом, чтобы дать время для стабилизации силы электрода.
Продолжительность сварки или время сварки
Время сварки – это продолжительность, в течение которой ток применяется к заготовкам или металлическим листам во время процесса сварки. Это рассчитывается в циклах линейного напряжения. Однако время сварки трудно точно определить, потому что оно зависит от того, что нужно сделать для сварной точки.
Однако нужно соблюдать некоторые правила. Например:
- Время сварки должно быть как можно короче.
- Сила тока должна обеспечивать оптимальное качество сварки.
- Продолжительность сварного шва должна быть достаточной для того, чтобы отпечаток сварного шва был как можно меньше. Чем меньше время сварки, тем меньше отпечаток.
- За время сварки толстых листов должен получиться самородок большого диаметра.
- Параметры, выбранные для сварного шва, должны как можно меньше изнашивать электроды.
- Продолжительность сварного шва должна быть изменена в случае автоматической правки наконечника. В этом случае контактная поверхность электрода поддерживается на постоянной величине.
Другими словами, наилучшее время сварки для качественной сварки – это как можно более короткое время.
Время выдержки
Как следует из названия, время выдержки относится к продолжительности после сварки, когда электроды остаются в контакте с листом. Это делается для того, чтобы область сварного шва остыла. Затем сварной кусок затвердевает до того, как сваренные детали будут освобождены.
Если время выдержки увеличено, тепло в месте сварки может распространиться на электрод и нагреть его, что приведет к его износу.Кроме того, если материал имеет высокое содержание углерода и время выдержки велико, сварной шов может стать хрупким и образоваться трещины. Однако, если вы удалите электроды до того, как самородок станет твердым, он может разорваться, что приведет к слабому сварному шву.
Области применения точечной сварки
Автомобильная промышленность
Точечная сварка – популярный метод сварки в автомобильной промышленности, поскольку это дешевый, но эффективный способ соединения листового металла. Таким образом, его можно использовать либо с обученным элементарным персоналом, либо с роботами, поскольку это не требует особых навыков.Суть в том, что процесс сварки является быстрым и эффективным, а это означает, что за смену разрабатывается больше автомобилей.
Для электроники
Этот метод сварки широко используется в производстве электроники, такой как печатные платы, датчики газа и даже солнечные панели. Этот метод известен как электронная контактная сварка и также используется для создания сложных и хрупких электрических компонентов от кабелей до переключателей и ручных инструментов.
Сплавление гвоздей
Большинство людей не знают об этом, но точечная сварка также используется для соединения мотков гвоздей.Стальную проволоку приваривают к гвоздям на высоких скоростях с помощью магазинов пневматического пистолета для гвоздей. Если вы используете круги для сварки швов, вы можете получить 1200 гвоздей в минуту.
Конечно, для обеспечения точного крепления гвоздей к проволоке, прикладываемый ток должен быть максимально точным в точке, где острие гвоздя находится под сварочным колесом.
Связанные вопросы
Легко ли точечная сварка? Точечная сварка – одна из самых первых сварочных процедур, она хорошо известна и проста в выполнении даже начинающим сварщикам.Процедура полностью определена и легко применима к множеству тонких металлов, таких как нержавеющая сталь, никелевые сплавы и титан. Его часто используют в аэрокосмической и автомобильной промышленности, но улучшения очень желательны.
Какой толщины можно сваривать точечной сваркой? Точечная сварка в основном используется для соединения деталей, толщина которых обычно составляет около 3 миллиметров. Толщина свариваемых компонентов должна быть эквивалентной, или соотношение толщины должно быть меньше 3: 1.Прочность этого соединения зависит от количества и размера сварных швов. Диаметр точечной сварки варьируется от 3 мм до 12,5 мм.
Можно ли сваривать алюминий точечной сваркой? Точечная сварка алюминия становится все более распространенной, поскольку алюминий заменяет сталь во многих областях, где важен вес, например, в автомобилях. Вы можете использовать трехфазное питание для точечной сварки легкого алюминия. Точечная сварка обычно обеспечивает ток в течение 0,1 секунды или намного меньше, поэтому ток должен быть очень значительным.
Подобные сообщения:
Фотонных сварочных точек для произвольных встроенных оптических межсоединений
Фотонные интегральные схемы (PIC) являются идеальной платформой для вычислений и связи в масштабе кристалла. На сегодняшний день плотность интеграции остается нерешенной проблемой, которая ограничивает дальнейшее развитие фотонных сетей на основе PIC. Обеспечение разводки волноводов произвольной конфигурации с низкими потерями имеет решающее значение как для классических, так и для квантовых фотонных приложений. Традиционно для управления световыми потоками на кристалле используются изгибы волноводов с большими радиусами изгиба и преобразователи адиабатических мод, чтобы избежать вносимых потерь из-за утечки излучения и рассогласования мод, соответственно.Однако эти структуры обычно занимают большие площади и, таким образом, уменьшают плотность интеграции. Чтобы преодолеть эту трудность, в данной работе представлен принципиально новый подход к произвольному повороту световых потоков в пределах ультракомпактного основания. Был предложен и экспериментально продемонстрирован тип «точек фотонной сварки», соединяющих два волновода с произвольным углом пересечения. Эти устройства с площадью основания менее 4 мкм 2 могут работать в телекоммуникационном диапазоне в полосе пропускания не менее 140 нм с вносимыми потерями менее 0.
5 дБ. Их изготовление совместимо с процессами фотонного литья и не требует дополнительных операций, помимо тех, которые необходимы для волноводов. Следовательно, они подходят для массового производства PIC и повышают плотность интеграции до следующего уровня.
1 Введение
В эпоху информационных технологий фотоника превосходит электронику. Фотонные интегральные схемы (PIC) имеют много значительных преимуществ, таких как широкая полоса пропускания [1], низкое энергопотребление, высокая устойчивость к электромагнитным помехам и совместимость с квантово-оптическими устройствами [2], [3], [4], [5], [6].Люди разработали множество высокопроизводительных встроенных приложений, таких как оптические межсоединения [7], модуляция [8], биосенсинг [9], квантовая связь [2], [3], [4], [5], [6] , оптомеханика [10]. Однако по мере того, как сложность оптических соединений на кристалле продолжает расти, основной проблемой при разработке PIC является ограниченная плотность интеграции, поскольку размеры большинства фотонных устройств составляют десятки микрометров, а межсоединения на кристалле также занимают большую площадь. [11], [12]. Плазмоника, использующая такие материалы, как Au, Ag и TiN, для преодоления дифракционного предела [13], является одним из наиболее часто используемых подходов к уменьшению габаритов устройства [14], [15], но большие омические потери плазмонные материалы устанавливают ограничение на длину распространения волноводов [16] и время жизни фотонов в резонаторах [17], что приводит к ограниченным характеристикам и возможностям применения плазмонных схем и устройств.Помимо использования плазмонных материалов, реализация структурированных фотонных конструкций также является способом уменьшить площадь, занимаемую интегрированными фотонными устройствами. Волноводы на фотонных кристаллах, которые направляют распространение света с боковым ограничением через эффект фотонной запрещенной зоны, могут делать резкие повороты направления распространения в пределах сверхмалой области [18], [19], [20], [21]. Однако угол поворота имеет ограниченный выбор, поскольку направленный свет может распространяться только в определенных кристаллических направлениях.
Обратный дизайн, в котором используется алгоритм оптимизации, позволяет искать конструкции во всем пространстве для достижения функциональных возможностей, неожиданных для обычного дизайна. Метод проектирования широко применяется в междисциплинарных областях науки и техники [22]. В интегрированной фотонике были разработаны устройства обратной конструкции с ультракомпактными следами, которые могут быть на несколько порядков меньше, чем устройства, разработанные традиционными методами. Например, такие устройства, как вращатели поляризации [23], [24], поляризационные светоделители [25], демультиплексоры мод [26], [27], демультиплексоры длины волны [28], [29], [30], делители мощности [ 31], [32], отражатели [33], изгибы волновода [34] и маскировка волновода [35], как было продемонстрировано, имеют площадь основания всего в несколько квадратных микрометров.
Несмотря на то, что было приложено много усилий для уменьшения размеров отдельных устройств, уменьшение занимаемой площади межсоединения PIC не менее важно и еще предстоит продемонстрировать. Маршрутизация волноводов с низкими потерями в PIC имеет решающее значение как в классических, так и в квантовых фотонных приложениях для получения высокого отношения сигнал / шум или для поддержания высокой точности квантовых состояний. Традиционно для изменения направления световых потоков на кристалле используются изгибы волноводов с большими радиусами изгиба и преобразователи адиабатических мод, которые позволяют избежать чрезмерных вносимых потерь из-за утечки излучения (потери изгиба) и модального рассогласования (потерь на рассеяние) [36 ], соответственно.Известно, что эти структуры занимают большие площади и, следовательно, уменьшают плотность интеграции. Поэтому очень желательно найти способ произвольно изменять направление световых потоков с незначительными вносимыми потерями в пределах минимально возможной площади. Здесь мы применяем метод обратного проектирования для проектирования точек фотонной сварки, которые являются фотонным аналогом электрических соединений в интегральных схемах, для соединения волноводов произвольной ориентации на чрезвычайно небольшой площади.
Такие точки фотонной сварки имеют много явных преимуществ.Во-первых, в отличие от точек электрической сварки, которые могут вносить дополнительные вносимые потери из-за несоответствия импеданса для высокочастотных сигналов, такие точки фотонной сварки свободны от этой проблемы и, таким образом, могут безопасно использоваться в PIC для высокочастотных приложений. Во-вторых, конструкции оптимизируются только путем проектирования формы границ, которые можно описать непрерывной и дифференцируемой функцией. Такие структуры с постепенно изменяющимися границами можно изготавливать с высокой точностью, а также вносить минимальные потери на рассеяние для пропускающего света.В-третьих, процесс изготовления точек фотонной сварки совместим с КМОП и требует всего одного этапа литографии и травления. Конструкции также отличаются высокой надежностью и большим допуском на изготовление, что гарантирует высокую производительность сборных конструкций с отклонениями от разработанного рисунка.
2 Процедура проектирования
Традиционно два волновода могут быть соединены изгибом волновода для изменения направления распространения света, как показано на рисунке 1A, где серая часть обозначает SiO 2 , а фиолетовая часть обозначает кремний ( Si). Если радиус изгиба не намного превышает длину световой волны, модальное несоответствие между прямым и изогнутым волноводами и плохое ограничение изгиба волновода приведет к значительным вносимым потерям для света (вспомогательная информация). Кроме того, изгибы волновода с малым радиусом изгиба также вносят перекрестные помехи между различными оптическими модами [37]. Ожидается, что точка фотонной сварки, реализованная на небольшой площади, как показано на рисунке 1B, будет соединять волноводы с незначительными вносимыми потерями и перекрестными помехами.Мы возьмем точку фотонной сварки, показанную на рисунке 1C, в качестве примера, чтобы объяснить процесс проектирования. Устройства спроектированы на платформе кремний-на-изоляторе (КНИ) со слоем Si 220 нм на скрытом оксиде толщиной 3 мкм. Мы рисуем небольшой прямоугольник с оранжевой пунктирной линией, как показано на рисунке 1C, чтобы указать область оптимизации конструкции точки фотонной сварки. Две непрерывные линии AB и CD , которые определены зелеными дискретными точками, очерчивают границы структуры точки фотонной сварки, где фиолетовая область обозначает неотравленный Si, а белая область обозначает полностью протравленный Si.
Положение каждой дискретной точки описывается радиальными и угловыми координатами ( r i и θ i ). Окончательные значения r i и θ i определяются после нескольких раундов оптимизации.
Рисунок 1:
Традиционная и новая схемы поворота направления светового потока на микросхеме.
(A) Схема обычного изгиба волновода для соединения двух непараллельных волноводов. R – это внутренний радиус изгиба волновода, который должен составлять не менее десятков микрометров, чтобы избежать значительного модального несоответствия и потерь на изгибе. Серые и фиолетовые области представляют SiO 2 и Si соответственно. (B) Схема точки фотонной сварки для соединения двух непараллельных волноводов. (C) Вид сверху точки фотонной сварки, структура которой определяется двумя непрерывными линиями AB и CD , проходящими через зеленые точки. (D) Схема алгоритма процесса оптимизации.
Как показано на рисунке 1C, структура точки фотонной сварки определяется двумя непрерывными линиями AB и CD , которые построены из 2 дискретных зеленых точек N с помощью интерполяции тройным сплайном. Расстояние между соседними точками установлено больше 100 нм, чтобы гарантировать успешное изготовление оптимизированной структуры. Из-за зеркальной симметрии структуры относительно оси y нам нужно оптимизировать положение только половины этих дискретных точек.Во время оптимизации четыре точки от A до D фиксируются, обеспечивая постоянное соединение точки фотонной сварки с двумя волноводами. Угловые координаты θ i дискретных точек также фиксированы. Для определения радиальных координат r i дискретных точек был принят метод жадной оптимизации (эвристический метод). На рисунке 1D показана блок-схема алгоритма процесса оптимизации. Показателем качества для оптимизации является нормализованное пропускание основной поперечной электрической моды (TE 0 ) на 1,55 мкм. Сначала мы сгенерировали случайное значение для каждой точки, а затем оптимизировали их последовательно. Во время последовательной оптимизации мы изменили отдельные r i и ограничили точку внутри оранжевого пунктирного прямоугольника, зафиксировав все остальные точки. Временные наилучшие значения r i были получены после сравнения структурной передачи всех предпринятых значений.После нескольких раундов оптимизации r i от первой точки до последней, мы получили окончательную структуру точки фотонной сварки, когда вносимые потери не могли уменьшиться в дополнительных прогонах оптимизации. Вышеописанная процедура применялась для получения точек фотонной сварки для соединения волноводов с произвольным углом изгиба.
Не умаляя общности, мы разработали точки фотонной сварки для соединения двух волноводов шириной 0,5 мкм с углами изгиба 30 °, 60 °, 90 °, 120 ° и 150 °. Структуры для дополнительных типичных углов изгиба можно найти во вспомогательной информации. Несмотря на использование одной и той же процедуры для оптимизации конструкции, время вычислений, необходимое для получения оптимизированной точки фотонной сварки для соединения волноводов с разными углами изгиба, варьируется. Конструкции для больших углов изгиба обычно требуют большего времени расчета. Пять точек фотонной сварки, соединяющие волноводы с углами изгиба 30 °, 60 °, 90 °, 120 ° и 150 °, заняли в общей сложности ~ 5 дней при использовании обычного настольного компьютера с 16 ядрами.На рисунке 2A показаны структуры, соединенные оптимизированными точками фотонной сварки в зеленых областях. Их увеличенные изображения можно найти во вспомогательной информации. На рис. 2В показано смоделированное электрическое поле | E | профили моды TE 0 на 1,55 мкм, проходящие через точки фотонной сварки, которые ясно показывают, что свет плотно ограничен в точках фотонной сварки, что позволяет избежать потерь на изгиб, вызванных малым радиусом изгиба.
Равномерная картина интенсивности в выходном волноводе также доказывает отсутствие перекрестных помех, вносимых точками фотонной сварки.На рис. 2С показаны конструкции обычных изгибов волновода, соединяющих два волновода, с внутренним радиусом изгиба волновода 0,15 мкм для сохранения такой же площади основания соответствующих точек фотонной сварки. Для света в полосе связи около λ = 1,55 мкм изгиб волновода с внутренним радиусом ~ λ /10 неизбежно приведет к большим вносимым потерям из-за несовпадения мод и резкого изгиба. На рисунке 2D показано смоделированное электрическое поле | E | профили режима TE 0 на 1.55 мкм проходит через изгибы волновода, что четко указывает на утечку света из изгибов волновода. Колебания интенсивности света, видимые в выходном волноводе, указывают на то, что свет больше не является чистой модой TE 0 . На рисунке 2E показаны нормализованные спектры пропускания через точки фотонной сварки и изгибы волновода, где синие сплошные линии представляют передачу из точек фотонной сварки, а красные пунктирные линии представляют передачу из изгибов волновода.Сравнение синей сплошной и красной пунктирной линии показывает, что изгибы волновода приведут к значительно более высоким вносимым потерям, которые пропорциональны углу изгиба, но точки фотонной сварки могут избежать этих потерь и переносить свет из одного волновода в другой любым другим способом. угол изгиба.
Рисунок 2:
Расчет и результаты моделирования точек фотонной сварки и изгибов волновода.
(A) Оптимизированная структура точек фотонной сварки, соединяющих два волновода с углами изгиба 30 °, 60 °, 90 °, 120 ° и 150 °.(B) Смоделированные профили электрического поля моды TE 0 на 1,55 мкм, проходящие через точки фотонной сварки. (C) Схема изгиба волновода, соединяющего два волновода с углами изгиба 30 °, 60 °, 90 °, 120 ° и 150 °. Внутренний радиус всех изгибов волновода 0,15 мкм. (D) Смоделированные профили электрического поля моды TE 0 на 1,55 мкм, проходящей через изгибы волновода. Фиолетовые стрелки указывают направления входа и выхода света. (E) Нормализованные спектры пропускания точек фотонной сварки (синие сплошные линии) и изгибов волновода (красные пунктирные линии), соединяющих два волновода с углами изгиба 30 °, 60 °, 90 °, 120 ° и 150 °.(A – D) Масштабные полосы представляют 1 мкм.
3 Результаты экспериментов и обсуждение
Устройства точек фотонной сварки и изгибы волноводов были изготовлены на пластине КНИ с приборным слоем Si 220 нм на скрытом оксиде 3 мкм. Структуры устройств были определены вместе с входными и выходными волноводами и решетчатыми элементами связи за один этап электронно-лучевой литографии с резистом ZEP520A. Затем рисунки были перенесены на верхний слой Si с помощью реактивного ионного травления с индуктивно связанной плазмой с использованием газохимии SF 6 / C 4 F 8 .Устройства были закончены после удаления электронно-лучевого резиста и сушки феном.
На рис. 3A (вверху) представлены изображения устройств для определения вносимых потерь в точках фотонной сварки, соединяющих волноводы с углами изгиба 30 °, 60 °, 90 °, 120 ° и 150 °, с оптического микроскопа, а на рис. 3A (внизу) ) содержит соответствующие изображения, полученные с помощью сканирующего электронного микроскопа (СЭМ), увеличенные на стыке, все из которых имеют площадь основания менее 4 мкм 2 . Рисунок 3B (вверху) содержит изображения устройств для определения вносимых потерь в изгибах волновода, соединяющих два волновода с углами изгиба 30 °, 60 °, 90 °, 120 ° и 150 °, с оптического микроскопа, а Рисунок 3B (внизу) содержит СЭМ-изображения увеличились на стыке.Мы включили несколько точек фотонной сварки или изгибы волновода в каждое устройство, чтобы уменьшить ошибку измерения, поскольку вносимые потери в точке одиночной фотонной сварки по сути малы. Для связи света между волноводами на кристалле и оптическими волокнами использовались интегрированные на кристалле решетчатые элементы связи, поскольку решетчатые элементы связи могут работать не только как ответвитель мощности, но также как модовый фильтр для выбора желаемой моды TE 0 для включенного -чиповые волноводы. Устройства, состоящие из пары решетчатых элементов связи, напрямую соединенных с прямым волноводом, были изготовлены за один цикл для калибровки вносимых потерь, вносимых решетчатыми элементами связи.Мы также изготовили несколько устройств точек фотонной сварки и изгибов волноводов с решетчатыми элементами связи, покрывающими различные рабочие диапазоны, чтобы преодолеть ограничение узкой рабочей полосы пропускания решетчатых элементов связи.
Рисунок 3:
Изображения с устройства точек фотонной сварки и изгибов волновода.
(A) Оптический микроскоп и изображения с помощью сканирующего электронного микроскопа изготовленных устройств для измерения потерь пропускания в точках фотонной сварки, соединяющих два волновода с углами изгиба 30 °, 60 °, 90 °, 120 ° и 150 °.Устройства с углами изгиба 30 °, 60 °, 120 ° и 150 ° каждое содержат 12 точек фотонной сварки, а устройство с углом изгиба 90 ° содержит 8 точек фотонной сварки. (B) Оптический микроскоп и изображения СЭМ изготовленных устройств для измерения потерь пропускания изгибов волновода, соединяющих два волновода с углами изгиба 30 °, 60 °, 90 °, 120 ° и 150 °. Каждое устройство содержит четыре каскадных изгиба для уменьшения погрешности измерения. Масштабные полосы представляют 40 мкм на всех изображениях, полученных с помощью оптического микроскопа, и 1 мкм на всех изображениях, полученных с помощью SEM.
Изготовленные устройства характеризовались спектроскопическим измерением их оптического пропускания. Свет от перестраиваемого полупроводникового лазера (длина волны 1440–1580 нм) направлялся через одномодовое волокно, состояние поляризации которого регулировалось контроллером поляризации волокна, в тестируемое устройство через входную решетчатую ответвитель. Проходящий свет, выходящий из выходного решетчатого ответвителя, собирался фотодетектором. На рис. 4 показаны нормализованные спектры пропускания точки одиночной фотонной сварки и одиночного изгиба волновода, где моделирование изготовленной структуры было проведено путем импорта SEM-изображения устройства в Lumerical и пренебрежения шероховатостью вдоль направления вне плоскости.Ясно, что три спектра (измеренные, смоделированные для идеального и смоделированные для изготовленного) согласуются друг с другом. Вносимые потери в точках фотонной сварки не превышают 0,5 дБ во всем диапазоне длин волн 1440–1580 нм, тогда как потери изгиба волновода возрастают с увеличением угла изгиба и могут достигать 3,0 дБ.
Рис. 4:
Экспериментальные и смоделированные нормализованные спектры пропускания точки однофотонной сварки и изгиба волновода для соединения двух волноводов с углами изгиба 30 °, 60 °, 90 °, 120 ° и 150 °.
Синие сплошные линии представляют результаты экспериментальных измерений, красные пунктирные линии представляют результаты моделирования для идеальной структуры, а зеленые пунктирные линии представляют результаты моделирования для изготовленной конструкции.
Из-за неконтролируемого несовершенства нанообработки размеры изготовленных устройств часто могут отличаться на десятки нанометров от оригинального дизайна, например, из-за переэкспонирования / недоэкспонирования в процессе литографии или чрезмерного / недостаточного растяжения при сухом травлении.Следовательно, допуск на изготовление является важной характеристикой для оценки производительности устройств. Здесь мы смоделировали пропускание точек фотонной сварки с изменением размера ∆ w = ± 40 нм, как показано на рисунке 5A, и результаты представлены на рисунке 5B для структур с углами изгиба 30 °, 60 °, 90 °. °, 120 ° и 150 °. Нормализованные спектры пропускания идеальной структуры и структур с ∆ w = 40 и -40 нм ясно показывают, что точки фотонной сварки сохраняют аналогичные характеристики при изменении размера ∆ w = ± 40 нм, что находится в пределах типичные производственные ошибки фактического изготовления устройства.Основная причина такого большого производственного допуска заключается в том, что общее изменение положения всех отдельных точек r i , которые определяют границы точки фотонной сварки, не вносит значительных изменений пропускания.
Рис. 5:
Анализ допусков при изготовлении.
(A) Иллюстрация типичной ошибки изготовления точек фотонной сварки. Пурпурная область обозначает изготовленную структуру, а сплошная черная линия обозначает границу исходного дизайна.Ширина изготовленной конструкции может иметь отклонение ∆ w от проектного значения. (B) Анализ производственных отклонений в точках фотонной сварки для соединения двух волноводов с углами изгиба 30 °, 60 °, 90 °, 120 ° и 150 °. Сплошные синие, красные пунктирные и зеленые пунктирные линии представляют идеальную структуру, структуру с отклонением ширины ∆ w = 40 нм и структуру с отклонением ширины ∆ w = -40 нм соответственно.
4 Заключение
В заключение, мы разработали и экспериментально продемонстрировали новый тип структур, а именно «точки фотонной сварки», для соединения двух волноводов с произвольным углом изгиба на кристалле.Размеры элементов этих точек фотонной сварки примерно на два порядка меньше, чем у обычных изгибов волновода. Разработанные устройства имеют большой допуск на изготовление, а процесс изготовления прост и понятен, который включает только один этап электронно-лучевой литографии с последующим сухим травлением на пластине КНИ. Вносимые потери по результатам моделирования и измерений остаются ниже 0,5 дБ в диапазоне длин волн 1440–1580 нм. Поэтому предлагаемые нами точки фотонной сварки можно использовать в качестве стандартного модуля в PIC для повышения плотности фотонной интеграции до следующего уровня.
Эта работа была поддержана схемой ранней карьеры (проект № 24208915) и общим исследовательским фондом (проект № 14208717), спонсируемым Советом по исследовательским грантам Гонконга и схемой совместных исследований NSFC / RGC (проект № N_CUHK415 / 15) при финансовой поддержке Совета по исследовательским грантам Гонконга и Национального фонда естественных наук Китая.
Ссылки
[1] Zhang C, Zhang S, Peters JD, Bowers JE. Полностью интегрированная кремниевая фотонная сеть на кристалле 8 × 8 × 40 Гбит / с.Optica 2016; 3: 785–6.10.1364 / OPTICA.3.000785 Поиск в Google Scholar
[2] Сибсон П., Кеннард Дж. Э., Станисич С., Эрвен С., О’Брайен Дж. Л., Томпсон М. Г.. Интегрированная кремниевая фотоника для высокоскоростного квантового распределения ключей. Optica 2017; 4: 172–7.10.1364 / OPTICA.4.000172 Поиск в Google Scholar
[3] Сильверстоун Дж. У., Бонно Д., Охира К. и др. Встроенная квантовая интерференция между кремниевыми источниками пар фотонов. Nat Photonics 2013; 8: 104–8. Искать в Google Scholar
[4] Politi A, Matthews JCF, Thompson MG, Brien JLO.Интегрированная квантовая фотоника. IEEE J Sel Top Quantum Electron 2009; 15: 1673–84.10.1109 / JSTQE.2009.2026060 Поиск в Google Scholar
[5] Кус М., Реймер К., Розтоцкий П. и др. Встроенная генерация запутанных квантовых состояний большой размерности и их когерентное управление. Nature 2017; 546: 622–6.10.1038 / nature2298628658228 Поиск в Google Scholar
[6] Полити А., Крайан М.Дж., Рарити Дж. Г., Ю. С., О’Брайен Дж. Л.. Квантовые волноводные схемы кремния на кремнии. Наука 2008; 320: 646–9.10.1126 / наука.115544118369104 Искать в Google Scholar
[7] Dai D, Bowers JE. Технологии и устройства на основе кремния мультиплексирования на кристалле для петабитных оптических межсоединений. Нанофотоника 2014; 3: 283–311. Искать в Google Scholar
[8] Лю А., Джонс Р., Ляо Л. и др. Быстродействующий кремниевый оптический модулятор на основе металл-оксидно-полупроводникового конденсатора. Nature 2004; 427: 615–8.10.1038 / nature0231014961115 Искать в Google Scholar
[9] Эстевес М.К., Альварес М., Лечуга Л.М. Интегрированные оптические устройства для биодатчиков «лаборатория на кристалле».Laser Photon Rev 2012; 6: 463–87.10.1002 / lpor.201100025 Искать в Google Scholar
[10] Sun X, Xu K, Tang HX. Монолитно интегрированная нанооптоэлектромеханическая система с высокочастотным резонатором с германиевым волноводным фотодетектором на кристалле. Opt Lett 2014; 39: 2514–7.24970.1364 / OL.39.002514 Поиск в Google Scholar
[11] Li G, Yao J, Thacker H, et al. Маршрутизация оптических волноводов SOI со сверхнизкими потерями и высокой плотностью для межкомпонентных соединений на макрочипах. Opt Express 2012; 20: 12035–9.10.1364 / OE.20.01203522714189 Искать в Google Scholar
[12] Sun X, Liu H-C, Yariv A. Критерий адиабатичности и кратчайший преобразователь адиабатической моды в системе связанных волноводов. Opt Lett 2009; 34: 280–2.10.1364 / OL.34.000280 Поиск в Google Scholar
[13] Грамотнев Д.К., Божевольный С.И. Плазмоника за дифракционным пределом. Nat Photonics 2010; 4: 83–91.10.1038 / nphoton.2009.282 Поиск в Google Scholar
[14] Меликян А., Аллоатти Л., Муслия А. и др. Быстродействующие плазмонные модуляторы фазы.Nat Photonics 2014; 8: 229–33.10.1038 / nphoton.2014.9 Поиск в Google Scholar
[15] Haffner C, Heni W, Fedoryshyn Y, et al. Полностью плазмонный модулятор Маха-Цендера, обеспечивающий оптическую высокоскоростную связь на микромасштабе. Nat Photonics 2015; 9: 525–8.10.1038 / nphoton.2015.127 Поиск в Google Scholar
[16] Zhu BQ, Tsang HK. Кремниевый волновод с высокой эффективностью связи с преобразователем мод металл-изолятор-металлический волновод. J Lightwave Technol 2016; 34: 2467–72.10.1109 / JLT.2016.2535490 Поиск в Google Scholar
[17] Чу Х-С, Бай П, Ли Э-П, Хофер WRJ.Гибридный делитель мощности на основе плазмонного волновода с диэлектрической нагрузкой и кольцевой резонатор: компактный размер и высокие оптические характеристики для нанофотонных схем. Plasmonics 2011; 6: 591–7.10.1007 / s11468-011-9239-y Поиск в Google Scholar
[18] Франдсен Л.Х., Харпот А., Борель П.И., Кристенсен М., Дженсен Дж. С., Зигмунд О. Широкополосный фотонно-кристаллический волновод 60 ° изгиб, полученный с использованием оптимизации топологии. Opt Express 2004; 12: 5916–21.10.1364 / OPEX.12.00591619488232 Поиск в Google Scholar
[19] Лин С.-Й, Чоу Э, Хиетала В., Вильнёв П. Р., Жоаннопулос Дж. Д..Экспериментальная демонстрация направления и отклонения электромагнитных волн в фотонном кристалле. Science 1998; 282: 274–6.10.1126 / science.282.5387.274 Искать в Google Scholar
[20] Mekis A, Chen JC, Kurland I, Fan S, Villeneuve PR, Joannopoulos JD. Высокое пропускание через острые изгибы световодов на фотонных кристаллах. Phys Rev Lett 1996; 77: 3787–90.10.1103 / PhysRevLett.77.378710062308 Искать в Google Scholar
[21] Борель П.И., Харпот А., Франдсен Л.Х., Кристенсен М., Ши П., Йенсен Дж. С., Зигмунд О.Оптимизация топологии и изготовление фотонно-кристаллических структур. Opt Express 2004; 12: 1996–2001.1947503410.1364 / OPEX.12.001996 Поиск в Google Scholar
[22] Бендсо М., Зигмунд О. Оптимизация топологии: теория, методы и приложения. Berlin, Springer, 2003. Поиск в Google Scholar
[23] Yu Z, Cui H, Sun X. Широкополосный вращатель поляризации на кристалле, оптимизированный с помощью генетических алгоритмов, с очень малой площадью основания. Opt Lett 2017; 42: 3093–6.10.1364 / OL.42.00309328809881 Поиск в Google Scholar
[24] Маджумдер А., Шен Б., Полсон Р., Менон Р.Сверхкомпактное вращение поляризации в интегральной кремниевой фотонике с использованием цифровых метаматериалов. Opt Express 2017; 25: 19721–31.10.1364 / OE.25.019721260 Поиск в Google Scholar
[25] Шен Б., Ван П., Полсон Р., Менон Р. Интегрированный нанофотонный поляризационный светоделитель с размером 2,4 × 2,4 мкм 2 след. Nat Photonics 2015; 9: 378–82.10.1038 / nphoton.2015.80 Поиск в Google Scholar
[26] Пигготт А.Ю., Лу Дж., Лагоудакис К.Г., Петикевич Дж., Бабинец Т.М., Вучкович Дж. Обратный дизайн и демонстрация компактного и широкополосный встроенный демультиплексор длин волн.Nat Photonics 2015; 9: 374–7.10.1038 / nphoton.2015.69 Поиск в Google Scholar
[27] Чанг В., Лу Л., Рен Х и др. Сверхкомпактный режим (де) мультиплексор на субволновом асимметричном Y-переходе. Opt Express 2018; 26: 8162–70.10.1364 / OE.26.00816229715785 Поиск в Google Scholar
[28] Фреллсен Л.Ф., Динг Й., Зигмунд О., Франдсен Л.Х. Мультиплексирование мод с оптимизированной топологией в волноводах на основе фотонных проводов кремний на изоляторе. Opt Express 2016; 24: 16866–73.2746413810.1364 / OE.24.016866 Поиск в Google Scholar
[29] Су Л., Пигготт А.Ю., Сапра Н.В., Петикевич Ю., Вучкович Ю.Обратная конструкция и демонстрация компактного узкополосного трехканального демультиплексора на кристалле. ACS Photonics 2018; 5: 301–5.10.1021 / acsphotonics.7b00987 Поиск в Google Scholar
[30] Борель П.И., Биленберг Б., Франдсен Л.Х. и др. Запечатанная нанофотоника на основе кремния. Opt Express 2007; 15: 1261–6.1953235510.1364 / OE.15.001261 Поиск в Google Scholar
[31] Мак JCC, Сидерис С., Чон Дж., Хаджимири А., Пун Дж. Оптимизированный рой бинарных частиц делители мощности 2 × 2 в стандартной литейной кремниевой фотонной платформе.Opt Lett 2016; 41: 3868–71.10.1364 / OL.41.003868 Поиск в Google Scholar
[32] Xu K, Liu L, Wen X, et al. Встроенный фотонный делитель мощности с произвольным коэффициентом мощности. Opt Lett 2017; 42: 855–8.10.1364 / OL.42.00085528198882 Поиск в Google Scholar
[33] Yu Z, Cui H, Sun X. Генетически оптимизированные встроенные в кристалл широкополосные сверхкомпактные отражатели и полости Фабри-Перо. Photonics Res 2017; 5: B15–9.10.1364 / PRJ.5.000B15 Поиск в Google Scholar
[34] Шен Б., Полсон Р., Менон Р.Изгибы из метаматериала-волновода с эффективным радиусом изгиба <λ 0 /2. Opt Lett 2015; 40: 5750–3.10.1364 / OL.40.005750 Поиск в Google Scholar
[35] Шен Б., Полсон Р., Менон Р. Повышение плотности пассивных фотонно-интегральных схем с помощью нанофотонной маскировки. Nat Commun 2016; 7: 13126.10.1038 / ncomms1312627827391 Поиск в Google Scholar
[36] Власов Ю.А., Макнаб С.Дж. Потери в одномодовых ленточных волноводах кремний на изоляторе и изгибы. Opt Express 2004; 12: 1622–31.1947498810.1364 / OPEX.12.001622 Поиск в Google Scholar
[37] Ван Дж, Чжао С., Вэй Б. и др. Измерение интермодальных перекрестных помех изогнутого многомодового волновода. Appl Opt 2016; 55: 7619–23.10.1364 / AO.55.00761927661590 Поиск в Google Scholar
Дополнительные материалы
Онлайн-версия этой статьи предлагает дополнительные материалы (https://doi.org/10.1515/nanoph-2018-0078 ).
Получено: 27.06.2018
Исправлено: 27.08.2018
Принято: 07.09.2018
Опубликовано онлайн: 28.09.2018
© 2018 Xiankai Sun et al., опубликовано De Gruyter, Берлин / Бостон
Это произведение находится под лицензией Creative Commons Attribution-NonCommercial-NoDerivatives 4.0 License.
Руководство по температуре плавления металлов 2021
При нагревании металла он претерпевает различные изменения и достигает разных, но важных температурных точек. Температура плавления металла – одна из самых важных из этих температур.
Температура плавления важна из-за выхода из строя компонента (и связанных с ним опасностей), которые могут произойти, когда металл достигнет точки плавления.Обратите внимание, что некоторые поломки могут произойти до того, как металл достигнет температуры плавления. Например, трещины, вызванные ползучестью, могут произойти до того, как будет достигнута точка плавления.
Но когда металл начинает превращаться в жидкость, это может вызвать еще более катастрофические отказы, не говоря уже о неспособности служить своему назначению. Например, если металлический элемент печи начинает плавиться, печь не будет работать должным образом. Точно так же, если сопло в реактивном двигателе расплавится, отверстия будут закупориваться и иногда делать двигатель бесполезным.
Учитывая, что эти отказы могут иметь катастрофические последствия, важно провести тщательные исследования воздействия различных уровней температуры на металл. Такие исследования особенно бесполезны для металлов, используемых в высокотемпературных приложениях.
Температура плавления также используется для отличия чистых металлов от нечистых, поскольку последние имеют диапазон температур плавления вместо определенной температуры плавления.
Кроме того, важна температура плавления металла, потому что большинство металлов в расплавленном состоянии поддается формованию.Таким образом, металлы нагреваются до температуры плавления для множества производственных процессов. Например, плавка, литье и сварка плавлением могут выполняться только тогда, когда металл находится в жидком состоянии.
С этой целью важно знать температуру плавления рассматриваемого металла, чтобы подготовить соответствующие материалы и оборудование.
Например, при сварке выбранный сварочный пистолет / пруток должен выдерживать окружающее тепло расплавленного металла и электрическую дугу. Точно так же литейное оборудование должно иметь более высокую температуру плавления, чем у разливаемых металлов.
Принципы сварки | Что такое сварка? | Основы автоматизированной сварки
На этой странице в качестве примеров объясняются принципы сварки плавлением, сварки давлением и пайки / пайки посредством дуговой сварки, точечной контактной сварки и пайки.
Обязательно к прочтению всем, кто занимается сваркой! Это руководство включает в себя базовые знания о сварке, такие как типы и механизмы сварки, а также подробные знания, касающиеся автоматизации сварки и устранения неисправностей.Скачать Сварка плавлением – это наиболее распространенный метод сварки.
Сварка плавлением – это процесс сварки путем плавления одного или обоих из основного материала и присадочного материала.
Дуговая сварка – распространенный пример сварки плавлением. Дуговая сварка и лазерная сварка обычно используются для автоматической сварки с использованием манипуляторов. На сложных линиях сборки изделий, например, для автомобильных деталей, в зависимости от характеристик или условий процесса используются роботизированная сварка и сварка человеком.
- Дуговая сварка
Сварку давлением можно разделить на три типа: сварка трением использует свойство, при котором, когда материал деформируется под действием определенной силы, деформация сохраняется даже после снятия силы (пластичность). Сварка под давлением в газе соединяет два основных материала, приводя их в контакт под давлением и нагревая их газом. Точечная сварка сопротивлением соединяет два основных материала, удерживая их вместе и проводя электрический ток, чтобы нагреть их теплом, выделяемым электрическим сопротивлением.
Поскольку точечную сварку трением и сопротивлением можно автоматизировать без вмешательства человека, они широко используются в автоматах для сварки давлением на объектах FA (автоматизация производства).
- Точечная контактная сварка
- Сила давления
- Протекание электрического тока
- Электроды
- Сварные материалы
Пайка / пайка – это метод соединения основных материалов с использованием присадочного материала (паяльной пасты), который имеет более низкую температуру плавления (точку плавления).Присадочные материалы смешаны с флюсом, чтобы предотвратить плавление основного материала и обеспечить надлежащее соединение с основным материалом.
Присадочные материалы должны не только иметь температуру плавления ниже, чем у основного материала, но также обеспечивать высокое сродство для обеспечения атомной связи между расплавленным наполнителем и основными материалами.
В зависимости от соединяемых материалов используются различные присадочные материалы, такие как алюминий, серебро, фосфорная медь и латунь.Мягкие присадочные материалы с низкой температурой плавления, такие как цинк, свинец, олово и сплавы олово-свинец, обычно называют припоями.
Поскольку пайка и пайка могут легко соединять металлы, она широко используется в производстве товаров, изобразительного искусства и ремесел, а также в стоматологии. Пайка, которая использует проводимость присадочных материалов, используется для электронных схем и других устройств в различных отраслях промышленности, включая бытовую технику, авиацию, ядерную энергетику и химическое оборудование.
- Присадочный материал или припой
- Присоединенный раздел
Дом
.