Трансферные прессы для холодной штамповки | CFT
Характеристики пресса
Особенности пресса холодной штамповки AIDA CFT
- Стабильная точность продукта при постоянном качестве
- Поток материала более плавный благодаря непрерывной обработке и повышению прочности
- Уменьшение места для хранения полуфабрикатов
- Безопасность улучшается благодаря резкому сокращению времени автоматизации и настройки
- Простая замена матрицы благодаря подъемному оборудованию
- Повышенная точность изделия и увеличенный срок службы штампа являются результатом минимального наклона салазок, вызванного внецентренной нагрузкой
Запросить дополнительную информацию
Спецификации пресса
Спецификации пресса холодной штамповки CFT
903 Ton 6 | 400 Ton п |
800 тонн | 1000 тонн |
1 200 тонн | |
400 – 1 200 тонн |
CFT-4000, Технические характеристики пресса для холодной штамповки 400 тонн
МОДЕЛИ CFT-4000 | |||
Технические характеристики пресса | CFT- | Узел | |
Грузоподъемность | кН | 4000 | |
Тонны США | 440 | ||
Длина хода | мм | 250 | 3 дюймов.![]() |
ударов в минуту | ходов в минуту | 30~45 | |
Высота матрицы | мм | 600 | дюймов |
Область скольжения (LR x FB) | мм | 1200×750 | |
дюймов | 47,24×29,53 | ||
Площадь балки (LR x FB) | мм | 1200×909 9028 | 47,24×35,43 |
Номинальный тоннаж Пункт | мм | 7 | |
дюймов | 0,28 | ||
Выталкивающая способность | тонн | ) 20 | |
Количество ступеней | 3 |
CFT-6000, 600-тонный пресс для холодной штамповки Технические характеристики
МОДЕЛИ CFT-6000 | ||||
Технические характеристики пресса | Блок | CFT-6000 | ||
Мощность | кН | 6000 | ||
Тонн США | 0 60 70090 | |||
Длина хода | мм | 250 | ||
дюймов | 9,84 | |||
Число ударов в минуту | об/мин | 30~45 | ||
Высота штампа | мм 3 0 9030 | 6 028 | дюймов | 25,59 |
Площадь скольжения (LR x FB) | мм | 1200×750 | ||
дюймов | 47,24×29,58 | мм | 1200×900 | |
дюйм | 47,24×35,43 | |||
Номинальная грузоподъемность | мм | 7 | ||
028029 | ||||
Вместимость выталкивателя слоя | тонн | 30 (по 15 шт.![]() | ||
Количество ступеней | 3 |
2 0029 47,24×29,53
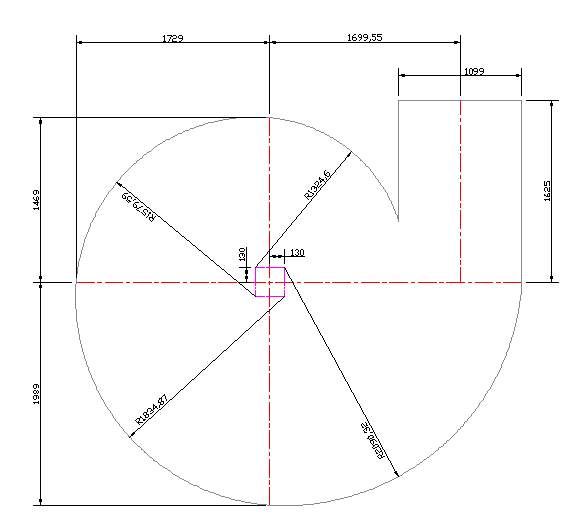
CFT-10000 МОДЕЛИ | |||
Технические характеристики пресса | Устройство | CFT-10000 | |
Мощность 9 кН 0 | 0 | 10000 | |
Тонны США | 1120 | ||
Длина хода | мм | 250 | |
дюймов | 9,84 | ||
Число ударов в минуту | об/мин | ||
Высота штампа | мм | 650 | |
дюймов | 25,59 | ||
Площадь скольжения (LR x FB) | 1 | 0 мм 1000||
дюймов | 59,06×39,37 | ||
Площадь надрессорной балки (LR x FB) | мм | 1500×1100 | |
дюймов | 59,06×43,31 | ||
Номинальная грузоподъемность 0 0 | 7 | ||
дюйма | 0,28 | ||
Вместимость заглушки слоя | тонн | 50 (по 25 шт.![]() | |
Количество ступеней | 3 | 74 |
CFT-12000, Технические характеристики пресса для холодной штамповки 1200 тонн
МОДЕЛИ CFT-12000 | ||
Технические характеристики пресса | Устройство | CFT-12000 |
Грузоподъемность | кН | 12000 |
Тонны США | 1350 | |
Длина хода | 250 | |
дюймов | 9,84 | |
Ходов в минуту | spm | 20~30 |
Высота матрицы | мм | 650 |
дюймов | 25,59 9008 | мм | 1500×1000 |
дюймов | 59,06×39,37 | |
Площадь балки (LR x FB) | 1 1 1мм | 00 |
дюймов | 59,06×43,31 | |
Номинальная грузоподъемность | мм | 7 |
дюймов | 0,28 | |
Выталкивающая способность | тонн | 0 90 |
Количество ступеней | 3 |
CFT, 400–1200 тонн Технические характеристики пресса для холодной штамповки
8 3 | 3 90 C0 MOD 028Технические характеристики пресса | Блок | CFT- 4000 | ЦФТ-6000 | ЦФТ-8000 | ЦФТ-10000 | ЦФТ-12000 | ||||
Грузоподъемность | кН 9002 0 | 6000 | 8000 | 10000 | 12000 | ||||||
Тонны США | 640 | 90 909 90 600 670 0301120 | 1350 | ||||||||
Длина хода | мм | 250 | 250 | 250 | 250 | 250 | |||||
дюймов | 9,84 | 9,84 | 9,84 | 9,0029 9029 9,84||||||||
ударов в минуту | spm | 30~45 | 30~45 | 25~35 | 25~35 | 20~30 | |||||
Высота матрицы | |||||||||||
600 | 650 | 650 | 650 | 650 | |||||||
дюймов | 23,62 | 25,59 | 25,59 | 25,59 | 25,59 | мм | 1200×750 | 1200×750 | 1200×750 | 1500×1000 | 1500×1000 |
дюймов | 47,24×29,53 | 47,24×29,53 | 30,547,24×29,53 029 59,06×39,37 | 59,06×39,37 | |||||||
Площадь балки (LR x FB) | мм | 1200×900 | 1200×900 | 1200×900 | 1500×1100 | 3 9000×1100 9002 029 дюймов | 47,24×35,43 | 47,24×35,43 | 47,24×35,43 | 59,06×43,31 | 59,06×43,31 |
Номинальная грузоподъемность | мм | 7 | 7 | 7 | 7 09029 397 9003 0033 | ||||||
дюймов | 0,28 | 0,28 | 0,28 | 0,28 | 0,28 | ||||||
Вместимость выбиваемого слоя | тонн | 20 (по 10 шт.![]() | 30 (по 15 шт.) | 40 (по 20 шт.) | 5 (5 00259 20 шт.) 9 60 (по 30 штук) | ||||||
Количество ступеней | 3 | 3 | 3 | 3 | 3 |
Часто задаваемые вопросы
- Что такое HOLP
- Механический пресс с щелевой рамой, тандемные линии
- Муфта и тормоз мокрого типа
- Конструкция рамы пресса с ЧПУ
- Ball Cup в сравнении с конструкцией наручных булавок
Мы предлагаем ответы на все типы распространенных вопросов, будь то технические вопросы или такие простые, как поиск возможностей для карьерного роста. Примеры некоторых вопросов: Что такое HOLP? Где находится ближайший центр AIDA? Как мы можем получить копию руководства для нашей печатной машины AIDA? Что такое реверсивный тоннаж? Посетите наш раздел часто задаваемых вопросов, чтобы найти ответы на свои вопросы.
Просмотреть Ч.А.В.
Технические документы AIDA-Tech
Белые книги AIDA-Tech содержат информацию по различным техническим темам, связанным со штамповочными прессами и операциями с прессами, по таким темам, как расстояние между соединениями, системы направляющих салазок, обратный тоннаж и т. д.
Посмотреть официальные документы AIDA-Tech
Отзывы пользователей
Пользователи пресс-службы AIDA описывают свои компании и бизнес-операции, а также то, как они использовали технологию AIDA для достижения своих производственных целей и расширения своих мощностей и возможностей. Приведены примеры из многих различных типов компаний, от мастерских до многоуровневых поставщиков и OEM-производителей. Читайте дальше, чтобы узнать, как лидеры во многих отраслях успешно сотрудничают с AIDA.
Просмотреть отзывы пользователей
Статьи по обработке металлов давлением
У нас имеется библиотека статей по обработке металлов давлением из различных отраслевых изданий, охватывающих широкий круг тем, связанных с штамповкой и штамповкой. Темы включают технологии печати, рыночные тенденции и области применения печати. Многие статьи, собранные здесь, были написаны или подготовлены сотрудниками AIDA.
View Metalforming Articles
Образовательные партнеры
AIDA не только инвестирует 5% годового дохода во внутренние исследования и разработки, но также активно ищет и участвует в исследованиях с образовательными учреждениями, такими как Центр точного формования (OSU), Institut für Umformtechnik, Edison Welding и другие.
Об образовательных партнерах
Исследования по применению и испытания штампов
Испытания штампов, проводимые AIDA, доказывают в режиме реального времени с вашими собственными штампами, как прессовая технология AIDA может иметь многочисленные преимущества для ваших штамповочных операций, включая увеличение производительности, более высокое качество частей, сокращение брака и сокращение технического обслуживания.
Исследования по применению и испытания штампов
Технология штамповочных прессов
На протяжении более 100 лет AIDA разрабатывает и производит специализированные изделия для обработки металлов давлением, такие как штамповочные прессы для металла и связанное с ними оборудование для автоматизации, такое как трансферы, роботы и питатели. Эксклюзивная технология штамповочных прессов AIDA используется во всем нашем широком диапазоне прессов мощностью от 30 до 4000 тонн.
Технология штамповочных прессов
Термины и глоссарий
Различные типы прессов могут выполнять различные функции в зависимости от инструмента. В этом разделе нашего веб-сайта объясняются типичные операции с прессами и другие термины, относящиеся к характеристикам и функциям прессов, а также основные характеристики и конструкции прессов.
Просмотреть термины и глоссарий
Глубокая вытяжка 101 | Macrodyne
Введение
Что такое глубокая вытяжка
Глубокая вытяжка — это процесс формовки металла для создания бесшовных деталей из листового металла, закрытых с одного конца и имеющих глубину, превышающую их радиус. Детали глубокой вытяжки приобретают свою форму за счет втягивания металла в полость, а не за счет растяжения или утончения на штампе, поэтому первоначальная толщина листа остается практически неизменной от начала до конца. Деталь с глубокой прорисовкой можно узнать по ее глубине и гладким закругленным углам. Примеры варьируются от банок, кастрюль, бочонков и баллонов со сжатым газом до проушин, раковин и панелей кузова автомобиля.
Простым деталям можно придать окончательную форму за один шаг, а сложные формы, в том числе особенно глубокие, могут потребовать нескольких шагов. Глубокая вытяжка обычно используется в сочетании с другими методами, такими как вырубка и прокалывание, для создания готового продукта. В некоторых случаях все шаги можно выполнить одним нажатием.
Преимущества глубокой вытяжки
Глубокая вытяжка существует уже много столетий, и на то есть веские причины. Процесс точен и воспроизводим со многими преимуществами:
- Без швов: Глубокая вытяжка создает однородные и цельные формы, уменьшая потенциальные слабые места в готовой детали.
- Прочность: В некоторых случаях упрочнение материала при деформации может повысить прочность деталей.
- Однородность: Детали глубокой вытяжки имеют высокую степень постоянства от начала производственного цикла до конца.
- Быстрое время цикла: Прессы, предназначенные для глубокой вытяжки, могут работать быстро, что делает этот способ очень эффективным для производства большого количества деталей.
- Сокращение технического труда: Глубокая вытяжка может быть автоматизирована, что значительно снижает трудозатраты.
- Низкие эксплуатационные расходы: Установки с глубокой вытяжкой требуют меньше текущего обслуживания, чем конкурирующие процессы.
- Быстрая сборка: Глубокая вытяжка позволяет создавать формы с закрытым концом, уменьшая или устраняя необходимость изготовления или сварки в качестве вторичных процессов.
Когда использовать глубокую вытяжку
Глубокая вытяжка лучше всего подходит для пластичных металлов. В общем, любой металл, который можно подвергнуть холодной прокатке в лист, должен иметь достаточную пластичность для глубокой вытяжки, но также может потребоваться учитывать такие свойства материала, как деформационное упрочнение или анизотропия. Подходящие материалы включают алюминиевые сплавы, латунь, медь и медные сплавы, титан, холоднокатаную низкоуглеродистую листовую сталь и некоторые нержавеющие стали.
Идеальные формы для глубокого рисования включают прямоугольники и осесимметричные структуры, такие как цилиндры или полусферы, но этот процесс может обрабатывать и более сложные формы.
В зависимости от изготавливаемой формы стоимость инструментов и настройки может сильно различаться. Для простых форм затраты могут быть ниже, чем для других процессов, но с увеличением сложности увеличивается стоимость. В некоторых случаях эти затраты могут быть компенсированы минимальным временем простоя глубокой вытяжки, низкими затратами на техническое обслуживание и сокращением технических трудозатрат в течение всего срока службы продукта. Факторы, которые могут увеличить сложность, включают:
- Наличие и расположение элементов детали
- Направление элементов
- Выступ элементов
- Размер и пропорции детали, включая толщину материала
Рассмотрение процесса
При проектировании детали глубокой вытяжки необходимо учитывать следующие соображения:
- Процесс
- Годовой объем производства
- Целевые объемы производства
- Целевые цены
- Форма и допуски готовой детали
- Ход формовки и количество этапов 9007 9007 8 Механические свойства
- Класс материала, термообработка
- Способность к вытягиванию: Коэффициент пластической деформации и деформационное упрочнение
- Анизотропия
- Размер заготовки, форма и толщина
- Прессы
- Многопозиционные или однопозиционные
- Передаточное или прогрессивное
- Одностороннего или двойного действия
6 - Возможности амортизации 0008
- Инструменты
- Возможность быстрой смены инструментов
- Плашки одинарного действия
- Матрицы двойного действия
- Составные матрицы
- Плашки прогрессивные
- Матрицы с несколькими механизмами переноса
Альтернативные процессы
В некоторых случаях для достижения аналогичных результатов можно использовать другие процессы.
Эти процессы включают:
- Гидроформинг: Усовершенствованный процесс формования листов и труб, в котором вместо фиксированного пуансона используется гидравлическое давление для получения геометрических форм, не подходящих для глубокой вытяжки, включая формы с подрезами или выпуклости.
- Прядение: Процесс, подходящий для некоторых осесимметричных деталей, при котором вращающаяся заготовка деформируется относительно концентрической вращающейся оправки. Стоимость инструмента обычно ниже, чем при глубокой вытяжке, но время цикла больше, и для настройки может потребоваться более квалифицированный программист станка.
- Изготовление: Для создания прототипов или небольших серий детали могут быть изготовлены из нескольких листов с помощью сварки или других способов соединения. В большинстве случаев изготовление подходит только тогда, когда объем производства недостаточно высок, чтобы оправдать стоимость специального инструмента.
Процесс глубокой вытяжки
Обзор
В своей основной форме глубокая вытяжка использует пуансон, чтобы вдавить заготовку из листового металла в полость штампа для получения высокой, гладкой детали с закрытыми концами из того же листа. толщина как заготовка. Чтобы металл мог течь, ввод матрицы и носик пуансона должны быть закруглены, диаметр пуансона должен находиться в допустимом диапазоне размеров для материала, а зазоры между пуансоном и матрицей должны быть тщательно отрегулированы. Слишком большой зазор, и деталь сморщится. Слишком мало, и деталь порвется. Многие установки для глубокой вытяжки добавляют держатель заготовки и прижимную пластину, чтобы свести к минимуму дефекты и обеспечить более глубокую вытяжку.
Настройка глубокой вытяжкиДержатель заготовок представляет собой плоскую или фигурную пластину с отверстием в центре для пуансона. Во время вытягивания держатель заготовки прикладывает давление, чтобы удерживать заготовку в контакте с поверхностью штампа.
Это давление помогает противодействовать склонности листового металла к сморщиванию из-за сжимающих кольцевых напряжений, которые накапливаются вокруг входного радиуса полости штампа. Требуемое усилие держателя заготовки зависит от толщины материала. Для толстых заготовок с отношением толщины к диаметру 0,03 или выше требуется незначительное усилие держателя заготовки или его отсутствие, в то время как для тонких заготовок может потребоваться до 30% усилия волочения.
В некоторых случаях необходимо также приложить амортизирующую силу, чтобы удерживать заготовку напротив носика пуансона, чтобы предотвратить истончение или разрыв. Во время вытягивания прижимная пластина давит на заготовку, удерживая ее в контакте с носиком пуансона. Это помогает противодействовать склонности листового металла к растяжению или разрыву из-за напряжения растяжения, когда заготовка оборачивается вокруг носика пуансона. Сила прижимной подушки обычно требует использования пресса двойного действия с возможностью подушки штампа.
Факторы успеха
Всестороннее изучение всех параметров, влияющих на глубокую вытяжку, выходит за рамки этой статьи. Вместо этого мы рассмотрим несколько ключевых факторов: зазор, коэффициент уменьшения вытяжки, силу пуансона и держателя заготовки, а также распространенные дефекты.
Зазор
Бездефектная глубокая вытяжка зависит от правильного зазора пуансона и матрицы. Слишком мало, и материал будет протыкаться или рваться вместо того, чтобы течь в полость штампа. Слишком много, и заготовка сморщится. При глубокой вытяжке значения зазора обычно составляют от 107 до 115 % толщины листа. Напротив, зазор при резке составляет от 3 до 8% толщины листа.
Коэффициент уменьшения вытяжки
Вдавливание заготовки в полость матрицы уменьшает диаметр заготовки и создает окружное сжимающее напряжение, поскольку заготовка деформируется по радиусу захода матрицы. Чем больше уменьшение диаметра, тем выше напряжение. Чем выше напряжение, тем больше сопротивление потоку.
Если сопротивление потоку превышает предел прочности бланка на растяжение, бланк растянется или порвется возле носика пуансона.
Чтобы избежать этой ситуации, процесс должен быть разработан таким образом, чтобы уменьшить диаметр заготовки не больше, чем позволяет материал. Этот предельный коэффициент вытяжки (LDR) варьируется в зависимости от материала, толщины и количества раз, когда деталь уже была вытянута. Коэффициенты вытяжки обычно включаются в спецификации сырья в диаграмме уменьшения вытяжки. Если обжатие при глубокой вытяжке превышает этот предел, деталь нужно будет вытягивать поэтапно.
Пример: расчет размера заготовки и количества вытяжек для цилиндрической чашки
Чтобы проиллюстрировать эту концепцию, мы проведем основные расчеты, чтобы определить, сколько вытяжек потребуется для изготовления безфланцевой цилиндрической чашки высотой 6 дюймов. диаметром 4 дюйма. Для чашки с оставшимся фланцем или более сложной формы потребуются более сложные расчеты, но основные концепции остаются прежними.
Сначала рассчитайте размер бланка. Поскольку во время глубокой вытяжки толщина листа практически не меняется, площадь поверхности готовой детали плюс остаточный материал фланца будет равна площади поверхности заготовки. В нашем примере цилиндрической чашки без фланца мы можем рассчитать требуемый размер заготовки по следующей формуле:
Где R b = радиус заготовки, R c = радиус чашки и H = высота чашки
диаметр 10,58″.
Затем рассчитайте уменьшение вытяжки, необходимое для достижения диаметра нашей окончательной детали. Для этого разделите диаметр детали на диаметр заготовки и вычтите это число из 1:
Где D c
Сокращение для чашки из нашего примера составляет около 62%. Для простоты расчетов предположим, что LDR нашего бланка равен 2,0 для первого розыгрыша, 1,5 для второго и 1,25 для третьего.
Это означает снижение на 50% для первого розыгрыша, 30% для второго и 20% для третьего. Поскольку чашка требует более чем 50% полного восстановления, процесс потребует более одной стадии.
На первом этапе диаметр чашки может быть уменьшен на 50 %, в результате чего диаметр промежуточной части составит 5,29.″. На втором этапе диаметр чашки может быть уменьшен до 30%. Доведение до этого предела приведет к диаметру детали 3,70 дюйма. Этот диаметр меньше указанных 4″, поэтому чашку можно смело вытягивать в 2 этапа.
Пресс глубокой вытяжки Macrodyne 100-150 тоннСила пуансона и сила держателя заготовки должны рассчитываться отдельно при определении и настройке пресса. Сила пробивки изменяется на протяжении всей операции, но, вероятно, достигает своего максимума примерно на 1/3 рабочего хода. Как правило, усилие держателя заготовки составляет не более 30–40 % от максимального усилия пуансона. В держатель заготовок можно добавить валики для вытягивания, чтобы уменьшить необходимое усилие или отрегулировать поток материала к определенным областям матрицы.
Факторы, влияющие на расчет усилия, включают способность материала вытягиваться, форму и толщину заготовки, форму пуансона и штампа, форму поверхности держателя заготовки, радиусы углов и величину обжатия. При разработке процесса эти факторы необходимо учитывать при определении желаемого усилия и производительности. В большинстве случаев пресс двойного действия лучше всего подходит для глубокой вытяжки. Калькулятор силы глубокой вытяжки может быть полезен при расчете необходимой силы и других параметров процесса.
Причины и предотвращение частых дефектов
При глубокой вытяжке многих дефектов можно избежать, тщательно спроектировав деталь. Стратегии проектирования включают:
- Уменьшение сложности и асимметрии
- Планирование геометрии заготовки для минимизации избыточного материала
- Корректировка ориентации зерна для минимизации напряжений в асимметричных конструкциях
- Использование САПР и моделирования методом конечных элементов для оптимизации конструкции последовательности и оснастки перед изготовлением инструментов .
Моделирование может значительно сэкономить трудозатраты и затраты на инструменты, избегая дорогостоящих изменений процесса методом проб и ошибок.
Успешная глубокая вытяжка требует знания принципов пластичности и текучести металла. Более толстые материалы лучше переносят глубокую вытяжку, чем тонкие, из-за их объема и способности растягиваться на большие расстояния; однако слишком большие заготовки могут ограничивать поток металла. Большинство дефектов глубокой вытяжки являются результатом одного или нескольких из следующих факторов:
- Неправильное распределение усилия
- Отсутствие учета свойств материала заготовки
- Неправильная степень вытяжки
- Неправильное управление трением
Ниже приведены краткие описания распространенных дефектов и способы их устранения.
Зазубренность
Волнистый верхний край на нарисованной детали, зазубренность является побочным эффектом использования анизотропных заготовок.
Если лист прочнее в одном плоскостном направлении, чем в других, предпочтительный направленный поток будет формировать выступы в верхней части детали. Наиболее распространенное решение — оставить достаточно лишнего материала на нарисованной детали, чтобы его можно было обрезать. Дополнительная обработка материала также может уменьшить анизотропию при увеличении стоимости.
Морщины
Ряд радиальных гребней на фланце детали, морщины обычно возникают из-за непостоянного течения металла. Морщины могут выглядеть как вертикальные дефекты, если гребни втянуты в матрицу. Надлежащее управление радиальным напряжением растяжения и окружным сжимающим напряжением может уменьшить или устранить морщины. В некоторых случаях может потребоваться несколько сокращений. Сморщивания можно избежать, используя держатели заготовок, изменяя радиусы пуансона и штампа, регулируя размер или форму заготовки и позиционируя заготовку на чертеже. При использовании держателя бланка недостаточное усилие держателя бланка может привести к образованию складок.
При соотношении толщин 0,5 % и менее держатели заготовок могут оказаться неэффективными.
Использование натяжных валиков
Натяжных валиков может помочь управлять потоком металла без необходимости чрезмерного усилия держателя заготовки. Приподнятый контур, окружающий полость штампа, вытяжной валик заставляет заготовку изгибаться и разгибаться по мере приближения к полости, регулируя поток материала без необходимости дополнительного усилия держателя заготовки.
Утончение и разрыв
Если не учитывать напряжения в вертикальной стенке детали, заготовка может истончиться или порваться вблизи передней кромки пуансона. Утончение и разрыв обычно являются результатом превышения предельного коэффициента вытяжки материала, слишком большого усилия держателя заготовки, недостаточного зазора между пуансоном и матрицей, неправильной формы заготовки, плохой смазки или дефектов инструмента, таких как царапины на поверхности или ямки, которые увеличивают трение.
Если в углах возникают разрывы, это может указывать на проблему с геометрией заготовки или слишком маленькими радиусами.
Управление трением: смазка и обработка поверхности
Трение между заготовкой и поверхностями оснастки может иметь большое влияние на качество готовой детали. Снижение коэффициента трения может способствовать текучести материала, улучшению распределения деформации материала и увеличению срока службы инструмента. Чтобы уменьшить трение, поверхности штампа и держателя заготовки должны быть отшлифованы и притерты, чтобы обеспечить их максимально гладкую поверхность, а перед волочением следует нанести смазку на обе стороны заготовки. Обычные смазочные материалы для глубокой вытяжки включают масло, мыло, эмульсии и воски. При использовании смазки может потребоваться увеличение усилия держателя заготовки, чтобы учесть повышенный поток металла. Убедитесь, что используемая смазка соответствует температуре и давлению технологического процесса.
Конфигурация пресса
Чтобы сконфигурировать пресс для производства детали глубокой вытяжки, важно начать с производственного процесса этой детали.
В идеальных условиях процесс будет основываться на типе материала, спецификациях деталей, объеме производства, скорости производства и целевых ценах. Затем эти факторы оказывают непосредственное влияние на процесс формирования детали, что, в свою очередь, влияет на характеристики пресса (прессов) и требуемой оснастки.
Следующие факторы помогают определить процесс формирования детали:
- Количество этапов: В зависимости от размера детали, материала и сложности может потребоваться многократное обжатие.
- Связанные процессы : Некоторые детали глубокой вытяжки требуют других процессов, таких как вырубка и прокалывание, для создания готовой детали.
- Способ переноса: В процессе формовки детали необходимо перемещать с одного этапа на другой. Это может быть выполнено в одном прессе с использованием прогрессивного штампа или с несколькими штампами. В прогрессивной матрице промежуточные детали остаются прикрепленными к каркасу отходов и перемещаются вместе с листом.
При использовании нескольких штампов каждая отдельная деталь должна перемещаться от станции к станции с помощью отдельного механизма перемещения. При использовании нескольких прессов отдельные детали должны перемещаться от пресса к прессу.
Прогрессию можно реализовать разными способами с разными преимуществами и недостатками. Лучший выбор обеспечивает баланс между экономическими факторами и качеством. Дополнительные соображения включают:
- Быстросменный инструмент: Для прессов, которые будут использоваться для нескольких продуктов, быстросменный инструмент может сократить дорогостоящее время простоя при переходе с одной линейки продуктов на другую. С другой стороны, прессе, предназначенной для одного продукта, эта функция может не понадобиться.
- Усовершенствованные функции : Особо сложные детали могут быть улучшены благодаря таким функциям, как многоточечные держатели заготовок или высокоточная многоточечная амортизация.
Основные параметры
Размер станины
Станина пресса должна вмещать в себя самый большой предполагаемый набор инструментов. Для прямоугольных или сложных форм заготовок ориентация детали внутри станины будет определять общие размеры станины. Если прогрессивный штамп будет использоваться для выполнения нескольких одновременных операций, станина должна быть достаточно большой, чтобы вместить весь набор штампов с учетом переноса. Грубая оценка размера кровати может быть рассчитана на основе размера бланка. Поскольку толщина материала детали глубокой вытяжки остается неизменной от начала до конца, площадь поверхности заготовки будет равна площади поверхности детали плюс любой оставшийся материал фланца. Это отношение площади поверхности можно использовать для определения размера заготовки. См. «Расчет размера заготовки и уменьшения вытяжки» для основного примера использования цилиндрической чашки без бортов.
Тоннаж и скорость
Для глубокой вытяжки необходимо управлять скоростью штамповки, чтобы обеспечить правильное течение материала заготовки во время вытяжки. Точно так же усилия, прилагаемые к пуансону, держателю бланка и подушке, также должны находиться в пределах допустимого диапазона бланка. В противном случае материал может истончиться, порваться или сморщиться. Гидравлические прессы преуспевают в этой области благодаря постоянной скорости ползуна.
Скорость протяжки сильно различается в зависимости от материала: от 18 дюймов/мин до 200 дюймов/мин. Скорость закрытия и зачистки может быть намного выше. Тоннажи также значительно различаются и напрямую связаны со скоростью пресса, размером заготовки, формой и материалом. В большинстве случаев потребуются отдельные усилия для пуансона, держателя заготовки и подушки.
Скорости глубокой вытяжки для обычных материалов 29 АлюминийМатериал Скорость (дюйм/мин) 150-175 Латунь 175- 200 Медь 125-150 Сталь 18-50 Нерж. 0033
Ход и дневной свет
Для фланцевых деталей, требующих зачистки, между полностью втянутым пуансоном и поверхностью штампа должно быть достаточно дневного света, чтобы можно было снять готовую деталь с пресса. На практике это означает дневной свет, вдвое превышающий ход пресса. Если пресс будет использоваться для производства более чем одной детали, ход и дневной свет должны соответствовать ожидаемому размеру инструмента. Если детали можно полностью втянуть в/через матрицу, то ход можно сократить, чтобы можно было извлечь из-под матрицы после завершения вытягивания. При многоступенчатом прессе необходимо учитывать все этапы. В некоторых случаях для промежуточной формы детали может потребоваться больше дневного света, чем для готовой детали.
Расширенные возможности
Многоточечные держатели и прокладки для заготовок
Детали глубокой вытяжки часто требуют использования держателя заготовок для предотвращения образования складок и прокладок для предотвращения растяжения, утончения и разрывов.
В зависимости от формы или сложности детали может потребоваться приложение различных усилий к разным участкам заготовки. В этом сценарии пресс может быть оснащен держателем заготовок с несколькими заостренными концами и/или системой демпфирования, в которой используется несколько гидравлических контуров, каждый со своим собственным управлением, для приложения дифференциального давления к держателю бланков и/или амортизатору. Например, для некоторых прямоугольных деталей требуются значительно разные усилия на их углах и на их сторонах. Это возможно благодаря многоцелевым держателям и/или подушкам. Для дальнейшего повышения точности обработки деталей сложной формы к многоточечным системам можно добавить управление с обратной связью.
Варианты амортизации
Системы амортизации обычно имеют регулируемые штифты для размещения нескольких инструментов. Пресс с подушкой может работать как с активированной подушкой, так и без нее. Автономные ящики для подушек также доступны в качестве модернизации для расширения возможностей существующего пресса.