станок | это… Что такое станок?
ТолкованиеПеревод
- станок
- стано́к
-
технологическая машина, предназначенная для обработки материалов с целью получения заготовок или готовых изделий либо для получения новых материалов из сырья. Станки являются основным видом оборудования механических цехов машиностроительных и приборостроительных заводов, деревообрабатывающих и камнерезных предприятий, ткацких и обувных фабрик, металлообрабатывающих и ремонтных мастерских и т. п.
Наибольшим разнообразием конструкций отличаются металлорежущие станки. К ним относятся токарные, фрезерные, сверлильные, строгальные, долбёжные, шлифовальные станки, название которых соответствует технологическим операциям, т. е. производимым на них видам обработки. В каждую из этих групп входит по несколько типов станков, отличающихся конструктивным исполнением, видом привода, возможностями осуществлять ту или иную операцию.
Многие деревообрабатывающие станки по конструкции и назначению аналогичны некоторым металлорежущим станкам (сверлильные, токарные, копировально-фрезерные, шлифовальные и др.
). Но есть и специализированные, к которым относятся лесопильный станок (лесопильная рама), фуговальный, рубильный, лобзиковый, лущильный и другие станки, предназначенные для выполнения определённых операций.
Ткацкий станок – особый вид станка, на котором из сырья получают новый материал, вырабатывают ткань. Для этого используют автоматические станки, обычно работающие в едином технологическом процессе и объединённые в линию, и механические с ручной сменой сырья (паковок) для прокладки поперечных нитей тканей (уткá). Продольные нити (основа) сматываются с большой катушки и проходят через отверстия особого прибора, который называют нитенаблюдателем, т. к. при обрыве нити прибор автоматически останавливает станок. Ткацкий станок – одно из самых древних орудий труда человека. Механический ткацкий станок изобретён в Великобритании в кон. 18 в. Э. Картрайтом.
Энциклопедия «Техника». — М.: Росмэн. 2006.
.
Поможем сделать НИР
Синонимы:
автомат, беннер, бобинорезка, бостонка, брусовал, брусорезка, бурстанок, бутара, вайма, вашгерд, велостанок, вибростанок, герт, девушка, жопа, зад, задница, зигмашина, кийстон, кровать, кромы, кросно, кросны, лафет, министанок, мольберт, мультстанок, наждак, нождак, опора, основание, пиломашина, пилоштамп, плавникорезка, подставка, полуавтомат, поселок, рельсорез, самоточка, сериплан, сновалка, спецстанок, станина, станок-автомат, станочек, станция, стойло, триммер, уставка, шепинг, электростанок
- стандартизация
- станок-качалка
Полезное
Что такое станок с ЧПУ: виды, характеристики ✭ «ЧПУ24»
В современном мире автоматизация производства является не элементом роскоши, а осознанной необходимостью. Хотя в нашей стране стоимость человеческого труда достаточно низкая и нет предпосылок к увеличению ее стоимости в ближней и среднесрочной перспективе, ЧПУ станки даже в этой ситуации выигрывают у человека.
Станок не уходит в отпуск и декрет, ему не нужны выходные, он не опаздывает и не прогуливает, его работоспособность не зависит от настроения и вчерашней вечеринки с друзьями. Каждое предприятие заинтересовано во внедрении высокоэффективных технологий. Поэтому подбирает надежное, функциональное оборудование для выполнения таких работ как фрезерные, токарные, раскрой металла, дерева, фанеры с помощью лазера, нанесению маркировки и гравировки на изделия и многие другие.
В этой статье мы расскажем, про ЧПУ станки, их виды, устройство конструкции, принцип работы. Предоставим основную информацию, чтобы вы могли решить, нужна вам такая техника или нет.
Станки с ЧПУ: что это такое?
Давайте разберемся, что такое ЧПУ станок, и какая расшифровка аббревиатуры. ЧПУ это числовое программное управление. Представляет собой компьютеризированную систему, которая направлена на проведение расчетов и автоматизацию технических операций. Контроль выполняется специальными командами ‒ G-кодами. Систему можно запрограммировать с внешних носителей или подключить к компьютеру.
Состоит из таких элементов:
- пульт оператора;
- дисплей;
- контроллер;
- ПЗУ ‒ память долговременного хранения;
- ОЗУ ‒ временное хранение программ, используемых в настоящий момент.
Многих интересует вопрос: что делает ЧПУ станок? Он относится к самому востребованному оборудованию основных сфер промышленности. Считается дорогой, инновационной техникой. На нем обрабатывают металл, обтачивают сложные заготовки, изготавливают корпусную мебель, пластиковые игрушки, сувениры. Устройство позволяет с высокой точностью выполнить даже самые сложные работы. Изготавливает детали, к которым выдвигаются самые строгие требования касаемо точности размеров и допусков. Компьютеризация и автоматизация исключает ошибки, присущие человеческому фактору. Если правильно пользоваться устройством, риск бракованной продукции снизится к нулю.
Возьмем для примера фрезерный станок и изготовление панно.
Для того чтобы изготовить такое панно, раньше человек должен был обладать художественным видением, чтобы вручную или используя полуавтоматический инструмент отсечь от заготовки все лишнее. Если нужно было изготовить таких штук 10, то это превращалось из творческого процесса в некую рутину для мастера. Все изделия были разными и непохожими друг на друга. Человек мог заболеть или потерять интерес. Могла дрогнуть рука мастера и т.д. Сегодня, при наличии 3D модели такого панно, любой человек, даже не обладающий художественным видением с помощью ЧПУ станка способен изготавливать такие изделия. Творчество все равно присутствует т.к. создание 3D модели — это творческий процесс, доступный немногим и неважно, что на выходе у вас будет физическая модель, воплощенная дереве или на компьютере. После того как мы выбрали модель для изготовления, нам нужно «рассказать» станку что необходимо делать – составить управляющую программу (УП). В ней мы сообщаем станку, какого размера заготовка, каким инструментом мы это делаем, с какой скоростью, где начать и где закончить и т.
Виды станков
Оборудование делится на несколько групп, которые отличаются способностью выполняемых операций. Виды станков с ЧПУ по типу воздействия на обрабатываемый материал:
- фрезерные, сверлильные, расточные ‒ используют для резки заготовок, раскроя листов, загибания углов, сверления отверстий;
- токарные ‒ для обработки наружной и внутренней поверхности, выполняют нарезку резьбы, позволяют создавать любые контуры.
- зубообрабатывающие ‒ позволяют создать необходимую геометрию шестеренок и других деталей;
- шлифовальные ‒ зачищают и выравнивают поверхность на конечном этапе обработки;
- многоцелевые ‒ сочетают в себе возможность выполнения всех видов работ;
- электромеханические ‒ включают в себя плазменные, лазерные, электрохимические, электроэрозионные агрегаты.
Фрезерный станок применяют на производстве, где важно соблюдать параметры точности. Бывает с вертикальным и горизонтальным расположением шпинделя. Работает с высокой скоростью. Есть габаритные и компактные модели.
Лазерный станок — это общее название станков, обработка материала на которых производится при помощи лазерного излучения (луча). Но источник этого излучения и соответственно его характеристики различаются. Например, источником луча может быть лазерная трубка с закаченной смесью различных газов основной из которых СО2. Это линейка станков применяется для обработки широкого спектра материалов, реже металла.
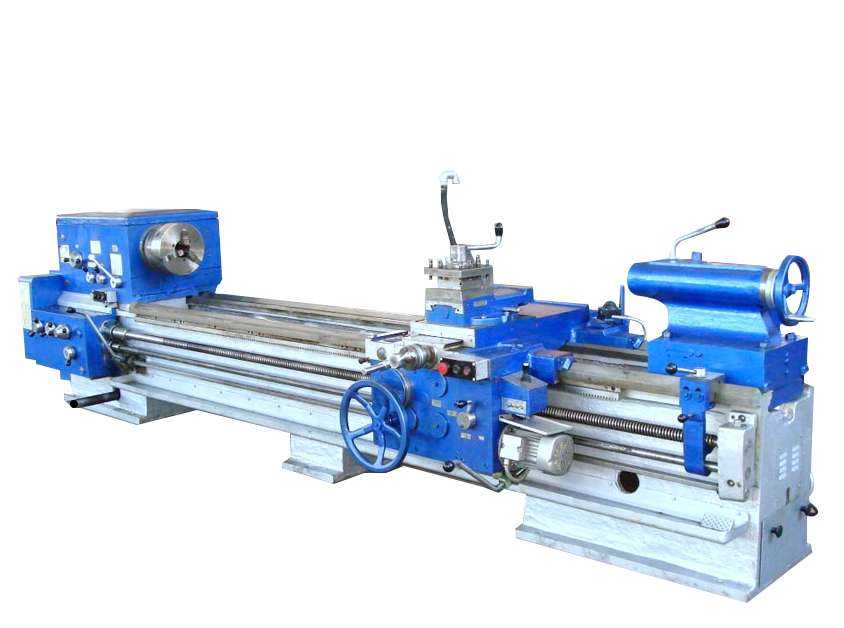
Плазменный предназначен для точного и качественного раскроя листов из металла любой толщины.
Основные характеристики
Те, кто знают, что такое ЧПУ в современных станках, уже давно оценили его преимущества. Оборудование значительно увеличивает производительность труда. Удешевляет себестоимость товаров. Один ЧПУ станок заменяет до 6 единиц обычных. Может бесперебойно работать многие годы, отменно выполняя заданные команды. Для обработки разных деталей нужно просто заменить программу. Устройство позволяет быстро изготовить спроектированное на компьютере изделие. Отличается надежностью, разнообразием функций, гибкостью настроек, точностью обработки. Благодаря данным характеристикам станки ЧПУ широко применяются на производствах, которые стремятся увеличить объемы выпускаемой продукции.
станок | Описание, история, типы и факты
сверлильный станок
Посмотреть все СМИ
- Ключевые сотрудники:
- Иоганн Георг Бодмер Сэр Джозеф Уитворт, баронет Джеймс Нэсмит Генри Модсли Джозеф Брама
- Похожие темы:
- шлифовальный станок расширитель токарный станок сверлильный станок буровая машина
Просмотреть весь соответствующий контент →
Резюме
Прочтите краткий обзор этой темы
станок , любая стационарная машина с механическим приводом, которая используется для формовки деталей из металла или других материалов. Формование осуществляется четырьмя основными способами: (1) путем срезания лишнего материала в виде стружки с детали; (2) путем разрезания материала; (3) сжимая металлические детали до нужной формы; и (4) путем воздействия на материал электричеством, ультразвуком или коррозионно-активными химическими веществами. Четвертая категория охватывает современные станки и процессы для обработки сверхтвердых металлов, не поддающихся обработке старыми методами.
Станки, формирующие детали путем удаления металлической стружки с заготовки, включают токарные, строгальные и строгальные станки, сверлильные станки, фрезерные станки, шлифовальные станки и электропилы. Холодная штамповка металлических деталей (кухонная утварь, кузова автомобилей и т. п.) производится на штамповочных прессах, горячая штамповка раскалённых заготовок в штампы соответствующей формы — на ковочных прессах.
Современные станки для резки или формовки деталей с допусками плюс или минус одна десятитысячная дюйма (0,0025 миллиметра). В особых случаях прецизионные притирочные станки могут изготавливать детали с точностью плюс-минус две миллионные доли дюйма (0,00005 миллиметра). Из-за требований к точным размерам деталей и больших сил резания, воздействующих на режущий инструмент, станки сочетают в себе вес и жесткость с деликатной точностью.
История
До промышленной революции 18 века ручные инструменты использовались для резки и формовки материалов для производства таких товаров, как кухонная утварь, фургоны, корабли, мебель и другие продукты. После появления паровой машины материальные блага производились машинами с механическим приводом, которые можно было изготовить только с помощью станков. Станки (способные производить детали с точными размерами в больших количествах), а также приспособления и приспособления (для удержания работы и направления инструмента) были незаменимыми новшествами, которые сделали массовое производство и взаимозаменяемые детали реальными в 19 веке.век.
Самые ранние паровые двигатели страдали от неточности ранних станков, а большие литые цилиндры двигателей часто неточно растачивались машинами, приводимыми в действие водяными колесами и изначально предназначенными для расточки пушек. В течение 50 лет после появления первых паровых двигателей были спроектированы и разработаны основные станки со всеми основными характеристиками, необходимыми для обработки деталей из тяжелых металлов. Некоторые из них были адаптацией более ранних деревообрабатывающих станков; токарный станок по металлу, созданный на основе токарных станков по дереву, использовавшихся во Франции еще в 16 веке. В 1775 году Джон Уилкинсон из Англии построил прецизионный станок для расточки цилиндров двигателя. В 1797 Генри Модслей, тоже англичанин и один из величайших гениев-изобретателей своего времени, спроектировал и построил токарно-винторезный станок. Отличительной чертой токарного станка Модслея был ходовой винт для привода каретки. Приведенный к шпинделю токарного станка ходовой винт продвигал инструмент с постоянной скоростью и гарантировал точную резьбу. К 1800 году Модслей оснастил свой токарный станок 28 сменными шестернями, которые нарезали резьбу с различным шагом, регулируя отношение скорости ходового винта к скорости вращения шпинделя.
Формирователь был изобретен Джеймсом Нэсмитом, который работал в магазине Генри Модслея в Лондоне. В станке Нэсмита заготовка могла быть закреплена горизонтально на столе и обработана фрезой с возвратно-поступательным движением для строгания небольших поверхностей, вырезания шпоночных пазов или обработки других прямолинейных поверхностей. Несколько лет спустя, в 1839 году, Несмит изобрел паровой молот для ковки тяжелых изделий. Другой ученик Модслея, Джозеф Уитворт, изобрел или усовершенствовал множество станков и стал доминировать в этой области; на Международной выставке 1862 г. экспонаты его фирмы заняли четверть всего места, посвященного станкам.
Оформите подписку Britannica Premium и получите доступ к эксклюзивному контенту. Подпишитесь сейчас
Великобритания пыталась сохранить лидерство в развитии станкостроения, запретив экспорт, но эта попытка была заранее обречена из-за промышленного развития в других странах. Британские инструменты экспортировались в континентальную Европу и США, несмотря на запрет, а новые инструменты разрабатывались за пределами Великобритании. Примечательным среди них был фрезерный станок, изобретенный Эли Уитни, произведенный в Соединенных Штатах в 1818 году и использовавшийся Симеоном Нортом для производства огнестрельного оружия. Первый полностью универсальный фрезерный станок был построен в 1862 году Дж. Р. Брауном из США и использовался для нарезания спиральных канавок в спиральных сверлах. Револьверный токарный станок, также разработанный в США в середине 19 века.20-го века, некоторые операции, такие как изготовление винтов, были полностью автоматизированы, и это предвещало важные события 20-го века. Различные зуборезные станки достигли своего полного развития в 1896 году, когда американец Ф. У. Феллоуз сконструировал зубодолбежный станок, который мог быстро обработать почти любой тип зубчатого колеса.
Производство искусственных абразивов в конце 19 века открыло новую область станков – шлифовальные станки. К.Х. Нортон из Массачусетса блестяще продемонстрировал потенциал шлифовального станка, создав такой, который мог шлифовать коленчатый вал автомобиля за 15 минут, на что ранее требовалось пять часов.
К концу 19 века в обработке и обработке металлов произошла полная революция, которая создала основу для массового производства и индустриального общества. 20-й век стал свидетелем внедрения многочисленных усовершенствований станков, таких как многоточечные фрезы для фрезерных станков, развитие автоматизированных операций, управляемых электронными и жидкостными системами управления, и нетрадиционных методов, таких как электрохимическая и ультразвуковая обработка. Тем не менее, даже сегодня основные станки остаются в значительной степени наследием 19-го века.век.
Характеристики станка
Все станки должны быть оснащены приспособлениями для закрепления заготовки и инструмента и средствами для точного контроля глубины резания. Относительное движение между режущей кромкой инструмента и заготовкой называется скоростью резания; скорость, с которой несрезанный материал входит в контакт с инструментом, называется движением подачи. Должны быть предусмотрены средства для изменения обоих.
Поскольку перегретый инструмент может потерять режущую способность, необходимо контролировать температуру. Количество выделяемого тепла зависит от силы сдвига и скорости резания. Поскольку усилие сдвига зависит от разрезаемого материала, а материал инструмента отличается устойчивостью к высоким температурам, оптимальная скорость резания зависит как от разрезаемого материала, так и от материала режущего инструмента. На него также влияет жесткость станка, форма заготовки и глубина реза.
Металлорежущие инструменты классифицируются как однолезвийные и многолезвийные. Одноточечный режущий инструмент можно использовать для увеличения размера отверстий или растачивания. Токарно-расточные работы выполняются на токарных и расточных станках. Многолезвийные режущие инструменты имеют две или более режущие кромки и включают фрезы, сверла и протяжки.
Существует два типа операции; либо инструмент движется по прямой к неподвижной заготовке, как на фрезерном станке, либо заготовка движется к неподвижному инструменту, как на рубанке. Для предотвращения трения поверхности инструмента под режущей кромкой о заготовку должны быть предусмотрены задние или задние углы. На режущих инструментах часто предусмотрены передние углы, чтобы вызвать расклинивание при образовании стружки и уменьшить трение и нагрев.
станок | Описание, история, типы и факты
сверлильный станок
Посмотреть все СМИ
- Ключевые сотрудники:
- Иоганн Георг Бодмер Сэр Джозеф Уитворт, баронет Джеймс Нэсмит Генри Модсли Джозеф Брама
- Похожие темы:
- шлифовальный станок расширитель токарный станок сверлильный станок буровая машина
Просмотреть весь соответствующий контент →
Резюме
Прочтите краткий обзор этой темы
станок , любая стационарная машина с механическим приводом, которая используется для формовки деталей из металла или других материалов. Формование осуществляется четырьмя основными способами: (1) путем срезания лишнего материала в виде стружки с детали; (2) путем разрезания материала; (3) сжимая металлические детали до нужной формы; и (4) путем воздействия на материал электричеством, ультразвуком или коррозионно-активными химическими веществами. Четвертая категория охватывает современные станки и процессы для обработки сверхтвердых металлов, не поддающихся обработке старыми методами.
Станки, формирующие детали путем удаления металлической стружки с заготовки, включают токарные, строгальные и строгальные станки, сверлильные станки, фрезерные станки, шлифовальные станки и электропилы. Холодная штамповка металлических деталей (кухонная утварь, кузова автомобилей и т. п.) производится на штамповочных прессах, горячая штамповка раскалённых заготовок в штампы соответствующей формы — на ковочных прессах.
Современные станки для резки или формовки деталей с допусками плюс или минус одна десятитысячная дюйма (0,0025 миллиметра). В особых случаях прецизионные притирочные станки могут изготавливать детали с точностью плюс-минус две миллионные доли дюйма (0,00005 миллиметра). Из-за требований к точным размерам деталей и больших сил резания, воздействующих на режущий инструмент, станки сочетают в себе вес и жесткость с деликатной точностью.
История
До промышленной революции 18 века ручные инструменты использовались для резки и формовки материалов для производства таких товаров, как кухонная утварь, фургоны, корабли, мебель и другие продукты. После появления паровой машины материальные блага производились машинами с механическим приводом, которые можно было изготовить только с помощью станков. Станки (способные производить детали с точными размерами в больших количествах), а также приспособления и приспособления (для удержания работы и направления инструмента) были незаменимыми новшествами, которые сделали массовое производство и взаимозаменяемые детали реальными в 19 веке.век.
Самые ранние паровые двигатели страдали от неточности ранних станков, а большие литые цилиндры двигателей часто неточно растачивались машинами, приводимыми в действие водяными колесами и изначально предназначенными для расточки пушек. В течение 50 лет после появления первых паровых двигателей были спроектированы и разработаны основные станки со всеми основными характеристиками, необходимыми для обработки деталей из тяжелых металлов. Некоторые из них были адаптацией более ранних деревообрабатывающих станков; токарный станок по металлу, созданный на основе токарных станков по дереву, использовавшихся во Франции еще в 16 веке. В 1775 году Джон Уилкинсон из Англии построил прецизионный станок для расточки цилиндров двигателя. В 1797 Генри Модслей, тоже англичанин и один из величайших гениев-изобретателей своего времени, спроектировал и построил токарно-винторезный станок. Отличительной чертой токарного станка Модслея был ходовой винт для привода каретки. Приведенный к шпинделю токарного станка ходовой винт продвигал инструмент с постоянной скоростью и гарантировал точную резьбу. К 1800 году Модслей оснастил свой токарный станок 28 сменными шестернями, которые нарезали резьбу с различным шагом, регулируя отношение скорости ходового винта к скорости вращения шпинделя.
Формирователь был изобретен Джеймсом Нэсмитом, который работал в магазине Генри Модслея в Лондоне. В станке Нэсмита заготовка могла быть закреплена горизонтально на столе и обработана фрезой с возвратно-поступательным движением для строгания небольших поверхностей, вырезания шпоночных пазов или обработки других прямолинейных поверхностей. Несколько лет спустя, в 1839 году, Несмит изобрел паровой молот для ковки тяжелых изделий. Другой ученик Модслея, Джозеф Уитворт, изобрел или усовершенствовал множество станков и стал доминировать в этой области; на Международной выставке 1862 г. экспонаты его фирмы заняли четверть всего места, посвященного станкам.
Оформите подписку Britannica Premium и получите доступ к эксклюзивному контенту. Подпишитесь сейчас
Великобритания пыталась сохранить лидерство в развитии станкостроения, запретив экспорт, но эта попытка была заранее обречена из-за промышленного развития в других странах. Британские инструменты экспортировались в континентальную Европу и США, несмотря на запрет, а новые инструменты разрабатывались за пределами Великобритании. Примечательным среди них был фрезерный станок, изобретенный Эли Уитни, произведенный в Соединенных Штатах в 1818 году и использовавшийся Симеоном Нортом для производства огнестрельного оружия. Первый полностью универсальный фрезерный станок был построен в 1862 году Дж. Р. Брауном из США и использовался для нарезания спиральных канавок в спиральных сверлах. Револьверный токарный станок, также разработанный в США в середине 19 века.20-го века, некоторые операции, такие как изготовление винтов, были полностью автоматизированы, и это предвещало важные события 20-го века. Различные зуборезные станки достигли своего полного развития в 1896 году, когда американец Ф. У. Феллоуз сконструировал зубодолбежный станок, который мог быстро обработать почти любой тип зубчатого колеса.
Производство искусственных абразивов в конце 19 века открыло новую область станков – шлифовальные станки. К.Х. Нортон из Массачусетса блестяще продемонстрировал потенциал шлифовального станка, создав такой, который мог шлифовать коленчатый вал автомобиля за 15 минут, на что ранее требовалось пять часов.
К концу 19 века в обработке и обработке металлов произошла полная революция, которая создала основу для массового производства и индустриального общества. 20-й век стал свидетелем внедрения многочисленных усовершенствований станков, таких как многоточечные фрезы для фрезерных станков, развитие автоматизированных операций, управляемых электронными и жидкостными системами управления, и нетрадиционных методов, таких как электрохимическая и ультразвуковая обработка. Тем не менее, даже сегодня основные станки остаются в значительной степени наследием 19-го века.век.
Характеристики станка
Все станки должны быть оснащены приспособлениями для закрепления заготовки и инструмента и средствами для точного контроля глубины резания. Относительное движение между режущей кромкой инструмента и заготовкой называется скоростью резания; скорость, с которой несрезанный материал входит в контакт с инструментом, называется движением подачи. Должны быть предусмотрены средства для изменения обоих.
Поскольку перегретый инструмент может потерять режущую способность, необходимо контролировать температуру. Количество выделяемого тепла зависит от силы сдвига и скорости резания. Поскольку усилие сдвига зависит от разрезаемого материала, а материал инструмента отличается устойчивостью к высоким температурам, оптимальная скорость резания зависит как от разрезаемого материала, так и от материала режущего инструмента. На него также влияет жесткость станка, форма заготовки и глубина реза.