Токарная обработка деталей на станках
Точение – один из самых распространенных методов механической обработки деталей. Принцип токарной обработки металла заключается в том, что механическое воздействие резца на заготовку происходит во время ее вращения. Современные токарные станки позволяют работать с любыми типами поверхностей, включая:
- цилиндрические,
- конические,
- фасонные,
- торцовые.
Преимуществом токарной обработки является возможность выточки канавок и проведения операций, отличающихся высокой точностью. Благодаря автоматизации процесса обработки не только снижается необходимость ручного труда, но и при этом повышается качество готовых деталей.
Сегодня обработка деталей на токарных станках используется во всем мире. Модернизация оборудования позволяет с каждым годом повышать точность изготовления металлических деталей. Этому результату способствует и внедрение ЧПУ, которые под управлением программного обеспечения полностью исключают вероятность ошибки или брака.
Процесс токарной обработки деталей
Обработка металлов на токарном станке требует использования специальных режущих инструментов, таких как:
- развертки,
- резцы,
- плашки,
- сверла.
Резка металлической заготовки происходит с помощью резца, совершающего поступательные движения во время вращения обрабатываемой детали. При этом движение ограничивается двумя плоскостями и может быть как поперечным, так и продольным. По большей части современная токарная обработка деталей проводится в полуавтоматическом режиме, поскольку наличие токаря все-таки необходимо. От него требуется постоянное слежение за проведением процесса обработки, а также внесение необходимых коррективов в зависимости от степени продвижения этапов обработки.
Что касается конструкционных параметров токарного станка, то базовым элементом служит станина, на которой закреплены все рабочие узлы. Стоит отметить, что в комплектации станка имеется «фартук», отвечающий за преобразование вращения винта в поступательное движение суппорта с рабочим инструментом.
Так, универсальные токарные станки позволяют производить широкий диапазон токарных работ. При использовании станков специального типа имеется возможность обработки деталей, обладающих строго определенными размерами и формами. Специализированные станки ориентированы на обработку деталей, которые выпускаются в массовом количестве или объемными партиями.
Отправить заявкуВиды токарных работ. Способы обработки на токарных станках
Самой популярной технологией обработки изделий из металла является токарная. Ее суть заключается в удалении лишнего слоя металлозаготовки, в результате чего получается деталь нужного размера, формы и с требуемой шероховатостью.
Особенности токарной обработки
Токарная обработка – один из способов работы с металлом, который применяется для изготовления деталей из металлических заготовок. Для решения данных задач используют специальные станки, которые оснащены сверлами, резцами и другими приспособлениями для резки.
Вращение детали, которая подвергается обработке, называют главным движением. Вращение инструмента, обеспечивающее резку до получения конечного продукта желаемых параметров, означает движение подачи. За счет того, что оборудование токарных станков способно выполнять различные движения, обеспечивается получение изделий практически любых форм.
- Нарезка резьбы.
- Расширение и раскатывание отверстий.
- Сверление и зенкеровка луз.
- Вытачивание канавок.
- Разделение деталей на несколько частей.
В процессе всех этих видов обработки не обойтись без измерительных приспособлений, которые представлены нутромерами, микрометрами, штангенциркулями и прочими приборами для измерения. С их помощью высчитывается размер деталей, а также контролируется конфигурация поверхностей обрабатываемого изделия. Это позволяет гарантировать получение безукоризненного результата.
Путем обтачивания наружных плоскостей изготавливают гладкие и ступенчатые детали разного типа. Последние формируют, пользуясь проходным резцом, передвижение которого должны осуществляться под определенным углом к заготовке.
Метод подрезания используют для торцевых конструкций. Для этого применяют специальные подрезные резцы поперечного типа. Таким же образом осуществляется изготовление канавок и обрезка изделий канавочными резцами.
Резьбу формируют специальными резчиками, которыми оснащены токарновинторезные станки. Сам резец имеет вид лузы, расположенной между оборотами. Для формирования резьбы кинематическую цепь подачи настраивают таким образом, чтобы за одно вращение получалось осевое передвижение на протяженность шага резьбы.
Выбор способа обработки металла на токарном станке зависит непосредственно от химического состава материала, а также его физических и механических свойств.
Существует следующие варианты токарной обработки:
- черновая – подразумевает под собой удаление дефектных слоев, разрезку, подрезку и срез торцов заготовки детали;
- чистовая – используется для получения конечного продукта нужной конструкции и параметров;
- получистовая – в процессе обработки снимается от 20 до 25% припуска в результате чего получают форму, близкую к проекту предполагаемой детали;
- тонкая – позволяет получить изделие низкой шероховатости путем срезания тонких стружек;
- специальная – включает в себя скоростное, силовое и виброточение, а также точение с предварительным подогревом.
Технологию и тип оборудования подбирают в зависимости от вида материала заготовок. Токарные автоматы позволяют получить детали точной формы с невысокой шероховатостью внешнего покрытия.
Обтачиванием обрабатывается внешняя поверхность изделий, а для внутренней используется растачивание. Для изготовления плоских торцевых плоскостей применяется подрезание. Резка разделяет заготовки изделий на части или отделяет готовые детали от заготовки.
Вы можете заказать услуги токаря прямо сейчас на нашем сайте – ОАО “РМС” выполнит все виды токарной обработки металла на станках ЧПУ.
Токарная обработка, виды токарных станков.
Токарная обработка – наиболее распространенный и востребованный способ обработки металлических деталей, в основном тел вращения, с помощью токарного станка. Токарная обработка деталей осуществляется при одновременном вращательном движении металлической заготовки и поступательном движении резца, которое регулирует глубину резания.
Токарная обработка является основополагающей операцией при различных производственных процессах и операциях. Без токарной обработки не нарезать внутреннюю или наружную резьбу на металлических деталях, не выточить торцы или уступы, а также пазы и канавки на металлических заготовках, не обработать поверхности деталей. Также токарная обработка детали подразумевает сверление, зенкерование и развертывание отверстий. Токарная обработка предполагает постепенное удаление лишнего материала заготовки путем снятия металлической стружки в тех местах, где это требуется по проекту детали.
Наиболее часто с помощью токарной обработки изготавливают такие детали как в валы, диски, втулки, гайки, муфты, фланцы и другие детали типа тел вращения.
Токарная обработка осуществляется на различного рода токарных станках, как с программным, так и с ручным управлением.
Наиболее распространенный вид станков для токарной обработки металла – токарно-винторезный станок, который используется для выполнения токарных и винторезных работ, нарезания резьб в условиях единичного производства или для изготовления мелких серий изделий.
Также востребованы для токарной обработки металлических заготовок токарно-карусельные станки. Они предназначены для токарной обработки деталей типа диск больших радиусов, а также для формирования торцов и канавок на металлических деталях, фрезеровочных и шлифовочных работ.
Для токарной обработки лобовых, цилиндрических и конических поверхностей труб или дисков используют лоботокарный станок. А на токарно-револьверных станках осуществляется токарная обработка заготовок и деталей из калиброванного прутка, их часто применяют в серийном производстве для токарной обработки деталей сложной конфигурации из прутков или штучных заготовок.
Токарная обработка в серийном производстве часто автоматизируется при применении станков с ЧПУ. Альтернативным методом автоматизации является проектирование и токарная обработка сложных деталей и использованием САМ-систем.
Токарная обработка не возможна без ряда деталей и приспособлений. Одним из первых является токарный станок.
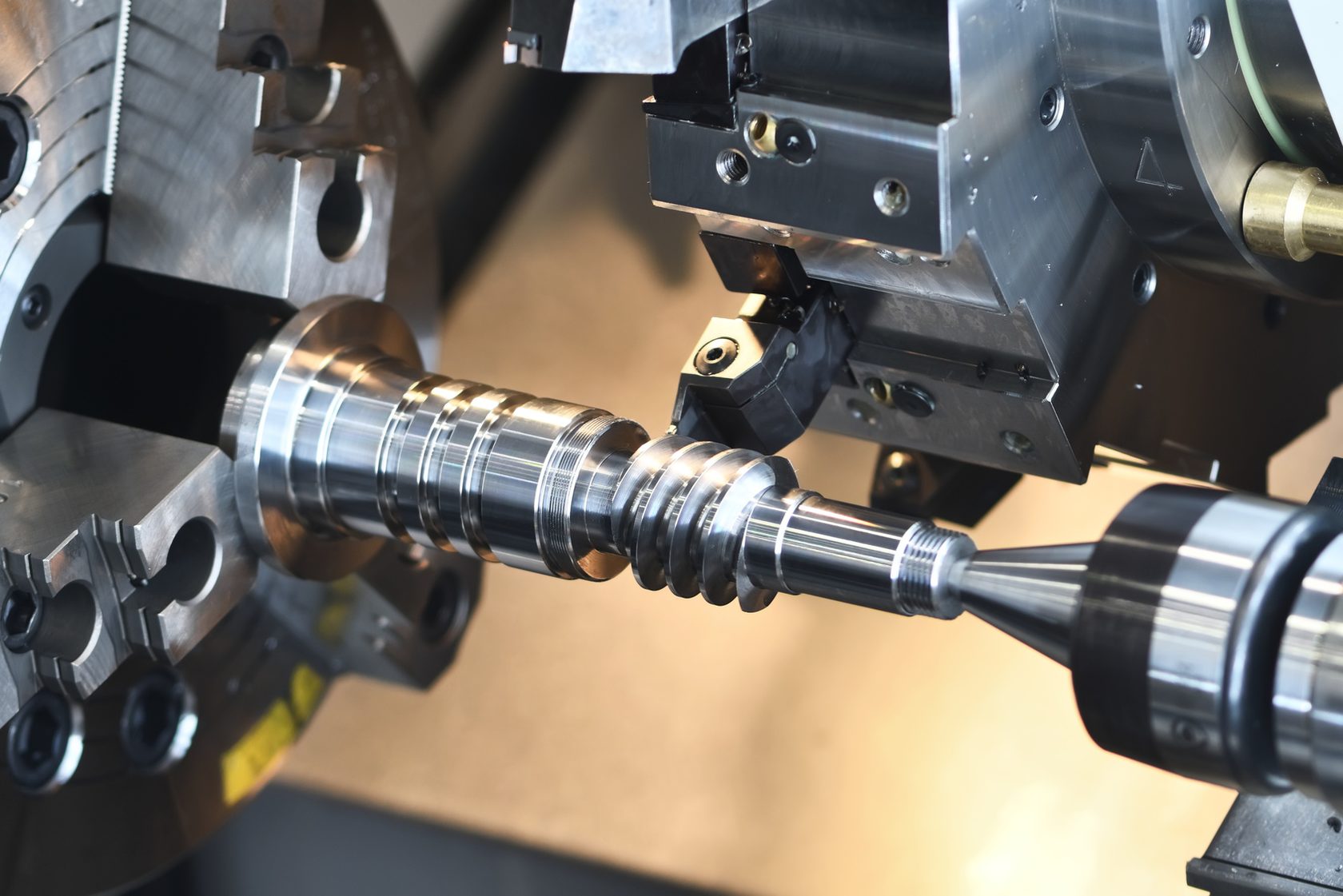
Токарная обработка это наиболее распространенный метод обработки резанием. Токарная обработка применяется при изготовлении деталей преимущественно типа тел вращения. Это всевозможные валы, диски, кольца, втулки, муфты, гайки и прочее.
1. Токарная обработка наружных цилиндрических поверхностей.
2. Токарная обработка наружных конических поверхностей.
3. Токарная обработка уступов и торцов.
4. Выточка канавок и пазов, отрезка заготовки.
5. Токарная обработка внутренних конических и цилиндрических поверхностей.
6. Зенкерование, сверление и развертывание отверстий.
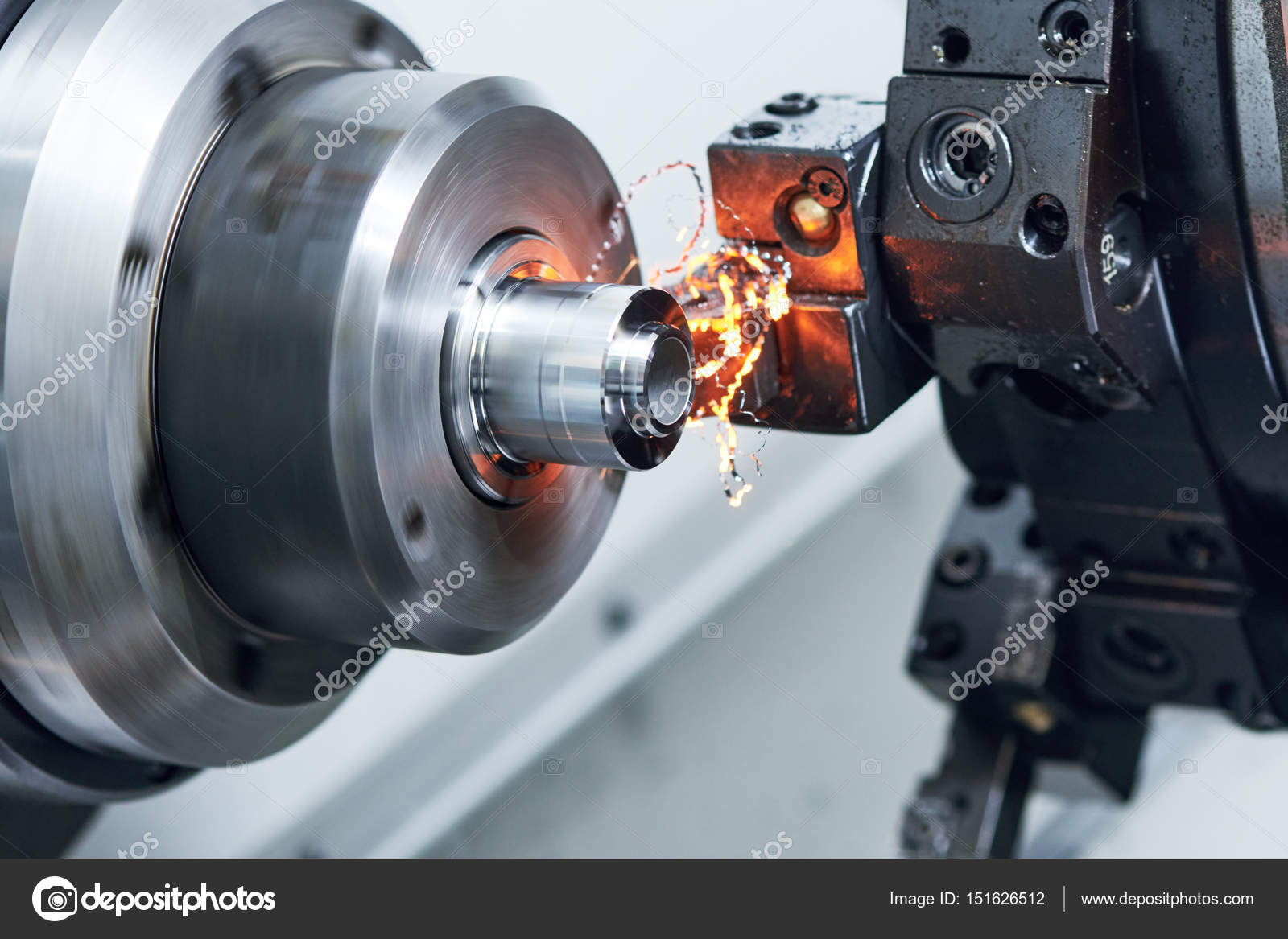
7. Нарезка наружной резьбы.
8. Токарная обработка фасонных поверхностей.
9. Накатывание рифлений.
В производстве большинство деталей получают свою окончательную форму и размер в результате токарной обработки, обработки заготовки с помощью резания. Резание заключается в последовательном удалении тонких слоев материала с поверхности заготовки резцом. При этом образуется стружка. Процесс токарной обработки на станках осуществляется при ускоренном вращении, которое передается обрабатываемой детали при поступательном движении резца.
Важнейшим элементом при токарной обработке является скорость вращения, глубина и подача резания. Скорость резания это путь, пройденный режущей кромкой инструмента относительно обрабатываемой поверхности в единицу времени.
Подача- величина перемещения режущей кромки за один оборот заготовки или за единицу времени. Она измеряется в мм/об или в мм/мин. Подача бывает поперечная и продольная. Поперечная подача – если инструмент перемещается перпендикулярно оси вращения. При продольной подаче инструмент перемещается параллельно оси вращения детали. Глубина резания это величина слоя металла, срезаемая за один подход резца. Глубина измеряется по перпендикуляру к обработанной поверхности заготовки. Измеряется в мм., Обозначается буквой t.
В процессе токарной обработки поверхность детали бывает нескольких видов. Сначала поверхность становится обрабатываемой, с которой снимают стружку. Поверхность резания – переходный этап между обрабатываемой и обработанной поверхностью, образуется режущим инструментом. Обработанная поверхность – конечный этап, получается после снятия стружки с детали.
Виды станков для токарной обработки:
1. Токарно-винторезный станок для токарной обработки.
Такой станок подходит для работ по черным и цветным металлам. На нем можно точить конусы, нарезать модульные, метрические, дюймовые и прочие резьбы. Такой вид станков для токарной обработки чаще всего применяют для единичного или мелкосерийного производства. Конструкция всех видов станков данной группы практически идентична. Типичный представитель группы – станок 16К20.
2. Токарно-карусельный станок для токарной обработки.
Данный станок используется для черновой и чистовой обработки крупных заготовок, таких как диск или вал. Имеет вертикальную ось вращения.
На токарно-карусельных станках можно производить:
– Прорезку канавок.
– Сверление, развертывание центральных отверстий и зенкерование.
– Протачивание торцовых поверхностей
– Растачивание и обтачивание конических и цилиндрических поверхностей.
3. Лоботокарный станок для токарной обработки.
Ось вращения в лоботокарных станках расположена горизонтально. Они подходят для обработки лобовых, конических, цилиндрических и прочих поверхностей типа труб, валов и дисков. Материал заготовки – чугун, сталь.
4. Токарно-револьверный станок для токарной обработки.
Такой станок применяется для токарной обработки заготовок из калиброванного прутка и обработки штучных деталей. На нем можно производить такие виды токарной обработки как: обточка, подрезка, расточка канавок, проточка, сверление, развертывание, зенкерование, обработка резьб метчиками, плашками и резцами, фасонное точение.
Название группы происходит от способа закрепления резцов в барабане. Большинство станков данной группы могут работать в полуавтоматическом режиме. Токарно-револьверные станки для токарной обработки широко используются в производстве. Применяются они для создания сложных заготовок.
5. Автомат продольного сечения.
Эти токарные станки применяются для изготовления мелких серийных деталей из холоднотянутого, калиброванного прутка, свернутой в бунт проволоки и фасонного профиля.
Станок может точить любые материалы, от меди до сталей. Автоматы продольного сечения применяются, в основном, в массовом производстве деталей, но применять их можно также и в серийном производстве. Внутри автомата находится станина, в которую вмонтирована система кулачков и распределительных валов. С их помощью и происходит управление аппаратом.
6. Многошпиндельный токарный автомат.
Многошпиндельные токарные автоматы подходят для токарной обработки точных и сложных деталей, изготовленных из калиброванного холоднотянутого прутка или из труб (в условиях серийного производства). Жесткая конструкция автомата в совокупностью с мощным приводом позволяет обеспечить высокую производительность. Некоторые модели мультифункциональны, то есть позволяют выполнять несколько операций одновременно.
Особенности и правила обработки металла на токарном станке
Токарный станок является распространенным устройством для обработки металлических заготовок. Он предназначен для работы с деталями цилиндрической, конической или округлой формы.
Принцип действия заключается в обработке вращающихся металлических заготовок методом точения с помощью резцов, зенкеров, сверл, плашек и прочих режущих инструментов. Такой станок используется для выполнения следующих операций:
- обтачивание (растачивание) наружной или внутренней поверхности детали цилиндрической формы;
- сверление и развертывание отверстий;
- отрезание заготовки нужных размеров;
- нарезание резьбы;
- подрезание торцов;
- удаление заусениц;
- снятие фасок;
- шлифование.
Устройство и принцип работы токарного станка
Токарно-винторезный станок состоит из горизонтальной станины на двух тумбах (на ней крепятся все механизмы), электродвигателя с коробкой передач, суппорта, передней и задней бабки.
Перед началом работы металлическая заготовка зажимается в специальном патроне, который получает вращательное движение от шпинделя. Тот в свою очередь приводится в движение электромотором, подключенным через коробку передач.
Обрабатывающий инструмент (резец) крепится в держателе. Он может перемещаться в продольном и поперечном направлении, а также изменять угол наклона с помощью специальной подачи.
В процессе работы сначала включается станок (придается вращение заготовке), а потом к ней плавно подводится резец и начинается проточка. В результате срезается определенный слой металла, что сопровождается появлением стружки, нагревом детали и режущего инструмента. Проточка повторяется столько раз, сколько нужно для достижения желаемого результата.
Разновидности используемых токарных резцов
В зависимости от особенностей выполняемой работы, используются различные режущие инструменты. Токарные резцы подразделяются на несколько типов.
- Проходные (прямые, отогнутые, упорные). Они являются основным рабочим инструментом токарного производства. Применяются для проточки наружных и внутренних поверхностей вращающихся деталей.
- Подрезные. Обработка торцевой части заготовок.
- Расточные. Доведение отверстий в деталях, полученных путем литья или штамповки, до нужного размера.
- Отрезные. Резка заготовки, проточка канавок.
- Резьбовые. Используются для механизированной нарезки резьбы.
- Фасонные. Производство деталей фигурной формы.
По своей конструкции резцы бывают цельными (изготовленными из единой заготовки) и составными (с напаянными или прикрученными режущими пластинами).
Некоторые правила работы на токарном станке
Обработка детали методом реза сопровождается появлением стружки, от которой токарю следует защищать глаза специальными очками. Кроме этого, длинные рукава и волосы должны быть убраны под спецодежду, а цепочки и прочие украшения сняты.
Особое внимание следует уделять надежности закрепления заготовки в патроне. Во избежание сильной вибрации обрабатываемая деталь должна быть отцентрирована. При работе с длинными заготовками противоположный патрону конец дополнительно закрепляется посредством вращающегося центра. Последний размещается на задней бабке станка.
При резке больших заготовок отрезным резцом необходимо остановить работу станка за 1,5-2 мм до центра и закончить операцию вручную. В противном случае под действием силы тяжести возможен изгиб «тонкой шейки» и поломка режущего инструмента.
Токарная обработка металла: обработка металла на станках ЧПУ
Токарная обработка металла представляет собой последовательное снятие металлических слоев с заготовки для получения изделия с заранее определенными параметрами. Процедура производится на токарных станках, в оснащение которых входят различные виды сверл, резцов и ряд других специнструментов.
Технология токарной обработки металлов осуществляется за счет одновременного выполнения двух движений:
- Главного. Производит вращение заготовки, зафиксированной в планшайбе либо патроне.
- Движения подачи. Совершается инструментом во время обработки изделия.
При обработке металла на токарном станке существует возможность разнообразного сочетания этих движений, что позволяет работать с заготовками различной конфигурации.
Возможно выполнение следующих технологических операций:
- сверление отверстий, включая выполнение зенкерования (проделывание цилиндрических и конических отверстий в деталях для увеличения диаметра), развертывания и растачивания;
- отрезание лишних частей заготовки;
- нарезка резьбы;
- вытачивание на внешней стороне детали различных канавок.
С учетом разновидности металла при обработке на токарном станке образуется стружка нескольких видов:
- Элементная (Скалывания). Появляется при работе с маловязкими и твердыми заготовками на малом скоростном режиме.
- Сливная. Образуется при обработке свинцовых, оловянных и медных заготовок. Функционирование агрегата осуществляется на повышенных скоростях.
- Ступенчатая. Формируется при работе оборудования на средних скоростях с заготовками из сплавов алюминия и из стали средней твердости.
- Стружка надлома, которая получается при резке материала с малой пластичностью.
Преимущества токарной обработки заготовок из металла
В сравнении с другими видами обработки металлических изделий применение токарного оборудования позволяет:
- получить готовую продукцию высокого качества, которая полностью соответствует заданным параметрам;
- минимизировать количество отходов, так как срезается только ненужная часть металла. Получаемая стружка подвергается прессованию и может быть отправлена на повторную переплавку;
- изготавливать изделия сложной конфигурации за один рабочий цикл;
- производить обработку разных типов металла, включая их сплавы;
- организовать серийное изготовление деталей различного назначения;
- получить абсолютно чистую поверхность готовых изделий;
- снизить стоимость готовой продукции, что достигается за счет высокой скорости производства.
Токарная обработка металла также отличается высоким уровнем автоматизации, поэтому существенно снижается вероятность выпуска брака.
Виды токарных станков
Классификация токарных станков организована в зависимости от того, какие изделия требуется получить и какой должна быть их точность. В зависимости от этого выполнение токарной обработки заготовок из металла производится на следующем оборудовании:
- Токарно-винторезные станки. Наиболее распространенный вид, который используется для получения цилиндрических поверхностей нужного диаметра. Заготовке можно придать конусность и нарезать резьбу.
- Токарно-револьверные станки. Они задействуются на предприятиях, которые занимаются массовым выпуском металлоизделий из поковок, прутка и отливок. Происхождение названия связано со способом крепления резцов, установленных, как в барабане у револьвера.
- Токарно-карусельные. Применяются для работы с габаритными заготовками, которые на станке устанавливаются в вертикальном положении. Основной критерий оборудования – диаметр планшайбы.
Токарная обработка металла ЧПУ
Станки с ЧПУ обеспечивают высокий уровень автоматизации и возможность внесения в компьютер множества готовых программ по изготовлению деталей. Благодаря этому повышается производительность труда, снижаются процент брака и стоимость готовой продукции.
Выделяют три типа систем, которые используются при токарной обработке металла на станках с ЧПУ:
- замкнутые. Обрабатывают два потока информации, которые исходят от считывающего и измеряющего устройств;
- разомкнутые. Здесь доступен только один поток информации, поэтому прибор сначала занимается расшифровкой данных, а затем передает их обрабатывающему механизму;
- самонастраивающиеся. В этом случае обработка металла на токарном станке характеризуется высокой точностью, так как система автоматически корректирует все данные.
Виды резцов и их особенности
Качество готовой продукции напрямую зависит от характеристик резца и его геометрических параметров. В зависимости от назначения выделяют следующие виды резцов:
- канавочные;
- проходные;
- фасонные;
- резьбовые;
- подрезные;
- расточные.
По направлению резания резцы делят на правые и левые, а по способу изготовления – цельные или составные.
Применение токарного оборудования является оптимальным выбором для получения деталей высокого качества.
Другие статьи
Рубка металла гильотиной: технологические особенности и преимущества |
Порошковая покраска: способы и преимущества технологии |
Лазерная резка металла: основные принципы производства |
Технология токарной обработки и оснастка
Самым популярным способом обработки заготовок режущими инструментами является токарная обработка. Она используется для получения деталей, представляющих собой тела вращения, симметричные по осям. К ним относятся:
- муфты;
- гайки;
- втулки;
- кольца;
- фланцы;
- цапфы;
- пальцы;
- оси;
- диски;
- валы.
Главные токарные операции видны на рис. 1.
Рис. 1. Токарные работы (стрелки указывают направления передвижения инструментов и вращения заготовки): а — внешняя обработка поверхностей в форме цилиндра; б — внешняя обработка поверхностей в форме конуса; в — выполнение токарной обработки торцов и уступов; г — выточка пазов, канавок, отрезание части заготовки; д — внутренняя обработка поверхностей в форме цилиндра либо конуса; е — обработка сверлением, зенкерованием и развертыванием отверстий; ж — нарезка резьбы снаружи; з — нарезка резьбы внутри детали; и — обработка фасонины; к — накатка рифленой поверхности.
При изготовлении деталей машин заготовки превращаются в изделия в результате их механической обработки режущими инструментами. При этом последовательно удаляется с заготовки тонкий слой металла в виде стружки.
Режущие инструментыНа токарных станках используется много различных режущих инструментов:
- фасонный инструмент;
- резьбонарезные головки;
- плашки;
- метчики;
- развертки;
- зенкеры;
- сверла;
- резцы.
Токарные резцы – наиболее популярные инструменты. Их используют для нарезания резьб, обработки фасонных, цилиндрических поверхностей, плоских деталей (рис. 2).
Рис. 2. Виды токарных резцов для обработки различных поверхностей:
а — внешняя расточка с помощью проходного отогнутого резца; б — внешняя расточка с помощью прямого проходного резца; в — расточка, выполненная с подрезом выступа под углом 90º; г — вырезание канавки по сечению вала; д — расточка галтели по радиусу; е — расточка отверстия; ж и з — нарезка внешней и внутренней резьбы.
Часто на токарных станках производится сверление различных отверстий. Это один из распространенных способов обработки. Его применяют с целью начальной обработки отверстий. Только сверлом можно выполнить черновую расточку отверстия в цельной заготовке. Сверла бывают:
- эжекторные;
- центровочные;
- глубинного сверления;
- перовые;
- спиральные.
Самую большую популярность получили спиральные сверла.
Крепеж режущих инструментов, их движение во время работы токарно-винторезного станка осуществляется различными узлами или сборочными единицами станка. Далее описываются схемы работы некоторых основных рабочих узлов.
Рис. 3. Суппорт:
1 — нижние направляющие продольного суппорта; 2 — винт подачи хода; 3 — поперечные направляющие суппорта; 4 — плита поворота; 5 — направляющие; 6 — держатель резца; 7 — головка поворота держателя резца: 8 — винт, крепящий резцы; 9 — рукоятка поворота держателя резцов; 10 — гайка; 11 — верхние направляющие продольного суппорта; 12 — направляющие; 13 и 14 — ручки; 15 — рукоятка для передвижения суппорта вдоль станка.
На рис. 3 изображен суппорт станка. Его устройство и работа: нижние направляющие 7 подаются по направляющим станины рукояткой 75 и резец двигается в нужном направлении. На салазках, расположенных внизу, по направляющим 12 передвигается поперечный суппорт 3. Он заставляет двигаться резец в сторону, перпендикулярную оси вращения обрабатываемой детали.
Рукояткой 13 по направляющим 5 поворотной станины подаются верхние салазки 77. Вместе со станиной 4 они прокручиваются в плоскости горизонта по отношению к поперечным салазкам 3 и заставляют резец подаваться под углом к оси вращения обрабатываемой детали.
Держатель резца или по-другому, резцовая головка на четыре позиции, прижимается ручкой 9 к верхним салазкам 77. С помощью этого универсального механизма резец мгновенно подается в работу с минимумом затрат времени.
Рис. 4. Держатель резцов:
1 — упорная шайба; 2 — поворотная головка; 3 — оправка с конусом; 4 — ручка; 5 — верхние салазки; 6 — головка с резцами четырехсторонняя; 7 — болт.
Как устроен держатель резцов, видно на рис 4. Центрирующая расточка верхних салазок 5 имеет оправку 3 конической формы с резьбой на конце. Четырехсторонняя резцовая головка 6 расположена на конусе оправки. Когда вращается рукоятка 4, головка 2 двигается вниз вдоль резьбы конической оправки 5.
Шайба 7 вместе с опорным подшипником жестко удерживают резцовую головку 6 на конусе оправки 3. Головка 2 закреплена к резцовой головке 6 с помощью винтов 7. От проворота резцедержатель предохраняет шарик. Он заклинивается между пазом, имеющимся в конусе оправки 3 и отверстием в резцедержателе 6.
В конструкции токарно-винторезного станка основное назначение задней бабки – поддержка слишком длинных деталей в момент обработки. Еще бабка применяется с целью крепежа инструментов, назначение которых – обработка различных отверстий. Это могут быть развертки, зенкера, сверла. И еще – нарезание резьбы – резьбонарезные головки, плашки, метчики.
Рис. 5. Задняя бабка:
1 — картер; 2 — центровочное приспособление; 3, 6 — ручки; 4 — пиноль; 5, 12 и 14 — болты; 7 — маховик; 8 — тяга; 9, 10 — рычаги; 11, 13 — гайки
Задняя бабка наглядно представлена на рис. 5. Маховик 7 раскручивает винт 5 и в корпусе 7 двигается пиноль 4. Она закрепляется ручкой 3. Режущий инструмент либо центр 2 установлен конусным хвостовиком в пиноли. Продольным суппортом либо вручную по салазкам станка задняя бабка совершает движение.
Если бабка неподвижна, она фиксируется ручкой 6. Ручка имеет связь с тягой 8 и рычагом 9. Винтом 72 и гайкой 77 регулируется мощность прижима рычага 9 тягой 8 к станине. Чтобы более жестко укрепить заднюю бабку, затягивают винт 14 и гайку 13. Рычаг 10 прижимает их к станине.
В револьверной поворотной головке, рассчитанной на много позиций, закрепляют разнообразные инструменты на токарно-винторезных станках, когда необходимо обрабатывать детали сложной формы и конструкции. Индексируя (поворачивая) ее, последовательно вводят в рабочий цикл настроенные инструменты.
Модификаторы для станков зависят от назначения и делятся на три группы:
- модификаторы для крепежа деталей на станке;
- механизмы для удержания режущего инструмента при обработке;
- модификаторы для модернизации технологических возможностей станков. Они дают возможность станку осуществлять не свойственные операции. Это фрезерование на токарном станке, выполнение нескольких отверстий одновременно и т. д.
Модификаторы для крепежа деталей на станке
Чтобы закрепить заготовки в рабочем пространстве станка, используются патроны на 2, 3 и 4 кулачка. Они могут быть с механизированным и ручным зажимным приводом. Самым популярным является самоцентрирующийся трехкулачковый патрон (рис. 6). Вместе с диском 4 синхронно передвигаются кулачки 3, 2, 1.
Рис. 6. Трехкулачковый самоцентрирующий патрон:
1, 2 и 3 — кулачки; 4 — диск; 5 — шестерня; 6 — шайба патрона
С одного торца диска изготовлены пазы в форме спирали Архимеда. В пазах установлены нижние выступы кулачков. С другого торца диска вырезана коническая шестерня. Она находится в зацеплении с тремя коническими шестернями 5. Проворачивая специальным универсальным ключом одну шестерню 5, диск 4 в результате зубчатого зацепления вынужден провернуться.
Через спираль синхронно передвигаются вдоль пазов корпуса 6 все кулачки патрона. Направлений движения всего два: кулачки стремятся к оси патрона, зажимая заготовку, либо отдаляются, отпуская ее. Конструктивно кулачки выполнены с тремя ступенями. Для сопротивления износу их подвергают закалке.
Кулачки могут захватывать детали во время обработки внешней и внутренней поверхности. Крепеж внутри заготовки предусматривает наличие технологического отверстия, куда заходят кулачки. Самоцентрирующиеся патроны с тремя кулачками удерживают детали шестигранного и круглого сечения, круглые прутки с большим сечением.
Самоцентрирующиеся патроны с двумя кулачками удерживают поковки и фасонные отливки. В кулачках подобных патронов крепят только одну заготовку. В самоцентрирующихся патронах на четыре кулачка крепят прутки с квадратным сечением. Патроны, где установлена индивидуальная регулировка кулачков, удерживают изделия несимметричной либо прямоугольной конфигурации.
Рис. 7. Разновидности центров:
а — центр с упором; б — обратный центр; в — полуцентр упорный; г — со сферой; д — рифленый конус; е — с наконечником из твердых сплавов; 1 — рабочая часть; 2 — хвостовик; 3 — опорный выступ.
Размеры и формы заготовок предоставляют возможность при обработке использовать различные центры (рис. 7). В вершине рабочего места центра угол равняется 60˚ (рис. 7, а). Конусные поверхности хвостовика 2 и рабочего места 1 должны быть гладкими, без забоин. В противном случае, обрабатывая детали, это приведет к погрешности.
Сечение опорного выступа 3 должно быть меньше, чем малое сечение конуса хвостовика. Данная пропорция дает возможность выбивать инструмент из гнезда, оставляя целым конус его рабочей части.
Работая с большими нагрузками и скоростями резания, используют задние центры вращения (рис. 8). Внутрь хвостовой части центра 4 на подшипниках качения 2, 3, 5 запрессована ось. Она заканчивается выходящей наружу рабочей частью 1. Это позволяет оси вращаться с деталью во время обработки.
Рис. 8. Устройство вращающегося центра:
1 — рабочая поверхность; 2, 3 и 5 — подшипник; 4 — хвостовик.
Чтобы передать вращение от патрона к заготовке, закрепленной в центрах станка, используются хомутики (рис. 9). Хомутик одевают на деталь и стягивают винтом 1 (рис. 9, а). Хвостовик 2 хомутика должен упираться в палец поводкового патрона.
Рис. 9. Токарные хомутики:
а —простой: 1 — болт; 2 — хвостовая часть; б — с самозатягиванием; 1 — упорный винт; 2 — хвостовая часть; 3 — пружинная пластина; 4 — палец; 5 — призматический корпус.
Когда деталь обрабатывается в центрах, движение ей передает поводковый патрон посредством пальца-поводка через хомутик, стянутый на заготовке винтом. Сократить время черновой обработки валов сечением 15…90 мм помогают поводковые самозажимные патроны.
Назначение цанговых патронов – крепеж холоднотянутого прутка. Также они применяются для повторного крепежа деталей на предварительно обработанной поверхности.
Мембранные патроны используются для получения деталей высокой точности центрирования.
Рис. 10. Расположение обрабатываемых деталей в патроне с использованием поджатия заднего центра:
1 — обрабатываемая деталь; 2 и 3 — резцы
Методы крепежа и установки обрабатываемых деталей на станок применяют исходя из их твердости, точности обработки, габаритных размеров. Если соотношение I/D<4, где I – длина заготовки, мм, D – сечение заготовки, мм, то заготовку крепят в патроне.
Если 4<I/D<10, заготовку крепят в патроне с поджимом задним центром либо в центрах (рис. 10). Если I/D>10, то заготовку помещают а центр либо патрон. Практикуется крепеж в центре задней бабки и поддержка с помощью люнета (рис. 11).
Рис. 11. Устройство люнетов:
а — с движением; б — без движения: 1 — откидывающийся механизм; 2 и 3 — болты; 4 — роликовый механизм; 5 — прижимная планка; 6 — гайка с винтом.
Наиболее популярной установкой обрабатываемой детали принято считать в центрах станка. Она установлена в центрах при необходимости придания ей концентричности поверхностей. Если дальнейшую обработку будут выполнять на шлифовальном станке – тоже в центрах. Это должно быть предусмотрено технологической картой обработки.
Детали, у которых имеются отверстия, крепятся в центрах с использованием токарных оправок (рис. 12). Облегчить труд станочника в операциях по закреплению деталей на станках способствуют механизированные приводы:
- магнитные;
- электрические;
- гидравлические;
- пневматические.
Рис. 12. Токарные оправки:
а — оправка с малой конусностью (обычно 1:2000): 1 — центровое отверстие; 2 — хомутик; 3 — оправка; 4 — заготовка; б — цилиндрическая оправка: 1 — заготовка; 2 — оправка; 3 — прижимная шайба; 4 — шайба; в — разжимная (цанговая) оправка: 1 — заготовка; 2 — коническая оправка; 3, 5 — гайки; 4 — полая оправка; г — шпиндельная оправка: 1 — цанга; 2 — заготовка; 3 — разжимная оправка; 4 — патрон; д — оправка с упругой оболочкой: 1 — план-шайба; 2 — втулка; 3 — заготовка; 4 — отверстие для ввода гидропласта; 5, 6 — винт
Данный инструмент служит для установки и крепежа режущего инструмента на станке. Он помогает добиться точности и повысить производительность токарной обработки. Его принципы работы одинаковые для всех токарных станков.
Разный по конфигурации только хвостовик, служащий для фиксации приспособления.
Виды вспомогательных инструментов:
- державки байонетного типа;
- державки со сложной конфигурацией и цилиндрическим хвостовиком;
- призматические державки с цилиндрическим хвостовиком;
- цилиндрические державки.
Ограничивают подачу валов и прутков, разворачивают револьверную головку, у которой горизонтальная ось вращения, набор специальных упоров. Они изготавливаются откидные, регулируемые, жесткие.
Интересные детали на токарном станке. Основные работы, выполняемые на токарном станке
Многие домашние мастера задумываются о том, как самостоятельно изготовить токарный станок по металлу. Такое желание объясняется тем, что при помощи подобного устройства, стоить которое будет совсем недорого, можно эффективно выполнять большой перечень токарных операций, придавая заготовкам из металла требуемые размеры и форму. Казалось бы, намного легче приобрести простейший настольный станок и использовать его в своей мастерской, но учитывая немалую стоимость такого оборудования, есть смысл потратить время на то, чтобы сделать его своими руками.
Самодельный токарный станок — это вполне реально
Использование токарного станка
Токарный станок, который одним из первых появился в линейке оборудования для обработки деталей из разных материалов, в том числе из металла, позволяет изготавливать изделия различных форм и размеров. С помощью такого агрегата можно выполнять обточку наружных и внутренних поверхностей заготовки, высверливать отверстия и растачивать их до требуемого размера, нарезать наружную или внутреннюю резьбу, выполнять накатку с целью придания поверхности изделия желаемого рельефа.
Серийный токарный станок по металлу – это габаритное устройство, управлять которым не так просто, а его стоимость очень сложно назвать доступной. Использовать такой агрегат в качестве настольного оборудования нелегко, поэтому есть смысл сделать самостоятельно. Используя такой мини-станок, можно оперативно производить обточку заготовок, выполненных не только из металла, но также из пластика и древесины.
На таком оборудовании обрабатываются детали, имеющие круглое сечение: оси, рукоятки инструментов, колеса, конструктивные элементы мебели и изделия любого другого назначения. В подобных устройствах заготовка располагается в горизонтальной плоскости, при этом ей придается вращение, а излишки материала снимает резец, надежно зафиксированный в суппорте станка.
Несмотря на простоту своей конструкции, такой агрегат требует четкой согласованности движений всех рабочих органов, чтобы обработка выполнялась с предельной точностью и наилучшим качеством исполнения.
Пример самодельного токарного станка с чертежами
Рассмотрим подробнее один из рабочих вариантов собранного собственными силами токарного станка, довольно высокое качество которого по праву заслуживает самого пристального внимания. Автор данной самоделки даже не поскупился на чертежи, по которым данное устройство и было успешно изготовлено.
Конечно, далеко не всем требуется настолько основательный подход к делу, зачастую для домашних нужд строятся более простые конструкции, но в качестве донора для хороших идей данный станок подходит как нельзя лучше.
Внешний вид станка
Основные узлы
Суппорт, резцедержатель и патрон
Вид сбоку
Задняя бабка
Вид снизу на заднюю бабку
Направляющие валы
Конструкция суппорта
Привод от двигателя
Чертеж №1
Чертеж №2
Чертеж №3
Конструкционные узлы
Любой, в том числе и самодельный, токарный станок состоит из следующих конструктивных элементов: несущей рамы – станины, двух центров – ведущего и ведомого, двух бабок – передней и задней, шпинделя, суппорта, приводного агрегата – электрического двигателя.
На станине размещают все элементы устройства, она является основным несущим элементом токарного станка. Передняя бабка – это неподвижный элемент конструкции, на котором располагается вращающийся шпиндель агрегата. В передней части рамы находится передаточный механизм станка, с помощью которого его вращающиеся элементы связаны с электродвигателем.
Именно благодаря такому передаточному механизму вращение получает обрабатываемая заготовка. Задняя бабка, в отличие от передней, может перемещаться параллельно направлению обработки, с ее помощью фиксируют свободный конец обрабатываемой заготовки.
Самодельный токарный станок по металлу можно оснастить любым электродвигателем даже не слишком высокой мощности, но такой двигатель может перегреться при обработке крупногабаритных заготовок, что приведет к его остановке и, возможно, выходу из строя.
Обычно на самодельный токарный станок устанавливают электродвигатели, мощность которых находится в пределах 800–1500 Вт.
Даже если такой электродвигатель отличается небольшим количеством оборотов, проблему решают при помощи выбора соответствующего передаточного механизма. Для передачи крутящего момента от таких электродвигателей обычно используют ременные передачи, очень редко применяются фрикционные или цепные механизмы.
Токарные мини-станки, которыми оснащаются домашние мастерские, могут даже не иметь в своей конструкции такого передаточного механизма: вращающийся патрон агрегата фиксируется непосредственно на валу электродвигателя.
Существует одно важное правило: оба центра станка, ведущий и ведомый, должны располагаться строго на одной оси, что позволит избежать вибрации заготовки в процессе ее обработки. Кроме того, необходимо обеспечить надежную фиксацию детали, что особенно важно для моделей лобового типа: с одним ведущим центром. Решается вопрос такой фиксации при помощи кулачкового патрона или планшайбы.
По сути, токарный станок своими руками можно сделать и с деревянной рамой, но, как правило, для этих целей применяют профили из металла. Высокая жесткость рамы токарного станка обязательна для того, чтобы на точность расположения ведущего и ведомого центра не оказывали влияние механические нагрузки, а его задняя бабка и суппорт с инструментом беспрепятственно перемещались вдоль оси агрегата.
Собирая токарный станок по металлу, важно обеспечить надежную фиксацию всех его элементов, обязательно учитывая нагрузки, которым они будут подвергаться в ходе работы. На то, какие габариты окажутся у вашего мини-станка, и из каких конструктивных элементов он будет состоять, станет оказывать влияние и назначение оборудования, а также размеры и форма заготовок, которые на нем планируется обрабатывать. От этих параметров, а также от величины планируемой нагрузки на агрегат будет зависеть и мощность электродвигателя, который вам необходимо будет использовать в качестве привода.
Для оснащения токарных станков по металлу не рекомендуется выбирать коллекторные электродвигатели, отличающиеся одной характерной особенностью. Количество оборотов вала таких электродвигателей, а также центробежная сила, которую развивает обрабатываемая заготовка, резко возрастают при уменьшении нагрузки, что может привести к тому, что деталь просто вылетит из патрона и может серьезно травмировать оператора.
Такие электродвигатели допускается использовать в том случае, если на своем мини-станке вы планируете обрабатывать некрупные и нетяжелые детали. Но даже в таком случае необходимо оснастить редуктором, который будет препятствовать бесконтрольному увеличению центробежной силы.
Уже доказано практикой и конструкторскими расчетами, что для токарных агрегатов, на которых будут обрабатываться заготовки из металла длиной до 70 см и диаметром до 10 см, лучше всего использовать асинхронные электродвигатели мощностью от 800 Вт. Двигатели такого типа характеризуются стабильностью частоты вращения при наличии нагрузки, а при ее снижении в них не происходит ее бесконтрольного увеличения.
Если вы собираетесь самостоятельно сделать мини-станок для выполнения токарных работ по металлу, то обязательно следует учитывать тот факт, что на его патрон будут воздействовать не только поперечные, но и продольные нагрузки. Такие нагрузки, если не предусмотреть ременную передачу, могут стать причиной разрушения подшипников электродвигателя, которые на них не рассчитаны.
Если использовать ременную передачу нет возможности, и ведущий центр устройства напрямую соединяется с валом электродвигателя, то можно предусмотреть ряд мер, которые защитят его подшипники от разрушения. Подобной мерой может стать упор, ограничивающий продольное перемещение вала двигателя, в качестве которого можно использовать шарик, устанавливаемый между корпусом электродвигателя и задним торцом его вала.
В задней бабке токарного станка располагается его ведомый центр, который может быть неподвижным или свободно вращаться. Наиболее простую конструкцию имеет неподвижный центр: его несложно сделать на основе обычного болта, заточив и отшлифовав под конус ту его часть, которая будет соприкасаться с заготовкой. За счет вкручивания или откручивания такого болта, перемещающегося по резьбовому отверстию в задней бабке, можно будет регулировать расстояние между центрами оборудования, тем самым обеспечивая надежную фиксацию заготовки. Обеспечивается такая фиксация и за счет перемещения самой задней бабки.
Чтобы обрабатываемая деталь беспрепятственно вращалась в таком неподвижном центре, заостренную часть болта, которая с ней соприкасается, нужно будет смазывать машинным маслом перед началом работы.
Сегодня не представляет сложности найти чертежи и фото токарных станков, по которым можно самостоятельно изготовить такое оборудование. Более того, несложно найти различные видео, демонстрирующие процесс их изготовления. Это может быть мини-станок с ЧПУ или очень простое устройство, которое, тем не менее, даст вам возможность оперативно и с минимальными трудозатратами изготавливать изделия из металла различной конфигурации.
Стойки простейшего токарного станка по металлу можно изготовить из древесины. Их необходимо будет надежно закрепить на станине агрегата при помощи болтовых соединений. Саму станину, если есть возможность, лучше изготовить из металлических уголков или швеллера, что обеспечит ей высокую надежность, но если их нет под рукой, можно также подобрать толстые деревянные бруски.
На видео ниже представлен процесс самостоятельного изготовления суппорта для токарного станка.
В качестве узла на таком станке, на котором будет фиксироваться и перемещаться режущий инструмент, выступит подручник, изготавливаемый из двух деревянных дощечек, соединенных под углом 90 градусов. На поверхности дощечки, где будет размещаться инструмент, необходимо зафиксировать лист металла, который защитит древесину от деформирования и обеспечит точное расположение резца по отношению к обрабатываемой детали. В опорной поверхности горизонтальной дощечки, перемещаемой по станине агрегата, необходимо сделать прорезь, за счет которой такое перемещение будет достаточно точным.
Современная обработка деталей из металла почти не возможна без токарного станка. Для экономии средств можно сделать это приспособление и самому.
Смастерить на самом деле эго не так сложно, как кажется, да и чертёж токарного станка легко можно найти в Интернете. Конструкция станка может быть самой разнообразной, также как и его габариты.
Материал для его изготовления в домашних условиях легко найти в любом гараже.
Устройство токарного станка
Сделать токарный станок своими руками невозможно без знания его устройства, поэтому ниже мы представлены его основные части:
- Привод. Основа механизма, генерирует мощность. Для маломощного станка подойдёт привод из дрели либо стиральной машинки;
- Станина. Для изготовления подойдёт стальной уголок или рама из дерева, это своего рода несущая рама, поэтому она должна быть прочной для выдерживания вибраций;
- Задняя бабка. Изготавливается методом приваривания уголка к железной пластинке. Она нужна для фиксации во время обработки изготавливаемого устройства;
- Передняя бабка. Устанавливается к подвижной раме, схожа с задней бабкой;
- Суппорт. Выполняет роль опоры рабочей части.
Момент вращения передаётся двигателем в рабочую часть с помощью следующих вариантов:
- Цепной;
- С помощью ремня;
- Фрикционный.
Каждый имеет свои как преимущества, так и недостатки. Ременной — наиболее дешевый и надёжный, легко изготовляется. Но ремень быстро изнашивается, нужно часто заменять.
Цепная стоит дороже, она более громоздкая, но служит долго. По своим достоинствам и недостаткам, фрикционная занимает срединное положение. Стоит отметить тот факт, что фото токарного станка с разными передачами имеются в Интернете, и Вы с легкостью можете подробно их изучить.
Суппорт — крайне важная деталь станка. Он регулирует и количество потраченных сил при работе, и качество детали.
Двигается в различных направлениях и поэтому сильно подвержен износу. Не забывайте его отрегулировать перед началом работ.
Последовательность сборки механизма
Собираем раму станка при помощи швеллеров и балок. Чем с более крупными деталями Вы планируете работать, тем из более прочных материалов должна быть рама.
Для производства передней бабки нам понадобится гидравлический цилиндр толщиной стенки 6 мм и более. В цилиндр запрессовываем 2 подшипника. При помощи подшипников большого диаметра прокладываем вал.
Необходимо залить смазывающую жидкость в гидравлический усилитель. После чего устанавливаем суппорт с направляющими и шкив.
Устанавливаем подручник для придания резцу устойчивости. Снизу крепим небольшую полоску металла, предающую рабочей части износоустойчивости.
Какой электродвигатель выбрать?
Мотор — самая главная часть любого станка, ведь без него он не будет функционировать. От его мощности зависит общая мощность станка. Мотор с мощностью до киловольта (старые машинки для шитья могут послужить донором), подойдёт для изготовления небольших деталей.
Моторы мощностью 1.5-2 Кв. используются при обработке крупных деталей. Ни в коем случае не забывайте про изоляцию всех электрических частей.
Для правильной установки мотора лучше позвать электрика, чем получить травму.
Как сделать токарный станок из дрели?
Для экономии на запчастях и упрощения сбора допускается применять дрель как привод. Эта конструкция имеет свои преимущества:
Обратите внимание!
- конструкция собирается и разбирается в любой момент;
- переносится и транспортируется достаточно просто, ведь разобрать его довольно просто;
- экономия средств;
Но у такого способа есть свои недостатки, ведь у дрели низкий крутящий оборот, из-за чего будет практически невозможно обрабатывать крупные детали.
Модифицировать токарный станок по металлу дрелью стоит только тогда, когда не планируется большой объём работ и нужно изготовить небольшие детали.
Для изготовки данной разновидности токарного станка по металлу, нужны обычные детали (за исключением мотора и передней бабки). Функцию передней бабки берёт на себя дрель.
Благодаря компактности станка, роль станин может выполнить ровная поверхность или верстак. Саму дрель можно закрепить благодаря струбцине или хомута.
Необходимо соблюдать следующие пункты техники безопасности:
Обратите внимание!
- по завершении компоновки станка необходимо проверить исправность.
- электродвигатель в станке должен быть защищён кожухом;
- мощность электродвигателя должна быть покрытой Вашей электросетью;
- рабочий инструмент может располагаться только параллельно к поверхности заготавливаемой детали. Иначе он отскочит;
- при обработке торцевых плоскостей последние должны быть упёрты в заднюю бабку;
- приступать к работе можно только используя средства защиты глаз от стружки;
- после работы необходимо рабочее место оставить в чистоте.
Деревообрабатывающий станок требует соблюдения такой же техники безопасности, что и металлообрабатывающий.
Изменение станка
Во время необходимости монтажа конусообразных отверстий крепим два напильника так, чтоб получилась форма трапеции. Дальше монтируем приспособление на пружинах для подвода напильника.
Для затачивания различных лезвий крепим к двигателю круг для шлифовки.
Подводя итоги, хочу сказать, что сборка станка достаточно простая. Смастерить самодельный токарный станок вполне возможно и дома при помощи подручных материалов, что является достаточно экономным мероприятием.
Можно самому регулировать размеры и мощность оборудования, а также проводить нужные модификации.
Обратите внимание!
Фото токарного станка своими руками
- Шахматы
- Делаем шкатулку
Если под рукой есть профессиональный инструмент, можно осваивать его возможности бесконечно. Так, например, обычная строительная токарка нередко используется в качестве основы для изготовления сувениров и различных декоративных изделий. Красиво сделанный деревянный подсвечник на токарном станке выглядит великолепно в классическом интерьере дома. Большая ваза, изготовленная из дерева способна поражать воображение. Иногда в руках опытного мастера обычная на первый взгляд чурка превращается в настоящий художественный шедевр. Как у них это получается? Что можно еще выточить самостоятельно?
Токарный станок по дереву позволяет делать не только строительные заготовки, но и различные декоративные изделия, которые призваны радовать глаз и демонстрировать возможности оборудования . Любые поделки из древесины очень практичны, им всегда найдется место в доме, поэтому можно смело поэкспериментировать и попробовать что-то сделать своими руками. Проще всего происходит точение вазы из дерева, легко может получиться кувшин, солонка и шкатулка для хранения всякой мелочи. Можно предложить сделать шахматы.
Ваза
Как можно сделать вазу на токарном станке? Для ее изготовления может понадобиться определенный инструмент. Кроме токарного станка необходимо взять резцы, рубанок, ножовка, линейка, циркуль, топор и пила, шлифовальные шкурки и стамеска.
Процесс точения вазочки предельно прост. Правда, необходимо отметить, что вазы бывают сложные по конфигурации и простые. Рассмотрим, как можно выточить несложный вариант.
- Сначала пилою вырезается чурбачок, длиною в 10-20 см.
- Его надо обязательно подработать рубанком, как с торцов, так и вдоль длины.
- Устанавливается заготовка в патрон станка.
- Станок включается и проверяется на предмет биения детали.
- Если оно присутствует, необходимо провести выравнивание.
- Производится снятие верхнего слоя древесины на глубину 1 см.
- Снимается фаска под углом 45° с внешнего торца.
- В заднюю бабку вставляется сверло.
- Высверливается отверстие глубиною меньше длины заготовки на 3-5 см. То есть, определяется дно вазы.
- Теперь с помощью резка, который называется косячок, вырезается полость изделия.
Так как вазочка может иметь разную форму: прямую, овальную и так далее, то соответственно и расточка верхней поверхности выдерживается точной формы. После чего производится шлифовка изделия снаружи и изнутри. Для чего используется наждачная бумага. Деревянное изделие снимается со станка, днище дорабатывается вручную с использованием рубанка и наждачки. После чего сувенир покрывается лаком.
Шахматы
Шахматы – фигурки маленькие, поэтому их изготовление требует определенного опыта и твердости руки токаря, а также его глазомера. Для изготовления фигуры вам потребуется небольшой чурбачок сечением 50х50 или 60х60 мм. Его с одной стороны формируют под более мелкое сечение, к примеру, 40х40 или 30х30 мм, как это показано на видео.
Этим меньшим концом заготовка вставляется и зажимается в патрон. Теперь необходимо резцом подрезать свободный торец болванки и прижать ее центром задней бабки. Снимается резцом слой древесины, чтобы заготовка стала круглого сечения. После чего можно приступать к изготовлению самой шахматной фигуры. Можно использовать традиционные формы, можно пофантазировать.
Как только фигура будет полностью готова, ее надо отшлифовать, а в конце отрезать от прижимаемой части заготовки. Остается только вручную ее обработать лаком или покрасить в черный или белый цвет. Кстати, подсвечник из дерева изготавливается на токарном станке точно также. Его длина больше, а значит, необходима будет более длинная заготовка.
Делаем шкатулку
Шкатулка – не самый сложный элемент, который можно обточить на токарном станке. Но если это будет изделие с крышкой, то чертежи здесь потребуются обязательно. Ведь крышка должна войти в шкатулку и сесть на паз, то есть, крышка должна стать вровень с краем самого изделия.
Для изготовления шкатулки потребуется цилиндрическая заготовка, которая устанавливается в токарный станок . Главное, чтобы заготовка не доставала до станины.
- Сначала снимается слой древесины полукруглым резцом, чтобы придать заготовке округлые формы.
- Затем косячком нужно подработать поверхность, то есть, сделать ее гладкой.
- После чего необходимо сформировать внутреннюю полость деревянного изделия. Для этого применяется узкий прямой резец. Одним проходом эту операцию не закончить, поэтому придется проводить ее ступенчато.
- Используя треугольный резец, можно расширить внутреннюю полость до толщины стенок.
- Дно шкатулки выравнивается прямым, но широким резцом. Им же делается паз для крышки.
- Проводится шлифовка внутренних и наружных плоскостей.
- Наносится лак сверху, воск изнутри.
Крышка изготавливается из того же материала, что и сама шкатулка. Просто для этого необходима тонкая заготовка, которая закрепляется в патроне деревообрабатывающего токарного станка. Сначала обработка проводится широким прямым резцом, то есть формируется внутренняя часть, она может быть плоской или вогнутой внутрь. Обязательно производится шлифовка .
Затем формируется внешняя часть, для чего заготовку придется перевернуть. То есть, отрезается полуготовая часть крышки и уже почти готовой внутренней стороной устанавливается в патрон. Затем тем же резцом производится формирование внешней стороны крышки. Она также может быть плоской или выпуклой. В конце проводится шлифовка. После чего готовое изделие покрывается лаком.
В принципе, очередность изготовления сторон можно поменять, если на крышке будет ручка-держатель. Для этого придется взять заготовку потолще, чтобы точить ручку. Она может быть круглой, овальной или фигурной. Можно ручку изготовить, как отдельно выточенный элемент, и прикрепить ее на крышку шкатулки клеевым составом.
Диаметр крышки должен соответствовать диаметру внутреннего паза шкатулки. То есть, крышка должна свободно войти в паз.
Вот такие изделия можно делать своими руками на токарном станке по дереву . Самое сложное из вышеописанных декоративных предметов – это шкатулка. Здесь необходимо точно придерживаться размеров, особенно это касается толщины стенки. Сделали чуть тоньше, и появится большая вероятность, что она со временем лопнет. К тому же придется точно придерживаться диаметров крышки и паза на самой шкатулке. Если один из размеров не совпадет, то или крышка упадет внутрь шкатулки, или она окажется на крае изделия.
Поэтому при вытачивании на токарном станке самодельных поделок из дерева требуется внимание и аккуратность (работа ведь не грубая). Конечно, надо обязательно в процесс работы снимать размеры штангенциркулем.
Элементы и режимы резания
Прежде чем говорить о способах обработки, познакомимся вкратце с элементами и режимом резания.
Здесь нам встретятся новые понятия: глубина резания, подача, скорость резания.
Все они связаны между собой, и величина их зависит от различных причин.
Глубиной резания называется толщина слоя металла, снимаемого за один проход резца. Она обозначается буквой t и колеблется от 0,5 до 3 и больше миллиметров при черновой обработке до десятых долей миллиметра при чистовой обточке.
Подача -это движение резца вдоль обрабатываемой поверхности. Численно она выражается в миллиметрах, обозначается буквой S и указывает на величину смещения резца за один оборот детали. В зависимости от прочности обрабатываемого материала, жесткости узлов станка и резца, величина подачи может меняться от 0,1-0,15 мм/об до 2-3 мм/об при скоростных режимах резания. Чем тверже металл, тем меньше должна быть подача.
Скорость резания зависит от числа оборотов шпинделя и диаметра детали и подсчитывается по формуле.
Выбирая ту или иную скорость резания, нужно учитывать твердость обрабатываемого материала и стойкость резца, которая измеряется временем непрерывной работы его до затупления в минутах. Она зависит от формы резца, его размеров, материала, из которого изготовлен резец, от точения с охлаждающей эмульсией или без нее.
Наибольшую стойкость имеют резцы с пластинками из твердых сплавов, наименьшую – резцы из углеродистой стали.
Вот, например, какие скорости резания можно рекомендовать при точении различных материалов резцом из быстрорежущей стали. Стойкость его без охлаждения равна 60 минутам.
Примерные данные о скорости резания металлов:
Обтачивание гладких цилиндрических поверхностей
Гладкие цилиндрические поверхности деталей обтачивают проходными резцами в два приема. Сначала черновым резцом производят обдирку – грубое обтачивание, – быстро снимая основную массу лишнего металла. На рисунке изображен прямой резец для черновой обработки:
Черновые резцы: а – прямой; б – отогнутый; в – конструкции Чекалина.
Отогнутый резец удобен при протачивании поверхности детали около кулачков патрона и для подрезания торцов. Обычно резцы имеют рабочий ход только в одну сторону, чаще всего справа налево. Двухсторонний проходной резец конструкции токаря-новатора Н. Чекалина позволяет ликвидировать обратный холостой ход резца, сокращая время обработки.
После обточки черновым резцом на поверхности детали остаются крупные риски и качество обработанной поверхности поэтому невысоко. Для окончательной обработки служат чистовые резцы:
Чистовые резцы: а – нормальный; б – с широкой режущей кромкой; в – отогнутый, конструкции А. В. Колесова.
Нормальный тип чистового резца применяется при точении с небольшой глубиной резания и малой подачей. Чистовой резец с широкой режущей кромкой позволяет работать на больших подачах и дает чистую и гладкую поверхность.
Подрезание торцов и уступов
Для подрезания торцов и уступов на токарном станке пользуются обычно подрезными резцами. Такой резец изображен на следующем рисунке:
Подрезание в центрах: а – подрезной резец; б – подрезание торца с полуцентром.
Его лучше употреблять при точении детали в центрах. Для того, чтобы торец можно было обрабатывать целиком, в заднюю бабку вставляется так называемый полуцентр.
Если деталь закреплена только одним своим концом – при обработке в патроне, – то для проточки торца может быть использован и проходной отогнутый резец. Для этой же цели и для проточки уступов используются и специальные подрезные упорные резцы, которые работают с поперечной и с продольной подачей.
Подрезание торцов: а – подрезание проходным отогнутым резцом, б – подрезной упорный резец и его работа.
При подрезании торцов и уступов юный мастер должен следить за тем, чтобы вершина резца была всегда установлена строго на уровне центров. Резец, установленный выше или ниже уровня центров, оставит на середине сплошного торца неподрезанный выступ.
Вытачивание канавок
Для вытачивания канавок служат прорезные резцы. Их режущая кромка точно воспроизводит форму канавки. Так как ширина канавок обычно невелика, режущую кромку прорезного резца приходится делать узкой, поэтому она получается довольно ломкой. Для повышения прочности такого резца высоту его головки делают в несколько раз больше ширины.
По этой же причине головка имеет небольшой передний угол.
Отрезные резцы очень похожи на прорезные, но имеют более длинную головку. Более узкая головка делается с целью сократить расход материала при отрезании.
Длина головки должна подбираться по размерам детали и быть несколько больше половины ее диаметра.
При установке прорезных и отрезных резцов нужно тоже быть очень внимательным и точным. Небрежная установка резца, например небольшой его перекос, вызовет трение резца о стенки канавки, брак в работе, поломку инструмента.
Вытачивание узких канавок производится за один проход резца, который подбирается по ширине будущей канавки. Широкие канавки вытачивают в несколько проходов.
Порядок работы таков: по линейке или другим мерительным инструментам намечают границу правой стенки канавки. Установив резец, протачивают узкую канавку, не доводя резец на 0,5 мм до нужной глубины – остаток для чистового прохода. Затем сдвигают резец вправо на ширину его режущей кромки и делают новую проточку. Выбрав таким образом канавку намеченной ширины, делают окончательный, чистовой проход резца, двигая его вдоль детали.
Установленную в центрах заготовку не следует разрезать до конца: обломившаяся часть может повредить инструмент. Короткую деталь, зажатую в патроне, можно отрезать начисто, пользуясь специальным отрезным резцом со скошенной кромкой.
Величина подачи и скорость резания при вытачивании канавок и отрезании должны быть меньше, чем при обработке цилиндров, потому что жесткость проходных и отрезных резцов не велика.
Вытачивание конусов
В практике юного токаря вытачивание конусов будет встречаться реже, чем другие работы. Наиболее простой способ- точение небольших конусов (не более 20 мм) специальным широким резцом.
При изготовлении наружного или внутреннего конуса на детали, закрепленной в патроне, пользуются другим приемом. Повернув верхнюю часть суппорта на угол, равный половине угла конуса при его вершине, протачивают деталь, двигая резец с помощью верхних салазок суппорта. Так точат относительно короткие конусы.
Для изготовления длинных и пологих конусов нужно сместить задний центр, передвинуть на определенное расстояние к себе или от себя заднюю бабку.
Если деталь закреплена в центрах таким образом, что широкая часть конуса будет у передней бабки, то заднюю бабку следует сместить к себе, и наоборот, при перемещении задней бабки от работающего широкая часть конуса будет находиться слева – у задней бабки.
Этот способ точения конусов имеет серьезный недостаток: вследствие смещения детали происходит быстрый и неравномерный износ центров и центровых отверстий.
Обработка внутренних поверхностей
Обработка отверстий может производиться различными инструментами, в зависимости от требуемой формы поверхности и точности обработки. На производстве встречаются заготовки с отверстиями, сделанными при отливке, ковке или штамповке. У юного металлиста готовые отверстия будут встречаться главным образом в отливках. Обработку отверстий в сплошных заготовках, не имеющих подготовленных отверстий, всегда придется начинать со сверления.
Сверление и рассверливание
Неглубокие отверстия на токарном станке сверлят перовыми и спиральными (цилиндрическими) сверлами.
Перовое сверло имеет плоскую лопатку с двумя режущими кромками, переходящую в стержень. Угол при вершине сверла обычно имеет 116-118°, однако он может быть, в зависимости от твердости материала, от 90 до 140°- чем тверже металл, тем больше угол. Точность отверстия при обработке перовым сверлом невелика, поэтому его употребляют тогда, когда большой точности не требуется.
Спиральные сверла – основной инструмент для сверления. Точность обработки этими сверлами достаточно высока. Спиральное сверло состоит из рабочей и части конического или цилиндрического хвостовика, которым сверло крепится в пиноли задней бабки или в патроне.
Спиральные сверла: а – с коническим хвостовиком; б – с цилиндрическим хвостовиком
Рабочая часть сверла – цилиндр с двумя винтовыми канавками, образующими режущие кромки сверла. По этим же канавкам выводится наружу стружка.
Головка сверла имеет переднюю и заднюю поверхности и две режущие кромки, соединенные перемычкой. Идущие вдоль винтовых канавок фаски направляют и центрируют сверло. Величина угла при вершине спирального сверла одинакова с перовым и может изменяться в тех же пределах. Изготовляются сверла из легированной или быстрорежущей стали. Иногда сверла из легированной стали оснащаются пластинками твердого сплава.
Закрепление сверла производится двумя способами, в зависимости от формы хвостовика. Сверла с цилиндрическим хвостовиком закрепляются в пиноли задней бабки при помощи специального патрона, сверла с коническим хвостовиком вставляются прямо в отверстие пиноли.
Может случиться, что конический хвостовик мал по своим размерам, не подходит к отверстию. Тогда придется воспользоваться переходной втулкой, которая вместе со сверлом вставляется в пиноль.
Переходная втулка к сверлам с коническими хвостовиками: 1 – хвостовик сверла; 2 – втулка.
Чтобы вытолкнуть сверло из пиноли, нужно вращением маховичка затянуть ее в корпус задней бабки. Винт упрется в хвостовик сверла и вытолкнет его. С помощью специальной державки можно закрепить сверло и в резцодержателе.
При сверлении нужно внимательно следить за тем, чтобы сверло не уводило в сторону, иначе отверстие будет неправильным, а инструмент может сломаться. Подачу сверла производят медленным и равномерным вращением маховичка задней бабки или перемещением суппорта, если сверло с державкой закреплено в резцодержателе.
Высверливая глубокие отверстия, нужно время от времени выводить сверло из отверстия и убирать из канавки стружку.
Глубина отверстия не должна превышать длины рабочей части сверла, в противном случае стружка не будет выводиться из отверстия и сверло сломается. При сверлении глухих отверстий на заданную глубину можно проверять глубину сверления по делениям на пиноли. Если их нет, то отметку ставят мелом на самом сверле. Когда при сверлении слышится характерный визг, это значит, что либо сверло имеет перекос, либо оно затупилось. Сверление нужно немедленно прекратить, убрав сверло из отверстия. После этого можно остановить станок, выяснить и устранить причину визга.
Рассверливание – это то же сверление, но сверлом большего диаметра по уже имеющемуся отверстию. Поэтому все правила сверления относятся и к рассверливанию.
Другие методы обработки внутренних поверхностей
В практике юного токаря может встретиться и такой случай, когда диаметр нужного отверстия гораздо больше диаметра самого большого сверла в его наборе, когда в отверстии нужно выточить канавку или сделать его конусным. Для каждого из этих случаев существует свой метод обработки.
Растачивание отверстий ведется специальными расточными резцами – черновыми и чистовыми, в зависимости от нужной чистоты и точности обработки. Черновые резцы для проточки глухих отверстий отличаются от черновых резцов для точения сквозных отверстий. Чистовую обработку сквозных и глухих отверстий проводят одним и тем же чистовым резцом.
Расточные резцы: а – черновой для сквозных отверстий; б – черновой для глухих отверстий; в – чистовой
Растачивание имеет свои трудности по сравнению с наружным точением. Расточные резцы обладают малой жесткостью, их приходится значительно выдвигать из резцодержателя. Поэтому резец.может пружинить и гнуться, что, конечно, отрицательно влияет на качество обработки. Кроме того, затруднено наблюдение за работой резца. Скорость резания и величина подачи резца должны быть поэтому меньше, чем при наружной обработке, на 10-20%.
Особую трудность представляет обработка тонкостенных деталей. Зажимая такую деталь в патроне, ее легко деформировать, и резец выберет на вдавленных частях более толстую стружку. Отверстие не будет строго цилиндрическим.
Для правильной обработки при растачивании резец устанавливается на уровне центров. Затем нужно расточить отверстие на 2-3 мм в длину и замерить диаметр.
Если размер верен, можно растачивать отверстие на всю длину. При растачивании глухих отверстий или отверстий с уступами, так же как и при сверлении, на резце делают мелом отметку, указывающую глубину растачивания.
Подрезание внутренних торцов производится подрезными резцами, а вытачивание внутренних канавок – специальными прорезными канавочными резцами, у которых ширина режущей кромки в точности соответствует ширине канавки. Резец устанавливается на соответствующую глубину по меловой риске на теле резца.
Измерение внутренней канавки: линейкой, штангенциркулем и шаблоном
Кроме расточных резцов, для растачивания цилиндрических отверстий употребляются зенкеры. Они похожи на спиральные сверла, но имеют три или четыре режущие кромки и не годятся для получения отверстий в сплошном материале.
Спиральные хвостовые зенкеры: а – из быстрорежущей стали; б – с пластинками из твердого сплава
Очень чистые и точные цилиндрические отверстия делают развертками. Оба эти инструмента применяют не для расширения отверстия, а для подгонки под точный размер и форму.
Развертки: а – хвостовая; б – назадная
Изготовление конических отверстий
Вытачивание внутренних конусов, пожалуй, наиболее трудное дело. Обработка ведется несколькими способами. Часто конические отверстия делают растачиванием резцом с поворотом верхней части суппорта.
В сплошном материале предварительно нужно высверлить отверстие. Для облегчения растачивания можно высверлить ступенчатое отверстие. Следует помнить, что диаметр сверла нужно подбирать с таким расчетом, чтобы оставался припуск в 1,5-2 мм на сторону, который затем снимается резцом. После точения можно воспользоваться коническим зенкером и разверткой. Если уклон конуса невелик, сразу же после сверления применяют набор конических разверток.
Последняя из основных операций, производимых на токарном станке, – нарезание резьбы.
Механическое изготовление резьбы возможно только на специальных винторезных станках. На простых станках эта операция производится вручную. Приемы ручного изготовления наружной и внутренней резьбы изложены выше .
Измерительный инструмент
В токарных работах используется тот же инструмент, что и при слесарной обработке: стальная линейка, кронциркуль, штангенциркуль и другие. О них уже было сказано раньше. Новыми здесь могут быть различные шаблоны, которые юный мастер будет изготовлять сам. Они особенно удобны при изготовлении нескольких одинаковых деталей.
Помните, что все измерения можно производить только после полной остановки станка. Будьте осторожны! Не производите замеров вращающейся детали!
Меры предосторожности
При работе на токарном станке нужно руководствоваться следующими правилами:
1) начинать работать на станке можно только после детального ознакомления со станком и методами обработки;
2) не работать на неисправном станке или негодным (тупым) инструментом;
3) прочно закреплять деталь и следить за исправностью ограждающих устройств;
4) не работать в свободной одежде: рукава завязывать у кисти, длинные волосы прятать под головной убор;
5) своевременно убирать стружку и следить за порядком на рабочем месте;
6) не останавливать руками вращающийся патрон;
7) в случае неисправности немедленно выключить станок.
Уход за станком
Чем тщательнее уход за станком, тем лучше и дольше он будет работать. Это простое правило следует твердо запомнить и аккуратно его выполнять. Уход за токарным станком сводится к следующему.
Основное – это смазка всех трущихся частей. Перед началом работы необходимо осмотреть станок и проверить, достаточно ли смазки. Наиболее внимательно нужно следить за смазкой подшипников, заполняя масленки и смазочные отверстия машинным маслом. Станок в это время, во избежание несчастного случая, должен быть остановлен.
После работы нужно вычистить станок, убрать стружку, протереть направляющие станины и суппорта, и смазать их тонким слоем масла.
Абсолютно чистыми должны быть и конические отверстия шпинделя и пиноли задней бабки. Точность работы станка будет зависеть от их хорошего состояния.
До начала работы нужно также проверить состояние приводного ремня. Его нужно оберегать от масляных брызг и капель, так как замасленный ремень проскальзывает и быстро срабатывается. Натяжение ремня должно быть не слишком сильным, но и не слишком слабым: слабо натянутый ремень проскальзывает, а при сильном его натяжении сильно греются и быстро изнашиваются подшипники. Ограждение приводного ремня тоже должно быть в порядке.
Читайте еще:
- Основные работы, выполняемые на токарном станке
Токарные станки предназначены для обработки тел вращения. При работе на токарном станке производится точение цилиндрических, конических и фасонных поверхностей, как внутренних, так и наружных, а также нарезание резьбы и накатку рифления. Помимо этого, на них можно производить операцию сверления, однако это возможно только в том случае, если отверстие находится в оси детали или же с некоторым смещение от нее.
Разновидности и характеристики станков для обработки дерева
Разнообразие типов, размеров и форм деревянных деталей предполагает многообразие оборудования, на котором происходит обработка.
В перечень разновидностей станков для деревообработки входят:
Пилильные
Данная группа используется для распиловки заготовок и целых древен, а также для придания формы плоским элементам. Пилильные в свою очередь следует разделить на следующие подгруппы:
- Пилорамы, при помощи которых осуществляется продольная и поперечная распиловка материала при помощи линейных пил, которые совершают возвратно-поступательные движения относительно заготовок. Данное оборудование не относится к экономичному оборудованию, к тому же оно достаточно громоздкое, поэтому встречается довольно редко.
- Круглопильные, которые представляют собой автоматические и ручные, выполняющие распиловку древесины в наклонной и вертикальной плоскостях при помощи круглых пил. Такое оборудование нашло применение при формовке. Классифицируется по количеству пил, их диаметру, мощности и производительности.
- Ленточные, функционирующие автоматически и с ручным управлением. Разрезание дерева происходит при линейном движении ленты. Используется как во время заготовки, так и при дальнейшей обработке. Достоинством данного оборудования можно назвать простоту обслуживания и экономичность, однако более низкую точность, если сравнивать с круглопильными.
Строгальные
Предназначены для снятия верхнего слоя материала при перемещении режущего инструмента. К основным разновидностям станков этого типа относятся:
- Рейсмусовые, одно и двухсторонние. Односторонние способны обрабатывать только верхнюю плоскость, так что их используют только при обработке только крупных заготовок. Получили большое распространение благодаря простоте своей конструкции, а значит простоте управления и обслуживания. Двухсторонние могут одновременно обработать нижнюю и верхнюю плоскость. Их достоинством является большая производительность, однако одновременно с этим с ними сложнее при обслуживании.
- Фуговальные, которые не только производят обработку плоскостей, но и способны снять фаски под определенных углом.
Токарные
Токарные станки подразделяются на большое количество разновидностей, исходя из точности, габаритов самих станков и обрабатываемых деталей и т.д. Деревообрабатывающие разновидности токарных станков используются при точении декоративных элементов, корпусных деталей и элементов крепежа. Основным параметром классификации является степень автоматизации и универсальности. По степени автоматизации существуют следующие разновидности:
- Станки с ручным управлением предполагают регулирование скорости вращения шпинделя, подачу деталей и прочие параметры рабочим.
- Автоматизированное оборудование оснащаются копированными устройствами, благодаря которым сокращается время обработки детали, однако все процессы по-прежнему под контролем человека.
- Автоматические процессы предполагают выполнение всех переходов в автоматическом режиме. Все параметры контролируются компьютером станка. стали особо популярны в последнее время.
Если говорить об универсальности, то стоит выделить:
- Универсальное оборудование, которое позволяет выполнять детали различной формы, размеров и сложности.
- Специализированное, которое предоставляет выполнять обработку деталей в определенной диапазоне размеров.
- Специальное, предназначенное для изготовления только одной определенной детали.
Сверлильные
Они необходимы для просверливания отверстий, которые находятся в оси или не в оси деталей, а также обработки отверстий. Классифицируются по многим параметром, однако основным можно назвать конфигурацию, по которому они разделяются на:
- Вертикально-сверлильные, которые выполняют работу только в вертикальной плоскости;
- Горизонтально-сверлильные, выполняющие обработку только в горизонтальной плоскости;
- Радиально-сверлильные, позволяющие изменять угол наклона инструмента.
Фрезерные
Такие станки используются для обработки плоских и фасонных поверхностей. Как и сверлильные, они разделяются по плоскостям, в которых работает фреза. По конфигурации их следует разделить:
- Горизонтально-фрезерные, у которых шпиндель расположен горизонтально относительно поверхности стола;
- Вертикально-фрезерные, инструмент которых расположен перпендикулярно относительно стола и закрепленной на нем детали;
- Универсальные, позволяющие менять расположение заготовки без ее переустановки.
Шлифовальные
Данные станки предназначены для чистовой обработки и предполагают снятие верхнего слоя небольшой толщины инструментом с абразивным покрытием. Различают:
- Плоскошлифовальные, на которых выполняется обработка плоских поверхностей;
- Круглошлифовальные, предназначенные для тел вращения;
- Специальные шлифовальные станки, которые предназначены для обработки сложных поверхностей;
- Кромкошлифовальные. Используются для окончательной обработки фигурных элементов.
Гнутарные
Представляют собой гидравлические прессы со специальными зажимами. Используются для придания элементом особой формы.
Сборочные
Чаще всего это автоматические устройства для сборки отдельных элементов в полуфабрикат или готовое изделие.
Технология проведения работ
Токарные станки предназначены для обработки тел вращения. На данном оборудовании выполняются следующие работы:
- Подрезка торцов;
- Точение наружных поверхностей;
- Нарезание резьбы любого типа;
- Отрезание деталей;
- Нанесение рифлений;
- Сверление и растачивание внутренних отверстий.
Однако это не единственное, что можно делать на данном станке. Помимо этого на нем можно выполнять полирование и притирку отверстия. Полирование может выполнять при помощи специального войлочного круга и пасты ГОИ. С их помощью изделие приобретает зеркальную поверхность, однако точность поверхности не обеспечивается. Доводка поверхности отверстия выполняется при помощи притира. Данная операция позволяет получить точное отверстие с низким показателем шероховатости.
Обработка на токарном станке обеспечивается путем вращения детали относительно закрепленного инструмента.
Инструмент может быть закреплен в шпинделе или в центрах. Центра – это специальные приспособления, которые закреплены в шпинделе и в задней бабке. Для ее обеспечения необходимо предварительно зацентровать (просверлить специальным сверлом отверстие в оси) заготовку с двух сторон. Установка для обработки в центрах позволяет выполнить все переходы за один установ.
Виды станков для выполнения токарных работ по металлу
По степени точности оборудование следует разделить на: нормальной точности; точные; особо точные; повышенной точности; сверхточности.
По типу подразделяются на:
- лоботокарные;
- карусельные;
- токарно-винторезные;
- токарно-револьверные.
Первые две разновидности предназначены для обработки крупногабаритных деталей, от полуметра до нескольких метров. Токарно-винторезные являются самыми распространенными, поскольку являются универсальными и предназначены для обработки деталей до пятисот миллиметров. Токарно-револьверные относятся к полуавтоматическим станка. Обработка на таком оборудовании осуществляется по упорам.
Методы выполнения токарных работ
На токарном станке производится точение деталей и сверление отверстий. Также выполняются комплексные работы, которая представляют собой выполнение точение и шлифование только на токарном станке. Для выполнения операции шлифования в этом случае может использоваться резцы высокой точности и притиры, если это отверстие. Подобная мера позволяет сократить время изготовления, а значит, и уменьшить стоимость деталей.
Проточки внутреннего диаметра выполняются при помощи сверла, зенкера и развертки, а также резцов. Помимо этого могут использовать метчики, которые нарезают резьбу внутри отверстия (для наружных поверхностей используется плашка).
Выверка размеров деталей происходит при помощи лимба (измерительной шкалы на суппорте), а также при помощи измерительных приборов (штангенциркулей, микрометров и т.д.).
Виды используемых резцов
Резцы для обработки на токарном стенке бывают:
- проходными, предназначенными для обработки плоских поверхностей торцов детали;
- подрезными, используемыми для точения цилиндрических поверхностей;
- отрезными, которые отрезают готовую деталь от заготовки;
- фасонные и галтельные, которые используются для точения фасонных поверхностей и скруглений;
- резьбовые, которые подразделяются на наружные и внутренние;
- расточные резцы, которые используются для обработки внутренних поверхностей;
- канавочные, похожие на отрезные, применяемые для точения канавок.
Помимо этого резцы подразделяются на:
- цельные, чаще всего изготовленные из быстрорежущей стали;
- составные с напаянными пластинами из твердого сплава, державка в этом случае изготовлена из углеродистой стали;
- ставные со съемной пластиной, которую можно заменить в случае износа или образования скола.
Техника безопасности
В ходе выполнения работ на токарном станке необходимо использовать защитный кожух, который закрывает зону вращения детали. Таким образом, рабочий защищен от отлетающией стружки.
Работник должен стоять на специальном деревянном настиле, это обеспечивает защиту от поражения током.
Одежда должна закрывать тело, оставляя открытыми только кисти рук, голову и шею. Обувь должна быть закрытой. Все это необходимо для защиты от стружки. Одежда не должна быть прилегающей или чересчур свободной. В первом случае она будет стеснять движения, а во втором может стать причиной травмы при затягивании одежды в шпиндель.
Рабочего перед началом работы должны выдать специальные очки, которые защищают органы зрения от попадания стружки или пыли. Если производится точение сыпучего материала (к примеру, графит или дерево), то помимо очков должны быть выданы респираторы для защиты органов зрения. Также при работе с сыпучими материала необходима вытяжка, которая позволит защитить не только того, что непосредственно точит, но и других работников цеха.
Перед снятием детали следует не только выключить вращение шпинделя, но и притупить острые кромки.
Самое главное: к работе на токарном станке человек допускается только после прохождения инструктажа.
Детали токарного станка – Rockler
Детали токарного станка – стенограмма видео
Опрашивающий: Давайте немного поговорим о токарном станке. В частности, начиная с головной части, чего мы хотим от мускулов нашей машины?
Опрашиваемый: Ну, конечно, он содержит двигатель, который приводит в движение этот шпиндель, и мы хотим иметь шпиндель с резьбой, на который мы можем устанавливать патроны, или конус Морзе, в который мы можем устанавливать патроны. Самый простой токарный станок имеет регулировку скорости это всего лишь несколько шкивов, на которых мы меняем ремень.Сегодня электроника стала очень сложной и недорогой, поэтому довольно легко добавить регулятор скорости в токарный станок. Обычно это используется в сочетании с набором шкивов, и вы можете сравнить этот набор скорости с акселератором в вашей машине, а шкивы с коробкой передач. Вы собираетесь использовать первую передачу для поворота планшайбы и вторую передачу для работы шпинделя.
Опрашивающий: Круто. Хорошо, начиная с передней бабки, давайте перейдем к задней бабке и поговорим немного о функциях задней бабки и пиноли.
Опрашиваемый: Ну, конечно, это другой конец группы поддержки. Он поддерживает внешнюю сторону токарной обработки, будь то лицевая панель или шпиндель, потому что мы поддерживаем и то, и другое. Мы хотим, чтобы он был тяжелым и прочным, с хорошим диаметром пиноли и желательным большим ходом, потому что мы можем просверлить более глубокое отверстие, не перемещая его, если мы вставим сверло в эту заднюю бабку.
Опрашивающий: Это было бы удобно.
Опрашиваемый: Мы могли протянуть руку помощи, поэтому много путешествовать – это здорово.
Опрашивающий: Задняя бабка здесь движется на этих двух чугунных кусках. Поговорим немного о способах.
Опрашиваемый: Ну, конечно, есть две магистрали, по которым задняя бабка и банджо движутся вперед и назад, и вес токарного станка желателен. Вибрация, о которой мы, токари, постоянно беспокоимся, прямо пропорциональна жесткости материала, из которого она сделана. Сталь не так хороша, потому что вибрация хорошо проходит по стали.Чугун имеет свойство всасывать вибрацию. Кроме того, чем больше масса токарного станка, тем лучше, поэтому наличие большого количества чугуна – вот почему нам нравятся большие старые тяжелые станки нашего дедушки.
Опрашивающий: Давайте немного поговорим о банджо, о котором вы упоминали ранее, и об упоре для инструментов.
Опрашиваемый: Что ж, банджо, важно, чтобы оно легко двигалось и было хорошо сбалансировано, но фиксировалось очень прочно с минимальными усилиями, а также чтобы эта подставка для инструмента двигалась вверх и вниз, назад и вперед и фиксировалась очень прочно, с минимальными усилиями. усилие.Также важна высота банджо. Производители указывают, что угол поворота их токарного станка равен удвоенной высоте центра, в данном случае 10 дюймов, но это над станиной. Истинное качание токарного станка – это качание над банджо. Более высокое банджо отнимает у качелей.
Опрашивающий: Отлично.
Опрашиваемый: Также, конечно, это то, на что мы опираем инструмент и манипулируем им, всегда принимая это скос.
Опрашивающий: Справа, скос.Что-то, о чем мне нравится думать в подставке для инструмента, – это также разные размеры, так что, если вы выполняете меньшую работу, вы можете быть уверены, что подставка для инструмента находится поближе.
Опрашиваемый: Я часто использую шестидюймовый инструмент для переворачивания коробок и подобных мелочей.
Опрашивающий: Хорошо. Приступим к повороту.
Опрашиваемый: Совершенно верно.
▷ Бывшие в употреблении инструменты, запчасти, принадлежности и приспособления для продажи
Бывшие в употреблении принадлежности и запасные части для токарных и токарных станков
Индекс
- Принадлежности и запасные части для токарных и токарных станков
- Широко используемые принадлежности для токарных и токарных станков токарные станки
- Стандартные аксессуары для токарных станков
- Специальные аксессуары для токарных станков
- Важные запасные части для токарных станков
- Купить бывшие в употреблении аксессуары и запасные части
Токарные станки – это универсальные инструментальные станки для производства точных, осесимметричных деталей.Ряд стандартных и специальных принадлежностей для токарных станков позволяет полностью использовать их производительность.
- Принадлежности позволяют полностью использовать производительность
- Токарный инструмент особого значения
- Зажимной патрон и токарный центр в качестве стандартных принадлежностей
Запасные части помогают поддерживать точность производства вашего токарного станка на высочайшем уровне.Какие аксессуары для токарных станков входят в стандартную комплектацию и какие дополнительные функции можно использовать со специализированными аксессуарами?
Токарный инструмент играет особую роль в принадлежностях токарных станков. Эти токарные инструменты, с одной стороны, являются быстроизнашивающимися деталями, которые требуют регулярной замены. Они также бывают разных форм и материалов, которые выбираются в зависимости от предполагаемого применения.
Для выполнения канавок или резьбы на токарном станке могут потребоваться специальные токарные инструменты. Простые токарные инструменты из быстрорежущей стали имеют меньший срок службы, чем инструменты из твердого металла, но их можно переточить.Инструменты из твердого металла также подходят для высоких скоростей резания, что особенно удобно при серийном и массовом производстве. Этот аксессуар для токарной обработки из твердого металла также состоит в основном из инструментальной стали, и используется только одна режущая кромка из твердого металла. Их можно припаять или прикрутить, чтобы их можно было легко заменить. Оксидная керамика и алмазы также используются в качестве режущих материалов для специальных применений. Керамика еще тверже и жаростойче, чем твердый металл, и поэтому подходит для очень высоких скоростей резания.Алмаз часто используется для чистовой обработки цветных металлов на очень высоких скоростях.
Самыми важными принадлежностями токарного станка являются зажимной патрон с усилителем, который устанавливается на приводном шпинделе и передает крутящий момент на заготовку, а также центр токарного станка в противоположной задней бабке. В токарных станках механика центр токарного станка, который установлен с возможностью вращения или подпружинен в подшипниках качения, расположен в пиноли задней бабки с конусом Морзе.Его также можно заменить другими принадлежностями для токарных станков для специальных производственных серий, такими как сверлильный патрон, который часто используется. Это позволяет делать центральные отверстия и используется, в частности, при производстве центрирующих отверстий, в которые при вращении защелкивается центр токарного станка. Специальные центрирующие сверла – еще одна разновидность стандартных принадлежностей для токарных станков. Они создают сложную геометрию центрирующего отверстия согласно DIN 332 за одну операцию.
Есть две причины использовать специальные принадлежности для токарных станков.Во-первых, они повышают точность производства, а во-вторых, они незаменимы при производстве деталей определенной геометрии. Люнеты обеспечивают дополнительную поддержку для длинных и тонких вращающихся деталей. Поворотные оправки позволяют зажимать полые детали.
Запасные части для токарных и токарных станков в первую очередь требуются для восстановления точности оборудования, которое было нарушено из-за износа. Это особенно полезно для подшипников приводных шпинделей и для регулировки шпинделей.
Вы хотите купить бывшие в употреблении инструменты, запасные части или принадлежности для токарного / токарного станка? Тогда Surplex – это то, что вам нужно! Мы регулярно используем предлагаемые аксессуары для токарных станков. Однако на одном из многочисленных промышленных аукционов вы найдете не только бывшие в употреблении аксессуары. Поскольку аукционы часто являются результатом банкротств или ликвидации компании, всегда есть шанс найти неиспользованные токарные инструменты, запасные части и принадлежности по очень привлекательным ценам. Если в настоящее время вы не можете найти подходящие принадлежности для токарных станков, посетите нас снова в ближайшем будущем.Или вы можете обратиться в службу поддержки клиентов Surplex, которая с радостью посоветует вам найти подходящий токарный инструмент или запасные части.
Что следует учитывать при токарной обработке микродеталей на токарном станке?
Производство миниатюрных деталей не ново, но в последние несколько лет наблюдается тенденция к продолжению миниатюризации в ряде отраслей, включая аэрокосмическую, автомобильную, медицинскую и электронную. Майк Смуди, инженер по применению в HORN USA, говорит, что необходимо обрабатывать детали с наружным диаметром (OD) всего 0.0039 дюймов, нужно смотреть на весь процесс, потому что здесь довольно много проблем. Малейшие отклонения в процессе, вызванные характеристиками материала или режущего инструмента, тепловыми изменениями в станке или вибрациями, будут иметь прямое влияние на возможность создания деталей этого типа.
Существует множество различных определений микрообработки. Для Horn под микрообработкой на токарных станках подразумевается внешний диаметр всего 0,0039 дюйма, внутренний диаметр (ВД) всего 0,0078 дюйма и врезное резание от 0.0197 дюймов. Кроме того, эти операции требуют чрезвычайно низкой глубины резания (менее 0,0039 дюйма), чрезвычайно низкой скорости подачи (0,00019 дюймов в минуту), низких усилий резания и высокого качества поверхности.
Необходимо учитывать несколько факторов для разработки процесса успешной обработки деталей такого размера. Как объясняет г-н Смуди, трое из них – это оператор, станок и режущие инструменты:
Оператор
Не каждый оператор подходит для такой работы. Помимо возможности обработки микрочастиц и деталей, простое обращение с микродетями и инструментами может создавать уникальные проблемы.Точность приобретает совершенно новое значение. Для процесса с допуском менее 1 микрона добиться повторяемости нелегко. Оператор должен быть спокойным и терпеливым.
Станок
Конструкция шпинделя станка имеет решающее значение для достижения точности, необходимой для эффективной микрообработки. Высокоскоростные шпиндели на большинстве новых станков имеют масляное охлаждение и должны обеспечивать высокую скорость ускорения и замедления, сводя к минимуму возникновение вибрации.
Для сбора мелких деталей некоторые производители станков предлагают бесконтактный сборный желоб с продувкой воздухом, который также отделяет стружку от обрабатываемых компонентов.Кроме того, системы подачи СОЖ под высоким давлением удаляют стружку с заготовки и стабилизируют температуру как режущего инструмента, так и обрабатываемой детали во время операции. Сборщики тумана также должны отфильтровывать туман смазочно-охлаждающей жидкости из рабочей зоны.
Режущие инструменты
В целом, инструменты для микроточения требуют исключительной остроты, хороших характеристик скольжения, чрезвычайно высокого качества поверхности, высокой точности переключения, высокой точности высоты наконечника и стабильного интерфейса.Поломка инструмента является более серьезной проблемой при микрообработке, потому что любое незначительное смещение может привести к защелкиванию инструмента.
Факторами, влияющими на процесс, являются зажим пластины, подложка, микрогеометрия (размер фаски или радиус кромки) и покрытие. Благодаря чрезвычайно низкой скорости подачи острые режущие кромки пластины с радиусом 1,44 мкм и углом, например, 80 градусов, обеспечивают низкие усилия резания, хорошее качество поверхности и высокую точность размеров. И наоборот, режущая кромка с радиусом 50 микрон рекомендуется для черновой обработки или прерывистой обработки.
Результат также зависит от стабильности системы в целом. Когда вставка зажимается, необходимо следить за тем, чтобы это было сделано с высочайшим уровнем стабильности и точности. Кроме того, при работе с очень маленькими диаметрами деталей чрезвычайно важна точность центровки по высоте. В идеале установка должна быть такой, чтобы оператору не приходилось регулировать высоту центра при индексации вставки. С этой целью пластины Horn µ-Finish производятся с допуском по высоте центра ± 0.0001 дюйм, чтобы обеспечить такую точность при индексировании.
Острая режущая кромка улучшает качество обработки за счет минимизации склонности к вибрации. Для сохранения острой режущей кромки идеально подойдет пластина без покрытия, но многие обрабатываемые материалы требуют покрытия пластины. (Кроме того, пластины без покрытия обычно создают меньшие силы резания по сравнению с пластинами с покрытием.) В случае режущих инструментов с покрытием предварительная обработка поверхности и нанесение покрытий значительно влияют на микрогеометрию режущей кромки, особенно при обработке инструментами малого диаметра.
В результате компания Horn разработала инструментальную систему S274 с пластинами µ-Finish. Каждая режущая кромка проверяется под 200-кратным увеличением в качестве дополнительной меры контроля качества. Такое внимание к деталям гарантирует, что после установки инструмента больше не потребуется регулировка высоты при замене изношенной пластины.
Карбид с мелкими зернами и специально разработанная геометрия хорошо подходят для обработки стали, нержавеющей стали и латуни. Новое покрытие типа AC25 (разработанное для точения, обработки канавок и отрезки) препятствует износу и отложению материала на режущих кромках.
Система µ-Finish S274 компанииHorn, а также ее система концевых фрез Supermini и DS Micro были использованы для обработки показанного выше крошечного компонента вала, длина которого составляет 0,08 дюйма. Первая операция торцевания с помощью системы S274 была выполнена со скоростью резания 80 метров в минуту и скоростью подачи 0,003 миллиметра на оборот. Та же самая инструментальная система использовалась для операций продольной токарной обработки, обработки канавок и отрезки.
Для операций внутреннего профилирования (для диаметра 0.009 дюймов) система Supermini использовалась при скорости резания 12 метров в минуту и скорости подачи 0,003 миллиметра на оборот. Г-н Смуди говорит, что новая основа, покрытие и подготовка кромок режущего инструмента Supermini увеличивают срок службы инструмента. Например, по его словам, сплав EG35 продемонстрировал увеличение стойкости инструмента на 60% при токарной обработке кобальт-хрома с усилием 1000 Н / мм 2 . Этот сплав позволяет инструменту обрабатывать твердые материалы диаметром от 0,008 до 0,268 дюйма, увеличивая при этом возврат инвестиций.Он добавляет, что помимо острых, чистых кромок без стружки поддержание правильной скорости подачи поможет избежать проблем со стружкой.
Пять основных частей токарного станка: станина, передняя бабка, каретка, задняя бабка и коробка передач.Ниже представлены иллюстрации различных токарных станков и детали токарных станков. Изучите эти части и будьте готовы ответить на вопросы, касающиеся их названий и локации.
Верх |
Типы и детали токарных станков с ЧПУ – 8 различных частей и типов токарных станков с ЧПУ
1. Передняя бабка
Первая часть токарного станка с ЧПУ – это передняя бабка, которая расположена с левой стороны станка. Основным элементом передней бабки является мастер-шпиндель, обработка выполняется вращением заготовки с определенной скоростью, это выполняется шпинделем на левой стороне шпинделя.Привод главного шпинделя обычно подключается к станкам с ЧПУ. Серводвигатели используются в качестве приводов шпинделя и правого торца. Крепление к стене фиксируется, стенка в сборе известна как шпиндельная бабка.
2. Задняя бабка
В токарных станках с ЧПУ задняя бабка используется для поддержки заготовки в осевом направлении. Когда у нас есть длинная заготовка для обработки, мы берем на себя центр задней бабки. Положение задней бабки можно регулировать по продольной оси.
3.Патрон (рабочий зажим)
Третья деталь токарного станка с ЧПУ – это зажимное приспособление. Обычно трехкулачковые гидравлические патроны широко используются для зажима рабочих мест, цилиндрическая и шестигранная форма могут легко удерживаться в патроне. Мы можем использовать патрон в двух режимах: они уже зажимают и зажимают в соответствии с формой заготовки и процессом, другие зажимные приспособления также могут использоваться в токарных станках с ЧПУ, например, лицевая пластина цанги или специальное приспособление.
4.Режущий инструмент токарного станка с ЧПУ
При точении деталей на токарном станке с ЧПУ или токарном обрабатывающем центре положение инструмента на держателе инструмента должно быть разумно и научно обосновано в соответствии с конструкцией держателя инструмента токарного станка и количеством инструментов, которые можно установить. Вмешательство в станки, инструменты и детали, а также инструменты.
5. Револьверная головка
Другой важной частью токарного станка с ЧПУ является револьверная головка. Револьверная головка – это элемент для переноски инструментов, в котором мы можем хранить несколько инструментов, необходимых для выполнения различных операций.Револьверная головка может быть загружена внешними инструментами, такими как токарная обработка, нарезание канавок, нарезание резьбы и т. Д., А также внутренними инструментами, такими как сверлильный расточный стержень и т. Д. Обычно револьверная головка имеет движение по двум осям: x и set.
6. Панель управления с ЧПУ (MCU)
Следующая часть токарного станка с ЧПУ – это панель управления с ЧПУ, это очень важная часть любого станка с ЧПУ. Это также называется блоком управления машиной. Панель управления включает в себя экран и клавиатуру для программирования, редактирования моделирования и других данных настроек, связанных с машиной.На панели управления ЧПУ доступно множество различных средств управления станком и программой для управления станком. В основном контроллер ЧПУ работает с программным обеспечением операционной системы.
7. Станина токарного станка
Это нижняя часть токарного станка. Обычно на станках с ЧПУ используется специальное основание для неподвижного станка, чтобы станина токарного станка не двигалась и не вибрировала.
8. Педальный переключатель и ножные педали
Последней частью токарного станка с ЧПУ являются ножные переключатели.Он расположен ниже стороны оператора, оператор может быстро активировать и деактивировать удержание заготовки и поддержку работы с помощью этих педалей питания. Обычно левый используется для зажима и опускания патрона, а другой – для зажима и опускания вкусового стыка.
Детали токарного станка по дереву: описание принадлежностей и компонентов
Детали токарного станка по дереву очень сложны и многочисленны. Эта статья о деталях токарного станка , которая даст вам краткую информацию о каждой детали и ее важности.Прочтите статью ниже, чтобы узнать больше:
Детали токарного станка по деревуСтанина
Подобно основанию и фундаменту каждого станка, токарный станок по дереву также имеет основание, известное как «Станина». На этой кровати делается операция, и монтируются разные детали. Кровать должна выдерживать всю операцию, поэтому она сделана из полустали и стального хлама . Основание сделано очень прочным, чтобы образовать тяжелую жесткую конструкцию.
Передняя бабкаПередняя бабка является головкой токарного станка.Это участок, где начинается вся сила и действие токарного станка. Наряду с этим, на конце мотора вы можете найти натяжной ролик и приводной ремень. Это зависит от производителя и модели токарного станка.
Шпиндель передней бабкиШпиндель передней бабки представляет собой резьбу, выдавленную из передней бабки. Есть два важных измерения шпинделя. Первый – это размер и количество ниток. Второй – конус Морзе.Вы можете найти схематическое описание инструментов в данном буклете с руководством пользователя.
Маховик передней бабкиМаховик передней бабки находится с левой стороны передней бабки. Маховик помогает вращать токарный станок быстро и плавно. Можно получить и электронный, и ручной дублер. Маховик также помогает токарному станку по дереву замедлиться вскоре после выключения.
Индексное колесоИндексное колесо расположено на внутренней стороне передней бабки и рядом со шпинделем.Для токарного станка индексное колесо – это направляющая, которая измеряет градусы вращения. Это самая продвинутая функция современного токарного станка по дереву. Я бы порекомендовал всем использовать колесо указателя, чтобы отмечать места.
Совет: перед выключением токарного станка ослабьте установочный штифт, чтобы предотвратить проблемы.
Опора для инструмента / Каретка / БанджоНаиболее важной опорой для токарного станка является опора для инструмента. Он прикреплен к кровати, также его можно назвать кареткой или банджо.Конструкция упора для инструмента – это лучшая опора, которая удерживает все важные инструменты. У банджо фиксирующий рычаг должен находиться на станине токарного станка.
Управление мощностью и скоростьюУправление мощностью и скоростью зависит от производителя и модели машины. На токарном станке регулятор скорости и кнопка включения имеют фиксированное положение. Благодаря новым технологиям, некоторые машины могут перемещаться к месту, имея только доступ.
Задняя бабкаЗадняя бабка находится с правой стороны токарного станка по дереву.Он может скользить вперед и назад по станине токарного станка. Основной мотив задней бабки – закрепление рельсов токарного станка. Он крепится к рельсам станины токарного станка и очень прочен.
Центр содержания животныхЦентр содержания животных расположен в верхнем левом углу задней бабки. Интересно, что живой центр еще называют гусиным.
Маховик задней бабки
Если смотреть в сторону крайней правой стороны задней бабки. Вы можете найти маховик задней бабки . Это опора и манипулятор задней бабки.Он блокирует и удерживает шпиндель в целости и сохранности.
Каретка
Во время массивных операций каретка удерживает и поддерживает инструменты. В основном, он служит для того, чтобы направлять и поддерживать инструменты в работе. Он состоит из таких частей, как седло, поперечный суппорт, резцедержатель со сложной опорой и фартук. Одна из важнейших частей токарного станка по дереву.
СедлоКак сказано выше. Седло – одна из частей коляски. Седло скользит по станине и поддерживает резцедержатель, составную опору и поперечные салазки.
Поперечный суппортКогда возникает необходимость в резании инструмента во время операции, для резания используется функция поперечного суппорта. Механизм работает перпендикулярно центру и улучшает края.
Комбинированная опора
Комбинированная опора имеет круглое основание с функцией поворота. Он размещается над поперечными салазками и оказывает массивную поддержку во время операции. Это особенно необходимо вашему токарному станку по дереву.
Резцедержатель
Резцедержатель удерживает самую верхнюю часть каретки и также известен как держатель инструмента.Во время работы основная функция резцедержателя – надежно удерживать и собирать инструменты. Если резцедержатель не работает функционально, то разрезы могут быть неровными, и даже работа на этом может остановиться сама.
ФартукФартук играет важную роль в работе. Он прикреплен к передней части седла и производит выбор / управление передачами. Без выбора фартука каретка не может питать кровать. У него очень жесткий механизм и сложное управление.Он находится на передней стороне станины токарного станка, что полезно для обеспечения питания поперечных салазок и каретки.
НожкиТокарный станок по дереву громоздок, и переносить нагрузку на устройство затруднительно. Ноги полностью поддерживают машину и принимают на себя нагрузку. Ножки крепятся к основанию болтами для предотвращения вибраций во время работы. Он имеет очень прочную конструкцию с обеих сторон машины.
Итак, это основные части токарного станка по дереву, благодаря которым станок работает эффективно и плавно.Надеюсь, вам понравилась статья и вы узнали о деталях машины.
Обработканекруглых деталей на любом хорошем токарном станке с ЧПУ
Автономная бескулачковая система с точностью до нескольких микрон.
Новый высокоскоростной твердотельный привод лежит в основе новой системы токарной обработки с ЧПУ под названием Pulse-Turn, которая может поворачивать юбки поршней и другие некруглые детали в несколько раз быстрее, чем современные традиционные технологии.Хотя эта технология была разработана для обработки поршней, она показала большие перспективы и оценивается для таких разнообразных применений, как токарная обработка гидростатических подшипников и корпусов реактивных двигателей.
Поршни и другие некруглые детали можно обрабатывать с помощью бескулачковой системы Pulse-Turn на любом точном токарном станке с ЧПУ хорошего качества.Бескулачковая система Pulse-Turn полностью программируется и работает с точностью до нескольких микрон при вращении поршней и других сложных форм со скоростью до 6000 об / мин.Для поворота поршня контроллер Pulse-Turn Model 25 может быть запрограммирован на создание одно-, двух- и трехкоординатной овальности; переменная овальность; и профильные формы.
Pulse-Turn – это автономный аксессуар, который устанавливается на «подходящие» стандартные токарные станки с ЧПУ и состоит из державки / привода с режущим инструментом, усилителя и контроллера. Решающим моментом в пригодности токарного станка с ЧПУ является то, что он должен быть качественным и точным, будь то старинный или новый.Единственный необходимый интерфейс для токарного станка с ЧПУ – это подключение к подходящему датчику положения шпинделя.
Регулятор Pulse-Turn Model 25 можно запрограммировать на создание одно-, двух- и трехкоординатной овальности; переменная овальность и формы профиля.Механический режим Pulse-Turn значительно отличается от обычных современных методов обработки поршней. Большинство поршней с овальной юбкой обрабатываются токарными станками с кулачковым приводом или специализированными токарными станками с сервосистемами.Обе технологии управления обеспечивают большие перемещения инструмента при относительно низких скоростях. Когда целью является выполнение коротких перемещений со скоростью несколько тысяч циклов в минуту, особенно когда требуется высокая точность, их большие динамические массы представляют собой непреодолимые препятствия.
Привод Pulse-Turn представляет собой стержень, сделанный из «умного материала», называемый так потому, что он способен изменять свою физическую форму при воздействии внешнего раздражителя. В этом случае стимул представляет собой переменное программируемое магнитное поле, и это явление известно как магнитострикция.Материал, который был разработан в Военно-морской артиллерийской лаборатории в поисках лучшего преобразователя гидролокатора, создает силу тяги в 600 фунтов и, следовательно, имеет высокое ускорение.
Стержень импульсно-поворотного привода изготовлен из «интеллектуального материала», который создает тягу в 600 фунтов и быстрое ускорение при внешнем физическом воздействии переменного программируемого магнитного поля.При токарной обработке он производит деформацию до 1500 частей на миллион, т.е.е. стержень длиной 10 дюймов может расшириться на 0,015 дюйма от состояния покоя. Поскольку действие происходит на молекулярном уровне, количество движения может быть очень маленьким и очень повторяемым. Его реакция практически мгновенная, и его характеристики не ухудшаются со временем.
Резцедержатель / привод состоит из очень небольшого количества деталей, без прерывистого скольжения и поверхностей скольжения. Шток привода толкает рычажный механизм, который управляет державкой инструмента, которая подвешена на гибком звене. Общая движущаяся масса ограничена менее 2 фунтами.Pulse-Turn развивает силу тяги максимум 2670 Н (600 фунтов) и имеет точность позиционирования ± 1,1 мкм (0,000 044 дюйма) и 1% фактического хода. Повторяемость позиционирования составляет 2,2 мкм (0,000 088). Размер привода составляет 70x130x460 мм (6,7×5,15×18,2 дюйма), а вес – 22 кг (48,4 фунта).
Контроллер Pulse-Turn Model 25 включает в себя пользовательский интерфейс на базе Windows, высокоскоростной DSP и усилитель.
Active Technologies Inc, P.O. Box 1691, Morristown, NY 07962-1691; телефон: 973-889-9426
Под редакцией Джима Лоринца.