Для чего нужны токарные станки?
Токарный станок являлся одним из первых станков, придуманных человеком. Именно на его основе создавались позднее станки других групп, такие как сверлильные, расточные и пр. Токарные станки сегодня отличаются исключительным разнообразием. В общем смысле, токарный станок необходим для обработки тел вращения путём снятия с них при точении стружки. При этом он позволяет производить множество различных видов токарной обработки, которые возможны при помощи определённых приспособлений. Современные технические характеристики токарных станков настолько высоки, что делают их пригодными для решения огромного количества задач и незаменимыми практически для любого промышленного предприятия в сфере металлообработки. Технология работы токарного станка актуальна уже более 2х веков, а самые первые подобные станки появились ещё в 650 году до н.э. Сегодня же общий перечень работ, производимых на токарном станке, можно условно свести к резке, сверлению и обтачиванию.
Высокий уровень автоматизации промышленного производства привёл к появлению токарных станков с числовым программным управлением (ЧПУ). Такие станки обладают рядом особенностей. Это и закрытая кожухами зона резания, и наклонные направляющие для удаления стружки с рабочей зоны. Программирование станков с ЧПУ позволяет автоматически сменять инструменты, производить запуск, остановку и реверс привода главного движения, переключать скорости шпинделя и проводить многие другие операции. Такие универсальные станки используются, в основном, в мелкосерийном производстве, но при наличии определённых приспособлений пригодны и для серийного производства. Автоматические станки нуждаются в регулярной наладке и подаче материала. Полуавтоматические же не обладают автоматизированными движениями, связанными с установкой и снятием изделий. Станки с ЧПУ способны решать задачи, связанные с высокой точностью исполнения.
Сегодня владельцы мелких мастерских предпочитают использовать малогабаритные станки, вес которых позволяет переносить их без использования дополнительных инструментов. Такие станки занимают немного места и не требуют больших энергозатрат. Ими оборудуются даже мастерские в учебных заведениях.
Другие статьи
Для чего нужен токарный станок?
Что и говорить, а ответ на этот вопрос не предполагает множества вариантов. Естественно, для вытачки деталей. Казалось бы все очень просто. Но на самом деле количество и разнообразие таких деталей достаточно сложно перечислить. Потому как оно поражает своими размерами.
Естественно, все это правдиво лишь в том случае, когда используются исключительно качественные современные токарные станки. И здесь сайт http://16k20.ru/catalog/tokarnye-stanki/ придет на помощь. Потому как в каталоге представлено достаточное количество токарных станков, которое в состоянии удовлетворить потребности любого предприятия.
В настоящий момент особой популярностью пользуются станки с числовым программным управлением. Принцип их работы предельно прост. На начальной стадии в программу обработки детали вносятся необходимые данные, путем переноса их с носителя информации. Потому уже контроллер ЧПУ на основании этих данных и производит управление станком, благодаря чему и достигается полностью автоматическая обработка заданной детали.
Что и говорить, а при помощи такой системы, преимущества перед ручным станком налицо. Самое главное – это высокая производительность. Ведь здесь участие оператора необходимо только на начальной стадии, а, машина, естественно, работает быстрее.
Второй положительный момент – это обработка деталей абсолютно любой сложности. Конечно, есть специалисты высокого уровня, которые могут посоперничать с точностью с машиной, но всем же в большинстве случаев, автоматическая обработка выигрывает.
Кстати, при использовании токарного станка с ЧПУК необходимость в высококвалифицированных рабочих также сокращается. И еще одно неоспоримое достоинство – это возможность быстро перенастроить оборудование на изготовление новых деталей.
Вот и получается, что токарный станок при помощи модернизации переживает свое втрое рождение. И необходимость в таком оборудовании будет всегда.
Токарный станок – виды, принцип работы и применение, оcобенности
Токарный станок – это металлорежущее оборудование для обработки металлических деталей точением, а также используемый для ряда других операций. Основным рабочим инструментом является резец. Благодаря большому разнообразию форм и размеров резцов на токарном станке можно изготавливать самые различные детали с цилиндрическими, коническими и сферическими поверхностями, производить обработку различных металлов.
Виды оборудования
Токарные станки классифицируются по ряду параметров, в первую очередь по назначению, универсальности или специализации оборудования, по его конструктивным особенностям. Также они подразделяются по:
- классу точности при обработке детали;
- автоматизации;
- массе;
- мощности двигателя и другим параметрам.
По действующей в РФ классификации существуют следующие типы токарных станков:
- одно- и многошпиндельные автоматы и полуавтоматы;
- отрезные;
- винторезные;
- револьверные;
- карусельные;
- лобовые;
- специализированные;
- специальные.
Принцип работы
Обработка резанием производится при контакте резца с вращающейся заготовкой. Вращательное движение осуществляет шпиндель или планшайба, необходимое усилие и частоту обеспечивает электродвигатель через ременную передачу и коробку скоростей. Резец крепится в суппорте и может передвигаться в поперечном и продольном направлении. От скорости движения суппорта зависит амплитуда подачи.
Станки могут быть с вертикальной или горизонтальной компоновкой. Это зависит от положения шпинделя, на который устанавливается заготовка. Вертикальная компоновка оптимальна для обработки тяжелых и коротких деталей, горизонтальная – для длинных с небольшим или средним диаметром.
Основные преимущества токарной обработки:
- Высокая сложность изготавливаемых деталей.
- Возможность работы с любыми металлами.
- Высокое качество и точность обработки.
- Большая производительность.
Конструкция
Независимо от типа и модели, в конструкции станка есть несколько основных частей:
- Станина – основной элемент оборудования предназначенный для размещения всех узлов и систем.
- Фартук – узел преобразующий вращательное движение винта или вала в поступательное перемещение суппорта.
- Шпиндельная бабка. Состоит из шпинделя и коробки скоростей.
- Суппорт – узел станка для крепления рабочего инструмента и обеспечения требуемой для обработки заготовки движения подачи. Конструкция включает одну или несколько нижних кареток и верхнюю для установки резцедержателя.
- Коробка подач – обеспечивает передачу движения на суппорт с помощью ходового винта.
- Электрооборудование – электромотор, специальные элементы и органы управления.
Практически все элементы токарного оборудования унифицированы для упрощения технического обслуживания и ремонта.
Особенности токарной обработки
Качество и производительность токарной обработки напрямую зависит от правильности выбора режима реза. Для расчета берутся справочные данные о скорости для различных материалов – сталь, медь, чугун и т. д. Также необходимы данные о плотности материала и других его параметрах. При правильном определении режима реза обеспечивается высокоэффективная и экономичная обработка, увеличивается срок службы инструмента и оборудования.
Основными параметрами являются глубина резания, подача и скорость вращения. Также учитывается форма резца, материал инструмента и заготовки. При расчете определяется шероховатость заготовки и на основании этих данных – параметры обточки поверхностей.
ГОСТ
Основные параметры и нормы точности токарных станков регулирует ГОСТ 18097-93. Действуют и другие стандартны на различные типы токарного оборудования.
История токарного станка – полезная информация Токарно-винторезные станки по металлу
История относит изобретение токарного станка к 650 гг. до н. э. Станок представлял собой два установленных центра, между которыми зажималась заготовка из дерева, кости или рога. Раб или подмастерье вращал заготовку (один или несколько оборотов в одну сторону, затем в другую). Мастер держал резец в руках и, прижимая его в нужном месте к заготовке, снимал стружку, придавая заготовке требуемую форму.
Позднее для приведения заготовки в движение применяли лук со слабо натянутой (провисающей) тетивой. Тетиву оборачивали вокруг цилиндрической части заготовки так, чтобы она образовала петлю вокруг заготовки.
В XIV – XV веках были распространены токарные станки с ножным приводом. Ножной привод состоял из очепа – упругой жерди, консольно закрепленной над станком. К концу жерди крепилась бечевка, которая была обернута на один оборот вокруг заготовки и нижним концом крепилась к педали. При нажатии на педаль бечевка натягивалась, заставляя заготовку сделать один – два оборота, а жердь – согнуться. При отпускании педали жердь выпрямлялась, тянула вверх бечевку, и заготовка делала те же обороты в другую сторону.

В 1500 г. токарный станок уже имел стальные центры и люнет, который мог быть укреплен в любом месте между центрами.
На таких станках обрабатывали довольно сложные детали, представляющие собой тела вращения, – вплоть до шара. Но привод существовавших тогда станков был слишком маломощным для обработки металла, а усилия руки, держащей резец, недостаточными, чтобы снимать большую стружку с заготовки. В результате обработка металла оказывалась малоэффективной. Необходимо было заменить руку рабочего специальным механизмом, а мускульную силу, приводящую станок в движение, более мощным двигателем.
Появление водяного колеса привело к повышению производительности труда, оказав при этом мощное революционизирующее действие на развитие техники. А с середины XIV в. водяные приводы стали распространяться в металлообработке.
В середине XVI Жак Бессон (умер в 1569 г.) – изобрел токарный станок для нарезки цилиндрических и конических винтов.
В начале XVIII века Андрей Константинович Нартов (1693-1756), механик Петра первого, изобретает оригинальный токарно-копировальный и винторезный станок с механизированным суппортом и набором сменных зубчатых колес. Чтобы по-настоящему понять мировое значение этих изобретений, вернемся к эволюции токарного станка.
В XVII в. появились токарные станки, в которых обрабатываемое изделие приводилось в движение уже не мускульной силой токаря, а с помощью водяного колеса, но резец, как и раньше, держал в руке токарь. В начале XVIII в. токарные станки все чаще использовали для резания металлов, а не дерева, и поэтому проблема жесткого крепления резца и перемещения его вдоль обрабатываемой поверхности стола весьма актуальной. И вот впервые проблема самоходного суппорта была успешно решена в копировальном станке А.К.Нартова в 1712 г.
К идее механизированного передвижения резца изобретатели шли долго. Впервые эта проблема особенно остро встала при решении таких технических задач, как нарезание резьбы, нанесение сложных узоров на предметы роскоши, изготовление зубчатых колес и т.д. Для получения резьбы на валу, например, сначала производили разметку, для чего на вал навивали бумажную ленту нужной ширины, по краям которой наносили контур будущей резьбы. После разметки резьбу опиливали напильником вручную. Не говоря уже о трудоемкости такого процесса, получить удовлетворительное качество резьбы таким способом весьма трудно.
А Нартов не только решил задачу механизации этой операции, но в 1718-1729 гг. сам усовершенствовал схему. Копировальный палец и суппорт приводились в движение одним ходовым винтом, но с разным шагом нарезки под резцом и под копиром. Таким образом, было обеспечено автоматическое перемещение суппорта вдоль оси обрабатываемой заготовки. Правда, поперечной подачи еще не было, вместо нее было введено качание системы “копир-заготовка”. Поэтому работы над созданием суппорта продолжались. Свой суппорт создали, в частности, тульские механики Алексей Сурнин и Павел Захава. Более совершенную конструкцию суппорта, близкую к современной, создал английский станкостроитель Модсли, но А.К. Нартов остается первым, кто нашел путь к решению этой задачи.
Вторая половина XVIII в. в станкостроении ознаменовалась резким увеличением сферы применения металлорежущих станков и поисками удовлетворительной схемы универсального токарного станка, который мог бы использоваться в различных целях.
В 1751 г. Ж. Вокансон во Франции построил станок, который по своим техническим данным уже походил на универсальный. Он был выполнен из металла, имел мощную станину, два металлических центра, две направляющие V-образной формы, медный суппорт, обеспечивающий механизированное перемещение инструмента в продольном и поперечном направлениях. В то же время в этом станке отсутствовала система зажима заготовки в патроне, хотя это устройство существовало в других конструкциях станков. Здесь предусматривалось крепление заготовки только в центрах. Расстояние между центрами можно было менять в пределах 10 см. Поэтому обрабатывать на станке Вокансона можно было лишь детали примерно одинаковой длины.
В 1778 г. англичанин Д. Рамедон разработал два типа станков для нарезания резьб. В одном станке вдоль вращаемой заготовки по параллельным направляющим передвигался алмазный режущий инструмент, скорость перемещения которого задавалась вращением эталонного винта. Сменные шестерни позволяли получать резьбы с разным шагом. Второй станок давал возможность изготавливать резьбу с различным шагом на детали большей длины, чем длина эталона. Резец продвигался вдоль заготовки с помощью струны, накручивавшейся на центральную шпонку.
В 1795 г. французский механик Сено изготовил специализированный токарный станок для нарезки винтов. Конструктор предусмотрел сменные шестерни, большой ходовой винт, простой механизированный суппорт. Станок был лишен каких-либо украшений, которыми любили украшать свои изделия мастера прежде.
Накопленный опыт позволил к концу XVIII века создать универсальный токарный станок, ставший основой машиностроения. Его автором стал Генри Модсли. В 1794 г. он создал конструкцию суппорта, довольно несовершенную. В 1798 г., основав собственную мастерскую по производству станков, он значительно улучшил суппорт, что позволило создать вариант универсального токарного станка.
В 1800 г. Модсли усовершенствовал этот станок, а затем создал и третий вариант, содержавший все элементы, которые имеют токарно-винторезные станки сегодня. При этом существенно то, что Модсли понял необходимость унификации некоторых видов деталей и первым стал внедрять стандартизацию резьб на винтах и гайках. Он начал выпускать наборы метчиков и плашек для нарезки резьб.
Одним из учеников и продолжателей дела Модсли был Р. Робертс. Он улучшил токарный станок тем, что расположил ходовой винт перед станиной, добавил зубчатый перебор, ручки управления вынес на переднюю па нель станка, что сделало более удобным управление станком. Этот станок работал до 1909 г.
Другой бывший сотрудник Модсли – Д. Клемент создал лоботокарный станок для обработки деталей большого диаметра. Он учел, что при постоянной скорости вращения детали и постоянной скорости подачи по мере движения резца от периферии к центру скорость резания будет падать, и создал систему увеличения скорости.
В 1835 г. Д. Витворт изобрел автоматическую подачу в поперечном направлении, которая была связана с механизмом продольной подачи. Этим было завершено принципиальное совершенствование токарного оборудования.
Следующий этап – автоматизация токарных станков. Здесь пальма первенства принадлежала американцам. В США развитие техники обработки металлов началось позднее, чем в Европе. Американские станки первой половины XIХ в. значительно уступали станкам Модсли.
Во второй половине XIХ в. качество американских станков было уже достаточно высоким. Станки выпускались серийно, причем вводилась полная взаимозаменяемость деталей и блоков, выпускаемых одной фирмой. При поломке детали достаточно было выписать с завода аналогичную и заменить сломанную деталь на целую без всякой подгонки.
Во второй половине XIХ в. были введены элементы, обеспечивающие полную механизацию обработки – блок автоматической подачи по обеим координатам, совершенную систему крепления резца и детали. Режимы резания и подач изменялись быстро и без значительных усилий. В токарных станках имелись элементы автоматики – автоматический останов станка при достижении определенного размера, система автоматического регулирования скорости лобового точения и т. д.
Однако основным достижением американского станкостроения было не развитие традиционного токарного станка, а создание его модификации – револьверного станка. В связи с необходимостью изготовления нового стрелкового оружия (револьверов) С. Фитч в 1845 г. разработал и построил револьверный станок с восемью режущими инструментами в револьверной головке. Быстрота смены инструмента резко повысила производительность станка при изготовлении серийной продукции. Это был серьезный шаг к созданию станков-автоматов.
В деревообработке первые станки-автоматы уже появились: в 1842 г. такой автомат построил К. Випиль, а в 1846 г. Т. Слоан.
Первый универсальный токарный автомат изобрел в 1873г. Хр. Спенсер.
Суппорт токарного станка
Одним из важнейших достижений машиностроения в начале XIX века стало распространение металлорежущих станков с суппортами – механическими держателями для резца. Введение суппорта разом повлекло за собой усовершенствование и удешевление всех машин, дало толчок к новым усовершенствованиям и изобретениям.
Суппорт предназначен для перемещения во время обработки режущего инструмента, закрепленного в резцедержателе. Он состоит из нижних салазок (продольного суппорта) 1, которые перемещаются по направляющим станины с помощью рукоятки 15 и обеспечивают перемещение резца вдоль заготовки. На нижних салазках по направляющим 12 перемещаются поперечные салазки (поперечный суппорт) 3, которые обеспечивают перемещение резца перпендикулярно оси вращения заготовки (детали).
На поперечных салазках 3 расположена поворотная плита 4, которая закрепляется гайкой 10. По направляющим 5 поворотной плиты 4 перемещаются (с помощью рукоятки 13) верхние салазки 11, которые вместе с плитой 4 могут поворачиваться в горизонтальной плоскости относительно поперечных салазок и обеспечивать перемещение резца под углом к оси вращения заготовки (детали).
Резцедержатель (резцовая головка) 6 с болтами 8 крепится к верхним салазкам с помощью рукоятки 9, которая перемещается по винту 7. Привод перемещения суппорта производится от ходового винта 2, от ходового вала, расположенного под ходовым винтом, или вручную. Включение автоматических подач производится рукояткой 14.
Устройство поперечного суппорта показано на рисунке ниже. По направляющим продольного суппорта 1 ходовым винтом 12, оснащенным рукояткой 10, перемещаются салазки поперечного суппорта. Ходовой винт 12 закреплен одним концом в продольном суппорте 1, а другим – связан с гайкой (состоящей из двух частей 15 и 13 и клина 14), которая крепится к поперечным салазкам 9. Затягивая винт 16, раздвигают (клином 14) гайки 15 и 13, благодаря чему выбирается зазор между ходовым винтом 12 и гайкой 15.
Величину перемещения поперечного суппорта определяют по лимбу 11. К поперечному суппорту крепится (гайками 7) поворотная плита 8, вместе с которой поворачиваются верхние салазки 6 и резцедержатель 5. На некоторых станках на поперечных салазках 9 устанавливается задний резцедержатель 2 для проточки канавок, отрезки и других работ, которые могут быть выполнены перемещением поперечного суппорта, а также кронштейн 3 с щитком 4, защищающим рабочего от попадания стружки и смазочно-охлаждающей жидкости.
Токарный станок имеет весьма древнюю историю, причем с годами его конструкция менялась очень незначительно. Приводя во вращение кусок дерева, мастер с помощью долота мог придать ему самую причудливую цилиндрическую форму. Для этого он прижимал долото к быстро вращающемуся куску дерева, отделял от него круговую стружку и постепенно давал заготовке нужные очертания. В деталях своего устройства станки могли довольно значительно отличаться друг от друга, но вплоть до конца XVIII века все они имели одну принципиальную особенность: при обработке заготовка вращалась, а резец находился в руках мастера.
Исключения из этого правила были очень редкими, и их ни в коем случае нельзя считать типичными для этой эпохи. Например, держатели для резца получили распространение в копировальных станках. С помощью таких станков работник, не обладавший особыми навыками, мог изготовлять затейливые изделия очень сложной формы. Для этого пользовались бронзовой моделью, имевшей вид изделия, но большего размера (обычно 2:1). Нужное изображение получали на заготовке следующим образом.
Станок оборудовался двумя суппортами, позволявшими вытачивать изделия без участия руки работника: в одном был закреплен копировальный палец, в другом – резец. Неподвижный копировальный палец имел вид стержня, на заостренном конце которого помешался маленький ролик. К ролику копировального пальца специальной пружиной постоянно прижималась модель. Во время работы станка она начинала вращаться и в соответствии с выступами и впадинами на своей поверхности совершала колебательные движения.
Эти движения модели через систему зубчатых колес передавались вращающейся заготовке, которая повторяла их. Заготовка находилась в контакте с резцом, подобно тому, как модель находилась в контакте с копировальным пальцем. В зависимости от рельефа модели заготовка то приближалась к резцу, то удалялась от него. При этом менялась и толщина стружки. После многих проходов резца по поверхности заготовки возникал рельеф, аналогичный имевшемуся на модели, но в меньшем масштабе.
Копировальный станок был очень сложным и дорогим инструментом. Приобрести его могли лишь весьма состоятельные люди. В первой половине XVIII века, когда возникла мода на точеные изделия из дерева и кости, токарными работами занимались многие европейские монархи и титулованная знать. Для них большей частью и предназначались копировальные станки.
Но широкого распространения в токарном деле эти приспособления не получили. Простой токарный станок вполне удовлетворял всем потребностям человека вплоть до второй половины XVIII века. Однако с середины столетия все чаще стала возникать необходимость обрабатывать с большой точностью массивные железные детали. Валы, винты различной величины, зубчатые колеса были первыми деталями машин, о механическом изготовлении которых встал вопрос тотчас же после их появления, так как они требовались в огромном количестве.
Особенно остро нужда в высокоточной обработке металлических заготовок стала ощущаться после внедрения в жизнь великого изобретения Уатта. Изготовление деталей для паровых машин оказалось очень сложной технической задачей для того уровня, которого достигло машиностроение XVIII века.
Обычно резец укреплялся на длинной крючкообразной палке. Рабочий держал его в руках, опираясь как на рычаг на специальную подставку. Этот труд требовал больших профессиональных навыков и большой физической силы. Любая ошибка приводила к порче всей заготовки или к слишком большой погрешности обработки.
В 1765 году из-за невозможности рассверлить с достаточной точностью цилиндр длиной в два фута и диаметром в шесть дюймов Уатт вынужден был прибегнуть к ковкому цилиндру. Расточка цилиндра длиною в девять футов и диаметром в 28 дюймов допускала точность до “толщины маленького пальца”.
С начала XIX века начался постепенный переворот в машиностроении. На место старому токарному станку один за другим приходят новые высокоточные автоматические станки, оснащенные суппортами. Начало этой революции положил токарный винторезный станок английского механика Генри Модсли, позволявший автоматически вытачивать винты и болты с любой нарезкой.
Нарезка винтов долго оставалась сложной технической задачей, поскольку требовала высокой точности и мастерства. Механики давно задумывались над тем, как упростить эту операцию. Еще в 1701 году в труде Ш. Плюме описывался способ нарезки винтов с помощью примитивного суппорта.
Для этого к заготовке припаивали отрезок винта в качестве хвостовика. Шаг напаиваемого винта должен был быть равен шагу того винта, который нужно было нарезать на заготовке. Затем заготовку устанавливали в простейших разъемных деревянных бабках; передняя бабка поддерживала тело заготовки, а в заднюю вставлялся припаянный винт. При вращении винта деревянное гнездо задней бабки сминалось по форме винта и служило гайкой, вследствие чего вся заготовка перемещалась в сторону передней бабки. Подача на оборот была такова, что позволяла неподвижному резцу резать винт с требуемым шагом.
Подобного же рода приспособление было на токарно-винторезном станке 1785 года, который был непосредственным предшественником станка Модсли. Здесь нарезка резьбы, служившая образцом для изготавливаемого винта, наносилась непосредственно на шпиндель, удерживавший заготовку и приводивший ее во вращение. (Шпинделем называют вращающийся вал токарного станка с устройством для зажима обрабатываемой детали.) Это давало возможность делать нарезку на винтах машинным способом: рабочий приводил во вращение заготовку, которая за счет резьбы шпинделя, точно так же как и в приспособлении Плюме, начинала поступательно перемещаться относительно неподвижного резца, который рабочий держал на палке.
Таким образом, на изделии получалась резьба, точно соответствующая резьбе шпинделя. Впрочем, точность и прямолинейность обработки зависели здесь исключительно от силы и твердости руки рабочего, направлявшего инструмент. В этом заключалось большое неудобство. Кроме того, резьба на шпинделе была всего 8-10 мм, что позволяло нарезать только очень короткие винты.
Винторезный станок, сконструированный Модсли, представлял собой значительный шаг вперед. История его изобретения так описывается современниками. В 1794-1795 годах Модсли, еще молодой, но уже весьма опытный механик, работал в мастерской известного изобретателя Брамы.
Перед Брамой и Модсли стояла задача увеличить число деталей, изготавливаемых на станках. Однако старый токарный станок был для этого неудобен. Начав работу по его усовершенствованию, Модсли в 1794 году снабдил его крестовым суппортом.
Нижняя часть суппорта (салазки) устанавливались на одной раме с задней бабкой станка и могла скользить вдоль ее направляющей. В любом ее месте суппорт мог быть прочно закреплен при помощи винта. На нижних салазках находились верхние, устроенные подобным же образом. С помощью них резец, закрепленный винтом в прорези на конце стального бруска, мог перемещаться в поперечном направлении.
Движение суппорта в продольном и поперечном направлениях происходило с помощью двух ходовых винтов. Подвинув резец с помощью суппорта вплотную к заготовке, жестко установив его на поперечных салазках, а затем перемещая вдоль обрабатываемой поверхности, можно было с большой точностью срезать лишний металл. При этом суппорт выполнял функцию руки рабочего, удерживающего резец. В описываемой конструкции, собственно, не было еще ничего нового, но она была необходимым шагом к дальнейшим усовершенствованиям.
Уйдя вскоре после своего изобретения от Брамы, Модсли основал собственную мастерскую и в 1798 году создал более совершенный токарный станок. Этот станок стал важной вехой в развитии станкостроения, так как он впервые позволил автоматически производить нарезку винтов любой длины и любого шага.
Слабым местом прежнего токарного станка было то, что на нем можно было нарезать только короткие винты. Иначе и быть не могло ведь там не было суппорта, рука рабочего должна была оставаться неподвижной, а двигалась сама заготовка вместе с шпинделем. В станке Модсли заготовка оставалась неподвижной, а двигался суппорт с закрепленным в нем резцом.
Для того чтобы заставить суппорт перемещаться на нижних салазках вдоль станка, Модсли соединил с помощью двух зубчатых колес шпиндель передней бабки с ходовым винтом суппорта. Вращающийся винт вкручивался в гайку, которая тянула за собой салазки суппорта и заставляла их скользить вдоль станины. Поскольку ходовой винт вращался с той же скоростью, что и шпиндель, то на заготовке нарезалась резьба с тем же шагом, что была на этом винте. Для нарезки винтов с различным шагом при станке имелся запас ходовых винтов.
Автоматическое нарезание винта на станке происходило следующим образом. Заготовку зажимали и обтачивали до нужных размеров, не включая механической подачи суппорта. После этого соединяли ходовой винт со шпинделем, и винтовая нарезка осуществлялась за несколько проходов резца. Обратный отход суппорта каждый делался вручную после отключения самоходной подачи. Таким образом, ходовой винт и суппорт полностью заменяли руку рабочего. Мало того, они позволяли нарезать резьбу гораздо точнее и быстрее, чем на прежних станках.
В 1800 году Модсли внес замечательное усовершенствование в свой станок – взамен набора сменных ходовых винтов он применил набор сменных зубчатых колес, которые соединяли шпиндель и ходовой винт (их было 28 с числом зубьев от 15 до 50).
На своем станке Модсли выполнял нарезку резьб с такой изумительной точностью и аккуратностью, что это казалось современникам почти чудом. Он, в частности, нарезал регулировочные винт и гайку для астрономического прибора, который в течение долгого времени считался непревзойденным шедевром точности. Винт имел пять футов длины и два дюйма в диаметре с 50-ю витками на каждый дюйм. Резьба была такой мелкой, что ее невозможно было рассмотреть невооруженным глазом. В скором времени усовершенствованный Модсли станок получил повсеместное распространение и послужил образцом для многих других металлорежущих станков. В 1817 году был создан строгальный станок с суппортом, позволивший быстро обрабатывать плоские поверхности. В 1818 году Уитни придумал фрезерный станок. В 1839 году появился карусельный станок и т.д.
Нартов Андрей Константинович (1683 – 1756)
Деятель времени Петра Великого. Русский механик и изобретатель. Учился в Школе математических и навигацких наук в Москве. Около 1718 года был послан царем за границу для усовершенствования в токарном искусстве и “приобретения знаний в механике и математике”. По указанию Петра I, Нартов вскоре был переведен в Петербург и назначен личным токарем царя в дворцовой токарной мастерской.
Работая здесь в 1712-1725, Нартов изобрел и построил ряд совершенных и оригинальных по кинематической схеме токарных станков (в том числе копировальных), часть которых была снабжена механическими суппортами. С появлением суппорта решалась задача изготовления частей машин строго определенной геометрической формы, задача производства машин машинами.
В 1726-1727 и в 1733 Нартов работал при Московском монетном дворе, где создал оригинальные монетные станки. В том же 1733 году Нартов создал механизм для подъема “Царь колокола”. После смерти Петра, Нартову было поручено сделать “триумфальный столп” в честь императора, с изображением всех его “баталий”.
Когда в Академию Наук были сданы все токарные принадлежности и предметы Петра, а также и “триумфальный столп”, то, по настоянию начальника академии, барона Корфа, считавшего Нартова единственным человеком, способным окончить “столп”, он был переведен в академию “к токарным станкам”, для заведывания учениками токарного и механического дела и слесарями. Петровская токарня, превращенная Нартовым в академические мастерские, послужила базой для последующих работ М. В. Ломоносова, а затем И. П. Кулибина (особенно в области приборостроения).
В 1742 году Нартов принес Сенату жалобу на советника академии Шумахера, с которым у него происходили пререкания по денежному вопросу, а затем добился назначения следствия над Шумахером, на место которого был определен сам Нартов. В этой должности он пробыл только 1,5 года, потому что оказался “ничего кроме токарного художества незнающим и самовластным”; он велел запечатать архив академической канцелярии, грубо обращался с академиками, и наконец, довел дело до того, что Ломоносов и другие члены стали просить возвращения Шумахера, который вновь вступил в управление академией в 1744 году, а Нартов сосредоточил свою деятельность “на пушечно-артиллерийском деле”.
1738-1756, работая в Артиллерийском ведомстве, Нартов создал станки для сверления канала и обточки цапф пушек, оригинальные запалы, оптический прицел; предложил новые способы отливки пушек и заделки раковин в канале орудия. В 1741 Нартов изобрел скорострельную батарею из 44 трехфунтовых мортирок. В этой батарее впервые в истории артиллерии был применен винтовой подъемный механизм, который позволял придавать мортиркам желаемый угол возвышения.
В обнаруженной рукописи Нартова “Ясное зрелище махин” описывается более 20 токарных, токарно-копировальных, токарно-винторезных станков различных конструкций. Выполненные Нартовым чертежи и технические описания свидетельствуют о его больших инженерных познаниях. Он издал также: “Достопамятные повествования и речи Петра Великого” и “Театрум махинарум”.
Генри Модсли (Maudslay Henry 1771-1831)
Английский механик и промышленник. Создал токарно-винторезный станок с механизированным суппортом (1797), механизировал производство винтов, гаек и др. Ранние годы провел в Вулвиче под Лондоном.
В 12 лет стал работать набивальщиком патронов в Вулвичском арсенале, а в 18 лет он лучший кузнец арсенала и слесарь-механик, в мастерской Дж. Брама – лучшей мастерской Лондона. Позже открыл собственную мастерскую, потом завод в Ламбете.
Создал “Лабораторию Модсли”. Дизайнер. Машиностроитель. Создал механизированный суппорт токарного станка, собственной конструкции. Придумал оригинальный набор сменных зубчатых колес. Изобрел поперечно-строгальный станок с кривошипно-шатунным механизмом. Создал или усовершенствовал большое количество различных металлорежущих станков. Строил для России паровые корабельный машины.
Токарно винторезный станок
Общее описание токарно-винторезного станка
Токарно винторезный станок – оборудование, которое используется для обработки заготовок из металлов и других материалов точением (резанием). С помощью токарных станков осуществляют расточку и обточку цилиндрических, конических и фасонных поверхностей, нарезание резьбы, подрезку и обработку торцов, сверление, зенкерование, развертывание отверстий и другие работы.
На Токарно винторезном станке простой принцип работы: заготовка, которая зажата в горизонтальном положении, начинает вращаться и резцом, который подвижен, снимается не нужный материал. Но для того чтобы осуществить этот принцип, нужен механизм, который состоит из большого количества точно пригнанных элементов.
Токарные станки объединяют девять видов станков, которые отличаются по различным признакам: по конструктивной компоновке, по назначению, по степени автоматизации.
Использование на станках специальных дополнительных устройств (для фрезерования, для шлифования, для сверления радиальных отверстий) сильно расширяет технологическую функциональность оборудования.
Токарные станки, автоматы и полуавтоматы, делятся на вертикальные и горизонтальные, в зависимости от размещения шпинделя, который несет приспособление для установки заготовки детали, которая обрабатывается.
Вертикальные станки в основном используются для обработки деталей крупных размеров и массы, но небольшой
длины. Наиболее известные токарные станки во времена советского союза – 16К20 и 1К62.
Токарный станок предназначен для обработки материалов резанием, для того чтобы получить детали в форме тел вращения. На сегодняшний день есть несколько основных видов токарных станков. Самая универсальная техника токарной группы – это токарно-винторезные станки, которые применяют в условиях мелкосерийного
производства. А токарно-винторезные станки, в свою очередь, тоже разделяются на виды:
Устройство токарно винторезного станка
Токарно-винторезный станок имеет свое индивидуальное устройство. Основной корпус техники является неподвижным, а инструмент начинает свою работу, нажатием специальных головок. Деталь, которая получается в процессе обработки можно применять в таких операциях. Сейчас многие считают, что использование токарно- винторезного станка осуществляется не оптимально. Обработку материалов можно увеличить и проводить с большей эффективностью. Но элементом, получаемым производителями после работы, обычно довольны.
Токарно-винторезный станок – оси
Токарно-винторезный станок оси – это достаточно новое оборудование.
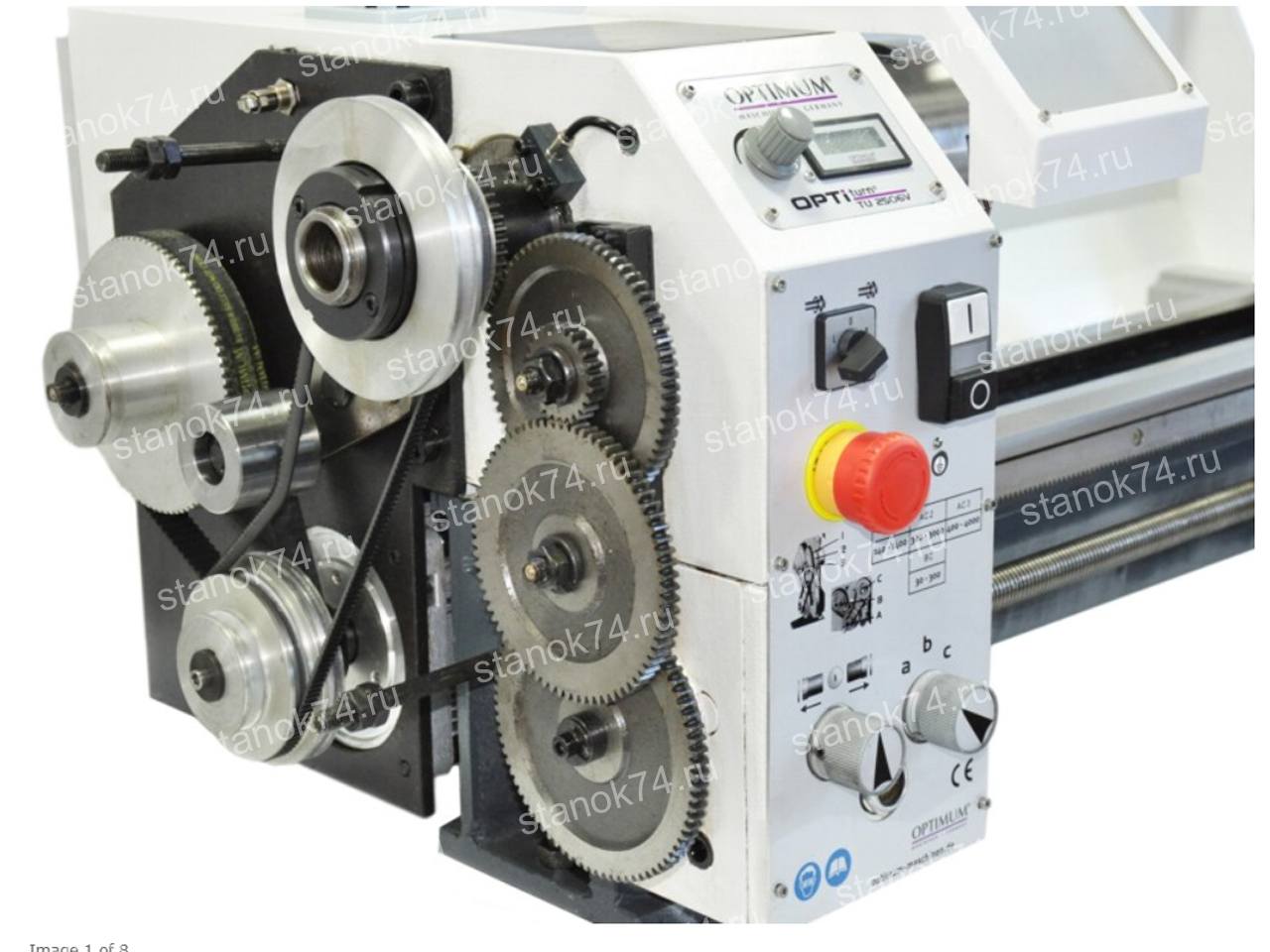
На токарном станке данного типа принцип работы достаточно простой и понятный даже тем людям, которые никогда не сталкивались с промышленностью. В момент, когда оборудование стыкуется с заготовкой, которую нужно обработать, то он начинает скользить по её поверхности. И поэтому процесс обработки становится быстрым, легким, ну и качественным.
Токарно-винторезный станок типа CNC
Данный станок в состоянии заменить старый вид оборудования. Мультишпиндель и другие инструменты станков CNC имеют ряд преимуществ: просты в установке и легки в эксплуатации. Такая техника в полном объеме отвечает тенденциям сегодняшней разработки рабочих мест.
Показатели токарно-винторезных станков CNC намного
выше других существующих типов оборудования данного класса. Можно отметить, что организации, которые
приобретают такие станки, решают свои проблемы с производительностью на все сто процентов.
Токарно-винторезный станок с легкостью можно считать наиболее универсальным станком из всех существующих
станков токарной группы. Он используется в условиях мелкосерийного и единичного производства разнообразных
деталей. Сейчас за счет своей универсальности он пользуется большим спросом во многих организациях, которые
работают в металлообрабатывающей промышленности.
Такую популярность обеспечивает большой спектр
задач, которые он выполняет. Это и большая степень производительности, и надежность, и высокая точность
обработки деталей. Наиболее известным токарно-винторезным станком в советском союзе был 16К20. Работа этого
станка базируется на снятии стружки с заготовок продукции при точении, таким образом обрабатываются чаще
всего тела вращения. Также к станкам токарной группый входят и токарно карусельные станки.
Токарные станки позволяют обрабатывать внутренние и наружные поверхности. Техника дает возможность обтачивать детали разнообразных форм (фасонных, конических, цилиндрических), выполнять сверление, растачивание, развертывание отверстий, подрезку торцов, накатку рифлений, нарезание резьбы и другие операции. Также возможность применения специального оборудования даст вам возможность выполнять и другую работу. К примеру, вы сможете осуществлять фрезерование, шлифование, нарезание зубьев и другие.
Токарно-винторезная техника, в первую очередь, предназначена для единичного и мелкосерийного
производства. Но, если необходимо, его можно будет оборудовать дополнительными приспособлениями и
устройствами, которые дадут возможность расшириться до серийного производства. В массовом производстве
используются токарные и револьверные полуавтоматы и автоматы. Обслуживание автомата подразумевает
периодическую наладку, подачу материала на станок и контроль обрабатываемых деталей.
В полуавтомате же движения, которые связаны со снятием и загрузкой заготовок, не автоматизированы. Автоматическое управление рабочим процессом таких токарно-винторезных станков выполняется благодаря распределительному валу, где установлены кулачки.
Какие бывают основные принадлежности для токарных станков?
Содержание:
- 1. Для крепления заготовки
- 2. Приспособления для крепления оснастки
Хотите переоборудовать Ваш токарный станок под деревообработку (Jet BD-7) или планируете обрабатывать заготовки не только цилиндрической, но и призматической формы? Для этого Вам понадобятся дополнительные принадлежности. А именно упор и цанговый патрон. Но они не поставляются в комплекте к оборудованию, что же делать? Ответ прост – их всегда можно подобрать отдельно. Встречаются и другие случаи, когда требуются приспособления такого рода. Какие они бывают, когда нужны и как правильно выбрать наиболее подходящие? Это мы расскажем в данной статье.
Для крепления заготовки
Патрон
Цанговый для зажима имеет цанги (пружинящие разрезные втулки). Они могут иметь цилиндрическую или призматическую форму. Особенно удобны такие патроны при производстве металлических деталей различных форм. В цанге можно зажать как обычный прут, так и шести- или четырехгранную заготовку, без опасности, что грани деформируются, или такая деталь будет закреплена недостаточно надежно. Кроме того цанги имеют разный диаметр и очень легко заменяются в патроне, что позволит обрабатывать самые различные заготовки с минимальными потерями по времени. Если втулки подходящего калибра не было в наборе, её всегда можно докупить. Обратите внимание, что далеко не на каждый станок можно установить патрон этого вида, к примеру, его можно закрепить на токарных станках по металлу Jet (BD-7, BD-8).
Кулачковый – самый распространенный вид патрона. Обычно он имеет несколько (от 2 до 6) цельных или сборных кулачков и устанавливается на шпиндель станка через переходной фланец, который можно приобрести отдельно, к примеру, для замены при износе.
Лучше всего такой патрон подходит для работ с круглыми заготовками. Диаметр патрона может быть от 80 до 400 мм. В зависимости от выбранного значения в нем можно будет закреплять прут с максимальным диаметром от 25 до 200 мм. Данное приспособление бывает быстрозажимным или ключевым. У последнего сила зажима регулируется вручную. Это очень важно, например, при обработке мягких металлов или дерева, где есть опасность повредить деталь при слишком сильном зажатии. Кроме того, это является гарантией, что фиксация всегда будет надежной и не будет опасности, что из-за изношенного быстрозажимного механизма заготовка вылетит или уйдет вглубь патрона.
Обратите внимание: после длительного использования может возникать незначительное биение детали при вращении, из-за стачивания одного или нескольких кулачков и соответственно смещения центра. Чтобы это исправить, кулачки растачиваются. При расточке важно учесть, из какого материала они выполнены, чтобы правильно подобрать резец. К примеру, закаленные кулачки растачивают твердосплавным расточным резцом. Отметим, что рано или поздно растачивать кулачки будет некуда и патрон придется заменять полностью.
Поводковый – применяется на токарных станках по дереву (Jet MK-2, Энкор Корвет-76). Он имеет несколько зубцов, которые захватывают заготовку. Для крепления детали необходимо с помощью углового центроискателя карандашом отметить на бруске центр, просверлить там отверстие 3-5 мм глубиной, туда установить центральный зуб патрона и ударить по хвостовику киянкой для лучшего сцепления. Далее следует вставить приспособление в переднюю бабку и надеть на него заготовку. Преимущества такого патрона в более простом и быстром способе крепления бруска и в доступной цене.
Планшайба
Крепежная принадлежность, представляющая собой металлическую шайбу толщиной 10-15 мм с отверстиями различной формы. Она накручивается на шпиндель станка и применяется для фиксации заготовок большого диаметра или деталей с несимметричным сечением. Для крепления используются болты. Причем в случае зажатия деревянных заготовок они выполняют функцию зубцов, как у поводкового патрона. А когда закрепляются металлические детали, используется система резьбового соединения. Главный плюс такого устройства – очень надежное крепление заготовки на станке без необходимости дополнительной фиксации со стороны задней бабки.
Вращающийся центр
Приспособление, которое применяется при обработке металлических и деревянных деталей большой длины для исключения биения заготовки. А также при обработке материалов небольшой жесткости и в прочих случаях, когда требуется фиксация детали с обоих концов. Устанавливается центр в пиноль задней бабки. В своей конструкции он имеет вращающуюся на роликовом и шариковом подшипниках головку. Самая распространенная её форма – конус, но есть вращающиеся центры со сменными насадками в виде трех или четырехгранной пирамиды разных размеров, параллелепипеда и пр. Такой вид приспособления удобен при обработке деталей с различными отверстиями в основании. Конус Морзе (хвостовик) центра, который закрепляется в пиноли, может иметь номер от 1 до 6. Выбор подходящего следует производить в зависимости от модели станка. Обратите на это внимание, в противном случае Вы попросту не сможете установить оснастку на оборудование.
Люнеты
Основное назначение этого приспособления – организация дополнительной опоры для металлических заготовок с длиной, в 10-12 раз превышающей их диаметр. Используются люнеты для предотвращения прогибов и биения деталей, без них работа значительно усложняется. Встречаются два вида данных элементов:
Приспособления для крепления оснастки
Резцедержатель
Также важная деталь любого токарного станка по металлу, она служит для крепления оснастки.
Позиционный – самый распространенный тип, на котором можно закрепить от 1 до 4-х различных режущих инструментов с квадратной державкой (Резцедержатель двухпозиционный для токарного станка BD-7 Jet 50000914). Смена установленной оснастки производится поворотом держателя с помощью специальной рукоятки. Преимущество данной принадлежности в доступной цене.
Картриджный – резцедержатель, представляющий собой основу, на которую закрепляется сменный картридж с резцом (Резцедержатель MultiFix для токарно-винторезных станков серии ZX Jet 956602А). Удобно такое устройство тем, что количество картриджей, а соответственно и оснастки, не ограничено, как в случае с позиционным приспособлением. При этом картриджи бывают двух типов:
- D – для закрепления резцов с квадратной державкой.
- H – для фиксации оснастки с цилиндрическим основанием.
Упор
Приспособление, также называемое подручником, которое служит как подставка для стамески. Используется оно на токарных станках для деревообработки и представляет собой металлическую пластину, на которую при обточке опирается резец. Упор является регулируемым по высоте для настройки на различные виды обточки, например, при тангенциальном резание оснастка должна находиться выше оси заготовки. Данная принадлежность Вам может понадобиться, если старая пришла в негодность или если Вы переоборудуете токарный станок по металлу под деревообработку.
Внимание: переоборудовать можно не каждую модель техники. Предварительно уточните в инструкции по эксплуатации, допускает ли это Ваша.
Совет: важно чтобы подручник легко перемещался как параллельно, так и перпендикулярно детали, а также, чтобы его можно было быстро зафиксировать в необходимом положении. Это ускорит Вашу работу и исключит рывки, из-за которых стамеска может соскочить.
Сверлильный патрон
Специальный вид патрона для закрепления сверел, зенкеров и разверток. Данное приспособление по строению идентично с кулачковым патроном электродрели, закрепляется в пиноли задней бабки с помощью конуса Морзе, также как и вращающийся центр. Без него не обойтись, если Вы планируете изготавливать детали с отверстиями. Обратите внимание, для его установки важно чтобы у станка был ход пиноли задней бабки (в некоторых моделях он составляет 100 мм – Токарный станок JWL-1442 708358LM).
Не важно какая из дополнительных принадлежностей Вам понадобилась, в нашем интернет-магазине представлены все из перечисленных. Выбор подходящей осуществить очень просто – в её названии всегда указывается, для какого станка эта оснастка предназначена, причем это может быть как целая группа оборудования, так и конкретные модели. Чтобы оформить заказ того или иного приспособления – позвоните нашим менеджерам по бесплатному телефону.
Бывший в употреблении токарный станок — стоит ли покупать?
Для домашней мастерской не всегда нужно дорогостоящее новое оборудование. Не помешает купить бывший в употреблении токарный станок и для производственного предприятия, если предстоит обрабатывать небольшие по объемам детали. В любом случае, необходимо определить уровень работоспособности технического устройства, состояние его основных механизмов.
Для чего нужен токарный станок
На токарном станке обрабатывают заготовки из различных материалов. По конструктивным особенностям основных узлов можно выделить:
- Электрический двигатель, расположенный на передней панели. Запуск силового агрегата происходит от нажатой кнопки. Мотор скрыт внутри корпуса, наиболее частые поломки –это выход из строя подшипников, которые заменяют при ремонте.
- В тумбе поместили щит электрооборудования, которым регулируют режим проведения операций.
- На станину прикреплены рабочие механизмы с деталями.
- На передней бабке установлен шпиндель.
- Подвижная часть состоит из задней бабки, куда фиксируют заготовку.
- Резец получает силовое движение от суппорта.
Техническое оборудование для выполнения токарных обработок классифицируются по виду работ:
- Винторезному.
- Фрезерному.
- Карусельному.
- Лобовому.
- Затыловочному.
Станки бывают:
- Специализированными.
- Автоматами и полуавтоматами.
При покупке бывшего в употреблении устройства нужно обращать внимание на технические характеристики по параметрам:
- Массы.
- Производственной мощности.
- Количества производимых оборотов.
- Центровых высот.
- Максимальных размеров обрабатываемых заготовок.
- Скорости.
Механические приспособления всегда имеют положительные и отрицательные свойства.
Плюсы оборудования
Даже старый станок, если был в руках у мастера, который следил за оборудованием, вовремя смазывал соприкасаемые детали, был выпущен хорошим производителем, принесет много пользы.
Такое механическое устройство позволяет:
- Создавать внешнюю и внутреннюю резьбу с разными шагами.
- Вытачивать изделия по требуемым размерам.
- Производить конусные и цилиндрические предметы.
- Растачивать болванки.
- Отделывать грани по боковым поверхностям.
- Высверливать разъемы.
- Обрезать лишние фрагменты.
Цена подержанных механизмов значительно меньше чем у новой техники, поэтому не стоит тратиться на дорогостоящие инструменты, если поставленные задачи выполнит бывший в употреблении прибор.
Какие минусы сопровождают покупку
Токарный станок является техническим средством, которое выполняет скоростные вращения, имеет острую режущую часть, поэтому опасен для новичков.
Недостатки работы на токарных станках как старых, так и новых, заключены в следующих моментах:
- Мастер должен иметь навыки производства, эксплуатации, знать свойства металлов, дерева, всех материалов, чтобы не было брака.
- Часто для выполнения операций нужно читать чертежи, понимать размеры, допуски – только так можно добиться качественной обработки.
- Токарю необходимо соблюдать технику безопасности для защиты своего здоровья от травм.
Обслуживание станка трудоемкая деятельность, где:
- Удаляют остаточные скопления стружки.
- Смазывают детали, выполняющие роль направляющих.
- Заменяют машинное масло.
- Проверяют электропроводку с двигателем.
- Протирают ветошью загрязненные места.
Минус старых станков в том, что они должны соответствовать времени по техническому состоянию, которое на месте не стоит, появляются совершенные устройства, их не нужно постоянно ремонтировать. На бывшей в употреблении технике могут быть сильно изношены детали, а в продаже многих аналогов для замены не найти. Придется делать чертеж и обращаться к токарю, работающему на новом оборудовании, чтобы он выточил запасную часть.
Рекомендации мастерам от токарей
Существует определенный порядок при покупке оборудования:
- Необходима личная встреча с продавцом.
- Не следует спешить совершать дистанционные сделки или нужно потребовать показать фото, переговорить по телефону, чтобы узнать параметры.
При контрольном осмотре б/у устройств можно заметить царапины на станине, что не всегда подтверждает её износ. Возможно хозяин был не аккуратный, который не проводил систематической смазки и правильной уборки. Но покупать нужно станок с направляющими, у которых минимальный износ по всей длине поверхности.
Перед покупкой проводят диагностику, где:
- Корпус должен быть без дефектов.
- Работа всех узлов четкая и бесперебойная на любой заявленной скорости.
- Подвижные детали действуют без люфтов.
- Рабочий ход плавный.
- Заготовки после обработки получаются с точными размерами.
Каждый станок выбирают для выполнения работ по его предназначению:
- Винторезное устройство используют для обработки металлических заготовок, они не должны быть большими по диаметру.
- Карусельные механизмы применяют для деталей объемных, где их растачивают, подрезают торцы, точат болванки.
- На лоботокарных станках отделывают конические, цилиндрические и фасонные поверхности.
- Револьверным приспособлением отрабатывают заготовки из калиброванных прутков, они подвергаются обточке, резке, сверлению отверстий.
- Агрегаты для проточного точения применяют в мелкосерийных партиях, куда идут калиброванные прутки или фасонная проволока.
В продаже много разных механизированных инструментов. Перед выбором не только проверяют на износ каждую деталь, но и определяются с индивидуальным направлением работ. В домашнюю мастерскую можно установить мини-станок. Такое оборудование скопировали по чертежам больших заводских механизмов. На установках можно производить изделия маленькие по размерам, но с аналогичными формами:
- Сферическими.
- Цилиндрическими.
- Конусными.
Такие аппараты подойдут для:
- Автомастерской.
- Обучения школьников.
- Цеха в научном институте, где проводят различные исследования с металлами.
Несмотря на высокую функциональность, миниатюрные технические средства не подойдут для работы на промышленных производствах, где необходимы большие объемы.
Похожие записи
Что такое токарный станок и как он работает
Сегодня мы собираемся ответить на популярный вопрос обработки:
Что такое токарный станок?
Если вы подумываете о токарных работах и хотите узнать больше о том, что делает этот инструмент, вы попали в нужное место. Вот некоторые основы токарного станка, которые помогут вам понять, что это такое, как он работает и почему он может быть полезен в вашем следующем проекте:
1.
Токарный станок – это обрабатывающий инструмент, который используется в основном для обработки металла или дерева.Он работает, вращая заготовку вокруг неподвижного режущего инструмента. Основное применение – удаление ненужных частей материала, после чего остается заготовка красивой формы.
Есть много типов токарных станков, которые специализируются на различных материалах и технологиях. Здесь, в All Metals Fabricating, у нас есть четыре различных типа токарных станков, в том числе токарный станок с активными инструментами для многозадачных работ.
Люди использовали токарные станки для изготовления деталей для другого оборудования, а также для изготовления специальных предметов, таких как чаши и музыкальные инструменты.Независимо от типа и функции, все они работают с использованием этого основного механизма удержания и вращения.
2. Детали токарного станка Основными частями токарного станка являются станина, передняя бабка, задняя бабка, шпиндели, опора для инструмента и двигатель. Вот как это работает:
Все части токарного станка прикреплены к станине. Это составляет основу токарного станка и является одним из факторов, определяющих размер детали. То есть расстояние от главного шпинделя до станины покажет вам максимальный предел диаметра.
Правильная ориентацияПередняя бабка должна быть слева, а задняя бабка – справа. Если вы видите обратное, проверьте и убедитесь, что вы не стоите не с той стороны токарного станка.
На передней бабке происходит основное действие. Здесь мощность двигателя передается на заготовку. Частично его предназначение – удерживать главный шпиндель, поэтому вы также должны увидеть этот шпиндель здесь.
Двигатель находится на нижней стороне станины токарного станка, слева возле передней бабки.Часто это какой-то тип электродвигателя, но токарный станок также может иметь гидравлический двигатель.
Регулируемые деталиВы можете отрегулировать подставку для инструментов по высоте и повороту, но по соображениям безопасности вы должны делать это только при выключенном станке. После того, как вы ослабите его для регулировки, дважды проверьте, чтобы убедиться, что он снова затянут, прежде чем продолжить.
Задняя бабка также регулируется, и вы, вероятно, сможете полностью ее снять. Как и в случае с подставкой для инструмента, вы никогда не должны выполнять эти регулировки во время работы токарного станка.Подробнее об этом читайте в разделе «Безопасность токарного станка».
Приспособления и аксессуарыШпиндели, включая вращающийся главный шпиндель, который удерживает заготовку, могут быть оснащены различными насадками и принадлежностями. Чтобы учесть эти фитинги, главный шпиндель часто бывает полым и имеет резьбу снаружи.
Некоторые полезные насадки для главного шпинделя включают центры, патроны и лицевые панели. Вы можете использовать их, чтобы позиционировать заготовку и удерживать ее на месте.
3. Кому подойдет токарный станок?Токарные станки, известные как «мать обрабатывающих инструментов», могут использоваться для различных целей. К ним относятся формование, сверление, шлифование, накатка, токарная обработка, резка и деформация. Такую универсальность инструмента трудно превзойти, и поэтому многие мастера по металлу и дереву полагаются на токарные станки как на основу своей работы.
Если вам нужен прецизионный инструмент для резки и формовки, токарный станок может идеально подойти для вашего проекта. Токарные станки хороши для команд, которым требуется универсальное оборудование, способное выполнять работу с несколькими инструментами.
4. Безопасность токарного станкаВам следует освоиться с токарным станком, если вы хотите использовать его хорошо, но не слишком удобно.
Вы знаете момент, когда вы используете машину, делаете какое-то повторяющееся движение, и ваш мозг медленно переключается на автопилот? Как вы, возможно, знаете по опыту, именно в эти моменты случаются ошибки.
Эти инструкции по безопасности для токарных станков от Университета Пердью и Университета Западной Вирджинии содержат некоторые важные вещи, на которые следует обратить внимание:
Надевайте правильную передачуЕсли вы работаете в механическом цехе, вы уже должны носить защитные очки сбоку. протекторы, а может быть, даже маска для лица.Если нет, то подходящее время для оснащения – перед операцией на токарном станке .
Соберите волосы, если они длинные, и закатайте длинные рукава. Никогда не надевайте перчатки, кольца или часы при работе на токарном станке. Если какой-либо из этих предметов застрянет в сверле или шпинделе, вы быстро окажетесь в смертельной ситуации.
Проверьте щитки и огражденияПеред тем, как начать работу на токарном станке, убедитесь, что все находится на своих местах. Если что-то не так, четко обозначьте это, прежде чем покинуть это место.Вы можете написать что-то вроде «Не работает». Вы не хотите, чтобы кто-то пришел за вами и столкнулся с проблемами, которые вы могли бы предотвратить.
Держите инструменты острымиТупые и поврежденные токарные инструменты не только неэффективны, но и опасны в использовании. Пометьте и исправьте, прежде чем двигаться дальше.
Отключение питания перед выполнением регулировокНикогда не регулируйте токарный станок во время его работы. Если вы заметили что-то, что хотите переместить, подождите, пока токарный станок полностью выключится, прежде чем делать это.Аналогичным образом, если вам нужно выполнить какое-либо техническое обслуживание токарного станка, вам следует заранее полностью отключить источник питания.
Партнерство с опытным механическим цехомСамое большое преимущество, когда речь идет о безопасности токарных станков, – это то, что нелегко исправить: опыт и навыки. Если вам не хватает собственных отбивных, не волнуйтесь. Все, что вам нужно сделать, это найти хороший механический цех, который знает, что они делают, и создать надежные партнерские отношения, чтобы выполнить свою работу.
Вы готовы использовать токарный станок!Итак, что такое токарный станок?
Токарный станок – это, помимо прочего, формирователь, резак, шлифовальный станок и деформатор.Он использует навесное оборудование для специальных работ и дает результаты, достаточно точные, чтобы их можно было использовать в другом оборудовании. Короче говоря, токарный станок – это незаменимая часть металло- и деревообрабатывающего оборудования и один из самых универсальных инструментов.
Обращайтесь к нам, если у вас есть какие-либо вопросы об этом удивительном инструменте, и узнайте, что мы можем для вас сделать!
Для чего нужен токарный станок?
Многие инструменты для деревообработки или механических цехов легко узнаваемы. Сверла, пробойники, тиски – все это довольно простые инструменты с понятным назначением.Другие машины могут быть немного сложнее, и их значение не совсем понятно. Токарные станки, особенно высокопроизводительные, относятся к последней категории.
По своей сути токарный станок – это простое устройство, предназначенное для удерживания части материала, который нужно вырезать, вырезать или придать форму. Это называется заготовкой. В отличие от простых тисков, токарный станок не только удерживает заготовку, но и вращает ее. Это позволяет другой части станка, головке, перемещаться вдоль заготовки, используя различные насадки или режущие инструменты, чтобы удалить материал по мере необходимости и придать форму заготовке.
Время для примера. Представьте гончарный круг:
В данном случае глина является заготовкой. Колесо представляет собой элементарный токарный станок, который вращает заготовку с заданной скоростью и удерживает ее на одном месте. Головка и режущие коронки в приведенном выше примере – это руки рабочего. Они являются движущейся частью – движутся по длине заготовки (ось «y»), а также внутрь и наружу по направлению к центру заготовки (ось «x»).
Начинаете видеть, как это работает? Хорошо, а теперь давайте немного поговорим о том, как появились токарные станки.
Краткая история токарных станков
Теперь, когда мы посмотрели на токарный станок в действии, давайте вернемся назад. Токарные станки в той или иной форме существуют со времен египтян. Подумайте о сходстве с гончарным кругом; Что ж, керамика существует уже тысячи лет, поэтому логично, что токарные станки, работающие по схожему принципу, вскоре появятся на свет.
Самые простые токарные станки позволяли и все еще позволяют мастерам снимать материал вручную, как на видео выше.С течением веков, и особенно во время промышленной революции, развивались токарные станки со встроенными головками, установленными на поперечных салазках, проходящих по всей длине станины токарного станка, по которой могла вращаться заготовка. Также во время промышленной революции появились токарные станки с паровым приводом, способные увеличивать скорость вращения и крутящий момент для вращения более тяжелых деталей. На токарных станках теперь обрабатывали не только деревянные детали, но и металлические.
Следующий большой скачок произошел во второй половине двадцатого века с появлением компьютерного числового управления (ЧПУ).Токарные станки с ЧПУ позволяли операторам программировать набор инструкций для станка. Это позволяло точно дублировать эти инструкции, что означало, что части становились все более точными, и уменьшало количество операторов, необходимых для одновременной работы нескольких машин. Сегодняшние инновации обеспечивают все более точное программирование ЧПУ с постоянно растущим числом осей.
Промышленное применение токарных станков
В промышленности токарные станки производят бесчисленное количество деталей: карданные валы автомобилей, ножки для столов и т. Д.На сверхмощных крупногабаритных токарных станках можно повернуть гигантский металлический конус или диск, а на небольших станках можно вырезать металлическую фишку.
Современные промышленные токарные станки полностью автоматизированы с головками, вмещающими несколько бит. Это означает, что один и тот же токарный станок может выполнять множество процессов – черновые коронки для шлифования материала, более тонкие для обработки деталей, даже сверла для шлифовки и полировки. Используя технологию ЧПУ, обученный оператор может запрограммировать токарный станок на доведение одной заготовки от сырья до готового продукта без участия человека вообще после запуска программы.Несколько человек могут контролировать весь производственный цех, оборудованный токарными станками с ЧПУ.
Мелкосерийное использование токарных станков
Токарные станки в промышленных масштабах могут быть довольно большими, но большинство токарных станков, как правило, немного меньше. Токарный станок по металлу является опорой многих небольших механических мастерских или инструментальных компаний из-за его универсальности. Помимо механического цеха, многие другие мастера и любители считают токарный станок незаменимым. На токарном станке можно создать детали для старой машины:
Или простая чаша:
Умелый мастер может превратить кусок металла в чашку, светильник или даже шахматную фигуру.Существует огромное множество потенциальных применений, а возможность от руки выполнять этапы резки и резьбы означает, что каждая деталь по-прежнему сохраняет уникальные черты мастера.
Токарный станок по металлу не ограничивается определенными сплавами или металлами: с некоторыми металлами может быть легче работать, но теоретически любой металл можно токарно обработать. Вот такая изящная детская чашка из олова:
Для чего-то более декоративного, но особенно яркого, попробуйте эту великолепную фишку:
Для чего нужен токарный станок? Почти все! Но сегодня они, как правило, попадают в категории «промышленные» и «ремесленные».«Промышленное использование охватывает все: от местного механического цеха, производящего запчасти для старых автомобилей, до государственных предприятий, производящих тяжелую технику. С другой стороны, мастера используют токарные станки для производства уникальных и захватывающих дух изделий из дерева, металла, стекла, эпоксидной смолы и почти любого другого материала, который только можно вообразить.
Для чего нужен токарный станок? Все, что вы хотите или что вам нужно! Выйди и посмотри, что ты можешь сделать!
и токарные станки по металлу: в чем разница?
Токарный станок – один из самых универсальных станков, используемых в обрабатывающей промышленности.Он может резать, шлифовать, сверлить, торцевать, поворачивать и деформировать заготовки. Токарные станки отличаются тем, как они удерживают заготовки. В то время как фрезерные станки подвергают неподвижную деталь воздействию вращающегося режущего инструмента, токарные станки подвергают вращающуюся деталь воздействию неподвижного режущего инструмента.
Все токарные станки используют один и тот же метод работы: заготовка закрепляется на токарном станке, после чего она вращается против неподвижного режущего инструмента. Однако токарные станки часто классифицируют как «деревянные» или «металлические». Итак, в чем разница между токарными станками по дереву и токарными станками по металлу?
Что такое токарный станок по дереву?
Токарный станок по дереву – это токарный станок, разработанный специально для обработки дерева.Другими словами, они используются для резки, шлифования, сверления, торцевания, поворота и деформации деревянных заготовок. Они по-прежнему работают, как и все другие токарные станки, подвергая вращающуюся заготовку неподвижному режущему инструменту. Но токарные станки по дереву используются именно для обработки деревянных деталей. Они не подходят для деталей из более твердых материалов, в том числе из металла.
Токарные станки по дереву меньше и проще своих собратьев по металлу. Скорость, с которой они вращают заготовки, контролируется базовой системой шкивов.Они не обладают такой мощностью, как токарные станки по металлу, но токарные станки по дереву очень эффективны при работе с деревянными заготовками.
Что такое токарный станок по металлу?
Токарный станок по металлу, с другой стороны, представляет собой тип токарного станка, который может выполнять операции по металлообработке. Поскольку металлические детали более твердые, чем деревянные, токарные станки по металлу чрезвычайно мощны. Они способны агрессивно манипулировать и деформировать детали из стали, железа, алюминия и других обычных металлов.
Также известный как токарный станок по металлу, это мощный станок, который часто используется при производстве металлических деталей. Токарные станки по металлу используются вместе с закаленным режущим инструментом, который закреплен на вращающейся монтажной поверхности. Металлическая заготовка размещается на токарном станке, после чего закаленный режущий инструмент прижимается к ней.
Важно отметить, что токарные станки по металлу все еще можно использовать с деревянными заготовками. Токарные станки по дереву поддерживают только деревянные заготовки, а токарные станки по металлу поддерживают как деревянные, так и металлические заготовки.
Заключение
Разница между токарными станками по дереву и токарными станками по металлу заключается в том, что первые предназначены для обработки деревянных деталей, а вторые – как для металлических, так и для деревянных деталей. Помимо соответствующих областей применения, токарные станки по дереву меньше и проще токарных станков по металлу. Из-за этого они, как правило, дешевле.
Нет тегов для этого сообщения.Что такое токарный станок? Краткое чтение!
Токарный станок – один из старейших станков, используемых в основном для обработки металла или дерева.Он работает, вращая заготовку на оси вращения неподвижного режущего инструмента. Токарный станок выполняет такие операции, как шлифование, накатка, резка, сверление, точение, деформация и торцевание.
Удаляет ненужные части изделия, оставляя заготовку желаемой формы. Токарный станок часто используется для создания цилиндрических и плоских поверхностей под прямым углом к оси.
Такие изделия, как чаши, музыкальные инструменты, винты, подсвечники, стволы для ружей и ножки стола, изготавливаются с использованием механизма удержания и вращения.
- Токарная обработка древесины
- Металлообработка
- Прядение металла
- термическое напыление
- обработка стекла и
- формовка керамических изделий
Это одни из наиболее известных функций токарного станка.
Детали токарного станкаСтанина – это прочная конструкция; основание станка и направляющий элемент. Станина должна выдерживать нагрузки режущей силы инструмента и скручивания.Обычно его делают из чугуна.
Передняя бабка – Крепится внутренними направляющими на левом конце станины токарного станка. Он состоит из полого шпинделя и механизма привода скорости шпинделя.
Задняя бабка – Задняя бабка расположена с правой стороны станины. Он поддерживает другой конец заготовки, когда она перемещается между двумя центрами.
Каретка – Она состоит из различных частей для поддержки, перемещения и управления режущим инструментом.
Механизм подачи – Присутствует на передней бабке и используется для определения направления подачи; продольные, поперечные или угловые.
Различные типы токарных станковТокарный станок можно разделить на различные типы в зависимости от конструкции и конструкции.
Настольный токарный станокЭто небольшой станок, который используется для высокоточных работ, требующих высокой точности. Его чаще всего используют производители.Настольный токарный станок монтируется отдельно на подготовленном станке. Он вмещает все навесное оборудование более крупного токарного станка и способен выполнять те же функции. Единственное отличие – размер.
Скоростной токарный станокСкоростной токарный станок предназначен для токарной обработки древесины, полировки, центрирования и прядения металла. Это высокоскоростной шпиндель, используемый для изготовления чаш, бейсбольных бит и деталей мебели. Скоростной токарный станок имеет опорные ножки, отлитые и прикрепленные к станине.
Токарный станок состоит из передней бабки, задней бабки и револьверной головки.У него нет редуктора, каретки, ходового винта и приспособления для подачи питания. Инструмент установлен на резцедержателе на регулируемом суппорте. Следовательно, приводится в действие вручную.
Токарный станок с двигателемЭто наиболее часто используемый тип станка. Названия образованы от 19-го и 20-го исторических памятников. Он был приведен в действие паровым двигателем, хотя современный токарный станок приводится в движение моторными приводами.
Токарный станок для двигателей идеально подходит для металлообрабатывающих предприятий, таких как сверление, растачивание и развёртывание.Он похож на скоростной токарный станок, но больше и сложнее. Большой механизм обеспечивает несколько скоростей вращения шпинделя.
Механизм подачи может управлять режущим инструментом как в продольном, так и в поперечном направлениях. Доступен в 3-х типах.
Ременные передачиЭтот токарный станок для двигателей имеет ременную передачу и получает энергию от продольного вала. Оснащен коническим шкивом с задними шестернями. Это помогает настроить желаемую скорость.
С приводом от двигателяОн получает энергию от отдельного встроенного двигателя.
Головка с редукторомОна получает свою силу от двигателя с постоянной скоростью, а диапазон скорости достигается за счет переключения передач.
Токарный станок с шпилем и револьверной головкойЭтот токарный станок используется для массового производства. Вместо задней бабки токарно-револьверный станок имеет шестигранную револьверную головку, установленную на суппорте. В шестигранную револьверную головку можно вставить множество инструментов.
Следовательно, несколько операций могут выполняться последовательно. Несколько операций позволяют производить большие объемы продукции.Токарно-револьверный станок с револьверной головкой является полуавтоматическим, и для работы с ним не требуется особых навыков. Различные операции, выполняемые на одной машине, сокращают количество ошибок и экономят время.
Токарный станок для инструментального цехаТокарный станок для инструментального цеха повышенной точности является образцовым выбором. У него относительно больший угол скорости и подачи. Коробка передач обеспечивает широкий диапазон скоростей от очень низкой до высокой до 2500 об / мин.
Эксклюзивные особенности включают патрон, приспособление для точения конуса, люнет и подпорку, насос для всасывания охлаждающей жидкости в приспособлении для сбора.Он пригоден для сверления, точения, развёртывания и растачивания.
Токарный автоматЭтот станок чрезвычайно продвинут для автоматического производства продукции. После настройки инструмент выполняет все операции автоматически. Смена кормов и инструментов автоматизирована. Один оператор может одновременно управлять 5-6 токарными станками. Это высокоскоростная и сверхмощная машина, призванная повысить качество и количество продукции.
Токарный станок с ЧПУТокарный станок с числовым программным управлением предоставляет программы ЧПУ для выполнения этой задачи.Благодаря этому токарному станку можно за короткий промежуток времени достичь высокого уровня точности. Токарный станок с ЧПУ состоит из тех же компонентов, что и ручной токарный станок, но дополнительно оснащен панелью управления с ЧПУ.
После установки кода операции его можно применять без повторного ввода во второй раз. Это самый современный токарный станок, используемый в различных отраслях промышленности, от автомобильной до авиакосмической.
Специальный токарный станокНекоторые токарные станки специально разработаны для удовлетворения особых требований.Специальный токарный станок эффективен для конкретного проекта. Некоторые специальные токарные станки:
Колесотокарный станок : Предназначен для обработки цапф и нарезания резьбы на колесах железных дорог, легковых автомобилей и локомотивов.
Т-токарный станок : Применяется для обработки роторов реактивных двигателей. Ось станины токарного станка расположена под прямым углом к оси шпинделя передней бабки.
Дубликат токарного станка: Он имеет трассирующее устройство, подключенное к каретке, которая движется вместе с шаблоном.Механические, пневматические и гидравлические устройства используются для координации движения инструмента. Используется для массового производства идентичных предметов.
Вертикальный токарный станок: Он несет вертикальную стойку, в которую вставляются поперечные и вертикальные направляющие. Он используется для растачивания и точения тяжелых вращающихся деталей, таких как маховик и зубчатые передачи.
Это различные типы токарных станков, предлагаемые производителями. Выдержка поможет вам определить, какой тип лучше всего подходит для ваших нужд.Некоторые токарные станки используются для обеспечения точности, а некоторые – для массового производства. Есть и продвинутые, чтобы удовлетворить особые потребности.
Сравнение фрезерных станков и токарных станков
Большинство современных производственных центров имеют как фрезерные, так и токарные станки. Каждый станок следует одному и тому же принципу обработки, известному как субтрактивная обработка, когда вы начинаете с блока материала, а затем формируете этот материал в соответствии с желаемыми характеристиками. Как на самом деле форма детали – это ключевое различие между двумя станками.Более глубокое понимание различий поможет установить нужную деталь в нужную машину, чтобы максимизировать их возможности.
Пример токарного станка
Пример фрезерного станка
Операция
Основное различие между фрезерным станком и токарным станком – это соотношение заготовки и инструмента.
Станки токарные
В токарном станке обрабатываемая деталь вращается вокруг своей оси, а режущий инструмент – нет.Это называется «точением» и эффективно для создания цилиндрических деталей. Общие операции, выполняемые на токарном станке, включают сверление, растачивание, нарезание резьбы, нарезание внутренних и наружных канавок и отрезку. Токарный станок – лучший выбор для создания быстрых, воспроизводимых и симметричных цилиндрических деталей.
Станки фрезерные
Для фрезерных станков все наоборот. Инструмент фрезерного станка вращается вокруг своей оси, а заготовка – нет. Это позволяет инструменту приближаться к заготовке во многих различных направлениях, которые требуются для более сложных и сложных деталей.Если вы можете запрограммировать это, вы можете сделать это на фрезерном станке, если у вас есть правильный зазор и вы выберете подходящий инструмент.
Лучшая практика
Лучшая причина использовать фрезерный станок для предстоящего проекта – универсальность. Варианты оснастки для фрезерного станка безграничны, с сотнями доступных специальных режущих инструментов и концевых фрез различных стилей, которые гарантируют, что вы от начала до конца выполняете каждую работу. Фреза также может резать более сложные детали, чем токарный станок.Например, невозможно эффективно обработать на токарном станке что-то вроде впускного коллектора двигателя. Для успешной обработки таких сложных деталей потребуется фрезерный станок.
Хотя токарные станки более ограничены в использовании, чем фрезерные станки, они лучше подходят для обработки цилиндрических деталей. Хотя фрезерный станок может делать те же пропилы, что и токарный станок, для создания одной и той же детали может потребоваться несколько настроек. Когда необходимо непрерывное производство цилиндрических деталей, токарный станок превосходит мельницу и увеличивает как производительность, так и эффективность.
Команда инженеровHarvey Performance Company работает вместе над тем, чтобы каждая ваша задача обработки – от выбора инструмента и поддержки приложений до разработки идеального индивидуального инструмента для вашей следующей работы – была решена с помощью продуманного комплексного решения.
Что такое токарный станок ?. Один из старейших станков – это… | by mechstuff4u
Один из старейших станков – токарный станок. В 1797 году англичанин Генри Модслей сконструировал первый токарно-винторезный станок, который является предшественником современного высокоскоростного высокопроизводительного токарного станка.
Функции токарного станка:
Удаление металла с детали для придания ей необходимой формы и размера – основная функция токарного станка.
Для этого нужно надежно и жестко удерживать изделие на станке, а затем повернуть его против режущего инструмента, который удалит металл в виде стружки.
Типы токарных станков:
1. Скоростной токарный станок
- Деревообработка
- Центровка
- Полировка
- Прядение
2.Токарный станок с двигателем
- Ременный привод
- Индивидуальный моторный привод
- Токарный станок с зубчатой головкой
3. Станок токарный
4. Инструментальный станок
5. Токарно-револьверный станок
6. Специального назначения
- Колесотокарный станок
- Станок токарный с зазором
- Станок Т-образный
7. Токарный автомат
Описание и назначение деталей токарного станка:
1. Станина
Станина токарного станка образует основание станка, переднюю бабку и Задняя бабка расположена на обоих концах станины, а каретка опирается на станину токарного станка и скользит по ней.
Станина токарного станка является направляющим элементом токарного станка, поэтому она должна удовлетворять следующему условию.
- Он должен быть достаточно жестким, чтобы предотвратить прогиб
- Он должен быть массивным, с достаточной глубиной и шириной, чтобы поглощать вибрацию
- Он должен сопротивляться скручиванию
- Чтобы избежать деформации
С этой точки зрения материал станины должен иметь высокую прочность на сжатие, быть износостойкими и поглощать вибрацию.
Чугун, легированный никелем и хромом, является хорошим материалом, подходящим для станины токарного станка.
2. Передняя бабка
Передняя бабка прочно закреплена на внутренних направляющих на левом конце станины токарного станка.
По сути, он состоит из полого шпинделя и механизма для приведения в движение и изменения скорости шпинделя.
3. Задняя бабка
Задняя бабка расположена на внутренних направляющих на правом конце станины.
Он имеет два основных назначения:
- Он поддерживает другой конец работы
- Он содержит инструмент для выполнения таких операций, как сверление, развертывание, нарезание резьбы и т. Д.
4. Каретка
Каретка токарного станка состоит из различных частей, которые служат для поддержки, перемещения и управления режущим инструментом. Ниже представлены следующие детали:
- Седло
- Поперечные салазки
- Составные салазки
- Стойка для инструмента
- Фартук
Седло представляет собой H-образную отливку, которая надевается на станину и скользит по ее пути. Он нес поперечный суппорт и резцедержатель.
Поперечный суппорт состоит из отливки, обработанной на нижней стороне для крепления к седлу, и имеет место на верхней поверхности для резцедержателя или составной опоры.
Составная опора установлена на верхней части поперечной салазки, которая используется для получения угловых пропилов и короткого конуса.
Резцедержатель, расположенный в верхней части составной опоры, для удержания инструмента и возможности его установки в рабочее положение.
Тип стойки для инструмента:
- Стойка для инструмента с одним винтом
- Стойка для инструмента с четырьмя болтами
- Открытая боковая стойка для инструмента
- Стойка для инструмента с четырьмя направлениями
Фартук прикреплен к седлу и нависает над передней частью станины .
Фартук содержит шестерни, муфты и рычаги для ручного управления кареткой и механических подач.
5. Механизм подачи
Подача – это движение инструмента относительно работы.
Токарный инструмент может иметь три типа подачи:
Токарный станок работает:
Токарный станок – это станок, который удерживает обрабатываемую деталь между двумя жесткими и прочными опорами, называемыми центрами, или в патроне или планшайбе, которая вращается. .
В стойке для инструмента, которая подается против вращающейся части, режущий инструмент жестко удерживается и поддерживается.
Когда режущий инструмент подается параллельно или под прямым углом к рабочей оси, выполняются обычные операции резания.
Операция, которая выполняется на токарном станке, удерживая заготовку между центрами или с помощью патрона, следующая:
- Прямое точение
- Токарная обработка плеча
- Снятие фаски
- Нарезание резьбы
- Торцевание
- Накатка
- Заполнение
- Точение конуса
- Эксцентриковое точение
- Полировка
- Обработка канавок
- Прядение
- Обмотка пружины
- Формование
Операция, которая выполняется путем удержания заготовки за угол патрона или планшайбы следующие:
- Сверление
- Развертка
- Расточка
- Зенковка
- Расточка
- Нарезание внутренней резьбы
- Нарезание резьбы
- Подрезание
- Отрезка
с помощью специальных приспособлений следующие: 90 010
Скорость резания:
Скорость резания токарного станка – это скорость, с которой инструмент удаляет металл из заготовки.
В токарном станке – окружная скорость работы за режущим инструментом, выраженная в метрах в минуту.
Скорость резания = Πdn / 1000 м / мин
Где
d = диаметр заготовки (мм)
n = об / мин работы
Подача:
При работе на токарном станке подача режущего инструмента – это расстояние, на которое инструмент продвигается за каждый оборот работы.
Подача выражается в миллиметрах на оборот.
Глубина резания:
Глубина резания – это расстояние по перпендикуляру от поверхности станка до неизрезанной поверхности заготовки.
Глубина резания = d1-d2 / 2
Где,
d1 = диаметр поверхности до обработки
d2 = диаметр обработанной поверхности
Глубина резания изменяется обратно пропорционально скорости резания.
Для общего назначения соотношение глубины резания и подачи варьируется и обычно составляет 10: 1.
Время обработки:
Время обработки на токарном станке можно рассчитать для конкретной операции, если известны скорость выполнения задания, длина подачи задания.
Время обработки = л / с * n мин
Где
l = длина задания в мм
с = подача задания в мм
n = об / мин работы
Безопасность токарного станка меры предосторожности:
При использовании токарного станка необходимо соблюдать меры безопасности, чтобы избежать несчастного случая. Когда мы работаем на токарном станке, нужно помнить следующее.
- Не поддерживайте обрабатываемую деталь руками. Используйте удерживающее устройство.
- Вместо использования кисти используйте щетку для очистки стружки.
- Никакой регулировки во время работы машины.
- Не пытайтесь измерять вращающиеся детали.
- Перед началом работы убедитесь, что все детали надежно закреплены в токарном станке.
- Никогда не кладите инструменты на сверлильный стол.
- Носите защитные очки и избегайте свободной одежды.
- Не держитесь за ручку патрона, прикрепленную к патрону, и она слетает в момент поворота токарного станка.
- Не касайтесь таблицы байтов вращающимся патроном, иначе вы можете повредить не только байт, но и сам стол.
Токарный станок – один из самых универсальных станков, используемых сегодня в промышленности. Это важный станок в обрабатывающей промышленности из-за его универсальности. На одной детали можно изготовить ряд профилей на токарном станке.
Ознакомьтесь со статьями по теме:
Введение в токарный станок
Функции токарного станка
Детали и функции токарного станка
Типы токарных станков
Токарный станок в рабочем состоянии
Работа на токарном станке
Типы режущего инструмента для токарного станка
Сигнатура режущего инструмента
Меры безопасности на токарном станке
Скорость резания на токарном станке
Глубина подачи резания и время обработки на токарном станке
Токарные станки – обзор | Темы ScienceDirect
11.5.1 Процесс и инструменты
Обработка – это процесс, при котором изготавливаются детали желаемого размера и формы путем удаления материала в виде мелких стружек с твердой заготовки с помощью одно- или многолезвийного режущего инструмента. Поскольку в процессе удаляется уже оплаченный материал, механическая обработка не является экономичным процессом и обычно не используется для производства деталей специального назначения для потребительских товаров. Однако его часто используют для улучшения допусков или обработки поверхности деталей, изготовленных с помощью других процессов (например,например, литье в песчаные формы, ковка и т. д.) путем аккуратного удаления небольшого количества материала с выбранных участков поверхности. Кроме того, механическая обработка используется для производства инструментов, штампов и штампов, используемых в большинстве процессов, таких как литье под давлением, литье под давлением, штамповка и другие процессы.
Есть несколько видов станков, но не все они здесь будут рассмотрены. Среди наиболее распространенных можно выделить следующие.
Токарные станки
Токарные станки используются в основном для изготовления цилиндрических или конических наружных и внутренних поверхностей путем токарной обработки, торцевания, расточки и сверления (см. Рисунок 11.12). Токарные станки также используются для изготовления винтовой резьбы. В токарном станке заготовка вращается, в то время как режущий инструмент перемещается («подается») в заготовку в направлении, параллельном и / или перпендикулярном оси вращения заготовки.
РИСУНОК 11.12. Основные узлы и движения токарного станка, а также основные операции, которые на нем можно выполнять.
Вертикальные и горизонтально-расточные станки
Эти станки используются вместо токарных станков для обработки больших деталей.Их можно использовать для точения, торцевания и растачивания. Расточные станки также используются для формирования канавок и увеличения диаметра существующих отверстий.
Вертикальные и горизонтальные фрезерные станки
Эти станки (рисунок 11.13) используются для формирования пазов, карманов, углублений, отверстий и других элементов. В этом случае режущий инструмент вращается, и заготовка подается.
РИСУНОК 11.13. Основные узлы и движения горизонтальных и вертикальных фрезерных станков, а также основные операции, которые на них можно выполнять.
Строгальные и формовочные станки
Эти станки используются, прежде всего, для уменьшения толщины блоков и листов и для квадратной обработки блоков и листов. Формовщики также используются для обработки пазов и шпоночных пазов и для формирования плоских поверхностей на деталях, сформированных другими процессами, такими как литье и ковка. В формовочной машине, показанной на рис. 11.14, заготовка зажимается на столе, в то время как режущий инструмент, прикрепленный к тяжелому плунжеру, перемещается горизонтально. При движении вперед режущий инструмент удаляет металл.После обратного хода ползуна рабочий стол отводится в сторону для подготовки к следующему ходу резания.
РИСУНОК 11.14. Горизонтальный формирователь, используемый в основном для уменьшения толщины блоков и плит.
Плоскошлифовальные и цилиндрические станки
В плоскошлифовальном станке заготовка закреплена на столе, который совершает возвратно-поступательное движение в продольном направлении и подается в боковом направлении. Шлифовальный круг закреплен на вращающемся горизонтальном шпинделе и шлифует заготовку, когда стол совершает возвратно-поступательное движение и подается.Плоскошлифовальные станки используются в первую очередь для улучшения точности и чистоты плоских поверхностей. Цилиндрические шлифовальные станки также используются для улучшения допусков и качества поверхности цилиндрических поверхностей. В этом случае вращаются и заготовка, и шлифовальный круг.
Электроэрозионные машины (EDM)
Электроэрозионная обработка (EDM) – это процесс удаления металла с помощью искры электрического разряда. Есть два типа электроэрозионных станков: «твердые» электроэрозионные станки (Рисунок 11.15) и «проволочный» электроэрозионный станок. В твердотельном электроэрозионном станке инструмент (обычно графитовый, но иногда медный или латунный), который содержит форму, которую нужно обработать в заготовке, вместе с самой заготовкой, подключен к источнику питания постоянного тока. Заготовка помещается в емкость, заполненную жидким диэлектриком. Инструмент подается в заготовку. Когда электрический потенциал между ними достаточно высок, возникает искра, которая удаляет небольшое количество материала с детали.
РИСУНОК 11.15. Основные элементы электроэрозионных машин (ЭЭМ).
Процесс твердотельной электроэрозионной обработки используется для обработки узких пазов, небольших отверстий и сложных форм. Его можно использовать на любом материале, проводящем электричество, и на него существенно не влияют твердость или прочность материала. Процесс электроэрозионной обработки намного медленнее, чем традиционный процесс обработки, описанный в разделе 11.5, и оставляет поверхность с изъязвлениями, что может потребовать дополнительной шлифовки или ручной обработки. По этим причинам EDM по возможности избегают.
Процесс электроэрозионной обработки проволоки является разновидностью этого процесса и часто используется для изготовления штампов и пуансонов. В этом случае разрабатывается компьютерная программа для создания желаемой формы.