принцип работы и технология обработки
Электроэрозионную обработку металла достаточно широко применяют для изменения размеров металлических деталей, не нарушая их физических свойств. Такой процесс осуществляется при помощи специального оборудования и требует хорошего знания необходимых технологий.Кроме того, такая обработка дает возможность получить отверстия нужной формы и конфигурации, при необходимости – сделать фасонные полости, и изготовить профильные пазы и канавки на заготовках, созданных на основе твердых сплавов.
Такое электроэрозионное воздействие делает различные инструменты гораздо прочнее, обеспечивает производство качественного электропечатания, высокоточного шлифования, осуществлять резку деталей и многое другое. Выполняется обработка при полном соблюдении всех необходимых правил техники безопасности.
Принцип работы
Перед тем как приступить к выполнению этого вида обработки, необходимо вначале правильно собрать все требуемые элементы в единую цепь и предварительно подготовить детали, которые понадобятся для работы.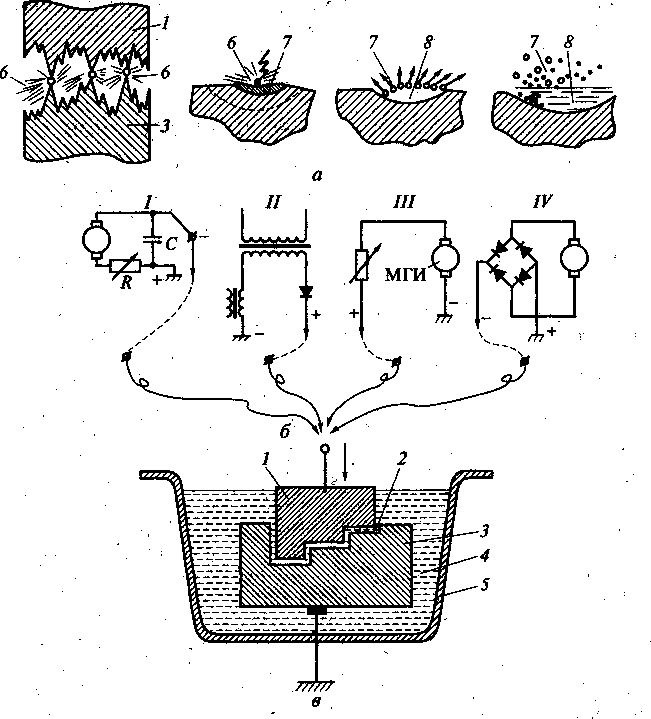
Нужно отметить, что важнейшим элементом в схеме, необходимой для выполнения электроэрозионной обработки, является электрод, который должен иметь достаточную эрозионную стойкость. В этом случае в качестве электрода можно использовать такие металлы, как:
- графит;
- медь;
- вольфрам;
- алюминий;
- латунь.
Довольно часто, чтобы обработать металл, применяют электроискровой и электроимпульсный методы. Также встречаются электроконтактный и анодно-механический способы.
Если для деталей из металла потребуется черновая обработка, то обычно применяют электроимпульсную схему. При этом во время работ температура вырабатываемых импульсов может достигать 5 000 градусов. Это увеличивает такой параметр, как производительность.
Если требуется обработать заготовки с небольшими размерами и габаритами, то в основном используется электроискровой способ.
Электроконтактная обработка применяется при работе со сплавами, осуществляемой в жидкой среде. Необходимо отметить, что приобретенные свойства металла после такого воздействия могут по-разному отразиться на эксплуатационных характеристиках деталей.
Практически всегда из-за воздействия токов и высоких температур у обрабатываемых деталей очень сильно повышается прочность, а в самой структуре сохраняется мягкость.
Виды используемого оборудования
Известно, что существуют разнообразные способы и методы обработки поверхностей металлов, и такой вид считается более эффективным, чем механический. В основном это связано с тем, что применяемый для проведения механической обработки инструмент стоит значительно дороже, чем проволока, используемая при электроэрозионной обработке.
Промышленные предприятия для электроэрозионной обработки металла применяют специальное оборудование, такое как:
- проволочно- электроэрозионное;
- копировально-прошивочное.
Если возникает необходимость изготовить детали со сложной формой и пресс-формы, а также для производства некоторых материалов с высокой точностью обработки, применяют проволочно- электроэрозионные агрегаты. Чаще всего такое оборудование используется для изготовления различных деталей для электроники, самолетов, и даже космической сферы.
Копировально-прошивочные агрегаты в основном применяются для серийного и массового производства деталей. Благодаря таким станкам получаются довольно точные сквозные контуры и мелкие отверстия, что с успехом используется при изготовлении сеток и штампов в инструментальной промышленной сфере. Такое оборудование подбирают, ориентируясь на поставленные цели и финансовую окупаемость. Электроэрозионная обработка металла считается сложным и довольно трудоемким рабочим процессом.
Выполняя электроэрозионную обработку, не стоит забывать о технике безопасности и использовании спецодежды.
Преимущества электроэрозионной обработки
Такие работы должны осуществляться только на специальном оборудовании под обязательным присмотром квалифицированного специалиста, имеющего соответствующий допуск. Хотя такой способ делает заготовку более точной и качественной, промышленные предприятия предпочитают применять механическую обработку металла.
Поэтому необходимо отметить основные достоинства электроэрозионного воздействия на разнообразные виды заготовок.
Используя такой метод, практически всегда удается добиться самого высокого качества поверхности металла, в результате чего она становится максимально точной и однородной. При этом полностью исключается необходимость проведения финишной обработки. Также этот метод гарантирует получение на выходе поверхности разнообразной структуры.
Также к достоинствам электроэрозионной обработки металла относят возможность осуществлять работу с поверхностью любой твердости.
Электроэрозионное воздействие полностью исключает возникновение деформации поверхности у деталей, имеющих небольшую толщину. Это возможно из-за того, что при таком методе не возникает никакой механической нагрузки, а рабочий анод имеет минимальный износ. Кроме того, электроэрозионная обработка способствует получению поверхности разнообразных геометрических форм и конфигураций при минимальных усилиях.Также к преимуществам такого процесса относят полное отсутствие шума при работе на специальном оборудовании.
Конечно, есть и недостатки при электроэрозионном воздействии на деталь из металла, но на ее эксплуатационных свойствах сказываются они несущественно.
Технология обработки
Чтобы до конца выяснить все преимущества электроэрозионной обработки и понять принцип воздействия на металлическую заготовку, следует более подробно рассмотреть следующий пример.
Итак, простая электроэрозионная схема должна обязательно состоять из следующих элементов:
- электрод;
- конденсатор;
- емкость для рабочей среды;
- реостат;
- источник, обеспечивающий электропитание.
Питание этой схемы обеспечивается напряжением импульсного типа, которое должно иметь разную полярность. Благодаря этому можно получить электроискровый и электроимпульсный режимы, которые требуются для работы.
Во время подачи напряжения осуществляется зарядка конденсата, от которого на электрод поступает разрядный ток. Этот электрод заранее опускают в емкость с заготовкой и рабочим составом. Как только на конденсаторе напряжение достигнет нужного потенциала, происходит пробой жидкости. Она начинает очень быстро нагреваться до температуры кипения, а также в ней возникает пузырь из газов, который способствует локальному нагреву заготовки.
Заключение
Современные станки для электроэрозионной обработки призваны выполнять как массовые, так и единичные задачи эстетического (декорирование, шлифовка и т. п.) и практического (формирование пазов, перфорация сквозных и глухих отверстий, заточка режущего инструмента) характера. Себестоимость обработки на таком оборудовании значительно ниже аналогичного показателя, который характерен для металлорежущих станков.
Оцените статью: Поделитесь с друзьями!Особенности и принцип электроэрозионной обработки
Принцип обработки
Для электроэрозионной обработки нужна предварительная подготовка деталей и создание единой цепи всех элементов. В промышленности применяется несколько способов такой обработки.
Важнейший элемент схемы электроэрозионной обработки – это электрод. Он должен обладать высокой эрозийной стойкостью. Не рекомендуется использовать алюминий, латунь, вольфрам, графит и медь.
С точки зрения химии, процесс электроэрозионной обработки представляет собой термическое воздействие на металл определенным образом. Вследствие воздействия разрушается кристаллическая решетка, что освобождает некоторые виды ионов.
Чаще всего на предприятиях используют электроискровую и электроимпульсную методики. Также иногда применяют анодно-механическое и электроконтактное воздействие.
Если металл изначально подвергается черновой обработке, то выгодней использовать электроимпульсную методику. В процессе работы температура импульсов поднимается до 5 тысяч градусов, что существенно повышает производительность.
Электроискровая обработка металла становится оптимальным выбором для заготовок небольшого размера. А для сплавов в жидкой среде подойдет электроконтактная обработка.
Примечательно, что обработка заготовки может повлиять на дальнейшие эксплуатационные характеристики. Зачастую после этого детали приобретают большую прочность структуры.
Виды применяемого оборудования
Существует множество самых разных методов обработки металлических изделий. Однако электроэрозионная обработка дает гораздо лучший результат, чем механическая. Обосновано это задействованием специализированного оборудования.
Для изготовления пресс-форм, деталей сложных форм и изделий, для которых важную роль играет точность обработки, задействуется проволочно-вырезные электроэрозионные станки. К примеру, с помощью электроэррозионных агрегатов создают детали механизмов в авиастроении и даже космической промышленности.
В серийном производстве разнообразных деталей удобно использовать копировально-прошивочное оборудование. Такие агрегаты дают возможность создавать мелкие элементы. Так, оборудование задействуется для изготовления сеток и всевозможных штампов.
Подбирать станки электроэрозионной обработки следует исходя из особенностей поставленных задач. Также следует понимать, что работать с агрегатом могут только квалифицированные специалисты при тщательном соблюдении техники безопасности. Провести обработку в кустарных условиях не удастся.
Преимущества обработки
На некоторых промышленных предприятиях сегодня по-прежнему используют механическую обработку металлических заготовок. Однако метод электроэрозионной обработки показал себя куда более эффективным. Можно выделить несколько очевидных преимуществ:
- высочайшее качество и точность;
- нет необходимости проводить финишную обработку;
- возможность получить поверхность с заданной структурой;
- можно проводить обработку поверхностей различной степени твёрдости;
- при обработке деталей полностью исключена вероятность деформации.
Электроэрозионная обработка открывает широкие возможности и позволяет работать с различными видами металлов. Это становится возможным благодаря тому, что нет необходимости проводить какое-либо механическое воздействие. Также в процессе работы с оборудованием не возникает шума.
Процедура обработки
В полной мере понять принцип электроэрозионной обработки можно, если рассмотреть пример наиболее простой электроэрозионной схемы.
Выстроена схема должна быть следующим образом: электрод, емкость рабочей среды, конденсатор, реостат и источник электропитания.
Электрод обязательно должен быть опущен в емкость с рабочим составом и деталью для обработки. После подачи напряжения заряжается конденсатор, ток которого подается на электрод.
Когда на конденсаторе происходит пробой жидкости, вследствие достижения нужного потенциала, появляются газы и пузыри. Они способны осуществлять локальный нагрев металла, что и вызывает плавление верхних слоев.
Электроэрозионная схема хоть и является наиболее простой, она требует определенных профессиональных навыков и постоянного контроля. Существуют более эффективные методы электроэрозионной обработки, позволяющие добиваться наилучшего результата. При этом методики обработки металла способны друг друга дополнять.
30 января 2017
Эрозионные станки
Всемирная локализация производственных процессов привела к расширению номенклатурных позиций для всех ведущих производителей технических средств, осуществляющих механическую обработку металлов.
Технологическая схема электроэрозионной проволочно-вырезной обработки, которую предлагает наша компания, гарантирует повышенные качественные характеристики конечного продукта. Одновременно работа наших станков и оборудования сопровождается чрезвычайно низкими затратами на их эксплуатацию, высокой надежностью, полнейшей автоматизацией, экономящей время пользователей.
Расширенный ассортиментный ряд массогабаритных показателей, технического оснащения, классов точности, и, как следствие, диапазонов стоимости привлекает все больше предприятий, заинтересованных в нашей продукции. Клиентская база концерна Knuth неуклонно расширяется, номенклатура растет соответственно спросу. Нашими постоянными заказчиками есть как небольшие частные предприятия, так и промышленные гиганты мирового значения.
Раздел «Эрозионные станки» в настоящее время представляют три наиболее популярные позиции:
1. Электроэрозионные проволочно-вырезные станки.
2. Электроэрозионные сверлильные станки (Супердрель).
3. Электроэрозионные копировально-прошивные станки.
Ниже предлагается подробное описание каждой позиции.
Сферы использования
Данная группа станков предназначена для пространственной обработки металла с соблюдением высокой точности. Машина осуществляет контурную обработку узлов, деталей, механизмов, изготовленных из электропроводящих материалов. Это могут быть: алюминиевые, медные, стальные заготовки любой твердости, твердые сплавы, цветные металлы.
Электроэрозионные проволочно-вырезные станки применяются для производства деталей, инструментов, оборудования со сложной геометрической формой: токарные кулачки, фасонные резцы, копиры, пуансоны, матрицы, постоянно задействованные в условиях серийного и мелкосерийного производства. Главной конструктивной особенностью данного оборудования является использование координат на линейных двигателях с прецизионными направляющими.
Станки оборудованы точными датчиками линейного перемещения. Это позволяет получать самую высокую степень точности при изготовлении ответственных деталей. Постоянный контроль с помощью высокоточных датчиков полностью исключает износ механики станка. Протяжка проволоки осуществляется через алмазные направляющие, имеющие чрезвычайно высокие прочностные характеристики.
Принцип работы
Электроэрозионные проволочно-вырезные станки производятся компанией Knuth с наличием числового программного управления. Система включает в себя:
- режим детального позиционирования от пункта к пункту;
- винтовую, круговую, линейную, сферическую интерполяции;
- профилирование скоростей;
- электронную синхронизацию;
- перемены траекторий;
- высокоскоростные входы и выходы.
Связь между приводами и контроллером осуществляется по интерфейсу с коммерческой доступностью. Цифровой токопроводящий контур обеспечивает высокую управляемость и устойчивость для всей системы. Программное обеспечение данной группы станков позволяет осуществлять обработку деталей, выполняя файлы-задания.
Информеры состоят из чертежей, характеристик для технологических процессов обработки, необходимых генератору с движущей системой. ПО способно выполнять функции самодиагностики для всей системы в процессе работы. Станки с успехом могут получать задание для обработки деталей, введенное в виде управляющих чертежей формата .dxf из любых САПР.
Группы, виды станков
Компания Knuth изготавливает и реализует электроэрозионные проволочно-вырезные станки близко 20 конструктивных исполнений. Это агрегаты общим весом от 800 кг до 14000 кг. Станки выполнены в различных функциональных категориях:
- однопроходные;
- многопроходные;
- станки с ЧПУ.
Размеры столов для каждой машины различные. Основные типоразмеры рабочих станин варьируются от 380х490 мм до 2600х1680 мм. Мощность генераторной установки находится в пределах от <1 кВт до 4,5 кВА. Минимальные габаритные размеры станка 1200х900х1300 мм, максимальные 5300х4800х3000 мм.
Особенности выбора
Для правильного выбора электроэрозионного станка со всей массы предложений, необходимо четко представлять себе особенности собственного производства, характеристики обрабатываемых деталей, ежедневную, месячную, годичную загруженность станков.
Остановив свой выбор на оборудовании концерна Knuth, каждый потребитель имеет возможность гарантированно выбрать станок необходимого типа и результативности. Поставка с центрального склада в Германии занимает всего от 2 до 8 недель, начиная от даты заявки.
Применяемость
Основная производственная задача оборудования, принадлежащего к большой группе, называемой электроэрозионные сверлильные станки (Супердрель), заключается в получении глубоких отверстий сечением 0,2 – 3,0 мм. Отверстия такого диаметра необходимы в материалах, проводящих электрический ток. Вещества могут быть любой твердости, толщины. Также различная геометрическая форма их поверхности.
Благодаря высокой степени универсальности, станки супердрель получили широкое распространение во многих сферах промышленности. Их используют в машиностроении при нарезании шлицевых, шпоночных пазов, выполнении отверстий в труднодоступных местах. Штампы, элементы прессформ также изготовлены на данном оборудовании. Оно применяется при обработке медицинских изделий, высокоточных деталей аэрокосмических механизмов, лазерной техники.
Устройство
Повышенная степень надежности, долговечность агрегатов позволяет их успешно использовать в процессах выпуска крупносерийной и мелкосерийной продукции. Супердрели работают на повышенных рабочих скоростях. По сравнению с обычными, привычными для нас дрелями, электроэрозионные сверлильные станки (Супердрель) имеют существенные принципиальные различия по ряду характеристик:
- конструкция;
- принцип работы;
- сечение обрабатываемых поверхностей.
Простые, но вместе с тем надежные механизмы позволяют быстро добиваться успеха в местах, труднодоступных и сложновыполнимых при использовании традиционных механических способов обработки. Единственное обязательное условие гарантированного успешного сверления нашим станком – хорошая проводимость электрического тока используемым материалом.
Супердрель электроэрозионного принципа действия состоит из двух электродов. Один из них представляет режущий инструмент. Это углеродный контакт, выдерживающий большую силу тока. Он помещается в одну из оправок, набор которых входит в базовую комплектацию станка. Другим электродом является зажимное устройство для обрабатываемой заготовки. Ток от механизма переходит к токопроводящей детали.
Принцип действия
Настроив углеродный контакт на сверление отверстий необходимого сечения, зажав заготовку в специальном кондукторе, оператор включает подачу электрического напряжения к исполнительным механизмам. За счет разницы потенциалов, на электроде возникает режущая сила. Параметры сверления заданы заранее электронной программой.
Электроэрозионные сверлильные станки (Супердрель) быстро, аккуратно, надежно справляются со всеми поставленными задачами. Исходя из высоких скоростей резания, агрегаты могут выполнять повышенные объемы обработки на любых участках обработки металлов.
Виды станков
Компания Knuth производит и реализует следующие виды станков типа супердрель:
Выбор
При необходимости покупки и эксплуатации высокотехнологичных станков моделей супердрель, изготовленных концерном Knuth, каждый потребитель должен сначала определиться с уровнем собственного производства, программой выпуска тех или иных деталей.
Наше оборудование, работая в условиях крупносерийного и мелкосерийного изготовления продукции, приносит значительную экономию времени, трудовых ресурсов, денежных средств. Работать с электроэрозионными сверлильными станками выгодно, экономично, целесообразно.
Принцип действия
Процесс электрической эрозии заключается в разрушении поверхностного слоя металлического изделия в результате воздействия на него электрического разряда. На данном принципе построена большая группа металлообрабатывающих станков немецкого концерна Knuth. Технологию работы с электрической эрозией разработали советские ученые-технологи Лазаренко Б. Р. и Лазаренко Н. И.
В настоящее время электроэрозионная обработка – ЭЭО, массово используется при изменении параметров металлических заготовок, проводящих электрический ток. Благодаря данной методике, получают отверстия различных сечений и конфигураций, фасонные полости, профильные канавки, пазы в деталях из твердосплавных материалов.
Наиболее популярной продукцией компании Knuth являются малогабаритные электроэрозионные копировально-прошивные станки модели D7120. Для различных производственных нужд предприятие производит станки различной мощности, исполнения, габаритных размеров. Оборудование имеет разные размеры станин, они различные по массе и выполняемым операциям.
Группы станков
Немецкая фирма Knuth производит и реализует по всей территории Российской Федерации уникальные высокоэффективные станки для электроэрозионной обработки металлов и сплавов. Самые компактные станки имеют массу от 1000 кг, наиболее металлоемкие выпускаются весом до 5500. Габаритные размеры выпускаемого оборудования: от 1200х1000х1800 мм до 2200х3600х2920 мм.
Электроэрозионные копировально-прошивные станки производятся с различной мощностью генераторной установки: от 2 кВт до 10 кВт. Предприятие изготавливает 14 моделей копировально-прошивных станков, предназначенных для выполнения самых разнообразных операций по обработке металлических заготовок по всему технологическому циклу. При этом используются различные размеры станин: от 200х160 мм до 1250х800 мм.
Устройство
Основные технологические функции предлагаемого оборудования будут рассмотрены на примере однокоординатного прошивного станка. Данный тип станков имеет только одну управляемую ось Z. Это вертикальная функция, которая определяет глубину электроэрозионного прожига. Перемещение по осям X, Y производится либо вручную, путем вращения рукояток, либо с помощью автоматики.
Когда на данном типе станка обрабатывается заготовка, оси X и Y должны оставаться неподвижными. С этой целью в районе рукояток установлены зажимы для фиксации. Они не позволяют ШВП проворачиваться. На все три оси станков: X, Y, Z, помещены оптические линейки с дискретностью 0,005 мм.
Выполняемые операции
Станки подобного типа с ЧПУ оснащены двумя системами координат. Осуществляя операции по обработке заготовок, одну из них удобно будет принять за абсолютную, вторую – за относительную. Данное обстоятельство, а также то, что полученное значение координат можно разделить на 2, позволяет легко базироваться, прожигать многоместные формы, измерять геометрические характеристики деталей, точно находить центры отверстий, более совершенно работать над производством и совершенствованием каждой отдельной детали.
Эксплуатируя электроэрозионные копировально-прошивные станки, операции эффективного прожига металла можно разбить на несколько этапов. Это усовершенствование позволит в процессе изготовления деталей обходиться одним электродом. Доглаживание обрабатываемой поверхности осуществляется на последнем этапе пониженными токами.
Данная хитрость позволяет значительно уменьшить износ электрода. На начальном этапе обработки ток прожига будет соблюдаться меньший. Постепенно увеличивая ток и глубину прожига, площадь обрабатываемой поверхности, добиваемся поставленной цели и экономим на расходе используемых электродов.
Разряды “Гризли” или супер дрель / Хабр
В этой статье хочу рассказать об электрических разрядах, которые способны грызть различные металлы и стали. Речь пойдет в основном про электроэрозионную обработку.Предположу, что большинство из вас знакомо с электродуговой сваркой и принципами работы этого технологического процесса. Похожий принцип лежит в основе электроэрозионной обработки, создаваемой электрическим разрядом, переходящим в дугу между двумя электродами. Если при сварке дуга должна гореть постоянно для получения наиболее качественного и ровного шва, то при эрозионной обработке эта дуга прерывается с некой частотой. В начальный момент каждого пробоя происходит вырывание части металла с поверхности обрабатываемого материала. Процесс представляет собой разрушение металла или иного токопроводящего материала в результате локального воздействия кратковременных электрических разрядов между двумя электродами, один из которых является обрабатываемой деталью, а другой – электродом-инструментом. Под воздействием высоких температур в зоне разряда происходит нагрев, расплавление и частичное испарение металла. Интенсивность вгрызания зависит от мощности импульсов, вкладываемых в разряды, которые в свою очередь зависят от характеристик источника питания, ширины импульса и паузы, за время которой разряд должен успеть затухнуть.
Еще следует отметить такой немаловажный параметр как: межэлектродное расстояние, которое варьируется в пределах нескольких микрометров. При длительной обработке межэлектродное расстояние должно поддерживаться постоянным и за это отвечает система позиционирования координат (применительно к чпу станкам). Разряд поджигается самостоятельно при достаточном для этого зазоре и напряжении (амплитуды импульсов). Этот зазор нельзя сводить к нулю, так как это чревато коротким замыканием и процесс обработки будет приостановлен или затянут по времени.
Все процессы электро-эрозии протекают в жидкой среде. Чаще всего применяют обыкновенную водопроводную воду либо керосин для наиболее ответственных деталей. Используемая жидкость служит в основном для отвода тепла и шлама из зоны воздействия импульсов, поэтому ее дополнительно прогоняют через ряд фильтров, очищая от продуктов реакции, таких как оксиды обрабатываемого металла и электрода – инструмента, так как последний тоже разрушается.
Существует ряд разновидностей электроэрозионной обработки: проволочная вырезка, копирование, фрезерование, прошивка отверстий, легирование. Электроэрозионная обработка применяется при изготовлении большого количества классов деталей: матриц штампов, полостей пресс-форм и литейных форм, фильер деталей машин, твердосплавных профилированных резцов и других.
Теперь давайте перейдем к практической части.
Я не я, если бы не попробовал сделать самостоятельно прототип генератор импульсов, хотя бы в простом исполнении.
Сам по себе генератор бесполезен, так как он должен входить в состав какой- либо технологической машины для эрозионной обработки. В связи с этим было решено сделать подобие эрозионного прошивного станка, так как от одного из прошлых проектов у меня осталась механическая часть, представляющая из себя основание с вертикально перемещающейся консольной траверсой.
Единственное что я изменил в ней, так это поменял привод на шаговый двигатель с энкодером и соединил вал двигателя с винтом ременной зубчатой передачи.
Управление шаговым двигателем осуществляется через китайскую программу (WireCut) для управления эрозионным вырезным станком. Эту программу в основном ставят китайцы на свои электроэрозионные станки, у нас в России ее тоже много кто устанавливает в качестве модернизации старых станков. Она идет в комплекте вместе с платой расширения AutoCut. На этом особо останавливаться не хочу, так как это сильно может раздуть статью. Помимо этого, программуля — так себе, но работать с ней можно.
За основу источника импульсов взял блок питания постоянного напряжения на 90В 20А. Потом надо перевести это напряжение в импульсы. Из самого простого, что мне пришло в голову – это взять ардуинку и подцепить к ней драйвер нижнего или верхнего ключа с силовым транзистором. Можно конечно использовать специальную ШИМ микросхему, но так как я подумывал в последующем несколько расширить функционал, то остановился все же на микроконтроллере.
Итак, что же за импульсы нам нужны? А нужны нам импульсы в виде меандра с постоянной частотой до 30 кГц и с возможностью менять ширину импульса.
Для изменения ширины импульса, я подцепил к контроллеру переменный резистор на 10кОм, который изменяет скважность от 0 до 50%, частоту установил статическую, начал с 20 кГц.
Дополнительно вывел на дисплей основные данные, то есть ширину импульса в микросекундах и скважность в процентах. Развел небольшую платку и изготовил ее на своем маленьком чпу станке. Опыта у меня в этих делах немного, но все же получилось довольно хорошо.
После распайки платы настал черед все соединить в единое целое:
Для контроля тока в цепь встроил амперметр, по нему буду отслеживать потребление тока в процессе обработки.
Плюсовой провод соединил с рабочим электродом, в качестве которого применил кусок медной проволоки диаметром 1,5 мм, то есть прошивать будем отверстие.
Минусовой провод от блока питания подключил через плату генератора и прикрепил к жертвенной металлической детали, которую предстоит дырявить.
Деталь представляет собой фланец, изготовленный из стали марки 40Х толщиной 5мм.
Разумеется, что такую технологию лучше использовать для обработки более прочного металла.
Фланец поместил в герметичный пластиковый контейнер наполненный водопроводной водой объемом 1 литр. Вода в ходе работы не циркулировала и никак, не очищалась.
После всех подсоединений, настал черед все включить и проверить работоспособность. Первым делом включил генератор и установил уровень ШИМ в 0%. Далее включил силовой блок питания и потихоньку начал прибавлять скважность. На рабочем электроде начали выделяться мелкие пузырьки кислорода. В ручном режиме подвел электрод к детали до появления первой искры, после чего запустил автоматическое опускание электрода со скоростью 1мкм/сек при ширине импульса в 1,5 мкс. Это дало слабенькие импульсы и быстро привело к короткому замыканию. В дальнейших попытках стал увеличивать ширину импульсов, до тех пор, пока при автоматическом опускании электрода не возникало постоянного искрения без “затыков”.
Остановился на ширине импульса 5 мкс при частоте 20 кГц. Дальнейшее увеличение ширины импульса приводит к более мощным импульсам и возрастанию тока, что перегревало мой балластный резистор и силовые транзисторы.
Снижение частоты дало лучшие результаты в связи с увеличением ширины паузы. Это позволило увеличить скорость опускания электрода до 5мкм/с, разряды стали стабильными, а ток увеличился до 6А. Сделал несколько сквозных отверстий, “сверловка” длилась в среднем мин 15, в зависимости от “затыков” в начале обработки и на выходе из отверстия.
Подводя итоги можно сказать, что данная упрощенная конструкция (прототип) генератора импульсов работает. Схема генератора далека от идеала и планируется ее усовершенствование параллельно с добавлением новых режимов генерации импульсов.
Данная статья не претендует на истинность всего изложенного, так как существует много нюансов, которые в ней возможно не раскрыты.
Все мы художники и видим по-разному.
Спасибо за внимание!
Электроэрозионная резка металла в Москве по бюджетным расценкам
Для просмотра видео требуется современный браузер с поддержкой видео HTML5.
Наравне с плазменной, лазерной и гидроабразивной резкой существует еще один способ высокоточной обработки металла, предназначенный для изготовления сложных по контуру деталей. Это электроэрозионная резка металла на проволочном станке. Данная технология была открыта еще в середине прошлого века, но долгое время не использовалась. Сегодня она относится к числу передовых.Технология электроэрозионной обработки металла
Главной “движущей силой” при электроэрозионных работах становится постоянный ток. А “инструментом”, непосредственно контактирующим с металлом, – проволока. В ней возникает электрическая дуга, благодаря которой катод и анод теряют вещество. Чтобы оно исчезло с анода, необходим непродолжительный по времени импульс. Чтобы такое же влияние испытал катод, требуется более длительное воздействие импульса.Таким образом, электроэрозионную резку в обиходе часто именуют резкой металла проволокой. В результате этой операции происходит разрушение металла. Конечно же, в тех участках, где это необходимо и в строгом соответствии с чертежами.
Важным условием для проведения проволочной резки является создание диэлектрической среды. В ее качестве чаще применяют дистиллированную воду, масло или керосин. Такие действия, как наращивание, напыление или укрепление, производятся в условиях вакуума.
Объявления по запросу “электроэрозионная резка” в России
Если вы поинтересуетесь электроэрозионной резкой, ценой на эту услугу в сети Интернет, любой поисковик предложит вам сотни ссылок – полезных и не очень. Одни будут вести на каталоги производств, готовых выполнить эту работу. Вторые направят вас на сайты предприятий по металлообработке. Третьи попытаются убедить, что простейшие станки проволочной резки можно собрать чуть ли не своими руками.Чтобы не потеряться в море предложений, доверьтесь опыту. И прежде всего оцените стоимость электроэрозионной резки у нескольких исполнителей и оборудование, на котором они работают. Поверьте: ни один “кустарный” станок, стоящий в чьем-то гараже, не сможет выполнить ваш заказ настолько качественно, как профессиональное оборудование нашего цеха.
Электроэрозия металла
Принцип электроэрозионной обработки металла, услуг, связанных с ней, базируется на таком явлении, как электроэрозия металла. При котором, по сути, происходит перенос частиц вещества при помощи электрических разрядов. Кстати, пальма первенства в открытии этого процесса принадлежит советским ученым, начавшим разработки незадолго до Великой Отечественной войны. Сегодня электроэрозионная резка в Москве, да и во всем мире, считается одним из самых эффективных способов обработки.Услуги электроэрозионной, проволочной резки металла на заказ
Наш цех готов предложить вам полный спектр услуг по электроэрозионной резке металла, цена на которую ниже, чем у большинства наших конкурентов. Мы в кратчайшие сроки и очень недорого:- изготовим для вас любые приспособления и детали;
- выполним фигурную резку металла;
- “подгоним” имеющиеся у вас заготовки под детали требуемых размеров;
- обработаем изделия повышенной сложности: с ячеистой структурой или изготовленные из труднообрабатываемых материалов.
Этапы электроэрозионной резки металла
Резка проволокой электроэрозионная может проводиться в режиме электроискровой или электроимпульсной обработки. В первом случае заготовка представляет собой анод, на который оказывает воздействие электронный поток. Чтобы не начался процесс разрушения электрода ионным потоком, длительность напряжения не должна превышать 10-3 с. Так как при этом процессе электроэрозионных работ удаляется лишь небольшой слой металла, его используют для проведения “чистовых” операций.При электроимпульсной обработке заготовка играет роль катода. Она подвергается воздействию отрицательного импульса, превышающего 10-3 с. Мощный дуговой разряд, возникающий между электродами, способен снимать металл в намного больших объемах и с высокой скоростью, хотя чистовая обработка при этом страдает. Для обработки особо чувствительных металлов, например, для электроэрозионной резки алюминия, этот способ лучше не использовать.
Преимущества электроэрозионной резки
Одно из главных преимуществ электроэрозионной резки металла на проволочном станке – в ее способности достичь труднодоступных мест. Например, проделать в заготовке закрытую внутреннюю полость. Эта методика пригодна в работе с любыми металлами как отличными проводниками электричества.Современное станочное оборудование полностью исключает брак при проведении данной операции. Несколько уступая в эффективности лазерной и плазменной резкам, резка металла проволокой намного опережает механические способы разделения металла.
Электроэрозионная обработка отверстий
Особенность технологии проволочной резки позволяет работать только со сквозными отверстиями, исключая глухие. Если в детали уже имеется отверстие и требуется его дальнейшая обработка, проволока просто продевается в него, что позволяет выполнить все необходимые манипуляции. В случае, когда такого отверстия нет, может быть произведен технический рез из-за одной из сторон периметра. Но только если это допускают техусловия.Границы применения электроэрозионной обработки
В обращении с металлами электроэрозионная резка в Москве не ограничивается практически ничем, ведь, как мы уже говорили, любой металл и сплав является отличным проводником электрического тока. Тончайшая проволока позволяет выполнить над материалом такие виды работ, как:- шлифовку,
- гравировку,
- упрочнение,
- напыление,
- прошивку,
- наращивание,
- копирование.
Нужна электроэрозионная обработка в Москве?
Обращайтесь: техническое оснащение цеха позволяет нам выполнить заказы по резке проволокой электроэрозионной любых объемов: от мелких до серийных. Мы внимательно изучим ваши чертежи, а если у вас их нет, готовы дополнительно оказать вам инженерно-конструкторскую поддержку.Самодельные электроэрозионные станки
Мы уже упоминали, что в Сети можно обнаружить множество мануалов, как изготовить станки проволочной резки самостоятельно. На самом деле даже собранный своими руками станок – сложное устройство, состоящее из станины, генератора, рабочего стола, ванны для диэлектрика и блока прокачки.Кроме того, в станке должны размещаться и успешно функционировать системы подачи проволоки, управления, запуска, установки и, конечно же, управления электродом. На самодельном устройстве качественная обработка металла абсолютно не гарантирована. Не лучше ли сэкономить время, нервные клетки и заказать электроэрозионную обработку, цена на которую так невысока?…
Электроэрозионные прошивные станки
В арсенале цеха имеется и сверхточное прошивное электроэрозионное оборудование для обработки сферических элементов заготовок как снаружи, так и во внутренних полостях. Некоторые марки таких станков могут одновременно выполнять и копировальные функции. Наши прошивные станки и регулирующие их работу специалисты в любое время готовы взяться за выполнение сложных заказов, в том числе по электроэрозионной резке алюминия.Электроэрозионный прожиг
Наравне с резкой в электроэрозионной обработке металла как услуге выделяют процесс электроэрозионного прожига. Эта операция во многом напоминает штамповку. С тем отличием, что во время нее происходит не деформация материала, а его удаление электрической искрой. И когда к детали подносят инструмент, ее поверхность, как зеркало, приобретает его очертания.Цены на услугу электроэрозии металла
Поскольку стоимость электроэрозионной резки зависит от сложности деталей, а ее трудно подвергнуть классификации, большинство предприятий измеряют свой труд не в количестве заготовок, а в часах. И назначают договорную цену на свои услуги. На формирование цены могут оказывать влияние:- диаметр проволоки, которой производится работа;
- степень твердости металла или сплава;
- тип операции, которую необходимо выполнить: резка, прошивка, прожиг и т.п.
Услуги электроэрозионной обработки
Мы выполним для вас качественную электроэрозионную обработку, цена которой настолько умеренна, что вы сможете израсходовать часть средств на другие нужды. Мощности нашего оборудования хватит, чтобы обработать не только стали, но и особо стойкие к воздействию сплавы, в том числе жаропрочные.Производственные возможности по электроэрозионной обработке
К вашим услугам – прошивка в заготовках сложнейших полостей и углублений, профилирование поверхностей, а также художественные виды обработки: гравировка и нанесение надписей. И на все эти услуги по электроэрозионной резке цена в любом случае не превысит указанной в прайс-листе.Как сделать электроискровой станок своими руками? Электроискровые станки
В направлении металлообработки широкое распространение получил метод электроэрозионной обработки (ЭЭО). Электроэрозионный метод обработки был открыт советскими учеными в 1947 году.
Эта технология смогла значительно облегчить процесс обработки металла, особенно это помогло при обработке металлов высокой прочности, при изготовлении деталей сложной конструкции, а также в других направлениях.
Работа метода основана на воздействии на деталь электрическими разрядами в диэлектрической среде, вследствие чего происходит разрушение металла или изменение его физических свойств.
Применение метода ЭЭО:
- При обработке деталей из металлов со сложными физико-химическими свойствами;
- При изготовлении деталей сложных геометрических параметров, со сложно выполнимой механической обработкой;
- При легировании поверхности для повышения показателей износоустойчивости и придания деталям требуемых качеств;
- Повышение характеристик верхнего слоя металлической поверхности (упрочнение) за счет окисления материала под воздействием электрического разряда;
- Маркирование изделий без вредоносного влияния, что присутствует при механическом клеймлении.
Для выполнения различных операций применяются разные виды электроэрозионной обработки. На промышленных станках устанавливаются устройства числового программного управления (ЧПУ), что значительно упрощает применение любого вида обработки.
Виды электроэрозионной обработки материала:
- Электроискровой вид обработки применяется при резке твердосплавных материалов, фигурной резке и для проделывания отверстий в металлах высокой прочности. Дает высокую точность, но скорость работы невелика. Применяется в прошивных станках.
- Электроконтактный способ обработки основан на местном расплавлении металла дуговыми разрядами с последующим удалением отработанного материала. Метод имеет более низкую точность, но более высокую скорость работы, чем электроискровой способ. Применяется при работе с большими деталями из чугуна, легированной стали, тугоплавких и других металлов.
- Электроимпульсный метод сродни электроискровому, но применяются дуговые разряды продолжительностью до 0.01 секунды. Это дает высокую производительность при относительно хорошем качестве.
- Анодно-механический метод основан на сочетании электрического и механического воздействия на металл. Рабочий инструмент – диск, а рабочая среда – жидкое стекло или сходное по характеристикам вещество. На обрабатываемую деталь и диск подают определенное напряжение, при разряде металл расплавляется, а шлам удаляется диском механически.
В промышленности применяются станки, работающие на основе метода электроэрозионной обработки металла. Они классифицируются по нескольким параметрам: принцип работы, управление, наличие ЧПУ и т.д.
Виды станков, работающих на принципе ЭЭО:
- Электроэрозионный проволочный станок;
- Электроэрозионный проволочно-вырезной станок;
- Электроэрозионный прошивной станок.
Станок ЭЭО в связи со своей многофункциональностью в хозяйстве нужен, а порой и вовсе не заменим. Заиметь такой аппарат в своем гараже хотел бы каждый. К сожалению, купить такой станок заводской сборки очень накладно и зачастую не представляется возможным. Выход из такой ситуации есть – собрать своими руками.
Вырезной и прошивной станок
Вопреки предвзятому мнению о сложности и невыполнимости такой задачи это не так. Это вполне посильная задача для простого обывателя, хотя все не так просто. Самый простой вид станка – это вырезной станок, предназначается для обработки деталей из легированных, тугоплавких и других прочных металлов.
В электрической схеме присутствуют: источник питания, диодный мост, лампочка и набор конденсаторов, соединенных в параллельную цепь. На выход подключаются электрод и обрабатываемая деталь. Отметим еще раз, что это принципиальная схема для образного понятия принципа работы устройства. На практике схема дополнена различными элементами, позволяющими отрегулировать прошивной станок под требуемые параметры.
Общие требования к электрической схеме вырезного станка:
- Учитывайте необходимую мощность станка при выборе трансформатора;
- Напряжение на конденсаторе должно быть больше 320 В;
- Общая емкость конденсаторов должна быть не меньше значения в 1000 мкФ;
- Кабель, идущий от схемы к контактам, должен быть только медным и сечением не меньше 10 мм;
Один из примеров рабочей схемы:
Как сразу видно, схема значительно отличается от принципиальной, но в то же время не является чем-то сверхъестественным. Все детали электрической схемы можно найти в специализированных магазинах или просто в старых электронных приборах, давно пылящихся где-нибудь в гараже. Отличное решение – применить ЧПУ для управления станком, но такой способ управления стоит немало, да и подключение его на самодельный станок требует определенных навыков и знаний.
Конструкция станка
Все элементы электрической схемы необходимо надежно закрепить в корпусе из диэлектрика, в качестве материала желательно использовать фторопласт или другой с похожими характеристиками. На панель можно вывести необходимые тумблеры, регуляторы и измерительные приборы.
На станине нужно закрепить держатель для электрода (должен быть закреплен подвижно) и обрабатываемой детали, а также ванночку для диэлектрика, в которой и будет проходить весь процесс. Как дополнение можно поставить автоматическую подачу электрода, это будет очень удобно. Процесс работы такого станка очень медленный, и для проделывания глубокого отверстия уходит много времени.
Проволочный станок своими руками
Электрическая схема проволочного станка та же, что и на вырезном станке, за исключением некоторых нюансов. Рассмотрим другие отличия проволочного станка. Конструктивно проволочный станок тоже похож на вырезной, но есть отличие – это рабочий элемент станка. На проволочном станке, в отличие от вырезного, – это тонкая медная проволока на двух барабанах, и в процессе работы проволока перематывается с одного барабана на другой.
Сделано это для снижения износа рабочего инструмента. Неподвижная проволока быстро придет в негодность. Это усложняет конструкцию механизмом движения проволоки, который необходимо установить на станину для удобной обработки деталей. В то же время дает станку дополнительный функционал. При вырезании сложных элементов оптимальным вариантом будет поставить ЧПУ, но, как сказано выше, это обусловлено некоторыми сложностями.
Для тех, кто не в курсе возможностей такого агрегата, целесообразно указать, что только с его помощью можно выполнять отверстия любого диаметра на самых твердых и прочных материалах, вне зависимости от их толщины и плотности. Кроме того, электроискровой станок способен гравировать поверхности, затачивать насадки инструментов, выполнять самые тонкие просветы и щели и даже высверливать резьбовые инструменты, которые сломались и безнадежно застряли, делая дальнейшее использование устройства невозможным. Вполне естественно, что наличие такого агрегата на подсобном хозяйстве открывает совершенно новые горизонты возможностей, однако стоимость и габариты готовых электроискровых станков делают их, мягко говоря, трудно доступными. Однако, подобное положение вещей не должно заставлять мастера отказываться от своей мечты, ведь при большом желании можно попытаться изготовить такое устройство самостоятельно.
На самом деле в этом нет ничего сложного, да и себестоимость самодельного электроискрового станка приятно удивит своей бюджетностью, ведь в ход можно пустить многие имеющиеся в наличии подручные средства. Однако, перед тем, как приступить к выполнению поставленной задачи, целесообразно более подробно описать устройство электроискрового станка, а самое главное, принцип его действия. Так, вся суть работы данного приспособления сводится к полному либо частичному разрушению обрабатываемой поверхности, которое происходит в результате воздействия импульсного электроразряда. Говоря проще, металл или любой другой материал попросту расплавляются от выделяемого установкой тепла, причем для усиления эффекта желательно использовать вспомогательную жидкость. Так, в идеале на потенциально контактное место наносить обычный керосин, который всегда найдется на хозяйстве.
Между тем, вспомогательная жидкость способна не только омывать само место соединения вибрирующей насадки и обрабатываемой поверхности, но и смывать все продукты эрозии. Что касается электродов, то в их качестве лучше всего использовать специальные стержни из такого жесткого материала, как латунь, причем они должны иметь ту же форму и габариты, что и у выполняемого отверстия. Не должно возникнуть трудностей и с принципиальной схемой электроискрового станка, ведь при желании подробный аналог подобного рода мини-установки можно отыскать на любом интернет-ресурсе. Так, весь принцип работы готового устройства подразумевает собой следующий процесс: контактный “плюс” разрядного конденсатора подводится к обрабатываемой детали, в то время, как его же “минус” подключают к самому инструменту, после чего приводится в действие электромагнитный вибратор.
В результате выделяемых искр удается блокировать сварку инструмента с обрабатываемой поверхностью, которая для обеспечения элементарных мер безопасности закрепляется в специальном зажимном устройстве, оборудованном дополнительным электрическим контактом со специальной “ванночкой”. Для того, чтобы собрать силовой трансформатор своими руками, лучше всего использовать сердечник (модификация Ш-32), выполненный из обычных трансформаторных стальных листов с толщиной набора не менее 4 сантиметров. Что касается самих подмоток, то первичная должна содержать не менее тысячи витков (отвод на 650 витке), в то время как вторичная – до 200 витков. В первом случае лучше всего использовать стальные провода модификации ПЭВ/0,41, а во втором – ПЭВ/2, диаметр которых составляет целых 125 миллиметров.
Не следует забывать и о таком важнейшем нюансе, как обеспечение промежуточной экранирующей обмотки, предусматриваемой между первичной и вторичной обмотками. Небольшие трудности могут возникнуть с созданием емкости конденсатора, которая должна расположить в себе сразу два приспособления по 50 Вольт каждое. Что касается реостата, то максимальное сила тока, на которую он рассчитан, составляет от трех до пяти Ампер, причем использовать следует лишь приспособление с нахромовой обмоткой.
Основу электроискрового метода обработки металлов составляет процесс электроэрозии металлов. Сущность его заключается в том, что под воздействием коротких искровых разрядов, посылаемых источником электрического тока, металл разрушается. При обработке на электроискровом станке для прошивки отверстий (рис. 18.3, а) заготовку 2 погружают в бак с жидкостью и соединяют с положительным полюсом, выполняющим функции анода. Электрод (инструмент) 4, являющийся катодом, соединяют с отрицательным полюсом и укрепляют на ползуне 5, имеющем вертикальное перемещение по направляющим 6. Заготовка 2, стол 1, на котором ее закрепляют, корпус бака и станина станка электрически соединены между собой и заземлены, так что их электрический потенциал всегда равен нулю. Это необходимо для безопасности работы на станке.
Если, опустив ползун 5, прикоснуться электродом 4 к заготовке 2, то в электрической цепи пойдет электрический ток от отрицательной клеммы 7 генератора Г к положительной клемме 8. В электрическую цепь включен резистор 11. Это катушка из длинной тонкой проволоки Изменяя сопротивление, можно регулировать силу тока, контролируя ее по амперметру 10.
Для того чтобы получить импульсные разряды, непрерывно следующие друг за другом, между электродом 4 и заготовкой 2 в электрическую схему стайка включается конденсаторная батарея 12. Ее включают параллельно заготовке 2 и электроду 4. Если замкнуть выключатель электрической цепи при разведенных электродах станка, то в первый момент стрелка амперметра 10 резко отклонится и постепенно возвратится на 0. Стрелка вольтметра 9, наоборот, плавно отклонится от того значения напряжения, которое создается генератором. Это означает, что произошла зарядка конденсаторов. Теперь можно приблизить электрод к заготовке. Как только расстояние между ними станет Небольшим, произойдет электрический разряд. При этом вся энергия, накопленная в конденсаторах, разрядится в промежутке между электродом и заготовкой, и чем больше запас энергии, тем больше будет электрическая эрозия анода (заготовки).
После разряда электрический ток между электродом и деталью исчезнет, так как вся энергия, накопленная в конденсаторах, израсходована, и снова начинается зарядка конденсаторной батареи. Следующий разряд произойдет, как только конденсаторы зарядятся. Этот процесс происходит непрерывно, импульсные разряды следуют один за другим до тех пор, пока не закончится обработка.
Во время обработки электрод 4 не должен касаться заготовки, иначе произойдет короткое замыкание. Между электродом 4 и заготовкой всегда должен поддерживаться небольшой, так называемый искровой промежуток. Это достигается с помощью различных устройств. Наиболее простое устройство – соленоидный регулятор (рис, 18.3, б). К верхнему концу ползуна 5 прикреплен стальной стержень-сердечник 13, который входит внутрь катушки (соленоида) 14, присоединенной к основной цепи. Присоединение сделано по разным сторонам резистора 11 так, что концы проводов 15 находятся под разными потенциалами.
Когда электрод 4 прикоснется к заготовке, электрическая цепь станка замкнется и в ней потечет электрический ток. Тогда на концах катушки 14 создается разность потенциалов, и в ней также потечет электрический ток. Сердечник 13 намагнитится и втянется в катушку 14, т. е. поднимется, поднимая вместе с собой ползун 5 и электрод 4. Искровой промежуток 3 между электродом 4 и заготовкой 2 восстановится, и основная электрическая цепь окажется разорванной – ток в ней исчезнет. Одновременно исчезнет ток и в катушке соленоида. Сердечник 13 размагнитится, перестанет втягиваться в катушку и под действием собственной массы опустится. Вместе с ним опустятся ползун 5 и электрод 4. Между электродом и заготовкой снова произойдет электрический разряд. По мере углубления отверстия электрод будет опускаться под действием силы тяжести.
Так будет продолжаться, пока идет процесс прошивки отверстия. Соленоидный регулятор автоматически постепенно опускает электрод по мере увеличения глубины отверстия. Если электрод можно сравнить с инструментом, то соленоидный регулятор может быть уподоблен механизму подачи. Электроды, применяемые при электроискровой прошивке, делают из мягкой латуни. Электрод должен иметь профиль, подобный профилю прошиваемого отверстия. Если диаметр отверстия больше 6 мм, то электрод лучше делать пустотелым.
Электроискровой прошивкой удается изготовлять отверстия с криволинейной осью (рис. 18.4) Электрод 2 из латунной проволоки изогнут по дуге окружности, радиус которой равен радиусу закрепления оси отверстия. Электрод укреплен в держателе 3, который может поворачиваться вокруг оси 1. Держатель 3 вокруг оси 1 поворачивается с помощью шнура 4, верхний конец которого прикреплен к соленоидному регулятору. В остальном процесс совершается так же, как и при прошивке отверстий с прямолинейной осью.
Универсальные электроискровые станки обычно имеют вертикальную компоновку (рис. 18.5). Автоматический регулятор подач 7 сообщает вертикальные перемещения электроду-инструменту 8. Ванну 4 с заготовкой 9, установленной на столе 3, можно перемещать в вертикальном направлении с помощью электродвигателя. Суппорт 5 при обработке отверстий с криволинейной осью поворачивается вокруг горизонтальной оси. Поперечный суппорт 6 перемещается по направляющим продольного суппорта. Продольный суппорт 5 установлен на направляющих 2 станины. Механизмы станка находятся внутри корпуса 1.
Для получения элементов со сложным профилем из труднообрабатываемых металлов используется электроэрозионный станок. Его работа основана на воздействии разрядов электрического тока, которые создают в зоне обработки высокую температуру, из-за чего металл испаряется. Такой эффект именуется электрической эрозией. Промышленность уже больше 50 лет использует станки, работающие по этому принципу.
Виды оборудования и методы обработки
Описать работу электроэрозионного станка можно так : взять заряженный конденсатор и поднести его электродами к металлической пластине. Во время короткого замыкания происходит разряд конденсатора. Яркая вспышка сопровождается выходом энергии (высокой температуры). В месте замыкания образуется углубление вследствие испарения некоторого количества металла от высокой температуры.
На технологическом оборудовании реализованы различные виды получения электрических разрядов. Среди основных схем выделяются:
- электроискровая;
- электроконтактная;
- электроимпульсная;
- анодно-механическая.
Реализуя одну из схем на практике, изготавливают станки . На принципе электрической эрозии были выпущены следующие станки в разных модификациях:
- вырезной;
- проволочный;
- прошивной.
Для получения точных размеров и автоматизации процесса оборудование комплектуется числовым программным управлением (ЧПУ).
Электроискровой станок работает за счет искрового генератора. Генератор – это накопитель энергии, который дает электрический импульс. Для постоянной подачи импульсов организуется конденсаторная батарея.
Чтобы организовать электрическую цепь, катод подключают к исполнительному инструменту, а анод – к обрабатываемой детали. Постоянное расстояние между электродом и деталью гарантирует однородность протекания процесса. При вертикальном опускании электрода на деталь происходит прошивка металла и образование отверстия, форма которого задается формой электрода. Так работает электроэрозионный прошивной станок.
Для изготовления деталей из твердосплавных и труднообрабатываемых деталей используется электроэрозионный проволочный станок. В качестве электрода в нем выступает тонкая проволока. При испарении металла на поверхности обрабатываемой детали образуются окислы, обладающие высокой температурой плавления. Для защиты от них процесс проводят в жидкой среде или масле. Во время искрообразования жидкость начинает гореть, забирая кислород и другие газы из рабочей зоны.
Станки такого типа иногда бывают единственно возможным способом изготовления конструкционного элемента. Но покупка оборудования для электроэрозионной обработки для выполнения нечастых работ – разорительное занятие. Поэтому если возникла необходимость, то можно изготовить электроэрозионный станок своими руками.
Особенности самодельного устройства
Перед тем как приступить к изготовлению самодельного электроэрозионного станка, необходимо разобраться в его устройстве. К основным конструкционным элементам относятся:
Изготовление искрового генеротора
Для изготовления искрового генератора детали можно найти везде (в старых телевизорах, мониторах блоков питания и т. д.). Принцип его работы таков :
Меры безопасности при работе
Так как организованная электроэрозия своими руками сопряжена с возможностью поражения электрическим током, к технике безопасности необходимо подойти со всей ответственностью. Обрабатываемая деталь не должна быть заземлена. В противном случае произойдет ЧП – короткое замыкание в питающей сети. Конденсаторы, рассчитанные на 400 В, могут привести к летальному исходу при их емкости всего в 1000 мкФ.
Подключение приборов исключает контакт с корпусом. Для подключения конденсатора к электроду требуется медный провод сечением 6−10 кв. мм. Большой объем масла, используемого для предотвращения образования окислов, может загореться и привести к пожару.
При помощи электроискровых станков изготовляются сквозные и глухие отверстия любой формы, отверстия с криволинейными осями, вырезают заготовки из листа, выполняют плоское, круглое и внутреннее шлифование. Изготавливают штампы, пресс-формы, фильеры, режущий инструмент. Такие станки способны резать металл, сверлить отверстия любого диаметра, наращивать дефектные области деталей, производить ювелирные работы с драгоценными металлами, упрочнять поверхность изделий, шлифовать изделия самой сложной формы, извлекать застрявшие сломанные сверла и резцы.
На базе электроискрового метода обработки металлов создано немало станков промышленного назначения. Это высокоточная и дорогая техника, которую могут позволить себе купить только крупные предприятия, специализирующиеся на металлообработке.
Выбор технических характеристик станкаОписывающие технологические свойства станков данной модели параметры являются: точность выполнения операций, перемещения по координатам, режимы и скорость подач, режимы резания и нагрузки, наличие механизированной смены инструмента, возможность установки дополнительного оборудования, потребляемая мощность. Приводимые данные по производительности, чистоте поверхности и энергоемкости относятся к обработке различных по величине площадей на режимах, обусловливающих отсутствие участков оплавления и покрытия, т. е. при оптимальных плотностях токов.
Рассмотрим основные технологические характеристики. Например, скорость съема металла на максимальных режимах при обработке стали составляет в среднем 600 мм3/мин и близка к предельно возможной для этого способа обработки металлов. Удельный расход энергии на жестких режимах составляет 20-50 квт-ч/кг диспергированного металла. Износ инструмента по отношению к объему снятого металла достигает 25-120 и более процентов. Чистота поверхности на мягких режимах достигает 4-го класса при скорости съема 10-15 мм3/мин. Дальнейшее повышение чистоты поверхности сопровождается резким уменьшением скорости съема. Так, при получении 5-го класса чистоты поверхности, производительность электроискрового способа обработки меньше 5 мм3/мин. Удельный расход энергии на мягких режимах в десятки и сотни раз выше, чем на жестких.
При обработке твердого сплава производительность процесса на мягких режимах, примерно, в два-три раза меньше, чем при обработке стали, однако при этом получается несколько лучшая чистота поверхности. Применение более жестких режимов при обработке твердых сплавов лимитируется образованием на них трещин.
Компоновка станкаОсновными узлами электроискровых станков являются: станина, механизм для установочных перемещений, рабочая ванна, насосная установка, генератор электрических импульсов и регулятор подачи. Станина является связующим звеном для основных узлов.
Механизм перемещений установки деталей и инструмента применяется, как и в металлорежущих станках.
Состав: ходовая часть, которая перемещается с помощью винтовых или шестеренных пар.
Рабочая ванна состоит из тонкой листовой стали и представляет собой цельносварную конструкцию. Клеммник крепится «на боку» рабочей ванны для того чтобы электроды присоединялись к разрядному контуру. От насосной установки подается рабочая жидкость. Размеры ванны зависят от деталей. Насосная установка представляется в виде емкости 50-60 литров.
Генератор импульсов. Для получения разрядов используется схема, которая включает в себя рабочие электроды, батарею, измерительную аппаратуру, источник постоянного тока и регулируемое сопротивление. Подробнее о нем рассмотрим ниже.
Электроэрозионный станок имеет искровой генератор, который выступает в качестве конденсатора. Принцип обработки заключается в накоплении энергии в течение длительного времени, а затем ее выброс в течение короткого промежутка времени.
Принцип работы генератора, который установлен на электроискровой станок, заключается в следующем:
Диодный мост проводит выпрямление промышленного тока напряжением 220 или 380 Вольт;
Установленная лампа ограничивает ток короткого замыкания и защиту диодного моста;
Чем выше показатель нагрузки, тем быстрее проходит зарядка электроискрового станка;
После того как зарядка закончится, лампа погаснет;
Зарядив установленный накопитель можно поднести электрод к обрабатываемой заготовке;
После того как проводится размыкание цепи, конденсатор снова начинает заряжаться;
Время зарядки установленного накопительного элемента зависит от его емкости. Как правило, временной промежуток от 0,5 до 1 секунды;
На момент разряда сила тока достигает несколько тысяч ампер;
Провод от конденсатора к электроду должен иметь большое поперечное сечение, около 10 квадратных миллиметров. При этом провод должен быть изготовлен исключительно из меди.
Линейный привод – это конструкция с бесконтактной передачей усилия, прямой привод без какой-либо кинематической цепи преобразования энергии в движение и вращательного движения в линейное, без люфтов, зоны нечувствительности и неравномерных подач. Все, что происходит при отработке каждого перемещения, это:
Командный импульс => Энергия взаимодействия магнитных полей => Линейное движение
В линейных приводах отсутствует многоступенчатое преобразование энергии в движение, что вызывает возникновение люфтов и неравномерных подач. Линейные приводы электроискрового станка способны корректировать зазор 500 раз в секунду с дискретностью подач 0,1 мкм. Выходит, оптимальный зазор практически в любой момент. И в итоге получаем оптимальные режимы, стабильно максимальный съем, высокую скорость обработки и качество поверхности.
Направляющие станкаНаправляющие служат для перемещения по станине подвижных узлов станка, обеспечивая правильность траектории движения заготовки или детали и для восприятия внешних сил. Во всех металлорежущих станках применяются направляющие: скольжения, качения, комбинированные, жидкостного трения, аэростатические.
Предъявляющие требования: первоначальная точность изготовления, долговечность, высокая жесткость, высокие демпфирующие свойства, малые силы трения, простота конструкции, возможность обеспечения, регулирования зазора-натяга.
В зависимости от расположения направляющие делятся также на горизонтальные, вертикальные, наклонные.
Шпиндельные узлы станкаШпиндель выполнен в виде массивного ротора, с расположенной внутри него крепежной цангой, а в верхней точке полости, образованной двумя встречно обращенными коническими поверхностями, установлен заборник(улавливатель) рабочей жидкости. Такая конструкция шпинделя улучшает условия работы на станке.
Рис.1 – Шпиндель электроискрового станка
В скользящем подшипнике 1 расположен вращающийся посредством клиноременной передачи 2 шпиндель 3, выполненный в виде ротора, в концентрической расточке которого расположена на напряженной или тугой посадке цанга 4, для крепления по внешней поверхности обрабатываемой детали 5. Внутренняя полость ротора образована двумя встречно обращенными коническими поверхностями 6 и 7, Рабочая жидкость, подаваемая от гидронасоса по трубке 8 в отверстие обрабатываемой детали, под действием центробежных сил вращающегося шпинделя собирается на периферии внутренней полости (кармана) ротора, откуда через заборник 9 по трубке 10 поступает в фильтрующий элемент гидронасоса.
Приводы подач станкаЛишь с недавнего времени начался выпуск электроискровых станков, а именно с совершенно новыми линейными двигателями. В данном выпуске были совершены и исправлены работы над регулированием скорости и ускорении, равномерным движением, реверсом, легкостью обслуживания и др.
Линейный двигатель в данном выпуске станков имеет двигатель, содержащий всего несколько элементов: электромагнитный статор и плоский ротор, которые содержат между собой только зазор из воздуха. Также имеется еще один немаловажный элемент и это оптическая измерительная линейка с высокой дискретностью (0.1 мкм). Без этого измерительного прибора система управления не сможет распознать координаты.
Но также ближе рассмотрим статор и ротор. Оба выполнены в виде плоских и легко снимаемых блоков. Но крепится статор к станине или колонне станка, а ротор – к рабочему органу.
В конструкции ротор совершенно прост. Он состоит из прямоугольных сильных постоянных магнитов. А магниты на тонкой плите из специальной высокопрочной керамики, коэффициент температурного расширения которой в два раза меньше чем у гранита.
Множество проблем линейного привода решились, так как стали использовать керамику одновременно с системой охлаждения. Соответственно «ушли» и проблемы с температурными факторами, с жесткостью конструкции, с наличием сильных магнитных полей и т.д.
Несущая система станкаСтанина, колонна, каретка стола и др. являются несущей конструкцией, обычно состоящей из чугуна. Шабренные посадочные поверхности предназначены для направляющих, а также для состыковки двух конструкций между собой.
Типичные представителиВ процессе подготовки данного реферата были разобраны несколько современных представителей станков электроискрового типа, оснащенных системой числового программного управления. Были представлены такие станки как, ALC 800G и AQ 15L . Их основные технические характеристики приведены ниже в таблицах 1 и 2.
Электроэрозионная обработка металлов: режимы, методы, технология
Суть технологии
Электрический разряд между проволокой и заготовкой приводит к удалению части металла. Выделенные частицы выводятся в объем рабочей жидкости. Шлам (кристаллизующиеся частицы) отфильтровывается и удаляется в конце реза. Скорость обработки регулируется силой тока. Но должны быть подобраны оптимальные режимы, при которых не образуются наплывы в процессе реза.
Электроэрозия помогает изготовить изделия с очень тонкими стенками, обрабатывать мягкие металлы без механических повреждений. Данный способ резки используется для прошивки на большую глубину. Толщина проволоки минимальна, лишь этим параметром ограничен диаметр получаемых отверстий.
Дополнительной обработки не требуется, так как после реза импульсами тока не остается заусенцев. Также не требуется дорогостоящего инструмента, применяемого при классических методах фрезерования. Это становится актуально при заготовках из вязких материалов.
Виды электроэрозионной обработки металлов
На современных предприятиях используется несколько видов электроэрозионной обработки металлов:
- Комбинированная. В данном случае электроэрозионная обработка осуществляется в комплексе с другими типами работ.
- Абразивная. Подразумевает электроэрозионное разрушение обрабатываемого металла.
Химическая. Сложная технология, в соответствии с которой материал заготовки одновременно растворяется в электролите (электрохимическим способом).
Анодно-механическая. В данном случае обработка осуществляется в жидкой среде, сопровождаясь растворением заготовки под воздействием импульсов электрического тока с одновременным образованием на поверхности металла окисных пленок, которые удаляются механически. Рассматриваемый процесс сопровождается электроэрозионной обработкой для придания материалу заготовки необходимых свойств и физико-химических характеристик.
Объемное копирование. Подразумевает отображение формы поверхности рабочего инструмента на поверхности заготовки (оба являются электродами).
Упрочнение. В данном случае электроэрозионная обработка металлов подразумевает повышение прочности поверхностного слоя металлической заготовки.
Прошивание. Технология подразумевает, что рабочий инструмент погружается в заготовку, создавая в ней отверстия постоянного сечения.
Маркирование.
Вырезание. Электрод-инструмент в данном случае имеет вид проволоки и постоянно находится в состоянии перематывания. Он осуществляет обход металлической заготовки в период движения подачи, и от траектории обхода непосредственно зависит контур создаваемой поверхности.
Отрезка. Такая электроэрозионная обработка позволяет разделить заготовку на несколько частей.
Шлифование. В соответствии с рассматриваемой методикой шлифование металла производится посредством его электроэрозионного разрушения.
Доводка.
Обработка заготовок с прямой или обратной полярностью.
Многоконтурная обработка.
Многоэлектродная эрозионная обработка.
Принцип работы станков
Электроэрозионная обработка материалов выполняется с использованием особого оборудования. Рядом с помещенной в станок деталью устанавливается специализированный инструмент — электрод, который может иметь вид бесконечного проводника (проволочная электроэрозионная резка) или заданную форму для прошивки фасонных отверстий и окон. Обрабатываемая деталь и инструмент подключаются к источнику питания.
Комплекс деталь-инструмент помещают в ванну с жидкой диэлектрической рабочей средой или обеспечивают подачу жидкого диэлектрика в искровой рабочий промежуток между инструментом и деталью. При включении силовой части станка между ними появляется разность потенциалов, что приводит к возникновению направленного электрического разряда.
При пробивании слоя диэлектрической жидкости происходит электрическая эрозия материала. Продукты эрозии из межэлектродного промежутка удаляются принудительной подачей диэлектрической жидкости или устраняются при ее естественной циркуляции и оседают на дне ванны.
Существует разница между электроискровой технологией и режимом электроимпульсной обработки материала. Электроимпульсный режим подразумевает наличие шагового генератора, который обеспечивает периодические разряды высокого напряжения импульсного типа. В период прохождения импульса происходит испарение и плавление материала проводника. Меняя параметры продолжительности и мощности одного импульса, можно регулировать скорость и глубину обработки, а также полярность проводников.
Сущность электроэрозионного метода
При обработке электроэрозией заготовка и инструмент присоединяются к разным полюсам источника постоянного тока. Предмет у положительного полюса становится анодом, у отрицательного — катодом. Между ними пропускаются короткие импульсы, вызывающие искровой разряд. Меняя длительность импульсов, можно добиться, чтобы преобладала эрозия катода или анода. Энергия импульсов ограничена, что позволяет избежать перегрева заготовки и добиться очень высокой точности манипуляций.
Как правило, в качестве инструмента применяется проволока, что во много раз уменьшает стоимость по сравнению с механическими станками. К инструменту не прилагается больших усилий, его износ минимален.
Поскольку при эрозии происходит перенос материала, можно не только убирать объем, но и наращивать, восстанавливать поверхность и получать рельефные оттиски. Появляется возможность обработки заготовок из сверхтвёрдых материалов, для которых нельзя подобрать механический режущий инструмент.
Станки для электроэрозии металлов
Перечислим основные модели станков, которые представлены в России:
- INTEGRAL 2 (AGIE). Производится одноименной швейцарской компанией. Позволяет работать с деталями размером не более 80 х 60 х 25 сантиметров. Основной режим работы — электроискровая эрозия в защитной среде диэлектрической жидкости. Имеет встроенную панель ЧПУ, которая позволяет контролировать технологические особенности операции (мощность ионного потока, точность обработки, итоговый уровень шероховатости).
- AQ535 (SODICK). Производится японской компанией. Позволяет обрабатывать заготовки, размеры которых составляют не более 105 x 65 x 30 сантиметров. Электроэрозионная обработка выполняется с помощью режущей проволоки, которая может делать все основные операции (создание отверстий, маркировка, шлифовка, вырезание). Модель оснащена продвинутой ЧПУ-панелью и имеет встроенную систему, экономящую электричество, что снижает себестоимость обработки.
- Модель 4531. Производилась в СССР; новые станки 4531 больше не выпускаются. Однако в продаже можно встретить множество неиспользованных моделей, а также станков Б/У. Для работы применяется электроискровая обработка металлических заготовок. Максимальные габариты обрабатываемых деталей — 16 x 12 x 3 сантиметра. Управление осуществляется в основном механическим способом + есть несколько информационных панелей, позволяющих узнать технологические особенности процедуры.
Типы оборудования для электроэрозии
В промышленности применяют два вида эрозионных станков — проволочный вырезной и прошивочный, принципиальное отличие которых заключается в технологии.
Проволочно-вырезной станок
В качестве инструмента используется очень тонкая, диаметром всего 0,1- 0,2 мм, проволока из тугоплавкого материала, обычно вольфрама или молибдена. Проволока намотана на барабаны и при движении вдоль поверхности заготовки вырезает линии по заданному контуру.
Проволочно-вырезной станок выполняет функции фрезерного оборудования. Однако точность получается намного выше, чем при традиционной механической обработке, в том числе при работе с металлами особой прочности.
Электроэрозионные прошивные станки
Прошивочные станки выпускаются как в стационарном, так и в настольном исполнении. В качестве рабочего инструмента служит электрод заданной формы. Углубление или отверстие в заготовке копирует форму электрода. На таких станках обрабатывают:
- сталь нержавеющих, инструментальных и закаленных марок;
- титан и прочие электропроводные материалы.
На таких станках получают глубокие отверстия очень малого диаметра или сложной формы. С помощью метода электроэрозии можно получать очень точные копии пресс-форм, штампов или иных деталей. Электрод, который в этом случае служит шаблоном, изготавливается из податливого материала, например, графита или меди. Меняя полярность подключения заготовки, можно получить на ее поверхности углубления или выпуклый рельеф с оттиском электрода.
Одной из самых трудоемких операций является нарезка резьбы в тугоплавких и особо прочных материалах. Движением электрода внутри отверстия в этом случае управляет станок с ЧПУ.
Электроэрозия — современный высокотехнологичный метод обработки металлов. Электроэрозионные станки приходят на замену традиционным механическим там, где необходима высокая точность, создание поверхностей или полостей сложной конфигурации, работа с заготовками из особо прочных металлов, легированных и закаленных сталей.
Выбираем электроэрозионный станок
Электроэрозия – разрушение металлических поверхностей под воздействием на них электрических зарядов. В основу этой технологии положены работы советских учёных Н. И. Лазаренко и Б. Р. Лазаренко.
Этим методом можно легко изменять размеры изделий из металла, получать в них отверстия различной формы и глубины. Отличные результаты даёт электроэрозионная обработка профильных пазов и канавок, полостей фасонного вида в деталях машин и механизмов.
Особенно сильно востребовано такое оборудование для изготовления деталей из твёрдых сплавов, где обычная механическая обработка затруднена.
Станки электроэрозионного типа обладают универсальными возможностями в обработке материалов, имеющих плотную структуру поверхностей. Этот вид обработки материалов выгодно отличается от других способов изменения формы и размеров деталей, так как трудоёмкость операций благодаря электроэрозионной технологии резко снижается.
Принцип работы электроэрозионного станка показан на приведенной схеме-рисунке. Под действием импульсного электрического генератора в зазоре между электродом и поверхностью детали образуются искровые разряды или иное электрическое взаимодействие.
Пространство искрового промежутка непрерывно омывается потоком охлаждающей жидкости, за счёт которой происходит удаление с обрабатываемой поверхности разрушенного металла. Под управлением блока ЧПУ процесс протекает в заданном направлении и в требуемом количестве.
В качестве электрода чаще всего используется латунная проволока, которая по мере расхода подаётся в зону электроэрозионной обработки. Более современный расходный материал для электроэрозии – молибденовая проволока, расход которой на осуществление обработки одной детали ничтожен.
Однако эти станки имеют и существенные ограничения по сравнению с аппаратами для механической обработки деталей. Ведь они подходят для обработки лишь токопроводящих металлов и их сплавов.
Воздействовать на металл электроэрозионным путём можно различными способами: подавая на искровой промежуток как электрические разряды, так и импульсы параметрического вида.
В зависимости от требуемого результата обработки выбирается и более подходящий путь её выполнения.
Очень важным элементов этого воздействия на металлические поверхности является то, что при нём можно вести обработку заготовки по различным направлениям в одно и то же время.
Среди способов электроэрозионной обработки изделий различают:
- электроимпульсный;
- электроискровой;
- электроконтактный;
- анодномеханический.
К технологическим операциям, которые выполняются электроэрозионным путём, относятся:
- структурное упрочнение;
- шлифование;
- маркировка;
- резание;
- доводка;
- копирование объёмное;
- доводка.
С помощью электрической эрозии на этих станках можно выполнять различные глухие проёмы, углубления и отверстия не геометрической конфигурации. Возможно также выполнение на поверхности отверстий резьбы любого профиля.
Станки способны производить выборку металла с внутренней поверхности изделий на заданную глубину, тем самым выполнять операции, заменяющие фрезерную и токарную обработки.
Технология электрической эрозии используется при обработке металлов, которые трудно поддаются классическому механическому станочному воздействию. К ним, в частности, относятся титан и его сплавы.
Вполне допустимо для выполнения определённых технологических операций в цехе купить б/у станок, предварительно проверив его работоспособность.
Практика показывает, что даже при большом количестве часов наработки оборудование для электроэрозионной обработки почти не подвержено износу.
Электроэрозионная резка металла
Метод электроэрозионной резки металла (ЭЭР) позволяет выполнять обработку заготовки с более высокой скоростью, чем метод электроэрозионной контурной прошивки, т. к. площадь обрабатываемой поверхности в единицу времени ограничена диаметром проволоки или единичного электрода инструмента. Электроэрозионная резка не требует использования черновых и чистовых контуров-электродов, а сразу вырезает требуемый контур детали.
Электрод-проволока изготавливается из металлов и сплавов с высокой эрозионной стойкостью (латунь, вольфрам) и в процессе работы при постоянной протяжке через искровой промежуток имеет минимальный износ и постоянный диаметр. Это позволяет добиться сверхвысокой точности обработки изделия. Данный метод дает возможность проводить чистовую шлифовку деталей независимо от формы, размеров и шероховатости обрабатываемой поверхности.
Электроэрозионная резка позволяет изменять размеры металлической заготовки без нарушения ее физических свойств, что существенно увеличивает технологическую вариативность производства. Появляется возможность расширить спектр используемых металлов, материалов и сплавов в технологической линейке производства.
Электроэрозионная резка проволокой чаще всего применяется на крупных промышленных предприятиях для производства высокоточных серийных деталей, поскольку позволяет придать заготовке сложный контур и производить вырезку конических отверстий с углами до 30° при высоте обрабатываемой заготовки до 400 мм. Несомненным преимуществом данного вида обработки является тот факт, что после окончания резки деталь не требует дополнительной шлифовки, а это существенно влияет на себестоимость и скорость полного цикла изготовления.
По этой же схеме осуществляется резка заготовок с малой толщиной и различной степенью обработки поверхности металлов, т. к. воздействие электрического разряда при резке не деформирует обрабатываемую поверхность. Электроэрозионная резка нашла широкое применение в производстве ювелирных изделий. Технология ЭЭО позволяет также поместить нужную информацию или рисунок на тонкую заготовку без ее деформации, при этом возможно нанесение не только на металл, но и на другие виды токопроводящих материалов.
Принцип рассматриваемого метода обработки
Особенностью обработки электроискровой установкой можно назвать то, что испарение металла происходит из-за воздействия определенного заряда на поверхность заготовки. Примером подобного воздействия можно назвать замыкание конденсатора на металлической пластинке – образуется лунка определенных размеров. Электроэрозионный разряд создает высокую температуру, которая просто испаряет металл с поверхности. Стоит отметить, что станок из этой группы уже используется на протяжении последних 50 лет в различных сферах промышленности. Главным условием использования подобного электроискрового станка можно назвать то, что заготовка должна быть изготовлена из определенного металла. При этом учитывается не степень обрабатываемости, а электропроводящие свойства.
Электроды
Рабочая часть для электроэрозионного оборудования — электроды. Они отличаются конструкцией, материалом.
Материал
Материал электродов должен иметь:
- эрозионную стойкость;
- высокую прочность;
- низкую цену.
Лучшие варианты:
- молибден;
- латунь;
- серый чугун;
- алюминиевые сплавы или чистый алюминий;
- электролитическая медь;
- медные сплавы;
- смесь вольфрама с медью.
Молибден (Фото: Instagram / ferroprofi)
Конструкция
Конструкция электродов:
- Форма инструмента должна быть обратной той поверхности, с которой будет проводиться рабочий процесс.
- Чтобы подводить рабочую жидкость к электроду, в нем высверливается небольшое отверстие.
- Чтобы снизить массу электрода, их могут изготавливать пустотелыми.
Чистовая обработка металла выполняется с помощью ступенчатых рабочих частей, а черновая — с помощью стержневой части.
Станки для электроэрозионной обработки
Первые образцы электроэрозионных станков появились в середине сороковых годов, в СССР. Ну а первый станок с числовым программным управлением создали вначале 60-х, в Швейцарии.
Современные станки позволяют решать, как массовые, так и мелкосерийные или единичные задачи, как эстетического (шлифовка, декорирование и прочее), так и практического (перфорация сквозных и глухих отверстий, формирование пазов, заточка режущего инструмента) характера. Причем и с теми и с другими целями электроэрозионные станки справляются с одинаковой эффективностью.
К тому же, себестоимость обработки на подобном оборудовании намного ниже аналогичного показателя, характерного для классических, металлорежущих станков.
Поэтому аппараты электроэрозионной обработки используются для создания высокоточных деталей, применяемых в аэрокосмической отрасли, приборостроении, станкостроении, автомобилестроении и прочих отраслях, испытывающих потребность в подобных изделиях.
Принцип работы электроэрозионного станка
После того как выше были рассмотрены конструктивные аспекты существующих электроэрозионных станков, следует разобраться в принципе их работы. Нельзя не упомянуть, что процедуры обработки деталей, которые применяются на устройствах такого типа, позволяют достигать просто поразительных результатов.
Для начала пару слов о том, что такое электрическая эрозия, ведь как мог уже догадаться читатель из названия станка, именно эта реакция стоит в основе работы таких устройств.
Разрушение верхнего слоя поверхности материала под влиянием внешнего воздействия, осуществляемого электрическими разрядами, называется электрической эрозией. Именно этот процесс и стал основой для обработки различных материалов и деталей, который называется электроэрозионным.
Сама электроэрозионная обработка осуществляется путём изменения размеров, формы, шероховатости и свойств поверхности обрабатываемой заготовки под влиянием электрических разрядов в результате электрической эрозии, воздействующих на заготовку при обработке.
Из-за того, что в зоне разряда действуют весьма высокие температуры (8000 — 12000 градусов по Цельсию), металл подвергается следующим изменениям: нагрев, затем последующее расплавление и даже частичное испарение. Для того чтобы получить такие высокие температуры в зоне разряда, создаётся большая концентрация энергии, которая достигается благодаря генератору электрических импульсов. Сам процесс электроэрозионной обработки происходит в рабочей жидкости, а именно в дистиллированной воде. Она заполняет пространство между имеющимися электродами. Одним из этих электродов является сама заготовка, а вторым — электрод-инструмент (электрод трубчатый).
Под действием сил, которые возникают в канале разряда, а также благодаря тому, что электрод быстро вращается, происходит выброс уже жидкого и парообразного металла из зоны разряда в окружающую его рабочую жидкость, а затем его застывание в ней с образованием отдельных мелких частей. В заготовке, под действием импульса тока, образуется отверстие. Кроме этого, можно наблюдать угар электрода-инструмента, происходящий параллельно образованию отверстия.
Следует заметить, что электрод-инструмент обязательно должен быть изготовлен из материала с высокой эрозионной стойкостью. Такими материалами, которые обладают таким важным качеством и которые способны обеспечить стабильность протекания процесса электроэрозии, являются: вольфрам, графит, алюминий, латунь, медь и графитовые материалы. Обычно в таких станках используются медные или латунные трубчатые электроды.
Краткое описание самодельной установки
В корпусе 2 установлен электрод 1. Его возвратно-поступательное перемещение производится электромагнитом из катушки 7. К направляющей втулке подведена клемма 3 (подается положительный потенциал).
На рабочем столе 4 крепится деталь, которую нужно обработать. На столе имеется клемма 5, к ней подключается отрицательный проводник. По трубке 6 внутрь корпуса подается смазка.
Через фильтры производится подключение преобразователя напряжения, от них положительный и отрицательный провода соединяются на соответствующих клеммах 3 и 5. На столе 4 фиксируется деталь, в которой можно проводить разные виды обработки, например, прожечь отверстие в закаленной детали.
Включив преобразователь, на токонесущих проводах будет получено рабочее напряжение. Дополнительно подается напряжение на индукционную катушку 7. Она создает вибрацию электрода 1, направляя его движение вправо и влево. Электрод 1 касается обрабатываемой детали. В зоне контакта возникает ток величиной 7000…9000 А.
При каждом движении инструмента в сторону детали выжигается небольшое количество металла. В течение 10…12 минут работы электроэрозионного станка в детали будет получено сквозное отверстие. Получено отверстие в хвостовике сверла. Обычным способом просверлить подобное отверстие довольно сложно.
Основные узлы ЭЭО-станков и их действие
Копировально-прошивочный станок
Типовой копировально-прошивочный станок вертикальной компоновки, снабжённый электрогидравлической системой привода рабочих органов, состоит из следующих узлов:
- Г-образной станины, регулируемой по высоте.
- Рабочей головки, в которой смонтирован узел электрода-инструмента.
- Привода двухкоординатного перемещения рабочей головки (на некоторых типоразмерах станков имеется ещё и орбитальная головка, благодаря которой электрод-инструмент может вращаться).
- Рабочего стола, на котором закрепляется обрабатываемая заготовка.
- Ванна с рабочей жидкостью, которая снабжена винтовой передачей для своего подъёма-опускания.
- Электродвигателей: главного привода, привода рабочей ёмкости и орбитальной головки.
- Системы управления.
В самостоятельном корпусе размещается шаговый генератор импульсов, который включается в общую электрическую схему станка. Эти устройства должны отвечать следующим требованиям:
- Отличаться возможно более высоким КПД;
- Стабилизировать во времени все параметры электрического разряда;
- Иметь возможность максимального регулирования рабочей частоты импульса;
- Обеспечивать такие параметры электрического разряда, при которых износ электрода-инструмента, производительность процесса и качество обработки заготовки будут оптимальными.
Отечественные генераторы импульсов системы ШГИ оснащаются встроенными регуляторами подачи электрода-инструмента и блоками предотвращения короткого замыкания.
Узлы подачи рабочей головки в станках, использующих для ЭЭО нестационарный электрический разряд, могут быть трёх основных типов – соленоидного, электромеханического и электрогидравлического. Первый применяется в установках малой мощности, второй – преимущественно для агрегатов, производящих электроискровое разрезание. Наиболее универсальным считается электрогидравлический привод. Его недостатки – несколько меньшая производительность на вспомогательных переходах и необходимость в дополнительных площадях под гидравлические компоненты, ответственные для очистки и перекачки рабочей среды.
Электродуговые станки
Электродуговые станки состоят из:
- Станины рамного типа.
- Рабочей головки с электродом-инструментом и контрольно-следящей системой его перемещения во время ЭЭО.
- Насосной станции для прокачки рабочей жидкости под повышенным давлением (это необходимо для повышения качества ЭЭО стационарным дуговым разрядом).
- Герметизирующей камеры, внутрь которой устанавливается заготовка.
- Рабочего стола.
- Источника питания постоянного тока.
Рабочий цикл такого оборудования включает в себя установку на стол заготовки, подлежащей ЭЭО, последующего размещения герметизирующей камеры, подвода инструментальной головки с электродом-инструментом и включения насосного привода подачи рабочей среды. После этого включается источник питания, возбуждается дуговой разряд и производится обработка. Подача электрода-инструмента выполняется автоматически. По достижении требуемого значения напряжения на дуге происходит пробой межэлектродного промежутка, и возникающий столб дуги, сжатый потоком рабочей среды производит размерное формообразование. Продукты эрозии удаляются насосной установкой через рабочие отверстия в электроде-инструменте.
Типы используемого оборудования
Как известно, существуют самые разные методы и способы обработки поверхностей металлов, при этом данный вид является более эффективным, чем механические.
Связано это главным образом с тем, что тот инструмент, который используется для проведения механических типов обработки, стоит гораздо дороже, чем проволока, которая применяется при электроэрозионной обработке.
В том случае, когда необходимо изготовить пресс-формы и детали со сложной формой, а также при производстве некоторых материалов, к которым применяются высокие требования к точности обработки, используют проволочно-вырезные электроэрозионные агрегаты.
Как правило, на таком типе оборудования изготавливают самые разные детали для самолетов, электроники и даже космической сферы.
На видео, которое размещено ниже, можно увидеть, как проводится такая обработка с использованием электроэрозионного оборудования.
Для массового и серийного производства деталей по данному методу в большинстве случаев используют копировально-прошивочные агрегаты.
Такие станки позволяют получить достаточно точные сквозные контуры, а также мелкие отверстия, что успешно используется при производстве сеток, а также штампов в инструментальной сфере промышленности.
Как правило, оборудование данного типа подбирается, исходя из поставленных задач, а также финансовой окупаемости. Следует отметить и то, что электроэрозионную обработку относят к сложным и достаточно трудоемким рабочим процессам.
Ее невозможно провести в домашних условиях своими руками. К работе на станках для данного вида обработки деталей допускаются только квалифицированные и аттестованные люди, которые имеют соответствующий опыт работы в данной сфере.
При выполнении электроэрозионной обработки необходимо не только соблюдать технику безопасности, но и обязательно надеть спецодежду. Видео:
Электроэрозионная резка металла
Метод электроэрозионной резки металла (ЭЭР) позволяет выполнять обработку заготовки с более высокой скоростью, чем метод электроэрозионной контурной прошивки, т. к. площадь обрабатываемой поверхности в единицу времени ограничена диаметром проволоки или единичного электрода инструмента. Электроэрозионная резка не требует использования черновых и чистовых контуров-электродов, а сразу вырезает требуемый контур детали.
Электрод-проволока изготавливается из металлов и сплавов с высокой эрозионной стойкостью (латунь, вольфрам) и в процессе работы при постоянной протяжке через искровой промежуток имеет минимальный износ и постоянный диаметр. Это позволяет добиться сверхвысокой точности обработки изделия. Данный метод дает возможность проводить чистовую шлифовку деталей независимо от формы, размеров и шероховатости обрабатываемой поверхности.
Электроэрозионная резка позволяет изменять размеры металлической заготовки без нарушения ее физических свойств, что существенно увеличивает технологическую вариативность производства. Появляется возможность расширить спектр используемых металлов, материалов и сплавов в технологической линейке производства.
Электроэрозионная резка проволокой чаще всего применяется на крупных промышленных предприятиях для производства высокоточных серийных деталей, поскольку позволяет придать заготовке сложный контур и производить вырезку конических отверстий с углами до 30° при высоте обрабатываемой заготовки до 400 мм. Несомненным преимуществом данного вида обработки является тот факт, что после окончания резки деталь не требует дополнительной шлифовки, а это существенно влияет на себестоимость и скорость полного цикла изготовления.
По этой же схеме осуществляется резка заготовок с малой толщиной и различной степенью обработки поверхности металлов, т. к. воздействие электрического разряда при резке не деформирует обрабатываемую поверхность. Электроэрозионная резка нашла широкое применение в производстве ювелирных изделий. Технология ЭЭО позволяет также поместить нужную информацию или рисунок на тонкую заготовку без ее деформации, при этом возможно нанесение не только на металл, но и на другие виды токопроводящих материалов.
На каком оборудовании и какие заказы делаются?
Наименование | Количество | Параметры |
Электроэрозионный вырезной станок А207.86М | 1 | 250*160*100mm |
Наименьшая шероховатость обработанной поверхности Ra 1.25мкм , точность образца изделия по ГОСТ 20551
Даже простое перечисление оборудования, на котором в «Зубиксе» осуществляется электроэрозионная обработка металлов заслуживает того, чтобы доверить нам выполнение самых сложных работ. Это вырезные станки, работающие по методу электроэрозии, с маркировкой А207.79 и А207.86, электропрошивной EDM450 и даже электроэрозионный вырезной станок 7740F с пятью координатами.
Поэтому спектр работ, выполняемых с их помощью, очень широк:
- проволочная резка, дающая уникальные возможности электроэрозионного раскроя заготовок и изготовления сложнейших прорезей;
- резка сверхпрочных сплавов, быстрая и не вызывающая износ инструмента;
- нарезка шлицев и шпоночных пазов;
- обработка используемых поверхностей пуансонов, матриц, фильер экструдеров, восстановление их эффективности;
- частичное производство пресс-форм, обработка профилей колес с зубьями, изготовление штампов и многие другие квалифицированные работы.
Суть и применение методики
Работа метода основана на воздействии на деталь электрическими разрядами в диэлектрической среде, вследствие чего происходит разрушение металла или изменение его физических свойств.
Применение метода ЭЭО:
- При обработке деталей из металлов со сложными физико-химическими свойствами;
- При изготовлении деталей сложных геометрических параметров, со сложно выполнимой механической обработкой;
- При легировании поверхности для повышения показателей износоустойчивости и придания деталям требуемых качеств;
- Повышение характеристик верхнего слоя металлической поверхности (упрочнение) за счет окисления материала под воздействием электрического разряда;
- Высокоточная шлифовка детали;
- Маркирование изделий без вредоносного влияния, что присутствует при механическом клеймлении.
Высокоточная шлифовка детали
Для выполнения различных операций применяются разные виды электроэрозионной обработки. На промышленных станках устанавливаются устройства числового программного управления (ЧПУ), что значительно упрощает применение любого вида обработки.
Виды электроэрозионной обработки материала:
- Электроискровой вид обработки применяется при резке твердосплавных материалов, фигурной резке и для проделывания отверстий в металлах высокой прочности. Дает высокую точность, но скорость работы невелика. Применяется в прошивных станках.
- Электроконтактный способ обработки основан на местном расплавлении металла дуговыми разрядами с последующим удалением отработанного материала. Метод имеет более низкую точность, но более высокую скорость работы, чем электроискровой способ. Применяется при работе с большими деталями из чугуна, легированной стали, тугоплавких и других металлов.
- Электроимпульсный метод сродни электроискровому, но применяются дуговые разряды продолжительностью до 0.01 секунды. Это дает высокую производительность при относительно хорошем качестве.
- Анодно-механический метод основан на сочетании электрического и механического воздействия на металл. Рабочий инструмент – диск, а рабочая среда – жидкое стекло или сходное по характеристикам вещество. На обрабатываемую деталь и диск подают определенное напряжение, при разряде металл расплавляется, а шлам удаляется диском механически.
Электроконтактный способ обработки
В промышленности применяются станки, работающие на основе метода электроэрозионной обработки металла. Они классифицируются по нескольким параметрам: принцип работы, управление, наличие ЧПУ и т.д.
Виды станков, работающих на принципе ЭЭО:
- Электроэрозионный вырезной станок;
- Электроэрозионный проволочный станок;
- Электроэрозионный проволочно-вырезной станок;
- Электроэрозионный проволочный с ЧПУ;
- Электроэрозионный прошивной станок.
Электроэрозионный проволочный с ЧПУ
Станок ЭЭО в связи со своей многофункциональностью в хозяйстве нужен, а порой и вовсе не заменим. Заиметь такой аппарат в своем гараже хотел бы каждый. К сожалению, купить такой станок заводской сборки очень накладно и зачастую не представляется возможным. Выход из такой ситуации есть – собрать своими руками.
Выводы
Целый ряд достоинств, а также нетипичный принцип работы, которые позволяет достигать выдающихся результатов при обработке различных заготовок, делают это обрабатывающее оборудование настоящим титаном среди устройств другого типа, но предназначенных также для обработки различных заготовок.
Простота эксплуатации электроэрозионных станков позволяет осуществлять на нём работу даже тем пользователям, которые ранее не имели опыта или определённых навыков работы с таки оборудованием.
Принцип работы электроэрозионных станков, заключающийся в использовании электрической эрозии для обработки заготовок, позволяет добиваться очень качественных результатов.
Источники
- https://obrabotkametalla.info/stanki/rabota-samodelnogo-elektroerozionnogo-stanka
- https://metmastanki.ru/elektroerozionnyy-stanok-svoimi-rukami
- https://stankiexpert.ru/stanki/stanki-dlya-rezki/elekroerozionnye-stanki.html
- https://ometalledo.ru/elektroerozionnyj-stanok-svoimi-rukami.html
- https://ice-people.ru/raznoe-2/elektroerozionnyj-stanok-svoimi-rukami-elektroerozionnyj-stanok-svoimi-rukami-zakonchennye-proekty.html
- https://WikiMetall.ru/metalloobrabotka/elektroerozionnaya-obrabotka.html
- https://stanok.guru/stanki/elektroerozionnye-stanki-i-princip-raboty.html
- https://www.softelectro.ru/5_2.html
- https://stanki-info.com/elektroerozionnyy-stanok-svoimi-rukami/
Электроэрозионная обработка – обзор
8.1 Введение
Электроэрозионная обработка (EDM) стала наиболее популярным нетрадиционным процессом удаления материала в современной производственной практике. Это связано с рядом причин. 1 , 2 EDM позволяет обрабатывать чрезвычайно твердые материалы, а изделия сложной формы могут изготавливаться с высокой точностью. Его неотъемлемая способность к автоматизации – еще одна особенность, отвечающая ожиданиям современного производства.Поэтому электроэрозионная обработка в основном применяется в производстве штампов и пресс-форм, а также при изготовлении прототипов. Появление оборудования с числовым программным управлением позволило использовать различные новые технологии электроэрозионной обработки, такие как электроэрозионная обработка с глубоким проходом по нескольким осям, контурная электроэрозионная обработка, проволочная и фрезерная электроэрозионная обработка. Это, вместе с более высокой производительностью и большей точностью, привело к функциональному расширению, которое частично отвечает за растущий интерес к EDM. В вышеупомянутых отраслях электроэрозионная обработка в основном применяется для обработки металлов, например, высоколегированных сталей.Одним из условий, необходимых для выполнения электроэрозионной обработки, является электропроводность материала.
Передовая инженерная керамика все больше и больше используется в современной промышленности из-за ее превосходных механических свойств, таких как высокая твердость, высокая прочность на сжатие, химическая и абразивная стойкость. Важным требованием к этой керамике является возможность экономичного формования. Для простых форм подойдет обычная распиловка и шлифование в оптимальных условиях.Большинство керамических материалов получают с помощью обычного процесса порошковой металлургии (ПМ). Хотя PM – это процесс, близкий к конечной, исследование рынка PM показывает, что около 60% всех компонентов нуждаются в какой-либо операции последующей обработки. Одним из объяснений этого является невозможность создания геометрии с поперечными отверстиями, поднутрениями, скосами, пазами и резьбой во время операции прессования порошка. Другое объяснение – это общая тенденция к разработке более сложных деталей с более жесткими допусками, которые требуют механической обработки.Операции по механической обработке могут составлять более 20% общих затрат на производство керамических компонентов.
EDM – это процесс, с помощью которого можно обрабатывать эти твердые материалы при условии, что керамика имеет достаточно низкое удельное электрическое сопротивление (<100 Ом · см). 3 Удельное электрическое сопротивление спеченного SiC (0,05 Ом · м) и B 4 C (0,01 Ом · м) как раз достаточно, чтобы обеспечить электроэрозионную обработку. Но на практике для некоторых технологий электроэрозионной обработки, таких как глубинная электроэрозионная обработка, процесс очень сложен из-за сложных условий промывки и охлаждения. 4 Для большинства керамических материалов, предназначенных для электроэрозионной обработки, добавляются другие электропроводящие фазы (например, TiN), что приводит к так называемым керамическим композитам (например, ZrO 2 – TiN, Si3N4-TiN, B4C-TiB2). 5
Наиболее изученным электроэродируемым керамическим композитом является Si3N4-TiN. Хотя это доступно на рынке, литературные отчеты очень фрагментированы и их трудно сравнивать, особенно в отношении настроек используемого электроэрозионного станка. Электроэрозионный ZrO 2 -TiN и Al 2 O 3 -SiC w -TiC также недавно были представлены на рынке, но их метод использования (как установить настройки генератора, применяемые стратегии обработки , так далее.) пока не сообщалось. Таким образом, даже несмотря на то, что электроэрозионные керамические композиты коммерчески доступны, подходящие технологии электроэрозионной обработки часто отсутствуют. Хотя современные генераторы EDM могут обрабатывать электропроводящие керамические материалы, они не предназначены для этого.
Чтобы обеспечить эффективную электроэрозионную обработку керамических композитов, необходимо хорошее понимание взаимодействия обрабатываемых материалов. В рамках нескольких исследовательских проектов, таких как проект ЕС MONCERAT, К.У. Левен работал вместе (в основном в качестве координатора) с другими институтами и отраслями, чтобы расширить область применения керамических компонентов путем совместных и интерактивных исследований в области электроэрозионной обработки и новых керамических материалов.
В следующем разделе кратко описаны принципы EDM. Эти знания необходимы для полного понимания взаимодействия технологического материала при обработке керамических композитов. Затем следует раздел 8.3, посвященный электропроводным керамическим материалам и композитам, подходящим для электроэрозионной обработки. В разделе 8.4 дается подробное описание электроэрозионной обработки керамических композитов. Влияние микроструктуры материала на характеристики электроэрозионной обработки (скорость съема материала, качество поверхности и т. Д.)) объясняется. Это объяснение дается для наиболее распространенных классов керамических композитов на основе Si 3 N 4 , ZrO 2 , B 4 C и нескольких боридов переходных металлов. Потребность в усовершенствованных генераторах машин кратко описана в Разделе 8.5. Некоторые приложения, разработанные в рамках проекта MONCERAT EU, описаны в Разделе 8.6.
Электроэрозионная обработка: принцип, работа, оборудование, преимущества и недостатки со схемой
Сегодня мы познакомимся со схемой электроэрозионной обработки, принципом работы, оборудованием, преимуществами и недостатками.Этот процесс обработки использует электрическую искру для удаления металлической формы. Эта обработка аналогична удалению металлического заусенца при наличии электрической искры. Электрическая искра, используемая в качестве режущего инструмента для резки заготовки и получения желаемой формы. Этот процесс осуществляется путем подачи высокочастотного тока через электрод к заготовке. Искровой продукт удаляет металл в виде очень мелких стружек. Этот процесс осуществляется в диэлектрической жидкости.
Электроэрозионная обработка:
Принцип:
Процесс электроэрозионной обработки основан на основном принципе искрообразования и удаления металла путем искровой эрозии.Электроэрозионная электроэрозия аналогична электрической искре, которая прожигает небольшое отверстие в куске металла через контакт с ним. Искра, образующаяся при этом процессе, выделяет тепло, которое удаляет металл за счет эрозии и испарения. В этом процессе обработки и заготовка, и инструмент должны быть изготовлены из проводящего материала.Схема электроэрозионной обработки |
Оборудования:
Электроэрозионный процесс включает следующее оборудование.
Источник питания:
В процессе электроэрозионной обработки ток высокой частоты, используемый для образования искры между электродом и заготовкой. Эта искра выделяет тепло и удаляет металлическую форму заготовки.
Система подачи и промывки диэлектрической жидкости:
Диэлектрическая жидкость действует как средство, отгоняющее стружку и предотвращая ее прилипание к поверхности. Эта жидкость действует как система промывки стружки. Это также помогает увеличить скорость съема металла, способствуя возникновению искры между инструментом и заготовкой.Эта жидкость также работает как охлаждающая среда.
Инструмент и держатели инструмента:
В процессе электроэрозионной обработки инструмент также разрушается из-за искры, поэтому выбор инструмента зависит от степени износа, простоты изготовления инструмента и стоимости материала. Наиболее часто используемые электродные материалы – это медь, вольфрамовый сплав, чугун, сталь, серебряно-вольфрамовый сплав, графит.
Заготовка и удерживающие устройства:
В этом процессе можно обрабатывать только хорошие проводники электричества.Таким образом, заготовка должна иметь хорошую электропроводность. Этот процесс не зависит от твердости заготовки, поэтому критерии твердости отсутствуют.
В рабочем состоянии:
В этом процессе заготовка должна быть хорошо проводящей электричество. Этим методом можно обрабатывать только электропроводящий материал. Работа EDM следующая.
- Сначала и заготовка, и инструмент погружаются в диэлектрическую жидкость. Диэлектрическая жидкость помогает контролировать дуговую разрядку. Это также удаляет взвешенные частицы материала детали и инструмента из рабочей полости.
- Используется сервомеханизм, который поддерживает очень маленький зазор между заготовкой и инструментом. Этот зазор желателен для правильного образования дуги. Речь идет о толщине человеческого волоса.
- Инструмент выполнен как форма, противоположная заготовке.
- На электрод подается высокочастотный ток, который вызывает искру между инструментом и заготовкой. Эта искра генерируется высоко в рабочей полости.
- Металл, удаленный с детали из-за эрозии и испарения ионов.
- Стружку или взвешенные частицы между инструментом и заготовкой следует удалить, чтобы они не образовали мостик, вызывающий короткое замыкание. Это достигается за счет непрерывной подачи диэлектрической жидкости.
- Из-за перереза на электроэрозионном станке образуется полость немного больше, чем на электроде.
Для лучшего понимания рабочего процесса EDM посмотрите следующее видео.
Преимущества и недостатки:
Преимущества:
- С помощью этого процесса можно разрезать любой проводящий материал.
- Он не зависит от твердости заготовки, поэтому закаленную заготовку легко обрабатывать.
- Сложное сечение матрицы и сложные формы можно изготавливать с высокой точностью.
- Этот процесс без заусенцев.
- Тонкий профиль легко обрабатывается без деформации детали.
Недостатки:
- В этом процессе обработки происходит сильный износ инструмента.
- Износ инструмента ограничивает точность и чистоту поверхности металла.
- С помощью электроэрозионной обработки можно обрабатывать только хорошие электрические проводники.
Это все об электроэрозионной обработке, принципах, работе, оборудовании, преимуществах и недостатках со схемой. Если у вас есть какие-либо вопросы относительно этой статьи, задавайте их в комментариях. Если вам понравилась эта статья, не забудьте поделиться ею в социальных сетях. Спасибо, что прочитали.
Процесс электроэрозионной обработки (EDM)
Электроэрозионная обработка или электроэрозионная обработка описывается вместе с определением, принципом действия, компонентами, типами, принципами работы, преимуществами, недостатками и т. Д.
Имеет несколько других названий, например,
- Искровая обработка
- Погонная обработка
- Искровая эрозия
- Эрозия или выгорание проволоки
Давайте приветствуем электроэрозионную обработку или электроэрозионную обработку!
Электроэрозионная обработка или основы электроэрозионной обработки
Начнем с основ электроэрозионной обработки или электроэрозионной обработки! Грань между изобретениями, открытиями и инновациями тонкая. С учетом наших требований с течением времени мы обнаружили и внедрили различные решения любой проблемы.
Одно из практических решений для обработки жестких материалов при электроэрозионной обработке.
- В системе обработки, когда традиционные процессы становятся исчерпывающими, становится важным вводить что-то новое.
- Поэтому, когда традиционные методы обработки устарели, была внедрена электроэрозионная обработка.
- Из этого отрывка вы узнаете о процессе электроэрозионной обработки.
К концу этой статьи вы сможете понять весь процесс электроэрозионной обработки.
А теперь давайте начнем без лишних слов.
Что такое электроэрозионная обработка?Определение EDM
Электроэрозионная обработка или электроэрозионная обработка – это производственная операция, используемая для формирования сложных деталей из различных деталей. Вы не знаете, что многие изделия изготавливаются с помощью электроэрозионной обработки.
- Это может быть пластик, металл, любой материал, из которого может получиться конкретный объект.
- Вы можете подумать, что каждая пластиковая вещь, которую вы выбираете, изготовлена в процессе электроэрозионной обработки.
Чтобы вы поняли, электроэрозионная обработка – это процесс, в котором используются очень сложные станки с компьютерным управлением для вырезания множества сложных конструкций из различных типов материалов.
Все, от пластиковых предметов до грифеля для карандашей, прошло электроэрозионную обработку.
Функция EDM
Функции электроэрозионных станков следующие:
- Есть много сложных контуров или, можно сказать, тонких отверстий, которые невозможно изготовить на стандартном производственном оборудовании.
- Это исключительно точный процесс обработки, который широко используется при производстве сложных компонентов.
- Кроме того, это процесс обработки даже самых твердых материалов, таких как закаленная сталь, титан и многие другие материалы.
Принцип работы электроэрозионного станка заключается в подаче электричества на заготовку, а также на формовочный инструмент. Тогда инструмент окажется в непосредственной близости от детали, погруженной в резервуар с диэлектрической жидкостью.
Операции электроэрозионной обработки- Близость инструмента к заготовке создает напряженность электрического поля для преодоления прочности диэлектрической жидкости.
- Это приведет к серии электрических разрядов между инструментом и заготовкой.
- Этот разряд позволяет выполнять удаление материала с заготовки и процесс отверждения любого рисунка или формы материала.
После всего процесса обработки диэлектрическая жидкость заменяется электродами.Эта диэлектрическая жидкость является неотъемлемой частью всего процесса обработки, поскольку она отвечает за вымывание оставшегося материала и обеспечивает охлаждение зоны обработки.
Периодическая замена охлаждающих электродов является обязательной из-за эрозии инструментальных электродов, возникающих в процессе обработки материала.
- Весь процесс электроэрозионной обработки можно использовать только при использовании проводящего материала.
- Периодические электрические разряды между электродами вызывают удаление материала с заготовки.
- Один из электродов известен как инструментальный электрод, инструмент или электрод.
- Другой известен как электрод заготовки или заготовка.
- Расстояние между обоими электродами определяет силу тока.
Посмотрите КРАСИВЫЕ ВИДЕО на Toolin U-SME!
История электроэрозионной обработки
В 1770 году одна из английских фраз по имени Джозеф Пристли началась о влиянии электрических разрядов.Продолжая исследовательский процесс Пристли, в 1943 году изобретение EDM-процесса было выполнено двумя российскими учеными по имени доктор Б. Лазаренко и д-р Н.И. Лазаренко. В контролируемом процессе обработки металлов использовалось разрушающее действие электрического разряда.
- Первоначально первый метод обработки назывался «Искровой».
- Искровое слово берется из серии искр, наблюдаемых между двумя разными электрическими проводниками, погруженными в диэлектрическую жидкость.
В этой машине использовался эффект электрического разряда, известный как схема Лазаренко. Схема Лазаренко широко использовалась в конструкции генератора с использованием электрического разряда.
С момента изобретения электроэрозионного станка многие новые виды исследований внесли огромный вклад в методы обработки, известные нам сегодня.
Сколько импровизации было сделано в процессе обработки, что привело к увеличению скорости в 20 раз, чем раньше?
Когда скорость обработки достигла нового пика, затраты на обработку снизились на 30% с 1.В 5 раз больше чистоты поверхности.
Компоненты EDMЭлектроэрозионная обработка включает в себя несколько компонентов во всей системе, а также помогает в решении задач по изготовлению различных верхних материалов.
Процесс электроэрозионной обработки включает в себя станок, состоящий из нескольких частей, в том числе:
Детали электроэрозионной обработки EDM- Электрооборудование / генератор
- Подвижный электрод или инструмент и держатель инструмента
- Бак
- Диэлектрическая среда
- Насосно-фильтрующий блок
- Заготовка, стол и приспособления
- Инструменты
Корпуса электропитания или выпрямителя и блока управления током.Есть две коммерчески доступные генераторы двух категорий, которые обычно используются в EDM.
Политики управления и импульсы на основе RC-цепочки.
Подвижный электрод и держательВ данном элементе электроэрозионной обработки под инструментом понимается электрод. Материал электродов должен иметь менее локализованную температуру, иначе при повышении температуры будет меньше плавления.
- Материал электрода должен обладать высокой электропроводностью, теплопроводностью, температурой плавления, плотностью, доступностью и невысокой стоимостью.
- Графит, латунь, теллур, медь и электролитическая бескислородная медь являются одними из распространенных материалов, широко используемых в различных отраслях промышленности.
- Электрод или инструмент поддерживается держателем инструмента.
Резервуар является важным компонентом электроэрозионного станка, поскольку он содержит диэлектрическую жидкость, в которую погружены инструмент и заготовка.
Таким образом, он становится неотъемлемой частью всей системы.
Диэлектрическая средаВ диэлектрической среде происходит термическое испарение и плавление, что приводит к удалению материала.
- Диэлектрическая среда должна создавать бескислородную среду обработки.
- Он должен обладать сильным диэлектрическим сопротивлением и не должен легко ломаться.
- Диэлектрическая среда должна ионизироваться, когда происходит столкновение электронов с молекулой. Термостойкость диэлектрика улучшает процесс обработки.
Керосин и деионизированная вода являются двумя из обычно используемых диэлектрических сред в процессе электроэрозионной обработки.
Насосно-фильтровальный агрегат
Насос, используемый для циркуляции диэлектрической жидкости от резервуара к заготовке. Фильтрующий блок используется после насоса для фильтрации жидкости от пыли и любых других посторонних частиц.
Электроэрозионный насос для механической обработки Заготовка , стол и приспособленияЗаготовка – это сырье, на котором происходит обработка. Обычно обработка происходит из твердых металлов или сплавов.
- Стол используется для удержания заготовки.
- Крепление используется для крепления стола.
Инструменты
В электроэрозионной машине есть несколько инструментов, например,
- Вольтметр: используется для измерения напряжения
- Амперметр: используется для измерения силы тока.
Система подачи
Для управления скоростью инструмента используется отдельная система управления. Он поддерживает достаточный зазор между электродом и заготовкой. Эта система известна как сервосистема.
EDM
Принцип работы Электроэрозионные машиныработают по принципу удаления материала с помощью серии электрических искровых разрядов, возникающих между электродным инструментом и заготовкой.
- Между электродным инструментом и заготовкой создается разность потенциалов.
- Оба они должны быть электропроводными.
- Погружен в диэлектрическую среду.
Обычно керосин или деионизированная вода используются в качестве диэлектрической жидкости в EDM.Между электродным инструментом и заготовкой сохраняется определенный зазор.
Шаг №1
Между инструментом и заготовкой возникает электрическое поле, которое будет зависеть от приложенной разности потенциалов и зазора.
Шаг №2
Затем электродный инструмент и заготовка соединяются с катодом и анодом генератора соответственно.
- Теперь свободные электроны имеют тенденцию приобретать электростатические силы на заготовке.
- Это происходит из-за наличия электрического поля между электродным инструментом и заготовкой.
Шаг № 3
Электроны будут выходить из инструмента, если энергия связи станет меньше. Этот процесс эмиссии электронов называется холодной эмиссией.
Электроэрозионная обработка работаетТеперь эти холодно испускаемые электроны ускоряются по направлению к заготовке, проходя через диэлектрическую среду.
Шаг № 4
По мере того, как электроны набирают скорость и энергию, они движутся к заготовке, где происходит столкновение между молекулами диэлектрика и электронами.
Шаг №5
Теперь эти столкновения приведут к ионизации молекул, присутствующих в диэлектрической жидкости.
Обычно ионизация во многом зависит от энергии ионизации молекул, присутствующих в диэлектрической жидкости, и энергии, запасенной в электроне.
Шаг №6
Когда происходит ускорение электронов, происходит генерация ионов и электронов из-за более высокой частоты столкновений.
Шаг № 7
Этот систематический процесс приведет к более высокой концентрации ионов и электронов в диэлектрической жидкости между электродом и заготовкой.
Когда концентрация становится выше, чем существующее вещество, будет называться плазмой.
Эта плазма будет обладать значительно меньшим электрическим сопротивлением.
Шаг № 8
Внезапно поток электронов и ионов от заготовки к электроду будет затоплен, что приведет к лавинному движению.Такое внезапное повышенное движение электронов и ионов считается искрой.
Рабочий процесс электроэрозионной обработкиШаг №9
Следовательно, энергия, запасенная в диэлектрической среде, будет рассеиваться как тепловая энергия искры.
Шаг № 10
Повышенная скорость электронов оказывает влияние на деталь и ионы электрода.
Шаг №11
Кинетическая энергия, запасенная в ионах и электронах на поверхности электродного инструмента и детали, будет преобразована в тепловой поток для тепловой энергии.
- Сильный тепловой поток приведет к более высокой температуре, которая будет более 10000 градусов по Цельсию.
- Ограниченный тепловой поток приведет к удалению материала.
Этот процесс удаления материала происходит из-за мгновенного испарения и плавления материала. Постоянная разность потенциалов при образовании ударных волн в плазменном канале приводит к удалению материала.
Вся эта серия операций выполняется за несколько микросекунд.
Типы электроэрозионных станковПо сути, существует два разных типа электроэрозионных машин, которые различаются в зависимости от типа инструмента, используемого для электрода, вписанного в машину.
Электроэрозионные станки двух типов:
Электроэрозионная машина с грузилойSinker EDM предполагает использование электродов формовочного инструмента для выполнения механической обработки. Его также называют объемным или резонаторным электроэрозионным методом.
- Этот EDM содержит электрод, а рабочая поверхность погружена в жидкость, которая является изолирующей по своей природе.
- Оба они подключены к источнику питания, что приводит к генерации электрического потенциала между ними.
Как только электроды продвигаются к заготовке, в канале происходит разделение диэлектрика, образуя плазменный канал, и возникает небольшая искра.
- Внезапно возникающие при использовании искры оказываются в случайных местах диэлектрической среды.
- Когда мозоль основного металла подвергается эрозии, искровой промежуток увеличивается, и электрод автоматически опускается для продолжения процесса.
- Несколько сотен тысяч искр в секунду возникают в канале, и заданные параметры обрабатывают это.
- Кроме того, эти циклы управления известны как время выключения и время включения.
- Цикл своевременного контроля отвечает за определение продолжительности существования искры.
- Время выключения – это продолжительность искры, в которой другая искра заменяет одну.
Впоследствии более длительное время работы создает больше резонансных полостей для всей искры в этом цикле, что приводит к более шероховатой отделке работы.Точно так же более длительное время простоя будет создано из-за внезапной промывки диэлектрической среды.
Электроэрозионная машина для проволокиЭтот тип идиомы широко известен как электроэрозионный электроэрозионный станок с проволочной резкой.
- Этот процесс обработки с электрическим разрядом состоит из одножильной металлической проволоки, размещенной на заготовке и выходящей в диэлектрическую среду.
- В электроэрозионных станках этой категории в качестве диэлектрической среды используется вода из-за ее резистивных и других электрических характеристик.
- В основном используется для резки толстых листов и изготовления штампов, инструментов, пуансонов из твердых металлов.
Электроэрозионный электроэрозионный станок подходит для процесса обработки, который требует низкого остаточного напряжения, так как не требует больших усилий для удаления материала.
Факторы, касающиеся EDMКаждый из нас, читающий эту статью, должен знать много факторов об электроэрозионной обработке.Мы зарегистрировали его ниже:
- Процесс EDM был адаптирован для жестких материалов, которые нельзя обрабатывать обычными методами.
- Этот процесс обработки обычно используется для обработки электропроводящих материалов. В настоящее время его можно использовать для обработки изоляционной керамики.
- Электроэрозионная обработка позволяет вырезать более глубокие и изысканные фигуры или полые участки в закаленной стали.
- При этом нет необходимости проводить термообработку для размягчения и повторного упрочнения жестких материалов.
- Это метод, который также можно использовать с любым другим немного твердым материалом, который раньше было трудно резать.
- Согласно отчету, было упомянуто, что электроэрозионная обработка применяется для формования инструментов из поликристаллического алмаза.
Электроэрозионная обработка применяется при изготовлении различных инструментов, оборудования и предметов.
- Он используется во всем процессе микропросверления, нарезания резьбы, фрезерования спирального профиля, сверления по всей кривой и вращательной формовки.
- EDM может изготавливать деликатные детали, например медные.
- Этот нетрадиционный процесс обработки может применяться ко всем проводящим металлам и сплавам.
- Он может копать глубокие отверстия малого диаметра, отверстия для охлаждения в лопатках турбины, узкие щели и многие замысловатые формы.
- Для очень твердых деталей EDM будет экономичным выбором.
- Этот процесс может происходить без каких-либо искажений, поскольку в нем нет механического напряжения.
- Этот процесс обработки позволяет создавать твердые и устойчивые к коррозии объекты.
- При промывке диэлектрика используется пластинчатый электрод.
- Предварительно просверленные отверстия используются для подачи диэлектрика путем дозирования или впрыска. Это требуется при использовании сплошных стержней.
- EDM может производить конические, криволинейные, наклонные и неровные полости.
- Idiom Drilling отвечает за создание каналов в лопатках турбины для охлаждения.
- Не беспокойтесь об обработке твердых и жестких материалов.
- Сложные полости можно быстро разработать с помощью электроэрозионной обработки, что, как правило, трудно сделать обычными методами.
- Обладает способностью превращать твердый материал с очень жесткими допусками.
- С его помощью можно обрабатывать небольшие детали.
- Обеспечивает хорошее качество поверхности.
- Поскольку нет прямого контакта между электродом и заготовкой, с помощью этого процесса также можно обрабатывать хрупкие и непрочные участки.
- Чрезмерный износ инструмента происходит в процессе обработки.
- Не обрабатывает непроводящие материалы.
- Иногда допускаются перерезы.
- Повышенное энергопотребление
- Из-за износа электродов воспроизвести острые углы довольно сложно. Если вам нужна определенная отделка поверхности, то этот процесс не будет работать для экономичного производства.
- Низкая скорость съема материала
- Создание электродов, в основном используемых в различных типах электроэрозионных станков, требует дополнительных затрат, а также времени.
Дальнейшее изучение
Ознакомьтесь с несколькими нашими интересными статьями,
Заключение
Это были основы процесса обработки с электрическим зарядом, который широко используется в обрабатывающей промышленности. Это один из важных способов превращения идей в продукты.
Появление электроэрозионных машин дает людям возможность создавать и вырезать замысловатые формы и переходные узоры. Наконец, речь идет об электроэрозионных машинах.
Однако он содержит более подробную информацию о перепрошивке и многих других концепциях.
Механика, принципы работы и схемы (со схемой)
В этой статье мы обсудим электроэрозионную обработку (EDM): – 1. Введение в электроэрозионную обработку (EDM) 2. Механика EDM 3. Схемы и принципы работы EDM (со схемой) 4. Обработка поверхности и обработка Точность 5. Роль инструментальных электродов и диэлектрических жидкостей в электроэрозионных станках 6.Воздействие электроэрозионной обработки на металлические поверхности 7. Характеристики.
Состав:
- Введение в электроэрозионную обработку (EDM)
- Механика электроэрозионного станка
- Цепи и принципы работы EDM (со схемой)
- Чистовая обработка поверхности и точность электроэрозионной обработки
- Роль инструментальных электродов и диэлектрических жидкостей в электроэрозионной обработке
- Воздействие электроэрозионной обработки на металлические поверхности
- Характеристики EDM
1.Введение в электроэрозионную обработку (EDM):
Использование термоэлектрического источника энергии при разработке нетрадиционных технологий в значительной степени помогло в достижении экономичной обработки материалов с чрезвычайно низкой обрабатываемостью и выполнения сложных работ. Процесс удаления материала путем контролируемой эрозии с помощью серии электрических искр, широко известный как электроэрозионная обработка, был впервые начат в СССР примерно в 1943 году. Затем исследования и разработки довели этот процесс до нынешнего уровня.
Когда разряд происходит между двумя точками анода и катода, сильное тепло, генерируемое около зоны, плавится и испаряет материалы в зоне искрообразования. Для повышения эффективности обрабатываемая деталь и инструмент погружаются в диэлектрическую жидкость (углеводородное или минеральное масло). Было замечено, что если оба электрода изготовлены из одного и того же материала, электрод, подключенный к положительному выводу, обычно разрушается с большей скоростью. По этой причине обрабатываемая деталь обычно является анодом.Между инструментом и поверхностями заготовки поддерживается подходящий зазор, известный как искровой разрядник.
Искры разряжаются с высокой частотой с помощью подходящего источника. Поскольку искра возникает в месте, где поверхность инструмента и обрабатываемой детали находится ближе всего, и поскольку пятно меняется после каждой искры (из-за удаления материала после каждой искры), искры распространяются по всей поверхности. Это приводит к равномерному снятию материала по всей поверхности, и, наконец, рабочая поверхность соответствует поверхности инструмента.Таким образом, инструмент производит необходимый отпечаток на заготовке.
Для поддержания заданного искрового промежутка обычно используется блок сервоуправления. Промежуток определяется по среднему напряжению на нем, и это напряжение сравнивается с заданным значением. Разница используется для управления серводвигателем. Иногда вместо серводвигателя используют шаговый двигатель. Конечно, для очень примитивных операций также возможно управление соленоидом, благодаря чему машина становится чрезвычайно недорогой и простой в сборке.
Частота искры обычно находится в диапазоне 200-500 000 Гц, искровой промежуток составляет порядка 0,025-0,05 мм. Пиковое напряжение на промежутке поддерживается в диапазоне 30-250 вольт. С помощью этого процесса можно получить MRR до 300 мм 3 / мин, при этом удельная мощность порядка 10 Вт / мм 3 / мин. Было обнаружено, что эффективность и точность рабочих характеристик улучшаются, когда обеспечивается принудительная циркуляция диэлектрической жидкости. Наиболее часто используемая диэлектрическая жидкость – керосин.Инструмент обычно изготавливается из латуни или медного сплава.
2. Механика электроэрозионного станка:
На Рис. 6.52 показаны детали поверхностей электродов. Хотя поверхности могут казаться гладкими, неровности и неровности всегда присутствуют, как указано (конечно, с преувеличением). В результате локальный зазор меняется, и в данный момент он минимален в одной точке (скажем, A). Когда на инструменте и на заготовке (катоде и аноде соответственно) создается подходящее напряжение, создается электростатическое поле достаточной силы, вызывающее холодную эмиссию электронов с катода при A.
Эти высвободившиеся электроны ускоряются по направлению к аноду. Набрав достаточную скорость, электроны сталкиваются с молекулами диэлектрической жидкости, разбивая их на электроны и положительные ионы. Образованные таким образом электроны также ускоряются и могут в конечном итоге вытеснить другие электроны из молекул диэлектрической жидкости. В конечном счете, узкий столб ионизированных молекул диэлектрической жидкости образуется в точке А, соединяющей два электрода (вызывая лавину электронов, поскольку проводимость ионизированного столба очень велика, что обычно воспринимается как искра).
В результате этой искры генерируется ударная волна сжатия, и электроды нагреваются до очень высокой температуры (10 000–12 000 ° C). Эта высокая температура вызывает плавление и испарение материалов электродов, а расплавленные металлы удаляются механическим ударом, что приводит к образованию небольших кратеров на обоих электродах в точке A. Как только это происходит, зазор между электродами в точке A увеличивается, и следующее место кратчайшего разрыва находится где-то еще (скажем, B).
Следовательно, когда цикл повторяется, следующая искра возникает в точке B. Таким образом, искры блуждают по всей поверхности электрода и, в конечном итоге, процесс приводит к равномерному зазору. Таким образом, в зависимости от формы отрицательного электрода на другом электроде создается отпечаток.
Как правило, скорость удаления материала с катода сравнительно меньше, чем с анода, по следующим причинам:
(i) Импульс, с которым поток электронов ударяется об анод, намного больше, чем из-за потока положительных ионов, падающих на катод, хотя масса отдельного электрона меньше, чем масса положительных ионов.
(ii) Пиролиз жидкого диэлектрика (обычно углеводорода) создает тонкую пленку углерода на катоде.
(iii) На поверхности катода создается сжимающая сила. Поэтому обычно инструмент подключается к отрицательной клемме источника постоянного тока.
Если инструмент неподвижен относительно обрабатываемой детали, зазор увеличивается по мере удаления материала, что требует увеличения напряжения для возникновения искры. Чтобы избежать этой проблемы, инструмент питается с помощью сервопривода, который определяет величину среднего зазора и поддерживает его постоянным.
Ниже мы попытаемся теоретически определить скорость съема материала при электроэрозионной обработке. При этом, хотя количественные результаты не будут получены, многие важные особенности станут очевидными. Пока достаточно понять действие только одной искры.
Количество материала, удаляемого за один разряд, можно определить, учитывая диаметр кратера и глубину, до которой достигается температура плавления.
Для этого сделаем следующие предположения:
(i) Искра представляет собой однородный круглый источник тепла на поверхности электрода, и диаметр (= 2a) этого круглого источника остается постоянным.
(ii) Поверхность электрода представляет собой полубесконечную область.
(iii) За исключением части источника тепла, поверхность электрода изолирована.
(iv) Скорость подводимого тепла остается постоянной в течение всего времени разряда.
(v) Свойства материала электрода не меняются с температурой.
(vi) Испарением электродного материала пренебрегают.
На рис. 6.53 показаны детали идеализированного источника тепла. В нашем анализе H- количество подводимого тепла (кал), θ = температура (° C), t = время (сек), k = теплопроводность (кал / см-сек- ° C), α = коэффициент температуропроводности (см 2 / сек), t d = продолжительность разряда (сек) и θ м = температура плавления (° C).
Из-за круговой симметрии температура в любой точке зависит от r и z. Уравнение теплопроводности –
Поскольку интуитивно видно, что глубина, на которой достигается максимальная температура плавления в центре, нас интересует решение при r = 0. Температура в точке на оси в конце разряда (предполагая, что максимальная температура достигается при t = t d , поскольку подвод тепла прекращается в этот момент) определяется как –
Итак, очевидно, что Z указывает объем материала, удаляемого каждой искрой.На рис. 6.54a показаны теоретические значения Z для заданной энергии искры и постоянного диаметра искры для Cu, Al и Zn в качестве материалов электродов. На рисунке 6.54b показан реальный характер изменения объема кратера в зависимости от t d для различных энергий искры. Тенденции очень похожи.
Одна важная особенность, которая становится очевидной из этих результатов, заключается в том, что съем материала очень низкий при небольшом времени разряда и увеличивается с t d . Затем, достигнув пикового значения, оно внезапно падает до нуля.Также было установлено, что количество материала, удаляемого за один разряд, сильно зависит от температуры плавления материала.
Эффект кавитации в процессе механического удаления также важен. График зависимости mrr во время одной искры от времени показан на рис. 6.55. Очевидно, что mrr является максимальным, когда давление ниже атмосферного, что свидетельствует о важности кавитации.
Для получения приблизительной оценки были разработаны эмпирические зависимости для скорости съема материала во время электроэрозионной обработки.Поскольку размер кратера зависит от энергии искры (при условии, что все другие условия остаются неизменными), глубина и диаметр кратера определяются как –
В этом отношении мы приняли условия среднего искрообразования.
MRR также сильно зависит от циркуляции диэлектрической жидкости. Без принудительной циркуляции частицы износа многократно плавятся и снова соединяются с электродом. На рис. 6.56 показан характер характеристик MRR без и с принудительной циркуляцией диэлектрика.
После завершения разряда диэлектрическая среда вокруг последней искры должна деионизироваться. Для этого напряжение на промежутке должно поддерживаться ниже напряжения разряда до завершения деионизации; в противном случае ток снова начинает течь через зазор в месте предыдущего разряда. Время, необходимое для полной деионизации, зависит от энергии, выделенной предыдущим разрядом. Большее выделение энергии приводит к увеличению времени деионизации.
3. Цепи и принципы работы EDM (со схемой):
Доступно несколько принципиально различных электрических цепей для создания пульсирующего постоянного тока через зазор рабочего инструмента. Хотя рабочие характеристики отличаются, почти во всех таких схемах конденсатор используется для хранения электрического заряда до того, как разряд произойдет через промежуток. Пригодность схемы зависит от условий обработки и требований.
Обычно используемые принципы подачи пульсирующего постоянного тока можно разделить на следующие три группы:
(i) Схема релаксации емкостного сопротивления с постоянным источником постоянного тока.
(ii) Роторный импульсный генератор.
(iii) Контролируемая импульсная цепь.
(i) Цепь релаксации сопротивления-емкости:
Схема релаксации резистивно-емкостного сопротивления использовалась при первой разработке электроэрозионных машин.На рисунке 6.57a показана простая RC-цепь. Как видно из этого рисунка, конденсатор C (который можно изменять) заряжается через переменное сопротивление R от источника постоянного напряжения V 0 .
Напряжение на зазоре (которое почти такое же, как и на конденсаторе) V изменяется со временем в соответствии с соотношением, где t обозначает время, начиная с момента подачи напряжения V 0 .
Итак, V будет асимптотически приближаться к V 0 , как показано на рис.6.57b, если это разрешено. Если инструментальный зазор и диэлектрическая жидкость таковы, что может возникнуть искра, когда напряжение на зазоре достигает значения V d (обычно известного как напряжение разряда), возникнет искра, полностью разряжая конденсатор всякий раз, когда напряжение на зазоре инструмента (В) достигает V d .
Время разряда намного меньше (около 10%), чем время зарядки, а частота искрения (v) приблизительно определяется следующим уравнением (поскольку время, необходимое для деионизации, также очень мало при нормальных обстоятельствах) –
Таким образом, для обеспечения максимальной мощности напряжение разряда должно составлять 72% от напряжения питания V 0 .
Если предположить, что количество материала, удаляемого за искру, пропорционально энергии, выделяемой за искру, то mrr может быть выражено как –
(ii) Роторный импульсный генератор:
Схема релаксации для генерации искры хоть и проста, но имеет определенные недостатки. Из них важным недостатком является то, что MRR невысокий. Для увеличения скорости съема используется генератор импульсов для генерации искры. На рисунке 6.59 показана принципиальная схема такой системы.Конденсатор заряжается через диод в течение первого полупериода. В течение следующего полупериода сумма напряжений, генерируемых генератором и заряженным конденсатором, подается в зазор рабочего инструмента.
Рабочая частота – это частота генерации синусоидальной волны, которая зависит от скорости двигателя. Хотя mrr выше, такая система не обеспечивает хорошего качества поверхности.
(iii) Контролируемые импульсные цепи:
В двух рассмотренных нами системах не предусмотрено автоматическое предотвращение протекания тока при возникновении короткого замыкания.Чтобы добиться такого автоматического управления, в качестве переключающего устройства используется вакуумная лампа (или транзистор). Эта система известна как управляемая импульсная схема. На рисунке 6.60 схематично показана такая система. Во время искрения ток, протекающий через зазор, исходит от конденсатора.
Когда ток течет через зазор, трубка клапана (VT) смещается, чтобы отключиться, и ведет себя как бесконечное сопротивление. Контроль смещения осуществляется с помощью электронного управления (EC). Как только ток в зазоре прекращается, проводимость трубки увеличивается, позволяя протеканию тока заряжать конденсатор для следующего цикла.
Схема может быть упрощена, а стабильность работы улучшена, если протекание тока разрешено циклически с заданной частотой. Это можно сделать, управляя смещением с помощью осциллятора. В этом случае конденсатор не нужен. На рисунке 6.61 показана такая схема, использующая транзистор.
4. Чистовая обработка поверхности и точность обработки EDM:
Поскольку удаление материала при электроэрозионной обработке достигается за счет образования кратеров из-за искр, очевидно, что кратеры больших размеров (особенно глубина) приводят к шероховатости поверхности.Таким образом, размер кратера, который в основном зависит от энергии / искры, определяет качество поверхности. На рисунке 6.62 показано, как H rms (среднеквадратичное значение неровности поверхности) зависит от C и V 0 .
Глубина кратера (h c ) может быть приблизительно выражена в единицах энергии, выделяемой на искру (E) как –
Зависимость шероховатости поверхности от энергии импульса E и сравнение чистоты поверхности с обработкой, полученной обычными способами, показаны на рис.6,63. Много усилий было потрачено на определение подходящего соотношения между скоростью съема материала и качеством обработки поверхности. Но очень надежное соотношение общего применения еще не появилось. Однако mrr и неровность поверхности при обработке стали в нормальных условиях примерно связаны как –
Где H rms – это среднеквадратическое значение неровности поверхности в микронах, а Q – скорость съема материала в мм 3 / мин.
Было обнаружено, что принудительная циркуляция диэлектрика в целом улучшает качество поверхности. Сечения поверхности латунного электрода, полученного электроэрозионным электродом с принудительной циркуляцией и без нее (напряжение 40 В, ток 0,2 А, частота 1,12 кГц), показаны на рис. 6.64. Понятно, что принудительная циркуляция приводит к значительному улучшению качества поверхности.
5. Роль инструментальных электродов и диэлектрических жидкостей в электроэрозионной обработке:
Электроды играют чрезвычайно важную роль в процессе электроэрозионной обработки, поэтому для достижения лучших результатов следует учитывать определенные аспекты электрода инструмента.
а. Износ электродов инструмента:
Во время электроэрозионной обработки электрод (т.е. инструмент), как уже упоминалось, также подвергается эрозии из-за искрообразования. Материалы, обладающие хорошими характеристиками износа электродов, такие же, как и материалы, которые обычно трудно обрабатывать. Одним из основных материалов, используемых для изготовления инструмента, является графит, который напрямую переходит в паровую фазу, не плавясь. Коэффициент износа (r Q ), определяемый отношением материала, удаленного из заготовки, к материалу, удаленному из инструмента, оказывается связанным с r θ (= температура плавления работы / температура плавления инструмент) as –
г.Материал электрода:
Выбор материала электродов зависит от:
(i) Скорость съема материала,
(ii) Коэффициент износа,
(iii) Простота формования электрода,
(iv) Стоимость.
Наиболее часто используемые электродные материалы – это латунь, медь, графит, сплавы A1, сплавы медь-вольфрам и сплавы серебра-вольфрама.
Методы изготовления электродов:
(i) Обычная обработка (используется для меди, латуни, сплавов Cu-W, сплавов Ag-W и графита),
(ii) Отливка (используется для литья под давлением сплава на основе Zn, сплавов Zn-Sn и сплавов Al),
(iii) Металлическое напыление,
(iv) Формование прессом.
Отверстия для потока обычно предусмотрены для циркуляции диэлектрика, и эти отверстия должны быть как можно больше для черновой резки, чтобы обеспечить большую скорость потока при низком давлении.
г. Диэлектрические жидкости:
Основные требования к идеальной диэлектрической жидкости:
(i) Низкая вязкость,
(ii) Отсутствие токсичных паров,
(iii) Химическая нейтральность,
(iv) Отсутствие склонности к воспалительным процессам,
(v) Низкая стоимость.
Обычная вода обладает почти всеми этими свойствами, но, поскольку она вызывает ржавчину в работе и в машине, ее не используют. Еще одна причина, по которой не рекомендуется использовать воду, заключается в следующем. Электроды постоянно находятся под некоторой разностью потенциалов, и из-за хорошей проводимости воды процесс ECM начинает искажать заготовку. Кроме того, энергия тратится зря. Однако в некоторых случаях используется деионизированная вода.
Наиболее часто используемый тип жидкости – углеводородное (нефтяное) масло.Керосин, жидкий парафин и силиконовые масла также используются в качестве диэлектрических жидкостей.
6. Воздействие электроэрозионной обработки на металлические поверхности:
Высокая температура, создаваемая искрами, вызывает плавление и испарение металла и, очевидно, эта высокая температура влияет на свойства мелких слоев (2,5–150 мкм) обработанной поверхности.
Самый внешний слой быстро охлаждается, поэтому он очень твердый. Слой непосредственно под ним находится в несколько закаленном состоянии.На рис. 6.67 показано изменение твердости в зависимости от глубины как для черновой, так и для чистовой электроэрозионной обработки стали. Понятно, что при чистовой обработке такое упрочнение не заметно. Однако внешний слой закален, а твердость невысока.
Упрочнение поверхностного слоя во время электроэрозионной обработки обеспечивает лучшую износостойкость. Однако усталостная прочность снижается из-за микротрещин, которые образуются в поверхностном слое при охлаждении. Рисунок 6.68 показано сравнение усталостной прочности идентичных деталей, изготовленных обычным фрезерованием и электроэрозионным фрезерованием. Свойства тонких поверхностных слоев не оказывают большого влияния на предел прочности. Их структура трансформируется, а из-за искр в некоторой степени изменяется их химический состав. Обычно они снижают сопротивление эрозии.
7. Характеристики электроэрозионного станка:
Что такое электроэрозионная обработка и понимаете ли вы принцип?
Даже если вы можете заниматься электромеханической обработкой, но действительно ли вы понимаете принцип электромеханической обработки?
Следующее видео полностью демонстрирует микропроцесс электромеханической обработки:
Как мы все знаем, традиционная обработка использует особенность, заключающуюся в том, что инструмент тверже заготовки и полагается на механическую энергию. удалить металл, чтобы добиться обработки.Суть в том, чтобы противопоставить стойкость стойкости.
В 1870 году британский ученый Пристли обнаружил, что разряды оказывают коррозионное воздействие на металлы.
В течение долгого времени коррозия при разрядке считалась вредным явлением.
Например, в повседневной жизни можно обнаружить, что, когда вилка вставляется и вынимается, разряд часто опаляет контактную поверхность и разъедает неровные ямки.
С развитием науки и техники, до 1943 года Лазаренко из бывшего Советского Союза изучали явление и причины повреждения контактов переключателя искровым разрядом и обнаружили, что мгновенная высокая температура электрических искр может вызвать локальные металл плавится, испаряется и подвергается коррозии.
Тогда был изобретен метод электроэрозионной обработки.
На этом этапе люди впервые отклонились от традиционной обработки старой дорожки и успешно получили метод обработки, заключающийся в использовании мягкости для преодоления твердости.
Электрообработка в основном включает два технологических метода: электроэрозионное формование и WEDM.
Электроэрозионная обработка (EDM)
Инструментальный электрод обычно представляет собой формованный электрод из меди или графита, который может иметь любую форму, которая может быть изготовлена, а обработанная форма представляет собой соответствующую полость.
Электроэрозионная обработка проволоки (WEDM)
WEDM подразделяется на низкоскоростную проволочную резку и высокоскоростное перемещение проволоки. Обычно электродная проволока диаметром от 0,1 до 0,3 мм используется для обработки деталей с линейчатой поверхностью, которые могут быть охватываемыми матрицами или охватывающими отверстиями матрицы.
Проверьте этиПринцип резки проволоки EDM
2011-11-04
Электроэрозионный электроэрозионный станок с ЧПУподает импульсное напряжение между электродной проволокой и заготовкой через источник импульсов, управляемый сервосистемой, чтобы получить определенный зазор и реализовать импульсный разряд в рабочей жидкости между электродной проволокой и заготовкой.Многочисленные крошечные отверстия появляются из-за эрозии импульсного разряда и, следовательно, приобретают необходимую форму заготовки (как показано на рисунке 1-1).
Электродная проволока подключается к катоду импульсного источника питания, а деталь – к аноду импульсного источника питания. Когда деталь приближается к электродной проволоке в изолирующей жидкости и зазор между ними уменьшается до определенной величины, изолирующая жидкость прорывается; очень скоро образуется разрядный канал и происходит электрический разряд.И мгновенно высвобождая огромную высокую температуру, до более чем 10000 градусов по Цельсию, эродированная заготовка быстро остывает в рабочей жидкости и смывается. Как показано на рисунке 1-2
Три основных условия, при которых электроэрозионный электроэрозионный станок работает правильно:
- Зазор между электродной проволокой и заготовкой обязательно должен поддерживаться в необходимом диапазоне. В этом диапазоне не только импульсная мощность может пробить изолирующую жидкость, чтобы вызвать искровой разряд, но также эродированная деталь может быть смыта после процесса разряда.Если зазор слишком большой, изолирующая жидкость не может пробиться, и искрового разряда не будет; если зазор слишком мал, легко может произойти короткое замыкание, искры тоже не будет.
- Процедура должна происходить в жидкости с изолирующей способностью, например омыление и деионизированная вода, жидкость может действовать как среда выпускного канала и обеспечивать охлаждение и промывку.
- Электрический разряд должен быть кратковременным импульсным разрядом. Как и в случае короткого времени разряда, выделяемое тепло не влияет на внутренний материал заготовки, ограничивает энергию крошечным полем и сохраняет характеристики холодной обработки на электроэрозионных станках с проволочной резкой.