ΠΈΠ½ΠΆΠ΅Π½Π΅Ρ ΠΏΠΎΠΌΠΎΠΆΠ΅Ρ – ΠΠ»Π΅ΠΊΡΡΠΎΠΈΡΠΊΡΠΎΠ²ΠΎΠΉ ΡΡΠ°Π½ΠΎΠΊ
Β
ΠΡΠΈ ΠΏΠΎΠΌΠΎΡΠΈ ΡΠ»Π΅ΠΊΡΡΠΎΠΈΡΠΊΡΠΎΠ²ΡΡ ΡΡΠ°Π½ΠΊΠΎΠ² ΠΈΠ·Π³ΠΎΡΠΎΠ²Π»ΡΡΡΡΡ ΡΠΊΠ²ΠΎΠ·Π½ΡΠ΅ ΠΈ Π³Π»ΡΡ ΠΈΠ΅ ΠΎΡΠ²Π΅ΡΡΡΠΈΡ Π»ΡΠ±ΠΎΠΉ ΡΠΎΡΠΌΡ, ΠΎΡΠ²Π΅ΡΡΡΠΈΡ Ρ ΠΊΡΠΈΠ²ΠΎΠ»ΠΈΠ½Π΅ΠΉΠ½ΡΠΌΠΈ ΠΎΡΡΠΌΠΈ, Π²ΡΡΠ΅Π·Π°ΡΡ Π·Π°Π³ΠΎΡΠΎΠ²ΠΊΠΈ ΠΈΠ· Π»ΠΈΡΡΠ°, Π²ΡΠΏΠΎΠ»Π½ΡΡΡ ΠΏΠ»ΠΎΡΠΊΠΎΠ΅, ΠΊΡΡΠ³Π»ΠΎΠ΅ ΠΈ Π²Π½ΡΡΡΠ΅Π½Π½Π΅Π΅ ΡΠ»ΠΈΡΠΎΠ²Π°Π½ΠΈΠ΅. ΠΠ·Π³ΠΎΡΠ°Π²Π»ΠΈΠ²Π°ΡΡ ΡΡΠ°ΠΌΠΏΡ, ΠΏΡΠ΅ΡΡ-ΡΠΎΡΠΌΡ, ΡΠΈΠ»ΡΠ΅ΡΡ, ΡΠ΅ΠΆΡΡΠΈΠΉ ΠΈΠ½ΡΡΡΡΠΌΠ΅Π½Ρ. Π’Π°ΠΊΠΈΠ΅ ΡΡΠ°Π½ΠΊΠΈ ΡΠΏΠΎΡΠΎΠ±Π½Ρ ΡΠ΅Π·Π°ΡΡ ΠΌΠ΅ΡΠ°Π»Π», ΡΠ²Π΅ΡΠ»ΠΈΡΡ ΠΎΡΠ²Π΅ΡΡΡΠΈΡ Π»ΡΠ±ΠΎΠ³ΠΎ Π΄ΠΈΠ°ΠΌΠ΅ΡΡΠ°, Π½Π°ΡΠ°ΡΠΈΠ²Π°ΡΡ Π΄Π΅ΡΠ΅ΠΊΡΠ½ΡΠ΅ ΠΎΠ±Π»Π°ΡΡΠΈ Π΄Π΅ΡΠ°Π»Π΅ΠΉ, ΠΏΡΠΎΠΈΠ·Π²ΠΎΠ΄ΠΈΡΡ ΡΠ²Π΅Π»ΠΈΡΠ½ΡΠ΅ ΡΠ°Π±ΠΎΡΡ Ρ Π΄ΡΠ°Π³ΠΎΡΠ΅Π½Π½ΡΠΌΠΈ ΠΌΠ΅ΡΠ°Π»Π»Π°ΠΌΠΈ, ΡΠΏΡΠΎΡΠ½ΡΡΡ ΠΏΠΎΠ²Π΅ΡΡ Π½ΠΎΡΡΡ ΠΈΠ·Π΄Π΅Π»ΠΈΠΉ, ΡΠ»ΠΈΡΠΎΠ²Π°ΡΡ ΠΈΠ·Π΄Π΅Π»ΠΈΡ ΡΠ°ΠΌΠΎΠΉ ΡΠ»ΠΎΠΆΠ½ΠΎΠΉ ΡΠΎΡΠΌΡ, ΠΈΠ·Π²Π»Π΅ΠΊΠ°ΡΡ Π·Π°ΡΡΡΡΠ²ΡΠΈΠ΅ ΡΠ»ΠΎΠΌΠ°Π½Π½ΡΠ΅ ΡΠ²Π΅ΡΠ»Π° ΠΈ ΡΠ΅Π·ΡΡ.
ΠΠ° Π±Π°Π·Π΅ ΡΠ»Π΅ΠΊΡΡΠΎΠΈΡΠΊΡΠΎΠ²ΠΎΠ³ΠΎ ΠΌΠ΅ΡΠΎΠ΄Π° ΠΎΠ±ΡΠ°Π±ΠΎΡΠΊΠΈ ΠΌΠ΅ΡΠ°Π»Π»ΠΎΠ² ΡΠΎΠ·Π΄Π°Π½ΠΎ Π½Π΅ΠΌΠ°Π»ΠΎ ΡΡΠ°Π½ΠΊΠΎΠ² ΠΏΡΠΎΠΌΡΡΠ»Π΅Π½Π½ΠΎΠ³ΠΎ Π½Π°Π·Π½Π°ΡΠ΅Π½ΠΈΡ. ΠΡΠΎ Π²ΡΡΠΎΠΊΠΎΡΠΎΡΠ½Π°Ρ ΠΈ Π΄ΠΎΡΠΎΠ³Π°Ρ ΡΠ΅Ρ Π½ΠΈΠΊΠ°, ΠΊΠΎΡΠΎΡΡΡ ΠΌΠΎΠ³ΡΡ ΠΏΠΎΠ·Π²ΠΎΠ»ΠΈΡΡ ΡΠ΅Π±Π΅ ΠΊΡΠΏΠΈΡΡ ΡΠΎΠ»ΡΠΊΠΎ ΠΊΡΡΠΏΠ½ΡΠ΅ ΠΏΡΠ΅Π΄ΠΏΡΠΈΡΡΠΈΡ, ΡΠΏΠ΅ΡΠΈΠ°Π»ΠΈΠ·ΠΈΡΡΡΡΠΈΠ΅ΡΡ Π½Π° ΠΌΠ΅ΡΠ°Π»Π»ΠΎΠΎΠ±ΡΠ°Π±ΠΎΡΠΊΠ΅.
Β
Β
ΠΡΠ±ΠΎΡ ΡΠ΅Ρ
Π½ΠΈΡΠ΅ΡΠΊΠΈΡ
Ρ
Π°ΡΠ°ΠΊΡΠ΅ΡΠΈΡΡΠΈΠΊ ΡΡΠ°Π½ΠΊΠ°
Β
ΠΠΏΠΈΡΡΠ²Π°ΡΡΠΈΠ΅ ΡΠ΅Ρ Π½ΠΎΠ»ΠΎΠ³ΠΈΡΠ΅ΡΠΊΠΈΠ΅ ΡΠ²ΠΎΠΉΡΡΠ²Π° ΡΡΠ°Π½ΠΊΠΎΠ² Π΄Π°Π½Π½ΠΎΠΉ ΠΌΠΎΠ΄Π΅Π»ΠΈ ΠΏΠ°ΡΠ°ΠΌΠ΅ΡΡΡ ΡΠ²Π»ΡΡΡΡΡ: ΡΠΎΡΠ½ΠΎΡΡΡ Π²ΡΠΏΠΎΠ»Π½Π΅Π½ΠΈΡ ΠΎΠΏΠ΅ΡΠ°ΡΠΈΠΉ, ΠΏΠ΅ΡΠ΅ΠΌΠ΅ΡΠ΅Π½ΠΈΡ ΠΏΠΎ ΠΊΠΎΠΎΡΠ΄ΠΈΠ½Π°ΡΠ°ΠΌ, ΡΠ΅ΠΆΠΈΠΌΡ ΠΈ ΡΠΊΠΎΡΠΎΡΡΡ ΠΏΠΎΠ΄Π°Ρ, ΡΠ΅ΠΆΠΈΠΌΡ ΡΠ΅Π·Π°Π½ΠΈΡ ΠΈ Π½Π°Π³ΡΡΠ·ΠΊΠΈ, Π½Π°Π»ΠΈΡΠΈΠ΅ ΠΌΠ΅Ρ Π°Π½ΠΈΠ·ΠΈΡΠΎΠ²Π°Π½Π½ΠΎΠΉ ΡΠΌΠ΅Π½Ρ ΠΈΠ½ΡΡΡΡΠΌΠ΅Π½ΡΠ°, Π²ΠΎΠ·ΠΌΠΎΠΆΠ½ΠΎΡΡΡ ΡΡΡΠ°Π½ΠΎΠ²ΠΊΠΈ Π΄ΠΎΠΏΠΎΠ»Π½ΠΈΡΠ΅Π»ΡΠ½ΠΎΠ³ΠΎ ΠΎΠ±ΠΎΡΡΠ΄ΠΎΠ²Π°Π½ΠΈΡ, ΠΏΠΎΡΡΠ΅Π±Π»ΡΠ΅ΠΌΠ°Ρ ΠΌΠΎΡΠ½ΠΎΡΡΡ. ΠΡΠΈΠ²ΠΎΠ΄ΠΈΠΌΡΠ΅ Π΄Π°Π½Π½ΡΠ΅ ΠΏΠΎ ΠΏΡΠΎΠΈΠ·Π²ΠΎΠ΄ΠΈΡΠ΅Π»ΡΠ½ΠΎΡΡΠΈ, ΡΠΈΡΡΠΎΡΠ΅ ΠΏΠΎΠ²Π΅ΡΡ Π½ΠΎΡΡΠΈ ΠΈ ΡΠ½Π΅ΡΠ³ΠΎΠ΅ΠΌΠΊΠΎΡΡΠΈ ΠΎΡΠ½ΠΎΡΡΡΡΡ ΠΊ ΠΎΠ±ΡΠ°Π±ΠΎΡΠΊΠ΅ ΡΠ°Π·Π»ΠΈΡΠ½ΡΡ ΠΏΠΎ Π²Π΅Π»ΠΈΡΠΈΠ½Π΅ ΠΏΠ»ΠΎΡΠ°Π΄Π΅ΠΉ Π½Π° ΡΠ΅ΠΆΠΈΠΌΠ°Ρ , ΠΎΠ±ΡΡΠ»ΠΎΠ²Π»ΠΈΠ²Π°ΡΡΠΈΡ ΠΎΡΡΡΡΡΡΠ²ΠΈΠ΅ ΡΡΠ°ΡΡΠΊΠΎΠ² ΠΎΠΏΠ»Π°Π²Π»Π΅Π½ΠΈΡ ΠΈ ΠΏΠΎΠΊΡΡΡΠΈΡ, Ρ. Π΅. ΠΏΡΠΈ ΠΎΠΏΡΠΈΠΌΠ°Π»ΡΠ½ΡΡ ΠΏΠ»ΠΎΡΠ½ΠΎΡΡΡΡ ΡΠΎΠΊΠΎΠ².
Β
Π Π°ΡΡΠΌΠΎΡΡΠΈΠΌ ΠΎΡΠ½ΠΎΠ²Π½ΡΠ΅ ΡΠ΅Ρ Π½ΠΎΠ»ΠΎΠ³ΠΈΡΠ΅ΡΠΊΠΈΠ΅ Ρ Π°ΡΠ°ΠΊΡΠ΅ΡΠΈΡΡΠΈΠΊΠΈ. ΠΠ°ΠΏΡΠΈΠΌΠ΅Ρ, ΡΠΊΠΎΡΠΎΡΡΡ ΡΡΠ΅ΠΌΠ° ΠΌΠ΅ΡΠ°Π»Π»Π° Π½Π° ΠΌΠ°ΠΊΡΠΈΠΌΠ°Π»ΡΠ½ΡΡ ΡΠ΅ΠΆΠΈΠΌΠ°Ρ ΠΏΡΠΈ ΠΎΠ±ΡΠ°Π±ΠΎΡΠΊΠ΅ ΡΡΠ°Π»ΠΈ ΡΠΎΡΡΠ°Π²Π»ΡΠ΅Ρ Π² ΡΡΠ΅Π΄Π½Π΅ΠΌ 600 ΠΌΠΌ3/ΠΌΠΈΠ½ ΠΈ Π±Π»ΠΈΠ·ΠΊΠ° ΠΊ ΠΏΡΠ΅Π΄Π΅Π»ΡΠ½ΠΎ Π²ΠΎΠ·ΠΌΠΎΠΆΠ½ΠΎΠΉ Π΄Π»Ρ ΡΡΠΎΠ³ΠΎ ΡΠΏΠΎΡΠΎΠ±Π° ΠΎΠ±ΡΠ°Π±ΠΎΡΠΊΠΈ ΠΌΠ΅ΡΠ°Π»Π»ΠΎΠ². Π£Π΄Π΅Π»ΡΠ½ΡΠΉ ΡΠ°ΡΡ ΠΎΠ΄ ΡΠ½Π΅ΡΠ³ΠΈΠΈ Π½Π° ΠΆΠ΅ΡΡΠΊΠΈΡ ΡΠ΅ΠΆΠΈΠΌΠ°Ρ ΡΠΎΡΡΠ°Π²Π»ΡΠ΅Ρ 20-50 ΠΊΠ²Ρ-Ρ/ΠΊΠ³ Π΄ΠΈΡΠΏΠ΅ΡΠ³ΠΈΡΠΎΠ²Π°Π½Π½ΠΎΠ³ΠΎ ΠΌΠ΅ΡΠ°Π»Π»Π°. ΠΠ·Π½ΠΎΡ ΠΈΠ½ΡΡΡΡΠΌΠ΅Π½ΡΠ° ΠΏΠΎ ΠΎΡΠ½ΠΎΡΠ΅Π½ΠΈΡ ΠΊ ΠΎΠ±ΡΠ΅ΠΌΡ ΡΠ½ΡΡΠΎΠ³ΠΎ ΠΌΠ΅ΡΠ°Π»Π»Π° Π΄ΠΎΡΡΠΈΠ³Π°Π΅Ρ 25-120 ΠΈ Π±ΠΎΠ»Π΅Π΅ ΠΏΡΠΎΡΠ΅Π½ΡΠΎΠ². Π§ΠΈΡΡΠΎΡΠ° ΠΏΠΎΠ²Π΅ΡΡ Π½ΠΎΡΡΠΈ Π½Π° ΠΌΡΠ³ΠΊΠΈΡ ΡΠ΅ΠΆΠΈΠΌΠ°Ρ Π΄ΠΎΡΡΠΈΠ³Π°Π΅Ρ 4-Π³ΠΎ ΠΊΠ»Π°ΡΡΠ° ΠΏΡΠΈ ΡΠΊΠΎΡΠΎΡΡΠΈ ΡΡΠ΅ΠΌΠ° 10-15 ΠΌΠΌ3/ΠΌΠΈΠ½. ΠΠ°Π»ΡΠ½Π΅ΠΉΡΠ΅Π΅ ΠΏΠΎΠ²ΡΡΠ΅Π½ΠΈΠ΅ ΡΠΈΡΡΠΎΡΡ ΠΏΠΎΠ²Π΅ΡΡ Π½ΠΎΡΡΠΈ ΡΠΎΠΏΡΠΎΠ²ΠΎΠΆΠ΄Π°Π΅ΡΡΡ ΡΠ΅Π·ΠΊΠΈΠΌ ΡΠΌΠ΅Π½ΡΡΠ΅Π½ΠΈΠ΅ΠΌ ΡΠΊΠΎΡΠΎΡΡΠΈ ΡΡΠ΅ΠΌΠ°. Π’Π°ΠΊ, ΠΏΡΠΈ ΠΏΠΎΠ»ΡΡΠ΅Π½ΠΈΠΈ 5-Π³ΠΎ ΠΊΠ»Π°ΡΡΠ° ΡΠΈΡΡΠΎΡΡ ΠΏΠΎΠ²Π΅ΡΡ Π½ΠΎΡΡΠΈ, ΠΏΡΠΎΠΈΠ·Π²ΠΎΠ΄ΠΈΡΠ΅Π»ΡΠ½ΠΎΡΡΡ ΡΠ»Π΅ΠΊΡΡΠΎΠΈΡΠΊΡΠΎΠ²ΠΎΠ³ΠΎ ΡΠΏΠΎΡΠΎΠ±Π° ΠΎΠ±ΡΠ°Π±ΠΎΡΠΊΠΈ ΠΌΠ΅Π½ΡΡΠ΅ 5 ΠΌΠΌ3/ΠΌΠΈΠ½. Π£Π΄Π΅Π»ΡΠ½ΡΠΉ ΡΠ°ΡΡ ΠΎΠ΄ ΡΠ½Π΅ΡΠ³ΠΈΠΈ Π½Π° ΠΌΡΠ³ΠΊΠΈΡ ΡΠ΅ΠΆΠΈΠΌΠ°Ρ Π² Π΄Π΅ΡΡΡΠΊΠΈ ΠΈ ΡΠΎΡΠ½ΠΈ ΡΠ°Π· Π²ΡΡΠ΅, ΡΠ΅ΠΌ Π½Π° ΠΆΠ΅ΡΡΠΊΠΈΡ .
ΠΡΠΈ ΠΎΠ±ΡΠ°Π±ΠΎΡΠΊΠ΅ ΡΠ²Π΅ΡΠ΄ΠΎΠ³ΠΎ ΡΠΏΠ»Π°Π²Π° ΠΏΡΠΎΠΈΠ·Π²ΠΎΠ΄ΠΈΡΠ΅Π»ΡΠ½ΠΎΡΡΡ ΠΏΡΠΎΡΠ΅ΡΡΠ° Π½Π° ΠΌΡΠ³ΠΊΠΈΡ ΡΠ΅ΠΆΠΈΠΌΠ°Ρ , ΠΏΡΠΈΠΌΠ΅ΡΠ½ΠΎ, Π² Π΄Π²Π°-ΡΡΠΈ ΡΠ°Π·Π° ΠΌΠ΅Π½ΡΡΠ΅, ΡΠ΅ΠΌ ΠΏΡΠΈ ΠΎΠ±ΡΠ°Π±ΠΎΡΠΊΠ΅ ΡΡΠ°Π»ΠΈ, ΠΎΠ΄Π½Π°ΠΊΠΎ ΠΏΡΠΈ ΡΡΠΎΠΌ ΠΏΠΎΠ»ΡΡΠ°Π΅ΡΡΡ Π½Π΅ΡΠΊΠΎΠ»ΡΠΊΠΎ Π»ΡΡΡΠ°Ρ ΡΠΈΡΡΠΎΡΠ° ΠΏΠΎΠ²Π΅ΡΡ Π½ΠΎΡΡΠΈ. ΠΡΠΈΠΌΠ΅Π½Π΅Π½ΠΈΠ΅ Π±ΠΎΠ»Π΅Π΅ ΠΆΠ΅ΡΡΠΊΠΈΡ ΡΠ΅ΠΆΠΈΠΌΠΎΠ² ΠΏΡΠΈ ΠΎΠ±ΡΠ°Π±ΠΎΡΠΊΠ΅ ΡΠ²Π΅ΡΠ΄ΡΡ ΡΠΏΠ»Π°Π²ΠΎΠ² Π»ΠΈΠΌΠΈΡΠΈΡΡΠ΅ΡΡΡ ΠΎΠ±ΡΠ°Π·ΠΎΠ²Π°Π½ΠΈΠ΅ΠΌ Π½Π° Π½ΠΈΡ ΡΡΠ΅ΡΠΈΠ½.
Β
Β
ΠΠΎΠΌΠΏΠΎΠ½ΠΎΠ²ΠΊΠ° ΡΡΠ°Π½ΠΊΠ°
Β
ΠΡΠ½ΠΎΠ²Π½ΡΠΌΠΈ ΡΠ·Π»Π°ΠΌΠΈ ΡΠ»Π΅ΠΊΡΡΠΎΠΈΡΠΊΡΠΎΠ²ΡΡ ΡΡΠ°Π½ΠΊΠΎΠ² ΡΠ²Π»ΡΡΡΡΡ: ΡΡΠ°Π½ΠΈΠ½Π°, ΠΌΠ΅Ρ Π°Π½ΠΈΠ·ΠΌ Π΄Π»Ρ ΡΡΡΠ°Π½ΠΎΠ²ΠΎΡΠ½ΡΡ ΠΏΠ΅ΡΠ΅ΠΌΠ΅ΡΠ΅Π½ΠΈΠΉ, ΡΠ°Π±ΠΎΡΠ°Ρ Π²Π°Π½Π½Π°, Π½Π°ΡΠΎΡΠ½Π°Ρ ΡΡΡΠ°Π½ΠΎΠ²ΠΊΠ°, Π³Π΅Π½Π΅ΡΠ°ΡΠΎΡ ΡΠ»Π΅ΠΊΡΡΠΈΡΠ΅ΡΠΊΠΈΡ ΠΈΠΌΠΏΡΠ»ΡΡΠΎΠ² ΠΈ ΡΠ΅Π³ΡΠ»ΡΡΠΎΡ ΠΏΠΎΠ΄Π°ΡΠΈ. Π‘ΡΠ°Π½ΠΈΠ½Π° ΡΠ²Π»ΡΠ΅ΡΡΡ ΡΠ²ΡΠ·ΡΡΡΠΈΠΌ Π·Π²Π΅Π½ΠΎΠΌ Π΄Π»Ρ ΠΎΡΠ½ΠΎΠ²Π½ΡΡ ΡΠ·Π»ΠΎΠ².
ΠΠ΅Ρ Π°Π½ΠΈΠ·ΠΌ ΠΏΠ΅ΡΠ΅ΠΌΠ΅ΡΠ΅Π½ΠΈΠΉ ΡΡΡΠ°Π½ΠΎΠ²ΠΊΠΈ Π΄Π΅ΡΠ°Π»Π΅ΠΉ ΠΈ ΠΈΠ½ΡΡΡΡΠΌΠ΅Π½ΡΠ° ΠΏΡΠΈΠΌΠ΅Π½ΡΠ΅ΡΡΡ, ΠΊΠ°ΠΊ ΠΈ Π² ΠΌΠ΅ΡΠ°Π»Π»ΠΎΡΠ΅ΠΆΡΡΠΈΡ ΡΡΠ°Π½ΠΊΠ°Ρ .
Π‘ΠΎΡΡΠ°Π²: Ρ ΠΎΠ΄ΠΎΠ²Π°Ρ ΡΠ°ΡΡΡ, ΠΊΠΎΡΠΎΡΠ°Ρ ΠΏΠ΅ΡΠ΅ΠΌΠ΅ΡΠ°Π΅ΡΡΡ Ρ ΠΏΠΎΠΌΠΎΡΡΡ Π²ΠΈΠ½ΡΠΎΠ²ΡΡ ΠΈΠ»ΠΈ ΡΠ΅ΡΡΠ΅ΡΠ΅Π½Π½ΡΡ ΠΏΠ°Ρ.
Β
Π Π°Π±ΠΎΡΠ°Ρ Π²Π°Π½Π½Π° ΡΠΎΡΡΠΎΠΈΡ ΠΈΠ· ΡΠΎΠ½ΠΊΠΎΠΉ Π»ΠΈΡΡΠΎΠ²ΠΎΠΉ ΡΡΠ°Π»ΠΈ ΠΈ ΠΏΡΠ΅Π΄ΡΡΠ°Π²Π»ΡΠ΅Ρ ΡΠΎΠ±ΠΎΠΉ ΡΠ΅Π»ΡΠ½ΠΎΡΠ²Π°ΡΠ½ΡΡ ΠΊΠΎΠ½ΡΡΡΡΠΊΡΠΈΡ. ΠΠ»Π΅ΠΌΠΌΠ½ΠΈΠΊ ΠΊΡΠ΅ΠΏΠΈΡΡΡ Β«Π½Π° Π±ΠΎΠΊΡΒ» ΡΠ°Π±ΠΎΡΠ΅ΠΉ Π²Π°Π½Π½Ρ Π΄Π»Ρ ΡΠΎΠ³ΠΎ ΡΡΠΎΠ±Ρ ΡΠ»Π΅ΠΊΡΡΠΎΠ΄Ρ ΠΏΡΠΈΡΠΎΠ΅Π΄ΠΈΠ½ΡΠ»ΠΈΡΡ ΠΊ ΡΠ°Π·ΡΡΠ΄Π½ΠΎΠΌΡ ΠΊΠΎΠ½ΡΡΡΡ. ΠΡ Π½Π°ΡΠΎΡΠ½ΠΎΠΉ ΡΡΡΠ°Π½ΠΎΠ²ΠΊΠΈ ΠΏΠΎΠ΄Π°Π΅ΡΡΡ ΡΠ°Π±ΠΎΡΠ°Ρ ΠΆΠΈΠ΄ΠΊΠΎΡΡΡ. Π Π°Π·ΠΌΠ΅ΡΡ Π²Π°Π½Π½Ρ Π·Π°Π²ΠΈΡΡΡ ΠΎΡ Π΄Π΅ΡΠ°Π»Π΅ΠΉ. ΠΠ°ΡΠΎΡΠ½Π°Ρ ΡΡΡΠ°Π½ΠΎΠ²ΠΊΠ° ΠΏΡΠ΅Π΄ΡΡΠ°Π²Π»ΡΠ΅ΡΡΡ Π² Π²ΠΈΠ΄Π΅ Π΅ΠΌΠΊΠΎΡΡΠΈ 50-60 Π»ΠΈΡΡΠΎΠ².
ΠΠ΅Π½Π΅ΡΠ°ΡΠΎΡ ΠΈΠΌΠΏΡΠ»ΡΡΠΎΠ². ΠΠ»Ρ ΠΏΠΎΠ»ΡΡΠ΅Π½ΠΈΡ ΡΠ°Π·ΡΡΠ΄ΠΎΠ² ΠΈΡΠΏΠΎΠ»ΡΠ·ΡΠ΅ΡΡΡ ΡΡ Π΅ΠΌΠ°, ΠΊΠΎΡΠΎΡΠ°Ρ Π²ΠΊΠ»ΡΡΠ°Π΅Ρ Π² ΡΠ΅Π±Ρ ΡΠ°Π±ΠΎΡΠΈΠ΅ ΡΠ»Π΅ΠΊΡΡΠΎΠ΄Ρ, Π±Π°ΡΠ°ΡΠ΅Ρ, ΠΈΠ·ΠΌΠ΅ΡΠΈΡΠ΅Π»ΡΠ½ΡΡ Π°ΠΏΠΏΠ°ΡΠ°ΡΡΡΡ, ΠΈΡΡΠΎΡΠ½ΠΈΠΊ ΠΏΠΎΡΡΠΎΡΠ½Π½ΠΎΠ³ΠΎ ΡΠΎΠΊΠ° ΠΈ ΡΠ΅Π³ΡΠ»ΠΈΡΡΠ΅ΠΌΠΎΠ΅ ΡΠΎΠΏΡΠΎΡΠΈΠ²Π»Π΅Π½ΠΈΠ΅. ΠΠΎΠ΄ΡΠΎΠ±Π½Π΅Π΅ ΠΎ Π½Π΅ΠΌ ΡΠ°ΡΡΠΌΠΎΡΡΠΈΠΌ Π½ΠΈΠΆΠ΅.
ΠΠ»Π΅ΠΊΡΡΠΎΡΡΠΎΠ·ΠΈΠΎΠ½Π½ΡΠΉ ΡΡΠ°Π½ΠΎΠΊ ΠΈΠΌΠ΅Π΅Ρ ΠΈΡΠΊΡΠΎΠ²ΠΎΠΉ Π³Π΅Π½Π΅ΡΠ°ΡΠΎΡ, ΠΊΠΎΡΠΎΡΡΠΉ Π²ΡΡΡΡΠΏΠ°Π΅Ρ Π² ΠΊΠ°ΡΠ΅ΡΡΠ²Π΅ ΠΊΠΎΠ½Π΄Π΅Π½ΡΠ°ΡΠΎΡΠ°. ΠΡΠΈΠ½ΡΠΈΠΏ ΠΎΠ±ΡΠ°Π±ΠΎΡΠΊΠΈ Π·Π°ΠΊΠ»ΡΡΠ°Π΅ΡΡΡ Π² Π½Π°ΠΊΠΎΠΏΠ»Π΅Π½ΠΈΠΈ ΡΠ½Π΅ΡΠ³ΠΈΠΈ Π² ΡΠ΅ΡΠ΅Π½ΠΈΠ΅ Π΄Π»ΠΈΡΠ΅Π»ΡΠ½ΠΎΠ³ΠΎ Π²ΡΠ΅ΠΌΠ΅Π½ΠΈ, Π° Π·Π°ΡΠ΅ΠΌ Π΅Π΅ Π²ΡΠ±ΡΠΎΡ Π² ΡΠ΅ΡΠ΅Π½ΠΈΠ΅ ΠΊΠΎΡΠΎΡΠΊΠΎΠ³ΠΎ ΠΏΡΠΎΠΌΠ΅ΠΆΡΡΠΊΠ° Π²ΡΠ΅ΠΌΠ΅Π½ΠΈ.
Β
ΠΡΠΈΠ½ΡΠΈΠΏ ΡΠ°Π±ΠΎΡΡ Π³Π΅Π½Π΅ΡΠ°ΡΠΎΡΠ°, ΠΊΠΎΡΠΎΡΡΠΉ ΡΡΡΠ°Π½ΠΎΠ²Π»Π΅Π½ Π½Π° ΡΠ»Π΅ΠΊΡΡΠΎΠΈΡΠΊΡΠΎΠ²ΠΎΠΉ ΡΡΠ°Π½ΠΎΠΊ, Π·Π°ΠΊΠ»ΡΡΠ°Π΅ΡΡΡ Π² ΡΠ»Π΅Π΄ΡΡΡΠ΅ΠΌ:
Β
-
ΠΠΈΠΎΠ΄Π½ΡΠΉ ΠΌΠΎΡΡ ΠΏΡΠΎΠ²ΠΎΠ΄ΠΈΡ Π²ΡΠΏΡΡΠΌΠ»Π΅Π½ΠΈΠ΅ ΠΏΡΠΎΠΌΡΡΠ»Π΅Π½Π½ΠΎΠ³ΠΎ ΡΠΎΠΊΠ° Π½Π°ΠΏΡΡΠΆΠ΅Π½ΠΈΠ΅ΠΌ 220 ΠΈΠ»ΠΈ 380 ΠΠΎΠ»ΡΡ;
Β
-
Π£ΡΡΠ°Π½ΠΎΠ²Π»Π΅Π½Π½Π°Ρ Π»Π°ΠΌΠΏΠ° ΠΎΠ³ΡΠ°Π½ΠΈΡΠΈΠ²Π°Π΅Ρ ΡΠΎΠΊ ΠΊΠΎΡΠΎΡΠΊΠΎΠ³ΠΎ Π·Π°ΠΌΡΠΊΠ°Π½ΠΈΡ ΠΈ Π·Π°ΡΠΈΡΡ Π΄ΠΈΠΎΠ΄Π½ΠΎΠ³ΠΎ ΠΌΠΎΡΡΠ°;
Β
-
Π§Π΅ΠΌ Π²ΡΡΠ΅ ΠΏΠΎΠΊΠ°Π·Π°ΡΠ΅Π»Ρ Π½Π°Π³ΡΡΠ·ΠΊΠΈ, ΡΠ΅ΠΌ Π±ΡΡΡΡΠ΅Π΅ ΠΏΡΠΎΡ ΠΎΠ΄ΠΈΡ Π·Π°ΡΡΠ΄ΠΊΠ° ΡΠ»Π΅ΠΊΡΡΠΎΠΈΡΠΊΡΠΎΠ²ΠΎΠ³ΠΎ ΡΡΠ°Π½ΠΊΠ°;
Β
-
ΠΠΎΡΠ»Π΅ ΡΠΎΠ³ΠΎ ΠΊΠ°ΠΊ Π·Π°ΡΡΠ΄ΠΊΠ° Π·Π°ΠΊΠΎΠ½ΡΠΈΡΡΡ, Π»Π°ΠΌΠΏΠ° ΠΏΠΎΠ³Π°ΡΠ½Π΅Ρ;
Β
-
ΠΠ°ΡΡΠ΄ΠΈΠ² ΡΡΡΠ°Π½ΠΎΠ²Π»Π΅Π½Π½ΡΠΉ Π½Π°ΠΊΠΎΠΏΠΈΡΠ΅Π»Ρ ΠΌΠΎΠΆΠ½ΠΎ ΠΏΠΎΠ΄Π½Π΅ΡΡΠΈ ΡΠ»Π΅ΠΊΡΡΠΎΠ΄ ΠΊ ΠΎΠ±ΡΠ°Π±Π°ΡΡΠ²Π°Π΅ΠΌΠΎΠΉ Π·Π°Π³ΠΎΡΠΎΠ²ΠΊΠ΅;
Β
-
ΠΠΎΡΠ»Π΅ ΡΠΎΠ³ΠΎ ΠΊΠ°ΠΊ ΠΏΡΠΎΠ²ΠΎΠ΄ΠΈΡΡΡ ΡΠ°Π·ΠΌΡΠΊΠ°Π½ΠΈΠ΅ ΡΠ΅ΠΏΠΈ, ΠΊΠΎΠ½Π΄Π΅Π½ΡΠ°ΡΠΎΡ ΡΠ½ΠΎΠ²Π° Π½Π°ΡΠΈΠ½Π°Π΅Ρ Π·Π°ΡΡΠΆΠ°ΡΡΡΡ;
Β
-
ΠΡΠ΅ΠΌΡ Π·Π°ΡΡΠ΄ΠΊΠΈ ΡΡΡΠ°Π½ΠΎΠ²Π»Π΅Π½Π½ΠΎΠ³ΠΎ Π½Π°ΠΊΠΎΠΏΠΈΡΠ΅Π»ΡΠ½ΠΎΠ³ΠΎ ΡΠ»Π΅ΠΌΠ΅Π½ΡΠ° Π·Π°Π²ΠΈΡΠΈΡ ΠΎΡ Π΅Π³ΠΎ Π΅ΠΌΠΊΠΎΡΡΠΈ. ΠΠ°ΠΊ ΠΏΡΠ°Π²ΠΈΠ»ΠΎ, Π²ΡΠ΅ΠΌΠ΅Π½Π½ΠΎΠΉ ΠΏΡΠΎΠΌΠ΅ΠΆΡΡΠΎΠΊ ΠΎΡ 0,5 Π΄ΠΎ 1 ΡΠ΅ΠΊΡΠ½Π΄Ρ;
Β
-
ΠΠ° ΠΌΠΎΠΌΠ΅Π½Ρ ΡΠ°Π·ΡΡΠ΄Π° ΡΠΈΠ»Π° ΡΠΎΠΊΠ° Π΄ΠΎΡΡΠΈΠ³Π°Π΅Ρ Π½Π΅ΡΠΊΠΎΠ»ΡΠΊΠΎ ΡΡΡΡΡ Π°ΠΌΠΏΠ΅Ρ;
Β
-
ΠΡΠΎΠ²ΠΎΠ΄ ΠΎΡ ΠΊΠΎΠ½Π΄Π΅Π½ΡΠ°ΡΠΎΡΠ° ΠΊ ΡΠ»Π΅ΠΊΡΡΠΎΠ΄Ρ Π΄ΠΎΠ»ΠΆΠ΅Π½ ΠΈΠΌΠ΅ΡΡ Π±ΠΎΠ»ΡΡΠΎΠ΅ ΠΏΠΎΠΏΠ΅ΡΠ΅ΡΠ½ΠΎΠ΅ ΡΠ΅ΡΠ΅Π½ΠΈΠ΅, ΠΎΠΊΠΎΠ»ΠΎ 10 ΠΊΠ²Π°Π΄ΡΠ°ΡΠ½ΡΡ ΠΌΠΈΠ»Π»ΠΈΠΌΠ΅ΡΡΠΎΠ². ΠΡΠΈ ΡΡΠΎΠΌ ΠΏΡΠΎΠ²ΠΎΠ΄ Π΄ΠΎΠ»ΠΆΠ΅Π½ Π±ΡΡΡ ΠΈΠ·Π³ΠΎΡΠΎΠ²Π»Π΅Π½ ΠΈΡΠΊΠ»ΡΡΠΈΡΠ΅Π»ΡΠ½ΠΎ ΠΈΠ· ΠΌΠ΅Π΄ΠΈ.
Β
Β
ΠΡΠΈΠ²ΠΎΠ΄ Π³Π»Π°Π²Π½ΠΎΠ³ΠΎ Π΄Π²ΠΈΠΆΠ΅Π½ΠΈΡ Π² ΡΡΠ°Π½ΠΊΠ΅
Β
ΠΠΈΠ½Π΅ΠΉΠ½ΡΠΉ ΠΏΡΠΈΠ²ΠΎΠ΄ β ΡΡΠΎ ΠΊΠΎΠ½ΡΡΡΡΠΊΡΠΈΡ Ρ Π±Π΅ΡΠΊΠΎΠ½ΡΠ°ΠΊΡΠ½ΠΎΠΉ ΠΏΠ΅ΡΠ΅Π΄Π°ΡΠ΅ΠΉ ΡΡΠΈΠ»ΠΈΡ, ΠΏΡΡΠΌΠΎΠΉ ΠΏΡΠΈΠ²ΠΎΠ΄ Π±Π΅Π· ΠΊΠ°ΠΊΠΎΠΉ-Π»ΠΈΠ±ΠΎ ΠΊΠΈΠ½Π΅ΠΌΠ°ΡΠΈΡΠ΅ΡΠΊΠΎΠΉ ΡΠ΅ΠΏΠΈ ΠΏΡΠ΅ΠΎΠ±ΡΠ°Π·ΠΎΠ²Π°Π½ΠΈΡ ΡΠ½Π΅ΡΠ³ΠΈΠΈ Π² Π΄Π²ΠΈΠΆΠ΅Π½ΠΈΠ΅ ΠΈ Π²ΡΠ°ΡΠ°ΡΠ΅Π»ΡΠ½ΠΎΠ³ΠΎ Π΄Π²ΠΈΠΆΠ΅Π½ΠΈΡ Π² Π»ΠΈΠ½Π΅ΠΉΠ½ΠΎΠ΅, Π±Π΅Π· Π»ΡΡΡΠΎΠ², Π·ΠΎΠ½Ρ Π½Π΅ΡΡΠ²ΡΡΠ²ΠΈΡΠ΅Π»ΡΠ½ΠΎΡΡΠΈ ΠΈ Π½Π΅ΡΠ°Π²Π½ΠΎΠΌΠ΅ΡΠ½ΡΡ ΠΏΠΎΠ΄Π°Ρ. ΠΡΠ΅, ΡΡΠΎ ΠΏΡΠΎΠΈΡΡ ΠΎΠ΄ΠΈΡ ΠΏΡΠΈ ΠΎΡΡΠ°Π±ΠΎΡΠΊΠ΅ ΠΊΠ°ΠΆΠ΄ΠΎΠ³ΠΎ ΠΏΠ΅ΡΠ΅ΠΌΠ΅ΡΠ΅Π½ΠΈΡ, ΡΡΠΎ:
Β
ΠΠΎΠΌΠ°Π½Π΄Π½ΡΠΉ ΠΈΠΌΠΏΡΠ»ΡΡ => ΠΠ½Π΅ΡΠ³ΠΈΡ Π²Π·Π°ΠΈΠΌΠΎΠ΄Π΅ΠΉΡΡΠ²ΠΈΡ ΠΌΠ°Π³Π½ΠΈΡΠ½ΡΡ ΠΏΠΎΠ»Π΅ΠΉ => ΠΠΈΠ½Π΅ΠΉΠ½ΠΎΠ΅ Π΄Π²ΠΈΠΆΠ΅Π½ΠΈΠ΅
Β
Π Π»ΠΈΠ½Π΅ΠΉΠ½ΡΡ ΠΏΡΠΈΠ²ΠΎΠ΄Π°Ρ ΠΎΡΡΡΡΡΡΠ²ΡΠ΅Ρ ΠΌΠ½ΠΎΠ³ΠΎΡΡΡΠΏΠ΅Π½ΡΠ°ΡΠΎΠ΅ ΠΏΡΠ΅ΠΎΠ±ΡΠ°Π·ΠΎΠ²Π°Π½ΠΈΠ΅ ΡΠ½Π΅ΡΠ³ΠΈΠΈ Π² Π΄Π²ΠΈΠΆΠ΅Π½ΠΈΠ΅, ΡΡΠΎ Π²ΡΠ·ΡΠ²Π°Π΅Ρ Π²ΠΎΠ·Π½ΠΈΠΊΠ½ΠΎΠ²Π΅Π½ΠΈΠ΅ Π»ΡΡΡΠΎΠ² ΠΈ Π½Π΅ΡΠ°Π²Π½ΠΎΠΌΠ΅ΡΠ½ΡΡ ΠΏΠΎΠ΄Π°Ρ. ΠΠΈΠ½Π΅ΠΉΠ½ΡΠ΅ ΠΏΡΠΈΠ²ΠΎΠ΄Ρ ΡΠ»Π΅ΠΊΡΡΠΎΠΈΡΠΊΡΠΎΠ²ΠΎΠ³ΠΎ ΡΡΠ°Π½ΠΊΠ° ΡΠΏΠΎΡΠΎΠ±Π½Ρ ΠΊΠΎΡΡΠ΅ΠΊΡΠΈΡΠΎΠ²Π°ΡΡ Π·Π°Π·ΠΎΡ 500 ΡΠ°Π· Π² ΡΠ΅ΠΊΡΠ½Π΄Ρ Ρ Π΄ΠΈΡΠΊΡΠ΅ΡΠ½ΠΎΡΡΡΡ ΠΏΠΎΠ΄Π°Ρ 0,1 ΠΌΠΊΠΌ. ΠΡΡ ΠΎΠ΄ΠΈΡ, ΠΎΠΏΡΠΈΠΌΠ°Π»ΡΠ½ΡΠΉ Π·Π°Π·ΠΎΡ ΠΏΡΠ°ΠΊΡΠΈΡΠ΅ΡΠΊΠΈ Π² Π»ΡΠ±ΠΎΠΉ ΠΌΠΎΠΌΠ΅Π½Ρ. Π Π² ΠΈΡΠΎΠ³Π΅ ΠΏΠΎΠ»ΡΡΠ°Π΅ΠΌ ΠΎΠΏΡΠΈΠΌΠ°Π»ΡΠ½ΡΠ΅ ΡΠ΅ΠΆΠΈΠΌΡ, ΡΡΠ°Π±ΠΈΠ»ΡΠ½ΠΎ ΠΌΠ°ΠΊΡΠΈΠΌΠ°Π»ΡΠ½ΡΠΉ ΡΡΠ΅ΠΌ, Π²ΡΡΠΎΠΊΡΡ ΡΠΊΠΎΡΠΎΡΡΡ ΠΎΠ±ΡΠ°Π±ΠΎΡΠΊΠΈ ΠΈ ΠΊΠ°ΡΠ΅ΡΡΠ²ΠΎ ΠΏΠΎΠ²Π΅ΡΡ Π½ΠΎΡΡΠΈ.
Β
Β
ΠΠ°ΠΏΡΠ°Π²Π»ΡΡΡΠΈΠ΅ ΡΡΠ°Π½ΠΊΠ°
Β
ΠΠ°ΠΏΡΠ°Π²Π»ΡΡΡΠΈΠ΅ ΡΠ»ΡΠΆΠ°Ρ Π΄Π»Ρ ΠΏΠ΅ΡΠ΅ΠΌΠ΅ΡΠ΅Π½ΠΈΡ ΠΏΠΎ ΡΡΠ°Π½ΠΈΠ½Π΅ ΠΏΠΎΠ΄Π²ΠΈΠΆΠ½ΡΡ ΡΠ·Π»ΠΎΠ² ΡΡΠ°Π½ΠΊΠ°, ΠΎΠ±Π΅ΡΠΏΠ΅ΡΠΈΠ²Π°Ρ ΠΏΡΠ°Π²ΠΈΠ»ΡΠ½ΠΎΡΡΡ ΡΡΠ°Π΅ΠΊΡΠΎΡΠΈΠΈ Π΄Π²ΠΈΠΆΠ΅Π½ΠΈΡ Π·Π°Π³ΠΎΡΠΎΠ²ΠΊΠΈ ΠΈΠ»ΠΈ Π΄Π΅ΡΠ°Π»ΠΈ ΠΈ Π΄Π»Ρ Π²ΠΎΡΠΏΡΠΈΡΡΠΈΡ Π²Π½Π΅ΡΠ½ΠΈΡ ΡΠΈΠ». ΠΠΎ Π²ΡΠ΅Ρ ΠΌΠ΅ΡΠ°Π»Π»ΠΎΡΠ΅ΠΆΡΡΠΈΡ ΡΡΠ°Π½ΠΊΠ°Ρ ΠΏΡΠΈΠΌΠ΅Π½ΡΡΡΡΡ Π½Π°ΠΏΡΠ°Π²Π»ΡΡΡΠΈΠ΅: ΡΠΊΠΎΠ»ΡΠΆΠ΅Π½ΠΈΡ, ΠΊΠ°ΡΠ΅Π½ΠΈΡ, ΠΊΠΎΠΌΠ±ΠΈΠ½ΠΈΡΠΎΠ²Π°Π½Π½ΡΠ΅, ΠΆΠΈΠ΄ΠΊΠΎΡΡΠ½ΠΎΠ³ΠΎ ΡΡΠ΅Π½ΠΈΡ, Π°ΡΡΠΎΡΡΠ°ΡΠΈΡΠ΅ΡΠΊΠΈΠ΅.
ΠΡΠ΅Π΄ΡΡΠ²Π»ΡΡΡΠΈΠ΅ ΡΡΠ΅Π±ΠΎΠ²Π°Π½ΠΈΡ: ΠΏΠ΅ΡΠ²ΠΎΠ½Π°ΡΠ°Π»ΡΠ½Π°Ρ ΡΠΎΡΠ½ΠΎΡΡΡ ΠΈΠ·Π³ΠΎΡΠΎΠ²Π»Π΅Π½ΠΈΡ, Π΄ΠΎΠ»Π³ΠΎΠ²Π΅ΡΠ½ΠΎΡΡΡ, Π²ΡΡΠΎΠΊΠ°Ρ ΠΆΠ΅ΡΡΠΊΠΎΡΡΡ, Π²ΡΡΠΎΠΊΠΈΠ΅ Π΄Π΅ΠΌΠΏΡΠΈΡΡΡΡΠΈΠ΅ ΡΠ²ΠΎΠΉΡΡΠ²Π°, ΠΌΠ°Π»ΡΠ΅ ΡΠΈΠ»Ρ ΡΡΠ΅Π½ΠΈΡ, ΠΏΡΠΎΡΡΠΎΡΠ° ΠΊΠΎΠ½ΡΡΡΡΠΊΡΠΈΠΈ, Π²ΠΎΠ·ΠΌΠΎΠΆΠ½ΠΎΡΡΡ ΠΎΠ±Π΅ΡΠΏΠ΅ΡΠ΅Π½ΠΈΡ, ΡΠ΅Π³ΡΠ»ΠΈΡΠΎΠ²Π°Π½ΠΈΡ Π·Π°Π·ΠΎΡΠ°-Π½Π°ΡΡΠ³Π°.
Β
Π Π·Π°Π²ΠΈΡΠΈΠΌΠΎΡΡΠΈ ΠΎΡ ΡΠ°ΡΠΏΠΎΠ»ΠΎΠΆΠ΅Π½ΠΈΡ Π½Π°ΠΏΡΠ°Π²Π»ΡΡΡΠΈΠ΅ Π΄Π΅Π»ΡΡΡΡ ΡΠ°ΠΊΠΆΠ΅ Π½Π° Π³ΠΎΡΠΈΠ·ΠΎΠ½ΡΠ°Π»ΡΠ½ΡΠ΅, Π²Π΅ΡΡΠΈΠΊΠ°Π»ΡΠ½ΡΠ΅, Π½Π°ΠΊΠ»ΠΎΠ½Π½ΡΠ΅.
Β
Β
Π¨ΠΏΠΈΠ½Π΄Π΅Π»ΡΠ½ΡΠ΅ ΡΠ·Π»Ρ ΡΡΠ°Π½ΠΊΠ°
Β
Π¨ΠΏΠΈΠ½Π΄Π΅Π»Ρ Π²ΡΠΏΠΎΠ»Π½Π΅Π½ Π² Π²ΠΈΠ΄Π΅ ΠΌΠ°ΡΡΠΈΠ²Π½ΠΎΠ³ΠΎ ΡΠΎΡΠΎΡΠ°, Ρ ΡΠ°ΡΠΏΠΎΠ»ΠΎΠΆΠ΅Π½Π½ΠΎΠΉ Π²Π½ΡΡΡΠΈ Π½Π΅Π³ΠΎ ΠΊΡΠ΅ΠΏΠ΅ΠΆΠ½ΠΎΠΉ ΡΠ°Π½Π³ΠΎΠΉ, Π° Π² Π²Π΅ΡΡ Π½Π΅ΠΉ ΡΠΎΡΠΊΠ΅ ΠΏΠΎΠ»ΠΎΡΡΠΈ, ΠΎΠ±ΡΠ°Π·ΠΎΠ²Π°Π½Π½ΠΎΠΉ Π΄Π²ΡΠΌΡ Π²ΡΡΡΠ΅ΡΠ½ΠΎ ΠΎΠ±ΡΠ°ΡΠ΅Π½Π½ΡΠΌΠΈ ΠΊΠΎΠ½ΠΈΡΠ΅ΡΠΊΠΈΠΌΠΈ ΠΏΠΎΠ²Π΅ΡΡ Π½ΠΎΡΡΡΠΌΠΈ, ΡΡΡΠ°Π½ΠΎΠ²Π»Π΅Π½ Π·Π°Π±ΠΎΡΠ½ΠΈΠΊ(ΡΠ»Π°Π²Π»ΠΈΠ²Π°ΡΠ΅Π»Ρ) ΡΠ°Π±ΠΎΡΠ΅ΠΉ ΠΆΠΈΠ΄ΠΊΠΎΡΡΠΈ. Π’Π°ΠΊΠ°Ρ ΠΊΠΎΠ½ΡΡΡΡΠΊΡΠΈΡ ΡΠΏΠΈΠ½Π΄Π΅Π»Ρ ΡΠ»ΡΡΡΠ°Π΅Ρ ΡΡΠ»ΠΎΠ²ΠΈΡ ΡΠ°Π±ΠΎΡΡ Π½Π° ΡΡΠ°Π½ΠΊΠ΅.
Β
Β
Π ΠΈΡ.1 β Π¨ΠΏΠΈΠ½Π΄Π΅Π»Ρ ΡΠ»Π΅ΠΊΡΡΠΎΠΈΡΠΊΡΠΎΠ²ΠΎΠ³ΠΎ ΡΡΠ°Π½ΠΊΠ°
Β
Π ΡΠΊΠΎΠ»ΡΠ·ΡΡΠ΅ΠΌ ΠΏΠΎΠ΄ΡΠΈΠΏΠ½ΠΈΠΊΠ΅ 1 ΡΠ°ΡΠΏΠΎΠ»ΠΎΠΆΠ΅Π½ Π²ΡΠ°ΡΠ°ΡΡΠΈΠΉΡΡ ΠΏΠΎΡΡΠ΅Π΄ΡΡΠ²ΠΎΠΌ ΠΊΠ»ΠΈΠ½ΠΎΡΠ΅ΠΌΠ΅Π½Π½ΠΎΠΉ ΠΏΠ΅ΡΠ΅Π΄Π°ΡΠΈ 2 ΡΠΏΠΈΠ½Π΄Π΅Π»Ρ 3, Π²ΡΠΏΠΎΠ»Π½Π΅Π½Π½ΡΠΉ Π² Π²ΠΈΠ΄Π΅ ΡΠΎΡΠΎΡΠ°, Π² ΠΊΠΎΠ½ΡΠ΅Π½ΡΡΠΈΡΠ΅ΡΠΊΠΎΠΉ ΡΠ°ΡΡΠΎΡΠΊΠ΅ ΠΊΠΎΡΠΎΡΠΎΠ³ΠΎ ΡΠ°ΡΠΏΠΎΠ»ΠΎΠΆΠ΅Π½Π° Π½Π° Π½Π°ΠΏΡΡΠΆΠ΅Π½Π½ΠΎΠΉ ΠΈΠ»ΠΈ ΡΡΠ³ΠΎΠΉ ΠΏΠΎΡΠ°Π΄ΠΊΠ΅ ΡΠ°Π½Π³Π° 4, Π΄Π»Ρ ΠΊΡΠ΅ΠΏΠ»Π΅Π½ΠΈΡ ΠΏΠΎ Π²Π½Π΅ΡΠ½Π΅ΠΉ ΠΏΠΎΠ²Π΅ΡΡ Π½ΠΎΡΡΠΈ ΠΎΠ±ΡΠ°Π±Π°ΡΡΠ²Π°Π΅ΠΌΠΎΠΉ Π΄Π΅ΡΠ°Π»ΠΈ 5. ΠΠ½ΡΡΡΠ΅Π½Π½ΡΡ ΠΏΠΎΠ»ΠΎΡΡΡ ΡΠΎΡΠΎΡΠ° ΠΎΠ±ΡΠ°Π·ΠΎΠ²Π°Π½Π° Π΄Π²ΡΠΌΡ Π²ΡΡΡΠ΅ΡΠ½ΠΎ ΠΎΠ±ΡΠ°ΡΠ΅Π½Π½ΡΠΌΠΈ ΠΊΠΎΠ½ΠΈΡΠ΅ΡΠΊΠΈΠΌΠΈ ΠΏΠΎΠ²Π΅ΡΡ Π½ΠΎΡΡΡΠΌΠΈ 6 ΠΈ 7, Π Π°Π±ΠΎΡΠ°Ρ ΠΆΠΈΠ΄ΠΊΠΎΡΡΡ, ΠΏΠΎΠ΄Π°Π²Π°Π΅ΠΌΠ°Ρ ΠΎΡ Π³ΠΈΠ΄ΡΠΎΠ½Π°ΡΠΎΡΠ° ΠΏΠΎ ΡΡΡΠ±ΠΊΠ΅ 8 Π² ΠΎΡΠ²Π΅ΡΡΡΠΈΠ΅ ΠΎΠ±ΡΠ°Π±Π°ΡΡΠ²Π°Π΅ΠΌΠΎΠΉ Π΄Π΅ΡΠ°Π»ΠΈ, ΠΏΠΎΠ΄ Π΄Π΅ΠΉΡΡΠ²ΠΈΠ΅ΠΌ ΡΠ΅Π½ΡΡΠΎΠ±Π΅ΠΆΠ½ΡΡ ΡΠΈΠ» Π²ΡΠ°ΡΠ°ΡΡΠ΅Π³ΠΎΡΡ ΡΠΏΠΈΠ½Π΄Π΅Π»Ρ ΡΠΎΠ±ΠΈΡΠ°Π΅ΡΡΡ Π½Π° ΠΏΠ΅ΡΠΈΡΠ΅ΡΠΈΠΈ Π²Π½ΡΡΡΠ΅Π½Π½Π΅ΠΉ ΠΏΠΎΠ»ΠΎΡΡΠΈ (ΠΊΠ°ΡΠΌΠ°Π½Π°) ΡΠΎΡΠΎΡΠ°, ΠΎΡΠΊΡΠ΄Π° ΡΠ΅ΡΠ΅Π· Π·Π°Π±ΠΎΡΠ½ΠΈΠΊ 9 ΠΏΠΎ ΡΡΡΠ±ΠΊΠ΅ 10 ΠΏΠΎΡΡΡΠΏΠ°Π΅Ρ Π² ΡΠΈΠ»ΡΡΡΡΡΡΠΈΠΉ ΡΠ»Π΅ΠΌΠ΅Π½Ρ Π³ΠΈΠ΄ΡΠΎΠ½Π°ΡΠΎΡΠ°.
Β
Β
ΠΡΠΈΠ²ΠΎΠ΄Ρ ΠΏΠΎΠ΄Π°Ρ ΡΡΠ°Π½ΠΊΠ°
Β
ΠΠΈΡΡ Ρ Π½Π΅Π΄Π°Π²Π½Π΅Π³ΠΎ Π²ΡΠ΅ΠΌΠ΅Π½ΠΈ Π½Π°ΡΠ°Π»ΡΡ Π²ΡΠΏΡΡΠΊ ΡΠ»Π΅ΠΊΡΡΠΎΠΈΡΠΊΡΠΎΠ²ΡΡ ΡΡΠ°Π½ΠΊΠΎΠ², Π° ΠΈΠΌΠ΅Π½Π½ΠΎ Ρ ΡΠΎΠ²Π΅ΡΡΠ΅Π½Π½ΠΎ Π½ΠΎΠ²ΡΠΌΠΈ Π»ΠΈΠ½Π΅ΠΉΠ½ΡΠΌΠΈ Π΄Π²ΠΈΠ³Π°ΡΠ΅Π»ΡΠΌΠΈ. Π Π΄Π°Π½Π½ΠΎΠΌ Π²ΡΠΏΡΡΠΊΠ΅ Π±ΡΠ»ΠΈ ΡΠΎΠ²Π΅ΡΡΠ΅Π½Ρ ΠΈ ΠΈΡΠΏΡΠ°Π²Π»Π΅Π½Ρ ΡΠ°Π±ΠΎΡΡ Π½Π°Π΄ ΡΠ΅Π³ΡΠ»ΠΈΡΠΎΠ²Π°Π½ΠΈΠ΅ΠΌ ΡΠΊΠΎΡΠΎΡΡΠΈ ΠΈ ΡΡΠΊΠΎΡΠ΅Π½ΠΈΠΈ, ΡΠ°Π²Π½ΠΎΠΌΠ΅ΡΠ½ΡΠΌ Π΄Π²ΠΈΠΆΠ΅Π½ΠΈΠ΅ΠΌ, ΡΠ΅Π²Π΅ΡΡΠΎΠΌ, Π»Π΅Π³ΠΊΠΎΡΡΡΡ ΠΎΠ±ΡΠ»ΡΠΆΠΈΠ²Π°Π½ΠΈΡ ΠΈ Π΄Ρ.
ΠΠΈΠ½Π΅ΠΉΠ½ΡΠΉ Π΄Π²ΠΈΠ³Π°ΡΠ΅Π»Ρ Π² Π΄Π°Π½Π½ΠΎΠΌ Π²ΡΠΏΡΡΠΊΠ΅ ΡΡΠ°Π½ΠΊΠΎΠ² ΠΈΠΌΠ΅Π΅Ρ Π΄Π²ΠΈΠ³Π°ΡΠ΅Π»Ρ, ΡΠΎΠ΄Π΅ΡΠΆΠ°ΡΠΈΠΉ Π²ΡΠ΅Π³ΠΎ Π½Π΅ΡΠΊΠΎΠ»ΡΠΊΠΎ ΡΠ»Π΅ΠΌΠ΅Π½ΡΠΎΠ²: ΡΠ»Π΅ΠΊΡΡΠΎΠΌΠ°Π³Π½ΠΈΡΠ½ΡΠΉ ΡΡΠ°ΡΠΎΡ ΠΈ ΠΏΠ»ΠΎΡΠΊΠΈΠΉ ΡΠΎΡΠΎΡ, ΠΊΠΎΡΠΎΡΡΠ΅ ΡΠΎΠ΄Π΅ΡΠΆΠ°Ρ ΠΌΠ΅ΠΆΠ΄Ρ ΡΠΎΠ±ΠΎΠΉ ΡΠΎΠ»ΡΠΊΠΎ Π·Π°Π·ΠΎΡ ΠΈΠ· Π²ΠΎΠ·Π΄ΡΡ Π°. Π’Π°ΠΊΠΆΠ΅ ΠΈΠΌΠ΅Π΅ΡΡΡ Π΅ΡΠ΅ ΠΎΠ΄ΠΈΠ½ Π½Π΅ΠΌΠ°Π»ΠΎΠ²Π°ΠΆΠ½ΡΠΉ ΡΠ»Π΅ΠΌΠ΅Π½Ρ ΠΈ ΡΡΠΎ ΠΎΠΏΡΠΈΡΠ΅ΡΠΊΠ°Ρ ΠΈΠ·ΠΌΠ΅ΡΠΈΡΠ΅Π»ΡΠ½Π°Ρ Π»ΠΈΠ½Π΅ΠΉΠΊΠ° Ρ Π²ΡΡΠΎΠΊΠΎΠΉ Π΄ΠΈΡΠΊΡΠ΅ΡΠ½ΠΎΡΡΡΡ (0.1 ΠΌΠΊΠΌ). ΠΠ΅Π· ΡΡΠΎΠ³ΠΎ ΠΈΠ·ΠΌΠ΅ΡΠΈΡΠ΅Π»ΡΠ½ΠΎΠ³ΠΎ ΠΏΡΠΈΠ±ΠΎΡΠ° ΡΠΈΡΡΠ΅ΠΌΠ° ΡΠΏΡΠ°Π²Π»Π΅Π½ΠΈΡ Π½Π΅ ΡΠΌΠΎΠΆΠ΅Ρ ΡΠ°ΡΠΏΠΎΠ·Π½Π°ΡΡ ΠΊΠΎΠΎΡΠ΄ΠΈΠ½Π°ΡΡ.
Β
Β
ΠΠΎ ΡΠ°ΠΊΠΆΠ΅ Π±Π»ΠΈΠΆΠ΅ ΡΠ°ΡΡΠΌΠΎΡΡΠΈΠΌ ΡΡΠ°ΡΠΎΡ ΠΈ ΡΠΎΡΠΎΡ. ΠΠ±Π° Π²ΡΠΏΠΎΠ»Π½Π΅Π½Ρ Π² Π²ΠΈΠ΄Π΅ ΠΏΠ»ΠΎΡΠΊΠΈΡ ΠΈ Π»Π΅Π³ΠΊΠΎ ΡΠ½ΠΈΠΌΠ°Π΅ΠΌΡΡ Π±Π»ΠΎΠΊΠΎΠ². ΠΠΎ ΠΊΡΠ΅ΠΏΠΈΡΡΡ ΡΡΠ°ΡΠΎΡ ΠΊ ΡΡΠ°Π½ΠΈΠ½Π΅ ΠΈΠ»ΠΈ ΠΊΠΎΠ»ΠΎΠ½Π½Π΅ ΡΡΠ°Π½ΠΊΠ°, Π° ΡΠΎΡΠΎΡ β ΠΊ ΡΠ°Π±ΠΎΡΠ΅ΠΌΡ ΠΎΡΠ³Π°Π½Ρ.
Π ΠΊΠΎΠ½ΡΡΡΡΠΊΡΠΈΠΈ ΡΠΎΡΠΎΡ ΡΠΎΠ²Π΅ΡΡΠ΅Π½Π½ΠΎ ΠΏΡΠΎΡΡ. ΠΠ½ ΡΠΎΡΡΠΎΠΈΡ ΠΈΠ· ΠΏΡΡΠΌΠΎΡΠ³ΠΎΠ»ΡΠ½ΡΡ ΡΠΈΠ»ΡΠ½ΡΡ ΠΏΠΎΡΡΠΎΡΠ½Π½ΡΡ ΠΌΠ°Π³Π½ΠΈΡΠΎΠ². Π ΠΌΠ°Π³Π½ΠΈΡΡ Π½Π° ΡΠΎΠ½ΠΊΠΎΠΉ ΠΏΠ»ΠΈΡΠ΅ ΠΈΠ· ΡΠΏΠ΅ΡΠΈΠ°Π»ΡΠ½ΠΎΠΉ Π²ΡΡΠΎΠΊΠΎΠΏΡΠΎΡΠ½ΠΎΠΉ ΠΊΠ΅ΡΠ°ΠΌΠΈΠΊΠΈ, ΠΊΠΎΡΡΡΠΈΡΠΈΠ΅Π½Ρ ΡΠ΅ΠΌΠΏΠ΅ΡΠ°ΡΡΡΠ½ΠΎΠ³ΠΎ ΡΠ°ΡΡΠΈΡΠ΅Π½ΠΈΡ ΠΊΠΎΡΠΎΡΠΎΠΉ Π² Π΄Π²Π° ΡΠ°Π·Π° ΠΌΠ΅Π½ΡΡΠ΅ ΡΠ΅ΠΌ Ρ Π³ΡΠ°Π½ΠΈΡΠ°.
ΠΠ½ΠΎΠΆΠ΅ΡΡΠ²ΠΎ ΠΏΡΠΎΠ±Π»Π΅ΠΌ Π»ΠΈΠ½Π΅ΠΉΠ½ΠΎΠ³ΠΎ ΠΏΡΠΈΠ²ΠΎΠ΄Π° ΡΠ΅ΡΠΈΠ»ΠΈΡΡ, ΡΠ°ΠΊ ΠΊΠ°ΠΊ ΡΡΠ°Π»ΠΈ ΠΈΡΠΏΠΎΠ»ΡΠ·ΠΎΠ²Π°ΡΡ ΠΊΠ΅ΡΠ°ΠΌΠΈΠΊΡ ΠΎΠ΄Π½ΠΎΠ²ΡΠ΅ΠΌΠ΅Π½Π½ΠΎ Ρ ΡΠΈΡΡΠ΅ΠΌΠΎΠΉ ΠΎΡ Π»Π°ΠΆΠ΄Π΅Π½ΠΈΡ. Π‘ΠΎΠΎΡΠ²Π΅ΡΡΡΠ²Π΅Π½Π½ΠΎ Β«ΡΡΠ»ΠΈΒ» ΠΈ ΠΏΡΠΎΠ±Π»Π΅ΠΌΡ Ρ ΡΠ΅ΠΌΠΏΠ΅ΡΠ°ΡΡΡΠ½ΡΠΌΠΈ ΡΠ°ΠΊΡΠΎΡΠ°ΠΌΠΈ, Ρ ΠΆΠ΅ΡΡΠΊΠΎΡΡΡΡ ΠΊΠΎΠ½ΡΡΡΡΠΊΡΠΈΠΈ, Ρ Π½Π°Π»ΠΈΡΠΈΠ΅ΠΌ ΡΠΈΠ»ΡΠ½ΡΡ ΠΌΠ°Π³Π½ΠΈΡΠ½ΡΡ ΠΏΠΎΠ»Π΅ΠΉ ΠΈ Ρ.Π΄.
Β
Β
Β
ΠΠ΅ΡΡΡΠ°Ρ ΡΠΈΡΡΠ΅ΠΌΠ° ΡΡΠ°Π½ΠΊΠ°
Β
Π‘ΡΠ°Π½ΠΈΠ½Π°, ΠΊΠΎΠ»ΠΎΠ½Π½Π°, ΠΊΠ°ΡΠ΅ΡΠΊΠ° ΡΡΠΎΠ»Π° ΠΈ Π΄Ρ. ΡΠ²Π»ΡΡΡΡΡ Π½Π΅ΡΡΡΠ΅ΠΉ ΠΊΠΎΠ½ΡΡΡΡΠΊΡΠΈΠ΅ΠΉ, ΠΎΠ±ΡΡΠ½ΠΎ ΡΠΎΡΡΠΎΡΡΠ΅ΠΉ ΠΈΠ· ΡΡΠ³ΡΠ½Π°. Π¨Π°Π±ΡΠ΅Π½Π½ΡΠ΅ ΠΏΠΎΡΠ°Π΄ΠΎΡΠ½ΡΠ΅ ΠΏΠΎΠ²Π΅ΡΡ Π½ΠΎΡΡΠΈ ΠΏΡΠ΅Π΄Π½Π°Π·Π½Π°ΡΠ΅Π½Ρ Π΄Π»Ρ Π½Π°ΠΏΡΠ°Π²Π»ΡΡΡΠΈΡ , Π° ΡΠ°ΠΊΠΆΠ΅ Π΄Π»Ρ ΡΠΎΡΡΡΠΊΠΎΠ²ΠΊΠΈ Π΄Π²ΡΡ ΠΊΠΎΠ½ΡΡΡΡΠΊΡΠΈΠΉ ΠΌΠ΅ΠΆΠ΄Ρ ΡΠΎΠ±ΠΎΠΉ.
Β
Β
Π’ΠΈΠΏΠΈΡΠ½ΡΠ΅ ΠΏΡΠ΅Π΄ΡΡΠ°Π²ΠΈΡΠ΅Π»ΠΈ
Β
Π ΠΏΡΠΎΡΠ΅ΡΡΠ΅ ΠΏΠΎΠ΄Π³ΠΎΡΠΎΠ²ΠΊΠΈ Π΄Π°Π½Π½ΠΎΠ³ΠΎ ΡΠ΅ΡΠ΅ΡΠ°ΡΠ° Π±ΡΠ»ΠΈ ΡΠ°Π·ΠΎΠ±ΡΠ°Π½Ρ Π½Π΅ΡΠΊΠΎΠ»ΡΠΊΠΎ ΡΠΎΠ²ΡΠ΅ΠΌΠ΅Π½Π½ΡΡ ΠΏΡΠ΅Π΄ΡΡΠ°Π²ΠΈΡΠ΅Π»Π΅ΠΉ ΡΡΠ°Π½ΠΊΠΎΠ² ΡΠ»Π΅ΠΊΡΡΠΎΠΈΡΠΊΡΠΎΠ²ΠΎΠ³ΠΎ ΡΠΈΠΏΠ°, ΠΎΡΠ½Π°ΡΠ΅Π½Π½ΡΡ ΡΠΈΡΡΠ΅ΠΌΠΎΠΉ ΡΠΈΡΠ»ΠΎΠ²ΠΎΠ³ΠΎ ΠΏΡΠΎΠ³ΡΠ°ΠΌΠΌΠ½ΠΎΠ³ΠΎ ΡΠΏΡΠ°Π²Π»Π΅Π½ΠΈΡ. ΠΡΠ»ΠΈ ΠΏΡΠ΅Π΄ΡΡΠ°Π²Π»Π΅Π½Ρ ΡΠ°ΠΊΠΈΠ΅ ΡΡΠ°Π½ΠΊΠΈ ΠΊΠ°ΠΊ, ALC800G ΠΈ AQ15L. ΠΡ ΠΎΡΠ½ΠΎΠ²Π½ΡΠ΅ ΡΠ΅Ρ Π½ΠΈΡΠ΅ΡΠΊΠΈΠ΅ Ρ Π°ΡΠ°ΠΊΡΠ΅ΡΠΈΡΡΠΈΠΊΠΈ ΠΏΡΠΈΠ²Π΅Π΄Π΅Π½Ρ Π½ΠΈΠΆΠ΅ Π² ΡΠ°Π±Π»ΠΈΡΠ°Ρ 1 ΠΈ 2.
Π’Π΅Ρ Π½ΠΈΡΠ΅ΡΠΊΠΈΠ΅ Ρ Π°ΡΠ°ΠΊΡΠ΅ΡΠΈΡΡΠΈΠΊΠΈ ALC800G
Β
Π’Π΅Ρ Π½ΠΈΡΠ΅ΡΠΊΠΈΠ΅ Ρ Π°ΡΠ°ΠΊΡΠ΅ΡΠΈΡΡΠΈΠΊΠΈ AQ15L
engcrafts.com
ΠΠ»Π΅ΠΊΡΡΠΎΠΈΡΠΊΡΠΎΠ²Π°Ρ ΠΎΠ±ΡΠ°Π±ΠΎΡΠΊΠ° ΠΌΠ΅ΡΠ°Π»Π»Π° – Π³Π°ΡΠ°ΠΆΠ½Π°Ρ ΡΡ Π΅ΠΌΠ°
ΠΡΠΎΠΌΡΡΠ»Π΅Π½Π½Π°Ρ ΠΎΠ±ΡΠ°Π±ΠΎΡΠΊΠ° ΠΌΠ΅ΡΠ°Π»Π»ΠΎΠ² Π²ΠΊΠ»ΡΡΠ°Π΅Ρ Π² ΡΠ΅Π±Ρ Π½Π΅ΡΠΊΠΎΠ»ΡΠΊΠΎ Π΄Π΅ΡΡΡΠΊΠΎΠ² ΡΠΏΠΎΡΠΎΠ±ΠΎΠ² ΠΈ ΠΌΠ΅ΡΠΎΠ΄ΠΎΠ² ΠΈΠ·ΠΌΠ΅Π½Π΅Π½ΠΈΡ ΡΠΎΡΠΌΡ, ΠΎΠ±ΡΠ΅ΠΌΠ° ΠΈ, Π΄Π°ΠΆΠ΅ ΠΌΠΎΠ»Π΅ΠΊΡΠ»ΡΡΠ½ΠΎΠΉ ΡΡΡΡΠΊΡΡΡΡ ΠΌΠ°ΡΠ΅ΡΠΈΠ°Π»Π°. ΠΠ»Π΅ΠΊΡΡΠΎΠΈΡΠΊΡΠΎΠ²Π°Ρ ΠΎΠ±ΡΠ°Π±ΠΎΡΠΊΠ° ΠΌΠ΅ΡΠ°Π»Π»ΠΎΠ² β ΠΎΠ΄Π½Π° ΠΈΠ· ΡΠ°ΡΠΏΡΠΎΡΡΡΠ°Π½Π΅Π½Π½ΡΡ ΡΠ΅Ρ Π½ΠΎΠ»ΠΎΠ³ΠΈΠΉ ΡΠ°Π±ΠΎΡΡ Ρ ΠΌΠ΅ΡΠ°Π»Π»ΠΎΠΌ, ΠΎΡΠ»ΠΈΡΠ°ΡΡΠ°ΡΡΡ Π²ΡΡΠΎΠΊΠΎΠΉ ΡΠΎΡΠ½ΠΎΡΡΡΡ ΠΈ ΠΏΡΠΎΠΈΠ·Π²ΠΎΠ΄ΠΈΡΠ΅Π»ΡΠ½ΠΎΡΡΡΡ. ΠΡΠΈ ΠΏΠΎΠΌΠΎΡΠΈ ΡΠ»Π΅ΠΊΡΡΠΎΠΈΡΠΊΡΠΎΠ²ΡΡ ΡΡΠ°Π½ΠΊΠΎΠ² ΠΌΠΎΠΆΠ½ΠΎ:
- ΡΠ΅Π·Π°ΡΡ ΠΌΠ΅ΡΠ°Π»Π»;
- ΡΠ²Π΅ΡΠ»ΠΈΡΡ ΠΎΡΠ²Π΅ΡΡΡΠΈΡ ΠΌΠΈΠΊΡΠΎΡΠΊΠΎΠΏΠΈΡΠ΅ΡΠΊΠΎΠ³ΠΎ Π΄ΠΈΠ°ΠΌΠ΅ΡΡΠ°;
- Π½Π°ΡΠ°ΡΠΈΠ²Π°ΡΡ Π΄Π΅ΡΠ΅ΠΊΡΠ½ΡΠ΅ ΠΎΠ±Π»Π°ΡΡΠΈ Π΄Π΅ΡΠ°Π»Π΅ΠΉ;
- ΠΏΡΠΎΠΈΠ·Π²ΠΎΠ΄ΠΈΡΡ ΡΠ²Π΅Π»ΠΈΡΠ½ΡΠ΅ ΡΠ°Π±ΠΎΡΡ Ρ Π΄ΡΠ°Π³ΠΎΡΠ΅Π½Π½ΡΠΌΠΈ ΠΌΠ΅ΡΠ°Π»Π»Π°ΠΌΠΈ;
- ΡΠΏΡΠΎΡΠ½ΡΡΡ ΠΏΠΎΠ²Π΅ΡΡ Π½ΠΎΡΡΡ ΠΈΠ·Π΄Π΅Π»ΠΈΠΉ;
- ΡΠ»ΠΈΡΠΎΠ²Π°ΡΡ ΠΈΠ·Π΄Π΅Π»ΠΈΡ ΡΠ°ΠΌΠΎΠΉ ΡΠ»ΠΎΠΆΠ½ΠΎΠΉ ΡΠΎΡΠΌΡ;
- ΠΈΠ·Π²Π»Π΅ΠΊΠ°ΡΡ Π·Π°ΡΡΡΡΠ²ΡΠΈΠ΅ ΡΠ»ΠΎΠΌΠ°Π½Π½ΡΠ΅ ΡΠ²Π΅ΡΠ»Π° ΠΈ ΡΠ΅Π·ΡΡ.
ΠΠ° Π±Π°Π·Π΅ ΡΠ»Π΅ΠΊΡΡΠΎΠΈΡΠΊΡΠΎΠ²ΠΎΠ³ΠΎ ΠΌΠ΅ΡΠΎΠ΄Π° ΠΎΠ±ΡΠ°Π±ΠΎΡΠΊΠΈ ΠΌΠ΅ΡΠ°Π»Π»ΠΎΠ² ΡΠΎΠ·Π΄Π°Π½ΠΎ Π½Π΅ΠΌΠ°Π»ΠΎ ΡΡΠ°Π½ΠΊΠΎΠ² ΠΏΡΠΎΠΌΡΡΠ»Π΅Π½Π½ΠΎΠ³ΠΎ Π½Π°Π·Π½Π°ΡΠ΅Π½ΠΈΡ. ΠΡΠΎ Π²ΡΡΠΎΠΊΠΎΡΠΎΡΠ½Π°Ρ ΠΈ Π΄ΠΎΡΠΎΠ³Π°Ρ ΡΠ΅Ρ Π½ΠΈΠΊΠ°, ΠΊΠΎΡΠΎΡΡΡ ΠΌΠΎΠ³ΡΡ ΠΏΠΎΠ·Π²ΠΎΠ»ΠΈΡΡ ΡΠ΅Π±Π΅ ΠΊΡΠΏΠΈΡΡ ΡΠΎΠ»ΡΠΊΠΎ ΠΊΡΡΠΏΠ½ΡΠ΅ ΠΏΡΠ΅Π΄ΠΏΡΠΈΡΡΠΈΡ, ΡΠΏΠ΅ΡΠΈΠ°Π»ΠΈΠ·ΠΈΡΡΡΡΠΈΠ΅ΡΡ Π½Π° ΠΌΠ΅ΡΠ°Π»Π»ΠΎΠΎΠ±ΡΠ°Π±ΠΎΡΠΊΠ΅.
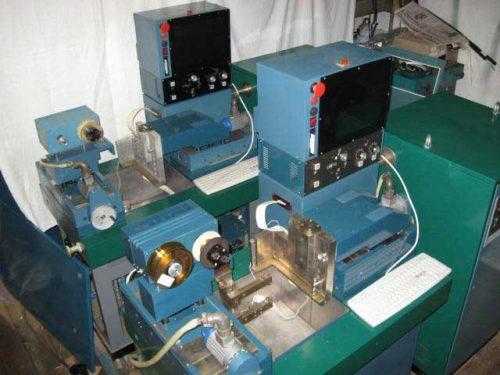
ΠΠ»Π΅ΠΊΡΡΠΎΠΈΡΠΊΡΠΎΠ²ΠΎΠΉ ΡΡΠ°Π½ΠΎΠΊ
ΠΠΎ ΠΈΠ½ΠΎΠ³Π΄Π° ΡΠ»Π΅ΠΊΡΡΠΎΠΈΡΠΊΡΠΎΠ²ΡΠ΅ ΡΡΠ°Π½ΠΊΠΈ ΡΡΠ΅Π±ΡΡΡΡΡ ΠΈ Π² ΠΌΠ°ΡΡΠ΅ΡΡΠΊΠΈΡ ΠΈΠ»ΠΈ ΡΠ΅Ρ Π°Ρ , Π³Π΄Π΅ ΠΈΡ ΡΡΠ»ΡΠ³ΠΈ ΡΡΠ΅Π±ΡΡΡΡΡ Π²ΡΠ΅ΠΌΡ ΠΎΡ Π²ΡΠ΅ΠΌΠ΅Π½ΠΈ. ΠΠ»Ρ ΡΡΠΎΠ³ΠΎ ΠΌΠΎΠΆΠ½ΠΎ ΠΊΡΠΏΠΈΡΡ ΠΏΡΠΎΠΌΡΡΠ»Π΅Π½Π½ΠΎΠ΅ ΡΡΡΡΠΎΠΉΡΡΠ²ΠΎ Ρ Π½Π΅ΡΠΊΠΎΠ»ΡΠΊΠΎ ΠΎΠ³ΡΠ°Π½ΠΈΡΠ΅Π½Π½ΡΠΌΠΈ Π²ΠΎΠ·ΠΌΠΎΠΆΠ½ΠΎΡΡΡΠΌΠΈ (ΡΡΠ½ΠΊΡΠΈΠΎΠ½Π°Π» Π² ΠΏΡΠ΅Π΄Π΅Π»Π°Ρ ΡΠ°ΠΌΡΡ Π²ΠΎΡΡΡΠ΅Π±ΠΎΠ²Π°Π½Π½ΡΡ ΠΎΠΏΠ΅ΡΠ°ΡΠΈΠΉ), ΠΈΠ»ΠΈ ΠΏΠΎΡΡΡΠΎΠΈΡΡ ΡΠ°ΠΌΠΎΠ΄Π΅Π»ΡΠ½ΡΠΉ ΡΠ»Π΅ΠΊΡΡΠΎΠΈΡΠΊΡΠΎΠ²ΠΎΠΉ ΡΡΠ°Π½ΠΎΠΊ. ΠΡΠΎ Π²ΠΏΠΎΠ»Π½Π΅ Π²ΠΎΠ·ΠΌΠΎΠΆΠ½ΠΎ Π΄Π°ΠΆΠ΅ Π² Π΄ΠΎΠΌΠ°ΡΠ½ΠΈΡ ΡΡΠ»ΠΎΠ²ΠΈΡΡ , Π½Π΅ Π³ΠΎΠ²ΠΎΡΡ ΡΠΆΠ΅ ΠΎ ΠΏΡΠ΅Π΄ΠΏΡΠΈΡΡΠΈΡΡ , Π² ΡΠΎΡΡΠ°Π²Π΅ ΠΊΠΎΡΠΎΡΡΡ Π΅ΡΡΡ ΡΠΎΠΊΠ°ΡΠ½ΡΠ΅ ΠΈ ΡΠ»Π΅ΠΊΡΡΠΎΠΌΠ΅Ρ Π°Π½ΠΈΡΠ΅ΡΠΊΠΈΠ΅ ΡΠ΅Ρ Π° ΠΈΠ»ΠΈ ΡΡΠ°ΡΡΠΊΠΈ.
ΠΡΠΈΠ½ΡΠΈΠΏ ΡΠ°Π±ΠΎΡΡ ΡΠ»Π΅ΠΊΡΡΠΎΠΈΡΠΊΡΠΎΠ²ΠΎΠ³ΠΎ ΡΡΠ°Π½ΠΊΠ°
ΠΠ°Π·ΠΈΡΡΠ΅ΡΡΡ ΠΎΠ±ΡΠ°Π±ΠΎΡΠΊΠ° ΠΌΠ΅ΡΠ°Π»Π»ΠΎΠ² ΡΠ»Π΅ΠΊΡΡΠΎΠΈΡΠΊΡΠΎΠ²ΡΠΌ ΡΠΏΠΎΡΠΎΠ±ΠΎΠΌ Π½Π° ΡΠ²ΠΎΠΉΡΡΠ²Π΅ ΡΠ»Π΅ΠΊΡΡΠΈΡΠ΅ΡΠΊΠΎΠ³ΠΎ ΡΠΎΠΊΠ° ΠΏΠ΅ΡΠ΅Π½ΠΎΡΠΈΡΡ Π²Π΅ΡΠ΅ΡΡΠ²ΠΎ ΠΏΡΠΈ ΠΏΡΠΎΠ±ΠΎΠ΅. ΠΡΠΈ Π²ΡΡΠΎΠΊΠΎΠΌ Π½Π°ΠΏΡΡΠΆΠ΅Π½ΠΈΠΈ ΠΈ ΡΠΈΠ»Π΅ ΠΏΠΎΡΡΠΎΡΠ½Π½ΠΎΠ³ΠΎ ΡΠΎΠΊΠ° (1-60 Π) Π°Π½ΠΎΠ΄ (ΠΏΠΎΠ»ΠΎΠΆΠΈΡΠ΅Π»ΡΠ½ΠΎ Π·Π°ΡΡΠΆΠ΅Π½Π½ΡΠΉ ΡΠ»Π΅ΠΊΡΡΠΎΠ΄) Π½Π°Π³ΡΠ΅Π²Π°Π΅ΡΡΡ Π΄ΠΎ Π²ΡΡΠΎΠΊΠΎΠΉ ΡΠ΅ΠΌΠΏΠ΅ΡΠ°ΡΡΡΡ Π² ΠΏΡΠ΅Π΄Π΅Π»Π°Ρ 10-15 ΡΡΡΡΡ Π³ΡΠ°Π΄ΡΡΠΎΠ² Π¦Π΅Π»ΡΡΠΈΡ, ΡΠ°ΡΠΏΠ»Π°Π²Π»ΡΠ΅ΡΡΡ, ΠΈΠΎΠ½ΠΈΠ·ΠΈΡΡΠ΅ΡΡΡ ΠΈ ΡΡΡΡΠ΅ΠΌΠ»ΡΠ΅ΡΡΡ ΠΊ ΠΊΠ°ΡΠΎΠ΄Ρ. Π’Π°ΠΌ, Π² ΡΠΈΠ»Ρ ΡΠ»Π΅ΠΊΡΡΠΈΡΠ΅ΡΠΊΠΈΡ Π²Π·Π°ΠΈΠΌΠΎΠ΄Π΅ΠΉΡΡΠ²ΠΈΠΉ ΠΎΠ½ ΠΎΡΠ°ΠΆΠΈΠ²Π°Π΅ΡΡΡ.
Π§ΡΠΎΠ±Ρ Π² ΠΏΡΠΎΡΠ΅ΡΡΠ΅ ΡΠ°Π±ΠΎΡΡ Π½Π΅ Π²ΠΎΠ·Π½ΠΈΠΊΠ°Π»Π° ΠΏΠΎΠ»Π½ΠΎΡΠ΅Π½Π½Π°Ρ ΡΠ»Π΅ΠΊΡΡΠΈΡΠ΅ΡΠΊΠ°Ρ Π΄ΡΠ³Π°, ΡΠ»Π΅ΠΊΡΡΠΎΠ΄Ρ ΡΠ±Π»ΠΈΠΆΠ°ΡΡΡΡ ΡΠΎΠ»ΡΠΊΠΎ Π½Π° ΠΊΠΎΡΠΎΡΠΊΠΈΠ΅ ΠΌΠ³Π½ΠΎΠ²Π΅Π½ΠΈΡ, Π΄Π»ΡΡΠΈΠ΅ΡΡ Π΄ΠΎΠ»ΠΈ ΡΠ΅ΠΊΡΠ½Π΄Π°. ΠΠ° ΡΡΠΎ Π²ΡΠ΅ΠΌΡ Π²ΠΎΠ·Π½ΠΈΠΊΠ°Π΅Ρ ΠΈΡΠΊΡΠ°, ΡΠ°Π·ΡΡΡΠ°ΡΡΠ°Ρ Π°Π½ΠΎΠ΄ ΠΈ Π½Π°ΡΠ°ΡΠΈΠ²Π°ΡΡΠ°Ρ ΠΊΠ°ΡΠΎΠ΄. ΠΠ±ΡΠ°Π±Π°ΡΡΠ²Π°Π΅ΠΌΡΠΉ ΡΡΠ°ΡΡΠΎΠΊ ΠΏΠΎΠ΄Π²Π΅ΡΠ³Π°Π΅ΡΡΡ Π½Π°Π³ΡΠ΅Π²Ρ ΠΈ Π²ΠΎΠ·Π΄Π΅ΠΉΡΡΠ²ΠΈΡ ΡΠ»Π΅ΠΊΡΡΠΎΡΠΎΠΊΠ° Π½Π° ΠΏΡΠΎΡΡΠΆΠ΅Π½ΠΈΠΈ ΠΌΠΈΠ»Π»ΠΈΡΠ΅ΠΊΡΠ½Π΄, ΠΏΡΠΈ ΡΡΠΎΠΌ ΡΠΎΡΠ΅Π΄Π½ΠΈΠ΅ ΠΎΠ±Π»Π°ΡΡΠΈ ΠΈ Π»Π΅ΠΆΠ°ΡΠΈΠΉ Π½ΠΈΠΆΠ΅ ΡΠ»ΠΎΠΉ Π½Π΅ ΡΡΠΏΠ΅Π²Π°ΡΡ ΠΏΡΠΎΠ³ΡΠ΅ΡΡΡΡ ΠΈ ΡΡΡΡΠΊΡΡΡΠ° ΠΈΡ Π½Π΅ Π½Π°ΡΡΡΠ°Π΅ΡΡΡ. ΠΡΠΎΠ±Π»Π΅ΠΌΠ° ΠΏΠΎΠ³ΡΠ°Π½ΠΈΡΠ½ΡΡ ΡΠΎΡΡΠΎΡΠ½ΠΈΠΉ Π½Π΅ Π²ΠΎΠ·Π½ΠΈΠΊΠ°Π΅Ρ Π² ΠΏΡΠΈΠ½ΡΠΈΠΏΠ΅.
ΠΡΠ»ΠΈ ΡΡΠ΅Π±ΡΠ΅ΡΡΡ ΡΠ΅Π·ΠΊΠ° ΠΈΠ»ΠΈ ΡΠ²Π΅ΡΠ»Π΅Π½ΠΈΠ΅ β ΠΊΠ°ΡΠΎΠ΄ΠΎΠΌ ΡΠ»ΡΠΆΠΈΡ ΡΠ°Π±ΠΎΡΠΈΠΉ ΠΈΠ½ΡΡΡΡΠΌΠ΅Π½Ρ, Π° Π°Π½ΠΎΠ΄ΠΎΠΌ β ΠΎΠ±ΡΠ°Π±Π°ΡΡΠ²Π°Π΅ΠΌΠ°Ρ Π΄Π΅ΡΠ°Π»Ρ. ΠΡΠΈ Π½Π°ΡΠ°ΡΠΈΠ²Π°Π½ΠΈΠΈ, ΡΠΊΡΠ΅ΠΏΠ»Π΅Π½ΠΈΠΈ ΠΏΠΎΠ²Π΅ΡΡ Π½ΠΎΡΡΠΈ ΠΈΠ»ΠΈ Π²ΠΎΡΡΡΠ°Π½ΠΎΠ²Π»Π΅Π½ΠΈΠΈ ΡΠΎΡΠΌΡ Π΄Π΅ΡΠ°Π»ΠΈ, ΠΎΠ½ΠΈ ΠΌΠ΅Π½ΡΡΡΡΡ ΠΌΠ΅ΡΡΠ°ΠΌΠΈ. ΠΠ»Ρ ΡΡΠΈΡ Π²ΠΈΠ΄ΠΎΠ² ΠΎΠ±ΡΠ°Π±ΠΎΡΠΊΠΈ ΡΠΎΠ·Π΄Π°Π½Ρ ΡΠΏΠ΅ΡΠΈΠ°Π»ΡΠ½ΡΠ΅ ΡΡΠ°Π½ΠΊΠΈ, ΠΊΠ°ΠΆΠ΄ΡΠΉ ΠΈΠ· ΠΊΠΎΡΠΎΡΡΡ Π²ΡΠΏΠΎΠ»Π½ΡΠ΅Ρ ΡΠ²ΠΎΠΈ ΠΎΠΏΠ΅ΡΠ°ΡΠΈΠΈ.
ΠΠ½ΡΡΡΡΠΌΠ΅Π½ΡΠΎΠΌ Π² ΡΡΡΠ°Π½ΠΎΠ²ΠΊΠ°Ρ ΡΠ»Π΅ΠΊΡΡΠΎΡΡΠΎΠ·ΠΈΠΎΠ½Π½ΠΎΠ³ΠΎ Π΄Π΅ΠΉΡΡΠ²ΠΈΡ ΡΠ»ΡΠΆΠ°Ρ Π»Π°ΡΡΠ½Π½ΡΠ΅ ΠΈΠ»ΠΈ ΠΌΠ΅Π΄Π½ΠΎ-Π³ΡΠ°ΡΠΈΡΠ½ΡΠ΅ ΡΠ»Π΅ΠΊΡΡΠΎΠ΄Ρ, Ρ ΠΎΡΠΎΡΠΎ ΠΏΡΠΎΠ²ΠΎΠ΄ΡΡΠΈΠ΅ ΡΠΎΠΊ ΠΈ Π½Π΅Π΄ΠΎΡΠΎΠ³ΠΈΠ΅ Π² ΠΈΠ·Π³ΠΎΡΠΎΠ²Π»Π΅Π½ΠΈΠΈ. Π‘ ΠΈΡ ΠΏΠΎΠΌΠΎΡΡΡ ΠΌΠΎΠΆΠ½ΠΎ ΡΠ΅Π·Π°ΡΡ ΠΈ ΡΠ²Π΅ΡΠ»ΠΈΡΡ ΡΠ°ΠΌΡΠ΅ ΡΠ²Π΅ΡΠ΄ΡΠ΅ ΡΠΏΠ»Π°Π²Ρ. Π§ΡΠΎΠ±Ρ ΠΌΠ΅ΡΠ°Π»Π» ΠΊΠ°ΡΠΎΠ΄Π° Π½Π΅ ΠΎΡΠ΅Π΄Π°Π» Π½Π° ΡΠ»Π΅ΠΊΡΡΠΎΠ΄Π΅ ΠΈ Π½Π΅ ΡΠ²Π΅Π»ΠΈΡΠΈΠ²Π°Π» Π΅Π³ΠΎ ΡΠ°Π·ΠΌΠ΅ΡΠ°, ΠΏΡΠΎΡΠ΅ΡΡ ΠΏΡΠΎΠΈΡΡ ΠΎΠ΄ΠΈΡ Π² ΠΆΠΈΠ΄ΠΊΠΎΠΉ ΡΡΠ΅Π΄Π΅ β ΠΆΠΈΠ΄ΠΊΠΎΡΡΡ ΠΎΡ Π»Π°ΠΆΠ΄Π°Π΅Ρ ΠΊΠ°ΠΏΠ»ΠΈ ΡΠ°ΡΠΏΠ»Π°Π²Π°, ΠΈ ΠΎΠ½ Π½Π΅ ΠΌΠΎΠΆΠ΅Ρ ΠΎΡΠ΅ΡΡΡ Π½Π° ΡΠ»Π΅ΠΊΡΡΠΎΠ΄Π΅, Π΄Π°ΠΆΠ΅ Π΅ΡΠ»ΠΈ ΠΈ Π΄ΠΎΡΡΠΈΠ³Π°Π΅Ρ Π΅Π³ΠΎ. ΠΡΠ·ΠΊΠΎΡΡΡ ΠΆΠΈΠ΄ΠΊΠΎΡΡΠΈ ΠΎΠΏΡΠ΅Π΄Π΅Π»ΡΠ΅Ρ ΡΠΊΠΎΡΠΎΡΡΡ Π΄Π²ΠΈΠΆΠ΅Π½ΠΈΡ ΠΌΠ°ΡΠ΅ΡΠΈΠ°Π»ΡΠ½ΡΡ ΡΠ°ΡΡΠΈΡ, ΠΈ ΠΎΠ½ΠΈ Π½Π΅ ΡΡΠΏΠ΅Π²Π°ΡΡ Π·Π° ΡΠΎΠΊΠΎΠΌ. ΠΠ΅ΡΠ°Π»Π» ΠΎΡΠ΅Π΄Π°Π΅Ρ Π² Π²Π°Π½Π½Π΅ Π² Π²ΠΈΠ΄Π΅ ΠΎΡΠ°Π΄ΠΊΠ° ΠΈ Π½Π΅ ΠΌΠ΅ΡΠ°Π΅Ρ Π΄Π°Π»ΡΠ½Π΅ΠΉΡΠ΅ΠΌΡ ΠΏΡΠΎΡ ΠΎΠΆΠ΄Π΅Π½ΠΈΡ ΡΠΎΠΊΠ°.
ΠΡΠΈ Π½Π°ΡΠ°ΡΠΈΠ²Π°Π½ΠΈΠΈ ΠΏΠΎΠ²Π΅ΡΡ Π½ΠΎΡΡΠΈ Π΄Π΅ΡΠ°Π»Π΅ΠΉ ΠΈΠ»ΠΈ ΡΠΊΡΠ΅ΠΏΠ»Π΅Π½ΠΈΠΈ, ΠΌΠ΅ΡΠ°Π»Π» Ρ Π°Π½ΠΎΠ΄Π° ΠΏΠ΅ΡΠ΅Π½ΠΎΡΠΈΡΡΡ Π½Π° ΠΊΠ°ΡΠΎΠ΄. Π ΡΡΠΎΠΌ ΡΠ»ΡΡΠ°Π΅ Π½Π° Π²ΠΈΠ±ΡΠ°ΡΠΈΠΎΠ½Π½ΠΎΠΉ ΡΡΡΠ°Π½ΠΎΠ²ΠΊΠ΅ Π·Π°ΠΊΡΠ΅ΠΏΠ»ΡΠ΅ΡΡΡ ΠΏΠΎΠ»ΠΎΠΆΠΈΡΠ΅Π»ΡΠ½ΡΠΉ ΡΠ»Π΅ΠΊΡΡΠΎΠ΄, ΡΠ»ΡΠΆΠ°ΡΠΈΠΉ Π΄ΠΎΠ½ΠΎΡΠΎΠΌ ΠΌΠ΅ΡΠ°Π»Π»Π°, Π° Π΄Π΅ΡΠ°Π»Ρ ΠΏΡΠΈΡΠΎΠ΅Π΄ΠΈΠ½ΡΠ΅ΡΡΡ ΠΊ ΠΎΡΡΠΈΡΠ°ΡΠ΅Π»ΡΠ½ΠΎΠΌΡ ΠΏΠΎΠ»ΡΡΡ. ΠΠΎΠ΄Π° ΠΈΠ»ΠΈ ΠΌΠ°ΡΠ»ΠΎ Π² ΡΡΠΎΠΌ ΠΏΡΠΎΡΠ΅ΡΡΠ΅ Π½Π΅ ΠΈΡΠΏΠΎΠ»ΡΠ·ΡΡΡΡΡ, Π²ΡΠ΅ ΠΏΡΠΎΠΈΡΡ ΠΎΠ΄ΠΈΡ Π² Π²ΠΎΠ·Π΄ΡΡ Π΅.
Π’Π΅Ρ Π½ΠΎΠ»ΠΎΠ³ΠΈΡΠ΅ΡΠΊΠΈΠ΅ ΠΏΠΎΠΊΠ°Π·Π°ΡΠ΅Π»ΠΈ
ΠΠ»Π΅ΠΊΡΡΠΎΠΈΡΠΊΡΠΎΠ²Π°Ρ ΡΡΡΠ°Π½ΠΎΠ²ΠΊΠ°, Π² Π·Π°Π²ΠΈΡΠΈΠΌΠΎΡΠΈ ΠΎΡ ΡΠ΅ΠΆΠΈΠΌΠ° ΡΠΎΠ±ΠΎΡΡ, ΠΌΠΎΠΆΠ΅Ρ ΠΎΠ±Π΅ΡΠΏΠ΅ΡΠΈΠ²Π°ΡΡ ΡΠΎΡΠ½ΠΎΡΡΡ ΡΠ΅Π·ΡΠ»ΡΡΠ°ΡΠ° Π² ΡΠΈΡΠΎΠΊΠΈΡ ΠΏΡΠ΅Π΄Π΅Π»Π°Ρ . ΠΡΠ»ΠΈ ΡΡΠ΅Π±ΡΠ΅ΡΡΡ Π²ΡΡΠΎΠΊΠ°Ρ ΠΏΡΠΎΠΈΠ·Π²ΠΎΠ΄ΠΈΡΠ΅Π»ΡΠ½ΠΎΡΡΡ ΠΏΡΠΈ ΠΎΡΠ½ΠΎΡΠΈΡΠ΅Π»ΡΠ½ΠΎ Π½Π΅Π²ΡΡΠΎΠΊΠΈΡ ΡΡΠ΅Π±ΠΎΠ²Π°Π½ΠΈΡΡ ΠΊ ΡΠΎΡΡΠΎΡΠ½ΠΈΡ ΠΏΠΎΠ²Π΅ΡΡ Π½ΠΎΡΡΠΈ (I ΠΈ II ΠΊΠ»Π°ΡΡ), ΡΠΎ ΠΈΡΠΏΠΎΠ»ΡΠ·ΡΡΡΡΡ ΡΠΎΠΊΠΈ 10-60 Π ΠΏΡΠΈ Π½Π°ΠΏΡΡΠΆΠ΅Π½ΠΈΠΈ Π΄ΠΎ 220Π. Π ΡΡΠΎΠΌ ΡΠ»ΡΡΠ°Π΅ ΡΠ»Π΅ΠΊΡΡΠΎΠΈΡΠΊΡΠΎΠ²Π°Ρ ΡΡΠΎΠ·ΠΈΡ ΠΌΠΎΠΆΠ΅Ρ ΡΠ΄Π°Π»ΠΈΡΡ ΠΈΠ· Π·ΠΎΠ½Ρ ΡΠ΅Π·Π° ΠΈΠ»ΠΈ ΡΠ²Π΅ΡΠ»Π΅Π½ΠΈΡ ΠΌΠ΅ΡΠ°Π»Π» Π² ΠΎΠ±ΡΠ΅ΠΌΠ΅ Π΄ΠΎ 300 ΠΌΠΌ3/ΠΌΠΈΠ½. ΠΡΠΈ Π±ΠΎΠ»Π΅Π΅ Π²ΡΡΠΎΠΊΠΈΡ ΠΏΠΎΠΊΠ°Π·Π°ΡΠ΅Π»ΡΡ ΠΊΠ»Π°ΡΡΠ° ΡΠΎΡΠ½ΠΎΡΡΠΈ β VI ΠΈ VII, ΠΏΡΠΎΠΈΠ·Π²ΠΎΠ΄ΠΈΡΠ΅Π»ΡΠ½ΠΎΡΡΡ ΡΠ½ΠΈΠΆΠ°Π΅ΡΡΡ Π΄ΠΎ 20-30 ΠΌΠΌ3/ΠΌΠΈΠ½, Π½ΠΎ ΠΈ ΡΠΎΠΊΠΈ ΡΡΠ΅Π±ΡΡΡΡΡ ΠΏΠΎΠΌΠ΅Π½ΡΡΠ΅, Π½Π΅ Π±ΠΎΠ»Π΅Π΅ 1 Π ΠΏΡΠΈ Π½Π°ΠΏΡΡΠΆΠ΅Π½ΠΈΠΈ Π΄ΠΎ 40 Π.
Π’Π°ΠΊΠΎΠΉ ΡΠΈΡΠΎΠΊΠΈΠΉ Π΄ΠΈΠ°ΠΏΠ°Π·ΠΎΠ½ ΡΠ΅Π³ΡΠ»ΠΈΡΠΎΠ²ΠΎΠΊ ΠΏΠΎΠΊΠ°Π·ΡΠ²Π°Π΅Ρ, ΡΡΠΎ ΡΠ»Π΅ΠΊΡΡΠΎΠΈΡΠΊΡΠΎΠ²Π°Ρ ΠΎΠ±ΡΠ°Π±ΠΎΡΠΊΠ° ΠΌΠ΅ΡΠ°Π»Π»Π° ΠΌΠΎΠΆΠ΅Ρ ΠΈΡΠΏΠΎΠ»ΡΠ·ΠΎΠ²Π°ΡΡΡΡ Π² ΡΠ°Π·Π»ΠΈΡΠ½ΡΡ ΠΎΠ±Π»Π°ΡΡΡΡ , ΠΊΠ°ΠΊ Π΄Π»Ρ ΠΏΡΠΎΠΈΠ·Π²ΠΎΠ΄ΡΡΠ²Π° ΠΊΡΡΠΏΠ½ΡΡ ΡΠ΅ΡΠΈΠΉ Π΄Π΅ΡΠ°Π»Π΅ΠΉ, ΡΠ°ΠΊ ΠΈ Π΄Π»Ρ ΡΠ°Π·ΠΎΠ²ΡΡ ΡΠ°Π±ΠΎΡ, Π²ΠΊΠ»ΡΡΠ°Ρ ΡΠ²Π΅Π»ΠΈΡΠ½ΡΠ΅.
ΠΡΠΎΠ±Π΅Π½Π½ΠΎΡΡΡΡ ΠΏΡΠΈΠΌΠ΅Π½Π΅Π½ΠΈΡ ΡΠ»Π΅ΠΊΡΡΠΎΠΈΡΠΊΡΠΎΠ²ΡΡ ΡΡΡΠ°Π½ΠΎΠ²ΠΎΠΊ ΠΌΠΎΠΆΠ½ΠΎ ΡΡΠΈΡΠ°ΡΡ Π²ΠΎΠ·ΠΌΠΎΠΆΠ½ΠΎΡΡΡ ΡΠΊΡΠ΅ΠΏΠ»Π΅Π½ΠΈΡ Π΄Π΅ΡΠ°Π»Π΅ΠΉ ΡΠ°Π·Π»ΠΈΡΠ½ΠΎΠΉ ΠΊΠΎΠ½ΡΠΈΠ³ΡΡΠ°ΡΠΈΠΈ. ΠΠ° ΠΏΠΎΠ²Π΅ΡΡ Π½ΠΎΡΡΡ Π·Π°Π³ΠΎΡΠΎΠ²ΠΊΠΈ Π½Π°Π½ΠΎΡΠΈΡΡΡΡ ΡΠΎΠ½ΡΠ°ΠΉΡΠΈΠΉ ΡΠ»ΠΎΠΉ Π±ΠΎΠ»Π΅Π΅ ΠΏΡΠΎΡΠ½ΠΎΠ³ΠΎ ΡΠΏΠ»Π°Π²Π° ΠΈΠ»ΠΈ ΠΌΠ΅ΡΠ°Π»Π»Π° Π±Π΅Π· Π½Π°Π³ΡΠ΅Π²Π° ΠΎΡΠ½ΠΎΠ²Π°Π½ΠΈΡ Π½Π° Π±ΠΎΠ»ΡΡΡΡ Π³Π»ΡΠ±ΠΈΠ½Ρ. ΠΡΠΎ ΠΏΠΎΠ·Π²ΠΎΠ»ΡΠ΅Ρ ΡΠΎΡ ΡΠ°Π½ΠΈΡΡ ΡΡΡΡΠΊΡΡΡΡ ΠΌΠ΅ΡΠ°Π»Π»Π° Π±Π°Π·ΠΎΠ²ΠΎΠ³ΠΎ ΠΈΠ·Π΄Π΅Π»ΠΈΡ ΠΈ Π·Π½Π°ΡΠΈΡΠ΅Π»ΡΠ½ΠΎ ΠΈΠ·ΠΌΠ΅Π½ΠΈΡΡ ΡΠ²ΠΎΠΉΡΡΠ²Π° Π΅Π³ΠΎ ΠΏΠΎΠ²Π΅ΡΡ Π½ΠΎΡΡΠΈ. Π Π½Π΅ΠΊΠΎΡΠΎΡΡΡ ΡΠ»ΡΡΠ°ΡΡ ΡΡΠ΅Π±ΡΠ΅ΡΡΡ Π²ΡΠ·ΠΊΠΎΡΡΡ ΠΎΡΠ½ΠΎΠ²Π°Π½ΠΈΡ ΠΈ Π²ΡΡΠΎΠΊΠ°Ρ ΡΠ²Π΅ΡΠ΄ΠΎΡΡΡ ΠΏΠΎΠ²Π΅ΡΡ Π½ΠΎΡΡΠΈ, ΠΈΠ»ΠΈ Π² ΠΎΠ±ΡΠ°ΡΠ½ΠΎΠΌ ΠΏΠΎΡΡΠ΄ΠΊΠ΅. Π Π΅ΡΠΈΡΡ ΡΡΡ Π·Π°Π΄Π°ΡΡ ΠΌΠΎΠΆΠ΅Ρ ΡΠΎΠ»ΡΠΊΠΎ ΡΠ»Π΅ΠΊΡΡΠΎΠΈΡΠΊΡΠΎΠ²ΠΎΠΉ ΡΡΠ°Π½ΠΎΠΊ.
Π‘Ρ Π΅ΠΌΠ° ΡΠ»Π΅ΠΊΡΡΠΎΠΈΡΠΊΡΠΎΠ²ΠΎΠ³ΠΎ ΡΡΠ°Π½ΠΊΠ°
ΠΠ±ΡΠ°Π±ΠΎΡΠΊΠΈ ΠΌΠ΅ΡΠ°Π»Π»ΠΎΠ² ΡΠ»Π΅ΠΊΡΡΠΎΠΈΡΠΊΡΠΎΠ²ΡΠΌ ΡΠΏΠΎΡΠΎΠ±ΠΎΠΌ ΠΎΡΠ΅Π½Ρ ΡΠ°ΡΠΏΡΠΎΡΡΡΠ°Π½Π΅Π½Π°, ΠΏΠΎΡΡΠΎΠΌΡ ΠΎΡΠ΅Π½Ρ ΡΠ»ΠΎΠΆΠ½ΠΎ ΡΠ°ΡΡΠΌΠΎΡΡΠ΅ΡΡ Π²ΡΠ΅ Π²ΠΈΠ΄Ρ ΠΎΠ±ΠΎΡΡΠ΄ΠΎΠ²Π°Π½ΠΈΡ ΠΈ ΠΌΠΎΠ΄Π΅Π»ΠΈ ΠΊΠΎΠ½ΠΊΡΠ΅ΡΠ½ΡΡ ΡΡΡΠ°Π½ΠΎΠ²ΠΎΠΊ. ΠΠ½ΠΈ Π²ΡΠ΅ ΠΎΠ±ΡΠ΅Π΄ΠΈΠ½Π΅Π½Ρ ΠΎΠ±ΡΠΈΠΌΠΈ ΠΊΠΎΠ½ΡΡΡΡΠΊΡΠΈΠ²Π½ΡΠΌΠΈ ΡΠ»Π΅ΠΌΠ΅Π½ΡΠ°ΠΌΠΈ:
- ΠΈΡΡΠΎΡΠ½ΠΈΠΊΠΎΠΌ ΠΏΠΎΡΡΠΎΡΠ½Π½ΠΎΠ³ΠΎ ΡΠΎΠΊΠ°;
- ΠΊΠΎΠ½Π΄Π΅Π½ΡΠ°ΡΠΎΡΠΎΠΌ;
- Π²ΠΈΠ±ΡΠ°ΡΠΎΡΠΎΠΌ;
- ΠΏΠ΅ΡΠ΅ΠΊΠ»ΡΡΠ°ΡΠ΅Π»Π΅ΠΌ ΡΠ΅ΠΆΠΈΠΌΠΎΠ².
ΠΠΎΠ½ΡΡΡΡΠΊΡΠΈΡ, ΡΠ°Π±ΠΎΡΠ°ΡΡΠ°Ρ Π² ΡΠ»Π΅ΠΊΡΡΠΎΠΈΡΠΊΡΠΎΠ²ΠΎΠΌ ΡΠ΅ΠΆΠΈΠΌΠ΅, ΠΌΠΎΠΆΠ΅Ρ ΠΎΡΠ»ΠΈΡΠ°ΡΡΡΡ ΡΡΠ΄ΠΎΠΌ Ρ Π°ΡΠ°ΠΊΡΠ΅ΡΠΈΡΡΠΈΠΊ, Π΄ΠΎΠΏΡΡΠΊΠ°ΡΡΠΈΡ ΡΠ°Π±ΠΎΡΡ Ρ ΡΠ΅ΠΌ ΠΈΠ»ΠΈ ΠΈΠ½ΡΠΌ ΠΌΠ°ΡΠ΅ΡΠΈΠ°Π»ΠΎΠΌ, Π½ΠΎ ΠΎΠ±ΡΠΈΠ΅ ΠΏΡΠΈΠ½ΡΠΈΠΏΡ ΠΏΠΎΡΡΡΠΎΠ΅Π½ΠΈΡ ΡΠ°Π±ΠΎΡΠ΅ΠΉ ΡΡ Π΅ΠΌΡ ΠΎΠ΄ΠΈΠ½Π°ΠΊΠΎΠ²Ρ.
ΠΠ°ΡΠ°ΡΠ΅Ρ ΠΊΠΎΠ½Π΄Π΅Π½ΡΠ°ΡΠΎΡΠΎΠ² ΡΠΎΠ³Π»Π°ΡΠΎΠ²Π°Π½Π° Ρ ΠΌΠ΅Ρ Π°Π½ΠΈΡΠ΅ΡΠΊΠΈΠΌ Π΄Π²ΠΈΠΆΠ΅Π½ΠΈΠ΅ΠΌ ΡΠ»Π΅ΠΊΡΡΠΎΠ΄Π°, ΡΠ°Π·ΡΡΠ΄ ΠΏΡΠΎΠΈΡΡ ΠΎΠ΄ΠΈΡ Π² ΠΌΠΎΠΌΠ΅Π½Ρ ΠΌΠ°ΠΊΡΠΈΠΌΠ°Π»ΡΠ½ΠΎΠ³ΠΎ ΡΠ±Π»ΠΈΠΆΠ΅Π½ΠΈΡ ΡΠ°Π±ΠΎΡΠΈΡ ΠΏΠΎΠ²Π΅ΡΡ Π½ΠΎΡΡΠ΅ΠΉ. Π Π΅Π»Π°ΠΊΡΠ°ΡΠΈΠΎΠ½Π½ΡΠ΅ Π³Π΅Π½Π΅ΡΠ°ΡΠΎΡΡ ΠΈΠΌΠΏΡΠ»ΡΡΠΎΠ² ΠΎΠΏΡΠ΅Π΄Π΅Π»ΡΡΡ ΠΌΠ°ΠΊΡΠΈΠΌΠ°Π»ΡΠ½ΡΠΉ Π·Π°ΡΡΠ΄ ΠΊΠΎΠ½Π΄Π΅Π½ΡΠ°ΡΠΎΡΠ° ΠΏΡΠΈ ΠΌΠ°ΠΊΡΠΈΠΌΠ°Π»ΡΠ½ΠΎΠΉ Π°ΠΌΠΏΠ»ΠΈΡΡΠ΄Π΅ ΠΎΡΠΊΠ»ΠΎΠ½Π΅Π½ΠΈΡ ΠΎΡ ΡΠΎΡΠΊΠΈ ΡΠ±Π»ΠΈΠΆΠ΅Π½ΠΈΡ. ΠΠΎΡΠ»Π΅ ΠΈΡΠΊΡΠΎΠ²ΠΎΠ³ΠΎ ΡΠ°Π·ΡΡΠ΄Π° ΠΊΠΎΠ½Π΄Π΅Π½ΡΠ°ΡΠΎΡ ΡΡΠΏΠ΅Π²Π°Π΅Ρ Π·Π°ΡΡΠ΄ΠΈΡΡΡΡ Π² ΠΏΠΎΠ»Π½ΠΎΠΌ ΠΎΠ±ΡΠ΅ΠΌΠ΅.
ΠΡΠ»ΠΈΡΠΈΠ΅ ΡΠ»Π΅ΠΊΡΡΠΎΠΈΡΠΊΡΠΎΠ²ΠΎΠΉ ΡΡΠΎΠ·ΠΈΠΈ ΠΎΡ Π΄ΡΠ³ΠΎΠ²ΠΎΠΉ ΡΠ²Π°ΡΠΊΠΈ ΠΈ ΡΠ΅Π·ΠΊΠΈ
ΠΡΠΏΠΎΠ»ΡΠ·ΠΎΠ²Π°Π½ΠΈΠ΅ ΠΈΠΌΠΏΡΠ»ΡΡΠ½ΠΎΠ³ΠΎ Π²ΠΎΠ·Π΄Π΅ΠΉΡΡΠ²ΠΈΡ ΡΠ»Π΅ΠΊΡΡΠΈΡΠ΅ΡΠΊΠΎΠ³ΠΎ ΡΠΎΠΊΠ° ΠΎΡΠ»ΠΈΡΠ°Π΅ΡΡΡ ΠΎΡ Π²ΠΎΠ·Π΄Π΅ΠΉΡΡΠ²ΠΈΡ Π΄ΡΠ³ΠΈ. ΠΠΌΠΏΡΠ»ΡΡ ΡΠ°Π±ΠΎΡΠ°Π΅Ρ Π² ΠΎΡΠ΅Π½Ρ ΠΎΠ³ΡΠ°Π½ΠΈΡΠ΅Π½Π½ΠΎΠΌ ΠΏΡΠΎΡΡΡΠ°Π½ΡΡΠ²Π΅, Π½Π΅ ΡΡΠΏΠ΅Π²Π°Ρ ΠΏΡΠΎΠ³ΡΠ΅ΡΡ ΡΠΎΡΠ΅Π΄Π½ΠΈΠ΅ ΡΡΠ°ΡΡΠΊΠΈ. ΠΠ°ΠΆΠ΅ Π½Π° ΡΠ°ΠΌΡΡ ΡΠ»ΠΎΠΆΠ½ΡΡ Π² ΠΏΠ»Π°Π½Π΅ ΡΠ΅ΡΠΌΠΈΡΠ΅ΡΠΊΠΎΠ³ΠΎ ΠΎΠΊΠΈΡΠ»Π΅Π½ΠΈΡ ΡΠΏΠ»Π°Π²Π°Ρ ΠΈΠ½Π΅ΡΡΠ½Π°Ρ Π°ΡΠΌΠΎΡΡΠ΅ΡΠ° Π½Π΅ ΠΏΠΎΡΡΠ΅Π±ΡΠ΅ΡΡΡ β Π²Π·Π°ΠΈΠΌΠΎΠ΄Π΅ΠΉΡΡΠ²ΠΈΠ΅ ΠΏΡΠΎΠΈΡΡ ΠΎΠ΄ΠΈΡ Π½Π° ΠΏΠ»ΠΎΡΠ°Π΄ΡΡ Π½Π΅ Π±ΠΎΠ»Π΅Π΅ 0,05-1 ΠΌΠΌ2 ΠΏΡΠΈ Π³Π»ΡΠ±ΠΈΠ½Π΅ Π²ΠΎΠ·Π΄Π΅ΠΉΡΡΠ²ΠΈΡ 0,05-0,3 ΠΌΠΌ. ΠΠ°ΠΆΠ΅ Π² ΡΠ°ΠΌΠΎΠΉ Π°Π³ΡΠ΅ΡΡΠΈΠ²Π½ΠΎΠΉ Π°ΡΠΌΠΎΡΡΠ΅ΡΠ΅ Π½Π΅ ΡΡΠΏΠ΅Π²Π°ΡΡ Π²ΠΎΠ·Π½ΠΈΠΊΠ½ΡΡΡ ΡΡΠ»ΠΎΠ²ΠΈΡ Π΄Π»Ρ Π°ΠΊΡΠΈΠ²Π½ΠΎΠ³ΠΎ ΠΎΠΊΠΈΡΠ»Π΅Π½ΠΈΡ.
ΠΠ»Π΅ΠΊΡΡΠΎΠΈΡΠΊΡΠΎΠ²ΠΎΠΉ ΡΡΠ°Π½ΠΎΠΊ ΡΠ²ΠΎΠΈΠΌΠΈ ΡΡΠΊΠ°ΠΌΠΈ
ΠΠ΄Π½ΠΎΠΉ ΠΈΠ· Π³Π»Π°Π²Π½ΡΡ Π΄Π΅ΡΠ°Π»Π΅ΠΉ ΡΠ»Π΅ΠΊΡΡΠΎΠΈΡΠΊΡΠΎΠ²ΠΎΠΉ ΡΡΡΠ°Π½ΠΎΠ²ΠΊΠΈ, ΠΊΠΎΡΠΎΡΡΡ ΠΌΠΎΠΆΠ½ΠΎ ΡΠ΅Π°Π»ΠΈΠ·ΠΎΠ²Π°ΡΡ ΡΠ²ΠΎΠΈΠΌΠΈ ΡΡΠΊΠ°ΠΌΠΈ, ΠΊΠΎΠ½Π΅ΡΠ½ΠΎ, ΠΏΡΠΈ ΡΠΎΠ±Π»ΡΠ΄Π΅Π½ΠΈΠΈ Π²ΡΠ΅Ρ ΠΏΡΠ°Π²ΠΈΠ» ΡΠ΅Ρ Π½ΠΈΠΊΠΈ Π±Π΅Π·ΠΎΠΏΠ°ΡΠ½ΠΎΡΡΠΈ, ΠΏΡΠΈΠ²Π΅Π΄Π΅Π½Π° Π½ΠΈΠΆΠ΅. Π‘Π»Π΅Π΄ΡΠ΅Ρ ΠΎΡΠΌΠ΅ΡΠΈΡΡ, ΡΡΠΎ ΡΡΠΎ ΡΠΎΠ»ΡΠΊΠΎ ΠΎΠ΄Π½Π° ΠΈΠ· ΠΌΠ½ΠΎΠ³ΠΈΡ ΡΡ Π΅ΠΌ, ΠΊΠΎΡΠΎΡΡΠ΅ ΠΌΠΎΠΆΠ½ΠΎ ΠΈΡΠΏΠΎΠ»ΡΠ·ΠΎΠ²Π°ΡΡ Π² ΠΊΠΎΠ½ΡΡΡΡΠΊΡΠΈΠΈ ΡΡΠ°Π½ΠΊΠ°.
ΠΡΠΈΠ΅Π½ΡΠΈΡΠΎΠ²ΠΎΡΠ½Π°Ρ ΡΡ Π΅ΠΌΠ° Π³Π΅Π½Π΅ΡΠ°ΡΠΎΡΠ° ΠΈΡΠΊΡΠΎΠ²ΡΡ ΡΠ°Π·ΡΡΠ΄ΠΎΠ²
Π Π°Π±ΠΎΡΠΈΠΉ ΡΡΠΎΠ» ΡΡΠ°Π½ΠΊΠ° Π΄ΠΎΠ»ΠΆΠ΅Π½ Π±ΡΡΡ ΠΎΠ±ΠΎΡΡΠ΄ΠΎΠ²Π°Π½ ΡΠΈΡΡΠ΅ΠΌΠΎΠΉ ΡΠ΄Π°Π»Π΅Π½ΠΈΡ ΠΎΠΊΠΈΡΠ»ΠΎΠ² (Π½Π΅ΠΏΡΠ΅ΡΡΠ²Π½ΠΎΠΉ ΠΏΠΎΠ΄Π°ΡΠ΅ΠΉ ΠΌΠ°ΡΠ»Π° ΠΈΠ»ΠΈ ΠΊΠ΅ΡΠΎΡΠΈΠ½Π°). ΠΠ½ΠΈ ΡΠ½ΠΈΠΆΠ°ΡΡ Π²Π΅ΡΠΎΡΡΠ½ΠΎΡΡΡ ΠΎΡΠ»ΠΎΠΆΠ΅Π½ΠΈΡ ΠΎΠΊΡΠΈΠ΄Π½ΠΎΠΉ ΠΏΠ»Π΅Π½ΠΊΠΈ Π½Π° ΠΏΠΎΠ²Π΅ΡΡ Π½ΠΎΡΡΠΈ Π΄Π΅ΡΠ°Π»ΠΈ ΠΈ, Π² ΡΠ΅Π·ΡΠ»ΡΡΠ°ΡΠ΅, ΠΏΡΠ΅ΠΊΡΠ°ΡΠ΅Π½ΠΈΡ ΠΈΡΠΊΡΠΎΠΎΠ±ΡΠ°Π·ΠΎΠ²Π°Π½ΠΈΡ. ΠΠ»Ρ ΠΏΡΠΎΠ±ΠΎΡ Π½Π΅ΠΎΠ±Ρ ΠΎΠ΄ΠΈΠΌ Π½Π°Π΄Π΅ΠΆΠ½ΡΠΉ ΡΠ»Π΅ΠΊΡΡΠΈΡΠ΅ΡΠΊΠΈΠΉ ΠΊΠΎΠ½ΡΠ°ΠΊΡ. ΠΠ°ΠΊ ΠΎΡΠ½ΠΎΠ²Π½ΠΎΠΉ Π²Π°ΡΠΈΠ°Π½Ρ ΠΌΠΎΠΆΠ½ΠΎ ΠΈΡΠΏΠΎΠ»ΡΠ·ΠΎΠ²Π°ΡΡ Π²Π°Π½Π½ΠΎΡΠΊΡ, Π·Π°ΠΏΠΎΠ»Π½Π΅Π½Π½ΡΡ ΠΆΠΈΠ΄ΠΊΠΎΡΡΡΡ.
ΠΠ»Π΅ΠΊΡΡΠΎΠ΄ ΠΏΡΠ΅Π΄ΡΡΠ°Π²Π»ΡΠ΅Ρ ΡΠΎΠ±ΠΎΠΉ Π»Π°ΡΡΠ½Π½ΡΡ ΠΈΠ»ΠΈ ΠΌΠ΅Π΄Π½ΡΡ ΠΏΡΠΎΠ²ΠΎΠ»ΠΎΡΠΊΡ ΡΡΠ΅Π±ΡΠ΅ΠΌΠΎΠ³ΠΎ Π΄ΠΈΠ°ΠΌΠ΅ΡΡΠ°, ΠΊΠΎΡΠΎΡΠ°Ρ Π·Π°ΠΊΡΠ΅ΠΏΠ»Π΅Π½Π° Π² Π·Π°ΠΆΠΈΠΌΠ΅. ΠΠ°ΠΆΠΈΠΌ, Π² ΡΠ²ΠΎΡ ΠΎΡΠ΅ΡΠ΅Π΄Ρ, ΠΏΡΠ΅Π΄ΡΡΠ°Π²Π»ΡΠ΅Ρ ΡΠΎΠ±ΠΎΠΉ Π΄Π΅ΡΠ°Π»Ρ Π²Π΅ΡΡΠΈΠΊΠ°Π»ΡΠ½ΠΎΠ³ΠΎ ΡΡΠΎΠΊΠ° ΠΊΡΠΈΠ²ΠΎΡΠΈΠΏΠ½ΠΎ-ΡΠ°ΡΡΠ½Π½ΠΎΠ³ΠΎ ΠΌΠ΅Ρ Π°Π½ΠΈΠ·ΠΌΠ°, ΠΊΠΎΡΠΎΡΡΠΉ ΠΏΡΠΈΠ²ΠΎΠ΄ΠΈΡΡΡ Π² Π΄Π²ΠΈΠΆΠ΅Π½ΠΈΠ΅ ΠΎΡ ΡΠ»Π΅ΠΊΡΡΠΎΠ΄Π²ΠΈΠ³Π°ΡΠ΅Π»Ρ. Π§Π°ΡΡΠΎΡΠ° Π²ΠΎΠ·Π²ΡΠ°ΡΠ½ΠΎ-ΠΏΠΎΡΡΡΠΏΠ°ΡΠ΅Π»ΡΠ½ΠΎΠ³ΠΎ Π΄Π²ΠΈΠΆΠ΅Π½ΠΈΡ ΡΠ»Π΅ΠΊΡΡΠΎΠ΄Π° Π²ΡΠ±ΠΈΡΠ°Π΅ΡΡΡ Π² Π·Π°Π²ΠΈΡΠΈΠΌΠΎΡΡΠΈ ΠΎΡ ΠΎΡΠΎΠ±Π΅Π½Π½ΠΎΡΡΠ΅ΠΉ ΠΎΠ±ΡΠ°Π±Π°ΡΡΠ²Π°Π΅ΠΌΠΎΠ³ΠΎ ΠΌΠ°ΡΠ΅ΡΠΈΠ°Π»Π°.
ΠΡΠ΅ ΡΠΎΠΊΠΎΠΏΡΠΎΠ²ΠΎΠ΄ΡΡΠΈΠ΅ Π΄Π΅ΡΠ°Π»ΠΈ ΠΈ ΠΊΠ°Π±Π΅Π»ΠΈ Π΄ΠΎΠ»ΠΆΠ½Ρ Π±ΡΡΡ ΠΊΠ°ΡΠ΅ΡΡΠ²Π΅Π½Π½ΠΎ ΠΈ Π½Π°Π΄Π΅ΠΆΠ½ΠΎ ΠΈΠ·ΠΎΠ»ΠΈΡΠΎΠ²Π°Π½Ρ, ΡΠ°ΠΌΠ° ΡΡΡΠ°Π½ΠΎΠ²ΠΊΠ° Π·Π°Π·Π΅ΠΌΠ»Π΅Π½Π°. ΠΠΎΡΠΌΠΎΡΡΠ΅ΡΡ, ΠΊΠ°ΠΊ ΡΠ°Π±ΠΎΡΠ°ΡΡ Π±ΡΡΠΎΠ²ΡΠ΅ ΡΠ°ΠΌΠΎΠ΄Π΅Π»ΡΠ½ΡΠ΅ ΡΡΡΠ°Π½ΠΎΠ²ΠΊΠΈ ΠΌΠΎΠΆΠ½ΠΎ Π½Π° Π²ΠΈΠ΄Π΅ΠΎ:
Π‘Π»Π΅Π΄ΡΠ΅Ρ ΠΎΡΠΌΠ΅ΡΠΈΡΡ, ΡΡΠΎ ΡΠ°ΠΌΠΎΠ΄Π΅Π»ΡΠ½ΡΠ΅ ΡΡΠ°Π½ΠΊΠΈ Π½ΠΈΠΊΠΎΠ³Π΄Π° Π½Π΅ ΡΡΠ°Π²Π½ΡΡΡΡΡ ΠΏΠΎ Π²ΠΎΠ·ΠΌΠΎΠΆΠ½ΠΎΡΡΡΠΌ Ρ ΠΏΡΠΎΠΌΡΡΠ»Π΅Π½Π½ΡΠΌΠΈ, Π½Π°ΠΏΡΠΈΠΌΠ΅Ρ ΡΠ΅ΡΠΈΠ΅ΠΉ ΠΠ Π’Π. ΠΠ»Ρ ΠΏΡΠΎΠΈΠ·Π²ΠΎΠ΄ΡΡΠ²Π° ΠΊΡΡΡΠ°ΡΠ½ΡΡ ΠΈΠ·Π΄Π΅Π»ΠΈΠΉ ΠΈΠ»ΠΈ ΠΈΡΠΏΠΎΠ»ΡΠ·ΠΎΠ²Π°Π½ΠΈΡ Π² ΠΊΠ°ΡΠ΅ΡΡΠ²Π΅ ΠΎΠ΄Π½ΠΎΠ³ΠΎ ΠΈΠ· Π²ΠΈΠ΄ΠΎΠ² Ρ ΠΎΠ±Π±ΠΈ, ΠΎΠ½ΠΈ, ΠΌΠΎΠΆΠ΅Ρ Π±ΡΡΡ ΠΈ ΠΏΡΠΈΠ³ΠΎΠ΄Π½Ρ, Π½ΠΎ Π΄Π»Ρ ΡΠ°Π±ΠΎΡΡ Π² ΠΌΠ°ΡΡΠ΅ΡΡΠΊΠΎΠΉ ΠΈΠ»ΠΈ ΡΠ»Π΅ΡΠ°ΡΠ½ΠΎΠΌ ΡΠ΅Ρ Π΅ Π½Π΅ Β«Π΄ΠΎΡΡΠ³ΠΈΠ²Π°ΡΡΒ». ΠΠ΅ Π³ΠΎΠ²ΠΎΡΡ ΡΠΆΠ΅ ΠΎ ΡΠΎΠΌ, ΡΡΠΎ ΡΠ»ΠΎΠΆΠ½ΠΎΡΡΡ ΡΠ»Π΅ΠΊΡΡΠΈΡΠ΅ΡΠΊΠΎΠΉ ΡΡ Π΅ΠΌΡ ΠΈ Π½Π΅ΠΎΠ±Ρ ΠΎΠ΄ΠΈΠΌΠΎΡΡΡ ΡΠΎΡΠ½ΠΎΠ³ΠΎ ΡΠΎΠ³Π»Π°ΡΠΎΠ²Π°Π½ΠΈΡ ΠΊΠΈΠ½Π΅ΠΌΠ°ΡΠΈΠΊΠΈ ΠΈ ΡΠ°Π·ΡΡΠ΄Π° ΠΊΠΎΠ½Π΄Π΅Π½ΡΠ°ΡΠΎΡΠ° Π΄Π΅Π»Π°ΡΡ ΠΈΡ ΠΎΡΠ΅Π½Ρ ΡΠ»ΠΎΠΆΠ½ΡΠΌΠΈ Π² ΡΠ΅Π³ΡΠ»ΠΈΡΠΎΠ²ΠΊΠ΅.
wikimetall.ru
ΠΠ»Π΅ΠΊΡΡΠΎΠΈΡΠΊΡΠΎΠ²ΠΎΠΉ ΡΡΠ°Π½ΠΎΠΊ.(Π³Π°ΡΠ°ΠΆΠ½ΡΠΉ) – ΠΠ°ΠΊΠΎΠ½ΡΠ΅Π½Π½ΡΠ΅ ΠΏΡΠΎΠ΅ΠΊΡΡ
Π‘Π»ΡΡΠ°ΠΉΠ½ΠΎ Π½Π° Π²ΡΠΎΡΡΠ΅ΡΠΌΠ΅ΡΠ΅ ΠΊΡΠΏΠΈΠ» ΠΏΠΎ ΡΠ΅Π½Π΅ ΠΌΠ΅ΡΠ°Π»ΠΎΠ»ΠΎΠΌΠ° Π²ΠΎΡ ΡΠ°ΠΊΠΎΠΉ ΡΡΠ°ΡΠΈΠ²ΡΠΈΠΊ.ΠΠ° ΡΠ°ΠΊ,ΠΏΠΎΠ½ΡΠ°Π²ΠΈΠ»ΡΡ ΠΎΠ½ ΠΌΠ½Π΅,Π΄ΠΎΠ»Π³ΠΎ ΡΡΠΎΡΠ» ΠΈ ΠΆΠ΄Π°Π» ΡΠ²ΠΎΠ΅Π³ΠΎ ΡΠ°ΡΠ°.ΠΡ ΠΈ Π²ΠΎΡ ΡΠΎΠ·ΡΠ΅Π»ΠΎ.
ΠΠ»Ρ Π½Π΅Π³ΠΎ ΠΏΡΠΈΠ³ΠΎΡΠΎΠ²ΠΈΠ» Π²ΠΎΡ ΡΠ°ΠΊΡΡ Π³ΠΎΠ»ΠΎΠ²ΠΊΡ.
Π―ΡΠΌΠΎ ΠΆΠ΅Π»Π΅Π·ΠΎ Π΄ΠΎ ΡΠ΅ΡΠ΅Π΄ΠΈΠ½Ρ,Π° Π²ΡΡΠ΅ ΡΠ΅ΠΊΡΡΠΎΠ»ΠΈΡ,Π² ΠΊΠΎΠ½ΡΠ΅ ΡΠ°ΠΉΠ±Π° ΠΏΠΎΠ΄ΠΏΡΡΠΆΡΠ½Π΅Π½Π½Π°Ρ Ρ Π΄Π²ΡΡ ΡΡΠΎΡΠΎΠ½. ΠΠ°ΡΠΊΠ°Ρ ΠΊΠ°ΡΡΡΠΊΠΈ ΠΈΠ· ΡΠ΅ΠΊΡΡΠΎΠ»ΠΈΡΠ°,ΠΏΡΠΎΠ²ΠΎΠ΄ ΠΠΠ 0,71ΠΌΠΌ.Π΄ΠΎ Π·Π°ΠΏΠΎΠ»Π½Π΅Π½ΠΈΡ. Π ΡΡΠΌΠ΅ Π²ΡΡΡΠ΅Π·ΠΈΡΠΎΠ²Π°Π½ ΠΏΡΠΎΠ΄ΠΎΠ»ΡΠ½ΡΠΉ ΠΏΠ°Π· Π΄Π»Ρ ΡΠ΄Π΅ΡΠΆΠ°Π½ΠΈΡ ΠΎΡ ΠΏΡΠΎΠΊΡΡΡΠΈΠ²Π°Π½ΠΈΡ.
Π Π½ΠΈΠΆΠ½Π΅ΠΉ ΡΠ°ΡΡΠΈ Π²Π°Π½ΠΎΡΠΊΠ° Π΄Π»Ρ ΠΊΠ΅ΡΠΎΡΠΈΠ½Π° (ΠΌΠ°ΡΠ»ΠΎ ΠΈΠ»ΠΈ Π2Π).
ΠΠ»Π΅ΠΊΡΡΠΈΡΠ΅ΡΠΊΠ°Ρ ΡΡ Π΅ΠΌΠ° ΡΡΠ°Π½ΠΊΠ°.
Π Π½Π°Π»ΠΈΡΠΈΠΈ Π΅ΠΌΠ΅Π»ΡΡ ΠΊΠΎΡΠΏΡΡ ΠΎΡ Π½Π΅ΡΠ°Π±ΠΎΡΠ΅Π³ΠΎ Π²ΠΎΠ»ΡΡΠΌΠ΅ΡΡΠ°. ΠΡΠ΅ ΠΏΠΎΡΡΠ°Ρ Π° Π±ΡΠ»ΠΈ ΡΠΎΠ±ΡΠ°Π½Ρ Π² Π½ΡΠΌ. ΠΡΡ ΡΠΌΠ΅ΡΡΠΈΠ» Π² ΠΎΠ΄Π½Ρ ΡΡΠΎΡΠΎΠ½Ρ Ρ ΡΠ°ΡΡΡΡΡΠ° ΡΡΠΎ ΡΠΎΠ±Π΅ΡΡ ΠΈ ΡΠ»Π΅ΠΊΡΡΠΎΠ½Π½ΡΠΉ Π³Π΅Π½Π΅ΡΠ°ΡΠΎΡ.
Π― Π½Π° Π½ΡΠΌ Ρ ΠΎΡΡ ΡΠ΄Π΅Π»Π°ΡΡ ΠΊΠΎΠΊΠΈΠ»Ρ Π΄Π»Ρ Π»ΠΈΡΡΡ Π±ΡΠΎΠ½Π·Ρ. ΠΠ»Ρ ΡΡΠΎΠ³ΠΎ Ρ ΠΏΡΠΈΠ³ΠΎΡΠΎΠ²ΠΈΠ» Π²ΠΎΡ ΡΠ°ΠΊΡΡ ΡΡΡΠΊΡ,Π΄Π»Ρ ΠΏΡΠΎΠ±Ρ.
Π Π²ΠΎΡ ΡΡΠΎ Ρ ΠΌΠ΅Π½Ρ ΠΏΠΎΠ»ΡΡΠΈΠ»ΠΎΡΡ.
Π Π΅Π·ΡΠ»ΡΡΠ°Ρ Π½Π΅ ΡΡΡΡΠ°ΠΈΠ²Π°Π΅Ρ. Π₯ΠΎΡΠ΅Π»ΠΎΡΡ ΠΏΠΎΠ»ΡΡΠΈΡΡ Ρ ΠΎΡΡΠ± ΡΠ°ΠΊΠΎΠΉ ΡΠ΅Π·ΡΠ»ΡΡΠ°Ρ-Π½ΠΎ?
Π ΡΡΡ Π²ΠΈΠ΄Π΅ΠΎ.
ΠΡΠΎ Π½ΠΈΠ±ΡΠ΄Ρ ΠΌΠΎΠΆΠ΅Ρ ΠΏΠΎΠ΄ΡΠΊΠ°Π·Π°ΡΡ ΡΡΠΎ Π½ΠΈΡΠ°ΠΊ. π
ΠΠ·ΠΌΠ΅Π½Π΅Π½ΠΎ ΠΏΠΎΠ»ΡΠ·ΠΎΠ²Π°ΡΠ΅Π»Π΅ΠΌ culibinwww.chipmaker.ru
Π‘Π’ΠΠΠΠ ΠΠΠ― ΠΠΠ ΠΠΠΠ’ΠΠ Π£ΠΠ¬Π’Π ΠΠΠΠ£ΠΠΠ
Β
Π£Π»ΡΡΡΠ°Π·Π²ΡΠΊ β ΡΠΏΡΡΠ³ΠΈΠ΅ Π²ΠΎΠ»Π½Ρ Ρ ΡΠ°ΡΡΠΎΡΠΎΠΉ ΠΊΠΎΠ»Π΅Π±Π°Π½ΠΈΠΉ ΠΎΡ 20 ΠΊΠΡ Π΄ΠΎ 1 ΠΠΡ. ΠΠ»Ρ ΠΏΠΎΠ»ΡΡΠ΅Π½ΠΈΡ ΡΠ»ΡΡΡΠ°Π·Π²ΡΠΊΠΎΠ²ΡΡ ΠΊΠΎΠ»Π΅Π±Π°Π½ΠΈΠΉ ΠΈΠ½ΡΡΡΡΠΌΠ΅Π½ΡΠ° ΡΠ°ΡΠ΅ Π²ΡΠ΅Π³ΠΎ ΠΏΡΠΈΠΌΠ΅Π½ΡΡΡ ΠΌΠ°Π³Π½ΠΈΡΠΎΡΡΡΠΈΠΊΡΠΈΠΎΠ½Π½ΡΠ΅ ΠΏΡΠ΅ΠΎΠ±ΡΠ°Π·ΠΎΠ²Π°ΡΠ΅Π»ΠΈ. Π Π°Π±ΠΎΡΠ° ΡΠ»ΡΡΡΠ°Π·Π²ΡΠΊΠΎΠ²ΡΡ ΡΡΡΠ°Π½ΠΎΠ²ΠΎΠΊ ΠΎΡΠ½ΠΎΠ²Π°Π½Π° Π½Π° ΠΈΡΠΏΠΎΠ»ΡΠ·ΠΎΠ²Π°Π½ΠΈΠΈ ΡΠΏΠΎΡΠΎΠ±Π½ΠΎΡΡΠΈ ΠΆΠ΅Π»Π΅Π·Π°, Π½ΠΈΠΊΠ΅Π»Ρ, ΠΊΠΎΠ±Π°Π»ΡΡΠ° ΠΈ ΠΈΡ ΡΠΏΠ»Π°Π²ΠΎΠ² ΠΈΠ·ΠΌΠ΅Π½ΡΡΡ Π΄Π»ΠΈΠ½Ρ ΠΏΠΎΠ΄ Π΄Π΅ΠΉΡΡΠ²ΠΈΠ΅ΠΌ ΡΠ»Π΅ΠΊΡΡΠΈΡΠ΅ΡΠΊΠΎΠ³ΠΎ ΠΈΠ»ΠΈ ΠΌΠ°Π³Π½ΠΈΡΠ½ΠΎΠ³ΠΎ ΠΏΠΎΠ»Ρ, Π° ΠΏΡΠΈ ΡΠ½ΡΡΠΈΠΈ ΠΏΠΎΠ»Ρ Π²ΠΎΡΡΡΠ°Π½Π°Π²Π»ΠΈΠ²Π°ΡΡ ΠΏΠ΅ΡΠ²ΠΎΠ½Π°ΡΠ°Π»ΡΠ½ΡΠ΅ ΡΠ°Π·ΠΌΠ΅ΡΡ. ΠΡΠΎ ΡΠ²Π»Π΅Π½ΠΈΠ΅ Π½Π°Π·ΡΠ²Π°ΡΡ ΠΌΠ°Π³Π½ΠΈΡΠΎΡΡΡΠΈΠΊΡΠΈΠ΅ΠΉ.
Π Π°Π±ΠΎΡΠ° ΡΠ»ΡΡΡΠ°Π·Π²ΡΠΊΠΎΠ²ΠΎΠ³ΠΎ ΡΡΠ°Π½ΠΊΠ° Π·Π°ΠΊΠ»ΡΡΠ°Π΅ΡΡΡ Π² ΡΠ»Π΅Π΄ΡΡΡΠ΅ΠΌ. Π Π·ΠΎΠ½Ρ ΠΌΠ΅ΠΆΠ΄Ρ Π·Π°Π³ΠΎΡΠΎΠ²ΠΊΠΎΠΉ ΠΈ Π²ΠΈΠ±ΡΠΈΡΡΡΡΠΈΠΌ ΠΏΡΠ°Π½ΡΠΎΠ½ΠΎΠΌ (ΠΈΠ½ΡΡΡΡΠΌΠ΅Π½ΡΠΎΠΌ), ΠΊΠΎΡΠΎΡΡΠΉ ΠΎΡΠ΅Π½Ρ Π±Π»ΠΈΠ·ΠΊΠΎ ΠΏΠΎΠ΄Ρ ΠΎΠ΄ΠΈΡ ΠΊ Π·Π°Π³ΠΎΡΠΎΠ²ΠΊΠ΅, Π½ΠΎ Π½Π΅ ΠΊΠ°ΡΠ°Π΅ΡΡΡ Π΅Π΅, ΠΏΠΎΡΡΡΠΏΠ°Π΅Ρ Π°Π±ΡΠ°Π·ΠΈΠ²Π½ΡΠΉ ΠΏΠΎΡΠΎΡΠΎΠΊ, Π½Π°Ρ ΠΎΠ΄ΡΡΠΈΠΉΡΡ Π² ΠΆΠΈΠ΄ΠΊΠΎΡΡΠΈ Π²ΠΎ Π²Π·Π²Π΅ΡΠ΅Π½Π½ΠΎΠΌ ΡΠΎΡΡΠΎΡΠ½ΠΈΠΈ. ΠΡ Π²ΠΎΠ·Π΄Π΅ΠΉΡΡΠ²ΠΈΡ Π²ΠΈΠ±ΡΠ°ΡΠΎΡΠ° (ΠΏΡΠ΅ΠΎΠ±ΡΠ°Π·ΠΎΠ²Π°ΡΠ΅Π»Ρ) Π°Π±ΡΠ°Π·ΠΈΠ²Π½ΡΠ΅ Π·Π΅ΡΠ½Π° Ρ Π±ΠΎΠ»ΡΡΠΎΠΉ ΡΠΈΠ»ΠΎΠΉ ΡΠ΄Π°ΡΡΡΡΡΡ ΠΎ ΠΏΠΎΠ²Π΅ΡΡ Π½ΠΎΡΡΡ Π·Π°Π³ΠΎΡΠΎΠ²ΠΊΠΈ ΠΈ Ρ Π±ΠΎΠ»ΡΡΠΎΠΉ ΡΠΊΠΎΡΠΎΡΡΡΡ Π²ΡΠ±ΠΈΠ²Π°ΡΡ ΡΠ°ΡΡΠΈΡΡ ΠΌΠ°ΡΠ΅ΡΠΈΠ°Π»Π° (ΡΡΡΡΠΆΠΊΡ). ΠΠ΄Π½ΠΎΠ²ΡΠ΅ΠΌΠ΅Π½Π½ΠΎ ΠΏΡΠ°Π½ΡΠΎΠ½ ΠΏΠΎΡΡΠ΅ΠΏΠ΅Π½Π½ΠΎ ΠΎΠΏΡΡΠΊΠ°Π΅ΡΡΡ Π² Π²ΡΠ΄ΠΎΠ»Π±Π»Π΅Π½Π½ΠΎΠ΅ ΡΠ°ΠΊΠΈΠΌ ΡΠΏΠΎΡΠΎΠ±ΠΎΠΌ ΠΏΡΠΎΡΡΡΠ°Π½ΡΡΠ²ΠΎ, ΠΈ ΠΏΡΠΎΡΠ΅ΡΡ ΠΏΡΠΎΠ΄ΠΎΠ»ΠΆΠ°Π΅ΡΡΡ.
ΠΡΠΈΠ½ΡΠΈΠΏ ΡΠ°Π±ΠΎΡΡ Π³ΠΎΠ»ΠΎΠ²ΠΊΠΈ ΠΌΠ°Π³Π½ΠΈΡΠΎΡΡΡΠΈΠΊΡΠΈΠΎΠ½Π½ΠΎΠ³ΠΎ ΠΏΡΠ΅ΠΎΠ±ΡΠ°Π·ΠΎΠ²Π°ΡΠ΅Π»Ρ (ΡΠΈΡ. 18.1) Π·Π°ΠΊΠ»ΡΡΠ°Π΅ΡΡΡ Π² ΡΠΎΠΌ, ΡΡΠΎ ΡΠ΅ΡΠ΅Π· ΠΊΠ°ΡΡΡΠΊΡ Π²ΠΎΠ·Π±ΡΠΆΠ΄Π΅Π½ΠΈΡ 2 ΠΏΡΠΎΠΏΡΡΠΊΠ°Π΅ΡΡΡ ΡΠΎΠΊ Π²ΡΡΠΎΠΊΠΎΠΉ ΡΠ°ΡΡΠΎΡΡ, ΠΊΠΎΡΠΎΡΡΠΉ ΡΠΎΠ·Π΄Π°Π΅Ρ ΠΏΠ΅ΡΠ΅ΠΌΠ΅Π½Π½ΠΎΠ΅ ΠΌΠ°Π³Π½ΠΈΡΠ½ΠΎΠ΅ ΠΏΠΎΠ»Π΅ ΡΠ°ΠΊΠΎΠΉ ΠΆΠ΅ ΡΠ°ΡΡΠΎΡΡ, Π΄Π΅ΠΉΡΡΠ²ΡΡΡΠ΅Π΅ Π½Π° ΡΠ΅ΡΠ΄Π΅ΡΠ½ΠΈΠΊ 1 Π²ΠΈΠ±ΡΠ°ΡΠΎΡΠ°. ΠΠ»Ρ Π»ΡΡΡΠ΅Π³ΠΎ ΠΈΡΠΏΠΎΠ»ΡΠ·ΠΎΠ²Π°Π½ΠΈΡ ΠΌΠ°Π³Π½ΠΈΡΠΎΡΡΡΠΈΠΊΡΠΈΠΎΠ½Π½ΡΡ ΡΠ²ΠΎΠΉΡΡΠ² Π²ΠΈΠ±ΡΠ°ΡΠΎΡΠ° ΡΠΎΠ·Π΄Π°ΡΡ ΠΏΠΎΡΡΠΎΡΠ½Π½ΠΎΠ΅ ΠΌΠ°Π³Π½ΠΈΡΠ½ΠΎΠ΅ ΠΏΠΎΠ»Π΅ Π΄Π²ΡΠΌΡ ΠΊΠ°ΡΡΡΠΊΠ°ΠΌΠΈ ΠΏΠΎΠ΄ΠΌΠ°Π³Π½ΠΈΡΠΈΠ²Π°Π½ΠΈΡ 4 ΠΈ ΠΈΡ ΡΠ΅ΡΠ΄Π΅ΡΠ½ΠΈΠΊΠ°ΠΌΠΈ 3. ΠΠΎΠ»Π΅Π±Π°Π½ΠΈΡ, Π²ΠΎΠ·Π½ΠΈΠΊΠ°ΡΡΠΈΠ΅ Π½Π° Π²ΠΈΠ±ΡΠ°ΡΠΎΡΠ΅, ΠΏΠ΅ΡΠ΅Π΄Π°ΡΡΡΡ Π½Π° ΡΡΠ°Π½ΡΡΠΎΡΠΌΠ°ΡΠΎΡ ΡΠΊΠΎΡΠΎΡΡΠΈ 6, Π·Π°ΠΊΠ»ΡΡΠ΅Π½Π½ΡΠΉ ΠΌΠ΅ΠΆΠ΄Ρ Π΄Π²ΡΠΌΡ ΡΠΊΠΎΠ±Π°ΠΌΠΈ 5, ΠΈ, ΡΡΠΈΠ»Π΅Π½Π½ΡΠ΅ ΠΈΠΌ, ΡΠΎΠΎΠ±ΡΠ°ΡΡΡΡ ΠΈΠ½ΡΡΡΡΠΌΠ΅Π½ΡΡ 7. ΠΠΎΠ½ΡΠ°ΠΆΠ½ΡΡ ΠΏΠ°Π½Π΅Π»Ρ ΡΡΡΠ°Π½Π°Π²Π»ΠΈΠ²Π°ΡΡ Π½Π° ΡΠ°Π»Π°Π·ΠΊΠΈ, Π²ΠΌΠ΅ΡΡΠ΅ Ρ ΠΊΠΎΡΠΎΡΡΠΌΠΈ ΠΎΠ½Π° ΠΏΠ΅ΡΠ΅ΠΌΠ΅ΡΠ°Π΅ΡΡΡ ΠΏΠΎ Π½Π°ΠΏΡΠ°Π²Π»ΡΡΡΠΈΠΌ ΡΡΠ°Π½ΠΈΠ½Ρ.
Π£Π½ΠΈΠ²Π΅ΡΡΠ°Π»ΡΠ½ΡΠΉ Π½Π°ΡΡΠΎΠ»ΡΠ½ΡΠΉ ΠΏΡΠΎΡΠΈΠ²ΠΎΡΠ½ΡΠΉ ΡΠ»ΡΡΡΠ°Π·Π²ΡΠΊΠΎΠ²ΠΎΠΉ ΡΡΠ°Π½ΠΎΠΊ 4770 (ΡΠΈΡ. 18.2) ΠΏΡΠ΅Π΄Π½Π°Π·Π½Π°ΡΠ΅Π½ Π΄Π»Ρ ΠΎΠ±ΡΠ°Π±ΠΎΡΠΊΠΈ Π΄Π΅ΡΠ°Π»Π΅ΠΉ ΠΈΠ· ΡΠ²Π΅ΡΠ΄ΡΡ ΠΈ Ρ ΡΡΠΏΠΊΠΈΡ ΠΌΠ°ΡΠ΅ΡΠΈΠ°Π»ΠΎΠ²: ΡΡΠ΅ΠΊΠ»Π°, ΠΊΠ΅ΡΠ°ΠΌΠΈΠΊΠΈ, ΠΏΠΎΠ»ΡΠΏΡΠΎΠ²ΠΎΠ΄Π½ΠΈΠΊΠΎΠ²ΡΡ ΠΌΠ°ΡΠ΅ΡΠΈΠ°Π»ΠΎΠ², ΠΊΠ°ΠΌΠ½Ρ, ΡΠ²Π΅ΡΠ΄ΡΡ ΡΠΏΠ»Π°Π²ΠΎΠ² ΠΈ Ρ. ΠΏ. ΠΠ° ΡΡΠ°Π½ΠΊΠ΅ ΠΌΠΎΠΆΠ½ΠΎ Π²ΡΠΏΠΎΠ»Π½ΡΡΡ ΠΊΡΡΠ³Π»ΡΠ΅ ΠΈ ΡΠ°ΡΠΎΠ½Π½ΡΠ΅ ΠΎΡΠ²Π΅ΡΡΡΠΈΡ ΠΈ ΠΏΠΎΠ»ΠΎΡΡΠΈ, Π²ΡΡΠ΅Π·Π°ΡΡ Π·Π°Π³ΠΎΡΠΎΠ²ΠΊΡ, Π³ΡΠ°Π²ΠΈΡΠΎΠ²Π°ΡΡ, ΡΠ°Π·ΡΠ΅Π·Π°ΡΡ ΠΈ Π΄Ρ. ΠΠΎ Π²ΡΠ΅ΠΌΡ ΡΠ°Π±ΠΎΡΡ ΠΈΠ½ΡΡΡΡΠΌΠ΅Π½Ρ ΠΊΠΎΠ»Π΅Π±Π»Π΅ΡΡΡ Ρ ΡΠ»ΡΡΡΠ°Π·Π²ΡΠΊΠΎΠ²ΠΎΠΉ ΡΠ°ΡΡΠΎΡΠΎΠΉ Π² Π½Π°ΠΏΡΠ°Π²Π»Π΅Π½ΠΈΠΈ Π΅Π³ΠΎ ΠΏΠΎΠ΄Π°ΡΠΈ. ΠΠ΄Π½ΠΎΠ²ΡΠ΅ΠΌΠ΅Π½Π½ΠΎ ΡΠ΅Π½ΡΡΠΎΠ±Π΅ΠΆΠ½ΡΠΌ Π½Π°ΡΠΎΡΠΎΠΌ ΠΏΠΎΠ΄ ΡΠΎΡΠ΅Ρ ΠΈΠ½ΡΡΡΡΠΌΠ΅Π½ΡΠ° ΠΏΠΎΠ΄Π°Π΅ΡΡΡ Π°Π±ΡΠ°Π·ΠΈΠ²Π½Π°Ρ ΡΡΡΠΏΠ΅Π½Π·ΠΈΡ.
Π‘ΡΠΎΠ» 2 ΡΡΠ°Π½ΠΊΠ° ΠΈΠΌΠ΅Π΅Ρ ΠΊΠΎΠΎΡΠ΄ΠΈΠ½Π°ΡΠ½ΡΠ΅ ΡΡΡΠ°Π½ΠΎΠ²ΠΎΡΠ½ΡΠ΅ ΠΏΠ΅ΡΠ΅ΠΌΠ΅ΡΠ΅Π½ΠΈΡ Π² Π³ΠΎΡΠΈΠ·ΠΎΠ½ΡΠ°Π»ΡΠ½ΠΎΠΉ ΠΏΠ»ΠΎΡΠΊΠΎΡΡΠΈ ΠΏΠΎ Π½Π°ΠΏΡΠ°Π²Π»ΡΡΡΠΈΠΌ ΡΠΈΠΏΠ° Π»Π°ΡΡΠΎΡΠΊΠΈΠ½Π° Ρ Π²ΠΎΡΡΠ°. Π₯ΠΎΠ΄ΠΎΠ²ΡΠ΅ Π²ΠΈΠ½ΡΡ ΡΠ½Π°Π±ΠΆΠ΅Π½Ρ Π»ΠΈΠΌΠ±Π°ΠΌΠΈ Ρ ΡΠ΅Π½ΠΎΠΉ Π΄Π΅Π»Π΅Π½ΠΈΡ 0,02 ΠΌΠΌ. ΠΠΎΠ»Π·ΡΠ½Ρ 5 Π²ΡΡΡΠ½ΡΡ ΡΠΎΠΎΠ±ΡΠ°ΡΡ ΠΏΠ΅ΡΠ΅ΠΌΠ΅ΡΠ΅Π½ΠΈΠ΅ ΠΏΠΎ ΡΠ°ΡΠΈΠΊΠΎΠ²ΡΠΌ Π½Π°ΠΏΡΠ°Π²Π»ΡΡΡΠΈΠΌ ΡΡΠ°Π½ΠΈΠ½Ρ 1 ΡΠ΅ΡΠ΅Π· ΡΠ΅Π΅ΡΠ½ΡΡ ΠΏΠ΅ΡΠ΅Π΄Π°ΡΡ z1β z2 ΠΈΠ»ΠΈ ΠΌΠ΅Ρ Π°Π½ΠΈΡΠ΅ΡΠΊΠΈ ΠΎΡ ΡΠ΅Π³ΡΠ»ΠΈΡΡΠ΅ΠΌΠΎΠ³ΠΎ Π΄Π²ΡΡ ΡΠ°Π·Π½ΠΎΠ³ΠΎ Π°ΡΠΈΠ½Ρ ΡΠΎΠ½Π½ΠΎΠ³ΠΎ ΡΠ»Π΅ΠΊΒΡΡΠΎΠ΄Π²ΠΈΠ³Π°ΡΠ΅Π»Ρ 8 ΡΠ΅ΡΠ΅Π· ΡΠ΅Π΄ΡΠΊΡΠΎΡ ΠΈ ΡΠ΅Π΅ΡΠ½ΡΡ ΠΏΠ΅ΡΠ΅Π΄Π°ΡΡ.
ΠΠ»Π΅ΠΊΡΡΠΎΠ΄Π²ΠΈΠ³Π°ΡΠ΅Π»Ρ ΡΠ°Π±ΠΎΡΠ°Π΅Ρ Π½Π° Π·Π°ΡΠΎΡΠΌΠΎΠΆΠ΅Π½Π½ΠΎΠΌ ΡΠ΅ΠΆΠΈΠΌΠ΅, ΡΠ°Π·Π²ΠΈΠ²Π°Ρ ΠΊΡΡΡΡΡΠΈΠΉΡΡ ΠΌΠΎΠΌΠ΅Π½Ρ Π² ΡΠΎΠΎΡΠ²Π΅ΡΡΡΠ²ΠΈΠΈ Ρ ΡΠΈΠ»ΠΎΠΉ ΠΏΠΎΠ΄Π°ΡΠΈ ΠΈΠ½ΡΡΡΡΠΌΠ΅Π½ΡΠ°. ΠΠΎΠ»Π·ΡΠ½ Π²ΠΌΠ΅ΡΡΠ΅ Ρ ΡΠΊΡΠ΅ΠΏΠ»Π΅Π½Π½ΠΎΠΉ Π½Π° Π½Π΅ΠΌ Π³ΠΎΠ»ΠΎΠ²ΠΊΠΎΠΉ ΡΡΠ°Π²Π½ΠΎΠ²Π΅ΡΠ΅Π½ Π³ΡΡΠ·ΠΎΠΌ 11, ΠΏΠΎΠ΄Π²Π΅ΡΠ΅Π½Π½ΡΠΌ Π½Π° Π»Π΅Π½ΡΠ΅ 10, Π½Π°ΠΌΠΎΡΠ°Π½Π½ΠΎΠΉ Π½Π° Π±Π°ΡΠ°Π±Π°Π½ 9 Π²Π°Π»ΠΈΠΊΠ° ΠΏΡΠΈΠ²ΠΎΠ΄Π° ΡΡΡΠ½ΠΎΠΉ ΠΏΠΎΠ΄Π°ΡΠΈ. ΠΠ»Ρ ΠΏΠ»Π°Π²Π½ΠΎΡΡΠΈ Ρ ΠΎΠ΄Π° ΠΏΠΎΠ»Π·ΡΠ½Π° ΠΈΠΌΠ΅Π΅ΡΡΡ ΠΌΠ°ΡΠ»ΡΒΠ½ΡΠΉ Π΄Π΅ΠΌΠΏΡΠ΅Ρ, ΡΠΈΠ»ΠΈΠ½Π΄Ρ 4 ΠΊΠΎΡΠΎΡΠΎΠ³ΠΎ ΠΊΡΠ΅ΠΏΡΡ ΠΊ ΠΊΠΎΡΠΏΡΡΡ ΠΊΠ°ΡΠ΅ΡΠΊΠΈ 7, Π° ΡΡΠΎΠΊ 6 β ΠΊ ΠΏΠΎΠ»Π·ΡΠ½Ρ. Π‘ΠΊΠΎΡΠΎΡΡΡ ΠΏΠΎΠ»Π·ΡΠ½Π° ΡΠ΅Π³ΡΠ»ΠΈΡΡΠ΅ΡΡΡ ΠΈΠ³Π»ΠΎΠΉ, ΠΏΠ΅ΡΠ΅ΠΊΡΡΠ²Π°ΡΡΠ΅ΠΉ ΠΏΡΠΎΠΏΡΡΠΊΠ½ΠΎΠ΅ ΠΎΡΠ²Π΅ΡΡΡΠΈΠ΅ Π² ΡΡΠΎΠΊΠ΅. ΠΠ»Ρ ΡΡΠΊΠΎΡΠ΅Π½Π½ΠΎΠ³ΠΎ ΠΎΡΠ²ΠΎΠ΄Π° ΠΏΠΎΡΡΠ½Ρ ΠΈΠΌΠ΅Π΅ΡΡΡ ΠΎΠ±ΡΠ°ΡΠ½ΡΠΉ ΠΊΠ»Π°ΠΏΠ°Π½.
Β
ΠΡΠ½ΠΎΠ²Π½ΠΎΠΉ ΡΠ°ΡΡΡΡ ΡΡΠ°Π½ΠΊΠ° ΡΠ²Π»ΡΠ΅ΡΡΡ Π°ΠΊΡΡΡΠΈΡΠ΅ΡΠΊΠ°Ρ Π³ΠΎΠ»ΠΎΠ²ΠΊΠ° 3, ΠΊΠΎΡΠΎΡΠ°Ρ ΡΠΎΠΎΠ±ΡΠ°Π΅Ρ ΠΈΠ½ΡΡΡΡΠΌΠ΅Π½ΡΡ ΠΊΠΎΠ»Π΅Π±Π°ΡΠ΅Π»ΡΠ½ΠΎΠ΅ Π΄Π²ΠΈΠΆΠ΅Π½ΠΈΠ΅. Π Π³ΠΎΠ»ΠΎΠ²ΠΊΠ΅ ΠΏΡΠΈΠΌΠ΅Π½Π΅Π½ Π΄Π²ΡΡ ΡΡΠ΅ΡΠΆΠ½Π΅Π²ΠΎΠΉ Π½ΠΈΠΊΠ΅Π»Π΅Π²ΡΠΉ ΠΌΠ°Π³Π½ΠΈΡΠΎΡΡΡΠΈΠΊΡΠΈΠΎΠ½Π½ΡΠΉ Π²ΠΈΠ±ΡΠ°ΡΠΎΡ (ΠΏΡΠ΅ΠΎΠ±ΡΠ°Π·ΠΎΠ²Π°ΡΠ΅Π»Ρ).
Π’Π΅Ρ Π½ΠΈΡΠ΅ΡΠΊΠ°Ρ Ρ Π°ΡΠ°ΠΊΡΠ΅ΡΠΈΡΡΠΈΠΊΠ° ΡΡΠ°Π½ΠΊΠ°:
ΠΠΈΠ°ΠΌΠ΅ΡΡ ΠΎΠ±ΡΠ°Π±Π°ΡΡΠ²Π°Π΅ΠΌΠΎΠ³ΠΎ ΠΎΡΠ²Π΅ΡΡΡΠΈΡ, ΠΌΠΌ 0,5β10
ΠΠ°ΠΈΠ±ΠΎΠ»ΡΡΠ°Ρ Π³Π»ΡΠ±ΠΈΠ½Π° ΠΎΠ±ΡΠ°Π±ΠΎΡΠΊΠΈ, ΠΌΠΌ …. (2β5) d
ΠΡΠΎΠ΄ΠΎΠ»ΡΠ½ΠΎΠ΅ ΠΏΠ΅ΡΠ΅ΠΌΠ΅ΡΠ΅Π½ΠΈΠ΅ ΡΡΠΎΠ»Π°, ΠΌΠΌ…………. 80
Π₯ΠΎΠ΄ ΠΏΠΎΠ»Π·ΡΠ½Π°, ΠΌΠΌ …………………………… 100
ΠΠ΅ΡΠ΅ΠΌΠ΅ΡΠ΅Π½ΠΈΠ΅ Π³ΠΎΠ»ΠΎΠ²ΠΊΠΈ ΠΏΠΎ ΠΏΠΎΠ»Π·ΡΠ½Ρ, ΠΌΠΌ… 110
Π§ΡΠ²ΡΡΠ²ΠΈΡΠ΅Π»ΡΠ½ΠΎΡΡΡ ΠΌΠ΅Ρ Π°Π½ΠΈΠ·ΠΌΠ° ΠΏΠΎΠ΄Π°ΡΠΈ, Π (686β980) 10~3
Π Π°Π±ΠΎΡΠ°Ρ ΡΠ°ΡΡΠΎΡΠ°, ΠΊΠΡ ……………………… 18β19
ΠΠΎΡΠ½ΠΎΡΡΡ Π³Π΅Π½Π΅ΡΠ°ΡΠΎΡΠ°, ΠΊΠΡ…………………….. 0,25.
ΠΠΠΠΠ’Π ΠΠΠ‘ΠΠ ΠΠΠ«Π Π‘Π’ΠΠΠΠ
Β
ΠΡΠ½ΠΎΠ²Ρ ΡΠ»Π΅ΠΊΡΡΠΎΠΈΡΠΊΡΠΎΠ²ΠΎΠ³ΠΎ ΠΌΠ΅ΡΠΎΠ΄Π° ΠΎΠ±ΡΠ°Π±ΠΎΡΠΊΠΈ ΠΌΠ΅ΡΠ°Π»Π»ΠΎΠ² ΡΠΎΡΡΠ°Π²Π»ΡΠ΅Ρ ΠΏΡΠΎΡΠ΅ΡΡ ΡΠ»Π΅ΠΊΡΡΠΎΡΡΠΎΠ·ΠΈΠΈ ΠΌΠ΅ΡΠ°Π»Π»ΠΎΠ². Π‘ΡΡΠ½ΠΎΡΡΡ Π΅Π³ΠΎ Π·Π°ΠΊΠ»ΡΡΠ°Π΅ΡΡΡ Π² ΡΠΎΠΌ, ΡΡΠΎ ΠΏΠΎΠ΄ Π²ΠΎΠ·Π΄Π΅ΠΉΡΡΠ²ΠΈΠ΅ΠΌ ΠΊΠΎΡΠΎΡΠΊΠΈΡ ΠΈΡΠΊΡΠΎΠ²ΡΡ ΡΠ°Π·ΡΡΠ΄ΠΎΠ², ΠΏΠΎΡΡΠ»Π°Π΅ΠΌΡΡ ΠΈΡΡΠΎΡΠ½ΠΈΠΊΠΎΠΌ ΡΠ»Π΅ΠΊΡΡΠΈΡΠ΅ΡΠΊΠΎΠ³ΠΎ ΡΠΎΠΊΠ°, ΠΌΠ΅ΡΠ°Π»Π» ΡΠ°Π·ΡΡΡΠ°Π΅ΡΡΡ. ΠΡΠΈ ΠΎΠ±ΡΠ°Π±ΠΎΡΠΊΠ΅ Π½Π° ΡΠ»Π΅ΠΊΡΡΠΎΠΈΡΠΊΡΠΎΠ²ΠΎΠΌ ΡΡΠ°Π½ΠΊΠ΅ Π΄Π»Ρ ΠΏΡΠΎΡΠΈΠ²ΠΊΠΈ ΠΎΡΠ²Π΅ΡΡΡΠΈΠΉ (ΡΠΈΡ. 18.3, Π°) Π·Π°Π³ΠΎΡΠΎΠ²ΠΊΡ 2 ΠΏΠΎΠ³ΡΡΠΆΠ°ΡΡ Π² Π±Π°ΠΊ Ρ ΠΆΠΈΠ΄ΠΊΠΎΡΡΡΡ ΠΈ ΡΠΎΠ΅Π΄ΠΈΠ½ΡΡΡ Ρ ΠΏΠΎΠ»ΠΎΠΆΠΈΡΠ΅Π»ΡΠ½ΡΠΌ ΠΏΠΎΠ»ΡΡΠΎΠΌ, Π²ΡΠΏΠΎΠ»Π½ΡΡΡΠΈΠΌ ΡΡΠ½ΠΊΡΠΈΠΈ Π°Π½ΠΎΠ΄Π°. ΠΠ»Π΅ΠΊΡΡΠΎΠ΄ (ΠΈΠ½ΡΡΡΡΠΌΠ΅Π½Ρ) 4, ΡΠ²Π»ΡΡΡΠΈΠΉΡΡ ΠΊΠ°ΡΠΎΠ΄ΠΎΠΌ, ΡΠΎΠ΅Π΄ΠΈΠ½ΡΡΡ Ρ ΠΎΡΡΠΈΡΠ°ΡΠ΅Π»ΡΠ½ΡΠΌ ΠΏΠΎΠ»ΡΡΠΎΠΌ ΠΈ ΡΠΊΡΠ΅ΠΏΠ»ΡΡΡ Π½Π° ΠΏΠΎΠ»Π·ΡΠ½Π΅ 5, ΠΈΠΌΠ΅ΡΡΠ΅ΠΌ Π²Π΅ΡΡΠΈΠΊΠ°Π»ΡΠ½ΠΎΠ΅ ΠΏΠ΅ΡΠ΅ΠΌΠ΅ΡΠ΅Π½ΠΈΠ΅ ΠΏΠΎ Π½Π°ΠΏΡΠ°Π²Π»ΡΡΡΠΈΠΌ 6. ΠΠ°Π³ΠΎΡΠΎΠ²ΠΊΠ° 2, ΡΡΠΎΠ» 1, Π½Π° ΠΊΠΎΡΠΎΡΠΎΠΌ Π΅Π΅ Π·Π°ΠΊΡΠ΅ΠΏΠ»ΡΡΡ, ΠΊΠΎΡΠΏΡΡ Π±Π°ΠΊΠ° ΠΈ ΡΡΠ°Π½ΠΈΠ½Π° ΡΡΠ°Π½ΠΊΠ° ΡΠ»Π΅ΠΊΡΡΠΈΡΠ΅ΡΠΊΠΈ ΡΠΎΠ΅Π΄ΠΈΠ½Π΅Π½Ρ ΠΌΠ΅ΠΆΠ΄Ρ ΡΠΎΠ±ΠΎΠΉ ΠΈ Π·Π°Π·Π΅ΠΌΠ»Π΅Π½Ρ, ΡΠ°ΠΊ ΡΡΠΎ ΠΈΡ ΡΠ»Π΅ΠΊΡΡΠΈΡΠ΅ΡΠΊΠΈΠΉ ΠΏΠΎΡΠ΅Π½ΡΠΈΠ°Π» Π²ΡΠ΅Π³Π΄Π° ΡΠ°Π²Π΅Π½ Π½ΡΠ»Ρ. ΠΡΠΎ Π½Π΅ΠΎΠ±Ρ ΠΎΠ΄ΠΈΠΌΠΎ Π΄Π»Ρ Π±Π΅Π·ΠΎΠΏΠ°ΡΠ½ΠΎΡΡΠΈ ΡΠ°Π±ΠΎΡΡ Π½Π° ΡΡΠ°Π½ΠΊΠ΅.
Β
Β
ΠΡΠ»ΠΈ, ΠΎΠΏΡΡΡΠΈΠ² ΠΏΠΎΠ»Π·ΡΠ½ 5, ΠΏΡΠΈΠΊΠΎΡΠ½ΡΡΡΡΡ ΡΠ»Π΅ΠΊΡΡΠΎΠ΄ΠΎΠΌ 4 ΠΊ Π·Π°Π³ΠΎΡΠΎΠ²ΠΊΠ΅ 2, ΡΠΎ Π² ΡΠ»Π΅ΠΊΡΡΠΈΡΠ΅ΡΠΊΠΎΠΉ ΡΠ΅ΠΏΠΈ ΠΏΠΎΠΉΠ΄Π΅Ρ ΡΠ»Π΅ΠΊΡΡΠΈΡΠ΅ΡΠΊΠΈΠΉ ΡΠΎΠΊ ΠΎΡ ΠΎΡΡΠΈΡΠ°ΡΠ΅Π»ΡΠ½ΠΎΠΉ ΠΊΠ»Π΅ΠΌΠΌΡ 7 Π³Π΅Π½Π΅ΡΠ°ΡΠΎΡΠ° Π ΠΊ ΠΏΠΎΠ»ΠΎΠΆΠΈΡΠ΅Π»ΡΠ½ΠΎΠΉ ΠΊΠ»Π΅ΠΌΠΌΠ΅ 8. Π ΡΠ»Π΅ΠΊΡΡΠΈΡΠ΅ΡΠΊΡΡ ΡΠ΅ΠΏΡ Π²ΠΊΠ»ΡΡΠ΅Π½ ΡΠ΅Π·ΠΈΡΡΠΎΡ 11. ΠΡΠΎ ΠΊΠ°ΡΡΡΠΊΠ° ΠΈΠ· Π΄Π»ΠΈΠ½Π½ΠΎΠΉ ΡΠΎΠ½ΠΊΠΎΠΉ ΠΏΡΠΎΠ²ΠΎΠ»ΠΎΠΊΠΈ. ΠΠ·ΠΌΠ΅Π½ΡΡ ΡΠΎΠΏΡΠΎΡΠΈΠ²Π»Π΅Π½ΠΈΠ΅, ΠΌΠΎΠΆΠ½ΠΎ ΡΠ΅Π³ΡΠ»ΠΈΡΠΎΠ²Π°ΡΡ ΡΠΈΠ»Ρ ΡΠΎΠΊΠ°, ΠΊΠΎΠ½ΡΡΠΎΠ»ΠΈΡΡΡ Π΅Π΅ ΠΏΠΎ Π°ΠΌΠΏΠ΅ΡΠΌΠ΅ΡΡΡ 10.
ΠΠ»Ρ ΡΠΎΠ³ΠΎ ΡΡΠΎΠ±Ρ ΠΏΠΎΠ»ΡΡΠΈΡΡ ΠΈΠΌΠΏΡΠ»ΡΡΠ½ΡΠ΅ ΡΠ°Π·ΡΡΠ΄Ρ, Π½Π΅ΠΏΡΠ΅ΡΡΠ²Π½ΠΎ ΡΠ»Π΅Π΄ΡΡΡΠΈΠ΅ Π΄ΡΡΠ³ Π·Π° Π΄ΡΡΠ³ΠΎΠΌ, ΠΌΠ΅ΠΆΠ΄Ρ ΡΠ»Π΅ΠΊΡΡΠΎΠ΄ΠΎΠΌ 4 ΠΈ Π·Π°Π³ΠΎΡΠΎΠ²ΠΊΠΎΠΉ 2 Π² ΡΠ»Π΅ΠΊΡΡΠΈΡΠ΅ΡΠΊΡΡ ΡΡ Π΅ΠΌΡ ΡΡΠ°Π½ΠΊΠ° Π²ΠΊΠ»ΡΡΠ°Π΅ΡΡΡ ΠΊΠΎΠ½Π΄Π΅Π½ΡΠ°ΡΠΎΡΠ½Π°Ρ Π±Π°ΡΠ°ΡΠ΅Ρ 12. ΠΠ΅ Π²ΠΊΠ»ΡΡΠ°ΡΡ ΠΏΠ°ΡΠ°Π»Π»Π΅Π»ΡΠ½ΠΎ Π·Π°Π³ΠΎΡΠΎΠ²ΠΊΠ΅ 2 ΠΈ ΡΠ»Π΅ΠΊΡΡΠΎΠ΄Ρ 4. ΠΡΠ»ΠΈ Π·Π°ΠΌΠΊΠ½ΡΡΡ Π²ΡΠΊΠ»ΡΡΠ°ΡΠ΅Π»Ρ ΡΠ»Π΅ΠΊΡΡΠΈΡΠ΅ΡΠΊΠΎΠΉ ΡΠ΅ΠΏΠΈ ΠΏΡΠΈ ΡΠ°Π·Π²Π΅Π΄Π΅Π½Π½ΡΡ ΡΠ»Π΅ΠΊΡΡΠΎΠ΄Π°Ρ ΡΡΠ°Π½ΠΊΠ°, ΡΠΎ Π² ΠΏΠ΅ΡΠ²ΡΠΉ ΠΌΠΎΠΌΠ΅Π½Ρ ΡΡΡΠ΅Π»ΠΊΠ° Π°ΠΌΠΏΠ΅ΡΠΌΠ΅ΡΡΠ° 10 ΡΠ΅Π·ΠΊΠΎ ΠΎΡΠΊΠ»ΠΎΠ½ΠΈΡΡΡ ΠΈ ΠΏΠΎΡΡΠ΅ΠΏΠ΅Π½Π½ΠΎ Π²ΠΎΠ·Π²ΡΠ°ΡΠΈΡΡΡ Π½Π° 0. Π‘ΡΡΠ΅Π»ΠΊΠ° Π²ΠΎΠ»ΡΡΠΌΠ΅ΡΡΠ° 9, Π½Π°ΠΎΠ±ΠΎΡΠΎΡ, ΠΏΠ»Π°Π²Π½ΠΎ ΠΎΡΠΊΠ»ΠΎΠ½ΠΈΡΡΡ ΠΎΡ ΡΠΎΠ³ΠΎ Π·Π½Π°ΡΠ΅Π½ΠΈΡ Π½Π°ΠΏΡΡΠΆΠ΅Π½ΠΈΡ, ΠΊΠΎΡΠΎΡΠΎΠ΅ ΡΠΎΠ·Π΄Π°Π΅ΡΡΡ Π³Π΅Π½Π΅ΡΠ°ΡΠΎΡΠΎΠΌ. ΠΡΠΎ ΠΎΠ·Π½Π°ΡΠ°Π΅Ρ, ΡΡΠΎ ΠΏΡΠΎΠΈΠ·ΠΎΡΠ»Π° Π·Π°ΡΡΠ΄ΠΊΠ° ΠΊΠΎΠ½Π΄Π΅Π½ΡΠ°ΡΠΎΡΠΎΠ². Π’Π΅ΠΏΠ΅ΡΡ ΠΌΠΎΠΆΠ½ΠΎ ΠΏΡΠΈΠ±Π»ΠΈΠ·ΠΈΡΡ ΡΠ»Π΅ΠΊΡΡΠΎΠ΄ ΠΊ Π·Π°Π³ΠΎΡΠΎΠ²ΠΊΠ΅. ΠΠ°ΠΊ ΡΠΎΠ»ΡΠΊΠΎ ΡΠ°ΡΡΡΠΎΡΠ½ΠΈΠ΅ ΠΌΠ΅ΠΆΠ΄Ρ Π½ΠΈΠΌΠΈ ΡΡΠ°Π½Π΅Ρ Π½Π΅Π±ΠΎΠ»ΡΡΠΈΠΌ, ΠΏΡΠΎΠΈΠ·ΠΎΠΉΠ΄Π΅Ρ ΡΠ»Π΅ΠΊΡΡΠΈΡΠ΅ΡΠΊΠΈΠΉ ΡΠ°Π·ΡΡΠ΄. ΠΡΠΈ ΡΡΠΎΠΌ Π²ΡΡ ΡΠ½Π΅ΡΠ³ΠΈΡ, Π½Π°ΠΊΠΎΠΏΠ»Π΅Π½Π½Π°Ρ Π² ΠΊΠΎΠ½Π΄Π΅Π½ΡΠ°ΡΠΎΡΠ°Ρ , ΡΠ°Π·ΡΡΠ΄ΠΈΡΡΡ Π² ΠΏΡΠΎΠΌΠ΅ΠΆΡΡΠΊΠ΅ ΠΌΠ΅ΠΆΠ΄Ρ ΡΠ»Π΅ΠΊΡΡΠΎΠ΄ΠΎΠΌ ΠΈ Π·Π°Π³ΠΎΡΠΎΠ²ΠΊΠΎΠΉ, ΠΈ ΡΠ΅ΠΌ Π±ΠΎΠ»ΡΡΠ΅ Π·Π°ΠΏΠ°Ρ ΡΠ½Π΅ΡΠ³ΠΈΠΈ, ΡΠ΅ΠΌ Π±ΠΎΠ»ΡΡΠ΅ Π±ΡΠ΄Π΅Ρ ΡΠ»Π΅ΠΊΡΡΠΈΡΠ΅ΡΠΊΠ°Ρ ΡΡΠΎΠ·ΠΈΡ Π°Π½ΠΎΠ΄Π° (Π·Π°Π³ΠΎΡΠΎΠ²ΠΊΠΈ).
ΠΠΎΡΠ»Π΅ ΡΠ°Π·ΡΡΠ΄Π° ΡΠ»Π΅ΠΊΡΡΠΈΡΠ΅ΡΠΊΠΈΠΉ ΡΠΎΠΊ ΠΌΠ΅ΠΆΠ΄Ρ ΡΠ»Π΅ΠΊΡΡΠΎΠ΄ΠΎΠΌ ΠΈ Π΄Π΅ΡΠ°Π»ΡΡ ΠΈΡΡΠ΅Π·Π½Π΅Ρ, ΡΠ°ΠΊ ΠΊΠ°ΠΊ Π²ΡΡ ΡΠ½Π΅ΡΠ³ΠΈΡ, Π½Π°ΠΊΠΎΠΏΠ»Π΅Π½Π½Π°Ρ Π² ΠΊΠΎΠ½Π΄Π΅Π½ΡΠ°ΡΠΎΡΠ°Ρ , ΠΈΠ·ΡΠ°ΡΡ ΠΎΠ΄ΠΎΠ²Π°Π½Π°, ΠΈ ΡΠ½ΠΎΠ²Π° Π½Π°ΡΠΈΠ½Π°Π΅ΡΡΡ Π·Π°ΡΡΠ΄ΠΊΠ° ΠΊΠΎΠ½Π΄Π΅Π½ΡΠ°ΡΠΎΡΠ½ΠΎΠΉ Π±Π°ΡΠ°ΡΠ΅ΠΈ. Π‘Π»Π΅Π΄ΡΡΡΠΈΠΉ ΡΠ°Π·ΡΡΠ΄ ΠΏΡΠΎΠΈΠ·ΠΎΠΉΠ΄Π΅Ρ ΠΊΠ°ΠΊ ΡΠΎΠ»ΡΠΊΠΎ ΠΊΠΎΠ½Π΄Π΅Π½ΡΠ°ΡΠΎΡΡ Π·Π°ΡΡΠ΄ΡΡΡΡ. ΠΡΠΎΡ ΠΏΡΠΎΡΠ΅ΡΡ ΠΏΡΠΎΠΈΡΡ ΠΎΠ΄ΠΈΡ Π½Π΅ΠΏΡΠ΅ΡΡΠ²Π½ΠΎ, ΠΈΠΌΠΏΡΠ»ΡΡΠ½ΡΠ΅ ΡΠ°Π·ΡΡΠ΄Ρ ΡΠ»Π΅Π΄ΡΡΡ ΠΎΠ΄ΠΈΠ½ Π·Π° Π΄ΡΡΠ³ΠΈΠΌ Π΄ΠΎ ΡΠ΅Ρ ΠΏΠΎΡ, ΠΏΠΎΠΊΠ° Π½Π΅ Π·Π°ΠΊΠΎΠ½ΡΠΈΡΡΡ ΠΎΠ±ΡΠ°Π±ΠΎΡΠΊΠ°.
ΠΠΎ Π²ΡΠ΅ΠΌΡ ΠΎΠ±ΡΠ°Π±ΠΎΡΠΊΠΈ ΡΠ»Π΅ΠΊΡΡΠΎΠ΄ 4 Π½Π΅ Π΄ΠΎΠ»ΠΆΠ΅Π½ ΠΊΠ°ΡΠ°ΡΡΡΡ Π·Π°Π³ΠΎΡΠΎΠ²ΠΊΠΈ ΠΈΠ½Π°ΡΠ΅ ΠΏΡΠΎΠΈΠ·ΠΎΠΉΠ΄Π΅Ρ ΠΊΠΎΡΠΎΡΠΊΠΎΠ΅ Π·Π°ΠΌΡΠΊΠ°Π½ΠΈΠ΅. ΠΠ΅ΠΆΠ΄Ρ ΡΠ»Π΅ΠΊΡΡΠΎΠ΄ΠΎΠΌ 4 ΠΈ Π·Π°Π³ΠΎΡΠΎΠ²ΠΊΠΎΠΉ Π²ΡΠ΅Π³Π΄Π° Π΄ΠΎΠ»ΠΆΠ΅Π½ ΠΏΠΎΠ΄Π΄Π΅ΡΠΆΠΈΠ²Π°ΡΡΡΡ Π½Π΅Π±ΠΎΠ»ΡΡΠΎΠΉ, ΡΠ°ΠΊ Π½Π°Π·ΡΠ²Π°Π΅ΠΌΡΠΉ ΠΈΡΠΊΡΠΎΠ²ΠΎΠΉ ΠΏΡΠΎΠΌΠ΅ΠΆΡΡΠΎΠΊ. ΠΡΠΎ Π΄ΠΎΡΡΠΈΠ³Π°Π΅ΡΡΡ Ρ ΠΏΠΎΠΌΠΎΡΡΡ ΡΠ°Π·Π»ΠΈΡΠ½ΡΡ ΡΡΡΡΠΎΠΉΡΡΠ². ΠΠ°ΠΈΠ±ΠΎΠ»Π΅Π΅ ΠΏΡΠΎΡΡΠΎΠ΅ ΡΡΡΡΠΎΠΉΡΡΠ²ΠΎ β ΡΠΎΠ»Π΅Π½ΠΎΠΈΠ΄Π½ΡΠΉ ΡΠ΅Π³ΡΠ»ΡΡΠΎΡ (ΡΠΈΡ. 18.3, Π±). Π Π²Π΅ΡΡ Π½Π΅ΠΌΡ ΠΊΠΎΠ½ΡΡ ΠΏΠΎΠ»Π·ΡΠ½Π° 5 ΠΏΡΠΈΠΊΡΠ΅ΠΏΠ»Π΅Π½ ΡΡΠ°Π»ΡΠ½ΠΎΠΉ ΡΡΠ΅ΡΠΆΠ΅Π½Ρ-ΡΠ΅ΡΠ΄Π΅ΡΠ½ΠΈΠΊ 13, ΠΊΠΎΡΠΎΡΡΠΉ Π²Ρ ΠΎΠ΄ΠΈΡ Π²Π½ΡΡΡΡ ΠΊΠ°ΡΡΡΠΊΠΈ (ΡΠΎΠ»Π΅Π½ΠΎΠΈΠ΄Π°) 14, ΠΏΡΠΈΡΠΎΠ΅Π΄ΠΈΠ½Π΅Π½Π½ΠΎΠΉ ΠΊ ΠΎΡΠ½ΠΎΠ²Π½ΠΎΠΉ ΡΠ΅ΠΏΠΈ. ΠΡΠΈΡΠΎΠ΅Π΄ΠΈΠ½Π΅Π½ΠΈΠ΅ ΡΠ΄Π΅Π»Π°Π½ΠΎ ΠΏΠΎ ΡΠ°Π·Π½ΡΠΌ ΡΡΠΎΡΠΎΠ½Π°ΠΌ ΡΠ΅Π·ΠΈΡΡΠΎΡΠ° 11 ΡΠ°ΠΊ, ΡΡΠΎ ΠΊΠΎΠ½ΡΡ ΠΏΡΠΎΠ²ΠΎΠ΄ΠΎΠ² 15 Π½Π°Ρ ΠΎΠ΄ΡΡΡΡ ΠΏΠΎΠ΄ ΡΠ°Π·Π½ΡΠΌΠΈ ΠΏΠΎΡΠ΅Π½ΡΠΈΠ°Π»Π°ΠΌΠΈ.
ΠΠΎΠ³Π΄Π° ΡΠ»Π΅ΠΊΡΡΠΎΠ΄ 4 ΠΏΡΠΈΠΊΠΎΡΠ½Π΅ΡΡΡ ΠΊ Π·Π°Π³ΠΎΡΠΎΠ²ΠΊΠ΅, ΡΠ»Π΅ΠΊΡΡΠΈΡΠ΅ΡΠΊΠ°Ρ ΡΠ΅ΠΏΡ ΡΡΠ°Π½ΠΊΠ° Π·Π°ΠΌΠΊΠ½Π΅ΡΡΡ ΠΈ Π² Π½Π΅ΠΉ ΠΏΠΎΡΠ΅ΡΠ΅Ρ ΡΠ»Π΅ΠΊΡΡΠΈΡΠ΅ΡΠΊΠΈΠΉ ΡΠΎΠΊ. Π’ΠΎΠ³Π΄Π° Π½Π° ΠΊΠΎΠ½ΡΠ°Ρ ΠΊΠ°ΡΡΡΠΊΠΈ 14 ΡΠΎΠ·Π΄Π°Π΅ΡΡΡ ΡΠ°Π·Π½ΠΎΡΡΡ ΠΏΠΎΡΠ΅Π½ΡΠΈΠ°Π»ΠΎΠ², ΠΈ Π² Π½Π΅ΠΉ ΡΠ°ΠΊΠΆΠ΅ ΠΏΠΎΡΠ΅ΡΠ΅Ρ ΡΠ»Π΅ΠΊΡΡΠΈΡΠ΅ΡΠΊΠΈΠΉ ΡΠΎΠΊ. Π‘Π΅ΡΠ΄Π΅ΡΠ½ΠΈΠΊ 13 Π½Π°ΠΌΠ°Π³Π½ΠΈΡΠΈΡΡΡ ΠΈ Π²ΡΡΠ½Π΅ΡΡΡ Π² ΠΊΠ°ΡΡΡΠΊΡ 14, Ρ.Π΅. ΠΏΠΎΠ΄Π½ΠΈΠΌΠ΅ΡΡΡ, ΠΏΠΎΠ΄Π½ΠΈΠΌΠ°Ρ Π²ΠΌΠ΅ΡΡΠ΅ Ρ ΡΠΎΠ±ΠΎΠΉ ΠΏΠΎΠ»Π·ΡΠ½ 5 ΠΈ ΡΠ»Π΅ΠΊΡΡΠΎΠ΄ 4. ΠΡΠΊΡΠΎΠ²ΠΎΠΉ ΠΏΡΠΎΠΌΠ΅ΠΆΡΡΠΎΠΊ 3 ΠΌΠ΅ΠΆΠ΄Ρ ΡΠ»Π΅ΠΊΡΡΠΎΠ΄ΠΎΠΌ 4 ΠΈ Π·Π°Π³ΠΎΡΠΎΠ²ΠΊΠΎΠΉ 2 Π²ΠΎΡΡΡΠ°Π½ΠΎΠ²ΠΈΡΡΡ, ΠΈ ΠΎΡΠ½ΠΎΠ²Π½Π°Ρ ΡΠ»Π΅ΠΊΡΡΠΈΡΠ΅ΡΠΊΠ°Ρ ΡΠ΅ΠΏΡ ΠΎΠΊΠ°ΠΆΠ΅ΡΡΡ ΡΠ°Π·ΠΎΡΠ²Π°Π½Π½ΠΎΠΉ β ΡΠΎΠΊ Π² Π½Π΅ΠΉ ΠΈΡΡΠ΅Π·Π½Π΅Ρ. ΠΠ΄Π½ΠΎΠ²ΡΠ΅ΠΌΠ΅Π½Π½ΠΎ ΠΈΡΡΠ΅Π·Π½Π΅Ρ ΡΠΎΠΊ ΠΈ Π² ΠΊΠ°ΡΡΡΠΊΠ΅ ΡΠΎΠ»Π΅Π½ΠΎΠΈΠ΄Π°. Π‘Π΅ΡΠ΄Π΅ΡΠ½ΠΈΠΊ 13 ΡΠ°Π·ΠΌΠ°Π³Π½ΠΈΡΠΈΡΡΡ, ΠΏΠ΅ΡΠ΅ΡΡΠ°Π½Π΅Ρ Π²ΡΡΠ³ΠΈΠ²Π°ΡΡΡΡ Π² ΠΊΠ°ΡΡΡΠΊΡ ΠΈ ΠΏΠΎΠ΄ Π΄Π΅ΠΉΡΡΠ²ΠΈΠ΅ΠΌ ΡΠΎΠ±ΡΡΠ²Π΅Π½Π½ΠΎΠΉ ΠΌΠ°ΡΡΡ ΠΎΠΏΡΡΡΠΈΡΡΡ. ΠΠΌΠ΅ΡΡΠ΅ Ρ Π½ΠΈΠΌ ΠΎΠΏΡΡΡΡΡΡΡ ΠΏΠΎΠ»Π·ΡΠ½ 5 ΠΈ ΡΠ»Π΅ΠΊΡΡΠΎΠ΄ 4. ΠΠ΅ΠΆΠ΄Ρ ΡΠ»Π΅ΠΊΡΡΠΎΠ΄ΠΎΠΌ ΠΈ Π·Π°Π³ΠΎΡΠΎΠ²ΠΊΠΎΠΉ ΡΠ½ΠΎΠ²Π° ΠΏΡΠΎΠΈΠ·ΠΎΠΉΠ΄Π΅Ρ ΡΠ»Π΅ΠΊΡΡΠΈΡΠ΅ΡΠΊΠΈΠΉ ΡΠ°Π·ΡΡΠ΄. ΠΠΎ ΠΌΠ΅ΡΠ΅ ΡΠ³Π»ΡΠ±Π»Π΅Π½ΠΈΡ ΠΎΡΠ²Π΅ΡΡΡΠΈΡ ΡΠ»Π΅ΠΊΡΡΠΎΠ΄ Π±ΡΠ΄Π΅Ρ ΠΎΠΏΡΡΠΊΠ°ΡΡΡΡ ΠΏΠΎΠ΄ Π΄Π΅ΠΉΡΡΠ²ΠΈΠ΅ΠΌ ΡΠΈΠ»Ρ ΡΡΠΆΠ΅ΡΡΠΈ.
Π’Π°ΠΊ Π±ΡΠ΄Π΅Ρ ΠΏΡΠΎΠ΄ΠΎΠ»ΠΆΠ°ΡΡΡΡ, ΠΏΠΎΠΊΠ° ΠΈΠ΄Π΅Ρ ΠΏΡΠΎΡΠ΅ΡΡ ΠΏΡΠΎΡΠΈΠ²ΠΊΠΈ ΠΎΡΠ²Π΅ΡΡΡΠΈΡ. Π‘ΠΎΠ»Π΅Π½ΠΎΠΈΠ΄Π½ΡΠΉ ΡΠ΅Π³ΡΠ»ΡΡΠΎΡ Π°Π²ΡΠΎΠΌΠ°ΡΠΈΡΠ΅ΡΠΊΠΈ ΠΏΠΎΡΡΠ΅ΠΏΠ΅Π½Π½ΠΎ ΠΎΠΏΡΡΠΊΠ°Π΅Ρ ΡΠ»Π΅ΠΊΡΡΠΎΠ΄ ΠΏΠΎ ΠΌΠ΅ΡΠ΅ ΡΠ²Π΅Π»ΠΈΡΠ΅Π½ΠΈΡ Π³Π»ΡΠ±ΠΈΠ½Ρ ΠΎΡΠ²Π΅ΡΡΡΠΈΡ. ΠΡΠ»ΠΈ ΡΠ»Π΅ΠΊΡΡΠΎΠ΄ ΠΌΠΎΠΆΠ½ΠΎ ΡΡΠ°Π²Π½ΠΈΡΡ Ρ ΠΈΠ½ΡΡΡΡΠΌΠ΅Π½ΡΠΎΠΌ, ΡΠΎ ΡΠΎΠ»Π΅Π½ΠΎΠΈΠ΄Π½ΡΠΉ ΡΠ΅Π³ΡΠ»ΡΡΠΎΡ ΠΌΠΎΠΆΠ΅Ρ Π±ΡΡΡ ΡΠΏΠΎΠ΄ΠΎΠ±Π»Π΅Π½ ΠΌΠ΅Ρ Π°Π½ΠΈΠ·ΠΌΡ ΠΏΠΎΠ΄Π°ΡΠΈ. ΠΠ»Π΅ΠΊΡΡΠΎΠ΄Ρ, ΠΏΡΠΈΠΌΠ΅Π½ΡΠ΅ΠΌΡΠ΅ ΠΏΡΠΈ ΡΠ»Π΅ΠΊΡΡΠΎΠΈΡΠΊΡΠΎΠ²ΠΎΠΉ ΠΏΡΠΎΡΠΈΠ²ΠΊΠ΅, Π΄Π΅Π»Π°ΡΡ ΠΈΠ· ΠΌΡΠ³ΠΊΠΎΠΉ Π»Π°ΡΡΠ½ΠΈ. ΠΠ»Π΅ΠΊΡΡΠΎΠ΄ Π΄ΠΎΠ»ΠΆΠ΅Π½ ΠΈΠΌΠ΅ΡΡ ΠΏΡΠΎΡΠΈΠ»Ρ, ΠΏΠΎΠ΄ΠΎΠ±Π½ΡΠΉ ΠΏΡΠΎΡΠΈΠ»Ρ ΠΏΡΠΎΡΠΈΠ²Π°Π΅ΠΌΠΎΠ³ΠΎ ΠΎΡΠ²Π΅ΡΡΡΠΈΡ. ΠΡΠ»ΠΈ Π΄ΠΈΠ°ΠΌΠ΅ΡΡ ΠΎΡΠ²Π΅ΡΡΡΠΈΡ Π±ΠΎΠ»ΡΡΠ΅ 6 ΠΌΠΌ, ΡΠΎ ΡΠ»Π΅ΠΊΡΡΠΎΠ΄ Π»ΡΡΡΠ΅ Π΄Π΅Π»Π°ΡΡ ΠΏΡΡΡΠΎΡΠ΅Π»ΡΠΌ.
ΠΠ»Π΅ΠΊΡΡΠΎΠΈΡΠΊΡΠΎΠ²ΠΎΠΉ ΠΏΡΠΎΡΠΈΠ²ΠΊΠΎΠΉ ΡΠ΄Π°Π΅ΡΡΡ ΠΈΠ·Π³ΠΎΡΠΎΠ²Π»ΡΡΡ ΠΎΡΠ²Π΅ΡΡΡΠΈΡ Ρ ΠΊΡΠΈΠ²ΠΎΠ»ΠΈΠ½Π΅ΠΉΠ½ΠΎΠΉ ΠΎΡΡΡ (ΡΠΈΡ. 18.4). ΠΠ»Π΅ΠΊΡΡΠΎΠ΄ 2 ΠΈΠ· Π»Π°ΡΡΠ½Π½ΠΎΠΉ ΠΏΡΠΎΠ²ΠΎΠ»ΠΎΠΊΠΈ ΠΈΠ·ΠΎΠ³Π½ΡΡ ΠΏΠΎ Π΄ΡΠ³Π΅ ΠΎΠΊΡΡΠΆΠ½ΠΎΡΡΠΈ, ΡΠ°Π΄ΠΈΡΡ ΠΊΠΎΡΠΎΡΠΎΠΉ ΡΠ°Π²Π΅Π½ ΡΠ°Π΄ΠΈΡΡΡ Π·Π°ΠΊΡΠ΅ΠΏΠ»Π΅Π½ΠΈΡ ΠΎΡΠΈ ΠΎΡΠ²Π΅ΡΡΡΠΈΡ. ΠΠ»Π΅ΠΊΡΡΠΎΠ΄ ΡΠΊΡΠ΅ΠΏΠ»Π΅Π½ Π² Π΄Π΅ΡΠΆΠ°ΡΠ΅Π»Π΅ 3, ΠΊΠΎΡΠΎΡΡΠΉ ΠΌΠΎΠΆΠ΅Ρ ΠΏΠΎΠ²ΠΎΡΠ°ΡΠΈΠ²Π°ΡΡΡΡ Π²ΠΎΠΊΡΡΠ³ ΠΎΡΠΈ 1. ΠΠ΅ΡΠΆΠ°ΡΠ΅Π»Ρ 3 Π²ΠΎΠΊΡΡΠ³ ΠΎΡΠΈ ΠΏΠΎΠ²ΠΎΡΠ°ΡΠΈΠ²Π°Π΅ΡΡΡ Ρ ΠΏΠΎΠΌΠΎΡΡΡ ΡΠ½ΡΡΠ° 4, Π²Π΅ΡΡ Π½ΠΈΠΉ ΠΊΠΎΠ½Π΅Ρ ΠΊΠΎΡΠΎΡΠΎΠ³ΠΎ ΠΏΡΠΈΠΊΡΠ΅ΠΏΠ»Π΅Π½ ΠΊ ΡΠΎΠ»Π΅Π½ΠΎΠΈΠ΄Π½ΠΎΠΌΡ ΡΠ΅Π³ΡΠ»ΡΡΠΎΡΡ. Π ΠΎΡΡΠ°Π»ΡΠ½ΠΎΠΌ ΠΏΡΠΎΡΠ΅ΡΡ ΡΠΎΠ²Π΅ΡΡΠ°Π΅ΡΡΡ ΡΠ°ΠΊ ΠΆΠ΅, ΠΊΠ°ΠΊ ΠΈ ΠΏΡΠΈ ΠΏΡΠΎΡΠΈΠ²ΠΊΠ΅ ΠΎΡΠ²Π΅ΡΡΡΠΈΠΉ Ρ ΠΏΡΡΠΌΠΎΠ»ΠΈΠ½Π΅ΠΉΠ½ΠΎΠΉ ΠΎΡΡΡ.
Β
Π£Π½ΠΈΠ²Π΅ΡΡΠ°Π»ΡΠ½ΡΠ΅ ΡΠ»Π΅ΠΊΡΡΠΎΠΈΡΠΊΡΠΎΠ²ΡΠ΅ ΡΡΠ°Π½ΠΊΠΈ ΠΎΠ±ΡΡΠ½ΠΎ ΠΈΠΌΠ΅ΡΡ Π²Π΅ΡΡΠΈΠΊΠ°Π»ΡΠ½ΡΡ ΠΊΠΎΠΌΠΏΠΎΠ½ΠΎΠ²ΠΊΡ (ΡΠΈΡ. 18.5). ΠΠ²ΡΠΎΠΌΠ°ΡΠΈΡΠ΅ΡΠΊΠΈΠΉ ΡΠ΅Π³ΡΠ»ΡΡΠΎΡ ΠΏΠΎΠ΄Π°Ρ 7 ΡΠΎΠΎΠ±ΡΠ°Π΅Ρ Π²Π΅ΡΡΠΈΠΊΠ°Π»ΡΠ½ΡΠ΅ ΠΏΠ΅ΡΠ΅ΠΌΠ΅ΡΠ΅Π½ΠΈΡ ΡΠ»Π΅ΠΊΡΡΠΎΠ΄Ρ-ΠΈΠ½ΡΡΡΡΠΌΠ΅Π½ΡΡ 8. ΠΠ°Π½Π½Ρ 4 Ρ Π·Π°Π³ΠΎΡΠΎΠ²ΠΊΠΎΠΉ 9, ΡΡΡΠ°Π½ΠΎΠ²Π»Π΅Π½Π½ΠΎΠΉ Π½Π° ΡΡΠΎΠ»Π΅ 3, ΠΌΠΎΠΆΠ½ΠΎ ΠΏΠ΅ΡΠ΅ΠΌΠ΅ΡΠ°ΡΡ Π² Π²Π΅ΡΡΠΈΠΊΠ°Π»ΡΠ½ΠΎΠΌ Π½Π°ΠΏΡΠ°Π²Π»Π΅Π½ΠΈΠΈ Ρ ΠΏΠΎΠΌΠΎΡΡΡ ΡΠ»Π΅ΠΊΡΡΠΎΒΠ΄Π²ΠΈΠ³Π°ΡΠ΅Π»Ρ. Π‘ΡΠΏΠΏΠΎΡΡ 5 ΠΏΡΠΈ ΠΎΠ±ΡΠ°Π±ΠΎΡΠΊΠ΅ ΠΎΡΠ²Π΅ΡΡΡΠΈΠΉ Ρ ΠΊΡΠΈΠ²ΠΎΠ»ΠΈΠ½Π΅ΠΉΠ½ΠΎΠΉ ΠΎΡΡΡ ΠΏΠΎΠ²ΠΎΡΠ°ΡΠΈΠ²Π°Π΅ΡΡΡ Π²ΠΎΠΊΡΡΠ³ Π³ΠΎΡΠΈΠ·ΠΎΠ½ΡΠ°Π»ΡΠ½ΠΎΠΉ ΠΎΡΠΈ. ΠΠΎΠΏΠ΅ΡΠ΅ΡΠ½ΡΠΉ ΡΡΠΏΠΏΠΎΡΡ 6 ΠΏΠ΅ΡΠ΅ΠΌΠ΅ΡΠ°Π΅ΡΡΡ ΠΏΠΎ Π½Π°ΠΏΡΠ°Π²Π»ΡΡΡΠΈΠΌ ΠΏΡΠΎΠ΄ΠΎΠ»ΡΠ½ΠΎΠ³ΠΎ ΡΡΠΏΠΏΠΎΡΡΠ°. ΠΡΠΎΠ΄ΠΎΠ»ΡΠ½ΡΠΉ ΡΡΠΏΠΏΠΎΡΡ 5 ΡΡΡΠ°Π½ΠΎΠ²Π»Π΅Π½ Π½Π° Π½Π°ΠΏΡΠ°Π²Π»ΡΡΡΠΈΡ 2 ΡΡΠ°Π½ΠΈΠ½Ρ. ΠΠ΅Ρ Π°Π½ΠΈΠ·ΠΌΡ ΡΡΠ°Π½ΠΊΠ° Π½Π°Ρ ΠΎΠ΄ΡΡΡΡ Π²Π½ΡΡΡΠΈ ΠΊΠΎΡΠΏΡΡΠ° 1.
ΠΠΠΠΠ’Π ΠΠΠΠΠ£ΠΠ¬Π‘ΠΠ«Π Π‘Π’ΠΠΠΠ
Β
ΠΠ»Π΅ΠΊΡΡΠΎΠΈΡΠΊΡΠΎΠ²ΠΎΠΉ ΠΌΠ΅ΡΠΎΠ΄ ΠΎΠ±ΡΠ°Π±ΠΎΡΠΊΠΈ ΠΌΠ΅ΡΠ°Π»Π»ΠΎΠ² Π²ΡΡΠ΅ΡΠ½ΡΠ΅ΡΡΡ ΡΠ»Π΅ΠΊΡΡΠΎΠΈΠΌΠΏΡΠ»ΡΡΠ½ΠΎΠΉ ΠΎΠ±ΡΠ°Π±ΠΎΡΠΊΠΎΠΉ. ΠΡΠΎ ΠΎΠ±ΡΡΡΠ½ΡΠ΅ΡΡΡ ΡΠ΅ΠΌ, ΡΡΠΎ ΡΠ»Π΅ΠΊΡΡΠΎΠΈΡΠΊΡΠΎΠ²Π°Ρ ΠΎΠ±ΡΠ°Π±ΠΎΡΠΊΠ° ΠΈΠΌΠ΅Π΅Ρ ΡΡΠ΄ ΡΠ΅ΡΡΠ΅Π·Π½ΡΡ Π½Π΅Π΄ΠΎΡΡΠ°ΡΠΊΠΎΠ²: ΠΏΡΠΎΠΈΠ·Π²ΠΎΠ΄ΠΈΡΠ΅Π»ΡΠ½ΠΎΡΡΡ ΡΡΠ°Π²Π½ΠΈΡΠ΅Π»ΡΠ½ΠΎ Π½ΠΈΠ·ΠΊΠ°; ΠΈΠ·Π½ΠΎΡ ΡΠ»Π΅ΠΊΡΡΠΎΠ΄Π°-ΠΈΠ½ΡΡΡΡΠΌΠ΅Π½ΡΠ° ΠΎΡΠ½ΠΎΡΠΈΡΠ΅Π»ΡΠ½ΠΎ Π±ΠΎΠ»ΡΡΠΎΠΉ (Π½Π°ΠΏΡΠΈΠΌΠ΅Ρ, ΠΈΠ·Π½ΠΎΡ Π»Π°ΡΡΠ½Π½ΡΡ ΡΠ»Π΅ΠΊΡΡΠΎΠ΄ΠΎΠ² ΡΠΎΡΡΠ°Π²Π»ΡΠ΅Ρ 25β30 % ΠΎΠ±ΡΠ΅ΠΌΠ° ΠΌΠ΅ΡΠ°Π»Π»Π°, ΡΠ½ΡΡΠΎΠ³ΠΎ Ρ Π·Π°Π³ΠΎΡΠΎΠ²ΠΊΠΈ), ΡΡΠΎ Π·Π½Π°ΡΠΈΡΠ΅Π»ΡΠ½ΠΎ ΡΠ΄ΠΎΡΠΎΠΆΠ°Π΅Ρ ΡΡΠΎΡ Π²ΠΈΠ΄ ΠΎΠ±ΡΠ°Π±ΠΎΡΠΊΠΈ ΠΈ Π·Π°ΡΡΡΠ΄Π½ΡΠ΅Ρ ΠΏΠΎΠ»ΡΡΠ΅Π½ΠΈΠ΅ Π½Π΅ΠΎΠ±Ρ ΠΎΠ΄ΠΈΠΌΠΎΠΉ ΡΠΎΡΠ½ΠΎΡΡΠΈ. ΠΡΠΎΠΌΠ΅ ΡΠΎΠ³ΠΎ, ΡΠ»Π΅ΠΊΡΡΠΎΠΈΡΠΊΡΠΎΠ²Π°Ρ ΠΎΠ±ΡΠ°Π±ΠΎΡΠΊΠ° ΡΡΠ΅Π±ΡΠ΅Ρ Π±ΠΎΠ»ΡΡΠΎΠ³ΠΎ ΡΠ°ΡΡ ΠΎΠ΄Π° ΡΠ»Π΅ΠΊΡΡΠΎΡΠ½Π΅ΡΠ³ΠΈΠΈ. ΠΠ»Π΅ΠΊΡΡΠΎΠΈΠΌΠΏΡΠ»ΡΡΠ½ΡΠΉ ΡΠΏΠΎΡΠΎΠ± ΠΎΠ±ΡΠ°Π±ΠΎΡΠΊΠΈ ΠΌΠ΅ΡΠ°Π»Π»ΠΎΠ² Π½Π΅ Π»ΠΈΡΠ΅Π½ ΠΏΠΎΠ»Π½ΠΎΡΡΡΡ Π½Π΅Π΄ΠΎΡΡΠ°ΡΠΊΠΎΠ² ΡΠ»Π΅ΠΊΡΡΠΎΠΈΡΠΊΡΠΎΠ²ΠΎΠ³ΠΎ ΠΌΠ΅ΡΠΎΠ΄Π°, ΠΎΠ΄Π½Π°ΠΊΠΎ ΡΠ²Π»ΡΠ΅ΡΡΡ Π±ΠΎΠ»Π΅Π΅ ΠΏΡΠΎΠΈΠ·Π²ΠΎΠ΄ΠΈΡΠ΅Π»ΡΠ½ΡΠΌ.
Π ΡΠ»Π΅ΠΊΡΡΠΈΡΠ΅ΡΠΊΠΎΠΉ ΡΡ Π΅ΠΌΠ΅ (ΡΠΈΡ. 18.6) ΡΠ»Π΅ΠΊΡΡΠΎΠΈΠΌΠΏΡΠ»ΡΡΠ½ΠΎΠ³ΠΎ ΡΡΠ°Π½ΠΊΠ° ΠΎΡΡΡΡΡΡΠ²ΡΡΡ ΠΊΠΎΠ½Π΄Π΅Π½ΡΠ°ΡΠΎΡΡ, ΠΊΠΎΡΠΎΡΡΠ΅ Π±ΡΠ»ΠΈ Π½ΡΠΆΠ½Ρ Π² ΡΠ»Π΅ΠΊΡΡΠΎΠΈΡΠΊΡΠΎΠ²ΠΎΠΌ ΡΡΠ°Π½ΠΊΠ΅ Π΄Π»Ρ ΠΏΠΎΠ»ΡΡΠ΅Π½ΠΈΡ ΠΈΠΌΠΏΡΠ»ΡΡΠ½ΡΡ ΡΠ°Π·ΡΡΠ΄ΠΎΠ². Π ΡΠ»Π΅ΠΊΡΡΠΎΠΈΠΌΠΏΡΠ»ΡΡΠ½ΠΎΠΌ ΡΡΠ°Π½ΠΊΠ΅ ΠΈΠΌΠΏΡΠ»ΡΡΠ½ΡΠ΅ ΡΠ°Π·ΡΡΠ΄Ρ, Π½Π΅ΠΎΠ±Ρ ΠΎΠ΄ΠΈΠΌΡΠ΅ Π΄Π»Ρ ΡΠ»Π΅ΠΊΡΡΠΈΡΠ΅ΡΠΊΠΎΠΉ ΡΡΠΎΠ·ΠΈΠΈ, ΡΠΎΠ·Π΄Π°ΡΡΡΡ (Π³Π΅Π½Π΅ΡΠΈΡΡΡΡΡΡ) Π² ΡΠΏΠ΅ΡΠΈΠ°Π»ΡΠ½ΠΎΠΌ Π³Π΅Π½Π΅ΡΠ°ΡΠΎΡΠ΅ ΠΈΠΌΠΏΡΠ»ΡΡΠΎΠ². Π ΠΎΠ»Ρ ΡΠ°ΠΊΠΎΠ³ΠΎ Π³Π΅Π½Π΅ΡΠ°ΡΠΎΡΠ° ΠΈΠΌΠΏΡΠ»ΡΡΠΎΠ² ΠΈΠ³ΡΠ°ΡΡ ΠΏΡΠ΅ΠΎΠ±ΡΠ°Π·ΠΎΠ²Π°ΡΠ΅Π»Ρ 1 ΠΈ ΡΠ΅Π»Π΅Π½ΠΎΠ²ΡΠΉ Π²ΡΠΏΡΡΠΌΠΈΡΠ΅Π»Ρ 2. ΠΡΠ΅ΠΎΠ±ΡΠ°Π·ΠΎΠ²Π°ΡΠ΅Π»Ρ 1 ΠΈΠ·ΠΌΠ΅Π½ΡΠ΅Ρ (ΠΏΡΠ΅ΠΎΠ±ΡΠ°Π·ΡΠ΅Ρ) Π½Π°ΠΏΡΡΠΆΠ΅Π½ΠΈΠ΅ ΠΈ ΡΠ°ΡΡΠΎΡΡ ΠΏΠ΅ΡΠ΅ΠΌΠ΅Π½Π½ΠΎΠ³ΠΎ ΡΠΎΠΊΠ°; Π΅Π³ΠΎ ΠΏΠΎΠ΄ΠΊΠ»ΡΡΠ°ΡΡ ΠΊ Π·Π°Π²ΠΎΠ΄ΡΠΊΠΎΠΉ ΡΠ΅ΡΠΈ (Π½Π°ΠΏΡΡΠΆΠ΅Π½ΠΈΠ΅ 380 Π, ΡΠ°ΡΡΠΎΡΠ° 50 ΠΡ). ΠΠ° Π²ΡΡ ΠΎΠ΄Π½ΡΡ Π·Π°ΠΆΠΈΠΌΠ°Ρ ΠΏΡΠ΅ΠΎΠ±ΡΠ°Π·ΠΎΠ²Π°ΡΠ΅Π»Ρ ΠΏΠΎΠ»ΡΡΠ°ΡΡ ΡΠΎΠΊ Ρ Π±ΠΎΠ»Π΅Π΅ Π½ΠΈΠ·ΠΊΠΈΠΌ Π½Π°ΠΏΡΡΠΆΠ΅Π½ΠΈΠ΅ΠΌ (50 Π) ΠΈ ΠΏΠΎΠ²ΡΡΠ΅Π½Π½ΠΎΠΉ ΡΠ°ΡΡΠΎΡΠΎΠΉ (490 ΠΡ). Π‘Π΅Π»Π΅Π½ΠΎΠ²ΡΠΉ Π²ΡΠΏΡΡΠΌΠΈΡΠ΅Π»Ρ 2 ΠΏΡΠΎΠΏΡΡΠΊΠ°Π΅Ρ ΡΠΎΠΊ ΡΠΎΠ»ΡΠΊΠΎ Π² ΠΎΠ΄Π½ΠΎΠΌ Π½Π°ΠΏΡΠ°Π²Π»Π΅Π½ΠΈΠΈ. Π’Π°ΠΊΠΈΠΌ ΠΎΠ±ΡΠ°Π·ΠΎΠΌ, Π² ΡΠ΅ΡΠ΅Π½ΠΈΠ΅ 1 Ρ ΠΏΠΎΠ»ΡΡΠ°ΡΡ 490 ΠΈΠΌΠΏΡΠ»ΡΡΠΎΠ². ΠΡΠΈ ΡΡΠΎΠΌ ΠΌΠ΅ΠΆΠ΄Ρ ΡΠ»Π΅ΠΊΡΡΠΎΠ΄ΠΎΠΌ 3 ΠΈ Π·Π°Π³ΠΎΡΠΎΠ²ΠΊΠΎΠΉ 4 ΠΏΡΠΎΠΈΡΡ ΠΎΠ΄ΡΡ ΡΠ»Π΅ΠΊΡΡΠΈΡΠ΅ΡΠΊΠΈΠ΅ ΡΠ°Π·ΡΡΠ΄Ρ. ΠΠ°Π³ΠΎΡΠΎΠ²ΠΊΠ΅ ΡΠΎΠΎΠ±ΡΠ°Π΅ΡΡΡ ΠΊΠΎΠ»Π΅Π±Π°ΡΠ΅Π»ΡΠ½ΠΎΠ΅ Π΄Π²ΠΈΠΆΠ΅Π½ΠΈΠ΅ Π² Π½Π°ΠΏΡΠ°Π²Π»Π΅Π½ΠΈΠΈ ΠΏΠΎΠ΄Π°ΡΠΈ, ΡΡΠΎ ΠΏΡΠ΅Π΄ΠΎΡ ΡΠ°Π½ΡΠ΅Ρ ΡΠ»Π΅ΠΊΡΡΠΎΠ΄Ρ ΠΎΡ ΠΊΠΎΡΠΎΡΠΊΠΎΠ³ΠΎ Π·Π°ΠΌΡΠΊΠ°Π½ΠΈΡ.
Π ΠΎΡΠ»ΠΈΡΠΈΠ΅ ΠΎΡ ΡΠ»Π΅ΠΊΡΡΠΎΠΈΡΠΊΡΠΎΠ²ΠΎΠΉ ΠΎΠ±ΡΠ°Π±ΠΎΡΠΊΠΈ ΠΏΡΠΈ ΡΠ»Π΅ΠΊΡΡΠΎΠΈΠΌΠΏΡΠ»ΡΡΠ½ΠΎΠΌ ΠΏΡΠΎΡΠ΅ΡΡΠ΅ Π·Π°Π³ΠΎΡΠΎΠ²ΠΊΠ° ΡΠΎΠ΅Π΄ΠΈΠ½Π΅Π½Π° Ρ ΠΊΠ°ΡΠΎΠ΄ΠΎΠΌ ΡΠ»Π΅ΠΊΡΡΠΈΡΠ΅ΡΠΊΠΎΠΉ ΡΠ΅ΠΏΠΈ, Π° ΠΈΠ½ΡΡΡΡΠΌΠ΅Π½Ρ β Ρ Π°Π½ΠΎΠ΄ΠΎΠΌ. ΠΠ±ΡΠ°Π±ΠΎΡΠΊΡ Π²Π΅Π΄ΡΡ Π² ΠΆΠΈΠ΄ΠΊΠΎΠΉ ΡΡΠ΅Π΄Π΅ (Π² ΠΌΠ°ΡΠ»Π°Ρ Π½ΠΈΠ·ΠΊΠΎΠΉ Π²ΡΠ·ΠΊΠΎΡΡΠΈ: ΠΈΠ½Π΄ΡΡΡΡΠΈΠ°Π»ΡΠ½ΠΎΠ΅ 12, ΡΡΠ°Π½ΡΡΠΎΡΠΌΠ°ΡΠΎΡΠ½ΠΎΠ΅, Π° ΡΠ°ΠΊΠΆΠ΅ Π² ΠΊΠ΅ΡΠΎΡΠΈΠ½Π΅ ΠΈ Π΄Ρ.). ΠΠ»Π΅ΠΊΡΡΠΎΠ΄Ρ ΠΈΠ·Π³ΠΎΡΠΎΠ²Π»ΡΡΡ ΠΈΠ· ΠΌΠ΅Π΄ΠΈ, Π°Π»ΡΠΌΠΈΠ½ΠΈΡ, ΡΡΠ³ΡΠ½Π°, Π³ΡΠ°ΡΠΈΡΠ° ΠΈ Ρ. Π΄. ΠΡΠΎΡΠ΅ΡΡ ΡΠ»Π΅ΠΊΡΡΠΎΠΈΠΌΠΏΡΠ»ΡΡΠ½ΠΎΠΉ ΠΎΠ±ΡΠ°Π±ΠΎΡΠΊΠΈ ΠΎΡΠ½ΠΎΠ²Π°Π½ Π½Π° ΡΠ°ΡΠΏΠ»Π°Π²Π»Π΅Π½ΠΈΠΈ ΠΌΠ°Π»ΡΡ ΠΎΠ±ΡΠ΅ΠΌΠΎΠ² ΠΌΠ΅ΡΠ°Π»Π»Π° ΡΠ»Π΅ΠΊΡΡΠΎΠ΄ΠΎΠ² Π² ΡΠ΅Ρ ΠΌΠ΅ΡΡΠ°Ρ , Π³Π΄Π΅ ΠΌΠ΅ΠΆΠ΄Ρ Π½ΠΈΠΌΠΈ ΠΏΡΠΎΡΠΊΠ°ΠΊΠΈΠ²Π°ΡΡ ΡΠ»Π΅ΠΊΡΡΠΈΡΠ΅ΡΠΊΠΈΠ΅ ΡΠ°Π·ΡΡΠ΄Ρ ΠΠ°ΠΆΠ΄ΡΠΉ ΡΠ°Π·ΡΡΠ΄ ΡΠ½ΠΈΠΌΠ°Π΅Ρ ΠΎΡΠ΅Π½Ρ Π½Π΅Π±ΠΎΠ»ΡΡΠΎΠ΅ ΠΊΠΎΠ»ΠΈΡΠ΅ΡΡΠ²ΠΎ ΠΌΠ΅ΡΠ°Π»Π»Π°, Π½ΠΎ ΡΠ°ΠΊ ΠΊΠ°ΠΊ ΡΠ°Π·ΡΡΠ΄Ρ ΠΏΡΠΎΠΈΡΡ ΠΎΠ΄ΡΡ ΠΎΡΠ΅Π½Ρ ΡΠ°ΡΡΠΎ, ΠΎΠ΄ΠΈΠ½ Π·Π° Π΄ΡΡΠ³ΠΈΠΌ, ΡΠΎ ΠΎΠ±ΡΠΈΠΉ ΠΎΠ±ΡΠ΅ΠΌ ΠΌΠ΅ΡΠ°Π»Π»Π° Π΄ΠΎΡΡΠ°ΡΠΎΡΠ½ΠΎ Π²Π΅Π»ΠΈΠΊ. ΠΠΎ ΠΌΠ΅ΡΠ΅ ΡΡΠ΅ΠΌΠ° ΠΌΠ΅ΡΠ°Π»Π»Π° ΡΠ»Π΅ΠΊΡΡΠΎΠ΄-ΠΈΠ½ΡΡΡΡΠΌΠ΅Π½ΡΡ ΡΠΎΠΎΠ±ΡΠ°Π΅ΡΡΡ ΠΏΠΎΠ΄Π°ΡΠ°.
ΠΠ»Π΅ΠΊΡΡΠΎΠΈΠΌΠΏΡΠ»ΡΡΠ½ΡΠΉ ΠΌΠ΅ΡΠΎΠ΄ ΠΏΠΎΠ·Π²ΠΎΠ»ΡΠ΅Ρ ΠΏΡΠΎΠΈΠ·Π²ΠΎΠ΄ΠΈΡΡ ΠΎΠ±ΡΠ°Π±ΠΎΡΠΊΡ Π½Π° Π½Π΅Π±ΠΎΠ»ΡΡΠΈΡ ΠΏΠ»ΠΎΡΠ°Π΄ΡΡ (Π΄ΠΎ 180 ΡΠΌ2) Ρ Π²ΡΡΠΎΠΊΠΎΠΉ ΠΏΡΠΎΠΈΠ·Π²ΠΎΠ΄ΠΈΡΠ΅Π»ΡΠ½ΠΎΡΡΡΡ (4000 ΠΌΠΌ3/ΠΌΠΈΠ½).
ΠΠΠΠΠΠ-ΠΠΠ₯ΠΠΠΠ§ΠΠ‘ΠΠΠ Π‘Π’ΠΠΠΠ
Β
ΠΡΠΈ Π°Π½ΠΎΠ΄Π½ΠΎ-ΠΌΠ΅Ρ Π°Π½ΠΈΡΠ΅ΡΠΊΠΎΠΉ ΡΠ΅Π·ΠΊΠ΅ (ΡΠΈΡ. 18.7) ΡΠ»Π΅ΠΊΡΡΠΎΠ΄-ΠΈΠ½ΡΡΡΡΠΌΠ΅Π½Ρ Π΄Π΅Π»Π°ΡΡ ΠΎΠ±ΡΡΠ½ΠΎ Π² Π²ΠΈΠ΄Π΅ Π΄ΠΈΡΠΊΠ°, Π±ΡΡΡΡΠΎ Π²ΡΠ°ΡΠ°ΡΡΠ΅Π³ΠΎΡΡ Π²ΠΎΠΊΡΡΠ³ ΡΠ²ΠΎΠ΅ΠΉ ΠΎΡΠΈ Π ΠΏΡΠΎΡΡΡΠ°Π½ΡΡΠ²ΠΎ ΠΌΠ΅ΠΆΠ΄Ρ ΠΎΠ±ΡΠ°Π±Π°ΡΡΠ²Π°Π΅ΠΌΠΎΠΉ Π·Π°Π³ΠΎΡΠΎΠ²ΠΊΠΎΠΉ 1 ΠΈ Π²ΡΠ°ΡΠ°ΡΡΠΈΠΌΡΡ ΡΠ»Π΅ΠΊΡΡΠΎΠ΄ΠΎΠΌ-Π΄ΠΈΡΠΊΠΎΠΌ 2 ΠΏΠΎΠ΄Π°Π΅ΡΡΡ ΠΏΠΎ ΡΡΡΠ±ΠΊΠ΅ 3 ΡΠ»Π΅ΠΊΡΡΠΎΠ»ΠΈΡ. ΠΠ»Π΅ΠΊΡΡΠΎΠ΄ β Π΄ΠΈΡΠΊ, ΠΈΠ·Π³ΠΎΡΠΎΠ²Π»Π΅Π½Π½ΡΠΉ ΠΈΠ· ΠΌΡΠ³ΠΊΠΎΠΉ ΡΡΠ°Π»ΠΈ, ΠΈ Π·Π°Π³ΠΎΡΠΎΠ²ΠΊΠ° ΠΏΡΠΈΡΠΎΠ΅Π΄ΠΈΠ½Π΅Π½Ρ, ΠΊΠ°ΠΊ ΠΏΡΠΈ ΡΠ»Π΅ΠΊΡΡΠΎΠΈΡΠΊΡΠΎΠ²ΠΎΠΉ ΠΎΠ±ΡΠ°Π±ΠΎΡΠΊΠ΅, ΠΊ Π³Π΅Π½Π΅ΡΠ°ΡΠΎΡΡ ΠΏΠΎΡΡΠΎΡΠ½Π½ΠΎΠ³ΠΎ ΡΠΎΠΊΠ° 4 (Π΄ΠΈΡΠΊ β ΠΊ ΠΎΡΡΠΈΡΠ°ΡΠ΅Π»ΡΠ½ΡΠΌ, Π° Π΄Π΅ΡΠ°Π»Ρ β ΠΊ ΠΏΠΎΠ»ΠΎΠΆΠΈΡΠ΅Π»ΡΠ½ΡΠΌ ΠΊΠ»Π΅ΠΌΠΌΠ°ΠΌ). Π ΠΎΡΠ»ΠΈΡΠΈΠ΅ ΠΎΡ ΡΠ»Π΅ΠΊΡΡΠΎΠΈΡΠΊΡΠΎΠ²ΠΎΠΉ ΠΎΠ±ΡΠ°Π±ΠΎΡΠΊΠΈ ΠΆΠΈΠ΄ΠΊΠΎΡΡΡ, ΠΊΠΎΡΠΎΡΠ°Ρ Π½Π°Ρ ΠΎΠ΄ΠΈΡΡΡ ΠΌΠ΅ΠΆΠ΄Ρ ΡΠ»Π΅ΠΊΡΡΠΎΠ΄ΠΎΠΌ-Π΄ΠΈΡΠΊΠΎΠΌ ΠΈ Π·Π°Π³ΠΎΡΠΎΠ²ΠΊΠΎΠΉ, ΠΏΡΠΎΠ²ΠΎΠ΄ΠΈΡ ΡΠ»Π΅ΠΊΡΡΠΈΡΠ΅ΡΠΊΠΈΠΉ ΡΠΎΠΊ.
Β
ΠΠ·-Π·Π° ΡΠΎΠΏΡΠΈΠΊΠΎΡΠ½ΠΎΠ²Π΅Π½ΠΈΡ Π΄ΠΈΡΠΊΠ° Ρ Π·Π°Π³ΠΎΡΠΎΠ²ΠΊΠΎΠΉ ΠΈ Π½Π°Π»ΠΈΡΠΈΡ ΡΠ»Π΅ΠΊΡΡΠΎΠ»ΠΈΡΠ° ΠΌΠ΅ΠΆΠ΄Ρ Π΄ΠΈΡΠΊΠΎΠΌ ΠΈ Π·Π°Π³ΠΎΡΠΎΠ²ΠΊΠΎΠΉ Π½Π΅ΠΏΡΠ΅ΡΡΠ²Π½ΠΎ ΠΏΡΠΎΡ ΠΎΠ΄ΠΈΡ ΡΠ»Π΅ΠΊΡΡΠΈΡΠ΅ΡΠΊΠΈΠΉ ΡΠΎΠΊ. ΠΡΠΈ Π°Π½ΠΎΠ΄Π½ΠΎ-ΠΌΠ΅Ρ Π°Π½ΠΈΡΠ΅ΡΠΊΠΎΠΉ ΡΠ΅Π·ΠΊΠ΅ Π΄ΠΈΡΠΊ ΠΈΠΌΠ΅Π΅Ρ ΠΌΠ΅Π΄Π»Π΅Π½Π½ΡΡ ΠΏΠΎΠΏΠ΅ΡΠ΅ΡΠ½ΡΡ ΠΏΠΎΠ΄Π°ΡΡ.
Π‘ΡΡΠ½ΠΎΡΡΡ ΠΏΡΠΎΡΠ΅ΡΡΠ° ΡΠΎΡΡΠΎΠΈΡ Π² ΡΠ»Π΅Π΄ΡΡΡΠ΅ΠΌ. ΠΠΈΠ΄ΠΊΠΎΡΡΡ-ΡΠ»Π΅ΠΊΡΡΠΎΠ»ΠΈΡ, ΠΊΠΎΡΠΎΡΠ°Ρ ΠΏΠΎΠ΄Π°Π΅ΡΡΡ Π² ΠΏΡΠΎΡΡΡΠ°Π½ΡΡΠ²ΠΎ ΠΌΠ΅ΠΆΠ΄Ρ Π΄ΠΈΡΠΊΠΎΠΌ 1 ΠΈ Π·Π°Π³ΠΎΡΠΎΠ²ΠΊΠΎΠΉ 2, ΡΠ°ΡΡΠ²ΠΎΡΡΠ΅Ρ ΠΏΠΎΠ΄ Π΄Π΅ΠΉΡΡΠ²ΠΈΠ΅ΠΌ ΡΠΎΠΊΠ° ΠΌΠ΅ΡΠ°Π»Π», ΠΎΠ±ΡΠ°Π·ΡΡ Π½Π° ΠΏΠΎΠ²Π΅ΡΡ Π½ΠΎΡΡΠΈ Π·Π°Π³ΠΎΡΠΎΠ²ΠΊΠΈ ΡΠΎΠ½ΠΊΡΡ ΠΏΠ»Π΅Π½ΠΊΡ 3 (ΡΠΈΡ. 18.8, Π°). Π’ΠΎΠ½ΠΊΠ°Ρ ΠΏΠ»Π΅Π½ΠΊΠ°, ΠΈΠΌΠ΅ΡΡΠ°Ρ Π½ΠΈΠ·ΠΊΡΡ ΠΏΡΠΎΡΠ½ΠΎΡΡΡ, Π»Π΅Π³ΠΊΠΎ ΡΠΎΡΠΊΠ°Π±Π»ΠΈΠ²Π°Π΅ΡΡΡ Π±ΡΡΡΡΠΎ Π²ΡΠ°ΡΠ°ΡΡΠΈΠΌΡΡ Π΄ΠΈΡΠΊΠΎΠΌ. ΠΠ° Π΅Π΅ ΠΌΠ΅ΡΡΠ΅ Π²Π½ΠΎΠ²Ρ ΠΎΠ±ΡΠ°Π·ΡΠ΅ΡΡΡ ΠΏΠ»Π΅Π½ΠΊΠ°, ΠΊΠΎΡΠΎΡΠ°Ρ Π²Π½ΠΎΠ²Ρ ΡΡΠΈΡΠ°Π΅ΡΡΡ Π΄ΠΈΡΠΊΠΎΠΌ ΠΏΡΠΈ Π΄Π°Π»ΡΠ½Π΅ΠΉΡΠ΅ΠΌ Π΅Π³ΠΎ Π²ΡΠ°ΡΠ΅Π½ΠΈΠΈ. Π’Π°ΠΊΠΈΠΌ ΠΎΠ±ΡΠ°Π·ΠΎΠΌ, Π½Π΅ΠΏΡΠ΅ΡΡΠ²Π½ΠΎ ΠΏΡΠΎΠΈΡΡ ΠΎΠ΄ΠΈΡ ΡΠ»Π΅ΠΊΡΡΠΎΡ ΠΈΠΌΠΈΡΠ΅ΡΠΊΠΎΠ΅ ΡΠ°Π·ΡΠ΅Π΄Π°Π½ΠΈΠ΅ ΠΏΠΎΠ²Π΅ΡΡ Π½ΠΎΡΡΠΈ Π΄Π΅ΡΠ°Π»ΠΈ.
ΠΠ΅ΡΡΠΈΠ½Ρ Π½Π΅ΡΠΎΠ²Π½ΠΎΡΡΠ΅ΠΉ Π½Π° ΠΏΠΎΠ²Π΅ΡΡ Π½ΠΎΡΡΠΈ Π·Π°Π³ΠΎΡΠΎΠ²ΠΊΠΈ (ΡΠΈΡ. 18.8, Π±) ΠΎΡΠ΄Π΅Π»Π΅Π½Ρ ΠΎΡ Π΄ΠΈΡΠΊΠ° ΠΎΡΠ΅Π½Ρ Π½Π΅Π±ΠΎΠ»ΡΡΠΈΠΌ ΠΏΡΠΎΠΌΠ΅ΠΆΡΡΠΊΠΎΠΌ, ΡΠ΅ΡΠ΅Π· ΠΊΠΎΡΠΎΡΡΠΉ Π»Π΅Π³ΠΊΠΎ ΠΏΡΠΎΡΠΊΠ°ΠΊΠΈΠ²Π°Π΅Ρ ΡΠ°Π·ΡΡΠ΄, ΠΈ ΠΏΠΎΠ΄Π²Π΅ΡΠ³Π°ΡΡΡΡ ΡΠ»Π΅ΠΊΡΡΠΈΡΠ΅ΡΠΊΠΎΠΉ ΡΡΠΎΠ·ΠΈΠΈ: ΠΎΠ½ΠΈ ΡΠ°ΡΠΏΠ»Π°Π²Π»ΡΡΡΡΡ ΠΈ ΡΠ°ΡΡΠΈΡΠΊΠΈ Π²ΡΠ½ΠΎΡΡΡΡΡ Π²ΡΠ°ΡΠ°ΡΡΠΈΠΌΡΡ Π΄ΠΈΡΠΊΠΎΠΌ ΠΈΠ· ΠΌΠ΅ΡΡΠ° ΡΠ°Π·ΡΠ΅Π·Π° Π² Π²ΠΈΠ΄Π΅ ΡΠ½ΠΎΠΏΠ° ΠΈΡΠΊΡ. Π’Π°ΠΊΠΈΠΌ ΠΎΠ±ΡΠ°Π·ΠΎΠΌ, ΠΏΡΠΈ Π°Π½ΠΎΠ΄Π½ΠΎ-ΠΌΠ΅Ρ Π°Π½ΠΈΡΠ΅ΡΠΊΠΎΠΉ ΠΎΠ±ΡΠ°Π±ΠΎΡΠΊΠ΅ ΠΏΡΠΎΠΈΡΡ ΠΎΠ΄ΡΡ ΠΎΠ΄Π½ΠΎΠ²ΡΠ΅ΠΌΠ΅Π½Π½ΠΎ Π΄Π²Π° ΠΏΡΠΎΡΠ΅ΡΡΠ°: ΡΠ»Π΅ΠΊΡΡΠΎΠΌΠ΅Ρ Π°Π½ΠΈΡΠ΅ΡΠΊΠΎΠ΅ ΡΠ°Π·ΡΠ΅Π΄Π°Π½ΠΈΠ΅ ΠΏΠΎΠ²Π΅ΡΡ Π½ΠΎΡΡΠΈ ΠΈ ΡΠ»Π΅ΠΊΡΡΠΈΡΠ΅ΡΠΊΠ°Ρ ΡΡΠΎΠ·ΠΈΡ. Π ΠΊΠ°ΡΠ΅ΡΡΠ²Π΅ ΡΠ°Π±ΠΎΡΠ΅ΠΉ ΠΆΠΈΠ΄ΠΊΠΎΡΡΠΈ-ΡΠ»Π΅ΠΊΡΡΠΎΠ»ΠΈΡΠ° ΠΏΡΠΈΠΌΠ΅Π½ΡΡΡ Π²ΠΎΠ΄Π½ΡΠΉ ΡΠ°ΡΡΠ²ΠΎΡ ΠΆΠΈΠ΄ΠΊΠΎΠ³ΠΎ ΡΡΠ΅ΠΊΠ»Π°.
ΠΠ½ΠΎΠ΄Π½ΠΎ-ΠΌΠ΅Ρ Π°Π½ΠΈΡΠ΅ΡΠΊΠ°Ρ ΠΎΠ±ΡΠ°Π±ΠΎΡΠΊΠ° ΠΏΠΎΠ»ΡΡΠΈΠ»Π° Π½Π°ΠΈΠ±ΠΎΠ»ΡΡΠ΅Π΅ ΡΠ°ΡΠΏΡΠΎΡΡΡΠ°Π½Π΅Π½ΠΈΠ΅ ΠΏΡΠΈ ΡΠ΅Π·ΠΊΠ΅ ΠΌΠ΅ΡΠ°Π»Π»ΠΈΡΠ΅ΡΠΊΠΈΡ Π·Π°Π³ΠΎΡΠΎΠ²ΠΎΠΊ ΠΈ Π·Π°ΡΠΎΡΠΊΠ΅ ΡΠ΅ΠΆΡΡΠΈΡ ΠΈΠ½ΡΡΡΡΠΌΠ΅Π½ΡΠΎΠ²; ΡΡΡ ΠΎΠ±ΡΠ°Π±ΠΎΡΠΊΡ ΠΌΠΎΠΆΠ½ΠΎ ΠΈΡΠΏΠΎΠ»ΡΠ·ΠΎΠ²Π°ΡΡ ΠΈ Π΄Π»Ρ ΡΠΈΡΡΠΎΠ²ΠΎΠΉ Π΄ΠΎΠ²ΠΎΠ΄ΠΊΠΈ ΠΏΠΎΠ²Π΅ΡΡ Π½ΠΎΡΡΠ΅ΠΉ. ΠΠ»Ρ Π°Π½ΠΎΠ΄Π½ΠΎ-ΠΌΠ΅Ρ Π°Π½ΠΈΡΠ΅ΡΠΊΠΎΠΉ ΡΠ΅Π·ΠΊΠΈ ΠΏΡΠΈΠΌΠ΅Π½ΡΡΡ ΡΡΠ°Π½ΠΊΠΈ ΡΠ°Π·Π»ΠΈΡΠ½ΡΡ ΠΊΠΎΠ½ΡΡΡΡΠΊΡΠΈΠΉ. Π Π°Π·ΡΠ΅Π·Π°Π΅ΠΌΡΠΉ ΠΏΡΡΡΠΎΠΊ 10 (ΡΠΈΡ. 18.9) Π·Π°ΠΆΠΈΠΌΠ°ΡΡ Π² ΡΠΈΡΠΊΠ°Ρ 9. ΠΠΈΡΠΊ 3 ΠΈΠ· Π»ΠΈΡΡΠΎΠ²ΠΎΠΉ ΡΡΠ°Π»ΠΈ ΡΠΊΡΠ΅ΠΏΠ»Π΅Π½ Π½Π° ΠΎΡΠΈ, ΡΠ°ΡΠΏΠΎΠ»ΠΎΠΆΠ΅Π½Π½ΠΎΠΉ Π² ΠΌΠ°ΡΡΠ½ΠΈΠΊΠ΅ 4, ΠΊΠΎΡΠΎΡΡΠΉ ΠΌΠΎΠΆΠ΅Ρ ΠΏΠΎΠ²ΠΎΡΠ°ΡΠΈΠ²Π°ΡΡΡΡ Π²ΠΎΠΊΡΡΠ³ ΠΎΡΠΈ 6. ΠΠΎΠ²ΠΎΡΠΎΡΠΎΠΌ ΠΌΠ°ΡΡΠ½ΠΈΠΊΠ° ΠΎΠ±Π΅ΡΠΏΠ΅ΡΠΈΠ²Π°Π΅ΡΡΡ Π½Π΅ΠΎΠ±Ρ ΠΎΠ΄ΠΈΠΌΠ°Ρ ΠΏΠΎΠ΄Π°ΡΠ°. ΠΠΎΠ΄Π°ΡΠ° ΡΠ΅Π³ΡΠ»ΠΈΡΡΠ΅ΡΡΡ Π³ΠΈΠ΄ΡΠ°Π²Π»ΠΈΡΠ΅ΡΠΊΠΈΠΌ ΡΠ΅Π³ΡΠ»ΡΡΠΎΡΠΎΠΌ 5. ΠΠΈΡΠΊ Π²ΡΠ°ΡΠ°Π΅ΡΡΡ ΠΎΡ ΡΠ»Π΅ΠΊΡΡΠΎΠ΄Π²ΠΈΠ³Π°ΡΠ΅Π»Ρ 7 Ρ ΠΏΠΎΠΌΠΎΡΡΡ ΡΠ΅ΠΌΠ΅Π½Π½ΠΎΠΉ ΠΏΠ΅ΡΠ΅Π΄Π°ΡΠΈ 8. Π Π°Π±ΠΎΡΠ°Ρ ΠΆΠΈΠ΄ΠΊΠΎΡΡΡ ΠΏΠΎΠ΄Π°Π΅ΡΡΡ Π½Π°ΡΠΎΡΠΎΠΌ 11 ΠΊ ΡΠΎΠΏΠ»Ρ 2. ΠΡΡΠ°Π±ΠΎΡΠ°Π½Π½Π°Ρ ΠΆΠΈΠ΄ΠΊΠΎΡΡΡ ΡΠΎΠ±ΠΈΡΠ°Π΅ΡΡΡ Π² ΠΊΠΎΡΠΎΠ±ΠΊΠ΅ 1. Π‘ΠΊΠΎΡΠΎΡΡΡ Π²ΡΠ°ΡΠ΅Π½ΠΈΡ Π΄ΠΈΡΠΊΠ° ΠΎΠ±ΡΡΠ½ΠΎ ΡΠ°Π²Π½Π° 15β25 ΠΌ/Ρ, Π½Π°ΠΏΡΡΠΆΠ΅Π½ΠΈΠ΅ ΡΠΎΠΊΠ° 20β30 Π. Π‘ΠΈΠ»Ρ ΡΠΎΠΊΠ° Π²ΡΠ±ΠΈΡΠ°ΡΡ Π² Π·Π°Π²ΠΈΡΠΈΠΌΠΎΡΡΠΈ ΠΎΡ Π΄ΠΈΠ°ΠΌΠ΅ΡΡΠ° ΡΠ°Π·ΡΠ΅Π·Π°Π΅ΠΌΠΎΠ³ΠΎ ΠΏΡΡΡΠΊΠ°. ΠΡΠΈ Π΄ΠΈΠ°ΠΌΠ΅ΡΡΠ΅ 40 ΠΌΠΌ ΡΠΈΠ»Π° ΡΠΎΠΊΠ° ΡΠ°Π²Π½Π° 80 Π, Π° ΠΏΡΠΈ Π΄ΠΈΠ°ΠΌΠ΅ΡΡΠ΅ 200-250 ΠΌΠΌ β 300β350 Π. ΠΠ»ΠΎΡΠΊΠΎΡΡΡ ΡΠ΅Π·Π° ΠΏΠΎΠ»ΡΡΠ°Π΅ΡΡΡ Π΄ΠΎΡΡΠ°ΡΠΎΡΠ½ΠΎ ΡΠΈΡΡΠΎΠΉ ΠΈ Π½Π΅ ΡΡΠ΅Π±ΡΠ΅ΡΡΡ Π½ΠΈΠΊΠ°ΠΊΠΎΠΉ Π΄ΠΎΠΏΠΎΠ»Π½ΠΈΡΠ΅Π»ΡΠ½ΠΎΠΉ ΠΎΠ±ΡΠ°Π±ΠΎΡΠΊΠΈ. ΠΡΠ»ΠΈ Π·Π°ΠΌΠ΅Π½ΠΈΡΡ Π΄ΠΈΡΠΊ ΡΡΠ°Π»ΡΠ½ΠΎΠΉ Π±Π΅ΡΠΊΠΎΠ½Π΅ΡΠ½ΠΎΠΉ Π»Π΅Π½ΡΠΎΠΉ ΡΠΎΠ»ΡΠΈΠ½ΠΎΠΉ 0,8β1,2 ΠΌΠΌ ΠΈ ΡΠΈΡΠΈΠ½ΠΎΠΉ 12β20 ΠΌΠΌ, ΡΠΎ ΠΌΠΎΠΆΠ½ΠΎ ΠΎΡΡΡΠ΅ΡΡΠ²ΠΈΡΡ ΡΠΈΠ³ΡΡΠ½ΡΡ ΡΠ΅Π·ΠΊΡ.
Β
ΠΡΠΈ Π°Π½ΠΎΠ΄Π½ΠΎ-ΠΌΠ΅Ρ Π°Π½ΠΈΡΠ΅ΡΠΊΠΎΠΈ Π·Π°ΡΠΎΡΠΊΠ΅ ΠΈΠ½ΡΡΡΡΠΌΠ΅Π½Ρ 6 (ΡΠΈΡ. 18.10) Π·Π°ΠΊΡΠ΅ΠΏΠ»ΡΡΡ Π² ΡΠΈΡΠΊΠ°Ρ 4, ΠΊΠΎΡΠΎΡΡΠ΅ ΠΏΡΠΈΡΠΎΠ΅Π΄ΠΈΠ½ΡΡΡ ΠΊ ΠΏΠΎΠ»ΠΎΠΆΠΈΡΠ΅Π»ΡΠ½ΠΎΠΌΡ Π·Π°ΠΆΠΈΠΌΡ Π³Π΅Π½Π΅ΡΠ°ΡΠΎΡΠ° ΠΏΠΎΡΡΠΎΡΠ½Π½ΠΎΠ³ΠΎ ΡΠΎΠΊΠ°. ΠΠ°ΡΠΎΡΠΊΠ° ΠΏΡΠΎΠΈΠ·Π²ΠΎΠ΄ΠΈΡΡΡ Π±ΡΡΡΡΠΎΠ²ΡΠ°ΡΠ°ΡΡΠΈΠΌΡΡ Π΄ΠΈΡΠΊΠΎΠΌ 1, ΠΈΠ·Π³ΠΎΡΠΎΠ²Π»Π΅Π½Π½ΡΠΌ ΠΈΠ· ΠΌΠ΅Π΄ΠΈ, ΡΡΠ³ΡΠ½Π° ΠΈΠ»ΠΈ Π½ΠΈΠ·ΠΊΠΎΡΠ³Π»Π΅ΡΠΎΠ΄ΠΈΡΡΠΎΠΉ ΡΡΠ°Π»ΠΈ. Π Π·ΠΎΠ½Ρ ΡΠΎΠΏΡΠΈΠΊΠΎΡΠ½ΠΎΠ²Π΅Π½ΠΈΡ Π·Π°ΡΠ°ΡΠΈΠ²Π°Π΅ΠΌΠΎΠ³ΠΎ ΠΈΠ½ΡΡΡΡΠΌΠ΅Π½ΡΠ° Ρ Π΄ΠΈΡΠΊΠΎΠΌ ΠΏΠΎΠ΄Π°Π΅ΡΡΡ ΡΠ΅ΡΠ΅Π· ΡΠΎΠΏΠ»ΠΎ 2 ΡΠ°Π±ΠΎΡΠ°Ρ ΠΆΠΈΠ΄ΠΊΠΎΡΡΡ (Π²ΠΎΠ΄Π½ΡΠΉ ΡΠ°ΡΡΠ²ΠΎΡ ΠΆΠΈΠ΄ΠΊΠΎΠ³ΠΎ ΡΡΠ΅ΠΊΠ»Π°).
Β
ΠΠ½ΠΎΠ΄Π½ΠΎ-ΠΌΠ΅Ρ Π°Π½ΠΈΡΠ΅ΡΠΊΡΡ Π·Π°ΡΠΎΡΠΊΡ ΠΈ Π΄ΠΎΠ²ΠΎΠ΄ΠΊΡ ΠΏΡΠΎΠΈΠ·Π²ΠΎΠ΄ΡΡ Π·Π° ΡΡΠΈ ΠΏΠ΅ΡΠ΅Ρ ΠΎΠ΄Π°: ΠΎΠ±Π΄ΠΈΡΠΊΠ°, ΡΠ»ΠΈΡΠΎΠ²Π°Π½ΠΈΠ΅ ΠΈ Π΄ΠΎΠ²ΠΎΠ΄ΠΊΠ°. ΠΡΠ΅ ΡΡΠΈ ΠΏΠ΅ΡΠ΅Ρ ΠΎΠ΄Ρ Π²ΡΠΏΠΎΠ»Π½ΡΡΡ Π½Π° ΠΎΠ΄Π½ΠΎΠΌ ΠΈ ΡΠΎΠΌ ΠΆΠ΅ ΡΡΠ°Π½ΠΊΠ΅ Π·Π° ΠΎΠ΄Π½Ρ ΡΡΡΠ°Π½ΠΎΠ²ΠΊΡ Π·Π°ΡΠ°ΡΠΈΠ²Π°Π΅ΠΌΠΎΠ³ΠΎ ΠΈΠ½ΡΡΡΡΠΌΠ΅Π½ΡΠ°, ΠΈΠ·ΠΌΠ΅Π½ΡΡΡ ΡΠΎΠ»ΡΠΊΠΎ ΡΠ»Π΅ΠΊΡΡΠΈΡΠ΅ΡΠΊΠΈΠ΅ ΡΠ΅ΠΆΠΈΠΌΡ ΠΎΠ±ΡΠ°Π±ΠΎΡΠΊΠΈ. ΠΠ±Π΄ΠΈΡΠΊΡ Π²Π΅Π΄ΡΡ ΠΏΡΠΈ Π½Π°ΠΏΡΡΠΆΠ΅Π½ΠΈΠΈ 20 Π, ΡΠ»ΠΈΡΠΎΠ²Π°Π½ΠΈΠ΅β ΠΏΡΠΈ Π½Π°ΠΏΡΡΠΆΠ΅Π½ΠΈΠΈ 15 Π; ΠΏΡΠΈ Π΄ΠΎΠ²ΠΎΠ΄ΠΊΠ΅ Π½Π°ΠΏΡΡΠΆΠ΅Π½ΠΈΠ΅ ΡΠ½ΠΈΠΆΠ°ΡΡ Π΄ΠΎ 10 Π. Π ΡΠ΅Π·ΡΠ»ΡΡΠ°ΡΠ΅ ΠΈΠ·ΠΌΠ΅Π½Π΅Π½ΠΈΡ Π½Π°ΠΏΡΡΠΆΠ΅Π½ΠΈΡ ΠΌΠ΅Π½ΡΠ΅ΡΡΡ ΠΈ Ρ Π°ΡΠ°ΠΊΡΠ΅Ρ ΠΎΠ±ΡΠ°Π±ΠΎΡΠΊΠΈ. ΠΡΠΈ ΠΎΠ±Π΄ΠΈΡΠΊΠ΅ ΡΠ½ΠΈΠΌΠ°Π΅ΡΡΡ Π±ΠΎΠ»ΡΡΠΎΠΉ ΡΠ»ΠΎΠΉ ΠΌΠ΅ΡΠ°Π»Π»Π° (1β1,5 ΠΌΠΌ). ΠΡΠΎ Π½Π΅ΠΎΠ±Ρ ΠΎΠ΄ΠΈΠΌΠΎ Π΄Π»Ρ ΡΠΎΠ³ΠΎ, ΡΡΠΎΠ±Ρ ΠΏΡΠΈΠ΄Π°ΡΡ ΠΈΠ½ΡΡΡΡΠΌΠ΅Π½ΡΡ ΡΡΠ΅Π±ΡΠ΅ΠΌΡΡ ΡΠΎΡΠΌΡ. ΠΡΠΈ ΡΠ»ΠΈΡΠΎΠ²Π°Π½ΠΈΠΈ Π³Π»ΡΠ±ΠΈΠ½Π° ΡΠ½ΠΈΠΌΠ°Π΅ΠΌΠΎΠ³ΠΎ ΡΠ»ΠΎΡ Π½Π΅ ΠΏΡΠ΅Π²ΡΡΠ°Π΅Ρ 0,1 ΠΌΠΌ. ΠΠΎΠ²ΠΎΠ΄ΠΊΠΎΠΉ ΡΠ½ΠΈΠΌΠ°Π΅ΡΡΡ Π½Π΅Π·Π½Π°ΡΠΈΡΠ΅Π»ΡΠ½ΡΠΉ ΠΏΠΎ ΡΠΎΠ»ΡΠΈΠ½Π΅ ΡΠ»ΠΎΠΉ, ΡΠΎΡΡΠ°Π²Π»ΡΡΡΠΈΠΉ Π²ΡΠ΅Π³ΠΎ 0,01β0,03 ΠΌΠΌ.
ο»Ώ
infopedia.su
ΠΠ»Π΅ΠΊΡΡΠΎΡΡΠΎΠ·ΠΈΠΎΠ½Π½Π°Ρ ΠΎΠ±ΡΠ°Π±ΠΎΡΠΊΠ° ΠΌΠ΅ΡΠ°Π»Π»ΠΎΠ²: ΡΠ΅Π·ΠΊΠ°, ΡΡΠ°Π½ΠΎΠΊ
Π§ΡΠΎΠ±Ρ ΠΏΡΠΈΠ΄Π°ΡΡ ΠΌΠ΅ΡΠ°Π»Π»ΠΈΡΠ΅ΡΠΊΠΎΠΌΡ ΠΈΠ·Π΄Π΅Π»ΠΈΡ ΠΎΠΏΡΠ΅Π΄Π΅Π»Π΅Π½Π½ΡΡ ΡΠΎΡΠΌΡ ΠΈ ΡΠ°Π·ΠΌΠ΅Ρ, ΠΌΠΎΠΆΠ½ΠΎ ΠΏΡΠΈΠΌΠ΅Π½ΡΡΡ ΡΠ°Π·Π½ΡΠ΅ ΡΠΏΠΎΡΠΎΠ±Ρ ΡΠΎΠΊΠ°ΡΠ½ΠΎΠΉ ΠΎΠ±ΡΠ°Π±ΠΎΡΠΊΠΈ.
ΠΠΎ ΠΈΠ½ΠΎΠ³Π΄Π° ΡΡΠ΅Π±ΠΎΠ²Π°Π½ΠΈΡ ΠΊ ΠΊΠ°ΡΠ΅ΡΡΠ²Ρ ΡΠ°ΠΊΠΎΠΉ ΠΎΠ±ΡΠ°Π±ΠΎΡΠΊΠΈ ΡΡΠ΅Π±ΡΠ΅Ρ ΠΏΠΎΠ²ΡΡΠ΅Π½Π½ΠΎΠΉ ΠΏΡΠΎΡΠ½ΠΎΡΡΠΈ Π² ΠΎΠ±Π»Π°ΡΡΠΈ Π²ΠΎΠ·Π΄Π΅ΠΉΡΡΠ²ΠΈΡ Π½Π° ΠΌΠ΅ΡΠ°Π»Π». Π‘ ΡΡΠΎΠΉ ΡΠ΅Π»ΡΡ ΠΌΠ΅ΡΠ°Π»Π»ΠΈΡΠ΅ΡΠΊΠΈΠ΅ ΠΈΠ·Π΄Π΅Π»ΠΈΡ ΠΎΠ±ΡΠ°Π±Π°ΡΡΠ²Π°ΡΡ ΡΠ»Π΅ΠΊΡΡΠΎΡΡΠΎΠ·ΠΈΠΎΠ½Π½ΡΠΌ ΡΠΏΠΎΡΠΎΠ±ΠΎΠΌ.
ΠΡΠΎΠΌΠ΅ ΠΏΠΎΠ»ΡΡΠ΅Π½ΠΈΡ Π½ΡΠΆΠ½ΠΎΠΉ ΡΠΎΡΠΌΡ ΠΈ ΠΏΠ°ΡΠ°ΠΌΠ΅ΡΡΠΎΠ² Π΄Π΅ΡΠ°Π»Π΅ΠΉ ΠΎΠ½ ΠΏΠΎΠ·Π²ΠΎΠ»ΡΠ΅Ρ ΠΏΠΎΠ»ΡΡΠ°ΡΡ ΡΠΊΠ²ΠΎΠ·Π½ΡΠ΅ ΠΎΡΠ²Π΅ΡΡΡΠΈΡ, ΡΠ°ΡΠΎΠ½Π½ΡΠ΅ ΠΊΠ°Π½Π°Π²ΠΊΠΈ Π² Π²ΠΈΠ΄Π΅ ΡΠ³Π»ΡΠ±Π»Π΅Π½ΠΈΠΉ ΠΈ ΠΏΠ°Π·Ρ Π² Π·Π°Π³ΠΎΡΠΎΠ²ΠΊΠ°Ρ . Π‘ ΠΏΠΎΠΌΠΎΡΡΡ ΡΠ»Π΅ΠΊΡΡΠΎΡΡΠΎΠ·ΠΈΠΎΠ½Π½ΠΎΠΉ ΠΎΠ±ΡΠ°Π±ΠΎΡΠΊΠΈ ΠΌΠ΅ΡΠ°Π»Π»ΠΎΠ² ΠΌΠΎΠΆΠ½ΠΎ ΠΈΠ·Π³ΠΎΡΠΎΠ²ΠΈΡΡ ΡΠ°Π·Π»ΠΈΡΠ½ΡΠ΅ Π²ΠΈΠ΄Ρ ΠΈΠ½ΡΡΡΡΠΌΠ΅Π½ΡΠΎΠ², ΠΏΡΠΎΡΠ½ΠΎΡΡΠ½ΡΠ΅ ΡΡΠ΅Π±ΠΎΠ²Π°Π½ΠΈΡ ΠΊ ΠΊΠΎΡΠΎΡΡΠΌ ΠΏΠΎΠ²ΡΡΠ΅Π½Ρ.
Π‘ΡΡΡ ΡΠ»Π΅ΠΊΡΡΠΎΡΡΠΎΠ·ΠΈΠΎΠ½Π½ΠΎΠΉ ΠΎΠ±ΡΠ°Π±ΠΎΡΠΊΠΈ
ΠΠ»Π΅ΠΊΡΡΠΎΡΡΠΎΠ·ΠΈΡ ΠΏΡΠ΅Π΄ΡΡΠ°Π²Π»ΡΠ΅Ρ ΡΠΎΠ±ΠΎΠΉ ΠΈΠ·ΠΌΠ΅Π½Π΅Π½ΠΈΠ΅ ΡΡΡΡΠΊΡΡΡΡ ΠΈ ΡΠΎΡΠΌΡ ΠΌΠ΅ΡΠ°Π»Π»Π° ΠΏΡΡΠ΅ΠΌ Π²ΠΎΠ·Π΄Π΅ΠΉΡΡΠ²ΠΈΡ ΡΠ»Π΅ΠΊΡΡΠΈΡΠ΅ΡΠΊΠΎΠ³ΠΎ ΡΠ°Π·ΡΡΠ΄Π°. ΠΠ½Π° Π²ΠΎΠ·Π½ΠΈΠΊΠ°Π΅Ρ ΠΏΡΠΈ ΡΠΎΠ·Π΄Π°Π½ΠΈΠΈ Π½Π°ΠΏΡΡΠΆΠ΅Π½ΠΈΡ ΠΌΠ΅ΠΆΠ΄Ρ ΡΠ»Π΅ΠΊΡΡΠΎΠ΄Π°ΠΌΠΈ. ΠΠ΄Π½ΠΈΠΌ ΠΈΠ· Π½ΠΈΡ ΡΠ»ΡΠΆΠΈΡ ΠΈΠ·Π΄Π΅Π»ΠΈΠ΅ ΠΈΠ· ΠΌΠ΅ΡΠ°Π»Π»Π°, Π° Π²ΡΠΎΡΡΠΌ β ΡΠ°Π±ΠΎΡΠΈΠΉ ΡΠ»Π΅ΠΊΡΡΠΎΠ΄.
ΠΡΠ»ΠΈ ΠΏΠΎ ΡΠ»Π΅ΠΊΡΡΠΎΠ΄Π°ΠΌ ΠΏΡΠΎΠΏΡΡΠΊΠ°ΡΡ ΡΠΎΠΊ, ΡΠΎ Π² ΠΏΡΠΎΡΡΡΠ°Π½ΡΡΠ²Π΅ ΠΌΠ΅ΠΆΠ΄Ρ Π½ΠΈΠΌΠΈ Π²ΠΎΠ·Π½ΠΈΠΊΠ½Π΅Ρ Π½Π°ΠΏΡΡΠΆΠ΅Π½ΠΈΠ΅ Π·Π° ΡΡΠ΅Ρ ΡΠ»Π΅ΠΊΡΡΠΈΡΠ΅ΡΠΊΠΎΠ³ΠΎ ΠΏΠΎΠ»Ρ. ΠΡΠΈ ΡΠ±Π»ΠΈΠΆΠ΅Π½ΠΈΠΈ ΡΠ°ΡΡΡΠΎΡΠ½ΠΈΡ ΠΌΠ΅ΠΆΠ΄Ρ ΡΠ»Π΅ΠΊΡΡΠΎΠ΄Π°ΠΌΠΈ Π΄ΠΎ ΠΊΡΠΈΡΠΈΡΠ΅ΡΠΊΠΎΠ³ΠΎ Π²ΠΎΠ·Π½ΠΈΠΊΠ½Π΅Ρ ΡΠ°Π·ΡΡΠ΄, ΡΠ»ΡΠΆΠ°ΡΠΈΠΉ ΠΏΡΠΎΠ²ΠΎΠ΄ΡΡΠΈΠΌ ΠΊΠ°Π½Π°Π»ΠΎΠΌ ΡΠ»Π΅ΠΊΡΡΠΈΡΠ΅ΡΡΠ²Π°.
Π§ΡΠΎΠ±Ρ ΠΏΠΎΠ²ΡΡΠΈΡΡ ΡΠΈΠ»Ρ ΡΠ°Π·ΡΡΠ΄Π° ΡΠ»Π΅ΠΊΡΡΠΎΠ΄Ρ ΠΏΠΎΠΌΠ΅ΡΠ°ΡΡΡΡ Π² ΠΆΠΈΠ΄ΠΊΠΎΡΡΡ, ΡΠ²Π»ΡΡΡΡΡΡΡ Π΄ΠΈΡΠ»Π΅ΠΊΡΡΠΈΠΊΠΎΠΌ, Π² ΠΊΠ°ΡΠ΅ΡΡΠ²Π΅ ΠΊΠΎΡΠΎΡΠΎΠΉ ΠΈΡΠΏΠΎΠ»ΡΠ·ΡΡΡ ΡΠ°Π·Π»ΠΈΡΠ½ΡΠ΅ ΠΌΠ°ΡΠ»Π° ΠΌΠΈΠ½Π΅ΡΠ°Π»ΡΠ½ΠΎΠ³ΠΎ Ρ Π°ΡΠ°ΠΊΡΠ΅ΡΠ° ΠΈΠ»ΠΈ ΠΊΠ΅ΡΠΎΡΠΈΠ½. ΠΡΠΎΡ ΠΎΠ΄ΡΡΠΈΠΉ ΠΏΠΎ ΠΎΠ±ΡΠ°Π·ΠΎΠ²Π°Π½Π½ΠΎΠΌΡ ΠΊΠ°Π½Π°Π»Ρ ΡΠΎΠΊ, Π½Π°Π³ΡΠ΅Π²Π°Π΅Ρ Π΄ΠΈΡΠ»Π΅ΠΊΡΡΠΈΡΠ΅ΡΠΊΡΡ ΠΆΠΈΠ΄ΠΊΠΎΡΡΡ, Π΄ΠΎΠ²ΠΎΠ΄Ρ Π΅Π΅ Π΄ΠΎ ΠΊΠΈΠΏΠ΅Π½ΠΈΡ ΠΈ ΠΏΠΎΡΠ»Π΅Π΄ΡΡΡΠ΅Π³ΠΎ ΠΈΡΠΏΠ°ΡΠ΅Π½ΠΈΡ Ρ ΠΎΠ±ΡΠ°Π·ΠΎΠ²Π°Π½ΠΈΠ΅ΠΌ Π³Π°Π·ΠΎΠ²ΠΎΠ³ΠΎ ΠΏΡΠ·ΡΡΡ. ΠΠ½ΡΡΡΠΈ ΡΡΠΎΠ³ΠΎ ΠΏΡΠ·ΡΡΡ Π²ΠΎΠ·Π½ΠΈΠΊΠ°Π΅Ρ ΠΌΠΎΡΠ½ΡΠΉ ΡΠ°Π·ΡΡΠ΄, ΡΠΎΠΏΡΠΎΠ²ΠΎΠΆΠ΄Π°ΡΡΠΈΠΉΡΡ ΠΏΠΎΡΠΎΠΊΠΎΠΌ ΡΠ»Π΅ΠΊΡΡΠΎΠ½ΠΎΠ² ΠΈ ΠΈΠΎΠ½ΠΎΠ².
ΠΠΎΠΌΠ±Π°ΡΠ΄ΠΈΡΡΡ ΡΠ»Π΅ΠΊΡΡΠΎΠ΄, ΠΎΠ½ΠΈ ΡΠΎΠ·Π΄Π°ΡΡ ΠΏΠ»Π°Π·ΠΌΠ΅Π½Π½ΡΠΉ ΠΏΠΎΡΠΎΠΊ. Π ΡΠ΅Π·ΡΠ»ΡΡΠ°ΡΠ΅ Π² Π·ΠΎΠ½Π΅ ΡΠ°Π·ΡΡΠ΄Π° ΡΠ΅ΠΌΠΏΠ΅ΡΠ°ΡΡΡΠ° ΠΏΠΎΠ²ΡΡΠ°Π΅ΡΡΡ Π΄ΠΎ 10000β12000Β°C ΠΈ ΠΌΠ³Π½ΠΎΠ²Π΅Π½Π½ΠΎ ΡΠ°ΡΠΏΠ»Π°Π²Π»ΡΠ΅Ρ ΠΌΠ΅ΡΠ°Π»Π» Ρ ΠΎΠ±ΡΠ°Π·ΠΎΠ²Π°Π½ΠΈΠ΅ΠΌ ΡΡΠΎΠ·ΠΈΠΎΠ½Π½ΠΎΠ³ΠΎ ΡΠ³Π»ΡΠ±Π»Π΅Π½ΠΈΡ Π² Π²ΠΈΠ΄Π΅ Π»ΡΠ½ΠΊΠΈ. ΠΠ½Π°ΡΠΈΡΠ΅Π»ΡΠ½Π°Ρ ΡΠ°ΡΡΡ ΡΠ°ΡΠΏΠ»Π°Π²Π° ΠΈΡΠΏΠ°ΡΡΠ΅ΡΡΡ, Π° Π½Π° ΠΏΠΎΠ²Π΅ΡΡ Π½ΠΎΡΡΠΈ ΠΌΠ΅ΡΠ°Π»Π»Π° Π² Π»ΡΠ½ΠΊΠ΅ ΠΏΠΎΡΠ»Π΅ Π΅Π³ΠΎ ΠΎΡΡΡΠ²Π°Π½ΠΈΡ ΠΎΡΡΠ°Π΅ΡΡΡ ΡΠ»ΠΎΠΉ, ΡΠΎΡΡΠ°Π² ΠΊΠΎΡΠΎΡΠΎΠ³ΠΎ ΠΎΡΠ»ΠΈΡΠ°Π΅ΡΡΡ ΠΎΡ ΡΠΎΡΡΠ°Π²Π° ΠΈΡΡ ΠΎΠ΄Π½ΠΎΠ³ΠΎ ΠΌΠ΅ΡΠ°Π»Π»Π°.
ΠΠ° ΡΠΈΡΡΠ½ΠΊΠ΅ (Π½ΠΈΠΆΠ΅) ΠΏΠΎΠΊΠ°Π·Π°Π½Π° Π»ΡΠ½ΠΊΠ°, Π²ΠΎΠ·Π½ΠΈΠΊΡΠ°Ρ ΠΏΡΠΈ Π²ΠΎΠ·Π΄Π΅ΠΉΡΡΠ²ΠΈΠΈ ΡΠ»Π΅ΠΊΡΡΠΈΡΠ΅ΡΠΊΠΎΠ³ΠΎ ΠΈΠΌΠΏΡΠ»ΡΡΠ°, Π³Π΄Π΅: 1β ΠΎΠ±ΡΠ΅ΠΌ Π»ΡΠ½ΠΊΠΈ, 2β Π»Π΅Π³ΠΈΡΠΎΠ²Π°Π½Π½ΡΠΉ ΡΠ»ΠΎΠΉ, 3 β Π»ΡΠ½ΠΎΡΠ½ΡΠΉ Π²Π°Π»ΠΈΠΊ, 4β ΠΌΠ΅ΡΠ°Π»Π»ΠΈΡΠ΅ΡΠΊΠ°Ρ Π΄Π΅ΡΠ°Π»Ρ.
Π ΡΠΎΡΡΠ°Π² ΠΏΠΎΠ²Π΅ΡΡ Π½ΠΎΡΡΠ½ΠΎΠ³ΠΎ ΡΠ»ΠΎΡ Π²Ρ ΠΎΠ΄ΡΡ ΠΊΠΎΠΌΠΏΠΎΠ½Π΅Π½ΡΡ Π½Π΅ ΡΠΎΠ»ΡΠΊΠΎ ΠΈΡΠΏΠ°ΡΠΈΠ²ΡΠ΅ΠΉΡΡ ΠΆΠΈΠ΄ΠΊΠΎΡΡΠΈ, Π½Π°ΡΡΡΠ°ΡΡΠΈΠ΅ ΠΌΠ΅ΡΠ°Π»Π» ΡΠ³Π»Π΅ΡΠΎΠ΄ΠΎΠΌ Ρ ΠΎΠ±ΡΠ°Π·ΠΎΠ²Π°Π½ΠΈΠ΅ΠΌ ΠΊΠ°ΡΠ±ΠΈΠ΄ΠΎΠ² ΠΆΠ΅Π»Π΅Π·Π°, Π½ΠΎ ΠΈ ΡΠ»Π΅ΠΌΠ΅Π½ΡΡ ΡΠ°ΡΠΏΠ»Π°Π²Π° ΠΌΠ΅ΡΠ°Π»Π»Π° ΡΠ°Π±ΠΎΡΠ΅Π³ΠΎ ΡΠ»Π΅ΠΊΡΡΠΎΠ΄Π°.
Π ΡΠ΅Π·ΡΠ»ΡΡΠ°ΡΠ΅ ΡΠ°ΠΊΠΎΠΉ ΡΠ»Π΅ΠΊΡΡΠΎΡΡΠΎΠ·ΠΈΠΎΠ½Π½ΠΎΠΉ ΠΎΠ±ΡΠ°Π±ΠΎΡΠΊΠΈ ΡΡΠ°Π»ΡΠ½ΡΠ΅ Π·Π°Π³ΠΎΡΠΎΠ²ΠΊΠΈ Π² ΠΌΠ΅ΡΡΠ΅ Π²ΠΎΠ·Π΄Π΅ΠΉΡΡΠ²ΠΈΡ ΠΌΠΎΠΆΠ½ΠΎ Π»Π΅Π³ΠΈΡΠΎΠ²Π°ΡΡ ΡΠ°ΠΊΠΈΠΌΠΈ ΡΠ»Π΅ΠΌΠ΅Π½ΡΠ°ΠΌΠΈ, ΠΊΠ°ΠΊ Ρ ΡΠΎΠΌ, ΡΠΈΡΠ°Π½, Π²ΠΎΠ»ΡΡΡΠ°ΠΌ ΠΈ Π΄ΡΡΠ³ΠΈΠΌΠΈ. Π’Π°ΠΊΠΎΠ΅ Π»Π΅Π³ΠΈΡΠΎΠ²Π°Π½ΠΈΠ΅ Π·Π½Π°ΡΠΈΡΠ΅Π»ΡΠ½ΠΎ ΡΠΏΡΠΎΡΠ½ΡΠ΅Ρ ΠΏΠΎΠ²Π΅ΡΡ Π½ΠΎΡΡΡ ΠΌΠ΅ΡΠ°Π»Π»ΠΈΡΠ΅ΡΠΊΠΎΠΉ Π·Π°Π³ΠΎΡΠΎΠ²ΠΊΠΈ Π² ΠΌΠ΅ΡΡΠ΅ ΡΠ»Π΅ΠΊΡΡΠΎΡΡΠΎΠ·ΠΈΠΎΠ½Π½ΠΎΠΉ ΠΎΠ±ΡΠ°Π±ΠΎΡΠΊΠΈ.
ΠΠ»Π΅ΠΊΡΡΠΎΡΡΠΎΠ·ΠΈΠΎΠ½Π½Π°Ρ ΡΠ΅Π·ΠΊΠ°
ΠΠ°ΠΈΠ±ΠΎΠ»Π΅Π΅ Π²ΠΎΡΡΡΠ΅Π±ΠΎΠ²Π°Π½Π½ΠΎΠΉ ΡΠ²Π»ΡΠ΅ΡΡΡ ΡΠ»Π΅ΠΊΡΡΠΎΡΡΠΎΠ·ΠΈΠΎΠ½Π½Π°Ρ ΡΠ΅Π·ΠΊΠ° ΠΌΠ΅ΡΠ°Π»Π»ΠΎΠ². ΠΠ΅ ΡΡΡΠ½ΠΎΡΡΡΡ ΡΠ²Π»ΡΠ΅ΡΡΡ Π΄Π΅ΠΉΡΡΠ²ΠΈΠ΅ Π½Π° ΠΌΠ΅ΡΠ°Π»Π»ΠΈΡΠ΅ΡΠΊΡΡ Π·Π°Π³ΠΎΡΠΎΠ²ΠΊΡ ΠΈΡΠΊΡΠΎΠ²ΡΡ ΡΠ»Π΅ΠΊΡΡΠΈΡΠ΅ΡΠΊΠΈΡ ΡΠ°Π·ΡΡΠ΄ΠΎΠ², ΠΎΠ±ΡΠ°Π·ΠΎΠ²Π°Π½Π½ΡΡ ΠΏΡΠΈ ΠΏΡΠΎΡΠ΅ΠΊΠ°Π½ΠΈΠΈ Π² ΡΠ»Π΅ΠΊΡΡΠΎΠ΄Π°Ρ ΠΈΠΌΠΏΡΠ»ΡΡΠ½ΠΎΠ³ΠΎ ΡΠΎΠΊΠ°, ΠΏΡΠΈ ΠΈΡ ΠΌΠ°ΠΊΡΠΈΠΌΠ°Π»ΡΠ½ΠΎΠΌ ΡΠ±Π»ΠΈΠΆΠ΅Π½ΠΈΠΈ ΠΈ Π½Π°Ρ ΠΎΠΆΠ΄Π΅Π½ΠΈΠΈ Π² ΠΆΠΈΠ΄ΠΊΠΎΠΉ ΡΡΠ΅Π΄Π΅ Π΄ΠΈΡΠ»Π΅ΠΊΡΡΠΈΠΊΠ°.
Π’Π°ΠΊΠΈΠΌ ΠΎΠ±ΡΠ°Π·ΠΎΠΌ, Π΄Π»Ρ ΠΏΡΠΎΠ²Π΅Π΄Π΅Π½ΠΈΡ ΡΠ»Π΅ΠΊΡΡΠΎΡΡΠΎΠ·ΠΈΠΎΠ½Π½ΠΎΠΉ ΡΠ΅Π·ΠΊΠΈ Π½Π° ΠΏΡΠΎΡΡΠΆΠ΅Π½ΠΈΠΈ Π²ΡΠ΅Π³ΠΎ ΠΏΡΠΎΡΠ΅ΡΡΠ° ΡΠ΅Π·Π°Π½ΠΈΡ Π½ΡΠΆΠ½ΠΎ ΠΎΠ±Π΅ΡΠΏΠ΅ΡΠΈΡΡ:
- ΠΏΠΎΠ΄Π°ΡΡ Π½Π°ΠΏΡΡΠΆΠ΅Π½ΠΈΡ ΠΊ ΡΠ»Π΅ΠΊΡΡΠΎΠ΄Π°ΠΌ Π² Π²ΠΈΠ΄Π΅ ΠΈΠΌΠΏΡΠ»ΡΡΠΎΠ²;
- ΠΏΠ΅ΡΠΈΠΎΠ΄ΠΈΡΠ΅ΡΠΊΠΈ ΡΠΎΠΊΡΠ°ΡΠ°ΡΡ ΠΌΠ΅ΠΆΠ΄Ρ ΡΠ»Π΅ΠΊΡΡΠΎΠ΄Π°ΠΌΠΈ ΡΠ°ΡΡΡΠΎΡΠ½ΠΈΠ΅ Π΄ΠΎ ΠΊΡΠΈΡΠΈΡΠ΅ΡΠΊΠΎΠ³ΠΎ ΡΠ°Π·ΠΌΠ΅ΡΠ°;
- ΠΎΠ±Π΅ΡΠΏΠ΅ΡΠΈΡΡ Π½Π°Π»ΠΈΡΠΈΠ΅ ΠΆΠΈΠ΄ΠΊΠΎΠΉ ΡΡΠ΅Π΄Ρ (ΠΊΠ΅ΡΠΎΡΠΈΠ½Π° ΠΈΠ»ΠΈ ΠΌΠ°ΡΠ»Π°).
ΠΡΠΈ ΠΎΠ±Π΅ΡΠΏΠ΅ΡΠ΅Π½ΠΈΠΈ ΡΠ°ΠΊΠΈΡ ΡΡΠ»ΠΎΠ²ΠΈΠΉ ΠΈΠ· ΠΌΠ΅ΡΠ°Π»Π»ΠΈΡΠ΅ΡΠΊΠΎΠΉ Π΄Π΅ΡΠ°Π»ΠΈ ΠΏΠΎΠ΄ Π²Π»ΠΈΡΠ½ΠΈΠ΅ΠΌ Π²ΡΡΠΎΠΊΠΎΠΉ ΡΠ΅ΠΌΠΏΠ΅ΡΠ°ΡΡΡΡ, Π²ΠΎΠ·Π½ΠΈΠΊΠ°ΡΡΠ΅ΠΉ Π·Π° ΡΡΠ΅Ρ Π΄Π΅ΠΉΡΡΠ²ΠΈΡ ΡΠ°Π·ΡΡΠ΄Π½ΠΎΠΉ Π΄ΡΠ³ΠΈ, Π²ΡΠ±ΠΈΠ²Π°ΡΡΡΡ ΡΠ°ΡΡΠΈΡΡ, ΠΊΠΎΡΠΎΡΡΠ΅ Π·Π°ΡΠ΅ΠΌ Π²ΡΠΌΡΠ²Π°ΡΡΡΡ Π΄ΠΈΡΠ»Π΅ΠΊΡΡΠΈΡΠ΅ΡΠΊΠΎΠΉ ΠΆΠΈΠ΄ΠΊΠΎΡΡΡΡ. ΠΠΈΡΠ»Π΅ΠΊΡΡΠΈΠΊ ΡΠ°ΠΊΠΆΠ΅ Π²ΡΠΏΠΎΠ»Π½ΡΠ΅Ρ ΡΡΠ½ΠΊΡΠΈΡ ΠΊΠ°ΡΠ°Π»ΠΈΠ·Π°ΡΠΎΡΠ° ΡΠ°ΡΠΏΠ°Π΄Π° ΡΠ°ΡΡΠΈΡ ΠΌΠ΅ΡΠ°Π»Π»Π°, Ρ. ΠΊ. ΠΏΡΠΈ Π²ΡΡΠΎΠΊΠΈΡ ΡΠ΅ΠΌΠΏΠ΅ΡΠ°ΡΡΡΠ°Ρ ΠΈΡΠΏΠ°ΡΡΠ΅ΡΡΡ.
ΠΠΎΡΠΊΠΎΠ»ΡΠΊΡ Π΅Π΄ΠΈΠ½ΠΈΡΠ½ΡΠΉ ΡΠ°Π·ΡΡΠ΄ Π΄ΠΎΠ»ΠΆΠ΅Π½ ΠΏΡΠΎΠΈΡΡ ΠΎΠ΄ΠΈΡΡ Ρ ΠΏΠ΅ΡΠΈΠΎΠ΄ΠΈΡΠ΅ΡΠΊΠΈΠΌ ΠΏΠΎΡΡΠΎΡΠ½ΡΡΠ²ΠΎΠΌ Π² Π²ΠΈΠ΄Π΅ ΠΊΡΠ°ΡΠΊΠΎΡΡΠΎΡΠ½ΡΡ ΠΈΡΠΊΡ, ΡΡΠΎΠ±Ρ Π΄ΠΎΡΡΠΈΡΡ ΡΠ°Π·ΡΠ΅Π·Π°Π½ΠΈΡ Π·Π°Π³ΠΎΡΠΎΠ²ΠΊΠΈ ΠΏΠΎ Π½Π°ΠΌΠ΅ΡΠ΅Π½Π½ΠΎΠΌΡ ΠΊΠΎΠ½ΡΡΡΡ, Π½ΡΠΆΠ½ΠΎ ΡΠΎΠ±Π»ΡΠ΄Π°ΡΡ ΠΎΠΏΡΠ΅Π΄Π΅Π»Π΅Π½Π½ΡΠΉ ΡΠ΅ΠΆΠΈΠΌ ΡΠ°Π±ΠΎΡΡ. Π Π°Π·Π»ΠΈΡΠ°ΡΡ Π΄Π²Π° ΡΠ΅ΠΆΠΈΠΌΠ° ΠΎΠ±ΡΠ°Π±ΠΎΡΠΊΠΈ: ΡΠ»Π΅ΠΊΡΡΠΎΠΈΡΠΊΡΠΎΠ²ΠΎΠΉ ΠΈ ΡΠ»Π΅ΠΊΡΡΠΎΠΈΠΌΠΏΡΠ»ΡΡΠ½ΡΠΉ Π²ΠΈΠ΄.
ΠΠΈΠ΄Π΅ΠΎ:
ΠΠ»Π΅ΠΊΡΡΠΎΠΈΡΠΊΡΠΎΠ²Π°Ρ ΠΎΠ±ΡΠ°Π±ΠΎΡΠΊΠ°
ΠΡΠΈ ΡΠ΅ΠΆΠΈΠΌΠ΅ ΡΠ»Π΅ΠΊΡΡΠΎΠΈΡΠΊΡΠΎΠ²ΠΎΠΉ ΠΎΠ±ΡΠ°Π±ΠΎΡΠΊΠΈ Π·Π°Π³ΠΎΡΠΎΠ²ΠΎΠΊ ΠΏΡΠΎΠ²ΠΎΠ΄ΠΈΡΡΡ Ρ ΠΈΡΠΏΠΎΠ»ΡΠ·ΠΎΠ²Π°Π½ΠΈΠ΅ΠΌ ΠΊΡΠ°ΡΠΊΠΎΠ²ΡΠ΅ΠΌΠ΅Π½Π½ΡΡ ΡΠ°Π·ΡΡΠ΄ΠΎΠ², ΠΏΡΠΎΠΈΡΡ ΠΎΠ΄ΡΡΠΈΡ Π² ΡΠΎΡΠΌΠ΅ ΠΈΡΠΊΡ ΡΠ΅ΡΠ΅Π· Π΄ΠΈΡΠ»Π΅ΠΊΡΡΠΈΡΠ΅ΡΠΊΡΡ ΠΆΠΈΠ΄ΠΊΠΎΡΡΡ.
ΠΡΠΈ ΡΠ°ΠΊΠΎΠΌ ΡΠ΅ΠΆΠΈΠΌΠ΅ ΡΠΎΠ±Π»ΡΠ΄Π°Π΅ΡΡΡ ΡΠ»Π΅Π΄ΡΡΡΠ°Ρ ΡΡ Π΅ΠΌΠ° ΠΏΠΎΠ΄Π°ΡΠΈ ΠΈΠΌΠΏΡΠ»ΡΡΠΎΠ²:
- ΠΎΠ±ΡΠ°Π±Π°ΡΡΠ²Π°Π΅ΠΌΠ°Ρ Π·Π°Π³ΠΎΡΠΎΠ²ΠΊΠ° ΡΠ»ΡΠΆΠΈΡ Π°Π½ΠΎΠ΄ΠΎΠΌ Ρ ΠΏΠΎΠ»ΠΎΠΆΠΈΡΠ΅Π»ΡΠ½ΡΠΌ Π·Π°ΡΡΠ΄ΠΎΠΌ, ΠΊ ΠΊΠΎΡΠΎΡΠΎΠΉ ΡΡΡΡΠ΅ΠΌΠ»ΡΠ΅ΡΡΡ ΠΏΠΎΡΠΎΠΊ ΡΠ»Π΅ΠΊΡΡΠΎΠ½ΠΎΠ² Ρ ΡΠ°Π±ΠΎΡΠ΅Π³ΠΎ ΡΠ»Π΅ΠΊΡΡΠΎΠ΄Π°.
- ΠΈΠΎΠ½Ρ ΠΌΠ΅ΡΠ°Π»Π»Π° Π΄Π΅ΡΠ°Π»ΠΈ Π²ΠΎΠ·Π΄Π΅ΠΉΡΡΠ²ΡΡΡ Π½Π° ΡΠ°Π±ΠΎΡΠΈΠΉ ΡΠ»Π΅ΠΊΡΡΠΎΠ΄. Π§ΡΠΎΠ±Ρ ΠΎΠ½ Π½Π΅ ΡΠ°Π·ΡΡΡΠΈΠ»ΡΡ, ΠΈΡΠΏΠΎΠ»ΡΠ·ΡΡΡ ΠΈΠΌΠΏΡΠ»ΡΡΠ½ΠΎΠ΅ Π½Π°ΠΏΡΡΠΆΠ΅Π½ΠΈΠ΅ Π½Π° ΠΏΡΠΎΡΡΠΆΠ΅Π½ΠΈΠΈ 10-3 Ρ.
ΠΠΈΠ΄Π΅ΠΎ:
ΠΠ»Π΅ΠΊΡΡΠΎΠΈΠΌΠΏΡΠ»ΡΡΠ½Π°Ρ ΠΎΠ±ΡΠ°Π±ΠΎΡΠΊΠ°
ΠΡΠΈ ΡΠ΅ΠΆΠΈΠΌΠ΅ ΡΠ»Π΅ΠΊΡΡΠΎΠΈΠΌΠΏΡΠ»ΡΡΠ° Π·Π°Π³ΠΎΡΠΎΠ²ΠΊΠ° ΡΠ»ΡΠΆΠΈΡ ΠΊΠ°ΡΠΎΠ΄ΠΎΠΌ Ρ ΠΎΡΡΠΈΡΠ°ΡΠ΅Π»ΡΠ½ΡΠΌ ΠΈΠΌΠΏΡΠ»ΡΡΠΎΠΌ, ΠΊΠΎΡΠΎΡΡΠΉ Π΄Π΅ΠΉΡΡΠ²ΡΠ΅Ρ Π΄ΠΎΠ»ΠΈ ΡΠ΅ΠΊΡΠ½Π΄Ρ. Π‘ΠΎΠ·Π΄Π°Π΅ΡΡΡ Π΄ΡΠ³ΠΎΠ²ΠΎΠΉ ΡΠ°Π·ΡΡΠ΄, Π½Π°ΠΏΡΠ°Π²Π»ΡΡΡΠΈΠΉ ΠΏΠΎΡΠΎΠΊ ΠΈΠΎΠ½ΠΎΠ² Π² ΡΡΠΎΡΠΎΠ½Ρ Π΄Π΅ΡΠ°Π»ΠΈ. Π ΡΠ°ΠΊΠΎΠΌ ΡΠ΅ΠΆΠΈΠΌΠ΅ ΠΎΠ±Π΅ΡΠΏΠ΅ΡΠΈΠ²Π°Π΅ΡΡΡ Π±ΠΎΠ»ΡΡΠ°Ρ ΡΠΊΠΎΡΠΎΡΡΡ ΠΌΠ΅ΡΠ°Π»Π»ΠΈΡΠ΅ΡΠΊΠΎΠ³ΠΎ ΡΡΠ΅ΠΌΠ°, Π½ΠΎ ΡΠΈΡΡΠΎΡΠ° ΠΎΠ±ΡΠ°Π±ΠΎΡΠΊΠΈ ΠΌΠ΅ΡΠ°Π»Π»Π° Ρ ΡΠΆΠ΅, ΡΠ΅ΠΌ ΠΏΡΠΈ ΡΠ»Π΅ΠΊΡΡΠΎΠΈΡΠΊΡΠΎΠ²ΠΎΠΌ ΡΠ΅ΠΆΠΈΠΌΠ΅.
ΠΡΠΈ ΡΠ»Π΅ΠΊΡΡΠΎΡΡΠΎΠ·ΠΈΠΎΠ½Π½ΠΎΠΉ ΡΠ΅Π·ΠΊΠ΅ ΠΈΡΠΏΠΎΠ»ΡΠ·ΡΡΡΡΡ ΠΈΡΠΊΡΠΎΠ²ΡΠ΅ ΡΠ°Π·ΡΡΠ΄Ρ, ΠΊΠΎΡΠΎΡΡΠ΅ ΠΎΠ±Π΅ΡΠΏΠ΅ΡΠΈΠ²Π°ΡΡΡΡ ΠΈΠΌΠΏΡΠ»ΡΡΠ°ΠΌΠΈ ΡΠ»Π΅ΠΊΡΡΠΈΡΠ΅ΡΠΊΠΎΠ³ΠΎ ΡΠΎΠΊΠ°, Π²ΡΡΠ°Π±Π°ΡΡΠ²Π°Π΅ΠΌΠΎΠ³ΠΎ Π³Π΅Π½Π΅ΡΠ°ΡΠΎΡΠΎΠΌ ΡΠΏΠ΅ΡΠΈΠ°Π»ΡΠ½ΠΎΠ³ΠΎ ΡΡΠ°Π½ΠΊΠ°, ΠΏΡΠ΅Π΄Π½Π°Π·Π½Π°ΡΠ΅Π½Π½ΠΎΠ³ΠΎ Π΄Π»Ρ ΡΠ°ΠΊΠΎΠΉ ΠΎΠ±ΡΠ°Π±ΠΎΡΠΊΠΈ.
ΠΠ»Π΅ΠΊΡΡΠΎΡΡΠΎΠ·ΠΈΠΎΠ½Π½ΡΠΉ ΡΡΠ°Π½ΠΎΠΊ
Π£ΠΏΡΠΎΡΠ΅Π½Π½ΠΎ ΡΠ°Π±ΠΎΡΠ° Π½Π° ΡΠ»Π΅ΠΊΡΡΠΎΡΡΠΎΠ·ΠΈΠΎΠ½Π½ΠΎΠΌ ΡΡΠ°Π½ΠΊΠ΅ ΠΏΡΠΎΠΈΡΡ ΠΎΠ΄ΠΈΡ ΡΠ°ΠΊ:
- ΠΠΌΠΏΡΠ»ΡΡΠ½ΡΠΉ ΡΠΎΠΊ ΠΏΠΎΠ΄Π°Π΅ΡΡΡ Π΄Π΅ΡΠ°Π»Ρ ΠΈ ΠΏΡΠΎΠ²ΠΎΠ»ΠΎΡΠ½ΡΠΉ ΡΠ»Π΅ΠΊΡΡΠΎΠ΄ ΠΈΠ· ΠΌΠΎΠ»ΠΈΠ±Π΄Π΅Π½Π°. Π’Π°ΠΊΠΆΠ΅ ΠΌΠΎΠ³ΡΡ Π±ΡΡΡ ΠΈΡΠΏΠΎΠ»ΡΠ·ΠΎΠ²Π°Π½Ρ Π²ΠΎΠ»ΡΡΡΠ°ΠΌ, Π»Π°ΡΡΠ½Ρ, ΠΌΠ΅Π΄Ρ ΠΈ Π΄ΡΡΠ³ΠΈΠ΅ ΠΌΠ΅ΡΠ°Π»Π»Ρ.
- ΠΠ΄Π½ΠΎΠ²ΡΠ΅ΠΌΠ΅Π½Π½ΠΎ Ρ ΠΏΠΎΠ΄Π°ΡΠ΅ΠΉ ΠΈΠΌΠΏΡΠ»ΡΡΠ½ΠΎΠ³ΠΎ ΡΠΎΠΊΠ° Π½Π° ΡΠ»Π΅ΠΊΡΡΠΎΠ΄ ΠΏΡΠΎΠΈΡΡ ΠΎΠ΄ΠΈΡ ΠΏΠ΅ΡΠ΅ΠΌΠ΅ΡΠ΅Π½ΠΈΠ΅ Π΄Π΅ΡΠ°Π»ΠΈ Ρ ΠΏΠΎΠΌΠΎΡΡΡ Π½Π°ΠΏΡΠ°Π²Π»ΡΡΡΠΈΡ ΡΡΠ°Π½ΠΊΠ° Π§ΠΠ£ Π² Π½ΡΠΆΠ½ΠΎΠΌ Π½Π°ΠΏΡΠ°Π²Π»Π΅Π½ΠΈΠΈ.
- ΠΠΎΠ·Π½ΠΈΠΊΠ°ΡΡΠΈΠ΅ ΠΈΡΠΊΡΠΎΠ²ΡΠ΅ ΠΈΠΌΠΏΡΠ»ΡΡΡ ΡΠ°Π·ΡΡΠ΄ΠΎΠ² Π²ΡΠΆΠΈΠ³Π°ΡΡ ΠΎΠ±Π»Π°ΡΡΡ ΠΌΠ΅ΡΠ°Π»Π»Π° Π² ΠΌΠ΅ΡΡΠ΅ ΡΠ°Π·ΡΠ΅Π·Π°.
- Π Π°ΡΠΏΠ»Π°Π²Π»Π΅Π½Π½ΡΠΉ ΠΌΠ΅ΡΠ°Π»Π» ΡΠΌΡΠ²Π°Π΅ΡΡΡ ΠΎΡ Π»Π°ΠΆΠ΄Π°ΡΡΠ΅ΠΉ ΠΆΠΈΠ΄ΠΊΠΎΡΡΡΡ.
- ΠΡΠΈ ΡΠ°Π±ΠΎΡΠ΅ ΠΎΠ±Π΅ΡΠΏΠ΅ΡΠΈΠ²Π°Π΅ΡΡΡ ΠΎΠ΄Π½ΠΎΠ²ΡΠ΅ΠΌΠ΅Π½Π½ΠΎΠ΅ ΠΏΠ΅ΡΠ΅ΠΌΠ΅ΡΠ΅Π½ΠΈΠ΅ ΠΏΡΠΎΠ²ΠΎΠ»ΠΎΠΊΠΈ, Π½Π°ΠΌΠΎΡΠ°Π½Π½ΠΎΠΉ Π½Π° ΡΠΏΠ΅ΡΠΈΠ°Π»ΡΠ½ΡΠΉ Π±Π°ΡΠ°Π±Π°Π½.
ΠΠ»Π΅ΠΊΡΡΠΎΡΡΠΎΠ·ΠΈΠΎΠ½Π½ΠΎΠ΅ ΠΎΠ±ΠΎΡΡΠ΄ΠΎΠ²Π°Π½ΠΈΠ΅ Π²ΠΊΠ»ΡΡΠ°Π΅Ρ:
- ΡΡΠ°Π½ΠΎΠΊ, Π½Π° ΠΊΠΎΡΠΎΡΠΎΠΌ ΠΎΡΡΡΠ΅ΡΡΠ²Π»ΡΠ΅ΡΡΡ ΠΎΠΏΠ΅ΡΠ°ΡΠΈΡ;
- Π³Π΅Π½Π΅ΡΠ°ΡΠΎΡ Π½Π°ΠΏΡΡΠΆΠ΅Π½ΠΈΡ, ΠΎΠ±Π΅ΡΠΏΠ΅ΡΠΈΠ²Π°ΡΡΠΈΠΉ ΠΈΠΌΠΏΡΠ»ΡΡΠ½ΡΠΉ ΡΠ΅ΠΆΠΈΠΌ;
- ΡΡΡΡΠΎΠΉΡΡΠ²ΠΎ ΠΏΠΎΠ΄Π°ΡΠΈ Π΄ΠΈΡΠ»Π΅ΠΊΡΡΠΈΡΠ΅ΡΠΊΠΎΠΉ ΠΆΠΈΠ΄ΠΊΠΎΡΡΠΈ ΠΈ Π΅Π΅ ΠΎΡΠΈΡΡΠΊΠΈ;
- ΡΠΈΡΡΠ΅ΠΌΡ ΠΎΡΠΊΠ°ΡΠΊΠΈ ΠΈΠ· ΡΠ°Π±ΠΎΡΠ΅ΠΉ ΠΎΠ±Π»Π°ΡΡΠΈ ΠΎΠ±ΡΠ°Π·ΠΎΠ²Π°Π½Π½ΡΡ Π³Π°Π·ΠΎΠ².
ΠΠ΅ΠΏΠΎΡΡΠ΅Π΄ΡΡΠ²Π΅Π½Π½ΠΎ ΡΡΠ°Π½ΠΎΠΊ ΡΠΎΡΡΠΎΠΈΡ ΠΈΠ·:
- ΠΎΡΠ½ΠΎΠ²Π°Π½ΠΈΡ Π² Π²ΠΈΠ΄Π΅ ΡΡΠ°Π½ΠΈΠ½Ρ;
- Π²Π°Π½Π½Ρ, ΡΠ°Π·ΠΌΠ΅ΡΠ΅Π½Π½ΠΎΠΉ Π½Π° ΡΡΠΎΠ»Π΅;
- Π³ΠΎΠ»ΠΎΠ²ΠΊΠΈ ΡΠΏΠΈΠ½Π΄Π΅Π»Ρ;
- ΠΏΡΠ»ΡΡΠ° Π΄Π»Ρ ΡΠΏΡΠ°Π²Π»Π΅Π½ΠΈΡ ΠΏΡΠΎΡΠ΅ΡΡΠΎΠΌ;
- ΡΠΈΡΡΠ΅ΠΌΡ ΠΎΠ±Π΅ΡΠΏΠ΅ΡΠ΅Π½ΠΈΡ ΠΏΠΎΠ΄Π°ΡΠΈ ΠΈΠΌΠΏΡΠ»ΡΡΠΎΠ² Π½Π° Π΄Π΅ΡΠ°Π»Ρ;
- ΡΠΈΡΡΠ΅ΠΌΡ Π°Π²ΡΠΎΠΌΠ°ΡΠΈΡΠ΅ΡΠΊΠΎΠΉ ΡΠ΅Π³ΡΠ»ΠΈΡΠΎΠ²ΠΊΠΈ ΠΏΡΠΎΡΠ΅ΡΡΠΎΠ².
ΠΠΈΠ΄Π΅ΠΎ:
ΠΡΡΡΠ΅ΡΠ°ΡΡΡΡ ΡΡΠ°Π½ΠΊΠΈ, ΠΊΠΎΡΠΎΡΡΠ΅ ΠΌΠΎΠ³ΡΡ ΠΈΠΌΠ΅ΡΡ Π½Π΅ΠΊΠΎΡΠΎΡΠΎΠ΅ ΠΎΡΠ»ΠΈΡΠΈΠ΅ Π² ΡΡΡΡΠΎΠΉΡΡΠ²Π΅. ΠΠ°ΠΏΡΠΈΠΌΠ΅Ρ, ΠΌΠΎΠ³ΡΡ ΠΈΠΌΠ΅ΡΡ ΡΠΈΡΡΠ΅ΠΌΡ ΠΎΡΠΈΡΡΠΊΠΈ Π² Π²ΠΈΠ΄Π΅ ΠΎΡΠ΄Π΅Π»ΡΠ½ΠΎΠ³ΠΎ ΡΡΡΡΠΎΠΉΡΡΠ²Π°.
ΠΠΌΠΏΡΠ»ΡΡΠ½ΡΠ΅ Π³Π΅Π½Π΅ΡΠ°ΡΠΎΡΡ ΡΠ²Π»ΡΡΡΡΡ ΠΎΡΠ΄Π΅Π»ΡΠ½ΡΠΌΠΈ Π°Π³ΡΠ΅Π³Π°ΡΠ°ΠΌΠΈ, ΡΠ°Π·ΠΌΠ΅ΡΠ΅Π½Π½ΡΠΌΠΈ ΡΡΠ΄ΠΎΠΌ Ρ ΠΎΡΠ½ΠΎΠ²Π½ΡΠΌ ΡΡΠ°Π½ΠΊΠΎΠΌ. ΠΡΡΡ Π²ΠΈΠ΄Ρ ΡΡΡΡΠΎΠΉΡΡΠ², Π² ΠΊΠΎΡΠΎΡΡΡ Π³Π΅Π½Π΅ΡΠ°ΡΠΎΡ Π²ΡΡΡΠΎΠ΅Π½ Π² ΡΡΠ°Π½ΠΎΠΊ.
Π£ΠΏΡΠΎΡΠ΅Π½Π½ΡΠΉ Π²Π°ΡΠΈΠ°Π½Ρ ΡΠ»Π΅ΠΊΡΡΠΎΠΈΡΠΊΡΠΎΠ²ΠΎΠ³ΠΎ ΡΡΠ°Π½ΠΊΠ° Π½Π΅ Π²ΠΊΠ»ΡΡΠ°Π΅Ρ ΡΠΈΡΡΠ΅ΠΌΡ ΠΏΠΎΠ΄Π°ΡΠΈ ΠΆΠΈΠ΄ΠΊΠΎΡΡΠΈ ΠΈ Π΅Π΅ ΠΎΡΠΈΡΡΠΊΠΈ. ΠΠ±ΡΠ°Π±ΠΎΡΠΊΠ° Π²ΠΊΠ»ΡΡΠ°Π΅Ρ ΠΏΠΎΠ³ΡΡΠΆΠ΅Π½ΠΈΠ΅ ΡΡΠΎΠ»Π° Ρ Π΄Π΅ΡΠ°Π»ΡΡ Π·Π°Π³ΠΎΡΠΎΠ²ΠΊΠΈ Π² Π²ΠΎΠ΄Ρ, Π½Π°Ρ ΠΎΠ΄ΡΡΡΡΡΡ Π² Π²Π°Π½Π½Π΅. ΠΡΠ»ΠΈ ΠΎΠ±ΡΠ°Π±ΠΎΡΠΊΠ° ΠΏΡΠΎΠ²ΠΎΠ΄ΠΈΡΡΡ Ρ ΠΈΡΠΏΠΎΠ»ΡΠ·ΠΎΠ²Π°Π½ΠΈΠ΅ΠΌ ΠΊΠ΅ΡΠΎΡΠΈΠ½Π°, ΡΠΎ ΠΎΠ±ΡΠ°Π·ΡΡΡΠΈΠ΅ΡΡ Π³Π°Π·Ρ ΡΠ΄Π°Π»ΡΡΡΡΡ ΡΠ΅ΡΠ΅Π· ΠΎΠ±ΡΡΡ Π²Π΅Π½ΡΠΈΠ»ΡΡΠΈΡ.
ΠΡΠΈ ΡΠΊΡΠΏΠ»ΡΠ°ΡΠ°ΡΠΈΠΈ ΡΡΠΎΠ³ΠΎ ΠΎΠ±ΠΎΡΡΠ΄ΠΎΠ²Π°Π½ΠΈΡ ΡΡΠ΅Π±ΡΡΡΡΡ ΠΊΠ²Π°Π»ΠΈΡΠΈΠΊΠ°ΡΠΈΡ ΠΈ Π·Π½Π°Π½ΠΈΠ΅ ΡΠ΅Ρ Π½ΠΎΠ»ΠΎΠ³ΠΈΡΠ΅ΡΠΊΠΎΠ³ΠΎ ΠΏΡΠΎΡΠ΅ΡΡΠ°, ΠΊΠΎΡΠΎΡΡΠ΅ ΠΏΠΎΠ·Π²ΠΎΠ»ΡΡ Π²ΡΠΏΠΎΠ»Π½ΡΡΡ ΠΏΡΠΎΡΠ΅ΡΡ Ρ ΡΠΎΠ±Π»ΡΠ΄Π΅Π½ΠΈΠ΅ΠΌ Π²ΡΠ΅Ρ ΡΡΠ΅Π±ΠΎΠ²Π°Π½ΠΈΠΉ, ΠΎΡΡΠ°ΠΆΠ΅Π½Π½ΡΡ Π² Π΄ΠΎΠΊΡΠΌΠ΅Π½ΡΠ°ΡΠΈΠΈ.
ΠΠ°Π³ΡΡΠ·ΠΊΠ°…plavitmetall.ru
ΠΠ»Π΅ΠΊΡΡΠΎΠΈΡΠΊΡΠΎΠ²ΡΠ΅ ΡΡΠ°Π½ΠΊΠΈ – ΠΠΎΠ»ΡΡΠ°Ρ ΠΠ½ΡΠΈΠΊΠ»ΠΎΠΏΠ΅Π΄ΠΈΡ ΠΠ΅ΡΡΠΈ ΠΈ ΠΠ°Π·Π°, ΡΡΠ°ΡΡΡ, ΡΡΡΠ°Π½ΠΈΡΠ° 1
ΠΠ»Π΅ΠΊΡΡΠΎΠΈΡΠΊΡΠΎΠ²ΡΠ΅ ΡΡΠ°Π½ΠΊΠΈ
CΡΡΠ°Π½ΠΈΡΠ° 1
ΠΠ»Π΅ΠΊΡΡΠΎΠΈΡΠΊΡΠΎΠ²ΡΠ΅ ΡΡΠ°Π½ΠΊΠΈ ΠΈΡΠΏΠΎΠ»ΡΠ·ΡΡΡ ΠΏΡΠΈ ΠΎΠ±ΡΠ°Π±ΠΎΡΠΊΠ΅ ΠΎΡΠ²Π΅ΡΡΡΠΈΠΉ ΠΌΠ°Π»ΠΎΠ³ΠΎ Π΄ΠΈΠ°ΠΌΠ΅ΡΡΠ°, ΡΠ·ΠΊΠΈΡ ΡΠ΅Π»Π΅ΠΉ ΠΈ Π΄ΡΡΠ³ΠΈΡ ΠΏΠΎΠ²Π΅ΡΡ Π½ΠΎΡΡΠ΅ΠΉ Π΄Π΅ΡΠ°Π»Π΅ΠΉ ΠΈΠ· ΡΡΡΠ΄Π½ΠΎΠΎΠ±ΡΠ°Π±Π°ΡΡΠ²Π°Π΅ΠΌΡΡ ΠΌΠ°ΡΠ΅ΡΠΈΠ°Π»ΠΎΠ². ΠΡΠΎΠΈΠ·Π²ΠΎΠ΄ΠΈΡΠ΅Π»ΡΠ½ΠΎΡΡΡ ΡΡΠ°Π½ΠΊΠΎΠ² Π½Π΅Π²Π΅Π»ΠΈΠΊΠ° – ΠΏΠΎΡΡΠ΄ΠΊΠ° 20 ΠΌ3 / ΠΌΠΈΠ½. β[1]
ΠΠ»Π΅ΠΊΡΡΠΎΠΈΡΠΊΡΠΎΠ²ΡΠ΅ ΡΡΠ°Π½ΠΊΠΈ ΠΈΡΠΏΠΎΠ»ΡΠ·ΡΡΡ ΠΏΡΠΈ ΠΎΠ±ΡΠ°Π±ΠΎΡΠΊΠ΅ ΠΎΡΠ²Π΅ΡΡΡΠΈΠΉ ΠΌΠ°Π»ΠΎΠ³ΠΎ Π΄ΠΈΠ°ΠΌΠ΅ΡΡΠ°, ΡΠ·ΠΊΠΈΡ ΡΠ΅Π»Π΅ΠΉ ΠΈ Π΄ΡΡΠ³ΠΈΡ ΠΏΠΎΠ²Π΅ΡΡ Π½ΠΎΡΡΠ΅ΠΉ Π΄Π΅ΡΠ°Π»Π΅ΠΉ ΠΈΠ· ΡΡΡΠ΄Π½ΠΎΠΎΠ±ΡΠ°Π±Π°ΡΡΠ²Π°Π΅ΠΌΡΡ ΠΌΠ°ΡΠ΅ΡΠΈΠ°Π»ΠΎΠ². β[3]
Π‘ΠΏΠ΅ΡΠΈΠ°Π»ΡΠ½ΡΠ΅ ΡΠ»Π΅ΠΊΡΡΠΎΠΈΡΠΊΡΠΎΠ²ΡΠ΅ ΡΡΠ°Π½ΠΊΠΈ ΠΌΠΎΠ΄Π΅Π»Π΅ΠΉ 159 – 162 ΠΏΡΠ΅Π΄Π½Π°Π·Π½Π°ΡΠ΅Π½Ρ Π΄Π»Ρ ΠΏΠΎΠ»ΡΡΠ΅Π½ΠΈΡ ΠΎΡΠ²Π΅ΡΡΡΠΈΠΈ Π² ΡΠ°ΡΠΏΡΠ»ΠΈΡΠ΅Π»ΡΡ Π΄ΠΈΠ·Π΅Π»ΡΠ½ΠΎΠΉ ΡΠΎΠΏΠ»ΠΈΠ²Π½ΠΎΠΉ Π°ΠΏΠΏΠ°ΡΠ°ΡΡΡΡ ΠΈ Π² Π΄ΡΡΠ³ΠΈΡ Π°Π½Π°Π»ΠΎΠ³ΠΈΡΠ½ΡΡ Π΄Π΅ΡΠ°Π»ΡΡ . β[4]
Π‘ΠΏΠ΅ΡΠΈΠ°Π»ΡΠ½ΡΠ΅ ΡΠ»Π΅ΠΊΡΡΠΎΠΈΡΠΊΡΠΎΠ²ΡΠ΅ ΡΡΠ°Π½ΠΊΠΈ ΠΌΠΎΠ΄Π΅Π»Π΅ΠΉ 159 – 162 ΠΏΡΠ΅Π΄Π½Π°Π·Π½Π°ΡΠ΅Π½Ρ Π΄Π»Ρ ΠΏΠΎΠ»ΡΡΠ΅Π½ΠΈΡ ΠΎΡΠ²Π΅ΡΡΡΠΈΠΉ Π² ΡΠ°ΡΠΏΡΠ»ΠΈΡΠ΅Π»ΡΡ Π΄ΠΈΠ·Π΅Π»ΡΠ½ΠΎΠΉ ΡΠΎΠΏΠ»ΠΈΠ²Π½ΠΎΠΉ Π°ΠΏΠΏΠ°ΡΠ°ΡΡΡΡ ΠΈ Π² Π΄ΡΡΠ³ΠΈΡ Π°Π½Π°Π»ΠΎΠ³ΠΈΡΠ½ΡΡ Π΄Π΅ΡΠ°Π»ΡΡ . β[5]
ΠΡΠΎΠΌΡΡΠ»Π΅Π½Π½ΠΎΡΡΡΡ Π²ΡΠΏΡΡΠΊΠ°ΡΡΡΡ ΡΠ»Π΅ΠΊΡΡΠΎΠΈΡΠΊΡΠΎΠ²ΡΠ΅ ΡΡΠ°Π½ΠΊΠΈ ΠΌΠΎΠ΄Π΅Π»ΠΈ 18Π Π΄Π»Ρ ΠΈΠ·Π²Π»Π΅ΡΠ΅Π½ΠΈΡ ΠΎΠ±Π»ΠΎΠΌΠΊΠΎΠ² ΡΠ²Π΅ΡΠ» ΠΈ Π΄ΡΡΠ³ΠΈΡ ΠΈΠ½ΡΡΡΡΠΌΠ΅Π½ΡΠΎΠ² ΠΈΠ· Π³Π»ΡΠ±ΠΎΠΊΠΈΡ ΠΎΡΠ²Π΅ΡΡΡΠΈΠΉ, ΡΡΠ°Π½ΠΊΠΈ ΠΌΠΎΠ΄Π΅Π»ΠΈ 37Π Π΄Π»Ρ ΠΏΠ»ΠΎΡΠΊΠΎΠ³ΠΎ ΡΠ»ΠΈΡΠΎΠ²Π°Π½ΠΈΡ ΠΈ Π°Π²ΡΠΎΠΌΠ°ΡΠΈΡΠ΅ΡΠΊΠΈΠ΅ ΡΡΠ°Π½ΠΊΠΈ ΠΌΠΎΠ΄Π΅Π»ΠΈ 62 Π΄Π»Ρ ΠΏΠΎΠ»ΡΡΠ΅Π½ΠΈΡ ΠΎΡΠ²Π΅ΡΡΡΠΈΠΉ Π΄ΠΈΠ°ΠΌΠ΅ΡΡΠΎΠΌ Π΄ΠΎ 0 15 ΠΌΠΌ Ρ ΡΠΎΡΠ½ΠΎΡΡΡΡ ΠΎΠ±ΡΠ°Π±ΠΎΡΠΊΠΈ Π΄ΠΎ 0 01 ΠΌΠΌ. β[6]
ΠΡΠΎΠΌΡΡΠ»Π΅Π½Π½ΠΎΡΡΡ Π²ΡΠΏΡΡΠΊΠ°Π΅Ρ ΡΠ»Π΅ΠΊΡΡΠΎΠΈΡΠΊΡΠΎΠ²ΡΠ΅ ΡΡΠ°Π½ΠΊΠΈ ΠΌΠΎΠ΄Π΅Π»ΠΈ 18Π Π΄Π»Ρ ΠΈΠ·Π²Π»Π΅ΡΠ΅Π½ΠΈΡ ΠΎΠ±Π»ΠΎΠΌΠΊΠΎΠ² ΡΠ²Π΅ΡΠ» ΠΈ Π΄ΡΡΠ³ΠΈΡ ΠΈΠ½ΡΡΡΡΠΌΠ΅Π½ΡΠΎΠ² ΠΈΠ· Π³Π»ΡΠ±ΠΎΠΊΠΈΡ ΠΎΡΠ²Π΅ΡΡΡΠΈΠΉ, ΡΡΠ°Π½ΠΊΠΈ ΠΌΠΎΠ΄Π΅Π»ΠΈ 37Π Π΄Π»Ρ ΠΏΠ»ΠΎΡΠΊΠΎΠ³ΠΎ ΡΠ»ΠΈΡΠΎΠ²Π°Π½ΠΈΡ ΠΈ Π°Π²ΡΠΎΠΌΠ°ΡΠΈΡΠ΅ΡΠΊΠΈΠ΅ ΡΡΠ°Π½ΠΊΠΈ ΠΌΠΎΠ΄Π΅Π»ΠΈ 62 Π΄Π»Ρ ΠΏΠΎΠ»ΡΡΠ΅Π½ΠΈΡ ΠΎΡΠ²Π΅ΡΡΡΠΈΠΉ Π΄ΠΈΠ°ΠΌΠ΅ΡΡΠΎΠΌ Π΄ΠΎ 0 15 ΠΌΠΌ Ρ ΡΠΎΡΠ½ΠΎΡΡΡΡ ΠΎΠ±ΡΠ°Π±ΠΎΡΠΊΠΈ Π΄ΠΎ 0 01 ΠΌΠΌ. β[7]
ΠΠ½Π°ΡΠΈΡΠ΅Π»ΡΠ½ΠΎ Π±ΠΎΠ»Π΅Π΅ ΠΏΡΠΎΠΈΠ·Π²ΠΎΠ΄ΠΈΡΠ΅Π»ΡΠ½Ρ ΠΌΠ½ΠΎΠ³ΠΎΠΊΠ°Π½Π°Π»ΡΠ½ΡΠ΅ ΡΠ»Π΅ΠΊΡΡΠΎΠΈΡΠΊΡΠΎΠ²ΡΠ΅ ΡΡΠ°Π½ΠΊΠΈ, ΠΏΠΎΠ·Π²ΠΎΠ»ΡΡΡΠΈΠ΅ ΡΠ°Π±ΠΎΡΠ°ΡΡ Ρ ΠΌΠ½ΠΎΠ³ΠΎΠΈΠ½ΡΡΡΡΠΌΠ΅Π½ΡΠ°Π»ΡΠ½ΠΎΠΉ Π½Π°ΡΡΡΠΎΠΉΠΊΠΎΠΉ. ΠΠΈΠΆΠ΅ ΡΠ°ΡΡΠΌΠΎΡΡΠ΅Π½ΠΎ Π½Π΅ΡΠΊΠΎΠ»ΡΠΊΠΎ ΡΠ΅Π»Π΅ΡΠΎΠΎΠ±ΡΠ°Π·Π½ΡΡ Π²Π°ΡΠΈΠ°Π½ΡΠΎΠ² ΠΊΠΎΠ½ΡΡΡΡΠΊΡΠΈΠΈ ΡΠ°ΠΊΠΈΡ ΡΡΠ°Π½ΠΊΠΎΠ². β[8]
ΠΠ°ΠΈΠ±ΠΎΠ»Π΅Π΅ ΡΠ΄ΠΎΠ±Π½ΡΠΌΠΈ Π΄Π»Ρ ΠΏΠ΅ΡΠ΅ΠΎΠ±ΠΎΡΡΠ΄ΠΎΠ²Π°Π½ΠΈΡ ΠΏΠΎΠ΄ ΡΠ»Π΅ΠΊΡΡΠΎΠΈΡΠΊΡΠΎΠ²ΡΠ΅ ΡΡΠ°Π½ΠΊΠΈ ΡΠ²Π»ΡΡΡΡΡ ΡΠ²Π΅ΡΠ»ΠΈΠ»ΡΠ½ΡΠ΅ ΠΈ ΡΡΠ΅Π·Π΅ΡΠ½ΡΠ΅ ΡΡΠ°Π½ΠΊΠΈ, ΠΏΡΠΈΡΠ΅ΠΌ Ρ ΠΏΠΎΡΠ»Π΅Π΄Π½ΠΈΡ ΠΏΡΠ΅ΠΈΠΌΡΡΠ΅ΡΡΠ²ΠΎ – Π²ΠΎΠ·ΠΌΠΎΠΆΠ½ΠΎΡΡΡ ΠΊΠΎΠΎΡΠ΄ΠΈΠ½Π°ΡΠ½ΠΎΠ³ΠΎ ΠΏΠ΅ΡΠ΅ΠΌΠ΅ΡΠ΅Π½ΠΈΡ ΡΡΠΎΠ»Π°. β[9]
Π Π½Π°ΡΡΠΎΡΡΠ΅Π΅ Π²ΡΠ΅ΠΌΡ ΠΎΡΠ΅ΡΠ΅ΡΡΠ²Π΅Π½Π½Π°Ρ ΠΏΡΠΎΠΌΡΡΠ»Π΅Π½Π½ΠΎΡΡΡ Π²ΡΠΏΡΡΠΊΠ°Π΅Ρ ΡΠ»Π΅ΠΊΡΡΠΎΠΈΡΠΊΡΠΎΠ²ΡΠ΅ ΡΡΠ°Π½ΠΊΠΈ ΠΊΠΎΠ½Π΄Π΅Π½ΡΠ°ΡΠΎΡΠ½ΠΎΠ³ΠΎ Π΄Π΅ΠΉΡΡΠ²ΠΈΡ, ΡΠ°Π·Π»ΠΈΡΠ°ΡΡΠΈΠ΅ΡΡ ΠΏΠΎ Π½Π°Π·Π½Π°ΡΠ΅Π½ΠΈΡ, ΠΊΠΎΠ½ΡΡΡΡΠΊΡΠΈΠΈ, ΠΏΡΠΎΠΈΠ·Π²ΠΎΠ΄ΠΈΡΠ΅Π»ΡΠ½ΠΎΡΡΠΈ ΠΈ Π΄ΡΡΠ³ΠΈΠΌ ΠΏΠ°ΡΠ°ΠΌΠ΅ΡΡΠ°ΠΌ. Π§ΡΠΎ ΠΆΠ΅ ΠΊΠ°ΡΠ°Π΅ΡΡΡ ΡΠ»Π΅ΠΊΡΡΠΎΠΈΡΠΊΡΠΎΠ²ΡΡ ΡΡΠ°Π½ΠΊΠΎΠ² Π±Π΅ΡΠΊΠΎΠ½Π΄Π΅Π½ΡΠ°ΡΠΎΡΠ½ΠΎΠ³ΠΎ Π΄Π΅ΠΉΡΡΠ²ΠΈΡ, ΡΠΎ ΡΠ°ΠΊΠΎΠ²ΡΠ΅ ΠΏΠΎΠΊΠ° Π½Π΅ ΠΈΠ·Π³ΠΎΡΠΎΠ²Π»ΡΡΡΡΡ ΠΏΡΠΎΠΌΡΡΠ»Π΅Π½Π½ΠΎΡΡΡΡ. β[10]
ΠΠ»Ρ ΠΎΡΠ²Π΅ΡΡΡΠΈΠΉ Π΄ΠΈΠ°ΠΌΠ΅ΡΡΠΎΠΌ ΠΌΠ΅Π½Π΅Π΅ 1 ΠΌΠΌ ΠΎΠ±ΡΡΠ½ΠΎ ΠΏΡΠΈΠΌΠ΅Π½ΡΡΡ ΡΠ»Π΅ΠΊΡΡΠΎΠΈΡΠΊΡΠΎΠ²ΡΠ΅ ΡΡΠ°Π½ΠΊΠΈ Ρ ΡΠ΅Π»Π°ΠΊΡΠ°ΡΠΈΠΎΠ½Π½ΡΠΌΠΈ Π³Π΅Π½Π΅ΡΠ°ΡΠΎΡΠ°ΠΌΠΈ. ΠΠ΄Π½Π°ΠΊΠΎ ΠΏΡΠΈ ΠΈΠ·Π³ΠΎΡΠΎΠ²Π»Π΅Π½ΠΈΠΈ ΡΠ΅Π»Π΅ΠΉ ( Π²ΡΠ»Π΅Π΄ΡΡΠ²ΠΈΠ΅ ΡΠ²Π΅Π»ΠΈΡΠ΅Π½ΠΈΡ ΠΏΠ»ΠΎΡΠ°Π΄ΠΈ Π·Π° ΡΡΠ΅Ρ Π΄Π»ΠΈΠ½Ρ ΡΠ΅Π»ΠΈ) ΡΠ»Π΅ΠΊΡΡΠΎΠΈΠΌΠΏΡΠ»ΡΡΠ½ΡΠ΅ ΠΈΡΡΠΎΡΠ½ΠΈΠΊΠΈ ΠΌΠΎΠ³ΡΡ ΠΏΡΠΈΠΌΠ΅Π½ΡΡΡΡΡ ΠΏΡΠΈ ΡΠΈΡΠΈΠ½Π΅ ΡΠ΅Π»ΠΈ ΠΈ ΠΌΠ΅Π½Π΅Π΅ 1 ΠΌΠΌ. Π’Π°ΠΊ, ΡΠΏΠ΅ΡΠΈΠ°Π»ΡΠ½ΡΠΉ Π΄Π²ΡΡ ΡΠΏΠΈΠ½Π΄Π΅Π»Ρ-Π½ΡΠΉ ΡΠ»Π΅ΠΊΡΡΠΎΠΈΠΌΠΏΡΠ»ΡΡΠ½ΡΠΉ ΡΡΠ°Π½ΠΎΠΊ ΠΌΠΎΠ΄Π΅Π»ΠΈ 4Π¦24Π ΠΏΠΎΠ·Π²ΠΎΠ»ΡΠ΅Ρ ΠΈΠ·Π³ΠΎΡΠΎΠ²Π»ΡΡΡ ΡΠ΅Π»ΠΈ ΡΠΈΡΠΈΠ½ΠΎΠΉ ΠΎΡ 0 5 ΠΌΠΌ, Π΄Π»ΠΈΠ½ΠΎΠΉ Π΄ΠΎ 75 – 80 ΠΌΠΌ ΠΈ Π³Π»ΡΠ±ΠΈΠ½ΠΎΠΉ Π΄ΠΎ 5 ΠΌΠΌ. β[11]
ΠΡΠΎΠΌΠ΅ ΡΠΎΠ³ΠΎ, Π²ΡΠ΅ ΠΊΠΎΠ»Π΅Π±Π°Π½ΠΈΡ Π½Π°ΠΏΡΡΠΆΠ΅Π½ΠΈΡ ΡΠ΅ΡΠΈ, ΠΏΠΈΡΠ°ΡΡΠ΅ΠΉ ΡΠ»Π΅ΠΊΡΡΠΎΠΈΡΠΊΡΠΎΠ²ΡΠ΅ ΡΡΠ°Π½ΠΊΠΈ, ΡΠΊΠ°ΠΆΡΡΡΡ Π½Π° ΡΠ°Π±ΠΎΡΠ΅ ΡΠ΅Π³ΡΠ»ΡΡΠΎΡΠ° ΠΏΠΎΠ΄Π°ΡΠΈ ΠΈ, Π² CBOIO ΠΎΡΠ΅ΡΠ΅Π΄Ρ, ΡΠ°ΠΊΠΆΠ΅ ΠΏΡΠΈΠ²Π΅Π΄ΡΡ ΠΊ ΠΊΠΎΠ»Π΅Π±Π°Π½ΠΈΡΠΌ Π²Π΅Π»ΠΈΡΠΈΠ½Ρ Π·Π°Π·ΠΎΡΠ°. β[12]
Π Π°Π±ΠΎΡΠΈΠΉ ΠΈΠ½ΡΡΡΡΠΌΠ΅Π½Ρ ΠΈ ΠΈΠ·Π΄Π΅Π»ΠΈΠ΅, ΠΊ ΠΊΠΎΡΠΎΡΡΠΌ ΠΏΠΎ ΡΡΠ»ΠΎΠ²ΠΈΡΠΌ ΡΠ°Π±ΠΎΡΡ ΠΏΠΎΠ΄Π²ΠΎΠ΄ΠΈΡΡΡ ΡΠ»Π΅ΠΊΡΡΠΈΡΠ΅ΡΠΊΠΈΠΉ ΡΠΎΠΊ, Π½Π°ΠΏΡΠΈΠΌΠ΅Ρ ΡΠ»Π΅ΠΊΡΡΠΎΠΈΡΠΊΡΠΎΠ²ΡΠ΅ ΡΡΠ°Π½ΠΊΠΈ, ΡΡΡΠ°Π½ΠΎΠ²ΠΊΠΈ Π΄Π»Ρ ΡΠ»Π΅ΠΊΡΡΠΎΠ³ΠΈΠ΄ΡΠ°Π²Π»ΠΈΡΠ΅ΡΠΊΠΎΠ³ΠΎ ΡΠ΄Π°ΡΠ°, ΡΠ»Π΅Π΄ΡΠ΅Ρ ΠΈΠ·ΠΎΠ»ΠΈΡΠΎΠ²Π°ΡΡ ΠΎΡ ΠΊΠΎΡΠΏΡΡΠ° ΠΎΠ±ΠΎΡΡΠ΄ΠΎΠ²Π°Π½ΠΈΡ. ΠΠΎΡΠΏΡΡΠ° ΡΠΊΠ°Π·Π°Π½Π½ΠΎΠ³ΠΎ ΠΈ Π°Π½Π°Π»ΠΎΠ³ΠΈΡΠ½ΠΎΠ³ΠΎ ΠΎΠ±ΠΎΡΡΠ΄ΠΎΠ²Π°Π½ΠΈΡ Π½Π΅ ΡΠ»Π΅Π΄ΡΠ΅Ρ Π·Π°Π·Π΅ΠΌΠ»ΡΡΡ, ΡΡΠΎΠ±Ρ ΠΈΡΠΊΠ»ΡΡΠΈΡΡ Π²ΠΎΠ·ΠΌΠΎΠΆΠ½ΡΡ ΠΎΠΏΠ°ΡΠ½ΠΎΡΡΡ ΠΏΠΎΡΠ°ΠΆΠ΅Π½ΠΈΡ ΡΠΎΠΊΠΎΠΌ ΡΠ°Π±ΠΎΡΠΈΡ , ΠΎΠ±ΡΠ»ΡΠΆΠΈΠ²Π°ΡΡΠΈΡ ΡΠ°ΠΊΠΎΠ΅ ΠΎΠ±ΠΎΡΡΠ΄ΠΎΠ²Π°Π½ΠΈΠ΅. β[13]
ΠΠ° Π½Π΅Π±ΠΎΠ»ΡΡΠΈΡ ΠΏΡΠ΅Π΄ΠΏΡΠΈΡΡΠΈΡΡ Ρ ΠΌΠ°Π»ΠΎΠΉ ΠΏΠΎΡΡΠ΅Π±Π½ΠΎΡΡΡΡ Π² ΡΠ΅Π·ΡΠ°Ρ Π΄Π»Ρ ΠΈΠ·Π³ΠΎΡΠΎΠ²Π»Π΅Π½ΠΈΡ ΡΡΡΡΠΆΠΊΠΎΠ·Π°Π²ΠΈΠ²Π°ΡΠ΅Π»ΡΠ½ΡΡ ΠΊΠ°Π½Π°Π²ΠΎΠΊ ΠΌΠΎΠ³ΡΡ Π±ΡΡΡ ΠΈΡΠΏΠΎΠ»ΡΠ·ΠΎΠ²Π°Π½Ρ ΡΠ»Π΅ΠΊΡΡΠΎΠΈΡΠΊΡΠΎΠ²ΡΠ΅ ΡΡΠ°Π½ΠΊΠΈ ΡΠΈΠΏΠ° Π½Π°ΡΡΠΎΠ»ΡΠ½ΠΎΠ³ΠΎ ΡΡΠ°Π½ΠΊΠ° ΠΠΠ ΠΠ. ΠΠ° ΡΡΠΎΠΌ ΡΡΠ°Π½ΠΊΠ΅ ΠΌΠΎΠΆΠ½ΠΎ ΠΎΠ±ΡΠ°Π±ΠΎΡΠ°ΡΡ Π΄ΠΎ 150 ΡΠ΅Π·ΡΠΎΠ² Π² ΡΠΌΠ΅Π½Ρ. ΠΠ° ΠΊΡΡΠΏΠ½ΡΡ ΠΏΡΠ΅Π΄ΠΏΡΠΈΡΡΠΈΡΡ , ΠΈΡΠΏΠΎΠ»ΡΠ·ΡΡΡΠΈΡ ΡΠ²Π΅ΡΠ΄ΠΎΡΠΏΠ»Π°Π²Π½ΡΠ΅ ΡΠ΅Π·ΡΡ ΡΠΎ ΡΡΡΡΠΆΠΊΠΎΠ·Π°Π²ΠΈΠ²Π°ΡΠ΅Π»ΡΠ½ΡΠΌΠΈ ΠΊΠ°Π½Π°Π²ΠΊΠ°ΠΌΠΈ Π² Π±ΠΎΠ»ΡΡΠΎΠΌ ΠΊΠΎΠ»ΠΈΡΠ΅ΡΡΠ²Π΅, ΠΎΠ±ΡΡΠ½ΠΎ ΠΏΡΠΈΠΌΠ΅Π½ΡΡΡ ΡΠΏΠ΅ΡΠΈΠ°Π»ΠΈΠ·ΠΈΡΠΎΠ²Π°Π½Π½ΡΠΉ ΡΠ»Π΅ΠΊΡΡΠΎΠΈΡΠΊΡΠΎΠ²ΡΠΉ ΡΡΠ°Π½ΠΎΠΊ Ρ Π±ΠΎΠ»ΡΡΠΎΠΉ ΠΏΡΠΎΠΈΠ·Π²ΠΎΠ΄ΠΈΡΠ΅Π»ΡΠ½ΠΎΡΡΡΡ, Π½Π°ΠΏΡΠΈΠΌΠ΅Ρ, ΡΡΠ°Π½ΠΎΠΊ ΠΌΠΎΠ΄Π΅Π»ΠΈ 4382, Π²ΡΠΏΡΡΠΊΠ°Π΅ΠΌΡΠΉ ΠΠΠΠΠ, ΠΎΠΏΠΈΡΠ°Π½ΠΈΠ΅ ΠΊΠΎΡΠΎΡΠΎΠ³ΠΎ ΠΏΡΠΈΠ²Π΅Π΄Π΅Π½ΠΎ Π½ΠΈΠΆΠ΅. β[14]
Π‘ΡΡΠ°Π½ΠΈΡΡ: β βββ1 βββ2
www.ngpedia.ru
Π‘ΡΠ°Π½ΠΊΠΈ ΡΠ»Π΅ΠΊΡΡΠΎΠΈΡΠΊΡΠΎΠ²ΡΠ΅ – ΠΠ½ΡΠΈΠΊΠ»ΠΎΠΏΠ΅Π΄ΠΈΡ ΠΏΠΎ ΠΌΠ°ΡΠΈΠ½ΠΎΡΡΡΠΎΠ΅Π½ΠΈΡ XXL
Π§ΠΈΡΠ»ΠΎ ΡΡΡΠΏΠ΅Π½Π΅ΠΉ ΠΏΠΎΠ΄Π°Ρ 9 β 38 ΠΠ΅ΡΠ°Π»Π»ΠΎΡΠ΅ΠΆΡΡΠΈΠ΅ ΡΡΠ°Π½ΠΊΠΈ ΡΠ»Π΅ΠΊΡΡΠΎΠΈΡΠΊΡΠΎΠ²ΡΠ΅ β[c.149]ΠΠ±ΡΠ΅Π΅ ΡΡΡΡΠΎΠΉΡΡΠ²ΠΎ ΡΡΠ°Π½ΠΊΠΎΠ² ΡΠ»Π΅ΠΊΡΡΠΎΠΈΡΠΊΡΠΎΠ²ΠΎΠ³ΠΎ Π΄Π΅ΠΉΡΡΠ²ΠΈΡ. Π ΡΡΠ°Π½ΠΊΠ°Ρ ΡΠ»Π΅ΠΊΡΡΠΎΠΈΡΠΊΡΠΎΠ²ΠΎΠ³ΠΎ Π΄Π΅ΠΉΡΡΠ²ΠΈΡ ΠΎΡΠ½ΠΎΠ²Π½ΠΎΠΉ ΡΠ°Π±ΠΎΡΠ΅ΠΉ ΡΠ°ΡΡΡΡ ΡΠ²Π»ΡΠ΅ΡΡΡ ΡΠ»Π΅ΠΊΡΡΠΈΡΠ΅ΡΠΊΠ°Ρ ΡΡ Π΅ΠΌΠ°, Π° ΠΊΠΈΠ½Π΅ΠΌΠ°ΡΠΈΡΠ΅ΡΠΊΠ°Ρ ΡΠ°ΡΡΡ ΡΡΠ°Π½ΠΊΠ° ΡΠ²Π»ΡΠ΅ΡΡΡ Π²ΡΠΏΠΎΠΌΠΎΠ³Π°ΡΠ΅Π»ΡΠ½ΡΠΌ ΡΠ»Π΅ΠΌΠ΅Π½ΡΠΎΠΌ, Π½Π°Π·Π½Π°ΡΠ΅Π½ΠΈΠ΅ ΠΊΠΎΡΠΎΡΠΎΠ³ΠΎ ΡΠ²ΠΎΠ΄ΠΈΡΡΡ ΠΊ ΡΠΎΡ ΡΠ°Π½Π΅Π½ΠΈΡ Π²ΠΎ Π²ΡΠ΅ΠΌΡ ΡΠ°Π±ΠΎΡΡ Π·Π°Π·ΠΎΡΠ° ΠΌΠ΅ΠΆΠ΄Ρ ΡΠ»Π΅ΠΊΡΡΠΎΠ΄ΠΎΠΌ – ΠΈΠ½ΡΡΡΡΠΌΠ΅Π½ΡΠΎΠΌ ΠΈ ΡΠ»Π΅ΠΊΡΡΠΎΠ΄ΠΎΠΌ-ΠΈΠ·Π΄Π΅Π»ΠΈΠ΅ΠΌ, Π° ΡΠ°ΠΊΠΆΠ΅ ΠΊ ΠΎΠ±Π΅ΡΠΏΠ΅ΡΠ΅Π½ΠΈΡ ΡΡΡΠ°Π½ΠΎΠ²ΠΎΡΠ½ΡΡ , Π° ΠΈΠ½ΠΎΠ³Π΄Π° ΠΈ ΡΠ°Π±ΠΎΡΠΈΡ ΠΏΠ΅ΡΠ΅ΠΌΠ΅ΡΠ΅Π½ΠΈΠΉ ΠΎΠ±ΡΠ°Π±Π°ΡΡΠ²Π°Π΅ΠΌΠΎΠΉ Π΄Π΅ΡΠ°Π»ΠΈ ΠΎΡΠ½ΠΎΡΠΈΡΠ΅Π»ΡΠ½ΠΎ ΠΈΠ½ΡΡΡΡΠΌΠ΅Π½ΡΠ°. ΠΡΠΈΠ½ΡΠΈΠΏΠΈΠ°Π»ΡΠ½Π°Ρ ΡΡ Π΅ΠΌΠ° ΡΡΠ°Π½ΠΊΠ° ΡΠ»Π΅ΠΊΡΡΠΎΠΈΡΠΊΡΠΎΠ²ΠΎΠ³ΠΎ Π΄Π΅ΠΉΡΡΠ²ΠΈΡ ΠΏΡΠ΅Π΄ΡΡΠ°Π²Π»Π΅Π½Π° Π½Π° ΡΠΈΠ³. 82. ΠΠ½Π° ΡΠΎΡΡΠΎΠΈΡ ΠΈΠ· ΡΠ»Π΅ΠΊΡΡΠΈ- β[c.64]
ΠΡΠΈ ΡΠ°Π±ΠΎΡΠ΅ Π½Π° ΡΡΠ°Π½ΠΊΠ°Ρ ΡΠ»Π΅ΠΊΡΡΠΎΠΈΡΠΊΡΠΎΠ²ΠΎΠ³ΠΎ Π΄Π΅ΠΉΡΡΠ²ΠΈΡ Π½Π΅ΠΎΠ±Ρ ΠΎΠ΄ΠΈΠΌΠΎ ΡΠΎΠ±Π»ΡΠ΄Π°ΡΡ Π²ΡΠ΅ ΠΏΡΠ°Π²ΠΈΠ»Π° ΠΏΠΎ ΡΠ΅Ρ Π½ΠΈΠΊΠ΅ Π±Π΅Π·ΠΎΠΏΠ°ΡΠ½ΠΎΡΡΠΈ ΡΠ°Π±ΠΎΡΡ Ρ ΡΠ»Π΅ΠΊΡΡΠΎΡΠ΅ΡΡΠΌΠΈ ΠΈ ΡΡΡΠ°Π½ΠΎΠ²ΠΊΠ°ΠΌΠΈ ΡΠΎΠΎΡΠ²Π΅ΡΡΡΠ²ΡΡΡΠ΅Π³ΠΎ Π½Π°ΠΏΡΡΠΆΠ΅Π½ΠΈΡ. β[c.67]
ΠΠ²ΡΠΎΠΌΠ°ΡΠΈΠ·Π°ΡΠΈΡ Π²ΡΠ΅ Π±ΠΎΠ»ΡΡΠ΅ ΠΏΡΠΎΠ½ΠΈΠΊΠ°Π΅Ρ Π²ΠΎ Π²ΡΠΏΠΎΠΌΠΎΠ³Π°ΡΠ΅Π»ΡΠ½ΡΠ΅ ΡΠ΅Ρ ΠΈ (ΠΈΠ½ΡΡΡΡΠΌΠ΅Π½ΡΠ°Π»ΡΠ½ΡΠΉ, ΡΠ΅ΠΌΠΎΠ½ΡΠ½ΡΠΉ, ΠΌΠΎΠ΄Π΅Π»ΡΠ½ΡΠΉ ΠΈ Π΄Ρ.), ΠΏΡΠΎΠ΄ΡΠΊΡΠΈΡ ΠΊΠΎΡΠΎΡΡΡ ΡΠ²Π»ΡΠ΅ΡΡΡ ΠΈΠ½Π΄ΠΈΠ²ΠΈΠ΄ΡΠ°Π»ΡΠ½ΠΎΠΉ ΠΈ ΡΠ΅ΡΠΈΠΉΠ½ΠΎΠΉ Π΄Π°ΠΆΠ΅ ΠΏΡΠΈ ΠΌΠ°ΡΡΠΎΠ²ΠΎΠΌ Ρ Π°ΡΠ°ΠΊΡΠ΅ΡΠ΅ ΠΎΡΠ½ΠΎΠ²Π½ΠΎΠ³ΠΎ ΠΏΡΠΎΠΈΠ·Π²ΠΎΠ΄ΡΡΠ²Π°. Π Π°Π·Π²ΠΈΡΠΈΠ΅ Π³ΠΈΠ΄ΡΠΎΠΊΠΎΠΏΠΈΡΠΎΠ²Π°Π»ΡΠ½ΡΡ ΡΡΠ°Π½ΠΊΠΎΠ², ΡΠ»Π΅ΠΊΡΡΠΎΠΈΡΠΊΡΠΎΠ²ΠΎΠΉ ΠΎΠ±ΡΠ°Π±ΠΎΡΠΊΠΈ ΠΈ ΡΡΠ°Π½ΠΊΠΎΠ² Ρ ΠΏΡΠΎΠ³ΡΠ°ΠΌΠΌΠ½ΡΠΌ ΡΠΏΡΠ°Π²Π»Π΅Π½ΠΈΠ΅ΠΌ ΠΏΠΎΠ·Π²ΠΎΠ»ΠΈΠ»ΠΎ ΡΠ΅ΡΠΈΡΡ ΠΏΡΠΎΠ±Π»Π΅ΠΌΡ Π°Π²ΡΠΎΠΌΠ°ΡΠΈΠ·ΠΈΡΠΎΠ²Π°Π½Π½ΠΎΠ³ΠΎ ΠΈΠ·Π³ΠΎΡΠΎΠ²Π»Π΅Π½ΠΈΡ ΡΡΠ°ΠΌΠΏΠΎΠ² ΠΈ Π΄ΡΡΠ³ΠΈΡ ΡΠ»ΠΎΠΆΠ½ΡΡ ΠΈΠ·Π΄Π΅Π»ΠΈΠΉ. Π‘ΡΠ°Π½ΠΊΠΈ Ρ ΠΏΡΠΎΠ³ΡΠ°ΠΌΠΌΠ½ΡΠΌ ΡΠΏΡΠ°Π²Π»Π΅Π½ΠΈΠ΅ΠΌ ΡΡΡΠ΅ΠΊΡΠΈΠ²Π½Ρ ΠΈ Π² ΡΡΠ»ΠΎΠ²ΠΈΡΡ ΡΠ΅ΡΠΈΠΉΠ½ΠΎΠ³ΠΎ ΠΏΡΠΎΠΈΠ·Π²ΠΎΠ΄ΡΡΠ²Π°. β[c.13]
Π€ΡΠ΅Π·Π΅ΡΠ½Π°Ρ Π½Π° ΠΏΠΎΠ»ΠΈΡΠΎΠ²Π°Π»ΡΠ½ΡΡ ΡΡΠ°Π½ΠΊΠ°Ρ . . ΠΠ»Π΅ΠΊΡΡΠΎΠΈΡΠΊΡΠΎΠ²Π°Ρ Π°Π»ΡΠΌΠΈΠ½ΠΈΠ΅Π²ΡΠΌΠΈ ΡΠ»Π΅ΠΊΡΡΠΎΠ΄Π°ΠΌΠΈ. …………….. β[c.389]
ΠΠ»Π΅ΠΊΡΡΠΎΡΡΠΎΠ·ΠΈΠΎΠ½Π½ΡΠ΅ ΡΡΠ°Π½ΠΊΠΈ. Π Π·Π°Π²ΠΈΡΠΈΠΌΠΎΡΡΠΈ ΠΎΡ Π²ΠΈΠ΄Π° ΠΏΡΠΈΠΌΠ΅Π½ΡΠ΅ΠΌΡΡ ΡΠ°Π·ΡΡΠ΄ΠΎΠ² ΡΠ°Π·Π»ΠΈΡΠ°ΡΡ ΡΠ»Π΅ΠΊΡΡΠΎΡΡΠΎΠ·ΠΈΠΎΠ½Π½ΡΠ΅ ΡΡΠ°Π½ΠΊΠΈ ΡΠ»Π΅ΠΊΡΡΠΎΠΈΡΠΊΡΠΎΠ²ΡΠ΅ (ΡΠΈΡ. 2), ΡΠ»Π΅ΠΊΡΡΠΎΠΈΠΌΠΏΡΠ»ΡΡΠ½ΡΠ΅ ΠΈ Π°Π½ΠΎΠ΄Π½ΠΎ-ΠΌΠ΅Ρ Π°Π½ΠΈΡΠ΅ΡΠΊΠΈΠ΅. ΠΠ° ΡΠ»Π΅ΠΊΡΡΠΎΠΈΡΠΊΡΠΎΠ²ΠΎΠΌ ΡΡΠ°Π½ΠΊΠ΅ ΠΎΠ±ΡΠ°Π±Π°ΡΡΠ²Π°Π΅ΠΌΡΡ Π΄Π΅ΡΠ°Π»Ρ 2 Π·Π°ΠΊΡΠ΅ΠΏΠ»ΡΡΡ Π½Π° ΡΡΠΎΠ»Π΅ β[c.14]
ΠΡΠ΅ΡΠ΅ΡΡΠ²Π΅Π½Π½Π°Ρ ΠΏΡΠΎΠΌΡΡΠ»Π΅Π½Π½ΠΎΡΡΡ Π²ΡΠΏΡΡΠΊΠ°Π΅Ρ ΡΠ°Π·Π½ΠΎΠΎΠ±ΡΠ°Π·Π½ΡΠ΅ ΡΡΠ°Π½ΠΊΠΈ ΡΠ»Π΅ΠΊΡΡΠΎΠΈΡΠΊΡΠΎΠ²ΠΎΠ³ΠΎ Π΄Π΅ΠΉΡΡΠ²ΠΈΡ Π΄Π»Ρ ΠΎΠ±ΡΠ°Π±ΠΎΡΠΊΠΈ ΠΎΡΠ²Π΅ΡΡΡΠΈΠΉ. β[c.158]
Π‘Ρ Π΅ΠΌΠ° ΡΠ»Π΅ΠΊΡΡΠΎΠΈΡΠΊΡΠΎΠ²ΠΎΠ³ΠΎ ΡΡΠ°Π½ΠΊΠ° Ρ Π³Π΅Π½Π΅ΡΠ°ΡΠΎΡΠΎΠΌ ΠΈΠΌΠΏΡΠ»ΡΡΠΎΠ² R ΠΏΠΎΠΊΠ°Π·Π°Π½Π° Π½Π° ΡΠΈΡ. 7.1. ΠΠΎΠ½Π΄Π΅Π½ΡΠ°ΡΠΎΡ Π‘, Π²ΠΊΠ»ΡΡΠ΅Π½Π½ΡΠΉ Π² Π·Π°ΡΡΠ΄Π½ΡΠΉ ΠΊΠΎΠ½ΡΡΡ, Π·Π°ΡΡΠΆΠ°Π΅ΡΡΡ ΡΠ΅ΡΠ΅Π· ΡΠ΅Π·ΠΈΡΡΠΎΡ R ΠΎΡ ΠΈΡΡΠΎΡΠ½ΠΈΠΊΠ° ΠΏΠΎΡΡΠΎΡΠ½Π½ΠΎΠ³ΠΎ ΡΠΎΠΊΠ° Π½Π°ΠΏΡΡΠΆΠ΅Π½ΠΈΠ΅ΠΌ 100β200 Π. ΠΠΎΠ³Π΄Π° Π½Π°ΠΏΡΡΠΆΠ΅Π½ΠΈΠ΅ Π½Π° ΡΠ»Π΅ΠΊΡΡΠΎΠ΄Π°Ρ 1 Π½ 3, ΠΎΠ±ΡΠ°Π·ΡΡΡΠΈΡ ΡΠ°Π·ΡΡΠ΄Π½ΡΠΉ ΠΊΠΎΠ½ΡΡΡ, Π΄ΠΎΡΡΠΈΠ³Π½Π΅Ρ ΠΏΡΠΎΠ±ΠΎΠΉΠ½ΠΎΠ³ΠΎ, ΠΎΠ±ΡΠ°Π·ΡΠ΅ΡΡΡ β[c.401]
Π ΠΈΡ. 7.1. Π‘Ρ Π΅ΠΌΠ° ΡΠ»Π΅ΠΊΡΡΠΎΠΈΡΠΊΡΠΎΠ²ΠΎΠ³ΠΎ ΡΡΠ°Π½ΠΊΠ° | ![]() |
ΠΠ»Ρ ΠΎΠ±Π΅ΡΠΏΠ΅ΡΠ΅Π½ΠΈΡ Π½Π΅ΠΏΡΠ΅ΡΡΠ²Π½ΠΎΡΡΠΈ ΠΏΡΠΎΡΠ΅ΡΡΠ° ΠΎΠ±ΡΠ°Π±ΠΎΡΠΊΠΈ Π½Π΅ΠΎΠ±Ρ ΠΎΠ΄ΠΈΠΌΠΎ, ΡΡΠΎΠ±Ρ Π·Π°Π·ΠΎΡ ΠΌΠ΅ΠΆΠ΄Ρ ΠΈΠ½ΡΡΡΡΠΌΠ΅Π½ΡΠΎΠΌ-ΡΠ»Π΅ΠΊΡΡΠΎΠ΄ΠΎΠΌ ΠΈ Π·Π°Π³ΠΎΡΠΎΠ²ΠΊΠΎΠΉ Π±ΡΠ» ΠΏΠΎΡΡΠΎΡΠ½Π½ΡΠΌ. ΠΠ»Ρ ΡΡΠΎΠ³ΠΎ ΡΠ»Π΅ΠΊΡΡΠΎΠΈΡΠΊΡΠΎΠ²ΡΠ΅ ΡΡΠ°Π½ΠΊΠΈ ΡΠ½Π°Π±ΠΆΠ°ΡΡ ΡΠ»Π΅Π΄ΡΡΠ΅ΠΉ ΡΠΈΡΡΠ΅ΠΌΠΎΠΉ ΠΈ ΠΌΠ΅Ρ Π°Π½ΠΈΠ·ΠΌΠΎΠΌ Π°Π²ΡΠΎΠΌΠ°ΡΠΈΡΠ΅ΡΠΊΠΎΠΉ ΠΏΠΎΠ΄Π°ΡΠΈ ΠΈΠ½ΡΡΡΡΠΌΠ΅Π½ΡΠ°. ΠΠ½ΡΡΡΡΠΌΠ΅Π½ΡΡ-ΡΠ»Π΅ΠΊΡΡΠΎΠ΄Ρ ΠΈΠ·Π³ΠΎΡΠΎΠ²Π»ΡΡΡ ΠΈΠ· ΠΌΠ΅Π΄Π½ΠΎ-Π³ΡΠ°ΡΠΈΡΠΎΠ²ΡΡ ΠΈ Π΄ΡΡΠ³ΠΈΡ ΠΌΠ°ΡΠ΅ΡΠΈΠ°Π»ΠΎΠ². β[c.402]
ΠΡΡΡΠ½Π΅Π½ΠΈΠ΅ Ρ Π°ΡΠ°ΠΊΡΠ΅ΡΠ° ΡΡΠΎΠ·ΠΈΠΈ ΠΏΡΠΈ ΡΠ°Π·ΡΡΠ΄Π°Ρ ΡΠ°Π·Π»ΠΈΡΠ½ΠΎΠΉ ΡΠΎΡΠΌΡ Π΄Π°Π΅Ρ Π²ΠΎΠ·ΠΌΠΎΠΆΠ½ΠΎΡΡΡ Π²ΡΠ±ΠΎΡΠ° ΠΎΠΏΡΠΈΠΌΠ°Π»ΡΠ½ΡΡ ΡΡΠ»ΠΎΠ²ΠΈΠΉ Π΄Π»Ρ ΡΠ°Π·Π½ΠΎΠΎΠ±ΡΠ°Π·Π½ΡΡ ΡΠ΅Ρ Π½ΠΎΠ»ΠΎΠ³ΠΈΡΠ΅ΡΠΊΠΈΡ ΡΠ΅ΠΆΠΈΠΌΠΎΠ². Π Π°Π·Π²ΠΈΡΠΈΠ΅ ΡΠ»Π΅ΠΊΡΡΠΎΠΈΡΠΊΡΠΎΠ²ΠΎΠ³ΠΎ ΡΠΏΠΎΡΠΎΠ±Π° ΠΏΡΠΈΠ²Π΅Π»ΠΎ ΠΊ ΡΠ°Π·ΡΠ°Π±ΠΎΡΠΊΠ΅ Π² 1950β 1951 Π³Π³. ΡΠ»Π΅ΠΊΡΡΠΎΠΈΠΌΠΏΡΠ»ΡΡΠ½ΠΎΠ³ΠΎ ΡΠΏΠΎΡΠΎΠ±Π° (Π½Π°ΡΡΠ½ΡΠ΅ ΠΊΠΎΠ»Π»Π΅ΠΊΡΠΈΠ²Ρ ΠΠΠ ΠΠΈΠ½ΠΈΡΡΠ΅ΡΡΡΠ²Π° ΡΡΠ°Π½ΠΊΠΎΡΡΡΠΎΠΈΡΠ΅Π»ΡΠ½ΠΎΠΉ ΠΈ ΠΈΠ½ΡΡΡΡΠΌΠ΅Π½ΡΠ°Π»ΡΠ½ΠΎΠΉ ΠΏΡΠΎΠΌΡΡΠ»Π΅Π½Π½ΠΎΡΡΠΈ, ΠΠΊΡΠΏΠ΅ΡΠΈΠΌΠ΅Π½ΡΠ°Π»ΡΠ½ΠΎΠ³ΠΎ Π½Π°ΡΡΠ½ΠΎ-ΠΈΡΡΠ»Π΅Π΄ΠΎΠ²Π°ΡΠ΅Π»ΡΡΠΊΠΎΠ³ΠΎ ΠΈΠ½ΡΡΠΈΡΡΡΠ° ΠΌΠ΅ΡΠ°Π»Π»ΠΎΡΠ΅ΠΆΡΡΠΈΡ ΡΡΠ°Π½ΠΊΠΎΠ² β ΠΠΠΠΠ‘Π°, Π₯Π°ΡΡΠΊΠΎΠ²ΡΠΊΠΎΠ³ΠΎ ΠΈ ΠΠ΄Π΅ΡΡΠΊΠΎΠ³ΠΎ ΠΏΠΎΠ»ΠΈΡΠ΅Ρ Π½ΠΈΡΠ΅ΡΠΊΠΈΡ ΠΈΠ½ΡΡΠΈΡΡΡΠΎΠ²). β[c.126]
ΠΠΎΠΆΠ½ΠΎ ΡΠ΅ΠΊΠΎΠΌΠ΅Π½Π΄ΠΎΠ²Π°ΡΡ ΡΠ»Π΅Π΄ΡΡΡ ΠΈΠ΅ ΡΠ΅ΠΆΠΈΠΌΡ ΠΌΠ΅Ρ Π°Π½ΠΈΡΠ΅ΡΠΊΠΎΠΉ ΠΎΠ±ΡΠ°Π±ΠΎΡΠΊΠΈ Π»ΠΈΡΡΠΎΠ²ΠΎΠ³ΠΎ Π±ΠΎΡΠ°Π»ΡΠΌΠΈΠ½ΠΈΡ ΠΏΡΠΈ ΡΠ΅Π·ΠΊΠ΅ ΡΠ°ΡΡΠΎΡΠ° 8 ΠΊΠΡ, ΡΠΈΠ»Π° ΡΠΎΠΊΠ° 15β20 Π, Π½Π°ΠΏΡΡΠΆΠ΅Π½ΠΈΠ΅ 25β30 Π ΠΏΡΠΈ ΠΏΡΠΎΡΠΈΠ²ΠΊΠ΅ ΠΎΡΠ²Π΅ΡΡΡΠΈΡ Π΄ΠΈΠ°ΠΌΠ΅ΡΡΠΎΠΌ 6 ΠΌΠΌ ΡΠ°ΡΡΠΎΡΠ° 8 ΠΊΠΡ, ΡΠΈΠ»Π° ΡΠΎΠΊΠ° 4β5 Π, Π½Π°ΠΏΡΡΠΆΠ΅Π½ΠΈΠ΅ 25 Π. ΠΠΈΠ½Π΅ΠΉΠ½Π°Ρ ΡΠΊΠΎΡΠΎΡΡΡ ΠΏΡΠΎΡΠΈΠ²ΠΊΠΈ ΠΈ ΡΠ΅Π·ΠΊΠΈ ΡΠΎΡΡΠ°Π²Π»ΡΠ΅Ρ ΠΎΡ 0,6 Π΄ΠΎ 5 ΠΌΠΌ/ΠΌΠΈΠ½. ΠΠ»Ρ ΡΠ°Π·ΡΠ΅Π·Π°Π½ΠΈΡ Π»ΠΈΡΡΠΎΠ² Π½Π° Π΄Π΅ΡΠ°Π»ΠΈ ΡΠ»ΠΎΠΆΠ½ΠΎΠ³ΠΎ ΠΏΡΠΎΡΠΈΠ»Ρ ΠΏΡΠΈΠ³ΠΎΠ΄Π½Ρ ΡΠ»Π΅ΠΊΡΡΠΎΠΈΡΠΊΡΠΎΠ²ΡΠ΅ ΡΡΠ°Π½ΠΊΠΈ Ρ Π΄Π²ΠΈΠΆΡΡΠΈΠΌΡΡ ΠΏΡΠΎΠ²ΠΎΠ»ΠΎΡΠ½ΡΠΌ ΡΠ΅ΠΆΡΡΠΈΠΌ ΠΈΠ½ΡΡΡΡΠΌΠ΅Π½ΡΠΎΠΌ (ΡΠ΅Π·ΠΊΠ° ΠΏΠΎ ΠΏΡΠΎΡΠΈΠ»Ρ, ΠΏΠΎ ΡΠ°Π±Π»ΠΎΠ½Ρ) ΠΈ Ρ ΠΏΡΠΎΠ³ΡΠ°ΠΌΠΌΠ½ΡΠΌ ΡΠΏΡΠ°Π²Π»Π΅Π½ΠΈΠ΅ΠΌ. β[c.202]
Π‘ΡΠ°Π½ΠΊΠΈ Ρ Π³Π΅Π½Π΅ΡΠ°ΡΠΎΡΠ°ΠΌΠΈ ΠΈΠΌΠΏΡΠ»ΡΡΠΎΠ², ΡΠ°Π±ΠΎΡΠ° ΠΊΠΎΡΠΎΡΡΡ Π½Π΅ Π·Π°Π²ΠΈΡΠΈΡ ΠΎΡ ΡΠΎΡΡΠΎΡΠ½ΠΈΡ ΠΌΠ΅ΠΆΡΠ»Π΅ΠΊΡΡΠΎΠ΄Π½ΠΎΠ³ΠΎ ΠΏΡΠΎΠΌΠ΅ΠΆΡΡΠΊΠ° Π² ΠΎΡΠ»ΠΈΡΠΈΠ΅ ΠΎΡ ΡΠ»Π΅ΠΊΡΡΠΎΠΈΡΠΊΡΠΎΠ²ΡΡ ΠΏΠΎΠ»ΡΡΠΈΠ»ΠΈ Π½Π°Π·Π²Π°Π½ΠΈΠ΅ ΡΠ»Π΅ΠΊΡΡΠΎΠΈΠΌΠΏΡΠ»ΡΡΠ½ΡΡ . ΠΠ½ΠΈ ΠΎΠ±Π΅ΡΠΏΠ΅ΡΠΈΠ»ΠΈ ΠΏΡΠΈΠΌΠ΅ΡΠ½ΠΎ Π΄Π΅ΡΡΡΠΈΠΊΡΠ°ΡΠ½ΠΎΠ΅ ΡΠ²Π΅Π»ΠΈΡΠ΅Π½ΠΈΠ΅ ΠΏΡΠΎΠΈΠ·Π²ΠΎΠ΄ΠΈΡΠ΅Π»ΡΠ½ΠΎΡΡΠΈ ΠΏΠΎ ΡΡΠ°Π²Π½Π΅Π½ΠΈΡ ΡΠΎ ΡΡΠ°Π½ΠΊΠ°ΠΌΠΈ, ΠΎΡΠ½Π°ΡΠ΅Π½Π½ΡΠΌΠΈ Π³Π΅Π½Π΅ΡΠ°ΡΠΎΡΠ°ΠΌΠΈ R . β[c.150]
ΠΡΡΡΠ±Π½ΡΠ΅ ΠΈ Π²ΡΡΡΠΆΠ½ΡΠ΅ ΡΡΠ°ΠΌΠΏΡ, ΠΈΠ·Π³ΠΎΡΠΎΠ²Π»Π΅Π½Π½ΡΠ΅ ΠΈΠ· ΡΠ²Π΅ΡΠ΄ΠΎΠ³ΠΎ ΡΠΏΠ»Π°Π²Π°, ΡΠ»ΡΠΆΠ°Ρ Π² Π΄Π΅ΡΡΡΠΊΠΈ ΡΠ°Π· Π΄ΠΎΠ»ΡΡΠ΅ ΡΡΠ°Π»ΡΠ½ΡΡ . ΠΠ±ΡΠ°Π±ΠΎΡΠΊΡ ΠΈΡ ΡΠ°ΡΡΠΎ ΠΏΡΠΎΠΈΠ·Π²ΠΎΠ΄ΡΡ ΠΊΠΎΠΌΠ±ΠΈΠ½ΠΈΡΠΎΠ²Π°Π½Π½ΡΠΌ ΡΠΏΠΎΡΠΎΠ±ΠΎΠΌ ΡΠ½Π°ΡΠ°Π»Π° Π½Π° ΡΠ»Π΅ΠΊΡΡΠΎΠΈΡΠΊΡΠΎΠ²ΡΡ , Π·Π°ΡΠ΅ΠΌ Π½Π° ΡΠ»ΡΡΡΠ°Π·Π²ΡΠΊΠΎΠ²ΡΡ ΡΡΠ°Π½ΠΊΠ°Ρ . Π Π²ΡΡΡΠ±Π½ΡΡ ΡΡΠ°ΠΌΠΏΠ°Ρ ΡΠ»Π΅ΠΊΡΡΠΎΠΈΡΠΊΡΠΎΠ²ΡΠΌ ΠΌΠ΅ΡΠΎΠ΄ΠΎΠΌ ΠΏΡΠΎΡΠΈΠ²Π°ΡΡ ΠΎΡΠ²Π΅ΡΡΡΠΈΡ, ΠΏΡΠΈ ΡΡΠΎΠΌ Π½Π° ΡΠ»ΡΡΡΠ°Π·Π²ΡΠΊΠΎΠ²ΡΡ ΠΎΠ±ΡΠ°Π±ΠΎΡΠΊΡ ΠΎΡΡΠ°Π²Π»ΡΠ΅ΡΡΡ ΠΏΡΠΈΠΏΡΡΠΊ ΠΏΠΎΡΡΠ΄ΠΊΠ° 1 ΠΌΠΌ. Π Π²ΡΡΡΠΆΠ½ΡΡ ΡΡΠ°ΠΌΠΏΠ°Ρ ΠΈ Π²ΠΎΠ»ΠΎΠΊΠ°Ρ ΡΠ½Π°ΡΠ°Π»Π° ΠΎΠ±ΡΠ°Π±Π°ΡΡΠ²Π°ΡΡ ΡΠΈΠ»ΠΈΠ½Π΄ΡΠΈΡΠ΅ΡΠΊΡΡ ΡΠ°ΡΡΡ, Π·Π°ΡΠ΅ΠΌ Π·Π°Π±ΠΎΡΠ½ΡΠΉ ΠΈ Π²ΡΡ ΠΎΠ΄Π½ΠΎΠΉ ΠΊΠΎΠ½ΡΡΡ. ΠΠ° ΠΎΠ±ΡΠ°Π±ΠΎΡΠΊΡ Π²ΡΡΡΠΆΠ½ΠΎΠΉ ΠΌΠ°ΡΡΠΈΡΡ (ΡΠΈΡ. 100, Π°) Π·Π°ΡΡΠ°ΡΠΈΠ²Π°Π΅ΡΡΡ 1 Ρ, Π° Π½Π° ΠΎΠ±ΡΠ°Π±ΠΎΡΠΊΡ ΡΠ²Π΅ΡΠ΄ΠΎΡΠΏΠ»Π°Π²Π½ΠΎΠΉ ΠΏΡΠ΅ΡΡ-ΡΠΎΡΠΌΡ (ΡΠΈΡ. 100, Π±) ΠΎΠΊΠΎΠ»ΠΎ 4 Ρ. β[c.167]
ΠΠ·Π²Π΅ΡΡΠ½Ρ ΡΠ°Π·Π»ΠΈΡΠ½ΡΠ΅ ΠΌΠ΅ΡΠΎΠ΄Ρ Π½Π°Π½Π΅ΡΠ΅Π½ΠΈΡ ΠΊΠ°ΡΠ±ΠΈΠ΄Π½ΡΡ ΠΏΠΎΠΊΡΡΡΠΈΠΉ. ΠΡΠΈΠΌΠ΅ΡΠΎΠΌ Π½Π°ΠΈΠ±ΠΎΠ»Π΅Π΅ ΠΏΡΠΎΡΡΠΎΠ³ΠΎ ΡΠΏΠΎΡΠΎΠ±Π° Π½Π°Π½Π΅ΡΠ΅Π½ΠΈΡ ΠΊΠ°ΡΠ±ΠΈΠ΄Π½ΠΎΠ³ΠΎ ΠΏΠΎΠΊΡΡΡΠΈΡ ΡΠ²Π»ΡΠ΅ΡΡΡ ΠΎΠ±ΠΌΠ°Π·ΠΊΠ° Π³ΡΠ°ΡΠΈΡΠΎΠ²ΡΡ Π½Π°Π³ΡΠ΅Π²Π°ΡΠ΅Π»Π΅ΠΉ ΠΏΡΡΠΈΠΎΠΊΠΈΡΡΡ Π½ΠΈΠΎΠ±ΠΈΡ Ρ ΠΏΡΠ΅Π²ΡΠ°ΡΠ΅Π½ΠΈΠ΅ΠΌ ΠΏΠΎΡΠ»Π΅Π΄Π½Π΅ΠΉ Π² ΠΏΡΠΎΡΠ΅ΡΡΠ΅ Π½Π°Π³ΡΠ΅Π²Π° Π² ΠΊΠ°ΡΠ±ΠΈΠ΄ Π½ΠΈΠΎΠ±ΠΈΡ [4]. ΠΠ±ΡΠ°Π·ΠΎΠ²Π°Π½ΠΈΠ΅ ΡΠΏΠ»ΠΎΡΠ½ΠΎΠ³ΠΎ ΠΊΠ°ΡΠ±ΠΈΠ΄Π½ΠΎΠ³ΠΎ ΠΏΠΎΠΊΡΡΡΠΈΡ (ΠΎΠ±ΠΎΠ»ΠΎΡΠΊΠΈ) ΠΈΠ· ΠΊΠ°ΡΠ±ΠΈΠ΄Π° Π½ΠΈΠΎΠ±ΠΈΡ Π½Π° Π³ΡΠ°ΡΠΈΡΠΎΠ²ΡΡ Π½Π°Π³ΡΠ΅Π²Π°ΡΠ΅Π»ΡΡ ΠΏΠΎΠ·Π²ΠΎΠ»ΠΈΠ»ΠΎ Π·Π½Π°ΡΠΈΡΠ΅Π»ΡΠ½ΠΎ ΠΏΠΎΠ²ΡΡΠΈΡΡ ΡΠ°Π±ΠΎΡΡΡ ΡΠ΅ΠΌΠΏΠ΅ΡΠ°ΡΡΡΡ ΠΈΠ½Π΄ΡΠΊΡΠΈΠΎΠ½Π½ΡΡ Π²Π°ΠΊΡΡΠΌΠ½ΡΡ ΠΏΠ΅ΡΠ΅ΠΉ. ΠΠ΅ΡΡΠΏΠ΅ΠΊΡΠΈΠ²Π½ΡΠΌΠΈ ΡΠ²Π»ΡΡΡΡΡ ΠΏΠΎΠΊΡΡΡΠΈΡ ΠΊΠ°ΡΠ±ΠΈΠ΄Π°ΠΌΠΈ ΠΌΠ΅ΡΠΎΠ΄ΠΎΠΌ ΡΠ»Π΅ΠΊΡΡΠΎΠΈΡΠΊΡΠΎΠ²ΠΎΠ³ΠΎ ΠΎΡΠ°ΠΆΠ΄Π΅Π½ΠΈΡ Π΄Π»Ρ ΠΏΠΎΠ²ΡΡΠ΅Π½ΠΈΡ ΠΈΠ·Π½ΠΎΡΠΎΡΡΠΎΠΉΠΊΠΎΡΡΠΈ ΡΡΠ°ΠΌΠΏΠΎΠ² ΠΏΡΠ΅ΡΡΠΎΠ²ΠΎΠ³ΠΎ ΠΈΠ½ΡΡΡΡΠΌΠ΅Π½ΡΠ°, ΠΌΠ΅ΡΠ°Π»Π»ΠΎΡΠ΅ΠΆΡΡΠΈΡ ΡΡΠ°Π½ΠΊΠΎΠ² ΠΈ Ρ, Π΄. β[c.425]
ΠΠ΅Ρ Π°Π½ΠΈ- ΡΠ΅ΡΠΊΠΈΠ΅ ΠΠ±ΡΠ°Π±ΠΎΡΠΊΠ° Π½Π° ΠΌΠ΅ΡΠ°Π»Π»ΠΎΡΠ΅ΠΆΡΡΠΈΡ ΠΈ ΡΠ»Π΅ΠΊΡΡΠΎΠΈΡΠΊΡΠΎΠ²ΡΡ ΡΡΠ°Π½ΠΊΠ°Ρ . . . + + + -4- β[c.236]
ΠΠ»Π΅ΠΊΡΡΠΎΠΈΡΠΊΡΠΎΠ²Π°Ρ ΡΠ°Π·ΡΠ΅Π·ΠΊΠ° ΠΌΠ΅ΡΠ°Π»Π»ΠΎΠ² 7 β 68 ΠΠ»Π΅ΠΊΡΡΠΎΠΈΡΠΊΡΠΎΠ²Π°Ρ ΡΠ²Π°ΡΠΊΠ° 7 β 69 ΠΠ»Π΅ΠΊΡΡΠΎΠΈΡΠΊΡΠΎΠ²ΡΠ΅ ΠΏΠΈΠ»Ρ 7 β 66 ΠΠ»Π΅ΠΊΡΡΠΎΠΈΡΠΊΡΠΎΠ²ΡΠ΅ ΡΡΠ°Π½ΠΊΠΈ β Π₯Π°ΡΠ°ΠΊΡΠ΅ΡΠΈΡΡΠΈΠΊΠ° β[c.358]
Π€ΠΈΠ³. 86. ΠΠ½Π΅ΡΠ½ΠΈΠΉ Π²ΠΈΠ΄ ΡΡΠ°Π½ΠΊΠ° Π΄Π»Ρ Π³ΡΠ°Π²ΠΈΡΠΎΠ²ΠΊΠΈ ΠΌΠ΅ΡΠ°Π»Π»ΠΎΠ² ΡΠ»Π΅ΠΊΡΡΠΎΠΈΡΠΊΡΠΎΠ²ΡΠΌ ΡΠΏΠΎΡΠΎΠ±ΠΎΠΌ. | ![]() |
ΠΠ°ΡΠΎΡΠΊΠ° Ρ ΠΏΠΎΠΌΠΎΡΡΡ ΡΠ»Π΅ΠΊΡΡΠΎΠΈΡΠΊΡΠΎΠ²ΠΎΠ³ΠΎ ΡΠΏΠΎΡΠΎΠ±Π° ΡΠ°ΡΠΎΠ½Π½ΡΡ ΡΠ΅Π·ΡΠΎΠ², Π°ΡΠΌΠΈΡΠΎΠ²Π°Π½Π½ΡΡ ΡΠ²ΡΡΠ΄ΡΠΌ ΡΠΏΠ»Π°Π²ΠΎΠΌ, ΠΌΠΎΠΆΠ΅Ρ Π±ΡΡΡ ΠΎΡΡΡΠ΅ΡΡΠ²Π»Π΅Π½Π° ΠΏΠΎ ΡΠ»Π΅Π΄ΡΡΡΠ΅ΠΉ ΡΡ Π΅ΠΌΠ΅. Π ΠΏΠ°ΡΡΠΎΠ½ ΡΠΎΠΊΠ°ΡΠ½ΠΎΠ³ΠΎ ΡΡΠ°Π½ΠΊΠ° Π·Π°ΠΊΡΠ΅ΠΏΠ»ΡΠ΅ΡΡΡ Π»Π°ΡΡΠ½Π½ΡΠΉ ΠΈΠ»ΠΈ ΡΡΠ³ΡΠ½Π½ΡΠΉ Π΄ΠΈΡΠΊ. Π‘ ΠΏΠΎΠΌΠΎΡΡΡ ΡΠΏΠ΅ΡΠΈΠ°Π»ΡΠ½ΠΎ ΠΈΠ·Π³ΠΎΡΠΎΠ²Π»Π΅Π½Π½ΠΎΠ³ΠΎ ΡΠ΅Π·ΡΠ° ΠΈΠ· ΡΡΠ°Π»ΠΈ ΡΡΠΎΠΌΡ Π΄ΠΈΡΠΊΡ Π·Π°Π΄Π°ΡΡΡΡ Π½Π΅ΠΎΠ±Ρ ΠΎΠ΄ΠΈΠΌΡΠΉ ΠΏΡΠΎΡΠΈΠ»Ρ. Π Π΄ΠΈΡΠΊΡ ΠΏΠΎΠ΄Π²ΠΎΠ΄ΠΈΡΡΡ ΠΎΠ±ΡΠ°Π±Π°ΡΡΠ²Π°Π΅ΠΌΡΠΉ ΡΠ΅Π·Π΅Ρ Ρ ΡΠ²ΡΡΠ΄ΡΠΌ ΡΠΏΠ»Π°Π²ΠΎΠΌ, ΠΈ Π² ΠΏΡΠΎΡΠ΅ΡΡΠ΅ ΠΏΠΎΡΠ»Π΅Π΄ΡΡΡΠ΅ΠΉ ΡΡΠΎΠ·ΠΈΠΎΠ½Π½ΠΎΠΉ ΠΎΠ±ΡΠ°Π±ΠΎΡΠΊΠΈ, Π³Π΄Π΅ Π΄ΠΈΡΠΊ ΠΈ ΡΠ΅Π·Π΅Ρ ΡΠ²Π»ΡΡΡΡΡ ΡΠ»Π΅ΠΊΡΡΠΎΠ΄Π°ΠΌΠΈ ΠΊΠΎΠ»Π΅Π±Π°ΡΠ΅Π»ΡΠ½ΠΎΠ³ΠΎ ΠΊΠΎΠ½ΡΡΡΠ°, ΡΠ΅Π·Π΅Ρ ΠΏΡΠΈΠΎΠ±ΡΠ΅ΡΠ°Π΅Ρ ΠΏΡΠΎΡΠΈΠ»Ρ Π΄ΠΈΡΠΊΠ°. β[c.68] ΠΡΠΎΠΌΠ΅ ΠΏΡΠΎΡΡΠ΅ΠΉΡΠ΅ΠΉ ΡΠΈΠΏΠΎΠ²ΠΎΠΉ ΠΊΠΎΠ½Π΄Π΅Π½ΡΠ°-ΡΠΎΡ-Π½ΠΎΠΉ ΡΡ Π΅ΠΌΡ R , Π² ΡΠ»Π΅ΠΊΡΡΠΎΠΈΡΠΊΡΠΎΠ²ΡΡ ΡΡΠ°Π½ΠΊΠ°Ρ ΠΏΡΠΈΠΌΠ΅Π½ΡΡΡΡΡ ΡΠ»Π΅Π΄ΡΡΡΠΈΠ΅ ΡΡ Π΅ΠΌΡ (ΡΠΈΠ³. 9). β[c.651]
Π’ΠΎΡΠ½ΠΎΡΡΡ ΡΠ»Π΅ΠΊΡΡΠΎΠΈΡΠΊΡΠΎΠ²ΠΎΠΉ ΠΎΠ±ΡΠ°Π±ΠΎΡΠΊΠΈ ΠΎΠΏΡΠ΅Π΄Π΅Π»ΡΠ΅ΡΡΡ ΡΠΎΡΠ½ΠΎΡΡΡΡ ΠΈΠ·Π³ΠΎΡΠΎΠ²Π»Π΅Π½ΠΈΡ ΡΠ»Π΅ΠΊΡΡΠΎΠ΄Π°-ΠΈΠ½ΡΡΡΡΠΌΠ΅Π½ΡΠ°, ΡΠΎΡΠ½ΠΎΡΡΡΡ Π΅Π³ΠΎ ΠΏΠ΅ΡΠ΅ΠΌΠ΅ΡΠ΅Π½ΠΈΡ (ΡΠΎΡΠ½ΠΎΡΡΡΡ ΡΡΠ°Π½ΠΊΠ°), ΠΆΠ΅ΡΡΠΊΠΎΡΡΡΡ ΠΌΠ΅Ρ Π°Π½ΠΈΡΠ΅ΡΠΊΠΎΠΉ ΡΠ°ΡΡΠΈ ΡΡΠ°Π½ΠΊΠ°. β[c.653]
Π ΡΠ°Π±Π» 22 ΠΏΠ΅ΡΠ΅ΡΠΈΡΠ»Π΅Π½Ρ ΠΎΡΠ½ΠΎΠ²Π½ΡΠ΅ ΠΌΠΎΠ΄Π΅Π»ΠΈ ΡΠ½ΠΈΠ²Π΅ΡΡΠ°Π»ΡΠ½ΡΡ ΠΈ ΡΠΏΠ΅ΡΠΈΠ°Π»ΡΠ½ΡΡ ΡΠ»Π΅ΠΊΡΡΠΎΠΈΡΠΊΡΠΎΠ²ΡΡ ΡΡΠ°Π½ΠΊΠΎΠ², Π²ΡΠΏΡΡΠΊΠ°Π΅ΠΌΡ n Π² Π‘Π‘Π‘Π ΡΠ΅ΡΠΈΠΉΠ½ΠΎ. β[c.656]
Π₯Π°ΡΠ°ΠΊΡΠ΅ΡΠΈΡΡΠΈΠΊΠΈ Π½Π΅ΠΊΠΎΡΠΎΡΡΡ ΡΠ»Π΅ΠΊΡΡΠΎΠΈΡΠΊΡΠΎΠ²ΡΡ ΡΡΠ°Π½ΠΊΠΎΠ² ΠΈ ΡΡΡΠ°Π½ΠΎΠ²ΠΎΠΊ β[c.661]
ΠΠ»Π΅ΠΊΡΡΠΎΠΈΡΠΊΡΠΎΠ²ΡΠ΅ ΡΡΠ°Π½ΠΊΠΈ β Π‘Ρ Π΅ΠΌΡ 650, 651 β[c.795]
Π Π°ΡΡΠΎΡΠΊΠ° ΠΎΡΠ²Π΅ΡΡΡΠΈΠΉ ΠΠ»Π΅ΠΊΡΡΠΎΠΈΡΠΊΡΠΎΠ²ΠΎΠ΅ Π½Π°ΡΠ΅Π·Π°Π½ΠΈΠ΅ ΡΠ΅Π·ΡΠ± 30β100 Π‘ΠΈΠ»Π° ΡΠΎΠΊΠ° 0,5βΠ¨ Π° – ΠΠΎΡΠ½ΠΎΡΡΡ ΡΡΠ°Π½ΠΊΠΎΠ² 0,5β10 ΠΊΠ΅Ρ – – 2β3 Π§Π· ΠΎ β[c.988]
Π’Π΅Ρ Π½ΠΈΡΠ΅ΡΠΊΠ°Ρ Ρ Π°ΡΠ°ΠΊΡΠ΅ΡΠΈΡΡΠΈΠΊΠ° ΡΡΠ°Π½ΠΊΠΎΠ² Π΄Π»Ρ ΡΠ»Π΅ΠΊΡΡΠΎΠΈΡΠΊΡΠΎΠ²ΠΎΠΉ ΠΎΠ±ΡΠ°Π±ΠΎΡΠΊΠΈ ΠΌΠ΅ΡΠ°Π»Π»ΠΎΠ² Π²ΡΠΏΡΡΠΊΠ° ΠΠ΅Π½ΠΈΠ½Π³ΡΠ°Π΄ΡΠΊΠΎΠ³ΠΎ Π·Π°Π²ΠΎΠ΄Π° ΠΡΠ°ΡΠ½ΠΎΠ³Π²Π°ΡΠ΄Π΅Π΅Ρ β[c.95]
ΠΠ»Π΅ΠΊΡΡΠΎΠ΄Π²ΠΈΠ³Π°ΡΠ΅Π»Ρ ΠΏΠΎΠ»ΡΡΠ°Π΅Ρ ΠΏΠΎΡΡΠΎΡΠ½Π½ΠΎΠ΅ ΠΈ Π½Π΅Π·Π°Π²ΠΈΡΠΈΠΌΠΎΠ΅ ΠΏΠΈΡΠ°Π½ΠΈΠ΅ ΠΎΠ±ΠΌΠΎΡΠΊΠΈ Π²ΠΎΠ·Π±ΡΠΆΠ΄Π΅Π½ΠΈΡ, Π° ΡΠΎΠΊ Π² ΡΠΊΠΎΡΠ΅ Π·Π°Π²ΠΈΡΠΈΡ ΠΎΡ ΡΠΎΡΡΠΎΡΠ½ΠΈΡ ΠΌΠ΅ΠΆΡΠ»Π΅ΠΊΡΡΠΎΠ΄Π½ΠΎΠ³ΠΎ Π·Π°Π·ΠΎΡΠ°, Π ΡΠ΅Π°Π»ΡΠ½ΡΡ ΡΡΠ»ΠΎΠ²ΠΈΡΡ ΡΠ°Π±ΠΎΡΡ ΡΠ»Π΅ΠΊΡΡΠΎΠΈΡΠΊΡΠΎΠ²ΠΎΠ³ΠΎ ΡΡΠ°Π½ΠΊΠ° ΡΠΎΠΊ Π½Π΅ΠΏΡΠ΅ΡΡΠ²Π½ΠΎ ΠΈΠ·ΠΌΠ΅Π½ΡΠ΅ΡΡΡ ΠΊΠ°ΠΊ ΠΏΠΎ Π²Π΅Π»ΠΈΡΠΈΠ½Π΅, ΡΠ°ΠΊ ΠΈ ΠΏΠΎ Π½Π°ΠΏΡΠ°Π²Π»Π΅Π½ΠΈΡ (ΡΠΈΠ³, 48, Π±,48,Π²). β[c.96]
Π‘ΡΠ°Π½ΠΎΠΊ Π ΠΠ-51 (ΡΠΈΠ³. 50) ΠΏΡΠ΅Π΄Π½Π°Π·Π½Π°ΡΠ΅Π½ Π΄Π»Ρ ΡΠ»Π΅ΠΊΡΡΠΎΠΈΡΠΊΡΠΎΠ²ΠΎΠ³ΠΎ ΡΠ»ΠΈΡΠΎΠ²Π°Π½ΠΈΡ Π½Π΅-Π±ΠΎΠ»ΡΡ.ΠΈΡ Π΄Π΅ΡΠ°Π»Π΅ΠΉ ΠΈΠ· ΡΠ²Π΅ΡΠ΄ΠΎΠ³ΠΎ ΡΠΏΠ»Π°Π²Π°, Ρ ΠΊΠΎΡΠΎΡΡΡ ΠΌΠΎΠ³ΡΡ ΠΎΠ±ΡΠ°Π±Π°ΡΡΠ²Π°ΡΡΡΡ ΡΠΈΠ»ΠΈΠ½Π΄ΡΠΈΡΠ΅ΡΠΊΠΈΠ΅ ΠΈ ΠΊΠΎΠ½ΡΡΠ½ΡΠ΅ ΠΎΡΠ²Π΅ΡΡΡΠΈΡ, Π° ΡΠ°ΠΊΠΆΠ΅ β[c.96]
Π’Π΅Ρ Π½ΠΈΡΠ΅ΡΠΊΠΈΠ΅ Ρ Π°ΡΠ°ΠΊΡΠ΅ΡΠΈΡΡΠΈΠΊΠΈ ΡΡΠ°Π½ΠΊΠΎΠ² Π΄Π»Ρ ΡΠ»Π΅ΠΊΡΡΠΎΠΈΡΠΊΡΠΎΠ²ΠΎΠΉ ΠΎΠ±ΡΠ°Π±ΠΎΡΠΊΠΈ, Π²ΡΠΏΡΡΠΊΠ°Π΅ΠΌΡΡ ΠΠ΅Π½ΠΈΠ½Π³ΡΠ°Π΄ΡΠΊΠΈΠΌ ΠΊΠ°ΡΠ±ΡΡΠ°ΡΠΎΡΠ½ΡΠΌ Π·Π°Π²ΠΎΠ΄ΠΎΠΌ ΠΈΠΌ. ΠΡΠΉΠ±ΡΡΠ΅Π²Π° β[c.97]
Π€ΠΈΠ³, 85 ΠΠ½Π΅ΡΠ½ΠΈΠΉ Π²ΠΈΠ΄ ΡΡΠ°Π½ΠΊΠ° ΡΠ»Π΅ΠΊΡΡΠΎΠΈΡΠΊΡΠΎΠ²ΠΎΠ³ΠΎ Π΄Π΅ΠΉΡΡΠ²ΠΈΡ Ρ ΡΠ»Π΅ΠΊΡΡΠΎΠΌΠ°Π³Π½ΠΈΡΠ½ΠΎΠΉ ΠΏΠΎΠ΄Π°ΡΠ΅1). β[c.66]
ΠΠ΅ΡΠ°Π»ΠΈ ΡΡΠΎΠΉ Π³ΡΡΠΏΠΏΡ ΠΌΠΎΠ³ΡΡ Π±ΡΡΡ ΠΈΠ·Π³ΠΎΡΠΎΠ²Π»Π΅Π½Ρ Π½Π° ΠΊΠΎΠΏΠΈΡΠΎΠ²Π°Π»ΡΠ½ΠΎΡΡΠ΅Π·Π΅ΡΠ½ΡΡ ΡΡΠ°Π½ΠΊΠ°Ρ , ΠΏΠΎΠ»ΡΠ°Π²ΡΠΎΠΌΠ°ΡΠΈΡΠ΅ΡΠΊΠΈΡ , Π°Π²ΡΠΎΠΌΠ°ΡΠΈΡΠ΅ΡΠΊΠΈΡ , ΡΠΎ ΡΠ»Π΅Π΄ΡΡΠΈΠΌΠΈ ΡΠΈΡΡΠ΅ΠΌΠ°ΠΌΠΈ ΠΈ ΠΏΡΠΎΠ³ΡΠ°ΠΌΠΌΠ½ΡΠΌ ΡΠΏΡΠ°Π²Π»Π΅Π½ΠΈΠ΅ΠΌ. ΠΡΠΈΠ²ΠΎΠ»ΠΈΠ½Π΅ΠΉΠ½ΡΠ΅ ΠΊΠ°Π½Π°Π»Ρ Π² Π΄Π΅ΡΠ°Π»ΡΡ ΠΌΠΎΠΆΠ½ΠΎ ΠΏΠΎΠ»ΡΡΠ°ΡΡ, Π½Π°ΠΏΡΠΈΠΌΠ΅Ρ, ΡΠ»Π΅ΠΊΡΡΠΎΠΈΡΠΊΡΠΎΠ²ΠΎΠΉ ΠΎΠ±ΡΠ°Π±ΠΎΡΠΊΠΎΠΉ Ρ ΠΏΡΠΈΠΌΠ΅Π½Π΅Π½ΠΈΠ΅ΠΌ ΡΠΏΠ΅ΡΠΈΠ°Π»ΡΠ½ΡΡ ΠΏΡΠΈΡΠΏΠΎΡΠΎΠ±Π»Π΅Π½ΠΈΠΉ. β[c.202]ΠΠ·Π΄Π΅Π»ΠΈΡ ΠΈΠ· ΡΠΏΠ»Π°Π²ΠΎΠ² ΠΏΠΎΠ»ΡΡΠ°ΡΡ Π² ΠΎΡΠ½ΠΎΠ²Π½ΠΎΠΌ ΠΌΠ΅ΡΠΎΠ΄ΠΎΠΌ Π»ΠΈΡΡΡ. ΠΠ΅Π΄ΠΎΡΡΠ°ΡΠΊΠ°ΠΌΠΈ ΡΠΏΠ»Π°Π²ΠΎΠ² ΡΠ²Π»ΡΡΡΡΡ ΠΎΡΠΎΠ±Π°Ρ Ρ ΡΡΠΏΠΊΠΎΡΡΡ ΠΈ Π²ΡΡΠΎΠΊΠ°Ρ ΡΠ²Π΅ΡΠ΄ΠΎΡΡΡ, ΠΏΠΎΡΡΠΎΠΌΡ ΠΎΠ±ΡΠ°Π±ΠΎΡΠΊΠ° ΠΈΡ Π½Π° ΠΌΠ΅ΡΠ°Π»Π»ΠΎΡΠ΅ΠΆΡΡΠΈΡ ΡΡΠ°Π½ΠΊΠ°Ρ Π·Π°ΡΡΡΠ΄Π½Π΅Π½Π°. ΠΠ΅Ρ Π°Π½ΠΈΡΠ΅ΡΠΊΠΎΠΉ ΠΎΠ±ΡΠ°Π±ΠΎΡΠΊΠ΅ Π² Π²ΠΈΠ΄Π΅ Π³ΡΡΠ±ΠΎΠΉ ΠΎΠ±Π΄ΠΈΡΠΊΠΈ ΡΠ΅Π·Π°Π½ΠΈΠ΅ΠΌ Ρ ΠΏΡΠΈΠΌΠ΅Π½Π΅Π½ΠΈΠ΅ΠΌ ΡΠ²Π΅ΡΠ΄ΠΎΡΠΏΠ»Π°Π²Π½ΡΡ ΡΠ΅Π·ΡΠΎΠ² ΠΏΠΎΠ΄Π΄Π°ΡΡΡΡ ΡΠΏΠ»Π°Π²Ρ, Π½Π΅ ΡΠΎΠ΄Π΅ΡΠΆΠ°ΡΠΈΠ΅ ΠΊΠΎΠ±Π°Π»ΡΡΠ°. ΠΠ΅ΡΠ°Π»ΠΈ ΠΈΠ· Π²ΡΠ΅Ρ ΡΠΏΠ»Π°Π²ΠΎΠ² ΠΌΠΎΠΆΠ½ΠΎ ΡΠ»ΠΈΡΠΎΠ²Π°ΡΡ Π½Π° ΠΏΠ»ΠΎΡΠΊΠΎΡΠ»Π½-ΡΠΎΠ²Π°Π»ΡΠ½ΡΡ ΠΈΠ»ΠΈ ΠΊΡΡΠ³Π»ΠΎΡΠ»ΠΈΡΠΎΠ²Π°Π»ΡΠ½ΡΡ ΡΡΠ°Π½ΠΊΠ°Ρ Π² Π΄Π²Π° ΠΏΡΠΈΠ΅ΠΌΠ° Π³ΡΡΠ±Π°Ρ ΡΠ»ΠΈΡΠΎΠ²ΠΊΠ° β Π΄ΠΎ ΡΠ΅ΡΠΌΠΈΡΠ΅ΡΠΊΠΎΠΉ ΠΎΠ±ΡΠ°Π±ΠΎΡΠΊΠΈ, ΡΠΈΡΡΠΎΠ²Π°Ρ β ΠΏΠΎΡΠ»Π΅ ΡΠ΅ΡΠΌΠΈ-ΡΠ΅ΡΠΊΠΎΠΉ ΠΎΠ±ΡΠ°Π±ΠΎΡΠΊΠ½. Π»Ρ Π³ΡΡΠ±ΠΎΠΉ Π±ΡΠ°Π±ΠΎΡΠΊΠΈ ΠΏΡΠΈΠΌΠ΅Π½ΡΡΡ ΡΠ°ΠΊΠΆΠ΅ ΡΠ»Π΅ΠΊΡΡΠΎΠΈΡΠΊΡΠΎΠ²ΠΎΠΉ ΠΌΠ΅ΡΠΎΠ΄ ΠΎΠ±ΡΠ°Π±ΠΎΡΠΊΠΈ. β[c.108]
ΠΠ»Π΅ΠΊΡΡΠΎΠΈΡΠΊΡΠΎΠ²Π°Ρ ΠΎΠ±ΡΠ°Π±ΠΎΡΠΊΠ° ΠΌΠ΅ΡΠ°Π»Π»ΠΎΠ² Π² Π½Π°ΡΡΠΎΡΡΠ΅Π΅ Π²ΡΠ΅ΠΌΡ ΠΏΡΠΈΠΌΠ΅Π½ΡΠ΅ΡΡΡ Π²ΠΎ ΠΌΠ½ΠΎΠ³ΠΈΡ ΠΎΡΡΠ°ΡΠ»ΡΡ ΠΏΡΠΎΠΌΡΡΠ»Π΅Π½Π½ΠΎΡΡΠΈ ΠΈ Π² ΠΎΡΠΎΠ±Π΅Π½Π½ΠΎΡΡΠΈ Π½Π° ΡΠΏΠ΅ΡΠΈΠ°Π»ΠΈΠ·ΠΈΡΠΎΠ²Π°Π½Π½ΡΡ Π·Π°Π²ΠΎΠ΄Π°Ρ ΡΠ²Π΅ΡΠ΄ΠΎΡΠΏΠ»Π°Π²Π½ΠΎΠ³ΠΎ ΠΈΠ½ΡΡΡΡΠΌΠ΅Π½ΡΠ° ΠΈ ΠΎΡΠ½Π°ΡΡΠΊΠΈ. Π ΠΏΡΠ°ΠΊΡΠΈΠΊΡ Π²Π½Π΅Π΄ΡΡΡΡΡΡ Π½ΠΎΠ²ΡΠ΅ ΡΠ΅Ρ Π½ΠΎΠ»ΠΎΠ³ΠΈΡΠ΅ΡΠΊΠΈΠ΅ ΠΏΡΠΎΡΠ΅ΡΡΡ, Π½ΠΎΠ²ΡΠ΅ Π²ΡΡΠΎΠΊΠΎΡΠ°ΡΡΠΎΡΠ½ΡΠ΅ Π³Π΅Π½Π΅ΡΠ°ΡΠΎΡΡ ΠΈ ΡΠ»Π΅ΠΊΡ-ΡΠΎΡΡΠΎΠ·ΠΈΠΎΠ½Π½ΡΠ΅ ΡΡΠ°Π½ΠΊΠΈ [57]. β[c.126]
ΠΠ»ΠΌΠ°Π·Π½ΡΠ΅ Π±ΡΡΡΠΊΠΈ, Π² ΠΎΡΠ»ΠΈΡΠΈΠ΅ ΠΎΡ Π°Π±ΡΠ°Π·ΠΈΠ²Π½ΡΡ , ΡΡΠ΅Π±ΡΡΡ ΠΎΠ±ΡΠ·Π°ΡΠ΅Π»ΡΠ½ΠΎΠΉ ΠΏΡΠ΅Π΄Π²Π°ΡΠΈΡΠ΅Π»ΡΠ½ΠΎΠΉ ΠΏΡΠΈΡΠ°Π±ΠΎΡΠΊΠΈ (ΠΏΡΠΎΡΠΈΠ»ΠΈΡΠΎΠ²Π°Π½ΠΈΡ). Π§Π°ΡΡΠΎ ΡΡΠ° ΠΎΠΏΠ΅ΡΠ°ΡΠΈΡ Π²ΡΠΏΠΎΠ»Π½ΡΠ΅ΡΡΡ ΠΏΠΎ ΡΠ΅Ρ Π½ΠΎΠ»ΠΎΠ³ΠΈΡΠ΅ΡΠΊΠΎΠΉ Π΄Π΅ΡΠ°Π»ΠΈ Π°Π±ΡΠ°Π·ΠΈΠ²Π½ΡΠΌ ΠΏΠΎΡΠΎΡΠΊΠΎΠΌ, Π½Π° ΡΡΠΎ Π·Π°ΡΡΠ°ΡΠΈΠ²Π°Π΅ΡΡΡ Π·Π½Π°ΡΠΈΡΠ΅Π»ΡΠ½ΠΎΠ΅ Π²ΡΠ΅ΠΌΡ. ΠΠΎΠ»Π΅ ΡΠ°Π΄ΠΈΠΊΠ°Π»ΡΠ½ΡΠΌ ΡΠ΅ΡΠ΅Π½ΠΈΠ΅ΠΌ ΡΠ²Π»ΡΠ΅ΡΡΡ ΠΏΡΠΎΡΠΈΠ»ΠΈΡΠΎΠ²Π°Π½ΠΈΠ΅ ΡΠ»Π΅ΠΊΡΡΠΎΠΈΡΠΊΡΠΎΠ²ΡΠΌ ΠΌΠ΅ΡΠΎΠ΄ΠΎΠΌ [113]. ΠΠ° ΡΠΈΡ. 29 ΠΏΡΠ΅Π΄ΡΡΠ°Π²Π»Π΅Π½Π° ΡΡ Π΅ΠΌΠ° ΠΏΡΠΈΡΠΏΠΎΡΠΎΠ±Π»Π΅Π½ΠΈΡ, ΠΏΡΠΈΠΌΠ΅Π½ΡΠ΅ΠΌΠΎΠ³ΠΎ Π΄Π»Ρ ΡΡΠΈΡ ΡΠ΅Π»Π΅ΠΉ. ΠΠ΅ΡΠΆΠ°Π²ΠΊΡ 1 Ρ Π±ΡΡΡΠΊΠ°ΠΌΠΈ 2 ΠΊΡΠ΅ΠΏΡΡ Π½Π΅ΠΏΠΎΠ΄Π²ΠΈΠΆΠ½ΠΎ Π½Π° ΡΡΠΎΠ»Π΅ ΡΠ»Π΅ΠΊΡΡΠΎΡΡΠΎΠ·ΠΈΠΎΠ½Π½ΠΎΠ³ΠΎ ΠΏΡΠΎΡΠΈΠ²ΠΎΡΠ½ΠΎΠ³ΠΎ ΡΡΠ°Π½ΠΊΠ° 4Π721. ΠΡΠΎΡΠΈΠ»ΠΈΡΠΎΠ²Π°Π½ΠΈΠ΅ Π²Π΅Π΄ΡΡ Π΄ΠΈΡΠΊΠΎΠΌ 3, Π΄ΠΈΠ°ΠΌΠ΅ΡΡ ΠΊΠΎΡΠΎΡΠΎΠ³ΠΎ ΡΠ°Π²Π΅Π½ Π΄ΠΈΠ°ΠΌΠ΅ΡΡΡ Π΄Π΅ΡΠ°Π»ΠΈ, Π΄Π»Ρ Π΄ΠΎΠ²ΠΎΠ΄ΠΊΠΈ ΠΊΠΎΡΠΎΡΠΎΠΉ Π±ΡΡΡΠΊΠΈ ΠΏΡΠ΅Π΄Π½Π°Π·Π½Π°ΡΠ΅Π½Ρ. Π¨ΠΏΠΈΠ½Π΄Π΅Π»Ρ ΡΡΠ°Π½ΠΊΠ° Ρ Π΄ΠΈΡΠΊΠΎΠΌ ΡΠΎΠ²Π΅ΡΡΠ°Π΅Ρ Π²ΡΠ°Ρ,Π°ΡΠ΅Π»ΡΠ½ΠΎΠ΅ ΠΈ Π²ΠΎΠ·Π²ΡΠ°ΡΠ½ΠΎ-ΠΏΠΎΡΡΡΠΏΠ°ΡΠ΅Π»ΡΠ½ΠΎΠ΅ Π΄Π²ΠΈΠΆΠ΅Π½ΠΈΠ΅. Π‘ΡΠ°Π½ΠΎΠΊ ΡΠ°Π±ΠΎΡΠ°Π΅Ρ Π½Π° ΡΠ²ΠΎΠ΅ΠΌ ΠΏΠ΅ΡΠ²ΠΎΠΌ ΡΠ΅ΠΆΠΈΠΌΠ΅. ΠΠ° 3β5 ΠΌΠΈΠ½ Ρ Π±ΡΡΡΠΊΠΎΠ² ΡΠ½ΠΈΠΌΠ°Π΅ΡΡΡ ΡΠ»ΠΎΠΉ 0,2β0,3 ΠΌΠΌ. ΠΡΡΡΠΊΠΈ ΠΏΠΎΠ»ΡΡΠ°ΡΡΡΡ Π΄ΠΎΡΡΠ°ΡΠΎΡΠ½ΠΎ ΠΏΡΡΠΌΠΎΠ»ΠΈΠ½Π΅ΠΉΠ½ΡΠΌΠΈ, ΠΏΡΠΈΠ»Π΅Π³Π°Π΅ΠΌΠΎΡΡΡ ΠΈΡ ΠΊ ΠΎΠ±ΡΠ°Π±Π°ΡΡΠ²Π°Π΅ΠΌΠΎΠΉ Π΄Π΅ΡΠ°Π»ΠΈ ΡΠΎΡΡΠ°Π²Π»ΡΠ΅Ρ β[c.77]
ΠΡΠ΅ΡΠ΅ΡΡΠ²Π΅Π½Π½Π°Ρ ΠΏΡΠΎΠΌΡΡΠ»Π΅Π½Π½ΠΎΡΡΡ Π²ΡΠΏΡΡΠΊΠ°Π΅Ρ Π½Π΅ΡΠΊΠΎΠ»ΡΠΊΠΎ ΡΠΈΠΏΠΎΠ² ΡΠ»Π΅ΠΊΡΡΠΎΠΈΡΠΊΡΠΎΠ²ΡΡ ΡΡΠ°Π½ΠΊΠΎΠ² ΠΌΠΎΠ΄Π΅Π»ΠΈ 4Π721, ΠΠΠ-18, 4722 ΠΈ Π΄Ρ. ΠΠ°ΡΡΠΎΠ»ΡΠ½ΡΠΉ ΡΠ½ΠΈΠ²Π΅ΡΡΠ°Π»ΡΠ½ΡΠΉ ΡΡΠ°Π½ΠΎΠΊ ΠΌΠΎΠ΄. 4Π721, Π½Π°ΠΏΡΠΈΠΌΠ΅Ρ, ΠΏΡΠ΅Π΄Π½Π°Π·Π½Π°ΡΠ΅Π½ Π΄Π»Ρ ΠΎΠ±ΡΠ°Π±ΠΎΡΠΊΠΈ ΠΎΡΠ²Π΅ΡΡΡΠΈΠΉ Π΄ΠΈΠ°ΠΌΠ΅ΡΡΠΎΠΌ 0,15β5 ΠΌΠΌ Ρ Π½Π°ΠΈΠ±ΠΎΠ»ΡΡΠ΅ΠΉ Π³Π»ΡΠ±ΠΈΠΈΠΎΠΉ 20 ΠΌΠΌ. β[c.388]
ΠΡΠΈΡΡΠ°Π»Π»-7 . Π£ΡΡΠ°Π½ΠΎΠ²ΠΊΠ° Ρ Π»Π°Π·Π΅ΡΠΎΠΌ Π½Π° ΡΡΠ΅ΠΊΠ»Π΅ Ρ Π½Π΅ΠΎΠ΄ΠΈΠΌΠΎΠΌ ΡΠ»ΡΠΆΠΈΡ Π΄Π»Ρ ΡΠ²Π΅ΡΠ»Π΅Π½ΠΈΡ Π² Π΄Π΅ΡΠ°Π»ΡΡ ΠΈΠ½ΡΡΡΡΠΌΠ΅Π½ΡΠ°Π»ΡΠ½ΠΎΠΉ ΠΎΡΠ½Π°ΡΡΠΊΠΈ ΡΠΊΠ²ΠΎΠ·Π½ΡΡ ΠΎΡΠ²Π΅ΡΡΡΠΈΠΉ ΠΏΠ΅ΡΠ΅Π΄ ΠΈΡ Π΄Π°Π»ΡΠ½Π΅ΠΉΡΠ΅ΠΉ ΠΊΠΎΠ½ΡΡΡΠ½ΠΎΠΉ ΠΎΠ±ΡΠ°Π±ΠΎΡΠΊΠΎΠΉ Π½Π° ΡΠ»Π΅ΠΊΡΡΠΎΠΈΡΠΊΡΠΎΠ²ΡΡ ΡΡΠ°Π½ΠΊΠ°Ρ . ΠΠ»ΠΈΡΠ΅Π»ΡΠ½ΠΎΡΡΡ ΠΈΠΌΠΏΡΠ»ΡΡΠ° 150β200 ΠΌΠΊΡ, ΡΠ½Π΅ΡΠ³ΠΈΡ ΠΈΠΌΠΏΡΠ»ΡΡΠ° ΠΈΠ·Π»ΡΡΠ΅Π½ΠΈΡ 0,1β5 ΠΠΆ, ΡΠ°ΡΡΠΎΡΠ° ΡΠ»Π΅Π΄ΠΎΠ²Π°Π½ΠΈΡ ΠΈΠΌΠΏΡΠ»ΡΡΠΎΠ² 0,5β10 ΠΡ. ΠΠΈΠ°ΠΌΠ΅ΡΡ ΠΎΠ±ΡΠ°Π±Π°ΡΡΠ²Π°Π΅ΠΌΡΡ ΠΎΡΠ²Π΅ΡΡΡΠΈΠΉ 0,05β 0,4 ΠΌΠΌ. ΠΠ»ΡΠ±ΠΈΠ½Π° ΠΎΠ±ΡΠ°Π±ΠΎΡΠΊΠΈ Π΄ΠΎ 4 ΠΌΠΌ, ΡΠΎΡΠ½ΠΎΡΡΡ ΠΎΠ±ΡΠ°Π±ΠΎΡΠΊΠΈ ΠΏΠΎ 5-ΠΌΡ ΠΊΠ»Π°ΡΡΡ. ΠΠΎΡΡΠ΅Π±Π»ΡΠ΅ΠΌΠ°Ρ ΠΌΠΎΡΠ½ΠΎΡΡΡ 4,5 ΠΊΠΡ. ΠΠ°Π±Π°ΡΠΈΡΠ½ΡΠ΅ ΡΠ°Π·ΠΌΠ΅ΡΡ ΡΡΡΠ°Π½ΠΎΠ²ΠΊΠΈ 1700X900X1500 ΠΌΠΌ. β[c.308]
ΠΠ±ΠΎΡΡΠ΄ΠΎΠ²Π°Π½ΠΈΠ΅. Π‘Π΅ΡΠΈΠΉΠ½ΡΠΉ Π²ΡΠΏΡΡΠΊ ΠΎΠ±ΠΎΡΡΠ΄ΠΎΠ²Π°Π½ΠΈΡ Π΄Π»Ρ ΡΠ»Π΅ΠΊΡΡΠΎΠΈΡΠΊΡΠΎΠ²ΠΎΠΉ ΠΎΠ±ΡΠ°Π±ΠΎΡΠΊΠΈ ΠΎΠ³ΡΠ°Π½ΠΈΡΠ΅Π½ ΠΏΡΠ΅ΠΈΠΌΡΡΠ΅ΡΡΠ²Π΅Π½Π½ΠΎ ΡΠ½ΠΈΠ²Π΅ΡΡΠ°Π»ΡΠ½ΡΠΌΠΈ ΡΡ Π½ΠΊΠ°ΠΌΠΈ. Π‘ΠΏΠ΅ΡΠΈΠ°Π»ΠΈΠ·ΠΈΡΠΎΠ²Π°Π½Π½ΡΠ΅ ΡΡΠ°Π½ΠΊΠΈ ΡΠ°ΡΡΠΎ ΠΈΠ·Π³ΠΎΡΠΎΠ²Π»ΡΡΡΡΡ Π½Π΅ΠΏΠΎΡΡΠ΅Π΄ΡΡΠ²Π΅Π½Π½ΠΎ ΠΏΠΎΡΡΠ΅Π±ΠΈΡΠ΅Π»ΡΠΌΠΈ β[c.656]
ΠΠ΅ΡΠΊΠΎΡΡΡΡΠΉΠ½Π°Ρ ΠΎΡΠΈΡΡΠΊΠ° ΡΡΡ ΠΈΠΌ ΠΊΡΡΠΏΠ½ΠΎΠ·Π΅ΡΠ½ΠΈΡΡΡΠΌ ΠΎΡΡΡΠΎΠ³ΡΠ°Π½Π½ΡΠΌ ΠΊΠ²Π°ΡΡΠ΅Π²ΡΠΌ ΠΏΠ΅ΡΠΊΠΎΠΌ ΡΠ°Π·ΠΌΠ΅ΡΠΎΠΌ ΡΠ°ΡΡΠΈΡ 1β2 ΠΌΠΌ. ΠΡΠΈ Π½Π΅Π±ΠΎΠ»ΡΡΠΈΡ ΡΠ°Π·ΠΌΠ΅ΡΠ°Ρ ΠΈΠ·Π΄Π΅Π»ΠΈΠΉ ΠΏΡΠΎΠΈΠ·Π²ΠΎΠ΄ΠΈΡΡΡ Π²ΡΡΡΠ½ΡΡ Π² ΠΏΠ΅ΡΠΊΠΎΡΡΡΡΠΉΠ½ΠΎΠΌ ΡΠΊΠ°ΡΡ ΠΏΡΠΈ Π΄Π°Π²Π»Π΅Π½ΠΈΠΈ ΡΠΆΠ°ΡΠΎΠ³ΠΎ Π²ΠΎΠ·Π΄ΡΡ Π° 4β6 Π°ΡΠΈ ΠΠ±ΡΠΎΡΠΊΠ° Π½Π° ΡΠΎΠΊΠ°ΡΠ½ΠΎΠΌ ΡΡΠ°Π½ΠΊΠ΅ Π»ΡΠ±ΠΎΠ³ΠΎ ΡΠΈΠΏΠ°. ΠΠΎΠ·ΠΌΠΎΠΆΠ½ΠΎ ΠΈΡΠΏΠΎΠ»ΡΠ·ΠΎΠ²Π°Π½ΠΈΠ΅ ΠΎΠ΄Π½ΠΎΠ³ΠΎ ΡΡΠ°Π½ΠΊΠ° ΠΊΠ°ΠΊ Π΄Π»Ρ ΠΏΠΎΠ΄Π³ΠΎΡΠΎΠ²ΠΊΠΈ ΠΏΠΎΠ²Π΅ΡΡ Π½ΠΎΡΡΠΈ, ΡΠ°ΠΊ ΠΈ Π΄Π»Ρ ΠΌΠ΅ΡΠ°Π»Π»ΠΈΠ·Π°ΡΠΈΠΈ ΠΠ°ΡΠ΅Π·ΠΊΠ° Π½Π° ΡΠΎΠΊΠ°ΡΠ½ΠΎ-Π²ΠΈΠ½ΡΠΎΡΠ΅Π·Π½ΠΎΠΌ ΡΡΠ°Π½ΠΊΠ΅ ΡΠ²Π°Π½ΠΎΠΉ ΡΠ΅Π·ΡΠ±Ρ ΠΈΠ»ΠΈ ΠΎΠ±ΡΠ°Π±ΠΎΡΠΊΠ° ΠΏΠΎΠ²Π΅ΡΡ Π½ΠΎΡΡΠΈ ΠΏΡΡΠΊΠΎΠΌ ΡΠ»Π΅ΠΊΡΡΠΎΠ΄ΠΎΠ², ΡΠ»Π΅ΠΊΡΡΠΎΠΈΡΠΊΡΠΎΠ²ΡΠΌ, ΡΠ»Π΅ΠΊΡΡΠΎΠ²ΠΈΠ±ΡΠ°ΡΠΈΠΎΠ½Π½ΡΠΌ ΠΈΠ»ΠΈ Π΄ΡΡΠ³ΠΈΠΌ ΡΠΏΠΎΡΠΎΠ±ΠΎΠΌ β[c.35]
Π ΡΠ°Π±Π». 63 ΠΏΡΠΈΠ²Π΅Π΄Π΅Π½Ρ ΠΊΡΠ°ΡΠΊΠΈΠ΅ ΡΠ΅Ρ Π½ΠΈΡΠ΅ΡΠΊΠΈΠ΅ Ρ Π°ΡΠ°ΠΊΡΠ΅ΡΠΈΡΡΠΈΠΊΠΈ ΡΠ»Π΅ΠΊΡΡΠΎΠΈΡΠΊΡΠΎΠ²ΡΡ ΡΡΠ°Π½ΠΊΠΎΠ² Π΄Π»Ρ ΠΊΠΎΠΏΠΈΡΠΎΠ²Π°Π»ΡΠ½ΠΎ-ΠΏΡΠΎΡΠΈΠ²ΠΎΡΠ½ΡΡ ΡΠ°Π±ΠΎΡ, Π²ΡΠΏΡΡΠΊΠ°Π΅ΠΌΡΡ ΠΠ΅Π½ΠΈΠ½Π³ΡΠ°Π΄ΡΠΊΠΈΠΌ Π·Π°Π²ΠΎΠ΄ΠΎΠΌ ΠΡΠ°ΡΠ½ΠΎΠ³Π²Π°ΡΠ΄Π΅Π΅Ρ . ΠΠ°ΠΈΠ±ΠΎΠ»Π΅Π΅ ΡΠΎΠ²Π΅ΡΡΠ΅Π½Π½ΡΠΌ ΠΈΠ· Π½ΠΈΡ ΡΠ²Π»ΡΠ΅ΡΡΡ ΡΡΠ°Π½ΠΎΠΊ ΠΠΠ‘Π-3. β[c.95]
mash-xxl.info