Формулы фрезерования / Milling formulas
Режущий инструмент, инструментальная оснастка и приспособления / Cutting tools, tooling system and workholding | |||||
Подборка ссылок из каталогов производителей инструмента для словаря по машиностроению | |||||
811 Формулы при фрезеровании для расчета режимов резания на фрезерных станках Расчет мощности Подача на зуб Частота вращения шпинделя Угол контакта Средняя толщина стружки | 812 Расчет режимов резания для фрезерных станков с ЧПУ Расчетные формулы для винтовой интерполяции наружного и внутреннего контуров Радиальная глубина резания | 190 Основные расчетные формулы при механической обработке на станках Расчет скорости и подачи Производительность резания Параметры поверхности | 193 Мощность и сила резания при фрезеровании металла на станках Расчетные формулы для торцевой и периферийной фрезерной обработки | 267 Расчет режимов резания при фрезеровании на фрезерных станках Расчетные формулы Скорость резания Подача на зуб Необходимая мощность главного привода | 266 Условные обозначения, понятия и размерности принятые при механической фрезерной обработке на металлообрабатывающем оборудовании Symbols Обозначение Term |
256 Основные формулы фрезеровщика фрезерного станка по металлу Скорость из оборотов шпинделя Минутная подача Толщина срезаемой стружки Крутящий момент | 512 Механическая обработка деталей на металлорежущих станках Основные определения при фрезеровании vc Скорость резания м/мин n частота вращения шпинделя | 527 Формулы для расчета режимов резания при фрезерования на фрезерных станках по металлу Скорость резания Машинное время Потребляемая мощность Подача | 352 Формулы и определения для фрезерной обработки на металлорежущем оборудовании и станках Скорость подачи, мм/мин Vf = fz X n X zc Скорость резания, | 1064 Геометрические особенности корпусных фрез по металлу с режущими сменными пластинами из твердого сплава Расчетные формулы при фрезеровке на станке | 1070 Цельные концевые фрезы по металлу Основные элементы конструкции металлорежущего фрезерного инструмента Отличия между высокоскоростными и стандартными |
См. | |||||
Перевод оборотов в скорость / Surface speed to RPM conversion | Встречное и попутное фрезерование / Up and down cut milling | ||||
Фрезерная обработка металла / Basics of milling | Резьбовые фрезы / Thread milling | ||||
Фрезы со сменными пластинами / Parts of a milling cutter | Твердосплавные концевые фрезы | ||||
Основное машинное время обработки / Machining time | Оснастка для фрезерных станков по металлу / Мilling tool holders | ||||
Примеры страниц из каталогов инструмента для металлообработки | |||||
811 Каталог WALTER 2013 Дополнение к общему Стр.H-7 | |||||
Формулы при фрезеровании для расчета режимов резания на фрезерных станках Расчет мощности Подача на зуб Частота вращения шпинделя Угол контакта Средняя толщина стружки Формулы при фрезеровании для расчета режимов резания на фрезерных станках Расчет мощности Подача на зуб Частота вращения шпинделя Угол контакта Средняя толщина стружки _ Удельная сила резания Угол в плане Частота вращения vmnn min vc x 1000 Dcx7t Скорость резания Dcxj xn Vr = m/min c 1000 Подача Vf = fz x z x n mm/min Скорость подачи на один зуб U = mm/z zxn Удельный съём материала ае х а0 х Vf Q = cm 3/min 1000 Мощность aD х a х Vf х kc Pm0t= a W tkWl 6 x 107 x Ti Средняя толщина стружки 114,7 xfzxsinicx(ae/Dc) = фз mm – hm X фз mm 114,7xsinKX(ae/Dc) I cle hmsfzx- 5 mm fz = – =- mm ae (Dc приближённая формула для ae Dc 30% Угол контакта фрезы Центральное позиционирование фрезы (ps = 2xarcsin(j ) Позиционирование со смещением от центра фз = 90°+arcsin ае(р )/2) Удельная сила резания кс = 1 х ci-i N/mm2 или n Частота вращения мин-1 Dc Обрабатываемый диаметр мм ap Глубина резания мм ae Ширина резания мм z Количество зубьев Vc Скорость резания м/мин Vf Подача мм/мин fz Подача на зуб мм Q Удельный съём материала см3/мин P mot Потребляемая мощность кВт hm Средняя толщина стружки мм kc Удельная сила резания Н/мм2 n КПД станка (0,7-0,95) К Угол в плане Ф5 Угол контакта фрезы Ф1 Зона фрезерования против подачи Ф2 Зона фрезерования по подаче kc Удельная сила резания Н/мм2 kc1. | |||||
936 Каталог SUMITOMO 2016 Металлорежущий инструмент Пластины Сверла Фрезы Резцы для станков Стр.N6 | |||||
Конструкция корпусной фрезы по металлу Станочный металлорежущий инструмент со сменными режущими пластинами Вычисление требуемой мощности при фрезеровании Конструкция корпусной фрезы по металлу Станочный металлорежущий инструмент со сменными режущими пластинами Вычисление требуемой мощности при фрезеровании _ Вычисление силы резания n doc Woe Vf Ко . . Рс = (кВт) 60 х 106 х I Коэффициент силы резания Мощность (л.с.) Рс 0,75 Н = Производительность doc х Woe х Vf Q = 1.000 (сма/мин) Pc : Требуемая мощность (кВт) Н : Требуемая мощность (л.с.) Q : Производительность (см3/мин) woc: Ширина фрезерования (мм) Vf : Подача (мм/мин) doc: Глубина резания (мм) П : КПД (0,7-0,85) Кс : Коэффициент силы резания (Н/мм2) Приблизительное значение j Сталь: 2500-3000 \ ( Чугун: 1500 ) А Q X \мат-л No>\ Легированная сталь Углеродистая стал. Чугун Алюминиевый сплав 1.800 800 200 – 1.400 600 160 – 1.000 400 120 – О 0,10,2 0,4 0,6 0,8 1,0 Подача (мм/зуб) В таблице указаны: – Предел прочности для сталей – Твердость (НВ) для чугуна > Вычисление скорости резания Vc = 71 X D X 1.000 9 Вычисление минутной подачи Vf = ft X Z X n vf Скорость резания(м/мин) 3,14 Диаметр фрезы (мм) Частота вращения (об/мин)) Минутная подача (мм/мин) Подача (мм/зуб) Количество зубьев N6 Техническое Руководство Техническое руководство Основы фрезерования | |||||
352 Пособие SANDVIK COROMANT 2009 Обработка металлов резанием Инструмент и оснастка Стр. | |||||
Формулы и определения для фрезерной обработки на металлорежущем оборудовании и станках Скорость подачи, мм/мин Vf = fz X n X zc Скорость резания, Формулы и определения для фрезерной обработки на металлорежущем оборудовании и станках Скорость подачи, мм/мин Vf = fz X n X zc Скорость резания, м/мин Vc = П X Dcap X n 1000 Частота вращения шпинделя, об/мин n = vc X 1000 П X D cap Подача на зуб, мм Vf fz = n X Zc Подача на оборот, мм/об fn = Скорость съёма материала, см3/мин Q = ap x ae x Vf Q 1000 Потребляемая мощность, кВт ae x ap x vf x kc Pc = 60 X 106 Крутящий момент, Нм Mc = Pc X 30 X 103 П X n Параметр Значение Единицы измерения Se Ширина фрезерования мм aP Глубина резания мм Dcap Диаметр резания при фактической глубине резания ap мм Dm Обрабатываемый диаметр (диаметр детали) мм fz Подача на зуб мм fn Подача на оборот мм/об n Частота вращения шпинделя об/мин vc Скорость резания м/мин vf Скорость подачи мм/мин c Эффективное число зубьев шт hex Максимальная толщина стружки мм hm Средняя толщина стружки мм kc Удельная сила резания Н/мм2 Pc Потребляемая мощность кВт Mc Крутящий момент Н/м Q Скорость съёма материала см3/мин k Угол в плане град SANDVIK H 77 n Формулы и определения | |||||
Подборка ссылок иллюстрированных из промышленных каталогов | |||||
5 Расчет режимов резания при фрезеровании на металлорежущих станках Основные формулы Крутящий момент Мощность Минутная подача Обороты на шпинделе | 7 Основные формулы для расчета сверления и фрезерования на станках по металлу (в дюймовой системе) Скорость и обороты в минуту Минутная подача | 936 Конструкция корпусной фрезы по металлу Станочный металлорежущий инструмент со сменными режущими пластинами Вычисление требуемой мощности при фрезеровании | 940 Конструкция цельной концевой фрезы из твердого сплава или инструментальной быстрорежущей стали Основные конструкционные элементы фрезерного инструмента | ||
1298 Фрезерные расчетный формулы при фрезеровании плоскостей Расчет скорости резания Подача на зуб режущего инструмента Машинное время обработки | 1299 Рекомендации по расчету потребляемой мощности при фрезерной обработке на металлообрабатывающем оборудовании Расчетные формулы Пример расчета | 1682 Расчетные формулы для фрезерования металла на станках Угол вхождения и число рабочих пластин фрезерного инструмента | 493 Формулы расчета для профильного фрезерования концевыми монолитными фрезами Расчет расстояния между проходами Расчет теоретической глубины прохода | ||
1672 Расчет потребляемой мощности при фрезеровании металла на фрезерных станках | 1673 Расчет режимов резания при фрезерной обработке металла на станках Расчет тангенциальной силы, крутящего момента и мощности при торцевом фрезеровании | 1674 Расчет тангенциальной силы, крутящего момента и мощности при торцевом фрезеровании на фрезерных станках и обрабатывающих центрах с ЧПУ | 1675 Пример пошагового расчета мощности при фрезеровании металла на станках Расчет тангенциальной силы и крутящего момента на фрезе | 1628 Formulae for face milling Cutting speed Feed per Tooth Cutting Time vf (mm/min) Table Feed per Min L (mm) Total Table Feed Length (Workpiece Length | 1629 Formulae for face milling CUTTING POWER (Pc) PC ap ae vf Kc 60 106xt7 Pc (kW) Actual Cutting Power ae (mm) Cutting Width Kc (MPa) Specific Cutting |
Пример иллюстрации инструмента из промышленного каталога (из подборки фото инструментов для металлообработки / Metal cutting tools images) | |||||
1118 Каталог KENNAMETAL 2018 Инструмент для обработки отверстий Метчики Фрезы Стр. | |||||
Красочная фотография фрезы сборной торцевой со сменными режущими шестигранными пластинами из твердого сплава и без задних углов Иллюстрация из каталога Красочная фотография фрезы сборной торцевой со сменными режущими шестигранными пластинами из твердого сплава и без задних углов Иллюстрация из каталога _ Kennametal | |||||
Каталоги инструмента и оснастки для металлообработки на станках / | |||||
Режимы резания при фрезеровании: таблица, элементы, выбор режимов
Поверхностная обработка заготовок методом фрезерования может проводиться исключительно после разработки технологической карты, в которой указываются основные режимы обработки. Подобной работой, как правило, занимается специалист, прошедший специальную подготовку. Режимы резания при фрезеровании могут зависеть от самых различных показателей, к примеру, типа материала и используемого инструмента. Основные показатели на фрезерном станке могут устанавливаться вручную, также проводится указание показателей на блоке числового программного управления. Особое внимание заслуживает резьбофрезерование, так как получаемые изделия характеризуются довольно большим количеством различных параметров. Рассмотрим особенности выбора режимов резания при фрезеровании подробно.
Скорость резания
Наиболее важным режимом при фрезеровании можно назвать скорость резания. Он определяет то, за какой период времени будет снят определенный слой материала с поверхности. На большинстве станков устанавливается постоянная скорость резания. При выборе подходящего показателя учитывается тип материала заготовки:
- При работе с нержавейкой скорость резания 45-95 м/мин. За счет добавления в состав различных химических элементов твердость и другие показатели меняются, снижается степень обрабатываемости.
- Бронза считается более мягким составом, поэтому подобный режим при фрезеровании может выбираться в диапазоне от 90-150 м/мин. Она применяется при изготовлении самых различных изделий.
- Довольно большое распространение получила латунь. Она применяется при изготовлении запорных элементов и различных клапанов. Мягкость сплава позволяет повысить скорость резания до 130-320 м/мин. Латуни склонны к повышению пластичности при сильном нагреве.
- Алюминиевые сплавы сегодня весьма распространены. При этом встречается несколько вариантов исполнения, которые обладают различными эксплуатационными характеристиками. Именно поэтому режим фрезерования варьирует в пределе от 200 до 420 м/мин. Стоит учитывать, что алюминий относится к сплавам с низкой температурой плавления. Именно поэтому при высокой скорости обработки есть вероятность существенного повышения показателя пластичности.
Встречается довольно большое количество таблиц, которые применяются для определения основных режимов работы. Формула для определения оборотов скорости резания выглядит следующим образом: n=1000 V/D, где учитывается рекомендуемая скорость резания и диаметр применяемой фрезы. Подобная формула позволяет определить количество оборотов для всех видов обрабатываемых материалов.
Рассматриваемый режим фрезерования измеряется в метрах в минуту режущие части. Стоит учитывать, что специалисты не рекомендуют гонять шпиндель на максимальных оборотах, так как существенно повышается износ и есть вероятность повреждения инструмента. Поэтому полученный результат уменьшается примерно на 10-15%. С учетом этого параметра проводится выбор наиболее подходящего инструмента.
Скорость вращения инструмента определяет следующее:
- Качество получаемой поверхности. Для финишной технологической операции выбирается наибольший параметр. За счет осевого вращения с большим количеством оборотов стружка получается слишком мелкой. Для черновой технологической операции, наоборот, выбираются низкие значения, фреза вращается с меньшей скоростью, и размер стружки увеличивается.
За счет быстрого вращения достигается низкий показатель шероховатости поверхности. Современные установки и оснастка позволяют получить поверхность зеркального типа.
- Производительность труда. При наладке производства уделяется внимание и тому, какова производительность применяемого оборудования. Примером можно назвать цех машиностроительного завода, где налаживается массовое производство. Существенное снижение показателя режимов обработки становится причиной уменьшения производительности. Наиболее оптимальный показатель существенно повышает эффективность труда.
- Степень износа устанавливаемого инструмента. Не стоит забывать о том, что при трении режущей кромки об обрабатываемую поверхность происходит ее сильный износ. При сильном изнашивании происходит изменение показателей точности изделия, снижается эффективность труда. Как правило, износ связан с сильным нагревом поверхности. Именно поэтому на производственной линии с высокой производительностью применяется оборудование, способное подавать СОЖ в зону снятия материала.
При этом данный параметр выбирается с учетом других показателей, к примеру, глубины подачи. Поэтому технологическая карта составляется с одновременным выбором всех параметров.
Глубина резания
Другим наиболее важным параметром является глубина фрезерования. Она характеризуется следующими особенностями:
- Глубина врезания выбирается в зависимости от материала заготовки.
- При выборе уделяется внимание тому, проводится черновая или чистовая обработка. При черновой выбирается большая глубина врезания, так как устанавливается меньшая скорость. При чистовой снимается небольшой слой металла за счет установки большой скорости вращения инструмента.
- Ограничивается показатель также конструктивными особенностями инструмента. Это связано с тем, что режущая часть может иметь различные размеры.
Глубина резания во многом определяет производительность оборудования. Кроме этого, подобный показатель в некоторых случаях выбирается в зависимости от того, какую нужно получить поверхность.
Мощность силы резания при фрезеровании зависит от типа применяемой фрезы и вида оборудования. Кроме этого, черновое фрезерование плоской поверхности проводится в несколько проходов в случае, когда нужно снять большой слой материала.
Особым технологическим процессом можно назвать работу по получению пазов. Это связано с тем, что их глубина может быть довольно большой, а образование подобных технологических выемок проводится исключительно после чистовой обработки поверхности. Фрезерование т-образных пазов проводится при применении специального инструмента.
Подача
Понятие подачи напоминает глубину врезания. Подача при фрезеровании, как и при проведении любой другой операции по механической обработке металлических заготовок, считается наиболее важным параметром. Долговечность применяемого инструмента во многом зависит от подачи. К особенностям этой характеристики можно отнести нижеприведенные моменты:
- Какой толщины материал снимается за один проход.
- Производительность применяемого оборудования.
- Возможность проведения черновой или чистовой обработки.
Довольно распространенным понятием можно назвать подачу на зуб. Этот показатель указывается производителем инструмента, зависит от глубины резания и конструктивных особенностей изделия.
Как ранее было отмечено, многие показатели режимом резания связаны между собой. Примером можно назвать скорость резания и подачу:
- При увеличении значения подачи скорость резания снижается. Это связано с тем, что при снятии большого количества металла за один проход существенно повышается осевая нагрузка. Если выбрать высокую скорость и подачу, то инструмент будет быстро изнашиваться или попросту поломается.
- За счет снижения показателя подачи повышается и допустимая скорость обработки. При быстром вращении фрезы возможно существенно повысить качество поверхности.
На момент чистового фрезерования выбирается минимальное значение подачи и максимальная скорость, при применении определенного оборудования можно получить практически зеркальную поверхность.
Довольно распространенным значением подачи можно назвать 0,1-0,25. Его вполне достаточно для обработки самых распространенных материалов в различных отраслях промышленности.
Ширина фрезерования
Еще одним параметром, который учитывается при механической обработки заготовок считается ширина фрезерования. Она может варьировать в достаточно большом диапазоне. Ширина выбирается при фрезеровке на станке Have или другом оборудовании. Среди особенностей отметим следующие моменты:
- Ширина фрезерования зависит от диаметра фрезы. Подобные параметры, которые зависят от геометрических особенностей режущей части, не могут регулироваться, учитываются при непосредственном выборе инструмента.
- Ширина фрезерования также оказывает влияние на выбор других параметров. Это связано с тем, что при увеличении значения также увеличивается количество материала, который снимается за один проход.
В некоторых случаях ширина фрезерования позволяет получить требуемую поверхность за один проход. Примером можно назвать случай получения неглубоких канавок. Если проводится резание плоской поверхности большой ширины, то число проходов может несколько отличаться, рассчитывается в зависимости от ширины фрезерования.
Как выбрать режим на практике?
Как ранее было отмечено, в большинстве случаев технологические карты разработаны специалистом и мастеру остается лишь выбрать подходящий инструмент и задать указанные параметры. Кроме этого, мастер должен учитывать то, в каком состоянии находится оборудование, так как предельные значения могут привести к возникновению поломок. При отсутствии технологической карты приходится проводить выбор режимов фрезерования самостоятельно. Расчет режимов резания при фрезеровании проводится с учетом следующих моментов:
- Типа применяемого оборудования.
Примером можно назвать случай резания при фрезеровании на станках ЧПУ, когда могут выбираться более высокие параметры обработки по причине высоких технологических возможностей устройства. На старых станках, которые были введены в эксплуатацию несколько десятков лет назад, выбираются более низкие параметры. На момент определения подходящих параметров уделяется внимание и техническому состоянию оборудования.
- Следующий критерий выбора заключается в типе применяемого инструмента. При изготовлении фрезы могут применяться различные материалы. К примеру, вариант исполнения из быстрорежущей качественной стали подходит для обработки металла с высокой скоростью резания, фреза с тугоплавкими напайками предпочтительно выбирается в случае, когда нужно проводить фрезерование твердого сплава с высоким показателем подачи при фрезеровании. Имеет значение и угол заточки режущей кромки, а также диаметральные размер. К примеру, с увеличением диаметра режущего инструмента снижается подача и скорость резания.
- Тип обрабатываемого материала можно назвать одним из наиболее важных критериев, по которым проводится выбор режима резания. Все сплавы характеризуются определенной твердостью и степенью обрабатываемости. К примеру, при работе с мягкими цветными сплавами могут выбираться более высокие показатели скорости и подачи, в случае с каленной сталью или титаном все параметры снижаются. Немаловажным моментом назовем то, что фреза подбирается не только с учетом режимов резания, но и типа материала, из которого изготовлена заготовка.
- Режим резания выбирается в зависимости от поставленной задачи. Примером можно назвать черновое и чистовое резание. Для черного свойственна большая подача и небольшой показатель скорости обработки, для чистовой все наоборот. Для получения канавок и других технологических отверстий и вовсе показатели подбираются индивидуально.
Как показывает практика, глубина резания в большинстве случаев делится на несколько проходов при черновой обработке, при чистовой он только один. Для различных изделий может применяться таблица режимов, которая существенно упрощает поставленную задачу. Встречаются и специальные калькуляторы, проводящие вычисление требуемых значений в автоматическом режиме по введенным данным.
Выбор режима в зависимости от типа фрезы
Для получения одного и того же изделия могут применяться самые различные виды фрез. Выбор основных режимов фрезерования проводится в зависимости от конструктивных и других особенностей изделия. Режимы резания при фрезеровании дисковыми фрезами или другими вариантами исполнения выбираются в зависимости от нижеприведенных моментов:
- Жесткости применяемой системы. Примером можно назвать особенности станка и различной оснастки. Новое оборудование характеризуется повышенной жесткостью, за счет чего появляется возможность применения более высоких параметров обработки. На старых станках жесткость применяемой системы снижается.
- Уделяется внимание и процессу охлаждения. Довольно большое количество оборудования предусматривает подачу СОЖ в зону обработки. За счет подобного вещества существенно снижается температура режущей кромки. СОЖ должна подаваться в зону снятия материала постоянно. При этом также удаляется и образующаяся стружка, что существенно повышает качество резания.
- Стратегия обработки также имеет значение. Примером можно назвать то, что получение одной и той же поверхности может проводится при чередовании различных технологических операций.
- Высота слоя, который может сниматься за один проход инструмента. Ограничение может зависеть от размера инструмента и многих других геометрических особенностей.
- Размер обрабатываемых заготовок. Для больших заготовок требуется инструмент с износостойкими свойствами, который при определенных режимах резания сможет не нагреваться.
Учет всех этих параметров позволяет подобрать наиболее подходящие параметры фрезерования. При этом учитывается распределение припуска при фрезеровании сферическими фрезами, а также особенности обработки концевой фрезой.
Классификация рассматриваемого инструмента проводится по достаточно большому количеству признаков. Основным можно назвать тип применяемого материала при изготовлении режущей кромки. К примеру, фреза ВК8 предназначена для работы с заготовками из твердых сплавов и закаленной стали. Рекомендуется применять подобный вариант исполнения при невысокой скорости резания и достаточной подаче. В тоже время скоростные фрезы могут применяться для обработки с высоким показателем резания.
Как правило, выбор проводится с учетом распространенных таблиц. Основными свойствами можно назвать:
- Скорость резания.
- Тип обрабатываемого материала.
- Тип фрезы.
- Частота оборотов.
- Подача.
- Тип проведенной работы.
- Рекомендуемая подача на зуб в зависимости от диаметра фрезы.
Использование нормативной документации позволяет подобрать наиболее подходящие режимы. Как ранее было отмечено, разрабатывать технологический процесс должен исключительно специалист. Допущенные ошибки могут привести к поломке инструмента, снижению качества поверхности заготовки и допущению погрешностей в инструментах, в некоторых случаях, поломке оборудования. Именно поэтому нужно уделять много внимания выбору наиболее подходящего режима резания.
Выбор режима в зависимости от материала
Все материалы характеризуются определенными эксплуатационными характеристиками, которые также должны учитываться. Примером можно назвать фрезерование бронзы, которое проводится при скорости резания от 90 до 150 м/мин. В зависимости от этого значения выбирается величина подачи. Сталь ПШ15 и изделия из нержавейки обрабатываются при применении других показателей.
При рассмотрении типа обрабатываемого материала уделяется внимание также нижеприведенным моментам:
- Твердости. Наиболее важной характеристикой материалов можно назвать именно твердость. Она может варьировать в большом диапазоне. Слишком большая твердость делает деталь прочной и износостойкой, но при этом усложняется процесс обработки.
- Степени обрабатываемости. Все материалы характеризуются определенной степенью обрабатываемостью, зависящая также от пластичности и других показателей.
- Применение технологии улучшения свойств.
Довольно распространенным примером можно назвать проведение закалки. Подобная технология предусматривает нагрев материала с последующим охлаждением, после чего показатель твердости существенно повышается. Также часто проводится ковка, отпуск и другие процедуры изменения химического состава поверхностного слоя.
В заключение отметим, что сегодня можно встретить просто огромное количество различных технологических карт, которые достаточно скачать и использовать для получения требуемых деталей. При их рассмотрении уделяется внимание типу материала заготовки, виду инструмента, рекомендуемому оборудованию. Самостоятельно разработать режимы резания достаточно сложно, при этом нужно делать предварительную проверку выбранных параметров. В противном случае может пострадать как инструмент, так и применяемое оборудование.
Режимы резания при фрезеровании на ЧПУ станках
Правильно подобранный режим резания при фрезеровании обеспечивает надежную работу ЧПУ станка без перебоев в работе. При несоблюдении требований производителя к нагрузке агрегата, происходит поломка режущего инструмента, порча обрабатываемого материала. Чтобы избежать подобных поломок, специалисты рекомендуют учитывать мощность рабочего шпинделя, качество режущего элемента, тип и толщину сырья.
Какая информация нужна для выбора режима?
Расчет режимов резания при фрезеровании происходит на основании таких показателей, как скорость вращения фрезы и интенсивность подачи. Первый критерий характеризует быстроту резания инструмента, второй — передвижение заготовки относительно фрезы.
Скорость вращения инструмента зависит от свойств шпинделя. Для современных инструментов показатель варьируется от 12 до 24 тыс. об/мин. Для вычисления показателя специалисты пользуются формулой:
Показатель V (скорость резания) можно брать из таблицы режимов резания для фрезерования.
п — это число Пи, значение которого 3,14.
d — диаметр режущего элемента.
Скорость подачи это также расчетная величина. Она рассчитывается умножением количества зубьев фрезы на количество оборотов при ее вращении и табличное значение подачи на зуб.
На что обратить внимание при подборе фрезы?
Рационально подобранный инструмент — это половина успешно выполненной работы. Специалисты рекомендуют выбирать фрезу с максимально возможным рабочим диаметром и наименьшим значением длины. Это предотвращает появление вибраций во время работы и позволяет рационально подобрать режущий элемент в соответствии с мощностью станка. Нужно быть осторожным при установке фрезы с большим диаметром, поскольку шпиндель и привод станка могут не выдержать такой нагрузки.
Канавка для стружки должна быть немного большего размера, чем количество снимаемого материала. В противном случае стружка будет скапливаться и мешать работе инструмента. Фреза будет не резать материал, а продавливать его.
Бывают одно-, двух- и трехзаходные фрезы. Каждая из них предназначена для определенного качества сырья. Первый тип используется для мягких материалов, второй — для средней жесткости, третий — для обработки жесткого сырья.
Даже для одинакового материала, который обрабатывается на одном и том же станке, режим резания при фрезеровке может зависеть от работы охлаждающей системы, способа обработки, высоты снимаемого слоя и размера обрабатываемой заготовки. Опытные специалисты практикуют корректировку режима в процессе работы станка, если инструмент начинает вибрировать или делать бракованные резы.
СМОТРИТЕ ТАКЖЕ: Подача на зуб при фрезеровании • Фрезы для изготовления филенок • Фрезы для мебельных фасадов
Скорость резания 358-361 – Формула
Скорость резания — Формулы 481 [c.456]Скорость резания. Формулы для расчета скорости резания приведены в табл. 23, значения коэффициентов и показателей степени в этих формулах — в табл. 24 и 26, поправочные коэффициенты на скорость резания — в табл. 25 и 27. [c.254]
Скорость резания. Формулы для расчета скорости резания при работа резцами из быстрорежущей стали (м/мин) [c.242]
После выбора по справочным таблицам стойкости инструмента определяют скорость резания (формулы см. в 44). Далее подсчитывают число оборотов, которое затем корректируют по паспортным данным станка (па). По принятому числу. оборотов находят действительную скорость резания. [c.134]
С учетом всех факторов, влияющих на скорость резания, формула для ее определения выглядит так [c.324]
Определяются скорость резания и число оборотов шпинделя в зависимости от ранее выбранных факторов по формуле [c.137]
Скорость резания и при заданном числе оборотов определяется по формуле, [c.138]
По выбранной скорости резания определяется число оборотов по формуле [c.138]
Если исходить из производительности, то необходимо работать с максимальной по мощности и кинематическим возможностям станка скоростью резания. Однако в реальных условиях скорость резания часто лимитируется не станком, а стойкостью инструмента, т. е. временем его работы до предельно-допустимого износа — принятого критерия затупления, по достижении которого инструмент должен быть снят для переточки. В общем виде связь между скоростью резания V и стойкостью Т инструмента выражается формулой
[c. 47]
Таким образом, чтобы получить максимальную производительность, необходимо скорость резания увеличить на 24 % при этом производительность полуавтомата, как это можно рассчитать по формуле (4.26), повышается в 1,1 раза. [c.99]
Стойкость зависит от материала инструмента, скорости резания, подачи, глубины резания, обрабатываемого материала и других факторов. Так как наибольшее влияние иа стойкость оказывает скорость резания, то эта зависимость может быть выражена следующей формулой [c.321]
Скорость резания при вращательном движении определяется по формуле [c.470]
При поступательном движении скорость резания определяется по формуле [c.470]
Скорость резания определяется по формуле und, [c.110]
Если при обработке вращается не изделие, а режущий инструмент, например при фрезеровании, то скорость-резания можно определить по приведенной выше формуле, подставив в нее вместо dun диаметр и число оборотов в минуту режущего инструмента (фрезы). [c.110]
При шлифовании скорость резания всегда является скоростью вращения шлифовального круга и определяется по формуле [c.110]
При строгании на поперечно-строгальном станке скоростью резания следует считать среднюю скорость движения ползуна. Скорость рабочего хода подсчитывается по формуле [c.111]
Скорость резания при точении определяется по формуле [c.165]
Предположим, что в своем стремлении повысить скорость резания мы добились величины, при которой время tp стало ничтожно мало, т. е. практически близко к нулю. Что тогда произошло бы с производительностью По формуле она была [c.95]
В этих случаях устанавливается лишь характер ветви функциональной кривой PyQ = f (v), проходяш,ей в зоне технологически возможных скоростей резания v ], и принимается в качестве экономичной скорости резания та ее величина или v , которая соответствует наибольшей возможно достижимой вели чине прибыли. Технически этот прием весьма прост если — Г > О, то в качестве наиболее эффективной скорости резания принимают величину v , т. е. наименьшую технологически допустимую скорость. А соответствующее ей значение стойкости и -струмента определяется из формулы (121), в которой вместо подставляется значение и уравнение решается относительно Т если Гэ— допустимую скорость резания) как наиболее элективную. Т,-любое значение стойкости инструмента, соответствующее зоне технологически возможных скоростей резания [и , v ]. Таким образом, если величины и v , рассчитанные по формулам (120) и (121), выходят за пределы технологически возможной зоны использования станка, то в качестве экономичных принимают те предельные технологически возможные параметры режимов, которые наиболее близки к экономичным.
[c.118]
Правильнее бы-ло бы рассматривать в качестве. характеристики производительности среднюю скорость резания при работе с экономической скоростью резания Из, которую можно представить формулой [c.163]
Условия применения формулы (27) Скорость резания [c.179]
Основные скорости резания могут быть определены по формуле [c.126]
Шевингование осуществляют на зубошевинговальных станках. Скорость резания при шевинговании (скорость продольного скольжения в сопряженных зубьях шевера и колеса) подсчитывают по формуле [c.607]
Количественные связи, выраженные формулами (2), (3) и (4) с учетом действительных чисел оборотов шпинделя и подач на станке, а также некоторых частных ограничений, как, например, диапазона скоростей резания, при которых рационально использовать данный инструментальный материал, ограничивают область допустимых режимов обработки. Графическое изображение сказанного в логарифмической системе координат представлено на рис. 2. [c.112]
Систематическое исследование закономерностей износа рабочих поверхностей инструментов было впервые выполнено на кафедре в 1931 — 1932 гг. под руководством проф. С. С. Рудника (проведено более тысячи трудоемких стойкостных опытов). В результате впервые были выведены основные законы скорости резания для победитовых резцов при обработке чугуна, стального литья и проката. При этом установлены оптимальные углы заточки резцов, составлены формулы, таблицы и номограммы для определения экономической скорости резания. Результаты проведенного исследования были широко использованы машиностроительными заводами страны.
[c.18]
Влияние вибраций на стойкость резца. Многие исследователи полагают, что в процессе резания при вибрациях снижается стойкость режущего инструмента Т лишь в результате изменения скорости резания v, выражаемой формулой [c.332]
Однако с этим нельзя согласиться, так как средняя результирующая стойкость при изменении скорости резания в связи с возникновением вибраций может не снижаться, а повышаться, если учитывать взаимосвязь между стойкостью резца и скоростью резания, согласно приведенной выше формуле. [c.332]
Анализ приведенной формулы для определения скорости резания, допустимой свойствами режущего инструмента, показывает, что для повышения производительности выгодней работать с большей глубиной резания, на втором месте идет увеличение подачи [c.84]
Анализ влияния отдельных факторов на допустимую скорость резания при фрезеровании разрешает сделать следующие общие выводы. При увеличении диаметра допустимая скорость резания должна возрастать, но значительно меньше, чем растет диаметр фрезы. Производительность при фрезеровании подсчитывается по формуле [c.86]
Поскольку допускаемое сечение стружки при предчистовых и чистовых проходах не ограничивает подачу, а на скорость резания влияют те же факторы, что и при черновой расточке, то формула примет следующий вид [c.131]
Вторая часть графика (//) разрешает по скорости резания подобрать число оборотов станка. Построена она на основании формулы
[c.139]
На данном графике по оси ординат отложены значения скорости резания, а на оси абсцисс — обрабатываемые диаметры. Линии, нанесенные на графике, соответствуют числам оборотов планшайбы станка 1531. Для нашего примера находим требуемое число оборотов на пересечении вертикали, проведенной из точки D=500 мм, с горизонтальной линией, проведенной из точки о=53 м/мин. Принимаем ближайшее меньшее из имеющихся на станке чисел оборотов fi=31,5 об/мин. Третья часть графика (III) служит для определения силы резания по глубине и подаче. Построена она по формуле [c.139]
На базе температурной зависимости (б) может быть получена формула дяя определения скорости резания [c.155]
Скорость — Расчётные формулы 7—101 Резание металлов абразивными кругами 7 — 3 [c.238]
Скорость резания х)-р, соответствующая заданной стойкости инструмента при определённом сечении стружки, выражается формулой [c.283]
Скорость резания, м/мин, например, при точении, определяют по следующей эминрнческой формуле [c.276]
При нарезании резьбы резцами и гребенками определяются число проходов и скорость резания (в м1мин) подачей (в мм/об) обрабатываемой детали является шаг нарезаемой резьбы (в мм), число оборотов нарезаемой детали определяется по формуле скорости резания при нарезании резьбы на резьбофрезерных станках дисковыми и групповыми фрезами определяются скорость резания (в м1мин) и подача для дисковой фрезы — в мм мин, для групповой фрезы — в мм1зуб. [c.141]
Такие критерии, впрочем, существовали и даже были общепринятыми. В те времена производительность металлорежущих станков любых типов, с любой степенью автоматизации оценивали количеством или объемом стружки, снимаемой в единицу времени. Расчеты производились по формулам стружечной производительности Q = vsty, где и —скорость резания s —подача в миллиметрах на оборот t — глубина резания у — удельный вес обрабатываемого материала произведение vst определяло объем металла, переводимого в стружку на данном станке в единицу времени.
[c.37]
В описываемых опытах установлено, что при внутреннем протягивании в деталь переходит от 45 до 70% общего количества образующейся 1)1еплоты. В зависимости от способа подвода смазочно-охлаждающей жидкости количество оставшейся в детали теплоты может меняться в два-три раза. Предложена формула для определения количества теплоты, образующегося при протягивании. Тепловой баланс зависит от скорости резания, толщины, стенки детали и площади контакта с планшайбой. [c.49]
Приближенная оценка амплитуды автоколебаний. Как известно, в случае /г-неустойчивости , вызванной отрицательным слагаемым уравнения движения, содержащим первую производную агрумента q, скорость предельного цикла не выходит далеко за пределы зоны возбуждения. Например, в случае возбуждения автоколебаний падающей характеристикой силы резания от скорости резания Р — v, при аппроксимации ее кубическим трехчленом, амплитуду автоколебаний в системе без рассеивания энергии в первом приближении можно оценить формулой [3] [c.73]
Практически на каждом станке сравниваются три варианта режимов скорость резания при минимальной себестоимости операции скорость резания при максимальной выработке скорость резания при максимальной прибыли за определенное время t. Им соответствуют свои величины прибыли Ру Ру , Ру опт и выработки 4qy произведение которых обусловит свою, соответствующую режиму величину прибыли за определенный период работы t, где Ру. скачестве критерия следует принимать величину, полученную по формуле (125). [c.121]
При обработке стальных зубчатых колес с т=16Ч-30 мм при предчистовом и чистовом проходах работают со скоростью резания от 12 до 20 mImuh и подачей от 1,6 до 3 мм/об. При чистовом проходе подачи более 1,6 мм/об не дают. При нарезании зубчатых валов или шестерен больших размеров после настройки гитар, установки и выверки заготовки к ней подводится инструмент, по касанию которого проверяется правильность настройки гитары деления. При обработке винтовых или шевронных колес берут касание, на ускоренном ходу наносят направление винтовой линии, а ее угол контролируется калькой, на которой нанесен наружный угол наклона винтовой линии нарезаемого колеса или вала. В чертеже этот угол наклона задается по начальному диаметру, а для определения по наружному диаметру он подсчитывается по формуле
[c.435]
На базе температурной зависимости получена формула для определения скорости резания (9). Причем,степенные показатели при Sj и t достаточно близки (показатель степени при 2г), либо совпадают (показатель степевм при t ) соответственно с показателями степени в формулах для определения скорости и стойкости, полученных на основании обычных экспериментов, положенных в основу для составления режимов резания /б/. [c.156]
Режимы резания при фрезеровании – таблица, параметры, подача и др.
Выбор режима резания играет основную роль при любой металлорежущей операции, и особенно при фрезеровании. От этого зависит производительность работ, возможность максимального использования ресурсов станка, стойкость инструмента и качество конечного результата. Для выбора режима резания разработаны специальные таблицы, но есть ряд общих понятий, которые необходимо знать любому фрезеровщику.
Особенности фрезерования
Процесс фрезерования является одним их наиболее сложных из всех видов металлообработки. Основной фактор – это прерывистый характер работы, когда каждый из зубьев инструмента входит в кратковременный контакт с обрабатываемой поверхностью. При этом каждый контакт сопровождается ударной нагрузкой. Дополнительные факторы сложности – более одной режущей поверхности и образование прерывистой стружки переменной толщины, что может стать серьёзным препятствием для работы.
Поэтому очень важен правильный подбор режима резания, что позволяет добиться максимальной производительности оборудования. Сюда входит правильный выбор подачи, скорости и силы реза, а также глубины удаляемого слоя что позволяет получить необходимую точность при минимальных затратах и износе инструмента.
Параметры режима резания
Основными характеристиками, которые регулируются в процессе фрезерования и являющиеся составляющими режима резания являются:
- глубина реза – это толщина металла снимаемая за один проход. Выбирается с учетом припуска на обработку;
- ширина реза – показатель ширины снимаемого слоя металла по направлению перпендикулярному направлению подачи;
- подача инструмента – перемещение обрабатываемой поверхности относительно оси фрезы. В расчете режима используются такие показатели как подача на один зуб, в минуту и на один оборот. На величину подачи влияет прочность инструмента и характеристики оборудования.
Ширина и глубина
Данные параметры имеют важное значение для рационального выбора режима фрезерования. Глубина, как правило, устанавливается на максимально допустимое значение для уменьшения количества проходов. При повышенных требованиях к чистоте и точности обработки применяются черновой и чистовой проходы, соответственно, для съёма основной массы металла и калибровки поверхности. Количество черновых проходов может быть увеличено для повышения качества реза.
При выборе глубины также необходимо учесть припуск на обработку. Как правило, несколько проходов применяется при значении припуска более 5 мм. При последнем черновом проходе оставляют около 1 мм на чистовую обработку.
При подборе ширины необходимо учесть, что при одновременной обработке нескольких деталей учитывается общее значение. Выбирая данные значения необходимо учесть и состояние поверхности заготовки. При наличии следов литья, окалины или загрязнений необходимо увеличить глубину реза. В противном случае возможно скольжение зуба, дефекты поверхности, быстрый износ режущих кромок.
При выборе глубины реза существуют следующие типовые рекомендации:
- Чистовая обработка – до 1 мм.
- Черновая по чугуну и стали – от 5 до 7 мм.
- Черновая для разных марок стали – от 3 до 5 мм.
Подача и скорость фрезы
Величина подачи зависит, в первую очередь от типа обработки – черновая или чистовая. При чистовом резе подача определяется требованиями к качеству поверхности. При черновом необходимо учесть несколько факторов:
- жесткость заготовки, инструмента и станка;
- материал заготовки и фрезы;
- угол заточки фрез;
- мощность привода станка.
Скорость обработки определяется по нормативам, в которых учитывается тип инструмента и материал заготовки. Данный параметр выбирается по стандартной таблице.
Необходимо учесть, что значения в таблице приведены для стандартной стойкости инструмента. Если фреза не соответствует стандартным параметрам, то необходимо учесть поправочный коэффициент который зависит от ширины инструмента (для торцовых фрез), свойств заготовки, угла фрезы и наличия окалины.
Рекомендации при выборе режима
Идеально подобрать режим обработки практически невозможно, но есть ряд рекомендаций, которым желательно следовать:
- Диаметр инструмента должен соответствовать глубине обработки. Это позволяет провести обработку в один проход, но для слишком мягких материалов есть риск снятия стружки большей толщины, чем необходимо.
- По причине ударов и вибрации желательно начать с подачи порядка 0,15 мм на зуб и затем регулировать в большую или меньшую сторону.
- Не желательно использовать максимальное количество оборотов, это может привести к падению скорости реза. Повысить частоту можно при увеличении диаметра инструмента.
Определение режима реза производится не только с помощью таблиц. Большую роль играет знание особенностей станка и личный опыт фрезеровщика.
Расчет и табличное определение режимов резания при фрезеровании | Методическая разработка на тему:
Расчёт и табличное определение режимов резания при фрезеровании
Дано: Материал заготовки – Серый чугун, 210 НВ
Вид обработки – черновое торцовое фрезерование плоскости шириной В=80 мм, длиной l = 120 мм.
Припуск на обработку h = 2мм.
Заготовка – отливка.
Обработка без охлаждения.
Станок вертикально-фрезерный 6Т12
Необходимо: выбрать режущий инструмент; назначить режим резания; определить основное время.
Решение
1 Выбираем фрезу и устанавливаем её геометрические параметры (см. Приложение 1). Для торцового фрезерования диаметр фрезы определяется по формуле
Dф = 1,6 · В (1)
где В – ширина фрезерования, мм.
Dф = 1,6 · 80 = 128 мм
Принимаем стандартное значение диаметра торцовой насадной фрезы со вставными ножами, оснащенными пластинами из твердого сплава ВК6 по ГОСТ 9473-80 Dф = 125 мм [1, с.187].
Число зубьев фрезы, оснащенной твердым сплавом, определяется по формуле
z = (0,08÷0,1)·D, (2)
где обозначения прежние
z = (0,08÷0,1)·125 = 10 шт.
Определим геометрические параметры торцовой фрезы: ω=35 °; φ1 = 1; φ=30 °; α1 = 8 °; αn = 12 °; γ = 10 ° [4, с.390].* 1
2 Назначаем режим резания
Глубина резания определяется по заданию t=h=2мм
Назначаем стойкость инструмента и его допустимый износ: Т = 180 мин [1, с.290], hз = 2 мм [5, с.50]* 2
Назначаем подачу, мм/зуб* 3
Sz = 0,2 – 0,4 мм/зуб.
Принимаем Sz = 0,3 мм/зуб [1, с.283].
Определяем скорость резания, допускаемую режущими свойствами фрезы, аналитическим методом по формуле
, (3)
где Сv , q, m, x, y, u, p – коэффициент и показатели степени,
Сv = 445, q = 0,2, m = 0,32, x = 0,15, y =0,35, u = 0,2, p = 0 [1, с.286]
Dф – диаметр фрезы, мм;
Т – стойкость инструмента, мин;
t – глубина резания, мм;
Sz –подача на зуб, мм/зуб;
В – ширина фрезерования, мм;
z – число зубьев фрезы;
Кv – поправочный коэффициент на скорость резания
(4)
где Км – коэффициент, зависящий от обрабатываемого материала;
____________________________________________________________________________________
* 1 Дополнительные источники: [2, с. 248] [4, с.369] [4, с.676, 790, 945] [6, с.366]
* 2 Дополнительные источники: [2, с.444] [4, с.400] [6, с.203]
* 3 Если в справочной литературе дана подача на оборот Sо, мм/об, необходимо найти подачу на зуб по формуле Sz = So/z, где z – число зубье
[1, с.262] (5)
где НВ – фактические параметры обрабатываемого материала;
n – показатель степени,
n = 0,95 [1, с.262];
Кп – коэффициент, учитывающий влияние состояния поверхности заготовки,
Кп = 0,8 [1, с.263];
Ки – коэффициент, учитывающий влияние инструментального материала,
Ки = 1 [1, с.263];
м/мин
Определим скорость резания табличным методом
v = vТ · Kv , (6)
где vТ – табличное значение скорости резания,
vТ = 126 м/мин [9, с.307]
Кv – поправочный коэффициент на скорость резания
Kv = Kм· Kи· Kn· Кс· Кф· Kо · Kв · Kφ, (7)
где Kм – коэффициент, учитывающий марку обрабатываемого материала
Kм = 0,89 [9, с.20];
Kи – коэффициент, учитывающий материал инструмента
Kи = 1,0 [9, с.308];
Kn – коэффициент, учитывающий состояние обрабатываемой поверхности
Kn = 0,8 [9, с.308];
Кс – коэффициент, учитывающий шифр типовой схемы фрезерования
Кс = –
Кф – коэффициент, учитывающий форму обрабатываемой поверхности
Кф = –
Kо – коэффициент, учитывающий условия обработки
Kо = 1,0 [9, с.308];
Kв – коэффициент, учитывающий отношение фактической ширины фрезерования к нормативной
Kв = 1,0 [9, с.309];
K φ – коэффициент, учитывающий влияние главного угла в плане
K φ = 1,3 [9, с. 308].
Подставляя значения в формулу 7 и 6, получим
Кv = 0,89 · 1 · 0,8 · 1 · 1 · 1,3 = 0,92
v = 126 · 0,92 = 116,6 м/мин
Определим частоту вращения шпинделя по формуле
(8)
где Vрез – аналитическая скорость резания;
остальные обозначения прежние
об/мин
Корректируем частоту вращения по паспорту станка
nд = 315 об/мин [7, с.422]
Определим действительную скорость резания, м/мин, по формуле
(9)
где обозначения прежние
м/мин
Находим минутную подачу, м/мин, по формуле
SM = Sz · z ·nд (10)
где Sz – подача на зуб, мм/зуб;
z – число зубьев фрезы, шт;
nд – действительная частота вращения шпинделя, об/мин
SM = 0,3 · 10 · 315 = 945 м/мин
Корректируем подачу по паспорту станка. Принимаем SMд = 1000 м/мин [7, с.422]
Из формулы 10 найдем подачу на зуб
Sz = мм/зуб
Определяем силу резания, Н, по формуле
, (11)
где Сp , x, y, u, q, w – коэффициент и показатели степени,
Ср = 54,5; x = 0,9, y =0,74, u = 1,0, q = 1, w = 0 [1, с.291]
Dф – диаметр фрезы, мм;
t – глубина резания, мм;
Sz –подача на зуб, мм/зуб;
В – ширина фрезерования, мм;
z – число зубьев фрезы;
n – действительная частота вращения шпинделя, об/мин;
Кмр – поправочный коэффициент на силу резания, учитывающий обрабатываемый материал
[1, с.264] (12)
где НВ – фактические параметры обрабатываемого материала;
n – показатель степени,
n = 1,0 [1, с. 264];
Н
Сравниваем силу резания с допустимой силой механизма станка
Pz zдоп (13)
где Pzдоп = 15000 Н [7, с.422];
2639
следовательно, выбранная подача допустима
Определяем крутящий момент, Н·м
(14)
где обозначения прежние
Н·м
Находим мощность, затрачиваемую на резание, по формуле
, (15)
где Рz – сила резания, Н;
vд – действительная скорость резания, м/мин
Сравниваем мощность резания с мощностью привода станка
Nрез ≤ Nшп , (16)
где Nшп – мощность шпинделя станка
Nшп = Nэ.дв · η, (17)
где Nэ.дв – мощность электродвигателя станка, кВт
Nэ.дв = 7,5 кВт [7, с.422];
η – КПД станка
η = 0,8 [7, с.422]
Nшп = 7,5 · 0,8 = 6 кВт
Так как 5,4
3 Определяем основное время, мин, по формуле
, (18)
где L – длина пути инструмента или детали в направлении подачи, мм, определяется по формуле
L = l + l1 + l2 , (19)
где l – длина обрабатываемой поверхности, мм;
l1 – длина врезания, мм
l1 = 19 мм [3, с.84];
l2 – длина перебега фрезы, мм
l2 = 1 ÷ 6 мм [3, с.84]. Принимаем l2 = 5 мм
L = 120 + 19 + 5 = 144 мм
SМ – минутная подача, м/мин;
i – число проходов
i = h|t (20)
где h – припуск на обработку, мм;
t – глубина резания, мм.
Так как h = t, то i = 1
По формуле 18
мм
Рисунок 1 – Схема фрезерования плоскости торцовой фрезой
Перечень использованной литературы
1 Косилова А.Г., Мещеряков Р.К. Справочник технолога – машиностроителя, Т2. М.: Машиностроение, 1986. 496 с.
2 Малов А.Н. Справочник технолога – машиностроителя, Т2 М.: Машиностроение, 1973 г.
3 Антонюк В.Е. и др. Краткий справочник технолога механического цеха. Минск: Беларусь, 1968 г.
4 Малов А.Н. Справочник металлиста., Т3 М.: Машиностроение, 1977 г.
5 Абрамов Ф.Н. Справочник по обработке металлов резанием. К.: Машиностроение, 1983. 239 с.
6 Общемашиностроительные нормативы режимов резания, 4.1 – М.: Машиностроение, 1974 г.
7 Нефедов Н.А., Осипов К.А. Сборник задач и примеров по резанию металлов и режущему инструменту. М.: Машиностроение, 1990.-448 с.
8 Долматовский Г.А. Справочник технолога, М.: Машиностроение, 1956 г.
9 Баранчиков В.И., Жаринов А.В. Прогрессивные режущие инструменты и режимы резания металлов. – М.: Машиностроение, 1990.-400 с.
Приложение 1
Выбор диаметра фрезы в зависимости от вида фрезерования
При торцовом фрезеровании диаметр фрезы определяется по формуле
Dф = 1,6 · В,
где В – ширина фрезерования, мм.
При фрезеровании дисковыми фрезами диаметр фрезы выбирается по ГОСТ в зависимости от ширины фрезерования В.
При фрезеровании концевыми и шпоночными фрезами диаметр фрезы можно принимать равным ширине фрезерования В.
Определение числа зубьев фрезы
Число зубьев фрезы из быстрорежущей стали при черновой обработке определяется по формуле
,
где Dф – диаметр фрезы, мм
При чистовой обработке
Для фрез, оснащенных твердым сплавом, число зубьев определяется следующим образом:
- для обработки чугуна z = (0,08÷0,1)·D;
- для обработки стали z = (0,04÷0,06)·D;
Для цилиндрических фрез число зубьев определяется по формуле
,
где m – коэффициент, определяется по таблице 1
Таблица 1
Цилиндрические фрезы | Угол наклона зуба ω | Коэффициент m |
С крупным зубом цельные | ° | 1,05 |
С мелким зубом цельные | 15 – 20 ° | 2 |
С крупным зубом сборные | 20 ° 45 ° 55 – 60 ° | 0,9 0,8 0,5 |
Выбор рациональных режимов фрезерования – Фрезерные работы
Выбор рациональных режимов фрезерования
Категория:
Фрезерные работы
Выбор рациональных режимов фрезерования
Выбрать рациональный режим фрезерования на данном станке означает, что для данных условий обработки (материал и марка заготовки, ее профиль и размеры, припуск на обработку) надо выбрать оптимальный тип и размер фрезы, марку материала и геометрические параметры режущей части фрезы, смазочно-охлаждаю-щую жидкость и назначить оптимальные значения следующих параметров режима резания: В, t, sz. v, п, Ne, Тм.
Из формулы (32) следует, что на объемную производительность фрезерования параметры В, t, sz и v оказывают одинаковое влияние, так как каждый из них входит в формулу в первой степени. Это означает, что при увеличении любого из них, например, в два раза (при прочих неизменных параметрах) объемная производительность увеличится также в два раза. Однако на стойкость инструмента указанные параметры оказывают далеко не одинаковое влияние (см. § 58). Поэтому с учетом стойкости инструмента выгоднее прежде всего выбирать максимально допустимые значения тех параметров, которые в меньшей степени влияют на стойкость инструмента, т. е. в такой последовательности: глубина резания, подача на зуб и скорость резания. Поэтому и выбор этих параметров режимов резания при фрезеровании на данном станке следует начинать в той же последовательности, а именно:
1. Назначается глубина резания в зависимости от припуска на обработку, требований к шероховатости поверхности и мощности станка. Припуск на обработку желательно снять за один проход с учетом мощности станка. Обычно глубина резания при черновом фрезеровании не превышает 4—5 мм. При черновом фрезеровании торцовыми твердосплавными фрезами (головками) на мощных фрезерных станках она может достигать 20—25 мм и более. При чистовом фрезеровании глубина резания не превышает 1—2 мм.
2. Назначается максимально допустимая по условиям обработки подача. При установлении максимально допустимых подач следует применять подачи на зуб, близкие к «ломающим».
Последняя формула выражает зависимость подачи на зуб от глубины фрезерования и диаметра фрезы. Величина максимальной толщины среза, т. е. значение постоянного коэффициента I с в формуле (21), зависит от физико-механических свойств обрабатываемого материала \ (для данного типа и конструкции фрезы). Значения максимально допустимых подач ограни- j чиваются различными факторами:
а) при черновой обработке — жесткостью и виброустойчивостью инструмента (при доста- i точной жесткости и виброустойчивости станка),’ жесткостью обрабатываемой заготовки и прочностью режущей части инструмента, например зуба фрезы, недостаточным объемом стружечных канавок, например, для дисковых фрез и др. ) определяется ближайшая ступень частоты вращения шпинделя станка из числа имеющихся на данном станке по формуле (2) или по графику (рис. 174). Из точки, соответствующей принятой скорости резания (например, 42 м/мин), проводят горизонтальную линию, а из точки с отметкой выбранного диаметра фрезы (например, 110 мм) — вертикальную. По точке пересечения указанных линий определяют ближайшую ступень чисел оборотов шпинделя. Так, в примере, показанном на рис. 172, при фрезеровании фрезой диаметром D = 110 мм со скоростью резания 42 м/мин частота вращения шпинделя будет равна 125 об/мин.
Рис.174 Номограмма частоты вращения фрезы
6. Определяется минутная подача по формуле (4) или по графику (рис. 175). Так, при фрезеровании фрезой D = 110 мм, z = 10 при sz = = 0,2 мм/зуб и п = 125 об/мин минутная подача по графику определяется следующим образом. Из точки, соответствующей подаче на зуб sг = 0,2 мм/ зуб, проводим вертикальную линию до пересечения с наклонной линией, соответствующей числу зубьев фрезы г = 10. Из полученной точки проводим горизонтальную линию до пересечения с наклонной линией, соответствующей принятой частоте вращения шпинделя л = 125 об/мин. Далее из полученной точки проводим вертикальную линию. Точка пересечения этой линии с нижней шкалой минутных подач, имеющихся на данном станке, определяет ближайшую ступень минутных подач.
7. Определяется машинное время.
Машинное время. Время, в течение которого происходит процесс снятия стружки без непосредственного участия рабочего, называется машинным временем (например, на фрезерование плоскости заготовки с момента включения механической продольной подачи до момента ее выключения).
Рис. 1. Номограмма минутной подачи
Повышение производительности при обработке на металлорежущих станках ограничивается двумя основными факторами: производственными возможностями станка и режущими свойствами инструмента. Если производственные возможности станка малы и не позволяют полностью использовать режущие свойства инструмента, то производительность такого станка будет составлять лишь некоторую часть от возможной производительности при максимальном использовании инструмента. В том случае, когда производственные возможности станка значительно превышают режущие свойства инструмента, на станке может быть достигнута максимально возможная при данном инструменте производительность, но при этом не будут полностью использованы возможности станка, т. е. мощность станка, максимально допустимые силы резания и т. д. Оптимальными с точки зрения производительности и экономичности использования станка и инструмента будут такие случаи, когда производственные мощности станка и режущие свойства инструмента будут совпадать или близки друг к другу.
Это условие положено в основу так называемых производственных характеристик станков, которые были предложены и разработаны проф. А. И. Кашириным. Производственная характеристика станка представляет собой график зависимостей возможностей станка и инструмента. Производственные характеристики позволяют облегчить и упростить определение оптимальных режимов резания при обработке на данном станке.
Режущие свойства того или иного инструмента характеризуются режимами резания, которые допускаются в процессе обработки. Скорость резания при заданных условиях обработки можно определить по формуле (42, а). Практически же ее находят по таблице режимов резания, которые приведены в справочниках нормировщика или технолога. Однако следует отметить, что нормативы по режимам резания как для фрезерования, так и для других видов обработки разрабатываются, исходя из режущих свойств инструмента для различных случаев обработки (тип и размер инструмента, вид и марка материала режущей части, обрабатываемый материал и др.), и не связаны со станками, на которых будет производиться обработка. Так как производственные возможности различных станков разные, то практически осуществимый оптимальный режим обработки на разных станках будет различным для одних и тех же условий обработки. Производственные возможности станков зависят прежде всего от эффективной мощности станка, частоты вращения, подач и др.
Рис. 2. Врезание и перебег
Производственные характеристики фрезерных стянкои для случая (Ьпезепования тогшо-выми фрезами были разработаны проф. А. И. Кашириным и автором.
Принцип построения производственных характеристик фрезерных станков (номограмм) для работы торцовыми фрезами основан на совместном графическом решении двух уравнений, которые характеризуют зависимость скорости резания vT по формуле (42) при -Bz’ = const, с одной стороны, и скорости резания ид„ допускаемой мощностью станка, — с другой. Скорость резания vN может быть определена по формуле
Рис. 3. Производственная характеристика консольно-фрезерного станка 6Р13
Реклама:
Читать далее:
Классификация фрез
Статьи по теме:
ЧПУ | Скорости резания и формулы подачи
В этой статье мы опишем, как рассчитать подачу и скорость для наиболее часто используемых инструментов на станках с ЧПУ, со всеми формулами и примерами.
Инструмент перемещается через материал с заданной скоростью вращения, определенной в оборотах в минуту (RPM), и скоростью подачи, определенной в дюймах в минуту (IPM). Вероятно, самая неприятная проблема для начинающего станочника с ЧПУ – это выбор правильных скоростей резания и подачи. Этот выбор на самом деле сложнее на ЧПУ, чем на ручном фрезерном станке, потому что на ручном фрезерном станке оператор может почувствовать давление резания и изменить подачу, частично основываясь на силе резания.Для фрезерных станков
с ЧПУ необходимо заранее рассчитывать скорость и подачу. Эти скорости и подачи могут и часто регулируются на станке в зависимости от формы и цвета стружки, звука резания и показаний счетчика мощности машины.
Лучшим источником данных о скоростях резания и подачах для конкретного инструмента, приложения и материала является поставщик инструмента. Многие из этих данных можно найти на веб-сайтах производителей или в печатных каталогах инструментов. Торговые представители инструмента могут быть ценным ресурсом, поэтому, если вы много занимаетесь механической обработкой, установите хорошие отношения со знающим представителем.
Еще одним источником данных о скоростях и подачах является программное обеспечение CAD / CAM. Они становятся все более сложными и часто обеспечивают хорошие параметры резания.
Но даже самые лучшие данные о скорости и подаче – это только отправная точка. Скорости и подачи требуют регулировки из-за многих факторов, включая максимальную скорость шпинделя или мощность станка, жесткость крепления заготовки, а также качество и состояние самого станка.
Возможно, вас заинтересует «ЧПУ | Основные сведения о режущем инструменте »
Следующие подробности предоставляют данные резания для наиболее часто обрабатываемых материалов и методику расчета скоростей и подач.Как всегда, руководствуйтесь здравым смыслом. Если деталь удерживается двусторонней лентой, подача, основанная на удержании заготовки в тисках, вероятно, будет слишком высокой. Если инструмент очень длинный и тонкий, скорее всего, потребуется уменьшить скорость и подачу.
Содержание статьи
Формула скорости
Скорости резания фрезерного станка вычисляются по следующей формуле:
Рисунок 14: Формула скорости Скорость – это частота вращения инструмента (скорость шпинделя) в оборотах в минуту (Об / мин) .
SFM (Количество футов в минуту) – это скорость, с которой материал перемещается за режущую кромку (внешний диаметр) инструмента, в футах в минуту. Значения SFM зависят от типа инструмента, материала инструмента и обрабатываемого материала.
Окружность – это окружность режущего инструмента в футах.
Как выводится формула скорости
Как выводится формула скорости
Поскольку режущие инструменты определяются их диаметром в дюймах, эта формула переписывается и упрощается следующим образом:
Рисунок 15: Формула скорости (упрощенная) DIA – это диаметр инструмента в дюймах.
3,82 – постоянная, производная от 12/, которая преобразует длину окружности инструмента в футах в диаметр в дюймах.
Формула подачи
Режущие подачи указаны в (IPM) и используют следующую формулу:
Рисунок 16: Формула подачи Подача – это линейная подача инструмента через материал в дюймах в минуту.
Скорость – это результат формулы скорости (Рисунок 15) в оборотах в минуту.
CL – нагрузка стружки или количество материала, которое каждая режущая кромка инструмента снимает за оборот.Нагрузка на стружку иногда обозначается как подача на зуб (FPT) или дюймов на оборот (IPR).
NumFlutes – количество режущих канавок. (Для спирального сверла это значение равно единице.)
Формула подачи метчика
Для операций нарезания резьбы подача основана на количестве резьбы на дюйм и скорости подачи:
Рисунок 17: Формула подачи метчика Подача – это линейная подача инструмента через материал в дюймах в минуту.
Скорость – результат предыдущей формулы в оборотах в минуту.
TPI – количество резьбы на дюйм метчика. Например, TPI метчика ¼-20 составляет 20.
Примеры скорости / подачи
Пример скорости / подачи фрезерования
Задача : Рассчитайте скорость резания и подачу для операции фрезерования при следующих значениях:
Примечание. Округлите скорость фрезерования и подачи до ближайшего целого числа.
Пример скорости сверления / подачи
Проблема: Рассчитайте скорость резания и подачу для операции сверления с учетом следующих значений:
Примечание: округлите подачу сверления до первого десятичного знака.
Пример скорости нарезания резьбы / подачи
Проблема: Рассчитайте скорость резания и подачу для операции резания ¼-24 при следующих значениях:
Примечание: округлите подачу нарезания резьбы до трех десятичных знаков или максимального числа, допускаемого станком.
Пример максимальной скорости шпинделя
В случаях, когда вычисленная скорость шпинделя превышает возможности станка, запрограммируйте максимальную скорость шпинделя станка и используйте это значение при вычислении подачи.
Проблема: Рассчитайте скорость резания и подачу для операции фрезерования при следующих значениях:
Нужно больше?
Наши волонтеры работали вместе, и тщательно подготовили статьи , опубликованные здесь на их родном языке без использования машинного перевода. Вы можете выполнить поиск по всему сайту для получения дополнительной информации по этому вопросу. Вы можете, , начать обсуждение на форуме CNCarea.com и присоединиться к нам, чтобы получить поддержку, задать вопросы, улучшить опубликованную статью или высказать свое мнение.
MITSUBISHI MATERIALS CORPORATION Формулы для резки
СКОРОСТЬ РЕЗКИ (vc)
- ВК (SFM)
- : Скорость резания
- Dm (дюйм)
- : Диаметр заготовки
- π (3.14)
- : Пи
- н (мин -1 )
- : Скорость шпинделя главной оси
(Проблема):
Какова скорость резания, когда скорость вращения шпинделя главной оси составляет 700 мин. -1 , а внешний диаметр составляет Ø2 “?
(Ответ):
Подставьте π = 3,14, Dm = 2, n = 700 в формулы.
vc = π × Dm × n ÷ 12 = 3,14 × 2 × 700 ÷ 12 = 366,33SFM
Скорость резания составляет 366,33SFM.
КОРМА (ж)
- ф (IPR)
- : Подача на оборот
- I (дюйм / мин)
- : Мин. Длина реза
- н (мин -1 )
- : Скорость шпинделя главной оси
(Проблема):
Какова подача на оборот, когда скорость шпинделя главной оси составляет 500 мин. -1 , а длина резки в минуту составляет 120 мм / мин?
(ответ):
Подставить в формулы n = 500, I = 4,72.
f = I ÷ n = 4,72 ÷ 500 = 0,009IPR
Ответ: 0,009IPR.
ВРЕМЯ РЕЗКИ (Tc)
- Tc (мин)
- : Время резания
- Im (дюйм)
- : Длина заготовки
- I (дюйм / мин)
- : Мин. Длина реза
Каково время резания при обработке 4-дюймовой заготовки при 1000 мин. -1 с подачей = 0,008IPR?
(ответ):
Сначала рассчитайте длину реза в минуту. от скорости подачи и шпинделя.
I = f × n = 0,008 × 1000 = 8 дюймов / мин
Подставьте полученный выше ответ в формулы.
Tc = Im ÷ I = 4 ÷ 8 = 0,5мин
0,5×60 = 30 (сек) Ответ 30 сек.
ТЕОРЕТИЧЕСКАЯ ШЕРОХОВАТОСТЬ ПОВЕРХНОСТИ (ч)
- ч (мкдюйм)
- : Шероховатость готовой поверхности
- ф (IPR)
- : Подача на оборот
- Re (дюйм)
- : Радиус угла вставки
Какова теоретическая шероховатость поверхности при угловом радиусе пластины.031 дюйм и корма .008 IPR?
(ответ):
Подставить в формулы f = .008IPR, Re = .031.
h = (. 008) 2 ÷ (8 × 0,031) × 1000 2 = 258 мкм
Теоретическая шероховатость готовой поверхности составляет 258 мкм.
СКОРОСТЬ РЕЗКИ (шт.)
* Разделите на 1000, чтобы сменить миллиметры на m.
- vc (м / мин)
- Скорость резания
- Дм (мм)
- Диаметр детали
- π (3,14)
- Пи
- n (мин -1 )
- Скорость вращения шпинделя главной оси
(Проблема)
Какова скорость резания, когда скорость вращения шпинделя главной оси составляет 700 мин.

(Ответ)
Подставляем в формулу π = 3,14, Dm = 50, n = 700.
vc = (π × Dm × n) ÷ 1000 = (3,14 × 50 × 700) ÷ 1000 = 110 (м / мин)
Скорость резания 110 м / мин.
КОРМА (ж)
- f (мм / об)
- Подача на оборот
- л (мм / мин)
- Мин. Длина реза
- n (мин -1 )
- Скорость шпинделя главной оси
(Проблема)
Какова подача на оборот, когда скорость шпинделя главной оси составляет 500 мин. -1 , а длина резания в минуту составляет 120 мм / мин?
(Ответ)
Подставляем в формулу n = 500, I = 120.
f = l ÷ n = 120 ÷ 500 = 0,24 (мм / об)
Ответ: 0,24 мм / об.
ВРЕМЯ РЕЗКИ (Tc)
- Tc (мин.)
- Время резки
- пм (мм)
- Длина детали
- л (мм / мин)
- Мин. Длина реза
(Проблема)
Какое время резания при обработке 100-миллиметровой заготовки за 1000 мин. -1 , с подачей = 0,2 мм / об?
(Ответ)
Сначала рассчитайте длину реза в минуту.от скорости подачи и шпинделя. l = f × n = 0,2 × 1000 = 200 (мм / мин)
Подставьте ответ в формулы.
Tc = lm ÷ l = 100 ÷ 200 = 0,5 (мин)
0,5 × 60 = 30 (сек.) Ответ – 30 секунд.
ТЕОРЕТИЧЕСКАЯ ШЕРОХОВАТОСТЬ ПОВЕРХНОСТИ (ч)
- h (мкм)
- Шероховатость готовой поверхности
- f (мм / об)
- Подача на оборот
- Re (мм)
- Радиус при вершине пластины
(Проблема)
Какова теоретическая шероховатость готовой поверхности при радиусе закругления пластины 0.8 мм и подача 0,2 мм / об?
(Ответ)
Подставьте в формулы f = 0,2 мм / об, R = 0,8.
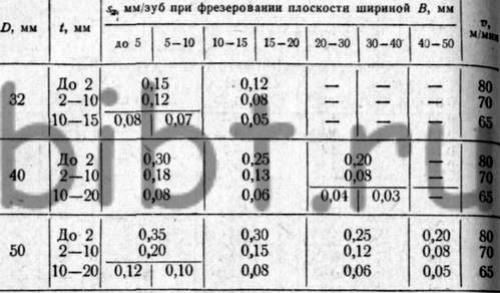
h = f 2 ÷ (8 × Re) × 1000 = 0,2 2 ÷ (8 × 0,8) × 1000 = 6,25 мкм
Теоретическая шероховатость готовой поверхности составляет 6 мкм.
Как улучшить качество обработки с помощью скоростей и подачи
Включает ли ваше производство обработку металлических деталей с ЧПУ? У вас могут периодически возникать проблемы с отделкой.
Одной из основных проблем, с которой ежедневно сталкивается программист ЧПУ, является определение критических параметров обработки металла, таких как глубина резания, скорость шпинделя и скорость подачи.Традиционно отправной точкой для этого был справочник данных по обработке или опыт старших механиков в цехе.
Получение наилучших результатов от станка с ЧПУ требует огромных усилий. Начнем с того, что оператор может попытаться оптимизировать несколько целей:
- Наилучшая производительность съема материала
- Увеличение срока службы инструмента
- Хорошая обработка поверхности
Лучшая практика для определения оптимальных подач и скоростей для обрабатываемого материала – использование калькулятора подачи и скорости.Используя базу данных материалов и зная очень конкретные спецификации для каждого станка с ЧПУ, можно рассчитать оптимальные подачи и скорости, которые обеспечивают три цели, указанные выше.
Для разных типов инструментов, используемых на станке с ЧПУ, необходимы разные формулы. Здесь мы рассмотрим формулы фрезерования.
Скорость резания
Поверхностных футов в минуту (SFPM) для обычных металлов:
- Низкоуглеродистая сталь 100
- Инструментальная сталь 70
- Чугун 60
- Алюминий 250
- Латунь 300+
SFPM – это единица измерения скорости, которая описывает, насколько быстро движется режущая кромка режущего инструмента, или, другими словами, это скорость, с которой материал движется за режущую кромку (внешний диаметр) инструмента в футах в минуту.
Простой расчет для определения числа оборотов режущего инструмента составляет:
(4 x SFPM) / Диаметр фрезы
Пример концевой фрезы 5/8 дюйма (0,625) для резки низкоуглеродистой стали:
(4×100) / 0,625 = 640 об / мин
>> Узнайте все, что вам нужно знать о процессе обработки металлов. Запросите наш БЕСПЛАТНЫЙ технический документ здесь <<
Скорость подачи
Скорость подачи – это скорость, с которой резец подается или продвигается по заготовке.Он выражается в единицах расстояния на оборот для точения и растачивания (обычно дюймов на оборот [ ipr ] или мм на оборот ).
Это может быть выражено таким же образом для фрезерования, но часто выражается в единицах расстояния за время фрезерования (обычно дюймов в минуту [ ipm ] или миллиметров в минуту ), с учетом количества зубьев ( или канавки) резак затем определяет, что это означает для каждого зуба.
FR = об / мин x T x CL
Где:
- FR = расчетная скорость подачи в дюймах в минуту или мм в минуту.
- об / мин = расчетная скорость фрезы (согласно расчету выше).
- T = Количество зубьев фрезы.
- CL = нагрузка стружки или подача на зуб . Нагрузка на стружку – это термин, используемый для описания толщины стружки, удаляемой одной режущей кромкой инструмента.Нагрузку на стружку иногда называют «подачей на зуб». Нагрузка на стружку – это радиальная глубина резания режущего инструмента за один оборот. Величина нагрузки стружки обычно предоставляется поставщиком инструмента, как в примере, показанном ниже:
Пример, который использует ту же концевую фрезу 5/8 дюйма, описанную выше, и предполагает, что у нее 4 канавки:
FR = 640 x 4 x 0,004
FR = 10,24 дюйма в минуту (ipm)
Контрольная точка
Фактические значения скоростей резания и подачи являются хорошей отправной точкой для начала и должны быть проверены экспериментально в зависимости от задания.
Обычно при определении скорости резания учитывается время, необходимое для затупления инструмента. Может быть выгоднее работать быстрее для увеличения производительности и более частой замены инструментов. Другой способ – использовать инструменты медленнее для повышения выносливости и оставить машину без присмотра. Здесь существует большой разброс, поэтому после выбора начальной скорости настройте ее в соответствии с выполняемой работой и желаемой производительностью.
Выбор СОЖ / СОЖ
Сегодня доступно большое количество смазочно-охлаждающих жидкостей.Многие новые охлаждающие жидкости были разработаны для удовлетворения потребностей в новых материалах, новых режущих инструментах и новых покрытиях на режущих инструментах.
Целью операций по механической обработке металлов должно быть повышение производительности и снижение затрат. Это достигается за счет обработки на максимальной практической скорости при сохранении практического срока службы инструмента, сокращении брака и производстве деталей с желаемым качеством поверхности. Правильный выбор и использование смазочно-охлаждающих жидкостей может помочь в достижении всех этих целей.
При механической обработке почти вся энергия, расходуемая на резку, преобразуется в тепло.Деформация металла с образованием стружки и трение стружки, скользящей по режущему инструменту, выделяют тепло.
Основная функция СОЖ – охлаждение инструмента, заготовки и стружки, уменьшение трения на скользящих контактах, а также предотвращение или уменьшение сварки или адгезии на контактных кромках, которые вызывают образование наростов на режущем инструменте или вставлять. Смазочно-охлаждающие жидкости также помогают предотвратить ржавчину и коррозию и смыть стружку.
Считаете ли вы этот блог полезным? У вас есть вопросы о том, как улучшить чистовую скорость и подачу при обработке металла? Оставьте комментарий ниже, мы будем рады услышать от вас!
Скорости и подачи – LittleMachineShop.

|
|
1.3: Блок 2: Скорость, подача и нарезание резьбы
ОбъективПосле завершения этого модуля вы должны уметь:
- Определять и выбирать настройки и операции вертикального фрезерного станка для различных задач обработки.
- Выберите подходящую скорость резания для различных типов материалов.
- Расчет скорости резания и подачи для концевых фрезерных операций.
- Объясните, как правильно настроить нарезку резьбы с механической подачей.
Скорость резания определяется как скорость на внешней кромке инструмента во время резания. Это также известно как поверхностная скорость. Скорость на поверхности, длина поверхности и площадь поверхности напрямую связаны. Если два инструмента разных размеров вращаются с одинаковыми оборотами в минуту (об / мин), у большего инструмента будет более высокая скорость резания. Скорость на поверхности измеряется в поверхностных футах в минуту (SFM).Все режущие инструменты работают по принципу метража поверхности. Скорость резания зависит, прежде всего, от типа материала, который вы режете, и от типа режущего инструмента, который вы используете. Твердость обрабатываемого материала во многом зависит от рекомендуемой скорости резания. Чем тверже обрабатываемый материал, тем меньше скорость резания. Чем мягче обрабатываемый материал, тем выше рекомендуемая скорость резания (см. Рисунок 1).
Сталь Чугун Алюминий Свинец
Рисунок 1: Увеличение скорости резания в зависимости от твердости рабочего материала
Твердость материала режущего инструмента также во многом зависит от рекомендуемой скорости резания.Чем тверже сверло, тем выше скорость резания. Чем мягче сверло, тем ниже рекомендуемая скорость резания (см. Рисунок 2).
Углеродистая сталь Карбид быстрорежущей стали
Рисунок 2: Увеличение скорости резания в зависимости от твердости режущего инструмента
Таблица 1: Скорости резания для типов материаловВысокоуглеродистая сталь 9015 100 9058 9058 Легированная сталь, SAE 4030 из бронзы 70-90
Тип материала | Скорость резания (SFM) |
---|---|
Низкоуглеродистая сталь | 40-140 |
Среднеуглеродистая сталь | 70-120 |
Свободная обработка Сталь | 100-150 |
Нержавеющая сталь, C1 302, 304 | 60 |
Нержавеющая сталь, C1 310, 316 | 70 |
Нержавеющая сталь, C1 410 | 100 |
Нержавеющая сталь, C1 416 | 140 |
Нержавеющая сталь, C1 17-4, pH | 50 |
Легированная сталь, SAE 4130, 4140 | 70 |
90 | |
Инструментальная сталь | 40-70 |
Чугун – обычный | 80-120 |
Твердый чугун | 5-30 |
Серый чугун | 50-80 |
Алюминиевые сплавы | 300-400 |
Никелевый сплав, Монель 400 | 40-60 |
Никелевый сплав, монель K500 | 30-60 |
Никелевый сплав, инконель | 5-10 |
Сплавы на основе кобальта | 5-10 |
Титановый сплав 20578 | |
Нелегированный титан | 35-55 |
Медь | 100-500 |
Бронза – обычная | 90–150 |
Бронза – Жесткая | 6 |
Латунь и алюминий | 200-350 |
Неметаллические соединения без кремния | 100-300 |
Кремнийсодержащие неметаллические соединения | 30-70 |
После определения SFM для данного материала и инструмента можно рассчитать шпиндель, поскольку это значение зависит от скорости резания и диаметра инструмента.
Где:
- об / мин = число оборотов в минуту.
- CS = Скорость резания в SFM.
- D = Диаметр инструмента в дюймах.
Подача (подача фрезерного станка) может быть определена как расстояние в дюймах в минуту, на которое деталь перемещается в фрезу.
На фрезерных станках, которые мы имеем здесь, в LBCC, подача не зависит от скорости шпинделя.Это хорошее расположение, позволяющее ускорить подачу больших, медленно вращающихся фрез.
Скорость подачи на фрезерном станке зависит от следующих факторов:
- Глубина и ширина резания.
- Тип фрезы.
- Резкость фрезы.
- Материал заготовки.
- Прочность и однородность заготовки.
- Требуемая отделка.
- Требуемая точность.
- Мощность и жесткость станка, удерживающего устройства и оснастки.
Подача на зуб
Подача на зуб – это количество материала, которое должно быть удалено каждым зубом фрезы при ее вращении и продвижении к работе.
По мере того, как деталь продвигается к фрезу, каждый зуб фрезы продвигается в работу на равное количество, образуя стружку одинаковой толщины.
Толщина стружки или подача на зуб вместе с количеством зубьев фрезы формируют основу для определения скорости подачи.
Идеальная скорость подачи для фрезерования измеряется в дюймах в минуту (IPM) и рассчитывается по следующей формуле:
IPM = F x N x RPMГде:
- IPM = скорость подачи в дюймах в минуту
- F = подача на зуб
- N = количество зубьев
- об / мин = оборотов в минуту
Например:
Подачи для концевых фрез, используемых в вертикальных фрезерных станках, варьируются от.Подача от 001 до 0,002 дюйма на зуб для фрез очень малого диаметра по стальному материалу до подачи 0,010 дюйма на зуб для больших фрез по алюминиевым заготовкам. Поскольку скорость резания для низкоуглеродистой стали составляет 90, частота вращения 3/8 дюймовой высокоскоростной концевой фрезы с двумя канавками составляет
Для расчета скорости подачи выберем 0,002 дюйма на зуб
IPM = F x N x RPM = 0,002 x 2 x 960 = 3.84 дюймов в минутуМашинная подача
Движение станка, которое заставляет режущий инструмент врезаться в или вдоль поверхности заготовки, называется подачей.
Количество подачи обычно измеряется в тысячных долях дюйма при резке металла.
Каналы выражаются немного по-разному на разных типах машин.
Сверлильные станки с механической подачей предназначены для продвижения сверла на заданную величину за каждый оборот шпинделя.Если мы настроим машину на подачу на 0,006 дюйма, машина будет подавать на 0,006 дюйма за каждый оборот шпинделя. Это выражается в (IPR) дюймах на оборот
Процедуры нарезания резьбы
Передовой опыт:
Использование направляющих для метчика
Направляющие для метчиков являются неотъемлемой частью удобной и прямой резьбы. При использовании токарного станка или фрезы метчик уже ровный и отцентрованный. При выравнивании метчика вручную будьте осторожны, так как направление метчика на 90 ° намного точнее, чем человеческий глаз.
Использование масла
При сверлении и нарезании резьбы критически важно использовать масло. Он предохраняет сверла от визга, делает рез более гладким, удаляет стружку и предохраняет сверло и инструмент от перегрева.
Клевка
Клевок помогает предотвратить перегрев и поломку сверл при использовании их для сверления или нарезания резьбы. Клевое сверление включает в себя просверливание части детали с последующим ее втягиванием для удаления стружки и одновременного охлаждения детали. Поворот ручки на полный оборот, а затем на пол-оборота назад – обычная практика. Каждый раз, когда сверло или метчик откручивается, удалите как можно больше стружки и добавьте масло на поверхность между сверлом или метчиком и заготовкой.
Процедура нарезания резьбы вручную
- Выберите размер сверла из таблицы.
При выборе размера крана в первую очередь следует обратить внимание на эту таблицу.
- При необходимости добавьте фаску к отверстию перед нарезанием резьбы.
Фаски и зенковки – это дополнительные элементы, которые иногда требуются для винтов. Для достижения наилучших результатов скорость шпинделя должна быть от 150 до 250 об / мин. - Получите направляющую для метчика.
Отверстие готово для нарезания резьбы. Для этого используйте метчики и направляющие блоки возле ручных фрез. В направляющих блоках будет несколько отверстий для метчиков разного размера. Выберите тот, который ближе всего к размеру используемого метчика, и поместите его над просверленным отверстием. - Постучите по резьбе.
Подбейте метчик с помощью гаечного ключа. Слегка надавите, поворачивая ключ до упора, а затем на пол-оборота. Клевать метчик на нужную глубину. - Заполните кран.
Если кран не идет дальше или желаемая глубина достигнута, ослабьте давление на кран; он, вероятно, достиг дна. Выньте кран из отверстия. Если приложить дополнительное давление, кран может сломаться. Чем меньше размер крана, тем больше вероятность его поломки.
Процедура нарезания резьбы с механической подачей (вертикальная фреза)
- Нарезание резьбы с подачей электроэнергии аналогично ручному нарезанию резьбы.Однако вместо нарезания резьбы вручную используйте вертикальную фрезу для нарезания резьбы по заготовке.
- Перед запуском машины переключите фрезу на низшую передачу.
- Освободите фиксатор пера и переместите перо как можно ниже. Это гарантирует, что будет достаточно места для установки на желаемую глубину.
- Включите шпиндель ВПЕРЕД и установите скорость вращения шпинделя на 60 об / мин.
- Опустите кран. Когда метчик захватывает приклад, он автоматически входит в отверстие.
- Когда желаемая глубина будет достигнута, быстро переведите переключатель направления шпинделя из прямого в обратное. Это изменит направление крана и вытащит его из отверстия. Изменение направления одним плавным движением предотвратит повреждение резьбового отверстия и крана.
- Выключите машину.
- Очистите резьбовое отверстие, метчик и механический подающий механизм перед тем, как уйти.
- Объясните скорость резания для более твердых и мягких материалов.
- Какова скорость резания инструментальной стали и алюминия?
- Рассчитайте число оборотов в минуту для концевой фрезы из быстрорежущей стали диаметром ½ дюйма для обработки алюминия.
- Рассчитайте подачу для инструмента с тремя зубьями. Используйте RPM из вопроса 3.
- Рассчитайте число оборотов в минуту для концевой фрезы из быстрорежущей стали диаметром ¾ дюйма для обработки бронзы.
- Рассчитайте скорость подачи твердосплавной концевой фрезы с двумя канавками диаметром ½ дюйма для обработки низкоуглеродистой стали.
- Какова цель клевания при использовании их для сверления или метчика?
- Выберите подходящий размер сверла для метчиков 5/16 – 24.
- Почему используются смазочно-охлаждающие жидкости?
- Опишите разницу между нарезанием резьбы вручную и механической подачей.
Калькулятор подачи и скорости фрезерования
Знаете ли вы, что плагины MecSoft MILL Module имеют встроенный Feeds & Speeds Calculator ? Правильно, вы можете попросить программу предложить значения подачи и скорости на основе вашего текущего материала заготовки и параметров активного инструмента! После того, как подача на резание рассчитана, вы можете выбрать автоматическое присвоение значений скорости подачи для различных движений траектории в вашей операции, включая врезание , заход , Engage , Retract и Departure ! Процентное соотношение Cut Feed , которое нужно назначить, контролируется в диалоговом окне CAM Preferences . Калькулятор подачи и скорости фрезерования
Конечно, вы можете изменить любое из этих вычисленных значений в любое время, для любого инструмента и для любой операции. В части 1 ниже мы обсудим, как назначаются подачи и скорости, основы работы с калькулятором подачи и скорости и как он работает. Для более опытных пользователей следите за обновлениями в Части 2, где мы обсудим, как можно настроить калькулятор Feeds & Speeds Calculator для добавления дополнительных исходных материалов.
Подачи и скорости, связанные с инструментом
В модуле MILL можно определить подачу и скорость и связать их с конкретным инструментом.Это позволяет гибко использовать различные определения инструментов в зависимости от типа обрабатываемого материала (например, сталь, дерево, акрил и т. Д.) Или типа операции (обработка карманов, торцевание и т. Д.). Диалоговое окно Create / Select Tool включает вкладку Feeds & Speeds , где определяются эти значения. Когда инструмент сохранен, значения подачи и скорости сохраняются вместе с ним.
Диалог создания / выбора инструмента
Каналы и скорости, связанные с операцией
У каждого типа операции траектории также есть вкладка Feeds & Speeds в своем диалоговом окне.Это позволяет гибко назначать значения подачи и скорости для конкретной операции. Здесь показан диалог операции 2½ Axis Pocketing .
Каждая вкладка Feeds & Speeds также содержит кнопку под названием Load from Tool . Это позволяет загружать значения подачи и скорости, которые вы ранее связали с активным инструментом. Активный инструмент просто относится к инструменту, который вы выбрали на вкладке Инструменты диалогового окна.
Как видите, только между инструментом и типом операции у вас есть широкий диапазон гибкости для определения стратегии подачи и скорости.
Калькулятор подачи и скорости
Возможно, вы заметили, что на вкладке Feeds & Speeds диалогового окна Create / Select Tool и на вкладке Feeds & Speeds диалогового окна операции есть кнопка под названием Load from File. При выборе этой кнопки откроется диалоговое окно « Feeds & Speeds Calculator ».Это диалоговое окно позволяет загружать значения подачи и скорости, которые рассчитываются на основе информации, хранящейся во внешнем файле Materials XML .
Как это работает?
Калькулятор состоит из двух частей.
Данные из таблицы
Эта информация извлекается из файла таблицы XML материалов по умолчанию и основывается на следующих параметрах:
- Материал заготовки выбирается в диалоговом окне Материалы , расположенном на вкладке Программа .
- Материал инструмента выбирается на вкладке Свойства диалогового окна Создание / выбор инструментов .
Значения поверхностной скорости (измеряется в единицах в минуту) и подачи на зуб (измеряется в единицах) извлекаются из файла XML и отображаются в диалоговом окне. Единицы относятся к текущему значению Единицы файла детали.
Входные переменные
Значения для Диаметр инструмента и # канавок загружаются автоматически в зависимости от инструмента, выбранного для операции (т.е.е., активный инструмент). На основе этих параметров программа вычисляет значение Скорость шпинделя , измеренное в об / мин ( оборотов в минуту ).
Расчетная скорость подачи нарезки
A Подача резания также рассчитывается для вас (измеряется в единиц / минуту ) на основе материала заготовки , материала инструмента , диаметра инструмента и количества канавок . Изменение скорости шпинделя обновляет Cut Feed и наоборот.
Когда вы выбираете OK из этого диалогового окна, вычисленные значения Feeds & Speeds передаются либо активному инструменту, либо активной операции траектории.
Формулы, используемые для расчета подачи нарезки
Единицы измерения в дюймах | |
Скорость шпинделя (об / мин) | Скорость резания (SFM) x 12 / (x Диаметр инструмента (дюйм)) |
Режущая подача (IPM) | Подача на зуб (IPT) x количество канавок x скорость шпинделя (об / мин) |
SFM: количество футов в минуту IPT: дюймов на зуб RPM: оборотов в минуту IPM: дюймов в минуту |
Единицы измерения в миллиметрах | |
Скорость шпинделя (об / мин) | Поверхностная скорость (SMM) * 1000 / (x Диаметр инструмента (мм)) |
Режущая подача (MMPM) | Подача на зуб (MMPT) x Количество канавок x Скорость шпинделя (об / мин) |
SMM: метров поверхности в минуту MMPT: миллиметров на зуб RPM: оборотов в минуту MMPM: миллиметров в минуту |
Давайте рассмотрим:
- Вы можете связать уникальные значения подачи и скорости с каждым инструментом или с каждой операцией.
- Вы можете вызвать Feeds & Speeds Calculator либо из диалогового окна Create / Select Tool , либо из любого диалогового окна операции с траекторией.
- Калькулятор подачи и скорости извлекает данные из внешнего файла XML и объединяет их с вашим материалом заготовки и параметрами инструмента для расчета предлагаемой скорости шпинделя и Подача при нарезке
- Изменение таких параметров, как Диаметр инструмента , Скорость резания , Материал и т. Д.автоматически рассчитает новые значения Скорость шпинделя и Подача резания .
- Процент от расчетной Подачи нарезки может быть назначен для Врезание , Подвод , Зацепление , Отвод и Отвод
- Вы можете изменить ЛЮБОЕ или ВСЕ предложенные значения подачи и скорости в любое время!
См. Также:
Дон ЛаКурс (Don LaCourse) – разработчик приложений в MecSoft Corporation.Дон обладает более чем 20-летним опытом работы в CAD / CAM-приложениях как для автомобилей, так и для проектирования пресс-форм. Дон также имеет обширный опыт в документировании продуктов CAD / CAM и активно участвует в написании интерактивной справки, а также в создании учебных пособий по продуктам MecSoft.
Правильная скорость и подача
Программисты обрабатывающих центров указывают скорость шпинделя в оборотах в минуту (об / мин). Многие также указывают скорость подачи в поминутном режиме, либо в дюймах в минуту (ipm), либо в миллиметрах в минуту (мм / мин).С режущими инструментами, используемыми на обрабатывающих центрах, диаметр инструмента не меняется во время операции обработки, поэтому для большинства операций обработки это означает, что для каждого режущего инструмента определяется одна скорость (в об / мин) и одна скорость подачи (в дюйм / мин или мм / мин).
Исключением может быть фреза, которая может как врезная, так и боковая фреза. В таком случае обычно требуется одна скорость подачи для врезания, а другая – для бокового фрезерования. Даже в этом случае, по сравнению с различными диаметрами, обрабатываемыми на токарных центрах, которые требуют использования постоянной скорости резания, изменение условий резания внутри данного режущего инструмента относительно минимально в применениях обрабатывающих центров.
Рассмотрим твердосплавное сверло диаметром 0,5 дюйма. В зависимости от обрабатываемого материала производитель режущего инструмента может рекомендовать скорость 250 футов на поверхность в минуту (sfm) и скорость подачи 0,004 дюйма на оборот (ipr). Используя эти рекомендации, программист применит следующую формулу:
об / мин = 3,82 * SFM / диаметр режущего инструмента
Результат скорости, 1 910 об / мин (3,82 * 250 / 0,5), будет запрограммирован как S1910.
После определения скорости шпинделя скорость подачи в дюйм / мин рассчитывается по следующей формуле:
дюйм / мин = об / мин * ipr
Используя скорость 1910 об / мин и скорость подачи 0.004 ipr, скорость подачи будет 7,64 ipm. Опять же, в программе для этого сверла потребуется только одно слово скорости (S1910) и одно слово скорости подачи (F7.64), независимо от того, сколько отверстий необходимо просверлить.
Все изложенное здесь довольно условно для программирования обрабатывающих центров. Единственным исключением может быть то, что скорость подачи часто программируется непосредственно на оборот, что исключает расчет скорости подачи.
Теперь рассмотрим компенсацию радиуса фрезы элемента.Это позволяет использовать резцы различных размеров (диаметров). Программист может запланировать использование фрезы диаметром 1,0 дюйма, но в действительности – на станке – фактически используется фреза диаметром 0,75 или 1,25 дюйма. Если программист задает скорость шпинделя и скорость подачи на основе запланированного размера фрезы, фактические условия резания, используемые в программе, будут неправильными, если используется другая фреза. Обработка будет либо слишком медленной, либо чрезмерно агрессивной.
Эту проблему можно легко преодолеть с помощью специального макроса, так как можно получить доступ к значению, хранящемуся в регистре коррекции радиуса фрезы, из программы ЧПУ.Мы можем определить фактический размер (диаметр) фрезы, используемой при запуске программы, а затем вычислить прямо в программе точные значения оборотов и дюймов в минуту.
Есть два способа использовать компенсацию радиуса фрезы: 1) запрограммировать траекторию рабочей поверхности, которая требует, чтобы размер фрезы был помещен в регистр смещения, или 2) запрограммировать траекторию центральной линии фрезы, которая требует отклонения от запланированный размер фрезы для размещения в регистре смещения. Кроме того, значение, помещенное в регистр смещения компенсации радиуса фрезы, может быть радиальным значением или значением диаметра, поэтому вы, конечно, должны знать, что представляет собой значение регистра смещения, если хотите использовать этот метод.
В нашем примере мы скажем, что программист задает траекторию рабочей поверхности, а значение в регистре смещения – это фактический радиус фрезы (очень распространенный метод).
Для ЧПУ FANUC текущей модели системные переменные, начинающиеся с # 2401, обычно обеспечивают доступ к регистрам геометрии для компенсации радиуса фрезы (вы должны подтвердить это в документации, поставляемой с вашим станком). В этом случае системная переменная # 2403 обеспечивает доступ к значению регистра геометрии коррекции радиуса фрезы смещения номер 3, которым в нашем примере будет радиус фрезы.
Рассмотрим эти команды, которые определяют скорость и подачу фрезы, работающей со скоростью 240 футов в минуту и 0,005 IPR:
N340 T03 M06 (твердосплавная концевая фреза 1,0)
# 1 = 3,82 * 240 / [# 2403 * 2] (Сохранить соответствующая частота вращения в локальной переменной # 1)
N345 G54 G94 G90 S # 1 M03 (рабочее смещение, режим подачи, абсолютный режим, стартовый шпиндель)
N350 G00 X-0,75 Y-0,75 (первый ход XY)
N355 G43 H03 Z -0,6 M08 (Установить коррекцию на длину инструмента, первый ход Z, подача СОЖ)
N360 G42 D03 Y0.