Обзор способов нарезания резьбы: взгляд изнутри
Анализ способов нарезания резьбы позволяет производителям налаживать эффективную и рентабельную нарезку резьбовых отверстий. Здесь представлены достоинства и недостатки четырёх ключевых методов машинного нарезания резьбы: нарезание метчиками, фрезерование, нарезание на токарных станках и шлифование.
Нарезание метчиками

Метчики Emuge Multi TAP-Form накатывают резьбу на детали, отлитой из алюминия. Метчики-раскатники деформируют материал заготовки, тем самым создавая резьбу нужной формы. При этом процессе стружка не образуется
Применение метчиков для нарезания резьбы является эффективной и популярной практикой. «Нарезание резьбы метчиками–самый распространённый способ, так как он является наименее затратным на начальном этапе производства, но не всегда оказывается самым экономичным в итоге», – говорит Каллен Морисон, специалист по развитию бизнеса американской компании КОМЕТ, производящей метчики и резьбонарезные фрезы.
Нарезание резьбы метчиками – это продолжительный процесс, при котором снятие материала производится режущими кромками, расположенными на определенном расстоянии друг от друга. Окончательные размеры резьбы достигаются за один проход. «Метчик сконструирован под размеры конкретной резьбы: ей соответствуют диаметры заборной и калибрующей частей и шаг резьбы», – поясняет Марк Хэтч, менеджер по продукции корпорации Emuge, расположенной в городе Вест Бойлстон штата Массачусетс, производящей метчики и резьбонарезные фрезы. Марк также добавляет, что, поскольку метчик производит черновую и чистовую обработку за один проход, производится большое количество стружки, которую нужно эффективно отводить. В противном случае существует вероятность возникновения чрезмерного давления, которое может привести к повреждению резьбы или метчика.
Контролирование отвода стружки – это большая проблема при нарезании резьбы, особенно в мягких материалах, ведь при обработке такого материала получается сливная стружка. Такая стружка может образовывать заторы вокруг метчика или забивать его канавки, что может привести к обламыванию метчика в отверстии. «Алюминий, углеродистые и нержавеющие стали 300 серии являются наиболее сложными материалами для контроля отвода стружки», – отмечает Шерил Стюарт, инженер по применению метчиков и резьбонарезных фрез, сотрудник компании OSG Tap & Die Inc., расположенной в Глендейл Хайтс, штат Иллинойс.
Метчики могут быть использованы при обработке практически любого материала твердостью до 50 HRC, но некоторые производители предлагают метчики, эффективные и до 65 HRC.
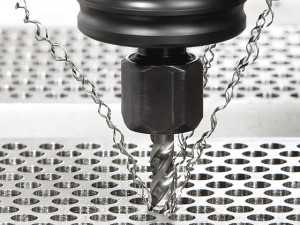
Спиралевидный метчик для нержавеющей стали EXOPROCC-SUS от OSG имеет изменяемую геометрию стружечных канавок с улучшенным контролем отвода стружки
Также нужно обращать внимание и на диметр отверстия под резьбу. Большинство предприятий нарезают резьбу в отверстиях диаметром не более 16 мм. Моррисон отмечает, что «при нарезании резьбы в отверстиях большего диаметра у станка может просто не хватить мощности для поворота метчика, контактирующего с заготовкой»
Также он добавил, что при нарезании резьбовых отверстий диаметром 6 мм и менее существует проблема отвода стружки, так как пространство очень ограничено, а инструменты маленького размера относительно хрупкие.
Вдобавок, метчики могут нарезать резьбу в отверстиях глубиной более трёх диаметров самого инструмента. «Как раз в этом случае метчики обычно работают намного быстрее, чем резьбонарезные фрезы с одной режущей кромкой», –говорит Мориссон. «До тех пор, пока у вас не возникает никаких проблем при отводе стружки, вы можете углублять инструмент настолько, насколько это позволяет сделать его конструкция».
Поскольку диаметр и шаг резьбы всегда остаются неизменными, один и тот же метчик не может использоваться для нарезания отверстий разного размера. Более того, нарезание резьбы подразумевает очень тесный контакт инструмента с заготовкой, из-за чего инструмент подвергается воздействию больших сил. Метчик может сломаться и застрять в отверстии, при этом деталь может уйти в брак. Поэтому при использовании метчиков нужно позаботиться о достаточном количестве смазки.
Накатка резьбы

Процесс резьбообразования при накатке
Метчики-раскатники используются для накатки внутренней резьбы глубиной до четырёх диаметров самого инструмента. Накатные метчики не режут, а деформируют материал, поэтому стружка при этом процессе не образуется и отсутствует вероятность возникновения заторов стружки, но твёрдость заготовки при такой обработке ограничивается 40 HRC. Поскольку накатка резьбы подразумевает пластическую деформацию, материал должен быть пластичен или обладать низким коэффициентом растяжения.
Накатные метчики обычно имеют диаметр от 0.5 до 19 мм. Инструменты большего размера создают и большее трение, поэтому требуют большей мощности станка.
По сравнению с обычными метчиками, метчики-раскатники обладают большей жесткостью и менее подвержены излому. «Давление, действующее на метчик, направлено тангенциально, метчик испытывает скручивающие напряжения, в то время как давление на метчик-раскатник направлено по радиусу в центр, поэтому он гораздо надежнее,» – говорит Моррисон.
«Накатанная резьба прочнее резьбы, получаемой нарезкой, так как зернистый по своей структуре металл подвергается сдавливанию, что делает его более однородным», – объясняет Хетч, работник компании Emuge.
Недостаток накатных метчиков заключается в том, что они требуют больший крутящий момент и большую мощность от станка, кроме того, инструмент должен быть крепче зажат в державке станка. «Для пластической деформации требуется приложить большую силу, чем при его резке», – поясняет Стюарт.
Ещё одним ограничением является то, что отверстие должно быть просверлено более точно, чем таковое отверстие при нарезании резьбы.
Кроме того, резьбы, полученные путем пластической деформации материала, не подходят для некоторых отраслей промышленности, таких как медицинская и авиационно-космическая. «При накатке резьбы внутренний диаметр не идеален», – отмечает Хэтч. «Авиационно-космическая отрасль не допускает такой изгиб (U-образный профиль) на внутреннем диаметре резьбы. Хотя, этот дефект не влияет на прочность резьбы, поэтому это не считается дефектом для деталей общего назначения».
Резьбонарезные фрезы
Фрезы для нарезания резьбы используют спиральную интерполяцию для нарезания как внутренней, так и наружной резьбы. Большинство станков ЧПУ, произведенных за последние 10 -15 лет, поддерживают спиральную интерполяцию.
Для нарезания резьбы применяются цельные твердосплавные фрезы и сменные твердосплавные пластины (стальное тело фрезы с карбидными вставками). Многовитковые резьбонарезные фрезы нарезают резьбу сразу на всю глубину за один полный поворот фрезы. Одновитковые фрезы нарезают один виток резьбы за оборот. Большинство фрез для нарезания резьбы – многовитковые.
Фрезы для нарезания резьбы подходят для обработки материала прочностью до 65 HRC, что существенно расширяет область их применения. «Фреза одной и той же геометрии, но с одним или двумя слоями различных покрытий, позволяет обрабатывать множество разнообразных материалов», – объясняет Моррисон.
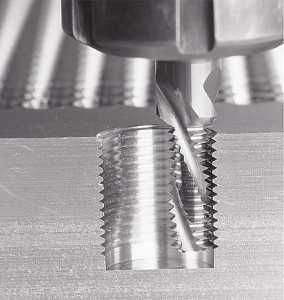
Одна и та же резьбонарезная фреза может применяться для отверстий, имеющих различный диаметр, но одинаковый шаг резьбы. Так как нижняя поверхность фрезы является плоской, она может быть использования для нарезания резьбы в непосредственной близости к нижней части глухого отверстия. KOMET, Америка
Отвод стружки обычно не является проблемой при нарезании резьбы фрезами. «Нарезание резьбы фрезами — это резание с остановками, поэтому, независимо от свойств материала, всегда получается стружка надлома с короткими частицами», – говорит г-н Хэтч из компании Emuge.
Резьбонарезные фрезы имеют большой диапазон применения, их диаметр начинается от 1.5 мм и заканчивается самыми большими размерами. Но по большому счету оптимальная глубина резки фрезой ограничивается 2.5 диаметрами самой фрезы. «При использовании фрезы для нарезания резьбы силы резания не сбалансированы», – отмечает Хетч. «При нарезании резьбы большой длины создается большое давление на боковую поверхность фрезы, так как на нее воздействует большая радиальная сила. Это может приводить к проблемам в виде отскакивания режущей кромки от заготовки и появлению на ней сколов, и даже к обламыванию фрез небольшого диаметра».
Однако одновитковая фреза может работать и на большой глубине. «Вы даже можете врезаться на 20 диаметров, если вам это действительно нужно», – говорит Моррисон. «У вас не будет проблемы отскакивания режущей кромки фрезы от края заготовки, так как в таком случае силы резания воздействуют только одну режущую кромку, находящуюся на самом конце фрезы. У нас много покупателей, работающих в области нефтедобывающей промышленности и электроэнергетики, закупающих одновитковые фрезы с длинным хвостовиком. Для них гораздо рентабельнее иметь в своем распоряжении фрезу, подходящую для нарезания множества различных видов резьбы, даже с учетом того, что процесс идет несколько медленнее. Иначе им бы пришлось приобретать метчики длиной 250 мм стоимостью под 1000 долларов».
Использование фрез имеет множество преимуществ. Один и тот же инструмент может применяться для отверстий разного диаметра, при этом используется один шаг резьбы. Фреза с одной режущей кромкой может быть использована для обработки отверстий различных диаметров, а также и нарезания резьбы различного шага.
К тому же одновитковая резьбонарезная фреза может быть применена для обработки глухих и сквозных отверстий, а также для нарезания правой и левой резьбы. Так как фреза имеет плоскую нижнюю поверхность, она может нарезать резьбу в непосредственной близости от днища глухого отверстия, и даже если фреза сломается, она не приведет к выбраковыванию детали. В заключение, фреза для нарезания резьбы может быть совмещена в одном корпусе с другими инструментами для сверления отверстий, тем самым образовывая комбинированный инструмент, который может одновременно сверлить, делать фаски и нарезать резьбу.
Тем не менее цикл обработки фрезой обычно дольше цикла обработки метчиками. «Так как использование фрез для нарезания резьбы требует специальной программы для станка, некоторые люди могут побояться их использовать», – говорит г-н Стюарт из компании OSG. «И всё же алгоритм достаточно прост и может быть реализован множеством управляющих программ станков ЧПУ».
Некоторые компании всё же предпочитают использовать метчики, так как хотят минимизировать вмешательство оператора в процесс работы. Использование фрез для нарезания резьбы подразумевает, что оператор должен постоянно производить необходимые регулировки. «Так как инструмент стачивается в процессе нормального износа, оператору необходимо регулировать режущий процесс, чтобы подстроится под текущий износ инструмента и сохранить правильные размеры получаемой резьбы», – говорит Хэтч. «Обязанность оператора – измерять допустимые отклонения в размерах резьбы и следить за износом инструмента, а затем, на основе полученных данных, производить регулировку оборудования».
«Размеры метчика всегда остаются неизменными, метчик изготовлен по размерам нарезаемой им резьбы. Оператор просто время от времени сверяет размеры при помощи измерительных инструментов и калибров, и если эти размеры вышли за пределы допустимого, метчик просто выбрасывается».
Токарная обработка резьбы
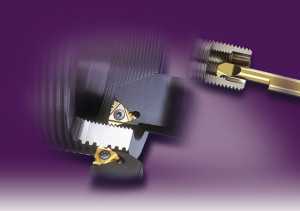
Твердосплавные пластины для токарных станков от компании Carmex могут использоваться для нарезания как внутренней, так и наружной резьбы
Токарная обработка является ещё одним способом нанесения внутренней резьбы. При этом используются либо сменные твердосплавные пластины, либо миниатюрный инструмент наподобие расточного резца. Обработка производится на многоосевых или токарных станках. Возможно применение однозубых и многозубых твердосплавных пластин. Многозубые пластины имеют по несколько зубцов на каждой режущей кромке, причем каждый зубец врезается глубже предыдущего, тем самым сокращается количество проходов, требуемых для нарезания резьбы.
Однако многозубые пластины достаточно дороги. «Большие производства, конечно, выиграют от использования таких пластин, но для маленьких производств польза может быть весьма сомнительной», – говорит Джеф Дей, президент компании Carmex Precision Tools LLC, Ричфилд, Висконсин, производящей инструменты для нарезания резьбы на токарных и фрезерных станках.
Кроме того, многозубые резьбонарезные пластины не могут нарезать наружную резьбу на деталях с фланцами. «В зависимости от шага резьбы, глубина врезания первого и последнего зубцов различается примерно на 3 мм», – говорит Майк Тримбл, менеджер по продукции компании Vargus (США, Дженесвилль, штат Висконсин), также производящей инструменты для нарезания резьбы на токарных и фрезерных станках. «При наличии на детали фланца или выступа, режущая пластина не может подойти к нему вплотную последним зубом, поэтому последние витки резьбы нужно дорезать другим способом».
При нарезании резьбы на токарном станке оператор может применять режущие пластины как полного, так и частичного профиля (многозубые пластины могут быть только полнопрофильными). Пластины полного профиля формируют полный профиль резьбы, включая вершину витка резьбы (при этом внутренний диаметр резьбы выбирается зубцами режущей пластины). При таком подходе для нарезания каждого шага резьбы требуется отдельная пластина.

Твердосплавные пластины для токарных станков марки V6 от компании Vargus имеют 6 режущих кромок. Доступны пластины для нарезания резьбы как полного, так и частичного профиля (т. е. без торцевания вершины витков резьбы)
Пластины полного профиля нарезают более прочную, более прецизионную резьбу, чем пластины частичного профиля, причем за меньшее число проходов. Тримбл говорит, что это происходит из-за того, что они одновременно создают наружный, внутренний и номинальный диаметры резьбы.
Пластины частичного профиля нарезают резьбу без торцовки вершин витков (они не формируют внешний диаметр). Пластины частичного профиля имеют только одну режущую кромку, поэтому они могут нарезать резьбу различного шага, варьируя глубину проникновения режущей кромки в материал. «У такой пластины очень острый кончик зуба, поэтому при большем шаге резьбы теряется ее прочность, и это может привести к более долгому процессу нарезания резьбы», – говорит Дей.
Нарезание резьбы на токарных станках при использовании сменных твердосплавных пластин позволяет нарезать резьбу в отверстиях диаметром 6 мм и больше. Для нарезания резьбы в меньших по диаметру отверстиях требуется цельный твердосплавный инструмент, при помощи которого возможно нарезать резьбу в отверстиях диаметром до 1.3 мм.
Что касается отверстий большого диаметра, компания Vargus сумела нарезать резьбу в отверстии диаметром 914 мм. Тримбл сказал: «Мы сделали это на вертикальном токарно-револьверном станке возрастом примерно в 100 лет. Не было никакого другого способа сделать это, кроме как точить эту резьбу, так как на таких станках не бывает спиральной интерполяции».
Нарезание резьбы на токарных станках подходит для отверстий глубиной до 3 его диаметров при использовании инструмента со стальными державками, и даже глубиной в 4-5 диаметров при использовании инструмента с державками из твердых сплавов.
Нарезание резьбы на токарных станках подходит для целого ряда материалов. «Мы каждый день нарезаем резьбу в материалах твердостью до 50 HRC», – говорит Тримбл. «Мы также нарезаем резьбу в экзотических материалах, таких как хастеллой и инконель 718, но это приводит к сокращению срока службы инструментов, так как такие материалы очень тверды или абразивны».
Отвод стружки является большой проблемой при нарезании внутренней резьбы на токарных станках, особенно остро проблема проявляется при нарезании резьбы в глухих отверстиях. Операторы могут компенсировать это, выбрав режущий инструмент с определенной геометрией, а также используя какой-либо вид поперечной подачи (прямо поперечная, по углу профиля резьбы, модифицированная угловая или попеременная угловая) используемый для облегчения отвода стружки, или метод обратной спирали. Тримбл объяснил, что «при последнем способе вместо того, чтобы нарезать резьбу по направлению к шпинделю, вы делаете это в обратном направлении, для облегчения отвода стружки».
«Применение того или иного вида поперечной подачи при нарезании резьбы зависит от конкретной детали, но в большинстве случаев при выборе модифицированной угловой подачи, вы не испортите работу», – говорит Тримбл. «Вы всегда можете использовать его в качестве способа по умолчанию. Но в 99% случаев, если вы сами не поменяете параметры программы станка, будет применяться прямо поперечная подача».
Как же производителю выбрать способ нарезания резьбы? Нарезание резьбы метчиками, фрезерование или токарная обработка? «Путем проб и ошибок», – ответил нам Дей. «Если один из способов не приносит удовлетворительного результата, нужно пробовать другой. У каждого из них есть свои достоинства и недостатки. Самое главное: решая взяться за нарезку резьбы, посмотрите на имеющиеся станки и подсчитайте стоимость инструментов, время цикла резки и сроки эксплуатации инструментов».
Метод шлифования для высокопрецизионной резьбы
Нарезание резьбы методом шлифования позволяет нарезать высокопрецизионные внутренние резьбы и является высокоэффективным решением для производства деталей с низким допустимым отклонением от размеров. При помощи одного станка можно вышлифовывать широкое разнообразие внутренних видов резьбы, а также пазы, желоба и другие формы. Типичными деталями, которые производятся методом внутреннего шлифования, являются резьбоизмерительные калибры, гайки для обычных и шариковых винтовых передач.
Нарезание внутренней резьбы методом шлифования обычно производится на специализированных станках. Для шлифования прецизионного профиля резьбы, ход шлифовальной головки должен осуществляться согласно углу спирали резьбы. Такой подход требует от станка наличия переменной оси вращения, которую абсолютное большинство шлифовальных станков не имеет. Даже при том, что наружная резьба может быть нарезана на шлифовальном станке с использованием профилированного многозубого шлифовального круга, профиль шлифовального круга должен быть модифицирован под спиралевидную форму (параллельное шлифование по оси А). Для нарезания внутренней резьбы требуется шлифовальный круг с одним шлифующим зубом и ось А должна быть настроена под спираль.
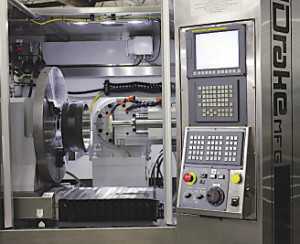
Нарезание внутренней резьбы на плашечном резьбовом калибре на шлифовальном оборудовании компании Drake
Типичные размеры, обеспечивающие экономически выгодный процесс шлифования, варьируются от 10 до 533 мм. Согласно материалам производителя шлифовальных станков компании Drake Manufacturing Services Co., Уоррен, штат Огайо, золотым правилом при шлифовании резьбы в глубоких отверстиях является наличие пропорционального соотношения между длиной и диаметром шлифовальной державки 7:1. Но при этом возникает проблема отношения угла подъема витка к диаметру отверстия. По мере увеличения длины резьбы и уменьшения диаметра отверстия возникают трудности при шлифовании деталей с большим углом подъема витка. Появляются границы, при достижении которых шлифовальная державка будет ударяться об заготовку.
Проблемы отвода стружки при нарезании резьбы методом шлифования заключаются в своевременном поступлении охлаждающей жидкости и смыве стружки из зоны шлифования. Опять же, из-за очень ограниченного пространства при шлифовании внутренней резьбы малого диаметра, в зону шлифования очень сложно доставить охлаждающую жидкость и направить поток в направлении движения ходового вала и при этом не препятствовать движению шлифовальной державки и закрепленной на ней головки.
Нарезание внутренней резьбы методом шлифования является очень точным процессом. Необходимо очень точно установить шлифовальную головку, но после того, как сделаны все настройки, головка может быть очень быстро заменена впоследствии. Также, по словам Дрейка, шлифование внутренней резьбы может увеличить производительность, поскольку замена шлифовальной головки на головку для резьбы другого типа происходит быстрее, чем замена всей державки.
Дрейк утверждает, что для эффективного нарезания внутренней резьбы методом шлифования станок должен обладать несколькими важными свойствами. Этими свойствами являются: жесткость конструкции, стабильная температура, точное перемещение по осям, способность выполнять точные циклические перемещения и наличие прецизионных шпинделей с датчиками контроля температуры.
В рубрике «Нарезание резьбы» находятся материалы по данной теме: анонсы нового инструмента – современных моделей метчиков, плашек и разверток, описание решений технологических проблем, авторские статьи о современных технологиях, новости производителей инструмента.
Источник материала: перевод статьи
Insider trading: evaluating internal threading methods,
Ctemag.com
Автор статьи—оригинала:
Сьюзан Вудс (Susan Woods), редактор
Также советуем прочитать:
Нет связанных записей.
Понравилась статья? Поделитесь:
tverdysplav.ru
ГОСТ 1336-77 Фрезы резьбовые гребенчатые. Технические условия
ГОСТ 1336-77
Группа Г23
ОКП 39 1810
Дата введения 1978-07-01
1. РАЗРАБОТАН И ВНЕСЕН Министерством станкостроительной и инструментальной промышленности СССР
2. РАЗРАБОТЧИКИ
Д.И.Семенченко, канд. техн. наук; Н.И.Минаева, Н.А.Коптева
3. УТВЕРЖДЕН И ВВЕДЕН В ДЕЙСТВИЕ Постановлением Государственного комитета СССР по стандартам от 04.05.77 N 1132
4. Срок проверки – 1996 г., периодичность проверки – 5 лет
5. Стандарт полностью соответствует СТ СЭВ 6291-88, СТ СЭВ 6292-88, СТ СЭВ 6293-88
6. ВЗАМЕН ГОСТ 1336-62
7. ССЫЛОЧНЫЕ НОРМАТИВНО-ТЕХНИЧЕСКИЕ ДОКУМЕНТЫ
8. Ограничение срока действия снято Постановлением Госстандарта от 24.05.91 N 736
9. ПЕРЕИЗДАНИЕ (октябрь 1997 г.) с Изменениями N 1, 2, 3, 4, 5, утвержденными в апреле 1982 г., марте 1985 г., марте 1987 г., апреле 1989 г., мае 1991 г. (ИУС 7-82, 6-85, 6-87, 7-89, 8-91)
Настоящий стандарт распространяется на резьбовые гребенчатые фрезы, предназначенные для нарезания наружных 6-й и 8-й степеней точности и внутренних 6-й и 7-й степеней точности метрических резьб с профилем по ГОСТ 24705 в изделиях из конструкционной стали.
Требования разд.1, 2, 4, 5, а также пп.3.2, 3.3 настоящего стандарта являются обязательными, другие требования – рекомендуемыми.
(Измененная редакция, Изм. N 2-5).
1. ТИПЫ, КОНСТРУКЦИЯ И ОСНОВНЫЕ РАЗМЕРЫ
1.1. Фрезы должны изготовляться типов:
1 – концевые фрезы с коническим хвостовиком;
2 – насадные фрезы.
1.2. Конструкция и основные размеры фрез типа 1 должны соответствовать указанным на черт.1 и в табл.1.
Черт.1. Конструкция и основные размеры фрез типа 1
Черт.1
Таблица 1
Размеры в мм
Праворежущие | Леворежущие | js16 | Шаг резьбы | Конус Морзе | Число зубьев | ||||||
Обозначение | Приме- няе- мость | Обозначение | Приме- няе- мость | ||||||||
2672-0001 | 2672-0002 | 10 | 0,50 | (92) | 10 | 10,00 | 10 | 2 | 6 | ||
2672-0003 | 2672-0004 | 0,60 | 10,20 | ||||||||
2672-0005 | 2672-0006 | 0,70 | 9,80 | ||||||||
2672-0007 | 2672-0008 | 0,75 | 9,75 | ||||||||
2672-0011 | 2672-0012 | 0,80 | 9,60 | ||||||||
2672-0013 | 2672-0014 | 1,00 | 10,00 | ||||||||
2672-0015 | 2672-0016 | 1,25 | 10,00 | ||||||||
2672-0017 | 2672-0018 | 1,50 | 9,00 | ||||||||
2672-0021 | 2672-0022 | 0,50 | 98 | 16 | 16,00 | ||||||
2672-0023 | 2672-0024 | 0,60 | 16,20 | ||||||||
2672-0025 | 2672-0026 | 0,70 | 16,10 | ||||||||
2672-0027 | 2672-0028 | 0,75 | 15,75 | ||||||||
2672-0031 | 2672-0032 | 0,80 | 16,00 | ||||||||
2672-0033 | 2672-0034 | 1,00 | 16,00 | ||||||||
2672-0035 | 2672-0036 | 1,25 | 16,25 | ||||||||
2672-0037 | 2672-0038 | 1,50 | 16,50 | ||||||||
2672-0041 | 2672-0042 | 12 | 0,50 | (94) | 12 | 12,00 | 12 | ||||
2672-0043 | 2672-0044 | 0,60 | 12,00 | ||||||||
2672-0045 | 2672-0046 | 0,70 | 11,90 | ||||||||
2672-0047 | 2672-0048 | 0,75 | 12,00 | ||||||||
2672-0051 | 2672-0052 | 0,80 | 12,00 | ||||||||
2672-0053 | 2672-0054 | 1,00 | 12,00 | ||||||||
2672-0055 | 2672-0056 | 1,25 | 12,50 | ||||||||
2672-0057 | 2672-0058 | 1,50 | 12,00 | ||||||||
2672-0061 | 2672-0062 | 1,75 | 12,25 | ||||||||
2672-0063 | 2672-0064 | 0,50 | 102 | 20 | 20,00 | ||||||
2672-0065 | 2672-0066 | 0,60 | 19,80 | ||||||||
2672-0067 | 2672-0068 | 0,70 | 20,30 | ||||||||
2672-0071 | 2672-0072 | 0,75 | 20,25 | ||||||||
2672-0073 | 2672-0074 | 0,80 | 20,00 | ||||||||
2672-0075 | 2672-0076 | 1,00 | 20,00 | ||||||||
2672-0077 | 2672-0078 | 1,25 | 20,00 | ||||||||
2672-0081 | 2672-0082 | 1,50 | 19,50 | ||||||||
2672-0083 | 2672-0084 | 1,75 | 19,25 | ||||||||
2672-0085 | 2672-0086 | 16 | 0,50 | 98 | 16 | 16,00 | 16 | ||||
2672-0087 | 2672-0088 | 0,60 | 16,20 | ||||||||
2672-0091 | 2672-0092 | 0,70 | 16,10 | ||||||||
2672-0093 | 2672-0094 | 0,75 | 15,75 | ||||||||
2672-0095 | 2672-0096 | 0,80 | 16,00 | ||||||||
2672-0097 | 2672-0098 | 1,00 | 16,00 | ||||||||
2672-0101 | 2672-0102 | 1,25 | 16,25 | ||||||||
2672-0103 | 2672-0104 | 1,50 | 16,50 | ||||||||
2672-0105 | 2672-0106 | 1,75 | 15,75 | ||||||||
2672-0107 | 2672-0108 | 2,00 | 16,00 | ||||||||
2672-0111 | 2672-0112 | 0,50 | 107 | 25 | 25,00 | ||||||
2672-0113 | 2672-0114 | 0,60 | 25,20 | ||||||||
2672-0115 | 2672-0116 | 0,70 | 25,20 | ||||||||
2672-0117 | 2672-0118 | 0,75 | 24,75 | ||||||||
2672-0121 | 2672-0122 | 0,80 | 24,80 | ||||||||
2672-0123 | 2672-0124 | 1,00 | 25,00 | ||||||||
2672-0125 | 2672-0126 | 1,25 | 25,00 | ||||||||
2672-0127 | 2672-0128 | 1,50 | 25,50 | ||||||||
2672-0131 | 2672-0132 | 1,75 | 24,50 | ||||||||
2672-0133 | 2672-0134 | 2,00 | 24,00 | ||||||||
2672-0135 | 2672-0136 | 20 | 0,75 | 102 | 20 | 20,25 | |||||
2672-0137 | 2672-0138 | 0,80 | 20,00 | ||||||||
2672-0141 | 2672-0142 | 1,00 | 20,00 | ||||||||
2672-0143 | 2672-0144 | 1,25 | 20,00 | ||||||||
2672-0145 | 2672-0146 | 1,50 | 19,50 | ||||||||
2672-0147 | 2672-0148 | 1,75 | 19,25 | ||||||||
2672-0151 | 2672-0152 | 2,00 | 20,00 | ||||||||
2672-0153 | 2672-0154 | 2,50 | 20,00 | ||||||||
2672-0155 | 2672-0156 | 3,00 | 21,00 | ||||||||
2672-0157 | 2672-0158 | 0,75 | 114 | 32 | 32,25 | ||||||
2672-0161 | 2672-0162 | 0,80 | 32,00 | ||||||||
2672-0163 | 2672-0164 | 1,00 | 32,00 | ||||||||
2672-0165 | 2672-0166 | 1,25 | 32,50 | ||||||||
2672-0167 | 2672-0168 | 1,50 | 31,50 | ||||||||
2672-0171 | 2672-0172 | 1,75 | 31,50 | ||||||||
2672-0173 | 2672-0174 | 2,00 | 32,00 | ||||||||
2672-0175 | 2672-0176 | 2,50 | 32,50 | ||||||||
2672-0177 | 2672-0178 | 3,00 | 30,00 | ||||||||
2672-0181 | 2672-0182 | 25 | 1,00 |
docs.cntd.ru
Резьбофрезерование, фрезерование резьбы, резьбофрезерование в NX, обработка резьбы, резьбофрезы, резьбовые фрезы, стратегии резьбофрезерования, резьбофреза, программирование резьбофрезерования в NX, особенности резьбофрезерования, преимущества резьбофрезерования, недостатки резьбофрезерования.
Главная страница » Резьбофрезерование
Резьбофрезерование
Для фрезерования резьб используются резьбовые фрезы или резьбофрезы. Сегодня существует большое разнообразие резьбофрез, как монолитных, так и с пластинами. Резьба образуется путем винтовой траектории вращающегося инструмента вдоль оси отверстия (винтовая интерполяция). То есть перемещение инструмента осуществляется по трем осям X, Y, Z. Причем смещение инструмента вдоль оси отверстия за один оборот равен шагу резьбы.
Каждая резьбофреза имеет свой шаг и тип резьбы, таким образом одна резьбофреза может фрезеровать резьбу в отверстиях различных размеров только с шагом и типом резьбы, соответствующей этой фрезе. Однако, используя одновитковые резьбофрезы возможно обрабатывать резьбы с разным шагом.
А при использовании сборных фрез смена пластины позволяет обрабатывать вовсе совершенно различные резьбы.
Резьбофрезы позволяют избавиться от большого количества метчиков, раскатников, плашек и резьбовых резцов. Одна резьбофреза способна заменить все эти инструменты, естественно на каждый шаг и тип резьбы желательно своя резьбофреза.
Преимущества резьбофрез
1. Снижение номенклатуры рузьбовых инструментов. Одна резьбофреза способна нарезать резьбу в отверстиях разных диаметров.
2. Твердосплавные резьбофрезы обладают большой стойкостью. Даже на экзотических сплавах на никелевой основе и т.д. резьбофрезы показывают отличную стойкость при грамотном их применении. Кроме того, при обработке труднообрабатываемых материалов возникают высокие силы резания и резьбофрезы для этого подходят лучше. Метчики же при малейших включениях в обрабатываемых материалах часто ломаются.
3. Резьбофрезы позволяют фрезеровать резьбу в больших отверстиях.
4. В случае поломки резьбофрезу легко извлечь из отверстия, нежели метчик. Резьбофреза – это первый выбор в дорогостоящей детали, когда резьба нарезается уже практически готовой детали.
5. При выходе из строя пластины, нет необходимости покупать новую фрезу, стоит только заменить пластину и фреза готова к работе. Это выгодно.
7. Фрезы позволяют обрабатывать резьбу в глубоких отверстиях. Здесь рекомендуется использовать одновитковые фрезы. Сила резания и момент в них не значительны, они действуют на один зуб.
8. Резьбофрезерование обеспечивает высокое качество резьбы.
9. Возможно нарезать как правую, так и левую резьбу. Одна пластина подходит как для левой так и для правой резьбы.
10. В глухом отверстии возможно нарезать резьбу практически до самого дна.
11. Резьбофрезы с кромкой для снятия фасок способны обработать не только резьбу, но и фаску для захода резьбы, что экономит время и снижает количество инструментов. Также возможны другие комбинированные резьбофрезы, которые фрезеруют/сверлят отверстие и нарезают в нем резьбу и фрезеруют фаску (3 в 1).

12. В случае износа резьбофрезы или непрохождения проходной пробки в резьбовое отверстие всегда можно скорректировать траекторию фрезы и получить годное отверстие, что невозможно при использовании метчика.
13. Нет необходимости в приобретении компенсирующих вспомогательных инструментов, которые необходимы при использовании метчиков.
14. Использование резьбофрез с внутренним подводом СОЖ еще более повышает производительность, а также стойкость и качество резьбовых отверстий.
15. Резьбофрезы позволяют фрезеровать специальные резьбы.
16. Резьбофрезы позволяют обрабатывать высокоточные резьбы.
17. С помощью резьбофрезы возможно обрабатывать как внутренние, так и наружные резьбы.
18. При использовании резьбофрез резко снижается количество режущих и вспомогательных инструментов, необходимых для обработки детали и соответственно не нужно большое количество инструментальных гнезд в магазине станка. Ведь теперь нет столько метчиков, фасочных фрез и т.д. Они здорово позволяют снизить издержки предприятия на закупке инструментов.
19. При обработке детали за один установ резьбофрезы обеспечивают высокую точность перпендикулярности и соосности резьбы относительно других элементов детали.
20. Снижение себестоимости изделия. Мало того, что требуется меньшее количество инструментов, так и, используя резьбофрезы, отпала необходимость в отдельных резьбонарезных операциях.
21. Рекомендуется использовать резьбофрезы при обработке тонкостенных деталях за счет низких усилий резания.
22. При недостаточно жестком закреплении заготовки опять же рекомендуется применять резьбофрезы.
23. Резьбофрезы отлично подходят для обработки невращающихся деталей, или которые сложно установить на токарном станке.
24. Нет необходимости в канавке под выход резьбы. Еще одним инструментом меньше для изготовления деталей.
25. Резьбофрезы обеспечивают лучший отвод стружки. Первый выбор для материалов, дающих сливную стружку.
26. Не требуется СОЖ. Даже рекомендуется работать без СОЖ, чтобы не было термических трещин.
К недостаткам резьбофрез можно отнести
1. Время обработки, зачастую метчики оказываются быстрее резьбофрез. А как всем известно, в большинстве случаев надо стремиться к снижению времени обработки, а не к снижению стоимости инструментов. То в каждом случае необходимо считать экономическую эффективность. И только так делать выбор в пользу метчика или резьбофрезы.
2. Невозможно использовать резьбофрезы вручную. Для использования резьбофрез необходимы станки с ЧПУ.
Поэтому метчики вполне актуальны и имеют свои преимущества, что отражает широкое их применение.
Типы резьбовых пластин

Программирование резьбофрезерования
Современные CAM-системы позволяют создавать управляющие программы для операций резьбофрезерования. В системе NX для этого имеется специальная операция резьбонарезания. Это будет показано в видео.
Разберем некоторые особенности резьбофрезерования
Часто полезным бывает начать резьбофрезерование сразу несколькими витками фрезы снизу вверх, а не наоборот, это уменьшает износ инструмента, и снижает время обработки.
Возможно фрезеровать с шагом вдоль оси отверстия несколькими витками или зубьями фрезы, но в ряде случаев желательно использовать непрерывное резание.
Для получения резьб высокого качества выбирайте меньший диаметр фрезы.
При выборе фрезы выбирайте диаметр фрезы не больше 70% от диаметра резьбы, иначе возможны погрешности и неточности профиля резьбы.
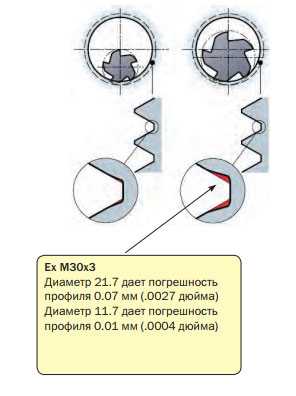
Для обработки труднообрабатываемых сплавов, или резьб с большим шагом, или в ряде других случаев используйте несколько радиальных проходов. Каждый следующий проход должен осуществлять меньший съем металла. Величину съема за проход необходимо брать из каталога инструментов.
Внутренняя резьба правого исполнения: Резьбофреза подводится к дну отверстия, и вращаясь по часовой стрелке, но двигаясь по спирали против часовой стрелки вверх на выход из отверстия. Осуществляется попутное фрезерование. При встречном фрезеровании фреза вращается по часовой стрелке и движется по спирали по часовой стрелке.

Используем минимальный вылет резьбофрезы и стараемся снизить холостые проходы, т.е. начинать подход не из центра отверстия, а вблизи стенки отверстия.
Всегда осуществляем плавный вход и выход из резания по плавной дуге.
Для достижения более высокого качества назначайте подачу на зуб поменьше.
При фрезеровании с небольшой глубиной резания подача не должна превышать 0,15 мм/зуб.
Старайтесь выбирать жесткие, мощные резьбофрезы, особенно при жесткой технологической системе.


Резюме
Резьбофрезы позволяют упростить технологический процесс, снизить количество инструментов для обработки детали, снизить время обработки, сделать производство более гибким, эффективным и более производительным.
Их использование экономически выгодно со всех сторон. Применение резьбофрез уже само за себя говорит о большой экономии временных, экономических, трудовых и других ресурсов предприятия, и повышении ее прибыли. Резьбофрезы не только окупаются, но и приносят значительный экономический эффект.
Программирование резьбофрезерования не составляет труда с этим отлично справляются все CAM-системы.
Тем не менее выбор в пользу резьбофрезы или метчика всегда индивидуален и нужно подходить к этому со здравым смыслом и делать выбор, основанным на расчете экономической эффективности и действительных условий предприятия.
Похожие записи:
vys-tech.ru
Резьбовые фрезы | Методы получения резьб и режущий инструмент
Резьбовые фрезы применяют для нарезания наружных и внутренних резьб различного профиля фрезерованием. По конструкции они делятся на дисковые (рис. 17, а) и гребенчатые (рис. 17, б). Последние — как бы собой несколько дисковых фрез, расположенных рядом. Дисковые фрезы применяют в основном для фрезерования длинных резьб и резьб с крупным шагом, а гребенчатые для фрезерования коротких резьб треугольного профиля (длина фрезы при этом больше длины нарезаемой резьбы).
Рис. 17. Резьбовые фрезы:
а — дисковая; б — гребенчатая
Профиль витков гребенчатой фрезы выполняют подобным впадине нарезаемой резьбы, при этом погрешность нарезаемого профиля резьбы незначительна. Профиль дисковой фрезы, особенно предназначенный для нарезания резьбы с большим шагом, выполняют криволинейным, так как в противном случае погрешности профиля резьбы при бесцентровом огибании будут велики. Трапецеидальный профиль для дисковых фрез делают только при черновом фрезеровании.
Дисковые фрезы по отношению к заготовке устанавливают вдоль винтовой линии на среднем диаметре резьбы, а гребенчатые фрезы — параллельно оси заготовки. Нарезание резьбы фрезой происходит в результате ее вращения и согласованных между собой вращательного движения заготовки и поступательного перемещения заготовки или фрезы вдоль оси заготовки. При нарезании резьбы дисковой фрезой заготовка за период обработки делает столько оборотов, сколько витков имеет резьба. При нарезании резьбы гребенчатой фрезой процесс нарезания заканчивается за 1 — 1¼ оборота заготовки (¼ оборота заготовки затрачивается на врезание фрезы на полную высоту профиля резьбы).
Гребенчатые фрезы применяют для нарезания не только цилиндрических резьб, но и конических. При нарезании конических резьб поступательное перемещение гребенчатой фрезы относительно заготовки происходит не вдоль оси заготовки, а параллельно образующей конуса.
Резьбу можно нарезать червячной резьбовой фрезой соответствующего профиля и шага. Условия резания в этом случае будут аналогичны резанию гребенчатой фрезой, однако условия согласования движений фрезы и заготовки существенно отличаются—червячная фреза за один оборот заготовки должна сделать один оборот, в то время как вращение гребенчатой фрезы не ограничивается вращением заготовки. Следует заметить, что если оставить только указанное согласование движений червячной фрезы и заготовки, то виток резьбы будет сформирован при небольшом числе резов (на длине одного шага число резов будет равно числу стружечных канавок фрезы). Для снижения шероховатости обработанной поверхности резьбы червячной фрезе и заготовке сообщают медленные дополнительные согласованные движения, например червячную фрезу смещают вдоль оси заготовки, а заготовке соответственно сообщают дополнительное вращение; при этом одному дополнительному обороту заготовки соответствует перемещение червячной фрезы на шаг резьбы. В результате число резов, формирующих резьбу, существенно увеличится.
www.stroitelstvo-new.ru
28. Резьбонарезные головки , Резьбовые фрезы и головки для скоростного нарезания резьбы. Виды, особенности конструкций.
Резьбонарезные головки
Сборный инструмент, в корпусе которого
устанавливаются гребенки (плоские радиаль-
ные, тангенциальные и круглые). Ось
детали и ось инструмента совместны.
Особенность – после нарезания резьб
гребенки выводятся из контакта с деталью
перемещением в радиальном направлении.
Что обеспечивает быстрый отвод инструмента
Фрезы:
Дисковые резьбонар фрезы – фасонные фрезы. Фрезы затылуются, примен для нарезания крупных ходовых резьб. Инструмент и деталь скрещиваются.
Гребенчатые фрезы предназн для нарезания креп резьб. Длина резьбы равна длине раб части (ширине фрезы) ось инстр и ось загот параллельны. Обраб выполн за 1 оборот вокруг оси загот. При этом в осевом напр-и загот и инстр смещ на шаг р. Насадные греб фрезы – для нарезания нар резьб, концевые – для внутр и нар резьб.
Охватыв фрезы – нар нар резьб. Обесп по ср-ю с гребенчат более высокое качество обраб, но они явл универс.
Головки для скор нарезания:
Примен для обраб нар и внутр резьб на ток-винтор станке. В корпусе инстр закрепл резцы (чаще – в радиал), корпус в виде кольцевой головки, устанавл на суп станка и имеет индивид привод. Ось загот и ось головки скрещены.
29.Зуборезный инструмент, работающий по методу копирования. Виды, особенности конструкций.
Зубор протяжки и зубодолб головки. Это сложные сборные констр, яв-ся высокопроизв инстр-ми специального назначения.
Применение: крупносер-е, массовое пр-во цил прямо- и косозубых колес, а также блочных ЗК, т.е. возм-ть обр-ки в упор. Дв-е деления отсутств так же, как и дв-е подачи. Они реализуются конструкцией инструмента. Число реж кромок на зубе равно числу впадин.
У зубодолб головки засчет перемещ резцов в радиальном напр-и за двойной ход осуществляется движение подачи.
2.Дисковые зуборезные фрезы.
Прим-ся для нарез-я цилиндр-х прямо- и косозубых колес; если позволяет констр (р-ы) колеса – то и шевронных; с модулем от 0,2 до 16 мм. 9 степени точн-ти в един пр-ве. Иногда исп-ся для нар-я прямозубых конич колес. Низкая произв-ть объясн необх-ю дв-я деления.
Различают следующие типы фрез:
а) Стандартные комплектные – 8,15,26 фрез в комплекте для каждого модуля. Нарезание зубчатых колес с числом зубьев от 12 до ∞.
Каждая фреза предн для зк с числом зубьев в опред-м диапозоне.
γ = 0 – с целью уменьшения искажения профиля
α = 10…15º (полученные в результате затылования) – обеспечивает боковой задний угол 1,5…3º
б) Специальные чистовые – профиль режущей кромки идентичен профилю впадины нарезаемого колеса. По сравнению со стандартными обладают увеличенным диаметром и числом зубьев. Повыш произв-ть и повыш точность.
в) Черновые фрезы с прямолинейным профилем зуба. Для улучшения процесса резания выполняют с γ › 0, а для повышения производительности используют наборы из 2,3,4 фрез, установленных на одной оправке, нарезают неполную впадину
3.Пальцевые зуборезные фрезы.
Нарезание крупномодульных (8…50 мм) прямо-, косозубых и шевронных колес. Используются в случае отсутствия альтернативы
Ø40…200 мм., z = 2…8.
Особенности:
-низкая производительность – из-за малого числа зубьев и нерациональной геометрии (γ = 0 с целью уменьшения искажения профиля)
-низкая точность – из-за погрешности при движении деления и искажения профиля зуба при повторной заточке.
Для предварительного нарезания зубья оснащаются стружкоразделительными канавками. Стружки канавки выполняются винтовыми. Для предварительной обработки используются фрезы с трапециидальным профилем.
studfiles.net
инженер поможет – Нарезание резьбы на станке с ЧПУ
Наиболее распространенные инструменты для получения внутренней резьбы на станках с СЧПУ – это метчики и фрезы. Сложность получения резьбы с помощью фрезы связана со сложностью программирования интерполирующего движения, поэтому чем проще система ЧПУ, тем чаще используются метчики.
Принцип получения резьбы фрезерованием
При фрезеровании профиль резьбы формируется с помощью движения специальной фрезы по винтовой линии. Подача в этом случае должна совпадать с шагом метчика.
Технология получения резьбы фрезерованием
Сверлят отверстие
Резьбовая фреза опускается в отверстие на нужную глубину резьбы и врезается по дуге 90° на глубину. Фреза при врезании поднимается на ¼ шага резьбы (участок 1-2).
Ось фрезы М делает оборот на диаметре m (участок 2-3) при этом фреза одновременно поднимается на шаг резьбы Р и выходит из профиля по дуге 90° (участок 3-4).
В случае, если глубина резьбы в полученном ранее отверстии больше длины режущей части фрезы, то обработку на участке 2-3 повторяется несколько раз.
Есть несколько типов резьбовых фрез используемых для нарезания резьбы в станках с ЧПУ
твердосплавные фрезы
резьбовые фрезы со сменными пластинами
комбинированные резьбовые фрезы – это фрезы позволяющие сначала сверлить отверстие под резьбу, а потом фрезеровать резьбу
Поэтому есть 2 основных технологии получения резьбы фрезами
Получение резьбы одним инструментом
Получение резьбы несколькими режущими инструментами
Виды метчиков для нарезания резьбы
Метчики с прямыми стружечными канавками
Метчик с прямыми канавками это самый широко используемый вид метчика. Этот метчик применяется для материалов, которые дают короткую стружку, например для стали или чугуна.
Метчики с шахматным зубом
Использование метчика с шахматным зубом уменьшает трение и сопротивление процессу резания, что очень важно при обработке труднообрабатываемых материалах (алюминии и бронзе). Шахматное расположение зубьев у метчика облегчает доступ СОЖ в зону резания.
Метчики со спиральной подточкой
Метчик со спиральной подточкой имеет прямые неглубокие стружечные канавки. Спиральная подточка предназначена для выталкивания стружки вперед. Сравнительно неглубокие стружечные канавки гарантируют максимальную прочность метчика на скручивание. Они также облегчают подвод СОЖ в зону резания. Этот тип метчиков рекомендуется для обработки сквозных отверстий.
Метчики со стружечными канавками только на заборной части
Режущая часть данного метчика имеет аналогичную спиральную подточку, предназначенную для выталкивания стружки вперед. Этот метчик имеет чрезвычайно жесткую конструкцию. Рекомендуется для обработки отверстий глубиной до 1.5 х 0.
Метчики со спиральными зубьями
Метчики со спиральными зубьями предназначены в основном для нарезания резьбы в глухих отверстиях. Спиральная стружечная канавка выталкивает стружку назад, что предотвращает пакетирование стружки на дне отверстия или в стружечных канавках. Поэтому спиральная канавка у метчика снижает риск поломки или повреждения метчика.
Бесстружечные метчики (раскатники)
Бесстружечные метчики отличаются от обычных тем, что образуют профиль резьбы за счет пластической деформации , а не за счет снятия стружки. Рекомендуются для материалов с высокой пластичностью. Такие материалы имеют предел прочности не более 1200 Н/ммг, а относительное удлинение не менее 10%.
Бесстружечные метчики можно использовать в обычных условиях, но лучшие результаты они показывают при обработке вертикальных глухих отверстий. Выпускаются также с внутренним подводом СОЖ.
Резьбонарезные фрезы имеют огромное преимущество при обработке глухих отверстий. Метчику всегда нужен зазор между дном отверстия и торцом метчика из-за заборного конуса метчика. Поэтому метчик не нарезает резьбу в глухом отверстии. Использование фрезы решет эту проблему, так как расстояние от торца фрезы до первой режущей резьбовой кромки очень мало. Также большим преимуществом фрез для резьбы является возможность изменять параметры резьбы, что не возможно при использовании метчика. Эта возможность существенно снижает затраты на нарезание резьбы.
Запомните, что подача равна при работе метчиком оборотам шпинделя умноженным на шаг резьбы.
Резьба может срезается при остановке шпинделя перед реверсом – ось Z уже остановилась, а вот шпиндель по инерции делает ещё какую-то часть оборота. При нарезании резьбы метчиком в стали при этом обрывает метчик, а Д16Т мягче и поэтому резьбу слизывает. Поэтому для нарезания резьбы на станке с ЧПУ нужно использовать специальный патрон – плавающий или его еще называют компенсирующий. Этот патрон имеет подпружиненную часть с цангой, которая может перемещается относительно неподвижной на несколько миллиметров вдоль оси патрона в обоих направлениях.
Привожу общие указания по нарезанию резьбы метчиками
Результат любой операции по нарезанию резьбы зависит от ряда факторов, каждый из которых, в конечном счете, влияет на качество готовой детали.
1. Выберите правильную конструкцию метчика для данного обрабатываемого материала и типа отверстия.
2. Убедитесь, что деталь надежно закреплена – перемещения в процессе обработки могут привести к поломке метчика или плохому качеству резьбы.
3. Выберите правильный размер сверла из соответствующих таблиц. Диаметр необходимого сверла также указан на страницах каталога с метчиками. Помните, что для метчиков-раскатников необходимы сверла других диаметров. Всегда контролируйте наклеп обрабатываемого материала.
4. Выберите правильное значение скорости резания, как показано в каталоге режущего метчиков.
5. Используйте СОЖ, соответствующую выполняемой операции.
6. При нарезании резьбы на станках с ЧПУ проверьте значение подачи, указанное в программе. При использовании резьбонарезного патрона значение подачи на оборот должно составлять от 95 до 97 % от шага для самозатягивания метчика.
7. По возможности используйте качественные патроны с компенсацией для ограничения крутящего момента, которые гарантируют осевое перемещение метчика и устанавливают его прямо в отверстии. Также это предохранит метчик от поломки при случайном столкновении одном отверстия.
8. Убедитесь в том, что метчик плавно входит в отверстие, прерывистая подача может привести к колоколообразной форме начальных витков.
engcrafts.com
Резьбовые фрезы по конструкции разделяют на дисковые (одно-ниточные) и цилиндрические (гребенчатые), представляющие собой как бы набор дисковых резьбовых фрез. Форма зуба дисковой резьбовой фрезы соответствует профилю нарезаемой резьбы. Фрезы для нарезания трапецеидальной резьбы большей частью применяют для нарезания резьб с крупным шагом, многоходовых и длинных. Для изготовления коротких резьб применяют в основном цилиндрические фрезы с формой зуба, соответствующей профилю нарезаемой резьбы. Цилиндрические фрезы бывают хвостовые (концевые) и насадные. Они стандартизованы по ГОСТ 1336—62. По предельным отклонениям профиля нарезки оба вида фрез разделяются на две степени точности, обозначаемые буками Е и Н. Хвостовые фрезыХвостовые фрезы применяют для фрезерования внутренних резьб. Эти фрезы изготовляют с конусными хвостовиками и разделяют на праворежущие и леворежущие. Насадные фрезы снабжены прямыми или винтовыми канавками. Неравномерность работы фрезы с прямыми канавками обусловлена тем, что все зубья фрезы начинают и заканчивают свою работу в процессе нарезания одновременно. Это приводит к возникновению вибрации при резании и, как следствие, к получению нечистой резьбы. Более сложные в изготовлении фрезы с винтовыми канавками лишены этого недостатка, но не обеспечивают одинакового резания всеми режущими кромками, так как с одной стороны профиля острые, а с другой – тупые, что приводит к возникновению осевого усилия во время резания. Для компенсации этих недостатков обычно применяют небольшой угол наклона зубьев в пределах 5—10°. Расчет отдельных элементов дисковых и цилиндрических резьбовых фрез производят теми же методами, как и обычных фрез. Передний угол фрез следует принимать в зависимости от материала обрабатываемой детали в пределах от 4 до 22°. Если передний угол у превышает 4°, то угол профиля нарезки должен быть скорректирован. Предыдущие статьи: Похожие статьи: Следующие статьи: |
www.instrument-osnastka.ru