Основные части сверла
Рис. 1 Части сверла
Основные части сверла.Режущая часть (рис.1). Калибрующая (направляющая, транспортирующая) часть. Эти две части образуют рабочую часть сверла. Соединительная часть (шейка). Хвостовая часть.
Рабочая частьсовместно с режущей и калибрующей частями образует две винтовые канавки и два зуба (пера), обеспечивающих процесс резания.
Калибрующая частьсверла, предназначенная для удаления стружки из зоны резания. Калибрующая часть по всей своей длине имеет ленточку и совместно с ней служит для направления сверла в отверстии.
Шейкау сверл служит для выхода шлифовального круга, а также для маркировки сверл.
Хвостовая частьбывает цилиндрической или конической с конусом Морзе. На конце хвостовой части имеется поводок или лапка.
Конструктивные элементы сверла
Сверло имеет сложную конструкцию и характеризуется диаметром и длиной сверла, шириной и высотой ленточки, диаметром спинки, центральным углом канавки, шириной зуба (пера) и диаметром (толщиной) сердцевины.
Диаметр сверла (d).Выбор диаметра сверла зависит от технологического процесса получения данного отверстия.
Ленточка сверла.Обеспечивает направление сверла в процессе резания, уменьшает трение об поверхность отверстия и уменьшает теплообразование.
Ширина
ленточки бывает от0,2–2мм в зависимости
от диаметра сверла. Ширину ленточки
выбирают:
при обработке легких сплавов равной
f=1,2+0,2682ln{d-18+[(d-18)2+1]1/2};
при обработке других материалов
f=(0,1…0,5)d1/3.
Высота ленточки обычно составляет 0,025dмм.
Для уменьшения трения при работе на ленточках делают утонение по направлению к хвостовику, т.е. обратную конусность по диаметру на каждые 100 мм длины. Для быстрорежущих сверл обратная конусность по диаметру составляет 0,03-0,12 мм. Для твердосплавных сверл – 0,1-0,12 мм.
Сердцевина
сверлавлияет на прочность и жесткость,
характеризуется диаметром сердцевины
–dо. Величина
диаметра сердцевины выбирается в
зависимости от диаметра сверла. Для
повышения жесткости и прочности сверла
его сердцевина утолщается к хвостовику
на 1,4-1,8 мм на каждые 100 мм длины.
Перемычка сверла оказывает влияние на процесс резания.
Режущие элементы сверла. Рабочая часть сверла (см. рис.) имеет шесть лезвий (режущих кромок). Двеглавные режущие кромки(1-2, 1’-2’). Двевспомогательных кромки(1-3, 1’-3’) расположенных на калибрующей части и служащие для направления сверла в процессе работы. Двепоперечные кромки(0-2, 0-2’) образующие перемычку. Все эти лезвия расположены на двух зубьях и имеют непрерывную пространственную режущую кромку, состоящую из пяти разнонаправленных отрезков (3-1, 1-2, 2-2’, 2’-1’, 1’-3’).
Геометрические параметры сверла
Угол при вершине сверла – 2.Для быстрорежущих сверл 118-120о, для твердосплавных 130-140о. Угол влияет на производительность и стойкость сверла, на силы резания, длину режущей кромки и элементы сечения стружки.
Угол наклона поперечного лезвия(перемычки)-(=50-55о).
Угол наклона винтовых канавок сверла оказывает влияние на прочность, жесткость сверла и стружкоотвод.
Рекомендуется для хрупких материалов =10-16о, для обработки материалов средней прочности и вязкости –=25-35о, для обработки вязких материалов –=35-45о.
Угол наклона винтовой канавки в данном сечении хопределяется по формуле
где r– радиус сверла;
rх– радиус сверла в рассматриваемой точке.
Шаг винтовых канавок р.
где D– диаметр сверла.
Диаметр сердцевины сверла – do или К принимают равнымК=(0,125…0,145)D.
Для упрочнения инструмента диаметр Кувеличивается к хвостовику сверла на 1,4 – 1,8 мм на 100 мм длины.
Диаметр спинки зуба сверлаqвыбирают по зависимостиq= (0,99…0,98)D.
Профиль
стружечных канавок.
Угол стружечной канавкиθпри обработке легких сплавов равен 116о, других материалов 90…93о.
Радиусы дуг, образующих профиль винтовой канавки сверла принимаются равнымиRк=(0,75…0,9)D, rк=(0,22…0,28)D, а центры дуг лежат на прямой, проходящей через центр поперечного сечения сверла.Ширина пера.Различают ширину пера в нормальном к оси сечениюВои в сечении, нормальном направлению стружечной канавкиВ, которую указывают на чертеже инструмента. Ширину пераВоопределяют в нормальном к оси сверла сечении по формуле:
Передний угол главных режущих кромок .Угол является величиной переменной, наибольшее его значении на периферии сверла, а наименьшее – в центре. Угол может быть определен в нормальномN–N(
Передние углы на поперечной режущей кромкеимеют большие отрицательные значения (могут достигать -60о). Меняются по длине кромки. Наибольшее значение в центре сверла.
Это приводит к следующему: режущая кромка не режет, а вдавливается в металл. На это тратится 65% осевой силы резания и 15% крутящего момента. Для уменьшения осевой силы уменьшают угол при вершине сверла, при этом крутящий момент возрастает и улучшаются его режущие свойства.
Задний угол главных режущих кромок –образуется на режущей части сверла на главных и поперечных режущих кромках. Является переменным и измеряется в нормальном и цилиндрическом сечениях.
Минимальное значение принимает на периферии сверла, максимальное – в центре. Эпюра углов показана на рисунке. Для сверл из быстрорежущих сталей принимается =8-15о. Для твердосплавных=4-6о.
Изменение передних и задних углов в процессе резания. В процессе резания передние и задние углы меняются и отличаются от углов заточки. Их называют кинематическими или действительными углами резания. Наибольшее значение при сверлении имеет кинематический задний угол.
Кинематический задний угол кизменяется вдоль главной режущей кромки сверла. Зависит от подачи и радиуса рассматриваемой точки режущего лезвия. Для обеспечения достаточного значения заднего угла в процессе резания его делают переменным вдоль режущей кромки. На периферии 8-14о, а у сердцевины 20-25ов зависимости от диаметра сверла.
Формы
задней поверхности сверл.Различают
одноплоскостные и двухплоскостные
формы задней поверхности.
Оформление задней поверхности по плоскости. Это наиболее простой одноплоскостной способ заточки сверл, при нем необходимо иметь задние углы не менее 20 – 25°. При этом способе заточки значения заднего углаи угла наклона поперечной кромки зависят от угла при вершине сверла2 и заднего угла на периферии.
Недостатком таких сверл является прямолинейная поперечная кромка, которая при работе без кондуктора не обеспечивает правильного центрирования сверла.
Кдвухплоскостной форме задней поверхности
сверл относится коническая, цилиндрическая
и винтовая форма задней поверхности.
Такая форма задней поверхности позволяет получить независимые значения заднего угла на периферии , угла при вершине2 и угла наклона поперечной кромки.
Коническая форма задней поверхности сверлаявляется участком конической поверхности.
Для образования задних углов вершина конуса смещается относительно оси сверла на величину Н, равную или больше радиуса перемычки, и ось конуса наклонена к продольной оси сверла под углом.
Цилиндрическая форма задней поверхности сверла является участком цилиндрической поверхности. Этот метод применяют редко.
Винтовая форма задней поверхности сверлаявляется развертывающейся винтовой поверхностью. Она позволяет получить рациональное распределение значений задних углов
У таких сверл увеличиваются значения задних углов на поперечной режущей кромке, что приводит к уменьшению осевых нагрузок. Большим преимуществом винтовой заточки является возможность автоматизации процесса заточки.
studfile.net
Геометрия режущей части сверла
⇐ ПредыдущаяСтр 11 из 11
Геометрия режущей части спирального сверла представлена на рис. 17.3. Главные режущие кромки перекрещиваются под углом 2φ, который называется углом при вершине и равен сумме двух углов в плане φ. Угол 2φ образуется проекциями главных режущих кромок на параллельную им плоскость, проходящую через ось сверла. Величина этого угла зависит от твёрдости и прочности обрабатываемого материала, возрастая при их увеличении. Чаще всего угол 2φ колеблется в пределах 90…160°. При обработке пластмасс угол при вершине может иметь значения меньше 90°.
Рис. 17.3. Геометрические параметры спирального сверла
Для исключения защемления сверла в отверстии направляющая часть делается с обратной конусностью, т. е. диаметр рабочей части сверла у режущих кромок больше, чем на другом конце у хвостовика. Такая разница составляет 0,04…0,1 мм на 100 мм длины сверла.
Угол ψ называется углом наклона поперечной режущей кромки. Это угол между проекциями главной режущей кромки и перемычки на плоскость, перпендикулярную оси сверла. Чаще всего величина этого угла находится в пределах 50…55°.
Угол ω называется углом наклона винтовой канавки. Он образуется касательной к винтовой линии канавки и осью сверла. У стандартных свёрл угол ω принимается равным 25…30°, а у специальных – в зависимости от твёрдости материала. Для различных материалов угол колеблется в пределах 15…45°.
Передний угол γ – это угол между плоскостью, касательной к передней поверхности, и плоскостью, проходящей через главную режущую кромку параллельно оси сверла. Его величина определяется параметрами винтовой поверхности и носит изменяющийся характер, уменьшаясь в точках главной режущей кромки по мере приближения к поперечной кромке. Задний угол α – угол между плоскостью, касательной к задней поверхности, и плоскостью, перпендикулярной оси сверла. При заточке сверла по конической поверхности задний угол в различных точках главной режущей кромки является переменным, увеличиваясь (в отличие от переднего угла) по мере приближения к поперечной режущей кромке. На чертежах задний угол даётся в периферийной точке главной режущей кромки, так как здесь его легче замерить. Для свёрл диаметром до 15 мм в периферийной точке
α = 11…14°, а для свёрл диаметром от 15 до 80 мм α = 8…11°.
Свёрла стандартной конструкции имеют ряд недостатков в геометрии режущих кромок. Для того чтобы улучшить геометрию, повысить качество обрабатываемой поверхности, увеличить производительность свёрл, используется так называемая подточка поперечной кромки и ленточки (рис. 17.4).
Рис. 17.4. Некоторые формы подточек спирального сверла:
а – подточка поперечной кромки; б – подточка ленточки; в – двойная заточка главной режущей кромки; г – срез поперечной кромки с двойной заточкой главной режущей кромки
Подточка поперечной кромки уменьшает её длину и увеличивает передний угол вблизи оси сверла. Уменьшение поперечной кромки резко уменьшает осевую силу при обработке твердых и хрупких (например, чугун) материалов.
Подточка ленточки делается обычно на длине 1,5…2,5 мм. Двойная заточка разделяет стружку на два потока и улучшает отвод тепла на наибольшем диаметре. Переходную кромку делают под углом 2φ =70°.
Порядок выполнения работы
1. Нарисовать эскиз сверла с обозначением основных размеров и геометрии.
2. Измерить параметры, указанные в табл. 17.1, используя штангенциркуль, микрометр, угломер и линейку. При определении углов ψ и ω, длины главных режущих кромок и перемычки можно пользоваться отпечатками режущих кромок и ленточки на листе бумаги.
Таблица 17.1
Результаты измерений параметров сверла
Измеряемые параметры | Обозначение | Величины |
Общая длина сверла, мм Длина рабочей части, мм Длина шейки, мм Длина хвостовика, мм Длина лапки, мм Длина главных режущих кромок, мм Длина поперечной режущей кромки, мм Наибольший диаметр рабочей части, мм Конусность рабочей части Диаметр шейки, мм Наибольший диаметр хвостовика, мм Наименьший диаметр хвостовика, мм Конусность хвостовика Толщина лапки, мм Ширина ленточки, мм Высота ленточки, мм Угол при вершине, град Угол наклона поперечной кромки, град Угол наклона винтовой канавки, град | L lр lш lх lл lрк lпк Dр Кр Dш Dх dх Кх a Hл hл 2φ ψ ω |
Содержание отчёта
1. Описание цели работы.
2. Эскиз исследуемого сверла.
3. Таблица результатов измерения параметров сверла.
4. Краткая характеристика исследуемого сверла: марка материала режущей части, форма заточки, тип хвостовика, номинальный диаметр, назначение.
17.4. Контрольные вопросы
1. Каково назначение свёрл, их типы?
2. Из какого материала изготовляется режущая часть сверла?
3. Из каких частей состоит сверло?
4. Для чего нужна ленточка сверла?
5. Какие существуют типы хвостовиков свёрл?
6. Каково назначение лапки хвостовика?
7.Что такое передний угол? Его влияние на процесс сверления.
8. Каковы функции поперечной режущей кромки?
9. Для чего делается подточка поперечной кромки?
10. Что такое двойная заточка сверла?
11. Каково значение угла при вершине?
Рекомендуемая литература [3, 13–17].
Изучение конструкции фрез
Цель работы:изучить конструкции фрез, определить радиальное и торцовое биения режущих кромок.
Приборы и оборудование: фрезы различных конструкций, микрометр, штангенциркуль, индикатор, стойка индикаторная.
infopedia.su
Сверла — Геометрические параметры режущей части
ГЕОМЕТРИЧЕСКИЕ ПАРАМЕТРЫ РЕЖУЩЕЙ ЧАСТИ ЗУБА СВЕРЛА. Определение геометрических параметров режущей части производится на основе общих положений кинематики резания. [c.202]Геометрия режущей части сверла. К геометрическим параметрам режущей части сверла относятся угол при вершине сверла, угол наклона винтовой канавки, передний и задний углы, угол наклона поперечного лезвия или лезвия перемычки . (рис. 28, б). [c.73]
Форма заточки и геометрические параметры режущей части сверл по нормали МН 70 65 для обработки легких сплавов Размеры в мм [c.337]
Сверла — Геометрические параметры режущей части 140 — 141, 200—208 [c.566]
Основные размеры, градация диаметров, геометрические параметры режущей части сверл приведены в табл. 3-6. [c.370]
По конструкции различают сверла спиральные, с прямыми канавками, перовые, для глубоких отверстий, для кольцевого сверления, центровочные и специальные комбинированные. К конструктивным элементам относятся диаметр сверла D угол режущей части 2ф (угол при вершине) угол наклона винтовой канавки м геометрические параметры режущей части сверла, т. е. соответственно передний а и задний y углы и угол резания б, толщина сердцевины (или диаметр сердцевины) Ф, толщина пера (зуба) Ь ширина ленточки / обратная конусность форма режущей кромки и профиль канавки сверла длина рабочей части /о общая длина сверла L. [c.206]
Геометрическими параметрами режущей части свер-,ла являются задний угол а, передний угол у, углы при вершине 2ф и 2фо и угол наклона поперечной кромки ij (рис. 138), Величина заднего угла изменяется вдоль режущей кромки. Наименьшее значение (7—15°) задний угол имеет в наружной поверхности сверла, а наибольшее (20—26°) — около поперечной режущей кромки. Величина переднего угла в разных точках рел[c.241]
Геометрические параметры режущей части сверл цилиндрических полых с выталкивателем для обработки отверстий и пробок имеют профиль, аналогичный профилю зубьев круглых пил для поперечной распиловки древесины. Угловые параметры зубьев и развертка цилиндрической части сверла представлены на рис. 8. [c.242]
На фиг. 180 приведены геометрические параметры режущей части сверла, предназначенного для обработки чугуна. Угол наклона винтовой канавки принимается равным 20, пластинка же наклонена к оси под углом 6°. Задний угол на периферии по пластинке 10— 12°, а по корпусу 18—20″. Угол при вершине 118—120″. Угол переходной кромки 75° на длине 0,2 диаметра сверла. Важное значение для работоспособности сверла имеет утонение калибрующей части. Оно принимается на длине пластинки для сверл. [c.377]
Сверла. Основные размеры, геометрические параметры режущей части сверл приведены в табл. 2 — 7. [c.420]
Основные геометрические параметры режущей части сверла для сверления пластмасс (см. рис. 154), мм [c.146]
Геометрические параметры режущей части сверл установлены ГОСТ и рекомендуются для сверл диаметром от 0,25 до 80 мм при обработке стали и чугуна. Формы заточек сверл в зависимости от размера сверла и обрабатываемого материала следует выбирать ио табл. 36. [c.219]
Своеобразие заточки сверл по коническим поверхностям заключается в том, что сверло относительно конуса заточки надо расположить так, чтобы получить на сверле необходимые величины геометрических параметров режущей части задних углов а, угла наклона поперечной кромки 1(), угла при вершине сверла 2ф. Положение сверла относительно вершины конуса заточки с углом при вершине 2р характеризуется расстоянием I (фиг. 123,а), смещением к осей конуса и сверла [c.229]
В соответствии с режимами резания металлов инструментами из быстрорежущей стали выбираем форму заточки сверл и устанавливаем геометрические параметры режущей части сверла. [c.297]
Устанавливаем геометрические параметры режущей части. Для сверла 013,5 мм [c.306]
На рис. У1-41 приведены элементы конструкции спиральных сверл с коническим и цилиндрическим хвостами. На рис. У1-42 показаны геометрические параметры режущей части сверла, где 1—2 [c.377]
По табл. 8, ч. II для сверла диаметром 9,8 мм геометрические параметры режущей части, в соответствии с ко- [c.383]
Геометрические параметры режущей части сверл для сверления жаропрочных сталей (фиг. 10) [c.247]
Значения геометрических параметров режущей части оказывают влияние на ресурс и стойкость всех видов осевых режущих инструментов (сверл, зенкеров, разверток), а также на точность размеров и шероховатость поверхности обработанных отверстий. Те значения геометрических параметров режущей части, при которых ресурс и стойкость инструмента максимальны и одновременно получаются наилучшие результаты по точности размеров и шероховатости поверхности обработанных отверстий, принято называть оптимальными. Оптимальные значения геометрических параметров, установленные на основе обобщения результатов экспериментальных исследований и передового производственного опыта, приведены в табл. 13.1. [c.213]
Геометрические параметры режущих частей сверл [c.482]
Геометрические параметры режущей части сверл Сверла из стали Р9 и Р18 [c.902]
Геометрические параметры режущей части цельных твердосплавных сверл угол при вершине 2ф, задний угол а и передний угол у/ упрочняющей фаски выбираются в зависимости от обрабатываемого материала и его прочности. Рекомендуемые значения углов приведены в табл. 42. [c.195]
Геометрическими параметрами режущей части сверла являются задний угол , передний угол у, углы при вершине 2угол наклона поперечной кромки i > (рис. 16). Величина заднего угла изменяется вдаль режущей кромки. Наименьшее значение (7—15°) задний угол имеет у наружной поверхности сверла, а наибольшее (20—26°) — около поперечной режущей кромки. Величина переднего угла в разных точках режущей кромки неодинакова наибольшее значение (25—30°) угол имеет у наруж-ной-ЛОверхности сверла, а наименьшее — около поперечной кромки, где бн мс жет быть и отрицательным. [c.65]
Геометрические параметры режущей части сверла состоят из заднего угла а, переднего угла т углов при вершине 2о и угла наклона поперечной кромки сверла Ф (рис. 21). [c.28]
На рис. 261 показаны углы спирального сверла. Передняя поверхность зуба (клина) сверла образуется спиральной канавкой, задняя— боковой поверхностью конуса. Геометрические параметры режущей части сверла показаны на рис. 262 (см. сечение N—Л ). [c.267]
Выполняем рабочий чертеж (рис. 41). Рабочий чертеж должен иметь три проекции (винтовые линии при черчении заменяют прямыми линиями). Форма заточки сверла с геометрическими параметрами режущей части, а также профиль канавочной фрезы вычерчивают отдельно в большом масштабе (см. рис. 41, в). На чертен1б также указывают основные технические требования к сверлу (см. указания на с. 19). [c.128]Геометрические параметры режущей части сверл установлены ГОСТ 2322-43 и рекомендуются для сверления отверстий диаметоом от 0,25 до 80 мм в стали и чугуне. [c.322]
Геометрические параметры (…°) режущей части сверл для обрабопл [c.430]
На фиг. 432 приведены элементы конструкции винтовых сверл с коническим и цилиндрическим хвостовиком. На фиг. 433, а показаны геометрические параметры режущей части сверла, где 1—2 и 3—4 главные режущие кромки 1—3 лезвие перемычки 2—5 и 4—6 — вспомогательные лезвия круглошлифованных ленточек а — задний угол в точке на режущей кромке в цилиндрическом сечении сверл — передний угол в плоскости, перпендикулярной к режущей кромке ср — главный угол в плане (фиг. 433, б) — угол в плане переходной кромки /о — ширина переходной кро . ки в мм I — угол наклона режущей кромки в град. (фиг. 433, а). [c.629]
Выбор формы заточки и геометрических параметров режущей части сверла. По табл. 6 (стр. 97) выбирают форму заточки сверла для обработки стали с пределом прочности =68 кг1мм ,.ДХ1 — двойная с подточкой перемычки. [c.82]
Геометрические параметры режущей части сверла (рис. 24) состоят из переднего угла Т (гам1ма), заднего угла а (альфа), угла при вершше 2ф (фи), угла наклона поперечной кромки сверл ijj (пси) и угла наклона винтовой канавки со (омега), указанного на рис. 23. [c.86]
Геометрические параметры режущей части сверла (рис. 11) состоят из переднего угла у (гамма), заднего угла а (альфа), угла при вершине 2ф (фи), угла наклона поперечной кромки сверл (пен) и угла наклона винтовой канавкп о (омега), указанного на рис. 10. [c.55]
Мо.мент и сила иодачи ири сверлении зависят в основном от геометрических параметров режущей части сверла, диаметра сверла, подачи, охлаждающе-смазывающей жидкости и физикомеханических свойств обрабатываемого материала. [c.165]
mash-xxl.info
инженер поможет – Геометрия сверла
Сверло – это инструмент, комбинирующий для проделывания отверстий вращательное движение и осевое движение подачи. Оно позволяет выполнить сквозные и глухие проемы в любой основе. В слесарных работах обычно используются спиральные сверла различного диаметра и размера рабочей части.
Инструмент состоит несколько частей – рабочей, разделенной на режущую и калибрующую, соединительную и хвостовую части. На режущей части находятся две основные режущие кромки, они образуются пересекающимися поверхностями винтовых канавок, служащих для отведения возникающей стружки. Здесь же расположена режущая перемычка, которая формируется при скрещивании задних поверхностей сверла.
Вспомогательные режущие кромки находятся на направляющей (калибрующей) части. Они образуются в месте пересечения передних поверхностей и ленточки – узкой полосы, расположенной по длине винтовой канавки и направляющей инструмент при работе.
Параметрами, определяющими геометрию сверла, считаются:
1. Угол при вершине режущей части 2 φ – он образуется основными режущими кромками. Оказывает значимое воздействие на процесс резания. С увеличением его значения усиливается прочность сверла, но требуется увеличение усилия подачи. Уменьшение угла приводит к упрощению процесса, но снижает ресурс прочности режущей части. Для каждого вида материала подбирается значение угла:
- алюминий, латунь – 130…140º
- медь – 125
- магниевые сплавы – 110…120°
- чугун, сталь – 116..118º
- мрамор – 90…100º
- пластмассы – 50…60º
2. Угол наклона ω винтовой канавки определяет удобство отведения стружки, его увеличение способствует облегчению процесса, но снижает жесткость сверла, увеличивая объем канавок на рабочей части. На его размер влияет диаметр сверла и вид растачиваемого материала.
3. Передний угол γ находится в плоскости перпендикулярной режущей кромке, облегчает врезание инструмента и отделение стружки. Величина угла уменьшается по направлению к поперечной кромке. Большое значение угла γ снижает необходимое усилие резания, но снижает прочность режущей части и приводит к скорому нагреву. Для работы с твердым материалом используются сверла с маленьким значением переднего угла, а при работе с пластичными материалами размер угла γ увеличивают.
4. Задний угол α определяется в плоскости, которая параллельна оси сверла. Значение угла отличается на различных участках режущей кромки, оно максимально у оси и уменьшается к наружной поверхности инструмента. Малый размер угла способствует преумножению трения задней поверхности, нагревая и повреждая инструмент.
Величина переднего угла задается при изготовлении, а задний измеряется специальным шаблоном.
5. Угол наклона поперечной кромки имеет постоянное значение 55°.
engcrafts.com
ГОСТ 22735-77 Сверла спиральные с цилиндрическим хвостовиком, оснащенные пластинами из твердого сплава. Основные размеры (с Изменением N 1)
ГОСТ 22735-77
Группа Г23
МКС 25.100.30
Дата введения 1979-01-01
ВВЕДЕН В ДЕЙСТВИЕ постановлением Государственного комитета стандартов Совета Министров СССР от 14 октября 1977 г. N 2442
Ограничение срока действия снято Постановлением Госстандарта СССР от 22.07.82 N 2774
ВЗАМЕН ГОСТ 6647-64 в части типа I; МН 316-65; MH 317-65 в части типа Б
ИЗДАНИЕ с Изменением N 1, утвержденным в июле 1982 г. (ИУС 11-82).
1. Настоящий стандарт распространяется на спиральные сверла с цилиндрическим хвостовиком, оснащенные пластинами из твердого сплава диаметром от 5 до 16 мм.
(Измененная редакция, Изм. N 1).
2. Основные размеры сверл должны соответствовать указанным на чертеже и в таблице.
Чертеж. Основные размеры сверл
мм | ||||||||||||||||||||
Сверла повышенной точности класса А | Сверла нормальной точности классов В1 и В | |||||||||||||||||||
Исполнение 1 | Исполнение 2 | Исполнение 1 | Исполнение 2 | |||||||||||||||||
Укороченные | Нормальные | Укороченные | Нормальные | Укороченные | Нормальные | Укороченные | Нормальные | |||||||||||||
Обозна- | При- | Обозна- | При- | Обозна- | При- | Обозна- | При- | Обозна- | При- | Обозна- | При- | Обозна- | При- | Обозна- | При- | уко- | нор- | уко- | нор- | |
2300-8261 | 2300-8262 | 2300-8263 | 2300-8264 | 2300-1201 | 2300-8265 | 2300-2001 | 2300-8266 | 5,00 | ||||||||||||
2300-8267 | 2300-8268 | 2300-8269 | 2300-8271 | 2300-1202 | 2300-8272 | 2300-2002 | 2300-8273 | 5,10 | 70 | 86 | 36 | 52 | ||||||||
2300-8274 | 2300-8275 | 2300-8276 | 2300-8277 | 2300-1203 | 2300-8278 | 2300-2003 | 2300-8279 | 5,20 | ||||||||||||
2300-8281 | 2300-8282 | 2300-8283 | 2300-8284 | 2300-1247 | 2300-8285 | 2300-2004 | 2300-8286 | 5,30 | ||||||||||||
2300-8287 | 2300-8288 | 2300-8289 | 2300-8291 | 2300-1248 | 2300-8292 | 2300-2005 | 2300-8293 | 5,40 | ||||||||||||
2300-8294 | 2300-8295 | 2300-8296 | 2300-8297 | 2300-1204 | 2300-8298 | 2300-2006 | 2300-8299 | 5,50 | ||||||||||||
2300-8301 | 2300-8302 | 2300-8303 | 2300-8304 | 2300-1205 | 2300-8305 | 2300-2007 | 2300-8306 | 5,60 | ||||||||||||
2300-8307 | 2300-8308 | 2300-8309 | 2300-8311 | 2300-1206 | 2300-8312 | 2300-2008 | 2300-8313 | 5,70 | 75 | 93 | 40 | 57 | ||||||||
2300-8314 | 2300-8315 | 2300-8316 | 2300-8317 | 2300-1207 | 2300-8318 | 2300-2009 | 2300-8319 | 5,80 | ||||||||||||
2300-8321 | 2300-8322 | 2300-8323 | 2300-8324 | 2300-1249 | 2300-8325 | 2300-2010 | 2300-8326 | 5,90 | ||||||||||||
2300-8327 | 2300-8328 | 2300-8329 | 2300-8331 | 2300-1208 | 2300-8332 | 2300-2011 | 2300-8333 | 6,00 | ||||||||||||
2300-8334 | 2300-8335 | 2300-8336 | 2300-8337 | 2300-1209 | 2300-8338 | 2300-2012 | 2300-8339 | 6,10 | ||||||||||||
2300-8341 | 2300-8342 | 2300-8343 | 2300-8344 | 2300-1210 | 2300-8345 | 2300-2013 | 2300-8346 | 6,20 | ||||||||||||
2300-8347 | 2300-8348 | 2300-8349 | 2300-8351 | 2300-1211 | 2300-8352 | 2300-2014 | 2300-8353 | 6,30 | ||||||||||||
2300-8354 | 2300-8355 | 2300-8356 | 2300-8357 | 2300-1250 | 2300-8358 | 2300-2015 | 2300-8359 | 6,40 | 80 | 101 | 42 | 63 | ||||||||
2300-8361 | 2300-8362 | 2300-8363 | 2300-8364 | 2300-1212 | 2300-8365 | 2300-2016 | 2300-8366 | 6,50 | ||||||||||||
2300-8367 | 2300-8368 | 2300-8369 | 2300-8371 | 2300-1251 | 2300-8372 | 2300-2017 | 2300-8373 | 6,60 | ||||||||||||
2300-8374 | 2300-8375 | 2300-8376 | 2300-8377 | 2300-1213 | 2300-8378 | 2300-2018 | 2300-8379 | 6,70 | ||||||||||||
2300-8381 | 2300-8382 | 2300-8383 | 2300-8384 | 2300-1252 | 2300-8385 | 2300-2019 | 2300-8386 | 6,80 | ||||||||||||
2300-8387 | 2300-8388 | 2300-8389 | 2300-8391 | 2300-1253 | 2300-8392 | 2300-2020 | 2300-8393 | 6,90 | ||||||||||||
2300-8394 | 2300-8395 | 2300-8396 | 2300-8397 | 2300-1214 | 2300-8398 | 2300-2021 | 2300-8399 | 7,00 | 85 | 109 | 45 | 69 | ||||||||
2300-8401 | 2300-8402 | 2300-8403 | 2300-8404 | 2300-1215 | 2300-8405 | 2300-2022 | 2300-8406 | 7,10 | ||||||||||||
2300-8407 | 2300-8408 | 2300-8409 | 2300-8411 | 2300-1216 | 2300-8412 | 2300-2023 | 2300-8413 | 7,20 | ||||||||||||
2300-8414 | 2300-8415 | 2300-8416 | 2300-8417 | 2300-1217 | 2300-8418 | 2300-2024 | 2300-8419 | 7,30 | ||||||||||||
2300-8421 | 2300-8422 | 2300-8423 | 2300-8424 | 2300-8992 | 2300-8425 | 2300-8993 | 2300-8426 | 7,40 | ||||||||||||
2300-8427 | 2300-8428 | 2300-8429 | 2300-8431 | 2300-1218 | 2300-8432 | 2300-2025 | 2300-8433 | 7,50 | ||||||||||||
2300-8434 | 2300-8435 | 2300-8436 | 2300-8437 | 2300-1219 | 2300-8438 | 2300-2026 | 2300-8439 | 7,60 | ||||||||||||
2300-8441 | 2300-8442 | 2300-8443 | 2300-8444 | 2300-1220 | 2300-8445 | 2300-2027 | 2300-8446 | 7,70 | ||||||||||||
2300-8447 | 2300-8448 | 2300-8449 | 2300-8451 | 2300-1221 | 2300-8452 | 2300-2028 | 2300-8453 | 7,80 | ||||||||||||
2300-8454 | 2300-8455 | 2300-8456 | 2300-8457 | 2300-1254 | 2300-8458 | 2300-2029 | 2300-8459 | 7,90 | ||||||||||||
2300-8461 | 2300-8462 | 2300-8463 | 2300-8464 | 2300-1222 | 2300-8465 | 2300-2030 | 2300-8466 | 8,00 | 95 | 117 | 52 | 75 | ||||||||
2300-8467 | 2300-8468 | 2300-8469 | 2300-8471 | 2300-1223 | 2300-8472 | 2300-2031 | 2300-8473 | 8,10 | ||||||||||||
2300-8474 | 2300-8475 | 2300-8476 | 2300-8477 | 2300-1224 | 2300-8478 | 2300-2032 | 2300-8479 | 8,20 | ||||||||||||
2300-8481 | 2300-8482 | 2300-8483 | 2300-8484 | 2300-1225 | 2300-8485 | 2300-2033 | 2300-8486 | 8,30 | ||||||||||||
2300-8487 | 2300-8488 | 2300-8489 | 2300-8491 | 2300-1226 | 2300-8492 | 2300-2034 | 2300-8493 | 8,40 | ||||||||||||
2300-8494 | 2300-8495 | 2300-8496 | 2300-8497 | 2300-1227 | 2300-8498 | 2300-2035 | 2300-8499 | 8,50 | ||||||||||||
2300-8501 | 2300-8502 | 2300-8503 | 2300-8504 |
docs.cntd.ru
Угол заточки сверла по металлу: таблица и рекомендации
Сверла по металлу, как и любой другой режущий инструмент, изнашиваются в процессе эксплуатации, что делает их непригодными к использованию. Между тем в большинстве случаев режущие и другие углы сверла по металлу можно восстановить, выбрав их значения по специальной таблице и выполнив заточку.
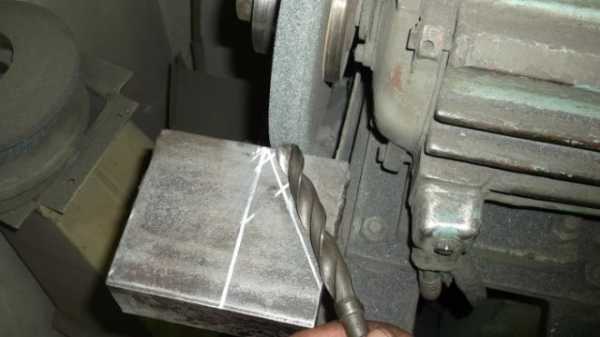
Ручная заточка сверла по металлу
Назначение и конструктивные особенности инструмента
Сверла по металлу, для изготовления которых используются стальные сплавы быстрорежущей группы, применяются для создания в металлических деталях как сквозных, так и глухих отверстий. Наиболее распространенными являются спиральные сверла, конструкция которых включает в себя следующие элементы:
- режущую часть;
- рабочее тело;
- хвостовик;
- лапку.
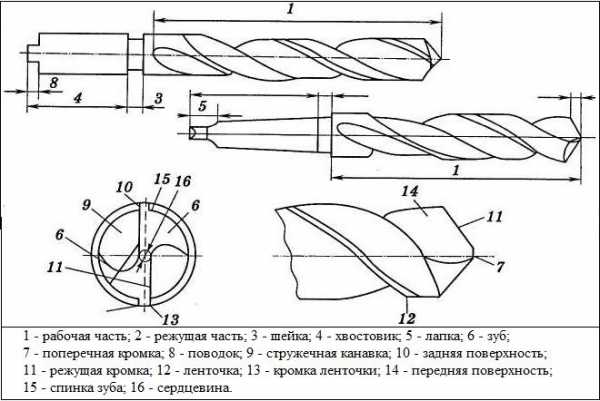
Конструктивные элементы спирального сверла
Если хвостовик, который может быть как цилиндрическим, так и коническим, предназначен для надежной фиксации инструмента в патроне используемого оборудования, то рабочая часть одновременно выполняет сразу несколько важных функций. Именно геометрией сверла определяются его работоспособность и режущие свойства.
Важнейшими элементами рабочей части сверла по металлу являются винтовые канавки. Их задача состоит в том, чтобы выводить из зоны обработки стружку. Геометрия спирального сверла по металлу предусматривает, что передняя сторона спиральной канавки выполняется под определенным углом, величина которого по направлению от оси инструмента к его периферийной части меняется. В процессе изготовления сверла по металлу на боковой области его спиральных элементов формируются узкие ленточки, несколько выступающие над основной поверхностью. Задача таких ленточек состоит в том, чтобы уменьшить величину трения инструмента о стенки формируемого отверстия.
Особенности различных видов заточки сверл
Заточка сверл, как уже говорилось выше, необходима для того, чтобы восстановить их геометрические параметры. Выбор определенного вида заточки сверла зависит от ряда факторов (диаметра инструмента, характеристик обрабатываемого металла и др.).
Наиболее универсальной является нормальная заточка (Н), при выполнении которой на рабочей части сверла формируются одна поперечная и две режущие кромки. Угол заточки сверла в данном случае составляет 118–120°. Выбирая такой вид заточки сверл, следует иметь в виду, что использовать его можно по отношению к инструментам, диаметр которых не превышает 12 мм.
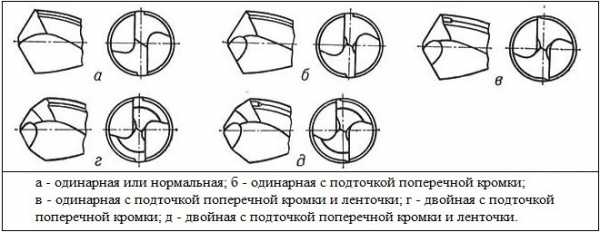
Типы заточек сверл по металлу
Все остальные виды заточки, которые обозначаются буквосочетаниями НП, НПЛ, ДП, ДПЛ, можно применять для инструментов с диаметром до 80 мм. Каждый из указанных типов заточки предполагает доведение геометрии сверла по металлу до требуемых параметров.
НПТакая заточка подразумевает подточку поперечной кромки, что делается для уменьшения ее длины и, соответственно, для снижения нагрузок, воспринимаемых инструментом в процессе сверления.
НПЛВ данном случае кроме поперечной кромки подточке подвергается и ленточка, что позволяет уменьшить ее ширину в области режущей части. Подточка ленточки помимо уменьшения силы трения, создаваемой при сверлении, позволяет сформировать дополнительный задний угол сверла, что способствует облегчению процесса обработки.
ДПЭто двойная заточка, совмещенная с подточкой поперечной кромки. Выполнение заточки данного вида позволяет сформировать на рабочей части сверла по металлу одну поперечную и четыре режущие кромки, имеющие вид ломаных линий.
ДПЛЭто аналогичный предыдущему вид заточки, при котором дополнительно подтачивают ленточку. Создание четырех режущих кромок при выполнении двойной заточки необходимо для того, чтобы уменьшить угол между периферийными участками режущих кромок. Такой подход позволяет улучшить отвод тепла от режущей части инструмента и, соответственно, значительно повысить его стойкость.
Как правильно выбрать углы заточки
Углы заточки сверла, как уже говорилось выше, выбираются по специальным таблицам, где их значения представлены в зависимости от того, в каком именно материале необходимо сформировать отверстие.
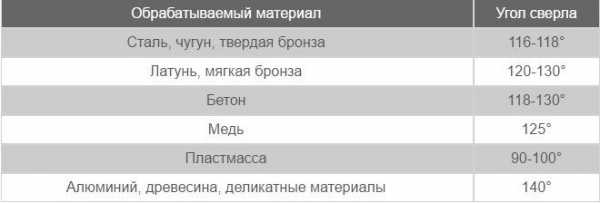
Таблица 1. Углы заточки сверла по металлу для различных материалов
Если неправильно выбрать углы, под которыми будет затачиваться сверло, то это приведет к тому, что оно в процессе работы будет сильно нагреваться. Это в итоге может привести к его поломке. Кроме того, именно неправильно выбранные углы, используемые для заточки сверла по металлу, часто становятся основной причиной некачественно выполненного сверления.
Выполнение операции
Традиционно заточка сверл по металлу спирального типа выполняется на наждачном станке, оснащенном точильным кругом соответствующей твердости. Начинать затачивать их следует с обработки задней поверхности. Прижимая инструмент данной поверхностью к вращающемуся точильному кругу под определенным углом, надо следить за тем, чтобы на ней формировался правильный уклон.
При заточке передней режущей поверхности необходимо контролировать не только угол, под которым выполняется операция, но и размер перемычки. Очень важно, чтобы при заточке на рабочей части сверла по металлу были сформированы режущие кромки равной длины, расположенные под одним углом. Если просверлить отверстие сверлом, при заточке которого не соблюдены эти важные требования, то диаметр такого отверстия будет больше, чем поперечный размер самого инструмента.
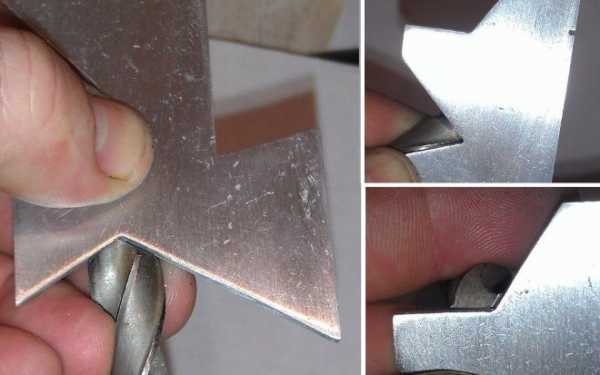
Проверка углов заточки с помощью шаблона
Проверить соответствие основных геометрических параметров (в том числе угла заточки) сверла требуемым характеристикам можно при помощи одного шаблона, который несложно приобрести в серийном исполнении или изготовить самостоятельно.
И в заключение небольшой видеоролик о том, как самостоятельно заточить сверло по металлу.
Оценка статьи:
Загрузка…Поделиться с друзьями:
met-all.org
Составные части сверла. Геометрические параметры режущей части Конструктивные элементы сверла
Геометрические параметры резца влияют на силы резания и износ режущих кромок лезвия.
Термины и определения элементов резцов приведены в ГОСТ 25751-83.
Геометрические параметры головки резца определяют положение его передних и задних поверхностей относительно основной опорной поверхности.
Угол наклона l главной режущей кромки может быть положительным, отрицательным или равным нулю.От утла l зависят форма стружки, направление ее схода по передней поверхности лезвия и упрочнение.Если главная режущая кромка совпадает с основной плоскостью, проходящей через вершину лезвия, l =0, если направлена вверх, угол l положительный, если вниз, угол l отрицательный.
Главный угол в плане j определяет соотношение между шириной и толщиной среза при постоянных значениях подачи и глубины резания. Вспомогательный угол в плане j 1 рекомендуется при жесткой системе принимать в пределах 10-15°,при нежесткой системе 20-30 о, при обработке деталей с врезанием 30-45 о.
Рис. 10 Рабочая часть резца
Переходную режущую кромку выполняют или по радиусу или в видефаски под углом jо= j/2 и длиной f =0,5…3,0 мм в зависимости от размероврезца,Задний угол на переходнойкромке a о = a.
Рис. 11 Геометрические параметры резца
Главный передний угол g уменьшает деформацию стружки и обрабатываемой поверхности,влияет на величину и направление сил резания, прочность режущей кромки, стойкость резца и качество обработанной поверхности.
Главный задний угол a выбирают взависимости от обрабатываемого материала.
Вспомогательный задний уголa 1 назначают одинаковым с принятым задним углом a . Для отрезных и прорезных рездов a 1 = l – 2°.
Радиус вершты лезвия влияетна работурезца также, как угол j 1 . С увеличением радиусаокругления повышаются качество обработанной поверхности и стойкость резца. Увеличение радиуса возможно толькопри жестких условиях работы во избежание вибраций.
Главная режущая кромка выполняет основную работу резания и теоретически должна быть острой. Практическиже всегда имеется некоторый радиус, называемый радиусом округления режущей кромки r (рис. 12). При работе с малой толщиной среза а радиус округления существенновлияет на процесс резания, так как изменяет передний угол.
Значение радиуса r зависит от зернистости инструментального материала и способа обработки передней и задней поверхностей:
r = 6…8 мкм для резцов из быстрорежущих сталей, алмазов, СТМ; r = 1,5…17 мкм для резцов с пластинами из твердого сплава и r = 30…40мкм для резпов, оснащенных минерало-керамическими пластинами.
Рис. 12. Форма режушей кромки в поперечом сечен и ее влияние на передний угол
Передняя поверхность лезвия выполняется плоской иликриволинейной. Плоскую поверхность применяют для обработки хрупких и очень твердых материалов, криволинейную – для обработки вязких,мягкихи средней твердости материалов. Передняя поверхность снабжается упрочняющей ленточкой f =0,2…1,0 мм (меньшиезначения-для малых подач). Размеры фасок, канавок зависят от режимов резания и в основном от подачи. Большей подаче соответствуют большие значения f, r .
СВЕРЛА
Сверло – осевой режущий инструмент для образования отверстий в сплошном материале и увеличения диаметра имеющегося отверстия. Сверла являются одним из самых распространенных видов инструментов. В промышленности применяют сверла: спиральные, перовые, одностороннего резания, эжекторные, кольцевого сверления, а также специальные комбинированные. Сверла изготавливают из легированной стали 9ХС, быстрорежущих сталей Р6М5 и др., и оснащенные твердым сплавом ВК6, ВК6-М, ВК8, ВКЮ-М и др.
Спиральные сверла. Спиральные сверла имеют наибольшее распространение и состоят из следующих основных частей: режущей, калибрующей или направляющей, хвостовой и соединительной. Главные режущие кромки сверла (рис. 13) прямолинейны и наклонены к оси сверла под главным углом в плане j .
Рис. 13 Спиральное сверло
Рис.14 Геометрические параметры спирального сверла
Режущая и калибрирующая части сверла составляют ее рабочую часть, на которой образованы две винтовые канавки, создающие два зуба, обеспечивающие процесс резания. На рабочей части сверла (рис. 15) имеется шесть лезвий: два главных (1 – 2 и 1″ – 2″), два вспомогательных (1 – 3 и 1″ – 3″), расположенны
mirhat.ru