Угол заточки сверла по металлу: таблица и рекомендации
Сверла по металлу, как и любой другой режущий инструмент, изнашиваются в процессе эксплуатации, что делает их непригодными к использованию. Между тем в большинстве случаев режущие и другие углы сверла по металлу можно восстановить, выбрав их значения по специальной таблице и выполнив заточку.
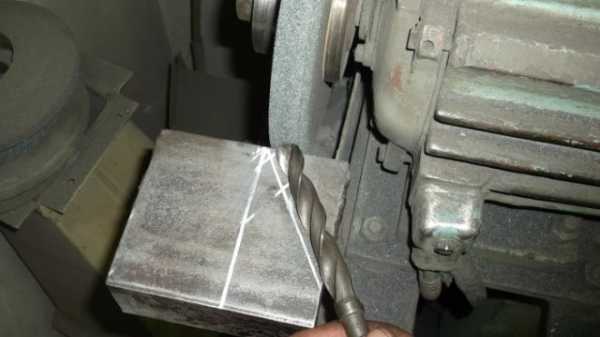
Ручная заточка сверла по металлу
Назначение и конструктивные особенности инструмента
Сверла по металлу, для изготовления которых используются стальные сплавы быстрорежущей группы, применяются для создания в металлических деталях как сквозных, так и глухих отверстий. Наиболее распространенными являются спиральные сверла, конструкция которых включает в себя следующие элементы:
- режущую часть;
- рабочее тело;
- хвостовик;
- лапку.

Конструктивные элементы спирального сверла
Если хвостовик, который может быть как цилиндрическим, так и коническим, предназначен для надежной фиксации инструмента в патроне используемого оборудования, то рабочая часть одновременно выполняет сразу несколько важных функций. Именно геометрией сверла определяются его работоспособность и режущие свойства.
Важнейшими элементами рабочей части сверла по металлу являются винтовые канавки. Их задача состоит в том, чтобы выводить из зоны обработки стружку. Геометрия спирального сверла по металлу предусматривает, что передняя сторона спиральной канавки выполняется под определенным углом, величина которого по направлению от оси инструмента к его периферийной части меняется. В процессе изготовления сверла по металлу на боковой области его спиральных элементов формируются узкие ленточки, несколько выступающие над основной поверхностью. Задача таких ленточек состоит в том, чтобы уменьшить величину трения инструмента о стенки формируемого отверстия.
Особенности различных видов заточки сверл
Заточка сверл, как уже говорилось выше, необходима для того, чтобы восстановить их геометрические параметры. Выбор определенного вида заточки сверла зависит от ряда факторов (диаметра инструмента, характеристик обрабатываемого металла и др.).
Наиболее универсальной является нормальная заточка (Н), при выполнении которой на рабочей части сверла формируются одна поперечная и две режущие кромки. Угол заточки сверла в данном случае составляет 118–120°. Выбирая такой вид заточки сверл, следует иметь в виду, что использовать его можно по отношению к инструментам, диаметр которых не превышает 12 мм.

Типы заточек сверл по металлу
Все остальные виды заточки, которые обозначаются буквосочетаниями НП, НПЛ, ДП, ДПЛ, можно применять для инструментов с диаметром до 80 мм. Каждый из указанных типов заточки предполагает доведение геометрии сверла по металлу до требуемых параметров.
Такая заточка подразумевает подточку поперечной кромки, что делается для уменьшения ее длины и, соответственно, для снижения нагрузок, воспринимаемых инструментом в процессе сверления.
НПЛВ данном случае кроме поперечной кромки подточке подвергается и ленточка, что позволяет уменьшить ее ширину в области режущей части. Подточка ленточки помимо уменьшения силы трения, создаваемой при сверлении, позволяет сформировать дополнительный задний угол сверла, что способствует облегчению процесса обработки.
ДПЭто двойная заточка, совмещенная с подточкой поперечной кромки. Выполнение заточки данного вида позволяет сформировать на рабочей части сверла по металлу одну поперечную и четыре режущие кромки, имеющие вид ломаных линий.
ДПЛЭто аналогичный предыдущему вид заточки, при котором дополнительно подтачивают ленточку. Создание четырех режущих кромок при выполнении двойной заточки необходимо для того, чтобы уменьшить угол между периферийными участками режущих кромок. Такой подход позволяет улучшить отвод тепла от режущей части инструмента и, соответственно, значительно повысить его стойкость.
Как правильно выбрать углы заточки
Углы заточки сверла, как уже говорилось выше, выбираются по специальным таблицам, где их значения представлены в зависимости от того, в каком именно материале необходимо сформировать отверстие.
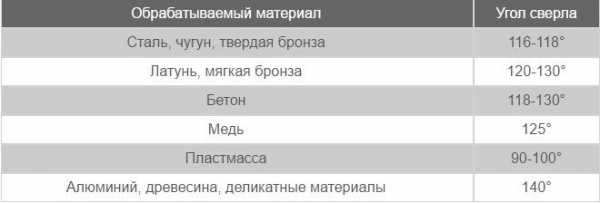
Таблица 1. Углы заточки сверла по металлу для различных материалов
Если неправильно выбрать углы, под которыми будет затачиваться сверло, то это приведет к тому, что оно в процессе работы будет сильно нагреваться. Это в итоге может привести к его поломке. Кроме того, именно неправильно выбранные углы, используемые для заточки сверла по металлу, часто становятся основной причиной некачественно выполненного сверления.
Выполнение операции
Традиционно заточка сверл по металлу спирального типа выполняется на наждачном станке, оснащенном точильным кругом соответствующей твердости. Начинать затачивать их следует с обработки задней поверхности. Прижимая инструмент данной поверхностью к вращающемуся точильному кругу под определенным углом, надо следить за тем, чтобы на ней формировался правильный уклон.
При заточке передней режущей поверхности необходимо контролировать не только угол, под которым выполняется операция, но и размер перемычки. Очень важно, чтобы при заточке на рабочей части сверла по металлу были сформированы режущие кромки равной длины, расположенные под одним углом. Если просверлить отверстие сверлом, при заточке которого не соблюдены эти важные требования, то диаметр такого отверстия будет больше, чем поперечный размер самого инструмента.

Проверка углов заточки с помощью шаблона
Проверить соответствие основных геометрических параметров (в том числе угла заточки) сверла требуемым характеристикам можно при помощи одного шаблона, который несложно приобрести в серийном исполнении или изготовить самостоятельно.
И в заключение небольшой видеоролик о том, как самостоятельно заточить сверло по металлу.
Оценка статьи:
Загрузка…Поделиться с друзьями:
Цилиндрические сверла по металлу: элементы и геометрия, ГОСТы
Цилиндрическое сверло по металлу является наиболее известным инструментом для выполнения отверстий. История приспособлений ведет свой отсчет с 1867 года, когда на Всемирной торговой выставке американской компанией Морзе был представлен первый инструмент. По настоящее время конструкция цилиндрических сверл практически не менялась – основные изменения относились к используемым конструкционным материалам.
В настоящей статье мы рассмотрим разновидность сверлильных приспособлений винтового типа, которые используют для выполнения сквозных и глухих отверстий в металлических изделиях.
Характеристики и назначение цилиндрических сверл
Цилиндрические сверла известны и под другими именами: их также называют спиральными или винтовыми.
Современные изделия различаются по следующим параметрам:
- Используемый материал. Инструменты профессионального назначения изготавливают из быстрорежущей стали. Наибольшей популярностью у отечественных производителей пользуется сорт Р6М5. Его ценят за хорошую прочность и устойчивость к износу: сверла из данного материала отлично держат заточку и не теряют эксплуатационных качеств даже под действием высокой температуры.
- Метод получения профиля. Для повышения точности инструмента используют метод шлифования. Кроме того, такой подход позволяет продлить срок службы приспособления.
- Наличие дополнительной заточки. Острие сверла подвергают дополнительной обработке. Метод используют при производстве изделий профессиональной серии для повышения центровки и снижения нагрузки в процессе эксплуатации.
- Максимальный диаметр отверстия. У самых крупных экземпляров этот показатель может достигать 80 мм.
Изготовление цилиндрических сверл по металлу осуществляется в условиях массового производства. К готовым изделиям предъявляют повышенные требования, которые регламентированы различными межгосударственными стандартами. Несмотря на это, себестоимость сверл по металлу невелика.
Геометрия спиральных сверл практически не менялась с момента выпуска первых экземпляров. Именно благодаря продуманной конструкции рабочей части приспособление получило широкое распространение.
- Винтовые каналы обеспечивают хороший отвод побочных продуктов сверления.
- Острый угол между касательной и режущей кромками облегчает процесс выполнения работ.
- Сверло по металлу цилиндрического типа является многоразовым инструментом: оно выдерживает большое количество переточек, которые выполняются вручную или с помощью станков.
- На наружной поверхности калибрующей части имеются специальные ленточки: они обеспечивают устойчивое направление движения в отверстии.
Особенности конструкции
Основными элементами конструкции спиральных сверл по металлу являются:
- Рабочая часть. Состоит из двух спиральных (винтовых) каналов. Их пересечение формирует режущую часть. Каналы обеспечивают подачу охлаждающей жидкости в зону сверления и отвечают за вывод стружки в процессе выполнения работ.
- Хвостовик. Эта часть фиксируется в патроне рабочего оборудования. Различают два типа хвостовиков: конические (типа Морзе) с лапкой на конце и цилиндрические.
Хвостовик не подвергают термической обработке. Это необходимо для повышения силы трения в патроне и возможности правки по длине. Для инструмента с диаметром рабочей части свыше 8 мм основным материалом хвостовика является конструкционная сталь типа 40Х. Этот элемент является отдельным узлом, который впоследствии приваривают к рабочей части изделия. При этом лапки сверла подвергают закалке с целью повышения прочности, поскольку их используют для выбивания инструмента из шпинделя или переходной втулки.
- Шейка. Здесь находится маркировка инструмента: рабочий диаметр, тип материала, а также информация об изготовителе.
Рассмотрим подробнее рабочую поверхность. Она состоит из двух частей: калибровочной и режущей. Первая представляет собой узкую полоску, расположенную вдоль винтовых каналов. Она придает инструменту дополнительную устойчивость в процессе резания. Режущая часть состоит из нескольких кромок:
- Главная (2 ед.). Она образована пересечением передних и задних канавок.
- Вспомогательная (2 ед.). Эти кромки расположены вдоль спирали сверла. Они образованы пересечением передних каналов с калибровочной частью.
- Дополнительная (1 ед.). Кромка конусной формы, расположенная в задней части инструмента.
Важную роль играет угол вершины. На изображении он имеет обозначение 2φ. Его величина зависит от типа обрабатываемого материала. Например, для высокопрочных сортов стали этот показатель варьируется в диапазоне от 125 до 150 ºC, а для чугуна и бронзы – 90–100 ºC.
Перейдем к особенностям сверл с разными хвостовыми частями.
Сверла цилиндрические с конической хвостовой частью
Данные изделия отличаются длиной и типом. Их используют для обработки различных металлических деталей с помощью стационарных станков. Благодаря конической форме хвостовика увеличивается контактная площадь, что гарантирует надежность крепления и способствует повышению точности сверления.
Посадочная часть конусной формы соответствует стандарту Морзе: от 1 до 6.
На оборудовании с патроном цилиндрической формы используют специальные переходные втулки.
Сверла с хвостовиками конического типа отличаются большим рабочим диаметром: этот параметр может достигать 90 мм. Для сравнения: для изделий цилиндрической формы показатель редко превышает 25 мм.
Сверла с хвостовиками цилиндрической формы
Основное отличие подобных изделий заключается в длине. Существуют линейки короткой, средней и длинной серий. Это позволяет подобрать оптимальный размер сверла спирального с цилиндрическим хвостовиком под любые условия выполнения работ.
Помимо длины, инструменты отличаются классом точности. Основными категориями являются:
Межгосударственный стандарт
Как было указано выше, все изделия отечественного производства подчиняются требованиям ГОСТов. Основными межгосударственными стандартами, которые регламентируют производство рассматриваемых инструментов, являются:
- 10903-77;
- 22736-77;
- 4010-77;
- 19544-74;
- 20694-75.
Цилиндрические сверла по металлу используют в различных отраслях промышленности для выполнения глухих и сквозных отверстий. Как вы считаете, какое покрытие изделий обеспечивает наибольшую износостойкость? Напишите ваше мнение в блоке комментариев.
wikimetall.ru
Угол заточки сверла по металлу:таблица,рекомендации по заточке
Виды заточек сверл по металлу
Заточка сверл осуществляется с целью реанимации инструментов после интенсивной эксплуатации. Существует несколько форм заточки. Выбор в пользу конкретного варианта зависит от диаметра спирального сверла, обрабатываемого материала и других факторов.
Универсальной считается нормальная форма заточки под углом 118-120 градусов. Она позволяет подобрать угол сверла, оптимальный для любых материалов. Единственный минус – ограничение диаметра сверла 12 миллиметрами. Нижеизложенные варианты применяются для инструментов с диаметром до 80 мм.
фото:углы заточки сверла по металлу
К примеру, форма обработки НП включает подточку поперечной кромки. Уменьшение длины способствует снижению усилия и, как следствие, предотвращает излишнее повреждение обтачиваемой детали. Сфера применения – подготовка бура к созданию отверстий в стали.
Разновидность этого способа – НЛП. Помимо описанной подточки кромки, аналогичное действие проводят с ленточками. В результате образуется дополнительный задний угол сверла, который значительно облегчает процесс резки и уменьшает трение функциональной части при проходе сквозь обрабатываемый материал.
В некоторых случаях применяется и двойное затачивание. Методы ДП, ДЛП и аналоги рассчитаны на улучшение характеристик периферийных узлов сверла. Изменение угловой точки между кромками до 75 градусов снижает теплоотвод от сверла и повышает его стойкость.
Рекомендуемые углы заточки сверла по металлу
Ниже представлена таблица углов заточки сверла по металлу для разных видов материала.
Обрабатываемый материал | Угол сверла |
---|---|
Сталь, чугун, твердая бронза | 116-118° |
Латунь, мягкая бронза | 120-130° |
Бетон | 118-130° |
Медь | 125° |
Пластмасса | 90-100° |
Алюминий, древесина, деликатные материалы | 140° |
Неправильно подобранный угол заточки сверла приводит к быстрому нагреву, плохому сверлению и возможной последующей поломке сверла.
Процесс заточки и проверки угла сверла по металлу
Процедуру выполняют на точильном круге. Первый этап – заточка задней поверхности спирали. Для этого инструмент уверенно прижимают к поверхности круга. Обращайте внимание на стабильность – угол заточки сверла по металлу должен быть одинаковым. В итоге, если смотреть на перку сбоку, должен получиться правильный конус.
Далее производится обработка режущей поверхности. Здесь следует обратить внимание не только на постоянство угла, но и на величину перемычки. Для крупных буравчиков ее размер не должен превышать полутора миллиметров.
Правильность заточки бура проверяется по шаблону, который изготавливается мастером вручную или приобретается фабричный. В основе проверки сверла – треугольник Рело, на основе которого создают режущие инструменты для создания квадратных отверстий.фото:шаблон для проверки угла заточки сверла
Он состоит из трех частей. Первая сторона используется для контроля поперечной кромки, вторая представляет собой эталон угла винтовой линии, третья измеряет длину режущей части и проверяет угол при вершине. Качественная работа не вызывает отклонений – все параметры соответствуют линиям шаблона по мере прилегания.
Угол заточки сверла по металлу:Видео
Спиральное сверло – конструкция и геометрия по ГОСТу + Видео
Сверление – один из распространенных способов изготовления отверстий. Исходя из того, каких размеров они должны получаться и в каком материале их делают, выбирают инструмент. Спиральное сверло – самое универсальное и востребованное.
1 Спиральные сверла – конструкция и основные характеристики
Спиральное сверло (или, по-другому, винтовое) конструктивно представляет собой стержень цилиндрической формы, состоящий из элементов:
- Рабочей части – снабжена двумя спиральными винтовыми канавками, которые образуют режущие элементы и предназначены для эффективного отвода стружки, а также подачи смазки в зону сверления.
- Хвостовика – предназначен для надежного закрепления сверла в ручном инструменте или на станке. Может иметь лапку для извлечения сверла из гнезда конусной формы или поводок, обеспечивающий передачу крутящего момента от патрона оборудования.
- Шейки – обеспечивает выход абразивного круга в процессе шлифовки рабочей части.
Рабочая часть состоит из:
- Калибровочной (направляющей) части – это узкая полоска, продолжающая поверхность канавки на окружности сечения сверла. Еще ее называют ленточкой.
- Режущей части – включает две главные и две вспомогательные, расположенные вдоль сверла по спирали, а также одну поперечную (конусообразную на конце сверла) режущие кромки. Все они образованы пересечением поверхностей канавок: главные – передних с задними, вспомогательные – передних с поверхностью ленточки, поперечная – обеих задних.
Рекомендуем ознакомиться
Из всех сверл известных на сегодняшний день конструкций спиральные нашли наиболее широкое применение за счет следующих достоинств:
- большому запасу под переточку;
- хорошему направлению в отверстии;
- отличному отводу стружки.
Основные геометрические параметры спирального сверла:
- угол на кончике при вершине – обозначается 2φ;
- угол наклона канавки ω;
- передний угол γ;
- задний угол α;
- угол наклона концевой поперечной кромки ψ.
Значения этих параметров зависят от типа, вида и назначения сверла.
Спиральные сверла по металлу также отличаются от прочих винтовых (по бетону, дереву, универсальных и других) размерами, формами и протяженностью своих конструктивных элементов. По форме хвостовика они бывают:
- с цилиндрическим хвостовиком;
- с коническим.
Для установки последних на станок используют универсальные специальные переходные втулки – конусы Морзе. Для наиболее распространенных видов инструмента по металлу ниже даны короткие описания.
2 Сверла с цилиндрическим хвостовиком
Сверло спиральное с цилиндрическим хвостовиком выпускается короткой, средней и длинной серий по соответствующим стандартам. Такое разнообразие обеспечивает оптимальный подбор нужного инструмента для выполнения каждой конкретной задачи.
Для всех сверл центровые отверстия выполняются согласно ГОСТ 14034. Допустимо выпускать инструмент без центровочных отверстий. Изделия средней и длинной серии согласно своим стандартам могут изготавливаться с шейкой или без нее. Ее размеры не регламентируются.
ГОСТ 4010-77 распространяется на левые и правые сверла короткой серии диаметром 0,5–40 мм. Согласно этому стандарту, в зависимости от диаметра выпускаемого сверла длина составляет (мм):
- общая всего инструмента – 20–200;
- рабочей части – 3–100.
ГОСТ 10902-77 распространяется на левые и правые сверла средней серии диаметром 0,25–20 мм. Длина составляет (мм):
- общая всего инструмента – 19–205;
- рабочей части – 3–140.
ГОСТ 886-77 распространяется на сверла длинной серии диаметром 1–31,5 мм. Длина составляет (мм):
- общая всего инструмента – 56–316;
- рабочей части – 33–207.
У данных изделий направление спирали – правое. С левым изготовляются по согласованию с заказчиком.
Для всего этого инструмента технические требования к изготовлению регламентируются ГОСТ 2034-80. Согласно этого документа данные сверла производятся из быстрорежущей стали и предназначены для просверливания отверстий в ковких и серых чугунах, легированных и углеродистых конструкционных и инструментальных сталях, конструкционных сталях высокой и повышенной обрабатываемости. Этот инструмент изготовляется 3 классов точности:
- повышенной точности – А1;
- нормальной – В1;
- нормальной – В.
Помимо инструмента из быстрорежущей стали допускается по заказу потребителя изготовление сверл также из легированной стали 9ХС. Инструмент может производиться не только цельным, но и сварным. Хвостовики сварных изделий должны быть выполнены из стали 45 или 40Х. Не допускаются в зоне сварки: непровар, поверхностные раковины и кольцевые трещины.
3 Сверла с коническим хвостовиком по ГОСТ 10903 и другие
Сверло спиральное с коническим хвостовиком выпускается разных типов и, соответственно, по различным стандартам. Это позволяет оптимально подобрать именно тот инструмент, который лучше всего подойдет для того или иного вида работ. Существуют следующие ГОСТы:
- 10903-77 – для сверл нормальной длины;
- 12121-77 – длинных;
- 2092-77 – удлиненных;
- 22736-77 – с твердосплавными пластинами.
Весь этот инструмент согласно своим стандартам может изготавливаться с шейкой или без нее. Ее размеры не регламентируются.
ГОСТ 10903 распространяется на сверла нормальной длины диаметром 5–80 мм, которые выпускаются в двух исполнениях: с нормальным и усиленным хвостовиком. Согласно ГОСТ 10903, в зависимости от диаметра выпускаемого сверла с нормальным хвостовиком длина составляет (мм):
- общая всего инструмента – 133–514;
- рабочей части – 52–260.
С усиленным хвостовиком сверла ГОСТ 10903 выпускаются диаметрами 12–76 мм. Длина их рабочей части такая же, как и у с нормальным хвостовиком. Длины следующие (мм):
- общая – 199–514;
- рабочей части – 101–260.
Размеры используемых для крепления в патроне станка конусов Морзе от 1 до 6.
ГОСТ 12121 распространяется на длинные сверла диаметром 5–50 мм, которые предназначены для выполнения сверления через специальные кондукторные втулки. Длина составляет (мм):
- общая всего инструмента – 155–470;
- рабочей части – 74–321.
Размеры используемых для крепления в патроне станка конусов Морзе от 1 до 4. У инструмента этих двух стандартов направление спирали – правое. С левым изготовляются по согласованию с заказчиком.
ГОСТ 2092 распространяется на удлиненные сверла диаметром 6–30 мм. Длина составляет (мм):
- общая всего инструмента – 225–395;
- рабочей части – 145–275.
Размеры используемых для крепления в патроне станка конусов Морзе от 1 до 3.
4 Сверла с коническим хвостовиком ГОСТ 22736
ГОСТ 22736 распространяется на сверла диаметром 10–30 мм, оснащенные твердосплавными пластинами. Инструмент производится в укороченном и нормальном исполнении. Длина составляет (мм):
- общая всего инструмента в укороченном исполнении – 140–275, нормальном – 168–324;
- рабочей части в укороченном исполнении – 60–125, нормальном – 87–175.
Размеры используемых для крепления в патроне станка конусов Морзе от 1 до 4.
Для этого инструмента технические требования к изготовлению регламентируются ГОСТ 5756-81. В соответствии с ним данные сверла предназначены для сверления различных деталей из чугуна. Должны изготавливаться классов:
- повышенной точности – А;
- нормальной – В.
В качестве режущей оснастки должны применяться твердосплавные пластины типа ВК. Корпуса изделий выполняются из быстрорежущей стали или сплава 9ХС. Допускается производство корпусов из иных марок с содержанием вольфрама в пределах до 6 %. Недопустимо использовать стальные сплавы, содержащие кобальт.
Инструмент с рабочей частью диаметром от 6 мм и больше, корпус которого выполнен из быстрорежущего сплава, должен изготавливаться сварным. Хвостовики сварных изделий должны быть выполнены из стали 45 или 40Х. Не допускаются в зоне сварки: непровар, поверхностные раковины и кольцевые трещины.
tutmet.ru
Геометрия сверла
(рис.3.)
Угол конуса при вершине 2φ определяет производительность и стойкость сверла. Играет роль главного угла в плане, подобно ему влияет на составляющие силы резания, длину режущей кромки и параметры сечения срезаемого слоя.
При уменьшении 2φ сила подачи снижается, а крутящий момент возрастает. Длина режущей кромки увеличивается – отвод тепла улучшается. Толщина стружки уменьшается. Снижается прочность вершины сверла. Угол 2φ выбирается экспериментально в зависимости от обрабатываемого материала.
Рис.3. Геометрия спирального сверла
,
где
Pz – шаг винтовой стружечной канавки.
От угла ω зависят:
сход стружки, с увеличением этого угла отвод стружки улучшается;
прочность и жесткость сверла, с увеличением ω жесткость на изгиб снижается, а жесткость на кручение возрастает;
величина переднего угла, с увеличением ω передний угол возрастает.
Международная организация по стандартизации ISO рекомендует три типа сверл:
ω = 25…350;
ω = 35…450
Передний угол γ главных режущих кромок в рабочей плоскости 0-0 (рис.3.) для каждой точки режущей кромки равняется углу наклона винтовой канавки на диаметре рассматриваемой точки:
, где
ωА – угол наклона винтовой канавки в данном сечении.
Передний угол в главной секущей плоскости N-N
,
Как видно из формулы, передний угол зависит от угла ω и уменьшается на режущей кромке от периферии к центру. На поперечной кромке передний угол имеет отрицательные значения.
Кинематический задний угол ρ (Рис.4.) определяют как угол между винтовой траекторией результирую-щего движения резания и касательной к задней поверхности ρi = i– μi , где μi– угол скорости резания
Угол скорости резания увеличивается с ростом подачи и уменьшением диаметра рассматриваемой точки. Для выравнивания кинематических задних углов инструментальный задний угол делают переменным вдоль режущей кромки. На периферии он равен 8…140 , а у сердце-вины 20…250
Рис.4. Геометрия задней поверхности сверла
Способы заточки спиральных сверл
(рис.5).
Рис. 5. Схемы заточки сверл.
Одноплоскостная (г) – наиболее простая в технологическом плане, но требует больших задних углов, дает прямолинейную поперечную кромку, не обеспечивающую правильного центрирования сверла при работе без кондуктора. Значения заднего угла и угла наклона поперечной кромки зависят от угла при вершине и заднего угла на периферии. Используют для мелких сверл диаметром до 3 мм.
Двухплоскостная (д)- устраняет возможность затирания поверхности детали. Распространена для заточки твердосплавных сверл
Коническая форма (а, б ) – обеспечивает изменение инструментальных задних углов вдоль режущей кромки, способ (б) дает более резкое изменение этих углов, поэтому он более распространен.
Винтовая форма(в) – позволяет получить более рациональное распределение значений задних углов и более выпуклую поперечную кромку сверла, что улучшает самоцентрирование сверла. Возможна автоматизация процесса заточки.
studfiles.net
инженер поможет – Геометрия сверла
Сверло – это инструмент, комбинирующий для проделывания отверстий вращательное движение и осевое движение подачи. Оно позволяет выполнить сквозные и глухие проемы в любой основе. В слесарных работах обычно используются спиральные сверла различного диаметра и размера рабочей части.
Инструмент состоит несколько частей – рабочей, разделенной на режущую и калибрующую, соединительную и хвостовую части. На режущей части находятся две основные режущие кромки, они образуются пересекающимися поверхностями винтовых канавок, служащих для отведения возникающей стружки. Здесь же расположена режущая перемычка, которая формируется при скрещивании задних поверхностей сверла.
Вспомогательные режущие кромки находятся на направляющей (калибрующей) части. Они образуются в месте пересечения передних поверхностей и ленточки – узкой полосы, расположенной по длине винтовой канавки и направляющей инструмент при работе.
Параметрами, определяющими геометрию сверла, считаются:
1. Угол при вершине режущей части 2 φ – он образуется основными режущими кромками. Оказывает значимое воздействие на процесс резания. С увеличением его значения усиливается прочность сверла, но требуется увеличение усилия подачи. Уменьшение угла приводит к упрощению процесса, но снижает ресурс прочности режущей части. Для каждого вида материала подбирается значение угла:
- алюминий, латунь – 130…140º
- медь – 125
- магниевые сплавы – 110…120°
- чугун, сталь – 116..118º
- мрамор – 90…100º
- пластмассы – 50…60º
2. Угол наклона ω винтовой канавки определяет удобство отведения стружки, его увеличение способствует облегчению процесса, но снижает жесткость сверла, увеличивая объем канавок на рабочей части. На его размер влияет диаметр сверла и вид растачиваемого материала.
3. Передний угол γ находится в плоскости перпендикулярной режущей кромке, облегчает врезание инструмента и отделение стружки. Величина угла уменьшается по направлению к поперечной кромке. Большое значение угла γ снижает необходимое усилие резания, но снижает прочность режущей части и приводит к скорому нагреву. Для работы с твердым материалом используются сверла с маленьким значением переднего угла, а при работе с пластичными материалами размер угла γ увеличивают.
4. Задний угол α определяется в плоскости, которая параллельна оси сверла. Значение угла отличается на различных участках режущей кромки, оно максимально у оси и уменьшается к наружной поверхности инструмента. Малый размер угла способствует преумножению трения задней поверхности, нагревая и повреждая инструмент.
Величина переднего угла задается при изготовлении, а задний измеряется специальным шаблоном.
5. Угол наклона поперечной кромки имеет постоянное значение 55°.
engcrafts.com
вопросы 8 и 16
8.Сверление. Геометрия спирального сверла
Сверление-это процесс получения резанием глухих и сквозных цилиндрич. отверстий в сплошном материале на станках сверлильной и токарной групп. Если диаметр отв.,которое требуется получить в процессе обработки 30 мм, то обработку производят в 2 этапа. На 1 этапе произв. сверление, а на 2 этапе рассверливание Дсв=Дотв.
При обработке отв. сверлами из быстрорежущей стали обеспечивает точность по 11…13 квалитетам и шероховатость поверхности Rz=80..32мкм. Сверла с пластинами из тв. сплавов, работающих на более высоких скоростях резания, позволяют получать отверстия с точностью по 8..11 кв. и Rz=40..20 мкм.
Выпускаются следующие разновидности сверл: спиральные, перовые кольцевые, одностороннего резания (рутейные и пушечные) и комбинированные. Наибольшее распространение при обработке отверстий глубиной (5..10)D получили спиральные сверла. Конструкция спирального сверла приведена на рис.10
Спиральное сверло состоит из рабочей части и из хвостовика . На рабочей части можно выделить режущую часть и направляющую часть . Для выбивания сверла с коническим хвостовиком из отверстия шпинделя станка предусмотрена лапка ; м/у рабочей частью и хвостовиком довольно часто имеется переходная часть, которая называется шейкой . Спиральные сверла могут иметь цилиндрический хвостовик Ø(0,1..20 мм) и конический хвостовик Ø(6..80мм).
Геометрия спирального сверла
Рабочая часть сверла осуществляет процесс резания,отвод стружки из зоны резания, формирует обработанную пов-ть и направляет сверло при обработке.
Рабочая
часть выполняется в виде 2х зубьев,образов.
спиральными канавками и связ. между
собой сердцевиной диам. dc
(рис. 11), величина,которая составляет
0,12;0,3 от диаметра сверла.
Режущая часть сверла выполнена в виде усеченного конуса и имеет 2 режущих лезвия. На режущем лезвии следует различать: 1-переднюю поа-ть,2-главную заднюю пов-ть.На направляющей части располагаются 2 вспом. задние пов-ти (направляющие ленточки 3), выступающие над спинкой сверла 7.
Передние пов-ти предст.собой линейчатые винтовые пов-ти, плавно сопрягающиеся со стружкоотводящими канавками. Главные задние пов-ти обращены к пов-ти резания. Направляющие ленточки, ширина которых составляет f=(0,06..0,07)d обеспечивают в процессе резания направление движения сверла II оси обрабат. отверстия.
Рабочая часть сверла имеет 5 режущих кромок: 2 главные(4),2 вспомогательные(5) и поперечная кромка(6). Главные режущие кромки образуют между собой угол при вершине 2. Величина этого угла при обработке конструкционных сталей нормальной прочности и чугунов составляет 118..120 градусов. Условия отвода стружки и охлаждения сверла в значительной мере зависят от размеров и формы поперечного сечения канавок, от шероховатости их пов-ти и угла наклона винтовой канавки . Под углом понимается угол между осью сверла и касательной к ленточке сверла. Величина этого угла в зависимости от диаметра сверла и свойств обрабат. материала изменяется в пределах 18..30 град.
Поперечная кромка образуется в рез-те заточки задних пов-тей. Величина ее наклона составляет обычно 55 град. Геометрия режущей части сверла рассматрив. в главной секущей пл-ти – и осевой –. В главной секущей пл-ти геометрия сверла хар-ся передним углом и задним углом .
Передний угол – угол между касательной передней пов-ти лезвия инструмента в какой-либо точке, например т.А режущей кромки и основной пл-тью, след которой обознач. –. Задний угол – это угол между касательной к задней пов-ти лезвия инструмента в какой-либо точке режущей кромки и пл-тью резания –.
Для удобства контроля задний угол рассматривают и измеряют в осевой (рабочей пл-ти). Этот угол предст. собой угол между касательной к задней пов-ти и в рассматр. точке режущей кромки и касательной в этой же точке к окружности, образующ. при вращении этой точки вокруг оси сверла.В отличие от резцов,передние и задние углы сверла не остаются постоянными, а измеряются по длине режущей кромки. Изменение переднего угла связано с тем,что передняя пов-ть сверла, как правило,предст.собой винтовую пов-ть и величина переднего угла определяется углом наклона винтовой линии, который уменьшается от периферии к центру сверла, а следовательно уменьшается передний угол.
2 причина, вызывающая изменение переднего и заднего углов связана с кинематикой процесса резания, а именно с наличием движение подачи. Если учесть движение подачи, то оказывается, что действит. передний угол при резании увеличивается по сравнению с углом, получ. при заточке, а действит. задний угол уменьшается и тем значительнее,чем ближе рассматриваемая точка к центру сверла.Увеличение действительного переднего угла существенно не отражается на работоспособности сверла, а уменьшение действительного заднего угла напротив приводит к увеличению площади контакта по задней пов-ти сверла и более интенсивному его износу, особенно вблизи поперечной кромки. Во избежание этого сверла затачивают таким образом,чтобы задний угол в статическом состоянии увеличивался от периферии к центру сверла. =8..12 град.,=20..25 град.(в центре сверла)
16. Дисковое фрезерование. Фасонное фрезерование.
На операциях дискового фрезерования у обрабатываем.заготовок получают пазы, уступы канавки. Этот вид фрезерования использ.также при разрезке металла. Схема дискового фрезерования представлена на рис.24.
Обработка заготовок на данных операциях осуществл.на горизонт.-фрезерных станках дисковыми фрезами.
Различают след.типы дисковых фрез: 1)Односторонние, с режущими кромками только на цилиндрической части, 2)Двухсторонние,с режущими кромками на 1 торцовой и цилиндрической части, 3)3-х сторонние с режущ.кромками на обеих торцах и цилиндрической части.
Односторонние дисковые фрезы явл.прямозубыми и по назначению подразделяются на
-пазовые(шпоночные),-прорезные,-отрезные.
Основные пар-ры у этих фрез имеют след.значения:
Пазовые фрезы. Ø50..100мм, В=3..6мм, =10..15 град, =15..20град.
Прорезные фрезы. Ø40..75мм, В=2..5мм, =5..10 град, =25..40град.
Отрезные фрезы. Ø60..200мм, В=1..3мм, =10..15 град, =5..20град.
Во избежание трения фрезы о стенки прорезаемой канавки, боковые стороны фрезы шлифуют с поднетрением с углом =0,5..1,5град.
2х сторонние дисковые фрезы имеют на цилиндрической части винтовые зубья. Основные диаметральные линейные и угловые размеры этих фрез лежат в следующих диапазонах:
Ø90..350мм, В=16..30мм, =-5..+5 град, =10..15град.
3-х сторонние дисковые фрезы могут выполн.как прямозубыми, т.е. зубьями располож.II оси, так и зубьями, располож.наклонно к оси и напр. В разные стороны(разнонаправленными).
Изготавл.вышеуказанные фрезы как из быстрорежущих сталей, так и с пластинами из тв.сплавов. В последнем случае корпус изготавливается из конструкционных сталей, а зубья из тв.сплава.
Фасонное фрезерование
Фасонное фрезерование получило распространение на операциях,связ.с изготовлением пов-тей со сложным фасонным профилем.
Инструментом при данном виде фрезеров-я явл.фасонные фрезы с различным профилем, обработка которыми ведется на горизонт.-фрезерных и универс.-фрезерных станках.
Типовые фасонные фрезы – это полукруглая выпуклая и полукруглая вогнутая. Основные конструктивные эл-ты фасонных фрез аналогичны конструктивным эл-там дисковых фрез. Фасонные фрезы изготавливаются всегда с крупным зубом, при этом число зубьев всегда зависит от диаметра фрезы и ее конструкции.
Z=1,8-число зубьев у цельных фрез
Z=1,2-число зубьев у сборных фрез
Для того, чтобы не искажать профиль режущей кромки фасонной фрезы, ее зубья затачивают с передним углом =0. В ряде случаев при обработке труднообрабатываемого мат-ла передний угол делают 5..10 град.
Однако в этом случае происходит искажение профиля фрезы. Для того, чтобы получить заданный профиль на заготовке нужно иметь либо комплект фрез (черновую с =5..10 и чистовую с =0) либо произвести корректировку профиля.
Форма режущих зубьев фрез может быть как острозаточенной, так и затылованной. Остроконечную форму зуба имеют практически все фрезы за исключением фасонных фрез. У фрез с остроконечной формой зуба рабочие пов-ти зуба затачиваются по плоскости. У фрез с затылованной формой зуба передняя пов-ть затачивается по пл-ти, а задняя пов-ть по спирали Архимеда.
Затылование задней пов-ти по спирали Архимеда позволяет при переточке зуба, осуществл.по передней пов-ти,сохранить неизменным профиль инструмента и задний угол .
Важной хар-кой у затылованных фрез явл.величина падения затылка К, опред. На передней пов-ти последующего зуба фасонной фрезы по отношению к предыдущей.
Величина затылования предст.собой расстояние между окружностью, провед.через вершину зуба и точкой пересечения Архимедовой спирали с передней пов-тью последнего зуба.
И расчитывается по ф-ле:
У фрез со шлифов.профилем для обеспечения выхода шлифовального круга делается 2-ное затылованные, величина которых составляет (1,2..1,7)К.
studfiles.net