Рекомендации по демонтажу
- Маломощные транзисторы и микросхемы в круглых корпусах с позолоченными выводами следует выпаять или аккуратно выкусить под корень, оставляя максимально возможную длину ног. Ни в коем случае не вырывайте их плоскогубцами, в этом случае теряются выводы и сильно падает стоимость микросхемы! Лучше всего купить для этого газовую горелку с пьезоподжигом или термофен. Для распайки возьмите плоскогубцы, горелку, зажмите плату в тиски стороной пайки к себе. Возьмите корпус транзистора плоскогубцами и нагрейте горелкой место пайки, и через пару секунд его транзистор можно извлечь. Не мучайте себя разнообразными паяльниками и т.д. Горелкой лучше всего распаивать на улице или в гараже. Не нужно обкусывать у транзисторов ни выводы, ни шляпки, даже если они и “белые”.
- Микросхемы в планарных корпусах нужно отпаивать, нагревая горелкой саму микросхему до плавления припоя, и после плавления нужно убрать горелку и пинцетом снять микросхему.
- Вертолеты лучше отпаивать паяльником, нагревая и отгибая каждую “лопасть” отдельно. Выводы от болтов типа КТ904 и прочих можно просто пооткусывать.
- Транзисторы в пластиковых корпусах, такие как КТ814, 502 и подобные разбирать нельзя, они принимаются только целиком. После разборки дороже не станет. а вот дешевле, при неверном подходе, может быть.
- Микросхемы в прямоугольных керамических корпусах, панельки, индикаторы АЛС и подобное нужно выпаивать горелкой, нагревая противоположную сторону платы. Не нагревайте сами микросхемы, они от этого очень сильно портятся 🙂 и соответственно может уменьшиться стоимость. Также не нужно отпаивать или отрывать никелевые крышки от микросхем, кварцевые окна серии 537РФ и так далее.
Для продажи достаточно просто аккуратно выпаять микросхему и отсортировать их.
- Микросхемы в пластиковых корпусах идут только с желтизной внутри, так что не стоит снимать микросхемы, в которых ее точно нет (главным образом это 580 серия в пластике). Для снятия нужно взять стамеску и молоток, либо топор, и срубить микросхемы, стараясь не разрушать сами корпуса. Выводы можно осталять в таком виде, как после срубания.
- Микросборки для извлечения керамики из них стоит обточить на точиле по пермиетру наружные 0.5мм ободка, после чего крышка отваливается, а нагревом на горелке можно отклеить керамику. Керамику складывайте в металлическую, стеклянную, деревянную или керамическую коробку, или на лист бумаги (т.к. после отклеивания она горячая и может разрушить пластик). После этого пересыпьте керамику, включая весь сор, в плотный пакет, не теряя при это даже малейших крох.
- Конденсаторы типа КМ, К52-2 и прочие выкусывайте с плат, сразу обкусывая под корень выводы.
Конденсаторы К10-17 в прямоугольных корпусах (“трусы”) – можно аккуратно отрывать плоскогубцами. Для этого надо взять плоскогубцами конденсаторы и повернуть его вокруг своей оси. К конденсаторам с остатками выводов применяется скидка от 0 до 20% (новые).
- Бескорпусные КМ отпаивайте паяльником или горелкой, не нужно пробовать срывать их кусачками – они могут покрошиться.
- Резисторы типа СП5 достаточно отрывать от плат плоскогубцами. Ценные составляющие при этом не теряются. Не нужно выпаивать их. торчащие выводы добавляют сложности при разборке, да и выпаивание тоже сложнее. Для резисторов ПП3, переключателей, шаговых искателей и т.д. провода нужно откусывать вблизи к самому выводу, но это не особо критично и на цену не влияет. Не нужно отпаивать провода от переключателей ПР, лучше откусите в любом месте, не повреждая сами выводы переключателя.
- Разьемы стоит выпаивать с плат, а такие у которых выводы с намотанными проводами – лучше по возможности провода разматывать.
Разьемы типа СНП59 “папы” можно снимать с плат зубилом. Для этого отрубите зубилом концы разьема, чтобы отделить его от винтов, потом стамеской срубите с платы под корень выводы. Нужно оставлять максимально возможную длину выводов на разьеме, не загрязняя поверхность припоем.
- Реле, запаянные в плату, нужно только выпаивать, особенно это касается РЭС-7,8,9,10,15,48, РПВ, РПА а также всех РПС. При выламывании реле кусачками или плоскогубцами некоторые контакты могут остаться в плате благодаря разрушившимся стеклянным вставкам или пластиковым корпусам. В таком случае часть стоимости потеряется вместе с контактми.
- Ламели нужно отрезать от плат, минимально захватывая саму плату. Для этого лучше всего использовать ножницы по металлу, не отламывайте их плоскогубцами, т.к. можете потерять некоторую часть контактов. Провода авиационные покупаем по результатам разборки одного метра провода и взвешивания получившейся жилы и оплетки.
- Индикаторные лампы новые покупаем в любом виде, как в упаковке, так и без.
Индикаторные лампы б/у, запаянные в плату, нужно сдавать вместе с платой и родным креплением, при необходимости обрезав лишнее. Не нужно выпаивать лампы или вытаскивать из панелек, т.к. есть риск их повредить. Нельзя также откусывать запаянные выводы. Корпус ламп должен оставаться без сколов и других дефектов.
Помните два главных правила: если выводы желтые, то чем большая часть их останется, тем выше будет и цена. Старайтесь по максимуму сохранять выводы. И второе – если желтый вывод покрыт припоем, то он теряет свою стоимость. Так что если у микросхемы выводы до основания будут покрыты припоем, то цена будет как за “без выводов”, а если будут загрязнены припоем прочие желтые части деталей, то цена будет еще ниже.
как выбрать паяльник и микроскоп? Как правильно выпаять микросхему из платы? Наборы с маленькими паяльниками
Довольно часто электронные устройства бытового назначения выходят из строя по причине того, что перегорела какая-либо микросхема, называемая чипом. Исправить поломку можно, обратившись к услугам сервисной мастерской, но нужно быть готовыми к тому, что ремонт там обойдется недешево. Если у вас имеются хотя бы минимальные навыки работы с паяльником, заменить электронный чип можно своими силами. Справиться с такой задачей поможет электрический паяльник, предназначенный для паяния мелких деталей. Вооружившись этим устройством, вы сможете выпаять старый сгоревший микрочип и выполнить пайку нового чипа к печатной плате.
Какой паяльник выбрать?
Маленький электрический паяльник является важным инструментом, предназначенным для работ с микросхемами. Модификации такого микропаяльника могут обладать различными свойствами и характеристиками.
Хороший профессиональный паяльник, выполненный в формате мини, обладает регулятором температуры нагрева.
С его помощью можно нанести тончайший слой компонентов расплавленного припоя, а также нагреть контактные выводы у радиодетали для монтажа или демонтажа микросхемы из печатной платы. Некоторые виды электрических миниатюрных паяльников обладают особенностями, которые могут быть пригодны только для выполнения одного типа работ.
Разновидности
Электрические профессиональные паяльники позволяют ремонтировать даже лазерный тип устройств. В соответствии с тем, какой тип нагрева предусмотрен у этого инструмента, паяльники разделяют на следующие виды.
Нихромовый
Нагревательным элементом паяльника является проволока из нихрома, не только хорошо проводящая электрический ток, но и быстро нагревающаяся.
Импульсный
Обладает способностью быстро нагреваться и стоек к механическим воздействиям. Конструкция содержит образователь частот со встроенным трансформатором.
Жало паяльника входит в состав электроцепи путем подключения к токосъемникам, расположенным на вторичной обмотке. Модель оснащена кнопкой включения, которая при нажатии мгновенно разогревает паяльник, а при ее отпускании инструмент остывает.При нагреве частота повышается, а затем снижается до необходимых рабочих параметров.

Керамический
Дорогая, но хрупкая модель, быстро разогревающаяся для работы. Конструкция содержит керамические стержни, подсоединенные к контактам напряжения, благодаря которым происходит разогрев паяльника. Паяльник служит долго, но у него высок риск механического повреждения: если жало выйдет из строя, заменить его не получится.
Индукционный
Конструкция содержит катушку индуктора и специальное ферромагнитное напыление на жале, обеспечивающее создание магнитного поля.
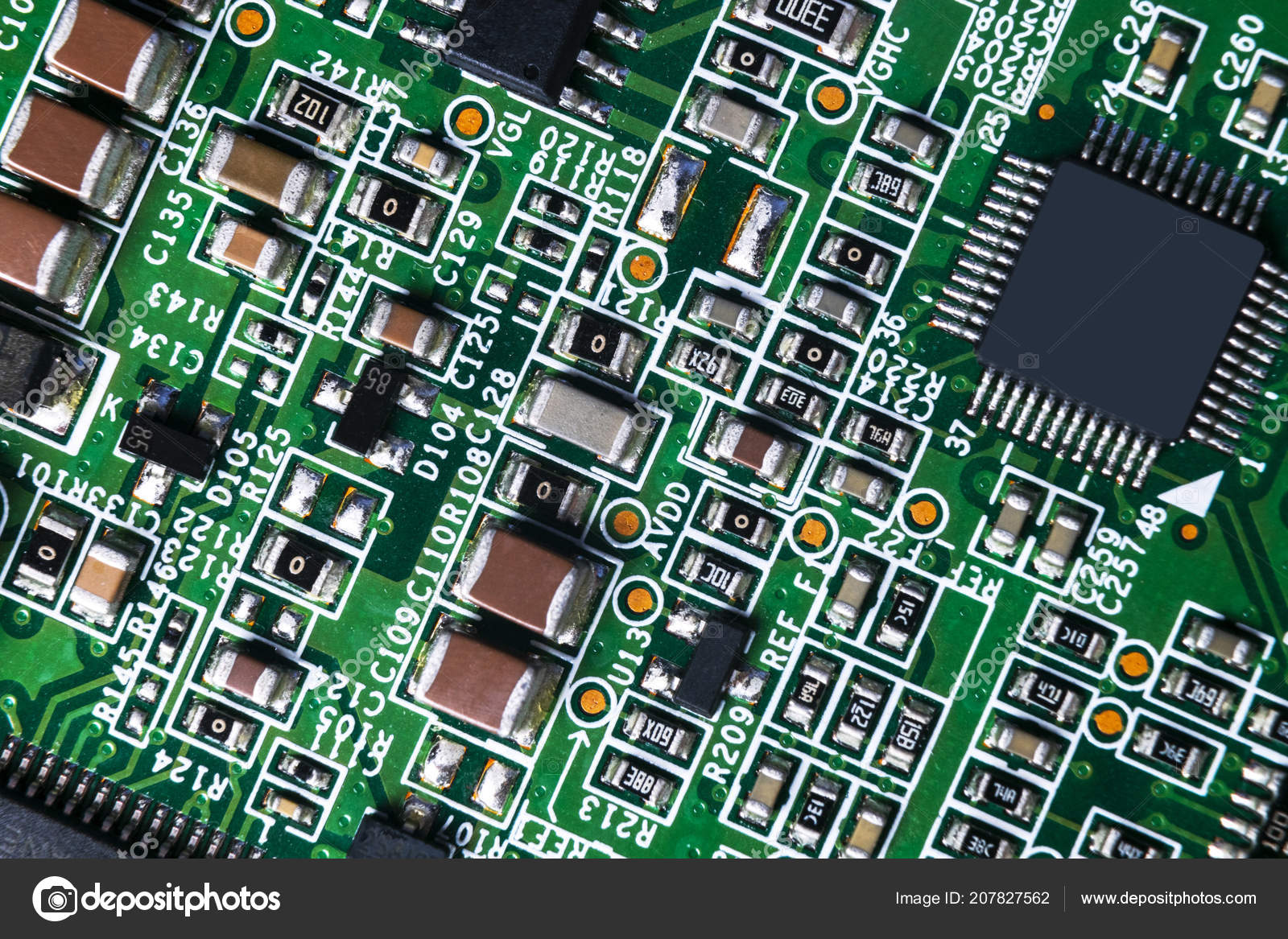
Специалисты в области радиоэлектроники рекомендуют обратить внимание на специальные паяльные станции, где нагрев происходит за счет индукторной катушки.
Электропаяльнику в этом случае не требуется автоматический терморегулятор, но выбор температурного режима придется подбирать путем смены жал, входящих в комплект такой паяльной станции.
Паяльная станция – дорогой инструмент, предназначенный для выполнения объемных и множественных работ. Паяльная станция оснащена автоматическим термостатом и контроллером, к которым при необходимости через специальные гнезда можно подключить не только паяльник, но и другие электроинструменты для паяния.
Характеристики
У паяльника с тонким жалом, используемого для паяния микрочипа, имеются следующие характеристики.
- Рабочая мощность. Оптимальным вариантом будут модели будет параметр в 20-35 Вт, так как более высокая мощность электроинструмента спровоцирует перегрев или прожог микросхемы.
- Контроллер (термостат). Удобный в применении инструмент должен иметь приспособление, которое удерживает нагрев жала до параметров, не превышающих 300°C.
- Вид жала. Удобно, если у электрического паяльника имеется набор сменных насадок в виде срезанного жала под углом 45°, а также комплект тонких конусных вариантов. Поверхность жала у хорошего паяльника покрыта защитным слоем, который препятствует образованию нагара. Такой вариант предпочтительнее медного жала, которое требуется постоянно зачищать.
- Конструкция. Кабель паяльника должен обладать удвоенной изоляцией, сечение провода выбирают от 2,5 мм. Шнур должен быть пластичным и не перекручиваться. Ручка инструмента не может быть тяжелой и выскальзывать из пальцев.
- Размеры и вес. Устройство выбирают легкое и небольшое по размеру, так как в процессе работы его принято держать так же, как и карандаш.
Большие паяльники с рукояткой из дерева будут неудобными из-за веса, их не получится правильно захватить пальцами.
Чтобы успешно осуществить пайку микросхем, необходимо выбирать маломощные устройства: чем ниже данный показатель, тем больше будет возможностей не испортить дорогостоящие радиоэлементы во время паяния.
Популярные модели
Теперь дадим краткий обзор популярных моделей, применяемых для паяния радиодеталей.
Другие приспособления и материалы
Процесс паяния микрочипов и радиодеталей подразумевает наличие не только паяльника, но и дополнительного оборудования.
Можно также приобрести:
- флюс для защиты поверхности металла от образования окислительной пленки;
- проволоку припоя для выполнения процесса паяния, толщина которой – 0,5-1 мм;
- набор сменных насадок (жал) различных форм и размеров;
- увеличительное стекло с держателем или очки-лупу, увеличивающие в 10-20 крат;
- бинокулярный стереоскопический микроскоп с длинным фокусом и подсветкой рабочей области;
- держатель-подставку, куда можно положить разогретый в процессе работы паяльник;
- специальный антистатический коврик и браслет для защиты микросхем от действия статического электричества;
- влажную ткань или специальное приспособление для очистки жала паяльника от нагара;
- металлическую плетенку для удаления лишнего количества припоя;
- шприц для удаления остатков припоя, оставшихся от демонтажа старого микрочипа и для переноса припоя во время работы в область паяния;
- пинцет для удерживания миниатюрных микросхем;
- органический растворитель либо этиловый спирт для удаления заводского защитного лака на микросхеме, а также для удаления остатков флюса после выполнения работы;
- небольшую кисточку для нанесения жидких составов.
Для удобства выполнения паяльных работ перечисленные инструменты необходимо приготовить заранее и расположить на столе в удобном порядке.
Технологии пайки
Для начинающих радиолюбителей научиться правильно паять в домашних условиях помогут пошаговые инструкции. Перед работой важно изучить подготовку деталей к работе, температуру плавления олова, правила нанесения флюса. Работу с микросхемами можно осваивать поэтапно. Например, для начала выпаять из платы старую деталь. Потренироваться выпаивать можно на каких-либо старых бытовых приборах, вышедших из строя.
После того как будет освоено выпаивание, можно переходить к процессу паяния и попробовать спаять дорожку в радиодетали.
Микросхемы производятся двух типов. DIP-чипы имеют штырьковые выводы, которые запаивают в отверстия с обратной стороны платы. SOIC-чипы имеют планарные выводы, которые паяют с лицевой стороны микросхемы к ее площадкам.
Последовательность паяльных работ зависит от вида детали. Есть следующие виды паяния.
Радиоэлементов
Чтобы отпаять SOIC-чип, нужно смыть растворителем защитный лак с выводов микросхемы, а затем очистить от лака и саму плату, используя этиловый спирт. Затем на выводы при помощи кисточки наносят флюс. Далее потребуется взять припой и запаять все выводы чипа с каждой стороны, замкнув их. Для этого жалом проходят по всем точкам выводов, распределяя по ним припой. Припоя рекомендуется брать много, чтобы после того, как вы уберете паяльник, он оставался в расплавленном состоянии. Только в этом случае у вас получится взять чип пинцетом и удалить его. Если микросхема приклеена в области платы, потребуется обрабатывать припоем каждый вывод поочередно, а затем поднимать его с помощью пинцета вверх, над платой. После завершения отпаивания вводов потребуется взять нож и удалить чип, стараясь не повредить при этом плату.
Припаять SOIC-чип можно, применяя метод «волны припоя», суть которого сводится к эффекту капилляра, когда расплавленный состав припоя протекает между площадкой платы и выводом микрочипа, образуя там каплю.
Последовательность действий в этом случае начинается с того, что на контакты вывода наносят жидкий флюс, чтобы облудить их. Затем микросхему помещают на плату и располагают точки ввода с соответствующими местами крепления. Далее нужно припаять по диагонали каждый вывод, чтобы не было перекоса и смещения чипа. После этого флюс вновь наносят на припаянные точки вывода и при помощи жала с припоем распределяют припой по выводам равномерно. Если между двумя выводами образуется мостик из припоя, его удаляют металлической плетенкой, помещая ее поверх образовавшейся перемычки.
Чипов
Чтобы отпаять DIP-чип, нужно смыть лаковое покрытие в области паяния при помощи ацетона, следы которого затем убирают этиловым спиртом. Разогретой насадкой-жалом прикасаются к ножке чипа, расположенной с оборотной стороны платы. Жало удерживают в этом месте до тех пор, пока имеющийся припой не расплавится. Затем припой собирают шприцем, втягивая внутрь. Подобное действие выполняют со всеми выводами чипа, после чего их можно будет вынуть из отверстий платы.
При выполнении процесса припаивания потребуется следить за тем, чтобы чип не перегревался, поэтому прикасаться жалом к ножке чипа можно только 2-3 секунды, а затем, чтобы выполнить повторные касания, потребуется охлаждать рабочую область пайки.
Перед выполнением процесса паяния выводы чипа необходимо облудить. Для этого на выводы чипа наносят флюс, не касаясь самой микросхемы, и обрабатывают насадкой с набранным на нее припоем. После лужения выводы чипа имеют гладкую и серебристую поверхность. Далее микрочип закрепляют на плате, используя для этого припой и фиксируя деталь на отведенном участке платы.
Рекомендации
Для правильного выполнения паяльных работ рекомендуется использовать мощность паяльника, не превышающую 10 Вт. Большинство электроинструментов работает от напряжения сети в 220 В, но в некоторых моделях предусмотрен блок питания, понижающий напряжение до показателей 36 или 12 В. Паяльники, способные понижать электрическое напряжение, считаются лучшим вариантом для работы с микросхемами.
Что касается толщины жала электропаяльника, то этот параметр колеблется от 1 до 2 мм. В большинстве случаев для работы удобно пользоваться конусовидными насадками. Выбирая модель электрического паяльника, целесообразно отдать предпочтение варианту с автоматическим терморегулятором, который поддерживает заданную температуру и позволяет добиться отличных результатов в процессе паяльных работ.
Как паять микродетали обычным паяльником, смотрите далее.
Как выпаять микросхему из платы паяльником: 4 способа
Оловоотсос: как правильно пользоваться
Вакуумный оловоотсос, является очень полезным инструментом при выпаивании различных радиодеталей, будь это микросхемы, транзистор или, например диод. Так же, качественно удаленное олово с контактов поможет без особых трудностей припаять рабочую деталь.
Оловоотсос состоит из:
- Вакуумной колбы, носика изготовленного из термоматериала;
- Обратной пружины;
- Поршня.
Выпаивать радиодетали оловоотсосом довольно просто. В первую очередь необходимо «взвести» оловоотсос. Для этого нужно путем нажатия на поршень зафиксировать его стопорным механизмом (фиксация происходит автоматически). Далее, разогретым до оптимальной температуры паяльником, расплавляем олово на контакте детали, предварительно приставив к контакту оловоотсос.
После того, как олово расплавилось, убираем паяльник, прижимаем оловоотсос к месту выпайки и плотно прижимаем. Нажимаем на кнопку стопорного механизма. Поршень, двигаясь обратно по колбе, создает вакуум, за счет которого и происходит засасывание олова.
Выпаивая большое количество радиодеталей, не забывайте периодически разбирать и чистить оловоотсос.
Если оловоотсоса под рукой нет, а деталь необходимо отпаять, то его можно сделать из обычного шприца своими руками. Для этого, нужно взять шприц (по возможности 50 кубов). Вынимаем поршень и помещаем в колбу шприца обратную пружину (пружина должна быть не длиннее колбы, что бы не выдавить поршень). Осталось защитить носик. Сделать это можно любой металлической трубкой соответствующего диаметра. И самодельный оловоотсос готов к использованию.
Оплетка для выпайки деталей
Многие профессионалы, а так же радиолюбители не понаслышке знают о достоинствах такого вспомогательного «инструмента», как оплетка для выпайки. Правильное ее применение в работе, позволяет быстро и качественно избавляться от олова на контактах, без их повреждения.
Оплетку можно:
- Приобрести в магазине. Насчитывается огромное количество видов;
- Изготовить самостоятельно из подручных материалов.
Выпаивание деталей при помощи оплетки происходит следующим образом. Нагревается до нужной температуры паяльник. К нужному контакту прикладывается оплетка и производится нагрев контакта паяльником. Затем небольшими круговыми движениями убирается олово с контакта.
Оплетка хорошего качества, всегда пропитывается канифолью на заводе изготовителе. При покупке проверяйте это важное условие.
Покупка оплетки не составит огромного труда. Но из – за ее немалой стоимости и высокого расхода при работе, отличным решением будет, изготовить ее своими руками. Для этого понадобится коаксиальный (радиочастотный) кабель или старые многожильные провода небольшого сечения.
Для изготовления оплетки из кабеля, понадобится небольшой его отрезок. Удаляется верхняя изоляция. Затем снимается медная оплетка кабеля (берите небольшие отрезки, это обеспечить удобное снятие оплетки). Снятую оплетку необходимо сплющить и пропитать спирто – канифольным флюсом.
Что бы сделать оплетку из проводов, понадобиться несколько мелких проводов (подойдут от наушников). Снимается изоляция, несколько проводков скручиваются вместе. Далее их нужно расплющить при помощи молотка. Осталось пропитать флюсом.
Как выпаять микросхему из платы феном
Самым быстрым способом отпаять радиодеталь, или распаять большие схемы, это применение фена. Стоит учитывать, что данный способ может нарушить работу или вывести из строя деталь. Поэтому в последующем, перед тем как паять деталь, извлеченную при помощи фена, необходимо проверить ее на работоспособность мультиметром.
Для работы потребуется:
- Фен;
- Плоская отвертка.
Фиксируем в удобном положении плату, из которой будет выпаиваться нужная микросхема. Под нее поддевается плоская отвертка (используется в качестве рычага). С обратной стороны платы, потоком горячего воздуха от фена разогреваются все контакты микросхемы.
При нагревании контактов феном, старайтесь не задерживать поток воздуха на одном участке. Так снижается вероятность вывода из строя микросхемы.
После того, как олово начинает плавиться, при помощи отвертки начинаем приподнимать микросхему. Проделываем данную работу до полного извлечения микросхемы. После этого (при замене детали), удаляются остатки олова с поверхности платы, и осуществляется пайка рабочей микросхемы.
Как выпаять конденсаторы из материнской платы
Конденсаторы различных видов, выполняют важную функцию в работе любой микросхемы. Пропускают или не пропускают ток, накапливают определенный заряд, сдвигают фазу и еще много функций. И выход из строя одного из них, влияет на работу всей системы. Поэтому своевременная замена способствует бесперебойной работе схемы.
Для замены потребуется:
- Паяльник;
- Припой.
Не многие знают, что конденсаторы имеют одну особенность – толстые контактные ножки. Пайка конденсаторов не составляет труда. Но процесс их выпаивания из – за данной особенности, несколько сложнее. Определяется это тем, что ножки очень трудно прогреть. Для того, что бы сделать работы легче и быстрее, воспользуйтесь предложенным способом.
Данный способ поможет гораздо качественнее прогреть ножки конденсатора, и избежать повреждения находящихся рядом токопроводящих дорожек на плате.
Паяльник или паяльная станция, разогревается до максимальной температуры. На жало наносится определенное количество припоя (что бы получилась небольшая капля). Далее, используя разогретую каплю припоя, нагреваем ножки конденсатора до нужной температуры.
Оловоотсос своими руками (видео)
Теперь, зная несколько способов выпаивания радиодеталей и микросхем, вы с легкостью сможете определить каким, и в каком случае воспользоваться. А применение некоторых хитростей, поможет сделать работу грамотно и с пониманием.
Как выпаивать smd компоненты. Быстрая распайка SMD компонентов с помощью утюга
Многие задаются вопросом, как правильно паять SMD-компоненты. Но перед тем как разобраться с этой проблемой, необходимо уточнить, что же это за элементы. Surface Mounted Devices – в переводе с английского это выражение означает компоненты для поверхностного монтажа. Главным их достоинством является большая, нежели у обычных деталей, монтажная плотность. Этот аспект влияет на использование SMD-элементов в массовом производстве печатных плат, а также на их экономичность и технологичность монтажа. Обычные детали, у которых выводы проволочного типа, утратили свое широкое применение наряду с быстрорастущей популярностью SMD-компонентов.
Ошибки и основные принцип пайки
Некоторые умельцы утверждают, что паять такие элементы своими руками очень сложно и довольно неудобно. На самом деле, аналогичные работы с ТН-компонентами проводить намного труднее. И вообще эти два вида деталей применяются в различных областях электроники. Однако многие совершают определенные ошибки при пайке SMD-компонентов в домашних условиях.
SMD-компоненты
Главной проблемой, с которой сталкиваются любители, является выбор тонкого жала на паяльник. Это связано с существованием мнения о том, что при паянии обычным паяльником можно заляпать оловом ножки SMD-контактов. В итоге процесс паяния проходит долго и мучительно. Такое суждение нельзя считать верным, так как в этих процессах существенную роль играет капиллярный эффект, поверхностное натяжение, а также сила смачивания. Игнорирование этих дополнительных хитростей усложняет выполнение работы своими руками.
Пайка SMD-компонентов
Чтобы правильно паять SMD-компоненты, необходимо придерживаться определенных действий. Для начала прикладывают жало паяльника к ножкам взятого элемента. Вследствие этого начинает расти температура и плавиться олово, которое в итоге полностью обтекает ножку данного компонента. Этот процесс называется силой смачивания. В это же мгновение происходит затекание олова под ножку, что объясняется капиллярным эффектом. Вместе со смачиванием ножки происходит аналогичное действие на самой плате. В итоге получается равномерно залитая связка платы с ножками.
Контакта припоя с соседними ножками не происходит из-за того, что начинает действовать сила натяжения, формирующая отдельные капли олова. Очевидно, что описанные процессы протекают сами по себе, лишь с небольшим участием паяльщика, который только разогревает паяльником ножки детали. При работе с очень маленькими элементами возможно их прилипание к жалу паяльника. Чтобы этого не произошло, обе стороны припаивают по отдельности.
Пайка в заводских условиях
Этот процесс происходит на основе группового метода. Пайка SMD-компонентов выполняется с помощью специальной паяльной пасты, которая равномерно распределяется тончайшим слоем на подготовленную печатную плату, где уже имеются контактные площадки. Этот способ нанесения называется шелкографией. Применяемый материал по своему виду и консистенции напоминает зубную пасту. Этот порошок состоит из припоя, в который добавлен и перемешан флюс. Процесс нанесения выполняется автоматически при прохождении печатной платы по конвейеру.
Заводская пайка SMD-деталей
Далее установленные по ленте движения роботы раскладывают в нужном порядке все необходимые элементы. Детали в процессе передвижения платы прочно удерживаются на установленном месте за счет достаточной липкости паяльной пасты. Следующим этапом происходит нагрев конструкции в специальной печи до температуры, которая немного больше той, при которой плавится припой. В итоге такого нагрева происходит расплавление припоя и обтекание его вокруг ножек компонентов, а флюс испаряется. Этот процесс и делает детали припаянными на свои посадочные места. После печки плате дают остыть, и все готово.
Необходимые материалы и инструменты
Для того чтобы своими руками выполнять работы по впаиванию SMD-компонентов, понадобится наличие определенных инструментов и расходных материалов, к которым можно отнести следующие:
- паяльник для пайки SMD-контактов;
- пинцет и бокорезы;
- шило или игла с острым концом;
- припой;
- увеличительное стекло или лупа, которые необходимы при работе с очень мелкими деталями;
- нейтральный жидкий флюс безотмывочного типа;
- шприц, с помощью которого можно наносить флюс;
- при отсутствии последнего материала можно обойтись спиртовым раствором канифоли;
- для удобства паяния мастера пользуются специальным паяльным феном.
Пинцет для установки и снятия SMD-компонентов
Использование флюса просто необходимо, и он должен быть жидким. В таком состоянии этот материал обезжиривает рабочую поверхность, а также убирает образовавшиеся окислы на паяемом металле. В результате этого на припое появляется оптимальная сила смачивания, и капля для пайки лучше сохраняет свою форму, что облегчает весь процесс работы и исключает образование «соплей». Использование спиртового раствора канифоли не позволит добиться значимого результата, да и образовавшийся белый налет вряд ли удастся убрать.
Очень важен выбор паяльника. Лучше всего подходит такой инструмент, у которого возможна регулировка температуры. Это позволяет не переживать за возможность повреждения деталей перегревом, но этот нюанс не касается моментов, когда требуется выпаивать SMD-компоненты. Любая паяемая деталь способна выдерживать температуру около 250–300 °С, что обеспечивает регулируемый паяльник. При отсутствии такого устройства можно воспользоваться аналогичным инструментом мощностью от 20 до 30 Вт, рассчитанным на напряжение 12–36 В.
Использование паяльника на 220 В приведет к не лучшим последствиям. Это связано с высокой температурой нагрева его жала, под действием которой жидкий флюс быстро улетучивается и не позволяет эффективно смачивать детали припоем.
Специалисты не советуют пользоваться паяльником с конусным жалом, так как припой трудно наносить на детали и тратится уйма времени. Наиболее эффективным считается жало под названием «Микроволна». Очевидным его преимуществом является небольшое отверстие на срезе для более удобного захвата припоя в нужном количестве. Еще с таким жалом на паяльнике удобно собирать излишки пайки.
Использовать припой можно любой, но лучше применять тонкую проволочку, с помощью которой комфортно дозировать количество используемого материала. Паяемая деталь при помощи такой проволочки будет лучше обработана за счет более удобного доступа к ней.
Как паять SMD-компоненты?
Порядок работ
Процесс пайки при тщательном подходе к теории и получении определенного опыта не является сложным. Итак, можно всю процедуру разделить на несколько пунктов:
- Необходимо поместить SMD-компоненты на специальные контактные площадки, расположенные на плате.
- Наносится жидкий флюс на ножки детали и нагревается компонент при помощи жала паяльника.
- Под действием температуры происходит заливание контактных площадок и самих ножек детали.
- После заливки отводится паяльник и дается время на остывание компонента. Когда припой остыл – работа выполнена.
Процесс пайки SMD-компонентов
При выполнении аналогичных действий с микросхемой процесс пайки немного отличается от вышеприведенного. Технология будет выглядеть следующим образом:
- Ножки SMD-компонентов устанавливаются точно на свои контактные места.
- В местах контактных площадок выполняется смачивание флюсом.
- Для точного попадания детали на посадочное место необходимо сначала припаять одну ее крайнюю ножку, после чего компонент легко выставляется.
- Дальнейшая пайка выполняется с предельной аккуратностью, и припой наносится на все ножки. Излишки припоя устраняются жалом паяльника.
Как паять при помощи фена?
При таком способе пайки необходимо смазать посадочные места специальной пастой. Затем на контактную площадку укладывается необходимая деталь – помимо компонентов это могут быть резисторы, транзисторы, конденсаторы и т. д. Для удобства можно воспользоваться пинцетом. После этого деталь нагревается горячим воздухом, подаваемым из фена, температурой около 250º C. Как и в предыдущих примерах пайки, флюс под действием температуры испаряется и плавится припой, тем самым заливая контактные дорожки и ножки деталей. Затем отводится фен, и плата начинает остывать. При полном остывании можно считать пайку оконченной.
Все чаще применяются SMD детали в производстве, а так же среди радиолюбителей. Работать с ними удобней, так как сверлить отверстия для выводов не нужно, а устройства получаются очень миниатюрными.
SMD компоненты вполне можно использовать и повторно. Тут опять появляется очевидное превосходство поверхностного монтажа, потому что выпаивать мелкие детали гораздо проще. Их очень просто сдувать специальным паяльным феном с платы. Но если у вас такого не окажется под рукой, то вас выручит обычный бытовой утюг.
Демонтаж SMD деталей
Итак, у меня сгорела светодиодная лампа, и я не буду её чинить. Я её распаяю на детали для будущих своих самоделок.Разбираем лампочку, снимаем верхний колпак.
Вытаскиваем плату из основания цоколя.
Отпаиваем навесные компоненты и детали, провода. В общем должна быть плата только с SMD деталями.
Закрепляем утюг вверх тормашками. Делать это нужно жестко, чтобы он в процессе пайки не опрокинулся.
Использование утюга ещё хорошо тем, что в нем есть регулятор, который будет довольно точно поддерживать установленную температуру поверхности подошвы. Это огромный плюс, так как поверхностные компоненты очень боятся перегрева.
Выставляем температуру около 180 градусов Цельсия. Это второй режим глажки белья, если мне не изменяет моя память. Если пайка не пойдет – постепенно увеличивайте температуру.
Кладем плату от лампочки на подошву перевернутого утюга.
Ждем 15-20 секунд пока плата прогреется. В это время смачиваем флюсом каждую детальку. Флюс не даст перегрева, это будет своеобразный помощник при распайки. С ним все элементы снимаются без труда.
Как только все хорошо разогреется, все детали можно смахнуть с платы, ударив плату о какую-нибудь поверхность. Но я сделаю все аккуратно. Для этого возьмем деревянную палочку для удержания платы на месте и с помощью пинцета будем отсоединять каждый компонент платы.
Голая плата в конце работы:
Выпаянные детали:
Ко мне было много вопросов на тему
демонтажа микросхем в различных корпусах. Предлагаю вам ознакомиться с самыми распространенными вариантами выпаивания микросхем в dip и smd корпусах.В первую очередь, следует рассказать о
демонтаже микросхем процессом, являющимся наиболее доступным радиолюбителям, но и несколько сложным, по сравнению с тем, который будет описан чуть позже.Способ демонтажа микросхем в dip — корпусе с помощью паяльника и нескольких предметов, которые можно найти в доме.
Нужен паяльник и иголка от десятикубового шприца. Отрезаем острие иглы так, чтобы она была ровной, без острия. Вставляем полым отверстием иглу в ножку микросхемы с нижней стороны, потихоньку нагревая ее, пока игла не пройдет насквозь отверстие в плате. Не вынимая иглы, даем остыть поверхности и припою, вынимаем иглу. Удаляем излишки припоя с иглы, повторяем процесс на остальных выводах микросхемы. При некоторой сноровке получается аккуратно и эффективно – микросхема сама выпадает из платы без усилия со стороны.
Потребуется паяльник и оплетка медного кабеля. Наносим слой флюса на медную оплетку, накладываем на одну сторону ножки микросхемы и прогреваем. При нагревании оплетка «вытягивает» на себя припой с поверхности платы, на которой расположена микросхема. При насыщении оплетки просто отрезается ненужная часть, и продолжается демонтаж. Надо сказать, что этот способ подходит как для демонтажа Dip — компонентов, так и для Smd — компонентов.
Нужен для работы все тот же паяльник и что-то тонкое, типа пинцета или часовой отвертки с плоским жалом. Аккуратно подсовываем плоскую часть отвертки (или пинцета) между микросхемой и платой на некоторую разумную глубину, нагреваем ножки с обратной стороны, и медленно приподнимаем сторону. Повторяем тот же процесс, но теперь с другой стороны детали: вставляем отвертку, нагреваем ножки, приподнимаем. И повторяем этот процесс до тех пор, пока микросхема не будет удалена с платы. Способ очень быстрый, простой и даже грубоватый. Но не надо забывать, что и у дорожек на плате и у самой микросхемы есть свой температурный предел. Иначе есть возможность остаться без рабочей микросхемы, или с отслоившимися дорожками.
Необходим паяльник и отсос для припоя. Отсос для припоя представляет из себя нечто вроде шприца, но с поршнем, работающим по принципу отсоса. Нагреваем вывод микросхемы, тут же прикладываем отсос для припоя, нажимаем кнопку и создавшаяся разреженность внутри отсоса «выкачивает» припой с дорожки. К сожалению, все так легко и просто выглядит только на словах. На деле же, нагрев ножку, нужно почти мгновенно попасть на ножку отсосом, и «выкачать» припой, что требует высокой скорости исполнения, ибо припой застывает почти мгновенно, а если держать паяльник дольше, есть риск получить опять-таки отслоившиеся дорожки или сгоревший компонент.
Сейчас пойдет речь про демонтаж компонентов с помощью паяльного фена. Способ наиболее простой, эффективный, быстрый и качественный. Но, к сожалению, паяльный фен является инструментом не из дешевых.
Способ демонтажа микросхемы в dip — корпусе.Нужен паяльный фен, пинцет, желательно немагнитный. Со стороны ножек наносится флюс, и начинается прогрев с той же самой стороны. Визуально ведется контроль над состоянием олова на выводах – когда он стал достаточно жидким, аккуратно прихватываем пинцетом деталь со стороны корпуса и вытягиваем из платы.
Демонтаж микросхемы в smd исполнении.
Принцип все тот же – наносится флюс вдоль дорожек, нагревается при определенной температуре, степень прогрева определяется путем легкого подталкивания детали пинцетом. Если деталь стала подвижна — медленно и аккуратно удаляем ее с поверхности платы пинцетом, придерживая за края, и стараясь не зацепить дорожек.
Очень важно не перегревать демонтируемые детали и поверхность! У каждой микросхемы и детали есть свой температурный предел, переступив который, деталь или плата окажется испорченной. Фен надо держать СТРОГО вертикально, подобрав нужную насадку, равномерно прогревая всю поверхность микросхемы. И не забыть выставить поток воздуха таковым, чтобы случайно не сдуть соседние компоненты.
Ну вот, пожалуй, все доступные способы демонтажа микросхем. Надеюсь, вы получили ответ на вопрос: как выпаять микросхему.
Появились желание и необходимость перейти на более компактные схемы, нежели собранные на обычной макетке. Перед тем, как основательно закупаться текстолитом, элементами и микросхемами для поверхностного монтажа, решил попробовать, а смогу ли я собрать такую мелочь. На просторах Алиэкспресс нашелся отличный «тренажер» за очень разумные деньги. Если у вас есть опыт пайки, большого смысла читать обзор нет
Набор представляет из себя светоэффект бегущие огни, скорость регулируется переменным резистором.
Приехало все в стандартном пупырчатом конверте, в зиппакете
Внешний вид набора
Помимо набора я пользовался припоем ПОС-61, флюсом RMA-223, пинцетом, паяльником.
Расходники
Если по припою никаких особых впечатлений быть не может, то по поводу флюса у меня есть что сказать.
Мне он показался излишне жирным, что ли. В общем, его достаточно сложно отмыть спиртом в компании с зубной щеткой, и я не вполне уверен, что под микросхемами не остались его остатки. Однако флюс рабочий и от пайки им у меня хорошие впечатления, особенно пока я не взялся за отмывку платы))). К плюсам добавлю, что флюс нейтральный и, в отличии от той же паяльной кислоты, его незначительные остатки не способны нанести вред компонентам. Так что флюсу зачет, а мои претензии к отмывке носят больше субъективный характер, до этого я пользовался водосмываемым флюсом ФТС и мне он казался проще в обращении.
К тому же у любого флюсгеля, по сравнению с жидким, есть очень удобный плюс, после его нанесения деталь можно «прилепить» к плате на гель и выровнять. Не ахти какое крепление, но случайно задеть плату или наклонить уже не страшно. Далее прижимаем элемент пинцетом и паяем. Пробовал несколько способов паять smd рассыпуху (резисторы, конденсаторы), самым удобным оказалось залудить одну контактную площадку, припаять ряд элементов с одной стороны, а уже потом пройтись по второй части. Причем форма жала оказалась не особенно и важна, подойдет практически любое, даже самое толстое.
Паяльник
Вот эти здоровым жалом я в итоге и пользовался… Им оказалось очень удобно поправлять криво вставшие элементы, поскольку его величины хватает, чтобы разогреть обе точки пайки, а потом мне было лень его сменить.
У микросхем похожая схема, сначала фиксируем одну ножку, затем паяем все остальное, фен не понравился категорически, часто сдувает компоненты, мне им сложно пользоваться. Отпаивать микросхемы феном – да, припаивать – нет.
Более крупные элементы, такие как ножки питания (как на этой плате) или радиаторы, толстые провода советую паять паяльной кислотой, она творит чудеса. Если же на проводах лак (например аудио, ради интереса можете разобрать старые наушники и попробовать припаять) его проще всего обжигать горелкой-зажигалкой, залудить кислотой и спокойно паять. Есть более удобный способ – использовать таблетку аспирина как флюс, на подобии канифоли – лак снимается на ура и провод имеет более аккуратный внешний вид. Здесь я проводами не пользовался, собрал «как есть».
Возможно кому-то будет удобнее паять не на столе, а зафиксировать плату в держателях
Держатели
третья рука, на крокодилах надета термоусадка, чтобы не царапать текстолит, и плата при этом держится в разы лучше
PCB Holder
Кому интересно, я добавил видео работы платы. Постарался как можно крупнее сфотографировать итог и название микросхем. Кстати, все заработало с первого раза, за пол бакса попробовать свои силы, флюсы, припои или обновить навык – самое то.
Еще пара фото
В этой статье будет рассмотрен один из работающих способов распайки smd компонентов. При чем распайка будет происходить не совсем стандартным способом но не смотря на это, он очень эффективный. Прогрев элементов проходит равномерно, без опасности перегрева, так как температуру можно регулировать!
Все чаще применяются SMD детали в производстве, а так же среди радиолюбителей. Работать с ними удобней, так как сверлить отверстия для выводов не нужно, а устройства получаются очень миниатюрными.
SMD компоненты вполне можно использовать и повторно. Тут опять появляется очевидное превосходство поверхностного монтажа, потому что выпаивать мелкие детали гораздо проще. Их очень просто сдувать специальным паяльным феном с платы. Но если у вас такого не окажется под рукой, то вас выручит обычный бытовой утюг.
Демонтаж SMD деталей
Итак, у меня сгорела светодиодная лампа, и я не буду её чинить. Я её распаяю на детали для будущих своих самоделок.
Разбираем лампочку, снимаем верхний колпак.
Вытаскиваем плату из основания цоколя.
Отпаиваем навесные компоненты и детали, провода. В общем должна быть плата только с SMD деталями.
Закрепляем утюг вверх тормашками. Делать это нужно жестко, чтобы он в процессе пайки не опрокинулся.
Использование утюга ещё хорошо тем, что в нем есть регулятор, который будет довольно точно поддерживать установленную температуру поверхности подошвы. Это огромный плюс, так как поверхностные компоненты очень боятся перегрева.
Выставляем температуру около 180 градусов Цельсия. Это второй режим глажки белья, если мне не изменяет моя память. Если пайка не пойдет — постепенно увеличивайте температуру.
Кладем плату от лампочки на подошву перевернутого утюга.
Ждем 15-20 секунд пока плата прогреется. В это время смачиваем флюсом каждую детальку. Флюс не даст перегрева, это будет своеобразный помощник при распайки. С ним все элементы снимаются без труда.
Как только все хорошо разогреется, все детали можно смахнуть с платы, ударив плату о какую-нибудь поверхность. Но я сделаю все аккуратно. Для этого возьмем деревянную палочку для удержания платы на месте и с помощью пинцета будем отсоединять каждый компонент платы.
Голая плата в конце работы:
Выпаянные детали:
Этот способ позволит вам очень быстро распаивать любые платы с SMD деталями. Берите на вооружение друзья!
Рекомендуем также
Как паять smd компоненты. Быстрая распайка SMD компонентов с помощью утюга
Многие задаются вопросом, как правильно паять SMD компоненты. Но прежде чем заняться этой проблемой, необходимо уточнить, что это за элементы. Surface Mounted Devices – в переводе с английского это выражение означает компоненты для поверхностного монтажа. Их главное преимущество – большая плотность сборки, чем у обычных деталей. Этот аспект влияет на использование SMD-элементов в массовом производстве печатных плат, а также на их эффективность и технологичность установки.Обычные детали с проволочными выводами утратили свое широкое распространение вместе с быстро растущей популярностью SMD-компонентов.
Ошибки и основной принцип пайки
Некоторые умельцы утверждают, что паять такие элементы своими руками очень сложно и достаточно неудобно. На самом деле, аналогичную работу с компонентами TH провести намного сложнее. Как правило, эти два типа деталей используются в различных областях электроники. Однако многие допускают определенные ошибки при пайке SMD компонентов в домашних условиях.
SMD-компоненты
Основная проблема дилетантов – выбор тонкого жала для паяльника. Это связано с существованием мнения, что при пайке обычным паяльником можно смазать оловом ножки SMD-контактов. В результате процесс пайки получается долгим и болезненным. Это суждение нельзя считать правильным, так как капиллярный эффект, поверхностное натяжение, а также сила смачивания играют существенную роль в этих процессах. Игнорирование этих дополнительных приемов затрудняет выполнение работы самостоятельно.
Пайка компонентов SMD
Для правильной пайки компонентов SMD вы должны придерживаться определенных шагов. Для начала приложите жало паяльника к ножкам взятого элемента. В результате температура начинает расти и олово плавится, которое в конечном итоге полностью обтекает ножку этого компонента. Этот процесс называется силой смачивания. При этом олово течет под шток, что объясняется капиллярным эффектом. Вместе с смачиванием ноги аналогичный эффект происходит и на самой доске.В результате получается равномерно набитый пучок доски с ножками.
Контакт припоя с соседними ножками не происходит из-за того, что начинает действовать растягивающая сила, образуя отдельные капли олова. Очевидно, что описанные процессы протекают сами по себе, только при небольшом участии паяльника, который только нагревает паяльником ножки детали. При работе с очень маленькими элементами они могут прилипнуть к жало паяльника. Чтобы этого не произошло, обе стороны припаяны по отдельности.
Заводская пайка
Этот процесс основан на групповом методе. Пайка SMD компонентов производится с помощью специальной паяльной пасты, которая равномерно распределяется тончайшим слоем на подготовленной печатной плате, где уже есть контактные площадки. Этот метод нанесения называется шелкографией. Используемый материал по внешнему виду и консистенции похож на зубную пасту. Этот порошок состоит из припоя, к которому добавлен и перемешан флюс. Процесс подачи заявки осуществляется автоматически по мере прохождения печатной платы по конвейеру.
Заводская пайка SMD деталей
Далее роботы, установленные на приводном ремне, раскладывают все необходимые элементы в нужном порядке. Во время движения платы детали надежно удерживаются на месте за счет достаточной липкости паяльной пасты. Следующий этап – это нагрев конструкции в специальной печи до температуры немного выше той, при которой плавится припой. В результате такого нагрева припой плавится и обтекает ножки компонентов, а флюс испаряется.В результате этого процесса детали впаяны в свои гнезда. После печки доске дают остыть, и все готово.
Необходимые материалы и инструменты
Для того, чтобы выполнить работы по пайке SMD компонентов своими руками, вам потребуются определенные инструменты и расходные материалы, в том числе:
- паяльник для пайки SMD контактов;
- пинцет и бокорезы;
- шило или игла с острым концом; Припой
- ;
- лупа или лупа, которая необходима при работе с очень мелкими деталями;
- нейтральный жидкий флюс типа no-clean;
- шприц, которым можно нанести флюс; №
- : при отсутствии последнего материала можно отказаться от спиртового раствора канифоли;
- для удобства пайки умельцы используют специальный паяльный фен.
Пинцет для установки и снятия компонентов SMD
Использование флюса необходимо и должно быть жидким. В этом состоянии этот материал обезжиривает рабочую поверхность, а также удаляет образовавшиеся оксиды на паяемом металле. В результате на припое появляется оптимальная сила смачивания, а капля припоя лучше сохраняет форму, что облегчает весь процесс работы и исключает образование «соплей». Применение спиртового раствора канифоли не позволит добиться значительного результата, а образовавшийся белый налет вряд ли удастся удалить.
Выбор паяльника очень важен. Лучше всего подойдет средство, которое можно подогнать под температуру. Это позволяет не беспокоиться о возможности повреждения деталей перегревом, но этот нюанс не касается моментов, когда нужно паять SMD компоненты. Любая паяная деталь способна выдерживать температуру порядка 250-300 ° C, что обеспечивает регулируемый паяльник. При отсутствии такого устройства можно использовать аналогичный инструмент мощностью от 20 до 30 Вт, рассчитанный на напряжение 12-36 В.
Использование паяльника 220 В приведет к плохим последствиям. Это связано с высокой температурой нагрева его наконечника, под действием которого жидкий флюс быстро испаряется и не дает деталям эффективно смачиваться припоем.
Специалисты не рекомендуют использовать паяльник с коническим наконечником, так как припой трудно нанести на детали, и на них уходит много времени. Самым эффективным считается жало под названием «Микроволновка». Его очевидное преимущество – небольшое отверстие в срезе для более удобного захвата припоя в нужном количестве.Даже с таким жалом на паяльнике удобно собирать лишнюю пайку.
Припой можно использовать любой, но лучше использовать тонкую проволоку, которой удобно дозировать количество используемого материала. Паяная деталь с такой проволокой будет лучше обрабатываться за счет более удобного доступа к ней.
Как паять SMD компоненты?
Наряд на работу
Процесс пайки, с осторожным подходом к теории и некоторым опытом, не сложен.Итак, всю процедуру можно разделить на несколько пунктов:
- SMD компоненты необходимо размещать на специальных контактных площадках, расположенных на плате.
- На ножки детали наносится жидкий флюс, и компонент нагревается с помощью жала паяльника.
- Под воздействием температуры переливаются контактные площадки и сами ножки детали.
- После заливки паяльник убирается и дается время, чтобы компонент остыл.Когда припой остынет, работа окончена.
Процесс пайки SMD компонентов
При выполнении аналогичных действий с микросхемой процесс пайки немного отличается от описанного выше. Технология будет выглядеть так:
- Ножки SMD компонентов устанавливаются точно в места контакта.
- В местах контактных площадок производится смачивание флюсом.
- Чтобы деталь точно вошла в гнездо, необходимо сначала припаять одну из ее крайних ножек, после чего деталь легко обнажится.
- Дальнейшая пайка проводится с особой тщательностью, причем припой наносится на все ножки. Излишки припоя удаляются жало паяльника.
Как паять феном?
При таком способе пайки необходимо смазать посадочные места специальной пастой. Затем на контактную площадку кладется необходимая деталь – помимо компонентов это могут быть резисторы, транзисторы, конденсаторы и т. Д. Для удобства можно воспользоваться пинцетом. После этого деталь нагревается горячим воздухом, подаваемым из фена, с температурой около 250 ° C.Как и в предыдущих примерах пайки, флюс испаряется под действием температуры, а припой плавится, заполняя контактные дорожки и ветви деталей. Затем фен убирают, и доска начинает остывать. Когда он полностью остынет, пайку можно считать завершенной.
SMD детали все чаще используются на производстве, а также среди радиолюбителей. С ними удобнее работать, так как не нужно сверлить отверстия под клеммы, а устройства очень миниатюрные.Компоненты
SMD можно использовать повторно и повторно. Здесь снова проявляется очевидное превосходство поверхностного монтажа, ведь припаять мелкие детали гораздо проще. Их очень легко сдувать с платы специальной паяльной сушилкой. Но если под рукой этого нет, то выручит обычный бытовой утюг.
Разборка SMD частей
Итак, моя светодиодная лампа перегорела, и я не буду ее ремонтировать. Распаяю на части для будущих самоделок.Разбираем лампочку, снимаем верхнюю крышку.
Вытаскиваем доску из основания цоколя.
Распаиваем прилагаемые комплектующие и детали, провода. В общем, должна быть плата только с SMD частями.
Закрепляем утюг вверх ногами. Делать это нужно жестко, чтобы в процессе пайки он не опрокинулся.
Использование утюга хорошо еще и тем, что в нем есть регулятор, который достаточно точно будет поддерживать заданную температуру поверхности подошвы.Это огромный плюс, так как поверхностные компоненты очень боятся перегрева.
Устанавливаем температуру примерно 180 градусов по Цельсию. Это второй режим глажки, если мне не изменяет память. Если пайка не работает, постепенно увеличивайте температуру.
Ставим плату от лампочки на подошву перевернутого утюга.
Ждем 15-20 секунд прогрева платы. В это время смачиваем каждую деталь флюсом. Флюс не перегреется, будет своеобразным помощником при распайке.С ним все элементы снимаются без труда.
Как только все хорошо нагреется, все детали можно смахнуть с доски, ударив доской о какую-либо поверхность. Но сделаю все аккуратно. Для этого возьмите деревянную палку, чтобы удерживать доску на месте, и с помощью пинцета отсоедините каждый компонент платы.
Голая плата по окончании работы:
Паяных деталей:
У меня было много вопросов по теме
разборка микросхем в разных постройках.Предлагаю вам ознакомиться с наиболее распространенными вариантами распайки микросхем в дип и smd корпусах.В первую очередь следует рассказать о
демонтаже микросхем – процессе, наиболее доступном для радиолюбителей, но и несколько сложном по сравнению с тем, о котором будет рассказано чуть позже.Способ демонтажа микросхем в погружном корпусе с помощью паяльника и некоторых предметов, которые можно найти в доме.
Вам понадобится паяльник и игла от десяти кубического шприца.Отрежьте кончик иглы так, чтобы он был прямым, без кончика. Вставляем иглу с полым отверстием в ножку микросхемы с нижней стороны, медленно нагревая ее, пока игла не пройдет через отверстие в плате. Не снимая иглы, дать поверхности остыть и припаять, вынуть иглу. Удаляем излишки припоя с иглы, повторяем процесс на оставшихся выводах микросхемы. При некоторой сноровке получается аккуратно и качественно – сама микросхема без усилия извне выпадает из платы.
Вам понадобится паяльник и оплетка медного кабеля. На медную оплетку наносим слой флюса, кладем на одну сторону ножки микросхемы и прогреваем. При нагревании оплетка «вытаскивает» припой с поверхности платы, на которой расположена микросхема. Когда коса пропитается, ненужная часть просто отрезается, и демонтаж продолжается. Надо сказать, что этот метод подходит как для демонтажа Dip-компонентов, так и для Smd-компонентов.
Для работы понадобится тот же паяльник и что-нибудь тонкое, например, пинцет или отвертка с плоским лезвием. Осторожно проденьте плоскую часть отвертки (или пинцета) между микросхемой и и до некоторой разумной глубины, нагрейте ножки с тыльной стороны и медленно поднимите сторону. Повторяем тот же процесс, но теперь с другой стороны детали: вставляем отвертку, нагреваем ножки, приподнимаем. И повторяем этот процесс до тех пор, пока микросхема не будет снята с платы.Метод очень быстрый, простой и даже грубый. Но не забывайте, что и дорожки на плате, и сама микросхема имеют свой температурный предел. Иначе можно остаться без исправной микросхемы, либо с отклеенными дорожками.
Требуется паяльник и отсос для припоя. Отсос для припоя представляет собой что-то вроде шприца, но с поршнем, работающим по принципу отсоса. Нагреваем вывод микросхемы, сразу прикладываем отсос для припоя, нажимаем кнопку и созданное разрежение внутри отсоса «выкачивает» припой из дорожки.К сожалению, все выглядит так просто и просто только на словах. На самом деле, нагревая ножку, нужно практически мгновенно попасть на ножку присосом, и «выкачать» припой, что требует высокой скорости исполнения, потому что припой замерзает практически мгновенно, а если держать паяльник дольше, есть риск получить отслаивающиеся следы или обгоревшую деталь …
Теперь поговорим о демонтаже компонентов с помощью паяльного фена. Метод самый простой, эффективный, быстрый и качественный.Но, к сожалению, паяльный фен – средство недешевое.
Способ демонтажа микросхемы в дип-корпусе .Вам понадобится паяльный фен, пинцет, желательно немагнитный. Со стороны ножек наносится флюс, с этой же стороны начинается нагрев. Визуально контроль за состоянием жести на выводах осуществляется – когда она стала достаточно жидкой, аккуратно захватываем пинцетом деталь сбоку корпуса и вытаскиваем из платы.
Разборка микросхемы в smd исполнении.
Принцип все тот же – по дорожкам наносится флюс, нагревается до определенной температуры, степень нагрева определяется легким нажатием на деталь пинцетом. Если деталь стала подвижной, медленно и осторожно снимите ее с поверхности доски пинцетом, придерживая за края и стараясь не цепляться за гусеницы.
Очень важно не перегревать разбираемые детали и поверхность! Каждая микросхема и деталь имеют свой температурный предел, при превышении которого деталь или плата будут повреждены.Фен нужно держать СТРОГО вертикально, подбирая нужную насадку, равномерно прогревая всю поверхность микросхемы. И не забудьте настроить подачу воздуха, чтобы случайно не сдувать соседние компоненты.
Ну вот, пожалуй, все доступные способы разборки микросхем. Надеюсь, вы получили ответ на свой вопрос: как паять микросхему.
Было желание и необходимость перейти на более компактные схемы, чем те, что собраны на обычной макетной плате.Прежде чем основательно закупить текстолит, элементы и микросхемы для поверхностного монтажа, решил попробовать, а можно ли собрать такую мелочь. На просторах Алиэкспресс нашелся отличный «симулятор» за вполне разумные деньги. Если есть опыт пайки, читать обзор смысла нет.
Комплект светового эффекта ходовых огней, скорость регулируется переменным резистором.
Все пришло в стандартном пузырчатом конверте, в застежке-молнии
Внешний вид комплекта
В дополнение к набору я использовал припой ПОС-61, флюс РМА-223, пинцет, паяльник.
Расходные материалы
Если на припое особых отпечатков не может быть, то по флюсу есть что сказать.
Мне показалось слишком толстым, что ли. Вообще, смыть спиртом в компании с зубной щеткой довольно сложно, да и не совсем уверен, что под микросхемами не осталось остатков. Однако флюс рабочий и впечатления от его пайки хорошие, особенно пока не занялся чисткой платы))).К плюсам добавлю, что флюс нейтральный и, в отличие от той же паяльной кислоты, его незначительные остатки не способны навредить компонентам. Так что флюс засветился, и мои жалобы на чистку более субъективны, до этого я использовал водосмываемый флюс FCS, и мне показалось, что с ним проще обращаться.
Кроме того, у любого флюксгеля, по сравнению с жидкостью, есть очень удобный плюс, после его нанесения деталь можно «приклеить» к доске на геле и выровнять. Не ахти, но случайно прикоснуться к доске или наклонить ее уже не страшно.Далее прижимаем элемент пинцетом и припаяем. Я пробовал несколько способов припаять smd отдельно (резисторы, конденсаторы), удобнее всего было залудить одну контактную площадку, припаять несколько элементов с одной стороны и только потом пройти вторую часть. Причем форма жала оказалась не особо важной, подойдет практически любое, даже самое толстое.
Паяльник
Вот и закончился вот этими здоровыми жалами … Исправить кривые элементы им оказалось очень удобно, так как его размера хватило на то, чтобы прогреть обе точки пайки, а потом поменять поленился.
У микросхем аналогичная схема, сначала фиксируем одну ножку, потом все остальное припаиваем, фен категорически не нравился, часто срывает компоненты, мне сложно пользоваться. Паять микросхемы феном – да, паять – нет.
Элементы большего размера, например силовые ножки (как на этой плате) или радиаторы, советую припаять толстые провода паяльной кислотой, творит чудеса. Если на проводах есть лак (например, аудиосистема, ради интереса можно разобрать старые наушники и попробовать припаять) проще всего обжечь зажигалкой, залудить кислотой и спокойно припаять.Есть более удобный способ – использовать таблетку аспирина в качестве флюса, похожего на канифоль – лак удаляется на ура и проволока имеет более аккуратный вид. Здесь провода не использовал, собрал “как есть”.
Возможно, кому-то будет удобнее паять не на столе, а закрепить плату в держателях
Держатели
третья рука, крокодилы снабжены термоусадкой, чтобы не царапать текстолит, да и плата держится намного лучше
PCB Holder
Кому интересно, я добавил видео работы платы.Я постарался сфотографировать результат и название микросхем как можно больше. Кстати, с первого раза все заработало, за полдоллара попробовать свои силы, флюсы, припои или прокачать мастерство – вот и все.
Еще пара фото
В данной статье пойдет речь об одном из рабочих приемов распайки smd компонентов. Причем распайка будет происходить не совсем стандартным способом, но, несмотря на это, очень эффективным.Элементы нагреваются равномерно, без опасности перегрева, так как температуру можно регулировать!
ДеталиSMD все чаще используются на производстве, а также среди радиолюбителей. С ними удобнее работать, так как не нужно сверлить отверстия под клеммы, а устройства получаются очень миниатюрными.
КомпонентыSMD можно использовать повторно и повторно. Здесь снова проявляется очевидное превосходство поверхностного монтажа, ведь припаять мелкие детали гораздо проще.Их очень легко сдувать с платы специальной паяльной сушилкой. Но если под рукой этого нет, то выручит обычный бытовой утюг.
Разборка деталей SMD
Итак, у меня перегорела светодиодная лампа, и я не буду ее чинить. Распаяю на части для будущих самоделок.
Разбираем лампочку, снимаем верхнюю крышку.
Вытаскиваем доску из цоколя цоколя.
Распаиваем прилагаемые комплектующие и детали, провода. В общем, должна быть плата только с SMD частями.
Закрепляем утюг вверх ногами. Делать это нужно жестко, чтобы в процессе пайки он не опрокинулся.
Использование утюга хорошо еще и тем, что в нем есть регулятор, который достаточно точно будет поддерживать заданную температуру поверхности подошвы. Это огромный плюс, так как поверхностные компоненты очень боятся перегрева.
Устанавливаем температуру около 180 градусов по Цельсию. Это второй режим глажки, если мне не изменяет память. Если пайка не работает, постепенно увеличивайте температуру.
Ставим плату от лампочки на подошву перевернутого утюга.
Ждем 15-20 секунд прогрева платы. В это время смачиваем каждую деталь флюсом. Флюс не перегреется, будет своеобразным помощником при распайке.С ним все элементы снимаются без труда.
Как только все хорошо нагреется, все детали можно смахнуть с доски, ударив доской о какую-либо поверхность. Но сделаю все аккуратно. Для этого возьмите деревянную палку, чтобы удерживать доску на месте, и с помощью пинцета отсоедините каждый компонент платы.
Пустая доска по окончании работы:
Паяных деталей:
Этот метод позволит очень быстро паять любые платы с SMD деталями.Примите друзей!
Как правильно паять SMD компоненты. О демонтаже SMD компонентов с печатных плат
Когда я в очередной раз разобрал в своих «закромах» радиолюбителей, то обнаружил большое количество плат с SMD компонентами, которые занимают довольно много места. Выбрасывать вроде бы жалко, так как платы содержат большое количество радиодеталей, которые могут пригодиться в работе. Поэтому я решил убрать с этих плат наиболее ценные детали – полупроводники, микросхемы, индукторы, кварц и т. Д.Те. те элементы, которые можно идентифицировать по маркировке.
Паять платы с SMD-компонентами можно несколькими способами, в том числе обычным паяльником. Но это очень неудобный способ, приводящий к перегреву деталей и отслаиванию контактных площадок. Особенно сложна пайка микросхем с большим количеством выводов. Самый удобный инструмент для этого бизнеса – промышленный фен или паяльная станция со встроенным феном. К сожалению, таких устройств у меня нет, поэтому я решил соорудить небольшую «печку» для массовой пайки SMD элементов.
Проект
Основа устройства – жестяная коробка от мультитула Leatherman размером 15х12х3,5 см. Используется как нагревательный элемент 118 мм. Галогенная лампа 300 Вт с цоколем R7s. Патронов для установки этих ламп я не нашел и в результате пришлось немного переделать керамический патрон от другого типа лампы (штыря).
Изначально сделал крепления для двух ламп, но как показала практика, одной лампы хватит «за глаза»
Галогенная лампа подключается к любому регулятору соответствующей мощности.Он у меня самодельный, собран на интегральном регуляторе PR1500ST. Использование регулятора позволяет не перегревать плату и поддерживать «рабочую» температуру платы, чтобы легко снимать элементы.
Работа
Процесс демонтажа элементов довольно простой. Участок платы, который нужно распаивать, размещают над лампой на высоте 1-3 см. Лампа включается почти на полную мощность. Через некоторое время – обычно 30-60 секунд. доска начинает слегка дымиться (при этом испаряется защитный лак, остатки флюсов или клея).В это время я пытаюсь удалить пинцетом элементы в зоне нагрева. Обычно это легко сделать через 30-40 секунд после дыма. Как только элементы начинают легко сниматься с платы, уменьшаю мощность и начинаю методично «чистить» плату. Снятые детали кладут на лист бумаги или картона. Таким образом, элементы снимаются легко, без «соплей», даже если они ранее были приклеены к доске (такие доски встречаются довольно часто).
Чтобы нагреть узкую плату, как сотовый телефон, я использую две металлические полоски.
Заключение
Вот и все. Конечным результатом является аккуратная стопка деталей, которые затем сортируются, каталогизируются и готовы к повторному использованию в любительских радиоустройствах.
Было желание и необходимость перейти на более компактные схемы, чем те, что собраны на обычной макетной плате. Прежде чем основательно закупить текстолит, элементы и микросхемы для поверхностного монтажа, решил попробовать, а можно ли собрать такую мелочь. На просторах Алиэкспресс нашелся отличный «симулятор» за вполне разумные деньги.Если у вас есть опыт пайки, нет смысла читать обзор
В комплекте световые ходовые огни, скорость регулируется переменным резистором.
Все пришло в стандартном пузырчатом конверте, в застежке-молнии
Внешний вид комплекта
В дополнение к набору я использовал припой ПОС-61, флюс РМА-223, пинцет, паяльник.
Расходные материалы
Если на припое особых отпечатков не может быть, то по флюсу есть что сказать.
Мне показалось слишком толстым, что ли. Вообще, смыть спиртом в компании с зубной щеткой довольно сложно, да и не совсем уверен, что под микросхемами не осталось остатков. Однако флюс рабочий и впечатления от его пайки хорошие, особенно пока не занялся чисткой платы))). Из плюсов добавлю, что флюс нейтральный и, в отличие от той же паяльной кислоты, его незначительные остатки не способны навредить компонентам.Так что флюс засветился, и мои жалобы на чистку более субъективны, до этого я использовал водосмываемый флюс FCS и мне показалось, что он проще в использовании.
Кроме того, у любого флюксгеля, по сравнению с жидкостью, есть очень удобный плюс, после его нанесения деталь можно «приклеить» к доске на геле и выровнять. Не ахти, но случайно прикоснуться к доске или наклонить ее уже не страшно. Далее прижимаем элемент пинцетом и припаяем. Я пробовал несколько способов припаять smd отдельно (резисторы, конденсаторы), удобнее всего было залудить одну контактную площадку, припаять несколько элементов с одной стороны и только потом пройти вторую часть.Причем форма жала не имела особого значения, подойдет практически любое, даже самое толстое.
Паяльник
Вот и закончился вот этими здоровыми жалами … Исправить кривые элементы им оказалось очень удобно, так как его размера хватило на то, чтобы прогреть обе точки пайки, а потом поменять поленился.
В микросхемах аналогичная схема, сначала фиксируем одну ножку, потом все остальное припаиваем, фен категорически не нравился, часто сдувает компоненты, мне сложно пользоваться.Паять микросхемы феном – да, припаять – нет.
Элементы большего размера, например силовые ножки (как на этой плате) или радиаторы, советую припаять толстые провода паяльной кислотой, творит чудеса. Если на проводах есть лак (например, аудиосистема, ради интереса можно разобрать старые наушники и попробовать припаять) проще всего обжечь зажигалкой, залудить кислотой и спокойно припаять. Есть более удобный способ – использовать таблетку аспирина в качестве флюса, похожего на канифоль – лак удаляется на ура и проволока имеет более аккуратный вид.Здесь провода не использовал, собрал их «как есть».
Возможно, кому-то будет удобнее паять не на столе, а закрепить плату в держателях
Держатели
третья рука, крокодилы снабжены термоусадкой, чтобы не царапать текстолит, да и плата держится намного лучше
PCB Holder
Кому интересно, я добавил видео работы платы. Я постарался сфотографировать результат и название микросхем как можно больше.Кстати, с первого раза все заработало, за полдоллара попробовать свои силы, флюсы, припои или апгрейд навыка – вот и все.
Еще пара фото
При выходе из строя какого-либо оборудования вовсе не обязательно сразу выбрасывать его в мусорное ведро. Если вы увлекаетесь электроникой и радиотехникой, разумнее будет припаять рабочие элементы микросхемы. Неожиданно в будущем вам понадобится конденсатор, транзистор или резистор, если вы решите это сделать.В этой статье мы расскажем, как снять радиодетали с платы, чтобы ничего не повредить.
Что для этого нужно?
Есть много устройств для распайки деталей. Конечно, радиолюбителю не обойтись без паяльника, который будет в этом деле главным помощником. Однако, помимо паяльника, для того, чтобы припаять элемент вам потребуется:
Также необходимо подготовить рабочее место. Он должен быть хорошо освещен.Лучше всего, если лампа будет находиться над рабочей зоной, чтобы свет падал вертикально, не создавая теней.
Техника демонтажа
Итак, сначала поговорим о самой популярной технологии – как припаять деталь с платы паяльником без дополнительных приспособлений. Затем кратко рассмотрим более простые методы.
Если вы хотите испарить электролитический конденсатор, просто возьмите его пинцетом (или крокодилом), разогрейте 2 вывода и быстро, но осторожно снимите их с платы.
То же самое и с транзисторами. Капаем припой на все 3 вывода и снимаем радиодеталь с платы.
Что касается резисторов, диодов и неполярных конденсаторов, то очень часто их ноги погнуты при пайке с обратной стороны платы, что затруднительно при пайке без дополнительных устройств. В этом случае рекомендуется сначала прогреть одну клемму и при помощи крокодила с небольшим усилием вытащить часть детали из цепи (ножка должна согнуться).Затем проделываем аналогичную процедуру со вторым выходом.
Рассматривали эту технику, когда кроме паяльника под рукой ничего нет. Но если вы приобрели набор игл, то припаять элемент будет еще проще: сначала прогрейте контакт паяльником, затем наденьте на вывод иглу подходящего диаметра (она должна пройти через отверстие в микросхему) и подождите, пока остынет припой. После этого вынимаем иглу и получаем оголенную булавку, которую легко вынимаем.Если у радиокомпонента несколько ножек, тоже действуем – прогреваем контакт, надеваем иголки, ждем и снимаем.
Все, о чем мы говорили в этой статье, хорошо видно на видео, где представлена технология пайки элементов с платы:
Кстати, вместо специальных игл можно использовать даже обычные иглы, которые идут в комплекте со шприцем. Однако в этом случае сначала нужно сточить конец иглы, чтобы он находился под прямым углом.
Запаять деталь с помощью демонтажной тесьмы тоже несложно. Перед началом работы смочите конец обмотки спиртово-канифольным флюсом. После этого поместите оплетку в место пайки (на припой) и прогрейте ее кончиком паяльника. В результате нагретый припой должен впитаться в оплетку, что освободит выводы радиодеталей.
С демонтажным насосом дела обстоят так же – пружина заряжается, контакт нагревается, после чего жало подводится к расплавленному припою и нажимается кнопка.Создается вакуум, который втягивает припой внутрь демонтажного насоса.
Вот и все, что я хотел рассказать о том, как снять радиодетали с платы в домашних условиях. Надеемся, предоставленные методики и видеоуроки были для вас полезны и интересны. Напоследок хотелось бы отметить, что элементы микросхемы можно припаять строительным феном, но мы не рекомендуем этого делать. Фен может повредить близлежащие детали, а также ту, которую нужно удалить!
Интересное
В данной статье пойдет речь об одном из рабочих приемов распайки smd компонентов.Причем распайка будет происходить не совсем стандартным способом, но, несмотря на это, очень эффективным. Элементы нагреваются равномерно, без опасности перегрева, так как температуру можно регулировать!
ДеталиSMD все чаще используются на производстве, а также среди радиолюбителей. С ними удобнее работать, так как не нужно сверлить отверстия под клеммы, а устройства очень миниатюрные.
КомпонентыSMD можно использовать повторно и повторно. Здесь снова проявляется очевидное превосходство SMT, потому что паять мелкие детали намного проще.Их очень легко сдувать с платы специальной паяльной сушилкой. Но если под рукой этого нет, то выручит обычный бытовой утюг.
Разборка деталей SMD
Значит, у меня перегорела светодиодная лампа, чинить не буду. Распаяю на части для будущих самоделок.
Разбираем лампочку, снимаем верхнюю крышку.
Вытаскиваем доску из цоколя цоколя.
Распаиваем прилагаемые комплектующие и детали, провода.В общем, должна быть плата только с SMD частями.
Закрепляем утюг вверх ногами. Делать это нужно жестко, чтобы в процессе пайки он не опрокинулся.
Использование утюга хорошо еще и тем, что в нем есть регулятор, который достаточно точно будет поддерживать заданную температуру поверхности подошвы. Это огромный плюс, так как поверхностные компоненты очень боятся перегрева.
Устанавливаем температуру около 180 градусов по Цельсию.Это второй режим глажки, если мне не изменяет память. Если пайка не работает, постепенно увеличивайте температуру.
Ставим плату от лампочки на подошву перевернутого утюга.
Ждем 15-20 секунд прогрева платы. В это время смачиваем каждую деталь флюсом. Флюс не перегреется, будет своеобразным помощником при распайке. С его помощью без труда снимаются все элементы.
Как только все хорошо нагреется, все детали можно смахнуть с доски, ударив доской по какой-либо поверхности.Но сделаю все аккуратно. Для этого возьмите деревянную палку, чтобы удерживать плату на месте, и с помощью пинцета отсоедините каждый компонент платы.
Пустая доска по окончании работы:
Паяных деталей:
Этот метод позволит очень быстро паять любые платы с SMD деталями. Примите друзей!
SMD детали все чаще используются на производстве, а также среди радиолюбителей.С ними удобнее работать, так как не нужно сверлить отверстия под клеммы, а устройства очень миниатюрные. Компоненты
SMD можно использовать повторно и повторно. Здесь снова проявляется очевидное превосходство SMT, потому что паять мелкие детали намного проще. Их очень легко сдувать с платы специальной паяльной сушилкой. Но если под рукой этого нет, то выручит обычный бытовой утюг.
Разборка SMD частей
Итак, моя светодиодная лампа перегорела и я не буду ее ремонтировать.Распаяю на части для будущих самоделок.Разбираем лампочку, снимаем верхнюю крышку.
Вытаскиваем доску из основания цоколя.
Распаиваем прилагаемые комплектующие и детали, провода. В общем, должна быть плата только с SMD частями.
Закрепляем утюг вверх ногами. Делать это нужно жестко, чтобы в процессе пайки он не опрокинулся.
Использование утюга хорошо еще и тем, что в нем есть регулятор, который достаточно точно будет поддерживать заданную температуру поверхности подошвы. Это огромный плюс, так как поверхностные компоненты очень боятся перегрева.
Устанавливаем температуру примерно 180 градусов по Цельсию. Это второй режим глажки, если мне не изменяет память. Если пайка не работает, постепенно увеличивайте температуру.
Ставим плату от лампочки на подошву перевернутого утюга.
Ждем 15-20 секунд прогрева платы.В это время смачиваем каждую деталь флюсом. Флюс не перегреется, будет своеобразным помощником при распайке. С его помощью без труда снимаются все элементы.
Как только все хорошо нагреется, все детали можно смахнуть с доски, ударив доской по какой-либо поверхности. Но сделаю все аккуратно. Для этого возьмите деревянную палку, чтобы удерживать плату на месте, и с помощью пинцета отсоедините каждый компонент платы.
Голая плата в конце работы:
Паяные детали:
домой »Расчет кровли» Как правильно паять SMD компоненты.О демонтаже SMD компонентов с печатных плат
Заявка на патент США на теплопроводы и оконечный радиатор для упаковки микросхем и производственного процесса Заявка на патент (заявка № 20030131476 от 17 июля 2003 г.)
ОБЛАСТЬ ИЗОБРЕТЕНИЯ& lsqb; 0001 & rsqb; Это изобретение относится к порошковой металлургии, а точнее к рассеивающим тепло элементам для упаковки микроэлектроники, выбранным так, чтобы иметь коэффициент теплового расширения, совместимый с материалом, используемым при изготовлении микросхем.
Уровень техники& lsqb; 0002 & rsqb; Большинство компонентов электронных микросхем требуют использования структур, способных рассеивать тепло, выделяемое активными частями микросхемы. Более того, эти конструкции, находящиеся в непосредственном контакте друг с другом, должны иметь совместимые характеристики теплового расширения. В противном случае напряжения, вызванные непропорциональным расширением, могут повредить компоненты, создать разделение между элементами или иным образом снизить эффективность рассеивания тепла.
& lsqb; 0003 & rsqb; Коэффициент теплового расширения («КТР») или просто тепловое расширение материала определяется как отношение изменения длины на градус Цельсия к длине при 25 ° C. Обычно он дается как среднее значение по диапазону температур.
& lsqb; 0004 & rsqb; Теплопроводность («K» или «TC») материала определяется как скорость передачи тепла через единицу толщины на единицу площади при единице разницы в температуре или K & равно WL / AT, где W & равно; Вт, L & равно ; толщина в метрах, A & равняется; площадь в квадратных метрах, а T & равно; разница температур в OK или ° C.
& lsqb; 0005 & rsqb; В этом описании в отношении микроэлектронного поддержания тепла термин «высокая теплопроводность» обычно означает те материалы, которые имеют коэффициент теплопроводности, превышающий 120 ватт на метр по Цельсию. Аналогичным образом, в отношении коэффициентов теплового расширения те материалы, имеющие КТР ниже приблизительно 10,0 × 10-6 / ° C, будут считаться имеющими «низкий» КТР. Те материалы, у которых КТР выше примерно 12 × 10-6 / ° C.будет сказано, что они имеют «высокий» КТР.
& lsqb; 0006 & rsqb; К сожалению, такие материалы, как медь, серебро, золото и алюминий, которые демонстрируют высокий коэффициент теплопроводности, также имеют тенденцию иметь КТР намного выше, чем такие материалы, как арсенид галлия, кремний и оксид алюминия, используемые в элементах микросхем реализации или их корпусах.
& lsqb; 0007 & rsqb; Как раскрыто в патенте США No. В US 4680618 Курода и др. Было обнаружено, что удобно использовать композиты из меди и других более плотных металлов, таких как вольфрам или молибден, при изготовлении радиаторов, подложек и других рассеивающих тепло элементов корпусов микросхем.Пропорции металлов в композите выбираются в соответствии с КТР материала, используемого при изготовлении активного компонента схемы.
& lsqb; 0008 & rsqb; Из-за больших различий в удельном весе и температурах плавления, а также из-за отсутствия взаимной растворимости металлов, таких как медь и вольфрам, например, трудно сформировать композиты из этих двух металлов, которые демонстрируют надежную степень однородности, с использованием обычных процессы плавления.
& lsqb; 0009 & rsqb; Как указано в U.С. Пат. В US 5086333 Osada et al., Включенном в настоящий документ посредством этой ссылки, было обнаружено, что более практично прессовать и спекать порошок плотного материала с более высокой точкой плавления, например, вольфрама, с образованием пористой прессованной массы, а затем для ее пропитывания. с расплавленной медью или другим материалом, имеющим более низкую температуру плавления. Полученный композит с металлической матрицей обладает как согласованными характеристиками расширения, так и повышенной теплопроводностью. Плита из композита может быть разрезана и обработана для образования радиаторов, соединителей, подложек и других теплоотводящих компонентов или элементов.
& lsqb; 0010 & rsqb; Однако по мере развития конструкций микросхем с еще большей плотностью населения возникает необходимость в обеспечении еще больших тепловых потоков при меньших затратах.
& lsqb; 0011 & rsqb; Что касается более крупных элементов или компонентов, таких как рассеивающие тепло подложки для высокомощных компонентов, стоимость металла становится важным фактором. Следовательно, есть преимущество в уменьшении зависимости от дорогостоящих металлов.
& lsqb; 0012 & rsqb; Что касается теплоотводящих элементов для корпусных микропроцессоров, популярной конструкцией является так называемый корпус типа «перевернутый кристалл», описанный в U.С. Пат. № 5,585,671 Nagesh et al. и в патенте США No. No. 6250127 B1, Polese, et al. включены в настоящий документ посредством ссылки. Как показано на фиг. 1, в этой конструкции корпуса была разработана рассеивающая тепло крышка или конструкция крышки 5, также известная как теплоотвод, которая прикреплена к задней стороне или, в показанной ориентации, к верхней поверхности матрицы 1 с использованием слоя теплопроводного клея 6, такого как проводящая эпоксидная смола или припой. Элемент жесткости 7 с боков окружает матрицу и связывает периферию 8 крышки с соединяющей керамической подложкой или печатной платой 3, таким образом закрывая и защищая матрицу, сохраняя хороший контакт на границе раздела между кристаллом и крышкой и позволяя использовать неклейкие материалы. например, термопаста на стыке.Кристалл 1 имеет множество паяных выступов 2, расположенных на его активной стороне или в показанной ориентации, на нижней стороне для электрического соединения кристалла с печатной платой 3. Как правило, нижний слой 4 из электроизолирующего полимера дополнительно связывает кристалл с печатной платой. печатная плата снижает механические нагрузки, возникающие из-за несоответствия CTE между кристаллом и платой. Поскольку большинство практичных изолирующих полимеров имеют относительно низкую теплопроводность, важно, чтобы крышка отводила большую часть тепла от матрицы.
& lsqb; 0013 & rsqb; Фиг. 2 и 3 показано, что элемент жесткости может быть объединен с крышкой путем формирования крышки 9 с утолщенной периферией или фланцем 10, заканчивающимся на внутреннем крае (стенки 11, 12 образуют внутреннюю полость 13. Фиг. 2 также показывает необходимость в крышки, имеющие равномерно гладкую и плоскую верхнюю поверхность для плотного контакта с установленным сверху радиатором 14. Из-за важности рассеивания тепла, связанного с радиатором, существует потребность в максимальном увеличении теплопередающей способности крышки.
& lsqb; 0014 & rsqb; Из-за относительно низкой теплопроводности промежуточного слоя между матрицей и крышкой желательна минимальная толщина, что приводит к необходимости в гладкой, плоской нижней поверхности крышки и хорошо подобранных характеристиках теплового расширения. Однако, если используется клей, более тонкий эпоксидный слой менее способен компенсировать любое несоответствие расширения между матрицей, крышкой и керамической подложкой, приводящее к разрывам контактных поверхностей.
& lsqb; 0015 & rsqb; Во многих устройствах на микросхемах в определенных местах кристалла может выделяться больше тепла, чем в других.Кроме того, тепловая мощность может колебаться в любом конкретном месте с течением времени. Следовательно, существует необходимость учитывать изменения тепловой мощности во времени и в зависимости от местоположения.
& lsqb; 0016 & rsqb; Таким образом, настоящее изобретение является результатом попытки разработать более простую, более практичную и более экономичную конструкцию теплоотводящего элемента и процесс изготовления, которые решают проблемы, описанные выше.
СУЩНОСТЬ ИЗОБРЕТЕНИЯ& lsqb; 0017 & rsqb; Основными и второстепенными задачами этого изобретения являются создание недорогого тепловыделяющего элемента для использования в упаковке тепловыделяющих микросхем, при этом элемент имеет улучшенную способность к теплопередаче и рассеиванию и имеет КТР, совместимый с материалом микросхемы, в то время как поддержание достаточно равномерной гладкости и плоскостности.
& lsqb; 0018 & rsqb; Эти и другие цели достигаются с помощью композита с металлической матрицей, согласованного по КТР, сочетающего материал с более высокой теплопроводностью с материалом с более низкой КТР, в котором композит имеет теплопроводы, образованные через него материалом с более высокой теплопроводностью. Каждый теплопровод расположен так, чтобы иметь первую торцевую поверхность или площадку в непосредственной близости от источника тепла, например, полупроводникового кристалла, и вторую торцевую поверхность или площадку в непосредственной близости от других рассеивающих тепло структур.
& lsqb; 0019 & rsqb; Различные варианты осуществления обеспечивают улучшенный конический или конусообразный теплопровод, снижающий механические напряжения, при сохранении высокой теплопередачи, отличающийся размером и ориентацией теплопроводов в зависимости от размера и места контакта матрицы.
& lsqb; 0020 & rsqb; В дополнительном варианте осуществления местоположения теплопроводов могут быть выбраны для образования символов, букв и слов, чтобы обеспечить уникальную информационную среду.
& lsqb; 0021 & rsqb; В дополнительном варианте осуществления теплопроводы могут соединять параллельные пластины, между которыми находится материал с согласованным КТР.
& lsqb; 0022 & rsqb; Эти элементы формируются с помощью процесса согласно изобретению, который включает создание пористой заготовки с более высокой температурой плавления, материалом с низким КТР, таким как вольфрам, которая имеет множество разнесенных отверстий, соответствующих трубопроводам. Затем в преформу пропитывают материал с более низкой температурой плавления и высокой теплопроводностью, такой как медь, с образованием композиционного материала с металлической матрицей и для заполнения отверстий.
& lsqb; 0023 & rsqb; В другом варианте осуществления изобретения отверстия в преформе формируются за один процесс прессования с использованием штамповочного пресса, имеющего выступы, связанные с отверстиями.
& lsqb; 0024 & rsqb; В дополнительном варианте осуществления изобретения трубопроводы проходят через соединяющийся между собой тепловой резервуар и заканчиваются конструкцией радиатора.
КРАТКОЕ ОПИСАНИЕ ЧЕРТЕЖА& lsqb; 0025 & rsqb; ИНЖИР. 1 представляет собой схематический вид в разрезе известного уровня техники кристалла интегральной схемы с перевернутой микросхемой, установленного на печатной плате и имеющего рассеивающую тепло крышку с элементом жесткости;
& lsqb; 0026 & rsqb; ИНЖИР. 2 – схематический вид в разрезе известного уровня техники кристалла интегральной схемы с перевернутым кристаллом, установленного на печатной плате и имеющего рассеивающую тепло крышку и радиатор;
& lsqb; 0027 & rsqb; ИНЖИР.3 представляет собой схематический вид в перспективе перевернутой крышки для откидной крышки, показывающий ее нижнюю сторону;
& lsqb; 0028 & rsqb; ИНЖИР. 4 – схематический вид в перспективе перевернутой крышки с откидной крышкой в соответствии с изобретением, показывающий ее нижнюю сторону и прокладки для теплопровода;
& lsqb; 0029 & rsqb; ИНЖИР. 5 – схематический вид в разрезе крышки, показанной на фиг. 4 взяты по линии 5-5 и поставлены вертикально;
& lsqb; 0030 & rsqb; ИНЖИР. 6 – увеличенный схематический вид в разрезе крышки, показанной на фиг.5, показывающий теплопроводы и прикрепленную матрицу;
& lsqb; 0031 & rsqb; ИНЖИР. 7 – схематический вид сверху ряда трубопроводов с одинаковым размером и разнесением;
& lsqb; 0032 & rsqb; ИНЖИР. 8 – схематический вид в разрезе альтернативного варианта осуществления изобретения, показывающий теплопроводы и рассеивающие пластины переменного размера;
& lsqb; 0033 & rsqb; ИНЖИР. 9 – схематический вид в разрезе альтернативного варианта осуществления изобретения, показывающий ориентированные и изменяемые формы теплопровода;
& lsqb; 0034 & rsqb; ИНЖИР.10 – схематический вид в перспективе подложки мощного транзистора, имеющей теплопроводы, образующие слово;
& lsqb; 0035 & rsqb; ИНЖИР. 11 – блок-схема обобщенного процесса изобретения;
& lsqb; 0036 & rsqb; ИНЖИР. 12 – блок-схема первого варианта осуществления способа изобретения;
& lsqb; 0037 & rsqb; ИНЖИР. 13 – схематический вид в разрезе штамповочного пресса согласно альтернативному варианту осуществления способа изобретения;
& lsqb; 0038 & rsqb; ИНЖИР.14 – схематический вид в разрезе пресс-формы в соответствии с другим альтернативным вариантом осуществления способа изобретения;
& lsqb; 0039 & rsqb; ИНЖИР. 15 – схематический вид в перспективе крышки с откидной крышкой, имеющей интегрированную конструкцию резервуара / радиатора в соответствии с настоящим изобретением;
& lsqb; 0040 & rsqb; ИНЖИР. 16 – схематический вид в разрезе крышки, показанной на фиг. 15 по линии 16-16;
& lsqb; 0041 & rsqb; ИНЖИР. 17 – схематический вид в разрезе крышки, показанной на фиг.16, прикрепленный к установленному на подложке флип-чипу;
& lsqb; 0042 & rsqb; ИНЖИР. 19 – схематический вид в перспективе с пространственным разделением деталей предварительно собранных компонентов варианта осуществления резервуара / радиатора в соответствии с настоящим изобретением;
& lsqb; 0043 & rsqb; ИНЖИР. 20 – схематическая пиктограмма, показывающая первую часть варианта осуществления процесса изготовления конструкции резервуара / радиатора;
& lsqb; 0044 & rsqb; ИНЖИР. 21 – схематическая пиктограмма, показывающая среднюю часть варианта осуществления процесса изготовления конструкции резервуара / радиатора;
& lsqb; 0045 & rsqb; ИНЖИР.22 – схематическая пиктограмма, показывающая последнюю часть варианта осуществления процесса изготовления конструкции резервуара / радиатора; и
& lsqb; 0046 & rsqb; ИНЖИР. 23 – схематический вид в разрезе альтернативного варианта осуществления способа, в котором наложенная пластина пропитывающего материала заменяет стержни более раннего варианта осуществления.
ОПИСАНИЕ ПРЕДПОЧТИТЕЛЬНОГО ВАРИАНТА ОСУЩЕСТВЛЕНИЯ ИЗОБРЕТЕНИЯ& lsqb; 0047 & rsqb; Предпочтительный вариант осуществления изобретения будет описан в отношении изготовления теплораспределителя из композитного медно-вольфрамового сплава с металлической матрицей в виде крышки с откидной крышкой.Специалистам в данной области техники ясно, что изобретение применимо для производства других теплоотводящих структур, таких как радиаторы, подложки мощных транзисторов, подложки оптических переключателей, крышки, базовые пластины, корпуса, другие теплоотводы и другие теплоотводы. элементы для терморегулирования компонентов микроэлектроники.
& lsqb; 0048 & rsqb; Обращаясь теперь к чертежам, на фиг. 4-6, крышка с откидной крышкой в соответствии с изобретением. Крышка 15 имеет утолщенную периферию или фланец 16, заканчивающийся на внутренних краевых стенках 17, 18, и нижнюю поверхность 19, образующую полость 20.Средняя область 21 нижней поверхности соответствует области, с которой контактирует микроэлектронная матрица 22 или слой 23 ее монтажного материала, такого как термопластическая смола, термопаста или зона эвтектического соединения. Внутри области контакта 21 расположены первые концы или площадки множества теплопроводов 25, образованных из материала с высокой теплопроводностью, такого как медь. Остальная часть крышки сформирована из материала с согласованным КТР, такого как по существу гомогенный композит из вольфрама и меди.
& lsqb; 0049 & rsqb; Каждый теплопровод 25 содержит в основном цилиндрический, сужающийся или конический корпус, имеющий круглую нижнюю торцевую поверхность или подушку 26 на уровне нижней поверхности полости 19 и круглую противоположную верхнюю торцевую поверхность или подушку 27 на уровне верхней поверхности 30 крышки. Поверхности прокладки выровнены со своими прилегающими поверхностями, чтобы поддерживать плоскостность для улучшения тесного контакта с матрицей или радиатором соответственно.
& lsqb; 0050 & rsqb; Специалисты в данной области техники легко оценят другие формы и трехмерные структуры трубопроводов в зависимости от применения.Размер, плотность и рисунок кабелепровода также будут зависеть от области применения. Как правило, местная теплопроводность максимизируется за счет большего количества или большего размера трубопроводов в данной области. Однако это должно быть сбалансировано с учетом простоты изготовления, структурной целостности и допустимости несоответствия CTE. Простые геометрические поперечные сечения предпочтительны для простоты изготовления. Гладкие формы, такие как цилиндры с круглым поперечным сечением, предпочтительны, если отверстия преформы формируются путем сверления, как описано ниже.Частичные конусы предпочтительны для штампованных отверстий, как описано ниже.
& lsqb; 0051 & rsqb; Например, с функциональной точки зрения предпочтительно поддерживать локализованный объемный баланс между медными теплопроводами и композитным материалом медь-вольфрам, чтобы максимизировать локализованную теплопроводность, в то же время поддерживая приемлемый локализованный КТР. Кроме того, этот баланс помогает минимизировать термические напряжения, возникающие между двумя материалами в рабочем диапазоне температур.Эти конструктивные соображения обычно определяются требованиями конкретного приложения в отношении теплопроводности и теплового расширения.
& lsqb; 0052 & rsqb; Если каждый канал имеет однородную форму и разнесен, специалисты в данной области техники легко поймут, что плотность канала максимизируется для данной области за счет рисунка, показанного на фиг. 7, где четыре канала образуют углы квадрата, который имеет пятый канал в центре, причем угловые каналы являются общими с соседними квадратами.
& lsqb; 0053 & rsqb; Как показано на фиг. 6, каждый из конических каналов 25 ориентирован так, чтобы площадка 26 с меньшей площадью поверхности была обращена к штампу, чтобы уменьшить влияние несоответствия CTE между материалом канала и материалом штампа. Площадь поверхности верхней подушки 27 больше, чтобы усилить многомерный тепловой поток и соответствовать КТР конструкции, такой как медный радиатор или другой рассеиватель тепла.
& lsqb; 0054 & rsqb; Если для теплопроводов используется коническая форма, а большая ось 28 перпендикулярна параллельным верхним и нижним поверхностям 30, 19 крышки, нижняя круглая прокладка будет иметь диаметр DL, который меньше диаметра круглой верхней прокладки. .Соответствующие площади поверхности также будут функцией угла конуса A.
& lsqb; 0055 & rsqb; Достаточное расстояние S между теплопроводами требуется для сохранения совместимости с тепловым расширением. Расстояние, конечно, зависит от размера и формы теплопровода.
& lsqb; 0056 & rsqb; Для многих компонентов, таких как микропроцессоры, разные части матрицы могут выделять больше тепла. Если такие участки известны, можно выборочно размещать трубы с большей плотностью или большими размерами, которые соответствуют этим участкам.Обратимся теперь к фиг. 8 показана композитная подложка 40 с металлической матрицей, имеющая сформированные в ней теплопроводы 41, 42, 43, проходящие через подложку. Трубопроводы имеют цилиндрическую форму, а их размеры и расположение выбраны таким образом, чтобы обеспечить максимальную теплопередачу при сохранении адекватных характеристик расширения. В этом случае центральный теплопровод 41 первого диаметра D1 больше, чем его соседние теплопроводы 42, которые, в свою очередь, имеют диаметры D2 больше, чем диаметры D3 следующих дополнительных соседних теплопроводов 43.В этой конфигурации соотношение между диаметрами соседних теплопроводов следует выбирать так, чтобы поддерживать локальный объемный баланс. Кроме того, использование теплоотводящих верхней и нижней пластин или слоев 44, 45 может быть сформировано во время процесса инфильтрации с использованием хорошо известных технологий для обеспечения избыточного расплавленного металла. Толщина T1, T2 верхней и нижней пластин выбирается близкой к одинаковой, чтобы избежать коробления, которое могло бы произойти из-за непропорционального расширения пластин, если бы они имели разную толщину.Эти две особенности, а именно трубы разного размера и многослойные пластины, раскрыты вместе только для краткости и никоим образом не требуются для совместного использования, как показано.
& lsqb; 0057 & rsqb; Как показано на фиг. 9, в альтернативном варианте осуществления сужающиеся или конические теплопроводы 47 имеют неперпендикулярные большие оси 48, а другие теплопроводы 49 имеют несимметричную форму для отвода тепла от микрочипа 50.
& lsqb; 0058 & rsqb; В дополнительном варианте осуществления, как показано на фиг.10, из-за визуального контраста, создаваемого различными материалами, используемыми для теплопроводов и окружающей подложки, выбор и расположение теплопроводов 51 может быть выполнено для создания букв или других символов, которые будут передавать информацию об устройстве, такую как его характеристики. , его изготовителя или для передачи другой информации для различных целей, включая рекламу. В настоящем варианте осуществления слово «SEMX» образовано заглавными буквами множеством теплопроводов 51, проходящих от верхней поверхности 53 подложки 52 мощного транзистора LDMOS-типа до нижней поверхности 54, которая, в свою очередь, контактировать с теплоотводящим носителем.Таким образом, силовой транзистор будет установлен на верхней поверхности подложки, закрывающей верхние контактные площадки теплопровода.
& lsqb; 0059 & rsqb; Обратимся теперь к фиг. 11, предпочтительный процесс изготовления рассеивающего тепло элемента для микроэлектронной упаковки будет включать сначала создание пористой преформы из материала с высокой температурой плавления, имеющей отверстия, соединяющие разделенные поверхности 61, затем проникновение инфильтрационного материала с низкой температурой плавления в преформу и полное заполнение преформы. отверстия 62, а затем отделка компонента 63 для образования поверхностей, которые будут соединять мощный источник тепла с теплоотводом через теплопроводы.
& lsqb; 0060 & rsqb; Обратимся теперь к фиг. 12, преформа создается путем выбора 71 первого количества частиц порошка первого материала, имеющего относительно низкий КТР и относительно высокую температуру плавления, такого как вольфрам, молибден, рений, железо-никелевые сплавы, сплавы железо-никель-кобальт. и их композиты и сплавы. Частицы могли быть сформированы методами, хорошо известными специалистам в области порошкового материаловедения, порошковой металлургии и традиционной металлургии.Частицы также могут быть предварительно агломерированными частицами металлов с другими металлами, такими как кобальт и никель, для повышения спекаемости.
& lsqb; 0061 & rsqb; Порошок первого материала затем формуют прессованием для образования пористого прессованного зерна 72. Плотность прессованного материала должна быть меньше теоретической, чтобы оставалось
пустот. ПРИМЕР 1& lsqb; 0062 & rsqb; Было предпринято множество попыток откидных крышек. Ниже представлен ряд параметров и наиболее предпочтительных в данном конкретном примере.Предпочтительные и наиболее предпочтительные значения будут сильно различаться в зависимости от приложения.
& lsqb; 0063 & rsqb; Выбирается количество порошка вольфрама, имеющее диаметр частиц от примерно 0,1 до 100 микрон, а более предпочтительно, средний диаметр частиц от примерно 0,5 до 25 микрон. Порошок состоит, по меньшей мере, на приблизительно 99,0% вольфрама, а остальное составляет связующее или примеси. Такой порошок можно приобрести в компании Osram-Sylvania, Тованда, Пенсильвания,
.& lsqb; 0064 & rsqb; Порошок вольфрама загружается в бункер, который подает порошок в пресс-формовочный инструмент поршневого типа, который работает при комнатной температуре под давлением от 35 до 75 тонн на квадратный дюйм («tsi»), а наиболее предпочтительно около 55 tsi. .Скорость подъемника была выбрана в диапазоне от примерно 2 до 30 дюймов в секунду («дюймов в секунду»), а наиболее предпочтительно – около 10 дюймов в секунду. Время выдержки под давлением было выбрано в диапазоне от около 2 до 20 секунд, а наиболее предпочтительно – около 5 секунд. Скорость выброса выбиралась в диапазоне от примерно 2 до 25 дюймов в секунду, а наиболее предпочтительно примерно 10 дюймов в секунду.
& lsqb; 0065 & rsqb; Пресс выталкивает пористую компактную структуру размером примерно 2,5 дюйма × 2,5 дюйма × 0,2 дюйма в форме крышки с откидной крышкой.Полученная пористая сырая прессовка имела плотность от примерно 63% до 89% от теоретической и наиболее предпочтительно примерно 76% от теоретической.
& lsqb; 0066 & rsqb; Компакт помещали в печь для спекания непрерывного действия, имеющую зоны предварительного нагрева, высокой температуры и охлаждения, а также восстановительную атмосферу. Зона высокой температуры, которая оказывает наибольшее влияние на спекание, была установлена в диапазоне от примерно 1150 до 1350 градусов по Цельсию, наиболее предпочтительно примерно от 1250 градусов по Цельсию. Время воздействия составляло примерно от 15 до 120 минут, наиболее предпочтительно примерно 60 минут. .
& lsqb; 0067 & rsqb; После охлаждения спеченную пористую заготовку просверливали на сверлильном станке с ЧПУ для образования цилиндрических отверстий диаметром от примерно 0,031 до 0,0625 дюйма, наиболее предпочтительно примерно 0,040 дюйма. Расстояние между центрами отверстий было, по меньшей мере, в 1,5 раза больше диаметра отверстия, а наиболее предпочтительно примерно в 2 раза больше диаметра отверстия. Расположение отверстий было таким, как показано на фиг. 7 и другие узоры, в том числе образующие символы.
& lsqb; 0068 & rsqb; Достаточное количество меди типа «бескислородная высокая проводимость», имеющая 99.Минимальное содержание меди 9%, остальное – другие легирующие элементы и примеси, в форме пластины размером 2,5 дюйма × 2,5 дюйма × 0,050 дюйма помещали с преформой в графитовую лодочку и помещали в печь для спекания непрерывного действия. В этой печи для инфильтрации высокотемпературная зона была установлена от примерно 1100 ° C до 1350 ° C, наиболее предпочтительно примерно 1150 ° C. Время воздействия составляло от примерно 1 часа до 8 часов, наиболее предпочтительно примерно 5 часов.
& lsqb; 0069 & rsqb; После охлаждения полученную пропитанную преформу затем измельчили для удаления излишков меди и очистили с использованием методов, хорошо известных в отрасли, для формирования готовой крышки откидного кристалла.
& lsqb; 0070 & rsqb; Как показано на фиг. 13, в альтернативном варианте изготовления некоторое количество порошка 81 преформы прессуется в прессе, имеющем выступы 80, соответствующие формированию отверстий в прессовке.
& lsqb; 0071 & rsqb; Обратимся теперь к фиг. 14, отверстия формируются во время стадии компактного прессования с использованием стержневых штифтов 90, установленных внутри полости 91 штампа. Достаточная тяга на стержневых стержнях требует общего сужения диаметра снизу вверх, что позволяет с небольшими затратами создавать конические или конические отверстия, описанные выше.
& lsqb; 0072 & rsqb; Теперь будет описан альтернативный вариант осуществления изобретения, обеспечивающий интегрированные конструкции теплопровода, теплового резервуара и теплового радиатора в корпусе микросхемы. Как и в предыдущих вариантах осуществления, этот вариант осуществления будет описан в отношении изготовления крышки с откидной крышкой. Специалистам в данной области техники ясно, что изобретение применимо для производства других теплоотводящих структур, как упомянуто выше в связи с предыдущими вариантами осуществления.
& lsqb; 0073 & rsqb; Обратимся теперь к фиг. 15-17 показана откидная крышка 100, имеющая интегрированную конструкцию 101 радиатора, состоящую из множества излучающих выступов 102, идущих вверх от верхней поверхности 103 в целом четырехугольного корпуса 104, имеющего утолщенную периферию или фланец 105, заканчивающийся на внутренней стороне. краевые стенки 106, 107 и нижняя поверхность 108, образующая внутреннюю полость 109. Средняя область 110 нижней поверхности соответствует области, контактирующей с микроэлектронной матрицей 111 или ее связующим слоем 112 из материала, такого как припой, термопластическая смола или термопаста.
& lsqb; 0074 & rsqb; Каждое из выступов 102 проходит вниз через корпус 104, образуя теплопровод 115, который заканчивается нижней обращенной к нему концевой площадкой 116. Расположенные посередине выступы / каналы заканчиваются подушечками в области контакта 110 с матрицей, тогда как выступы / каналы 116, расположенные более периферически. оканчиваются концевыми площадками 118 на нижней поверхности 117 периферийного фланца 105 корпуса 104.
& lsqb; 0075 & rsqb; Таким образом, медиальные прокладки расположены близко к тепловыделяющему кристаллу 111 и разделены слоем 112 связывания чипа с крышкой.Периферийные контактные площадки 118 расположены рядом с держателем микросхемы или подложкой 120, разделенные слоем 121 соединения подложки с крышкой. Таким образом, тепловой путь 122 создается от кристалла через подложку, а затем обратно. через периферийные теплопроводы к радиатору для отвода большего количества тепла от матрицы.
& lsqb; 0076 & rsqb; Предпочтительно, каждый из трубопроводов 115 проходит через резервуар 125 тепла, сформированный в корпусе 104 крышки между верхней и нижней поверхностями 103, 117.Конструкция теплового резервуара соединяет между собой два или более трубопроводов, а наиболее предпочтительно все каналы, так что тепловые колебания между трубопроводами эффективно устраняются. Другими словами, вся способность радиатора рассеивать тепло доступна каждому из трубопроводов. Это также способствует поддержанию однородной температуры по всей поверхности штампа, тем самым сводя к минимуму местные термические напряжения.
& lsqb; 0077 & rsqb; Конструкция 101 радиатора, теплопроводы 115 и резервуар 125 тепла выполнены из материала с высокой теплопроводностью, такого как медь.Остальная часть корпуса 104 крышки сформирована из CTE-совместимого материала, такого как однородный композит с металлической матрицей из вольфрама и меди. Специалисты в данной области легко оценят другие материалы, которые могут быть адекватно использованы. Например, помимо меди материалом с высокой теплопроводностью могут быть серебро, карбид кремния и композиты углерод-медь. Если для материала, совместимого с КТР, используется композит с металлической матрицей, то этот материал может быть, помимо вольфрама-меди, например, молибден-медь, медь-графит и молибден.
& lsqb; 0078 & rsqb; Как показано на фиг. 17, интегрированная крышка 100 прикреплена к откидной микросхеме 111 и подложке 120 с использованием связующего слоя 121, 112 из материала, такого как припой, для образования корпуса 126, охватывающего перевернутую микросхему. Необходимо соблюдать осторожность при выборе типа припоя для соединения. слой так, чтобы температура, необходимая для его оплавления во время прикрепления к микросхеме и подложке, не повредила существующие связи, такие как типичное паяное соединение 127 между микросхемой и подложкой. Кроме того, тип припоя, выбранный для связующего слоя, должен быть способен образовывать связи, которые выдерживают температуру любых процессов оплавления припоя, таких как решетка микрошариков золота и олова (Micro BGA), используемая для поверхностного монтажа подложки на печатной плате. .
& lsqb; 0079 & rsqb; В альтернативном варианте осуществления, как показано на фиг. 18, конструкция 130 теплового резервуара сформирована на верхней поверхности 131 корпуса 132 крышки. Этот вариант осуществления подходит для менее требовательных условий теплового расширения и, как правило, дешевле в изготовлении.
& lsqb; 0080 & rsqb; Обратимся теперь к фиг. 19-22, теперь будет описан предпочтительный процесс изготовления вышеописанной крышки с откидной крышкой. Как правило, корпус крышки изготовлен из композитного материала с металлической матрицей, сочетающего в себе более высокую температуру плавления, матричный материал с низким тепловым расширением, такой как вольфрам, с более низкой температурой плавления, более высокое тепловое расширение и пропитывающий материал с высокой теплопроводностью, такой как медь.Чтобы сократить количество этапов обработки, предпочтительно, чтобы теплопроводы, тепловые резервуары и радиаторные конструкции были выполнены из того же проникающего металла с более низкой температурой плавления, который использовался для формирования корпуса, такого как медь.
& lsqb; 0081 & rsqb; Как показано на фиг. 19 крышка начинается как предварительно просверленная предварительная сборка 140, в которой корпус образован из нижней заготовки 141 и верхней заготовки 142 из пористого матричного материала, между которыми находится пластина 143 из пропитывающего материала. Верхняя преформа имеет ряд перфорационных отверстий 144, проникающих от верхней поверхности 145 к нижней поверхности 146.Пластина 143 имеет соответствующий набор отверстий 147, коаксиально расположенных по отношению к перфорационным отверстиям и проникающих через верхнюю поверхность 148 к нижней поверхности 149. Аналогично, нижняя заготовка 141 имеет соответствующий набор отверстий 150, расположенных соосно относительно перфорации. перфорации и проходят от верхней поверхности 151 на некоторое расстояние в преформу. Стержни 152 из проникающего материала выбираются для вставки в перфорационные отверстия / отверстия / скважины. Перфорация, отверстия, колодцы и стержни имеют размер и расположение, соответствующие конструкции теплопровода и выступа радиатора в готовой крышке.
& lsqb; 0082 & rsqb; Будет описана следующая стадия процесса, на которой вольфрам выбран в качестве материала матрицы, а медь выбрана в качестве пропитывающего материала. Специалисты в данной области легко оценят применимость этапов с использованием других материалов.
& lsqb; 0083 & rsqb; Как показано на фиг. 20 верхняя часть 160 преформы формируется 161 методами порошковой металлургии, хорошо известными в данной области техники. Некоторое количество порошка вольфрама выбирается и прессуется, чтобы сформировать прессовку, которую затем спекают в пористую заготовку, имеющую пористость, которая может быть позже пропитана расплавленной медью.Верх либо сформирован, либо обработан так, чтобы на нижней стороне была полость 162, размер которой соответствовал бы медной пластине. Затем верх пористой преформы перфорируют 163, чтобы иметь набор перфораций 164 по размеру и местоположению, чтобы соответствовать более поздним структурам теплопровода и, возможно, более поздним структурам выступа радиатора. Следует отметить, что размер, количество и форма теплопроводов и выступающих структур радиатора предпочтительно выбираются после тщательного анализа терморегулирования в данном устройстве и применении.Такие анализы хорошо известны специалистам в данной области.
& lsqb; 0084 & rsqb; Нижняя часть 165 преформы формируется отдельно 166 посредством процесса, аналогичного описанному выше верху преформы, и просверливается 167 для образования ряда правых цилиндрических колодцев 168, равных количеству перфораций, размер и расположение которых соответствуют более поздним конструкциям теплопроводов. .
& lsqb; 0085 & rsqb; Медная пластина 169 сформирована 170 с возможностью вставки в полость верхней преформы.В пластине также просверливают 171 отверстия для образования отверстий 172, коаксиально совпадающих с перфорационными отверстиями и лунками.
& lsqb; 0086 & rsqb; Затем предварительно собирают 173 пористую верхнюю заготовку из вольфрама, медную вставку и нижнюю заготовку из пористого вольфрама, чтобы сформировать предварительную сборку 174 корпуса крышки.
& lsqb; 0087 & rsqb; Как показано на фиг. 21 предварительная сборка 174 корпуса крышки загружается 175 в удерживающую прорезь 176 графитовой лодочки 177. Затем крышка 178 графитовой лодочки точно позиционируется 179 с помощью выравнивающих направляющих штифтов 180 на верхней части предварительной сборки корпуса крышки так, чтобы цилиндрические каналы 181 в крышке совмещены с отверстиями в предварительной сборке корпуса.
& lsqb; 0088 & rsqb; Формованные медные стержни 182 имеют длину и диаметр 183, которые позволяют вводить 184 в выровненные каналы, перфорации, отверстия и лунки для образования предварительно отфильтрованной крышки в лодочке для спекания 185.
& lsqb; 0089 & rsqb; Лодочка с предварительно отфильтрованной крышкой затем спекается 186 путем помещения в печь для спекания, в результате чего медь плавится и течет в поры преформ и полностью заполняет перфорационные отверстия / отверстия / лунки с образованием теплопроводов.Полость между заготовками заполняется для образования теплового резервуара. Медь, остающаяся в каналах крышки, образует выступы теплоотводящей конструкции радиатора предварительно обработанной спеченной интегрированной крышки 187.
& lsqb; 0090 & rsqb; После охлаждения пропитанная крышка затем подвергается механической обработке 188 для формирования готовой крышки 189 перед прикреплением матрицы путем правильного определения размеров выступов и создания полости 190, содержащей матрицу.
& lsqb; 0091 & rsqb; Как показано на фиг. 22, перед формированием корпуса flip-chip формируют 192 связующий слой 191 припоя на нижней поверхности 193 крышки и нижних поверхностях 194 периферии 195 крышки.Крышка затем прикрепляется 196 к кристаллу 197 и подложке 198 для формирования готовой упаковки 200.
& lsqb; 0092 & rsqb; Обратимся теперь к фиг. 23, в альтернативном варианте осуществления процесса стержни могут быть заменены пластиной 201 из меди, размещенной над каналами перед спеканием, которая будет стекать по каналам с образованием необходимых структур. Этот процесс показан, когда требуется особенно большое количество выступов / теплопроводов.
ПРИМЕР 2& lsqb; 0093 & rsqb; Ниже представлен ряд параметров и наиболее предпочтительных в данном конкретном примере.Предпочтительные и наиболее предпочтительные значения будут сильно различаться в зависимости от приложения.
& lsqb; 0094 & rsqb; Выбирается количество порошка вольфрама, имеющее диаметр частиц от примерно 0,1 до 100 микрон, а более предпочтительно, средний диаметр частиц от примерно 0,5 до 25 микрон. Порошок состоит, по меньшей мере, на приблизительно 99,0% вольфрама, а остальное составляет связующее или примеси. Такой порошок можно приобрести в компании Osram-Sylvania, Тованда, Пенсильвания,
.& lsqb; 0095 & rsqb; Порошок вольфрама загружается в бункер, который подает порошок в пресс-формовочный инструмент поршневого типа, который работает при комнатной температуре под давлением от 35 до 75 тонн на квадратный дюйм («tsi»), а наиболее предпочтительно около 55 tsi. .Скорость подъемника была выбрана в диапазоне от примерно 2 до 30 дюймов в секунду («дюймов в секунду»), а наиболее предпочтительно – около 10 дюймов в секунду. Время выдержки под давлением было выбрано в диапазоне от около 2 до 20 секунд, а наиболее предпочтительно – около 5 секунд. Скорость выброса выбиралась в диапазоне от примерно 2 до 25 дюймов в секунду, а наиболее предпочтительно примерно 10 дюймов в секунду.
& lsqb; 0096 & rsqb; Пресс выталкивает пористую компактную структуру размером приблизительно 2,5 дюйма × 2,5 дюйма × 0,2 дюйма в форме верхней и нижней структуры корпуса крышки.Верх был сформирован так, чтобы иметь полость на нижней стороне, размеры которой позволяют разместить пластину преформ резервуара. Полученные пористые сырые прессовки имели плотность от примерно 63% до 89% от теоретической и наиболее предпочтительно примерно 76% от теоретической.
& lsqb; 0097 & rsqb; Компакт помещали в печь для спекания непрерывного действия, имеющую зоны предварительного нагрева, высокой температуры и охлаждения, а также восстановительную атмосферу. Зона высокой температуры, которая оказывает наибольшее влияние на спекание, была установлена в пределах примерно 1150 ° C.и 1350 градусов по Цельсию, наиболее предпочтительно около 1250 градусов по Цельсию. Время воздействия составляло от примерно 15 до 120 минут, наиболее предпочтительно примерно 60 минут.
& lsqb; 0098 & rsqb; Полученные спеченные пористые заготовки верхней и нижней структурных частей имеют плотность от примерно 65% до 90% от теоретической и наиболее предпочтительно примерно 85% от теоретической.
& lsqb; 0099 & rsqb; После охлаждения спеченные пористые заготовки просверливали на сверлильном станке с ЧПУ.В верхней преформе просверливали цилиндрические отверстия диаметром от примерно 0,031 до 0,0625 дюйма, наиболее предпочтительно примерно 0,040 дюйма. Расстояние между центрами отверстий было, по меньшей мере, в 1,5 раза больше диаметра отверстия, а наиболее предпочтительно примерно в 2 раза больше диаметра отверстия. Рисунок отверстий представлял собой ортогональную сетку. Нижняя заготовка просверливалась с помощью долота с плоской головкой типа концевой фрезы для создания по существу правильных цилиндрических лунок глубиной от примерно 0,05 дюйма до 0,15 дюйма и наиболее предпочтительно примерно 0.1 дюйм.
& lsqb; 0100 & rsqb; Была выбрана четырехугольная медная пластина типа «бескислородная высокая проводимость», имеющая минимальное содержание меди 99,9%, остальное – другие легирующие элементы и примеси, размером приблизительно 2,3 дюйма × 2,3 дюйма × 0,1 дюйма, чтобы поместиться в верхней полости преформы. В пластине просверливали сквозные отверстия, чтобы сформировать цилиндрические отверстия, соизмеримые с отверстиями и углублениями заготовок корпуса.
& lsqb; 0101 & rsqb; Серия правильных цилиндрических медных стержней того же типа, что и пластина, размером около 0.5 дюймов в длину и около 0,04 дюйма в диаметре были получены методами, хорошо известными в данной области. Такие стержни коммерчески доступны от компании McMaster Catalog Company, хорошо известной в данной области техники.
& lsqb; 0102 & rsqb; Верхняя и нижняя заготовки, а также медная пластина были предварительно собраны, помещая пластину между заготовками. Предварительная сборка была размещена в графитовой лодке и закрыта графитовой крышкой, имеющей цилиндрические каналы, соразмерные перфорациям, отверстиям и колодцам предварительной сборки.Затем в каждый из совмещенных каналов / перфораций / отверстий / лунок вставляли медный стержень.
& lsqb; 0103 & rsqb; Затем загруженную лодочку помещали в печь для спекания непрерывного действия. В этой печи для инфильтрации высокотемпературная зона была установлена от примерно 1100 ° C до 1350 ° C, наиболее предпочтительно примерно 1150 ° C. Время воздействия составляло от примерно 1 часа до 8 часов, наиболее предпочтительно примерно 5 часов.
& lsqb; 0104 & rsqb; После охлаждения полученная крышка была извлечена из лодки и обработана для удаления излишков меди и образования полости на нижней стороне матрицы.Затем крышка была очищена с использованием методов, хорошо известных в отрасли, для формирования готовой крышки с откидной крышкой.
& lsqb; 0105 & rsqb; Затем крышки загружали в автоматический дозатор припоя, имеющий температуру плавления от 200 ° C до 240 ° C, а наиболее предпочтительно от примерно 220 ° C до 230 ° C для размещения ранее нанесенных материалов и более поздние температуры процесса. Затем крышки нагревали для оплавления припоя с образованием линии соединения связующего слоя припоя менее примерно 0.001 дюйм.
& lsqb; 0106 & rsqb; Хотя были описаны предпочтительные варианты осуществления изобретения, могут быть выполнены модификации и другие варианты осуществления, не выходящие за рамки сущности изобретения и объема прилагаемой формулы изобретения.
Патент США на патент на металлизацию микросхем (Патент № 4,113,578, выдан 12 сентября 1978 г.)
Уровень техникиЭто изобретение относится к формированию выступов контактных электродов в таких структурах, как пластины интегральных схем и монтажные подложки.
Для упаковки микроэлектронных компонентов разрабатываются крупносерийные, быстрые в обращении и экономичные системы упаковки для удовлетворения растущего спроса на такие компоненты и системы таких компонентов по разумной цене. Одним из методов монтажа компонентов в рамках одного из этих методов упаковки является так называемая техника соединения «лицевой стороной вниз». В этом методе контактные электроды в виде небольших металлических выступов предусмотрены на выбранных участках сети межсоединений металлизации, обычно там, где требуются электрические соединения с внешними компонентами.Эта сеть межсоединений металлизации предусмотрена в устанавливаемом компоненте, обычно в интегральной микросхеме. Компонент должен как устанавливаться, так и обеспечивать электрическое соединение через эти выступы.
Микросхемы интегральной схемы, имеющие эти выступы, размещаются сетевой стороной, обращенной к поверхности монтажной подложки, и размещаются так, чтобы выступы контактировали с токопроводящими выводами, предусмотренными на подложке, к которой должны быть прикреплены выступы. Затем нагревание выступов заставляет их течь и, таким образом, вступать в тесный контакт с этими проводящими свинцовыми частями подложки, так что при охлаждении возникает желаемое соединение.Следовательно, требуется, чтобы (1) металл, используемый для изготовления выступов, и (2) материалы и структура, с которыми этот металл выступа должен взаимодействовать в связке друг с другом, приводили к выступам, имеющим достаточную когезионную способность в расплавленном состоянии, чтобы обеспечить поддержку для фишка – т.е. чтобы неровности при расплавлении не разрушались. Такое сжатие приведет к тому, что чип окажется в непосредственной близости от подложки или прямо на ней, а металлический выступ будет распространяться настолько, насколько он будет течь. Выступ зазора, не используемый для плотного соединения с проводящими выводами подложки и, возможно, не сформированный в сети межсоединений, может использоваться для отделения чипа от подложки, хотя он не может препятствовать течению расплавленного металла выступа.Вытекание металлического выступа можно предотвратить независимо от того, используется ли выступ зазора или нет, путем использования, например, стеклянной перегородки на подложке, окружающей точку, на которой должно быть выполнено соединение.
Другой метод упаковки также имеет металлические выступы, обычно образующиеся на сети межсоединений с металлизацией, снабженной компонентом, который должен быть упакован, опять же, как правило, микросхемой интегральной схемы, выступы должны быть обеспечены в выбранных частях сети, где желателен контакт с внешними компонентами.Контакт с внешними компонентами снова обеспечивается посредством соединения с токопроводящими выводами, предусмотренными на монтажной подложке. Однако метод монтажа микросхемы в этом способе упаковки отличается от техники «лицевой стороной вниз» тем, что поверхность микросхемы, противоположная поверхности, имеющей предусмотренную на ней сеть межсоединений, также должна быть установлена на поверхности монтажной подложки. Для этого требуется выводная рамка, имеющая проводящие выводы внутри, с этими проводящими выводами, прикрепленными к выступам, чтобы обеспечить выводы для соединения с участками проводящих выводов, предусмотренными на подложке.Этот метод соединения можно назвать методом монтажа выводной рамки.
Выпуклости в этой технике соединения не предназначены для значительного протекания при воздействии на них тепла с целью их соединения с проводящими выводами выводной рамки. Скорее, эвтектическая связь должна образовываться между выступами и токопроводящими выводами, требующими, чтобы (1) металл выступа и (2) проводящий металлический свинец рамки выводов мог образовывать удовлетворительную эвтектическую связь. Поскольку не должно происходить заметного потока, не требуется никаких мер для предотвращения потока металла выступа по проводящему проводу выводной рамки.
В первом методе монтажа, упомянутом выше, было указано, что необходимо принять некоторые меры в отношении подложки и металла выступов, чтобы не допустить, чтобы выступы, которые должны течь, проходить через подложку на любое большое расстояние. Эта необходимость ограничить поток расплавленных выступов существует, как изложено выше, потому что неограниченный поток приведет к уменьшению выступов и оставит мало, чтобы обеспечить зазор между микросхемой интегральной схемы и подложкой. Даже если предусмотрен выступ зазора, неограниченный поток металла выступа не приведет к тесному электрическому контакту или неправильному контакту между микросхемой и подложкой.
Как указано выше, выбор метода упаковки и, следовательно, метода монтажа компонентов (1) ограничивает виды металлов, которые подходят для создания выступов контактного электрода, например, на межсоединительной сети металлизации компонентов и (2) ограничивает виды материалов и / или структур, которые могут использоваться в сети или рядом с ней, и предметом, который должен быть соединен, в точках, где выступы контактного электрода должны быть сформированы или связаны, соответственно. Опять же, например, сеть межсоединений берется такой, которая предусмотрена на микросхеме интегральной схемы, и микросхема должна быть установлена на монтажной подложке и обеспечивать электрический контакт с монтажной подложкой.В технике «лицевой стороной вниз» металл контактного электрода должен обладать способностью течь, и обычно нельзя допускать, чтобы большая часть поверхности смачивалась в его непосредственной области на микросхеме интегральной схемы или в непосредственной близости от предполагаемого соединения на микросхеме. проводящая свинцовая часть подложки. В этом случае поверхностное натяжение расплавленного металла, составляющего большую часть выступа, служит для придания расплавленному выступу достаточной структурной целостности для сохранения зазора между чипом и подложкой.
Хорошо известная металлургическая система для выступа, используемая в технике монтажа «лицевой стороной вниз», представлена в четырех слоях на выбранной части межсоединительной сети. Выбранный участок обычно доступен в качестве обнажения сети через отверстие в изолирующем слое. Межкомпонентная сеть обычно изготавливается из алюминия.
Для создания металлургической системы на изолирующий верхний слой помещается металлическая маска, при этом маска имеет отверстие, которое концентрично, но больше, чем отверстие в изолирующем верхнем слое.При использовании методов напыления на алюминий через отверстие в металлической маске и отверстие в изолирующем верхнем слое наносится слой хрома. За этим следует испарение меди на хром, которое, в свою очередь, сопровождается испарением золота на меди. Эти три металлических слоя служат для герметизации, предотвращения образования нежелательных интерметаллических соединений и для обеспечения надлежащего прилипания пленок к различным поверхностям. Общая толщина этих трех слоев обычно составляет 10 000 А или меньше.Важно, чтобы не было слишком много золота, потому что оно образует нежелательные интерметаллические соединения с оловом в припое, которые затем испаряются на золото. Затем припой испаряется на золото и образует основную часть выступа, обычно имеющую высоту в несколько милов.
Однако использование выводной рамы обычно предотвращает использование припоя в качестве основного компонента в корпусе выступа. Обычно припой не используется и не образует эвтектическую связь с другим металлом, соединенным с ним таким образом, чтобы включить в качестве составной части этот другой металл в металлургическую связь, которая должна быть образована.Скорее, припой используется для соединения с другим металлом из-за его адгезионных свойств к поверхности другого металла, когда припой затвердевает из расплавленного состояния, в котором он смачивал поверхность другого металла. Если, однако, выводная рамка находится в контакте с выступом из расплавленного припоя, в результате припой будет течь по выводной рамке в таком количестве, чтобы значительно уменьшить выступ. Кроме того, приложение давления через вывод выводной рамки к выступу из расплавленного припоя неизбежно при контакте выводной рамки с выступом.Это давление на выступ расплавленного припоя преодолеет поверхностное натяжение выступа расплавленного припоя, придав выступу необходимую когезионную способность, чтобы предотвратить его растекание, и, таким образом, поток через поверхность, на которой образован выступ, будет происходить, что усугубит проблему текучести в расплавленном состоянии.
Таким образом, припой обычно не является подходящим металлом для большей части тела выступа, где должна быть образована эвтектическая связь с выводом рамки с выводами, изготовленным из металла, обычно используемого для таких выводов. Использование паяного выступа в расплавленном состоянии для прикрепления вывода выводной рамки было бы затруднительным без внесения нежелательных изменений в сам вывод выводной рамки и / или в окрестности точки на поверхности, где предусмотрен вывод.
Использование эвтектического соединения для техники монтажа выводной рамки требует, чтобы металл для использования в основной части корпуса выступа и металл, который будет использоваться для токопроводящих выводов в выводной рамке, были способны образовывать эвтектическую связь при давлениях и температурах. не слишком экстремально, учитывая чип и подложку, после чего должен быть функциональным. Температура эвтектики, которая будет ниже точки плавления любого из задействованных металлов, должна быть существенно выше, чем температура, при которой соединение с проводящими выводами подложки формируется на противоположном конце выводного вывода рамки.Эта последняя связь с проводящим проводом подложки обычно представляет собой соединение припоя. Эти критерии гарантируют, что металл, составляющий основную часть выпуклого электрода, может образовывать эвтектическую связь с относительно небольшим количеством металла в выводной рамке без заметной потери выпуклостью своих структурных и формовых характеристик при достижении температуры эвтектики, и дополнительно гарантирует, что соединение не будет ухудшено из-за образования соединения с проводящими выводами подложки на противоположном конце вывода рамки.Еще одна желательная особенность металла, который должен составлять основную часть тела выпуклости, состоит в том, что он является относительно инертным, чтобы не образовывать нежелательные соединения, которые могут влиять на целостность связей или иным образом влиять на материалы, окружающие связь.
Удовлетворительным сочетанием металлов для монтажа выводной рамки являются золото для большей части корпуса выступа и олово, которое может быть нанесено на медный проводящий провод выводной рамки. Эта комбинация металлов является удовлетворительной, поэтому для создания выступов в методике монтажа выводной рамки можно использовать ту же структуру слоев, что и при методе монтажа «лицевой стороной вниз» вплоть до нанесения припоя, причем это хром на поверхности. Алюминиевая соединительная сеть, затем медь и, наконец, золото, причем золото присутствует в гораздо большем количестве, чем в технике «лицевой стороной вниз», чтобы обеспечить желаемую высоту выступа.Вместо меди и хрома можно использовать другие металлы. Кроме того, также возможны комбинации металлов, отличных от золота и олова.
Поскольку такой же рисунок слоев металлов может быть нанесен на алюминиевую межсоединительную сеть, может показаться, что для их размещения можно использовать ту же технику осаждения, то есть испарение. Однако использование испарения для нанесения большого количества дорогостоящего металла, такого как здесь золото, неэкономично, потому что такая небольшая часть испарившегося металла достигает положения, необходимого для осаждения, но скорее осаждается во многих местах камеры для осаждения, поскольку испаренный металл заполняет камеру с небольшой направленностью.
Методы гальваники также использовались для создания выступов контактных электродов в соединительных сетях. Однако в известных методах нанесения покрытия металлическая маска не используется. Скорее, необходимые слои металлов, одинаковый узор из хрома, меди и золота, испаряются по всей поверхности изолирующего слоя, покрывающего сеть межсоединений, и на открытых выбранных участках сети межсоединений. Нежелательным результатом этого является то, что при охлаждении, особенно в случае интегральных схем, быстрое сжатие теперь сконденсированных металлов имеет тенденцию вызывать микротрещины в различных местах изоляционного слоя, нанесенного на межсоединительную сеть, что приводит к потере урожайности в последующих операциях. .
После испарения бланкета слой фоторезиста помещается на последний испарившийся металл, и в фоторезисте создаются отверстия напротив выбранных участков межсоединительной сети, где желательно разместить неровности на последнем испаренном металле. Используется процесс позолоты поверх результата, но золото будет прилипать и покрывать только участки последнего испаренного металла в отверстиях слоя фоторезиста. Затем фоторезист удаляется, как и те большие части нескольких слоев испаренного металла, которые не служат основой для выпуклости.Удаление этих испаренных металлов требует нежелательного множества стадий травления. Если микротрещины, упомянутые выше, возникли в точках, чтобы обнажить части сети межсоединений ниже, на одном или нескольких этапах травления может также протравиться алюминий, используемый в сети межсоединений.
На этом этапе требуется термическая обработка спеканием в сухом азоте, чтобы заставить материал межсоединительной сети, обычно алюминий, диффундировать как через его собственные оксиды, так и через любые остатки материала изоляционного слоя, образующиеся на выбранных участках, чтобы обеспечить хороший контакт. с нанесением покрывающих слоев испаренного металла, если требуется относительно небольшое сопротивление электрода.Это спекание необходимо, поскольку методы очистки ограничены без использования металлической маски для защиты поверхностей из-за результирующего ухудшения характеристик поверхности тех поверхностей, которые не участвуют в поддержании неровностей.
Техника монтажа компонентов выводной рамки, особенно для интегральных схем, является весьма желательной техникой, когда рассматривается схемная работа компонентов в том виде, в каком они установлены, потому что лицевая сторона компонента, не имеющая выступов, монтируется непосредственно на подложке.Это обеспечивает, в качестве естественного шага метода, гораздо лучший отвод тепла, выделяемого компонентом во время работы схемы, чем метод монтажа «лицевой стороной вниз», когда большая часть тепла рассеивается только через выступы, если не будут приняты дополнительные меры. предпринято. Таким образом, желательно иметь экономичный и эффективный способ создания выступов контактного электрода на компоненте для использования в технике монтажа компонента выводной рамки.
СУЩНОСТЬ ИЗОБРЕТЕНИЯВ настоящем изобретении используются методы напыления и гальваники для создания выступов контактного электрода.Процесс может включать только этапы распыления для выполнения осаждения металлов или может включать распыление, дополненное этапами нанесения покрытия для создания выступов контактного электрода. Гальваника также может использоваться в дополнение к другим типам начальных этапов осаждения.
Выбираются части структуры, обычно части сети межсоединений металлизации, на которых создаются выступы контактного электрода. Маска, обычно из металла, имеющая рисунок отверстий в ней, соответствующий выбранным частям, помещается напротив конструкции так, чтобы отверстия были концентричными с областями, выбранными для создания выступов.
Эта замаскированная структура должна быть предусмотрена в камере распылительного аппарата. Устройство для распыления содержит электроды истока, каждый из которых имеет тип металла, который желательно наносить через отверстия в маске. В этой камере предусмотрена газовая атмосфера.
Выбранные части, на которых должны быть сформированы выступы контактных электродов, которые, возможно, были сделаны частично доступными ранее, сначала полностью обнажаются за счет использования стадии очистки распылением. После этого каждый тип металла, который требуется осаждать через отверстия в металлической маске, распыляется через эти отверстия в желаемом порядке осаждения.Хорошая направленность выброшенных атомов металла, возникающая в результате использования метода распыления, приводит к использованию меньших количеств каждого типа металла, чем было бы в случае использования метода испарения. Кроме того, образование выступов путем распыления означает, что каждый распыленный слой имеет лучшую адгезию к материалу, находящемуся под ним, что дает лучшее сцепление с неровностями из-за свойства самоочищения метода распыления и из-за большей вероятности образования химических связей в каждом распыляемом материале. слой.Если должны использоваться только стадии распыления металла, распыленные металлы должны достигать достаточной высоты для образования выступа контактного электрода, который составляет около 0,2 мил или более.
Если этапы распыления должны быть дополнены этапом нанесения гальванического покрытия, маска удаляется после того, как металлы были распылены через ее отверстия, чтобы сформировать металлическую основу для гальванической выпуклости с высотой основания меньше, чем требуется для выпуклости. . Металлический мгновенный слой, обычно тот же металл, что и последний напыленный металл, представляет собой покрытие, испаряющееся над поверхностью конструкции, когда должны использоваться методы гальваники.Затем на этом слое металлической вспышки наносят слой фоторезиста с отверстиями в слое фоторезиста, которые концентричны выбранным участкам. Затем на металл, открывающийся в отверстиях в слое фоторезиста, наносят металлический слой, как правило, металл, напыленный последним. Гальванический металл не отслаивается и не прилипает к слою фоторезиста. Слой фоторезиста затем удаляется, как и слой металлической вспышки, оставляющий неровности контактного электрода.
Формирование основы из напыленных металлических слоев с использованием маски означает, что этап очистки распылением доступен для использования на начальном этапе в процессе нанесения покрытия, поэтому этап спекания не требуется для достижения относительно низкого сопротивления электрода, если это желательно.Слои напыленного металла также обеспечивают прочно прилегающую металлическую основу, на которую накладывается оставшийся металл для образования выступов контактного электрода. Микротрещины сводятся к минимуму, поскольку напыленные слои покрывают лишь небольшую часть поверхности конструкции.
Электролитическое покрытие может использоваться вместо гальванического покрытия для химического нанесения покрытия на часть металла, используемого для обеспечения большей части выпуклости. Этот метод нанесения покрытия исключает использование металлического флеш-слоя и слоя фоторезиста.
КРАТКОЕ ОПИСАНИЕ ЧЕРТЕЖЕЙРИС. С 1 по 5 показаны результаты этапов процесса распыления, приводящих к выступам контактного электрода, а
РИС. С 6 по 8 показаны результаты этапов процесса дополнительного покрытия, которые приводят к появлению неровностей на контактных электродах.
ОПИСАНИЕ ПРЕДПОЧТИТЕЛЬНЫХ ВАРИАНТОВ ОСУЩЕСТВЛЕНИЯРИС. 1 показывает часть монолитной пластины интегральной схемы после металлизации и пассивации и до начала обработки для размещения выступов контактных электродов на межсоединительной сети.Кремниевый материал 10 показан поддерживающим алюминиевую межсоединительную сеть 11 электронного устройства, которая, как показано, соединяется со слоем кремния 10. Межкомпонентная сеть 11 по большей части поддерживается на слое 12 диоксида кремния, а также покрыта слоем 12 диоксида кремния, который предусмотрен для пассивация и защита.
РИС. 2 показано отверстие 13, выполненное в слое 12 диоксида кремния для обнажения выбранного участка 14 межсоединительной сети 11. Кремниевый участок 10 на фиг.1 исключен из остальных чертежей, поскольку он не играет прямой роли в описанном здесь процессе. Отверстие 13 может быть выполнено хорошо известными методами травления с последующей стадией очистки распылением, описанной ниже. В некоторых случаях отверстие 13 может быть выполнено полностью методами очистки распылением. Существуют ситуации, в которых может быть желательно сформировать выступы на частях конструкции, которые не являются частью сети межсоединений. Тогда металл 11 не будет частью межсоединительной сети, и действительно, при правильном выборе материалов для образования выступа, выступ может быть сформирован на кремнии, диоксиде кремния или другом материале, поэтому металл не потребуется там, где алюминий металл 11 показан.
Также показано на фиг. 2 представляет собой часть металлической маски 15, которая все еще отделена от структуры, содержащей слой 12 диоксида кремния, межсоединительную сеть 11 и кремний, который теперь не используется, но вот-вот будет помещен напротив нее.
Отверстие 16 в маске должно располагаться по существу соосно с выбранной частью межсоединительной сети 14 и, следовательно, с отверстием 13, оставляя часть диоксида кремния 12 открытой. Металлические маски в виде листа металла с предусмотренными в нем отдельными отверстиями хорошо известны, и материалом, подходящим для такой маски, является молибден.
РИС. 3 показывает металлическую маску 15 на месте напротив слоя 12 диоксида кремния. На этом этапе процесса выполняется упомянутый выше этап очистки распылением после травления. Этот этап выполняется для удаления остатков диоксида кремния, оксидов металлов и любых других загрязнений на выбранной части 14 межсоединительной сети 11, чтобы сначала полностью обнажить эту выбранную часть и удалить загрязнения с поверхностей слоя 12 диоксида кремния, остающегося открытыми в отверстии 16 в отверстии. маска 15.Эта очистка будет выполняться в тех случаях, когда отверстие 13 обеспечивается методами очистки распылением. Эффективная очистка здесь устраняет необходимость в стадии спекания на более позднем этапе процесса, если желательно очень низкое контактное сопротивление. Очистка распылением выполняется в вакуумной камере распылительного устройства, в котором размещается пластина, замаскированная выше. Стандартное распылительное устройство того типа, которое используется для осаждения тонких пленок, обычно является удовлетворительным.
Вакуумная камера откачивается и в нее помещается атмосфера инертного газа, обычно аргона, хотя в этих и других обстоятельствах могут использоваться другие газы или газовые смеси, включая, в некоторых случаях, газы, которые не являются инертными. Непрерывный поток аргона через вакуумную камеру путем удаления и добавления помогает удалить и таким образом уменьшить загрязняющие вещества, образующиеся в ней во время распыления. Эта вакуумная откачка и обеспечение выбранной газовой атмосферы происходит только один раз на этапах распыления в этом процессе.Обычная атмосфера не попадает в камеру после начальной откачки, предшествующей использованию этапов очистки распылением, до тех пор, пока этапы распыления металла не будут завершены. В общем, давление выбранной атмосферы для камеры никогда не должно приближаться к обычному атмосферному давлению после начальной откачки, то есть начального значительного снижения давления, до тех пор, пока распыление не будет завершено. Такое выполнение этапов распыления во время единственного обеспечения выбранной атмосферы в значительной степени способствует предотвращению загрязнения открытых поверхностей, происходящего во время этапов распыления в процессе.Как правило, во время обработки избегают затратных по времени дополнительных откачиваний.
Неактивный электрод содержится в вакуумной камере, как и электроды источника, каждый из которых имеет предусмотренный в нем тип металла, который желательно наносить через отверстие 16 металлической маски 15. Для очистки распылением достаточно большой Между неактивным электродом и структурой пластины прикладывается потенциал, при этом пластина является отрицательной по отношению к неактивному электроду, чтобы вызвать ионизацию газообразного аргона между неактивным электродом и структурой пластины.Образующиеся в результате ионы аргона затем ударяются о структуру пластины с достаточным импульсом для удаления с нее поверхностных частиц и атомов в ней. Это столкновение ионов аргона продолжается до тех пор, пока несколько сотен ангстрем (порядка 300 А) диоксида кремния, остатков диоксида кремния, оксидов металлов и / или алюминия не будут удалены после травления. Парциальное давление газообразного аргона для операции очистки обычно составляет 20 микрон ртутного столба.
После операции очистки первый тип металла, который требуется нанести через отверстие 16 в металлической маске 15 и на выбранный участок 14, затем распыляется как на эту область, так и на те участки слоя диоксида кремния 12, открытые в отверстиях 16.Для распыления выбранного металла между неактивным электродом и электродом источника (отрицательным электродом источника во время распыления металла) прикладывается достаточный потенциал, содержащий этот металл для ионизации газа в вакуумной камере между этими двумя электродами. Опять же, этим газом является аргон, и земная атмосфера не попадает в камеру между этапом очистки распылением и распылением металлов. Маскируемая пластина помещается рядом с неактивным электродом (в темном пространстве катода) или на нем (в темном пространстве катода) так, чтобы области, на которых должно происходить осаждение, были обращены к электроду истока.
Распыление может выполняться с использованием постоянного (DC) напряжения или радиочастотного (RF) напряжения и с мишенью, на которой должно происходить напыление, либо имеющей, либо не имеющей постоянного напряжения смещения относительно анода, обычно анода находясь под потенциалом земли. Распыление постоянным напряжением, хотя и удобно с точки зрения источника питания, должно производиться при относительно высоких давлениях газовой атмосферы, в данном случае аргона, в камере для распыления. Такое распыление можно проводить в диапазоне давлений от 10 до 100 микрон ртутного столба с учетом особых обстоятельств, но обычно оно проводится при давлении от 40 до 50 микрон ртутного столба.Напыление радиочастотным напряжением, с другой стороны, обычно проводится при рабочем давлении менее 20 микрон ртутного столба. Поскольку более высокое давление газа означает, что большая часть распыленного металла отклоняется на пути к цели, более высокое давление газа в камере распыления приводит к снижению эффективности количества металла, достигающего нужных мест, по сравнению с количеством металла, распыляемого из мишени.
Работа мишени, на которой должно происходить напыление, со смещением по отношению к аноду, может улучшить адгезию из-за очищающего действия, которое ионы, притянутые к мишени, оказывают на нее.Однако и здесь это приводит к снижению эффективности использования распыляемого металла.
Таким образом, распыление высокочастотным напряжением часто предпочтительнее, когда дорогие металлы должны распыляться на мишень из-за его более высокой эффективности при использовании таких металлов. Кроме того, распыление высокочастотным напряжением позволяет использовать изолирующие мишени, такие как подложка, на которой должны быть сформированы контактные электроды, а также мишени, которые являются проводниками, как здесь, где мишенью является замаскированная пластина с открытыми проводящими отверстиями.
В этом расположении атомы, выброшенные из электрода истока из-за столкновения ионов аргона, имеют сильную тенденцию (1) быть направленными к неактивному электроду и замаскированной пластине и (2) столкнуться с ними довольно значительным Скорость намного выше, чем при ударе о пластинчатую структуру из-за осаждения при испарении. Это дает два существенных преимущества для распыления выступов контактного электрода, когда большая часть выступа состоит из дорогостоящего металла.
Первое преимущество связано с относительно высокой направленностью выброшенных атомов электрода истока на пластинчатую структуру. Это приводит к тому, что гораздо большая часть металла, поступающего из источника, осаждается на структуре пластины, а не на других поверхностях камеры осаждения, по сравнению с испарением. В свою очередь, это означает, что расходуется гораздо меньшее количество дорогостоящего металла, необходимого для наплавки.
Второе преимущество связано с относительно высокой скоростью, с которой выброшенные атомы ударяются о структуру пластины.Процесс имеет тенденцию быть самоочищающимся, поскольку он протекает из-за высокоскоростного удара атомов, стремящихся очистить от загрязнений и очистить плохо связанные атомы металла, выброшенные из электрода источника, которые были ранее осаждены. Это, в свою очередь, приводит к тому, что выпуклости контактного электрода имеют значительно большую адгезию к структуре пластины и большую адгезию между ее составляющими через каждый слой металла выпуклости, нанесенного распылением.
Как показано на фиг.4, хром является первым металлом, нанесенным распылением с образованием слоя 17 на выбранной части 14 и на открытых частях слоя диоксида кремния 12. Хром проявляет сильную адгезию как к алюминию, так и к диоксиду кремния, что является основанием для выбора его для первый слой. Обычно предусматривается слой хрома на 1500 А.
Следующий слой металла, медь, показанный как слой 18, обычно наносится совместно с последними 500 А слоя хрома, чтобы создать двухфазный слой хрома и меди.Этот двухфазный слой отдельно не показан на фиг. 4 и обычно не является необходимым, хотя помогает обеспечить хорошее сцепление между слоями. Совместное осаждение заканчивается доведением слоя 17 хрома до желаемой высоты, после чего наносится полностью медный слой 18 силой до 5000 А путем распыления. Этот медный слой хорошо сцепляется с хромом и третьим используемым слоем металла – золотом. Как слой 18 меди, так и слой 17 хрома ограничивают диффузию металла, так что материалы, лежащие в основе этих соответствующих слоев, не могут образовывать нежелательные интерметаллические соединения с золотом.Для любого из этих слоев можно использовать другие металлы, в частности, заменяя медь на никель или серебро.
Третий слой, наносимый распылением, – это золото. Когда распыление должно быть единственным методом осаждения металла, используемым для образования выступов контактного электрода, как показано на фиг. 4, золото напылено до желаемой высоты выступа контактного электрода. Высота выступа составляет минимум около 0,2 мил, если должно быть достигнуто надлежащее соединение, так как давление и тепло соединения заставят выступ разрушиться на одну десятую миллиарда или около того.Более желательная высота выступа для склеивания будет 0,5 мил.
Затем пластина с маской удаляется из вакуумной камеры устройства для напыления, а маска, в свою очередь, снимается с пластины. Удаление маски должно происходить в направлении, перпендикулярном поверхности пластины, чтобы избежать срезания любых образовавшихся выступов контактного электрода. Затем пластину помещают в травильный раствор для легкого протравливания для удаления любого металлического золота, которое могло «разбрызгиваться» под маской во время распыления золота.Затем пластину ополаскивают в деионизированной воде. Результат показан на фиг. 5.
Хотя распыление является более эффективным способом нанесения металла на неровности контактных электродов с целью экономии используемого металла, чем испарение, в случае дорогостоящего металла все же может оказаться желательным дальнейшее снижение потерь металла, которые происходят из-за его отсутствия. размещается только там, где это необходимо, на конструкции. Нанесение металлического покрытия на дорогой металл может повысить эффективность его использования, а любой «неправильно направленный» или избыточный металл может быть вытравлен и восстановлен из травильного раствора, используемого в процессе нанесения покрытия.Тем не менее, все еще возможно напыление слоев других металлов на выбранные области межсоединительной сети до нанесения покрытия на дорогостоящий металл, чтобы обеспечить металлическую основу для нанесения покрытия, чтобы обеспечить как очистку распылением, так и лучшие адгезионные свойства металлов, нанесенных распылением. процесс можно сохранить. Эти небольшие разбросанные выбранные области, на которых формируются металлические основания, ограничивают любые микротрещины, возникающие приблизительно только на поверхностях, которые будут покрыты выступами после завершения, поскольку металлический металл должен прилипать только к этим металлическим основаниям для завершения выступов.
Чтобы дополнить описанный выше процесс распыления путем добавления этапов нанесения покрытия, только тонкий слой золота 20 напыляется на слой 18 меди, как показано на фиг. 6 вместо распыления золота до тех пор, пока не будет достигнута желаемая высота выступа, как показано на фиг. 4. Затем металлическую маску 15 удаляют, и при первом способе нанесения покрытия на всю поверхность пластины напыляется очень тонкий золотой слой. Этот очень тонкий слой не вызовет микротрещин. Слой золотой вспышки объединяется со слоем 20 напыленного золота и показан как слой 20, 21 на фиг.7. В этом первом методе нанесения покрытия используется гальваническое покрытие, и необходимость соединения всех оснований металлического покрытия в один электрод для нанесения покрытия требует нанесения золотого слоя 21.
Затем стандартными методами наносится слой 22 фоторезиста на золотом слое вспышки, и в слое фоторезиста создается отверстие поверх осажденных слоев хрома 17 и меди 18, а также части слоя золота 20, 21, расположенной поверх слоя меди. 18, как показано на фиг. 8. Затем, используя стандартные методы гальваники, на обнаженный слой золота 20, 21 наносят золото.Золото, поставляемое в этом процессе нанесения покрытия, будет прилипать только к слою золота 20, 21 и не будет накапливаться или прилипать к слою фоторезиста 22. Золото наносится на желаемую высоту выступа контактного электрода с образованием слоя золота 20, 21, 23.
Затем слой 22 фоторезиста удаляют стандартными методами. Затем протравливается слой золотого отлива, за исключением тех мест, где он покрыт золотым покрытием, образующим выпуклость. Небольшая часть нанесенного золота также протравлена. Для достижения этого травления открываются небольшие микротрещины, и, поскольку также требуется очень небольшое травление для удаления очень тонкого мигающего слоя, значительного травления межсоединительной сети не происходит.Спекание не требуется, как в противном случае, если требуется относительно низкое сопротивление электрода из-за стадии очистки распылением, выполняемой перед напылением слоя 17 хрома. Результирующая выпуклость примерно такая же, как показано на фиг. 5.
Доступен второй метод нанесения покрытия, альтернативный вышеуказанному способу нанесения покрытия, который несколько менее эффективен при использовании золота, но исключает необходимость использования металлического светосильного слоя и слоя фоторезиста.В этом альтернативном методе используются стандартные методы химического или химического нанесения покрытия. Такие методы, пока они разработаны, не являются полностью удовлетворительными для обеспечения всего золота (то есть золота сверх того, которое требуется для формирования металлической основы) для полной выпуклости золотого контактного электрода 0,5 мил, но могут быть удовлетворительно использованы для обеспечения последних 0,2 или 0,3 миллиона золота, необходимого для образования такой выпуклости. Для получения первых 0,2 мил или около того золота перед этапом химического нанесения покрытия требуется дополнительное распыление золота.Дополнительное распыление в некоторой степени снижает эффективность использования золота, достигаемую указанным выше способом гальваники.
Для использования химического нанесения покрытия повторяются те же этапы, которые выполняются для получения полностью распыленного выступа, за исключением того, что процесс завершается до того, как последние 0,2 или 0,3 мил золота, использованные для создания выступа, будут распылены на место. Здесь, как показано на фиг. 4 слой 19 золота будет тоньше, чем показано на фиг. 4 на 0,2 или 0,3 мил, которые необходимо сформировать методом химического нанесения покрытия.Затем на этом этапе распыление золота прекращают и металлическую маску 15 удаляют. Затем пластина погружается в ванну для химического покрытия, и тем самым золото наносится на золото, уже нанесенное напылением, чтобы обеспечить выступ контактного электрода, примерно показанный на фиг. 5. Золото не будет химически наноситься на слой 12 диоксида кремния, который имеет неактивированную поверхность. Таким образом, хотя распыление золота обеспечивает большую долю золота в выступе контактного электрода, чем в способе гальваники, этапы создания металлического светового слоя и обеспечения слоя фоторезиста были устранены.
При использовании тех же дополнительных этапов нанесения покрытия, что и в любом из вышеуказанных способов нанесения покрытия, но с металлической основной структурой, содержащей слои хрома 17, меди 18 и золота 20, показанные на фиг. 6 или какой-либо другой металлический каркас, размещенный там с использованием хорошо известных методов напыления, обеспечит процесс, имеющий почти такое же эффективное использование золота. На удовлетворительном металлическом основании будет обеспечена позолоченная выпуклость. Если перед испарением используется очистка распылением, спекания после завершения этапов нанесения покрытия обычно можно избежать, также при желании обеспечивая относительно низкое сопротивление электрода.В некоторых обстоятельствах могут использоваться другие методы для обеспечения металлических оснований на конструкции, на которой можно наносить неровности, такие как «печать» через трафареты. Наложенные структуры, отличные от выступов контактных электродов, могут быть образованы дополнительными методами покрытия, такими как пути межсоединения электронных устройств.
Ножки могут быть обеспечены на многих типах структур, отличных от пластин интегральных схем, описанными здесь способами с подложками, на которых должны быть установлены различные виды электронных компонентов, включая микросхемы интегральных схем, что является типичным примером.