Строим Сами – Токарный станок своими руками
Сделать токарный станок своими руками не так сложно как могло бы казаться на первый взгляд. Если вы всё-таки решили не покупать, а сделать токарный станок своими руками, то эта статья как раз поможет вам в этом. И если даже вы не будите делать его один в один, как делал я, то всё равно вам будет понятно, что к чему.
Если вы не читали статью строение токарного станка, то очень советую для начала ознакомиться с ней.
Я делал станок практически весь из дерева, и времени у меня ушло на это всего ничего – около дня, с небольшими доработками в последующем. Думаю, не стоит объяснять, что для сборки токарного станка нужно использовать только сухой и качественный материал.
Одной из главных целей
Так как у меня дома есть лестница, то и балясны предполагалось выточить самостоятельно. Поэтому ширину рабочей части я сделал 1 м.
Для работы мне понадобилось
- Из материалов:
- берёзовая доска
- пара реек
- металлические уголки
- уголок 30х30 мм
- саморезы
- фанера (ОСП)
- пара длинных болтов с гайками и шайбами
- шпилька Ø18 мм и 3 гайки
- двигатель от старой стиральной машинки, со скоростью 1200 об/мин.
- пара брусков 50х50 мм
- Из инструмента:
- Ножовка
- Шуруповёрт
- Болгарка
- Электрорубанок
И так приступим.
Для начала готовим из доски два куска длинной примерно по полтора метра, из них будет сделана станина – основа
токарного станка. Чем крепче будет материал древесины, тем лучше.
Затем необходимо прогнать обе части через рубанок для того что бы поверхность была ровная и без заноз.
Соединяем обе части при помощи саморезов. Между досками вкладываем рейку в трёх местах поперёк доски,
для того что бы на станине можно было крепить подручник, заднюю бабку, люнет и прочие приспособления.
Далее из брусков готовим две ножки, они повысят устойчивость станка и позволят прикрепить станок к верстаку или столу, на котором будет стоять токарный станок.
Когда всё готово на этом этапе приступаем к установке электродвигателя. В отличие от остальных составляющих электродвигатель,
скорее всего, будет отличаться, поэтому придумываете, как прикрепить его к станине.
Для того что бы выставить центр станка на необходимую высоту я использовал бруски,
так у меня получилась высота около 20 см.
Всё выше перечисленное было не самым сложным. Следующим этапом будет изготовление задней бабки.
Для этого я использовал ОСП, на тот момент у меня не было под рукой фанеры, но лучше использовать её.
На фото видны все элементы. Для поддержки центра задней бабки я использовал брусок. Он был просверлен строго по центру.
Отверстие диаметром 18 мм или другого размера в зависимости от того какого диаметра была выбрана шпилька.
Затем с двух сторон отверстие было расширено до размера чуть меньше размера гайки, куда впоследствии и были впрессованы гайки.
Центр задней бабки из шпильки делается просто: отрезаем шпильку необходимой длины и затачиваем с одной стороны на конус.
Советую использовать для заточки болгарку с чашкой на липучке и нождачную бумагу разной зернистости.
Чем чище и гладше будет отполирована поверхность конуса, тем лучше.
Подручник токарного станка очень советую сделать из металлического уголка. В моём первом варианте подручник был сделан из ОСП и очень сильно вибрировал при работе, что не только очень осложняло работу, но и было просто опасно. При помощи болгарки я разрезал уголок на необходимые куски сварены в подручник, который вы видите на фото. Подручник должен быть ниже оси точения на 5-7 мм.
Как видите сборных элементов токарного станка не так уж и много.
Крепиться подручник и задняя бабка будут при помощи длинных болтов, гаек и шайб.
Согласен, не очень удобно, но для начала пойдёт, если придумаю что-нибудь по лучше, то обязательно напишу.
Ну, вот как бы и всё: токарный станок в рабочей комплектации полностью готов к работе. В других статьях я расскажу о том, как сделать токарные стамески, дополнительные устройства к станку и расскажу о методах работы.
Спасибо за внимание.
Автор статьи:
Самородов Вадим
2015-11-09
Как сделать своими руками самодельный токарный станок по металлу для маленького домашнего стола
Предлагаем построить токарный станок по металлу своими руками с плавной регулировкой скорости вращения шпинделя.
Для создания такого небольшого токарного станка по металлу потребуются запчасти от разных неисправных электроинструментов.
Станок имеет небольшие размеры и мощный двигатель.
Изготовление регулятора скорости будет показано на шаге 5.
На видео ниже показана работа миниатюрного токарного станка по металлу на различной скорости. Соединительная муфта вызывает вибрацию, которая становится тем больше, чем больше число оборотов.
На шаге 9 имеется еще одно видео.
Содержание статьи
Шаг 1: Материалы
Вам потребуются некоторые специализированные узлы для самодельного токарного мини станка по металлу.
Основные из них выпускает компания Bosch Rexroth: механический алюминиевый профильный элемент, болты, шайбы, торцевые заглушки. Алюминиевый профиль имеет сечение 45*90 мм и длину 350 мм.
Опорные блоки можно приобрести на сайте VXB.COM. Номер детали Wh22A.
Подшипники 608ZZ тоже есть на этом же сайте. Для нашего проекта желательно использовать радиально-упорные роликовые подшипники, но подойдут и шариковые.
Мягкая моторная муфта с резиновой крестовиной с сайта PrincessAuto.com. Электродвигатель 12 В постоянного тока – от беспроводного триммера фирмы Black & Decker. Выключатель с регулятором скорости вращения от литий-ионной аккумуляторной 18-вольтовой дрели Milwaukee.
Остальные необходимые материалы для домашнего токарного станка по металлу будут указаны по мере их появления в инструкции.
Шаг 2: Делаем опоры
Показать еще 11 изображений
Внутренний диаметр опорных блоков равен 20 мм. Вам нужно рассверлить их до 22 мм под наружный диаметр подшипников. Это можно сделать при помощи ручной дрели или сверлильного станка.
Подшипники устанавливаются заподлицо с одной стороны блоков и закрепляются с помощью винтов на блоках.
В качестве пиноля на задней опоре используем коническое бурильное долото диаметром 12 мм, которое будет вращаться вместе с заготовкой. Диаметр зажимного хвостовика пиноля равен 6 мм. Для того, чтобы пиноль плотно вставлялся во внутреннее кольцо подшипника, диаметр которого составляет 8 мм, используем медную трубку-переходник.
В опору со стороны привода устанавливается гибкая полумуфта со шпилькой диаметром 8 мм. Нарежьте резьбу М8 в отверстии полумуфты, вкрутите шпильку и зафиксируйте двумя шестигранными гайками. Возможно, вам придется отрегулировать длину вала установкой на шпильку дополнительных шайб. Затем вставьте свободный конец шпильки в подшипник и зажмите его самостопорящейся гайкой. Постарайтесь собрать узлы как можно аккуратнее.
Шаг 3: Собираем станок
Показать еще 11 изображений
Установите собранные опорные блоки и угловые опоры для двигателя на профильное основание.
В качестве крепления для двигателя используйте металлическую пластину. Просверлите в ней отверстие под вал двигателя, а также отверстия для крепления к двигателю и к угловым опорам. Т.к. вал двигателя меньше отверстия во второй полумуфте, намотайте полоску алюминиевой фольги на вал и насадите на него полумуфту. Далее установите между полумуфтами резиновую крестовину, закрепите на раме-основании двигатель и подшипниковый опорный блок привода.
Зафиксируйте на раме при помощи болтов задний опорный блок.
Установите две дополнительные угловые опоры между опорными блоками. Они будут использоваться в качестве упора для инструмента. Торцы профильного основания можете закрыть специальными торцевыми заглушками.
Шаг 4: Изготавливаем 3-кулачковый патрон
Показать еще 4 изображения
Для изготовления 3-кулачкового зажимного патрона нужны навыки пайки или сварки.
В качестве основания патрона вам потребуется шайба увеличенного диаметра с отверстием 6 мм. Еще нужна гайка с резьбой М8 и установочный винт длиной 12 мм. Вкрутите установочный винт в гайку так, чтобы фаска болта выступала и по ней можно было выровнять отверстия в шайбе и гайке. Они не должны смещаться относительно друг друга. Спаяйте или сварите между их собой. Выверните установочный винт и переверните получившийся узел.
Поместите шестигранную М12 в центр шайбы и установите три шестигранные гайки М8 по трем граням гайки М12.
Припаяйте или приварите гайки М8 к шайбе и удалите М12. Очистите места пайки (сварки) от шлака и обработайте швы напильником. Загрунтуйте и покрасьте патрон в черный цвет (по желанию).
Вкрутите три зажимных винта М8 длиной 12 мм. Теперь у вас есть зажимной патрон с тремя кулачками. Перед работой на настольном станке полностью затягивайте зажимные винты, иначе при работе на высокой скорости обрабатываемую заготовку может сорвать.
Шаг 5: Делаем регулятор скорости вращения
Показать еще 11 изображений
В конструкцию станка рекомендуется добавить регулятор скорости вращения шпинделя, т.к. ротор двигателя крутится с огромной скоростью и, при работе на максимальных оборотах, это становится небезопасно.
Для изготовления регулятора вам понадобится кнопка-регулятор от аккумуляторного электроинструмента. Желательно найти кнопку без блокировки включения.
Соберите регулировочный механизм, как показано на фото. Детали для его изготовления можно найти в металлоломе. В качестве основы для регулировочного механизма можете использовать струбцину.
Посмотрите на регулятор. Вы можете заметить, что кроме толстых красного и черного провода, к нему подходят еще тонкие провода. Для работы регулятора необходимо питание 3,6 В подключить к тонким красному и черному проводам. Для этой цели добавим литий-ионную батарею напряжением 3,6 В, подключенную положительным полюсом – к черному проводу, а отрицательным – к красному (обратная полярность). Выключатель-регулятор работает так: чем сильнее его нажимать, тем выше скорость вращения ротора.
Выключатель имеет рычажок переключения направления вращения. Нужно выбрать такое направление, чтобы патрон при вращении накручивался на резьбу шпильки, иначе при работе станка он просто-напросто открутится.
Для изготовления регулятора используйте отрезок квадратного алюминиевого профиля Bosch Rexroth, несколько болтов М8 и рычаг, изготовленный из металлических обрезков с помощью сварки или пайки (см. фото). Выключатель приклейте к профилю. Регулировка осуществляется с помощью резьбового соединения М8. При завинчивании – кнопка-регулятор постепенно нажимается, и увеличивается скорость вращения ротора двигателя, а при выкручивании – кнопка постепенно отжимается, и скорость уменьшается. При полностью отжатой кнопке, подача питания на электродвигатель прекращается.
Батарейный отсек для литий-ионного элемента питания 3,6 В можно найти в разных устройствах, где такой элемент используется в качестве резервного источника питания, например, в датчике движения.
Провода от источника питания подключаются к нижней части регулятора (там-же, где и тонкие провода цепи управления). Двигатель подключается к клеммам в верхней части регулятора.
Шаг 6: Выбираем источник питания
Для работы станка потребуется напряжение не менее 10 В. Для этого нужно подобрать подходящий источник питания, например, на 12 В. Можете подключить 12-вольтовую батарею, если нет блока питания, но ее не хватит на долгое время работы.
Для обеспечения безопасности, закройте защитными кожухами вращающиеся части станка.
На фотографии можно видеть обработанную с помощью напильника алюминиевую деталь. Деталь была обточена на низкой скорости без охлаждения. Упор для режущего инструмента представляет собой болт М6, установленный в угловые опоры.
Если муфтовое соединение плохо сбалансировано, у станка будет большая вибрация, и его нужно будет жестко крепить на верстак.
Шаг 7: Конструируем двухосевой держатель инструмента
Показать еще 11 изображений
В качестве основания возьмите стальную заготовку размером 125*25*3 мм.
Еще понадобятся болты М8: два – длиной 150 мм и один длиной 200 мм с резьбой по всей длине.
Также нужны одиннадцать гаек М8.
Высверлите резьбу у 8 гаек сверлом на 8 мм. На 4 гайках сточите немного одну из граней. Наденьте по 3 просверленных гайки на два 150-миллиметровых болта и накрутите по одной гайке с резьбой на каждый. Две просверленных гайки наденьте на 200-миллиметровый болт.
Разложите все болты с гайками на стальное основание как показано на фото. Болты должны располагаться как можно более параллельно друг другу. Убедитесь, что две средние гайки на каждом из двух крайних болтов обращены сточенной гранью к пластине-основанию. Эти 4 гайки припаивать не нужно, т.к. они будут двигаться свободно по болтам (скользящие гайки). Крайние 6 гаек припаяйте (приварите) к пластине.
Выньте центральный 200-миллиметровый болт. Возьмите еще одну гайку, сточите немного одну грань и припаяйте эту гайку ребром, противоположным сточенному, в центре стальной квадратной пластины (см. фото).
Поместите эту квадратную пластину в центр нашей конструкции гайкой вниз, затем вставьте 200-миллиметровый болт обратно, вкрутив его в гайку на квадратной пластине. Болт нужно вставить слева-направо, чтобы свободная резьба болта была с правой стороны.
Расположите верхнюю пластину по центру крайних болтов, затем придвиньте скользящие гайки под углы этой пластины и аккуратно припаяйте их к пластине, следя за тем, чтобы они не припаялись к болтам.
Убедитесь, что квадратная пластина свободно перемещается по болтам. Вначале она может двигаться туго, пока шлак не отвалится.
Крайние болты не привариваются к основанию, а держатся на резьбе. Это делается для того, чтобы у них был небольшой люфт, который позволит свободнее перемещаться верхней пластине, если болты были установлены не достаточно параллельно.
Отрежьте концы крайних болтов заподлицо с крайними. Средний болт обрезать не надо, он будет являться винтом подачи.
Весь процесс изготовления, изложенный выше в этом шаге, нужно повторить для болтов М6. Вам понадобится 6 скользящих гаек, два болта длиной 60 мм и один – длиной 75 мм с резьбой по всей длине.
Высверлите 6 гаек сверлом на 6 мм. На 4 гайках сточите немного одну из граней. Наденьте 2 скользящие на каждый 60-миллиметровый болт и навинтите по одной с резьбой.
Наденьте 2 скользящие на 75-миллиметровый болт.
Уложите и выровняйте болты с гайками на верхней квадратной пластине перпендикулярно болтам М8. Убедитесь, что со сточенной гранью обращены этой гранью к поверхности пластины. Осторожно приварите 6 концевых гаек, не трогая скользящие.
Выньте центральный болт и обточите у него головку.
Отрежьте крайние болты заподлицо с припаянными гайками.
Поместите гайку с резьбой М6 в центр между крайними болтами и вставьте центральный болт через эту гайку головкой в сторону от вас, свободным концом с резьбой – к вам. Это будет верхний винт подачи.
Возьмите еще одну стальную квадратную пластину такого же размера, как и предыдущая. Просверлите отверстие в центре этой пластины и снимите у него фаску. Установите пластину по центру верхних салазок. Передвиньте скользящие гайки так, чтобы между ними было примерно 6 мм.
Приварите центральную гайку через отверстие на пластине. Попробуйте подвигать винт подачи. Он должен свободно перемещаться. Затем приварите или припаяйте боковые скользящие. Проверьте скольжение.
Приварите 4 маленьких болта головками по углам верхней пластины.
Изготовьте алюминиевую пластину с четырьмя отверстиями по краям, которыми она надевается и прикручивается к болтам на верхней стальной пластине. Режущий инструмент зажимается между верхней стальной и алюминиевой пластинами.
Винты подачи должны быть надежно зафиксированы, но не должны затягиваться. Для нижнего винта подачи используйте стопорную гайку и муфту (удлиненную гайку): накрутите их, стяните между собой, затем просверлите в гайке-муфте тонкое сквозное отверстие (которое должно пройти через болт в гайке). Вставьте в отверстие маленький гвоздь, обрежьте его до необходимой длины и заклепайте (см. фото). На верхний болт накрутите три гайки и припаяйте их к нему.
Чтобы закрепить получившийся держатель инструмента на станке, приварите 4 шайбы увеличенного диаметра к нижней пластине. Держатель будет прикручиваться к профилю винтами.
Загрунтуйте и покрасьте держатель в черный цвет.
Шаг 8: Настраиваем и регулируем станок
Возможно, вам придется отрегулировать высоту двигателя: резец должен находиться по центру обрабатываемой детали.
Желательно заменить фольгу, намотанную на вал двигателя под полумуфту, на подходящего размера втулку из мягкого металла. Это значительно уменьшит вибрации.
Шаг 9: Доработка станка
Со временем, можно будет сделать некоторые улучшения для вашего станка. Рекомендуется добавить второй подшипник в передний опорный блок.
Электрический токарный станок в японском стилеСборка
Я должен начать этот пост с четкого заявления, что это абсолютно новая для меня территория. Я очень мало знаю о японских токарных станках, кроме того, что узнал из постов в блогах и постах в Instagram Джаррода Даля. Я знаю, что Джаррод был первым, кто изготовил электрический токарный станок в японском стиле на Западе. Он ездил в Японию, чтобы исследовать токарные станки, инструменты и методы токарной обработки японских токарных станков, и уже довольно давно использует один из них, наряду с токарным станком с шестом и стандартным электрическим токарным станком в западном стиле. Зайдите в его блог и поищите в его Instagram, если вы еще этого не сделали. Там можно найти массу вдохновения и информации. Я благодарен Джарроду за то, что он обратил наше внимание на этот стиль дерева в своих трудах и работах.
Я почти ничего не знаю о двигателях, инверторах, шкивах, подшипниках и приводных ремнях, кроме того, что узнал за последние несколько недель, пытаясь собрать все эти компоненты вместе. Однажды один из моих друзей описал меня как луддита, что, вероятно, не так уж далеко от истины. Пожалуйста, имейте это в виду. Когда я пишу это, я использовал токарный станок всего пару раз. Я понятия не имею, развалится ли он или будет поврежден из-за неправильной сборки или использования неподходящих деталей и т. д. Пожалуйста, проведите собственное исследование, прежде чем покупать какие-либо из перечисленных ниже деталей, и примите собственные решения о том, могут ли другие детали или продукты быть неисправными. лучше машина. Или подождите год или около того и посмотрите, как мои поживают после этого времени!
Я в долгу перед Оуэном Томасом, который пригласил меня, Йоава Элькаяма и Мэтта Уиттакера в свою мастерскую, чтобы посмотреть на токарный станок в японском стиле, который он построил. Без этого приглашения и возможности посмотреть на токарный станок Оуэнса, задать ему вопросы и посмотреть, как он работает, мне потребовались бы целые века, чтобы понять, как его построить. До того дня я никогда не пользовался каким-либо электрическим токарным станком, поэтому в тот момент был в полном неведении и совершенно невежественен. Любые ошибки, которые я допустил со своими, — это исключительно моя вина и никакого отношения к Оуэну! Большая часть того, что я купил, точно такое же, как и он, за исключением опорных блоков и подшипников. Подробнее об этом см. ниже.
Теперь с этим покончено. Перейду к сути этого поста. По сути, это не более чем ответ на множество вопросов, которые я получил после того, как опубликовал в Instagram информацию о своей сборке электротокарного станка. Несколько человек спрашивали, есть ли в Интернете какая-либо информация о том, как его собрать, о различных деталях, характеристиках двигателя и т. д. На момент написания этой статьи ее не было, хотя Джаррод, к счастью, планирует вскоре написать об этих токарных станках. Для меня просто имело смысл написать это здесь, а не отвечать на множество отдельных вопросов в Instagram через DM.
Я надеюсь, что это будет интересным проектом для вас, если вы один из тех, кто заинтересован в его создании. Другой, более простой вариант — купить подержанный западный электрический токарный станок с чашей и просто установить его на рабочую поверхность. Но если это слишком просто, то читайте дальше. Эти три предмета были куплены в комплекте на eBay. Ссылка на страницу здесь;
https://www.ebay.co.uk/itm/164494188809?ul_ref=https%253A%252F%252Frover.ebay.com%252Frover%252F1%252F710-53481-19255-0%252F1%253Fff3%253D2% 2526pub%253D5575376664%2526toolid%253D10044%2526campid%253D5338268676%2526customid%253DEAIaIQobChMI8baztfjw7AIVKoBQBh24ognUEAQYASABEGJvY_D_BwE%252 6lgeo%253D1%2526item%253D164494188809%2526srcrot%253D710-53481-19255-0%2526rvr_id%253D2674947040062%2526rvr_ts%253Da3b8234f1750ac3c22 c694acff8b8284&ul_noapp=true
– Двигатель
Технические характеристики двигателя (взято из рекламного проспекта)
Универсальный IE2 0,75 кВт (1 л. с.), трехфазный, 4 полюса B3 Асинхронный двигатель переменного тока с рамой 80 для крепления на лапах для трехфазного питания 400 В. Подходит для использования с частотно-регулируемым преобразователем частоты.
Выходная мощность: 750 Вт (1 л.с.) x 1410 об/мин при 230 В или 400 В x 50 Гц 3-фазный диапазон скоростей от инвертора: диапазон 15:1 от 141 до 2115 об/мин для частот от 5 до 75 Гц, при уменьшении номинальных значений на более низких скоростях. Диапазон: от 1410 об/мин до 2115 об/мин непрерывно.
Размеры: 163 мм в ширину, 290 мм в длину и 213 мм в высоту. Крепление: опора на 10-миллиметровых отверстиях с шириной 125 мм и расстоянием между центрами 100 мм в 50 мм от плеча вала. Вал: диаметр 19 мм, длина 40 мм со шпонкой на 6 мм. .
– Инвертор
Размер: 165*115*100 мм
Мощность: 0,75 кВт
Номинальный ток: 5 А
Частота: 50 Гц/60 Гц
Мощность: 2,0 кВА (0,75 кВт/1 л. с.)
Режим регулирования выходного напряжения : ШИМ-управление
-Контроллер
Старт-Стоп – Вперед – Назад – Быстрый набор.
Кнопка мгновенного запуска – действует как функция сброса напряжения без напряжения.
Кнопка «Стоп»
Поворотный переключатель «Вперед/Назад» — для изменения направления вращения двигателя.
Потенциометр переменной скорости — для плавного изменения скорости вращения двигателя.
-Шпиндель
Шпиндель является запасным валом для токарных станков серии Record Power CL. Стайлз и Бейтс продают полный комплект узла вала и подшипника, который включает в себя основной шпиндель, бронзовый подшипник внутренней передней бабки, 2 стопорных кольца, внешний подшипник передней бабки и сменный ремень. Оуэн Томас купил этот комплект и сделал деревянные подушки для размещения подшипников. Этот вариант хорош с точки зрения наличия точно правильного размера подшипника шпинделя. Однако я не хотел использовать бронзовый подшипник и не хотел возиться с изготовлением деревянных корпусов для подшипников. Поэтому я купил опорные блоки и подшипники отдельно и купил только шпиндель напрямую у Record Power.
Обратите внимание, что диаметр шпинделя изменяется по его длине и на резьбовом конце не является стандартным размером. Это означает, что ближайший стандартный подшипник, который подходит к этому концу, немного больше. Чтобы решить эту проблему, я поэкспериментировал со стальными прокладками разных размеров, купленными на eBay, и обнаружил, что стальная прокладка толщиной 0,005 была примерно подходящего размера, чтобы компенсировать любой очевидный свободный ход после обрезки по размеру и использования между подшипником и шпинделем на резьбовом конце. . Возможно, вам будет лучше провести некоторые исследования и найти другой шпиндель, который имеет стандартный диаметр, чтобы соответствовать легко доступным подшипникам.
-Шпоночная сталь
Для фиксации шкива на шпинделе. Я купил на eBay набор стальных ключей с круглым концом 6 мм x 6 мм x 20 мм и немного отшлифовал каждый конец, так как прорезь в шпинделе составляет 19 мм. Было бы достаточно легко сделать его из мягкой стали.
На следующем фото мой счет-фактура от Simply Bearings Ltd, где я купил все остальные биты, опорные блоки, подшипники, конические стопорные втулки, клиновой ремень, шкив и т. д.
Вот и все. Двигатель, частотно-регулируемый привод и контроллер поставляются с подробными примечаниями о том, как все это подключить и как их использовать, а на YouTube есть видеоролики, в которых подробно описаны все многочисленные функции и настройки частотно-регулируемого привода. Это довольно удивительный комплект.
У меня было много предложений, как сделать регулируемую систему натяжения ремня. Это было то, на чем настаивал мой отец (он очень помог мне во время визита сюда своим инженерным умом, когда я начал строить), но в конце концов я решил не делать этого. Монтажные отверстия в опорных блоках предназначены для движения, поэтому я просто натягиваю ремень вручную, оттягивая блоки от двигателя, а затем затягивая гайки, когда ремень чувствует себя правильно. Вроде все в порядке, но я уверен, что было бы полезно приложить дополнительные усилия и разработать какую-нибудь скользящую пластину и натяжной рычаг, как предлагал мой отец.
Все это нужно как-то защитить, чтобы стружка не попала на движущиеся части. В основном люди делают для этого деревянный ящик, но я использовал потрепанный старинный сундук, который нашел мой партнер Ферн. Кто-то собирался бросить его в контейнер, поэтому она спасла его, а я переделал его. Ему, наверное, около ста лет, и я его очень люблю. все это нужно как-то закрепить на рабочей поверхности. Я использую L-образные кронштейны, чтобы держать его неподвижным во время использования, прикрепляя его к деревянной основе через сундук, а затем к поверхности стола.
Японские инструменты с крючками сильно отличаются от крючков, которые мы используем на наших токарных станках. Но я очень мало знаю о них прямо сейчас. Много экспериментов на горизонте. Сейчас я использую крюки для токарного станка.
Кто-то спросил, буду ли я указывать, когда буду продавать миски или чашки, изготовлены ли они на токарном станке или на электрическом станке. Надеюсь, само собой разумеется, что я никогда не стал бы продавать чашу электротокарного станка как чашу токарного станка. Все будет продано за то, что они есть. В любом случае, у них обоих разные качества, и я не собираюсь отказываться от своего токарного станка. В душе я токарь на токарном станке, и я не мог бы отказаться от использования этого архаичного станка, даже если бы захотел. Если я хотя бы несколько дней не захожу за токарный станок, я начинаю нервничать! Я надеюсь, что эти два стиля токарной обработки со временем будут дополнять друг друга и по-новому наполнять мою работу. На данный момент для меня это новое путешествие, полное открытий, много обучения и веселья. Я действительно чувствую, что последнее десятилетие токарной обработки на токарном станке позволило мне с определенной легкостью освоить другой стиль. В конце концов, основные принципы в основном одинаковы. Надеюсь, он и впредь сослужит мне хорошую службу, пока я буду исследовать больше возможностей, которые могут предложить эти новые (для меня) техники.
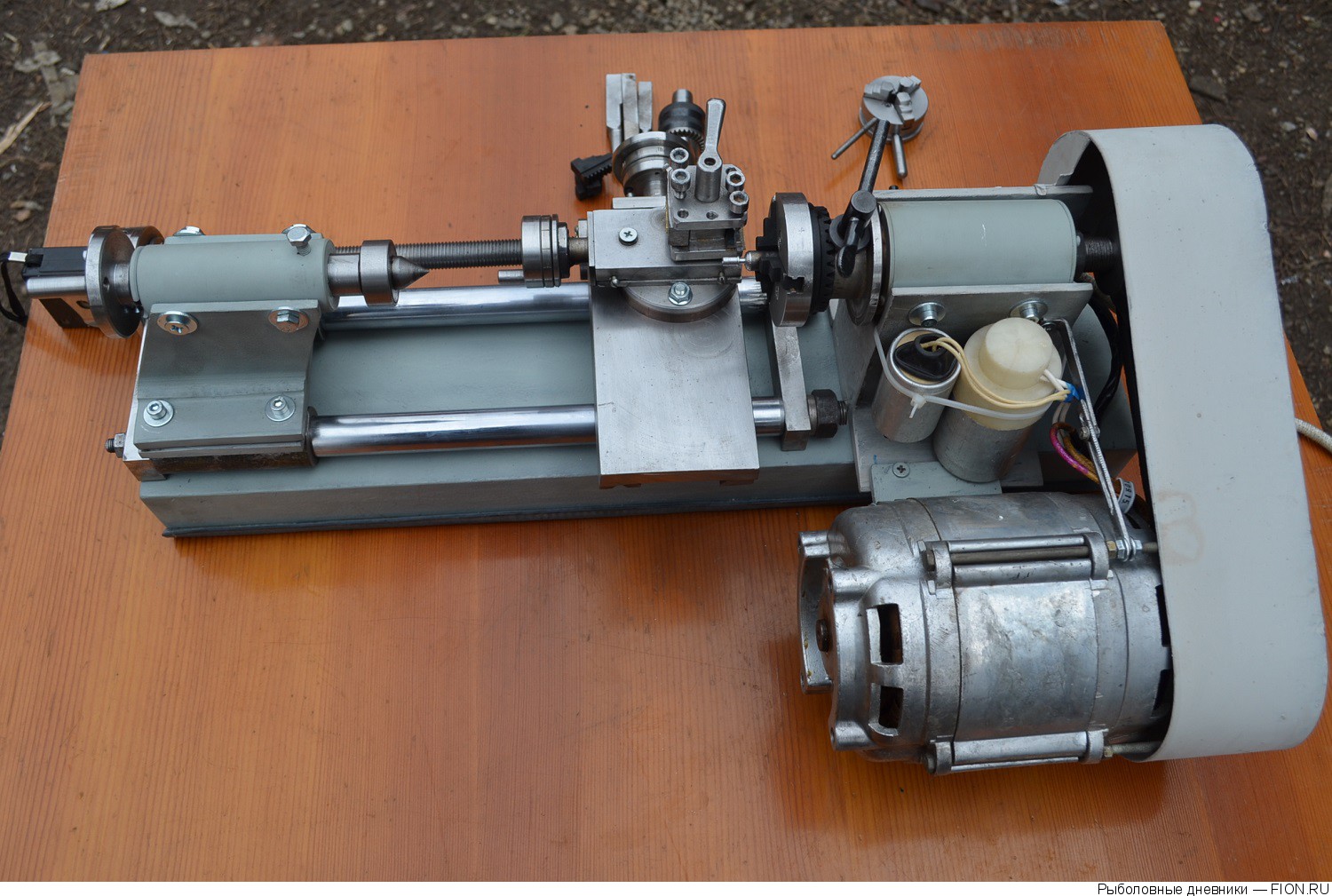
Нравится:
Нравится Загрузка…
Сделать подставку для станка | Деревообрабатывающий проект
Чтобы получить токарный станок, нужно сделать для него подставку. Я сделал эту подставку для токарного станка прочной, с большим количеством места для хранения и возможностью расширения по мере будущих обновлений. Эта подставка изготовлена из твердого клена и кленовой фанеры и весит более 200 фунтов без токарного станка! Он имеет много места для хранения токарных инструментов, а также токарных заготовок. Я также добавил ящик с песком, чтобы увеличить вес и гасить вибрацию подставки. Следуйте ниже, чтобы увидеть, как я сделал этот единственный в своем роде предмет мебели для магазина!
ЗНАЕТЕ ЛИ ВЫ: Вы можете следить за мной в этих социальных сетях!
Instagram · YouTube · Facebook · Pinterest
Материалы и принадлежности* | Инструменты* |
(1 ) Лист 3/4″ фанеры | Погружной фрезер Bosch (если нет ЧПУ) |
Шипы Domino 10 мм | Набор сверл и отверток DeWalt |
В качестве альтернативы можно использовать дюбели или шурупы с гнездом | Квадрат |
Сверло с зенковкой | |
( 1) Лист 1/2″ Ply | Торцовочная пила |
Твердый кленовый пиломатериал 8/4 | Настольная пила |
Твердый кленовый пиломатериал 4/4 | Фуганок/строгальный станок при использовании грубых пиломатериалов |
Клей для дерева | Параллельные зажимы |
(3) Наборы направляющих для 12″ ящиков | |
(2) Наборы еврочашечных петель | |
Строительные винты 2,5″ | |
70 фунтов Все специальный песок | |
Винты 1 1/4″ |
3 .
Фрезерование грубых пиломатериалов
Этот проект представляет собой наполовину мебель из твердого дерева и наполовину краснодеревщик. Поэтому для деталей из твердой древесины я начал с грубо распиленного клена.
Полный набор “Энчилада”
Полный набор “Энчилада”! Вы хотите все это? Ты получил это! Получите все планы, которые я предлагаю, в одном пакете со скидкой 65%!
69,99 $
Если сначала вырезать все мои грубые детали на торцовочной пиле, с ними будет легче работать на настольной пиле.
Затем я иду к настольной пиле, чтобы обрезать все до грубых размеров перед фрезерованием.
У меня есть смесь 4/4 и 8/4 для разных деталей.
Полный набор “Энчилада”
Полный набор “Энчилада”! Вы хотите все это? Ты получил это! Получите все планы, которые я предлагаю, в одном пакете со скидкой 65%!
69,99 $
Формирование заготовок для ножек
Чтобы сформировать ножки станины, я склеиваю пары заготовок 8/4 вместе (все четыре ножки сразу помещаю в зажимы, как большую разделочную доску). Только будьте осторожны, наносите клей только на те части, которые хотите склеить!
После того, как клей высохнет, я подравниваю детали на фуганке с двух сторон.
Все, что мне нужно сделать, это выровнять одну грань, а затем выровнять соседнюю грань, а затем рубанок сможет обработать две другие стороны!
Приклейте одну из сплющенных лицевых сторон на стол рубанка и пропустите ее. Волшебным образом противоположная сторона будет плоской и параллельной! Затем просто поверните на 90 градусов к другой стороне, которую вы сплющили на фуганке, и снова сделайте противоположную сторону параллельной, и вы получите 4 квадратных стороны! Просто не забудьте пропустить все четыре ножки одновременно, чтобы убедиться, что каждая из них обрезана до одинаковых размеров.
Затем я отрезаю по одному концу каждой ножки, чтобы получился чистый и прямоугольный конец. Затем я отложил эти заготовки для ножек на некоторое время, потому что мне нужно построить ножки подставки.
Полный набор “Энчилада”
Полный набор “Энчилада”! Вы хотите все это? Ты получил это! Получите все планы, которые я предлагаю, в одном пакете со скидкой 65%!
69,99 $
Фрезерование фартука и верхней части стойки токарного станка
После повторения процесса фрезерования на фуганке…. .
….а затем рубанок, у меня этот запас 8/4 фрезерован до 1,5″. В основном я сделал жесткий клен 2х4. Я также потратил время, чтобы фрезеровать детали фартука, а также доски, которые будут формировать верхнюю часть подставки. Все из 8/4 запаса фрезеровано до 1,5 дюймов.
Вот изображение деталей для изготовления верха, фартука, ножек и ступней. Это не так уж и много (но я очищал пылесборник несколько раз, ха!) Я хотел, чтобы на концах ножек был радиус 1,5 дюйма, чтобы они не были заостренными. Я могу только представить, как споткнусь ногой, поворачивая проект. Это плохо кончится.
После того, как я обрезал эти радиусы, я закруглил верхний край каждой части ноги для контура и чтобы края не затупились.
Мне нужно было прорезать сквозные пазы на каждом конце ножек, чтобы вставить в них ножки. Теперь я использовал для этого свой ЧПУ, но вы также можете сделать это с помощью маршрутизатора и шаблона. В этом проекте нет части, для выполнения которой требуется ЧПУ, но у меня он есть, и я использую его, чтобы облегчить себе работу.
Для нижней части ножек мне нужно сделать соответствующие пазы, но они не проходят насквозь, а глубиной в дюйм. Оглядываясь назад, мне, вероятно, не нужно было делать этот шаг, так как сквозных пазов в верхней части, вероятно, было достаточно, но я сделал это, и теперь это сделано. Что я могу сделать?
Далее мне нужно склеить их вместе с помощью клея и выровнять пазы. Опять же, я думаю, что мог бы облегчить себе задачу, просто вырезав пазы в верхней части ножек.
К счастью, пазы выстроились!
Я просто скрепил детали и дал им высохнуть.
Полный набор “Энчилада”
Полный набор “Энчилада”! Вы хотите все это? Ты получил это! Получите все планы, которые я предлагаю, в одном пакете со скидкой 65%!
$69.99
Резка столярных изделий в ножках
Когда они высохли, я измерил общую глубину с помощью глубиномера. Я сделал это, чтобы установить высоту лезвия настольной пилы, когда я обрезал шип на конце ножек, чтобы он поместился в эти пазы.
Сначала я установил расстояние до забора и вырезал выступы для шипов на основе снятых мерок.
Затем я обрезал щеки шипов, используя приспособление для шипов.
Я обрезал каждую сторону одинаково, чтобы шип оказался по центру ножки.
, поскольку мои пазы были закруглены из-за фрезы, мне пришлось сбрить углы шипов, чтобы они подходили. Не нужно делать их идеальными, их никто никогда не увидит!
Время пробной посадки…….
Ах, как мило! Именно то, что я был после. Хорошие чистые плечи и хорошая посадка.
Последние надрезы на ногах должны были сделать выемку наверху, чтобы надеть фартук. Сначала я разрезал плечо…..
А затем разрезал щеку, сделав надрез.
Будьте осторожны, удаляя обрезки. Обязательно держитесь подальше от лезвия.
Затем я предварительно просверлил отверстия для последующей сборки. Я буду использовать винты, которые позже будут скрыты за шкафом.
Сборка основания стойки токарного станка
Я добавил немного клея для прочности в выемку на верхней части ножек.
Затем я прикрепил детали фартука к ногам.
Наконец я загнал винты домой. Они будут находиться ВНУТРИ стойки токарного станка и позже будут полностью скрыты за шкафом, так что не нужно беспокоиться о заглушках и т. д.
Я снова проверил, чтобы убедиться, что все осталось ровно.
Затем я зажал ножку/фартук и вставил пазы домино там, где будут соединяться фартуки короткой стороны. Вы можете использовать дюбели здесь, если хотите.
вы можете увидеть здесь Я использую домино XL, чтобы сделать это соединение с короткими боковыми фартуками.
Затем я добавляю клей в паз.
Затем вставьте шип и добавьте к нему клей.
Наконец, я прикрепляю короткие кусочки фартука, в которых есть соответствующие пазы домино.
Дайте высохнуть примерно 2 часа.
Затем я добавил костяшки костяшек и клей на другую сторону.
Затем я прикрепил другую пару ножек. Я перевернул всю сборку вверх дном, чтобы упростить задачу.
Несколько зажимов на стыках и многое другое ждет, пока высохнет клей.
Пока клей сохнет, прикрепил ножки. Сначала я добавил клей на шипы на ножках.
Затем я выровнял пазы в ножках.
После того, как я подвигал их из стороны в сторону, я усадил их на плечи.
Затем я закрепил это соединение винтами, которые будут действовать как зажимы. Так как это дно, эти винты не будут видны.
Затем я перевернул всю сборку вертикально, и вы можете видеть, что основание подставки готово. Ну, почти. Далее мне нужно было добавить подрамник, но не просто подрамник. Я хотел добавить песочницу! Что?…. Продолжай читать.
Изготовление ящика с песком
Полный набор планов Энчилада
Полный набор планов Энчилада! Вы хотите все это? Ты получил это! Получите все планы, которые я предлагаю, в одном пакете со скидкой 65%!
69,99 $
После фрезеровки клена размером 4/4 до 3/4 я обрезал его по ширине.
Затем я обрезал все по длине.
Здесь вы можете увидеть, как это будет работать вместе.
Я намазал все детали клеем.
Скрепил зажимами, добавил концы (не показаны) и дал коробке высохнуть.
Затем я установил это между двумя ногами, создав носилки.
Я предварительно просверлил и прикрутил его на место.
Затем я добавил в коробку песок. Это делает две вещи…. это увеличивает вес (это было 70 фунтов песка) и добавляет гашение вибрации. Это хорошо для токарной обработки, так как вибрация может вызвать плохие порезы на токарном станке и, как правило, раздражает ваши ноги.
Я прикрутил кусок 1/4 слоя к верхней части, чтобы закрыть коробку, а также создать платформу для шкафа, на которой он будет стоять.
Изготовление столешницы для стойки токарного станка
После того, как я склеил верхнюю часть стола, я обрезал концы своей гусеничной пилой. Верхняя часть была слишком длинной и тяжелой, чтобы резать ее поперечными салазками на настольной пиле.
Затем хорошая шлифовка верхней части зернистостью 120 и 180 (я проигнорировал нижнюю часть, так как ее никогда не увидишь и не потрогаешь).
Наконец я сбил края своим рубанком.
Я поставил крышку на основание и расположил ее там, где хотел.
Затем я приклеил эти скобы к среднему подрамнику и добавил такие же скобы к двум концам. Я вкрутил их в верхнюю часть, чтобы закрепить ее посередине. Это дает верхней части возможность расширяться и сжиматься.
Полный набор “Энчилада”
Полный набор “Энчилада”! Вы хотите все это? Ты получил это! Получите все планы, которые я предлагаю, в одном пакете со скидкой 65%!
69,99 $
Добавление места для хранения к станине для токарного станка
После того, как основание станка для станка в основном готово, мы можем перейти к хранилищу (шкафу). Я сделал свой из предварительно обработанной кленовой фанеры толщиной 3/4 дюйма.
С помощью гусеничной пилы я разрезаю фанеру на полоски, с которыми можно было бы справиться.
Затем я отнес их к настольной пиле, где разрезал их на части, необходимые для шкафов. Сначала я оторвал заводской край фанеры.
Затем я перевернул слой и вырезал детали. Все на столе видели.
Это очень просто, нужно всего 9 деталей (четыре для левого шкафа и пять для правого).
Сборка шкафов
Затем я выровнял все детали для проверки, чтобы убедиться, что размеры подходят и подходят под станину токарного станка.
Затем я отнес все части обратно на верстак, чтобы добавить ко всему пазы домино. Эту конструкцию можно легко сделать с помощью дюбелей или карманных отверстий без необходимости изменения размеров деталей!
горизонтальные детали имеют пазы на торцах, а не на торце.
А в правом шкафчике есть пазы посередине для удержания полки.
Когда все пазы были вырезаны, я добавил к ним клей и вставил домино перед сборкой шкафов.
Вот где блестит сборка домино. Все легко стыкуется, просто зажимаешь и ждешь.
После того, как первый шкаф будет склеен и высушен, я могу заняться вторым.
Этот собирается так же, но с полкой посередине. Вы можете видеть, что мои пазы домино немного ослаблены, чтобы дать мне некоторую свободу при сборке шкафов. Я вырезал пазы в горизонтальных частях наглухо. Только вертикальные части должны быть свободными.
Снова зажмите и подождите, пока он высохнет. Около часа нормально.
Установка шкафов
Хорошо, когда шкафы высохнут, я могу добавить их на стенд токарного станка. Они просто вставляются на место один слева и один справа.
Я только что прикрепил шкаф к ножкам подставки с помощью винтов, которые предварительно просверлил в фанере.
Второй шкаф проскальзывает рядом с ним.
И крепится так же. Вы можете решить, с какой стороны вы хотите, чтобы ваши шкафы были на. Тумбу без полки ставлю слева. В этом шкафу будут выдвижные ящики. В другом шкафу будут двери.
Затем я прикрепил кусок 1/4″ фанеры к задней части шкафов. Я использовал одну большую полосу, чтобы покрыть их обоих, чтобы они выглядели бесшовно.
Вот как выглядит вся эта готовая фанера, когда она собрана вместе. Так приятно и так удобно, что не нужно распылять все эти детали.
ОК! Теперь пришло время сделать шаг назад и проверить нашу работу! Подставка более-менее готова, осталось только обрезать края фанеры, а затем добавить ящики и дверцы. Вы можете добавить сколько угодно ящиков, но я выбрал три. Вы даже можете сделать ящики с обеих сторон, если хотите, СУМАСШЕСТВИЕ! Так много вариантов HA!
Вот вид сверху.
Изготовление дверей шкафа
Начните с изготовления деталей, которые будут формировать рамы дверей. Это каркасно-панельные двери, и мы делаем их две, поэтому нам понадобится всего восемь (8) деталей.
Это 3/4-дюймовая заготовка, которую я распилил по ширине на настольной пиле.
Затем отрежьте каждую часть по длине. Вы также можете использовать для этого матовую пилу.
Затем я добавил 1/4-дюймовую канавку прямо по центру каждой детали. Этот паз будет удерживать панель в центре, а также служить пазом для удержания шипов на концах горизонтальных частей рамы (подробнее об этом через минуту).
Чтобы отцентрировать канавку, нужно провести деталь поперек лезвия в одном направлении, затем перевернуть ее так, чтобы противоположная сторона была у упора, и снова провести ею.
Затем я обрезал шипы на концах горизонтальных частей рамы, пропустив их вертикально поперек лезвия с помощью приспособления для шипов. У меня есть руководство по изготовлению рамных и филенчатых дверей, если вы хотите узнать больше об этой процедуре.
Все 8 частей рамы можно целиком распилить на настольной пиле.
Вот шипы на концах коротких горизонтальных частей крупным планом.
Двери легко собираются. Вклейте одну короткую горизонтальную деталь в канавку более длинной вертикальной детали, чтобы получилась буква «L». Затем добавьте центральную панель в пазы обеих частей.
Добавьте другой конец, повторив этот процесс, а затем приклейте последнюю сторону на место. Проверьте квадрат, когда закончите, прежде чем зажать их.
Я прикрепил к зажимам сразу обе двери, так как они были маленькими.
Вот последние двери, все высохшие и снятые с зажимов. Идите вперед и отшлифуйте их с зернистостью 120 и 180, убедившись, что стыки ровные и все гладкое на ощупь. Я был осторожен, чтобы шлифовальный станок не ударил по центральной панели, так как они уже были готовы, и я не хотел их поцарапать.
Изготовление ящиков шкафа
Затем я сделал детали ящиков, для которых использовал фанеру толщиной 1/2″. Я вырвал все стороны ящиков и обрезал их по длине, чтобы они поместились в моем шкафу.
Затем я вырезал канавки вдоль каждой стороны и сопрягаемый шпунт, чтобы создать запирающее соединение выдвижного ящика.
Этот паз принимает язычок передней панели ящика для создания прочного соединения.
Вы также можете увидеть тот же паз, прорезанный по всей длине, чтобы принять дно ящика.
После того, как вы обрежете все четыре стороны, вы можете разложить их для сухой примерки.
Вставьте язычок на передней части ящика в паз сбоку.
Повторяйте этот процесс, пока не приклеите все четыре стороны и не установите их в зажимы. Я укрепил свои суставы штифтовыми гвоздями.
Наконец, вы можете вставить дно на место, используя канавки, которые проходят вдоль дна.
Я закрепил дно с помощью гвоздей.
Проверяйте все на ровность, чтобы ящики правильно входили в шкаф.
Я повторил этот процесс для всех трех ящиков.
Вот! Три выдвижных ящика готовы к работе.
Добавление лицевой рамки
Я вырезал 3/4-дюймовую квадратную кромку, чтобы применить ее к фасадам шкафа. Я просто обрезал их по длине и собрал все вместе, пока ходил по шкафу.
Синяя лента — отличный зажимной механизм, позволяющий клею высохнуть.
Установка ящиков и дверей
Далее дело за направляющими ящиков. Я использовал прокладку, чтобы установить их там, где я хотел.
С первым ящиком я могу подняться наверх.
Я также установил свой ящик на распорки, чтобы обеспечить правильное расстояние между ящиками.
Я прикрепил направляющие к ящику таким образом, чтобы обеспечить правильное размещение.
Установив последний ящик, я могу перейти к фасадам ящиков.
Я использую больше предварительно обработанного слоя толщиной 3/4″ для фасадов, чтобы соответствовать центральным панелям дверей, которые я сделал.
Используя прокладки, я выравниваю фасады по вертикали.
Привинчивание фасадов ящиков сзади двумя винтами завершает эту задачу.
Используя сверло Форстнера 35 мм, я просверлил отверстия для чашечных петель на дверях.
Вот вырезанная петля, установленная на двери.
Вот установленные двери. Я выровнял петли со стороны двери с петлями со стороны шкафа и прикрепил их к шкафу.
После небольшой регулировки выравнивания все выглядит равномерно!
Добавление последних штрихов к стенду токарного станка
Этот стенд токарного станка почти готов. Просто несколько других мелких вещей, чтобы решить.
Я добавил ручки для ящиков из нержавеющей стали, потому что они смотрятся оооочень хорошо рядом с кленовым деревом.