Назначение и основные виды точения
Обычно диапазон значений скорости резания — 0,005…3,5 м/с. Минимальное значение подачи составляет 0,0125 мм/об, а для очень тяжелых режимов резания — 2,5 мм/об. Глубина резания может достигать 25 мм и более.
Разновидностью токарной обработки заготовок являются растачивание отверстий и обработка торцовых плоскостей.
Растачивание проводят по той же принципиальной схеме, что и наружное точение. Особенностью растачивания отверстий является ограниченный обзор зоны резания и малая жесткость расточного резца. Под действием сил резания инструмент изгибается и вибрирует, что влияет не только на размеры и шероховатость обрабатываемой поверхности, но и на стойкость режущего инструмента.
Для повышения точности выполняемых отверстий и качества обработанных поверхностей вместо расточного резца консольного типа предпочтительнее использовать более жесткие расточные оправки, в которых закреплены два резца (рис. 30.2). В процессе механической обработки расточной станок сообщает оправке два вида движения: вращательное — вокруг ее оси, и поступательное — вдоль оси. При этом окружная скорость вращения вершин резцов является скоростью резания.
Точение торцовых плоскостей заготовок удобно выполнять токарными резцами. В этом случае механическая обработка может осуществляться при перемещении резца как от периферии к центру вращения заготовки, так и от оси к периферии.
17
МИНИСТЕРСТВО ОБРАЗОВАНИЯ РЕСПУБЛИКИ БЕЛАРУСЬ
УЧРЕЖДЕНИЕ ОБРАЗОВАНИЯ
МОЗЫРЬСКИЙ ГОСУДАРСТВЕННЫЙ ПЕДАГОГИЧЕСКИЙ УНИВЕРСИТЕТ ИМЕНИ И.П. ШАМЯКИНА
КУРСОВАЯ РАБОТА
по предмету: Технология обработки древесины
Технология точения внутренних цилиндрических поверхностей древесины на токарных станках
Разработал:
студент 3 курса, 3 группы
Шиманович Ю.С.
Мозырь 2011
Содержание
Введение
1. Точение внутренних поверхностей древесины на токарных станках
1.1 Процесс точения; виды
1.2 Устройство станка, инструменты и приспособления
1.3 Вытачивание внутренних поверхностей на токарных станках
1. 4 Правила безопасной работы при точении
2. Методические рекомендации для точения внутренних поверхностей
Заключение
Литература
Введение
Тема
курсовой работы
: «Технология точения внутренних цилиндрических поверхностей древесины на токарных станках».
Цель:
изучить процесс точения древесины на примере внутреннего точения.
Задачи:
— изучить точение внутренних поверхностей;
— ознакомиться с материалами, инструментами и приспособлениями, необходимыми для точения древесины;
— описать методические рекомендации при работе на станке;
— начертить графическое изображение и составить технологическую карту на разрабатываемое изделие;
— подготовить сувенирное изделие.
Объект исследования
: процесс точения внутренних цилиндрических поверхностей.
Предмет исследования
: токарный станок;
Методы исследования
: теоретический анализ и справочной литературы по художественной обработке и токарному делу (Карабанов И. А., Астрейко С.Я.), а также опираясь на свой личный опыт преподавания трудового обучения в средней общеобразовательной школе.
1. Точение внутренних поверхностей древесины на токарных станках
1.1 Процесс точения; виды
Токарная обработка
— это обработка резанием наружных и внутренних поверхностей вращения, в том числе цилиндрических и конических, торцевание, отрезание, снятие фасок, обработка галтелей, прорезание канавок, нарезание внутренних и наружных резьб на токарных станках.
Точение — одна из самых древних технических операций, которая была механизирована с помощью примитивного токарного станка. [5, с.15-17]
Вращательное движение заготовки называют главным движением резания, а поступательное движение режущего инструмента — движением подачи. Различают также вспомогательные движения, которые не имеют непосредственного отношения к процессу резания, но обеспечивают транспортирование и закрепление заготовки на станке, его включение и изменение частоты вращения заготовки или скорости поступательного движения инструмента и др. [8, с. 375]
Разновидности точения
§ Обтачивание — обработка наружных поверхностей.
§ Растачивание — обработка внутренних поверхностей.
§ Подрезание — обработка плоских торцевых поверхностей.
§ Резка — разделение заготовки на части или отделение готовой детали от заготовки.
1.2 Устройство станка, инструменты и приспособления
Точение — это лезвийная обработка резанием поверхностей вращения и торцовых поверхностей. Обработку наружных поверхностей называют точением или обтачиванием, обработку внутренних поверхностей называют растачиванием. Детали и изделия цилиндрической формы быстро и точно изготавливают на токарном станке
.[2, с. 26]
Токарный станок по обработке древесины- это технологическая машина для получения изделий путем снятия стружки с заготовки.
Основными частями станка являются электродвигатель, ременная передача, передняя и задняя бабки, подручник с кареткой, кнопочная станция.
Все они крепятся на станине.
Для закрепления заготовки служат передняя и задняя бабки станка.
Режущий инструмент опирают на
подручник.
От электродвигателя
через
ременную передачу
вращение передается
шпинделю
(рабочий орган). Заготовку закрепляют в приспособлении, которое фиксируется на шпинделе. Шпиндель размещается в передней бабке. Резец при точении перемещают вручную, опирая его на
подручник.
[10, 118-120 с.]
Пуск и остановку производят при помощи кнопочной станции.
Для закрепления заготовок применяют такие приспособления, как патрон,
планшайба, трезубец.
В патроне крепят небольшие заготовки с длиной до 150 мм, в планшайбе ? заготовки небольшой толщины, но значительного диаметра. При обработке длинной заготовки ее закрепляют одним концом в трезубце, другим ? в задней бабке.
На торцах заготовки проводят диагонали квадрата и в центре накалывают шилом. С заготовки состругивают ребра, придавая ей форму восьмигранника, и закрепляют на станке. [9, с. 203]
По качеству обработки различают черновое (первоначальное) и чистовое (окончательное) точение.
Основными инструментами для точения служат резцы. Полукруглой стамеской (рейер
) осуществляют черновое точение, косой стамеской (
майзель
) — чистовое.
Подручник при закреплении заготовки устанавливают так, чтобы он был выше оси вращения на 1-3 мм. Заготовку проворачивают на один оборот, чтобы проверить зазор между ею и подручником. [3, 70-72 с.]
При черновом точении рейер держат двумя руками, прижимая его левой рукой к подручнику, лезвие слегка отклоняют вверх. За первый проход снимают стружку толщиной 1-2 мм серединой лезвия рейера. Дальнейшее точение выполняют боковыми частями закругления лезвия, двигая стамеску влево и вправо. После 2-3 мин работы станок выключают и проверяют крепление заготовки.
Рис. 1
Для черновой
обработки применяют
полукруглую стамеску
(см. рис.1-
а
), для
чистового
точения, подрезания торцов и отрезания детали —
косую стамеску
(см. рис. 1-
б
).
Прежде чем отрезать деталь ее обрабатывают шлифовальной шкуркой, затем полируют брусочком более твердой породы при включенном станке. Деталь снимают со станка, отрезают ее концы мелкозубой ножовкой, торцы зачищают. Все операции выполняют по технологической карте.
На производстве точение деталей и изделий выполняют станочники токарных станков. Они должны хорошо знать свойства древесины, устройство станков, владеть приемами наладки станка, заточки инструмента, точения. [1, 17-19 с.]
Для изготовления большого количества одинаковых деталей
на токарном станке применяют
кондукторы
(
ограничители
) для стамесок или
станки с копировальным приспособлением
. Кондукторы несложно изготовить самому и легко установить как на токарной стамеске, так и на подручнике (см. рис.2).
Рис. 2
При чистовом точении майзель подводят к заготовке тупым углом книзу и в сторону вращения. Срезают слой древесины серединой лезвия; чем древесина тверже, тем больше должен быть угол наклона.
Для подрезания торцов майзель ставят острым углом вниз и делают легкий надрез. Наклонив лезвие, срезают часть заготовки до образования шейки.
Контроль качества точения деталей цилиндрических поверхностей (чистоты обработки, формы, размеров) осуществляют кронциркулем, шаблоном или линейкой «на просвет». Это делается после остановки станка, причем измерения проводят в нескольких местах. [6, 48-53 с.]
1.3 Вытачивание внутренних поверхностей на токарных станках
Для вытачивания внутренних выемок изделий с использованием патрона
(различные ёмкости, шкатулки, солонки и т.д.) — сначала высверливают сверлом отверстие по центру заготовки. Затем стамеской с полукруглым концом выбирают лишнюю древесину. Напоследок, для выравнивания стенок, используют стамеску с изогнутым концом (см. рис. слева).
Рис. 3
Для точения изделий с помощью планшайбы
сначала делают заготовку в виде квадрата. На этой заготовке проводят диагонали и чертят окружность чуть больше, чем диаметр предполагаемого изделия. Пилой обрезают лишние углы до получения восьмигранника, который прикручивают к планшайбе шурупами. Планшайбу накручивают на шпиндель и проверяют — не цепляется ли заготовка за подручник. После этого станок включают и восьмигранник обтачивают до нужного диаметра. Потом подручник устанавливают параллельно плоскости заготовки и вытачивают её внутреннюю часть. Передвинув подручник, вытачивают внешнюю сторону изделия. [9, 14-18 с.]
Сразу после обтачивания поверхность детали зачищают шлифовальной шкуркой, прикрепленной к деревянному бруску (см. рис.4). Чтобы ярче выделить текстуру древесины, поверхность изделия можно отполировать бруском более твердой древесины. Эту операцию выполняют при вращении детали, так же как и шлифование. [9, с. 29]
Рис.4
Для получения нужных контуров на изготавливаемых деталях иногда применяют и специфические стамески (см. рис.4).
Древесину для точения готовят, не только вырезая бруски или куски досок, но и используют высушенные ветки деревьев, а также склеивая куски брусков или досок (т. е. — из сегментов). Нередко для точения таких “блочных” изделий применяют древесину разных пород. Благодаря этому, добиваются весьма необычных по окраске и текстуре изделий.
При работе смотровой экран на станке должен быть опущен. Если на станке нет такого экрана, работать надо в защитных очках. Режущий инструмент подводят к заготовке только после того, как шпиндель наберет полное число оборотов.
При включенном станке запрещается подправлять заготовку и измерять ее размеры, перемещать узлы станка. После выключения станка нельзя тормозить руками заготовку, патрон или планшайбу.
Нельзя оставлять работающий станок без надзора. По окончании работы следует положить инструменты на установленные места, смести стружку щеткой.[10, 69-73 с.]
1.4 Правила безопасной работы при точении
ДО НАЧАЛА РАБОТЫ
1. Правильно надеть спецодежду (фартук с нарукавниками или халат и головной убор: мальчики — берет, девочки — косынки).
2. Проверить надежность крепления защитного кожуха ременной передачи.
3. Осмотреть надежность присоединения защитного заземления (зануления) к корпусу станка.
4. Убрать со станка все посторонние предметы, инструменты разложить на установленные места.
5. Проверить, нет ли в заготовке сучков и трещин, обтесать заготовку до нужной формы, после чего надежно закрепить на станке.
6. Установить подручник с зазором 2-3 мм от обрабатываемой детали и закрепить его на высоте центровой линии заготовки.
7. Проверить исправность режущего инструмента и правильность его заточки.
8. На холостом ходу проверить работу станка, а также исправность пусковой коробки путем включения и выключения его кнопок.
9. Перед началом работы надеть защитные очки.
ВО ВРЕМЯ РАБОТЫ
1. Подачу режущего инструмента на материал следует производить только после того, как рабочий вал наберет полное число оборотов. Подача инструмента должна быть плавной, без сильного нажима.
2. Своевременно подвигать подручник обрабатываемой детали, не допускать увеличения зазора.
3. Во избежание травм во время работы на станке ЗАПРЕЩАЕТСЯ:
а) близко наклонять голову к станку;
б) принимать и передавать предметы через работающий станок
в) замерять обрабатываемую деталь до полной остановки ее вращения;
г) останавливать станок путем торможения рукой обрабатываемой детали;
ПОСЛЕ ОКОНЧАНИЯ РАБОТЫ
1. Уложить на свои места инструменты.
2. Удалить со станка стружку при помощи щетки. Сдувать стружку ртом и сметать ее рукой запрещается.
Общие требования по охране труда
— К самостоятельной работе на токарном станке допускаются лица не моложе 18 лет, имеющие соответствующую квалификацию, получившие вводный и первичный инструктажи на рабочем месте, а также прошедшие проверку знаний по электробезопасности.
— Работник, не пошедший ежегодную проверку знаний и своевременно повторный инструктаж по охране труда, к работе не допускается.
— Запрещается пользоваться инструментом, приспособлениями, оборудованием, обращению с которыми работник не обучен.
— Работник должен соблюдать правила пожарной безопасности, а также Правила внутреннего трудового распорядка. Курить разрешается только в специально отведенных местах. Употреблять алкогольные, наркотические и токсические средства перед работой и в процессе работы запрещается.
— Работник должен знать, что опасными производственными факторами, которые могут действовать на него в процессе выполнения работ, являются:
— оборудование, инструмент и приспособления. В результате применения неисправного инструмента и приспособлений, неправильных приемов выполнения работы может произойти травмирование;
— заготовки, изделия, стружка. В результате падения или неправильного обращения может произойти травмирование;
— электрический ток. Нарушение требований нормативно-технических документов может привести к опасным электротравмам (ожог, электрометаллизация и т.д.) или к смертельным электроударам.
2. Методические рекомендации для точения внутренних поверхностей
станок древесина поверхность точение
Заготовку для точения внутренней поверхности закрепляют только в передней бабке станка (с помощью патрона или планшайбы). Инструментом служат резцы с рабочей поверхностью в виде крючка
или
ложечки.
Для работы берут заготовку (брусок) с учетом припуска. Выбрав базовую сторону (торец), заготовку размечают с помощью линейки и карандашом, затем плотно вгоняют заготовку в патрон станка и закрепляют шурупами. Патрон навинчивают на шпиндель. Если на наружной поверхности будущего изделия не будет резких перепадов диаметра, то сначала заготовку обтачивают. Затем точат ее внутреннюю поверхность. [3, с. 60]
Если же изделие должно иметь резкие перепады диаметров (например, спортивный кубок с ножкой), то сначала обтачивают наружную
поверхность большего диаметра, затем ?
внутреннюю
и только после этого вытачивают наружные элементы
малых
диаметров.
Для точения внутренней
поверхности в торце заготовки просверливают отверстия на полную глубину будущего изделия. Сверлят в 2-3 приема с увеличением диаметра сверла. Растачивают внутреннюю поверхность
крючком
.
Внутренние сферические
поверхности большого диаметра обрабатывают крючком другого типа. Для обработки перехода от дна изделия к стенке и выравнивания дна используют ложечный резец, а также специальные токарные стамески. Инструмент ставят на правое ребро, прижав лезвие к плоскости торца заготовки. Точение начинают с небольшой стружки, которую получают при обработке заготовки вершиной лезвия, отводя ручку вправо. Продолжают точение от края торца к центру, постепенно поднимая ручку инструмента вверх и отводя ее вправо. Металлическая часть резца не должна тереться о края получаемого углубления. Контроль качества ведут по толщине стенок с помощью штангенциркуля, предварительно остановив станок. [9, с.47-49]
Для получения изделий большого диаметра (например, тарелок) заготовку привинчивают шурупами к планшайбе.
Планшайбу с заготовкой навинчивают на шпиндель станка.
Следует помнить, что шурупы, которыми крепиться заготовка к планшайбе, не должны попасть под резец.
При точении на планшайбе вначале обрабатывают наружную поверхность заготовки. Затем подручник поворачивают и закрепляют параллельно плоскости планшайбы или под незначительным к ней углом. После этого приступают к внутреннему точению,
перемещая резец от центра к краям заготовки.
В процессе окончательной обработки поверхности изделий из древесины шлифуют стеклянной шлифовальной шкуркой. Наждачная шлифовальная шкурка образует темную пыль и загрязняет поверхность изделия. Работают на токарном станке в соответствии с технологическими картами.
На производстве конические и фасонные поверхности изделий из древесины вытачивают станочники токарных станков. Шлифуют их на шлифовальных станках шлифовщики по древесине. [8, с.386-393]
Заключение
Учебно-воспитательная работа в процессе токарной обработки древесины направлена на развитие трудового, эстетического и нравственного воспитания, расширение их кругозора, формирование устойчивого интереса к творческой деятельности.
Учитывая, что при токарной обработке лучше раскрываются декоративные свойства древесины, предоставляется возможность использования различных пород древесины, имеющих даже не чётко выраженную текстуру.
При изучении технологической операции «Точение древесины» можно познакомиться познакомятся с различными видами точения и отделки точеных поверхностей.
Практические работы включают изучение токарного станка, заточку инструмента, приемы работы рабочим и контрольно-измерительным инструментом, составление эскизов и чертежей изделий, разработку творческих проектов. [7, с. 483]
Работа на токарных станках по изготовлению изделия занимает главное место на практических занятиях. Обучение этому следует начинать с изготовления изделий по образцам. Такие учебные задания выполняются при точении цилиндрических, конических наружных и внутренних поверхностей.
При выполнении заданий предусматривается сообщение теоретических сведений по основам материаловедения, технологии точения древесины, о породах и пороках древесины, об отделке изделий.
В процессе изучения технологии точения древесины проводятся экскурсии на деревообрабатывающие предприятия и по возможности на предприятия народных художественных промыслов. В плане работы следует также предусмотреть посещение музеев, выставок технического и художественного творчества с последующим обсуждением увиденного.
После выполнения учебного задания по каждому виду точения древесины составляют рисунки (эскизы, чертежи) с элементами выжигания, росписи, аппликации, резьбы и др., для выполнения индивидуальных и коллективных работ.
В конце курса обучения можно выполнять задания по собственному замыслу. Выбор тематики, отбор эскизов изделий и их выполнение должны носить коллективно-творческий характер. Это способствует развитию чувства коллективизма, взаимопомощи, ответственности за общее дело.
В процессе обучения нужно уделять особое внимание правилам безопасной работы и противопожарной безопасности, а также санитарно-гигиеническим условиям труда.
В зависимости от национальных традиций народного искусства региона, а также индивидуальных и возрастных особенностей обучающего можно вносить изменения. Последовательность изучения токарной работы должна сохранить принципы «от простого к сложному» и «от частного к общему». [6, с.171-172]
Литература
1. Астрейко С.Я. Ручная отделка изделий из древесины (с основами материаловедения) / С.Я. Астрейко. — Мозырь: МГПИ, 1996. — Вып.1. — 34 с.; 2002. — Вып.2. — 36 с.
2. Барташевич А.А. Художественная обработка дерева / А.А. Барташевич, А.М. Романовский. — Минск: Выш. шк., 2003. — 230 с.
3. Гликин М.С. Декоративные работы по дереву на станках / М.С. Гликин. — М.: Изд-во «Народное творчество», «Искона», 1990. — 280 с.
4. Гостомыслов А.П. Токарное художество / А.П. Гостомыслов. — Л.: Дет. лит., 1999. — 165 с.
5. Карабанов И.А. Технология обработки древесины, 5-9: учеб. для учащ. 5-9 классов общеобр. учреждений / И.А. Карабанов. — М.: Просвещение, 2002. — 192 с.
6. Коваленко В.И. Объекты труда: 7 кл.: обраб. древ. и металла, электротехн. работы: пос. для учителя / В.И. Коваленко, В.В. Куленёнок. — М. : Просвещение,1993. — 191 с.
7. Работы по дереву / сост. В.И. Рыженко. — М.: ООО «Гамма Пресс-2000», 2001. — 512 с.
8. Резьба по дереву / авт.-сост. В.В. Новиков. — М.: Лабиринт Пресс, 2002. — 416 с.
9. Резьба по дереву / Сост. А.С. Лихонин — Нижний Новгород: Изд-во «Времена», 2000. — 224 с.
10. Справочник мастера деревообработки / под ред. Ю.Р. Бокшанова. — М.: Лесная промышленность, 1997. — 277 с.
11. Шпаковский, В.О. Для тех, кто любит мастерить / В.О. Шпаковский. — М., 1990. — 192 с.
Размещено на stud.wiki
виды чашек (тарелок), выбор инструмента
Режущий инструмент тупится во время работы. Это естественный процесс. Качество металла резца или пилы может повлиять разве что на скорость изнашивания, но в любом случае от операции заточки не уйти. Именно для этой процедуры существуют специальные круги алмазные заточные. Их закрепляют на точильный станок или шлифовальную угловую машинку.
Конструкции заточных дисков бывают разными, например, есть алмазная тарелка, инструмент в виде чашки, просто плоский диск либо любой другой формы. Все это множество конфигураций обусловлено целью сделать удобным выполнение шлифования или заточки разного инструмента.
Наиболее востребованы алмазные круги для заточки дисковых пил. Они рассчитаны на работу с твердыми победитовыми напайками, с которыми тяжело справиться обычному заточному инструменту. Попробуем разобраться в вопросах, как устроены алмазные круги, какими бывают и для чего конкретно предназначен тот или иной тип изделия.
Типы алмазных дисков для заточки
Алмазные круги для заточки инструмента имеют свою классификацию. Заводы по изготовлению абразивного инструмента выпускают алмазные диски трех форм:
- В виде чашечки – это полый внутри конус с основанием из металла и напыленным на рабочую часть слоем алмазной крошки.
- Наподобие тарелки, где бывает односторонняя или двухсторонняя выточка, профиль смотрится полукругло-выпуклым.
- Диски с прямым профилем.
Кроме этого, имеются две основные группы инструмента, в каждой из которых применяют различный алмазный материал для заточки:
- Абразив из штучно созданных алмазов, который отличается высокой однородностью зерна.
- Абразив, выполненный из натуральных кристаллов алмазов, которые относятся к техническим.
И одна из самых важных категорий, определяющая назначение алмазного диска для обработки инструмента, – это категория по величине основной массы зерна в напыленном слое:
- Мелкая фракция абразивного алмаза, используемая для шлифовок, доводок и финишных работ по обработке материала (100/80).
- Средняя фракция абразивного алмаза, используемая для целевых задач заточки, а также при чистовых операциях шлифовки (125/100).
- Крупная фракция абразивного алмаза, применяемая в черновых работах шлифовки или грубого обдира обрабатываемого материала (200/160–160/125).
Кроме всего перечисленного, выбирая алмазный диск для конкретного шлифовального станка, нужно учитывать диаметр посадочного места, ширину рабочей поверхности абразива, материал основы инструмента.
Назначение абразивов
В зависимости от вида абразива, из которого изготовлен шлифовальный круг, меняется сфера его применения.
Нормальный электрокорунд обладает хорошей вязкостью, сцеплением со связкой, термостоек хорошо подходит для работы со сталью, чугуном, бронзой и латунью ввиду своих физических свойств.
Белый электрокорунд имеет более однородную структуру, острые кромки, более твердый чем обычный корунд и имеет меньшую шероховатость поверхности. Предназначен для обработки тех же материалов, что и обычный электрокорунд, но за счет меньшего нагрева и износа, применяется также для легированных и инструментальных сталей, заточки зубьев пил, режущих кромок фрез, ножей, сверл. Хорошо подходит для полировки изделий.
Карбид кремния тверже, но хрупче электрокорунда. У него выше абразивная способность, но сцепление зерна со связкой слабее, чем у корунда.
Используется для работы с твердыми, но хрупкими веществами – стеклом, фарфором, керамикой, гранитом, а также для составов с повышенной вязкостью – резины, меди, алюминия, жаропрочных сталей.
Алмаз имеет большую механическую прочность, но чувствителен к высоким температурам, реагирует с железом, хрупок, имеет очень хорошие самозатачивающиеся свойства, что придает диску долговечности.
Алмазные круги для шлифовки используются для обработки таких материалов, как чугун, стекло, керамика, твердые сплавы. Хорошо подходит для финишной доводки изделий, заточки сверл, фрез, пил, ножей.
Эльбор второй после алмаза по твердости, не реагирует с железом, теплостоек, хрупок, обладает хорошей абразивной способностью.
Применяется для шлифовки и обработки твердых сталей, заточки инструмента, чистовой обработки, сфера применения эльбора включает в себя участки, где другие абразивы не применяются вследствие высоких рабочих температур.
Конструкция алмазных кругов для заточки инструмента
Диски алмазные заточные представляют собой изделия круглой формы с основанием из металла и нанесенным на него покрытием алмазного порошка, который закрепляется на металле связующим веществом, также там присутствует наполнитель.
Марка диска характеризуется:
- конфигурацией корпуса и видом материала, из которого он изготовлен;
- размером окружности;
- величиной концентрации абразивных зерен;
- фракцией алмазов;
- типом вещества, используемого в качестве связки;
- степенью точности;
- классом неуравновешенности.
Одним из важных параметров является износостойкость диска.
Корпуса алмазных заточных кругов могут быть изготовлены из стальных заготовок, марок Ст-25, 30, 20 или 3, либо сплавов из алюминия АК-6 или Д-16, либо полимерных материалов. Для некоторых шлифкругов типа А1ПП, АГЦ делают еще хвостовики из стальных У7 и У8 марок.
Что касается применяемых связующих веществ, которые скрепляют алмазные зерна в единую форму, то выпускаются диски на основе:
- Связок металлического характера на основе алюминия, меди, цинка или олова. В маркировке таких изделий указывается литера М.
- Связок керамических на основе шамота либо стекла, куда добавляют составляющую алюминия.
В маркировке здесь будет присутствовать литера К.
- Связок на основе органики – это пульвербакелитные и карболитные вещества. Присутствие такой связки обозначают в маркировочном коде литерами КБ.
В качестве наполнителей используют электрокорунд, графитовый порошок, медь, карбид бора и глинозем.
Виды зернистости в зависимости от вида обработки
Под зернистостью понимают размер основной массы зерен среди общего количества алмазных частиц в абразиве. Размер зерна обычно определяется тремя параметрами: высотой, шириной и толщиной, но на практике за основу берут ширину. Чистота обработки поверхности материала зависит от степени зернистости круга для заточки. Также этот параметр влияет на оперативность проведения работ, количество металла, который можно удалить за один проход инструмента по заготовке и изнашиваемость рабочей области алмазного диска для заточки.
Согласно нормам стандартизации международного уровня FEPA маркировка алмазного заточного инструмента должна содержать код зернистости: сочетание литеры F и определенного числа за ним. Возрастание числа указывает на присутствие в абразиве более мелких зерен. Чтобы правильно подобрать круг для заточки, нужно знать марку материала, какую необходимо получить в итоге шероховатость, допустимый припуск.
Между размером зерна в абразиве и чистотой поверхности металла после обработки существует обратно пропорциональная зависимость. Поэтому для финишных работ применяют заточные круги с самыми маленькими алмазными зернами.
Наиболее правильный подход к обработке и заточке инструмента лежит в последовательном применении алмазных кругов, начиная с более грубых и заканчивая финишными. Применение только последних может привести к пригоранию обрабатываемой поверхности, засаливанию и быстрому выходу из строя заточного круга.
По размеру фракции зерна его можно отнести к тому или другому типу зернистости:
- 100/80 – мелкие алмазные зерна. С их применением выполняют окончательную доводку тонких лезвий, заточку металлообрабатывающих резцов, операции финишной шлифовки.
- 125/100 – средние алмазные зерна. Заточка изделий до состояния необходимой остроты.
- 160/125 – крупные.
- 200/160 – очень крупные алмазные зерна. Абразивы подходят для выравнивания поверхности режущего инструмента.
Особенности кругов на органических связках
Все органические связки не могут обходиться без наполнителя. Они обладают слабыми показателями твердости, устойчивости к повышенным температурным режимам и плохо проводят тепло, но зато отличаются хорошей производительностью и высокой скоростью проведения операций заточки инструмента.
Алмазные диски на основе органического компонента целенаправленно применяют в доводочных обработках и когда выполняют чистовые работы. Они отлично справляются при заточке победитовых материалов, твердокомпонентных сплавов, любых металлов и материалов из сверхтвердых структур. Выводят обрабатываемую поверхность на уровень 12 и 11 класса шероховатости. Диски мало подвержены засаливанию, но очень быстро изнашиваются.
Профили на керамических связках
В связках на керамике используется покрытие из алмазоникеля. Это покрытие бывает однослойным либо может наноситься в несколько слоев. Толщина связующего вещества на керамической основе не превышает 2/3 величины зерен алмаза. Благодаря тому что между вершинами кристаллов и связкой имеется свободный промежуток, стружка, снятая с обрабатываемой поверхности, автоматически удаляется, не создавая дополнительных препятствий процессу заточки.
Основные свойства заточных дисков на керамической связке:
- отличная способность к снятию слоя металла во время заточки;
- возможность создавать абразивный инструмент любой конфигурации;
- высокая проводимость тепла;
- приемлемая стоимость изделий.
Что представляет собой шлифовальный круг
Является абразивным инструментом для обработки изделий как на стационарных станках, так и при помощи ручного инструмента. Существует несколько параметров, по которым можно классифицировать шлифовочные круги.
Для их изготовления может использоваться:
- карбид кремния;
- алмаз искусственного либо природного происхождения;
- электрокорунд;
- эльбор.
В зависимости от размеров зерна диски различаются по своему назначению. Между зернами расположен клеящий и заполняющий состав – связка, придающий ему абразивные свойства за счет пор. Абразив снимает частицы с обрабатываемого материала.
Некоторые диски обрабатываются специальными импрегнированными пропитками, чтобы уменьшить температуру при шлифовке.
Характеристики и особенности алмазных кругов для заточки резцов
Алмазные круги для заточки резцов токарных и другого режущего инструмента в зависимости от формы профиля и типа абразива целенаправленно подходят для следующих операций:
- С формой прямого плоского профиля марки 1A1 – для проведения обработки изделий цилиндрической формы, плоских деталей и затачивания резцов из сплавов твердой структуры.
- С формой тарельчатого профиля марки 12A2-20* – для проведения операций заточки передней части инструмента, который имеет много лезвий, выполненных из сплавов твердой структуры, фрез, состоящих из сборочных единиц либо цельнометаллических, фрез червячного типа, пил дисковых.
- С формой чашечного профиля марки 12A2-45* – для работ с задними и передними поверхностями твердосплавных резцов и шлифования торцов.
- С формой тарельчатого профиля марки 12R4 – для проведения операций доводки и заточки, как в случае с диском марки 12A2-20*.
- С формой прямого плоского профиля и устроенными по обе стороны выточками марки 9A3 – для работы с резцами из твердых сплавов, конструктивными элементами машин, материалов полупроводниковой структуры, инструментом для измерений.
- С формой плоского выпукло-полукруглого профиля марки 1FF1 – для заточки и шлифовки изделий из твердых сплавов.
- С формой плоского конического по двум сторонам профиля для работы с фасонными поверхностями и резьбой.
Следует сказать о концентрации алмазной составляющей, которая имеет влияние на режим заточки. При стопроцентном показателе круги имеют высокую производительность и способны выдерживать жесткие режимы обработки, не подвергаясь при этом деформации. При 50%-м показателе диски применяют чаще всего для любых видов работ. При 20%-м показателе – доводочные круги для ручной подачи инструмента.
Инструменты для токарного оборудования
Для того чтобы разбираться в правилах заточки резцов для токарных станков по металлу, недостаточно просто посмотреть обучающее видео. Необходимо иметь представление о том, как классифицируются такие инструменты. Самым главным параметром, по которому токарные резцы относят к различным видам, является тип обработки, выполняемой с их помощью. По этому признаку выделяют следующие виды токарных резцов.
Основные типы токарных резцов
Проходные
Такими резцами заготовки обрабатываются вдоль оси вращения.
Подрезные
Используя эти резцы на токарном станке, уменьшают уступы и выполняют торцевание заготовок.
Канавочные
Как следует из названия, ими формируют наружные и внутренние канавки на поверхностях цилиндрической формы. Создавать канавки на наружных сторонах заготовок можно и при помощи отрезных резцов по металлу. Кроме того, такие резцы позволяют отрезать части заготовки под прямым углом.
Расточные
С помощью таких инструментов на станках выполняют обработку отверстий.
Резьбонарезные
Такие резцы специально предназначены для нарезания резьбы.
Фасонные
С помощью резцов этого вида на внешней стороне цилиндрических заготовок формируют фасонные выступы или канавки.
Фасочные
С помощью этих резцов на заготовках снимаются фаски.
Операции, проводимые резцами различного типа
Токарные резцы также подразделяются на виды в зависимости от того, в каком направлении с их помощью выполняется обработка заготовки. Так, среди них бывают правые (обработка выполняется по направлению к передней бабке) и левые (обработка по направлению к задней бабке).
Классифицируется токарный инструмент и по материалу изготовления, по способу соединения режущей части с державкой, а также по ряду других параметров.
На что стоит обратить внимание при выборе алмазного диска
От правильного выбора алмазного диска напрямую зависит удобство и быстрота работы на заточном станке. В некоторых случаях неправильный выбор может послужить причиной деформации диска или порчи резца. Вот что нужно проанализировать, прежде чем выбрать конкретный диск:
- марку металла, который будет подвержен заточке или тип твердого сплава;
- обороты и мощность заточного станка;
- форму обрабатываемой поверхности;
- степень допустимой шероховатости.
Приобретаемый алмазный диск должен строго соответствовать всем этим параметрам.
Если вы профессионал, работающий с токарным оборудованием, или человек, имеющий опыт применения алмазных заточных кругов, поучаствуйте в обсуждении темы в комментариях. Знания специалиста всегда в цене!
Неглубокая тарелка.

По внешнем виду тарелка заметно отличается от чашки глубиной, как правило, высота тут всего 18 мм. В другом все стандартно, алмазный заточной круг 12А220 150*10*2*18*32 160/125 — тарелка диаметром 150 мм, ширина алмазного слоя 10 мм, толщина 2 мм, глубина — 18 мм(неглубокая), посадка 32 мм. Зерно 165/100 — достаточно крупное по сравнению с другими.
Тарелки бывают на 150 мм и на 125 мм диаметром.
Они отлично подходят для заточки инструмента, более того, на них точат твердосплавные напайки на дисковых пилах. Для того, чтобы заточить такие напайки, понадобится тонкая тарелка, чтобы край смог пролезть между зубьями.
Краткое руководство по плоскому и круглому шлифованию
16 декабря 2020 г. 0 0
Два наиболее распространенных метода шлифования — плоское и круглое. Вот руководство, чтобы узнать больше.
Согласно Amon Engineering:
«Существует множество методов шлифования, но два наиболее распространенных — это плоское и круглое шлифование. Различия между процессами действительно сводятся к форме, которую вы пытаетесь создать. Плоское шлифование режет плоско, круглое шлифование режет круглое. Вы можете использовать один и тот же носитель в обоих процессах. Еще одно замечание: обычно вы монтируете цилиндрическую деталь между центрами или в цангу. Для плоского шлифования вам понадобится магнитный патрон или вам нужно покрыть детали воском. Таким образом, круглое шлифование снижает потребность в очистке. Ниже приведено краткое руководство по плоскому и круглому шлифованию.
Плоское шлифование
«Плоское шлифование обычно является наиболее распространенным методом шлифования. Абразивный круг вращается на шпинделе и перемещается, как правило, над куском материала, будь он металлическим или неметаллическим. Это обеспечивает желаемую чистоту поверхности, а также возможность шлифования с чрезвычайно высокими допусками. Обычно +/-0,0001” или +/-0,002 мм. Заготовка удерживается на патроне, обычно магнитного типа, в другом варианте для немагнитных компонентов используется вакуумный патрон.
«Требуемый шлифовальный круг зависит от типа шлифуемого компонента, существует множество различных составов для шлифования различных материалов. После того, как вы выбрали правильный круг, вы можете либо шлифовать плоским кругом, создавая плоскую поверхность, либо вы можете поместить форму снаружи круга, чтобы получить определенную форму, это будет зеркальное отражение формы на круге. .
Круглое шлифование
«Круглое шлифование — еще один вид шлифования. Это позволяет шлифовать наружный и внутренний диаметры. Основное различие между этими двумя методами заключается в том, что при круглом шлифовании заготовка, удерживаемая либо в патроне, либо между центрами, и абразивный круг будут вращаться. Достижим тот же уровень допусков, что и при обработке поверхности.
«Станки круглошлифовальные применяются в основном для прецизионного шлифования торцов, наружных и конических поверхностей деталей валов партий и являются основным оборудованием в автомобильном двигателестроении. Он также подходит для обработки деталей вала с небольшими партиями и высокими требованиями к точности в военных, аэрокосмических и общих цехах прецизионной обработки.
«Используется в текстильной прядильной промышленности, машинах для толстой пряжи, ленточных машинах, гребнечесальных машинах, машинах для текстурирования и другой обработке верхних валков. Используется в производстве оргтехники, факсимильных аппаратов, копировальных аппаратов, принтеров, режущих плоттеров и других резиновых валиков. Он также применим к фармацевтической промышленности, автоматическим конвейерным устройствам, верхним роликам и обработке пластмасс.
«Для получения дополнительной информации о плоском и круглом шлифовании обратитесь в компанию Amon Engineering. Мы предоставляем нашим клиентам полный спектр прецизионных компонентов, включая прототипирование малых и средних партий деталей из широкого выбора материалов. Мы умеем работать с черными металлами, карбидом вольфрама, инструментальной сталью, алюминием, нержавеющей сталью, аэрокосмическими сплавами, конструкционными пластиками, цветными металлами, усовершенствованной технической керамикой и другими материалами».
Первоисточник
Теги: круглое шлифование, плоское шлифование
Конические и плоские кофемолки [My No *BS Explanation]
Кофе — это сложно. Особенно, когда речь идет о множестве различных шлифовальных станков.
Вам не нужно долго искать, прежде чем вы поймете, что жерновная мельница — это способ прокатки; лезвийные кофемолки просто не приготовят вам вкусную чашку кофе.
Но достать кофемолку не так-то просто. Вы можете рассмотреть как конические, так и плоские модели жерновов.
Что означают эти технические различия?
И один лучше для эспрессо, чем другой?
Пришло время стать занудой 🤓
Что такое кофемолки с коническими и плоскими жерновами?
Жернова являются основным механизмом «дробления/резки», на который полагаются кофемолки для измельчения целых кофейных зерен в порошок.
Плоские жернова (как следует из названия) плоские и имеют крошечные зубья, которые используются для измельчения кофейных зерен на более мелкие частицы.
Конические борфрезы имеют конусообразный внутренний вращающийся бор и неподвижный внешний бор.
Примечание: Есть несколько исключений из этого правила. Например, Baratza Sette. Он имеет вращающийся внешний заусенец.
Как плоские, так и конические жернова можно использовать для эспрессо- и капельных кофемашин. Однако некоторые люди будут утверждать, что одно лучше другого, но на самом деле это не так.
Зависит от того, какой кофе вы будете варить и какие характеристики кофемолки вы цените.
С учетом этого, мы можем сказать одну вещь об этих кофемолках: самые дешевые кофемолки с жерновами, как правило, имеют коническую форму.
Другими словами; если вы ищете кофемолки начального уровня, большинство из них будут оснащены коническими жерновами.
То же самое касается ручных шлифовальных машин. Большинство ручных шлифовальных машин имеют конические жернова, так как очень сложно вставить большие плоские жернова в такую конструкцию. Поэтому, если вы цените что-то портативное, у него обычно будут конические заусенцы.
Опять же, это не обязательно плохо. Многие заядлые кофеманы используют ручную кофемолку с коническими жерновами и просто обожают ее!
Плоские жернова сверху, конические снизуКак форма жерновов влияет на качество кофе?
Жерновая мельница работает по принципу трения между двумя поверхностями.
При использовании конического жернова каждое кофейное зерно должно подвергаться увеличивающемуся уровню трения по мере того, как оно раздавливается вращающимся жерновом.
Зерна затягиваются во все более узкое пространство сначала под действием силы тяжести, а затем под действием заусенцев, действующих как шнек.
В конце концов, все кофейные зерна должны пройти через один и тот же тонкий зазор между внутренним и внешним жерновами, что означает, что все частицы должны иметь одинаковый диаметр.
Однако в действительности будут некоторые отличия. Часто вы также получаете немного пыли/очень крошечных частиц, которые на кофейном жаргоне называются «мелочью».
Плоские борфрезы работают немного по-другому, так как они вращаются на более высоких скоростях. Зубья и непрерывное вращение медленно выталкивают все более мелкие кофейные стружки к выходу из камеры помола.
Такой равномерный размер помола важен для равномерной экстракции.Консистенция помола
Вот как они работают. Но какой из них лучше?
Чтобы ответить на этот вопрос, нам нужно рассмотреть множество параметров.
В первую очередь следует позаботиться о равномерности помола, или , однородности частиц.
Допустим, мы размалываем одну мерную ложку кофе. Возможно, половина совка будет содержать частицы размером 600 микрон. Остальные частицы будут падать в форме колоколообразной кривой, состоящей из более мелких и более крупных частиц. Когда мы говорим о таких вещах, как распределение частиц и «пик», мы имеем в виду эту кривую.
Обычно желательно иметь высокий пик и узкое распределение. Это связано с тем, что это гарантирует, что большая часть частиц извлекается с одинаковой скоростью.
Мелкие частицы (пыльные, сверхмалые частицы) обычно считаются нежелательными, поскольку они склонны к переэкстракции и создают горечь.
Они также забивают фильтры или сетчатые фильтры при приготовлении пуровер-кофе, что приводит к остановке и засорению.
Если кофемолка имеет два слегка разделенных пика, один больше, а другой меньше, мы называем это бимодальной кофемолкой, когда смотрим на распределение. Если есть только один пик, мы называем его унимодальным.
Унимодальный кофе считается святым Граалем для фильтрованного кофе, тогда как бимодальный считается более подходящим для эспрессо.
Узнайте больше: Как очистить кофемолку
Различия во вкусе
Что касается вкуса, бимодальный напиток создает более текстурированную чашку с консистенцией, востребованной многими бариста.
С другой стороны, унимодальный способ дает чашку большей четкости. Вот почему многие кофейные снобы предпочитают кофемолку с плоскими жерновами для фильтрованного кофе.
Однако многие бариста предпочитают плоские жернова для эспрессо, поскольку они обеспечивают более округлый и комплексный вкусовой профиль.
Также стоит отметить, что некоторые плоские борфрезы, например, раскрученный многоцелевой набор SSP, обеспечивают то, что можно назвать невероятно чистым профилем выстрела.
Напротив, многие другие плоские жернова дают распределение, которое подчеркивает тело и сладость. Таким образом, даже в мире плоских жерновов могут быть значительные различия во вкусе.
Размер помола и настройки
Универсальные борфрезы SSP имеют одномодальное распределение с высоким пиком. Они популярны как для эспрессо, так и для капельного приготовления. Нам также необходимо кратко коснуться настроек помола. Для эспрессо и кофе по-турецки лучше использовать мелкий помол. Именно здесь заусенцы расположены очень близко, так что они могут производить крошечные частицы.
Для френч-пресса и капельного кофе следует использовать среднюю настройку. При таком размере помола жернова находятся где-то между мелким и грубым.
Большинство (если не все) жерновных кофемолок могут производить хороший средний помол. Однако, как правило, сделать очень мелкий или грубый помол сложнее, так как он требует лучшей калибровки и точности между каждым жерновом.
Конические жернова
Pros- Как правило, они намного дешевле, чем кофемолки с плоскими жерновами, даже несмотря на то, что они доступны во всех ценовых категориях. Коническая керамическая мельница может стоить менее 20$
- Калибровка и юстировка пользователем обычно не требуются
- Стань менее горячим. Однако этот фактор необходим только в среде кофейни.
- Как правило, легче набрать на эспрессо-выстрелах с кониками
- , как правило, более бимодальные
- . Это может быть более активизирующим
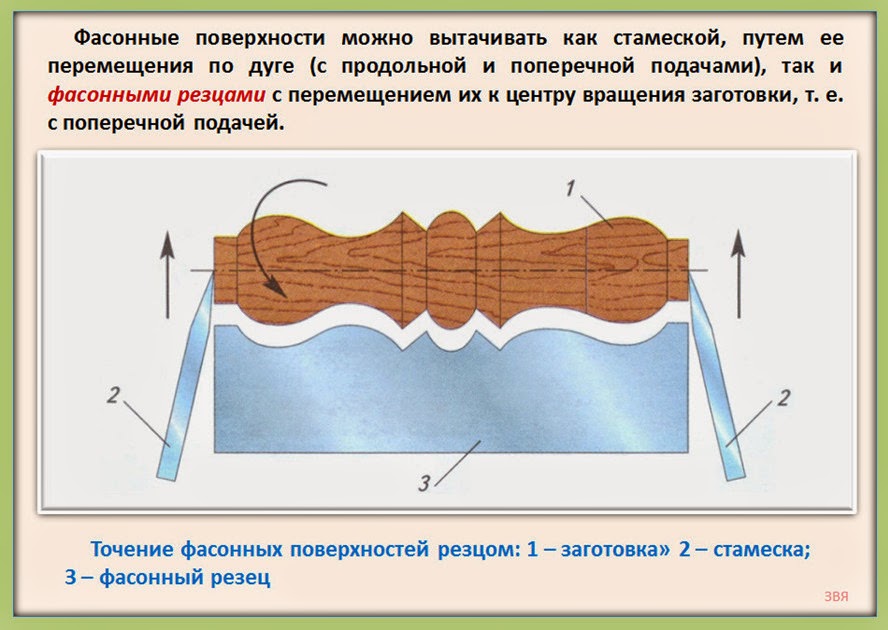
- Может быть сложно настроить для домашних пользователей
- Более дорогой
- Легко настроить размер помола и удержание. Хотя эти факторы имеют решающее значение, они не имеют большого отношения к типу бора, используемому в устройстве. Обычно шум определяется материалом корпуса, числом оборотов и геометрией жерновов, а также общей конструкцией.
Удержание измеряется тем, сколько старого кофе осталось в кофемолке. Обычно он застревает в камере измельчения, желобе или различных уголках устройства.
Высокое удержание — это проблема, поскольку это означает, что каждый раз, когда вы гриндите, будет происходить некоторый «обмен».
Другими словами, это означает, что вы можете получить немного старого кофе в свой портафильтр.
Использование плоского или конического бора не является самым важным аспектом ретенции. Вместо этого общий дизайн кофемолки гораздо более важен.
Например, Niche Zero, кофемолка с коническими жерновами, имеет очень низкое удержание. Тем не менее, Iberital MC2, еще одна кофемолка с коническими жерновами, имеет превосходное удержание.
Керамический конический бор Hario Skerton Pro (справа) по сравнению с обычным коническим стальным бором (слева). Керамические конические борфрезы обычно являются самым дешевым вариантом.Заключение
В заключение мы рассмотрели все основные плюсы и минусы кофемолок с коническими и плоскими жерновами.
В зависимости от ваших потребностей и предпочтений один вариант может быть более подходящим, чем другой.
Если вы впервые покупаете и ищете что-то дешевое и простое в использовании, обратите внимание на коническую борфрезу.
С помощью такой кофемолки можно сварить вкусный кофе. Из-за цены он, вероятно, должен быть вариантом по умолчанию для большинства покупателей впервые.
Вы всегда можете обновить кофемолку на более позднем этапе, если вы одержимы кофе и готовы потратить больше денег на кофемолку с плоскими жерновами.
С другой стороны, если вы уже знаете, чего хотите, и ищете что-то сверхчистое и высококачественное, выбирайте плоскую борфрезу.
Часто задаваемые вопросы
Какая кофемолка лучше с плоским или коническим жерновом?
Этот вопрос довольно субъективен. Здесь нет правильных ответов. Это зависит от ваших вкусовых предпочтений.
Лично я предпочитаю кофемолки с плоскими жерновами, потому что они дают мне более чистую чашку кофе со сладостью.Каковы преимущества кофемолок с коническими жерновами по сравнению с плоскими жерновами?
Кофемолки с коническими жерновами имеют тенденцию создавать эспрессо с большей густотой и текстурой.