Кругорез по металлу своими руками: фото и описание конструкции
Самодельный кругорез по металлу, сделанный своими руками, фото и описание конструкции самоделки.
Станок собран из того что было, на коленке, в гаражных условиях.
Конструкция кругореза простая, поворотный стол карусельного типа, вместо резца — ролик от трубореза. Перемещением каретки выбираем радиус резки.
Вот на таком самодельном станке, режу нержавейку 0,5 мм. В результате: получается ровный круги, деталь с отверстием тоже ровная, так сказать, безотходное производство.
Правда у станка есть свои минусы: круг прорезается, где то за десяток оборотов, острые края, ограниченный ресурс поворотного стола (ролик не только прорезает жестянку но и делает канавку в столе). Ну а в остальном меня всё устраивает.
Автор самоделки: Игорь. г. Ульяновск.
Загрузка…Кругорез по металлу своими руками
24 февраля 2016 г.
Больно смотреть, когда при вырезании круглых отверстий в листах фанеры, пластика и металла применяют зубило, ножовку или высверливают отверстия по периметру.
Я изготовил своими руками простое приспособление — станок-кругорез. Для него необходимы два куска стального угольника 32х32, два прутка диаметром 12 мм, гайки M12 и болты М6. Устройство самодельного кругореза ясно из рисунка. С его помощью можно вырезать круги диаметром от 40 до 500 мм практически в любом материале — дереве, фанере, металле, различных пластиках и т. п.
Устройство самодельного кругореза
1 — угольник 3х32х32; 2 — штанга Ø12, L=350; 3 — каретка из угольника 3х32х32 для установки резца; 4 — болт М6, фиксирующий каретку на штанге; 5 — резец; 6 — рукоятка; 7 — болт М6 для крепления резца; 8 — центрирующий болт.
Для установки кругореза в центре вырезаемого круга просверливается отверстие, в которое вставляется центрирующий болт 8 и фиксируется гайкой. Взяв за ручку, совершают кругорезом вращательные движения. Дорезав до половины толщины, переставляют приспособление на другую сторону заготовки и продолжают резать до конца. Это необходимо делать при вырезании отверстий в дереве, фанере и других волокнистых материалах, чтобы избежать обрывов наружных слоев.
В качестве резцов применяются отработавшие свой срок надфили, ножовочные полотна, стальная проволока. Формы заточки резцов самые различные в зависимости от обрабатываемых материалов. Например, резину хорошо режет игла. Укрепив стеклорез, можно вырезать круги и круглые отверстия в стекле, при этом на центр кругореза надевается металлический наконечник, обклеенный резиной, чтобы он не скользил. Одной рукой нажимают на центр сверху, а второй ведут стеклорез.
Порекомендуйте эту страницу друзьям или добавьте в закладки: |
—>
Другие материалы о самодельных станках и приспособлениях на сайте: |
---|
Самодельный сверлильный станок из фотоувеличителя |
Токарный станок по дереву из электродрели |
Простой самодельный гравировальный станок |
Приспособление для нарезки зубьев пилы |
Главная
Последние публикации, новое на сайте.
Ремонт и строительство
Дом и квартира, дизайн и архитектура, проекты домов. Обзоры, советы.
Сад, огород, усадьба
Садоводство и огородничество, приусадебное хозяйство.
Декоративно — прикладное искусство
Резьба по дереву, выжигание, чеканка, плетение и многое другое.
Идеи мастеру
Сделай сам, различные оригинальные и полезные самоделки.
Мебель своими руками
Самостоятельное изготовление мебели, чертежи, схемы.
Рекомендованные сообщения
Создайте аккаунт или войдите в него для комментирования
Вы должны быть пользователем, чтобы оставить комментарий
Создать аккаунт
Зарегистрируйтесь для получения аккаунта. Это просто!
Войти
Уже зарегистрированы? Войдите здесь.
Сейчас на странице 0 пользователей
Нет пользователей, просматривающих эту страницу.
Здравствуйте. Сегодня я хочу рассказать о том, как я сделал из не нужной мне болгарки отрезной станок. Мне часто приходится резать трубы. Особенно, профильные. Кто это делал, знает, что отрезать ровно профильную трубу болгаркой достаточно сложно. Это занимает много времени — приходится при помощи угольника отчерчивать под прямой угол каждую сторону, потом аккуратно прорезать по одной грани. И всё равно, бывает, что одна сторона получается на полмиллиметра короче, и потом, при сваривании тонкий металл стенки в этом месте начинает гореть из за неплотного прилегания. В идеале ровно можно отрезать только за один рез. А для этого нужен отрезной станок.
У меня была не нужная мне УШМ “DWT ws-180s”. Её мне отдали бесплатно по причине неисправности — оторвалась крыльчатка ротора и болгарка заклинила. Хозяин хотел её выбрасывать и предложил отдать мне её на запчасти бесплатно. Я отремонтировал ротор, заменил щётки и подшипники.
..Но оказалось, что такая болгарка мне не нужна. Она очень тяжёлая и массивная для 180-го круга. Мощности там хватает и для 230-го (2200 Вт), но, почему-то, производитель оборудовал её защитой именно под 180-й круг. Поэтому она у меня несколько лет висела в мастерской невостребованная — у меня есть более лёгкая “180-ка”. Я собирался переделать защиту под 230-й круг (тогда она пригодится для работ по бетону, например), но так и не собрался! )))). Ведь 230-я у меня тоже есть.
И вот мне пришла в голову мысль купить для неё станину и сделать отрезной стационарный станок. Но рассмотрев покупные варианты, я обнаружил, что они, в большинстве своём, не обладают достаточной жёсткостью, а значит, и точностью! Поэтому, я пришёл к выводу,что нужно сделать самому.
Что мне понадобилось:
1. Собственно УШМ.
2. Уголок стальной 50 на 50 и 40 на 40.
3. Обрезок водопроводной трубы ДУ32-3,5
4. Обрезок водопроводной трубы ДУ-25
5. Подшипник 6202 (2 шт)
6. Подшипник опорный.
7. Шпилька М14.
8. Профильные трубы 15 на 15, 20 на 20, 25 на 25
9. Болты и гайки М6, М8, М14.
10. Обрезки жести.
Итак, для начала я решил собрать крепление болгарки. В покупных вариантах, рассчитанных на различные болгарки, крепление осуществляется тремя длинными болтами с контргайками, что сказывается на жёсткости. К тому же, закрепив УШМ в трёх точках, её приходится располагать вертикально, что немного “ворует” глубину реза — как правило, впереди корпус редуктора чуть вытянут. А посему я решил закрепить её горизонтально, в двух точках, с плотным прилеганием рамы к редуктору.. Минус такого крепления — оно подходит только к одной модели УШМ. Но я решил этим пренебречь, посчитав, что если мне и придётся заменить болгарку, то я просто сварю новое крепление.))))

Теперь подошла очередь стола. Его я изготовил из листа стали, толщиной 4мм, размером 60 на 60 см:
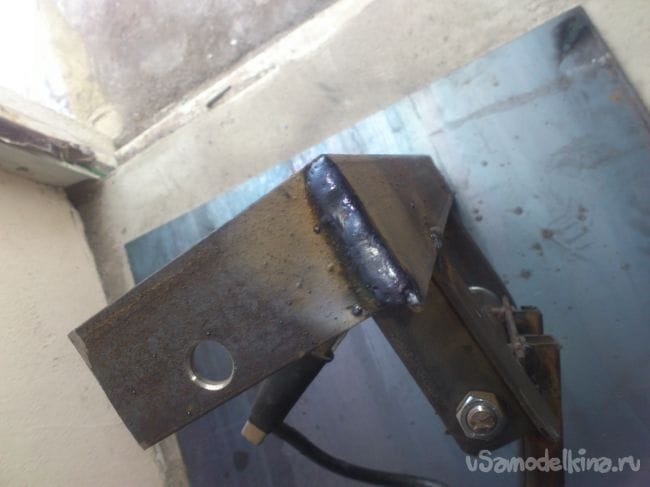
Из профильной трубы 15 на 15 сделал две квадратных рамки, размером 50 на 50 см. При этом в трубе, в местах сгиба прорезал только по три стенки, четвёртую оставил.
После этого вварил в углах вертикальные стойки из той-же трубы, и на получившийся параллелепипед закрепил мою конструкцию.
На данном этапе возникла необходимость выставить прямой угол между отрезным кругом и столом. Как я уже говорил, я исключил все регулировки в угоду жёсткости (читай: точности) конструкции. В моих планах было просто подогнуть тяги, а потом укрепить их в нужном положении, приварив к ним в качестве усиления уголки. Но, когда я попробовал их подогнуть сперва двумя монтажками. (У-у-у! Какой я оптимист! )))). Потом ломом! (Результат тот же). Я понял, что усиливать конструкцию не придётся!! Две толстостенные профильные трубы небольшой длины, к тому-же, проваренные на концах к уголкам швами по 5 см длиной с каждой стороны, дают неимоверную жёсткость! .
. Подогнуть я смог, лишь вставив между ними двухметровую (!) трубу, сечением 60 на 20. (Благо, между тягами как раз 60 мм.
После этого расширил и удлинил прорезь малой болгаркой. (На случай установки, к примеру, круга по дереву.)
..Кстати. Изначально у меня возникла мысль сделать “2 в 1”. Т.е., предусмотреть возможность переворачивания стола болгаркой вниз, с целью получения циркулярки! И я даже начал это воплощать. К примеру, шляпки всех крепёжных болтов с обратной стороны я проварил, расплавил и зачистил, чтобы получить ровный циркулярочный стол:
По той же причине сделал симметрично отверстия для крепёжных болтов, которыми стол крепится к “параллелепипеду”. Но эйфория от того, что “классно я придумал” прошла, и я понял, что я просто “повёлся”, и погнался не за практичностью, а за “классно получилось”.))))))
. А на деле я НЕ БУДУ ЭТИМ ПОЛЬЗОВАТЬСЯ. Ведь у меня циркулярка есть. И она, в любом случае, лучше, чем сделанная из болгарки! К тому-же, работая циркуляркой с деревом, хорошо поставить рядом этот станок с кругом по дереву, чтобы торцевать. А не переворачивать стол ради каждой доски.
В общем, отбросил я эту глупую затею.
..
Дальше я приступил к сооружению упора для заготовки. Я приложил угольник к кругу, отчертил линию под прямым углом, и закрепил по ней упорный уголок 40 на 40.
После этого я открутил уголок и по его отверстиям, приложив на этот раз угольник 45 градусов, просверлил отверстие в столе.
Забыл сфотографировать, но тут, думаю, понятно. Теперь, чтобы отрезать под 45, нужно извлечь один болт, повернуть уголок и закрепить в другое отверстие.
Следующий этап. Я приступил к сборке инструментальных тисков. Ведь точно отрезать можно только хорошо закреплённую заготовку.Вырезал кусок трубы 20 на 20.
При вращении маховичка, труба с приваренной гайкой вылезает из направляющей и плотно прижимает заготовку к упору. Единственное неудобство — вращать нужно влево.))). Зато надёжней, чем эксцентриковый зажим.
Далее, я приступил к изготовлению защитного кожуха. Как я уже говорил, кожух на болгарке был под 180-й круг, а я решил использовать 230-й. (Мощности хватает. Обороты тоже подходящие.). К тому-же, так как мне нужна точность, то резать я буду толстыми кругами (2,6, или 3 мм). Потому как более тонкие немного болтаются при нажиме. А посему количество искр будет неимоверным. Поэтому я решил сделать наиболее закрытый кожух, и закрепить его непосредственно к станине.
Сперва я сделал шаблон из картона:
Планирую ещё продлить на правую сторону упор. Так будет удобно что-то к примеру, подторцевать. И закрепить на нём металлическую слесарную линейку — так удобно будет отрезать небольшие куски, не отмеряя каждый раз. Поддвинул трубу до нужного размера по линейке, зажал, отрезал.Только линейка должна иметь регулировку, чтобы компенсировать разность толщины отрезных кругов. И разные мелочи, вроде крепления кабеля и отдельностоящую подставку-упор с регулируемой высотой, если надо резать длинные трубы.
. А пока я экстренно “ввёл его в эксплуатацию”, потому что делаю сейчас трубогиб, и там очень много чего резать нужно.
Угол держит идеально. Разрезал им даже валы к трубогибу (круг 40 мм), и потом на станке биение было настолько мизерным, что от торцовки отказался. Трубы профильные вообще идеально режутся — потом угольник на свет никакой, даже мизерной щёлочки не даёт.
Вот небольшой видеообзор. Простите за шмурыганье носом! )))). Было довольно холодно. ))))
crast.ru
Кругорезы своими руками конструкция и чертежи — Оборудование
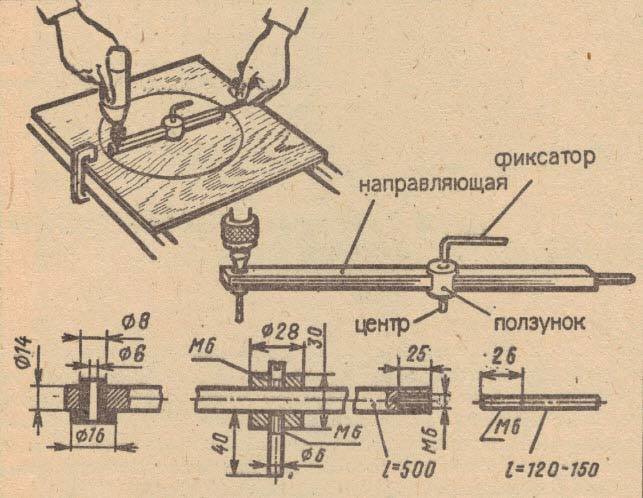
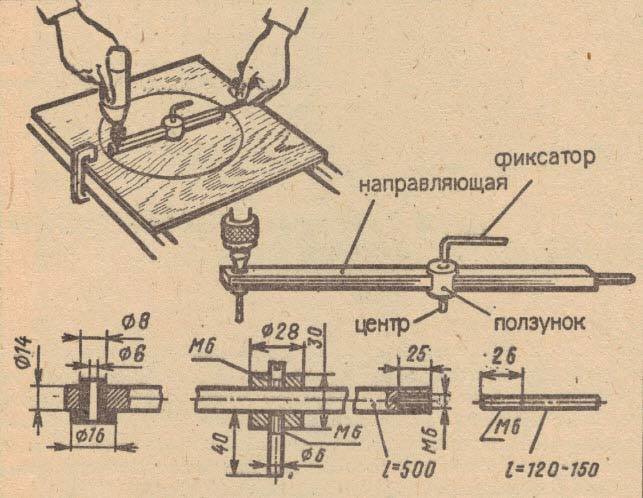
Автор Admin На чтение 2 мин. Опубликовано
На занятиях школьного технического кружка часто необходимо получить отверстие большого диаметра в фанере, оргстекле или листовом металле. Сделать его можно разными способами, в том числе и кругорезами различных конструкций.
На рис. 1. показано приспособление, в котором резцом является зажатая в патроне электродрели пальчиковая фреза.
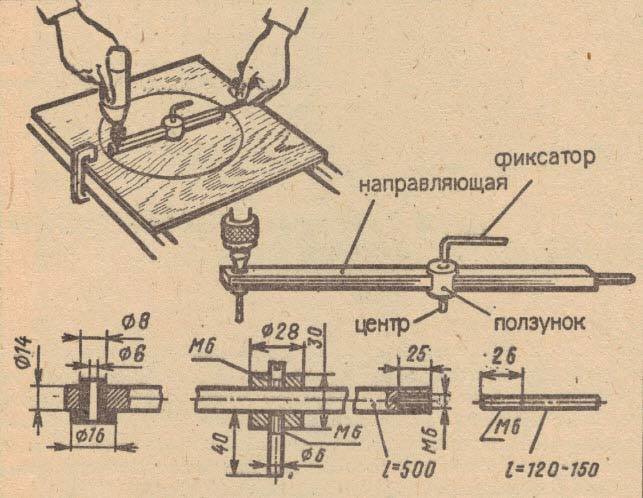
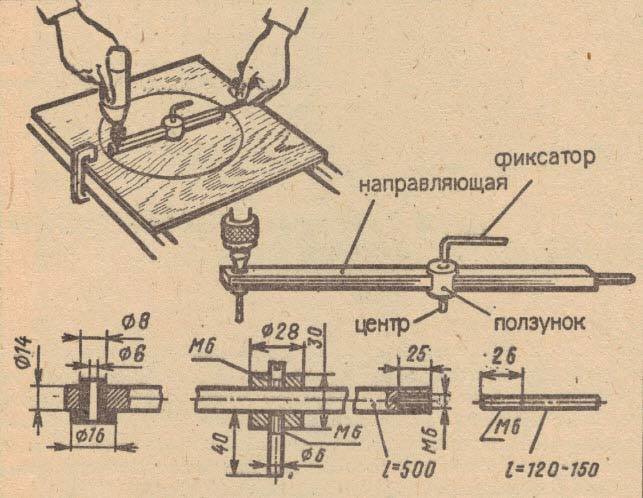
В качестве направляющей может быть испольована рейка А из древесины твердой породы или металлический стержень Б. Центр приспособления жестко закрепляется в ползунке, положение которого на направляющей фиксируется. Для удобства пользования направляющую рейку можно дбполнить ручкой-стержнем длиной 120—150 мм. Втулку-кондуктор, в которой вращается фреза, вытачивают из конструкционной стали и закаливают.
Самодельный кругорез для столярных работ
На рис. 2 представлена конструкция кругореза, предназначенного для столярных работ. Две металлические трубки диаметром 12—14 мм и длиной 500—700 свободно проходят в отверстиях направляющих брусков. Примерные размеры их 25X30X55 мм.
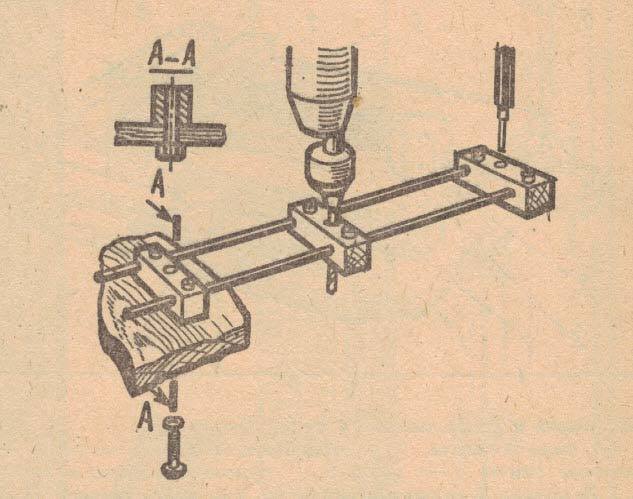
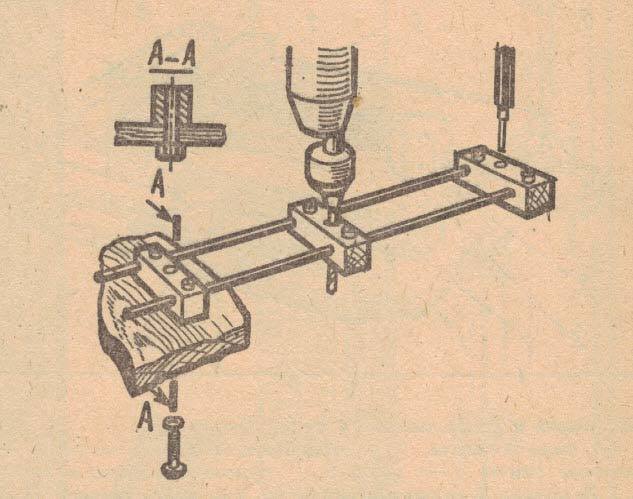
Сделать бруски лучше из дюралюминия: вначале сверлят отверстия для направляющих, а затем для фиксирующих винтов М6. Направляющая втулка запрессовывается в центр одного из брусков. В других же должны быть отверстия для удерживающего центра. Им может быть стержень, укрепленный в ручке от напильника, или сломанная отвертка. Можно использовать для этой- цели и резьбовой штырь (см. А—А). Применение его оправданно в том случае, когда предстоит вырезать круг большого диаметра.
arxipedia.ru
Самодельный кругорез для вырезания больших отверстий » Полезные самоделки
Идеально круглую резиновую прокладку любого размера или пассик для лентопротяжного механизма магнитофона вы сможете вырезать из листа резины с помощью этого несложного приспособления. Кроме этого, оно может быть использовано для прорезания отверстий большого диаметра в фанере, пластмассе, оргстекле, картоне и других подобных материалах.
Смастерить его самому совсем несложно. Из листа фанеры толщиной 10 мм выпилите три квадрата размером 300х300 мм. В центре одного из них просверлите отверстие ?8 мм, а в двух других – ?25 мм. Склеив заготовки, как показано на чертеже, получим основание приспособления. В его центральном отверстии закрепите гайкой болт М8.
Центральную стойку выточите из латунного прутка ?12 мм и длиной 80 мм. Нарежьте на одном конце наружную резьбу М12, а в торцевом отверстии с другой стороны – внутреннюю М8.
Поворотная втулка имеет осевое отверстие ?12 мм и перпендикулярное ему резьбовое М10.
Водилом служит латунный пруток ?10 мм. На одном его конце нарезается резьба М10 длиной 10 мм, а радиальное отверстие М3 на другом конце изготавливается после подсборки водила с поворотной втулкой: оно должно быть параллельно его отверстию ?12 мм.
Ползун в виде уголка вырезается из дюралюминиевого бруска. В его вертикальной стенке выполняются два отверстия ?10 мм – одно под водило, второе, перпендикулярное ему и смещенное вниз на 5 мм, – для фиксатора – резьбового штифта с полукруглым пазом. В горизонтальной стенке пропиливается паз сечением 14X3 мм – под нож. Материалом для его изготовления служит обломок ножовочного полотна. В вертикальном пазу ползуна нож фиксируется винтом М6.
Прижимной диск вырезается на токарном станке из металлической пластины толщиной 2 мм или более толстого листа пластмассы. Его центральное отверстие должно иметь ?8 мм, а наружный диаметр – чуть меньше вырезаемого.
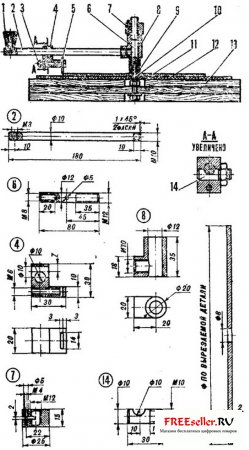
Рис. 1 Приспособление для вырезания отверстий большого диаметра:
1 – ручка, 2 – водило, 3 – винт М6, 4 – ползун, 5 – нож, 6 – центральная стойка, 7 – стопорная гайка, 8 – поворотная втулка, 9 – пружина, 10 – болт М8, 11 – прижимной диск, 12 – заготовка, 13 – основание, 14 – резьбовой штифт-фиксатор.
Стопорная гайка втулки с центральной резьбой M12 имеет наружный ?25 мм и высоту 15 мм. Пропилите в ней поперечный паз на полдиаметра и в этой части сделайте продольное отверстие. Затем в нижней его половине нарежьте резьбу М4, а в верхней – рассверлите до ?5 мм. Теперь стяните половинки гайки винтом, этим самым вы сможете стопорить ее в любом положении на центральной стойке.
Порядок сборки приспособления следующий. Заверните водило резьбовым хвостовиком в поворотную втулку до упора. В ползун вставьте фиксатор-штифт так, чтобы его цилиндрическая выточка совпадала с продольным отверстием. Надев ползун на водило, вставьте в его паз нож и зажмите винтом. Закрепите на конце водила вращающуюся ручку.
На выступающий из основания стержень болта надевается заготовка. На нее устанавливается прижимной диск, а затем центральная стойка. Подтянуть резьбу можно воротком – для этого предназначено радиальное отверстие ?5 мм. На стойку надевается пружина, за ней – водило в сборе и, наконец, стопорная гайка.
Подрегулировав положение ползуна на водиле и втулки на стойке (по высоте), можно приступать к работе.
Размеры основных деталей позволяют вырезать на этом приспособлении отверстия диаметром до 240 мм, однако, если вам требуется большая величина, достаточно заменить всего три элемента: водило, основание и прижимной диск. А для быстрой настройки приспособления на заданный размер на водило можно нанести риски-нониус.
Ю. ОРЛОВ, г. Троицк, Московская обл.
“Моделист-Конструктор” 1985, №5
www.freeseller.ru
Самодельное приспособление для вырезания кругов в листовом металле болгаркой
Удобное и простое, самодельное приспособление для вырезания кругов в листовом металле, фото и описание изготовления.
С помощью этого нехитрого съёмного приспособления для болгарки, можно быстро и легко, вырезать круги из листового металла.
Понадобятся материалы:
- Круглый магнит от динамика.
- Стальной уголок.
- Гайки удлиненные, болты и шайбы.
- Шпилька с резьбой по всей длине.
- Металлическая полоса.
- Винты, хомут.
- Клей.
Процесс изготовления самоделки, подробно показан на этих фото.
Нам нужно из звукового динамика извлечь магнит. Для этого зажимаем в тиски и высверливаем головки винтов, которыми корзина прикручена к верхнему фланцу. Отделяем корзину с верхним фланцем от постоянного кольцевого магнита и нижнего фланца со стальным цилиндром (керном). Снова зажимаем в тиски корзину с верхним фланцем и с помощью молотка и наставки выбиваем фланец из корзины.
Нам понадобится постоянный кольцевой магнит, верхний и нижний фланец.
Зажимаем нижний фланец в тиски и болгаркой отрезаем керн у самого основания.
Затем, переворачиваем деталь, в центре сверлим отверстие. Поверхность нижнего фланца со стороны остатка керна и кольцевого магнита покрываем клеем и фланец отростком вниз накладываем на магнит и после центровки фиксируем их.
Затем, от уголка отрезаем две одинаковые заготовки длиной по 35 мм. Заготовки привариваем между собой.
Привариваем вертикально по центру стыка уголков, удлиненную шестигранную гайку, ввернув в нее сверху болт для фиксации гайки при ее обваривании.
Теперь сверлим два отверстия напротив друг друга.
Берём металлическую полосу, металлическую полоску, делаем изгиб, разводящий концы полоски по двум вертикальным плоскостям.
Располагаем ее поверх и продольно сварочному шву уголков без упора в удлиненную гайку и завариваем полоску-ручку в таком положении.
Берём магнит, вкручиваем с лицевой стороны фланца болт с шайбой и гайкой. Поверх головки болта располагаем удлиненную шестигранную гайку и привариваем ее в таком положении.
К шпильке, вкрученной в удлиненную гайку на головке болта, с другого конца привариваем такую же гайку, но меньшего диаметра.
Детали окрашиваем.
Первый узел накладываем на болгарку так, чтобы отверстия в полках уголков совпали с отверстиями на УШМ, а ручка узла была направлена вдоль корпуса инструмента сверху.
Закрепляем узел на болгарке болтами с двух сторон, а ручку крепим к корпусу хомутом.
В удлиненную гайку узла с постоянным магнитом вкручиваем шпильку, на конце которой приварена гайка меньшего диаметра.
В гайку на конце стержня вкручиваем ручку с резьбой.
Вращая узел с постоянным магнитом вокруг шпильки, можно увеличивать или уменьшать расстояние между центром гайки (осью вращения) и диском болгарки, что будет равно радиусу круга, который мы собираемся вырезать в листовом металле.
Магнит ставим в центр вырезаемого круга, а болгарку с диском перемещаем за ручку по заданному радиусу, прижимая инструмент к металлу.
Таким образом вырезаем круг из листового металла, нужного диаметра.
Также рекомендуем посмотреть видео, где автор подробно показывает процесс изготовления этой самоделки.
sam-stroitel.com
Дырокол по металлу своими руками

Привет всем любителям самоделок. В данной статье я расскажу как сделать дырокол по металлу своими руками, который пригодится в создании отверстий в листовом металле, а также других материалах.
В сборке данной самоделки не нужны какие-либо труднодоступные детали, достаточно автомобильных запчастей.
Перед тем, как начать читать статью, предлагаю посмотреть видеоролик, в котором подробно показан процесс сборки и тестирование самодельного инструмента.
Для того, чтобы сделать дырокол по металлу своими руками, понадобится:
* Автомобильная рулевая тяга
* Клапан
* Отрезки от токарных резцов
* Дисковая фреза
* Токарный станок по металлу
* Сварочный аппарат
* Сварочная маска, краги
* Молоток
* Металлическая пластина толщиной 2 мм
* Два болта М6
* Пружинка, шайба
* Перчатки, защитные очки, наушники
* Углошлифовальная машинка, отрезной диск
Шаг первый.
Устанавливаем дисковую фрезу в трехкулачковый патрон токарного станка по металлу при помощи специальной оправки, если же у вас есть фрезерный станок, то можно сделать паз на нем.
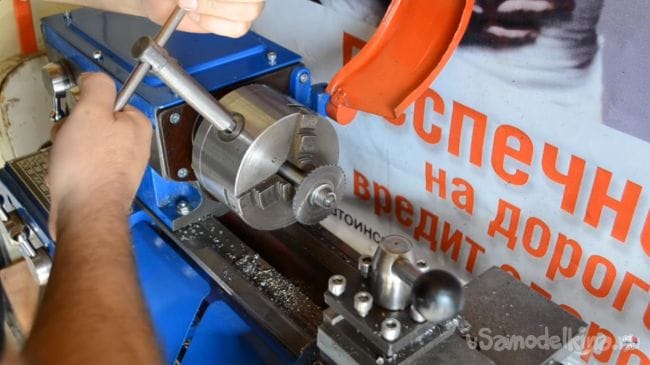
Затем в резцедержке закрепляем отрезок ненужного резца и фрезеруем в нем паз. В процессе фрезерования капаем немного технического масла на режущую кромку, так фреза прослужит дольше и не будет подклинивать в детали.

В итоге по завершению фрезеровки получается такой паз.

Шаг второй.
Зажимаем рулевую тягу в резцедержку и делаем такой же паз дисковой фрезой на токарном станке.
Затем устанавливаем тягу в тиски и при помощи сверлильного станка делаем отверстие диаметром 6 мм.

В итоге получается такое отверстие, сверлом побольше делаем небольшую фаску.

В отрезке резца с пазом делаем такое же отверстие, как и в рулевой тяге. В двух заготовках в одном из двух отверстий нарезаем резьбу М6 при помощи метчика.

Шаг третий.
Далее нужно сделать подвижную часть дырокола. Для этого подойдет сломанное сверло, метчик или же, как в данном случае автомобильный клапан. Клапан зажимаем в тисках и при помощи углошлифовальной машинки с отрезным диском отпиливаем шток длиной около 3 см. При работе с углошлифовальной машинкой будьте осторожны, одевайте защитные очки, перчатки и наушники.

На этом штоке делаем небольшое углубление для крепления в ручке с двух сторон, а также затачиваем его обратную сторону таким образом, как показано на фото.

Шаг четвертый.
Для установки штока в ручку делаем углубление при помощи сверлильного станка, по бокам сверлим отверстия поменьше, в них будут устанавливаться штифты, сделанные из обычных гвоздей.

Также нужно вырезать из листового металла пластинку толщиной 2 мм, а затем просверлить в них два отверстия сверлом на 6 мм.
Шаг пятый.
Пришло время сварочных работ.
Привариваем два отреза резца к рулевой тяге с небольшим зазором относительно друг друга, причем один должен быть длиннее другого примерно на 15 мм.
При работе со сварочным аппаратом будьте осторожны, а также используйте сварочную маску и краги.

После сварки удаляем шлак при помощи молотка и зачищаем шов металлической щеткой, установленной на шуруповерт.
Далее нужно просверлить отверстие в приваренных отрезках резцов на сверлильном станке с сверлом по металлу на 6 мм. Все детали данной самоделки готовы, теперь можно собирать инструмент и тестировать его в реальных условиях.

Шаг шестой.
После сборки получается такой дырокол, сделанный своими руками.
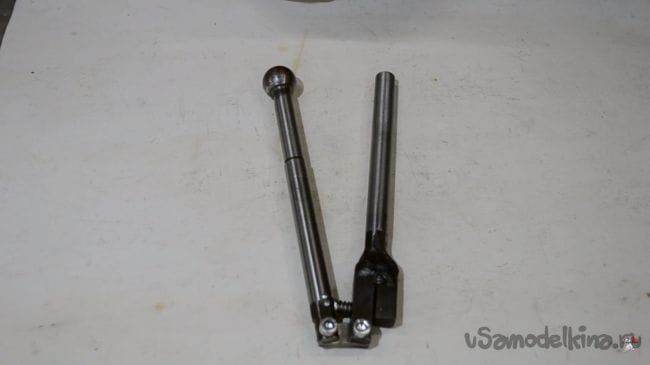
Проверим его на пароните толщиной 2 мм, отверстия делаются легко и без особых усилий, а установленная пружина на подвижном штоке возвращает ручку в исходное рабочее положение.

Пробуем инструмент на листе металла, справляется он с данной задачей вполне хорошо. При складывании листа вдвое дырокол также отлично проделывает отверстия, не смотря на то, что большого рычага тут нет.

Данный дырокол пригодится при работе с листовыми материалами, в которых необходимо быстро и ровно сделать отверстия одинакового диаметра. В данном случае диаметр отверстий, сделанных при помощи самодельного дырокола равен 6 мм, при необходимости этот параметр можно изменить, если изготовить шток требуемого диаметра.
На этом у меня все, всем спасибо за внимание и творческих успехов.

Получайте на почту подборку новых самоделок. Никакого спама, только полезные идеи!
*Заполняя форму вы соглашаетесь на обработку персональных данных
Становитесь автором сайта, публикуйте собственные статьи, описания самоделок с оплатой за текст. Подробнее здесь.usamodelkina.ru