Обучение операторов и наладчиков ЧПУ
Проводим обучение по ЧПУ для операторов, наладчиков, программистов и начинающих специалистов из Перми.
Обучение проводится по нескольких программам, которые адаптированы под разные уровни учащихся и базируются на двух курсах «Основы работы на фрезерных станках с числовым программным управлением» и «Наладчик станков с программным управлением».
В ходе обучения слушатели формируют теоретические и практические навыки в сфере обработки деталей на станках с ЧПУ, включая материаловедение, технологию обработки, устройство, безопасную эксплуатацию и наладку фрезерных станков, составление управляющих программ как в системах ЧПУ, так и в системах геометрического моделирования обработки (CAD/САМ-системы).
Внимание! В данный момент проводится только выездное обучение на предприятиях.
Набор групп для обучения частных лиц временно приостановлен.
Программы обучения
Основные курсы по ЧПУ:
- обучение операторов ЧПУ: курс для широкого круга слушателей с выдачей удостоверения о повышении квалификации;
- повышение квалификации операторов ЧПУ – курс для действующих операторов ЧПУ с выдачей удостоверения о повышении квалификации;
- обучение наладчиков ЧПУ – курс для действующих наладчиков и операторов ЧПУ с выдачей удостоверения о повышении квалификации или свидетельства о присвоении разряда;
- курс “ЧПУ с нуля” - специальный курс для начинающих операторов ЧПУ и любителей с выдачей сертификата о прохождении курса “Основы работы на фрезерных станках с числовым программным управлением”;
- дистанционное обучение по ЧПУ – заочный онлайн курс для операторов и программистов ЧПУ.
Полный список курсов представлен на этой странице.
Внимание! В данный момент проводится только выездное обучение на предприятиях.
Форма обучения
В нашем учебном центре предусмотрены четыре формы обучения по курсам ЧПУ:
- дневная;
- вечерняя;
- дистанционная;
- выездное обучение на предприятии заказчика.
Вы можете заниматься по любой удобной для вас форме. При обучении по дневной или вечерней форме оказываем содействие в организации проживания и питания специалистов из Перми на период прохождения курса.
Внимание! В данный момент проводится только выездное обучение на предприятиях.
Набор групп для обучения частных лиц временно приостановлен.
Результат обучения и прохождения курса
В зависимости от выбранной программы выдаётся:
- удостоверение о повышении квалификации по программе дополнительного профессионального образования;
- свидетельство о присвоении разряда;
- свидетельство центра о прохождении обучения по соответствующей программе.
Обучение на станках с ЧПУ Пермь
Компания «Obuchenie – chpu.ru» имеет богатый опыт работы с обучением на станках с ЧПУ в Перми. За длительный срок работы компании было выпущено огромное количество настоящих профессионалов.
Данный центр по обучению имеет возможность дать квалификацию по работе с:
- деревообрабатывающими,
- электроэрозионными,
- металлообрабатывающими станками.
Есть три ветки курсов по подготовке наладчиков и операторов:
- токарных,
- фрезерных,
- токарно-фрезерных станков ЧПУ.
Во время обучения на станках ЧПУ рабочие получают те знания, которые им пригодятся каждый день в процессе производства, в том числе и практические занятия. Примечательно, что специалисты «Obuchenie–chpu.ru» производят обучение таким образом, что процесс производства не останавливается и не замедляется, за счет совмещения практики, обучения и производства.
Высылайте вашу заявку на обучение на станках ЧПУ на [email protected]
Ведется набор в группы наладчиков, операторов, механиков и электриков.
Обучение инструкторы начинают с самых азов, т.е. включения станка, за этим следует объяснение всего процесса по этапам. Условия договора предусматривают некоторое количество дней, чтобы можно было провести обучение и подготовку всего персонала предприятия. После этого компания «Obuchenie–chpu.ru», обязуется консультировать своих учащихся по любому вопросу, связанный с обучением на станках с ЧПУ в Перми.
Данный курс рассчитан в основном на рабочих с базовыми техническими знаниями, а также теми, кто желает обучиться навыкам работы на станках. Мы осуществляем обучение во многих городах страны. Наша компания также предлагает обучение на станках с ЧПУ в Нижнем Новгороде, Москве и Челябинске.
В первую очередь, цели компании – это обучение знаниями и навыкам по работе со станками ЧПУ, а также произвести обучение таким образом, чтобы рабочий смог изготовить деталь от чертежа и до самого последнего этапа.
Каким образом строится курс?
Сначала учащиеся проходят ознакомление с теорией, т.е. основам строения фрезерных и токарных станков ЧПУ, а также современными технологиями и вспомогательными инструментами. В теоретический курс также входит информация о наладке станка, основы автоматизированных систем современного образца.
После ознакомления с теорией учащиеся переходят непосредственно к практическим занятиям. Обучение проходит на специализированных тренажерах, которые абсолютно ничем не отличаются от настоящего фрезерного или токарного станка со стойкой Fanuc 0i. Учащиеся сдают зачет по производству инструмента на станке, а также каждому предоставляется индивидуальное задание по написанию программы на компьютерном стимуляторе. В целом зачет состоит из полной обработки, изготовления, прогона программы на современном станке ЧПУ. Обучение на станках с ЧПУ в Перми в нашей компании не простое, а как видите профессиональное.
Высылайте вашу заявку на обучение на станках ЧПУ на [email protected]
Ведется набор в группы наладчиков, операторов, механиков и электриков.
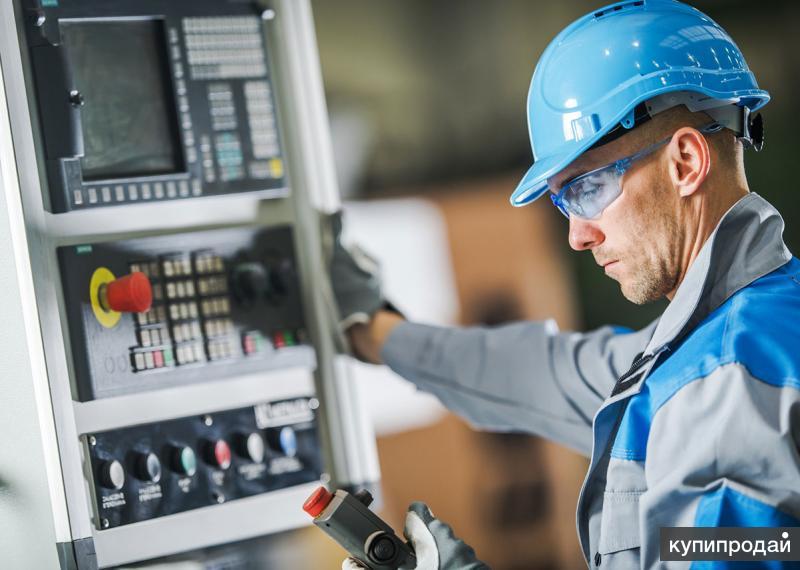
Длительность всего курса составляет сорок часов, в которые входят пять дней двенадцатичасового обучения с небольшим перерывом. В период работы учащимся предоставляются пособия, которыми они могут пользоваться весь курс. Кроме того, все желающие могут приобрести специальный комплект документации, который предполагает набор различных руководств по эксплуатации токарного и фрезерного станков ЧПУ.
Огромным достоинством работы именно на таких станках является способность изготовления и обработки таких сложных деталей, которые не под силу малоквалифицированным операторам. То же самое касается и подготовки машины к производству, а именно корректной установки деталей по картам накладки, правильная работа с системой координат. Одним словом вся система изготовления деталей на современном оборудовании требует квалифицированного исполнения, так как человеку, не получившему соответствующих знаний и умений это не под силу.
Во время того, как проходит этап внедрения таких станков, всю работу над ними осуществляют квалифицированные технологические службы, они совершают обработку программ, внедряют машины и совершенствуют управление. После того, как станки полностью пройдут подготовку и будут переданы для эксплуатации, все остальные операции по подготовке станков и производству изделий выполняют сотрудники цеха.
Идеальный интерфейс для обработки
Когда-нибудь запрограммировать станок с ЧПУ будет так же просто, как загрузить CAD-модель с прикрепленной информацией о производстве продукта.
Fagor использует язык программирования HTML 5 в своем интерфейсе управления HMIelite. По словам компании, это изменение откроет множество дополнительных функций, сделает настройку чрезвычайно простой и представляет собой «будущее интерфейсов станков». (Предоставлено Fagor Automation) Система управления станком будет использовать искусственный интеллект (ИИ) для анализа геометрии детали и свойств материала, выбора правильных режущих инструментов, применения соответствующих подач и скоростей, проверки отсутствия столкновений и самопроизвольного срабатывания. сгенерированные траектории не будут выдалбливать заготовку и не оставят материал необрезанным, а также предписывают станку начать резку. Затем он будет контролировать процесс обработки, корректировать параметры и заменять режущие инструменты по мере необходимости, обеспечивая при этом, чтобы деталь находилась в пределах допусков, указанных для GD&T. А если что-то пойдет не так, что не в силах исправить самостоятельно, управление остановит машину и будет терпеливо ждать помощи от своих хозяев-людей.
Этот будущий ЧПУ будет выполнять каждую из этих функций автономно, так же, как самоуправляемые автомобили, которые каждый день доставляют на работу живых спутников машины, роботы, которые загружают грузовик и моют детали, или бесчисленное множество других скоро — самые распространенные примеры технологий на базе ИИ.
До того знаменательного дня люди должны продолжать программировать старомодным способом — с помощью программного обеспечения CAM, систем диалогового программирования или вводить G-код на машине по одному символу за раз. Хорошей новостью является то, что первые два из этих методов становятся проще и эффективнее, в то время как даже последний становится менее болезненным благодаря интерфейсам управления, которые делают работу машины похожей на отправку текстовых сообщений близкому другу или посещение вашего любимого веб-сайта.
Путешествие по веб-управлению
Больше всего Сурового Бибру волнует технология, лежащая в основе этого последнего действия. Генеральный менеджер по Северной Америке в Fagor Automation Corp., Элк-Гроув-Виллидж, штат Иллинойс, Бибра объяснил, что он и другие сотрудники Fagor потратили последние несколько лет на разработку HMIelite, «масштабируемого, портативного, настраиваемого и интерактивного» интерфейса управления, основанного на языком программирования, с которым знакомы даже многие дети школьного возраста: HTML 5, язык Интернета.
«Любой молодой человек сразу это поймет, что, учитывая нехватку квалифицированной рабочей силы и необходимость привлечения следующего поколения к профессии, было по крайней мере частью нашей цели», — сказал Бибра.
Как следует из названия, HTML 5 является пятой и последней версией вездесущего стандарта языка гипертекстовой разметки, или HTML. Согласно консорциуму World Wide Web Consortium (W3C), HTML дает веб-разработчикам возможность «публиковать онлайн-документы с заголовками, текстом, таблицами и фотографиями, извлекать онлайн-информацию через гипертекстовые ссылки, создавать формы для транзакций с удаленными службами и включать электронные таблицы. , медиаклипы и другие приложения прямо в их документах». Проще говоря, если вы видите это в Интернете, вы можете поблагодарить HTML.
Но какое отношение программирование станков и изготовление деталей имеет к созданию веб-страниц? Ничего, по крайней мере пока. Однако, разработав интерфейс управления, которым может легко манипулировать практически каждый, Fagor предоставил машиностроителям и конечным пользователям мощный инструмент, за которым, по мнению Bibra, будущее интерфейсов станков. «По сути, HTML 5 позволяет нашим клиентам модифицировать любой экран или создавать совершенно новый интерфейс очень быстро и легко, используя доступные таланты».
Он также отметил, что HMIelite в настоящее время является опцией и что стандартный интерфейс компании остается в силе. Тем не менее, для тех, кто ищет максимальную гибкость, HTML-совместимый элемент управления дает пользователям некоторые интригующие возможности. Производитель медицинского оборудования может использовать его для создания «удобных для хирургов» станков. Автопроизводитель может легко настроить интерфейс для конкретного крупномасштабного приложения, в то время как глобальная производственная компания может добавить геотеги, безопасный удаленный мониторинг с любого мобильного устройства и аналогичные функции определения местоположения к своему парку оборудования с ЧПУ.
Бибра сказал: «Потребности и навыки людей, работающих на машине, в каждом из этих примеров совершенно разные, поэтому возможность настройки управления для уникальных условий так важна. Тем не менее, у вас все еще есть все важные технологии, находящиеся внутри ЧПУ; поэтому человеко-машинный интерфейс на основе HTML 5, или HMI, не требует подключения к Интернету или облаку для работы».
Clear Text
Гисберт Ледвон, директор по развитию бизнеса станков в Heidenhain Corp., Шаумбург, Иллинойс, согласился с необходимостью простой настройки. «Наша последняя система управления, TNC7, выводит ее на новый уровень с точки зрения удобства использования», — сказал он.
Благодаря возможности самопрограммирования с использованием диалогового программирования, называемого Klartext (открытый текст), новое высокоточное управление Heidenhain TNC7 обеспечивает новый уровень удобства для пользователя. (Предоставлено Heidenhain)
Однако подождите: диалоговые элементы управления с возможностями графического программирования существуют с тех пор, как Фрэнсис Рейнджес и Дуглас Росс из Лаборатории сервомеханизмов Массачусетского технологического института впервые представили APT (автоматически программируемый инструмент), то есть более 60 лет назад. Тем не менее, Ледвон имеет в виду возможность самопрограммирования наравне с описанной в начале этой статьи, которая не требует ничего, кроме твердотельной модели для генерации кода обработки.
Ледвон описал элемент управления, который принимает файлы САПР так же легко, как и произвольные формы, нарисованные на сенсорном экране. В последнем случае операторы могут использовать свои пальцы для рисования окружностей, линий и других геометрий деталей, присваивать им размерные значения и, когда закончите, нажать кнопку, чтобы начать процесс программирования. «Когда я впервые увидел это, я был совершенно потрясен», — сказал он. «Система управления пишет для вас всю программу на Klartext, человекочитаемом языке. Вы можете идти вперед и назад, внося изменения и имитируя их на экране, пока все не станет так, как вы хотите, прежде чем запускать программу».
Конструктор элементов управления упростил процесс программирования и другими способами. Например, там, где обычная программа на G-коде может использовать десятки или даже сотни команд для выполнения определенной операции, Klartext от Heidenhain может использовать всего одну строку кода для выполнения той же задачи.
Ледвон также отметил, что из-за своей компактной длины эти многофункциональные команды упрощают устранение неполадок в программах. «У нас уже некоторое время есть такие расширенные функции, но мы продолжаем расширять их возможности», — сказал он. «Одним из недавних примеров этого является OCM, сокращение от оптимизированного контурного фрезерования. Эта функция позволяет оператору в интерактивном режиме программировать трохоидальную траекторию фрезерования, моделировать ее и проверять на помехи, а затем нажимать кнопку, чтобы снять фаску со всего профиля детали, или перемещать ползунок для автоматического определения идеальной подачи и скорости на основе материала, режущий инструмент и насколько агрессивно вы хотите обрабатывать деталь».
Протянуть руку помощи
Автоматическое программирование станков не является чем-то новым. Sodick и другие разработчики EDM уже много десятилетий используют «нечеткую логику» в своих системах управления. Здесь оператор вводит значения желаемой шероховатости поверхности, скорости износа электрода, скорости обработки и других переменных; Затем система управления определяет, какие рабочие параметры лучше всего подходят для достижения этих целей. Интерактивные функции управления, которые только что описал Ледвон, не являются особенно новыми, хотя они явно намного мощнее, чем когда-то.
То же самое можно сказать и о диалоговом программировании, дебютировавшем примерно за десять лет до появления нечеткой логики. Пол Вебстер, директор FA Engineering в FANUC America Corp. в Рочестере-Хиллз, штат Мичиган, отметил, что FAPT — версия APT FANUC — с тех пор была заменена на MANUAL GUIDE i, вариант управления, который на веб-сайте компании описан как «пользовательский – удобная диалоговая платформа программирования, которая позволяет легко создавать программы обработки деталей прямо в цеху, не зная G-кода».
Однако то же самое можно сказать и о многих CAM-системах, в связи с чем возникает вопрос: неужели диалоговое программирование уступило место бумажной ленте и инструментам HSS? Вовсе нет, сказал Вебстер. «CAM-системы и портативные компьютеры сейчас настолько недороги, что их может позволить себе практически каждый, поэтому многие производители пошли по этому пути, но для мастерских, производителей инструментов и штампов и других сред, где люди создают один или два конкретных предмета, MANUAL GUIDE i остается весьма популярным».
Диалоговый или нет, Вебстер отметил, что пользовательский интерфейс новых элементов управления FANUC балансирует между традиционными интерфейсами, состоящими только из G-кода, и интерфейсами, управляемыми графикой. «Наши 30iB или 0iF гораздо больше ориентированы на оператора, чем устаревшие элементы управления», — сказал он. «Оба имеют наш интерфейс iHMI, который помогает оператору выполнять повседневные задачи. Например, элемент управления будет подсказывать пользователям, когда они вводят значения для цикла обработки, и стал намного более графическим и простым в использовании, чем когда-либо прежде».
Стремление к большему удобству использования в значительной степени обусловлено продолжающимся дефицитом рабочей силы, добавил он, и выходом на рынок труда молодых людей, привыкших к приложениям для смартфонов и браузерным интерфейсам. Но, несмотря на этот более мягкий и мягкий мир ЧПУ, элементы управления FANUC остаются обратно совместимыми, и старожилы, привыкшие к системам управления 16B или более ранних версий, без проблем приобретут текущую модель 30iB.
Что касается настройки, Вебстер указал на FANUC FOCAS API (интерфейс прикладного программирования), который в настоящее время находится во втором поколении. С его помощью машиностроители могут изменять экраны управления, создавать программные интерфейсы и подключаться к сторонним системам, а также собирать данные с FANUC и MTConnect или оборудования с ЧПУ, совместимых с OPC. «FOCAS поддерживает эти и другие функции разработки программного обеспечения с использованием C++, C#, Visual Basic или любых других языков программирования, которые вы хотите использовать», — сказал он. «Кроме того, сам iHMI легко настраивается, поэтому у наших клиентов есть много вариантов, когда речь идет о совместимости и модификации интерфейса».
Все дело в командной работе
Джим Космала видит ту же потребность в диалоговом программировании, по крайней мере, когда речь идет о только что описанном базовом сценарии. Тем не менее, для больших объемов или более сложных работ вице-президент по инженерии и технологиям Okuma America Corp. Шарлотта, Северная Каролина, предположила, что система CAM является практически необходимым условием. «Наш Advanced OneTouch, или AOT, хорош для первой группы магазинов, но, честно говоря, человеческий мозг просто не может обрабатывать больше нескольких осей одновременно. Вот почему любой, кто хочет использовать все возможности своих пятиосевых обрабатывающих центров и многозадачных токарных станков, обычно программирует в автономном режиме».
И тем не менее офлайн не исключает общения. Как и многие подобные системы программирования, AOT можно использовать как на ПК, так и на машине. В этом отношении многие ЧПУ в настоящее время поддерживают множество программных приложений для ПК, в том числе средства управления станком Okuma. Это оказалось удачным за последние два года, поскольку магазины во всем мире боролись с поддержкой и обучением перед лицом ограничений и запретов на поездки, связанных с COVID, что побудило команду Космалы использовать решение, с которым многие из нас познакомились во время пандемии: Microsoft Teams. .
«Поскольку наши элементы управления OSP работают на чипе Intel с операционной системой Windows, они поддерживают большинство программных пакетов для ПК, — сказал он. «Поэтому, когда в начале прошлого года у одного из наших дистрибьюторов возникла проблема с машиной в Мексике, и мы не могли туда поехать из-за ограничений на поездки, мы посоветовали им установить MS Teams непосредственно на станок Okuma. Затем один из наших инженеров-электриков в Шарлотте смог удаленно подключиться, диагностировать ошибку и быстро запустить их. Не нужно было садиться в самолет, не нужно было платить за аренду автомобиля или гостиницу, а время простоя было минимальным. Всем понравилось, особенно заказчику.
С тех пор MS Teams нашла более постоянный дом в Okuma America для целей обучения и предоставления клиентам ответов на вопросы, связанные с приложением. На самом деле производитель машин, так сказать, перевернул камеру, пригласив клиентов посетить виртуальные занятия по программированию и обслуживанию в MS Teams через Интернет. Космала добавил: «Как говорится, необходимость — мать всех изобретений, и в этом случае COVID подтолкнул нас к использованию команд MS, работающих непосредственно на управлении станком. Оглядываясь назад, мы могли бы использовать эти инструменты до появления COVID».
На вопрос, что ждет Okuma дальше, Космала ответил: «Как и все остальные, мы постоянно разрабатываем новые технологии и усердно работаем над тем, чтобы сделать наши продукты более удобными и мощными. Часть этих усилий будет сосредоточена на функциях на основе ИИ, таких как ИИ шпинделя, ИИ оси подачи, Machining Navi и других адаптивных элементах управления, а также функциях обработки с обратной связью, оптимизированной резке и сборе данных».
Natively Digital
И последнее, но не менее важное: Siemens Industry U.S., Элк-Гроув-Виллидж, штат Иллинойс, где менеджер центра виртуальных технических приложений Крис Поллак подчеркнул важность цифрового двойника и его использования в моделировании механической обработки. «Мы создаем передовые системы управления станками на протяжении многих десятилетий, и наш новейший продукт, Sinumerik One, является последним воплощением этой технологии», — сказал он. «Его главная цель — наконец объединить цифровой и физический миры воедино, что позволит производителям концептуализировать, проектировать, тестировать и виртуально обрабатывать детали перед тем, как вырезать первый чип».
Эти возможности могут показаться чем-то новым для тех, кто инвестировал средства в стороннее программное обеспечение для моделирования траекторий, однако Поллак сказал, что они похожи на яблоки и апельсины. «В ЧПУ есть мозг, которого нет у сторонней компании-разработчика программного обеспечения и никогда не будет. Имея цифровую версию этого мозга, вы получаете доступ к наиболее точному и точному представлению о том, что будет делать физическая машина, когда вы нажмете кнопку запуска цикла. Это действительно единственный способ добиться этого».
Как объяснил Поллак, этот виртуальный мозг может находиться в программном обеспечении, расположенном на ПК системы управления, ПК в офисе программиста или ПК рядом с токарным станком с ЧПУ или обрабатывающим центром. Независимо от местоположения и способа создания программы ЧПУ ее пользователь имеет возможность моделировать весь процесс обработки. Они могут загружать виртуальные тиски и держатели инструментов, проверять наличие помех, проверять процедуры измерения и следить за тем, чтобы все в настройке работало должным образом, пока станок занят изготовлением деталей.
Как это делает программирование или эксплуатацию машины более удобными? Это не так, пока вы не поймете, что стоять перед разбитой машиной — явно недружелюбное место, событие, которое цифровой двойник призван предотвратить. Это также служит для увеличения времени безотказной работы шпинделя и дает всем участникам возможность улучшить все, что касается процесса обработки, заблаговременно. И хотя может показаться, что Поллок выступает против диалогового управления, внешний вид может быть обманчивым — в 2010 году компания представила обновленный элемент управления и ориентированный на пользователя интерфейс, дополненный графическими и простыми в использовании циклами обработки.
«Еще задолго до выпуска нашего HMI Sinumerik Operate мы поняли, что уровень квалификации рабочей силы снижается, и что нам нужно отказаться от того, что, по общему признанию, было очень сложным управлением, которое многим было трудно использовать», — сказал он. «Сегодня наши элементы управления полностью разговорные. Вы можете управлять всем, даже не зная простейших кодов G и M. На самом деле, мы разработали элемент управления, очень похожий на технологию, к которой люди начали двигаться, а именно смартфоны, приложения и жесты на сенсорном экране. Это так просто».
Защита машин — навыки безопасности
Производители разрабатывают свои машины таким образом, чтобы защитить операторов от контакта с опасными частями. Несмотря на это, машины ежегодно вызывают в США более 18 000 травм, включая ампутации, рваные раны и размозжения. Многие из этих травм были вызваны небезопасной эксплуатацией или неправильным обслуживанием. Защитные кожухи , или барьеры между оператором и опасными частями, являются одной из наиболее распространенных стратегий, которые производители используют для повышения безопасности своих инструментов.
Типы ограждений машин
Существует несколько различных типов ограждений машин . Защитные ограждения — это материалы, которые удерживают рабочих от прямого контакта с движущимися частями и другими опасными участками машины. Некоторые ограждения также защищают рабочих от стружек, летящих осколков или металлических искр, создаваемых работающими машинами. Управление по безопасности и гигиене труда (OSHA) требует ограждения любой части машины, которая может привести к травме. Конструкция и материал защитного кожуха будут варьироваться от машины к машине и от инструмента к инструменту. Наиболее распространенные типы ограждений машин:
- Фиксированные ограждения
- Блокирующие ограждения
- Регулируемые защитные кожухи
- Саморегулирующиеся кожухи
Фиксированные ограждения
Фиксированные ограждения постоянно прикреплены к станку или инструменту, не имеют движущихся частей и не могут перемещаться во время работы станка. Чаще всего они используются для ограждения рабочей точки или других опасностей, с которыми оператору не нужно взаимодействовать, таких как лопасти вентилятора или маховики. Поскольку фиксированные ограждения являются постоянными элементами машины, их необходимо разбирать и снимать для выполнения любых регулировок или технического обслуживания.
Регулируемые ограждения
Регулируемые ограждения, как и фиксированные ограждения, являются постоянными, но их можно отрегулировать, чтобы машина могла работать с материалами разных размеров. Они должны быть отрегулированы вручную и зафиксированы на месте, поэтому все сотрудники, которые будут управлять регулируемыми ограждениями, должны быть обучены их использованию. Если регулируемые ограждения неправильно отрегулированы или заблокированы, они могут не предотвратить контакт с движущимися частями, что может привести к серьезным или даже смертельным травмам.
Саморегулирующиеся ограждения
Саморегулирующиеся ограждения служат для тех же целей, что и регулируемые ограждения, но автоматически адаптируются к размеру материала. Когда машина находится в состоянии покоя, эти ограждения полностью опущены. Когда машина используется, оператор подает материал в машину, которая открывает защитный кожух ровно настолько, чтобы впустить материал. Эти защитные кожухи обычно встречаются на настольных пилах и деревообрабатывающих инструментах.
Блокирующие ограждения
Блокирующие ограждения, также известные как барьерные ограждения, автоматически отключают или отключают источник питания, когда ограждение открывается или снимается. Они особенно полезны в ситуациях, когда операторам необходимо открыть ограждение или получить доступ к защищенным частям машины, например, при устранении замятий. Эти ограждения обеспечивают безопасный доступ к внутренним частям машины, не требуя полной разборки. Однако их легко открыть случайно, и они требуют тщательной регулировки и обслуживания.
Общие меры предосторожности
Во избежание потенциально опасных для жизни травм сотрудники должны пройти надлежащее обучение перед началом работы с любыми машинами или электроинструментами.
- Осматривать все инструменты и ограждения перед каждым использованием
- При необходимости выполните все надлежащие процедуры блокировки/маркировки
- Соблюдайте надлежащие процедуры при настройке машины, регулировке машины, устранении замятий, очистке или смазке деталей
- Никогда не снимайте ограждения во время работы на машине
- Пометьте все поврежденные ограждения и механизмы «Не использовать» и немедленно сообщите о них
Резюме
Большинство травм, связанных с машинами, можно полностью предотвратить. Чтобы сохранить свое рабочее место в безопасности и избежать дорогостоящих травм и судебных исков, проведите надлежащее обучение всех сотрудников, прежде чем они будут работать с каким-либо оборудованием или охраной, и регулярно выполняйте техническое обслуживание и ремонт. Проинструктируйте сотрудников никогда не снимать ограждения машины до или во время работы на машине.