Наладка станков с чпу.
Наладка станков является одним из ответственных этапов его эксплуатации. Правильная наладка способствует повышению производительности труда, качества продукции и сохранению долговечности оборудования.
Налалдка – подготовка технологического оборудования и оснастки к выполнению технологической операции.
Подналадка – дополнительная регулировка технологического оборудования и (или) технологической оснастки при выполнении технологической операции для восстановления достигнутых при наладке значений параметров.
Наладка станка с ЧПУ включает
в себя подготовку режущего инструмента
и технологической оснастки, размещение
рабочих органов станка в исходном
положении, пробную обработки первой
детали, внесение корректив в положение
инструмента и режим обработки, исправление
погрешностей и недочетов в управляющей
программе.
Важным этапом наладки является базирование и закрепление заготовок. При определении схемы базирования необходимо знать конструктивные особенности налаживаемого оборудования в частности элементов обеспечивающих базирование приспособления или заготовки.
Для токарных станков с ЧПУ выбор схемы базирования сводится к выбору используемого приспособления для закрепления заготовок (различные зажимные патроны), а также к выбору наладочных элементов выбранного приспособления (например, обычные или сырые кулачки).
Для станков сверлильно-фрезерно-расточной группы возможны различные схемы базирования:
Непосредственно на столе станка с ЧПУ;
В приспособлении, которое установлено на столе станка;
В приспособлении установленном на координатной плите;
Непосредственно на координатной плите.
Непосредственно на столе
станка устанавливают заготовку, имеющую
большие размеры, хорошую опорную
поверхность и удобные поверхности для
закрепления. Кроме того, объем выпуска
должен быть сравнительно небольшим, а
трудоемкость обработки сравнительно
высокой (например, обработка малых
партий корпусных деталей на фрезерных
и многоцелевых станках при высокой
концентрации операций). При этом процент
времени затрачиваемого на установку
будет незначительным.
Если деталь имеет небольшие размеры, отсутствуют удобные поверхности для закрепления, повышается объем выпуска, сокращается концентрация операций и как следствие возникает необходимость сокращения времени на переустановку заготовок, то целесообразно применять приспособления. При этом приспособление может быть установлено на столе станка или на координатной плите. Координатная плита позволяет повысить точность установки приспособления и его быстросменность.
Существует несколько вариантов расположения приспособлений на станках с ЧПУ.
Приспособление может занять единственно возможное положение. В этом случае не требуется его выверять.
Пример – крепление токарного патрона к шпинделю станка, установка вращающегося центра в пиноль задней бабки.
Произвольное расположение приспособления вдоль осей координат, допускаемое управляющей программой. Характерно для фрезерных, сверлильных и расточных станков в том случае если обработка ведется с одной стороны. Приспособление должно бать выверено в угловом направлении относительно линейных координат.
Приспособление должно занять относительно рабочих органов единственно допустимое управляющей программой положение. Примером является наладка станка на обработку детали с нескольких сторон при повороте стола станка. Приспособление должно быть выверено в угловом направлении относительно линейных координат, а также в линейном направлении по отношению к оси поворота.
Для правильной установки
приспособления имеют соответствующие
базовые элемента (шпонки, пальцы), которые
соответствуют базовым элементом стола
станка (пазы, центральное отверстие). Совмещая указанные базовые элементы
добиваются правильного размещения
приспособления в координатах станка.
В случае если такие элементы отсутствуют или требуется более точная установка приспособления применяют мерные оправки. При этом мерная оправка закрепляется в шпинделе станка, перемещая стол в нужном направлении добиваются касания оправки базовых элементов приспособления, если это необходимо используют набор мерных плиток. Для совмещения оси шпинделя и центра детали применяют оптический или индикаторный центроискатели.
Наладка
режущего инструмента на размер.
В современном производстве возможно
определение положения вершины резца
при помощи специальных приборов. Такие
приборы имеют подставку, имитирующую
присоединительные поверхности станка,
подвижную каретку, измерительное
устройство (микроскоп, проектор,
индикатор). Установив режущий инструмента
на подставке, при помощи каретки
перемещают его до нужного положения,
отслеживая все перемещения на измерительном
устройстве. Полученную информацию
заносят в автоматическом или ручном
режиме в УЧПУ станка. Такие устройства
позволяют, кроме того, проверить
правильность и точность исполнения
режущей части.
Современные устройства
ЧПУ позволяют автоматически осуществлять
«привязку» инструмента к координатной
системе станка. Для этого система должна
иметь специальный цикл, а также устройство
позволяющее отследить местоположение
режущей кромки инструмента.
В случае отсутствия указанных систем «привязка» инструмента осуществляется оператором методом пробных проточек. Для этого оператору необходимо в ручном режиме осуществить проточку заготовки на небольшую длину, отвести инструмент, от заготовки не перемещая его по фиксируемой координате. Произвести замер, включить режим привязки инструмента, записать измеренную информацию в УЧПУ. Такую процедуру необходимо провести по всем координатам.
Режимы работы станков с ЧПУ. Станки с ЧПУ могут работать в нескольких режимах: автоматический, полуавтоматический, ручной ввод, ручной, режим привязки инструмента.
В автоматическом режиме осуществляется отработка управляющей программы безостановочно до одной из вспомогательных команд останова.
В полуавтоматическом режиме осуществляется покадровая
отработка управляющей программы. После
чего выполнение программы приостанавливается
до нажатия клавиши «Пуск».
В режиме ручного ввода оператор имеет возможность откорректировать управляющую программу или создать новую, а также ввести константы (параметры) станка.
В ручном режиме оператор имеет возможность перемещать рабочее органы, задавать технологические команды (пуск-останов шпинделя, включение охлаждения, смена инструмента, установка рабочее подачи), выполнять простейшие переходы (проточить диаметр, подрезать торец).
В режиме привязки инструмента вводится информация о фактическом положении режущего инструмента в системе координат станка, а также вводится коррекция на износ инструмента.
Органы
управления. Для работы
оператора в ручном режиме предусмотрены
следующие органы управления: кнопки
включения и отключения шпинделя,
зажима-отжима инструмента и шпинделя,
смены инструмента, клавиши или манипулятор
типа джойстик управления перемещениями
рабочих органов вдоль координатных
осей на рабочей подаче или ускоренном
ходу, штурвал для дискретных перемещений
рабочих органов, кнопка возврата рабочих
органов в «Нуль» станка. Почти на всех
станках с ЧПУ имеются корректоры рабочей
подачи, а на станках с регулируемым
приводом и частоты вращения шпинделя
в пределах от 0-120%.
Органы сигнализации. Органы сигнализации можно разделить на три группы: оперативные сигнальные группы, оперативные сигнальные лампы, диагностические сигнальные лампы, устройство цифровой индикации.
Оперативные лампы сигнализируют о готовности к выполнению цикла соответствующими агрегатами: включение станка в сеть, включение выбранного режима и др. В качестве диагностических лам, т.е. свидетельствующих о неисправности или некорректной работе обычно используются те же. Современные УЧПУ немыслимы без дисплея, на который выводится полная информация о местоположении рабочих органов, и протекании технологического процесса. Также на экран монитора может выводится управляющая программа.
Управление
точностью. Одним из
непременных условий обеспечивающих
получение требуемой точности детали
при обработке на станках, работающих в
автоматическом цикле, является
соответствие фактических размеров,
размерам, заданным в управляющей
программе. Выполнение этого условия
зависит от сохранения положения режущих
кромок инструмента и баз станка
относительно начала отсчета. Для этого
необходимо компенсировать погрешности
статической наладки, развивающиеся в
результате изнашивания режущего
инструмента и температурных деформаций
системы СПИД, а также в результате замены
инструмента.
Для решения этой задачи
используются автоматические системы,
обеспечивающие коррекцию точности
статической наладки в сходном положении.
Коррекция точности статической наладки
в исходном положении необходима при
переналадке станка непосредственно
перед обработкой первой детали очередной
партии. Именно на этом этапе погрешность
составляет наибольшее значение.
Автоматическую коррекцию наладки можно
выполнять также непосредственно в
процессе обработки партии деталей,
после одного или нескольких циклов
обработки. Такая коррекция позволяет
уменьшить влияние систематически
действующих факторов. Современные
станки с ЧПУ имеют специальную систему
управления точностью.
Рассмотрим систему автоматической коррекции для токарного станка с ЧПУ. Это устройство фиксирует отклонения вершины режущей кромки инструмента вследствие изнашивания, температурных деформаций или замены пластины. Отклонение положения вершины резца измеряется в двух перпендикулярных направлениях, соответствующих образованию линейных и радиальных размеров детали. Процесс измерения осуществляется по определенной программе системы ЧПУ. По команде системы ЧПУ револьверная головка выводится в определенное положение, при котором резец устанавливается в измерительной позиции. Далее происходит установочное перемещение револьверной головки до касания режущей кромкой измерительного наконечника датчика. Затем револьверная головка возвращается, в измерительную позицию, после чего установочное перемещение осуществляется для другой координаты.
На основании результатов
измерения производится автоматическая
коррекция в блоке ЧПУ, позволяющая
компенсировать изменение положения
режущей кромки инструмента. Такую
коррекцию целесообразно производить
непосредственно перед чистовым проходом.
Проверка и оценка новой управляющей программы. Весьма ответственным этапом работы является отладка новой УП. Этот этап наладки осуществляет чаще всего наладчик или наладчик совместно с технологом программистом. В ходе отладки УП проверяют ее оптимальность по параметрам производительности, качества обработки, отсутствия вибраций, стойкости инструмента, приемлемого схода стружки. По результатам обработки пробной детали УП редактируют. Наиболее высокий результат редактирования УП может быть достигнут только с использованием теоретических знаний в области металлообработки, а также творческого подхода.
Работа начинается чаще
всего с устранения ошибок не позволяющих
начать процесс обработки. Такие ошибке
могут быть сведены к минимуму при
применении современных способов
составления УП, который заключается в
использовании средств автоматизированного
проектирования CAD и CAM. Чаще всего встречаются следующие ошибки
первоначальной редакции:
– нуль программы выбран за пределами рабочей зоны, т.е.;
– использованы технологические команды невыполняемые станком;
– инструменты при холостых перемещениях и сменах задевают за элементы станка, крепежную оснастку или обрабатываемую деталь.
Наибольшего внимания требует
проверка вероятности наличия в программе
третьего вида ошибок, которые могут
привести к возникновению аварийной
ситуации, поломке дорогостоящего
инструмента. Новую программу целесообразно
отрабатывать в полуавтоматическом
режиме, проверяя каждый кадр программ
перед его отработкой. Ситуация связанная
с нежелательными столкновениями
инструмента с элементами станка могут
возникнуть также при неправильном вводе
информации о коррекции инструмента.
Поэтому при пробной отработке УП следует
также перед началом работы нового
инструмента проверять правильность
его «привязки».
При первой отработке УП целесообразно снижать скорость перемещения рабочих органов, пользуясь регулятором подачи. При незапланированном контакте инструмента с заготовкой или другими элементами необходимо остановить подачу при помощи соответствующего переключателя. При встрече препятствия инструментами во время его смены следует воспользоваться кнопкой аварийного отключения.
В целях экономии материала, в случае больших деталей, отработку УП осуществляют с использованием более дешевого и легкообрабатываемого материала.
Для оценки оптимальности УП руководствуются принципами построения технологических процессов на станках с ЧПУ. Основная характерная черта – интеграция обработки, т.е. последовательное выполнение большого числа переходов, выполняемых различными инструментами. При этом характерен последовательный переход от черновой обработке к чистовой.
Следующий этап проверки
оптимальности УП – оценка правильного
выбора режимов резания. При черновой
обработке необходимо достичь максимальной
производительности, при этом критерием
выбора режима резания является
экономическая стойкость инструмента.
При чистовой обработке определяющую
роль играют требования точности и
шероховатости обработанной поверхности.
В процессе отладки программы
необходимо проверить соответствие
заложенных режимов резания возможностям
инструмента и станка, надежности
закрепления заготовки. Особое внимание
следует уделить возникновению вибраций,
т.к. вибрации способствуют разрушению
инструмента и повышенному износу узлов
станка. Погасить вибрацию можно путем
изменения скорости резания, подачи или
глубины резания. Наиболее часто вибрации
возникают при срезании тонких стружек,
поэтому самый простой прием гашения
вибрации – увеличение подачи на оборот.
Возникновению вибраций способствует
также очень острая кромка, при ее
затуплении вибрации могут прекратится
самопроизвольно. Надежно гасит вибрации
фаска на режущей кромке, притупляющая
лезвие инструмента. Фаску выполняют на
передней поверхности режущей части
инструмента под углом -15 º. Фаску можно
выполнить при помощи алмазного бруска
не снимая инструмент со станка.
При токарной обработке и сверлении существенным показателем правильно выбранных режимов резания является характер схода стружки. Сливная стружка представляет угрозу для инструмента т.к. не удаляется самостоятельно из зоны резания. Наилучшей по всем показателям является дробленая стружка. Решить проблему дробления стружки можно тремя способами:
Изменением движения рабочих органов;
Приданием передней поверхности инструмента соответствующей формы;
Режимами резания.
Изменение движения рабочих
органов приводит к усложнению УП, а
также к увеличению времени обработки.
Наиболее перспективным является
применение специальной заточки
инструмента или применение инструмента
с СМП с заложенными функциями
стружкодробления. Также дробления
стружки можно достичь увеличивая подачу
и (или) снижая скорость резания.
В ряде случаев, например при программировании сложного контура детали целесообразно выполнить прорисовку движения режущего инструмента при помощи программных средств.
Наладка токарного станка с ЧПУ — Национальная сборная Worldskills Россия
“
В этом видео мы рассмотрим процесс наладки токарного станка с ЧПУ.
Глоссарий
Для успешного освоения материала рекомендуем вам изучить следующие понятия:
Обработка заготовки со снятием металла для подготовки к чистовой обработке
Обработка заготовки для достижения жестких допусков и высокого качества обработанной поверхности
Резец, у которого при наложении на него сверху ладони правой руки так, чтобы пальцы были направлены к его вершине, главная режущая кромка будет находиться под большим пальцем
Резец, у которого при наложении на него левой руки указанным выше способом главная режущая кромка окажется под большим пальцем
Подготовка технологического оборудования и оснастки к выполнению определенной технологической операции или набора операций
Язык программирования устройств с ЧПУ
Программное обеспечение, позволяющее быстро создавать программы для обработки деталей непосредственно на станке с ЧПУ
Автоматизированная система либо модуль автоматизированной системы, предназначенные для подготовки управляющих программ для станков с ЧПУ. Под термином понимаются как сам процесс компьютеризированной подготовки производства, так и программно-вычислительные комплексы, используемые инженерами-технологами
Видеолекция
Конспект
Инструменты и материалы для наладки
Правый черновой резец с пластиной 55°, R = 0,4 мм
Правый чистовой резец с пластиной 35°, R = 0,4 мм
Правый канавочный резец, R = 0,2 мм
Корпусное сверло, D = 30 мм
Правый расточной резец с пластиной 55°, D =16 мм, R = 0,4 мм
Концевая фреза, D = 10 мм
Твердосплавное спиральное сверло, D = 4 мм
Инструментальные блоки
Приводные блоки
Материал заготовки — алюминиевый сплав Д16Т
Сборка инструмента
1. Прикручиваем все пластины к резцам.
Важно
Обратите внимание на правильность подбора ключей. Неправильно подобранный ключ может слизать грани винта
3. Прикручиваем пластины к сверлу.
4. Вставляем резцы в подходящие блоки.
Совет
Не стоит делать слишком большой вылет резца из блока. Это может привести к вибрациям и к тому, что при повороте револьвера инструмент упрется в кожух станка
5. Вставляем в блок сверло.
7. Собираем осевой инструмент.
8. Загружаем инструмент в револьвер.
Создание инструмента в системе ЧПУ
- радиус — 0.4 мм,
- угол державки — 93°,
- угол между плитами — 55°,
- направление по часовой стрелке,
- включаем СОЖ.
- радиус — 0.4 мм,
- угол державки — 93°,
- угол между плитами — 35°,
- направление по часовой стрелке,
- включаем СОЖ.
3. Создаем резец с корректором слева. Меняем имя и вводим параметры инструмента:
- радиус — 0.2 мм,
- ширина пластины — 4 мм,
- длина пластины — 13 мм,
- направление по часовой стрелке,
- включаем СОЖ.
- диаметр — 30 мм,
- направление по часовой стрелке,
- включаем СОЖ.
- радиус — 0.
4 мм,
- угол державки — 93°,
- угол между плитами — 55°,
- ширина плиты — 7 мм,
- направление по часовой стрелке,
- включаем СОЖ.
6. Снова пропускаем одно место. Затем создаем концевую фрезу. Вводим параметры:
- диаметр — 10 мм,
- количество зубьев — 3,
- направление по часовой стрелке,
- включаем СОЖ.
- диаметр — 4 мм,
- угол при вершине — 118°,
- направление по часовой стрелке,
- включаем СОЖ.
9. Опускаем датчик.
10. Подводим инструмент над датчиком.
11. Выбираем ось X, устанавливаем подачу на 100% и нажимаем Cycle Start.
12. Переключаемся на ось Z и повторяем измерения.
13. Измеряем все остальные инструменты.
14. Убираем датчик.
Сборка кулачков
Инструменты
Сухари
Кулачки
Процесс сборки
1. Располагаем сухарь внутри паза кулачка. Далее совмещаем отверстие на сухаре с отверстием на кулачке, переворачиваем его и опускаем в отверстие два болта. Затем необходимо притянуть болты, но не затягивать их до конца.
2. Аналогично собираем каждый кулачок.
Установка заготовки в патрон
1. Устанавливаем кулачки в патрон.
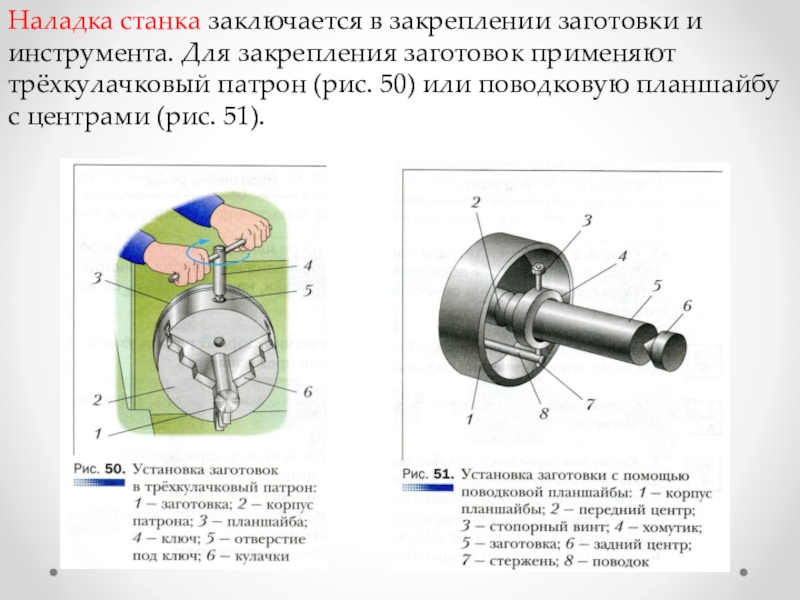
3. Выставим давление в патроне 28 бар.
5. Указываем нулевую точку. Для этого переходим в режим Machine и на вкладке TSM вводим:
- номер места — 1,
- число оборотов шпинделя — 1500 об/мин,
- направление вращения по часовой стрелке.
6. Закрываем дверь и нажимаем Cycle Start. После этого подъезжаем к заготовке и торцуем.
Запуск программы
1. Чтобы отправить программу на исполнение в режим Auto, переходим в начало программы и нажимаем «Выбор».2. Программа откроется в новом окне, запускаем ее кнопкой Cycle Start.
3. Чтобы запустить программу в G-коде с определенного кадра, предварительно задайте поиск. Это позволит станку прочитать все условия, которые были в программе ранее.
Совет
Перед запуском программы рекомендуется установить рабочую и ускоренную подачу на ноль, а уже затем постепенно добавлять подачу
“
Вы узнали, как осуществить наладку станка и запустить программу. Закрепите новые знания с помощью теста и интерактивного задания.
Интерактивное задание
Для закрепления полученных знаний пройдите тест
Стартуем! |
Дальше |
Проверить |
Узнать результат |
Offset
MachineProgram Manager
Дальше |
Проверить |
Узнать результат |
К сожалению, вы ответили неправильно на все вопросы
Прочитайте лекцию и посмотрите видео еще раз
Пройти еще раз |
Неплохо!
Но можно лучше. Прочитайте лекцию и посмотрите видео еще раз
Пройти еще раз |
Отлично!
Вы отлично справились. Теперь можете ознакомиться с другими компетенциями
Пройти еще раз |
Введение в настройку станка
Руководства по проектам тонкой деревообработки
Магазинные машины
Video
Когда станок правильно настроен и обслуживается, это не только сделает вашу работу по дереву более точной, но и сделает ваше времяпрепровождение в мастерской более приятным.
Мэтт Вайда, Эллен Касперн № 270–сентябрь/октябрь 2018 г., выпуск
Если станок правильно настроен и обслуживается, это не только сделает вашу работу по дереву более точной, но и сделает ваше пребывание в мастерской более приятным. И Мэтт Вайда, и Эллен Касперн провели бесчисленное количество часов за станками, изготавливающими мебель, а также вели занятия по настройке и обслуживанию машин.
В этом видео-семинаре Эллен покажет вам, как настроить настольную пилу: сделать угловые пазы параллельными лезвию, установить упор параллельно угловым пазам, установить столешницу параллельно углу диска и, наконец, смазать все подвижные части.
Для фуганка Мэтт проследит, чтобы кровати лежали в одной плоскости, проверяя на ветер и регулировку при необходимости. Затем он установит ножи, ориентируясь на разгрузочный стол, и установит глубину резания.
На ленточной пиле Эллен проследит, чтобы полотно двигалось правильно, установив колеса в одной плоскости друг с другом, закрепив шины и отрегулировав наклон и натяжение верхнего колеса. Наконец, она установит подшипники и направляющие блоки.
На рубанке Мэтт установит станину параллельно ножевой головке и установит ножи. Затем он использует калибровочный блок и регулировочную прокладку для установки режущего круга, подающих роликов, прижимной планки и разгрузочных роликов. Чтобы закончить, он почистит и смажет машину.
Наконец, Мэтт настроит долбежный станок с полым долотом, установив упор параллельно долоту, убедившись, что станина перпендикулярна упору, а долото и столы двигаются плавно и точно.
Видео из серии
- Введение в настройку машины
23 июля 2018 г.
Когда станок правильно настроен и обслуживается, это не только сделает вашу работу по дереву более точной, но и сделает ваше время в мастерской более приятным.
- Настройка машины: Настольная пила
23 июля 2018 г.
Как идеально настроить настольную пилу, используя только комбинированный угольник и циферблатный индикатор.
- Настройка станка: настройка фуганочных столов
30 июля 2018 г.
Инструктор по деревообработке Мэтт Вайда показывает, как установить фуганочные столы, используя только линейку и несколько клочек бумаги.
- Настройка станка: установка фуганковых ножей
30 июля 2018 г.
В этом выпуске Мэтт Вайда решает часто разочаровывающую задачу правильной настройки фуганочных ножей.
- Настройка станка: ленточная пила
7 августа 2018 г.
Инструктор по деревообработке Эллен Касперн демонстрирует, как настроить 14-дюймовый столярный станок. ленточная пила.
- Настройка станка: сверлильный станок с полым долотом
13 августа 2018 г.
Узнайте, как установить упор параллельно долоту, убедиться, что станина перпендикулярна упору, а долото и столы перемещаются плавно и точно.
- Настройка станка: Строгальный станок
20 августа 2018 г.
Узнайте, как настроить рубанок, а также как его чистить и смазывать, чтобы обеспечить его бесперебойную работу и безупречные результаты.
Предыдущий: Вощение машины против использования керосина Следующий: Прислушивание к инструментам — хороший способ выявить потенциальные проблемы
Магазинные машины
Магазинные машины
В этом руководстве вы найдете все необходимое от настройки до безопасного использования.
Посмотреть руководство по проекту
Просмотреть все руководства по проектам »
Станьте участником и получите неограниченный доступ к сайту, включая Руководство по проекту цеховых машин.
Начать бесплатную пробную версию
Знакомство с магазинными машинами
Ленточные пилы
- Основы ленточной пилы
- Ленточные пилы
- Настраивать
- Техники: перепиливание и распиловка
- Техники: вырезание кривых
- Джиги
Настольные пилы
- Настраивать
- Техники
- Лезвия пилы
Фуганки и строгальные станки
- Фуганки
- Рубанки
Сверлильные и долбежные станки
- Сверлильные станки
- Полые долота долбежные
Станочные приспособления и приспособления
Дальнейшие мысли по сокращению времени настройки станка
Опубликовано
На протяжении многих лет я работал со многими компаниями, пытаясь найти способы сократить время простоя их машин при переключении с одной работы на другую. Когда машина настраивается, она не производит детали.
Уэйн Чанески
Президент, Интеллектуальные производственные решения
Доля
Читать далее
- История американского производства
- Правильный выбор шлифовального круга
- Почему городам нужны производственные предприятия
На протяжении многих лет я работал со многими компаниями, пытающимися найти способы сократить время простоя их машин при переключении с одной работы на другую. Когда машина настраивается, она не производит детали. В течение года минуты, потерянные на время настройки, могут привести к многочасовым простоям производства.
Теория сокращения времени установки не претерпела существенных изменений с тех пор, как Шигео Синго более двадцати лет назад представил свою новаторскую концепцию одноминутной замены штампов (SMED). Применяя эти концепции, тысячи производителей сократили время настройки с 50 до 75 и более процентов. Кроме того, производители станков и инструментальной оснастки внедрили новые технологии, такие как устройство смены паллет, увеличенная емкость устройства смены инструмента, конвейеры для стружки, упрощенное программирование ЧПУ, быстросменный инструмент и упрощенная предварительная настройка инструмента, все с явной целью сокращения времени настройки станка. .
Самый простой и наиболее эффективный способ сократить время наладки станка — это заранее подготовить три вещи, которые необходимы перед наладкой и эксплуатацией любой части оборудования: информацию, материалы и инструменты. Хотя вы можете начать настройку без всех трех, вы не сможете завершить настройку, если вам не хватает какой-либо из них. Сколько раз мы видели, как машина бездействует, ожидая появления хотя бы одной из этих вещей? Эффективная процедура настройки практически гарантирует наличие всего необходимого для выполнения работы заранее. Рассмотрим подробнее каждый из этих важнейших компонентов.
Информация. Какой бы очевидной ни была потребность в полной и точной информации, этот компонент часто упускается из виду, особенно когда машина настраивается для выполнения повторяющегося задания. Информация, необходимая для настройки, может различаться, но обычно она включает в себя распечатку детали или спецификацию, описывающую характеристики детали; запись настройки с указанием необходимых инструментов, приспособлений и настроек станка; программа для любого станка с ЧПУ с числовым программным управлением; и заказ на работу с указанием количества деталей и любых инструкций для конкретного клиента. Всю эту информацию необходимо прочитать и понять до того, как начнется фактическая установка. Поэтому важно, чтобы информация о настройке была доставлена на машину и размещена на видном месте до того, как предыдущее задание будет завершено.
Материал . Без материала невозможно изготовить детали. Как только наладчик получает информацию о следующей работе, он может проверить потребности в материалах и либо получить материал (если он хранится поблизости), либо предпринять действия, чтобы доставить его к станку. В идеале у каждой машины должна быть четко обозначенная площадка для хранения материала, необходимого для следующей работы.
Инструменты. Инструменты могут охватывать целый ряд предметов. Режущие инструменты, необходимые для машины, должны быть легко доступны. Если позволяют возможности хранения станка, идеальным местом для хранения инструментов является сам станок. Ручные инструменты, необходимые для измерения или дополнительных операций, выполняемых на станке, также должны быть доступны заранее. Этого намного легче достичь, если они регулярно хранятся в месте использования. Однако политика компании может требовать, чтобы такие продукты, как контрольно-измерительные приборы, приобретались в контролируемой зоне. Точно так же любые специальные приспособления, необходимые для следующей работы, также должны быть доставлены к машине и проверены заранее. Поддержание таких приспособлений на машине или рядом с ней облегчит эту задачу.
Просмотрите некоторые ожидающие настройки машины и ответьте на следующие вопросы словами «всегда», «обычно», «иногда» или «никогда».
- Доступна ли информация о следующей работе и в этом районе заранее?
- Материал для следующего задания хранится рядом со станком?
- Готовы ли инструменты для следующей работы в этом районе и готовы ли к использованию?
Ответ «всегда» на все три вопроса гарантирует более короткое время настройки и повышенную вероятность того, что ваши станки начнут резать стружку раньше.