инженер поможет – Нарезание резьбы на станке с ЧПУ
Наиболее распространенные инструменты для получения внутренней резьбы на станках с СЧПУ – это метчики и фрезы. Сложность получения резьбы с помощью фрезы связана со сложностью программирования интерполирующего движения, поэтому чем проще система ЧПУ, тем чаще используются метчики.
Принцип получения резьбы фрезерованием
При фрезеровании профиль резьбы формируется с помощью движения специальной фрезы по винтовой линии. Подача в этом случае должна совпадать с шагом метчика.
Технология получения резьбы фрезерованием
Сверлят отверстие
Резьбовая фреза опускается в отверстие на нужную глубину резьбы и врезается по дуге 90° на глубину. Фреза при врезании поднимается на ¼ шага резьбы (участок 1-2).
Ось фрезы М делает оборот на диаметре m (участок 2-3) при этом фреза одновременно поднимается на шаг резьбы Р и выходит из профиля по дуге 90° (участок 3-4).
В случае, если глубина резьбы в полученном ранее отверстии больше длины режущей части фрезы, то обработку на участке 2-3 повторяется несколько раз.
Есть несколько типов резьбовых фрез используемых для нарезания резьбы в станках с ЧПУ
твердосплавные фрезы
резьбовые фрезы со сменными пластинами
комбинированные резьбовые фрезы – это фрезы позволяющие сначала сверлить отверстие под резьбу, а потом фрезеровать резьбу
Поэтому есть 2 основных технологии получения резьбы фрезами
Получение резьбы одним инструментом
Получение резьбы несколькими режущими инструментами
Виды метчиков для нарезания резьбы
Метчики с прямыми стружечными канавками
Метчик с прямыми канавками это самый широко используемый вид метчика. Этот метчик применяется для материалов, которые дают короткую стружку, например для стали или чугуна.
Метчики с шахматным зубом
Использование метчика с шахматным зубом уменьшает трение и сопротивление процессу резания, что очень важно при обработке труднообрабатываемых материалах (алюминии и бронзе).
Метчики со спиральной подточкой
Метчик со спиральной подточкой имеет прямые неглубокие стружечные канавки. Спиральная подточка предназначена для выталкивания стружки вперед. Сравнительно неглубокие стружечные канавки гарантируют максимальную прочность метчика на скручивание. Они также облегчают подвод СОЖ в зону резания. Этот тип метчиков рекомендуется для обработки сквозных отверстий.
Метчики со стружечными канавками только на заборной части
Режущая часть данного метчика имеет аналогичную спиральную подточку, предназначенную для выталкивания стружки вперед. Этот метчик имеет чрезвычайно жесткую конструкцию. Рекомендуется для обработки отверстий глубиной до 1.5 х 0.
Метчики со спиральными зубьями
Метчики со спиральными зубьями предназначены в основном для нарезания резьбы в глухих отверстиях. Спиральная стружечная канавка выталкивает стружку назад, что предотвращает пакетирование стружки на дне отверстия или в стружечных канавках.
Бесстружечные метчики (раскатники)
Бесстружечные метчики отличаются от обычных тем, что образуют профиль резьбы за счет пластической деформации , а не за счет снятия стружки. Рекомендуются для материалов с высокой пластичностью. Такие материалы имеют предел прочности не более 1200 Н/ммг, а относительное удлинение не менее 10%.
Бесстружечные метчики можно использовать в обычных условиях, но лучшие результаты они показывают при обработке вертикальных глухих отверстий. Выпускаются также с внутренним подводом СОЖ.
Резьбонарезные фрезы имеют огромное преимущество при обработке глухих отверстий. Метчику всегда нужен зазор между дном отверстия и торцом метчика из-за заборного конуса метчика. Поэтому метчик не нарезает резьбу в глухом отверстии. Использование фрезы решет эту проблему, так как расстояние от торца фрезы до первой режущей резьбовой кромки очень мало. Также большим преимуществом фрез для резьбы является возможность изменять параметры резьбы, что не возможно при использовании метчика.
Запомните, что подача равна при работе метчиком оборотам шпинделя умноженным на шаг резьбы.
Резьба может срезается при остановке шпинделя перед реверсом – ось Z уже остановилась, а вот шпиндель по инерции делает ещё какую-то часть оборота. При нарезании резьбы метчиком в стали при этом обрывает метчик, а Д16Т мягче и поэтому резьбу слизывает. Поэтому для нарезания резьбы на станке с ЧПУ нужно использовать специальный патрон – плавающий или его еще называют компенсирующий. Этот патрон имеет подпружиненную часть с цангой, которая может перемещается относительно неподвижной на несколько миллиметров вдоль оси патрона в обоих направлениях.
Привожу общие указания по нарезанию резьбы метчиками
Результат любой операции по нарезанию резьбы зависит от ряда факторов, каждый из которых, в конечном счете, влияет на качество готовой детали.
1. Выберите правильную конструкцию метчика для данного обрабатываемого материала и типа отверстия.
2. Убедитесь, что деталь надежно закреплена – перемещения в процессе обработки могут привести к поломке метчика или плохому качеству резьбы.
3. Выберите правильный размер сверла из соответствующих таблиц. Диаметр необходимого сверла также указан на страницах каталога с метчиками. Помните, что для метчиков-раскатников необходимы сверла других диаметров. Всегда контролируйте наклеп обрабатываемого материала.
4. Выберите правильное значение скорости резания, как показано в каталоге режущего метчиков.
5. Используйте СОЖ, соответствующую выполняемой операции.
6. При нарезании резьбы на станках с ЧПУ проверьте значение подачи, указанное в программе. При использовании резьбонарезного патрона значение подачи на оборот должно составлять от 95 до 97 % от шага для самозатягивания метчика.
7. По возможности используйте качественные патроны с компенсацией для ограничения крутящего момента, которые гарантируют осевое перемещение метчика и устанавливают его прямо в отверстии. Также это предохранит метчик от поломки при случайном столкновении одном отверстия.
8. Убедитесь в том, что метчик плавно входит в отверстие, прерывистая подача может привести к колоколообразной форме начальных витков.
нарезание резьбы резцом на токарном станке, нарезание резьбы чпу, точение резьбы, способы нарезания резьбы, инструмент для нарезания наружной резьбы, нарезание наружной и внутренней резьбы, технология нарезания наружной резьбы, технология нарезания резьбы, инструмент для нарезания наружной резьбы, пластины для нарезания резьбы, резьбовые пластины
Главная страница » Нарезание резьбы ЧПУ
Нарезание резьбы на токарном станке является распространенной обработкой, как наружной, так и внутренней. Это частая операция и о ней необходимо знать всё. И в первую очередь знать технологию нарезания резьбы, способы нарезания резьбы, а также уметь правильно подбирать

Нарезание резьбы резцом на токарном станке является наиболее производительным и эффективным способом обработки резьбы, он обеспечивает высокое качество поверхности резьбы.
Помним и применяем:
1. Подача равна шагу резьбы.
2. Для нарезания резьбы на нержавеющей стали и других материалах, склонных к наклёпу, не выбираем слишком малые глубины резания.
3. Резьбу с большим шагом сначала точим обычными токарными пластинами треугольными, а на чистовом проходе используем резьбовую пластину, для повышения стойкости резьбовых пластин. При черново_й разгрузке применяем наиболее подходящее врезание (одностороннее боковое, двухстороннее боковое, радиальное врезание).
4. Использует пластины с полным профилем, так как они обеспечивают максимальную производительность. Иногда имеет смысл брать многозубые пластины для еще большей производительности, но необходима повышенная жесткость системы.
5. Применяем СОЖ желательно под давлением (10…70 бар). Для эвакуации стружки, охлаждения, смазки, снижения трения, повышения качества поверхности резьбы и повышения стойкости инструмента для нарезания резьбы на токарном станке.
6. Преимущественно применяем одностороннее боковое врезание, так как обеспечивает_ся лучшее стружкодробление, процесс напоминает простое точение, высокое качество обработки.
7. Стараемся снизить вибрации путем: минимальный вылет инструмента, жесткие инструменты, разумное кол-во проходов и глубина врезания.
8. Следим, чтобы вершина резца точно была настроена по центру заготовки.
9. Крепление пластин с помощью динамометрического ключа. Нельзя перетягивать или не дотягивать винты крепления пластин. Момент затяжки смотреть в каталоге инструментов.
10. Следим за стружкодроблением, не допускаем наматывания стружки на инструмент, особенно на токарных автоматах, где нет контроля оператора.
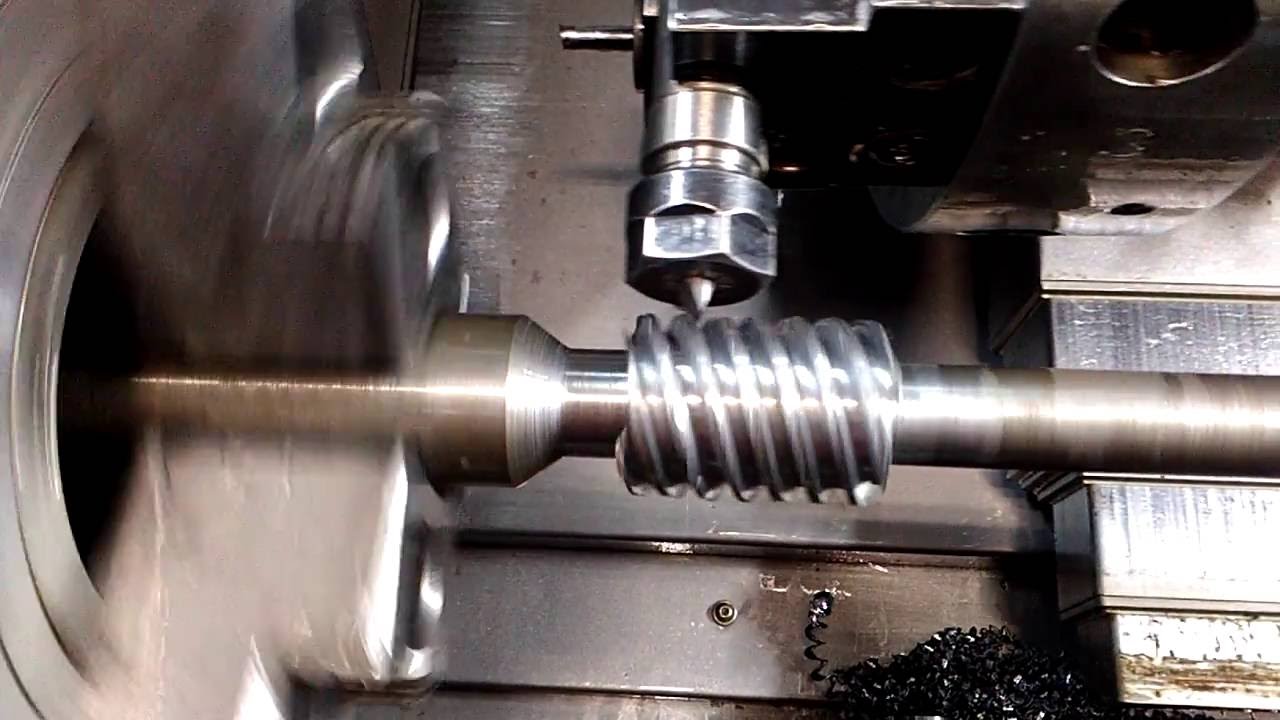
12. При нарезании внутренней резьбы на токарном станке обеспечиваем безпрепятственный выход стружки, желательно внутренний подвод СОЖ.
13. При нарезании внутренней резьбы желательно работать от патрона, это обеспечит выход стружки из отверстия.
14. Направление подачи от патрона или к патрону не влияет на качество резьбы.
15. Не забываем добавлять припуск на диаметр 0,03…0,07 мм на радиус при работе пластиной с полным профилем.
16. Используем твердосплавные оправки при большом вылете инструмента, а также антивибрационные оправки, особенно при внутреннем нарезании резьбы с большим вылетом.
Инструменты для нарезания резьбы на токарном станке
В основном используются резцы со сменными твердосплавными пластинами для нарезания резьбы. Давайте рассмотрим основные типы резьбовых пластин. На сегодняшний день применяются три типа резьбовых пластин.
Пластины с полным профилем
Обеспечивают высокопроизводительное нарезание резьбы, являются частым выбором, они:
1. Полностью формируют профиль резьбы и впадину, и вершину, и радиусы на вершине и впадине резьбы. Поэтому данные пластины гарантированно выдерживают все параметры резьбы и обеспечивают требуемую прочность. Обеспечивают более высокое качество резьбы.
17. Не нужна точная предварительная обработка диаметра под резьбу, и последующем снятии заусенцев после нарезания резьбы.
19. Соответственно для каждого шага и профиля резьбы применяется своя резьбовая пластина.
20. Требуется выполнять несколько проходов, т.к. пластины имеют большой радиус.
Пластины с не полным профилем
1. Не обрабатывают вершину резьбы.
2. Поэтому нужна точная обработка диаметра вала или отверстия под нарезание резьбы.
3. Одна пластина может нарезать резьбу с разным шагом, но одного профиля.

4. Поэтому нет необходимости закупать большое количество инструментов под каждый шаг резьбы.
5. Пластины имеют низкую стойкость, так как радиус на вершине минимален и рассчитан на наименьший шаг. Каждый профиль резьбы имеет свой радиус.
Пластины многозубые
Обеспечивают максимальную производительность нарезания резьбы на токарном станке.
1. Работают аналогично, как и пластины с полным профилем, однако имеют более одного зуба и требуют меньшего количества проходов.
2. Производительность увеличивается в 2 раза при 2 зубьях, в 3 при 3-х зубьях и т.д.
3. Платины требуют больше места под выход из резания.
4. Необходима высокая жесткость технологической системы, так как возникают большие силы резания.
5. Такие пластины имеются только для распространенных размеров резьбы.
Количество проходов и глубина резания при нарезании резьбы
Резьба нарезается за несколько проходов, при этом важное значение имеет глубина резания на каждом проходе. Стоит отметить, что глубина врезания не зависит от способа врезания (одностороннее боковое, двухстороннее боковое, радиальное врезание).
В зависимости от глубины врезания можно выделить два способа обработки резьбы.
1. Постоянная площадь сечения стружки и разная глубина врезания. Наиболее популярный способ, так как обеспечивает максимальную производительность. В данном способе каждый последующий проход имеет меньшую глубину врезания, и она уменьшается до 0,09…0,02 мм на последнем проходе. Так пластина срезает стружку с одинаковой площадью сечения, соответственно воспринимает постоянные нагрузки и равномерный износ, что увеличивает ее стойкость.
2. Постоянная глубина врезания. Используется, когда есть проблемы со стружкодроблением. Каждый проход имеет одинаковую глубину врезания. Обычно данный способ требует большего количества проходов, чем первый. Толщина стружки постоянная на каждом проходе, но площадь сечения стружки на последующих проходах больше, соответственно нагрузка на инструмент увеличивается на каждом проходе.
Последний зачистной проход выполняют без врезания. Его делают для устранения погрешностей. Рекомендации по количеству проходов обычно приводятся в каталоге инструментов.
Нарезание наружной и внутренней резьбы на токарном станке довольно широкий вопрос, имеет много тонкостей, но применяя основные вышеперечисленные рекомендации точения резьбы, способы нарезания резьбы и технологию нарезания резьбы, а также подбирая правильные инструменты для нарезания резьбы Вы добьетесь высокой производительности при нарезании наружной и внутренней резьбы на токарном станке.
Возможно Вам также будет интересно:
Фрезерование резьбы
Точение канавок
Обработка канавок
Фрезерование канавок
Похожие записи:
Режущий инструмент, инструментальная оснастка и приспособления / Cutting tools, tooling system and workholding | |||||
Подборка ссылок из каталогов инструмента для словаря по машиностроению | |||||
1610 Для международной унификации резьбы была создана резьба ISO Метрическая резьба ISO является сегодня самым распространенным видом резьбы Этот факт отра | 1611 Резьбовые посадки при различном зазоре профиля Диаметр D внутренней резьбы гайки Диаметр d наружней резьбы болта Диаметр d наружней резьбы болта Диаме | 1612 Проблемы и их решения при нарезании внутренней резьбы в отверстиях новыми метчиками Резьба слишком большая Режущая геометрия резьбонарезного инструмен | 1613 Проблемы и их решения при нарезки резьбы в отверстиях стальных заготовок новыми метчиками Продолжение Поверхность резьбы рваная Геометрия метчика для | 1614 Типовые проблемы и их решение при нарезании внутренней резьбы переточенными метчиками Проблема Причина Решение Резьба слишком большая Имеется заусенец | |
190 Технологии нарезания резьбы метчиком на станке При обработке глухих отверстий стружка должна измельчаться в точке переключения направления вращен | 778 Основные элементы и параметры стандартной резьбы Угол профиля Шаг Наружный внутренний и средний диаметры Подъем резьбы Определение допусков | 782 Нарезание внутренней резьбы метчиком на станке Основные факторы влияющие при определении скорости станочного резьбонарезания Материал заготовки | 784 Технология нарезания резьбы метчиком Рекомендации производителя инструмента по выявлению и устранению проблем при обработке резьбы на станках | ||
См. | |||||
Устройство метчика / Thread taps for metal | Диаметр под резьбу / Tap drill sizes | ||||
Метчики раскатники / Cold forming roll taps | Резьбонарезные патроны для метчиков / Tapping chucks | ||||
Перевод дюймов в мм Таблица / Inches to mm Conversion table | Типы резьб / Thread types and applications | ||||
Резьбовые фрезы / Thread milling | Нарезание резьбы на токарном станке / Thread turning | ||||
Примеры страниц из каталогов инструмента для металлообработки | |||||
782 Каталог KENNAMETAL 2018 Инструмент для обработки отверстий Метчики Фрезы Стр. | |||||
Нарезание внутренней резьбы метчиком на станке Основные факторы влияющие при определении скорости станочного резьбонарезания Материал заготовки Нарезание внутренней резьбы метчиком на станке Основные факторы влияющие при определении скорости станочного резьбонарезания Материал заготовки _ Факторы, которые следует учесть при выборе оптимальных скоростей для резьбонарезания: Обрабатываемый материал Длина заходной части метчика Доля обрабатываемого профиля резьбы Глубина отверстия (длина резьбы) Шаг резьбы Смазочно-охлаждающие жидкости Станок Горизонтальное или вертикальное нарезание резьбы Определение эффективных рабочих скоростей для метчиков с такой же точностью, как для многих других металлорежущих инструментов, невозможно. В случае с другими токарными инструментами подача на оборот может быть установлена произвольно, а в процессе обработки меняться по мере необходимости. Метчики, напротив, всегда должны перемещаться с подачей, равной одному шагу за оборот. | |||||
1612 Каталог GUHRING 2012 Режущий инструмент и инструментальная оснастка Стр. | |||||
Проблемы и их решения при нарезании внутренней резьбы в отверстиях новыми метчиками Резьба слишком большая Режущая геометрия резьбонарезного инструмен Проблемы и их решения при нарезании внутренней резьбы в отверстиях новыми метчиками Резьба слишком большая Режущая геометрия резьбонарезного инструмента для данного применения не пригодна Предварительно просверленное отверстие мало Позиционная или угловая ошибка отверстия под резьбу Использовать метчик рекомендуемый для данного обрабатываемого материала Изготовить отверстие под резьбу с необходимым диаметром см. табл. Диаметры отверстий под резьбу” в общей технической части – Проверить крепление инструмента – Использовать резьбонарезной патрон с компенсацией несоосности – Проверить сверло для отверстия под резьбу Ошибка хода шпинделя станка – Использовать машинную подачу – использовать резьбонарезные патроны с компенсацией длины Метчик с наростом на режущей кромке – Использовать новый метчик или метчик с улучшенной поверхностью – Оптимизировать СОЖ Плохое направление метчика из-за недостаточ- – Резать с при нудит подачей ной глубины резьбы – Использовать метчик с улучшенными свойствами направляющей Слишком высокая скорость резания – Согласовать скорость резания – Оптимизировать СОЖ Неправильный выбор СОЖ или недостаточный Обеспечить подходящую СОЖ подвод СОЖ в достаточном количестве Допуск метчика не соответствует данным черте- Использовать метчик жа и или резьбового калибра с соответствующим допуском Резьба осевая подточка 1 Метчики спиральными канавками используются слишком сильным усилием врезания 1 Метчики при врезании только слегка прижать. | |||||
6 Руководство DORMER 2008 Обработка металлов резанием на металлорежущих станках Стр. | |||||
Расчет режимов резания при нарезании резьбы метчиком на металлорежущем станке Формулы для расчета крутящего момента и мощности Скорость и обороты на шпинделе Расчет режимов резания при нарезании резьбы метчиком на металлорежущем станке Формулы для расчета крутящего момента и мощности Скорость и обороты на шпинделе _ p2 D kc Md = 8000 Мощность % n P = 60 M d = крутящий момент Нм p = шаг резьбы мм D = номинальный диаметр резьбы мм kC = удельное усилие резания H/мм2 n = об/мин P = мощность (КВт) 6 Общая информация Резьбонарезание Об/мин Vc 1000 П = п D | |||||
Подборка ссылок иллюстрированных из промышленных каталогов | |||||
361 Образование резьбы производится следующими основными способами Нарезание резьбы метчиками Формирование резьбы Резьбофрезерование Нарезание | 362 Форма метчика должна в первую очередь соответствовать виду стружки (мелкая или длинная стружка) и направлению её отвода (вперёд или назад) | 363 Срезание припуска и формирование профиля резьбы Форма поперечного сечения стружки A задается распределением резов, которое представлено на | 364 Усилия и потребляемая мощность при нарезании резьбы метчиками Расчёт силы резания Fc производится следующим образом z Количество режущих к | 365 Расчетные режимы нарезания резьбы твердосплавными машинными цельными метчиками Garant Hoffmann для обработки закалённых сталей 132080 1328 | 366 Сравнение процессов по нарезанию резьбы и формированию резьбы Стружечные канавки Заборная часть Материал обработан Формирование резьбы Наж |
787 Производственные испытания режущего инструмента Форма протокола для метчиков по металлу Режимы резания Информация об обрабатываемой детали и станке | 262 Нарезание резьбы метчиком на станке Типовые технологические проблемы при нарезке резьбы и пути их решения Слишком свободное резьбовое соединение | 263 Типовые технологические проблемы при нарезании резьбы метчиком и пути их решения Повреждение режущей кромки Рваная и грубая резьба Размер отверстия | |||
65 Общие указания по нарезанию резьбы метчиками Выберите правильную конструкцию резьбового инструмента для данного обрабатываемого материала и типа отверстия | 83 Нарезание внутренней резьбы метчиками в отверстиях заготовок из металлов и сплавов Возможные трудности и способы их устранения Выкрашивание инструмента | 84 Возможные трудности при нарезке резьбы метчиками и способы их устранения Поломка Быстрое изнашивание резьбонарезного инструмента Наростообразование | |||
6 Расчет режимов резания при нарезании резьбы метчиком на металлорежущем станке Формулы для расчета крутящего момента и мощности Скорость и обороты на шпинделе | 192 Мощность и крутящий момент при нарезании резьбы метчиком на станке Расчетные формулы для расчета режимов резания при механической обработке | 448 Инструментальные материалы для изготовления метчиков HM Твёрдый сплав HSS-E-PM Порошковая быстрорежущая сталь с кобальтом Изностойкие покрытия TiCN | 449 Нарезание резьбы метчиком на станке Общие рекомендации по резьбонарезной технологической операции Заготовка детали должно быть надежна закреплена | ||
Пример иллюстрации инструмента из промышленного каталога (из подборки фото инструментов для металлообработки / Metal cutting tools images) | |||||
392 Каталог WALTER 2013 Дополнение к общему Стр. | |||||
Фото спирального метчика с винтовыми стружечными канавками Иллюстрация процесса нарезания внутренней метрической резьбы в глухом отверстии заготовки детали на станке Фото спирального метчика с винтовыми стружечными канавками Иллюстрация процесса нарезания внутренней метрической резьбы в глухом отверстии заготовки детали на станке _ метчиком Walter Prototyp Красочная иллюстрация из дополнительного каталога продукции немецкого производителя за 2013 год на русском языке Общий вид обработки на вертикально-фрезерном станке | |||||
Каталоги металлорежущего инструмента, оснастки и приспособлений для станков / | |||||
Накатывание резьбы на станках с ЧПУ?
Все фотографии предоставлены LMT India Pvt LtdПри работе на большинстве станков с ЧПУ наилучшим вариантом создания высококачественной наружной резьбы за один проход является метод накатывания, исключающий образование стружки.
На протяжении десятилетий накатывание резьбы производилось на многошпиндельных, токарно-винторезных и специализированных резьбонакатных станках. Новым направлением является накатывание резьбы на станках, не специализированных под производство определенных деталей/операций. Он дает определенные преимущества при использовании на станках с ЧПУ, поскольку такой метод исключает дорогостоящие многократные проходы, обязательные при нарезании резьбы резцом. Накатывание резьбы за один проход экономит до 90% времени!
Современные станки с ЧПУ универсальны и отличаются оперативностью переналадки, отвечая требованиям производства «точно в срок». Еще более важным преимуществом станков с ЧПУ является быстрота и эффективность, с которой они обрабатывают детали. Смена инструментов на них происходит быстрее, а операции по наладке можно выполнять во время работы станка.
Так же как использование станка с ЧПУ, нарезание резьбы резцом является универсальным методом. Современный процесс нарезания резьбы в основном происходит с применением инструментов со сменными пластинами и является частью процесса высокоскоростной программируемой обработки. Обрабатываемая деталь, как правило, проходит через стандартные циклы программы и множество разнообразных механизмов станка. Этот способ может быть очень экономичным при изготовлении небольшого количества деталей.
Однако при обработке большого количества деталей нарезание резьбы резцом дает меньше преимуществ. Это обусловлено тем, что для увеличения срока эффективной работы инструмента сменные пластины производятся с ограниченной глубиной резания, и для достижения требуемой глубины резьбы необходимо несколько проходов. Это замедляет процесс производства. Дополнительные проходы также могут потребоваться для снятия заусенцев с резьбы. Несмотря на то, что ЧПУ сокращает общее время обработки за счет повышения эффективности нерабочего хода, эта экономия сводится на нет временем, необходимым на дополнительную обработку. С другой стороны, при накатывании резьбы за один проход сокращается дорогостоящее время работы станка с ЧПУ. Кроме того, использование резьбонакатной головки на станке ЧПУ позволяет обрабатывать детали с одного установа, исключая тем самым необходимость в дополнительной обработке на специальном резьбонакатном станке.
Бесстружечная холодная формовка
Технические преимущества
В дополнение к тому, что метод накатки резьбы позволяет выполнять больший объем работ за меньшее время на одном станке, он также имеет целый ряд технических преимуществ перед методом нарезания. Вместо резания материала в процессе накатки формируется необходимый профиль. В ходе этого процесса обрабатываемый материал испытывает напряжение, превышающее его предел текучести, и подвергается пластической, а значит, постоянной деформации. Усиленный накатный ролик, изготовленный из инструментальной или быстрорежущей стали, смещает материал по контуру резьбы, подвергая его пластической деформации и придавая ему окончательную форму. На материал заготовки действует напряжение, превышающее его предел текучести, вследствие чего он деформируется, принимая зеркально отраженную форму накатного ролика (см. рисунок).
- Увеличение прочности
Линии зерен подвергшегося накатке материала непрерывны в отличие от линий при нарезании: они спрессованы и направлены перпендикулярно осевой линии заготовки, что увеличивает прочность резьбы на 10-30% по сравнению с процессом нарезания. Это важно при воздействии на резьбу растягивающего усилия, направленного вдоль осевой линии заготовки. Такое увеличение прочности дает наибольшие преимущества при обработке цилиндров, штоков поршней, рулевых тяг и т.п.
- Чистота поверхности
Сжатие материала во время операции накатки приводит к деформационному упрочнению поверхности резьбы, особенно на впадинах и боковых сторонах ее профиля, что приводит к повышению ее износостойкости. Сжатие материала накатным роликом дает более точный профиль с более высоким качеством обработки, чем можно достичь при помощи шлифовки. При резании материала получается более грубая поверхность, чем при сжатии, когда поверхность приобретает большую гладкость и прочность, а значит, повышенную стойкость к износу, коррозии и истиранию. Данное качество особенно важно для штоков клапанов и других деталей, подверженных воздействию агрессивной, коррозионно-активной среды. Гладкая поверхность резьбы также необходима для гаек, которые должны обеспечивать свободное движение на большие расстояния в загрязненной атмосфере.
- Повышенная износостойкость
Накатанная резьба также на 70% больше устойчива к усталости металла, чем нарезанная. Благодаря тому, что процесс накатывания проходит без образования стружки, на профиле не образуются шероховатости, следы вибрации и острые точки выхода, наиболее подверженные напряжению. При накатке обеспечивается гладкая, начисто обработанная поверхность резьбы, с минимальными неровностями в местах концентрации напряжений, что предотвращает образование усталостных дефектов. Это особенно важно в месте сбега и на участках неполной или неиспользуемой резьбы. Резьба особенно подвержена усталости на конце, в месте концентрации нагрузки. Детали, постоянно находящиеся под действием нагрузки, выигрывают от метода накатки, поскольку он обеспечивает округлую форму сбега резьбы, гладкость и повышенную прочность.
- Точность профиля
При накатывании качество резьбы более постоянно, чем в случае нарезания резцом. Даже при самой лучшей шлифовке контакт резца с материалом приводит к его износу. Чем длиннее резьба, тем больше отклоняющее напряжение и вибрация, сокращающие срок службы инструмента. Однако накатные ролики также претерпевают изменения в процессе эксплуатации, в частности, в плане размеров. С каждым оборотом действующее на ролик напряжение возрастает. Это напряжение концентрируется в точке наибольшей усталости материала, в результате чего от гребня, который активнее всего задействован в процессе, откалываются небольшие частицы. До этого момента форма профиля сохраняется неизменной. На протяжении срока своей службы (обычно десятки тысяч обработанных деталей) накатные ролики не требуют практически никакой корректировки.
Экономические преимущества
- Экономия материала
Поскольку при накатывании материал скорее смещается, чем удаляется, это позволяет экономить на инструментах по сравнению с нарезанием. Если в процессе нарезания заготовка уменьшается, то при накатывании ее диаметр увеличивается до наружного диаметра резьбы. Поэтому диаметр круглой заготовки при накатке отличается от диаметра при нарезании, где он совпадает с наружным диаметром резьбы, но при этом является ее средним диаметром. При большом количестве обрабатываемых заготовок это означает значительную экономию материала, в особенности, если при достижении среднего диаметра резьба уже готова к использованию. Кроме того, накатывание позволяет избежать многих трудностей, связанных с образованием стружки при работе с такими материалами, как нержавеющая сталь 304, Инконель и титан.
- Чрезвычайно малое время обработки
Скорость накатывания резьбы варьируется от 20 до 90 м/мин и значительно превышает скорость нарезания. При нарезании резьбы гребенкой скорость редко превышает 10 м/мин. Поэтому в процессе накатки чистое время обработки никогда не является решающим фактором.
Пример:
Время нарезания резьбы M16, 19 мм на одной шейке вала из литой стали составляет 4,8 секунды. При этом время накатывания данной резьбы составляет лишь 0,8 секунды с использованием аксиальной (осевой) резьбонакатной головки, и 0,2 секунды – с использованием радиальной головки.
- Длительный срок службы инструментов
Использование для накатывания резьбы роликов и головок LMT FETTE с длительным сроком службы гарантирует максимальное снижение затрат на инструмент. Примеры приведены в таблице:
Резьба | Длина резьбы | Материал | Система | Срок службы одного комплекта роликов |
M5 x 0,8 | 15 мм | AISI 1117 | Осевая | 120 000 заготовок |
Tr.30 x 6 | 600 мм | AISI 1020 | Осевая | 35 000 заготовок |
M16 x 1,5 | 22 мм | AISI 5140 | Осевая | 30 000 заготовок |
M20 x 1,5 | 16 мм | AISI 1213 | Радиальная | 250 000 заготовок |
- Полное использование возможностей станка
Разработанные LMT FETTE резьбонакатные головки представляют собой компактные устройства, которые для правильной работы должны испытывать вращательное движение. Удовлетворить эти требования способен обычный токарный станок. Тем не менее, данные головки можно также использовать на токарно-револьверных станках, токарных автоматах и токарных станках с ЧПУ для накатывания резьбы на любых подходящих для этих станков заготовках при минимальных временных затратах.
Форма резьбы
Метод накатки применим как ко многим стандартным, так и особым типам резьбы. Помимо стандартных профилей 60°, этим методом изготавливается параллельная и коническая треугольная резьба, трапецеидальная резьба ACME, круговая и в некоторых случаях трапецеидальная трубная резьба. Однако необходимо заметить, что если угол профиля резьбы больше 10°, практически любая резьба, имеющая особую форму, может накатываться от 1,4 мм примерно до 230 мм. При этом в зависимости от назначения можно уменьшать диаметр труб, обжимать их концы, выполнять кольцевые профили, ставить фирменные знаки, символы и номера.
Материал заготовки
Накатывание резьбы можно производить практически на любой заготовке, удовлетворяющей определенным физическим параметрам. Это может быть конструкционная сталь, цементируемая сталь, нержавеющая сталь, улучшаемая сталь, алюминий и сплавы никеля, такие как Инконель 718.
Возможность накатывания резьбы определяется тремя основными параметрами:
- Коэффициент удлинения
Поскольку под давлением материал деформируется, коэффициент его удлинения должен быть минимум 5-7%. Материалы, имеющие меньший коэффициент удлинения, такие как чугун, чистая бронза, твердые латунные сплавы и другие упрочненные материалы, слишком хрупки для накатки.
- Твердость и предел прочности
В общем случае твердость не должна превышать Rc 40, а предел прочности материала должен быть не более 1700 Н/мм2. Имеет значение и химический состав. Для обеспечения нормальной обработки материал заготовки не должен содержать более 1% свинцовых добавок. Кроме того, возможность накатывания резьбы на материале зависит от типа профиля и количества вытесняемого материала.
Материал заготовки определяет выбор резьбонакатной головки и роликов, типа обработки поверхности ролика и системы накатывания резьбы. Существует три основные системы: осевая, тангенциальная и радиальная.
Осевая
Осевая система предусматривает процесс обработки от переднего конца детали вдоль осевой линии – см. рисунок 6. Если в других системах накатки длина резьбы ограничена шириной роликов, то осевая не предполагает никаких ограничений. Профиль резьбы на осевых роликах представляет собой ряд кольцевых канавок, выполненных с шагом накатываемой резьбы. Ролики расположены в головке под углом, примерно соответствующим углу подъема резьбы, и совершают поступательное движение, в результате чего заготовка движется самостоятельно.
Если первое кольцо осевого ролика имеет полный профиль, основную работу выполняет именно оно. Поэтому, как в случае с метчиком, ролики оснащаются заборной частью для захвата заготовки и обеспечения длительного срока службы. Наличие большего числа колец на заборной части ролика способствует повышению стойкости инструмента при большей длине профиля.
Для накатывания резьбы ближе к буртику можно уменьшить размеры заборной части, однако это сократит срок службы роликов. Наименьшее расстояние между резьбой и буртиком составляет примерно 1,5 шага резьбы. Если резьба должна находиться еще ближе, лучше воспользоваться тангенциальной или радиальной системой накатки.
Хотя осевая система и не позволяет накатывать резьбу так близко к буртику, как две другие, она обеспечивает уникальную возможность обработки больших диаметров. Поскольку осевые ролики за один цикл могут накатывать только одну резьбу, их устройство проще. Это позволяет обрабатывать больший диапазон диаметров. В настоящее время осевые системы FETTE способны накатывать резьбу диаметром до 230 мм.
Тангенциальная
В тангенциальной системе один ролик расположен сверху, а другой – снизу заготовки. Подача роликов осуществляется сбоку (ось X), их давление увеличивается с каждым оборотом заготовки. При совпадении оси роликов с осью заготовки для завершения процесса обычно требуется от 15 до 30 оборотов, см. рис. 7. Ни заготовка, ни ролики не движутся по оси. Таким образом, длина накатываемой резьбы зависит от ширины роликов.
Все фотографии предоставлены LMT India Pvt LtdВ тангенциальной системе используется ролик с винтовой нарезкой, установленный на шпинделе неподвижной головки. Угол подъема резьбы, нанесенной на ролики, соответствует углу подъема накатываемой резьбы, другими словами, форма роликов представляет собой зеркальное отражение резьбы. Таким образом, ролик с левой резьбой используется для накатывания левой резьбы, а правый – для правой. При этом на каждую головку можно устанавливать оба типа ролика.
На обоих концах ролики имеют скошенную кромку, что способствует продлению срока их службы. Длина скоса соответствует сбегу резьбы, или участку неиспользуемой или неполной резьбы до буртика, что составляет примерно от ½ до 1 шага резьбы. Поэтому резьба может быть максимально приближена к буртику.
Тангенциальную систему можно устанавливать на поперечном суппорте токарно-винторезных станов, токарных автоматов и токарных станков с ЧПУ.
Время обработки
Все системы обеспечивают накатывание резьбы за ОДИН проход, что исключает затраты на дополнительные проходы, неизбежные при нарезании резьбы резцом, и сокращает время обработки на 90%.
Поскольку только осевая система предусматривает обработку одной резьбы за один цикл, время обработки в этом случае определяется длиной резьбы. В качестве примера рассчитаем время накатывания резьбы М20 х 1,5 длиной 40 мм. При использовании осевой системы время накатывания будет следующим:
Экономия времени обработки, которую дает метод накатки по сравнению с нарезанием резьбы, полностью оправдывает вложения в резьбонакатную систему.
Затраты на инструмент, время обработки, количество деталей за смену
Поскольку цикл накатывания резьбы занимает очень мало времени, это положительно сказывается на общем времени обработки и коэффициенте использования станка. Более того, использование метода накатки позволяет снизить затраты на инструмент и сократить непроизводительное время. Срок службы роликов в большинстве случаев достаточно велик, что гарантирует меньшее время простоя. Применение метода накатки также значительно увеличивает количество обрабатываемых за смену деталей по сравнению с методом нарезания резьбы.
Характеристики станка
Так как накатывание резьбы происходит за один проход, этот процесс требует большей мощности, чем при нарезании. Однако эти требования к мощности, как правило, вполне удовлетворяются современными станками.
При накатке резьбы происходит выделение невероятно большого количества тепла за короткое время. Поскольку в процессе обработки давлением поверхность резьбы постоянно меняется, это тепло свободно рассеивается в воздухе вокруг вращающейся заготовки или резьбонакатной головки – отсюда термин «холодная формовка». Использование водоэмульсионной СОЖ также помогает рассеивать тепло, продлевая срок службы ролика.
Резьбонакатные головки и ролики FETTE можно использовать практически на любых станках, включая токарные автоматы с ЧПУ, обычные токарно-винторезные станки, роторные автоматические линии и обрабатывающие центры.
При правильном расположении головки и заготовки процесс накатывания не имеет практически никаких ограничений. Однако из-за того что современные станки с ЧПУ имеют небольшие размеры, при выборе следует обращать внимание на зазор резьбонакатной головки.
Первоначальная стоимость
Для потенциальных покупателей первоначальная стоимость резьбонакатной системы может стать серьезным препятствием, так как она значительно превышает стоимость системы нарезания резьбы.
Однако при более высокой первоначальной стоимости описанных резьбонакатных систем они имеют более низкую долгосрочную стоимость благодаря долговечности инструмента и существенному сокращению времени обработки. И хотя экономия при покупке может быть более ощутима, покупателям следует подумать о технических и экономических преимуществах, которые накатывание резьбы предоставляет в долгосрочной перспективе.
Источник материала: перевод статьи
Thread Rolling on CNC?
Mfgtechupdate.com
LMT India Pvt Ltd
Нет связанных записей.
Нарезание резьбы на станке с ЧПУ
Нарезание резьбы на станке с ЧПУ
Наиболее распространенные инструменты для получения внутренней резьбы на станках с ЧПУ – это метчики и фрезы. Сложность получения резьбы с помощью фрезы связана со сложностью программирования интерполирующего движения, поэтому чем проще система ЧПУ, тем чаще используются метчики.
Принцип получения резьбы фрезерованием
При фрезеровании профиль резьбы формируется с помощью движения специальной фрезы по винтовой линии. Подача в этом случае должна совпадать с шагом метчика.
Технология получения резьбы фрезерованием
Сверлят отверстие. Резьбовая фреза опускается в отверстие на нужную глубину резьбы и врезается по дуге 90° на глубину. Фреза при врезании поднимается на ¼ шага резьбы. Ось фрезы М делает оборот на диаметре m, при этом фреза одновременно поднимается на шаг резьбы Р и выходит из профиля по дуге 90°. В случае, если глубина резьбы в полученном ранее отверстии больше длины режущей части фрезы, то обработку повторяют несколько раз.
Есть несколько типов резьбовых фрез используемых для нарезания резьбы в станках с ЧПУ
– твердосплавные фрезы;
– резьбовые фрезы со сменными пластинами;
– комбинированные резьбовые фрезы – это фрезы позволяющие сначала сверлить отверстие под резьбу, а потом фрезеровать резьбу.
Есть 2 основных технологии получения резьбы фрезами
Получение резьбы одним инструментом
Получение резьбы несколькими режущими инструментами
Виды метчиков для нарезания резьбы
Метчики с прямыми стружечными канавками
Метчик с прямыми канавками это самый широко используемый вид метчика. Этот метчик применяется для материалов, которые дают короткую стружку, например для стали или чугуна.
Метчики с шахматным зубом
Использование метчика с шахматным зубом уменьшает трение и сопротивление процессу резания, что очень важно при обработке труднообрабатываемых материалах (алюминии и бронзе). Шахматное расположение зубьев у метчика облегчает доступ СОЖ в зону резания.
Метчики со спиральной подточкой
Метчик со спиральной подточкой имеет прямые неглубокие стружечные канавки. Спиральная подточка предназначена для выталкивания стружки вперед. Сравнительно неглубокие стружечные канавки гарантируют максимальную прочность метчика на скручивание. Они также облегчают подвод СОЖ в зону резания. Этот тип метчиков рекомендуется для обработки сквозных отверстий.
Метчики со стружечными канавками только на заборной части
Режущая часть данного метчика имеет аналогичную спиральную подточку, предназначенную для выталкивания стружки вперед. Этот метчик имеет чрезвычайно жесткую конструкцию. Рекомендуется для обработки отверстий глубиной до 1.5 х 0.
Метчики со спиральными зубьями
Метчики со спиральными зубьями предназначены в основном для нарезания резьбы в глухих отверстиях. Спиральная стружечная канавка выталкивает стружку назад, что предотвращает пакетирование стружки на дне отверстия или в стружечных канавках. Поэтому спиральная канавка у метчика снижает риск поломки или повреждения метчика.
Бесстружечные метчики (раскатники)
Бесстружечные метчики отличаются от обычных тем, что образуют профиль резьбы за счет пластической деформации , а не за счет снятия стружки. Рекомендуются для материалов с высокой пластичностью. Такие материалы имеют предел прочности не более 1200 Н/ммг, а относительное удлинение не менее 10%.
Бесстружечные метчики можно использовать в обычных условиях, но лучшие результаты они показывают при обработке вертикальных глухих отверстий. Выпускаются также с внутренним подводом СОЖ.
Резьбонарезные фрезы имеют огромное преимущество при обработке глухих отверстий. Метчику всегда нужен зазор между дном отверстия и торцом метчика из-за заборного конуса метчика. Поэтому метчик не нарезает резьбу в глухом отверстии. Использование фрезы решет эту проблему, так как расстояние от торца фрезы до первой режущей резьбовой кромки очень мало. Также большим преимуществом фрез для резьбы является возможность изменять параметры резьбы, что не возможно при использовании метчика. Эта возможность существенно снижает затраты на нарезание резьбы.
Запомните, что подача равна при работе метчиком оборотам шпинделя умноженным на шаг резьбы.
Резьба может срезается при остановке шпинделя перед реверсом – ось Z уже остановилась, а вот шпиндель по инерции делает ещё какую-то часть оборота. При нарезании резьбы метчиком в стали при этом обрывает метчик, а Д16Т мягче и поэтому резьбу слизывает. Поэтому для нарезания резьбы на станке с ЧПУ нужно использовать специальный патрон – плавающий или его еще называют компенсирующий. Этот патрон имеет подпружиненную часть с цангой, которая может перемещается относительно неподвижной на несколько миллиметров вдоль оси патрона в обоих направлениях.
Привожу общие указания по нарезанию резьбы метчиками
Результат любой операции по нарезанию резьбы зависит от ряда факторов, каждый из которых, в конечном счете, влияет на качество готовой детали.
1. Выберите правильную конструкцию метчика для данного обрабатываемого материала и типа отверстия.
2. Убедитесь, что деталь надежно закреплена – перемещения в процессе обработки могут привести к поломке метчика или плохому качеству резьбы.
3. Выберите правильный размер сверла из соответствующих таблиц. Диаметр необходимого сверла также указан на страницах каталога с метчиками. Помните, что для метчиков-раскатников необходимы сверла других диаметров. Всегда контролируйте наклеп обрабатываемого материала.
4. Выберите правильное значение скорости резания, как показано в каталоге режущего метчиков.
5. Используйте СОЖ, соответствующую выполняемой операции.
6. При нарезании резьбы на станках с ЧПУ проверьте значение подачи, указанное в программе. При использовании резьбонарезного патрона значение подачи на оборот должно составлять от 95 до 97 % от шага для самозатягивания метчика.
7. По возможности используйте качественные патроны с компенсацией для ограничения крутящего момента, которые гарантируют осевое перемещение метчика и устанавливают его прямо в отверстии. Также это предохранит метчик от поломки при случайном столкновении одном отверстия.
8. Убедитесь в том, что метчик плавно входит в отверстие, прерывистая подача может привести к колоколообразной форме начальных витков.
Материал для статьи предоставлен нашим партнером: Компания “ИнженерПоможет”
Нарезание резьбы на токарном чпу
Плашка это изделие, которое изготавливается из инструментальной стали, основное назначение которой является нарезание резьбы. Обычно внешний диаметр плашек имеет цилиндрическую форму для установки в отверстие плашкодержателя или оправки, но бывают также и шестигранные поверхности. Поэтому плашку можно сравнить с той же закалённой гайкой, у которой имеются дополнительные отверстия, смещённые от центра для выхода стружки. В местах пересечения этих отверстий с резьбовым отверстием образуются режущие кромки.
До того, как начать выполнение работ связанных с нарезанием резьбы, плашку необходимо установить в специальный держатель и закрепить её с внешних сторон винтами. Деталь, на поверхности которой планируется нарезание резьбы, обычно закрепляется в токарном патроне. На её торце делается фаска не меньше профиля резьбы, для облегчения захода плашки в процессе резания, а обрабатываемый диаметр занижается на одну или две десятые миллиметра от номинального значения.
С помощью пиноли задней бабки осуществляется прижим плашкодержателя, это позволяет задавать правильное направление для самой плашки, которая устанавливается в специальное для нарезания резьбы положение. После этого можно включать вращение шпинделя, причём желательно это делать на минимальных оборотах.
Чтобы деталь соответствовала надлежащему качеству, необходимо отслеживать положение плашки. Во время технологического процесса она должна постоянно находиться перпендикулярно оси цилиндрического изделия, а давление, оказываемое на неё пинолью задней бабки, должно быть равномерным.
Если имеется оснастка и соответствующее оборудование, то плашку можно устанавливать в специальный держатель. Его закрепляют в гнездо револьверной головки или в пиноли задней бабки. При этом плашка будет изначально находиться на оси задней бабки, которая соосна со шпинделем станка.
Предварительно обработанная поверхность перед нарезанием резьбы должна иметь диаметр меньше, чем номинальный диаметр:
- Диаметры под резьбу от Ø 6 до 10 мм занижаются на 0,1 – 0,2мм ;
- Диаметры заготовки от Ø 11 до 18 мм на 0,12 – 0,24 мм ;
- Для диаметров от Ø 20 до 30 мм на 0,14 – 0,28 мм .
Рекомендуемые скорости резания v при нарезании резьбы составляют: для стали от З до 5 м/мин ; для чугуна от 2 до 3 м/мин ; для латуни от 10 до 15 м/мин .
Для того чтобы процесс нарезания резьбы и конечный результат был на высоком качественном уровне необходимо использовать смазочно-охлаждающие жидкости обеспечивающие хорошую чистоту поверхностей обрабатываемым изделиям.
Нарезание резьбы метчиками
Метчик представляет собой изделие, изготовленное из закалённой инструментальной стали, назначением которого является нарезание внутренней резьбы. По форме метчик схож с обычным винтом, но в отличие от последнего он имеет продольные канавки, для выхода стружки, они же, образуют в свою очередь режущие кромки в местах пересечения с резьбовой поверхностью.
В состав этого инструмента входит рабочая часть и хвостовик. Коническая резьбовая часть метчика предназначена для постепенного срезания слоя материала при ввинчивании инструмента в просверленное заранее отверстие, а цилиндрическая часть для окончательной калибровки. Хвостовик, окончание которого имеет, как правило, квадратную форму, служит для закрепления его в специальных удерживающих приспособлениях. Таковыми могут быть, как воротки, так и специальные оправки.
При нарезании резьбы, на универсальных токарных станках выполняется такой технологический процесс, при котором происходит постепенное срезание слоя материала, чем обеспечивается надлежащее качество. Для этого применяют два и даже три метчика входящие в комплект для первоначального и окончательного нарезания резьбы. Обычно, их обозначают поперечными рисками. Для первого одна риска, для второго две, а для третьего соответственно три.
На токарном станке нередко применяют и машинные метчики, что позволяет нарезать резьбу за один рабочий ход. В отличие от обычных резьбонарезных инструментов машинные метчики обладают увеличенным режущим коническим участком. Это способствует постепенному срезанию слоя металла. Чаще всего их применяют для того, чтобы обеспечить нарезку резьбы в сквозных отверстиях – гайках и похожих элементах.
Известно, что перед нарезанием внутренней резьбы необходимо просверлить отверстие, причём если оно имеет небольшой диаметр, то для его обработки требуется, только сверло, а при больших диаметрах они подвергаются расточке после сверления. Сами отверстия делаются чуть больше номинального значения на 0,1 – 0,3 миллиметра в зависимости от диаметра резьбы и используемого материала, чтобы избежать смятия и даже срыва ниток резьбы.
Диаметры отверстий под метрическую резьбу, нарезаемых метчиками, выбирают по специальным таблицам.
Приёмы нарезания резьбы метчиками
До начала процесса метчик должен быть установлен в исходное положение. Это обеспечивается, если заборную часть инструмента вводят в отверстие, а хвостовую при этом поддерживают с помощью центра задней бабки. Чтобы не допустить проворачивания метчика на его квадрат закрепляется вороток, который своей ручкой упирается на суппорт.
Чтобы нарезать первые нитки резьбы необходимо равномерно и осторожно двигать шпиндель задней бабки с помощью маховика. Когда метчик начнет врезаться в отверстие заготовки, дальше он будет продолжать движение по нарезаемым виткам. Однако и после этого перемещение пиноли задней бабки надо продолжать, слегка поджимая инструмент. Это необходимо для того, чтобы хвостовая часть метчика, поддерживаемая центром, оставалась на оси вращения, также как и режущая часть, входящая в отверстие. При этом, во время всего процесса, важно обеспечить обильное охлаждение.
Для нарезания резьбы рекомендуемая скорость резания должна составлять v = 5 – 12 м/мин для нарезания резьбы метчиками в стальных заготовках; v = 6 – 22 м/мин – в чугунных, бронзовых и алюминиевых заготовках.
Самой ответственной операцией при отделке труб и муфт является нарезание резьбы. Оно производится методом многопроходного нарезания на станках с ЧПУ либо на обычных токарно-винторезных станках. При работе на универсальном оборудовании к квалификации и опыту токаря предъявляются особенно высокие требования, так как многопроходное нарезание резьбы на довольно высоких скоростях резания требует от него очень большого внимания и хорошей реакции. Особенно это касается нарезания резьбы в муфтах. Работа на станках с ЧПУ не требует от токаря столь высоких профессиональных навыков, однако в этом случае нужно иметь специалиста или специалистов, умеющих составлять программы для станков с ЧПУ и обслуживать электронные системы станков.
Для многопроходного нарезания резьбы могут быть использованы призматические многозубые гребенки или неперетачиваемые многозубые твердосплавные пластины с износостойким покрытием и без него. Для нарезания резьбы на трубах наиболее часто пользуются пластинами Т1 22НП 2. 54 НКТ, Т1 22НП 3.175 НКТ – для треугольных и Т1 22НП 5.08 ОГМ – для трапецеидальных резьб. При работе гребенками – ПГ 20НП 2.54 НКТ для треугольной и . для трапецеидальной резьбы.
При обработке муфт соответственно применяют пластины с треугольным профилем: Т1 22ВП 3.175 НКТ и с трапецеидальным – Т1 22ВП 5.08 ОТМ. В качестве гребенок используют ПГ 12ВП 2.54 НКТ, ПГ 12ВП 3.175 НКТ – для треугольной резьбы и . – для трапецеидальной).
Специфика обработки муфт, заключающаяся в большом вылете инструмента и, следовательно, повышении опасности вибраций, часто заставляет отказаться от использования многозубого инструмента. Особенно это касается обработки муфт малого диаметра. В этих случаях используется однозубый инструмент, например, резьбовая пластина Т4 22ВП 2.54 НКТ. В некоторых случаях применению многозубого инструмента препятствуют конструктивные особенности муфт, не дающие пространства для свободного выхода предварительных режущих зубьев. Это относится, например, к соединениям ОТТГ. В этом случае приходится уменьшать количество режущих зубьев.
Общий вид призматических гребенок и резьбовых пластин приведен на рис. 17, 18.
Рис. 17 Твердосплавные призматические резьбовые гребенки | Рис. 18 Твердосплавные резьбовые пластины. |
Применение призматических гребенок, инструмента исторически более старого, целесообразно только при организации хорошего заточного хозяйства, оснащенного соответствующим оборудованием (желательно для электрохимической алмазной заточки), обслуживаемого высококвалифицированным персоналом. Если такой инструмент затачивать на обычном точиле, то существенно ухудшаются физико-механические свойства сплава, что ведет к снижению стойкости инструмента после переточки. Кроме того, отклонения переднего угла при заточке ведет к искажению профиля нарезаемой резьбы. Следует также отметить, что твердый сплав, используемый для изготовления этого инструмента, обеспечивает более низкие скорости резания, чем современные сплавы с износостойкими покрытиями, из которых обычно делают неперетачиваемые пластины.
Современная технология инструментального производства позволяет производить твердосплавный многозубый инструмент почти по тем же ценам, что и однозубый. В то же время, такой инструмент имеет два серьезных преимущества. Его стойкость выше, чем у однозубого, так как калибрующий зуб, размерный износ которого определяет выход инструмента из строя, разгружен за счет предварительно работающих зубьев. Кроме того, наличие нескольких одновременно работающих зубьев позволяет сократить число проходов, что существенно повышает производительность резьбообработки.
Типаж твердосплавного резьбового инструмента очень широк. Он предусматривает учет самых различных пожеланий заказчика с учетом имеющегося у него оборудования.
Ассортимент серийно выпускаемых резьбовых пластин и гребенок приведен в Каталоге.
Некоторые рекомендации по технологии многопроходного резьбонарезания.
Рис.19 Многопроходное нарезание наружной резьбы многозубой резьбовой пластиной.
Нарезание наружной и внутренней резьбы многозубым инструментом рекомендуется проводить в три прохода – для треугольных резьб с шагами 2. 54 и 3.175 мм и в 4-6 проходов – для трапецеидальных резьб с шагом 5.08 мм. Количество проходов во многом зависит от состояния станка. Ясно, что на разболтанном старом станке при уменьшении числа проходов поломки инструмента могут создать серьезные проблемы. Поэтому число проходов должно выбираться, исходя из соотношения производительности обработки и расхода дорогостоящего инструмента. В случае необходимости использования однозубого резьбового инструмента, число проходов соответственно увеличивается.
Рис. 20 Многопроходное нарезание внутренней резьбы однозубой резьбовой пластиной.
Особо следует предостеречь от необоснованного увеличения числа проходов. Несмотря на кажущееся облегчение условий работы инструмента и станка, в ряде случаев мы можем получить.
Это связано с тем, что при неоправданно завышенном числе проходов мы уменьшаем припуск на проход (толщину срезаемой в каждом конкретном проходе стружки). При достижении этого припуска величин, измеряемых в сотых долях миллиметра, мы делаем толщина среза сопоставимой с радиусом округления режущей кромки инструмента.
При этом мы получаем резание с большими отрицательными значениями переднего угла (см. рис. 21). Практически происходит смятие, пластическая деформация. Поперечные силы резания резко возрастают. Это ведет к появлению вибраций, быстрому выходу инструмента из строя, ухудшению качества обрабатываемой поверхности.
Рис. 21 Геометрия резания при толщине среза, сопоставимым с величиной радиуса округления.
Неоправданно малый припуск на проход может быть связан не только с большим числом проходов, но и с неправильным распределением припуска между проходами, например, оставлению слишком малого припуска на последний проход. Лучше, чтобы минимальная толщина среза не превышала 0.04-0.05 мм.
Учитывая, что в многозубом инструменте припуск между зубьями определяется самой конструкцией, этому вопросу при его проектировании всегда уделяется большое внимание.
Серьезным вопросом при резьбонарезании является правильная установка инструмента. На станках с ЧПУ инструмент, как правило, настраивается вне станка на специальных оптических приборах. Данные по настройке вносятся потом в специальные корректора системы ЧПУ. Правильность установки инструмента в резцедержателе обеспечивается его конструкцией и конструкцией инструментальной оснастки.
При установке инструмента на универсальных токарно-винторезных станках дело обстоит сложнее. Следует отметить, что неправильная установка может привести к получению бракованной резьбы даже при использовании вполне годного инструмента. Необходимо обеспечение двух условий: правильного расположения режущей кромки относительно оси изделия, правильной ориентации инструмента относительно вертикальной оси. Первое требование является достаточно привычным, правда, для резьбообработки оно приобретает особое значение из-за дополнительных искажений профиля при неправильной установке инструмента. К выполнению второго условия, к сожалению, иногда относятся недостаточно серьезно, хотя оно может самым непосредственным образом сказаться на качестве резьбы. Допуск на половину угла профиля треугольной резьбы составляет 1° 15′ ± 1°, а на углы уклона профиля трапецеидальных резьб – 1° 30′ до ± 45′ в зависимости от ГОСТа. Нужно учитывать, что около трети этого допуска может “съесть” допуск на изготовление профиля инструмента, свою лепту в искажения вносит и сам станок, точнее, погрешности изготовления и перемещения его узлов. Поэтому к вопросу установки резьбового инструмента нужно отнестись достаточно серьезно.
Рис. 22 Установка резьбового инструмента под угол уклона конуса на универсальном станке.
Если у Вас нет специальных приспособлений для выверки правильности установки инструмента, можно использовать, например, подрезанный торец трубы для проверки параллельности ему державки инструмента. Однако ни в коем случае нельзя настраивать инструмент путем установки параллельности верхушек его зубьев проточенному конусу трубы. Угол наклона линии, проходящей через вершины зубьев гребенки или пластины, никогда не равняется углу уклона конуса! Настраивая инструмент подобным образом, Вы гарантированно получаете искаженные углы профиля. (См. рис.22).
Хотя режущий инструмент изготовлен из достаточно износостойкого материала, он все равно подвержен износу. Следует помнить, что в случае с резьбовым инструментом критерием его выхода из строя является не просто физический износ, когда инструмент ломается или об износе свидетельствуют специфические звуки, сопровождающие работу, а размерный износ. То есть о выходе инструмента из строя свидетельствует несоответствие нарезанной резьбы предъявляемым требованиям. Таким образом, для получения качественной резьбы необходимо менять резьбовой инструмент, не дожидаясь его физического выхода из строя (поломки или катастрофического износа). В то же время, при резьбонарезании могут возникнуть проблемы, связанные с ускоренным износом инструмента, не связанным с потерей размеров.
Следует обратить особое внимание на необходимость использования при резьбонарезании смазочно-охлаждающей жидкости (СОЖ). При этом особенно важно следить за тем, что струя охлаждающей жидкости попадала в зону резания. Грамотное применение СОЖ может существенно повысить стойкость режущего инструмента.
В целом, опыт эксплуатации твердосплавного резьбового инструмента показывает, что его стойкость в случае обработки резьб насосно-компрессорных труб и муфт по ГОСТ 631-75 с треугольной резьба с шагом 2. 54 мм составляет в среднем от 60 до 80 обработанных концов в случае применения многозубых резьбовых пластин и 30-50 концов – для однозубого инструмента. При этом подразумевается, что для нарезания резьбы используется смазочно-охлаждающая жидкость, состояние оборудования соответствует стандартным требованиям по жесткости и точности, обрабатывается сталь группы прочности Д, скорость резания составляет 80-120 м/мин, число проходов 3-4 для многозубого инструмента и 9-12 – для однозубого. Изменение этих параметров, естественно, ведет к изменению стойкости.
При обработке трапецеидальных резьб на трубах и муфтах с более высокими физико-механическими свойствами значения стойкости отличаются от вышеприведенных в меньшую сторону.
Для повышения стойкости инструмента в конкретных условиях эксплуатации необходимо проведение дополнительной работы по подбору конструктивных параметров, марок покрытия, и режимов резания. Кроме того, необходимо обратить внимание на станочный парк, используемый при резьбонарезании, так как его состояние оказывает на стойкость инструмента самое серьезное влияние.
Особенности инструмента для обработки замковых резьб.
Нарезание замковых резьб на ниппелях и муфтах замков бурильных труб, в принципе, производится аналогично нарезанию резьбы на трубах и муфтах. В то же время, следует отметить, что инструмент для нарезания замковых резьб, как правило, однозубый. Это связано с двумя причинами. Во-первых, из-за больших размеров профиля этих резьб нарезание их многозубым инструментом будет сопровождаться слишком большими усилиями резания, что может сопровождаться повышенными вибрациями. Это чревато ухудшением качества резьбы, поломками инструмента. Потребуется использование более мощного и дорогостоящего оборудования. Во-вторых, по тем же причинам для получения многозубого инструмента понадобится использование твердосплавных пластин очень большого размера, что вызовет неоправданное увеличение их стоимости.
Широкая гамма резьбовых пластин для нарезания замковых резьб также приведена в Каталоге.
Главная Статьи G76 – цикл автоматического нарезания резьбы [9]
G76 – цикл автоматического нарезания резьбы [9]Рубрика: “Циклы FANUC понятным языком”
Цикл G76 является стандартным циклом, применяемым на токарных станках с ЧПУ Fanuc. Резьбовое соединение – это вид разъёмного соединения, который очень часто применяется в машиностроении. Около 70% деталей, изготовленных на токарных станках, будут содержать элементы резьбы. Соответственно, операторы ЧПУ работающие со стойкой Fanuc, должны уметь правильно запрограммировать цикл резьбы G76.
Раньше, когда станков с ЧПУ практически не было, нарезать резьбу можно было на токарно-винторезном станке. Во-первых, этот процесс занимал много времени. Во-вторых, нельзя было нарезать резьбу произвольного шага, так как шаг резьбы задавался с помощью коробки подач. В настоящее время цикл ЧПУ G76, применяемый для нарезки резьбы на токарных станках с ЧПУ, существенно облегчил эту задачу.
Предлагаем Вам разобрать на примере, как правильно запрограммировать цикл G76. Fanuc поддерживает огромное количество циклов, в данной статье мы разберем только один из них. Описание всех остальных токарных циклов Вы сможете найти в статье стандартные токарные циклы Fanuc.
Давайте посмотрим, как запрограммировать резьбу M16х2. По стандартам ЕСКД данная запись гласит, что нам нужна метрическая резьба с внешним диаметром 16 мм и шагом 2 мм.
Для начала нам нужно выбрать подходящий резьбовой резец. Основным параметром резьбовой пластины будет её угол при вершине. В нашем случае угол пластины должен быть 60° (т.к. резьба метрическая). Вы должны убедиться, что оправка резца по своим габаритам позволяет выполнить данную операцию. Это очень важно, так как при запуске цикла в автоматическом режиме во время реза не будет работать кнопка «CYCLE STOP». Если вы нажмёте кнопку «CYCLE STOP», то станок остановится только после возвращения резца в стартовую точку цикла. Соответственно, остановить станок получится только кнопкой «emergency stop» или «RESET».
Затем нам необходимо привязать нулевую точку резца. Мы можем привязывать ноль к кончику резца или к боковой поверхности. Если Вы планируете нарезать резьбу на прутке, то Вам подойдёт первый вариант. Однако, если резьба будет заканчиваться уступом (например, шляпкой болта), то предпочтительнее второй вариант.
Теперь мы можем перейти непосредственно к программированию. Цикл нарезания резьбы G76 программируется с помощью 2-х строк. А также, перед включением цикла необходимо переместить инструмент в стартовую точку цикла. Стартовую точку цикла следует указывать на безопасном расстоянии от заготовки, чтобы стружка могла спокойно выводиться из зоны резания.
G76 – описание цикла (первая строка)Теперь разберёмся с первой строкой цикла. Первый параметр в ней комплексный и определяет сразу 3 параметра: количество чистовых проходов, величину сбега резьбы и способ съёма материала. Задаётся буквой Р и далее следует три двузначных числа, которые должны быть написаны слитно.
- Количество чистовых проходов как правило составляет от «01» до «03» и подбирается опытным путем.
При этом следует помнить, что припуск на чистовой проход R разделится на такое количество чистовых проходов, которое мы укажем.
- R – размер припуска на чистовые проходы;
- r – величина одного чистового прохода;
- N – количество чистовых проходов.
- Величину сбега резьбы необходимо указывать для более плавного выхода резца из материала. Если на детали предусмотрена выточка под выход резьбы, то значение этого параметра принимается равным «00».
Параметр может принимать любые целые значения в интервале от «00» до «99». Длинна самого сбега рассчитывается по вышеуказанной формуле.
- Способ съёма материала бывает с прямым врезанием и боковым врезанием. Прямое врезание лучше применять на резьбовых резцах, обладающих низкой боковой жёсткостью.
Оно обеспечивает распределённую нагрузку на резец.
Но если требуется нарезать резьбу большой глубины, то правильнее применять боковое врезание. Благодаря этому снижается площадь контакта кромки резца с заготовкой. Если на поверхности резьбы образуется дробление, то применение бокового врезания может помочь в этой ситуации. Данный параметр может принимать значения от «00» до «99», в зависимости от угла нарезаемой резьбы. Для метрической резьбы не более «60»
Ещё два параметра, прописываемых в первой строке цикла, отмечены на следующем рисунке:
- Q – величина съёма материала при проходах, которые следуют за первым проходом. Задаётся в микрометрах.
- R – значение припуска на чистовые проходы. Задаётся в миллиметрах.
Во второй строке цикла параметров больше чем в первой. Обратите внимание, что программисты компании Fanuc разработали цикл нарезания резьбы G76 таким образом, что в двух строках используются параметры, имеющие одинаковые буквенные обозначения. Так что будьте очень внимательны!
Графическое описание токарного цикла G76:
- P – это высота профиля резьбы. Этот параметр рассчитывается по формуле:
- F – шаг резьбы;
- α – коэффициент, зависящий от угла резьбы. Для метрической резьбы α = 0,542.
Полученное значение умножаем на 1000, поскольку параметр Р задаётся в микрометрах и для нашего примера получаем P = 1083.
- X – это внутренний диаметр резьбы. Его можно рассчитать по формуле:
- D – это внешний диаметр резьбы.
В нашем примере он равен 16 мм.
- Z – это длина резьбы. Не забывайте, что этот параметр указывается в абсолютной системе координат, то есть со знаком «минус». В нашем примере Z = -30.
- Q – это величина съёма при первом проходе. Из-за того, что при первом проходе нагрузка на резец минимальная, то первый проход можно делать чуть большим, чем последующие. Выберем значение Q равным 0,5 миллиметров. Так как этот параметр задаётся в микрометрах, то Q = 500.
- F – это шаг резьбы. По факту этот параметр обозначает подачу, но так как на токарном станке мы задаём подачу в мм/оборот, то подача будет равна шагу резьбы. Для нашего примера F =2.
В конечном итоге цикл G76 (цикл нарезки резьбы) для нашего примера будет выглядеть следующим образом:
На этом описание токарного цикла G76 подошло к концу. В следующей статье мы рассмотрим нюансы нарезания внутренней, левой, многозаходной и конической резьбы.
Нарезание внешней и внутренней резьбы в СПБ на современном станке с ЧПУ
Резьбовое соединение широко применяется в качестве крепежа в различных механизмов и устройств.
Нарезание резьбы – это специализированная методика по снятию металлической стружки на стержне или в отверстии специализированным инструментом на токарном станке.
По методике, нарезание разделается на два типа:
- наружное;
- внутренние;
Нарезание наружной резьбы плашкой в Санкт-Петербурге
Если вам требуется нарезание наружных резьб для болтов, трубных соединений или шпильки, то вам потребуется, простой, но эффективный инструмент- плашка.
У нас вы сможете заказать услугу по нарезанию наружной резьбы резцом по доступной стоимости. Для обработки металла у нас имеются все необходимые инструменты и станковое оборудование. Большой опыт работы и мастерство наших специалистов обеспечит вам за короткое время качественное нарезание металлических изделий.
Нарезание внутренней резьбы метчиком на токарном станке СПБ
Процесс нарезание внутренней резьбы – это процесс который требует, куда более сложные инструменты и оборудование. Чаще всего для обработки внутренней поверхности металла применяется такой инструмент как метчик.
Компания «ПФ Ресурс» готова выполнить работы по формированию внутренней резьбы метчиком любой сложности и весьма сжатые для этого сроки. Точность обработки деталей обеспечивается благодаря опыту сотрудников и современным оборудованием.
Нарезка резьбы цена работы от «ПФ Ресурс»
Стоимость на услуги по нарезке резьбы формируется в зависимости от:
- вид обработки. Наружная или внутренняя;
- параметры. Размер, диаметр и вид материала;
- объем заказа. Серийный или штучный;
Для уточнее стоимости, свяжитесь с нашим менеджером.
+7 812 980-24-86
pf-resurs@mail. ru
G76 Цикл нарезания резьбы для токарных станков с ЧПУ (Fanuc)
Пасс
Количество проходов, которое необходимо обрезать для нарезания резьбы, очень важно. Выполните слишком мало проходов, и качество поверхности может быть плохим, и вы можете даже сломать резьбонарезной инструмент, заставив его работать слишком интенсивно. Сделайте слишком много проходов, и вы потеряете много времени.
Вы не можете изменить большую часть информации, относящейся к характеристикам резьбы, поэтому ваши основные инструменты для управления количеством проходов включают:
– Начальное положение: поверните все вниз, как я описал выше, чтобы свести к минимуму работу, которую должен выполнять резьбонарезной инструмент.
– Глубина первого прохода: выберите самый большой проход, который вы можете. G-Wizard Calculator даст вам здесь хорошую рекомендацию.
– Минимальная глубина прохода: Старайтесь не использовать этот параметр слишком часто и установите его равным допустимому финишу.
– Припуск на чистовую обработку: меньший припуск на чистовую обработку может означать, что большие проходы черновой обработки удаляют большую часть материала. Просто помните, слишком маленький припуск заставит резак тереться.
– Весенние проходы: вам не нужно больше двух проходов, и одного может хватить.Поэкспериментируйте с вашей конкретной ситуацией, чтобы увидеть, сможете ли вы обойтись одним весенним проходом или даже без него.
Ваша следующая задача будет заключаться в том, чтобы определить, сколько проходов фактически сделает цикл. Это непросто, поскольку G76 будет динамически изменять глубину каждого прохода после первого, чтобы уравнять количество удаленного материала. Чтобы точно определить, сколько проходов будет сделано, вам придется проделать довольно много вычислений.
Но там, если у вас есть GCode Simulator, он может помочь.Взгляните на этот снимок экрана G-Wizard Editor:
G-Wizard Editor сообщит вам в подсказке под графиком, сколько проходов займет цикл G76…
G-Wizard Editor сообщит вам в подсказке под графиком, сколько проходов займет цикл G76. Вы можете использовать его, чтобы настроить цикл G76, чтобы в нем не было чрезмерного количества проходов. Обратите внимание на сообщение ПРЕДУПРЕЖДЕНИЕ, в котором говорится, что припуск на чистовую обработку не будет использоваться из-за того, что минимальная глубина реза больше.Это также полезно при настройке всего этого.
У многих токарных станков возникают проблемы с синхронизацией шпинделя при слишком быстрой подаче. Если проходы потоковой передачи не синхронизируются, попробуйте замедлить работу, пока не станет лучше. Как правило, это означает снижение числа оборотов в минуту, которое определяет, насколько быстро вы будете подавать, в зависимости от шага резьбы.
Кодовые диалекты для цикла нарезания резьбы G76 Надеюсь, вы собрали значения для всех параметров, описанных выше.Возможно, вы можете использовать электронную таблицу, чтобы упростить и сделать этот процесс более полным. Теперь вы готовы вставить параметры в конкретный диалект GCode, используемый вашим элементом управления:
G76 P (м) (r) (a) Q (dmin) R (d)
G76 X (U) Z (W) R (i) P (k) Q (d) F (L)
P-слово: P-слово состоит из 6 цифр, состоящих из трех двухзначных групп для m, r и a.
м: Повторный счет чистовой обработки (от 1 до 99) – пружинных проходов.
r: величина снятия фаски (от 1 до 99)
a: Угол вершины инструмента. Выберите 80, 60, 55, 30, 29 или 0 градусов.
Q Word: dmin – минимальная глубина резания. Если глубина чернового или чистового прохода меньше этой, она фиксируется, по крайней мере, на эту величину.
R Word: d – припуск на чистовую обработку.
слов X / Z / U / W (2-я строка): укажите координаты конечной точки. X, Z используют текущий режим (абсолютный или относительный), а U, W могут использоваться для указания относительного положения.
Слово R (2-я строка): i – величина конуса при нарезании конической резьбы.
Слово P (2-я строка): k – высота резьбы, выраженная как значение радиуса (а не диаметра).
Q Word (2-я строка): d – глубина первого реза.
Слово F (2-я строка): L – шаг резьбы.
Пример: Fanuc 2 line G76 нарезание конической трубной резьбы:
G-Wizard Editor расскажет вам в подсказке под графиком, что делают все параметры G76…
Fanuc Однолинейный цикл нарезания резьбы G76Цикл нарезания резьбы Haas G76G76 X.. Z .. I .. K .. D .. F .. A .. P ..
X = Диаметр последнего прохода резьбы
Z = Положение конца резьбы
I = Конус по всей длине
K = Одна глубина резьбы – положительный
D = Глубина первого прохода резьбы – положительный
A = Включенный угол пластины – положительный
P = Метод подачи (один из 4)
LinuxCNC / PathPilot G76 Цикл потоковой обработкиG76 D .
. K .. X .. Z .. U .. W .. I .. P .. F .. A ..
D = Начальная глубина резания
K = высота резьбы
X * = абсолютное конечное положение оси X
Z * = абсолютное конечное положение оси Z.Определяет длину резьбы.
U * = инкрементное расстояние по оси X до конца. Может использоваться вместо X.
W * = инкрементное расстояние по оси Z до конца. Может использоваться вместо Z.
I * = величина конуса резьбы (размер радиуса).
P * = Метод позиционирования последующего прохода (1-4)
F * = скорость подачи
A * = угол при вершине инструмента (0-120 градусов. 0 предполагается, если не указано)
Мах 3 G76 Цикл нарезания резьбыG76 П.. Z .. I .. J .. R .. K .. Q .. H .. E .. L ..
P = Шаг резьбы в расстоянии на оборот
Z = Конечное положение резьбы
I = Смещение вершины резьбы . Отрицательный для внешнего, положительный для внутреннего.![]()
J = Начальная глубина резания
K = Полная глубина резьбы
R = Глубина отклонения (опция). R = 1 – постоянная глубина, R = 2 – постоянные площади.
Q = Составной угол скольжения (опция)
H = Пружина (опция)
E = Расстояние вдоль линии привода для конуса
L = Какой конец резьбы сужается.L0 = без конуса. L1 = входной конус. L2 = выходной конус. L3 = входной и выходной конус.
G76 X .. Z .. Q .. P .. H .. I .. R .. K .. L .. C .. B .. T .. J ..
X = X конец
Z = Z конец
Q = Пружина (опция)
P = Шаг
H = Глубина первого прохода
I = Угол подачи
R = X начало (опция)
K = Z начало (опция)
L = фаска (опция)
C = X зазор
B = глубина последнего прохода (опция)
T = конус (опция)
J = минимальная глубина за проход (опция)
Рекомендации по нарезанию резьбы для обработки с ЧПУ
Шаг резьбы
Когда мы говорим о резьбе на болтах и винтах, это не универсальный сценарий. Помимо метрической резьбы, есть три основных вида резьбы с британской мерой, которые входят в серию унифицированных резьб.
- UNC (крупный шаг): 20 ниток на дюйм (tpi)
- UNF (мелкий шаг): 28 tpi
- UNEF (сверхмелкий шаг): 32 tpi
Обратите внимание, что для добавления шага резьбы UNEF требуется наша служба точной обработки, доступная через нашу систему расценок. Например, если вы хотите использовать винт № 4-40, вы знаете, что этот винт № 4 имеет диаметр резьбы 0.11 дюймов (2,794 мм) имеют 40 витков резьбы на дюйм, что означает очень мелкий шаг.
Хорошая новость заключается в том, что когда вы используете нашу систему для привязки определенного типа винта к отверстию, желаемый шаг резьбы зависит от хода. Меньше забот всегда хорошо, правда?
Где я могу разместить нить?
На самом деле, резьбу можно разместить практически в любом месте, которое имеет смысл для токарной или фрезерованной детали и требований вашей сборки. Пока область, в которой будет проходить резьба, доступна для нашего оборудования, все в порядке, но если возникнут препятствия, наше программное обеспечение для анализа проекта сообщит вам, что в этом месте создание потоков невозможно, но это всегда Хорошая идея – следовать нашим рекомендациям, чтобы не сбиться с пути.
Несмотря на то, что кажется, что ограничений по размещению не так много, когда дело доходит до нарезания резьбы, важно учитывать глубину внутренней резьбы. Если глубина резьбы превышает максимальную глубину для инструмента, возможно, нам придется просверлить отверстие с обеих сторон, чтобы завершить процесс. Когда это произойдет, важно знать, что ваши цепочки не будут непрерывными от одного конца до другого, но есть варианты, которые мы рассмотрим в следующем разделе.
В точеных деталях есть три типа отверстий, которые можно использовать для внутренней резьбы:
- На оси: отверстия, проходящие прямо через центр токарной детали, начиная с одного конца
- Осевое: отверстия, начинающиеся на одном конце детали, но не полностью проходящие через центр
- Радиально: отверстия, которые проходят через внешнюю дугу токарной детали
G76 Цикл резьбы винта
При обработке резьбы на токарном станке с ЧПУ у нас есть несколько вариантов. В зависимости от версии элементов управления FANUC мы можем
используйте одну или две строчки кода. Оба метода используют команду G76 и содержат информацию, которая сообщает органам управления машиной
детали нити, которую мы хотим обрезать. Нарезание резьбы также может выполняться с использованием кодов G32 G и G92. Мы возьмем
посмотрите, как они работают вместе с более распространенным G76.
G76 X, Z, I, K, D, A, F;
Пример:
T1212 M06;
G97 S400 M03;
G76 X18.2 Z-18.0 I-0.1 K900 D100 A60 F1.5;
G00 X25.0 Z10.0;
Этот цикл содержит много информации в строке G76. Размер X – это диаметр сердцевины резьбы, расстояние между основанием зуба резьбы и осевой линией, умноженное на 2. Размер Z – это расстояние до конца резьбы от исходного положения. Мы предполагаем, что база данных находится на передней поверхности детали в нашем примере.
«I» сообщает машине величину конуса резьбы по всей длине.Нам часто нужно добавить конус, чтобы иметь возможность нарезать параллельную резьбу, особенно если это длинная резьба небольшого диаметра. Это связано с отражением материала. Это регулируется во время настройки, если калибр резьбы затянут или теряется на одном конце резьбы. Это значение также можно использовать для нарезания конической резьбы при необходимости.
Значение «K» используется, чтобы сообщить органам управления глубину зубца резьбы. Эту информацию можно найти в диаграммах потоков, таких как диаграммы, доступные в моей бесплатной электронной книге.
«D» обозначает глубину первого прохода, глубина автоматически уменьшается по мере нарезания резьбы из-за того, что на каждом проходе удаляется больше материала. При использовании однострочного G76 элементы управления решают эту проблему с помощью встроенных функций.
«А» определяет угол зуба резьбы. Например, стандартная метрическая резьба составляет 60 градусов, а британская резьба BSF – 55 градусов.
Наконец, «F» используется, чтобы сообщить органам управления шаг резьбы.Расстояние между каждым зубом.
G76 P (1) (2) (3), Q, R;
G76 X, Z, P, Q, F;
Первая строка
Пример:
T1212 M06;
G97 S400 M03;
G76 P040060 Q100 R0.2
G76 X18.2 Z-18.0 P180 Q160 F1.5;
G00 X25.0 Z10.0;
Двухстрочный метод G76 дает нам немного больше контроля над обработкой резьбы, некоторые версии элементов управления FANUC позволяют нам использовать этот стиль нарезания резьбы.
Слово «P» дает нам три команды в одной, каждое значение представляет собой двузначное число. Первый определяет количество проходов пружины, которое машина сделает после того, как резьба будет нарезана на глубину. Это помогает улучшить качество поверхности и повторяемость, чтобы наши резьбы оставались в пределах допусков на многих деталях.Второе значение определяет угол фаски биения на конце резьбы, а третье – угол зубьев резьбы (т.е. 60 градусов для метрической резьбы или 55 градусов для резьбы BSF).
Слово «Q» определяет наш минимальный разрез. Это сделано для того, чтобы станок не начинал резать 0,001 мм по мере приближения к диаметру сердечника.
‘R’ – это количество материала, которое мы оставляем перед выполнением чистовых проходов.
X и Z – это диаметр сердцевины резьбы и конечная точка резьбы от исходной точки соответственно.
Слово «P» во второй строке обозначает глубину резьбы в микронах, а буква «Q» определяет глубину первого прохода.
Наконец, мы сообщаем контроллеру шаг резьбы, используя значение «F». Когда G76 активен, машина знает, что мы используем подачу за оборот, а не подачу за минуту.
G-код нарезания резьбы G32 не является постоянным циклом. Он используется как способ зафиксировать вращение патрона в соответствии с шагом ходового винта, чтобы мы могли полностью контролировать глубину каждого прохода.Это больше похоже на команду G01, где каждую строку нужно программировать отдельно, но позволяет нам установить высоту тона. Это классифицируется как модельная операция. G32 также можно использовать для нарезания резьбы торцом.
Пример:
G00 X8.0 Z5.0; (Исходное положение)
G32 X5.0 F0.8; (Глубина и шаг первого прохода резьбы)
Z-15.0; (Конечная точка резьбы по Z)
G00 X8.0; (Убрать в X)
G00 Z5.0; (Убрать по Z)
G32 X4.8 F0.8; (Глубина и шаг прохода второй резьбы)
Z-15.0; (Конечная точка резьбы по Z)
G00 X8.0; (Убрать в X)
G00 Z5.0; (Убрать по Z)
G32 X4.6 F0.8; (Глубина и шаг третьей резьбы)
Z-15.0; (Конечная точка резьбы по Z)
И т.п.
G92 – это цикл нарезания винта, который позволяет нам программировать глубину каждого прохода. Это дает нам полный контроль над диаметром X для каждого прохода. Его нужно программировать для каждого прохода, как показано ниже.
Пример:
G00 X5.0 Z5.0; (Исходное положение)
G92 X5.0 Z-15.0 F0.8; (Внешний диаметр резьбы, конечная точка резьбы и шаг)
X4.8; (Второй проход)
X4.65; (Третий проход)
X4.5; (Четвертый проход)
X4.4; (Пятый проход)
И т.п.
G76 Цикл нарезания резьбы Сколько проходов
G76 Цикл нарезания резьбы Сколько проходов
G76 Threading Cycle Согласитесь, что пользоваться им непросто.
Прочтите эту статью, больше никаких бессонных ночей, беспокоясь о G76 Threading Cycle. Информация, разрушающая мифы, которая упрощает и развеивает мифы. Применимо к Haas, Fanuc и Mazak ISO
Обязательно прочтите конец этой статьи, чтобы увидеть простой способ расчета количества необходимых проходов.
Я заметил, что довольно много людей публикуют сообщения о проблемах на форумах Machining и т. Д. И, как обычно, массу дезинформации. Я решил поискать это, и, честно говоря, есть «Bugger All».Итак, мы здесь.
Что такое цикл нарезания резьбы G76?
Чтобы нарезать резьбу с помощью программы G-кода длинной рукой, потребуется много времени. Всего одному потоку может потребоваться 30 строк кода. Для меня это означает массу возможностей облажаться, и это сложно.
Ох, и становится еще хуже.
Если вы хотите что-то изменить, это кошмар. Вам придется перепрограммировать его только для того, чтобы изменить глубину резания.
И не говоря уже о той скучной математике, которую вам придется делать.Вы помните того учителя с бородой, который постоянно твердил о соотношениях и различиях? Что ж, может тебе стоило обратить внимание.
Всего одна или две строчки, и готово.
Читайте дальше, это просто и сложно.
Звучит глупо, я знаю, но вы можете пропустить много сложных вещей в цикле, поскольку многие значения имеют значения по умолчанию (что означает, что вы можете их пропустить).
G76 X16.93 Z-25. K1.534 D.485 F2.5 (Простой как это)
Многократные повторяющиеся циклы вы знаете, что это такое?
На самом деле, тебе не нужно знать, это просто я пытаюсь произвести впечатление.Большинство циклов на токарном станке с ЧПУ ошибочно называют постоянными циклами. Правильное название для таких циклов, как цикл нарезания резьбы G76 и цикл черновой обработки G71, – это многократно повторяющийся цикл. Нет, это не болезнь, это правильное название.
Постоянные циклы повторяются каждый раз, когда задается позиция. Многократные повторяющиеся циклы делают то, что предлагает название, они повторяют ходы внутри процесса. При нарезании резьбы цикл создает все повторяющиеся движения, необходимые для создания резьбы.
G76 Цикл нарезания резьбы.Итак, как это работает?
В системе управления Fanuc это либо цикл с одной строкой, либо с циклом с двумя строками, в зависимости от возраста элемента управления и настройки параметров. Haas – это однолинейный цикл.
Вы указываете циклу глубину, шаг, диаметр сердечника, длину и, возможно, еще несколько «долот и бобов». Затем при нажатии кнопки появляется ваша ветка.
Haas and Some Fanucs
G76 X16.93 Z-25. K1.534 D.485 A60 Q0 P2 F2.5
X = Диаметр сердцевины резьбы
Z = Конечная точка резьбы
K = Глубина резьбы (в виде радиуса)
D = Глубина первого прохода
A = Угол пластины (предполагается, что A0, если не указан)
Q = Начальный угол резьбы это используется для многозадачных потоков и может быть опущено.
P = Метод нарезания (см. Пояснение ниже, можно не указывать)
F = Шаг резьбы
Обратите внимание, что в системе управления Fanuc вам придется вводить значение D без десятичной точки (D485)
Итак, цикл нарезания резьбы G76 в простейшей форме
Можно было написать:
G76 X16.93 Z-25. K1.534 D.485 F2.5
Fanuc
G76 P010060 Q20 R.02
G76 X16.93 Z-25. P1534 Q485 F2.5
G76 Цикл нарезания резьбы Первая строка
P01 Один проход пружины 00 Фаска 60 Угол резьбы
Q Минимальная глубина резания
R Припуск на чистовую обработку
G76 Цикл нарезания резьбы Вторая строка
X Диаметр сердцевины резьбы
Z Конечная точка резьбы
P Глубина резьбы (как радиус без десятичной точки)
Q Глубина первой нарезки без десятичной точки.
F Шаг резьбы
В системе управления Fanuc используется двухстрочный дисплей, P010060 разделен на три набора по две цифры.
Первые два – количество ходов пружины.
Вторые две – фаска. (Подробнее)
Третьи два – угол инструмента.
Итак, G76 Цикл нарезания резьбы (двухстрочный) в простейшей форме
Извините, нет, это сложно!
Что такое весенние пассы?
Когда вы обрезаете нить, она отталкивается на последнем отрезке, поэтому вы можете повторить это несколько раз, чтобы получить правильный размер.Эти дополнительные разрезы называются пружинными проходами. Сколько вам понадобится, это зависит от материала.
Да, и, кстати, не ищите глубину резьбы в каких-нибудь Zeus Book или чем-то подобном. Просто умножьте высоту на 0,614
Давайте нарежем резьбу M20 x 2,5 с помощью цикла нарезания резьбы G76
Глубина резьбы = 0,614 x шаг
. 614 x 2,5 = 1,535
X Малый диаметр для резки = 20 – (1.535 х 2)
X Малый диаметр для резки = 16,93
G76 X16.93 Z-25. K1.535 D.485 F2.5
Вы годами поступали неправильно?
Как я уже сказал выше, когда начал гуглить G76, зрелище не очень приятное. Во-первых, информации не так много, и что немаловажно, часть ее неверна.
То, как вы используете этот цикл, сильно влияет на работу инструмента.Вышеупомянутое значение по умолчанию для цикла нарезания резьбы Haas G76 даст вам так называемое «врезание».
Это буквально то место, где инструмент врезается в резьбу, и рез становится шире и, следовательно, более склонен к вибрации по мере углубления. Он идет прямо по центру V-образной резьбы.
Если вы вставите A60, цикл будет обрезать по бокам.
Фланговый разрез ?????
См. Ниже:
Помощь под рукой
Способы обрезки нити
(1) Врезание: обрезайте прямо посередине программы резьбы.A0 или просто пропустите.
(2) Боковая резка: обрезает боковую сторону резьбы. A60 на форме резьбы 60 градусов.
(3) Альтернативная боковая резка: переключалась из стороны в сторону, обрезая боковую сторону резьбы. A60 P2, если у вас есть возможность.
Итак, какой из них лучший.
Последнее число (3) является лучшим, а число (1) – худшим.
Извините, выродки, но я собираюсь слишком упростить его.
Почему?
С помощью третьего метода вы получите ровный рез с меньшим количеством вибраций и меньшим износом инструмента.К тому же это лучше для вашей вставки.
Если вы мне не верите, поговорите со своим мастером по инструментам. В любом случае он знает больше, чем я.
G76 имеет значение P от 1 до 4 (P1 P2 и т. Д.). Это определяет четыре различных метода, которые вы можете использовать. Мой совет – просто игнорируйте их все и используйте P2. Это означает, что инструмент режет, чередуя две стороны резьбы, как указано выше. Вам также необходимо ввести A60 для угла протектора.
G76 D.485 K1.534 X16.93 Z-25.A60 P2 F2.5
Да, и всегда есть улов
У вас будет только альтернативная боковая резка на новом станке, если у вас старый бандаж, то вы набиты.
Не беспокойтесь, просто воспользуйтесь методом (2), боковая резка – это нормально.
Если вы введете угол пластины A60 на форме резьбы 60 градусов, вы получите резку по бокам.
Глубина разреза (Слон в комнате)
Как рассчитать количество разрезов?
Если честно, я знаю, что ты делаешь, ты думаешь.Что ж, на самом деле вы не одиноки, я думаю, что многие люди делают это. Они угадывают глубину первого прохода, затем просто запускают цикл и смотрят, сколько проходов они получат.
Это ты?
Давай, это нехорошо.
В течение многих лет я видел эту формулу в большом желтом Fanuc Manual .
Если честно, это выглядело слишком сложно. Однажды, когда мои консультации закончились, я осторожно открыл большую желтую книгу и решил раз и навсегда завоевать ее.
Wooppee It’s Easy
Это просто глубина резьбы, деленная на квадратный корень из числа проходов. Немного набитый ртом.
Итак, на вашем калькуляторе:
(1) Нажмите кнопки для определения глубины резьбы, например, 1,534
(2) Нажмите кнопку разделения (÷)
, затем нажмите кнопку √
(3) Введите число, затем нажмите 10, затем нажмите =
1,534 ÷ √10 = 0.4854
Это значение, которое нужно ввести для
KК.485
Так просто, вы можете сделать это задом наперед
Итак, ваш цикл показывает
G76 D.485 K1.534 X16.93 Z-25. A60 P2 F2.5
Так сколько проходов я получу от этого?
- Введите глубину резьбы (значение K) .
- Пресс ÷
- Введите глубину первого прохода (значение D)
- Нажмите =
- Нажмите кнопку в квадрате (²)
Ответ:
10.01689871 вот вам 10.
Так что в следующий раз, когда вы нарежете резьбу, не угадайте количество проходов, используя эту формулу, это очень просто.
Как я уже сказал, вы можете сделать это задом наперед
Глубина резьбы, деленная на квадрат глубины первого прохода.
Как в примере выше.
Я знаю, что у меня глубина резьбы 1,534, а у меня
(1,534 / .4854) ²
1,534 / 0,4854 = 3,1602
3,1602 х 3,1602 = 9.98737 (10 к вам)
Прочтите, чтобы узнать, как получить каждый пропуск.
Таким образом, вы можете использовать эту формулу для расчета глубины каждого прохода.
1,534 ÷ √1 = 1,534 Cut = 0,000
1,534 ÷ √2 = 1,084 Cut = 0,450
1,534 ÷ √3 = 0,885 Cut = 0,199
1,534 ÷ √4 = 0,767 Cut = 0,118
1,534 ÷ √5 = 0,686 Cut = 0,081
1,534 ÷ √6 = 0,626 Cut = 0,060
1.534 ÷ √7 = 0,579 Cut = 0,047
1,534 ÷ √8 = 0,542 Cut = 0,037
1,534 ÷ √9 = 0,511 Cut = 0,031
1,534 ÷ √10 = 0,485 Cut = 0,026
Обратите внимание, что по мере того, как резьба становится глубже, разрезы становятся меньше. Это потому, что ширина разреза становится больше.
Таким образом, уменьшение глубины выравнивает нагрузку на инструмент.
Дружелюбный совет
Будьте проще с первой попытки.Это означает упустить как можно больше. Обрежьте резьбу на свежем воздухе (в патроне нет компонентов). Затем вы можете поиграть со всеми небольшими корректировками и посмотреть, что они делают. Этот инженерный бизнес – это очень весело. О, и снизьте скорость, когда вы его тестируете, чтобы вы могли точно видеть, что происходит. Вы можете подготовиться с помощью E Stop.
О, да, вот еще один совет
Запускайте шпиндель очень медленно (например, 100 об / мин). Таким образом вы можете остановить станок с помощью E Stop , если похоже, что он собирается столкнуться с уступом.
Вам нужно выполнить только один такой проход. Это может просто поцарапать первый проход. Увеличьте скорость, и вы этого не увидите. (Это может быть наш секрет)
Single Block, что насчет этого?
При использовании G76 вы не можете использовать подпорку.
Почему? ……. Давай, подумай об этом.
Вы также не можете использовать коррекцию шпинделя. Они оба блокируются циклом, чтобы вы не испортили свою драгоценную нить.
В «Single Block» каждое нажатие запуска цикла дает вам один полный проход.
Несколько правил
Правила правила всегда тупые правила тупой жопы.
- Всегда используйте скорость G97 в об / мин, G96 использовать нельзя.
- Не перемещайте начальную позицию Z, если она не кратна шагу.
- Не меняйте скорость.
- Станок должен ускориться в резьбу, поэтому начните с Z5. в зависимости от скорости и шага может потребоваться больше.
- Остерегайтесь этого Z и точки. Это тот, который заставит его попасть в патрон, если вы ошибетесь.
- Приходите и тренируйтесь с нами.
Еще немного полезной информации от Vardex.
Спасибо за чтение
Не забывайте, что есть еще много людей.
И канал на YouTube
Свяжитесь с нами
Услуги, предлагаемые в Учебном центре с ЧПУ
Siemens Sinumerik Training
Обучение Edgecam.
Аудиторная подготовка программистов.
Обучение работе с ЧПУ на месте.
Обучение ЧПУ по всем элементам управления и станкам.
Mazak Training Fanuc Training
Не забывайте, что мы предлагаем обучение на всех типах станков Mazak и всех контроллерах Fanuc Controls от 6 мес до 31 года.
[contact-form-7 id = ”2706 ″ title =” Contact Form ”]
Опыт и методики нарезания резьбы – Hastings Machine
Существуют различные методы создания резьбы. Метод, выбранный для любого приложения, выбирается на основе ограничений и доступных опций; время отклика, стоимость, степень точности, прочность, доступность оборудования и т. д.В общем, определенные процессы создания резьбы имеют тенденцию попадать в определенные части спектра от нестандартной до серийно выпускаемой оснастки, при этом может быть значительное перекрытие. Например, притирка резьбы после шлифования резьбы попала бы только в крайнюю нестандартную область спектра, в то время как накатка резьбы – это большая и разнообразная область практики с широким спектром применения. Нити металлических креплений обычно создаются на резьбонакатном станке. Их также можно вырезать на токарном станке. Накатанная резьба прочнее, чем нарезанная резьба, с увеличением прочности на разрыв от 10% до 20% и, возможно, более высокой усталостной и износостойкостью.Субтрактивные методы (удаление материала)
Нарезание резьбы
Нарезание резьбы по сравнению с нарезанием и накатыванием резьбы может использоваться, когда требуется полная глубина резьбы, когда количество небольшое, когда заготовка не очень точна, когда требуется нарезание резьбы до заплечика, при нарезании конической резьбы, или когда материал хрупкий.Нарезание резьбы
Нарезание метчиками – распространенный метод нарезания резьбы. В отличие от сверл, метчики не удаляют автоматически стружку, которую они создают.Метчик поочередно обрезает резьбу, образуя длинные стружки, которые могут быстро заклинить метчик (эффект, известный как «скучивание»), что может привести к поломке инструмента. Для непрерывного нарезания резьбы используются специальные метчики со спиральным острием, которые разбивают и выбрасывают стружку, чтобы предотвратить скучивание.Нарезание одноточечной резьбы
Одноточечная нарезка резьбы, чаще называемая просто однонаправленной, представляет собой операцию, в которой используется одноточечный инструмент для создания формы резьбы на или внутри цилиндрического или конусообразного элемента. Инструмент движется линейно, в то время как точное вращение детали определяет переднюю кромку резьбы.Процесс может быть выполнен для создания внешней или внутренней резьбы (мужской или женской). При нарезании наружной резьбы деталь может либо удерживаться в патроне, либо устанавливаться между двумя центрами. При нарезании внутренней резьбы деталь удерживается в патроне. Инструмент движется по заготовке линейно, снимая стружку с заготовки при каждом проходе. Согласование различных элементов станка, включая ходовой винт, опору скольжения и переключающие шестерни, явилось технологическим достижением, позволившим изобрести токарно-винторезный станок, который положил начало тому, как мы знаем его сегодня, нарезания одноточечной резьбы.Горизонтальные токарные станки и токарные станки с ЧПУ являются наиболее часто используемым оборудованием для нарезания точечной резьбы. Станки с ЧПУ обрабатывают быстро и эффективно благодаря способности станка постоянно отслеживать взаимосвязь положения инструмента и положения шпинделя. Программное обеспечение ЧПУ упрощает настройку оборудования с помощью предварительно запрограммированных подпрограмм, которые исключают ручное программирование цикла настройки. Параметры вводятся (например, размер резьбы, коррекция инструмента, длина резьбы) через клавиатуру компьютера или непосредственно с компьютера программиста, все остальное делает машина.Всю нарезку резьбы можно выполнить с помощью одноточечного инструмента, но из-за высокой скорости и низкой стоимости единицы других методов (например, нарезания резьбы, нарезания резьбы, накатки резьбы и формовки) одноточечная нарезка резьбы обычно используется, когда другие факторы технологического процесса в пользу этого (т. е. низкая потребность в количестве, уникальные требования к резьбе, крутящий момент и / или мощность, препятствующие нарезанию резьбы, физический размер и т. д.).Фрезерование резьбы
Резьба может быть нарезана вращающейся фрезерной коронкой по запрограммированной спиральной траектории инструмента.Фрезерование резьбы подходит для массового производства, как таковое не является обычным для работы в мастерской. С повсеместным распространением доступных, быстрых и точных станков с ЧПУ, это стало гораздо более распространенным, внутренняя и внешняя резьба часто фрезеровалась на деталях, которые раньше нарезались метчиками, штамповочными головками или однонаправленными. Преимуществами резьбофрезерования являются более короткое время цикла, меньшее количество поломок инструмента и гибкость левой или правой резьбы при использовании одного и того же инструмента. Для больших и неудобных деталей проще оставить деталь неподвижной, в то время как все операции обработки выполняются с помощью вращающихся инструментов.Существуют различные типы резьбофрезеровки, в том числе несколько вариантов формофрезеровки и сочетание сверления и нарезания резьбы одним инструментом. При фрезеровании формы используются инструменты одной или нескольких форм. Один из примеров формовочного фрезерования: цельный инструмент наклоняется под углом спирали резьбы и затем подается радиально в заготовку. Заготовка медленно вращается, так как инструмент точно перемещается по оси заготовки, нарезая резьбу. Достигается за один проход, если инструмент подается на полную глубину резьбы, или за последовательные проходы с меньшим съемом материала.Этот процесс обычно используется для больших потоков. Он обычно используется для нарезания крупно- или многозаходной резьбы. В аналогичном примере с использованием многоформного инструмента вся резьба получается за один оборот вокруг заготовки. Инструмент должен быть длиннее необходимой длины резьбы. Использование инструмента с несколькими формами быстрее, чем с использованием инструмента с одной формой, но он ограничен по углу наклона спирали. Еще один вариант формовочного фрезерования включает в себя удерживание оси инструмента перпендикулярно (без перекоса к спирали резьбы) и подачу инструмента по траектории, образующей резьбу.Деталь обычно представляет собой неподвижную заготовку, такую как выступ на корпусе клапана (внешняя резьба) или отверстие в пластине или блоке (внутренняя резьба). Этот тип резьбового фрезерования использует, по сути, ту же концепцию, что и контурное концевое фрезерование, но инструмент и траектория расположены специально для определения «контура» резьбы. Геометрия инструмента отражает шаг резьбы, но не шаг резьбы. Коническая резьба может быть нарезана либо коническим инструментом различной формы, который завершает резьбу за один оборот, либо прямым или коническим монолитным инструментом.Инструмент, используемый для фрезерования резьбы, может быть цельным или сменным. Для внутренней резьбы цельные инструменты обычно ограничиваются отверстиями размером более 0,24 дюйма (6 мм), инструменты для нарезания внутренней резьбы со сменными пластинами ограничиваются отверстиями размером более 0,47 дюйма (12 мм). Преимущество; поскольку вставка изнашивается, ее можно легко и более экономично заменить. Недостаток; время цикла обычно больше, чем у твердых инструментов. Цельнометаллические инструменты для нарезания резьбы разной формы похожи на метчики, но отличаются режущей кромкой, отсутствием конуса и входной фаски.Отсутствие входной фаски позволяет формировать резьбу в пределах одного шага от дна глухого отверстия.Нарезание резьбы
Нарезание коронки – это процесс корончатого сверления / нарезания внутренней резьбы с использованием специального режущего инструмента на фрезерном станке с ЧПУ или аналогичном приводном механизме. Наконечник режущего инструмента имеет форму сверла, а хвостовик имеет форму метчика. Преимущество процесса исключает замену инструмента. Недостатком является то, что процесс обычно ограничивается глубиной отверстия, не превышающей трехкратный диаметр инструмента.Закручивающаяся резьба
Завихрение резьбы – это форма процесса резьбового фрезерования, за исключением того, что режущие коронки устанавливаются внутри режущего кольца или держателя инструмента, а не снаружи фрезерного инструмента. Завихрение нити дает несколько преимуществ по сравнению с одноточечной резьбой:- Глубокая резьба – как и в случае костных винтов, обычно имеет глубокую резьбу, аналогичную формам Acme и другим резьбам с увеличенным шагом.
- Резьба от длины до диаметра – при использовании на станке швейцарского типа вращающийся шпиндель работает близко к направляющей втулке, что увеличивает поддержку и жесткость при резке от длины до диаметра.Процесс обычно выполняется за один проход от диаметра заготовки, что обеспечивает постоянную поддержку материала.
- Faster Setup – устраняя необходимость согласования черновой и чистовой форм пластин, процесс вихревой обработки сокращает время настройки и точной настройки.
- Повышенная производительность – сокращение времени цикла и увеличенное время работы приводит к повышению производительности. Завихрение резьбы обычно выполняется за один проход от диаметра заготовки, что исключает необходимость в нескольких проходах, необходимых для одноточечной нарезания резьбы.
Деформационные методы (перемещение материала)
Нарезание резьбы и накатка резьбы
Это процессы формирования резьбы, первая из которых относится к созданию внутренней резьбы, а вторая – внешней резьбы. В обоих процессах резьбу формуют в заготовку путем прижатия профилированного инструмента, обычно называемого «штампик для накатывания резьбы», на заготовку в процессе, аналогичном накатке. Эти процессы обычно используются для крупных производственных циклов или конкретных приложений, когда прочность резьбы должна соответствовать минимальному пределу текучести.Формовка и прокатка не производят стружки (стружки, стружки и т. Д.), Требуется меньше материала, поскольку размер заготовки начинается меньше, чем размер заготовки, необходимой для нарезания резьбы. Накатанную резьбу часто можно распознать по диаметру резьбы большего диаметра, чем диаметр заготовки, из которой она была изготовлена; шейки и поднутрения можно нарезать или накатить на заготовки с нескрученной резьбой. Материалы ограничиваются пластичными материалами, поскольку резьба формируется в холодном состоянии. Процесс улучшает поток; предел текучести, чистота поверхности, твердость и износостойкость.Для прокатки необходимы материалы с хорошими деформационными характеристиками, а также исключают хрупкие материалы. Существует четыре основных типа накатки резьбы, названные так в соответствии с конфигурацией технологических штампов: плоские штампы, цилиндрические штампы с двумя штампами, цилиндрические штампы с тремя штампами и планетарные штампы. В системе плоских матриц используются две матрицы, нижняя удерживается неподвижно, а вторая скользит. Заготовка помещается на один конец неподвижной матрицы, подвижная матрица скользит по заготовке, заставляя заготовку катиться между двумя матрицами, формируя нити.Прежде чем движущийся штамп достигает конца своего хода, заготовка скатывается с неподвижного штампа в готовой форме. Цилиндрический процесс с двумя головками используется для получения резьбы диаметром до 6 дюймов (150 мм) и длиной до 20 дюймов (510 мм). Есть два типа процессов с тремя головками; в первом три матрицы перемещаются радиально из центра, позволяя заготовке входить в матрицы, а затем закрываются и вращаются для наматывания резьбы. Этот тип процесса обычно используется на токарно-револьверных станках и винтовых станках. Второй тип представляет собой самооткрывающуюся штамповочную головку.Этот тип более распространен, чем первый, но ограничен тем, что не может сформировать последние 1,5–2 нитки на плечах. Планетарные матрицы используются для массового производства резьбы диаметром до 1 дюйма (25 мм). В отличие от операций нарезания резьбы с использованием метчиков с канавками, метчики для нарезания резьбы не образуют стружки. Вместо этого они перемещают или перемещают материал, чтобы сформировать форму нити. Метчики имеют многоугольное поперечное сечение с образующими клиньями, отражающими профиль резьбы. Их входной конус формирует профиль резьбы, материал постепенно стекает с вершин резьбы вдоль боковых сторон резьбы в область малого диаметра.Поскольку материал сжимается, а его зернистость перенаправляется, а не разрезается или прерывается, прочность на боковых сторонах резьбы и в основании увеличивается. Нарезание резьбы методом холодной штамповки подходит для материалов с пределом прочности на разрыв менее 1200 Н / мм2 и деформацией разрушения 5 процентов. Как показывает опыт, если при сверлении образуется непрерывная стружка, материал, вероятно, является хорошим кандидатом для резьбы холодной штамповки. Однако подходящие материалы по-разному реагируют на холодную штамповку. Именно по этой причине метчики для нарезания резьбы имеют особые комбинации геометрии и покрытий для резьбонарезания стандартных сталей; мягкие стали; закаленные стали; нержавеющие стали; литой алюминий; деформируемые алюминиевые сплавы и цветные металлы; и материалы с ограниченной пластичностью.Покрытия включают нитрид титана, карбонитрид титана и алмазоподобный аморфный углерод. Антифрикционные покрытия также могут использоваться для таких материалов, как кованый алюминий, чтобы предотвратить прилипание материала к метчику. Учитывая высокое трение, возникающее во время процесса формовки, рекомендуются смазочные материалы или эмульсионные охлаждающие жидкости. Для определенных применений также можно использовать минимальное количество смазки. Некоторые версии инструментов имеют подачу СОЖ через инструмент для облегчения нарезания резьбы в глухих отверстиях.Другие выводят охлаждающую жидкость на инструмент в продольные канавки, чтобы повысить скорость нарезания резьбы и качество резьбы.Возможности нарезания резьбы
Резьба, обычно производимая Hastings Machine Company, включает, но не ограничивается: Unified National Coarse (UNC), Unified National Fine (UNF), National Pipe Thread (NPT), Coil, Metric, Tapered, Transitional (т.е. от №8 до №10 ), Евро, ACME, 8 Round (API) и т. Д. Возможности материалов включают: холоднотянутую углеродистую сталь, сплав, нержавеющую сталь, дуплекс, алюминий, латунь, чугун с шаровидным графитом и некоторые полимеры.Наши возможности потоковой передачи включают:- Многопозиционный поворотный стол
- Вертикальные и горизонтальные операции
- Диаметр от 1/4 ″ до 2 ″
- Головки нарезные и сверлильные
- Самонарезающие головки для вертикального сверления
- Автоматическая обработка
- Специальное вертикальное нарезание резьбы
- Диаметр от 1/4 ″ до 2 3/8 ″
- , ход 12 дюймов
- Многошпиндельное вертикальное сверление
- Диаметр от 1/4 ″ до 2 ″
- Автомат для нарезания гаек
- Диаметр от 1/2 ″ до 1 3/8 ″
- Плоское шлифование
- Фиксированные и многоосные возможности
- Автоматическая обработка
- Ленточнопильный станок
- Станок токарный
- Одношпиндель, горизонтальная опора
6.1.3. G76 Цикл нарезания резьбы
Для правильного отображения этой страницы вам необходим браузер с поддержкой JavaScript.
С помощью этого двухблочного постоянного цикла нарезания резьбы можно выполнять внешнюю или внутреннюю резьбу. Вот краткое описание цикла и его параметров.
Параметры первого блока:
P: этот параметр состоит из трех значений, которые управляют поведением резьбы.
В приведенном выше примере у нас P010060. Давайте разберем цифры.
01: Количество пружин. Это означает, что после выполнения нарезки резьбы машину можно запрограммировать на выполнение ряда дополнительных проходов на той же глубине для сглаживания конечной резьбы.
00: Угол биения. Угол, используемый для выхода резьбы.
60: Угол подачи. Угол, используемый при вводе резьбы.
Q: Глубина каждого нормального реза.Это значение дано в сотнях, поэтому Q500 выше означает 0,5.
R: Глубина последнего или чистового пропила.
Параметры второго блока:
X: конечное значение по оси X.
Z: Конечное значение по оси Z.
P: Глубина резьбы (радиальное значение).
Q: Глубина первого реза.
F: Шаг резьбы.
Примечание! CNCSimulator Pro упрощает процесс нарезания резьбы, игнорируя некоторые параметры, так как для моделирования не важно принимать каждый параметр литературным.Важные параметры симулятора следующие:
Параметр Q в первом блоке сообщает симулятору, сколько нужно брать на каждый проход.
Значения X и Z второго блока говорят симулятору завершить поток.
Параметр F второго блока сообщает симулятору шаг резьбы.
Среди демонстрационных программ есть пример под названием Sample4_G76_Threading_units.cnc, который вы можете запустить, чтобы увидеть цикл в действии.
QK1319 Токарно-винторезный станок с ЧПУ
ТРУБОПРОВОДНОЙ ТОКАРНЫЙ СТАНОК с ЧПУ ВВЕДЕНИЕ
Эта серия токарно-резьбонарезных станков с ЧПУ в основном предназначена для обработки внутренней и внешней трубной резьбы, включая метрическую, дюймовую, модульную DP и коническую резьбу, а также имеет все общие функции обычных токарных станков с ЧПУ, такие как как обработка внутреннего отверстия и торца валов и дисков.Токарный станок этой серии широко используется в таких отраслях, как нефтедобыча, добыча полезных ископаемых, химические трубопроводы и геологоразведочные работы, это высокоэффективное оборудование для обработки и ремонта бурильных труб, буровых штанг, резьбовых соединений и т. Д.
ХАРАКТЕРИСТИКИ
Большое отверстие шпинделя и двойной патрон для обеспечения обработки трубы большого диаметра
В цельной станине используется высокопрочный чугун для обеспечения жесткости и точности
Направляющие, закаленные ультразвуковой частотой, обеспечивают хорошую износостойкость
Каретка и контактная поверхность направляющего канала используйте Turcite B для поддержания точности
СТАНДАРТНЫЕ ПРИНАДЛЕЖНОСТИ | ДОПОЛНИТЕЛЬНЫЕ ПРИНАДЛЕЖНОСТИ |
револьверная головка с ЧПУ 4 положения, ручная пила с 3 лапками , насос охлаждающей жидкости, полушиток | Контроллер ЧПУ Fanuc или другой марки, быстросменный резцедержатель, гидравлическая револьверная или механическая револьверная головка, пневматический патрон, гидравлическая задняя бабка, пневматический ограничитель положения, рычаг для установки инструмента, полный щит |
Технические характеристики
ТЕХНИЧЕСКИЕ ХАРАКТЕРИСТИКИ | Шт. | QK1319 | |||||||||||||||||||||||||||||
Поворот над станиной | мм | 630/800 |
Расстояние между центрами | мм | 1000/1500/3000 | |||||||||||||||||||||||||||||
Диапазон нарезки трубной резьбы | 0265 | ||||||||||||||||||||||||||||||
Ширина направляющей | мм | 550 | |||||||||||||||||||||||||||||
Макс.грузоподъемность | T | 3 | |||||||||||||||||||||||||||||
Отверстие шпинделя | мм | 200 | |||||||||||||||||||||||||||||
05 05 | |||||||||||||||||||||||||||||||
Диапазон скорости вращения шпинделя | об / мин | 20-550 | | ||||||||||||||||||||||||||||
Патрон | мм | мм||||||||||||||||||||||||||||||
Револьверная головка / резцедержатель | – | Револьверная головка с ЧПУ, 4 позиции | |||||||||||||||||||||||||||||
Размер хвостовика инструмента | мм | 9103 9103 | мм | 320/420 | |||||||||||||||||||||||||||
Ход оси Z | мм | 850/1350/2850 |
/ мин | 4000 | |||||||||
Ускоренный ход оси Z | мм / мин | 6000 | ||||||||
Диаметр пиноли задней бабки | мм | φ100 | ||||||||
Конус пиноли задней бабки 4
|