Делаем арболитовые блоки своими руками. Оборудование для производства арболитовых блоков
Арболит – это строительные блоки на основе цемента и древесной щепки. Он обладает хорошими характеристиками, которые существенно лучше, чем у опилкобетона. В статье речь пойдет о том, в каких сферах применяются арболитовые блоки, об их достоинствах и недостатках, а также о технологии изготовления.
Содержание:
- Что такое арболитовые блоки
- Преимущества и недостатки арболитовых блоков
- Виды арболитовых блоков
- Технология производства арболитовых блоков
- Производители арболитовых блоков
- Инструмент для арболитовых блоков
- Подготовка щепы для изготовления арболитовых блоков
- Раствор для арболитовых блоков и заливка в формы
- Советы для изготовления арболитовых блоков
Что такое арболитовые блоки
Бетон – это универсальный строительный материал.
- В основе арболитовых блоков лежит древесная щепка. К ее размеру и количеству применяются строгие требования – эти два параметра влияют на качество материала и его марку. Кроме этого, есть производства арболита, которые используют стебли хлопчатника, рисовую солому или кору.
- Вяжущим компонентом выступает цемент марки не ниже М300. Его марка влияет на прочность готового изделия и, следовательно, на его маркировку.
- Для улучшения соединения компонентов смеси, в нее добавляют специальные добавки, обеспечивающие быстрое затвердение и т.д. В большинстве случаев это жидкое стекло, хлористые соли калия или алюминия.
- Изначально древесная щепка и цемент плохо сочетаются, чтобы доиться качественных и равномерных по прочности блоков требуется правильно поставить производство с четким технологическим процессом.
Во время которого важную роль играет продолжительное и тщательное перемешивание всех составляющих.
- Щепка, отбираемая для изготовления должна проходить жесткий контроль. Лучше всего подходят сосна, ель или бук. Немаловажен и характер древесины – поздняя или ранняя заготовка. Размер щепки не должен превышать 10 мм в ширину и 25 мм в длину. Соблюдая эти условия, материал получится с высокой паропроницаемостью, но прочный.
- Для достижения лучших теплоизоляционных показателей. Смесь делается из щепы, вяжущего (цемент с добавками) и воды в пропорции 1:1:1,5. Если нужен более прочный блок для стены с высокой несущей нагрузкой, то пропорции вяжущего соответственно меняются
Арболитовые блоки видео
Преимущества и недостатки арболитовых блоков
Самое главное – это высокие энергоэффективные показатели при строительстве внешних стен дома и невысокая стоимость материала. Но из-за невысокой прочности, допустим только для строительства малоэтажных домов.
Достоинства арболита
- По теплоизоляционным качествам он опережает обычный бетон или кирпич. Его теплопроводность составляет всего 0,08 Вт/(м*С).
- Он обладает лучшими качествами древесины, но в отличие от нее, является пожаробезопасным. Арболит трудновоспламеняемый материал, который во время пожара образует мало дыма.
- При нагревании дома и последующем отключении системы отопления, тепло в помещении будет сохраняться еще долгое время даже при отрицательной температуре снаружи.
- По своим паропроницаемым характеристикам он уступает только древесине. Поэтому внутри помещения будет всегда хороший микроклимат, даже при высокой влажности. Вот почему этот материал выбирают для строительства сауны или бани.
- Несмотря на невысокую прочность (допускается строительство зданий из арболитовых блоков не выше 3 этажей), он хорошо противостоит нагрузкам на растяжении.
Что особенно важно при сезонном пучении грунта, когда дом начинает «ходить». Это свойства материала убережет строение от появления трещин.
- Морозостойкость в зависимости от марки изделия может быть в пределах F25 – F50, Но если зимой чередуются влажность и отрицательная температура, срок годности арболита значительно снижается.
- Этот недорогой материал легко подгонять под нужные размеры, в нем достаточно прочно держится закрепленные предметы. Он станет лучшим вариантом для небольших хозяйственных построек или гаражей.
- Небольшой вес блоков позволяет экономить на фундаменте, так как на последний не будет оказываться высоких нагрузок.
Недостатки арболита
- Невысокая прочность ставит использование арболитовых блоков в узкие рамки. Разрешено только малоэтажное строительство, межкомнатные перегородки или в качестве дополнительной теплоизоляции.
- Долговечность материала зависит от его качества. Помимо специализирующихся крупных заводов, сегодня по стране очень много частных маленьких фирм, которые изготавливают блоки и продают их по более низким ценам.
Но, к несчастью, качество их продукции зачастую остается низким из-за желания максимально удешевить товар и сделать его привлекательным для покупателя.
- Изготовленный по ГОСТу материал имеет стоимость, практически равную пенобетону. Это связано с тем, что при его изготовлении не обойтись без человеческого труда.
- Из-за погрешностей в размерах блоков, во время кладки швы получаются неравномерными. Да и сам материал не отличается красивым внешним видом, поэтому требуется финишная декоративная облицовка фасадов дома.
Виды арболитовых блоков
Всего производят 2 основных вида:
- Конструкционный. Отличается наивысшей плотностью – 500-800 кг/куб.м. В нем пропорционально больше содержание цемента по отношению к щепе. По характеристикам он пригоден для кладки несущих стен и опор. Для большей прочности допускается его армирование стержнями или сеткой.
- Теплоизоляционный. Плотность в пределах 500 кг/куб.м. Предназначается для строительства межкомнатных перегородок, на которые не оказывается нагрузки и в качестве теплоизоляционного слоя.
Арболит может иметь 2 формы:
В виде блоков. Это уже готовый к использованию материал определенных размеров. Но из-за особенностей материала и его изготовления в размерах могут быть существенные погрешности. Хотя они регламентированы ГОСТом, на деле чаще нестыковки превышают эти параметры. Это надо учитывать еще на стадии проектирования и подсчета требуемого количества материалов. Блоки имеют большой размер, поэтому темпы строительства высокие.- Монолитный. Его изготавливают непосредственно перед использованием прямо на строительной площадке. После замеса сразу же используют полностью. Такой способ подойдет для создания тонкого теплоизоляционного слоя (когда арболит заливается в несъемную опалубку из пеноплэкса или пенопласта). После заливки придется остановить на работы на время схватывания состава. Это не менее 7 дней.
Технические характеристики арболитовых блоков
- Хоть в арболите и присутствует древесина на равне с бетоном, все же этот класс материала относится именно к строительному камню.
Поэтому его маркируют и дают класс прочности именно как любому другому изделию из бетона.
По форме арболитовые блоки могут быть:
- с U-образным углублением. Удобны для дверных или оконных поемов с перемычками;
- стеновые блоки могут быть крупными, средними или узкими;
- плоты. Но они обязательно имеют слой прочного и плотного бетона, так как характеристики арболита не могут отвечать необходимым, в данном случае, требованиям. Допустимая длина по ГОСТу не превышает 480 см.
Технология производства арболитовых блоков
Сам технологический процесс довольно прост, поэтому для небольших построек, например сарая или курятника, арболитовые блоки моно сделать своими руками. Но из-за медленного отвердения состава, изготовление займет очень много времени, особенно если форм для заливки немного. Особенно при условии, что арболит будет набирать необходимую прочность только при температуре от 12 градусов и выше. Конечно, можно добавить специальные химические компоненты, которые сделают возможным работы и при более низких температурах, но это приведет к удорожанию материала.
Этапы технологического процесса
- Получение деревянных щепок. Для этого подойдут отходы от деревообработки, которые имеются в большом количестве на любой лесопилке. Подходят практически все сорта древесины, кроме лиственницы и тополя. Нельзя забывать и про строгие ограничения в размере, которые являются основополагающими качества арболита. Поэтому изготовители изготавливают щепу самостоятельно при помощи различных дробилок (шредера, молотковой, дисковой или роторно-ножевой).
- Пропорции. Если профессионалы используют специализированные дозаторы, то при самостоятельном изготовлении придется руководствоваться весом или объемом.
- Соединение компонентов. Вначале соединяют щепку и цемент. Сделать это вручную лопатой не получится, допускается только длительный замес в бетономешалке.
- Заливка формы. Готовая смесь по желобу подается в специальные формы из металла или дерева.
- Трамбовка. Это очень ответственный этап, который нельзя упускать. Здесь используется ручной труд, так как сначала смесь надо проколоть, чтобы удалить пузырьки воздуха. Далее утрамбовка производится на вибростоле.
Совет: из-за плохой адгезии цемента с щепой, утрамбовка должна продолжаться не более 20 мин, иначе бетон начнет отделяться от щепы и утрамбовываться на дне.
- Отвердение. Происходит на проветриваемых складах, где нет прямых солнечных лучей. Формы снимаются через сутки. Дальнейшая транспортировка возможна через 2-3 недели.
Производители арболитовых блоков
В каждом городе есть не одно производство арболитовых блоков. Но чаще всего их производят в кустарных условиях и продают через объявления на местных ресурсах. Если поблизости нет крупного завода, то лучше обратиться в компании, которые занимаются строительством арболитовых домов. Как правило, у них всегда есть свое производство, на котором соблюдаются все технологии.
- Наиболее крупное предприятие в России, занимающееся арболитовыми блоками – «ЭкоДрев Продукт». Они поставляют свою продукцию на крупные рынки строительных материалов. В среднем стоимость конструкционного материала составляет 5500 – 6000 руб/м3, а теплоизоляционного 4500 руб/м3.
- Более низкие цены у производителя «Арболит Трейд» – 5300 руб/м3 с доставкой. Они производят не только полнотелый, но и пустотелый кирпич.
- Вологодский завод арболита также предлагает свою продукцию в большинстве регионов. Цена конструкционного блока от 4100 руб/м3.
Покупая большие объемы напрямую от изготовителя, всегда можно договориться о дополнительной скидке.
Инструмент для арболитовых блоков
Специального оборудования для арболитовых блоков не потребуется, достаточно подготовить стандартные инструменты:
- бетономешалка;
- большой металлический поддон;
- форма для заливки арболита;
- разделитель.
Он нужен, если в одной форме планируется залить несколько более маленьких блоков или сделать пустоты;
- большое сито с вибрацией;
- вибростол или молоток;
- вилы, лопата и ведро;
- мастерок.
Чертежи арболитовых блоков
Подготовка щепы для изготовления арболитовых блоков
Делается это двумя методами.
Выдержка на открытом воздухе
- Вначале на любой пилораме приобретается большой объем стружки или щепки подходящей породы древесины. Как правило, ее всегда отдают бесплатно, понадобится только оплатить доставку.
- Если такой возможности нет или материал там низкого качества, тогда при помощи рубильной машины (которую можно взять в аренду) материал подготавливается самостоятельно из пиломатериала.
- Перед использованием, щепу выдерживают на открытом воздухе 2-2,5 мес. За это время опил очищается от присутствующей в нем сахарозы, которая отрицательно влияет на качество готовых блоков (может начаться брожение).
На протяжении этого времени несколько раз щепу тормошат и обрабатывают оксидом кальция, переворачивают. Желается это для того, чтобы воздух попал и в нижний слой. Это предотвратит загнивание материала.
Обработка известняком
- Известняк смешивают с водой до получения 1,5% раствора. Для этого потребуется очень большая емкость. В полученный раствор засыпают щепку из расчета 200 л/1м3 щепы. Перемешивают 2 раза в день на протяжении 4 дней.
- Потом просеивают через крупное сито, чтобы отделить крупный мусор и оставляют просыхать.
Раствор для арболитовых блоков и заливка в формы
- Примерные пропорции для арболитовых блоков выглядят так: 25-30 кг цемента М400/25-30 кг щепы/1 кг жидкого стекла/35-40 л воды.
- Для замеса нужна электрическая бетономешалка. Вначале заливают нужный объем воды, добавляют жидкое стекло и начинают перемешивать в течение нескольких минут, для качественного смешивания.
- Затем засыпается щепа и перемешивается.
Она должна вся намокнуть, чтобы не оставалось сухих участков.
- Далее идет очереди цемента. Если засыпать сразу весь объем, неизбежно образуются комки. Поэтому засыпать надо постепенно в работающую бетономешалку.
- Не останавливая работы бетономешалки, добавляется весь цемент, пока он не образует со щепой однородной массы. Это возможно только в том случае, если щепа вся равномерно намокла.
- Готовую арболитовую смесь раскладывают в разъемные формы или опалубку. Если есть вибростол, то процесс очень упрощается. После заполнения форм только остается дождаться результата и извлечь готовые блоки.
- При самостоятельном изготовлении арболитовых блоков кустарным методом, чаще всего используется ручной труд при уплотнении. Для этого нужно подготовить трамбовалку в виде листа металла по размеру формы с ручкой.
- Форма представляет собой ящик из металла или досок без дна. Устанавливают его на абсолютно ровную поверхность, наливают слой смеси и утрамбовывают. Количество слоев зависит от высоты формы.
Чем их больше, тем более качественный и прочный получится блок. В среднем заливают примерно 5 слоев. Для удаления лишнего воздуха, смесь после каждой заливки протыкают вилами или металлическим прутом.
- Для наивысшей плотности, трамбовать нужно так, чтобы наименьше проявлялась распрессовка. Лучше всего поочередно чередовать сильные и более слабые нажимы.
- По окончанию излишки раствора счищаются мастерком.
- Наилучшей прочности добиваются посредством вибростола. В этом случае трамбовать вручную не надо. После заливки смеси в форму ее прижимают грузом и включают вибрацию на 15-20 мин.
- Дальше происходит момент сушки. Если прочность арболитового раствора высокая, форму допускается снимать сразу с сырых блоков и отправлять их на досушку. Но при более жидкой консистенции делать это нельзя. Так как блок потеряет свою геометрию.
- Технологический процесс подразумевает просушку блоков в течение 2 суток при температуре 60°C. Но в домашних условиях их сушат просто на улице в течение 2-3 недель, предварительно накрыв пленкой.
Производство арболитовых блоков видео
Советы для изготовления арболитовых блоков
- Готовую щепу можно купить у небольших производителей арболитовых блоков.
- Для более легкого извлечения блока из формы, ее внутреннюю часть отделывают гладким материалом, например, линолеумом.
- Для набора прочности блоки должны проходить гидратацию. Первые 10 дней они должны сохнуть под пленкой при температуре 13-15 °C.
- Если арболитовые блоки нужны только для утепления несущих стен, то технологический процесс можно незначительно упростить.
- Можно изготовить сразу отделочные блоки. Для этого на сырой блок прямо в форме наносят шпателем слой шпаклевки и разравнивают.
Бизнес план производства арболитовых блоков. Свой цех с нуля.
Арболит в народе еще называют древесным кирпичом. Это недорогой, а главное экологически чистый материал, который используется при малоэтажном строительстве или в качестве утеплителя для несущих стен. В его состав входит деревянная щепа или стружка, цемент и вода. А для организации всего бизнеса на производстве арболита, вам потребуется совсем немного оборудования, которое можно будет окупить в течение года.
Если говорить о процентном соотношении состава этих блоков, то в большинстве случаев стружка занимает около 60% – 85%, а цемент 15% – 40%, в зависимости от рецептуры.
Где брать сырье?
Содержание статьи
Наверное, это один из наиболее часто задаваемых вопросов, который касается этой бизнес идеи. Основным материалом, из которого изготавливаются эти блоки – это отходы от древесного производства (опилки, стружка). Часто это сырье можно купить по невысокой цене, или же и вовсе доставать бесплатно. За счет такой экономии, получается и невысокая себестоимость произведенной единицы блока, а рентабельность при этом растет. Главное подписать договор с несколькими деревообрабатывающими предприятиями, для того чтобы иметь стабильный поток нужного сырья для бизнеса на арболите.
Преимущества материала
В строительстве арболит позиционируется как материал для возведения малоэтажных конструкций, с отличными техническими показателями. К тому же ценник его ниже чем, скажем того же газоблока, что тоже играет важную роль для многих клиентов. Вот основные плюсы, которые вам нужно знать об арболите.
1.) Этот материал является экологически чистым, что в свою очередь привлекает клиентов, которые заботятся о здоровье своей семьи.
2.) Такие блоки при правильной технологии изготовления не подвергаются действию грибка и гниению, а также с ними удобно производить любые нужные операции – распил, шлифовка.
3.) Высокие звуко и теплоизоляционные характеристики.
4.) Высокие показатели огнестойкости. Из такого материала можно строить объекты, которые имеют повышенный показатель пожарной безопасности.
5.) За счет своей структуры, которая состоит из пор, обеспечивает конвекцию воздуха в помещении, а также нормальный уровень влажности.
6.) Арболит достаточно легкий, и здания, построенные с его использованием достаточно долговечны.
7.) Хорошая рентабельность, простой процесс производства, а также минимальная себестоимость.
Весь этот перечень характеристик и обеспечил арболиту популярность на рынке строительных материалов.
Из таких блоков возводят не только жилые дома, но и летние кухни, подсобные помещения, гаражи и прочее.
Еще один вариант бизнеса на производстве пеллет. О материале, оборудование, технология и расчет бизнеса.Документы
Перед тем как запустить производство вам нужно зарегистрироваться как ИП или как юр. лицо. Вторым шагом станет подбор системы налогообложения и указание ОКВЭ на деятельность.
Из разрешительной документации нужно будет еще разрешение от СЭС и пожарного надзора.
Поскольку данный вид деятельности подразумевает под собой подключение рабочих (4 разнорабочих, бухгалтер, менеджер по продажам), вам нужно будет оформить их и платить ежемесячные взносы.
Не забудьте заключить договор аренды или купли-продажи на помещение.
Технология производства арболитовых блоков
Стоит сразу отметить, что арболитовые блоки бывают также разных марок, которые в зависимости от процента в составе древесной стружки используются для различных целей. Например, марки: М5, М10, М15 используются для утепления стен, а от марки: М25, М35 для возведения несущих конструкций.
Для запуска технологического процесса вам нужно будет следующее сырье:
- цемент марки 400 или 500.
- деревянная щепа и опилки.
- химические смеси для обработки древесины.
- вода.
К примеру, для изготовления 1 куб.м. арболитного блока марки М15 используют следующую рецептуру:
- щепа — 240-300 кг.
- цемент — 250-280 кг.
- химические смеси — 12 кг.
- вода 350-400 л.
Для следующих марок, уменьшают объем щепы и увеличивают процент цементного состава.
Сам технологический процесс производства можно разделить на несколько этапов:
- загрузка отходов древесины в устройство для рубки.
Также сюда добавляют сернокислый алюминий или хлористый калий и прочие химические добавки, для обработки древесины. В установке производит разрубка отходов до необходимых размеров.
- далее в смесительную установку (бетономешалку) кроме щепы добавляют цемент и воду. На этом этапе получаем готовую арблитную смесь.
- готовый раствор разливают по пресс формам, и с помощью ручной трамбовки производится ее уплотнение. Если позволяет бюджет для этого этапа покупают вибростол.
- после завершения предыдущего процесса, блоки извлекаются из формы и отправляются в сушильную камеру на 2-3 дня.
- перемещение готовых блоков можно производить только через неделю. А сам материал можно использовать для строительства только через месяц.
Как видите, производство арболита, как бизнес не содержит в себе каких-то сложных технологических решений. Здесь главное соблюдать рецептуру и этапы трамбовки и сушки блоков в целом.
Помещение
Для небольшого цеха нужно будет арендовать как минимум 200 кв. м. 50 кв.м. площади, из которых выделить на цех, 75кв.м. на сушильную камеру и 75 кв.м. на складские помещения для готовой продукции.
Помещение должно быть вентилируемым, а также нужно, чтобы была подведена холодная вода. Обязательно наличие электросети 380В.
Не забывайте о системе пожарной безопасности, а также видеонаблюдении и охранной сигнализации. Это снизит риски потери оборудования, и вы точно будете спать спокойней.
Узнайте, как запустить собственное производство брусчатки. Выбор сырья, оборудования и технологии изготовления.
Оборудование
Комплект оборудования можно покупать либо в формате готовой производственной линии, либо формировать его самостоятельно. К тому же можно сэкономить, покупая б/у установки, и снизить ценник на оборудование до 40%. Но нужно внимательно смотреть на степень износа станков и просчитывать реальную выгоду от такого шага.
1.) Смесительная станция — $3750.
2.) Ручные трамбовки — $500/комплект. Или же вибростол – $700 за шт.
3.) Пресс формы — $120 за штуку. Для начала вам нужно будет закупить около 25 – 35 штук. Приблизительная сумма будет около $3600.
4.) Камера для сушки продукции – $8000.
5.) Устройство для рубки щепы — $4600.
6.) Поддоны для готовой продукции — $1000.
7.) Машина для транспортировки готовой продукции на поддонах (при наличии достаточного финансирования). В общие расходы мы не будем включать этот пункт.
Общая сумма – около $21 450.
Ту же сушильную камеру, которая съедает львиную долю бюджета, на первых порах можно не покупать и использовать для этого просто сухие помещения с отоплением, а со временем уже задуматься о таком профессиональном оборудовании.
Рынки сбыта
Наилучшим решением будет наладить оптовый сбыт продукции. В таком случае вы сможете работать с большими объемами.
Реализовывать можно на:
- оптовые и розничные базы и магазины строительных материалов;
- напрямую через менеджеров продаж с личными связями;
- через объявления в СМИ.
Но не стоит полностью отказываться от розничных продаж. Ведь даже частный клиент при постройке дома может закупать неплохие партии блока, да еще и по розничной цене. Поэтому тут, скорее всего, нужно комбинировать и то и другое. И очень большую роль в росте продаж будет отыгрывать менеджер по реализации арболита.
Расходы на бизнес
Какой же бизнес план без расчета основных затратных частей. Тут стоит выделить что в случае с арболитом стартовый капитал нужен совсем небольшой, и при этом его всегда можно подкорректировать за счет покупки того или иного оборудования. Мы будем разбирать покупку сразу готовой производственной линии.
Базовые затраты:
- покупка и наладка оборудования – $21000
- ремонт в помещении и подвод нужных коммуникаций – $80 на 1 кв.м.
- закупка сырья – $8000
- оформление документов – $200
Ежемесячные вложения:
- арендная плата за помещение – $9 — $12 за 1 кв.м.
- коммунальные платежи
- налоги – от $150
- заработная плата – от $200 на одного сотрудника
- транспортные расходы – $100
Стоимость ежемесячного содержания бизнеса можно снизить за счет работы в своем помещении, или же сокращении штата сотрудников, для более эффективного использования рабочей силы в целом.
Сколько можно заработать?
Допустим, что объем вашего производства будет равен 450 куб.м. арболита в месяц. Так в случае реализации по оптовой цене, которая в среднем равна $40/куб.м. тогда сумма выручки составит – $18000 в месяц. При розничной реализации ($50/куб.м.) выйдет – $22500.
Из этих сумм можно вычесть ежемесячные расходы, а также себестоимость производства блока. Чистая прибыль будет в районе $5000 – $7000.
Окупаемость бизнеса при таких объемах продаж составит около 9 – 14 месяцев.
Выводы. Заработок на арболитовых блоках – это вполне реализуемая бизнес идея малого производства, которая при сравнительно небольших денежных вложениях может приносить хороший доход. Важно только найти рынки сбыта и закупить хорошее оборудование для получения качественных блоков, а далее можно масштабировать бизнес.
Есть опыт работы в этом сегменте рынка? Ждем ваших отзывов и рекомендаций.
Производство арболитовых блоков: станки, оборудование
Технологии изготовления арболита своими руками и промышленным методом не должны иметь особых различий в наличии и последовательности следующих технологических процессов для подготовки сырья:
- производство щепы – если производство щепы осуществляется на месте, то для этой операции необходимым оборудованием является щепорез, для изготовления арболита выбирают агрегат производительностью, сопоставимой объёмам производства готовой продукции.
Для производства арболитовых блоков наилучше подходит древесина хвойных видов деревьев;
- просушка материала – для качественной просушки, древесный материл выдерживают на открытом воздухе в течение трёх месяцев. Временами материал переворачивают для лучшей просушки нижних слоёв;
- придание древесине биологической стойкости – делают это для препятствия её гниению уже будучи в составе арболитовых блоков. Для этого удаляют из щепы сахар и минерализируют её при помощи обработки в растворе гашеной извести, хлористого кальция, сернокислых алюминия или кальция, жидкого стекла. Раствор может быть как однокомпонентным, так и комбинированным. Щепу выдерживают в растворе в течение четырёх суток, перемешивая по три раза на день. Объёмное соотношение в смеси должно составлять пять частей щепы и одна раствора.
Необходимое оборудование для производства арболитовых блоков
От предполагаемой производительности будет зависеть, какое оборудование необходимо применять и, соответственно, его цена. Стоит понимать, что чем более высока технологичность всего процесса, тем менее выраженными будут недостатки арболита.
В любом случае Вам понадобится:
- растворосмеситель, лучше принудительного действия;
- станок для вибрационной трамбовки либо ручной инструмент для трамбовки;
- формы для блоков с подставками к ним.
Перечисленный набор – это самый минимум, и он больше подходит для домашней мини-фабрики. Если же продукцию планируется выпускать в промышленных масштабах, то необходима целая производственная линия, где уже не обойтись без вибрационных столов, дорогостоящих смесительных, транспортировочных, сушильных и прочих установок и станков.
Совет прораба: при изготовлении арболитовых блоков своими руками можно прибегать ко всяческим хитростям для снижения цены оснащения. К примеру, можно собственноручно изготовить формы для заливки при помощи досок, которые сколачиваются вместе. Затем они оббиваются из внутренней стороны фанерой и покрываются слоем гидроизолирующего материала, будь то полиэтиленовая плёнка, линолеум или что-то другое, что не пропускает воду. Если вы решили провести собственноручное изготовление форм для арболитовых блоков, то стоит знать, что считаются стандартными их размеры — 20-30*20*50 сантиметров, но, конечно же, они могут иметь и другой размер, на Ваше усмотрение.
Также можно приспособить какой-либо вибрирующий инструмент для виброусадки смеси, помещённой в формы.
Фото: вибростанок
Форма для арболитового блока
Изготовление арболитовых блоков
Для начала необходимо приготовить смесь для производства арболитовых блоков, которая должна состоять из трёх частей древесной составляющей, четырёх частей воды и трёх – цемента. В имеющееся у Вас смесительное оборудование ингредиенты загружаются в очерёдности, соответствующей изложенной выше. В норме образовавшаяся смесь должна выглядеть рассыпчатой, но в то же время сохранять форму, приобретённую сжатием в руке.
Далее, полученный арболит помещают в форму для формирования блока. Излишки удаляют шпателем либо мастерком, форму накрывают крышкой и в течение пяти-десяти секунд подвергают вибротрамбовке. Лучше, когда операция проводится при помощи специального вибрационного станка, но можно обойтись ручной трамбовкой либо же модернизированным Вами виброинструментом.
Следующий этап производства – это сушка арболита. Для сушки с блока снимают форму, при этом он остаётся на подставке формы, на ней он и остаётся до полного затвердевания и высыхания. Также для повышения прочности изделий можно их заворачивать в плёнку на срок до десяти дней, для более медленной влагопотери.
Подводя итоги, можно сказать, что производство арболитовых блоков вполне возможно в домашних условиях, даже без использования дорогостоящих вибрационных станков и другого подобного оборудования, что значительно снижает цену на налаживание производства. С другой стороны, есть чёткая зависимость между ценой оборудования и качеством готовой продукции, снижение одного показателя неминуемо тянет за собой вниз второй, даже при соблюдении тончайших аспектов технологии.
Видео
youtube.com/embed/WcjJ6dF6Lr4″ frameborder=”0″ allowfullscreen=”allowfullscreen”/>
Автоматизированная линия СГС-Л4 Арболит(380В/220Вт)
Универсальный комплекс оборудования для производства арболитовых и опилкобетонных блоков СГС-Л4 Арболит(380В/220В).
Возможность производить арболитовые блоки и опилкобетонные стеновые блоки размером 200х300х600мм, 200х300х500(под заказ), перегородочные 100х300х600мм, 200х200х400мм, 100х200х400мм.
Оборудование СГС-Л4 Арболит(380) позволяет производить арболитовые блоки по уникальной технологии, разработанной научными сотрудниками МГТУ им. Баумана, которая значительно экономит цемент и увеличивает марку прочности арболитовых блоков. Вы можете использовать и комбинировать любые материалы: щепа, опилки, шлак, стружка, керамзит и т.д. При этом Вы всегда получите отличный строительный материал – блоки.
На нашем оборудовании Вы получаете сразу готовое изделие, которое укладывается на стеллаж или любую ровную поверхность и для этого не требуется специальных поддонов под каждый готовый блок. Производительность оборудования 50м.куб. в сутки и больше. Минимальная площадь производственного помещения от 100м.кв.
Комплектация СГС-Л4 Арболит(380В/220В):
- Вибропресс СГС-3 (скорость производства 20секунд – 1 блок)
- Бетоносмеситель СГС-М500(принудительный, четыре лопасти, броня 12мм).
- Транспортер ленточный с приемочным бункером (длинна 5м. желобчатый)
- Бункер дозатор
- Обучение (налоги, зарплата, кадры, сырьё, поставщики)
- Рецептуры смесей (различная прочность и плотность, комбинированные смеси)
- Пробный пуск, изготовление блоков (вместе мы изготовим пробную партию, можно на Вашем сырье).
- Гарантия 1 год
ВЕС СГС-Л4 Арболит(380В/220В)- 1137/987 кг.
Предлагаем посмотреть видеоролики, где представлено в работе наше оборудование для производства арболитовых блоков:
1. Автоматизированная линия СГС-Л4 Арболит под управлением трех красавиц На оборудование СГС могут работать даже девушки. Смотреть видео
2. Видеоролик демонстрирует работу оборудования СГС-Л4 Арболит по изготовлению арболитовых блоков. Смотреть видео
НОВИНКА !
Пресс “МАСТЕР” для производства всех типов блоков и плитки !
Может работать в составе любой линии СГС !
Узнать подробности !
Оборудование для производства арболитовых блоков
Перечень необходимых механизмов
Оборудование для производства арболитовых блоков формирует линию, при помощи которой можно осуществить весь перечень операций, предвиденных технологией. В стандартную комплектацию промышленного цеха по изготовлению данного конструкционно-теплоизоляционного материала обычно входят следующие агрегаты:
- щепорез, использующийся для измельчения всех ингредиентов до оптимального размера фракции;
- растворомешалки промышленного типа, предназначенные для соединения компонентов арболита;
- формовочные дозаторы для получения материала определенного веса;
- вибростолы для удаления пузырьков воздуха из материала;
- сушка для готовых блоков и исходного сырья;
- бункеры для хранения сыпучих материалов (цемента и песка), применяющихся для изготовления арболита;
- конвейер для подачи материалов.
Конвейер для подачи материалов
Технология производства
Первоначальным этапом производства арболита является тщательная подготовка всех необходимых компонентов, затем следует приготовление основы, ее отлив в формы для дальнейшего получения блоков.
Подготовка основы
Наполнитель для блоков включает в себя стружки и опилки в пропорции 1:2 или 1:1. они должны быть хорошо просушены, для этого их выдерживают 3-4 месяца на открытом воздухе, периодически переворачивая и обрабатывая раствором извести.
В последнем случае на 1 куб. метр сырья необходимо около 200 л раствора извести 15%. В нем будут находиться древесные компоненты в течение 4 дней, которые требуется перемешивать 2-4 раза в день.
На данном этапе главная цель – это убрать сахар, содержащийся в опилках. Он может стать причиной их дальнейшего гниения.
Щепу можно купить готовую, а можно сделать самим, соорудив щепорез. Что это такое и как он работает, расскажет видео:
https://youtube. com/watch?v=9xZYAv1u9is
Необходимые компоненты
После того как опилки подготовлены, к ним присоединяют следующие добавки:
- Гашеная известь;
- Сернокислый кальций и алюминий;
- Портландцемент 400 марки;
- Растворимое жидкое стекло;
- Хлористый кальций.
Как правило, доля этих компонентов в арболитовой смеси не превышает 4% от массы цемента. Они придают конечному продукту устойчивость к гниению, обеспечивают высокую огнеупорность и пластичность.
Технология изготовления
Арболитовые блоки имеют оптимальные параметры 25 см*25 см*50 см. они удобны не только в процессе изготовления, но и при укладке. Процесс отливки заключается в следующем: блоки заполняются арболитовой смесью из трех слоев. После каждого подхода следует тщательное уплотнение деревянным молотком, обшитым жестью.
Лишняя масса ударяется при помощи линейки, а форма выдерживается сутки с температурой воздуха от +18оС. По истечению времени блоки извлекаются из форм путем небольшого постукивания и выкладываются на ровное основание для полного затвердения на 2 дня и просушивания на срок от 10 дней.
На фото — процесс выемки арболитового блока из станка после формовки:
Оборудование
Чтобы производить арболитовые блоки может потребоваться различное оборудование в зависимости от объема производства и используемого сырья. Процесс изготовления данного строительного материала и его конечный результат должны отвечать ряду критериям: ГОСТ 19222-84 и СН 549-82.
Чаще всего для производства арболита используются остатки деревьев хвойных пород. Их измельчение производится на рубильной машине (РРМ-5, ДУ-2 и прочие). Более тщательный процесс дробления производится на дробилках (ДМ-1) или молотковых мельницах. На вибростолах из измельченной древесной смеси отделяются кусочки земли и коры.
Саму арболитовую смесь рекомендуется приготавливать на лопастных растворосмесителях или смесителях принудительного цикличного действия. Перевозить готовую смесь к специальным формам можно с помощью кюбелей или бетонораздатчиков. А сам подъем транспортера не должен превышать 15о вверх и 10о вниз при скорости движения до 1 м/с. Падение смеси осуществлять на высоте не более одного метра.
Уплотнение конструкций можно произвести как ручными трамбовками, так и вибропрессом (Рифей и прочие). Если изготовить блоки из арболита необходимо в небольших объемах, то можно воспользоваться специальным мини-станком. Если речь идет о промышленных масштабах, то используют целые линии по производству арболитовых блоков, которые включают в себя станки для изготовления блоков, прессы и смесители.
Так выглядит линия по производству арболитовых блоков
Лучший процесс затвердения достигается путем использования тепловых камер с ТЭНом, ИК-излучением и т. д. В них можно контролировать необходимую температуру и уровень влажности.
Щепорезы
Щепорезом называют промышленный измельчитель, который способен работать с деревянными щепами, соломой или опилками. Порезка материалов на частицы нужного размера осуществляется в барабане при помощи нескольких ножей, изготовленных из инструментальной стали. В конструкции щепореза присутствует молоток. Он осуществляет автоматическую подачу материала при измельчении массивных досок или веток.
Рабочие инструменты щепореза окружены по контуру специальным барабаном с перфорированными стенками. Именно через эти отверстия пересыпается готовая деревянная щепа. Наружный кожух из листовой стали предотвращает рассыпание опилок по помещению и выполняет защитную функцию. Эффективная работа данного оборудования обеспечивается наличием трехфазного двигателя, ременных приводов и пусковых устройств.
Сушка
Изготовленная щепа в обязательном порядке подвергается сушке.
Это может происходить природным путем или при помощи специальных агрегатов. От качества проведения сушки сырья зависят эксплуатационные характеристики арболитовых блоков.
Для повышения эффективности данного процесса промышленное оборудование отличается следующими конструкционными особенностями:
- сушка представляет собой двойной барабан, имеющий диаметр около 2,2 м;
- наружный кожух агрегата оснащен перфорированными стенками, что обеспечивает проникновение теплого воздуха внутрь;
- в конструкции сушки присутствуют асбестовые трубы или специальные гибкие шланги.
Они предназначены для подачи теплого воздуха;
- барабан постоянно крутится, что позволяет перемешать щепу и равномерно ее подсушить;
- тепловая энергия производится пушками, мощность которых может достигать 4 кВт.
В зависимости от технических характеристик оборудования за одну смену удается просушить сырье для изготовления 100 блоков.
Технология изготовления арболитовых блоков + Видео как делают
Наиболее востребованными изделиями из данного вида бетона, являются кладочные блоки большого формата. Производители наладили выпуск различных типоразмеров этого строительного материала, но самым ходовым считается формат 500х300х200 мм.
Технология производства регламентируются следующими государственными документами:
- СН 549-84 «Инструкция по проектированию, изготовлению, применению конструкций и изделий из арболита»;
- ГОСТ 19222-84 «Арболит и изделия из него. Общие технические условия».
Согласно этим стандартам, в составе блоков должны присутствовать следующие компоненты:
- вода;
- цемент;
- щепа древесная;
- химические, в том числе регулирующие пористость, добавки.
Наполнитель
В качестве него обычно используют древесную щепу. ГОСТ 19222-84 также допускает для производства использование измельчённых стеблей риса, хлопка, костра льна или конопли.
Частицы древесины не должны быть больше следующих размеров: 40х10х5 мм. Массовая доля коры не должна превышать 10%, а хвои и листьев – 5% в смеси заполнителей.
Для остальных материалов/сырья регламентируются только длина частиц – не более 40 мм и содержание очёсов и пакли – до 5% от общей массы.
Химические добавки
Используются для улучшения свойств смеси и готового арболита. Их разделяют на несколько групп:
- регуляторы пористости смеси;
- ускорители отвердения;
- ингибиторы коррозии стали;
- добавки, придающие арболиту инсектицидные и бактерицидные свойства;
- компоненты, увеличивающие адгезию цементного теста с деревянной щепой;
- полифункциональные присадки.
Вода
На производстве для приготовления смеси используют воду, соответствующую ГОСТ 23732-79. Сначала приготавливают водный раствор минерализаторов для увеличения адгезии (хлорид кальция, известь, жидкое стекло и пр.) в специальном смесителе. После этого к раствору добавляется древесная щепа и перемешивается 20 секунд. Затем раствор заливается цементом с остальными добавками и перемешивается до однородной массы в течении 3 минут.
Цемент
Прочность изделий будет сильно зависеть от выбранной марки этого материала. Для производства теплоизоляционного арболита нужен портландцемент марки 300. А для конструкционного потребуется марка не ниже 400.
Процесс формирования
Закончить придание окончательной формы необходимо не позже 15 минут после приготовления смеси. Для этого используют методы ручного и механического формирования:
- ручное без вибрирования;
- ручное с вибрированием;
- с использованием вибростанка;
- на вибростанке с пригрузом.
Естественно, блоки, при производстве которых использовался метод ручного формирования, обладают более низкими показателями механических параметров, меньшей точностью геометрических размеров по сравнению с изделиями из арболита, производимыми на вибростанках. Сырые блоки подвергают вибрации не с целью повысить их плотность. Эта процедура необходима на производстве для равномерного распределения древесных частиц в цементном растворе и их произвольного переориентирования. Размеры блока при этом остаются неизменными. Прочностные характеристики изделий, прошедших процедуру уплотнения, будут отличаться в зависимости от степени вибрации. Слишком интенсивное воздействие может привести к опусканию цементного теста. Поэтому здесь применяют умеренную вибрацию.
Видео как делают арболитовые блоки:
Готовые изделия из арболита должны выдержать испытания, описанные в ГОСТ 19222-84. Ответственность за проведение испытаний и их результаты возлагаются на производителя арболитовых блоков.
Смесительные станции или растворомешалки
Во время производства арболитовых блоков чаще всего используют мешалки периодического действия, иногда строительные миксеры. На крупных линиях, где изготовление материала происходит большими партиями, устанавливается оборудование с непрерывным характером работы.
Для обеспечения потребностей небольших производств в основном используют обычные растворомешалки, которые имеют следующие конструкционные особенности:
- представляют собой большие чаны с боковой загрузкой компонентов и нижней выгрузкой готовой смеси;
- агрегат оснащен двигателем с редуктором, максимальной мощностью 6 кВт;
- для смешивания компонентов арболита используются специальные лопасти.
Объем растворомешалки рассчитывается на основании суточной потребности в материалах для организации эффективного производственного процесса.
Линия для производства арболитовых блоков
Схема вибростола для арболита
Оптимальным вариантом является производство самодельного вибростола, а также небольшого ручного пресса для окончательного формирования строительного материала. В дальнейшем их можно использовать в оборудовании по производству шлакоблока, тротуарной плитки и т.д.
Для производства вибростола понадобится опорная рама и стальная столешница. Последняя будет крепиться на опорных пружинах. Вибрация происходит за счет движения эксцентрика, расположенного в центре столешницы.
Прессовальная форма должна иметь съемное дно. После окончательного формирования изделия оно помещается на деревянную подставку и переносится в зону просушки. В качестве пресса можно использовать любую самодельную конструкции. Оптимальной является рычажная схема.
Для массового производства блоков своими руками необходима профессиональная линия. Ее стоимость зависит от производительности и комплектации.
В видеоматериале показан пример производства с минимальной комплектацией линии:
youtube.com/embed/3jtCxXHROsw?feature=oembed” frameborder=”0″ allow=”accelerometer; autoplay; clipboard-write; encrypted-media; gyroscope; picture-in-picture” allowfullscreen=””/>Формы для арболита
Готовая смесь для изготовления блоков распределяется по съемным формам.
Они представляют собой специальный короб, изготовленный из стали. Для облегчения эксплуатации каждая форма оснащается боковыми ручками и съемными крышками (верхней и нижней). От количества форм и их качества зависит мощность производства, что напрямую влияет на прибыль предприятия.
Другое оборудование для формирования блоков
Нагретые и очищенные формы наполняются готовым раствором. Данный процесс осуществляется при помощи формовочных дозаторов шнекового типа. При небольших объемах производства распределения раствора по формам может осуществляться вручную.
Когда данный процесс закончен, приступают к трамбовке, которая позволяет уплотнить арболитовую смесь и удалить из нее пузырьки воздуха. В данном случае применение ручных инструментов нецелесообразно. Ручная трамбовка не обеспечивает достаточных показателей прочности готовых блоков.
Поэтому для уплотнения раствора чаще применяют статические или вибрационные станки.
Вибрационные станки для арболита
Первый тип оборудования встречается на небольших производствах, а вторая разновидность является частью оснащения мощных конвейерных линий. Вибростолы, которые чаще всего можно встретить в цехах по выпуску арболита, отличается следующими характеристиками и конструкционными особенностями:
- представляет собой стальной стол;
- на станине, являющейся частью оборудования, находится трехфазовый двигатель мощностью 1,6 кВт или меньше;
- на ось мотора установлены эксцентрики или специальные грузы. Их центр тяжести смешен, что позволяет создать вибрацию.
Достоинства и недостатки арболитовых блоков
Калькулятор расчета арболитовых блоков
Следует отметить, что в прошлом веке арболит использовался не только для изготовления стеновых блоков, но также выпускался в виде листов, которые применяли для утепления и звукоизоляции полов.
Сегодня в этом качестве древобетон практически не используется, потому что его основные достоинства раскрываются при возведении малоэтажных зданий. Перечислим их более подробно.
— Низкая теплопроводность
Стеновые блоки из арболита относятся к категории эффективных теплоизолирующих материалов. Об этом говорит следующий факт: стена из арболита толщиной всего в 30 см так же хорошо удерживает тепло, как кирпичная кладка метровой толщины.
Поэтому в отзывах владельцев домов из арболитовых блоков в первую очередь отмечается существенная экономия топлива даже в самые холодные зимы.
— Прочность
Прочность арболитовых блоков напрямую зависит от их плотности. Для конструкционно-теплоизоляционного древобетона плотностью 600-650 кг/м3 она составляет от 20 до 35 кг/см2. По данному показателю арболит практически не отличается от своих главных конкурентов – пено и газобетона.
Важным плюсом является пластичность этого материала. Данный факт объясняется тем, что в состав арболитовых блоков входит древесная щепа, армирующая этот материал. Поэтому под нагрузкой древобетон не трескается, а только немного деформируется без потери целостности.
Возводя дом из арболита, вам не придется тратить лишние деньги и время на заливку бетонного армированного пояса, который необходим для хрупких стен из газо и пенобетонных блоков.
— Морозостойкость
У арболита морозостойкость (количество циклов замерзания-оттаивания в водонасыщенном состоянии) составляет от 25 до 50. На практике это означает, что дом из этого материала простоит не менее 50 лет (подтверждено исследованиями существующих зданий). У пеноблоков сопротивляемость замораживанию и оттаиванию не превышает 35 циклов.
Говоря о плюсах арболита, следует также сказать о его низкой карбонизационной усадке. Этим термином обозначают процесс потери прочности цементным камнем из-за реакции с атмосферным углекислым газом, в результате которой получается мягкий мел.
— Хорошая звукоизоляция
У арболитовых блоков в акустическом диапазоне от 125 до 2000 Гц коэффициент звукопоглощения составляет от 0,17 – 0,6. У кирпича этот показатель хуже почти в четыре раза. У древесины он находится в границах от 0,06 до 0,1, что так же существенно меньше, чем у древобетона.
— Легкий вес
1 м3 блоков из конструкционно-теплоизоляционного арболита весит почти в 3 раза меньше кирпича и почти в 1,5 раза меньше керамзитобетона. Это позволяет существенно снизить затраты на возведение фундаментов под арболитовые стены.
— Экологичность и долговечность
Древобетон – один из самых экологичных строительных материалов, поскольку в его состав входят только натуральные компоненты – цементный камень, древесная щепа, вода, хлористый кальций (используется в пищевой промышленности) или обычное известковое молоко.
В стене этот материал ведет себя превосходно, поскольку не гниет, не боится плесневых грибков и не горит. Кроме этого, древобетон хорошо дышит и регулирует влажность воздуха в помещении, поглощая избыток влаги и отдавая ее при недостатке.
— Негорючесть
Арболит относится к группе трудногорючих материалов (группа горючести Г1). Кроме этого, древобетон является трудновоспламеняемым (группа воспламенямемости В1) и малодымообразующим материалом (Д1).
— Легкость обработки
Древобетон легко обрабатывается любым механическим инструментом. Его можно пилить и сверлить, он хорошо держит гвозди и шурупы. Шероховатая поверхность блоков является идеальной основой для нанесения штукатурных растворов без использования армирующих сеток.
К минусам арболитовых блоков можно отнести невысокую точность геометрических размеров. Поэтому стены из этого материала требуют выравнивания штукатурными растворами или листовыми отделочными материалами (гипсокартон, магнезит, вагонка, сайдинг).
Поскольку технология изготовления арболита основана на использовании древесной щепы – достаточно дорогого материала, то стоимость блоков из древобетона превышает цену газобетона в среднем на 15-20%.
Камеры для сушки готовых блоков
Готовые блоки, которые спрессованы должным образом, вместе с формами подаются в специальное помещение. В нем влажность воздуха строго контролируется, что позволяет создать лучшие условия для высушивания материала. Блоки в обязательном порядке раскладываются по поддонам и освобождаются от форм. Это облегчает доступ воздуха до материала, что положительно сказывается на его свойствах.
Камера для сушки арболита
Схватывание смеси обычно происходит через 2 суток. Проектная мощность материала достигается только спустя 18-28 дней. Все это время арболит должен находиться в условиях достаточной влажности и стабильной температуры.
В условиях ограниченных ресурсов допускается сушка блоков в любом затемненном месте. В таком случае их необходимо накрыть полиэтиленовой пленкой и защитным тканевым тентом. Через несколько дней такие материалы переносят в помещение с бетонным полом и складывают в один слой.
Вибропресс для арболитовых блоков от ТМ БУМ Вибропресс
Вибропрессы
Формовочная зона 0,36 м²
Вибропресс БП-120Мощность потребляемая:
9,0 кВт 380 В 50 ГцПроизводственный цикл:
60 сек.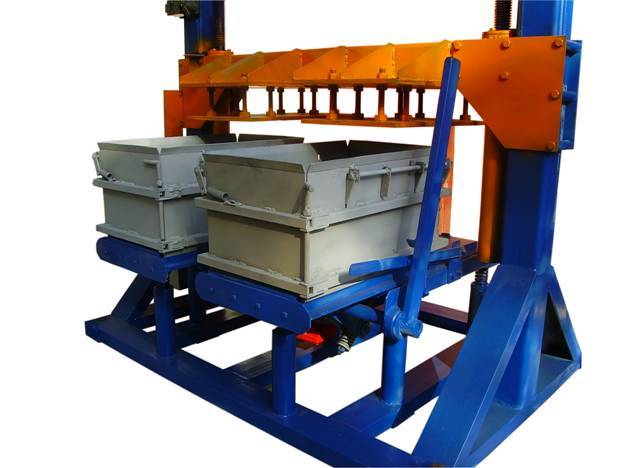
Количество циклов в час:
60 шт.Управление:
полуавтоматическоеОбслуживающий персонал:
3 чел. Вибропресс БП-160Мощность потребляемая:
13 кВт 380 В 50 ГцПроизводственный цикл:
45 сек.
Количество циклов в час:
80 шт.Управление:
автоматическоеОбслуживающий персонал:
3 чел.Формовочная зона 0,6 м²
Вибропресс БП-200Мощность потребляемая:
15 кВт 380 В 50 ГцПроизводственный цикл:
60-90 сек.
Количество циклов в час:
40-60 шт.Управление:
полуавтоматическоеОбслуживающий персонал:
3 чел. Вибропресс БП-250Мощность потребляемая:
21 кВт 380 В 50 ГцПроизводственный цикл:
45 сек.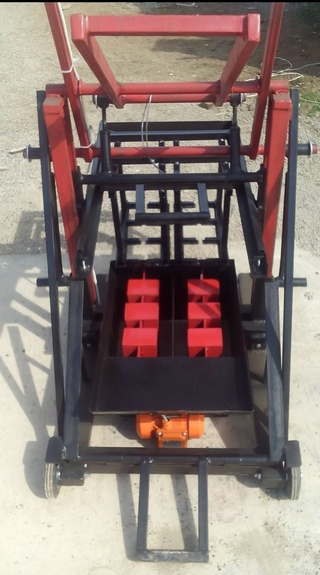
Количество циклов в час:
80 шт.Управление:
автоматическоеОбслуживающий персонал:
3 чел. Вибропресс БП-350Мощность потребляемая:
23 кВт 380 В 50 ГцПроизводственный цикл:
30 сек.
Количество циклов в час:
120 шт.Управление:
автоматическоеОбслуживающий персонал:
2 чел. Вибропресс БП-550Мощность потребляемая:
37,0 кВт 380 В 50 ГцПроизводственный цикл:
20 сек.
Количество циклов в час:
180 шт.Управление:
автоматическоеОбслуживающий персонал:
2 чел.Формовочная зона 1 м²
Вибропресс БП-1000Мощность потребляемая:
65,0 кВт 380 В 50 ГцПроизводственный цикл:
18 сек.
Количество циклов в час:
200 шт.Управление:
автоматическоеОбслуживающий персонал:
2 чел.Нужен вибропресс для арболитовых блоков? Заказать оборудование вы можете в компании «БУМ Вибропресс» с доставкой по Украине. Мы предлагаем современные и рентабельные машины, которые смогут экономить потребление электроэнергии. Станки удобны и просты в эксплуатации и техническом обслуживании. Готовы предложить вам модели оборудования с различными модификациями и техническими характеристиками.
Что такое арболитовые строительные блоки?
Арболитовые блоки имеют в своем составе щепу хвойных или лиственных пород деревьев. За счет смешивания с бетоном и присадками получаются прочные и морозостойкие стройматериалы. Дома, построенные из таких блоков, стоят более 50 лет.
Кроме того, изделия отличаются небольшой массой, что значительно облегчает процесс строительства и транспортировки. За счет этого постройки можно возводить на облегченных фундаментах (столбчатых, свайно-винтовых и так далее).
Производство стройматериалов путем вибропрессования
Для изготовления стройматериала применяется метод вибпропрессования. За счет использования при производстве жесткой бетонной смеси с минимальным количеством воды, готовое изделие получается прочным, износостойким и более плотным, несмотря на свою небольшую массу.
Вибропресс для производства арболитовых блоков позволяет:
- Ускорить процесс. Благодаря высокой производительности станки способны производить большие партии в минимальные сроки.
- Сэкономить электроэнергию. Современные устройства позволяют сократить расход электричества в несколько раз.
- Минимизирует человеческий фактор. Для управления установкой требуется максимум два оператора.
Новые модели вибропрессов удобны и просты в обслуживании. Кроме того, они быстро окупаются, что является довольно весомым преимуществом.
Как заказать оборудование?
Чтобы оформить заказ на станок для производства арболитовых блоков, вам нужно связаться с менеджером компании «БУМ вибропресс» в телефонном режиме. Актуальная контактная информация и график работы указаны на сайте. Мы предлагаем удобные способы оплаты продукции, а также доставку по всей территории страны.
Другие статьи:
Оборудование для производства арболитовых блоков
Автор статьи: Судаков А. П.
Уникальные свойства бетона используются при производстве различных материалов, одним из которых является арболит. Его отличительные характеристики обусловлены добавлением в раствор опилок. В некоторых технологиях допускается их замена на рисовую солому, кору или на измельченные стебли хлопчатника. Размер включений добавок и их примененное количество, оказывают влияние на качество готовой продукции и отнесение ее к определенной марке. Какова технология производства строительного материала и можно ли его изготовить своими руками?
Арболитовый блок
Общая информация о строительном материале
Бетон считается универсальным строительным материалом, свойства которого зависят от наполнителя. Его жидкая консистенция на сырьевом и полуфабрикатном этапе производства обуславливает простоту работы с ним. После залития подготовленного бетонного раствора в специальную форму или в опалубку, спустя некоторое время, необходимое для высыхания материала, получается прочное изделие нужных размеров.
На прочность готового изделия оказывают влияние добавки в раствор вяжущих компонентов, в качестве которых актуально применение цементной смеси, маркировка которой не должна быть ниже М 300. Для улучшения соединения всех компонентов раствора и ускорения его затвердевания, используются специальные добавки, такие как хлористый калий, алюминий или жидкое стекло.
Критерием качества готовых блоков является равномерное распределение включений по изделию, что обеспечивает его одинаковую прочность по всему его объему. Для обеспечения таких характеристик необходимо учитывать требования технологического процесса, особенно уделяя внимание продолжительности и тщательности перемешивания составляющих элементов, поскольку в сырьевом состоянии древесная щепка и цемент сочетаются плохо.
Оборудование для производства
Для блоков используются опилки из ели, сосны или бука. Размер частиц оказывает влияние на теплопроводность, парапроницаемость и прочность готового изделия. Оптимальные параметры соответствуют величине 10х25 мм.
Преимущества и недостатки строительного материала
Для арболитовых блоков характерны высокие показатели энергоэффективности, что позволяет использовать их для оборудования стен дома с внешней стороны. Плотность строительного материала не позволяет его применять при возведении многоэтажных домов, поэтому такие блоки актуальны только для строительства малоэтажных объектов. Материал выдерживает нагрузки при резких температурных колебаниях, способствующих образованию трещин на стенах дома.
Теплоизоляционные свойства материала превышают характеристики кирпича и стандартных блоков из чистого бетона. Он вобрал в себя все лучшие качества древесины, при этом оставаясь пожаробезопасным, не разрушающимся и не дымящим под воздействием высоких температур и прямого огня. Дом из арболитовых блоков надолго сохраняет тепло при отключении отопления даже при отрицательной температуре за его пределами. Срок службы материала напрямую зависит от его качества и порядка эксплуатации. Он сохраняет свои свойства в температурном пределе от +25 до -500С. При чередовании сильных морозов и оттепелей, срок годности арболита сокращается.
Материал сравнительно недорогой, его несложно подгонять под нужный размер, однако блоки не отличаются эстетичным внешним видом, поэтому для придания сооружению респектабельного вида, понадобится облицовка. Погрешности в размерах блока, избежать которые в процессе производства сложно, могут стать причиной неравномерностей кладок шва. Небольшой вес блоков позволяет сэкономить на качестве фундамента, поскольку на него не будут оказаны высокие нагрузки.
Бизнес решение
Технологическая линия
На его производстве специализируются не только крупные заводы, но и небольшие частные фирмы, что обусловлено несложными технологическими операциями. Предприниматель, решив открыть линию по изготовлению арболитовых блоков не должен ориентироваться на дешевизну готового изделия. Несмотря на ценовую привлекательность, повторно клиенты не обратятся за строительным материалом и не порекомендуют продавца свои знакомым, ввиду низких качественных характеристик. Производителю рекомендуется ориентироваться на нормы ГОСТов, при соблюдении которых показатели прочности блоков будут идентичны пеноблоку.
Виды продукции
Различают конструкционные и теплоизоляционные арболитовые блоки. Конструкционные модели отличаются высокой плотностью за счет большего содержания цемента по отношению к опилкам. Они применимы для возведения несущих опор и стен. Для их большей плотности допускается армирование блоков стержнями или сеткой.
При изготовлении теплоизоляционного материала щепки используют в больших пропорциях, чем цемент. Готовое изделие может быть использовано в качестве теплоизоляционного слоя, а также для строительства межкомнатных перегородок.
Планируя производство, необходимо учитывать, что арболит выпускается в виде монолита или блоков.
Монолитные блоки изготавливаются на строительной площадке. После замеса раствор используется полностью. Он заливается в несъемную опалубку из пенопласта. Для дальнейшей деятельности придется неделю подождать для схватывания и застывания состава. Такой метод производства актуален при необходимости теплоизолировать помещение.
Стандартная блоковая продукция изготавливается в соответствии с требованиями нормативно-правовых актов. Готовое изделие имеет вид блоков, что достигается посредством залития раствора в заранее подготовленные формы.
Технология производства
Производство арболитовых блоков не отличается сложностью. Для его обеспечения не требуется громоздкого оборудования, поэтому для его размещения достаточно небольшой постройки, в качестве которой можно использовать гараж или сарай.
Процедура занимает много времени, поскольку для получения готового изделия необходимо ожидать затвердевания состава, который приобретает нужную плотность только при температуре выше 120С. Это обуславливает невозможность обеспечения больших производственных объемов, особенно в случае ограниченного количества форм для заливки. Ускорить процесс возможно за счет применения специальных добавок, ускоряющих затвердевание при любом температурном режиме. Однако, их использование приведет к удорожанию строительного материала.
Общий технологический процесс проводится в соответствии с алгоритмом:
- приобретение сырьевой продукции;
- подготовка сырья;
- смешивание;
- разлив по формам;
- тромбовка;
- сушка.
Подготовка опилок
В качестве сырьевых материалов используются опилки и цемент.
Деревянные щепки можно достать на лесопилке. Допускается использовать продукт из любого дерева, кроме тополя и лиственницы. Чтобы снизить транспортные расходы, рекомендуется открывать производство неподалеку от источника сырья, поскольку в противном случае, расходы на его доставку, могут придать бизнесу нерентабельный статус.
Прежде чем загружать щепу в аппарат для смешивания, необходимо привести ее в размерное соответствие. Стандарты ГОСТ предъявляют к параметрам включений жесткие требования, поскольку их характеристика влияет на качество готового изделия. Поэтому, самостоятельное изготовление арболитовых блоков, требует включения в алгоритм этапа мероприятия, предполагающего измельчение опилок при помощи дробилки. Для этого можно использовать любой вид оборудования, измельчение в котором может быть основано на молотковом, дисковом или роторно-ножовом принципе.
Приготовление раствора
При подготовке рабочего раствора должны быть соблюдены строгие пропорции его составляющих элементов, поскольку каждый из них влияет на характеристику готовой продукции. Несоблюдение нормативов может стать причиной изготовления непрочного или крошащегося продукта, который сложно будет применить в строительных целях.
При приготовлении раствора опытные специалисты пользуются специализированными дозаторами. При их отсутствии можно ориентироваться на весовые или объемные показатели.
Перемешивание
В емкость для перемешивания помещают опилки и цемент. Для равномерного смешивания лучше использовать специальное оборудование для производства арболитовых блоков. При его отсутствии достаточно иметь бетономешалку для обеспечения длительного замеса. Стоит отметить, что ручного перемешивания лопатой недостаточно, поскольку таким методом невозможно добиться хорошего качества смеси.
Заливка, трамбовка, отвердевание
Готовая смесь размещается в специальных металлических или деревянных формах. Оборудование для производства арболита упрощает проведение процедуры за счет возможности заливки форм через желоб. Профессиональные устройства позволят хорошо затрамбовать смесь на вибростоле. Поскольку цемент очень плохо смешивается с щепой, то нормативные требования регламентируются проведение трамбовки не менее 20 минут. Плохо выполненная работа на этом этапе может стать причиной отделения бетона от щепы и его утрамбовка на дне.
На отвердевание выделяется до трех недель при условии размещения полуфабрикатов в проветриваемом складе. Снятие форм допускается через сутки. Для ускорения процедуры на этапе смешивания в раствор необходимо добавить вещества, выполняющие функции катализаторов.
Какое оборудование применяется в производстве
Производство арболитовых блоков не предусматривает необходимость приобретения специальной линии. Достаточно купить оборудование для реализации отдельных операций. Станок для производства арболитовых блоков представлен в виде бетономешалки, поддона из металла для удобства размещения на нем полуфабрикатов. Отдельно придется приобрести формы, вибросито и вибростол. В качестве вспомогательных элементов пригодятся лопата, ведро и мастерок.
Вконтакте
Одноклассники
Google+
Прочный деревянный поддон для машины для производства бетонных блоков Для легкого подъема и несения нагрузки Услуги по проектированию и настройке
Перейдите на сайт Alibaba. com и откройте для себя удивительную коллекцию деревянных поддонов для машины для производства бетонных блоков . Этот выбор включает невероятное разнообразие деревянных поддонов для машины для производства бетонных блоков размеров, конструкций и материалов и специально используется для удовлетворения разнообразных потребностей разных покупателей. Вы найдете самый практичный деревянный поддон для машины для производства бетонных блоков , чтобы повысить вашу производительность, независимо от того, нужны ли вам поддоны для крупных грузов или для небольших подъемов.Их заманчивые предложения делают их доступными.
Деревянный поддон для машины для производства бетонных блоков , изготовленный из прочных материалов, отличается невероятной долговечностью и прочностью, что обеспечивает превосходную производительность. Исключительная грузоподъемность этих деревянных поддонов для машины для производства бетонных блоков делает их идеальным вариантом в различных условиях. Несмотря на свою огромную прочность и несущую способность, деревянный поддон для машины для изготовления бетонных блоков имеет небольшой вес, поэтому избегайте лишнего веса в процессе подъема.Их совместимость с различными продуктами и погрузчиками делает их идеальными для всех отраслей промышленности.
Деревянный поддон для машины для производства бетонных блоков , представленный на Alibaba.com, имеет атрибуты высшего качества, соответствующие всем нормативным стандартам и спецификациям. Их поставляют проверенные и проверенные деревянные поддоны для машины для производства бетонных блоков , оптовые торговцы и поставщики, которые соблюдают все требования. Их низкие эксплуатационные расходы и низкие затраты гарантируют, что они предложат вам максимальную ценность.Деревянный поддон для машины для производства бетонных блоков не наносит вреда окружающей среде и способствует устойчивости благодаря возможности повторного использования. Даже если они повреждены, их можно отремонтировать или переработать для непрерывного использования.
Пусть ваши инвестиции принесут вам максимальную прибыль, поскольку вы будете удобно совершать покупки в Интернете на Alibaba.com. Вы сэкономите много времени и энергии, исследуя площадку для поиска идеального деревянного поддона для машины для производства бетонных блоков серии . Выберите наиболее подходящий вариант в соответствии с вашими требованиями и поймите, что они стоят каждого доллара, который вы на них потратите.
Изолированные бетонные формы против деревянного каркаса: выбор лучшей конструкции
Изолированные бетонные формы (ICF) создают более энергоэффективное, тихое и здоровое здание, чем здание, построенное с использованием деревянного каркаса. Здания ICF также более устойчивы к стихийным бедствиям, пожарам, насекомым и проникновению влаги, чем конструкции с деревянным каркасом.
Кроме того, строители и архитекторы могут избежать нестабильности и увеличения стоимости пиломатериалов, используя простую в установке стеновую систему ICF, такую как Fox Block, в качестве отличной альтернативы деревянному каркасу.
На протяжении более 100 лет строительство с деревянным каркасом было обычным явлением в Соединенных Штатах, потому что оно быстрое, легкое, возобновляемое и легко настраиваемое. Деревянное строительство также не требует тяжелого оборудования или инструментов.
Однако архитекторы, подрядчики и владельцы зданий должны столкнуться с несколькими проблемами при строительстве деревянных каркасов: устойчивость к стихийным бедствиям, пожарам и термитам, проникновение влаги, ухудшение качества воздуха в помещении (IAQ), контроль шума, низкая тепловая масса, и рост цен на древесину.
7 Проблемы с деревянным каркасом1. Дополнительные расходы
Устойчивое к стихийным бедствиям здание с деревянным каркасом должно выдерживать постоянную нагрузку на землю и быть устойчивым к ракетам. Построение устойчивой к стихийным бедствиям конструкции с деревянным каркасом выполнимо, но это дорого и трудоемко. Фактически, строительство устойчивого к стихийным бедствиям здания с деревянным каркасом может стоить на 25–30 процентов дороже, чем строительство стандартного деревянного каркаса.
2.Повышенный риск пожара
Построить огнестойкую деревянную каркасную конструкцию сложно, потому что древесина горючая и трудно уменьшить распространение пламени. Здания с деревянным каркасом особенно уязвимы для возгорания во время строительства до установки противопожарной защиты на каркас.
3. Привлекательность для термитов
Деревянное каркасное строительство подвержено проблемам термитов. Термиты могут повредить здание, а их ремонт будет стоить тысячи долларов.Фактически, ежегодные предполагаемые расходы на нанесение ущерба термитам и меры борьбы с ними в США составляют 5 миллиардов долларов. Защита от термитов для деревянного каркаса является сложной задачей и требует квалифицированного профессионального и специализированного оборудования.
4. Накопление влаги
Каркасные конструкции из дерева склонны к накоплению влаги в полостях стен. Контроль влажности в системе стен деревянного каркасного здания затруднен, поскольку эффективные методы, предотвращающие попадание влаги в полость стены, также могут препятствовать выходу влаги из полости стены.
5. Летучие органические соединения
Деревянные каркасные здания могут содержать клеи, химические вещества и летучие органические соединения (ЛОС), ухудшающие качество воздуха в помещении. Выбросы ЛОС могут вызывать раздражение глаз, носа и горла, головные боли, тошноту и повреждение почек, печени и центральной нервной системы.
6. Более высокая звукоизоляция
При строительстве стен с деревянным каркасом требуются звукоизоляционные свойства, чтобы дом был тихим и спокойным. Снижение шума в здании с деревянным каркасом достигается за счет ограничения звуковых колебаний с помощью изоляции, размещения стоек или дополнительной массы в полости стены.
7. Низкая тепловая масса
Древесина имеет низкую тепловую массу. Следовательно, конструкции с деревянным каркасом не так энергоэффективны по своей природе, как здания, построенные из материалов с высокой тепловой массой, таких как камень, саман и изолированные бетонные формы Fox Blocks.
ICFs Vs. Конструкция с деревянным каркасомСтеновая система Fox Block ICF проще в установке, более энергоэффективна и снижает уровень шума, чем конструкция с деревянным каркасом. Система Fox Block также более здоровая и более устойчива к стихийным бедствиям, пожарам, термитам и влаге, чем системы деревянных стен.Наконец, строительство ICF дает строителям возможность избежать нестабильности и роста цен на пиломатериалы.
10 причин выбрать Fox Blocks ICF вместо деревянных каркасных стеновых систем1. Сведение к минимуму ненужных шагов
Fox Block – это сборка стен «все в одном», которая объединяет пять этапов строительства в один, включая конструкцию, изоляция, воздушный барьер, пароизоляция и крепление для внутренней и внешней отделки. Эта функция значительно ускоряет реализацию проекта, устраняя необходимость координировать несколько сделок при достижении всех целей настенной системы.
2. Повышенная энергоэффективность
Fox Blocks со значением R 23 являются энергоэффективными и превышают требования энергетического кодекса ASHRAE / ANSI 90.1. Фактически, дома, построенные с внешними стенами ICF, обычно требуют на 32 процента меньше энергии для охлаждения и на 44 процента меньше энергии для обогрева, чем сопоставимые дома с деревянным каркасом.
3. Высокая тепловая масса
Высокая тепловая масса блоков Fox способствует созданию высокоэффективной и энергоэффективной конструкции.Материалы с высокой термальной массой поглощают и накапливают тепловую энергию и помогают стабилизировать температурные сдвиги внутри конструкции за счет снижения скорости теплопередачи.
4. Снижение передачи шума
Испытания на передачу звука показали, что менее трети звука проходит через стены ICF, чем стены с деревянным каркасом, заполненные изоляцией из стекловолокна. Блоки Fox Blocks соответствуют классификации передачи звука (ASTM E90): 4 дюйма = STC 46, 6 и 8 дюймов = STC 50+.
5.Лучшее качество воздуха
Fox Blocks практически не содержат летучих органических соединений, что позволяет поддерживать качество воздуха на более высоком уровне.
6. Исключительная прочность
Fox Blocks устойчивы к бедствиям: Fox Blocks, армированные сталью, устойчивы к стихийным бедствиям и могут противостоять торнадо и ураганным ветрам со скоростью более 200 миль в час, а также обломкам снарядов, движущимся со скоростью более 100 миль в час.
7. Пониженный риск возгорания
Fox Blocks огнестойкие. Блоки Fox имеют рейтинг огнестойкости (ASTM E119): 4 часа для 6-дюймовых блоков и 2 часа для 4-дюймовых блоков.
8. Сдерживает термитов и вредителей
Лисица меньше подвержена повреждению термитами, потому что в них отсутствует органический материал, который поедают такие вредители, как термиты.
9. Контроль проникновения влаги
Fox Blocks обеспечивает прочную непрерывную монолитную бетонную стену с рейтингом проницаемости менее 1,0, который контролирует проникновение влаги и предотвращает рост плесени, грибка и гниения.
10. Меньшая изменчивость цен на материалы
Строители и архитекторы могут избежать нестабильности и увеличения стоимости пиломатериалов, выбрав альтернативу стенам с деревянным каркасом, например, изолированные бетонные формы Fox Blocks.
Выбор альтернативы деревянному каркасуОтличной альтернативой деревянному каркасу является настенный монтаж Fox Block ICF.
Конструкции Fox Block ICF более устойчивы к стихийным бедствиям, пожарам, насекомым и проникновению влаги, чем здания с деревянным каркасом.
Кроме того, Fox Blocks создает более эффективное, шумоподавляющее и здоровое здание, чем деревянные конструкции. Более того, Fox Blocks также просты в установке и представляют собой альтернативный продукт для борьбы с ростом цен на пиломатериалы.
Посетите Fox Blocks для получения дополнительной информации о конструкциях ICF и деревянных каркасов.
Объяснение сверл по камню | Лучшие сверла 2021
Чтобы проделать отверстие в каменной кладке и камне, вам понадобится сверло для каменной кладки – и знать, как правильно ее использовать. Это может быть не часто, что вам действительно нужно делать это, но задача возникает время от времени, как мы сейчас переживаем, когда цех готов в новом офисе Popular Mechanics , и мы приступили к строительству и установка всего необходимого нам оборудования.Пол в магазинах бетонный, стены – бетонные.
Выполните сверление кирпичной кладки правильно, и тяжелая работа станет намного более предсказуемой с желаемыми результатами: круглое отверстие, проделанное на нужную глубину, без поломки сверла или выгорания электроинструмента.
Здесь мы расскажем об умных технологиях, лежащих в основе этих специализированных сверл, а также о том, как вы можете наилучшим образом использовать их в своих проектах.
Твердосплавный наконечник делает сверло
Вы используете сверло по камню в специальной дрели, называемой перфоратором (например, аккумуляторная дрель-шуруповерт с функцией перфоратора) или перфоратором. Эти сверла похожи на сверла для сверления отверстий в дереве и металле, поскольку они имеют цилиндрическую форму со спиральными канавками по длине. Однако биты для каменной кладки имеют кусок карбида вольфрама (композитный материал, состоящий из вольфрама и углерода), припаянный к наконечнику. Твердый сплав чрезвычайно прочный и износостойкий, что позволяет сверлу пробивать себе путь сквозь кладку или камень.Насадки для каменной кладки доступны в различных диаметрах и длинах, и мы рекомендуем их от DeWalt.
Типичное сверло по камню – это просто спиральное сверло с припаянным к его наконечнику треугольным куском карбида вольфрама.Персонал
Промышленные насадки по камню для проделывания глубоких отверстий в бетоне могут иметь несколько кусков твердого сплава, припаянных к концу в форме X. Либо весь наконечник сверла может быть твердосплавным, как он находится ниже на долоте для перфоратора MX4 от Milwaukee.
Персонал
Другие варианты
Существуют сверла для различных материалов, которые могут просверливать все распространенные строительные материалы, кроме стекла. Чаще всего они используются для сверления дерева и кирпичной кладки. Один из примеров – биты MP500 от Bosch. У меня есть их набор, и я считаю их незаменимыми для проделывания отверстий в дереве, бетоне, кирпиче и растворе. В крайнем случае, я даже использую их в стали. Я использую их не только в перфораторе, но и в ударном шуруповерте.
Чтобы использовать их в ударном отвертке, вы вставляете их так же, как и любую другую шестигранную головку. Чтобы использовать их в шуруповерте, вы затягиваете на них патрон так же, как если бы вы слегка затягивали хвостовик с круглым хвостовиком. Примечание. Не используйте ударную отвертку для проделывания отверстий в кирпичной кладке, иначе она может выгореть. Вместо этого вставьте эти биты из нескольких материалов в перфоратор, чтобы проделать отверстие в кирпиче, бетоне, бетонном блоке, растворе или камне.
Имейте в виду, что эти биты – мастера на все руки, но не мастера ни в одном; они позволяют быстро переключаться между сверлением различных материалов и завинчиванием крепежа в тех же материалах.Вы можете использовать их, чтобы проделывать отверстия в дереве любой толщины, но я обнаружил, что они не особенно эффективны в толстой стали; Я ограничиваю их использование легким металлом, толщиной не более 3⁄16 дюйма. Существуют лучшие и более быстрые способы сверления стали и даже дерева, но вы обнаружите, что ударный отвертка хорошо работает с этими сверлами, чтобы проделывать отверстия небольшого диаметра в тонком материале. Если в ходе той же работы вам нужно пробить отверстие в кирпичной кладке, просто вытащите сверло из ударного шуруповерта и вставьте его в перфоратор.
Биты из различных материалов могут проделывать отверстия в кирпичной кладке, дереве и стали.
Персонал
Немецкий SDS
Так называемые биты SDS сегодня широко используются в Соединенных Штатах, но они были разработаны в Европе, где в жилом (и коммерческом) строительстве используется больше каменных материалов, чем в США. биты для каменной кладки, которые обеспечивали быструю замену, либо из-за затупления биты, либо для перехода на другой размер.SDS – это немецкая аббревиатура от Streck-Dreh-Sitz, или «растягивающееся поворотное сиденье», отсылка к первому поколению этих бит и их предназначению для вставки в патрон перфоратора.
Американская версия аббревиатуры остается той же (SDS), но понимается как означающая Spline Drive System или Slotted Drive System, возможно, лучшее описание этих бит и того, как они удерживаются в патроне, не путем затягивания, а с помощью паза на конец бита. Вы просто совмещаете современную коронку SDS с патроном сверла и вставляете ее. Если она не сядет, слегка поверните биту (в любом направлении), пока она не встанет. Сверло готово к работе. Перфораторы имеют две или три настройки. Двухступенчатые перфораторы могут сверлить (по дереву или стали) или сверлить с ударным действием. Перфораторы с тремя настройками могут сверлить, перфорировать или перемещать долото линейным возвратно-поступательным движением (очевидно, никогда не пытайтесь использовать долото в режиме перфорации или сверления, и никогда не используйте сверло в режиме долота. ). Настроить перфоратор для сверления кирпичной кладки так же просто, как повернуть циферблат на двойной значок, на котором есть и сверло, и молоток.
Персонал
The Famous Tapcon Все они хороши для создания отверстия, но затем следует крепление. Это было в год двухсотлетия Америки, в 1976 году, когда компания Illinois Tool Works (ITW) запатентовала то, что впоследствии стало одной из самых производительных систем крепежа, когда-либо изобретенных, – винт Tapcon и подходящее сверло для кирпичной кладки. Если вы достаточно взрослые, чтобы крепить к бетону с помощью различных систем, предшествовавших эпохе Tapcon, таких как свинцовые заглушки и анкеры, вклинивающиеся в отверстие, вы оцените прекрасную простоту этих вещей. Просверлите отверстие, прочистите, закрутите винт. Но вам не нужно быть старожилом (как я, кхм), чтобы приветствовать Tapcon.
Tapcon (для нарезания резьбы по бетону) представляет собой винт из закаленной стали. Он предназначен для использования с подходящей по размеру битой для кирпичной кладки.Система проста. Установите перфоратор в режим сверления кирпичной кладки и затяните бит Tapcon в патроне. Просверлите отверстие и удалите пыль пылесосом. Переведите дрель в режим заворачивания шурупов и проденьте шуруп в направляющее отверстие в том, что вы крепите к бетону: в пиломатериалах, металлическом кронштейне или каком-либо другом приспособлении. Винт врезается в бетон собственной резьбой, и крепеж красиво прижимается к поверхности того, что вам нужно было закрепить.
Персонал
Best Practices
Сверление кирпичной кладки – это просто, но есть некоторые вещи, в которых вы можете ошибиться. Вот список советов, которые помогут вам этого не делать.
Не используйте стандартное сверло.Да, вы можете проделать отверстие в мягкой кладке, например в кирпиче, с помощью обычного сверла, но это медленно и неэффективно. Используйте перфоратор для работы в режиме перфорации.
Не применяйте силу к биту.Сверление кирпичной кладки по своей природе является медленным, особенно в бетоне, когда вы ударяете много камня. Не торопитесь и работайте над этим. В противном случае вы рискуете сломать биту.
Будьте осторожны при сверлении бетона. В бетоне есть все, от арматурных стержней (арматуры) до металлической проволочной сетки и больших кусков камня. Иногда в него даже встроен электрический провод. Чаще всего ударяют по арматуре. Это остановит каменную кладку, которая не успеет замерзнуть.У вас есть два варианта: переместить отверстие в направлении, в котором вероятность попадания в арматуру меньше, или купить или арендовать специальную коронку для резки арматуры.
Используйте промышленный пылесос для удаления пыли и кладки перед ввинчиванием винта Tapcon, используя стеновой анкер или заливочные материалы, такие как эпоксидная смола, раствор или строительный раствор, чтобы удерживать резьбовую шпильку. Все системы крепления кладки (шурупы, анкеры и закладные материалы) имеют рейтинг прочности, основанный на предположении, что отверстие было очищено от мусора.Чтобы достичь расчетной прочности системы, очистите отверстие.
Используйте специальные биты для гранита. Не пытайтесь сверлить каменными коронками гранитные или мраморные столешницы. Это быстрый способ получить в них довольно неприятные трещины. Вместо этого вам понадобится специальный бит.
Этот контент создается и поддерживается третьей стороной и импортируется на эту страницу, чтобы помочь пользователям указать свои адреса электронной почты. Вы можете найти больше информации об этом и подобном контенте на сайте piano.io.
Работа с лепниной и бетонным блоком в Неаполе, Флорида
(Уровень: средний)
Возведение фундаментов и стен из бетонных блоков – более простая и обычно менее дорогая альтернатива, чем бетонные или каменные конструкции, но результат не очень привлекателен.Штукатурка, изготовленная на заказ или приготовленная на заводе цементная штукатурка, обеспечивает недорогую, долговечную, привлекательную и не требующую особого ухода отделку внутреннего или внешнего фундамента и садовых стен в любом климате.
Как правило, в качестве основного покрытия можно использовать проверенную временем штукатурку из портландцемента (1 часть портландцемента, 1 часть извести и 4 части мелкого песка). Хотя известь не нужна, она продлевает срок службы лепнины – плюс для неопытного рабочего. Для получения более однородной консистенции и цвета от партии к партии безопаснее выбрать штукатурку, приготовленную на заводе, для второго, финишного слоя.
Наносите штукатурку в мягкую (от 50 до 70 градусов F) погоду. Приложение может быть настолько простым или сложным, насколько позволяют ваши навыки и опыт; а текстуры, которые вы можете получить, ограничены только вашим воображением. Основные шаги описаны ниже. Местные условия, качество песка и особенности вашего проекта могут потребовать специальных смесей или добавок. Например, белый цемент и белый песок могут быть лучшим выбором для белой или светлой штукатурки. Для некоторых неабсорбирующих поверхностей могут потребоваться связующие добавки.Ваш дилер по каменной кладке лучше всего сможет посоветовать вам, какую смесь использовать для вашего конкретного применения. Для получения дополнительной информации мы рекомендуем вам получить копию Руководства по портландцементной штукатурке (штукатурке), опубликованное Портлендской цементной ассоциацией, и ознакомиться с инструкциями по установке финишного покрытия производителя.
Необходимые инструменты и материалы:
- Миксер для строительного раствора (показан пункт проката)
- Мойка усиленная (аренда)
- Мотыга
- Гвозди для реек и кладок по дереву
- Лопата
- Молот
- Hawk (доска с ручкой для загрузки цемента)
- Рабочие перчатки
- Садовый шланг и насадка
- Очки защитные
- Мастерок каменщик обыкновенный
- Портландцемент I типа
- Мастерок по камню остроконечный
- Лайм
- Длинная металлическая или деревянная линейка
- Мелкий чистый песок
- Деревянный поплавок (деревянный брусок с ручкой)
- Губчатый поплавок
- Тачка
- Съёмник для гвоздей
Шаг 1. Осмотрите и подготовьте поверхность
Стена из блоков должна быть прочной и правильной, а значительные дыры или трещины должны быть отремонтированы.На поверхности также не должно быть грязи, плесени, высолов, краски или других поверхностных загрязнений, которые могут помешать склеиванию. Обычно для старых необработанных стен требуется механическая мойка, хотя в некоторых случаях необходима пескоструйная очистка.
Шаг 2: Установите стяжку
Прикрепите временные полоски деревянной рейки толщиной 3/8 дюйма по горизонтали к верхней и нижней (а на высокой стене – к середине) стены, используя кладочные гвозди. Эти стяжки будут направлять линейку (называемую стержнем), которая используется для выравнивания поверхности на шаге 7.
Шаг 3: Получение материалов
Один кубический фут штукатурки покроет около 17 квадратных футов стены для основного покрытия. Предполагаемый охват штукатурки заводской отделки указан на этикетке. Вам понадобится примерно 1 кубический фут влажного песка, от 1/4 до 1/3 мешка цемента и такое же количество извести, чтобы сделать кубический фут гипса.
Шаг 4: Увлажните стену
Штукатурку лучше всего наносить на влажную стену, поэтому перед нанесением опрыскайте (не пропитывайте) поверхность садовым шлангом и насадкой.
Осторожно: Цемент и известь едкие. Перед тем, как начать перемешивание, защитите руки тяжелыми рабочими перчатками, а глаза – очками.
Шаг 5: Смешайте базовый слой штукатурки
Для больших работ вам понадобится арендовать механический растворный миксер. Сначала добавьте примерно 2/3 воды и включите миксер. Последовательно добавьте примерно половину песка, цемент, известь и оставшуюся часть песка. Перемешивайте несколько минут, добавляя оставшуюся воду по мере необходимости для получения однородной смеси.Если вы перемешиваете мотыгу в тачке, сначала смешайте сухие ингредиенты и сразу же добавьте половину воды, а затем добавьте остальные по мере необходимости. Хотя сухие ингредиенты можно отмерять ведрами, обычно вы просто считаете их лопатками, загружая миксер или тачку.
Совет: Взвесьте лопаты извести и цемента по отдельности, чтобы вы могли приблизительно рассчитать потребность в воде для вашей смеси. Вода, которая весит около 7,8 фунтов на галлон, должна составлять примерно половину веса вяжущего материала (цемента и извести) в смеси.Сначала поэкспериментируйте с парой небольших порций, чтобы определить необходимое количество воды. Смесь должна иметь консистенцию пудинга или мягкого сливочного масла. Вы можете повторно темперировать смесь (добавить воду, когда смесь стала слишком густой) в течение 30 минут после первоначального перемешивания.
Шаг 6: Нанесите базовое покрытие
Нанесите штукатурку на ястреб, а затем на шпатель. Сначала держите затирку под углом 45 градусов к стене и медленно уменьшайте угол до 30 градусов, нанося штукатурку широкими движениями.Приложите давление, достаточное для того, чтобы штукатурка прижалась к шероховатой поверхности стены. На вертикальных поверхностях вам, вероятно, будет проще работать снизу вверх. Базовое покрытие должно быть примерно 3/8 дюйма. толстая по всей площади. Избегайте чрезмерного затирки, так как это может вызвать проблемы с приклеиванием. Нанесите штукатурку на ястреб, а затем на мастерок. Сначала держите затирку под углом 45 градусов к стене и медленно уменьшайте угол до 30 градусов, нанося штукатурку широкими движениями. Приложите достаточное усилие, чтобы прижать штукатурку к шероховатой поверхности стены.На вертикальных поверхностях вам, вероятно, будет проще работать снизу вверх. Базовое покрытие должно быть примерно 3/8 дюйма. толстая по всей площади. Избегайте чрезмерного затирки, так как это может вызвать проблемы с приклеиванием.
Шаг 7: Выровняйте плоскость
Спустя всего несколько минут с помощью линейки (металлической или деревянной) выровняйте поверхность до равномерного 3/8 дюйма. толщина. Поместите концы линейки на деревянную или металлическую стяжку (см. Шаг 2) и, используя движения вверх и вниз, медленно проведите линейкой по стене, чтобы удалить излишки материала.Заполните все углубления и повторите выравнивание.
Шаг 8: Удаление стяжки
Удалите деревянные стяжки с помощью съемника для гвоздей и молотка, как можно меньше нарушая штукатурку.
Шаг 9: Плавайте на поверхности
После исчезновения блеска поверхности, но до того, как штукатурка затвердеет слишком сильно, чтобы ее можно было обрабатывать, пройдитесь по всей поверхности деревянной или пенопластовой теркой, вращая ее. Это укрепляет штукатурку и снижает усадку и растрескивание, возникающие при отверждении основного покрытия.
Шаг 10: Смешайте и нанесите финишное покрытие
Перемешать и на следующий день нанести финишное покрытие. Это покрытие обычно имеет толщину от 1/8 до 1/4 дюйма, поэтому стяжки не нужны. В остальном процедура аналогична описанной выше. Однако существуют различия от продукта к продукту, поэтому следуйте инструкциям производителя.
Шаг 11. Текстурирование поверхности
Возможны десятки текстур. К простейшим из них относится несколько шероховатая, но однородная поверхность, достигаемая за счет обработки финишного покрытия губкой или кистью.В некоторых случаях поверх исходного финишного слоя наносится дополнительный текстурный слой отделочного материала и обрабатывается шпателем или другим инструментом.
Здание с бетонным блоком и конструкция с деревянным каркасом
Крис Берч
С тех пор, как я начал строить дома в округе Уолтон в 2005 году, я заметил многочисленные изменения в методах строительства и материалах, используемых в жилых домах. Одним из них является тенденция к строительству домов из бетонных блоков, которые обычно называют бетонными каменными блоками (CMU).
Строительство из бетонных блоков традиционно более распространено в центральной и южной Флориде, в то время как конструкция наружных стен с деревянным каркасом преобладает вдоль панно, но теперь у тех, кто строит новые дома, есть больше вариантов, если только кодексы дизайна района не поощряют или не диктуют тип экстерьера. стеновая конструкция, которую необходимо утилизировать. Давайте рассмотрим некоторые преимущества и недостатки использования бетонных блоков по сравнению с деревянным каркасом.
ПРЕИМУЩЕСТВА КОНСТРУКЦИИ БЕТОННЫХ БЛОКОВ НАД ДЕРЕВЯННЫМ КАРКАСОМ:
Strength – сопротивление урагану
Существует предубеждение, что дом из бетонных блоков прочнее каркасного дома 2 × 6.Хотя я согласен с этим мнением, любой тип конструкции, в зависимости от местоположения, спроектирован инженером в соответствии с действующими строительными нормами и выдерживает скорость ветра 140 миль в час, независимо от того, построен ли он из CMU или деревянного каркаса (с различными обвязочные и застегивающие механизмы).
Огнестойкость
CMU действительно более огнестойкий, чем деревянные стойки и фанерная обшивка, хотя деревянные каркасы по-прежнему используются и прикрепляются к внутренней части стен CMU, чтобы скрыть механические трубопроводы и проводку.Если пожар произойдет там, где используются стены CMU, деревянные стойки (шпалы), скорее всего, будут повреждены, в то время как CMU может быть или не подлежит утилизации.
Штукатурка стен – лучшая основа
Учитывая наше расположение в непосредственной близости от Мексиканского залива и в зоне сильных ветров, стены CMU с меньшей вероятностью будут двигаться во время сильных ветров, чем стены с деревянным каркасом. Кроме того, деревянный каркас имеет больший потенциал двигаться, поскольку древесина со временем высыхает. Штукатурка на подложке из CMU работает намного лучше в долгосрочной перспективе по сравнению с деревянным каркасом, при условии правильного использования компенсаторов, поскольку бетон и штукатурка также имеют некоторое движение из-за тепловых изменений.
Термитное сопротивление
Обрамление стенCMU имеет преимущество перед конструкцией с деревянным каркасом. Тем не менее, шпалы или деревянные части каркаса, прикрепленные к внутренней стороне стен из бетонных блоков, все еще подвержены воздействию термитов, но потенциальное повреждение всей конструкции уменьшается, поскольку деревянные полосы не являются структурной частью дома и могут быть легко заменены. В то время как популяция термитов жива и здорова во Флориде, поддержание осмотра и лечения термитов (привязка) снижает количество термитов как определяющий фактор при выборе того, какую систему внешних стен использовать.
Устойчивость к наводнениям и погодным условиям – проникновение влаги
Бетонный блок более устойчив к проникновению воды и влаги. Например, если бы гараж затопил, было бы намного проще просушить или отремонтировать поврежденные стены CMU. Поступающая вода со временем гниет наружное покрытие, оконные и дверные коллекторы, а также структурные деревянные каркасы.
В многоэтажных проектах в округе Уолтон мы наблюдали более широкое использование CMU на первом уровне с деревянным каркасом 2 × 6 на верхних уровнях.Это выгодно с точки зрения затрат, в то время как комбинация по-прежнему отражает преимущества наличия лучшего основания для штукатурки и упрощения ремонта после потенциального наводнения из-за сильных дождей, как мы наблюдали за последние несколько лет.
НЕДОСТАТКИ БЕТОННОБЛОКНОГО СТРОИТЕЛЬСТВА:
Стоимость
Бетонный блок значительно дороже, чем конструкция из стержневого каркаса. Затраты на рабочую силу и материалы для бетонного блока выше.Во-первых, кадровый резерв для блочной кладки намного меньше, чем
рабочей силы, доступной для строительства рамного каркаса. Во-вторых, стоимость КМУ, арматуры, раствора, бетонной заливки и т. Д. Дороже фанерной обшивки. В обоих случаях по-прежнему требуются материалы для обрамления деревянных стоек. В-третьих, для возведения блочной стены требуется больше труда и оборудования (например, строительных лесов) по сравнению со стеной с деревянным каркасом. Наконец, даже после того, как каменщики построили стену, необходимы деревянные каркасы и плотники, чтобы построить вторую стену внутри CMU для размещения механических трубопроводов и проводки.
Время сборки
Время строительства также увеличивается, когда подрядчики используют конструкцию CMU. Стену CMU можно поднимать только на определенную высоту каждый день, поэтому для установки арматуры и заполнения ячеек CMU требуется больше времени. Кроме того, необходимы дополнительные проверки. Только после того, как стены CMU будут подняты, можно начинать каркас из дерева. В типичном проекте дома, в котором для наружных стен
используется каркас из каркаса CMU, время строительства может быть легко увеличено на три-пять месяцев.
Меньше изоляции (R-значение)
R-значение – это мера способности теплопередачи от горячего к холодному через такие материалы, как изоляция. Чем выше значение R, тем больше материал препятствует передаче тепла. Типичный каркас из деревянных шпилек 2 × 6 с изоляцией из стекловолокна или изоляцией из распыляемой пены достигает значения R примерно 19. 8-дюймовый блок CMU с изоляцией с закрытыми порами имеет значение R примерно 7. Значение R
в древесине- каркасная конструкция (2 × 6 стен) превосходит конструкцию блока КМУ и утеплителя с закрытыми порами.
Сложнее реконструировать
Вырезать окно большего размера во время будущей реконструкции легче при работе с деревянным каркасом, чем с конструкцией из бетонных блоков.
Требуемое пространство
Многие дома не пострадают, если откажутся от небольших дополнительных квадратных футов для строительства 8-дюймовых стен CMU. Однако, если размер партии невелик и / или требования к снижению являются ограничительными, как в случае участков с нулевой линией партии, толщина внешней стенки может быть проблемой.Стены из бетонных блоков могут быть на четыре дюйма толще (или больше), чем обычные наружные стены размером 2 × 6. При рассмотрении четырех внешних стен конструкции можно потерять в общей сложности восемь дюймов на погонный фут как в направлениях север-юг, так и в направлениях восток-запад.
Если вы строите новый дом, вы должны решить, какой материал использовать для внешних стен. Обдумайте и обсудите вышеперечисленные моменты со своим профессиональным дизайнером, чтобы принять лучшее решение для вашего конкретного проекта.
Инновационный блок, прочнее дерева
Бетонный блок, открытый заново – новый лучший для домашнего строительства – Реклама –Роберто Уго Гонсалес
В начале нового века предприниматель и дальновидный человек обнаружил потребность в компания-производитель, чтобы помочь обеспечить строителей лучшими блочными и бетонными изделиями для строительства.
Это было в 2004 году, когда Чарльз Мюллер помог основать компанию и начал строительство с нуля. Выбранная недвижимость была старой промышленной площадкой. «Перед возведением здания на этом участке необходимо было провести обширные ремонтные работы», – сказал Мюллер. Он добавил: «Город Ла-Ферия сыграл важную роль в первоначальном запуске».
Основание для этого объекта потребовало нескольких равных, чтобы компенсировать 20-тонное давление, которое пресс оказывает каждые 20 секунд или около того. Потребовались значительные фундаментальные работы для подготовки к давлению, создаваемому тяжелым прессом и оборудованием.Когда все необходимые фундаментные работы были завершены, Innovative построила современное здание для размещения точного оборудования для производства бетонных блоков и прочего. «Каким бы крупным это ни был проект, на его завершение ушло почти два года», – сказал Мюллер.
Innovative Block of South Texas начал производство в 2006 году и на сегодняшний день является единственным производителем бетонных блоков и брусчатки к югу от Сан-Антонио.
«Мы изучили рынок и увидели потребность. Мы собрали лучшее оборудование, которое только можно найти по всему миру, для производства высококачественных блоков, но, что более важно, чтобы обеспечить гибкость в будущем для включения новых продуктов, таких как Omni Block », – сказал он.
У Мюллера отличная команда, многие были там с самого начала, он добавил, они знали, что если они будут постоянно предоставлять качественные продукты, они будут успешными, и успешными они являются во всех подразделениях компании. «Наше подразделение по литью самостоятельно изготавливает формы, чтобы быстро реализовать ваш проект».
– Объявление –Он добавил, что бетонный блок или бетонные блоки для каменной кладки (CMU) более огнестойки и устойчивы к ошибкам, чем деревянные шпильки или фанера обшивка . Мюллер отметил, что деревянные каркасы иногда все еще используются и прикрепляются к внутренней части бетонной стены, чтобы скрыть механические трубопроводы и проводку, но это не самый эффективный способ строительства в настоящее время.
Бетонный блок не подвержен воздействию экстремальных температур, термитов, плесени или грибка. Он также может обеспечить звукоизоляцию и лучшую защиту от наводнений и штормовых нагонов.
Хорошо это или плохо, деревянные каркасы остаются доминирующим методом строительства домов на одну семью в США.S., согласно проведенному Национальной ассоциацией домостроителей анализу данных Бюро переписи населения. На момент завершения 2020 года 90% новых домов были с деревянным каркасом и только 10% были с каменным каркасом. Тем не менее, блочная кладка предлагает потребителям множество преимуществ, включая устойчивость к экстремальным погодным условиям и ураганам.
Проекты, построенные с инновационным блоком
Innovative Block – компания, занимающая уникальное положение, которое может предоставить вам бетонные блоки, архитектурные блоки, брусчатку из Голландии, литой камень, системы подпорных стен и заполнители.
Некоторые из самых красивых и знаковых зданий и школ в Долине были построены из блоков, произведенных компанией Innovative Block of South Texas из Ла-Фериа, штат Техас.
Большинство строителей знают компанию и ее продукцию. По мере того, как потребители узнают больше о том, насколько эффективны и прочные бетонные блоки, они могут информировать своих строителей о затратах на жизненный цикл и экономии, которую дает бетон.
Хотя большинство людей понимают, что бетонный блок прочнее дерева, существует множество других факторов, которые следует учитывать: в долгосрочной перспективе владелец дома или бизнеса сэкономит больше на расходах на электроэнергию и страховку, используя блоки по сравнению с деревом.
Завод Innovative Block в Южном Техасе загружен в трейлеры своей продукцией для доставки строителям и поставщикам, которых они обслуживают по всему Южному Техасу.20-25% экономии затрат на электроэнергию
По данным Юго-восточной ассоциации каменщиков (SCMA), Мюллер сказал, что они рассмотрели факты в отношении затрат на отопление и охлаждение. Дома с каркасом из бетонной кладки обеспечивают от 20 до 25 процентов ежегодной экономии на отоплении и охлаждении, но при этом более комфортны.
А что со страховкой? Та же самая национальная организация SCMA, беседуя с Национальной ассоциацией строителей жилья (NAHB), обнаружила, что большинство потребителей даже не знают, что могут окупить свои вложения в дом из каменной кладки со значительной экономией на страховании. Многие агентства предлагают скидки на полисы домовладельцев до 25% из-за их устойчивости к огню, торнадо, ураганам и землетрясениям.
Обе ассоциации согласны с тем, что все сбережения начинаются с образования.Для сравнения: если ваша страховка стоит 2500 долларов в год, вы можете сэкономить примерно 625 долларов в год. За десять лет это 6250 долларов, что позволит вам вложить эти деньги обратно в другие жизненные инвестиции.
Наличие компании по производству бетонных блоков в долине Рио-Гранде – благословение для строителей и потребителей, которые хотели бы построить новый дом. Бетонный блок имеет смысл построить дом где угодно; однако, поскольку мы находимся недалеко от Мексиканского залива, нам постоянно напоминают об опасности урагана.Мы должны быть хорошо защищены, а бетонный блок является наиболее эффективным строительным продуктом, «если он затоплен, просто вылейте его из шланга», – сказал Мюллер. На нем не будет плесени и грибка, поэтому он идеально подходит для побережья.
Innovative Block имеет обширную линейку продуктов, первые бетонные блоки, блоки с гладкой и гладкой поверхностью, архитектурные блоки, голландские асфальтоукладчики. Компания гордится тем, что производит лучшую продукцию для ваших строительных нужд.
Innovative Block of South Texas также производит литые камни, системы подпорных стен, заполнители, бетон и цемент в мешках.«Мы прямо находимся в середине роста долины». Мюллер добавил: «Я думаю, что сейчас, когда пиломатериалы так дороги, люди заново открывают для себя бетон как жизнеспособный метод строительства».
Во время экскурсии по заводу мы воочию увидели преданную делу команду, выполняющую свою работу. В то время машина производила цельные блоки, а другая – брусчатку.
Innovative Block использует большой участок земли для обработки своей продукции, где они хранят камни для озеленения, груды заполнителя и линии мешковины.На заводе также есть зоны дробления и смешивания, а также впечатляющие силосы, которые видны издалека.
Innovative Block в Южном Техасе активно работает на заводе. В трейлеры загружали продукцию для доставки строителям, обслуживающим территорию Южного Техаса.
Крупные клиенты могут делать заказы непосредственно в Innovative Block или через многочисленных местных дистрибьюторов, включая McCoy’s Building Supply, The Home Depot, Do-it Best Alamo Lumber, Builders First Source и другие.
Innovative Block также является крупным поставщиком основных каменщиков и подрядчиков в Южном и Центральном Техасе, а также крупных подрядчиков, включая Noble Texas Builders, D. Wilson Construction, Peterson Construction, Granchelli Construction LLC, EB Merit Construction и других.
Профессиональные строители знают, что они могут рассчитывать на Innovative Block of South Texas в производстве продукции высочайшего качества, теперь можете и вы.
Для получения дополнительной информации посетите их веб-сайт по адресу https: //www.innovativeblock.com /.
В следующем месяце мы представим Omni Block, также продаваемый Innovative Block. Omni Block – одно из лучших новых изобретений этого века, которое значительно повысило эффективность и стоимость.
– Реклама –Как построить 6 различных фундаментов сараев
Успех или неудача вашего сарая во многом зависит от его фундамента. Даже самые хорошо спроектированные и построенные сараи не прослужат долго, если они установлены на слабом или плохо построенном основании. Поэтому создание прочного и прочного фундамента, возможно, является самым важным шагом в строительстве сарая.Давайте рассмотрим лучшие варианты фундамента для вашего сарая.
по классу против морозостойкости
Существует несколько различных типов фундаментов навесов, но их можно разделить всего на две категории: грунтовые и морозостойкие.
Нестандартные фонды
Другое название грунтового фундамента – плавучий фундамент. Этот тип сидит прямо на земле. Одним из их преимуществ является то, что их легко и быстро построить. Для этого типа фундамента не нужно копать ямы или заливать бетон.Фундамент на уровне грунта достаточен для большинства сараев малого и среднего размера.
Морозостойкие фундаменты
Морозостойкие фундаменты создают больше проблем, чем обычные, но они намного прочнее и долговечнее. По этой причине морозостойкие фундаменты часто называют постоянными фундаментами . Хотя этот тип фундамента можно построить практически где угодно, он хорошо работает в местах с более холодной погодой и морозным пучком.Морозостойкие фундаменты обычно изготавливают путем заливки бетонных фундаментов, опор или монолитной плиты. Но вы также можете создать один из столбов-сараев, в котором используется серия высоких круглых столбов или квадратных столбов, вставленных в глубокие ямы. Морозостойкий фундамент идеален – и часто требуется кодекс – для больших навесов.
Нестандартные фундаменты
Фундамент на уровне грунта – это фундамент, который стоит на земле. Это не постоянный фундамент навеса. Поэтому при необходимости его можно переместить. Это может быть моноблочный, полозьевый или каркасный фундамент.Вы бы выбрали один из них, если у вас есть сарай маленького или среднего размера, если вы можете захотеть переместить сарай в какой-то момент или если вы не можете копать землю.
Бетонный блок
Фундамент из монолитных блоков под навес 10х12Для сооружения этого типа фундамента используется серия моноблоков. Их следует раскладывать прямыми рядами, на равном расстоянии друг от друга. Размер вашего сарая и древесина, используемая для перекрытия перекрытий, определят, сколько блоков вам нужно и сколько места будет между ними.
Важно: Не используйте пустотелые стеновые блоки. Со временем они могут треснуть и рассыпаться из-за веса вашего сарая.
Блоки, наиболее часто используемые для наземных фундаментов, имеют толщину 4 дюйма, ширину 8 дюймов и длину 16 дюймов. Существуют также блоки толщиной 2 дюйма, называемые блоками для патио, которые можно установить поверх более толстых блоков, когда необходимо поднять один блок вместе с другими.
Совет: Удалите траву под каждым монолитным бетонным блоком, чтобы представить эрозию почвы.Мы рекомендуем использовать 2-3 дюйма гравия, чтобы покрыть грязь. Утрамбуйте гравий ручным трамбовкой, а затем поместите на него блок.
Фундамент на салазках
Фундамент на салазках 4 × 8Фундаменты с салазками используются для поддержки сараев и других уличных построек более 300 лет. Построить такой фундамент на грунте очень просто. Используя две или более длинные прямые полозья (бревна), положите их на землю параллельно друг другу и на равном расстоянии друг от друга. Постройте на них каркас пола сарая.
На возведение салазок требуется совсем немного времени, и это один из самых простых вариантов. Одним из их преимуществ является то, что они равномерно распределяют вес здания по широкой поверхности. Но лучше всего их использовать на достаточно ровных участках. Обычно салазки изготавливаются из обработанных давлением 4×6, 6×6 и 8×8. Размер может варьироваться в зависимости от размера строящегося сарая.
Наконечник: Если длинные прямые бревна недоступны, салазки можно сделать, забив 3–4 гвоздями 2×6 или 2×8, обработанных давлением.После соединения их следует поставить на край.
Деревянная рама
Фундамент с деревянным каркасом для навеса 10 × 12Фундамент с деревянным каркасом изготавливается путем сооружения прямоугольного деревянного каркаса и его размещения на гравийной подушке. Строить очень легко. Затем поверх каркаса возводятся стены сарая. Одна из причин, по которой фундаменты с деревянным каркасом так популярны, заключается в том, что они допускают множество вариантов напольного покрытия. Например, пространство пола внутри рамы может быть заполнено кирпичом, бетоном, гравием, мраморной крошкой или плитами из голубого камня.Вы также можете просто прикрутить настил, обработанный под давлением. Обработанные давлением 4×4, 4×6 или 6×6 обычно используются для изготовления деревянных каркасов. Угловые соединения внахлест используются для соединения бревен вместе, или они также могут быть уложены друг на друга по два или три бруса и скреплены друг с другом. Для этого подойдут конструкционные шурупы или длинные ландшафтные шипы.
В качестве альтернативы можно использовать доски 2 × 8 как для внешнего контура, так и для внутренних балок. Обратите внимание, что короткие внутренние балки расположены в шахматном порядке для облегчения установки.
Если участок не выровнен предварительно, можно использовать опоры из бруса 6 × 6 и средней длиной 3 фута (в зависимости от уклона рельефа, который необходимо компенсировать)
Совет: Чтобы древесина не гнила преждевременно, обязательно используйте пиломатериалы, обработанные под давлением, которые рассчитаны на контакт с землей.
Морозостойкие фундаменты
Морозостойкие фундаменты способны выдерживать больший вес, чем обычные фундаменты, поэтому их часто выбирают.Они постоянные, и строительство одного требует нескольких дополнительных шагов. Вы должны копать ниже линии промерзания и использовать бетон и опоры для поддержания структурной целостности фундамента. Этот тип фундамента не сдвинется. Некоторые примеры этого типа включают в себя амбары с столбами, бетонные опоры и фундаменты из бетонных плит. Этот вариант очень полезен для более холодных мест, где отрицательные температуры могут вызвать повреждение фундамента сарая.
Бетонные опоры
Фундамент бетонной опоры для навеса 12 × 12 Фундамент бетонной опоры – это просто бетонный столб, залитый в отверстие в земле.Если вы строите сарай в регионе с холодной погодой, проследите, чтобы отверстия выходили ниже линии замерзания. Это может предотвратить негативное воздействие морозного пучения на ваш сарай. Два или более рядов опор поддерживают каркас перекрытия сарая. Если вам нужно увеличить высоту опоры над землей, выровняйте отверстия трубками из волокнистой формы, которые широко известны под торговым названием Sonotube, а затем заполните трубы бетоном. Каркас перекрытия сарая может быть прикреплен к бетонным опорам с помощью оборудования из оцинкованного металла, например, анкеров для столбов или соединителей балок.Только не забудьте установить оборудование в опоры до того, как бетон затвердеет.
Совет: Морозостойкие фундаменты обычно требуются по нормам для навесов площадью более 200 кв. Футов или выше 12 футов. Однако строительные нормы и правила в разных штатах различаются, поэтому обязательно уточняйте у местного строительного департамента точные требования в вашем районе.
Монолитно-бетонная плита
Фундамент из бетонных плитФундамент из бетонных плит – лучший выбор для больших хозяйственных построек, которые будут использоваться для хранения тяжелого оборудования, такого как деревообрабатывающие станки, тракторы, лодки, мотоциклы, снегоходы и автомобили.Есть два основных способа заливки бетонной плиты, но только один можно отнести к морозостойкому фундаменту. Это называется монолитной плитой, и пол сарая и стены фундамента по периметру заливаются одновременно. Стены доходят до линии замерзания и обычно имеют толщину от 8 до 12 дюймов. Пол имеет толщину всего от 4 до 6 дюймов, но он армирован проволочной сеткой или металлическими арматурными стержнями.
Фундамент с плавающими плитамиВторой тип бетонного пола известен как плавающая плита или плита на уровне грунта.Это просто слой бетона толщиной от 4 до 6 дюймов, который лежит прямо на земле. Этот тип одноэтажного перекрытия никогда не следует использовать, если строительные нормы и правила требуют наличия морозостойкого фундамента.
Полюс-сарай
Все ранее упомянутые фундаменты предназначены для поддержки каркаса перекрытия сарая. Каркас пола, в свою очередь, поддерживает стены. Совсем другое дело – фундамент сарая: у него технически даже пола нет.
Конструкция столбов-сараев состоит из нескольких ям, вырытых ниже линии промерзания по периметру фундамента.В каждое отверстие заливают бетонные опоры, а в отверстия вставляют высокие круглые столбы или бревна. Поперек опор крепятся горизонтальные балки, а затем к балкам крепятся стены. Голую землю в фундаменте столбов-сараев можно засыпать обработанным камнем, мелким гравием или древесной стружкой. Или вы можете залить бетонный пол.
Предварительно сформованная бетонная подушка для фундаментаОдин из вариантов – использовать предварительно отформованную бетонную подушку для печенья, она должна быть толщиной 6 дюймов и диаметром 12-16 дюймов.Поместите бетонную подушку в подготовленную яму и поместите в проем пиломатериал, обработанный давлением. Сам яму можно засыпать гравием или другими сыпучими материалами средней фракции, которые будут действовать как дренаж и удалять влагу из пиломатериалов.
Бетонный столб для фундамента сараяСледующий способ – бетонировать всю стойку. В зависимости от региона, в котором происходит строительство, может потребоваться дополнительная обработка от гниения части столба, находящейся в бетоне.Пока бетон застывает, необходимо закрепить брус, предварительно выровняв его в вертикальном положении с помощью строительного уровня.
Стойка из пиломатериалов, обработанных давлением,Третий метод предполагает использование опоры, монтажная арматура которой устанавливается в еще не затвердевший бетон, что и дало само название. После затвердевания пиломатериал, обработанный давлением, устанавливается в опорную стойку с помощью соответствующих креплений.
Бетонный блок с колонной в подготовленной ямеИ, наконец, последний метод, который максимально поднимает столб над землей и тем самым лучше всего защищает его от гниения, – это использование пермских колонн.Готовый бетонный блок с колонной опускается в подготовленную яму, на которую с помощью опорной стойки устанавливается пропущенный под давлением брус. Яму можно засыпать чем угодно, поскольку бетон не требует дренажа.
Совет: Так как пол сарая почти на одном уровне с окружающим грунтом, он обеспечивает легкий доступ для тракторов-газонокосилок, лодочных прицепов, сельскохозяйственной техники и домашнего скота.
Дополнительные типы фундаментов для рассмотрения
Когда дело доходит до строительства фундамента сарая, у вас есть из чего выбрать.Вот еще несколько вариантов, которые вы, возможно, захотите рассмотреть.
Регулируемое пластиковое основание Регулируемое пластиковое основаниеНебольшие навесы могут не нуждаться в большом фундаменте; особенно, если нынешний ландшафт может хорошо его поддерживать. Для обеспечения твердости и уровня фундамента можно использовать пластиковые домкраты для сараев.
Плюсы:
- Установить очень быстро и легко
- Выравнивание можно сделать быстро
- Сарай будет очень близко к уровню земли
- Отличный вариант как для маленьких, так и для больших навесов
Минусы:
- Есть вероятность затопления со временем
- Этот тип фундаментного материала доступен не везде
- Возможно, это не лучший выбор, если земля наклонная.
Домкраты для сарая работают так же, но они могут быть более подходящими, в зависимости от того, на чем строится сарай.Они хорошо работают, когда земля имеет уклон и ее нужно сделать ровной.
Плюсы:
- Относительно недорого
- Легко установить
- Их можно перемещать вверх и вниз с помощью лишь некоторых основных инструментов
Минусы:
- Важно проявлять большую осторожность, чтобы фундамент мог выдержать нагрузку сарая и всего, что находится внутри.
- Навес будет сложнее переместить, если его нужно переместить
- Вам понадобятся люди, которые помогут вам убедиться, что он установлен правильно
Фундамент с пластиковой решеткой
Пластиковая решетчатая фундаментная системаЕсть несколько пластиковых решетчатых систем, специально разработанных для использования в качестве фундамента навеса.Они могут стать прекрасной альтернативой использованию бетонных плит. Пластик легкий, поэтому с сетками очень легко обращаться. Обычная ручная пила может вырезать и придавать им форму, а их воздушные ячейки сохранят сарай сухим.
Плюсы:
- Пластик – отличный вариант для легкого навеса, потому что он будет выглядеть более естественным
- Пластик для естественного слива воды
- Пластик устойчив к ультрафиолетовому излучению
- Этот тип фундамента под навес очень легко установить самим людям
- Переезд очень прост
Минусы:
- Этот тип фундамента склонен к гниению и может не прослужить так долго, как хотелось бы
- Пластик очень легкий, что может означать, что он легко перемещается
- Сарай необходимо закрепить, чтобы его нельзя было сдвинуть с места
Есть несколько пластиковых решетчатых систем, специально разработанных для использования в качестве фундамента сарая.Они могут стать прекрасной альтернативой использованию бетонных плит. Пластик легкий, поэтому с сетками очень легко обращаться. Обычная ручная пила может разрезать их и придать им форму, а их воздушные ячейки сохранят сарай сухим.
Основание для подпорной стенки
Фундамент с подпорной стенкойНаконец, если эрозия вызывает у вас беспокойство вокруг участка, на котором вы собираетесь построить сарай, вы можете рассмотреть вариант фундамента с подпорной стенкой. Конечно, это требует немного больше работы. Но выгода того стоит.
Плюсы:
- В зависимости от используемого материала фундамент будет очень прочным
- Этот тип фундамента для сарая обычно является очень привлекательным вариантом
- В зависимости от используемого материала фундамент этого типа может выдерживать любые погодные условия
Минусы:
- Фундамент может сломаться и требует ремонта
- Этот тип фундамента, вероятно, будет дороже построить
- Особое внимание следует уделить правильной опоре и дренажу
Сравнение фундаментов навесов
У каждого типа фундамента под навес есть свои достоинства и недостатки.Выбор подходящего типа навеса действительно зависит от нескольких факторов:
- Сарай какого типа вы строите.
- Благоустройство территории, на которой вы работаете.
- Какая погода обычно бывает в вашем районе.
Следующая таблица может помочь вам в принятии решения.
Сарай Тип | Экономичный | Легко перемещать | Водонепроницаемость | Хорошо для склонов | Отличная поддержка | Подходит для автомобилей |
Регулируемое пластиковое основание | ✓ | ✓ | ✓ | ✓ | ✓ | |
Регулируемое металлическое основание | ✓ | ✓ | ✓ | ✓ | ||
Пластик | ✓ | ✓ | ✓ | ✓ | ||
Древесина | ✓ | |||||
Бетонная тротуарная плитка | ✓ | ✓ | ||||
Заливное бетонное основание | ✓ | ✓ | ||||
Фундамент для пирса | ✓ | ✓ | ✓ | |||
Основание типа подпорной стенки | ✓ | ✓ |
Начните работу над фундаментом под навес сегодня
Теперь, когда вы знаете, какой фундамент под навес подходит вам, узнайте, как построить пол под навес.