Обработка заготовок на фрезерных станках
Содержание страницы
- 1. Схемы обработки поверхностей на станках фрезерной группы
- 2. Схемы фрезерования
- 3. Особенности процесса и режимы резания при фрезеровании
- 4. Виды фрез, их элементы и геометрия
- 5. Станки фрезерной группы
Фрезерование – высокопроизводительная обработка поверхностей многолезвийным инструментом – фрезой. Фрезерованием обрабатывают горизонтальные, вертикальные и наклонные плоскости, фасонные и винтовые поверхности, нарезают шлицы и зубчатые колеса, получают винтовые канавки и пазы. При фрезеровании главное движение вращения совершает инструмент; поступательное движение подачи придается заготовке в направлении любой из координатных осей.
1. Схемы обработки поверхностей на станках фрезерной группы
Рассмотрим схемы обработки поверхностей на универсальных горизонтально-фрезерном (ГФС; имеет горизонтальную ось вращения фрезы) и вертикально-фрезерном (ВФС; имеет вертикальную ось вращения фрезы) станках.
Горизонтальные плоскости фрезеруют цилиндрическими фрезами на ГФС (рис. 24, а) или торцевыми фрезами на ВФС (рис. 25, а). Горизонтальные плоскости чаще обрабатывают торцевыми насадными фрезами, так как они имеют более жесткое закрепление и обеспечивают плавное, безвибрационное резание. При большой ширине обрабатываемой плоскости используют торцевые фрезы и обработку ведут в несколько последовательных рабочих ходов. Узкие горизонтальные плоскости удобно обрабатывать концевыми фрезами.
Вертикальные плоскости на ГФС обрабатывают торцевыми насадными фрезами (рис. 24, б) или фрезерными головками, а на ВФС – концевыми фрезами (рис. 25, б). Большие по высоте вертикальные плоскости удобнее обрабатывать на ГФС с использованием вертикальной подачи. Обработку небольших по высоте вертикальных плоскостей можно производить на ГФС с помощью концевых или дисковых фрез. Наклонные плоскости небольшой ширины обрабатывают на ГФС одноугловой фрезой.
Широкие наклонные плоскости обрабатывают на ВФС с поворотом шпиндельной головки (рис. 25, в) торцевой насадной или концевыми фрезами. Одновременную обработку нескольких поверхностей (вертикальных, горизонтальных и наклонных) ведут на ГФС (рис. 24, г), установив на оправку набор фрез.
Рис. 24. Обработка плоскостей на ГФС: а – горизонтальных; б – вертикальных; в – наклонных; г – нескольких плоскостей одновременно; д – уступов; Dr – движение резания; Ds – движение подачи
Рис. 25. Обработка на ВФС плоскостей: а – горизонтальных; б – вертикальных; в – наклонных; г – уступов
Рис. 26. Фрезерование пазов: а, б – прямоугольных; в – полукруглых; г – типа «ласточкин хвост»; д – Т-образных; е, ж – шпоночных
Горизонтальные уступы и пазы обрабатывают дисковыми односторонними (рис. 24, д) и трехсторонними (рис. 26, а) фрезами на ГФС или концевыми фрезами (рис. 25, г; 26, б) на ВФС.
Фасонные пазы с криволинейной образующей обрабатывают на ГФС фасонными дисковыми фрезами (рис. 26, в). Пазы типа «ласточкин хвост» или Т-образные обрабатывают на ВФС (рис. 26, г, д). Вначале концевой фрезой получают прямоугольный паз, затем используют концевую одноугловую фрезу или специальную концевую фрезу для Т-образных пазов.
Шпоночные пазы для сегментных шпонок фрезеруют на ГФС дисковой трехсторонней фрезой (рис. 26, е), для прямоугольных шпонок – на ВФС концевой фрезой (рис. 26, ж).
2. Схемы фрезерования
Цилиндрическое и торцевое фрезерование в зависимости от направления движений резания и подачи можно осуществить двумя способами: попутным фрезерованием, когда совпадают направления главного движения и движения подачи, и встречным фрезерованием, когда направления главного движения и движения подачи не совпадают.
При попутном фрезеровании (рис. 27, а) толщина срезаемого слоя изменяется от максимальной до нуля, зуб врезается в заготовку с ударом. Горизонтальная составляющая силы резания направлена по подаче, а вертикальная – вниз, на заготовку. При встречном фрезеровании (рис. 27, б) толщина срезаемого слоя изменяется от нуля до максимальной (зуб плавно врезается в заготовку). Горизонтальная составляющая силы резания направлена против подачи, а вертикальная – вверх.
Рис. 27. Фрезерование: а – попутное; б – встречное; Dr – движение резания; DSпр – движение продольной подачи; Рг, Рв – соответственно горизонтальная и вертикальная составляющие силы резания; Sz – подача на зуб; v – скорость резания
Рациональность использования какой-либо схемы обусловлена требованием к качеству обработки, условиями обработки заготовки и состоянием фрезерного станка. При черновой обработке литых заготовок (особенно литья в песчано-глинистые формы), имеющих твердую поверхностную корку, использование попутного фрезерования нерационально, так как удар зуба фрезы об эту корку приводит к его выкрашиванию или поломке.
Лучше использовать встречное фрезерование. Зуб начинает работу в мягком материале сердцевины заготовки, подходя к корке, он взламывает ее. При чистовом фрезеровании, наоборот, рациональнее использовать попутное фрезерование. Теоретически при встречном фрезеровании резание начинается с нулевой толщины срезаемого слоя, которая постепенно увеличивается. Однако режущая кромка зуба фрезы имеет радиус округления, равный 0,03–0,05 мм. При чистовом фрезеровании толщина резания невелика. В начале резания зуб не режет, а скользит по обрабатываемой поверхности без снятия стружки. При этом создаются значительные напряжения сжатия в поверхностных слоях заготовки, приводящие к значительному наклепу, повышенному истиранию режущей кромки зуба, вибрациям в системе СПИД и плохому качеству обработанной поверхности. При попутном фрезеровании толщина срезаемого слоя невелика, поэтому ударное вхождение зуба в материал заготовки не вызывает существенных колебаний в системе СПИД, что способствует стабильной работе фрезы, а шероховатость обработанной поверхности улучшается на один класс. Особенно эффективно попутное фрезерование при обработке вязких материалов, склонных к наклепу и налипанию.
При обработке встречным фрезерованием горизонтальных плоско стей нежестких заготовок или заготовок относительно небольшой толщины (до 30 мм) вертикальная составляющая силы резания будет отрывать заготовку от стола, это может привести к неравномерности глубины срезаемого слоя (большая погрешность обработки по толщине заготовки) или к большим усилиям на закрепление заготовки (возможны деформации заготовки). Лучше использовать попутное фрезерование, когда вертикальная составляющая силы резания прижимает заготовку к столу.
3. Особенности процесса и режимы резания при фрезеровании
Особенностями процесса фрезерования является прерывистый характер процесса резания каждым зубом фрезы и переменность толщины срезаемого слоя. Каждый зуб фрезы участвует в резании только на определенной части оборота фрезы, остальную часть проходит по воздуху, вхолостую, что обеспечивает охлаждение зуба и дробление стружки.
При цилиндрическом фрезеровании плоскостей работу резания осуществляют зубья, расположенные на цилиндрической поверхности фрезы. При торцевом фрезеровании плоскостей работу резания осуществляют зубья, расположенные на цилиндрической и торцевой поверхностях фрезы. К режимам резания при фрезеровании относят скорость резания, подачу (минутную, на оборот и на зуб), глубину резания и ширину фрезерования В. Скорость резания, мм/мин, рассчитывается как окружная скорость вращения фрезы:
V = πDфn/1 000,
где Dф – наружный диаметр фрезы, мм; n – частота вращения шпинделя станка, мм/об.
Зависимости между подачами: минутной Sм, на оборот So и на зуб Sz:
Sм= Son = Sznz = S2x,
где z – число зубьев инструмента.
Влияние диаметра фрезы на производительность обработки неоднозначно. С увеличением диаметра фрезы повышается расчетная скорость резания при постоянной стойкости; это объясняется тем, что уменьшается средняя толщина срезаемого слоя, улучшаются условия охлаждения зуба фрезы, так как удлиняется время нахождения зуба вне зоны резания.
С целью повышения производительности лучше выбирать фрезы большего диаметра, поскольку с увеличением скорости резания пропорционально увеличиваются частота вращения фрезы и минутная подача (при пропорциональном увеличении числа зубьев фрезы). Возможности увеличения диаметра фрез ограничиваются мощностью и жесткостью станка, размерами инструментального отверстия в шпинделе станка.
4. Виды фрез, их элементы и геометрия
Фреза – многолезвийный инструмент, у которого по окружности или на торце расположены режущие зубья, представляющие собой простейшие резцы. На рис. 28 показаны основные типы фрез, применяемых в машиностроении.
Фрезы подразделяют по типам: цилиндрические (рис. 28, а, б) и торцевые (рис. 28, е), предназначенные для обработки плоских поверхностей; дисковые (рис. 28, в–д), концевые (рис. 28, ж) и угловые – для обработки пазов, канавок и шлицов; фасонные – для обработки фасонных поверхностей; модульные (рис. 28, з) – для нарезания зубьев; червячные (рис. 28, и) – для нарезания зубьев цилиндрических и червячных колес.
Зуб 4 цилиндрической фрезы (рис. 28, а) имеет режущую кромку 2; переднюю 1, заднюю 3 и затылочную 5 поверхности. Между зубьями фрезы находится канавка 6. В сечении фрезы рассматриваются следующие углы: передний γ, задний α, заострения β и резания δ.
Передний угол γ служит для облегчения схода срезаемых элементов стружки и уменьшения их усадки.
При обработке стали γ = 10–20°, чугуна – γ = 10–15°. Для твердых материалов угол γ принимают меньшим, чем для мягких.
Задний угол α выбирают с таким расчетом, чтобы снизить трение между затылочной поверхностью зуба и поверхностью резания. Для различных фрез угол α = 12–25°.
Зубья цилиндрических фрез могут быть прямыми и винтовыми под углом наклона ω к оси фрезы (см. рис. 28, б). У цилиндрических фрез угол ω = 30–40°, у дисковых и торцевых ω = 10–25°.
Фреза изготавливают цельными из инструментальных сталей и сборными, у которых зубья выполняют из быстрорежущих сталей или оснащают пластинками из твердых сплавов и закрепляют в корпусе фрезы пайкой или механически (ГОСТ Р 53413–2009).
Рис. 28. Основные типы фрез: а – цилиндрическая прямозубая, где 1, 3, 5 – соответственно передняя, задняя и затылочная поверхности; 2 – режущая кромка; 4 – зуб; 6 – канавка; α – задний угол; β – угол заострения; γ – передний угол; δ – угол резания; ω – угол наклона зубьев к оси фрезы; б – цилиндрическая с винтовыми зубьями; в – дисковая пазовая; г – дисковая двухсторонняя; д – дисковая трехсторонняя; е – торцевая; ж – концевая; з – пальцевая модульная; и – червячная
Фреза с прямыми зубьями врезается в обрабатываемую поверхность сразу по всей длине зуба, что приводит к переменной (толчковой) нагрузке на станок и некоторому ухудшению качества обработанной поверхности. Фрезы с винтовыми зубьями работают более плавно, так как зубья фрезы врезаются в деталь постепенно, при этом станок нагружен равномернее.
5. Станки фрезерной группы
В условиях единичного и мелкосерийного производства широко используются универсальные консольно-фрезерные станки: горизонтальнофрезерные без поворотного стола; горизонтально-фрезерные с поворотным столом; вертикально-фрезерные.
Рис. 29. Универсальные фрезерные станки: а – горизонтально-фрезерный; б – вертикально-фрезерный; 1 – фундаментная плита; 2 – станина; 3 – коробка скоростей; 4 – хобот; 5 – шпиндельный узел; 6 – поперечные салазки; 7 – стол; 8 – серьга; 9 – поворотные салазки; 10 – продольные салазки; 11 – консоль; 12 – поворотная планшайба; 13 – шпиндель; в – ГФС MMF-125PD
На рис. 29, а показаны основные узлы горизонтально-фрезерного станка с поворотным столом. На фундаментной плите 1 установлена чугунная станина 2, внутри которой расположены отсек для электрооборудования, коробка скоростей 3 и шпиндельный узел 5.
Серьга 8, совместно с хоботом обеспечивающая жесткость фрезерной оправки, перемещается по его направляющим и закрепляется гайкой. С помощью винтового домкрата по вертикальным направляющим станины перемещается консоль 11.
По горизонтальным направляющим консоли перемещаются продольные салазки 10, по верхним направляющим которых перемещаются поперечные салазки 6, а на них установлены поворотные салазки 9 и стол 7. Вертикальное, продольное и поперечное движения подачи стола могут осуществляться вручную или коробкой подач, размещенной в консоли. Вращательное движение выходного вала коробки подач преобразуется в поступательное перемещение стола с помощью механизмов «ходовой винт – гайка». На верхней части стола выполнены поперечные Т-образные пазы для установки заготовки или рабочих приспособлений.
На рис. 29, б показаны основные узлы вертикально-фрезерного станка. Эти станки имеют много общих унифицированных узлов и деталей с горизонтально-фрезерными станками, но отличаются от них вертикальным расположением шпинделя 13, который можно поворачивать под углом до 45° в обе стороны с помощью поворотной планшайбы 12. На фундаментной плите 1 установлена чугунная станина 2. Внутри станины расположены отсек для электрооборудования, коробка скоростей. В верхней части станины установ лена поворотная планшайба 12 с фрезерной головкой и шпинделем 13. С помощью винтового домкрата по вертикальным направляющим станины перемещается консоль 11 с продольными 10, поперечными 6 салазками и столом.
Просмотров: 1 786
Обработка деталей на фрезерных станках. Фрезерная обработка на станках с ЧПУ
Обработка деталей на фрезерных станках ЧПУ.

- пластик ПВХ;
- оргстекло;
- дерево;
- МДФ;
- фанеру;
- композит;
- поликарбонат;
- полистирол и другие.
Преимущества обработки деталей на фрезерных станках.
Фрезеровка с использованием числового программного управления дает ряд преимуществ по сравнению с отделкой на обыкновенном фрезерном станке.
- Точность.
- Производительность.
- Контроль.
- Скорость.
- Возможность передачи с макета на материал мельчайших деталей.
- Получение на только прямых, но и криволинейных, радиусных конструкций разного размера.
Технология фрезеровки используется в промышленности уже более 200 лет, и только станки с ЧПУ помогли значительно расширить потенциал данной технологии обработки деталей. Фрезерная обработка деталей на станках с ЧПУ чаще всего используется в мебельном производстве, дизайне, архитектуре и строительстве, отделке интерьеров помещений и экстерьеров зданий, изготовлении конструкций для наружной и внутренней рекламы, выставочных стендов, торгового оборудования, оригинальных подарков и упаковочных материалов.
Фрезерная обработка на станках ЧПУ – наши особенности.
Для изготовления заготовок и готовых изделий в нашей компании используются фрезерные станки с ЧПУ. Фрезерная обработка на данных станках позволяет добиться высочайшего качества продукции при минимальных затратах времени.
Процесс фрезеровки выполняется специальным режущим элементом станка – фрезой. Они выпускаются разной длины, диаметра сечения. Для каждого вида обрабатываемого материала применяется специально разработанная программа, учитывающая особенности обработки.
Через компьютер, подключенный к станку, осуществляется управление скоростью и направлением движения фрезы, глубиной проникновения в материал. При помощи фрезерной обработки на станках с ЧПУ получают сложные по конструкции детали, заготовки, целые изделия, полностью соответствующие исходному электронному макету.
Собственное производство. Наша компания имеет собственное оборудование ЧПУ. Мы всегда рады видеть Вас у нас на производстве для ознакомления и показа наших потенциалов.
Наши цены конкурентоспособны. За счет увеличения производства, высокой квалификации наших сотрудников, беспрерывного процесса производства мы смогли снизить цены и сделать их ниже рыночных.
Фрезерная обработка деталей на заказ.
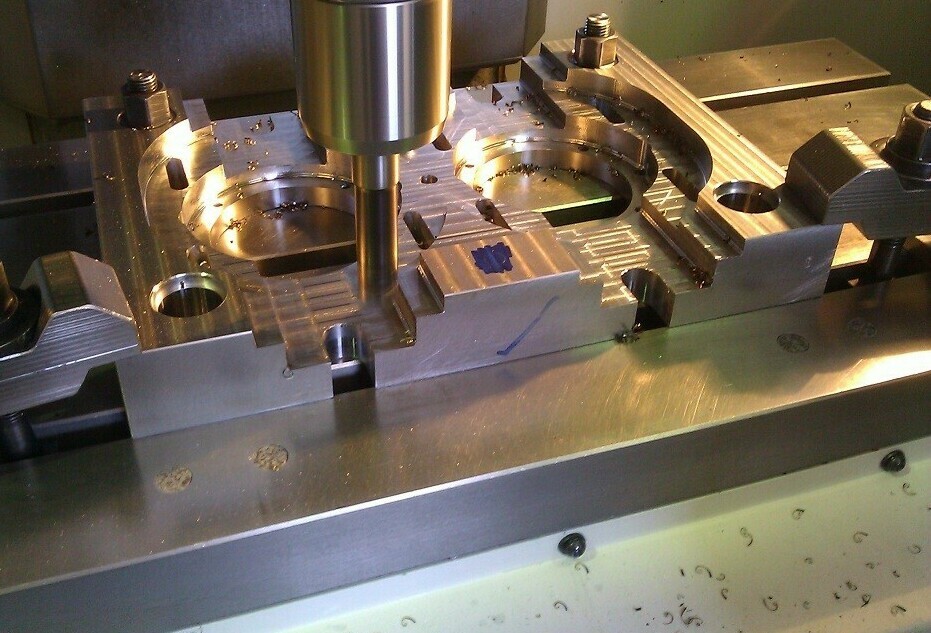
Фрезерная обработка на заказ выполняется нашими специалистами быстро и качественно. Заявки принимаются по телефону, электронной почте, в офисе компании и на сайте. Менеджер обрабатывает заказ, уточняет с клиентом все детали, выполняет просчет стоимости.
Пошаговая инструкция заказа услуг по фрезерной обработке деталей.К каждому клиенту у нас особый подход. Подготовка к работе в нашей компании строиться следующим образом:
- Оформление заявки;
- Оговорка всех нюансов заказа;
- Формирование пакета технической документации;
- Оплата заказа по счету;
- Срок выполнение заказа от 3 дней.
Заказчик предоставляет готовый эскиз или описание нужной детали. Наши сотрудники разрабатывают электронный макет. Затем выполняется фрезерная обработка на ЧПУ, при необходимости оказываются дополнительные услуги по покраске, сборке изделий, конструкций, доставке продукции клиенту.
Процесс фрезерного станка: типы деталей и их применение
Фрезерование — это процесс удаления металла, который включает подачу заготовки на вращающийся резец с одним или несколькими режущими лезвиями. Фрезерные станки могут обрабатывать плоские или криволинейные поверхности различных заготовок с хорошей отделкой и точностью. Фрезерный станок также можно использовать для сверления, прорезания пазов, создания круглого профиля и нарезания зубчатых колес с помощью соответствующих насадок.
Что такое фрезерный станок?
Фрезерный станок является одним из самых универсальных традиционных станков, способных резать широкий спектр металлов. Фрезерный станок может выполнять различные сложные операции, такие как индексация, групповое фрезерование, разветвление и так далее.
Детали, используемые во фрезерных станках
Различные части фрезерного станка:
Колонна и основание – Колонна и основание фрезерного станка поддерживают другие компоненты.
Колено – Винт вертикального позиционирования, часто называемый подъемным винтом, поддерживает и регулирует колено.
Седло и поворотный стол – Седло находится на колене и поддерживает стол, а поворотный стол прикреплен к седлу, которое поворачивается (вращается) горизонтально в обоих направлениях.
Механизм механической подачи – Механизм механической подачи расположен в колене. Продольная (левая и правая), поперечная (внутрь и наружу) и вертикальная (вверх и вниз) подачи контролируются им.
Стол – В верхней части седла находится прямоугольная отливка, называемая столом.
Шпиндель – Шпиндель фрезерного станка представляет собой вал, удерживающий и приводящий в движение режущие инструменты.
Консоль/консоль – Это горизонтальная балка, которая проходит по всей длине верхней грани колонны. Это может быть одна отливка, которая скользит по каналам типа «ласточкин хвост» на верхней поверхности колонны.
Опора вала – Опора вала представляет собой отливку с подшипником, который поддерживает внешний край вала. Это также помогает выровнять внешний конец оправки со шпинделем.
Поршень – Подвесной рычаг вертикальной машины называется поршнем.
Различные типы фрезерных станков
> ● Вертикально-фрезерные станки
Вертикально-фрезерный станок вращается, оставаясь на одной оси, и имеет вертикально расположенную ось шпинделя. Шпиндель также можно удлинить для выполнения операций сверления и резки. Существует два типа вертикальных мельниц: револьверная мельница и станина.
Револьверная мельница использует стол, который перемещается перпендикулярно и параллельно оси шпинделя для резки материала. Веретено, с другой стороны, остается неподвижным. Возможны два метода резки: смещение колена и опускание или подъем пера.
С другой стороны, станок для станины имеет стол, который перемещается перпендикулярно оси шпинделя, и шпиндель, который перемещается параллельно его оси.
● Горизонтальные фрезерные станки
Горизонтальная фреза — это фреза, идентичная вертикальной фрезе, за исключением того, что она установлена на горизонтальной оправке. Многие горизонтальные мельницы используют поворотные столы для фрезерования под разными углами. Такие таблицы называются универсальными. Кроме того, все инструменты, используемые в вертикальной мельнице, можно использовать и в горизонтальной мельнице.
Процесс фрезерования
Различные типы фрезерных операций проходят через следующие процессы или этапы резки:
● Фрезы
В процессе фрезерования используется много различных режущих инструментов. Фрезерные станки могут одновременно работать с несколькими фрезами. Концевые фрезы представляют собой фрезы со специальными режущими поверхностями на их торцевых поверхностях, которые позволяют всверливать их в заготовку. Для периферийного фрезерования они также имеют расширенные режущие поверхности с обеих сторон. На концевых углах фрез расположены маленькие резцы. Резцы изготовлены из высокопрочных, долговечных материалов, которые вызывают минимальное трение.
● Обработка поверхности
Фрезерный станок режет материалы, проходящие через его зону резания через равные промежутки времени. На боковых резцах можно обнаружить регулярные гребни. Расстояние между гребнями определяется скоростью подачи, диаметром фрезы и количеством режущих поверхностей. Между поверхностями могут быть значительные перепады высот.
● Групповое фрезерование
В системе горизонтального фрезерования это означает, что используется более двух фрез. Возможно, что все фрезы выполняют одну и ту же операцию или каждая фреза выполняет разную работу.
Применение фрезерных станков
Вот некоторые из областей, где фрезерные станки используются для:
● С помощью фрезерного станка можно создавать различные шестерни.
● В большинстве случаев он используется для создания пазов или канавок в заготовках. ● Имеет возможность обрабатывать как плоские, так и неровные поверхности.
● Используется в обрабатывающей промышленности для создания сложных форм.
Заключение
Хотя фрезерные станки бывают разных форм и размеров, их основная функция остается неизменной. Тем не менее, выбор правильной машины для работы имеет решающее значение. Мы надеемся, что эта информация помогла вам лучше узнать о фрезерных станках и их отличиях.
Читайте также: Что такое станок с ЧПУ и как он работает?
Что такое процесс измельчения?
Фрезерование — метод механической обработки, при котором фреза используется в качестве инструмента для обработки поверхности объекта. Фрезерование — это высокоэффективный метод обработки, при котором для резки заготовки используется вращающийся многолезвийный инструмент.
Что такое процесс измельчения?
Фрезерование относится к методу перемещения относительного положения заготовки, такой как металл, к инструменту при резке или сверлении отверстия в материале для придания материалу желаемой формы. При работе инструмент вращается как основное движение, заготовка движется как движение подачи, и заготовка также может быть зафиксирована, но вращающийся инструмент должен выполнять основное движение и движение подачи одновременно. Станки для фрезерования включают горизонтальные фрезерные станки, вертикально-фрезерные станки или портальные фрезерные станки. Эти станки могут быть обычными станками или станками с ЧПУ. Резка вращающейся фрезой как инструментом. Фрезерование обычно выполняется на фрезерном или расточном станке и подходит для обработки плоскостей, канавок, различных формообразующих поверхностей и специальных форм форм.
Фрезерование можно условно разделить на два типа: фрезерование, при котором обрабатываемая заготовка фиксируется и вращается инструмент, и точение, при котором заготовка вращается.
Что такое обработка на фрезерном станке?
Фрезерная обработка – это метод обработки режущим инструментом, называемым фрезерным станком, установленным на вращающемся валу. Поскольку это позволяет инструменту периодически контактировать и резать неподвижную заготовку, он может не только обрабатывать поверхность заготовки до плоской или изогнутой поверхности, но также выполнять различные операции, такие как сверление и нарезание канавок.
Фрезерные станки можно разделить на горизонтальные и вертикальные типы в зависимости от направления шпинделя установочного инструмента, а также существуют фрезерные станки портального типа, которые могут использовать такие инструменты, как торцевые фрезы, концевые фрезы и пазовые фрезы для обработки заготовок. в целевые формы.
Что такое токарная обработка?
Токарная обработка обычно делится на две категории: перемещение материала, перемещение инструмента и перемещение инструмента и перемещение материала. Технология токарной обработки может использоваться для обработки заготовки на токарном станке, чтобы придать внешней периферии заготовки круглую форму или форму с тонким концом, или выполнить сверление, растачивание для увеличения диаметра отверстия, нарезание резьбы и нарезание канавок. Заготовку можно полностью отрезать.
Коррекция точности для фрезерования:
- Калибровка оси X фрезерного станка:
Слегка ослабьте 4 болта, но убедитесь, что 4 болта все еще имеют некоторое сопротивление трению. В настоящее время используйте головку для вращения болтов, чтобы отрегулировать левый и правый углы. Во время процесса на торец главного вала необходимо поместить циферблатный индикатор для измерения правильного положения рабочего стола. - Калибровка оси Y фрезерного станка:
Слегка ослабьте три болта, но убедитесь, что три болта не слишком ослаблены, чтобы облегчить работу по точной настройке. Используйте поворотный болт рычага, чтобы поместить циферблатный индикатор на торец вала, чтобы измерить правильное положение рабочего стола. - Выравнивание фрезерного станка:
Поместите спиртовой уровень на рабочую поверхность.
Что такое объекты обработки?
- Плоские детали:
Характеристики плоских деталей заключаются в том, что обработанная поверхность может быть параллельна горизонтальной плоскости, перпендикулярна горизонтальной плоскости, а также может образовывать фиксированный угол с горизонтальной плоскостью.Самый простой тип деталей при фрезеровании с ЧПУ, как правило, для обработки требуется использовать только двухосную связь или трехосную связь трехкоординатного фрезерного станка с ЧПУ. В процессе обработки обрабатываемая поверхность находится в поверхностном контакте с инструментом, а концевые фрезы можно использовать как для черновой, так и для чистовой обработки.
- Поверхностные детали
Характеристики поверхностных деталей заключаются в том, что обрабатываемая поверхность представляет собой пространственную поверхность, и во время процесса обработки обрабатываемая поверхность и фреза всегда находятся в точечном контакте. Обработка поверхности в основном выполняется шаровыми фрезами.
Какие факторы влияют на точность обработки?
- Жесткость:
Как только к объекту приложена сила, объект деформируется, но, с другой стороны, создается сила, противодействующая деформации, такое свойство называется жесткостью. При использовании станка необходимо преодолеть жесткость станка, если обработка должна выполняться с заданной точностью.Хотя способность современных станков справляться с жесткостью довольно высока, для выполнения обработки с микронной точностью необходимо понимать характеристики жесткости. Жесткость делится на статическую силу (статическую жесткость) и динамическую силу (динамическую жесткость). При выполнении механической обработки, такой как резка заготовки, необходимо одновременно учитывать как статическую, так и динамическую жесткость.
- Статическая жесткость: Относится к состоянию, в котором направление и величина действующей силы остаются фиксированными в любое время. В станке можно сказать, что рабочая часть находится в состоянии неподвижности на рабочей плите. В настоящее время, со строгой точки зрения, можно считать, что рабочее место деформировано под действием силы тяжести рабочей части. Хотя фактический эффект невелик, в некоторых случаях он все же может снизить точность обработки.
- Динамическая жесткость: Относится к состоянию, в котором изменяется направление или величина приложенной силы.
В случае станка вибрация генерируется, когда переключатель включен, чтобы заставить станок работать. Это может вызвать такие симптомы, как вибрация станка, влияющая на точность обработки.
- Термическая деформация:
Объекты расширяются при повышении их температуры. Поэтому для точного измерения длины необходимо выполнять работы в измерительной комнате, в которой досконально реализован температурный режим. При обработке особое внимание следует обращать на деформацию предметов, вызванную нагреванием. Это связано с тем, что каждая деталь нагревается после запуска станка. Кроме того, при выполнении таких операций, как резка, также повышается температура целевого объекта. И чем дольше работает станок, тем меньше можно пренебречь влиянием термической деформации. Поэтому можно сказать, что знание того, как долго время работы будет доводить станок до высокой температуры, важно для точной обработки.
Базовые знания о резке:
- Режущее действие:
Резание относится к действию использования инструмента для сбривания части мишени, за которым должны следовать два действия.Резка – это действие по срезанию части мишени, которое выполняется путем перемещения инструмента, такого как токарный инструмент, по прямой линии. Подача относится к действию перемещения инструмента, чтобы станок мог резать другие детали. Например, после нанесения прямой линии можно вырезать новую грань, подавая инструмент в направлении, перпендикулярном направлению резания. Просто повторите это действие, чтобы создать плоскость.
- Обработка и сопротивление:
Поскольку инструмент и цель в процессе обработки соприкасаются друг с другом, а силы мешают друг другу, возникает сопротивление. При работе необходимо учитывать, что сопротивление, создаваемое разными инструментами, различно. При резке токарным инструментом сопротивление будет варьироваться в зависимости от таких факторов, как материал заготовки, площадь резания или тип токарного инструмента. Среди них площадь резания имеет большое отношение к сопротивлению, и во время обработки необходимо уделять особое внимание.Кроме того, при сверлении дрелью также необходимо учитывать сопротивление по крутящему моменту и подаче. Момент относится к силе кручения, также известной как крутящий момент. Подача относится к действию продвижения направления сверла. При сверлении, помимо материала цели, величина сопротивления меняется в зависимости от типа сверла (формы наконечника), скорости вращения сверла и скорости подачи. На месте обработки можно добиваться качества, эффективности и долговечности инструмента, если метод обработки рассматривается с учетом влияния сопротивления.
- Обработка и скорость:
На участке обработки важным вопросом является эффективность работы, а также контроль качества. Использование механической обработки заключается в повышении эффективности за счет увеличения скорости обработки. Однако особое внимание следует также уделять увеличению скорости машин и обработки, что может вызвать негативные последствия, такие как повышенное сопротивление и термическая деформация. Кроме того, увеличение скорости обработки также может сократить срок службы токарного инструмента.Это может увеличить частоту смены токарных инструментов, что приведет к увеличению стоимости единицы механической обработки. Поэтому перед обработкой важно учитывать скорость и точность, а также стойкость инструмента.
- Обработка и температура:
При выполнении механической обработки, такой как резка, выделяется тепло, когда цель и инструмент сталкиваются друг с другом. Это может повысить температуру внутри мишени, что повлияет на точность обработки или долговечность инструмента. Чем выше скорость обработки, тем больше тепла выделяется. Чем больше площадь обработки, тем больше трение, что увеличивает температуру. Поэтому при выполнении механической обработки следите за изменениями температуры во время работы. Смазочно-охлаждающие жидкости играют важную роль в управлении температурой при механической обработке. Это может уменьшить разницу в износе между целью и инструментом, поэтому он может уменьшить тепло, выделяемое в процессе охлаждения, и уменьшить количество отходов, образующихся в процессе.Раньше большинство смазочно-охлаждающих жидкостей были на масляной основе. Но теперь, в связи с повышенным вниманием к защите окружающей среды, большинство из них перешли на водорастворимые смазочно-охлаждающие жидкости. Кроме того, поскольку для механической обработки требуется большое количество смазочно-охлаждающей жидкости, большинство производителей в настоящее время используют устройства циркуляционного типа для фильтрации отработанной смазочно-охлаждающей жидкости и ее повторного использования.
Важные советы по техническому обслуживанию фрезерных станков:
- Смазка:
Одним из способов поддержания инструментов фрезерной головки в хорошем состоянии является их хорошая смазка. Для правильной работы фрезерных головок они должны иметь соответствующую смазку, чтобы все детали двигались плавно. - Очистка:
Еще одним важным условием поддержания работоспособности машины является правильная очистка после использования. Многие детали станков регулярно подвергаются воздействию пыли и других загрязнений, поэтому во избежание каких-либо проблем держите фрезерную головку в чистоте.