что это и для чего он нужен?
Плазматроны, или плазменные резаки – это устройства, которые формируют плазменный поток (высокотемпературный ионизированный воздух) из электрического тока и сжатого воздуха. Они предназначены для высокоточного раскроя различных металлов и могут выполнять резы любой конфигурации.
Как работает оборудование?
Принцип работы плазматрона основан на том, что воздух в состоянии ионизации начинает проводить электроток. Устройство создает поток высокотемпературного ионизированного воздуха и сварочную электродугу, с помощью которых и осуществляется резка металлических материалов. Применение плазматронов обеспечивает высокую производительность раскроя и не наносит вред здоровью людей и окружающей среде.
Чтобы создать систему плазменной резки, плазматрон комбинируют с источником электропитания и компрессором, который подает сжатый воздух. Установки резки металлов ионизированным газом используются на производстве, в жилищно-коммунальном хозяйстве, строительстве, автомобиле- и машиностроении, а также многих других отраслях.
Типы устройств
Плазмотроны делятся на две группы: для ручной и машинной резки. Для небольших производственных предприятий и автомастерских подойдут устройства, управляемые вручную. Купить плазмотроны в Астане для ручной резки металлических сплавов можно по приемлемой стоимости. Цена устройства зависит от рабочих характеристик: силы тока, типа и максимальной толщины металла, других параметров. Главный минус таких аппаратов – в том, что необходимо держать и направлять резак на весу.
Автоматические установки плазменной резки функционируют при минимальном участии оператора. Это обеспечивает высокую производительность и идеальное качество реза, а также позволяет выполнять фигурный раскрой металлов любой сложности.
Что учесть при выборе плазмотрона?
Главный критерий выбора плазмотрона – толщина разрезаемого металла и сила тока. Важно выбирать характеристики с существенным запасом, поскольку в инструкции к аппаратам обычно указываются не номинальные, а максимальные характеристики.
Компания «ИТС-Астана» предлагает купить плазмотроны в Астане для ручной и автоматической резки металлов ионизированным газом. В нашем каталоге представлен широкий ассортимент установок известных производителей рынка для воздушной-плазменной резки сталей, меди, никеля, титана и других металлов.
Преимущества и недостатки плазменной резки
Преимущества и недостатки плазменной резки по сравнению с другими методами резки металлов?
Резка металлов – проблема, с которой приходится сталкиваться и в цеху, и на стройплощадке, и в мастерской. Простые решения вроде автогена устроят многих, но не всех. Если объем работ по резке металла большой, а требования к качеству реза высоки, то стоит подумать об использовании аппарата плазменной резки (плазмореза).
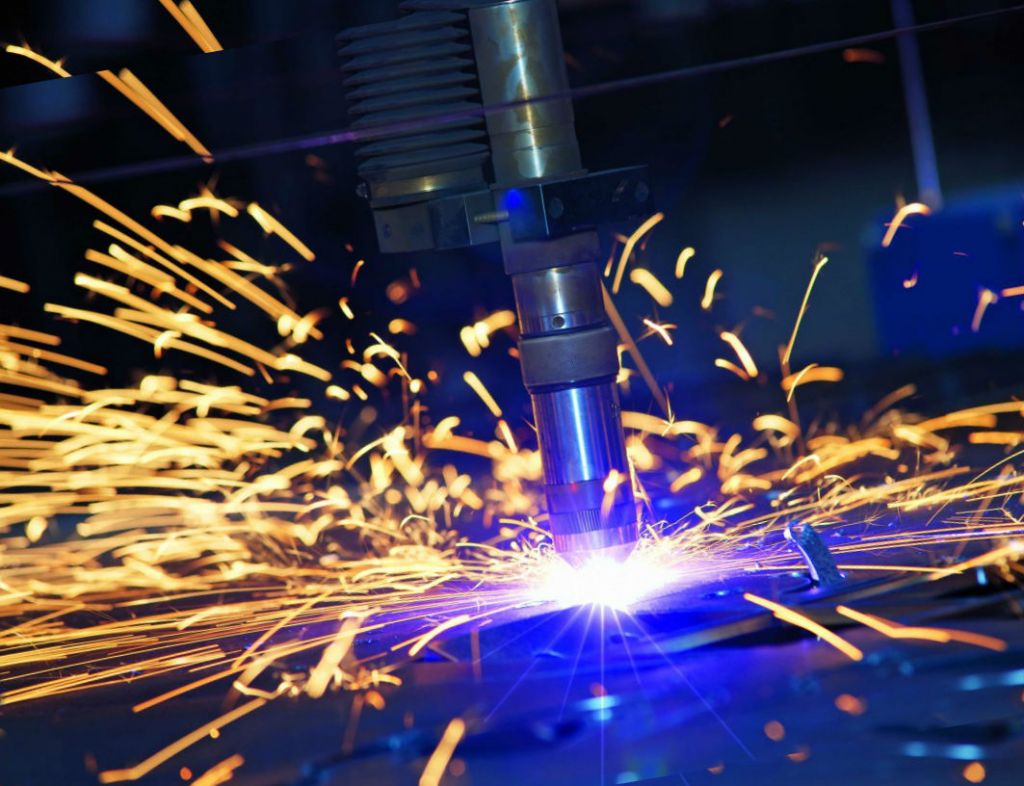
ПРЕИМУЩЕСТВА:
Какие преимущества в работе дает аппарат или станок плазменной резки металла в работе?
1. При правильном подборе мощности он позволит в 4-10 раз (по сравнению кислородной горелкой) повысить производительность. По этому параметру плазморез уступит лишь промышленной лазерной установке, зато намного выиграет в себестоимости. Экономически целесообразно использовать плазменную резку на толщинах металла до 50-60мм. Кислородная же резка более предпочтительна при раскрое стальных листов толщиной свыше 50 мм.
2. УНИВЕРСАЛЬНОСТЬ. Плазменная резка позволяет обрабатывать и сталь, и чугун, и алюминий, и медь, и титан, и любой другой металл, причем работы выполняются с использованием одного и того же оборудования: достаточно выбрать оптимальный режим по мощности и выставить необходимое давление воздуха. Важно отметить и то, что качество подготовки поверхности материала особого значения не имеет: ржавчина, краска или грязь помехой не станут.
3. ТОЧНОСТЬ и ВЫСОКОЕ КАЧЕСТВО РЕЗА. Современные плазморезы обеспечивают минимальную ширину реза и “чистые” без наплывов, перекаливания и грата кромки, почти не требующие дополнительной обработки. Немаловажно и то, что зона нагрева обрабатываемого материала намного меньше, чем при использовании автогена, а поскольку термическое воздействие на участке реза минимально, то и тепловые деформации вырезанных деталей незначительны, даже если они небольшой толщины.
4. БЕЗОПАСНОСТЬ, обусловленная отсутствием взрывоопасных газовых баллонов.
5. НИЗКИЙ уровень загрязнения окружающей среды. Касательно экономической стороны вопроса, то совершенно очевидно, что при больших объемах работ плазменная резка выгоднее той же кислородной или, например, механической. В остальных же случаях нужно учитывать не материалы, а трудоемкость использования. Например, сделать фигурный рез в толстом листе недолго и автогеном, но может потребоваться продолжительная шлифовка краев.
НЕДОСТАТКИ:
Ну а теперь поговорим о недостатках. Первый из них – относительно скромная максимально допустимая толщина реза, которая даже у мощных аппаратов редко превышает 80-100 мм. В случае же с кислородной резкой максимально допустимая толщина реза для стали и чугуна может достигать 500 мм.
Следующий недостаток метода – довольно жесткие требования к отклонению от перпендикулярности реза. В зависимости от толщины детали угол отклонения не должен превышать 10-50°. При выходе за эти пределы наблюдается значительное расширение реза и, как одно из следствий, быстрый износ расходных материалов.
Наконец, сложность рабочего оборудования делает практически невозможным одновременное использование двух резаков, подключенных к одному аппарату, что с успехом применяется при резке штучным электродом.
Процесс плазменной резки (принцип работы плазмореза)
Для начала определим, что же есть плазма. В данном случае это нагретый электрической дугой до высокой температуры (порядка 25000 °C) воздух в ионизированном состоянии. Последнее означает, что он утрачивает свойства диэлектрика и приобретает способность проводить электрический ток. В процессе резки плазменный поток становится проводником для тока, расплавляющего металл, и сам же его выдувает.
Для начала определим, что же есть плазма. В данном случае это нагретый электрической дугой до высокой температуры (порядка 25000 °C) воздух в ионизированном состоянии. Последнее означает, что он утрачивает свойства диэлектрика и приобретает способность проводить электрический ток. В процессе резки плазменный поток становится проводником для тока, расплавляющего металл, и сам же его выдувает.
Рабочий орган аппарата называется плазмотрон. Под этим словом подразумевается плазменный резак с кабель-шланговым пакетом, подключаемый к аппарату. Иногда плазмотроном ошибочно называют аппарат плазменной резки целиком. Разновидностей плазмотронов достаточно много. Но наиболее распространены и более всего пригодны для резки металлов плазмотроны постоянного тока прямой полярности. По виду дуги различают плазмотроны прямого и косвенного действия. В первом случае разрезаемое изделие включено в электрическую цепь, и дуговой разряд возникает между металлической деталью и электродом плазматрона. Именно такие плазмотроны применяются в устройствах, предназначенных для обработки металлов, включая и аппараты воздушно-плазменной резки. Плазматроны косвенного действия применяются, в основном, для обработки неэлектропроводных материалов (у них электрическая дуга возникает в самом резаке).
Сопло – важнейший элемент, определяющий возможности плазмотрона. При плазменной резке применяются сопла небольшого (до 3 мм) диаметра и большой (9-12 мм) длины. От размера диаметра сопла плазмотрона зависит количество воздуха, которое способен пропустить плазмотрон, этот параметр необходимо учитывать при подборе компрессора. Это также влияет на ширину реза и охлаждение плазмотрона. Что касается длины, то чем она больше, тем выше качество реза. Однако чрезмерное увеличение этого параметра ведет к снижению надежности работы и быстрому разрушению сопла. Считается, что длина канала должна быть больше диаметра в 1,5-1,8 раза.
Электродом (катодом) внутри плазматрона служит металлический стержень – другие конструкции в недорогих аппаратах не применяются. То же можно сказать и о материале: разновидностей изобилие, но массово используется лишь электрод из гафния.
Теперь пару слов о рабочих газах, используемых при плазменной резке. Их можно разделить на плазмообразующие и защитные (транспортирующие). Для резки в обычных плазменных системах бытового назначения (сила тока дуги – ниже 200 А, максимальная толщина реза – до 50 мм) сжатый воздух применяют и как плазмообразующий, и как защитный газ. При этом достигается удовлетворительное качество реза, хотя и наблюдается некоторое азотирование и окисление обрабатываемой поверхности. В более сложных системах применяются иные газовые смеси, содержащие кислород, азот, водород, гелий, аргон.
Выбор аппарата плазменной резки
Даже самые доступные аппараты плазменной резки сложны и довольно дороги в сравнении, например, со сварочными, поэтому к выбору недешевой техники нужно подходить осознанно.
Первый параметр, без учета которого бесполезно учитывать остальные, – это максимально допустимая толщина реза. Данная величина обычно приводится для углеродистой стали, реже – для нержавеющей, еще реже – для алюминия и очень редко – для меди. Поскольку на максимально допустимую глубину реза сильно влияет теплопроводность материала, то для сплавов на основе меди этот показатель примерно на 30% ниже, чем для сплавов на основе железа. И если в технических характеристиках аппарата заявлена максимально допустимая толщина реза стали в 10 мм, это будет означать, что максимальная глубина реза медных сплавов составит 7 мм. Таким образом, вторым по важности показателем станет тип сплава, с которым предстоит работать.
Следующий фактор – планируемый режим эксплуатации плазмореза. Как и в случае со сварочными аппаратами, он определяется параметром “ПВ” (продолжительность включения), который определяет отношение времени работы аппарата ко времени, необходимому для его охлаждения.
На практике это выглядит следующим образом. Если ПВ плазмореза составляет 50%, то в течение часа эксплуатации он должен 30 минут работать и 30 минут остывать. При ручной резке приходится время от времени перемещаться или перемещать изделие и периодически выключать кнопку поджига на плазмотроне. Это время как раз и идет в зачет охлаждения, и поэтому работа кажется непрерывной. Такая формула дает сбой при работе с толстыми листами металла или при автоматической плазменной резке с ЧПУ, когда время реза может быть значительным. Дело в том, что параметр ПВ определяется для 10-минутного цикла, поэтому в начале смены, пока аппарат холодный, он будет отработать без перерыва и 15 минут даже при низком ПВ, а вот при цикличной работе может отключиться и после 5 минут непрерывной резки.
Когда ключевые параметры, определяющие принципиальную возможность использования аппарата, определены, следует уделить внимание такому аспекту, как удобство использования. Тут первостепенное значение приобретает мобильность, точнее, радиус действия, на который можно свободно удаляться от малоподвижного аппарата, “прикованного” к своему месту компрессором. Так, длина кабель-шлангового пакета плазмотрона может варьироваться до десятков метров. Кстати, важна не только длина: некоторые производители заявляют ее на уровне 30 м и более, но “забывают” сообщить о том, имеются ли евроразъемы на плазмотроне и источнике. Если таких разъемов нет, то укоротить или удлинить плазмотрон вряд ли получится, и всякий раз разматывать его для того, чтобы резать небольшие по размерам листы, будет утомительно. Главный же минус длинного плазматрона не в этом, а в том (и производители об этом, как правило, тоже умалчивают!), что при его длине свыше 20 метров наблюдается потеря мощности, причем довольно ощутимая. Поэтому разумнее всего выбирать плазмотрон небольшой (6-12 м) длины, оснащенный евроразъемом, чтобы при необходимости была возможность удлинить конструкцию, используя быстронаращиванмый удлинитель плазмотрона.
Это будет, кстати, удобно и при работе на открытом воздухе в неблагоприятных условиях, когда выносить из помещения аппарат нежелательно. Однако, как уже отмечалось, использовать удлинитель нужно лишь в случае действительной необходимости.
Очень важный вопрос – проблема расходных материалов: электродов (катодов) и сопел. Важно, чтобы они были доступны и недороги. Как правило, износ этих деталей происходит или одновременно или с небольшим “разбросом” (один катод на два сопла). Одного сопла в среднем хватает на целую рабочую смену (при работе с деталями, толщиной до 10 мм).
Момент, не относящийся напрямую к плазматрону, но требующий обязательного учета, – это система подачи воздуха. Если отбросить самые маломощные модели, оборудованные встроенным компрессором и воспринимаемые многими профессионалами как малополезные игрушки, то следует помнить, что для работы плазматрону нужен мощный компрессор. И не он один: при достаточно большом расходе воздуха (100-250 л/мин при 0,4-0,6 МПа) жесткие требования предъявляются и к его качеству, а значит не обойтись без вспомогательных устройств – таких как влаго- и маслоотделители, фильтры. Поступать в аппарат воздух должен равномерно, без пульсаций, поскольку они серьезно влияют на стойкость сопел и электродов, на стабильность поджига дуги и, как следствие, на качество реза, а значит, нужен объемный ресивер.
ПРЕДЛОЖЕНИЕ ДЛЯ ЛЮБИТЕЛЯ
Среди современных устройств плазменной резки можно выделить отдельную и наиболее интересную для рядового потребителя категорию – переносные инверторные источники плазмы, применяемые при ручной резке. Их основные достоинства: низкое энергопотребление, компактность, небольшой вес, эргономичный дизайн. Недостатки: ограничение по максимальной мощности (не более 70 А), и, как следствие, по максимальной толщине реза (до 15-20 мм). Также придется мириться с невысокой продолжительностью включения и чувствительностью к перепадам напряжения. Оборудование, выходящие за рамки этого типа, как правило, рассчитано на промышленное применение.
Большинство аппаратов с плазмотронами воздушного охлаждения пригодны для резки металлических деталей толщиной до 50 мм. Для резки деталей толщиной свыше 50 мм или для увеличения производительности применяют более сложные и дорогие аппараты с плазмотронами водяного охлаждения
Максимальная глубина реза определяет толщину материала, которая может быть разрезана данным аппаратом в принципе. Скорость работы при этом в расчет не берется. Чтобы комфортно и быстро работать с деталями толщиной 3-4 мм, следует выбирать аппарат, максимально допустимая глубина реза которого – 8-10 мм.
Унифицированные разъемы для плазмотронов производятся в соответствии с европейскими стандартами и состоят из розеток (со стороны источника плазмы) и вилок (со стороны резака). Преимущество подобной системы заключается в возможности при необходимости удлинить или укоротить конструкцию без ощутимой потери мощности, прочности и электрического контакта.
Износ сопла заключается в нарушении его геометрической формы, что негативно влияет на качество реза. Износ же катода приводит к выработке стержня (допустимая глубина выработки – не более 1,5 мм), в результате чего может произойти пригорание катода к головке плазмотрона и его (плазмотрона) перегрев.
При минусовых температурах необходимо соблюдать определенные меры предосторожности. Поскольку в ресивере и шлангах образуется конденсат, который в случае замерзания может вывести из строя оборудование, то после окончания работ шланги обязательно продувают, а сам компрессор хранят в помещении с плюсовой температурой.
Типичные ошибки при плазменной резке металла
При выполнении работ связанных с резкой металла на станках с ЧПУ можно выделить наиболее типичные ошибки, которые гарантированно ведут к повышению итоговой стоимости таких работ:
1. Первой ошибкой зачастую является несвоевременная замена расходки плазмотрона (сопла, электроды, завихритель и т.п.).Использование расходных частей с дефектами, выходящими за расчетные параметры – типичное нарушение, при запоздалой замене, ведет к ухудшению качества реза, неровной кромке, сокращению срока службы остальных деталей и самого резака. При преждевременной замене элементов(когда все параметры расходных частей ещё находятся в пределах нормы), нет абсолютно никаких негативных последствий для оборудования, но расходные части не отрабатывают свой полный ресурс, заложенный заводом производителем, что в свою очередь увеличивает себестоимость такой работы.
Опытный оператор оборудования в состоянии исключить ошибки такого характера, осматривая состояние расходных частей визуально, через регламентированные промежутки времени, оценивая пригодность и уровень выработки деталей для дальнейшей работы.
2. Вторая распространенная ошибка в условиях производства – применение не соответствующих режимов резки, что значительно сокращает срок службы расходки.
Крайне не рекомендуется долговременное использование оборудования, на тока превышающих 95% от максимального значения, заявленного производителем. Не стоит с попустительством относиться к состоянию плазменного источника в процессе работы – должны быть запланированы мероприятия по техническому обслуживанию, исходя из состояния оборудования и условий, в которых оно работает. В процессе работы узлы плазмотрона загрязняются нагаром от обрабатываемого металла, грязью, пылью, металлическими частицами и прочим, что при не своевременном уходе так же может привести к преждевременному выходу оборудования из строя, за счет электрического пробоя или недостатка охлаждения, при работе на режимах близких к максимальным. Для минимизации влияния внешних факторов на плазмотрон одевается защитный кожух, с последующей переодической ревизией.
3. Отсутствующий контроль за расходом охлаждающего газа. Для стабильной работы оборудования плазмообразующий газ должен соответствовать расчетным характеристикам – по содержанию воды, масляной взвеси, давлению и количеству подачи (производительность подачи).
В случае большой влажности воздуха и/или присутствию обильных маслянных паров в подаваемом воздухе чрезвычайно повышается вероятность электрического пробоя внутри плазмотрона. При несоттветствии давления подачи газа, или производительности насоса (при длинном резе насос может не успевать подавать необходимое давление на плазмотрон, например при опустошенном рессивере) возникает чрезвычайная нестабильность диаметра дуги – диаметр дуги начинает “плавать”, что отражается на точности и качестве реза, а так же получаемой кромки, значительно сокращает срок службы электродов и сопел. При существенном недостатке охлаждающего газа, либо при неправильно подключенном охладителе происходит перегрев плазмотрона, при котором с большой долей вероятности выйдут из строя раньше времени различные его части.
4. Неправильная сборка резака – плазмотрон должен быть собран так, чтобы все его части были выровненны относительно другдруга и плотно прилегали друг к другу, что обеспечит отличный контакт при работе с резаком.
Храните запасные и расходные части в чистом месте, чтобы избежать загрязнения металлической стружкой и пылью. При сборке стоит смазать уплотнительное кольцо – но лишь чтобы оно слегка блестело – это важно. Завихритель может забиться излишним количеством смазки, нанесенным при сборке, при том на смазку отлично налипает металлическая пыль, которая приводит к неконтролируемому процессу образования плазмы внутри резака, что грозит выходом плазмотрона из строя.
5. Непрорез – при неудачной пробивке металла и непрорезе брызги расплавленного металла устремляются вверх, в сопло плазмотрона.

При нормальном процессе резки металла все искры, расплавленный метал, окалины и металлосодержащая пыль должны быть сдуты вниз в поддерживающий стол или вбок, вдоль металла, кроме того, в то самое время, пока не зажглась стабильная плазменная дуга, плазмотрон работает на повышенных токах, что значительно сокращает срок его службы, срок службы расходных частей и может привести к значительным повреждениям высоковольтной части оборудования.
6. Слишком большая или малая скорость резки. При наличии трудноотделимого от заготовки грата на нижней кромке резки стоит задуматься о целесообразности подбора отличной от текущей скорости реза.
При слишком медленной резке листа значительно увеличивается ширина получаемого разреза, что приводит к снижению точности соответствия заготовки и чертежа, заложенного в программу ЧПУ. Завышение же скорости резки увеличивает шансы на “непрорез” металла доконца и приводит к “отставанию дуги” от плазмотрона, что может сместить получаемую кромку вырезаемой заготовки от заданных параметров (не перпендикулярность кромки реза оси плазмотрона). Увидеть слишком быстрый рез можно по направлению температурного рисунка на срезе металла. При слишком быстром резе металл не успевает выдуть из разреза и рез идет наискосок, как бы не поспевая за плазмотроном.
7. Растянутая дуга реза. При растяжении дуги возможно повреждения узлов плазмотрона нестабильно горящей дугой.
Дуга “растягивается”, рез становится не перпендикулярным, увеличивается шероховатость поверхности, когда разрезаемая заготовка или лист металла имеет неровности, а станок с ЧПУ не имеет стабилизатора высоты и не может компенсировать подобные огрехи. Самое безобидное что может случиться – плазмотрон встретиться с разрезаемым листом металла, получая повреждения расходных частей, которые зачастую уносят с собой элементы крепления к плазмотрону, в худшем же случае он может отдалиться от разрезаемой заготовки на столько, что начнется нестабильное горение дуги, произойдет пробой, который выведет из строя плазмотрон.
Для устранения неполадок, связанных с изменением высоты плазмотрона над заготовкой целесообразно применять качественные контроллеры высоты, например датчик производства Hypertherm – “Система Sensor™ PHC” или “Система регулировки высоты резака Sensor”, ведь из за высоких скоростей резки устройства низкого качества могут не успевать срабатывать, что повлечет за собой длительные простои для выявления поломки, определения перечня необходимых запасных частей (которые в таких случаях не всегда имеются на производстве) и устранение неисправности, что влечет за собой дополнительное удорожание цены производства конечного изделия.
8. Применение правильного угла резки для используемого типа расходных частей плазмотрона.
Для резки под прямым углом стоит использовать специальные расходые части Hypertherm – FineCut, при использовании которых стоит ожидать, что на поверхности металла останется менее 5 мм металла, оставшегося от срезанного профиля или проушины.
Вы всегда можете заказать новые запасные части, расходные материалы и сервисное обслуживание, обратившись к нашим Менеджерам, по телефону 8(800)775-08-50 или написать на почту [email protected]
Плазморезы АПР
Наша компания проектируем, производит и поставляет установки для плазменной резки металлов АПР. Многолетний опыт работы в сфере производства оборудования для раскроя металлов является гарантией того, что наша продукция удовлетворит любого клиента имеющего прямой интерес к данному оборудованию. Аппараты плазменной резки нашего производства отличает применение систем энергосбережения (начиная с АПР-91), использование плазмотронов (резаков) итальянского производства (Trafimet) с евроразъемами, что позволяет наращивать длину кабель-шлангового пакета, а также применять самые оптимальные по соотношению цена-качество-стойкость расходные материалы (сопла и катоды).
НАШИ АППАРАТЫ ПЛАЗМЕННОЙ РЕЗКИ АПР: (нажмите на картинку чтобы перейти)
Стандартная комплектация с АПР – резак ручной 6м. (Trafimet – Италия), зажим на массу, паспорт АПР, 5 сопел, 5 катодов
Расходные материалы для АПР (катоды, сопла, диффузоры, насадки и т.д. ) …
ПАСПОРТ АПР
Воздушно-плазменная резка является наиболее прогрессивным методам обработки металла и позволяют выполнять работы с минимальной зоной теплового воздействия, деформацией и отпуском металла. Также не маловажно то, что плазмотроны установленные на источники – немецкого производства. В них применены новейшие мировые достижения, что позволяет снизить себестоимость, как самой резки, так и оборудования в целом. Качество реза и скорость резки многократно превосходят российские аналоги. При этом отсутствуют такие недостатки как выставление вручную зазора между электродом (катодом) и соплом, что в свою очередь многократно повышает производительность труда резчика. Вся рукоятка плазмотрона выполнена из специального ударо-жаропрочного пластика (исключает попадание резчика под напряжение, при падении плазмотрон не выходит из строя). Кабель-шланговый пакет находится в специальной оболочке (состав резины и пластика) который сохраняет эластичность до -50 С и не подвержен процессу прожига при попадании на него искр или расплавленного металла. Плазмотрон подсоединяется к источнику с помощью евроразъема, который позволяет использовать плазмотроны и других известных мировых производителей. Аппарат укомплектован стандартным плазмотроном, длиной 6м. Также, возможны нестандартные решения: 12м, 18м. Существуют 12-метровые удлинители.
КРАТКАЯ КЛАССИФИКАЦИЯ АППАРАТОВ и УСТАНОВОК ПЛАЗМЕННОЙ РЕЗКИ
- Плазмотрон.
- Плазматрон.
- Плазморез.
- Плазмарез.
- Плазморезка.
- Аппарат воздушно-плазменной резки.
- Установка плазменной резки.
Краткий справочник.
Очень часто плазмотроном ошибочно называют целиком устройство – установку плазменной резки, хотя на самом деле плазмотрон – это непосредственно резак с кабель-шланговым пакетом, который подключается кисточнику плазменной резки ( к аппарату, источнику или установке плазменной резки), который может работать как в режиме ручной плазменной резки, так и в составе установки плазменной резки с ЧПУ(портальная машины термической резки с ЧПУ).
Под установкой плазменной резки чаще всего принимается именно машина термической резки с ЧПУ, хотя иногда так называют и аппараты или источники плазменной резки. Допустимо называть как ручные аппараты плазменной резки так и установки плазменной резки с ЧПУ.
Согласно правилам русского языка, в середине слов плазмотрон, плазморез, плазморезка, правильно писать букву «О», т.к. эти слова – двухкорневые, а в русском языке соеденительной буквы «А» нет.
В английском языке наоборот: plasmacutting (Plasma Cutting).
Система задержки воздуха – система которая автоматически отключает подаваемый сжатый воздух для резки через 15 секунд после того как плазморезчик отпустит кнопку включения на плазмотроне (окончание резки)
Система старта с маленького тока – система при которой процесс плазменной резки всегда начинается с тока резки в 30-40 Ампер. Эта система позволяет уменьшить износ сопел и катодов в 3-4 раза.
ПОДРОБНЕЕ:
Как работает плазменная резка?
Что такое плазма?
Чтобы разъяснить принцип действия плазменной резки, сначала нужно ответить на вопрос «Что такое плазма?» Плазма — это четвертое состояние вещества. Обычно мы сталкиваемся только с тремя состояниями вещества: твердым, жидким и газообразным. При поступлении или утрате энергии, например, тепла, вещество может переходить из одного состояния в другое. Например, при поступлении достаточного количества тепла вода переходит из твердого состояния (лед) в жидкое. Если тепла поступит еще больше, она перейдет в газообразное состояние (пар). Если добавить еще больше тепла, пар ионизируется и станет электропроводящим — превратится в плазму. Устройство плазменной резки сможет использовать этот электропроводящий газ для передачи энергии от источника питания к любому материалу-проводнику, что позволяет обеспечить более качественную и быструю резку по сравнению с газовой.
Образование плазменной дуги начинается с пропускания газа, например, кислорода, азота, аргона или даже обычного воздуха, через узкое сопло внутри плазмотрона под высоким давлением. Затем к этому потоку сжатого газа подается ток от источника питания, в результате чего возникает электродуга. В результате образовывается «струя плазмы». Плазма мгновенно достигает температуры до 22000°C, достаточной для быстрого разрезания рабочего изделия и сдувания расплавленного металла.
Составляющие системы плазменной резки
-
Источник питания — источник питания для плазменной резки преобразует одно- или трехфазный переменный ток в постоянный ток напряжением от 200 до 400В. Постоянный ток требуется для поддержания стабильной плазменной дуги на всем протяжении резки. Также источник питания позволяет регулировать силу тока в зависимости от типа и толщины материала.
-
Система поджига дуги — этот контур генерирует переменный ток напряжением около 5000 В и частотой 2 МГц, который образует внутри плазмотрона искру, поджигающую плазменную дугу.
-
Плазмотрон — плазмотрон служит для выравнивания и охлаждения расходных материалов. Основные расходные материалы для плазменной резки — это электрод, завихритель и сопло. Для повышения качества резки также может потребоваться дополнительный защитный колпачок, а для удержания всех деталей вместе используются внутренний и внешний поджимные колпачки.
Большинство современных систем плазменной резки делятся на традиционные и высокоточные.
В традиционных системах в качестве плазменного газа используется окружающий воздух, а форма плазменной дуги зависит от отверстия сопла. Приблизительная сила тока дуги таких систем составляет примерно 12 000-20 000 ампер на квадратный дюйм. Подобная схема используется во всех системах для ручной резки и некоторых механизированных системах, если это позволяют допуски. | ||
Высокоточные системы плазменной резки (с высокой плотностью тока) используются для особо высококачественной и точной плазменной резки. |
Ручная резка В большинстве систем ручной плазменной резки, например, Tomahawk® Air Plasma, в выключенном состоянии электрод и детали сопла находятся в контакте. При нажатии триггера источник питания начинает вырабатывать постоянный ток, который проходит через это соединение и запускает поток плазменного газа. После того, как плазменный газ (сжатый воздух) достигает достаточного давления, электрод и сопло размыкаются, что приводит к возникновению электрической искры, которая преобразует поток воздуха в струю плазмы. |
Высокоточная плазменная резка
Электрод и сопло внутри плазмотрона для высокоточной резки не соприкасаются и изолированы друг от друга завихрителем, который имеет небольшие вентиляционные отверстия, преобразующие плазменный газ в вихрь. Когда в источник питания поступает команда включения, он начинает подачу постоянного тока с напряжением холостого хода до 400В и начинает предварительную подачу газа через шланг к плазмотрону. Сопло в данный момент подключено к положительному потенциалу источника питания через контур вспомогательной дуги, а электрод — к отрицательному.
После этого система поджига дуги вырабатывает высокочастотную искру, из-за которой плазменный газ ионизируется и становится проводником тока от электрода к соплу. В результате образуется вспомогательная дуга плазмы.
После того, как вспомогательная дуга вступит в контакт с рабочим изделием (заземленному через пластины стола для резки), контур тока перемещается от электрода к рабочему изделию, высокочастотный разряд отключается и включается контур вспомогательной дуги.
После этого источник питания наращивает постоянный ток до выбранной оператором силы тока и меняет предварительную скорость потока газа на оптимальную скорость для данного материала. Также используется вспомогательный поток защитного газа, который подается вне сопла через защитный колпачок.
Форма и диаметр отверстия защитного колпачка заставляют защитный газ еще больше сужать плазменную дугу, что позволяет обеспечить чистую резку с минимальными углами скоса и небольшой шириной линии разреза.
Что такое плазменная резка – CyberSTEP
Плазменной резкой называют процесс резки металла раскаленной струей плазмы.
Первоначальным источником нагрева выступает электрическая дуга, но в отличие от дуговой сварки,
где дуга горит абсолютно свободно между изделием и электродом, при плазменной резке дуга обжимается газом,
чтобы на обрабатываемом предмете повысилась концентрация тепловой энергии.
Плазмотрон – это основной инструмент, который используется при плазменной сварке и резке.
В этих устройствах газ поступает в специальную разрядную камеру. В этой камере горит мощная дуга. Поступающий в камеру газ нагревается от горения мощной дуги. Так же газ ионизируется и выходит через специальное отверстие, называемое соплом, в виде струи плазмы, которая и используется как источник нагрева. Газ принято считать плазмой, когда он полностью или частично ионизирован.
Температура плазмы газового разряда зависит от состава среды и характеризуется температурами от 2 000 до 50 000 градусов Цельсия.
Струя плазмы, выходящая из сопла объединена со столбом дуги.
Следовательно теплопередача на воздействующий металл осуществляется, как за счёт тепла дуги, так и за счёт конвективного нагрева этого металла,
плазменной струёй. Всё это повышает энергетический коэффициент полезного действия процессов резки и сварки.
Аппараты плазменной резки могут:
- резать любой материал, проводящий электричество
- резать с минимальной деформацией или с полным её отсутствием без необходимости последующей обработки
- осуществлять резку быстрее, чем другими методами
- выполнять строжку любого токопроводящего материала
- использоваться вместе с установками для прямой и фигурной резки
- эксплуатироваться в полевых условиях от генераторов с автономным двигателем
Из истории появления плазменной резки:
В середине пятидесятых годов двадцатого века использование плазмотронов плотно вошло в сварочную технику.
Это произошло, тогда, когда аргонно-дуговая сварка с специальным неплавящемся электродом начала применяться для соединения
тонких металлических листов. Само – собой разуметься, что первый сварочный плазмотрон был разработан на базе горелок,
которые применялись в аргонно-дуговой сварке. Отличие первого плазмотрона от нынешнего заключалась в том,
что в первом плазмотроне применялась водоохлаждаемая металлическая камера, а не керамическое защитное сопло,
которое используется в нынешних плазмотронах. Камера, используемая в первоначальных плазмотронах,
полностью охватывала вольфрамовый электрод и кончалась соплом, соединённым с электродом и такого же диаметра, как диаметр столба дуги.
Газ, который проходил под давлением между столбом дуги и водоохлаждаемыми стенками камеры, воздействовал на столб, охлаждая и сжимая его при этом.
Газ так же обеспечивал электрическую и тепловую изоляцию столба от стенок самого сопла.
За счёт исследований, которые проводились в Институте металлов имени Байкова и определялось применение в нашей стране плазменной резки и сварки.
Исследования проводились под руководством Н. Н. Рыкалина.
В проводимых исследованиях были изучены многие энергетические и физические свойства сжатой дуги, находящейся в аргоне.
Так же были определены технологические возможности сжатой дуги.
При проведении опытов, было выявлено то, что струя плазмы имеет отчётливо выраженные режущие свойства.
Это и обусловило очень высокие темпы развития сварочного оборудования в этом направлении.
Оборудование для плазменной резки металла в нашем каталоге.
Принцип и технология плазменной резки металла — Плазменная резка
Плазменная резка позволяет разрезать металл, но не резцом — этот агрегат имеет струю плазмы.
Суть работы плазморезки такова: между соплом, электродом или разрезаемым материалом образовывается электрическая дуга.
Из сопла выходит газ, он преобразовывается в плазму после воздействия электричеством.
Виды плазменной резки
Резка металла с помощью плазмы бывает нескольких видов.
Это зависит от того, в какой среде происходит процесс:
- Простой — при разрезании используется электрический ток, воздух, иногда вместо воздуха применяют азот. При таком способе длина электрической дуги ограничивается. Если толщина листа несколько миллиметров, то параллельность поверхностей можно сравнить с лазерной резкой. Данный параметр можно соблюсти, разрезая металл, толщина которого 10 мм. Такой способ применяется при разрезании низколегированной или мягкой стали. Кислород применяют в качестве режущего элемента. Кромка после разреза остается ровной, заусенцы не образовываются. Кроме этого, в обработанной кромке металла содержится пониженное содержание азота;
- С применением защитного газа — в качестве такого газа используются защитный, плазмообразующий. С применением такой резки качество разрезания металла увеличивается, так как срез защищен от воздействия окружающей среды;
- С водой — вода во время разрезания металла защищает срез от влияния окружающей среды, охлаждает плазмотрон, все вредные испарения поглощаются водой.
Плазменная резка может быть разделительной, поверхностной. Чаще всего применяют разделительную резку.
Также разделяют резку по способам: дугой — при разрезании металла материал является частью электроцепи и струей — при разрезании металл не является частью электроцепи, дуга образовывается между электродами.
Преимущества резки плазмой
Плазменная резка имеет свои плюсы перед лазерной резкой:
- плазморезкой можно обработать любой металл: цветной, черный, тугоплавкий;
- скорость разрезания проходит быстрее, чем работа газовой резкой;
- плазморезкой доступна художественная работа — заготовки можно делать любой геометрической формы, доступна фигурная резка повышенной сложности, художественная резка металла плазмой и деталей;
- независимо от того, какова толщина разрезаемого металла, можно разрезать заготовку быстро, точно;
- плазморезкой можно разрезать не только металл, но и материалы, не содержащие в своем составе железа;
- разрезание материалов с помощью плазмы проходит гораздо эффективнее, быстрее, чем обычная резка механическим способом;
- в сравнении с лазерной резкой, плазморезка способна обрабатывать листы материала большой ширины, под углом.
Изделия получаются с наименьшим количеством дефектов, загрязнений;
- при работе в воздух выбрасывается минимальное количество загрязняющих веществ;
- перед тем, как разрезать металл, его не нужно прогревать, таким образом сокращается время прожига;
- безопасность во время плазменной резки на высоком уровне, так как нет необходимости использовать газовые баллоны, которые очень взрывоопасны.
Наряду с преимуществами плазморезка имеет некоторые недостатки:
- высокая стоимость плазмотрона;
- толщина металла, который можно разрезать плазмотроном, не должна быть более 10 см;
- во время работы агрегат издает большой шум, так как газ подается на высокой скорости, близкой к скорости звука;
- плазмотрон необходимо правильно обслуживать;
- к плазмотрону нельзя прикрепить резаки, чтобы металл обрабатывать вручную.
Принцип действия плазмотрона
Плазменная резка металла проводится своими руками, которые не имеют в этом деле большого опыта. В данном разделе рассмотрен принцип действия прибора для плазменной резки.
Если в наличии есть специальный аппарат, то с легкостью можно разрезать металл, плитку из керамики, дерево или пластик своими руками, доступна также фигурная резка.
Кроме этого, аппаратом можно производить сварку цветных, черных металлов, закаливать элементы, выполнять огневую зачистку или отжиг поверхностей, производить художественную резку.
В отличие от лазерной, принцип резки плазмой заключается в нагревании до высокой температуры места нагрева именно плазмой. Она образуется в сопле из пара. Сопло имеет узкий канал.
В нем образовывается электродуга. Пар проходит через канал под давлением, вместе с этим дуга охлаждается.
Пар при выходе ионизируется, затем возникает струя плазмы, имеющая высокую температуру — до 6 тысяч градусов.
Схемы и чертежи помогут разобраться в конструкции плазморезки и в принципах образования режущей струи.
При проведении работ плазма не нагревает большой участок материала. Место, где разрез делала плазморезка, остывает гораздо быстрее, чем резка лазерной, механической техникой.
Рабочая жидкость в плазморезке призвана охлаждать сопло и катод, так как это самые нагруженные части аппарата.
Дуга стабилизируется в результате определенного отношения катода, сопла с паром. Резервуар плазмотрона содержит специальный материал, который впитывает влагу.
Он помогает рабочей жидкости переноситься к нагревателю. На катоде образовывается отрицательный заряд, на сопле — противоположный, в результате возникает дуга.
При воздействии плазморезкой своими руками, как и при лазерной, механической резке, следует быть осторожным и соблюдать правила безопасности.
Аппарат крайне травматичен для человека — высокое напряжение, нагрев, расплавленный материал.
При проведении резки специалисты рекомендуют одевать защитный костюм, иметь специальный щиток, у которого стекла затемненные. Видео в статье наглядно покажет, как проводить резку.
Перед тем как приступать к работе, важно внимательно изучить схемы аппарата, осмотреть сопло, электрод, щиток на предмет закрепления.
Если они закреплены не надежно, работать плазморезкой нельзя. Также нельзя ударять аппаратом о металл с целью удаления брызг — так аппарат может повредиться.
Рекомендуется экономить материал при работе. Для этого не стоит часто зажигать плазменную дугу и обрывать ее.
Резка с помощью плазмы своими руками будет выполнена качественно, на срезе не будет окалины, заусенец, материал не деформируется, если при работе правильно рассчитать ток.
Чтобы это сделать, нужно применить действия, согласно схеме: подать высокий ток, произвести пару разрезов. По материалу будет видно, нужно снизить ток или оставить высоким.
Если для материала ток большой, то на нем будет образовываться окалина в результате его перегрева.
Технология работы плазморезкой
Перед тем как начать разрезание плазмой, стоит знать, как проходит весь процесс. В отличие от лазерной резки, горелку плазмы стоит разместить близко к краю материала.
После включения кнопки «пуск» будет зажжена сначала дежурная дуга, потом режущая. Горелку с режущей дугой необходимо медленно вести по материалу.
Для регулировки скорости разрезания, рекомендуется контролировать появление искр с другой стороны металла. Когда их нет, то полностью материал разрезать не удалось.
Причин можно отметить несколько: высокая скорость прохождения аппарата, низкий ток, горелка не находилась под углом в 90 гр. к разрезаемому металлу. Как правильно установить угол резки, показано на видео.
После завершения процесса, горелку нужно наклонить, как показывают схемы. Стоит помнить, что после выключения пуска, воздух будет идти еще какое-то время.
Проплавить полностью металл плазморезка сможет в тот момент, когда наклон составит 90 градусов и выше.
После включения аппарата — дождаться появления режущей дуги, создать между горелкой и материалом прямой угол. Так любая фигурная конструкция может получить отверстие.
При работе с плазморезкой стоит изучить схемы аппарата — в них указана наибольшая толщина металла, в котором можно сделать отверстие. Технология плазменной резки подробно показана на видео.
Как выбрать плазмотрон?
Чтобы производить резку металла плазморезкой своими руками, важно купить оборудование.
Перед тем как совершить покупку, рекомендовано учесть свойства и параметры прибора. Они будут оказывать большое влияние на функции плазмотрона. Цена также будет отличаться.
Резка с помощью плазмы может производиться двумя видами плазморезки:
- Инвенторная — имеет компактные размеры, для ее работы необходимо малое количество энергии, аппарат легкий с привлекательным дизайном. В то же время у него непродолжительное включение, перепады напряжения негативно скажутся на аппарате;
- Трансформаторная — высокая длительность включения, если напряжение будет скакать, плазморезка не выходит из строя. Размер, вес агрегата достаточно большие, энергии такая плазморезка также потребляет много.
При выборе плазмотрона для резки своими руками, рекомендуется обратить внимание на параметры.
Такая плазморезка сможет максимально удовлетворить потребности мастера и выполнить работу.
Мощность
В зависимости от того, каковы характеристики изделия, которое необходимо разрезать, выбирается мощность. Будет отличаться и размер сопла, тип газа.
Так, при мощности 60-90А плазморезка сможет справиться с металлом толщиной 30 мм.
Если необходимо разрезать большую толщину, то рекомендуется купить плазморезку с мощностью 90-170А.
Выбирая агрегат, учтите силу тока, напряжение, которое он сможет выдержать.
Время, скорость разрезания материала
Этот показатель меряют в см, которые аппарат сможет разрезать за 1 минуту. Одни плазморезки смогут разрезать металл за 1 минуту, а другие за 5.
При этом толщина материала будет одинаковая.
Если важно сократить время на резку, то стоит учесть скорость разрезания.
Аппараты отличаются временем работы — длительность разрезания металла, не перегреваясь.
Если указано, что длительность работы составляет 70 процентов, то это значит, что плазморезка будет работать 7 минут, после чего 3 минуты она должна остывать.
Если необходимо сделать длинные разрезы, то рекомендуется выбирать агрегаты с высокой продолжительностью работы.
Горелка плазморезки
Стоит оценить материал, который придется разрезать. Горелка плазморезки должна обладать мощностью, чтобы качественно его разрезать.
При этом стоит учесть, что условия работы могут быть сложными, резка — интенсивной.
Считается, что агрегаты с медным соплом очень прочные, почти не бьются, охлаждаются воздухом очень быстро.
На рукоятки таких плазморезок можно закрепить дополнительные элементы, поддерживающие наконечник сопла на определенном расстоянии. Это во много раз облегчает работу.
Если плазморезкой будет проводиться разрезание тонкого металла, то можно выбрать агрегат, в горелку которого поступает воздух.
Если планируется плазменная резка толстого металла, нужно предпочесть плазмотрон, в горелку которого будет подаваться азот.
Внешние характеристики
При плазморезке своими руками чаще всего выбирают переносные плазморезки, которые отличаются компактными размерами.
Ими не сложно управлять, не имея достаточного опыта, доступна фигурная резка.
Стационарные агрегаты имеют большой вес, предназначены для разрезания более толстых материалов, их цена соответственно будет больше.
осциллятор для плазмореза
плазморез бытовой
плазморез чпу своими руками
как выбрать плазморез
плазменная сварка видео
Выбор между плазменной или газокислородной резкой?
Почему бы не рассмотреть оба варианта?
Если вы проводите много времени с производителями металла, любителями или кем-либо, кто занимается сваркой, вы обязательно услышите споры о том, что лучше – плазма или кислородное топливо?
Я вырос на ферме, и, как и в большинстве фермерских магазинов того времени, у нас не было плазменного резака. У нас была только кислородно-ацетиленовая горелка. Единственным местом, где был плазменный резак, был местный магазин, и, увидев его в действии, нам просто нужно было купить его! Это были значительные вложения, но мы были впечатлены качеством резки.
Новый плазменный резак быстро занял почетное место в нашем магазине, поскольку оборудование с газокислородной горелкой было отброшено в угол (думая, что мы никогда не сможем его снова использовать). Это, конечно, быстро изменилось, когда мы поняли, что первым делом в тот день были ремонтные работы, которые предполагали нагрев и гибку стали на 1/2 дюйма. Аппарат газокислородной горелки вернулся и занял свое законное место рядом с плазменным резаком. Дело в том, что ни один магазин не обходится без обоих инструментов, поэтому давайте обсудим приложения, преимущества и ограничения каждого из них.
3 Вопрос, который укажет вам верное направление
- Какой металл вы обычно режете?
- Какой металл самый толстый, в пределах разумного, из того, что вы когда-либо резали?
- Вам нужен только инструмент для резки или вам также нужны возможности нагрева, сварки или пайки?
Плазменная резка
Плазменная резка предлагает быстрых запусков и быстрых скоростей резки на тонких и умеренных металлах, включая алюминий и нержавеющую сталь.Обычно это чистый срез с минимальной очисткой . В зависимости от входной мощности и толщины материала скорость плазменной резки может составлять от 6 до 50+ дюймов в минуту. По мере увеличения толщины материала преимущество в скорости резки по сравнению с кислородно-топливными системами уменьшается.
Еще одно существенное преимущество плазмы связано с короблением. При резке тонких металлов тепло, выделяемое в процессе газокислородной резки, может вызвать деформацию материала. Плазменная резка дает очень узкую зону теплового воздействия, минимизируя коробление .Это может быть большим преимуществом при работе с листовым металлом толщиной 3/16 дюйма или меньше.
Для работы аппарата плазменной резки и воздушного компрессора вам потребуются воздушный компрессор и основной источник питания. Первоначальная стоимость установки плазменной резки колеблется от 850 до 1700 долларов в зависимости от требуемого максимального номинального размера резки. Линия плазменных резаков AirForce® компании Hobart® позволяет выполнять чистую резку стали толщиной от 1/8 до 5/8 дюймов.
Добавьте e Отличное качество резки, простая кривая обучения и возможность резать практически любой токопроводящий материал в приведенный выше список, и легко понять, почему плазменный резак является незаменимым инструментом для множества операций резки и строжки.
Для резки с кислородно-топливной системой необходимо предварительно нагреть углеродистую сталь до температуры возгорания (около 1600 F) перед нажатием на рычаг подачи кислорода для резки. Существуют ( 2) основные типы ручных газокислородных горелок – односекционные (резаки ), и двухсекционные (комбинированные горелки , ). Цельные резаки предназначены только для резки. Вам следует выбрать комбинированный резак, если для вас важны другие процессы, кроме резки.
На более толстых материалах газокислородная резка может быть намного быстрее, чем плазменная. Например, кусок углеродистой стали толщиной 2 дюйма, требующий длинного разреза 4 дюйма, потребует плазменной резке 120-A примерно 1 минуту для завершения резки, в то время как газокислородная горелка может сделать такой же разрез за 15-20 минут. секунд. Комбинированные горелки могут быть оснащены режущими насадками, наконечниками для нагрева, строжки или сварки, специально разработанными для различных топливных газов, толщины материалов и областей применения.
Кислородно-топливные системы обычно на дешевле, и более универсальны. Кислородно-топливные системы на более портативны, , потому что они полностью автономны. Они не требуют источника электроэнергии или воздушного компрессора . Как правило, газокислородная резка ограничивается углеродистой сталью, но режущая способность может варьироваться от 1/8 дюйма до 22 дюймов или более .
Вам понадобятся топливный баллон и кислородный баллон для работы кислородно-топливной системы в любое время и в любом месте. Первоначальная стоимость установки типичной кислородно-топливной системы средней мощности составляет 230-500 долларов.Hobart предлагает комбинированный резак средней мощности, который позволяет резать сталь толщиной до 1/2 дюйма и сваривать сталь толщиной до 3/32 дюйма. Также доступны дополнительные насадки, которые могут резать сталь толщиной до 6 дюймов и сваривать сталь толщиной до 1-1 / 4 дюйма.
Последние мысли
В руках опытного оператора кислородно-топливная система обеспечивает отличное качество резки, требует небольшого обслуживания и относительно невысоких затрат на расходные материалы. При правильной настройке, эксплуатации и настройке пламени один режущий наконечник может проработать 50–90 часов.резки (или даже больше, в зависимости от оператора и области применения). С другой стороны, плазменная резка может потребовать больших первоначальных вложений, но обеспечивает более быстрый запуск и позволяет резать материалы, отличные от углеродистой стали, такие как нержавеющая, алюминий и медь. Оба инструмента заполняют пробелы и дополняют друг друга, и оба инструмента незаменимы, . Доверяете ли вы дуге или пламени, зависит от того, что вы делаете.
Автор: Джо Бевинг – эксперт по резке с опытом более 40 лет
Плазменный резакпротив резака: что лучше
Я слышал, что многие производители и металлурги спрашивают об этом.Их эффективность настолько сильно зависит от типа и толщины материалов и энергоресурсов, что многим из нас, особенно новичкам, трудно решить, предпочтительнее ли плазменный резак резаку, системе столетней давности, которую мы называем « кислородно-топливная »горелка в наши дни. Что ж, вот что я могу вам сказать.
Плазменный резак лучше резака, поскольку вы хотите резать и строжать тонкие цветные металлы с большей точностью, более узким пропилом, меньшими деформациями и образованием шлака и без предварительного нагрева.Но плазменные системы стоят дороже, чем газокислородный резак. Это также дает большую универсальность.
Я знаю, что это краткое заявление оставляет мне многое для объяснения, и именно этим я буду заниматься в следующих разделах этой статьи.
Темы, затронутые в этой статье
Плазменный резак против резака: выбор лучшегоПоскольку ни один из режущих инструментов не является абсолютно лучше другого, я думаю, вам следует как можно больше узнать об обоих инструментах и методах их работы, прежде чем начинать проект.
Как работает плазменный резак?В процессе используется специализированная горелка с отверстием сопла, расположенным внутри. Это требует образования плазменной дуги, которая начинается с подачи газов, таких как производственный воздух, аргон, азот или кислород, через это отверстие.
Затем дуга, представляющая собой поток газа под высоким давлением, вводится в электрическую дугу, создаваемую от внешнего источника питания. Таким образом, возникает плазменная струя, максимальная температура которой достигает 40000 ° F.
Эта струя может нагревать, плавить и пробивать самые разные электропроводящие материалы, такие как алюминий, нержавеющая сталь, чугун и т. Д., С получением нестандартных конструкций и форм.
Итак, запомните один момент о плазменной резке. Насколько ловко и эффективно ваш аппарат плазменной резки может резать, зависит от того, насколько сильно нагревается плазменная дуга. Чем больше энергии вырабатывается вашим плазменным резаком, тем горячее и мощнее плазменная дуга.
Конструкция / ТипВ настоящее время мы видим два типа плазмотронов, такие как высокочастотные (ВЧ) и контактные пускатели, в зависимости от способа пуска.
Горелкис ВЧ-пуском не используют движущихся частей, а это значит, что мало что может пойти не так с точки зрения эффективности и удобства использования. В горелках с контактным зажиганием используется движущийся электрод для создания искры для зажигания дуги. Эти модели более безопасны, чем ВЧ-фонари, из-за того, что они не могут что-либо сделать с другими предметами, использующими электричество.
Опять же, это еще один аспект, на который я должен обратить внимание. Плазменная горелка может быть как однопоточной, так и двухпоточной. Запомните эти точки:
- Однопоточный резак хорош для резки тонких материалов при низком выходном токе, не требуя, чтобы поток защитных газов сам охлаждался.
- Плазменный резак с двойным потоком подходит для резки толстых листов при высоком выходном токе.
Для заданного качества, скорости и бюджета требуются различные комбинации плазмы и защитных газов. Для вашего понимания я помещаю комбинации в следующем порядке (защитный газ + плазменный газ) в этот список:
- Мягкая сталь: воздух + кислород , углекислый газ + азот , воздух + азот
- Алюминий и нержавеющая сталь: воздух + воздух , воздух + азот , диоксид углерода + азот , азот + водород + аргон
Доказано, что вышеуказанные газовые смеси обеспечивают отличное качество резки, небольшое количество окалины, экономичную работу и срок службы деталей.Не используйте смесь азота, водорода и аргона для мягкой стали. Точно так же смесь воздуха и кислорода не рекомендуется для алюминия и нержавеющей стали.
Материал и толщинаВ отличие от резака, плазменный резак не использует процесс «окисления» для резки металла. Идеальный выбор для этого метода – токопроводящие и цветные металлы, такие как алюминий, медь, латунь, сталь и т. Д.
Для уложенных друг на друга металлов плазменная резка оказывается более подходящей, чем кислородно-топливная система.Вы также можете резать некоторые черные металлы. Но чем тоньше материал вы выберете, тем лучше будет результат. Плазменная резка – практически хороший выбор для резки фасонных металлов, таких как уголки, трубы, каналы и т. Д.
Средний плазменный резак может обрабатывать материал толщиной от 1/4 дюйма до 1 дюйма. Некоторые модели с более высокими характеристиками (выходы усилителя) могут выдерживать до 2 дюймов. Плазменные машины высокой четкости могут резать сталь до 6 дюймов. Если не считать намеченных деталей и сложностей разрезов, резак – хороший выбор, когда рабочий материал толще 1 дюйма.
ПриложенияБольшая часть универсальности, которую предлагает плазменный резак, ограничивается резкой и / или строжкой. Оборудование значительно помогает при выполнении работ по искусству, вентиляции и кондиционирования воздуха и сантехнических работах, производстве и ремонте металлов, переработке и сносе зданий, строительных и автомобильных проектах.
Качество резки и угловатостьПлазменный резак производит минимум шлака, но облегчает работу своей точностью и быстротой работы. Вам не нужно тратить много энергии на уборку.Качественный пропил должен быть ровным, а пропил – узким. Эти факторы отличают оборудование от резака, делая его более подходящим.
Еще одним очевидным преимуществом является то, что вам не нужно предварительно нагревать заготовку. Это значительно экономит время до начала процесса. Кроме того, этот процесс не оставляет значительных искажений металла, что является очень распространенной проблемой для тонких материалов.
Если вам нужно разрезать большой объем тонкого металлического листа или листа и вы ожидаете отличной производительности резки, не затрачивая много времени, плазменный резак – это то, что вам нужно.Кроме того, плазменная резка обеспечивает приемлемый угол наклона с учетом отклонения кромки и качества.
СтоимостьПомимо толщины металла, с которой может работать плазменный резак, стоимость среднего станка выше, чем стоимость кислородно-топливной установки. Даже если вы рассматриваете типичную плазменную систему, вам потребуется не менее 500 долларов, а стоимость может достигать 4000 долларов, и я не говорю о системе высокой четкости, которая будет стоить еще больше.
Другие факторы, увеличивающие эксплуатационные расходы, включают электроды и плазменные наконечники, которые могут составлять от 15 до 20 долларов за комплект.Стоимость коммунальных услуг (электричество) также значительна, но она не будет такой же, как стоимость топлива, необходимого для резаков.
Теперь я рассмотрю те же факторы, что и для газокислородного резака, чтобы вы могли определить, какой из них превосходит другой и по каким параметрам.
Как работает резак?В резаке используется термический процесс, в котором используется смесь кислорода и горючего газа. Газовая смесь требуется для предварительного нагрева заготовки (металла) до температуры воспламенения, сохраняя при этом температуру ниже точки плавления металла.
Чистый кислород в виде струи или струи направляется через сопло горелки в предварительно нагретую зону металла. Это конкретное действие вызывает сильную экзотермическую реакцию между металлом и кислородом и приводит к образованию шлака или оксида железа, температура плавления которого ниже, чем у металла, с которым обрабатывается.
Затем поток кислорода сдувает шлак без какого-либо воздействия на неокисленную часть металла. Процесс непрерывный, и при перемещении резака создается разрез.Режущий металл обязательно должен оставаться горячим во время процесса, потому что от этого зависит длительность экзотермической реакции.
Вы можете выбирать из различных конструкций форсунок и топливных газов, чтобы оптимизировать качество и скорость резки с учетом потребностей вашего проекта. Из-за использования кислорода с топливными газами этот метод известен как газокислородная резка.
Конструкция / ТипРаспространены две конструкции, например горелки с инжектором и соплом.
- Модель инжектора требует, чтобы газы предварительного нагрева смешивались либо в трубке подачи газа в корпусе, либо в головке. Такая конструкция позволяет кислороду под высоким давлением втягивать газ в горелку.
- Смесь в сопле требует, чтобы в сопле горелки предварительно нагревали кислород и топливный газ.
Инжекторные модели более универсальны, чем горелки со смешиванием с соплами, потому что первые позволяют без проблем использовать резак при перепаде давления газа или низком давлении, что может быть обычным для длинных шлангов.
Требования к газуВ резаке используется любой из ацетилена, пропана, MAPP, природного газа и пропилена, а кислород используется в любом процессе. Каждый из этих топливных газов влияет на скорость и качество резки следующим образом:
- Ацетилен образует самую высокую температуру и зону минимального термического влияния со строго сфокусированным пламенем для операций многократного прожига и небольших разрезов на высокой скорости.
- Более дешевый, чем ацетилен, пропан обеспечивает относительно низкую температуру для получения гладких кромок, снижения адгезии шлака и упрочнения кромок листа.
- Смесь пропадиена и метилацетилена, MAPP более устойчива к колебаниям расстояния между горелками и идеально подходит для подводной резки.
- Пропилен предлагает почти те же преимущества, что и пропан, но за счет кислорода в более высокой доле в кислородно-топливном отношении.
- Природный газ обеспечивает самую низкую температуру пламени и самую медленную прошивку.
Выбор материалов в этом случае крайне ограничен.Чтобы металл был идеальным для газокислородной резки, его оксиды должны иметь температуру плавления ниже, чем у самого металла. Некоторые низколегированные и низкоуглеродистые стали подпадают под эту категорию, поэтому резаком можно резать только эти материалы.
Вы должны исключить алюминий, латунь, медь, нержавеющую сталь и все другие цветные металлы. Я собираюсь объяснить состав стали, чтобы вы могли понять, когда она подходит для работы, а когда нет.
Углерод является важным элементом в составе.Если количество углерода превышает 0,3%, следует избегать газокислородной резки. Другие элементы в этой категории – хром, кремний, никель, молибден и марганец. Эти элементы вызывают загрязнение вашей заготовки, и их концентрация очень трудно окислить.
Следовательно, ваш проект может страдать от таких проблем, как шероховатость реза, увеличенное лобовое сопротивление, потеря частоты и скорости, повышенная потребность в интенсивности предварительного нагрева и трудности с контролем закругления верхней кромки.
Марганец, фосфор, кремний и сера оказывают минимальное действие, если их количество в основном металле составляет всего 1% или меньше.Мягкая сталь содержит до 98% железа, 0,3% углерода, 1% марганца и несколько других элементов в очень небольших количествах. Итак, выбирайте черные металлы, которые содержат железо в качестве основной части.
Резак подходит для резки толстой низкоуглеродистой стали или любого подходящего металла. Средняя толщина колеблется от 6 дюймов до 12 дюймов. Некоторые модели работают со сталью толще 20 дюймов.
Итак, вы видите, что материал и толщина, с которыми вы хотите работать, очень важны при выборе между плазменной и газокислородной резкой.
ПриложенияКислородно-топливные резаки более универсальны, чем плазменные резаки, но в другом отношении. Вы можете использовать резак для нагрева (формование и обработка), пайки, резки, строжки, пайки и даже сварки. Таким образом, эти инструменты популярны среди рабочих-автомобилестроителей, каменщиков и в других отраслях промышленности, включая производство стекла, ювелирных изделий и платины.
Качество резки и угловатостьРезак предназначен для работы с толстыми материалами, которые содержат в основном железо и другие элементы в очень малых размерах.Точность может быть достигнута при правильной концентрации и выборе кислорода и топливных газов. Также пропил может быть узким, если не таким, как у плазменного резака.
При правильном расположении всего можно ожидать порезы следующего качества:
- Квадратный верхний угол с минимальным радиусом
- Плоская поверхность без подрезов
- Квадратная грань, совпадающая с верхней поверхностью
- Гладкая поверхность с почти вертикальными линиями сопротивления
- Минимальный шлак, удаляемый соскабливанием
Однако резак не выполняет работу быстрее, чем система плазменной резки.Итак, вам нужно терпение и безраздельное внимание, чтобы обеспечить качественную резку. Любая неспособность сделать это правильно, может привести к серьезному компромиссу в отношении качества кромки и отклонения.
СтоимостьГазокислородная горелка может стоить от 200 до 1200 долларов плюс 10-20 долларов на замену наконечников. Стоимость кислорода и другого топлива значительно увеличивает стоимость установки, но именно эти расходы требуются каждый раз, когда вы начинаете проект.
Теперь вы можете сказать, какой вариант более доступный.Верно ли это даже по эксплуатационным расходам? Да, это! Позволь мне объяснить. Предположим, у вас есть плазменная система на 450 А, потому что это хороший выбор для большинства проектов DIY, а материалы, которые вы собираетесь резать, не толще 1 дюйма.
Независимо от того, используете ли вы одну или несколько газокислородных горелок (до 4), стоимость каждого дюйма будет ниже, чем при использовании плазменного резака на 450 А. Используя 4 резака вместо одного плазменного резака, вы также можете рассчитывать на почти такую же скорость. Однако стоимость настройки в этом случае значительно возрастет.
Последние мыслиИтак, есть ли в плазменном резаке что-то особенное, чего нельзя добиться с помощью резака? Даже если вы можете оптимизировать стоимость и скорость при использовании резака, плазменный аппарат все же более желателен, когда важны качество резки и кромок, точность и сложность.
Наконец, я расскажу о портативности и безопасности, которые отличают плазменную систему от кислородно-топливной. Плазменные машины не требуют обращения или хранения взрывоопасных газов.Кроме того, вы не будете работать с открытым пламенем.
С газокислородной горелкой, которая позволяет работать на расстоянии, вы можете избежать тепла или пламени, но их не избежать. Таким образом, плазменные системы дают вам преимущество с точки зрения безопасности. Вы так не думаете?
Обе системы предлагают портативность в том смысле, что плазменную установку удобнее переносить, в то время как вы можете наслаждаться тем же самым с любым кислородно-топливным оборудованием со шлангами резака длиной от 75 до 200 футов.
И это подводит вас к концу моего обсуждения.Напишите мне, если вам нужна дополнительная информация о порядке работы или что-нибудь, что поможет вам выбрать лучшее из двух.
4 основных различия между плазменным резаком и кислородно-ацетиленовым резаком
Вы когда-нибудь задумывались, в чем разница между плазменным резаком и кислородно-ацетиленовым резаком? Сварку металлов можно выполнять с помощью ряда методов нагрева для соединения или разделения этих прочных материалов. Газовая сварка, кислородно-ацетиленовая сварка и плазменная резка – это два способа резки металлов и манипуляций с ними.Сравнение этих двух методов даст вам наилучшую информацию при выборе метода, более идеального для ваших сварочных работ.
В чем основные различия между плазменным резаком и кислородно-ацетиленовым резаком? Кислородно-ацетиленовый резак использует сжигание газов для плавления металлов, а плазменная резка сочетает электричество с газом. Если вы цените чистые и точные линии, плазменная резка – лучший вариант. Если вы ищете более универсальный инструмент, для работы которого вам не нужен источник питания, вам могут пригодиться резаки.
Создание источника тепла | Кислородно-ацетилен использует сжигание газов для плавления металлов, в то время как плазменная резка сочетает электричество с газом |
Применение материалов | Горелки могут резать более толстые металлы, чем плазменные резаки |
Точность резки | Плазменная резка часто приводит к более чистой и быстрой резке |
Портативность | Кислородное топливо обычно более портативно без потребности в электричестве |
Универсальность | Оба метода предлагают уникальное использование и области применения |
Хотя оба метода подходят для резки металлов, один метод может быть предпочтительнее другого в зависимости от типа используемого металла, а также ваших предпочтений в отношении деталей, упомянутых выше.Мы подробно рассмотрим каждую из этих категорий, предложив преимущества и различия между резаком и плазменной резкой, а также их технические конфигурации.
Различия между резаками и плазменными резаками
Давайте сначала рассмотрим технические различия между двумя процессами, которые используются для резки металла, а также рассмотрим различные методы обработки металла. Для выполнения процессов потребуется различное оборудование и материалы. Понимание этапов выполнения каждого из них позволит заметить их различия и позволит вам использовать оба метода резки металла.
Как работает горелка (кислородно-ацетиленовая) сварка?
Метод кислородно-топливной сварки сочетает кислород и газ (обычно ацетилен) для создания очень горячего пламени, которое может прорезать металл. Уровни кислорода и ацетилена можно регулировать на горелке, чтобы создать идеальное пламя для резки металла или их сплавления. В контексте сравнения резаков с плазменной резкой мы сосредоточимся на режущих возможностях резака.
Статья по теме : Здесь вы можете найти статью с нашего веб-сайта по теме: Сварочный кислород – это то же самое, что и медицинский кислород?
Чтобы резать металл с помощью резака, вам необходимо выполнить следующие действия и инструкции:
1. Получите материалы: Вам понадобятся кислородный баллон, баллон с ацетиленом и фонарик. Размер бака будет зависеть от количества сварочных работ, которое вы планируете сделать, при этом баки большего размера более экономичны, чем частое использование. Соответствующие шланги прикрепляют баллоны к горелке.
2. Открытые газовые баллоны: Толщина металла будет определять ваше давление кислорода и газа (а также наконечник, который вы используете на резаке). Это полезное руководство даст вам подходящие уровни для обоих. Оба должны быть открыты и настроены для подачи в горелку достаточного количества топлива и кислорода.
3. Пусковая горелка: Сначала откройте ацетиленовую ручку на резаке и дайте возможность выветриться черному дыму. Затем введите кислород, чтобы создать точное пламя. Для лучшей резки вам понадобится нейтральное пламя, которое включает 50% кислорода и 50% ацетилена. Вы увидите маленькие конусы, которые должны быть одинаковыми при использовании кислородного рычага.
4. Предварительный нагрев металла: При газокислородной сварке вам необходимо предварительно нагреть металл перед резкой. Перед резкой необходимо нагреть металл до температуры воспламенения, чтобы предотвратить растрескивание.
5. Начало резки: Нажав кислородный рычаг до конца вниз, медленно и точно перемещайте резак через идеальную зону резки. Старайтесь держать резак как можно устойчивее, чтобы резка была ровной и прямой.
Основные принципы этого метода сварки заключаются в том, что вам нужен кислород и источник топлива, чтобы прорезать металл . Для этого требуется предварительный нагрев, и для достижения наилучших результатов вы должны использовать нейтральное пламя.Материалы, которые можно разрезать во время этого процесса, должны содержать железо, которое может окисляться при сварке горелкой. Посмотрите видео ниже
Как работает плазменная резка?
При плазменной резке вы можете работать с широким спектром материалов, если они могут электрически проводиться. Для этого процесса требуется источник электричества, сжатый воздух и металлическая деталь. Использование электрической дуги, создаваемой вашим источником питания, и добавленного газа (воздуха), при прохождении через небольшое сопло в плазменном резаке создает плазму.
По сравнению с кислородно-топливным процессом, создание этого плазменного пламени имеет значительно более высокую температуру, что обеспечивает более быструю резку. Вам не нужно предварительно нагревать металл из-за этой более высокой температуры, но вам также понадобится источник электроэнергии, в отличие от газокислородной сварки.
Процесс резки металла плазменным резаком сильно отличается от кислородно-топливного процесса, который описан в следующих шагах:
1. Приобретите материалы: Используйте источник газа или воздуха (обычно используется цеховой воздух) и машину плазменной резки.Эта машина должна быть подключена к источнику питания, чтобы использовать ее, и к ней должен быть прикреплен резак для выполнения операций резки. Для достижения наилучших результатов к горелке подключаются отдельные воздушные компрессоры.
2. Включите воздушный компрессор: Это позволит создать необходимое давление. Обратитесь к конкретному руководству пользователя, чтобы узнать необходимое давление воздуха и силу тока, поскольку они меняются от машины к машине.
3. Используйте заземляющий зажим: Поскольку вы проводите электричество, использование заземляющего зажима и прикрепление его к куску металла гарантирует, что электрический цикл не повредит вам.
4. Подключите резак для воздушной и плазменной резки: Вы должны убедиться, что резак и воздух надежно подключены к устройству для плазменной резки.
5. Начало резки: Удерживайте кнопку, чтобы включить резак. Держите резак близко к металлическому предмету, но не прикасайтесь к нему для получения наилучшего результата. Быстро перемещайтесь одним плавным движением, пока не проработаете весь кусок металла.
В процессе плазменной резки ваши разрезы часто будут более эффективными и быстрыми, без необходимости предварительного нагрева или манипулирования несколькими газами.Предварительная подготовка воздушного компрессора обеспечит достаточное давление воздуха для выполнения разрезов. Будьте осторожны в этом процессе и используйте средства защиты, так как при этом образуются искры.
Дополнительные различия между кислородно-ацетиленовым резаком и плазменным резаком
Как подробно описано выше, наибольшая разница между двумя процессами резки металла заключается в используемом оборудовании и в том, как оно влияет на выполненную резку. При сварке горелкой происходит химическая реакция между источником топлива, кислородом и металлом.При плазменной резке электричество и газ работают в замкнутом пространстве, создавая материю четвертого состояния.
Помимо различных процессов, существуют важные различия между двумя методами сварки:
- Совместимость с металлами: Сварка горелкой может использоваться только для черных металлов (металлов, содержащих железо), в то время как плазменная резка работает с металлами, которые могут быть электрически проводимыми.
- Мощность: Для работы плазменного резака потребуется источник электроэнергии, в отличие от сварки горелкой.Это влияет на мобильность и работу на любом рабочем месте.
- Эффективность: Плазменные резаки могут работать с металлами намного быстрее, чем резаки, но для работы с ними должны быть более тонкие детали.
Преимущества каждого типа резки, которые мы подробно рассмотрим в следующем разделе, еще более четко разграничим эти два метода и объясним, почему вы можете использовать один по сравнению с другим.
Подробнее о плазменном резаке – Здесь вы можете найти статью с нашего веб-сайта о : Чем отличается лазерный резак от плазменного резака?
Преимущества использования кислородно-ацетиленовой горелки для резки металла
Сварка горелкой – один из самых популярных и надежных способов резки металла, поскольку ее можно выполнять практически из любого места и обрабатывать самые разные материалы.Мы объединили ключевые преимущества использования резака перед плазменным резаком для резки металла и манипуляций с ним.
Способность резать более толстые металлы
Сильный запас топливного газа и кислорода сгорает, чтобы создать очень мощное пламя, способное прорезать толстые куски металла. Одно из наиболее полезных применений для этого – обработка стали, которую может быть труднее прорезать, чем множество других типов металлов. Кислородная сварка может эффективно использоваться для металлов толщиной до 24 дюймов.
Ваш плазменный резак не сможет с успехом обрабатывать эти более толстые материалы. Обычно они более эффективны и предпочтительнее для тонких металлических деталей. Если вам нужно выбрать один из двух вариантов для работы с большим разнообразием металлических заготовок, резак прорежет гораздо большее разнообразие толщин.
В то же время вы можете снизить качество резки более тонкого металла при использовании резака. Мы более подробно остановимся на этом, когда укажем на преимущества плазменного резака.
Повышенная мобильность
Поскольку для питания горелки вам нужны только кислородные и топливные баки, вы можете использовать кислородно-топливную сварку где угодно. Это особенно полезно, если вы находитесь на стройплощадке или вам нужно работать с металлами в удаленных местах. Вы можете легко транспортировать резервуары (меньшие резервуары легче перемещать) в нужное место для различных применений.
Этого нельзя сказать о методе плазменной резки, который требует использования источника питания.Электрическая составляющая использования плазменного резака накладывает некоторые ограничения на то, где вы сможете резать металлы. Основной способ решения этой проблемы – предоставить вам генератор. Это часто случается на стройплощадке, но не во всех местах.
Что касается общей возможности транспортировки и использования этих систем в любом месте, то сварка горелкой выигрывает. Вам не нужно беспокоиться о добавлении достаточно мощного источника питания или о наличии достаточного количества сжатого воздуха.
При транспортировке газовых баллонов убедитесь, что вы делаете это безопасно.При транспортировке баллонов с ацетиленом следует учитывать следующее:
- Держите их в вертикальном положении: По возможности держите баллоны в вертикальном положении, чтобы поддерживать надлежащий баланс между газовыми элементами. Если резервуар необходимо хранить в горизонтальном положении, вы должны позволить резервуарам вернуться в свое вертикальное положение в течение как минимум 30 минут, чтобы материалы могли должным образом воссоединиться перед использованием.
- Закрепите их: Если баки не закреплены, особенно в автомобиле, они могут случайно открыть клапаны при контакте друг с другом и создать опасность возгорания.
- Вентиляция: Обеспечьте доступ к вентиляции при транспортировке в случае утечки. Это может привести к возгоранию или взрыву, особенно в течение длительного времени.
Универсальность использования
Резка – не единственное полезное приложение для газокислородной горелки, так как вы можете применять самые разные методы работы с металлом. Это будет разумным вложением средств, если вы планируете работать с металлом различными способами.
К основным областям применения газокислородной горелки помимо резки относятся:
- Сварка: Это процесс плавления основного металла для соединения или склеивания двух металлических частей вместе.Чаще всего для этого используются горелки.
- Пайка : Горелки можно использовать для плавления присадки, которая будет служить соединением между двумя или более металлами.
- Пайка: Этот процесс аналогичен пайке, но выполняется при более низкой температуре. Пайка плавит присадочные металлы при температуре ниже 450 градусов Цельсия, а пайка плавит их выше.
- Строжка: Строжку можно использовать для удаления металла с помощью значительного источника тепла.
- Гибка: Гибка металла может выполняться путем нагревания и размягчения заготовки без разрезания металла.
Широкий спектр применений делает резак полезным и подходящим инструментом для использования на рабочем месте. Плазменные резаки не так успешны в выполнении многих из этих задач, потому что их выходная температура значительно выше (более 20000 градусов по Цельсию), и они не используют присадочные металлы для выполнения задач.
Преимущества использования плазменных резаков для резки металла
Плазменная резка стала популярной альтернативой газокислородной сварке из-за множества преимуществ, которые она дает в плане точности и эффективности.Давайте подробнее рассмотрим преимущества использования плазменных резаков перед резаками для резки металла.
Точность и скорость резки
Чрезвычайно высокая температура и точность плазменной струи через установку плазменной резки делают его идеальным выбором для работы над проектами, требующими действительно чистых линий. Повышенная скорость, с которой плазма рассекает металл по сравнению с резаком, позволяет линии быть плавной и точной. Это важно в приложениях, где ценится визуальное представление, таких как искусство или архитектура.
Плазменным резаком легко манипулировать и перемещать, что позволяет вырезать из металлических деталей интересные формы и конструкции. Это было бы намного сложнее с горелкой, которая оставляет менее точную линию из-за избыточного тепла. Если вы хотите сделать очень тонкие или тонкие линии для резки металла, мы рекомендуем выбрать плазменный резак.
Связанная статья : Каковы преимущества и ограничения плазменно-дуговой обработки?
Скорость и точность плазменного резака – его самое значительное преимущество, и поэтому слесарии предпочитают его резакам.Плазменные резаки предпочтительны при резке штабелированных металлов и формовании металлов, особенно на более тонких заготовках. Вам также будет проще использовать плазменную резку для просечно-вытяжного металла, чем альтернативу горелке.
Предварительный нагрев не требуется
Если вы не хотите полагаться на то, что у вас будет достаточно времени на подготовку перед началом резки, предпочтительнее будет плазменная резка. В отличие от кислородно-топливной резки, вам не нужно предварительно нагревать металл перед тем, как начать. Это позволяет легко настроить плазменный резак и быстро работать, особенно если вы работаете с большим количеством металлических деталей.
Если вам нужно разрезать много металлических деталей, плазменный резак со временем станет более производительным и эффективным.
Резка цветных металлов
Плазменные резакичасто могут быть более универсальным и предпочтительным вариантом, когда дело доходит до резки различных типов металлов. Единственное требование для резки металла – это электрическая проводимость. В отличие от газокислородных горелок (которым для химической реакции требуются черные металлы), плазменные резаки могут работать через нержавеющую сталь и алюминий.
Если вы планируете работать с любым из этих материалов, плазменный резак будет вашим оптимальным выбором. При плазменной резке можно использовать множество металлов, каждый из которых может проводить электричество. Наиболее распространенными видами металла для плазменной резки являются алюминий, сталь и нержавеющая сталь.
Выбор кислородно-ацетиленовой горелки по сравнению с плазменным резаком
Выделив различные процессы и преимущества между двумя системами, предпочтение во многом зависит от вашего применения в металле.Тип металла (черный или цветной) и толщина заготовки будут вашими первыми индикаторами того, следует ли вам использовать резак или плазменный резак.
Ключом к выбору любого метода резки металла является безопасность. Убедитесь, что у вас есть все необходимое оборудование для выполнения работы, в том числе средства индивидуальной безопасности и организованное рабочее место на случай аварии. Повышенное внимание к безопасности не только минимизирует опасность, но и позволит применять более осторожные и точные методы резки.
источники:
linde-gas.com
twi-global.com/technical-knowledge
tibtech.com/conductivite.php
grainger.com/content/supplylink-great-debate-cutter-or-torch
Рекомендуемая литература
В чем разница между лазерным резаком и плазменным резаком?
Каковы преимущества и ограничения плазменно-дуговой обработки?
Может ли плазменный резак резать алюминий? | Полное руководство – 2020
Услуги плазменной и газовой резки
Прецизионная резка металла
Плазменная резка (пламенная — кислородно-топливная — термическая)
Компания по производству отработанного газа Услуги плазменной и газовой резки
Высококачественная прецизионная плазменная резка входит в число многих услуг по изготовлению углеродистой, легированной и нержавеющей стали, предлагаемых компанией Waste Gas Fabricating Co.Наши высококвалифицированные сотрудники используют передовые системы плазменной и газовой резки, такие как плазменные резаки Whitney и Messer, а также кислородно-топливные резаки для всех нужд газовой и плазменной резки, включая снятие фаски с пластин плазменной резки, прецизионную газовую резку, плазменную резку высокого разрешения и кислородно-кислородную резку. резка топлива. Эти передовые инструменты позволяют выполнять сложные проекты газовой и плазменной резки с высочайшими отраслевыми допусками, изготавливать из любой марки стали или другого металла, который вам может потребоваться, и доставлять в кратчайшие сроки и в рамках бюджета.
Линия систем газовой и плазменной резки компании Waste Gas Fabricating включает следующие современные машины:
- Whitney 3400-XP / 60 “x 120” с плазменной панелью HP2000 и системой управления GE-Fanuc
- Оснащен: прецизионным плазменным резаком Hypertherm Truecut HT-2000 (в сочетании с 40-тонным пуансоном с устройством смены инструмента на 9 позиций)
- A Система погрузки / разгрузки Part handler II в сочетании с системой полного удаления и обработки лома
- Messer TMC-4518 с (1) плазменными горелками Hypertherm HPR400 с технологией снятия фаски и (8) кислородно-топливными резаками Alfa
- Messser MPC2018 с (2) плазменными горелками Hypertherm HPR260 и (2) кислородно-топливными резаками Alfa
Эти передовые системы обслуживаются и эксплуатируются в соответствии с высочайшими отраслевыми стандартами для превосходной плазменной и газовой резки и пробивки отверстий, а также для автоматической резки кромок листов.
Производственный процессWGF, сертифицированный по ISO, и безупречное современное оборудование обеспечивают лучшие услуги плазменной и газовой резки для многих областей применения. Спектр отраслей, которые мы обслуживаем, разнообразен, в том числе: производство взрывного оборудования, тяжелого строительного оборудования, систем обработки жидкостей и судостроения всех типов. Своевременная инвентаризация обеспечивает высокую производительность всех изготовленных компонентов. Сроки всегда являются приоритетом для WGF, и парк грузовых автомобилей нашей компании обеспечивает своевременную доставку, поэтому WGF готова справиться и с вашими срочными работами.
Если вам требуется лучшая высококачественная прецизионная обработка, резка, формовка, обработка и изготовление тяжелых нержавеющих и конструкционных сталей и металлических листов в Среднеатлантическом регионе, не ищите ничего, кроме Waste Gas Fabricating Co.
Дом ” Услуги по изготовлению » Прецизионная резка металла » Плазменная резка
Что такое плазменная резка
Что такое плазменная резка / Как работает плазменный резак?
Плазменная резка – это процесс, используемый для резки стали и других металлов различной толщины с помощью сжатого воздуха.Плазменная резка
, широко известная как убийца кислородно-ацетиленового ряда.История плазменного резака
Process намного чище, быстрее и эффективнее резать металл. Процесс плазменной резки начинается с подачи сжатого воздуха из сопла (части плазменной горелки) с чрезвычайно высокой скоростью, в то же время электрическая дуга формируется через сопло с помощью высокочастотных методов или методов запуска пилотной дуги через сопло, чтобы разрезаемая поверхность превращает газ в плазму.
При добавлении электричества через электрод (гафний) газ становится несбалансированным и проводит электричество. Чем больше добавляется электроэнергии, тем горячее становится плазменная дуга.
Плазменные резакисуществуют уже более 50 лет. Плазменные резаки были важной частью эпохи Второй мировой войны. Во время войны существовала потребность в более эффективном и быстром способе резки и формования металла для обслуживания и производства самолетов.
После войны процесс плазменной резки был настолько эффективным, что он был широко принят производственными и производственными компаниями, поскольку считался лучшим способом резки металла.Производители осознали, что качество резки и эффективность резки были отличным дополнением к миру производства.
В последние годы, с развитием трансформаторного блока и инверторной технологии плазменной резки, плазменные резаки стали более доступными и доступными для небольших производственных цехов, автомастерских, заводов-изготовителей, специалистов по сварке, любителей сварки и владельцев гаражных мастерских.
Longevity является ведущим производителем доступного оборудования для плазменной резки и сварки, что дает возможность большему количеству людей использовать, чувствовать и владеть аппаратом плазменной резки благодаря низкой цене.
Сегодня Longevity® производит качественные и доступные по цене аппараты плазменной резки для всех людей и незаменимый инструмент на вашем заводе, в магазине или в гараже.
Плазменная резка и кислородное топливо (кислородно-ацетиленовый)
Поскольку плазменная резка является довольно новой технологией по сравнению с резкой OxyFuel, велись большие споры о том, какой процесс более эффективен, какой купить и стоит ли переход на плазменную резку своих денег. Чтобы ответить на некоторые из обсуждаемых тем, Долголетие объяснит
.различие двух процессов и укажите некоторые ключевые факты, которые помогут вам принять обоснованное решение о том, является ли плазменный резак хорошей инвестицией.Есть различные факторы, которые вы должны учитывать, прежде чем покупать инструмент, который будет резать металл в соответствии с вашими потребностями. Некоторые из этих факторов – это толщина пропила, место работы, тип металла, энергоресурсы и эксплуатационные расходы – это лишь некоторые из них.
Как работает каждый процесс?
Плазменный резак:
Процесс плазменной резки работает, когда газ (в основном сжатый воздух) проходит с высокой скоростью в сочетании с электричеством, образуя очень горячую дугу, вызывающую плавление металла при выдувании шлака.
Основные сведения о плазменном резаке :
Имея источник питания 110/220 В, резак, расходные материалы и сжатый воздух, вы можете использовать плазменный резак Longevity практически в любом месте и в любое время.
Кислородное топливо:
Оксицетелен, также известный как кислородная резка, работает путем предварительного нагрева металла до температуры воспламенения с помощью струи кислорода высокой мощности, направляемой на металл, создавая химическую реакцию между кислородом и металлом, образуя оксид железа, который более известен как шлак.
Затем мощная струя кислорода удаляет шлак из пропила. Качество резки, время предварительного нагрева и толщина могут зависеть от типа используемого газа. Кислородная резка используется для обработки черных (железосодержащих), низкоуглеродистых и низколегированных сталей толщиной до 2 футов или 24 дюймов.
Основы OxyFuel.
С топливным баком, кислородным баллоном и горелкой вы можете резать сталь где угодно – кроме цветных металлов, таких как алюминий и нержавеющая сталь.Кислородная резка позволяет с легкостью резать очень толстые металлы, а различные варианты горелок позволяют пользователям паять, паять, сваривать плавлением, строжку, подогревать и гнуть металлы по мере необходимости. Этот процесс требует намного больше работы по очистке, чем плазменная резка.
Longevity® предоставляет отличную диаграмму, которая четко показывает каждый процесс и возможности каждого метода:
Плазменно-дуговая резка кислородно-топливная резка
| ||||||||||||||||||||||||
Аргументы в пользу долговечности плазменных резаков и процесса плазменной резки:
Плазменные резакиLongevity позволяют слесарям быстрее резать металлы без предварительного нагрева или тщательной очистки до 2 дюймов с однофазной вилкой 220 В, рассчитанной на 100 ампер.Процесс плазменной резки – это метод резки новейшего поколения, поскольку он портативен, может использоваться где угодно и обеспечивает более быстрые и чистые на вид разрезы по сравнению с резкой Oxy Fuel.
Плазменные резакитакже широко используются со столами с ЧПУ (автоматическими станками для резки) из-за их точной резки. Кроме того, плазменные резаки могут резать любой металл
Аргументы для резки OxyCetelene (OxyFuel):
Кислородная резка – это проверенная временем традиция резки.Для некоторых металлов Oxyfuel требуется меньше времени для резки различной толщины по сравнению с плазменным резаком. В отличие от плазменных резаков, кислородное топливо не имеет номинальных значений толщины резки. Толщина реза зависит от используемого газа и наконечника на конце кислородной горелки, что делает кислородное топливо более универсальным для резки различной толщины.
Основные сведения о кислородно-топливном газе
Ацетилен
Обладает самой высокой температурой пламени среди всех обычных топливных газов.Чем горячее пламя, тем быстрее происходит пробивание. Более высокая теплотворная способность внутреннего пламени по сравнению с другими газами делает ацетилен самым быстрым режущим газом с наименьшим количеством искажений и самой узкой зоной термического воздействия – вот почему это, пожалуй, самый популярный газ. Также имеет самое низкое соотношение кислорода к газу (1,2: 1).
Пропан
Более низкая температура пламени, чем у ацетилена, но имеет большую общую теплоту сгорания, что делает его одинаково быстрым при резке.Но поскольку большая часть тепла генерируется во вторичном пламени, пламя менее сфокусировано, что приводит к более медленному прожигу. Имеет относительно высокое отношение кислорода к топливному газу (4,3: 1), необходимое для достижения максимальной температуры пламени.
Метилацетилен-пропадиен (МАПП)
Более медленное время прошивки и резки по сравнению с ацетиленом из-за более низкой температуры пламени, большего распределенного источника тепла и потоков газа, но может использоваться при более высоких давлениях, чем ацетилен (т.е. менее горючий). Соотношение газ-кислород составляет (2: 5: 1).
Пропилен
По температуре аналогичен MAPP, горячее, чем пропан, холоднее, чем ацетилен, но требует высокого отношения кислорода к топливному газу (3,7: 1).
Природный газ
Самый медленный газ для прошивки, с самой низкой температурой пламени и самой низкой общей теплотой сгорания.
Плазма против OxyFuel Цена:
До того, как Longevity® представила доступные плазменные резаки, плазменная резка обычно была дороже, чем кислородная резка.Благодаря тому, что Longevity обеспечивает качественные устройства плазменной резки по доступным ценам, вы можете приобрести устройство плазменной резки с высоким током, которое позволит резать толстые металлы быстрее, эффективнее и эффективнее с меньшими затратами на очистку и меньшими эксплуатационными расходами. Компания Longevity®, выпустившая доступные станки плазменной резки, в значительной степени способствовала результату, подтолкнув все больше металлистов к использованию метода резки новейшего поколения: плазменной резки.
Портативность:
До того, как Longevity® представила свою линейку инверторных аппаратов плазменной резки, большинство аппаратов плазменной резки были аппаратами на основе трансформатора, которые вообще нельзя было переносить.Инверторные плазменные резаки Longevity® позволили слесарам резать ¾ дюйма портативного станка весом 25 фунтов. Благодаря такому малому весу и такой мощности, Longevity® сделал плазменную резку наиболее портативным и эффективным методом резки на сегодняшний день.
Безопасность:
Как плазменная резка, так и методы газокислородной резки могут быть опасными при неправильном использовании и соблюдении всех мер безопасности. Оба метода могут вызвать пожар и несут особую опасность. Чтобы безопасно использовать каждый метод резки, необходимо соблюдать правила техники безопасности для каждого метода – выбор более безопасного невозможен, учитывая, что вы используете мощные процессы резки.Если бы нам пришлось выбирать одно или другое, мы бы заявили, что плазменная резка более безопасна, потому что от горелки нет открытого пламени.
Заключение:
Плазменная резка – это новейший и лучший метод резки металла из-за портативности, мощности резки и текущих затрат на запуск с Longevity®, что делает доступные плазменные резаки доступными для всех и каждого. Плазменные резаки Longevity® начинаются с 549,99 долларов США с бесплатной доставкой и 1-летней гарантией на 40-амперный станок, способный резать до ½ дюйма.Это выгодная сделка!
Все, что вам нужно знать о плазменной резке
Если вы рабочий на верфи, строящей грузовые корабли, или художник, пытающийся превратить свое последнее видение в металлический шедевр, скорее всего, вы собираетесь использовать плазменную резку в какой-то момент во время процесс.
Разработанный для быстрой и точной резки, неудивительно, что плазменная резка получила такое широкое распространение во всем мире. Скорее всего, вы используете продукты, которые были частично изготовлены с помощью плазменной резки, каждый день.
Итак, что такое плазменная резка? А как именно это работает?
Что такое плазма?
Чтобы понять, как работает плазменная резка, сначала необходимо понять основы. Начнем с ответа на простой вопрос: что такое плазма?
Не путать с прозрачной жидкостью в крови, в которой взвешены жировые шарики (что бы это ни значило). Плазма, о которой мы говорим, представляет собой ионизированный газ – газ, который был возбужден до такой степени, что электроны вырывались из своих атомов, но все же путешествовали вместе с ядром.
Этот возбужденный газ является плазмой. Плазма фактически упоминается как четвертое состояние материи, помещая ее рядом с другими тремя хорошо известными и широко преподаваемыми состояниями. Правильно, на самом деле состояния материи следующие: твердое, жидкое, газообразное и ПЛАЗМА.
Интересно, что согласно науке, плазма на самом деле является наиболее распространенным состоянием материи во Вселенной! Здесь, на Земле, мы в значительной степени полагаемся на плазму. Я уверен, что тебе знакомо солнце. Что ж, наш большой желтый друг в небе, как и большинство других звезд, на самом деле представляет собой гигантский плазменный шар.Вроде круто, правда?
Есть несколько различных способов превращения газа в плазму, но это всегда включает закачку газа полной энергии. В этом случае искра – очень эффективный источник энергии. Когда мы пропускаем сжатый газ (например, кислород, азот, аргон или даже производственный воздух) через большую искру, он ионизирует газ и создает контролируемый поток плазмы.
Вы можете спросить себя: «Как нам использовать газ, чтобы прорезать самые твердые материалы, известные человеку?» Ну, плазменные резаки могут достигать ошеломляющих 40 000 ° F почти мгновенно.Поток плазмы такой температуры может быстро и легко пройти через большинство материалов.
Даю Вам …
ПЛАЗМЕННЫЙ ФАКЕЛ!
Каждая система плазменной резки состоит из следующих трех компонентов:
- Блок питания – Блок питания плазменной резки отвечает за поддержание плазменной дуги на протяжении всей резки.
- Консоль зажигания дуги – Или ASC создает искру внутри плазменной горелки, которая создает плазменную дугу.
- Плазменный резак – Плазменный резак обеспечивает юстировку, необходимую для точной резки, а также для охлаждения расходных деталей.
Теперь, когда вы понимаете, что такое плазма, давайте перейдем к применению плазмотрона.
Виды плазменной резкиПочти все системы плазменной резки подразделяются на две категории: обычные и прецизионные системы плазменной резки.
Обычные плазменные системы – Обычно в качестве плазменного газа используется производственный воздух, а форма дуги определяется соплом горелки.Ручные системы относятся к категории обычных систем плазменной резки, а также к приложениям, в которых разрезаемые материалы имеют более низкие допуски. Хотя эти типы широко распространены, они менее точны, чем другие формы плазменной резки.
Прецизионные плазменные системы – Используйте различные газы, такие как кислород, азот или смесь водорода / аргона / азота, для достижения оптимальной резки широкого диапазона проводящих материалов. Эти типы систем управляются ЧПУ и предназначены для выполнения самых точных резов, достижимых с помощью плазмы.Резаки и вырезаемые ими конструкции более сложные, а форма дуги сужена для большей точности.
Зачем нужна плазма?
К этому моменту вы должны хорошо понимать, что такое плазма и как работает плазменная резка, но при этом остается без ответа один очень важный вопрос – почему?
Есть много других способов резки металла – пилы, лазеры, гидроабразивная резка и кислородно-топливные системы. Мы не будем вдаваться в подробности каждого из них прямо сейчас, так как вы захотите использовать разные методы для разных заданий.
При принятии решения о том, какой метод резки использовать, играют роль несколько факторов. Важно учитывать толщину обрабатываемого материала, требуемое качество кромки и то, что важнее – производительность или стоимость.
Наиболее заметные различия между плазменной резкой и другими методами резки – это раз и стоимость . Плазменная резка работает быстрее, чем другие методы, особенно при работе с более толстыми материалами, а недавние достижения в технологии плазменной резки снижают влияние плазменной резки на вашу прибыль.
По сравнению с этим стоимость гидроабразивного или лазерного резака очень высока. Как правило, гидроабразивная резка стоит в три раза дороже, чем плазменная и лазерная резка может стоить в восемь раз дороже! Плазменная резка – очень практичный метод резки, и он достаточно точен для почти любых ваших потребностей в фигурном вырезании.
Итак, вот оно! Полное изложение – от науки, лежащей в основе того, что такое плазма, до принципов работы плазменных резаков и преимуществ плазменной резки.
Если окажется, что это не все, что вы хотели знать, и даже больше, позвоните в один из наших офисов, и мы будем рады поговорить подробнее о том, как ваш бизнес может воспользоваться преимуществами плазменной резки.
Вы нашли эту информацию интересной? Посетите страницу блога Boyd Metals, чтобы получить больше интересной информации о металлургической промышленности, и не забудьте проверить эту бесплатную загрузку с фактами о стали!
Сталь – удивительный, многогранный материал, который люди используют каждый день , часто даже не учитывая его важность. Для вашего развлечения и просветления мы составили бесплатное руководство: 12 впечатляющих и интригующих фактов о нержавеющей стали!
Мы надеемся, что вы найдете эту информацию
такой же захватывающей, как и мы!
Газовая резка vs.Плазменная резка нержавеющей стали и алюминия
Любой, кто работает с металлами, знает, как важно понимать несколько различных методов резки. К сожалению, те же производители, которые могут потратить месяцы на исследования, испытания и создание прототипов продуктов из самых разных металлических сплавов, некоторые из которых едва различимы друг от друга, чтобы получить только правильный материал, будут использовать любой режущий инструмент, который у них есть. под рукой.Умные производители знают, что то, что вы используете для резки материалов, так же важно, как и сам материал.
Вот почему производителям очень важно понимать разницу между газовой и плазменной резкой и знать, какие операции лучше всего подходят для каждой из них. В конечном итоге решение будет зависеть от ряда факторов, в том числе от того, какой сплав вы используете, его толщину, местоположение, разнообразие работ, ваши энергоресурсы, бюджет и многое другое.
Нас часто спрашивают о различиях между газовой и плазменной резкой.В следующих параграфах мы рассмотрим оба аспекта и объясним, почему, когда дело касается алюминия и нержавеющей стали, плазменная резка действительно является единственным жизнеспособным вариантом.
Что такое газовая резка?
Газовая резка имеет множество названий, включая газокислородную резку, кислородно-ацетиленовую резку и кислородную резку. Это процесс, в котором для резки металлов используются топливные газы и кислород. Он был создан французскими инженерами Эдмоном Фуше и Шарлем Пикаром в 1903 году как метод газовой сварки. Он полагается на чистый кислород, а не на воздух, для повышения температуры пламени.Это позволяет локализовать плавление материала заготовки.
При газокислородной резке пламя не предназначено для плавления металла, а скорее должно довести материал до температуры воспламенения. Затем поток кислорода направляется на металл и разрезает его, образуя шлак из оксида металла. Для быстрого сравнения, обычное пламя пропана / воздуха горит при температуре около 3590 ° F, пламя пропана / кислорода горит при температуре около 4087 ° F, кислородно-водородное пламя горит при температуре 5072 ° F, а пламя ацетилен / кислород горит при температуре около 6332 °. Ф.
Резак обычно имеет головку под углом 60 или 90 градусов с отверстиями, расположенными вокруг центральной струи. Внешние форсунки представляют собой пламя, состоящее из кислорода и ацетилена, которые предназначены для предварительного нагрева. В центральной форсунке только кислород. Используя пламя предварительного нагрева, можно изменить направление реза без изменения положения сопла или угла.
Подобная резка очень хорошо работает с железом и сталью. Разрез инициируется нагревом кромки металла до температуры воспламенения.Когда режущий клапан выпускает кислород из центральной струи, он химически соединяется с железом и превращается в расплавленный оксид железа, образуя разрез.
К сожалению, хотя газовая резка является дешевым и эффективным вариантом для работы с черными металлами, такими как железо и сталь, ее практически невозможно эффективно использовать с алюминием или нержавеющей сталью. С алюминием это не работает, потому что оксид алюминия плавится при более высокой температуре (это причина, по которой высококачественный алюминий является популярным выбором в аэрокосмических двигателях и вокруг них).С другой стороны, поскольку нержавеющая сталь не окисляется, она также не подходит.
По этим причинам при работе с нержавеющей сталью и алюминием производители обычно обращаются к плазменной резке как альтернативе газовой резке.
Что такое плазменная резка?
Плазменная резка, как и газовая резка, представляет собой процесс, при котором струя ионизированного газа проходит через отверстие с высокой скоростью. Газ, будучи перегретым и электрически ионизированным электрическим каналом, образует замкнутую цепь обратно к резаку через заземляющий зажим.Мы называем этот ионизированный газ плазмой. Чем больше добавляется электроэнергии, тем горячее становится плазменная дуга. Эта дуга способна нагревать металл, и газ сдувает материал после того, как он расплавился, создавая разрез в желаемой точке.
Плазменный резак очень эффективен с любым электропроводящим металлом, включая алюминий и нержавеющую сталь. Используемый сжатый газ может быть воздухом, кислородом, инертным газом или другим газом, в зависимости от того, какой материал разрезается. Когда газ проходит через сопло, между электродом в сопле и материалом образуется электрическая дуга.Затем газ ионизируется с достаточной интенсивностью тепла, чтобы проплавить материал.
Каковы преимущества плазменной резки?
Известно, что плазменная резка очень хорошо работает с материалами толщиной менее полутора дюймов. Его также можно использовать с многослойным материалом или просечно-вытяжным металлом. В этих случаях, скорее всего, подойдут ручные фонарики. Для более толстых материалов, до 6 дюймов, доступны станки с компьютерным управлением. Кроме того, плазма обычно образует чрезвычайно локализованный конус, который эффективен при резке листового металла угловой или изогнутой формы.
К другим преимуществам относится то, что время подготовки к плазменной резке сводится к минимуму, без необходимости предварительного нагрева. Резак производит чрезвычайно точный пропил. Универсальность огромна, и можно использовать плазменные резаки для резки штабелей, снятия фаски, фигурной резки, строжки и пробивки отверстий. Кроме того, зона термического влияния мала, поэтому деформация или другие повреждения очень незначительны. Очистить также относительно легко.
Что касается портативности, это зависит от используемой машины, размера требуемого источника питания и размера воздушных резервуаров.Доступно множество видов портативных плазменных резаков, которые идеально подходят для полевых работ и полагаются на генераторы с приводом от двигателя или первичные источники энергии. Для более крупных разрезов потребуются специальные станки.
Ваш партнер по техническим ресурсам
Хотя и газовая резка, и плазменная резка имеют свое место, если вы работаете с алюминием или нержавеющей сталью, плазменная резка будет вашим единственным вариантом. В Clinton Aluminium and Steel мы гордимся тем, что помогаем производителям сочетать правильный инструмент с правильным материалом.