Проверка токарных станков на точность: ГОСТ, видео
Говоря о точности токарного станка имеется ввиду соответствие данных паспорта оборудования следующим параметрам:
- перемещение тех элементов, на которых располагается заготовка;
- расположение тех поверхностей, с помощью которых базируется инструмент или заготовка;
- форма базовых поверхностей.
После окончательной сборки и проверки на заводе, а также после ремонтов станки получают акт о приемке, и только после этого, вводятся в эксплуатацию.
Требования к точности указываются в паспорте станков.
Выполнение измерения для выявления погрешностей следует производить регулярно в соответствии с нормативами ГОСТ.
Скачать ГОСТ 8-82 «Станки металлорежущие. Общие требования к испытаниям на точность»
Скачать ГОСТ 18097-93 «Станки токарно-винторезные и токарные. Основные размеры. Нормы точности».
В процессе использования токарного оборудования происходит износ его деталей, т.
Качественное испытание токарных станков в соответствии с государственным стандартом во многом зависит от того, насколько правильно он установлен на испытательном стенде. Установка на стенд должна происходить строго, соблюдая установочный чертеж. Самым распространенным методом, является установка на количество опор более 3-х. Отметим, что все двигающиеся части проверяемого станка должны находится в средних положениях.
Геометрическая точность токарного станка характеризует качество изготовления деталей, поэтому установка заготовки должна осуществляться на геометрическую правильную поверхность.
Для определения степени износа нужно установить линейку поочередно на каждую из направляющих станины. После этого, щупом определяется расстояние между направляющими и контрольной линейкой. Допустимое значение такого износа согласно государственного стандарта не должно превышать 0,02 мм.
Не мало важным фактором является соответствие горизонтальности направляющих станины. Определить ее можно с помощью перемещения специального уровня вдоль поверхности направляющих, который покажет значение имеющегося отклонения. Предельно допустимое отклонение по ГОСТ не может превышать значение 0,05 мм. А параллельность между направляющими станины для упорной (задней бабки) и каретки можно проверить с помощью специального измерительного индикатора. Его необходимо закрепить на каретке с суппортом и с помощью перемещения каретки выявить величину отклонения.
- Проверка параллельности направляющих
- Проверка горизонтальности направляющих станины
Также точность токарного станка поможет определить биение вращающегося шпинделя, в который крепится заготовка. Обязательно при этом соблюдать параллельность между осью шпинделя и направляющими станины. Во время проверки в отверстие вала устанавливают специальную контрольную оправку и на протяжении всей ее длины проверяют ее на биение.
Проверка биения шпинделя: а — проверка биения шейки шпинделя; б — проверка осевого перемещения шпинделя; в — проверка биения переднего центра
Также одним из важных измерений при проверке токарного станка на точность является определение точности шага ходового винта. Величина отклонения в соответствии с ГОСТ определяется с помощью следующей методики:
- в центры передней и задней бабки устанавливают резьбовую оправку;
- на эту оправку накручивают гайку в форме цилиндра и имеющую паз;
- индикатор, закрепленный в державке, упирается в торцевую часть цилиндрической гайки;
- токарный станок настраивается на шаг резьбы;
- индикатор определяет отклонения.
Проверка точности шага ходового винта
Основные погрешности формы обрабатываемых заготовок:
- непрямолинейность;
- конуснообразность;
- отсутствие параллельности;
- некруглость;
- неконцентричность.
Инструмент, применяемые при испытаниях:
- контрольная линейка;
- уровень;
- щуп;
- угольник;
- измерительный индикатор;
- резьбовая оправка;
- контрольная оправка;
- цилиндрическая гайка;
- державка.
При выполнении измерений следует использовать только те инструменты, которые прошли метрологическую поверку с учтенной погрешностью.
Рекомендуем приобрести: Установки для автоматической сварки продольных швов обечаек – в наличии на складе! Сварочные экраны и защитные шторки – в наличии на складе! Станки после ремонта должны быть подвергнуты внешнему осмотру, испытанию на холостом ходу, под нагрузкой в процессе работы, на точность и жесткость. Все это осуществляется на специальных стендах, имеющихся в ремонтно-механическом цехе. После внешнего осмотра станка приступают к его испытанию на холостом ходу. В процессе испытания станка проверяется взаимодействие всех его механизмов, безотказность и своевременность действия различных автоматических устройств, выключателей, тормозных и защитных устройств по технике безопасности и т. д. Особое внимание следует уделять проверке исправности действия системы смазки, системы охлаждения, гидравлических и пневматических устройств. В процессе испытания станка работа должна быть плавной, без толчков, без сильного шума, стуков или сотрясений, вызывающих вибрацию станка. ![]() Кроме испытания станка под нагрузкой, производят испытание станка на точность и жесткость. Собранный после ремонта станок перед его эксплуатацией проверяют на точность. Проверку на точность станка осуществляет контрольный мастер с обязательным участием представителей ремонтно-механического цеха. Технический контроль предусматривает проверку геометрической точности и жесткости станка и измерение точности обрабатываемых на станке деталей. Проверка точности станков, вышедших из ремонта, выполняется по нормам точности для приемки новых станков согласно ГОСТу 8—53 «Станки металлорежущие. Общие условия к стандартам на нормы точности». Испытание на жесткость станков соответствующих групп производится в соответствии с требованиями ГОСТа 7035—54 «Станки металлорежущие. Общие условия к стандартам на нормы жесткости» по нормам, установленным в соответствующих стандартах. |
Паспорт токарного станка. Испытание и проверка станка на геометрическую точность.
Токарный станок
Паспорт токарного станка
Испытание и проверка станка на геометрическую точность

В паспорте описывается комплект приспособлений
и принадлежностей, поставляемых заказчику со станком: сменные и
запасные зубчатые колеса; инструмент для обслуживания станка; ремни
для главного привода и других сборочных единиц; патроны; оправки;
люнеты; центры упорные и вращающиеся; шкивы; вспомогательный инструмент
и др. В паспорте приводятся результаты испытания токарного станка на
соответствие нормам точности и жесткости, которые показывают допускаемые
и фактические значения точности перемещения сборочных единиц (узлов)
станка, а также точности обработки и качества обработанной поверхности
изделия – образца.
Одним из необходимых условий для обеспечения
требуемой точности и долговечности работы станка является его
правильная установка и крепление на фундаменте. Тип фундамента зависит
от нагрузки, передаваемой основанию станка, массы станка и сил инерции,
действующих во время работы станка. Фундаменты под металлорежущие
станки бывают двух типов: первый – фундаменты, которые являются
только основанием для станка, второй – фундаменты, которые жестко
связаны со станком и придают станку дополнительную устойчивость и
жесткость. Токарные станки устанавливают, как правило, на фундаментах
второго типа согласно установочному чертежу, который дается в руководстве
по эксплуатации станка. В чертеже указываются необходимые размеры для
изготовления фундамента, а также расположение станка в помещении с учетом
свободного пространства для выступающих и движущихся частей станка.
При установке станка на бетонное основание размечают гнезда по размерам,
соответствующим отверстиям крепления станины станка, а затем гнезда
вырубают. После установки и выверки станка по уровню фундаментные болты
заливают цементным раствором. Установку станка в горизонтальной
плоскости выверяют с помощью уровня, устанавливаемого в средней части
суппорта параллельно и перпендикулярно оси центров. В любом положении
каретки суппорта на направляющих станка отклонение уровня не должно
превышать 0,04 мм на 1000 мм. Если фундаментные болты предварительно
залиты в фундаменте, то выверку производят, когда они не затянуты.
После установки и выверки производят внешний осмотр станка и испытывают
его на холостом ходу, под нагрузкой, на точность и жесткость.
Испытание станка на холостом ходу. Привод
главного движения последовательно проверяют на всех ступенях частоты
вращения. Затем проверяют взаимодействие всех механизмов станка;
безотказность и своевременность, включения и выключения механизмов
от различных управляющих устройств; работу органов управления;
исправность системы подачи СОЖ и гидро- и пневмооборудования станка. В процессе испытания на холостом ходу станок должен на всех режимах
работать устойчиво, без стуков и сотрясений, вызывающих вибрации.
Перемещение рабочих органов станка механическим или гидравлическим
приводом должно происходить плавно, без скачков и заеданий. При
испытании станка на холостом ходу проверяются также его паспортные
данные (частота вращения шпинделя, подача, перемещения кареток суппорта
и др.). Фактические данные должны соответствовать значениям, указанным
в паспорте.
Испытание станка под нагрузкой позволяет
выявить качество его работы и проводится в условиях, близких к
производственным. Испытание производят путем обработки образцов на
таких режимах, при которых нагрузка не превышает номинальной мощности
привода в течение основного времени испытания. В процессе испытания
допускается кратковременная перегрузка станка по мощности, но не более
чем на 25%. Время испытания станка под полной нагрузкой должно быть не
менее 0,5 ч. При этом все механизмы и рабочие органы станка должны
работать исправно; система подачи СОЖ должна работать безотказно;
температура подшипников скольжения и качения не должна превышать
70-80 градусов С, механизмов подач 50 градусов С, масла в резервуаре 60 С.
Новые станки в процессе эксплуатации, а также после ремонта проверяют на геометрическую точность в ненагруженном состоянии, на точность обработанных деталей и на получаемую при этом шероховатость обработанной поверхности. Требования к точности изложены в руководстве по эксплуатации станка. При проверке на точность станка проверяют прямолинейность продольного перемещения суппорта в горизонтальной плоскости; одновысотность оси вращения шпинделя передней бабки и оси отверстия пиноли задней бабки по отношению к направляющим станины в вертикальной плоскости; радиальное биение центрирующей поверхности шпинделя передней бабки под установку патрона; осевое биение шпинделя передней бабки и др.
Прямолинейность продольного перемещения суппорта в
горизонтальной плоскости проверяют с помощью цилиндрической оправки,
закрепленной в центрах передней и задней бабки, и индикатора, установленного
на суппорте, рисунок ниже – а). Смещением задней бабки в поперечном
направлении добиваются, чтобы показания индикатора на концах оправки
были одинаковы или отличались не более чем на 0,02 мм на 1 м хода суппорта.
Одновысотность оси вращения шпинделя передней бабки и оси отверстия пиноли задней бабки по отношению к направляющим станины в вертикальной плоскости проверяют при удалении задней бабки от передней на 1/4 наибольшего расстояния между центрами, рисунок выше – б). Проверку выполняют с помощью цилиндрических оправок, вставленных в отверстия шпинделя и пиноли задней бабки, и индикатора, установленного на суппорте. Наибольшее показание индикатора на образующей оправки шпинделя определяют возвратно-поступательным поперечным перемещением суппорта в горизонтальной плоскости относительно линии центров. Не изменяя положения индикатора, таким же способом определяют его показания на образующей оправки задней бабки. Разница в показаниях индикатоpa не должна превышать 0,06 мм у станков для обработки деталей с наибольшим диаметром 400 мм. Допускается только превышение оси отверстия пиноли над осью шпинделя передней бабки.
Радиальное биение центрирующей поверхности шпинделя
передней бабки под патрон проверяют с помощью индикатора, рисунок выше – в). При этом измерительный стержень индикатора устанавливают перпендикулярно
образующей центрирующей шейки шпинделя. Радиальное биение шейки
вращающегося шпинделя для патрона с наибольшим диаметром обрабатываемой
детали 400 мм не должно превышать 0,01 мм.
Осевое биение шпинделя передней бабки измеряют с помощью оправки, вставленной в отверстие шпинделя, и индикатора, установленного на станке при вращающемся шпинделе, рисунок ниже – г). Измерительный стержень индикатора с плоским наконечником упирается в шарик, который установлен в центровое отверстие оправки. Осевое биение шпинделя для установки деталей с наибольшим диаметром 400 мм не должно превышать 0,01 мм.
Радиальное биение конического отверстия шпинделя
передней бабки проверяют с помощью оправки длиной L=300 мм, вставленной
в отверстие шпинделя, и индикатором, установленным в резцедержатель
станка при вращающемся шпинделе, рисунок выше – д).
Для станков с наибольшим диаметром обрабатываемой детали 400 мм радиальное
биение оправки у торца шпинделя (положение 1) не должно превышать 0,01 мм,
а на расстоянии L=300 мм от торца шпинделя (положение 2) – 0,02 мм.
Параллельность оси вращения шпинделя передней бабки
продольному перемещению суппорта проверяют с помощью оправки длиной
L=300 мм, установленной в отверстие шпинделя, и индикатором, установленным
на суппорте станка, рисунок выше – е). Измерение производят по образующей
оправки в вертикальной (положение 3) и горизонтальной (положение 4)
плоскостях. При этом снимают показания индикатора по двум диаметрально
расположенным образующим оправки (при повороте шпинделя на 180 градусов),
перемещая суппорт с индикатором от торца шпинделя на расстояние
L=300 мм. Затем определяют среднеарифметическое значение отклонений,
измеренных по двум образующим (отдельно для горизонтальной и для
вертикальной плоскостей). Для станков с наибольшим диаметром обрабатываемой
детали 400 мм допускаемая непараллельность оси шпинделя направлению
продольного перемещения суппорта в вертикальной плоскости не должна
превышать 0,03 мм (причем непараллельность должна быть направлена
только вверх), а в горизонтальной плоскости – 0,012 мм (непараллельность
должна быть направлена только в сторону суппорта).
Точность работы токарных станков проверяют при обработке образцов. На станках с наибольшим диаметром обрабатываемой детали 400 мм точность геометрической формы цилиндрической поверхности проверяют при обработке образцов длиной 200 мм. Предварительно обработанный образец с тремя поясками, расположенными по концам и в середине образца, устанавливают в патрон или в центры станка и обрабатывают по наружной поверхности поясков. Проверяют постоянство диаметра в любом поперечном сечении, при этом разность между измеренными максимальным и минимальным значениями не должна превышать 0,02 мм. Измерение производят пассиметром, микрометром или другими инструментами.
Плоскостность торцовой поверхности проверяют при
обработке образцов диаметром d=200 мм, установленных в кулачки патрона.
Торцовая поверхность образца может иметь кольцевые канавки (у периферии,
в середине и в центре) и должна быть предварительно обработана.
После проточки торцовой поверхности образец не снимают со станка. Результаты обработки могут быть проверены индикатором, установленным
на суппорте так, чтобы наконечник индикатора был перпендикулярен
измеряемой поверхности. Измерение производят путем перемещения в
поперечном направлении верхней части суппорта на длину, равную или
больше D. Отклонение, определяемое как половина наибольшей алгебраической
разности показаний индикатора, не должно превышать 0,016 мм.
Плоскостность торцовой поверхности можно также проверить, касаясь
наконечником индикатора контрольной линейки, приложенной к обработанному
торцу образца. Линейку прикладывают в разных осевых сечениях проверяемой
поверхности и определяют отклонение так же, как описано выше.
Точность нарезаемой резьбы проверяют на образце
(диаметр которого примерно равен диаметру ходового винта станка),
закрепленном в центры станка, при нарезании трапецеидальной резьбы
длиной не более 500 мм с шагом, примерно равным шагу ходового винта станка.
При этом ходовой винт непосредственно соединяют со шпинделем через сменные
зубчатые колеса с отключением механизма коробки подач. После чистовой
обработки проверяют равномерность резьбы с помощью соответствующих
приборов и методов проверки. По результатам измерений определяют
накопленную погрешность шага резьбы – разность между фактическим и
заданным расстоянием между любыми одноименными (не соседними) профилями
витка резьбы в осевом сечении по линии, параллельной оси винта.
Величина накопленной погрешности шага резьбы не должна превышать 0,04 мм
на длине 300 мм.
Станок геометрическая точность – Энциклопедия по машиностроению XXL
Проверка геометрической точности станков. Геометрическая точность станка является одним из факторов, определяющих точность обработки изделий (формы и размеров). [c.292]Новые или отремонтированные станки проходят испытания для проверки качества их изготовления или ремонта. С этой целью станки подвергают испытанию на геометрическую точность, на шероховатость поверхности и точность обработанных деталей. Перед испытанием станок устанавливают на фундамент, выверяют по уровню и проверяют геометрическую точность станка. Геометрическая точность станка определяется проверкой точности взаиморасположения, перемещения и соотношения движения рабочих органов, несущих обрабатываемую деталь и инструмент. Проверяемые параметры, методы контроля и нормы точности, в зависимости от конструкции станка и его точности, регламентированы соответствующими ГОСТами или специальными техническими условиями.
[c.246]
При производстве зубчатых колес осуществляют три вида контроля профилактический, текущий и приемочный. Профилактический контроль включает в себя контроль средств производства станка — геометрический и кинематический инструмента — нового и после заточки приспособления — вне станка и на станке заготовки — после ее обработки, на станке — перед выполнением технологических операций обработки изделия, с целью обеспечения требуемой точности изготовления зубчатых колес.
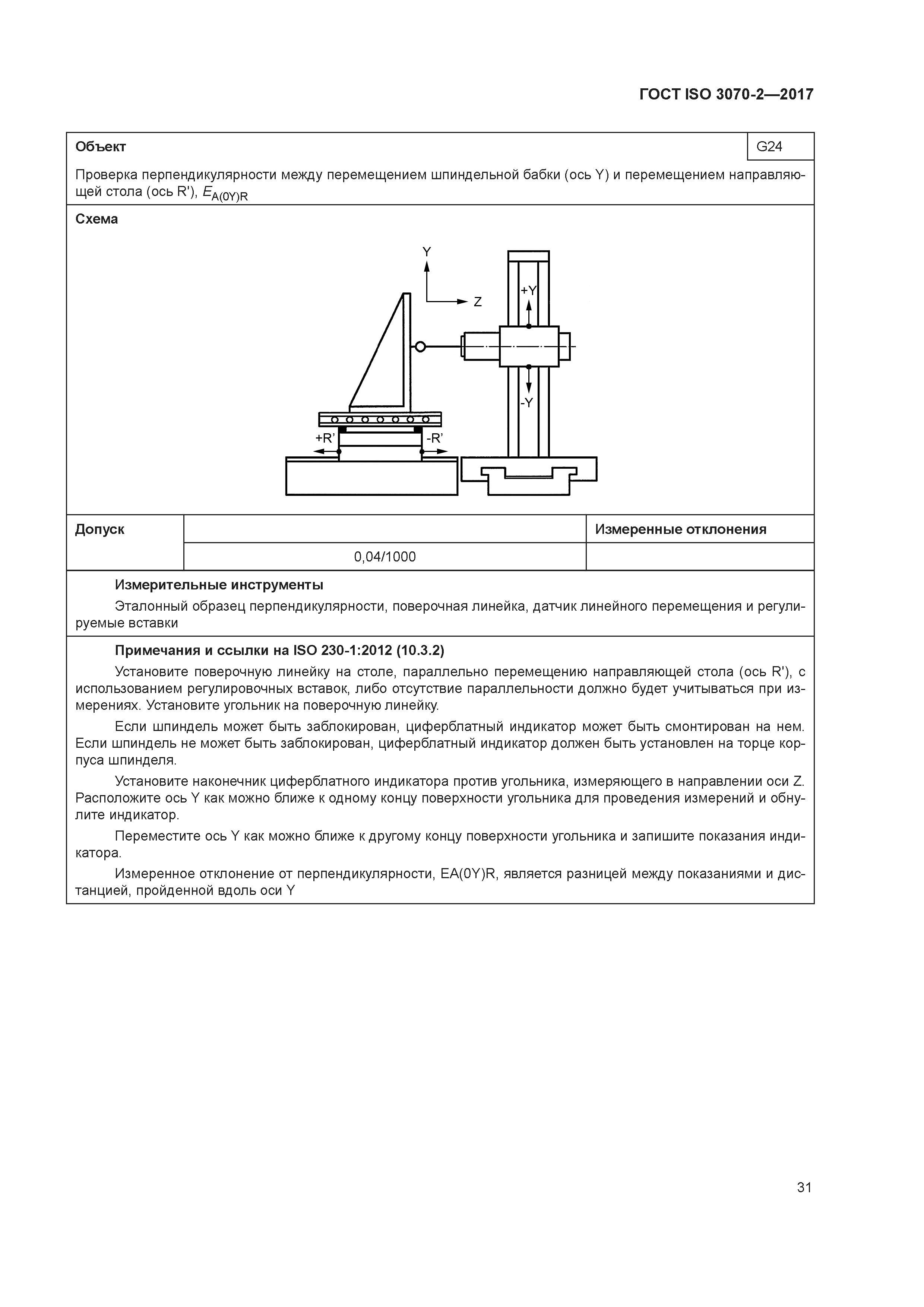
На начальные параметры точности станка влияет геометрическая точность изготовления и сборки его узлов, жесткость и виброустойчивость системы, а также ее тепловые деформации. В стадии проектирования эти показатели должны быть регламентированы соответствующими нормативами, а при наличии” опытного образца подтверждены его испытанием. Погрешности обработки, вызванные перечисленными факторами, определяют запас надежности, т. е. ту часть допуска на обработку, которая будет не израсходована и оставлена в качестве запаса на износ. Хотя оценка начальных параметров машины на стадии ее проектирования является сложной самостоятельной проблемой, она не несет в себе опасности эксплуатации некачественной машины, поскольку неточность предварительной оценки начальных показателей проявится сразу же при испытании первого образца. После этого можно внести исправления в серийную модель или в данный образец. Вместе с тем прогнозирование потери точности от износа имеет большое значение потому, что результат износа проявится лишь после достаточно длительного периода эксплуатации машины.
[c.371]
Так, из рассмотренного примера расчета ресурса видно, что основное внимание для повышения параметрической надежности следует уделить повышению жесткости, начальной геометрической точности и уменьшению тепловых деформаций станка, которые занимают в балансе точности значительную долю. При уменьшении начальных погрешностей и ужесточении требований к выходным параметрам станка вновь станет вопрос о необходимости повышения износостойкости его сопряжений. Кроме того,, если данный класс износостойкости не будет обеспечен условиями эксплуатации станка, то расчетные показатели надежности соответственно изменят свое значение.- [c.377]
Непрерывное функционирование оборудования неизбежно сопровождается ухудшением таких его характеристик, как жесткость и геометрическая точность узлов, виброустойчивость и др.

Интерес представляет и обратная проектная задача — определение возможности путем совершенствования токарной обработки и повышения точности формообразования (использование оборудования с повышенной жесткостью и геометрической точностью, занижение технологических режимов и др.) сокращение числа шлифовальных станков, ограничиваясь, топ например, только двукратным [c.181]
Проверка геометрической точности взаимного расположения и движения узлов металлорежущего станка [c.625]
Таким образом, испытание станков на точность производят измерением геометрических точностей станка, а также определением точности обработки изделия.
[c.625]
Контроль точности и качества изготовления и сборки отдельных узлов линии заключается в выполнении отдельных замеров параметров узлов и деталей, от которых зависит надежность оборудования, а также в выборочной проверке геометрической точности технологического оборудования (станков) и точности монтажа линии (после испытания линии в работе). Проверка проводится по внутризаводским приемно-сдаточным нормам точности методика проверки — по действующим техническим условиям. [c.242]
Не разбирая подробно вопросов проверки на геометрическую точность, отметим одно обстоятельство, имеющее значение и при монтаже станков при контроле точности станка необходимо учитывать величину собственного прогиба оправок. Величина [c.417]
Работа системы П происходит следующим образом. Величины задаваемых координат через УВП или У ПН подаются в АУ, откуда поступают в регистры Рхг и Ру устройства позиционирования. Технологические команды, содержащие информацию о номере инструмента, скорости вращения шпинделя, величине подачи и т. п., подаются в регистры памяти команд Р к устройства технологических команд, а оттуда через дешифраторы Дш и усилители Ус — на исполнительные органы станка. После окончания ввода программы происходит ввод величин коррекций (коррекций на длину и диаметр инструмента, коррекции геометрической точности). Отработка задаваемых координат осуществляется путем сравнения в АУ текущих значений координат, хранящихся в Рпп с заданными программой величинами, хранящимися в Рхг, Ру устройства позиционирования.
[c.9]
Экспериментами было установлено, что система отрабатывает рассогласование практически независимо от величины и характера изменения исходной погрешности обработки А , материала и размеров детали, глубины резания и продольной геометрической точности станка. При этом погрешность Ар г составляет около 3—5 мкм. Др . значительно возрастает при прерывистом включении системы в работу. [c.359]
После окончания общей сборки, регулировки, обкатки и предварительной проверки оборудование предъявляется отделу технического контроля. Контроль качества капитального и среднего ремонтов заключается в проведении технических испытаний работы станка под нагрузкой, проверке геометрической точности в соответствии с нормами ГОСТа.
[c.205]
Точность станка определяют измерением его геометрических точностей и точности обработки образцов. Станок при этом устанавливают и выверяют на фундаменте на стальных клиньях. [c.609]
Определение геометрической точности станка не исключает всех его проверок на точность по стандарту. Однако проверки точности, которые проводятся в этом случае, имеют следующие принципиальные отличия [c.167]
Для этого при проверке геометрической точности станка погрешности следует разделять на скалярные и векторные. Векторные величины, в свою очередь, разделяются на действующие вдоль заданного направления (например, осевое биение шпинделя), в заданной плоскости (например, биение шпинделя в плоскости перпендикулярной оси, погрешность траектории суппорта или стола в плоскости его движения). В последнем случае по стандарту проверка осуществляется с помощью одного индикатора. При этой проверке получаемой информации не достаточно для суждения о погрешности траектории резца необходима постановка двух индикаторов (датчиков), как показано на рис. 2. Этот пример иллюстрирует отличие применяемых проверок от стандартных. Для оценки влияния точности основных узлов станка на выходные параметры необходимо составление расчетных схем. Следует иметь в виду, что на один и тот же выходной параметр типовой детали может влиять несколько видов исходных погрешностей.
[c.169]
В соответствии с этим лабораторные испытания станков предусматривают 1) проверку геометрической точности станка и точности обработки 2) испытание жёсткости станка 3) исследование вибраций станка 4) энергетическое испытание привода станка 5) проверку работы электрооборудования станка [c.663]
Методы измерений при проверке геометрической точности и других величин при испытании станков приведены в табл. 1.
[c.664]
Проверка станка на геометрическую точность по ГОСТ или по техническим условиям. [c.205]
Правильность установки станков, имеющих три опорные точки, следует контролировать в те же сроки, что п их геометрическую точность. [c.21]
МЕТОДЫ ИЗМЕРЕНИЯ ГЕОМЕТРИЧЕСКОЙ ТОЧНОСТИ СТАНКОВ [c.616]
Соответственно указанному, контроль точности таких станков, как например, зуборезные или винторезные, должен слагаться из двух этапов 1) контроля геометрической точности станка, ставящего своей целью выявление его геометрических ошибок и 2) контроля кинематической точности станка, задачей которого является определение кинематических ошибок. [c.625]
Контроль геометрической точности станков может быть только поэлементным, поскольку геометрические ошибки станка в отрыве от его кинематических ошибок не создают какого-либо комплекса, поддающегося контролю как единое целое. Поэтому стремление к максимальной детализации геометрического контроля является всегда оправданным.
[c.625]
На стадии отбора факторов требуется установить их области определения. Это связано с установлением законов распределения технологических факторов. Необходимо учитывать условия изменения факторов во времени. Естественно, что при изучении хода процесса во времени надо учитывать износ режущего инструмента и его затупление. Следует также учитывать потери первичной геометрической точности станка вследствие износа рабочих поверхностей. [c.256]
Данные произведенных проверок станков токарного типа на геометрическую точность после капитального ремонта часто расходились с данными практической точности, получаемой при обработке деталей на станках, причем точность в последнем случае была недостаточной. [c.342]
Собранный станок проверяют по нормам геометрической точности (рис. 112, а—г). Проверяется биение конца главного вала, которое не должно превышать 0,2 мм (рис. 112, а) совпадение осей главного вала и вала левой группы — 1,0 в горизонтальной плоскости и 1,7 в вертикальной (рис. 112, б) несоосность шаблона и рычажного механизма — 1 мм (рис. 112, в). Точность расположения обжимных рычагов и кольцевой пружины— 1,8 мм (рис. 112, г).
[c.166]
Качество обработки на станке непосредственно связано с его точностью, которая характеризует степень влияния различных погрешностей станка (геометрических, кинематических, упругих, температурных и динамических) на точность изготовляемых деталей. [c.9]
Температурные погрешности возникают, главным образом, вследствие неравномерного нагрева различных элементов станка в процессе его работы (что приводит к изменению начальной геометрической точности) и оказывают существенное влияние на качество обработки деталей, особенно высокоточных. [c.10]
В процессе наладки и эксплуатации металлорежущих станков периодически осуществляют проверку их геометрической точности (например, биение шпинделя) на соответствие нормам, указанным в паспорте оборудования.
[c.295]
По точности металлорежущие станки классифицируются на 5 групп. Геометрические пофешности станков более высоких точностных групп значительно уменьшаются, а трудоемкость их изготовления резко возрастает. По отношению к характеристикам станков нормальной точности погрешности станков других групп и трудоемкость их изготовления составляют в процентах к погрешностям и трудоемкости изготовления станков нормальной точности величины, приведенные в табл. 2.10. [c.97]
К основным характеристикам геометрической точности станков относят [c.97]
Погрешности геометрической точности станков полностью или частично переносятся на обрабатываемые заготовки в виде систематических погрешностей. Например, отклонение от параллельности оси шпинделя токарного станка направлению движения суппорта в горизонтальной плоскости приводит к появлению конусообразности у обрабатываемой заготовки в вертикальной плоскости — к гиперболоиду вращения.
[c.98]
Точность станка в ненагруженном состоянии, называемая геометрической точностью станка, зависит главным образом от точности изготовления основных деталей и узлов станка и точности их сборки. Погрешности, допущенные в размерах и форме этих деталей и их взаимном расположении (плсскостность, цилиндрич-ность, параллельность и перпендикулярность осей и плоскостей, концентричность, соосность и т. д.), называют иногда геометрическими погрешностями станка. [c.48]
Отклонение геометрической формы опорных шеек по овальности и конусности для станков нормальной точности обычно не должно превышать 50% допуска на диаметральные размеры шеек. Для станков повышенной точности эта величина не превьшаает 25%, а для прецизионных лежит в пределах 5—10% от допуска на диаметр шеек. Шпиндели современных прецизионных шлифовальных станков имеют овальность не выше 0,3—0,5 мкм, конусность не выше 0,25—0,5 мкм на длине 300 мм при допуске на диаметр шейки 1,5—3 мкм.
[c.369]
Для станочных линий в этом разделе указывают нормы и методы контроля геометрической точности оборудования, его жесткости, нормы и методы контроля шума и другие требования. С целью обеспечения сроков сохранения заданной точности обработки деталей и норм геометрической точности станочных АЛ в технических условиях дают виутрисдаточные нормы точности, которые должны быть ужесточены по сравнению с установленными нормами на 40 %. Нормы геометрической точности агрегатных станков установлены 0СТ2 Н72-5—80. [c.32]
Обработка заготовок со стабильным по величине припуском и однородными физико-механическими свойствами, использование в АЛ станков с высокой жесткостью и геометрической точностью, применение высококачественного инструмента, контрольных автоматов и автоподналадчиков, рациональная система обслуживания и ремонта оборудования — все эти факторы позво- [c.
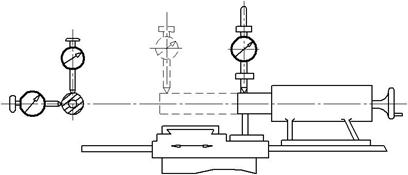
В курсе лекций, читаемых в МАТИ, большой раздел посвящается вопросам технологической надежности станков, зависящей от процессов, происходящих в самих станках во время их работы вибрации, изменений жесткости, температурных деформаций, износа и др. Для закрепления знаний по вопросу влияния изменений температурных полей станка на точность параметров изготавливаемых на этом станке деталей, сборник включает лабораторную работу Исследование влияния тепловых деформаций станка на его технологическую надежность . В работе студенты знакомятся с методикой исследования температурных полей и тепловых деформаций стенда на базе токарно-револьверного автомата 1Б118, изучают приборы и аппаратуру для измерения температуры и тепловых деформаций, производят настройку станка и необходимые измерения, а также оценивают во времени смещение уровня настройки станка и стенда. Смещение настройки станка из-за тепловых деформаций оценивается по изменению выбранных геометрических параметров типич ной детали, обрабатываемой на станке.
[c.307]
Вновь смопт11])ованные станки, подливаемые цементным раствором, первые шесть месяцев следует проверять с такой же частотой, как многоопорные. Если на протяжении полугодия не будет обнаружена осадка фундамента, можно дальнейшую проверку правильности установки совместить с проверкой геометрической точности станков. [c.21]
При работе на высоких режимах резания современные зубофрезерные станки для крупносерийного и массового производства должны иметь высокие статическую и динамическую жесткости [достигаемые вследствие большей массы (1,2 —1,5 т на модуль), обре-бренных и толстых стенок станины, короткой кинематической цепи], большую мощность главного электродвигателя (1,8 —2,5 кВт на модуль), длинные и широкие направляющие, гидростатичёские подшипники, большое осевое перемещение фрезы (160 — 200 мм), обильное охлаждение (200 — 400 л/мин), возможность автоматизации. Станки должны быть удобными в обслуживании и наладке, иметь хорошие условия отвода теплоты, выделяющейся в процессе резания. У новых станков, кроме контроля норм геометрической точности и точности обрабатываемой детали, контролируют синхронность вращения шпинделей инструмента и детали. Зубчатые колеса обрабатывают на скорости резания 50—80 м/мин и подаче 3 — 6 мм/об с обеспечением 6 —7-й степени точности.
[c.342]
В ряде случаев целесообразно заменять непосредственный контроль параметров зацепления профилактическим контролем кинематической и геометрической точностей станка, точности режущего инструмента, заготовки и их установки. Профилактический контроль особенно эффективен при производстве крупногабаритных колес. Его можно осуществлять также дифференцированной проверкой отдельных параметров зубчатых колес, по результатам которой выявляют погрешностп технологического процесса и производят его подна-ладку. [c.520]
Как известно, станки испытывают на геометрическую точность по ГОСТ, т. е. в ненагруженном состоянии. Профессор А. П. Со-КОЛОНСКИЙ в опубликованных им работах справедливо утверждал, что эти испытания не дают возможности оценить реальную точность станка даже в ненагруженном состоянии. Тем более, по его мнению, недопустимо ограничиваться подобными статическими испытаниями на точность для оценки эксплуатационной точности, т. е. технологической. Наша практика подтвердила бесспорность этих утверждений.
[c.342]
Проверка геометрической точности – Энциклопедия по машиностроению XXL
Проверка геометрической точности взаимного расположения и движения узлов металлорежущего станка [c.625]Контроль точности и качества изготовления и сборки отдельных узлов линии заключается в выполнении отдельных замеров параметров узлов и деталей, от которых зависит надежность оборудования, а также в выборочной проверке геометрической точности технологического оборудования (станков) и точности монтажа линии (после испытания линии в работе). Проверка проводится по внутризаводским приемно-сдаточным нормам точности методика проверки — по действующим техническим условиям. [c.242]
После окончания общей сборки, регулировки, обкатки и предварительной проверки оборудование предъявляется отделу технического контроля.

Для этого при проверке геометрической точности станка погрешности следует разделять на скалярные и векторные. Векторные величины, в свою очередь, разделяются на действующие вдоль заданного направления (например, осевое биение шпинделя), в заданной плоскости (например, биение шпинделя в плоскости перпендикулярной оси, погрешность траектории суппорта или стола в плоскости его движения). В последнем случае по стандарту проверка осуществляется с помощью одного индикатора. При этой проверке получаемой информации не достаточно для суждения о погрешности траектории резца необходима постановка двух индикаторов (датчиков), как показано на рис. 2. Этот пример иллюстрирует отличие применяемых проверок от стандартных. Для оценки влияния точности основных узлов станка на выходные параметры необходимо составление расчетных схем. Следует иметь в виду, что на один и тот же выходной параметр типовой детали может влиять несколько видов исходных погрешностей.
[c.169]
Методы измерений при проверке геометрической точности и других величин при испытании станков приведены в табл. 1. [c.664]
ПРОВЕРКА ГЕОМЕТРИЧЕСКОЙ ТОЧНОСТИ [c.302]
Проверка геометрической точности автоматов производится при ручном перемещении отдельных узлов (в нерабочем состоянии станка) и состоит в контроле взаимного расположения основных деталей и узлов станин, колонн, столов, суппортов, шпинделей и пр. Целью проверки геометрической точности является выявление фактических отклонений от прямолинейности, плоскостности, цилиндричности, параллельности, перпендикулярности, от точного вращения и т. д.
[c.463]
Сущность и метод проверки геометрической точности лучше всего проследить на следующем примере. На станине револьверного автомата имеются направляющие, по которым перемещаются суппорты (рис. 233). Для того чтобы вершина резца при движении суппорта по продольным направляющим перемещалась по прямой линии, параллельной оси станка, без чего нельзя получить на станке деталь правильной цилиндрической формы, необходима прямолинейность направляющих в горизонтальной и вертикальной плоскостях, а также параллельность направляющих оси станка. Совпадение направляющих с горизонтальной или вертикальной плоскостью (плоскостность) проверяется обычным или рамным уровнем с ценой деления 0,02—0,04 мм на 1 м длины (рис.
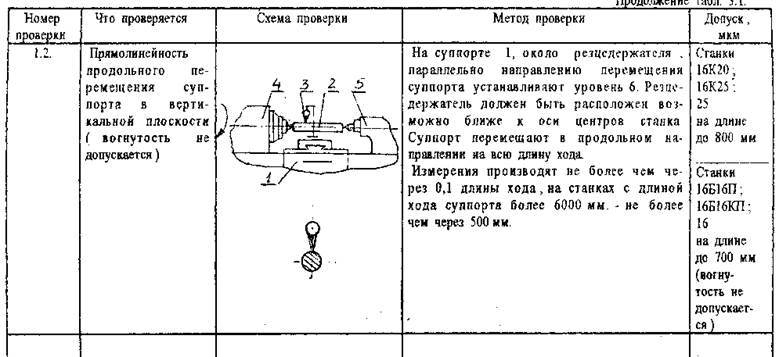
Для проверки геометрической точности станков применяются следующие инструменты уровень, эталонная линейка, угольник, индикатор, стойка для индикатора, щупы и контрольная оправка (рис. 234). [c.466]
Рис. 234. Измерительные приборы, применяемые при проверке геометрической точности а —уровень, б — эталонная линейка, в — угольник, г — индикатор 5 — стойка для индикатора, е — щупы, ж — контрольная оправка |
Проверка геометрической точности станка выполняется после точной установки его на стенде в ремонтном цехе или на фундаменте в производственном цехе и после испытания станка на холостом ходу и в работе. Проверяют
[c.330]
При проверке геометрической точности вращающихся рабочих органов контролируются биение оси и правильность расположения опорных поверхностей и посадочных мест. Если шпиндель имеет центрирующую шейку и упорный буртик для посадки зажимных приспособлений, то проверяется биение центрирующей шейки и упорного буртика. Биение центрирующей шейки проверяется с помощью индикатора штифт которого опирается на центрирующую шейку. Так как перемещение штифта индикатора яв- [c.160]
Проверка геометрической точности оборудования [c.192]
Проверка геометрической точности и жесткости производится после плановых ремонтов в соответствии с нормами, предусмотренными ГОСТ или техническими условиями. [c.344]
Проверку геометрической точности выполняет контролер отдела технического контроля с привлечением ремонтных слесарей.
[c.344]
I. Проверка геометрической точности токарного станка [c.19]
Сущность н метод проверки геометрической точности лучше всего проследить на следующем примере. На станине револьверного автомата имеются направляющие, по которым перемещаются суппорты (рис. 241). Для того чтобы вершина резца при дви- [c.551]
Рис. 242. Измерительные инструменты, применяемые при проверке геометрической точности а —уровень, б — эталонная линейка, в — стойка для индикатора |
Для проверки геометрической точности станков применяются следующие инструменты уровень (рис. 242, а), эталонная линейка (рис. 242, б), угольник, индикатор, стойка для индикатора (рис. 242, в), щупы я контрольная оправка. [c.552]
Упражнение 2. Ознакомиться с ГОСТами по проверке геометрической точности одного полуавтомата или автомата.
[c.556]
При проверке геометрической точности проводится определение точности размеров, ( рмы и взаимного расположения тех деталей автомата и полуавтомата, от вращения или перемещения которых в первую очередь зависит получение требуемой точности обработки. [c.364]
Так как проверка геометрической точности автоматов и полуавтоматов дает представление о возможной точности обработки, наладчику необходимо хорошо знать назначение и способы выполнения этих проверок. [c.364]
Проверка геометрической точности многошпиндельных автоматов и полуавтоматов несколько сложнее, чем для одношпиндельных, так как необходимо определить погрешности, появляющиеся из-за последовательной обработки заготовки на нескольких позициях. [c.367]
Наряду с рассмотренными проверками геометрической точности, проводимыми для каждого автомата или полуавтомата, в необходимых случаях выборочно проводятся их испытание и проверки на жесткость, виброустойчивость, потребляемую мощность, к. п.д. и др.
[c.367]
При проверке геометрической точности автоматов и полуавтоматов применяются измерительные инструменты, для приведения в действие которых требуются ничтожно малые по сравнению с возможными во время обработки усилия. Поэтому полученные при этих проверках результаты будут показы-вать,какую степень точности можно получить при чистовой обработке весьма жестких заготовок жестким режущим инструментом. [c.367]
В чем заключается проверка геометрической точности токарных автоматов и полуавтоматов Приведите примеры проверок геометрической точности. [c.369]
Кроме испытания станка под нагрузкой, производят испытание станка на точность и жесткость. Собранный после ремонта станок перед его эксплуатацией проверяют на точность. Проверку на точность станка осуществляет контрольный мастер с обязательным участием представителей ремонтно-механического цеха. Технический контроль предусматривает проверку геометрической точности и жесткости станка и измерение точности обрабатываемых на станке деталей. Проверка точности станков, вышедших из ремонта, выполняется по нормам точности для приемки новых станков согласно ГОСТу 8—53 Станки металлорежущие. Общие условия к стандартам на нормы точности . Испытание на жесткость станков соответствующих групп производится в соответствии с требованиями ГОСТа 7035—54 Станки металлорежущие. Общие условия к стандартам на нормы жесткости по нормам, установленным в соответствующих стандартах. Выявленные в процессе испытания дефекты заносят в ведомость дефектов и передают для устранения ремонтной бригаде. Осмотр, испытание и проверка собранного станка производится в присутствии бригадира слесарей-сборщиков, мастера ремонтно-механического цеха и контрольного мастера. Затем проверяют отдельные узлы станка, наличие таблиц, ограждения, необходимые при обслуживании станка, и др. После окончательной проверки станок обезжиривают, грунтуют и красят. Станок передается в цех по акту для его эксплуатации.
[c.415]
Вновь смопт11])ованные станки, подливаемые цементным раствором, первые шесть месяцев следует проверять с такой же частотой, как многоопорные. Если на протяжении полугодия не будет обнаружена осадка фундамента, можно дальнейшую проверку правильности установки совместить с проверкой геометрической точности станков.
[c.21]
П0МЙ1М0 перечисленных, делают еще некоторые проверки геометрической точности, на которых здесь нет надобности останавливаться. При всех проверках руководствуются нормативами, установленны.ми ГОСТ 42—56. [c.331]
Рис. и. Методы проверки геометрической точности токарного станва общего назначения [c.50]
Проверку геометрической точности для соответствующих типов станков проводят по нормам ГОСТов, которые приводятся в техническом паспорте на оборудование. В тех случаях, когда подобная документация отсуствует или имеется несерийное оборудование, можно провести типовую проверку (табл. 111). [c.191]
Технический надзор и уход за оборудованием включает межремонтное обслуживание промывку смену и пополнение масел проверку геометрической точности и жесткости осмотр профилактите-ские испытан 1я электрооборудования.
[c.342]
Проверка геометрической точности проводится по ГОСТ 8831—70 — для автоматов продольного точения, по ГОСТ 11578—65 для токарно-револь-верных автоматов, по ГОСТ 43—73 для горизонтальных многошпиндельных автоматов, по ГОСТ 6819—70 и ГОСТ 6820—54 — соответственно для горизонтальных и вертикальных многошпиндельных полуавто 1атов. [c.365]
На рис. 260 показано несколько схем различных проверок для многошпиндельных атоматов и полуавтоматов. Наряду с проверкой геометрической точности каждого автомата и полуавтомата в нерабочем состоянии проводится также их проверка на постоянство получаемых размеров и погрешность геометрической формы при изготовлении определенной партии типовых деталей. При этом определяется постоянство диаметров и длины деталей, их овальность и конусность. Погрешности постоянства диаметров и длины деталей определяются наибольшей разностью диаметров и длин для всех измеренных деталей в партии. Овальность и конусность проверяются не менее чем на 25% деталей от всей партии.
[c.367]
Проверка станков на технологическую точность – «Nord West Tool»
Точность металлообработки является базовым критерием для оценки качества металлических изделий. Приоритетная задача состоит в минимизации отклонений размеров изготавливаемой продукции от заданных параметров. Для решения этой проблемы проводится периодический контроль станков на технологическую точность. При этом следует понимать, что подобная проверка – это больше чем просто осмотр и измерения соответствующих частей оборудования. В ходе этой работы осуществляется целый комплекс мероприятий.
Цель проверок на технологическую точность
Главной целью проведения контроля является проверка совпадения текущих параметров станка с характеристиками, указанными в паспорте на оборудование. Необходимость в этой процедуре диктуется износом оснащения в процессе эксплуатации. И речь здесь идёт не о сменных инструментах – резцы, фрезы, свёрла и точильные камни проверяются в текущем режиме. При проверках технологической точности исследуются постоянные компоненты конструкции станков, в числе которых следующие.
- Шпиндели.
- Суппорты.
- Консоли.
- Приводы.
В оборудовании, оснащённом системой ЧПУ, проверке подвергаются также измерительные устройства (датчики), которые используются для автоматического управления металлообработкой.
Итогом контрольных мероприятий становится вывод о возможности дальнейшего использования машины на данном производственном участке. Снижение технологической точности до недопустимых пределов становится основанием для коренной модернизации или замены станка.
Измеряемые параметры
Измерениям подлежат все параметры станка, которые так или иначе влияют на точность металлообработки. Прежде всего, измеряются линейные и угловые перемещения частей машины, удерживающих заготовку и инструменты. Помимо этого определяется скорость подачи обрабатываемого проката. Все подвижные компоненты исследуются на наличие свободных биений (люфтов). Этой процедуре в обязательном порядке подвергаются узлы на подшипниках.
Технические средства для проведения измерений
Очевидно, что качество проверок технологической точности напрямую определяется характеристиками измерительных приборов. При проведении контроля используются следующие технические средства:
- штангенциркули;
- микрометры;
- угломеры;
- калибры;
- индикаторы перемещений.
В большинстве случаев измерения выполняются типовыми механическими приборами, но существуют и более точные измерители – лазерные. Эти устройства применяются сегодня всё чаще и чаще.
Регламент контроля
Плановый контроль технологической точности металлообрабатывающей техники проводится по графику, который составляется согласно специальному документу – ведомости станочного оборудования. В неё заносятся сведения о периодичности технологических операций, влияющих на точность изготовления продукции. Этот документ содержит также сведения о режимах работы станков.
Проверка может носить не только плановый характер, но и выполняться при аварийных отказах оборудования. В этом случае контрольные мероприятия проводятся в соответствии с регламентами, разработанными для устранения форс-мажорных обстоятельств.
Любые проверки – как плановые, так и аварийные – проводятся при условии временного вывода машин из эксплуатации. По этой причине разработка графика контрольных мероприятий является весьма важной для планирования как производственной деятельности, так и модернизации оборудования. Остаётся добавить, что ответственным за это направление работы предприятия отвечает, как правило, главный технолог завода.
Сервисный пакет Проверка геометрической точности станка
Сервисный пакет – Проверка геометрической точности станка
- Для станка OPTIMUM с системой ЧПУ Siemens. Пакет включает транспортные расходы на 400 км пути в общей сложности (200 км в одну сторону)
- Каждый последующий км будет рассчитываться по цене 0,59 ЕВРО
- В пакет не входят Транспортные расходы в размере 60,00 ЕВРО за каждый начавшийся час
- Проживание и суточные по фактическим расходам
Тип станка:
- Токарные / фрезерные станки.
Услуги:
Проверка геометрической точности- Проверка круглости с помощью системы Renishaw QC20 (фрезерные станки)
- Подробный протокол проверки с указанием всех результатов измерений
- Анализ и оценка результатов измерений
- Предварительная смета для устранения выявленных несоответствий
Преимущества:
- Ранее выявление наличия износа станка;
- Возможность заблаговременно запланировать работы по техобслуживанию станка ;
- Повышение качества обработки;
- Предсказуемые расходы на обслуживание;
- Безопасность производства.
Дополнительная информация:
- Срок действия сервисного пакета устанавливается индивидуально;
Метрология станков
16.1.
Введение Размеры калибра, его поверхность и геометрия зависят от качества и точности станка для его изготовления. Также при массовом производстве различные производимые компоненты должны иметь такую точность, чтобы их можно было собирать на неизбирательной основе. Точное производство комплектующих зависит от точности станков.
Постоянно растущий спрос на высокоточные обрабатываемые компоненты привел к серьезным исследованиям в отношении средств, с помощью которых геометрическая точность станков может быть улучшена и сохранена. Поэтому очень важно, чтобы в статических условиях точность центровки станков проверялась с помощью некоторых геометрических тестов. Испытания, которые проверяют точность центровки различных частей станка, называются статическими упорами.
Станок, в то же время, должен иметь возможность отображать желаемое поведение и характеристики в нормальных рабочих условиях, поскольку оператор озабочен фактической работой станка.Поэтому некоторые испытания на центровку выполняются в условиях динамической нагрузки, и они называются динамическими испытаниями. Таким образом, очевидно, что удовлетворительной работы машины только при статической нагрузке недостаточно, но следует также учитывать вибрацию и прогиб различных частей машины при реальной динамической нагрузке. В динамических испытаниях различные элементы фактически нагружаются, и проводятся испытания на центровку. Также различные части возбуждаются на рабочей частоте и наблюдают за поведением машины.
Другими словами, можно сказать, что станки для мастерской должны иметь возможность производить детали заданной точности в заданных пределах последовательно и без необходимости художественного мастерства со стороны оператора, и что качество деталей зависит от:
(i) Жесткость и жесткость станка и его составных частей.
(ii) Выравнивание различных частей машины относительно друг друга. Это очень важно, потому что геометрия различных форм основана на относительном движении между различными частями машины и, следовательно, на совмещении различных частей.
(iii) Качество и точность устройств управления и приводного механизма. Жесткость и жесткость – это вопрос конструктора, и как только испытания прототипа определенной конструкции дали удовлетворительные результаты, отпадает необходимость снова и снова испытывать машину той же конструкции. Точность изготовления, точность устройств управления и приводных механизмов, таких как ходовой винт токарного станка, – все должно иметь как можно более точное относительное выравнивание. Это зависит от качества изготовления и может варьироваться от машины к машине.Поэтому каждая машина подвергается приемочным испытаниям по пунктам {ii) и (iii).
Точность станков (которые режут металл путем удаления стружки или стружки) проверяется посредством геометрических проверок и практических испытаний.
К геометрическим проверкам относится проверка размеров форм и положений компонентов, а также проверка их смещения относительно друг друга. Они включают в себя все операции, которые влияют на компоненты станка и касаются только размеров, форм, положений и относительных перемещений, которые могут повлиять на точность станка.Следует понимать, что геометрические определения являются абстрактными и относятся только к воображаемым линиям и поверхностям. Поэтому на практике соблюдаются метрологические определения, которые являются конкретными и учитывают реальные линии и поверхности, доступные для измерения. Метрологические определения охватывают в одном результате все макро- и микрогеометрические ошибки и позволяют достичь результата, охватывающего все причины ошибок, не различая их друг от друга.
Практические испытания включают механическую обработку испытательных образцов, соответствующих основным целям, для которых был разработан станок, и имеющим заранее определенные пределы и допуски.
Результаты практических испытаний и геометрических проверок можно сравнивать только постольку, поскольку эти два вида испытаний имеют один и тот же объект; в случае, если оба результата не дают одинакового результата, результаты, полученные при проведении практических испытаний, принимаются как действительные. В случае, если проведение обоих типов испытаний является дорогостоящим или трудным, точность машины может быть проверена только геометрическими проверками или только практическими испытаниями.
Различные геометрические проверки, обычно выполняемые на станках: (Перед проведением этих испытаний важно, чтобы станок был настроен и основные горизонтальные и практические плоскости и оси были проверены с помощью спиртовых уровней и т. Д.
(а) Прямолинейность
(i) прямолинейность линии в двух плоскостях;
(ii) прямолинейность направляющих скольжения станков; (iii) прямолинейное движение.
(б) Плоскостность
(c) Параллельность, равноудаленность и совпадение.
Параллельность включает (i) параллельность прямых и плоскостей; (ii) параллельное движение.
(d) Прямолинейные движения или прямоугольность прямых линий и плоскостей.
Также проверяется качество направляющих и опорных поверхностей станины, стоек и опорных плит.
(e) Вращение
Это включает (i) вне круга, (ii) эксцентриситета, (iii) радикального отклонения оси в заданной точке, (iv) отклонение от истинного положения (биение) , (v) периодическое осевое скольжение, (vi) кулачок.
Главный шпиндель является основным элементом станка и проверяется на концентричность, осевое скольжение, точность оси и положения относительно других осей и поверхностей.
(f) Перемещение всех рабочих компонентов.
Теперь мы обсудим определения и различные тесты для выполнения этих геометрических проверок.
Прямолинейность.
Определение прямолинейности штрафа в двух плоскостях дается в главе 7. Существуют различные методы проверки прямолинейности:
(i) Метод прямой кромки. Этот метод описан в главе 7 и ограничен длиной менее 1600 мм.
(ii) Спиртовой уровень и оптические методы. Они также описаны в главе 7.Метод спиртового уровня позволяет проверить прямолинейность только в вертикальной плоскости и может использоваться для длин как ниже, так и выше 1600 мм. Оптические методы используются только для длин более 1800 мм.
(iii) Натянутая проволока и микроскопический метод. В этом методе стальная проволока диаметром 0,1 мм растягивается и располагается примерно параллельно проверяемой линии. Микроскоп
, снабженный устройством горизонтального перемещения в микрометрах, помещают вертикально на поверхность тестируемой линии и перемещают вдоль линии, которая должна быть протестирована.Таким образом, можно отметить отклонение линии от натянутого провода в горизонтальной плоскости измерения. Этого метода следует избегать, если необходимо учитывать провисание проволоки, поскольку провисание чрезвычайно трудно определить с большой точностью.
Условия прямолинейности направляющих станков такие же, как и для линии. Указанные выше методы применимы для плоских направляющих: однако, для V-образных направляющих испытания проводятся на поверхности цилиндра или промежуточной детали (выполненной по форме направляющих), размещенной на V-образных направляющих.
Можно отметить, что проверка прямолинейности направляющих или грядок не так важна, как проверка движения по прямой, которая учитывает все факторы, которые могут повлиять на движение. Выражение «точность движения по прямой» относится к траектории точки на компоненте машины при воздействии на рабочее или установочное движение. Различные возможные случаи движения по прямой:
(i) движение оси на самой себе, когда эта ось остается в пределах двух прямоугольных плоскостей, которые содержат ее в состоянии покоя;
(ii) движение плоской поверхности в своей собственной плоскости, когда эта поверхность остается в своей собственной плоскости;
(iii ) движение компонента параллельно прямой линии или поверхности, когда любая точка на этом компоненте остается на равном расстоянии от линии или от поверхности;
(iv) движение компонента перпендикулярно заданной плоскости, когда каждая точка компонента описывает траекторию, перпендикулярную заданной плоскости.
Прямолинейное движение может быть проверено для меньших перемещений с помощью линейки и индикатора часового типа и для более длинных перемещений с помощью микроскопа и натянутого провода. В методе проверки с помощью линейки и индикатора часового типа циферблатный индикатор прикреплен к движущемуся компоненту машины, прямолинейное движение которой должно быть проверено, а щуп скользит по линейке, представляющей контрольную линию. В методе проверки с помощью микроскопа и натянутой проволоки контрольная линия представлена слегка натянутой тонкой стальной проволокой, а индикатор часового типа заменяется микроскопом, отклонения считываются непосредственно со шкалы окуляра путем визирования проволоки через микроскоп. .
Прямолинейность перемещения суппортов токарного станка для длин менее 1600 мм может быть проверена методом оправки и щупа, а для длин более 1600 мм – методом натянутой проволоки и микроскопом. В первом методе оправка устанавливается между двумя центрами токарного станка и регулируется так, чтобы показания индикатора часового типа были одинаковыми на двух концах. На седле на месте инструмента установлен индикатор с круговой шкалой, а его щуп соприкасается с поверхностью оправки. Первый набор показаний снимается при перемещении индикатора часового типа по поверхности оправки, второй – путем поворота оправки на 180 °.трасса может быть разрешена только в одном направлении. Это должно быть четко указано, например, как «траектория вогнута только в горизонтальной плоскости».
Тесты для оставшихся геометрических проверок описаны в главе 7.
Доктор Г. Шелезинджер в течение многих лет занимался различными испытаниями соосности станков для обеспечения удовлетворительной работы, и им было проделано много новаторской работы по разработке и оценке подходящие тесты. Здесь мы будем иметь дело с новейшими методами, используемыми при проверке центровки машин.
Высокоточный, геометрический и полносистемный метод тестирования адаптивной SRS, продемонстрированный на Gamma Knife® Icon ™
J Radiosurg SBRT. 2019; 6 (2): 121–129.
, PhD, 1 , M.Phil, 1 , MSc, 1 , HNC, 1 и, MSc 1Майкл Никс
1 Онкологический центр Лидса, Сент-Джеймс Университетская больница, Лидс, LS9 7TF, Великобритания
Гэвин Райт
1 Онкологический центр Лидса, Св.Университетская больница Джеймса, Лидс, LS9 7TF, Великобритания
Питер Фаллоус
1 Онкологический центр Лидса, Университетская больница Св. Джеймса, Лидс, LS9 7TF, Великобритания
Уэйн Сайкс
1 Онкологический центр Лидса, St. Университетская больница Джеймса, Лидс, LS9 7TF, Великобритания
Питер Баунс
1 Онкологический центр Лидса, Университетская больница Св. Джеймса, Лидс, LS9 7TF, Великобритания
1 Онкологический центр Лидса, Университетская больница Сент-Джеймс, Лидс, LS9 7TF, UK
Автор, ответственный за переписку.Для корреспонденции: Майклу Никсу, Онкологический центр Лидса, Университетская больница Св. Джеймса, Лидс, LS9 7TF, Великобритания; Электронная почта: [email protected]Поступила в редакцию 29 сентября 2018 г .; Принято 11 декабря 2018 г.
Опубликовано по лицензии издательством OCP Science, членом издательской группы Old City Publishing Group.
Abstract
Новый фантом и метод полносистемного тестирования (FST) были разработаны для демонстрации и обеспечения качества геометрической точности совместной регистрации изображений и общей доставки кадра в контексте SRS с использованием Gamma Knife® Icon ™.В этом методе используются масштабные линейки Вернье для достижения субвоксельной точности измерений совместной регистрации и радиохромные пленки с расположением штифтов для определения общей точности доставки кадра. Проверочные испытания показали, что искусственно примененные ошибки регистрации <0,15 мм могут быть точно обнаружены и количественно определены. Перекрестная проверка результатов тестирования всей системы со стандартным тестом фокусной точности производителя показала, что оба подхода измеряют схожие ошибки фокусной точности с точностью до <0.1 мм, и что компоненты регистрации и фокальной точности геометрической ошибки всей системы могут быть успешно разделены с помощью нашего подхода Vernier FST. Было показано, что ошибки совместной регистрации КЛКТ сопоставимы по величине с ошибками фокусной точности, демонстрируя, что лечение в маске на основе регистрации КЛКТ может достигать субвоксельной геометрической точности, конкурируя с традиционной иммобилизацией на основе кадра. Этот метод геометрического тестирования всей системы и концепция фантомного дизайна в принципе применимы к любой методике SRS, включающей совместную регистрацию изображений.
Ключевые слова: Гамма-нож, Icon, компьютерная томография с коническим лучом, совместная регистрация, полносистемный тест
Введение
Геометрическая точность имеет первостепенное значение в стереотаксической радиохирургии (SRS) и стереотаксической радиотерапии тела (SBRT). Традиционные методы SRS, включающие иммобилизацию черепа на основе рамки, по своей сути позволяют проводить геометрическое тестирование всей системы с помощью пленочного облучения. Однако точное измерение геометрической точности без стереотаксической индексации является сложной задачей, особенно когда регистрация изображения участвует в пути лечения.В частности, для внутричерепной SRS требуется субмиллиметровая геометрическая точность. Существует необходимость продемонстрировать, что такое требование может быть выполнено с использованием современных методов SRS, основанных на использовании нежесткой иммобилизации и совместной регистрации изображений с размером вокселя, превышающим требования геометрической точности. Эти проблемы могут также повлиять на высокоточные методы SBRT (например, спинномозговую SABR), где геометрическая проверка достигается путем сопоставления изображений.
Одним из распространенных способов интракраниальной доставки SRS является установка Gamma Knife® (GK) Co60.Запущенная в 2015 году модель Icon ™ GK (Elekta Instrument AB, Стокгольм, Швеция) представила использование конусно-лучевой КТ (КЛКТ) GK SRS. С помощью калибровки, установленной при установке, встроенная система КЛКТ Icon ™ отображает кубический объем 448 × 448 × 448 вокселей, в которых каждый воксель размером 0,5 × 0,5 × 0,5 мм 3 имеет четко определенные стереотаксические координаты. Стереотаксическая система координат GK, которая используется для определения местоположения изоцентров излучения (так называемых «выстрелов») во время GK SRS, обычно накладывается на томографические изображения при планировании лечения через реперные маркеры, прикрепленные к титановой раме, привинченной к черепу пациента. .Помимо определения стереотаксической системы координат, эта титановая рама также обеспечивает жесткую иммобилизацию пациента для обеспечения точно воспроизводимой установки пациента.
В качестве альтернативы использованию реперных маркеров стереотаксическая система КЛКТ от Icon ™ предлагает возможность наложить необходимую стереотаксическую систему координат на изображения для планирования лечения посредством совместной регистрации. Используя Icon ™, изображения для планирования лечения (обычно МРТ) могут быть зарегистрированы совместно с эталонным исследованием КЛКТ, полученным во время планирования.Без необходимости в реперных маркерах и рамке для определения стереотаксической системы координат, Icon ™, таким образом, впервые позволяет выполнять GK SRS без рамки, используя иммобилизацию на основе термопластической маски. В свою очередь, иммобилизация на основе маски предлагает практическое решение для фракционированного GK SRS и большую степень гибкости рабочего процесса.
Сдвиг парадигмы в сторону подхода на основе фракционированной маски, который предлагает Icon ™, тем не менее, представляет собой потерю уверенности в воспроизводимости настроек пациента, которая хорошо зарекомендовала себя при использовании традиционного подхода на основе кадров.Чтобы решить проблему межфракционных изменений, присущих иммобилизации на основе маски, Icon ™ дополнительно использует встроенную стереотаксическую систему КЛКТ. Выполняя КЛКТ перед лечением непосредственно перед доставкой каждой фракции и последовательно регистрируя каждое сканирование перед лечением относительно эталонной КЛКТ, полученной во время планирования, Icon ™ может автоматически корректировать любые межфракционные вариации в настройке. . Жесткие переводы и повороты совместной регистрации применяются к запланированным координатам выстрела, таким образом создавая адаптированный план лечения, состоящий из снимков, местоположения которых смещены относительно стереотаксической системы отсчета, чтобы они сохраняли свои запланированные положения относительно анатомической основы. Рамка.Таким образом, этот автоматически адаптированный план лечения поддерживает доставку дозы в смещенный целевой объем.
Геометрическая точность и, следовательно, безопасность рабочего процесса адаптивного лечения Icon ™ в решающей степени зависят от точности жесткой совместной регистрации каждой КЛКТ перед лечением по сравнению с эталонной КЛКТ. Эта жесткая совместная регистрация выполняется автоматически в связанной системе планирования лечения GK, Leksell GammaPlan (LGP) (Elekta Instruments AB, Стокгольм, Швеция), с помощью числового оптимизатора моделирования отжига, направленного на максимизацию метрики взаимного сходства информации 1 .Это геометрическая точность процесса адаптивного проведения лечения Icon ™, о котором идет речь в текущем исследовании. Авторы представляют новый фантом и инструмент для выполнения сквозного теста геометрической точности адаптивно доставленных радиационных выстрелов, а также для оценки точности самих трансляций и вращений совместной регистрации КЛКТ, о которых сообщается LGP. Представленные инструмент и фантом призваны дать пользователю Icon ™ уверенность в том, что новый рабочий процесс на основе адаптивной маски, включенный в Icon ™, может поддерживать геометрическую точность, хорошо известную с традиционной техникой, основанной на кадрах.
Предпосылки
Идеальный фантом для тестирования всей системы (FST) для GK-Icon ™ оценил бы дозиметрическую и геометрическую точность доставки выстрела. Для этого радиометрическую пленку необходимо поместить в строго определенное место и подвергнуть лечебному облучению. Дозиметрическую точность можно установить путем тщательной калибровки пленки в соответствии с общепринятыми методами 2,3 . Для ГК SRS на базе кадра геометрическая точность доставки излучения зависит от позиционной точности движения кушетки относительно фокуса излучения.Так называемая «фокусная точность» проверяется отдельно от других факторов с помощью поставляемого производителем инструмента для точного фокусирования, который позволяет размещать пленку с четко определенной стереотаксической координатой, местоположение которой отмечается через отверстие, пробитое на пленке с помощью булавка. Экспонируя две пленки в ортогональных плоскостях, можно проверить трехмерную геометрическую точность. Процедуры на основе масок подвержены двум дополнительным источникам ошибок. Во-первых, в отличие от жесткого каркаса, маска не устраняет внутрифракционное движение; с этой целью Icon ™ обеспечивает доставку излучения на основе стереоскопической камеры, которая отслеживает движения пациента во время лечения 4 .Во-вторых, и предметом беспокойства в текущей работе является ошибка в координатах выстрела адаптированного плана, которая распространяется от неопределенности в совместной регистрации КЛКТ-сканирования до лечения до стереотаксического эталонного КЛКТ-сканирования.
Следовательно, существует необходимость в надежной методологии тестирования, чтобы продемонстрировать и гарантировать, что общая геометрическая точность обработки с использованием маски Icon ™ сравнима с традиционной стереотаксической техникой кадра. С этой целью был разработан инструмент для полного тестирования системы, который вставляется в коммерчески доступный фантом антропоморфной головы RANDO® (The Phantom Laboratory, Нью-Йорк, США), а также инструмент программного анализа, который обеспечивает общую геометрическую точность доставляемый импульс излучения должен быть оценен с точки зрения ошибки регистрации КЛКТ и ошибки точности фокусировки.
Наш инструмент FST предназначен для непосредственного измерения остаточной ошибки регистрации после регистрации жесткого изображения (RIR) данных предварительной обработки и стереотаксических эталонных данных КЛКТ с использованием физических шкал Вернье. Первоначально разработанные в качестве навигационного средства для точного измерения углов, эти шкалы долгое время использовались для измерения расстояний с большей точностью, чем позволяет единое правило, чаще всего в физических штангенциркулях или микрометрах. Поскольку две одинаковые шкалы с немного разным шагом перемещаются относительно друг друга, разрешающая способность измерения определяется разницей в шаге шкалы, а не самим шагом.В нашей реализации две масштабные линейки, составляющие каждую меру Вернье, физически фиксированы относительно друг друга. Способность одного столбца «перемещаться» относительно другого является результатом только свободы КЛКТ-изображения перед обработкой перемещаться по эталонному изображению во время регистрации изображения. Путем наложения зарегистрированных изображений таким образом, чтобы одна сторона шкалы Нони происходила из эталонного изображения, а другая сторона – из изображения до обработки, можно измерить ошибки регистрации порядка разрешения Нониуса.В случае идеального совмещения два изображения идеально выровняли бы центральную пару полосок каждой шкалы Нони, что привело бы к нулевой ошибке измерения.
Материалы и методы
Модель фантома
Инструмент предназначен для прямой замены одного среза толщиной 2,5 см (срез 2) коммерчески доступного фантома антропоморфной головы RANDO®, чтобы обеспечить максимально реалистичный сценарий регистрации изображения для ФСТ. Фантомная вставка изготовлена из ПММА и включает два держателя пленки с маркерами в осевой и корональной плоскостях соответственно.Плоскости пленки и расположение штифтов могут быть идентифицированы на КЛКТ для определения положений лечебных снимков. Осевая прорезь для пленки может вместить 16-миллиметровый выстрел, в то время как корональная прорезь ограничена 8-миллиметровым выстрелом из-за необходимости использования инструмента для замены 2,5-сантиметрового среза фантома RANDO®. Из этих двух ортогональных пленок измерение фактических центров выстрелов относительно центров, отмеченных точечными отверстиями, позволяет количественно оценить геометрические ошибки во всех трех направлениях.
Для оценки совмещения изображения на субвоксельной шкале восемь шкал Вернье (четыре в аксиальной плоскости и четыре перпендикулярно ей) с парами металлических стержней устанавливаются в фантом в четко определенных положениях (), а также шарикоподшипник для определения геометрического центра массива Вернье.Эти шкалы используются для определения ошибки жесткой регистрации с 6 степенями свободы (DoF), выполняемой как часть процесса планирования до субвоксельной точности. Масштабные линейки в каждом блоке Вернье () расположены на расстоянии 1,0 и 1,1 мм с каждой стороны блока. В отличие от физической шкалы Вернье, где две стороны движутся независимо, две шкалы находятся в фиксированном относительном положении с выровненными центральными парами полос. При просмотре наложенного изображения КЛКТ перед обработкой после регистрации на эталонной КЛКТ с наложением изображения перед обработкой, показывающим более короткую сторону блока Вернье (), любую ошибку совмещения можно измерить как видимое смещение положения пары стержней с наилучшим выравниванием.Поскольку расстояние между каждой парой стержней смещено на 0,1 мм, и на практике можно определить, что две соседние пары стержней одинаково хорошо выровнены, предел разрешения каждой осевой шкалы нониуса составляет 0,05 мм. Из-за размера вокселя Icon ™ КЛКТ 0,5 * 0,5 * 0,5 мм масштабные линейки размещаются под углом 45 o к сетке вокселей, используя эффект частичного объема, так что смещения субвокселей легче визуализировать. Из-за ограниченного пространства в фантомном срезе вертикальные масштабные линейки имеют меньше пар полос с интервалом 1.0 и 1,2 мм, что дает теоретический предел разрешения 0,1 мм. Чтение таких ошибок требует, чтобы два набора изображений были соответствующим образом наложены и ориентированы. Внутреннее программное обеспечение для анализа (Matlab 2015b) позволяет наложить эталонные и пострегистрационные изображения в общую систему отсчета, используя регистрацию, полученную из LGP. Прямая визуализация каждой шкалы Нониус в наложении позволяет визуализировать ошибки в каждой точке измерения.
a) Фантомное изображение, показывающее положение шкалы Нониуса (все размеры в мм) и расположение прорезей для пленки.б) Фотография фантома в том виде, в котором он был изготовлен.
a) Деталь дизайна масштабной линейки Вернье. Металлические стержни (черные) точно вставляли в блок подложки из полиметилметакрилата (серый), который затем вставляли в прорезь на фантоме (). б) Фотография изготовленного блока шкалы Вернье.
Анализ ошибки регистрации по шкале Вернье. Движущееся изображение (синее) накладывается на эталонное изображение (оттенки серого), и пары столбиков Вернье выравниваются по шести парам от центральной пары, что указывает на 0.Смещение 6 мм вдоль направления масштабной линейки в этом месте из-за несовпадения.
Каждая масштабная линейка обеспечивает измерение геометрической погрешности на определенной оси в определенном месте. В принципе, шести таких измерений должно быть достаточно, чтобы определить жесткие (6 степеней свободы поступательного и вращательного движения) ошибки регистрации относительно центра вращения. Однако в идеале эти точки измерения должны быть распределены на равном расстоянии от точки измерения по всем трем декартовым осям. Поскольку «срезанная» конструкция фантома не может приспособиться к такому расположению, вертикальные стержни Вернье имеют более низкое разрешение, чем осевые стержни, и не могут быть размещены в идеальных местах.Поэтому мы измеряем четыре вертикальные ошибки для избыточности и повышения чувствительности к небольшим поворотам вне плоскости.
Методология анализа
Восемь измеренных ошибок и номинальные координаты шкал Вернье используются в качестве входных данных для обычного анализа Прокруста 5 . Этот анализ направлен на поиск оптимального вектора сдвига и матрицы вращения для выравнивания двух наборов точек, в данном случае номинальных и измеренных координат выровненных пар стержней Вернье.
В каждой из четырех точек измерения показания горизонтальной и вертикальной шкалы нониуса объединяются, что дает трехмерные ошибки. Эти смещения точек используются для определения координат Прокруста и, следовательно, расстояния Прокруста между эталонным и совместно зарегистрированным наборами изображений. Оптимальное преобразование для полного выравнивания наборов точек восстанавливается с помощью частичного «обычного анализа Прокруста» 5 , в котором масштабирование не допускается. Поступательные смещения сначала удаляются путем выравнивания центроидов облака точек, сводя проблему к ограниченной ортогональной проблеме Прокруста, решаемой алгоритмом Кабша 6 .Здесь используется итеративная реализация, после Umeyama 7 .
В контексте текущей работы этот анализ Прокруста дает оценку основных поступательных и вращательных компонентов ошибки RIR в системе отсчета центрального шарикоподшипника фантома.
Фактическое положение центра каждой шкалы Вернье (пересечение пары центральных стержней) относительно эталонного центра шарикоподшипника было определено с помощью компьютерной томографии с высоким разрешением и оказалось в пределах 0.1 мм проектного положения во всех случаях.
Координаты вокселей центрального шарикоподшипника были измерены на эталонном изображении, установленном в LGP. Они были преобразованы в местоположения в стереотаксическом пространстве через внутреннюю взаимосвязь между CBCT и стереотаксической (STX) системой отсчета, как определено при установке машины (находится в файлах установки LGP). Номинальные местоположения Вернье были преобразованы в координаты STX таким же образом. С этого момента все расчеты проводились в физических единицах (мм, градусах) и стереотаксическом пространстве с поворотами вокруг центральной точки (100, 100, 100) мм.
Измерения по шкале Вернье представляют собой смещение эталонного и совместно зарегистрированного наборов изображений с помощью 4 измерений в плоскости X-Y и 4 измерений по оси Z. Эти измеренные данные используются вместе с известными местоположениями центров шкалы Вернье на эталонном изображении для получения координат центров шкалы Вернье на совместно зарегистрированном изображении относительно исходной точки, определенной на центральном шарикоподшипнике. Эти точки представляют собой «движущийся» набор с известными опорными точками как «фиксированный» набор.Таким образом, каждый набор точек представлен в виде матрицы 4 × 3, которая является входными данными для анализа Прокруста, описанного выше.
Согласно методу Обычного Прокруста, смещения определялись как среднее значение смещений по каждой оси. Поскольку плоскостные шкалы Вернье лежат под углом 45 o к декартовой оси, эти средние ошибки лежат в направлениях X + Y и X-Y (). Эти ошибки преобразуются матрицей вращения 45 o 2 × 2 для нахождения ошибок перевода по декартовым осям X (слева направо) и Y (передне-заднее).Ошибка оси Z (верхняя-нижняя) измерялась непосредственно по среднему наблюдаемому смещению в верхнем-нижнем направлении.
После того, как эти средние погрешности перевода были установлены, они были вычтены из координат STX местоположений центров Вернье, удалив трансляционный компонент и совместив эталонные и пострегистрационные изображения в эталонной точке STX (100,100,100) мм. Любые остаточные ошибки не могут быть исправлены переводом и должны возникать в результате вращения в случае жесткой регистрации.Нахождение оптимальной матрицы вращения (определитель = 1) соответствует ортогональной задаче Прокруста с ограничениями. Хотя существуют аналитические подходы, такие как алгоритм Кабша 6 , здесь элементы матрицы вращения оптимизировались итеративно посредством минимизации остаточной ошибки 7 методом наименьших квадратов. Благодаря ортогональности и симметрии матрицы вращения, три независимых вращения (вокруг осей измерения X + Y, X-Y и Z) могут быть оптимизированы одновременно. Эта оптимизация сводит к минимуму остаточную ошибку (с поправкой на пост-трансляцию) повернутых координат выровненной пары стержней Вернье относительно их номинальных координат STX.Опять же, вращения вокруг осей X + Y и X-Y преобразуются в декартовы вращения с помощью стандартной матрицы вращения 45 o 2 × 2.
Если восемь измеренных ошибок могут быть представлены как чистое перемещение и вращение, остаточная ошибка RMS должна быть строго равна нулю. На практике небольшие ненулевые остатки являются результатом ограниченного разрешения измерения, что подразумевает малые масштабные или сдвиговые составляющие. Хотя в принципе они могут быть представлены в полностью аффинной регистрации, фантом является физически жестким, и регистрация не содержит таких степеней свободы, поэтому эти (обычно очень маленькие) дополнительные термины не имеют физического значения.
Проверка инструмента точности регистрации
Работоспособность тестового фантома оценивалась в первую очередь путем внесения известных искусственных ошибок в референсную регистрацию. Из-за ожидаемого предела разрешения 0,1 мм в плоскости и 0,2 мм вне плоскости, погрешности перевода 0,15 мм и 0,3 мм применялись в плоскости, а погрешности 0,2 и 0,4 мм применялись вне плоскости. Прикладные ошибки вращения составляли 0,15 / 0,3 и 0,2 / 0,4 градуса по плоскости и вне плоскости соответственно. Известные ошибки применялись как по отдельности, так и в сочетании.Таким образом, восстановление ошибок в каждой глубине резкости было тщательно протестировано, чтобы гарантировать точное воспроизведение геометрических ошибок.
После этой первоначальной проверки шесть наборов случайно сгенерированных ошибок регистрации (величины ошибок 0-0,5 мм и 0-0,5 градуса) были применены к контрольным данным и измерены с использованием инструмента и алгоритма анализа. В связи с необходимостью оценки шкал Вернье человеком, также оценивалась изменчивость анализа между наблюдателями (4 наблюдателя).Таким образом, средние ошибки измерения и их стандартные отклонения были измерены для каждой глубины резкости.
FST в сравнении с тестом на точность фокусировки
Контрольные КЛКТ для планирования и предварительной обработки были получены путем настройки и сканирования фантома, применения небольшого возмущения к положению установки и повторного сканирования перед доставкой снимка. Планирование было выполнено на начальной КЛКТ с выстрелами по центру обоих маркеров. КЛКТ после возмущения жестко регистрировали в КЛКТ планирования (LGP) и преобразовании регистрации (T), извлеченном из выходного файла LGP.Впоследствии оба набора данных КЛКТ были наложены с использованием преобразования, полученного из LGP, и оценены на предмет ошибок регистрации, как описано выше. В соответствии со стандартным рабочим процессом Icon ™ с иммобилизованной маской, план лечения был автоматически адаптирован LGP на основе результата регистрации и проведенного лечения. Общие ошибки поступательного движения в доставленной дозе определялись по положениям центра выстрела, измеренным на вставках из радиохромной пленки, и вычитались измеренные ошибки регистрации (включая поправки на вращение).Остаточные ошибки, которые должны соответствовать ошибке позиционирования кушетки, сравнивались с ошибкой кушетки, определенной в ходе отдельного теста на точность фокусировки GK Icon ™, указанного производителем, который проводился сразу после FST. В каждом случае местоположения центров выстрелов определялись по радиохромной пленке путем сканирования (300 dpi), установления порога на уровне 80% от максимальной интенсивности выстрела и центроида с использованием функции «Анализ частиц» в пакете анализа биологических изображений FIJI 8 .Центры точечных отверстий определялись визуальным осмотром отсканированного изображения пленки.
Результаты
Проверка инструмента точности совмещения
Все примененные ошибки были исправлены на соответствующей оси и с правильным знаком. 94% восстановленных величин погрешности находились в пределах 0,1 мм и 0,1 град от примененного значения (максимальное отклонение 0,17 мм).
Оценка случайно сгенерированных ошибок показала средние невязки <0,02 мм и <0,02 град, за исключением случаев вращения осей X и Y, которые показали остаточные ошибки 0.06 и +0,07 град. Соответственно. Средние остаточные ошибки и стандартные отклонения (представляющие вариации между наблюдениями) показаны на.
Таблица 1
Средние остаточные ошибки регистрации после вычитания прикладных ошибок из измеренных ошибок для диапазона случайно сгенерированных сценариев неправильной регистрации до и после исправления систематической производственной ошибки (см. Текст и рис. 4)
Степень свободы Средняя остаточная ошибка (sd) Систематическая ошибка, вызванная производством Средняя остаточная ошибка после исправления X / мм 0.01 (0,09) 0,00 0,01 Y / мм 0,00 (0,08) 0,00 0,00 Z / мм 0,01 0,02 -0,01 X Rot / град. -0,06 (0,02) -0,07 0,01 Y Rot / град. 0.02 Z Rot / град. 0,00 (0,03) 0,00 0,00
Вращение по оси X и Y показало большие средние ошибки, предполагающие систематическое смещение. При проверке правильного совмещения пар стержней внутри фантома было обнаружено, что вертикальная шкала в позиции 4 незначительно смещена (), так что шкала показывает +0,2 мм даже при идеальном совмещении. Меньшее смещение 0,1 мм было обнаружено на вертикальной шкале в позиции 1.В совокупности эти производственные неточности приводят к очевидной ошибке регистрации при перемещении по оси Z, повороте по оси X и повороте по оси Y, как показано на рис.
На одной вертикально выровненной шкале Вернье смещение 0,3 мм было заметно только на фиксированном изображении из-за небольшой производственной неточности. Шкала выравнивается по позиции между 7-й и 8-й парами столбцов (красная стрелка), а не между 6-й (центральной) парой столбцов (желтые линии). Это привело к систематической ошибке во всех степенях свободы, которая была идентифицирована и удалена из представленных результатов (см. Текст и)
Исправление измеренных данных для этих систематических производственных ошибок дает распределение остаточных ошибок, показанное в ошибки <0.1 мм и <0,1 град. Примечательно, что перемещение по оси X, перемещение по оси Y и вращение оси Y показывают большие стандартные отклонения, чем другие степени свободы.
Распределение остаточных ошибок после вычитания приложенных ошибок из измеренных ошибок. Распределения были получены путем взаимного сравнения 4 наблюдателей на основе 6 случайно сгенерированных синтетических ошибок регистрации. а) поступательные и б) вращательные остатки до исправления систематической неточности производства. в) поступательные и г) угловые остатки после систематической коррекции.
FST в сравнении с тестом на точность фокусировки
Ошибки позиционирования кушетки, полученные из двух независимых FST (после исправления ошибок регистрации), сравнивались с ошибками положения кушетки по результатам теста точности фокусировки (FPT), выполненного сразу после второго FST (). Все средние ошибки, полученные с помощью FST, были в пределах 0,1 мм от результатов FPT производителя. Общие ошибки FST были чрезвычайно малы в направлениях X и Y из-за отмены кушетки и ошибок регистрации. В направлении Z большая общая ошибка возникла в результате суммирования ошибок регистрации и позиционирования кушетки.Общие погрешности и ошибки позиционирования кушетки, полученные от фантома FST и непосредственно измеренные с помощью FPT, во всех случаях оказались в пределах допуска 0,3 мм, указанного Elekta.
Таблица 2
Среднее значение Общие, регистрационные и остаточные трансляционные ошибки полного теста системы (FST), измеренные на практике, с ошибками теста фокусной точности (FPT) и разницей между геометрическими ошибками, определенными с помощью методов FST и FPT.
Ось | Общая ошибка FST / мм | Ошибка регистрации FST / мм | Геометрическая ошибка FST / мм | Геометрическая ошибка FPT / мм | Ошибка разницы FST-FPT / мм | -0.013 | -0,023 | 0,011 | 0,025 | -0,015 |
Y | 0,013 | -0,106 | 0,119 | 0,051 | 0,068 | |
0,140 | -0,005 | |||||
dr | 0,242 | 0,152 | 0,180 | 0,151 | 0,070 |
Phaussion жесткое обсуждение описанной здесь возможности
9000nt2 для точного определения подгруппы Ошибки в КЛКТ демонстрируются небольшими средними остаточными ошибками и узкими стандартными отклонениями, полученными в результате анализа с участием нескольких наблюдателей.После учета производственных дефектов средние остаточные ошибки очень близки к нулю, что указывает на отсутствие систематических факторов. Точность обнаружения ошибок регистрации ограничена способностью наблюдателя идентифицировать совпадающую пару столбцов, где соседние пары, по-видимому, имеют одинаковое качество совпадения. Со временем можно использовать визуальную интерполяцию, чтобы найти центральное положение совпадения с более высокой точностью, чем позволяет номинальное расстояние между парами стержней.Все отдельные прикладные ошибки регистрации были исправлены с точностью до <0.2 мм и <0,2 градуса от их номинальных значений, что указывает на надежную работу субвокселей. Эта субвоксельная точность подтверждает результаты исследования, в котором сравниваются точно известные сдвиги, применяемые к тестируемому объекту, с перемещениями и поворотами при совместной регистрации от LGP, в котором сообщается о согласовании в пределах 0,2 градуса и 0,1 мм 9 . Дальнейшее исследование с использованием изменения координат ориентиров для оценки точности совместной регистрации Icon TM CBCT-to-CBCT аналогичным образом сообщает о средней ошибке (стандартное отклонение), равной 0.2 (0,1) мм 10 . Более поздняя работа Chung et. al. сообщает о несколько большей ошибке тестирования всей системы (0,5 ± 0,6 мм) из 3 тестов 11 . Несмотря на то, что мы сообщаем о меньшей погрешности в 0,24 мм по результатам двух испытаний, учитывая небольшие размеры выборки и ожидаемые межмашинные механические отклонения, мы считаем эти результаты согласованными. Кроме того, они сопоставимы с таковыми Sarfehnia et. al. 9 , которые сообщают о максимальной погрешности 0,27 мм по результатам четырех сквозных испытаний.
После исправления неточностей базового производства, средние ошибки наблюдателей были <0.02 мм и <0,02 градуса, демонстрируя возможности метода шкалы Вернье для точного обнаружения геометрического смещения, где бы оно ни возникло. Различия между наблюдателями (4 наблюдателя) при измерении, количественно оцененные с помощью стандартного отклонения остаточных ошибок, показали, что повороты по осям X (LR) и Z (AP) (sd 0,03 градуса) вместе с перемещениями оси Z (SI) (sd 0,03 мм) ) были восстановлены с более высокой точностью, чем вращения оси Y (sd 0,08 градуса) и перемещения оси X или Y (sd 0,08 и 0.06 мм соответственно).
Из-за конструкции фантома перемещение оси Z измеряется с помощью шкалы с более низким разрешением 0,2 мм, установленной вдоль кранио-каудальной оси. Однако точность этого измерения не ухудшается из-за возможности присвоения промежуточного значения, когда две пары полосок совпадают одинаково хорошо. Фактически, наличие четырех масштабных полос на этой оси обеспечивает более высокую точность измерения, чем для перемещений осей X и Y, каждый из которых измеряется с помощью двух плоскостных шкал Вернье с 0.Номинальное разрешение 1 мм. В то время как в принципе визуальная интерполяция допускает точность 0,05 мм с этими масштабами, обеспечивая точность, аналогичную той, которая наблюдается при перемещении по оси Z, на практике сетка вокселей слишком грубая, чтобы допускать такую интерполяцию. Следовательно, точность перемещения по осям X и Y примерно вдвое выше, чем при перемещении по оси Z.
Точность вращения также зависит от оси из-за конструкции фантома. На всех трех осях доступны четыре масштабных линейки для измерения углового перекоса.Однако в случае ошибок оси Y (A-P) расстояние от центральной оси до точки измерения составляет 35 мм по сравнению с 65 мм и 74 мм для вращения осей X и Z. Это увеличивает неопределенность вращения оси Y даже при фиксированной точности измерения на каждой шкале масштаба. Уменьшение расстояния в этом измерении является результатом формы головы человека, которую этот тестовый объект предназначен для приближения.
Способность этого подхода к фантому и анализу позволяет проводить субвоксельный анализ регистрации изображений как часть полного системного тестирования GK Icon ™.В сочетании с геометрически и дозиметрически точными пленочными измерениями в известных местах этот тип фантома должен повысить уверенность в способности КЛКТ и регистрации изображений обеспечивать высокоточное лечение в отсутствие традиционной инвазивной стереотаксической иммобилизации. Это, в свою очередь, открывает путь к многофракционному SRS с точностью обычных однофракционных обработок.
Сравнение полученных ошибок положения кушетки (FST) и измерений FPT показало, что тестовый объект смог отделить ошибку регистрации от общей ошибки и что остаточная ошибка была очень похожа на ошибку, полученную в результате теста позиционирования кушетки FPT.Поэтому кажется разумным сделать вывод, что полная системная ошибка имеет два важных компонента (регистрация и позиционирование кушетки), которые точно и точно измеряются до субвоксельных масштабов с помощью описанного фантома FST. Кроме того, было обнаружено, что общие ошибки, включая регистрацию, находятся в пределах допустимых отклонений, рекомендованных производителем.
Этот фантом позволяет однозначно продемонстрировать, что точность регистрации, достигаемая на практике с помощью GK Icon ™, находится в масштабе, значительно меньшем, чем у вокселей визуализации КЛКТ, без ошибок больше 0.Точность 1 мм / 0,1 градуса инструмента FST. Таким образом, учитывая уже продемонстрированную высокую точность 1,9 для системы внутрифракционного обнаружения движения IFMM, ожидается, что точность адаптивной доставки GK на основе маски с использованием Icon ™ будет сравнима с традиционной доставкой G-кадра. был оптимизирован и продемонстрирован для конкретного случая Gamma Knife® Icon ™, аналогичный подход с модифицированным фантомом может найти применение при вводе в эксплуатацию и обеспечении качества других методов SBRT, требующих высокой геометрической точности.В настройке SBRT потребуется дополнительная проверка.
Выводы
Точность стереотаксической радиохирургии на основе маски на основе КЛКТ с использованием GK Icon ™ была подтверждена с использованием нового полностью системного тестового объекта, встроенного в антропоморфный фантом головы RANDO®. Использование физических шкал Вернье для точности регистрации позволяет измерять ошибки регистрации с субвоксельной точностью. Продемонстрирована способность этого метода восстанавливать случайно сгенерированные искусственные ошибки регистрации с правильным направлением, знаком и величиной.
В сочетании с точно расположенными радиохромными пленками этот анализ ошибок совмещения позволяет разделить геометрические ошибки совмещения и механические (движение кушетки). Ошибки регистрации обычно составляют <0,2 мм и 0,2 градуса после автоматического RIR в LGP. Ошибки позиционирования кушетки, которые суммируются с ошибками регистрации в квадратуре, оказались аналогичной величины. Следовательно, потеря точности из-за межфракционного движения, связанного с переходом от кадра к лечению на основе маски, вероятно, будет порядка 0.1 мм и 0,1 градуса на степень свободы. Однако следует отметить, что движение пациента внутри фракции может также ухудшить точность лечения на основе маски по сравнению с традиционными методами на основе кадров. Учитывая продемонстрированный уровень субвоксельной точности, наряду с удобным инструментом FST для проверки регистрации, позиционирования кушетки и выполнения выстрела, возможна повышенная уверенность в геометрической и, следовательно, дозиметрической точности стереотаксической обработки на основе маски. Продемонстрированный здесь подход к высокоточной проверке совпадения изображений может быть распространен на другие стереотаксические методы (на основе линейного ускорителя) с соответствующими модификациями.
Благодарности
Раскрытие авторами потенциальных конфликтов интересов
Гэвин Райт сообщает о посещаемости собраний группы пользователей первых пользователей Icon и встреч, организованных и проводимых компанией Elekta, а также о предоставлении консультационных услуг компании Elekta, для которых его отдел имеет получил гонорар. Всем остальным авторам нечего раскрывать.
ПредоставленоВклад авторов
Концепция и дизайн: Майкл Никс, Гэвин Райт, Уэйн Сайкс, Питер БоунсСбор данных: Майкл Никс, Гэвин Райт, Питер Фаллоуз
Анализ и интерпретация данных: Майкл Никс, Гэвин Райт
Написание рукописи: Майкл Никс, Гэвин Райт
Окончательное утверждение рукописи: Майкл Никс, Гэвин Райт, Питер Фаллоуз, Уэйн Сайкс, Питер Баунс
Ссылки
1.Стадхольм К., Хилл Д., Хоукс Д. Инвариантная перекрывающаяся мера энтропии совмещения трехмерных медицинских изображений. Распознавание образов. 1999; 32 (1): 71–86 [Google Scholar] 2. Мик А., Льюис Д. Ф., Ю. X. Многоканальная пленочная дозиметрия с коррекцией неоднородности. Медицинская физика 2011; 38: 2523-2534; doi: 10.1118 / 1.3576105 [PubMed] [CrossRef] [Google Scholar] 3. ван Хоф С.Дж., Грантон П.В., Ландри Г., Подеста М., Верхаеген Ф. Оценка новой процедуры трехканального радиохромного анализа пленки с использованием EBT2. Phys. Med.Биол. 2012; 57: 4353–4368; DOI: 10.1088 / 0031-9155 / 57/13/4353 [PubMed] [CrossRef] [Google Scholar] 4. Райт Г., Харролд Н., Хэтфилд П., Боунс П. Обоснованность использования движения кончика носа в качестве заменителя внутричерепного движения в безрамной терапии Gamma Knife® Icon ™ с фиксацией маски, Jour. радиохирургии и SBRT 2017; 4 (4): 289-301 [Бесплатная статья PMC] [PubMed] [Google Scholar] 5. Schönemann PH. Обобщенное решение проблемы ортогональных прокрастов. Психометрика. 1966; 31 (1): 1-10. doi: 10.1007 / BF02289451 [CrossRef] [Google Scholar] 6.Кабш В. Решение для наилучшего вращения для связи двух наборов векторов. Acta Crystallogr Sect A. 1976; 32 (5): 922-923. DOI: 10.1107 / S0567739476001873 [CrossRef] [Google Scholar] 7. Умэяма С. Оценка параметров преобразования между двумя точечными шаблонами методом наименьших квадратов. IEEE Trans Pattern Anal Mach Intell. 1991; 13 (4): 376-380. DOI: 10.1109 / 34.88573 [CrossRef] [Google Scholar] 8. Schindelin J, Arganda-Carreras I, Frize E, et al. Фиджи: платформа с открытым исходным кодом для анализа биологических изображений. Нат методы.2012; 9 (7): 676-682. doi: 10.1038 / nmeth.2019 [Бесплатная статья PMC] [PubMed] [CrossRef] [Google Scholar] 9. Сарфехния А., Рушин М., Чу Б., Йебоа К., Беккер Н., Чо Ю. Б., Ли Ю. Характеристика характеристик интегрированной системы компьютерной томографии с коническим лучом для специализированной гамма-радиохирургии. Med Phys. 2018; 29. DOI: 10.1002 / mp.13073. [Epub перед печатью] [PubMed] [CrossRef] [Google Scholar] 10. Чунг Х.Т., Ким Дж.Х., Ким Дж.В., Пэк С.Х., Ким Д.Г., Чун К.Дж., Ким Т.Х., Ким Ю.К. Оценка точности совмещения изображений при безрамной хирургии гамма-ножом.PLoS One. 2018; 13 (3): e0193809. doi: 10.1371 / journal.pone.0193809 .. eCollection 2018. [Бесплатная статья PMC] [PubMed] [CrossRef] [Google Scholar] 11. Чунг Х.Т., Пак В., Тэ Х.К., Йонг К.К., Чун К.Дж. Оценка точности и стабильности радиохирургии безрамным гамма-ножом. J Appl Clin Med Phys. 2018. июль; 19 (4): 148-154. doi: 10.1002 / acm2.12365 .. [Бесплатная статья PMC] [PubMed] [CrossRef] [Google Scholar]Как проверить точность обработки на станке
Измерительные щупы обеспечивают дополнительную поддержку в достижении своевременности, высокого качества и стоимости -эффективное производство, чем просто наладка детали, а это означает, что проверка геометрической точности обрабатываемых деталей непосредственно на станке не менее ценна.
Благодаря этой прямой проверке точности могут быть быстро обнаружены ошибки программирования и дефекты инструмента, а также неблагоприятные последствия процесса обработки.
Однако такие методы контроля часто не используются из-за сложности программирования или отсутствия доверия к точности станка.
В то время как базовая точность станка является важным условием для обработки прецизионных деталей.
Следовательно, машину следует периодически проверять (пересматривать) по геометрическим параметрам, например, по лазерному интерферометру.,
Для таких мер компания Renishaw рекомендует систему лазерного интерферометра ML10 GoldStandard.
Кроме того, для проверки следует периодически использовать круговые калибры QC10.
Таким образом, последующее измерение на станке также создает условия для управления процессом.
Измерение на координатно-измерительной машине показывает только, была ли обработана деталь в соответствии с требованиями.
Невозможно различить эффекты, производимые станком, инструментом и процессом.
Если для детали измеряются отклонения при обработке, то определить действительную причину отклонения трудно.
Следовательно, соответствующие или необходимые корректирующие меры не могут быть надежно получены на основе результатов таких измерений.
Измерительные задачи на станкахСуществует четыре основных требования к пользователю для выполнения измерительных задач на станках:
(1) Это просто наладка или наладка заготовки.
(2) Он выполняет ряд случайных задач измерения на основе чертежей, где цикл измерения интегрирован в поток программы, управляет процессом на основе результатов измерения и просто выводит результаты измерения.
(3) Все измерительные задачи напрямую и полностью интегрированы с программой обработки, обработка контролируется в соответствии с результатами измерений, программа подготовлена в соответствии с данными САПР, проверка столкновений выполняется посредством графического моделирования, а измерение результаты выводятся в виде таблиц.
(4) После обработки геометрическая точность детали проверяется, программируется в соответствии с данными САПР, проверяется столкновение с помощью графического моделирования, измеренные значения статистически, аналитически и обрабатываются, а результаты выражаются и анализируются в виде таблиц. и графики.
Таким образом, измерительные техники компании Renishaw предлагают несколько пакетов, разработанных для удовлетворения различных требований.
Если пользователь хочет только установить деталь и измерить инструмент, то следует использовать широко популярный пакет измерения цикла для управления.
С помощью этого пакета можно легко и удобно запрограммировать наладку детали и измерение инструмента.
Контроль точности вместо простой проверки точностиВ Renishaw производительность семейства программного обеспечения может не зависеть от используемой системы управления машиной.
А благодаря поддержке графического взаимодействия очень просто запрограммировать все измерительные программы фрезерного станка.
ActiveEditor и ActiveEditorPro используются для включения всех программ измерения деталей и инструментов в программу обработки с вводом дополнительных данных САПР при программировании программы.
Таким образом, эти программы могут быть адаптированы к процессу путем прямой обратной связи по результатам измерений.
Это позволяет не только корректировать систему координат станка и данные инструмента, но также до определенной степени автоматически реализовывать логические решения на основе этих данных без необходимости распознавать инструкции, необходимые для управления.
Таким образом, простая и иерархическая структура правил также позволяет пользователю использовать специальные команды ЧПУ без необходимости детального знания структуры программы.
Для этой цели интерфейс оператора предоставляет подходящие предварительно определенные значения и проверяет, были ли реализованы все абсолютно необходимые вводы.
Программа и инструкции для выбранного элемента управления генерируются только в результате работы постпроцессора.
В результате отдельные параметры могут быть точно отрегулированы, как если бы они были обращены вспять при резком изменении графика обработки станка.
Благодаря входу CAD ActiveEditorPro, он не только упрощает программирование, но также позволяет получить полное представление измеренного движения и моделирование измерений, включая проверку столкновений.
Это моделирование также учитывает зажимной инструмент.
После обработки для проверки образца непосредственно на станке. При проверке сложных или крупных деталей компания Renishaw разработала программное обеспечение Renishaw OMV в сотрудничестве с экспертами по CAD / CAM в Delcam UK.
При нажатии на элементы и поверхности введенной модели детали САПР программное обеспечение OMV генерирует необходимую программу измерения.
Например, ActiveEditor предоставляет заранее определенные значения, подходящие для фактического использования, и проводит проверку достоверности во время ввода.
После ввода данных программа отображает графическое моделирование процедуры измерения, что, несомненно, повышает уверенность пользователя в правильности процесса измерения.
Во всех направлениях измерения используется высокоточный резистивный тензодатчик на основе триггерного датчика шпинделя.
С новым компактным датчиком OMP400, например, или с проверенным датчиком касания MP700, измеряются точки на поверхности, а затем измерительный прибор передает данные на ПК.
Анализ и обработка данных выполняются с помощью специального метода расчета измерений, который аналогичен методу КИМ и, следовательно, может также использоваться для измерения сложных поверхностей произвольной формы.
По этой причине сенсорные датчики MP700 и OMP400 необходимо не только калибровать по всем векторным направлениям, но и сразу же выполнять измерения во всех векторных направлениях.
Это также значительно сокращает время цикла, так как каждая деталь должна иметь небольшое количество точек измерения.
Программное обеспечение Renishaw OMV, основанное на модели CAD, не только показывает измеренное отклонение, но также указывает значение этого отклонения в цветных точках.
Эти точки образуют цветной график, который позволяет быстро оценить точность детали, что предоставляет многочисленные возможности для статистического анализа и графического представления результатов измерений.
Набор точек измерения может быть адаптирован к модели CAD (функция оптимальной подгонки), чтобы избежать ошибок во время настройки детали и выбора опорной точки.
В результате ошибки могут быть обнаружены и исправлены до того, как деталь будет снята со станка.
Возможность проверки точности размеров деталей в различных режимах обработки не только экономит время, но и повышает надежность обработки.
Поделиться – это забота!
[1] | Швенке, Х.и другие. Измерение геометрических погрешностей и компенсация машин – обновление. CIRP Annals 57, 660-675 (2008). |
[2] | Liu, K. et al. Интеллектуализация станков: комплексная компенсация тепловых погрешностей системы машина-деталь. Международный журнал передовых производственных технологий 102, 3865-3877 (2019). |
[3] | Лю, Д.и другие. Динамическая погрешность станков с ЧПУ: современный обзор. Международный журнал передовых производственных технологий 106, 1869-1891 (2020). |
[4] | Tonnellier, X. et al. Прецизионное шлифование для быстрого изготовления сегментов для очень больших телескопов с использованием Cranfield BoX. Труды SPIE 7739, Современные технологии в космических и наземных телескопах и инструментах, Сан-Диего, SPIE, 2010. |
[5] | Comley, P. et al. Шлифовка сегментов зеркала метровой шкалы для наземного телескопа E-ELT. Анналы CIRP 60, 379-382 (2011). |
[6] | Йошиока, Х., Кодзима, К. и Тойота, Д. Создание микротекстур на изогнутой поверхности с помощью быстрой сервосистемы инструмента для процесса микропереработки. CIRP Annals 69, 325-328 (2020). |
[7] | Tong, Z. et al. Быстрая обработка микроканавок на поверхностях произвольной формы с сервоприводом и встроенной метрологией. CIRP Annals 69, 505-508 (2020). |
[8] | Zhu, Z. et al. Настроенное алмазное точение микроструктурированных поверхностей на хрупких материалах для повышения эффективности обработки. CIRP Annals 68, 559-562 (2019). |
[9] | Brinksmeier, E. et al. Сверхточное шлифование. CIRP Annals 59, 652-671 (2010). |
[10] | Slocum, A.H. Прецизионное проектирование машин (Englewood Cliffs: Society of Manufacturing Engineers, 1992). |
[11] | Лич, Р.И Смит, С. Основы точного машиностроения (Бока-Ратон: CRC Press, 2018). |
[12] | Vermeulen, J.P.M.B., Rosielle, P.C.J.N. И Schellekens, P.H.J. Конструкция усовершенствованного станка для токарной обработки оптического алмаза по керамике и разработка прототипа. Анналы CIRP 49, 407-410 (2000). |
[13] | Лян, Ю.и другие. Термическая оптимизация сверхточного станка методом термического разложения и противодействия. Международный журнал передовых производственных технологий 76, 635-645 (2015). |
[14] | Brecher, C., Utsch, P. & Wenzel, C. Повышение точности по пяти осям за счет компактной и цельной конструкции. CIRP Annals 58, 355-358 (2009). |
[15] | Thompson, D.C. & McKeown, P. Конструкция сверхточной измерительной машины с ЧПУ. Анналы CIRP 38, 501-504 (1989). |
[16] | Florussen, G.H.J. и другие. Оценка геометрических погрешностей многоосных станков с помощью трехмерных измерений длины. Измерение 30, 241-255 (2001). |
[17] | Gao, W. et al. Машинная и производственная метрология поверхностей для прецизионного производства. CIRP Annals 68, 843-866 (2019). |
[18] | Li, D. et al. Измерение поверхности на станке и приложения для сверхточной обработки: современный обзор. Международный журнал передовых производственных технологий 104, 831-847 (2019). |
[19] | ISO. Код испытаний для станков – Часть 11: измерительные приборы, подходящие для испытаний геометрии станков. (Женева, Швейцария: Международная организация по стандартам, 2018 г.). |
[20] | ISO.Кодекс испытаний для станков, часть 6: определение точности позиционирования по диагоналям тела и лица (испытания на диагональное смещение). Международная организация по стандартизации , Женева, Швейцария (2002 г.). |
[21] | ISO. Код испытаний для станков – часть 7: геометрическая точность осей вращения. Международная организация по стандартизации , Женева, Швейцария. (2015). |
[22] | ISO.230-1 Код испытаний для станков – Часть 1: Геометрическая точность станков, работающих на холостом ходу или чистовых условиях. Международная организация по стандартизации , Женева, Швейцария. (2012). |
[23] | Smith, G.T. Метрология станков: промышленный справочник (Cham: Springer, 2016). |
[24] | Рамеш Р., Маннан, М. и Пу, А. Компенсация ошибок в станках – обзор: часть I: геометрические ошибки, ошибки, вызванные силой резания, и ошибки, связанные с приспособлением. Международный журнал станков и производства 40, 1235-1256 (2000). |
[25] | Шривастава А., Велдхуис С. и Эльбеставит М. Моделирование геометрических и тепловых ошибок на пятиосевом станке с ЧПУ. Международный журнал станков и производства 35, 1321-1337 (1995). |
[26] | Zhu, S. et al. Комплексное моделирование геометрических ошибок, идентификация и компенсация станков с ЧПУ. Международный журнал станков и производства 52, 24-29 (2012). |
[27] | Хан, А. И Чен, В. Методология систематической компенсации геометрической погрешности в пятикоординатных станках. Международный журнал передовых производственных технологий 53, 615-628 (2011). |
[28] | Peng, F. et al. Универсальный алгоритм постобработки на основе тотальных дифференциальных методов с учетом геометрической погрешности для многоосных станков с ЧПУ. Международный журнал станков и производства 70, 53-62 (2013). |
[29] | Чен, Дж., Лин, С. и Хе, Б. Компенсация геометрической погрешности для многоосных станков с ЧПУ на основе дифференциального преобразования. Международный журнал передовых производственных технологий 71, 635-642 (2014). |
[30] | Cheng, Q. et al. Анализ чувствительности точности обработки многоосевого станка на основе теории винта POE и метода Морриса. Международный журнал передовых производственных технологий 84, 2301-2318 (2016). |
[31] | Xiang, S. & Altintas, Y. Моделирование и компенсация объемных ошибок для пятиосевых станков. Международный журнал станков и производства 101, 65-78 (2016). |
[32] | Янг Дж., Майер Дж. И Алтинтас Ю. Метод определения и исправления геометрических ошибок, не зависящий от положения, для пятикоординатных серийных станков, основанный на теории винта. Международный журнал станков и производства 95, 52-66 (2015). |
[33] | Fu, G. et al. Повышение точности пятикоординатного станка на основе матрицы дифференциального движения: моделирование геометрической погрешности, идентификация и компенсация. Международный журнал станков и производства 89, 170-181 (2015). |
[34] | Ю., З., Tiemin, L. & Xiaoqiang, T. Моделирование геометрических ошибок станков на основе теории винта. Разработка процедур 24, 845-849 (2011). |
[35] | Lion Precision. Анализатор ошибок шпинделя (SEA). https://www.lionprecision.com/products/machine-tool-inspection/spindle-error-analyzer/. |
[36] | Рейншоу.Лазерная измерительная система XL-80 Станки и КИМ. https://www.renishaw.com/en/xl-80-laser-system–8268. |
[37] | Заргарбаши, С. и Майер, Дж. Оценка погрешности движения оси цапфы станка с использованием магнитного двойного шарикового стержня. Международный журнал станков и производства 46, 1823-1834 (2006). |
[38] | Ли, К.-И., Ли, Д.-М. И Ян, С.-Х. Параметрическое моделирование и оценка геометрических погрешностей поворотной оси с использованием двойной шариковой штанги. Международный журнал передовых производственных технологий 62, 741-750 (2012). |
[39] | Hsieh, H.-L. И Пан, С.-В. Разработка интерферометра на основе решеток для измерения перемещений и углов с шестью степенями свободы. Оптика Экспресс 23, 2451-2465 (2015). |
[40] | Ибараки, С., Ояма, К. и Оцубо, Х. Построение карты ошибок осей вращения на пятикоординатном обрабатывающем центре с помощью статического R-теста. Международный журнал станков и производства 51, 190-200 (2011). |
[41] | Бармен, С. и Сен, Р.Повышение точности многокоординатных станков за счет измерения ошибок и компенсации ошибок с помощью лазерной интерферометрии. МАПАН 25, 79-87 (2010). |
[42] | Рахман М., Хейккала Дж. И Лаппалайнен К. Моделирование, измерение и компенсация ошибок многоосных станков. Часть I: теория. Международный журнал станков и производства 40, 1535-1546 (2000). |
[43] | Kong, L. et al. Кинематика и экспериментальный анализ компенсации погрешности формы при сверхточной обработке. Международный журнал станков и производства 48, 1408-1419 (2008). |
[44] | Huang, N. et al. Встроенный постпроцессор для 5-осевых станков с компенсацией геометрических ошибок. Международный журнал станков и производства 94, 65-73 (2015). |
[45] | Bi, Q. et al. Выявление и компенсация геометрических погрешностей осей вращения на пятикоординатном станке путем измерения на станке. Международный журнал станков и производства 89, 182-191 (2015). |
[46] | Лю, Ю.и другие. Обобщенная реальная модель обратной кинематики для компенсации геометрических ошибок в пятикоординатных станках. Международный журнал механических наук 145, 299-317 (2018). |
[47] | Tlusty, J. Методы проверки точности станков с ЧПУ. в материалах Двенадцатой Международной конференции по проектированию и исследованиям станков (ред. Кенигсбергер, Ф. и Тобиас, С.A.) 333-345 (Лондон: PalgraveSpringer, 1972), 333-345. |
[48] | Hocken, R. et al. Трехмерная метрология. CIRP Annals 26, 403-408 (1977). |
[49] | Брайан Дж. Простой метод тестирования измерительных машин и станков. Часть 2: Детали конструкции. Точное машиностроение 4, 125–138 (1982). |
[50] | Estler, W.T. Калибровка и использование оптических линейок в метрологии прецизионных машин. Optical Engineering 24, 243372 (1985). |
[51] | Теймель А. Технология и применение решетчатых интерферометров в высокоточных измерениях. Точное машиностроение 14, 147-154 (1992). |
[52] | Gao, W. et al. Измерение движений с ошибками с несколькими степенями свободы прецизионной линейной ступени с воздушным подшипником. Точное машиностроение 30, 96-103 (2006). |
[53] | Hwang, J. et al. Трехзондовая система для измерения параллельности и прямолинейности пары рельсов для сверхточных направляющих. Международный журнал станков и производства 47, 1053-1058 (2007). |
[54] | Кэмпбелл, А. Измерение прямолинейности и параллельности Z-образных суппортов токарного станка с использованием плоской площадки. Точное машиностроение 17, 207-210 (1995). |
[55] | Гао, W.и другие. Измерение погрешности скольжения сверхточного алмазного токарного станка с использованием вращающейся цилиндрической заготовки. Международный журнал станков и производства 50, 404-410 (2010). |
[56] | Niu, Z. et al. Прецизионное измерение вертикального отклонения Z-образных салазок на сверхточном токарном станке с использованием трехзондового метода. Международный журнал точного машиностроения и производства 18, 651-660 (2017). |
[57] | Donaldson, R.R. Простой метод отделения ошибки шпинделя от ошибки круглости тестового шара. CIRP Annals 21, 125-126 (1972). |
[58] | Брайан, Дж. И Дж. Б., Б. Унификация терминологии, касающейся погрешности движения осей вращения. CIRP Annals 24, 555-562 (1975). |
[59] | Me, S. Объединительный документ Me: оси вращения. CIRP Annals 25, 545-564 (1976). |
[60] | Marsh, E. & Grejda, R. Опыт применения метода ведущей оси для измерения ошибочных движений шпинделя. Точное машиностроение 24, 50-57 (2000). |
[61] | Zhang, G. et al. Многоточечный метод измерения ошибочного движения шпинделя. CIRP Annals 46, 441-445 (1997). |
[62] | Salsbury, J.G. Реализация техники обратного движения лица Эстлера. Точное машиностроение 27, 189–194 (2003). |
[63] | Грейда, Р., Марш, Э. и Валланс, Р. Методы калибровки шпинделей с ошибкой движения нанометров. Точное машиностроение 29, 113-123 (2005). |
[64] | Марш, Э. Р., Арнесон, Д. А. И Мартин, Д. Сравнение реверсивного и многозондового разделения ошибок. Точное машиностроение 34, 85-91 (2010). |
[65] | Linxiang, C. Точность измерения многоступенчатого метода в методе разделения ошибок. Journal of Physics E: Scientific Instruments 22, 903-906 (1989). |
[66] | Buajarern, J.и другие. Влияние номера шага на определение округлости многоступенчатым методом. Международный журнал точного машиностроения и производства 14, 2047-2050 (2013). |
[67] | Haitjema, H. Возвращаясь к многоступенчатому методу: улучшенное разделение ошибок и уменьшенное количество измерений. CIRP Annals 64, 491-494 (2015). |
[68] | Марш, Э., Couey, J. & Vallance, R. Сравнение на нанометровом уровне трех методов разделения ошибочного движения шпинделя. Journal of Manufacturing Science and Engineering 128, 180-187 (2006). |
[69] | Cappa, S., Reynaerts, D. & Al-Bender, F. Техника разделения движений ошибки шпинделя субнанометрового диапазона. Точное машиностроение 38, 458-471 (2014). |
[70] | Куй, Х.и другие. Измерение и анализ погрешности радиального движения аэростатического сверхточного шпинделя. Измерение 137, 624-635 (2019). |
[71] | Лев. Точность. Осмотр станков. https://www.lionprecision.com/products/machine-tool-inspection/spindle-error-analyzer/. |
[72] | Чен, Ю.и другие. Новый метод с несколькими датчиками для отделения радиальной ошибки шпинделя от ошибки округлости артефакта. Международный журнал передовых производственных технологий 93, 623-634 (2017). |
[73] | Shi, S. et al. Оценка погрешности и снижение трехконтактного измерения профиля округлости на основе передаточной функции системы. Точное машиностроение 68, 139-157 (2021). |
[74] | ISO. Неопределенность измерения – Часть 3: Руководство по выражению неопределенности измерения. Международная организация по стандартизации (1995). |
[75] | Ma, P. et al. Технология измерения погрешности вращения и экспериментальные исследования высокоточного гидростатического шпинделя. Международный журнал передовых производственных технологий 73, 1313-1320 (2014). |
[76] | Lee, J. et al. Погрешность измерения движения шпинделя на токарном станке с большим прецизионным валком. Международный журнал точного машиностроения и производства 13, 861-867 (2012). |
[77] | Дин, Ф.и другие. Измерение на месте радиальных перемещений и отклонений от наклона шпинделя дополнительным многопозиционным методом. Нанопроизводство и метрология 2, 225-234 (2019). |
[78] | Анандан, К. И Оздоганлар, О. Метод разделения ошибок по разным направлениям для метрологии шпинделя миниатюрных сверхвысокоскоростных шпинделей. Точное машиностроение 43, 119-131 (2016). |
[79] | Shi, S. et al. Гибридный трехзондовый метод измерения погрешности округлости и погрешности шпинделя. Точное машиностроение 45, 403-413 (2016). |
[80] | Pezeshki, M. & Arezoo, B. Идентификация кинематических ошибок трехкоординатных станков на основе обработанных деталей. Точное машиностроение 43, 493-504 (2016). |
[81] | Ibaraki, S. et al. Испытания на обработку для выявления кинематических ошибок на пятиосевых станках. Точное машиностроение 34, 387-398 (2010). |
[82] | Гао, Х., Фанг, Ф. и Чжан, X. Обратный анализ геометрических ошибок сверхточного станка. Международный журнал передовых производственных технологий 73, 1615-1624 (2014). |
[83] | Liu, X. et al. Выявление и компенсация основных ошибок обработки по точности формы поверхности при сверхточном алмазном точении. Международный журнал станков и производства 105, 45-57 (2016). |
[84] | Гао, W.и другие. Измерение и компенсация ошибочных движений алмазного токарного станка. Точное машиностроение 31, 310-316 (2007). |
[85] | Хонг, Г.С. и Сан Вонг, Ю. Компенсация погрешности профиля при быстрой алмазной токарной обработке с сервоприводом инструмента микроструктурированных поверхностей. Международный журнал станков и производства 52, 13-23 (2012). |
[86] | Тао, Х.и другие. Новый подход к выявлению геометрических ошибок непосредственно по топографии поверхности заготовки при сверхточной обработке. Международный журнал станков и производства 106, 5159-5173 (2020). |
[87] | Боргоново, Э. и Плишке, Э. Анализ чувствительности: обзор последних достижений. Европейский журнал операционных исследований 248, 869-887 (2016). |
[88] | Li, Q. et al. Метод чувствительности для анализа объемной погрешности пятиосевого станка. Международный журнал передовых производственных технологий 98, 1791-1805 (2018). |
[89] | Saltelli, A. et al. Анализ глобальной чувствительности: учебник (John Wiley & Sons, 2008). |
[90] | Fu, G. et al. Моделирование влияния геометрической ошибки и оценка чувствительности для каждой оси пятиосевых станков на основе теории POE и преобразования дифференциальных изменений между системами координат. Международный журнал станков и производства 147, 103455 (2019). |
[91] | Чжан, X., Zhang, Y. & Pandey, M.D. Анализ глобальной чувствительности станка с ЧПУ: применение MDRM. Международный журнал передовых производственных технологий 81, 159-169 (2015). |
[92] | Li, J., Xie, F. & Liu, X.-J. Моделирование геометрической погрешности и анализ чувствительности пятиосевого станка. Международный журнал передовых производственных технологий 82, 2037-2051 (2016). |
[93] | Сальтелли А., Андрес Т. и Хомма Т. Анализ чувствительности выходных данных модели. Выполнение повторного дробно-факторного метода проектирования. Вычислительная статистика и анализ данных 20, 387-407 (1995). |
[94] | Zou, X. et al. Анализ чувствительности с использованием дисперсионного метода для трехосного алмазного токарного станка. Международный журнал передовых производственных технологий 92, 4429-4443 (2017). |
[95] | Li, D. et al. Компенсация кинематической погрешности для измерительного щупа на сверхточном токарном станке. Микромашины 9, 334 (2018). |
[96] | Лю, X.и другие. Производство оптических поверхностей с контролируемой производительностью путем сверхточной обработки. Международный журнал передовых производственных технологий 94, 4289-4299 (2018). |
ПРАЙМ PubMed | Оценка геометрических характеристик машины для проверки рабочих характеристик (MPC) для ежедневного контроля качества геометрической точности IGRT
Abstract
Machine Performance Check (MPC) – это автоматизированный и интегрированный инструмент на основе изображений для проверки характеристик пучка и геометрических характеристик линейного ускорителя TrueBeam .Цели исследования заключались в оценке эффективности геометрических тестов MPC, относящихся к геометрической точности OBI / CBCT IGRT. Это включало оценку изоцентра MPC и тестов кушетки. Оценка проводилась путем сравнения MPC с тестами QA, которые обычно выполнялись в отделении в течение 4-месячного периода. Изоцентрические тесты MPC сравнивались с тестом Winston-Lutz, разработанным собственными силами, и кушетка сравнивалась с обычными механическими процедурами типа QA. Во всех случаях результаты рутинной процедуры контроля качества были представлены в форме, непосредственно сопоставимой с ПДК, чтобы можно было провести сопоставимое сравнение.Чувствительность MPC также была проверена путем преднамеренной неправильной калибровки соответствующего параметра линейного ускорителя. Было обнаружено, что размер изоцентра MPC и смещение формирователя изображения MPC кВ согласуются с данными Уинстона-Лутца с точностью 0,2 мм и 0,22 мм соответственно. Испытания на кушетке MPC согласовывались с обычным контролем качества с точностью до 0,12 мм и 0,15 °. Было обнаружено, что на размер изоцентра MPC и параметры смещения тепловизора в кВ влияет изменение положения фокусного пятна луча при более чувствительном смещении тепловизора в кВ. На все тесты кушетки MPC не повлияло смещение калибровки кушетки, но три оси, в которых использовались двухточечные калибровки, были чувствительны к ошибочной калибровке размера в диапазоне калибровки.На все тесты MPC не повлияло преднамеренное смещение фантома MPC и крена порядка одного градуса.
Citation
Барнс, Майкл П. и Питер Б. Грир. «Оценка геометрических проверок машины Truebeam (MPC) для ежедневного контроля качества геометрической точности IGRT». Журнал прикладной клинической медицинской физики, т. 18, нет. 3, 2017, с. 200-206.
Барнс М.П., Грир ПБ. Оценка геометрических проверок при проверке рабочих характеристик станка с истинным лучом (MPC) для ежедневного контроля качества геометрической точности IGRT. J Appl Clin Med Phys . 2017; 18 (3): 200-206.
Барнс, М. П., и Грир, П. Б. (2017). Оценка геометрических проверок при проверке рабочих характеристик станка с истинным лучом (MPC) для ежедневного контроля качества геометрической точности IGRT. Журнал прикладной клинической медицинской физики , 18 (3), 200-206. https://doi.org/10.1002/acm2.12064
Барнс MP, Грир ПБ. Оценка геометрических проверок Truebeam Machine Performance Check (MPC) для ежедневного контроля качества геометрической точности IGRT. J Appl Clin Med Phys. 2017; 18 (3): 200-206. PubMed PMID: 28332342.
TY – JOUR T1 – Оценка геометрических проверок при проверке рабочих характеристик станка с истинным лучом (MPC) для ежедневного контроля качества геометрической точности IGRT. AU – Барнс, Майкл П., AU – Грир, Питер Б, 1 год – 2017/03/22 / PY – 2016/10/31 / получено PY – 2017/02/02 / исправлено PY – 2017/02/04 / принято PY – 2017/3/24 / pubmed PY – 2018/3/31 / medline PY – 2017/3/24 / entrez KW – гарантия качества линейного ускорителя KW – проверка работоспособности машины (MPC) СП – 200 EP – 206 JF – Журнал прикладной клинической медицинской физики JO – J Appl Clin Med Phys. ВЛ – 18 ИС – 3 N2 – Machine Performance Check (MPC) – это автоматизированный и интегрированный инструмент на основе изображений для проверки характеристик луча и геометрических характеристик линейного ускорителя TrueBeam.Цели исследования заключались в оценке эффективности геометрических тестов MPC, относящихся к геометрической точности OBI / CBCT IGRT. Это включало оценку изоцентра MPC и тестов кушетки. Оценка проводилась путем сравнения MPC с тестами QA, которые обычно выполнялись в отделении в течение 4-месячного периода. Изоцентрические тесты MPC сравнивались с тестом Winston-Lutz, разработанным собственными силами, и кушетка сравнивалась с обычными механическими процедурами типа QA. Во всех случаях результаты рутинной процедуры контроля качества были представлены в форме, непосредственно сопоставимой с ПДК, чтобы можно было провести сопоставимое сравнение.Чувствительность MPC также была проверена путем преднамеренной неправильной калибровки соответствующего параметра линейного ускорителя. Было обнаружено, что размер изоцентра MPC и смещение формирователя изображения MPC кВ согласуются с данными Уинстона-Лутца с точностью 0,2 мм и 0,22 мм соответственно. Испытания на кушетке MPC согласовывались с обычным контролем качества с точностью до 0,12 мм и 0,15 °. Было обнаружено, что на размер изоцентра MPC и параметры смещения тепловизора в кВ влияет изменение положения фокусного пятна луча при более чувствительном смещении тепловизора в кВ. На все тесты кушетки MPC не повлияло смещение калибровки кушетки, но три оси, в которых использовались двухточечные калибровки, были чувствительны к ошибочной калибровке размера в диапазоне калибровки.На все тесты MPC не повлияло преднамеренное смещение фантома MPC и крена порядка одного градуса. СН – 1526-9914 UR – https://www.unboundmedicine.com/medline/citation/28332342/evaluation_of_the_truebeam_machine_performance_check__mpc__geometric_checks_for_daily_igrt_geometric_accuracy_quality_assurance_ L2 – https://doi.org/10.1002/acm2.12064 БД – ПРЕМЬЕР DP – Unbound Medicine ER –
Геометрические ошибки машин – эталонная часть Hexagon
Станки и измерительные машины с 3–5 осями можно найти в большом количестве и во всех областях современного производства: от автомобилестроения до авиакосмической промышленности, от производства товаров народного потребления до товаров медицинского назначения.Точные детали можно получить только с помощью контролируемого и детерминированного производственного процесса. В то время как повторяемость станка является необходимым требованием для хорошо контролируемого процесса, геометрическая точность детали может быть достигнута либо с помощью контура обратной связи через метрологию детали, либо с помощью точно откалиброванных станков. Из-за более короткого жизненного цикла продукции и мелкосерийного производства абсолютная точность станков приобретает все большее значение.
Источники геометрических ошибок
На точность станков и КИМ влияет множество источников ошибок.Следующие сообщаемые источники ошибок могут повлиять на точность обработанной детали:
- Кинематические ошибки: Кинематические ошибки – это ошибки из-за несовершенной геометрии, центровки и размеров компонентов машины. Они стабильны или медленно меняются с течением времени, например. из-за выемок фундамента, износа или старения материала. Но и столкновения могут изменить эти ошибки.
- Термомеханические ошибки: внутренние и внешние источники тепла в машине могут привести к термомеханической деформации компонентов машины и, следовательно, к изменению кинематических погрешностей.Постоянная времени и амплитуда геометрических изменений зависит от постоянной времени причин, а также от тепловой массы и демпфирования конструкции машины.
- Нагрузки: в некоторых случаях вес и положение заготовки оказывают значительное влияние на геометрию станка. Воспроизводимые деформации из-за массы заготовки могут быть охвачены описанием кинематической ошибки станка, но иногда также может потребоваться дополнительное моделирование и измерение.
- Динамические силы: На траекторию, которую должна реализовать машина, также влияет динамическая жесткость структурной петли машины.В этом случае различные силы, такие как силы обработки или силы, вызванные ускорениями или замедлениями, вызывают деформации. Однако прецизионная обработка или измерения часто выполняются при малых скоростях подачи, с небольшими ускорениями и замедлениями, а также небольшими силами резания.
Кинематические конструкции станков
Кинематическая структура определяется расположением компонентов машины и их осей. Большинство станков и измерительных машин имеют последовательную структуру: одна ось движения накладывается на другую.Обозначения, основанные на Шверде, могут использоваться для описания последовательной кинематической структуры от инструмента до детали [РИСУНОК 1].
Описание геометрических ошибок
Соответствующие ошибки станка – это относительные ошибочные движения между инструментом и заготовкой. Каждое движение оси станка можно описать шестью степенями свободы: тремя перемещениями и тремя поворотами. Обозначения движения оси стандартизированы в ISO 841: X, Y и Z обозначают линейные перемещения, A, B и C – вращения вокруг X, Y и Z соответственно.
Для номинального линейного перемещения шесть составляющих ошибок – это ошибка положения, два движения с ошибкой прямолинейности, движение с ошибкой по крену и два движения с ошибкой наклона, которые называются движением с ошибкой по тангажу и рысканью для горизонтальных осей. В предположении поведения твердого тела эти ошибки являются функциями только номинального движения и не зависят от расположения других осей (см. Анимацию).
Для номинального вращательного движения шесть составляющих ошибок – это два движения с радиальной ошибкой, одно движение с осевой ошибкой, ошибка углового положения и два движения с ошибкой наклона.На Рисунке 6 показаны эти ошибки компонентов для движения C [РИСУНОК 3].
Etalon предлагает эффективный и точный способ измерения и компенсации этих ошибок.
FS-Laboratorij za odrezavanje (LABOD)
Геометрическая точность станка с ЧПУТребования к точности обрабатываемых изделий постоянно повышаются. Высокие стандарты для точных продуктов «крутят колесо» для постоянного развития компьютерного программного и аппаратного обеспечения, а также для точных продуктов и усовершенствований машин и инструментов.Уровень точности обрабатываемых изделий напрямую зависит от производительности станков, используемых в производственной линии. Конкурентоспособная продукция и эффективная производственная линия на современном предприятии требуют постоянной проверки производительности станков для предотвращения брака продукции. Геометрическую точность станка с ЧПУ можно определить разными способами. Очень быстрый и успешный метод определения уровня точности станка с ЧПУ основан на тесте Ballbar.
Устройство Ballbar QC10
Ballbar QC10 – это измерительная система для определения геометрической точности различных станков с ЧПУ.Стандартный комплект разработан для быстрой проверки 3-х осевых станков с ЧПУ (вертикальные и горизонтальные центры), с дополнительными элементами, испытание Ballbar может быть выполнено также на нескольких типах 2-х осевых станков (токарный станок с ЧПУ, Wire EMD , …)
Назначение теста Ballbar, выполненного на станке с ЧПУ
Тест Ballabar на станке с ЧПУ выполняется за 10 минут. Выбранные условия испытаний и результаты испытаний представляют собой основу для определения фактической геометрической точности станка с ЧПУ.В соответствии с результатами испытаний Ballbar, которые отображаются в графическом и табличном режимах, и анализом результатов испытаний, можно определить различные меры для повышения геометрической точности станка с ЧПУ.
Лазер ML10 Gold Standard
Лазерная система ML10 Gold Standard представляет собой второй режим для верхнего уровня идентификации и компенсации ошибок на станках с ЧПУ, а также на координатно-измерительных машинах (КИМ). С высокой точностью лазерного луча можно выполнять нанометрические измерения.С помощью специального оборудования и дополнительных оптических устройств можно выполнить несколько измерений на станке с ЧПУ; линейная точность и повторяемость измерений, измерение углового шага и рыскания, измерение прямолинейности, измерение прямоугольности, измерение плоскостности, измерение осей вращения и т. д.
Назначение лазерной измерительной сети на станке с ЧПУ
Одночастотный лазер содержит сложную электронику для стабилизации, интерполяции и подсчета интерференционных полос.Вместе с устройством компенсации окружающей среды EC10 (для компенсации рабочей температуры, влажности и давления воздуха) могут быть достигнуты измерения с нанометровым разрешением при скорости подачи до 1 м / с. На основе данных карты компенсации ошибок, подходящие для указанного типа контроллера, могут быть легко созданы в программном обеспечении Laser 10, а затем через кабель передачи данных, также переданы в схему контроллера. Карты компенсации ошибок являются основой для точного рабочего эффекта по всей рабочей зоне на станке с ЧПУ или координатно-измерительной машине (КИМ).
Следует использовать оба устройства …
Оба устройства (Ballbar QC10 и лазерная система ML10) могут использоваться для идентификации точности станков с ЧПУ. Лучшее решение – совместное использование обоих устройств, как показано на рисунке ниже. На рисунке представлены последовательные действия по определению геометрической точности станков с ЧПУ. В этом случае лазерная система используется для калибровки после серьезного механического вмешательства на станке с ЧПУ, а устройство Ballbar QC10, напротив, используется для быстрой и частой проверки точности станка с ЧПУ.Такие действия могут потребовать регулярного или профилактического обслуживания деталей станков с ЧПУ.
Стоимость услуги
На данный момент услуга включает измерение с помощью измерительного прибора Ballbar QC10 на станке с ЧПУ. Мы также предлагаем анализ результатов испытаний с предложением мер по повышению производительности станка с ЧПУ.
Шт. | Описание услуги / работы | Цена не указана.НДС |
1 | Тест Ballbar (тест на ЧПУ – станке) | 200 / станок |
1 | Анализ испытаний с предложением меры | 100-200 / станок |
Прочие расходы (проезд, проезд)
расходы, …) |
«Назад
.