🛠 ЧПУ своими руками v1.0 👈
Это мой первый станок с ЧПУ собранный своими руками из доступных материалов. Себестоимость станка около 170$.
Собрать станок с ЧПУ мечтал уже давно. В основном он мне нужен для резки фанеры и пластика, раскрой каких-то деталей для моделизма, самоделок и других станков. Собрать станок руки чесались почти два года, за это время собирал детали, электронику и знания.
Станок бюджетный, стоимость его минимальна. Далее я буду употреблять слова, которые обычному человеку могут показаться очень страшными и это может отпугнуть от самостоятельной постройки станка, но на самом деле это всё очень просто и легко осваивается за несколько дней.
Электроника собрана на Arduino + прошивка GRBL
Плата Ардуино R3
Плата CNC shield v3 Update: есть новая версия платы v4
Шаговые моторы NEMA 17
Блок питания 24 вольта 15 ампер
Видео о том как поют 🙂 моторы ЧПУ станка.
Механика самая простая, станина из фанеры 10мм + шурупы и болты 8мм, линейные направляющие из металического уголка 25*25*3 мм + подшипники 8*7*22 мм.
Шпиндель для ЧПУ самодельный, собран из бесколлекторного мотора и цангового зажима + зубчатая ременная передача. Надо отметить, что мотор шпинделя питается от основного блока питания 24 вольта. В технических характеристиках указано, что мотор на 80 ампер, но реально он потребляет 4 ампера под серьёзной нагрузкой. Почему так происходит я объяснить не могу, но мотор работает отлично и справляется со своей задачей.
Изначально ось Z была на самодельных линейных направляющих из уголков и подшипников, позже я переделал её, фотки и описание ниже.
Рабочее пространство примерно 45 см по X и 33 см по Y, по Z 4 см. Учитывая первый опыт, следующий станок я буду делать с большими габаритами и на ось X буду ставить два мотора, по одному с каждой строны. Это связано с большим плечом и нагрузкой на него, когда работа ведётся на максимальном удалении по оси Y.
Родные подшипники у мотора быстро разболтались, потому что не рассчитаны на боковую нагрузку, а она тут серьёзная. Поэтому сверху и снизу на оси установил два больших подшипника диаметром 8 мм, это надо было бы делать сразу, сейчас из-за этого есть вибрация.
Здесь на фото видно, что ось Z уже на других линейных направляющих, описание будет ниже.
Сами направляющие имеют очень простую конструкцию, её я как-то случайно нашел на Youtube. Тогда мне эта конструкция показалась идеальной со всех сторон, минимум усилий, минимум деталей, простая сборка. Но как показала практика эти направляющие работают не долго. На фото видно какая канавка образовалась на оси Z после недели моих тестовых запусков ЧПУ станка.
Самодельные направляющие на оси Z я заменил на мебельные, стоили меньше доллара за две штуки. Я их укоротил, оставил ход 8 см. На осях X и Y ещё остались направляющие старые, менять пока не буду, планирую на этом станке вырезать детали для нового станка, потом этот просто разберу.
Пару слов о фрезах. Я никогда не работал с ЧПУ и опыт фрезерования у меня тоже очень маленький. Купил я в Китае несколько фрез, у всех 3 и 4 канавки, позже я понял, что эти фрезы хороши для металла, для фрезерования фанеры нужны другие фрезы. Пока новые фрезы преодолевают расстояние от Китая до Беларуси я пытаюсь работать с тем, что есть.
На фото видно как фреза 4 мм горела на берёзовой фанере 10 мм, я так и не понял почему, фанера чистая, а на фрезе нагар похожий на смолу от сосны.
Далее на фото фреза 2 мм четырёхзаходная после попытки фрезерования пластика. Этот кусок расплавленного пластика потом очень плохо снимался, откусывал по чуть-чуть кусачками. Даже на малых оборотах фреза все равно вязнет, 4 канавки явно для металла 🙂
На днях у дяди был день рождения, по этому случаю решил сделать подарок на своей игрушке 🙂
В качестве подарка сделал аншлаг на дом из фанеры. Первым делом попробовал фрезеровать на пенопласте, чтобы проверить программу и не портить фанеру.
Из-за люфтов и прогибаний подкову получилось вырезать только с седьмого раза.
В общей сложности этот аншлаг (в чистом виде) фрезеровался около 5 часов + куча времени на то, что было испорчено.
Как-то я публиковал статью про ключницу, ниже на фото эта же ключница, но уже вырезанная на станке с ЧПУ. Минимум усилий, максимум точность. Из-за люфтов точность конечно не максимум, но второй станок я сделаю более жестким.
А ещё на станке с ЧПУ я вырезал шестерёнки из фанеры, это намного удобнее и быстрее, чем резать своими руками лобзиком.
Позже вырезал и квадратные шестерёнки из фанеры, они на самом деле крутятся 🙂
Итоги положительные. Сейчас займусь разработкой нового станка, буду вырезать детали уже на этом станке, ручной труд практически сводится к сборке.
Нужно освоить резку пластика, потому как встала работа над самодельным роботом-пылесосом. Собственно робот тоже подтолкнул меня на создание своего ЧПУ. Для робота буду резать из пластика шестерни и другие детали.
Update: Теперь покупаю фрезы прямые с двумя кромками (3.175*2.0*12 mm), режут без сильных задиров с обоих сторон фанеры.
Механика ЧПУ станка
Механика ЧПУ станка
Сегодняшняя статья является продолжением статьи Хоббийный ЧПУ станок. В данной статье мы продолжим изготовление ЧПУ станка для домашних нужд из подручных средств.
Одним из важных компонентов самодельного ЧПУ станка является контроллер, я рекомендую воспользоваться книгой Контроллеры ЧПУ станков и шаговые двигатели или собрать контроллер из статьи Простой контроллер для ЧПУ станка.
Сам я возиться с паяльником не слишком люблю, так что расписывать
вторично, то, что уже описывал не буду.
В прошлой статье я рассматривал схему на базе роликовых подшипников. Такая схема хорошо работает для сверлильного ЧПУ станка, на нем можно разводить платы, но вот с гравировкой будут проблемы. Поэтому сегодня рассмотрим вариант небольшого самодельного фрезерного станка на базе втулок.
Если вы помните, для сборки нашего станка мы использовали старые матричные принтеры. В основном из за хороших шаговых двигателей в них. Так же из этих принтеров были взяты стальные шлифованные направляющие.
Но кроме направляющих в принтерах используются и механизм скольжения головки принтера.
Именно их и можно использовать! Ведь данные механизмы и предназначены для скольжения по направляющим. Причем эти механизмы можно взять от любых принтеров. Даже от дешевых струйников в которых нет шаговых двигателей.
Если принтеров под рукой нет, не беда. Можно использовать медные или
алюминиевые втулки. Медные лучше. Они не будут заедать на направляющей.
Можно использовать для изготовления втулок и прочный скользкий пластик.
Так как выставить направляющие параллельно с большой точностью в домашних условиях очень сложно, то втулку используем только на одной направляющей,так сказать – одна втулка на одну ось ЧПУ станка.
Теперь хотелось бы остановиться на самой конструкции нашего домашнего мини фрезера.
Готовые схемы и чертежи чпу станков это хорошо, но часто приходится переделывать готовое под желаемое.
На этом этапе главное – прикинуть какой материал у нас есть и что мы будем из него делать.
Потратьте немного времени для прорисовки каждой оси.
Затем разбейте ее на компоненты, тогда вы сможете приступить к изготовлению механики без проблем на этапе сборки.
Первая ось очень проста в изготовлении. единственным нюансом является крепление ходовой гайки.
Ходовая гайка вставлена в резиновую втулку и затем затягивается с помощью шурупа.
Как можно видеть – все крепления выполнены с помощью шурупов. Для домашнего ЧПУ станка этого вполне достаточно. В прикрепляемой детали отверстие сверлится с запасом, а во второй детали – используется более тонкое сверло, что бы шуруп смог прочно закрепиться в пластике. Перед окончательной сборкой не лишнем будет смазать винты каплей фиксатора резьбы Локтайт. Это позволит избежать ситуации с самораскручиванием от вибрации.
Теперь приступаем к изготовлению оси Y и Z. В данном станке это самая сложная операция.
Делаем башню – она будет нести на себе всю нагрузку.
И крепление фрезера, в качестве которого используется насадка для Дремеля подключенная к китайской минидрели.
Собираем механизм перемещения и станок почти готов. Для крепления ходовых винтов используются подшипники качения.
Это можно делать только с одной стороны, с другой стороны ходовой винт должен или быть свободным или подшипник должен быть зажат в крепление через большую резиновую амортизирующую прокладку. Если подобной нет под рукой, то ее можно изготовить самостоятельно из ластика (стирательной резинки).
Остается только закрепить шаговые двигатели. Это удобно делать, если при вытаскивании шаговиков из принтера вы сохранили крепления. Как крепить вал двигателя к ходовой оси – смотрите в первой части статьи.
Наш самодельный ЧПУ станок готов.
Рекомендуется оборудовать его концевыми выключателями из микровыключтелей. Их можно купить в магазине типа ЧипИДип или выдрать из ненужной компьютерной мышки.
Конечные выключатели очень полезны для предотвращения
саморазрушения. Переключатель устанавливается на границе каждой оси и
соединяются параллельно. Когда ось достигает края – цепь замыкается и
контроллер ЧПУ станка получает сигнал. Главная опасность в том, что
переключатель может загрязниться мусором от работы станка. Но можно
засунуть концевик в презерватив или воздушный шарик, это убережет его
от мусора и пыли.
В качестве ПО управления станком я рекомендую LinuxCNC или KCam. О преимуществах и недостатках вы можете почитать по ссылкам.
Самодельный ЧПУ станок
Самодельный ЧПУ станок – rodan.ru
Самодельный ЧПУ станок – это устройство, которое может производить резку, фрезеровку любых материалов. Каждый мастер мечтает заиметь в своей мастерской агрегат, который откроет большие возможности для творчества.
Содержание- Фрезерные станки – назначение
- Станок с ЧПУ своими руками
- ЧПУ станок своими руками – схема
- Подготовка к процессу
- Алгоритм сборки
- Конструктивные особенности станков с ЧПУ
- В заключение
Фрезерные станки – назначение
Широкое распространение станков ЧПУ в промышленности и среди частных мастеров обусловлено возможностью точно обработать дерево, металл или пластмассу. Кроме этого они применяются при сверлильных и гравировочных работах.
Все самодельные станки по дереву с ЧПУ могут справиться с любой поставленной задачей. Если использовать высококачественные узлы и настроить устройство должным образом, исключив даже минимальный люфт, то можно добиться высокой точности обработки деталей.
Станок с ЧПУ своими руками
Перед сборкой конструкции, нужно потратить время и создать проект ЧПУ станка – для этого можно ознакомиться с различными моделями заводского производства. Благодаря этим двум пунктам можно избежать ошибок, которые часто совершают новички.
Многие мастера считают, что сделать самостоятельно данную конструкцию невозможно, так как устройство имеет сложное электронное наполнение. Но это ошибочное мнение, достаточно подготовить чертеж, специальный набор инструментов и необходимые детали.
Также нужны не только временные, но и денежные расходы. Если эти проблемы не пугают, то изготовить агрегат для фрезеровки материалов с ПУ не будет слишком сложным процессом. Достаточно запастись терпением и необходимыми элементами.
ЧПУ станок своими руками – схема
Это самый важный этап работы над формированием станка ЧПУ – план нужно начертить на бумаге, описав все необходимые нюансы, он должен иметь оптимальные параметры, которые определяются исходя из размеров обрабатываемых заготовок.
Если устройство будет применяться в бытовых целях для фрезеровки небольших деталей, то желательно отдать предпочтение компактному оборудованию с оптимальным набором функций.
Самый простой вариант – конструкция, которая состоит из 2 кареток, двигающихся по плоскости. В качестве базы прекрасно подходят стальные прутки, отшлифованные до идеальной гладкости, на них монтируются каретки.
Также следует подготовить крепежи с подшипниками качения и ШД, для обеспечения трансмиссии. Самодельный станок ЧПУ будет управляться специальным ПО, которое необходимо будет установить после монтажа.
Подготовка к процессу
Электроника в агрегате должна быть продумана до мельчайших подробностей. Необходимо подготовить следующие элементы:
- блок питания – он будет обеспечивать подачу электричества на контроллер и ШД;
- драйвер – будет обеспечивать стабильную работу движущихся элементов конструкции;
- контроллер – многоцепная коммутационная микросхема управляющая устройствами в электронике.
В отличие от фрезерного, самодельный лазерный ЧПУ станок – действует при помощи луча, воздействуя максимальной температурой на металл, расплавляя его и создавая на нем необходимый рисунок. Изготовление подобного устройства процесс сложный и трудоемкий.
Итак для самостоятельной сборки, нужно приготовить детали, подойдут материалы, которые есть под рукой. Это поможет снизить расходы на создание устройства до минимума.
Основание для устройства делают из металла либо дерева. Немаловажно чтобы в период работы суппортов не было колебаний, которые приводят к неточной работе устройства. Поэтому необходимо разрабатывать аппарат правильно. Какие составляющие подойдут:
- прутки сечением 12 мм – как направляющие;
- текстолит – это оптимальный вариант для суппорта;
- Ш-двигатель – обычно используют от матричного принтера их понадобиться 3 шт;
- блок фиксации для фрезы.
Алгоритм сборки
После того, как все будет готово, можно начинать производство фрезеровального станка ЧПУ для шлифования металлических и деревянных болванок. Порядок действий следующий:
- закрепить к боковым поверхностям конструкции направляющие суппорта;
- чтобы ход был плавным, суппорты нужно тщательно притереть, путем многократного перемещения;
- затянуть болты;
- смонтировать все компоненты на станину;
- установить ходовые муфты с винтами;
- закрепить шаговые двигатели к муфтовым винтам.
Всю электронику необходимо разместить в отдельном блоке. Это позволит устройству работать бесперебойно на протяжении всего срока эксплуатации.
Важно! Увеличению точности содействует ликвидация зазоров во всех приводах подачи, которые применяются в механизмах, сокращение потерь на трение в направляющих и других узлах, улучшение устойчивости к вибрации, сокращение деформации при перегреве, использование обратных датчиков связи.
Приводы станков с управлением должны гарантировать максимальное быстродействие.
Конструктивные особенности станков с ЧПУ
Механизмы устройств с ЧПУ обеспечивает совмещение разных типов обработки, удобную загрузку заготовок простое снятие деталей. Кроме этого должна быть возможность быстро поменять программное обеспечение.
Как только собраны все составляющие самодельного устройства, можно начинать испытания.
Контроль над действиями аппарата будет проводиться за счет программного обеспечения, которое должно работать бесперебойно, поэтому его выбирают с особой тщательностью.
Первое – программа должна по максимуму реализовывать все без исключения возможности оснащения. Необходимо установить драйверы для контроллеров в программном обеспечении.
Второе – подбирать нужно оптимальный вариант ПО, на котором могут работать новички, и со временем его усовершенствовать.
Не нужно на первом этапе замахиваться на сложные программы – установите простое ПО. При первом запуске станка, необходимо строго следить за работой фрезы, только так можно определить насколько правильно работает устройство и обрабатывает болванку, как по глубине, так и по ширине. Особого внимания требует трехмерный вариант ЧПУ станков, изготовленных самостоятельно в домашних условиях.
В заключение
Аппараты для фрезеровки и обработки различных материалов со специальным ПУ, состоят из отдельных составляющих и имеют разную электронику в своей конструкции. Но, не смотря на это, самостоятельное изготовление подобного аппарата не составит труда, если правильно подойти к процессу подготовки и сборки. Каждый человек, которых хоть немного знаком с техникой и электроникой сможет сделать станок ЧПУ, и работать на нем длительное время с максимальной эффективностью и точностью.
Но если нет времени на занятие подобного рода, компания РОДАН, может предложить поставки профессиональных станков с ЧПУ, и Вы сразу можете приступить к делу.
Самодельный Лазерный гравёр с ЧПУ, в домашних условиях.
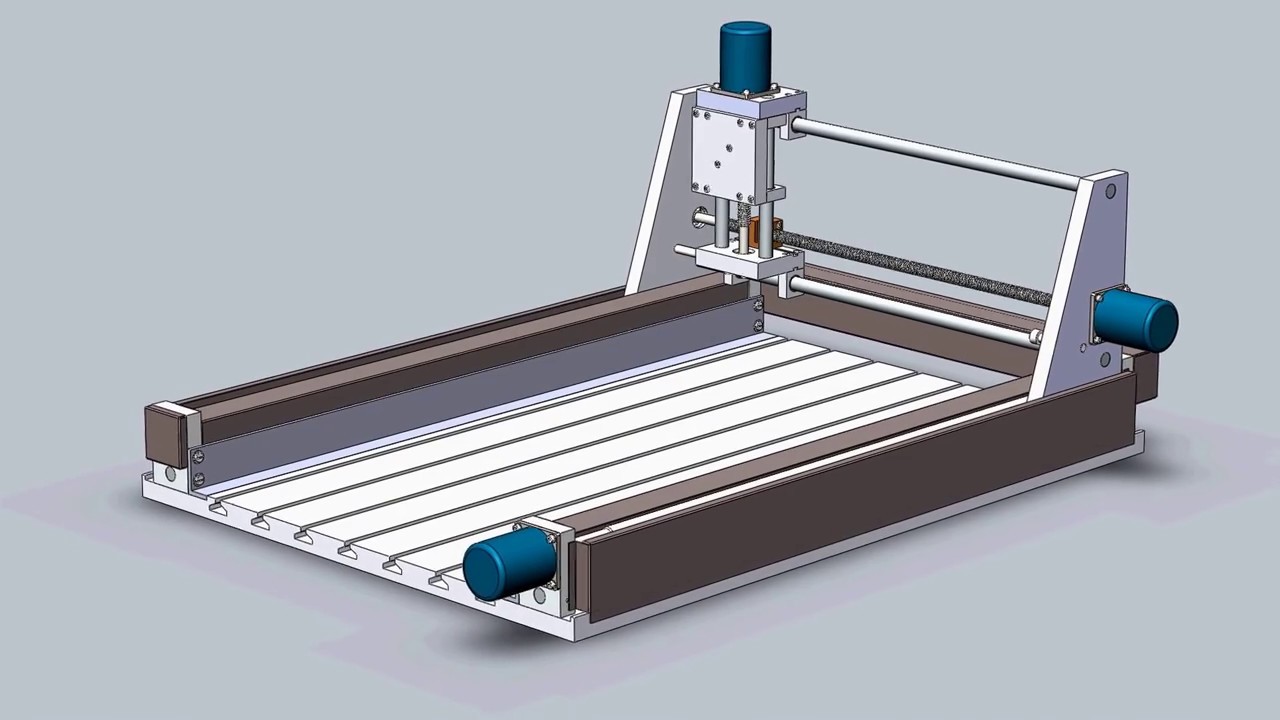
Кроме созданий проектов на Arduino, ещё я увлекаюсь созданием самодельных станков с ЧПУ. На счету у меня собрано больше 5 штук самодельных ЧПУ станков с различной кинематикой перемещения и разнообразного назначения. Сегодня пойдет речь о самодельном лазерном гравере, который я собрал в домашних условиях, а точнее в квартире. При этом использовал подручные материалы, которые лежат без дела, или которые можно не задорого купить в ближайшем магазине. С чего все началось, и для чего я собрал лазерный гравировальный станок из хлама, сейчас расскажу.
Зачем собирать самодельный ЧПУ станок из хлама?
Один знакомый сказал, что ЧПУ станки это сложно и для того, чтобы собрать работающий станок нужно очень много знать и уметь. Я ответил, что я собираю ЧПУ станки из подручных материалов, и многие работают у меня больше 2 лет верой и правдой. Показал, что я на них делаю, и где можно почитать описание моих проектов.
Спустя некоторое время этот знакомый мне говорит, что он рассказал друзьям, и они не верят, что можно собрать ЧПУ станок в домашних условиях. Да даже не то, чтобы он работал, как из магазина, а хотя бы выполнял какую-нибудь работу. И тут он меня спрашивает: «Ты можешь собрать станок не из старых принтеров, мебельных направляющих, а из материалов, которые я бы купил сам, и повторил бы станок?» Я сказал, что это вполне возможно, и приступил к реализации мини станка с ЧПУ. Скорее всего, это не последний мини ЧПУ станок в домашних условиях. В ближайшее время сделаю еще пару вариантов.
Сборка самодельного лазерного гравера с ЧПУ.
Механическая часть самодельного лазерного гравера.
Недавно делал узел из карандашей (каретку для ЧПУ), и на основе данной каретки решил собрать лазерный гравер с ЧПУ. Но нужно, как минимум, 2 оси, поэтому собрал второй узел, но немного уже. Вот так выглядят узлы оси X и Y для самодельного лазерного гравера.
Как собирал каретку, можете почитать в предыдущей статье. Про нее могу сказать одно: сделана она из карандашей, строительной шпильки и фанеры.
Закрепил с помощью реек и фанеры узлы осей Y и X. Вот такой каркас станка получился. Пора приступить к электронной составляющей самодельного ЧПУ гравировального станка.
Электроника самодельного лазерного гравера.
Доставать лазер из старого DVD привода не стал, так как меня просили сделать ЧПУ станок, который можно повторить, и все узлы можно было бы купить, например, на AliExpress. Поэтому буду использовать лазерный модуль с TTL контролером от моего лазерного гравера. Обзор гравера можно посмотреть тут.
Лазерный модуль можно использовать в такой самоделке и подешевле, например, на 500 mw.
Так как я увлекаюсь еще и Arduin, то мозгом станка будет Arduino UNO и CNC shield v3. Драйвера буду использовать самые дешёвые A4988. Описание драйверов A4988 читайте в этой статье:
Описание CNC shield v3 читайте в статье:
Для того, чтобы закрепить электронику, сделал заготовку из фанеры, которая будет крепиться с задней стороны гравера.
После чего, закрепил электронику и установил на место, где будет все стоять.
Пришло время все подключить и запрограммировать.
Схема подключения cnc shield v3.0 + arduino uno + TTl и лазер.
Подключаем все компоненты по схеме.
Правда, у меня не установлены концевые выключатели. Схему взял из интернета, самому рисовать стало лень. Но когда буду писать обзорную статью про подключение электроники, обязательно все нарисую.
Как видим, схема достаточно простая, и запутаться тут сложно. Нам нужно к шилду подключить 2 шаговых двигателя. Один подключаем в разъем, где написано X, второй в разъем с надписью Y. Соответственно, один двигатель перемещает по оси X, второй по оси Y.
C подключением лазера будьте внимательны, в зависимости от версии прошивки, подключение TTL к Arduino может быть разным.
Внимание!!! С прошивки GBRL 9.0i были поменяны местами Z-Max (D12) и Spn_EN (D11).
TTL модуль подключаем к D11, который является ШИМ портом, – это необходимо для управления мощностью лазера, с помощью ШИМ.
Теперь, если вы желаете подключить концевик Z_Max, то его необходимо подключить в Spn_EN, а включение лазера необходимо подключать в Z+. Вот такая путаница с распиновкой на шилде.
После подключения уложил провода, чтобы ничего не торчало и не мешало работе станка.
Прошивка для лазерного гравёра на Arduino.
Для того, чтобы гравер заработал, в Arduino нужно загрузить код. Где же его взять? Код писать самостоятельно не нужно. Добрые люди уже написали и проверили работу прошивки на тысячах, а может и на сотнях тысяч различных станках с ЧПУ. Скачать прошивку GRBL 1.1 можно с репозитория, или внизу статьи, в разделе Материалы для скачивания.
Более подробно о прошивке и настройке GRBL 1.1 буду рассказывать в следующей статье.
Настройка и калибровка самодельного станка с ЧПУ.
После того, как мы загрузили прошивку, все настройки будут стандартные, и их нужно поменять под ваш станок. Это не так и сложно, но процесс занимает некоторое время. Для калибровки нужно перемещать по оси лазерный модуль, и смотреть, как точно происходит перемещение. Например, вы переместили на 100 мм, а станок переместился на 102 мм. Это все настраивается в прошивке. Полный процесс калибровки буду рассказывать в следующей статье. А сейчас выложу скриншот моих настроек GRBL 1.1 для лазерного гравировального станка.
Программа LaserGRBL для управления лазерным гравером на Arduino.

Осталось установить программное обеспечения для компьютера, которое позволит гравировать, выбрав понравившуюся картинку. Я буду гравировать векторный логотип сайта и елочную игрушку. Исходники будут в разделе материалы для скачивания.
LaserGRBL поддерживает гравировку растровой и векторной графики, что позволяет облегчить поиск материала для гравировки.
Подробнее о программе LaserGRBL напишу отдельную статью, так как там есть некоторые фишки, которые упрощают работу с лазерным гравером. Некоторые из них вы можете увидеть в видео.
А сейчас покажу, как выглядит исходное изображение, загруженное в программу LaserGRBL, и что получается после гравировки.
Подведём итог.
В домашних условиях собрать лазерный гравер не составит большого труда. Но перед сборкой нужно определиться, чего мы ожидаем. В связи с тем, что данный станок я собрал попутно, то лазерный гравер не является первоначальной задачей. И выбор ходового винта, для данного станка, является не правильным решением. Потому что перемещение происходит медленно, а гравировка делается быстро, и я использовал только 50% мощности лазера. Это не приемлемо. Что же делать? Нужно использовать не ходовые винты, а ременную передачу, что увеличит скорость и плавность перемещения.
Если присмотреться на гравированные изделия, то можно увидеть небольшую рябь. Это связанно с тем, что по оси X ходовой винт имеет изгиб и при перемещении происходит раскачивание лазерной головы. Если такое колебание будет при фрезеровке, то зажатая фреза в материал просто не допустит такие небольшие колебания.
Более подробно настройку станка и программное обеспечение разберу в следующих статьях:
Понравился проект Самодельный Лазерный гравёр с ЧПУ, в домашних условиях? Не забудь поделиться с друзьями в соц. сетях.
А также подписаться на наш канал на YouTube, вступить в группу Вконтакте, в группу на Facebook.
Спасибо за внимание!
Технологии начинаются с простого!
Фотографии к статье
Файлы для скачивания
логотип сайта .svg | 10 Kb | 114 | Скачать Вы можете скачать файл. | |
елочнаяигрушка.svg | 8 Kb | 115 | Скачать Вы можете скачать файл. | |
grbl_v1.1h.zip | 301 Kb | 118 | Скачать Вы можете скачать файл. |
Как сделать фрезерный станок с чпу по дереву своими руками?
Сегодня производитель предлагает множество станков для обработки дерева. Однако стоимость их доступна не каждому. Человек, который обладает теоретическими основами фрезеровки и минимальным набором навыков в сфере данных работ, может изготовить и станки по дереву и лазер для резки дерева своими руками.
Качество функционирования при этом самодельных станков ничуть не уступает промышленным аналогам.
Функции фрезерного станка
Фрезерный станок по дереву выполняет следующие функции:
- поперечное строгание;
- вырезание неровных поверхностей;
- вырезание неправильных форм, их корректура;
- калибровка заготовок;
- распиловка;
- выборка шпунтов, пазов.
Преимущества фрезерных станков с чпу по дереву
Фрезерный станок по дереву своими руками характеризуется многочисленными преимуществами:
- высокая производительность;
- минимизация временных и трудовых затрат;
- возможность получения идентичных деталей;
- длительный срок службы изделия;
- универсальная технологическая оснащённость.
Комплектация фрезерного станка
Базовая комплектация станка для осуществления фрезеровальных работ включает в себя следующие компоненты:
- вращающийся вал;
- режущий инструмент;
- рабочая поверхность;
- суппорт;
- станина;
- двигатель.
Изготовление привода
Для осуществления оперативной и точной фрезеровки необходимо оснастить станок электрическим двигателем. Наиболее оптимальным вариантом будет использование готовых двигателей от различных бытовых электроприборов. Мощность станкового двигателя должна равняться 1 кВт.
Далее на вал электродвигателя необходимо прикрепить насадку, в которую монтируется фреза. Её можно будет снимать и менять. Желательно, чтобы двигатель осуществлял большое количество оборотов. Для того, чтобы фреза вращалась равномерно, необходимо прикрепить маховик на оборотную сторону вала.
Изготовление рабочей поверхности
Рама, или рабочая поверхность, должна иметь горизонтальную поверхность. Поэтому здесь можно использовать готовый столик небольших размеров. Другой вариант исполнения рамы – толстый лист фанеры, обрамленный металлическими уголками.
Поверх столика необходимо прорезать окно для рабочей части фрезы. Под окном, снизу стола, необходимо прикрепить несущий корпус лифта. Эта конструкция позволяет перемещаться электродвигателю с фрезой.
Изготовление лифта для фрезерного станка
Функция лифта – регулирование высоты фрезы над рабочим столом. Лифт состоит из 2 направляющих, каретки с электродвигателем, устройство для подъёма и фиксации фрезы. Для того, чтобы фреза не шаталась, нужно тщательно прикрепить каретку с направляющим. По последним и осуществляет своё движение каретка, изменяя местоположение фрезы. Активируется каретка путём вращения подъёмного механизма.
Фрезерный станок с чпу по дереву своими руками может стать серьезным подспорьем при обработке изделий. Возможности и функции таких станков могут быть самыми различными. Они зависят от того, какие материалы использовались при изготовлении станка, а также от точности следования алгоритма его изготовления.
– Самодельный станок с ЧПУ –
Данный сайт посвящен самодельному станку который подключается к компьютеру.
Разработанный и изготовленный
самостоятельно станок с ЧПУ может выполнять механическую обработку
(сверление, фрезерование) пластмасс, текстолита. Гравировка по стали. Также
может использоваться как графопостроитель, можно рисовать печатные платы. Я
например еще на CD
дисках рисую.
Точность станка 0.0025 мм на 1 шаг, но по факту (с учетом неточности изготовления узлов станка, зазоры в узлах, в паре винт- гайка) точность составляет 0.1мм. Станок без обратной связи, т.е. положение инструмента отслеживается программно, за точность перемещения отвечают шаговые двигатели.
Станок подключается к компьютеру через LPT порт, работает под Windows 98 и XP.
Хотелось бы отметить, что предложенная конструкция станка не является идеальной, а также существует множество конструкций аналогичных станков. В этой статье я лишь опишу станок сделанный мной.
На моем ФОРУМЕ уже 3000 сообщений и информации
больше чем на сайте. И информация свежей. Также там можно задать любой вопрос
по самодельному станку с ЧПУ.
07.11.08 запущен новый сайт VRI-cnc.ru.
Постепенно туда перенесу всю информацию с этого сайта.
На этом сайте обновлений больше не будет!
старый ФОРУМ cnc.4bb.ru для чтения будет доступен
(многим пользователям из Казахстана форум не доступен. Обратитесь к своему провайдеру или используйте прокси)
Новости (статьи):
– 22.10.08 статья о изготовлении станка. Автор Sementon
– 3.09.08 Программа для намоточного станка (станок для намотки трансформаторов и катушек) и описание конструкции станка
– 5.05.08 свежие версии демо 7.3
– 20.04.08 Станок с ЧПУ своими руками.
– 9.04.08 Статья Николая Филенко Актуатор “Супер Мощный Жак”.
– 7.04.08 Статья Николая Филенко КАК РАБОТАЕТ L298?
– 20.03.08 фото станка автор – Ав Эдуард
– 16.03.08 198 фотографий самодельных станков
– 11. 03.08 дополнение к статье Николая Филенко
по ШИМ шаговых движков
– 10.03.08 статья Николая Филенко по ускорению (разгону) шаговых движков
или о при применении ШИМ
– 10.03.08 версия демо обновлена до 7.3 http://vri-cnc.narod.ru/load/VRI73D.ZIP
после тестов выйдет полная версия 7.3. Добавлена поддержка Step/Dir и конечников.
– 24.01.08 вышла следующая версия VRI-cnc 7.2 см. http://cnc.4bb.ru/viewtopic.php?pid=1384#p1384
– 03.11.07 забущен новый форум мой ФОРУМ добро пожаловать!
– 29.09.07 на форум выложил разработки по конвертору BMP в 3D DXF
– 17.09.07 запущен данный сайт.
Прочие увлечения.’) //–> полярные поисковые фразы полярные поисковые фразы2
Самодельный лазерный станок с ЧПУ — libixur — Мой блог
Этим летом прикупил новый Синий лазерный модуль на 2Вт и сразу решил собрать под него станок на ремнях, так как первый мой станок был бы слишком медленным для этого лазера. Для этого станка прикупил более серьезные комплектующие:
- Красный китайский контроллер-драйвер на 4 оси.
- Валы на 12 и 16 мм по одному метру.
- Линейные подшипники на 12 и 16 мм соответственно.
- Шаговые двигателя. Уже не от флоппи дисков.
Долго ломал голову как сделать крепление для подшипников, пока мой друг которого я тоже заразил идеей станкостроения не подсказал мне замечательную идею от которой я рад до сих пор:) И так, первые фото, сегодня их будет много:
На фото присутствует кнопка СТОП которая пока не используется. В будущем соберу корпус для контроллера и поставлю в него кнопку. По поводу креплений, то клипсы для пластиковых труб в этом варианте просто идеальны! Подшипники держат так что я с трудом их мог снять, поэтому даже не пришлось их сажать на клей или закреплять с боков что бы они не выезжали.
Перейдем к сборке. Кстати станок я собрал в удивительно быстрые сроки, всего за 2 дня (нужно было срочно). Первым делом я разрезал купленные валы пополам. Следовательно размеры станка будут 500х500мм:
Дальше изготовление оси Y из фанеры 10мм. Без промежуточных фото, но думаю и так все понятно:
Сделал отверстия и вставил валы. Все сидит туго, поэтому дополнительно не закреплял:
Крепление подшипников на 16 по оси X:
Изготовил переднюю и заднюю стенки станка, а так же сам рабочий стол из фанеры 15мм:
Вставляю валы на 16 и только что изготовленную часть станка. Уже на что-то похоже:
Двигателя и ременная передача.
Ремни, и шкивы были извлечены из 2х старых принтеров:
По скольку шкивы оказались меньше чем я ожидал, и их нельзя было надеть на мои двигателя, пришлось их вставить шкивы которые стояли на шаговом двигателе:
Снял основу лазера, прикрутил к ней подшипники, ремень и с другой стороны пружину для его натяжки:
Установил двигатель, шкив с обратной стороны. По скольку ремень короткий, а лишнего под рукой нет пришлось добавить веревкой. Станок наездил уже примерно 1км и веревка себя нормально чувствует:
Делаю аналогичное для оси X:
Все закрутил, установил лазер и вот результат:
Вот и получился станок без особых наворотов. Как для меня собрать станок за 2 дня уже хорошо:) Скорости передвижения получились хорошие: по Y до 7000 мм/мин, работаю на 5000. По X максимальную не замерял, работаю на 3000 мм/мин. Теоретически скорость могла бы быть больше, но на униполярных двигателях с биполярным контроллером мощность двигателей меньше паспортной. Работаю под управление программы ПАУК, выжигаю портреты и картинки. Изображение выжигается линиями с постоянной мощностью лазера, но с разной скорость передвижения на разных оттенках изображения. Так же пробовал выжигать точками, тоже хорошо получается. Скорость такой гравировки на слух примерно 5-10 точек/сек.
Вот еще дополнительно несколько фотографий:
Сразу хочу предупредить кому будут интересны чертежи — их нет! 🙂 Все продумывалось и расчитывалось на месте.
Фото первых работ. К сожалению на тот момент у меня уже не было цифровика, так что простите за качество фото. Так же видно что были проблемы со съездом картинки:
Человек который подкинул мне идею и креплением подшипников:
Так же сделал себе гравировку на крышку телефона:
На данный момент это все, потом добавлю видео и добавлю фото новых работ.
Добавление: 04.09.2013
Как и обещал, вот видео:
——
—Добавление: 06.

Добавление: 20.12.2013
Станок продан. В новом году будет новый вариант о котором обязательно напишу.
Добавление: 13.07.2015
Нашел качественную фотографию крышки телефона:
VN:F [1.9.20_1166]
Rating: 9.5/10 (120 votes cast)
Самодельный лазерный станок с ЧПУ, 9.5 out of 10 based on 120 ratingsПоделиться ссылкой с друзьями:
Как выбрать шаговые двигатели и контроллеры для станков с ЧПУ своими руками
Когда я решил построить свой первый станок с ЧПУ, резак для пенопласта, я не имел никакого реального представления о том, что мне нужно использовать для шаговых двигателей или контроллера ЧПУ. Я провел довольно много исследований и был поражен объемом информации. Итак, как я выбрал правильные детали?
Ну, в основном я проверил, какие товары наиболее популярны в Интернете для проектов, очень похожих на мой, и надеялся, что все будет в порядке. Это было примерно в 2010 году, когда любители 3D-печати еще ничего не слышали. К счастью, я сделал правильный выбор, и все по-прежнему работает и на 100% надежно.
Я многому научился и теперь у меня есть фрезерный станок с ЧПУ и 3D-принтер. ЧПУ может вызвать привыкание и очень полезно, когда все работает. Но когда это не работает должным образом или не работает вообще, это может быть очень неприятно. Я помог нескольким ребятам по всему миру заставить их машину работать, и восторг, который они проявляют, когда она работает, бесценен.Надеюсь, этот пост поможет вам принять осознанное решение.
Есть так много шаговых двигателей и контроллеров ЧПУ, из которых можно выбирать, как узнать, какой из них выбрать. Если вы будете искать ответы в Интернете, вы, вероятно, будете завалены всей технической информацией.
У меня есть простой метод, который работает без особых технических проблем.
Время от времени я получаю вопросы, например, будут ли эти шаговые двигатели в порядке, какой контроллер ЧПУ мне следует использовать.
Мой метод – посмотреть, какие двигатели используются продавцами, которые продают полные комплекты, очень похожие на мою сборку, и использовать это в качестве отправной точки. Есть способы сделать это с научной точки зрения, которые включают много математических вычислений и инерционных расчетов, но это очень трудоемкий процесс. Если вы заинтересованы, проверьте эту ссылку здесь
После того, как мы выбрали двигатели, все остальное довольно просто. У меня это сработало, и если ваша сборка представляет собой довольно простой маршрутизатор или машину с горячей проволокой, читайте дальше.
Я увлекаюсь своими руками и уже несколько лет использую резак для пенопласта, фрезерный станок с ЧПУ и 3D-принтер, так что я ни в коем случае не эксперт.Но я могу поделиться с вами своим опытом при скромном бюджете с большим успехом, который поможет вам сделать осознанный выбор. Ознакомьтесь с некоторыми из моих проектов с ЧПУ, чтобы увидеть, чего можно достичь.
Шаговые двигатели
Давайте начнем с них в первую очередь, а остальные должны встать на свои места. Вы, вероятно, решили, что собираетесь построить резак для пенопласта или маршрутизатор, и первое, на что вы обычно начинаете смотреть, – это шаговые двигатели. Итак, о чем все это NEMA?
NEMA ( Национальная ассоциация производителей электрооборудования, ) – это стандарт, определяющий размер лицевой панели двигателя. Именно здесь крепежные винты крепят двигатель к раме машины.Это не имеет ничего общего с мощностью двигателя.
Два самых популярных размера для DIY-машин – это NEMA17 (1,7 дюйма x 1,7 дюйма) и NEMA23 (2,3 дюйма x 2,3 дюйма).
В моем 3d-принтере Anet A8 использовалось 4 NEMA17, но мой ЧПУ оригинальный резак для пенопласта и маршрутизатор использовали NEMA23.
Номинальный крутящий момент
Шаговые двигатели рассчитываются по их удерживающему моменту в унциях / дюймах или НМ, Н. см Ньютонах на метр или сантиметр. Например, NEMA23 может указывать 175 унций на дюйм (унций на дюйм).Таким образом, он может удерживать 175 унций на рычаге длиной 1 дюйм, прикрепленном к валу двигателя. Это удерживающий момент. Это полезно для сравнения двигателей
. Нам также необходимо отметить, какой ток будет потреблять двигатель, и какое напряжение необходимо для работы.
Что такое биполярный униполярный
Шаговые двигатели могут быть биполярными или униполярными. Это связано со способом подключения катушек. Не вдаваясь в технические подробности почти во всех случаях, мы используем биполярные двигатели. Биполярные двигатели имеют высокий выходной крутящий момент из-за способа подключения катушек.Но для переключения катушек требуется более сложная схема, это не проблема, потому что драйверные модули делают это за нас. Вы можете заставить однополярный двигатель работать как биполярный, подключив катушки определенным образом, но мы не будем здесь вдаваться в подробности. Почти все двигатели для любительских станков с ЧПУ продаются как биполярные.
Выбор шаговых двигателей
Выбор шагового двигателя во многом зависит от типа станка, который у вас есть или вы собираетесь построить, и от материала, который вы собираетесь резать. Итак, я покажу вам свой подход к выбору двигателей для резака для пенопласта и маршрутизатора.
Для 3D-принтеров в основном используется NEMA17, и из-за их популярности их можно довольно дешево приобрести в виде полных комплектов. Мой ANET A8 сейчас можно купить примерно за 120 фунтов стерлингов / 170 долларов, так что вряд ли он стоит усилий по его созданию. Проверьте мой пост здесь на моем ANET A8
Шаговые двигатели для пенопластов с ЧПУ с горячей проволокой
Когда мы разрезаем пену на станке для резки горячей проволокой, она на самом деле не разрезается, а плавится. Это называется срезанием сиянием. Таким образом, нагрузка на шаговые двигатели практически не связана с горячей проволокой, если ее температура и скорость подачи правильные. Почти вся нагрузка приходится на движущиеся части машины.
Так что NEMA17 подойдет, если ваша машина не слишком тяжелая, что-то около 50-80 унций / дюйм должно быть в порядке. Vortec RC использует NEMA17 в своем наборе. http://www.vortex-rc.com/product/4-axis-diy-hot-wire-cnc-for-rc-hobbyists-aeromodellers-and-designers/
FoamLinx предлагает несколько машин, но на самом деле они не предназначены для любитель, стоимостью несколько тысяч долларов. Однако мы видим, что они используют NEMA23 с номинальной плотностью 220 унций на дюйм на своей небольшой машине.
Мой старый резак для пенопласта с ЧПУ использовал NEMA23 175 унций на дюйм с номиналом 2,8 А. Движущиеся части моей сборки весят немногим более 11 кг или 25 фунтов, так что это немного тяжеловато. Он изготовлен из 3/4 ″ (18 мм) FIbreBoad высокой плотности (HDF), который очень прочный и устойчивый, но довольно тяжелый. Поэтому я решил использовать более крупные шаговые двигатели с рекомендованным источником питания 24 Вольт.
В моем новом обновленном дизайне на 2021 год используется МДФ толщиной 12 мм, в него внесены некоторые изменения и улучшения. Это значительно снижает вес и позволяет использовать степперы NEMA17.Следите за обновлениями, которые скоро выйдут.
Шаговые двигатели для фрезерных станков с ЧПУ
Как правило, вам понадобится NEMA23 от 175 унций и выше, если только ваш станок не очень маленький, например гравер с ЧПУ. Они довольно часто используются для изготовления печатных плат (PCB), и если вы посмотрите описание, они скажут только о мягких материалах.
Итак, давайте рассмотрим пару примеров.
В случае маршрутизаторов режущий материал играет большую роль в нашем решении.Для более твердых материалов потребуется более мощный шаговый двигатель, потому что режущая коронка врезается в материал.
WorkBee от Ooznest в Великобритании, основанный на дизайне OpenBuilds. Он использует NEMA23 175 унций / дюйм. Если вы проверите некоторые из предложений в Интернете для маршрутизаторов 6040 с ЧПУ, вы довольно часто увидите в описании двигатели размером 57, что является метрическим эквивалентом 2,3 дюйма или NEMA23, и они обычно поставляются с двигателями на 175-200 унций
Если вы намеревались резать очень твердые материалы, вам потребуются шаговые двигатели с высоким крутящим моментом, обычно около 300-400 унций / дюйм, и вам, возможно, придется перейти на NEMA34, и вам понадобится прочная рама для поддержки этого.
Контроллеры ЧПУ для станка DIY
Теперь, когда мы знаем, какие шаговые двигатели требуются для нашего проекта, мы можем сопоставить их с подходящим контроллером ЧПУ. Контроллер преобразует созданный нами g-код и отправляет пошаговые импульсы на шаговые двигатели. Он также принимает входные сигналы от машины, такие как концевые выключатели и аварийные остановки.
Итак, нам нужно знать 3 вещи: –
- Кол-во осей. Обычно 3 для маршрутизаторов и 4 для резака для пенопласта
- Ток и напряжение, которые нам нужно подать на шаговые двигатели
- Как мы собираемся подключить компьютер к контроллеру ЧПУ
Количество осей
Фрезерные станки с ЧПУ могут использовать контроллеры с 3 или 4 осями.Есть только 3 плоскости движения X, Y и Z, но в некоторых конструкциях используются два шаговых двигателя на одной оси. Мой фрезерный станок с ЧПУ OX использует два NEMA 23 на оси Y в качестве фрезерного станка портального типа. Некоторые перемещают столик для оси Y на ползунках, и для оси Y требуется только 1 двигатель. Как кровать для 3d принтера
требуются 4 оси, чтобы горячая проволока могла перемещаться в любом направлении в 4-х плоскостях, обычно X, Y, Z и U.
New Foam CutterНеобходимый ток и напряжение для шаговых двигателей
Итак, вы решили, сколько шаговых двигателей вам нужно и какой крутящий момент вам нужен.Тогда остается только подобрать подходящий контроллер. Все контроллеры будут иметь драйверы шагового двигателя, которые могут быть отдельными модулями или интегрированы в плату контроллера. Драйверы шагового двигателя предназначены для подачи тока и напряжения, которые в большинстве случаев регулируются. Важно согласовать ток с шаговым двигателем. Шаговые двигатели могут работать при очень низких напряжениях, но они обычно приводятся в действие при гораздо более высоких напряжениях до 8 раз с помощью драйвера прерывателя. Если вам нужна дополнительная информация, проверьте эту ссылку. Это дает более высокий крутящий момент и скорость.
Если вы используете шаговый двигатель, которому требуется 2,8 А, а ваши драйверы выдают только 1,5 А, он все равно может работать, но медленно и может быть недостаточным для преодоления нагрузки.
Обычно NEMA17 работают от 12 вольт, а NEMA23 24 вольт. Если вы поставите меньше, двигатели будут вращаться медленно или не вращаться совсем. Это связано с тем, что называется ЭДС. Поэтому, когда вы выбираете контроллер, проверьте текущий рейтинг шаговых двигателей и убедитесь, что модули контроллера или драйверов можно отрегулировать так, чтобы они соответствовали как можно точнее, но не подавать больше, иначе двигатель может выйти из строя.
Мой старый резак для пенопласта использовал 57BYGH56-401A NEMA 23, которые рассчитаны на 2,8 А и 3,36 В на фазу. Я использую источник питания на 24 В, а сила тока составляет 2,25 А, установленная с помощью DIP-переключателей на плате. Это работало несколько лет без проблем
Источник питания
Блок питания должен обеспечивать напряжение и ток для выбранных вами двигателей и контроллера. Увеличение тока не повредит, но напряжение должно соответствовать напряжению контроллера.Итак, для моего старого резака для пенопласта я использовал 4 x 57BYGH56-401A NEMA 23 с номиналом 2,8 А, а контроллеру нужно 2 А. Таким образом, 4 x 2,8 ампера плюс 2 ампера для контроллера дают 13,2 ампера. Если мы умножим это на 24 вольта, мы получим ватт в 316,8 ватт. Источники питания могут быть оценены в амперах или ваттах, поэтому я использую источник питания на 15 ампер и 350 ватт.
Для моего последнего резака для пенопласта он использует 4 x 0,9 А, а для контроллера требуется 1 А. Так что мне нужно всего 4 x 0,9 + 1 = 4,6 ампер x 12 В, поэтому мне понадобится только блок питания на 55 Вт.Я бы использовал блок питания 12v 120 Вт. Если мне когда-нибудь понадобится заменить двигатели, я хочу использовать немного более высокий ток, тогда все будет в порядке.
Подключение компьютера к контроллеру ЧПУ
Существует довольно много вариантов подключения вашего компьютера, будь то ноутбук или настольный компьютер, к контроллеру ЧПУ. Подключение также зависит от программного обеспечения, которое вы собираетесь использовать. Mach4, вероятно, наиболее широко используется для маршрутизаторов с ЧПУ. Он был разработан для использования параллельного порта с кабелем DB25 (25 контактов).Параллельный порт теперь устарел, и Mach4 будет работать только на 32-битных компьютерах с Windows с драйвером параллельного порта. Это означало, что Windows XP была последней версией, которую вы могли использовать. Но вы можете использовать его на современных компьютерах со специализированным оборудованием и драйверами. В моей статье содержится более подробная информация о 6 решениях для устаревшего интерфейса параллельного порта Mach4
. Не сбрасывайте со счетов старый параллельный порт, если у вас есть старый настольный компьютер с парой гигабайт оперативной памяти, он будет отлично работать с Mach4 и LinuxCNC. Вы также можете получить их очень дешево. Это очень надежное решение, и я уже много лет его использую на Mach4 и LinuxCNC. Вы также можете купить карты параллельного порта, чтобы добавить их к более современному настольному компьютеру. Таким образом, вы можете выделить компьютер только для ЧПУ. Большинство контроллеров ЧПУ, продаваемых на eBay и Amazon, которые поддерживают Mach4 и LinuxCNC, по-прежнему являются версиями с параллельным портом.
Если вы предпочитаете USB, у вас есть несколько вариантов.
- Используйте контроллер на базе Arduino
- Используйте плату контроллера USB или адаптер для Mach4 или Mach5.LinuxCNC не поддерживает USB
USB-контроллеры на базе Arduino
В 3D-принтерах используется плата на базе Arduino, и они очень популярны. Фрезеры с ЧПУ и резаки для пенопласта также могут использовать их. Единственным недостатком является то, что вам нужно иметь возможность загружать скомпилированную и выгружать прошивку на плату. Это довольно просто, и есть много руководств о том, как это сделать. Вы не сможете использовать Mach4 или Mach5 с этой настройкой. Универсальный отправитель G-кода (UGS), вероятно, является самым популярным программным обеспечением для управления платой.Также есть несколько вилок для резаков для пенопласта. У меня есть подробная статья
USB для Mach4
Для использования USB с Mach4 вы можете купить специализированную плату контроллера с драйверами, поддерживающими Mach4, или переходник USB-параллельный для подключения к старому контроллеру параллельного порта. Это не универсальный адаптер, а специализированный USB-адаптер для ЧПУ. Лучшим из них является UC100. Подробнее здесь
Контроллеры Ethernet
Они используют ваш сетевой порт для подключения к специализированной плате контроллера или адаптеру, который может подключаться к контроллеру параллельного порта, известному как BOB (Break Out Boards). Это работает как для Mach4 / 4, так и для LinuxCNC
.
Предлагаемые конфигурации
В предлагаемых конфигурациях я покажу, что бы я купил, используя следующие критерии.Назначение машины, бюджет и подключение к компьютеру
Фрезерный станок с ЧПУ для резки материалов от древесины мягких пород до алюминия
Если ваш бюджет ограничен и у вас есть старый настольный компьютер с параллельным портом, используйте LinuxCNC с 3- или 4-осевым контроллером и шаговыми двигателями NEMA23, рассчитанными на 175 унций или лучше. Mach4 стоит 175 долларов, так что вы сэкономите на этом, и я сделал полное руководство по этой конфигурации с видео здесь
TB6560 отдельные драйверыЕсли ваш бюджет позволяет, и вы предпочитаете использовать USB с Mach4 / 4, я бы использовал одну из этих коммутационных плат USB с модулями драйверов TB6600 или драйверами Geckodrive G251X.
Устройство для резки пеноматериала с ЧПУ Hot Wire
Если ваш бюджет ограничен, я бы использовал тот же вариант, что и бюджетный маршрутизатор. Если вы предпочитаете использовать USB и с удовольствием загружаете прошивку на платы Arduino, то вариант ниже будет хорошим выбором.
Вам нужно постоянно строить свет, поскольку в нем используются двигатели NEMA17. Моя новая сборка USB Foam Cutter находится здесь http://rckeith.co.uk/how-to-build-a-usb-cnc-hot-wire-foam-cutter/
Я предпочитаю использовать модули драйверов DRV8255 или TMC2100 потому что они могут выдерживать немного больший ток, чем A4988, и всегда используют охлаждающий вентилятор.
Если вы предпочитаете использовать Mach4 / 4 с USB, то подойдет и вариант, описанный выше, для маршрутизатора и с шаговыми двигателями NEMA17 облегченной сборки.
Последние мысли
Как видите, при выборе деталей для сборки нужно многое учитывать. Как я уже говорил ранее, я не являюсь экспертом в этом вопросе, но у меня был хороший опыт фрезерования с ЧПУ, резки пенопласта и 3D-печати, и я надеюсь, что это поможет вам в принятии решений.
Пожалуйста, используйте этот пост в качестве руководства и ознакомьтесь с другими ресурсами, и вы сможете принимать обоснованные решения по своим покупкам.
Ссылки в этом посте являются партнерскими ссылками, что означает, что если вы совершаете покупку у них, я получаю небольшую комиссию. Вы не платите больше, а если и платите, то спасибо. Все это помогает финансировать сайт.
Самодельный станок с ЧПУ
На фото ниже мой самодельный станок с ЧПУ. Он был построен для ускорения сверления отверстий в самодельных печатных платах для других электронных проектов. Это был увлеченный проект, который разрабатывался в течение года по вечерам и по выходным, работая штатным инженером.Для его создания потребовались все мои навыки и изучение новых, включая проектирование и обработку механических деталей, проектирование электронных схем и, конечно же, много программирования. Он максимально самодельный, большинство механических компонентов делаю сам на фрезерном станке G0704, а его дизайн, вдохновленный другими проектами DIY, полностью мой.
Ниже приводится краткое видео о работе станка с ЧПУ, сверление 0. Отверстия 7мм в пустой плате.
Блок-схема системы
Основные части системы показаны на схеме ниже. Основа системы – микроконтроллер ATmega328P, который получает команды GCODE от управляющего ПК через UART. ATmega328P получает местоположение для перемещения шпинделя ЧПУ, вычисляет путь и дает команду шаговым двигателям двигаться по осям X, Y и / или Z.
Каждый из трех шаговых двигателей приводится в действие платой EasyDriver.Это упрощает управление с точки зрения микроконтроллера и уменьшает количество требуемых выводов, поскольку каждый шаг управляется импульсом от одного соединения. Кроме того, каждый драйвер имеет соединение для управления направлением и одно для управления режимом (1/8 шага против полного шага).
Программа главного компьютера
Чтобы отправлять команды микроконтроллеру, запускать сценарии, отображать местоположение и т. Д., Я написал программу для хост-компьютера или консоль GCODE, как я буду называть ее с этого момента.Он полностью написан на Python и использует библиотеку wxWidgets для графического интерфейса. Снимок экрана этой программы показан ниже.
Программа использует потоки для постоянного обновления отображения на главном экране, одновременно выполняя сценарии в фоновом режиме.
Краткое изложение основных функциональных областей программы показано ниже.
ATmega328P Программа
Atmega328P требовалась способность переводить команды, поступающие с главного ПК, в движение шаговых двигателей.Исходный код этой программы можно найти здесь. Общий вид программы показан на диаграмме UML ниже. Программа Atmega328P считывает команды через свое оборудование UART и сравнивает их со списком допустимых команд. Если команда запрашивает перемещение по диагональной линии или по кривой, координаты команды пропускаются через алгоритм, который вычисляет наиболее близкое приближение к указанной линии или кривой с использованием дискретных шагов. Эти шаги отправляются в виде импульсов на микросхемы ИС шагового двигателя, которые перенаправляют мощность от источника 12 В для управления отдельными линиями шагового двигателя.
Алгоритм определения шаговых импульсов для аппроксимации диагональной линии или кривой был адаптирован из этой статьи Кеннета и Мелвина Голдбергов, озаглавленной «Алгоритмы интерполяции XY».
Макет
В настоящее время схема все еще находится в макетной форме. В настоящее время я работаю над дизайном в EAGLE, чтобы преобразовать его во что-то более постоянное.
Механические и электрические детали
Шпиндель, используемый в этом проекте, имеет воздушное охлаждение мощностью 400 Вт и был приобретен здесь у RATTMMOTOR. Он использует отдельную плату управления для установки скорости и работает от этого источника питания 48 В.
Ходовой винт и соответствующее оборудование, используемое в этом проекте для управления осями, являются общими для большинства 3D-принтеров.
Остальные детали были изготовлены из 6061 алюминиевых прямоугольных профилей толщиной 1/4 дюйма.
Зачем?
Этот проект был попыткой упростить изготовление печатных плат для других проектов. До сих пор я вручную обрабатывал каждое отверстие в плате, которое делаю, что может занимать очень много времени. Например, на плате ниже, разработанной мною для ATmega328P, более 50 отверстий!
Шаг за шагом к созданию домашнего фрезерного станка с ЧПУ | by Roctech CNC Router
Одним из аспектов любого домашнего фрезерного станка с ЧПУ является использование каждого материала в конструкции станка по сравнению с количеством этого материала, которое вы должны купить. Вы строите только одну машину, поэтому вам не нужно покупать больше материалов, чем нужно для сборки этой машины. Это особенно необходимо учитывать при выборе желаемой длины хода для каждой оси, потому что это решение влияет почти на все остальные части станка. Это был основной процесс проектирования моего станка с ЧПУ.
1. Решите, какая длина хода вам нужна для каждой оси (если у вас есть конкретный проект для вашего ЧПУ, начните с требований к его размерам)
2.Решите, какой тип системы линейного перемещения вы будете использовать для станка
3. Решите, какой тип линейного привода вы будете использовать для каждой оси
4. Решите, какой тип приводного двигателя и контроллера вы будете использовать
5. Определитесь с выбором материал, который вы будете использовать для создания машины
6. Основываясь на предыдущих решениях, спроектируйте машину на бумаге или в программном обеспечении САПР по вашему выбору (это не обязательно должен быть полный дизайн, достаточно, чтобы вы знали общее количество необходимые материалы)
7. Определите, понадобятся ли вам какие-либо специальные инструменты для вашей конструкции.
8. Определите общую стоимость вашей конструкции, которая включает стоимость инструментов, которых у вас может не быть.
9. Решите, что вы не можете тратить столько денег на машину. и вернуться к шагу 1
Я прошел через этот процесс 5 раз, прежде чем перейти к окончательному дизайну. На фотографиях показаны различные версии маршрутизатора по мере развития моего дизайна. Я знаю, что большинство людей сочли бы это излишним, но для меня все это важно.Я знал, что как только я закончу сборку машины, у меня будет что-то, что соответствует моим потребностям и моему бюджету, без каких-либо проблем с плохим планированием.
Вот мои мысли по каждому из описанных мною этапов проектирования:
1. Travel : Моей первой мыслью о фрезерном станке с ЧПУ было создание форм для вакуумно-формовочной машины, которую я уже построил. Поэтому я решил построить машину с ходом примерно 12 x 24 x 6 дюймов, потому что именно так велика формующая плита на моем вакуум-формовочном станке.
2. Линейное перемещение : Есть много вариантов линейного перемещения. Обычно используемые методы для фрезерных станков с ЧПУ включают в себя направляющие выдвижных ящиков, подшипники скольжения, подшипники с V-образной канавкой, круглую линейную направляющую и профильную линейную направляющую. Они заказаны с точки зрения стоимости, я бы порекомендовал выбрать лучшую систему, которую вы можете себе позволить. Вы можете сэкономить деньги на других частях станка, но хорошая система движения окупится качеством резки. Я выбрал круглую линейную направляющую. В этой системе используются прецизионные шлифованные и закаленные стальные валы и линейные подшипники, в которых используются маленькие стальные шарики, которые катятся по валу и рециркулируют по каналам внутри подшипника.Это обеспечивает плавное движение с низким коэффициентом трения и хорошее сопротивление силам, действующим на подшипник в любом направлении. Есть много разных производителей этих типов рельсов и подшипников, и их стоимость может сильно отличаться. Рельсы и подшипники я купил у продавца в Китае на ebay. Магазин ebay – это линейные двигатели, и цены были лучшими, которые я нашел в Интернете. Они часто продают комплекты с тремя наборами направляющих и двумя подшипниками для каждой направляющей, что необходимо для 3-осевого ЧПУ. В комплекте, который я получил, используются длинные направляющие 20 мм x 800 мм для оси x, длинные направляющие 16 мм x 500 мм для оси Y и длинные направляющие 12 мм x 300 мм для оси z.Этот комплект стоил мне 223 доллара с доставкой.
3. Линейный привод : Три основных варианта привода каждой оси фрезерного станка с ЧПУ – это поликлиновые ремни, винты и зубчатая рейка. Самыми распространенными на DIY-маршрутизаторах с ЧПУ являются винты ACME, шарико-винтовые пары, а также реечные установки. Системы винтовых приводов работают, прикрепляя гайку к подвижной части каждой оси, затем резьбовой стержень пропускается через гайку и фиксируется на обоих концах. Винт вращается приводными двигателями, и гайка перемещается по винту. Винты ACME имеют трапециевидную резьбу, которую нарезают или скручивают в стальной стержень. Резьба ACME используется на обычных C-образных зажимах. Их форма резьбы делает винт более прочным, чем резьба на стандартных болтах. Когда эти резьбы нарезаны с высокой точностью, они идеально подходят для работы на фрезерном станке с ЧПУ. Вероятно, самый распространенный и дешевый размер резьбы ACME составляет 1/2 “-10”. Это означает 1/2 “в диаметре и 10 витков на дюйм. Десять витков на дюйм означает, что если винт закручен примерно в 10 раз, прикрепленная гайка сдвинется на 1 дюйм вдоль винта.Для винта любого размера на винте можно нарезать несколько отдельных резьб, это называется числом заходов винта. Однозаходный винт имеет одну резьбу, двухзаходной – две, а пятизаходной – пять. Какое значение имеет несколько резьб на винте? Есть две вещи, которые делают несколько стартовых винтов лучше для станков с ЧПУ. Первые несколько пусковых винтов более эффективны при превращении вращающей силы на винте в линейную силу на гайке.
Это означает, что приводным двигателям требуется меньший крутящий момент для перемещения каждой оси.Во-вторых, несколько стартовых винтов увеличивают шаг винта, то есть то, насколько далеко гайка переместилась бы, если бы винт был повернут один раз. Чтобы определить шаг винта, разделите количество заходов на количество витков на дюйм. Например, винт ACME 1/2 дюйма -10,5 дюйма будет иметь шаг 5/10 или 1/2 дюйма. Это означает, что при каждом обороте винта гайка перемещается на 1/2 дюйма. Это важно, потому что электродвигатель привода может создавать наибольший крутящий момент на низких скоростях, а с более высоким шагом гайка будет перемещаться дальше за один оборот винта, а это означает, что двигатель может вращаться на более низкой скорости для перемещения оси станка. .Для своей машины я выбрал прецизионный винт ACME 1/2 ”-10, 5 пусков от Mcmaster Carr для всех трех осей.
Еще одна важная вещь, которую следует отметить, – это точность посадки между гайкой и винтом. Стандартная гайка на болте будет немного покачиваться вперед и назад, и в терминах ЧПУ это называется люфтом. Вы хотите уменьшить количество люфта между гайкой и винтом, потому что каждый раз, когда винт меняет направление вращения, этот небольшой люфт в гайке смещает ваше положение ЧПУ, и ваши детали могут выходить неверного размера.Есть способы как с аппаратным, так и с программным обеспечением, которое вы используете, чтобы уменьшить количество люфтов, которые у вас есть. Со стороны программного обеспечения есть простые настройки, которые могут компенсировать люфт, а со стороны оборудования вы можете использовать гайку против люфта. Я купил гайки с люфтом в dumpsterCNC, и снова вы можете найти номера деталей в списке деталей. Обычно эффект люфта может быть уменьшен до такой степени, что детали можно изготавливать с точностью до нескольких тысяч дюймов.
1. Приводной двигатель : Для фрезерных станков с ЧПУ существует два основных варианта: шаговые двигатели или серводвигатели.Шаговые двигатели используются в подавляющем большинстве DIY-маршрутизаторов с ЧПУ. У CNCroutersource есть отличная информация, сравнивающая эти два типа двигателей. Ключевое различие в этих двигателях заключается в том, что серводвигатели обеспечивают обратную связь по положению, чтобы гарантировать правильное позиционирование, а шаговые двигатели – нет. Я решил использовать для своей машины шаговые двигатели в основном из-за стоимости. Серводвигатели более дорогие и требуют более дорогих контроллеров, чем сопоставимые шаговые двигатели для типоразмеров, которые обычно используются на маршрутизаторах с ЧПУ.Также шаговые двигатели широко поддерживаются сообществом DIY-маршрутизаторов и доступны во многих розничных магазинах. Изучая шаговые двигатели и контроллеры, я обнаружил множество вариантов и цен в диапазоне от менее 100 до более 500 долларов. Решая, что приобрести для своего станка, я пришел к выводу, что эти системы настолько универсальны, что я мог бы использовать свой контроллер и даже шаговые двигатели для других проектов с ЧПУ в будущем. Зная, что я хочу получить хорошую производительность и долгосрочную надежность, я решил использовать компоненты американского производства от Gecko.
Я купил шаговый контроллер Gecko G540, который может управлять до 4 шаговых двигателей одновременно и подключается к компьютеру через параллельный порт. Я также купил 4 шаговых двигателя NEMA 23 на 280 унций у компании Gecko, которые также производятся в Америке. Управляющее программное обеспечение, которое я решил использовать, называется Mach4 и использует параллельный порт компьютера для отправки сигналов на G540, который управляет шаговыми двигателями. Управляющее программное обеспечение Mach4 с ЧПУ можно загрузить и использовать бесплатно, но его действие ограничено, пока вы не купите программное обеспечение за 150 долларов.Mach4, вероятно, является наиболее широко используемым программным обеспечением для DIY-станков с ЧПУ и хорошо поддерживается.
2. Конструкционный материал : Большинство DIY-фрезерных станков с ЧПУ построено из МДФ, алюминиевого профиля или стали. С МДФ легко работать и дешево покупать, и многие строители-новички используют этот материал. Щелевой алюминиевый профиль, обычно выпускаемый компанией 80/20, используется во многих чертежах DIY-маршрутизаторов с ЧПУ, доступных в Интернете. Он предлагает множество вариантов дизайна из-за большого количества монтажных кронштейнов и конфигураций, которые позволяет конструкция с прорезями.Экструзия алюминия также будет самым дорогим из трех методов, которые я перечислил. Сталь также используется для изготовления многих маршрутизаторов своими руками. Квадратные, угловые и плоские трубы – обычное дело, и их обычно можно купить на месте. В большинстве случаев стальные станки свариваются друг с другом, поэтому необходимы сварщик и способность сваривать. Сталь, как правило, будет дешевле, чем экструзия алюминия. Я решил использовать стальную трубу размером 1 x 2 x 0,065 дюйма для изготовления фрезерного станка с ЧПУ. Мне удалось купить одну 24-футовую деталь у местного поставщика стали, Industrial Tube and Steel.Они даже разрезали его пополам, чтобы я мог погрузить его в машину. Если у вас нет местного поставщика стали, я бы посоветовал обратить внимание на speedymetals, я покупал у них раньше, у них хорошие цены и быстрая доставка.
У меня есть опыт сварки и я работаю сварщиком с флюсовым сердечником, который похож на сварочный аппарат MIG, но не требует защитного газа. Если вы хотите получить больше информации о сварке, взгляните на это замечательное руководство от Фила Б. Обучение сварке. Использование стали также требует использования инструментов для обработки металла.Я использовал небольшую горизонтальную ленточную пилу, чтобы разрезать трубы, и небольшой настольный сверлильный станок, чтобы просверлить отверстия. Я включил в это руководство несколько советов по работе с металлом и некоторые инструменты, которые значительно облегчают жизнь.
3. Дизайн : Вы можете использовать любое удобное программное обеспечение при проектировании машины. Можно даже просто нарисовать машинку на бумаге. 123D от Autodesk и SketchUp от Google – это бесплатные программы для 3D-моделирования, которые вы можете использовать. Многие детали, которые я использовал в этой машине, были произведены компанией McMaster-Carr. На их веб-сайте представлены чертежи многих товаров, которые они продают, включая 3D-модели, которые можно загрузить бесплатно.
4. Инструменты : Я использовал ряд инструментов для создания своего станка с ЧПУ, и они перечислены на шаге Инструменты. Некоторые инструменты предназначены только для работы с металлом и необходимы для получения наилучших результатов. Я также сделал несколько собственных инструментов, чтобы упростить сборку этой машины.
5. Стоимость : Я оценил свои затраты на полную машину и электронику примерно в 1500 долларов.
Теперь вы знаете мои решения и, надеюсь, понимаете мои рассуждения. Думаю, у меня неплохая комбинация деталей, которая превзошла мои ожидания. Если вы решите построить машину на основе моих планов, у меня все изложено в следующих шагах.
фрезерный станок с ЧПУ по дереву
Фрезерный станок с ЧПУ
Фрезерный станок с ЧПУ 4 оси
Фрезерный станок с ЧПУ 3 оси
Фрезерный станок с ЧПУ
5-осевой фрезерный станок с ЧПУ
Самодельный фрезерный станок с ЧПУ
В этой статье я описываю конструкцию механики моей собственной разработки , фрезерный станок с компьютерным управлением.
Зачем мне делать фрезерный станок с ЧПУ?
Когда я делал свои проекты, я дошел до того, что некоторые вещи я просто не мог реализовать. Итак, было ясно, что мне нужен фрезерный станок с ЧПУ.
Конечно, купить фрезерный станок было бы не вариант, потому что это было бы очень скучно (правда?). Я бы показал вам чертеж в САПР моего фрезерного станка с ЧПУ, но, к сожалению, он существует только в моей голове.
Алюминиевые профили с линейными подшипниками в качестве базовой конструкции
Я решил построить фрезерный станок с алюминиевыми профилями и алюминиевыми пластинами.
На следующих фотографиях вы можете увидеть алюминиевые профили, которые я полностью засыпал песком и заделал концы эпоксидной смолой, чтобы машина была более устойчивой и имела меньше вибрации.
На эти алюминиевые профили я наконец установил линейные подшипники. Здесь вы можете увидеть ось Y:
Т-образные гайки очень дороги, поэтому я решил изготовить свои собственные для установки линейных подшипников. Купил плоский прокат, просверлил отверстия и нарезал в нем резьбу.
Конструкция базовой рамы
В то время у меня не было фрезерного станка, поэтому мне пришлось обрабатывать все алюминиевые пластины и профили напильником и пилой.Для следующих двух алюминиевых пластин толщиной 15 мм мне потребовалось много времени, чтобы распилить их лобзиком: 2–3 часа на пластину.
Здесь вы можете увидеть окончательную базовую раму:
Вся рама прикручена с помощью болтов. На правом рисунке вы можете видеть ось Y, которая в то время не была прикручена к базовой раме.
Поворотные шариковые шпиндели для высокой точности
Из-за того, что я установил линейные подшипники, мне также пришлось использовать вращающиеся шариковые шпиндели.На стороне двигателя вращающиеся шариковые шпиндели установлены на неподвижных подшипниках (каждый состоит из двух угловых шарикоподшипников), а на другой стороне – на плавающих подшипниках (каждый состоит из одного радиального шарикоподшипника).
Конструкция оси Z
Изображения оси Z не самые лучшие, но я думаю, что вы можете увидеть основную конструкцию:
Двигатель
Вначале двигатель (включая неподвижный подшипник) закреплялся несколькими алюминиевыми пластинами, в которых просверливались отверстия разного размера.Позже, когда я наконец смог фрезеровать, их заменили обработанные алюминиевые блоки, показанные на правом рисунке. Двигатель имеет крутящий момент 3 Нм и разрешение 200 шагов на оборот. При работе с 16-ю ступенями на один оборот приходится 3200 шагов.
Окончательный фрезерный станок с держателем для ноутбука
Здесь вы можете увидеть финальный фрезерный станок с ЧПУ:
Конечно, я также установил подходящий держатель для ноутбука …
Make CNC DIY Projects & Products
Добро пожаловать в makeCNC
Лучший маленький проект с ЧПУ и магазин моделей в сети!
Мы также на Facebook с еженедельными новостями!
https: // www. facebook.com/MakeCNC
Мы предоставляем загружаемые шаблоны, программное обеспечение, оборудование и другой контент для лазерных резаков, фрезерных станков с ЧПУ, плазменных, гидроабразивных станков, фрезерных станков с ЧПУ и других роботизированных инструментов. Мы также предоставляем наши файлы шаблонов в формате PDF для пользователей спиральной пилы. Мы известны своим дружелюбным и эффективным обслуживанием клиентов, и мы часто предоставляем новые шаблоны и контент
Что можно построить с помощью фрезерного станка с ЧПУ?
Фрезерный станок с ЧПУ (или фрезерный станок с ЧПУ) – это универсальный станок, который используется для резки различных материалов, а именно пластика, пенопласта, дерева, стали, алюминия и композитов.
Аспект «числового программного управления» – это способность станка планировать траектории движения инструмента, что позволяет ему создавать несколько типов продуктов с высоким уровнем точности и низким уровнем потерь материала. Может показаться, что это займет некоторое время, но это просто неверно, фрезерные станки с ЧПУ работают на удивление быстро, так что вы увидите свой шедевр в кратчайшие сроки.
Кроме того, вы можете купить множество различных «бит» для своей машины. Назовем несколько: стружколомы, фрезы с прямой канавкой, алмазные фрезы и компрессионные фрезы.Все они имеют разное использование и стоимость, которые, в зависимости от вашего проекта, могут вам понадобиться, а могут и не понадобиться.
Деревянные Проекты
Вы можете использовать фрезерные станки с ЧПУ для работы с деревом, вырезая на нем изображения или вырезая его насквозь, а затем собирая его с помощью шурупов, гвоздей или столярного клея.
Дизайнеры, художники и любители любят использовать эту машину для изготовления рам, сложной резьбы на дверях, декоративных панелей, сырных досок, пазлов и даже музыкальных инструментов.
После того, как вы вырезали и собрали свою деталь (например, после того, как вы сделали каждый компонент для стула и зафиксировали все вместе), некоторые люди любят добавлять дополнительные украшения, выполняя пирографию (сжигание дерева с помощью специального инструмента для создания искусства) .
Металл Проекты
Эти устройства могут измельчать металл в больших или малых масштабах, но в основном они используются для изготовления деталей машин на заводах. Благодаря мелким деталям их можно запрограммировать на производство любого размера и формы, в зависимости от работы, которую необходимо выполнить.
Каменные Проекты
Вы можете купить специальные фрезерные станки с ЧПУ для каменных проектов, однако, если вы не работаете только с этим материалом, вам будет лучше приобрести универсальный.
Фрезы по камню специально изготовлены для резки искусственного камня, гранита, надгробий и даже стекла. На изделиях можно вырезать предметы искусства и узоры, а также аккуратно вырезать их.
Проекты пенополиуритана
Резать этот материал вручную может быть довольно сложно, особенно если вам нужны сложные формы.К счастью, фрезерные станки с ЧПУ легко сделают это за вас. В зависимости от типа пены они могут даже вырезать рисунки на поверхности, если вы захотите.
Прочие проекты
Большинство владельцев фрезерных станков с ЧПУ, как правило, занимаются деревообработкой и художественными проектами, но машины также используются в машиностроении для изготовления прототипов.
Производители используют эти маршрутизаторы, чтобы предоставлять своим клиентам стабильную и качественную продукцию без необходимости выполнения каких-либо ручных работ по резьбе или дизайну, что экономит время и деньги компании.
Проектирование напильников
Красота владения фрезерным станком с ЧПУ заключается в том, что вы можете создавать свои собственные вырезанные файлы, позволяющие создавать совершенно индивидуальные проекты.
AutoCAD (CAD означает автоматизированное проектирование) – это программа для рисования, используемая для запуска процесса создания вашего продукта. В AutoCAD вы создадите свой проект и создадите файл DXF (формат обмена чертежами).
На ваш выбор доступно различное программное обеспечение, имеющее разный ценовой диапазон и простоту использования.Тем не менее, в Интернете есть множество руководств, которые шаг за шагом показывают, как работает каждое конкретное программное обеспечение, так что, если у вас есть глаз на дизайн, все готово.
После рисования программа CAM (автоматизированное производство) преобразует ваше изображение в G-код, который затем управляет вашим маршрутизатором с ЧПУ. Ваш дизайн никуда не денется, поэтому вы можете воссоздавать одно и то же снова и снова – идеально для оптовых заказов.
Покупка напильников
однако вы просто хотите начать работу и быстро увидеть готовый продукт, вы можете приобрести огромное количество файлов нарезки в Интернете!
Дизайн включает в себя все, от динозавров, транспортных средств, держателей для ручек и ящиков для хранения до мини-головоломок, замков, велосипедов и даже мебели.
Теперь мы уверены, что вы знаете, что художественные работы и объекты, которые вы можете создать с помощью этого станка, безграничны, и, с быстрым ростом области технологий, маршрутизаторы с ЧПУ будут становиться все более совершенными с точки зрения их общих возможностей и поразительной точности .
Как настроить Arduino и gShield
gShield потрясающий. Вы можете построить 3-осевой контроллер ЧПУ своими руками менее чем за 80 долларов!
Этот пост проведет вас через пошаговый процесс настройки вашего собственного контроллера ЧПУ DIY. Если вы хотите сразу погрузиться в работу, загрузите Quick Start Guide здесь. Если вы застряли, вернитесь сюда, чтобы найти подробные инструкции по установке. Удачи!
Введение
Мне нравится gShield от Synthetos! Нет, мне не платят за это. Электроника пугает меня, как твердолобого механика. Я не могу сказать почему, они просто кажутся загадкой. Я получаю механические вещи. Я вижу, как это работает. Я не вижу электронов на печатной плате или нулей в программном обеспечении.
Введите Arduino. Это создало для меня совершенно новый мир. Это почти неразрушимо. Я имею в виду, что уже несколько лет пытаюсь дать производителям курить из устройства. (Давняя шутка заключается в том, что производители вкладывают дым в электрические компоненты, который выпускается, когда кто-то облажается, и они поджаривают чип, что демонстрирует выходящий дым.) Комбинация Arduino с grblShield позволила мне создать контроллер ЧПУ своими руками для менее 80 долларов! Это безумие! И что самое приятное, я не привязан к якорю ПК с параллельным портом, который обычно требуется для работы драйверов шагового двигателя.
Поправьте меня, если я ошибаюсь, но я не знаю ни одного промышленного контроллера ЧПУ, который использует что-либо, кроме параллельного порта. Я имею в виду давай! Я не знаю ни одного принтера, который все еще использует параллельный порт. Пожалуйста, помогите ему избавиться от страданий. Хорошо, моя тирада закончена.
Одним из огромных преимуществ grblShield с Arduino является возможность использовать обычное старое USB-соединение. Добро пожаловать в 21 -й век. Я знаю, что не падай со стульев. Моя мини-фабрика по страхованию гавани не такая уж и большая.Я действительно не хотел, чтобы контроллер был больше мельницы. Если бы мне пришлось использовать параллельный порт, это означало бы найти старый ПК со стабильной версией Windows и, вероятно, использовать Mach4. Я не хотел с этим связываться.
Нажмите здесь, чтобы посмотреть видео на YouTube.
Ниже приводится пошаговое руководство по созданию 3-осевого контроллера ЧПУ DIY.

Обратите внимание, что некоторые из приведенных ниже ссылок являются партнерскими. Если вы решите совершить покупку по одной из приведенных ниже ссылок, я получу небольшую комиссию, которая поможет поддерживать этот сайт. Если нет, то это тоже хорошо. В любом случае ваша цена, которую вы платите, не изменится. Вы можете узнать больше о раскрытии информации о моей партнерской программе здесь.
Необходимое оборудование…
- Arduino UNO или клон Я неравнодушен к SparkFun RedBoard – запрограммирован с Arduino
- gShield можно приобрести у Synthetos
- Источник питания (12 или 24 В) импульсный источник питания с одним выходом Mean Well SE-200-24 24 В 8.8A Я использовал источник питания 24 В, потому что grblShield рассчитан на 30 В и 2,5 А на драйвер. Я хочу увеличить мощность, насколько я могу вспомнить, P = IV, где P = мощность, I = ток и V = вольт.
Если я скажу, что удвоить напряжение с 12 до 24, я удвою мощность, если ток I.
Пример 12 В – 2,5 А x 12 В = 30 Вт
Пример 24 В – 2,5 А x 24 В = 60 Вт
Кроме того, у большинства источников питания на 24 В есть винт регулировки напряжения, который позволяет мне получить около 28 В и еще больше увеличивает мощность на шаговый двигатель.
- Шаговый двигатель (и) NEMA23 425 унций / дюйм 2,8 A Шаговый двигатель ¼ ”Двойной вал
- ПК или ноутбук с USB-портом ASUS Netbook
- Монтажный провод (многожильный калибр 14 или 16) 4-жильный экранированный кабель 18 AWG (25 футов)
- Штекерный конец для блока питания Шнур питания переменного тока 6 футов 18 AWG 3 штыря
Вам также необходимо иметь под рукой следующие инструменты…
- Мультиметр – У меня есть измеритель плавности хода, который я купил в продаже несколько лет назад для других вещей.Они работают очень хорошо, но вы можете получить хороший счетчик за 10-20 долларов.
- Маленькая отвертка Паяльник
- – в зависимости от возраста вашего Arduino вам может потребоваться переставить перемычку
- Кусачки
- Инструмент для зачистки проводов
- Нож X-acto или аналог
Получите краткое руководство здесь
Обзор
- Загрузите и установите программное обеспечение grbl на свой Arduino
- Загрузите и установите универсальный отправитель Gcode на свой компьютер
- Подключите источник питания (подтвердите полярность источника питания и установите напряжение 110 В переменного тока)
- Подключаем блок питания к grblShield и тестируем
- Подключите grblShield к Arduino
- Проверить соединение
- Подключите шаговый двигатель к grblShield
- Проверить шаговый двигатель
Шаг 1. Загрузите и установите программное обеспечение grbl на свой Arduino
Следующий метод использует Arduino IDE (интегрированная среда разработки) для загрузки программного обеспечения grbl в Arduino. Этот процесс очень похож на загрузку «скетча» в ваш Arduino. Если вы не знакомы с загрузкой программного обеспечения в Arduino или у вас нет последней версии программного обеспечения Arduino на вашем ПК, то потратьте несколько минут, чтобы загрузить последнюю доступную IDE, нажав здесь.
- Перейдите на домашнюю страницу grbl на GitHub, нажав здесь.
- Щелкните по кнопке «Загрузить ZIP» в правой части экрана. См. Рисунок ниже.
Скриншот страницы GitHub для программы grbl.
- Сохраните файл на свой компьютер и разархивируйте, чтобы создать папку grbl-master. Я поместил папку grbl-master в свою папку Arduino. Файловая структура будет выглядеть примерно так… / Arduino / grbl-master (обратите внимание, что путь установки Arduino по умолчанию – «C: \ Program Files (x86) \ Arduino»)
- Откройте Arduino IDE и убедитесь, что у вас установлена как минимум версия 1.8.10 (вы можете проверить, какая у вас версия Arduino IDE, перейдя в раскрывающееся меню «Справка» и выбрав «Об Arduino»).
- Затем вам нужно добавить библиотеку GRBL в IDE Arduino.Щелкните меню « Sketch », затем выберите « Включить библиотеку », затем выберите « Добавить библиотеку .ZIP »
- Найдите папку «Grbl», загруженную с сайта GRBL github (обратите внимание, что вам нужно будет щелкнуть папку «Grbl-Master», чтобы перейти в папку «Grbl». Если нет, вы получите сообщение об ошибке.)
- Щелкните раскрывающееся меню « Файл », затем « Примеры », затем « grbl » (это, вероятно, будет в самом низу меню) и, наконец, « grblUpload ».Откроется эскиз GRBL, который необходимо загрузить в Arduino.
- Подключите ваш Arduino и выберите com-порт, используемый вашим Arduino, используя раскрывающееся меню « Tools », затем « Port ».
- Загрузите эскиз GRBL на свой Arduino – обязательно выберите com-порт, который использует ваш Arduino
Обратите внимание, когда я писал этот пост, последняя версия Arduino была 1. 61
Шаг 2 – Загрузите и установите отправитель Gcode на свой компьютер
Это программное обеспечение загружается на ваш компьютер и отправляет Gcode в Arduino.UniversalGcodeSender – это программное обеспечение на основе Java, для которого на вашем компьютере должна быть установлена как минимум Java 7. Вы можете проверить, установлена ли на вашем компьютере Java, перейдя сюда.
Нажмите кнопку «Активировать Java» в центре экрана, чтобы определить, установлена ли Java на вашем компьютере.
Чтобы загрузить последнюю версию Java, перейдите сюда. Обязательно обратите внимание при установке. Существует флажок, который позволяет изменить вашу поисковую систему и домашнюю страницу на «Yahoo.«Если вы не хотите, чтобы это произошло, обязательно снимите флажок. См. Снимок экрана ниже.
Обязательно снимите этот флажок во время установки Java, иначе поисковой системой по умолчанию будет Yahoo.
Теперь об установке универсального отправителя Gcode…
- Перейдите на домашнюю страницу Universal gCode Sender на GitHub, нажав здесь.
- Прокрутите страницу вниз до раздела «Загрузки». Мне нравится работать с последней стабильной сборкой в корпусе
1.0,81,0,9
- Щелкните номер версии, которую хотите загрузить.
- Распакуйте папку и поместите ее в папку «Program Files».
- Наконец, создайте ярлык на рабочем столе для расширения UniversalGcodeSender.jar, щелкнув файл правой кнопкой мыши и выбрав «отправить на», затем «рабочий стол (создать ярлык)».
- Дважды щелкните файл UniversalGcodeSender.jar
Вот и все! Программный бит готов. А теперь давайте соберем оборудование.Вы на правильном пути к запуску своего DIY-контроллера ЧПУ.
Шаг 3. Подключите источник питания (подтвердите полярность и установите 110 В переменного тока)
ПРЕДУПРЕЖДЕНИЕ – Будьте здесь предельно осторожны. Вы имеете дело с переменным током 115 В (бытовая сеть), что может быть очень опасно. Если вы не знаете, что делаете, обратитесь к лицензированному специалисту, который поможет вам.
- Найдите переключатель входной мощности на источнике питания и установите его в соответствии с напряжением сети переменного тока, которое вы планируете использовать.Это действительно важно. Если переключатель установлен неправильно, вы выведите из строя блок питания. В моем случае я установил переключатель в положение «115 В переменного тока». См. Рисунок ниже.
Селекторный переключатель входа напряжения переменного тока, расположенный сбоку источника питания.
- Найдите донорский шнур питания для блока питания. Я использовал старый шнур питания ПК и отрезал женский конец.
- Удалите примерно 1,5 дюйма (дюйма) внешней оболочки кабеля. Будьте осторожны, чтобы не порезать проводники внутри кабеля.Я использовал острый нож Xacto с несколькими световыми проходами. Я не прорезаю полностью. Вместо этого я беру конец и разрезаю оболочку кабеля по линии разреза.
- Зачистите изоляцию примерно на 1/4 дюйма с каждого зеленого, черного и белого проводов.
- Затем подключите зеленый провод (заземление) к клемме заземления, помеченной «⏚» на задней панели источника питания.
- Подключите белый провод (нейтраль) к клемме с надписью «N».
- Наконец, подключите черный провод (линию) к клемме с надписью «L».
- Дважды проверьте все ваши соединения и убедитесь, что клеммы напряжения постоянного тока свободны.
- Подключите блок питания и убедитесь, что он работает. Вы увидите, что рядом с клеммами загорится зеленый светодиод. Не прикасайтесь ни к каким клеммам!
Щелкните эту ссылку, чтобы просмотреть техническое описание MeanWell SE-200, чтобы узнать об источнике питания, который я использую. Я купил свой у Mouser на общую сумму 46,10 доллара, включая налоги и доставку. Я знаю, что вы можете получить более дешевые блоки питания, но мне всегда везло с продуктами MeanWell.
Шаг 4 – Подключите блок питания к grblShield и проверьте
Теперь, когда ваш блок питания подключен, пора подключить его к grblShield.
ВНИМАНИЕ! – grblShield не имеет защиты от обратной полярности. Если вы подключите напряжение питания наоборот, вы разрушите свой grblShield и вам придется отправить его обратно для замены.
- С помощью мультиметра проверьте выходное напряжение и полярность источника питания. Вы должны увидеть примерно 24 вольта.
- Отключите блок питания.
- Подключите клемму V + источника питания к винтовой клемме Vmot на grblShield.Я использовал многожильный провод 16 AWG.
- Подключите клемму V- на источнике питания к винтовой клемме GND на grblShield.
- Убедитесь, что провода между источником питания и grblShield правильно подключены. Я не хочу, чтобы вас тормозили отправка grblShield обратно в Synthetos.
- Подключите блок питания и убедитесь, что ваш grblShield работает. Вы увидите, что рядом с винтовыми клеммами загорится синий светодиод. Опять же, не трогайте никакие клеммы!
- Отключите блок питания.
Щелкните здесь, чтобы получить дополнительные сведения о начале работы с grblShield.
Шаг 5 – Подключите grblShield к Arduino
Если у вас установлена последняя версия Arduino UNO rev 3 (R3), вы можете просто подключить Arduino к grblShield. Версия Arduino R3 имеет 8-контактный разъем в качестве источника питания. Если у вас R3, просто перейдите к шагу 6.
Однако, если вы похожи на меня и у вас более старая Arduino, тогда вам нужно будет сделать быстрый мод для grblShield, который включает вырезание следа на печатной плате и добавление перемычки.Звучит устрашающе, но это займет всего несколько минут. В следующем процессе рассматриваются модификации, необходимые, если у вас более старая версия Arduino.
- Отключите все питание от grblShield.
- Обрежьте крайний левый след в секции перемычки питания J11, используя острый нож x-acto. См. Изображение ниже. Секция перемычки питания представляет собой расположение 2 × 3 металлических сквозных отверстий в печатной плате под приводом шагового двигателя оси Z.
- Добавьте перемычку к крайней правой паре металлических сквозных отверстий в секции перемычки питания J11.Они наиболее близки к маркировке J5 и J6 на печатной плате. Я использовал обрезок провода, отрезанный от резистора, и припаял перемычку на место.
Щелкните здесь для дополнительных настроек логической мощности на grblShield.
Перемещение перемычки питания grblShield для установки старых Arduinos.
Шаг 6 – Проверьте соединение
Теперь пора проверить, хорошо ли работают вместе ваш компьютер, Arduino и grblShield.
- Подключите кабель USB к Arduino и ПК
- Подключите блок питания к grblShield
- Включите компьютер и запустите Universal gCode Sender, щелкнув ярлык на рабочем столе
- Установите скорость передачи данных в универсальном отправителе gCode на 115200.(Обратите внимание, если вы используете grbl версии v0.8 или ниже, установите скорость передачи на 9600.) См. Рисунок ниже.
- Затем выберите COM-порт, используемый для подключения к Arduino.
если вы не знаете, какой из них, попробуйте первый из перечисленных COM-портов.
- Нажмите кнопку «Открыть» рядом с полем выбора скорости передачи.
- Если все системы отключены, вы увидите приветственное сообщение в окне консоли «grbl v0.9 [‘ $ ’for help]».
- Если вы получили приветственное сообщение, отключите питание и отсоедините Arduino от ПК.
Выберите скорость передачи в раскрывающемся меню. Для grbl версии v0.9 используйте 115200.
Шаг 7. Подключите шаговые двигатели
Следующий процесс относится к шаговым двигателям на 425 унций (425 унций), поставляемым Automation Technologies Inc.
Это 8-проводные шаговые двигатели. Но подождите, у grblShield только 4 точки подключения для каждого двигателя. Эти шаговые двигатели имеют 4 катушки. Нам нужно настроить эти катушки таким образом, чтобы в итоге получилось 4 точки подключения.Существует множество данных, описывающих оптимальный способ подключения шагового двигателя. Я выбрал биполярную (параллельную) конфигурацию. Это позволит мне максимально использовать возможности этих двигателей. В этой конфигурации двигатели потребляют 2,8 А (чуть выше 2,5 рейтинга grblShield), но, судя по информации от Synthetos, они работают очень хорошо.
Двигатели имеют следующие 8 проводов, каждый из которых имеет цветовую маркировку:
Синий / Белый, Синий, Красный / Белый, Красный, Зеленый / Белый, Зеленый, Черный / Белый, Черный
Вы можете использовать технический паспорт для подтверждения следующей схемы подключения.
A + = синий / белый и красный / белый
A – = синий и красный
B + = зеленый / белый и черный / белый
B- = зеленый и черный
Я скрутил пары проводов перед установкой в grblShield. В клеммных зажимах используются крошечные винты с плоской головкой, и вам понадобится хорошая небольшая отвертка.
- Убедитесь, что питание между grblShield и Arduino отключено. Сюда входит USB-кабель, соединяющий ПК с Arduino.
Перед подключением шаговых двигателей убедитесь, что он снят.
- Подключите пары проводов к клеммам шагового двигателя оси X в указанном выше порядке. Смотрите картинку ниже
Порядок подключения шагового двигателя.
Шаг 8 – Проверьте шаговый двигатель
А теперь давайте соберем все вместе и пошумим!
- Найдите потенциометр ограничения тока на grblShield для оси, которую вы используете для тестирования. Я использовал ось x.
- Осторожно поверните потенциометр против часовой стрелки до упора. Принудительное перемещение потенциометров за упор приведет к неработоспособности оси.
- Включите компьютер и запустите универсальный отправитель gCode, щелкнув ярлык на рабочем столе.
- Подключите блок питания к grblShield.
- Затем подключите кабель USB к Arduino и ПК.
- Подтвердите, что ваш компьютер обращается к grblShield, проверив приветственное сообщение в окне консоли «grbl v0.9 [‘$’ за помощь] ».
- Затем введите «G0 X1000» в командном окне. Это команда g-кода, которая сообщает оси x, чтобы она сместилась на 1000 мм от ее текущего положения. (По умолчанию grblShield имеет мм, но это может быть изменено на дюймы, если вам удобнее использовать эту систему единиц.)
- Осторожно поверните потенциометр по часовой стрелке, пока двигатель не начнет вращаться. Продолжайте движение, пока двигатель не заработает плавно. Обратите внимание, что вам, вероятно, придется повторить этот шаг после того, как в машине будут установлены шаговые двигатели.
- Отправьте еще несколько команд g-кода или поиграйте с кнопками на вкладке «Управление машиной».
У хороших ребят из Synthetos есть хорошая начальная страница для grblShield здесь.
Последние мысли
Вау, это куча информации, которую нужно усвоить. Если у вас есть какие-либо вопросы или вы застряли в пути, напишите мне на почту [email protected]
Не забудьте скачать Quick Start Guide здесь. Если вы визуальный человек, это больше ваш стиль.
Удачи в вашем проекте. Я хотел бы услышать, что вы создаете с помощью своего DIY-контроллера ЧПУ. Оставьте небольшую заметку в комментариях ниже.
Спасибо за внимание. До следующего раза… Тим
Как собрать самодельный лазерный гравер с ЧПУ
Сделай сам, чтобы помочь тебе с самодельными проектами? Это издание Gadget Freak выходит на рынок с лазерным гравером с ЧПУ, созданным Эми Киппен и ее однокурсниками из Университета штата Колорадо.
Лазерный гравер с ЧПУ состоит из управляемого пользователем лазера, установленного на оси Y, и гравировальной пластины, установленной на оси X. Движение лазера и гравировальной пластины контролируется с помощью G-кода, который позволяет лазеру гравировать двухмерные рисунки или изображения на древесине.
Пользователь может ввести G-код через SD-карту на задней панели ЖК-дисплея. Используя кнопку / диск для управления ЖК-экраном, пользователь выбирает правильный G-код. ЖК-дисплей также предоставляет пользователям возможность визуализировать и контролировать температуру корпуса лазера путем изменения скорости вращения вентилятора.Каждая из осей X и Y управляется шаговым двигателем, а бесконтактные переключатели используются для ограничения движения каждой оси мимо стен конструкции.
Гравер также оснащен функцией безопасности, которая отключает лазер, когда дверца открыта и выполняется программа. Во время работы гравера горит зеленый светодиод. Если дверь открыта, концевой выключатель внутри двери отключается, и отправляется сигнал для выключения зеленого светодиода и включения функции безопасности, которая включает красный светодиод и предупреждающий зуммер.Отключение концевого выключателя также включает реле, отключающее лазер. Как только дверца закрывается, лазер возобновляет гравировку.
Щелкните изображение ниже, чтобы просмотреть слайд-шоу с инструкциями по сборке.
И нажмите здесь, чтобы загрузить полные инструкции по сборке, включая схемы, диаграммы и код.
У вас есть крутой оригинальный самодельный гаджет, которым вы бы хотели поделиться со всем миром? Сообщите нам подробности на DesignNews.com / GF, и вы можете получить 500 долларов и автоматическое участие в нашем конкурсе на звание “Гаджет-урод” на 6000 долларов!
Список деталей | |||
Сумма | Описание детали | Партия союзников № | Банкноты |
1 | Arduino Mega | ||
1 | регулятор напряжения | 70099596 | LM317T Регулируемый 2.2-3.7 Регулятор напряжения |
1 | стеклянная линза | Стеклянная линза 405-G-2 для лазерного модуля Aixiz 405 нм | |
1 | диод | Cassio- 2W 445nm M140 Синий диод | |
1 | упор механический | Концевой упор Signwise из 3 шт.![]() | |
2 | шаговый двигатель | ZJchao 57-ox-in 1Nm Nema 17 Stepper Motor 1.3A 40 мм | |
1 | блок питания | NEWSTYLE 12V 30A DC Универсальный блок питания 360W | |
1 | Комплект контроллера Комплект для принтера OSOYOO Контроллер RAMPS 1,4 Mega 2560 R3 Драйвер шагового двигателя LCD 1286 Графический дисплей | ||
8 | линейный подшипник | Sprite Science 12LM8U Подшипники линейного перемещения | |
4 | линейные стержни | Линейное движение, вал 8 мм, длина 406 мм, хромированный корпус, закаленный | |
1 | вентилятор охлаждения | Uxcell 92 x 25 мм DC 12 В 2 клеммы 65. ![]() | |
2 | ремень и шкив | Алюминиевый шкив GT2 16T и ремень 2M | |
2 | PIC16F88 | 70045634 | 18-контактный PDIP, SOIC |
1 | прозрачная стенка | Экранирование лазера от 250 нм до 520 нм – 12 ”X 12” | |
1 | зуммер оповещения | Диаметр 12 мм.Электронный зуммер непрерывного звука с 2 клеммами, 5 В постоянного тока, | |
1 | Детали, напечатанные на 3D-принтере | 70369255 | 3 мм нить ABS |
1 | лазер | 2 Вт 445 нм M140 Синий диод в медном модуле с выводами и трехэлементной стеклянной линзой | |
1 | дисплей регулятора напряжения и тока | Дисплей понижающего преобразователя напряжения постоянного тока в постоянный, дисплей | |
1 | термопары | Алюминиевое крепление и радиатор для модулей 12 мм | |
1 | 13 футов алюминиевой трубки 1 x 1 дюйм | ||
1 | Алюминиевый уголок 2 фута 2 x 2 дюйма | ||
100 | гайки | Гайка крепежного винта с шестигранной головкой, 8-32 | |
100 | болты | Винт со шлицевой головкой для фермы, 8-32 x 1-1½ ” | |
4 | лазерные очки | Защитные очки HDE для лазерной защиты глаз для зеленого и синего лазеров |
У вас в гараже стоит крутой оригинальный самодельный гаджет, который пылится? Сообщите нам подробности на DesignNews.