16. Методы обработки отверстий.
После выполнения отверстий в сплошном материале производится их обработка для увеличения размеров и снижения шероховатости поверхностей, а также обработка предварительно полученных отверстий (например, литьем, продавливанием и т.п.).Обработка отверстий выполняется несколькими способами, в зависимости от того, какие параметры точности и шероховатости поверхности отверстия заданы чертежом. В соответствии с выбранным способом обработки выбирается и инструмент для ее осуществления. При обработке отверстий различают три основных вида операций: сверление, зенкерование, развертывание и их разновидности: рассверливание, зенкование, цекование.
Сверление –
это операция по образованию сквозных
и глухих отверстий в сплошном материале,
выполняемая при помощи режущего
инструмента – сверла. Различают сверление
ручное – ручными пневматическими и
электрическими сверлильными устройствами
(дрелями) и сверление на сверлильных
станках.
Одной из разновидностей
сверления является рассверливание –
увеличение диаметра отверстия,
просверленного ранее. В качестве
инструментов для рассверливания
отверстий, также как и для сверления,
используют сверла. Не рекомендуется
рассверливать отверстия, полученные в
заготовке методом литья, ковки или
штамповки. Такие отверстия имеют
различную твердость по поверхности
отверстия из-за окалины, образующейся
при литье, а также из-за неравномерной
концентрации внутренних напряжений в
металле на различных участках поверхности
отверстий, полученных методом ковки
или штамповки.
Зенкерованием называется операция, связанная с обработкой предварительно просверленных, штампованных, литых или полученных другими методами отверстий с целью придания им более правильной геометрической формы (устранение отклонений от круглости и других дефектов), а также достижения более высокой, по сравнению со сверлением, точности (до 8-го квалитета) и более низкой шероховатости (до Ra 1,25). Зенкерование ведут

Виды отверстий и способы их обработки
Отверстия по способам обработки подразделяют на:
- крепежные отверстия в различных деталях (отверстия для крепежных болтов, винтов, шпилек, заклепок и т. п.). Точность изготовления таких отверстий невысокая (11…12-й квалитеты и грубее). Такие обычно сверлят на одно- или многошпиндельных сверлильных станках;
- ступенчатые или гладкие отверстия в деталях, представляющих собой тела вращения. Их обрабатывают сверлом (в ряде случаев с последующим зенкерованием или развертыванием) или резцом совместно с токарной обработкой наружных цилиндрических поверхностей;
- ответственные отверстия в корпусных деталях, точность обработки которых определяет правильность работы и долговечность узлов машины (например, редуктора) или качество работы всей машины (например, для шпинделей в корпусных деталях станков и т.
п.). Такие отверстия изготовляют обычно не хуже, чем по 7-му квалитету. Обрабатывают такие отверстия на различных станках универсальных или специального назначения;
- глубокие отверстия с отношением длины l к диаметру d больше пяти (l/d>5), например, отверстия шпинделей станков, пустотелых валов и т. п. Эти отверстия обрабатывают на станках специального назначения;
- конические и фасонные (с криволинейной образующей) отверстия, которые обрабатывают инструментом с коническими или криволинейными режущими кромками либо растачивают с помощью копирного приспособления;
- профильные (некруглого сечения) отверстия, обрабатываемые протягиванием, прошиванием и долблением.
В зависимости от назначения отверстий к ним могут предъявляться следующие требования: выдерживание размера отверстия по диаметру с заданной точностью, прямолинейность оси отверстия и образующей его поверхности, правильность цилиндрической формы отверстия (отсутствие конусности, овальности и огранки), перпендикулярность оси торцевым поверхностям детали.
Обработка отверстий круглого сечения производится на сверлильных, расточных, токарных, карусельных, револьверных станках, токарно-револьверных полуавтоматах и автоматах, протяжных и шлифовальных станках.
Обработка точных отверстий всегда требует больших затрат станочного времени и средств на инструмент, чем аналогичная обработка таких же по размерам наружных поверхностей с той же степенью точности, так как режущий инструмент для обработки отверстий не обладает такой же жесткостью конструкции, особенно конструкции его крепления (расточные оправки — борштанги, длинные расточные резцы и т. п.), как инструмент для обработки наружных цилиндрических поверхностей.
Для повышения точности при обработке отверстий увеличивают число рабочих ходов, чтобы таким образом постепенно довести погрешности первоначальной обработки до допустимых размеров. Так, если для обтачивания гладкого вала по 8-му квалитету точности достаточно двух рабочих ходов, то для обработки отверстия того же диаметра и с той же точностью понадобится не менее четырех операций или переходов: сверление двумя сверлами, зенкерование и одно-или двукратное развертывание.
При обработке отверстий даже с относительно большим числом переходов в обычных условиях не удается достигнуть высокой точности по соосности обрабатываемого отверстия и какой-либо наружной цилиндрической поверхности обрабатываемой заготовки. Поэтому, когда требуется обеспечить соосность отверстия с другими поверхностями, необходимо сначала окончательно обработать отверстие, а затем, установив заготовку этим отверстием на точную оправку, обработать наружные поверхности заготовки.
Отверстия диаметром до 80 мм в сплошном металле сверлят спиральными сверлами на сверлильных станках, а также на различных станках токарной группы. Для сверления отверстий диаметром свыше 80 мм применяют сверлильные головки специальных конструкций; эту операцию, как правило, выполняют на расточных станках.
Метки: Виды отверстий и способы их обработки
- Вперед Виды сложных поверхностей и их классификация
- Назад Обработка на токарно-карусельных и токарно-лобовых станках
Обработка мелких отверстий | Адамант Намики Precision Jewel Co.
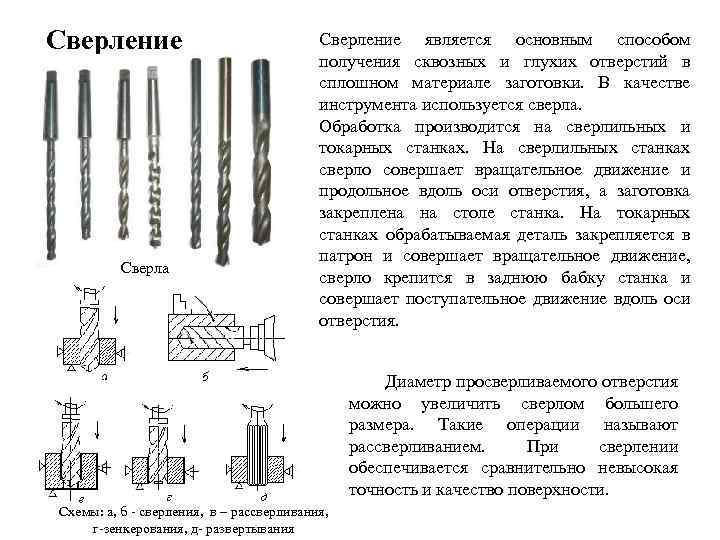
Технология обработки мелких отверстий Adamant Namiki эволюционировала от микронного до наноуровня. Применяя технику полировки, которую мы используем для нашего алмазного наконечника, мы разработали собственное алмазное сверло для точного сверления. Кроме того, мы внедрили передовую технологию фемтосекундной лазерной обработки. Объединив фемтосекундный лазер и алмазное микросверло, мы добились сверхточной обработки отверстий от микронного до наноуровня.
Эти сверхтонкие отверстия массово производятся в качестве насадок для микрожидкостных устройств. Можно точно контролировать мельчайшие объемы различных жидкостей и газов.
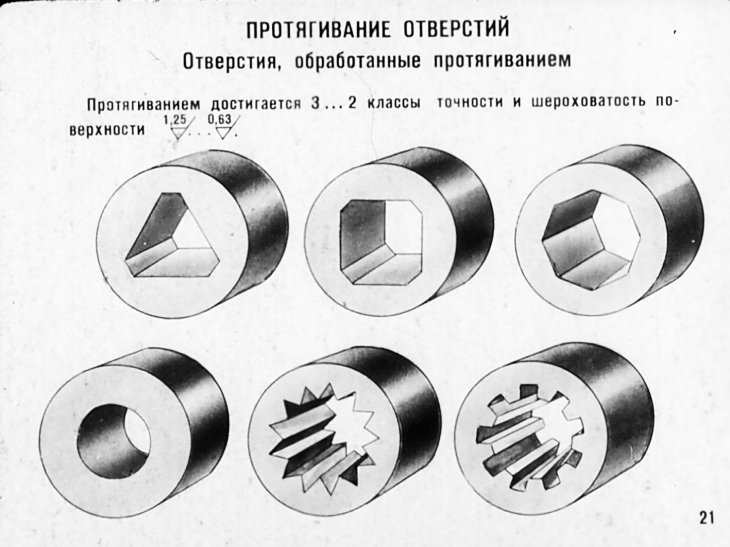
Мы можем удовлетворить различные запросы, такие как разработка деталей для промышленного и лабораторного аналитического оборудования, для которых требуются микроотверстия. Основная технология нашей компании (резка, шлифовка и полировка) основана на обработке твердых материалов, и мы можем предложить вам лучшие решения для таких материалов, как кварцевое стекло, сапфир и керамика.
Лазерное сверление
Помимо цементированного карбида, наша компания также специализируется на обработке тонкой керамики, такой как оксид алюминия, диоксид циркония и монокристаллический рубин.
В случаях, когда обработка традиционными методами затруднена, шлифование и полирование иногда выполняются с помощью алмазных абразивных зерен или с помощью ультразвуковой или электроэрозионной обработки. Однако эти методы не могут сохранить присущие керамике физические свойства, поэтому возникают проблемы, когда требуемая точность не может быть достигнута или время обработки слишком велико.
В нашей компании мы разработали технологию обработки тонкой керамики, объединив нашу личную технологию с мощным сфокусированным лазером и специальной оптической системой.
В процессе сверления мы внедрили высокоточную технологию микроперфорации, которая позволяет обрабатывать такие материалы, как керамика, глиноземная керамика, нитрид кремния и нитрид алюминия.
Кроме того, вокруг отверстия нет мусора, обработанная поверхность гладкая, вторичная обработка не требуется.
Фемтосекундный лазер
ЕЩЕ
УФ-лазер
ЕЩЕ
Прецизионная обработка отверстий
Алмазное микросверление
ЕЩЕ
Цилиндрическая обработка
Хотя на первый взгляд феррула из диоксида циркония выглядит как простой керамический цилиндр, наша технология цилиндрической обработки незаменима для механической обработки и представляет собой очень сложную технологию обработки.
Внешний диаметр шлифуется и полируется на субмикронном уровне, и он может соответствовать допуску ± 0,0005 мм.
Сверление Обработка
Сверление цилиндрического отверстия или расширение просверленного отверстия.
Мы можем выполнять высокоточную обработку с помощью собственных станков и специальных инструментов.
Обработка внутреннего диаметра
Сложность обработки отверстия заключается в том, что, например, когда рабочий материал представляет собой твердый материал, такой как керамика, его нельзя легко обработать с помощью инструмента, такого как лезвие, поэтому цилиндричность и поверхность шероховатости внутреннего диаметра становятся неравномерными.
Мы занимаемся производством, используя наши ноу-хау, чтобы получить точность на уровне нанометров, сохраняя при этом округлость и оставаясь верными характерной природе материала.
Хотя типичное применение для каждого продукта отличается, например, одно изделие с одним или несколькими сквозными отверстиями диаметром от 0,1 до 1,2 мм в центре можно использовать в таких деталях, как форсунки для впрыска жидкости (для распыления пестицидов и т. д.). .).
С помощью нашей технологии обработки можно обрабатывать отверстия диаметром 0,01 мм в различных керамических материалах.
Точность обработки отверстия (цилиндричность, соосность, округлость)Цилиндричность: 0,280 мкм Коаксиальность: 0,350 мкм Круглость: 0,190 мкм
Результаты измерения коаксиального распределениякоаксиальность (мкм) | |
---|---|
МАКС. | 0,97 |
МИН | 0,12 |
АВЭ | 0,35 |
σ | 0,114 |
Сп | 1,908 |
нет | 1 255 |
Обработка овального отверстия
Эллиптическое отверстие обрабатывается с применением лазерной обработки и обработки канавок.
Сквозное отверстие овальной формы шириной 0,02 мм и длиной около 0,1 мм.
Материал: Карбид вольфрама
*Если вы не можете найти контактную форму, нажмите здесь.
В вашем браузере должен быть включен JavaScript.
- Связаться по телефону
- Онлайн контактная форма
Практический пример: Моделирование процесса расширения холодного ствола
Расширение в холодном состоянии (сокращенно CX или холодное расширение) отверстий для крепежных деталей — это метод, который широко используется в авиационной промышленности для улучшения усталостных характеристик компонентов конструкции. Процесс расширения холодного отверстия создает остаточное сжимающее напряжение вблизи отверстия, что замедляет рост трещины и может значительно улучшить усталостные характеристики. Этот процесс вызывает пластическую деформацию вблизи отверстия из-за протягивания оправки слишком большого размера через отверстие. Упругое восстановление окружающего материала приводит к возникновению остаточного напряжения сжатия вблизи поверхности отверстия, которое уравновешивается остаточным напряжением растяжения дальше от отверстия. Преимущества холодного расширения в отношении усталостных характеристик были продемонстрированы в нескольких исследованиях. Корреляция роста усталостной трещины в холоднорасширенных отверстиях проиллюстрирована в [1].
В этом тематическом исследовании основное внимание уделяется нелинейному моделированию процесса холодного расширения с использованием анализа методом конечных элементов. Рассматривается алюминиевый образец размерами 50,8 х 50,8 х 6,35 мм (2,0 х 2,0 х 0,25 дюйма) и отверстием в центре диаметром 12,12 мм (0,477 дюйма). Отверстие претерпевает приложенное расширение на 3,16% в процессе расширения холодного отверстия, т. е. при максимальном расширении радиус отверстия увеличивается на 3,16%. На рис. 1 показана геометрия купона.
Геометрия купона, используемая для моделирования процесса расширения холодного ствола. Размеры без скобок указаны в дюймах, а размеры в скобках – в мм.
Анализ учитывает упруго-пластическое поведение материала и использует реальную кривую напряжения-деформации, полученную в результате экспериментальных испытаний с использованием рассматриваемого здесь конкретного материала.
Как правило, усталостные трещины возникают на краях отверстий под крепеж. Кольцевое остаточное напряжение в сочетании с приложенной нагрузкой изменяет движущую силу трещины и важно при анализе роста усталостной трещины с учетом холодных расширенных отверстий. Используемая здесь модель процесса обеспечивает кольцевое остаточное напряжение, как показано на рис. 2. Карта сквозной толщины, полученная в плоскости y = 25,4 мм (1,0 дюйм), показана на рис. 2а, где высокое остаточное напряжение сжатия наблюдается вблизи краев отверстие, в то время как растягивающее остаточное напряжение возникает дальше от края отверстия, чтобы обеспечить механическое равновесие. На рис. 2b также показано кольцевое остаточное напряжение, но в средней плоскости xy (z = 3,175 мм (0,125 дюйма)). Высокое остаточное напряжение сжатия локализовано вблизи края отверстия и приблизительно осесимметрично. Линейный график кольцевого остаточного напряжения вдоль заданного пути дает более количественные результаты, как показано на рисунке 2c, где выбранный путь находится в плоскости y = 25,4 мм и в середине толщины пластины (z = 3,175 мм). (0,125 дюйма)). Кривая на этом графике относится только к правой стороне отверстия (x > 30 мм).
Распределение показывает пиковое остаточное напряжение сжатия на краю отверстия, которое затухает и в конечном итоге становится растягивающим. Пиковое остаточное напряжение сжатия на краю отверстия составляет -480 МПа (приблизительно -70 тысяч фунтов на квадратный дюйм). Размер зоны остаточного напряжения сжатия, т. е. расстояние, на котором RS пересекает 0, составляет около 4,4 мм (0,17 дюйма), что соответствует примерно 0,7R (R = радиус отверстия). За пределами зоны остаточного напряжения сжатия развивается остаточное напряжение растяжения с пиком около 115 МПа (приблизительно 17 тысяч фунтов на квадратный дюйм) на расстоянии 7,2 мм (0,28 дюйма) от края отверстия, что соответствует 1,1R.
Остаточное кольцевое напряжение из модели процесса с приложенным расширением 3,16 % a) по толщине образца, b) на средней плоскости xy при z = 3,175 мм (0,125 дюйма), c) линейный график вдоль направления x при y = 25,4 мм, Z = 3,175 мм
Имея установленную выше модель процесса, полезно оценить влияние уровня радиального расширения на результирующее кольцевое остаточное напряжение. Запуск модели процесса с приложенным расширением 4,16% обеспечивает кольцевое остаточное напряжение, как показано на рисунке 3. Карты кольцевого остаточного напряжения показаны на рисунках 3a и 3b и показывают несколько более высокие величины остаточного напряжения по сравнению с результатами на рисунке 2a. и Рисунок 2b. На рис. 3с показан линейный график по тому же пути, что и для предыдущей модели, и сравниваются результаты, полученные для обоих уровней расширения. В целом более высокий уровень расширения привел к увеличению пикового остаточного напряжения сжатия на краю отверстия примерно на 5% и к увеличению размера зоны остаточного напряжения сжатия вокруг отверстия на 10%.
Остаточное кольцевое напряжение из модели процесса с приложенным расширением 4,16% a) по толщине образца, b) на средней плоскости xy при z = 3,175 мм (0,125 дюйма), c) линейный график вдоль направления x при y = 25,4 мм, Z = 3,175 мм
В этом тематическом исследовании основное внимание уделяется моделированию процессов с использованием анализа методом конечных элементов для прогнозирования остаточного напряжения в результате холодного расширения отверстий под крепеж. Разработана модель процесса для имитации расширения отверстия из-за операции протягивания оправки, и представлено результирующее кольцевое остаточное напряжение после упругого восстановления материала. Результаты моделирования показывают высокое остаточное напряжение сжатия на краю и вблизи отверстия, которое уменьшается по мере удаления от отверстия и в конечном итоге становится растягивающим. Увеличение величины применяемого расширения, используемого в модели, вызывает увеличение пикового остаточного напряжения сжатия на краю отверстия, а также увеличение размера зоны остаточного напряжения сжатия вблизи отверстия.