Токарно-винторезный станок 1К625 – цена, отзывы, характеристики с фото, инструкция, видео
Токарно-винторезный станок 1К625 предназначен для выполнения разнообразных токарных работ, в том числе для нарезания метрической, модульной, дюймовой и питчевой резьб на заготовках, устанавливаемых в центрах или патроне.
Основные достоинства предлагаемой серии станков – высокая мощность главного привода, большая жесткость и прочность всех звеньев кинематической цепи, надежность и виброустойчивость конструкции, широкий диапазон частот вращения шпинделя, рассчитанных на скоростное и силовое резание.
Базовая модель серии – универсальный токарно-винторезный станок 1К62Д, который является усовершенствованным прототипом хорошо зарекомендовавшего себя во многих странах мира станка 1К62, выпускавшегося ранее заводом “Красный пролетарий”.
Пример обозначения станка: станок токарно-винторезный модели 1К625ДГУ. 1500.
(У базовой модели – станка 1К62Д – наибольший диаметр обработки 435мм).
- Шпиндель станков установлен на специальных подшипниках, которые обеспечивают необходимую жесткость и высокую точность обработки.
- Обработка разнообразных материалов может производиться с ударными нагрузками без потери точности.
- Станки могут использоваться для обработки закаленных заготовок из жаропрочной и инструментальной стали, требующих тяжелых режимов резания.
- Выемка в станине (ГАП) позволяет устанавливать и обрабатывать заготовки, радиус которых превышает расстояние, ограниченное высотой центров
Например, наибольший диаметр заготовки, устанавливаемой над станиной станка 1К62Д- 435мм, а станок 1К62ДГ с ГАПом дает возможность изготавливать деталь с наружным диаметром 630 мм.
Сравнительная техническая характеристики токарного станка 1К625Д, 1К625ДГ, 1К62
Параметры станка | 1К62Д 1К62ДГ | 1К625Д 1К625ДГ |
---|---|---|
Наибольший диаметр обрабатываемой заготовки, мм: | ||
– над станиной | 435 | 500 |
– над суппортом | 224 | 290 |
Наибольшая длина обрабатываемой заготовки, мм | 1000,1500 | 1000, 1500, 2000 |
Размер внутреннего конуса в шпинделе | Морзе 6 | |
Диаметр цилиндрического отверстия в шпинделе | 55 (62*) | |
Число ступеней частот вращения шпинделя | 23 | |
Частота вращения шпинделя | 12,5.![]() | |
Число ступеней рабочих подач: | ||
– продольных | 42(56*) | |
– поперечных | 42(56*) | |
Рабочие подачи, мм/об: | ||
– продольные | 0,70…4,16 (0,036…7,54*) | |
– поперечные | 0,035…2,08 (0,018…3,77*) | |
Число нарезаемых резьб: | ||
– метрических | 45(53*) | |
– дюймовых | 28(57*) | |
– модульных | 38 | |
– питчевых | 37 | |
– архимедовой спирали | 5 | |
Шаг нарезаемой резьбы: | ||
– метрической | 0,5…192 мм | |
– модульной | 0,5.![]() | |
– дюймовой | 24…15/8 ниток на дюйм | |
– питчевой | 96…1 питч | |
– архимедовой спирали | 3/8″, 7/16″, 8; 10 и 12 мм | |
Быстрые установочные перемещения суппорта, м/мин: | ||
– продольного | 4,5 | |
– поперечного | 2,25 | |
Размер внутреннего конуса в задней бабке | Морзе 5 | |
Наибольшее перемещение пиноли задней бабки, мм | 200 | |
Поперечное смещение корпуса задней бабки, мм | ±15 | |
Наибольшее сечение резца | 25 | |
Давление воздуха, МПа | 0,4…0,6 | |
Питание от электросети напряжением | 220/380 В (50Гц) | |
Мощность электродвигателя главного привода, кВт | 11 (7,5*) | |
Габаритные размеры станка, мм: | ||
– длина | 2786, 3286, 3786 | |
– ширина | 1200 | 1221 |
– высота | 1500 | |
Масса станка, кг, при длине обработки: | ||
– 1000мм | 3080 | 3124 |
– 1500мм | 3440 | 3484 |
– 2000мм | 3800 | 3844 |
Возможности токарных станков с ГАПом
Параметры станка | 1К62ДГ | 1К625ДГ |
---|---|---|
Наибольший диаметр изделия, устанавливаемого над выемкой в станине, мм | 630 | 700 |
Расстояние от торца фланца шпинделя до правого края выемки, мм | 348 | 348 |
Длина выемки в станине, мм | 355 | 355 |
Станок токарный 1к625 технические характеристики
Iht625 Китай 3-в-1 мини-токарный станок с ЧПУ Спецификация Цена Серия IHT Тюнинг-машина с системой управления FANUC, включенным стандартным оборудованием и стандартными функциями системы управления. Цельнолитая отливная станина с низким центром тяжести, седло 30 ° благодаря оптимизированной конструкции, имеет большое демпфирование и меньшую степень деформации, коробку главной оси, револьверную головку. Обеспечение структуры высокой жесткости. 30 ° наклонная конструкция кровати, чтобы облегчить верхнюю и нижнюю части оператора, но и для обеспечения.Плавная откачка стружки.
IHT625 Миниатюрный токарный станок с ЧПУ Китай 3 в 1 Спецификация Цена
Жесткость 1.Super
Конструкция машины объединена в прочную основу, нижний барицентр, опору седла 30 ° для лучшего демпфирования вибрации и уменьшения деформации , обеспечивая переднюю бабку и револьверную головку с очень устойчивой структурой наклонного основания 30 °, более удобной для загрузки и разгрузки стержня, более гладкой для удаления стружки
2.Современные популярные блоки управления
серии iHT имеют опциональный блок управления FAUNC 0iTF и блок управления Siemens 828D, дисплей 8,4 “, дисплей 10,4”, дополнительные интерфейсы и т. Д., Готовые для клиентов.
3. Высокая стоимость исполнения
Немецкая линейка серии iHT может похвастаться лучшими компонентами, такими как револьверная головка SAUTER, подшипники NSK и т. Д., Что гарантирует высокую точность исполнения. В то же время мы предлагаем конкурентоспособную цену, чтобы сделать серию iHT супер высокой стоимостью.
4. Удобный для пользователя дизайн
Минимальная занимаемая площадь, но в основном соответствующая фактической рабочей зоне, полный защитный кожух с эстетичным дизайном человека, крышка из нержавеющей телескопа, обеспечивают безопасную и чистую рабочую среду и лучшую долговечность.
5. Дополнительные опции
Электрическая револьверная головка, серворезка, механическая револьверная головка, модернизировать мощность шпинделя, модернизировать крутящий момент шпинделя, модернизировать отверстие цилиндра и патрона, бак охлаждающей жидкости выдвижного типа, зонд инструмента, сепаратор масляного тумана и т. Д.варианты готовы для клиентов.
Что такое токарный станок с ЧПУ серии IHT?
1.Компактная конструкция с чугунной станиной Mehhanite высокого напряжения HT300.
2. Идеальная доступность и оптимальная рабочая глубина.
3. Идеальный станок для обучения, занимающий всего 3,5 м 2 и рабочую глубину всего 350 мм до шпинделя.
4. Повышение производительности благодаря использованию до 12 приводных инструментов (опция).
5.Новейшая обновленная технология управления: FANUC 0i-TF с панелью 20,4 “(опция) или SIEMENS 828D (опция 840D)
Технические характеристики | CZ1237G | CZ1337G | ||||||||||||||||||||||
Качели над кроватью | мм | 305 | 330 | |||||||||||||||||||||
Поворотная каретка | мм | 173 | 215 | |||||||||||||||||||||
000 | ||||||||||||||||||||||||
Ширина проходного пути | мм | 182 | ||||||||||||||||||||||
Расстояние между центрами | мм | M T5 | ||||||||||||||||||||||
отверстие шпинделя | мм | 38 | ||||||||||||||||||||||
ступень скорости | об / мин | 64-1500 | ||||||||||||||||||||||
Метрическая резьба | мм | Закрытая коробка: 11 видов (0. | ||||||||||||||||||||||
Коробка Norton: 15 видов (0,25 ~ 47,5) | ||||||||||||||||||||||||
дюймовая резьба | ТПИ | Закрытая коробка: 14 000 сторон ~ 48) | ||||||||||||||||||||||
Коробка Norton: 40 видов (4 ~ 112) | ||||||||||||||||||||||||
Диапазон подачи | мм / р | Закрытая коробка: 0.051 ~ 0.303 0,002 ” – 0,012 ”) | ||||||||||||||||||||||
Коробка Нортона: 0.12 ~ 0,42 (0,0047 ” – 0,0165 ”) | ||||||||||||||||||||||||
Диаметр ходового винта | мм | 22 (7/8 ”) | ||||||||||||||||||||||
шаг вперед Винт | 3 мм или 8 TPI | |||||||||||||||||||||||
Ход седла | мм | 510 | ||||||||||||||||||||||
000000000 | ||||||||||||||||||||||||
составное перемещение | мм | 85 | ||||||||||||||||||||||
перемещение ствола | 000000000 | 32 | ||||||||||||||||||||||
Конус центра | мм 90 007 | MT3 | ||||||||||||||||||||||
Мощность двигателя | кВт | 1. | ||||||||||||||||||||||
Двигатель для питания системы охлаждения | кВт | 0,04 (0,055 л.с.) | ||||||||||||||||||||||
Машина | мм | 1420x750x760 | ||||||||||||||||||||||
Стенд (левый) (Д × Ш × В) | мм | 400x370x700 |
(0005) | (0005) ( ) ( ) | ( ) ( ) ( ) ( ) 00000000000 H) | мм | 300x370x700 |
Машина | кг | 380/430 |
C6256 Токарный станок
Описание продукта
Основные рабочие характеристики :
Направляющий путь и все шестерни в бабке закалены и точны.
Шпиндельная система отличается высокой жесткостью и точностью.
Станки имеют мощную зубчатую передачу, высокую точность вращения и плавный ход с шумом Iow.
На фартуке предусмотрено устройство защиты от перегрузки.
Педальное или электромагнитное тормозное устройство.
Свидетельство об испытании на допуск, прилагаемая технологическая схема испытаний
СТАНДАРТНЫЕ АКСЕССУАРЫ
1 Патрон с тремя кулачками и адаптер
2 Патрон с четырьмя зажимами и адаптер
3 Лицевые панели
4 Устойчивый отдых
5 Следовать за
5 Следовать
5 Следовать
5 Следить за
5 Следить за 5 Следовать 5 Следовать Остальное Масляный пистолет7 Циферблат для нарезания резьбы
8 Руководство по эксплуатации
9 Один комплект гаечных ключей
10 Втулка 7/5 MT и центр 5 MT
СПЕЦИАЛЬНЫЕ ПРИНАДЛЕЖНОСТИ
1 Приводная пластина
2 Стойка для быстрой смены инструмента
3 Приспособление для точения конуса
4. переменная скорость
Основные технические характеристики продукта :
ТЕХНИЧЕСКИЕ ХАРАКТЕРИСТИКИ | C6256 |
Поворот красного цвета | 9 5 000 000 (20 000 000) 5 000 000 (20 000 000) |
Поворотный поперечный суппорт | 355 мм (11-7 / 8 “) |
Поворотный зазор | 785 мм (29″) |
Станок токарно-винторезный универсальный 1К625 (РМЦ 2000)
Если Вам необходимо купить Станок токарно-винторезный универсальный 1К625 (РМЦ 2000) звоните по телефонам:
в Москве +7 (499) 372-31-73
в Санкт-Петербурге +7 (812) 245-28-87
в Минске +375 (17) 246-40-09
в Екатеринбурге +7 (343) 289-16-76
в Новосибирске +7 (383) 284-08-84
в Челябинске +7 (351) 951-00-26
в Тюмени +7 (3452) 514-886
в Нижнем Новгороде +7 (831) 218-06-78
в Самаре +7 (846) 201-07-64
в Перми +7 (342) 207-43-05
в Ростове-на-Дону +7 (863) 310-03-86
в Воронеже +7 (473) 202-33-64
в Красноярске +7 (391) 216-42-04
в Нур-Султане +7 (7172) 69-62-30;
в Абакане, Альметьевске, Архангельске, Астрахани, Барнауле, Белгороде, Благовещенске, Брянске, Владивостоке, Владимире, Волгограде, Вологде, Иваново, Ижевске, Иркутске, Йошкар-Оле, Казани, Калуге, Кемерово, Кирове, Краснодаре, Красноярске, Кургане, Курске, Кызыле, Липецке, Магадане, Магнитогорске, Майкопе, Мурманске, Набережных Челнах, Нижнекамске, Великом Новгороде, Новокузнецке, Новороссийске, Новом Уренгое, Норильске, Омске, Орле, Оренбурге, Пензе, Перми, Петрозаводске, Пскове, Рязани, Саранске, Саратове, Севастополе, Симферополе, Смоленске, Сыктывкаре, Тамбове, Твери, Томске, Туле, Улан-Удэ, Ульяновске, Уфе, Хабаровске, Чебоксарах, Чите, Элисте, Якутске, Ярославле и в других городах
По всей России бесплатный номер 8 (800) 775-16-64.
В странах СНГ — Беларуси, Казахстане, Туркменистане, Узбекистане, Украине, Таджикистане, Молдове, Азербайджане, Кыргызстане, Армении в городах Нур-Султан, Бишкек, Баку, Ереван, Минск, Ашхабад, Кишинев, Душанбе, Ташкент, Киев и других для покупки оборудования типа Станок токарно-винторезный универсальный 1К625 (РМЦ 2000) звоните на любой удобный номер, указанный на нашем сайте, или оставьте свои контакты под кнопкой ЗАКАЗАТЬ ЗВОНОК вверху сайта – мы сами Вам перезвоним.
Токарный станок 1К62, 1К625 и их аналоги Запчасти к металлорежущему оборудованию
Станок токарно-винторезный модели 1К62 предназначен для выполнения разнообразных токарных работ: для нарезания метрической, дюймовой, модульной, питчевой, правой и левой, с нормальным и увеличенным шагом, одно- и многозаходной резьбы, для нарезания торцовой резьбы и для копировальных работ (с помощью прилагаемого к станку гидрокопировального устройства). Станок применяется в условиях индивидуального и мелкосерийного производства
Класс точности по ГОСТ 8-82 H
Технические характеристики
Наибольший диаметр обрабатываемого изделия, мм: | |
– над станиной | 400 |
– над суппортом | 220 |
Наибольшая длина обрабатываемого изделия, мм | 710, 1000, 1400 |
Наибольшая длина хода каретки, мм | 640, 930, 1330 |
Центр в шпинделе передней бабки по ГОСТ 13214-67 | конус Морзе 6 |
Конец шпинделя по ГОСТ 12593-72 | 6К |
Диаметр прутка, проходящего через отверстие в шпинделе, мм | 45 |
Высота резца, установленного в резцедержателе,мм | 25 |
Наибольшая масса устанавливаемого изделия в Т: | |
– закрепленного в патроне | 0,5 |
– закрепленного в центрах | 1,5 |
Количество скоростей шпинделя: | |
– прямого вращения | 23 |
– обратного вращения | 12 |
Пределы частоты вращения шпинделя, об/мин | |
– прямого вращения | 12,5-2000 |
– обратного вращения | 19-2420 |
Количество подач: | |
– продольных | 42 |
– поперечных | 42 |
Пределы подач, мм/об | |
– продольных | 0.![]() |
– поперечных | 0.035-2.08 |
Количество нарезаемых резьб, единиц: | |
– метрических | 44 |
– модульных | 20 |
– модульных | 38 |
– питчевых | 37 |
Наибольший крутящий момент, кНм | 2 |
Наибольшее перемещение пиноли, мм | 200 |
Поперечное смещение корпуса, мм | ±15 |
Габаритные размеры станка, мм | |
– длина | 2522 ; 2812 ; 3212 |
– ширина | 1166 |
– высота | 1324 |
Масса станка, кг | 2080 ; 2200 ; 2300 |
Токарно-винторезный станок SN 500SA – Поставки станков
Станок токарно-винторезный Trens SN 500SA – более мощный аналог модели Trens SN 50C. Выполняет обточку деталей тел вращения из металла и других материалов по наружной и внутренней поверхности, в прямолинейном и ступенчатом профиле. Режущий инструмент: резцы, метчики, сверла, развертки, плашки изготавливаются из быстрорежущей стали. Применяются станки в производственных цехах и ремонтных мастерских.
Данная модель по техническим характеристикам соответствует следующим позициям: 1К62, 16К20, 16В20, 1К625, 16К25, 1В625М.
Отличительные особенности
- повышенный класс точности
- увеличенное отверстие в шпинделе для прохождения прутков
- большой выбор, применяемой оснастки увеличивает возможности станка
- возможность установки быстросменной инструментальной системы MultiSuisse
- самые ответственные поверхности обработаны методом ручной шабровки
- надежность, безопасность, долговечность
Технические характеристики | SN 500SA |
Диаметр установки над выемкой, мм | 700 |
Наибольший диаметр обработки, мм | |
над станиной | 505 |
над суппортом | 270 |
Расстояние между центрами, мм | 1000/1500/2000 |
Класс точности | П |
Диаметр проходного отверстия в шпинделе, мм | 77/105 |
Конус в шпинделе | Морзе 6 |
Передний конец шпинделя | B6/D6 |
Крутящий момент, Нм | 1450 |
Число оборотов шпинделя, мин-1 | 12,5-2000 |
Продольные рабочие подачи, мм/об | 0,05-6,4 |
Диапазон поперечных подач суппорта, мм/об | 0,025-3,2 |
Поперечное сечение резца, мм | 32х32 |
Внутренний конус пиноли задней бабки | Морзе 5 |
Ход пиноли, мм | 180 |
Диапазон шагов метрической резьбы, мм | 0,5-40 |
Диапазон шагов дюймовой резьбы, ниток | 1-80 |
Диапазон шагов модульной резьбы, мм | 0,25-20 |
Диапазон шагов питчевой резьбы, количество ходов DP | 2-72 |
Мощность электродвигателя главного движения, кВт | 7,5 |
Габаритные размеры, мм | |
длина | 2595/3095/3595 |
ширина | 1100 |
высота | 1525 |
Масса станка, кг | 2300/2400/2600 |
Оснащение оборудования
Базовое | Дополнительное |
|
|
Цена станка
Всю дополнительную информацию на токарно-винторезный станок SN 500SA, Вы можете запросить через электронную почту info@standart-st. ru или по телефону +7(4852) 66-40-25.Производим таможенное оформление и транспортировку оборудования до предприятия заказчика. Предоставляем гарантию на токарно-винторезный станок SN 500SA сроком 12 месяцев.
технические характеристики фрезерного станка
Обзор фрезерного станка 6Р12 конструкция
Основные технические характеристики модели 6Р12 подробно указаны в паспорте Но для выбора правильного режима работы следует знать такие параметры станка габариты рабочего стола
Получить ценусхемы описание характеристики
Сведения о производителе Консольно Фрезерного станка 6Р13ф3 6Р13ф3 37 Получить ценуКинематическая схема вертикально
Технические характеристики станка мод 6Р13 ФЗ Класс точности станка по ГОСТ 8 82 Н Размеры рабочей поверхности стола по ГОСТ 165 81 мм ширина длина
Получить ценуEsferoРоссийские Фрезерные 3D станки с
Технические характеристики фрезерного станка с ЧПУ Esfero 3D 014 Модель Esfero 3D 01 4 Размер стола 810 х 1180 Рабочая область X Y Z 650 x 9 50 х 1 20 мм Шаг 0 006 мм Повторяемость 0 0 5 мм Процессор ЧПУ NC Studio v5
Получить ценуТехнические характеристики фрезерного
Технические характеристики фрезерного станка IMPULS RTM 2 Модель АБ 02 02ВМЕ68 Рабочая зона X x Y x Z мм 1080 х 900 х 350
Получить ценуТехнические характеристики фрезерного
Технические характеристики Основные технические характеристики фрезерного станка ФСШ 1А максимальная ширина заготовки которую можно установить на столе при глубине шипа в 10 см70 см номинальный диаметр шпиндельной насадки
Получить ценуТехнические характеристики универсального
Технические характеристики универсального фрезерного станка 6М82 6М82современный высокотехнологичный фрезерный станок Его технические характеристики особенности габариты параметры Содержание Сведения о производителе консольно фрезерного станка 6М82
Получить ценуФрезерный станок характеристики и
Фрезерный станок характеристики и устройство станка Назначение и классификация фрезерных станков По принятой классификации фрезерные станки относят к шестой группе но часть фрезерных станков входит и в пятую
Получить ценуТехнические характеристики фрезерного
Технические характеристики фрезерного станка IMPULS RTM 3 Габариты станка мм стойки ЧПУ мм 2400 х 2250 х 2050 600 х 700 х 2000 Питающая сеть
Получить ценуДиплом на тему Техническая эксплуатация и
Технические характеристики фрезерного станка модели 6Ф410 Характер и виды технического обслуживания станков
Получить цену679 Станок фрезерный
Основные характеристики фрезерного широкоуниверсального станка 679 Разработчик Одесский
Получить ценуКупить Широкоуниверсальный фрезерный
Технические характеристики фрезерного станка TOS FGS 32/40 Рабочея поверхност стола мм 1405 x 400 Наибольшая масса обрабатываемой детали кг 800
Получить ценуТехнические характеристики и эксплуатация
Технические характеристики фрезерного станка ВМ127 Назначение агрегата общий вид конструкция Кинематическая и электрическая схема
Получить ценуВМ127важнейшие технические параметры
Видео работы консольного вертикально фрезерного станка ВМ127 характеристики и особенности его конструкции описание всех достоинств данной установки 3 Кинематика и электрическое оборудование консольно фрезерного
Получить ценусхемы описание характеристики
6Т10 Станок фрезерный вертикальный консольный Паспорт схемы описание характеристики Обозначение консольно фрезерных станков 6фрезерный станок номер группы по классификации ЭНИМС Тсерия поколение станка Б
Получить ценуТех характеристики фрезерного станка СПП 30
Внедрение станка позволит улучшить метрологические характеристики анализа и обеспечит их соответствие требованиям ГОСТ для различных материалов
Получить ценуУстройство консольно фрезерного станка
Салазки 13 консольно фрезерного станка рис 5 4 перемещаются на консоли 16 в поперечном направлении На салазках смонтирована поворотная плита 11 а на ней в продольных направляющих стол 9 перемещающийся ходовым
Получить цену1 1 Основные технические данные
Основные технические характеристики фрезерного станка представлены в таблице 1 Таблица 1Технические характеристики 6Н82
Получить ценуТехнические характеристики
Технические характеристики и принцип работы плоскошлифовального станка модели 3Б172
Получить ценуСхема электрическая 6р126Р12 станок
Технические характеристики консольного фрезерного станка 6Р13 6Р13Б Наименование параметра 6Р12
Получить ценуOkuma GENOS M технические
центров Okuma серии GENOS M по всей России Технические характеристики Склад станков в Полное название станка с указанием модели Серийный номер указанный на шильдике станка Укажите
Получить ценуТехнические характеристики фрезерного
Технические характеристики фрезерного станка ФСШ 1 Доски обшивочные вагонка и для настила пола плинтуса наличники штапики и другие отделочные материалы из дерева применяемые в
Получить ценуТехнические характеристики токарно
Технические характеристики токарно винторезного станка 1К625 Токарно винторезный станок 1К625 Является удлиненной модификацией станка 1К62 Предназначен для обработки деталей длиной до 1000
Получить ценуЧертежи и схемы Фрезерных станков
Чертежи и схемы 53А80Д зубофрезерного полуавтомата Чертежи и схемы 676 фрезерного станка Всего записей 100 Показано с 1 по 48 записи Схема транспортировки 675П Схема транспортировки 675П
Получить ценуТехнические характеристики схемы и
Технические характеристики схемы и эксплуатация фрезерного станка 6Р12 Сведения о производителе фрезерного станка модели 6Р12 особенности описание Основные технические характеристики
Получить ценуУстройство и технические характеристики
Устройство и технические характеристики горизонтально фрезерного станка Содержание статьи Особенности конструкции
Получить ценуТехнические характеристики фрезерного
Технические характеристики фрезерного станка IMPULS RTM 2 Габариты станка мм 2300 х 1450 х 2250 Комплектация станков может быть дооснащена различным опциональным оборудованием При
Получить ценуВМ127важнейшие технические параметры
Видео работы консольного вертикально фрезерного станка ВМ127 характеристики и особенности его конструкции описание всех достоинств данной установки 3 Кинематика и электрическое оборудование консольно фрезерного
Получить ценуФрезерно центровальный станок 2г942
Технические характеристики Станки модели 2г942 00 предназначены для обработки торцов деталей типа валов в серийном и массовом производстве со встройкой автоматических загрузочных устройств и в составе
Получить ценуТехнические характеристики
Технические характеристики и принцип работы плоскошлифовального станка модели 3Б172
Получить ценуОписание параметров горизонтально
Описание параметров горизонтально фрезерного станка 6р82 Станок 6р82 способен фрезеровать изделия как из чугуна так из стали и цветных металлов
Получить ценуТехнические характеристики фрезерного
Технические характеристики вертикального фрезерного станка 6Т13 Вертикально фрезерный станок 6р13 Едва ли найдется отрасль тяжелой промышленности и машиностроения где не задействуются так или иначе фрезерные
Получить ценусхемы описание характеристики
Технические характеристики фрезерного станка с ЧПУ 6Р13Ф3 37 Наименование параметра 6Р13Ф3 37
Получить ценуТехнические характеристики станка СТХ 310
Технические характеристики станка СТХ 310 ecoline От 700 руб Получить выполненную работу или консультацию специалиста по вашему учебному проекту Узнать стоимость Величина перемещения по оси
Получить цену(PDF) Оценка износа токарного инструмента на основе расчетных значений параметров термодинамической подсистемы режущей системы
Материалы 2021,14, 6492 16 из 16
9.
Лапшин В.П .; Бабенко, Т.С.; Моисеев, Д. Экспериментальная оценка влияния износа инструмента на качество токарной обработки. В ICIE 2018,
Труды 4-й Международной конференции по промышленной инженерии (ICIEA); Спрингер: Чам, Швейцария, 2018; С. 853–859.
[CrossRef]
10.
Лапшин В.П .; Христофорова, В.В .; Носачев, С.В. Связь температуры и силы резания с износом инструмента и вибрациями при токарной обработке металла
. Металл. Работа. Матер. Sci. 2020,22, 44–58. [CrossRef]
11.
Wang, J .; Куриягава, Т .; Wei, X.P .; Го, Д. Оптимизация режимов резания для однопроходных токарных операций с использованием детерминированного подхода
. Int. J. Mach. Инструменты Manuf. 2002,42, 1023–1033. [CrossRef]
12.Астахов, В. Оценка износа режущего инструмента. Int. J. Mach. Инструменты Manuf. 2004, 44, 637–647. [CrossRef]
13.
Rao, K.V .; Murthy, B.S.N .; Рао, Н.М. Прогнозирование износа режущего инструмента, шероховатости поверхности и вибрации заготовки при растачивании стали
AISI 316 с помощью искусственной нейронной сети. Измерение 2014,51, 63–70. [CrossRef]
14.
Marani, M .; Zeinali, M .; Kouam, J .; Songmene, V .; Mechefske, C.K. Прогнозирование износа режущего инструмента в процессе токарной обработки с использованием методов искусственного интеллекта
.Int. J. Adv. Manuf. Syst. 2020, 111, 505–515. [CrossRef]
15. Sharma, V.S .; Шарма, С.К .; Шарма, А. Оценка износа режущего инструмента при токарной обработке. J. Intell. Manuf. 2008,19, 99–108. [CrossRef]
16.
Chen, Y .; Jin, Y .; Джири, Дж. Прогнозирование износа инструмента с помощью данных с нескольких датчиков с использованием сетей глубокого убеждения. Int. J. Adv. Manuf. Syst.
2018
, 99,
1917–1926. [CrossRef]
17.
Намаччивая, Н.С .; Беддини, Р. Изменение скорости вращения шпинделя для подавления регенеративного вибрации.J. Nonlinear Sci.
2003
, 13,
265–288. [CrossRef]
18.
Wahi, P .; Чаттерджи, А. Регенеративный дребезг инструмента возле точки Хопфа коразмерности 2 с использованием нескольких весов. Нелинейный Дин.
2005
,
40, 323–338. [CrossRef]
19.
Moradi, H .; Бахтиари-Неджад, Ф .; Movahhedy, M.R .; Ахмадиан, М. Нелинейное поведение регенеративного вибрации в процессе токарной обработки
с изношенным инструментом: анализ вынужденных колебаний и устойчивости.Мех. Мах. Теория 2010,45, 1050–1066. [CrossRef]
20. Литак Г. Хаотические колебания в процессе регенеративного резания. Фракталы Солитонов Хаоса 2002,13, 1531–1535. [CrossRef]
21.
Заковоротный, В.Л .; Лапшин, В.П .; Бабенко, Т. Оценка влияния регенеративного эффекта на динамику деформации
Движения инструмента во время токарной обработки. Процедуры Eng. 2017, 206, 68–73. [CrossRef]
22.
Заковоротный, В.Л .; Лукьянов, А.Д .; Губанова, А.А .; Христофорова, В. Бифуркация стационарных многообразий, образующихся в окрестности положения равновесия
в динамической системе резания. J. Sound Vib. 2016, 368, 174–190. [CrossRef]
23.
Гусков А.М.; Воронов, С.А .; Paris, H .; Батцер С.А.Нелинейная динамика обрабатывающей системы с двумя взаимозависимыми задержками.
Commun. Нелинейные науки. Нумер. Simul. 2002,7, 207–221. [CrossRef]
24.
Металлопродукция из нелегированных конструкционных качественных и специальных сталей.Общие характеристики. Доступно в Интернете: https: // docs.
cntd.ru (дата обращения 28 октября 2021 г.).
25. Американский стандарт ASTM A568M. Доступно в Интернете: https://www.astm.org (по состоянию на 28 октября 2021 г.).
26. Стандарты DIN. Доступно в Интернете: https://www.din.de (по состоянию на 28 октября 2021 г.).
27.
Бордачёв Е.В .; Лапшин, В. Математическое моделирование температуры в зоне контакта инструмента с деталью при точении металла. Adv. Англ.
Рез. 2019,19, 130–137.[CrossRef]
28.
Лапшин В.П .; Туркин, И.А .; Христофорова, В.В .; Бабенко, Т. Влияние температуры в зоне контакта инструмента с деталью
на динамику деформации при токарной обработке. Русь. Англ. Res. 2020,40, 259–265. [CrossRef]
29.
Рыжкин А.А .; Щучев, К.Г .; Климов, М. Обработка материалов резанием; Феникс: Ростов-на-
Дон, Россия, 2008.
30.
Kim, E.J .; Ли, К.М.А. Исследование оптимальных параметров обработки для индукционного фрезерования с использованием Inconel 718. Материалы
2019,12, 233. [CrossRef]
31.
Qian, X .; Дуан, X. Материальная модель и моделирование резания титанового сплава Ti6Al4V после термообработки. Материалы
2019
,
12, 4145. [CrossRef]
32.
Беляев Н.М .; Рядно, А.А. Методы теории теплопроводности. Высшая школа: Москва,
Россия, 1982.
33.
Иванов Е.А .; Положий, Г. Уравнения математической физики. [Уравнения математической физики]; Высшая школа: Москва,
Россия, 1964. Дифференц. Уравн. 1965,1, 701–704.
34. Graupe, D .; Чаки, Ф. Идентификация систем. IEEE Trans. Syst. Человек Киберн. 1978,8, 835. [CrossRef]
35.
Rizzo, A .; Goel, S .; Grilli, M.L .; Iglesias, R .; Jaworska, L .; Лапковскис, В .; Новак, П .; Постольный, Б.О .; Валерини, Д.Критическое сырье
Материалыв режущих инструментах для обработки: обзор. Материалы 2020,13, 1377. [CrossRef] [PubMed]
Концепция оценки прочности трубопровода из-за …
Контекст 1
… распределительные станции являются важными звеньями в газо- система снабжения, осуществляющая подготовку и распределение газа между потребителями в стране. Как показала эксплуатационная практика, строительство промышленных трубопроводов газораспределительных станций не обеспечивает длительной безаварийной эксплуатации.Вибрации, превышающие уровни силы, могут привести к разрушению трубопровода, и этот фактор необходимо учитывать [1]. В результате чрезмерной вибрации в трубопроводах возникают различные отказы, такие как трещины из-за усталости материала, самораскручивающиеся фитинги, путевые соединения и регулирующая арматура, разгерметизация трубопроводов. Колебания трубопроводов по характеру проявления, причинам, а, следовательно, и способам устранения, существенно отличаются от машинной.Если вибрация насосных агрегатов и их оснований в большинстве случаев возникает из-за инерционных сил движущихся частей агрегата и может быть устранена механическими средствами, то вибрация возникает в трубах в результате действия инерционных сил среды. перекачивается (что менее существенно), а также в результате пульсаций давления в трубопроводе [2]. Если частота вынужденных колебаний системы, обычно совпадающая с циклами работы машины, близка к частоте автоколебаний системы трубопроводов, это означает, что система будет резонировать, что приведет к интенсивной вибрации большей части напорные трубы и, в меньшей степени, всасывающие трубы.Зона распространения вибрации обычно ограничивается системой трубопроводов насосной станции или компрессорной станции, пульсации давления среды быстро затухают после достижения прямых участков труб [3]. В этой статье различные методы определения виброакустических характеристик были объединены для прогнозирования прочности трубопровода.
Как видно на рисунке 1, прочностные характеристики можно рассчитать по нескольким различным последовательностям. В зависимости от типа данных (измеренные виброакустические характеристики, геометрические характеристики элемента, входные параметры) для получения желаемых результатов можно использовать разные способы (сплошная линия – расчет, пунктирная линия – сравнение).Рассмотрим пример расчета на прочность по известным параметрам режима работы магистрального газопровода газораспределительной станции № 19 А г. Тольятти. План расчета представлен на рис. 2. Первый шаг – необходимо рассчитать уровень звуковой мощности и убедиться, что рабочие значения соответствуют …
Материалы | Бесплатный полнотекстовый | Оценка износа токарного инструмента по расчетным значениям параметров термодинамической подсистемы режущей системы
1.Введение
Мировые производители металлорежущего оборудования, такие как Siemens and Fanuc Co., Ltd. (Мюнхен, Германия), используют передовые технологии, разработанные сегодня в мире.

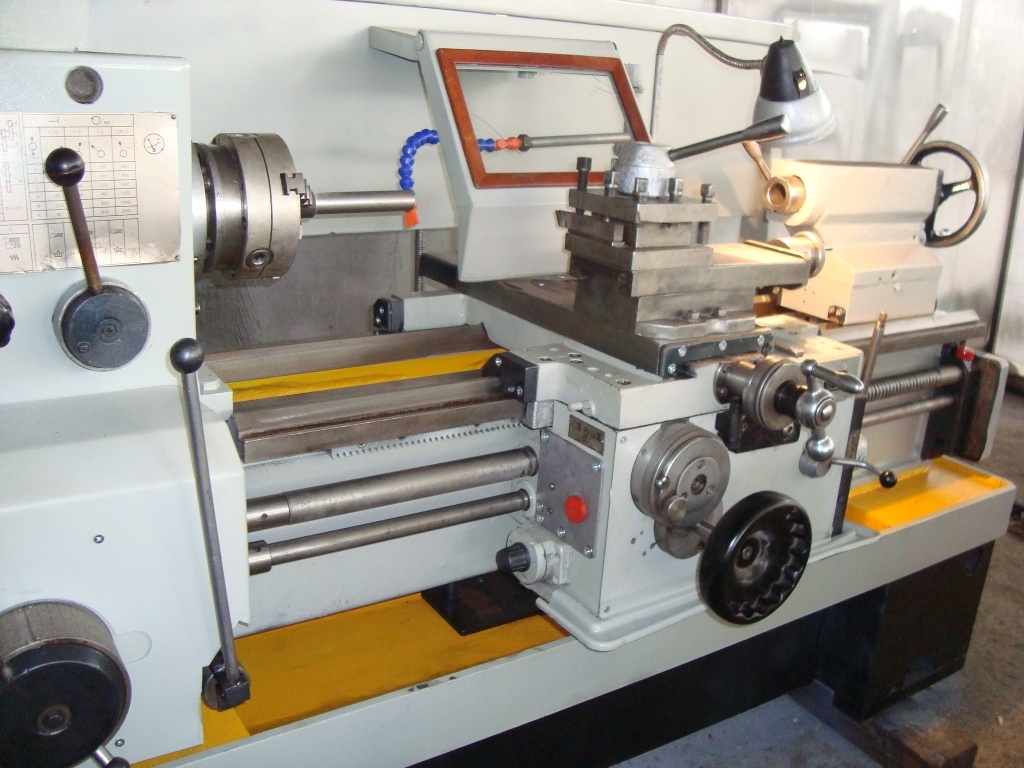
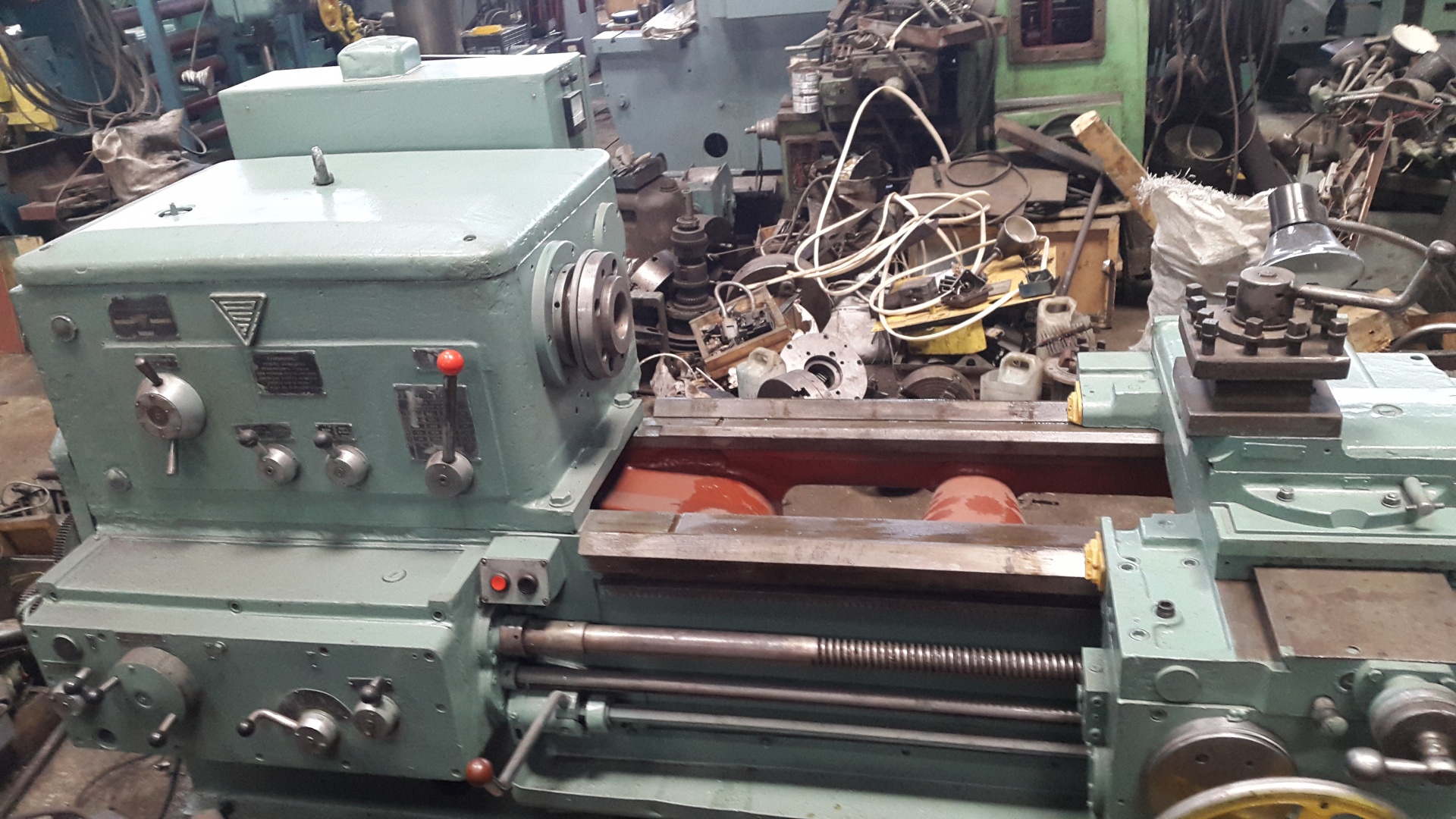
Здесь под интеллектуальными системами мы подразумеваем системы, которые имеют алгоритмы обработки данных, подобные человеческим, такие как нечеткие алгоритмы и / или алгоритмы, построенные на основе нейросетевого подхода.Несмотря на достаточно хорошие результаты использования таких систем для прогнозирования и оценки скорости износа инструмента в металлообработке, широкое внедрение этого подхода в массовое производство имеет существенные ограничения. Это ограничение связано с тем, что на каждом новом станке сложная динамика резания будет уникальной, и применение интуитивно понятного диагностического алгоритма для конкретного станка становится невозможным на другом станке.
Решение этой проблемы, на наш взгляд, заключается в применении существующих научных подходов к описанию взаимосвязанной сложной нелинейной динамики процесса резания с учетом регенеративного характера самовозбуждения обрабатываемых колебаний [ 17,18,19,20,21].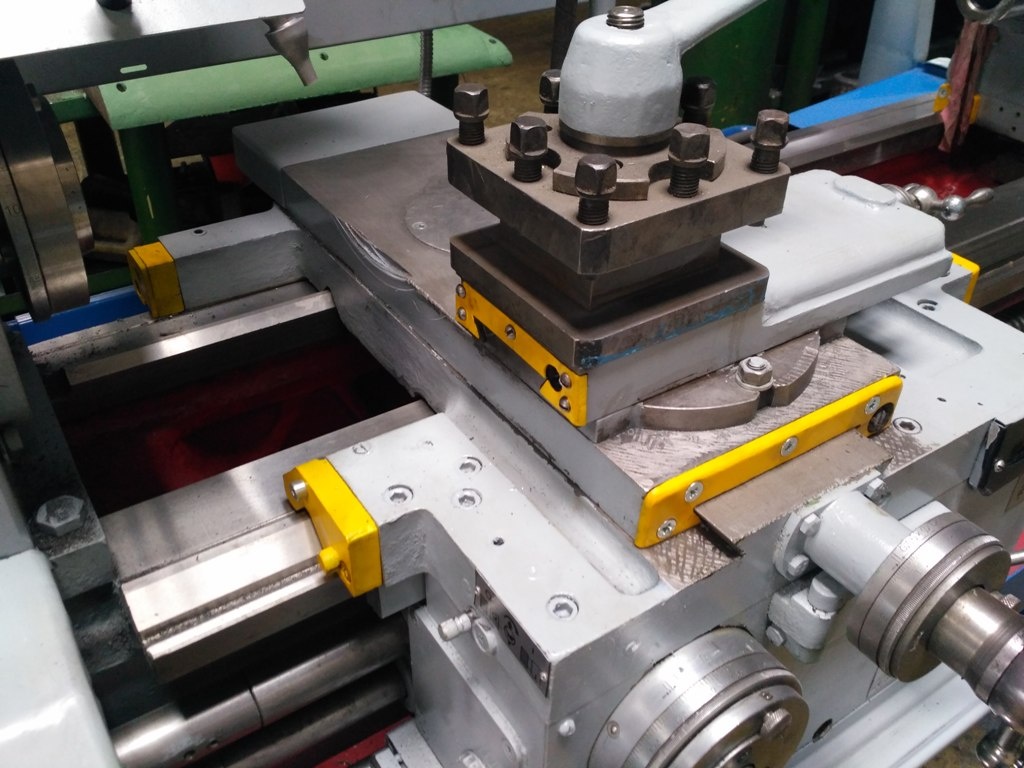
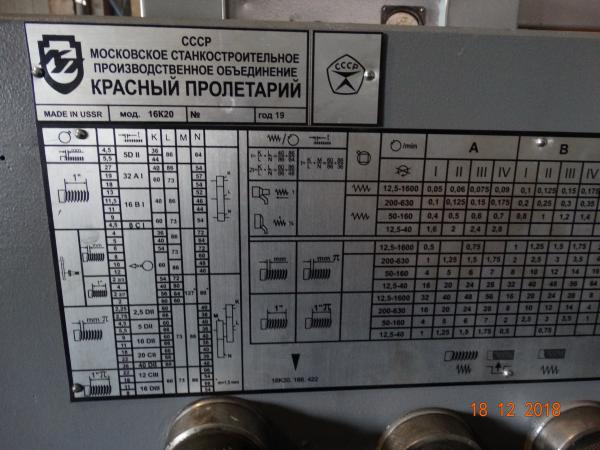
В связи с этим в качестве цели исследования была выбрана разработка нового метода оценки степени износа режущего инструмента, который будет опираться на математический аппарат, описывающий взаимосвязанную измеримую динамику процесса резания на металле. станки для резки.
В качестве оценки новизны исследования и научного вклада отмечу, что подход, предложенный в этой работе, ранее никем не использовался; то есть исследования носят новаторский характер. В целом толчком к формированию названного метода моделирования и основанного на нем подхода к оценке степени износа инструмента по параметрам термодинамической подсистемы является быстрое развитие и внедрение измерительных систем для контроля динамики процессов в металле. -резальные машины.То есть раньше такая математическая модель не была нужна, поэтому невозможно было измерить и обработать данные о динамике температуры и вибрации процесса обработки в реальном времени. Эти аргументы позволяют говорить о высокой научной и практической значимости исследования.
2. Материалы и методы
Для синтеза математической модели взаимосвязи между износом, измеренной температурой в зоне контакта инструмент-заготовка, силой резания и вибрационной активностью инструмента мы провели серию натурных экспериментов. на токарном станке 1К625 (см. рис. 1а) с СТД.На нем установлен стенд 201-1 для исследования режимов резания при токарной обработке (см. Рис. 1б), а также экспериментов на экспериментальном комплексе собственной конструкции (см. Рис. 1в, г). Стенд измерительный СТД. 201-1 позволяет измерять силовую реакцию, разложенную по осям деформации инструмента, температуру в зоне резания, используя эффект естественной термо-ЭДС, образующейся при контакте инструмента и заготовки. Измерительный стенд также включает в себя три виброакселерометра, измеряющих колебания по осям деформации инструмента.Опытная машина была предварительно модернизирована, управление двигателем, обеспечивающее режимы работы на машине, переведено на частотное управление. Благодаря этому появилась возможность плавно регулировать скорость резания внутри выбранного режима работы станка. Станок 1К625, изображенный на рисунке 1, был модернизирован; В частности, управление двигателем, обеспечивающим режимы работы на машине, было переведено на частотное регулирование. Преобразователь частоты представлен в правом верхнем углу рисунка 1а.В результате появилась возможность плавно регулировать скорость резания в рамках выбранного режима работы станка. Параметры режима в экспериментах были следующие: скорость резания V c = 124 м / мин, подача fr = 0,11 мм / об, глубина резания a p = 0,1 мм на весь период эксперимента, параметры резания остались без изменений. Выбор этих параметров связан с возможностями самого станка, для которого с учетом обрабатываемого материала это самые оптимальные режущие элементы.В качестве инструмента использовали держатель MR TNR 2020 K11 и фрезу на нем пятигранную пластину 10113-110408 T15K6, а также КЗТС WNUM 120,612 (02114-120612) h40 (T5K10) – сменную шестигранную пластину «ломаный треугольник», режущая пластина с углом вверху (угол атаки) γ 0 = 35 °, а главный угол в плане φ = 80 ° (угол между выступом главной режущей кромки на главную плоскость и подачей направление), как держатели, так и режущие пластины российского производства (г. Елец, ул., 3, из 2). В обоих экспериментах держатель был изолирован от опоры станка и внутренних стенок стенда с помощью текстолитовых пластин. Обработан вал из стали марки 45 (ГОСТ), эта марка стали широко применяется как в России (ГОСТ 2591-2006 – Сталь 45 (ст45) – конструкционный углерод качественный), так и в США и Германии. Американский стандарт ASTM A568M маркирует этот тип стали как AISI 1045, а в Германии стандарт DIN17200 – Ck45. Сталь 45 (Ст45) содержит от 0,42 до 0,5% углерода (это можно проследить по названию марки стали), 97% железа, а также процентное содержание кремния, марганца, никеля, серы, фосфора, хрома, меди, мышьяка. [24,25,26].Вал из стали на 45% изготовлен по технологии горячей прокатки; перед экспериментом вал обрезали на длину 75 см, затем производилась предварительная обработка поверхности вала и точная центровка. Выбор этой марки стали связан с ее широким использованием в машиностроении, что обусловлено высоким качеством конструкционной стали и ее относительно невысокой ценой на рынке стали. Всего было проведено более 15 серий экспериментов; в статье представлена лишь часть результатов этих экспериментов.Во втором эксперименте использовались датчики вибрации производства GLOBAL TEST AR2081-10 (Саров, Россия), подключенные к кабелю GLOBALTEST AR13. Эти преобразователи вибрации имеют аналоговый выход с сигналом, имеющим очень высокую естественную частоту среза 48 кГц; сам процесс обработки имеет базовую частоту колебаний в диапазоне от 1 до 4 кГц. Для оцифровки такого сигнала необходима частота квантования не менее 8 кГц; в связи с этим, АЦП компании L-CARD (Москва, Россия) E14-440 AD / DA CONVERTER с USB 2.0 (USB тип B). Сам эксперимент и его результаты также описаны в наших предыдущих статьях, в которых рассматривается интерпретация результатов другими методами [23,27]. Разработанный нами экспериментальный комплекс (см. Рис. 1в, г) содержит три виброакселерометра и искусственный Термопара встроена в режущий клин вблизи зоны контакта задней кромки инструмента и заготовки. Для врезки термопары в режущий клин ее предварительно прорезали электроэрозионной резкой металла, а термопару наплавляли в подготовленном отверстии.Износ инструмента в эксперименте оценивали по задней кромке. Для этого после каждого шага обработки делалось фото режущего клина; Примеры этих фотографий показаны на рисунке 2. Рисунок 2а, б – увеличенные фотографии режущей пластины, прошедшей предварительную приработку, и режущей пластины с критическим износом по задней поверхности. Видно, что степень износа по задней поверхности изменилась с почти нуля до значения, близкого к 0,45 мм. Из рис. 2в, г видно, что эксперимент также проводился с момента приработки до образования значительного участка износа задней поверхности инструмента.3. Синтез базовой математической модели
Что касается моделирования температуры в зоне контакта инструмента с заготовкой, я исходил из гипотезы температурного наследования результатов температурной изоляции по всей траектории резания в точке контакта. То есть значение температуры в данный момент времени и в данной зоне контакта инструмента с заготовкой будет определяться не только текущим значением выделяемого здесь тепла, но и влиянием мощности необратимых преобразований на всем предыдущем пути время обработки продукта.Предположим, что N (n) – текущее значение мощности необратимых преобразований, L (n) – текущее значение пути, пройденного инструментом во время обработки, а t (n) – текущее значение времени обработки. Тогда в каждой точке обрабатываемой поверхности заготовки, пройденной инструментом, будет выделяться определенное количество тепла, пропорциональное мощности необратимых преобразований. Текущее значение температуры в рассматриваемой зоне будет определяться как величиной выделяемого здесь количества тепла, так и влиянием ранее выделенного тепла на пути, пройденном инструментом (L), с учетом времени рассеяния энергии ( т).В качестве базовой модели для описания этого явления я рассмотрел модернизированный оператор Вольтерра, представленный в виде следующего двойного интеграла [27]:Qz = Qs + kT∬DwL (ξ − L) wt (η − t) N (γ, η) dγdη
(1)
где Qz – значение температуры в точке контакта инструмента с заготовкой, Qs – температура окружающей среды, wL (ξ − L) – ядро оператора Вольтерра, которое характеризует рассеяние мощности, преобразованной в температуру, в пространстве, задаваемом формулой геометрическая форма детали wt (η − t) – ядро оператора Вольтерра, характеризующее рассеяние мощности, преобразованной в температуру, за время, заданное программой обработки.Для конкретности рассмотрим механизм передачи температуры через заднюю кромку инструмента при токарной обработке металлов на металлорежущих станках (см. Рисунок 3) [9]. Как видно из рисунка 3, задняя кромка, образованная под обработка, контактирует во время резки с той частью заготовки, которая будет вращаться в течение периода вращения шпинделя. Как правило, температура в зоне контакта инструмента с заготовкой стабилизируется в течение нескольких секунд после начала резания. За это время инструмент прогревается; формируется температурное поле, градиент которого направлен в сторону инструмента; температурный поток направлен к той части заготовки, которая будет повернута за период вращения шпинделя, то есть в направлении образовавшейся области контакта инструмента с заготовкой (на рис. 3а это зона, обозначенная h 3 , где h 3 – глубина этой области в мм).Благодаря этому зона резания предварительно нагревается из-за температуры, сбрасываемой ранее при резке. Таким образом, вся температура, ранее назначенная во время обработки, влияет на текущую температуру в зоне контакта инструмента с заготовкой через соединение, образованное областью контакта вдоль задней кромки. Именно этот процесс можно описать с помощью математического аппарата, основанного на операторе Вольтерра второго рода. Следовательно, в качестве базовой модели он будет принимать мультипликативный критерий для оценки влияния предыдущего повышения температуры на ее текущее значение в виде следующего двойного интеграла [27]:Qz = Qs + kQ∫0L (t) eα1λ (ξ − L) dξ∫0teα2Th (η − t) N (η) dη
(2)
где α 1 , α 2 – параметры безразмерного масштабирования определяемого интегрального оператора, λ – коэффициент теплопроводности, Qz – значение температуры в зоне контакта инструмента с заготовкой, Qs – температура окружающей среды, kQ – коэффициент, характеризующий преобразование мощности необратимых преобразований, выделяемых в зоне контакта инструмента – детали в температуру, L (t) = Vct – путь, пройденный инструментом при резании, V c – скорость резания в мм / s, N (η) – мощность, выделяемая в контакте инструмент – заготовка при резании.Чтобы описать мощность, выделяемую в зоне резания, рассмотрим диаграмму разложения силового отклика от процесса резания на движения формовочного инструмента по осям деформации этого инструмента во время токарной обработки (см. Рисунок 4). (Рисунок 4) принято разложение деформаций на три основные оси: ось x – осевое направление деформаций (мм), ось y – радиальное направление деформаций (мм), ось z – тангенциальное направление. деформаций (мм).Вдоль тех же осей силовая реакция раскладывается от процесса резания до формующих движений инструмента (F f , F p , F c (N)), V f и V c (мм / с) скорости подачи и резания, соответственно, ω – угловая скорость шпинделя (рад / с). Соотношение между составляющими силы Ff, Fp, Fc зависит от многих факторов, таких как геометрия фрезы, скорость износа резца и др. [28]. Так, в [29] при обработке острой фрезой с передними углами основного инструмента γ 0 = 35 °, φ = 80 ° соотношение компонентов в среднем равно:Ff, Fp, Fc = (0.3-0,4), (0,4-0,5), (1)
(3)
Принимая во внимание диаграмму, показанную на рисунке 4, мы представляем мощность обратимых преобразований как:N = (Fc) 2+ (Fp) 2+ (Ff) 2 (Vf − dxdt) 2 + dydt2 + (Vc − dzdt) 2
(4)
где Ff, Fp, Fc – компоненты силового отклика, сформированные на передней кромке инструмента, Vf, Vc – скорости, установленные программой ЧПУ, скорость подачи и скорость резания соответственно, dxdt, dydt.dzdt – скорости деформационных движений инструмента.На основе проведенного анализа формулируем представление о механизме взаимного влияния силы и температуры в зоне резания, износа и вибрации режущего инструмента, которое удобно осуществлять путем построения обратных связей в процессе резания.Таким образом, мы получаем систему, состоящую из следующих подсистем:
- –
механическая подсистема или подсистема, которая формирует силовой ответ на формообразующие движения инструмента;
- –
термодинамическая подсистема, отвечающая за формирование температуры в зоне контакта инструмента и заготовки;
- –
подсистема деформации, описывающая динамику деформационных движений инструмента;
- –
эволюция (износ) инструмента, подсистема, описывающая процесс изнашивания инструмента при резании.
ВА = 1Тв (∫0Твдыдт2дт)
(6)
здесь VA – можно интерпретировать как фоновый шум сигнала или энергию сигнала вибрации за период наблюдения (эксперимент) – Tv, h 3 – износ по задней поверхности инструмента.Фактически, чем больше износ и чем ниже вибрационная активность инструмента, тем больше эта константа. В целом влияние введенной константы на температуру в зоне обработки можно описать следующим образом: чем выше значение T h , тем сильнее влияние на текущую температуру в зоне контакта инструмента с заготовкой, выбранную ранее в разделе температура резки; чем ниже Т х , тем меньше такое влияние. Другими словами, чем больше T h , тем выше температура в зоне обработки.Аналогичные аргументы справедливы и для λ – коэффициента теплопроводности. Никаких дополнительных пояснений здесь не требуется, поскольку этот коэффициент напрямую входит в уравнение Фурье, и чем больше этот коэффициент, тем сильнее влияние градиента температуры на количество теплового потока, направляемого в заготовку. Интегральный оператор (2) имеет решение для случая, когда мощность необратимых преобразований является постоянной величиной N0 = N (t).Qz = Qs + kQN0λThα1α2Vc (1 − e − α1Vλt) (1 − e − α2Tht) = Qs + kQN0λh4VAα1α2Vc (1 − e − α1Vcλt) (1 − e − α2VAh4t)
(7)
Уравнение (7) по существу является решением стандартного линейного дифференциального уравнения второго порядка, такого как приведенное ниже:Qz = Qs + кН (1 − e − tT1) (1 − e − tT2)
(8)
или само дифференциальное уравнение:T1T2d2Qzdt2 + (T1 + T2) dQzdt + Qz = кН
(9)
где T1 = λα1Vc, T2 = Thα2 = h4VAα2, k = kQλh4VAα1α2Vc – коэффициент передачи.Уравнение, полученное в уравнении (9), представляет собой математическую модель термодинамической подсистемы режущей системы с некоторыми ранее предложенными допущениями. Здесь в уравнении (9):Т = Т1Т2 = λh4VAα1α2V
(10)
Постоянная времени этой термодинамической подсистемы режущей системы. Как видно из уравнения (10), эта константа включает данные, полученные от подсистемы вибрационных движений инструмента (VA), и данные от подсистемы, отражающие скорость износа (h 3 ).В терминах уравнения моделирования (9) константа (10) отражает наклон переходной характеристики термодинамической подсистемы режущей системы. Другими словами, постоянная времени термодинамической подсистемы определяет скорость реакции со стороны этой подсистемы на изменение мощности необратимых превращений. Температура в контакте инструмент – заготовка при точении металлов на металлорежущих станках измеряется следующим образом: с помощью искусственной термопары, встроенной в инструмент (см. Рис. 1в), и посредством естественного термоэлектрического эффекта ЭДС, измеряемого измерительным стендом STD. .201-1 (см. Рисунок 1b). В этом случае можно получить кривую увеличения температуры резания, скорость изменения которой будет правильно оценена, даже если эти два метода измерения имеют несовершенную точность.4. Обсуждение и результаты
Результаты экспериментов, проведенных с использованием измерительного стенда STD.201-1, показаны на рис. 6. Результаты испытаний представлены на графиках силы резания на рис. 6a – c, разложенных по осям. деформации и график повышения температуры в зоне резания Рис. 6г.Помимо этих данных, я получил результаты измерения вибрационной активности инструмента по осям деформации. На основании этих значений я рассчитал дискретные значения мощности необратимых преобразований, используя уравнение (4). Данные, полученные в эксперименте, позволяют получить график расчетных значений температуры с помощью интегрального оператора (2). Однако этот оператор нельзя использовать напрямую, поскольку эти данные имеют дискретный (цифровой) характер. Основываясь на полученном математическом аппарате (см. Уравнение (2)), я представлю интегральный оператор в дискретной форме, как он представлен в уравнении (10):Qzn = kQe − α1λL (tn) e − α2ThtnλThα1α2 [N2 (eα1λL (t2) −eα1λL (t1)) (eα2Tht2 − eα2Tht1) +…..]
(11)
где N2, N3 – рассчитанные значения мощности, полученные путем умножения измеренного значения силы на скорость обработки, tn – последний из выборки дискретного времени обработки, L (tn) – последнее значение из выборки траектории инструмента. Здесь отмечу, что принятый подход к описанию взаимосвязи между энергетической и термодинамической подсистемами режущей системы прекрасно укладывается в современные представления о температурно-силовом характере резания [31]. Результаты моделирования дискретной версии интегрального оператора , представленные уравнением (10), приведены здесь вместе с графиком начальной температуры, измеренным в эксперименте с помощью STD.201-1 стенд. Это наглядно демонстрирует адекватность математического аппарата, разработанного и представленного в статье ранее (см. Рисунок 7). На рисунке 7 смоделированная температурная характеристика показана красным цветом, а температурная характеристика, измеренная в эксперименте, показана черным. Здесь интегральный оператор (2), представленный дискретным уравнением (10), адекватно отражает зависимость температуры в зоне контакта инструмент – заготовка от изменения (увеличения) мощности необратимых преобразований.Видно, что в рассматриваемом эксперименте стабилизация температуры происходит за время, близкое к 3 с. При этом максимальное несовпадение модельных и экспериментальных характеристик наблюдается в начале графика и в интервале от 15 до 17 с, где разница составляет почти 45 ° С. Результаты моделирования для случая измерения вибрации на экспериментальное оборудование, разработанное автором статьи, показано на рисунке 8. На рисунке 9 показаны результаты измерения температуры термопарой, встроенной в прибор (см. рисунок 1c), а также результаты моделирования температурных характеристик по уравнению ( 9) с учетом значения ВА-сигнала, взятого в эксперименте (около 30 мм / с), и параметров резки, принятых здесь.Как видно из рисунка 9, измерение температуры с помощью искусственной термопары (черная линия на графике) показывает время повышения температуры примерно за то же время, что и в случае, показанном на рисунке 7, примерно за 3 с. Тем не менее, температурная характеристика на рисунке 7 все еще является некоторым отклонением, и характеристика, измеренная с помощью искусственной термопары, монотонно увеличивается до определенного установившегося значения. Это связано с принципами измерения температуры через термоэдс, снимаемую с инструмента и шпинделя с закрепленной в нем заготовкой.При этом в начале измерений термо-ЭДС покажет более высокую температуру, чем есть на самом деле. Дело в том, что чем выше градиент температуры, тем выше термо-ЭДС; то есть в начальный момент времени температура в контакте инструмента и заготовки показывает большее значение, чем в последующий момент времени после стабилизации процесса и распространения теплового поля из зоны резания вглубь инструмента и инструмента. заготовка. В результате рассеивания тепловой энергии в инструменте и заготовке градиент температуры уменьшается, и значение температуры, измеренное этим методом, также немного уменьшается.В связи с этим я считаю, что экспериментальная характеристика повышения температуры, представленная на рисунке 9, более точно отражает характер повышения температуры в течение начального периода обработки. График моделируемой температуры (рисунок 9) статистически менее точно отражает изменения в экспериментально определенная температура в зоне резания, поэтому в интервале от 1 до 2 с разница между графиками достигает 160 ° C, а в интервале от 2 до 3 с – 140 ° C.Что касается моделирования повышения температуры в зоне резания, метод, основанный на использовании дискретной версии модифицированного оператора Вольтерра (см. Уравнение (10)), дает более точное значение температуры, чем метод, основанный на реализации того же оператора в предположении стационарности значений мощности необратимых преобразований (см. уравнение (9)). Это хорошо видно на начальной части температурной характеристики, показанной на рисунке 9, где расхождение между измеренным значением температуры и наблюдаемым значением достаточно велико.Для большей уверенности в этом несоответствии давайте рассмотрим, является ли уравнение (7) решением задачи Коши для дифференциального уравнения теплопроводности. Уравнение теплопроводности для этого случая примет следующий вид [32,33]:dQdt = λ2∂2Q∂L2 + Vc∂Q∂L
(12)
где Q (L, t) – функция, задающая температуру в точке с координатой L в момент времени t. Подставляя (7) в дифференциальное уравнение теплопроводности (11), получаем:α1Vce − α1λL (1 − e − α2Tht) + α2e − α2Tht (1 − e − α1λL) = – (α1λ) 2e − α1λL (1 − e − α2Tht) + α1λVce − α1λL (1 − e − α2Tht)
(13)
или разрешение относительно времени и расстояния:α2e − α2tTh (1 − e − α2t) = – α12e − α1Lλ2 (1 − e − α1L)
(14)
Анализ уравнения (13) показывает, что вариант стационарного развития температуры, предложенный в уравнении (7) в зоне контакта инструмент-заготовка, действителен только для больших значений времени (t) из-за принятого стационарного движения источника температуры L = Vt.Отчасти это связано с тем, что в случае металлообработки приближение температурного поля к стационарному состоянию возможно только после некоторого переходного процесса, связанного с проникновением инструмента в заготовку. При этом время установления определенного квазистационарного состояния в случае измеряемой характеристики и стационарного состояния в случае моделируемой характеристики значения температуры совпадает (см. Рисунок 9). Результаты измерений и моделирования, представленные на рисунке 9, позволяют Нам необходимо определить скорость износа задней поверхности инструмента на основе анализа параметров уравнения (9), полученных при моделировании.Под этими параметрами понимают постоянную времени термодинамической системы T = λh4VAα1α2Vc и коэффициент усиления этой системы k = kQλh4VAα1α2Vc. В представленном имитационном случае (см. Рисунок 9) величина износа h 3 составила около 0,1 мм. Это значение было определено экспериментально из увеличенной фотографии задней кромки режущей пластины (см. Рисунок 2). Однако значения этих констант были получены с использованием коэффициентов масштабирования α1α2, которые заранее не были известны. В связи с этим на практике для оценки скорости износа задней поверхности инструмента требуется проведение предварительных исследований.То есть в начале обработки, когда степень износа либо равна нулю, либо известна, необходимо провести предварительное проплавление инструмента в заготовку. Затем на основе результатов выберите значения этих коэффициентов масштабирования путем сравнения экспериментальных и смоделированных характеристик. После этого эти значения можно будет использовать в дальнейшем без изменений. В этом случае постоянную времени термодинамической подсистемы режущей системы удобно задавать с помощью метода определения постоянной времени инерционного звена второго порядка [34].Значение коэффициента передачи термодинамической подсистемы может быть определено из усредненного установившегося значения экспериментальной температурной характеристики в зоне контакта инструмента с заготовкой. По обоим этим параметрам (T = λh4VAα1α2Vc, k = kQλh4VAα1α2Vc) можно рассчитать скорость износа задней поверхности инструмента (h4). Для упрощения расчетов можно использовать только значение коэффициента передачи. Для пояснения, вы можете рассчитать оба значения и получить оценку износа путем усреднения этих двух результатов.В целом проведенное исследование соответствует многим из тех же современных работ в области описания взаимосвязанной динамики процессов резки металла на металлорежущих станках [35]. Однако представленный метод математического моделирования температуры в зоне обработки и основанный на нем способ косвенной оценки скорости износа инструмента предлагаются впервые.5. Выводы
Основными научными результатами являются синтезированная математическая модель, представленная уравнением (9), а также, основанный на использовании этой модели, метод оценки степени износа инструмента по идентифицируемым параметрам.В то же время этот метод и используемая в нем модель позволяют оценить степень износа инструмента по совокупности косвенно наблюдаемых параметров процесса резания. Такими наблюдаемыми параметрами являются время повышения температуры в зоне контакта инструмента и заготовки; окончательное среднее измеренное значение температуры в зоне обработки и среднеквадратичное значение мощности вибросигнала берутся либо с инструмента, либо с опоры станка. Благодаря этому при мониторинге динамики процесса резания с целью оценки износа режущего клина можно опираться в расчетах на усредненные расчетные характеристики, что должно исключать влияние случайных колебаний в процессе обработки.Исходя из этого, в качестве основной научной позиции, вытекающей из анализа полученных результатов, я вижу следующее: эволюция (износ) инструмента при резке металлов на металлорежущих станках в полной мере отражается в изменении параметров термодинамическая подсистема режущего аппарата.
С точки зрения возможности практического применения полученных научных результатов это следует из непосредственного использования методики оценки степени износа инструмента, предложенной в данной работе.Для непосредственного измерения и возможного расчета усредненных характеристик вибрации, температуры и времени реакции термодинамической подсистемы потребуется разработать и внедрить в современное производство интеллектуальный режущий инструмент, включающий в себя встроенный датчик температуры и встроенный преобразователь вибросигнала. Расчет параметров термодинамической подсистемы должен производиться на микроконтроллере, встроенном в инструментальную оправку, с которого полученное значение степени износа инструмента может быть напрямую передано в сеть предприятия, где осуществляется система управления всем предприятием. на основании этих данных принимает решения о планируемых операциях на конкретных металлорежущих станках или металлообрабатывающих центрах.Реализация метода оценки степени износа в этой форме, как я уже описал, по своей сути соответствует основному направлению развития современного промышленного производства в рамках Индустрии 4.0.
% PDF-1.4 % 1 0 объект > поток 2021-11-11T07: 42: 06-08: 002019-10-30T11: 12: 26-04: 002021-11-11T07: 42: 06-08: 00Acrobat PDFMaker 10.1 для Worduuid: 27ae426f-fac9-4d94-868d- d3f3e33cf1b5uuid: 9498a96e-9126-451b-9e3b-5ed2dfc28855uuid: 27ae426f-fac9-4d94-868d-d3f3e33cf1b5
сек.gov | Превышен порог скорости запросов
Чтобы обеспечить равный доступ для всех пользователей, SEC оставляет за собой право ограничивать запросы, исходящие от необъявленных автоматизированных инструментов. Ваш запрос был идентифицирован как часть сети автоматизированных инструментов за пределами допустимой политики и будет обрабатываться до тех пор, пока не будут приняты меры по объявлению вашего трафика.
Пожалуйста, объявите свой трафик, обновив свой пользовательский агент, чтобы включить в него информацию о компании.
Для лучших практик по эффективной загрузке информации из SEC.gov, включая последние документы EDGAR, посетите sec.gov/developer. Вы также можете подписаться на рассылку обновлений по электронной почте о программе открытых данных SEC, включая передовые методы, которые делают загрузку данных более эффективной, и улучшения SEC.gov, которые могут повлиять на процессы загрузки по сценарию. Для получения дополнительной информации обращайтесь по адресу [email protected].
Для получения дополнительной информации см. Политику конфиденциальности и безопасности веб-сайта SEC. Благодарим вас за интерес к Комиссии по ценным бумагам и биржам США.
Идентификатор ссылки: 0.14ecef50.1636645362.5c47acd8
Дополнительная информация
Политика безопасности в Интернете
Используя этот сайт, вы соглашаетесь на мониторинг и аудит безопасности. В целях безопасности и обеспечения того, чтобы общедоступная услуга оставалась доступной для пользователей, эта правительственная компьютерная система использует программы для мониторинга сетевого трафика для выявления несанкционированных попыток загрузки или изменения информации или иного причинения ущерба, включая попытки отказать пользователям в обслуживании.
Несанкционированные попытки загрузить информацию и / или изменить информацию в любой части этого сайта строго запрещены и подлежат судебному преследованию в соответствии с Законом о компьютерном мошенничестве и злоупотреблениях 1986 года и Законом о защите национальной информационной инфраструктуры 1996 года (см. Раздел 18 U.S.C. §§ 1001 и 1030).
Чтобы обеспечить хорошую работу нашего веб-сайта для всех пользователей, SEC отслеживает частоту запросов на контент SEC.gov, чтобы гарантировать, что автоматический поиск не влияет на возможность доступа других лиц к контенту SEC.gov. Мы оставляем за собой право блокировать IP-адреса, которые отправляют чрезмерное количество запросов. Текущие правила ограничивают пользователей до 10 запросов в секунду, независимо от количества машин, используемых для отправки запросов.
Если пользователь или приложение отправляет более 10 запросов в секунду, дальнейшие запросы с IP-адреса (-ов) могут быть ограничены на короткий период.Как только количество запросов упадет ниже порогового значения на 10 минут, пользователь может возобновить доступ к контенту на SEC.gov. Эта практика SEC предназначена для ограничения чрезмерного автоматического поиска на SEC.gov и не предназначена и не ожидается, чтобы повлиять на людей, просматривающих веб-сайт SEC.gov.
Обратите внимание, что эта политика может измениться, поскольку SEC управляет SEC.gov, чтобы гарантировать, что веб-сайт работает эффективно и остается доступным для всех пользователей.
Примечание: Мы не предлагаем техническую поддержку для разработки или отладки процессов загрузки по сценарию.
Расчет технических показателей участка механической обработки пресс-диска. Расчет технико-экономических показателей участка механообработки части складского техника экономические показатели участка механообработки
Калужский государственный машиностроительный техникум
КУРСОВАЯ РАБОТА
По предмету:
«Экономика и управление производством»
Задание на курсовую работу по экономике и управлению предприятием
Тема проекта: «Расчет технико-экономических параметров предприятия». участок механический для изготовления детали «шайба», материал – сталь 3Сп, штамповка, цена материала 50 руб / кг, цена отходов 300 руб / тн.Масса детали 0,18кг., Вес заготовки 0,23кг. “.
Исходные данные:
Годовая программа: n = 2100 шт. CNR = 210%
Режим работы сайта: S = 2 SNR смещения = 370%
Нормальный коэффициент полезного действия: K. = 1,1 к Ом. = 3,3%
Сложность обработки узла: Т о = 48н / час n = 17%
по типу оборудования:
оп.1 – Токарная обработка 16К20: 4 мин.
оп.2 – сверление с ЧПУ 2П132Ф2 16мин.
оп. 3 – Улавливание щелчков 3E711V 12мин.
оп. 4 – круговой пух 3м151: 6 мин.
оп. 5 -VTRISHLIFICAL 3K228V 6мин:
oP.6-очистка 3мин.
Введение
2. Раздел: «Расчет площади участка»
4. Раздел: «Расчет фонда оплаты труда»
5. Раздел: «Расчет продолжительности технологического цикла»
6. Раздел: «Расчет срока запуска – выпуск продукции и строительство незавершенного производства»
7.Раздел: «Расчет стоимости основных материалов»
8. Раздел: «Составление расчета, определение себестоимости и цены продукта»
9. Раздел: «График технико-экономических показателей
Библиография
Введение
В условиях рыночных отношений Центр экономической деятельности Перемещается к главному звену всей экономики – предприятию
Именно на этом уровне товары и услуги, выпуск необходимой продукции создаются обществом.На предприятии сосредоточены самые квалифицированные кадры. Здесь возникают вопросы экономного расходования ресурсов, использования высокопроизводительного оборудования, техники. Компания добилась минимума затрат на производство и реализацию продукции. Разрабатываются бизнес-планы, применяется маркетинг, осуществляется эффективное управление – менеджмент.
Все это требует глубоких экономических знаний. В условиях рыночной экономики только тот, кто наиболее грамотно и грамотно определяет потребности рынка, превзойдет, создаст и наладит производство востребованной продукции, обеспечит высокий доход высококвалифицированным работникам.Задания из заданий сможет выполнить только тот, кто изучил основы экономики предприятия.
1. Раздел: «Расчет необходимого количества оборудования»
Расчет необходимого количества оборудования, необходимого для изготовления планового количества деталей, производится по типам (моделям) оборудования по следующей формуле:
|
N – годовая программа выпуска продукции;
Кому. – Планируемый коэффициент правил. Он устанавливается с учетом фактического выполнения нормативов по исходным данным и предусмотренной планом степени дальнейшего повышения производительности труда.
F EF – Эффективный годовой фонд оборудования оборудования (одна машина).
Определение трудоемкости по типу оборудования производится по данным базового предприятия по согласованию с преподавателем и пропорционально сложности изготовления представительной части по следующей формуле:
|
Таблица 1: «Определение затрат времени по типу оборудования».
№ п / п | наименование операции | Модель машины | T / Clee. Heot. Дети. – Perst. (Н / час) | Всего т / цистерна. узел (н / час) | т / кли. узел по типу Оборудование. (LF) |
1. | Токар | 16к20 | 0,06 | 48 | 3,06 |
2. | Сверлильный станок с ЧПУ | 2п132ф2. | 0,43 | 21,9 | |
3. | СамолетШлилифовал | 3Е711В. | 0,2 | 10,2 | |
4. | Круглохлифовал | 3м151 | 0,1 | 5,1 | |
5. | Интрагелифовальный | 3k228V. | 0,1 | 5,1 | |
Сантехника | Сантехника | 0,05 | 2,55 | ||
ИТОГО: | ∑0,94 | ∑48 |
Эффективность работы оборудования в течение года определяется по формуле:
|
D год – количество дней в году.
D дюйм – Количество выходных в году.
пр.Д – Количество праздничных дней в году.
Т, см – продолжительность рабочей смены в часах (8 часов).
S – количество смен оборудования.
K – коэффициент потерь времени на ремонт оборудования.
1 – Сокращение продолжительности рабочего дня на 1 час в праздничные дни.
F EF = [(365-105-11) * 8-6 * 1] * 2 * 0,97 = 3852,84 часа
Эффективное поле работы участка на 2009 год составит:
FEF = 3852,84 ч. .
При расчете количества оборудования с расчетом. (Количество станков) получается дробной величиной, поэтому необходимо решить вопрос о том, какое количество оборудования необходимо взять для выполнения производственной программы на участке, то есть определить с помощью пр.
Правило округления: если дробная часть с вычислить.> 0,1, то округление производится в большую сторону, если дробная часть
В данном случае, в данном случае, ряд технических мероприятий направлен на уменьшение с расчетом. :
а) совершенствуется технологический процесс с целью снижения Т шт.
б) повышается квалификация рабочих, с целью повышения К.
в) переносить часть работы кафедры группы оборудования на аналогичную.
г) увеличена производительность существующего оборудования.
По результатам расчетов с расчетом. И после определения с принципом. Расчет КПД оборудования для данного типа оборудования производим по формуле:
|
С расчетом = Н * Т шт. / F EF * К.
1.Определите количество оборотов модов 16к20, необходимое для выполнения токарной операции.
Станок
Мы принимаем 2 станка, тогда процент использования этих станков будет:
2. Определите количество сверлильных станков с ЧПУ мод. 2R132F2, необходимое для токарной обработки:
Станок
Мы принимаем 11 машин, то процент использования этих машин будет:
3. Определить количество плоских оксильных осветительных машин мод.3E711B, необходимый для выполнения операции сверления:
Станок
Мы принимаем 6 станков, тогда процент использования этих станков будет:
4. Определите количество станков для круглых печей mod 3 mM151, необходимое для операции шлифования:
Станок
5. Определите количество внутриплоскостных станков мод. 3K228B, необходимых для операции шлифования:
Станок
Мы принимаем 3 станка, тогда процент использования этих станков будет:
6.Определить количество слесарных жилетов станков, используемых для выполнения сантехнической программы:
Верстак напольный
Принимаем 2 жилета для резки.
Определить средний уровень загрузки оборудования
Результаты расчета необходимого количества оборудования и его использования сведены в таблицу.
Сводная таблица № I «Расчет оборудования и его загрузка» | Сантехника | для прога | 105 | 5250 | 5355 | 1,1 | 4868 | 3852,84 | 1,26 | 2 | KZ.О.С. = 90% | |
по 1 шт. | 0,05 | 2,5 | 2,55 | 2,3 | – | – | – | |||||
Intrahelifoval | для программы | 210 | 10500 | 10710 | 9736 | 2,52 | 3 | 84 | ||||
по 1 штуке | 0,1 | 5 | 5,1 | 4,6 | – | – | – | |||||
Круглохлифовал | Для программы | 210 | 10500 | 10710 | 9736 | 2,52 | 3 | 84 | ||||
по 1 штуке | 0,1 | 5 | 5,1 | 4,6 | – | – | – | |||||
PlaneShlylifoval | для прог | 420 | 21000 | 21420 | 19472 | 5,05 | 6 | 84,2 | ||||
по 1 шт. | 0,2 | 10 | 10,2 | 9,3 | – | – | – | |||||
Бурение | для программы | 903 | 45087 | 45990 | 41809 | 10 | 11 | 98,6 | ||||
по 1 шт. | 0,43 | 21,47 | 21,9 | 20 | – | – | – | |||||
Tokar | для программы | 126 | 6300 | 6426 | 5842 | 1,5 | 2 | 75 | ||||
по 1 шт. | 0,06 | 3 | 3,06 | 2,8 | – | – | – | |||||
Имя узла | 1.Прошний | 2. ОСТ. Дочерние узлы | 3. Общее количество н / ч (на узле) | 4. Планируемый коэффициент NT | 5. Фактическое количество н / ч | 6. Полезный фонд рабочего времени 1-я машина, час | 7 Расчет. Количество станков, раздел | 8. Допустимое количество станков, Sprin | 9.% Загрузки и стропы | 10. Оборудование CP% |
2 Раздел: «Расчет площади участка»
При расчете общей производственной площади участка необходимо рассчитать площадь, занимаемую станками (Производственная площадь), и прибавить вспомогательная площадь к ней:
Склад заготовок – 7-8% производственной площади;
Склад готовой продукции – 5-6% производственных площадей;
Земельный участок технического контроля – 2-3% производственной площади;
Мастерские комнаты – 5-6 м 2 на мастера;
Отделение заточки – 5-6% производственной площади.
Средняя площадь, занимаемая одним станком, указана в справочнике, в зависимости от размера станка. В этой же литературе указаны нормы расчета подсобных помещений.
Средняя удельная площадь, занимаемая одной машиной, с учетом проходов и хода:
а) для малых машин – 10 – 12 м 2;
б) для средних машин – 20-25 м 2;
в) для больших машин – 35-40 м 2;
Найдите на участке участки, занятые машинами:
1.Текущий мод. 16к20 (относится к среднему):
S = 25 * 2 = 50 м 2
2. Сверло с ЧПУ мод. 2п132ф2 (относится к среднему):
ST-CNC. = 25 * 11 = 275 м 2
3. PlaneShlylifed мод. 3E711B (относится к среднему):
SSV = 25 * 6 = 150м 2
4. Круговые режимы. 3м151 (относится к среднему):
СКС = 25 * 3 = 75 м 2
5. Внутрипосеточная мод. 3k228B (относится к среднему):
SVS.= 25 * 3 = 75 м 2
6. Слесарь (верстак):
SSL = 10 * 2 = 20 м 2
Определите производственную площадь:
Sprove = SCT. + SP. + Слос. + Скрик. + СВНТР. = 50 + 275 + 150 + 75 + 75 + 20 = 645 м 2
Площадь склада заготовок составляет 7-8% производства:
СС.З. = 645 * 0,08 = 51,6м 2
Площадь склада готовой продукции 5-6 от производства:
СС.Г.И. = 645 * 0,06 = 38,7 м 2
Площадь ОТП составляет 2-3% от производства
СОТК = 645 * 0,03 = 19,35м 2
Комната мастера занимает 5-6 м 2 на мастера:
SM. = 6 * 1 = 6 м 2
Определяем общую производственную площадь участка:
Сингч. = Ss.z. + SS.G.I. + SCCE. + СОТК + СМ. = 645 + 51,6 + 38,7 + 19,35 + 6 = 760,65м 2
Расчетную производственную площадь необходимо разделить на количество рабочих мест и полученную удельную площадь по сравнению с характеристиками расхода цехов.
Sud. = СПР. / Весна. [м 2]
Sud. = 645/25 = 25,8м 2
3. Раздел: «Расчет численности рабочих и определение состояния участка»
Производственный участок может включать следующие категории рабочих:
1. Основные рабочие.
2. Вспомогательные рабочие.
3. Инженерно-технические работники.
4. Сотрудники.
Расчет количества основных рабочих.
Расчет количества основных рабочих, работающих на универсальном оборудовании, производится по профессиям:
РО = N * ТСТ./ (FEF * sq.) [Люди]
Где n – годовая программа выпуска продукции;
Т шт. – норма штук (рассмотрение) по типу оборудования для изготовления всех деталей узла;
Кому. – Планируемый коэффициент правил.
FEF. – Фактический годовой полезный фонд работы одного работника, определяем, заполняя Таблицу № 3.
Сводная таблица 3: «Расчет рабочего баланса».
Временные категории | Количество часов |
1.Календарное время | 365 * 8 = 2920 |
2. Потери времени, связанные с выходными и праздниками. | 116 * 8 = 928 |
3. Потери времени, связанные с сокращением предпраздничных дней. | 6 * 1 = 6 |
4. Номинальный ход времени. | 2920-928-6 = 1986 |
5. Еще один отпуск. | 24 * 8 = 192 |
6. Временной фонд, который можно использовать. | 1984–192 = 1794 |
7.Неявка по причине а) болезни (2% от номинального фонда) б) казенного общества. и государственные обязанности (0,5%) в) Академический отпуск (1% от номинального фонда) | ИТОГО: 69,51 |
8. Срочный фонд | 1794-69,51 = 1724,5 |
9. Потери внутри рабочего дня по льготному дежурству подростка (0,5% фонтана) | 1724,5 * 0,005 = 8,62 |
10.Полезный фонд времени | 1724,5-8,62 = 1715,88 |
Учет количества основных рабочих.
Для определения объема работ необходимо округлить расчетную цифру с учетом имеющегося количества рабочих мест.
1. Определите количество токов, необходимых для выполнения заданной программы на токарной операции:
Мы принимаем 4 человека.
2. Определите количество операторов:
Производство Большие работы 2 заменяемых, рекомендуемый уровень обслуживания станков с ЧПУ от 2 до 3 станков.Количество таких машин на участке 11, примите ставку обслуживания -8. На сайте будет 8 операторов.
3. Определите количество шлифовальных машин, необходимых для выполнения данной программы на операции шлифования:
Мы принимаем 12 человек.
4. Определите количество шлифовальных машин, необходимое для выполнения операции шлифования:
Принимаем 6 человек.
5. Определите количество шлифовальных машин, необходимое для выполнения операции шлифования:
Мы принимаем 6 человек.
6. Определить количество замков, необходимых для выполнения сантехнических работ:
Принимаем 3 человека.
Данные расчета сводятся к таблице:
Таблица 4: «Количество основных рабочих на участке».
ПП | Профессия | План, шт. | Ставка времени, час | План. Кофф. Норма производительности | Факт. время, в н / ч | Страна | ||
По 1 шт. | Для прог. | По расчету | Принято | |||||
1 | Тернер | 2100 | 3,06 | 6426 | 1,1 | 5841,8 | 3,38 | 2 |
2 | Шлифовальный станок | 10,2 | 21420 | 19472,7 | 11,3 | 8 | ||
3 | Шлифовальный станок | 5,1 | 10710 | 9736 | 5,6 | 10 | ||
4 | Шлифовальный станок | 5,1 | 10710 | 9736 | 5,6 | |||
5 | Слесарь | 2,55 | 5355 | 4868 | 2,8 | 2 | ||
6 | Оператор | – | – | – | 8 | 8 | ||
Расчет количества вспомогательных рабочих
Количество вспомогательных рабочих можно определить тремя способами:
а) сложность вспомогательных работ.
б) о нормах службы труда.
в) увеличенный, в процентах от основного.
При расчете используем третий метод, величина процента зависит от типа производства:
При серийном производстве – 10-15%
При крупносерийном производстве – 15-18%
При массовом производстве – 18 – 25%
Так как производство мелкое, количество вспомогательных рабочих составляет 15% от основного.
РВСП. = 36 * 0.2 = 7,2 (человек)
Принимаем 7 человек.
Производственная площадка может включать следующие профессии вспомогательных рабочих:
а) слесарь по ремонту оборудования,
б) легковые автомобилисты,
в) электрика,
г) точилки
д) регулировка.
Определить количество наладчиков:
На участке будет наладчик, так как производство мелкоячеистых, работа 2см.
Количество станков, обслуживаемых одним наладчиком от 7 до 9
Производим разбивку по профессиям:
Слесарь по ремонту оборудования -2.
Водитель автомобиля -1.
Электрики -1.
Точилка -1.
Регуляторы -2.
Расчет количества I.T.R. и M.O.P.
Количество инженерно-технических работников и младшего обслуживающего персонала определяется в соответствии со штатным расписанием.
Мы используем следующие нормы стандартного расписания:
I.T.R. – 1 мастер – на 20 – 25 осн. Рабочие
1 старший мастер – на 3 мастера
1 Заведующий участком на 2 ст.Мастера
1 технолог на участке средней сложности обработки деталей
1 Нормализатор на 40 рабочих партнеры
M.O.P. – 1 уборщица на производственной площади 400 м 2.
Мастера -2 ч.
Технолог -2ч.
Нормализатор -1 ч.
Очиститель – 2 ч.
Таблица 5: «Сводная ведомость земельных работников»
Категория рабочих | номер | Удельный вес в% |
Основные рабочие | 39 | 73,6 |
Вспомогательные рабочие | 7 |
Расчет технико-экономических показателей участка в базовой и модернизированной версии представлена в таблице 4.
Таблица 4 – Технико-экономические показатели участка в модернизированной версии
Показатели | Модернизированный вариант |
Годовая программа выпуска продукции, шт. | |
Количество рабочих смен | |
Количество единиц промышленного оборудования | |
Общая площадь, м 2 в том числе производство | |
Количество работ на сайте, чел. | |
в том числе: Мачников Мастера Контроллеры | |
Мощность установленного оборудования, кВт: | |
Средняя мощность оборудования, кВт. | |
Годовое производство, штук: На единицу производственного оборудования 1 м 2 производственная площадь | |
Общая производственная площадь на единицу оборудования, м 2 | |
Коэффициент загрузки среднего оборудования | |
Сложность труда: Одна деталь, мин. Детализация программ вывода, час. |
В данной работе спроектирован механический участок для изготовления детали «Вал»: определено количество необходимого оборудования, его передача, количество сотрудников, составлен макет участка, определены его основные параметры. .
Для изготовления требуются детали общей площадью 180 (м 2), на которых размещается 6 станков в ходе технологического маршрута. В качестве подъемно-транспортного средства выбран мостовой кран, грузоподъемностью 5 тонн.
1. Гручева Н.Н. Проектирование механических мест и мастерских. Руководство. / Н.Н. Гиршева, В.В. Гришев, В. Casmun.- Чита: Читгу, 2001. – 119С.
2. Соломенцы Ю.М. Дизайн автоматизированных сайтов и мастерских. / Ю.М. Соломенцы, А.Г. Схиртладзе, Ю.В. Копыленко. – М .: Высшая школа, 2000. – 266с.
3. Схиртладзе А.Г. Основы механического производства. Руководство. / А.Г. Ширтладзе, В. Осетр, т.н. Иванова.- Олдакол: ТНТ, 2009.- 292С.
4. Гиршева Н.Н. Проектирование машиностроительных производств (механических участков и цехов): Учебное пособие / Н.Н. Перешева.- Чита: Рик Заббе, 2011.- 80с.
вспомогательный механический вал
Отправить свою хорошую работу в базу знаний просто. Используйте форму ниже
Студенты, аспиранты, молодые ученые, использующие базу знаний в учебе и работе, будут Вам очень благодарны.
Размещено на http://www.allbest.ru/
Расчет технико-экономических показателей части механической обработки деталей
1. Организационная часть
Выполнение организационной части проекта осуществляется на основе разработанного технологического процесса обработки детали – представителя.
Для лучшего обзора и анализа результатов, полученных в технологической части проекта, а также для удобства проведения расчетов в данном разделе составлена таблица 1 исходных данных.
Таблица 1. Исходные данные
Имя | Нормы времени | |||||||
операций | ||||||||
Фрезерование | ||||||||
Токар | ||||||||
Протяжка | ||||||||
Бурение | ||||||||
Шлифовальный | ||||||||
Токарная обработка с ЧПУ | ||||||||
Фрезерование | ||||||||
с резьбой | ||||||||
Сантехника |
Определение годового представления представителя представителя и количества наименований однородных частей, обрабатываемых на сайте.Расчет количества деталей в партии, норм поштучного времени и расценок.
Ежегодная презентация деталей NPR., Т.е. Условное количество типовых деталей, время обработки которых равно сложности всех деталей, закрепленных на объекте, определяется исходя из производственной мощности участка и наиболее рационального использования оборудования по формуле:
НПР = МГ КЗ =, шт. (один)
где мг – годовая производственная мощность
KZ – коэффициент загрузки оборудования принимаем 0.8 – 0,85, что характеризует достаточно полное использование оборудования и наличие необходимого запаса времени.
FD – действующий годовой фонд оборудования оборудования (4015 часов).
ТШМ – норма штук на ведущей операции для представительной части, (мин)
В некоторых случаях рекомендуется совмещать операции небольшой продолжительности (менее минуты) одной модели, выполняемые на станках.
Коэффициент допустимой эталонной потери.
0,05 – 0,08 для среднего производства.
0,08 – 0,1 для мелкосерийного производства.
Расчетное значение NPR округлено до целого значения, удобного для последующих расчетов.
Ведущее предприятие
НПР = 4015 * 0,85 * 60 / 2,3 * (1 + 0,1) = 80935 шт.
НПР = 80000, шт.
Годовой выпуск части представителя Национального представителя определен в пределах
NAW = NPR / KZOMAX… NPR / CW MIN, шт. (2)
, где КЗО – коэффициент обеспеченности операций (по ГОСТ 3.1108-74 для средней продукции 11-20, для мелкосерийной 21-40).
Наид = 2023 … 3854, шт.
Принято Народное = 2500, шт.
Количество деталей деталей обрабатываемых на сайте деталей определяется по формуле:
МД = НПР / Н., шт. (3)
MD = 80000/2500 = 32, шт.
При систематическом течении года изготовления и закреплении каждого рабочего места одной операции КВК = МД
В данном случае MD = 32 шт.Находится в пределах КЗО = 21 … 40 для производства, что соответствует задаче проекта.
Определение количества деталей в партии. Минимальное количество деталей в партии определяется по формуле:
ПД = ТПЗВ / (ТСТ), шт. (четыре)
ПД = 16 / 2,3 * 0,1 = 70
, где TPZV – подготовительно-заключительное время на ведущей операции в мин. Остальные обозначения старые.
Расчетная стоимость партии корректируется таким образом, чтобы в ней было не меньше выбранных деталей и больше годового выпуска.
Выпуск деталей за половину смены 1 / 2N см определяется из следующей зависимости.
1/2 н см = верх. СМ / 2Верх, мин. (пять)
ТОП = ТО + ТВ = 1,2 + 0,9 = 2,3, мин
где верх. CM – время работы на переключение принято равным 300 минутам.
Top – показатель наработки на ведущую операцию (ТО + ТВ)
1/2 n см = 300/2 * 2,3 = 71, мин
Принят ПД = 50 шт., Что близко к расчетной стоимости и многократному годовому выпуску.
Нетто / ПД = 100 шт.
Норма расчетного времени ТСК на эксплуатацию определяется по формуле:
ТСК = (ТСТ + ТПЗ) / ПД, Мин (6)
TSK005 = 2,4 + 23/100 = 2,63, мин
Операция рассчитывается по формуле
RSD = (ТСТТШ) / 60, руб. (7)
RSD005 = (29,2 * 2,63) / 60 = 1,28, руб.
Результаты расчетов представлены в таблице 2.
где ТСТ – почасовая тарифная ставка соответствующего выполнения работы.
, где обозначения старые.
Расчет норм сдельного времени и расценок желательно представить в таблице 2.
Таблица 2. Расчет норм ТСК и сдельной оплаты
ТСК = 43,7 мин.
Всего трудозатрат на детали
ТД = ТСК = 0,73, n – h
Суммарная производительность труда при годовом выпуске деталей
Всего переключателей.В норме
Переключить обычно. = (ЦКНПР) / 60, н-ч. (восемь)
Всего переключателей. = (43,780000) / 60 = 58267н-ч
Определение необходимого количества оборудования и коэффициента его загрузки. Необходимое количество машин рассчитывается на основе временной консультации с ежегодным выпуском релиза для каждой операции.
Расчетное количество машин в ПОКУПКЕ. Каждая операция определяется по формуле:
ПОКУПКА = (ЦКНПР) / (FD60), шт.(девять)
SOSCH005 = 2,6380000 / 401560 = 0,87
Принимается СРАСЧ2 = 0,87
Результаты расчета представлены в таблице.
Расчетное количество станков (дробное) округляем в большую сторону, т.е. получаем полученное количество станков SPR Коэффициент загрузки оборудования KZ на этой операции определяется по формуле:
KZ = SURCH / SPR (10)
KZ005 = 0,87 / 1 = 0,87
Результаты расчетов приведены в таблице 3.
Средний коэффициент загрузки оборудования на площадке определяется по формуле:
KZ ср. = ПОКУПКА. / SPR (11)
KZ ср. = 13,69 / 17 = 0,81
Результаты расчета приведены в таблице 3.
Таблица 3. Расчет количества необходимого оборудования
Тип и модель станка | ||||||||
Фрезерный 6м82ш | ||||||||
Токарный 1К625 | ||||||||
Протяжка 7A534 | ||||||||
Буровая С-12М | ||||||||
Шлифовальный 3К161 | ||||||||
Токарная обработка с ЧПУ 1K625DF1 | ||||||||
Фрезерный 6Т80 | ||||||||
С резьбой ET-28 | ||||||||
Сантехника |
ИТОГО: СРЕЩ = 13.69 СПР = 17
KZ ср. = 0,81.
Определение численности производственных рабочих, их средней квалификации и уровня производительности труда.
Анализ возможности мультисервисного обслуживания.
Многократное обслуживание – одно из направлений повышения эффективности производства, так как обеспечивается численность производственных рабочих и рост производительности труда.
Многократное обслуживание применяется на машинах с достаточно высоким уровнем автоматизации.Лучшие возможности Наличие нескольких одинаковых машин, выполняющих одну и ту же операцию, т.е. двойных машин.
При выполнении операций, включающих два или более переходов, выполняемых на универсальных машинах с ручным управлением, необходимо сконструировать мультисервисную циклическую машину для определения возможности мультисервисного обслуживания.
Количество станков-дублеров, которые могут обслуживать один рабочий СМ, определяется исходя из соотношения машинно-автоматического и ручного времени по формуле:
где TM.Авто – машинное и автоматическое время, мин.
Truch. – Время выполнения ручных приемов, а также время контроля работы станков и переходов от станка к станку, мин. (можно взять 0,1-0,5).
SM принимается округлением расчетной величины в меньшую сторону с учетом фактического (принятого) количества машин на этой операции и равномерного распределения работы между рабочими.
Для станков с ЧПУ
Труч = ТВ + (1.0 … 0,5), мин. (13)
где ваше – вспомогательное время на установку и снятие детали, мин
TM. Авто = ТО + ТМВ, Мин. (четырнадцать)
где TM.V-machine – вспомогательное время, мин.
Расчет для работы ЧПУ: ТО = 5; ТВ = 3,5; ТВ = ТВ + ТМВ;
ТВ = 1,5; ТМБ = 2;
Truch. = 1,5 + 1 = 2,5
TM.Avt. = 5 + 2 = 7
SM = 7 / 2,5+ 1 = 3,8
Принят СМ = 3 шт.Так как операция проводится на трех машинах.
Для остальных моделей машин значение SM принимается равным единице, так как операции, выполняемые на этих машинах, состоят из двух или более переходных и непрерывных машинных и автоматических по времени коротких.
Расчет численности производственных рабочих РП производится по каждой профессии в категории (по операциям) исходя из сложности работы за год по формуле:
Р.П. Ш. = (ЦКНПР) / (FDR60SM), чел (пятнадцать)
RP.Ветчина.005 = 2,63? 80000/1860? 60? 1 = 1,9
, где FDRF – действительный годовой производственный фонд. (1860 г.).
Остальные обозначения старые.
Результаты расчета приведены в таблице 5.
Таблица 5. Расчет численности производственных рабочих
Рабочие профессии | Гудрон. Рейд | Количество рабочих, чел. | |||||||||
Фрезерование | |||||||||||
Токар | |||||||||||
Протяжка | |||||||||||
Бурение | |||||||||||
Шлифовальный | |||||||||||
Токарная обработка с ЧПУ | |||||||||||
Фрезерование | |||||||||||
с резьбой | |||||||||||
Сантехника |
ИТОГО: RP = 26
Средняя категория производственных рабочих по МСФО.Определяется по формуле:
iSR = (IRP) / RP (16)
иср = (2? (2 + 2 + 3) +3? (5 + 2 + 5 + 4) +4? 4) / 25 = 2,88
где i – увольнение рабочего
Производительность труда работающих ПТР производственной площадки определяется как производство продукции в норме-часах на одного промышленного рабочего по формуле:
ПТР = ТГРЕСС / РП, Н-Н (17)
ПТР = 58267/26 = 2041,04 Н-ч
, где обозначения старые.
Вывод: Выработка на рабочий 1833,04 N-час в год при FDRF = 1860 ч. Недостаточно высокая и достигается за счет мультисервисного обслуживания, необходимо ее увеличивать, уменьшая количество рабочих на участке на 1 человека.
2. Хозяйственная часть
Определение годового расхода и стоимости материалов. Стоимость материалов определяется исходя из стоимости заготовки с учетом возврата за реализованные отходы по формулам:
М = СЗ – мед, руб.(восемнадцать)
М = 88,05 – 6 = 82,05, руб.
Мэн = м НПР, руб. (девятнадцать)
Мужчины = 82,05? 80000 = 6564000, руб.
ЦО = 10% СМ = 29,35, руб.
К = МЗ – МД = 3 – 2 = 1, кг
Соты = цо перед, руб. (двадцать)
От = 6? 1 = 6, руб.
где М – стоимость основных материалов на деталь, руб.
Разное – стоимость основных материалов в годовом объеме выпуска продукции, руб.
С3 – стоимость заготовки, руб.
Цо – цена за 1 кг. Отходы, руб.
До – масса отходов до 1 части, кг.
Расчетприведен в таблице 6.
Таблица 6. Расход и стоимость основных материалов
Имя | ||||
Годовой выпуск, шт. (NPR) | ||||
одна деталь, кг (MD) | ||||
Годовой выпуск, т | ||||
Материал | ||||
загрузка | Вид заготовки | Прокатный | ||
на 1 заготовку, кг (МЗ) | ||||
по годовому выпуску, т | ||||
Стоимость материалов | Цена металла, руб.(СМ) | |||
На 1 заготовку, руб. (SZ) | ||||
Для детали, кг (вверх) | ||||
По годовому выпущенному выпуску, т | ||||
Стоимость отходов | За 1 кг, руб.(TSO) | |||
На 1 детали, руб. (Из s) | ||||
О годовом выпущенном выпуске, руб. | ||||
Стоимость материалов без учета отходов | На 1 детали, руб. (М) | |||
О годовом выпущенном выпуске, руб.(М) |
фонд годовой заработной платы производственных рабочих и значения их среднемесячной заработной платы.
Заработная плата по тарифу ТС за единицу:
ЗТ = (РСДКМН), руб. (21)
ZT = 83,54, руб.
пр = 1,6; РК = 1,15
Базовая заработная плата На детали:
ЗО = ЗТ ПР РК, руб. (22)
ЗО = 83,54? 1,6? 1,15 = 153.71
Годовой фонд основной заработной платы производственных рабочих определяется по:
Зо год = зо спр, руб. (23)
Партия Детальный расчет Стоимость
Zo год = 153,71? 80000 = 12296800, руб.
Годовой фонд оплаты труда производственных рабочих:
Zd = (zo 18%) / 100%, руб. (24)
Zd = 153,71? 0,18 = 11,65, руб.
HD Год = (Zo год 18%) / 100%, руб. (25)
Год здоровья = 12296800? 0.18 = 2213424
Фонд оплаты труда производственных рабочих состоит из основной и дополнительной заработной платы.
Зерри = zo год + zh год, руб. (26)
Зерри = 12296800+ 2213424 = 14510224, руб.
ZSR. Мем = зерри / (RP12), руб. (27)
ZSR. Монс = 14510224/26? 12 = 46567,13
где ZT – заработная плата из расчета за одну позицию (без доплаты по системам прогрессивной премии).
пр – коэффициент, учитывающий приобретения.Пр = 1,6
RSD – операция по операции.
рК – районный коэффициент, РК = 1,15
KMN – коэффициент, учитывающий мультисервисную услугу.
M оп – количество операций технологического процесса.
Зо год – годовой фонд основной заработной платы производственных рабочих.
Здоровье – Доплата по каждой позиции определяется в размере 18% от основной заработной платы.
Здоровый год – Годовой фонд дополнительной заработной платы для производственных рабочих.
Зенч – полный годовой фонд оплаты труда производственных рабочих.
ZSR. Mem. – Среднемесячная заработная плата производственных рабочих.
Таблица 7. Расчет фонда оплаты труда производственных рабочих и среднемесячной заработной платы
График расценок РСД., Руб. | Коэффициент кратный КМН | динаров кмн руб. | ||
ИТОГО: (МЦД КМН) = 83,54
Расчет мастерской представителя представителя и определение стоимости годового объема выпуска деталей.
Социальные отчисления определяются в размере 27,9% от размера основной и дополнительной заработной платы по формуле:
Зстр = ((ЗО + ЗД) 27,9%) / 100%, руб. (28)
Zстр = (153,71 + 11,65)? 0,377 = 18,7, руб.
Рекламные расходы определены в размере 300% от основной заработной платы производственных рабочих.
ORD = (ZO 300) / 100, руб. (29)
ORD = 153,71? 300/100 = 194 руб.
Стоимость мастерской определяется по:
С = М + ТЗР + ЗО + ЗД + Зстро + ЗАКАЗ, руб.(тридцать)
СК = 82,05 + 10,5 + 153,71 + 11,65 + 30,92 + 194 = 287,3, руб.
Транспорт – затраты на закупку определены в размере 12% от стоимости заготовки:
ТЗР = 12% СЗ, руб. (31)
ТЗР = 0,12? 88,05 = 10,5
Определена стоимость годового объема выпуска деталей:
СК Год = СК НПР, руб. (32)
СБ Год = 287,3? 80000 = 22984000, руб.
Таблица 8.Расчет стоимости работ по детали
Расходы | Сумма, руб. | ||
Материалы (сетевые). (М) | |||
Транспортно-закупочные расходы. (TZR) | |||
Основная заработная плата коммунальщиков.(ZO) | |||
Дополнительная заработная плата производственных рабочих. (Zd) | |||
Социальный вычет. (Заста) | |||
Объективные затраты. (ОПР) | |||
Итого: детализация стоимости мастерской (SC). | |||
Годовой объем выпуска детали (NPR). | |||
Стоимость годового объема выпуска деталей (год SC) |
Заключение
Курсовая работа по организации производства выполнялась по теме «Расчет технико-экономических показателей части механической обработки деталей» на основании следующих исходных данных: тип производства малый, масса детали 3. .1 кг и масса заготовки 4,8 кг. Остальные исходные данные, такие как перечень операций, модели станков, штучно-подготовительное и конечное время, а также расчеты рабочих, приводятся в соответствующей таблице.
По расчетам установлено, что годовой объем выкладки деталей на сайте составил 134 тысячи штук, а годовой объем детали «вал» – 5000 штук. На сайте обрабатывается 26 наименований. Валы запущены в производство в количестве 125 штук.
Затем был произведен расчет норм сдельного времени и сдельных ставок по каждой операции. Сложность обработки одной детали составляет 0,41 н.д., а общая производительность труда при годовом выпуске деталей составляет 55188 н-ч.
Литература
1. Планово-профилактический ремонт и рациональная эксплуатация технологического оборудования машиностроительных предприятий / Под ред. Д.н., профессора М.О. Якобсон, изд. “Машиностроение”.М. 1967, 592 с.
2. А.К. Кучер, М. Киватицкий, А.А. Покровские металлорежущие станки. / Кромочное машиностроение. Ленинград. 1972 г., 307 с.
Каталог – Справочник по металлорежущим станкам. М: Миимаш, 1973 I, 297 с.
Методическое пособие, курсовая работа. Организация планирования и управления производством. 55 с.
Размещено на Allbest.ru.
Похожие документы
Организация производственного процесса, расчет части деталей, количества оборудования и коэффициента его загрузки, количества рабочих.Определение основных технико-экономических показателей: стоимость основных материалов, себестоимость продукции.
курсовая, добавлен 27.03.2010
Определение эффективности части механической обработки детали с помощью обобщающих показателей. Определение эффективного оборудования для работы оборудования, типа производства и размеров детали. Составление сметы на производство.
курсовая работа, добавлен 10.11.2014
Расчет эффективного оборудования для работы оборудования.Определение необходимого количества рабочих по увольнению и фонда их заработной платы. Расчет затрат на обслуживание и эксплуатацию оборудования. Планируемые расчетные единицы продукции.
курсовая работа, добавлен 26.03.2012
Расчет необходимого количества оборудования, определение его коэффициента загрузки, количества всех категорий работ. Расчет стоимости основного материала на деталь, фонда оплаты труда, стоимости основных производственных тканей и отчислений.
курсовая, добавлен 19.04.2010
Технико-экономические показатели деятельности участка по производству деталей «Вал», производимых на предприятии «НЕФАЗ». Расчет технологической стоимости детали, основы оплаты труда производственных рабочих и отчислений на социальные нужды.
курсовая, добавлен 08.08.2010
Расчет необходимого количества оборудования, количества рабочих, фонда оплаты труда. Определение площади участка, стоимости основных и вспомогательных материалов, общих расходов, полной стоимости.Прибыль и цена изготовления кронштейна запчастей.
курсовая работа, добавлен 21.02.2013
Особенности расчета необходимого количества оборудования для производства данного продукта. Определение количества рабочих и персонала, анализ методики расчета фонда оплаты труда. Подготовка расчета и определение затрат и цены на продукцию.
курсовая, добавлен 26.02.2010
Расчет программы сюжета механико-механического цеха и ритма выпуска деталей.Определение количества деталей в партии, железа и его загрузки. Расчет заработной платы основных рабочих. Затраты на компенсацию износа специального инструмента.
курсовая, добавлен 30.10.2012
Определение производственной программы и эффективное оборудование для работы оборудования. Расчет продолжительности производственного цикла детали детали детали. Составление сметы затрат: материальных, по заработной плате, отчислениям на социальные нужды.
курсовая, добавлен 17.12.2014
Расчет количества оборудования и его загрузки, стоимости основных средств участка механообработки, амортизации основных средств, стоимости основных материалов для изготовления деталей.Составление сметы затрат на изготовление деталей «Кейса».
Краткое описание
1. Реализация организационной части проекта осуществляется на основе разработанного технологического процесса обработки детали – представителя.
Для лучшего обзора и анализа результатов, полученных в технологической части проекта, а также для удобства проведения расчетов составлена таблица 1 исходных данных.
1.
Организационная часть.
1.1.
Определение годового выпуска
Сведения о производительности.
1.2.
Определение необходимого количества оборудования.
1.3.
Определение численности производственных рабочих.
2.
Хозяйственная часть.
2.1.
2.2.
Определение годового фонда оплаты труда.
2.3.
Расчет стоимости работ по детали.
3.
Результирующая часть.
3.1.
Определение экономической эффективности.
3.2.
3.3.
Расчет суммы капитальных вложений.
3.4.
Расчет стоимости механообработки.
3.5.
Определение годового экономического эффекта.
3.6.
Расчет роста производительности и снижения затрат.
3,7
Обоснование экономической эффективности.
4.
Заключение.
5.
Приложение: Компьютерный расчет на листах А4.
6.
Литература.
Вложенные файлы: 1 файл
Министерство образования и науки Российской Федерации
Кафедра: «Технология машиностроения, станки»
Курсовая работа
«Организация производства и управления»
Выполнено:
группа ученика
Устюгова Е.А.
Усть-Катав.
Южно-Уральский государственный университет
филиал в г. Усть-Катава
Кафедра: «Технологические процессы и машиностроительное оборудование
»производство »
Для курсовой работы
по курсу «Организация производства и менеджмент»
Курсовая группа __________
Тема задания: Расчет технико-экономических показателей участка механообработки части запаса __
Исходные данные:
Массовые части _0.52 ____________
Масса заготовки _0,74 __________
Детали материала_ст45 __________
Вид заготовки __Стамповка _____
Производство _ Мелкоэриан ___
Режим работы 2 смены по ____8_________ час.
Трудоемкость, объемность выполняемых и применяемых работ оснащена ИЭ:
наименование операции | Модельное оборудование | ||||
Токарная обработка с ЧПУ | |||||
Токар | |||||
Бурение | |||||
Токар | |||||
Бурение | |||||
Фрезерный | |||||
Шлифовальный | |||||
Фрезерный | |||||
Сантехника | моторная станция | ||||
Шлифовальный |
Дата защиты _________________ Вскрытие выдано _________________
Заведующая курсовой работой ____________________ / Устюгова Е.А. /
Аннотация.
Расчет технико-экономических показателей площадки для торговли деталями “_stock_” с расчетом производительности труда и стоимости изготовления детали на месте.
Усть-Катав, У-КФ СУУРГУ, 151001, 2009 г., _31_С, библиография – _4_ имен.
Рассчитано: количество станков на участке, сдельные цены, возможность многоцелевого обслуживания станков, количество рабочих, их разработка и среднемесячная заработная плата.Анализ применения в машинном процессе станка с ПУ модели ___ 16Б16Т1 ____ взамен станка с ручным управлением модели __16б16 ____. Применение станка с ПУ позволило снизить себестоимость изготовления на _1,89_%, годовой экономический эффект – на _352 958_ руб.
Организационная часть. | ||
Определение годового выпуска сведения о производительности. | ||
Определение необходимого количества оборудования. | ||
Определение численности производственных рабочих. | ||
Хозяйственная часть. | ||
Определение годового расхода материалов. | ||
Определение годового фонда оплаты труда. | ||
Расчет стоимости работ по детали. | ||
Результирующая часть. | ||
Определение экономической эффективности. | ||
Определение дополнительных данных. | ||
Расчет суммы капитальных вложений. | ||
Расчет стоимости механообработки. | ||
Определение годового экономического эффекта. | ||
Расчет роста производительности и снижения затрат. | ||
Обоснование экономической эффективности. | ||
Заключение. | ||
Приложение: Компьютерный расчет на листах А4. | ||
Литература. |
Организационная часть
1. Реализация организационной части проекта осуществляется на основе разработанного технологического процесса обработки детали – представителя.
Для лучшего обзора и анализа результатов, полученных в технологической части проекта, а также для удобства проведения расчетов составлена таблица 1 исходных данных.
Таблица 1. Исходные данные:
Подробный представитель – Skot
Масса детали – 0,52
Масса заготовки – 0,74
Цена 1т. Отходы – 15900.
Производство – Melkossilee
Имя операций | Нормы времени | ||||||
Токарная обработка с ЧПУ | |||||||
Токар | |||||||
Бурение | |||||||
Токар | |||||||
Бурение | |||||||
Фрезерный | |||||||
Шлифовальный | |||||||
Фрезерный | |||||||
Сантехника | моторная станция | ||||||
Шлифовальный |
- Определение годового представления представителя представителя и количества наименований однородных деталей, обрабатываемых на сайте.Расчет количества деталей в партии, норм поштучного времени и расценок.
- Ежегодное представление деталей NPR., Т.е. Условное количество типовых деталей, время обработки которых равно сложности всех деталей, закрепленных на объекте, определяется исходя из производственной мощности участка и наиболее рационального использования оборудования по формуле:
НПР = MG KZ =, шт (1)
где мг – годовая производственная мощность
KZ – коэффициент загрузки оборудования принимаем 0.8 – 0,85, что характеризует достаточно полное использование оборудования и наличие необходимого запаса времени.
FD – действующий годовой фонд оборудования оборудования (4015 часов).
ТШМ – норма штук на ведущей операции для представительной части, (мин)
В некоторых случаях рекомендуется совмещать операции небольшой продолжительности (менее минуты) одной модели, выполняемые на станках.
Коэффициент допустимой эталонной потери.
0,05 – 0,08 для среднего производства.
0,08 – 0,1 для мелкосерийного производства.
Расчетное значение NPR округлено до целого значения, удобного для последующих расчетов.
Ведущая операция –
НПР = 105000
1.1.2. Годовой выпуск части представителя Национального представителя определен в пределах
.NAW = NPR / KZOMAX … NPR / CW MIN, шт. (2)
где КЗО – коэффициент операций крепления (по ГОСТ 3.1108-74 для среднего производства 11-20, для мелкого 21-40).
Принято Народное = 4000шт
1.1.3. Количество деталей деталей обрабатываемых на сайте деталей определяется по формуле:
MD = NPR / N., Шт. (3)
При систематическом течении года изготовления и закреплении каждого рабочего места одной операции КВК = МД
В данном случае MD = 27 шт. Находится в пределах КЗО = 21-40 по производству, что соответствует задаче проекта.
1.1.4. Определение количества деталей в партии. Минимальное количество деталей в партии определяется по формуле:
ПД = ТПЗВ / (ТСТ), шт. (четыре)
, где TPZV – подготовительно-заключительное время на ведущей операции в мин. Остальные обозначения старые.
Расчетная стоимость партии скорректирована так, чтобы она не равнялась
. Наменьше пол съемного выпуска деталей и многократный годовой выпуск.
Выпуск деталей за половину смены 1 / 2N см определяется из следующей зависимости.
1/2 н см = верх. См / 2 верх, мин. (пять)
Верх = ТО + ТВ = 1 + 0,7 = 1,7
где верх. CM – время работы на переключение принято равным 300 минутам.
Top – показатель наработки на ведущую операцию (ТО + ТВ)
ПД = 200 шт, что близко к расчетной стоимости и многократному годовому выпуску.
Нетто / ПД = 20 шт.
1.1.5. Норма расчетного времени ТСК на эксплуатацию определяется по формуле:
TSH = TCT + (TPZ / PD), Мин (6)
1.1.6. Кусок операции рассчитывается по формуле
RSD = (ТШК) / 60, руб. (7)
RSD005 =
руб.Результаты расчетов представлены в таблице 2.
где ТСТ – почасовая тарифная ставка соответствующего выполнения работы.
, где обозначения старые.
Расчет норм времени и ставок рассмотрения дел желательно представить в таблице 2.
Таблица 2. Расчет норм ТСК и сдельной оплаты труда.
DAC Concepts Высокоскоростные преобразователи данных Texas Instruments
DAC Concepts Высокоскоростные преобразователи данных Texas Instruments Июнь 2014 г. 1
Краткое описание • Текущая архитектура управления, используемая в высокоскоростных ЦАП – что находится внутри • Полномасштабный расчет ЦАП • Характеристики ЦАП – SNR, SFDR, IMD – Гармоники в дискретных системах • Шум и искажения в высокоскоростных ЦАП • Тактирование высокоскоростных ЦАП – фаза шум, джиттер, скорость нарастания • Улучшение SFDR ЦАП с помощью дизеринга 2 Информация TI – Требуется NDA
High Speed Current Steering DACs – что находится внутри 3 TI Information – требуется NDA
IOUT 1 Полная шкала = 30 м.A IOUT 1 IOUT 2 30 мес. А 15 м. А 0 м. А 30 м. A Коммутатор Драйверы Декодер Логика = ЦАП Цифровые входные данные IOUT 2 Аналоговый выход Управление током ЦАП «под капотом» цепи смещения массива переключателей Источник тока массива 4 Информация TI – требуется NDA
ЦАПмогут быть источниками или приемниками NMOS PMOS (источник) VCC + 0. 5 Вольт Каскоды источника тока VCC Ioutb Iout Переключатели Каскоды стока тока Переключатели VCC – 0. 5 Вольт +1/0. 5 Вольт – 1/0. 5 В (сток) Ioutb Iout DAC (2) 90 x, DAC 2932, DAC 56 x 2, DAC 38 J 84 DAC 34 xx, DAC 3174 Информация TI – требуется NDA DAC 5686/87/88/89, DAC 5681/82 Z, ЦАП 3282/83 ЦАП 3152/62 5
Простой 3-битный двоичный ЦАП AVDD Pro: наименьшее количество источников тока и переключателей.Против: более высокие искажения. AVDD 1000 Vout бит 3 1 0 бит 2 500 u. A 1 0 бит 1 250 ед. А 1 0 125 шт. A (875 u * 1 K) (625 u * 1 K) (375 u * 1 K) (125 u * 1 K) – (125 u * 1 K) Vout – (375 u * 1 K) – (625 u * 1 K) – (875 u * 1 K) 000 бит 1 и бит 2 отключаются, бит 3 включается 001010011100101110111 бит 3 бит 2 бит 1 6 Информация TI – Требуется NDA
Эквивалентный 3-битный ЦАП с термометрическим кодированием AVDD Pro: уменьшенные искажения (легче сопоставить одинаковые источники тока). Недостаток: требуется больше источников тока и переключателей.AVDD 1000 Vout therm 7 1 0 therm 2 125 ед. A 1 0 therm 1 125 ед. А 1 0 125 шт. A (875 u * 1 K) (625 u * 1 K) (375 u * 1 K) (125 u * 1 K) – (125 u * 1 K) Vout – (375 u * 1 K) – (625 u * 1 K) – (875 u * 1 K) бит 3 бит 2 бит 1 0000000 включается еще один равный источник тока 00000011 00001111 00111111 1111111 7 Информация TI – Требуется NDA
ЦАП могут быть сегментированы и смешаны с кодировкой ввода 6 b word therm (7: 1) в логику декодера сегмента MSB бит AVDD (3: 1) в сегмент LSB 1000 AVDD 1000 Vout therm 7 1 0 therm 2 125 u.A 1 0 1 therm 1 125 ед. Немного 3 1 62. 5 шт. A 0 бит 2 0 Термометр 3 b MSB DAC 125 u. А 1 31.25 шт. A 0 бит 1 1 0 двоичный 3 b LSB ЦАП 15.625 u. Информация A 8 TI – Требуется NDA
Упрощенный TI 16 b Топология ЦАП Пример: DAC 34 xx D (15: 10) (6 битов MSB) D (9: 0) (10 битов LSB) IOUT 1 декодирование сегмента MSB Декодирование сегмента LSB IOUT 2 MSB Thermo (63: 0 ) LSB двоичный (9: 0) 73 драйверы переключателей 73 переключатели 63 цепи смещения EXTIO RBIAS 10 MSB каскоды LSB каскоды Источники тока LSB Источники тока LSB 9 Информация TI – Требуется NDA
Полномасштабный расчет DAC 10 Информация TI – требуется NDA
Двоичное смещение vs.Дополнение 2 • Большинство наших ЦАП могут принимать режим двоичного смещения или дополнения до двух. • Формат данных зависит от предпочтений пользователя. • Чтобы преобразовать двоичный код смещения в код с дополнением до двух, просто инвертируйте старший бит. 11 Информация TI – Требуется NDA
ЦАП приемника тока NMOS (C 05 – 180 нм) AVDD + 0. 5 Вольт Ioutp Ioutn AVDD – 0. 5 Вольт NPN (биполярный) AVDD + 0. 3 Вольта Ioutp Ioutn Каскодирование стока тока Переключатели AVDD – 1,0 В DAC 5686 / 87/88, DAC 5681/82 Z TI Информация – Требуется NDA DAC 5675, DAC 5675 A, Биполярный DAC 5675 / A использует архитектуру типа приемника NPN, поскольку большинство биполярных технологий не включают высокоскоростной PNP.12
Работа ЦАП с потребителем тока (показан пример с нагрузкой 25 Вт для AVDD) Ток потребления: минимальное напряжение Без тока: максимальное напряжение 13 Информация TI – требуется NDA
Источник тока DAC PMOS (C 05–180 нм) PMOS (C 027–90 нм) AVDD переключает каскоды источника тока AVDD +1. 25 Вольт -1. 0 Вольт +0. 6 Вольт Ioutp Ioutn DAC 90 x, DAC 2932, DAC 56 x 2, DAC 5674-0. 5 Вольт Ioutp Ioutn DAC 348 x Семейство 14 Информация TI – Требуется NDA
Работа ЦАП источника тока (показан пример с нагрузкой 25 Вт на заземление) Ток источника: максимальное напряжение Нет тока: минимальное напряжение 15 Информация TI – требуется NDA
Три способа программирования тока полной шкалы: DAC_Gain, VEXTIO и RBIAS • Ток полной шкалы можно регулировать тремя различными факторами: – DAC_gain: это 4-битный программируемый регистр в ЦАП.Это масштабирует выходной ток по 16 ступеням. – VEXTIO: внутреннее или внешнее опорное напряжение. Внутреннее генерируемое напряжение обычно составляет 1,2 В. – RBIAS: внешний резистор смещения. 16 Информация TI – Требуется NDA
DAC Технические характеристики 17 Информация TI – Требуется NDA
Сравнение частотной и временной областей 18 Информация TI – требуется NDA
DAC SNR Ø SNR измеряется с выходным сигналом Ø Noise = сумма выходного сигнала по 1-й зоне Найквиста (fs / 2), исключая паразиты, и сигнал Ø SNR = сигнал / шум fs = 1 GSPS f out = 20 МГц Сигнальный шум Ø Выходной шум ЦАП состоит из – шума квантования – теплового шума – шума дрожания – шума, зависящего от данных 19 Информация TI – Требуется NDA
DAC SFDR Ø SFDR измеряется с помощью однотонального сигнала Ø SFDR = Сигнал / самый высокий паразитный сигнал Ø Шпоры представляют собой смесь гармоник, продукты дискретизации fs = 1 GSPS f out = 20 МГц SFDR Другие ответвления 20 Информация TI – Требуется NDA
DAC IMDx Ø IMDx – это интермодуляционные искажения x-го порядка, которые измеряются с помощью двухтонального сигнала.Ø IMD 3, 3-е IMD, обычно сложнее всего удалить с помощью фильтрации. fs = 1 GSPS f 1 = 39,5 МГц f 2 = 40,5 МГц 3-е ответвления IMD 21 Информация TI – Требуется NDA
Гармоники в дискретизированных системах Аналоговый сигнал гармоник HD 2 HD 3 HD 4 HD 5… fo 2 * fo 3 * fo 4 * fo 5 * fo Сигнал дискретизированной системы 2 nd Nyquist HD 5 fo HD 2 HD 3 2 * fo 3 * fo Fs – 5 * fo HD 3 HD 4 4 * fo Fs / 2 Fs – 4 * fo Fs – 3 * fo HD 2 HD 5 5 * fo… Fs – fo Fs Fs – 2 * fo • Образцы систем имеют дополнительные гармоники на Fs – N * fo 22 TI Information – Требуется NDA
Шум и искажения в высокоскоростных ЦАП 23 Информация TI – требуется NDA
Шум и искажения в высокоскоростных ЦАП Ошибка амплитуды амплитуды, джиттер 1 ограничение полосы пропускания 2 3 4 5 6 7 8 Время (Tsample) • Выход DAC имеет желаемую амплитуду (напряжение или ток) в зависимости отвремя • Для вывода с удержанием нулевого порядка (ZOH) новая амплитуда устанавливается в начале периода выборки и удерживается до конца периода выборки • Шум и искажения возникают из-за ошибки либо амплитуды, либо времени переключения (джиттера) • Полоса пропускания ограничения не создают шума или искажений, просто сглаживают переходы 24 Информация TI – Требуется NDA
Источники шума и искажений переменного тока: ошибки амплитуды IOUT • Ошибки амплитуды IOUTB • • INL, DNL Скорректировано в ходе производственного испытания Ограничение на низкой выходной частоте Гармоники высокого порядка – шум источника тока (1 / f) • Создает низкочастотный шум (<1 МГц) Время - линейность постоянного тока (согласование источника тока) 73 драйверы переключателей 73 переключатели 63 10 каскоды MSB Каскоды LSB Источники тока LSB Источники тока LSB Амплитуда 25 25 Информация TI - требуется NDA
Источники шума и искажений переменного тока: ошибки синхронизации (джиттер) IOUT 1 • Случайное дрожание часов – ФАПЧ / ГУН – Буферы часов – – Согласование случайного времени переключения Время переключения, зависящее от кода Время переключения, зависящее от выходного напряжения. Внешние побочные источники – другие тактовые генераторы, гетеродины, импульсные регуляторы – Внутренние источники – тактовые импульсы цифровых схем Информация TI – Требуемое время NDA • Детерминированный джиттер IOUT 2 73 драйверы переключателей 73 переключателя 63 10 Каскоды MSB Каскоды LSB Источники тока LSB Источники тока LSB Амплитуда 26
Источники шума и искажений переменного тока: детерминированный джиттер • Согласование времени случайного переключения – – Транзисторы драйвера переключателя Согласование улучшается с увеличением площади транзистора. Зависимость от времени нарастания / спада – более быстрые транзисторы лучше.грамм. HD 2 – HD 7) доминируют и варьируются от устройства к устройству • Время переключения в зависимости от кода – – Увеличивается с увеличением емкости нагрузки драйвера, например. Cload = Коммутатор Улучшается с помощью агрессивной технологии в драйвере переключателя. Ухудшается с увеличением площади транзистора. Результаты в гармониках низкого порядка • Время переключения, зависящее от выходного напряжения – Время переключения зависит от выходного напряжения, воспринимаемого переключателем – Результаты в гармониках низкого порядка. Информация TI – Требуется NDA 27
Отмена гармоник четного порядка • Iout и Iout.B являются зеркальными отображениями друг друга: • Iout. B = FS – Iout • Гармоники четного порядка компенсируют друг друга, нечетные – не Iout HD 2 Iout. B + = 0 HD 3 Iвых. B + ¹ 0 • На практике выходы не совсем совпадают, и часто HD 2 ограничивает характеристики искажения 28 Информация TI – Требуется NDA
Тактирование высокоскоростных ЦАП 29 Информация TI – требуется NDA
Оценка SNR и джиттера для ЦАП • Общее SNR – это векторная сумма всех индивидуальных вкладов SNR SNRQUANT = SNR из-за квантования SNRCLK = SNR из-за дрожания тактовой частоты и апертуры SNRTHERM = SNR из-за теплового и транзисторного шума • Аналогичная обработка тактового джиттера (интегрированный фазовый шум) для предела SNR системы дискретизации DAC 30 Информация TI – Требуется NDA
DAC NSD или спецификация SNR • Более новая таблица данных определяет NSD (d.Бк / Гц). Это разница мощности между выходной мощностью основного тона и минимальным уровнем шума в полосе пропускания 1 Гц. fs = 1 GSPS f out = 20 МГц Шум сигнала 31 Информация TI – Требуется NDA
Почему НРД по SNR? • В реальных системах часто существует жесткая фильтрация вокруг интересующей полосы, где отфильтровывается весь шум за пределами этой полосы. • Вместо того, чтобы показывать ОСШ сигнала в первой зоне Найквиста, удобнее показывать мощность шума, чтобы можно было легко вычислить общую мощность шума в нефильтрованном диапазоне. • Например, рассмотрим ЦАП 3484, работающий на 1228.8 MSPS с интересующей полосой 100 МГц и следующими фильтрами: – Фильтр нижних частот 614,4 МГц (полностью пропускающий первую зону Найквиста): – Фильтр нижних частот 100 МГц: 32 Информация TI – Требуется NDA
Преобразование NSD в SNR • SNR DAC можно вычислить из спецификации NSD • SNR традиционно определялся как отношение мощности основной гармоники к мощности шума, интегрированного по первой зоне Найквиста. • Его также можно рассчитать непосредственно в d. БФС от НРД в д.Бит / Гц • Пример: DAC 3484 работает на 1,25 GSPS с выходом 10 МГц 33 Информация TI – Требуется NDA
Компромисс между NSD и SNR – Джиттер / Фазовый шум • Оценки SNR, основанные на Джиттере, являются хорошими оценками для SNR для всего диапазона Найквиста – могут быть слишком пессимистичными для приложений с ограничением BW. • Оценки SNR, основанные на NSD (обычно измеряемые с некоторым сдвигом в МГц), не учитывают близкий фазовый шум, который может повлиять на внутриполосный EVM – было бы хорошо для внеполосных оценок, таких как ACPR. • Использование тактовых NSD и расчетов ограниченного шума BW могло бы быть идеальным решением для внеполосных измерений в полосе частот.34 Информация TI – Требуется NDA
Влияние фазового шума CLK на системы с дискретизацией • Для систем с дискретизацией АЦП и ЦАП фазовый шум CLK будет транслироваться с тактовой частоты на дискретизированные выходы со следующим соотношением • Все внутриполосные (% EVM, чувствительность RX) и выходят. -of-band (ACPR, TX Mask) измерения могут быть основаны на измеренном графике фазового шума источника тактовых импульсов АЦП и ЦАП 35 Информация TI – Требуется NDA
Внутренние шумовые эффекты ЦАП • При более высоких смещениях частоты, когда фазовый шум тактовых импульсов падает, собственный шум ЦАП будет играть роль в общем уровне шума выходного спектра • Измерения CLK NSD и выходного NSD ЦАП показывают, что существует некоторое расхождение между оценками – это объясняется собственным шумом ЦАП из-за теплового воздействия / воздействия устройства 36 Информация TI – Требуется NDA
Влияние внутреннего шума ЦАП • Внутренний шум ЦАП зависит от частоты и измеренный на определенной частоте смещения будет только приблизительно точным для других частот смещения.• Оценки собственного шума, сделанные при отстройке 40 МГц, в некоторой степени точны для оценок NSD при одном и том же частотном смещении с использованием разных источников тактовой частоты. Ошибка во всех случаях Собственный шум ЦАП при 40 МГц -146 2 0 50100150200250300350400450500 1 пс_ пик 200 фс_ пик 500 фс_1 МГц 1. 5 Ошибка (d. B) Шум ЦАП -148-150-152-154 1 500 fs_peaking 1 ps_1 MHz 200 fs_1 MHz 0. 5 0 0 -156-0. 5 -158-1-160-1. 5-162 50100150200250300350400450-2 Выходная частота ЦАП (МГц) 37 Информация TI – требуется NDA 500
DAC NSD Измерение приложений – EVM • Сигнал WCDMA 3.Полоса пропускания 84 МГц, ПЧ = 122. 88 M, частота дискретизации 983. 04 Msps, 1% EVM (40 d. Bc SNR эквивалентно) • Предполагая, что% EVM является мерой отношения SNR средней мощности внутриполосного сигнала к средней внутриполосной NSD, мы можем оценить требуемое среднее NSD частоты тактовых импульсов (-105. 84 d. Bc / Hz avg на выходе DAC) • Масштабирование по IF и частоте дискретизации (-87. 78 d. Bc / Hz avg на источнике синхронизации) 38 Информация TI – Требуется NDA
DAC NSD Application Измерение – EVM • Средняя тактовая частота NSD в пределах 3.84 МГц вокруг основной тактовой частоты должна быть меньше -87.78 дн. Bc / Hz • Средняя частота NSD должна быть меньше, чем прогнозируемая частота NSD, чтобы соответствовать системным требованиям для EVM Пик фазового шума NSD – вызвать флуктуацию EVM Прогнозируемая частота NSD Среднее значение внутриполосной частоты NSD @ clock – определить EVM 1. Информация о TI 92 МГц – NDA Требуемый сдвиг частоты 39
DAC NSD Application Измерение ACPR • Сигнал WCDMA 3. Полоса пропускания 84 МГц, IF = 122. 88 M, частота дискретизации 983. 04 Msps, ACPR = 70 d. Б, Альт АКПР = 75 дн. Bc • Тактовый сигнал NSD как для ACPR, так и для альтернативного ACPR задается следующим образом: • Тактовый сигнал NSD ACPR = -118 d.Bc / Hz, Часы NSD Alt ACPR = -123 d. Bc / Hz 40 Информация TI – Требуется NDA
DAC NSD Application Measurement ACPR • Используя некоторые распространенные источники тактовой частоты, мы можем увидеть, что тактовая частота NSD при смещениях частоты ACPR и Alt ACPR значительно ниже этих значений NSD. Характеристики фазового шума 1. 00 E + 02 1. 00 E + 03 1. 00 E + 04 1. 00 E + 05 1. 00 E + 06 1. 00 E + 07 1. 00 E + 08 -60. 00 Фазовый шум -80. 00 -100. 00 -120. 00-140. 00 -160. 00 1 ps_close_in 1 ps_peaking 500 fs_close_in 500 fs_peaking 200 fs_wide_band 41 Информация TI – требуется NDA
DAC NSD Application Measurement ACPR • Тактовая частота NSD на ACPR и Alt ACPR смещает незначительную разницу между использованием разных тактовых импульсов на разных частотах ПЧ.Повторяет форму внутреннего шума ЦАП. 42 Информация TI – Требуется NDA
DAC NSD Application Measurement – ACPR • Те же результаты с альтернативным ACPR. 43 Информация TI – Требуется NDA
Скорость нарастания и характеристики джиттера • Как показано в предыдущем примере, добавление фильтра может снизить скорость нарастания сигнала синхронизации за счет фильтрации гармоник • Более низкая скорость нарастания более восприимчива к изменениям точки пересечения нуля из-за шума 44 TI Информация – требуется NDA
Зависимость амплитуды синусоидальной волны от скорости нарастания • Использование синусоидальной волны большего размера может преодолеть пониженную скорость нарастания, поскольку большая амплитуда приведет к более быстрому переходу через точку пересечения нуля.Это снизит влияние шума на точку пересечения нуля. 45 Информация TI – Требуется NDA
Фазовый шум для более медленной скорости нарастания • Для часов с ~ 9 d. Bm меньше мощности, количество джиттера увеличено с 31,52 фс до 72,208 фс 6,11 d. Часы БМ: -3. 35 дн. Часы Bm: 46 Информация TI – Требуется NDA
Улучшение SFDR ЦАП с помощью дизеринга 47 Информация TI – требуется NDA
Интегральная нелинейность ЦАП – это ошибка идеального линейного ЦАП IOUTS D (15: 11) (5 битов MSB) D (10: 7) Декодирование сегмента MSB Декодирование сегмента MID MSB Thermo (30: 0) MID Thermo (14: 0) (4 MID бита) D (6: 0) (7 LSB бит) декодирование сегмента LSB 53 переключателя 53 драйвера переключателя LSB двоичный (6: 0) 31 цепи смещения EXTIO RBIAS 15 7 MSB каскодов MID каскодов LSB каскодов Источники тока MSB Источники тока MID Источники тока LSB Переход от 1 текущего сегмента к следующему Несоответствие в источниках тока приводит к ошибкам в DAC INL 48 Информация TI – Требуется NDA
Ошибка INL ЦАП создает гармоники Синусоидальный сигнал Синусоидальная волна с ОГРОМНОЙ ошибкой INL * Выходной спектр = разрывы INL генерируют гармоники, особенно гармоники высокого порядка 49 Информация TI – Требуется NDA
Дизеринг • Дизеринг – это случайный сигнал, который может быть добавлен к выходу ЦАП • Добавление случайного дизеринга в прерывания INL Дизеринг случайным образом перемещается при возникновении прерываний INL • Дизеринг эффективен для улучшения гармоник высокого порядка из прерываний INL, не улучшает гармоники нижнего порядка из другие источники искажений Информация TI – Требуется NDA 50
Добавление дизеринга для улучшения гармоник высокого порядка • Дизеринг может быть ограничен по полосе, а затем отфильтрован на выходе ЦАП – система 0 ПЧ – дизеринг расположен около Fs / 2 – Комплексная система ПЧ – дизеринг размещен около 0 Гц • Точный спектр дизеринга не имеет значения • Амплитуда должна быть порядка сегментов источника тока MSB ЦАП • Будущие ЦАП будут включать в себя встроенные схемы генерации дизеринга 51 Информация TI – Требуется NDA
Демонстрация дизеринга: настройка • TSW 3100 + DAC 34 H 84 • Fs = 1228.8 МГц • NCO: отключен • Мощность выходного сигнала: -1. 95 дн. Bm • Частота выходного сигнала: 210 МГц • Генерация дизеринга – 200-тональный сигнал – Несущая WCDMA 52 Информация TI – Требуется NDA
Пример улучшения гармоник высокого порядка с помощью дизеринга HD 17 HD 5 HD 13 HD 11 Сигнал дизеринга Значительное улучшение для HD 11, HD 13, HD 17. Незначительное улучшение для HD 5. 53 Информация TI – требуется NDA
Сводка по влиянию дизеринг-шума Амплитуда дизеринг-шума (d.Bc) HD 5 (d. Bc) HD 11 (d. Bc) HD 13 (d. Bc) HD 17 (d. Bc) – Inf (без дизеринга) -69. 89 -77. 05-81-75. 09-35. 75-70. 23 <-84-80. 13-41. 77 -69. 86 <-84 -78. 2-45. 28 -69. 22 <-84-76. 6 Примечание: шум дизеринга BW = 20 МГц. Вывод: большая амплитуда может улучшить производительность, однако может вызвать перегрузку. 54 Информация TI - Требуется NDA
Резюме по влиянию шума дизеринга Ширина полосы 10 МГц 30 МГц Ширина полосы шума дизеринга (МГц) HD 5 (d. Bc) HD 11 (d.Bc) HD 13 (d. Bc) HD 17 (d.