Станок для балансировки коленчатых валов, маховиков, балансировка V8, развесовка шатунов, . Технобаланс
√ Дорезонансная система измерений дисбаланса
Работа на низких, дорезонансных частотах вращения балансируемого коленвала, повышает безопасность и сокращает время балансировки.
√ Жесткий подвес и портал со сверлильной головкой
Дает возможность осуществлять процесс корректировки масс без снятия коленвала со станка.
√ Система высокоточных линейных перемещений
Передвижение опорных стоек по системе линейных перемещений осуществляется с минимальным усилием, позволяет быстро производить перенастройку станка под другой тип коленвала.
√ Высококачественные комплектующие
Комплектующие европейского производства (ручки, ролики, шкивы и проч.) значительно повышают точность измерений, надежность и срок службы станка.
√ Станина из полимербетона с вибропоглощающим покрытием
Снижает зависимость измерений от внешних вибраций и позволяет организовывать участок балансировки рядом с другим работающим промышленным оборудованием.
√ Установка на виброопоры
Станок не требует специального фундамента (устанавливается на 4 виброопоры) и может быть легко перемещен с помощью ручной роклы.
√ Вывод результатов измерений на ПК
Удобство эксплуатации, универсальность, снижение стоимости станка.
Технические характеристики:
Предельные параметры балансируемого ротора | ||
максимальный вес | 300 кг | |
минимальный вес | 3кг | |
максимальное расстояние между шейками | 1300 мм | |
минимальное расстояние между шейками | 120 мм | |
максимальный диаметр балансируемого ротора | 700 мм | |
Параметры балансировки | ||
диапазон рабочих частот вращения | 200-2000 об/мин | |
минимально достижимый удельный остаточный дисбаланс | 0.5 г·мм/кг | |
вывод результатов измерения | дисплей, принтер, файл | |
Параметры станка | ||
электропитание | 220 В / 2.2 кВт | |
ширина | 950 мм | |
длина | 1900 мм | |
высота | 1800 мм | |
вес | 800 кг | |
Срок изготовления до 45 раб. дней. |
Данный станок прошёл процедуру сертификации на соответствие нормам технического регламента таможенного союза (EAC):
tehnobalans.ru
Станок для балансировки коленчатых валов – Вопросы балансировки
Сделал наконец станок для балансировки коленвалов. :rolleyes:
Особенности
-Жесткий подвес. Рассчитан на возможные большие начальные дисбалансы и на сверление противовесов прямо на станке.
– В ПО внесено изменение – линейный перерасчет из одних плоскостей коррекции в другие. Это необходимо когда негде сверлить на одной паре противовесов и можно легко “перейти” на соседние. Достаточно рулетки или линейки :rolleyes:
– Основание из натурального гранита. Виброгашение/термостабильность.
– Быстрое/удобное натяжение ремня. Легкость перемещения измерительных стоек, это сильно упрощает перенастройку на другой типоразмер.
Сегодня начал испытания. Пока, вроде, все хорошо…
Вот так5ую точность удалось получить. Причем и на 1000 и на 400 об. Это вес неуравновешенной массы :rolleyes:
За новогодние праздники надеюсь сделать сверлильный портал.
www.chipmaker.ru
Балансировочный станок для коленчатых валов 9Д715У
Диапазон масс балансируемых роторов на станке, кг | 2,5 – 250 |
Максимальный диаметр ротора, мм | 850 |
Максимальный диаметр ротора над ременным приводом, мм | 500 |
Расстояние между серединами опорных шеек ротора, мм | 150 – 1350* |
Диаметр опорных шеек ротора, мм | 20 – 140 |
Диапазон частот вращения ротора, об/мин | 300 – 1500 |
Минимальный достижимый остаточный удельный дисбаланс, гмм/кг | 1,0 |
Тип привода | Ременной |
Тип опор | Ролики + призмы |
Габаритные размеры станка (длина х ширина х высота), мм | 1600 х 1330 х 1268 |
Масса станка, кг (не более) | 480 |
Род тока питающей сети | ~ 3-х фазный |
Частота тока, Гц | 50 ± 1 |
Напряжения сети, В | 380 ± 10% |
Мощность электродвигателя привода вращения детали, не менее, кВт | 3,0 |
Балансировочная система станка (на выбор) | ПБ-02М или ПАК-1 |
www.vikatm.com
Подробная инструкция по балансировке коленвала в домашних условиях
Для экономии затрат, идущих на техническое обслуживание в автосервисе, можно выполнять балансирование коленчатого вала в условиях гаража. В статье описываются варианты, как можно проводить балансировку коленвала своими руками.
Содержание
[ Раскрыть]
[ Скрыть]
Зачем нужна балансировка коленчатых валов?
При дисбалансе коленчатого вала неравномерно распределяется масса вдоль и поперек оси, то есть нарушается баланс: один край легче другого. В основном причиной поперечного дисбаланса является износ деталей вала при продолжительной эксплуатации.
Балансировка коленвала проводится, чтобы снизить нагрузку и вибрации на узлы силового агрегата. Эта операция дает возможность поднять производительность двигателя, продлить срок эксплуатации. В основном балансировка необходима для изношенных элементов двигателя, но встречаются случаи, когда в балансировке нуждается новый автомобиль.
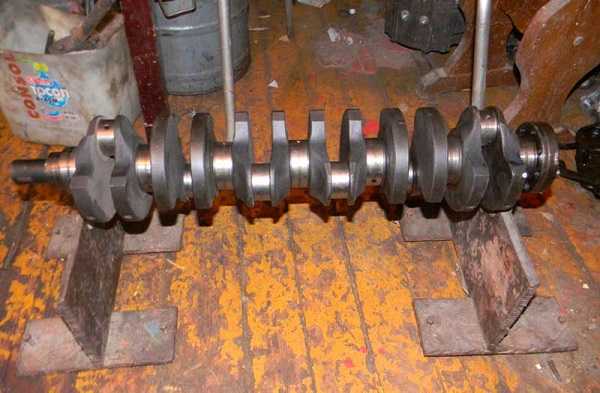
Определить, нужна ли балансировка коленвала, можно по поведению ручки переключения передач: она начинает болтаться при передвижении на холостом ходу. То же самое касается двигателя: если на холостом ходу мотор работает с рывками.
Причины появления неполадок могут быть разные:
- некачественное изготовление сопряженных деталей;
- неоднородность материала, который использован для коленчатого вала;
- люфты, возникшие в результате нарушения зазоров между сопряженными элементами;
- некачественная сборка;
- неточное центрирование;
- естественный износ.
После замены маховика или его зубчатого венца, корзины сцепления необходимо отбалансировать коленвал. Если не выполнить эту процедуру, то даже при небольших скоростях мотор начнет вибрировать из-за нарушения баланса.
Где отбалансировать коленвал – варианты ремонта
Отбалансировать коленчатый вал можно двумя способами:
- Статический способ применяется при незначительных нарушениях баланса. В этом случае коленчатый вал находится в неподвижном состоянии. При этом тяжелая сторона опущена вниз. Легкая часть уравновешивается с помощью грузов, которые крепятся на край легкой стороны. Затем с помощью специальных ножей снимается металл с тяжелой части, пока не опустится нагруженная часть.
Шлифовка коленчатого вала
- Динамический способ точнее статического. Его применяют для устранения существенного дисбаланса. В этом случае необходим специальный станок, на который устанавливается вал. Коленчатый вал начинают раскручивать до необходимых оборотов. С помощью лазера определяется точка, где находится наиболее тяжелая точка. С этого места снимается лишний металл.
Процедура балансировки своими руками
Балансировку можно выполнить в автосервисе, где, естественно, процедура будет проведена более точно, либо в собственном гараже. Для проведения процедуры в домашних условиях нужно изготовить специальное приспособление – станок, на который будет устанавливаться маховик. Сложного ничего нет. Сделать такой станок своими руками сможет даже человек, неимеющий слесарного опыта.
Приспособление
В первую очередь нужно сварить рамку, которая служить будет основой станка. Размеры рамки и приспособления зависят от длины коленчатого вала. Для изготовления нужна профильная труба и уголок. После изготовления рамки и затирки швов, в двух уголках рамки и в середине противоположной трубы, нужно просверлить отверстия для трех шпилек. К отверстиям приваривают гайки с диаметром внутренней резьбы равным диаметру шпилек, которые изготавливаются из железных прутов.
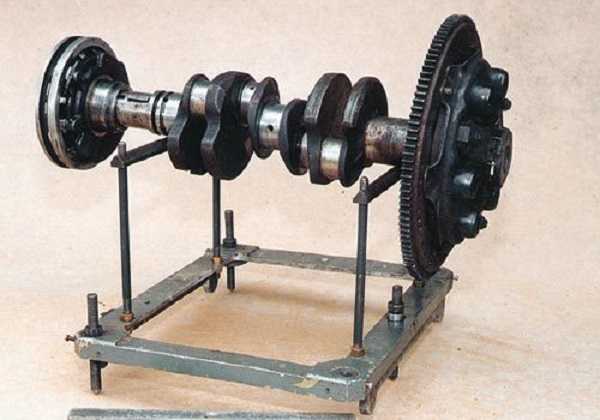
Перед балансировкой рамку нужно выставить с помощью уровня строго горизонтально. Это легче сделать, если она будет стоять на трех штырях, чем на четырех. После регулировки на приваренные гайки сверху следует накрутить контргайки. Далее нужно сделать недалеко от каждого угла рамки отверстия для 4 прутов диаметром 14-16 мм, которые будут исполнять роль стоек. Длина прутов должна быть одинаковой – примерно 250 мм.
Теперь нужно взять 4 уголка шириной 2-4 см и длиной около 30 см и просверлить в них отверстия диаметром, соответствующим диаметру стоек. На каждую пару стоек надевается уголок ребрами вверх. Уголки нужно приварить. Получается приспособление напоминающее турник с брусьями: напротив друг друга устанавливаются стойки в виде буквы «П». На эти стойки будет устанавливаться коленчатый вал. Таким образом, станок для балансировки коленвала готов.
Последовательность действий
Балансировка коленчатого вала с помощью устройства, сделанного своими руками, состоит из следующих шагов:
- В первую очередь нужно выставить станок строго горизонтально. Для этого уровень укладывается сначала на одну перекладину-уголок. Затем следует подкручивать шпильки-стойки, пока уголок не будет расположен строго горизонтально. Далее уровень поворачиваем перпендикулярно, кладем его на два уголка-перекладины одновременно и крутим шпильку, высверленную посередине трубы. Добиваемся полной горизонтальности всей конструкции.
- Когда станок выставлен, на него можно устанавливать коленчатый вал в сборе с комплектующими. Если присутствует дисбаланс, вал начнет проворачиваться по уголку, пока самая тяжелая точка не окажется в нижней точке. Этот дисбаланс (перевес) нужно ликвидировать.
Приспособление для балансировки
- Для устранения перевеса нужно убрать лишнюю часть металла в нижней (тяжелой) точке маховика. Определить точный вес металла, который нужно высверлить, можно с помощью небольших магнитиков. Их нужно цеплять на противоположной – легкой стороне маховика. Цеплять магнитики следует до тех пор, пока коленвал в сборе с деталями не будет переворачиваться, а будет лежать неподвижно.
- Добившись неподвижного положения коленчатого вала, нужно снять магнитики и взвесить их на весах. Это и будет тот вес, который нужно убрать, чтобы устранить дисбаланс.
- Теперь с маховика снимается столько стружки, чтобы ее вес был равен весу магнитов, которые мы перед этим взвешивали. Под приспособлением нужно постелить ветошь, чтобы собрать и взвесить стружку. Высверливать приходится порой несколько отверстий, так как одного диаметром 7-8 мм обычно не достаточно. Главное, не высверлить больше, чем нужно, иначе придется сверлить маховик с противоположной стороны.
Процедура балансирования на СТО
- Если тяжелая точка приходится на какую-то деталь маховика, которая менялась, например, шкив. То высверливать нужно эту деталь. Если менялась корзина сцепления, то в ней удаляется лишний металл около отверстий ее крепления.
С данным приспособлением, изготовленным своими руками, можно легко отбалансировать коленчатый вал. Конечно, без специального оборудования достичь точности трудно, зато можно сэкономить на посещении автосервиса.
Видео «Балансировка коленчатого вала»
В этом видео демонстрируется, как правильно отбалансировать коленвал.
avtozam.com
Мифы и реальность о балансировке коленчатого вала
К сожалению, вопросы балансировки коленчатого вала (маховика, корзины сцепления, демпфера) в доступной литературе практически не раскрыты, а если что и можно найти, то это ГОСТы и научная литература. Однако осмысление и понимание того, что там написано, требует определенной подготовки и наличия самого балансировочного станка. Это, естественно, отбивает у автомехаников все желание разобраться с этими вопросами с точки зрения ремонта ДВС. В этой короткой статье мы попытаемся раскрыть вопросы балансировки с позиции автомеханика, не вдаваясь в сложные математические расчеты и больше акцентируя внимание на практическом опыте.
Итак, наиболее частый вопрос возникающий при ремонте двигателя: нужно ли проводить балансировку после шлифовки коленчатого вала?
Для этого мы покажем все этапы балансировки коленчатого вала, которые выполняются в нашей фирме при ремонте коленчатого вала. В качестве примера возьмем коленчатый вал двигателя МВ 603.973. Это рядный 6 цилиндровый дизельный двигатель. Допустимый дисбаланс завода изготовителя на данный вал 100 гмм. Много это или мало? Что будет если дисбаланс будет меньше или больше данной цифры? Эти вопросы мы не будем рассматривать в этой статье, а опишем их позже. Но можно с уверенностью говорить, что завод изготовитель берет эти цифры не с потолка, а проводит достаточное количество экспериментов для того, чтобы найти компромисс между допустимым значением дисбаланса для нормальной эксплуатации двигателя и себестоимостью производства для обеспечения данного допуска. Просто для сравнения, допустимый дисбаланс завода изготовителя на коленчатый вал двигателя ЗМЗ 406 360 гмм. Чтобы легче представить и понять эти цифры, вспомним простую формулу из курса физики. Для вращательного движения сила инерции равна:
где:
m – неуравновешенная масса, кг;
r – радиус ее вращения, м;
w – угловая скорость вращения, рад/с;
n – частота вращения, об/мин.
Итак, подставляем цифры в формулу и принимаем частоту вращения от 1000 до 10 000 об/мин, получаем следующее:
F1000 = 0.1х 0,001х( 3,14х1000/30)2= 1,1 Н
F2000 = 0.1х 0,001х( 3,14х2000/30)2= 4,4 Н
F3000 = 0.1х 0,001х( 3,14х3000/30)2= 9,9 Н
F4000 = 0.1х 0,001х( 3,14х4000/30)2= 17,55 Н
F5000 = 0.1х 0,001х( 3,14х5000/30)2= 27,4 Н
F6000 = 0.1х 0,001х( 3,14х6000/30)2= 39,5 Н
F7000 = 0.1х 0,001х( 3,14х7000/30)2= 53,8 Н
F8000 = 0.1х 0,001х( 3,14х8000/30)2= 70,2 Н
F9000 = 0.1х 0,001х( 3,14х9000/30)2= 88,9 Н
F10000 = 0.1х 0,001х( 3,14х10000/30)2= 109,7 Н
Все конечно понимают, что этот мотор никогда не выйдет на частоту вращения 10 000 об/мин, но этот простенький расчет сделан для того, что бы «почувствовать» цифры и понять как важна балансировка при увеличении частоты вращения. Какие можно сделать предварительные выводы? Во первых, вы «почувствовали», что такое дисбаланс 100 гмм, ну и, во вторых, убедились, что это действительно достаточно жесткий допуск для данного двигателя, и нет никакой необходимости делать этот допуск жестче.
Теперь давайте покончим с цифрами и наконец-то вернемся к этому валу. Данный вал был предварительно отшлифован и после попал к нам на балансировку. И вот какие результаты мы получили при измерении дисбаланса.
Что обозначают эти цифры? На данном рисунке мы видим, что дисбаланс на левой плоскости равен 378 гмм, и дисбаланс на правой плоскости равен 301 гмм. То есть условно можно принять, что общий дисбаланс на вал получается 679 гмм, что почти в 7 раз превышает допуск, заложенный заводом изготовителем.
Вот фото этого вала на станке:
Сейчас конечно Вы начнете во всем обвинять «криворукого» шлифовщика или плохой станок. Но давайте вернемся опять к простеньким расчетам и попробуем понять, почему так получается. Для простоты расчета примем вес вала 20 кг (этот вес очень близок к истине для 6 цилиндрового коленчатого вала). Вал имеет остаточный дисбаланс допустим 0 гмм ( что является полной утопией).
И так теперь шлифовщик этот вал прошлифовал в ремонтный размер. Но при установке вала он сместил ось вращения от оси инерции всего на 0,01 мм (чтобы проще понять – у шлифовщика не совпала старая и новая ось вращения всего на 0,01 мм), и мы получили сразу же дисбаланс в 200 гмм. А если учесть, что у заводского вала всегда присутствует дисбаланс, то картина будет еще хуже. Поэтому те цифры, что мы получили, не являются из ряда вон выходящими, а являются нормой после шлифовки вала.
А если учесть, что не всегда завод изготовитель выдерживает свои же допуска, то обвинения в адрес шлифовщика или станка просто отпадают. Только не надо теперь стоять над шлифовщиком и требовать, что бы он выставлял вал с микронной точностью, все равно это не принесет желаемого результата. Единственным правильным выходом из данной ситуации является обязательная балансировка коленчатого вала после его шлифовки. Традиционно балансировку коленчатого вала выполняют высверливанием противовеса (иногда правда приходится утяжелять противовесы, но это достаточно редкий случай).
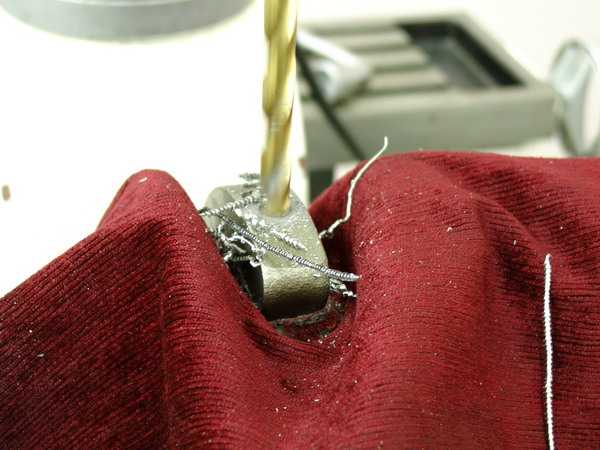
Остаточный дисбаланс по левой плоскости 7 гмм и 4 гмм по правой плоскости. То есть общий дисбаланс на вал 11 гмм. Такая точность делалась специально, чтобы показать возможности данного станка и, как вы поняли теперь, необходимости выполнять такие требования при балансировке после шлифовки вала нет. Требований завода изготовителя вполне достаточно. Итак, с валом мы закончили, и, естественно, возникает вопрос, а нужно ли балансировать передний демпфер (шкив), маховик, корзину сцепления. Обратимся опять к ремонтной литературе. Что рекомендует тот же ЗМЗ, например, на допустимый дисбаланс этих деталей? На шкив передний с демпфером 100 гмм, на маховик 150 гмм, на корзину сцепления 100 гмм. Но есть очень важное примечание.
Все эти детали балансируются отдельно от вала ( то есть на оправках), и коленчатый вал в сборе на современных моторостроительных заводах в серию не балансируется. То есть Вы понимаете, что при установке вышеперечисленных деталей на коленчатый вал остаточный дисбаланс естественно изменится, так как совпадение осей вращения практически невозможно. Ниже представлены фото балансировки данных деталей.
Опять же, как показала практика, эти детали вносят ощутимый вклад в дисбаланс коленчатого вала, и, как показал наш опыт, дисбаланс каждой из этой детали существенно перекрывает допуски на остаточный дисбаланс. Так, цифра 150-300 гмм является «нормой» для переднего шкива (демпфера), для маховика 200-500 гмм, и 200-700 гмм для корзины сцепления. И это относится не только к российскому автопрому. Как показал наш опыт, примерно эти же цифры получаются и у зарубежного автопрома.
И есть обязательно еще один очень важный момент: после балансировки деталей по отдельности надо провести балансировку в сборе, но она должна делаться на последнем этапе. Предварительная балансировка по отдельности является также обязательной. Это надо для того, чтобы в случае, если выйдет из строя маховик или сцепление, Вам не пришлось снимать колено для повторной перебалансировки.
Итак, вот, что мы получаем окончательно при балансировке в сборе.
Итоговый дисбаланс коленчатого вала в сборе 37 гмм.
При этом следует учесть, что вес вала в сборе был около 43 кг.
Но, выполнив балансировку коленчатого вала в сборе, не стоит забывать о развесовке поршней и шатунов. Причем развесовку шатунов надо делать не просто по весу, а развесовку по центру масс, так как разница в весе этих деталей также вносит свой вклад в дисбаланс двигателя и строго регламентируется заводом изготовителем.
И вот, что хотелось бы отметить в заключении: очень многие автомеханики, прочитав эту статью, скажут, что это все ерунда. Что они собрали не один десяток моторов, и что все они без балансировки прекрасно работают, и они будут правы- действительно работают. Но давайте вспомним, сколько приходилось видеть моторов, которые работали …. при поломанных направляющих, со стертыми кулачками распредвала, с фрезерованными по плоскости ГБЦ выше нормы в 2-3 раза, с изношенными цилиндрами в 0,3 мм, с неправильно установленными поршнями- этот список можно продолжать до бесконечности.
У каждого, наверно, найдется парочка своих примеров, когда двигатель работал вопреки всем законам. Зачем хонинговать цилиндры, ведь раньше только точили и все работало? или: Зачем пользоваться хон-брусками, когда можно обычной шкуркой нанести сетку? Зачем «ловить» эти сотки, ведь это и так работает? Так почему, следуя одним требованиям завода изготовителя, пренебрегают другими? Только не надо думать, что, выполнив балансировку коленчатого вала в сборе и развесовку поршней и шатунов, Вы получите «чудо», что у Вас штатный мотор от Ваза по характеристикам станет, как мотор от болида Формулы 1. Этого у Вас не произойдет то же. Ведь балансировка – это один из кирпичиков, который вместе с выполнением остальных требований по ремонту дает Вам уверенность в том, что отремонтированный Вами двигатель отработает как минимум ресурс нового двигателя. И чем больше мотористов будут следовать требованиям автопроизводителей при ремонте двигателя, тем меньше будет автолюбителей, которые считают, что двигатель после капитального ремонта больше 50-70 тыс. км не работает.
motortehn.com
Станок для балансировки коленчатых валов
Забытая балансировка
Балансировка коленчатого вала – процедура, о которой, при проведении ремонта ДВС, очень часто стараются не вспоминать и балансировочное оборудование оказывается, подчас, последним, что приобретается из оборудования. Дороговизна станка, отсутствие в штате балансировщика, мнимая «невостребованность» данной операции со стороны клиента…
Все это переводит участок балансировки в разряд экзотики и не нужной роскоши ремонтного предприятия. Вроде как «…появятся лишние деньги, тогда, может быть…». Между тем, как показывает практика, эксплуатация коленчатого вала, имеющего дисбаланс, ведет к снижению мощности двигателя до 10% и уменьшению ресурса его работы на 25-40%. Один этот факт подводит нас к простому и понятному выводу – балансировка не роскошь, а жизненно необходимая процедура при проведении ремонта двигателя внутреннего сгорания. Ничуть не менее важная, чем, например, восстановление фаски клапана или хонингование цилиндров. Все коленчатые валы в обязательном порядке балансируются производителем на заводах. Но ведь при шлифовке шеек при ремонте, центр масс смещается в любом случае, поэтому после шлифовки шеек во всех технологических картах ремонта ДВС значится балансировка. Балансировка имеет смысл, если предприятие ставит своей целью обеспечить качественный ремонт, а не его видимость. Если это о Вас, возможно, Вам будет полезна изложенная ниже информация о нашей продукции, как минимум, не уступающей (а по ряду технических решений и превосходящей) продукцию известных европейских и американских брэндов.
Занимаясь разработкой и производством балансировочного оборудования, самого разного по назначению и возможностям, от небольших настольных станков для балансировки легких роторов, до пятиметровых, шеститонных станков для балансировки турбин электростанций, мы не могли, разумеется, обойти вниманием узкоспециализированный сектор рынка станков для балансировки коленчатых валов. При проектировании ставились следующие задачи: качество на уровне ведущих немецких и итальянских производителей, простота в использовании, чтобы балансировщиком мог выступать практически любой слесарь, умеющий работать с ПК, но при всем этом стоимостью, ниже чем у коллег из России и Украины. Задачи, казавшиеся невыполнимыми, если не учитывать наличие колоссального опыта практической работы по балансировке, кропотливого изучения образцов всех ведущих производителей и большого конструкторского и инженерного таланта. Давайте посмотрим, оценим и сравним нашу гордость – серийно выпускаемый станок ТБ300.
Cтанок для балансировки коленвалов ДВС, модель ТБ 300.
Итак, начнем с технических характеристик. ТБ 300 позволяет балансировать коленчатые валы весом от 5 до 300 кг, с расстоянием между шейками, от 120 до 1450 мм. Такой диапазон обеспечивает возможность обрабатывать практически все коленчатые валы, используемые в двигателях, начиная от мотоциклов и заканчивая тяжелой спецтехникой. Исключение составит лишь минимальный процент грузовой техники, преимущественно американского производства, с поистине гигантскими, 2-х и более метровыми коленвалами. Есть станок и для таких валов, но речь о таком оборудовании мы поведем в следующих наших статьях.
Традиционно, станины станков изготавливаются либо чугунными, цельнолитыми, либо бетонными (в частности американские образцы не имеют даже металлической арматуры и опалубки). Также, есть «умельцы», использующие в качестве станины швеллер или трубы, заполненные песком. В нашем случае мы разработали сложную каркасную конструкцию из стали, с рассчитанными ребрами жесткости внутри, заполненную специальным, вибропоглощающим полимербетоном. Зачем? Дело в том, что мы разрабатывали станок для реальных производственных участков, когда в непосредственной близости с ним будет другое работающее оборудование.
Станок устанавливется на 4 регулируемых виброопоры, дополнительно гасящих колебания и одновременно позволяющих легко выравнивать станок при размещении в цеху строго в горизонтальной плоскости. Отдельно отметим, что наша конструкции позволяет также легко, с помощью простой роклы, осуществлять транспортировку станка, что порой бывает очень желательно в условиях перепланировки или расширения ремонтного участка. А попробуйте переместить балансировочный станок, «станиной» которого является залитый фундамент, как у некоторых производителей.
Станина перед покраской обрабатывается специальным упругим полимерным составом, который дополнительно защищает поверхность от возможного повреждения, коррозии и уменьшает вибрацию.
Теперь стойки, на которых размещается балансируемый коленвал. Практически во всех моделях балансировочного оборудования, они подвижные, обеспечивающие возможность укладки на них коленвалов разной длины. Вопрос в том, насколько они подвижны. Постоянно перемещать двумя руками не легкую стойку по салазкам, либо с помощью ключа передвигать её по цепи задача хоть и не для спортсмена-армрестлера, но явно не самая приятная процедура для работающего со станком балансировщика. А если балансируемый вал весит килограммов этак 200? Учтя эти жалобы, мы использовали в своей конструкции системы линейных перемещений, позволяющие перемещать стойку буквально указательным пальцем. Аналогичное техническое решение применено в конструкции подвижного сверлильного портала. Также, мы комплектуем свой станок специальными укладчиками/домкратами. Когда тяжелый вал укладывается сначала на домкраты, а потом уже с них, без ударов, мягко, перекладывается на стойки. Да и при корректировки дисбаланса (сверлении), укладчики незаменимы, так как сверлить тяжелый вал на роликовом блоке сложно.
Теперь балансировка. Здесь, при разработке измерительной системы, мы попытались максимально снизить частоту вращения балансируемого ротора, превзойдя по этому параметру большинство аналогов. Согласитесь, как с точки зрения элементарной техники безопасности, так и по соображениям экономии времени и ресурса привода, лучше, чтобы трехсоткилограммовый вал, да ещё нагруженный противовесами вращался рядом с вами со скоростью не 500 или 800, а всего лишь 200 оборотов в минуту.
Еще одна «мелочь» из пожеланий балансировщиков-практиков – выносной пульт управления приводом вращения. Обычно управление приводом вращения осуществляется со стойки диагностического компьютера. Которая в лучшем случае, – где-то сбоку и к ней нужно поворачиваться, отвлекаясь от непосредственно балансируемой детали. Запустив вращение вала и увидев, что вал «пополз», немедленно остановить вращение с пульта гораздо безопаснее, чем бежать к стойке.
Отдельный разговор о качестве изготовления станка. Мы принципиально используем при производстве только качественные комплектующие, начиная от подшипников (только оригинальный немецкий SKF), и заканчивая ручками, натяжными роликами, соединительными элементами. Ни один, даже самый привередливый пользователь, «ощупывавший» станок и рассматривавший его чуть ли не через микроскоп, не смог придраться к качеству изделия, даже в сравнении с продукцией американских и европейских брэндов. И мы подтверждаем это, предоставляя на все механические части станка гарантию в 36 месяцев.
А как же на счет цены, спросите Вы? Наверняка наш станок должен бы
i-perf.ru
Балансировка коленчатых валов
Уравновешивание коленчатых валов нарушается вследствие износа трущихся поверхностей (при эксплуатации) и неравномерной наплавки и последующей механической обработки (при ремонте). Увеличенный в результате этого дисбаланс приводит к дополнительным вибрациям, ухудшающим работу двигателя.
Смещение оси маховика и сцепления относительно оси вала, особенно при обезличенном ремонте, — основной – источник дисбаланса. Кроме того, переход на ремонтные размеры, нарушение размеров отверстий во фланце и его толщины нарушают балансировку и увеличивают дисбаланс.
Исследованиями установлено, что после ремонта дисбаланс коленчатых валов в 5… 10 раз превышает установленный допустимый.
Коленчатые валы рекомендуется вначале балансировать отдельно, а затем в сборе с маховиком и сцеплением, также предварительно статически отбалансированными. Для этого используют станки КИ-4274 (БМ-У4) для динамической балансировки. Однако в отдельных случаях в качестве предварительной операции проводят статическую балансировку.
В зависимости от конструкции валов и возможностей производства их балансировка имеет свои особенности. Например, на каждую шатунную шейку двигателя ЗИЛ-130 устанавливают разъемный груз взамен массы шатунов и поршневых комплектов. Груз балансируют статически с допустимым дисбалансом 2 г-см, а массу подгоняют с точностью ± 1 г. При этом длина груза должна быть равна длине шатунной шейки, а центр тяжести располагаться на ее оси посередине длины шейки.
Статическую балансировку коленчатых валов в сборе с маховиком выполняют на стендах различной конструкции. Один из них показан на рисунке 43. Он состоит из рамы 1 сварной конструкции, опирающейся на четыре ножки, что позволяет его установить в строго горизонтальном положении. На переднем конце рамы на двух валиках 4, расположенных в кронштейнах 2, перемещается ползун 3. Его положение определяется расстоянием между крайними коренными шейками балансируемых валов. Ползун 3 стопорится винтом в нужном положении. На ползуне 3 и задней стойке 6 установлены по два диска 7 и 8, которые вращаются на подшипниках.
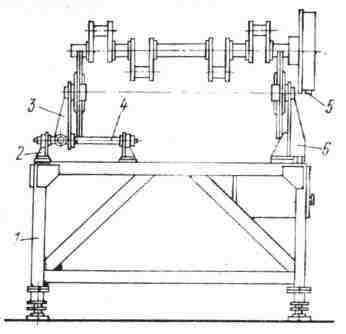
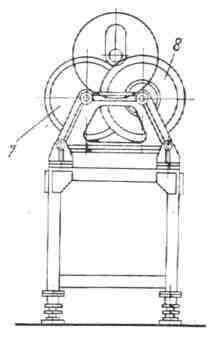
Рис. 43. Стенд для статической балансировки коленчатых валов в сборе с маховиком:
1 — рама; 2 — передний кронштейн; 3 — ползун; 4 — валик; 5 — грузик; 6 — задняя стойка; 7 и 8 — диски.
Коленчатый вал укладывают во впадины дисков. Если вал не сбалансирован, то он утяжеленной частью будет повертываться вниз. К торцу обода маховика с противоположной стороны приклеивают массу, равную массе металла, необходимую для уравновешивания вала. После проверки вращением вала на дисках 7 и 8 убеждаются в правильности подобранной массы груза.
Высверливают массу металла, равную приклеенной на том же радиусе. Если вал не поворачивается из любого установленного положения, то он отбалансирован правильно. После этого проводят динамическую балансировку,
В других случаях статическую и динамическую балансировку совмещают.
Универсальная балансировочная машина БМ-У4 предназначена для быстрой и точной балансировки деталей и изделий массой 10… 250 кг (рис. 44). Она пригодна для уравновешивания изделий, вращающихся на подшипниках качения и скольжения.
Балансируют детали, центр тяжести которых располагается между опорами (коленчатые валы, коленчатые валы в сборе с маховиками и со сцеплениями, роторы электродвигателей и т. д.).
Переключением на пульте измеряют дисбаланс в левой или правой плоскости. Высокая чувствительность и стабильность показаний приборов машины позволяют в течение 10…15 с после ее пуска определить неуравновешенность балансируемой детали с точностью 5… 10 г-см, а также место расположения грузов. В зависимости от длины балансируемых изделий балансировочные машины изготавливают трех размеров.
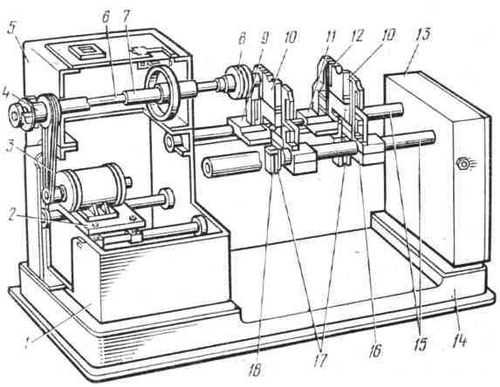
Рис. 44. Универсальная балансировочная машина БМ-У4 модели 4274:
1 и 13 — стойки; 2 — консольная плита; 3 — клиноременная передача; 4 и S — пружинные муфты; 5 — шпиндельная бабка; 6 — приводной вал; 7 — шпиндель; 9 и 11 — опоры люлек; 10 — люльки; 12 — стальная лента; 14 — плита; 15 — трубчатые направляющие; 16 — демпфер; 17 — электромагниты; 18 — кронштейн.
Основные технические данные машины БМ-У4
Наибольший диаметр балансируемой детали, мм 800
Наибольшее расстояние между опорными шейками балансируемой детали, мм 800
Наибольшая масса балансируемой детали, кг 250
Точность определения неуравновешенности балансируемой детали, г-см 5… 10
Ошибка определения места расположения неуравновешенности детали в плоскости вращения, градусов 0… 5
Машина состоит из механической части и измерительного устройства с датчиками и стробоскопом для определения места необходимой корректировки. Кроме того, в нее входят электропривод и устройство для автоматического смазывания вкладышей под шейки балансируемых деталей.
На плите 14 установлены стойки 1 и 13 и трубчатые направляющие 15. На последних расположены неподвижные опоры 9 и 11, которые в заданном положении фиксируются стопорами. На опорах находятся люльки 10. На стойке 1 жестко укреплена шпиндельная бабка 5, а внутри стойки смонтирован электропривод. Электродвигатель помещен на консольной плите 2 и приводит во вращение шпиндель 7 через клиноременную передачу 3. Для управления электродвигателем служит кнопочная станция, расположенная в шпиндельной бабке 5. В стойке 13 смонтирован щит с электрооборудованием, который включается с помощью переключателя, находящегося на передней панели.
На опорах 9 и 11 крепятся кронштейны 18 с электромагнитами 17, которые предназначены для автоматического запирания и отпирания люлек, а также приведения в действие масляных насосов, подающих масло к вкладышам опор. В корпусах опор 9 и 11 на стальных лентах 12 подвешены люльки 10, колебания которых гасятся демпферами 16. При включении электродвигателя через заданное время после его разгона автоматически растормаживаются люльки 10 включением электромагнитов 17. При выключении электродвигателя электромагниты обесточиваются и срабатывают клиновидные запоры люлек.
Балансируемый коленчатый вал укладывают крайними коренными шейками на вкладыш опор и через пружинную муфту соединяют с приводным валом. Вал приводится во вращение шпинделем 7, внутри которого проходят приводной вал 6 с двумя пружинными муфтами 4 и 8. Муфты устроены и расположены таким образом, что не препятствуют раскачиванию люлек в поперечном направлении в пределах 5… 10 мм.
Измерительное устройство включает два датчика, ламповый усилитель, стробоскопический осветитель и миллиамперметр. Датчики преобразуют механические колебания люлек в электрические. Электрические сигналы поступают на вход усилителя, а затем на измерительный прибор. Для настройки и контроля показаний миллиамперметра со шкалой балансировочную машину оборудуют контрольным валом с эталонным грузом, который можно ввертывать в отверстия левого и правого дисков. Вращение контрольного вала без эталонного груза не должно создавать его колебаний, при этом показания миллиамперметра должны равняться нулю. При постановке эталонного груза дисбаланс контрольного вала должен составлять 300 г-см.
При измерении неуравновешенности используют сигналы обоих датчиков. Сигналы поступают на вход усилителя, а после их усиления — на измерительный прибор и импульсную безынерционную лампу ИФК-120. Лампа освещает цифры лимба, показывающие, на каком градусе балансируемой детали находится дисбаланс. Уровень сигнала, поступающего из датчика через усилитель на миллиамперметр, определяет значение дисбаланса. Массу балансировочных грузов G определяют по формуле
G=M/r
где М — показания миллиамперметра, г-см; г — радиус смещения груза относительно оси вращения, см.
Коленчатый вал рекомендуется уравновешивать за счет его крайних щек, снимая или наплавляя с противоположной стороны массу металла G.
Исследования, проведенные в МИИСП, показали, что балансировочные стенды с фиксированной плоскостью колебания оси вращения ротора имеют недостаток, заключающийся в самокомпенсации, которая снижает его чувствительность к неуравновешенности в какой-либо плоскости коррекции. В связи с этим предложено изменение показаний балансировочного стенда оценивать двумя показателями: масштабным коэффициентом и коэффициентом влияния.
Масштабный коэффициент показывает, ЕО сколько раз занижены показания стенда в данной плоскости коррекции. Коэффициент влияния определяют как отношение дисбаланса в одной плоскости к мнимому дисбалансу в другой, действие которого вызвано дисбалансом первой плоскости. Он показывает, во сколько раз ослаблено влияние одной плоскости на другую. Для определения коэффициентов используют контрольный груз.
Рекомендуется вначале устранить неуравновешенность коленчатого вала в обеих плоскостях коррекции, а затем маховика и сцепления. В последнем случае достаточно устранить дисбаланс в плоскости маховика. Такая последовательность с учетом указанных коэффициентов обеспечивает более высокую точность балансировки.
Балансировке вращающихся деталей и сборочных единиц уделяется большое внимание на ремонтных предприятиях зарубежных стран. Ее проведение обосновано снижением вибраций на 10%, что способствует увеличению мощности двигателя. Ресурс двигателя при этом возрастает на 25 … 60 % за счет уменьшения динамических нагрузок, экономится топливо. За рубежом применяют последовательную балансировку отдельно коленчатого вала, вала с маховиком, а затем всей сборочной единицы в сборе со шкивом и сцеплением. Шатунно-поршневую группу комплектуют с допуском 2 г.
< Предыдущая | Следующая > |
---|
motoavto.su