Станок для шлифовки клапанов в категории “Промышленное оборудование и станки”
Войди и получай выгодные условия доставки
поиск в товарах / по продавцам
Шлифовальные станки по металлу
Оборудование для ремонта ДВС
Шлифовальные станки по дереву
Отрезные, зачистные, шлифовальные, пильные круги
Оборудование для автосервиса, общее
Пемзы, терки и наборы для педикюра
Головки блока цилиндров
Расточные станки
Оборудование для производства ремней
Инструмент для ремонта мототехники
Клапаны, оси, коромысла двигателя, толкатели клапанов
Комплектующие для шиномонтажа
Наборы инструментов
Токарные станки
Точильные станки
Оборудование для производства пластиковых изделий
Товары, общее
Промышленные смазки
Комплектующие и аксессуары для автомоек
Станки для проточки дисков и барабанов
Станок для шлифовки клапанов SJMC VG100
В наличии
от 120 000 ₴
Купить
Станок для шлифовки фаски клапана Poleks ST 080
В наличии
166 462 ₴
Купить
Станок для шлифовки клапанов Comec RV516 (Италия)
Под заказ
223 400 ₴
Купить
Станок для шлифовки клапанов MANEK модель VRM-150 (Индия)
Под заказ
107 900 ₴
Купить
Международное моторное бюроКиев
Ленточно-дисковый станок для шлифовки Scheppach BTS 800
Готово к отправке
6 999 ₴
Купить
Станок для шлифовки криволинейных деталей OKZ. Z DINCMAK
Готово к отправке
270 400 ₴
Купить
Ленточно-дисковый станок для шлифовки Scheppach BTS 800
Готово к отправке
7 779 ₴
Купить
Станок для шлифовки головок и блоков цилиндров Comec RP- 850
В наличии
588 000 ₴
Купить
DoneDeal DD 6698 Абразивная паста для притирки клапанов, для шлифовки металлов 2*25гр
Готово к отправке
Купить
2
3
Вперед
Показано 1 – 29 товаров из 100+
Смотрите также
Аппарат для удаления мозолей
Чулочно-носочные автоматы giovanni
Набор пружинок
Станок для шлифовки гбц
Шлифовальный аппарат
Шлифовочный станок
Ленточный гриндер
Автоматический шлифовально-полировальный станок
Профессиональный станок
Станок полировально-шлифовальный двухсторонний
Круглошлифовальный станок 3м151
Круглошлифовальный станок
Электрическая пемза для пяток
Станок для шлифовки дерева
Isitan
Станок для шлифовки клапанов со скидкой
Станок для шлифовки клапанов оптом
Популярные категории
Промышленное оборудование и станки
Станки
Металлообрабатывающие станки
Шлифовальные станки по металлу
Оборудование и товары для предоставления услуг
Оборудование для автосервиса
Оборудование для ремонта ДВС
Деревообрабатывающие станки
Шлифовальные станки по дереву
Инструмент
Оснастка для инструмента
Отрезные, зачистные, шлифовальные, пильные круги
Насколько вам
удобно на проме?
Не рассчитывать на меньшее качество, чем дает оборудование SERDI / Ремонт двигателей
Ремонт головок блока цилиндров в последние годы стал традиционной темой. Что совершенно неудивительно, поскольку средний уровень качества этой работы на российском рынке пока не просто далек от идеала, а вызывает самое удручающее впечатление. Одна из причин такого положения дел — отсутствие в российских цехах нормального оборудования для обработки седел и клапанов. Отсюда и всеобщие попытки ремонтировать головки блока всевозможными подручными средствами. А проще говоря — налицо непонимание сути проблемы.
Но потребности рынка уже диктуют свои правила, и время, когда придется приобретать хорошее оборудование для ремонта головок блока цилиндров, уже не за горами. Только вот вопрос — выбор оборудования большой, а что выбрать для конкретных условий работы, сразу и не скажешь. Поэтому сначала придется немного разобраться с теорией…
Качество бывает разное…
Основным видом работ при ремонте головок блока цилиндров (ГБЦ), безусловно, следует признать обработку седел с целью восстановления их геометрии. Дело в том, что качество этой работы в значительной степени определяет и надежность, и долговечность двигателя в эксплуатации после ремонта. Напротив, низкое качество обработки седел дает резкое снижение ресурса, появление дефектов в виде стука, повышенного расхода масла, падения компрессии и даже разрушения деталей, приводящего к выходу двигателя из строя.
В чем же заключается качество обработки седел? Ответ на этот вопрос является ключевым для понимания сути не только самого процесса обработки,но и ремонта двигателя в целом.
К сожалению, следует признать, что в основной массе работников автосервисов и мотористов понимания качества ремонта седел головки блока пока не наблюдается. Многие из сервисменов либо затрудняются ответить на вопрос, что такое качество, либо твердо убеждены, что для качественного ремонта вполне достаточно сделать сопряжение седла с клапаном абсолютно герметичным. При этом высшим уровнем качества ремонта считается такое, когда при проверке известным способом «на керосин» обеспечивается абсолютная герметичность.
Главным результатом данного весьма распространенного заблуждения является полное непонимание разницы в способах обработки седла. Многим кажется, что седло может быть отлично обработано любым доступным способом, например, ручным инструментом, а потом тщательно притерто к клапану. И все. А проблемы с качеством относятся исключительно к квалификации механика, выполняющего эту работу, и оцениваются только по принципу «течет — не течет».
Однако многолетняя практика ремонта седел и исследования последних лет показывают, что дело совсем не в исполнителе и уж тем более не в керосине. Исполнитель не в состоянии обеспечить правильную обработку седла, если этого не дает сделать сам инструмент. Керосин же просто обманет, когда покажет герметичность заведомо кривого седла с силой «пристукнутым» в него клапаном. При этом из поля зрения яростных сторонников «керосиновой герметичности» полностью исчезают такие важнейшие параметры седла, как равная ширина рабочей фаски по окружности и правильная форма этой фаски, особенно, после того, как она «убивается» большим количеством абразивной пасты во время притирки.
На самом деле, такая работа никак не может быть названа качественной, даже несмотря на «отличные» результаты проверки на керосин. Почему? Потому что, помимо профиля седла, никак не контролируется, более того, вообще игнорируется главный показатель качества обработки седла — его соосность с отверстием направляющей втулки клапана.
Именно соосность седла и втулки определяет долговечность клапанного механизма и хорошую герметичность посадки клапана после многих десятков и даже сотен тысяч километров пробега автомобиля. Заметьте — не сразу после ремонта седла, а, возможно, многие годы позже. Но на такой результат никак нельзя рассчитывать с кривыми после ручного инструмента седлами и с притертыми к ним клапанами — боковые нагрузки на клапан в момент его посадки в седло не только приведут к неравномерному износу седла, но и обеспечат быстрый износ направляющей втулки. А абразив, внедрившийся в седло во время притирки, довершит дело. Какие уж тут десятки тысяч километров?
Кривизна седла, точнее, большая несоосность седла и втулки, получается при работе ручным инструментом автоматически, даже против желания и старания механика. Причина кроется в нежесткости направляющего стержня (пилота), устанавливаемого в отверстие направляющей втулки для центрирования фрезы — пилот изгибается при малейшем боковом усилии от руки механика или при отжиме фрезы от седла. А это делает седло, обработанное таким способом, заведомо несоосным направляющей втулке. Да и время, затрачиваемое на ручную обработку, как правило, получается огромным.
Вот для устранения несоосности седла и втулки, получения оптимальной формы седла, обеспечения нормальной производительности и служат специализированные станки для ремонта седел. Такие станки выпускаются многими производителями, поэтому вопрос правильного выбора оборудования сегодня становится все более актуальным. Особенно для тех, кто не планирует тратить свои деньги впустую.
Жесткость или шарнир?
Итак, соосная обработка седла — как она реализуется на практике? В конструкциях станков для ремонта седел сегодня используются две принципиально различных схемы обеспечения соосности и обработки седла — жесткая и шарнирная. При этом выбор станка для ремонта седел фактически означает и выбор схемы. И вот почему.
Жесткая схема предполагает, что цилиндрический пилот и резцедержатель с резцом жестко закреплены на шпинделе станка. При такой конструкции обработке седла должна предшествовать операция точного центрирования шпинделя по отверстию направляющей втулки. А для этого шпиндель должен иметь на данной стадии подвижность как в горизонтальной плоскости (для точного попадания кончиком пилота в отверстие втулки), так и угловую (для обеспечения совпадения оси пилота с осью направляющей втулки). Затем, после центрирования, шпиндель жестко фиксируется, и производится собственно обработка седла. Разумеется, седло в таком случае получается соосным втулке автоматически.
В настоящее время жесткую схему применяют только ведущие мировые производители станочного оборудования для ремонта двигателей. Среди них датская фирма AMC-SCHOU, французские NEWEN и SERDI, причем две последних компании являются специализированными производителями оборудования для ремонта головок блока цилиндров.
Остальные фирмы, включая итальянские и американские, пока придерживаются шарнирной схемы. В такой схеме, как правило, применен легкоконусный пилот, заклинивающий в отверстии направляющей втулки, а резцедержатель имеет свободную посадку на пилоте и так называемый байонетный шарнир для соединения со шпинделем станка.
К сожалению, практика показала, что все станки шарнирного типа при значительной твердости седел, а также при уменьшении диаметра пилота менее 7-8 мм (а это все современные многоклапанные двигатели с клапанами малого диаметра) неспособны точно обрабатывать седла. Причина кроется в резком, в десятки раз, падении жесткости системы — тонкий пилот не может удержать резцедержатель с резцом от поворота в шарнире и качания в вертикальной плоскости под действием переменных сил резания. В результате происходит отжим резца от обрабатываемой поверхности, и возникают значительные трудности в сосной обработке седла, изначально расположенного несоосно втулке (такое часто наблюдается при значительном износе седел, перегреве двигателя, а также после замены втулок).
Указанные недостатки шарнирной схемы являются следствием ее морального устаревания — станки, работающие по данной схеме, разработаны более 30-40 лет назад, когда многоклапанных двигателей не было и в помине. Вот почему приобретение шарнирного станка сегодня не может быть оправдано ни его низкой ценой, ни звонким названием фирмы-изготовителя. Это как раз тот случай, когда деньги будут потрачены совершенно зря.
Таким образом, выбор «головочного» оборудования реально возможен только среди ведущих фирм, указанных выше, причем предпочтение следует отдать специализированным компаниям — у них есть довольно широкий ассортимент станков под конкретные условия работы.
Правда, станки этих фирм неравноценны — если многие модели станков SERDI имеют простое электромеханическое управление (хотя есть и образцы, оснащенные ЧПУ), то оборудование компании NEWEN заведомо сложнее — по причине использования в конструкции серьезных электронных систем. Естественно, имея более высокую точность, станки NEWEN получаются и существенно дороже. Но, как известно, обратной стороной сложности является пониженная надежность, что может создать дополнительные трудности ремонтному предприятию. К примеру, устранение практически любой, даже самой мелкой, неисправности такой сложной техники требует, как правило, приезда квалифицированных заводских специалистов. А это потери времени, да еще и дополнительные расходы…
В общем, применение такого сложного и дорогостоящего оборудования получается весьма ограниченным — это серийный ремонт в условиях ремзаводов или решение специальных задач (опытное и серийное производство, подготовка специальных двигателей и т. д.). К сожалению, в этот список с большим трудом попадает обычная работа в обычном цехе механической обработки — там такое оборудование будет слишком долго окупаться. А возможно, не окупится вообще.
Вот почему, выбирая вариант станка, оптимальный и по точности, и по цене для реальных условий работы в российских цехах, следует остановиться, прежде всего, на оборудовании фирмы SERDI.
«Хитрость» фирмы SERDI
Преимущества «головочных» станков SERDI заключены не только в жестком креплении пилота и резцедержателя на шпинделе. Основная «хитрость» кроется в системе точного центрирования шпинделя по отверстию направляющей втулки перед обработкой седла.
Надо сказать, что схема центрирования SERDI появилась не на голом месте — в 1980 году фирмой был получен патент на так называемую двойную воздушную подушку. Смысл схемы довольно прост — рабочий узел станка во время центрирования «плавает» по станине на плоской воздушной подушке, в то время как шпиндель имеет возможность свободно наклоняться в любую сторону на специальной сферической воздушной подушке. Далее, как только пилот зашел в направляющую втулку клапана, рабочий узел и шпиндель фиксируются специальными пневмо- или гидрозажимами, после чего выполняется обработка седла.
Такая схема благополучно дожила и до наших дней, но применяется сейчас только на станках для обработки седел грузовых ГБЦ. Дело в том, что при малых диаметрах пилота точность центрирования шпинделя ухудшается по причине влияния большой массы рабочего узла. Этот факт привел фирму к новой схеме — с тройной воздушной подушкой, патент на которую был выдан в 1996 году.
Суть новой схемы состоит в следующем. Рабочий узел станка по-прежнему имеет воздушную подушку, но она используется только для предварительного (грубого) центрирования шпинделя, после чего рабочий узел фиксируется на станине. Далее включаются сразу две воздушных подушки шпинделя, расположенные внутри рабочего устройства, — плоская и сферическая, и производится окончательное центрирование шпинделя.
Для повышения точности центрирования фирма внедрила еще одну новинку — шпиндель со встроенным двигателем. Тем самым удалось полностью разгрузить шпиндель от усилий со стороны элементов привода (шкивы, приводные ремни), а также существенно его облегчить, используя алюминиевые сплавы в конструкции. В результате точность центрирования и обработки достигла 0,01-0,02 мм даже на самых тонких пилотах 4-5 мм. Причем, что характерно, без малейшей притирки.
С тех пор по такой схеме построено подавляющее большинство станков SERDI для обработки седел. Это довольно внушительный ряд машин, включая станки с ЧПУ. Но нас больше интересует практическая сторона дела, а именно, та техника, которая может найти реальное применение в реальных российских цехах.
«Вы не можете себе позволить рассчитывать на меньшее качество…»
Наиболее мощной и универсальной машиной SERDI, без сомнения, является модель S4.5. Этот станок способен обрабатывать седла диаметром от 16 до 120 мм при диаметре стержня клапана от 4 мм в ГБЦ любых двигателей — от мотоциклетного до самого тяжелого дизеля. Для большей жесткости рабочий узел и шпиндель, помимо пневматических зажимов, имеют и гидрозажимы. Удобство в работе создает и четвертая воздушная подушка — на ней «плавает» рабочий стол, что позволяет без усилий перемещать в нужное положение самые тяжелые головки блока.
Для повышения точности обработки станок снабжен электронным указателем хода шпинделя, имеется также плавная регулировка скорости вращения шпинделя, встроенный вакуумтестер для проверки герметичности посадки клапана в седле и приспособление для заточки резцов. Рабочий стол станка комплектуется специальным зажимным устройством, способным зажать в нужном положении любую головку блока.
Кстати, после обработки на этом станке никакой притирки или контроля «на керосин» не предусматривается — внешний вид седла такой, какой никогда не получится после притирки. К тому же чувствительности встроенного вакуумтестера более чем достаточно для определения любого, даже самого незначительного, дефекта обработки. При необходимости можно использовать и специальный измерительный прибор для точного измерения биения седла относительно направляющей втулки.
Фирма SERDI также предоставляет огромный выбор инструмента — твердосплавных резцов и пилотов, что называется, на все случаи жизни. Кстати, резцы поставляются прямоугольные (для вырезания старых седел), одноугловые и профильные — с двумя, тремя углами и даже радиусные, причем все типы резцов с очень большим количеством сочетаний углов и размеров. С некоторых пор инструмент SERDI стал стандартным и для многих других производителей головочного оборудования.
Более простая модель — SERDI S3.5, предназначена, в основном, для ремонта седел ГБЦ легковых автомобилей, легких грузовиков и мотоциклов. Диапазон обработки здесь меньше и составляет 14-50 мм, хотя возможно увеличение диаметра седла до 60 мм при обработке простыми одноугловыми резцами. Поскольку усилия резания седел небольшого диаметра невелики, а головки блока имеют небольшую массу, фиксация рабочего узла и шпинделя осуществляется пневмозажимами, а рабочий стол не имеет воздушной подушки.
Для головок блока любых грузовых автомобилей и тяжелой техники предлагается мощный станок S100ES-L. Он отличается от S4.5, в основном, отсутствием плоской воздушной подушки шпинделя, которая, как указано выше, не требуется для сравнительно толстых пилотов, применяемых при ремонте грузовых ГБЦ. Диапазон обработки этого станка — 28-120 мм по диаметру седла и от 7 мм по диаметру стержня клапана.
Все указанные станки предназначены, в основном, для специализированных цехов по ремонту моторных деталей. Учитывая потребности небольших мастерских и автосервисов, на фирме был разработан ручной станок SERDI Micro 2000.
Эта модель представляет собой небольшой портативный аналог станка типа S3.5. Аналогия касается принципа центрирования шпинделя — Micro тоже имеет три подушки (одну плоскую для рабочего узла и две других — плоскую и сферическую, для шпинделя), но не воздушные, а механические. Это означает, что, ослабляя на рабочем устройстве соответствующие резьбовые фиксаторы, можно получить свободное плоское перемещение рабочего узла на станине или шпинделя в рабочем узле, а также наклон шпинделя в сферическом шарнире.
Данная схема позволяет весьма точно центрировать шпиндель и проводить обработку седел с точностью, лишь ненамного уступающей большим станкам SERDI. Станок снабжен вакуумтестером и специальной станиной Uniclampe 2000 для крепления любых легковых ГБЦ, а диапазон обработки примерно соответствует станку S3.5. Весь инструмент, включая пилоты и резцы, также соответствует стандарту SERDI. Благодаря этому модель Micro 2000 является одной из самых точных среди ручных станков и отлично обрабатывает седла в головках блока подавляющего большинства легковых автомобилей и мотоциклов, в том числе, самых современных многоклапанных.
Но станками для обработки седел производственная программа фирмы не ограничивается. Как не ограничивается обработкой седел и ремонт головки блока. Такая задача — контроль герметичности рубашек охлаждения и выявление дефектов типа трещин, пор и т. д. На самом деле, задача очень важная, поскольку многие двигатели поступают в ремонт после перегрева, когда образование трещин весьма и весьма вероятно. А найти место такого дефекта нетрудно — достаточно воспользоваться специальной установкой для проверки герметичности SERDI SPT1600L.
Установка SPT1600L представляет собой термоизолированный резервуар с крышкой и подвижным суппортом для крепления испытуемой детали. Суппорт посредством гидравлики может перемещаться вертикально, а его вращение производится электроприводом. Резервуар заполняется водой, температура которой автоматически поддерживается программируемым терморегулятором с таймером. Гидравлический и электрический приводы суппорта, а также наличие таймера делают эксплуатацию установки удобной и позволяют снизить затраты на электроэнергию, что выгодно отличает SPT1600L от более простых изделий других производителей.
Работает установка достаточно просто. У испытуемой детали (головка или блок цилиндров) с помощью фланцев и резиновых прокладок герметично глушатся все боковые каналы системы охлаждения. Деталь устанавливается на суппорт привалочной плоскостью вверх, на окна рубашки кладутся резиновые прокладки, после чего деталь сверху закрывается прозрачной плитой, и с помощью шпилек и штанг вся конструкция притягивается к суппорту.
На одном из боковых фланцев делается резьбовое отверстие для подключения шланга воздушной магистрали. После погружения детали в резервуар и выдержки для выравнивания ее температуры в рубашку дается давление воздуха (не более 4-5 кг/см2). Далее производится осмотр, при котором можно вращать деталь внутри резервуара, чтобы рассмотреть все возможные места утечки воздуха.
Данным способом удается испытывать на герметичность рубашки охлаждения практически любых головок и блоков цилиндров, включая V-образные, опрессовывать масляные каналы и даже проверять на герметичность посадку направляющих втулок клапанов.
В целом любой из описанных выше станков для обработки седел вместе со станком для шлифовки клапанов и опрессовочной установкой уже составляют практически готовый участок по ремонту головок блока цилиндров. Причем, заметьте — качественному ремонту с использованием самых современных технологий и оборудования, а не дедовских «крутилок», волшебных шарниров и прочего устаревшего хлама.
Поэтому неудивительно, что все описанные выше станки успешно прошли апробацию и давно работают в самых передовых российских цехах. Москва, С. Петербург, Ростов, Екатеринбург, Тюмень, Омск, Красноярск, Нижний Новгород — вот только неполный перечень городов, где уже достаточно хорошо знают, что такое качественный ремонт головки блока на оборудовании SERDI. И те автосервисы, где хоть раз попробовали сделать головку блока правильно, на меньшее качество уже не рассчитывают — прямо в соответствие с вынесенным в заголовок раздела девизом фирмы. А это лучшее подтверждение тому, что деньги на такое оборудование были потрачены не зря.
Самодельный станок для шлифовки клапанов Стоимость $0
JavaScript отключен. Для лучшего опыта, пожалуйста, включите JavaScript в вашем браузере, прежде чем продолжить.
- Автор темы Свомпратт
- Дата начала
Свомпратт
Снайпер
- #1
Так что я не мог просто притереть эти сильно изъеденные выпускные клапаны.
Бадди оставил здесь свою точилку для клапанов сиу, но уронил ее и погнул головку, и эта штука теперь бесполезна для притирки клапанов.
Я исследовал самодельные шлифовальные станки для клапанов, и какой-то чувак построил один. Мне понравилась концепция, и у меня были детали. Вот его видео.
Я взял очень изрытый клапан и заземлил его.. да, это заняло около 3 минут.
Затем, чтобы убедиться, что угол находится на деньгах, я притер клапан к седлу в головке 3-й рисунок. . Для меня достаточно. У меня пробег более 100 000 км намного хуже.
deerwhacker444
Снайпер
- #2
Мне нравится…
Catt57
Гуру Gill-Gun
- #3
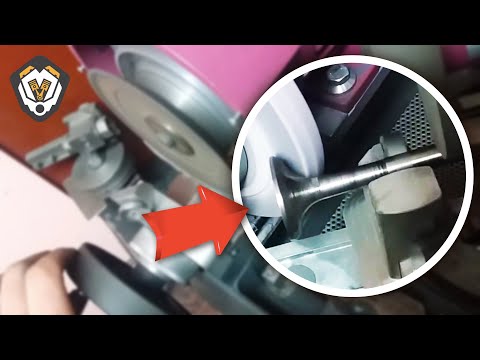
Свомпратт
Снайпер
- #4
Я установил тефлоновый блок на деревянную доску с 1 винтом, чтобы я мог изменить угол, поворачивая его.
Я посмотрел на диск резака дремелем, выровнял на нем седло клапана и вставил еще один винт через тефлон в дерево, чтобы закрепить его.
Затем я взял пробный клапан и посмотрел, на деньгах ли он.
Теперь седло бывшего в употреблении клапана будет утоплено.. и если вы посмотрите это видео выше и продвинетесь вперед на 1:30 секунды видео, вы увидите, где его клапан выходил на поверхность на внешнем и внутреннем краях седла.
Во время первого удара шлифовального круга.
Это поставило бы вас на деньги, чтобы быть в согласии с сиденьем. Или чертовски близко и достаточно близко, чтобы работать.
Так действовали мои клапаны, когда я начал шлифовать их на этом грубом инструменте.
Я заземлил их все и притер 2 клапана, и это выглядит великолепно.
Единственная проблема заключается в том, что диск малого диаметра позволит моему тефлоновому блоку работать только с клапанами 1,5 дюйма или 1,60 дюйма в текущем завинченном положении. Впускные клапаны 1,94 дюйма мне нужно будет переместить и отрегулировать.
Но эти впускные клапаны не имеют ямок и будут притерты как есть
Притирка не требуется
Gunbuffer
Снайпер
- #5
Вместо этих отрезных кругов я бы использовал насадку для барабанного шлифования. Они плохо переносят боковое давление, как я уверен, вы знаете. они легко отклоняются и взрываются
пара советов; используйте HD-диски, они толще обычных и складывайте их по 2-3 штуки, при условии, что на крепежном винте достаточно резьбы. это поможет укрепить его
Свомпратт
Снайпер
- #6
Я слегка надавил на диск, когда он вращался на высокой скорости, а моя дрель вращала клапан в другом направлении.
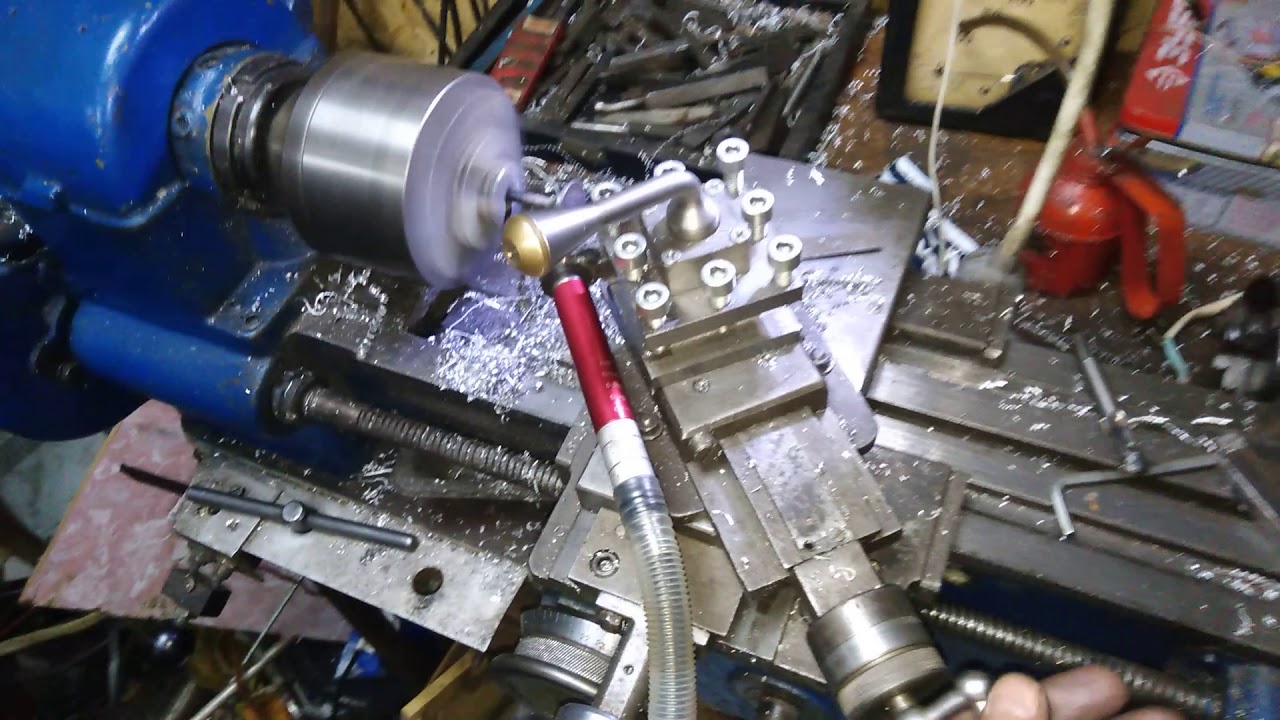
Поэтому Притирка клапана заняла 3 минуты, а не несколько секунд, как на видео.
Но мои клапаны были изъедены довольно глубоко.
Мой клапан соприкасался с диском в середине, а не на внешнем крае, так что там точно меньше прогибается.
доктор
Снайпер
- #7
Теперь используйте эту установку для работы с 3-угловым или 5-угловым клапаном, и я буду впечатлен! Просто шучу. Это на самом деле чертовски круто. Парень на видео выглядел так, будто у него за шлифовальным диском был какой-то покровитель, чтобы сделать его жестче.Свомпратт сказал:
Ты прав. В итоге я их удвоил. Я мог видеть, что он едва прогибается с 1 диском, а затем я добавил еще один.
Я слегка надавил на диск, когда он вращался на высокой скорости, а моя дрель вращала клапан в другом направлении.![]()
Поэтому Притирка клапана заняла 3 минуты, а не несколько секунд, как на видео.Но мои клапаны были сильно изъедены.
Мой клапан соприкасался с диском в середине, а не на внешнем крае, так что там точно меньше прогибается.Нажмите, чтобы развернуть…
Свомпратт
Снайпер
- #8

С другой стороны, я взял заводские клапаны GM в маленьком блоке Chevy и заводские клапаны и просто притер их без обрезки клапана или седла, и пробежал середину 11 на 1/4 мили без добавления мощности.
Народная мастерская в Нормане сделала для меня 5 угловых клапанов на некоторых головках 601, это головки 305 HO.
Затем я портировал головки и удалял все углы, кроме двух, и запускал 11-е на насосе с октановым числом 91 с двигателями 355 дюймов. Никаких усилителей мощности.
, возвращались за другими головками, потому что головки 305 не работали
Он хотел знать, что я сделал с ними после того, как они вышли из магазина
Однажды я пригласил его на обед и сказал ему… Я предупредил его, что ему не понравится то, что я собираюсь ему сказать.
он был полностью посвящен трубке Вентури на выпускном отверстии. . и, играя со стендом для измерения потока, вы обнаружите много воздуха в форме трубки Вентури.
Я сказал ему, что вынул трубку Вентури из выпускного отверстия и оставил 2 угла.
Он покачал головой, а затем сказал: Ну, конечно, получилось. Автомобиль разогнался до 117 миль в час на 1/4. Это был лучший MPH.
Эти камеры 305HO начинались с 53,5 куб. см, а после снятия кожуха я получил 61,5 куб. Удаление большого количества металла.
Вы можете оставить его в районе 57 куб. см с заводскими клапанами 1,84-1,50.. в этот клапан были вставлены 1,94-дюймовые клапаны. двигатель видит
Вы должны прибегнуть к испытанию своих вещей в реальных условиях
Как мы знаем
Карбюраторы Edelbrock Carter AFB LS тюнинг.
- Свомпратт
- Редукторы
- Ответы
- 1
- просмотров
Свомпратт
Делиться:Фейсбук Твиттер Реддит Пинтерест Тамблер WhatsApp Электронная почта Делиться Связь
Верх Низ
Art’s Automotive Machine Shop
Art’s Automotive Machine Shop Services
Как правило, мы не занимаемся самостоятельными машинными работами для других магазинов или частных лиц. Мы создали наш механический цех в первую очередь для контроля затрат, времени ремонта и качества машинной обработки автомобилей, которые мы ремонтируем здесь, в Art’s. Мы выполним нестандартный тормозной диск, маховик, восстановление поверхности головки или испытание под давлением, но в большинстве случаев мы рекомендуем вам доверить свое машинное дело компании Hasselgren Engineering. Их возможности намного превосходят наши, и они, похоже, готовы выполнять несколько небольших работ между высокотехнологичными гоночными моторами.
Капитальный ремонт двигателя
К счастью или к сожалению, в зависимости от того, как на это посмотреть, большинство японских автомобилей настолько стары и изношены к моменту, когда двигатель нуждается в восстановлении, что стоимость автомобиля не покрывает стоимость полная перестройка. В большинстве случаев мы делаем только ремонт двигателя, а не полную переборку. Однако время от времени мы находим владельца, который любит свою машину и хочет, чтобы двигатель работал как новый. Теперь мы предлагаем почти все операции по восстановлению двигателя, необходимые для восстановления его состояния, как у нового, собственными силами.
Преимущество ремонта здесь, по сравнению с доставкой восстановленного двигателя к нам, заключается в том, что мы контролируем все аспекты качества. Мы можем быть уверены, что вместо обычного чугуна используются азотированные кольца высшего качества. Мы можем убедиться, что отделка поверхности не только соответствует требованиям производителей, но и превосходит их. Мы можем загерметизировать двигатель способом, который, как мы знаем, будет работать. Мы можем потратить столько времени, сколько необходимо, чтобы получить зазоры такими, какими они были, когда двигатель был новым.
Есть производители двигателей, которые отлично работают. Многие даже лучше нас. К сожалению, есть также несколько очень плохих производителей двигателей, некоторые из которых имеют крупные контракты на восстановление оригинального оборудования. С некоторыми марками вы даже не можете доверять дорогому двигателю, купленному у дилера. Когда мы делаем это сами, мы, по крайней мере, точно знаем, на что ручаемся.
Шлифовка седла клапана
Седла клапана представляют собой стальные вставки, запрессованные в алюминиевую головку. Угол контакта седла с клапаном уменьшен до 45 градусов. Ширина и положение контакта на клапане обычно регулируются с помощью 60-градусной «горловой» фрезы и 30-градусной «верхней» фрезы. Некоторые автомобили используют разные углы; мы всегда следуем оригинальным спецификациям производителя при шлифовке сидений. Внимание, уделяемое обрезке сиденья, влияет на то, как долго продлится восстановление. Наш механик Сандор имеет необходимый опыт и приверженность качеству, чтобы гарантировать, что ваша восстановленная головка будет работать так же, как когда она была новой.
Шлифовка клапана
Мы берем 0,1 рабочего часа за шлифовку клапана. Большинство новых клапанов стоят от 15 до 35 долларов каждый. На 16-клапанной головке шлифовка вместо замены может сэкономить до 475 долларов. По-прежнему имеет смысл шлифовать, когда это возможно. Многие клапаны в новых автомобилях крошечные и не имеют большого запаса хода. Мы шлифуем клапаны только тогда, когда производитель говорит, что это приемлемая процедура, и мы всегда тщательно проверяем клапан на предмет износа перед механической обработкой и соблюдаем минимальные требования производителя. Для тех из вас, кто смотрит на картинку и думает: «Вау, это похоже на старую шлифовальную машину для клапанов!», вы правы. Но старое не равно плохое. Это очень хорошо сконструированное устройство Snap On, которое сегодня работает так же хорошо, как и тогда, когда оно было новым. У нас также есть редукционные цанги, и мы можем обрабатывать клапаны со штоками толщиной до 4 мм.
Фрезерование головки блока цилиндров
Это фрезерный станок Kwik-Way 855-5. Я потратил около 40 часов на восстановление и преобразование во фрезу. Направляющие были заново обработаны в Worrell Industries прямо здесь, в Беркли, а шлифовальный камень был заменен фрезерной головкой Jamison. Двигатель траверсы был заменен двигателем постоянного тока с регулируемой скоростью, чтобы снизить скорость подачи до едва заметного проскальзывания. Эта машина теперь производит *очень* гладкую поверхность 15 RA на алюминиевых головках, используя вставку CBN и WD40 в качестве смазки. Hasselgren Racing провела тест на шероховатость поверхности, так как это единственная механическая мастерская в этом районе, у которой есть пролифометр. Недавно мы перешли на вставку из поликристаллического алмаза и высокоэффективный спрей для обработки поверхностей Goodson. Наша поверхность выглядит более гладкой, чем когда-либо, но мы еще не тестировали еще один образец нашей работы. Тем не менее, 15 RA на 5 RA лучше, чем самая низкая характеристика чистоты поверхности, с которой мы сталкивались для двигателей с прокладками MLS до сих пор, поэтому насколько она лучше после нашего перехода на PCD, на самом деле не имеет значения.
Расточка цилиндра
Если износ стенки цилиндра выходит за пределы допусков изготовителя, ее необходимо расточить с запасом для использования с поршнями увеличенного размера. Растачивание должно сопровождаться несколькими этапами хонингования, чтобы создать поверхность, которая будет удерживать масло для смазки и обеспечивать хорошее уплотнение. Когда это возможно, мы будем следовать процедуре производителя для растачивания и хонингования. Например, для двигателя 5SFE Toyota рекомендует расточку на 0,0008 дюйма (чуть меньше 0,001 дюйма) ниже конечного размера. Затем с помощью жесткого хона с зернистостью 400 доведите отверстие до нужного размера. Однако часто нет опубликованной процедуры. Когда у нас нет доступа к процедуре, которую мы расточили до 0,002 дюйма под готовый размер, удалите дополнительный 0,0015 дюйма с помощью точилки Sunnen с зернистостью 280, затем удалите последний 0,0005 дюйма с помощью точилки Sunnen с зернистостью 400, чтобы создать плато. заканчивать. Мы следуем этому с нейлоновым ультрафинишным мягким хонингованием против часовой стрелки, чтобы удалить сложенный или порванный металл, оставшийся в процессе хонингования. После завершения растачивания и хонингования стенки цилиндра тщательно очищают горячей мыльной водой.
Настил блоков цилиндров
Иногда поверхность блока цилиндров необходимо обновить. Деформация деки чаще встречается на Subaru и других алюминиевых блоках с втулками, но может случиться с любым типом блока. Мы можем обрабатывать большинство 4-цилиндровых и рядных 6-цилиндровых блоков, но в настоящее время мы не можем обрабатывать блоки V6 и V8.
Шлифовка головки цилиндров
**УСТАРЕВШАЯ ПРОЦЕДУРА**
Одно время мы использовали плоскошлифовальный станок для обработки головок цилиндров. Для плоской шлифовки цилиндра используется лента из карбида кремния с зернистостью 80. Поскольку это «сухая» машина без циркулирующей охлаждающей жидкости/смазки, мы покрываем ремень средством Goodson’s Grind Aid. Это улучшило качество поверхности, которое мы получаем на этой машине. Однако во многих случаях используются прокладки MLS (многослойная сталь), которые требуют очень гладкой поверхности. Какое-то время мы притирали, чтобы получить гладкую поверхность, как у оригинала, но это было очень трудоемко. Теперь, когда у нас есть головная фреза со вставками PCD и CBN, мы редко используем эту машину для чего-либо, кроме шлифовки выпускных коллекторов.
Головка блока цилиндров Притирка
**УСТАРЕВШАЯ ПРОЦЕДУРА**
Двигатели с прокладками MLS требуют покрытия с очень низким среднеквадратичным значением для надлежащей герметизации. Поскольку зернистость 80 является самой тонкой лентой, изготавливаемой в настоящее время для ленточных шлифовальных станков, мы используем гранитную поверочную плиту (прецизионно обработанная гранитная плита, отшлифованная до идеально плоской толщины 0,00001″, изначально предназначенная в качестве основы для измерения). Мы наносим притирочный состав с зернистостью 400, затем 800, а затем 1200 на пластину, а затем перемещаем головку блока цилиндров в виде восьмерки, пока поверхность не станет очень гладкой. Изначально мы были обеспокоены тем, что этот метод создаст выпуклую поверхность на головке блока цилиндров. Тем не менее, мы не обнаружили заметного изменения плоскостности головок цилиндров, которое мы наблюдали до сих пор, и на самой пластине не наблюдается заметного износа. Эта техника физически утомительна, но дает красивый результат.
Замена направляющей клапана
Если расстояние между направляющей и штоком клапана слишком велико, это вызывает две проблемы: во-первых, седло клапана не может быть отрезано по центру, а во-вторых, двигатель потребляет больше масла, чем необходимо. О состоянии направляющих клапанов нельзя узнать, пока ГБЦ не будет снята с автомобиля и не будут измерены направляющие. Это означает, что когда мы обнаруживаем изношенные направляющие, нам необходимо позвонить вам для получения дополнительного разрешения на замену направляющих. Изношенные выпускные направляющие встречаются чаще, чем изношенные впускные, потому что выпускные клапаны нагреваются намного сильнее, чем впускные. Чтобы снять направляющие, нагреваем головку до 200 градусов (F), затем выбиваем направляющие с помощью отвертки, приводимой в действие пневматическим молотком. Чтобы установить направляющие, мы повторно нагреваем и охлаждаем направляющие клапанов перед тем, как вставить их обратно.
Расширение направляющей клапана
Входит в стоимость замены направляющей клапана. Размер новой направляющей клапана должен соответствовать указанному изготовителем масляному зазору. Это делается путем измерения штока клапана, добавления характеристик масляного зазора и использования развертки нужного размера для обрезания направляющей по размеру.
Пенетрантная краска Проверка наличия трещин
Первым шагом является очистка головки блока цилиндров. Необходимо соблюдать осторожность, чтобы не покрыть трещины проволочной щеткой. Алюминий — довольно мягкий металл, и энергичная очистка щеткой может фактически скрыть трещины, делая их незаметными для красителя. Затем на проверяемый участок распыляют проникающую краску и дают впитаться в течение 5 минут или около того. После замачивания весь краситель вытирается салфеткой. После того, как головка очищена, на нее распыляется проявитель. Трещины будут отображаться красными линиями. Простое выполнение движений пенетранта не гарантирует, что вы найдете трещину. Ключом к успеху является очень тщательный осмотр. Краска — это всего лишь инструмент, который немного облегчает поиск трещин. Реальный способ обнаружения трещин – это тщательность и опыт человека, проводящего тест, а не сам тест.
Теперь, когда у нас есть прибор для проверки давления головки блока цилиндров, мы почти всегда проверяем давление вместо проверки красителя. Тестер давления обнаружит трещины или пористость под седлами клапанов, которые было бы невозможно обнаружить с помощью красителя.
Краска все же пригодится. Это удобно для проверки пластиковых шестерен распредвала, установленных на Subaru 2.5 DOHC EJ25 1996-1999 годов, а также других деталей, кроме головок цилиндров.
Испытание под давлением головки блока цилиндров
Испытание под давлением является лучшим методом проверки на наличие трещин, поскольку трещины в невидимых областях все еще могут быть обнаружены, например, под седлом клапана или на полпути к отверстию под болт в головке. Это тестер давления Axe, который мы купили подержанным. Для каждой новой головки не требуется специальный набор пластин. Он использует 20 универсальных палубных пластин и универсальных пластин для блокировки портов различных размеров. Он охватывает 95% процентов всех голов и 100% голов мы ремонтируем здесь у Арта. Чтобы проверить наличие трещин, мы блокируем все порты системы охлаждения, затем создаем давление в водяной рубашке до 40 фунтов на квадратный дюйм (примерно в 3 раза больше нормального давления в системе охлаждения). Затем мы погружаем головку в нагретую воду, чтобы довести головку до нормальной рабочей температуры и облегчить обнаружение утечек по следу пузырьков.
Шлифовальный станок с маховиком
Компания Art купила этот станок с маховиком в 1990-х годах, и он более чем себя окупил. Покупка дорогой одноразовой машины может быть немного рискованной для независимого магазина. Тем не менее, возможность обрабатывать маховик на месте при каждой работе со сцеплением позволила нам предложить более качественную работу со сцеплением за один день, не выезжая в ремонтную мастерскую и обратно и не беспокоясь о том, сделает ли слесарь маховик за короткое время. время.
Мы только что перешли с камней из карбида кремния на алмазные фрезы и очень довольны результатами. Алмазный отрезной круг режет маховик намного быстрее и оставляет на маховике привлекательный острый выступ и очень красивую поверхность.
Тормозной диск и шлифовка барабана
Мы рекомендуем шлифовать тормозной диск при каждой замене колодок. Некоторые производители (например, Subaru) в настоящее время рекомендуют повторно использовать роторы как есть или заменять их. Их беспокоит то, что многие магазины не смогут произвести подходящую отделку поверхности.
На нашем токарном станке Hunter мы можем обрабатывать роторы с шероховатостью более 60 микродюймов (согласно измерению с помощью измерителя шероховатости поверхности). Затем мы используем шлифовальный диск с зернистостью 150, чтобы нанести перекрестную штриховку и улучшить отделку примерно до 45 микродюймов. Это сопоставимо с отделкой новых высококачественных тормозных дисков и намного лучше, чем у некоторых более дешевых брендов.
Прессование втулок и подшипников
Для ремонта рычагов подвески и других компонентов подвески доступно множество втулок. Наши клиенты могут сэкономить много денег, ремонтируя детали подвески, а не заменяя их. Рычаги, изображенные справа, новые стоили 262 доллара, а втулки стоили всего 26 долларов, что составляет одну десятую стоимости. Возможность выполнять этот тип работы на дому означает, что мы можем получать и сдавать автомобили в один и тот же день, а не полагаться на милость поставщика субаренды. Мы также прессуем собственные подшипники и шестерни.
Сварочный ремонт может сэкономить много денег по сравнению с покупкой новых деталей, а в некоторых случаях прочность детали может быть увеличена по сравнению с оригиналом. Теперь у нас есть сварочный аппарат Lincoln Electric Precision TIG 375, и мы предлагаем больше сварки алюминия, включая ремонт головки блока цилиндров. Сварка также очень удобна для чрезвычайных ситуаций в пятницу вечером; треснувший корпус термостата, из-за которого клиент может остаться без машины на выходные, можно в один миг починить с помощью сварочного аппарата TIG на месте.
Окси/ацетилен
Мы редко свариваем кислородно-ацетиленовую сварку. Мы в основном используем его для нагрева и резки.
GTAW (TIG)
Сварка TIG аналогична кислородно-ацетиленовой сварке тем, что горелку держат одной рукой, а присадку добавляют другой. Тепло может быть добавлено без добавления без добавления наполнителя. Если вы заметили плохой сплав в секции, которую вы сварили, вы можете просто вернуться и переплавить секцию. Силу тока можно регулировать с помощью ножного управления, чтобы компенсировать накопление тепла в заготовке во время сварки. Можно использовать любой наполнительный материал без необходимости замены катушек или вкладышей.
GMAW (MIG)
Мы используем MIG для сварки стали. Это самый простой и быстрый процесс, с его помощью получаются более мелкие и привлекательные шарики, чем у оксиацетилена.
Это изображение гибкого соединения, которое мы приварили к каталитическому нейтрализатору Camry 49 State. Старый гибкий шарнир треснул и начал течь. Новый преобразователь стоил 1100 долларов, только за деталь! Поскольку остальная часть трубы была в относительно хорошем состоянии, мы смогли приварить гибкое соединение вторичного рынка примерно за треть стоимости новой детали. Для этой работы мы использовали сварочный аппарат TIG, так как эта область выхлопа подвергается высоким нагрузкам, и мы хотели быть уверены, что наша работа выдержит испытание временем. Сварочный аппарат TIG использует высокочастотный импульс для запуска дуги и иногда может повредить чувствительное электронное оборудование (хотя это очень редко). Поскольку этот автомобиль загружен электронными блоками управления, мы прикрепили гибкое соединение на место с помощью MIG, а затем приварили автомобиль к TIG.
Это чугунный выпускной коллектор, треснувший в нескольких местах. Я использую сварочный аппарат TIG и присадочную проволоку из чистого никеля для сварки чугуна. Чугун — сложный материал для сварки, потому что он очень жесткий и скорее трескается, чем изгибается.