Самодельный токарный станок из двигателя от стиральной машины

Самый простой самодельный токарный станок по дереву, сделанный из двигателя от стиральной машины.
Токарный станок по дереву, можно собрать практически из подручных материалов, а двигатель подойдёт от старой стиральной машины.
Небольшой совет: лучше использовать двигатель от стиральной машины автомат, он более мощный и оборотистый чем моторы от советских стиральных машин.
В этой конструкции станка использован шкив с тремя ручейками, что позволяет переключать скорости в зависимости от потребностей, всего у станка три скорости.
Понадобятся материалы:
- — электродвигатель от стиральной машины;
- — ремень и пара шковов;
- — уголок;
- — швеллер;
- — кусок круглой трубы;
- — резьбовые шпильки;
- — болты и гайки;
- — кругляк;
- — листовая сталь;
- — подшипники (радиальные и упорные).
Процесс изготовления станка подробно показан на этих фото:
Сначала, изготовил крепеж для двигателя, использовал — уголок и стальные пластины. Крепежный кронштейн нужен для того, чтобы шарнирно подвесить двигатель на раму, это позволит быстро перекидывать ремень и тем самым переключать скорости.
Крепление готово, теперь можно изготовить станину, нам понадобится два куска швеллера.
Швеллеры нужно сварить друг с другом так, чтобы между ними свободно ездила задняя бабка и подручник. Для получения нужных зазоров, проложил обычную бумагу, а затем сварил швеллеры между собой при помощи стальных пластин.
Двигатель будет крепиться к станине шарнирно, через резьбовую ось, а ось вращается на подшипниках. Под подшипники делаем хомуты, для их изготовления использовал куски круглой трубы. Привариваем к хомутам уши для стягивания их болтами с гайками, ну а также привариваем сами хомуты к станине.
Сделал подручник.
Изготавливаем заднюю и переднюю бабку. Для изготовления осей и прочих деталей для бабок не обошлось без использования токарного станка, но такие детали можно заказать у токаря. Все оси вращаются на радиальных и упорных подшипниках, что значительно продлевает ресурс работы станка.
Покраска деталей станка и сборка.
В результате, получился вот такой простой самодельный станок по дереву. С его помощью можно вытачивать деревянные детали: — рукоятки для ручного инструмента, ножки для стульев и прочие декоративные элементы.
Также весь процесс изготовления токарного станка можно посмотреть в этом видео:
Автор самоделки: TeraFox.
sam-stroitel.com
Супер дешевый гриндер из двигателя от стиральной машины
Сегодня мы, вместе с автором YouTube канала «TeraFox», сделаем наиполезнейший станок в мастерскую с учетом минимальных затрат.

Профильная труба 20 на 40 послужит фундаментом нашего проекта. Разметив и нарезав трубу, складываем заготовки в стопочку и пока убираем в сторону.
И еще несколько отрезков проф трубы, которые пока подождут своей очереди.

Те части, которые нарезали первыми, раскладываем именно так, как нам придется их сварить. Единственное, пока не трогаем маленькой отрезок с отверстием, потому как в процессе станет понятно где его расположить лучше всего.
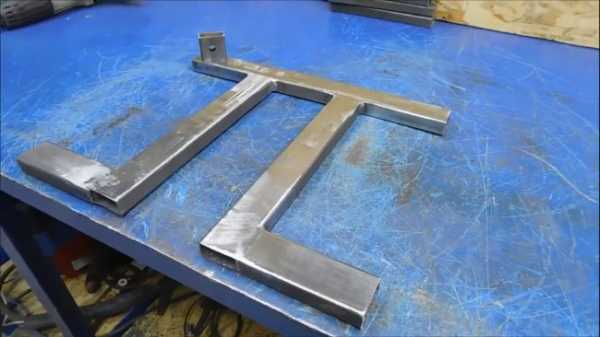
Ну а следом у нас вторая партия отрезков, которую тоже необходимо сварить.
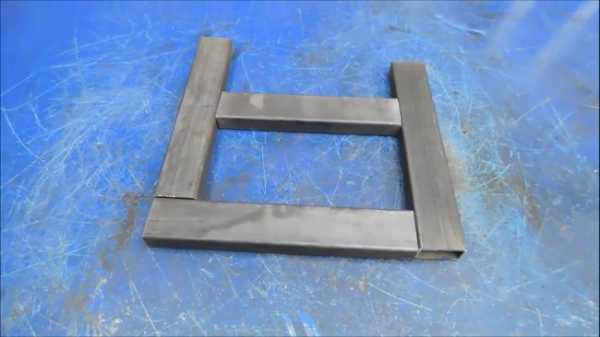
И вот, 2 части будущей конструкции уже готовы.

Далее необходимо сделать несколько отверстий для будущих креплений.
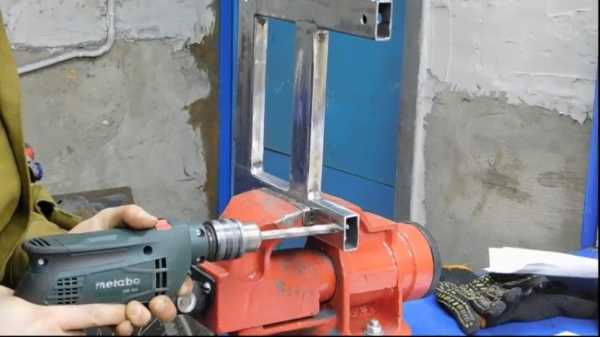
Теперь максимально точно под углом нужно приварить эти 2 элемента, в ход идут все магниты, имеющиеся в наличии.

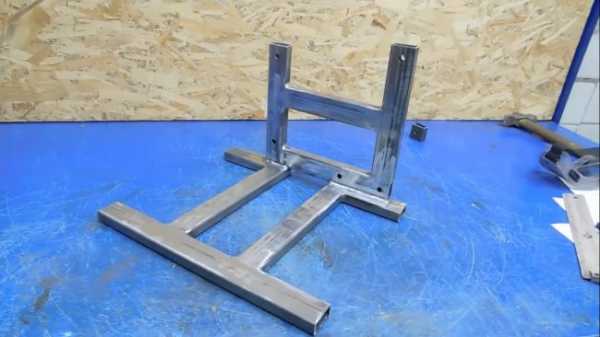
Далее нам потребуется 10-ая пластина. Размечаем чертилкой по металлу, точность при резке по выше в сравнении с маркером.
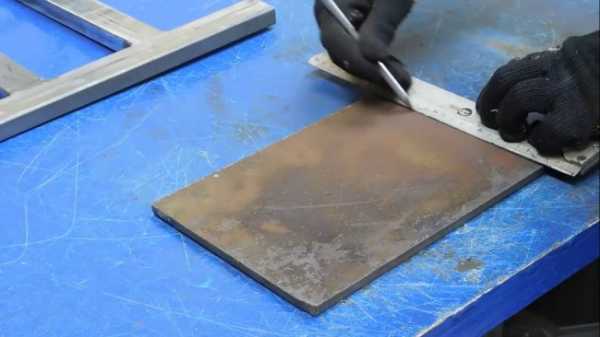
125-ой болгаркой делаем канавки, ей проще вести по линии разметки. Ну а 180-ой достается более тяжелая работа – сделать основной срез.
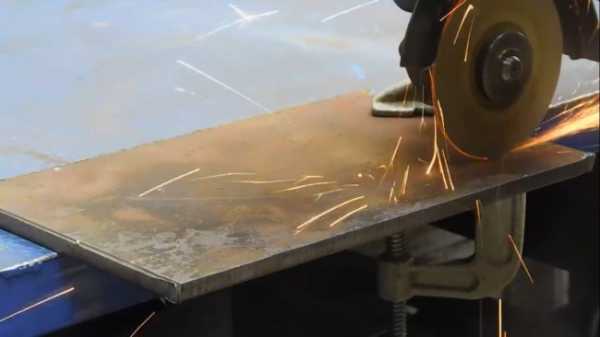
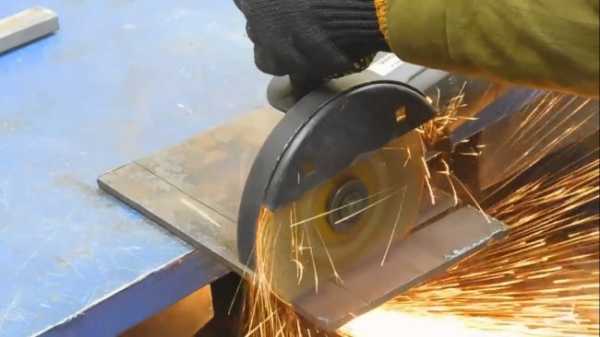
Затем разметка под вырез в пластине и аккуратное его воплощение.
Не на все 100% конечно, поэтому придется поработать напильником.
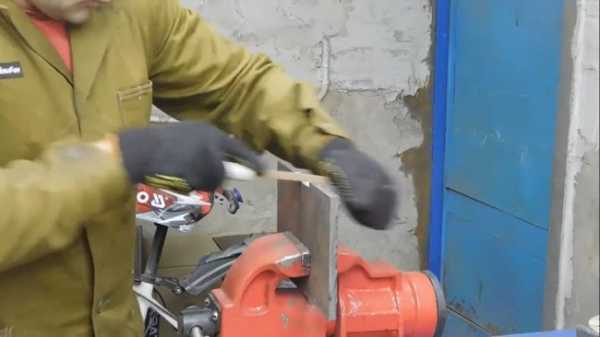
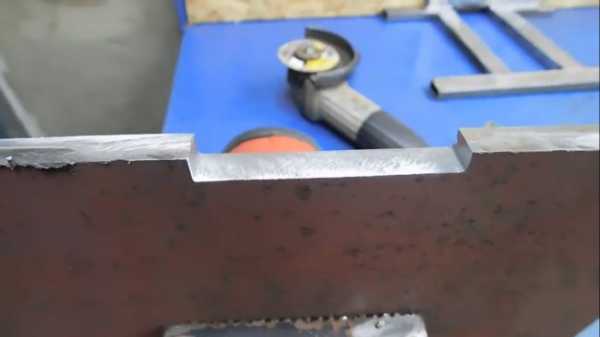
Далее следующая деталь.
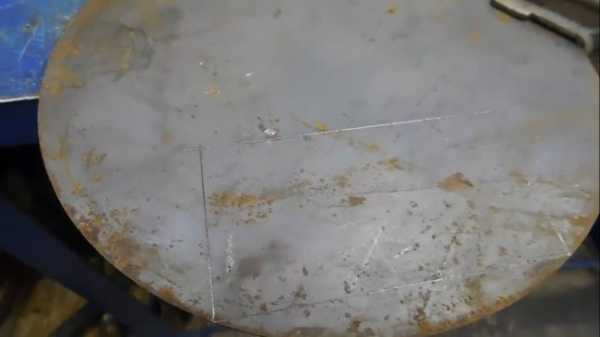
Толщина металла тут уже поменьше – 6мм. Вырезаем еще 1 прямоугольник размерами поменьше.
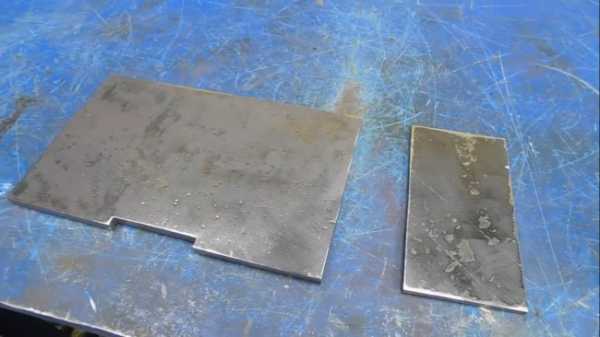
Опору под столешницу будем делать из 2-ух отрезков уголка, потому как прилегание 2-ух плоскостей к стенкам профильной трубы гарантирует четкий угол.
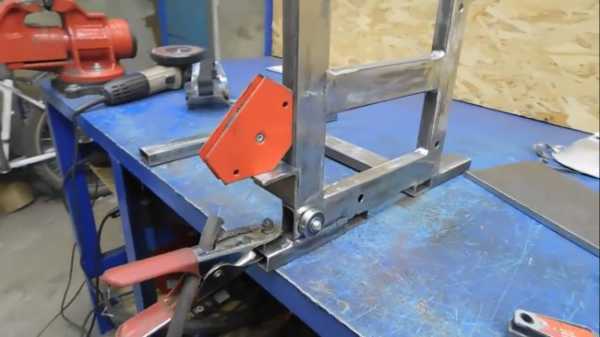
Упорная пластина расположена в одной плоскости с трубой, зафиксирована магнитами с обеих сторон, так чтобы наверняка, и прихвачена сваркой.
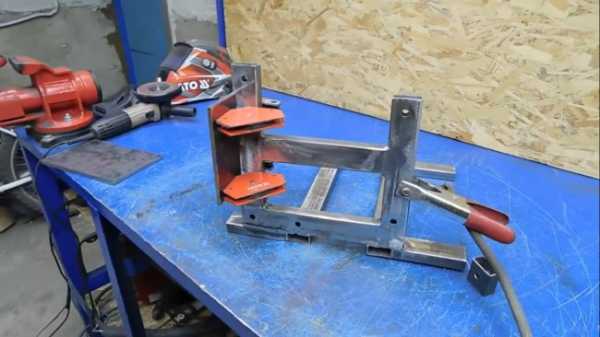
Теперь делаем 2 отверстия в столешнице, нарезаем резьбу.
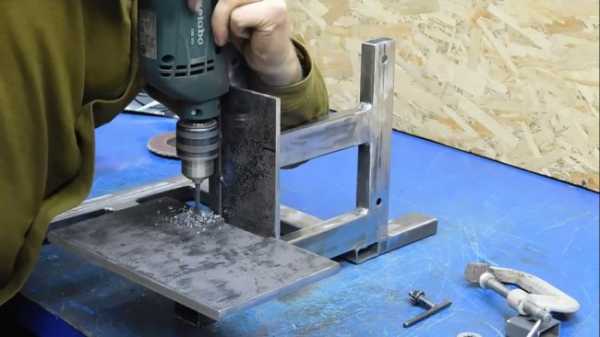

Плашкодержателем подобраться не вариант, пришлось использовать набор инструментов и вполне успешно. Столешница все это время также держалась на прихватках, что позволило точно просверлиться и нарезать резьбу. Болты на месте, в впоследствии их конечно подрежем.
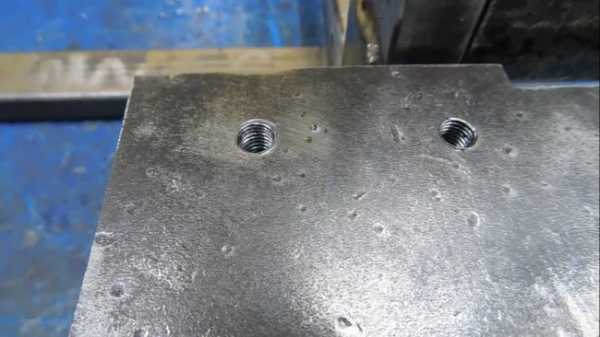
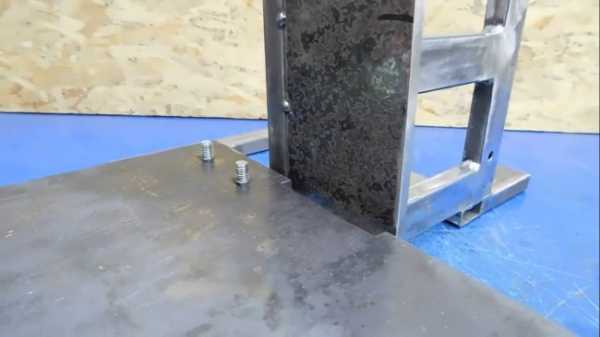
А вот и первая ошибка: отверстия расположены по центру, а подшипники, которые у автора были в наличии и должны были встать на это место, меньшего диаметра, нежели должны быть, поэтому отверстия нужно смещать.
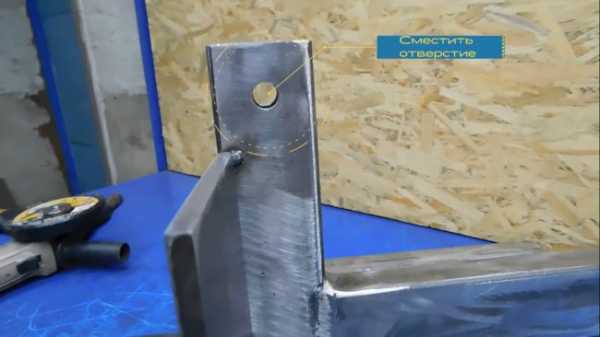
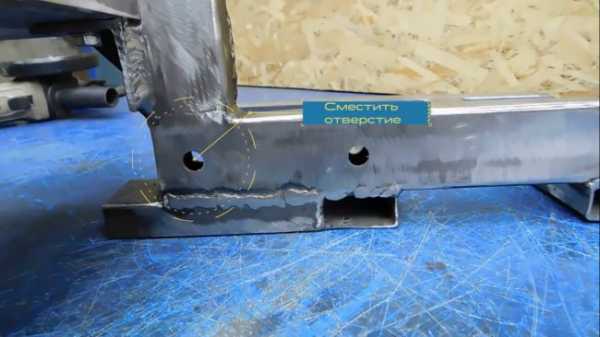
4 небольшие металлические подложки располагаем с внутренней стороны и завариваем отверстия по принципу электрозаклепки.
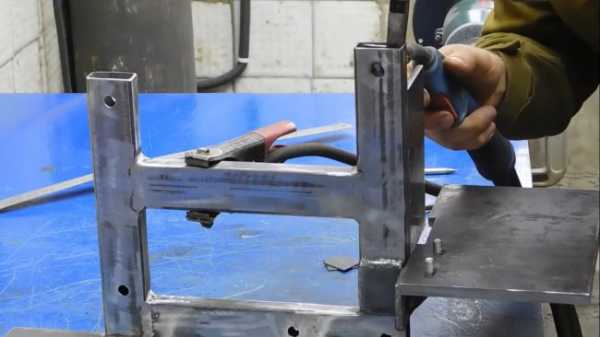
Вся работа по переделке заняла не так уж и много времени, так что ошибка, будем считать, незначительная. Далее необходимо набрать подшипники на шпильку и продеть через отверстия.
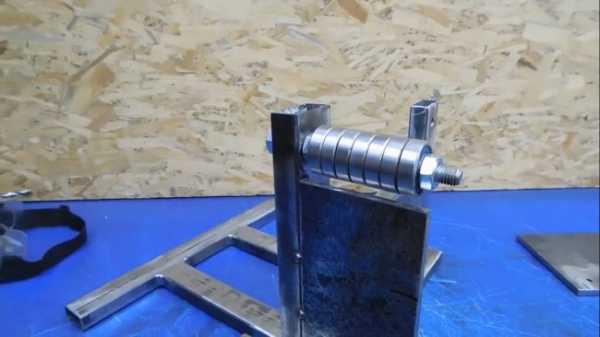
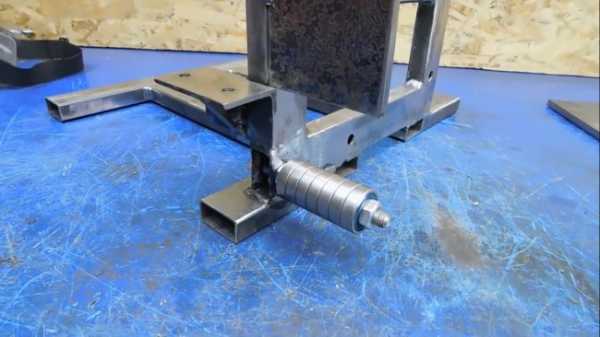
Автор использовал недорогие подшипники, так что пусть их количество никого не пугает. Зазор между упорной пластиной и линией подшипников около 3-ех миллиметров.
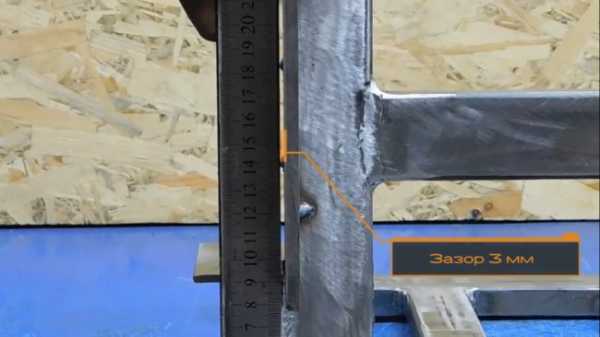
После того, как мы убедились в точности подгонки всех сопряженных элементов, пришло время приварить основательно пластину в стойке.
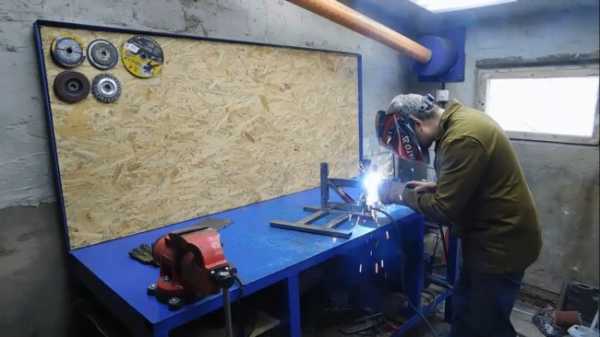
Теперь изготовим еще одну деталь, а точнее рычаг.
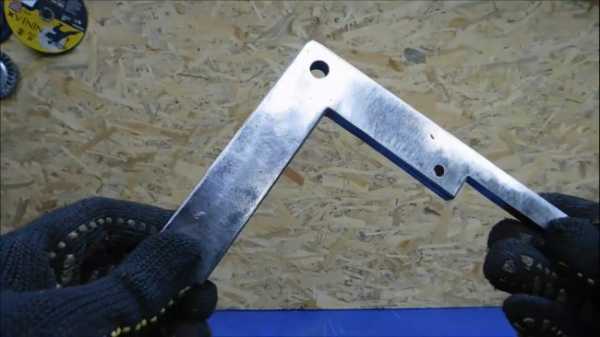
Болты, гайки и небольшая деталь с отверстием – это составные части натяжного механизма. Собираем воедино и свариваем их вместе.

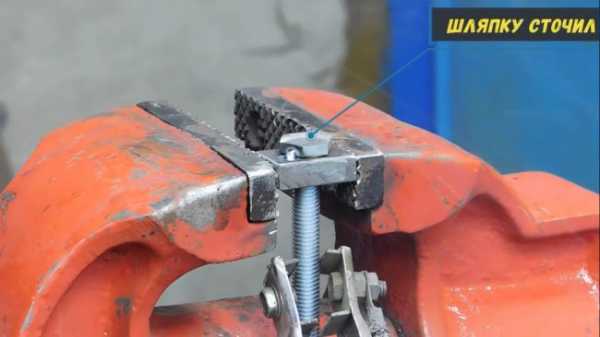
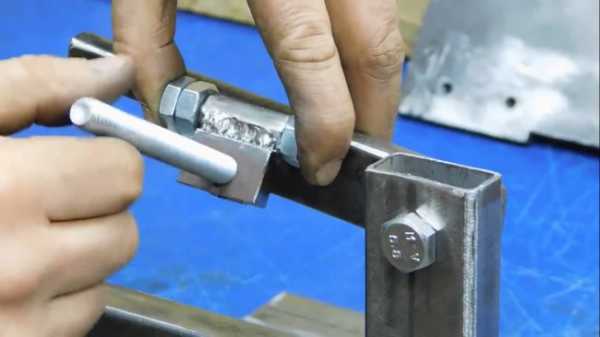
В рычаге отверстие с резьбой под болт с пружинкой.
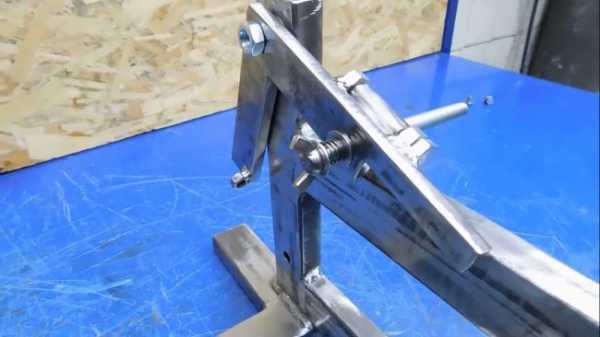
Принцип простой: вращением болта ось меняет угол наклона, таким образом и будет происходить регулировка ленты двигателя стиральной машины.

Данный двигатель от стиральной машины уже не советских времен, а более современный – коллекторного типа. Заявленная мощность 480Вт, 14000 оборотов в минуту.
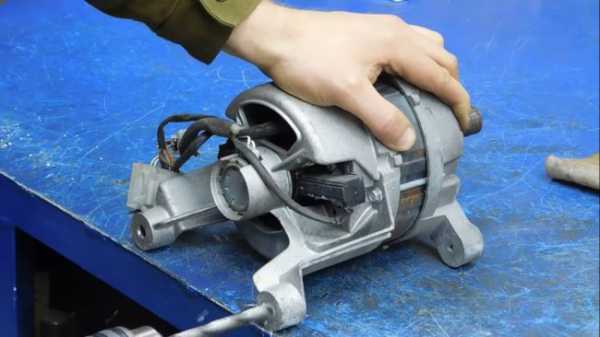
Автор впервые решил воспользоваться услугами лазерной резки, и для шкива заказал заготовки из 10-ой фанера. Качество отменное, по финансам совсем недорого.
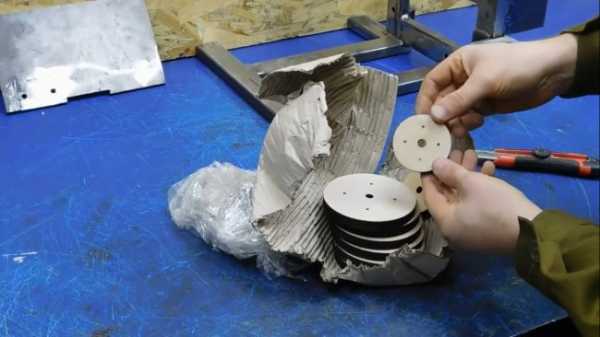
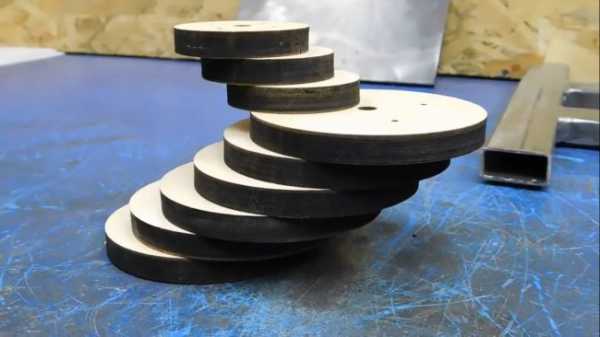
Как вы поняли, автор выбрал наипростейший путь, никаких обращений к токарю, посмотрим, что из этого получится. Отзывы по шкивам из фанеры в основном положительные. Осталось только склеить заготовки вместе и затянуть саморезами.
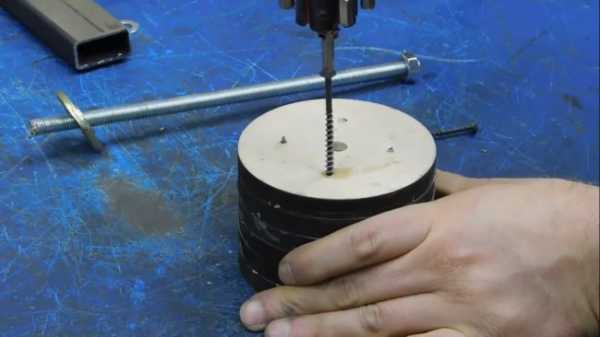
Теперь сверлим отверстие диаметром 20 мм.
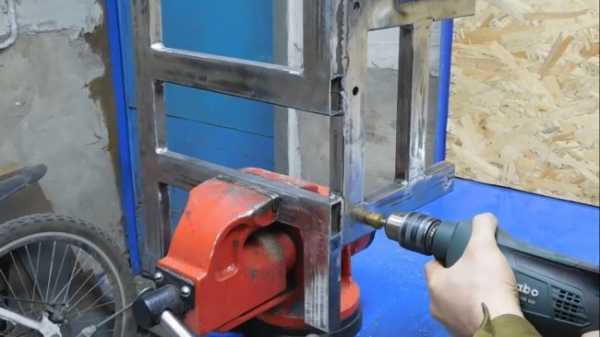
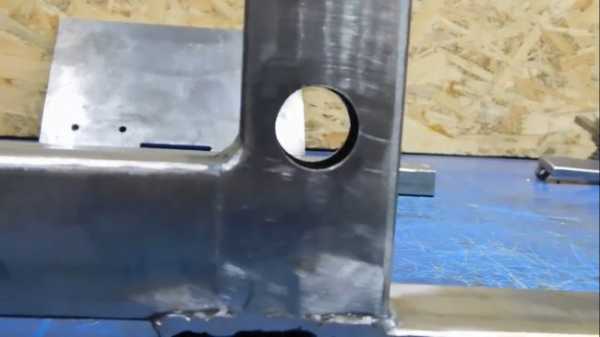
Также необходимо изготовить кольцо, которое послужит обоймой подшипника. Для фиксации сверлим отверстие и нарезаем резьбу под винт.

Подшипник сел довольно-таки плотно – то что нужно.
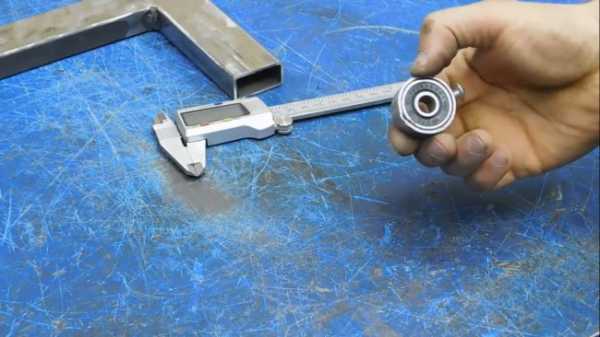
Перед сваркой подгоняем весь узел почти в сборе под отверстие для того, чтобы убедиться в беспрепятственном его вращении. Не забываем производить охлаждение сжатым воздухом, во избежание перегрева подшипника.
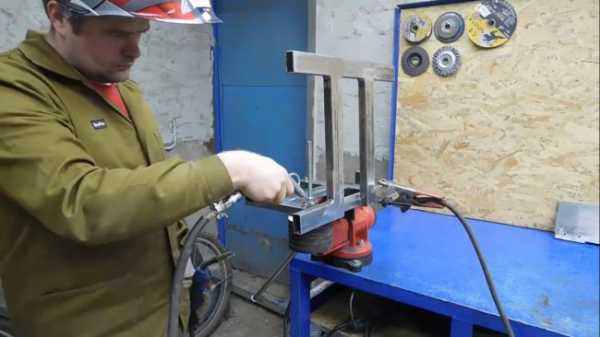
После можно одеть маленький шкив и затянуть гайкой. С этим узлом закончили, пришло время прикинуть, как встанет движок от стиралки и пора бы уже приварить маленькую стойку с отверстием под шпильку.
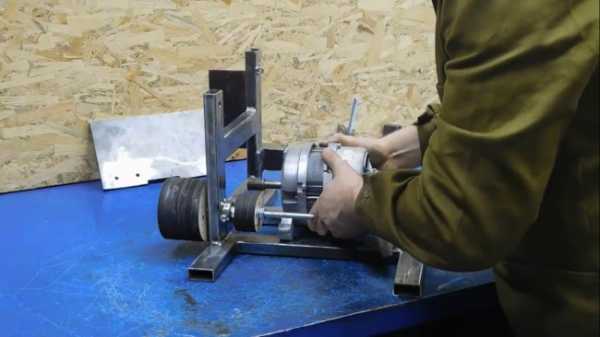
Из обычного болта и гайки, приваренной к шляпке, получается такой вот рым-болт.
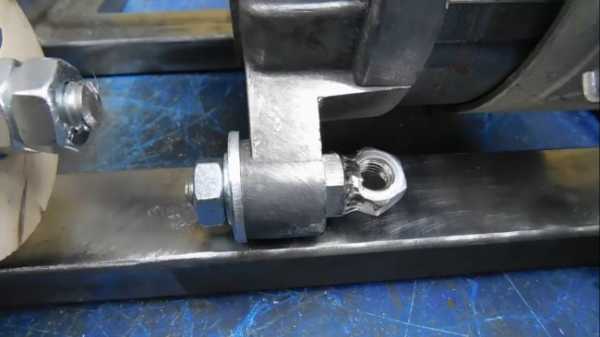
Ремень от стиральной машины автор подобрал на рынке. Последние 3 цифры обозначают его рабочую длину.
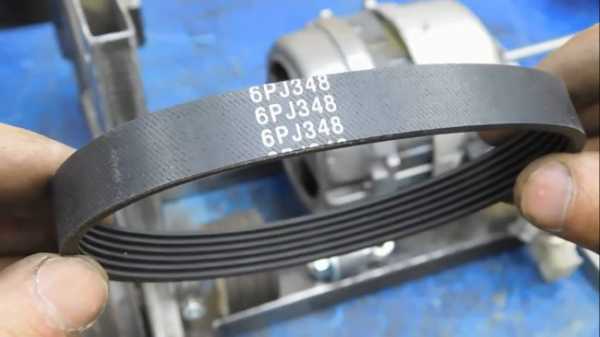
Закручиваем болт.
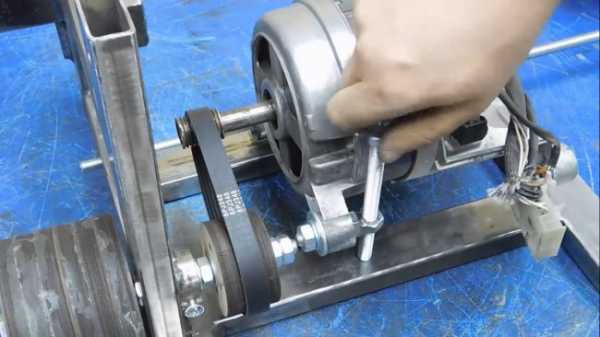
Таким образом происходит натяжение ремня. Кстати, канавки шкива вала двигателя стандартные, можно ставить любой коллекторный двигатель под этот ремень. Всего было использовано по 7 подшипников на каждой из 3-ёх шпилек и того 21 штука.
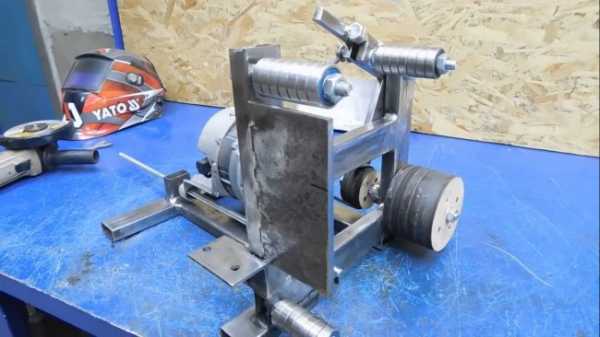
Возможно не самый лучший вариант, но автор собирает станок из того, что есть в наличии. Подключение коллекторного двигателя не составило большого труда. Визуально видно пару проводов, которые идут к щеткам, они-то нам и нужны. Теперь необходимо найти обмотку двигателя. Сопротивление 200 Ом, считанные секунды и обмотка найдена.
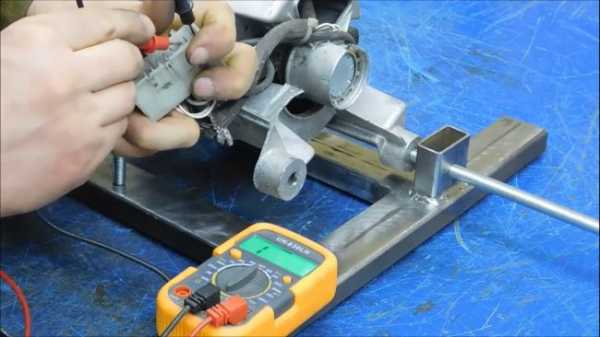
Для данного проекта автор приобрел вот такой регулятор мощности.
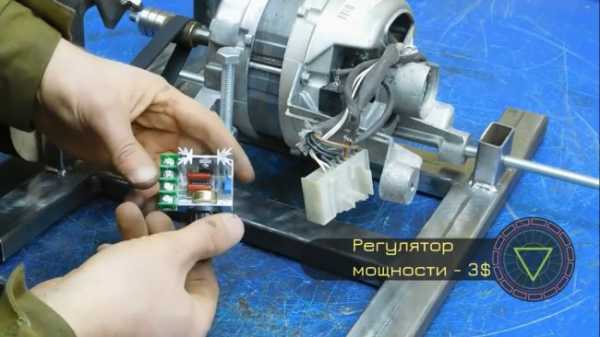
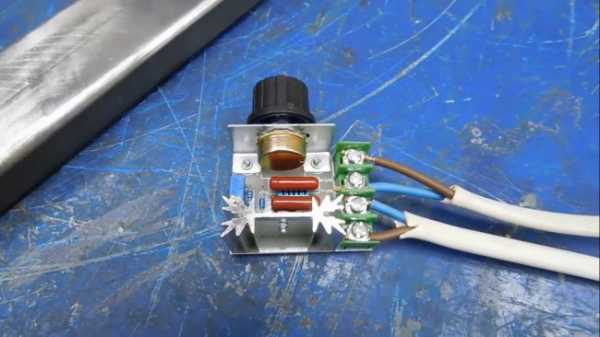
Двигатель работает.
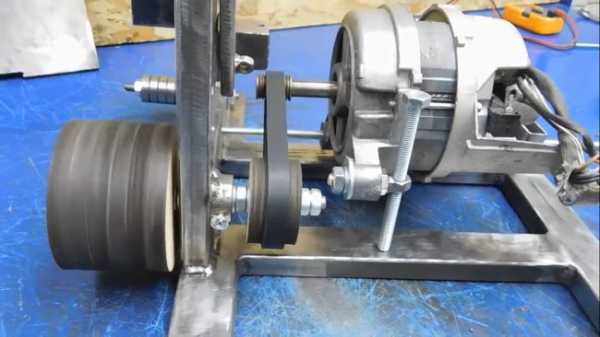
Шкив из фанеры требует обработки.
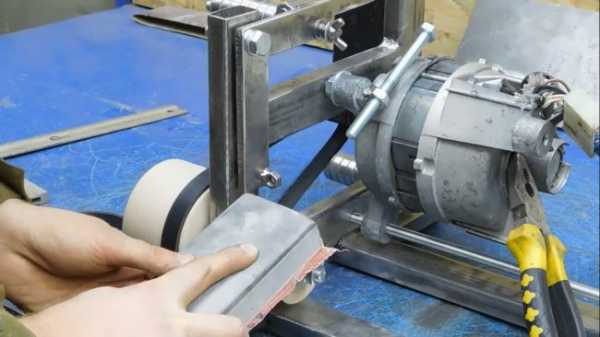

Далее устанавливаем пружину. Это обычная дверная пружина, точнее ее часть.
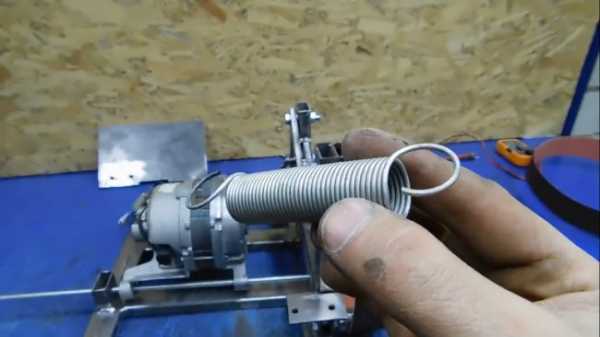
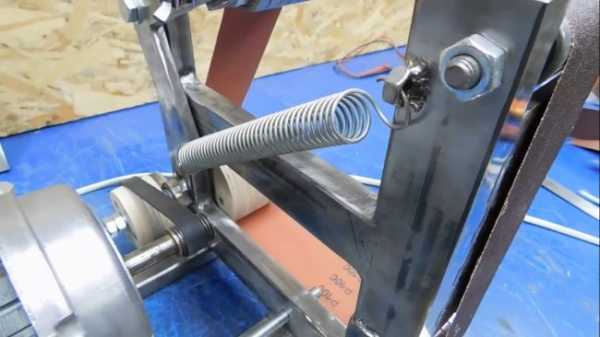
Один из вариантов придать бочкообразную форму натяжному ролику, это изолента и отрезок велосипедной камеры. Да, колхоз редкий, но жажда дешевых экспериментов никогда не оставляет.
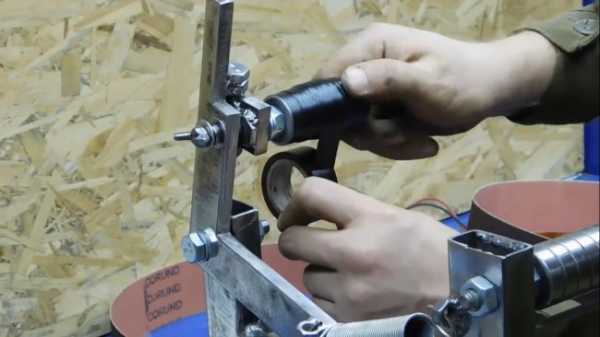
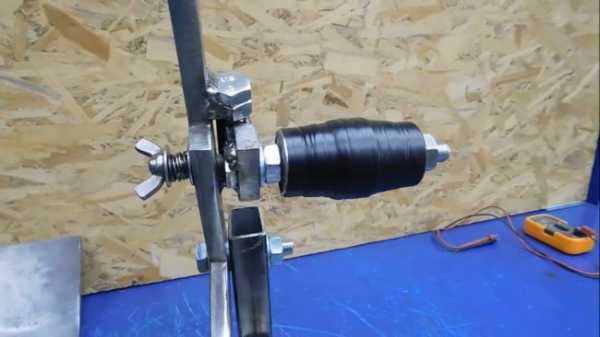
Но эксперимент не увенчался успехом, ленту настроить так и не получилось. Автор бросил пока эту затею, но вернулся к бочкообразности ролика скорее всего еще придется.
С регулятором запуск плавный, но есть минус том, что уменьшая обороты, падает и мощность двигателя. Скорость ленты по расчетам около 20 м/с.
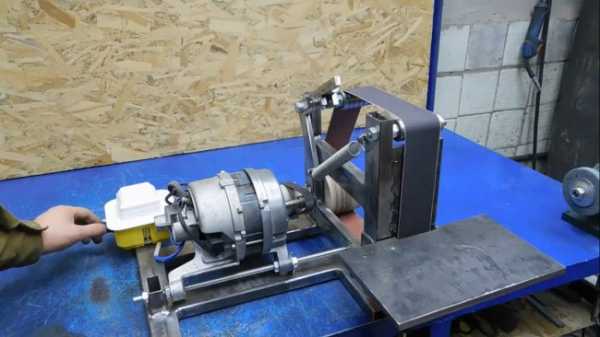
Лента подаётся смещению, реагирует на наклон ролика. Неужели будет работать без бочкообразной формы?
И напоследок шпилька с максимальной нагрузкой на ленту.
Остановить ленту так и не удалось. Станок автор преобразил покраской. Проект «гриндер» закончен. Благодарю за внимание. До новых встреч!
Видео:
Источник
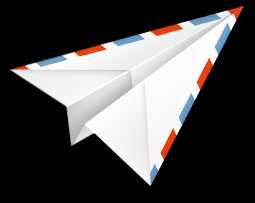
Получайте на почту подборку новых самоделок. Никакого спама, только полезные идеи!
*Заполняя форму вы соглашаетесь на обработку персональных данных
Становитесь автором сайта, публикуйте собственные статьи, описания самоделок с оплатой за текст. Подробнее здесь.usamodelkina.ru
Фрезерный станок из двигателя стиральной машинки
Фрезеры широко используются в мебельном производстве и поскольку относятся к профессиональному оборудованию, стоят недешево. Среди них самый универсальный и широко используемый – погружной (вертикальный или штанговый) фрезер, который можно сделать самому из отслуживших свой срок узлов и деталей.
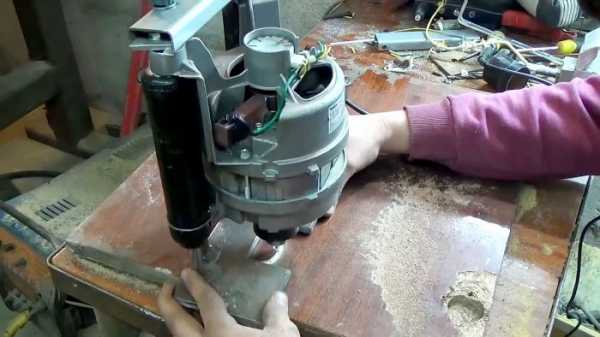
Понадобится
Чтобы изготовить самодельный фрезер, нам необходимо обзавестись:
- электродвигателем от старой стиральной машины;
- двумя амортизаторами передними от «Жигулей»;
- обычным цанговым патроном для дрели;
- кнопкой пуска;
- небольшим листом толстого металла;
- незамкнутым металлическим профилем и круглой трубкой;
- шпилькой, обычными гайками и гайкой-барашком.
Последовательность изготовления фрезера из двигателя стиралки
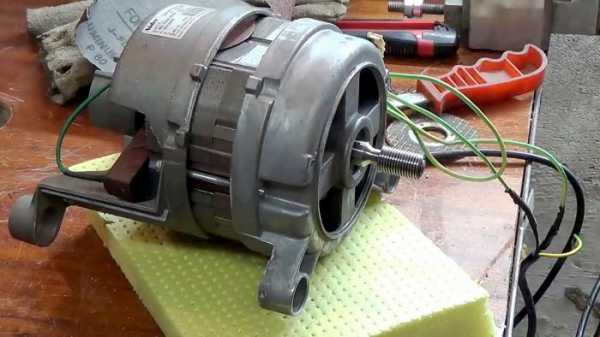
Один из главных узлов нашей самоделки – электродвигатель. Проверим его работоспособность и, убедившись, что с ним все в порядке, начинаем его модернизировать.
В первую очередь, болгаркой стачиваем резьбу на конце вала и протачиваем его под размер посадочного места патрона, которое также заранее было подготовлено на токарном станке.

Главное в этой операции – исключить биение и прочную посадку, чего мы добиваемся с помощью молотка.
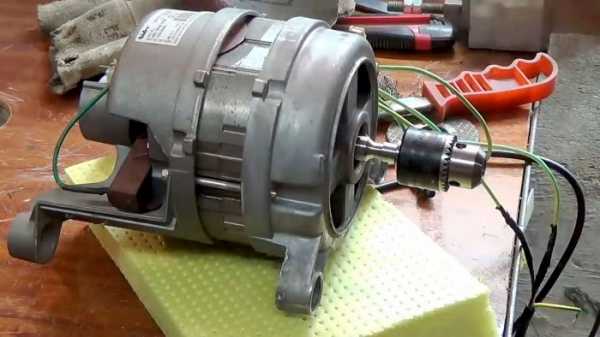
Для проверки качества посадки патрона на валу включаем двигатель и убеждаемся, что оно прочное и практически отсутствует вибрация. Для надежности в дальнейшем прихватываем патрон сваркой к валу.
В качестве вертикальных направляющих штанг используем негодные автомобильные амортизаторы. Для этого отрезаем от них с помощью болгарки верхние и нижние узлы крепления.
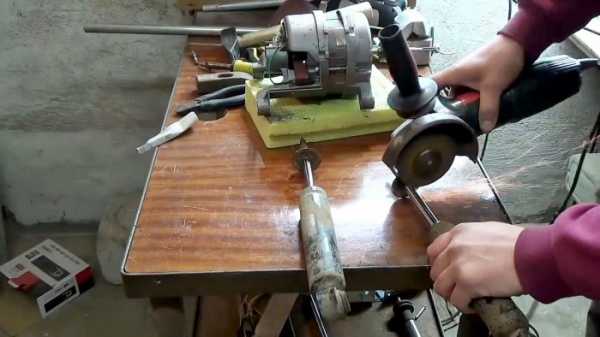
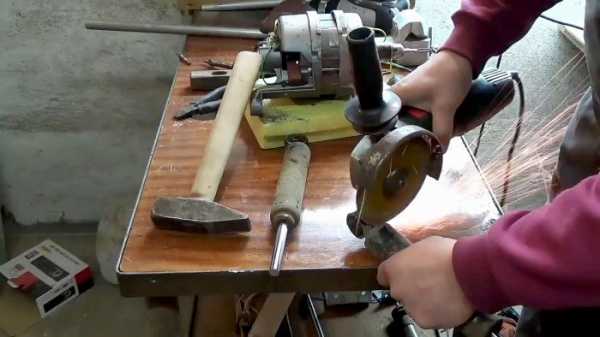
Подготавливаем на двигателе посадочные места под установку и закрепление амортизаторов, используя болгарку.
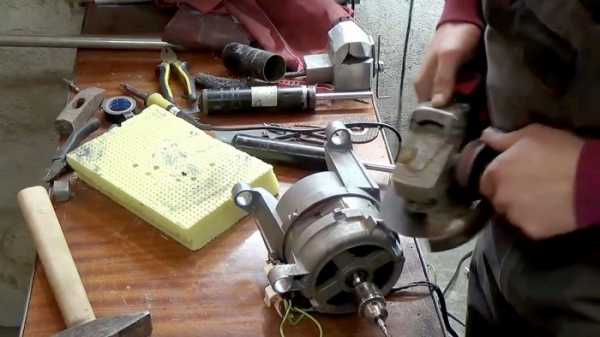
Заднее крепление производим с помощью болта и надежной шайбы через штатное отверстие на двигателе, вворачивая болт в резьбовое отверстие амортизатора.
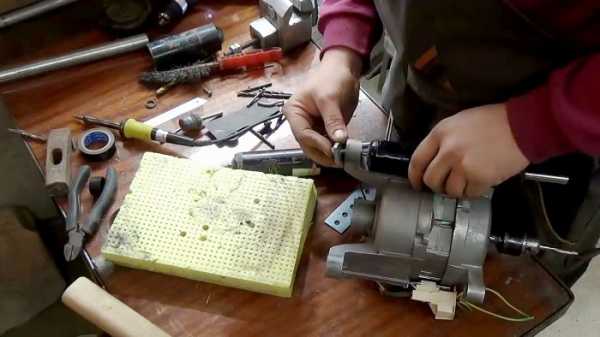
Перед окончательной установкой амортизаторов на электродвигатель в их донце сверлим отверстия и удаляем из их полости масло, несколько раз оттягивая и опуская шток.
Спереди амортизаторы крепим вязальной проволокой, пропустив их через заранее просверленные отверстия в «ушках» посадочных мест на двигателе, обхватывая ею корпус амортизаторов, и, связывая концы с помощью пассатижей.
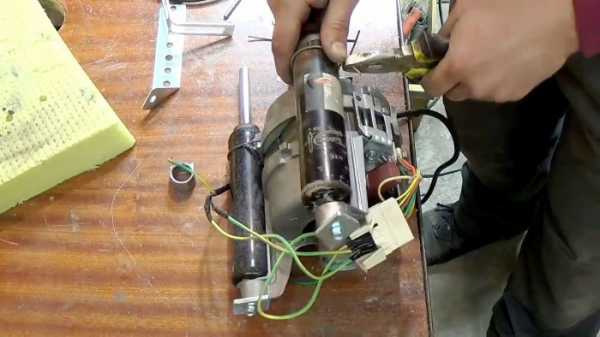
Беря в расчет расстояние в плане между штоками амортизаторов, размечаем толстую металлическую пластину, отрезаем ее от заготовки, удаляем заусенцы и обрабатываем кромки. Она будет исполнять функции подошвы в нашем самодельном фрезере.
В средней части пластины отрезным диском выполняем односторонний прямоугольный вырез, соразмерный с диаметром патрона и также обрабатываем его, удаляя заусенцы, и, скругляя кромки.
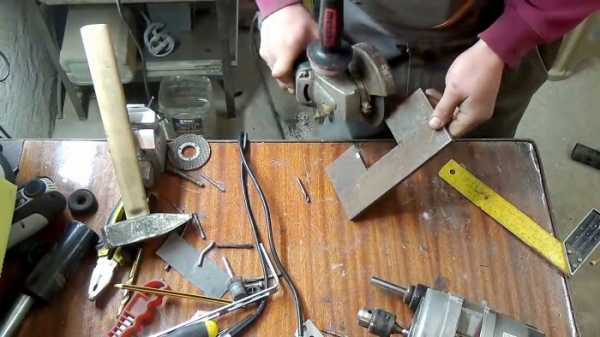
Привариваем концы штоков амортизаторов к пластине-подошве симметрично прямоугольного отверстия.
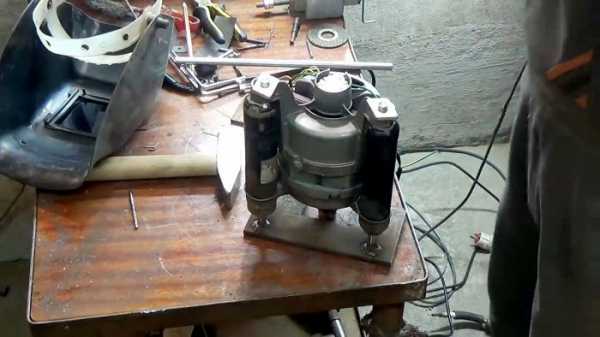
С тыльной стороны вертикально привариваем трубку необходимой высоты. На пластины, свободно закрепленные болтами к корпусу двигателя над верхним креплением амортизаторов, надвигаем незамкнутый стальной профиль и отрезаем лишнее. Профиль прижимаем пластинами к корпусу мотора за отбортовки, вкручивая болты.
Над вертикально установленной и приваренной к подошве трубкой, в стальном профиле сверлим отверстие.
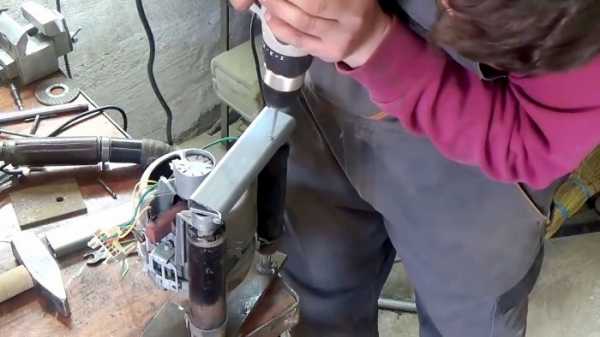
Вставляем в него шпильку с гайкой, чтобы она находилась под профилем. Нижний конец шпильки помещаем в трубку и опускаем ее до упора гайки в торец, которую затем привариваем к торцу трубки.
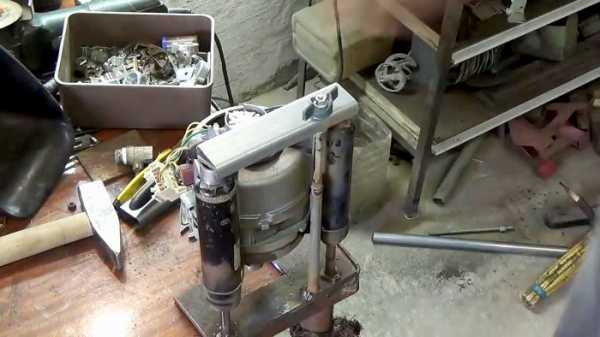
На конец шпильки сверху профиля навинчиваем гайку-барашек, с помощью которой можно регулировать высоту головки самодельного фрезера над подошвой и, тем самым, глубину обработки материла.
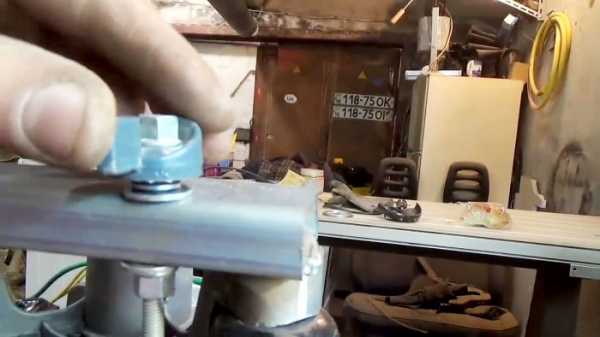
Для пуска и остановки двигателя нашего самодельного фрезера с лицевой стороны устанавливаем кнопку вкл./выкл.
Для безопасности поверх патрона устанавливаем и закрепляем кольцевой кожух, который защитит оператора, если вдруг патрон оторвется от вала электродвигателя.
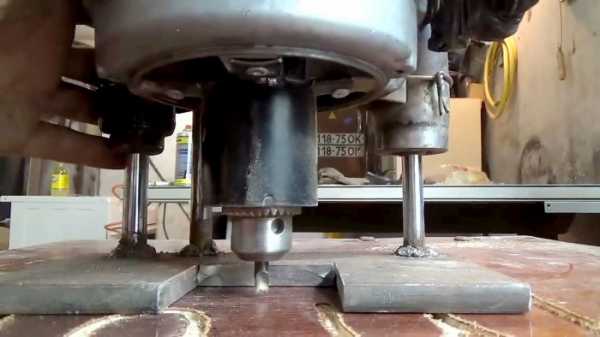
С помощью нашего самодельного фрезера можно осуществлять любые операции по дереву, вплоть до вырезания сложных криволинейных фигур, в том числе различных знаков: букв, цифр и т. д.
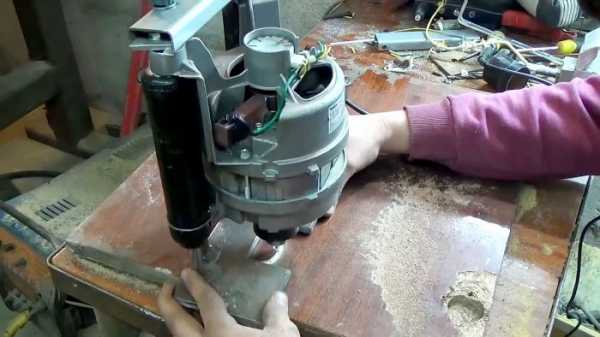

ИСТОЧНИК
coollifehack.ru
Токарный станок из двигателя от стиральной машины своими руками
У каждого запасливого хозяина имеется огромное количество работ, подразумевающих обработку заготовок из древесины. С такой задачей поможет справиться токарный станок. Приобрести такую технику в готовом виде – удовольствие дорогостоящее, и многие пытаются изготовить его из подручных материалов. Сегодня мы рассмотрим, как монтируется токарный станок из двигателя от стиральной машины.
Целесообразность самостоятельного изготовления
Автоматизированные устройства повышают эффективность обрабатывания древесины, что довольно актуально в организации производства или для исполнения бытовых заданий. Современные модификации позволяют не только работать по дереву, но и по мягкому металлу – бронзе, алюминию, меди. Широкий ассортиментный ряд представляет вашему вниманию не только станки для профессиональной обработки, но и оборудование, используемое в домашних условиях.
Правда, имеется один существенный недостаток покупного оборудования – стоит такой токарный станок достаточно дорого. Чтобы сэкономить бюджет, можно воспользоваться одним из трех вариантов – купить китайскую модель, приобрести советскую технику и постоянно ее ремонтировать либо изготовить такой станок своими руками.
В том случае, если станок предназначается для бытового применения и совершенствования собственного мастерства в столярном деле на уровне хобби, то станок, собранный самостоятельно, является отличным альтернативным решением дорогостоящему оборудованию. Естественно, самодельная модель не имеет разных особенностей заводского аналога, но ее функциональности окажется вполне достаточно, чтобы изготовить небольшую поделку из мягкого металла или древесины.
Что необходимо, чтобы изготовить станок
Ничего сложного в самостоятельной сборке оборудования нет. Возможно изготовить простейшую модель токарного станка, основу которой составляют подручник, задняя бабка и электрический мотор от стиральной машины автомат.
Чтобы изготовить станок, способный обрабатывать древесный материал, придется подготовить все необходимое. В перечень исходных материалов входят:
- мотор от старой машины для стирки вещей, сохранивший свою работоспособность;
- доска, из которой готовится основа прибора. В качестве варианта – токарный станок можно закрепить на рабочем столе;
- металлические уголки, длина которых составляет 19.5 см, а размер – 2 на 2 см. Потребуется также труба с квадратным сечением. Стальные заготовки будут использованы для изготовления подручников;
- уголок 6.2 на 6.2 см, длина 16.5 см – из него необходимо сделать заднюю бабку;
- подручник к основе необходимо закрепить болтом, длина которого должна быть не менее 7 см;
- отрезок стальной трубы, диаметр которой немного больше, чем размер вала электродвигателя;
- болт с заостренным наконечником, из которого можно сделать вращающийся узел бабки.
Основными исполнительными деталями токарного станка считаются подручник и бабка, между которыми вставляется заготовка из древесины. От подручника на изделие передается вращательное движение от электрического мотора. С помощью задней бабки изделие удерживается, сохраняя свою статичность. Бабку передвигают с помощью ручного привода.
Для удобства в работе потребуются определенный инструмент и крепеж:
- электродрель с набором сверел;
- болгарка с отрезными дисками;
- болты и гайки, с помощью которых будет собрана вся основная конструкция.
Как только все необходимое будет подготовлено, можно переходить к основной задаче. Только следует разобраться, как правильно сделать токарный станок, используя старый мотор от стиральной машины.
Как изготовить станину
Под самодельный токарный станок подходит каркас из дерева. Высокой жесткости не требуется, ведь обрабатывать предстоит не металл. Стандартные габариты самодельного станка, как правило, составляют 90 на 50 на 45 по длине, ширине и высоте соответственно. На таком станке возможно обрабатывать заготовки длиной в двадцать сантиметров и диаметром в двадцать пять.
Разберемся, как правильно сделать станину:
- пару уголков располагаем на ровной поверхности, направив полки друг к другу;
- для параллельности их размещения используем вкладыши через каждые пять сантиметров;
- направляющие в торцевых участках фиксируются уголками;
- детали соединяются струбцинами и привариваются;
- станина укрепляется на верстак или колоду.
Альтернативным решением для такой станины может быть основание из металла, как более жесткое и прочное. Чтобы изготовить центры под установку заготовки, понадобится помощь токаря.
Как сделать станок
Чтобы все сборочные работы выполнить самостоятельно, придется запастись терпением и достаточным количеством времени – процесс пойдет не так быстро, как предполагается. Изначально готовим основу, на которую будут установлены все элементы конструкции. Алгоритм действий выглядит следующим образом:
- столешница очищается от посторонних предметов;
- электрический мотор от стиральной машины крепится на подготовленной основе, для чего применяются уголки, соответствующие по размерам;
- подручник можно сделать из стальных уголков и квадратной трубы;
- с помощью подходящего сверла в столешнице устраивается отверстие под фиксацию подручника, для чего используется болт;
- теперь можно сделать станину из уголка с гранью 6.2 см и заостренным болтом;
- подручник и задняя бабка крепятся друг к другу;
- изготавливается насадка под вал электрического мотора. Сделать ее возможно из отрезка трубы. Для нарезки зубьев насадки понадобится болгарка;
- насадка приваривается к валу электромотора;
- остается подсоединить к мотору электрическую проводку.
Где применяется самодельное токарное оснащение?
Рассмотрим область использования такого оборудования. Токарный станок небольших размеров, собранный в домашних условиях из мотора старой стиральной машины, можно использовать при изготовлении массы вещей из древесины. Такое самодельное устройство поможет сделать:
- элементы для внешней или внутренней отделки;
- отдельные детали мебели;
- резные элементы лестничных перил;
- деревянные ручки на инструменты;
- табуретки и еще массу полезных в хозяйстве вещей.
Кроме того, на маленьком токарном станке по древесине возможно:
- шлифовать обрабатываемую поверхность;
- наносить резьбы с определенным шагом;
- высверливать в деталях необходимые разъемы;
- обтачивать элементы из древесного материала.
Оказывается, область использования токарного оборудования довольно большая. И если у вас есть мотор от старой стиральной машины, способный еще поработать, вполне можно сделать необходимое для дома оснащение.
Заключение
Следуя данной инструкции, вы сможете сделать маленький токарный станок, который всегда пригодится в домашних делах. Деревянную заготовку, которую необходимо будет обработать, следует насадить на острый конец вала двигателя и вращающийся узел расположенной сзади бабки. Включив устройство, можно приступать к работе.
Как видите, не следует утилизировать электромотор от старой стиральной машины. При достаточной смекалке из него можно сделать полезное в хозяйстве оборудование.
Кроме этого из б/у стиральной машины так же можно сконструировать:
- газонокосилку,
- траворезку,
- электровелосипед,
- медогонку,
- гончарный круг,
- дровокол,
- бетономешалку,
- фрезер,
- насос для полива,
- соковыжималку,
Вам также будет интересно почитать:
stiralkainfo.ru
Сверлильный станок с двигателем от стиральной машины часть 1 SW19.ru
Когда в твою голову постоянно приходит мысль «сделать», а не «купить» у тебя появляется потребность в инструменте и оборудование. Это невозможно выработать или приобрести в зрелом возрасте, это приходит к тебе в голову с молоком матери, когда бегая во дворе ты вместо слез и истеричных призывов «купи автомат» идешь в кусты и ломаешь подходящую палку, если она ломается, то превращается в пистолет, бац и у тебя в руках кортик. Тут то и зарождается конструкторская и изобретательская извилина в мозгу. С возрастом она больше и больше изгибается, создавая причудливый узор и одному богу известно, что может придти в такую голову. У меня эта извилина не такая загнутая как хотелось бы, но по счастливому стечению обстоятельств вокруг меня всегда есть гениальные (сильно отличающиеся мыслями и поступками) люди. Одно из таких проявлений симбиоза гениальности, опыта металлообработки и творческого полета конструкторской мысли является сверлильный станок, который уже в полной мере разрабатывает мой Отчим.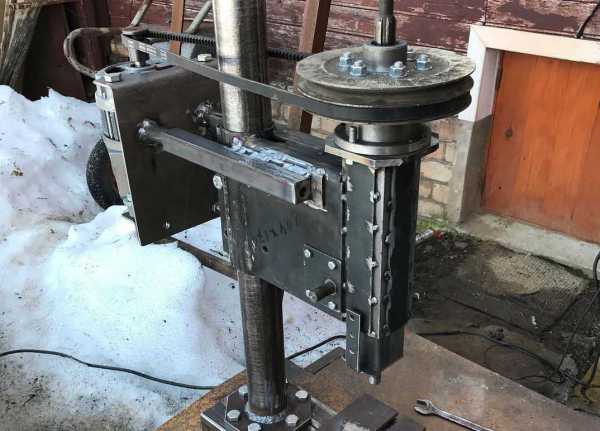
Самое гениальной в данном изобретении, то что оно выполнено из подручных материалов, как мальчик, который пошел в кусты за автоматом или саблей, мой Отчим взял подходящую квадратную (профильную) трубу и сделал увесистую станину.
СТАНИНА
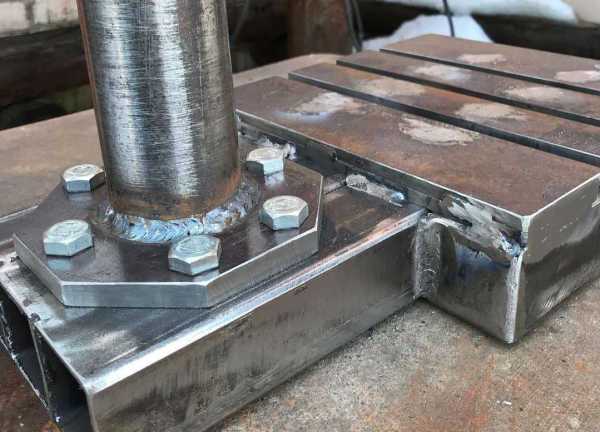
Одной из самых сложных задач было поймать плоскость стола и стойки. С этой задачей справились благодаря торцовки уже приваренной шайбы на большом токарном станке
Не скажу что мы получили идеальный угол, но для «гаражного рукоблудства» оно и не надо
Второй важный момент сделать пиноль, которую мы изготовили из той же трубы, что и станину, но сверху с небольшим зазором наварили уголок, который образовал корпус, как Вы понимаете чем меньше будет зазор, тем меньше будет люфт и биение, но и тем больше вероятность «закуса».
БАБКА

Третий важный момент были подшипники, благодаря которым происходит вращение, в нашей модели этих подшипников аж 4 штуки, две сверху, ну тут все понятно как их посадить и два снизу. Для посадки нижних подшипников нужно было изготовить квадратную обойму, которая встанет в квадратную трубу и сможет быть посадкой для подшипников. В изготовлении этих обойм помог наш горячёлюбимый 3D принтер, который уже не раз выручал нас, в 2019 году не представляю свою жизнь без подобного гаджета.
ДВИГАТЕЛЬ
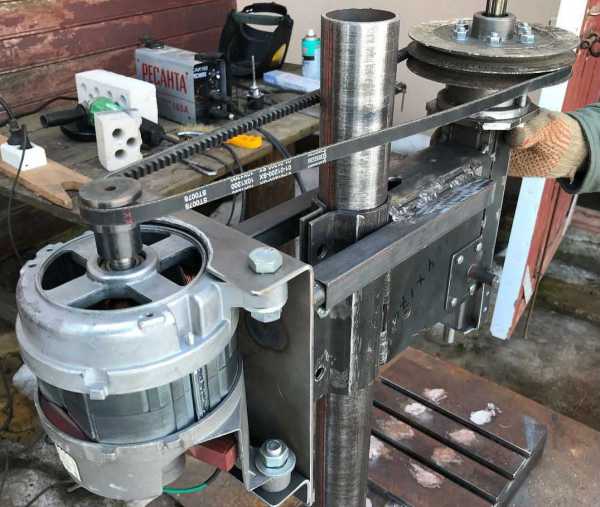
В нашем случае найти двигатель было одним из самых легких занятий, так как у нас все-таки сервисный центр по ремонту стиральных машин в Ярославле, мы без проблем можем найти нужную деталь и тем более ненужный движок. Взяли самый мощный из тех что есть в наличии, 480W, пока нет информации подойдет он или нет, расчеты очень сложные для нашего низкого уровня образованности, поэтому мы будем поступать как все выдающиеся физики, применять метод «научного тыка» или попросту проб и ошибок.
Если нужно будет убавить обороты и добавить мощности, будем играть диаметрами шкивов ременной передачи, если совсем не пролезем по мощности, то заменим моторчик на более мощный асинхронник с чистотником.
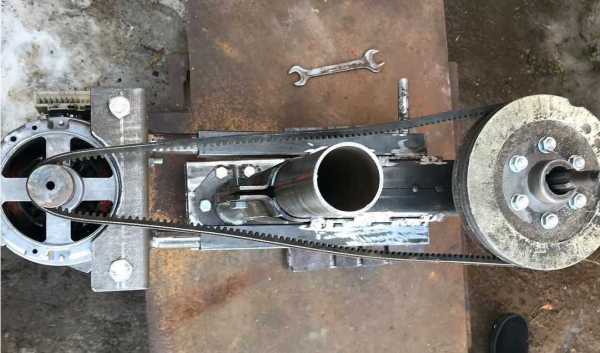
Пока мысль задействовать таходатчик для поддержания стабильных оборотов под нагрузкой и их регулировки, насколько будет жизнеспособна эта схема покажет практика и следующее видео
ПРОБЛЕМА
На данный момент проблема заключается в механизме подъема и опускания бабки с мотором, нужно это сделать более менее плавно, элегантно и с возможностью поворота всей конструкции на стойке, если у кого есть идеи реализации напишите пожалуйста в комментариях будем рады любым советам.
Если Вам понравилась данная статья или видео, то мы буем рады если Вы поделитесь ссылкой на наш ТЕХНОМАГ – магазин запчастей для бытовой техники, где можно купить щетки для такого и любого другого двигателя для стиральных машин.
Удачи в ремонте!
sw19.ru
Сверлильный станок из движка от старой стиральной машины
Приветствую, Самоделкины!Из этой статьи вы узнаете, как автор YouTube канала «Добрый Мастер» модернизировал и усовершенствовал свой сверлильный станок. Сегодня мы подберем для него двигатель, установим цифрового линейку, а также подсветку.

Итак, состояние у этого станка оставляет желать лучшего. После долгих подборов электродвигателя, выбор автора пал вот на этого малыша от советской стиральной машины.
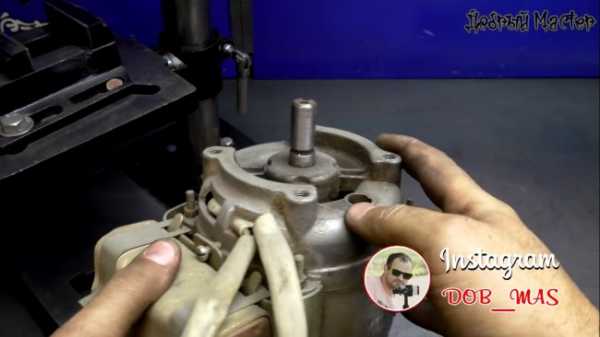
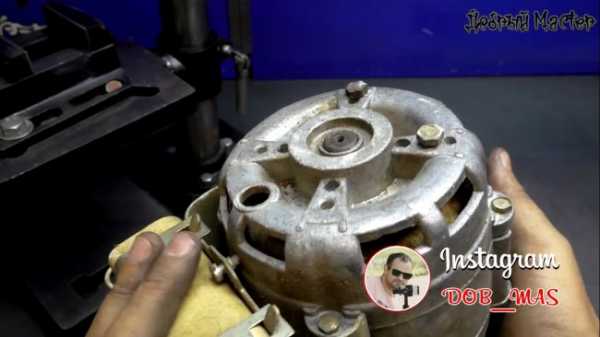
Данный двигатель полностью в рабочем состоянии и даже с пусковым конденсатором. Для начала давайте попробуем закрепить его на свое законное место на эту пластину с натяжителем.
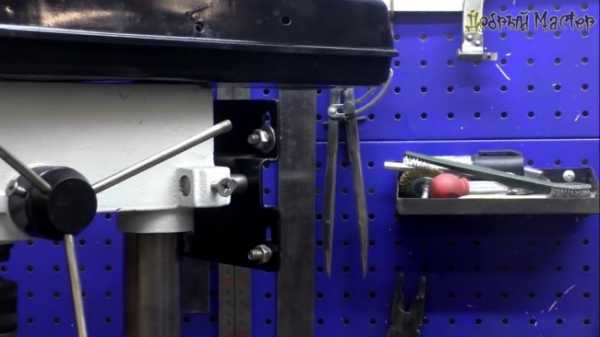
Поскольку у штатной пластины отверстия для крепления двигателя горизонтальные, а на новом моторе вертикальный, придется изготавливать переходные пластины. Делать их будем из полосы металла шириной 40 мм. Для этого размечаем линии реза и режем при помощи угловой шлифовальной машинки.
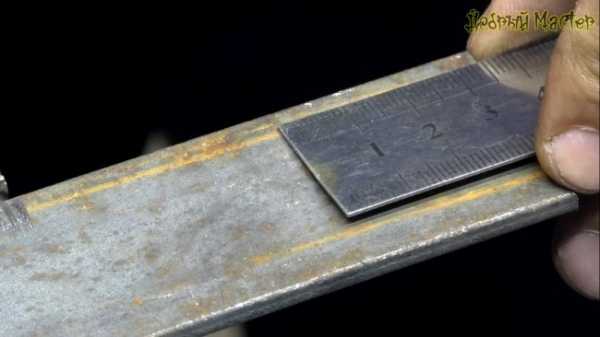
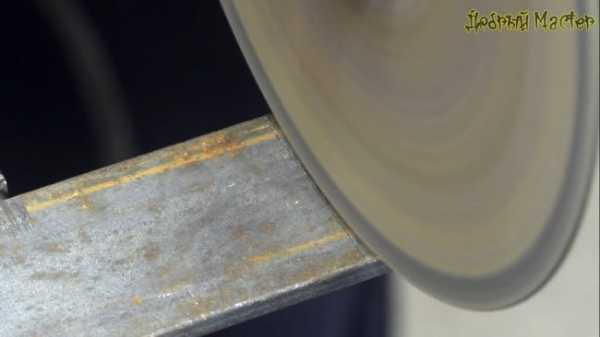
Не забываем при этом пользоваться средствами защиты. Чтобы отверстия получились соосными, пластины сверлим парами, как обычно, сначала тонким сверлом, а затем в нужный диаметр.
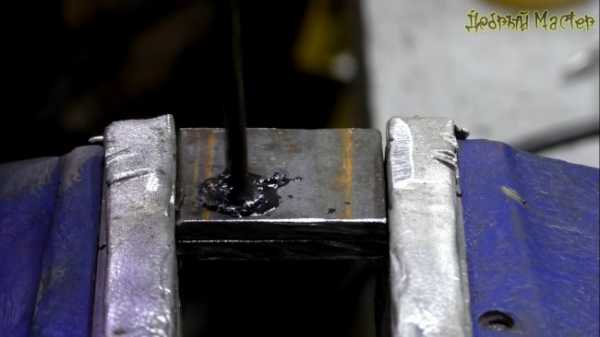
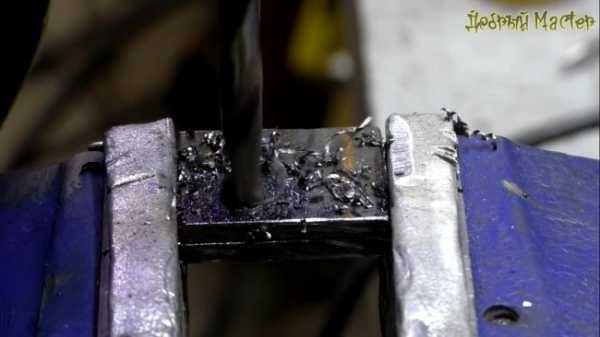
Верхние пластины готовы и теперь можно их примерять. Крепить их будем вот на такие винты м8.
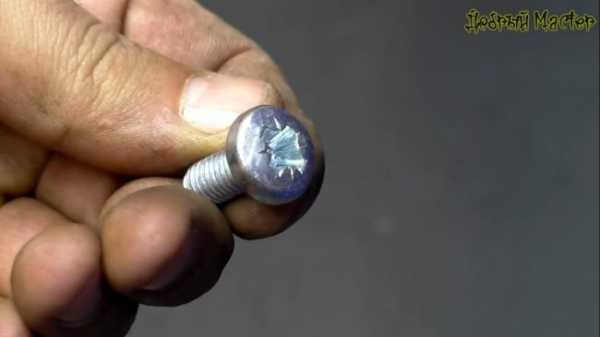
Остальные части будущего крепления автор решил варить по месту, так будет точнее.
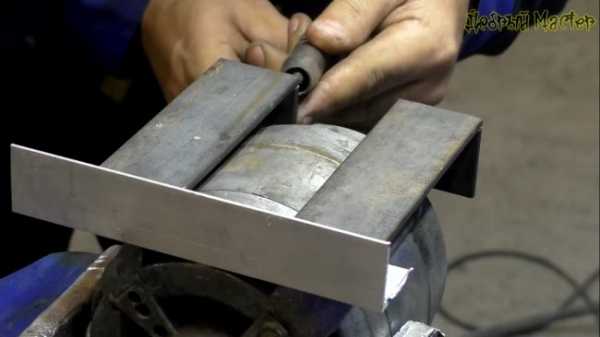
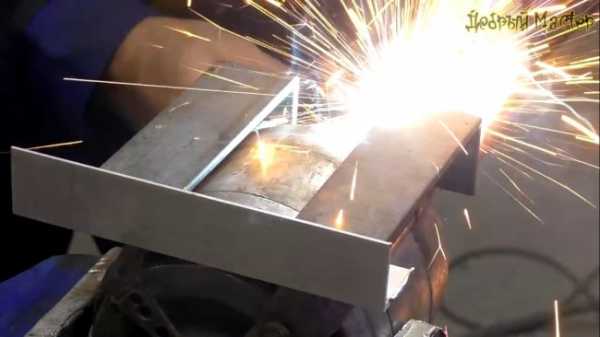
Теперь просто прикладываем заводской кронштейн к нашей конструкции и размечаем места будущих отверстий по середине пазов и сверлим.
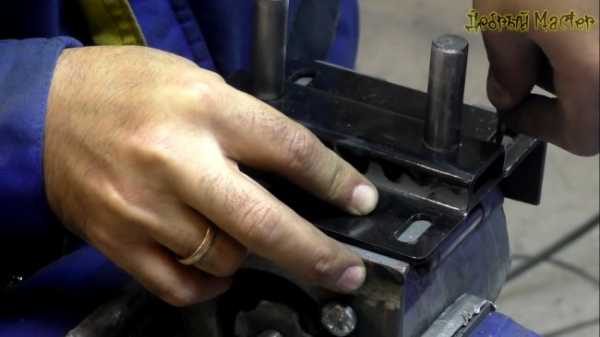
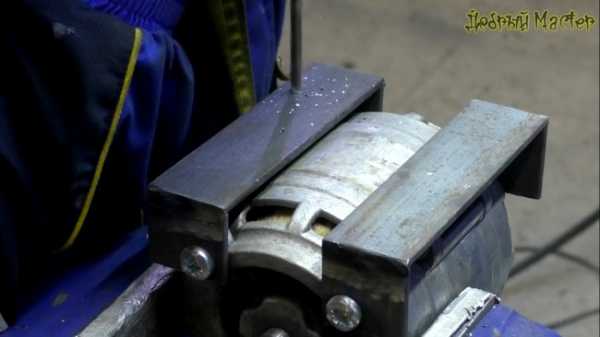
А вот так выглядит наш станок с установленным на него двигателем.
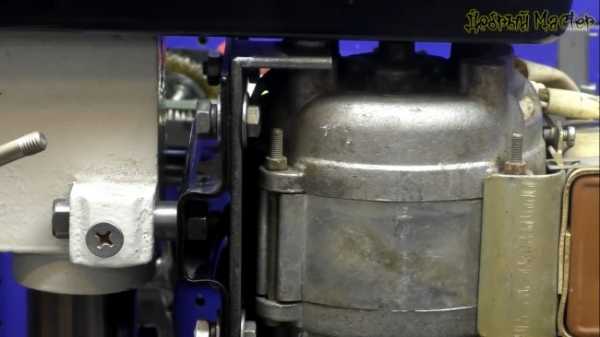
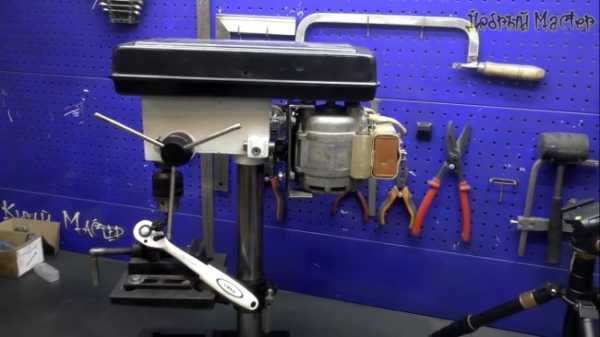
Теперь можно эту конструкцию разобрать для последующей покраски. А пока детали сохнут, перейдем к цифровой линейке.
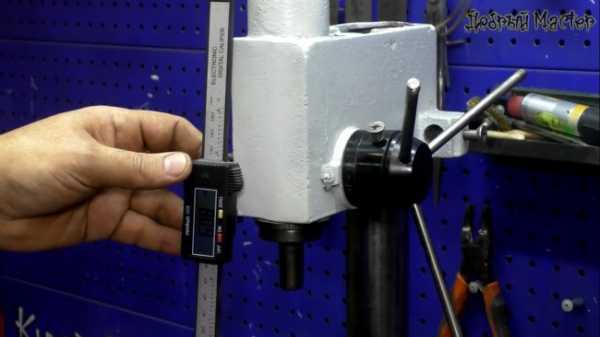
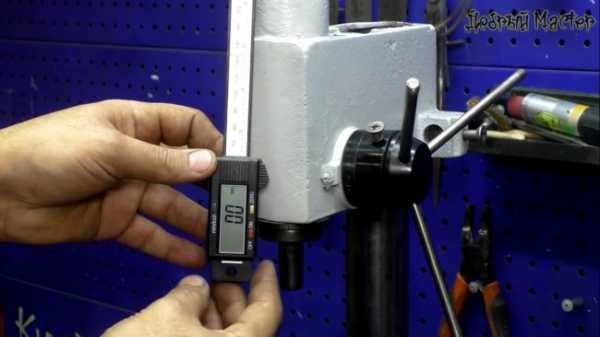
Данное устройство автор снял со своего старого самодельного сверлильного станка. Линейка пластиковая, сделана из китайского штангенциркуля. Подвижную часть мы будем крепить к пиноли сверлильного станка. На ней есть проточка, на которую раньше одевалась защита. Диаметр этой проточки 40 мм.
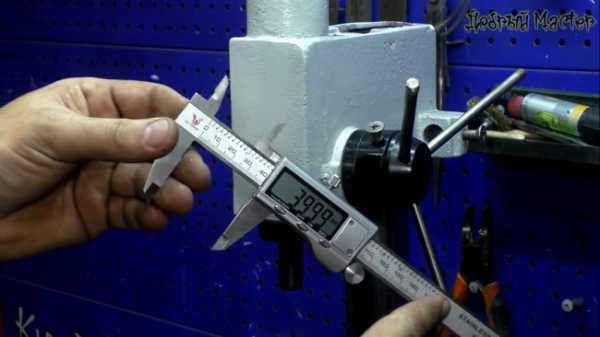
Поскольку кругляка нужного диаметра у автора в мастерской не нашлось, заготовку он решил делать из листового металла высотой (толщиной) 10 мм.
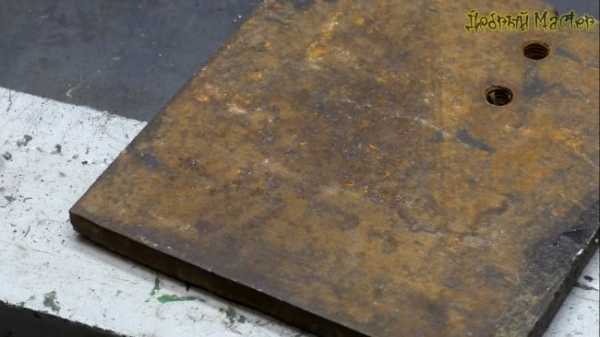
Размечаем примерную окружность будущей детали и обрезаем при помощи обыкновенной болгарки. Все острые углы так же срезаем, чтобы меньше потом снимать металла на токарном станке.
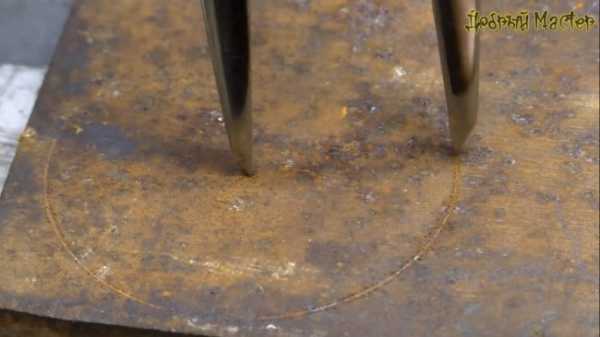
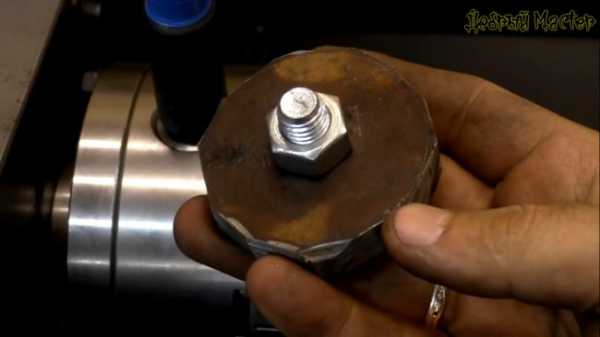
Вместо оправки для наружной обработки деталей автор решил использовать самый обыкновенный болт с гайкой. Затем просто зажмем нашу заготовку в обратных кулачках за внешнюю сторону и расточим внутреннюю часть.
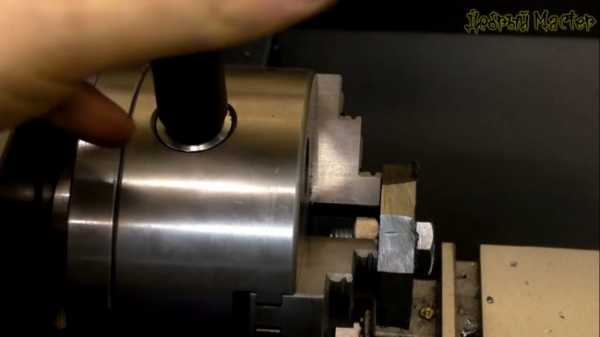
Автор признается, что, наверное, это его самая любимая часть, он может очень долго смотреть на то, как ведется металлообработка на токарном станке.
В итоге вот такая красота у нас получилась:
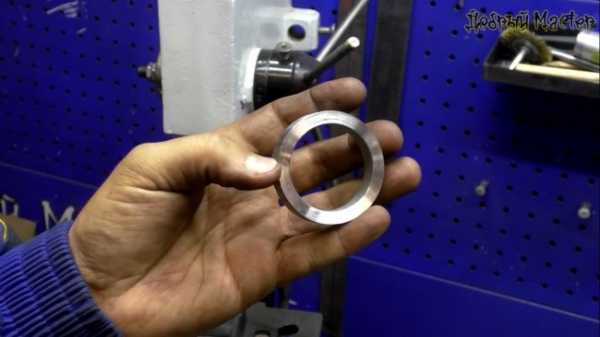
Одевается это кольцо на пиноль свободно, а впоследствии будет фиксироваться на ней при помощи пары гужонов.
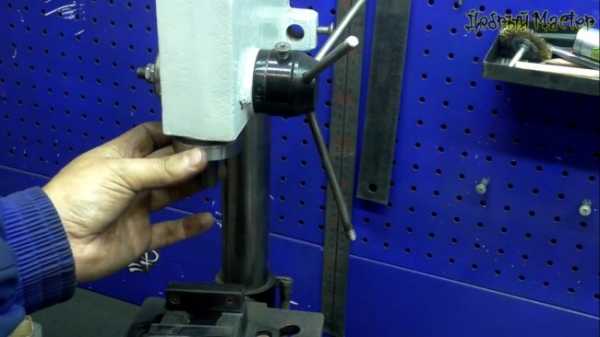
Сама же линейка будет крепиться через металлический уголок к корпусу станка.
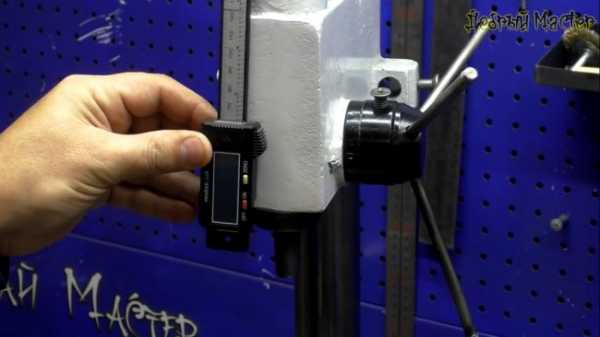
Для этого сверлим отверстия и нарезаем резьбу м3.
После крепления линейки удалось снять необходимые размеры. И вот еще одна деталь для крепления к пинолю станка.
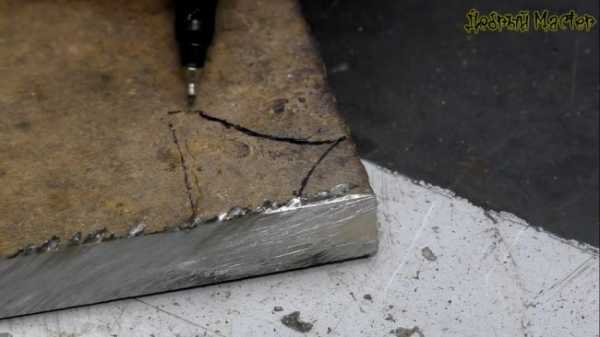
Вырезаем ее при помощи угловой шлифовальной машинки, а также необходимо сразу обработать некоторые края перед тем, как отрезать заготовку, так будет намного удобней.
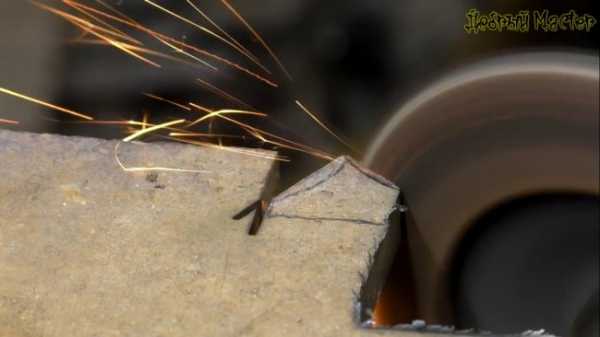
После грубой обработки можно приварить деталь к кольцу и можно будет устанавливать все на свои места.
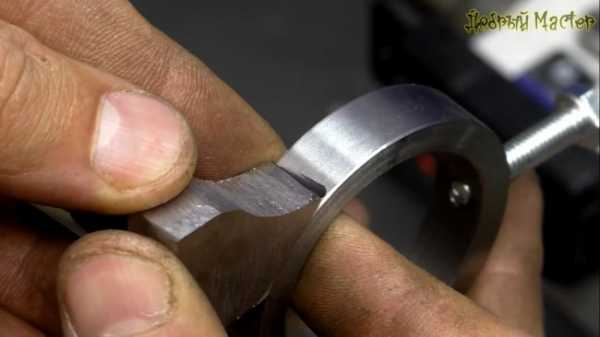
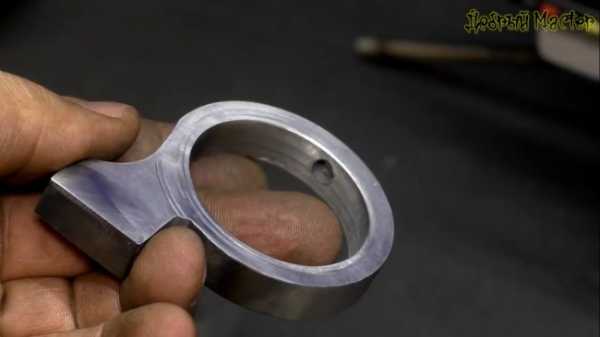
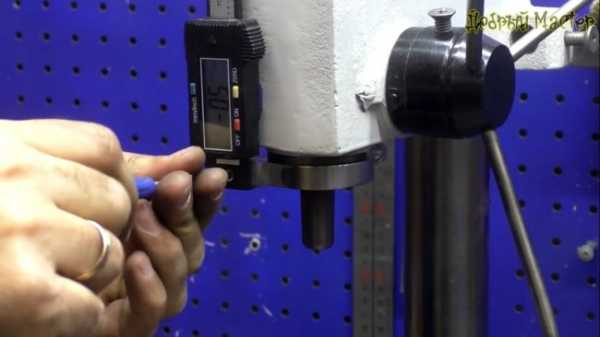
Как мы видим, линейка работает, но ее нужно немного укоротить.
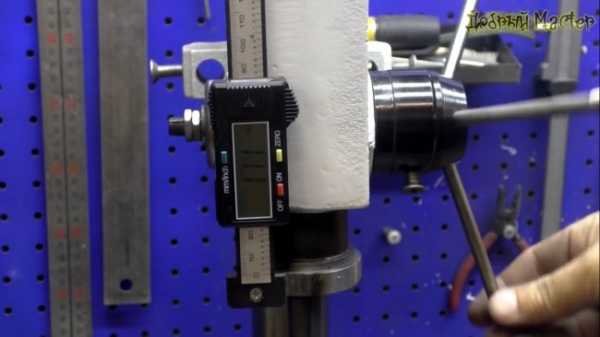
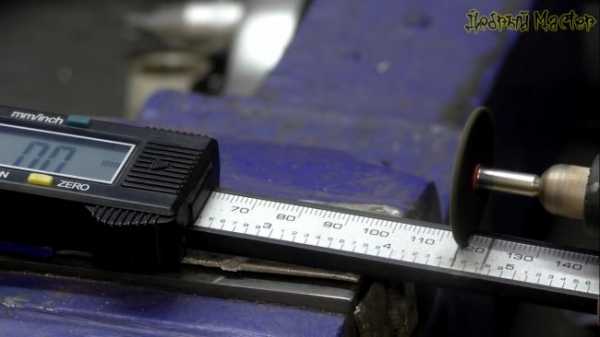
Автор признается, он думал, что после такой операции бывший китайский штангенциркуль просто перестанет работать, но все обошлось.
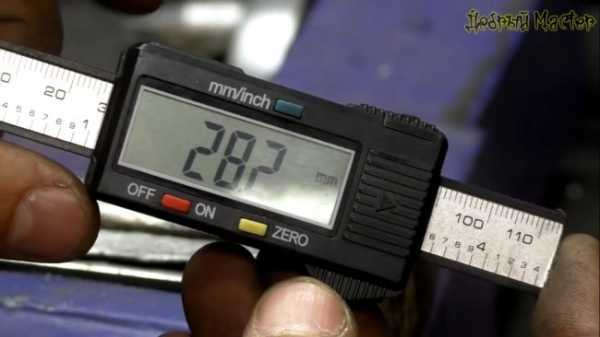

У себя в хламе автор нашел вот такой светильник.
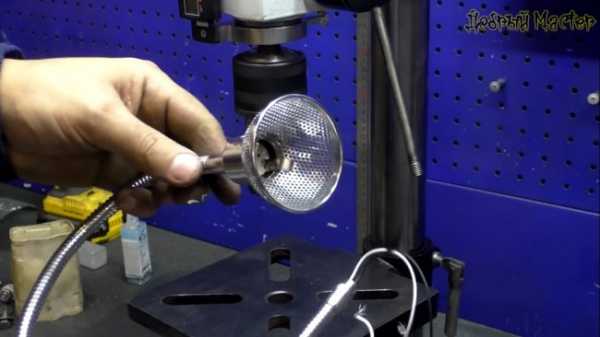
Этот светильник он когда-то принес из металлоприемки, смонтируем его на этот станок. Крепить его будем снизу станка параллельно стойке.
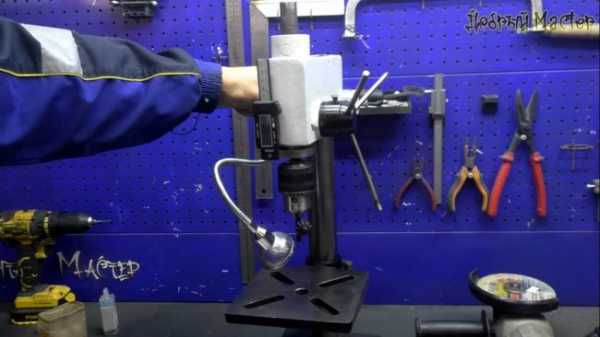
Здесь все просто, сверлим отверстие под гибкую ножку светильника и вклеиваем.
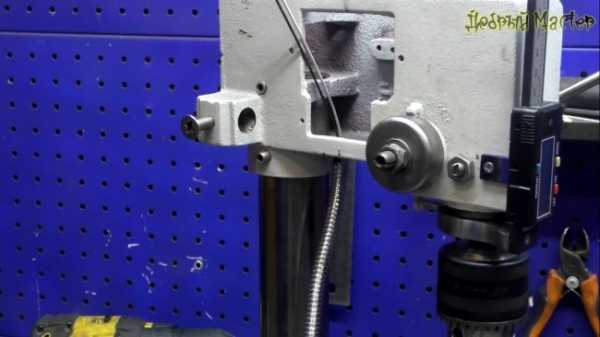
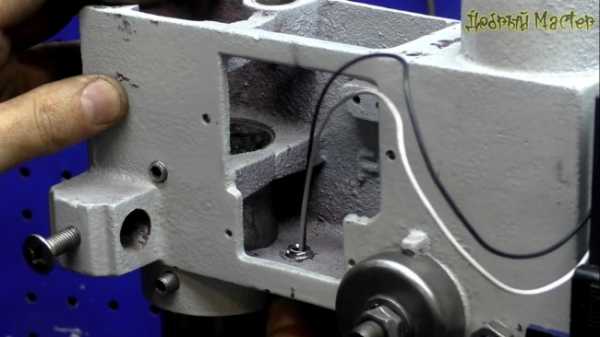
К этому моменту и двигатель подсох. Автор его перебрал, удлинил провода и надел термоусадку, правда желтую, но какая была в наличии.

Теперь можно установить двигатель.
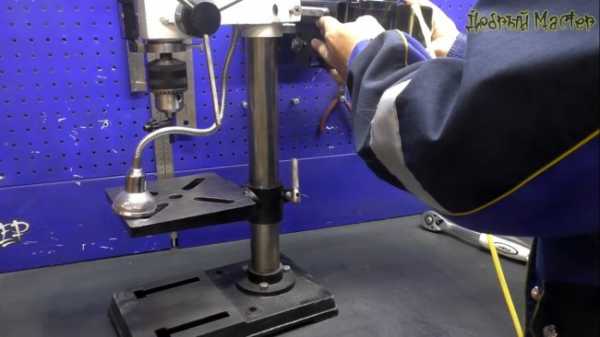
Вал двигателя придется наращивать, так как он намного ниже оси шкива.
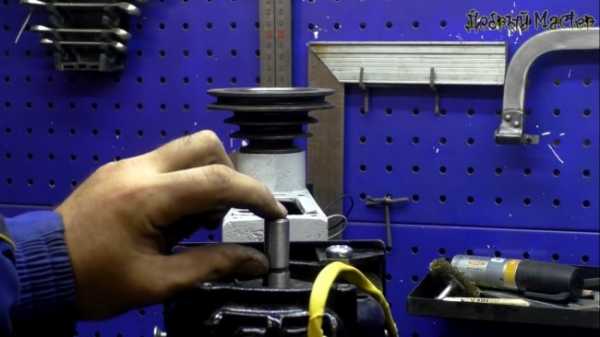
Идем к токарному станку. Автор не понимает, как же он раньше без него обходился.
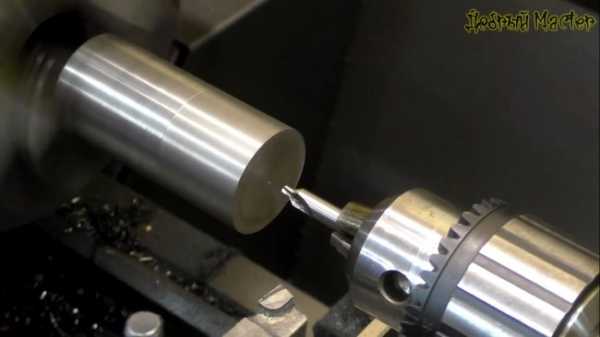
Центрируем, рассверливаем и растачиваем отверстие под диаметр вала двигателя, а также немного облегчим конструкцию.
Заготовку к сожалению, пришлось перевернуть, но автор выставил ее по индикатору и добился минимального биения. Теперь точим посадку под шкив.
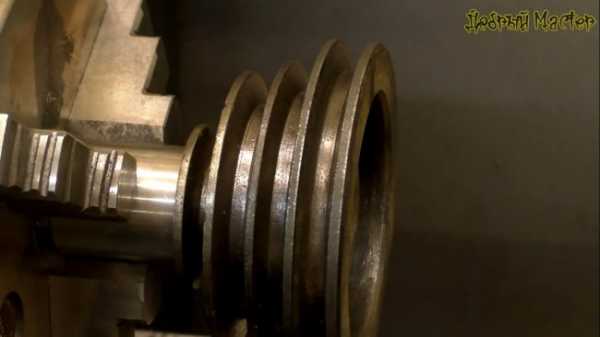
И как мы можем видеть, шкив сел очень плотно и люфтов нет.
Мастер решил не резать шпоночный паз в переходнике, а просто решил просверлить отверстия и вкрутить винты из нержавейки. Их не срежет, не такой уж и мощный этот двигатель.
В автомагазине был приобретен зубчатый ремень подходящего размера, а также автомобильная гофра. С ней подводящие к двигателю провода выглядят намного эстетичнее.
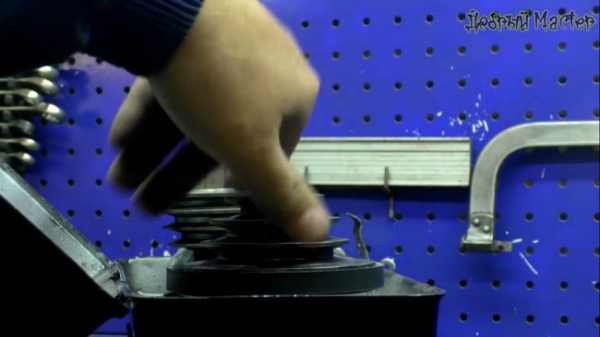
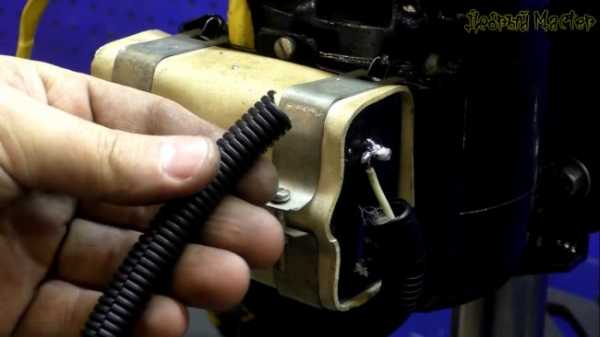
Провода пойдут к выключателю через верхний защитный кожух, а чтобы он внутри не болтался, закрепим его обычными пластиковыми хомутами.
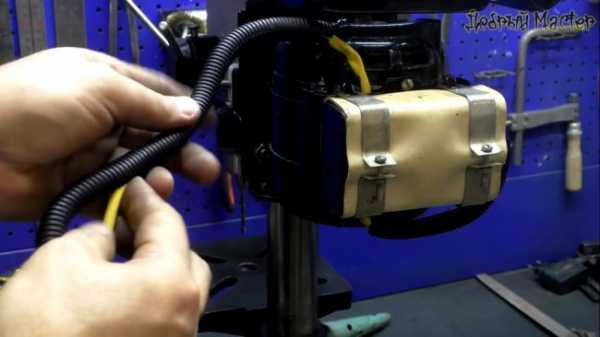
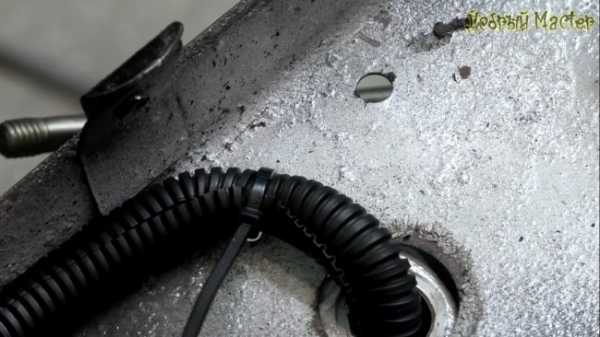
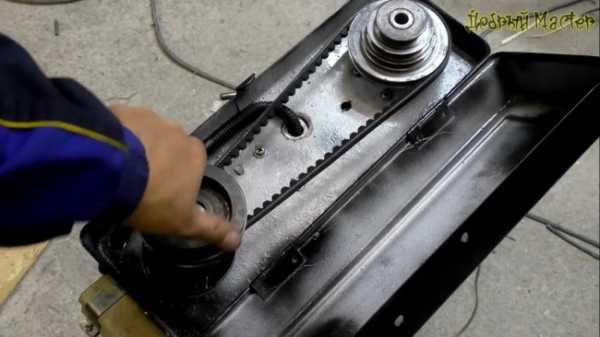
Для включения двигателя станка установим кнопку с фиксацией.
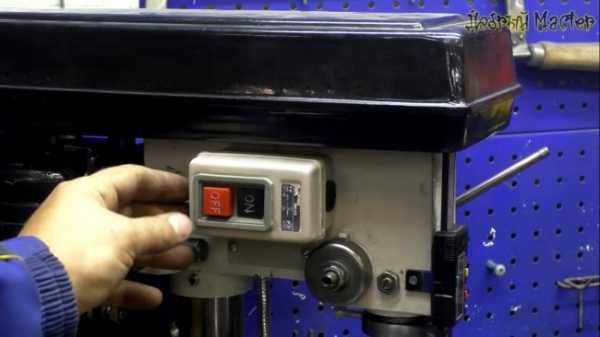
Теперь остается только лишь подключить эту вилку к сетевому проводу станка. Она рассчитана на ток до 16А и с нагрузкой этого станка должна справиться.
Ну вот, друзья, наш станок полностью собран. Все эти доработки получились довольно-таки неплохо, особенно мастера радует яркий свет в рабочей области.
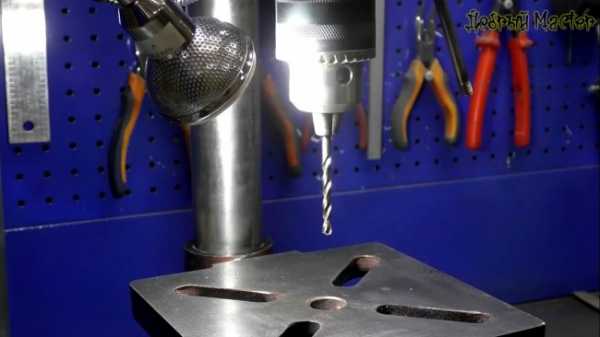

Для проверки автор установил самое большое сверло, которое было у него в арсенале диаметром 13 мм.
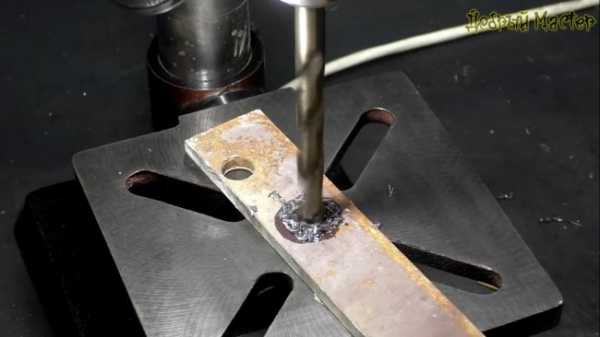

И как мы видим, мощности двигателя вполне достаточно для сверления. Вот таким получился у нас станок, осталось только накрутить шары на ручки, но их автор заказал в Китае, так что это он сделает в скором времени.
А на этом сегодня все. Благодарю за внимание. До новых встреч!
Видео:
Источник
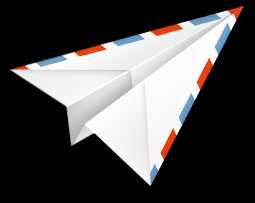
Получайте на почту подборку новых самоделок. Никакого спама, только полезные идеи!
*Заполняя форму вы соглашаетесь на обработку персональных данных
Становитесь автором сайта, публикуйте собственные статьи, описания самоделок с оплатой за текст. Подробнее здесь.usamodelkina.ru
Самоделки из двигателя от cтарой стиральной машины для различного применения
В современном ритме жизни время течет очень быстро и вот некогда качественная и надежная стиральная машина превращается в мусор из-за износа или по другим причинам. Что делать с любимой помощницей? Многие решат с тяжёлым сердцем выкинуть устройство. Но хозяева с фантазией и прямыми руками могут начать искать варианты применения различных работающих деталей. Этот текст призван помочь найти применение двигателя от стиральной машины. Итак, что можно сделать из старой стиральной машины , а, точнее, из ее двигателя?
Точильно-шлифовальный станок
Начать необходимо прежде всего с основы будущего станка. Этой платформой может послужить плита из старого ДСП из старой советской мебели, отличающейся своей прочностью и надежностью. Силовой частью агрегата выступает двигатель от стиральной машинки. На его корпусе расположены стандартные шпилечки, к которым нужно прикрепить монтажные уголки, которые потребуется заранее приобрести в любом строительном супермаркете или магазине. Соответственно, уголки крепим к подставке или непосредственно к основе, если это, конечно, удобно.
Не стоит забывать, что простое подключение двигателя из-под стиральной машины в 220 Вт не приведёт ни к чему хорошему. Необходимо сохранить родной конденсатор и произвести подключение мотора именно через него.
Так как вал двигателя от стиральной машинки-автомат не предназначен для закрепления на нем различных режущих, или точильных дисков, потребуется поискать на местных электронных досках переходник для точила или переходник для наждака и приобрести его, чтоб сделать аппарат на совесть.
Купленный переходник садится на 14 миллиметровый вал. Визуально его ни с чем не спутаешь — цилиндрический элемент, который фиксируется болтом с резьбой. Сам вал цилиндра имеет резьбу М 14. На него надевается шайба двухсторонняя с проточными диаметрами, позволяющими устанавливать все расходные материалы для точильно-шлифовального станка на основе старого двигателя от стиральной машинки.
На базе основания имеет смысл изготовить и установить съёмный столик из тех же плит ДВП. Для надежной фиксации столика, на основании потребуется использовать по два шканта с обеих сторон поверхности. В данном дополнении к станку необходимо сделать зазоры под самые различные диски. Это важно.
Таким образом, получается недорогой, но функциональный точильный или шлифовальный станок. Он прослужит долго и надежно, что весьма приятно, особенно в контексте того, что сделать его получилось из старого мотора от стиральной машинки. Кстати, некоторые взяли этот принцип за основу в изготовлении фрезера, хотя большинству эта идея все же кажется безумной.
Газонокосилка
Для того чтобы воплотить эту задумку в жизнь и сделать качественный аппарат, нужно использовать:
- стальная основа;
- колесики и рукоятка;
- провод;
- нож, который нужно изготовить самостоятельно.
Традиционно начать следует с основы из листовой стали 500-500-5 миллиметров. Подготовив колёсики из-под чего-либо, например, от старой коляски, крепим их к стальному листу. На готовую основу крепится непосредственно сам двигатель от старой стиральной машинки посредством стандартных шпилек на корпусе мотора. На сам вал агрегата, с помощью заранее выточенного на токарном станке переходника, фиксируется режущий нож. Затем, подготовив рукоятку из доступного материала, прикрепим её к стальной основе. По этой же рукояти выводим провод электропитания моторчика.
Плюсами этой газонокосилки является простота конструкции, а также ее функциональность. И самое приятное, что аналог заводской косилки на порядок дороже.
Токарный станок по дереву
Для основы изделия необходим брус 250-50 миллиметров на который крепится двигатель от стиральной машинки. Как? Ответ прост — с помощью монтажных уголков. Шпильки крепим болтами к уголкам, а их, в свою очередь, прикручиваем саморезами к основе. На вал моторчика садим переходник для точила. После накручиваем на резьбу переходника съёмную насадку, сваренную из болта с соответствующей резьбой и небольшого цилиндра с шипами. Таким образом, эта часть станка является неподвижной бабкой.
В роли подвижной бабки выступает сваренная конструкция, состоящая из:
- трубы с внутренней резьбой;
- вала от тисков, на конце которого расположен небольшой цилиндр с упорным подшипником и шипами.
Труба наваривается на пьедестал из квадрата 45-45-3 миллиметров. Основа для подвижной бабки выполнена из листовой стали, на которую также приваривается пьедестал. Затем основа бабки прикручивается к брусу, выступающему основой станка.
Следующей конструктивной частью токарного станка из двигателя от старой машинки является «упор». Выполнен он из уголка с выпиленным пазом, выступающим как направляющая, и второго уголка, который надежно ходит по пазам в направляющих благодаря болтам между этими двумя элементами. Этими же болтами и фиксируется уголок на направляющих. Крепится упор саморезами непосредственно к брусу.
Циркулярка
Вначале потребуется сворить станину из квадратной трубы в виде небольшого прямоугольного столика. По центру него необходимо сварить ушки под вал с креплением под циркулярку. На верхнюю часть станины следует прикрутить столешницу либо вырезанную пластину из листовой стали. Под верхние части станины потребуется сварить основу для двигателя от старой стиральной машинки с установкой впоследствии.
В виде ходовой части представлена ременная передача. На валу моторчика и циркулярки оба шкива имеют канавки, а ремень имеет пазы. Это позволяет ремню не слетать со шкивов во время работы. Для удобства использования и транспортировки этой циркулярки к ножкам станины с одной стороны крепятся два колесика от старой тележки, а с другой стороны — удобная ручка необходимой длинны. К советам по эксплуатации можно отнести правила безопасности при работе с циркуляркой, а также то, что необходимо всегда проверять натяжения ремня. Это сохранит пальцы и остальные части тела целыми.
Дровокол
Для начала стоит подготовить:
- заранее выточенный на токарном станке конус с резьбой;
- вал на одном конце которого нарезана резьба;
- два подшипника в корпусе;
- втулку под подшипники;
- шкив;
- втулку под шкив;
- гаечки и шайбочки с болтами.
В виде моторчика может выступать, естественно, двигатель от старой машинки. Стоит также отметить, что чем массивней шкив, тем мощнее будет дровокол.
Сперва вал стоит посадить во втулку, а затем собрать вал на подшипники. После надежно скрепляем конус с валом распорочными болтами таким образом, чтобы болты зашли в потаены в конусе. Затем насаживается шкив на вал и зажимается через контргайку шайбой. Всю механику располагают и крепят на пластине из листовой стали. В конце потребуется изготовить станину, расположить на ней двигатель от старой стиральной машинки автомат и натянуть ремень между шкивом моторчика и валом.
Некоторые идеи из других элементов
Область применения двигателя от старой, но такой дорогой сердцу стиральной машинки поистине велика. Варианты, что описаны выше — лишь некоторые из возможных. Больше информации о применении такого рода двигателя, или, вообще, всех деталей от старой стиральной машинки, включая барабан, можно найти в интернете.
«Лучше один раз увидеть, чем сто раз услышать» — эта непреложная истина применима к поиску интересных вариаций использования элементов стиральной машины в наши дни. Каким образом? В Сети очень много вариантов, что можно сделать не только из двигателя, но и из барабана, корпуса и даже ремня в отдельности. О чем идет речь? Некоторые части стиральной машины можно использовать для изготовления мельницы, фрезера, генератора, насоса, а из барабана можно сделать даже мангал и часть декора интерьера!
instrument.guru