Сварочная проволока (назначение, требования, химический состав, маркировка)
Для сварки сталей применяется специальная стальная проволока по ГОСТу 2246-70. Используется в основном низкоуглеродистая и низколегированная сталь. Предусмотрено 77 марок сварочной проволоки различного химического состава.
К сварочной проволоке предъявляются следующие требования:
• она должна расплавляться спокойно и равномерно;
• температура плавления должна быть меньше или равна температуре плавления основного металла;
• должна быть очищенной от ржавчины и грязи;
• должна по химическому составу соответствовать химическому составу свариваемого металла.
Условное обозначение проволоки рассмотрим на примере.
2Св-08А, где:
2 – диаметр проволоки 2 мм;
Св – сварочная проволока;
08 – 0,08% – содержание углерода;
А – повышенное качество металла.
В
марке могут присутствовать две буквы
АА (Св-08АА), что говорит о том, это материал
проволоки особо качественный.
Под качеством понимается пониженное содержание в стали вредных примесей – серы и фосфора. Повышенное содержание углерода в проволоке приводит к снижению пластичности металла.
В марке проволоки могут присутствовать легирующие элементы (Св-12ГС; Св-15ГСТЮЦА):
Г – 1% марганца; С – 1% кремния.
Если после буквы, обозначающей легирующий элемент, не стоит цифра, то содержание этого элемента в стали до 1%. Цифра показывает содержание элемента в целых долях процента.
Условные обозначения легирующих элементов:
С – кремний
Н – никель
М – молибден
Т – титан
Ю – алюминий
Ц – цирконий
Г – марганец
X – хром
В – вольфрам
Ф – ванадий
Проволока различается по диаметру. Диаметр проволоки – от 1 до 12 мм.
Проволока
диаметром от 1,6 до 6 мм применяется для
ручной дуговой сварки (металлический
стержень электрода). Проволока диаметром
более 6 мм называется прутами и применяется
для сварки чугуна и цветных металлов,
наплавочных работ.
Диаметр проволоки для газовой сварки выбирается в зависимости от толщины металла и способа сварки.
Для сварки правым способом диаметр присадочной проволоки равен d=S/2.
Для сварки левым способом диаметр присадочной проволоки равен d=S/2+1.
В покрытие электродов для сварки глубоким проплавлением вводят повышенное количество органического вещества – целлюлозы ( до 30 %), рутила, карбонатов и железа. [
В
том случае, когда нежелательно глубокое
проплавление основного металла, применяют
ток меньшей силы при соответствующем
снижении скорости подачи электродной
проволоки. Изменение силы тока и скорости
подачи проволоки влияет на величину
напряжения дуги. Последняя является
весьма важным фактором режима наплавки.
Повышение напряжения приводит к
увеличению ширины валика наплавляемого
металла, росту потерь металла на
разбрызгивание, угар и окисление;
ухудшается качество наплавки, появляются
поры.
Допустим, что швы сварены без глубокого проплавления. В горизонтальных швах образуется пара сил.
При многопроходной сварке узкими швами с глубоким проплавлением наряду с горячими трещинами в центре шва, по так называемой зоне слабины, возможно образование зашлаковок, особенно в местах переходов от свариваемой кромки к наплавленному металлу. Образованию указанных включений сопутствуют либо подрез кромки, либо несплавление. В образовавшихся полостях при подрезе кромки или несплавлении, как правило, и залегают протяженные шлаковые включения, вытянутые в направлении сварки.
Объем наплавленного металла у шва с глубоким проплавлением меньше чем у обычного шва, так как всегда делают fliQ2 – Это значительно повышает производительность процесса сварки швов с глубоким проплавлением. Такой шов будет и более экономичен по расходу электроэнергии и электродов, так как он образуется зз счет большей доли расплавленного металла в металле сварного шва.
В
чем заключается сущность сварки с
глубоким проплавлением.
В слунае применения автоматической сварки, обеспечивающей глубокое проплавление основного металла, применение углового шва допускается для штуцеров с толщиной стенки до 15 мм.
В случае применения автоматической сварки, обеспечивающей глубокое проплавление основного металла, применение углового шва допускается для штуцеров с толщиной стенки до 15 мм.
Высокопроизводительным методом ручной сварки является сварка с глубоким проплавлением, иначе называемая сваркой укороченной дугой ( УКД), которую производят электродами марок ЦМ-7.
Пистолет предназначен для дуговой сварки электрозаклепками при глубоком проплавлении нахлесточных соединений стальных деталей суммарной толщиной до 30 мм. Количество деталей может быть любым. Сварка осуществляется электродом с качественным покрытием.
Благодаря высокой плотности энергии электронный луч может обеспечивать глубокое проплавление.
В чем состоит принципиальное отличие лазерной сварки с глубоким проплавлением от сварки металлов малых толщин
БИЛЕТ 8
Проволока для полуавтомата: разновидности, состав
Проволока для полуавтомата — расходный материал, применяемый для соединения металлических заготовок. Она помогает создавать прочную связь между стыкуемыми поверхностями. Так как большинство металлоконструкций испытывает повышенные нагрузки, к выбору присадочного материала стоит относиться ответственно.
Изделие используется в качестве электрода, необходимого для возбуждения сварочной дуги.
Одновременно оно является источником расплава, формирующего соединение. Она имеет вид шнура того или иного диаметра. При изготовлении присадочных элементов применяют чистые металлы или их сплавы.
Сварочная проволока используется для соединения заготовок из следующих материалов:
- разные типы стали, в том числе легированные и нержавеющие;
- алюминий и сплавы на его основе;
- цветные металлы;
- чугун.
Проволоку для сварки применяют совместно с газовыми или простыми полуавтоматическими агрегатами.
Маркировки проволоки для полуавтоматических аппаратов
Присадочный материал относится к категории промышленной продукции, технические характеристики которой регулируются ГОСТом. Принятый в 1973 г. стандарт используется и сейчас. Маркировка содержит основные сведения об изделии.
Ее компоненты можно расшифровать на примере проволоки СВ08Г2С:
- Первые 2 буквы обозначают назначение продукта. СВ — материал для сварочных работ.
- Следующие 2 символа свидетельствуют о концентрации углерода. В рассматриваемом случае она не превышает 0,08%.
- Расположенные далее буква и цифра отображают содержание марганца (2%).
- Последний символ свидетельствует о присутствии в составе кремния. Если число после буквы отсутствует, содержание элемента не превышает 1%. Если в маркировке присутствует O, изделие является омедненным.
Общее количество легирующих присадок в составе рассматриваемого изделия превышает 2,5%.
Проволока СВ08Г2С наиболее часто применяется совместно с автоматическими и полуавтоматическими аппаратами.
Основные требования к расходнику
Чтобы проволока для сварки полуавтоматом формировала надежный шов, она должна соответствовать виду соединяемых металлов. Химический состав присадочного элемента регламентируется ГОСТом, что необходимо учитывать при выборе. Неправильно подобранное изделие приводит к деформации соединения, связанной с разностью температур плавления.
Разновидности изделий для полуавтомата
Присадочные материалы классифицируют по следующим критериям:
- Сфера применения. Изделия бывают универсальными или узкоспециализированными. Второй тип используется при работах под водой или в космосе, сборке арматурных каркасов. Первая группа предназначена для общестроительных и наплавных операций.
- Структура стержня. Изделия могут иметь сплошной, порошковый или активированный сердечник.
- Тип внешнего покрытия. Присадка бывает простой или омедненной. Самозащитная проволока используется для сварки низколегированной или углеродистой стали.
- Физико-химические свойства. Объясняются концентрацией легирующих присадок.
Омедненная проволока
Изделие используют при соединении деталей из низколегированных и малоуглеродистых типов стали. Металлы при расплавлении вступают в реакцию с кислородом, на поверхности образуется оксидный налет, снижающий прочность соединения. Устранить такой эффект помогает нанесение на поверхность электрода медного покрытия. Оболочка устойчива к коррозии, она формирует защитную оболочку вокруг шва. Омедненный электрод применяется в сочетании с газовым оборудованием.
К основным его преимуществам относятся:
- высокое качество получаемого шва;
- повышенная антикоррозионная защита;
- возможность использования при наплавочных работах;
- низкая стоимость.
Гибкая нержавейка
Изделия такого типа обладают высокой устойчивостью к окислению. Они могут иметь круглое, овальное, шестигранное, квадратное сечение.
Гибкие стержни из нержавеющей стали применяются при сварке следующих конструкций:
- медицинские инструменты и оборудование;
- нефтепроводы, резервуары для хранения углеводородов;
- оборудование, используемое в металлургической промышленности.
Состав гибкого изделия утвержден ГОСТ 18143-72.
Алюминиевые изделия
Такой тип расходного материала отличается повышенной прочностью, устойчивостью к окислению, пластичностью. Он предназначен для соединения деталей из алюминия и сплавов на его основе. В качестве легирующих присадок при изготовлении электродов используют магний, марганец, кремний. Сварка ведется в защитной газовой среде. После вскрытия упаковки приступать к работе нужно немедленно, т. к. проволока начинает окисляться, что негативно сказывается на качестве шва.
Порошковые присадки
Такой элемент имеет вид полой трубки. Внутреннее пространство заполнено порошком и флюсом. Состав способствует защите сварного соединения от кислорода и попадания шлака. Важным фактором является и обеспечение безопасности сварщика. Включение в состав порошка флюса ускоряет розжиг дуги, снижает вероятность образования брызг. Применение этой разновидности электродов не требует создания газовой среды.
Другие цветные металлы
Для работы с медью, латунью и алюминием предназначена специализированная проволока, изготавливаемая из соответствующих металлов. Выпуск таких электродов регулируется ГОСТ 7871-85, согласно которому диаметр элемента должен составлять 0,8-12,5 мм.
Активированное изделие
Является разновидностью порошковых электродов. Оболочка производится из стали марки 08Г2С. Отличается увеличенной толщиной. Полость содержит порошкообразный флюс, его масса не превышает 7%. Проволоку используют при сварке в среде инертного газа. Наполнитель содержит соли щелочноземельных металлов. Особый химический состав способствует стабильному горению электрической дуги.
Совместимость с полуавтоматическими устройствами
Выбор сварочной проволоки зависит от типа агрегатов, в сочетании с которыми можно использовать расходный материал:
- Газовое оборудование. С ним совместимо около 75 видов присадочных элементов. С их помощью можно варить большинство видов металлов — чугун, сталь, титан, алюминий.
- Аппараты, не формирующие газовую среду. В сочетании с таким оборудованием используют флюсовые виды расходного материала.
Проволока не должна содержать токсичных веществ, способных выделяться в окружающую среду при нагреве.
По каким критериям выбирать
При покупке присадочного материала учитывают следующие характеристики:
- Назначение. На упаковке указывается, в каких условиях используется та или иная марка. Если состав проволоки не соответствует типам свариваемых металлов, шов получается непрочным.
- Диаметр. Этот параметр выбирают в соответствии с толщиной соединяемых заготовок.
- Количество в упаковке. Изделие продается в мотках по 1, 5 или 15 кг. Последний вариант предназначен для применения в промышленных условиях.
- Температура плавления. Она должна быть ниже таковой у соединяемых деталей.
- Отсутствие внешних дефектов. На поверхности не должно иметься следов коррозии, краски, масла.
Производители расходников для сварки
Рейтинг лучших видов сварочной проволоки включает следующие бренды:
- «Кедр».
Продукция предназначена для работы в среде инертного газа. Удобные катушки легко вставляются в барабан. 5 кг изделия хватает надолго. Материал пригоден для сварки легированной и низкоуглеродистой стали. Недостатком считается несовместимость с некоторыми типами аппаратов.
- ESAB. Шведская продукция поставляется в катушках еврообразца. Она полностью соответствует требованиям ГОСТа. При использовании проволоки ESAB образуется прочный шов, выдерживающий удары и перепады температур. Электрическая дуга горит стабильно и мягко. Недостаток — неровность укладки.
- Elitech. Продукция этого бренда считается лучшей среди порошковых разновидностей. Она поддерживает стабильную дугу, защищает сварочную ванну от попадания посторонних включений. Ровная намотка облегчает работу.
- «СварМонтажСтрой». Российская компания производит расходный материал разных марок, используемый при сварке в любых условиях. Применение европейских технологий позволяет выпускать изделия, полностью соответствующие требованиям ГОСТа.
Также стоит обратить внимание на присадочную проволоку, выпускаемую компаниями «Петромет» и «Велд-Метиз».
Сварочная проволока для полуавтоматов. Советы по выбору
Берегите глаза |
24.06.2016
Поскольку полуавтоматы для сварки сейчас довольно востребованы, это позволило создать широкий рынок производства сварочной проволоки для полуавтомата. Правильный выбор проволоки позволяет существенно повысить производительность, а также качество самой сварки и сварного шва. Дополнительно повышается и безопасность, что тоже немаловажно для квалифицированных сварщиков.
Типы и маркировка проволоки для сварки
Сварочная проволока для полуавтоматов используется как плавящийся электрод при проведении сварочных работ на полуавтомате.
Существует около 77 марок проволоки для сварки, качество и состав которых регулирует ГОСТ 2246-70. Этому стандарту полностью соответствует выпускаемая холоднотянутая проволока из низкоуглеродистой стали, легированной, а также высоколегированной стали.
Сварочная проволока для полуавтоматов подразделяется по своему назначению на:
- непосредственно для сварки;
- для изготовления электродов (дополнительное обозначение Э).
Низкоуглеродистая и легированная проволоки сортируются по виду обработки поверхности на неомеднённую и омеднённую (О).
Несмотря на большое количество различных марок проволоки для сварки полуавтоматом, в производстве и строительстве широко используют для работы всего несколько. Остальные – это марки специальные, или узкопрофильные. При изготовлении к ним предъявляют особенные требования. Такая проволока предназначается для проведения сварочных работ при строительстве научных комплексов и лабораторий, объектов атомной промышленности и для других современных отраслей промышленности, которые используют высокие технологии.
В настоящее время применяются технологии, позволяющие проводить сварку полуавтоматами не только в нейтральной среде защитного газа, но и при помощи проволоки, под слоем флюса. Тип применяемой проволоки, её диаметр и марка всегда зависят от толщины и химического состава конструкций и деталей, подлежащих сварке. В связи с этим, сварочная проволока для полуавтоматов делится на три основные категории:
- низкоуглеродистая – такие марки проволоки, как Св-08АА, Св-08, Св-10ГА, Св-08ГА и Св-10Г2;
- легированная – марки проволоки Св-12ГС, Св-08ГС, Св-10ГН, Св-08Г2С, а также Св-08ГСМТ и др.;
- высоколегированная – марки Св-10Х11НВМФ, Св-12Х11НММФ, Св-Х13,Св-20Х13 и др.
Если знать маркировку, то одного взгляда на название будет достаточно, чтобы узнать её состав. Таким образом, название Св-08Г2С говорит о следующем:
Аббревиатура Св обозначает, что данная проволока сварочная. Буквы и цифры, идущие следом, рассказывают о содержании составляющих элементов в той или иной проволоке. Далее, цифры 08 говорят о массе углерода в сотых долях процента, в этом случае здесь 0,08%. Г – сообщает о том, что в состав проволоки входит марганец, следующая цифра 2 говорит о двухпроцентном его содержании. Буква С указывает на кремний в составе проволоки, если далее цифр нет, то его содержание не превышает 1%.
В некоторых случаях необходимо знать дополнительную маркировку проволоки:
А – стоящая в конце маркировки, означает, что эта проволока с уменьшенным содержанием вредных веществ, вроде серы или фосфора, а две буквы (АА) говорят о том, что проволока содержит минимум вредных примесей, а сама проволока сделана из металла высокой очистки. Кроме того, внутри маркировки А показывает наличие в составе азота.
Х и Н – (хром, никель), в основном используются как легирующие добавки, в том случае, если изготавливается сварочная проволока для нержавейки.
Остальные элементы, встречающихся в маркировках:
В — вольфрам;
Т — титан;
Ю — алюминий;
Ф — ванадий;
Б — ниобий;
Д — медь;
М — молибден;
С — кремний;
Ц — цирконий.
Можно выделить несколько самых известных производителей проволоки для сварки. Это Компания ООО «Петромет», выпускающая такие популярные в нашей промышленности марки проволоки, как Св-08ГСНТи Св-08Г2С, Св-08ГНМ, Св-08ХМ и др. ООО «Свармонтажстрой», производство которого основано на ряде иностранных технологий и качество выпускаемых изделий соответствует основным международным нормам. Московский производитель ООО «Велд – Метиз».
Диаметры сварочной проволоки
Номинальные диаметры проволоки применяемой для сварки полуавтоматом имеют размеры от 0,3 мм до 12 мм. Всего существует 17 стандартных диаметров.
Предварительно, при сварке автоматом выбирают проволоку диаметром до 5 мм, а при полуавтоматической, механизированной – до 2 мм, в основном её диаметр зависит от толщины металла.
Для достижения требуемого качества сварочного шва, при сварке деталей и конструкций из легированных и высоколегированных сталей, химический состав самой проволоки обязательно должен быть таким, чтобы в получаемом шве содержание углерода ограничивалось 0,10 – 0,12%, а кремния было менее 0,5%.
Для сварки специализированных сталей применяются высоколегированные аустенитные и ферритные сварочные проволоки. Однако аустенитная высоколегированная сварочная проволока для полуавтоматов после волочения нагартовывается (нагартовка – наклёп) и становится более жёсткой, а её пластичность снижается. В связи с этим подача проволоки такого малого диаметра от 2 – 3 мм по шлангам при сварке полуавтоматом, облегчается, в отличие от подачи проволоки большего диаметра.
Сварка с применением газовой смеси отличается лучшими техническими показателями. Поэтому в настоящее время повсеместно используют смесь углекислого газа и нейтрального аргона, имеющую процентное соотношение – 75-80% Ar и 20-25% CO2.
Контроль расхода сварочной проволоки
В процессе сварки на полуавтомате, необходимо вести учёт расхода проволоки для сварки и газовых смесей. Это обеспечивает экономию расходных материалов на производстве и ведёт к снижению себестоимости самих работ.
На расход проволоки для сварки оказывают влияние такие показатели как:
- химический состав металла;
- диаметр и качество самой проволоки;
- данные технических характеристик рабочего полуавтомата для сварки;
- проведение сварки в среде нейтрального газа.
Во многих случаях, расход используемой сварочной проволоки считается до 1,5 % от веса всей конструкции. А вес проволоки превышает вес наплавляемого материала до 6%, так как имеют место угар и отходы.
Нормы расхода определённых марок проволоки на метр сварочного шва определяются по формуле М = НР ∙ КР. (где М – масса наплавляемого металла, напрямую зависящая и от металла, и от вида сварочного шва). КР – коэффициент расхода используемой проволоки (значение берётся из таблиц).
Исходя из данной формулы рассчитывают потребность в сварочной проволоке не только для конкретного вида работ, но и для всего предприятия в течение времени.
Современные механизмы и скорость подачи сварочной проволоки
Сварочные полуавтоматы классифицируют следующим образом:
- для сварки изделий в защитных газах;
- для сварки с помощью порошковой проволоки;
- для выполнения сварки под флюсом;
- универсальные.
Полуавтоматы для сварки с применением защитных газов оборудованы специальным клапаном, прекращающим подачу рабочего газа по окончании сварки.
В полуавтоматах для сварки под флюсом всегда есть горелка с воронкой. Осуществляется более мощная подача проволоки, чем на другом оборудовании, поскольку для этой сварки необходима проволока большого диаметра.
Сварочные полуавтоматы разделяют на бытовые, полупрофессиональные и профессиональные, в зависимости от силы тока и длительности работы самого аппарата. А также бывают передвижными, стационарными и переносными. Промышленные полуавтоматы изготавливают только для работы в режиме трёхфазного тока. Швы, получаемые при использовании в работе таких аппаратов гораздо более качественные и ровные.
Полуавтоматы для сварки современной порошковой проволокой снабжены специальным устройством подающих роликов, чтобы не допустить деформации рабочей проволоки.
Универсальные полуавтоматы укомплектованы вспомогательными приспособлениями (сварочными горелками, роликами для подачи проволоки и др.), что даёт возможность с успехом использовать их для различных видов сварки.
К механизму подачи проволоки к горелке относятся – электродвигатель, редуктор и, конечно, подающие ролики. Вид подающего устройства (относительно газовой горелки), может быть тянущий, толкающий и универсальный. При подаче проволоки устройством толкающего типа, подающие ролики находятся у самого шланга сварочной горелки и равномерно толкают проволоку непосредственно в канал горелки. Используется всегда при сварке стали.
С помощью подачи проволоки на полуавтомате механизмом тянущего типа проволока попадает в канал горелки. Это придаёт ей дополнительный вес, но тем не менее, такой механизм часто устанавливают в полуавтоматах для сварки алюминия. Сварочная проволока для полуавтоматов служит не только для улучшения качества шва, но и непрерывности сварочных работ. Подачу тянуще – толкающего типа применяют для сварки алюминия в случае значительного удаления основного сварочного механизма от места сварки.
Скорость подачи проволоки необходимо настраивать для каждого случая и регулировать по ходу работ. Основную регулировку скорости подачи выполняет коробка передач и комплект шестерён. В таком случае приводом служит трёхфазный асинхронный двигатель. Недостатком данной регулировки скорости является трудность подбора необходимого режима для сварки. Особенно при работе с тонким металлом.
Плавное регулирование необходимой скорости подачи проволоки очень малого диаметра достигается при использовании в работе двигателя постоянного тока, путём плавного изменения числа оборотов головки двигателя. Скорость подачи может доходить до 150 м/ час.
При настройке скорости подачи важна толщина металла, состав и диаметр выбранной сварочной проволоки. Получить качественный сварочный шов возможно только при тщательной регулировке скорости путём нескольких пробных сварок.
Резиновая киянка. Молоток с мягким характером
Малка-угломер. Незаменимый транспортир строителя
Урок по теме: “Сварочная проволока”
Министерство образования и науки Пермского края
Государственное автономное профессиональное образовательное учреждение
«КРАЕВОЙ политехнический колледж»
ПЛАН УЧЕБНОГО ЗАНЯТИЯ
по теме: «Сварочная проволока»
Разработала преподаватель:
Чернов А. П.
План учебного занятия
Учебный предмет: «Специальная технология»
Специальность: «Электрогазосварщик» 3 разряд
Тема программы: «Сварочные материалы для газовой сварки и резки»
Тема учебного занятия: « Сварочная проволока»
Цели:
Обучающая: сформировать знания о сварочной проволоке, её маркировке и химическом составе, применяемой для газовой сварки сталей, чугуна и цветных металлов;
Развивающая: развивать у учащихся самостоятельное умение преодолевать трудности в учении;
Воспитательная: воспитание положительного интереса к изучаемому материалу;
Методическая: использование
учебной презентации и опорного конспекта для активизации учебно-познавательной
деятельности учащихся.
Материально-техническое оснащение: опорный конспект, мультимедийная установка, компьютер, экспресс-опрос, презентация.
Тип учебного занятия: формирование новых знаний.
Межпредметные связи: «Материаловедение», «Химия», «Охрана труда».
Структура учебного занятия
1. Организационный момент
2. Целевая установка мотивации предстоящей деятельности
3. Формирование новых знаний по теме
4. Закрепление нового материала
5. Подведение итогов
6. Информация о домашнем задании
Ход учебного занятия
I. Организационный момент
1. Проверка наличия учащихся
2. Отметка отсутствующих
3. Проверка готовности к учебному занятию
II. Целевая установка мотивации предстоящей деятельности
Преподаватель: объявляет тему и цели учебного занятия, обращая внимание на значимость темы

Мы начинаем с вами изучать новый раздел «Сварочные материалы для газовой сварки и резки». Этот раздел включает 6 учебных занятий.
Способ газовой сварки стал применяться в конце XX века, когда началось промышленное производство ацетилена и кислорода. Сравнительная простота и портативность оборудования, большая универсальность способа делают газовую сварку незаменимой для соединения деталей из низкоуглеродистых сталей, а также при сварке трубопроводов, чугуна, цветных металлов и сплавов.
Источником нагрева при газовой сварке служит пламя сварочной горелки, получаемое сжиганием горючего газа в смеси с чистым кислородом. Газовая сварка может выполняться без сварочной проволоки и с её применением.
III.Формирование новых знаний по теме
Преподаватель: тема нашего учебного занятия « Сварочная проволока» (приложение 1слайд 2).
На учебном занятии мы с вами рассмотрим следующие вопросы:
1.
Назначение и выбор сварочной проволоки.
2. Маркировка и химический состав стальной сварочной проволоки.
3. Маркировка и химический состав чугунных прутков для сварки чугуна.
4. Маркировка и химический состав присадочных материалов для сварки цветных металлов.
5.Требования, предъявляемые к присадочному металлу при газовой сварке и резке
1. Назначение и выбор сварочной проволоки (приложение 1слайд 3).
Преподаватель:
Сварочная проволока является присадочным материалом и служит для заполнения зазора между кромками свариваемого металла и образования валика шва. В процессе сварки двух элементов проволока подводится к месту шва и плавится вместе с кромками металлов, заполняя шов. Таким образом, присадочная проволока служит материалом, который восполняет потери на разбрызгивание металла при сварке. Помимо проволоки в качестве присадочного материала можно использовать присадочные прутки и ленты.
Диаметр сварочной проволоки для газовой
сварки выбирается в зависимости от состава, толщины металла и способа сварки.
2. Маркировка и химический состав стальной сварочной проволоки (приложение 1слайд 4,5,6)
Преподаватель:
Сварочная проволока поставляется в мотках массой не более 80 кг. На каждый моток проволоки крепят бирку, где указывается завод-изготовитель, условное обозначение проволоки, номер партии.
Марки сварочной проволоки применяют по ГОСТ 2246—70, который включает в себя 6 марок низкоуглеродистой, 30—легированной, 41—высоколегированной неомедненной и омедненной проволоки. Для сварки изготовляют стальную холоднотянутую проволоку диаметром 0,3; 0,5; 0,8; 1,0; 1,2; 1,4; 1,6; 2,0; 2,5; 3,0; 4,0; 5,0; 6,0; 8,0; 10,0; 12,0 мм.
Обозначение сварочной проволоки состоит из
букв Св (сварочная) и буквенно-цифрового обозначения ее состава. Легирующие
элементы, содержащиеся в металле проволок, обозначаются: Б — ниобий, В —
вольфрам, Г — марганец, Д—медь, М —молибден, Н — никель, С — кремний, Ф —
ванадий, X — хром, Ц — цирконий, Ю — алюминий. Цифры после букв Св указывают на
содержание в проволоке углерода в сотых долях процента, а цифры после
буквенного обозначения легирующего элемента указывают на содержание данного
элемента в составе проволоки в процентах. Отсутствие цифр после буквы означает,
что данного легирующего элемента в проволоке меньше одного процента. Буква А в
конце условного обозначения марок низкоуглеродистой и легированной проволоки
указывает на повышенную чистоту металла по содержанию серы и фосфора. Сдвоенная
буква А указывает на пониженное содержание серы и фосфора по сравнению с
проволокой, в обозначении которой одна буква А.
Например, проволока сварочная диаметром 4 мм, марки Св-08А, с омедненной поверхностью обозначается 4Св-08А-О ГОСТ 2246—70. Проволока сварочная диаметром 3 мм, марки Св-08Г2С, с неомедненной поверхностью —ЗСв-08Г2С ГОСТ 2246—70.
Химический состав некоторых марок сварочной проволоки, применяемой, для газовой сварки углеродистых и легированных сталей приведен в табл. 1.
3. Маркировка и химический состав чугунных прутков для сварки чугуна (приложение 1слайд 7,8,9)
Преподаватель:
Чугунные прутки для сварки и наплавки выпускаются по
ГОСТ 2671-70 и в зависимости от назначения изготовляются следующих марок: А –
для горячей газовой сварки, Б – для газовой сварки с местным подогревом и для
электродных стержней, НЧ-1 – для низкотемпературной газовой сварки тонкостенных
отливок, НЧ-2 – для низкотемпературной газовой сварки толстостенных отливок, БЧ
и ХЧ – для износостойкой наплавки.
Размеры и химический состав чугунных прутков всех марок приведены в табл. 2 и 3.
Прутки маркируются с одного торца краской следующих цветов:
· марки А – белой;
· марки Б – красной;
· марки НЧ-1 – зелёной;
· марки НЧ-2 – синей;
· марки БЧ – жёлтой;
· марки ХЧ – серой.
Таблица.1
Химический состав сварочной стальной проволоки
Таблица 2.
Размеры чугунных прутков
Диаметр прутка, мм | Длина прутка, мм | Стрела прогиба, мм, не более |
4 | 250 | 1,5 |
6 | 350 | 2,0 |
8-10 | 450 | 3,0 |
12-16 | 450 | 3,0 |
Таблица 3.
Марки и химический состав чугунных прутков для газовой сварки чугуна
Марка прутка | Химический состав, % | Ni
| Примеси, не более | |||||||
С | Si | Mn | S, не более | P | Ti | Cr | Cr | Ni | ||
А | 3-3,5 | 3-3,4 | 0,5-0,8 | 0,08 | 0,2-0,4 | – | – | – | 0,05 | 0,3 |
В | 3-3,5 | 3,5-4, | 0,5-0,8 | 0,08 | 0,3-0,5 | – | – | – | 0,05 | – |
НЧ-1 | 3-3,5 | 3-3,4 | 0,5-0,8 | 0,05 | 0,2-0,4 | 0,03-0,06 | – | 0,4-0,6 | 0,05 | – |
НЧ-2 | 3-3,5 | 3,5-4, | 0,5-0,8 | 0,05 | 0,2-0,4 | 0,03-0,06 | – | 0,4-0,6 | 0,05 | – |
БЧ | 2,5-3 | 1-1,5 | 0,2-0,6 | 0,05 | не более 0,1 | – | 1,2-2 | – | – | – |
ХЧ | 2,5-3 | 1,2-1,5 | 0,5-0,8 | 0,05 | не более 0,1 | – | 1,2-2 | – | – | – |
4. Маркировка и химический состав
присадочных материалов для сварки цветных металлов (приложение 1слайд
10,11,12,13)
Преподаватель:
Для сварки цветных металлов промышленность выпускает сварочную проволоку с соответствующим химическим составом.
Так, проволока для сварки алюминия и его сплавов выпускается диаметром от 0,8 до 12,0 мм. Она может быть тянутой или прессованной. Тянутая проволока поставляется в нагартованном состоянии только в бухтах. Горячепрессованная проволока может поставляться как бухтах, так и в виде прутков не короче 3 м. Бухты упаковывают во влагонепроницаемую бумагу, рогожу или мешковину. К каждой бухте прикрепляется бирка, на которой указываются: завод-изготовитель, номер плавки, условное обозначение проволоки, масса мотка и слова: «Боится сырости и ударов».
Химический состав алюминиевой проволоки указан в табл. 4. и должен соответствовать свариваемому сплаву.
При сварке меди в
качестве присадочного материала выступает медная проволока или прутки из чистой
меди или с небольшим содержанием примесей фосфора или фосфора и кремния.
Сварочная проволока изготавливается диаметром 0,8; 1,0; 1,2;,1,4; 1,6; 1,8; 2,0; 2,5; 3,0; 4,0; 5,0; 6,0 и 8,0 мм, а сварочные прутки диаметром 6,0 и 8,0 мм. Проволока и прутки могут поставляться как в мягком (отожженном), так и в твёрдом состоянии.
Таблица 4.
Маркировка и состав алюминиевой проволоки
Марки сплавов | Массовая доля элементов, % |
| |||||
| |||||||
Алюминий | Магний | Марганец | Железо | Кремний | Титан | ||
Св-А99 Св-А97 Св-А85Т | Не менее 99,99 Не менее 99,97 Остальное | — | — | 0,2—0,5 |
| ||
Св-А5, Св-АМн | Не менее 99,5 Остальное | — | 1,0-1,5 | 0,2-0,35 0,3-0,5 | 0,10—0,25 0,2—0,4 | — |
|
Св-АМгЗ | То же | 3,2-3,8 | 0,3—0,6 | — | 0,5—0,8 | — |
|
Св-АМг6 | » | 4,8-5,8 | 0,5-0,8 | — | — | 0,1—0,2 |
|
Св-1557 Св-АМг6 | 4,5-5,5 5,8—6,8 | 0,2-0,6 0,5-0,8 | — | — | Хром |
| |
Св-АМг63 | » | 5,8-6,8 | 0,5-0,3 | — | — | — |
|
СвА-Мг61 | » | 5,5—6,5 | 0,8-1,1 | — | — | — |
|
Св-АК5 | » | — | — | — | 4,5—6,0 . | 0,1-0,2 |
|
Св-АК10 | » | — | — | — | 7,0—10,0 | — |
|
Св-1201 | » | Медь 6,0—6,8 | 0,2-0,4 | — | Ванадий 0,05—0,15 | 0,1—0,2 |
|
- Ml – проволока для сварки неответственных конструкций на основе меди;
- М1р, МЗр – проволока для газовой сварки медных конструкций общего назначения;
- MCpl – для сварки ответственных электротехнических конструкций;
- JI63 – для газофлюсовой сварки латуни;
- ЛК62-0,5 – для газовой сварки латуни;
- JIO60-1 – для газофлюсовой сварки латуни, легированной оловом;
- ЛКБО62-0,2-0,04-0,5 – для газовой сварки и пайки меди и латуни без применения флюса;
- ЛМц58-2, ЛЖМц59-1-1, ЛОК59-1-0,3 – для сварки
латуни, пайки меди и меди с латунью.
5. Требования, предъявляемые к присадочному металлу при газовой сварке и резке (приложение 1слайд 14)
Преподаватель:
Присадочный металл при газовой сварке должен отвечать следующим требованиям:
· температура плавления присадочного металла должна быть не выше температуры плавления основного металла;
· поверхность проволоки и стержней должна быть ровной и чистой — без окалины, ржавчины, масла, краски и других загрязнений;
· присадочный металл должен плавиться спокойно, без разбрызгивания, способствуя получению наплавленного металла, по свойствам близкого к основному;
· присадочный металл должен содержать минимальное количество вредных примесей;
· диаметр присадочной проволоки и прутков должен соответствовать толщине свариваемых элементов;
· получившийся сварной шов должен быть ровным, без трещин и пор в металле.
IV. Закрепление нового материала:
Преподаватель: мы сегодня с
вами изучили тему «Сварочная проволока». Для закрепления темы необходимо
ответить на экспресс-опрос:
1. Пояснить назначение сварочной проволоки (приложение 1 слайд 15)
Эталон ответа:
Сварочная проволока является присадочным материалом и служит для заполнения зазора между кромками свариваемого металла и образования валика шва. В процессе сварки двух элементов проволока подводится к месту шва и плавится вместе с кромками металлов, заполняя шов. Таким образом, присадочная проволока служит материалом, который восполняет потери на разбрызгивание металла при сварке.
2. Перечислите, от чего зависит выбор диаметра сварочной проволоки (приложение 1 слайд 16).
Эталон ответа:
Диаметр сварочной проволоки для газовой сварки выбирается в зависимости от состава, толщины металла и способа сварки.
3. Поясните, каких диаметров выпускается стальная сварочная проволока (приложение 1 слайд 17)?
Эталон ответа:
Для сварки изготовляют
стальную холоднотянутую проволоку диаметром 0,3; 0,5; 0,8; 1,0; 1,2; 1,4; 1,6;
2,0; 2,5; 3,0; 4,0; 5,0; 6,0; 8,0; 10,0; 12,0 мм.
4. Поясните обозначение сварочной стальной проволоки (приложение 1 слайд 18).
Эталон ответа:
Обозначение сварочной
проволоки состоит из букв Св (сварочная) и буквенно-цифрового обозначения ее состава.
Легирующие элементы, содержащиеся в металле проволок, обозначаются: Б — ниобий,
В — вольфрам, Г — марганец, Д—медь, М —молибден, Н — никель, С — кремний, Ф —
ванадий, X — хром, Ц — цирконий, Ю — алюминий. Цифры после букв Св указывают на
содержание в проволоке углерода в сотых долях процента, а цифры после
буквенного обозначения легирующего элемента указывают на содержание данного
элемента в составе проволоки в процентах. Отсутствие цифр после буквы означает,
что данного легирующего элемента в проволоке меньше одного процента. Буква А в
конце условного обозначения марок низкоуглеродистой и легированной проволоки
указывает на повышенную чистоту металла по содержанию серы и фосфора. Сдвоенная
буква А указывает на пониженное содержание серы и фосфора по сравнению с
проволокой, в обозначении которой одна буква А.
5. Расшифруйте марку сварочной проволоки 3,0Св-08Г2С ГОСТ 2246—70 (приложение 1 слайд 19).
Эталон ответа:
Сварочная проволока диаметром 3мм, содержание углерода 0,08 %, легирована марганцем до 2 % и кремнием до 1%, с неомеднённой поверхностью.
6. Перечислите марки чугунных прутков и их назначение (приложение 1 слайд 20).
Эталон ответа:
Чугунные прутки для сварки и наплавки выпускаются по ГОСТ 2671-70 и в зависимости от назначения изготовляются следующих марок: А – для горячей газовой сварки, Б – для газовой сварки с местным подогревом и для электродных стержней, НЧ-1 – для низкотемпературной газовой сварки тонкостенных отливок, НЧ-2 – для низкотемпературной газовой сварки толстостенных отливок, БЧ и ХЧ – для износостойкой наплавки.
7. Поясните маркировку чугунных прутков (приложение 1слайд 21).
Эталон ответа: Прутки
маркируются с одного торца краской следующих цветов: марки А – белой; марки Б –
красной; марки НЧ-1 – зелёной; марки НЧ-2 – синей; марки БЧ – жёлтой; марки ХЧ
– серой.
8. Перечислите элементы, входящие в состав чугунных прутков (приложение 1 слайд 22).
Эталон ответа:
В состав чугунных прутков входят следующие химические элементы: железо, углерод, кремний, марганец, сера, фосфор, титан, хром, никель.
9. Перечислите виды проволоки для сварки алюминия и охарактеризуйте их (приложение 1 слайд 23).
Эталон ответа:
Проволока для сварки алюминия может быть тянутой или прессованной. Тянутая проволока поставляется в нагартованном состоянии только в бухтах. Горячепрессованная проволока может поставляться как бухтах, так и в виде прутков не короче 3 м.
10. Поясните условия упаковки проволоки для сварки алюминия (приложение 1 слайд 24).
Эталон ответа:
Бухты упаковывают во
влагонепроницаемую бумагу, рогожу или мешковину. К каждой бухте прикрепляется
бирка, на которой указываются: завод-изготовитель, номер плавки, условное
обозначение проволоки, масса мотка и слова: «Боится сырости и ударов».
11. Перечислите марки медной проволоки и ее назначение (приложение 1 слайд 25).
Эталон ответа:
Для сварки меди и её сплавов используются следующие марки:
- Ml – проволока для сварки неответственных конструкций на основе меди;
- М1р, М3р – проволока для газовой сварки медных конструкций общего назначения;
- MCpl – для сварки ответственных электротехнических конструкций;
- JI63 – для газофлюсовой сварки латуни;
- ЛК62-0,5 – для газовой сварки латуни;
- JIO60-1 – для газофлюсовой сварки латуни, легированной оловом;
- ЛКБО62-0,2-0,04-0,5 – для газовой сварки и пайки меди и латуни без применения флюса;
- ЛМц58-2, ЛЖМц59-1-1, ЛОК59-1-0,3 – для сварки латуни, пайки меди и меди с латунью.
12. Перечислить
основные требования, предъявляемые к присадочному металлу при газовой сварке и резке (приложение 1
слайд 26).
Эталон ответа:
Присадочный металл при газовой сварке должен отвечать следующим требованиям:
· температура плавления присадочного металла должна быть не выше температуры плавления основного металла;
· поверхность проволоки и стержней должна быть ровной и чистой — без окалины, ржавчины, масла, краски и других загрязнений;
· присадочный металл должен плавиться спокойно, без разбрызгивания, способствуя получению наплавленного металла, по свойствам близкого к основному;
· присадочный металл должен содержать минимальное количество вредных примесей;
· диаметр присадочной проволоки и прутков должен соответствовать толщине свариваемых элементов;
получившийся сварной шов должен быть ровным, без трещин и пор в металле.
V. Подведение итогов учебного занятия
Преподаватель
подводит итог работы пройденного учебного занятия в целом. Выставляет оценки с
мотивировкой. Организовывает проведение рефлексии по пройденному учебному
занятию: учащиеся поднимают заготовленные листы с рожицами:
побольше таких учебных занятий, поучительно
понравилось, но не всё, интересно
не понравилось, скучно
VI. Информация о домашнем задании
И.И.Соколов «Газовая сварка и резка металлов. -М.: Высшая школа, 1981, стр.34-37
Расшифруйте Св-08АА, Св-12Х11НМФ
Проволока сварочная СВ-08А — Ковка, сварка, кузнечное дело
Проволока сварочная СВ-08А применяется для автоматической сварки углеродистых сталей под флюсом с пределом текучести 235-285Мпа и для производства электродов с повышенной вязкостью и пластичностью шва, предназначенных для сваривания низколегированной и низкоуглеродистой стали.
Буква «А» в наименовании данной проволоки указывает на повышенную чистоту химического состава металла по содержанию фосфора и серы, «СВ» обозначает – сварочная, а «08» — содержание углерода (C).
Влияние содержания углерода, фосфора, марганца и серы в сварочной проволоке на механические характеристики шва
- Содержание углерода – с уменьшением содержания углерода (С) в сварочной проволоке наплавленный сварочный шов становится пластичнее.
- Содержание серы и фосфора — с уменьшением содержания фосфора (Р) и серы (S) увеличивается надежность сварного шва соединения.
- Содержание марганца – марганец (Мn) упрочняет сварной шов соединения.
Химический состав проволоки сварочной СВ-08А
- Углерод (С) — менее 0,10%.
- Марганец (Mn) — 0,35 — 0,60%.
- Кремний (Si) — менее 0,30%.
- Сера (S) — менее 0,03%.
- Фосфор (P) — менее 0,03%.
- Медь (Cu) — менее 0,25%.
- Хром (Cr) — менее 0,12%.
- Никель (Ni) — менее 0,25%.
Проволока поставляется в мотках, которые упакованы в полиэтилен и бумагу. Поставка может осуществляться также и без упаковки или в большегрузных бухтах весом 1-1,3 тонны. Проволока сварочная СВ-08А изготавливается диаметром от 0. 8 до 7.0мм. Для обеспечения хорошего контакта в сварочном аппарате с целью обеспечения минимальных потерь напряжения, проволока с диаметрами 0,8; 1,0; 1,2; 1,4 и 1,6мм производится с медным покрытием толщиной не менее 0,15мм.
Требования, предъявляемые к сварочной проволоке
Основным требованием, предъявляемым к сварочной проволоке, является соответствие состава проволоки составу металла, из которого изготовлены свариваемые детали и конструкции. Температура плавления сварочной проволоки должна практически равняться температуре свариваемого металла, сам процесс плавления должен происходить равномерно, а проволока должна быть чистой и не окисленной.
kovka-svarka.net
Характеристики проволоки сварочной
Св-08, Св-08А, Св-08АА
— автоматическая сварка под флюсом углеродистых сталей с пределом текучести 235-285 МПа, изготовление электродов, предназначенных для сварки низкоуглеродистой и низколегированной стали.
Св-08Г1НМА
— автоматическая сварка под флюсом низколегированных сталей повышенного уровня прочности и хладостойкости Предназначена для однопроходной одно- или двусторонней сварки под флюсом сталей толщиной до 25 мм различного типа легирования и категорий прочности. (К55-К65)
Св-08Г2С
— механизированная сварка в защитных газах конструкций ответственного и общего назначения.
Св-08ГА
— автоматическая сварка под флюсом углеродистых сталей с пределом текучести 235-440 МПа. (конструкций мостов, опор, труб, трубопроводов и котлов, работающих при высоких давлениях и температурах)
Св-08ГСНТ
— предназначена для механизированной сварки в защитных газах, применяется в судостроении и химическом машиностроении.
Св-08ХМ
— автоматическая сварка под флюсом нефтегазопроводных труб и металлоконструкций ответственного назначения из углеродистых и низколегированных сталей с пределом текучести 235-440 МПа. (конструкций мостов, опор, труб, трубопроводов и котлов, работающих при высоких давлениях и температурах)
Св-10Г2
— автоматическая сварка под флюсом углеродистых сталей с пределом текучести 235-440 МПа.
Св-10ГА
— автоматическая сварка под флюсом углеродистых и низколегированных сталей с пределом текучести 235-440 МПа Св-ЮГН — механизированная сварка под флюсом в судостроении и химическом машиностроении.
Св-10НМА
— автоматическая сварка под флюсом низколегированных сталей повышенного уровня прочности и хладостойкости металлоконструкций ответственного назначения. (конструкций мостов, опор, котлов, труб и трубопроводов работающих при высоких давлениях и температурах)
Низкоуглеродистая | Легированная | Высоколегированная |
СВ-08 СВ-08А СВ-08АА СВ-08ГА СВ-ЮГА СВ-10Г2 | СВ-08ГС СВ-12ГС СВ-08Г2С СВ-ЮГН СВ-08ГСМТ СВ-15ГСТЮЦА СВ-20ГСТЮА СВ-18ХГС СВ-ЮНМА СВ-08МХ СВ-08ХМ СВ-18ХМА СВ-08ХНМ СВ-08ХМФА СВ-10ХМФТ СВ-08ХГ2С СВ-08ХГСМА СВ-10ХГ2СМА СВ-08ХГСМФА СВ-04Х2МА СВ-13Х2МФТ СВ-08Х3Г2СМ СВ-08ХМНФБА СВ-08ХН2М СВ-10ХН2ГМТ СВ-08ХН2ГМТА СВ-08ХН2ГМЮ СВ-08ХН2Г2СМЮ СВ-06Н3 СВ-10Х5М | СВ-12Х11НМФ СВ-10Х11НВМФ СВ-12Х13 СВ-20Х13 СВ-06Х14 СВ-08Х14ГНТ СВ-10Х17Т СВ-13Х25Т СВ-01Х19Н9 СВ-04Х19Н9 СВ-08Х16Н8М2 СВ-08Х18Н8Г2Б СВ-07Х18Н9ТЮ СВ-06Х19Н9Т СВ-04Х19Н9С2 СВ-08Х19Н9Ф2С2 СВ-05Х19Н9ФЗС2 СВ-07Х19Н10Б СВ-08Х19Н10Г2Б СВ-06Х19Н10М3Т СВ-08Х19Н10М3Б СВ-04Х19Н11М3 СВ-05Х20Н9ФБС СВ-06Х20Н11М3ТБ СВ-10Х20Н15 СВ-07Х25Н12Г2Т СВ-06Х25Н12ТЮ СВ-07Х25Н13 СВ-08Х25Н13БТЮ СВ-13Х25Н18 СВ-08Х20Н9Г7Т СВ-08Х21Н10Г6 СВ-30Х25Н16Г7 СВ-10Х16Н25АМ6 СВ-09Х16Н25М6АФ СВ-01Х23Н28М3Д3Т СВ-30Х15Н35В3Б3Т СВ-08Н50 СВ-05Х15Н60М15 |
Проволока сварочная СВ08А 3.
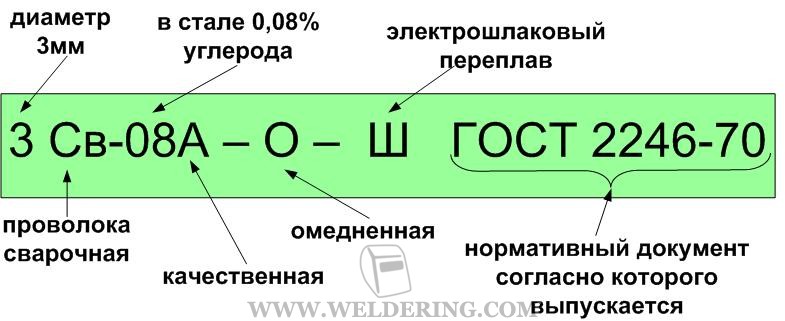
СВ08А (1000 кг) ТУ 14-4-828-77 диаметр от 2,0мм до 6,0мм Сварочная проволока СВ-08А применяется для сварки ацитиленокислородным пламенем углеродистых конструкци
Сварочная проволока это один из неотъемлемых элементов сварочного процесса, необходимая для обеспечения качественной сварки.
Сварочная проволока делится по назначению, способу обработки, составу и алгоритму производства.
Примеры применения сварочной проволоки:
1) сварочная проволока применяется как плавящийся электрод при использовании электродуговой полуавтоматической сварки. При этом сварочная проволока может быть как порошковой так и сплошной, самозащитной или газозащитной. Если сварочная проволока применяется в среде защитных газов, то при сварке можно изменять металлический состав шва, регулируя состав применяемой сварочной проволоки и защитного газа.
2) при использовании аргонодуговой сварки неплавящимся электродом, сварочная проволока применяется в качестве присадки. Использование присадки необходимо для того чтобы усилить шов или заполнить разделку кромок основного металла, при толщине более 3мм. Подаваться проволока может как в ручную так и механизмом подачи.
Сварочная проволока также может быть газосварочной, нержавеющей алюминиевой, омеднённой и неомеднённой.
Применение различных марок сварочных проволок:
Сварочная проволока СВ-08Г2С применяют для сварки низколегированных и низкоуглеродистых сталей в углекислом газе, в различных газовых смесях и под флюсом.
Стальная нержавеющая сварочная проволока применяется для сварки нержавеющих сталей таких как 08х18н10т, 12х18н9т, 08х18н10 и других. Отрасли в которых применяется данная проволока: изготовление трубопроводов, в нефтехиммашиностроении, в энергетике и пищевой промышленности и т.д.
Алюминиевая сварочная проволока применяется для сварки алюминиевых конструкций и сплавов Al-Mg, Al-Mn.
Омеднённая сварочная проволока применяется для дуговой сварки в газовой среде углеродистых и низкоуглеродистых сталей, судостроительной и конструкционной сталей, а так же стали для сосудов находящихся под высоким давлением.
Примененяется проволока сварочная для изготовления электродов и электродуговой сварки.
krafft.tiu.ru
Проволока ГОСТ 2246 для сварки. Проволока СВ08А
ГОСТ 2246-70 определяет характеристики проволоки для сварки различных марок. Кроме того, она может использоваться для наплавки и для производства электродов.
Проволоку ГОСТ 2246-70 для сварки делят в зависимости от марки стали на:
- проволоку низкоуглеродистую сварочную — марок СВ08, СВ08А, СВ08ГА
- проволоку легированную сварочную — марок СВ08ГС, СВ12ГС, СВ08Г2С, СВ10ГН, СВ08ГСМТ, СВ15ГСТЮЦА (ЭП-439), СВ20ГСТЮА, СВ18ХГС и других
- проволоку высоколегированную сварочную — марок СВ12Х13, СВ12Х11НМФ, СВ10Х11НВМФ, СВ13Х25Т, СВ01Х19Н9, СВ20Х13, СВ06Х14, СВ08Х14ГНТ, СВ10Х17Т и других.
По виду покрытия производится: черная и омедненная сварочная проволока.
Некоторые марки сварочной проволоки, например, проволока СВ08А и СВ08, применяется также для изготовления сварочных электродов разных марок — УОНИ 13/55, МР-3, УОНИ 13/45, АНО-21 и т. д.
Химсостав приведен в таблице:
Элемент, % Марка стали низкоуглеродистая легированная Св08 Св08А Св08ГА Св08ГС Св08Г2С Св08ХМ С не более Мn Si не более РS Сr не болееNi не болееAl не болееСu не более
0,10 | 0,10 | 0,10 | 0,10 | 0,10 | 0,06-0,10 |
0,35-0,60 | 0,35-0,60 | 0,80-1,1 | 1,40-1,70 | 1,80-2,10 | 0,35-0,60 |
0,03 | 0,03 | 0,06 | 0,60-0,85 | 0,70-0,95 | 0,12-0,30 |
0,040 | 0,030 | 0,030 | 0,030 | 0,030 | 0,030 |
0,040 | 0,030 | 0,025 | 0,025 | 0,025 | 0,025 |
0,15 | 0,12 | 0,10 | 0,20 | 0,20 | 0,9-1,2 |
0,30 | 0,25 | 0,25 | 0,25 | 0,25 | 0,30 |
0,01 | 0,01 | — | — | — | — |
0,25 | 0,25 | 0,25 | 0,25 | 0,25 | 0,25 |
Проволока ГОСТ 2246-70, в зависимости от диаметра и используемой марки стали может поставляться в мотках по 80-100 кг. , в больших бухтах по 800-1000 кг., а также на специальных пластиковых катушках или металлических каркасах.
Сварочная проволока обычно упаковывается в ткань или влагостойкую бумагу. Проволока для производства электродов СВ08А и СВ08 в бухтах поставляется без упаковки.
profmetiz.ru
Сварочная проволока для наплавки. Химический состав сварочной проволоки.
Сварочная проволока для наплавки. Химический состав сварочной проволоки. 5.00/5 (100.00%) проголосовало 11
Наплавочная проволока изготавливается согласно ГОСТ 2246-70, предназначена для всех видов наплавки и изготовления электродов. Согласно ГОСТа проволока выпускается диаметрами: 0,3; 0,5; 0,8; 1,0; 1,2; 1,4; 1,6; 2,0; 2,5; 3,0; 4,0; 5,0; 6,0; 6,5; 8,0; 10,0; 12 мм. При изготовлении электродов используют проволоку диаметром от 1,6 до 8,0 мм.
Поставка проволоки заказчику производится в мотках весом не более 40 кг и внутренними диаметрами от 150 до 750 мм. Для удобства установки на сварочный аппарат наплавочная проволока может наматываться на катушки. Мотки наплавочной проволоки должны быть обернуты в водонепроницаемую бумагу. На каждом мотке должна присутствовать бирка с названием предприятия, маркой проволоки и номером партии.
Хранят проволоку в сухим помещениях, защищающих от атмосферных осадков, коррозии и грязи. Возможно омеднение проволоки для лучшей защиты от коррозии.
ГОСТ 2246-70 проволока сварочная.
По ГОСТ 2246-70 выпускают 77 различных марок наплавочной проволоки, которые в свою очередь, в зависимости от химического состава, можно разделить на группы:
— низкоуглеродистая наплавочная проволока;
— легированная наплавочная проволока;
— высоколегированная наплавочная проволока.
В таблице 1 ниже представлены некоторые из этих марок.
Маркировка сварочной проволоки.
На примере проволоки Св-08А разберем что означает каждая буква и цифра.
Св-08А
— индекс Св означает, что она сварочная;
— цифры 08 указывают на содержание в проволоке углерода в процентах;
— буква А указывает на содержание в проволоке главных элементов. В высоколегированных проволоках буквой А обозначают азот, в низкоуглеродистых и легированных буква А указывает на повышенную чистоту металла по содержанию серы и фосфора.
Если в конце обозначения после буквы присутствуют еще цифры, значит они указывают на процентное содержание данного элемента, например:
Св-10Г2
Значит, что в данном составе проволоки содержится до 2% марганца. Буква Г означает марганец, а цифра рядом с ним его процентное содержание в сотых долях.
Если рядом с элементом отсутствует цифра, это означает, что его содержание в наплавочной проволоке незначительно и составляет менее одного процента.
Если в конце обозначения присутствует сдвоенная буква АА (Св-08АА), это означает о пониженном содержании серы и фосфора по сравнению с проволокой Св-08А.
Химический состав сварочной проволоки.
Таблица 1. Химический состав сварочной проволоки по ГОСТ 2246-70.
Марка проволоки | Химический состав, % | |||||||||
Углерод | Кремний | Марганец | Хром | Никель | Молибден | Титан | Сера | Фосфор | Прочие элементы | |
Не более | ||||||||||
Низкоуглеродистая проволока | ||||||||||
Св-08 | 0,10 | 0,03 | 0,35-0,60 | 0,15 | 0,30 | — | — | 0,040 | 0,040 | Алюм.![]() |
Св-08А | 0,10 | 0,03 | 0,35-0,60 | 0,12 | 0,25 | — | — | 0,030 | 0,030 | |
Св-08АА | 0,10 | 0,03 | 0,35-0,60 | 0,10 | 0,25 | — | — | 0,020 | 0,020 | — |
Св-08ГА | 0,10 | 0,03 | 0,80-1,10 | 0,10 | 0,25 | — | — | 0,025 | 0,030 | — |
Св-10ГА | 0,12 | 0,03 | 1,10-1,40 | 0,20 | 0,30 | — | — | 0,025 | 0,030 | — |
Св-10Г2 | 0,12 | 0,03 | 1,50-1,90 | 0,20 | 0,30 | — | — | 0,030 | 0,030 | — |
Легированная проволока | ||||||||||
Св-08ГС | 0,10 | 0,60-0,85 | 1,40-1,70 | 0,20 | 0,25 | — | — | 0,025 | 0,030 | — |
Св-12ГС | 0,14 | 0,60-0,90 | 0,80-1,10 | 0,20 | 0,30 | — | — | 0,025 | 0,030 | — |
Св-08Г2С | 0,05-0,11 | 0,70-0,95 | 1,80-2,10 | 0,20 | 0,25 | — | — | 0,025 | 0,030 | — |
Св-15ГСТЮЦА (ЭП-439) | 0,12-0,18 | 0,45-0,85 | 0,60-1,00 | 0,30 | 0,40 | — | 0,05-0,20 | 0,025 | 0,025 | Алюм.![]() Цирконий 0,05-0,15 Церий не менее 0,4 |
Св-18ХГС | 0,15-0,22 | 0,90-1,20 | 0,80-1,10 | 0,80-1,10 | 0,30 | — | — | 0,025 | 0,030 | — |
Высоколегированная проволока | ||||||||||
Св-12Х13 | 0,09-0,14 | 0,30-0,70 | 0,30-0,70 | 12,00-14,00 | Не более 0,60 | — | — | 0,025 | 0,030 | — |
Св-06Х19Н9Т | Не более 0,08 | 0,40-1,00 | 1,00-2,00 | 18,00-20,00 | 8,00-10,00 | — | 0,50-1,00 | 0,015 | 0,030 | — |
Св-07Х19Н10Б | 0,05-0,09 | Не более 0,70 | 1,50-2,00 | 18,50-20,50 | 9,00-10,50 | — | — | 0,018 | 0,025 | Ниобий 1,20-1,50 |
Св-10Х16Н25АМ6 | 0,08-0,12 | Не более 0,60 | 1,00-2,00 | 15,00-17,00 | 24,00-27,00 | 5,50-7,00 | — | 0,018 | 0,025 | Азот 0,10-0,20 |
Статья оказалась полезной?! Поделись с друзьями!!!
mechanicinfo. ru
Расшифруйте Св-08АА, Св-12Х11НМФ
Св- 08АА -Сварочная проволока, среднее содержание углерода-0,08%, с более пониженным содержанием серы и фосфора
Св-12Х11НМФ Сварочная проволока, среднее содержание углерода-0,12% , с содержанием хрома 11%, никеля, молибдена, ванадия по 1%
Билет №10
Гарячая сварка чугуна.
Назначение и устройство преобразователя.
3. Задача. Объясните причину и ваши действия в том случае, если при зажигании дуги она прилипает к металлу.
Ответы
1.
Горячую сварку можно применять для изделий ограниченных размеров и массы, практически до 2,5 т, так как при большом объеме нагретого металла производить сварку трудно. Горячая сварка чугуна выполняется в такой последовательности: 1. Подготовка к сварке. Раковины и шлаковые включения полностью удаляются обычно механическим способом — вырубкой или сверлением. Трещины, подлежащие заварке, вырубаются с V-образной или чашеобразной разделкой; невырубленным остается притупление в 3 — 6 мм. Если объем металла, подлежащего наплавке, велик и превышает 60 см3, то место, предназначенное к сварке, должно быть заформовано так, чтобы можно было обеспечить заполнение этой части ванны жидким чугуном. Формовку выполняют графитовыми пластинами или формовочным песком, замешанным на жидком стекле. Формовка должна исключить возможность вытекания жидкого металла из ванны. После заварки одной секции и затвердения заваренного участка вставка вынимается. 2. Подогрев изделий производится в печах или специальных нагревательных ямах. Обычно температура нагрева при газовой сварке поддерживается в пределах 450 — 600°С и при дуговой сварке — 700 — 850°С. Подогрев чугунных изделий перед сваркой до таких высоких температур требуется для того, чтобы снизить скорость охлаждения металла шва и придать ему относительно высокие пластические свойства и возможность обработки режущим инструментом; подогрев необходим также после сварки, чтобы происходило равномерное охлаждение всего изделия и не возникали трещины.
Присадочным материалом при горячей сварке служат чугунные прутки марок А и Б. 4. Выполнение сварки. Дуговая сварка чугуна выполняется как угольным электродом с применением чугунного присадочного прутка, так и покрытыми чугунными электродами. Для удаления окислов кремния при сварке угольной дугой используют те же флюсы. При дуговой сварке металл сварочной ванны также поддерживают в жидком состоянии до полного заполнения дефекта или заформованного блока. Это обеспечивает наиболее полное удаление газов и неметаллических включений из металла шва и равномерную структуру в металле шва и околошовном металле.
Качество соединения свариваемых частей и температура, от которой оно зависит, определяются формой сварочной ванны. Выпуклая поверхность ванны говорит о плохом соединении. В этом случае сварщик должен увеличить нагрев стенок изделия. Правильный процесс сварки характеризуется вогнутой поверхностью сварочной ванны без подреза; жидкий чугун хорошо смачивает стенки детали. 5. Охлаждение изделий производится с малой скоростью, иногда в течение 3 — 5 суток. Подготовка к охлаждению заключается в том, что после окончания сварки поверхность металла шва засыпается слоем мелкого порошка древесного угля, а все изделие со всех сторон закрывается асбестовыми листами и сухим песком. При дуговой сварке чугуна с подогревом применяют чугунные стержни с покрытием, например, ОМЧ-1. При диаметре чугунного электрода 6 — 8 мм сварочный ток 200 — 400 А. Род тока — любой, при постоянном токе применяют прямую полярность.
2.
Для питания электрической дуги постоянным током выпускаются
передвижные и стационарные сварочные преобразователи. На рис. показано устройство однопостового сварочного преобразователя ПСО-500, выпускаемого серийно нашей промышленностью.
Схема сварочного преобразователя ПСО-500: 1 — корпус, 2 — электродвигатель, 3 — вентилятор, 4 — катушка полюсов, 5 — якорь генератора, 6 — коллектор, 7 — токосъемник, 8 — маховичок для регулирования тока, 9 — сварочные зажимы, 10 — амперметр, 11 — пакетный выключатель, 12 — коробка пускорегулирующей и контрольной аппаратуры преобразователя.
Однопостовой сварочный преобразователь ПСО-500 состоит из двух машин: из приводного электродвигателя 2 и сварочного генератора ГСО-500 постоянного тока, расположенных в общем корпусе 1. Якорь 5 генератора и ротор двигателя расположены на общем валу, подшипники которого установлены в крышках корпуса преобразователя. На валу между электродвигателем и генератором находится вентилятор 3, предназначенный для охлаждения агрегата во время его работы. Якорь генератора набран из тонких пластин электротехнической стали толщиной до 1 мм и снабжен продольными пазами, в которых уложены изолированные витки обмотки якоря. Концы обмотки якоря припаяны к соответствующим пластинам коллектора 6. На полюсах магнитов насажены катушки 4 с обмотками из изолированной проволоки, которые включаются в электрическую цепь генератора. Генератор работает по принципу электромагнитной индукции. При вращении якоря 5 его обмотка пересекает магнитные силовые линии магнитов, в результате чего в обмотках якоря наводится переменный электрический ток, который с помощью коллектора 6 преобразуется в постоянный; с щеток токосъемника 7 при нагрузке в сварочной цепи ток течет с коллектора к зажимам 9. Пускорегулирующая и контрольная аппаратура преобразователя смонтирована на корпусе / в общей коробке 12. Преобразователь включается пакетным включателем 11. Величина тока возбуждения и режим работы сварочного генератора плавно регулируются реостатом в цепи независимого возбуждения маховичком 8. С помощью перемычки, соединяющей дополнительный зажим с одним из положительных выводов от последовательной обмотки, можно устанавливать сварочный ток до 300 и 500 А. Работа генератора на токах, превышающих верхние пределы (300 и 500 А), не рекомендуется, так как возможен перегрев машины и нарушение системы коммутации. Величина сварочного тока определяется амперметром 10, шунт которого включен в цепь якоря генератора, смонтированного внутри корпуса преобразователя. Перед пуском преобразователя в работу необходимо проверить заземление корпуса; состояние щеток коллектора; надежность контактов во внутренней и внешней цепях; штурвал реостата повернуть против часовой стрелки до упора; проверить, не касаются ли концы сварочных проводов друг друга; установить перемычку на доске зажимов соответственно требуемой величине сварочного тока (300 или 500 А).
Пуск преобразователя осуществляется включением двигателя в сеть (пакетным выключателем). После подсоединения к сети необходимо проверить направление вращения генератора (если смотреть со стороны коллектора, ротор должен вращаться против часовой стрелки) и в случае необходимости поменять местами провода в месте их подключения к питающей сети.
3. Задача. Объясните причину и ваши действия в том случае, если при зажигании дуги она прилипает к металлу
. Прилипание дуги связано с несоответствием силы тока диаметру электрода. Сила тока мала. Необходимо правильно рассчитать силу тока и установить ее на источнике питания. Если источник питания не позволяет это сделать точно, то силу тока увеличивают опытным путем.
Виды сварочных материалов и их основные характеристики
Для сварки используют специальные материалы — они обеспечивают стабильное горение дуги, хорошее качество сварных швов. Виды и назначение материалов для сварки различны.
Основные типы:
- сварочные электроды с различными покрытиями (кислым, смешанным, целлюлозным, рутиловым) и присадочные прутки;
- проволока — активированная.
порошковая, сплошная;
- флюсы;
- газы — защитные, горючие;
- керамические подкладки для соединения разных видов швов — всепозиционные, круглые и др.
Изделия делят на группы по типу свариваемых металлов: для соединения элементов из углеродистых сталей, для нержавеющих и низколегированных сталей, а также для меди, чугуна и т.д.
Электроды и проволока
Эти два вида сварочных материалов обеспечивают подачу питания в сварочную зону. Плавящиеся электроды с покрытием, отдельные разновидности проволоки и защитный флюс содержат компоненты, помогающие защитить металл от окисления. Они поддерживают стабильную работу, помогают получить нужный химический состав шва. Присадочный пруток вводится в шов непосредственно при сварке.
Плавящиеся проволоки используют под флюсом, в защитных газах и при электрошлаковой сварке. Технологические стандарты предполагают использование разных типов проволок из стали: легированных, высоколегированных и низкоуглеродистых. Легированная и низкоуглеродистая сталь бывает омедненной и неомедненной.
При выборе той или иной марки нужно учитывать, что от нее будет зависеть химический состав шва. Обычно используют материал, по составу наиболее близкий к обрабатываемому металлу. Он должен соответствовать требованиям ГОСТ — состав указывают на упаковке изделия.
При выборе сварочного материала для сварки обращайте внимание на качество изготовления. Поверхность изделия должна быть гладкой, без следов жира, окалины и ржавчины. Показатель плавления не должен быть ниже, чем у соединяемых материалов.
Стержни и пластины
Электрошлаковая сварка производится с использованием пластин, дуговая — с применением металлических стержней с покрытием на основе электрода. Электроды бывают тонкими, средней толщины и толстыми.
Изделия маркируют буквами в зависимости от типа покрытия:
- А — с кислотными добавками;
- Б — традиционный вариант;
- Ц — с содержанием целлюлозы;
- П — смешанные.
Газы
Для газовой сварки используют горючие газы и газы, поддерживающие горение, в частности:
- кислород;
- водород;
- ацетилен;
- пропанобутановую смесь;
- метилацетилен-алленовую фракцию.
Также применяют защитные газы для обеспечения защиты расплава от воздуха: углекислый газ, гелий, аргон и различные смеси.
Помните о безопасности: сжатый кислород при взаимодействии со смазкой и маслами может воспламениться или вызвать взрыв. Хранить сварочные материалы этого типа нужно со строгим соблюдением норм пожарной безопасности. Ацетилен при ускоренном нагревании до высоких температур также может привести к взрыву — важно строго соблюдать технологию работы.
Прочие изделия
Флюс имеет разное назначение: в процессе сварочных работ благодаря ему можно быстро и эффективно расстворить окислы на металлической поверхности, он образует барьер для доступа кислорода. Кроме того, расплав флюса при сварке может выступать в роли теплообменной среды — облегчать нагревание стыка.
По способу производства флюсы делят на плавленые и неплавленые. Состоят из порошка или пасты, изготовленной на основе борной кислоты или прокаленной буры. Для соединения легированных сталей данный вид сварочного материала не применяют.
Сравнительно недавно в сварке начали использовать керамические подкладки. Они обеспечивают качественный шов и служат для создания обратного валика. Универсальны, применять их можно для всех типов сварки, в любых положениях материалов (например, удобны при изготовлении изогнутых швов).
Общие требования
К сварочным материалам предъявляют определенные технологические требования Согласно принятым стандартам, все заводские изделия должны иметь сертификаты с указанием основных характеристик:
- товарный знак;
- маркировка, указывающая на тип изделия;
- заводской номер смены, номер партии;
- показатель поверхностного состояния;
- состав материала с указанием процентного соотношения компонентов;
- механические особенности направленного шва;
- вес нетто.
Одним из важнейших требований для электродов является хорошо сформированный шов и дуга со стабильным горением. Металл полученной направки должен соответствовать заданному химическому составу, стержень при сварке должен плавиться равномерно, без образования брызг и выделения токсичных веществ.
Для получения хорошего качественного шва необходимо соблюдать все условия, которых требует технология. Лучший вариант — приобрести сертифицированные изделия у проверенных поставщиков с гарантией качества.
1910.252 – Общие требования. | Управление по безопасности и гигиене труда
- По стандартному номеру
- 1910.252 – Общие требования.
1910.252(а)
Противопожарная защита и защита –
1910. 252(а)(1)
Основные меры предосторожности . Для разработки этих основных мер предосторожности и специальных мер предосторожности, указанных в параграфе (а)(2) настоящего раздела, а также для определения ответственности сварщиков и монтажников в области противопожарной защиты и предотвращения пожаров, их руководителей (включая внешних подрядчиков) и лиц, занимающих руководящие должности. на чьей собственности должны выполняться резка и сварка, см. Стандарт по предотвращению пожаров при использовании процессов резки и сварки, Стандарт NFPA 51B, 19.62, который включен посредством ссылки, как указано в § 1910.6. Основные меры предосторожности по предотвращению пожара при сварке или резке:
1910.252(а)(1)(и)
Пожароопасность . Если объект, подлежащий сварке или резке, не может быть легко перемещен, все подвижные источники возгорания поблизости должны быть перемещены в безопасное место.
1910.252(а)(1)(ii)
Охранники . Если свариваемый или разрезаемый объект не может быть перемещен, а все источники возгорания не могут быть устранены, то должны применяться ограждения для локализации тепла, искр и шлака, а также для защиты неподвижных источников возгорания.
1910.252(а)(1)(iii)
Ограничения . Если требования, изложенные в пунктах (а)(1)(i) и (а)(1)(ii) настоящего параграфа, не могут быть соблюдены, то сварка и резка не должны выполняться.
1910.252(а)(2)
Особые меры предосторожности . Если характер выполняемой работы подпадает под действие параграфа (a)(1)(ii) настоящего раздела, могут потребоваться определенные дополнительные меры предосторожности:
1910. 252(а)(2)(и)
Горючий материал . Везде, где имеются отверстия или трещины в полу, которые невозможно закрыть, должны быть приняты меры предосторожности, чтобы никакие легковоспламеняющиеся материалы на полу не подвергались воздействию искр, которые могут падать сквозь пол. Те же меры предосторожности должны соблюдаться в отношении трещин или отверстий в стенах, открытых дверных проемов и открытых или разбитых окон.
1910.252(а)(2)(ii)
Огнетушители . Подходящие средства пожаротушения должны содержаться в состоянии готовности к немедленному использованию. Такое оборудование может состоять из ведер с водой, ведер с песком, шланга или переносных огнетушителей, в зависимости от характера и количества горючего материала.
1910. 252(а)(2)(iii)
Пожарная служба .
1910.252(а)(2)(iii)(А)
Пожарные наблюдатели должны быть необходимы всякий раз, когда сварка или резка выполняются в местах, где возможно возникновение пожара, кроме незначительного, или существует любое из следующих условий:
1910.252(а)(2)(iii)(А)(1)
Заметный горючий материал в конструкции здания или его содержании, ближе 35 футов (10,7 м) к месту эксплуатации.
1910.252(а)(2)(iii)(А)(2)
Заметные горючие вещества находятся на расстоянии более 35 футов (10,7 м), но легко воспламеняются от искр.
1910.252(а)(2)(iii)(А)(3)
Отверстия в стенах или полу в радиусе 35 футов (10,7 м) обнажают горючие материалы в прилегающих областях, включая скрытые пространства в стенах или полах.
1910.252(а)(2)(iii)(А)(4)
Горючие материалы примыкают к противоположной стороне металлических перегородок, стен, потолков или крыш и могут воспламениться от теплопроводности или излучения.
1910.252(а)(2)(iii)(В)
Пожарные наблюдатели должны иметь в наличии средства пожаротушения и быть обучены их использованию. Они должны быть знакомы со средствами подачи сигнала тревоги в случае пожара. Они должны следить за пожарами во всех открытых зонах, пытаться тушить их только тогда, когда очевидно, что это позволяет имеющееся оборудование, или иным образом бить тревогу. По окончании сварочных или резочных работ в течение не менее получаса должно вестись пожарное дежурство для обнаружения и тушения возможного тлеющего пожара.
1910. 252(а)(2)(iv)
Авторизация . Прежде чем разрешить резку или сварку, участок должен быть осмотрен лицом, ответственным за разрешение операций по резке и сварке. Он должен указать меры предосторожности, которые необходимо соблюдать при выдаче разрешения на продолжение деятельности, предпочтительно в форме письменного разрешения.
1910.252(а)(2)(в)
Этажи . Если на полу находятся горючие материалы, такие как обрезки бумаги, древесная стружка или текстильные волокна, пол необходимо подмести в радиусе 35 футов (10,7 м). Горючие полы должны поддерживаться во влажном состоянии, засыпаться влажным песком или защищаться огнеупорными щитами. Если полы намокли, персонал, работающий с оборудованием для дуговой сварки или резки, должен быть защищен от возможного удара током.
1910. 252(а)(2)(vi)
Запрещенные зоны . Резка или сварка не допускаются в следующих ситуациях:
1910.252(а)(2)(vi)(А)
В местах, не разрешенных руководством.
1910.252(а)(2)(vi)(Б)
В обрызгиваемых зданиях при нарушении такой защиты.
1910.252(а)(2)(vi)(С)
При наличии взрывоопасных сред (смесей легковоспламеняющихся газов, паров, жидкостей или пыли с воздухом) или взрывоопасных сред, которые могут образоваться внутри неочищенных или неправильно подготовленных резервуаров или оборудования, ранее содержавших такие материалы, или которые могут образоваться в участки со скоплением горючей пыли.
1910. 252(а)(2)(vi)(D)
В местах хранения большого количества открытых легко воспламеняющихся материалов, таких как сера, кипы бумаги или хлопок.
1910.252(а)(2)(vii)
Перемещение горючих материалов . Там, где это возможно, все горючие материалы должны быть перемещены не менее чем на 35 футов (10,7 м) от рабочей площадки. Там, где перемещение невозможно, горючие материалы должны быть защищены огнеупорными крышками или иным образом ограждены металлическими или асбестовыми ограждениями или занавесками.
1910.252(а)(2)(viii)
Воздуховоды . Воздуховоды и конвейерные системы, по которым искры могут попасть в отдаленные горючие материалы, должны быть надлежащим образом защищены или закрыты.
1910. 252(а)(2)(ix)
Горючие стены . Если резка или сварка производятся вблизи стен, перегородок, потолка или крыши из горючих материалов, должны быть предусмотрены огнеупорные экраны или ограждения для предотвращения воспламенения.
1910.252(а)(2)(х)
Стены негорючие . Если сварка должна выполняться на металлической стене, перегородке, потолке или крыше, должны быть приняты меры предосторожности для предотвращения воспламенения горючих материалов с другой стороны из-за проводимости или излучения, предпочтительно путем перемещения горючих материалов. Если горючие материалы не перемещаются, должно быть обеспечено пожарное дежурство на противоположной стороне от места проведения работ.
1910.252(а)(2)(xi)
Горючая крышка . Сварку не следует проводить на металлической перегородке, стене, потолке или крыше с горючим покрытием, а также на стенах или перегородках из сэндвич-панелей из горючих материалов.
1910.252(а)(2)(xii)
Трубы . Резка или сварка труб или другого металла, соприкасающегося с горючими стенами, перегородками, потолками или крышами, не должны производиться, если работа проводится достаточно близко, чтобы вызвать воспламенение от проводимости.
1910.252(а)(2)(xiii)
Менеджмент . Руководство признает свою ответственность за безопасное использование режущего и сварочного оборудования на своей территории и:
1910.252(а)(2)(xiii)(А)
В зависимости от пожароопасности заводских сооружений установить зоны резки и сварки, а также установить процедуры резки и сварки в других зонах.
1910.252(а)(2)(xiii)(В)
Назначьте лицо, ответственное за разрешение операций по резке и сварке в зонах, специально не предназначенных для таких процессов.
1910.252(а)(2)(xiii)(С)
Настаивайте на том, чтобы резчики или сварщики и их руководители прошли надлежащую подготовку по безопасной эксплуатации своего оборудования и безопасному использованию процесса.
1910.252(а)(2)(xiii)(D)
Информируйте всех подрядчиков о легковоспламеняющихся материалах или опасных условиях, о которых они могут не знать.
1910.252(а)(2)(xiv)
Супервайзер . Супервайзер:
1910. 252(а)(2)(xiv)(А)
Должен нести ответственность за безопасное обращение с режущим или сварочным оборудованием и безопасное использование процесса резки или сварки.
1910.252(а)(2)(хiv)(Б)
Должен определить горючие материалы и опасные зоны, которые присутствуют или могут присутствовать на рабочем месте.
1910.252(а)(2)(xiv)(С)
Должны защищать горючие вещества от возгорания следующим образом:
1910.252(а)(2)(xiv)(С)(1)
Перенесите работу в место, свободное от опасных горючих материалов.
1910.252(а)(2)(xiv)(С)(2)
Если работа не может быть перемещена, переместите горючие материалы на безопасное расстояние от работы или защитите их должным образом от воспламенения.
1910.252(а)(2)(xiv)(С)(3)
Следите за тем, чтобы резка и сварка были спланированы таким образом, чтобы во время резки или сварки не запускались операции, которые могут привести к воспламенению горючих материалов.
1910.252(а)(2)(xiv)(D)
Необходимо получить разрешение на резку или сварку от назначенного представителя руководства.
1910.252(а)(2)(xiv)(Е)
Должен определить, что закройщик или сварщик получил свое одобрение о том, что условия безопасны, прежде чем продолжить работу.
1910.252(а)(2)(xiv)(F)
Должен определить, правильно ли расположены на площадке средства противопожарной защиты и пожаротушения.
1910.252(а)(2)(xiv)(Г)
Если требуются пожарные дежурства, он должен следить за их наличием на объекте.
1910.252(а)(2)(xv)
Противопожарные меры . Резка или сварка допускаются только в зонах, которые являются или были сделаны пожаробезопасными. Когда работа практически не может быть перемещена, как в большинстве строительных работ, зона должна быть безопасна путем удаления горючих материалов или защиты горючих материалов от источников воспламенения.
1910.252(а)(3)
Контейнеры для сварки или резки –
1910.252(а)(3)(и)
Использованные контейнеры . Запрещается выполнять сварку, резку или другие огневые работы на использованных барабанах, бочках, цистернах или других емкостях до тех пор, пока они не будут очищены настолько тщательно, чтобы быть абсолютно уверенным в отсутствии горючих материалов или любых веществ, таких как жиры, смолы, кислоты или другие материалы, которые при нагревании могут выделять легковоспламеняющиеся или токсичные пары. Любые трубопроводы или соединения с барабаном или сосудом должны быть отсоединены или заглушены.
1910.252(а)(3)(ii)
Вентиляция и очистка . Все полые пространства, полости или контейнеры должны вентилироваться, чтобы обеспечить выход воздуха или газов перед предварительным нагревом, резкой или сваркой. Рекомендуется продувка инертным газом.
1910.252(а)(4)
Закрытые помещения –
1910. 252(а)(4)(и)
Случайный контакт . Когда дуговая сварка должна быть приостановлена на какой-либо значительный период времени, например, во время обеда или на ночь, все электроды должны быть удалены из держателей, а держатели должны быть тщательно расположены так, чтобы не произошло случайного контакта, и машина должна быть отключена от источника питания.
1910.252(а)(4)(ii)
Клапан горелки . Чтобы исключить возможность утечки газа из-за утечек или неправильно закрытых клапанов, при газовой сварке или резке клапаны горелки должны быть закрыты, а подача газа к горелке должна быть принудительно перекрыта в какой-либо точке за пределами замкнутого пространства, когда горелка не находится в рабочем состоянии. для использования в течение значительного периода времени, например, в обеденный перерыв или на ночь. Там, где это практически возможно, горелка и шланг также должны быть удалены из замкнутого пространства.
1910.252(б)
Защита персонала –
1910.252(б)(1)
Общий –
1910.252(б)(1)(и)
Перила . Сварщик или помощник, работающий на платформах, подмостках или подмостках, должен быть защищен от падения. Этого можно добиться с помощью перил, ремней безопасности, страховочных тросов или других не менее эффективных средств защиты.
1910.252(б)(1)(ii)
Сварочный кабель . Сварщики должны размещать сварочный кабель и другое оборудование так, чтобы они не попадали в проходы, стремянки и лестничные марши.
1910.252(б)(2)
Защита глаз –
1910.252(б)(2)(и)
Выбор .
1910.252(б)(2)(я)(А)
Каски или щитки для рук должны использоваться во время всех операций дуговой сварки или дуговой резки, за исключением дуговой сварки под флюсом. Помощники или обслуживающий персонал должны быть обеспечены надлежащей защитой глаз.
1910.252(б)(2)(и)(Б)
Защитные очки или другие подходящие средства защиты глаз должны использоваться во время всех операций газовой сварки или кислородной резки. Очки без боковых щитков с соответствующими фильтрующими линзами разрешены для использования во время газовых сварочных работ на легких работах, для пайки горелкой или для осмотра.
1910.252(б)(2)(и)(С)
Все операторы и обслуживающий персонал оборудования для контактной сварки или контактной пайки должны использовать прозрачные лицевые щитки или защитные очки, в зависимости от конкретной работы, для защиты лица или глаз по мере необходимости.
1910.252(б)(2)(и)(Д)
Защита глаз в виде подходящих очков должна быть обеспечена там, где это необходимо для операций пайки, не указанных в пунктах (b)(2)(i)(A)–(b)(2)(i)(C) настоящего раздела .
1910.252(б)(2)(ii)
Технические характеристики протекторов .
1910.252(б)(2)(ii)(А)
Шлемы и щитки для рук должны быть изготовлены из материала, который является изолятором тепла и электричества. Шлемы, щитки и защитные очки не должны легко воспламеняться и должны выдерживать стерилизацию.
1910.252(б)(2)(ii)(В)
Шлемы и щитки для рук должны быть устроены таким образом, чтобы защищать лицо, шею и уши от прямой лучистой энергии дуги.
1910.252(б)(2)(ii)(С)
Каски должны быть снабжены фильтрующими пластинами и накладками, предназначенными для легкого снятия.
1910.252(б)(2)(ii)(D)
Все детали должны быть изготовлены из материала, который не будет быстро разъедать или обесцвечивать кожу.
1910.252(б)(2)(ii)(Е)
Защитные очки должны вентилироваться для предотвращения запотевания линз, насколько это практически возможно.
1910.252(б)(2)(ii)(Ф)
Все стекла для линз должны быть закаленными, практически без полос, пузырьков воздуха, волн и других дефектов. За исключением случаев, когда линза шлифуется для обеспечения надлежащей оптической коррекции дефектов зрения, передняя и задняя поверхности линз и окон должны быть гладкими и параллельными.
1910.252(б)(2)(ii)(Г)
Линзы должны иметь постоянную отличительную маркировку, по которой можно легко идентифицировать источник и оттенок.
1910.252(б)(2)(ii)(Н)
Ниже приведены рекомендации по выбору подходящего номера оттенка. Эти рекомендации могут варьироваться в зависимости от индивидуальных потребностей.
Сварка | Оттенок № |
---|---|
Дуговая сварка в среде защитного газа – электроды 1⁄16, 3⁄32, ⅛-, 5⁄32 дюйма | 10 |
Дуговая сварка в среде защитных газов (цветные металлы) – электроды 1⁄16, 3⁄32, ⅛, 5⁄32 дюйма | 11 |
Дуговая сварка в среде защитных газов (черные металлы) – электроды 1/16, 3/32, ⅛, 5/32 дюйма | 12 |
Дуговая сварка металлическим электродом в среде защитного газа: | |
Электроды 3⁄16-, 7⁄32-, ¼ дюйма | 12 |
Электроды 5⁄16, ⅜ дюйма | 14 |
Сварка атомным водородом | 10-14 |
Дуговая сварка углеродом | 14 |
Пайка | 2 |
Пайка горелкой | 3 или 4 |
Легкая резка, до 1 дюйма | 3 или 4 |
Средняя резка, от 1 до 6 дюймов | 4 или 5 |
Тяжелая резка, 6 дюймов и более | 5 или 6 |
Газовая сварка (легкая) до ⅛ дюйма | 4 или 5 |
Газовая сварка (средняя) от ⅛ дюйма до ½ дюйма | 5 или 6 |
Газовая сварка (тяжелая) ½ дюйма и более | 6 или 8 |
Примечание. При газовой сварке или кислородной резке, когда горелка излучает сильный желтый свет, желательно использовать фильтр или линзу, поглощающую желтую или натриевую полосу в видимом рабочем свете.
1910.252(б)(2)(ii)(I)
Линзы фильтров должны пройти тест на передачу лучистой энергии, предписанный любым из согласованных стандартов, перечисленных в 29CFR 1910.133(b)(1).
1910.252(б)(2)(iii)
Защита от лучей дуговой сварки . Там, где это позволяет работа, сварщик должен быть заключен в индивидуальную кабину, окрашенную с низким коэффициентом отражения, например, оксидом цинка (важный фактор поглощения ультрафиолетового излучения) и ламповой сажей, или должен быть огражден негорючими экранами с аналогичной окраской. Кабины и экраны должны обеспечивать циркуляцию воздуха на уровне пола. Рабочие или другие лица, находящиеся рядом с зонами сварки, должны быть защищены от лучей негорючими или огнестойкими экранами или щитами или должны носить соответствующие защитные очки.
1910.252(б)(3)
Защитная одежда. Общие требования . Работники, подвергающиеся опасности, создаваемой сваркой, резкой или пайкой, должны быть защищены средствами индивидуальной защиты в соответствии с требованиями § 1910.132 настоящей части. Соответствующая защитная одежда, необходимая для любой сварочной операции, зависит от размера, характера и места выполняемой работы.
1910.252(б)(4)
Работа в замкнутом пространстве –
1910.252(б)(4)(и)
Общий . Под ограниченным пространством здесь подразумевается относительно небольшое или ограниченное пространство, такое как резервуар, котел, сосуд высокого давления или небольшой отсек корабля.
1910.252(б)(4)(ii)
Вентиляция . Вентиляция является обязательным условием для работы в закрытых помещениях. Требования к вентиляции см. в параграфе (c) данного раздела.
1910.252(б)(4)(iii)
Крепление цилиндров и механизмов . При сварке или резке в любых замкнутых пространствах газовые баллоны и сварочные аппараты должны находиться снаружи. Перед началом работы тяжелое переносное оборудование, установленное на колесах, должно быть надежно заблокировано для предотвращения случайного перемещения.
1910. 252(б)(4)(iv)
Линии жизни . Если сварщику необходимо проникнуть в замкнутое пространство через люк или другое небольшое отверстие, должны быть предусмотрены средства для его быстрого удаления в случае возникновения чрезвычайной ситуации. При использовании для этой цели ремней безопасности и страховочных тросов они должны быть прикреплены к телу сварщика таким образом, чтобы его тело не могло быть зажато в небольшом выходном отверстии. Дежурный с заранее спланированной процедурой спасения должен находиться снаружи, чтобы постоянно наблюдать за сварщиком и иметь возможность проводить спасательные операции.
1910.252(б)(4)(в)
Снятие электрода . Когда дуговая сварка должна быть приостановлена на какой-либо значительный период времени, например, во время обеда или на ночь, все электроды должны быть удалены из держателей, а держатели должны быть тщательно расположены так, чтобы не произошло случайного контакта, и машина должна быть отключена от источника питания.
1910.252(б)(4)(vi)
Блокировка газового баллона . Чтобы исключить возможность утечки газа через негерметичность неправильно закрытых клапанов, при газовой сварке или резке клапаны горелки должны быть закрыты, а подача топливного газа и кислорода к горелке принудительно перекрыта в какой-либо точке за пределами замкнутого пространства всякий раз, когда фонарь нельзя использовать в течение длительного периода времени, например, в обеденный перерыв или на ночь. Там, где это возможно, горелку и шланг следует также удалить из замкнутого пространства.
1910.252(б)(4)(vii)
Предупреждающий знак . После завершения сварочных работ сварщик должен маркировать горячий металл или предусмотреть другие средства предупреждения других рабочих.
1910. 252(с)
Охрана здоровья и вентиляция –
1910.252(с)(1)
Общие –
1910.252(с)(1)(и)
Загрязнение . Требования в этом параграфе были установлены на основе следующих трех факторов дуговой и газовой сварки, которые определяют степень загрязнения, которому могут подвергаться сварщики:
1910.252(с)(1)(я)(А)
Размеры помещения, в котором должна производиться сварка (особенно с учетом высоты потолка).
1910.252(с)(1)(и)(Б)
Количество сварщиков.
1910. 252(с)(1)(я)(С)
Возможное выделение опасных паров, газов или пыли в зависимости от используемых металлов.
1910.252(с)(1)(ii)
Экраны . Если сварку необходимо проводить в помещении, полностью экранированном со всех сторон, экраны должны быть расположены таким образом, чтобы не возникало серьезного ограничения вентиляции. Желательно устанавливать экраны таким образом, чтобы они находились на высоте около 2 футов (0,61 м) над полом, за исключением случаев, когда работа выполняется на таком низком уровне, что экран должен быть выдвинут ближе к полу, чтобы защитить находящихся рядом рабочих от яркого света. сварка.
1910.252(с)(1)(iii)
ПДК . Должны быть предусмотрены и устроены местные вытяжные или общие вентиляционные системы, чтобы количество токсичных паров, газов или пыли было ниже максимально допустимой концентрации, как указано в § 1910. 1000 настоящей части.
1910.252(с)(1)(iv)
Сообщение об опасности . Работодатель должен включить потенциально опасные материалы, используемые во флюсах, покрытиях, покрытиях и присадочных металлах, которые потенциально могут использоваться при сварке и резке или выбрасываются в атмосферу во время сварки и резки, в программу, установленную в соответствии с Стандарт оповещения об опасности (HCS) (§ 1910.1200). Работодатель должен обеспечить, чтобы каждый сотрудник имел доступ к этикеткам на контейнерах с такими материалами и паспортам безопасности и прошел обучение в соответствии с положениями § 1910.1200. Потенциально опасные материалы должны включать, помимо прочего, материалы, перечисленные в параграфах (c)(5) – (c)(12) настоящего раздела.
1910.252(с)(1)(в)
Дополнительные сведения об опасности при сварке, резке и пайке .
1910.252(с)(1)(в)(А)
Поставщики должны определять и маркировать в соответствии с § 1910.1200 любые опасности, связанные с использованием их материалов при сварке, резке и пайке.
1910.252(с)(1)(в)(Б)
В дополнение к любым требованиям, установленным § 1910.1200, все присадочные металлы и плавкие гранулированные материалы должны иметь как минимум следующее уведомление на бирках, коробках или других контейнерах:
Не используйте в местах с недостаточной вентиляцией. См. документ ANSI Z49.1-1967 «Безопасность при сварке, резке и смежных процессах», опубликованный Американским обществом сварщиков.
1910.252(с)(1)(в)(С)
Если присадочные металлы для пайки (сварки) содержат кадмий в значительных количествах, на этикетках должны быть указаны опасности, связанные с кадмием, включая рак, воздействие на легкие и почки, а также острое токсическое воздействие.
1910.252(с)(1)(в)(Г)
Если флюсы для пайки и газовой сварки содержат соединения фтора, на этикетках должна быть указана опасность, связанная с соединениями фтора, включая воздействие на глаза и дыхательные пути.
1910.252(с)(1)(vi)
До 1 июня 2015 г. работодатели могут размещать на этикетках следующую информацию вместо требований к маркировке, изложенных в параграфе (c)(1)(v) настоящего раздела:
1910.252(с)(1)(vi)(А)
Все присадочные металлы и плавкие гранулированные материалы должны иметь как минимум следующую пометку на бирках, коробках или других контейнерах:
ВНИМАНИЕ
При сварке могут образовываться пары и газы, опасные для здоровья. Избегайте вдыхания этих паров и газов. Используйте адекватную вентиляцию. См. документ ANSI Z49.1-1967 «Безопасность при сварке и резке», опубликованный Американским обществом сварщиков.
1910.252(с)(1)(vi)(Б)
Присадочные металлы для пайки (сварки), содержащие кадмий в значительных количествах, должны иметь следующую пометку на бирках, коробках или других контейнерах:
ПРЕДУПРЕЖДЕНИЕ
СОДЕРЖИТ КАДМИЙ – ПРИ НАГРЕВАНИИ МОГУТ ОБРАЗОВАТЬСЯ ЯДОВИТЫЕ ПАРЫ
Не вдыхать пары. Используйте только при наличии адекватной вентиляции, такой как дымоуловители, вытяжные вентиляторы или респираторы с подачей воздуха. См. АНСИ Z49.1-1967. Если после использования появляется боль в груди, кашель или лихорадка, немедленно обратитесь к врачу.
1910.252(с)(1)(vi)(С)
Флюсы для пайки и газовой сварки, содержащие соединения фтора, должны иметь предупреждающую надпись, указывающую, что они содержат соединения фтора. Одна из таких предупредительных формулировок, рекомендованных Американским обществом сварщиков для флюсов для пайки и газовой сварки, гласит:
ОСТОРОЖНО
СОДЕРЖИТ ФТОРИДЫ
Этот флюс при нагревании выделяет пары, которые могут раздражать глаза, нос и горло.
1. Избегайте паров – используйте только в хорошо проветриваемых помещениях.
2. Избегайте попадания флюса в глаза или на кожу.
3. Не принимать внутрь.
1910.252(с)(2)
Вентиляция для общей сварки и резки –
1910.252(с)(2)(я)
Общий . Механическая вентиляция должна быть обеспечена при сварке или резке металлов, не указанных в параграфах (c)(5) – (c)(12) настоящего параграфа. (Для конкретных материалов см. требования к вентиляции в параграфах (c)(5) – (c)(12) данного раздела. )
1910.252(с)(2)(я)(А)
На площади менее 10 000 кубических футов (284 м 3 ) на сварщика.
1910.252(с)(2)(я)(Б)
В помещении с высотой потолков менее 16 футов (5 м).
1910.252(с)(2)(я)(С)
В замкнутых пространствах или там, где помещение для сварки содержит перегородки, балконы или другие конструктивные барьеры в такой степени, что они значительно препятствуют поперечной вентиляции.
1910.252(с)(2)(ii)
Минимальная ставка . Такая вентиляция должна обеспечиваться с минимальной скоростью 2000 кубических футов (57 м 3 ) в минуту на одного сварщика, за исключением случаев, когда используются местные вытяжные шкафы и кабины в соответствии с параграфом (c)(3) настоящего раздела или респираторы для воздушных судов, утвержденные В соответствии с положениями 30 CFR, часть 11, предоставляются Управление по охране труда и здоровья в шахтах и Национальный институт охраны труда и техники безопасности. Естественная вентиляция считается достаточной для операций сварки или резки, если ограничения, указанные в параграфе (c)(2)(i) данного раздела, отсутствуют.
1910.252(с)(3)
Местные вытяжные шкафы и кабины . Механическая местная вытяжная вентиляция может осуществляться одним из следующих способов:
1910.252(с)(3)(я)
Вытяжки . Свободно перемещаемые колпаки, предназначенные для размещения сварщиком как можно ближе к свариваемому объекту и обеспечивающие скорость воздушного потока, достаточную для поддержания скорости в направлении колпака 100 погонных футов (30 м) в минуту в зона сварки, когда вытяжка находится на максимально удаленном расстоянии от места сварки. Интенсивность вентиляции, необходимая для достижения этой контрольной скорости с использованием фланцевого всасывающего отверстия шириной 3 дюйма (7,6 см), показана в следующей таблице:
Зона сварки | Минимальный расход воздуха 1 кубических футов/минуту | Диаметр воздуховода, дюймы 2 |
---|---|---|
4–6 дюймов от дуги или горелки | 150 | 3 |
6-8 дюймов от дуги или горелки | 275 | 3½ |
8–10 дюймов от дуги или горелки | 425 | 4½ |
10–12 дюймов от дуги или горелки | 600 | 5½ |
1 При пайке материалов, содержащих кадмий, или при резке таких материалов может потребоваться повышенная скорость вентиляции.
2 Ближайший диаметр воздуховода полдюйма на основе скорости 4000 футов в минуту в трубе.
1910.252(с)(3)(ii)
Стационарный корпус . Стационарное ограждение с верхом и не менее чем с двух сторон, которое окружает места проведения операций сварки или резки, а также со скоростью воздушного потока, достаточной для поддержания скорости на расстоянии от сварщика не менее 100 погонных футов (30 м) в минуту.
1910.252(с)(4)
Вентиляция в закрытых помещениях –
1910.252(с)(4)(и)
Замена воздуха . Все операции по сварке и резке, проводимые в замкнутых пространствах, должны надлежащим образом вентилироваться, чтобы предотвратить накопление токсичных материалов или возможную нехватку кислорода. Это относится не только к сварщику, но и к помощникам и другому персоналу, находящемуся в непосредственной близости. Весь воздух, замещающий отбираемый, должен быть чистым и пригодным для дыхания.
1910.252(с)(4)(ii)
Респираторы для воздушных судов. В случаях, когда такая вентиляция невозможна, необходимо использовать воздушные респираторы или маски для шлангов, одобренные для этой цели Национальным институтом безопасности и гигиены труда (NIOSH) в соответствии с 42 CFR, часть 84.
1910.252(с)(4)(iii)
Автономные устройства. В зонах, представляющих непосредственную опасность для жизни, следует использовать полнолицевую маску, автономный дыхательный аппарат с принудительной подачей воздуха или комбинированный полнолицевой респиратор с принудительной подачей воздуха и вспомогательной автономной подачей воздуха, одобренный NIOSH в соответствии с Необходимо использовать 42 CFR, часть 84.
1910.252(с)(4)(iv)
Внешний помощник . Если сварочные работы проводятся в замкнутом пространстве и если сварщики и помощники обеспечены масками для шлангов, масками для шлангов с воздуходувками или автономными дыхательными аппаратами, одобренными Управлением по безопасности и гигиене труда в шахтах и Национальным институтом безопасности и гигиены труда, рабочий должны быть размещены снаружи таких замкнутых пространств для обеспечения безопасности тех, кто работает внутри.
1910.252(с)(4)(в)
Кислород для вентиляции . Кислород никогда не должен использоваться для вентиляции.
1910.252(с)(5)
Соединения фтора –
1910. 252(с)(5)(я)
Общий . В замкнутых пространствах сварка или резка с использованием флюсов, покрытий или других материалов, содержащих соединения фтора, должна выполняться в соответствии с пунктом (c)(4) настоящего раздела. Соединение фтора — это соединение, которое содержит фтор как элемент в химической комбинации, а не как свободный газ.
1910.252(с)(5)(ii)
ПДК . Необходимость в местной вытяжной вентиляции или воздушных респираторах для сварки или резки вне замкнутых пространств будет зависеть от индивидуальных обстоятельств. Однако опыт показал, что такая защита желательна для стационарной производственной сварки и для любой производственной сварки нержавеющих сталей. Если пробы воздуха, взятые в месте сварки, показывают, что концентрация выделяющихся фторидов ниже максимально допустимой, такая защита не требуется.
1910.252(с)(6)
Цинк –
1910.252(с)(6)(я)
Закрытые помещения . В замкнутых пространствах сварка или резка цинкосодержащих основных или присадочных металлов или металлов, покрытых цинкосодержащими материалами, должна выполняться в соответствии с параграфом (с)(4) настоящего раздела.
1910.252(с)(6)(ii)
В помещении . Внутри помещений сварка или резка цинкосодержащего основного металла или присадочного металла, покрытого цинкосодержащим материалом, должна выполняться в соответствии с параграфом (c)(3) настоящего раздела.
1910. 252(с)(7)
Свинец –
1910.252(с)(7)(я)
Закрытые помещения . В замкнутых пространствах сварка металлов на основе свинца (ошибочно называемая выжиганием свинца) должна выполняться в соответствии с пунктом (c)(4) настоящего раздела.
1910.252(с)(7)(ii)
В помещении . Сварка металлов на основе свинца внутри помещений должна выполняться в соответствии с параграфом (с)(3) настоящего параграфа.
1910.252(с)(7)(iii)
Местная вентиляция. В закрытых помещениях или в закрытых помещениях сварка или резка металлов, содержащих свинец, за исключением примеси, или металлов, покрытых свинецсодержащими материалами, включая краску, должна выполняться с использованием местной вытяжной вентиляции или воздушных респираторов. Такие операции, когда они выполняются на открытом воздухе, должны выполняться с использованием респираторов, одобренных для этой цели NIOSH в соответствии с 42 CFR, часть 84. Во всех случаях рабочие, находящиеся в непосредственной близости от места резки, должны быть защищены местной вытяжной вентиляцией или воздушными респираторами.
1910.252(с)(8)
Бериллий . Сварка или резка в помещении, на открытом воздухе или в замкнутых пространствах с использованием бериллийсодержащих основных или присадочных металлов должна производиться с использованием местной вытяжной вентиляции и воздушных респираторов, если атмосферные испытания в самых неблагоприятных условиях не установили, что воздействие на рабочих находится в пределах установленных допустимых концентраций. по § 1910.1000 настоящей части. Во всех случаях рабочие, находящиеся в непосредственной близости от сварочных или режущих работ, должны быть при необходимости защищены местной вытяжной вентиляцией или воздушными респираторами.
1910.252(с)(9)
Кадмий –
1910.252(с)(9)(я)
Общие. В замкнутых пространствах или в помещении операции по сварке или резке неблагородных металлов, содержащих кадмий или покрытых кадмием, должны выполняться с использованием местной вытяжной вентиляции или воздушных респираторов, если атмосферные испытания в наиболее неблагоприятных условиях не показывают, что воздействие на работника находится в пределах указанных допустимых концентраций к 29CFR 1910.1000. Такие операции, когда они выполняются на открытом воздухе, должны выполняться с использованием респираторов, таких как противодымные респираторы, одобренные для этой цели NIOSH в соответствии с 42 CFR, часть 84.
1910. 252(с)(9)(ii)
Замкнутое пространство . Сварка (пайка) кадмийсодержащих присадочных металлов должна производиться с использованием вентиляции, предусмотренной пунктами (в)(3) или (в)(4) настоящего параграфа, если работы должны выполняться в замкнутом пространстве.
1910.252(с)(10)
Меркурий. В замкнутых пространствах или в помещении операции по сварке или резке металлов, покрытых ртутьсодержащими материалами, включая краску, должны выполняться с использованием местной вытяжной вентиляции или воздушных респираторов, кроме случаев, когда атмосферные испытания в наиболее неблагоприятных условиях показывают, что воздействие на работника находится в пределах допустимого концентрации, указанные в 29 CFR 1910.1000. Такие операции, когда они выполняются на открытом воздухе, должны выполняться с использованием респираторов, одобренных для этой цели NIOSH в соответствии с 42 CFR, часть 84.
1910.252(с)(11)
Чистящие составы –
1910.252(с)(11)(и)
Инструкции производителя . При использовании чистящих средств из-за их возможной токсичности или воспламеняемости необходимо соблюдать соответствующие меры предосторожности, такие как инструкции производителя.
1910.252(с)(11)(ii)
Обезжиривание . Обезжиривание и другие операции по очистке с использованием хлорированных углеводородов должны быть расположены таким образом, чтобы пары от этих операций не попадали и не втягивались в атмосферу, окружающую любую сварочную операцию. Кроме того, трихлорэтилен и перхлорэтилен не должны попадать в атмосферу, через которую проникает ультрафиолетовое излучение сварочных работ в защитных газах.
1910.252(с)(12)
Резка нержавеющих сталей . Кислородная резка с использованием либо химического флюса, либо железного порошка, либо дуговая резка нержавеющей стали в среде защитного газа должна выполняться с использованием механической вентиляции, достаточной для удаления образующихся паров.
1910.252(с)(13)
Средства первой помощи . Средства первой помощи должны быть доступны в любое время. Обо всех травмах следует сообщать как можно скорее для оказания медицинской помощи. Первая помощь должна быть оказана до момента оказания медицинской помощи.
1910.252(г)
Промышленное применение –
1910. 252(д)(1)
Трубопровод –
1910.252(г)(1)(я)
Общий . Требования пунктов (b) и (c) настоящего раздела и § 1910.254 настоящей части.
1910.252(г)(1)(ii)
Операции на выезде . Если для изготовления арматуры, переходов через реки, дорог, насосно-компрессорных станций задействованы полевые цеха, требования пунктов (а), (б) и (в) настоящего параграфа и §§ 1910.253 и 1910.254 настоящей части должны соблюдаться.
1910.252(г)(1)(iii)
Поражение электрическим током . При дуговой сварке во влажных условиях или в условиях повышенной влажности должны быть предусмотрены специальные средства защиты от поражения электрическим током.
1910.252(г)(1)(iv)
Опрессовка . При опрессовке трубопроводов рабочие и население должны быть защищены от травм в результате срабатывания затворов или других устройств, ограничивающих давление. Кроме того, должна быть обеспечена защита от выброса рыхлой грязи, которая могла попасть в трубу.
1910.252(д)(1)(в)
Строительные стандарты . Сварные конструкции магистральных трубопроводов должны выполняться в соответствии со Стандартом сварки трубопроводов и связанных с ними сооружений, API Std. 1104–1968, который включен посредством ссылки, как указано в § 1910.6.
1910.252(г)(1)(vi)
Линии легковоспламеняющихся веществ . Соединение посредством сварки отводов к трубопроводам, транспортирующим легковоспламеняющиеся вещества, должно выполняться в соответствии с API Std. PSD № 2201 – 1963, который включен посредством ссылки, как указано в § 1910.6.
1910.252(г)(1)(vii)
Рентгенологическое обследование . Использование рентгеновских лучей и радиоактивных изотопов для контроля сварных соединений трубопроводов должно осуществляться в соответствии с Американским национальным стандартом безопасности для немедицинских источников рентгеновского излучения и закрытых источников гамма-излучения, ANSI Z54.1-19.63, который включен посредством ссылки, как указано в § 1910.6.
1910.252(г)(2)
Системы механических трубопроводов –
1910. 252(г)(2)(и)
Общий . Необходимо соблюдать требования параграфов (a), (b) и (c) настоящего раздела и §§ 1910.253 и 1910.254 настоящей части.
1910.252(г)(2)(ii)
Рентгенологическое обследование . Использование рентгеновских лучей и радиоактивных изотопов для контроля сварных соединений трубопроводов должно соответствовать Американскому национальному стандарту безопасности для немедицинских источников рентгеновского излучения и герметичных источников гамма-излучения, ANSI Z54.1 – 1963.
[39 FR 23502, 27 июня 1974 г., в редакции 40 FR 23073, 28 мая 1975 г.; 43 FR 49750, 24 октября 1978 г.; 49 ФР 5323, 10, 19 фев.84; 51 FR 34562, 29 сентября 1986 г.; 54 ФР 24334, 7 июня 1989 г.; 55 FR 13696, 11 апреля 1990 г.; 61 ФР 9227, 7 марта 1996 г.; 63 FR 1152, 8 января 1998 г.; 74 FR 46357, 9 сентября 2009 г. ; 77 ФР 17777, 26 марта 2012 г.]
Номер P, номер F и номер A в сварке (ASME Раздел IX) – сварка и неразрушающий контроль
15 комментариев / Номер P, номер F и номер A (ASME Раздел IX), Спецификация процедуры сварки (WPS) / By Сандип Ананд
Код ASME для котлов и сосудов под давлением (BPVC) присваивает определенные номера основным металлам (подлежащим сварке), а также присадочным металлам (электродам).
Для основных металлов ASME присвоил две системы нумерации:
- Номера P
- Номера групп
Для присадочных металлов присваивается следующая система нумерации;
- F-номер
- Номер А
Эти номера можно найти в разделе IX ASME BPVC, подробности см. в таблице –1 ;
Таблица – 1 .
- Подготовка испытательного купона
- приварка пробного образца и
- отправка в лабораторию для разрушающего испытания
Следовательно, чтобы сократить эти дорогостоящие и трудоемкие действия, ASME сгруппировал основные металлы и присвоил каждой группе металлов определенные номера P. Эта группировка неблагородных металлов была сделана на основе следующих параметров;
- Состав материала
- Свариваемость
- Механическое свойство
Хотя все материалы с одинаковым номером «P» не обладают одинаковыми свойствами, но после рассмотрения вышеупомянутых параметров ASME провел эту логическую группировку.
Зачем нужна эта группировка? Предположим, если мы меняем основной металл из существующей квалифицированной WPS и если новый основной металл попадает в тот же номер «P», то повторная квалификация существующей WPS не требуется, это означает, что нет необходимости в новом PQR.
Но это не означает, что можно в любое время легко заменить базовый материал из существующих WPS с тем же номером «P». Всякий раз, когда происходит изменение основного материала по сравнению с существующими WPS, совместимость должна учитываться в отношении следующих факторов:
- Металлургическое имущество
- Механическое свойство
- Вопросы дизайна
- Требования к обслуживанию
- Термическая обработка
Таблица 2 показывает группы назначения для различных металлов и их сплавов (согласно ASME BPVC).
Таблица – 2 Теперь, когда мы поняли числа «P», давайте перейдем к номерам групп. Номера групп являются подмножествами номеров «P» и присваиваются металлам на основе черных металлов . Групповые номера присваиваются только тем материалам , которые требуют испытаний на ударную вязкость для квалификации их WPS.
Возьмем в качестве примера SA516 Gr 65 из таблицы QW/QB-422 (Страница – 118 ASME Раздел IX, издание 2017 г.), мы можем узнать следующие значения;
Основной материал – SA516 Gr 65
- Прочность на растяжение (мин.) – 65 Ksi (или 450 МПа)
- P-№. – 1
- Номер группы – 1
- Номинальный состав – C-Mn-Si
- Типовая форма изделия – плита
Еще одной группой неблагородных металлов были номера «S», но в настоящее время номер «S» не используется. Он был исключен из ASME в 2009 году.
Номера S были присвоены тем материалам, которые были приемлемы для использования в соответствии со стандартом ASME B31 для трубопроводов под давлением или отдельными случаями кодов котлов и сосудов под давлением, но не были включены в раздел II ASME. Котел и сосуд под давлением (BPVC). Неблагородным металлам, которым ранее были присвоены номера «S», были присвоены соответствующие номера P или номера P и номера групп.
Номер F: Группировка номеров F (для присадочных металлов) выполняется для сокращения количества сварщиков и спецификаций процедуры (WPS) исполнительские квалификации. Основой для группировки номеров F являются характеристики удобства использования . Характеристики удобства в основном определяют способность сварщика производить качественные сварные швы с данным присадочным металлом . Следовательно, предполагается, что если сварщик может выполнить удовлетворительный сварной шов с определенным присадочным металлом, он сможет сваривать все присадочные металлы, относящиеся к этому конкретному номеру «F».
В таблице 3 приведен краткий обзор «F» и присадочных металлов (согласно ASME BPVC, таблица: QW-432).
Таблица – 3 Группировка номеров «F» не означает, что можно легко заменить присадочный металл (электрод/сварочный пруток) из существующих технологических карт на тот же номер «F» в любое время. . Всякий раз, когда происходит замена присадочного металла (электрод/сварочная проволока) по сравнению с существующими технологическими процессами, совместимость должна учитываться в отношении следующих факторов:
- Металлургическое имущество
- Механическое свойство
- Вопросы дизайна
- Требования к обслуживанию
- Термическая обработка
Номер A: Другим типом группировки присадочного металла или сварочной проволоки является номер «A». Группировка номеров «А» выполнена на основе химического состава наплавленного металла шва. Это можно найти в ASME BPVC Раздел IX, Таблица – QW-442).
Пожалуйста, посмотрите видео (приведенное ниже) для большей ясности по этой теме;Читайте также: Диапазон толщины для квалификации сварщика
Читайте также: Символы сварки
Читайте также: Как написать спецификацию процедуры сварки
МаркерыPaint для металла… что означает «низкая коррозия» и «низкая концентрация хлоридов»?
Дата: 17-03-2017
Внутренняя прихватка
Все о «низкой коррозии», почему это важно.

Почему так важен «низкий уровень коррозии»?
Поскольку технологии продолжают развиваться, многие отрасли, такие как производство и транспортировка продуктов питания, производство электроэнергии, нефтепереработка, газовые заводы, горнодобывающая промышленность, аэрокосмическая промышленность, судостроение и т. д., полагаются на нержавеющую сталь и различные сплавы металлов для использования в ответственном и чувствительном оборудовании.
Нежелательная коррозия может ослабить или загрязнить это важное оборудование и создать опасные риски для здоровья и безопасности.
Химические вещества, такие как хлориды, другие галогены, сера и металлы с низкой температурой плавления, которые часто встречаются в маркировке и красках, могут способствовать нежелательной коррозии, деградации, точечной коррозии или общему ослаблению чувствительных материалов.
Чтобы избежать этого, важно использовать маркеры с «низкой коррозией».
Каково определение лакокрасочного маркера с низким уровнем коррозии?
Хотя не существует национальных или международных стандартов, определяющих низкий уровень коррозии в отношении лакокрасочных маркеров, общепринятым пороговым значением для маркеров с низким уровнем коррозии являются те, которые содержат менее 250 ppm (частей на миллион) вызывающих коррозию веществ… Или, чтобы быть конкретным;
Менее 200 частей на миллион хлоридов и общего количества галогенов
Менее 250 частей на миллион каждого металла с низкой температурой плавления (включая: сурьму, висмут, кадмий, свинец, ртуть, фосфор, олово, цинк, медь, серебро)
Менее 250 частей на миллион серы
«Низкая коррозия» и «Низкая хлоридность» — в чем разница?
Чтобы быть действительно «низкокоррозийными», маркеры должны содержать не только мало хлоридов, но и другие коррозионно-активные вещества (сера, фториды, галогены, легкоплавкие металлы и т. д.).
Некоторые маркеры могут претендовать на «низкое содержание хлоридов», но имеют неприемлемо высокое содержание этих других веществ, вызывающих коррозию, поэтому они не являются действительно «низкокоррозионными».
Откуда мне знать, что маркеры Pro-Line HP не подвержены коррозии?
Все маркеры Pro-Line HP имеют минимально возможную коррозионную стойкость.
Определенные распространенные цвета Pro-Line HP прошли лабораторные испытания (с использованием стандартного анализа) на содержание менее n 250 ppm (частей на миллион) хлоридов и других веществ, вызывающих коррозию. Эти цвета: белый, желтый, красный, черный и розовый*
Вот почему эти маркеры Pro-Line HP рекомендуются многими мастерскими и предприятиями по всей Австралии. Использование Pro-Line HP дает вам уверенность в том, что маркер, который вы используете сегодня, не будет способствовать возникновению проблем, связанных с коррозией, на вашей металлической конструкции завтра .
Нажмите здесь, чтобы просмотреть и загрузить информационный бюллетень и отчеты об испытаниях Pro-Line HP.
Подходит ли Pro-Line HP только для критически важных приложений? …Или я могу использовать его как обычный маркер?
Pro-Line HP используется в Австралии и во всем мире в качестве универсального промышленного лакокрасочного маркера практически для любого применения, о котором вы только можете подумать… включая; все металлы, дерево, пластик, кирпичная кладка, стекло, керамика, резина и многое другое. А Pro-Line HP отлично работает на сложных поверхностях, таких как влажный, масляный или ржавый металл.
Pro-Line HP — действительно один из самых безопасных и универсальных промышленных красочных маркеров в мире!
Свяжитесь с Weldclass сегодня, чтобы запросить образцы и найти ближайшего дистрибьютора, или щелкните здесь для получения дополнительной информации.
youtube.com/embed/gorbZFivFw4″ frameborder=”0″ allowfullscreen=”allowfullscreen”>
Этот блог поможет: Предотвратить коррозию металла, ржавчину, окисление ручек, точечную коррозию и т. д., вызванные маркером краски | Какой маркер лучше всего использовать для нержавеющей стали? | Какой маркер для металла лучше?
Все технические характеристики могут быть изменены без предварительного уведомления. Несмотря на то, что были предприняты все меры предосторожности, Weldclass не несет ответственности за любые неточности, ошибки или упущения в этой информации или ссылках и приложениях. Любые комментарии относительно предполагаемого применения предназначены только для целей описания и идентификации. Пользователь, и/или владелец, и/или покупатель несут исключительную ответственность за выбор соответствующего продукта для его предполагаемой цели и за обеспечение того, чтобы выбранный продукт мог работать правильно и безопасно в предполагаемом применении. Э.&О.Э. *Розовые маркеры, предлагаемые Weldclass, относятся к серии Markal Valve-Action, которые сгруппированы вместе с серией Pro-Line HP для удобства и идентификации.
Метки
Металлические маркеры Изготовление из нержавеющей стали
КомментарииДата: 17-03-2020
Чарльз МатисСпасибо за информацию.
Дата: 22-03-2019
Команда Weldclass JWL Marketing Pty LtdАзеведо Хоана. По всем причинам, упомянутым в этом блоге, Pro-Line HP особенно подходит для обработки нержавеющей стали. Метки долговечны, однако, как и в случае с любым маркером, они не будут длиться бесконечно.
Если вам нужна маркировка, которая не сойдет ни при каких условиях, вам стоит подумать о травлении/гравировке.
Дата: 22-03-2019
Команда Weldclass JWL Marketing Pty LtdAtul – Pro-Line HP рекомендуется для маркировки как на окрашенных, так и на неокрашенных поверхностях.
Дата: 22-03-2019
Азеведо ДжоанаКакой черный маркер лучше всего подходит для маркировки нержавеющей стали? И мне нужно, чтобы он не отрывался. Спасибо
Дата: 31-12-2018
Атул Кумар Карн Tata сталь лимитедМы хотим писать на окрашенной поверхности, а также на стальных пластинах для идентификации (с целью отслеживания).
Пожалуйста, предложите соответствующие маркеры со всеми деталями.
Обратите внимание: спам-комментарии (или попытки создания обратных ссылок) будут УДАЛЕНЫ и НЕ будут опубликованы.
Стандартная спецификация штуцеров стальной трубы ASTM A234 WPB
Стандартные штуцеры стальной трубы ASTM A234 широко применялись в трубопроводных системах, они включают материал из углеродистой и легированной стали.
Что такое Фитинги для стальных труб
Фитинги для стальных труб изготавливаются из труб, пластин, профилей из углеродистой или легированной стали определенной формы, которая может выполнять функцию (изменение направления или расхода жидкости) в трубопроводных системах. В основном эти фитинги включают стальное колено (изгиб 45 или 90 градусов), тройник, переходник (концентрический или эксцентрический переходник), крестовину, заглушки, ниппель, фланцы, прокладку, шпильки и т. д.
В промышленных целях в трубопроводных системах обычно требуется изменить направление передачи; Отрегулируйте расход жидкости (нефть и газ, вода, шлам); Откройте или закройте трубопроводы и т. д. Таким образом, для выполнения этих действий будут применяться фитинги для стальных труб.
Что такое ASTM A234 WPB
ASTM A234 является стандартной спецификацией для фитингов из стальных труб, включая углеродистую и легированную сталь для эксплуатации при умеренных и высоких температурах. Он охватывает стальную арматуру бесшовного и сварного типов. Фитинги из стальных труб применяются в напорных трубопроводах и в конструкциях сосудов под давлением. Материал этих фитингов состоит из спокойной стали, поковок, стержней, пластин, бесшовных или HFW (сварных плавлением) трубных изделий с добавлением присадочного металла.
ASTM A234 включает фитинги из кованой углеродистой и легированной стали бесшовной и сварной конструкции, на которые распространяется последняя редакция ASTM B16. 9, B16.11, MSS-SP-79, MSS-SP-83, MSS-SP-95, и МСС-СП-97. и т.д.
Как известно, фитинги из стали ASTM A234 используются в трубопроводах под давлением и при изготовлении сосудов под давлением для работы при умеренных и повышенных температурах. Материал фитингов в этом стандарте состоит из спокойной стали, поковок, стержней, пластин, бесшовных или сваренных плавлением трубных изделий с добавлением присадочного металла.
В этом стандарте указаны характеристики отводов, тройников, переходников, заглушек и крестовин, обычно используются концы под приварку встык.
Классы ASTM A234
Спецификация ASTM A234 имеет множество классов, таких как WPB, WPC, WP5, WP9 WP11, WP12, WP22, WP91 и так далее.
В этих стандартах марка WPB является наиболее распространенным материалом, используемым для средне- и высокотемпературных трубопроводов. W означает свариваемый, P означает давление, B означает класс b, относится к минимальному пределу текучести.
Исходным сырьем для стальных трубных фитингов ASTM A234 WPB может быть стальная труба, такая как ASTM A106 Gr.B и C. Также из стального листа, как ASTM A285 Gr.C, ASTM A516 Gr 70, ASTM A572 и т. д.
ASTM A234 Фитинги для стальных труб WPB химические и механические характеристики
Фитинги WPB класса, изготовленные из стальных труб или пластин максимум C составляет 0,35%.
Кованая фурнитура Содержание углерода не более 0,35 % и не более 0,35 % содержания кремния, без минимума.
При каждом снижении содержания углерода на 0,01 максимальное содержание марганца увеличивается на 0,06%, до максимального значения 1,35% для Mn.
Суммарное содержание меди, никеля, ниобия и молибдена не должно превышать 1,00%.
Ниобий + Молибден не должен превышать 0,32%.
Для других классов:
Механические свойства ASTM A234 WPB Fipting Fitings
Прочность на растяжение 60 000 PIS 415 МПа
Выход 35 000 фунтов на квадратный дюйм 240 МПа
. , 2000 фунтов, 3000 фунтов до 9000 фунтов.
Для других марок по ASTM A234:
ASTM A234 включает бесшовные и сварные фитинги для труб
Под бесшовными фитингами для стальных труб понимается исходный материал для фитингов из бесшовных стальных труб и трубок;
Таким образом, сварные фитинги для стальных труб охватывают сырье для фитингов из сварных стальных труб.
Следует отметить, что спецификация
ASTM A234 не распространяется на литые сварные фитинги или фитинги, изготовленные из отливок.
Производство фитингов для стальных труб Процессы формовки
Процессы производства фитингов для труб включают операции ковки и формовки. А также прессование, ковка, прошивка, выдавливание, осадка, прокатка, гибка, сварка плавлением и механическая обработка. Или процессы совмещения двух и более этих операций.
При изготовлении арматуры для стальных труб необходимо отметить следующие мероприятия:
1, Не допускается образование вредных дефектов, дефектов сварки.
2. После придания формы или формирования фитингов при подходящей температуре их следует охладить в соответствующих условиях до температуры ниже критического диапазона. И никаких дефектов не должно быть сделано во время процедур охлаждения. Скорость охлаждения должна быть не выше, чем на воздухе.
3 Соответствующая проверка должна быть проведена после изготовления. (гидростатические испытания, испытания на твердость, испытания на растяжение и т. д.)
Размеры фитингов для стальных труб ASTM A234
Стандарты: ANSI/ASME B16.9, B16.28, MSS-SP-43.
Диапазон наружного диаметра: от 1/2” до 48”
Диапазон толщины: SCH 10, sch 20, SCH 40, SCH STD, SCH 80, SCH XS, SCH 160, SCH XXS и т. д.
Производство фитингов для стальных труб типы кованые, резьбовые, сварные встык и бесшовные.
Фитинги из легированной стали, классы ASTM A234
. Фитинги из легированной стали изготавливаются из таких сплавов, как хром, молибден, никелевый сплав, сплав Hastelloy, монель, инконель и т. д. Чтобы получить более высокие номинальные значения давления, лучшую прочность, хорошая коррозионная стойкость и длительный срок службы. Широко применяется на нефте- и газопроводах, химической промышленности, электростанциях, объектах атомной энергетики, в серверных условиях.
Фитинги для труб из легированной стали включают в себя фитинги для сварки встык, изгибы с большим радиусом из легированной стали, кованые фитинги из легированной стали и так далее.
Фитинги для сварки встык из легированной стали соответствуют стандарту ASTM A234, имеют классы WP1, WP5, WP11, WP12, WP22, WP23 и WP91. Уровень класса в CL1, CL2, CL3.
Фитинги из легированной стали ASTM A234 включают колена из легированной стали с длинным и коротким радиусом, эксцентриковый и концентрический редуктор из легированной стали, колпачки и крестовины из легированной стали, муфты из легированной стали, тройники из легированной стали, ниппели из легированной стали, колпачки из легированной стали и т. Д. Другие формы . Он бывает бесшовным, сварным и сборным.
Для кованых фитингов из легированной стали используется стандарт ASTM A182, относящийся к фланцам стальных труб. Стандарт материала в ASTM A182 F1, F5, F9, F11 класс 1, F12 класс 1, F22 класс 1 и т. д.
Химический состав
Класс и символ маркировки | Состав, % | ||||||
С | Мн | Р | С | Си | Кр | Пн | |
ВПБ | 0,30 макс. | 0,29-1,06 | 0,050 | 0,058 | 0,10 мин | 0,40 макс. | 0,15 макс. |
ВПК | 0,35 макс. | 0,29-1,06 | 0,050 | 0,058 | 0,10 мин | 0,40 макс. | 0,15 макс. |
РП1 | 0,28 макс. | 0,30-0,90 | 0,045 | 0,045 | 0,10-0,50 | … | 0,44-0,65 |
WP12 класс 1, WP12 класс 2 | 0,05-0,20 | 0,30-0,80 | 0,045 | 0,045 | 0,60 макс. | 0,80-1,25 | 0,44-0,65 |
WP11 CL1, | 0,05-0,15 | 0,30-0,60 | 0,030 | 0,030 | 0,50-1,00 | 1,00-1,50 | 0,44-0,65 |
WP11 класс 2, WP11 класс 3 | 0,05-0,20 | 0,30-0,80 | 0,040 | 0,040 | 0,50-1,00 | 1,00-1,50 | 0,44-0,65 |
WP22 класс 1, WP22 класс 3 | 0,05-0,15 | 0,30-0,60 | 0,040 | 0,040 | 0,50 макс. | 1,90-2,60 | 0,87-1,13 |
WP5 класс 1, WP5 класс 3 | 0,15 макс. | 0,30-0,60 | 0,040 | 0,030 | 0,50 макс. | 4,0-6,0 | 0,44-0,65 |
WP9 класс 1, WP9 класс 3 | 0,15 макс. | 0,30-0,60 | 0,030 | 0,030 | 1,00 макс. | 8,0-10,0 | 0,90-1,10 |
WPR | 0,20 макс. | 0,40-1,06 | 0,045 | 0,050 | … | … | … |
WP91 | 0,08-0,12 | 0,30-0,60 | 0,020 | 0,010 | 0,20-0,50 | 8,0-9,5 | 0,85-1,05 |
WP911 | 0,09-0,13 | 0,30-0,60 | 0,020 | 0,010 | 0,10-0,50 | 8,5-9,5 | 0,90-1,10 |
Требования к растяжению
Класс и символ маркировки | ВПБ | ДПК, WP11 класс 1, WP12 класс 2 | РП1 | WP11 класс 1, WP22 класс 1, WP5 класс 1, WP9 класс 1 | WPR | WP11 класс 3, WP22 класс 3, WP2 класс 3, WP9 класс 3 | WP91 | WP911 | WP12 CL1 |
Прочность на растяжение, диапазон Ksi [МПа] | 60-95 [415-655] | 70-95 [485-655] | 55-80 [380-550] | 60-85 [415-585] | 63-88 [435-605] | 75-100 [520-690] | 85-110 [585-760] | 90-120 [620-840] | 60-85 [415-585] |
Предел текучести, мин, Ksi [МПа] (смещение 0,2 % или удлинение 0,5 % под нагрузкой) | 35 [240] | 40 [275] | 30 [205] | 30 [205] | 46 [315] | 45 [310] | 60 [415] | 64 [440] | 32 [220] |
Запросить предложение
Краткое руководство по сварке нержавеющей стали
Сварка нержавеющей стали существенно отличается от сварки других материалов. Отличие начинается с уникального химического состава нержавеющей стали.
Что такое нержавеющая сталь?
Как и другие стали, нержавеющая сталь представляет собой сплав железа и углерода. Что отличает нержавеющую сталь, так это то, что она содержит не менее 10,5% хрома, элемента, который делает полученный сплав устойчивым к коррозии. Kloeckner Metals поставляет нержавеющую сталь различных форматов, включая листовую нержавеющую сталь, листовую нержавеющую сталь, трубы из нержавеющей стали и пруток из нержавеющей стали.
Нержавеющая сталь бывает пяти типов, но в производственных цехах обычно встречаются только три из них: аустенитная нержавеющая сталь, мартенситная нержавеющая сталь и ферритная нержавеющая сталь. Наиболее распространен аустенитный. Мартенситная нержавеющая сталь используется для наплавки. А ферритная сталь, самый дешевый вариант, чаще всего используется в потребительских товарах.
Загрузить нашу спецификацию на нержавеющую сталь сегодня Kloeckner Metals является поставщиком полного ассортимента нержавеющей стали и сервисным центром. Загрузите нашу спецификацию нержавеющей стали и узнайте, что Kloeckner Metals регулярно поставляет на склад.
Технические характеристики нержавеющей стали
Каждый из этих типов стали классифицируется на основе ее микроструктуры, которая влияет на ее пластичность и прочность. Микроструктура стали зависит от ее химического состава. Например, аустенитная сталь содержит 16-26% хрома (Cr) и 8-22% никеля (Ni). Мартенситная сталь имеет содержание Cr в пределах 11-28%. Ферритная сталь содержит 12-18% Cr. В результате материал, привариваемый к каждому типу стали, должен соответствовать составу этой стали.
Что усложняет сварку нержавеющей стали?
Сварка нержавеющей стали сложнее, чем сварка углеродистой стали.
Во-первых, нержавеющая сталь эффективно удерживает тепло, вызывая ее деформацию при воздействии высоких температур, создаваемых сваркой. Нержавеющая сталь также может деформироваться или растрескиваться в процессе охлаждения после того, как она была нагрета сварщиком. Даже если кусок нержавеющей стали не трескается и не деформируется после неудачной сварки, на нем почти всегда остаются царапины и пятна.
Каждый вид нержавеющей стали представляет собой сложную задачу для сварщиков. Аустенитная сталь может растрескиваться при высокой подводимой температуре или при выполнении вогнутого или плоского сварного шва. Мартенситная сталь может треснуть, если ее не подогреть должным образом. А с низкой максимальной межпроходной температурой 300°С ферритная сталь будет терять прочность, если ее не нагреть с низким погонным теплом.
Ключом к успешной сварке нержавеющей стали является выбор правильного присадочного материала. Марка присадочного материала должна соответствовать марке основного материала, чтобы получить хороший сварной шов.
Материалы и оборудование, необходимые для сварки нержавеющей стали
Почему для сварки нержавеющей стали требуется специальное оборудование и какие инструменты и материалы необходимы для сварки нержавеющей стали?
Нержавеющая сталь может подвергаться сварке электродуговой сваркой с защитным металлом (MIG) или дуговой сваркой вольфрамовым электродом в среде защитного газа (TIG). Лучший выбор зависит от того, чего вы пытаетесь достичь, поскольку каждый процесс приводит к разным результатам.
Нержавеющую сталь можно сваривать палкой, но, вероятно, не следует. Есть другие, лучшие варианты.
Сварочный аппарат MIG обеспечивает самые прочные и надежные сварные швы с нержавеющей сталью. Это особенно хороший выбор, если вы свариваете что-то толстое. Сварочные аппараты TIG могут быть правильным выбором для более тонких материалов и для сварки, требующей красоты и точности. Тем не менее, TIG — это сложная сварка, если у вас нет опыта и времени, чтобы сделать это правильно. Неопытный сварщик TIG может оставить неприятные следы или пятна на нержавеющей стали.
Несмотря на менее тонкий сварной шов, MIG-аппарат, как правило, является лучшим вариантом для сварки нержавеющей стали. Выберите аппарат, который поставляется со сварочным пистолетом и образцом сварочной проволоки. У большинства машин есть пистолет, но вы можете модернизировать свой, если вам нужно что-то, что обеспечит более точный сварной шов. Вы также захотите приобрести несколько насадок для сварочных пистолетов, чтобы заменить их, когда они изнашиваются.
Для защиты сварочного пистолета вы можете приобрести чехол. Это отличное дополнение, поскольку оно позволяет быстро и эффективно переключаться между различными типами металлической проволоки. Вам не нужен механизм подачи сварочной проволоки, если вы не профессиональный сварщик или не планируете много сваривать. Что касается самой проволоки, вы должны использовать подходящую сварочную проволоку из нержавеющей стали, которая обычно имеет диаметр 0,030 дюйма, но для более толстых деталей может подойти проволока от 0,035 до 0,045 дюйма.
Поскольку при сварке нержавеющей стали необходимо контролировать температуру, чтобы избежать проблем с производительностью, необходимо иметь под рукой устройство для отслеживания температуры. Вы можете использовать традиционную палку, но помните, что ее диапазон ограничен. Другие опции включают электронный инфракрасный термометр и электронный датчик температуры поверхности.
Вам также понадобится защитный газ. Инертные газы не рекомендуются, поэтому вам, вероятно, понадобится смесь из 7,5% аргона, 90% гелия и 2,5% углекислого газа. Наконец, вам нужно будет добавить щетку для соскабливания и очистки металла. Этот инструмент может помочь вам подготовить рабочее место и, в конечном итоге, добиться более прочного сварного шва.
Подготовка к сварке
На что следует обратить внимание при подготовке к сварке? Чем он отличается для разных марок стали?
Используйте металлическую щетку для удаления пыли, грязи, масла, жира или воды с рабочей станции. Вы также можете помочь предотвратить деформацию и растрескивание, зажав кусок латуни или меди за сварочным швом. Этот трюк может помочь поглотить тепло и сохранить вашу нержавеющую сталь достаточно прохладной.
Держите отдельный набор инструментов для сварки нержавеющей стали. Как только ваши инструменты коснутся углеродистой стали, на них останется нагар. Этот остаток перейдет на нержавеющую сталь во время сварки, что в конечном итоге может привести к ржавчине изделия.
Другие советы, которые следует учитывать при сварке нержавеющей стали
Как обеспечить наилучшие результаты сварки?
- При сварке TIG используйте отрицательную настройку электрода DCEN или постоянного тока и силу тока 1 ампер на каждые 1/1000 дюйма толщины металла.
- При сварке MIG используйте метод проталкивания. Этот подход позволяет вам более четко видеть, что вы делаете, и создает меньше бусинок. Используйте технику натяжения только тогда, когда вам нужно более глубокое проникновение.
- Держите сварочный пистолет под углом 90 градусов с углом перемещения 5–15 градусов. Для Т-образных соединений и соединений внахлестку попробуйте увеличить угол примерно на 45-70 градусов.
- Следите за чистотой, безопасностью и хорошей вентиляцией рабочего места.
Хотя сварка нержавеющей стали немного сложнее, чем другие сварные швы, ее можно сделать. Вы даже можете сваривать нержавеющую сталь с мягкой сталью. Используя правильное оборудование, регулируя температуру и используя правильный присадочный материал, можно получить прочный и долговечный сварной шов.
Kloeckner Metals является поставщиком и сервисным центром полного ассортимента нержавеющей стали. Kloeckner Metals сочетает в себе национальное присутствие с новейшими технологиями производства и обработки и самыми инновационными решениями для обслуживания клиентов.
Свяжитесь с нами сейчас
Распределение размеров частиц дыма и скорость образования дыма при дуговой сварке из чугуна
Ind Health. 2020 июль; 58(4): 325–334.
Опубликовано в Интернете 10 января 2020 г. doi: 10.2486/indhealth.2019-0161
, 1, * , 1 и 1
Информация об авторе Примечания к статье Информация об авторских правах и лицензии Отказ от ответственности
дуговой сварки чугуна и оценили скорость образования вдыхаемой пыли. В
Кроме того, скорость генерации частиц диаметром 0,3 мкм и менее была
оцененный. В этом эксперименте использовались три типа присадочных материалов (проволока из мягкой стали, нержавеющая сталь). стальная проволока и покрытые электроды из мягкой стали) с основными составляющими Fe или Fe-Cr-Ni,
как было предложено ранее авторами. Методы сварки: газовая дуга.
сварка и дуговая сварка защищенным металлом. Пары, измеренные в этом исследовании, содержали
73–91% вдыхаемой пыли, а скорость образования дыма находилась в диапазоне 1,96–12,2 мг/с.
Результаты этого исследования были следующими: (i) сварочный ток влияет на генерацию
скорость вдыхания пыли, и весьма вероятно, что чем выше скорость образования дыма,
образуется больше вдыхаемой пыли; (ii) скорости образования вдыхаемой пыли при низких
и большой ток были самыми высокими, когда электроды с покрытием из мягкой стали и проволока из нержавеющей стали
был использован соответственно; и (iii) скорость генерации частиц диаметром 0,3
мкм или меньше было самым высоким при использовании проволоки из нержавеющей стали.
Ключевые слова: Дуговая сварка, Чугун, Скорость образования дыма, Гранулометрический состав, Вдыхаемая пыль, Респираторы
очень опасны для человеческого организма. Так как эти пары обычно имеют чрезвычайно малую
(0,005–20 мкм) размер частиц 1 ) ,
частицы переносятся тепловыми восходящими потоками, создаваемыми горячей свариваемой деталью, и рассеиваются
по всему рабочему месту. Из-за этого чрезвычайно большое количество рабочих подвергается
к испарениям на рабочих местах, где выполняется дуговая сварка. Хотя количество людей
диагноз пневмокониоз и его осложнения в последнее время имеют тенденцию к снижению.
лет в Японии, в настоящее время около 160 рабочих в год заболевают 2 ) . Доля дуговых сварщиков среди этого числа составляет
высокая 3 ) . Кроме того, канцерогенное
риск дыма, образующегося при сварке, недавно был повышен с группы 2В до
группа 1 Международного агентства по изучению рака (2017) 4 ) . В связи с этим ожидается, что управление рисками и
контроль дыма станет строже, чем когда-либо.
Дым, образующийся при дуговой сварке, представляет собой твердые микрочастицы, в которых пары металла
образуется из капли на кончике сварочного электрода и на поверхности сварочной ванны
быстро остывает и затвердевает по мере окисления 5 ) . Эти твердые микрочастицы плавают в окружающем воздухе и
попадают в организм человека через рот и нос.
Размер частиц дыма является важным фактором, влияющим на осаждение частиц
внутри дыхательной системы человека. Поскольку частицы разного размера проявляют разные
аэродинамическое поведение, они откладываются в разных местах дыхательной системы.
зависимость от размера частиц доли частиц, которые проникают и оседают в
каждое место в дыхательной системе может быть рассчитано с использованием модели из
Международная комиссия по радиологической защите 6 ) . Согласно этой модели, скорость осаждения достигает пика примерно в
частицы диаметром 10 мкм во входах в дыхательную систему, таких как нос и
глотка. Как правило, частицы диаметром порядка 10 мкм и более прилипают к поверхности.
слизистых оболочек полости носа, трахеи и широкой бронхиальной стенки, а затем
выгнали из тела 7 ) . Однако хорошо
частицы диаметром 10 мкм и менее достигают альвеол легких, а
скорость отложения в альвеолах увеличивается по мере уменьшения размера частиц 6 ) .
Пары, отложившиеся внутри альвеол, включаются внутрь клеток путем фагоцитоза
альвеолярными макрофагами и выводятся из организма в виде мокроты цилиарным движением
дыхательные пути вместе с выделениями из дыхательных путей. Однако, если количество
вдыхаемые пары достаточно велики, чтобы превысить способность обработки альвеолярных макрофагов или
движение ресничек нарушено, альвеолярные макрофаги прилипают к альвеолам 7 ) . Это приводит к фиброзу легких, который вызывает
осложнения, такие как пневмокониоз и первичный рак легкого 8 ) . В настоящее время в области охраны труда и техники безопасности в Японии
пыль с диаметром частиц 4 мкм и менее (аэродинамический диаметр), которая является основным
причиной пневмокониоза, определяется как вдыхаемая пыль, и эти частицы подвержены
измерение рабочей среды в соответствии с законом 9 ) . Таким образом, измерение распределения частиц дыма по размерам и
Скорость образования дыма в процессе дуговой сварки важна для прогнозирования
опасность паров и принятие соответствующих защитных мер.
Хотя дуговая сварка в основном используется для низкоуглеродистой стали, ее также можно применять для соединения
различных металлических материалов, таких как нержавеющая сталь и алюминиевые сплавы. Среди них более 3
миллионов тонн чугуна производится ежегодно 10 ) . Это практически то же самое, что и количество алюминиевого сплава.
продукция производства Японии 10 ) . Чугун
является основным металлическим материалом, используемым в литых изделиях. Литье – это процесс, при котором расплавленная отливка
железо образуется при разливке в формы различной формы, а так как этот процесс относительно
простой, он подходит для массового производства крупных изделий и сложных форм. Для
По этим причинам литые изделия, в которых используется чугун, используются в самых разных областях,
особенно в автомобильных и инструментальных частях для различных отраслей промышленности. Дуговая сварка – это
необходимая технология для соединения этих чугунных деталей и для ремонта, когда
изделия из чугуна ломаются.
В прошлых исследованиях распределение частиц дыма по размерам и скорость образования дыма во время дугового разряда
сварка алюминиевых сплавов, нержавеющей стали и магниевых сплавов с упором на мягкую сталь
были измерены. Например, Heile and Hill 11 ) измерили распределение частиц дыма по размерам и образование дыма.
скорость при дуговой сварке алюминиевых сплавов или низкоуглеродистой стали с использованием различных присадочных материалов.
Hewett 12 ) измерил размер частиц
распределение дыма, образующегося при дуговой сварке в среде защитного газа (GMAW) и дуговой сварке в среде защитного газа
сварка (SMAW) низкоуглеродистой и нержавеющей стали. Кроме того, авторы ранее
измерил распределение частиц дыма по размерам и скорость образования дыма во время GMAW
алюминиевые и магниевые сплавы 13 ) . Эти
Исследования показали, что распределение частиц дыма по размерам и скорость образования дыма зависят от
различные условия, в том числе процесс сварки, условия сварки (сила тока, напряжение),
тип присадочного материала, состав защитного газа и основной металл. Поскольку эти условия различаются
широко на реальных рабочих местах, распределение размера частиц дыма и скорость образования дыма
также ожидается, что они будут отличаться. На самом деле опытным путем сварщики замечают, что дуговая сварка литых
железо производит больше дыма, чем сварка мягкой стали. Однако, насколько нам известно, ранее
исследования измеряли распределение частиц дыма по размерам и скорость образования дыма во время
дуговая сварка чугуна.
Хотя при дуговой сварке
чугуна, давно рекомендуется, чтобы присадочный материал с никелем
основной компонент (ок. 50–100 % Ni) использовать 14 , 15 ) . Однако, поскольку пары (пыль
содержащие соединения Ni), которые накапливаются в рабочей среде при использовании присадочных материалов.
которые содержат Ni в качестве основного компонента, являются высокотоксичными, соблюдаются строгие правила.
наложенный на их обращение 16 ) . Поэтому,
поскольку использование наполнителя, содержащего Ni в качестве основного компонента, может нанести вред
здоровью из-за никелевой пыли предпочтительно использовать присадочные материалы с низким содержанием никеля или
абсолютно без никеля при дуговой сварке чугуна. Ранее мы предлагали дуговую сварку
метод для чугуна, который использует присадочные материалы, где основными составляющими являются Fe и
Fe-Cr-Ni 17 , 18 ) . Эти методы сварки оказались экономически более выгодными и
более практичны, чем материалы-наполнители, содержащие Ni в качестве основного компонента.
Это исследование измеряло распределение размера частиц дыма и скорость образования дыма во время
дуговая сварка чугуна с использованием присадочных материалов, содержащих Fe и Fe-Cr-Ni в качестве основных
составляющие, как было предложено ранее. Скорость образования вдыхаемой пыли, т.
затем по полученным результатам была оценена высокая опасность для организма человека.
Кроме того, мы оценили скорость генерации частиц с диаметром частиц 0,3
мкм или менее, которые считаются трудноулавливаемыми пылевыми фильтрами.
маски 19 , 20 , 21 , 22 , 23 , 24 ) .
Измерение гранулометрического состава
Как показано на рисунке, генерация дуги выполнялась в камере сбора дыма, чтобы исключить влияние перекрестных токов на отбор проб. Образовавшиеся пары были частично отобраны всасывающий патрубок, установленный в передней части камеры сбора дыма. Сварка была выполняется путем перемещения дуги в направлении, показанном на . В это время расстояние между дугой и всасывающим соплом составляло диапазон 450–550 мм (). Это почти то же самое, что и фактическое расстояние между дугой и зона дыхания сварщика.
Открыть в отдельном окне
Камера сбора дыма, используемая в этом исследовании.
Открыть в отдельном окне
Экспериментальная установка для измерения гранулометрического состава дыма.
12-ступенчатый импактор низкого давления типа Андерсена (модель LP-20; Tokyo Dylec Corp., Токио,
Япония) использовали для измерения гранулометрического состава дыма. Размер частиц
диапазоны на каждой ступени этого ударника составляли >12,1 мкм, 8,5–12,1 мкм, 5,7–8,5 мкм, 3,9–5,7 мкм. мкм, 2,5–3,9мкм, 1,25–2,5 мкм, 0,76–1,25 мкм, 0,52–0,76 мкм, 0,33–0,52 мкм, 0,22–0,33 мкм,
0,13–0,22 мкм и 0,06–0,13 мкм. Скорость всасывания импактора составляла 20 л/мин.
фильтровальную бумагу из стекловолокна (Т60А20) диаметром 80 мм надевали на каждую
ступень для улавливания образующихся паров.
При измерении гранулометрического состава с помощью импактора Андерсена, если количество
собранных частиц невелико, влияние погрешности веса фильтра на вес
количество частиц, собранных на каждом этапе, увеличивается. Кроме того, если сумма собранных
частицы слишком велики, происходит повторное рассеивание частиц, что влияет на размер частиц
распределение, полученное измерением. Поэтому в данном исследовании предварительно
был проведен эксперимент, и время генерации дуги было определено равным 90 с (GMAW) или
60 с (SMAW). Время всасывания было установлено на 690 с (GMAW) и 660 с (SMAW), включая дугу.
время генерации. После двукратного отсасывания фильтровальная бумага, прикрепленная к каждой ступени
вынимали и измеряли их вес. Вес фильтровальной бумаги, прикрепленной к каждому
измеряли до и после отбора проб с точностью до 0,01 мг, а вес
(мг) дыма, загруженного на каждой ступени.
Сварка выполнялась сварщиком вручную. Сварщик представил сварочную горелку или держатель электрода через входное отверстие на передней поверхности камеры сбора дыма, и выполнена сварка валиком основного металла, размещенного на рабочем столе. Бусина на пластине сварка – это метод плавления основного металла с подачей присадочного материала в расплавленный участок поверхности основного металла.
Измерение скорости образования дыма
Скорость образования дыма была измерена методом полного отбора проб, который соответствует
Японские промышленные стандарты (JIS) 25 ) .
Внутри камеры для сбора дыма генерировалась дуга, как показано на рис. , и дым полностью собирался с помощью всасывающей трубы, установленной
в верхней части камеры сбора дыма (). Пробоотборник воздуха большого объема (HV-500F; Shibata Scientific Technology, Сайтама,
Япония) использовался для сбора дыма. После включения пробоотборника большого объема воздуха
скорость всасывания была установлена на 800 л/мин, и дуга генерировалась немедленно. Сгенерированный
все пары собирали фильтровальной бумагой (GB-100R; Advantec Toyo, Kaisha, Ltd., Токио,
Япония) диаметром 110 мм из стекловолокна, вставленного в пробоотборник большого объема.
Затем скорость образования дыма (мг/с) была получена путем деления изменения веса на
фильтровальная бумага до и после сбора по времени генерации дуги.
Открыть в отдельном окне
Экспериментальная установка для измерения скорости дымообразования.
Уравнение (1) показывает уравнение для определения скорости образования дыма:
Fs=(W2−W1)/T (1)
В этом уравнении F s скорость образования дыма (мг/с), Вт 1 вес фильтровальной бумаги до сбора паров (мг), W 2 – масса фильтровальной бумаги после сбора пары (мг) и T – время генерации дуги (с).
Наварка валиком на пластину, выполняемая сварщиком вручную так же, как и при
измерение распределения частиц по размерам использовалось для сварки, а генерация дуги
время установлено 10 сек. Время всасывания пробоотборника большого объема воздуха было установлено на 180 с,
включая время генерации дуги. Наплавку валика на пластину выполняли в пяти экспериментальных
работает с тремя различными наполнителями, а представленные данные представляют собой средние значения из
эти пять серий экспериментов.
Основным металлом, использованным в этом исследовании, была пластина из чугуна с шаровидным графитом (FCD450-10), как в соответствии с JIS 26 ) . Размеры основной металл был t18 мм × L300 мм × W300 мм. показывает химический состав основного металла.
Таблица 1.
Химический состав основного металла, сварочных проволок и покрытых электродов (масс.%)
Материал | C | Si | Mn | P | S | Ni | Cr | Mo | Cu | Mg | Fe | |
---|---|---|---|---|---|---|---|---|---|---|---|---|
Base metal | ||||||||||||
FCD450- 10 | 3,40 | 2,98 | 0,20 | 0,030 | 0,010 | ― | ― | ― | ― | ― | ― ― ― ― ― ― ―.||
Filler material | ||||||||||||
YGW12 (Mild steel wire) | 0.02–0.15 | 0.50–1.00 | 1.25–2.00 | ≤0.030 | ≤0.030 | ― | ― | ― | ≤0,50 | ― | Ре.![]() | |
YS308 (проволока из нержавеющей стали) | ≤0,08 | ≤0,65 | ≤1,0–2,5 | ≤0,03 | ≤0,03 | 9,0-11,0 | 19,5-22,0 | ≤0,75 | ≤0,75 | |||
E4916 (Mild steel covered electrode) | ≤0.15 | ≤0.75 | ≤1.60 | ≤0.035 | ≤0.035 | ≤0.![]() | ≤0.20 | ≤0.30 | ― | ― | Ре. |
Открыть в отдельном окне
Re.: остаток.
Дуговая сварка – это метод соединения путем создания дуги между металлическим электродом (присадочным материала) и основного металла (свариваемого металла), а также расплавление основного металла и присадочного материала материал с использованием тепла, выделяющегося в это время. Наполнитель плавится под действием тепла дуга образует усиление сварного шва, которое обеспечивает прочность зоны сварки и заполняет зазор между двумя соединяемыми металлами. В дуговой сварке чугуна уже давно рекомендуется использовать наполнитель с никелем в качестве основного компонента.
В качестве присадочного материала в данном исследовании использовалась сварочная проволока и электрод с покрытием из Fe
и Fe-Cr-Ni в качестве основных компонентов, которые оказались очень практичными в наших исследованиях. предыдущие исследования 17 , 18 ) .
Сварочная проволока YGW12 27 ) и YS308 28 ) согласно определению JIS. Главный составной частью YGW12 является Fe, и он не содержит Ni. Этот наполнитель в основном для сварки низкоуглеродистой стали и в дальнейшем именуется проволокой из низкоуглеродистой стали. Главный составляющими YS308 являются Fe-Cr-Ni, а содержание Ni составляет около 10%. Этот наполнительный материал в основном является присадочным материалом для сварки нержавеющей стали и далее именуется провод из нержавеющей стали. Оба представляют собой сплошную проволоку диаметром 1,2 мм.
Покрытый электрод был E4916 29 ) as
определяется JIS. Основным компонентом E4916 является Fe, и это в основном наполнительный материал.
для сварки мягкой стали. В дальнейшем этот присадочный материал называется мягкой сталью с покрытием.
электрод. Диаметры покрытых электродов из мягкой стали составляли 3,2 мм и 5,0 мм. в зависимости от величины сварочного тока. показаны типы и химические составы сварочных проволок и покрытых
электроды, используемые в этом исследовании, как определено JIS.
В этом исследовании использовались методы сварки GMAW и SMAW.
GMAW — это метод сварки, при котором к сварным швам подаются спиральные электроды (сварочная проволока).
автоматически при использовании защитного газа для защиты сварных швов. Защитный газ, используемый для
стальная проволока была 100% CO 2 . Скорость потока составляла 15 л/мин. Точно так же 98% Ar + 2%
O 2 использовали для проволоки из нержавеющей стали, а скорость потока составляла 20 л/мин.
сварочный аппарат, используемый для GMAW, представлял собой импульсный сварочный аппарат MAG с цифровым инвертором (DP350;
DAIHEN Corporation, Осака, Япония). Как показано на рисунке, сварщик выполнил сварку валиком на пластине, наклонив сварочную горелку примерно на
10–20° в направлении, противоположном направлению сварки.
Открыть в отдельном окне
Направление сварки при дуговой сварке металлическим газом (GMAW) и дуговой сварке защищенным металлом (СМАВ). (A) показывает направление сварки GMAW, а (B) показывает направление сварки СМАВ.
Сварочный ток был установлен на 100 А и 200 А. В это время скорость подачи мягкого стальная проволока составляла 2,4 м/мин (100 А) и 6,0 м/мин (200 А), а скорость подачи проволока из нержавеющей стали составляла 2,7 м/мин (100 А) и 7,5 м/мин (200 А). Используемое сварочное напряжение было значением, соответствующим сварочному току, установленному изготовителем сварочного аппарата. сварочный аппарат.
SMAW — это метод сварки, в котором используется электрод с флюсовым покрытием вокруг круглой
металлический стержень диаметром от 3,2 до 5,0 мм в качестве электрода. Сварочный аппарат, используемый для
SMAW представлял собой аппарат для дуговой сварки переменным током (YK-250AD2; Panasonic Corp., Осака, Япония). Как показано в
, сварщик выполнил валик на пластине
при сварке с наклоном покрытого электрода примерно на 10–20° в направлении сварки. сварочный ток был установлен таким же, как и для GMAW, на 100 A и 200 A. показаны основные условия сварки для GMAW и SMAW.
Таблица 2.
Условия сварки в дуговой сварке (Gmaw and Smaw) чугуна
СВОРИ. CO 2 (проволока из мягкой стали) | YS308-98% Ar + 2% O 2 (проволока из нержавеющей стали) | E4916 (электрод с покрытием из мягкой стали) | 1.2 | 3.2, 5.0 | |||||||||||
---|---|---|---|---|---|---|---|---|---|---|---|---|---|---|---|
Welding current (A) | 100, 200 | ||||||||||||||
Welding voltage (V) | 19.![]() | 16.7, 26.7 | 23.5, 24.5 | ||||||||||||
Скорость подачи провода (м/мин) | 2,4, 6,0 | 2,7, 7,5 | ― | ||||||||||||
Расширение проволоки (мм) | 10–15 | ° | 10–15 | ° 40437 277 2779279 29277 9237 9237 | 10–15 | ° | 10–15 | . ) | 15 | 20 | ― |
Открыть в отдельном окне
GMAW: Дуговая сварка металлическим электродом в среде защитного газа; SMAW: Дуговая сварка защищенным металлом.
показывает распределение частиц дыма по размерам, измеренное в этом исследовании, в виде частоты распределение 30 ) . W по вертикальной оси представляет собой общий вес частиц, собранных импактором, а ΔW представляет собой вес частиц, собранных на каждой ступени импактора. Горизонтальная ось показывает диапазон размеров частиц (аэродинамический диаметр) на каждой ступени импактора. Кроме того, показано распределение частиц дыма по размерам, измеренное в этом исследовании, в виде кумулятивного раздача 30 ) .
Открыть в отдельном окне
Гранулометрический состав дыма, образующегося при дуговой сварке чугуна. На графике показано частотное распределение на основе веса 30 ) . Диапазон размеров частиц указывает на аэродинамический диаметр.
Открыть в отдельном окне
Гранулометрический состав дыма, образующегося при дуговой сварке чугуна.
На графике показано совокупное распределение веса 30 ) . Диаметр частиц указывает на аэродинамическую
диаметр.
От , средний массовый аэродинамический диаметр (MMAD) при 100 А составлял 0,63 мкм (проволока из мягкой стали), 0,52 мкм (проволока из нержавеющей стали) и 0,77 мкм. (электрод с покрытием из мягкой стали). При 200 А MMAD составлял 0,88 мкм (проволока из мягкой стали), 0,72 мкм (проволока из нержавеющей стали) и 0,89 мкм (электрод с покрытием из мягкой стали). MMAD увеличился с увеличение сварочного тока в любых условиях. Кроме того, MMAD нержавеющей стали провод был меньше, чем в других условиях при любом значении тока.
Дым, образующийся при всех условиях сварки, измеренных в этом исследовании, содержал
73–91% вдыхаемой пыли с диаметром частиц 4 мкм или менее, которая осаждается на нижних
дыхательные пути, как показано на рис. Вес
процент вдыхаемой пыли был, в порядке от самого высокого к самому низкому, покрытой мягкой сталью
электрод, проволока из мягкой стали и проволока из нержавеющей стали. Кроме того, эти массовые проценты
имеет тенденцию к уменьшению по мере увеличения сварочного тока.
Обратите внимание, что порядок массовых процентов частиц диаметром около 1,0 мкм или менее было обратным, с порядком от самого высокого к самому низкому из нержавеющей стали. проволока, проволока из мягкой стали и электрод с покрытием из мягкой стали.
показывает скорость образования дыма, измеренную в этом исследовании. Скорость образования дыма измеренные в этом исследовании, находились в диапазоне 1,96–12,2 мг/с. Скорость образования дыма увеличивается по мере увеличения сварочного тока во всех условиях. Скорость образования дыма при 100 А в порядке от большего к меньшему: электрод с покрытием из мягкой стали, проволока из мягкой стали и проволока из нержавеющей стали, а при 200 А – проволока из нержавеющей стали, электрод с покрытием из мягкой стали, и проволока из мягкой стали.
Открыть в отдельном окне
Скорость образования дыма, измеренная при дуговой сварке чугуна. Планки погрешностей представляют собой стандартные отклонения.
Распределение частиц дыма по размерам и скорость образования дыма при дуговой сварке литых
железа с использованием трех различных типов наполнителя с основными составляющими Fe и
Fe-Cr-Ni были измерены экспериментально в этом исследовании.
Дым, измеренный в ходе этого исследования, содержал 73–91% вдыхаемой пыли (с диаметром частиц 4 мкм или менее) (). Это говорит о том, что дым очень опасные для человеческого организма, генерировались при любых условиях. Поэтому, при дуговой сварке чугуна необходимо удалять образующиеся пары, например, с помощью местной системы вытяжной вентиляции, а сварщики должны носить соответствующие респираторы. Кроме того, скорость образования дыма увеличивалась по мере увеличения сварочного тока. увеличился, как и в других исследованиях 11 , 31 ) ().
Как показано на , массовые проценты
вдыхаемая пыль: электрод с покрытием из мягкой стали > проволока из мягкой стали > нержавеющая сталь
проволока. Оценка скорости образования вдыхаемой пыли путем умножения весового процента
вдыхаемой пыли по скорости образования дыма при каждом условии (весовой процент
вдыхаемая пыль [%] × скорость образования дыма [мг/с]) дает 3,26 мг/с (91,4% × 3,57 мг/с: легкая
электрод со стальным покрытием), 1,80 мг/с (82,5% × 2,18 мг/с: проволока из мягкой стали) и 1,52 мг/с. (77,8% × 1,96 мг/с: проволока из нержавеющей стали) при 100 А и 8,35 мг/с (90,2% × 9,26 мг/с: мягкий
электрод со стальным покрытием), 3,68 мг/с (74,9% × 4,91 мг/с: проволока из мягкой стали) и 8,92 мг/с.
(73,1% × 12,2 мг/с: проволока из нержавеющей стали) при 200 А. Это дает скорость генерации
вдыхаемая пыль электрода с покрытием из мягкой стали>проволока из мягкой стали>проволока из нержавеющей стали
при 100 А, и проволока из нержавеющей стали>электрод с покрытием из мягкой стали>проволока из мягкой стали при 200
A. Это показывает, что скорость образования вдыхаемой пыли выше с более высоким дымом.
скорость генерации.
Если используются случаи 100 А и 200 А в
по сравнению с этим массовый процент вдыхаемой пыли имеет тенденцию к снижению по мере
сварочный ток увеличивается при любых условиях. Это показывает, что крупные частицы с
диаметр 4 мкм и более, содержащихся в дымах, увеличивается по мере увеличения сварочного тока,
что соответствует результатам Ojima 32 ) . Однако скорость образования вдыхаемой пыли увеличивается примерно в 2–6 раз по мере
сварочный ток увеличивается при любых условиях. Это говорит о том, что сварочный ток
является важным фактором, влияющим на скорость образования вдыхаемой пыли.
В настоящее время рабочие, выполняющие дуговую сварку, обязаны носить респираторы при дуговой сварке.
рабочие места 33 ) . Прежде всего, частицы
широко используются респираторы, а для дуговых сварочных работ – противопылевые респираторы с
производительность категории 2 или выше (эффективность фильтрации 95% или выше), указанная в
JIS 34 ) необходимо использовать 35 ) . Однако в целом известно, что частицы с
диаметром от 0,1 до 0,3 мкм не улавливаются фильтрами, используемыми для очистки от твердых частиц.
респираторы 19 , 20 , 21 , 22 , 23 , 24 ) .
Как показано на , массовые проценты частицы с близкими к этому диаметрами (в основном 0,3 мкм и менее) различаются в зависимости от условия с проволокой из нержавеющей стали > проволокой из мягкой стали > электродом с покрытием из мягкой стали. Оценка скорости генерации частиц диаметром 0,3 мкм и менее в одном и том же так как коэффициент образования вдыхаемой пыли дает 0,59мг/с (проволока из нержавеющей стали), 0,38 мг/с (проволока из мягкой стали) и 0,21 мг/с (электрод с покрытием из мягкой стали) при 100 А, и 2,6 мг/с (проволока из нержавеющей стали), 0,47 мг/с (проволока из мягкой стали) и 0,41 мг/с (проволока из мягкой стали). покрытым электродом) при 200 А. Это показывает, что скорость генерации самая высокая, когда нержавеющая сталь используется стальная проволока.
В соответствии с рекомендациями Национального института безопасности и гигиены труда 36 ) , если MMAD меньше 2 мкм или неизвестно,
высокоэффективный сажевый фильтр (эффективность фильтрации 99,97% или выше) или любой
фильтр сертифицирован по 42 CFR 84 37 ) (эффективность фильтрации 95% или выше). Поэтому при выполнении дуги
сварка чугуна с использованием присадочного материала, в основном состоящего из Fe и Fe-Cr-Ni,
следует надевать противоаэрозольный респиратор категории 2 или выше по стандарту JIS 34 ) или респираторы для очистки воздуха с электроприводом по стандарту JIS 38 ) . При дуговой сварке,
обычно используются противоаэрозольные респираторы категории 2. Однако следует соблюдать особую осторожность
при использовании проволоки из нержавеющей стали с высокой скоростью генерации частиц диаметром
0,3 мкм или менее.
Ранее авторы измеряли распределение частиц дыма по размерам и образование дыма.
скорость при дуговой сварке низкоуглеродистой стали проволокой из низкоуглеродистой стали 39 ) . В соответствии с этим скорость образования дыма из мягкой стали составляет
находится в диапазоне 2,13–4,18 мг/с, и существенной разницы от образования дыма не обнаружено
скорость чугуна (2,18–4,91 мг / с) в тех же условиях, как измерено
в этом исследовании. Однако в распределении частиц по размерам наблюдается тенденция к
весовой процент частиц диаметром 2,5 мкм и выше уменьшаться в случае мягкого
стальной дым. Это означает, что многие более крупные частицы, чем в случае мягкой стали,
содержится в дымах, образующихся при дуговой сварке чугуна. Поэтому сварщики могут
чувствую, что шлейф дыма от сварки чугуна относительно массивен.
Это исследование измеряло распределение размера частиц дыма и скорость образования дыма во время дуговая сварка чугуна с использованием присадочных материалов Fe и Fe-Cr-Ni в качестве основных составляющие. На основании этих результатов мы оценили скорость образования вдыхаемой пыли и скорость генерации частиц диаметром 0,3 мкм и менее. Следующее в результате были сделаны выводы.
(i) Скорость образования вдыхаемой пыли увеличивается по мере увеличения сварочного тока
(примерно от 2 до 6 раз). (ii) Настоятельно предполагается, что чем выше дым
скорость генерации, тем больше образуется вдыхаемой пыли. (iii) Скорость генерации
вдыхаемая пыль была самой высокой с электродом, покрытым мягкой сталью, при низком токе и
проволока из нержавеющей стали на большом токе. (iv) Скорость генерации частиц диаметром
0,3 мкм или менее было самым высоким, когда использовалась проволока из нержавеющей стали. (v) Чугунные пары
содержат намного больше крупных частиц, чем пары мягкой стали.
1. Опря М., Киро С., Воробец А., Хореманс Б., Дарчук Л., Новакович В., Эннан А., Ван Грикен Р. (2012) Распределение размеров и химический состав свойства сварочного дыма вдыхаемых частиц. Дж Аэрозоль Наука 45, 50–7. [Google Scholar]
2. Министерство здравоохранения, труда и Благосостояние. Heisei 30nen Gyoumujou shippei hassei joukyou to chousa kekka. https://www.mhlw.go.jp/content/11300000/000525946.pdf. Доступ 9 августа, 2019.
3. Кисимото Т. (2005) Nihon no jinhai no genjou ni костюм ДЖОМТ 53, 54–60. [Академия Google]
4. Международное агентство
Research on Cancer (2018) Сварка, триоксид молибдена и оксид индия-олова. Монографии IARC по оценке канцерогенных рисков для человека. Том 118. МАИР,
Лион. [Google Scholar]
5. Кобаяши М., Маки С., Хашимото Ю., Суга Т. (1980) Исследования образования дыма. явления дуговой сварки защищенным металлом. J японская сварка Соц 49, 454–61. [Google Scholar]
6. Международная комиссия по Радиологическая защита (1994 г.) Модель дыхательных путей человека для радиологической защиты. защита. В: Публикация МКРЗ 66. Ann. МКРЗ 24, Elsevier Science, Оксфорд. [Академия Google]
7. Yoshii C, Morimoto Y, Kido M. (2005) Пневмокониоз сварщика — легочный заболевание, вызванное вдыханием сварочного дыма. Дж Аэрозоль Рез. 20, 238–42. [Google Scholar]
8. Morimoto Y. (2013) [Закон о пневмокониозе и врач]. J UOEH 35 Suppl, 113–9. [PubMed] [Google Scholar]
9. Министерство здравоохранения, труда и
Благосостояние. Стандарты измерения рабочей среды, уведомление Министерства труда №
46. https://www.jniosh.johas.go.jp/icpro/jicosh-old/japanese/country/japan/laws/02_enf/1_metric_std/index. html.
По состоянию на 1 ноября 2019 г..
10. Исследования и статистика Департамент Секретариата Министра (2016 г.) Ежегодник текущей продукции статистика: железо и сталь, цветные металлы и готовые металлы, Министерство Экономика, торговля и промышленность, Токио (на японском языке). [Google Scholar]
11. Хайле Ф., Хилл, округ Колумбия. (1975) Образование твердых частиц дыма в дуге процесс сварки. Сварка J 54, 201с–10с. [Google Scholar]
12. Hewett P. (1995) Распределение частиц по размерам, плотность и удельная поверхность сварочных дымов от SMAW и GMAW легких и расходные материалы из нержавеющей стали. Am Ind Hyg Assoc J 56, 128–35. [PubMed] [Академия Google]
13. Takahashi J, Nakashima H, Hirabayashi R, Ojima J, Okuno T, Fujii N. (2018) Исследование дыма, образующегося при сварке MIG. из сплавов алюминия и магниевого сплава. Джей Лайт встретил Сварка 56, 13–9. [Google Scholar]
14. Паскуаль М., Феррер С., Район Э. (2009) Свариваемость сфероидального графита. ковкий чугун с использованием электродов Ni/NiFe. Преподобный
Металл 45, 334–8.
[Google Scholar]
15. Келли Т.Дж., Бишел Р.А., Уилсон Р.К. (1985) Сварка ковкого чугуна с Ni-Fe-Mn присадочный металл. Сварка J 64, 79–85. [Google Scholar]
16. Хатано И. (2017) Здоровье и безопасность. J Jpn Weld Soc 79, 508–10. [Google Scholar]
17. Fujii N, Takahashi J, Suzuki H, Yasuda K. (2005) Сравнение прочностных характеристик сварных соединений чугуна и низкоуглеродистой стали различными способами сварки. Q J Jpn Weld Soc 23, 302–10. [Google Scholar]
18. Fujii N, Honda H, Fukase A, Yasuda K. (2007) Сравнение прочностных характеристик сварных соединений чугуна с шаровидным графитом различными видами сварки процессы. Q J Jpn Weld Soc 25, 261–7. [Академия Google]
19. Hinds WC. (1999) Аэрозольная технология: свойства, поведение и измерение аэрозольных частиц, 2-е изд. 182–205, John Wiley & Sons, Лос-Анджелес Анджелес. [Google Scholar]
20. Martin SB, Jr, Moyer ES. (2000) Фильтрующий материал для электростатических респираторов:
эффективность фильтра и наиболее проникающие эффекты размера частиц.
Приложение Occup Environ Hyg 15,
609–17. [PubMed] [Google Scholar]
21. Балази А., Тойвола М., Репонен Т., Подгорский А., Циммер А., Гриншпун С.А. (2006) Оценка производительности на основе манекенов N95 фильтрующих респираторов с наночастицами. Энн Оккуп Хайг 50, 259–69. [PubMed] [Google Scholar]
22. Kim SC, Harrington MS, Pui DYH. (2007) Экспериментальное исследование наночастиц проникновение через коммерческие фильтрующие материалы. Дж Нанопарт Рез. 9, 117–25. [Google Scholar]
23. Энингер Р.М., Хонда Т., Репонен Т., Маккей Р., Гриншпун С.А. (2008) О чем говорит сертификация респираторов нам о фильтрации ультрадисперсных частиц? J Оккупация окружающей среды Хиг 5, 286–95. [Бесплатная статья PMC] [PubMed] [Google Scholar]
24. Rengasamy S, Eimer BC, Shaffer RE. (2009) Сравнение фильтрации наночастиц
производительность маски для защиты от твердых частиц, одобренной NIOSH и имеющей маркировку CE
респираторы. Энн Оккуп Хайг 53,
117–28. [PubMed] [Google Scholar]
25. Промышленные стандарты Японии Комитет (2013) JIS Z 3930: Определение скорости выброса дыма во время дуги сварки и сбора дыма для анализа, Японская ассоциация стандартов, Токио (в Японский язык). [Google Scholar]
26. Промышленные стандарты Японии Комитет (2001) JIS G 5502: Отливки из чугуна со сфероидальным графитом, Япония. Ассоциация стандартов, Токио (на японском языке). [Академия Google]
27. Промышленные стандарты Японии Комитет (2009 г.) JIS Z 3312: Сплошные проволоки для сварки MAG и MIG мягких сталь, высокопрочная сталь и низкотемпературная сталь, Японская ассоциация стандартов, Токио (на японском языке). [Google Scholar]
28. Промышленные стандарты Японии Комитет (2013) JIS Z 3321: Прутки, проволока и ленточные электроды из нержавеющей стали. для сварки, Японская ассоциация стандартов, Токио (на японском языке). [Google Scholar]
29. Промышленные стандарты Японии
Комитет (2008) JIS Z 3211: Покрытые электроды для низкоуглеродистой стали, высокопрочные. прочная сталь и низкотемпературная рабочая сталь, Японская ассоциация стандартов, Токио (в
Японский язык). [Академия Google]
30. Промышленные стандарты Японии Комитет (1989) JIS K 0302: Метод измерения гранулометрического состава. пыли в дымовых газах, Японская ассоциация стандартов, Токио (на японском языке). [Google Scholar]
31. Suga T, Kobayashi M. (1984) Генерация дыма в CO 2 arc сварка сплошной проволокой. J японская сварка Соц 2, 22–9. [Google Scholar]
32. Ojima J. (2002) [Измерение калибровочного коэффициента монитор светорассеивающей пыли для газов дуговой сварки CO 2 ]. Й УОЭХ 24, 439–44. [PubMed] [Google Scholar]
33. Министерство здравоохранения, труда и Благосостояние. Постановление о предотвращении опасностей, связанных с пылью, Постановление Министерства труда № 18. https://www.jniosh.johas.go.jp/icpro/jicosh-old/japanese/country/japan/laws/03_rel/13_dust_reg/index.html. По состоянию на 1 ноября 2019 г.
34. Японские промышленные стандарты.
Комитет (2018) JIS T 8151: респираторы для твердых частиц, стандарты Японии
Ассоциация, Токио (на японском языке). [Google Scholar]
35. Министерство здравоохранения, труда и Благосостояние. Boujin Masuku no sentaku to siyou ni tsuite. Уведомление Бюро трудовых норм № 0207006. https://www.jaish.gr.jp/anzen/hor/hombun/hor1-46/hor1-46-4-1-0.htm. Доступ 1 ноября 2019 г..
36. Национальный институт Безопасность и гигиена труда, руководство NIOSH по выбору и использованию твердых частиц респираторы. https://www.cdc.gov/niosh/docs/96–101/default.html. Доступ 9 декабря, 2019.
37. Национальная служба индивидуальной защиты Технологическая лаборатория, 42 CFR Part 84 Средства защиты органов дыхания. https://www.cdc.gov/niosh/npptl/topics/respirators/pt84abs2.html. Доступ 9 декабря 2019 г.
38. Промышленные стандарты Японии
Комитет (2018) JIS T 8157: Респиратор для очистки воздуха от твердых частиц.
материя, Японская ассоциация стандартов, Токио (на японском языке).