Таблица с режимами обработки для различных материалов – Производственные вопросы
#1 OFFLINE Космос
Отправлено 13 Январь 2013 – 17:35
Есть какая нить таблица для обработки различных материалов Или все самим необходимо подбирать!?
- Наверх
#2 OFFLINE Michael Yurov
Отправлено 13 Январь 2013 – 17:49
А таблица… есть таблица Скачать файл режимы резки.pdf (47.25 kB), но мне она не нравится, я режу намного быстрее и с меньшим заглублением. За годы работы я нашел оптимальные значения для себя, и материал не отрывает и фрезы не ломает и быстрее не получается.
Но я режу в основном пластики и обычно двухзаходными фрезами, так что опыт только в этой области.
- Наверх
#3 OFFLINE Космос
Отправлено 13 Январь 2013 – 18:00
Мы наружной рекламой занимаемся. Поэтому материал в основном пластик, дсп, оргстекло и композитные панели! Но хочется еще и что нить из 3d попробовать)). Фрезы используем китайские какие то цилиндрические 3мм.
- Наверх
#4 OFFLINE Michael Yurov
Отправлено 13 Январь 2013 – 18:57
Если фрезы 3 мм, то для оргстекла скорость подачи желательно установить около 3000 (максимум 5000) мм/мин (обороты шпинделя около 20 000 об/мин), заглубление за один проход желательно не более 3-4 мм, а еще лучше – .
Для дерева и вспененного ПВХ можно скорость подачи сделать больше – до 8000 мм/мин, если качество реза не очень важно, заглубление для дерева 3-6 мм, а для вспененного ПВХ можно до 10 мм (но тогда скорость лучше не более 5000 мм/мин).
Для полистирола можно чуть быстрее, чем для оргстекла, например, 4500 мм/мин и заглубление 3 мм.
Если обороты шпинделя ниже 20 000 об/мин, то и скорость нужно пропорционально уменьшить, если выше, то можно и быстрее резать, но может сорвать материал.
Вообще качество реза получается выше, если резать за много проходов с небольшим заглублением на относительно высоких подачах.
Для 3 мм фрезы оптимальная подача для пластиков – 3500 – 4000 мм/мин, для 2 мм фрезы – 2000 – 2500 мм/мин (заглубление за проход 2-2,5 мм), для 1 мм фрезы – 1000 – 1250 мм/мин, заглубление не более 1-1,5 мм
Оргстекло лучше всего использовать литое (ТОСП), а не тянутое (экструзионное), хотя бывает и тянутое тугоплавкое. У литого может гулять толщина, но зато оно не плавится и не налипает на фрезу.
Чтобы оргстекло не плавилось желательно использовать более быстрые подачи и меньшую глубину каждого прохода. Еще очень помогает, если брызгать (можно из ручного распылителя) место реза мыльной водой (добавить в воду немного fairy).
P.S. я привел режимы близкие к максимальным, если на таких резать тяжело, то, естественно, можно немного убавить скорость и глубину.
Про композитные панели не подскажу, знаю только что обязательно верхний слой алюминия срезать за 1 раз вместе с некоторым количеством пластика внутри панели, так же и с последним слоем.
Сообщение отредактировал Michael Yurov: 13 Январь 2013 – 19:03
- Наверх
#5 OFFLINE Космос
Отправлено 13 Январь 2013 – 19:09
Очень ценная информация! Спс огромноеее)))- Наверх
#6 OFFLINE lkbyysq
Отправлено 02 Январь 2015 – 04:23
Еще очень помогает, если брызгать (можно из ручного распылителя) место реза мыльной водой (добавить в воду немного fairy).
Нельзя fairy. Ржавеет все от фейри пипец как. Видать там кислотная среда.
Если уж пошла такая пьянка, то автошампунь безопаснее.
Сообщение отредактировал lkbyysq: 02 Январь 2015 – 10:17
- Наверх
#7 OFFLINE zenobond
Отправлено 03 Январь 2015 – 06:36
чем тоньше фреза тем легче ей резать материал… ЭТО НАДО ПОМНИТЬ!!!!
акрил, пвх достаточно фрезы 3,175 (стружка вверх, однозубая, однозаходная в 99% случаев достаточно)
акп, алюминий …. 4 мм (стружка вверх, однозубая, однозаходная в 99% случаев достаточно при чем покупать ВЫ её скорее всего будете по каталогу и значится она будет как по ПВХ), но надо чувствовать направление реза, как правило при резке снаружи контура надо ставить конвертал (как то так называется)
Если есть возможность отрезать одним проходом. ..надо резать одним…. это золотое правило экономии фрез и зарабатывание денег (ну если работать по серьезному по акп и алюмишке)….
если отрезать не получается значит Вы что-то не правильно делаете или фрезы не те (например алюминий до 4 мм режется в один проход это нормально при условии башки 5-6 квт)
Для всех материалов кроме акрила и вязких марок алюмишек, чем больше количество зубьев тем лучше… тем будет выше Ваша максимальная скорость реза … ВОТ ТИПА ТАКИХ
Фреза спиральная четырехзаходная со стружколомом K4LXS (твердосплавная с покрытием)
у нас они правда по другому называются…особенно хорошо такие фрезы себя показывают в черновой обработке 3D
( в любых материалах: МДФ,Модулан,ПВХ, и т.п.)
при чем маленькие диаметры таких фрез рекомендую также использовать при чистовой линейной обработке поверхностей с шагом не более 0,4..0,5, а в некоторых случаях и в спиральных траекториях
если все правильно делать. ..охлаждение зоны резки в обычной серой скучной cnc жизни практически не требуется
Сообщение отредактировал zenobond: 03 Январь 2015 – 06:38
- Наверх
#8 OFFLINE 3D-BiG
Отправлено 03 Январь 2015 – 08:40
чем тоньше фреза тем легче ей резать материал… ЭТО НАДО ПОМНИТЬ!!!!
Если есть возможность отрезать одним проходом…надо резать одним…. это золотое правило экономии фрез и зарабатывание денег (ну если работать по серьезному по акп и алюмишке)….
Очень спорные выводы – рассмотрю на примере акрила, ибо:
– 3. 175 мм однозаходкой можно и 12мм акрил резать в один проход, НО скорость реза будет низкой и будут периодически возникать проблемы из-за намотки полупасплавленной массы опилок на фрезу, в то время многопроходная резка по 3 мм с большими скоростями дает сухие, а не плавленные опилки и большую итоговую скорость реза, только надо станок иметь с достаточно хорошей динамикой…
– если по акрилу будем уменьшать диаметра фрезы, увеличивая соотношение глубины реза за проход к диаметру фрезы, то будут стремительно возрастать проблемы с намоткой на фрезу опилок…, т.е. уже 10мм акрил порезать за проход 2мм фрезой уже почти невозможно – будет постоянная борьба с намоткой опилок…
– при больших съемах возрастает усилие на сдвижку изделия, а значит появляется проблема удержания изделия, поэтому и приводил здесь давно вариант эффективного раскроя из 3мм акрила мелких изделий типа номерков 3.175 фрезой в два прохода, когда первым снимаем 2.5мм глубины, при этом делаем отступ от края на 0. 5мм, а затем проводим чистовую дорезку на полную глубину… В этом случае нет никаких проблем к удерживанию номерков скотчем, да при этом не нужны перемычки для удержания изделий, которые, если их делать, замаешься удалять…
если отрезать не получается значит Вы что-то не правильно делаете или фрезы не те (например алюминий до 4 мм режется в один проход это нормально при условии башки 5-6 квт) Для всех материалов кроме акрила и вязких марок алюмишек, чем больше количество зубьев тем лучше… тем будет выше Ваша максимальная скорость реза …
Что-то жестко, ибо при резе дюраля в 2мм за проход 3.175 фрезой с подачей 5мм/с реально потребная мощность порядка 75-80Вт. В свое время на таком режиме много дюраля перерезал на станках с мощностью шпинделя всего 400Вт. А вот уже 6мм фрезой на 400Вт шпинделе было эффективно резать уже проблемно – шпиндель захлебывался при поднятии скорости подачи, но если бы было хотя-бы 1.
Для всех материалов кроме акрила и вязких марок алюмишек, чем больше количество зубьев тем лучше… тем будет выше Ваша максимальная скорость реза
Эта закономерность хорошо работает на низких оборотах шпинделя, но на высоких начинает сильно влиять процесс выноса опилок по каналу фрезы, а у однозаходных канал шире, чем у много заходных, а также прочность фрезы – двух и трех заходные фрезы имеют большую жесткость, чем однозаходные, но далеко не всегда на 15тыс оборотов в мин мы поимеем тройное увеличение подачи для трехзаходной фрезы по сравнению с однозаходной, а тем более на 24тыс оборотов в мин…
А есть еще обработка на более высокооборотных шпинделях – там еще интереснее процессы реза проходят….
Так что не стоит так категорично утверждать. ..
Сообщение отредактировал 3D-BiG: 03 Январь 2015 – 08:41
- Наверх
#9 OFFLINE yaso73
Отправлено 03 Январь 2015 – 09:07
чем тоньше фреза тем легче ей резать материал… ЭТО НАДО ПОМНИТЬ!!!!
Пора подумать о диссертации…
- Наверх
#10 OFFLINE 369852
Отправлено 03 Январь 2015 – 12:24
10 мм акрил марки Plexiglass XT спокойно режется 3,175 мм фрезой в один проход при выполнении нескольких условий – новая либо не “”севшая” фреза, обороты не более 12-13 тыс, охлаждение либо водой либо керосином (с керосином торец вообще как полированный получается) Можно и просто воздухом дуть, но ресурс фрезы до затупления заметно меньше. Момент затупления довольно просто определить по стружке – при острой фрезе стружка мягкая и при растирании между пальцами рассыпается в труху. Скорость резки 15-20 мм/сек. Еще марка акрила Quinn Cast хороша для резки. Дзержинская “”Акрима” – быстрее всех “садит” фрезы.
Фрезы однозаходные с винтовой канавкой, желательно с полированной кромкой. Точу “на глаз” на алмазном круге – тупо подтачиваю торец. Угол заточки, конечно, не такой как в оригинале, но этого и не требуется.
Можно и 20 мм акрил порезать в один проход фрезой 4 мм, если резать в ванне с водой. Но мы, собственно, не о том у кого фреза длиннее
Как правильно заметил 3D-Big, чем больше съем за проход, тем больше усилие на сдвиг и “влетать” на материал заказчика желания нет. Поэтому обычно не вы*бываешься и режешь акрил в несколько проходов – дольше, но спокойнее.
Сообщение отредактировал 369852: 03 Январь 2015 – 12:24
- Наверх
#11 OFFLINE zenobond
Отправлено 03 Январь 2015 – 16:29
Очень спорные выводы – рассмотрю на примере акрила, ибо:
– 3.
175 мм однозаходкой можно и 12мм акрил резать в один проход, НО скорость реза будет низкой и будут периодически возникать проблемы из-за намотки полупасплавленной массы опилок на фрезу, в то время многопроходная резка по 3 мм с большими скоростями дает сухие, а не плавленные опилки и большую итоговую скорость реза, только надо станок иметь с достаточно хорошей динамикой…
– если по акрилу будем уменьшать диаметра фрезы, увеличивая соотношение глубины реза за проход к диаметру фрезы, то будут стремительно возрастать проблемы с намоткой на фрезу опилок…, т.е. уже 10мм акрил порезать за проход 2мм фрезой уже почти невозможно – будет постоянная борьба с намоткой опилок…
– при больших съемах возрастает усилие на сдвижку изделия, а значит появляется проблема удержания изделия, поэтому и приводил здесь давно вариант эффективного раскроя из 3мм акрила мелких изделий типа номерков 3.175 фрезой в два прохода, когда первым снимаем 2.5мм глубины, при этом делаем отступ от края на 0.
5мм, а затем проводим чистовую дорезку на полную глубину… В этом случае нет никаких проблем к удерживанию номерков скотчем, да при этом не нужны перемычки для удержания изделий, которые, если их делать, замаешься удалять…
Что-то жестко, ибо при резе дюраля в 2мм за проход 3.175 фрезой с подачей 5мм/с реально потребная мощность порядка 75-80Вт. В свое время на таком режиме много дюраля перерезал на станках с мощностью шпинделя всего 400Вт. А вот уже 6мм фрезой на 400Вт шпинделе было эффективно резать уже проблемно – шпиндель захлебывался при поднятии скорости подачи, но если бы было хотя-бы 1.5-2.2кВт , да с подачей СОЖ, то процесс резки на достаточно жестком станке шел бы эффективно…
Эта закономерность хорошо работает на низких оборотах шпинделя, но на высоких начинает сильно влиять процесс выноса опилок по каналу фрезы, а у однозаходных канал шире, чем у много заходных, а также прочность фрезы – двух и трех заходные фрезы имеют большую жесткость, чем однозаходные, но далеко не всегда на 15тыс оборотов в мин мы поимеем тройное увеличение подачи для трехзаходной фрезы по сравнению с однозаходной, а тем более на 24тыс оборотов в мин.
..
А есть еще обработка на более высокооборотных шпинделях – там еще интереснее процессы реза проходят….
Так что не стоит так категорично утверждать…
Я пишу про коммерческую резку (не думаю что чел будет режимы спрашивать что бы в гараже у себя что то точить)
90% случаев резки акрила это толщина максимум 10 мм и меньше… режется замечательно в один проход и на достаточно большой скорости (enroute показатель feeds 70..80)..при этом диаметр фрезы 3,175*15 это норма…. ввиду своей универсальности
резка меньшими диаметрами это экзотика…
при этом резка по слоям однозначно при затуплении фрезы Вам со временем даст полостность на торце.
Про номерки… это все таки редкие заказы…. топик не отменяет наличие МУДРОГО оператора станка…. я бы наверно просто не прорезал защитку на стекле и резал бы в шахматном порядке с зазорами 3 фрезы, что бы легче было вытаскивать…при этом что то можно закасячить а можно и НЕТ. … так что каждый выбирает сам.
Пора подумать о диссертации…
А что смешного если не секрет?
- Наверх
#12 OFFLINE yaso73
Отправлено 03 Январь 2015 – 21:03
А что смешного если не секрет?
Чушь несёте. Да так уверенно,что страшно становится.
Особенно про
до 4 мм режется в один проход это нормально при условии башки 5-6 квт
Как Вы изволили выразиться “башкой 6квт” можно и побольше прорезать.А обороты какие?
при этом резка по слоям однозначно при затуплении фрезы Вам со временем даст полостность на торце
ПОЛОСТНОСТЬ – насмерть
топик не отменяет наличие МУДРОГО оператора станка
Пойду и утоплюсь
- Наверх
#13 OFFLINE 3D-BiG
Отправлено 03 Январь 2015 – 22:05
при этом резка по слоям однозначно при затуплении фрезы Вам со временем даст полостность на торце
А про методику подчистки края последним проходом, что я привел на примере технологии номерков не думали? Вот вам и НЕ однозначность. ..
- Наверх
#14 OFFLINE vv92
Отправлено 03 Январь 2015 – 22:39
Припуск на последнем проходе не только вреден, но и полезен, так Вадим?
Знаю технику безопасности как свои три пальца.Эксперт – это существо, которое перестало мыслить, ибо оно знает!В мире еще много граблей, на которые не ступала нога человека.
Пожалуйста! Исправляйте мои глупые ошибки (но оставьте мои умные ошибки)!
- Наверх
#15 OFFLINE 3D-BiG
Отправлено 03 Январь 2015 – 23:10
Припуск НЕ на последнем проходе, а на предыдущих проходах, а на последнем делаем в размер. ..
- Наверх
#16 OFFLINE yaso73
Отправлено 03 Январь 2015 – 23:26
Про “черновую”(видимо послойную?) фрезами со стружколомом – тоже тронуло.Остался один вопрос:”на хрена?”
Ещё много зависимостей от жесткости станка,скорости перемещений и пр.Когда увидел(первый раз),как на скорости 12м/мин фреза диаметром 18мм входит в сталь на 40мм сразу. Жуткая картина.А оказалось,это по трохоиде траектория.И съёма там совсем чуть-чуть,но зрелищно – ипздец.
- Наверх
#17 OFFLINE sunny417
Отправлено 07 Январь 2015 – 19:55
Хотел бы уточнить, речь про прямые фрезы или про спиральные? Просто я считал, что спиральные для раскроя не подходят, так как торцом они, в отличие от прямых, работают плохо (будут отгибаться итд). Поэтому в случае спиральных, если нужно вырезать деталь, снимаю по 1/2 диаметра фрезы за проход на любом материале. Это вообще верное утверждение?Очень спорные выводы – рассмотрю на примере акрила, ибо:
– 3.175 мм однозаходкой можно и 12мм акрил резать в один проход, НО скорость реза будет низкой и будут периодически возникать проблемы из-за намотки полупасплавленной массы опилок на фрезу, в то время многопроходная
- Наверх
#18 OFFLINE lkbyysq
Отправлено 07 Январь 2015 – 20:02
спиральные … торцом .
.., в отличие от прямых, работают плохо (будут отгибаться итд).
Это вообще верное утверждение?
Нет, не верное.
Насколько фреза отгибается зависит в первую очередь от площади поперечного сечения (очень грубо) и вылета. Спиральная она или нет, роли практически не играет.
Сообщение отредактировал lkbyysq: 07 Январь 2015 – 20:51
- Наверх
#19 OFFLINE 3D-BiG
Отправлено 07 Январь 2015 – 20:37
Хотел бы уточнить, речь про прямые фрезы или про спиральные? Просто я считал, что спиральные для раскроя не подходят, так как торцом они, в отличие от прямых, работают плохо (будут отгибаться итд).
Крою акрил спиральными обычно с выводом опилок вверх. ..
- Наверх
Режимы резания для фрезерных станков с ЧПУ
JavaScript отключён. Чтобы полноценно использовать наш сайт, включите JavaScript в своём браузере.
- Автор темы Виталий
- Дата начала
- Последнее редактирование модератором: 03.2021″ data-time-string=”15:47″ title=”17.03.2021 в 15:47″>17.03.2021
- Ответы: 71
Последнее редактирование модератором:
PS в прикрепленном файле основная таблица.
Нажмите для раскрытия…
Автор
Виталий
МЕСТНЫЙ СТАРОЖИЛА · 39 · Из Чита
- Сообщения
- 627
- Реакции
- 553
- Баллы
- 188
exe
“/>
- #16
Последнее редактирование:
не нужно сверлами ничего снимать, они не предназначены для фрезеровкиpanov-05 написал(а):
скажите сколько можно снять сверлом 6мм два ножа у клена за проход чтоб не сломалось
Нажмите для раскрытия…
эти таблицы очень приблизительны, они годятся только для того, чтобы понять зависимость режимов в зависимости от того, какой обрабатывается материал.panov-05 написал(а):
таблицей вопрос как узнать скорость подачи на зуб
Нажмите для раскрытия.
..
что касается конкретно этой таблицы, то режимы там тем более более очень спорные и зачастую взяты с потолка, например смотрим режимы резания дюралюминия – инструмент – 1-2 заходный, подача – “с потолка”, обороты “с потолка”, глубина резания до 0.4мм, это вообще очень далеко от эффективной обработки алюминия и его сплавов…
уж лучше взять какой-нибудь HSMAdvisor, забить туда параметры шпинделя, указать параметры фрезы (рекомендованные для нее режимы, если фреза фирменная, то такая информация есть на сайте производителя), выбрать подходящий материал, и он выдаст гораздо более приближенные к реальности режимы, чем эта таблица.
вот например получившийся режим обработки твердого дерева с помощью 4 заходной фрезы, вполне подойдет для кукурузы, разумеется нужно сделать поправку на жесткость станка и возможности шпинделя, возможно стоковый 775й это не вытянет.
extrimus
- #17
Теория без практики мертва. (А. Суворов).Alexf написал(а):
Ок, предположим вы получили от мастеров режимы обработки под силовое резание (обороты в пределах нескольких тысяч), и что с этим будет делать человек, у которого станочек не отлит из полутонны чугуна, а состоит из хлипенького китайского профиля ? И зачем идти на какой-то завод, если есть интернет и доступна любая литература?Нажмите для раскрытия.
..
Ваши сообщения автоматически объединены:
Снять сверлом? Ножи у клена? Чего не сломалось, ножи или сверло?panov-05 написал(а):
скажите сколько можно снять сверлом 6мм два ножа у клена за проход чтоб не сломалось
Нажмите для раскрытия…
Alexf
- #18
Несомненноextrimus написал(а):
Теория без практики мертва. (А. Суворов)
Нажмите для раскрытия…
только я имел в виду то, что на тех же форумах можно точно так же узнать эти самые режимы резания, и для этого не обязательно идти на какой-то завод, где вы узнаете например режимы обработки от низкоскоростного шпинделя, которые вообще не применимы к станочкам типа cnc3018.
Дядя Вова
- 01.2021 в 08:01″>29.01.2021
- #19
Смешной Вы ей богу! CNC3018 в оригинальном исполнении это школьный станочек для ознакомления и обучения процессам фрезеровки, работе с постпроцесорами и прочими там камами. Предприимчивые улыбающиеся человечки из поднебесной решили, что для всего Китая их много не сделать и выложили их на Алли под брендом “Хоббийный”. Для гаражных российских предпринимателей это не подходит.Alexf написал(а):
Ок, предположим вы получили от мастеров режимы обработки под силовое резание (обороты в пределах нескольких тысяч), и что с этим будет делать человек, у которого станочек не отлит из полутонны чугуна, а состоит из хлипенького китайского профиля ? И зачем идти на какой-то завод, если есть интернет и доступна любая литература?Нажмите для раскрытия…

Потом Вы мне говорите о Интернете! Ради бога! Барабан на шею и флаг в руки! У нас на заводах рядом с каждым станком справочники лежат?
Вы сами понимаете что на нашем станочке и речи может не идти о силовом резании, только ладошкой по попе водить. Ну с деревом он как то справляется, с пластиком, максимум на нем делать макеты будущих изделий из других материалов.
Поскольку параметры фрез даны для силового резания такого то материала, нужно пересчитать соотношение параметров зверских станком с нашим и по этому соотношению вывести значение материала по которому ладошкой гладить.
Ваши сообщения автоматически объединены:
Вообще то в книжках и таблицах Вы ничего не найдете. А вот если приведете старого мастера к себе и дадите ему попробовать свой станочек, то парочку – троечку фрез и параметров к нему он Вам по рекомендует.Alexf написал(а):
Несомненно
только я имел в виду то, что на тех же форумах можно точно так же узнать эти самые режимы резания, и для этого не обязательно идти на какой-то завод, где вы узнаете например режимы обработки от низкоскоростного шпинделя, которые вообще не применимы к станочкам типа cnc3018.Нажмите для раскрытия…
Alexf
- #20
Этот форум про станочек cnc3018, который у большинства стоит дома, а не в гараже.Дядя Вова написал(а):
Смешной Вы ей богу! CNC3018 в оригинальном исполнении это школьный станочек для ознакомления и обучения процессам фрезеровки, работе с постпроцесорами и прочими там камами.
Предприимчивые улыбающиеся человечки из поднебесной решили, что для всего Китая их много не сделать и выложили их на Алли под брендом “Хоббийный”. Для гаражных российских предпринимателей это не подходит
Нажмите для раскрытия…
Что до предпринимателей и используемых ими чпу станков, то это уже совсем другой уровень и соответствующие станки, сдесь форум не про профф станки, а про cnc3018.
Я то как раз понимаю, однако вы несколькими постами выше предлагали прогуляться на завод, где попросить у мастера режимы:Дядя Вова написал(а):
Вы сами понимаете что на нашем станочке и речи может не идти о силовом резании, только ладошкой по попе водить
Нажмите для раскрытия…
Дядя Вова написал(а):
Там скорость вращения шпинделя может быть на много ниже нашего 3018.
И в работе надо учитывать, где ставить 3,175, а где 8 мм. Онозаходную, а где и пяти. Проще прийти на завод и в свой блокнотик табличку зарисовать под диктовку старых мастеров
Нажмите для раскрытия…
Странно, наверное мы пользуемся разными интернетами , вот я ни на какие заводы не ходил и ни у кого никакие режимы не спрашивал, почитал форумы, почитал статьи в интернете, прикинул режимы в калькуляторах и убедился в их работоспособности на практике.Дядя Вова написал(а):
Вообще то в книжках и таблицах Вы ничего не найдете. А вот если приведете старого мастера к себе и дадите ему попробовать свой станочек, то парочку – троечку фрез и параметров к нему он Вам по рекомендует.
Нажмите для раскрытия…
extrimus
“/>
- #21
А я ничего, ни на никаких калькуляторах не прикидывал. Тупо начинал с малых подач, и постепенно их увеличивал в реальном времени.Alexf написал(а):
Странно, наверное мы пользуемся разными интернетами , вот я ни на какие заводы не ходил и ни у кого никакие режимы не спрашивал, почитал форумы, почитал статьи в интернете, прикинул режимы в калькуляторах и убедился в их работоспособности на практике.Нажмите для раскрытия…
Geka
“/>
- #22
Подскажите, Вы делали этот расчет для какого станка и какого шпинделя?exe написал(а):
вот например получившийся режим обработки
Нажмите для раскрытия…
В представленном режиме указаны обороты шпинделя 12.000 – это реальные или заявленные обороты?
У меня например, заявленные 12.000 (при 48В), а реальные 10.600 (при 48В) на холостом ходу.
Смущают два представленных параметра:
Мощность – 0,007 kW – это же всего 7 Ватт и при таких то скоростях по твердой древесине.
Максимальный изгиб (я так понимаю фрезы) – 0,15875 мм – не многовато? Или это из характеристик фрезы, а не во время этой обработки?
Подача 911,29 мм/мин – это по Z (врезание)?
Скорость 113 м/мин – это по X, Y ?
Для 3018 имхо неподъемные режимы
Дядя Вова
“/>
- #23
Эка удивили! Я и сам это знаю, что форум о 3018. Только не предлагайте тем кто на основе знаний о 3018 перешел на другой уровень покинуть форум!Alexf написал(а):
Этот форум про станочек cnc3018, который у большинства стоит дома, а не в гараже.
Что до предпринимателей и используемых ими чпу станков, то это уже совсем другой уровень и соответствующие станки, сдесь форум не про профф станки, а про cnc3018.
Я то как раз понимаю, однако вы несколькими постами выше предлагали прогуляться на завод, где попросить у мастера режимы:
Странно, наверное мы пользуемся разными интернетами , вот я ни на какие заводы не ходил и ни у кого никакие режимы не спрашивал, почитал форумы, почитал статьи в интернете, прикинул режимы в калькуляторах и убедился в их работоспособности на практике.Нажмите для раскрытия…
А так иной раз не повредит уважить старичков своими вопросами и они с удовольствием расскажут Вам о том, о чем не поведают самые умные книжки.
Ну а если Вы нашли статьи и прикинули на калькуляторе так поделитесь опытом, откройте блог или публикацию!
Чего ради заниматься тем, что написано в подписи мох сообщений?
Samokatoff
- #24
Вот коллега дело говорит!extrimus написал(а):
А я ничего, ни на никаких калькуляторах не прикидывал.
Тупо начинал с малых подач, и постепенно их увеличивал в реальном времени.
Нажмите для раскрытия…
Таблицы и тЭория – это, конечно, очень хорошо для понимания происходящих процессов.
Но для 3018 режимы, рассчитанные для “взрослых” станков совершенно неприменимы.
У каждого свой собственный, уникальный 3018 и таблицы необходимо будет составлять именно для него.
Так что ориентируйтесь на плавность хода, отсутствие резонансов и прочих вибраций и ищите пределы возможностей конкретно для вашего станка.
exe
- #25
Последнее редактирование: 01.2021″ data-time-string=”10:34″ title=”29.01.2021 в 10:34″>29.01.2021
это линейная подачаGeka написал(а):
Подача 911,29 мм/мин – это по Z (врезание)?
Нажмите для раскрытия…
это скорость резания.Geka написал(а):
Скорость 113 м/мин – это по X, Y ?
Нажмите для раскрытия…
в CAM при настройке параметров фрезы вы будете указывать линейную подачу.
это то значение, на которое возможно отгибание фрезы при обработке на таком режиме, что при длине инструмента в 15мм вполне вероятно.Geka написал(а):
Максимальный изгиб (я так понимаю фрезы) – 0,15875 мм – не многовато? Или это из характеристик фрезы, а не во время этой обработки?
Нажмите для раскрытия…

этот расчет брался под шпиндель с пределом в 12000 оборотов, в настройках можно ограничить максимальные обороты, что отразится на вычислении режимов.Geka написал(а):
Подскажите, Вы делали этот расчет для какого станка и какого шпинделя?
В представленном режиме указаны обороты шпинделя 12.000 – это реальные или заявленные обороты?
У меня например, заявленные 12.000 (при 48В), а реальные 10.600 (при 48В) на холостом ходу.Нажмите для раскрытия…
разумеется калькулятор не способен учесть все ньюансы того или иного станка, поэтому при применении режимов всегда делается поправка с учетом конструкции вашего станка.
фрезой 3мм при подаче 900мм/мин, и заглублении 3мм вполне по силам 3018 при обработке древесины.Geka написал(а):
Для 3018 имхо неподъемные режимы
Нажмите для раскрытия…
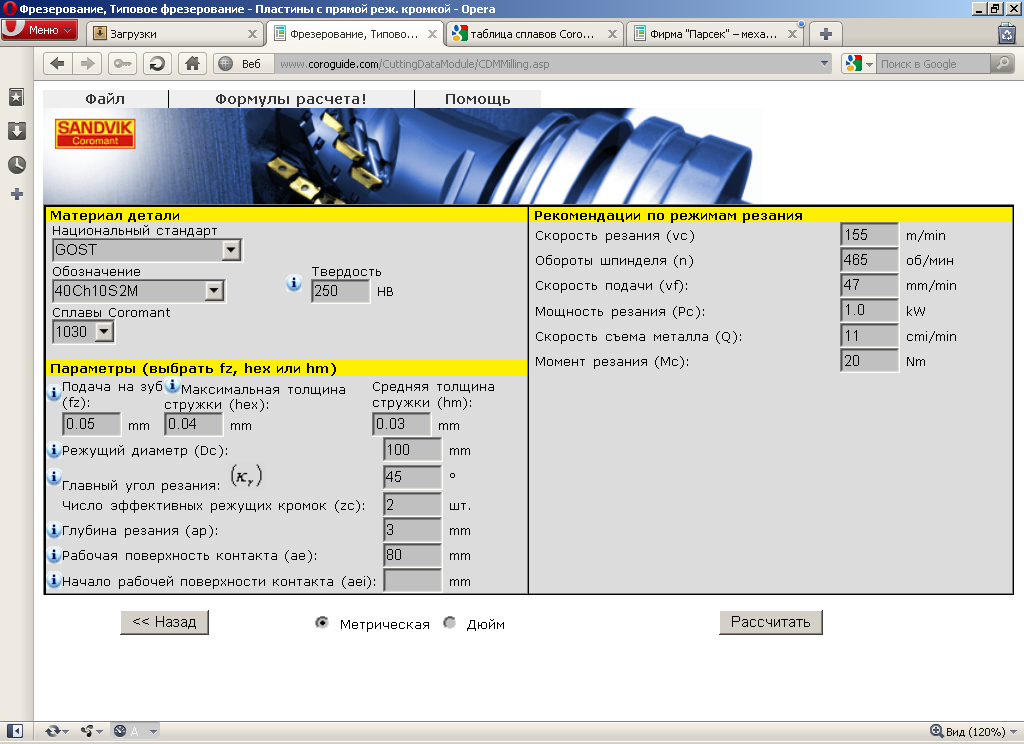
Alexf
- #26
А разве это кто-то предлагал?Дядя Вова написал(а):
Только не предлагайте тем кто на основе знаний о 3018 перешел на другой уровень покинуть форум
Нажмите для раскрытия…
Полагаю, что кто-нибудь, кто не сможет самостоятельно подобрать режимы обработки для своего станка возможно последует вашему совету.Дядя Вова написал(а):
А так иной раз не повредит уважить старичков своими вопросами и они с удовольствием расскажут Вам о том, о чем не поведают самые умные книжки.
Нажмите для раскрытия…
Однако если внимательно изучить данный форум, то не потребуются походы ни на какие заводы, тут уже более чем достаточно информации по настройкам фрез в той или иной САМ и режимов обработки для того или иного материала
exe
- #27
я точно так же свой станок осваивал, пару раз при первых пробах латуни и чермета заглянул в калькуляторы, а так в общем опирался на слух, внешний вид стружки и “научный метод тыка”Samokatoff написал(а):
Таблицы и тЭория – это, конечно, очень хорошо для понимания происходящих процессов.
![]()
Но для 3018 режимы, рассчитанные для “взрослых” станков совершенно неприменимы.
У каждого свой собственный, уникальный 3018 и таблицы необходимо будет составлять именно для него.
Так что ориентируйтесь на плавность хода, отсутствие резонансов и прочих вибраций и ищите пределы возможностей конкретно для вашего станка.Нажмите для раскрытия…
panov-05
- #28
вот темнота , у каждого сверла есть количесво ножей , однозаходные, двух , и четырех.extrimus написал(а):
Теория без практики мертва.(А. Суворов).
Ваши сообщения автоматически объединены:
Снять сверлом? Ножи у клена? Чего не сломалось, ножи или сверло?
Нажмите для раскрытия…
Еси сверло однозаходное то шпиндель должен вращаться в два раза больше .чтоб подача на зуб была как с двумя ножами.
следовательно если у сверла 4 ножа , то может в 4 раза медленней крутиться шпиндель как с одним ножом , но стоят такие сверла очень дорого ,хочу заказать но думаю надо ли мне это.
И еще на будущее , если сверло большего диаметра , то вращаться оно может медленней чем маленькое , на маленькие сверла нужны очень большие обороты шпинделя и стол и сам станок без люфта , (пока у меня такого станка нет , то высший пилотах исполнить не получится).

После таго как я себя случайно чуть два раза не убил фрезером , заготовка вылетела из под него со скоростью выстрела из пистолета макарова , одного раза было мало.я понял что это наука .И ее нужно побеждать.Бывают встречные подачи и попутные.Иди зубри двоечник.Уже на форуме как год скоро а ты во второй класс перейти не можешь.
Возможно чтоб процесс быстрей пошел возьми молоток и стукни себе по пальцу , начнешь быстрей соображать.
Вот фильм был Лечение смертью.Посмотри.
exe
- #29

panov-05
- #30
Войдите или зарегистрируйтесь для ответа.
Поделиться:Vkontakte Odnoklassniki Mail.ru WhatsApp Telegram Viber Skype Электронная почта Поделиться Ссылка
ТАБЛИЦА ПАРАМЕТРОВ РЕЗКИ ДЛЯ ОБРАБАТЫВАЮЩЕГО ЦЕНТРА作者 KYLT Precision CNC Machining
CNC-обработка может быть разделена на две категории: обычная обработка и высокоскоростная обработка .
Обычный станок обычно относится к станку с числом оборотов менее 8000; высокоскоростной станок обычно относится к станку с числом оборотов более 12000, а станок между 8000 и 12000 называется квазивысокоскоростным станком.
Процесс обработки с ЧПУ обычно делится на три категории: грубая резка, средняя легкая (полутонкая) и гладкая резка (тонкое фрезерование). Вообще говоря, лучше использовать большую фрезу (летающую фрезу и концевую фрезу) и большую глубину резания и шаг (тяжелую резку) для грубой резки, чтобы удалять материалы быстро и в больших количествах. Для получения идеальной точности поверхности используется легкое резание (малая глубина резания, малый шаг) с высокой скоростью и подачей. Концевая фреза (или угловая фреза) и летающая фреза для гладкой поверхности, концевая фреза для гладкой вертикальной стенки и шариковая фреза (или угловая фреза) для гладкой поверхности.
В процессе обработки следует выбирать соответствующие режущие инструменты в соответствии с твердостью материала обрабатываемых деталей, таких как пластик, дерево и т. Д. Можно выбрать отечественные ножи из белой стали.
Медь, алюминий и сталь с твердостью менее 38 градусов по Роквеллу (например, сталь 45 и козырный материал) должны быть импортными стальными ножами и отечественными ножами из высококачественной стали. Для материалов с высокой твердостью (таких как закаленная штамповая сталь) следует отдавать предпочтение ножу из легированного сплава, ножу с титановым покрытием или ножу из вольфрамовой стали.
В этой статье для справки приведены некоторые параметры резки популярного обрабатывающего центра с ЧПУ. Различные виды режущих инструментов (летающий нож, белая сталь, концевая фреза, плоская фреза из вольфрамовой стали, шаровая фреза из белой стали, шаровая фреза из вольфрамовой стали) описаны соответственно для шероховатой и гладкой фрезы. Из-за большого количества обрабатываемых материалов в этой таблице описаны только репрезентативные алюминиевый сплав, сталь 45 и нержавеющая сталь.
Таблица параметров резания инструмента 1
Метательный нож, черновая резка, сталь 45
Таблица параметров резания инструмента 1Таблица параметров резания 2
Плоское лезвие из импортной белой стали, черновая резка, алюминиевый сплав, сталь 45
Таблица параметров резания 2Таблица параметров резания 3
Белый стальной шариковый нож, гладкий нож, алюминиевый сплав, сталь 45
Таблица параметров резания 4
Шариковый нож из вольфрамовой стали, гладкий, сталь 45, нержавеющая сталь
Таблица параметров резания 4Таблица параметров резания 5
Плоский нож из вольфрамовой стали, гладкий нож, сталь 45, нержавеющая сталь
Параметры резки Таблица 5Параметры резки Таблица 6
Плоский нож из белой стали, гладкий нож, алюминиевый сплав, сталь 45
Параметры резки Таблица 6 Услуги по механической обработке с ЧПУ ( фрезерная обработка и токарная обработка услуга), быстрая прототипирование , Изготовление приспособления/приспособления/инструмента , Детали для литья под давлением из алюминия и пластика .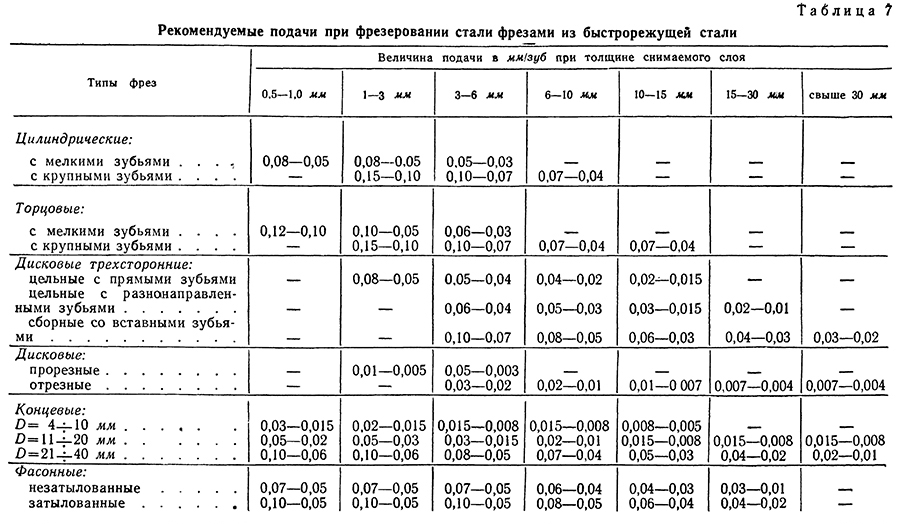
KYLT Услуги по обработке с ЧПУ:
Главная>Услуги по обработке с ЧПУ>Услуги по токарной обработке с ЧПУ
Главная>Услуги по обработке с ЧПУ>Услуги по быстрому прототипированию
Главная>Услуги по обработке с ЧПУ>Услуги по литью под давлением 9Главная>Точные детали с ЧПУ
Главная>Точные детали с ЧПУ>Точные токарные детали с ЧПУ
NC Precise Milled Parts
Главная>Точность Детали с ЧПУ>Обработка алюминия
Главная>Точные детали с ЧПУ>Обработка магния
Главная>Точные детали с ЧПУ>Обработка меди и латуни
Главная>Точные детали с ЧПУ>Обработка стали
Главная>Точные детали с ЧПУ>Обработка нержавеющей стали
Главная>Обработка Новости и блог
Скорости и подачи: Руководство для начинающих с таблицей
Каждая операция обработки на станке с ЧПУ требует установки оптимальных скоростей и подач для процесса.
Это два наиболее важных параметра обработки, которые напрямую влияют на качество, эффективность и срок службы инструмента.
Но какие факторы влияют на эти параметры и как определить оптимальные скорости и подачи для процесса?
В этой статье содержится подробное руководство по скорости и подаче операции обработки и объясняется, как рассчитать оптимальные значения.
Что в этой статье?
- Что такое скорость и подача при обработке с ЧПУ?
- Факторы, влияющие на скорости и подачи
- Расчет оптимальных скоростей и подач для процесса обработки
- Часто задаваемые вопросы (FAQ)
MellowPine поддерживается читателями. Когда вы покупаете по ссылкам на моем сайте, я могу получить партнерскую комиссию без каких-либо дополнительных затрат для вас.
Что такое скорости и подачи при обработке с ЧПУ?
Скорости и подачи относятся к разным скоростям процесса резания. В то время как скорость резания определяет количество удаляемого материала в футах с поверхности в минуту (SFM), скорость шпинделя — это скорость вращения режущего инструмента/заготовки (об/мин), а скорость подачи — это скорость, с которой режущий инструмент продвигается вдоль заготовки.
Для начала работы с ЧПУ требуется доскональное знание различных параметров, таких как скорость, подача, глубина резания, количество стружки и т. д., которые определяют его функциональность.
Для достижения наилучших результатов каждый процесс обработки с ЧПУ требует определенной комбинации этих параметров.
Как правило, для получения плавных резов рекомендуется высокая скорость с малой подачей, но обработка материала на очень высокой скорости может привести к перегреву и повреждению инструмента.
Аналогично, очень низкая скорость подачи увеличивает время цикла и снижает производительность процесса.
Поэтому важно установить оптимальное значение, обеспечивающее чистый срез с высокой производительностью.
Скоростные параметры станка с ЧПУ состоят из двух типов скоростей: скорости резания и скорости шпинделя.
Скорость резания
Скорость резания — это относительная скорость между заготовкой и режущим инструментом.
Можно определить как скорость, с которой конкретная точка заготовки проходит через режущую кромку.
Скорость резания обычно рассчитывается в метрах в минуту (MPM) или поверхностных футах в минуту (SFM).
Таким образом, скорость резания также можно определить как площадь поверхности, снимаемую режущими зубьями в минуту.
Скорость резания вместе со скоростью подачи и глубиной резания определяет скорость съема материала (MRR) в процессе обработки.
Скорость резания зависит от таких факторов, как материал заготовки, материал режущего инструмента и ожидаемая стойкость инструмента.
Как правило, оптимальную скорость резания инструмента можно определить из справочного руководства, предоставленного производителем.
Эти руководства обычно имеют цветовую маркировку и алфавит для каждой категории материалов.
P (синий) для стали, M (желтый) для нержавеющей стали, K (розовый) для чугуна, N (зеленый) для цветных металлов, таких как алюминий, S (коричневый) для жаропрочных сплавов, таких как титановые сплавы, и H (серый) для жаропрочных сплавов.
Скорость вращения шпинделя
Скорость вращения шпинделя определяет количество оборотов, которое режущий инструмент выполняет в минуту (об/мин).
Разницу между скоростью вращения шпинделя и скоростью резания можно понять по тому факту, что два круга разного диаметра, вращающиеся с одинаковыми оборотами, будут преодолевать разные расстояния.
Вращение режущих инструментов разного диаметраКруг большего диаметра имеет сравнительно большую длину окружности, и поэтому каждый оборот большего круга проходит большее расстояние, чем меньшего круга.
В результате при работе с одинаковыми настройками числа оборотов скорость резания (SFM) инструмента большего диаметра больше, чем инструмента меньшего диаметра.
Скорость шпинделя в первую очередь зависит от возможностей вашего станка с ЧПУ, режущего инструмента и типа обрабатываемого материала.
Обычно рекомендуется устанавливать высокие обороты для обработки мягких материалов и низкие обороты для обработки твердых материалов.
Однако обработка материала при слишком высокой или слишком низкой скорости вращения шпинделя может повредить заготовку и резко сократить срок службы инструмента.
Поэтому рекомендуется установить оптимальную скорость для вашего приложения.
Скорость подачи
Скорость подачи — это скорость, с которой режущий инструмент продвигается вдоль заготовки для удаления материала.
Зависит от частоты вращения фрезы, количества канавок режущего инструмента и количества стружки.
Как правило, медленная подача с высокой скоростью вращения обеспечивает чистый рез с высоким качеством поверхности, в то время как высокая скорость подачи может привести к грубому резу со сравнительно плохим качеством поверхности.
Факторы, влияющие на скорость и подачу
Параметры | Связь со скоростью или подачей |
---|---|
Скорость резания | 90 226 Прямо пропорциональна скорости шпинделя|
Диаметр инструмента | Обратно пропорциональна скорости шпинделя |
Скорость шпинделя | Прямо пропорциональна скорости подачи |
Количество зубьев | Прямо пропорциональна скорости подачи |
Chip load/ Feed per tooth | Directly proportional to the feed rate |
Machining parameters and their proportionality with speed and feed
Speeds and feeds of a machining process are directly dependent upon various factors such as the диаметр режущего инструмента, количество канавок и количество стружки.
Помимо этого, существует множество других факторов, таких как материал заготовки, материал режущего инструмента, жесткость станка с ЧПУ, отклонение инструмента и т. д., которые косвенно влияют на оптимальную скорость и конфигурацию подачи для операции обработки.
Диаметр инструмента
Диаметр инструментаДиаметр инструмента играет важную роль в настройке оптимального числа оборотов.
Инструмент большего диаметра может удалить больше материала, чем инструмент меньшего размера, при той же настройке скорости вращения.
Например, рассмотрим режущий инструмент 1/8″ и режущий инструмент 1/2″, оба вращаются с одинаковой скоростью вращения шпинделя.
Оба инструмента используются для аналогичной операции резания с одинаковым размером и глубиной резания.
Из-за своего большего размера режущий инструмент 1/2″ завершит операцию резания быстрее, чем инструмент 1/8″, независимо от качества резки.
Это связано с тем, что больший режущий инструмент удаляет сравнительно больше материала за каждый оборот.
Поэтому для достижения качественного реза важно учитывать диаметр инструмента при установке оптимальной скорости вращения для процесса.
Количество канавок
Количество канавок на режущем инструментеКоличество канавок (режущих зубьев) инструмента играет важную роль в установке оптимальной скорости подачи.
Режущий инструмент с одним зубом производит одну стружку за один оборот, что означает, что все режущее действие будет выполняться одним зубом.
Принимая во внимание, что в многолезвийной фрезе операция резания выполняется всеми канавками, и, как правило, количество стружки, производимой за один оборот, равно общему количеству канавок.
В результате сила резания равномерно распределяется между различными канавками, что снижает риск повреждения режущего инструмента.
Таким образом, по мере увеличения количества канавок оптимальная скорость подачи также увеличивается.
Нагрузка на стружку
Нагрузка на стружку Нагрузка на стружку, также известная как подача на зуб, может быть определена как толщина стружки, удаляемой в процессе обработки.
Это один из самых важных параметров обработки. Расчет оптимальной нагрузки стружки для процесса обработки может помочь установить оптимальную скорость подачи процесса.
По мере увеличения оптимальной нагрузки на стружку значение оптимальной скорости подачи также увеличивается.
Вы можете использовать калькулятор нагрузки на стружку, чтобы найти значение нагрузки на стружку для вашей настройки обработки.
Материал заготовки
Тип материала заготовки также играет важную роль в определении оптимальных скоростей и подач.
Как правило, твердые материалы, такие как металлы, плохо поддаются механической обработке, поэтому для них требуется меньшая скорость подачи, чем для мягких материалов, таких как дерево.
Кроме того, при обработке твердых металлов требуется большее усилие сдвига для выполнения режущего действия, поэтому конфигурация с низким числом оборотов в минуту и высоким крутящим моментом идеально подходит для таких операций.
В то время как мягкие материалы, такие как дерево, относительно легко обрабатываются и требуют высоких оборотов для скольжения режущего инструмента по заготовке.
Режущий инструмент Материал
Фрезы с твердосплавными напайкамиМатериал режущего инструмента определяет его способность выдерживать высокие силы резания.
Твердосплавный режущий инструмент может выдерживать большее усилие, чем инструменты из быстрорежущей стали, и поэтому может использоваться для обработки с более высокой скоростью и конфигурацией подачи.
Жесткость станка
Жесткость станка определяет максимальное усилие резания, которое может быть приложено к заготовке.
Как правило, станок с ЧПУ с жестким шасси может создавать сравнительно большие силы резания.
В то время как станок с менее жесткой конструкцией будет изгибаться под нагрузкой, возникающей из-за высоких сил резания.
Отклонение инструмента
Отклонение инструмента является одним из самых недооцененных параметров, влияющих на качество обработки.
Инструмент с длинным хвостовиком более склонен к отклонению под действием большой силы резания, поэтому его нельзя использовать для конфигураций с высокими скоростями и подачами.
В то время как инструмент с минимальным вылетом имеет очень меньшую возможность отклонения под действием силы резания и может использоваться для передачи сравнительно больших усилий.
Расчет оптимальных скоростей и подач
При расчете скоростей и подач для операции обработки следует учитывать, что оптимальную скорость резания (SFM) можно получить из справочного каталога, предоставленного производителем инструмента.
Точно так же оптимальную стружкообразование режущего инструмента для конкретного материала заготовки можно также получить из каталога инструментов, предоставленного производителем.
Затем вы можете выполнить следующие расчеты, чтобы получить оптимальную скорость шпинделя и скорость подачи для различных операций обработки.
Расчеты для фрезерных операций
Фрезерный станок с ЧПУ, работающий на металлической заготовке.
Уравнение для расчета оптимальной скорости шпинделя для фрезерной операции с ЧПУ:
S = (V с x 12)/(π x D)
Где S обозначает скорость шпинделя в об/мин, V с обозначает резку скорость в SFM, а D обозначает диаметр режущего инструмента в дюймах.
Вы также можете рассчитать скорость шпинделя в метрических единицах следующим образом:
S = (V s x 1000)/(π x D)
Где V s обозначает скорость резания в метрах в секунду (м/сек), а D обозначает диаметр инструмента в миллиметрах (мм).
Точно так же можно рассчитать оптимальную скорость подачи (в дюймах в минуту), используя следующую формулу:
Скорость подачи = скорость шпинделя x количество зубьев x количество стружки
Необходимо отметить, что произведение умножения количества стружки с количеством канавок дает подачу при резании в дюймах на оборот (IPR).
Следовательно, скорость подачи (IPM) также может быть определена как произведение скорости шпинделя (RPM) и рабочей подачи (IPR).
Расчеты для операций токарного станка
Токарная операция на токарном станкеОперации обработки на токарном станке с ЧПУ отличаются от других операций тем, что вместо вращающегося инструмента токарные станки состоят из вращающейся заготовки.
Таким образом, режущий инструмент токарного станка существенно отличается от фрез или концевых фрез.
Однако расчеты скорости и подачи для токарных операций аналогичны фрезерным и сверлильным, с той лишь разницей, что для расчетов используется диаметр.
Поскольку токарные станки состоят из вращающейся заготовки, мы учитываем диаметр обрабатываемой заготовки (а не диаметр инструмента) для расчета оптимальной скорости вращения шпинделя.
Оптимальную скорость для токарной операции можно рассчитать следующим образом:
S = (V с x 12)/(π x D)
Где S — скорость вращения шпинделя в об/мин, V с — скорость резания в SFM, а D — диаметр резания в дюймах.
Следует отметить, что произведение π на диаметр заготовки или режущего инструмента дает длину окружности.
Таким образом, скорость шпинделя также может быть определена как отношение скорости резания на границе инструмент-заготовка и ее окружности.
Кроме того, токарные инструменты, используемые для токарных операций, в основном являются одноточечными режущими инструментами, поэтому нагрузка на стружку равна рабочей подаче на оборот (в дюймах на оборот).
Скорость подачи (дюйм/мин) = скорость вращения шпинделя (об/мин) x подача на оборот (дюйм/об)
Расчеты для операций сверления
Иллюстрация сверления с ЧПУАналогично для операций сверления скорость и подачу можно рассчитать следующим образом.
S = (V с x 1000)/(π x D)
Где V с обозначает скорость резания в метрах в секунду (м/сек), а D обозначает диаметр инструмента в миллиметрах (мм) .
Скорость подачи (IPM) = Скорость шпинделя (RPM) x подача на оборот (IPR)
Часто задаваемые вопросы (FAQ)
Влияет ли глубина резания на скорость и подачу в процессе обработки?
Да, глубина резания является важным фактором, который влияет на количество стружки и, следовательно, влияет на оптимальную скорость и подачу для процесса обработки.