Трудовые действия | Проверка и корректировка управляющей программы |
Отладка управляющей программы | |
Уточнение эскиза карты наладки | |
Корректировка сопроводительной документации | |
Составление инструкций по работе с программами | |
Контроль соблюдения технологической дисциплины в цехах и правильной эксплуатации технологического оборудования с числовым программным управлением | |
Отладка управляющих программ многокоординатной и/или многошпиндельной обработки лезвийным инструментом | |
Корректировка синхронизации управляющих программ на разных каналах | |
Необходимые умения | Программировать станки на языках системы числового программного управления |
Программировать на языках высокого уровня | |
Работать в режиме верификации управляющих программ | |
Использовать методы поиска и выявления ошибок в управляющих программах | |
Выявлять геометрические, синтаксические и семантические ошибки в управляющих программах | |
Работать в режиме визуализации управляющих программ | |
Искать и выявлять технологические ошибки | |
Вносить изменения в техническую документацию в связи с корректировкой технологических процессов, управляющих программ и режимов производства | |
Составлять инструкции по работе с программами | |
Контролировать соблюдение технологической дисциплины в производствах и цехах, правильную эксплуатацию технологического оборудования | |
Синхронизировать управляющие программы на разных каналах | |
Разрабатывать управляющие программы для параллельного выполнения на нескольких каналах | |
Перебрасывать в управляющей программе оси и шпиндели между каналами | |
Запускать из управляющей программы, выполняемой на одном канале, управляющую программу, выполняемую на другом канале | |
Программировать в системе координат детали и в системе координат станка | |
Необходимые знания | Языки программирования систем числового программного управления |
Команды языка программирования систем числового программного управления | |
Основы языка высокого уровня | |
Диалекты языка программирования станков с числовым программным управлением и языка высокого уровня | |
Основы применения пакетов цехового программирования | |
Принципы построения управляющих программ | |
Функциональные возможности и принципы работы оборудования с числовым программным управлением | |
Современные инструменты и технологическая оснастка для станков с числовым программным управлением | |
Интерфейс оператора | |
Методы и средства контроля и редактирования управляющих программ | |
Методы поиска и выявления ошибок в управляющих программах | |
Руководящие и нормативные материалы, регламентирующие методы программирования систем числового программного управления, используемых для управления оборудования, для которого разрабатываются управляющие программы | |
Руководящие и нормативные материалы по эксплуатации систем числового программного управления, используемых для управления оборудования, для которого разрабатываются управляющие программы | |
Стандарты и технические условия | |
Методические и нормативные материалы по технологической подготовке производства | |
Основы применения систем автоматизированного проектирования | |
Проблемно ориентированные языки для программирования систем числового программного управления | |
Системы и методы разработки управляющих программ для оборудования с числовым программным управлением | |
Формы записи исходной информации для программирования | |
Принципы, методы и средства привязки “нуля детали” к “нулю станка” | |
Виды интерполяции и способы их программирования | |
Теория размерных цепей | |
Режимы резания материалов | |
Основные и вспомогательные команды, специальные функции, их свойства и правила применения | |
Режимы обработки материалов | |
Методы и средства постпроцессирования программ | |
Методы и средства контроля и редактирования управляющих программ | |
Средства вычислительной техники, коммуникации и связи | |
Современные системы автоматизированного проектирования технологических процессов | |
Виды брака и способы его предупреждения | |
Руководящие и нормативные материалы, регламентирующие методы программирования систем числового программного управления, используемых для управления оборудованием, для которого разрабатываются управляющие программы | |
Координатные трансформации | |
5-осевые трансформации | |
3D-коррекция инструмента в процессе обработки | |
Стратегии и методы обработки деталей сложных пространственных конфигураций | |
Многокоординатная обработка | |
Сплайновая интерполяция | |
Компрессия кадров | |
Методы обработки поверхностей свободной формы | |
Методы и режимы высокопроизводительной обработки | |
Стратегии и методы высокоскоростной обработки | |
Основы кинематических схем и принципы кинематические трансформации | |
Трансформации ориентации инструмента | |
Трудовое законодательство Российской Федерации | |
Другие характеристики | Деятельность, направленная на решение типовых задач технологического характера |
NCManager / Подготовка управляющих программ / Машиностроение / НИП-Информатика
Назначение программы
NCManager – программное обеспечение, служащее для визуального анализа и редактирования управляющих программ в кодах конкретного станка ЧПУ. Это программы для фрезерных, токарных, лазерных станков, листопробивных прессов и т.п.
NCManager обеспечивает возможность:
– проверить новую УП. После создания управляющей программы вручную или в любой CAM системе можно проверить, как она реально будет выполняться на конкретном станке с учетом коррекции, циклов, подпрограмм и т.д. При этом выявляются такие ошибки, как столкновение инструмента с заготовкой, зарезание, неправильная геометрия, неправильно установленные технологические параметры и т.д. Если программа содержит ошибки, то NCManager поможет их найти и немедленно исправить;
– просмотреть старую УП. С помощью NCManager можно мгновенно восстановить в памяти назначение имеющейся программы и, при необходимости, внести в нее изменения;
– восстановить форму детали по УП. NCManager отображает процесс удаления материала при обработке, поэтому можно восстановить все обрабатываемые поверхности детали, узнать координаты любых точек;
– обмерить деталь без изготовления.
На любом этапе имитации работы управляющей программы можно остановить ее выполнение и измерить реальные координаты и расстояния на детали, получающейся после обработки, т.е. проконтролировать деталь, не изготавливая ее;
– оптимизировать программу. Даже самый хороший постпроцессор не в состоянии выдать оптимальную программу во всех случаях. С помощью NCManager можно проанализировать любые участки программы с учетом времени, режимов и т.д. и оптимизировать ее;
– написать простейшую программу. Нередко возникает ситуация, когда необходимо очень быстро выдать на станок несложную программу. В этом случае можно написать ее непосредственно в NCManager. При этом одновременно с написанием можно видеть, как программа будет работать и, тем самым, избежать ошибок;
– отладить постпроцессор. При разработке постпроцессора возникает необходимость проверить его работу во всех возможных ситуациях. CAM система, для которой он разрабатывается, как правило не может ни чем помочь.
NCManager заменяет в этом случае эксперименты на станке, значительно упрощая весь процесс разработки;
– найти нужную программу в архиве. При просмотре архива имеющихся управляющих программ часто приходится ориентироваться только по их именам, что далеко не всегда удобно. Использование графических и измерительных возможностей NCManager позволяет значительно быстрее найти необходимую программу;
– заменить инструмент. Если вместо инструмента, для которого управляющая программа была изначально разработана, приходится использовать другой, NCManager позволит задать новый инструмент, ввести необходимые значения коррекции и увидеть (измерить) результат работы программы;
– обучить персонал. NCManager по существу представляет из себя симулятор станка с ЧПУ и может быть использован как тренажер для обучения новых сотрудников;
– учесть особенности стойки ЧПУ. NCManager можно настроить с учетом особенностей конкретного станка, даже если эти особенности не отражены в документации или являются результатом модернизаций.
- – перенести программу с одной системы ЧПУ (стойки) на другую. Экспорт программ в формате АРТ CL позволяет использовать программы, разработанные для одной стойки ЧПУ, для работы на другой стойке. В этом случае NC Manager считывает имеющуюся программу, интерпретирует и отображает ее и дает пользователю возможность перевести ее в АРТ CL файл. АРТ CL файл обрабатывается постпроцессором для нужной стойки. Полученный G-код снова загружается в NCManager. Таким образом, появляется возможность сравнить исходную и полученную программы и убедиться, что перевод осуществлен корректно.
– экспортировать геометрию программы в другие CAD/CAM системы. Наличие DXF интерфейса позволяет передать форму траектории инструмента практически в любую систему для дальнейшего использования.
Фотогаллерея
Демонстрационный проект:
Исходными данными для NCManager является текст программы для конкретного станка (G-код), файл определения стойки ЧПУ.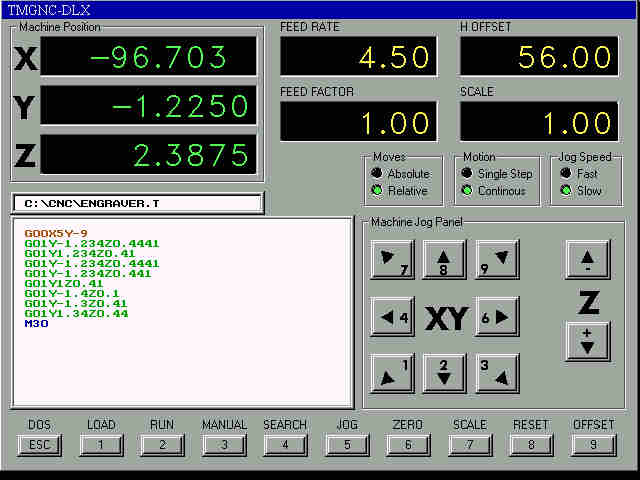
NCManager предназначен для работы, как с программами, подготовленными вручную, так и с программами, полученными при помощи любых CAM систем. Во втором случае вся необходимая дополнительная информация (инструменты, заготовка) могут быть импортированы из CAM системы. В обоих случаях эта информация может быть откорректирована или создана заново «внутри» NCManager. Кроме того, NCManager позволяет редактировать текст программы с немедленным отображением сделанных изменений в графическом окне.
В
вложении pdf с описаниям проекта(презентации), сделанного из присланной
УП. Прислали в следующей постановке, – выбираем симулятор,
рассматриваем и NCManager в том числе. Давайте проведем тесты и
подготовим презентацию.
—-
NCManager – пояснения к демопректу
Загружаем в NCManager УП, модель заготовки, модель детали. Определяем станок, стойку ЧПУ. Создаем режущий инструмент.
На
картинке вид NCManager после определения всех данных необходимых для
проверки УП. Показано основное Графическое окно Станок (Главное меню
Окно – Станок).
Скачать: itnc530-ux-600.pdf (760 кб)
NCManager обеспечивает возможность имитации выполнения программы в различных режимах: от простой прорисовки траектории до реалистической имитации процесса удаления материала заготовки. Во всех режимах пользователю доступна вся текущая информация о координатах любой точки заготовки, инструмента, траектории и вся информация о состоянии стойки ЧПУ (подача, скорость, режим и т.д.).
Таким образом, NCManager представляет собой компактный и простой в освоении продукт, способный существенно упростить работу со всем многообразием программ для станков с ЧПУ независимо от их происхождения.
Видео каталог:
youtube.com/embed/GSiGtWX_lYs” frameborder=”0″ title=”Симуляция 3-х координатной УП большого размера”>
Контроль управляющих программ | Техтран
Назначение программы
Программа предназначена для отображения, контроля и редактирования управляющих программ (УП) для станков с ЧПУ. Программа может использоваться во взаимодействии с другими программами семейства Техтран и как независимый продукт. При этом не имеет значения, как была получена УП: с использованием системы автоматизированного программирования или вручную.
Анализ УП
Программа производит анализ УП с учетом особенностей конкретной системы ЧПУ. В процессе анализа осуществляются синтаксический контроль кадров УП, проверка согласованности значений параметров и их корректности. Все диагностические сообщения заносятся в протокол анализа, по которому можно быстро определить ошибочное место в тексте УП.
Свойства УП
По результатам анализа УП заполняется окно Свойства УП, в котором отображаются списки объектов, используемых в УП: инструментов, подпрограмм, встроенных циклов, технологических команд (подача, скорость шпинделя, загрузка инструмента и др. ). Управление компонентами УП дает возможность локализовать область исследования УП, оставив на экране только те ее составляющие, которые требуется анализировать и сопоставлять друг с другом, и убрав из обозрения элементы, несущественные в данный момент. Например, можно прорисовать траекторию, пройденную только определенным инструментом, или временно отключить отображение команд переключения подачи.
Выполнение управляющей программы
Основным механизмом для контроля данных УП служит выполнение кадров УП в различных режимах. По мере выполнения программы производится прорисовка траектории инструмента и вывод текущих параметров обработки. УП отображается в текстовом окне и может выполняться как целиком, так и по частям. Это позволяет детально исследовать определенные команды УП и пропускать фрагменты, которые в данный момент несущественны.
Строка, на которой приостановлено выполнение, отмечается специальным маркером. Пошаговое выполнение УП дает представление о логике работы программы: перемещение маркера отслеживает запрограммированные повторы, переходы в подпрограммы и т. д. Кроме того, при таком режиме хорошо видно соответствие между кадрами УП и результатами их выполнения.
Графическое отображение
Графическое окно обеспечивает пространственное отображение траектории инструмента. Управление видами позволяет произвольно выбирать точку зрения, менять масштаб, устанавливать стандартные проекции, получать увеличенное изображение выбранной области рисунка и т.д.
Траектория каждого инструмента рисуется своим цветом. В процессе выполнения УП можно управлять видимостью таких участков независимым образом через список инструментов. Так же организовано управление отображением технологических команд, которые рисуются в графическом окне в виде различных значков. Для каждого перемещения инструмента в графическом окне может быть получена информация об его геометрических параметрах и соответствующем кадре УП.
Анимация выполнения
Режим анимации отображения обработки в графическом окне позволяет получить представление о том, как происходит движение инструмента по своей траектории с течением времени. Это автоматическое выполнение УП в пошаговом режиме с определенной скоростью.
Преобразование УП в программу на языке Техтран
При анализе УП в окне Обработка формируется программа на языке Техтран. Она состоит из операторов, которые соответствуют элементарным командам, составляющим кадры УП. Благодаря такому представлению, наглядно прослеживается фактическое восприятие системой ЧПУ текста УП. В процессе выполнения происходит синхронное перемещение маркеров текущего положения как в тексте УП, так и в соответствующей программе на Техтране. Таким образом видна связь между двумя различными представлениями программы. Управление выполнением может осуществляться из обоих окон.
Использование данных УП в программах семейства Техтран
Текст программы на языке Техтран, полученный по УП может использоваться для передачи данных в программы семейства Техтран, ориентированные на различные виды обработки. Эти данные могут быть использованы при программировании обработки аналогичных деталей и получении УП для различных систем ЧПУ. Благодаря тому, что Техтран основан на универсальной модели представления данных, не зависящей от системы ЧПУ, таким способом обеспечивается возможность преобразования УП для использования на другом оборудовании.
инженер поможет – Автоматизация подготовки управляющих программ для станков с ЧПУ
Проблема в особенности осложняется при ручной разработке управляющих программ для обработки непростых контурных заготовок. В следствии более современным становится использование для разработки УП применение САП (систем автоматизированной подготовки), применяемые для повышения их качества и сокращение сроков подготовки производства.
УП (управляющая программа) — совокупность команд на языке программирования, идентичная алгоритму работы станка при обработке заготовок.
Управляющая программа на языке PEPS содержит три части:
– “шапка” программы, показывающая постпроцессор станка с ЧПУ, материал и параметры заготовки, размеры рабочего окна;
– “геометрия” программы, в которой отображается конфигурация детали, т. е. путь движения режущих инструментов;
– “технология” программы, включающая в себя выбор (или назначение) режущих инструментов и их параметров, перемещения инструментов относительно заготовки, режимы резания, вспомогательные команды.
Технологический процесс изготовления деталей на станках с ЧПУ связан с получением, обработкой, передачей, хранением и управлением огромными информационными потоками. При этом важную роль играет человек (разработка ТП, работа в режиме диалога с ЭВМ, активное участие в организации и управлении процессом обработки, подготовка и отладка УП,). Поэтому с позиции кибернетики комплекс систем проектирования ТП (САПР), подготовки УП (систем автоматического программирования—САП) и управления процессом обработки (СЧПУ) можно рассматривать как человеко-машинную систему, где человек использует уникальные возможности электронной техники.
При разработке ТП и подготовке УП большой объём информации перерабатывается в определённой последовательности:
1.
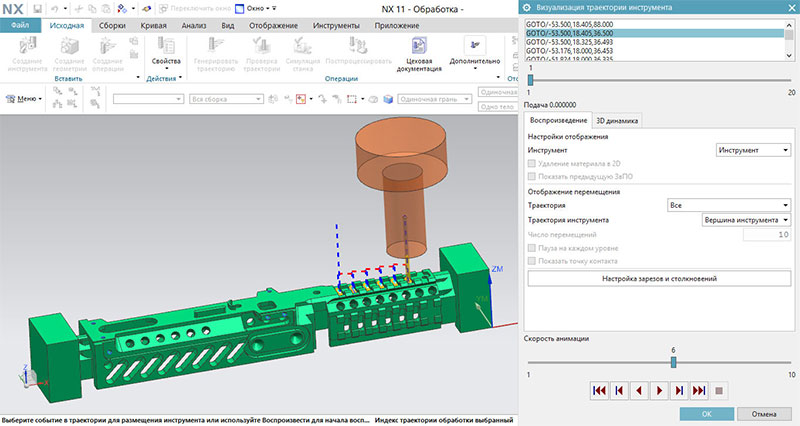
Проектирование технологического процесса считается сложной задачей и находится в зависимости от конструкции детали, материала, требований к ее качеству, вида заготовки, а также масштаба выпуска.
При классическом проектировании маршрута технологического процесса остаются не пользующиеся известностью величины снимаемых припусков, число рабочих ходов при обработке каждой поверхности детали, режимы обработки, затраты времени. Следовательно, маршрут не выделяет информации, которая разрешила бы на данном этапе разработки подсчитывать производительность и себестоимость изготовления детали. Вследствие обозначенного недочета расценить эффективность технологического процесса становится, вероятно, возможным только впоследствии проектирования операций, т. е. после абсолютной разработки процесса. Это существенно удлиняет поиск наиболее оптимального варианта разрабатываемого технологического процесса и увеличивает трудозатратность разработки. В то же время установленная маршрутом структура процесса: количество и порядок операций, способы обработки и оборудование – оказывают существенное воздействие на стоимость, производительность и, в конечном результате, на эффективность изготовления детали.
Разработка маршрута содержит:
1) выбор технологических баз и последовательности изготовления МП, МПИ детали;
2) определение заготовительных модулей и технологических переходов;
3) разработку последовательности обработки заготовки;
4) составление операций.
2. Разработка операционной технологии с расчетами режимов резания.
К режимам резания относятся:
Скорость резания V– это расстояние, пройденное точкой режущей кромки инструмента сравнительно заготовки в направленности главного движения в единицу времени;подачейS именуют путь точки режущей кромки инструмента сравнительно заготовки в направлении движения подачи за один оборот или же один ход заготовки или же инструмента; глубиной резания t именуют расстояние между обрабатываемой и обработанной поверхностями заготовки, измеренное перпендикулярно последней. Глубину резания относят к одному рабочему ходу инструмента сравнительно обрабатываемой поверхности. Глубина резания содержит размерность мм.
3. Построение траектории движения режущих инструментов и расчет координат опорных точек.
В ходе создания УП для станков с ЧПУ деталь рассматривается в системе СПИД (станок-приспособление-инструмент-деталь). Заготовка устанавливается на станке с поддержкой приспособления, которое закрепляет будущую деталь относительно исходного положения рабочих органов станка, определяющих состояние режущего инструмента. Траектория инструмента создаётся сравнительно контура детали, а потом преобразуется в перемещение надлежащих рабочих органов станка. Для этого применяются системы координат детали, станка и инструмента. Система координат детали нужна для пересчета размеров, данных на чертеже детали, в координаты опорных точек ее контура.
4. Создание команд и функций, кодирование информации.
Кодирование информации – это процесс формирования определенного представления информации. В более узком смысле под термином «кодирование» часто понимают переход от одной формы представления информации к другой, более удобной для хранения, передачи или обработки.
5. Запись управляющей программы на программоноситель.
Текст готовой УП либо записывается на программоноситель, либо вводится в устройство ЧПУ с помощью клавиатуры и переключателей на пульте управления. От способа ввода УП в систему ЧПУ зависит только вид документа, на котором фиксируются результаты программирования. Запись программы обработки осуществляется кадрами переменной длины, которые содержат информацию о технологических условиях обработки, длине перемещения и вспомогательных функциях. Порядок кадров определяется последовательностью обработки. Кадр состоит из информационных слов (команд), которые включают числовую информацию и символ, определяющий вид информации.
6. Проверка и отладка УП (внесение коррекции).
Отладка программ и обработка ошибок всегда выступает как часть процесса разработки. Если бы все программировали идеально, то необходимость отладки программ и обработки ошибок отпала бы сама собой: каждая создаваемая программа выполняла бы все требуемые действия с первого раза. Как правило, такого не бывает, поэтому в большинстве систем разработки имеются инструменты, с помощью которых можно решить проблемы, возникающие в процессе программирования. Отладка программ — это проверка и внесение исправлений в программу при ее разработке. Отладка позволяет идентифицировать ошибки, допущенные при программировании. Например, синтаксические ошибки в тексте программы, именах функций и переменных или логические ошибки.
Программирование ТП производства деталей на станках с ЧПУ — качественно новый этап, когда производится часть работы (этапы 3-6), перенесенная из сферы изготовления в область технологической подготовки. Влияния рабочего при обрабатывании заготовок на обычном станке (после этапов 1-2) осуществляются на станке с ЧПУ в автоматическом режиме по УП. Под обработкой понимается предложенное изменение формы, размеров или же шероховатости поверхности заготовок.
Технологический процесс обработки на станках с ЧПУ требует большой детализации — разбиения на составляющие, т. е. декомпозиции. Структурно ТП распределяется на операции, установы, позиции, переходы, рабочие и вспомогательные ходы, шаги и технологические команды.
Очередность элементарных перемещений и технологических команд определяет содержание УП.
При создании маршрутной технологии определяют состав операций, целесообразность выполнения которых на станках с ЧПУ устанавливают на основе технико-экономических расчетов.
Подготовка управляющей программы требует переработки больших размеров (объемов) специальной информации. Использование электронно-вычислительных машин (ЭВМ) для автоматизации программирования и подготовки УП потребовало разработки специального программно-математического обеспечения для решения всевозможных технологических и геометрических задач, встречающихся при подготовке УП.
Совокупность математического, программного обеспечения и проблемно-ориентированного языка для записи и ввода в ЭВМ первоначальной информации при организации УП называют САП. В настоящее время разработано множество различных САП. Они различаются степенью и уровнем автоматизации этапов подготовки управляющей программы (УП).
Чертеж изготовляемой детали представляют в виде технической документации (на электронных или магнитных носителях), полученной от САПР. Визуальный контроль такого чертежа возможен с помощью дисплея ЭВМ. Если чертеж представлен в традиционном виде, то данные чертежа вводятся в САП с помощью клавиатуры. САП перерабатывает данные чертежа и выдает УП в коде ISO (стандарт IS06983).
Полученная от САП УП обычно фиксируется на накопителе на магнитном диске (НМД — гибкая дискета или жесткий диск). Применяют также накопители на магнитной ленте (МЛ) или перфоленте (ПЛ).
Ввод УП совершается либо путем установки в дисковод устройства ЧПУ (УЧПУ) станка, либо пересылки УП из САП (жесткого диска) в оперативное запоминающее устройство (ОЗУ) процессорного модуля УЧПУ.
Процессорный модуль формирует сигналы управления, которые подаются на автоматический привод. При одновременном управлении движением по двум координатам можно обрабатывать конусообразные и криволинейные поверхности.
Системы автоматизации программирования (САП) возможно рассматривать как кибернетическую систему, обеспечивающую изменение информации. На вход системы попадает информация об обрабатываемой детали и указания ее технических требований, а на выходе принимают подготовленную УП. Обычно управляющая программа в САП создается в два этапа.
Важнейшие блоки САП, такие как: сервис, препроцессор, процессор, постпроцессор-это, как правило, файл и или несколько файлов, в которых заложена информация о конфигурации оборудования и системы ЧПУ, установленной на данное оборудование, наличии всевозможных функций. Блок сервис преобразовывает неизменную информацию о станках, материале заготовок, инструментах и др. Информация систематизируется и записывается в память ЭВМ как таблицы параметров.
На первом этапе переработка информации применяется в двух блоках, составляющих основу каждой САП, — процессоре и постпроцессоре. Процессор осуществляет геометрические и технологические расчеты «без привязки» к определенному станку и системе ЧПУ. Процессор предполагает траекторию перемещения инструмента. Данные вместе с данными о режимах резания выводятся на наружный носитель ЭВМ — диск или же магнитную ленту. Конфигурация представления этих данных называется CLDATA (от англ. CATTER Location Data — данные о расположении инструмента) и является установленным видом информации на конкретном языке.
Процессор САП состоит из трех один за другим работающих блоков: трансляции и геометрического формирования CLDATA.
Технологический блок самостоятельно делит область, подлежащую обработке, на переходы, рабочие ходы и рассчитывает оптимальные режимы резания.
Геометрический блок процессора постановляет задачи, объединенные с созданием траектории перемещения инструмента: определение точек и линий скрещивания всевозможных элементов; аппроксимация разнообразных кривых с определенным допуском; диагностика геометрических ошибок.
Блок трансляции (блок ввода и декодирования) реализовывает вытекающие функции: чтение первоначальной программы обработки изделия с наружного носителя; вывод программы на печать или же экран дисплея; изменение информации из символьной формы во внутреннее машинное представление. В препроцессоре готовятся данные для работы остальных блоков, операции подразделяются на установы и позиции, отбираются схемы крепления заготовки и оснащаются инструментальные наладки.
Блок формирования CLDATA ведет сбор сведений для работоспособности постпроцессора. Постпроцессор не прекращает переработку информации и сформировывает УП с ориентацией (т. е. с «привязкой») на конкретный станок и систему ЧПУ. Типовые функции постпроцессора: сканирование данных, которые разработаны процессором, перенос их в систему координат станка; составление команд на передвижение с учетом стоимости импульса СЧПУ и команд, обеспечивающих цикл замены инструмента; выдача в кадр значений подач и скоростей шпинделя, которые были закодированы; подача команд на включение и выключение охлаждения, зажима — разжима заготовок; выдача управляющей перфоленты и листинг (распечатки) УП; диагностика ошибок; выполнение сервисных функций. Это является вторым этапом переработки информации.
В большинстве случаев САП заключает в себе набор постпроцессоров, предоставляющие формирование УП (управляющей программы) для отдельных типов станков с ЧПУ. Вызов нужного постпроцессора выполняется автоматически по параметрам, которые технолог-программист укажет в тексте исходной программы.
Двухэтапная организация работы САП при подготовке УП содержит важное преимущество. На определенном языке САП на основе одной и той же начальной информации, имея данные CLDATA и применяя всевозможные постпроцессоры, можно получать УП для разнообразных моделей станков и УЧПУ. Кроме того, для подключения новейших моделей станков с ЧПУ к имеющейся на предприятии САП достаточно создать постпроцессор и состыковать с САП. Вместе с постпроцессором создается работа с программным блоком «редактор», который позволяет изменять УП, выводимую на экран дисплея.
Применение систем автоматизации проектировании в процессе подготовки производства способствует повышению технического уровня и качества проектируемых объектов, сокращению сроков их разработки и освоения в производстве.
Тем не менее, зачастую производство сталкивается с проблемой эффективности технологической организации производства, в частности
на этапе подготовки управляющих программ (УП) для станков с ЧПУ. Качество разработки конкретной управляющей программы зачастую связано с навыками технолога-программиста. Снижение квалификации возможно за счет внедрения типовых решений при подготовке управляющих программ.
Повысить качество процесса разработки управляющих программ возможно за счет:
повышения уровня автоматизации процесса организации управляющих программ;
совершенствования процедур отладки и верификации управляющих программ, в том числе и с привлечением специализированных средств автоматизации с расширенными возможностями.
Новизна проделанной работы заключается в:
в установлении связей между технологическими ограничениями в виде требований к точности изготавливаемой детали и правилами формирования операционной технологии, способствующей сокращению затрат времени и повышению качества организации управляющих программ для оборудования с ЧПУ;
в выявлении геометрических и технологических показателей, позволяющих представить деталь в виде набора параметрических элементов форм и определить их влияние на аналогичные технологические схемы обработки, используемые при формировании операционной технологии производства детали.
Эти результаты были достигнуты путем разработки следующих методик:
методики автоматизированной организации управляющих программ на основе технологии FBM системы Siemens NX;
методики классификации деталей на основе параметрических элементов форм, методики создания кинематической модели станка с помощью программ Machine Tool Builder и Siemens Machine Configurator.
Из статьи «Автоматизация подготовки управляющих программ для станков с ЧПУ (числовым программным управлением)», можно сделать вывод, о что использование систем автоматизации проектирования в процессе подготовки производства способствует повышению технического уровня и качества проектируемых объектов, сокращению сроков их разработки и освоения в производстве.
Повысить качество процесса разработки УП можно за счет: усовершенствования процедур верификации и отладки УП и повышения уровня автоматизации процесса подготовки УП.
Подготовка управляющих программ(УП) на базе САD/CAM системы SprutCAM. CAM-системы нужны для проектирования обработки деталей на станках с ЧПУ (числовым программным управлением) и выдачи программ для станков (фрезерных, сверлильных, токарных, шлифовальных и др.). CAM-системы так же называют системами технологической подготовки производства. Сейчас они являются почти единственным способом для изготовления деталей и сокращения цикла их производства.
Существуют программы для автоматизации подготовки УП, такие как:
ü Программа PowerMill
ü Программа PowerMill – профессиональный инструмент, который используется для составления УП для любого автоматизированного производства. Подходит для постановки задач для 2-х и 5-тиосного инструмента. PowerMill – программный продукт от американской компании Autodesk Inc, специализирующейся на разработке программного обеспечения для машиностроения, строительства, и производства. В свое время программа вышла на рынок как разработка Delcam plc, предложившей революционную систему построения УП, и работавшей над самой распространенной на тот момент операционной системой.
Уже тогда главной задачей программы было определить оптимальную траекторию движения режущего инструмента. Начиная с 1995 года и до наших дней на свет появилось 21 версия powermill. Начиная с 2002 года, обновления выпускались регулярно, а с 2010 по несколько версий в год. Это сделало Пауэр Милл одним из самых совершенных и конкурентно способных профессиональных программных продуктов в производственной среде.
ü CAM-система Mastercam нужна для создания управляющих программ для станков с ЧПУ фрезерной, токарной, токарно-фрезерной, электроэрозионной групп, а также для деревообрабатывающего оборудования. Mastercam позволяет разрабатывать в автоматизированном режиме управляющие программы по каркасной геометрии и по любым 3D-моделям — как созданным в Mastercam, так и переданным в него с помощью большого набора прямых и нейтральных трансляторов.
Трансляторы и модуль Design, включающий функционал для создания каркасной и поверхностной геометрии, входят в состав всех базовых модулей: Mill (фрезерование), Lathe (токарная обработка), Wire (электроэрозионная обработка) и Router (деревообработка). Создание и обработка рельефных художественных изображений осуществляются с помощью модуля Art, поставляемого совместно с модулем Mill или Router.
К ключевым преимуществам Mastercam относятся:
легкость изучения и удобство в эксплуатации; 2D- и 3D-каркасное, поверхностное, твердотельное моделирование, оформление эскизов; библиотека трансляторов из CAD-систем; надежность системы, высокая скорость расчетов; наглядная проверка созданных траекторий; полная ассоциативность геометрии и траекторий; настраиваемая конфигурация «станок-CЧПУ».
ü VisualMILL является флагманским продуктом компании Mecsoft и наиболее подходит для производства литейных форм, фильер и штампов, общего машиностроения, быстрого прототипирования и тд. VisualMILL является одним из пяти модулей обработки в программном пакете Visual CAD/CAM.
Факторы, влияющие на автоматизацию подготовки управляющей программы для станков с числовым программным управлением:
v Важные: отсутствие у предприятия должного финансирования отделов, отсутствие должной квалификации программистов, использование старых стоек ЧПУ.
v Менее важные: устаревшие базу CAM программ.
Источник статья «Автоматизация подготовки управляющих программ для станков с ЧПУ (числовым программным управлением)» авторов: Сергеева Олега Сергеевича, Гисметулина Альберта Растемовича, Маданова Александра Владимировича
Подготовка управляющих программ для станков с ЧПУ
1. Лекция 10 Подготовка управляющих программ для станков с ЧПУ Основные понятия и сведения о кодировании, управляющей программе. Определение
Лекция 10Подготовка управляющих программ для станков с
ЧПУ
Основные понятия и сведения о кодировании, управляющей
программе. Определение кода, кодирования. Характеристика
систем счисления: двоичная, двоично-десятичная система
счисления. Вес кода. Определение управляющей программы, кадра,
слова, адреса. Формат кадра управляющей программы
2. Основы программирования
Для разработки управляющей программы обработки деталей на станках сЧПУ необходимо:
1. Спроектировать маршрутную технологию обработки в виде последовательности операций с выбором режущих и вспомогательных
инструментов и приспособлений;
2. Разработать операционную технологию с расчетом режимов резания и определением траекторий движения режущих инструментов;
3. Определить координаты опорных точек для траекторий движения
режущих инструментов;
4. Составить расчетно-технологическую карту и карту наладки
станка;
5. Закодировать информацию;
6. Нанести информацию на программоноситель и переслать в память
устройства ЧПУ станка или вручную набрать на пульте устройства
ЧПУ;
6. Проконтролировать и при необходимости исправить программу.
Для программирования необходимы чертеж детали, руководство по
эксплуатации станка, инструкция по программированию, каталог
режущих инструментов и нормативы режимов резания
Понятия о коде, кодировании
Кодирование информации – процесс формирования определенного
представления информации.
В более узком смысле под термином «кодирование» понимают переход от
одной формы представления информации к другой, более удобной для хранения,
передачи или обработки, т.е. преобразование знаков или групп знаков одной
знаковой системы в знаки или группы знаков другой знаковой системы.
Декодирование – расшифровка кодированных знаков, преобразование кода
символа в его изображение
Код – система условных обозначений или сигналов используемых для кодирования
Длина ( значность) кода – количество знаков (разрядов) n в кодовой комбинации,
используемых для представления кодируемой информации. Каждый разряд может
принимать значение 0 или 1.
Вес кода – количество единиц в кодовой комбинации
Например: кодовая комбинация 100101100 характеризуется значностью n=9 и
весом =4.
Главнейшим показателем кода является значность кода или алфавит выбранных
элементарных символов (сигналов), используемых для записи информации в
выбранном коде. Если выбирается алфавит из двух элементов (букв), например, 0
и 1, то такой код (алфавит) называют двоичным или бинарным, если число
элементарных сигналов (букв) выбирают больше двух, то такой код (алфавит)
называют многозначным (например, если количество элементов алфавита –
десять: 0, 1, 2, 3, 4, 5, 6, 7, 8, 9 – такой код называют десятичным).
Десятичная система
Десятичные числа: ОСНОВАНИЕ 10
Наша десятичная система состоит из цифр от 0 до 9. Одна и та же
цифра внутри одного числа в зависимости от положения (разряда)
может иметь различное значение.
Пример: число 72075
Двоичная система
Двоичные числа:
ОСНОВАНИЕ 2
В устройствах обработки данных при обработке информации оперируют только импульсами тока. Это означает, что компьютер может понимать только два
состояния сигнала. Поэтому для представления знаков и цифр используется
числовая система, которая состоит только из цифр 0 и 1.
Элемент информации, у которого возможны только два состояния, называется бит (англ. binary digit = двоичный шаг). Информационная единица из 8 бит
называется байт.
Преобразование “двоичное число —
десятичное число”
Преобразование “десятичное
число — двоичное число”
Вычислительные операции
Все вычислительные операции в ЭВМ, такие как вычитание, умножение и деление,
сводятся к сложению. Правила вычисления в двоичной системе при сложении те
же, что и в десятичной системе, т. е. переносы прибавляются к следующему более
высокому разряду.
В двоично-десятичном кодировании, каждая десятичная
цифра (сообщение) представляется группой двоичных
символов, состоящих из 4-х элементов. Общее число
возможных комбинаций двоичного 4-х разрядного числа
составляет N = 24 = 16. Из них для представления
десятичного числа используется только 10 комбинаций.
Остальные 6 являются лишними (избыточными). 10
комбинаций дают возможность построить большее
количество вариантов кода.
При рассмотрении двоичного представления десятичных цифр видно, что использование
первых 4-х степеней цифры 2 (20, 21, 22, 23) приводит к одному из возможных кодов 8-4-2-1.
Каждый разряд этого кода имеет постоянный вес. Возможны и другие двоично-десятичные
.коды с другими весами разрядов двоичного числа, например:
Эти коды представляют десятичное число от 0 до 9, однако, они не имеют однозначности в
изображении десятичных чисел. Например, код 4-3-2-1 дает определение числа 6 в виде:
0111 или 1010
Управляющая программа
Согласно ГОСТ 20523-80 «Управляющей программой называется
совокупность команд на языке программирования, соответствующая
заданному алгоритму функционирования станка по обработке
конкретной заготовки».
Другими словами: УП для станка с ЧПУ представляет собой совокупность элементарных команд, определяющих последовательность и
характер перемещений и действий исполнительных органов станка при
обработке конкретной заготовки. При этом вид и состав элементарных
команд зависит от типа системы ЧПУ станка и языка программирования,
принятого для данной системы.
В настоящее время наибольшее распространение получил универсальный
международный язык программирования ИСО-7бит, который иногда еще
называют CNC-кодом или G и М -кодом. В нашей стране действует также
специальный государственный стандарт ГОСТ 20999-83 «Устройства числового программного управления для металлообрабатывающего оборудования.
Кодирование информации управляющих программ». Современные международные и отечественные требования к управляющим программам станков с
ЧПУ в основном соответствуют друг другу.
Код языка программирования ИСО-7бит относится к буквенно-цифровым кодам, в котором команды управляющей программы записываются в
виде последовательности кадров с использованием соответствующих символов
Кадр программы (фраза) – последовательность слов, расположенных в определенном порядке и несущих информацию об одной
технологической рабочей операции.
Кадр УП может состоять из одного или нескольких слов которые
воспринимаются системой ЧПУ как единое целое и содержат как минимум одну команду. Отличительным признаком кадров как совокупности слов является то, что в них содержится вся геометрическая,
технологическая и вспомогательная информация, необходимая для
выполнения рабочих или подготовительных действий исполнительных органов станка. Рабочее действие в данном случае означает
обработку заготовки за счет однократного перемещения инструмента по
одной элементарной траектории (прямолинейное перемещение,
перемещение по дуге и т. п.), а подготовительное действие – действие исполнительных органов станка для выполнения или завершения
рабочего действия.
Пример записи кадра:
N125 G01 Z-2.7 F30.
Данный кадр состоит из четырех слов: порядкового номера кадра
«N125» и трех слов «G01», «Z-2.7» и «F30», которыми задается прямолинейное перемещение инструмента по оси Z до точки с координатой
Z=–2,7 мм со скоростью подачи F = 30 мм/мин.
Слово программы – последовательность символов, находящихся в определенной связи как единое целое.
Слово представляет собой комбинацию прописной буквы латинского алфавита и некоторого числового значения, в качестве
которого может использоваться либо целое двузначное или трехзначное число, либо десятичная дробь, целая и дробная части которой
могут отделяться как запятой, так и точкой.
Пример записи слов:
G01
Х136.728
Z-4.87
В некоторых случаях в слове кроме буквы и числа могут использоваться и другие текстовые символы; например, между буквой и
числом при необходимости может находиться математический знак
«+» или «–».
Буквенная составляющая слова в теории ЧПУ называется
адресом, потому что она определяет «назначение следующих за
ним данных, содержащихся в этом слове» (ГОСТ 20523-80).
Системы ЧПУ разных производителей имеют свои индивидуальные особенности в отношении буквенных символов, применяемых при
составлении управляющих программ. Они во многом различаются как
по перечню букв, так и по смысловому назначению команд. Стандарт
РФ ГОСТ 20999-83 дает следующие определения значениям
буквенных символов (см. табл).
Буквы, используемые в качестве символов в управляющих программах,
выбраны не случайным образом. Большинство из них представляют собой
начальные буквы соответствующих терминов на английском языке. Например,
в качестве символа величины контурной скорости подачи выбрана буква «F» –
первая буква английского слова feed («подача»), в качестве символа скорости
вращения шпинделя – буква «S» – первая буква английского слова speed
(«скорость»), в качестве символа номера инструмента – буква «T» – первая
буква английского слова tool («инструмент»).
В качестве числовой составляющей слов с буквенными символами G и М
может использоваться только целое двузначное или трехзначное число.
Десятичная дробь в словах с символами G и М использоваться не
может, в отличие от слов с другими буквенными символами.
Если числовая составляющая слова представляет собой десятичную
дробь, в конце дробной части которой содержатся нули, то для упрощения
записи и чтения программ незначащие нули дробной части в большинстве
систем ЧПУ отбрасываются. В УП не принято записывать, например, числа
4,100 или 3,120, а принято писать 4,1 или 3,12.
Приведенные в таблице буквенные символы являются не обязательными, а только рекомендуемыми для языков программирования. Если
символы A, B, C, D, E, P, Q, R, U, V и W не используются для управления
станком по прямому назначению, то они могут применяться для программирования каких-то специальных функций, присущих данной системе ЧПУ.
Текст управляющей программы для станка с ЧПУ есть не
что иное, как сформированная по определенным правилам
совокупность кадров. В общем случае система ЧПУ станка выполняет команды управляющей программы строго в порядке следования кадров, при этом переход к каждому очередному кадру осуществляется только по окончании выполнения предыдущего кадра.
Чтобы отдельные кадры можно было связать в единую систему,
кроме буквенных символов, приведенных в табл. 1, при составлении
управляющих программ для систем ЧПУ применяют и многие другие
текстовые символы. В табл.приведены некоторые дополнительные
символы, которые рекомендованы к применению стандартами РФ
(ГОСТ 20999-83 и ГОСТ 19767-74).
Слова, произвольно расположенные в тексте управляющей
программы, воспринимаются системой ЧПУ всего лишь как некоторый
набор слов и не будут приняты к исполнению. Чтобы данные слова
представляли собой команду, понятную для системы ЧПУ, они должны
быть записаны в кадре управляющей программы в определенном виде
и порядке в соответствии с принятым для конкретной системы ЧПУ
форматом кадра. Формат кадра уточняется в руководстве
эксплуатации на конкретный станок
Международный стандарт содержит следующие общие
рекомендации, относящиеся к формату кадра при ручном
программировании:
1. Слова кадра, так же как и в обычном тексте, должны отделяться
друг от друга интервалами (пробелами). (Необходимо отметить, что
данное требование не всегда соблюдается во многих современных
системах ЧПУ).
2. Каждый кадр начинается словом, обозначающим номер кадра.
Данное слово – «номер кадра» – содержит буквенный символ N и
число, соответствующее порядковому номеру кадра.
3. Каждый кадр рекомендуют заканчивать словом, обозначающим
конец кадра. Рекомендуемый вариант написания данного слова для
большинства импортных систем ЧПУ – LF, для отечественных систем
ЧПУ – ПС. (В современных станках не пишут)
4. Командные и размерные слова, а также слова, задающие
величины технологических параметров обработки деталей, располагаются в тексте кадра между словами «номер кадра» и «конец кадра» в
порядке, определенным производителем системы ЧПУ.
В одних системах ЧПУ он может быть только строго определенным, в других – произвольным.
Для удобства работы международный стандарт рекомендует
следующий порядок расположения слов в кадре: N…, G…, X…, Y…,
Z…, U…, V…, W…, P…, Q…, R…, A…, B…, C…, I…, J…, K…, …, LF.
Если задается скорость подачи по одной определенной оси
координат, то слово, обозначающее скорость подачи, должно
следовать непосредственно за словом, задающим перемещение по
данной оси. Если задается скорость подачи одновременно по двум и
более осям координат, то слово, обозначающее скорость подачи,
должно следовать непосредственно за последним словом, задающим
перемещение по данным осям.
5. Не допускается наличие в одном кадре слов с одинаковыми
буквенными символами. В то же время любое слово может быть
пропущено, если оно не является обязательным в данном кадре.
6. С целью уменьшения объема текста управляющей программы в
каждом кадре записывается только новая информация по отношению к предыдущему кадру, при этом неизменяемая часть информации из предыдущего кадра воспринимается системой ЧПУ по
умолчанию как действующая.
Пример записи и анализа структуры кадра:
N75 G01 Z-10.75 F0.3 S1800 T03 M08 LF
Пример: формат кадра для системы ЧПУ «Размер- 4»
станков типа 2204ВМ1Ф4
N7 – семиразрядный номер кадра, т.е.сколько кадров может содержать УП;
9G2 – двухразрядная подготовительная функция, разбитая на 9 групп;
X+–43Y – семиразрядная функция перемещения по оси Х, последняя цифра
(3) означает количество знаков после запятой, т.е. тысячные доли мм;.
E7 – выдержка времени;
H7 – число повтора программы и т.д.
Число кадров в УП
различных систем ЧПУ
Структура управляющей программы
В соответствии с международными стандартами и ГОСТ 20999-83
структура управляющей программы в общем случае подчиняется
следующим правилам:
1. В тексте управляющей программы должна содержаться геометрическая, технологическая и вспомогательная информация,
которая необходима для проведения заданной обработки. В каждом
кадре программы записывается только та информация, которая
изменяется по отношению к предыдущему кадру. При этом выполнение системой ЧПУ оставшейся неизменной информации прекращается
только после поступления команды на ее отмену (вид этой команды и
способ отмены определяется особенностями конкретной системы
ЧПУ).
2. Каждая управляющая программа начинается символом «начало
программы», подающим системе управления сигнал о начале выполнения программы. Вид символа «начало программы» зависит от
особенностей применяемой системы ЧПУ. Наиболее часто в
отечественных и зарубежных системах ЧПУ используется символ %.
При этом кадр с символом «начало программы» не нумеруется.
Нумерация кадров начинается с последующего кадра.
3. Если управляющей программе необходимо присвоить обозначение, то его располагают в кадре с символом «начало программы»
непосредственно за символом.
4. Если текст управляющей программы необходимо сопроводить
комментарием, например сведениями об особенностях наладки
станка, то его размещают перед символом «начало программы».
5. Управляющая программа должна заканчиваться символом
«конец программы», подающим системе управления сигнал на
прекращение выполнения управляющей программы, останов
шпинделя, приводов подач и выключение охлаждения. Информация,
помещенная в тексте управляющей программы после этого символа
не должна восприниматься системой ЧПУ.
6. Информация, расположенная в тексте управляющей программы
между символами «начало программы» и «конец программы» и
заключенная в круглые скобки не должна приниматься системой
ЧПУ к исполнению. При этом в тексте внутри скобок не должны
применяться символы «начало программы» и «главный кадр».
Пример: распечатка текста управляющей программы с
точки зрения ее структуры
Вопросы для самоконтроля.
1. Какие подготовительные работы необходимо выполнить для
написания УП? Перевести число 42 в двоичный код.
2. Что такое кодирование, длина (значность) кода, вес кода?
Перевести кодовую комбинацию 1 0 11 00 в десятичное число.
3. Какой код называют двоичным и десятичным? Перевести число 56
в двоичный код.
4. Дайте определение управляющей программы. Перевести кодовую
комбинацию 1 1 0 1 0 в десятичное число.
5. Что такое кадр УП? Напишите пример кадра. Перевести число 17 в
двоичный код
6. Что такое слово УП?. Напишите пример слова. Перевести кодовую
комбинацию 1 1 0 1 0 в десятичное число.
7. Какие основные символы (буквы) используют при написании УП и
что они обозначают? Перевести число 71 в двоичный код
8. Что такое текст УП? Перевести кодовую комбинацию 1 0 0 1 1 в
десятичное число.
9. Как обозначают главный кадр в УП, пропуск кадра?
10. Что такое формат кадра?
11. Назовите общие рекомендации, относящиеся к формату кадра в
УП.
12. Какие правила регламентируют структуру УП?
Системы числового программного управления / CNC programming and machining | |||||
Подборка ссылок иллюстрированных из руководств производителей | |||||
51 Примеры простых программы ЧПУ для металлорежущего оборудования Первые шаги программирования Принцип действий Создание новой программы | 52 Пример написания токарной программы ЧПУ Он содержит программирование радиуса и коррекцию радиуса инструмента Представлен чертеж детали | 53 Пример простой ЧПУ программы Siemens Sinumerik 840D для токарной обработке на металлорежущем оборудовании с краткими комментариями | |||
54 Пример создания программы CNC Siemens Sinumerik для вертикально-фрезерного станка Данная ЧПУ программа содержит фрезерование поверхности | 55 Продолжение примера написания управляющей программы для фрезерного станка с ЧПУ по металлу Вид сверху обрабатываемой детали сверху Размеры | 56 Листинг примера программы Sinumerik 840D в руководстве по программированию Программный код и комментарии Предварительный выбор инструмента | 57 Продолжение текста примера управляющей программы для металлорежущего фрезерного станка с ЧПУ Программный код Комментарии к отдельным кадрам | ||
См.также / See also : | |||||
Перевод дюймов в мм / Inches to mm Conversion table | Аналоги сталей / Workpiece material conversion table | ||||
Формулы точения / Turning formulas | Предельные отклонения линейных размеров / Fit tolerance table | ||||
Формулы фрезерования / Milling formulas | Соответствие твердости и прочности Таблица / Hardness equivalent table | ||||
Формулы для расчета сверления / Formulas for drilling | Группы обрабатываемых резанием материалов / Workpiece material groups | ||||
Примеры страниц из каталогов инструмента для металлообработки | |||||
52 Справочник SIEMENS 2012 Программирование систем ЧПУ Sinumerik 840D sl 828D Основы Стр.52 | |||||
Пример написания токарной программы ЧПУ Он содержит программирование радиуса и коррекцию радиуса инструмента Представлен чертеж детали Пример написания токарной программы ЧПУ Он содержит программирование радиуса и коррекцию радиуса инструмента Представлен чертеж детали _ Примечание Для того чтобы программа работала на станке должны быть правильно установлены машинные данные ( изготовитель станка ). Габаритный чертеж детали – 15 18 20 40 57 60 62 70 80 Изображение 3-1 Вид сверху Создание программы ЧПУ 3.4 Примеры программы 3.4.2 Пример 2 Программа ЧПУ для токарной обработки Пример программы 2 предназначен для обработки детали на токарном станке. | |||||
| |||||
| |||||
53 Справочник SIEMENS 2012 Программирование систем ЧПУ Sinumerik 840D sl 828D Основы Стр.53 | |||||
Пример простой ЧПУ программы Siemens Sinumerik 840D для токарной обработке на металлорежущем оборудовании с краткими комментариями Пример простой ЧПУ программы Siemens Sinumerik 840D для токарной обработке на металлорежущем оборудовании с краткими комментариями _ Стартовая точка Смещение нулевой точки Ограничение числа оборотов (G96) Выбор постоянной скорости резания Выбор инструмента и коррекции Подвод инструмента в рабочее положение с коррекцией радиуса инструмента Обтачивание радиуса 10 Обтачивание радиуса 3 Обтачивание радиуса 3 Обтачивание радиуса 3 Отключение коррекции радиуса инструмента и подвод к точке смены инструмента Вызов инструмента и выбор коррекции Выбор постоянной скорости резания Подвод инструмента в рабочее положение с коррекцией радиуса инструмента Обтачивание диаметра 50 Обтачивание радиуса 8 Отвод инструмента и выключение коррекции радиуса инструмента Переход к точке смены инструмента Конец программы Основы 2 3.4 Примеры программы Программный код Комментарий N5 G0 G53 X2 8 0 Z380 D0 N10 TRANS X0 Z2 5 0 N15 LIMS4000 N20 G96 S2 5 0 M3 N25 G9 0 T1 D1 M8 N30 G0 G42 X-1.5 Z1 N35 G1 X0 Z0 F0.25 N40 G3 X16 Z-4 I0 K-10 N45 G1 Z-12 N50 G2 X22 Z-15 CR3 N55 G1 X24 N60 G3 X30 Z-18 I0 K-3 N65 G1 Z-2 0 N70 X35 Z-40 N75 Z-57 N80 G2 X41 Z-60 CR3 N85 G1 X4 6 N90 X52 Z-63 N95 G0 G40 G97 X100 Z50 M9 N100 T2 D2 N105 G96 S210 M3 N110 G0 G42 X50 Z-60 M8 N115 G1 Z-7 0 F0.12 N120 G2 X5 0 Z-8 0 I6.245 K-5 N125 G0 G40 X100 Z50 M9 N130 G0 G53 X280 Z380 D0 M5 N135 M30 Создание программы ЧПУ Пример программы | |||||
| |||||
| |||||
56 Справочник SIEMENS 2012 Программирование систем ЧПУ Sinumerik 840D sl 828D Основы Стр.56 | |||||
Листинг примера программы Sinumerik 840D в руководстве по программированию Программный код и комментарии Предварительный выбор инструмента Листинг примера программы Sinumerik 840D в руководстве по программированию Программный код и комментарии Предварительный выбор инструмента _ с именем PF60. Установить инструмент в шпиндель. Число оборотов направление вращения охлаждение вкл. Первичные установки геометрии и подвод к стартовой точке. Ось Z на безопасное расстояние. Поведение при активной G41 G42. Фреза на глубине контакта с подачей3 0 0 0мм/мин. Включение коррекции радиуса фрезы. Движение по контуру с подачей12 0 0мм/мин. Выключение коррекции радиуса фрезы. Подъем фрезы шпиндель + охлаждение выкл. Предварительный выбор инструмента с именем SF10. Установить инструмент в шпиндель. Число оборотов направление вращения охлаждение вкл. Первичные установки геометрии и подвод к стартовой точке. Вызов цикла фрезерования кармана. Подъем фрезы шпиндель + охлаждение выкл. Вызвать центровое сверло 6 мм. Точный останов G60 из-за N160 M6 Пример программы 3 Программный код Комментарий N10 T”PF60″ N20 M6 N30 S2000 M3 M8 N40 G9 0 G64 G54 G17 G0 X-72 Y-72 N50 G0 Z2 N6 0 G4 5 0 CFTCP N70 G1 Z-10 F3000 N80 G1 G41 X-4 0 N90 G1 X-4 0 Y3 0 RND10 F1200 N100 G1 X4 0 Y3 0 CHR10 N110 G1 X4 0 Y-3 0 N120 G1 X-41 Y-30 N130 G1 G4 0 Y-72 F3000 N140 G0 Z200 M5 M9 N150 T”SF10″ N170 S2800 M3 M8 N180 G9 0 G64 G54 G17 G0 X0 Y0 N190 G0 Z2 N2 0 0 POCKET4(201-515000008001300021520.5) N210 G0 Z2 0 0 M5 M9 N220 T”ZB6″ N230 M6 N240 S5000 M3 M8 N250 G9 0 G6 0 G54 G17 X25 Y0 Создание программы ЧПУ Примеры программы | |||||
Пример иллюстрации инструмента из промышленного каталога (из подборки фото инструментов для металлообработки / Metal cutting tools images) | |||||
225 Каталог KORLOY 2013 Металлорежущий инструмент и инструментальная оснастка Стр. | |||||
Иллюстрация современного токарного инструмента со сменными режущими пластинами для наружного профильного точения на металлорежущих станках Фото из каталога Иллюстрация современного токарного инструмента со сменными режущими пластинами для наружного профильного точения на металлорежущих станках Фото из каталога _ Токарная стандартная ISO державка Korloy с механическим креплением сменной режущей твердосплавной пластины повышенной жесткости Металлорежущий инструмент южнокорейского производителя крупным планом | |||||
Системы числового программного управления / CNC programming and machining | |||||
Доработки Creo для разработки управляющих программ для станков с ЧПУ – ПТС
Автоматическое получение карт наладки по ГОСТ
- Автоматическое получение карт наладки по ГОСТ 3.1404-86. Карта содержит описание переходов, режущего инструмента, режимы резания и основное время обработки.
- Создание карты наладки по ГОСТ 3.1105-84. Карта содержит вид детали, способ крепления, ноль программы.
- Возможно создание чертежа инструмента и автоматическое создание спецификации:
Карта наладки по операциям
Автоматическое получение карт наладки с отображением эскиза детали и списком и эскизами режущего инструмента. Все данные для карты хранятся в файле обработки. Для каждого инструмента можно выбрать эскиз из библиотеки символов, либо создать его самому (Рисунок 1, Рисунок 2). Карту наладки можно редактировать стандартными средствами создания чертежа.
Минимальные требования: Creo 3.0
Рисунок 1 – Эскиз детали
Рисунок 2 – Список инструментов
Карта наладки по переходам
Автоматическое получение карт для каждого токарного перехода с генерацией эскиза, траектории инструмента, эскиза инструмента и параметрами обработки. Карта представляет собой обычный чертеж CreoParametric, который можно редактировать стандартными средствами Creo (Рисунок 3).
Минимальные требования: Creo 3.0
Рисунок 3 – Карта наладки токарного перехода
Также автоматически генерируется сводная карта об использовании инструмента. В зависимости от стойкости пластины и времени обработки автоматически рассчитывается количество пластин, необходимых для обработки детали.
Утилита стойкости
Позволяет автоматически разбивать ЧПУ переходы на несколько частей. В конце каждой части осуществляется отвод инструмента по алгоритму, который выбрал пользователь. Для удобства задания параметров отвода и подвода инструмента разработал графический интерфейс (Рисунок 4).
Рисунок 4 – Утилита стойкости
Разбивка программы осуществляется в процессе вывода управляющей программы. Результат разбивки можно посмотреть во встроенном симуляторе.
Минимальные требования: Creo 2.0
Дополнительные инструкции и методические указания по разработке управляющих программ
CreoParametric содержит встроенную помощь на русском языке Однако нашей компанией разработаны дополнительные материалы, которые позволят быстрее освоить работу с системой.
- Базовый курс фрезерной 3-х координатной обработки
- Расширенный курс фрезерной 5-и координатной обработки
- Курс токарной обработки
- Курс токарно-фрезерной обработки
Разработаны методические указания по настройке модуля ЧПУ CreoParametric и приведены рекомендации по обработке сложных поверхностей (Рисунок 5).
Рисунок 5 – Обработка тонкой стенки
Расширенный перевод пользовательского интерфейса
Разработан дополнительный перевод ЧПУ параметров для более удобного использования системы (Рисунок 6).
Рисунок 6 – Параметры обработки
Команда для отображения только что созданной Управляющей программы
Для удобства работы создана горячая клавиша для отображения только что созданной Управляющей программы. Для удобства, программы отсортированы по времени создания. Таким образом для отображения последней программы необходимо нажать только кнопку ОК (Рисунок 7).
Рисунок 7. Отображение управляющей программы
Узнать подробнее
Типы программного обеспечения и систем управления станками с ЧПУ
В этой статье рассматриваются типы доступного программного обеспечения для управления станками с ЧПУ. Обработка с ЧПУ – это управляемый компьютером процесс формования металла в готовые компоненты. ЧПУ на самом деле означает «компьютерное числовое управление» и имеет уместное название – компьютер управляет режущим инструментом на основе ряда числовых кодов, которые можно изменять с помощью компьютерного программного обеспечения. Станок с ЧПУ, управляемый с помощью управляющего программного обеспечения ЧПУ
Изображение предоставлено: Shutterstock / Pixel B
Обработка с ЧПУ изменила отрасль производства металлов, упростив производство трехмерных структур и снизив уровень участия человека в обработке металлов.С момента внедрения обработки с ЧПУ качество и стабильность улучшились.
Типы программного обеспечения для управления станком с ЧПУ
Когда несколько станков с ЧПУ производят деталь, требующую нескольких операций, дизайнеры называют эту группу станков «ячейкой». Сегодня станки с ЧПУ – это, как правило, автоматы, поскольку они могут работать без помощи человека. Пакеты программного обеспечения, которые управляют этими станками с ЧПУ, представляют собой программы CAM (автоматизированное производство).
Происхождение программного обеспечения для обработки с ЧПУ
Обработка с ЧПУ (числовым управлением) предшествовала обработке с ЧПУ – эти более ранние станки отличались неизменными, фиксированными жестко запрограммированными рабочими параметрами. Станки с ЧПУ управлялись «G-кодами», которые представляют собой приложения с перфолентой, загружаемые в компьютер станка.
Программное обеспечение CAM
Специальные файлы, созданные программным обеспечением CAM, управляют современными станками с ЧПУ. Программное обеспечение CAM сокращает время производства, устраняя необходимость в создании бумажного чертежа желаемого производимого компонента.
Благодаря программному обеспечению CAM, управляющему станком с ЧПУ, станок может производить большое количество деталей без участия человека. Станки с ЧПУ, управляемые программным обеспечением CAM, также оснащены лазерами, способными обнаруживать даже незначительные дефекты в готовом продукте. Когда лазер обнаруживает проблему, компьютер автоматически звонит на мобильный телефон оператора и уведомляет его о ситуации.
Программное обеспечение САПР
Программное обеспечениеCAD (Computer-Aided Design) – это программа, используемая для разработки продукта, который в конечном итоге будет производить программа CAM.В большинстве современных программ САПР используются базовые системы 2D-векторных черчений или средства трехмерного твердотельного и поверхностного моделирования.
Программное обеспечениеCAD предоставляет дизайнерам свободу создавать свои изделия на экране компьютера и сохранять их для последующего редактирования и печати, что сокращает время проектирования и производства. Другие возможности программного обеспечения САПР включают:
- 3D параметрическое моделирование на основе элементов
- Твердое моделирование
- Моделирование поверхностей произвольной формы
- Повторное использование конструктивных элементов
- Создание геометрии каркаса
- Автоматизированное проектирование узлов
- Расчет массовых свойств узлов и деталей
- Вспомогательная визуализация с затенением и вращением
- Двунаправленное параметрическое объединение
- Прокладка кабеля
- Упаковка электрических компонентов
- Включение программного кода в модель для связи и управления желаемыми атрибутами модели
- Программируемая оптимизация конструкции
- Сложные процедуры визуального анализа
- Проверка конструкции на соответствие проектным нормам и спецификациям
- Автоматическое создание стандартных элементов дизайна
- Моделирование конструкций без создания физического прототипа
- Ведение библиотек деталей и узлов
- Выдача проектных данных непосредственно на производственные предприятия
- Вывод непосредственно на машину для быстрого прототипирования или быстрого производства промышленных прототипов
Программное обеспечение CAE
ИнструментыCAE (Computer-Aided Engineering) помогают инженерам в анализе, проектировании, моделировании, планировании, производстве, диагностике и ремонте операций механической обработки.Инструменты CAE управляют задачами в три этапа: предварительная обработка, анализ и постобработка. Области применения приложений CAE включают:
Расчет напряжений компонентов и узлов с использованием анализа методом конечных элементов
- Тепловой анализ и анализ потока жидкости
- Кинематика
- Моделирование механических событий (MES)
- Анализ для моделирования процесса для таких операций, как литье, штамповка и формование
- Оптимизация процесса или продукта
Программное обеспечение CAD / CAE / CAM
Некоторые компании-разработчики программного обеспечения объединили все три аспекта управляющих приложений с ЧПУ в один управляемый программный пакет, обозначенный как CAD / CAE / CAM.Эти программы обрабатывают весь процесс изготовления: исходный дизайн, созданный в САПР, анализ, выполняемый CAE, и окончательное производство, управляемое программным обеспечением CAM.
Другие изделия с ЧПУ
Прочие “виды” изделий
Больше от производства и изготовления на заказ
Что такое программа управления ЧПУ Mach 3
Что такое программа управления ЧПУ Mach 3?
Программное обеспечение для управления ЧПУMach 3 – это платформа, которая превращает большинство ПК с ОС Windows в контроллер станка с ЧПУ, который управляет движениями двигателей и генераторов.
Посредством процесса импорта, называемого LazyCam, управляющее программное обеспечение Mach 3 CNC обрабатывает язык программирования ЧПУ, называемый геометрическим кодом (G-code), который сообщает станку с ЧПУ, какой тип действия следует выполнять.
Третья версия программного обеспечения, Mach 3, считается самой удобной и надежной – от проектов DIY до промышленной обработки.
Область мехатроники направлена на создание проектного решения для создания более интеллектуальных и оптимизированных системных процессов для сложных или трудоемких задач.
Каковы некоторые особенности управляющего программного обеспечения Mach 3 с ЧПУ?
- Позволяет импортировать файлы формата обмена чертежами (DXF) непосредственно на ПК.
- Растровое изображение (BMP) и JPEG, формат для сжатия файлов изображений, можно быстро преобразовать в код .
- Может контролировать скорость шпинделя для более точных резов
- Полный видеодисплей и возможности сенсорного экрана
- Полностью настраиваемый пользовательский интерфейс
- Возможность расширения возможностей Mach 3 с помощью «мастеров» или мини-программ, позволяющих пользователям выполнять функции без предварительно написанного файла G-кода.
- Удаленное включение и выключение оборудования путем одновременного управления несколькими реле
- Пользователи могут писать разные инструкции с помощью M-кодов и макросов через Microsoft Visual Basic Scripting Edition или VBScript и
- С 6-осевым вводом-выводом – нет необходимости в дорогой панели контроллера
Какие машины могут управлять Mach 3?
Управляет Mach 3:
- Зуборезки
- Лазеры
- Токарные станки
- Мельницы Плазма
- и
- Маршрутизаторы
Хотите узнать больше о станках с ЧПУ? Ознакомьтесь с нашими программами ЧПУ!
Мы готовы, когда вы будете.
Свяжитесь с нами сегодня!
Запросить дополнительную информациюGoodwin University никогда не будет продавать вашу личную информацию третьим лицам. Отправляя свою контактную информацию, вы разрешаете Goodwin University связываться с вами по телефону, электронной почте, почте и текстовым сообщениям.
Решения и средства управления с ЧПУ | FlashCut с ЧПУ
Объявление: Наши офисы будут закрыты со 2 по 5 июля. С Днем независимости! ×
FlashCut предлагает надежное, мощное, интуитивно понятное и интегрированное программное обеспечение CAD / CAM / CNC и средства управления для любого приложения резки с ЧПУ.Это все, что мы делаем, и никто не делает это лучше. Наши пакеты включают программное обеспечение, электронику, двигатели и кабели для реального старта plug-n-play.
Какое у вас приложение? Простое, но мощное Интегрированное программное обеспечениеCAD / CAM / CNC
Плавно переходите от чертежа к траектории инструмента к резке в этой универсальной интегрированной программе на базе Windows-
.
- Интуитивно понятная настройка для любого типа механики станка и приводной техники.
- Интуитивно понятный пользовательский интерфейс, упрощающий рисование и редактирование любых 2D- и 2.5D-форм.
- FlashCut CAM мгновенно создает точные траектории инструмента с помощью кончика пальца для резки точных деталей.
- FlashCut 2D и 3D CAM генерирует идеальные траектории движения инструмента для плазменной резки, кислородной гидроабразивной резки, лазера или маркировки.
Существует множество разновидностей FlashCut CAD / CAM в соответствии с вашими уникальными потребностями, бюджетом или областью применения.
Партнерские отношения с ведущими производителями оборудования в отраслиНаша команда инженеров работает напрямую с нашими OEM-партнерами для разработки мощных и экономичных решений с ЧПУ, адаптированных к конкретному применению.Эти партнерские отношения обеспечивают передовые достижения, которые помогают позиционировать наших производителей оригинального оборудования как лидеров в своей отрасли.
Rock Solid, Адаптивная поддержкаFlashCut CNC предлагает самую оперативную и компетентную службу поддержки клиентов в отрасли. Мы тщательно разработали наше программное обеспечение, элементы управления и вспомогательную документацию, чтобы сделать их максимально удобными и интуитивно понятными.Мы всегда готовы удовлетворить ваши потребности по телефону, электронной почте или в режиме онлайн-конференции.
MicroSystems World CNC – Контроллер ЧПУ на базе ПК – Программное обеспечение ЧПУ WinCNC – Программное обеспечение Контроллера ЧПУ – Управление движением ЧПУ
Описание товараWinCNC – это программный и аппаратный пакет, который позволяет управлять станком с ЧПУ с помощью ПК с ОС Windows. Аппаратное обеспечение состоит из PCI карта и дочерняя плата, которые устанавливаются внутри ПК.Оба элемента необходимы для запуска WinCNC. Карта PCI является 64-битной. высокоскоростное цифровое устройство ввода / вывода и дочерняя плата представляют собой небольшую печатную плату, которая добавляет высокоскоростной микропроцессор для буферизации импульсов. Буфер высокоскоростных импульсов позволяет WinCNC выводить импульсы со 100% точностью при максимальной частоте и увеличивает его способность работать вместе с другими приложениями и процессами Windows без потери шагов. Компоненты станков с ЧПУ, такие как шаговые / сервоприводы, концевые выключатели или выходные реле подключаются к ПК через 37-контактные (стандартные) или 25-контактные (дополнительные) разъемы на задней панели ПК.Выходы WinCNC ТТЛ-сигналы шага и направления для моторных приводов и включают дополнительные входные и выходные контакты ТТЛ для вспомогательных функций для интерфейса ввода-вывода от станок с ЧПУ.
Чтобы упростить процесс электромонтажа и подключения вашего станка с ЧПУ к ПК без необходимости пайки или изготовления нестандартных кабелей, Пожалуйста, рассмотрите одну из наших интерфейсных плат WinCNC IO на базе винтовых клемм. Эти интерфейсные платы обеспечивают встроенную Питание 5 В постоянного тока, выходные реле, изоляция входа и легкий доступ к сигналам шага / направления для управления шаговыми или серводвигателями.
WinCNC предоставляет настраиваемый простой в использовании интерфейс для любых операций. Станком с ЧПУ можно полностью управлять с помощью мыши и клавиатуры ПК. Настройка кнопок позволяет управлять простым наведением и щелчком без необходимости вводить имена файлов или команды GCode. Размер кнопки и панели инструментов может быть увеличенным для использования на мониторе с сенсорным экраном. Дистанционное управление можно добавить с помощью одной из наших проводных или беспроводных портативных клавиатур.
КонтроллерWinCNC устанавливает стандарт управления движением на ПК.Невероятно плавное ускорение и движение машины – результат наших продвинутые алгоритмы. WinCNC использует большой упреждающий буфер, считывая вперед тысячи строк при запуске файлов GCode. Забегая вперед позволяет WinCNC для ускорения или замедления через множество небольших дуговых или линейных сегментов, обеспечивая более плавное движение и меньшее время выполнения. Каждый ход буферизируется и обрабатывается с использованием запатентованных подпрограмм сопоставления векторов в реальном времени. В результате ваша машина работает максимально плавно и эффективно. по возможности, снижая скорость только при необходимости и производя детали высокого качества.Регулируемая скорость, ускорение и сглаживание позволяют настроить WinCNC для максимально быстрой и бесперебойной работы на станках с ЧПУ любого размера и типа.
Конфигурации WinCNCПлазма Лазерный Маршрутизатор
Плазменная резка с ЧПУ становится все более популярной в последние годы. В WinCNC было добавлено множество новых функций и улучшений для поддержки требований плазменной резки и автоматического управления высотой резака.
Узнать больше
WinCNC уже много лет используется на лазерных станках многими довольными клиентами.WinCNC может использоваться на любом шаговом или серво лазере, а также с лазерами Synrad, Coherent и другими типами. WinCNC поддерживает гравировку растровых изображений и векторную гравировку и резку.
Узнать больше
WinCNC уже много лет используется на фрезерных станках с ЧПУ. Его использовали тысячи клиентов по всему миру. WinCNC широко используется с Cut 2D / 3D, VCarve Pro, Aspire, EnRoute, BobCAD, VisualMill и многими другими пакетами CAD / CAM.
Узнать больше
Совместимость и производительностьWinCNC Controller – это программный и аппаратный пакет для управления движением станка с ЧПУ, совместимый с Windows 7, 8 и 10 – 32- и 64-разрядные версии. Устаревшие версии WinCNC были совместимы с Windows 95, 98, ME, 2000 и XP. WinCNC требует включенного порта USB и свободного слота PCI или PCIe. WinCNC может одновременно управлять до 6 осями движения на частоте до 100 кГц. при этом оставаясь невероятно плавным и никогда не пропуская ни одного шага.
ПРИМЕЧАНИЕ. Для Windows 8 и 10 требуется WinCNC версии 2.6 или 3.0. Убедитесь, что ваша лицензия на программное обеспечение и оборудование способно поддерживать WinCNC версии 2.6 или 3.0 до обновления вашей ОС Windows.
ПРИМЕЧАНИЕ. WinCNC 3.0 требует другой дочерней платы, чем 2.6 или предыдущие версии. Если вы используете 2.6 или более старую версию WinCNC, вам необходимо обновить программное обеспечение и приобрести новую дочернюю плату, чтобы запустить WinCNC 3.0
Возможности программного обеспеченияЛюбая шаговая, микрошаговая или сервосистема с входами шага и направления может быть сопряжена с помощью прилагаемой карты PCI и дочерней платы микропроцессора. или одну из нескольких доступных плат расширения ввода-вывода PCI. В дополнение к перемещению оси, до 128 дополнительных выходов и 128 отдельных входы могут быть определены. Интуитивно понятный пользовательский интерфейс прост в освоении и удобен в использовании. Все функции, которые вам нужны и которые вы ожидаете, легко доступны доступны через стандартные отраслевые G-коды.Простые нажатия клавиш позволяют запускать, приостанавливать, перезапускать, перемещаться и быстро перемещаться по любой оси без навигации по нескольким экранам и окнам. При необходимости программы могут запускаться из любой строки. Запрограммированные скорости подачи можно регулировать от 1%. до 200% без остановки движения машины.
Возможности настройки программного обеспечения КонтроллерWinCNC работает на станках с фрезерными станками, сверлами, резьбонарезными головками, вращающимися пилами и ножами, плазменными резаками, газовыми резаками, гвоздезабивателями, шлифовальными машинами, струи воды и лазеры для обработки различных материалов, от древесины твердых пород, композитов и пластмасс до металлов, стекла и камня.Все основные CAM пакеты могут создавать файлы G-кода, готовые для работы на WinCNC Controller. Окно WinCNC легко настраивается, с несколькими типами компонентов. и кнопки, которые можно добавлять и настраивать. Настройка макроса позволяет создавать пользовательские коды G / L / M, связанные с редактируемыми подпрограммами, сохранять значения и выполнение основных математических операций, даже переопределение или отключение уже определенных кодов G / L / M.
ТехподдержкаЛюбая система управления движением хороша ровно настолько, насколько доступна поддержка, когда она вам нужна.Наши техники ежедневно используют нашу продукцию для производства. и прототипирование. Это означает, что мы можем говорить на вашем языке, когда дело касается оказания необходимой поддержки по телефону, через Интернет, или на месте по всему миру. В розничные пакеты программного обеспечения WinCNC входит 30 дней бесплатной технической поддержки по телефону / Интернету / электронной почте. Технические специалисты службы поддержки доступны по телефону. или по электронной почте с понедельника по пятницу с 9:00 до 17:00 по восточному стандартному времени, кроме праздников. Дополнительная техническая поддержка может быть приобретена почасово для существующих Лицензии на программное обеспечение WinCNC.Клиенты должны иметь доступ в Интернет и иметь возможность отправлять / получать файлы по электронной почте, чтобы получать техническую поддержку.
Новомодные решения Mach4
Mach4 превращает обычный компьютер в контроллер станка с ЧПУ. Он очень богат функциями и представляет большую ценность для тех, кому нужен пакет управления ЧПУ.
Mach4 работает на большинстве ПК с Windows для управления движением двигателей (шаговых и сервоприводов) путем обработки G-кода.
Обладая множеством расширенных функций, это наиболее интуитивно понятное программное обеспечение для управления ЧПУ.Mach4 настраивается и используется во многих приложениях с различными типами оборудования.
Приобрести лицензию Скачать Mach4- Контроль скорости шпинделя
- Управление несколькими реле
- Ручная генерация импульсов
- Видеодисплей станка
- Возможность сенсорного экрана
- Право на полноэкранный режим
- Преобразует стандартный ПК в полнофункциональный 6-осевой контроллер ЧПУ
- Позволяет напрямую импортировать файлы DXF, BMP, JPG и HPGL через LazyCam
- Визуальный дисплей Gcode
- Генерирует Gcode через LazyCam или Wizards
- Полностью настраиваемый интерфейс
- Настраиваемые M-коды и макросы с использованием VBscript
- Станки токарные
- Мельницы
- Маршрутизаторы
- Лазеры
- Плазма
- Граверы
- Зуборезное
Мастера
Мастера– это «мини-программы», расширяющие возможности Mach4.Мастера могут быть написаны кем угодно и предназначены для того, чтобы пользователи могли быстро выполнять рутинные или удобные операции без необходимости иметь предварительно написанный файл G-кода.
В состав Mach4 входит несколько бесплатных мастеров, добавленных пользователями. Эти ярлыки не следует путать с надстройкой для Mill или новым программным обеспечением Mill Wizard, которые представляют собой более продвинутые пакеты мастеров со встроенными операциями. Некоторые типичные операции мастера:
- Зуборезное
- Оцифровка
- отверстия
- Прорези и шпоночные пазы
- Гравировка текста
- Многие стандартные формы
- Наплавка
- МНОГОЕ БОЛЬШЕ
Без лицензии Mach4 будет работать в демонстрационном режиме.
В демонстрационном режиме программа имеет следующие ограничения:
- Mill & Plasma: ограничение gcode 500 строк (ограничение 10 000 000 после лицензирования)
- Turn: ограничение gcode 50 строк (лимит 10 000 000 после лицензирования)
- Частота ядра заблокирована на уровне 25 кГц (применимо только при использовании драйвера параллельного порта)
- Отключить функцию следующей строки
- Функция «Запуск отсюда» отключена
- Turn: Заправка резьбы отключена
- Плазма: функции THC отключены
Некоммерческим пользователям (также известным как любители) разрешается использовать одну лицензию Mach на столько машин, сколько им требуется.Для коммерческих пользователей (всех, кто использует программное обеспечение для получения прибыли) нам требуется отдельная покупка лицензии для каждой машины. Mach2, Mach3 и Mach4 могут использоваться на одном компьютере, но только одна версия каждого из них будет сосуществовать на одном компьютере.
Лицензия требуется только для компьютера, на котором фактически работает машина. Если компьютер, не подключенный к машине, используется для тестирования кода, используйте Mach4 в режиме моделирования – это снимет ограничение в 500 строк. Доступ к режиму моделирования можно получить, удалив (или не установив) драйвер параллельного порта.Дополнения для Mill будут работать только с лицензионной копией Mach4, поскольку это программное обеспечение является дополнением, а не отдельным продуктом.
Жесткие копии (диск) загружаемого содержимого доступны напрямую у третьих лиц.
Требования при использовании параллельного порта для управления станком:
- Настольный ПК как минимум с одним параллельным портом
- (Ноутбуки не поддерживаются )
- 32-битная версия Windows 2000, Windows XP, Windows Vista или Windows 7
- (64-битные версии не будут работать с )
- 1 ГГц процессор
- 512 МБ ОЗУ
- Неинтегрированная видеокарта с 32 МБ ОЗУ
- (для больших файлов G-кода, особенно 3D-файлов, потребуется видеокарта с 512 МБ ОЗУ или выше)
Требования при использовании внешнего устройства движения для управления станком:
- Соответствующий внешний контроллер движения
- (параметры можно найти на странице плагинов)
- Настольный компьютер или ноутбук с Windows 2000, Windows XP, Windows Vista, Windows 7, Windows 8 и Windows 10.
- 1 ГГц процессор
- 512 МБ ОЗУ
- Видеокарта с 32 МБ ОЗУ
- (для больших файлов G-кода, особенно 3D-файлов, потребуется видеокарта с 512 МБ ОЗУ или выше)
Шаг 1
Резервное копирование на рабочий стол или, что еще лучше, на USB-накопитель:
- XML (профиль) – в нем хранятся ваши настройки для Mach4. Если вы потеряете его, вам нужно будет заново настроить порты и контакты, настройку двигателя и т. Д.
- Наборы экранов
- Макросы / Мозги
Шаг 2
Загрузите текущую версию Mach4 со страницы «Загрузки и обновления».
папкаШаг 3
Установите скачанную версию; разрешите путь установки по умолчанию туда, где установлен Mach4.
ПРЕДУПРЕЖДЕНИЕ: Если вы не сделаете резервную копию файлов на шаге 1, вы потеряете ВСЕ настройки и конфигурации.
Прикладные науки | Бесплатный полнотекстовый | Интеллектуальный фрезерный станок с ЧПУ, совместимый со стандартом STEP-NC, с контроллером открытой архитектуры
1. Введение
Станки с числовым программным управлением (ЧПУ) играют жизненно важную роль в производстве продукции. Традиционно станки с ЧПУ программировались в соответствии со стандартом ISO6983 [1] на протяжении последних полувека или около того. Этот стандарт определяет язык программирования низкого уровня, который описывает только путь расположения резака и инструкции переключения [2].Ограниченный набор информации, записанный с помощью кодов G и M, отправляется на станок с ЧПУ для выполнения. Станок с ЧПУ просто действует как машина-исполнитель, не имея интеллекта. Следовательно, из-за недоступности информации о заготовке, режущем инструменте, особенностях обработки и параметрах обработки, изменения на уровне цеха не могут быть приняты, за исключением регулировки скорости подачи и скорости шпинделя. Эти данные не передаются в контроллер станка, хотя они доступны в программном обеспечении CAM.Поскольку ISO 6983 охватывает только ограниченный набор возможностей, поставщики станков с ЧПУ расширили коды G и M, чтобы определить свои собственные специфические функции, такие как настраиваемые фиксированные циклы. Это требует определенного постпроцессора для каждого контроллера ЧПУ из-за специфичных для производителя кодов G и M. Поэтому взаимозаменяемость программ обработки деталей ЧПУ между различными контроллерами ограничена [3]. Для решения этих проблем недавно был введен новый стандарт ISO 14649 [4], широко известный как STEP-NC.Этот новый стандарт обеспечивает модель данных для нового поколения интеллектуальных станков с ЧПУ [3]. Основная цель STEP-NC – объединить данные, доступные на этапе проектирования, с помощью CAM и ЧПУ. В новый стандарт включены специальные положения для предотвращения потери данных во время цепочки CAD-CAM-CNC [2]. Кроме того, стандарт ISO 14649 вводит новый формат данных для передачи информации, доступной на этапе CAD / CAM, такой как обрабатываемые детали, данные детали, данные режущего инструмента, технологические данные, операции и их последовательность и многое другое, в станок с ЧПУ.Соответственно, траектории движения инструмента могут быть сгенерированы самим контроллером ЧПУ, поскольку вся информация для создания местоположения резцов доступна на станке с ЧПУ. Поскольку информация о станках не используется в ISO 14649, требование постпроцессора устранено [5]. Практически все коммерческие контроллеры станков с ЧПУ в настоящее время были разработаны на основе архитектур конкретных производителей. Следовательно, для совместимости аппаратные и программные модули расширения должны быть приобретены у одного и того же поставщика. Доступность этих модулей ограничена и определяется поставщиком, а не заказчиком.Соответственно, эти коммерческие контроллеры не могут быть расширены до контроллеров, совместимых со STEP-NC. Таким образом, технология разработки контроллера открытой архитектуры (OAC) используется для разработки контроллеров, совместимых с STEP-NC [6,7,8]. OAC определяется как открытая система, которая предоставляет возможности, позволяющие правильно реализованным приложениям работать на различных платформах от разных поставщиков, взаимодействовать с другими системными приложениями и обеспечивать согласованный стиль взаимодействия с пользователем [9]. Кроме того, системы OAC не зависят от патентованных производителями, и, таким образом, заказчик предоставляет возможность гибкости встраивания в систему необходимого дополнительного оборудования и программного обеспечения от любого разработчика.Это позволяет интегрировать прикладные программы, алгоритмы управления и аппаратные аксессуары, разработанные различными производителями [10]. В целом технология OAC – это нейтральный интерфейс системы управления поставщиком, который обеспечивает взаимодействие, совместимость, переносимость и масштабируемость. По мере того, как персональные компьютеры (ПК) набирали популярность, она стала лучшим выбором в отрасли в качестве аппаратной платформы для систем ЧПУ с открытой архитектурой. Высокое соотношение производительности и цены ПК – одно из основных преимуществ использования ПК в системах ЧПУ с открытой архитектурой [11].Некоторые из разработок OAC на базе ПК, описанные в литературе, описаны ниже. OAC на базе ПК для существующего 3-осевого фрезерного станка с ЧПУ Denford Novamill ATC был разработан на программной платформе LabVIEW Elias et al. Два интерпретатора были разработаны для чтения файлов формата ISO 14649 и ISO 6983 и преобразования их в общие траектории инструмента [12]. Юсоф и Латиф внесли дальнейшие улучшения в вышеупомянутый контроллер, представив аппаратную платформу на базе ПК с картой управления движением и программную платформу с использованием Windows, JAVA / Visual Studio, разработчика ST и LabVIEW [13].Еще одно улучшение было сделано Latif et al. за счет внедрения 3D-моделирования и управления движением станка с помощью устройства смены сверл. Интеграция программного и аппаратного обеспечения была выполнена в среде LabVIEW [14]. Другой фрезерный станок для обработки жалоб STEP-NC на базе ПК был разработан совместно с OAC Ли и др. В этом аппарате используется STEP-NC в формате XML. Контроллер способен изменять данный файл STEP-NC в формате XML на ранних стадиях за счет своего ограниченного интеллекта и отправляет его обратно контроллеру для обработки [15].Calabrese et al. использовала встроенный микроконтроллер для разработки контроллера ЧПУ, совместимого со стандартом STEP-NC. Это было реализовано на станке с ЧПУ для плазменной резки с двумя степенями свободы с использованием микропроцессора Rabbit RCM3700 [16]. В приведенном выше кратком обзоре освещены фрезерные станки с ЧПУ типа OAC STEP-NC, разработанные различными исследователями. Для большинства этих разработок требуются дорогие карты управления движением и карты сбора данных [17]. Некоторые из них зависят от коммерчески доступного стороннего программного обеспечения, такого как LabVIEW, MATLAB [11,13,18] и т. Д.Мониторинг состояния машины и улучшение может быть достигнуто путем установки датчиков на станке с ЧПУ. Нараян и др. исследовали возможность использования акселерометра, датчика тока и детектора звука для сбора данных с станка с ЧПУ [19]. Дауни и др. использовал промышленный станок с ЧПУ для исследования износа режущего инструмента с помощью трех сенсорных технологий; сила, акустическая эмиссия и вибрация [20]. Система мониторинга состояния инструмента на основе нескольких датчиков была разработана Zhang et al.Данные о вибрации, силе резания и мощности были собраны с параметрами резания для контроля состояния инструмента и оценки срока службы инструмента [21]. Миколайчик сообщил об усовершенствовании существующего фрезерного станка на станке с числовым программным управлением с помощью разработанного программного обеспечения под названием PCMill [22]. В последнее десятилетие одноплатные компьютеры (SBC) стали популярными из-за их низкого энергопотребления, меньшего размера, низкой стоимости, способности взаимодействовать с внешним миром с помощью доступного средства ввода-вывода общего назначения (GPIO), способности работать в бесплатных операционных системах и иметь возможность беспроводного подключения.Почти все эти SBC используют различные разновидности операционных систем Linux с открытым исходным кодом. Из числа доступных на рынке SBC SBC на базе ARM становятся все более продвинутыми и сильными [23]. В последнее время Raspberry Pi считался одним из самых популярных SBC в области автоматизации и деятельности, связанной с Интернетом вещей. Григорьев провел расследование перехода от системы управления ЧПУ на базе ПК к системе управления Raspberry Pi на базе ARM. и другие. В рамках этого исследования контроллер на базе Raspberry pi SBC был разработан для существующего многозадачного токарно-фрезерного станка.Авторы пришли к выводу, что вычислительные ресурсы SBC на базе ARM достаточны для выполнения основных задач многоканальных многоосных станков с ЧПУ [24].Существует два популярных бесплатных программного обеспечения для управления станками с ЧПУ, 3D-принтерами, роботизированными манипуляторами и т. Д. Первое, LinuxCNC, работает в дистрибутивах Linux, Ubuntu и Debian. LinuxCNC имеет интерпретатор для ISO 6983, человеко-машинного интерфейса (HMI) и системы планирования движения в реальном времени. Второй – программа grbl, которая также облегчает интерпретацию данных стандарта ISO 6983.Программное обеспечение grbl может быть реализовано в микроконтроллере Arduino Uno для управления станком с ЧПУ. Кроссплатформенное приложение на основе Java под названием Universal Gcode Sender или аналогичное приложение может использоваться в качестве интерфейса между микроконтроллером и компьютером. Оба эти приложения могут интерпретировать только стандартные данные ISO 6983 и, следовательно, не соответствуют стандартам STEP-NC.
Вагнер К. продемонстрировал деревообрабатывающий маршрутизатор, работающий на Raspberry Pi с программным обеспечением Linux CNC [25]. Winegarner T. использовал Raspberry Pi и Universal Gcode Sender для управления существующим маршрутизатором [26].Обе эти реализации являются просто заменой ПК с Raspberry Pi SBC. Другая реализация маршрутизатора с ЧПУ была сделана Баллардом Р. на Raspberry Pi с новой версией grbl под названием grblHAL [27]. GrblHAL был разработан специально для 32-битных операционных систем и процессоров, таких как Raspberry Pi, в отличие от grbl, который был выпущен для 8-битных контроллеров, таких как Arduino Uno. Расширенный отправитель G-кода, bCNC, использовался с grblHAL вместо универсального отправителя G-кода. BCNC – это надежное и быстрое кроссплатформенное (Windows, Linux и Mac) приложение, написанное на Python для передачи данных и обработки других функций.Однако ни одна из этих разработок не соответствует стандартам STEP-NC.В этом исследовании авторы разработали фрезерный станок с ЧПУ с жалобой на STEP-NC, который можно использовать в качестве испытательного стенда для будущих исследований. Raspberry Pi 3 Model B + SBC использовался в качестве основного контроллера станка с ЧПУ. Для всех связанных разработок использовалась среда на основе операционной системы Raspberry Pi OS (ранее называвшаяся Raspbian). Основная кодировка была написана на языке программирования C ++, а HMI был запрограммирован с помощью Qt для обеспечения гибкости и быстрого обновления данных на экране.SBC Raspberry Pi легко доступны на рынке по невысокой цене. В отличие от систем на базе ПК, встроенные контакты GPIO SBC подключают сигналы от машины и к машине, что является дополнительным преимуществом. Полное автономное программное обеспечение OAC разрабатывается без использования дорогостоящего коммерческого программного обеспечения. Стоит отметить, что ни о каких разработках ЧПУ, совместимых с OAC STEP-NC, выполненных на SBC, в литературе не сообщается.
Разработанный станок может быть использован для расширения возможностей, представленных в стандарте STEP-NC.Подчиненная карта ввода-вывода поддерживает больше аналоговых и цифровых сигналов для подключения датчиков для контроля условий резания. Это будет полезно для прогнозирования лучших условий резания и восстановления траектории инструмента для обработки.
Технология микрофрезерования относится к сверхточной обработке с субмикронной точностью. Обычные режимы резания не могут быть использованы при микрообработке путем простого уменьшения размера. Uriarte et al. предложили инструмент для выбора параметров процесса микропереработки [28]. Lamikiz et al.предложил утилиту для оптимизации траектории инструмента и оценки сил резания при обработке сложных поверхностей [29]. Обе эти реализации запланированы на этапе CAM. Такие реализации могут быть интегрированы в сам недавно разработанный контроллер, поскольку он работает на OAC и STEP-NC. Качество обработанного продукта в основном зависит от точности станка. Ошибки при обработке снижают точность станка и влияют на качество конечного продукта. Геометрические ошибки, тепловые ошибки, кинематические ошибки, ошибки жесткости и ошибки из-за деформации режущих инструментов и станков считаются основными источниками ошибок, связанных со станками [30].Из всех этих ошибок геометрические ошибки, возникающие из-за механических дефектов, вносят наибольший вклад в ошибки в станках. Кроме того, тепловые ошибки из-за колебаний температуры станка, вызванные внутренним выделением тепла и изменениями окружающей среды, также оказывают значительное негативное влияние на точность станка [31]. В этой статье описывается разработка аппаратного обеспечения недавно разработанного ЧПУ. Описание машины приведено в разделе 2. Механическая система и электрическая система подробно описаны в этом разделе.Разработка программного обеспечения, включающая алгоритмы управления и проектирование HMI, описана в разделе 3. Раздел 4 включает проверку выполнения программы STEP-NC.3. Разработка программного обеспечения Ядро с числовым программным управлением
(NCK) было разработано на одноплатном компьютере Raspberry Pi 3 B + с использованием языка программирования C ++. HMI был разработан с помощью Qt. Пользователю доступны пять рабочих режимов, а именно: Home, Manual, MDI, Run и Edit (рисунок 6). Пять основных программных модулей (рисунок 7) включены в NCK, а именно: модули управления движением, чтение файлов, модуль интерполятора. , Модуль интерпретатора ISO 14649, модуль цифрового и аналогового ввода-вывода и модуль HMI.Модуль интерпретатора ISO 14649 начинает с чтения файла STEP-NC part21 в контроллер ЧПУ. Для интерпретации файла используется программное обеспечение с открытым исходным кодом, разработанное Национальным институтом стандартов и технологий (NIST). Интерпретированные и обработанные данные сохраняются как файл Canonical Machining Command (CMC) [34]. Канонические команды – это атомарные инструкции, которые производят движение инструмента или логическое действие [35]. Затем данные внутри файла CMC извлекаются модулем извлечения данных. Данные отправляются в модуль интерполятора, если извлекается команда движения инструмента.В противном случае извлеченная команда обрабатывается индивидуально. Модуль интерполятора принимает команды линейного движения STRAIGHT_TRAVERSE (), STRAIGHT_FEED () и команду кругового движения ARC_FEED (). Все остальные канонические команды направляются в модуль обработки логических действий.Траектория обработки планируется в соответствии с командами движения, переданными из файла CMC. Модуль интерполятора контролирует движение инструмента по правильной траектории. Линейная и круговая интерполяция используются для управления движением оси по ее траектории.
Для плавного движения машины ускорение и замедление должны применяться в начале и в конце кадра. Как правило, существует два вида методов управления ускорением и замедлением: управление ускорением / замедлением после интерполяции (ADCAI) и перед интерполяцией (ADCBI) [36]. Ошибки команды траектории не могут быть устранены в методе ADCAI, что ограничивает его точность обработки. Напротив, в методе ADCBI ошибки команд пути исключаются теоретически [37].Таким образом, в этой разработке используется метод ADCBI с трапециевидным профилем скорости.Применяется трапециевидный профиль скорости с предустановленными значениями ускорения и замедления для достижения заданного положения путем интерполяции. Трапециевидный профиль скорости прост в реализации, требует меньших вычислительных затрат и поэтому рекомендуется для низкоскоростных недорогих машин.
Существует два основных метода разработки алгоритмов линейной и круговой интерполяции. Первый метод – поддерживать постоянное смещение с переменным периодом интерполяции.Второй метод противоположен первому в том, что он поддерживает постоянный период интерполяции с изменяющимся смещением [38]. В этой разработке применяется первый метод алгоритма интерполяции с постоянным смещением. Алгоритм линейной интерполяции разработан на основе уравнения (1). Ожидается, что контроллер будет двигаться от точки P s (X s , Y s ) до P e (X e , Y e ) по линейной траектории, как показано на рисунке 8.Рассмотрим две точки на линии P n (X n , Y n ) и P n + 1 (X n + 1 , Y n + 1 ), расположенные на расстоянии δt друг от друга. . Интервал интерполяции δt считается постоянным смещением вдоль линии. Координаты новой точки P n + 1 относительно точки P n рассчитываются следующим образом:δx = δt cos (θ) Xn + 1 = Xn + δxYn + 1 = Yn + (Xn −Xs) (Xe − Xs) (Ye − Ys)
(1)
Точно так же уравнение (2) применяется, когда круговой путь, по которому должен следовать стол станка, от точки P s (X s , Y s ) до P e (X e , Y e ), как показано на рисунке 9.Рассмотрим две точки на дуге P n (X n , Y n ) и P n + 1 (X n + 1 , Y n + 1 ), расположенные под углом δθ друг от друга. . Следующую точку на дуге можно рассчитать по уравнению (2) следующим образом:Xn = Rcos (θn); Yn = R sin (θn) Xn + 1 = Rcos (θn + δθ); Yn + 1 = Rsin (θn + δθ) Xn + 1 = Xn cos (δθ) – Yn sin (δθ); Yn + 1 = Yn cos (δθ) + Xn sin (δθ)
(2)
В этой разработке используются шарико-винтовые пары с шагом 5 мм. Вращательное движение шарико-винтовой передачи измеряется двухканальным инкрементным энкодером с отдельным индексным каналом.Два сигнала энкодера, канал A и канал B, разделены на 90 °. Из-за квадратурного декодирования для каждого оборота генерируется четыре отсчета [39]. DIP-переключатели энкодера установлены на 1000 PPR, поскольку ожидаемое разрешение может быть достигнуто без каких-либо ошибок округления. Следовательно, для перемещения на расстояние 5 мм требуется 4000 чисел квадратурных импульсов. Ожидаемое разрешение новой машины – 0,01 мм. Количество импульсов N, необходимое для перемещения на расстояние d (мм), определяется уравнением (3).Последовательность импульсов отправляется на привод оси для вращения соответствующего серводвигателя станка и привода оси. Частота последовательности импульсов определяется требуемой скоростью подачи оси. В ручном режиме и режиме MDI скорость подачи определяется установкой поворотного переключателя на панели оператора, и частота рассчитывается соответствующим образом. Непрерывная последовательность импульсов отправляется на привод оси при активации ручного переключателя соответствующей оси в ручном режиме. В режимах MDI и работы на привод оси посылается предварительно рассчитанное количество импульсов в соответствии с заданным расстоянием.В рабочем режиме скорость подачи извлекается из файла CMC. В станках с ЧПУ HMI служит интерфейсом между NCK и оператором. Высокое удобство использования, быстрые и плавные варианты ввода и возможность отображения в реальном времени – вот некоторые из важных аспектов хорошего HMI. Чтобы охватить все вышеперечисленные аспекты, HMI контроллера запрограммирован на платформе Qt. На рисунке 10 показан общий вид разработанного HMI.Разработанный контроллер станка способен читать и интерпретировать описание продукта формата файла STEP-NC часть 21.В файле описываются материал и размер заготовки, план процесса, этапы работы, производственные данные и многое другое. Следовательно, сам контроллер может генерировать траектории инструмента и выполнять их на станке с ЧПУ для обработки продукта. Если в последний момент необходимо изменить какой-либо параметр процесса, это можно сделать с помощью редактора на контроллере. Одним из преимуществ системы является то, что без возврата к этапу CAD / CAM траектория инструмента может быть восстановлена на самом контроллере станка.
5. Выводы
Новый контроллер станка с ЧПУ, совместимый со стандартом STEP-NC, был разработан и успешно реализован в этом исследовании. В отличие от прошлых разработок контроллеров ЧПУ, совместимых с STEP-NC, о которых сообщалось в литературе, контроллер, разработанный в этом исследовании, не требует каких-либо высокопроизводительных вычислительных мощностей и, таким образом, может быть реализован в недорогих одноплатных компьютерах, таких как Raspberry Pi. Кроме того, все сопутствующие разработки программного обеспечения были выполнены на языке программирования C ++, поэтому дорогостоящее коммерческое программное обеспечение не использовалось в этой разработке.Соответственно, новый контроллер STEP-NC, предложенный в этом исследовании, считается недорогой альтернативой контроллеру STEP-NC, описанному в литературе [12,14,15].Станок с ЧПУ лабораторного масштаба был также разработан в рамках этого исследования для проверки производительности нового контроллера ЧПУ, совместимого со стандартом STEP-NC. Более того, ключевой целью этого исследования была разработка станка с ЧПУ, совместимого со стандартом STEP-NC; Следовательно, машина, разработанная в этом исследовании, может быть использована в качестве эффективного испытательного стенда для разработки контроллеров на основе STEP-NC с приемлемой точностью.Дальнейшие исследования также будут сосредоточены на изучении точности машины и поиске способов ее улучшения, если это необходимо.
Стоимость разработанного станка составляет 3840 долларов США, настольного фрезерного станка с ЧПУ аналогичной мощности на рынке – 23000 долларов США.
Эксперименты, проведенные на разработанной испытательной установке, показали, что новый контроллер ЧПУ, соответствующий стандарту STEP-NC, предложенный в данном исследовании, способен выполнять модификации параметров резки и геометрических характеристик на уровне цеха, как указано в ISO 14649.Пересмотренная программа, основанная на модификациях на уровне цеха, также может быть обратной связью с системой CAD / CAM для хранения и будущих требований.
В заключение, это исследование представляет собой недорогую, интеллектуальную, совместимую со STEP-NC систему OAC, работающую на разработанном и изготовленном на месте трехосевом фрезерном станке с ЧПУ. В будущем эта разработка будет расширена до четвертой категории контроллеров STEP-NC: интерактивного интеллектуального станка с ЧПУ с поддержкой STEP-NC. Кроме того, эта машина может быть использована для создания цифрового двойника машины за счет возможности удаленного мониторинга и управления.
Поскольку Raspberry Pi SBC упрощает взаимодействие с видеокамерой, мониторинг обработки в реальном времени может быть очень легко встроен в станок. Таким образом, это средство может быть расширено до стратегии визуального контроля для оценки параметров, таких как шероховатость поверхности. Кроме того, интеллектуальные возможности контроллера могут быть улучшены для расчета оптимальных параметров резания и восстановления программы обработки детали с учетом эмпирических данных.
Lopez et al. представила метод многоосной высокоскоростной обработки, основанный на оценке силы резания и создании траекторий движения инструмента с минимальной силой резания.Предлагаемая разработка централизована на CAM-системе [41]. Другая модель была разработана тем же исследователем для обработки прогрессивных высокопрочных сталей [42]. Эта модель фрезерования учитывала отклонение режущего инструмента и определяла силу резания. Модель отдельно обрабатывала участки с разной твердостью и плохо очерченными границами. Эти типы моделей могут быть включены в разработанный контроллер, поскольку OAC и STEP-NC способствуют этому. Исследования, проведенные Лакнером и Хардтом по условиям трения при резке металла при подаче СОЖ под высоким давлением, показали, что это снижает износ режущего инструмента. [43].Кроме того, эта недавно разработанная машина может быть использована в качестве испытательного стенда для исследования использования смазочно-охлаждающей жидкости для уменьшения износа режущего инструмента в будущих исследованиях.Машинист с ЧПУ, техник
Обучение на станка с ЧПУ предоставляет студентам возможности по всему региону. Программа дает навыки, необходимые для безопасной настройки и эксплуатации ручных станков, включая токарные, фрезерные, шлифовальные, пилы и ручные инструменты. Вы научитесь управлять, настраивать и программировать различные станки с ЧПУ, проектировать и программировать с использованием систем CAD / CAM, а также инструментов проектирования и приспособлений для повышения производительности.Программа CNC Machinist подготовит вас к успешному трудоустройству в производственной сфере.
Награда: Диплом
Кредиты: 43,5
Местоположение: Пеоста
Поступление: Осень
Оплата программы
$ 8,874 *
State Out Стоимость обучения и сборов: 9 918 долларов Аналитик EMSI, карьерный тренер и данные институциональных исследований.
Возможная карьера
- Оператор ЧПУ
- Станок с ЧПУ
- Программатор с ЧПУ
- Изготовитель инструментов и штампов
- Подайте заявку на зачисление.
- Отправьте официальные документы об окончании средней школы, эквивалентной средней школы и / или выписки из колледжа в приемную комиссию кампуса, который вы планируете посещать.
- Полный экзамен по чтению и письму ACCUPLACER® и экзамен по математике ALEKS® для размещения на курсах. От оценок можно отказаться на основании предыдущей курсовой работы в колледже или предоставления действительных результатов тестов ACT® или SAT®.Оценки по чтению и письму действительны в течение трех лет, а по математике – в течение двух лет.
Программа для технических специалистов по станкам с ЧПУ поддерживает официальные соглашения о артикуляции с учреждениями, перечисленными ниже. Студентам рекомендуется поговорить со своим переводным колледжем или университетом, чтобы убедиться, что их запланированные курсы в NICC будут соответствовать необходимым требованиям.