ΡΡΡΠ°Π½ΠΎΠ²ΠΊΠ° ΠΏΠΎ ΠΏΠ΅ΡΠ΅ΡΠ°Π±ΠΎΡΠΊΠ΅ ΠΏΠΎΠΊΡΡΡΠ΅ΠΊ ΡΠ²ΠΎΠΈΠΌΠΈ ΡΡΠΊΠ°ΠΌΠΈ
ΠΡΠ²ΠΎΠ·, ΠΏΠ΅ΡΠ΅ΡΠ°Π±ΠΎΡΠΊΠ° ΠΈ ΡΡΠΈΠ»ΠΈΠ·Π°ΡΠΈΡ ΠΎΡΡ ΠΎΠ΄ΠΎΠ² Ρ 1 ΠΏΠΎ 5 ΠΊΠ»Π°ΡΡ ΠΎΠΏΠ°ΡΠ½ΠΎΡΡΠΈ
Π Π°Π±ΠΎΡΠ°Π΅ΠΌ ΡΠΎ Π²ΡΠ΅ΠΌΠΈ ΡΠ΅Π³ΠΈΠΎΠ½Π°ΠΌΠΈ Π ΠΎΡΡΠΈΠΈ. ΠΠ΅ΠΉΡΡΠ²ΡΡΡΠ°Ρ Π»ΠΈΡΠ΅Π½Π·ΠΈΡ. ΠΠΎΠ»Π½ΡΠΉ ΠΊΠΎΠΌΠΏΠ»Π΅ΠΊΡ Π·Π°ΠΊΡΡΠ²Π°ΡΡΠΈΡ Π΄ΠΎΠΊΡΠΌΠ΅Π½ΡΠΎΠ². ΠΠ½Π΄ΠΈΠ²ΠΈΠ΄ΡΠ°Π»ΡΠ½ΡΠΉ ΠΏΠΎΠ΄Ρ ΠΎΠ΄ ΠΊ ΠΊΠ»ΠΈΠ΅Π½ΡΡ ΠΈ Π³ΠΈΠ±ΠΊΠ°Ρ ΡΠ΅Π½ΠΎΠ²Π°Ρ ΠΏΠΎΠ»ΠΈΡΠΈΠΊΠ°.
Π‘ ΠΏΠΎΠΌΠΎΡΡΡ Π΄Π°Π½Π½ΠΎΠΉ ΡΠΎΡΠΌΡ Π²Ρ ΠΌΠΎΠΆΠ΅ΡΠ΅ ΠΎΡΡΠ°Π²ΠΈΡΡ Π·Π°ΡΠ²ΠΊΡ Π½Π° ΠΎΠΊΠ°Π·Π°Π½ΠΈΠ΅ ΡΡΠ»ΡΠ³, Π·Π°ΠΏΡΠΎΡΠΈΡΡ ΠΊΠΎΠΌΠΌΠ΅ΡΡΠ΅ΡΠΊΠΎΠ΅ ΠΏΡΠ΅Π΄Π»ΠΎΠΆΠ΅Π½ΠΈΠ΅ ΠΈΠ»ΠΈ ΠΏΠΎΠ»ΡΡΠΈΡΡ Π±Π΅ΡΠΏΠ»Π°ΡΠ½ΡΡ ΠΊΠΎΠ½ΡΡΠ»ΡΡΠ°ΡΠΈΡ Π½Π°ΡΠΈΡ ΡΠΏΠ΅ΡΠΈΠ°Π»ΠΈΡΡΠΎΠ².
Π‘ΠΎΠ²ΡΠ΅ΠΌΠ΅Π½Π½ΠΎΠ΅ ΠΎΠ±ΡΠ΅ΡΡΠ²ΠΎ Π½Π΅ ΠΏΡΠ΅Π΄ΡΡΠ°Π²Π»ΡΠ΅Ρ ΡΠ²ΠΎΠ΅ΠΉ ΠΆΠΈΠ·Π½ΠΈ Π±Π΅Π· Π°Π²ΡΠΎΠΌΠΎΠ±ΠΈΠ»ΡΠ½ΠΎΠΉ ΡΠ΅Ρ Π½ΠΈΠΊΠΈ. Π‘ ΡΠΎΡΡΠΎΠΌ ΡΠΈΡΠ»Π° ΠΌΠ°ΡΠΈΠ½ ΠΏΡΠΎΠΏΠΎΡΡΠΈΠΎΠ½Π°Π»ΡΠ½ΠΎ ΡΠ°ΡΡΠ΅Ρ ΠΈ ΠΊΠΎΠ»ΠΈΡΠ΅ΡΡΠ²ΠΎ ΠΈΠ·Π½ΠΎΡΠ΅Π½Π½ΡΡ ΠΏΠΎΠΊΡΡΡΠ΅ΠΊ Π² ΠΌΠΈΡΠ΅. Π‘ΡΠ°Π½ΠΊΠΈ Π΄Π»Ρ ΠΏΠ΅ΡΠ΅ΡΠ°Π±ΠΎΡΠΊΠΈ Π°Π²ΡΠΎΡΠΈΠ½ Π² ΠΊΡΠΎΡΠΊΡ Π½Π΅ ΡΠΏΠΎΡΠΎΠ±Π½Ρ ΡΠΏΡΠ°Π²ΠΈΡΡΡΡ Ρ ΡΠ°ΠΊΠΈΠΌ ΠΎΠ±ΡΠ΅ΠΌΠΎΠΌ ΡΠ΅Π·ΠΈΠ½ΠΎΠ²ΡΡ ΠΎΡΡ ΠΎΠ΄ΠΎΠ².
Π ΡΠ΅Π·ΡΠ»ΡΡΠ°ΡΠ΅ Π±ΡΠ» ΡΠ°Π·ΡΠ°Π±ΠΎΡΠ°Π½ Π°Π»ΡΡΠ΅ΡΠ½Π°ΡΠΈΠ²Π½ΡΠΉ ΠΌΠ΅ΡΠΎΠ΄, ΠΏΡΠΈ ΠΊΠΎΡΠΎΡΠΎΠΌ Π°Π²ΡΠΎΠΌΠΎΠ±ΠΈΠ»ΡΠ½ΡΠ΅ ΡΠΈΠ½Ρ ΠΏΡΠΎΡ ΠΎΠ΄ΡΡ ΠΏΡΠΎΡΠ΅ΡΡ ΡΠ°Π·Π΄Π΅Π»Π΅Π½ΠΈΡ Π½Π° ΠΏΠΎΠ»Π΅Π·Π½ΡΠ΅ ΡΠ»Π΅ΠΌΠ΅Π½ΡΡ. Π’Π°ΠΊΠΎΠΉ ΠΌΠ΅ΡΠΎΠ΄ Π½Π°Π·ΡΠ²Π°Π΅ΡΡΡ ΠΏΠΈΡΠΎΠ»ΠΈΠ·.
ΠΠ°ΠΊ ΠΏΡΠΎΠΈΡΡ ΠΎΠ΄ΠΈΡ ΠΏΠΈΡΠΎΠ»ΠΈΠ·
ΠΠΈΡΠΎΠ»ΠΈΠ· ΡΠΈΠ½ ΠΏΡΠ΅Π΄ΡΡΠ°Π²Π»ΡΠ΅Ρ ΡΠΎΠ±ΠΎΠΉ Π²ΡΡΠΎΠΊΠΎΡΡΡΠ΅ΠΊΡΠΈΠ²Π½ΡΠΉ ΠΈ Π½Π΅Π΄ΠΎΡΠΎΠ³ΠΎΠΉ ΡΠΏΠΎΡΠΎΠ± ΠΏΠ΅ΡΠ΅ΡΠ°Π±ΠΎΡΠΊΠΈ ΡΠ΅Π·ΠΈΠ½ΠΎΡΠ΅Ρ
Π½ΠΈΡΠ΅ΡΠΊΠΈΡ
ΠΈΠ·Π΄Π΅Π»ΠΈΠΉ (ΡΡΠΈ), Π° ΡΠ°ΠΊΠΆΠ΅ ΠΎΡΡΠ»ΡΠΆΠΈΠ²ΡΠΈΡ
ΡΠ²ΠΎΠΉ ΡΡΠΎΠΊ Π°Π²ΡΠΎΠΌΠΎΠ±ΠΈΠ»ΡΠ½ΡΡ
ΠΏΠΎΠΊΡΡΡΠ΅ΠΊ. Π ΡΠ΅Π·ΡΠ»ΡΡΠ°ΡΠ΅ ΠΏΡΠΎΡΠ΅ΡΡΠ° Π½Π΅ ΠΏΡΠΎΠΈΡΡ
ΠΎΠ΄ΠΈΡ Π·Π°Π³ΡΡΠ·Π½Π΅Π½ΠΈΡ ΠΎΠΊΡΡΠΆΠ°ΡΡΠ΅ΠΉ ΡΡΠ΅Π΄Ρ.
ΠΡΠ½ΠΎΠ²Π½ΡΠ΅ ΡΡΠ°ΠΏΡ ΡΠ΅Ρ
Π½ΠΎΠ»ΠΎΠ³ΠΈΡΠ΅ΡΠΊΠΎΠ³ΠΎ ΠΏΡΠΎΡΠ΅ΡΡΠ°, Π² ΡΠ΅Π·ΡΠ»ΡΡΠ°ΡΠ΅ ΠΊΠΎΡΠΎΡΠΎΠ³ΠΎ ΡΡΠΈΠ»ΠΈΠ·ΠΈΡΡΡΡΡΡ ΡΠ΅Π·ΠΈΠ½ΠΎΠ²ΡΠ΅ ΠΎΡΡ
ΠΎΠ΄Ρ, Π° ΡΠ°ΠΊΠΆΠ΅ ΠΈΠ·Π½ΠΎΡΠ΅Π½Π½ΡΠ΅ Π°Π²ΡΠΎΠΌΠΎΠ±ΠΈΠ»ΡΠ½ΡΠ΅ ΡΠΈΠ½Ρ:
- ΠΡΠΈ ΠΏΠΎΠΌΠΎΡΠΈ ΡΠΏΠ΅ΡΠΈΠ°Π»ΡΠ½ΡΡ Π½ΠΎΠΆΠ΅ΠΉ ΠΏΠΎΠΊΡΡΡΠΊΠΈ ΡΠ°Π·Π΄Π΅Π»ΡΡΡΡΡ Π½Π° Π±ΠΎΠΊΠΎΠ²ΡΡ ΠΈ ΠΏΠ΅ΡΠ΅Π΄Π½ΡΡ ΡΠ°ΡΡΡ.
- ΠΠ°Π»Π΅Π΅ ΠΏΡΠΎΠΈΡΡ ΠΎΠ΄ΠΈΡ Π·Π°Π³ΡΡΠ·ΠΊΠ° ΡΡΡΡΡ. Π Π°Π·Π΄Π΅Π»Π΅Π½Π½ΡΠΉ ΠΌΠ°ΡΠ΅ΡΠΈΠ°Π» ΠΏΠΎΠΌΠ΅ΡΠ°ΡΡ Π² ΡΠ΅ΡΠΎΡΡΡ ΠΈ Π³Π΅ΡΠΌΠ΅ΡΠΈΡΠ½ΠΎ Π·Π°ΠΊΡΡΠ²Π°ΡΡ, Π° Π·Π°ΡΠ΅ΠΌ Π·Π°Π³ΡΡΠΆΠ°ΡΡ Π² ΠΏΠ΅ΡΡ.
- Π ΡΠ΅Π·ΡΠ»ΡΡΠ°ΡΠ΅ Π½Π°Π³ΡΠ΅Π²Π° ΠΏΡΠΎΠΈΡΡ ΠΎΠ΄ΠΈΡ ΡΠ°Π·Π»ΠΎΠΆΠ΅Π½ΠΈΠ΅ ΡΠ΅Π·ΠΈΠ½Ρ ΠΈ Π²ΡΠ΄Π΅Π»ΡΠ΅ΡΡΡ Π³Π°Π·. ΠΠΎΡΠ»Π΅ ΠΎΠΊΠΎΠ½ΡΠ°Π½ΠΈΡ ΠΏΡΠΎΡΠ΅ΡΡΠ° ΡΠ΅ΡΠΎΡΡΡ ΡΠ΄Π°Π»ΡΡΡ ΠΈΠ· Π½Π°Π³ΡΠ΅Π²Π°ΡΠ΅Π»ΡΠ½ΠΎΠΉ ΠΊΠ°ΠΌΠ΅ΡΡ ΠΈ ΠΏΡΠΎΠΈΡΡ ΠΎΠ΄ΠΈΡ Π·Π°ΠΌΠ΅Π½Π° Π½Π° Π½ΠΎΠ²ΡΡ. Π’Π΅ΠΌΠΏΠ΅ΡΠ°ΡΡΡΠ° Π² ΠΏΠ΅ΡΠΈ ΠΈΠΌΠ΅Π΅Ρ Π·Π½Π°ΡΠ΅Π½ΠΈΠ΅ 450Β°Π‘.
- ΠΠΎΡΠ»Π΅ Π΄Π»ΠΈΡΠ΅Π»ΡΠ½ΠΎΠ³ΠΎ ΠΎΡΡΡΠ²Π°Π½ΠΈΡ ΠΈΠ· Π΅ΠΌΠΊΠΎΡΡΠΈ Π²ΡΠ½ΠΈΠΌΠ°ΡΡ ΡΠΎΠ΄Π΅ΡΠΆΠΈΠΌΠΎΠ΅. ΠΡΠ΄Π΅Π»ΡΡΡΡΡ ΠΆΠΈΠ΄ΠΊΠΈΠ΅ ΡΠ³Π»Π΅Π²ΠΎΠ΄ΠΎΡΠΎΠ΄Ρ ΠΎΡ ΠΊΠΎΡΠ΄Π°.
Π Ρ ΠΎΠ΄Π΅ Π·Π°ΠΊΡΡΡΠΎΠ³ΠΎ ΡΠΆΠΈΠ³Π°Π½ΠΈΡ ΡΠ΅Π·ΠΈΠ½Ρ Π½Π΅ ΡΡΠ΅Π±ΡΠ΅ΡΡΡ ΠΊΠΈΡΠ»ΠΎΡΠΎΠ΄. ΠΠ΅ΡΠ΅ΡΠ°Π±ΠΎΡΠΊΠ° ΡΠΈΠ½ ΠΏΠΈΡΠΎΠ»ΠΈΠ·ΠΎΠΌ ΡΡΠΈΡΠ°Π΅ΡΡΡ ΠΏΠΎΠ»Π½ΠΎΡΡΡΡ Π±Π΅Π·ΠΎΡΡ ΠΎΠ΄Π½ΠΎΠΉ, Π²ΡΠ΅ ΠΏΡΠΎΠ΄ΡΠΊΡΡ Π² ΡΠ΅Π·ΡΠ»ΡΡΠ°ΡΠ΅ ΡΠ΅Π°ΠΊΡΠΈΠΈ ΡΠΈΡΠΎΠΊΠΎ ΠΏΡΠΈΠΌΠ΅Π½ΡΡΡΡΡ Π² Π½Π΅ΡΡΠ΅ΠΏΠ΅ΡΠ΅ΡΠ°Π±Π°ΡΡΠ²Π°ΡΡΠ΅ΠΉ ΠΏΡΠΎΠΌΡΡΠ»Π΅Π½Π½ΠΎΡΡΠΈ.
ΠΡΠΈ Π³ΠΎΡΠ΅Π½ΠΈΠΈ Π² ΠΏΠ΅ΡΠΈ ΠΏΡΠΎΠΈΡΡ ΠΎΠ΄ΡΡ Ρ ΠΈΠΌΠΈΡΠ΅ΡΠΊΠΈΠ΅ ΡΠ΅Π°ΠΊΡΠΈΠΈ ΡΠ°Π·Π»ΠΎΠΆΠ΅Π½ΠΈΡ ΡΠ΅Π·ΠΈΠ½Ρ Π½Π° Π³Π°Π·ΠΎΠΎΠ±ΡΠ°Π·Π½ΡΠ΅ Π½Π΅ΡΡΡΠ½ΡΠ΅ ΡΠΎΡΡΠ°Π²Π»ΡΡΡΠΈΠ΅, ΡΠ³Π»Π΅ΡΠΎΠ΄ΠΈΡΡΡΠΉ ΠΏΠΎΡΠΎΡΠΎΠΊ ΠΈ ΠΌΠ΅ΡΠ°Π»Π»ΠΈΡΠ΅ΡΠΊΠΈΠΉ ΠΊΠΎΡΠ΄.
ΠΡΠΎΠ΄ΡΠΊΡΡ ΡΠ΅Π°ΠΊΡΠΈΠΈ
Π ΡΠ΅Π·ΡΠ»ΡΡΠ°ΡΠ΅ ΠΏΠ΅ΡΠ΅ΡΠ°Π±ΠΎΡΠΊΠΈ ΡΠ΅Π·ΠΈΠ½ΠΎΠ²ΡΡ ΠΎΡΡ ΠΎΠ΄ΠΎΠ² ΠΏΡΠΎΠΈΡΡ ΠΎΠ΄ΠΈΡ Π²ΡΠ΄Π΅Π»Π΅Π½ΠΈΠ΅ Π½Π΅ΡΠΊΠΎΠ»ΡΠΊΠΈΡ Π²ΠΈΠ΄ΠΎΠ² ΠΏΡΠΎΠ΄ΡΠΊΡΠΈΠΈ:
- Π’ΠΎΠΏΠ»ΠΈΠ²ΠΎ ΠΆΠΈΠ΄ΠΊΠΎΠΉ ΡΠΎΡΠΌΡ.
- ΠΡΡΠ°ΡΠΎΠΊ, ΡΠΎΠ΄Π΅ΡΠΆΠ°ΡΠΈΠΉ ΡΠ³Π»Π΅ΡΠΎΠ΄.
- ΠΠ°Π· ΠΏΡΠΈ ΠΏΠΈΡΠΎΠ»ΠΈΠ·Π΅.
- ΠΠ΅ΡΠ°Π»Π»ΠΈΡΠ΅ΡΠΊΠ°Ρ Π°ΡΠΌΠΈΡΡΡΡΠ°Ρ ΠΏΡΠΎΠ²ΠΎΠ»ΠΎΠΊΠ°.
ΠΠΈΠ΄ΠΊΠΎΡΡΡ
ΠΠΈΠ΄ΠΊΠΈΠΉ ΠΎΡΡΠ°ΡΠΎΠΊ, ΠΏΠΎ ΡΡΡΠΈ, ΠΏΡΠ΅Π΄ΡΡΠ°Π²Π»ΡΠ΅Ρ ΡΠΎΠ±ΠΎΠΉ ΡΠΈΠ½ΡΠ΅ΡΠΈΡΠ΅ΡΠΊΡΡ Π½Π΅ΡΡΡ, ΡΡ ΠΎΠΆΡΡ ΠΏΠΎ ΡΠ²ΠΎΠ΅ΠΌΡ ΡΠΎΡΡΠ°Π²Ρ Ρ ΠΏΡΠΈΡΠΎΠ΄Π½ΠΎΠΉ. ΠΡΠΈ ΠΎΠ±ΡΠ°Π±ΠΎΡΠΊΠ΅ ΠΏΠΎΠ»ΡΡΠ΅Π½Π½ΠΎΠ³ΠΎ ΡΡΡΡΡ Π½Π° Π½Π΅ΡΡΠ΅ΠΏΠ΅ΡΠ΅ΡΠ°Π±Π°ΡΡΠ²Π°ΡΡΠΈΡ Π·Π°Π²ΠΎΠ΄Π°Ρ Π²ΠΎΠ·ΠΌΠΎΠΆΠ½ΠΎ ΠΏΠΎΠ»ΡΡΠΈΡΡ ΡΠ°ΠΊΠΈΠ΅ Π²ΠΈΠ΄Ρ ΠΌΠ°ΡΠ΅ΡΠΈΠ°Π»ΠΎΠ², ΠΊΠ°ΠΊ Π±Π΅Π½Π·ΠΈΠ½, ΠΌΠ°Π·ΡΡ, Π° ΡΠ°ΠΊΠΆΠ΅ ΡΠΈΠ½ΡΠ΅ΡΠΈΡΠ΅ΡΠΊΠΎΠ΅ ΠΌΠ°ΡΠ»ΠΎ Π΄Π»Ρ Π°Π²ΡΠΎΠΌΠΎΠ±ΠΈΠ»ΡΠ½ΠΎΠΉ ΡΠ΅Ρ Π½ΠΈΠΊΠΈ.
ΠΠΎ ΠΌΠ½ΠΎΠ³ΠΈΡ ΡΡΡΠ°Π½Π°Ρ ΡΠ°ΠΊΠΎΠΉ ΡΠΏΠΎΡΠΎΠ± ΡΡΠΈΠ»ΠΈΠ·Π°ΡΠΈΠΈ Π½Π°ΡΠ΅Π» ΡΠΈΡΠΎΠΊΠΎΠ΅ ΠΏΡΠΈΠΌΠ΅Π½Π΅Π½ΠΈΠ΅, ΠΈΠ· ΠΎΠ³ΡΠΎΠΌΠ½ΠΎΠ³ΠΎ ΡΠΈΡΠ»Π° Π°Π²ΡΠΎΡΠΈΠ½ ΠΏΡΠΎΠΈΠ·Π²ΠΎΠ΄ΡΡ Π΄ΠΈΠ·Π΅Π»ΡΠ½ΠΎΠ΅ ΡΠΎΠΏΠ»ΠΈΠ²ΠΎ. Π‘ ΠΎΠ΄Π½ΠΎΠΉ ΡΠΎΠ½Π½Ρ ΡΠΈΠ½ Π² ΡΠ΅Π·ΡΠ»ΡΡΠ°ΡΠ΅ ΠΏΠΈΡΠΎΠ»ΠΈΠ·Π° ΠΏΠΎΠ»ΡΡΠ°ΡΡ 500 Π» ΡΠΎΠΏΠ»ΠΈΠ²Π°. ΠΠΈΠ΄ΠΊΠΈΠΉ ΠΎΡΡΠ°ΡΠΎΠΊ ΠΌΠΎΠΆΠ½ΠΎ ΠΏΡΠΈΠΌΠ΅Π½ΡΡΡ Π±Π΅Π· ΠΎΠ±ΡΠ°Π±ΠΎΡΠΊΠΈ Π΄Π»Ρ ΠΏΠ΅ΡΠ΅ΠΉ ΠΈ ΠΊΠΎΡΠ»ΠΎΠ² Π² ΠΊΠ°ΡΠ΅ΡΡΠ²Π΅ ΠΎΡΠ½ΠΎΠ²Π½ΠΎΠ³ΠΎ ΡΠΎΠΏΠ»ΠΈΠ²Π°.
Π£Π³Π»Π΅ΡΠΎΠ΄ΡΠΎΠ΄Π΅ΡΠΆΠ°ΡΠΈΠΉ ΠΎΡΡΠ°ΡΠΎΠΊ
Π’Π²Π΅ΡΠ΄ΡΠΉ ΠΎΡΡΠ°ΡΠΎΠΊ Π½Π°ΡΠ΅Π» ΡΠΈΡΠΎΠΊΠΎΠ΅ ΠΏΡΠΈΠΌΠ΅Π½Π΅Π½ΠΈΠ΅ Π² Π½Π΅ΠΊΠΎΡΠΎΡΡΡ ΠΎΠ±Π»Π°ΡΡΡΡ :
- ΠΠ½ Π°Π½Π°Π»ΠΎΠ³ΠΈΡΠ΅Π½ Π°ΠΊΡΠΈΠ²ΠΈΡΠΎΠ²Π°Π½Π½ΠΎΠΌΡ ΡΠ³Π»Ρ ΠΏΠΎ ΡΠ²ΠΎΠΈΠΌ Π°Π±ΡΠΎΡΠ±Π΅Π½ΡΠ½ΡΠΌ ΡΠ²ΠΎΠΉΡΡΠ²Π°ΠΌ.
- ΠΠ°ΠΊ ΡΠ΅ΡΠ½ΡΠΉ ΠΊΡΠ°ΡΠΈΡΠ΅Π»Ρ Π² Π»Π°ΠΊΠΎΠΊΡΠ°ΡΠΎΡΠ½ΠΎΠΌ ΠΈ ΡΠ΅ΠΌΠ΅Π½ΡΠ½ΠΎΠΌ ΠΏΡΠΎΠΈΠ·Π²ΠΎΠ΄ΡΡΠ²Π΅.
- ΠΠ°ΠΊ ΡΡΡΡΠ΅ Π΄Π»Ρ ΠΈΠ·Π³ΠΎΡΠΎΠ²Π»Π΅Π½ΠΈΡ Π½ΠΎΠ²ΡΡ ΡΠ΅Π·ΠΈΠ½ΠΎΠ²ΡΡ ΠΈΠ·Π΄Π΅Π»ΠΈΠΉ, Π° ΡΠ°ΠΊΠΆΠ΅ ΠΏΠΎΠΊΡΡΡΠ΅ΠΊ.
- ΠΠΎΠ±Π°Π²Π»ΡΠ΅ΡΡΡ Π² ΠΆΠΈΠ΄ΠΊΠΎΠ΅ ΡΠΎΠΏΠ»ΠΈΠ²ΠΎ, Π»ΠΈΠ±ΠΎ ΡΠΆΠΈΠ³Π°Π΅ΡΡΡ ΡΠ°ΠΌ Π² ΡΠΏΠ΅ΡΠΈΠ°Π»ΡΠ½ΡΡ ΠΏΠ΅ΡΠ°Ρ .
ΠΠΈΡΠΎΠ»ΠΈΠ·Π½ΡΠΉ Π³Π°Π·
ΠΠΈΡΠΎΠ»ΠΈΠ· ΠΏΠΎΠΊΡΡΡΠ΅ΠΊ ΠΏΡΠΎΠΈΠ·Π²ΠΎΠ΄ΠΈΡΡΡ Ρ Π²ΡΠ΄Π΅Π»Π΅Π½ΠΈΠ΅ΠΌ Π³Π°Π·Π°, ΠΊΠΎΡΠΎΡΡΠΉ ΠΏΠΎ ΡΠ²ΠΎΠΈΠΌ Ρ Π°ΡΠ°ΠΊΡΠ΅ΡΠΈΡΡΠΈΠΊΠ°ΠΌ ΡΡ ΠΎΠΆ Ρ ΠΏΡΠΈΡΠΎΠ΄Π½ΡΠΌ. ΠΠΎΠ»ΡΡΠ°Ρ ΡΠ°ΡΡΡ Π΄Π°Π½Π½ΠΎΠ³ΠΎ Π³Π°Π·Π° Π² ΡΠ΅Π·ΡΠ»ΡΡΠ°ΡΠ΅ Π³ΠΎΡΠ΅Π½ΠΈΡ Π² ΠΏΠ΅ΡΠΈ ΡΠ°Π·Π΄Π΅Π»ΡΠ΅ΡΡΡ Π½Π° ΠΆΠΈΠ΄ΠΊΠΈΠ΅ ΡΡΠ°ΠΊΡΠΈΠΈ, Π° ΡΠ°ΠΊΠΆΠ΅ Π½Π΅Π²ΡΠΏΠ°Π΄Π°ΡΡΠΈΠ΅ Π² ΠΎΡΠ°Π΄ΠΎΠΊ ΠΎΡΡΠ°ΡΠΊΠΈ, ΠΊΠΎΡΠΎΡΡΠ΅ ΠΏΠΎΠ΄Π΄Π΅ΡΠΆΠΈΠ²Π°ΡΡ ΡΠ°Π·Π»ΠΎΠΆΠ΅Π½ΠΈΠ΅ ΡΠ΅Π·ΠΈΠ½Ρ.
ΠΠ΅ΡΠ°Π»Π»ΠΈΡΠ΅ΡΠΊΠΈΠΉ ΠΊΠΎΡΠ΄
ΠΠ΅ΡΠ°Π»Π»ΠΈΡΠ΅ΡΠΊΠ°Ρ ΠΏΡΠΎΠ²ΠΎΠ»ΠΎΠΊΠ° ΠΏΡΠΈ Π²ΠΎΠ·Π΄Π΅ΠΉΡΡΠ²ΠΈΠΈ Π²ΡΡΠΎΠΊΠΎΠΉ ΡΠ΅ΠΌΠΏΠ΅ΡΠ°ΡΡΡΡ Π½Π΅ ΠΏΠΎΠ΄Π²Π΅ΡΠΆΠ΅Π½Π° ΡΠ°Π·Π»ΠΎΠΆΠ΅Π½ΠΈΡ ΠΈ ΠΎΡΡΠ°Π΅ΡΡΡ Π² ΠΏΡΠ°ΠΊΡΠΈΡΠ΅ΡΠΊΠΈ Π½Π΅ΠΈΠ·ΠΌΠ΅Π½Π½ΠΎΠΌ Π²ΠΈΠ΄Π΅. Π‘Π΅ΡΠ΄Π΅ΡΠ½ΠΈΠΊ Π°Π²ΡΠΎΠΌΠΎΠ±ΠΈΠ»ΡΠ½ΡΡ
ΡΠΈΠ½ ΠΏΡΠΎΠΈΠ·Π²ΠΎΠ΄ΠΈΡΡΡ ΠΈΠ· ΠΊΠ°ΡΠ΅ΡΡΠ²Π΅Π½Π½ΠΎΠΉ ΡΡΠ°Π»ΠΈ, ΠΊΠΎΡΠΎΡΠ°Ρ ΠΏΡΠΈ Π΄Π°Π»ΡΠ½Π΅ΠΉΡΠ΅ΠΉ ΠΏΠ΅ΡΠ΅ΠΏΠ»Π°Π²ΠΊΠ΅ Π½Π°Ρ
ΠΎΠ΄ΠΈΡ ΡΠ²ΠΎΡ Π²ΡΠΎΡΡΡ ΠΆΠΈΠ·Π½Ρ
Π£ΡΡΡΠΎΠΉΡΡΠ²ΠΎ ΠΊΠΎΡΠ»ΠΎΠ²
ΠΠΈΡΠΎΠ»ΠΈΠ·Π½Π°Ρ ΡΡΡΠ°Π½ΠΎΠ²ΠΊΠ° ΠΏΠΎ ΠΏΠ΅ΡΠ΅ΡΠ°Π±ΠΎΡΠΊΠ΅ ΡΠΈΠ½ Π² ΡΠ²ΠΎΠ΅ΠΉ ΠΊΠΎΠ½ΡΡΡΡΠΊΡΠΈΠΈ ΠΈΠΌΠ΅Π΅Ρ ΡΠ»Π΅Π΄ΡΡΡΠΈΠ΅ ΠΎΡΠ½ΠΎΠ²Π½ΡΠ΅ ΡΠ»Π΅ΠΌΠ΅Π½ΡΡ:
- Π Π΅ΡΠΎΡΡΠ°.
- ΠΠ°ΠΌΠ΅ΡΠ° Π³ΠΎΡΠ΅Π½ΠΈΡ.
Π Π΅ΡΠΎΡΡΠ°
ΠΠ΅ΡΠΌΠ΅ΡΠΈΡΠ½Π°Ρ Π΅ΠΌΠΊΠΎΡΡΡ, Π² ΠΊΠΎΡΠΎΡΠΎΠΉ ΡΠ΅Π·ΠΈΠ½ΠΎΠ²ΡΠ΅ ΠΎΡΡ ΠΎΠ΄Ρ ΠΈ ΡΠΈΠ½Ρ ΠΏΠΎΡΠ»Π΅ ΠΏΡΠ΅Π΄Π²Π°ΡΠΈΡΠ΅Π»ΡΠ½ΠΎΠ³ΠΎ ΠΈΠ·ΠΌΠ΅Π»ΡΡΠ΅Π½ΠΈΡ ΠΏΡΠΎΡ ΠΎΠ΄ΡΡ ΠΏΡΠΎΡΠ΅ΡΡΡ ΡΠ°Π·Π»ΠΎΠΆΠ΅Π½ΠΈΡ Π² ΡΠ΅Π·ΡΠ»ΡΡΠ°ΡΠ΅ ΠΏΠΈΡΠΎΠ»ΠΈΠ·Π° Π½Π° ΠΎΡΠ½ΠΎΠ²Π½ΡΠ΅ ΡΠΎΡΡΠ°Π²Π»ΡΡΡΠΈΠ΅ ΠΏΠ΅ΡΠ΅Π΄ Π΄Π°Π»ΡΠ½Π΅ΠΉΡΠ΅ΠΉ ΠΏΠ΅ΡΠ΅ΡΠ°Π±ΠΎΡΠΊΠΎΠΉ.
ΠΡΠΈ ΠΏΠΎΠΏΠ°Π΄Π°Π½ΠΈΠΈ Π² ΡΠ΅ΡΠΎΡΡΡ Π²ΠΎΠ·Π΄ΡΡ Π°, Π² ΡΠ»ΡΡΠ°Π΅ ΡΠ°Π·Π³Π΅ΡΠΌΠ΅ΡΠΈΠ·Π°ΡΠΈΠΈ, ΠΌΠΎΠΆΠ΅Ρ ΠΏΡΠΎΠΈΠ·ΠΎΠΉΡΠΈ Π²Π·ΡΡΠ² ΠΎΠ±ΡΠ°Π·ΡΡΡΠ΅Π³ΠΎΡΡ ΠΏΠΈΡΠΎΠ»ΠΈΠ·Π½ΠΎΠ³ΠΎ Π³Π°Π·Π°.
ΠΠ·Π³ΠΎΡΠ°Π²Π»ΠΈΠ²Π°Π΅ΡΡΡ ΠΈΠ· ΠΏΡΠΎΡΠ½ΠΎΠ³ΠΎ ΠΌΠ΅ΡΠ°Π»Π»Π° Π²ΠΎ ΠΈΠ·Π±Π΅ΠΆΠ°Π½ΠΈΠ΅ ΠΏΡΠΎΠ³ΠΎΡΠ°Π½ΠΈΡ ΡΡΠ΅Π½ΠΎΠΊ.
ΠΠ°ΠΌΠ΅ΡΠ° Π³ΠΎΡΠ΅Π½ΠΈΡ
Π’ΠΎΠΏΠΊΠ° ΠΏΠΎ ΠΊΠΎΠ½ΡΡΡΡΠΊΡΠΈΠΈ ΠΏΡΠ΅Π΄ΡΡΠ°Π²Π»ΡΠ΅Ρ ΡΠΎΠ±ΠΎΠΉ Π΄Π²Π° ΠΎΡΡΠ΅ΠΊΠ° Π΄Π»Ρ Π³ΠΎΡΠ΅Π½ΠΈΡ ΡΠΎΠΏΠ»ΠΈΠ²Π°. Π ΠΏΠ΅ΡΠ²ΠΎΠΉ ΠΊΠ°ΠΌΠ΅ΡΠ΅ ΠΏΡΠΎΠΈΡΡ ΠΎΠ΄ΠΈΡ ΠΎΡΠ½ΠΎΠ²Π½ΠΎΠ΅ Π³ΠΎΡΠ΅Π½ΠΈΠ΅, Π³Π΄Π΅ ΠΏΠΎΠ΄Π΄Π΅ΡΠΆΠΈΠ²Π°Π΅ΡΡΡ Π½Π΅ΠΎΠ±Ρ ΠΎΠ΄ΠΈΠΌΠ°Ρ ΡΠ΅ΠΌΠΏΠ΅ΡΠ°ΡΡΡΠ° Π΄Π»Ρ ΡΠ΅Ρ Π½ΠΎΠ»ΠΎΠ³ΠΈΡΠ΅ΡΠΊΠΎΠ³ΠΎ ΠΏΡΠΎΡΠ΅ΡΡΠ°. Π Π²Π΅ΡΡ Π½Π΅ΠΌ ΠΎΡΡΠ΅ΠΊΠ΅ ΠΏΡΠΎΠΈΡΡ ΠΎΠ΄ΠΈΡ ΠΏΠΎΠ»Π½ΠΎΠ΅ Π΄ΠΎΠΆΠΈΠ³Π°Π½ΠΈΠ΅ ΡΠΎΠΏΠ»ΠΈΠ²Π° Π²ΠΎ ΠΈΠ·Π±Π΅ΠΆΠ°Π½ΠΈΠ΅ Π²ΡΠ±ΡΠΎΡΠΎΠ² Π²ΡΠ΅Π΄Π½ΡΡ Π²Π΅ΡΠ΅ΡΡΠ² Π² Π°ΡΠΌΠΎΡΡΠ΅ΡΡ. ΠΠ°ΠΌΠ΅ΡΠ° Π΄ΠΎΠΆΠΈΠ³Π°Π½ΠΈΡ ΡΠ½Π°Π±ΠΆΠ°Π΅ΡΡΡ ΠΎΡΠ²Π΅ΡΡΡΠΈΡΠΌΠΈ Π΄Π»Ρ Π΅ΡΡΠ΅ΡΡΠ²Π΅Π½Π½ΠΎΠΉ ΠΏΠΎΠ΄Π°ΡΠΈ Π²ΠΎΠ·Π΄ΡΡ Π°.
Π’Π΅ΠΏΠ»ΠΎΠΎΠ±ΠΌΠ΅Π½Π½ΠΈΠΊ
ΠΠ°Π½Π½Π°Ρ ΠΊΠΎΠ½ΡΡΡΡΠΊΡΠΈΡ ΠΏΡΠ΅Π΄ΡΡΠ°Π²Π»ΡΠ΅Ρ ΡΠΎΠ±ΠΎΠΉ ΡΠΎΠ΅Π΄ΠΈΠ½Π΅Π½ΠΈΠ΅ ΠΈΠ· ΠΌΠ΅ΡΠ°Π»Π»ΠΈΡΠ΅ΡΠΊΠΈΡ ΡΡΡΠ±, Π² ΠΊΠΎΡΠΎΡΡΡ ΠΏΡΠΎΠΈΡΡ ΠΎΠ΄ΠΈΡ ΠΎΡΡΡΠ²Π°Π½ΠΈΠ΅ ΠΈ ΡΠ°Π·Π΄Π΅Π»Π΅Π½ΠΈΠ΅ ΠΏΠΈΡΠΎΠ»ΠΈΠ·Π½ΠΎΠ³ΠΎ Π³Π°Π·Π° Π½Π° ΡΠΎΡΡΠ°Π²Π»ΡΡΡΠΈΠ΅. ΠΡΡΡΠ΅Π½Π½ΡΠΉ Π³Π°Π· ΠΏΡΠΈΠΌΠ΅Π½ΡΡΡ Π΄Π»Ρ Π΄Π°Π»ΡΠ½Π΅ΠΉΡΠ΅Π³ΠΎ ΡΠΆΠΈΠ³Π°Π½ΠΈΡ Π² ΠΏΠ΅ΡΠΈ. ΠΠΈΠ΄ΠΊΠ°Ρ ΡΠΎΡΡΠ°Π²Π»ΡΡΡΠ°Ρ ΠΏΡΠΎΡ ΠΎΠ΄ΠΈΡ ΠΏΠΎΡΠ»Π΅Π΄ΡΡΡΡΡ ΠΏΠ΅ΡΠ΅ΡΠ°Π±ΠΎΡΠΊΡ.
ΠΠΎΡΠ΅Π» Π΄Π»Ρ ΠΏΠΈΡΠΎΠ»ΠΈΠ·Π° ΡΠ²Π»ΡΠ΅ΡΡΡ ΡΠΊΠΎΠ»ΠΎΠ³ΠΈΡΠ΅ΡΠΊΠΈ Π±Π΅Π·ΠΎΠΏΠ°ΡΠ½ΡΠΌ ΠΎΠ±ΠΎΡΡΠ΄ΠΎΠ²Π°Π½ΠΈΠ΅ΠΌ ΠΏΡΠΈ ΡΠΎΠ±Π»ΡΠ΄Π΅Π½ΠΈΠΈ ΡΡΠ΅Π±ΠΎΠ²Π°Π½ΠΈΠΉ ΠΏΡΠ°Π²ΠΈΠ»ΡΠ½ΠΎΠΉ ΡΠΊΡΠΏΠ»ΡΠ°ΡΠ°ΡΠΈΠΈ.
ΠΠΎΠΆΠ½ΠΎ Π»ΠΈ ΡΠ΄Π΅Π»Π°ΡΡ ΠΎΠ±ΠΎΡΡΠ΄ΠΎΠ²Π°Π½ΠΈΠ΅ ΡΠ²ΠΎΠΈΠΌΠΈ ΡΡΠΊΠ°ΠΌΠΈ
ΠΠ±ΠΎΡΡΠ΄ΠΎΠ²Π°Π½ΠΈΠ΅ Π΄Π»Ρ ΠΏΠ΅ΡΠ΅ΡΠ°Π±ΠΎΡΠΊΠΈ ΡΠΈΠ½ ΠΌΠΎΠΆΠ½ΠΎ ΡΠΎΠ±ΡΠ°ΡΡ ΡΠ²ΠΎΠΈΠΌΠΈ ΡΡΠΊΠ°ΠΌΠΈ, ΠΊΠΎΠ½ΡΡΡΡΠΊΡΠΈΡ ΠΏΠΈΡΠΎΠ»ΠΈΠ·Π½ΠΎΠΉ ΡΡΡΠ°Π½ΠΎΠ²ΠΊΠΈ ΠΏΡΠΎΡΡΠ°. ΠΠ»Ρ ΠΈΠ·Π³ΠΎΡΠΎΠ²Π»Π΅Π½ΠΈΡ Π½Π΅ΠΎΠ±Ρ ΠΎΠ΄ΠΈΠΌΡ ΡΠ»Π΅Π΄ΡΡΡΠΈΠ΅ ΠΎΡΠ½ΠΎΠ²Π½ΡΠ΅ ΡΠ»Π΅ΠΌΠ΅Π½ΡΡ:
- ΠΠ΅ΡΠ°Π»Π»ΠΈΡΠ΅ΡΠΊΠΈΠ΅ ΡΡΡΠ±Ρ ΡΠ°Π·Π»ΠΈΡΠ½ΠΎΠ³ΠΎ Π΄ΠΈΠ°ΠΌΠ΅ΡΡΠ°, Π΄Π»Ρ ΠΎΡΠ΄Π΅Π»ΡΠ½ΡΡ ΡΠ·Π»ΠΎΠ² Π°ΠΏΠΏΠ°ΡΠ°ΡΠ°.
- ΠΡΠ°Π½Ρ ΠΈ Π²Π΅Π½ΡΠΈΠ»Ρ Π΄Π»Ρ ΠΊΠΎΠ½ΡΡΠΎΠ»Ρ ΠΏΠΎΠ΄Π°ΡΠΈ ΡΠΎΠΏΠ»ΠΈΠ²Π° Π΄Π»Ρ ΠΏΠ΅ΡΠΈ.
- Π’Π΅ΡΠΌΠΎΠΌΠ΅ΡΡΡ, Ρ ΠΏΠΎΠΌΠΎΡΡΡ ΠΊΠΎΡΠΎΡΡΡ Π±ΡΠ΄Π΅Ρ ΠΏΡΠΎΠΈΠ·Π²ΠΎΠ΄ΠΈΡΡΡΡ ΠΊΠΎΠ½ΡΡΠΎΠ»Ρ Π·Π° Π²Π½ΡΡΡΠ΅Π½Π½ΠΈΠΌΠΈ ΠΏΡΠΎΡΠ΅ΡΡΠ°ΠΌΠΈ ΠΈ Π·Π½Π°ΡΠ΅Π½ΠΈΠ΅ΠΌ ΠΏΠΎΠΊΠ°Π·Π°Π½ΠΈΠΉ ΡΠ΅ΠΌΠΏΠ΅ΡΠ°ΡΡΡΡ.
- ΠΠ΅ΡΠ°Π»Π»ΠΈΡΠ΅ΡΠΊΠ°Ρ Π±ΠΎΡΠΊΠ° ΠΎΠ±ΡΠ΅ΠΌΠΎΠΌ 200 Π», ΠΎΠ½Π° ΠΏΠΎΡΠ»ΡΠΆΠΈΡ Π΄Π»Ρ ΠΈΠ·Π³ΠΎΡΠΎΠ²Π»Π΅Π½ΠΈΡ ΠΊΠ°ΠΌΠ΅ΡΡ ΡΠ³ΠΎΡΠ°Π½ΠΈΡ.
- Π ΠΊΠ°ΡΠ΅ΡΡΠ²Π΅ ΡΠ΅ΡΠΎΡΡΡ ΠΏΠΎΠ΄ΠΎΠΉΠ΄Π΅Ρ ΠΎΠ±ΡΡΠ½ΡΠΉ Π±ΡΡΠΎΠ²ΠΎΠΉ Π±ΠΈΠ΄ΠΎΠ½, ΠΏΠΎΡΠ»Π΅ Π΄ΠΎΡΠ°Π±ΠΎΡΠΊΠΈ Π΅Π³ΠΎ Π³Π΅ΡΠΌΠ΅ΡΠΈΡΠ½ΡΠΌΠΈ ΡΠΎΠ΅Π΄ΠΈΠ½Π΅Π½ΠΈΡΠΌΠΈ.
ΠΠ΅ΠΉΡΡΠ²ΠΎΠ²Π°ΡΡ ΠΈΠ·Π³ΠΎΡΠΎΠ²Π»Π΅Π½Π½ΠΎΠ΅ ΡΠ²ΠΎΠΈΠΌΠΈ ΡΡΠΊΠ°ΠΌΠΈ ΠΎΠ±ΠΎΡΡΠ΄ΠΎΠ²Π°Π½ΠΈΠ΅ Π±ΡΠ΄Π΅Ρ, Π½ΠΎ ΡΠΎΠ»ΡΠΊΠΎ ΠΊΠ°ΠΊ Π±ΡΡΠΎΠ²ΠΎΠΉ ΠΏΡΠΈΠ±ΠΎΡ Π΄Π»Ρ Π½Π°ΡΡΠ½ΡΡ ΠΈΡΡΠ»Π΅Π΄ΠΎΠ²Π°Π½ΠΈΠΉ. ΠΠ΅Π· Π΄ΠΎΠΏΠΎΠ»Π½ΠΈΡΠ΅Π»ΡΠ½ΠΎΠ³ΠΎ ΠΎΠ±ΠΎΡΡΠ΄ΠΎΠ²Π°Π½ΠΈΡ Π΄Π»Ρ Π΄Π°Π»ΡΠ½Π΅ΠΉΡΠ΅ΠΉ ΠΏΠ΅ΡΠ΅ΡΠ°Π±ΠΎΡΠΊΠΈ ΠΏΠΎΠ»ΡΡΠ°Π΅ΠΌΠΎΠ³ΠΎ ΡΡΡΡΡ, ΠΏΡΠΎΠ΄ΡΠΊΡΡ Π±ΡΡΠΎΠ²ΠΎΠ³ΠΎ ΠΏΡΠΎΡΠ΅ΡΡΠ° ΠΏΠΈΡΠΎΠ»ΠΈΠ·Π° ΠΌΠ°Π»ΠΎΠΏΡΠΈΠ³ΠΎΠ΄Π½Ρ Π΄Π»Ρ ΠΏΡΠΈΠΌΠ΅Π½Π΅Π½ΠΈΡ ΠΏΠΎ ΡΠ²ΠΎΠ΅ΠΌΡ Π½Π°Π·Π½Π°ΡΠ΅Π½ΠΈΡ. ΠΠΊΠΎΠ½ΠΎΠΌΠΈΡΠ΅ΡΠΊΠ°Ρ Π²ΡΠ³ΠΎΠ΄Π° ΠΏΡΠΈ ΠΈΡΠΏΠΎΠ»ΡΠ·ΠΎΠ²Π°Π½ΠΈΠΈ ΡΠ°ΠΊΠΎΠΉ ΡΡΡΠ°Π½ΠΎΠ²ΠΊΠΈ Π±ΡΠ΄Π΅Ρ Π½Π΅Π·Π°ΠΌΠ΅ΡΠ½Π° Π² ΡΠ΅Π·ΡΠ»ΡΡΠ°ΡΠ΅ ΠΌΠ°Π»ΠΎΠ³ΠΎ Π²ΠΎΠ·ΠΌΠΎΠΆΠ½ΠΎΠ³ΠΎ ΠΎΠ±ΡΠ΅ΠΌΠ° ΡΠΈΠ½.
Π’Π΅Ρ Π½ΠΎΠ»ΠΎΠ³ΠΈΡΠ΅ΡΠΊΠΈΠΉ ΠΏΡΠΎΡΠ΅ΡΡ ΡΠ°Π·Π»ΠΎΠΆΠ΅Π½ΠΈΡ Π°Π²ΡΠΎΠΌΠΎΠ±ΠΈΠ»ΡΠ½ΡΡ ΠΏΠΎΠΊΡΡΡΠ΅ΠΊ ΡΠ²Π»ΡΠ΅ΡΡΡ Π²Π·ΡΡΠ²ΠΎΠΎΠΏΠ°ΡΠ½ΡΠΌ. ΠΡΠΈ ΠΏΠΎΠΏΠ°Π΄Π°Π½ΠΈΠΈ ΠΊΠΈΡΠ»ΠΎΡΠΎΠ΄Π° Π² ΡΠ°Π·Π³Π΅ΡΠΌΠ΅ΡΠΈΠ·ΠΈΡΠΎΠ²Π°Π½Π½ΡΡ ΡΠ΅ΡΠΎΡΡΡ ΠΌΠΎΠΆΠ΅Ρ ΠΏΡΠΎΠΈΠ·ΠΎΠΉΡΠΈ Π²Π·ΡΡΠ². Π’Π°ΠΊΠ°Ρ Π°Π²Π°ΡΠΈΠΉΠ½Π°Ρ ΡΠΈΡΡΠ°ΡΠΈΡ ΠΏΡΠΈΠ²Π΅Π΄Π΅Ρ ΠΊ Π²ΡΡ ΠΎΠ΄Ρ Π²ΡΠ΅Π³ΠΎ ΠΎΠ±ΠΎΡΡΠ΄ΠΎΠ²Π°Π½ΠΈΡ ΠΈΠ· ΡΡΡΠΎΡ, Π° ΡΠ°ΠΊΠΆΠ΅ ΠΊ Π½Π΅ΡΡΠ°ΡΡΠ½ΡΠΌ ΡΠ»ΡΡΠ°ΡΠΌ Π² ΠΏΡΠΎΡΠ΅ΡΡΠ΅ ΡΠΊΡΠΏΠ»ΡΠ°ΡΠ°ΡΠΈΠΈ.
ΠΠ»Ρ ΡΠ²Π΅Π»ΠΈΡΠ΅Π½ΠΈΡ Π²ΡΠ³ΠΎΠ΄Ρ ΠΏΡΠΈ ΠΏΠ΅ΡΠ΅ΡΠ°Π±ΠΎΡΠΊΠ΅ ΠΏΠΎΠΊΡΡΡΠ΅ΠΊ Π² ΠΏΡΠΈΠ³ΠΎΠ΄Π½ΠΎΠ΅ ΡΠΎΠΏΠ»ΠΈΠ²ΠΎ Π½Π΅ΠΎΠ±Ρ ΠΎΠ΄ΠΈΠΌΠΎ ΠΏΡΠΈΠΌΠ΅Π½ΡΡΡ Π³ΠΎΡΠΎΠ²ΡΠ΅ ΡΡΡΠ°Π½ΠΎΠ²ΠΊΠΈ ΠΏΠΈΡΠΎΠ»ΠΈΠ·Π°, ΠΈΠ·Π³ΠΎΡΠΎΠ²Π»Π΅Π½Π½ΡΠ΅ ΡΠΏΠ΅ΡΠΈΠ°Π»ΠΈΡΡΠ°ΠΌΠΈ.
Π‘ΠΎΠ²ΡΠ΅ΠΌΠ΅Π½Π½ΡΠΉ ΡΡΠ½ΠΎΠΊ ΠΈΠΌΠ΅Π΅Ρ Π²ΠΎΠ·ΠΌΠΎΠΆΠ½ΠΎΡΡΡ ΠΏΡΠ΅Π΄ΡΡΠ°Π²ΠΈΡΡ ΠΏΡΠΎΠΈΠ·Π²ΠΎΠ΄ΡΡΠ²Π΅Π½Π½ΠΎΠ΅ ΠΎΠ±ΠΎΡΡΠ΄ΠΎΠ²Π°Π½ΠΈΠ΅ ΡΠ°Π·Π»ΠΈΡΠ½ΡΡ Π·Π½Π°ΡΠ΅Π½ΠΈΠΉ ΠΏΡΠΎΠΈΠ·Π²ΠΎΠ΄ΠΈΡΠ΅Π»ΡΠ½ΠΎΡΡΠΈ.
ΠΠΎΠ»ΡΡΠ°Π΅ΠΌΠΎΠ΅ ΡΡΡΡΠ΅ Π½Π΅ΠΎΠ±Ρ ΠΎΠ΄ΠΈΠΌΠΎ Π² Π΄Π°Π»ΡΠ½Π΅ΠΉΡΠ΅ΠΌ ΡΠ»ΡΡΡΠ°ΡΡ ΠΈ ΠΏΠ΅ΡΠ΅ΡΠ°Π±Π°ΡΡΠ²Π°ΡΡ, Π΄Π»Ρ ΡΡΠΎΠ³ΠΎ Π² ΠΏΡΠΎΠΌΡΡΠ»Π΅Π½Π½ΡΡ Π°Π³ΡΠ΅Π³Π°ΡΠ°Ρ ΠΏΡΠΈΠΌΠ΅Π½ΡΡΡΡΡ Π΄ΠΎΠΏΠΎΠ»Π½ΠΈΡΠ΅Π»ΡΠ½ΡΠ΅ Π²ΡΠΏΠΎΠΌΠΎΠ³Π°ΡΠ΅Π»ΡΠ½ΡΠ΅ ΡΠ·Π»Ρ:
- Π‘ΠΊΡΡΠ±Π±Π΅Ρ. Π£ΡΡΡΠΎΠΉΡΡΠ²ΠΎ, ΠΊΠΎΡΠΎΡΠΎΠ΅ ΠΎΡ Π»Π°ΠΆΠ΄Π°Π΅Ρ ΠΏΠΎΠ»ΡΡΠ°Π΅ΠΌΡΠΉ Π² ΡΠ΅Π·ΡΠ»ΡΡΠ°ΡΠ΅ ΠΏΠΈΡΠΎΠ»ΠΈΠ· Π³Π°Π·, Ρ ΠΏΡΠΈΠΌΠ΅Π½Π΅Π½ΠΈΠ΅ΠΌ ΡΠΏΠ΅ΡΠΈΠ°Π»ΡΠ½ΡΡ Ρ ΠΈΠΌΠΈΡΠ΅ΡΠΊΠΈΡ Π²Π΅ΡΠ΅ΡΡΠ². ΠΡΠΎΠΈΡΡ ΠΎΠ΄ΠΈΡ ΡΠ°ΡΡΠΈΡΠ½Π°Ρ ΠΊΠΎΠ½Π΄Π΅Π½ΡΠ°ΡΠΈΡ Π² ΠΆΠΈΠ΄ΠΊΠΎΡΡΡ.
- Π‘Π΅ΠΏΠ°ΡΠ°ΡΠΎΡ. Π‘Π½ΠΈΠΆΠ°Π΅Ρ ΡΡΠΎΠ²Π΅Π½Ρ Π²Π»Π°ΠΆΠ½ΠΎΡΡΠΈ ΠΏΠΎΠ»ΡΡΠ΅Π½Π½ΠΎΠ³ΠΎ Π³Π°Π·Π° ΠΏΠ΅ΡΠ΅Π΄ Π΄Π°Π»ΡΠ½Π΅ΠΉΡΠ΅ΠΉ ΠΏΠΎΠ΄Π°ΡΠ΅ΠΉ Π² ΠΏΠ΅ΡΡ.
- ΠΠΎΠ½Π΄Π΅Π½ΡΠ°ΡΠΎΡ. ΠΠΊΠΎΠ½ΡΠ°ΡΠ΅Π»ΡΠ½ΠΎ ΠΏΡΠ΅ΠΎΠ±ΡΠ°Π·ΡΠ΅Ρ ΠΏΠΎΠ»ΡΡΠ΅Π½Π½ΡΡ Π³Π°Π·ΠΎΠΎΠ±ΡΠ°Π·Π½ΡΡ ΡΡΠ°ΠΊΡΠΈΡ Π² ΠΆΠΈΠ΄ΠΊΠΎΡΡΡ.
- Π€ΠΈΠ»ΡΡΡΡ. ΠΠ°ΡΠΈΡΠ°ΡΡ ΠΎΡ ΠΏΠΎΠΏΠ°Π΄Π°Π½ΠΈΡ Π²ΡΠ΅Π΄Π½ΡΡ Π²Π΅ΡΠ΅ΡΡΠ² Π² Π°ΡΠΌΠΎΡΡΠ΅ΡΡ, Π² ΡΠ΅Π·ΡΠ»ΡΡΠ°ΡΠ΅ Π³ΠΎΡΠ΅Π½ΠΈΡ.
Π Ρ ΠΎΠ΄Π΅ ΠΏΡΠΎΡΠ΅ΡΡΠ° ΠΏΠΈΡΠΎΠ»ΠΈΠ·Π° Π½Π΅ΠΎΠ±Ρ ΠΎΠ΄ΠΈΠΌΠΎ ΡΠΎΠ±Π»ΡΠ΄Π°ΡΡ ΠΏΡΠ°Π²ΠΈΠ»Π° Π±Π΅Π·ΠΎΠΏΠ°ΡΠ½ΠΎΠΉ ΡΠΊΡΠΏΠ»ΡΠ°ΡΠ°ΡΠΈΠΈ.
Π Π°Π±ΠΎΡΠ° ΠΏΠ΅ΡΠΈ
ΠΠ΅ΡΠΎΠ΄ ΡΠ°Π±ΠΎΡΡ ΠΏΡΠΎΠΌΡΡΠ»Π΅Π½Π½ΠΎΠΉ ΠΏΠΈΡΠΎΠ»ΠΈΠ·Π½ΠΎΠΉ ΡΡΡΠ°Π½ΠΎΠ²ΠΊΠΈ Π΄Π»Ρ ΠΏΠ΅ΡΠ΅ΡΠ°Π±ΠΎΡΠΊΠΈ ΡΠ΅Π·ΠΈΠ½ΠΎΠ²ΡΡ ΠΈΠ·Π΄Π΅Π»ΠΈΠΉ ΠΈ ΡΠΈΠ½ ΠΏΠΎΠ΄ΡΠ°Π·ΡΠΌΠ΅Π²Π°Π΅Ρ Π½Π΅ΡΠΊΠΎΠ»ΡΠΊΠΎ ΠΎΡΠ½ΠΎΠ²Π½ΡΡ ΡΡΠ°ΠΏΠΎΠ² ΠΏΡΠΎΠΈΠ·Π²ΠΎΠ΄ΡΡΠ²Π°:
- ΠΠΎΠ΄Π³ΠΎΡΠΎΠ²ΠΊΠ° ΠΌΠ°ΡΠ΅ΡΠΈΠ°Π»Π° Π΄Π»Ρ Π΅Π³ΠΎ Π΄Π°Π»ΡΠ½Π΅ΠΉΡΠ΅Π³ΠΎ ΡΠ°Π·Π»ΠΎΠΆΠ΅Π½ΠΈΡ Π² ΡΠ΅ΡΠΎΡΡΠ΅.
- ΠΠΎΠ»ΡΡΠ΅Π½Π½ΠΎΠ΅ ΡΡΡΡΠ΅ ΠΏΡΠΈ ΠΏΠΈΡΠΎΠ»ΠΈΠ·Π΅ ΠΏΠΎΠ΄Π°Π΅ΡΡΡ Π² ΡΡΡΡΠΎΠΉΡΡΠ²ΠΎ Π΄Π»Ρ ΠΎΡ Π»Π°ΠΆΠ΄Π΅Π½ΠΈΡ ΠΈ ΡΠ°ΡΡΠΈΡΠ½ΠΎΠΉ ΠΊΠΎΠ½Π΄Π΅Π½ΡΠ°ΡΠΈΠΈ ΠΏΠΈΡΠΎΠ»ΠΈΠ·Π½ΠΎΠ³ΠΎ Π³Π°Π·Π°.
- ΠΡΠΈ ΠΏΡΠΎΡ ΠΎΠΆΠ΄Π΅Π½ΠΈΠΈ ΡΠ΅ΡΠ΅Π· ΠΊΠΎΠ½Π΄Π΅Π½ΡΠΈΡΡΡΡΠΈΠΉ ΡΡΡΠ±ΠΎΠΏΡΠΎΠ²ΠΎΠ΄ ΠΏΡΠΎΠΈΡΡ ΠΎΠ΄ΠΈΡ ΠΎΠΊΠΎΠ½ΡΠ°ΡΠ΅Π»ΡΠ½ΠΎΠ΅ ΡΠ°Π·Π΄Π΅Π»Π΅Π½ΠΈΠ΅ Π½Π° ΠΆΠΈΠ΄ΠΊΡΡ ΠΈ Π³Π°Π·ΠΎΠΎΠ±ΡΠ°Π·Π½ΡΡ ΡΠΎΡΡΠ°Π²Π»ΡΡΡΡΡ.
- ΠΡΠΈ ΠΎΡΡΡΠ΅Π½ΠΈΠΈ ΠΎΡΡΠ°Π²ΡΠ΅Π³ΠΎΡΡ Π³Π°Π·Π° Π΅Π³ΠΎ ΠΏΠΎΠ΄Π°ΡΡ Π΄Π»Ρ Π΄Π°Π»ΡΠ½Π΅ΠΉΡΠ΅Π³ΠΎ ΡΠΆΠΈΠ³Π°Π½ΠΈΡ Π² ΠΏΠ΅ΡΠΈ.
ΠΠΎΠ»ΡΡΠΈΠ΅ ΠΏΠ΅ΡΠ΅ΡΠ°Π±Π°ΡΡΠ²Π°ΡΡΠΈΠ΅ Π·Π°Π²ΠΎΠ΄Ρ ΠΈΡΠΏΠΎΠ»ΡΠ·ΡΡΡ Π² ΠΏΡΠΎΡΠ΅ΡΡΠ΅ ΡΠ°Π·Π»ΠΎΠΆΠ΅Π½ΠΈΡ ΡΠ΅Π·ΠΈΠ½Ρ Π΄ΠΎΠΏΠΎΠ»Π½ΠΈΡΠ΅Π»ΡΠ½ΡΠ΅ ΠΊΠ°ΡΠ°Π»ΠΈΠ·Π°ΡΠΎΡΠ½ΡΠ΅ ΡΡΡΠ°Π½ΠΎΠ²ΠΊΠΈ.
Π ΡΠ°ΠΊΠΎΠΌ ΠΎΠ±ΠΎΡΡΠ΄ΠΎΠ²Π°Π½ΠΈΠΈ ΠΏΡΠΎΠΈΡΡ ΠΎΠ΄ΠΈΡ ΠΏΠ΅ΡΠ΅Π³ΠΎΠ½ΠΊΠ° ΠΏΠΈΡΠΎΠ»ΠΈΠ·Π½ΠΎΠ³ΠΎ ΡΡΡΡΡ Π² ΡΠ°Π·Π»ΠΈΡΠ½ΠΎΠ΅ ΡΠΎΠΏΠ»ΠΈΠ²ΠΎ, Π΄Π»Ρ Π΄Π°Π½Π½ΡΡ ΡΡΡΠ°Π½ΠΎΠ²ΠΎΠΊ Π½Π΅ΠΎΠ±Ρ ΠΎΠ΄ΠΈΠΌΡ Π±ΠΎΠ»ΡΡΠΈΠ΅ ΠΏΠ»ΠΎΡΠ°Π΄ΠΈ ΠΈ Π΄ΠΎΡΡΠ°ΡΠΎΡΠ½ΠΎΠ΅ ΡΠΈΠ½Π°Π½ΡΠΈΡΠΎΠ²Π°Π½ΠΈΠ΅.
Π Π½Π°ΡΠ΅ΠΉ ΡΡΡΠ°Π½Π΅ ΠΌΠ΅ΡΠΎΠ΄ ΡΠ΅Ρ Π½ΠΎΠ»ΠΎΠ³ΠΈΡΠ΅ΡΠΊΠΎΠΉ ΠΏΠ΅ΡΠ΅ΡΠ°Π±ΠΎΡΠΊΠΈ ΡΠ΅Π·ΠΈΠ½Ρ ΠΏΠΎΠΊΠ° Π½Π΅ ΠΈΡΠΏΠΎΠ»ΡΠ·ΡΠ΅ΡΡΡ ΡΠΈΡΠΎΠΊΠΎ, ΠΎΠ΄Π½Π°ΠΊΠΎ Π½Π° ΡΡΠ½ΠΊΠ΅ ΠΏΡΠ΅Π΄ΡΡΠ°Π²Π»ΡΡΡΡΡ Π΄ΠΎΡΡΠΎΠΉΠ½ΡΠ΅ ΠΎΠ±ΡΠ°Π·ΡΡ ΡΡΡΠ°Π½ΠΎΠ²ΠΎΠΊ ΠΎΡΠ΅ΡΠ΅ΡΡΠ²Π΅Π½Π½ΠΎΠ³ΠΎ ΠΏΡΠΎΠΈΠ·Π²ΠΎΠ΄ΡΡΠ²Π°.
stop-othod.ru
ΠΠΈΡΠΎΠ»ΠΈΠ·Π½Π°Ρ ΡΡΡΠ°Π½ΠΎΠ²ΠΊΠ° Π΄Π»Ρ ΠΏΠ΅ΡΠ΅ΡΠ°Π±ΠΎΡΠΊΠΈ ΡΠΈΠ½, ΠΏΠΎΠΊΡΡΡΠ΅ΠΊ. ΠΠΈΡΠΎΠ»ΠΈΠ·
ΠΠΈΡΠΎΠ»ΠΈΠ· ΡΠΈΠ½, ΠΏΠΎΠΊΡΡΡΠ΅ΠΊ, ΠΏΠ»Π°ΡΡΠΈΠΊΠΎΠ² ΠΈ Π΄ΡΡΠ³ΠΈΡ
ΠΎΡΡ
ΠΎΠ΄ΠΎΠ² ΠΏΠΎΠ·Π²ΠΎΠ»ΡΠ΅Ρ ΡΡΠΈΠ»ΠΈΠ·ΠΎΠ²Π°ΡΡ ΠΈ ΠΏΠ΅ΡΠ΅ΡΠ°Π±ΠΎΡΠ°ΡΡ ΡΠΎΠΊΡΠΈΡΠ½ΡΠ΅ ΠΎΡΡ
ΠΎΠ΄Ρ Π² ΡΠΎΠΏΠ»ΠΈΠ²ΠΎ, ΡΠ³Π»Π΅ΡΠΎΠ΄ ΠΈ ΠΌΠ΅ΡΠ°Π»Π»ΠΎΠΊΠΎΡΠ΄. ΠΠΈΡΠΎΠ»ΠΈΠ·Π½Π°Ρ ΡΡΡΠ°Π½ΠΎΠ²ΠΊΠ° ΠΏΡΠΎΡΡΠ° ΠΈ ΡΡΡΠ΅ΠΊΡΠΈΠ²Π½Π°. ΠΠ»ΠΎΠΆΠ΅Π½ΠΈΡ Π² ΠΏΠΈΡΠΎΠ»ΠΈΠ·Π½ΠΎΠ΅ ΠΎΠ±ΠΎΡΡΠ΄ΠΎΠ²Π°Π½ΠΈΠ΅ ΠΎΠΊΡΠΏΠ°Π΅ΡΡΡ ΠΌΠ΅Π½Π΅Π΅ ΡΠ΅ΠΌ Π·Π° Π³ΠΎΠ΄, ΠΏΡΠΈ ΠΏΡΠΈΠΎΠ±ΡΠ΅ΡΠ΅Π½ΠΈΠΈ ΠΎΠ±ΠΎΡΡΠ΄ΠΎΠ²Π°Π½ΠΈΡ Π² Π»ΠΈΠ·ΠΈΠ½Π³ ΡΡΠΎΠΊ ΠΎΠΊΡΠΏΠ°Π΅ΠΌΠΎΡΡΠΈ ΡΠ½ΠΈΠΆΠ°Π΅ΡΡΡ Π΄ΠΎ Π½Π΅ΡΠΊΠΎΠ»ΡΠΊΠΈΡ
ΠΌΠ΅ΡΡΡΠ΅Π². ΠΠΈΡΠΎΠ»ΠΈΠ·Π½Π°Ρ ΡΡΡΠ°Π½ΠΎΠ²ΠΊΠ° Π½Π΅ ΡΡΠ΅Π±ΡΠ΅Ρ ΠΌΠ½ΠΎΠ³ΠΎΡΠΈΡΠ»Π΅Π½Π½ΠΎΠ³ΠΎ ΠΏΠ΅ΡΡΠΎΠ½Π°Π»Π°. ΠΠ»Ρ ΠΎΠ±ΡΠ»ΡΠΆΠΈΠ²Π°Π½ΠΈΡ Π³ΠΎΡΠΈΠ·ΠΎΠ½ΡΠ°Π»ΡΠ½ΠΎΠΉ ΠΏΠΈΡΠΎΠ»ΠΈΠ·Π½ΠΎΠΉ ΡΡΡΠ°Π½ΠΎΠ²ΠΊΠΈ ΡΡΠ΅Π±ΡΠ΅ΡΡΡ 3-4 ΡΠ΅Π»ΠΎΠ²Π΅ΠΊΠ° Π² ΠΌΠΎΠΌΠ΅Π½Ρ Π·Π°Π³ΡΡΠ·ΠΊΠΈ (3 – 5 ΡΠ°ΡΠΎΠ² Π² Π·Π°Π²ΠΈΡΠΈΠΌΠΎΡΡΠΈ ΠΎΡ ΠΎΠ±ΡΠ΅ΠΌΠ°) ΠΈ Π΄Π΅ΠΆΡΡΠ½ΡΠΉ Π²ΠΎ Π²ΡΠ΅ΠΌΡ ΡΠ°Π±ΠΎΡΡ. Π‘ΡΠΎΠΊ ΡΠ»ΡΠΆΠ±Ρ ΠΏΠΈΡΠΎΠ»ΠΈΠ·Π½ΠΎΠ³ΠΎ ΡΠ΅Π°ΠΊΡΠΎΡΠ° ΠΈΠ· ΠΆΠ°ΡΠΎΠΏΡΠΎΡΠ½ΠΎΠΉ ΡΡΠ°Π»ΠΈ ΡΠΎΠ»ΡΠΈΠ½ΠΎΠΉ 16 -18 ΠΌΠΌ ΠΎΠΊΠΎΠ»ΠΎ 7-8 Π»Π΅Ρ. ΠΠΎΠ·ΠΌΠΎΠΆΠ½Π° ΠΏΠΎΡΡΠ°Π²ΠΊΠ° ΡΠ΅Π°ΠΊΡΠΎΡΠ° ΠΈΠ· ΠΆΠ°ΡΠΎΠΏΡΠΎΡΠ½ΠΎΠΉ Π½Π΅ΡΠΆΠ°Π²Π΅ΡΡΠ΅ΠΉ ΡΡΠ°Π»ΠΈ. ΠΠΎΡΠ»Π΅ 7 -8 Π»Π΅Ρ ΡΠΊΡΠΏΠ»ΡΠ°ΡΠ°ΡΠΈΠΈ ΡΠ΅Π°ΠΊΡΠΎΡ ΠΌΠ΅Π½ΡΠ΅ΡΡΡ Π½Π° Π½ΠΎΠ²ΡΠΉ. ΠΡΡΠ°Π»ΡΠ½ΡΠ΅ ΡΠ·Π»Ρ ΡΡΡΠ°Π½ΠΎΠ²ΠΊΠΈΒ Π·Π°ΠΌΠ΅Π½Ρ Π½Π΅ ΡΡΠ΅Π±ΡΡΡ. Π ΡΡΡΠ°Π½ΠΎΠ²ΠΊΠ΅ ΠΈΡΠΏΠΎΠ»ΡΠ·ΠΎΠ²Π°Π½Π° Π°Π²ΡΠΎΠΌΠ°ΡΠΈΠΊΠ°
ΠΠΎΠ·ΠΌΠΎΠΆΠ΅Π½ Π»ΠΈΠ·ΠΈΠ½Π³ ΠΎΠ±ΠΎΡΡΠ΄ΠΎΠ²Π°Π½ΠΈΡΒ Π½Π° 2 – 5 Π»Π΅Ρ, ΠΏΠ΅ΡΠ²ΡΠΉ Π²Π·Π½ΠΎΡ 10 -15%,Β ΡΠ΄ΠΎΡΠΎΠΆΠ°Π½ΠΈΠ΅ 5 -12% Π² Π³ΠΎΠ΄, Π²Π°Π»ΡΡΠ° – ΡΡΠ±Π»ΠΈ.
Β ΠΠΈΡΠΎΠ»ΠΈΠ· ΠΎΡΡ ΠΎΠ΄ΠΎΠ². Π Π·Π°Π²ΠΈΡΠΈΠΌΠΎΡΡΠΈ ΠΎΡ ΡΠ΅ΠΌΠΏΠ΅ΡΠ°ΡΡΡ ΠΈ ΠΌΠ°ΡΠ΅ΡΠΈΠ°Π»ΠΎΠ² ΠΏΡΠΈΠΌΠ΅Π½ΡΡΡΡΡ ΡΡΡΠ°Π½ΠΎΠ²ΠΊΠΈ Π½ΠΈΠ·ΠΊΠΎΡΠ΅ΠΌΠΏΠ΅ΡΠ°ΡΡΡΠ½ΠΎΠ³ΠΎ ΠΏΠΈΡΠΎΠ»ΠΈΠ·Π° ΠΈ Π²ΡΡΠΎΠΊΠΎΡΠ΅ΠΌΠΏΠ΅ΡΠ°ΡΡΡΠ½ΠΎΠ³ΠΎ ΠΏΠΈΡΠΎΠ»ΠΈΠ·Π° ΠΎΡΡ ΠΎΠ΄ΠΎΠ².
ΠΠΈΠ·ΠΊΠΎΡΠ΅ΠΌΠΏΠ΅ΡΠ°ΡΡΡΠ½ΡΠΉ ΠΏΠΈΡΠΎΠ»ΠΈΠ· – ΠΏΡΠΎΡΠ΅ΡΡ ΡΠ°Π·Π»ΠΎΠΆΠ΅Π½ΠΈΡ ΠΎΡΡ ΠΎΠ΄ΠΎΠ² Π±Π΅Π· Π΄ΠΎΡΡΡΠΏΠ° Π²ΠΎΠ·Π΄ΡΡ Π° ΠΏΡΠΈ ΡΠ΅ΠΌΠΏΠ΅ΡΠ°ΡΡΡΠ°Ρ – 300-600Β° C. ΠΡΠΎΡ ΡΠΏΠΎΡΠΎΠ± Ρ Π°ΡΠ°ΠΊΡΠ΅ΡΠΈΠ·ΡΠ΅ΡΡΡ ΠΌΠ°ΠΊΡΠΈΠΌΠ°Π»ΡΠ½ΡΠΌ Π²ΡΡ ΠΎΠ΄ΠΎΠΌ ΠΆΠΈΠ΄ΠΊΠΈΡ ΠΏΡΠΎΠ΄ΡΠΊΡΠΎΠ². Π ΠΏΡΠΎΡΠ΅ΡΡΠ΅ ΠΏΠΈΡΠΎΠ»ΠΈΠ·Π° ΠΌΡ ΠΏΠΎΠ»ΡΡΠ°Π΅ΠΌ ΡΠΎΠΏΠ»ΠΈΠ²ΠΎ ΠΈ Π΄ΡΡΠ³ΠΈΠ΅ ΡΠ΅Π½Π½ΡΠ΅ ΠΎΡΡ ΠΎΠ΄Ρ. Π Π½Π°ΡΠΈΡ ΡΡΡΠ°Π½ΠΎΠ²ΠΊΠ°Ρ ΠΈΡΠΏΠΎΠ»ΡΠ·ΡΠ΅ΡΡΡ ΠΏΡΠΎΡΠ΅ΡΡ ΠΊΠ°ΡΠ°Π»ΠΈΡΠΈΡΠ΅ΡΠΊΠΎΠ³ΠΎ ΠΏΠΈΡΠΎΠ»ΠΈΠ·Π° ΠΏΠΎΠ·Π²ΠΎΠ»ΡΡΡΠΈΠΉ ΡΠ²Π΅Π»ΠΈΡΠΈΡΡ ΡΡΡΠ΅ΠΊΡΠΈΠ²Π½ΠΎΡΡΡ ΠΈ ΡΠΊΠΎΡΠΎΡΡΡ ΠΏΡΠΎΡΠ΅ΡΡΠ°. Π ΡΡΡΠ°Π½ΠΎΠ²ΠΊΠ°Ρ Π½Π° Π²ΡΡ ΠΎΠ΄Π΅ ΠΌΡ ΠΏΠΎΠ»ΡΡΠ°Π΅ΠΌ ΡΡΠΆΠ΅Π»ΡΡ ΠΈ Π»Π΅Π³ΠΊΡΡ ΡΡΠ°ΠΊΡΠΈΠΈ ΡΠΎΠΏΠ»ΠΈΠ²Π°, Π½Π΅ΠΊΠΎΠ½Π΄Π΅Π½ΡΠΈΡΡΠ΅ΠΌΡΠ΅ ΡΡΠ°ΠΊΡΠΈΠΈ- Π³Π°Π· ΠΈΡΠΏΠΎΠ»ΡΠ·ΡΠ΅ΡΡΡ Π΄Π»Ρ ΠΏΠΎΠ΄ΠΎΠ³ΡΠ΅Π²Π° ΠΏΠΈΡΠΎΠ»ΠΈΠ·Π½ΠΎΠΉ ΠΏΠ΅ΡΠΈ, ΠΏΠΎΡΡΠΎΠΌΡ Π΄Π»Ρ ΡΠ°Π±ΠΎΡΡ ΠΏΠΈΡΠΎΠ»ΠΈΠ·Π½ΠΎΠΉ Π½Π΅ΠΎΠ±Ρ ΠΎΠ΄ΠΈΠΌ ΡΠΎΠ»ΡΠΊΠΎ ΠΏΠ΅ΡΠ²ΠΎΠ½Π°ΡΠ°Π»ΡΠ½ΡΠΉ ΠΏΠΎΠ΄ΠΎΠ³ΡΠ΅Π². ΠΠΎΡΠ»Π΅ Π½Π°ΡΠ°Π»Π° ΠΏΡΠΎΡΠ΅ΡΡΠ° ΠΏΠΈΡΠΎΠ»ΠΈΠ·Π° Π΄Π»Ρ ΠΏΠΎΠ΄ΠΎΠ³ΡΠ΅Π²Π° ΠΈΡΠΏΠΎΠ»ΡΠ·ΡΡΡΡΡ Π²ΡΠ΄Π΅Π»ΡΡΡΠΈΠΉΡΡ Π³Π°Π·. ΠΡΠ»ΠΈ ΠΡ ΠΏΡΠΈΠΎΠ±ΡΠ΅ΡΠ°Π΅ΡΠ΅ 2 ΡΡΡΠ°Π½ΠΎΠ²ΠΊΠΈ ΠΈ ΠΎΠ½ΠΈ ΡΠ°Π±ΠΎΡΠ°ΡΡ Π²ΠΌΠ΅ΡΡΠ΅, ΠΈΠ·Π»ΠΈΡΠΊΠΈ Π³Π°Π·Π° Π² ΠΎΠ΄Π½ΠΎΠΉ ΠΏΠΈΡΠΎΠ»ΠΈΠ·Π½ΠΎΠΉ ΡΡΡΠ°Π½ΠΎΠ²ΠΊΠ΅ ΠΈΡΠΏΠΎΠ»ΡΠ·ΡΡΡΡΡ Π΄Π»Ρ Π·Π°ΠΏΡΡΠΊΠ° ΠΏΡΠΎΡΠ΅ΡΡΠ° ΠΏΠΈΡΠΎΠ»ΠΈΠ·Π° Π²ΠΎ Π²ΡΠΎΡΠΎΠΉ ΡΡΡΠ°Π½ΠΎΠ²ΠΊΠ΅. ΠΡΠΏΠ°Π΄Π°Π΅Ρ ΠΏΠΎΡΡΠ΅Π±Π½ΠΎΡΡΡ Π² ΠΊΠ°ΠΊΠΎΠΌ Π»ΠΈΠ±ΠΎ Π΄ΠΎΠΏΠΎΠ»Π½ΠΈΡΠ΅Π»ΡΠ½ΠΎΠΌ Π²ΠΈΠ΄Π΅ ΡΠΎΠΏΠ»ΠΈΠ²Π° Π²ΠΎΠΎΠ±ΡΠ΅. ΠΠΈΡΠΎΠ»ΠΈΠ·Π½Π°Ρ ΡΡΡΠ°Π½ΠΎΠ²ΠΊΠ° ΠΊΠΎΠΌΠΏΠ»Π΅ΠΊΡΡΠ΅ΡΡΡ 4Ρ - ΡΡΡΠΏΠ΅Π½ΡΠ°ΡΠΎΠΉ ΡΠΈΡΡΠ΅ΠΌΠΎΠΉ ΠΎΡΠΈΡΡΠΊΠΈ Π³Π°Π·ΠΎΠ². ΠΡΠ°ΠΉΡ Π»ΠΈΡΡ Π½Π° ΠΏΠΈΡΠΎΠ»ΠΈΠ·Π½ΡΠ΅ ΡΡΡΠ°Π½ΠΎΠ²ΠΊΠΈ.
ΠΡΡΠΎΠΊΠΎΡΠ΅ΠΌΠΏΠ΅ΡΠ°ΡΡΡΠ½ΡΠΉ ΠΏΠΈΡΠΎΠ»ΠΈΠ· ΠΏΡΠΎΡΠ΅ΠΊΠ°Π΅Ρ ΠΏΡΠΈ ΡΠ΅ΠΌΠΏΠ΅ΡΠ°ΡΡΡΠ°Ρ ΠΎΠΊΠΎΠ»ΠΎ 1000- 1400 Π³ΡΠ°Π΄ΡΡΠΎΠ² ΠΈ Ρ Π°ΡΠ°ΠΊΡΠ΅ΡΠΈΠ·ΡΠ΅ΡΡΡ ΠΌΠ°ΠΊΡΠΈΠΌΠ°Π»ΡΠ½ΡΠΌ Π²ΡΡ ΠΎΠ΄ΠΎΠΌ Π³Π°Π·Π°. ΠΡΡΠΎΠΊΠΎΡΠ΅ΠΌΠΏΠ΅ΡΠ°ΡΡΡΠ½ΡΠΉ ΠΏΠΈΡΠΎΠ»ΠΈΠ· – ΠΎΠ΄ΠΈΠ½ Π»ΡΡΡΠΈΡ ΡΠΏΠΎΡΠΎΠ±ΠΎΠ² ΠΏΠ΅ΡΠ΅ΡΠ°Π±ΠΎΡΠΊΠΈ ΡΠ²Π΅ΡΠ΄ΡΡ Π±ΡΡΠΎΠ²ΡΡ ΠΎΡΡ ΠΎΠ΄ΠΎΠ², Π’ΠΠ, ΠΊΠ°ΠΊ Ρ ΡΠΎΡΠΊΠΈ Π·ΡΠ΅Π½ΠΈΡ ΠΊΠ°ΠΊ ΡΠΊΠΎΠ»ΠΎΠ³ΠΈΡΠ΅ΡΠΊΠΎΠΉ Π±Π΅Π·ΠΎΠΏΠ°ΡΠ½ΠΎΡΡΠΈ, ΡΠ°ΠΊ ΠΈ ΠΏΠΎΠ»ΡΡΠ΅Π½ΠΈΡ ΡΠΈΠ½ΡΠ΅Π·-Π³Π°Π·Π°, ΡΠ»Π°ΠΊΠ°, ΠΌΠ΅ΡΠ°Π»Π»ΠΎΠ² ΠΈ Π΄ΡΡΠ³ΠΈΡ ΠΌΠ°ΡΠ΅ΡΠΈΠ°Π»ΠΎΠ², ΠΊΠΎΡΠΎΡΡΠ΅ ΠΌΠΎΠ³ΡΡ Π½Π°ΠΉΡΠΈ ΡΠΈΡΠΎΠΊΠΎΠ΅ ΠΏΡΠΈΠΌΠ΅Π½Π΅Π½ΠΈΠ΅ Π² Π½Π°ΡΠΎΠ΄Π½ΠΎΠΌ Ρ ΠΎΠ·ΡΠΉΡΡΠ²Π΅. ΠΡΡΠΎΠΊΠΎΡΠ΅ΠΌΠΏΠ΅ΡΠ°ΡΡΡΠ½Π°Ρ Π³Π°Π·ΠΈΡΠΈΠΊΠ°ΡΠΈΡ Π΄Π°Π΅Ρ Π²ΠΎΠ·ΠΌΠΎΠΆΠ½ΠΎΡΡΡ ΡΠ΅Ρ Π½ΠΈΡΠ΅ΡΠΊΠΈ ΠΏΡΠΎΡΡΠΎ ΠΏΠ΅ΡΠ΅ΡΠ°Π±Π°ΡΡΠ²Π°ΡΡ ΡΠ²Π΅ΡΠ΄ΡΠ΅ Π±ΡΡΠΎΠ²ΡΠ΅ ΠΎΡΡ ΠΎΠ΄Ρ Π±Π΅Π· ΠΈΡ ΠΏΡΠ΅Π΄Π²Π°ΡΠΈΡΠ΅Π»ΡΠ½ΠΎΠΉ ΠΏΠΎΠ΄Π³ΠΎΡΠΎΠ²ΠΊΠΈ, ΡΠΎΡΡΠΈΡΠΎΠ²ΠΊΠΈ, ΡΡΡΠΊΠΈ ΠΈ Ρ. Π΄.
ΠΠ±ΠΎΡΡΠ΄ΠΎΠ²Π°Π½ΠΈΠ΅ Π΄Π»Ρ ΠΎΡΡ ΠΎΠ΄ΠΎΠ² – ΠΏΡΠ΅ΠΈΠΌΡΡΠ΅ΡΡΠ²ΠΎ ΠΏΠΈΡΠΎΠ»ΠΈΠ·Π°:
- ΠΠΈΡΠΎΠ»ΠΈΠ·Π½ΠΎΠ΅ ΠΎΠ±ΠΎΡΡΠ΄ΠΎΠ²Π°Π½ΠΈΠ΅ – ΠΎΠΏΡΠΈΠΌΠ°Π»ΡΠ½ΠΎΠ΅ ΡΠ΅ΡΠ΅Π½ΠΈΠ΅ Π΄Π»Ρ ΠΏΠ΅ΡΠ΅ΡΠ°Π±ΠΎΡΠΊΠΈ ΠΎΡΡ ΠΎΠ΄ΠΎΠ². ΠΠΈΡΠΎΠ»ΠΈΠ· ΠΌΠ°Π»ΠΎ ΡΡΠ²ΡΡΠ²ΠΈΡΠ΅Π»Π΅Π½ ΠΊ ΡΠΈΠΏΡ ΡΡΡΡΡ ΠΈ ΡΠΏΠΎΡΠΎΠ±Π΅Π½ ΠΏΠ΅ΡΠ΅ΡΠ°Π±Π°ΡΡΠ²Π°ΡΡ Π½Π΅ΡΠΎΡΡΠΈΡΠΎΠ²Π°Π½Π½ΡΠ΅ ΡΠ²Π΅ΡΠ΄ΡΠ΅ Π±ΡΡΠΎΠ²ΡΠ΅ ΠΎΡΡ ΠΎΠ΄Ρ, ΠΊΠ°Π½Π°Π»ΠΈΠ·Π°ΡΠΈΠΎΠ½Π½ΡΠΉ ΠΈΠ», Π½Π΅ΡΡΡΠ½ΡΠ΅ ΠΎΡΡΠ°ΡΠΊΠΈ, Π±ΡΠΌΠ°ΠΆΠ½ΡΡ ΠΏΡΠ»ΡΠΏΡ, ΡΠΌΠ΅ΡΠ°Π½Π½ΡΠ΅ ΠΏΠ»Π°ΡΡΠΈΠΊΠΈ ΠΈ ΠΈΠ·ΠΌΠ΅Π»ΡΡΠ΅Π½Π½ΡΠ΅ ΠΎΡΡΠ°ΡΠΊΠΈ Π°Π²ΡΠΎΠΌΠΎΠ±ΠΈΠ»Π΅ΠΉ, ΡΠ΅Π·ΠΈΠ½Ρ ΠΈ Π°Π²ΡΠΎΠΏΠΎΠΊΡΡΡΠΊΠΈ, ΠΎΡΡ ΠΎΠ΄Ρ Π΄Π΅ΡΠ΅Π²ΠΎΠΎΠ±ΡΠ°Π±ΠΎΡΠΊΠΈ, Π±ΠΎΠ»ΡΠ½ΠΈΡΠ½ΡΠ΅ ΠΎΡΡ ΠΎΠ΄Ρ ΠΈ Ρ.Π΄ ΠΠ²ΡΠΎΠΌΠ°ΡΠΈΠΊΠ° ΡΡΡΠ°Π½ΠΎΠ²ΠΊΠΈ ΠΏΡΠΈΡΠΏΠΎΡΠ°Π±Π»ΠΈΠ²Π°Π΅ΡΡΡ ΠΊ ΠΈΠ·ΠΌΠ΅Π½Π΅Π½ΠΈΡΠΌ ΡΠΎΡΡΠ°Π²Π° ΠΎΡΡ ΠΎΠ΄ΠΎΠ².
- ΠΠ΅Ρ ΠΎΡΡ ΠΎΠ΄ΠΎΠ² ΡΠ³ΠΎΡΠ°Π½ΠΈΡ, ΠΏΠΈΡΠΎΠ»ΠΈΠ·Π½Π°Ρ ΡΡΡΠ°Π½ΠΎΠ²ΠΊΠ° ΠΈΠΌΠ΅Π΅Ρ ΠΎΡΠ»ΠΈΡΠ½ΡΠ΅ ΠΏΠΎΠΊΠ°Π·Π°ΡΠ΅Π»ΠΈ ΠΏΠΎ Π²ΡΠ±ΡΠΎΡΠ°ΠΌ Π²ΡΠ΅Π΄Π½ΡΡ Π²Π΅ΡΠ΅ΡΡΠ² ΡΠ°ΠΊΠΈΡ ΠΊΠ°ΠΊ Π΄ΠΈΠΎΠΊΡΠΈΠ½Ρ, ΡΡΠΎΠ²Π΅Π½Ρ ΠΊΠΎΡΠΎΡΡΡ Π½ΠΈΠΆΠ΅ ΡΡΡΠ°Π½ΠΎΠ²Π»Π΅Π½Π½ΡΡ ΡΠΎΠΎΡΠ²Π΅ΡΡΡΠ²ΡΡΡΠΈΠΌ Π·Π°ΠΊΠΎΠ½ΠΎΠ΄Π°ΡΠ΅Π»ΡΡΡΠ²ΠΎΠΌ.
- Π£ΡΡΠ°Π½ΠΎΠ²ΠΊΠ° Π½Π΅ ΠΏΡΠΎΠΈΠ·Π²ΠΎΠ΄ΠΈΡ ΡΡΠΎΡΠ½ΡΡ Π²ΠΎΠ΄.
- ΠΠ΅ ΡΡΠ΅Π±ΡΠ΅ΡΡΡ Π²ΡΡΠΎΠΊΠΎΠΊΠ²Π°Π»ΠΈΡΠΈΡΠΈΡΠΎΠ²Π°Π½Π½ΡΠΉ ΠΏΠ΅ΡΡΠΎΠ½Π°Π», ΡΡΡΠ°Π½ΠΎΠ²ΠΊΠ° ΡΠ°Π±ΠΎΡΠ°Π΅Ρ Π² Π°Π²ΡΠΎΠΌΠ°ΡΠΈΡΠ΅ΡΠΊΠΎΠΌ ΡΠ΅ΠΆΠΈΠΌΠ΅.
- ΠΡΠΎΠΈΡΡ ΠΎΠ΄ΠΈΡ Π±ΠΎΠ»ΡΡΠΎΠ΅ ΡΠ½ΠΈΠΆΠ΅Π½ΠΈΠ΅ ΠΎΠ±ΡΠ΅ΠΌΠΎΠ² ΠΎΡΡ ΠΎΠ΄ΠΎΠ² Π΄Π»Ρ Π·Π°Ρ ΠΎΡΠΎΠ½Π΅Π½ΠΈΡ.
- ΠΠ΅Π·Π²ΡΠ΅Π΄Π½ΡΠ΅ ΠΎΡΡΠ°ΡΠΊΠΈ ΠΏΡΠΎΠΈΠ·Π²ΠΎΠ΄ΡΡΠ²Π° ΠΌΠΎΠ³ΡΡ ΠΈΡΠΏΠΎΠ»ΡΠ·ΠΎΠ²Π°ΡΡΡΡ Π² Π΄Π°Π»ΡΠ½Π΅ΠΉΡΠ΅ΠΌ, Π² ΠΏΡΠΎΠΈΠ·Π²ΠΎΠ΄ΡΡΠ²Π΅ ΡΠΈΠ½, Π΄ΠΎΡΠΎΠΆΠ½ΠΎΠΌ ΡΡΡΠΎΠΈΡΠ΅Π»ΡΡΡΠ²Π΅ ΠΈ.Ρ.Π΄.
- ΠΠΈΡΠΎΠ»ΠΈΠ·Π½Π°Ρ ΡΡΡΠ°Π½ΠΎΠ²ΠΊΠ° ΠΏΡΠΎΡΡΠ° Π² ΡΠ°Π±ΠΎΡΠ΅ ΠΈ ΠΎΠ±ΡΠ»ΡΠΆΠΈΠ²Π°Π½ΠΈΠΈ, Π° ΡΠ°ΠΊ ΠΆΠ΅ ΡΠΎ, ΡΡΠΎ ΠΏΠΈΡΠΎΠ»ΠΈΠ·Π½Π°Ρ ΡΡΡΠ°Π½ΠΎΠ²ΠΊΠ° ΠΎΠ±Π΅ΡΠΏΠ΅ΡΠΈΠ²Π°Π΅Ρ ΡΠ΅Π±Ρ Π½Π΅ΠΎΠ±Ρ ΠΎΠ΄ΠΈΠΌΠΎΠΉ Π΄Π»Ρ ΡΠ°Π±ΠΎΡΡ ΡΠ½Π΅ΡΠ³ΠΈΠ΅ΠΉ (ΡΡΠ΅Π±ΡΠ΅ΡΡΡ ΡΠΎΠ»ΡΠΊΠΎ Π΄Π»Ρ ΠΏΡΡΠΊΠ°), Π² ΡΠΎ Π²ΡΠ΅ΠΌΡ ΠΊΠ°ΠΊ ΠΈΠ·Π±ΡΡΠΎΠΊ Π³Π΅Π½Π΅ΡΠΈΡΡΠ΅ΠΌΠΎΠ³ΠΎ ΠΏΠ°ΡΠ° ΠΈ/ΠΈΠ»ΠΈ ΡΠ»Π΅ΠΊΡΡΠΈΡΠ΅ΡΡΠ²Π° ΠΏΠΎΡΡΠ°Π²Π»ΡΠ΅ΡΡΡ Π²Π½Π΅ΡΠ½Π΅ΠΌΡ ΠΏΠΎΡΡΠ΅Π±ΠΈΡΠ΅Π»Ρ.
ΠΠΈΡΠΎΠ»ΠΈΠ·Π½ΡΠ΅ ΠΌΠ°ΡΠΈΠ½Ρ Π²ΡΠΏΡΡΠΊΠ°ΡΡΡΡ Π² 2 ΠΈΡΠΏΠΎΠ»Π½Π΅Π½ΠΈΡΡ Π²Π΅ΡΡΠΈΠΊΠ°Π»ΡΠ½ΡΠ΅ ΠΈ Π³ΠΎΡΠΈΠ·ΠΎΠ½ΡΠ°Π»ΡΠ½ΡΠ΅. Π£ Π½Π°Ρ ΠΡ ΠΌΠΎΠΆΠ΅ΡΠ΅ ΠΏΡΠΈΠΎΠ±ΡΠ΅ΡΡΠΈ Π³ΠΎΡΠΈΠ·ΠΎΠ½ΡΠ°Π»ΡΠ½ΡΠ΅ ΠΏΠΈΡΠΎΠ»ΠΈΠ·Π½ΡΠ΅ ΠΌΠ°ΡΠΈΠ½Ρ Π΄Π»Ρ ΠΏΠ΅ΡΠ΅ΡΠ°Π±ΠΎΡΠΊΠΈ ΠΎΡΡ ΠΎΠ΄ΠΎΠ² ΡΠΈΠ½Ρ ΠΈ.Ρ.Π΄. ΠΈ Π²Π΅ΡΡΠΈΠΊΠ°Π»ΡΠ½ΡΠ΅ ΠΌΠ°ΡΠΈΠ½Ρ Π΄Π»Ρ ΠΏΠ΅ΡΠ΅ΡΠ°Π±ΠΎΡΠΊΠΈ ΠΎΡΡ ΠΎΠ΄ΠΎΠ² ΠΌΠ°ΡΠ»Π° ΠΈ Π½Π΅ΡΡΠ΅ΠΏΡΠΎΠ΄ΡΠΊΡΠΎΠ².
ΠΡΠ΅ΠΈΠΌΡΡΠ΅ΡΡΠ²Π° Π³ΠΎΡΠΈΠ·ΠΎΠ½ΡΠ°Π»ΡΠ½ΡΡ ΠΏΠΈΡΠΎΠ»ΠΈΠ·Π½ΡΡ ΡΡΡΠ°Π½ΠΎΠ²ΠΎΠΊ:
- Π ΡΠ΅Π°ΠΊΡΠΎΡΠ΅ ΠΈΠ΄Π΅Ρ ΠΏΠ΅ΡΠ΅ΠΌΠ΅ΡΠΈΠ²Π°Π½ΠΈΠ΅ ΠΌΠ°ΡΠ΅ΡΠΈΠ°Π»Π°, ΡΡΠΎ ΡΡΠΊΠΎΡΡΠ΅Ρ ΠΏΡΠΎΡΠ΅ΡΡ ΠΏΠΈΡΠΎΠ»ΠΈΠ·Π°.
- ΠΠ΅ Π½ΡΠΆΠ½Ρ ΠΊΡΠ°Π½-Π±Π°Π»ΠΊΠΈ Π΄Π»Ρ ΡΠ°Π·Π³ΡΡΠ·ΠΊΠΈ ΡΠ΅ΡΠΎΡΡ.
- Π¦Π΅Ρ ΠΌΠΎΠΆΠ΅Ρ ΠΈΠΌΠ΅ΡΡ ΠΌΠ΅Π½ΡΡΡΡ Π²ΡΡΠΎΡΡ.
- ΠΠΎΠ»ΡΡΠΈΠ΅ ΡΠ°Π·ΠΌΠ΅ΡΡ Π·Π°Π³ΡΡΠ·ΠΎΡΠ½ΡΡ Π΄Π²Π΅ΡΠ΅ΠΉ ΡΡΡΠ°Π½ΠΎΠ²ΠΊΠΈ.
- ΠΠΎΠ·ΠΌΠΎΠΆΠ½ΠΎΡΡΡ Π°Π²ΡΠΎΠΌΠ°ΡΠΈΠ·Π°ΡΠΈΠΈ Π·Π°Π³ΡΡΠ·ΠΊΠΈ, Π·Π°Π³ΡΡΠ·ΠΎΡΠ½ΠΎΠ΅ ΡΡΡΡΠΎΠΉΡΡΠ²ΠΎ ΠΌΠΎΠΆΠ΅Ρ Π±ΡΡΡ Π΄ΠΈΠ°ΠΌΠ΅ΡΡΠΎΠΌ ΡΠ°Π²Π½ΡΠΌ Π΄Π²Π΅ΡΠΈ ΠΌΠ°ΡΠΈΠ½Ρ.
- ΠΠΎΠ»Π½ΠΎΡΡΡΡ Π°Π²ΡΠΎΠΌΠ°ΡΠΈΡΠ΅ΡΠΊΠ°Ρ Π²ΡΠ³ΡΡΠ·ΠΊΠ° ΡΠ³Π»Π΅ΡΠΎΠ΄Π°, ΠΏΡΠΈΡΠΏΠΎΡΠΎΠ±Π»Π΅Π½ΠΈΠ΅ Π΄Π»Ρ Π²ΡΠ³ΡΡΠ·ΠΊΠΈ ΠΌΠ΅ΡΠ°Π»Π»ΠΎΠΊΠΎΡΠ΄Π°, ΠΠ΅Π±ΠΎΠ»ΡΡΠΎΠ΅ ΠΊΠΎΠ»ΠΈΡΠ΅ΡΡΠ²ΠΎ ΠΎΠ±ΡΠ»ΡΠΆΠΈΠ²Π°ΡΡΠ΅Π³ΠΎ ΠΏΠ΅ΡΡΠΎΠ½Π°Π»Π° 3-4 ΡΠ΅Π»ΠΎΠ²Π΅ΠΊΠ°, ΠΎΡΠΎΠ±Π΅Π½Π½ΠΎ Π²ΡΡΠΎΠΊΠ°Ρ ΡΠΊΠΎΠ½ΠΎΠΌΠΈΡ ΠΏΠΎΠ»ΡΡΠ°Π΅ΡΡΡ ΠΏΡΠΈ Π±ΠΎΠ»ΡΡΠΎΠΉ ΠΏΡΠΎΠΈΠ·Π²ΠΎΠ΄ΠΈΡΠ΅Π»ΡΠ½ΠΎΡΡΠΈ ΡΡΡΠ°Π½ΠΎΠ²ΠΊΠΈ ΠΈΠ»ΠΈ Π·Π°ΠΊΡΠΏΠΊΠ΅ 2 ΠΈ Π±ΠΎΠ»Π΅Π΅ Π±Π»ΠΎΠΊΠΎΠ².
- ΠΠΈΡΠΎΠ»ΠΈΠ· ΠΏΠ»Π°ΡΡΠΈΠΊΠ°, Π΅ΡΠ΅ ΠΎΠ΄Π½ΠΎ ΠΏΠΎΠΏΡΠ»ΡΡΠ½ΠΎΠ΅ Π½Π°ΠΏΡΠ°Π²Π»Π΅Π½ΠΈΠ΅ ΠΈΡΠΏΠΎΠ»ΡΠ·ΠΎΠ²Π°Π½ΠΈΡ ΠΏΠΈΡΠΎΠ»ΠΈΠ·Π½ΡΡ ΠΌΠ°ΡΠΈΠ½. Π§ΡΠΎ ΠΎΡΠΎΠ±Π΅Π½Π½ΠΎ Π²Π°ΠΆΠ½ΠΎ, ΡΡΠΎ ΠΏΠ»Π°ΡΡΠΈΠΊ ΡΠ°Π·Π»Π°Π³Π°Π΅ΡΡΡ Π² ΠΏΠΈΡΠΎΠ»ΠΈΠ·Π½ΠΎΠΉ ΠΌΠ°ΡΠΈΠ½Π΅ Π±Π΅Π· ΠΎΠ±ΡΠ°Π·ΠΎΠ²Π°Π½ΠΈΡ Π΄ΠΈΠΎΠΊΡΠΈΠ½ΠΎΠ². ΠΡΠΈ ΡΡΠΎΠΌ Π²ΡΡ ΠΎΠ΄ ΠΏΠΈΡΠΎΠ»ΠΈΠ·Π½ΠΎΠ³ΠΎ ΡΠΎΠΏΠ»ΠΈΠ²Π° ΡΠΎΡΡΠ°Π²Π»ΡΠ΅Ρ ΠΎΠΊΠΎΠ»ΠΎ 65% ΠΎΡ Π²Π΅ΡΠ° ΠΏΠ»Π°ΡΡΠΈΠΊΠ°. ΠΡΠΈ ΠΏΠΎΡΡΠ°Π²ΠΊΠ΅ Π±Π»ΠΎΠΊΠ° Π΄Π΅Ρ Π»ΠΎΡΠΈΡΠΎΠ²Π°Π½ΠΈΡ Π²ΠΎΠ·ΠΌΠΎΠΆΠ½Π° ΠΏΠ΅ΡΠ΅ΡΠ°Π±ΠΎΡΠΊΠ° ΠΏΠ»Π°ΡΡΠΈΠΊΠΎΠ² Ρ ΠΏΡΠΈΠΌΠ΅ΡΡΠΌΠΈ ΠΠΠ₯.
-
ΠΠΈΡΠΎΠ»ΠΈΠ· ΠΎΡΡ ΠΎΠ΄ΠΎΠ²
- Π ΠΏΠΈΡΠΎΠ»ΠΈΠ·Π½ΡΡ ΡΡΡΠ°Π½ΠΎΠ²ΠΊΠ°Ρ ΡΠ°ΠΊΠΆΠ΅ Π²ΠΎΠ·ΠΌΠΎΠΆΠ½Π° ΠΏΠ΅ΡΠ΅ΡΠ°Π±ΠΎΡΠΊΠ° ΠΎΡΡΠ°ΡΠΊΠΎΠ² ΠΊΠ°Π±Π΅Π»Ρ, ΠΊΠΎΠΆΠΈ (ΠΎΠ±ΠΎΡΡΠ΄ΠΎΠ²Π°Π½ΠΈΠ΅ Π΄Π»Ρ ΠΏΡΠ΅Π΄Π²Π°ΡΠΈΡΠ΅Π»ΡΠ½ΠΎΠΉ ΠΎΠ±ΡΠ°Π±ΠΎΡΠΊΠΈ ΠΏΠΎΡΡΠ°Π²Π»ΡΠ΅ΡΡΡ),
-
ΠΠΈΡΠΎΠ»ΠΈΠ· ΠΎΡΡΠ°Π±ΠΎΡΠ°Π½Π½ΠΎΠ³ΠΎ ΠΌΠ°ΡΠ»Π° ΠΈ Π½Π΅ΡΡΠ΅ΠΏΡΠΎΠ΄ΡΠΊΡΠΎΠ²
- ΠΠΎΠ·ΠΌΠΎΠΆΠ½Π° ΠΏΠ΅ΡΠ΅ΡΠ°Π±ΠΎΡΠΊΠ° ΠΎΡΡΠ°Π±ΠΎΡΠ°Π½Π½ΠΎΠ³ΠΎ ΠΌΠ°ΡΠ»Π° Π² Π³ΠΎΡΠΈΠ·ΠΎΠ½ΡΠ°Π»ΡΠ½ΡΡ ΠΏΠΈΡΠΎΠ»ΠΈΠ·Π½ΡΡ ΡΡΡΠ°Π½ΠΎΠ²ΠΊΠ°Ρ 10 -15 % ΠΎΡ ΠΎΠ±ΡΠ΅ΠΌΠ° Π·Π°Π³ΡΡΠ·ΠΊΠΈ ΡΡΡΠ°Π½ΠΎΠ²ΠΊΠΈ, Π² ΡΡΡΠ°Π½ΠΎΠ²ΠΊΠ°Ρ Π΄ΠΈΡΡΠΈΠ»Π»ΡΡΠΈΠΈ ΠΈΠ»ΠΈ Π² ΡΡΡΠ°Π½ΠΎΠ²ΠΊΠ°Ρ ΡΠ΅Π³Π΅Π½Π΅ΡΠ°ΡΠΈΠΈ ΠΌΠ°ΡΠ΅Π».
- Β Β ΠΡ ΠΏΡΠ΅Π΄Π»Π°Π³Π°Π΅ΠΌΒ 2 ΡΠΈΠΏΠ° ΡΡΡΠ°Π½ΠΎΠ²ΠΎΠΊ Π΄Π»Ρ ΠΏΠ΅ΡΠ΅ΡΠ°Π±ΠΎΡΠΊΠΈ ΠΌΠ°ΡΠ΅Π».
ΠΠΈΡΠΎΠ»ΠΈΠ· ΡΠ΅Π·ΠΈΠ½Ρ ΠΈ ΡΠΈΠ½.
ΠΠΈΡΠΎΠ»ΠΈΠ· ΡΠ΅Π·ΠΈΠ½Ρ ΠΈ ΡΡΠΈΠ»ΠΈΠ·Π°ΡΠΈΡ Π°Π²ΡΠΎΠΌΠΎΠ±ΠΈΠ»ΡΠ½ΡΡ ΠΏΠΎΠΊΡΡΡΠ΅ΠΊ – ΡΠ°ΠΌΠΎΠ΅ Π²ΠΎΡΡΡΠ΅Π±ΠΎΠ²Π°Π½Π½ΠΎΠ΅ Π½Π°ΠΏΡΠ°Π²Π»Π΅Π½ΠΈΠ΅, Π³Π΄Π΅ ΡΠΈΡΠΎΠΊΠΎ ΠΈΡΠΏΠΎΠ»ΡΠ·ΡΡΡΡΡ Π³ΠΎΡΠΈΠ·ΠΎΠ½ΡΠ°Π»ΡΠ½ΡΠ΅ ΠΏΠΈΡΠΎΠ»ΠΈΠ·Π½ΡΠ΅ ΡΡΡΠ°Π½ΠΎΠ²ΠΊΠΈ. ΠΠΎΠ»ΡΡΠΎΠΉ ΠΎΠ±ΡΠ΅ΠΌ ΡΠ΅Π°ΠΊΡΠΎΡΠ° ΠΎΡ 12 ΠΌ3 Π΄ΠΎ 50 ΠΌ3 Π±ΠΎΠ»ΡΡΠΈΠ΅ Π·Π°Π³ΡΡΠ·ΠΎΡΠ½ΡΠ΅ Π΄Π²Π΅ΡΠΈ ΠΎΡ 2,2 Π΄ΠΎ 2,8 ΠΌΠ΅ΡΡΠ° Π² Π΄ΠΈΠ°ΠΌΠ΅ΡΡΠ΅, Π°Π²ΡΠΎΠΌΠ°ΡΠΈΡΠ΅ΡΠΊΠ°Ρ ΡΠ°Π·Π³ΡΡΠ·ΠΊΠ° ΡΡΡΠ°Π½ΠΎΠ²ΠΊΠΈ, Π½Π΅Π±ΠΎΠ»ΡΡΠΎΠ΅ ΠΊΠΎΠ»ΠΈΡΠ΅ΡΡΠ²ΠΎ ΠΎΠ±ΡΠ»ΡΠΆΠΈΠ²Π°ΡΡΠ΅Π³ΠΎ ΠΏΠ΅ΡΡΠΎΠ½Π°Π»Π° Π΄Π΅Π»Π°ΡΡ Π³ΠΎΡΠΈΠ·ΠΎΠ½ΡΠ°Π»ΡΠ½ΡΠ΅ ΡΡΡΠ°Π½ΠΎΠ²ΠΊΠΈ Π½Π°ΠΈΠ±ΠΎΠ»Π΅Π΅ Π²ΡΠ³ΠΎΠ΄Π½ΡΠΌΠΈ Π² ΠΈΡΠΏΠΎΠ»ΡΠ·ΠΎΠ²Π°Π½ΠΈΠΈ Π΄Π»Ρ ΡΡΠΈΡ ΡΠ΅Π»Π΅ΠΉ.
ΠΠΈΡΠΎΠ»ΠΈΠ· ΠΏΠ»Π°ΡΡΠΈΠΊΠ°.
Π‘Π΅ΡΠΈΡ ΡΡΡΠ°Π½ΠΎΠ²ΠΎΠΊ Π΄ΠΈΡΡΠΈΠ»Π»ΡΡΠΈΠΈ ΠΊΠΎΡΠΎΡΡΠ΅ ΠΏΠΎΠ·Π²ΠΎΠ»ΡΡΡ ΠΏΠ΅ΡΠ΅ΡΠ°Π±ΠΎΡΠ°ΡΡ 5 Π΄ΠΎΒ 50ΡΠΎΠ½Π½ ΠΌΠ°ΡΠ»Π° Π² ΡΡΡΠΊΠΈ Π² ΡΡΠ°Π½Π΄Π°ΡΡΠ½ΠΎΠ΅ Π»Π΅ΡΠ½Π΅Π΅ Π΄ΠΈΠ·Π΅Π»ΡΠ½ΠΎΠ΅ ΡΠΎΠΏΠ»ΠΈΠ²ΠΎ ΠΈ Π±Π΅Π½Π·ΠΈΠ½Β ΠΠ 92.
Π£ΡΡΠ°Π½ΠΎΠ²ΠΊΠΈ ΡΠ΅Π³Π΅Π½Π΅ΡΠ°ΡΠΈΠΈ ΡΠ²ΠΎΠΉΡΡΠ² ΠΌΠ°ΡΠ΅Π» Ρ ΠΏΡΠΎΠΈΠ·Π²ΠΎΠ΄ΠΈΡΠ΅Π»ΡΠ½ΠΎΡΡΡΡ ΠΎΡ 62 Π΄ΠΎ 2000 Π»ΠΈΡΡΠΎΠ² Π² ΡΠ°Ρ. ΠΡΠΈ ΡΡΡΠ°Π½ΠΎΠ²ΠΊΠΈ ΠΏΠΎΠ·Π²ΠΎΠ»ΡΡΡ ΠΏΠΎΠ»ΡΡΠΈΡΡ ΠΌΠ°ΡΠ»ΠΎ ΡΠΎ ΡΠ²ΠΎΠΉΡΡΠ²Π°ΠΌΠΈ Π±Π»ΠΈΠ·ΠΊΠΈΠΌΠΈ ΠΊ ΠΈΡΡ ΠΎΠ΄Π½ΠΎΠΌΡ ΠΌΠ°ΡΠ»Ρ.
-
Β Π ΡΠ΅Π·ΡΠ»ΡΡΠ°ΡΠ΅ ΠΏΠΈΡΠΎΠ»ΠΈΠ·Π° ΠΏΠΎΠ»ΡΡΠ°ΡΡΡΡ ΡΠ»Π΅Π΄ΡΡΡΠΈΠ΅ ΠΏΡΠΎΠ΄ΡΠΊΡΡ:
|
Π Π°Π±ΠΎΡΠΈΠΉ ΠΏΡΠΎΡΠ΅ΡΡ:
Π Π·Π°Π³ΡΡΠ·ΠΎΡΠ½ΠΎΠ΅ Π²ΠΏΡΡΠΊΠ½ΠΎΠ΅ ΠΎΡΠ²Π΅ΡΡΡΠΈΠ΅ Π·Π°Π³ΡΡΠΆΠ°Π΅ΡΡΡ ΡΡΡΡΠ΅, Π² Π·Π°Π²ΠΈΡΠΈΠΌΠΎΡΡΠΈ ΠΎΡ ΠΎΠ±ΡΠ΅ΠΌΠΎΠ² ΠΈ ΠΌΠ°ΡΠ΅ΡΠΈΠ°Π»Π° ΠΌΠΎΠΆΠ΅Ρ ΠΏΠΎΡΡΠ°Π²Π»ΡΡΡΡΡ Π·Π°Π³ΡΡΠ·ΠΎΡΠ½ΡΠΉ ΠΊΠΎΠ½Π²Π΅ΠΉΠ΅Ρ. ΠΠ°ΡΠ΅ΠΌ, ΡΠ΅Π°ΠΊΡΠΎΡ ΠΏΠΈΡΠΎΠ»ΠΈΠ·Π½ΠΎΠΉ ΠΌΠ°ΡΠΈΠ½Ρ Π½Π°Π³ΡΠ΅Π²Π°Π΅ΡΡΡ Π³Π°Π·ΠΎΠ²ΠΎΠΉ ΠΈΠ»ΠΈ Π΄ΠΈΠ·Π΅Π»ΡΠ½ΠΎΠΉ Π³ΠΎΡΠ΅Π»ΠΊΠΎΠΉ, Π½Π° Π²ΡΠ±ΠΎΡ Π·Π°ΠΊΠ°Π·ΡΠΈΠΊΠ°. ΠΠΎΠ³Π΄Π° ΡΠ΅ΠΌΠΏΠ΅ΡΠ°ΡΡΡΠ° Π΄ΠΎΡΡΠΈΠ³Π°Π΅Ρ Π΄ΠΎ 350 Β° Π‘ 400 Β° C, Π² ΡΠ΅Π°ΠΊΡΠΎΡΠ΅ Π½Π°ΡΠΈΠ½Π°Π΅ΡΡΡ ΡΠ΅Π°ΠΊΡΠΈΡ ΠΏΠΈΡΠΎΠ»ΠΈΠ·Π°. ΠΡ ΠΎΠ±ΡΠ°Π·ΠΎΠ²Π°Π²ΡΠ΅Π³ΠΎΡΡ Π½Π΅ΡΡΡΠ½ΠΎΠ³ΠΎ Π³Π°Π·Π° Π±ΡΠ΄ΡΡ ΠΎΡΠ΄Π΅Π»ΡΡΡΡΡ Π»Π΅Π³ΠΊΠΈΠΉ ΠΈ ΡΡΠΆΠ΅Π»ΡΠΉ ΠΊΠΎΠΌΠΏΠΎΠ½Π΅Π½ΡΡ. Π‘Π²Π΅ΡΠ»ΡΠΉ ΠΊΠΎΠΌΠΏΠΎΠ½Π΅Π½Ρ ΠΎΡ Π»Π°ΠΆΠ΄Π°Π΅ΡΡΡ Π² ΠΊΠΎΠ½Π΄Π΅Π½ΡΠ°ΡΠΎΡΠ΅ ΠΈ Π½Π°ΠΊΠ°ΠΏΠ»ΠΈΠ²Π°Π΅ΡΡΡ Π² Π±Π°ΠΊΠ΅ Π΄Π»Ρ ΡΠΎΠΏΠ»ΠΈΠ²Π°, ΡΠ°ΠΊΠΆΠ΅ Π² ΡΠΈΡΡΠ΅ΠΌΠ΅ ΠΎΡΡΠ°ΡΡΡΡ Π³ΠΎΡΡΡΠΈΠ΅ Π³Π°Π·Ρ, ΠΊΠΎΡΠΎΡΡΠ΅ Π½Π΅ ΠΌΠΎΠ³ΡΡ Π±ΡΡΡ ΡΠΆΠΈΠΆΠ΅Π½Ρ, ΠΎΠ½ΠΈ Π²ΠΎΠ·Π²ΡΠ°ΡΠ°ΡΡΡΡ Π² ΡΠΈΡΡΠ΅ΠΌΡ ΡΠ΅ΠΏΠ»ΠΎΡΠ½Π°Π±ΠΆΠ΅Π½ΠΈΡ Π΄Π»Ρ ΡΠΆΠΈΠ³Π°Π½ΠΈΡ. ΠΠΈΡΠΎΠ»ΠΈΠ·Π½Π°Ρ ΠΌΠ°ΡΠΈΠ½Π° ΠΊΠΎΠΌΠΏΠ»Π΅ΠΊΡΡΠ΅ΡΡΡ ΡΠΈΡΡΠ΅ΠΌΠΎΠΉ ΠΎΡΠΈΡΡΠΊΠΈ Π³Π°Π·ΠΎΠ² Π² ΡΠΈΡΡΠ΅ΠΌΠ΅ ΡΠ΅ΠΏΠ»ΠΎΡΠ½Π°Π±ΠΆΠ΅Π½ΠΈΡ ΠΌΠ°ΡΠΈΠ½Ρ. ΠΡ ΠΌΠΎΠΆΠ΅ΠΌ ΠΠ°ΠΌ ΠΏΡΠ΅Π΄Π»ΠΎΠΆΠΈΡΡ ΡΠ»Π΅Π΄ΡΡΡΠΈΠΉ ΡΠΈΠΏΠΎΡΠ°Π·ΠΌΠ΅ΡΠ½ΡΠΉ ΡΡΠ΄ ΠΠΈΡΠΎΠ»ΠΈΠ·Π½ΡΡ ΠΌΠ°ΡΠΈΠ½ Ρ ΡΠ°Π·Π½ΠΎΠΉ ΠΏΡΠΎΠΈΠ·Π²ΠΎΠ΄ΠΈΡΠ΅Π»ΡΠ½ΠΎΡΡΡΡ:
Π¦Π΅Π½Ρ ΠΈ Ρ Π°ΡΠ°ΠΊΡΠ΅ΡΠΈΡΡΠΈΠΊΠΈΒ ΠΏΠΈΡΠΎΠ»ΠΈΠ·Π½ΡΡ ΡΡΡΠ°Π½ΠΎΠ²ΠΎΠΊ ΠΏΡΠΎΠΈΠ·Π²ΠΎΠ΄ΠΈΡΠ΅Π»ΡΠ½ΠΎΡΡΡΡ ΠΎΡΒ 4 Π΄ΠΎ 20 ΡΠΎΠ½Π½Β Β
βΒ | Β ΠΠ°ΠΈΠΌΠ΅Π½ΠΎΠ²Π°Π½ΠΈΠ΅Β | Β ΠΠΎΡΠ½ΠΎΡΡΡΒ Β ΠΊΠΡ. |
ΠΠ±ΡΠ΅ΠΌ Β ΡΠ΅Π°ΠΊΡΠΎΡΠ°Β Β ΠΌ3/ΡΠ°Ρ |
ΠΠ±ΡΠ΅ΠΌΒ Β Π·Π°Π³ΡΡΠ·ΠΊΠΈΒ ΡΠΎΠ½Π½. |
ΠΠ±ΡΠ΅ΠΌΒ Β Π² ΡΡΡΠΊΠΈΒ ΡΠΎΠ½Π½. |
Β ΠΠΎΠ»ΠΈΡΠ΅ΡΡΠ²ΠΎ Β Π·Π°Π³ΡΡΠ·ΠΎΠΊ Π² Π΄Π΅Π½Ρ |
Π¦Π΅Π½Π°* Β $ USA |
Π¦Π΅Π½Π°** $ USAΒ |
Π¦Π΅Π½Π°*** Β $ USA |
Π¦Π΅Π½Π° **** $ USA |
Β Π¦Π΅Π½Π°***** Β $ USA |
1 | LL-2200-6000 |
11 | 22 | 5 – 6 | 8 – 10 | Β 3 Π·Π° 2 Π΄Π½ΡΒ | 87000 | 102000Β | 115000 | 128000Β | 149000 |
2 | LL-2200-6000 |
11 | 22 | 5 -6 | 8 – 10 | 3 Π·Π° 2 Π΄Π½ΡΒ | 99000 | 115000 | 128000 | 140000 | 161000 |
3 | LL-2200-6600 |
11 | 25 | 7 | 10 -11 | 3 Π·Π° 2 Π΄Π½Ρ | 89000 | 104000Β | 117000 | 130000Β | 151000 |
4 | LL-2200-6600 |
11 | 25 | 7 | 10 -11 | 3 Π·Π° 2 Π΄Π½Ρ | 101000 | 117000 | 130000 | 142000 | 163000 |
5 | LL-2600-6000 |
16 | 32 | 8 -10 | 8 -10 | 1 Π² Π΄Π΅Π½Ρ | 98000 | 115000Β | 128000 | 141000Β | 163000 |
6 | LL-2600-6000 |
16 | 35 | 8 – 10 | 8 -10 |
1 Π² Π΄Π΅Π½Ρ | 110000 | 127000Β | 140000 | 153000Β | 175000 |
7 | LL-2800-6000 |
17 | 37 | 10 -11 | 10 -11 |
1 Π² Π΄Π΅Π½Ρ | 111000 | 129000Β | 143000 | 158000Β | 182000 |
8 | LL-2800-6000 |
22 | 37 | 10 – 11 | 10 -11 | 1 Π² Π΄Π΅Π½Ρ | 124000 | 142000 | 156000 | 171000 | 195000 |
9 | LL-2800-6600 |
22 | 40 | 12 – 13 | 12 – 13 |
1 Π² Π΄Π΅Π½Ρ | 128000 | 149000Β | 164000 | 180000Β | 209000 |
10 | LL-2800-6600 |
22 | 40 | 12 -13 | 12 – 13 | 1 Π² Π΄Π΅Π½Ρ | 137000 | 180000 | 177000 | 193000 | 221000 |
11 | LL-2800-7500 |
22 | 46 | 15 – 16 | 15 – 16 | 1 Π² Π΄Π΅Π½Ρ | 143000 | 168000Β | 184000 | 203000Β | 229000 |
12 | LL-2800-7500 |
22 | 46 | 15 – 16 | 12 – 13 | 1 Π² Π΄Π΅Π½Ρ | 158000 | 184000 | 199000 | 219000 | 245000 |
* –Β Β ΠΠΎΠ΄ΠΎΠ³ΡΠ΅Π² ΡΠ΅Π°ΠΊΡΠΎΡΠ° ΡΡΡΠ°Π½ΠΎΠ²ΠΊΠΈ Π³Π°Π·ΠΎΠΌ, ΡΠ³Π»Π΅ΠΌ ΠΈΠ»ΠΈ Π΄ΡΠΎΠ²Π°ΠΌΠΈ.
** – ΠΠΎΠ΄ΠΎΠ³ΡΠ΅Π² ΡΠ΅Π°ΠΊΡΠΎΡΠ° ΡΡΡΠ°Π½ΠΎΠ²ΠΊΠΈ ΠΌΡΠ»ΡΡΠΈΡΠΎΠΏΠ»ΠΈΠ²Π½ΡΠΌΠΈ Π³ΠΎΡΠ΅Π»ΠΊΠ°ΠΌΠΈ, ΡΠ°Π±ΠΎΡΠ°ΡΡΠΈΠΌΠΈ Π½Π° Π΄ΠΈΠ·Π΅Π»ΡΠ½ΠΎΠΌ ΡΠΎΠΏΠ»ΠΈΠ²Π΅, ΠΏΠΈΡΠΎΠ»ΠΈΠ·Π½ΠΎΠΌ ΠΌΠ°ΡΠ»Π΅, ΠΌΠ°Π·ΡΡΠ΅.
***Β ΠΠΎΠ΄ΠΎΠ³ΡΠ΅Π² ΡΠ΅Π°ΠΊΡΠΎΡΠ° ΡΡΡΠ°Π½ΠΎΠ²ΠΊΠΈ ΠΌΡΠ»ΡΡΠΈΡΠΎΠΏΠ»ΠΈΠ²Π½ΡΠΌΠΈ Π³ΠΎΡΠ΅Π»ΠΊΠ°ΠΌΠΈ, ΡΠ°Π±ΠΎΡΠ°ΡΡΠΈΠΌΠΈ Π½Π° Π΄ΠΈΠ·Π΅Π»ΡΠ½ΠΎΠΌ ΡΠΎΠΏΠ»ΠΈΠ²Π΅, ΠΏΠΈΡΠΎΠ»ΠΈΠ·Π½ΠΎΠΌ ΠΌΠ°ΡΠ»Π΅, ΠΌΠ°Π·ΡΡΠ΅. ΠΠ»ΡΡ Π°Π²ΡΠΎΠΌΠ°ΡΠΈΠ·ΠΈΡΠΎΠ²Π°Π½Π½Π°Ρ Π·Π°Π³ΡΡΠ·ΠΊΠ° ΡΠ΅Π°ΠΊΡΠΎΡΠ° ΡΡΡΠ°Π½ΠΎΠ²ΠΊΠΈ
**** ΠΠΎΠ»Π½ΠΎΡΡΡΡ Π°Π²ΡΠΎΠΌΠ°ΡΠΈΡΠ΅ΡΠΊΠ°Ρ ΡΠΈΡΡΠ΅ΠΌΠ° Π·Π°Π³ΡΡΠ·ΠΊΠΈ ΠΈ Π²ΡΠ³ΡΡΠ·ΠΊΠΈ ΠΌΠ°ΡΠ΅ΡΠΈΠ°Π»ΠΎΠ²
***** – ΡΠ΅Π½Π° ΠΏΠΈΡΠΎΠ»ΠΈΠ·Π½ΠΎΠΉ ΡΡΡΠ°Π½ΠΎΠ²ΠΊΠΈ Ρ ΡΠΈΡΡΠ΅ΠΌΠΎΠΉ ΠΎΡ Π»Π°ΠΆΠ΄Π΅Π½ΠΈΡ Π°Π΄Π°ΠΏΡΠΈΡΠΎΠ²Π°Π½Π½ΠΎΠΉ ΠΊ Ρ ΠΎΠ»ΠΎΠ΄Π½ΠΎΠΌΡ ΠΊΠ»ΠΈΠΌΠ°ΡΡ, Π±Π΅Π· ΠΎΡΠΊΡΡΡΠΎΠ³ΠΎ Π±Π°ΡΡΠ΅ΠΉΠ½Π° ΠΈ ΡΠΈΡΡΠ΅ΠΌΠΎΠΉ ΠΎΡ Π»Π°ΠΆΠ΄Π΅Π½ΠΈΡ, ΠΏΠΎΠ·Π²ΠΎΠ»ΡΡΡΠ΅ΠΉ ΠΈΡΠΏΠΎΠ»ΡΠ·ΠΎΠ²Π°Π½ΠΈΠ΅ Π²ΡΠ΄Π΅Π»ΡΠ΅ΠΌΠΎΠ³ΠΎ ΡΡΡΠ°Π½ΠΎΠ²ΠΊΠΎΠΉ ΡΠ΅ΠΏΠ»Π° Π΄Π»Ρ ΠΎΡΠΎΠΏΠ»Π΅Π½ΠΈΡ ΡΠ΅Ρ Π°. Π‘ΠΈΡΡΠ΅ΠΌΠ° ΠΏΡΠΈΡΠΎΡΠ½ΠΎΠΉ Π²Π΅Π½ΡΠΈΠ»ΡΡΠΈΠΈ. ΠΠ°Π³ΡΠ΅Π² ΡΡΡΠ°Π½ΠΎΠ²ΠΊΠΈ ΠΌΡΠ»ΡΡΠΈΡΠΎΠΏΠ»ΠΈΠ²Π½ΡΠΌΠΈ Π³ΠΎΡΠ΅Π»ΠΊΠ°ΠΌΠΈ, ΡΠ°Π±ΠΎΡΠ°ΡΡΠΈΠΌΠΈ Π½Π° Π΄ΠΈΠ·Π΅Π»ΡΠ½ΠΎΠΌ ΡΠΎΠΏΠ»ΠΈΠ²Π΅, ΠΏΠΈΡΠΎΠ»ΠΈΠ·Π½ΠΎΠΌ ΠΌΠ°ΡΠ»Π΅, ΠΌΠ°Π·ΡΡΠ΅.
Π‘ΡΠ°Π½Π΄Π°ΡΡΠ½ΡΠΉ ΡΠΈΠΊΠ» ΡΠ°Π±ΠΎΡΡ ΠΏΠΈΡΠΎΠ»ΠΈΠ·Π½ΠΎΠΉ ΠΌΠ°ΡΠΈΠ½Ρ.
Β βΒ | Β ΠΠ°ΠΈΠΌΠ΅Π½ΠΎΠ²Π°Π½ΠΈΠ΅Β | Β ΠΠ°Π³ΡΡΠ·ΠΊΠ° ΠΌΠ°ΡΠ΅ΡΠΈΠ°Π»Π°Β ΡΠ°Ρ. |
Β Π Π°Π±ΠΎΡΠ° ΠΌΠ°ΡΠΈΠ½ΡΒ ΡΠ°Ρ. |
Β ΠΡΡΡΠ²Π°Π½ΠΈΠ΅Β ΡΠ°Ρ |
Β Π Π°Π·Π³ΡΡΠ·ΠΊΠ°Β ΡΠ°Ρ. |
Β Π Π°Π±ΠΎΡΠΈΠΉ ΡΠΈΠΊΠ»Β ΡΠ°Ρ. |
Β 1 | LN-2200-5100Β | Β 1,5-2 | 6-7Β | 2Β | 1,5-2Β | Β 12 |
Β 2 | LN-2200-5100Β | 1,5-2Β | 6-7Β | 2Β | Β 1,5-2 | Β 12 |
Β 3 | LN-2200-5100Β | 1,5-2Β | Β 6-7 | 2 | Β 1,5-2 | Β 12 |
4 | LN-2200-5100 | 1,5-2 | 6-7 | 2 | 1,5-2 | 12 |
5 | LN-2200-6000 | 2 | 7 | 2 | 2 | 13 |
6 | LN-2200-6600 | 2 | 8 | 2 | 2 | 14 |
7 | LN-2600-6000 | 2-3 | 10 | 2 – 3 | 2-3 | 19 |
8 | LN-2800-6000 | 3 | 12 | 4 | 3 | 22 |
9 | LN-2800-6600 | 3 | 12 | 4 | 3 | 22 |
10 | LN-2800-7500 | 4 | 12 | 4 | 4 | 24 |
ΠΡ Π΄Π°Π΅ΠΌ Π³Π°ΡΠ°Π½ΡΠΈΡ Π½Π° ΠΌΠ°ΡΠΈΠ½Ρ 1 Π³ΠΎΠ΄, ΡΡΠΎΠΊ Π½Π° ΡΠ΅Π°ΠΊΡΠΎΡ ΠΈΠ· Π½Π΅ΡΠΆΠ°Π²Π΅ΡΡΠ΅ΠΉ ΡΡΠ°Π»ΠΈ ΡΠΎΠ»ΡΠΈΠ½ΠΎΠΉ 14 ΠΌΠΌ. 3 Π³ΠΎΠ΄Π°, Π΄ΡΡΠ³ΠΈΠ΅ ΡΠ°ΡΡΠΈ ΠΌΠ°ΡΠΈΠ½Ρ Π½Π΅Ρ Π½Π΅ΠΎΠ±Ρ ΠΎΠ΄ΠΈΠΌΠΎΡΡΠΈ ΠΌΠ΅Π½ΡΡΡ Π²Π΅ΡΡ Π΅Π΅ ΠΏΠ΅ΡΠΈΠΎΠ΄ ΡΠ°Π±ΠΎΡΡ Π·Π° ΠΈΡΠΊΠ»ΡΡΠ΅Π½ΠΈΠ΅ΠΌ ΠΈΠ·Π½Π°ΡΠΈΠ²Π°Π΅ΠΌΡΡ ΡΠ·Π»ΠΎΠ² ΠΈ Π΄Π΅ΡΠ°Π»Π΅ΠΉ.
Π‘ΠΎΡΡΠ°Π² ΠΌΠ°ΡΠΈΠ½Ρ Π΄Π»Ρ ΠΏΠΈΡΠΎΠ»ΠΈΠ·Π° Π²Ρ ΠΎΠ΄ΡΡ
- Π‘ΠΈΡΡΠ΅ΠΌΠ° Π½Π°Π³ΡΠ΅Π²Π° ΡΠ΅Π°ΠΊΡΠΎΡΠ°
- Π’Π΅ΠΏΠ»ΠΎΠΈΠ·ΠΎΠ»ΠΈΡΠΎΠ²Π°Π½Π½ΡΠΉ ΠΊΠΎΡΠΏΡΡ ΠΌΠ°ΡΠΈΠ½Ρ ΠΏΠΈΡΠΎΠ»ΠΈΠ·Π°
- ΠΠΈΡΠΎΠ»ΠΈΠ·Π½ΡΠΉ ΡΠ΅Π°ΠΊΡΠΎΡ, ΠΈΠ·Π³ΠΎΡΠ°Π²Π»ΠΈΠ²Π°Π΅ΡΡΡ ΠΈΠ· Π½Π΅ΡΠΆΠ°Π²Π΅ΡΡΠ΅ΠΉ ΡΡΠ°Π»ΠΈ ΡΠΎΠ»ΡΠΈΠ½ΠΎΠΉ 14 ΠΌΠΌ.
- ΠΡΠ»ΡΡ ΡΠΏΡΠ°Π²Π»Π΅Π½ΠΈΡ ΠΌΠ°ΡΠΈΠ½ΠΎΠΉ.
- ΠΠ°ΡΠ°Π»ΠΈΡΠΈΡΠ΅ΡΠΊΠ°Ρ ΠΊΠΎΠ»ΠΎΠ½Π½Π°
- ΠΠΌΠΊΠΎΡΡΡ Π΄Π»Ρ ΡΡΠΆΠ΅Π»ΠΎΠΉ ΡΡΠ°ΠΊΡΠΈΠΈ ΠΏΠΈΡΠΎΠ»ΠΈΠ·Π½ΠΎΠ³ΠΎ ΠΌΠ°ΡΠ»Π°
- Π‘ΠΈΡΡΠ΅ΠΌΠ° ΠΎΡ Π»Π°ΠΆΠ΄Π΅Π½ΠΈΡ ΠΏΠΈΡΠΎΠ»ΠΈΠ·Π½ΡΡ Π³Π°Π·ΠΎΠ²
- ΠΠΌΠΊΠΎΡΡΡ Π΄Π»Ρ Π»Π΅Π³ΠΊΠΎΠΉ ΡΡΠ°ΠΊΡΠΈΠΈ ΠΏΠΈΡΠΎΠ»ΠΈΠ·Π½ΠΎΠ³ΠΎ ΠΌΠ°ΡΠ»Π°
- ΠΠΈΠ΄ΡΠΎΠ·Π°ΡΠ²ΠΎΡ
- Π‘ΠΈΡΡΠ΅ΠΌΠ° ΠΎΡ Π»Π°ΠΆΠ΄Π΅Π½ΠΈΡ Π²ΠΎΠ΄Ρ. ΠΡΠ΅Π΄ΡΡΠΌΠΎΡΡΠ΅Π½Π° Π²ΠΎΠ·ΠΌΠΎΠΆΠ½ΠΎΡΡΡ ΠΈΡΠΏΠΎΠ»ΡΠ·ΠΎΠ²Π°Π½ΠΈΡ ΡΠ΅ΠΏΠ»Π° Π²ΡΡΠ°Π±Π°ΡΡΠ²Π°Π΅ΠΌΠΎΠ³ΠΎ Π² ΠΏΡΠΎΡΠ΅ΡΡΠ΅ ΠΏΠΈΡΠΎΠ»ΠΈΠ·Π° Π΄Π»Ρ ΠΏΠΎΠ΄ΠΎΠ³ΡΠ΅Π²Π° Π²ΠΎΠ·Π΄ΡΡ Π° Π² ΠΏΠΎΠΌΠ΅ΡΠ΅Π½ΠΈΠΈ ΡΠ΅Ρ Π° Π·ΠΈΠΌΠΎΠΉ
- ΠΡΡΡΠΎΠ΅Π½Π½ΡΠΉ Π²Π΅Π½ΡΠΈΠ»ΡΡΠΎΡ ΠΈ ΡΠΈΡΡΠ΅ΠΌΠ° ΠΊΠ»Π°ΠΏΠ°Π½ΠΎΠ².
- ΠΡΠΌΠΎΡ ΠΎΠ΄
- ΠΠ΅Π½ΡΠΈΠ»ΡΡΠΎΡ Π΄ΡΠΌΠΎΡΠ΄Π°Π»Π΅Π½ΠΈΡ
- Π‘ΠΈΡΡΠ΅ΠΌΠ° ΠΎΡΠΈΡΡΠΊΠΈ Π²ΡΡ Π»ΠΎΠΏΠ½ΡΡ Π³Π°Π·ΠΎΠ²
- ΠΠΎΡΠ΅Π»ΠΊΠ° Π΄Π»Ρ Π΄ΠΎΠΆΠΈΠ³Π° Π³Π°Π·Π°
- Π Π΅Π΄ΡΠΊΡΠΎΡ ΡΠΊΠΎΡΠΎΡΡΠΈ
- ΠΠ²ΡΠΎΠΌΠ°ΡΠΈΡΠ΅ΡΠΊΠΈΠΉ ΠΊΠΎΠ½Π²Π΅ΠΉΠ΅Ρ Π΄Π»Ρ ΡΠ΄Π°Π»Π΅Π½ΠΈΡ ΡΠ°ΠΆΠΈ
- ΠΠ»Π°ΡΡΠΎΡΠΌΡ ΠΎΠ±ΡΠ»ΡΠΆΠΈΠ²Π°Π½ΠΈΡ
- Π ΠΎΠ»Π»Π΅Ρ Π΄Π»Ρ Π²ΡΠ³ΡΡΠ·ΠΊΠΈ ΡΡΠ°Π»ΠΈ (ΠΊΠΎΡΠ΄Π°)
pyrolysisplant.ru
ΠΠ΅ΡΠ΅ΡΠ°Π±ΠΎΡΠΊΠ° ΡΠΈΠ½ ΠΌΠ΅ΡΠΎΠ΄ΠΎΠΌ ΠΏΠΈΡΠΎΠ»ΠΈΠ·Π° – ΠΠΎΡΡΠΊΠΎΠΉ ΡΠ»ΠΎΡ
Π‘ΠΎΠ²ΡΠ΅ΠΌΠ΅Π½Π½ΠΎΠ΅ ΠΎΠ±ΡΠ΅ΡΡΠ²ΠΎ Π½Π΅ ΠΏΡΠ΅Π΄ΡΡΠ°Π²Π»ΡΠ΅Ρ ΡΠ²ΠΎΠ΅ΠΉ ΠΆΠΈΠ·Π½ΠΈ Π±Π΅Π· Π°Π²ΡΠΎΠΌΠΎΠ±ΠΈΠ»ΡΠ½ΠΎΠΉ ΡΠ΅Ρ Π½ΠΈΠΊΠΈ. Π‘ ΡΠΎΡΡΠΎΠΌ ΡΠΈΡΠ»Π° ΠΌΠ°ΡΠΈΠ½ ΠΏΡΠΎΠΏΠΎΡΡΠΈΠΎΠ½Π°Π»ΡΠ½ΠΎ ΡΠ°ΡΡΠ΅Ρ ΠΈ ΠΊΠΎΠ»ΠΈΡΠ΅ΡΡΠ²ΠΎ ΠΈΠ·Π½ΠΎΡΠ΅Π½Π½ΡΡ ΠΏΠΎΠΊΡΡΡΠ΅ΠΊ Π² ΠΌΠΈΡΠ΅. Π‘ΡΠ°Π½ΠΊΠΈ Π΄Π»Ρ ΠΏΠ΅ΡΠ΅ΡΠ°Π±ΠΎΡΠΊΠΈ Π°Π²ΡΠΎΡΠΈΠ½ Π² ΠΊΡΠΎΡΠΊΡ Π½Π΅ ΡΠΏΠΎΡΠΎΠ±Π½Ρ ΡΠΏΡΠ°Π²ΠΈΡΡΡΡ Ρ ΡΠ°ΠΊΠΈΠΌ ΠΎΠ±ΡΠ΅ΠΌΠΎΠΌ ΡΠ΅Π·ΠΈΠ½ΠΎΠ²ΡΡ ΠΎΡΡ ΠΎΠ΄ΠΎΠ².
ΠΠ°ΠΊ ΠΏΡΠΎΠΈΡΡ ΠΎΠ΄ΠΈΡ ΠΏΠΈΡΠΎΠ»ΠΈΠ·
ΠΠΈΡΠΎΠ»ΠΈΠ· ΡΠΈΠ½ ΠΏΡΠ΅Π΄ΡΡΠ°Π²Π»ΡΠ΅Ρ ΡΠΎΠ±ΠΎΠΉ Π²ΡΡΠΎΠΊΠΎΡΡΡΠ΅ΠΊΡΠΈΠ²Π½ΡΠΉ ΠΈ Π½Π΅Π΄ΠΎΡΠΎΠ³ΠΎΠΉ ΡΠΏΠΎΡΠΎΠ± ΠΏΠ΅ΡΠ΅ΡΠ°Π±ΠΎΡΠΊΠΈ ΡΠ΅Π·ΠΈΠ½ΠΎΡΠ΅Ρ
Π½ΠΈΡΠ΅ΡΠΊΠΈΡ
ΠΈΠ·Π΄Π΅Π»ΠΈΠΉ (ΡΡΠΈ), Π° ΡΠ°ΠΊΠΆΠ΅ ΠΎΡΡΠ»ΡΠΆΠΈΠ²ΡΠΈΡ
ΡΠ²ΠΎΠΉ ΡΡΠΎΠΊ Π°Π²ΡΠΎΠΌΠΎΠ±ΠΈΠ»ΡΠ½ΡΡ
ΠΏΠΎΠΊΡΡΡΠ΅ΠΊ. Π ΡΠ΅Π·ΡΠ»ΡΡΠ°ΡΠ΅ ΠΏΡΠΎΡΠ΅ΡΡΠ° Π½Π΅ ΠΏΡΠΎΠΈΡΡ
ΠΎΠ΄ΠΈΡ Π·Π°Π³ΡΡΠ·Π½Π΅Π½ΠΈΡ ΠΎΠΊΡΡΠΆΠ°ΡΡΠ΅ΠΉ ΡΡΠ΅Π΄Ρ.
ΠΡΠ½ΠΎΠ²Π½ΡΠ΅ ΡΡΠ°ΠΏΡ ΡΠ΅Ρ
Π½ΠΎΠ»ΠΎΠ³ΠΈΡΠ΅ΡΠΊΠΎΠ³ΠΎ ΠΏΡΠΎΡΠ΅ΡΡΠ°, Π² ΡΠ΅Π·ΡΠ»ΡΡΠ°ΡΠ΅ ΠΊΠΎΡΠΎΡΠΎΠ³ΠΎ ΡΡΠΈΠ»ΠΈΠ·ΠΈΡΡΡΡΡΡ ΡΠ΅Π·ΠΈΠ½ΠΎΠ²ΡΠ΅ ΠΎΡΡ
ΠΎΠ΄Ρ, Π° ΡΠ°ΠΊΠΆΠ΅ ΠΈΠ·Π½ΠΎΡΠ΅Π½Π½ΡΠ΅ Π°Π²ΡΠΎΠΌΠΎΠ±ΠΈΠ»ΡΠ½ΡΠ΅ ΡΠΈΠ½Ρ:
- ΠΡΠΈ ΠΏΠΎΠΌΠΎΡΠΈ ΡΠΏΠ΅ΡΠΈΠ°Π»ΡΠ½ΡΡ Π½ΠΎΠΆΠ΅ΠΉ ΠΏΠΎΠΊΡΡΡΠΊΠΈ ΡΠ°Π·Π΄Π΅Π»ΡΡΡΡΡ Π½Π° Π±ΠΎΠΊΠΎΠ²ΡΡ ΠΈ ΠΏΠ΅ΡΠ΅Π΄Π½ΡΡ ΡΠ°ΡΡΡ.
- ΠΠ°Π»Π΅Π΅ ΠΏΡΠΎΠΈΡΡ ΠΎΠ΄ΠΈΡ Π·Π°Π³ΡΡΠ·ΠΊΠ° ΡΡΡΡΡ. Π Π°Π·Π΄Π΅Π»Π΅Π½Π½ΡΠΉ ΠΌΠ°ΡΠ΅ΡΠΈΠ°Π» ΠΏΠΎΠΌΠ΅ΡΠ°ΡΡ Π² ΡΠ΅ΡΠΎΡΡΡ ΠΈ Π³Π΅ΡΠΌΠ΅ΡΠΈΡΠ½ΠΎ Π·Π°ΠΊΡΡΠ²Π°ΡΡ, Π° Π·Π°ΡΠ΅ΠΌ Π·Π°Π³ΡΡΠΆΠ°ΡΡ Π² ΠΏΠ΅ΡΡ.
- Π ΡΠ΅Π·ΡΠ»ΡΡΠ°ΡΠ΅ Π½Π°Π³ΡΠ΅Π²Π° ΠΏΡΠΎΠΈΡΡ ΠΎΠ΄ΠΈΡ ΡΠ°Π·Π»ΠΎΠΆΠ΅Π½ΠΈΠ΅ ΡΠ΅Π·ΠΈΠ½Ρ ΠΈ Π²ΡΠ΄Π΅Π»ΡΠ΅ΡΡΡ Π³Π°Π·. ΠΠΎΡΠ»Π΅ ΠΎΠΊΠΎΠ½ΡΠ°Π½ΠΈΡ ΠΏΡΠΎΡΠ΅ΡΡΠ° ΡΠ΅ΡΠΎΡΡΡ ΡΠ΄Π°Π»ΡΡΡ ΠΈΠ· Π½Π°Π³ΡΠ΅Π²Π°ΡΠ΅Π»ΡΠ½ΠΎΠΉ ΠΊΠ°ΠΌΠ΅ΡΡ ΠΈ ΠΏΡΠΎΠΈΡΡ ΠΎΠ΄ΠΈΡ Π·Π°ΠΌΠ΅Π½Π° Π½Π° Π½ΠΎΠ²ΡΡ. Π’Π΅ΠΌΠΏΠ΅ΡΠ°ΡΡΡΠ° Π² ΠΏΠ΅ΡΠΈ ΠΈΠΌΠ΅Π΅Ρ Π·Π½Π°ΡΠ΅Π½ΠΈΠ΅ 450Β°Π‘.
- ΠΠΎΡΠ»Π΅ Π΄Π»ΠΈΡΠ΅Π»ΡΠ½ΠΎΠ³ΠΎ ΠΎΡΡΡΠ²Π°Π½ΠΈΡ ΠΈΠ· Π΅ΠΌΠΊΠΎΡΡΠΈ Π²ΡΠ½ΠΈΠΌΠ°ΡΡ ΡΠΎΠ΄Π΅ΡΠΆΠΈΠΌΠΎΠ΅. ΠΡΠ΄Π΅Π»ΡΡΡΡΡ ΠΆΠΈΠ΄ΠΊΠΈΠ΅ ΡΠ³Π»Π΅Π²ΠΎΠ΄ΠΎΡΠΎΠ΄Ρ ΠΎΡ ΠΊΠΎΡΠ΄Π°.
Π Ρ ΠΎΠ΄Π΅ Π·Π°ΠΊΡΡΡΠΎΠ³ΠΎ ΡΠΆΠΈΠ³Π°Π½ΠΈΡ ΡΠ΅Π·ΠΈΠ½Ρ Π½Π΅ ΡΡΠ΅Π±ΡΠ΅ΡΡΡ ΠΊΠΈΡΠ»ΠΎΡΠΎΠ΄. ΠΠ΅ΡΠ΅ΡΠ°Π±ΠΎΡΠΊΠ° ΡΠΈΠ½ ΠΏΠΈΡΠΎΠ»ΠΈΠ·ΠΎΠΌ ΡΡΠΈΡΠ°Π΅ΡΡΡ ΠΏΠΎΠ»Π½ΠΎΡΡΡΡ Π±Π΅Π·ΠΎΡΡ ΠΎΠ΄Π½ΠΎΠΉ, Π²ΡΠ΅ ΠΏΡΠΎΠ΄ΡΠΊΡΡ Π² ΡΠ΅Π·ΡΠ»ΡΡΠ°ΡΠ΅ ΡΠ΅Π°ΠΊΡΠΈΠΈ ΡΠΈΡΠΎΠΊΠΎ ΠΏΡΠΈΠΌΠ΅Π½ΡΡΡΡΡ Π² Π½Π΅ΡΡΠ΅ΠΏΠ΅ΡΠ΅ΡΠ°Π±Π°ΡΡΠ²Π°ΡΡΠ΅ΠΉ ΠΏΡΠΎΠΌΡΡΠ»Π΅Π½Π½ΠΎΡΡΠΈ.
ΠΡΠΈ Π³ΠΎΡΠ΅Π½ΠΈΠΈ Π² ΠΏΠ΅ΡΠΈ ΠΏΡΠΎΠΈΡΡ ΠΎΠ΄ΡΡ Ρ ΠΈΠΌΠΈΡΠ΅ΡΠΊΠΈΠ΅ ΡΠ΅Π°ΠΊΡΠΈΠΈ ΡΠ°Π·Π»ΠΎΠΆΠ΅Π½ΠΈΡ ΡΠ΅Π·ΠΈΠ½Ρ Π½Π° Π³Π°Π·ΠΎΠΎΠ±ΡΠ°Π·Π½ΡΠ΅ Π½Π΅ΡΡΡΠ½ΡΠ΅ ΡΠΎΡΡΠ°Π²Π»ΡΡΡΠΈΠ΅, ΡΠ³Π»Π΅ΡΠΎΠ΄ΠΈΡΡΡΠΉ ΠΏΠΎΡΠΎΡΠΎΠΊ ΠΈ ΠΌΠ΅ΡΠ°Π»Π»ΠΈΡΠ΅ΡΠΊΠΈΠΉ ΠΊΠΎΡΠ΄.
ΠΡΠΎΠ΄ΡΠΊΡΡ ΡΠ΅Π°ΠΊΡΠΈΠΈ
Π ΡΠ΅Π·ΡΠ»ΡΡΠ°ΡΠ΅ ΠΏΠ΅ΡΠ΅ΡΠ°Π±ΠΎΡΠΊΠΈ ΡΠ΅Π·ΠΈΠ½ΠΎΠ²ΡΡ ΠΎΡΡ ΠΎΠ΄ΠΎΠ² ΠΏΡΠΎΠΈΡΡ ΠΎΠ΄ΠΈΡ Π²ΡΠ΄Π΅Π»Π΅Π½ΠΈΠ΅ Π½Π΅ΡΠΊΠΎΠ»ΡΠΊΠΈΡ Π²ΠΈΠ΄ΠΎΠ² ΠΏΡΠΎΠ΄ΡΠΊΡΠΈΠΈ:
- Π’ΠΎΠΏΠ»ΠΈΠ²ΠΎ ΠΆΠΈΠ΄ΠΊΠΎΠΉ ΡΠΎΡΠΌΡ.
- ΠΡΡΠ°ΡΠΎΠΊ, ΡΠΎΠ΄Π΅ΡΠΆΠ°ΡΠΈΠΉ ΡΠ³Π»Π΅ΡΠΎΠ΄.
- ΠΠ°Π· ΠΏΡΠΈ ΠΏΠΈΡΠΎΠ»ΠΈΠ·Π΅.
- ΠΠ΅ΡΠ°Π»Π»ΠΈΡΠ΅ΡΠΊΠ°Ρ Π°ΡΠΌΠΈΡΡΡΡΠ°Ρ ΠΏΡΠΎΠ²ΠΎΠ»ΠΎΠΊΠ°.
ΠΠΈΠ΄ΠΊΠΎΡΡΡ
ΠΠΈΠ΄ΠΊΠΈΠΉ ΠΎΡΡΠ°ΡΠΎΠΊ, ΠΏΠΎ ΡΡΡΠΈ, ΠΏΡΠ΅Π΄ΡΡΠ°Π²Π»ΡΠ΅Ρ ΡΠΎΠ±ΠΎΠΉ ΡΠΈΠ½ΡΠ΅ΡΠΈΡΠ΅ΡΠΊΡΡ Π½Π΅ΡΡΡ, ΡΡ ΠΎΠΆΡΡ ΠΏΠΎ ΡΠ²ΠΎΠ΅ΠΌΡ ΡΠΎΡΡΠ°Π²Ρ Ρ ΠΏΡΠΈΡΠΎΠ΄Π½ΠΎΠΉ. ΠΡΠΈ ΠΎΠ±ΡΠ°Π±ΠΎΡΠΊΠ΅ ΠΏΠΎΠ»ΡΡΠ΅Π½Π½ΠΎΠ³ΠΎ ΡΡΡΡΡ Π½Π° Π½Π΅ΡΡΠ΅ΠΏΠ΅ΡΠ΅ΡΠ°Π±Π°ΡΡΠ²Π°ΡΡΠΈΡ Π·Π°Π²ΠΎΠ΄Π°Ρ Π²ΠΎΠ·ΠΌΠΎΠΆΠ½ΠΎ ΠΏΠΎΠ»ΡΡΠΈΡΡ ΡΠ°ΠΊΠΈΠ΅ Π²ΠΈΠ΄Ρ ΠΌΠ°ΡΠ΅ΡΠΈΠ°Π»ΠΎΠ², ΠΊΠ°ΠΊ Π±Π΅Π½Π·ΠΈΠ½, ΠΌΠ°Π·ΡΡ, Π° ΡΠ°ΠΊΠΆΠ΅ ΡΠΈΠ½ΡΠ΅ΡΠΈΡΠ΅ΡΠΊΠΎΠ΅ ΠΌΠ°ΡΠ»ΠΎ Π΄Π»Ρ Π°Π²ΡΠΎΠΌΠΎΠ±ΠΈΠ»ΡΠ½ΠΎΠΉ ΡΠ΅Ρ Π½ΠΈΠΊΠΈ.
Π£Π³Π»Π΅ΡΠΎΠ΄ΡΠΎΠ΄Π΅ΡΠΆΠ°ΡΠΈΠΉ ΠΎΡΡΠ°ΡΠΎΠΊ
Π’Π²Π΅ΡΠ΄ΡΠΉ ΠΎΡΡΠ°ΡΠΎΠΊ Π½Π°ΡΠ΅Π» ΡΠΈΡΠΎΠΊΠΎΠ΅ ΠΏΡΠΈΠΌΠ΅Π½Π΅Π½ΠΈΠ΅ Π² Π½Π΅ΠΊΠΎΡΠΎΡΡΡ ΠΎΠ±Π»Π°ΡΡΡΡ :
- ΠΠ½ Π°Π½Π°Π»ΠΎΠ³ΠΈΡΠ΅Π½ Π°ΠΊΡΠΈΠ²ΠΈΡΠΎΠ²Π°Π½Π½ΠΎΠΌΡ ΡΠ³Π»Ρ ΠΏΠΎ ΡΠ²ΠΎΠΈΠΌ Π°Π±ΡΠΎΡΠ±Π΅Π½ΡΠ½ΡΠΌ ΡΠ²ΠΎΠΉΡΡΠ²Π°ΠΌ.
- ΠΠ°ΠΊ ΡΠ΅ΡΠ½ΡΠΉ ΠΊΡΠ°ΡΠΈΡΠ΅Π»Ρ Π² Π»Π°ΠΊΠΎΠΊΡΠ°ΡΠΎΡΠ½ΠΎΠΌ ΠΈ ΡΠ΅ΠΌΠ΅Π½ΡΠ½ΠΎΠΌ ΠΏΡΠΎΠΈΠ·Π²ΠΎΠ΄ΡΡΠ²Π΅.
- ΠΠ°ΠΊ ΡΡΡΡΠ΅ Π΄Π»Ρ ΠΈΠ·Π³ΠΎΡΠΎΠ²Π»Π΅Π½ΠΈΡ Π½ΠΎΠ²ΡΡ ΡΠ΅Π·ΠΈΠ½ΠΎΠ²ΡΡ ΠΈΠ·Π΄Π΅Π»ΠΈΠΉ, Π° ΡΠ°ΠΊΠΆΠ΅ ΠΏΠΎΠΊΡΡΡΠ΅ΠΊ.
- ΠΠΎΠ±Π°Π²Π»ΡΠ΅ΡΡΡ Π² ΠΆΠΈΠ΄ΠΊΠΎΠ΅ ΡΠΎΠΏΠ»ΠΈΠ²ΠΎ, Π»ΠΈΠ±ΠΎ ΡΠΆΠΈΠ³Π°Π΅ΡΡΡ ΡΠ°ΠΌ Π² ΡΠΏΠ΅ΡΠΈΠ°Π»ΡΠ½ΡΡ ΠΏΠ΅ΡΠ°Ρ .
ΠΠΈΡΠΎΠ»ΠΈΠ·Π½ΡΠΉ Π³Π°Π·
ΠΠΈΡΠΎΠ»ΠΈΠ· ΠΏΠΎΠΊΡΡΡΠ΅ΠΊ ΠΏΡΠΎΠΈΠ·Π²ΠΎΠ΄ΠΈΡΡΡ Ρ Π²ΡΠ΄Π΅Π»Π΅Π½ΠΈΠ΅ΠΌ Π³Π°Π·Π°, ΠΊΠΎΡΠΎΡΡΠΉ ΠΏΠΎ ΡΠ²ΠΎΠΈΠΌ Ρ Π°ΡΠ°ΠΊΡΠ΅ΡΠΈΡΡΠΈΠΊΠ°ΠΌ ΡΡ ΠΎΠΆ Ρ ΠΏΡΠΈΡΠΎΠ΄Π½ΡΠΌ. ΠΠΎΠ»ΡΡΠ°Ρ ΡΠ°ΡΡΡ Π΄Π°Π½Π½ΠΎΠ³ΠΎ Π³Π°Π·Π° Π² ΡΠ΅Π·ΡΠ»ΡΡΠ°ΡΠ΅ Π³ΠΎΡΠ΅Π½ΠΈΡ Π² ΠΏΠ΅ΡΠΈ ΡΠ°Π·Π΄Π΅Π»ΡΠ΅ΡΡΡ Π½Π° ΠΆΠΈΠ΄ΠΊΠΈΠ΅ ΡΡΠ°ΠΊΡΠΈΠΈ, Π° ΡΠ°ΠΊΠΆΠ΅ Π½Π΅Π²ΡΠΏΠ°Π΄Π°ΡΡΠΈΠ΅ Π² ΠΎΡΠ°Π΄ΠΎΠΊ ΠΎΡΡΠ°ΡΠΊΠΈ, ΠΊΠΎΡΠΎΡΡΠ΅ ΠΏΠΎΠ΄Π΄Π΅ΡΠΆΠΈΠ²Π°ΡΡ ΡΠ°Π·Π»ΠΎΠΆΠ΅Π½ΠΈΠ΅ ΡΠ΅Π·ΠΈΠ½Ρ.
ΠΠ΅ΡΠ°Π»Π»ΠΈΡΠ΅ΡΠΊΠΈΠΉ ΠΊΠΎΡΠ΄
ΠΠ΅ΡΠ°Π»Π»ΠΈΡΠ΅ΡΠΊΠ°Ρ ΠΏΡΠΎΠ²ΠΎΠ»ΠΎΠΊΠ° ΠΏΡΠΈ Π²ΠΎΠ·Π΄Π΅ΠΉΡΡΠ²ΠΈΠΈ Π²ΡΡΠΎΠΊΠΎΠΉ ΡΠ΅ΠΌΠΏΠ΅ΡΠ°ΡΡΡΡ Π½Π΅ ΠΏΠΎΠ΄Π²Π΅ΡΠΆΠ΅Π½Π° ΡΠ°Π·Π»ΠΎΠΆΠ΅Π½ΠΈΡ ΠΈ ΠΎΡΡΠ°Π΅ΡΡΡ Π² ΠΏΡΠ°ΠΊΡΠΈΡΠ΅ΡΠΊΠΈ Π½Π΅ΠΈΠ·ΠΌΠ΅Π½Π½ΠΎΠΌ Π²ΠΈΠ΄Π΅. Π‘Π΅ΡΠ΄Π΅ΡΠ½ΠΈΠΊ Π°Π²ΡΠΎΠΌΠΎΠ±ΠΈΠ»ΡΠ½ΡΡ
ΡΠΈΠ½ ΠΏΡΠΎΠΈΠ·Π²ΠΎΠ΄ΠΈΡΡΡ ΠΈΠ· ΠΊΠ°ΡΠ΅ΡΡΠ²Π΅Π½Π½ΠΎΠΉ ΡΡΠ°Π»ΠΈ, ΠΊΠΎΡΠΎΡΠ°Ρ ΠΏΡΠΈ Π΄Π°Π»ΡΠ½Π΅ΠΉΡΠ΅ΠΉ ΠΏΠ΅ΡΠ΅ΠΏΠ»Π°Π²ΠΊΠ΅ Π½Π°Ρ
ΠΎΠ΄ΠΈΡ ΡΠ²ΠΎΡ Π²ΡΠΎΡΡΡ ΠΆΠΈΠ·Π½Ρ
Π£ΡΡΡΠΎΠΉΡΡΠ²ΠΎ ΠΊΠΎΡΠ»ΠΎΠ²
ΠΠΈΡΠΎΠ»ΠΈΠ·Π½Π°Ρ ΡΡΡΠ°Π½ΠΎΠ²ΠΊΠ° ΠΏΠΎ ΠΏΠ΅ΡΠ΅ΡΠ°Π±ΠΎΡΠΊΠ΅ ΡΠΈΠ½ Π² ΡΠ²ΠΎΠ΅ΠΉ ΠΊΠΎΠ½ΡΡΡΡΠΊΡΠΈΠΈ ΠΈΠΌΠ΅Π΅Ρ ΡΠ»Π΅Π΄ΡΡΡΠΈΠ΅ ΠΎΡΠ½ΠΎΠ²Π½ΡΠ΅ ΡΠ»Π΅ΠΌΠ΅Π½ΡΡ:
Π Π΅ΡΠΎΡΡΠ°
ΠΠ΅ΡΠΌΠ΅ΡΠΈΡΠ½Π°Ρ Π΅ΠΌΠΊΠΎΡΡΡ, Π² ΠΊΠΎΡΠΎΡΠΎΠΉ ΡΠ΅Π·ΠΈΠ½ΠΎΠ²ΡΠ΅ ΠΎΡΡ ΠΎΠ΄Ρ ΠΈ ΡΠΈΠ½Ρ ΠΏΠΎΡΠ»Π΅ ΠΏΡΠ΅Π΄Π²Π°ΡΠΈΡΠ΅Π»ΡΠ½ΠΎΠ³ΠΎ ΠΈΠ·ΠΌΠ΅Π»ΡΡΠ΅Π½ΠΈΡ ΠΏΡΠΎΡ ΠΎΠ΄ΡΡ ΠΏΡΠΎΡΠ΅ΡΡΡ ΡΠ°Π·Π»ΠΎΠΆΠ΅Π½ΠΈΡ Π² ΡΠ΅Π·ΡΠ»ΡΡΠ°ΡΠ΅ ΠΏΠΈΡΠΎΠ»ΠΈΠ·Π° Π½Π° ΠΎΡΠ½ΠΎΠ²Π½ΡΠ΅ ΡΠΎΡΡΠ°Π²Π»ΡΡΡΠΈΠ΅ ΠΏΠ΅ΡΠ΅Π΄ Π΄Π°Π»ΡΠ½Π΅ΠΉΡΠ΅ΠΉ ΠΏΠ΅ΡΠ΅ΡΠ°Π±ΠΎΡΠΊΠΎΠΉ.
ΠΠ·Π³ΠΎΡΠ°Π²Π»ΠΈΠ²Π°Π΅ΡΡΡ ΠΈΠ· ΠΏΡΠΎΡΠ½ΠΎΠ³ΠΎ ΠΌΠ΅ΡΠ°Π»Π»Π° Π²ΠΎ ΠΈΠ·Π±Π΅ΠΆΠ°Π½ΠΈΠ΅ ΠΏΡΠΎΠ³ΠΎΡΠ°Π½ΠΈΡ ΡΡΠ΅Π½ΠΎΠΊ.
ΠΠ°ΠΌΠ΅ΡΠ° Π³ΠΎΡΠ΅Π½ΠΈΡ
Π’ΠΎΠΏΠΊΠ° ΠΏΠΎ ΠΊΠΎΠ½ΡΡΡΡΠΊΡΠΈΠΈ ΠΏΡΠ΅Π΄ΡΡΠ°Π²Π»ΡΠ΅Ρ ΡΠΎΠ±ΠΎΠΉ Π΄Π²Π° ΠΎΡΡΠ΅ΠΊΠ° Π΄Π»Ρ Π³ΠΎΡΠ΅Π½ΠΈΡ ΡΠΎΠΏΠ»ΠΈΠ²Π°. Π ΠΏΠ΅ΡΠ²ΠΎΠΉ ΠΊΠ°ΠΌΠ΅ΡΠ΅ ΠΏΡΠΎΠΈΡΡ ΠΎΠ΄ΠΈΡ ΠΎΡΠ½ΠΎΠ²Π½ΠΎΠ΅ Π³ΠΎΡΠ΅Π½ΠΈΠ΅, Π³Π΄Π΅ ΠΏΠΎΠ΄Π΄Π΅ΡΠΆΠΈΠ²Π°Π΅ΡΡΡ Π½Π΅ΠΎΠ±Ρ ΠΎΠ΄ΠΈΠΌΠ°Ρ ΡΠ΅ΠΌΠΏΠ΅ΡΠ°ΡΡΡΠ° Π΄Π»Ρ ΡΠ΅Ρ Π½ΠΎΠ»ΠΎΠ³ΠΈΡΠ΅ΡΠΊΠΎΠ³ΠΎ ΠΏΡΠΎΡΠ΅ΡΡΠ°. Π Π²Π΅ΡΡ Π½Π΅ΠΌ ΠΎΡΡΠ΅ΠΊΠ΅ ΠΏΡΠΎΠΈΡΡ ΠΎΠ΄ΠΈΡ ΠΏΠΎΠ»Π½ΠΎΠ΅ Π΄ΠΎΠΆΠΈΠ³Π°Π½ΠΈΠ΅ ΡΠΎΠΏΠ»ΠΈΠ²Π° Π²ΠΎ ΠΈΠ·Π±Π΅ΠΆΠ°Π½ΠΈΠ΅ Π²ΡΠ±ΡΠΎΡΠΎΠ² Π²ΡΠ΅Π΄Π½ΡΡ Π²Π΅ΡΠ΅ΡΡΠ² Π² Π°ΡΠΌΠΎΡΡΠ΅ΡΡ. ΠΠ°ΠΌΠ΅ΡΠ° Π΄ΠΎΠΆΠΈΠ³Π°Π½ΠΈΡ ΡΠ½Π°Π±ΠΆΠ°Π΅ΡΡΡ ΠΎΡΠ²Π΅ΡΡΡΠΈΡΠΌΠΈ Π΄Π»Ρ Π΅ΡΡΠ΅ΡΡΠ²Π΅Π½Π½ΠΎΠΉ ΠΏΠΎΠ΄Π°ΡΠΈ Π²ΠΎΠ·Π΄ΡΡ Π°.
Π’Π΅ΠΏΠ»ΠΎΠΎΠ±ΠΌΠ΅Π½Π½ΠΈΠΊ
ΠΠ°Π½Π½Π°Ρ ΠΊΠΎΠ½ΡΡΡΡΠΊΡΠΈΡ ΠΏΡΠ΅Π΄ΡΡΠ°Π²Π»ΡΠ΅Ρ ΡΠΎΠ±ΠΎΠΉ ΡΠΎΠ΅Π΄ΠΈΠ½Π΅Π½ΠΈΠ΅ ΠΈΠ· ΠΌΠ΅ΡΠ°Π»Π»ΠΈΡΠ΅ΡΠΊΠΈΡ ΡΡΡΠ±, Π² ΠΊΠΎΡΠΎΡΡΡ ΠΏΡΠΎΠΈΡΡ ΠΎΠ΄ΠΈΡ ΠΎΡΡΡΠ²Π°Π½ΠΈΠ΅ ΠΈ ΡΠ°Π·Π΄Π΅Π»Π΅Π½ΠΈΠ΅ ΠΏΠΈΡΠΎΠ»ΠΈΠ·Π½ΠΎΠ³ΠΎ Π³Π°Π·Π° Π½Π° ΡΠΎΡΡΠ°Π²Π»ΡΡΡΠΈΠ΅. ΠΡΡΡΠ΅Π½Π½ΡΠΉ Π³Π°Π· ΠΏΡΠΈΠΌΠ΅Π½ΡΡΡ Π΄Π»Ρ Π΄Π°Π»ΡΠ½Π΅ΠΉΡΠ΅Π³ΠΎ ΡΠΆΠΈΠ³Π°Π½ΠΈΡ Π² ΠΏΠ΅ΡΠΈ. ΠΠΈΠ΄ΠΊΠ°Ρ ΡΠΎΡΡΠ°Π²Π»ΡΡΡΠ°Ρ ΠΏΡΠΎΡ ΠΎΠ΄ΠΈΡ ΠΏΠΎΡΠ»Π΅Π΄ΡΡΡΡΡ ΠΏΠ΅ΡΠ΅ΡΠ°Π±ΠΎΡΠΊΡ.
ΠΠΎΠΆΠ½ΠΎ Π»ΠΈ ΡΠ΄Π΅Π»Π°ΡΡ ΠΎΠ±ΠΎΡΡΠ΄ΠΎΠ²Π°Π½ΠΈΠ΅ ΡΠ²ΠΎΠΈΠΌΠΈ ΡΡΠΊΠ°ΠΌΠΈ
ΠΠ±ΠΎΡΡΠ΄ΠΎΠ²Π°Π½ΠΈΠ΅ Π΄Π»Ρ ΠΏΠ΅ΡΠ΅ΡΠ°Π±ΠΎΡΠΊΠΈ ΡΠΈΠ½ ΠΌΠΎΠΆΠ½ΠΎ ΡΠΎΠ±ΡΠ°ΡΡ ΡΠ²ΠΎΠΈΠΌΠΈ ΡΡΠΊΠ°ΠΌΠΈ, ΠΊΠΎΠ½ΡΡΡΡΠΊΡΠΈΡ ΠΏΠΈΡΠΎΠ»ΠΈΠ·Π½ΠΎΠΉ ΡΡΡΠ°Π½ΠΎΠ²ΠΊΠΈ ΠΏΡΠΎΡΡΠ°. ΠΠ»Ρ ΠΈΠ·Π³ΠΎΡΠΎΠ²Π»Π΅Π½ΠΈΡ Π½Π΅ΠΎΠ±Ρ ΠΎΠ΄ΠΈΠΌΡ ΡΠ»Π΅Π΄ΡΡΡΠΈΠ΅ ΠΎΡΠ½ΠΎΠ²Π½ΡΠ΅ ΡΠ»Π΅ΠΌΠ΅Π½ΡΡ:
- ΠΠ΅ΡΠ°Π»Π»ΠΈΡΠ΅ΡΠΊΠΈΠ΅ ΡΡΡΠ±Ρ ΡΠ°Π·Π»ΠΈΡΠ½ΠΎΠ³ΠΎ Π΄ΠΈΠ°ΠΌΠ΅ΡΡΠ°, Π΄Π»Ρ ΠΎΡΠ΄Π΅Π»ΡΠ½ΡΡ ΡΠ·Π»ΠΎΠ² Π°ΠΏΠΏΠ°ΡΠ°ΡΠ°.
- ΠΡΠ°Π½Ρ ΠΈ Π²Π΅Π½ΡΠΈΠ»Ρ Π΄Π»Ρ ΠΊΠΎΠ½ΡΡΠΎΠ»Ρ ΠΏΠΎΠ΄Π°ΡΠΈ ΡΠΎΠΏΠ»ΠΈΠ²Π° Π΄Π»Ρ ΠΏΠ΅ΡΠΈ.
- Π’Π΅ΡΠΌΠΎΠΌΠ΅ΡΡΡ, Ρ ΠΏΠΎΠΌΠΎΡΡΡ ΠΊΠΎΡΠΎΡΡΡ Π±ΡΠ΄Π΅Ρ ΠΏΡΠΎΠΈΠ·Π²ΠΎΠ΄ΠΈΡΡΡΡ ΠΊΠΎΠ½ΡΡΠΎΠ»Ρ Π·Π° Π²Π½ΡΡΡΠ΅Π½Π½ΠΈΠΌΠΈ ΠΏΡΠΎΡΠ΅ΡΡΠ°ΠΌΠΈ ΠΈ Π·Π½Π°ΡΠ΅Π½ΠΈΠ΅ΠΌ ΠΏΠΎΠΊΠ°Π·Π°Π½ΠΈΠΉ ΡΠ΅ΠΌΠΏΠ΅ΡΠ°ΡΡΡΡ.
- ΠΠ΅ΡΠ°Π»Π»ΠΈΡΠ΅ΡΠΊΠ°Ρ Π±ΠΎΡΠΊΠ° ΠΎΠ±ΡΠ΅ΠΌΠΎΠΌ 200 Π», ΠΎΠ½Π° ΠΏΠΎΡΠ»ΡΠΆΠΈΡ Π΄Π»Ρ ΠΈΠ·Π³ΠΎΡΠΎΠ²Π»Π΅Π½ΠΈΡ ΠΊΠ°ΠΌΠ΅ΡΡ ΡΠ³ΠΎΡΠ°Π½ΠΈΡ.
- Π ΠΊΠ°ΡΠ΅ΡΡΠ²Π΅ ΡΠ΅ΡΠΎΡΡΡ ΠΏΠΎΠ΄ΠΎΠΉΠ΄Π΅Ρ ΠΎΠ±ΡΡΠ½ΡΠΉ Π±ΡΡΠΎΠ²ΠΎΠΉ Π±ΠΈΠ΄ΠΎΠ½, ΠΏΠΎΡΠ»Π΅ Π΄ΠΎΡΠ°Π±ΠΎΡΠΊΠΈ Π΅Π³ΠΎ Π³Π΅ΡΠΌΠ΅ΡΠΈΡΠ½ΡΠΌΠΈ ΡΠΎΠ΅Π΄ΠΈΠ½Π΅Π½ΠΈΡΠΌΠΈ.
ΠΠ΅ΠΉΡΡΠ²ΠΎΠ²Π°ΡΡ ΠΈΠ·Π³ΠΎΡΠΎΠ²Π»Π΅Π½Π½ΠΎΠ΅ ΡΠ²ΠΎΠΈΠΌΠΈ ΡΡΠΊΠ°ΠΌΠΈ ΠΎΠ±ΠΎΡΡΠ΄ΠΎΠ²Π°Π½ΠΈΠ΅ Π±ΡΠ΄Π΅Ρ, Π½ΠΎ ΡΠΎΠ»ΡΠΊΠΎ ΠΊΠ°ΠΊ Π±ΡΡΠΎΠ²ΠΎΠΉ ΠΏΡΠΈΠ±ΠΎΡ Π΄Π»Ρ Π½Π°ΡΡΠ½ΡΡ ΠΈΡΡΠ»Π΅Π΄ΠΎΠ²Π°Π½ΠΈΠΉ. ΠΠ΅Π· Π΄ΠΎΠΏΠΎΠ»Π½ΠΈΡΠ΅Π»ΡΠ½ΠΎΠ³ΠΎ ΠΎΠ±ΠΎΡΡΠ΄ΠΎΠ²Π°Π½ΠΈΡ Π΄Π»Ρ Π΄Π°Π»ΡΠ½Π΅ΠΉΡΠ΅ΠΉ ΠΏΠ΅ΡΠ΅ΡΠ°Π±ΠΎΡΠΊΠΈ ΠΏΠΎΠ»ΡΡΠ°Π΅ΠΌΠΎΠ³ΠΎ ΡΡΡΡΡ, ΠΏΡΠΎΠ΄ΡΠΊΡΡ Π±ΡΡΠΎΠ²ΠΎΠ³ΠΎ ΠΏΡΠΎΡΠ΅ΡΡΠ° ΠΏΠΈΡΠΎΠ»ΠΈΠ·Π° ΠΌΠ°Π»ΠΎΠΏΡΠΈΠ³ΠΎΠ΄Π½Ρ Π΄Π»Ρ ΠΏΡΠΈΠΌΠ΅Π½Π΅Π½ΠΈΡ ΠΏΠΎ ΡΠ²ΠΎΠ΅ΠΌΡ Π½Π°Π·Π½Π°ΡΠ΅Π½ΠΈΡ. ΠΠΊΠΎΠ½ΠΎΠΌΠΈΡΠ΅ΡΠΊΠ°Ρ Π²ΡΠ³ΠΎΠ΄Π° ΠΏΡΠΈ ΠΈΡΠΏΠΎΠ»ΡΠ·ΠΎΠ²Π°Π½ΠΈΠΈ ΡΠ°ΠΊΠΎΠΉ ΡΡΡΠ°Π½ΠΎΠ²ΠΊΠΈ Π±ΡΠ΄Π΅Ρ Π½Π΅Π·Π°ΠΌΠ΅ΡΠ½Π° Π² ΡΠ΅Π·ΡΠ»ΡΡΠ°ΡΠ΅ ΠΌΠ°Π»ΠΎΠ³ΠΎ Π²ΠΎΠ·ΠΌΠΎΠΆΠ½ΠΎΠ³ΠΎ ΠΎΠ±ΡΠ΅ΠΌΠ° ΡΠΈΠ½.
ΠΠ»Ρ ΡΠ²Π΅Π»ΠΈΡΠ΅Π½ΠΈΡ Π²ΡΠ³ΠΎΠ΄Ρ ΠΏΡΠΈ ΠΏΠ΅ΡΠ΅ΡΠ°Π±ΠΎΡΠΊΠ΅ ΠΏΠΎΠΊΡΡΡΠ΅ΠΊ Π² ΠΏΡΠΈΠ³ΠΎΠ΄Π½ΠΎΠ΅ ΡΠΎΠΏΠ»ΠΈΠ²ΠΎ Π½Π΅ΠΎΠ±Ρ ΠΎΠ΄ΠΈΠΌΠΎ ΠΏΡΠΈΠΌΠ΅Π½ΡΡΡ Π³ΠΎΡΠΎΠ²ΡΠ΅ ΡΡΡΠ°Π½ΠΎΠ²ΠΊΠΈ ΠΏΠΈΡΠΎΠ»ΠΈΠ·Π°, ΠΈΠ·Π³ΠΎΡΠΎΠ²Π»Π΅Π½Π½ΡΠ΅ ΡΠΏΠ΅ΡΠΈΠ°Π»ΠΈΡΡΠ°ΠΌΠΈ.
ΠΠΎΠ»ΡΡΠ°Π΅ΠΌΠΎΠ΅ ΡΡΡΡΠ΅ Π½Π΅ΠΎΠ±Ρ ΠΎΠ΄ΠΈΠΌΠΎ Π² Π΄Π°Π»ΡΠ½Π΅ΠΉΡΠ΅ΠΌ ΡΠ»ΡΡΡΠ°ΡΡ ΠΈ ΠΏΠ΅ΡΠ΅ΡΠ°Π±Π°ΡΡΠ²Π°ΡΡ, Π΄Π»Ρ ΡΡΠΎΠ³ΠΎ Π² ΠΏΡΠΎΠΌΡΡΠ»Π΅Π½Π½ΡΡ Π°Π³ΡΠ΅Π³Π°ΡΠ°Ρ ΠΏΡΠΈΠΌΠ΅Π½ΡΡΡΡΡ Π΄ΠΎΠΏΠΎΠ»Π½ΠΈΡΠ΅Π»ΡΠ½ΡΠ΅ Π²ΡΠΏΠΎΠΌΠΎΠ³Π°ΡΠ΅Π»ΡΠ½ΡΠ΅ ΡΠ·Π»Ρ:
- Π‘ΠΊΡΡΠ±Π±Π΅Ρ. Π£ΡΡΡΠΎΠΉΡΡΠ²ΠΎ, ΠΊΠΎΡΠΎΡΠΎΠ΅ ΠΎΡ Π»Π°ΠΆΠ΄Π°Π΅Ρ ΠΏΠΎΠ»ΡΡΠ°Π΅ΠΌΡΠΉ Π² ΡΠ΅Π·ΡΠ»ΡΡΠ°ΡΠ΅ ΠΏΠΈΡΠΎΠ»ΠΈΠ· Π³Π°Π·, Ρ ΠΏΡΠΈΠΌΠ΅Π½Π΅Π½ΠΈΠ΅ΠΌ ΡΠΏΠ΅ΡΠΈΠ°Π»ΡΠ½ΡΡ Ρ ΠΈΠΌΠΈΡΠ΅ΡΠΊΠΈΡ Π²Π΅ΡΠ΅ΡΡΠ². ΠΡΠΎΠΈΡΡ ΠΎΠ΄ΠΈΡ ΡΠ°ΡΡΠΈΡΠ½Π°Ρ ΠΊΠΎΠ½Π΄Π΅Π½ΡΠ°ΡΠΈΡ Π² ΠΆΠΈΠ΄ΠΊΠΎΡΡΡ.
- Π‘Π΅ΠΏΠ°ΡΠ°ΡΠΎΡ. Π‘Π½ΠΈΠΆΠ°Π΅Ρ ΡΡΠΎΠ²Π΅Π½Ρ Π²Π»Π°ΠΆΠ½ΠΎΡΡΠΈ ΠΏΠΎΠ»ΡΡΠ΅Π½Π½ΠΎΠ³ΠΎ Π³Π°Π·Π° ΠΏΠ΅ΡΠ΅Π΄ Π΄Π°Π»ΡΠ½Π΅ΠΉΡΠ΅ΠΉ ΠΏΠΎΠ΄Π°ΡΠ΅ΠΉ Π² ΠΏΠ΅ΡΡ.
- ΠΠΎΠ½Π΄Π΅Π½ΡΠ°ΡΠΎΡ. ΠΠΊΠΎΠ½ΡΠ°ΡΠ΅Π»ΡΠ½ΠΎ ΠΏΡΠ΅ΠΎΠ±ΡΠ°Π·ΡΠ΅Ρ ΠΏΠΎΠ»ΡΡΠ΅Π½Π½ΡΡ Π³Π°Π·ΠΎΠΎΠ±ΡΠ°Π·Π½ΡΡ ΡΡΠ°ΠΊΡΠΈΡ Π² ΠΆΠΈΠ΄ΠΊΠΎΡΡΡ.
- Π€ΠΈΠ»ΡΡΡΡ. ΠΠ°ΡΠΈΡΠ°ΡΡ ΠΎΡ ΠΏΠΎΠΏΠ°Π΄Π°Π½ΠΈΡ Π²ΡΠ΅Π΄Π½ΡΡ Π²Π΅ΡΠ΅ΡΡΠ² Π² Π°ΡΠΌΠΎΡΡΠ΅ΡΡ, Π² ΡΠ΅Π·ΡΠ»ΡΡΠ°ΡΠ΅ Π³ΠΎΡΠ΅Π½ΠΈΡ.
Π Ρ ΠΎΠ΄Π΅ ΠΏΡΠΎΡΠ΅ΡΡΠ° ΠΏΠΈΡΠΎΠ»ΠΈΠ·Π° Π½Π΅ΠΎΠ±Ρ ΠΎΠ΄ΠΈΠΌΠΎ ΡΠΎΠ±Π»ΡΠ΄Π°ΡΡ ΠΏΡΠ°Π²ΠΈΠ»Π° Π±Π΅Π·ΠΎΠΏΠ°ΡΠ½ΠΎΠΉ ΡΠΊΡΠΏΠ»ΡΠ°ΡΠ°ΡΠΈΠΈ.
Π Π°Π±ΠΎΡΠ° ΠΏΠ΅ΡΠΈ
ΠΠ΅ΡΠΎΠ΄ ΡΠ°Π±ΠΎΡΡ ΠΏΡΠΎΠΌΡΡΠ»Π΅Π½Π½ΠΎΠΉ ΠΏΠΈΡΠΎΠ»ΠΈΠ·Π½ΠΎΠΉ ΡΡΡΠ°Π½ΠΎΠ²ΠΊΠΈ Π΄Π»Ρ ΠΏΠ΅ΡΠ΅ΡΠ°Π±ΠΎΡΠΊΠΈ ΡΠ΅Π·ΠΈΠ½ΠΎΠ²ΡΡ ΠΈΠ·Π΄Π΅Π»ΠΈΠΉ ΠΈ ΡΠΈΠ½ ΠΏΠΎΠ΄ΡΠ°Π·ΡΠΌΠ΅Π²Π°Π΅Ρ Π½Π΅ΡΠΊΠΎΠ»ΡΠΊΠΎ ΠΎΡΠ½ΠΎΠ²Π½ΡΡ ΡΡΠ°ΠΏΠΎΠ² ΠΏΡΠΎΠΈΠ·Π²ΠΎΠ΄ΡΡΠ²Π°:
- ΠΠΎΠ΄Π³ΠΎΡΠΎΠ²ΠΊΠ° ΠΌΠ°ΡΠ΅ΡΠΈΠ°Π»Π° Π΄Π»Ρ Π΅Π³ΠΎ Π΄Π°Π»ΡΠ½Π΅ΠΉΡΠ΅Π³ΠΎ ΡΠ°Π·Π»ΠΎΠΆΠ΅Π½ΠΈΡ Π² ΡΠ΅ΡΠΎΡΡΠ΅.
- ΠΠΎΠ»ΡΡΠ΅Π½Π½ΠΎΠ΅ ΡΡΡΡΠ΅ ΠΏΡΠΈ ΠΏΠΈΡΠΎΠ»ΠΈΠ·Π΅ ΠΏΠΎΠ΄Π°Π΅ΡΡΡ Π² ΡΡΡΡΠΎΠΉΡΡΠ²ΠΎ Π΄Π»Ρ ΠΎΡ Π»Π°ΠΆΠ΄Π΅Π½ΠΈΡ ΠΈ ΡΠ°ΡΡΠΈΡΠ½ΠΎΠΉ ΠΊΠΎΠ½Π΄Π΅Π½ΡΠ°ΡΠΈΠΈ ΠΏΠΈΡΠΎΠ»ΠΈΠ·Π½ΠΎΠ³ΠΎ Π³Π°Π·Π°.
- ΠΡΠΈ ΠΏΡΠΎΡ ΠΎΠΆΠ΄Π΅Π½ΠΈΠΈ ΡΠ΅ΡΠ΅Π· ΠΊΠΎΠ½Π΄Π΅Π½ΡΠΈΡΡΡΡΠΈΠΉ ΡΡΡΠ±ΠΎΠΏΡΠΎΠ²ΠΎΠ΄ ΠΏΡΠΎΠΈΡΡ ΠΎΠ΄ΠΈΡ ΠΎΠΊΠΎΠ½ΡΠ°ΡΠ΅Π»ΡΠ½ΠΎΠ΅ ΡΠ°Π·Π΄Π΅Π»Π΅Π½ΠΈΠ΅ Π½Π° ΠΆΠΈΠ΄ΠΊΡΡ ΠΈ Π³Π°Π·ΠΎΠΎΠ±ΡΠ°Π·Π½ΡΡ ΡΠΎΡΡΠ°Π²Π»ΡΡΡΡΡ.
- ΠΡΠΈ ΠΎΡΡΡΠ΅Π½ΠΈΠΈ ΠΎΡΡΠ°Π²ΡΠ΅Π³ΠΎΡΡ Π³Π°Π·Π° Π΅Π³ΠΎ ΠΏΠΎΠ΄Π°ΡΡ Π΄Π»Ρ Π΄Π°Π»ΡΠ½Π΅ΠΉΡΠ΅Π³ΠΎ ΡΠΆΠΈΠ³Π°Π½ΠΈΡ Π² ΠΏΠ΅ΡΠΈ.
ΠΠΎΠ»ΡΡΠΈΠ΅ ΠΏΠ΅ΡΠ΅ΡΠ°Π±Π°ΡΡΠ²Π°ΡΡΠΈΠ΅ Π·Π°Π²ΠΎΠ΄Ρ ΠΈΡΠΏΠΎΠ»ΡΠ·ΡΡΡ Π² ΠΏΡΠΎΡΠ΅ΡΡΠ΅ ΡΠ°Π·Π»ΠΎΠΆΠ΅Π½ΠΈΡ ΡΠ΅Π·ΠΈΠ½Ρ Π΄ΠΎΠΏΠΎΠ»Π½ΠΈΡΠ΅Π»ΡΠ½ΡΠ΅ ΠΊΠ°ΡΠ°Π»ΠΈΠ·Π°ΡΠΎΡΠ½ΡΠ΅ ΡΡΡΠ°Π½ΠΎΠ²ΠΊΠΈ.
Π Π½Π°ΡΠ΅ΠΉ ΡΡΡΠ°Π½Π΅ ΠΌΠ΅ΡΠΎΠ΄ ΡΠ΅Ρ Π½ΠΎΠ»ΠΎΠ³ΠΈΡΠ΅ΡΠΊΠΎΠΉ ΠΏΠ΅ΡΠ΅ΡΠ°Π±ΠΎΡΠΊΠΈ ΡΠ΅Π·ΠΈΠ½Ρ ΠΏΠΎΠΊΠ° Π½Π΅ ΠΈΡΠΏΠΎΠ»ΡΠ·ΡΠ΅ΡΡΡ ΡΠΈΡΠΎΠΊΠΎ, ΠΎΠ΄Π½Π°ΠΊΠΎ Π½Π° ΡΡΠ½ΠΊΠ΅ ΠΏΡΠ΅Π΄ΡΡΠ°Π²Π»ΡΡΡΡΡ Π΄ΠΎΡΡΠΎΠΉΠ½ΡΠ΅ ΠΎΠ±ΡΠ°Π·ΡΡ ΡΡΡΠ°Π½ΠΎΠ²ΠΎΠΊ ΠΎΡΠ΅ΡΠ΅ΡΡΠ²Π΅Π½Π½ΠΎΠ³ΠΎ ΠΏΡΠΎΠΈΠ·Π²ΠΎΠ΄ΡΡΠ²Π°.
Π‘ΡΡΠ΅ΠΌΠΈΡΠ΅Π»ΡΠ½ΠΎΠ΅ ΡΠ°Π·Π²ΠΈΡΠΈΠ΅ Π°Π²ΡΠΎΠΌΠΎΠ±ΠΈΠ»Π΅ΡΡΡΠΎΠ΅Π½ΠΈΡ ΠΈ Π΄ΠΎΡΡΡΠΏΠ½ΠΎΡΡΡ Π°Π²ΡΠΎΠΌΠΎΠ±ΠΈΠ»Π΅ΠΉ ΠΏΡΠΈΠ²ΠΎΠ΄ΠΈΡ ΠΊ ΡΠΎΠΌΡ, ΡΡΠΎ Ρ ΠΊΠ°ΠΆΠ΄ΡΠΌ Π³ΠΎΠ΄ΠΎΠΌ ΡΠ°ΡΡΠ΅Ρ ΠΊΠΎΠ»ΠΈΡΠ΅ΡΡΠ²ΠΎ ΠΎΡΡΠ°Π±ΠΎΡΠ°Π²ΡΠΈΡ ΡΠ²ΠΎΠΉ ΡΡΠΎΠΊ ΠΏΠΎΠΊΡΡΡΠ΅ΠΊ. ΠΠ°ΠΊΠΎΠΏΠ»Π΅Π½ΠΈΠ΅ ΡΠΈΠ½ ΠΈΠΌΠ΅Π΅Ρ ΠΎΡΡΠΈΡΠ°ΡΠ΅Π»ΡΠ½ΠΎΠ΅ Π²Π»ΠΈΡΠ½ΠΈΠ΅ Π½Π° ΠΎΠΊΡΡΠΆΠ°ΡΡΡΡ ΡΡΠ΅Π΄Ρ, ΠΏΠΎΡΠΊΠΎΠ»ΡΠΊΡ ΡΠ°ΠΊΠΎΠ³ΠΎ ΡΠΎΠ΄Π° ΠΌΡΡΠΎΡ ΠΏΡΠ°ΠΊΡΠΈΡΠ΅ΡΠΊΠΈ Π½Π΅ ΡΠ°Π·Π»Π°Π³Π°Π΅ΡΡΡ Π΅ΡΡΠ΅ΡΡΠ²Π΅Π½Π½ΡΠΌ ΡΠΏΠΎΡΠΎΠ±ΠΎΠΌ Π² ΠΏΡΠΈΡΠΎΠ΄Π΅ ΠΈ ΠΏΠΎΡΡΠΎΠΌΡ Π½Π΅ ΠΌΠΎΠΆΠ΅Ρ Π±ΡΡΡ ΠΏΡΠΎΡΡΠΎ ΡΡ ΠΎΡΠΎΠ½Π΅Π½Π½ΡΠΌ Π½Π° ΡΠΏΠ΅ΡΠΈΠ°Π»ΡΠ½ΡΡ ΡΠ²Π°Π»ΠΊΠ°Ρ . Π§ΡΠΎΠ±Ρ ΠΈΠ·Π±Π΅ΠΆΠ°ΡΡ ΡΠ΅Ρ Π½ΠΎΠ³Π΅Π½Π½ΠΎΠΉ ΠΊΠ°ΡΠ°ΡΡΡΠΎΡΡ ΡΠ»Π΅Π΄ΡΠ΅Ρ ΡΡΠΈΠ»ΠΈΠ·ΠΈΡΠΎΠ²Π°ΡΡ Π½Π΅Π½ΡΠΆΠ½ΡΠ΅ ΠΏΠΎΠΊΡΡΡΠΊΠΈ.
Π‘ΡΡΠ΅ΡΡΠ²ΡΠ΅Ρ Π½Π΅ΡΠΊΠΎΠ»ΡΠΊΠΎ ΡΠΏΠΎΡΠΎΠ±ΠΎΠ² ΡΡΠΈΠ»ΠΈΠ·Π°ΡΠΈΠΈ Π½Π΅Π½ΡΠΆΠ½ΡΡ ΡΠΈΠ½, Π½ΠΎ Π½Π°ΠΈΠ±ΠΎΠ»Π΅Π΅ ΠΏΠ΅ΡΡΠΏΠ΅ΠΊΡΠΈΠ²Π½ΡΠΌ ΠΈ ΡΠΊΠΎΠ»ΠΎΠ³ΠΈΡΠ΅ΡΠΊΠΈ ΠΏΡΠ°Π²ΠΈΠ»ΡΠ½ΡΠΌ ΡΡΠΈΡΠ°Π΅ΡΡΡ ΠΌΠ΅ΡΠΎΠ΄ ΠΏΠΈΡΠΎΠ»ΠΈΠ·Π°, ΡΠ΅Π°Π»ΠΈΠ·ΡΠ΅ΠΌΡΠΉ Π² ΡΠΏΠ΅ΡΠΈΠ°Π»ΡΠ½ΡΡ ΡΡΡΠ°Π½ΠΎΠ²ΠΊΠ°Ρ (ΠΏΠΈΡΠΎΠ»ΠΈΠ·Π½ΡΡ ΠΏΠ΅ΡΠ°Ρ ).
ΠΡΠΈΠ½ΡΠΈΠΏΠΈΠ°Π»ΡΠ½Π°Ρ ΡΡ Π΅ΠΌΠ° ΠΏΠΈΡΠΎΠ»ΠΈΠ·Π½ΠΎΠΉ ΠΏΠ΅ΡΠΈ Ρ ΠΎΡΠ½ΠΎΠ²Π½ΡΠΌΠΈ ΡΠ»Π΅ΠΌΠ΅Π½ΡΠ°ΠΌΠΈ
ΠΠ° ΡΠ΅Π³ΠΎΠ΄Π½Ρ ΠΏΠΈΡΠΎΠ»ΠΈΠ·Π½ΡΠ΅ ΠΊΠΎΡΠ»Ρ β ΡΡΠΈΠ»ΠΈΠ·Π°ΡΠΈΡ ΡΠΈΠ½ Ρ Π±ΠΎΠ»ΡΡΠΎΠΉ Π²ΡΠ³ΠΎΠ΄ΠΎΠΉ ΠΈ ΠΌΠΈΠ½ΠΈΠΌΠ°Π»ΡΠ½ΡΠΌ Π²ΠΎΠ·Π΄Π΅ΠΉΡΡΠ²ΠΈΠ΅ΠΌ Π½Π° ΠΎΠΊΡΡΠΆΠ°ΡΡΡΡ ΡΡΠ΅Π΄Ρ.
Π§ΡΠΎ ΡΠ²Π»ΡΠ΅Ρ ΡΠΎΠ±ΠΎΠΉ ΠΏΠΈΡΠΎΠ»ΠΈΠ·?
ΠΠΈΡΠΎΠ»ΠΈΠ· ΠΏΡΠ΅Π΄ΡΡΠ°Π²Π»ΡΠ΅Ρ ΡΠΎΠ±ΠΎΠΉ ΡΠΏΠ΅ΡΠΈΠ°Π»ΡΠ½ΡΠΉ ΡΠΈΠ·ΠΈΠΊΠΎ-Ρ ΠΈΠΌΠΈΡΠ΅ΡΠΊΠΈΠΉ ΠΏΡΠΎΡΠ΅ΡΡ, ΠΏΡΠ΅Π΄ΡΡΠΌΠ°ΡΡΠΈΠ²Π°ΡΡΠΈΠΉ ΡΠ°Π·Π»ΠΎΠΆΠ΅Π½ΠΈΠ΅ ΡΠ»Π΅ΠΌΠ΅Π½ΡΠΎΠ² ΡΠ΅Π·ΠΈΠ½ΠΎΠ²ΡΡ ΠΏΠΎΠΊΡΡΡΠ΅ΠΊ ΠΏΠΎΠ΄ Π²ΠΎΠ·Π΄Π΅ΠΉΡΡΠ²ΠΈΠ΅ΠΌ Π²ΡΡΠΎΠΊΠΎΠΉ ΡΠ΅ΠΌΠΏΠ΅ΡΠ°ΡΡΡΡ ΠΈ Π±Π΅Π· Π΄ΠΎΡΡΡΠΏΠ° Π²ΠΎΠ·Π΄ΡΡ Π°.
ΠΡΠ»ΠΈ ΡΠΈΠ½Ρ ΠΏΠΎΠΏΡΠΎΡΡΡ Π½Π°Π³ΡΠ΅Π²Π°ΡΡ Π² ΠΎΡΠΊΡΡΡΠΎΠΉ Π°ΡΠΌΠΎΡΡΠ΅ΡΠ½ΠΎΠΉ ΡΡΠ΅Π΄Π΅, ΡΠΎ ΡΠ½Π°ΡΠ°Π»Π° ΠΎΠ½ΠΈ Π±ΡΠ΄ΡΡ ΡΠ»Π΅ΡΡ ΠΈ Π²ΠΏΠΎΡΠ»Π΅Π΄ΡΡΠ²ΠΈΠΈ Π·Π°Π³ΠΎΡΡΡΡΡ, Π²ΡΠ΄Π΅Π»ΡΡ Π² Π°ΡΠΌΠΎΡΡΠ΅ΡΡ ΠΌΠ°ΡΡΡ Π²ΡΠ΅Π΄Π½ΡΡ Π²Π΅ΡΠ΅ΡΡΠ². ΠΠΎΠ³Π΄Π° Π½Π°Π³ΡΠ΅Π² ΠΏΡΠΎΠΈΡΡ ΠΎΠ΄ΠΈΡ Π±Π΅Π· Π΄ΠΎΡΡΡΠΏΠ° Π²ΠΎΠ·Π΄ΡΡ Π°, ΡΠΎ ΠΎΡΡΡΡΡΡΠ²ΡΡΡ ΡΡΠ»ΠΎΠ²ΠΈΡ Π΄Π»Ρ Π³ΠΎΡΠ΅Π½ΠΈΡ. Π ΡΠ°ΠΊΠΎΠΌ ΡΠ»ΡΡΠ°Π΅ Π½Π°ΡΠΈΠ½Π°ΡΡ ΠΏΡΠΎΡΠ΅ΠΊΠ°ΡΡ Ρ ΠΈΠΌΠΈΡΠ΅ΡΠΊΠΈΠ΅ ΡΠ΅Π°ΠΊΡΠΈΠΈ ΠΈΠ½ΠΎΠ³ΠΎ ΡΠΈΠΏΠ°, ΠΏΠΎΠ·Π²ΠΎΠ»ΡΡΡΠΈΠ΅ ΡΠ°Π·Π»ΠΎΠΆΠΈΡΡ ΠΎΠ±ΡΡΠ½ΡΡ ΡΠ΅Π·ΠΈΠ½Ρ Π½Π° Π½Π΅ΡΠΊΠΎΠ»ΡΠΊΠΎ Π½Π΅ΡΡΡΠ½ΡΡ ΡΡΠ°ΠΊΡΠΈΠΉ, ΠΊΠΎΡΠΎΡΡΠ΅ Π²ΡΠ»Π΅Π΄ΡΡΠ²ΠΈΠ΅ Π²ΡΡΠΎΠΊΠΈΡ ΡΠ΅ΠΌΠΏΠ΅ΡΠ°ΡΡΡ ΠΏΡΠ΅Π±ΡΠ²Π°ΡΡ Π² Π³Π°Π·ΠΎΠΎΠ±ΡΠ°Π·Π½ΠΎΠΌ ΡΠΎΡΡΠΎΡΠ½ΠΈΠΈ. ΠΡ ΠΌΠΎΠΆΠ½ΠΎ ΡΠΊΠΎΠ½Π΄Π΅Π½ΡΠΈΡΠΎΠ²Π°ΡΡ, ΡΡΠΎΠ±Ρ ΠΏΠΎΠ»ΡΡΠΈΡΡ ΠΏΠΈΡΠΎΠ»ΠΈΠ·Π½ΠΎΠ΅ ΠΌΠ°ΡΠ»ΠΎ, Π° ΡΠ°ΠΊΠΆΠ΅ Π½Π΅ΠΊΠΎΠ½Π΄Π΅Π½ΡΠΈΡΡΠ΅ΠΌΡΠΉ ΠΏΠΈΡΠΎΠ»ΠΈΠ·Π½ΡΠΉ Π³Π°Π·. ΠΡΠΎΡ Π³Π°Π· ΠΌΠΎΠΆΠ½ΠΎ ΠΏΠΎΠ²ΡΠΎΡΠ½ΠΎ Π½Π°ΠΏΡΠ°Π²Π»ΡΡΡ Π² ΡΠΎΠΏΠΊΡ ΡΠ΅Π°ΠΊΡΠΎΡΠ° Π΄Π»Ρ ΠΏΠΎΠ΄Π΄Π΅ΡΠΆΠΊΠΈ ΡΠΈΠΊΠ»ΠΈΡΠ½ΠΎΡΡΠΈ ΠΏΡΠΎΡΠ΅ΡΡΠ° ΠΈ ΠΈΡΠΊΠ»ΡΡΠ΅Π½ΠΈΠΈ ΠΏΠΎΡΡΠ΅Π±Π½ΠΎΡΡΠ΅ΠΉ Π² Π΄ΠΎΠΏΠΎΠ»Π½ΠΈΡΠ΅Π»ΡΠ½ΠΎΠΌ ΡΠΎΠΏΠ»ΠΈΠ²Π΅ Π΄Π»Ρ ΡΡΠ½ΠΊΡΠΈΠΎΠ½ΠΈΡΠΎΠ²Π°Π½ΠΈΡ ΠΏΠΈΡΠΎΠ»ΠΈΠ·Π½ΠΎΠΉ ΡΡΡΠ°Π½ΠΎΠ²ΠΊΠΈ.
ΠΠ»Π°Π³ΠΎΠ΄Π°ΡΡ ΡΠ°ΠΊΠΎΠΉ ΠΌΠ΅ΡΠΎΠ΄ΠΈΠΊΠ΅ ΠΌΠΎΠΆΠ½ΠΎ ΠΏΠΎΠ»ΡΡΠΈΡΡ Π±Π΅Π·ΠΎΡΡ ΠΎΠ΄Π½ΡΡ ΡΠ΅Ρ Π½ΠΎΠ»ΠΎΠ³ΠΈΡ ΡΡΠΈΠ»ΠΈΠ·Π°ΡΠΈΠΈ Ρ ΠΌΠΈΠ½ΠΈΠΌΠ°Π»ΡΠ½ΠΎΠΉ Π½Π°Π³ΡΡΠ·ΠΊΠΎΠΉ Π½Π° ΠΎΠΊΡΡΠΆΠ°ΡΡΡΡ ΡΡΠ΅Π΄Ρ. ΠΡΠ»ΠΈ ΡΡΠ°Π²Π½ΠΈΠ²Π°ΡΡ ΠΎΠ±ΡΡΠ½ΠΎΠ΅ ΡΠΆΠΈΠ³Π°Π½ΠΈΠ΅ ΡΠΈΠ½ Ρ ΠΏΡΠΎΡΠ΅ΡΡΠΎΠΌ ΠΏΠΈΡΠΎΠ»ΠΈΠ·Π°, ΡΠΎ ΡΠ»Π΅Π΄ΡΠ΅Ρ ΠΎΡΠΌΠ΅ΡΠΈΡΡ, ΡΡΠΎ ΠΏΠΎΡΠ»Π΅Π΄Π½ΠΈΠΉ Π² Π½Π΅ΡΠΊΠΎΠ»ΡΠΊΠΎ ΡΠ°Π· ΡΠΊΠΎΠ»ΠΎΠ³ΠΈΡΠ½Π΅Π΅ ΠΈ Π΄ΠΎΠΏΠΎΠ»Π½ΠΈΡΠ΅Π»ΡΠ½ΠΎ Π΅ΡΠ΅ ΠΏΠΎΠ·Π²ΠΎΠ»ΡΠ΅Ρ ΠΏΠΎΠ»ΡΡΠΈΡΡ Π²ΡΠΎΡΠΈΡΠ½ΠΎΠ΅ ΡΡΡΡΠ΅.
Π Π΅ΠΊΠΎΠΌΠ΅Π½Π΄ΡΠ΅ΠΌ ΡΠ°ΠΊΠΆΠ΅ ΠΏΠΎΡΠΌΠΎΡΡΠ΅ΡΡ Π²ΠΈΠ΄Π΅ΠΎ ΠΏΡΠΎ ΠΈΠ·Π³ΠΎΡΠΎΠ²Π»Π΅Π½ΠΈΡ ΠΏΠΈΡΠΎΠ»ΠΈΠ·Π½ΠΎΠ³ΠΎ ΠΊΠΎΡΠ»Π° ΡΠ²ΠΎΠΈΠΌΠΈ ΡΡΠΊΠ°ΠΌΠΈ Π½Π° 15-25 ΠΊΠΡ
ΠΡΠΎΡΠΈΡΠ½ΡΠ΅ ΠΏΡΠΎΠ΄ΡΠΊΡΡ, ΠΏΠΎΠ»ΡΡΠ°Π΅ΠΌΡΠ΅ ΠΏΡΠΈ ΠΏΠΈΡΠΎΠ»ΠΈΠ·Π΅
ΠΠΈΡΠΎΠ»ΠΈΠ· β ΡΡΠΎ ΠΏΡΠΎΡΠ΅ΡΡ, ΠΊΠΎΡΠΎΡΡΠΉ Π½Π΅ ΡΠΎΠ»ΡΠΊΠΎ ΠΎΠ±Π΅ΡΠΏΠ΅ΡΠΈΠ²Π°Π΅Ρ ΡΠΊΠΎΠ»ΠΎΠ³ΠΈΡΠ½ΠΎΡΡΡ, Π½ΠΎ ΠΈ ΡΠ²Π»ΡΠ΅ΡΡΡ Π²ΡΡΠΎΠΊΠΎΠΏΡΠ°ΠΊΡΠΈΡΠ½ΠΎΠΉ ΠΌΠ΅ΡΠΎΠ΄ΠΈΠΊΠΎΠΉ, Ρ ΠΏΠΎΠΌΠΎΡΡΡ ΠΊΠΎΡΠΎΡΠΎΠΉ ΠΌΠΎΠΆΠ½ΠΎ ΠΏΠΎΠ»ΡΡΠΈΡΡ ΡΠ°Π·Π»ΠΈΡΠ½ΠΎΠ΅ Π²ΡΠΎΡΠΈΡΠ½ΠΎΠ΅ ΡΡΡΡΠ΅.
Π ΠΏΡΠΎΡΠ΅ΡΡΠ΅ ΡΡΠΈΠ»ΠΈΠ·Π°ΡΠΈΠΈ ΡΠΈΠ½ Ρ ΠΏΠΎΠΌΠΎΡΡΡ ΠΏΠΈΡΠΎΠ»ΠΈΠ·Π° ΠΏΠΎΠ»ΡΡΠ°ΡΡ ΡΠ΅Ρ Π½ΠΈΡΠ΅ΡΠΊΠΈΠΉ ΡΠ³Π»Π΅ΡΠΎΠ΄, ΠΊΠΎΡΠΎΡΡΠΉ ΠΌΠΎΠΆΠ΅Ρ ΠΏΡΠΈΠΌΠ΅Π½ΡΡΡΡΡ Π² ΠΊΠ°ΡΠ΅ΡΡΠ²Π΅ Π½Π°ΠΏΠΎΠ»Π½ΠΈΡΠ΅Π»Ρ Π² ΠΏΡΠΎΡΠ΅ΡΡΠ΅ ΠΏΡΠΎΠΈΠ·Π²ΠΎΠ΄ΡΡΠ²Π° ΡΠ°Π·Π»ΠΈΡΠ½ΠΎΠΉ ΠΏΡΠΎΡΠ΅Π·ΠΈΠ½Π΅Π½Π½ΠΎΠΉ ΠΏΡΠΎΠ΄ΡΠΊΡΠΈΠΈ ΡΠ°ΠΊΠΎΠΉ, ΠΊΠ°ΠΊ ΡΡΠ°Π½ΡΠΏΠΎΡΡΠ½ΡΠ΅ Π»Π΅Π½ΡΡ, ΡΠΏΠ»ΠΎΡΠ½ΠΈΡΠ΅Π»ΠΈ, ΡΠ΅Ρ ΠΏΠ»Π°ΡΡΠΈΠ½Ρ ΠΈ ΠΏΡ. Π£Π³Π»Π΅ΡΠΎΠ΄Π½ΡΠ΅ ΡΡΠ°ΠΊΡΠΈΠΈ Π±ΠΎΠ»Π΅Π΅ Π½ΠΈΠ·ΠΊΠΎΠ³ΠΎ ΠΊΠ°ΡΠ΅ΡΡΠ²Π° ΠΏΡΠΈΠΌΠ΅Π½ΡΠ΅ΡΡΡ Π² ΡΡΡΠΎΠΈΡΠ΅Π»ΡΡΡΠ²Π΅ Π² ΡΠΎΠ»ΠΈ Π΄ΠΎΠ±Π°Π²ΠΎΠΊ ΠΏΡΠΈ ΠΏΡΠΎΠΈΠ·Π²ΠΎΠ΄ΡΡΠ²Π΅ ΡΠ°Π·Π»ΠΈΡΠ½ΡΡ ΠΈΠ·Π΄Π΅Π»ΠΈΠΉ ΠΈΠ· Π±Π΅ΡΠΎΠ½Π°, ΠΏΠ»ΠΈΡΠΎΠΊ Π΄Π»Ρ ΡΡΠΎΡΡΠ°ΡΠ° ΠΈ Π΄Ρ.
ΠΠΈΡΠΎΠ»ΠΈΠ·Π½ΡΠΉ Π³Π°Π·, ΠΏΠΎΠ»ΡΡΠ°Π΅ΠΌΡΠΉ ΠΏΡΠΈ ΡΡΠΈΠ»ΠΈΠ·Π°ΡΠΈΠΈ, Π½Π°ΠΏΠΎΠΌΠΈΠ½Π°Π΅Ρ ΠΏΡΠΈΡΠΎΠ΄Π½ΡΠΉ ΠΈ ΠΌΠΎΠΆΠ΅Ρ ΠΏΡΠΈΠΌΠ΅Π½ΡΡΡΡΡ Π΄Π»Ρ ΠΏΠΎΠ»ΡΡΠ΅Π½ΠΈΡ ΡΠ΅ΠΏΠ»ΠΎΠ²ΠΎΠΉ ΡΠ½Π΅ΡΠ³ΠΈΠΈ, Π° ΡΠ°ΠΊΠΆΠ΅ Π½Π° Π½Π΅Π±ΠΎΠ»ΡΡΠΈΡ ΡΠ»Π΅ΠΊΡΡΠΎΡΡΠ°Π½ΡΠΈΡΡ Π΄Π»Ρ Π³Π΅Π½Π΅ΡΠΈΡΠΎΠ²Π°Π½ΠΈΡ ΡΠ»Π΅ΠΊΡΡΠΈΡΠ΅ΡΡΠ²Π°.
ΠΠ΅ΡΠ°Π»Π»ΠΈΡΠ΅ΡΠΊΠΈΠ΅ ΠΊΠΎΡΠ΄Ρ, ΠΊΠΎΡΠΎΡΡΠ΅ ΠΎΡΡΠ°ΡΡΡΡ ΠΎΡ ΡΠΈΠ½ ΠΌΠΎΠ³ΡΡ ΠΏΠΎΠ²ΡΠΎΡΠ½ΠΎ ΠΈΡΠΏΠΎΠ»ΡΠ·ΠΎΠ²Π°ΡΡΡΡ Π² ΠΌΠ΅ΡΠ°Π»Π»ΡΡΠ³ΠΈΡΠ΅ΡΠΊΠΎΠΌ ΠΏΡΠΎΠΈΠ·Π²ΠΎΠ΄ΡΡΠ²Π΅ Π΄Π»Ρ ΠΏΠ΅ΡΠ΅ΠΏΠ»Π°Π²ΠΊΠΈ ΠΈ ΠΏΡΠΎΠΈΠ·Π²ΠΎΠ΄ΡΡΠ²Π° Π΄ΡΡΠ³ΠΎΠΉ ΠΌΠ΅ΡΠ°Π»Π»ΠΈΡΠ΅ΡΠΊΠΎΠΉ ΠΏΡΠΎΠ΄ΡΠΊΡΠΈΠΈ.
ΠΠΎΠ»ΡΡΠ°Π΅ΠΌΠ°Ρ ΡΠΈΠ½ΡΠ΅ΡΠΈΡΠ΅ΡΠΊΠ°Ρ Π½Π΅ΡΡΡ ΠΈΠΌΠ΅Π΅Ρ ΡΠΎΡΡΠ°Π², Π½Π°ΠΏΠΎΠΌΠΈΠ½Π°ΡΡΠΈΠΉ ΠΏΡΠΈΡΠΎΠ΄Π½ΠΎΠ΅ ΡΡΡΡΠ΅ ΠΈ ΠΌΠΎΠΆΠ΅Ρ Π·Π°ΠΌΠ΅Π½ΠΈΡΡ ΠΌΠ½ΠΎΠ³ΠΈΠ΅ ΠΈΠ· Π½Π΅ΡΡΠ΅ΠΏΡΠΎΠ΄ΡΠΊΡΠΎΠ².
ΠΠΈΠ·ΠΊΠΎΡΠ΅ΠΌΠΏΠ΅ΡΠ°ΡΡΡΠ½Π°Ρ ΡΡΠΈΠ»ΠΈΠ·Π°ΡΠΈΡ ΡΠΈΠ½
ΠΠΈΠ·ΠΊΠΎΡΠ΅ΠΌΠΏΠ΅ΡΠ°ΡΡΡΠ½ΡΠΉ ΠΏΠΈΡΠΎΠ»ΠΈΠ· ΠΎΡΠ½ΠΎΡΠΈΡΡΡ ΠΊ ΠΏΡΠΎΡΠ΅ΡΡΠ°ΠΌ, ΠΏΡΠΈ ΠΊΠΎΡΠΎΡΡΡ ΠΈΠ·ΠΌΠ΅Π»ΡΡΠ΅Π½Π½ΡΠ΅ ΠΏΠΎΠΊΡΡΡΠΊΠΈ ΠΏΠΎΠ΄Π²Π΅ΡΠ³Π°ΡΡΡΡ ΡΠ΅ΠΌΠΏΠ΅ΡΠ°ΡΡΡΠ½ΠΎΠΌΡ ΡΠ°Π·Π»ΠΎΠΆΠ΅Π½ΠΈΡ Π² Π±Π΅Π·Π²ΠΎΠ·Π΄ΡΡΠ½ΠΎΠΉ ΡΡΠ΅Π΄Π΅ ΠΏΡΠΈ Π’= 400ΒΊΠ‘β¦900ΒΊΠ‘. ΠΠΎΡΠ»Π΅ ΡΠ°ΠΊΠΎΠ³ΠΎ ΠΏΡΠΎΡΠ΅ΡΡΠ° Π² ΠΎΡΡ ΠΎΠ΄Π°Ρ ΠΎΡΡΡΡΡΡΠ²ΡΡΡ Π±ΠΈΠΎΠ»ΠΎΠ³ΠΈΡΠ΅ΡΠΊΠΈ Π°ΠΊΡΠΈΠ²Π½ΡΠ΅ Π²Π΅ΡΠ΅ΡΡΠ²Π°, ΠΏΠΎΡΡΠΎΠΌΡ ΠΈΡ ΠΌΠΎΠΆΠ½ΠΎ Ρ ΡΠ°Π½ΠΈΡΡ ΠΈΡΠΊΠ»ΡΡΠ°Ρ Π²ΡΠ΅Π΄ ΠΎΠΊΡΡΠΆΠ°ΡΡΠ΅ΠΉ ΡΡΠ΅Π΄Π΅. ΠΠ΅ΠΏΠ΅Π», ΠΊΠΎΡΠΎΡΡΠΉ ΠΏΡΠΈ ΡΡΠΎΠΌ ΠΎΠ±ΡΠ°Π·ΡΠ΅ΡΡΡ, ΠΎΡΠ»ΠΈΡΠ°Π΅ΡΡΡ Π²ΡΡΠΎΠΊΠΎΠΉ ΠΏΠ»ΠΎΡΠ½ΠΎΡΡΡΡ, ΡΡΠΎ ΠΌΠΈΠ½ΠΈΠΌΠΈΠ·ΠΈΡΡΠ΅Ρ ΠΎΠ±ΡΠ΅ΠΌ ΠΎΡΡΠ°ΡΠΊΠΎΠ², ΠΊΠΎΡΠΎΡΡΠ΅ ΠΌΠΎΠ³ΡΡ ΡΠΊΠ»Π°Π΄ΠΈΡΠΎΠ²Π°ΡΡΡΡ Π½Π° Π½Π΅Π±ΠΎΠ»ΡΡΠΎΠΉ ΠΏΠ»ΠΎΡΠ°Π΄ΠΈ.
ΠΡΠ΅ΠΈΠΌΡΡΠ΅ΡΡΠ²Π° Π½ΠΈΠ·ΠΊΠΎΡΠ΅ΠΌΠΏΠ΅ΡΠ°ΡΡΡΠ½ΠΎΠ³ΠΎ ΠΏΠΈΡΠΎΠ»ΠΈΠ·Π°
- ΠΏΡΠΎΡΡΠΎΡΠ° Ρ ΡΠ°Π½Π΅Π½ΠΈΡ ΠΈ ΡΡΠ°Π½ΡΠΏΠΎΡΡΠΈΡΠΎΠ²Π°Π½ΠΈΡ ΠΏΡΠΎΠ΄ΡΠΊΡΠΎΠ² ΠΏΠΈΡΠΎΠ»ΠΈΠ·Π°;
- ΠΌΠΈΠ½ΠΈΠΌΠ°Π»ΡΠ½ΡΠΉ ΠΎΠ±ΡΠ΅ΠΌ ΠΏΠΎΠ»ΡΡΠ°Π΅ΠΌΡΡ ΠΎΡΡ ΠΎΠ΄ΠΎΠ²;
- ΠΏΠΎΠ»ΡΡΠ΅Π½ΠΈΠ΅ Π²ΡΠΎΡΠΈΡΠ½ΠΎΠ³ΠΎ ΡΡΡΡΡ, ΠΊΠΎΡΠΎΡΠΎΠ΅ ΠΌΠΎΠΆΠ΅Ρ ΠΈΡΠΏΠΎΠ»ΡΠ·ΠΎΠ²Π°ΡΡΡΡ Π΄Π»Ρ ΠΏΠΎΠ»ΡΡΠ΅Π½ΠΈΡ ΡΠ΅ΠΏΠ»ΠΎΠ²ΠΎΠΉ ΡΠ½Π΅ΡΠ³ΠΈΠΈ.
ΠΠ΅Π΄ΠΎΡΡΠ°ΡΠΊΠΈ ΠΏΠΈΡΠΎΠ»ΠΈΠ·Π°
- Π½ΠΈΠ·ΠΊΠΎΡΠ΅ΠΌΠΏΠ΅ΡΠ°ΡΡΡΠ½ΡΠΉ ΠΏΠΈΡΠΎΠ»ΠΈΠ· Π½Π΅ ΠΌΠΎΠΆΠ΅Ρ ΠΎΠ±Π΅ΡΠΏΠ΅ΡΠΈΡΡ ΠΏΠΎΠ»Π½ΠΎΠ³ΠΎ ΡΠ°ΡΠΏΠ°Π΄Π° Π΄ΠΈΠΎΠΊΡΠΈΠ½ΠΎΠ²;
- Π½Π΅ ΠΏΡΠΎΠΈΡΡ ΠΎΠ΄ΠΈΡ ΠΏΠ»Π°Π²Π»Π΅Π½ΠΈΠ΅ ΡΡΠΆΠ΅Π»ΡΡ ΠΌΠ΅ΡΠ°Π»Π»ΠΎΠ², ΠΊΠΎΡΠΎΡΡΠ΅ Π²ΡΠΏΠ°Π΄Π°ΡΡ Π² ΠΎΡΠ°Π΄ΠΎΠΊ ΡΠΎ ΡΠ»Π°ΠΊΠΎΠΌ.
ΠΡΡΠΎΠΊΠΎΡΠ΅ΠΌΠΏΠ΅ΡΠ°ΡΡΡΠ½Π°Ρ ΡΡΠΈΠ»ΠΈΠ·Π°ΡΠΈΡ
ΠΡΡΠΎΠΊΠΎΡΠ΅ΠΌΠΏΠ΅ΡΠ°ΡΡΡΠ½ΡΠΉ ΠΏΠΈΡΠΎΠ»ΠΈΠ· ΠΎΡΠ½ΠΎΡΠΈΡΡΡ ΠΊ Π²ΡΡΠΎΠΊΠΎΡΠ΅ΠΌΠΏΠ΅ΡΠ°ΡΡΡΠ½ΡΠΌ ΠΏΡΠΎΡΠ΅ΡΡΠ°ΠΌ ΡΡΠΈΠ»ΠΈΠ·Π°ΡΠΈΠΈ ΠΎΡΡΠ°Π±ΠΎΡΠ°Π½Π½ΡΡ ΡΠΈΠ½, ΠΊΠΎΡΠΎΡΡΠΉ ΠΎΡΡΡΠ΅ΡΡΠ²Π»ΡΠ΅ΡΡΡ ΠΏΡΠΈ ΡΠ΅ΠΌΠΏΠ΅ΡΠ°ΡΡΡΠ½ΠΎΠΌ ΡΠ΅ΠΆΠΈΠΌΠ΅ 1000ΒΊΠ‘β¦1400ΒΊΠ‘. ΠΡΠΎΡ ΠΏΡΠΎΡΠ΅ΡΡ ΠΏΡΠ΅Π΄ΡΡΠΌΠ°ΡΡΠΈΠ²Π°Π΅Ρ ΠΌΠ°ΠΊΡΠΈΠΌΠ°Π»ΡΠ½ΡΡ Π³Π°Π·ΠΈΡΠΈΠΊΠ°ΡΠΈΡ ΡΠ΅Π·ΠΈΠ½ΠΎΠ²ΡΡ ΠΎΡΡ ΠΎΠ΄ΠΎΠ², Π² ΠΏΡΠΎΡΠ΅ΡΡΠ΅ ΠΊΠΎΡΠΎΡΠΎΠΉ ΠΈΠ· ΠΎΡΠ³Π°Π½ΠΈΡΠ΅ΡΠΊΠΈΡ ΡΠΎΡΡΠ°Π²Π»ΡΡΡΠΈΡ ΠΏΠΎΠΊΡΡΡΠ΅ΠΊ ΠΏΠΎΠ»ΡΡΠ°Π΅Ρ ΡΠΈΠ½ΡΠ΅Π·-Π³Π°Π·, ΠΊΠΎΡΠΎΡΡΠΉ Π²ΠΏΠΎΡΠ»Π΅Π΄ΡΡΠ²ΠΈΠΈ ΠΌΠΎΠΆΠ΅Ρ ΠΈΡΠΏΠΎΠ»ΡΠ·ΠΎΠ²Π°ΡΡΡΡ Π΄Π»Ρ ΠΏΠΎΠ»ΡΡΠ΅Π½ΠΈΡ ΡΠ»Π΅ΠΊΡΡΠΈΡΠ΅ΡΡΠ²Π° Π½Π° ΡΠ΅ΠΏΠ»ΠΎΠ²ΡΡ ΡΠ»Π΅ΠΊΡΡΠΎΡΡΠ°Π½ΡΠΈΡΡ ΠΈΠ»ΠΈ Π΄Π»Ρ ΠΏΠΎΠ΄ΠΎΠ³ΡΠ΅Π²Π° Π²ΠΎΠ΄Ρ ΡΠΈΡΡΠ΅ΠΌΠ°ΠΌΠΈ ΡΠ΅ΠΏΠ»ΠΎΠ²ΠΎΠ΄ΠΎΠΏΠΎΠ΄Π°ΡΠΈ.
Π£ΡΡΠ°Π½ΠΎΠ²ΠΊΠ° Π΄Π»Ρ ΠΏΠΈΡΠΎΠ»ΠΈΠ·Π° ΡΠΈΠ½
ΠΠΈΡΠΎΠ»ΠΈΠ·Π½ΡΠ΅ ΠΊΠΎΡΠ»Ρ ΠΏΡΠ΅Π΄ΡΡΠ°Π²Π»ΡΡΡ ΡΠΎΠ±ΠΎΠΉ ΡΠΏΠ΅ΡΠΈΠ°Π»ΡΠ½ΡΠ΅ ΡΡΡΠ°Π½ΠΎΠ²ΠΊΠΈ, Ρ ΠΏΠΎΠΌΠΎΡΡΡ ΠΊΠΎΡΠΎΡΡΡ ΠΌΠΎΠΆΠ½ΠΎ ΡΡΡΠ΅ΠΊΡΠΈΠ²Π½ΠΎ ΡΡΠΈΠ»ΠΈΠ·ΠΈΡΠΎΠ²Π°ΡΡ ΠΏΠΎΠΊΡΡΡΠΊΠΈ, ΠΈΡΠΏΠΎΠ»ΡΠ·ΡΡ ΡΠ΅Ρ Π½ΠΎΠ»ΠΎΠ³ΠΈΡ Π²ΡΡΠΎΠΊΠΎΡΠ΅ΠΌΠΏΠ΅ΡΠ°ΡΡΡΠ½ΠΎΠ³ΠΎ ΠΈΠ»ΠΈ Π½ΠΈΠ·ΠΊΠΎΡΠ΅ΠΌΠΏΠ΅ΡΠ°ΡΡΡΠ½ΠΎΠ³ΠΎ ΠΏΠΈΡΠΎΠ»ΠΈΠ·Π°. ΠΡ ΠΎΡΠ½ΠΎΠ²Π½ΡΠΌ ΡΠ»Π΅ΠΌΠ΅Π½ΡΠΎΠΌ ΡΠ²Π»ΡΠ΅ΡΡΡ ΡΠ΅Π°ΠΊΡΠΎΡ, ΠΊΠΎΡΠΎΡΡΠΉ Π²ΠΊΠ»ΡΡΠ°Π΅Ρ Π² ΡΠ²ΠΎΡ ΠΊΠΎΠ½ΡΡΡΡΠΊΡΠΈΡ ΡΠ²Π΅Π»ΡΡΠ°Ρ ΡΡ ΠΈ ΡΠ°Ρ ΡΠ½ΡΡ ΠΏΠ΅ΡΡ. Π’Π²Π΅ΡΠ΄ΡΠ΅ ΡΠ°ΡΡΠΈ ΠΏΡΠ΅Π΄Π²Π°ΡΠΈΡΠ΅Π»ΡΠ½ΠΎ ΡΠ°Π·Π΄Π΅Π»Π΅Π½Π½ΡΡ ΠΏΠΎΠΊΡΡΡΠ΅ΠΊ Π·Π°ΡΡΠΏΠ°ΡΡΡΡ Π² Π²Π΅ΡΡ Π½ΡΡ ΡΠ°ΡΡΡ ΡΠ΅Π°ΠΊΡΠΎΡΠ°, Π³Π΄Π΅ ΠΎΠ½ΠΈ ΠΎΠΏΡΡΠΊΠ°ΡΡΡΡ Π² ΡΠ²Π΅Π»ΡΡΠ°Ρ ΡΡ. Π Π²Π΅ΡΡ Π½Π΅ΠΉ ΡΠ°ΡΡΠΈ ΡΠ΅Π°ΠΊΡΠΎΡΠ° ΠΏΡΠΎΠΈΡΡ ΠΎΠ΄ΠΈΡ ΠΏΠΎΠ΄ΡΡΡΠΈΠ²Π°Π½ΠΈΠ΅ ΠΏΠ΅ΡΠ΅ΡΠ°Π±Π°ΡΡΠ²Π°Π΅ΠΌΠΎΠΉ ΡΠ΅Π·ΠΈΠ½Ρ Ρ ΠΏΠΎΡΠ»Π΅Π΄ΡΡΡΠΈΠΌ Π΅Π΅ ΠΎΠΏΡΡΠΊΠ°Π½ΠΈΠ΅ΠΌ ΠΊ ΡΠ΅ΡΠ΅Π΄ΠΈΠ½Π΅ ΡΠ΅Π°ΠΊΡΠΎΡΠ°, Π³Π΄Π΅ ΠΈ ΡΠ΅Π°Π»ΠΈΠ·ΡΠ΅ΡΡΡ ΡΠ°ΠΌ ΠΏΡΠΎΡΠ΅ΡΡ ΠΏΠΈΡΠΎΠ»ΠΈΠ·Π°.
Π Π±Π΅Π·Π²ΠΎΠ·Π΄ΡΡΠ½ΠΎΠΉ ΡΡΠ΅Π΄Π΅ ΠΏΡΠΎΠΈΡΡ ΠΎΠ΄ΠΈΡ ΠΏΠΎΡΡΠ΅ΠΏΠ΅Π½Π½ΠΎΠ΅ ΠΊΠΎΠΊΡΠΎΠ²Π°Π½ΠΈΠ΅ ΡΠ΅Π·ΠΈΠ½Ρ ΠΈ Π΅Π΅ ΡΠ΅ΡΠΌΠΈΡΠ΅ΡΠΊΠΎΠ΅ ΡΠ°Π·Π»ΠΎΠΆΠ΅Π½ΠΈΠ΅ Π½Π° ΠΎΡΠ΄Π΅Π»ΡΠ½ΡΠ΅ ΡΡΠ°ΠΊΡΠΈΠΈ. Π ΠΏΡΠΎΡΠ΅ΡΡΠ΅ ΠΏΠΈΡΠΎΠ»ΠΈΠ·Π° ΠΎΠ±ΡΠ°Π·ΡΡΡΡΡ Π³Π°Π·Ρ, ΠΊΠΎΡΠΎΡΡΠ΅ ΠΈΠ·Π½Π°ΡΠ°Π»ΡΠ½ΠΎ Π½Π°ΠΏΡΠ°Π²Π»ΡΡΡΡΡ ΠΊ ΠΊΠΎΡΠ»Ρ-ΡΡΠΈΠ»ΠΈΠ·Π°ΡΠΎΡΡ ΠΏΠΎΡΠ»Π΅ ΠΊΠΎΡΠΎΡΠΎΠ³ΠΎ ΠΏΡΠΎΡ ΠΎΠ΄ΡΡ ΡΠ΅ΡΠ΅Π· ΡΠ°ΡΠΏΡΠ»ΠΈΡΠ΅Π»ΡΠ½ΡΡ ΡΡΡΠΈΠ»ΠΊΡ ΠΈ Π½Π°ΠΏΡΠ°Π²Π»ΡΡΡΡΡ Π² ΡΠΏΠ΅ΡΠΈΠ°Π»ΡΠ½ΡΠΉ Π°Π±ΡΠΎΡΠ±Π΅Π½Ρ. ΠΡΠΈΡΡΠΊΠ° Π΄ΡΠΌΠΎΠ²ΡΡ Π³Π°Π·ΠΎΠ² Π°Π±ΡΠΎΡΠ±Π΅Π½ΡΠΎΠΌ ΠΏΠΎΠ·Π²ΠΎΠ»ΠΈΡ ΠΈΠ·Π²Π»Π΅ΡΡ Π²ΡΠ΅Π΄Π½ΡΠ΅ Π²Π΅ΡΠ΅ΡΡΠ²Π°, ΠΏΠΎΡΠ»Π΅ ΡΠ΅Π³ΠΎ Π³Π°Π·Ρ ΠΌΠΎΠ³ΡΡ Π²ΡΠ²ΠΎΠ΄ΠΈΡΡΡΡ Π² Π°ΡΠΌΠΎΡΡΠ΅ΡΡ, Π½Π΅ ΠΏΡΠΈΡΠΈΠ½ΡΡ Π΅ΠΉ Π²ΡΠ΅Π΄Π°.
ΠΡΠΎΠ΄ΡΠΊΡΡ ΠΏΠΈΡΠΎΠ»ΠΈΠ·Π° Π²ΡΠ²ΠΎΠ΄ΡΡΡΡ ΠΈΠ· ΡΠ΅Π°ΠΊΡΠΎΡΠ° Π΄Π»Ρ ΠΏΠΎΡΠ»Π΅Π΄ΡΡΡΠ΅Π³ΠΎ ΠΈΡ ΠΈΡΠΏΠΎΠ»ΡΠ·ΠΎΠ²Π°Π½ΠΈΡ Π² ΠΊΠ°ΡΠ΅ΡΡΠ²Π΅ Π²ΡΠΎΡΠΈΡΠ½ΠΎΠ³ΠΎ ΡΡΡΡΡ Π΄Π»Ρ ΠΏΡΠΎΠΌΡΡΠ»Π΅Π½Π½ΡΡ ΠΎΡΡΠ°ΡΠ»Π΅ΠΉ ΠΈΠ»ΠΈ Π½Π°ΡΠΎΠ΄Π½ΠΎΠ³ΠΎ Ρ ΠΎΠ·ΡΠΉΡΡΠ²Π°.
ΠΡΠ½ΠΎΠ²Π½ΡΠ΅ ΡΡΠ°ΠΏΡ ΠΏΠ΅ΡΠ΅ΡΠ°Π±ΠΎΡΠΊΠΈ ΡΠΈΠ½ ΠΏΠΈΡΠΎΠ»ΠΈΠ·ΠΎΠΌ
Π£ΡΠΈΠ»ΠΈΠ·Π°ΡΠΈΡ ΡΠΈΠ½ Ρ ΠΏΠΎΠΌΠΎΡΡΡ ΠΏΠΈΡΠΎΠ»ΠΈΠ·Π½ΡΡ ΡΡΡΠ°Π½ΠΎΠ²ΠΎΠΊ ΡΠ΅Π°Π»ΠΈΠ·ΡΠ΅ΡΡΡ Π² Π½Π΅ΡΠΊΠΎΠ»ΡΠΊΠΎ ΡΡΠ°ΠΏΠΎΠ²:
- ΠΏΠΎΠΊΡΡΡΠΊΠΈ Π΄Π»Ρ ΡΡΠΈΠ»ΠΈΠ·Π°ΡΠΈΠΈ ΠΎΡΠΏΡΠ°Π²Π»ΡΡΡΡΡ Π½Π° ΡΠΊΠ»Π°Π΄ Π²ΡΠΎΡΡΡΡΡΡ;
- ΠΈΡΠΏΠΎΠ»ΡΠ·ΡΡ Π±ΠΎΡΡΠΎΡΠ΅Π·Π½ΡΡ ΡΡΡΠ°Π½ΠΎΠ²ΠΊΡ, ΠΏΠΎΠΊΡΡΡΠΊΠΈ ΡΠ°Π·ΡΠ΅Π·Π°ΡΡ Π½Π° ΠΏΡΠΎΡΠ΅ΠΊΡΠΎΡΠ½ΡΡ ΠΈ Π±ΠΎΡΡΠΎΠ²ΡΡ ΡΠ°ΡΡΡ, ΡΡΠΎΠ±Ρ ΠΎΠ±Π΅ΡΠΏΠ΅ΡΠΈΡΡ ΠΌΠ°ΠΊΡΠΈΠΌΠ°Π»ΡΠ½ΠΎ ΠΏΠ»ΠΎΡΠ½ΡΡ ΡΠΏΠ°ΠΊΠΎΠ²ΠΊΡ ΠΏΠ΅ΡΠ΅Π΄ Π·Π°Π³ΡΡΠ·ΠΊΠΎΠΉ ΠΏΠΈΡΠΎΠ»ΠΈΠ·Π½ΠΎΠ³ΠΎ ΠΊΠΎΡΠ»Π°;
- ΠΏΠΎΡΠ΅Π·Π°Π½Π½ΡΠ΅ ΠΏΠΎΠΊΡΡΡΠΊΠΈ Π·Π°Π³ΡΡΠΆΠ°ΡΡΡΡ Π½Π° ΡΠ΅ΡΠΎΡΡΡ, ΠΊΠΎΡΠΎΡΡΠ΅ ΡΡΡΠ°Π½Π°Π²Π»ΠΈΠ²Π°ΡΡΡΡ Π² ΠΏΠΈΡΠΎΠ»ΠΈΠ·Π½ΡΠ΅ ΠΏΠ΅ΡΠΈ;
- Π² ΠΏΡΠΎΡΠ΅ΡΡΠ΅ ΡΠ΅ΡΠΌΠΈΡΠ΅ΡΠΊΠΎΠ³ΠΎ ΡΠ°Π·Π»ΠΎΠΆΠ΅Π½ΠΈΡ ΠΏΠΎΠΊΡΡΡΠΊΠΈ ΠΎΠ±ΡΠ°Π·ΡΠ΅ΡΡΡ Π³Π°Π·, ΠΊΠΎΡΠΎΡΡΠΉ ΠΈΡΠΏΠΎΠ»ΡΠ·ΡΠ΅ΡΡΡ Π² ΠΊΠ°ΡΠ΅ΡΡΠ²Π΅ Π³ΠΎΡΡΡΠ΅Π³ΠΎ Π³Π°Π·Π°, Π° ΡΠ°ΠΊΠΆΠ΅ Π΄Π»Ρ ΠΊΠΎΠ½Π΄Π΅Π½ΡΠ°ΡΠΈΠΈ Π² ΠΏΠΈΡΠΎΠ»ΠΈΠ·Π½ΠΎΠ΅ ΠΌΠ°ΡΠ»ΠΎ;
- ΠΏΠΎΡΠ»Π΅ Π·Π°Π²Π΅ΡΡΠ΅Π½ΠΈΡ ΠΏΡΠΎΡΠ΅Π΄ΡΡΡ ΠΏΠΈΡΠΎΠ»ΠΈΠ·Π° ΡΠ΅ΡΠΎΡΡΠ° ΠΈΠ·Π²Π»Π΅ΠΊΠ°Π΅ΡΡΡ ΠΈΠ· ΠΏΠ΅ΡΠΈ, Π° Π΅Π΅ ΠΌΠ΅ΡΡΠΎ Π·Π°Π½ΠΈΠΌΠ°Π΅Ρ Π½ΠΎΠ²Π°Ρ ΡΠΎ ΡΠ»Π΅Π΄ΡΡΡΠ΅ΠΉ ΠΏΠΎΡΡΠΈΠ΅ΠΉ ΠΏΠΎΠΊΡΡΡΠ΅ΠΊ Π½Π° ΠΏΠ΅ΡΠ΅ΡΠ°Π±ΠΎΡΠΊΡ;
- ΠΏΠΎΡΠ»Π΅ ΠΎΡΡΡΠ²Π°Π½ΠΈΡ ΡΠ΅ΡΠΎΡΡΡ ΠΏΡΠΎΠΈΠ·Π²ΠΎΠ΄ΠΈΡΡΡ ΠΎΡΠ΄Π΅Π»Π΅Π½ΠΈΠ΅ ΠΌΠ΅ΡΠ°Π»Π»ΠΈΡΠ΅ΡΠΊΠΈΡ ΠΊΠΎΡΠ΄ΠΎΠ² ΠΎΡ ΡΠ³Π»Π΅ΡΠΎΠ΄Π½ΡΡ ΠΎΡΡΠ°ΡΠΊΠΎΠ²;
- ΠΏΡΠΎΠ΄ΡΠΊΡΡ ΠΏΠΈΡΠΎΠ»ΠΈΠ·Π° ΡΠΎΠ±ΠΈΡΠ°ΡΡΡΡ ΠΈ ΠΎΡΠΏΡΠ°Π²Π»ΡΡΡΡΡ Π½Π° ΡΠΊΠ»Π°Π΄ Π΄Π»Ρ ΠΈΡΠΏΠΎΠ»ΡΠ·ΠΎΠ²Π°Π½ΠΈΡ Π² ΠΊΠ°ΡΠ΅ΡΡΠ²Π΅ Π²ΡΠΎΡΡΡΡΡΡ.
ΠΡΠ΅ΠΈΠΌΡΡΠ΅ΡΡΠ²Π° ΠΏΠΈΡΠΎΠ»ΠΈΠ·Π° ΡΠΈΠ½
Π£ΡΠΈΠ»ΠΈΠ·Π°ΡΠΈΡ ΠΎΡΡ ΠΎΠ΄ΠΎΠ² ΠΎΡΡΠ°Π±ΠΎΡΠ°Π½Π½ΡΡ ΠΏΠΎΠΊΡΡΡΠ΅ΠΊ Ρ ΠΏΠΎΠΌΠΎΡΡΡ ΡΡΡΠ°Π½ΠΎΠ²ΠΎΠΊ ΠΏΠΈΡΠΎΠ»ΠΈΠ·Π° ΠΈΠΌΠ΅Π΅Ρ ΡΠ΅Π»ΡΠΉ ΡΡΠ΄ Π½Π΅ΠΎΡΠΏΠΎΡΠΈΠΌΡΡ ΠΏΡΠ΅ΠΈΠΌΡΡΠ΅ΡΡΠ²:
- ΠΏΡΠΎΡΠ΅ΡΡ ΡΠ²Π»ΡΠ΅ΡΡΡ Π²ΡΡΠΎΠΊΠΎΠ±Π΅Π·ΠΎΠΏΠ°ΡΠ½ΡΠΌ ΠΈ ΡΠΊΠΎΠ»ΠΎΠ³ΠΈΡΠ½ΡΠΌ ΠΏΠΎ ΠΎΡΠ½ΠΎΡΠ΅Π½ΠΈΡ ΠΊ ΠΎΠΊΡΡΠΆΠ°ΡΡΠ΅ΠΉ ΡΡΠ΅Π΄Π΅;
- ΠΏΡΠΎΠ΄ΡΠΊΡΡ ΠΏΠΈΡΠΎΠ»ΠΈΠ·Π° Π½Π΅ ΠΈΠΌΠ΅ΡΡ Π² ΡΠ²ΠΎΠ΅ΠΌ ΡΠΎΡΡΠ°Π²Π΅ ΡΠΎΠΊΡΠΈΡΠ½ΡΡ ΠΈ ΠΎΠΏΠ°ΡΠ½ΡΡ Π²Π΅ΡΠ΅ΡΡΠ²;
- Π²Π΅ΡΠ΅ΡΡΠ²Π°, ΠΏΠΎΠ»ΡΡΠ°Π΅ΠΌΡΠ΅ Π² ΠΏΡΠΎΡΠ΅ΡΡΠ΅ ΡΡΠΈΠ»ΠΈΠ·Π°ΡΠΈΠΈ ΡΠΈΠ½ ΠΏΠΈΡΠΎΠ»ΠΈΠ·ΠΎΠΌ, ΠΌΠΎΠ³ΡΡ ΠΈΡΠΏΠΎΠ»ΡΠ·ΠΎΠ²Π°ΡΡΡΡ Π² ΠΊΠ°ΡΠ΅ΡΡΠ²Π΅ Π²ΡΠΎΡΠΈΡΠ½ΠΎΠ³ΠΎ ΡΡΡΡΡ Π² ΡΠ°Π·Π½ΡΡ ΠΎΡΡΠ°ΡΠ»ΡΡ ΠΏΡΠΎΠΌΡΡΠ»Π΅Π½Π½ΠΎΡΡΠΈ ΠΈ ΡΠ½Π΅ΡΠ³Π΅ΡΠΈΡΠ΅ΡΠΊΠΎΠΌ ΡΠ΅ΠΊΡΠΎΡΠ΅;
- ΠΏΡΠ°ΠΊΡΠΈΡΠ΅ΡΠΊΠΈ ΠΎΡΡΡΡΡΡΠ²ΡΡΡ ΠΎΡΡ ΠΎΠ΄Ρ β Π²ΡΠ΅ Π²Π΅ΡΠ΅ΡΡΠ²Π°, ΠΊΠΎΡΠΎΡΡΠ΅ ΠΏΡΠΎΠ΄ΡΡΠΈΡΡΡΡΡΡ ΠΏΠΎΡΠ»Π΅ ΠΏΠΈΡΠΎΠ»ΠΈΠ·Π° ΠΏΠΎΠΊΡΡΡΠ΅ΠΊ, ΡΠ²Π»ΡΡΡΡΡ Π»ΠΈΠΊΠ²ΠΈΠ΄Π½ΡΠΌΠΈ ΠΏΡΠΎΠ΄ΡΠΊΡΠ°ΠΌΠΈ ΠΈ ΠΌΠΎΠ³ΡΡ ΠΈΡΠΏΠΎΠ»ΡΠ·ΠΎΠ²Π°ΡΡΡΡ ΠΏΠΎΠ²ΡΠΎΡΠ½ΠΎ;
- ΡΡΡΠ°Π½ΠΎΠ²ΠΊΠ° Π΄Π»Ρ ΠΏΠΈΡΠΎΠ»ΠΈΠ·Π° Π½Π΅ ΡΡΠ΅Π±ΡΠ΅Ρ Π±ΠΎΠ»ΡΡΠΈΡ ΡΠ½Π΅ΡΠ³ΠΎΠ·Π°ΡΡΠ°Ρ ΠΈ ΠΎΡΠ»ΠΈΡΠ°Π΅ΡΡΡ Π²ΡΡΠΎΠΊΠΈΠΌΠΈ ΠΏΠΎΠΊΠ°Π·Π°ΡΠ΅Π»ΡΠΌΠΈ ΡΠΊΠΎΠ½ΠΎΠΌΠΈΡΠ½ΠΎΡΡΠΈ ΠΈ ΡΠ½Π΅ΡΠ³ΠΎΡΡΡΠ΅ΠΊΡΠΈΠ²Π½ΠΎΡΡΠΈ.
Π‘ΡΠΌΠΌΠΈΡΡΡ Π²ΡΡΠ΅ ΡΠΊΠ°Π·Π°Π½Π½ΠΎΠ΅ ΠΌΠΎΠΆΠ½ΠΎ ΡΠ΄Π΅Π»Π°ΡΡ Π²ΡΠ²ΠΎΠ΄Ρ, ΡΡΠΎ ΡΡΠΈΠ»ΠΈΠ·Π°ΡΠΈΡ Π½Π΅Π½ΡΠΆΠ½ΡΡ ΠΏΠΎΠΊΡΡΡΠ΅ΠΊ Ρ ΠΏΠΎΠΌΠΎΡΡΡ ΠΏΠΈΡΠΎΠ»ΠΈΠ·Π° ΡΠ²Π»ΡΠ΅ΡΡΡ Π΅Π΄ΠΈΠ½ΡΡΠ²Π΅Π½Π½ΠΎ Π²Π΅ΡΠ½ΡΠΌ ΡΠΏΠΎΡΠΎΠ±ΠΎΠΌ ΠΏΠ΅ΡΠ΅ΡΠ°Π±ΠΎΡΠΊΠΈ ΠΎΡΡ ΠΎΠ΄ΠΎΠ² Π°Π²ΡΠΎΠΌΠΎΠ±ΠΈΠ»ΡΠ½ΠΎΠΉ ΠΎΡΡΠ°ΡΠ»ΠΈ, ΠΊΠΎΡΠΎΡΡΠΉ ΠΌΠ°ΠΊΡΠΈΠΌΠ°Π»ΡΠ½ΠΎ Π·Π°ΡΠΈΡΠ°Π΅Ρ ΠΎΠΊΡΡΠΆΠ°ΡΡΡΡ ΡΡΠ΅Π΄Ρ ΠΎΡ Π·Π°Π³ΡΡΠ·Π½Π΅Π½ΠΈΠΉ Π²ΡΠ΅Π΄Π½ΡΠΌΠΈ Π²Π΅ΡΠ΅ΡΡΠ²Π°ΠΌΠΈ. ΠΡΠΎΠΌΠ΅ ΡΡΠΎΠ³ΠΎ, ΡΠ΅Ρ Π½ΠΎΠ»ΠΎΠ³ΠΈΡ ΠΏΠΈΡΠΎΠ»ΠΈΠ·Π° ΡΠ²Π»ΡΠ΅ΡΡΡ Π²ΡΠ³ΠΎΠ΄Π½ΠΎΠΉ ΠΈ Π΄Π»Ρ Π±ΠΈΠ·Π½Π΅ΡΠ°, Π²Π΅Π΄Ρ, ΠΏΡΠΈ ΠΌΠΈΠ½ΠΈΠΌΠ°Π»ΡΠ½ΡΡ Π·Π°ΡΡΠ°ΡΠ°Ρ , ΠΏΠΎΠ·Π²ΠΎΠ»ΡΠ΅Ρ ΠΏΠΎΠ»ΡΡΠΈΡΡ Π±ΠΎΠ»ΡΡΠΎΠ΅ ΠΊΠΎΠ»ΠΈΡΠ΅ΡΡΠ²ΠΎ ΡΠ°Π·Π»ΠΈΡΠ½ΡΡ Π²Π΅ΡΠ΅ΡΡΠ², ΠΊΠΎΡΠΎΡΡΠ΅ ΠΌΠΎΠ³ΡΡ ΠΈΡΠΏΠΎΠ»ΡΠ·ΠΎΠ²Π°ΡΡΡΡ Π² ΠΊΠ°ΡΠ΅ΡΡΠ²Π΅ Π²ΡΠΎΡΠΈΡΠ½ΠΎΠ³ΠΎ ΡΡΡΡΡ Π΄Π»Ρ ΠΏΡΠΎΠΈΠ·Π²ΠΎΠ΄ΡΡΠ²Π° Π½ΠΎΠ²ΠΎΠΉ ΠΏΡΠΎΠ΄ΡΠΊΡΠΈΠΈ, Π³Π΅Π½Π΅ΡΠΈΡΠΎΠ²Π°Π½ΠΈΡ ΡΠ΅ΠΏΠ»ΠΎΠ²ΠΎΠΉ ΡΠ½Π΅ΡΠ³ΠΈΠΈ, ΡΠ»Π΅ΠΊΡΡΠΈΡΠ΅ΡΡΠ²Π°.
ΠΡΠΎΠ±Π»Π΅ΠΌΠ° ΡΡΠΈΠ»ΠΈΠ·Π°ΡΠΈΠΈ Π±ΡΡΠΎΠ²ΡΡ ΠΎΡΡ ΠΎΠ΄ΠΎΠ² Π΄ΠΎΡΡΠ°ΡΠΎΡΠ½ΠΎ ΠΎΡΡΡΠΎ ΡΠ΅Π³ΠΎΠ΄Π½Ρ ΡΡΠΎΠΈΡ Π²ΠΎ Π²ΡΠ΅ΠΌ ΠΌΠΈΡΠ΅. ΠΡΠΈΡΠ΅ΠΌ, Π΅ΡΠ»ΠΈ Ρ Π±ΡΡΠΎΠ²ΡΠΌΠΈ ΠΎΡΡ ΠΎΠ΄Π°ΠΌΠΈ ΠΎΡΠ³Π°Π½ΠΈΡΠ΅ΡΠΊΠΎΠ³ΠΎ ΠΏΡΠΎΠΈΡΡ ΠΎΠΆΠ΄Π΅Π½ΠΈΡ ΠΌΠΎΠΆΠ½ΠΎ ΠΏΠΎΠ»ΠΎΠΆΠΈΡΡΡΡ Π½Π° ΡΠ°ΠΌΡ ΠΏΡΠΈΡΠΎΠ΄Ρ, ΡΠΎ Π½Π°Π΄ Π²ΠΎΠΏΡΠΎΡΠ°ΠΌΠΈ ΡΡΠΈΠ»ΠΈΠ·Π°ΡΠΈΠΈ ΠΏΠΎΠ»ΠΈΠΌΠ΅ΡΠΎΠ² Π½Π΅ΠΎΠ±Ρ ΠΎΠ΄ΠΈΠΌΠΎ ΠΎΠ±Π΅ΡΠΏΠΎΠΊΠΎΠΈΡΡΡΡ ΡΠ°ΠΌΠΎΠΌΡ ΡΠ΅Π»ΠΎΠ²Π΅ΠΊΡ. ΠΡΠ΅ Π΄Π΅Π»ΠΎ Π² ΡΠΎΠΌ, ΡΡΠΎ Π±ΠΎΠ»ΡΡΠΈΠ½ΡΡΠ²ΠΎ ΠΈΠ· Π½ΠΈΡ , Π½Π°ΠΏΡΠΈΠΌΠ΅Ρ, Π°Π²ΡΠΎΠΌΠΎΠ±ΠΈΠ»ΡΠ½ΡΠ΅ ΡΠΈΠ½Ρ, ΡΠ°ΠΌΠΎΡΡΠΎΡΡΠ΅Π»ΡΠ½ΠΎ Π½Π΅ ΡΠ°Π·Π»Π°Π³Π°ΡΡΡΡ, Π° Π·Π½Π°ΡΠΈΡ, Π΅ΡΠ»ΠΈ ΠΈΡ Π½Π΅ ΡΠ½ΠΈΡΡΠΎΠΆΠ°ΡΡ, ΡΠΎ ΠΎΠ½ΠΈ ΡΠΊΠΎΡΠΎ ΠΏΡΠ΅Π²ΡΠ°ΡΡΡ Π½Π°ΡΡ ΠΏΠ»Π°Π½Π΅ΡΡ Π² ΠΎΠ΄Π½Ρ Π±ΠΎΠ»ΡΡΡΡ ΡΠ²Π°Π»ΠΊΡ.
Π£ΡΠΈΠ»ΠΈΠ·Π°ΡΠΈΡ Π°Π²ΡΠΎΠΌΠΎΠ±ΠΈΠ»ΡΠ½ΡΡ ΡΠΈΠ½ Π½Π° Π΄Π°Π½Π½ΡΠΉ ΠΌΠΎΠΌΠ΅Π½Ρ Π²ΡΠ΅ΠΌΠ΅Π½ΠΈ ΠΏΡΠΎΠΈΠ·Π²ΠΎΠ΄ΠΈΡΡΡ Π½Π΅ΡΠΊΠΎΠ»ΡΠΊΠΈΠΌΠΈ ΡΠ°Π·Π»ΠΈΡΠ½ΡΠΌΠΈ ΡΠΏΠΎΡΠΎΠ±Π°ΠΌΠΈ.
ΠΠ΅ΡΠ΅ΡΠ°Π±ΠΎΡΠΊΠ° Π² ΠΊΡΠΎΡΠΊΡ. ΠΡΠΎΡΠΈΡΠ½Π°Ρ ΠΏΠ΅ΡΠ΅ΡΠ°Π±ΠΎΡΠΊΠ° ΡΠΈΠ½ ΠΏΡΠΈ ΠΏΠΎΠΌΠΎΡΠΈ ΠΈΠ·ΠΌΠ΅Π»ΡΡΠ΅Π½ΠΈΡ ΡΡΠΎ ΡΠ°ΠΌΡΠΉ ΠΏΡΠΎΡΡΠΎΠΉ ΠΈ Π΄ΠΎΡΡΠ°ΡΠΎΡΠ½ΠΎ ΡΠ°ΡΠΏΡΠΎΡΡΡΠ°Π½Π΅Π½Π½ΡΠΉ Π² Π½Π°ΡΠ΅ΠΉ ΡΡΡΠ°Π½Π΅ ΠΌΠ΅ΡΠΎΠ΄. ΠΠ½ ΠΏΠΎΠ·Π²ΠΎΠ»ΡΠ΅Ρ ΡΠΎΡ ΡΠ°Π½ΠΈΡΡ Ρ ΠΈΠΌΠΈΡΠ΅ΡΠΊΠΈΠ΅ ΠΈ ΡΠΈΠ·ΠΈΠΊΠΎ-ΠΌΠ΅Ρ Π°Π½ΠΈΡΠ΅ΡΠΊΠΈΠ΅ Ρ Π°ΡΠ°ΠΊΡΠ΅ΡΠΈΡΡΠΈΠΊΠΈ ΡΠ΅Π·ΠΈΠ½Ρ. ΠΠΎΡΠ»Π΅ ΠΈΠ·ΠΌΠ΅Π»ΡΡΠ΅Π½ΠΈΡ ΡΠ΅Π·ΠΈΠ½Π° ΠΌΠΎΠΆΠ΅Ρ Π±ΡΡΡ ΠΈΡΠΏΠΎΠ»ΡΠ·ΠΎΠ²Π°Π½Π° ΠΏΡΠΈ ΡΡΡΠΎΠΈΡΠ΅Π»ΡΡΡΠ²Π΅ Π΄ΠΎΡΠΎΠ³ ΠΈ ΡΠΎΠΎΡΡΠΆΠ΅Π½ΠΈΠΉ. Π’Π°ΠΊΠΆΠ΅ ΠΈΠ·ΠΌΠ΅Π»ΡΡΠ΅Π½ΠΈΠ΅ ΡΠ΅Π·ΠΈΠ½Ρ ΠΏΠΎΠ·Π²ΠΎΠ»ΡΠ΅Ρ ΠΊΠΎΠΌΠΏΠ°ΠΊΡΠ½ΠΎ Ρ ΡΠ°Π½ΠΈΡΡ ΠΈ ΡΡΠ°Π½ΡΠΏΠΎΡΡΠΈΡΠΎΠ²Π°ΡΡ Π΅Π΅ Π΄ΠΎ Π΄Π°Π»ΡΠ½Π΅ΠΉΡΠ΅ΠΉ ΠΏΠ΅ΡΠ΅ΡΠ°Π±ΠΎΡΠΊΠΈ ΠΌΠ΅ΡΠΎΠ΄ΠΎΠΌ ΠΏΠΈΡΠΎΠ»ΠΈΠ·Π°.
Π£ΡΠΈΠ»ΠΈΠ·Π°ΡΠΈΡ ΡΠΈΠ½ ΠΏΡΡΠ΅ΠΌ ΡΠΆΠΈΠ³Π°Π½ΠΈΡ. ΠΠ°Π½Π½ΡΠΉ ΠΌΠ΅ΡΠΎΠ΄ ΡΡΠΈΠ»ΠΈΠ·Π°ΡΠΈΠΈ Π±ΡΠ» ΠΏΡΠΈΠ΄ΡΠΌΠ°Π½ Π΅ΡΠ΅ Π² ΡΠ΅ Π²ΡΠ΅ΠΌΠ΅Π½Π°, ΠΊΠΎΠ³Π΄Π° ΡΠ΅Π»ΠΎΠ²Π΅ΡΠ΅ΡΡΠ²ΠΎ Π½Π΅ ΠΈΠ·ΠΎΠ±ΡΠ΅Π»ΠΎ Π½ΠΈΠΊΠ°ΠΊΠΈΡ Π°Π»ΡΡΠ΅ΡΠ½Π°ΡΠΈΠ² ΡΠ½ΠΈΡΡΠΎΠΆΠ΅Π½ΠΈΡ ΡΠ΅Π·ΠΈΠ½Ρ. Π¨ΠΈΠ½Ρ ΡΠΆΠΈΠ³Π°Π»ΠΈ Π² ΠΎΡΠ½ΠΎΠ²Π½ΠΎΠΌ Π½Π° ΠΏΡΠ΅Π΄ΠΏΡΠΈΡΡΠΈΡΡ ΡΠ΅ΠΌΠ΅Π½ΡΠ½ΠΎΠΉ ΠΏΡΠΎΠΌΡΡΠ»Π΅Π½Π½ΠΎΡΡΠΈ, Π³Π΄Π΅ ΠΎΠ½ΠΈ ΡΠ°ΡΡΠΈΡΠ½ΠΎ Π·Π°ΠΌΠ΅Π½ΡΠ»ΠΈ ΡΠ°ΠΊΠΎΠ΅ ΡΠΎΠΏΠ»ΠΈΠ²ΠΎ ΠΊΠ°ΠΊ ΠΌΠ°Π·ΡΡ ΠΈ ΡΠ³ΠΎΠ»Ρ. Π‘ΠΆΠΈΠ³Π°Π½ΠΈΠ΅ ΡΠΈΠ½ Π²ΡΠ³Π»ΡΠ΄ΠΈΡ ΠΏΡΠΎΡΡΠΎ Π½Π°ΡΡΠΎΡΡΠΈΠΌ Π²Π°ΡΠ²Π°ΡΡΡΠ²ΠΎΠΌ Ρ ΡΠΎΡΠΊΠΈ Π·ΡΠ΅Π½ΠΈΡ ΡΠΊΠΎΠ»ΠΎΠ³ΠΈΠΈ, ΠΏΠΎΡΠΊΠΎΠ»ΡΠΊΡ ΠΌΠ½ΠΎΠ³ΠΈΠ΅ Π²ΡΠ΅Π΄Π½ΡΠ΅ Π²Π΅ΡΠ΅ΡΡΠ²Π° Π² ΠΏΡΠΎΡΠ΅ΡΡΠ΅ ΡΠΆΠΈΠ³Π°Π½ΠΈΡ ΡΠ΅Π·ΠΈΠ½Ρ Π½Π΅ ΡΠ°ΡΠΏΠ°Π΄Π°ΡΡΡΡ, Π° ΠΏΠΎΠΏΠ°Π΄Π°ΡΡ Π² Π°ΡΠΌΠΎΡΡΠ΅ΡΡ. Π‘ΡΠ΅Π΄ΠΈ ΡΡΠΈΡ Π²Π΅ΡΠ΅ΡΡΠ² Π½Π°ΠΈΠ±ΠΎΠ»Π΅Π΅ Π²ΡΠ΅Π΄Π½Ρ:
ΠΡΠΎΠΌΠ΅ ΡΠΎΠ³ΠΎ, ΠΎΠ΄Π½Π° ΡΠΎΠ½Π½Π° Π°Π²ΡΠΎΡΠΈΠ½ ΡΠΎΠ΄Π΅ΡΠΆΠΈΡ ΠΏΡΠΈΠ±Π»ΠΈΠ·ΠΈΡΠ΅Π»ΡΠ½ΠΎ 700 ΠΊΠ³ ΡΠ΅Π·ΠΈΠ½Ρ, ΠΊΠΎΡΠΎΡΡΡ, Π±Π»Π°Π³ΠΎΠ΄Π°ΡΡ Π½ΠΎΠ²ΡΠΌ ΡΠ΅Ρ Π½ΠΎΠ»ΠΎΠ³ΠΈΡΠΌ, ΠΌΠΎΠΆΠ½ΠΎ ΠΏΠΎΠ²ΡΠΎΡΠ½ΠΎ ΠΈΡΠΏΠΎΠ»ΡΠ·ΠΎΠ²Π°ΡΡ Π΄Π»Ρ ΠΏΡΠΎΠΈΠ·Π²ΠΎΠ΄ΡΡΠ²Π° ΡΠΎΠΏΠ»ΠΈΠ²Π°. Π’Π°ΠΊΠΈΠΌ ΠΎΠ±ΡΠ°Π·ΠΎΠΌ, ΡΡΠ°Π½ΠΎΠ²ΠΈΡΡΡ ΠΏΠΎΠ½ΡΡΠ½ΠΎ, ΡΡΠΎ ΡΠΆΠΈΠ³Π°Π½ΠΈΠ΅ ΠΏΠΎΠΊΡΡΡΠ΅ΠΊ ΡΡΠΎ ΡΠΎΠ²Π΅ΡΡΠ΅Π½Π½ΠΎ Π½Π΅ ΠΎΠΏΡΠ°Π²Π΄Π°Π½Π½ΡΠΉ ΠΌΠ΅ΡΠΎΠ΄, ΠΏΡΠΈΡΠ΅ΠΌ ΠΊΠ°ΠΊ Ρ ΡΠΊΠΎΠ»ΠΎΠ³ΠΈΡΠ΅ΡΠΊΠΎΠΉ, ΡΠ°ΠΊ ΠΈ ΡΠΊΠΎΠ½ΠΎΠΌΠΈΡΠ΅ΡΠΊΠΎΠΉ ΡΡΠΎΡΠΎΠ½Ρ. ΠΠΎΠ»Π΅Π΅ ΠΏΡΠ°Π²ΠΈΠ»ΡΠ½ΡΠΌ ΡΠ²Π»ΡΠ΅ΡΡΡ ΠΌΠ΅ΡΠΎΠ΄ ΡΡΠΈΠ»ΠΈΠ·Π°ΡΠΈΠΈ ΡΠΈΠ½ ΠΏΡΠΈ ΠΏΠΎΠΌΠΎΡΠΈ ΠΏΠΈΡΠΎΠ»ΠΈΠ·Π°. ΠΠ°ΠΊ ΠΆΠ΅ ΠΎΠ½ ΠΏΡΠΎΠΈΡΡ ΠΎΠ΄ΠΈΡ?
ΠΠ΅ΡΠ΅ΡΠ°Π±ΠΎΡΠΊΠ° ΡΠΈΠ½ ΠΏΠΈΡΠΎΠ»ΠΈΠ·ΠΎΠΌ
ΠΠ»Ρ ΠΏΠΎΠ»ΡΡΠ΅Π½ΠΈΡ ΡΠΎΠΏΠ»ΠΈΠ²Π° ΠΏΡΠΈ Π²ΡΠΎΡΠΈΡΠ½ΠΎΠΉ ΠΏΠ΅ΡΠ΅ΡΠ°Π±ΠΎΡΠΊΠ΅ ΡΠΈΠ½ ΡΠ΅Π³ΠΎΠ΄Π½Ρ ΠΈΡΠΏΠΎΠ»ΡΠ·ΡΠ΅ΡΡΡ ΠΌΠ΅ΡΠΎΠ΄ ΠΏΠΈΡΠΎΠ»ΠΈΠ·Π°. ΠΠ½ ΠΏΡΠ΅Π΄ΡΡΠ°Π²Π»ΡΠ΅Ρ ΡΠΎΠ±ΠΎΠΉ ΠΏΡΠΎΡΠ΅ΡΡ ΡΠ΅ΡΠΌΠΈΡΠ΅ΡΠΊΠΎΠ³ΠΎ ΡΠ°Π·Π»ΠΎΠΆΠ΅Π½ΠΈΡ ΡΠΎΠ΄Π΅ΡΠΆΠ°ΡΠΈΡ ΡΡ Π² ΡΠΈΠ½Π°Ρ ΠΎΡΠ³Π°Π½ΠΈΡΠ΅ΡΠΊΠΈΡ ΡΠΎΠ΅Π΄ΠΈΠ½Π΅Π½ΠΈΠΉ Π±Π΅Π· Π΄ΠΎΡΡΡΠΏΠ° ΠΊΠΈΡΠ»ΠΎΡΠΎΠ΄Π°. ΠΠΈΡΠΎΠ»ΠΈΠ· ΡΠΈΠ½ ΡΠ΅Π³ΠΎΠ΄Π½Ρ ΡΠ²Π»ΡΠ΅ΡΡΡ Π½Π°ΠΈΠ±ΠΎΠ»Π΅Π΅ ΡΠΊΠΎΠ½ΠΎΠΌΠΈΡΠ½ΡΠΌ ΠΈ ΡΠΊΠΎΠ»ΠΎΠ³ΠΈΡΠ΅ΡΠΊΠΈ ΡΠΈΡΡΡΠΌ ΠΌΠ΅ΡΠΎΠ΄ΠΎΠΌ ΠΈΡ ΡΡΠΈΠ»ΠΈΠ·Π°ΡΠΈΠΈ, ΠΏΠΎΡΠΊΠΎΠ»ΡΠΊΡ ΠΎΠ½ Π½Π΅ ΡΠΎΠ»ΡΠΊΠΎ ΡΠ΅ΡΠ°Π΅Ρ ΡΠΎΠ»ΡΠΊΠΎ Π²ΠΎΠΏΡΠΎΡ ΠΏΠ΅ΡΠ΅ΡΠ°Π±ΠΎΡΠΊΠΈ Π²ΡΠΎΡΡΡΡΡΡ, Π½ΠΎ ΠΈ ΠΏΠΎΠ·Π²ΠΎΠ»ΡΠ΅Ρ ΠΏΠΎΠ»ΡΡΠ°ΡΡ ΡΠΎΠΏΠ»ΠΈΠ²ΠΎ Π±ΡΠΊΠ²Π°Π»ΡΠ½ΠΎ ΠΈΠ· ΠΌΡΡΠΎΡΠ°.
ΠΠΈΠ·ΠΊΠΎΡΠ΅ΠΌΠΏΠ΅ΡΠ°ΡΡΡΠ½ΡΠΉ ΠΏΠΈΡΠΎΠ»ΠΈΠ· ΠΏΠΎΠ·Π²ΠΎΠ»ΡΠ΅Ρ ΡΠ°Π·Π»ΠΎΠΆΠΈΡΡ ΠΏΠΎΠΊΡΡΡΠΊΠΈ Π½Π° ΡΠΎΡΡΠ°Π²Π»ΡΡΡΠΈΠ΅ ΠΊΠΎΠΌΠΏΠΎΠ½Π΅Π½ΡΡ, ΠΊΠ°ΠΆΠ΄ΡΠΉ ΠΈΠ· ΠΊΠΎΡΠΎΡΡΡ ΠΌΠΎΠΆΠ½ΠΎ ΠΈΡΠΏΠΎΠ»ΡΠ·ΠΎΠ²Π°ΡΡ Π² ΠΎΠΏΡΠ΅Π΄Π΅Π»Π΅Π½Π½ΡΡ ΡΠ΅Π»ΡΡ . ΠΠ΅ΡΠ΅ΡΠ°Π±ΠΎΡΠΊΠ° Π°Π²ΡΠΎΡΠΈΠ½ ΠΌΠ΅ΡΠΎΠ΄ΠΎΠΌ ΠΏΠΈΡΠΎΠ»ΠΈΠ·Π° Π΄ΠΎΡΡΠ°ΡΠΎΡΠ½ΠΎ Π΄Π°Π²Π½ΠΎ ΠΈΡΠΏΠΎΠ»ΡΠ·ΡΠ΅ΡΡΡ Π² Π΅Π²ΡΠΎΠΏΠ΅ΠΉΡΠΊΠΈΡ ΡΡΡΠ°Π½Π°Ρ , ΠΏΠΎΡΠΊΠΎΠ»ΡΠΊΡ ΠΏΠΎΠΌΠΈΠΌΠΎ ΡΠΊΠΎΠ»ΠΎΠ³ΠΈΡΠ΅ΡΠΊΠΈ ΡΠΈΡΡΠΎΠΉ ΡΡΠΈΠ»ΠΈΠ·Π°ΡΠΈΠΈ, Π΄Π°Π½Π½ΡΠΉ ΡΠΈΠΏ ΠΏΠ΅ΡΠ΅ΡΠ°Π±ΠΎΡΠΊΠΈ ΡΠΏΠΎΡΠΎΠ±Π΅Π½ ΠΏΡΠΈΠ½Π΅ΡΡΠΈ ΠΎΡΠ΅Π½Ρ Ρ ΠΎΡΠΎΡΡΡ ΠΏΡΠΈΠ±ΡΠ»Ρ. ΠΡΠ°ΠΊ, ΠΊΠ°ΠΊΠΈΠ΅ ΠΆΠ΅ ΠΏΡΠΎΠ΄ΡΠΊΡΡ ΠΌΠΎΠΆΠ΅Ρ ΠΏΡΠΎΠΈΠ·Π²ΠΎΠ΄ΠΈΡΡ ΠΎΠ±ΡΠΊΠ½ΠΎΠ²Π΅Π½Π½ΡΠΉ Π·Π°Π²ΠΎΠ΄ ΠΏΠΎ ΠΏΠ΅ΡΠ΅ΡΠ°Π±ΠΎΡΠΊΠ΅ Π°Π²ΡΠΎΡΠΈΠ½:
- Π’Π΅Ρ Π½ΠΈΡΠ΅ΡΠΊΠΈΠΉ ΡΠ³Π»Π΅ΡΠΎΠ΄, ΠΊΠΎΡΠΎΡΡΠΉ ΠΈΡΠΏΠΎΠ»ΡΠ·ΡΠ΅ΡΡΡ Π² ΠΊΠ°ΡΠ΅ΡΡΠ²Π΅ Π½Π°ΠΏΠΎΠ»Π½ΠΈΡΠ΅Π»Ρ Π² ΠΏΡΠΎΠΈΠ·Π²ΠΎΠ΄ΡΡΠ²Π΅ Π½Π΅ΠΎΡΠ²Π΅ΡΡΡΠ²Π΅Π½Π½ΡΡ ΡΠ΅Π·ΠΈΠ½, ΡΡΠ°Π½ΡΠΏΠΎΡΡΠ΅ΡΠ½ΡΡ Π»Π΅Π½Ρ, ΡΠ΅Ρ Π½ΠΈΡΠ΅ΡΠΊΠΈΡ ΠΏΠ»Π°ΡΡΠΈΠ½, ΠΈ ΠΌΠ½ΠΎΠ³ΠΎΠ³ΠΎ Π΄ΡΡΠ³ΠΎΠ³ΠΎ. Π’Π°ΠΊ ΠΆΠ΅ ΠΎΠ½ ΡΠ²Π»ΡΠ΅ΡΡΡ ΠΏΠΈΠ³ΠΌΠ΅Π½ΡΠΎΠΌ Π΄Π»Ρ ΠΏΡΠΎΠΈΠ·Π²ΠΎΠ΄ΡΡΠ²Π° ΠΊΡΠ°ΡΠΎΠΊ. Π’Π΅Ρ Π½ΠΈΡΠ΅ΡΠΊΠΈΠΉ ΡΠ³Π»Π΅ΡΠΎΠ΄ Π±ΠΎΠ»Π΅Π΅ Π½ΠΈΠ·ΠΊΠΎΠ³ΠΎ ΠΊΠ°ΡΠ΅ΡΡΠ²Π° ΡΠΈΡΠΎΠΊΠΎ ΠΈΡΠΏΠΎΠ»ΡΠ·ΡΠ΅ΡΡΡ Π² ΡΡΡΠΎΠΈΡΠ΅Π»ΡΡΡΠ²Π΅ (ΠΈΠ· Π½Π΅Π³ΠΎ Π΄Π΅Π»Π°Π΅ΡΡΡ ΡΡΠΎΡΡΠ°ΡΠ½Π°Ρ ΠΏΠ»ΠΈΡΠΊΠ°, Π±Π΅ΡΠΎΠ½Π½ΡΠ΅ ΠΈΠ·Π΄Π΅Π»ΠΈΡ ΠΈ ΠΊΠΈΡΠΏΠΈΡ).
- Π’Π΅ΡΠΌΠΎΠ»ΠΈΠ·Π½ΡΠΉ Π³Π°Π·, ΠΊΠΎΡΠΎΡΡΠΉ ΡΠ²Π»ΡΠ΅ΡΡΡ Π°Π½Π°Π»ΠΎΠ³ΠΎΠΌ ΠΏΡΠΈΡΠΎΠ΄Π½ΠΎΠ³ΠΎ Π³Π°Π·Π°. ΠΠ°Π½Π½ΡΠΉ Π³Π°Π· Π΄ΠΎΡΡΠ°ΡΠΎΡΠ½ΠΎ ΡΠΈΡΡΡΠΉ, ΠΈ ΠΌΠΎΠΆΠ΅Ρ ΡΠ²ΠΎΠ±ΠΎΠ΄Π½ΠΎ ΠΈΡΠΏΠΎΠ»ΡΠ·ΠΎΠ²Π°ΡΡΡΡ Π½Π° ΠΌΠΈΠ½ΠΈ-ΠΊΠΎΡΠ΅Π»ΡΠ½ΡΡ Π΄Π»Ρ ΠΏΠΎΠ»ΡΡΠ΅Π½ΠΈΡ ΡΠ΅ΠΏΠ»ΠΎ ΠΈ ΡΠ»Π΅ΠΊΡΡΠΎΡΠ½Π΅ΡΠ³ΠΈΠΈ.
- ΠΡΠ΅ΡΡΠΎΠ²Π°Π½Π½ΡΠΉ ΠΌΠ΅ΡΠ°Π»Π»ΠΎΠΊΠΎΡΠ΄, ΠΈΡΠΏΠΎΠ»ΡΠ·ΡΠ΅ΠΌΡΠΉ Π΄Π»Ρ Π½ΡΠΆΠ΄ ΠΌΠ΅ΡΠ°Π»Π»ΡΡΠ³ΠΈΡΠ΅ΡΠΊΠΎΠΉ ΠΏΡΠΎΠΌΡΡΠ»Π΅Π½Π½ΠΎΡΡΠΈ. ΠΠ½ ΠΌΠΎΠΆΠ΅Ρ ΡΠ΅Π°Π»ΠΈΠ·ΠΎΠ²ΡΠ²Π°ΡΡΡΡ ΠΊΠ°ΠΊ ΠΌΠ΅ΡΠ°Π»Π»ΠΎΠ»ΠΎΠΌ, ΡΠ°ΠΊ ΠΈ ΠΊΠ°ΠΊ Π²ΡΠ·Π°Π»ΡΠ½Π°Ρ ΠΏΡΠΎΠ²ΠΎΠ»ΠΎΠΊΠ° (ΠΏΡΠΈ ΡΡΠ»ΠΎΠ²ΠΈΠΈ Π΅Π³ΠΎ Π΄ΠΎΠΏΠΎΠ»Π½ΠΈΡΠ΅Π»ΡΠ½ΠΎΠ³ΠΎ ΠΎΠ±ΠΆΠΈΠ³Π°)
- Π‘ΠΈΠ½ΡΠ΅ΡΠΈΡΠ΅ΡΠΊΠ°Ρ Π½Π΅ΡΡΡ, ΠΊΠΎΡΠΎΡΠ°Ρ ΠΏΠΎ ΡΠ²ΠΎΠ΅ΠΌΡ ΡΠΎΡΡΠ°Π²Ρ ΠΏΡΠ°ΠΊΡΠΈΡΠ΅ΡΠΊΠΈ ΠΈΠ΄Π΅Π½ΡΠΈΡΠ½Π° ΠΏΡΠΈΡΠΎΠ΄Π½ΠΎΠΉ. ΠΡΠΈ ΡΡΠ»ΠΎΠ²ΠΈΠΈ Π΅Π΅ ΠΎΡΠΈΡΡΠΊΠΈ ΠΎΠ½Π° ΡΠΏΠΎΡΠΎΠ±Π½Π° Π·Π°ΠΌΠ΅ΡΡΠΈΡΡ ΠΌΠ½ΠΎΠ³ΠΈΠ΅ Π½Π΅ΡΡΠ΅ΠΏΡΠΎΠ΄ΡΠΊΡΡ.
ΠΡΠ΅ ΡΡΠΈ ΠΏΡΠΎΠ΄ΡΠΊΡΡ ΡΠ°ΠΊΠΎΠ³ΠΎ ΠΏΡΠΎΡΠ΅ΡΡΠ° ΠΊΠ°ΠΊ ΠΏΠΈΡΠΎΠ»ΠΈΠ· Π°Π²ΡΠΎΡΠΈΠ½ ΡΠ²Π»ΡΡΡΡΡ Π²ΠΎΡΡΡΠ΅Π±ΠΎΠ²Π°Π½Π½ΡΠΌΠΈ Π² ΡΠ°ΠΌΡΡ ΡΠ°Π·Π»ΠΈΡΠ½ΡΡ ΠΎΡΡΠ°ΡΠ»ΡΡ , ΠΏΠΎΡΡΠΎΠΌΡ ΠΏΠ΅ΡΠ΅ΡΠ°Π±ΠΎΡΠΊΠ° ΡΠΈΠ½ ΡΠ²Π»ΡΠ΅ΡΡΡ Π΄ΠΎΡΡΠ°ΡΠΎΡΠ½ΠΎ ΠΏΡΠΈΠ±ΡΠ»ΡΠ½ΡΠΌ Π±ΠΈΠ·Π½Π΅ΡΠΎΠΌ.
ΠΠΈΡΠΎΠ»ΠΈΠ· ΠΏΠΎΠΊΡΡΡΠ΅ΠΊ.
Π£ΡΠΈΠ»ΠΈΠ·Π°ΡΠΈΡ ΠΈ ΠΏΠΎΡΠ»Π΅Π΄ΡΡΡΠ°Ρ ΠΏΠ΅ΡΠ΅ΡΠ°Π±ΠΎΡΠΊΠ° ΡΠΈΠ½ ΠΎΡΡΡΠ΅ΡΡΠ²Π»ΡΠ΅ΡΡΡ Π² Π½Π΅ΡΠΊΠΎΠ»ΡΠΊΠΎ ΡΡΠ°ΠΏΠΎΠ²:
- ΠΡΠ΅Π΄Π½Π°Π·Π½Π°ΡΠ΅Π½Π½ΡΠ΅ Π΄Π»Ρ ΡΡΠΈΠ»ΠΈΠ·Π°ΡΠΈΠΈ Π°Π²ΡΠΎΠΌΠΎΠ±ΠΈΠ»ΡΠ½ΡΠ΅ ΡΠΈΠ½Ρ ΠΎΡΠΏΡΠ°Π²Π»ΡΡΡΡΡ Π½Π° ΡΠΊΠ»Π°Π΄ ΡΡΡΡΡ.
- Π‘ ΠΏΠΎΠΌΠΎΡΡΡ Π±ΠΎΡΡΠΎΡΠ΅Π·Π½ΠΎΠ³ΠΎ ΡΡΠ°Π½ΠΊΠ° ΡΠΈΠ½Ρ ΡΠ°Π·Π΄Π΅Π»ΡΠ²Π°ΡΡ Π½Π° ΠΏΡΠΎΡΠ΅ΠΊΡΠΎΡΠ½ΡΡ ΡΠ°ΡΡΡ ΠΈ Π±ΠΎΡΡΡ (Π΄Π»Ρ ΠΌΠ°ΠΊΡΠΈΠΌΠ°Π»ΡΠ½ΠΎ ΠΏΠ»ΠΎΡΠ½ΠΎΠΉ ΡΠΊΠ»Π°Π΄ΠΊΠΈ).
- Π Π΅ΡΠΎΡΡΠ° Π·Π°Π³ΡΡΠΆΠ°Π΅ΡΡΡ ΡΡΡΡΠ΅ΠΌ, Π·Π°ΡΠ΅ΠΌ ΠΎΠ½Π° Π·Π°ΠΊΡΡΠ²Π°Π΅ΡΡΡ ΠΊΡΡΡΠΊΠΎΠΉ ΠΈ ΠΏΠΎΠΌΠ΅ΡΠ°Π΅ΡΡΡ Π² ΠΏΠΈΡΠΎΠ»ΠΈΠ·Π½ΡΡ ΠΏΠ΅ΡΡ, Π³Π΄Π΅ Π½Π°Π³ΡΠ΅Π²Π°Π΅ΡΡΡ Π΄ΠΎ 450Β°Π‘. ΠΠΎ Π²ΡΠ΅ΠΌΡ ΡΠ΅ΡΠΌΠΈΡΠ΅ΡΠΊΠΎΠ³ΠΎ ΡΠ°Π·Π»ΠΎΠΆΠ΅Π½ΠΈΡ ΡΠ΅Π·ΠΈΠ½Ρ ΠΎΠ±ΡΠ°Π·ΡΠ΅ΡΡΡ ΠΏΠΈΡΠΎΠ»ΠΈΠ·Π½ΡΠΉ Π³Π°Π·, ΠΊΠΎΡΠΎΡΡΠΉ, ΠΏΡΠΎΡ ΠΎΠ΄ΠΈΡ ΡΠ΅ΡΠ΅Π· Ρ ΠΎΠ»ΠΎΠ΄ΠΈΠ»ΡΠ½ΠΈΠΊ, Π³Π΄Π΅ ΠΊΠΎΠ½Π΄Π΅Π½ΡΠΈΡΡΠ΅ΡΡΡ Π² ΠΏΠΈΡΠΎΠ»ΠΈΠ·Π½ΠΎΠ΅ ΠΌΠ°ΡΠ»ΠΎ. ΠΠ»Ρ ΠΏΠΎΠ΄Π΄Π΅ΡΠΆΠ°Π½ΠΈΡ ΠΏΡΠΎΡΠ΅ΡΡΠ° ΠΏΠΈΡΠΎΠ»ΠΈΠ·Π°, ΡΠ°ΡΡΡ ΠΏΠΎΠ»ΡΡΠ΅Π½Π½ΠΎΠ³ΠΎ Π³Π°Π·Π° ΠΏΠΎΠ΄Π°Π΅ΡΡΡ Π² ΠΏΠ΅ΡΠ½ΡΡ Π³ΠΎΡΠ΅Π»ΠΊΡ.
- ΠΠΎ Π·Π°Π²Π΅ΡΡΠ΅Π½ΠΈΡ ΠΏΡΠΎΡΠ΅ΡΡΠ° ΠΏΠΈΡΠΎΠ»ΠΈΠ·Π° ΡΠ΅ΡΠΎΡΡΡ ΠΈΠ·Π²Π»Π΅ΠΊΠ°ΡΡ ΠΈΠ· ΠΏΠ΅ΡΠΈ, Π° Π½Π° Π΅Π΅ ΠΌΠ΅ΡΡΠΎ Π·Π°Π³ΡΡΠΆΠ°ΡΡ ΡΠ»Π΅Π΄ΡΡΡΡΡ ΡΠ΅ΡΠΎΡΡΡ Ρ ΡΡΡΡΠ΅ΠΌ.
- ΠΠΎΡΠ»Π΅ ΠΎΡΡΡΠ²Π°Π½ΠΈΡ, ΡΠ΅ΡΠΎΡΡΠ° ΡΠ°Π·Π³ΡΡΠΆΠ°Π΅ΡΡΡ, ΠΈ ΠΌΠ΅ΡΠ°Π»Π»ΠΎΠΊΠΎΡΠ΄ ΠΎΡΠ΄Π΅Π»ΡΡΡ ΠΎΡ ΠΏΠΈΡΠΎΡΠ³Π»Π΅ΡΠΎΠ΄Π°.
- ΠΠΎΡΠΎΠ²ΡΠ΅ ΠΏΡΠΎΠ΄ΡΠΊΡΡ ΠΏΠΈΡΠΎΠ»ΠΈΠ·Π° ΠΎΡΠΏΡΠ°Π²Π»ΡΡΡ Π½Π° ΡΠΊΠ»Π°Π΄, Π³Π΄Π΅ ΠΎΠ½ΠΈ Ρ ΡΠ°Π½ΡΡΡΡ Π΄ΠΎ Π½Π΅ΠΏΠΎΡΡΠ΅Π΄ΡΡΠ²Π΅Π½Π½ΠΎΠΉ ΠΎΡΠ³ΡΡΠ·ΠΊΠΈ ΠΊΠΎΠ½Π΅ΡΠ½ΠΎΠΌΡ ΠΏΠΎΡΡΠ΅Π±ΠΈΡΠ΅Π»Ρ.
ΠΡΠ΅ΠΈΠΌΡΡΠ΅ΡΡΠ²Π° ΠΏΠΈΡΠΎΠ»ΠΈΠ·Π° Π°Π²ΡΠΎΠΌΠΎΠ±ΠΈΠ»ΡΠ½ΡΡ ΡΠΈΠ½ ΠΏΡΠΎΡΡΠΎ ΠΎΡΠ΅Π²ΠΈΠ΄Π½Ρ Π½Π΅Π²ΠΎΠΎΡΡΠΆΠ΅Π½Π½ΡΠΌ Π²Π·Π³Π»ΡΠ΄ΠΎΠΌ:
- ΠΠ°Π½Π½ΡΠΉ ΠΏΡΠΎΡΠ΅ΡΡ ΡΡΠΈΠ»ΠΈΠ·Π°ΡΠΈΠΈ ΡΠ²Π»ΡΠ΅ΡΡΡ Π±Π΅Π·ΠΎΠΏΠ°ΡΠ½ΡΠΌ Ρ ΡΠΊΠΎΠ»ΠΎΠ³ΠΈΡΠ΅ΡΠΊΠΎΠΉ ΡΠΎΡΠΊΠΈ Π·ΡΠ΅Π½ΠΈΡ, Π° Π² ΠΏΡΠΎΠ΄ΡΠΊΡΠ°Ρ ΠΏΠ΅ΡΠ΅ΡΠ°Π±ΠΎΡΠΊΠΈ ΠΎΡΡΡΡΡΡΠ²ΡΡΡ Π²ΡΡΠΎΠΊΠΎΡΠΎΠΊΡΠΈΡΠ½ΡΠ΅ Π²Π΅ΡΠ΅ΡΡΠ²Π°.
- ΠΡΡΡΡΡΡΠ²ΠΈΠ΅ ΠΎΡΡ ΠΎΠ΄ΠΎΠ² ΠΏΡΠΈ ΠΏΡΠΎΠΈΠ·Π²ΠΎΠ΄ΡΡΠ²Π΅ β Π°Π±ΡΠΎΠ»ΡΡΠ½ΠΎ Π²ΡΠ΅, ΡΡΠΎ ΠΎΠ±ΡΠ°Π·ΡΠ΅ΡΡΡ Π² ΠΏΡΠΎΡΠ΅ΡΡΠ΅ ΠΏΠ΅ΡΠ΅ΡΠ°Π±ΠΎΡΠΊΠΈ ΠΏΠΎΠΊΡΡΡΠ΅ΠΊ, ΡΠ²Π»ΡΠ΅ΡΡΡ Π»ΠΈΠΊΠ²ΠΈΠ΄Π½ΡΠΌ ΠΏΡΠΎΠ΄ΡΠΊΡΠΎΠΌ.
- ΠΠ°Π½Π½Π°Ρ ΠΏΠ΅ΡΠ΅ΡΠ°Π±ΠΎΡΠΊΠ° Π’ΠΠ Π½Π΅ ΡΡΠ΅Π±ΡΠ΅Ρ ΡΠ΅ΡΡΠ΅Π·Π½ΡΡ ΡΠ½Π΅ΡΠ³ΠΎΠ·Π°ΡΡΠ°Ρ, ΠΈ Π² ΡΠ΅Π»ΠΎΠΌ, ΠΎΠ½Π° ΠΎΡΠ΅Π½Ρ ΡΠΊΠΎΠ½ΠΎΠΌΠΈΡΠ½Π°;
- ΠΠΌΠ΅Π΅ΡΡΡ Π²ΠΎΠ·ΠΌΠΎΠΆΠ½ΠΎΡΡΡ ΠΈΡΠΏΠΎΠ»ΡΠ·ΠΎΠ²Π°Π½ΠΈΡ ΠΏΠΎΠ»ΡΡΠ°Π΅ΠΌΠΎΠ³ΠΎ ΠΎΡ ΠΏΠ΅ΡΠ΅ΡΠ°Π±ΠΎΡΠΊΠΈ ΡΠ΅Π·ΠΈΠ½Ρ ΡΠΎΠΏΠ»ΠΈΠ²Π°, Π΄Π»Ρ Π²Π½ΡΡΡΠ΅Π½Π½ΠΈΡ ΡΠ΅Ρ Π½ΠΎΠ»ΠΎΠ³ΠΈΡΠ΅ΡΠΊΠΈΡ ΠΏΡΠΎΡΠ΅ΡΡΠΎΠ².
Π Π΅Π·ΡΠΌΠΈΡΡΡ Π²ΡΠ΅ Π½Π°ΠΏΠΈΡΠ°Π½Π½ΠΎΠ΅ Π²ΡΡΠ΅, ΠΌΠΎΠΆΠ½ΠΎ ΡΠΊΠ°Π·Π°ΡΡ, ΡΡΠΎ ΠΏΠΈΡΠΎΠ»ΠΈΠ· ΡΠΈΠ½ ΡΠ²Π»ΡΠ΅ΡΡΡ Π΅Π΄ΠΈΠ½ΡΡΠ²Π΅Π½Π½ΠΎ Π²Π΅ΡΠ½ΡΠΌ ΡΠ΅ΡΠ΅Π½ΠΈΠ΅ΠΌ ΡΡΠΈΠ»ΠΈΠ·Π°ΡΠΈΠΈ ΡΠ΅Π·ΠΈΠ½Ρ Π΄Π»Ρ Π²ΡΠ΅Ρ ΡΠ΅Ρ , ΠΊΡΠΎ Π΄ΡΠΌΠ°Π΅Ρ ΠΎ Π±ΡΠ΄ΡΡΠ΅ΠΌ ΡΠ²ΠΎΠΈΡ Π΄Π΅ΡΠ΅ΠΉ ΠΈ Π·Π°Π±ΠΎΡΠΈΡΡΡ ΠΎΠ± ΠΎΠΊΡΡΠΆΠ°ΡΡΠ΅ΠΉ ΡΡΠ΅Π΄Π΅. Π Ρ ΡΠΎΡΠΊΠΈ Π·ΡΠ΅Π½ΠΈΡ Π΄Π»Ρ Π±ΠΈΠ·Π½Π΅ΡΠ° ΠΏΠΈΡΠΎΠ»ΠΈΠ· ΡΠ²Π»ΡΠ΅ΡΡΡ Π½Π°ΠΈΠ±ΠΎΠ»Π΅Π΅ Π²ΡΠ³ΠΎΠ΄Π½ΡΠΌ ΡΠΏΠΎΡΠΎΠ±ΠΎΠΌ Π²ΡΠΎΡΠΈΡΠ½ΠΎΠΉ ΠΏΠ΅ΡΠ΅ΡΠ°Π±ΠΎΡΠΊΠΈ ΡΡΠ°ΡΠΎΠΉ Π°Π²ΡΠΎΠΌΠΎΠ±ΠΈΠ»ΡΠ½ΠΎΠΉ ΡΠ΅Π·ΠΈΠ½Ρ.
morflot.su
ΠΎΠ±Π·ΠΎΡ ΡΠ°Π·Π»ΠΈΡΠ½ΡΡ ΡΡΠ°Π½ΠΊΠΎΠ² ΠΈ ΠΌΠΈΠ½ΠΈ-Π·Π°Π²ΠΎΠ΄ΠΎΠ² Π΄Π»Ρ ΡΡΠΈΠ»ΠΈΠ·Π°ΡΠΈΠΈ ΡΠ΅Π·ΠΈΠ½Ρ
Π‘ ΠΊΠ°ΠΆΠ΄ΡΠΌ Π³ΠΎΠ΄ΠΎΠΌ Π²ΡΠ΅ Π±ΠΎΠ»ΡΡΠ΅ ΡΠΆΠ΅ΡΡΠΎΡΠ°ΡΡΡΡ Π·Π°ΠΊΠΎΠ½Ρ, Π·Π°ΡΠΈΡΠ°ΡΡΠΈΠ΅ ΠΎΠΊΡΡΠΆΠ°ΡΡΡΡ ΡΡΠ΅Π΄Ρ ΠΈ ΡΠΊΠΎΠ»ΠΎΠ³ΠΈΡ. ΠΠ΅ ΡΠ°ΠΊ Π΄Π°Π²Π½ΠΎ ΡΡΠ°Π»ΠΎ ΠΏΠΎΠ»Π½ΠΎΡΡΡΡ Π·Π°ΠΏΡΠ΅ΡΠ΅Π½ΠΎ Π·Π°Ρ
ΠΎΡΠΎΠ½Π΅Π½ΠΈΠ΅ ΡΠ΅Π·ΠΈΠ½Ρ ΠΈ Π°Π²ΡΠΎΠΌΠΎΠ±ΠΈΠ»ΡΠ½ΡΡ
ΠΏΠΎΠΊΡΡΡΠ΅ΠΊ. ΠΡΠΈ ΡΠ΅ΡΠΎΡΠΌΡ Π΄ΠΎΠ»ΠΆΠ½Ρ ΡΡΠΈΠΌΡΠ»ΠΈΡΠΎΠ²Π°ΡΡ ΡΠ°Π·Π²ΠΈΡΠΈΠ΅ ΡΠ°ΠΊΠΎΠΉ ΠΎΡΡΠ°ΡΠ»ΠΈ, ΠΊΠ°ΠΊ Π²ΡΠΎΡΠΈΡΠ½Π°Ρ ΠΏΠ΅ΡΠ΅ΡΠ°Π±ΠΎΡΠΊΠ° ΡΡΡΡΡ. ΠΠ½ΠΎΠ³ΠΈΠ΅ ΡΠΆΠ΅ ΡΠ΅Π³ΠΎΠ΄Π½Ρ ΠΏΡΠΈΠΎΠ±ΡΠ΅ΡΠ°ΡΡ ΡΠΏΠ΅ΡΠΈΠ°Π»ΠΈΠ·ΠΈΡΠΎΠ²Π°Π½Π½ΠΎΠ΅ ΠΎΠ±ΠΎΡΡΠ΄ΠΎΠ²Π°Π½ΠΈΠ΅ Π΄Π»Ρ ΠΏΠ΅ΡΠ΅ΡΠ°Π±ΠΎΡΠΊΠΈ ΡΠΈΠ½, Π·Π°ΡΠ°Π±Π°ΡΡΠ²Π°Ρ Π½Π° ΡΡΠΎΠΌ Ρ
ΠΎΡΠΎΡΠΈΠ΅ Π΄Π΅Π½ΡΠ³ΠΈ. ΠΡΠΎΡΠΈΡΠ½ΡΠΉ ΠΌΠ°ΡΠ΅ΡΠΈΠ°Π» ΠΌΠΎΠΆΠ½ΠΎ ΠΈΡΠΏΠΎΠ»ΡΠ·ΠΎΠ²Π°ΡΡ Π²ΠΎ ΠΌΠ½ΠΎΠ³ΠΈΡ
ΠΎΡΡΠ°ΡΠ»ΡΡ
ΠΏΡΠΎΠΌΡΡΠ»Π΅Π½Π½ΠΎΡΡΠΈ.
ΠΠ±Π»Π°ΡΡΡ ΠΏΡΠΈΠΌΠ΅Π½Π΅Π½ΠΈΡ Π²ΡΠΎΡΠΈΡΠ½ΠΎΠ³ΠΎ ΡΡΡΡΡ
Π‘ΡΡΠ΅ΡΡΠ²ΡΠ΅Ρ Π½Π΅ΡΠΊΠΎΠ»ΡΠΊΠΎ Π½Π°ΠΏΡΠ°Π²Π»Π΅Π½ΠΈΠΉ ΡΡΠΈΠ»ΠΈΠ·Π°ΡΠΈΠΈ ΡΡΠ°ΡΠΎΠΉ ΡΠ΅Π·ΠΈΠ½Ρ: ΠΏΠΈΡΠΎΠ»ΠΈΠ· ΠΈ ΠΈΠ·ΠΌΠ΅Π»ΡΡΠ΅Π½ΠΈΠ΅ Π² ΠΊΡΠΎΡΠΊΡ. ΠΡ ΠΎΡΠ»ΠΈΡΠΈΠ΅ ΡΠΎΡΡΠΎΠΈΡ Π² ΠΎΠ±ΠΎΡΡΠ΄ΠΎΠ²Π°Π½ΠΈΠΈ, ΡΠ½Π΅ΡΠ³Π΅ΡΠΈΡΠ΅ΡΠΊΠΈΡ Π·Π°ΡΡΠ°ΡΠ°Ρ , ΡΠ°Π·ΠΌΠ΅ΡΠ°Ρ Π½Π°ΡΠ°Π»ΡΠ½ΠΎΠ³ΠΎ ΠΊΠ°ΠΏΠΈΡΠ°Π»Π° ΠΈ ΡΠΏΠΎΡΠΎΠ±Π΅ ΡΠ΅Π°Π»ΠΈΠ·Π°ΡΠΈΠΈ ΠΏΡΠΎΠ΄ΡΠΊΡΠΈΠΈ. ΠΡΠΈ ΠΏΠΈΡΠΎΠ»ΠΈΠ·Π½ΠΎΠΉ ΡΠ΅Ρ Π½ΠΎΠ»ΠΎΠ³ΠΈΠΈ ΡΠ΅Π·ΠΈΠ½Π° Π½Π°Π³ΡΠ΅Π²Π°Π΅ΡΡΡ Π΄ΠΎ 450β500 Π³ΡΠ°Π΄ΡΡΠΎΠ². ΠΡΠΈ ΡΡΠΎΠΌ Π²ΡΠ΄Π΅Π»ΡΠ΅ΡΡΡ:
- Π‘ΠΈΠ½ΡΠ΅ΡΠΈΡΠ΅ΡΠΊΠΎΠ΅ ΡΠΎΠΏΠ»ΠΈΠ²ΠΎ Π² ΠΆΠΈΠ΄ΠΊΠΎΠΌ Π²ΠΈΠ΄Π΅, ΠΊΠΎΡΠΎΡΠΎΠ΅ ΠΈΡΠΏΠΎΠ»ΡΠ·ΡΠ΅ΡΡΡ Π΄Π»Ρ ΠΎΡΠΎΠΏΠΈΡΠ΅Π»ΡΠ½ΡΡ ΡΡΡΠ°Π½ΠΎΠ²ΠΎΠΊ ΠΈ ΠΊΠΎΡΠ»ΠΎΠ². ΠΡΠΈ Π΅Π³ΠΎ ΠΏΠΎΡΠ»Π΅Π΄ΡΡΡΠ΅ΠΉ ΠΏΠ΅ΡΠ΅Π³ΠΎΠ½ΠΊΠ΅ ΠΏΠΎΠ»ΡΡΠ°ΡΡΡΡ ΡΠ°Π·Π»ΠΈΡΠ½ΡΠ΅ ΡΠ³Π»Π΅Π²ΠΎΠ΄ΠΎΡΠΎΠ΄Π½ΡΠ΅ ΡΡΠ°ΠΊΡΠΈΠΈ β Π΄ΠΈΠ·Π΅Π»ΡΠ½ΠΎΠ΅ ΡΠΎΠΏΠ»ΠΈΠ²ΠΎ, ΡΠΌΠΎΠ»Π°, Π±Π΅Π½Π·ΠΈΠ½ ΠΈ ΠΌΠ°Π·ΡΡ.
- Π’Π΅Ρ Π½ΠΈΡΠ΅ΡΠΊΠΈΠΉ ΡΠ³Π»Π΅ΡΠΎΠ΄, ΠΊΠΎΡΠΎΡΡΠΉ ΠΈΡΠΏΠΎΠ»ΡΠ·ΡΠ΅ΡΡΡ Π² Π²ΠΈΠ΄Π΅ Π°Π΄ΡΠΎΡΠ±Π΅Π½ΡΠ°, ΠΎΡΠ½ΠΎΠ²Ρ Π΄Π»Ρ Π±ΠΈΡΡΠΌΠ½ΠΎΠΉ ΠΌΠ°ΡΡΠΈΠΊΠΈ, Π½Π°ΠΏΠΎΠ»Π½ΠΈΡΠ΅Π»Ρ ΠΏΡΠΈ ΠΈΠ·Π³ΠΎΡΠΎΠ²Π»Π΅Π½ΠΈΠΈ ΡΠ΅Π·ΠΈΠ½ΠΎΠ²ΡΡ ΠΈΠ·Π΄Π΅Π»ΠΈΠΉ, ΠΊΡΠ°ΡΠΈΡΠ΅Π»Ρ Π² Π»Π°ΠΊΠΎΠΊΡΠ°ΡΠΎΡΠ½ΠΎΠΌ ΠΏΡΠΎΠΈΠ·Π²ΠΎΠ΄ΡΡΠ²Π΅.
- ΠΠ°Π·, ΠΊΠΎΡΠΎΡΡΠΉ ΠΈΡΠΏΠΎΠ»ΡΠ·ΡΡΡ ΠΏΡΠΈ ΠΏΠΎΠ²ΡΠΎΡΠ½ΠΎΠΌ ΡΠΆΠΈΠ³Π°Π½ΠΈΠΈ Π² ΠΏΠΈΡΠΎΠ»ΠΈΠ·Π½ΡΡ ΡΡΡΠ°Π½ΠΎΠ²ΠΊΠ°Ρ .
ΠΠ°ΡΠ°ΡΡΡΡ ΡΠΈΠ½Ρ ΠΏΡΠΎΠΈΠ·Π²ΠΎΠ΄ΡΡΡΡ ΠΈΠ· Π²ΡΡΠΎΠΊΠΎΠΊΠ°ΡΠ΅ΡΡΠ²Π΅Π½Π½ΠΎΠΉ ΡΠ΅Π·ΠΈΠ½Ρ, ΠΊΠΎΡΠΎΡΠ°Ρ Π΄Π°ΠΆΠ΅ ΠΏΠΎΡΠ»Π΅ ΠΈΠ·ΠΌΠ΅Π»ΡΡΠ΅Π½ΠΈΡ ΠΏΡΠΎΠ΄ΠΎΠ»ΠΆΠ°Π΅Ρ ΡΠΎΡ
ΡΠ°Π½ΡΡΡ ΡΠ²ΠΎΠΈ ΡΠ²ΠΎΠΉΡΡΠ²Π°: ΡΡΡΠΎΠΉΡΠΈΠ²ΠΎΡΡΡ ΠΊ Ρ
ΠΈΠΌΠΈΡΠ΅ΡΠΊΠΈΠΌ Π²ΠΎΠ·Π΄Π΅ΠΉΡΡΠ²ΠΈΡΠΌ, ΡΠ»Π°ΡΡΠΈΡΠ½ΠΎΡΡΡ ΠΈ ΠΏΡΠΎΡΠ½ΠΎΡΡΡ. ΠΡΠΈ ΠΏΠ΅ΡΠ΅ΡΠ°Π±ΠΎΡΠΊΠ΅ ΡΠ΅Π·ΠΈΠ½Ρ Π² ΠΊΡΠΎΡΠΊΡ ΠΎΡΠ½ΠΎΠ²Π½ΡΠΌ ΠΌΠ°ΡΠ΅ΡΠΈΠ°Π»ΠΎΠΌ ΡΠ²Π»ΡΡΡΡΡ ΡΠ°Π·Π»ΠΈΡΠ½ΡΠ΅ ΡΡΠ°ΠΊΡΠΈΠΈ Π΄ΠΈΠ°ΠΌΠ΅ΡΡΠΎΠΌ ΠΎΡ 0,25 Π΄ΠΎ 5 ΠΌΠΌ.
ΠΠΎΠ»ΡΡΠ΅Π½Π½ΡΠΉ ΠΌΠ°ΡΠ΅ΡΠΈΠ°Π» ΠΈΡΠΏΠΎΠ»ΡΠ·ΡΠ΅ΡΡΡ ΠΏΡΠΈ ΠΏΡΠΎΠΈΠ·Π²ΠΎΠ΄ΡΡΠ²Π΅ ΡΠ°Π·Π»ΠΈΡΠ½ΡΡ ΠΈΠ·Π΄Π΅Π»ΠΈΠΉ:
- ΡΠ΅Π·ΠΈΠ½ΠΎΠ²Π°Ρ ΠΏΠ»ΠΈΡΠΊΠ° Π΄Π»Ρ ΠΏΠΎΠΊΡΡΡΠΈΡ Π΄Π΅ΡΡΠΊΠΈΡ ΠΏΠ»ΠΎΡΠ°Π΄ΠΎΠΊ ΡΡΠ°Π΄ΠΈΠΎΠ½ΠΎΠ² ΠΈ Π΄Ρ;
- Π½Π°ΠΏΠΎΠ»Π½ΠΈΡΠ΅Π»Ρ Π΄Π»Ρ ΡΠΏΠΎΡΡΠΈΠ²Π½ΠΎΠ³ΠΎ ΠΈΠ½Π²Π΅Π½ΡΠ°ΡΡ;
- ΠΏΠΎΠ΄ΠΎΡΠ²Π° Π΄Π»Ρ ΡΠ΅Π·ΠΈΠ½ΠΎΠ²ΡΡ ΡΠ°ΠΏΠΎΠ³ ΠΈ Π΄ΡΡΠ³ΠΎΠΉ ΠΎΠ±ΡΠ²ΠΈ;
- ΠΆΠ΅Π»Π΅Π·Π½ΠΎΠ΄ΠΎΡΠΎΠΆΠ½ΡΠ΅ ΠΏΠ΅ΡΠ΅Π΅Π·Π΄Ρ, Β«Π»Π΅ΠΆΠ°ΡΠΈΠ΅ ΠΏΠΎΠ»ΠΈΡΠ΅ΠΉΡΠΊΠΈΠ΅Β»;
- ΠΎΡΠ±ΠΎΠΉΠ½ΠΈΠΊΠΈ, Π±Π°ΠΌΠΏΠ΅ΡΠ°, ΠΊΠΎΠ²ΡΠΈΠΊΠΈ ΠΈ Π΄ΡΡΠ³ΠΈΠ΅ ΡΠ΅Π·ΠΈΠ½ΠΎΠ²ΡΠ΅ ΠΈΠ·Π΄Π΅Π»ΠΈΡ Π΄Π»Ρ Π°Π²ΡΠΎΠΌΠΎΠ±ΠΈΠ»Π΅ΠΉ;
- ΠΏΠΎΠ΄ΠΊΠ»Π°Π΄ΠΊΠΈ Π΄Π»Ρ ΡΠΏΠ°Π» Π½Π° ΠΆΠ΅Π»Π΅Π·Π½ΠΎΠΉ Π΄ΠΎΡΠΎΠ³Π΅.
ΠΡΠΎΠΌΠ΅ ΡΡΠΎΠ³ΠΎ, Π² ΠΏΠΎΠΊΡΡΡΠΊΠ°Ρ ΡΠΎΠ΄Π΅ΡΠΆΠΈΡΡΡ ΡΠ΅ΠΊΡΡΠΈΠ»ΡΠ½ΡΠΉ ΠΊΠΎΡΠ΄, ΠΊΠΎΡΠΎΡΡΠΉ Π²ΠΎ Π²ΡΠ΅ΠΌΡ ΠΏΠΈΡΠΎΠ»ΠΈΠ·Π½ΠΎΠΉ ΠΎΠ±ΡΠ°Π±ΠΎΡΠΊΠΈ ΡΠΆΠΈΠ³Π°Π΅ΡΡΡ, Π° ΠΏΡΠΈ ΠΈΠ·ΠΌΠ΅Π»ΡΡΠ΅Π½ΠΈΠΈ ΡΠ΅Π·ΠΈΠ½Ρ Π² ΠΊΡΠΎΡΠΊΡ ΠΎΡΡΠ΅ΠΈΠ²Π°Π΅ΡΡΡ, Π° Π·Π°ΡΠ΅ΠΌ ΠΏΡΠΈΠΌΠ΅Π½ΡΠ΅ΡΡΡ Π² ΡΡΡΠΎΠΈΡΠ΅Π»ΡΡΡΠ²Π΅ (Π΄Π»Ρ ΡΡΠ΅ΠΏΠ»Π΅Π½ΠΈΡ, ΡΡΠΌΠΎΠΈΠ·ΠΎΠ»ΡΡΠΈΠΈ, ΠΏΡΠΈ ΠΈΠ·Π³ΠΎΡΠΎΠ²Π»Π΅Π½ΠΈΠΈ Π°ΡΠΌΠΈΡΠΎΠ²Π°Π½Π½ΠΎΠ³ΠΎ Π±Π΅ΡΠΎΠ½Π°).
Π‘ΡΠ°Π»ΡΠ½ΠΎΠΉ ΠΊΠΎΠΌΠΏΠΎΠ½Π΅Π½Ρ ΠΏΠΎΠΊΡΡΡΠ΅ΠΊ ΠΎΡΠ΄Π΅Π»ΡΠ΅ΡΡΡ ΠΎΡ ΡΠ΅Π·ΠΈΠ½Ρ ΠΈ ΠΈΡΠΏΠΎΠ»ΡΠ·ΡΠ΅ΡΡΡ Π² ΠΊΠ°ΡΠ΅ΡΡΠ²Π΅ Π°ΡΠΌΠΈΡΡΡΡΠ΅ΠΉ Π΄ΠΎΠ±Π°Π²ΠΊΠΈ ΠΊ Π±Π΅ΡΠΎΠ½Ρ ΠΏΡΠΈ ΡΡΡΠΎΠΈΡΠ΅Π»ΡΡΡΠ²Π΅ Π΄ΠΎΡΠΎΠ³ ΠΈΠ»ΠΈ Π² ΠΊΠ°ΡΠ΅ΡΡΠ²Π΅ ΡΡΡΡΡ Π΄Π»Ρ ΠΏΠΎΡΠ»Π΅Π΄ΡΡΡΠ΅ΠΉ ΠΏΠ΅ΡΠ΅ΠΏΠ»Π°Π²ΠΊΠΈ.
Π‘Π»Π΅Π΄ΡΠ΅Ρ ΠΎΡΠΌΠ΅ΡΠΈΡΡ, ΡΡΠΎ ΠΏΠ΅ΡΠ΅ΡΠ°Π±ΠΎΡΠΊΠ° ΡΠ΅Π·ΠΈΠ½Ρ Π»ΡΠ±ΡΠΌ ΠΈΠ· ΠΎΠΏΠΈΡΠ°Π½Π½ΡΡ ΡΠΏΠΎΡΠΎΠ±ΠΎΠ² ΡΠ²Π»ΡΠ΅ΡΡΡ Π±Π΅Π·ΠΎΡΡ ΠΎΠ΄Π½ΡΠΌ ΠΏΡΠΎΡΠ΅ΡΡΠΎΠΌ. Π ΠΈΡΠΎΠ³Π΅ ΠΏΠΎΠ»ΡΡΠ°Π΅ΡΡΡ Π²ΠΎΡΡΡΠ΅Π±ΠΎΠ²Π°Π½Π½Π°Ρ Π² ΠΏΡΠΎΠΌΡΡΠ»Π΅Π½Π½ΠΎΡΡΠΈ ΠΏΡΠΎΠ΄ΡΠΊΡΠΈΡ.
ΠΠΈΡΠΎΠ»ΠΈΠ· ΡΠΈΠ½
ΠΡΠΎΡΠ΅ΡΡ ΠΏΠ΅ΡΠ΅ΡΠ°Π±ΠΎΡΠΊΠΈ ΠΏΠΎΠΊΡΡΡΠ΅ΠΊ ΡΠ°ΠΊΠΈΠΌ ΠΎΠ±ΡΠ°Π·ΠΎΠΌ ΠΏΡΠΎΠΈΡΡ ΠΎΠ΄ΠΈΡ Π±Π΅Π· Π΄ΠΎΡΡΡΠΏΠ° Π²ΠΎΠ·Π΄ΡΡ Π°. ΠΠ· ΠΎΠ΄Π½ΠΎΠΉ ΡΠΎΠ½Π½Ρ ΠΏΠΎΠ»ΡΡΠ°Π΅ΡΡΡ ΠΏΡΠΈΠ±Π»ΠΈΠ·ΠΈΡΠ΅Π»ΡΠ½ΠΎ 500 ΠΊΠ³ ΡΠ³Π»Π΅Π²ΠΎΠ΄ΠΎΡΠΎΠ΄Π½ΠΎΠΉ ΠΆΠΈΠ΄ΠΊΠΎΡΡΠΈ, ΠΏΠΎ 200 ΠΊΠ³ Π³Π°Π·Π° ΠΈ ΡΠ΅Ρ Π½ΠΈΡΠ΅ΡΠΊΠΎΠ³ΠΎ ΡΠ³Π»Π΅ΡΠΎΠ΄Π°, Π° ΡΠ°ΠΊΠΆΠ΅ 100 ΠΊΠ³ ΠΌΠ΅ΡΠ°Π»Π»Π°. ΠΠ½ΠΎΠ³ΠΈΠ΅ Π»ΡΠ΄ΠΈ, Π·Π½Π°ΡΡΠΈΠ΅ Ρ ΠΈΠΌΠΈΡ, ΠΌΠΎΠ³ΡΡ ΠΎΠ·Π°Π΄Π°ΡΠΈΡΡΡΡ Π²ΠΏΠΎΠ»Π½Π΅ Π»ΠΎΠ³ΠΈΡΠ½ΡΠΌ Π²ΠΎΠΏΡΠΎΡΠΎΠΌ: ΠΊΡΠ΄Π° Π΄Π΅Π²Π°Π΅ΡΡΡ ΡΠ΅ΡΠ°, Π΅ΡΠ»ΠΈ Π² ΡΠΎΡΡΠ°Π²Π΅ ΠΏΡΠΈΡΡΡΡΡΠ²ΡΠ΅Ρ Π½Π΅ Π±ΠΎΠ»Π΅Π΅ 10% Π΄ΠΈΠΎΠΊΡΠΈΠ΄Π° ΠΊΡΠ΅ΠΌΠ½ΠΈΡ. ΠΡΠ΅ Π΄ΠΎΠ²ΠΎΠ»ΡΠ½ΠΎ ΠΏΡΠΎΡΡΠΎ β ΠΎΡΠ½ΠΎΠ²Π½Π°Ρ ΡΠ°ΡΡΡ ΠΏΡΠ΅Π²ΡΠ°ΡΠ°Π΅ΡΡΡ Π² ΡΠ΅ΡΠΎΠ²ΠΎΠ΄ΠΎΡΠΎΠ΄ (ΡΠΈΠ»ΡΠ½ΡΠΉ ΡΠ΄), ΡΠΎΠ΄Π΅ΡΠΆΠ°ΡΠΈΠ΅ΡΡ Π² ΠΏΠΈΡΠΎΠ»ΠΈΠ·Π½ΡΡ Π³Π°Π·Π°Ρ . ΠΠ· ΠΎΡΡΠ°Π²ΡΠ΅ΠΉΡΡ ΡΠ°ΡΡΠΈ ΠΏΠΎΠ»ΡΡΠ°Π΅ΡΡΡ ΡΠ΅ΡΠΎΡΠ³Π»Π΅ΡΠΎΠ΄ ΠΈ Π΄ΡΡΠ³ΠΈΠ΅ ΡΠΎΠ΅Π΄ΠΈΠ½Π΅Π½ΠΈΡ, ΠΊΠΎΡΠΎΡΡΠ΅ ΠΏΠ΅ΡΠ΅ΠΌΠ΅ΡΠ°ΡΡΡΡ Π² ΠΆΠΈΠ΄ΠΊΡΡ ΡΡΠ°ΠΊΡΠΈΡ.
Π ΠΊΠΎΠ½ΡΠ΅ ΠΎΡΡΠ°Π΅ΡΡΡ ΡΠ΅Ρ Π½ΠΈΡΠ΅ΡΠΊΠΈΠΉ ΡΠ³Π»Π΅ΡΠΎΠ΄, ΡΠΎΠ΄Π΅ΡΠΆΠ°ΡΠΈΠΉ ΡΡΠ»ΡΡΠΈΠ΄Ρ ΠΌΠ΅ΡΠ°Π»Π»ΠΎΠ². ΠΠΌΠ΅Π½Π½ΠΎ Π² ΡΡΠΎΠΌ ΠΎΡΡΠ°ΡΠΊΠ΅ ΠΈ Π½Π°Ρ ΠΎΠ΄ΠΈΡΡΡ Π΄ΠΈΠΎΠΊΡΠΈΠ΄ ΠΊΡΠ΅ΠΌΠ½ΠΈΡ.
ΠΠΎΠ»Π΅Π΅ ΡΠ»ΠΎΠΆΠ½Π°Ρ ΡΠΈΡΡΠ°ΡΠΈΡ ΡΠΎΡΡΠΎΠΈΡ Ρ ΠΏΠΎΠ»ΠΈΡ Π»ΠΎΡΠΈΠ΄Π°ΠΌΠΈ. ΠΠ΄Π½Π° ΠΈΡ ΡΠ°ΡΡΡ ΠΏΠ΅ΡΠ΅Ρ ΠΎΠ΄ΠΈΡ Π² ΠΎΡΡΠ°ΡΠΎΠΊ, Π° Π΄ΡΡΠ³Π°Ρ β ΠΎΠ±ΡΠ°Π·ΡΠ΅Ρ Π²Π΅ΡΠ΅ΡΡΠ²Π° ΠΏΠΎΠ΄ Π½Π°Π·Π²Π°Π½ΠΈΠ΅ΠΌ Π΄ΠΈΠΎΠΊΡΠΈΠ½Ρ, ΠΊΠΎΡΠΎΡΡΠ΅ ΠΌΠΎΠΆΠ½ΠΎ Π²ΡΡΡΠ΅ΡΠΈΡΡ Π²ΠΎ ΠΌΠ½ΠΎΠ³ΠΈΡ ΠΏΡΠΎΠ΄ΡΠΊΡΠ°Ρ .
Π‘Π»Π΅Π΄ΡΠ΅Ρ ΠΎΡΠΌΠ΅ΡΠΈΡΡ, ΡΡΠΎ Π½ΠΈ ΠΎΠ΄ΠΈΠ½ ΠΎΡΠ²Π΅ΡΡΡΠ²Π΅Π½Π½ΡΠΉ ΠΏΡΠΎΠΈΠ·Π²ΠΎΠ΄ΠΈΡΠ΅Π»Ρ Π½Π΅ ΡΡΠ°Π½Π΅Ρ ΠΈΡΠΏΠΎΠ»ΡΠ·ΠΎΠ²Π°ΡΡ ΡΠ΅Ρ Π½ΠΈΡΠ΅ΡΠΊΠΈΠΉ ΡΠ³Π»Π΅ΡΠΎΠ΄, Π½ΠΎ ΠΈ Π·Π°ΠΊΠΎΠΏΠ°ΡΡ Π΅Π³ΠΎ Π½Π΅Π»ΡΠ·Ρ. ΠΠΎΠ»ΡΡΠ°Π΅ΡΡΡ, ΡΡΠΎ ΠΏΡΠΈ ΡΠ°ΠΊΠΎΠΉ ΠΏΠ΅ΡΠ΅ΡΠ°Π±ΠΎΡΠΊΠ΅ ΠΏΠΎΡΠ²Π»ΡΠ΅ΡΡΡ ΠΌΠ½ΠΎΠΆΠ΅ΡΡΠ²ΠΎ Π½ΠΎΠ²ΡΡ ΠΏΡΠΎΠ±Π»Π΅ΠΌ. ΠΡ ΠΌΠΎΠΆΠ½ΠΎ ΡΠ΅ΡΠΈΡΡ, Π½ΠΎ Π½Π° ΡΡΠΎ ΡΡΠ΅Π±ΡΡΡΡΡ Π·Π½Π°ΡΠΈΡΠ΅Π»ΡΠ½ΡΠ΅ ΠΊΠ°ΠΏΠΈΡΠ°Π»ΠΎΠ²Π»ΠΎΠΆΠ΅Π½ΠΈΡ. Π‘Π»Π΅Π΄ΠΎΠ²Π°ΡΠ΅Π»ΡΠ½ΠΎ, ΠΏΠΎΡΠ²Π»ΡΠ΅ΡΡΡ Π²ΠΎΠΏΡΠΎΡ ΡΠ΅Π½ΡΠ°Π±Π΅Π»ΡΠ½ΠΎΡΡΠΈ ΡΡΠΎΠ³ΠΎ ΡΠΏΠΎΡΠΎΠ±Π° Π±Π΅Π· Π³ΠΎΡΡΠ΄Π°ΡΡΡΠ²Π΅Π½Π½ΠΎΠ³ΠΎ ΡΡΠ°ΡΡΠΈΡ.
ΠΠ·ΠΌΠ΅Π»ΡΡΠΈΡΠ΅Π»ΡΠ½ΠΎΠ΅ ΠΎΠ±ΠΎΡΡΠ΄ΠΎΠ²Π°Π½ΠΈΠ΅
Π‘ΠΏΠΎΡΠΎΠ± ΠΏΡΠΎΠΈΠ·Π²ΠΎΠ΄ΡΡΠ²Π° ΡΠ΅Π·ΠΈΠ½ΠΎΠ²ΠΎΠΉ ΠΊΡΠΎΡΠΊΠΈ ΠΈΠ· Π°Π²ΡΠΎΠΌΠΎΠ±ΠΈΠ»ΡΠ½ΡΡ
ΠΏΠΎΠΊΡΡΡΠ΅ΠΊ ΠΏΡΠ΅Π΄ΡΡΠ°Π²Π»ΡΠ΅Ρ ΡΠΎΠ±ΠΎΠΉ ΠΏΠΎΡΠ»Π΅Π΄ΠΎΠ²Π°ΡΠ΅Π»ΡΠ½ΠΎΠ΅ ΠΈΠ·ΠΌΠ΅Π»ΡΡΠ΅Π½ΠΈΠ΅ ΡΡΡΡΡ Π½Π° ΠΌΠ°Π»Π΅Π½ΡΠΊΠΈΠ΅ ΠΊΡΡΠΎΡΠΊΠΈ, ΠΊΠΎΡΠΎΡΡΠ΅ Π·Π°ΡΠ΅ΠΌ ΠΏΠ΅ΡΠ΅ΡΠΈΡΠ°ΡΡΡΡ Π² ΠΌΠ΅Π»ΠΊΠΎΠ΄ΠΈΡΠΏΠ΅ΡΡΠ½ΡΠ΅ ΡΡΠ°ΠΊΡΠΈΠΈ. Π‘Π΅Π³ΠΎΠ΄Π½Ρ ΠΏΡΠΎΠΈΠ·Π²ΠΎΠ΄ΠΈΡΠ΅Π»ΠΈ ΠΏΡΠ΅Π΄Π»Π°Π³Π°ΡΡ Π±ΠΎΠ»ΡΡΠΎΠΉ Π²ΡΠ±ΠΎΡ ΠΎΠ±ΠΎΡΡΠ΄ΠΎΠ²Π°Π½ΠΈΡ Π΄Π»Ρ ΡΠΎΠ·Π΄Π°Π½ΠΈΡ ΡΠ΅Π·ΠΈΠ½ΠΎΠ²ΠΎΠΉ ΠΊΡΠΎΡΠΊΠΈ, ΡΠ΅Π½Ρ Π·Π°Π²ΠΈΡΡΡ ΠΎΡ ΠΌΠΎΡΠ½ΠΎΡΡΠΈ ΠΈ ΠΏΡΠΎΠΈΠ·Π²ΠΎΠ΄ΠΈΡΠ΅Π»ΡΠ½ΠΎΡΡΠΈ.
ΠΠ΄Π½ΠΎΠ²Π°Π»ΡΠ½ΡΠΉ ΡΡΠ΅Π΄Π΅Ρ
ΠΡΠΈΠ½ΡΠΈΠΏ ΡΠ°Π±ΠΎΡΡ ΡΠ°ΠΊΠΎΠ³ΠΎ ΡΡΠ°Π½ΠΊΠ° Π΄Π»Ρ ΠΏΠ΅ΡΠ΅ΡΠ°Π±ΠΎΡΠΊΠΈ ΡΠΈΠ½ ΡΠΎΡΡΠΎΠΈΡ Π² ΡΠΎΠΌ, ΡΡΠΎ ΡΡΡΡΠ΅ ΠΈΠ·ΠΌΠ΅Π»ΡΡΠ°Π΅ΡΡΡ ΡΠΏΠ΅ΡΠΈΠ°Π»ΡΠ½ΡΠΌ ΡΠ΅ΠΆΡΡΠΈΠΌ Π²Π°Π»ΠΎΠΌ, ΠΊΠΎΡΠΎΡΡΠΉ ΡΠ°Π±ΠΎΡΠ°Π΅Ρ Π½Π° Π½ΠΈΠ·ΠΊΠΈΡ ΠΎΠ±ΠΎΡΠΎΡΠ°Ρ . Π£ΡΡΡΠΎΠΉΡΡΠ²ΠΎ ΠΏΠΎΡΠ»Π΅Π΄ΠΎΠ²Π°ΡΠ΅Π»ΡΠ½ΠΎ ΠΏΠΎΠ΄Π½ΠΈΠΌΠ°Π΅ΡΡΡ ΠΈ ΠΎΠΏΡΡΠΊΠ°Π΅ΡΡΡ. ΠΠ³ΠΎ ΡΠ°Π±ΠΎΡΠ° Π²ΡΠ³Π»ΡΠ΄ΠΈΡ ΡΠ°ΠΊΠΈΠΌ ΠΎΠ±ΡΠ°Π·ΠΎΠΌ:
- Π¨ΠΈΠ½Ρ ΠΏΠΎΠ΄Π°ΡΡΡΡ Π² ΠΊΠ°ΠΌΠ΅ΡΡ ΡΡΡΡΠΎΠΉΡΡΠ²Π° Π·Π°Π³ΡΡΠ·ΠΊΠΈ, Π° Π·Π°ΡΠ΅ΠΌ Ρ ΠΏΠΎΠΌΠΎΡΡΡ Π³ΠΈΠ΄ΡΠ°Π²Π»ΠΈΡΠ΅ΡΠΊΠΎΠ³ΠΎ ΠΏΡΠ΅ΡΡΠ° ΠΏΠΎΠΏΠ°Π΄Π°ΡΡ Π½Π° Π²ΡΠ°ΡΠ°ΡΡΠΈΠ΅ΡΡ Π½ΠΎΠΆΠΈ.
- ΠΡΠ΅ΡΡ Π΄Π²ΠΈΠΆΠ΅ΡΡΡ ΡΠ²Π΅ΡΡ Ρ Π²Π½ΠΈΠ·, Π·Π°ΡΠ΅ΠΌ ΠΏΠΎ Π΄ΠΎΡΡΠΈΠΆΠ΅Π½ΠΈΠΈ ΠΌΠ°ΠΊΡΠΈΠΌΠ°Π»ΡΠ½ΠΎΠ³ΠΎ Π΄Π°Π²Π»Π΅Π½ΠΈΡ Π½Π° Π²Π°Π» Π²ΠΎΠ·Π²ΡΠ°ΡΠ°Π΅ΡΡΡ Π² ΠΈΡΡ ΠΎΠ΄Π½ΠΎΠ΅ ΠΏΠΎΠ»ΠΎΠΆΠ΅Π½ΠΈΠ΅.
- ΠΠ·ΠΌΠ΅Π»ΡΡΠ΅Π½Π½ΡΠΉ ΠΌΠ°ΡΠ΅ΡΠΈΠ°Π» ΠΏΡΠΎΠ΄Π°Π²Π»ΠΈΠ²Π°Π΅ΡΡΡ ΡΠ΅ΡΠ΅Π· ΡΠΏΠ΅ΡΠΈΠ°Π»ΡΠ½ΠΎΠ΅ ΡΠΈΡΠΎ, ΠΊΠΎΡΠΎΡΠΎΠ΅ ΡΠ°Π·ΠΌΠ΅ΡΠ°Π΅ΡΡΡ ΠΏΠΎΠ΄ Π²Π°Π»ΠΎΠΌ.
Π‘Π»Π΅Π΄ΡΠ΅Ρ ΠΎΡΠΌΠ΅ΡΠΈΡΡ, ΡΡΠΎ Π½Π° ΡΡΠΎΠΌ ΡΡΡΡΠΎΠΉΡΡΠ²Π΅ Π½ΠΎΠΆΠΈ Π΄Π΅Π»Π°ΡΡΡΡ Π΄Π²ΡΡΡΠΎΡΠΎΠ½Π½ΠΈΠΌΠΈ, ΡΡΠΎΠ±Ρ ΠΏΠΎΡΠ»Π΅ ΠΈΠ·Π½ΠΎΡΠ° ΠΎΠ΄Π½ΠΎΠΉ Π³ΡΠ°Π½ΠΈ, ΠΈΡ ΠΌΠΎΠΆΠ½ΠΎ Π±ΡΠ»ΠΎ ΠΏΠ΅ΡΠ΅Π²Π΅ΡΠ½ΡΡΡ ΠΈ ΠΈΡΠΏΠΎΠ»ΡΠ·ΠΎΠ²Π°ΡΡ Π²ΡΠΎΡΠΈΡΠ½ΠΎ. ΠΡΠ° ΠΎΡΠΎΠ±Π΅Π½Π½ΠΎΡΡΡ ΡΠ²Π΅Π»ΠΈΡΠΈΠ²Π°Π΅Ρ ΡΡΠΎΠΊ ΡΠ»ΡΠΆΠ±Ρ ΡΡΠ΅Π΄Π΅ΡΠ°. ΠΠΎΠΆΠ½ΠΎ Π²ΡΠ΄Π΅Π»ΠΈΡΡ ΡΡΠ΄ ΠΏΡΠ΅ΠΈΠΌΡΡΠ΅ΡΡΠ² ΠΈΡΠΏΠΎΠ»ΡΠ·ΠΎΠ²Π°Π½ΠΈΡ ΡΡΠΎΠ³ΠΎ ΡΡΡΡΠΎΠΉΡΡΠ²Π°:
- Π»Π΅Π³ΠΊΠ°Ρ ΡΠΊΡΠΏΠ»ΡΠ°ΡΠ°ΡΠΈΡ;
- Π²ΠΎΠ·ΠΌΠΎΠΆΠ½ΠΎΡΡΡ ΠΏΠ΅ΡΠ΅ΡΠ°Π±Π°ΡΡΠ²Π°ΡΡ ΠΏΠΎΠΊΡΡΡΠΊΠΈ Π±ΠΎΠ»ΡΡΠΎΠΉ ΡΠΎΠ»ΡΠΈΠ½Ρ;
- ΠΏΡΠΎΡΡΠΎΡΠ° ΠΊΠΎΠ½ΡΡΡΡΠΊΡΠΈΠΈ;
- Π²ΠΎΠ·ΠΌΠΎΠΆΠ½ΠΎΡΡΡ ΠΈΡΠΏΠΎΠ»ΡΠ·ΠΎΠ²Π°ΡΡ ΡΡΡΡΠΎΠΉΡΡΠ²ΠΎ ΠΊΠ°ΠΊ ΠΈΠ½Π΄ΠΈΠ²ΠΈΠ΄ΡΠ°Π»ΡΠ½ΠΎ, ΡΠ°ΠΊ ΠΈ Π²ΠΊΠ»ΡΡΠΈΠ² Π΅Π³ΠΎ Π² ΠΏΡΠΎΠΈΠ·Π²ΠΎΠ΄ΡΡΠ²Π΅Π½Π½ΡΡ Π»ΠΈΠ½ΠΈΡ.
ΠΠ²ΡΡ Π²Π°Π»ΡΠ½ΡΠΉ Π°Π³ΡΠ΅Π³Π°Ρ
Π’Π°ΠΊΠΎΠ΅ ΠΎΠ±ΠΎΡΡΠ΄ΠΎΠ²Π°Π½ΠΈΠ΅ Π΄Π»Ρ ΠΏΠ΅ΡΠ΅ΡΠ°Π±ΠΎΡΠΊΠΈ ΡΠ΅Π·ΠΈΠ½Ρ ΠΈΡΠΏΠΎΠ»ΡΠ·ΡΠ΅ΡΡΡ Π΄Π»Ρ ΠΈΠ·Π³ΠΎΡΠΎΠ²Π»Π΅Π½ΠΈΡ ΠΊΡΡΠΎΡΠΊΠΎΠ² ΡΠ°Π·ΠΌΠ΅ΡΠΎΠΌ Π½Π΅ Π±ΠΎΠ»ΡΡΠ΅, ΡΠ΅ΠΌ 5 Π½Π° 5 ΡΠΌ. ΠΡΠΎΠ±Π΅Π½Π½ΠΎΡΡΡΡ ΡΡΡΡΠΎΠΉΡΡΠ²Π° ΡΠ²Π»ΡΠ΅ΡΡΡ ΡΠΎ, ΡΡΠΎ ΠΎΠ½ΠΎ ΠΌΠΎΠΆΠ΅Ρ ΠΏΠ΅ΡΠ΅ΡΠ°Π±Π°ΡΡΠ²Π°ΡΡ ΡΠ΅Π·ΠΈΠ½Ρ ΠΊΠ°ΠΊ Ρ Π»Π΅Π³ΠΊΠΎΠ²ΡΡ , ΡΠ°ΠΊ ΠΈ Π³ΡΡΠ·ΠΎΠ²ΡΡ Π°Π²ΡΠΎΠΌΠΎΠ±ΠΈΠ»Π΅ΠΉ. ΠΡΠΈΠ½ΡΠΈΠΏ ΡΠ°Π±ΠΎΡΡ ΡΠΎΡΡΠΎΠΈΡ Π² ΡΠ»Π΅Π΄ΡΡΡΠ΅ΠΌ:
Π‘Π½Π°ΡΠ°Π»Π° ΠΏΠΎΠΊΡΡΡΠΊΠ° ΠΏΠΎΠ΄Π°Π΅ΡΡΡ Π² ΡΠΏΠ΅ΡΠΈΠ°Π»ΡΠ½ΡΡ ΠΊΠ°ΠΌΠ΅ΡΡ Π΄Π»Ρ ΠΏΡΠΈΠ΅ΠΌΠ° ΡΡΡΡΡ. ΠΠΊΠ½ΠΎ Π±ΠΎΠ»ΡΡΠΎΠ³ΠΎ ΡΠ°Π·ΠΌΠ΅ΡΠ° ΠΏΠΎΠ·Π²ΠΎΠ»ΡΠ΅Ρ Π·Π°Π³ΡΡΠ·ΠΈΡΡ ΡΠΈΠ½Ρ ΠΏΠΎΠ»Π½ΠΎΡΡΡΡ. ΠΠ΄ΠΈΠ½ΡΡΠ²Π΅Π½Π½ΠΎΠ΅ ΡΡΠ»ΠΎΠ²ΠΈΠ΅ β ΠΏΡΠ΅Π΄Π²Π°ΡΠΈΡΠ΅Π»ΡΠ½ΠΎ Π½ΡΠΆΠ½ΠΎ ΠΈΠ·Π²Π»Π΅ΡΡ ΠΊΠΎΡΠ΄.
- ΠΠ·ΠΌΠ΅Π»ΡΡΠΈΡΠ΅Π»ΡΠ½ΡΠ΅ Π²Π°Π»Ρ Π²ΡΠ°ΡΠ°ΡΡΡΡ ΠΏΡΠΎΡΠΈΠ²ΠΎΠΏΠΎΠ»ΠΎΠΆΠ½ΠΎ Π΄ΡΡΠ³ Π΄ΡΡΠ³Ρ. Π Π°Π·ΠΌΠ΅ΡΠ΅Π½Π½ΡΠ΅ Π½Π° ΡΠΎΡΠΎΡΠ°Ρ ΠΊΡΡΠΊΠΈ Π·Π°Ρ Π²Π°ΡΡΠ²Π°ΡΡ ΡΠ΅Π·ΠΈΠ½Ρ, ΡΠ°Π·ΡΡΠ²Π°Ρ Π΅Π΅ Π½Π° ΡΠ°ΡΡΠΈ.
- ΠΠ°ΡΠ΅ΠΌ ΠΈΠ·ΠΌΠ΅Π»ΡΡΠ΅Π½Π½ΡΠΉ ΠΌΠ°ΡΠ΅ΡΠΈΠ°Π» ΠΏΡΠΎΡΠ΅ΠΈΠ²Π°Π΅ΡΡΡ ΡΠ΅ΡΠ΅Π· ΡΠΈΡΠΎ, ΠΊΠΎΡΠΎΡΠΎΠ΅ ΠΏΡΠ΅Π΄ΡΡΠ°Π²Π»Π΅Π½ΠΎ Π² Π²ΠΈΠ΄Π΅ ΠΊΡΡΡΡΡΠ΅Π³ΠΎΡΡ Π±Π°ΡΠ°Π±Π°Π½Π°. Π§Π°ΡΡΠΈΡΡ Π±ΠΎΠ»ΡΡΠΎΠ³ΠΎ ΡΠ°Π·ΠΌΠ΅ΡΠ° Π°Π²ΡΠΎΠΌΠ°ΡΠΈΡΠ΅ΡΠΊΠΈ Π·Π°Π±ΡΠ°ΡΡΠ²Π°ΡΡΡΡ Π² ΠΊΠ°ΠΌΠ΅ΡΡ Π΄Π»Ρ ΠΏΠΎΠ²ΡΠΎΡΠ½ΠΎΠΉ ΡΠ΅Π·ΠΊΠΈ.
- ΠΠΎΡΠΎΠ²ΠΎΠ΅ ΡΡΡΡΠ΅ ΡΠΎΡΡΠΈΡΡΡΡΡΡ Π½Π° ΡΡΠ°ΠΊΡΠΈΠΈ, Π° Π·Π°ΡΠ΅ΠΌ ΠΏΠΎΠΏΠ°Π΄Π°Π΅Ρ Π½Π° ΡΡΠ°Π½ΡΠΏΠΎΡΡΠ΅ΡΠ½ΡΡ Π»Π΅Π½ΡΡ ΠΈ ΠΎΡΠΏΡΠ°Π²Π»ΡΠ΅ΡΡΡ Π½Π° ΡΠ°ΡΠΎΠ²ΠΊΡ.
ΠΡΠΏΠΎΠ»ΡΠ·ΠΎΠ²Π°Π½ΠΈΠ΅ Π΄Π²ΡΡ Π²Π°Π»ΡΠ½ΡΡ ΡΡΠ°Π½ΠΊΠΎΠ² ΠΏΡΠΈ ΠΈΠ·Π³ΠΎΡΠΎΠ²Π»Π΅Π½ΠΈΠΈ ΡΠ΅Π·ΠΈΠ½ΠΎΠ²ΠΎΠΉ ΠΊΡΠΎΡΠΊΠΈ ΠΈΠΌΠ΅Π΅Ρ ΡΡΠ΄ ΠΏΡΠ΅ΠΈΠΌΡΡΠ΅ΡΡΠ². ΠΠ΅ΠΊΠΎΡΠΎΡΡΠ΅ ΠΈΠ· Π½ΠΈΡ :
- Π²ΠΎΠ·ΠΌΠΎΠΆΠ½ΠΎΡΡΡ ΡΠ°Π±ΠΎΡΡ Ρ ΠΊΡΡΠΏΠ½ΠΎΠ³Π°Π±Π°ΡΠΈΡΠ½ΡΠΌ ΡΡΡΡΠ΅ΠΌ;
- ΠΎΡΡΡΡΡΡΠ²ΠΈΠ΅ Π½Π°Π΄ΠΎΠ±Π½ΠΎΡΡΠΈ ΠΏΠ΅ΡΠ΅ΡΠ°ΡΠΈΠ²Π°ΡΡ Π»Π΅Π·Π²ΠΈΡ Π½Π° Π½ΠΎΠΆΠ°Ρ ΠΏΡΠΈ ΠΏΠ΅ΡΠ΅ΡΡΡΠ°Π½ΠΎΠ²ΠΊΠ΅.
ΠΡΠΎΠΈΠ·Π²ΠΎΠ΄ΡΡΠ²Π΅Π½Π½Π°Ρ ΠΌΠΎΡΠ½ΠΎΡΡΡ ΡΡΡΡΠΎΠΉΡΡΠ²Π° Π½Π°ΠΏΡΡΠΌΡΡ Π·Π°Π²ΠΈΡΠΈΡ ΠΎΡ Π·Π°Π΄Π°Π½Π½ΡΡ
ΠΏΠ°ΡΠ°ΠΌΠ΅ΡΡΠΎΠ² ΠΊΠΎΠ½Π΅ΡΠ½ΠΎΠΉ ΠΏΡΠΎΠ΄ΡΠΊΡΠΈΠΈ. ΠΠ°ΠΏΡΠΈΠΌΠ΅Ρ, ΠΏΡΠΈ ΠΏΡΠΎΠΈΠ·Π²ΠΎΠ΄ΡΡΠ²Π΅ ΠΊΡΡΠΊΠΎΠ² ΡΠ°Π·ΠΌΠ΅ΡΠΎΠΌ 5 Π½Π° 5 ΡΠΌ ΠΌΠΎΡΠ½ΠΎΡΡΡ ΠΎΠ΄Π½ΠΎΠ³ΠΎ ΡΡΠ°Π½ΠΊΠ° ΡΠΎΡΡΠ°Π²Π»ΡΠ΅Ρ 2 ΡΠΎΠ½Π½Ρ Π² ΡΠ°Ρ ΠΈ Π±ΠΎΠ»Π΅Π΅, ΠΏΡΠΈ ΠΈΠ·ΠΌΠ΅Π»ΡΡΠ΅Π½ΠΈΠΈ Π΄ΠΎ ΠΌΠ΅Π½ΡΡΠΈΡ
ΡΠ°Π·ΠΌΠ΅ΡΠΎΠ² β Π΄ΠΎ 2 ΡΠΎΠ½Π½ Π² ΡΠ°Ρ.
ΠΠ΅ΡΡΠΎΠ½Π°Π», ΠΊΠΎΡΠΎΡΡΠΉ ΠΎΠ±ΡΠ»ΡΠΆΠΈΠ²Π°Π΅Ρ ΡΡΠ°Π½ΠΊΠΈ, Π½Π΅ΠΎΠ±ΡΠ·Π°ΡΠ΅Π»ΡΠ½ΠΎ Π΄ΠΎΠ»ΠΆΠ΅Π½ ΠΎΠ±Π»Π°Π΄Π°ΡΡ ΠΊΠ°ΠΊΠΈΠΌΠΈ-ΡΠΎ ΡΠΏΠ΅ΡΠΈΠ°Π»ΡΠ½ΡΠΌΠΈ Π½Π°Π²ΡΠΊΠ°ΠΌΠΈ. ΠΠ»Ρ ΡΠ°Π±ΠΎΡΡ Π½Π° ΡΡΠΎΠΌ ΡΡΡΡΠΎΠΉΡΡΠ²Π΅ Π½Π΅ΠΎΠ±Ρ ΠΎΠ΄ΠΈΠΌΠΎ Π΄Π²Π° ΡΠ°Π±ΠΎΡΠ½ΠΈΠΊΠ°: ΠΏΠ΅ΡΠ²ΡΠΉ Π·Π°Π³ΡΡΠΆΠ°Π΅Ρ ΡΡΡΡΠ΅, Π²ΡΠΎΡΠΎΠΉ β ΠΏΡΠΈΠ½ΠΈΠΌΠ°Π΅Ρ Π³ΠΎΡΠΎΠ²ΡΡ ΠΏΡΠΎΠ΄ΡΠΊΡΠΈΡ.
Π‘ΠΏΠ΅ΡΠΈΠ°Π»ΡΠ½ΡΠ΅ ΡΡΡΠ°Π½ΠΎΠ²ΠΊΠΈ
Π Π°Π±ΠΎΡΡ ΡΠ°ΠΊΠΈΡ ΠΈΠ·ΠΌΠ΅Π»ΡΡΠΈΡΠ΅Π»ΡΠ½ΡΡ Π°Π³ΡΠ΅Π³Π°ΡΠΎΠ² ΠΌΠΎΠΆΠ½ΠΎ ΡΠ°ΡΡΠΌΠΎΡΡΠ΅ΡΡ Π½Π° ΠΏΡΠΈΠΌΠ΅ΡΠ΅ ΡΡΡΡΠΎΠΉΡΡΠ²Π° ΠΎΡ ΠΊΠΎΠΌΠΏΠ°Π½ΠΈΠΈ Β«Π’Π΅Ρ Π½ΠΎΡΠ΅ΡΡΡΡΡΒ». Π£ΡΡΠ°Π½ΠΎΠ²ΠΊΠ° ΠΏΡΠ΅Π΄ΡΡΠ°Π²Π»Π΅Π½Π° Π² Π²ΠΈΠ΄Π΅ Π²ΡΠ°ΡΠ°ΡΡΠ΅ΠΉΡΡ ΠΊΠΎΡΠΎΠ½ΠΊΠΈ. ΠΠ° Π½Π΅ΠΉ ΡΠ°ΡΠΏΠΎΠ»ΠΎΠΆΠ΅Π½Ρ 25 Π½ΠΎΠΆΠ΅ΠΉ, ΠΊΠΎΡΠΎΡΡΠ΅ Π°Π²ΡΠΎΠΌΠ°ΡΠΈΡΠ΅ΡΠΊΠΈ ΠΏΠΎΠ΄Π²ΠΎΠ΄ΡΡΡΡ ΠΊ ΠΏΠΎΠΊΡΡΡΠΊΠ΅. ΠΠΎΡΠ»Π΅Π΄Π½ΡΡ Π·Π°ΠΆΠΈΠΌΠ°Π΅ΡΡΡ Π² ΡΠΏΠ΅ΡΠΈΠ°Π»ΡΠ½ΠΎΠΌ ΠΏΠ°ΡΡΠΎΠ½Π΅. ΠΡΠΎΡΠ΅ΡΡ ΠΏΠ΅ΡΠ΅ΡΠ°Π±ΠΎΡΠΊΠΈ ΡΠ»Π΅Π΄ΡΡΡΠΈΠΉ:
- Π‘Π½Π°ΡΠ°Π»Π° ΠΏΠΎΠΊΡΡΡΠΊΠ° ΠΏΠΎΠ΄Π°Π΅ΡΡΡ ΠΊ Π·Π°ΠΆΠΈΠΌΠ½ΠΎΠΌΡ Π±Π°ΡΠ°Π±Π°Π½Ρ.
- ΠΠ°ΡΠ΅ΠΌ Π΅Π΅ Π½ΡΠΆΠ½ΠΎ ΡΡΡΠ°Π½ΠΎΠ²ΠΈΡΡ ΠΈ Π·Π°ΡΠΈΠΊΡΠΈΡΠΎΠ²Π°ΡΡ. ΠΡΠΎ ΠΌΠΎΠΆΠ½ΠΎ ΡΠ΄Π΅Π»Π°ΡΡ ΠΊΠ°ΠΊ ΡΡΡΠ½ΡΠΌ, ΡΠ°ΠΊ ΠΈ ΠΌΠ΅Ρ Π°Π½ΠΈΡΠ΅ΡΠΊΠΈΠΌ ΡΠΏΠΎΡΠΎΠ±ΠΎΠΌ (ΠΏΡΠΈ ΠΏΠΎΠΌΠΎΡΠΈ ΠΏΠΎΠ΄ΡΠ΅ΠΌΠ½ΠΎΠ³ΠΎ ΠΌΠ΅Ρ Π°Π½ΠΈΠ·ΠΌΠ°).
- ΠΠΎΡΠ»Π΅ ΡΡΡΠ°Π½ΠΎΠ²ΠΊΠΈ ΡΠΈΠ½Ρ ΠΏΡΠΎΠ²ΠΎΠ΄ΠΈΡΡΡ Π²ΠΊΠ»ΡΡΠ΅Π½ΠΈΠ΅ ΠΏΡΠΈΠ±ΠΎΡΠ° ΠΈ Π½Π°ΡΠΈΠ½Π°Π΅ΡΡΡ Π²ΡΠ°ΡΠ΅Π½ΠΈΠ΅ Π±Π°ΡΠ°Π±Π°Π½Π°. Π‘ΠΈΡΡΠ΅ΠΌΠΎΠΉ ΠΏΡΠ΅Π΄ΡΡΠΌΠΎΡΡΠ΅Π½ΠΎ 3 ΡΠΊΠΎΡΠΎΡΡΠΈ ΡΠΎΡΠΎΡΠ°. ΠΡ Π²ΡΠ±ΠΎΡ Π·Π°Π²ΠΈΡΠΈΡ ΠΎΡ Π½Π°ΡΡΠΆΠ½ΠΎΠ³ΠΎ Π΄ΠΈΠ°ΠΌΠ΅ΡΡΠ° ΠΈΠ·Π΄Π΅Π»ΠΈΡ.
- ΠΠΎΡΠΎΠ½ΠΊΠ° Π½Π°ΡΠΈΠ½Π°Π΅Ρ ΠΏΡΠΈΠ±Π»ΠΈΠΆΠ°ΡΡΡΡ ΠΊ Π±Π°ΡΠ°Π±Π°Π½Ρ, Π²ΡΠ°ΡΠ°ΡΡΡ Π² ΠΎΠ±ΡΠ°ΡΠ½ΡΡ ΡΡΠΎΡΠΎΠ½Ρ ΠΎΡ Π½Π΅Π³ΠΎ. Π‘ΠΊΠΎΡΠΎΡΡΡ Π΅Π΅ Π΄Π²ΠΈΠΆΠ΅Π½ΠΈΡ Π·Π°Π΄Π°Π΅Ρ ΠΎΠ±ΡΠ»ΡΠΆΠΈΠ²Π°ΡΡΠΈΠΉ ΠΏΠ΅ΡΡΠΎΠ½Π°Π», ΠΎΠ½Π° Π²Π°ΡΡΠΈΡΡΠ΅ΡΡΡ Π² Π·Π°Π²ΠΈΡΠΈΠΌΠΎΡΡΠΈ ΠΎΡ ΡΡΠ΅Π±ΡΠ΅ΠΌΠΎΠΉ Π²Π΅Π»ΠΈΡΠΈΠ½Ρ Π³ΠΎΡΠΎΠ²ΠΎΠΉ ΠΏΡΠΎΠ΄ΡΠΊΡΠΈΠΈ: ΡΡΠΎΠ±Ρ ΠΏΠΎΠ»ΡΡΠΈΡΡ Π±ΠΎΠ»Π΅Π΅ ΠΌΠ΅Π»ΠΊΡΡ ΠΊΡΠΎΡΠΊΡ, Π½Π΅ΠΎΠ±Ρ ΠΎΠ΄ΠΈΠΌΠΎ Π·Π°Π΄Π°ΡΡ ΠΌΠΈΠ½ΠΈΠΌΠ°Π»ΡΠ½ΡΡ ΡΠΊΠΎΡΠΎΡΡΡ Π΄Π²ΠΈΠΆΠ΅Π½ΠΈΡ.
Π‘Π½ΡΡΠΈΠ΅ ΡΠ΅Π·ΠΈΠ½Ρ Ρ ΡΠΈΠ½Ρ Π½Π°ΡΠΈΠ½Π°Π΅ΡΡΡ ΠΎΡ Π²Π½Π΅ΡΠ½Π΅Π³ΠΎ ΡΠ»ΠΎΡ ΠΈ ΠΎΡΡΡΠ΅ΡΡΠ²Π»ΡΠ΅ΡΡΡ Π΄ΠΎ Π΄ΠΎΡΡΠΈΠΆΠ΅Π½ΠΈΡ ΠΊΠΎΡΠ΄Π°. ΠΡΠ»ΠΈ ΠΏΠΎΡΠ»Π΅Π΄Π½Π΅ΠΉ ΡΠΎΡΡΠΎΠΈΡ ΠΈΠ· ΡΠ΅ΠΊΡΡΠΈΠ»Ρ, Π΅Π³ΠΎ ΠΌΠΎΠΆΠ½ΠΎ ΠΈΠ·ΠΌΠ΅Π»ΡΡΠΈΡΡ Π²ΠΌΠ΅ΡΡΠ΅ Ρ ΡΠ΅Π·ΠΈΠ½ΠΎΠΉ. ΠΠ΅ΡΠ°Π»Π»ΠΈΡΠ΅ΡΠΊΠ°Ρ ΠΊΠΎΠ½ΡΡΡΡΠΊΡΠΈΡ ΡΠ²Π»ΡΠ΅ΡΡΡ ΠΎΠ³ΡΠ°Π½ΠΈΡΠ΅Π½ΠΈΠ΅ΠΌ. ΠΠΎ Π΄ΠΎΡΡΠΈΠΆΠ΅Π½ΠΈΠΈ ΡΡΠΎΠΉ ΡΠ΅ΡΡΡ Π·Π°ΠΏΡΠ΅ΡΠ°Π΅ΡΡΡ ΠΈΡΠΏΠΎΠ»ΡΠ·ΠΎΠ²Π°ΡΡ ΡΡΡΠ°Π½ΠΎΠ²ΠΊΡ. ΠΡΠΎΡ Π²ΠΈΠ΄ ΠΎΠ±ΠΎΡΡΠ΄ΠΎΠ²Π°Π½ΠΈΡ ΠΈΠΌΠ΅Π΅Ρ ΡΡΠ΄ ΠΏΡΠ΅ΠΈΠΌΡΡΠ΅ΡΡΠ²:
- ΡΠΏΠΎΡΠΎΠ±Π΅Π½ Π·Π°ΠΌΠ΅Π½ΠΈΡΡ ΡΠ΅Π»ΡΡ ΠΈΠ·ΠΌΠ΅Π»ΡΡΠΈΡΠ΅Π»ΡΠ½ΡΡ Π»ΠΈΠ½ΠΈΡ;
- ΠΈΠΌΠ΅Π΅Ρ ΠΊΠΎΠ½ΠΊΡΡΠ΅Π½ΡΠ½ΡΡ ΡΠ΅Π½Ρ;
- ΡΠ΄ΠΎΠ±Π½ΠΎ ΡΡΠ°Π½ΡΠΏΠΎΡΡΠΈΡΡΠ΅ΡΡΡ;
- Π±ΡΡΡΡΠΎ ΠΌΠΎΠ½ΡΠΈΡΡΠ΅ΡΡΡ;
- ΠΌΠΎΠΌΠ΅Π½ΡΠ°Π»ΡΠ½ΠΎ ΠΏΠΎΠ΄ΠΊΠ»ΡΡΠ°Π΅ΡΡΡ ΠΊ ΡΠ½Π΅ΡΠ³ΠΎΡΠ½Π°Π±ΠΆΠ΅Π½ΠΈΡ;
- ΠΏΠ΅ΡΠ΅ΡΠ°Π±Π°ΡΡΠ²Π°Π΅Ρ ΠΏΠΎΠΊΡΡΡΠΊΠΈ ΡΠ°Π·Π½ΡΡ ΡΠ°Π·ΠΌΠ΅ΡΠΎΠ²;
- ΠΈΠΌΠ΅Π΅Ρ ΠΌΠ°Π»ΡΠΉ ΡΡΠΎΠΊ ΠΎΠΊΡΠΏΠ°Π΅ΠΌΠΎΡΡΠΈ.
ΠΠ±ΡΠ»ΡΠΆΠΈΠ²Π°Π½ΠΈΠ΅ ΡΡΡΡΠΎΠΉΡΡΠ²Π° ΠΏΡΠΎΠΈΠ·Π²ΠΎΠ΄ΠΈΡΡΡ ΠΎΠ΄Π½ΠΈΠΌ ΡΠ΅Π»ΠΎΠ²Π΅ΠΊΠΎΠΌ. Π’Π΅Ρ Π½ΠΎΠ»ΠΎΠ³ΠΈΡ ΠΏΡΠΎΡΡΠ°, ΠΏΠΎΡΡΠΎΠΌΡ ΡΠ°Π±ΠΎΡΠ΅ΠΌΡ Π½Π΅ ΡΡΠ΅Π±ΡΠ΅ΡΡΡ Π΄ΠΎΠΏΠΎΠ»Π½ΠΈΡΠ΅Π»ΡΠ½ΡΡ Π½Π°Π²ΡΠΊΠΎΠ² ΠΈ ΠΎΠ±ΡΡΠ΅Π½ΠΈΡ. ΠΡΠΎΠΈΠ·Π²ΠΎΠ΄ΡΡΠ²Π΅Π½Π½Π°Ρ ΠΌΠΎΡΠ½ΠΎΡΡΡ ΡΡΡΡΠΎΠΉΡΡΠ²Π° ΡΠΎΡΡΠ°Π²Π»ΡΠ΅Ρ 34 ΡΡΡ. ΠΊΠ³ ΡΠΈΡΡΠΎΠΉ ΠΊΡΠΎΡΠΊΠΈ Π² ΠΌΠ΅ΡΡΡ.
ΠΠΎΠΌΠΏΠ»Π΅ΠΊΡΠ½ΡΠ΅ Π»ΠΈΠ½ΠΈΠΈ
ΠΠΎΠ΄ΠΎΠΉΡΠΈ ΠΊ Π²ΠΎΠΏΡΠΎΡΡ ΠΈΠ·ΠΌΠ΅Π»ΡΡΠ΅Π½ΠΈΡ ΠΏΠΎΠΊΡΡΡΠ΅ΠΊ ΠΌΠΎΠΆΠ½ΠΎ ΠΊΠΎΠΌΠΏΠ»Π΅ΠΊΡΠ½ΠΎ Ρ ΠΏΠΎΠΌΠΎΡΡΡ ΡΠΏΠ΅ΡΠΈΠ°Π»ΠΈΠ·ΠΈΡΠΎΠ²Π°Π½Π½ΡΡ
Π»ΠΈΠ½ΠΈΠΉ. ΠΠ½ΠΎΠΆΠ΅ΡΡΠ²ΠΎ ΠΏΡΠΎΠΈΠ·Π²ΠΎΠ΄ΠΈΡΠ΅Π»Π΅ΠΉ ΠΏΡΠ΅Π΄Π»Π°Π³Π°ΡΡ ΡΠ°Π·Π»ΠΈΡΠ½ΠΎΠ΅ ΠΎΠ±ΠΎΡΡΠ΄ΠΎΠ²Π°Π½ΠΈΠ΅, ΠΊΠΎΡΠΎΡΠΎΠ΅ ΠΏΡΠ°ΠΊΡΠΈΡΠ΅ΡΠΊΠΈ Π½Π΅ ΠΎΡΠ»ΠΈΡΠ°Π΅ΡΡΡ Π΄ΡΡΠ³ ΠΎΡ Π΄ΡΡΠ³Π°. ΠΠ°ΡΠ°ΡΡΡΡ ΠΈΡ
ΠΊΠΎΠΌΠΏΠ»Π΅ΠΊΡΠ°ΡΠΈΡ ΡΠ»Π΅Π΄ΡΡΡΠ°Ρ:
- ΠΏΡΠΈΡΠΏΠΎΡΠΎΠ±Π»Π΅Π½ΠΈΠ΅ Π΄Π»Ρ ΡΠ΄Π°Π»Π΅Π½ΠΈΡ Π±ΠΎΡΡΠΊΠΎΠ»ΡΡΠ°;
- ΡΠΏΠ΅ΡΠΈΠ°Π»ΡΠ½Π°Ρ Π³ΠΈΠ»ΡΠΎΡΠΈΠ½Π° Π΄Π»Ρ ΡΠ°Π·ΡΠ΅Π·Π°Π½ΠΈΡ ΡΠΈΠ½ Π½Π° Π»Π΅Π½ΡΡ;
- ΡΡΠ°Π½ΠΎΠΊ Π΄Π»Ρ Π²ΡΠ΄Π°Π²Π»ΠΈΠ²Π°Π½ΠΈΡ ΠΌΠ΅ΡΠ°Π»Π»ΠΈΡΠ΅ΡΠΊΠΎΠ³ΠΎ ΠΊΠΎΡΠ΄Π°;
- Π²Π°Π»ΡΡΡ Π΄Π»Ρ ΠΏΡΠΎΠΈΠ·Π²ΠΎΠ΄ΡΡΠ²Π° ΠΊΡΠΎΡΠΊΠΈ;
- ΠΌΠ°Π³Π½ΠΈΡΠ½ΡΠ΅ ΠΈ Π²ΠΎΠ·Π΄ΡΡΠ½ΡΠ΅ ΡΠ΅ΠΏΠ°ΡΠ°ΡΠΎΡΡ;
- Π²ΠΈΠ±ΡΠΎΡΠΈΡΠΎ.
Π’Π΅Ρ Π½ΠΎΠ»ΠΎΠ³ΠΈΡ ΠΏΠ΅ΡΠ΅ΡΠ°Π±ΠΎΡΠΊΠΈ ΡΠΈΠ½ Π·Π°ΠΊΠ»ΡΡΠ°Π΅ΡΡΡ Π² ΠΏΠΎΡΠ»Π΅Π΄ΠΎΠ²Π°ΡΠ΅Π»ΡΠ½ΠΎΠΌ Π²ΡΠΏΠΎΠ»Π½Π΅Π½ΠΈΠΈ ΡΡΡΡΠΎΠΉΡΡΠ²ΠΎΠΌ ΠΎΠΏΡΠ΅Π΄Π΅Π»Π΅Π½Π½ΡΡ Π΄Π΅ΠΉΡΡΠ²ΠΈΠΉ. ΠΠΎΡΡΠ°ΠΏΠ½ΡΠΉ ΠΏΡΠΎΡΠ΅ΡΡ:
- Π‘Π½Π°ΡΠ°Π»Π° ΠΏΠΎΠΊΡΡΡΠΊΠΈ ΡΠ°Π·Π΄Π΅Π»ΡΡΡΡΡ ΠΏΠΎ Π²Π΅ΡΡ ΠΈ Π΄ΠΈΠ°ΠΌΠ΅ΡΡΡ, Π·Π°ΡΠ΅ΠΌ ΠΎΡΠΈΡΠ°ΡΡΡΡ ΠΎΡ ΠΊΡΡΠΏΠ½ΡΡ Π·Π°Π³ΡΡΠ·Π½Π΅Π½ΠΈΠΉ.
- Π¨ΠΈΠ½Ρ Π·Π°ΠΆΠΈΠΌΠ°Π΅Ρ ΡΠΈΡΠΊΠ°ΠΌΠΈ, ΡΡΠΎΠ±Ρ ΠΎΡΠ΄Π΅Π»ΠΈΡΡ ΠΎΡ ΡΠ΅Π·ΠΈΠ½Ρ Π±ΠΎΡΡΠΊΠΎΠ»ΡΡΠΎ.
- ΠΠΎΡΠ»Π΅ ΡΡΠΎΠ³ΠΎ ΠΏΡΠΎΠΈΡΡ ΠΎΠ΄ΠΈΡ Π½Π°ΡΠ΅Π·ΠΊΠ° Π»Π΅Π½Ρ ΡΠΈΡΠΈΠ½ΠΎΠΉ ΠΏΡΠΈΠΌΠ΅ΡΠ½ΠΎ 4 ΡΠΌ.
- ΠΠ°Π»Π΅Π΅ ΠΏΠΎΠ»ΠΎΡΡ ΡΠ°Π·Π΄Π΅Π»ΡΡΡΡΡ Π½Π° Π·Π°Π³ΠΎΡΠΎΠ²ΠΊΠΈ.
- ΠΠΎΡΠ»Π΅Π΄Π½ΠΈΠ΅ ΠΈΠ·ΠΌΠ΅Π»ΡΡΠ°ΡΡΡΡ Π² ΠΊΡΠΎΡΠΊΡ, Π° Π·Π°ΡΠ΅ΠΌ ΠΏΠΎΠ΄Π°ΡΡΡΡ Π½Π° ΡΡΠ°Π½ΡΠΏΠΎΡΡΠ΅ΡΠ½ΡΡ Π»Π΅Π½ΡΡ.
- Π‘Π»Π΅Π΄ΡΡΡΠΈΠΌ ΡΠ°Π³ΠΎΠΌ ΡΠ²Π»ΡΠ΅ΡΡΡ ΠΎΡΠΈΡΡΠΊΠ° ΠΊΡΠΎΡΠΊΠΈ Π² ΡΠ΅ΠΏΠ°ΡΠ°ΡΠΎΡΠ°Ρ . Π‘ ΠΏΠΎΠΌΠΎΡΡΡ ΠΌΠ°Π³Π½ΠΈΡΠ½ΡΡ ΠΏΠΎΠ»Π΅ΠΉ, ΠΊΠΎΡΠΎΡΡΠ΅ ΡΠΎΠ·Π΄Π°ΡΡΡΡ ΡΠ°ΠΌΠΈΠΌ ΡΡΡΡΠΎΠΉΡΡΠ²ΠΎΠΌ, ΡΠ°ΡΡΠΈΡΡ ΠΌΠ΅ΡΠ°Π»Π»ΠΎΠΊΠΎΡΠ΄Π° ΠΎΡΠ΄Π΅Π»ΡΡΡΡΡ ΠΎΡ ΠΎΠ±ΡΠ΅ΠΉ ΠΌΠ°ΡΡΡ. Π Π²ΠΎΠ·Π΄ΡΡΠ½ΠΎΠΌ ΡΠ΅ΠΏΠ°ΡΠ°ΡΠΎΡΠ΅ Ρ ΠΏΠΎΠΌΠΎΡΡΡ Π²ΠΈΡ ΡΠ΅Π²ΡΡ ΠΏΠΎΡΠΎΠΊΠΎΠ² ΠΎΠΊΠΎΠ½ΡΠ°ΡΠ΅Π»ΡΠ½ΠΎ ΠΎΡΠ΄Π΅Π»ΡΡΡΡΡ ΠΏΠΎΡΡΠΎΡΠΎΠ½Π½ΠΈΠ΅ ΠΏΡΠΈΠΌΠ΅ΡΠΈ ΠΎΡ ΡΠ΅Π·ΠΈΠ½Ρ.
ΠΠΎΡΠ»Π΅ ΠΎΠ±ΡΠ°Π±ΠΎΡΠΊΠΈ Π² ΡΠ΅ΠΏΠ°ΡΠ°ΡΠΈΠΎΠ½Π½ΡΡ ΠΊΠ°ΠΌΠ΅ΡΠ°Ρ ΠΊΡΠΎΡΠΊΠ° ΡΠΎΡΡΠΈΡΡΠ΅ΡΡΡ ΠΏΠΎ ΡΠ°Π·ΠΌΠ΅ΡΠ°ΠΌ. ΠΠΎΡΠΎΠ²ΡΡ ΠΏΡΠΎΠ΄ΡΠΊΡΠΈΡ ΡΠΏΠ°ΠΊΠΎΠ²ΡΠ²Π°ΡΡ, Π° Π·Π°ΡΠ΅ΠΌ ΠΎΡΠΏΡΠ°Π²Π»ΡΡΡ Π½Π° ΡΠ΅Π°Π»ΠΈΠ·Π°ΡΠΈΡ. Π‘Π»ΠΈΡΠΊΠΎΠΌ ΠΊΡΡΠΏΠ½ΡΠ΅ ΡΠ°ΡΡΠΈ Π²ΠΎΠ·Π²ΡΠ°ΡΠ°ΡΡ Π½Π° ΡΡΠ°Π½ΡΠΏΠΎΡΡΠ΅Ρ, Π° Π·Π°ΡΠ΅ΠΌ ΠΈΠ·ΠΌΠ΅Π»ΡΡΠ°ΡΡ ΠΏΠΎΠ²ΡΠΎΡΠ½ΠΎ. Π’Π°ΠΊΠ°Ρ Π»ΠΈΠ½ΠΈΡ ΠΌΠΎΠΆΠ΅Ρ ΠΏΡΠΎΠΈΠ·Π²ΠΎΠ΄ΠΈΡΡ Π½Π΅ ΠΌΠ΅Π½Π΅Π΅ 500 ΠΊΠ³ ΠΏΡΠΎΠ΄ΡΠΊΡΠΈΠΈ Π² ΡΠ°Ρ. ΠΠ»Ρ ΠΎΠ±ΡΠ»ΡΠΆΠΈΠ²Π°Π½ΠΈΡ ΠΎΠ±ΠΎΡΡΠ΄ΠΎΠ²Π°Π½ΠΈΡ Π½ΡΠΆΠ½ΠΎ 2β3 ΡΠ΅Π»ΠΎΠ²Π΅ΠΊΠ°, ΠΏΡΠΈ ΡΡΠΎΠΌ ΡΠΏΠ΅ΡΠΈΠ°Π»ΡΠ½ΡΡ Π½Π°Π²ΡΠΊΠΎΠ² Π½Π΅ ΡΡΠ΅Π±ΡΠ΅ΡΡΡ.
ΠΡΠΏΠΎΠ»ΡΠ·ΠΎΠ²Π°Π½ΠΈΠ΅ ΠΌΠΈΠ½ΠΈ-Π·Π°Π²ΠΎΠ΄ΠΎΠ²
ΠΠΏΡΠΈΠΌΠ°Π»ΡΠ½ΡΠΉ Π²Π°ΡΠΈΠ°Π½Ρ Π΄Π»Ρ ΡΠ΅Ρ
, ΠΊΡΠΎ ΠΏΠ»Π°Π½ΠΈΡΡΠ΅Ρ Π² Π±ΠΎΠ»ΡΡΠΈΡ
ΠΌΠ°ΡΡΡΠ°Π±Π°Ρ
ΠΏΠ΅ΡΠ΅ΡΠ°Π±Π°ΡΡΠ²Π°ΡΡ ΡΡΡΡΠ΅ β ΠΏΡΠΈΠΎΠ±ΡΠ΅ΡΠ΅Π½ΠΈΠ΅ ΠΌΠΈΠ½ΠΈ-Π·Π°Π²ΠΎΠ΄Π° Π² ΠΊΠ°ΡΠ΅ΡΡΠ²Π΅ ΠΎΠ±ΠΎΡΡΠ΄ΠΎΠ²Π°Π½ΠΈΡ Π΄Π»Ρ ΡΡΠΈΠ»ΠΈΠ·Π°ΡΠΈΠΈ ΡΠΈΠ½. Π’Π°ΠΊΠΎΠ΅ ΠΏΡΠΎΠΈΠ·Π²ΠΎΠ΄ΡΡΠ²ΠΎ Π±ΡΠ΄Π΅Ρ ΡΠΏΠΎΡΠΎΠ±ΡΡΠ²ΠΎΠ²Π°ΡΡ Π½Π΅ ΡΠΎΠ»ΡΠΊΠΎ Π»ΠΈΡΠ½ΠΎΠΌΡ ΡΠΊΠΎΠ½ΠΎΠΌΠΈΡΠ΅ΡΠΊΠΎΠΌΡ ΡΡΡΠ΅ΠΊΡΡ, Π½ΠΎ ΠΈ ΠΎΠ±ΡΠ΅ΡΡΠ²Π΅Π½Π½ΠΎΠΌΡ. ΠΠΎΡΠ»Π΅Π΄Π½ΠΈΠΉ ΠΎΠ±ΡΡΠ»ΠΎΠ²Π»Π΅Π½ ΡΠ΅ΠΌ, ΡΡΠΎ Π±ΡΠ΄ΡΡ ΡΠΎΠ·Π΄Π°Π½Ρ ΡΠ°Π±ΠΎΡΠΈΠ΅ ΠΌΠ΅ΡΡΠ°, ΡΠ΅ΠΌ ΡΠ°ΠΌΡΠΌ ΠΏΡΠΎΠΈΠ·ΠΎΠΉΠ΄Π΅Ρ ΡΠ½ΠΈΠΆΠ΅Π½ΠΈΠ΅ ΡΠΎΡΠΈΠ°Π»ΡΠ½ΠΎΠΉ Π½Π°ΠΏΡΡΠΆΠ΅Π½Π½ΠΎΡΡΠΈ. ΠΡΠΏΠΎΠ»ΡΠ·ΠΎΠ²Π°Π½ΠΈΠ΅ ΡΠ°ΠΊΠΎΠ³ΠΎ ΠΎΠ±ΠΎΡΡΠ΄ΠΎΠ²Π°Π½ΠΈΡ ΠΈΠΌΠ΅Π΅Ρ ΡΡΠ΄ ΠΏΡΠ΅ΠΈΠΌΡΡΠ΅ΡΡΠ²:
- ΠΌΠ°Π»ΡΠ΅ Π·Π°ΡΡΠ°ΡΡ ΡΠ½Π΅ΡΠ³ΠΈΠΈ, ΡΠ»Π΅Π΄ΠΎΠ²Π°ΡΠ΅Π»ΡΠ½ΠΎ ΡΠ½ΠΈΠΆΠ°Π΅ΡΡΡ ΡΠ΅Π±Π΅ΡΡΠΎΠΈΠΌΠΎΡΡΡ Π³ΠΎΡΠΎΠ²ΠΎΠΉ ΠΏΡΠΎΠ΄ΡΠΊΡΠΈΠΈ;
- ΠΊΠΎΠΌΠΏΠ°ΠΊΡΠ½ΠΎΡΡΡ ΠΎΠ±ΠΎΡΡΠ΄ΠΎΠ²Π°Π½ΠΈΡ;
- ΡΠ΄ΠΎΠ±ΡΡΠ²ΠΎ Π² ΠΎΠ±ΡΠ»ΡΠΆΠΈΠ²Π°Π½ΠΈΠΈ;
- Π΄Π°ΠΆΠ΅ ΠΏΡΠΈ Π½Π°ΡΡΡΠΎΠΉΠΊΠ΅ ΠΏΡΠΎΠΈΠ·Π²ΠΎΠ΄ΡΡΠ²Π° Π² ΠΎΠ΄ΠΈΠ½ ΡΠΈΠΊΠ» Π² ΠΈΡΠΎΠ³Π΅ ΠΏΠΎΠ»ΡΡΠ°Π΅ΡΡΡ Π²ΡΡΠΎΠΊΠΎΠΊΠ°ΡΠ΅ΡΡΠ²Π΅Π½Π½ΡΠΉ ΠΏΡΠΎΠ΄ΡΠΊΡ.
ΠΠΎΠΌΠΏΠ°ΠΊΡΠ½ΡΠ΅ ΠΌΠΈΠ½ΠΈ-Π·Π°Π²ΠΎΠ΄Ρ ΠΌΠΎΠ³ΡΡ ΠΏΠ΅ΡΠ΅ΡΠ°Π±Π°ΡΡΠ²Π°ΡΡ Π΄ΠΎ 350 ΠΊΠ³ ΠΊΡΠΎΡΠΊΠΈ. ΠΡΠΎΠ΄ΡΠΊΡΠΈΡ, ΠΈΠ·Π³ΠΎΡΠΎΠ²Π»Π΅Π½Π½Π°Ρ ΡΠ°ΠΊΠΈΠΌ ΡΡΡΡΠΎΠΉΡΡΠ²ΠΎΠΌ, ΠΎΠ±Π»Π°Π΄Π°Π΅Ρ Π²ΡΡΠΎΠΊΠΈΠΌ ΠΊΠ°ΡΠ΅ΡΡΠ²ΠΎΠΌ, ΡΠ»Π΅Π΄ΠΎΠ²Π°ΡΠ΅Π»ΡΠ½ΠΎ, Π±ΠΎΠ»ΡΡΠ΅ΠΉ ΡΠ΅Π½Π½ΠΎΡΡΡΡ Π΄Π»Ρ ΠΊΠΎΠ½Π΅ΡΠ½ΠΎΠ³ΠΎ ΠΏΠΎΡΡΠ΅Π±ΠΈΡΠ΅Π»Ρ. Π Π°Π±ΠΎΡΠ° ΡΡΡΡΠΎΠΉΡΡΠ²Π° ΡΠΎΡΡΠΎΠΈΡ ΠΈΠ· ΡΠ»Π΅Π΄ΡΡΡΠΈΡ
ΡΡΠ°ΠΏΠΎΠ²:
- Π‘Π½Π°ΡΠ°Π»Π° ΡΠ°Π±ΠΎΡΠ½ΠΈΠΊΠΈ Π²ΠΈΠ·ΡΠ°Π»ΡΠ½ΠΎ ΠΎΡΠΌΠ°ΡΡΠΈΠ²Π°ΡΡ ΡΡΡΡΠ΅ Π½Π° Π½Π°Π»ΠΈΡΠΈΠ΅ ΠΏΡΠΈΠΌΠ΅ΡΠ΅ΠΉ, ΠΊΠΎΡΠΎΡΡΠ΅ ΡΠΏΠΎΡΠΎΠ±Π½Ρ Π²ΡΠ²Π΅ΡΡΠΈ ΡΡΡΠ°Π½ΠΎΠ²ΠΊΡ ΠΈΠ· ΡΡΡΠΎΡ.
- ΠΠ°ΡΠ΅ΠΌ ΠΏΠΎΠΊΡΡΡΠΊΠΈ Ρ Π»Π΅Π³ΠΊΠΎΠ²ΡΡ Π°Π²ΡΠΎΠΌΠΎΠ±ΠΈΠ»Π΅ΠΉ ΠΏΠΎΠΌΠ΅ΡΠ°ΡΡΡΡ Π² Π·Π°Π³ΡΡΠ·ΠΎΡΠ½ΡΡ ΠΊΠ°ΠΌΠ΅ΡΡ ΡΠ΅Π»ΠΈΠΊΠΎΠΌ, Π±ΠΎΠ»Π΅Π΅ ΠΊΡΡΠΏΠ½ΡΠ΅ β ΠΈΠ·ΠΌΠ΅Π»ΡΡΠ°ΡΡΡΡ ΡΡΡΠ½ΡΠΌΠΈ ΠΈΠ½ΡΡΡΡΠΌΠ΅Π½ΡΠ°ΠΌΠΈ.
- ΠΠΎΡΠ»Π΅ ΡΡΠΎΠ³ΠΎ ΡΠ΅Π·ΠΈΠ½Π° ΡΠΈΠ½ΠΊΡΠ΅ΡΡΡ Ρ ΠΏΠΎΠΌΠΎΡΡΡ ΡΡΠ΅Π΄Π΅ΡΠΎΠ² Π½Π° ΠΌΠ΅Π»ΠΊΠΈΠ΅ ΡΡΠ°ΠΊΡΠΈΠΈ. ΠΠ° ΡΡΠΎΠΉ ΠΆΠ΅ ΡΡΠ°Π΄ΠΈΠΈ ΡΡΡΡΠ΅ ΠΎΡΠΈΡΠ°Π΅ΡΡΡ ΠΎΡ ΠΏΡΠΈΠΌΠ΅ΡΠΈ ΠΌΠ΅ΡΠ°Π»Π»Π°.
- ΠΠΎ ΠΎΠΊΠΎΠ½ΡΠ°Π½ΠΈΠΈ ΠΏΡΠΎΡΠ΅Π΄ΡΡΡ ΠΌΠ°ΡΠ΅ΡΠΈΠ°Π» ΠΏΠΎΠ΄Π°Π΅ΡΡΡ Π² ΠΎΡΡΠ΅ΠΊ, Π³Π΄Π΅ Π²ΡΠ°ΡΠ°ΡΡΠΈΠ΅ΡΡ Π½ΠΎΠΆΠΈ ΠΈΠ·ΠΌΠ΅Π»ΡΡΠ°ΡΡ Π΅Π³ΠΎ Π΄ΠΎ ΡΡΠ΅Π±ΡΠ΅ΠΌΡΡ ΡΠ°Π·ΠΌΠ΅ΡΠΎΠ². ΠΠΏΠ΅ΡΠ°ΡΠΎΡ ΠΌΠΎΠΆΠ΅Ρ Π·Π°ΠΏΡΡΡΠΈΡΡ ΠΎΠΏΡΠΈΡ Π΄Π»Ρ ΠΎΡΠΈΡΡΠΊΠΈ ΡΠ΅Π·ΠΈΠ½Ρ ΠΎΡ ΠΌΠ΅ΡΠ°Π»Π»ΠΈΡΠ΅ΡΠΊΠΎΠ³ΠΎ ΠΊΠΎΡΠ΄Π°.
- ΠΠΎΡΠ»Π΅ ΡΡΠΎΠ³ΠΎ ΡΠ΅Π·ΠΈΠ½Π° ΠΏΠΎΡΡΡΠΏΠ°Π΅Ρ Π² ΡΠ΅ΠΏΠ°ΡΠ°ΡΠΎΡ, Π³Π΄Π΅ ΠΏΡΠΎΠΈΡΡ ΠΎΠ΄ΠΈΡ ΠΎΠΊΠΎΠ½ΡΠ°ΡΠ΅Π»ΡΠ½Π°Ρ ΠΎΡΠΈΡΡΠΊΠ°.
- ΠΠΎΡΠΎΠ²Π°Ρ ΠΏΡΠΎΠ΄ΡΠΊΡΠΈΡ ΠΏΡΠΎΠΏΡΡΠΊΠ°Π΅ΡΡΡ ΡΠ΅ΡΠ΅Π· Π²ΠΈΠ±ΡΠΎΡΠΈΡΠΎ, Π³Π΄Π΅ ΡΠΎΡΡΠΈΡΡΠ΅ΡΡΡ ΠΏΠΎ ΡΡΠ°ΠΊΡΠΈΡΠΌ.
ΠΠ±ΠΎΡΡΠ΄ΠΎΠ²Π°Π½ΠΈΠ΅ Π΄Π»Ρ ΠΏΠ΅ΡΠ΅ΡΠ°Π±ΠΎΡΠΊΠΈ ΠΏΠΎΠΊΡΡΡΠ΅ΠΊ β Π½Π°Ρ ΠΎΠ΄ΠΊΠ° Π΄Π»Ρ ΡΠ΅Ρ , ΠΊΡΠΎ ΠΆΠ΅Π»Π°Π΅Ρ Π·Π°Π½ΡΡΡΡΡ Π±ΠΈΠ·Π½Π΅ΡΠΎΠΌ ΠΏΠΎ ΠΏΠ΅ΡΠ΅ΡΠ°Π±ΠΎΡΠΊΠ΅ Π²ΡΠΎΡΠΈΡΠ½ΠΎΠ³ΠΎ ΡΡΡΡΡ. Π‘Π΅Π³ΠΎΠ΄Π½Ρ ΡΡΡΠ΅ΡΡΠ²ΡΠ΅Ρ ΠΌΠ½ΠΎΠΆΠ΅ΡΡΠ²ΠΎ ΡΠ°Π·Π»ΠΈΡΠ½ΡΡ ΡΡΠ°Π½ΠΊΠΎΠ² ΠΈ Π»ΠΈΠ½ΠΈΠΉ, ΠΊΠΎΡΠΎΡΡΠ΅ ΠΌΠΎΠΆΠ½ΠΎ ΠΏΡΠΈΠΎΠ±ΡΠ΅ΡΡΠΈ, ΠΎΠΏΠΈΡΠ°ΡΡΡ Π½Π° ΡΠΎΠ±ΡΡΠ²Π΅Π½Π½ΡΠ΅ ΠΏΡΠ΅Π΄ΠΏΠΎΡΡΠ΅Π½ΠΈΡ ΠΈ ΡΠΈΠ½Π°Π½ΡΠΎΠ²ΡΠ΅ Π²ΠΎΠ·ΠΌΠΎΠΆΠ½ΠΎΡΡΠΈ.
vtothod.ru
ΠΠ·Π½ΠΎΡΠ΅Π½Π½ΡΠ΅ Π°Π²ΡΠΎΠΌΠΎΠ±ΠΈΠ»ΡΠ½ΡΠ΅ ΡΠΈΠ½Ρ ΠΊΠ°ΠΊ ΡΠΎΠΏΠ»ΠΈΠ²ΠΎ – ΠΠ½Π΅ΡΠ³Π΅ΡΠΈΠΊΠ° ΠΈ ΠΏΡΠΎΠΌΡΡΠ»Π΅Π½Π½ΠΎΡΡΡ Π ΠΎΡΡΠΈΠΈ – β 2 (30) ΡΠ΅Π²ΡΠ°Π»Ρ 2003 Π³ΠΎΠ΄Π° – WWW.EPRUSSIA.RU
ΠΠ°Π·Π΅ΡΠ° “ΠΠ½Π΅ΡΠ³Π΅ΡΠΈΠΊΠ° ΠΈ ΠΏΡΠΎΠΌΡΡΠ»Π΅Π½Π½ΠΎΡΡΡ Π ΠΎΡΡΠΈΠΈ” | β 2 (30) ΡΠ΅Π²ΡΠ°Π»Ρ 2003 Π³ΠΎΠ΄Π°
ΠΡΠΎΡΠΈΡΠ½ΡΠ΅ ΡΠ½Π΅ΡΠ³Π΅ΡΠΈΡΠ΅ΡΠΊΠΈΠ΅ ΡΠ΅ΡΡΡΡΡ (ΠΠΠ ) – ΡΡΠΎ ΡΠ½Π΅ΡΠ³ΠΈΡ ΡΠ°Π·Π»ΠΈΡΠ½ΡΡ Π²ΠΈΠ΄ΠΎΠ², ΠΏΠΎΠΊΠΈΠ΄Π°ΡΡΠ°Ρ ΡΠ΅Ρ Π½ΠΎΠ»ΠΎΠ³ΠΈΡΠ΅ΡΠΊΠΈΠΉ ΠΏΡΠΎΡΠ΅ΡΡ ΠΈΠ»ΠΈ ΡΡΡΠ°Π½ΠΎΠ²ΠΊΡ, ΠΈΡΠΏΠΎΠ»ΡΠ·ΠΎΠ²Π°Π½ΠΈΠ΅ ΠΊΠΎΡΠΎΡΠΎΠΉ Π½Π΅ ΡΠ²Π»ΡΠ΅ΡΡΡ ΠΎΠ±ΡΠ·Π°ΡΠ΅Π»ΡΠ½ΡΠΌ Π΄Π»Ρ ΠΎΡΡΡΠ΅ΡΡΠ²Π»Π΅Π½ΠΈΡ ΠΎΡΠ½ΠΎΠ²Π½ΠΎΠ³ΠΎ ΡΠ΅Ρ Π½ΠΎΠ»ΠΎΠ³ΠΈΡΠ΅ΡΠΊΠΎΠ³ΠΎ ΠΏΡΠΎΡΠ΅ΡΡΠ°. ΠΠΊΠΎΠ½ΠΎΠΌΠΈΡΠ΅ΡΠΊΠΈ ΠΎΠ½Π° ΠΏΡΠ΅Π΄ΡΡΠ°Π²Π»ΡΠ΅Ρ ΡΠΎΠ±ΠΎΠΉ ΠΏΠΎΠ±ΠΎΡΠ½ΡΡ ΠΏΡΠΎΠ΄ΡΠΊΡΠΈΡ, ΠΊΠΎΡΠΎΡΠ°Ρ ΠΏΡΠΈ ΡΠΎΠΎΡΠ²Π΅ΡΡΡΠ²ΡΡΡΠ΅ΠΌ ΡΡΠΎΠ²Π½Π΅ ΡΠ°Π·Π²ΠΈΡΠΈΡ ΡΠ΅Ρ Π½ΠΈΠΊΠΈ ΠΌΠΎΠΆΠ΅Ρ Π±ΡΡΡ ΡΠ°ΡΡΠΈΡΠ½ΠΎ ΠΈΠ»ΠΈ ΠΏΠΎΠ»Π½ΠΎΡΡΡΡ ΠΈΡΠΏΠΎΠ»ΡΠ·ΠΎΠ²Π°Π½Π° Π΄Π»Ρ Π½ΡΠΆΠ΄ Π½ΠΎΠ²ΠΎΠΉ ΡΠ΅Ρ Π½ΠΎΠ»ΠΎΠ³ΠΈΠΈ ΠΈΠ»ΠΈ ΡΠ½Π΅ΡΠ³ΠΎΡΠ½Π°Π±ΠΆΠ΅Π½ΠΈΡ Π΄ΡΡΠ³ΠΈΡ Π°Π³ΡΠ΅Π³Π°ΡΠΎΠ² (ΠΏΡΠΎΡΠ΅ΡΡΠΎΠ²) Π½Π° ΡΠ°ΠΌΠΎΠΌ ΠΏΡΠ΅Π΄ΠΏΡΠΈΡΡΠΈΠΈ ΠΈΠ»ΠΈ Π·Π° Π΅Π³ΠΎ ΠΏΡΠ΅Π΄Π΅Π»Π°ΠΌΠΈ.
ΠΠΊΠΎΠ½ΠΎΠΌΠΈΠΊΠ° ΡΡΠ°Π»Π° Π±Ρ Π·Π½Π°ΡΠΈΡΠ΅Π»ΡΠ½ΠΎ ΠΌΠ΅Π½Π΅Π΅ ΡΠ½Π΅ΡΠ³ΠΎΠ΅ΠΌΠΊΠΎΠΉ ΠΈ ΠΌΠ΅Π½Π΅Π΅ Π·Π°Π³ΡΡΠ·Π½ΡΡΡΠ΅ΠΉ ΠΎΠΊΡΡΠΆΠ°ΡΡΡΡ ΡΡΠ΅Π΄Ρ Π·Π° ΡΡΠ΅Ρ Π²ΡΠΎΡΠΈΡΠ½ΠΎΠ³ΠΎ ΠΈΡΠΏΠΎΠ»ΡΠ·ΠΎΠ²Π°Π½ΠΈΡ ΠΎΡΡ ΠΎΠ΄ΠΎΠ². ΠΠΎΠ»ΡΡΠ°Ρ ΡΠ°ΡΡΡ ΠΈΡΠΏΠΎΠ»ΡΠ·ΡΠ΅ΠΌΡΡ ΡΠ΅Π³ΠΎΠ΄Π½Ρ ΠΌΠ°ΡΠ΅ΡΠΈΠ°Π»ΠΎΠ² Π²ΡΠ±ΡΠ°ΡΡΠ²Π°Π΅ΡΡΡ ΠΏΠΎΡΠ»Π΅ ΠΎΠ΄Π½ΠΎΡΠ°Π·ΠΎΠ²ΠΎΠ³ΠΎ ΠΏΡΠΈΠΌΠ΅Π½Π΅Π½ΠΈΡ. ΠΡΠΎ ΠΏΡΠΈΠΌΠ΅ΡΠ½ΠΎ 2/3 Π²ΡΠ΅Π³ΠΎ Π°Π»ΡΠΌΠΈΠ½ΠΈΡ, 3/4 ΡΡΠ°Π»ΠΈ ΠΈ Π±ΡΠΌΠ°Π³ΠΈ ΠΈ Π΅ΡΠ΅ Π±ΠΎΠ»ΡΡΠ°Ρ ΡΠ°ΡΡΡ ΠΏΠ»Π°ΡΡΠΌΠ°ΡΡ. ΠΡΠ΅Π³ΠΎ Π»ΠΈΡΡ 5% ΡΠ½Π΅ΡΠ³ΠΈΠΈ, Π·Π°ΡΡΠ°ΡΠΈΠ²Π°Π΅ΠΌΠΎΠΉ Π½Π° Π΄ΠΎΠ±ΡΡΡ Π°Π»ΡΠΌΠΈΠ½ΠΈΡ ΠΈΠ· Π±ΠΎΠΊΡΠΈΡΠΎΠ², ΡΡΠ΅Π±ΡΠ΅ΡΡΡ Π΄Π»Ρ Π΅Π³ΠΎ ΡΠ΅Π³Π΅Π½Π΅ΡΠ°ΡΠΈΠΈ. ΠΠ»Ρ ΡΡΠ°Π»ΠΈ, ΠΈΠ·Π³ΠΎΡΠ°Π²Π»ΠΈΠ²Π°Π΅ΠΌΠΎΠΉ ΡΠΎΠ»ΡΠΊΠΎ ΠΈΠ· Π»ΠΎΠΌΠ°, ΡΠΊΠΎΠ½ΠΎΠΌΠΈΡ ΡΠ½Π΅ΡΠ³ΠΎΠ·Π°ΡΡΠ°Ρ ΡΠΎΡΡΠ°Π²Π»ΡΠ΅Ρ ΠΏΡΠΈΠΌΠ΅ΡΠ½ΠΎ 65%. ΠΡΠΎΠΈΠ·Π²ΠΎΠ΄ΡΡΠ²ΠΎ Π³Π°Π·Π΅ΡΠ½ΠΎΠΉ Π±ΡΠΌΠ°Π³ΠΈ ΠΈΠ· ΠΌΠ°ΠΊΡΠ»Π°ΡΡΡΡ ΡΡΠ΅Π±ΡΠ΅Ρ Π½Π° 25 – 60% ΠΌΠ΅Π½ΡΡΠ΅ ΡΠ½Π΅ΡΠ³ΠΈΠΈ, ΡΠ΅ΠΌ Π΅Π΅ ΠΈΠ·Π³ΠΎΡΠΎΠ²Π»Π΅Π½ΠΈΠ΅ ΠΈΠ· Π΄ΡΠ΅Π²Π΅ΡΠ½ΠΎΠΉ ΠΌΠ°ΡΡΡ. ΠΠΎΠ»ΡΡΠ΅Π½ΠΈΠ΅ ΡΡΠ΅ΠΊΠ»Π° ΠΈΠ· Π²ΡΠΎΡΡΡΡΡΡ ΡΠΊΠΎΠ½ΠΎΠΌΠΈΡ Π΄ΠΎ 33% ΡΠ½Π΅ΡΠ³ΠΈΠΈ, Π½Π΅ΠΎΠ±Ρ ΠΎΠ΄ΠΈΠΌΠΎΠΉ Π΄Π»Ρ Π΅Π³ΠΎ ΠΈΠ·Π³ΠΎΡΠΎΠ²Π»Π΅Π½ΠΈΡ ΠΈΠ· ΠΏΠ΅ΡΠ²ΠΈΡΠ½ΠΎΠ³ΠΎ ΡΡΡΡΡ.
Π Π½Π°ΡΡΠΎΡΡΠ΅Π΅ Π²ΡΠ΅ΠΌΡ ΠΎΡΠΎΠ±Π΅Π½Π½ΠΎ Π²Π΅Π»ΠΈΠΊΠΈ ΠΏΠΎΡΠ΅ΡΠΈ ΡΠ΅ΠΏΠ»ΠΎΡΡ Π½Π° ΡΠ»Π΅ΠΊΡΡΠΎΡΡΠ°Π½ΡΠΈΡΡ , Π² ΠΌΠ΅ΡΠ°Π»Π»ΡΡΠ³ΠΈΡΠ΅ΡΠΊΠΎΠΉ, Ρ ΠΈΠΌΠΈΡΠ΅ΡΠΊΠΎΠΉ, Π½Π΅ΡΡΠ΅Π΄ΠΎΠ±ΡΠ²Π°ΡΡΠ΅ΠΉ ΠΈ Π½Π΅ΡΡΠ΅ΠΏΠ΅ΡΠ΅ΡΠ°Π±Π°ΡΡΠ²Π°ΡΡΠ΅ΠΉ ΠΏΡΠΎΠΌΡΡΠ»Π΅Π½Π½ΠΎΡΡΠΈ, Π² ΡΠ΅Π»ΡΡΠΊΠΎΠΌ Ρ ΠΎΠ·ΡΠΉΡΡΠ²Π΅.
Π’Π΅ΠΏΠ»ΠΎΡΠ° ΡΠ½ΠΎΡΠΈΡΡΡ ΡΠ°ΠΊΠΆΠ΅ Ρ Π²Π΅Π½ΡΠΈΠ»ΡΡΠΈΠΎΠ½Π½ΡΠΌ Π²ΠΎΠ·Π΄ΡΡ ΠΎΠΌ, Ρ ΠΊΠ°Π½Π°Π»ΠΈΠ·Π°ΡΠΈΠΎΠ½Π½ΡΠΌΠΈ ΠΈ Π±ΡΡΠΎΠ²ΡΠΌΠΈ ΡΡΠΎΠΊΠ°ΠΌΠΈ. Π‘ΠΎΠ³Π»Π°ΡΠ½ΠΎ ΡΠ°ΡΡΠ΅ΡΠ°ΠΌ, ΠΈΠ· 1,7 ΠΌΠ»ΡΠ΄. Ρ Ρ. Ρ., ΡΠ°ΡΡ ΠΎΠ΄ΡΠ΅ΠΌΠΎΠ³ΠΎ Π² ΡΡΡΠ°Π½Π΅ Π·Π° Π³ΠΎΠ΄, ΠΏΠΎΠ»Π΅Π·Π½ΠΎ ΠΈΡΠΏΠΎΠ»ΡΠ·ΡΠ΅ΡΡΡ ΠΏΡΠΈΠΌΠ΅ΡΠ½ΠΎ 700 ΠΌΠ»Π½. Ρ. Π£ΡΠΈΠ»ΠΈΠ·Π°ΡΠΈΡ ΠΠΠ ΠΏΠΎΠ·Π²ΠΎΠ»ΠΈΡ ΠΏΠΎΠ»ΡΡΠΈΡΡ Π±ΠΎΠ»ΡΡΡΡ ΡΠΊΠΎΠ½ΠΎΠΌΠΈΡ ΡΠΎΠΏΠ»ΠΈΠ²Π° ΠΈ ΡΡΡΠ΅ΡΡΠ²Π΅Π½Π½ΠΎ ΡΠΌΠ΅Π½ΡΡΠΈΡΡ ΠΊΠ°ΠΏΠΈΡΠ°Π»ΡΠ½ΡΠ΅ Π·Π°ΡΡΠ°ΡΡ Π½Π° ΡΠΎΠ·Π΄Π°Π½ΠΈΠ΅ ΡΠΎΠΎΡΠ²Π΅ΡΡΡΠ²ΡΡΡΠΈΡ ΡΠ½Π΅ΡΠ³ΠΎΡΠ½Π°Π±ΠΆΠ°ΡΡΠΈΡ ΡΡΡΠ°Π½ΠΎΠ²ΠΎΠΊ, ΡΠ°ΠΊ ΠΊΠ°ΠΊ ΠΏΡΠΈ ΠΎΠ΄ΠΈΠ½Π°ΠΊΠΎΠ²ΠΎΠΌ ΡΡΡΠ΅ΠΊΡΠ΅ Π·Π°ΡΡΠ°ΡΡ Π½Π° ΡΠ»ΡΡΡΠ΅Π½ΠΈΠ΅ ΠΈΡΠΏΠΎΠ»ΡΠ·ΠΎΠ²Π°Π½ΠΈΡ ΡΠ½Π΅ΡΠ³ΠΎΡΠ΅ΡΡΡΡΠΎΠ² Π² 1,5-2 ΡΠ°Π·Π° Π½ΠΈΠΆΠ΅ Π·Π°ΡΡΠ°Ρ Π½Π° Π΄ΠΎΠ±ΡΡΡ ΡΠΎΠΏΠ»ΠΈΠ²Π°. Π Π°ΡΠΈΠΎΠ½Π°Π»ΡΠ½ΠΎΠ΅ ΠΈ Π²ΠΎΠ·ΠΌΠΎΠΆΠ½ΠΎ Π±ΠΎΠ»Π΅Π΅ ΠΏΠΎΠ»Π½ΠΎΠ΅ ΠΈΡΠΏΠΎΠ»ΡΠ·ΠΎΠ²Π°Π½ΠΈΠ΅ Π²ΡΠΎΡΠΈΡΠ½ΡΡ ΡΠ½Π΅ΡΠ³ΠΎΡΠ΅ΡΡΡΡΠΎΠ² Π΄Π°Π΅Ρ Π±ΠΎΠ»ΡΡΡΡ ΡΠΊΠΎΠ½ΠΎΠΌΠΈΡ ΠΌΠ°ΡΠ΅ΡΠΈΠ°Π»ΡΠ½ΡΡ , Π΄Π΅Π½Π΅ΠΆΠ½ΡΡ ΠΈ ΡΡΡΠ΄ΠΎΠ²ΡΡ Π·Π°ΡΡΠ°Ρ, ΠΎΠ±Π΅ΡΠΏΠ΅ΡΠΈΠ²Π°Π΅Ρ ΡΠ½ΠΈΠΆΠ΅Π½ΠΈΠ΅ Π²ΡΠ±ΡΠΎΡΠΎΠ² Π²ΡΠ΅Π΄Π½ΡΡ Π²Π΅ΡΠ΅ΡΡΠ², Π² ΡΠΎΠΌ ΡΠΈΡΠ»Π΅ ΠΈ ΡΠ΅ΠΏΠ»ΠΎΠ²ΡΡ .
ΠΠΠ ΡΠ°Π·Π΄Π΅Π»ΡΡΡΡΡ Π½Π° ΡΡΠΈ ΠΎΡΠ½ΠΎΠ²Π½ΡΠ΅ Π³ΡΡΠΏΠΏΡ: ΠΈΠ·Π±ΡΡΠΎΡΠ½ΠΎΠ³ΠΎ Π΄Π°Π²Π»Π΅Π½ΠΈΡ, Π³ΠΎΡΡΡΠΈΠ΅ ΠΈ ΡΠ΅ΠΏΠ»ΠΎΠ²ΡΠ΅.
Π Π‘Π¨Π Π΅ΠΆΠ΅Π³ΠΎΠ΄Π½ΠΎ ΠΊΠΎΠ»ΠΈΡΠ΅ΡΡΠ²ΠΎ ΠΈΠ·Π½ΠΎΡΠ΅Π½Π½ΡΡ ΡΠΈΠ½ ΡΠΎΡΡΠ°Π²Π»ΡΠ΅Ρ Π±ΠΎΠ»Π΅Π΅ 230 ΠΌΠ»Π½. ΡΡ. (190 ΠΌΠ»Π½. – ΠΎΡ Π»Π΅Π³ΠΊΠΎΠ²ΡΡ ΠΈ 47 ΠΌΠ»Π½. – ΠΎΡ Π³ΡΡΠ·ΠΎΠ²ΡΡ Π°Π²ΡΠΎΠΌΠΎΠ±ΠΈΠ»Π΅ΠΉ), ΠΈΠ»ΠΈ 1,9 ΠΌΠ»Π½. Ρ, ΠΏΡΠΈΡΠ΅ΠΌ ΡΠΆΠ΅ Π½Π°ΠΊΠΎΠΏΠ»Π΅Π½ΠΎ ΠΎΠΊΠΎΠ»ΠΎ 2 ΠΌΠ»ΡΠ΄. ΡΡΠ°ΡΡΡ ΡΠΈΠ½. Π ΠΠ½Π³Π»ΠΈΠΈ Π²ΡΡ ΠΎΠ΄ ΠΈΠ·Π½ΠΎΡΠ΅Π½Π½ΡΡ ΡΠΈΠ½ ΡΠΎΡΡΠ°Π²Π»ΡΠ΅Ρ 30 ΠΌΠ»Π½. ΡΡ., ΠΈΠ»ΠΈ Π±ΠΎΠ»Π΅Π΅ 200 ΡΡΡ. Ρ., Π² ΠΡΠ°Π»ΠΈΠΈ – ΠΎΠΊΠΎΠ»ΠΎ 400 ΡΡΡ. Ρ. Π ΡΡΡΠ°Π½Π°Ρ Π‘ΠΠ ΡΠΊΠΎΠΏΠΈΠ»ΠΎΡΡ 50 ΠΌΠ»Π½. ΠΈΠ·Π½ΠΎΡΠ΅Π½Π½ΡΡ ΡΠΈΠ½.
ΠΠ΅ΡΠΎΠ΄ΠΎΠΌ ΡΡΠΈΠ»ΠΈΠ·Π°ΡΠΈΠΈ ΠΈΠ·Π½ΠΎΡΠ΅Π½Π½ΡΡ ΡΠΈΠ½ ΡΠ²Π»ΡΠ΅ΡΡΡ ΠΈΡΠΏΠΎΠ»ΡΠ·ΠΎΠ²Π°Π½ΠΈΠ΅ ΠΈΡ Π² ΠΊΠ°ΡΠ΅ΡΡΠ²Π΅ ΡΠΎΠΏΠ»ΠΈΠ²Π°. Π’Π΅ΠΏΠ»ΠΎΡΠ° ΡΠ³ΠΎΡΠ°Π½ΠΈΡ ΡΠ΅Π·ΠΈΠ½Ρ ΡΠΎΡΡΠ°Π²Π»ΡΠ΅Ρ 32 ΠΠΠΆ/Ρ, Ρ. Π΅. ΡΠΎΠΎΡΠ²Π΅ΡΡΡΠ²ΡΠ΅Ρ ΡΠ³Π»Ρ Π²ΡΡΠΎΠΊΠΎΠ³ΠΎ ΠΊΠ°ΡΠ΅ΡΡΠ²Π°. ΠΠ΅ΡΠ²ΠΎΠ½Π°ΡΠ°Π»ΡΠ½ΠΎ ΡΠ΅Ρ Π½ΠΎΠ»ΠΎΠ³ΠΈΡ ΡΠΆΠΈΠ³Π°Π½ΠΈΡ ΡΠΎΡΠ΅ΡΠ°Π»Π°ΡΡ Ρ ΡΠ΅ΡΠΈΠΊΠ»ΠΈΠ½Π³ΠΎΠΌ ΡΠ΅Π·ΠΈΠ½Ρ, ΡΠΆΠΈΠ³Π°Π»ΠΈΡΡ ΠΊΡΡΠΏΠ½ΡΠ΅ ΡΡΠ°ΠΊΡΠΈΠΈ Π΄ΡΠΎΠ±Π»Π΅Π½ΠΎΠΉ ΡΠ΅Π·ΠΈΠ½Ρ, ΠΊΠΎΡΠΎΡΡΠ΅ Π½Π΅ ΠΎΡΠ²Π΅ΡΠ°ΡΡ ΡΡΠ΅Π±ΠΎΠ²Π°Π½ΠΈΡΠΌ ΡΠ΅Π·ΠΈΠ½ΠΎΡΠ΅Ρ Π½ΠΈΡΠ΅ΡΠΊΠΎΠ³ΠΎ ΠΏΡΠΎΠΈΠ·Π²ΠΎΠ΄ΡΡΠ²Π°. Π€ΠΈΡΠΌΠ° Β«Waste Management IncΒ» ΡΠΎΠΎΡΡΠΆΠ°Π΅Ρ ΡΡΡΠ°Π½ΠΎΠ²ΠΊΠΈ ΠΏΠΎ Π΄ΡΠΎΠ±Π»Π΅Π½ΠΈΡ ΡΠΈΠ½ ΠΌΠΎΡΠ½ΠΎΡΡΡΡ 5 ΡΡΡ. Ρ Π² Π³ΠΎΠ΄ Π½Π° ΡΠΏΠ΅ΡΠΈΠ°Π»ΠΈΠ·ΠΈΡΠΎΠ²Π°Π½Π½ΡΡ ΡΠ²Π°Π»ΠΊΠ°Ρ Π² ΡΡΠ°ΡΠ°Ρ Π€Π»ΠΎΡΠΈΠ΄Π°, ΠΠΈΡΠΊΠΎΠ½ΡΠΈΠ½, ΠΠΈΠ½Π½Π΅ΡΠΎΡΠ°. Π Π³ΠΎΡΠΎΠ΄Π°Ρ ΠΠ°Π»Π»Π°ΡΠ΅, ΠΠΎΡΡΠ»Π΅Π½Π΄Π΅, Π₯ΡΡΡΡΠΎΠ½Π΅ ΠΈ ΠΡΠ»Π°Π½ΡΠ΅ ΡΠΎΠ»ΡΠΊΠΎ Π² 1988 Π³. ΡΡΠ° ΡΠΈΡΠΌΠ° ΠΏΠ΅ΡΠ΅ΡΠ°Π±ΠΎΡΠ°Π»Π° Π±ΠΎΠ»Π΅Π΅ 4,5 ΠΌΠ»Π½. ΡΠΈΠ½, ΠΏΠΎΡΡΠ°Π²Π»ΡΡ ΡΠ΅Π·ΠΈΠ½ΠΎΠ²ΡΡ ΠΊΡΠΎΡΠΊΡ Π² ΠΊΠ°ΡΠ΅ΡΡΠ²Π΅ ΡΠΎΠΏΠ»ΠΈΠ²Π° Π½Π° ΡΠ΅Π»Π»ΡΠ»ΠΎΠ·Π½ΠΎ-Π±ΡΠΌΠ°ΠΆΠ½ΡΠ΅ ΠΊΠΎΠΌΠ±ΠΈΠ½Π°ΡΡ ΠΈ ΡΠ΅ΠΌΠ΅Π½ΡΠ½ΡΠ΅ Π·Π°Π²ΠΎΠ΄Ρ.
Π Π΅Π·ΠΈΠ½ΠΎΠ²Π°Ρ ΠΊΡΠΎΡΠΊΠ° ΠΊΠ°ΠΊ ΡΠΎΠΏΠ»ΠΈΠ²Π½ΡΠΉ ΠΌΠ°ΡΠ΅ΡΠΈΠ°Π» ΠΈΡΠΏΠΎΠ»ΡΠ·ΡΠ΅ΡΡΡ Π² Π²ΠΈΠ΄Π΅ 10%-Π½ΠΎΠΉ Π΄ΠΎΠ±Π°Π²ΠΊΠΈ ΠΏΡΠΈ ΡΠΆΠΈΠ³Π°Π½ΠΈΠΈ ΡΠ³Π»Ρ. Π Π‘Π¨Π ΠΏΡΠΎΠ²ΠΎΠ΄ΠΈΡΡΡ ΡΠΊΡΠΏΠ΅ΡΠΈΠΌΠ΅Π½Ρ ΠΏΠΎ ΡΠΆΠΈΠ³Π°Π½ΠΈΡ ΡΠ΅Π·ΠΈΠ½Ρ ΠΊΡΡΠΏΠ½ΠΎΠ³ΠΎ Π΄ΡΠΎΠ±Π»Π΅Π½ΠΈΡ (Π΄ΠΎ 25 ΠΌΠΌ) Π² ΡΠΈΠΊΠ»ΠΎΠ½Π½ΡΡ ΡΠΎΠΏΠΊΠ°Ρ ΡΠ½Π΅ΡΠ³Π΅ΡΠΈΡΠ΅ΡΠΊΠΈΡ ΠΊΠΎΡΠ»ΠΎΠ². ΠΠΎΠ»Ρ ΡΠ΅Π·ΠΈΠ½Ρ ΡΠΎΡΡΠ°Π²Π»ΡΠ΅Ρ 2-3% ΠΎΡ ΠΌΠ°ΡΡΡ ΡΠ³ΠΎΠ»ΡΠ½ΠΎΠ³ΠΎ ΡΠΎΠΏΠ»ΠΈΠ²Π°. Π ΠΠ΅ΡΠΌΠ°Π½ΠΈΠΈ Π΅ΠΆΠ΅Π³ΠΎΠ΄Π½ΠΎ ΠΈΠ· 400 ΡΡΡ. Ρ ΠΈΠ·Π½ΠΎΡΠ΅Π½Π½ΡΡ ΡΠΈΠ½ ΡΠΆΠΈΠ³Π°Π΅ΡΡΡ Π² ΠΎΠ±ΠΆΠΈΠ³ΠΎΠ²ΡΡ ΠΏΠ΅ΡΠ°Ρ 170 ΡΡΡ. Ρ.
Π‘Π»ΠΎΠΆΠ½ΠΎΡΡΡ ΠΏΡΠΎΡΠ΅ΡΡΠ° Π΄ΡΠΎΠ±Π»Π΅Π½ΠΈΡ ΠΈΠ·Π½ΠΎΡΠ΅Π½Π½ΡΡ ΡΠΈΠ½ (ΠΎΡΠΎΠ±Π΅Π½Π½ΠΎ Ρ ΠΌΠ΅ΡΠ°Π»Π»ΠΎΠΊΠΎΡΠ΄ΠΎΠΌ) ΡΡΠΈΠΌΡΠ»ΠΈΡΠΎΠ²Π°Π»Π° ΡΠ°Π·Π²ΠΈΡΠΈΠ΅ ΡΠ΅Ρ Π½ΠΎΠ»ΠΎΠ³ΠΈΠΈ ΡΠΆΠΈΠ³Π°Π½ΠΈΡ ΡΠΈΠ½ Π² ΡΠ΅Π»ΡΠ½ΠΎΠΌ Π²ΠΈΠ΄Π΅. Π ΠΠ½Π³Π»ΠΈΠΈ ΡΠΈΡΠΌΠ° Β«Avon RubberΒ» Ρ 1973 Π³. ΡΠΊΡΠΏΠ»ΡΠ°ΡΠΈΡΡΠ΅Ρ ΠΏΠ΅ΡΠΈ Π΄Π»Ρ ΡΠΆΠΈΠ³Π°Π½ΠΈΡ ΡΠΈΠ½ Π² ΡΠ΅Π»ΡΠ½ΠΎΠΌ Π²ΠΈΠ΄Π΅, Ρ. Π΅. ΠΈΠΌΠ΅Π΅Ρ ΡΠΆΠ΅ ΠΏΠΎΡΡΠΈ 30-Π»Π΅ΡΠ½ΠΈΠΉ ΠΎΠΏΡΡ Π² ΡΡΠΎΠΉ ΠΎΠ±Π»Π°ΡΡΠΈ.
Π ΠΡΠ°Π»ΠΈΠΈ ΠΏΡΠΎΠ²Π΅Π΄Π΅Π½Ρ ΠΎΠΏΡΡΡ Π½Π° ΡΠΊΡΠΏΠ΅ΡΠΈΠΌΠ΅Π½ΡΠ°Π»ΡΠ½ΠΎΠΉ ΡΡΡΠ°Π½ΠΎΠ²ΠΊΠ΅ ΠΏΠΎ ΡΠΆΠΈΠ³Π°Π½ΠΈΡ ΡΠΈΠ½ Π² ΡΠ΅Π»ΡΠ½ΠΎΠΌ Π²ΠΈΠ΄Π΅. Π€ΠΈΡΠΌΠΎΠΉ Β«Del MonegoΒ» ΡΠΎΠΎΡΡΠΆΠ΅Π½Π° ΡΡΡΠ°Π½ΠΎΠ²ΠΊΠ° Ρ Π²ΡΠ°ΡΠ°ΡΡΠ΅ΠΉΡΡ ΠΏΠ΅ΡΡΡ, ΠΊΠΎΡΠΎΡΠ°Ρ ΠΏΠΎΠ·Π²ΠΎΠ»ΡΠ΅Ρ Π·Π°Π³ΡΡΠΆΠ°ΡΡ ΡΠΈΠ½Ρ Π΄ΠΈΠ°ΠΌΠ΅ΡΡΠΎΠΌ Π΄ΠΎ 120 ΡΠΌ ΠΈ ΠΌΠ°ΡΡΠΎΠΉ 70 ΠΊΠ³.
Π Π‘Π¨Π ΡΠ°Π·Π²ΠΈΠ²Π°Π΅ΡΡΡ ΡΡΡΠΎΠΈΡΠ΅Π»ΡΡΡΠ²ΠΎ ΡΠ»Π΅ΠΊΡΡΠΎΡΡΠ°Π½ΡΠΈΠΉ, ΠΈΡΠΏΠΎΠ»ΡΠ·ΡΡΡΠΈΡ Π² ΠΊΠ°ΡΠ΅ΡΡΠ²Π΅ ΡΠΎΠΏΠ»ΠΈΠ²Π° ΡΠΎΠ»ΡΠΊΠΎ Π°Π²ΡΠΎΠΌΠΎΠ±ΠΈΠ»ΡΠ½ΡΠ΅ ΡΠΈΠ½Ρ. Π€ΠΈΡΠΌΠ° Β«Oxford EnergyΒ» ΠΏΠΎΡΡΡΠΎΠΈΠ»Π° ΠΈ ΡΠΊΡΠΏΠ»ΡΠ°ΡΠΈΡΡΠ΅Ρ Π² Π³. ΠΠΎΠ΄Π΅ΡΡΠΎ ΡΠ»Π΅ΠΊΡΡΠΎΡΡΠ°Π½ΡΠΈΡ ΠΌΠΎΡΠ½ΠΎΡΡΡΡ 14 ΠΠΡ Π΄Π»Ρ ΡΠΆΠΈΠ³Π°Π½ΠΈΡ 50 ΡΡΡ. Ρ ΡΠΈΠ½ Π² ΡΠ΅Π»ΡΠ½ΠΎΠΌ Π²ΠΈΠ΄Π΅. ΠΠ° ΠΎΡΠ½ΠΎΠ²Π°Π½ΠΈΠΈ ΡΡΠΏΠ΅ΡΠ½ΠΎΠ³ΠΎ ΠΎΠΏΡΡΠ° ΡΠΆΠΈΠ³Π°Π½ΠΈΡ ΡΠΈΠ½ Π² Π‘Π¨Π ΠΏΠ»Π°Π½ΠΈΡΡΠ΅ΡΡΡ ΠΏΠΎΡΡΡΠΎΠΈΡΡ 12 ΡΠ°ΠΊΠΈΡ ΡΠ»Π΅ΠΊΡΡΠΎΡΡΠ°Π½ΡΠΈΠΉ.
Π ΠΠ΅Π»ΠΈΠΊΠΎΠ±ΡΠΈΡΠ°Π½ΠΈΠΈ ΡΠ°ΡΡΠΌΠ°ΡΡΠΈΠ²Π°Π΅ΡΡΡ Π²ΠΎΠΏΡΠΎΡ ΡΡΡΠΎΠΈΡΠ΅Π»ΡΡΡΠ²Π° ΡΠ»Π΅ΠΊΡΡΠΎΡΡΠ°Π½ΡΠΈΠΉ ΠΌΠΎΡΠ½ΠΎΡΡΡΡ 20-30 ΠΠΡ Π΄Π»Ρ ΡΠΆΠΈΠ³Π°Π½ΠΈΡ 12 ΠΌΠ»Π½. ΡΠΈΠ½ Π² Π³ΠΎΠ΄ ΠΌΠ°ΡΡΠΎΠΉ 90 ΡΡΡ. Ρ.
ΠΡΠΎΠ³ΡΠ΅ΡΡΠΈΠ²Π½ΠΎΡΡΡ Π½Π°ΠΏΡΠ°Π²Π»Π΅Π½ΠΈΡ ΡΠΆΠΈΠ³Π°Π½ΠΈΡ ΡΠΈΠ½ (ΠΊΠ°ΠΊ Π΄ΡΠΎΠ±Π»Π΅Π½ΡΡ , ΡΠ°ΠΊ ΠΈ Π² ΡΠ΅Π»ΡΠ½ΠΎΠΌ Π²ΠΈΠ΄Π΅) ΠΏΠΎΠ΄ΡΠ²Π΅ΡΠΆΠ΄Π°Π΅ΡΡΡ ΡΠ΅ΠΌ, ΡΡΠΎ, Π½Π°ΠΏΡΠΈΠΌΠ΅Ρ, Π² Π‘Π¨Π Π³ΠΎΡΡΠ΄Π°ΡΡΡΠ²ΠΎ ΡΡΠΈΠΌΡΠ»ΠΈΡΡΠ΅Ρ ΠΏΡΠΈΠΌΠ΅Π½Π΅Π½ΠΈΠ΅ ΡΡΠΎΠΉ ΡΠ΅Ρ Π½ΠΎΠ»ΠΎΠ³ΠΈΠΈ ΡΠΊΠΎΠ½ΠΎΠΌΠΈΡΠ΅ΡΠΊΠΈΠΌ ΠΏΠΎΠΎΡΠ΅ΡΠ΅Π½ΠΈΠ΅ΠΌ. Π’Π°ΠΊ, Π·Π° ΠΏΠ΅ΡΠ΅ΡΠ°Π±ΠΎΡΠΊΡ 1 Ρ ΠΈΠ·Π½ΠΎΡΠ΅Π½Π½ΡΡ ΡΠΈΠ½ ΠΏΠΎ Π΄ΠΎΠ³ΠΎΠ²ΠΎΡΡ Ρ Π³ΠΎΡΡΠ΄Π°ΡΡΡΠ²Π΅Π½Π½ΡΠΌΠΈ ΡΠ»ΡΠΆΠ±Π°ΠΌΠΈ ΡΠΈΡΠΌΠ΅, Π·Π°Π½ΠΈΠΌΠ°ΡΡΠ΅ΠΉΡΡ ΠΏΠ΅ΡΠ΅ΡΠ°Π±ΠΎΡΠΊΠΎΠΉ ΡΠΈΠ½, Π²ΡΠΏΠ»Π°ΡΠΈΠ²Π°Π΅ΡΡΡ 50 Π΄ΠΎΠ»Π». ΠΡΠΎΠΌΠ΅ ΡΠΎΠ³ΠΎ, ΡΠΈΡΠΌΠ° ΠΏΠΎΠ»ΡΡΠ°Π΅Ρ Π΄ΠΎΡ ΠΎΠ΄ ΠΎΡ ΠΏΡΠΎΠ΄Π°ΠΆΠΈ ΡΠ΅Π·ΠΈΠ½ΠΎΠ²ΠΎΠΉ ΠΌΠ°ΡΡΡ ΠΊΠ°ΠΊ ΡΠΎΠΏΠ»ΠΈΠ²Π° ΠΏΠΎΡΡΠ΅Π±ΠΈΡΠ΅Π»ΡΠΌ.
Π‘ΠΆΠΈΠ³Π°Π½ΠΈΠ΅ ΡΠΈΠ½ Π΄Π»Ρ ΠΏΡΠΎΠΈΠ·Π²ΠΎΠ΄ΡΡΠ²Π° ΡΠ»Π΅ΠΊΡΡΠΎΡΠ½Π΅ΡΠ³ΠΈΠΈ ΡΠ²Π»ΡΠ΅ΡΡΡ ΠΏΡΠΎΠ³ΡΠ΅ΡΡΠΈΠ²Π½ΡΠΌ Π½Π°ΠΏΡΠ°Π²Π»Π΅Π½ΠΈΠ΅ΠΌ, ΠΏΠΎΡΠΊΠΎΠ»ΡΠΊΡ Π·Π° ΡΡΠ΅Ρ ΡΡΠΈΠ»ΠΈΠ·Π°ΡΠΈΠΈ ΠΎΡΡ ΠΎΠ΄ΠΎΠ² ΠΏΠΎΡΠ²Π»ΡΠ΅ΡΡΡ Π²ΠΎΠ·ΠΌΠΎΠΆΠ½ΠΎΡΡΡ ΠΏΠΎΠ»ΡΡΠ°ΡΡ Π²ΡΡΠΎΠΊΠΎΠΊΠ°ΡΠ΅ΡΡΠ²Π΅Π½Π½ΡΡ ΡΠ½ΠΈΠ²Π΅ΡΡΠ°Π»ΡΠ½ΡΡ ΡΠ½Π΅ΡΠ³ΠΈΡ Π² Π²ΠΈΠ΄Π΅ ΡΠ»Π΅ΠΊΡΡΠΈΡΠ΅ΡΡΠ²Π°. ΠΠ΄Π½Π°ΠΊΠΎ Π΄Π»Ρ ΠΎΡΡΡΠ΅ΡΡΠ²Π»Π΅Π½ΠΈΡ ΡΡΠΎΠ³ΠΎ ΡΡΠ΅Π±ΡΠ΅ΡΡΡ ΠΎΠΏΡΠ΅Π΄Π΅Π»Π΅Π½Π½ΡΠΉ Π½Π°Π±ΠΎΡ ΡΠ΅Ρ Π½ΠΎΠ»ΠΎΠ³ΠΈΡΠ΅ΡΠΊΠΈΡ ΡΠ»Π΅ΠΌΠ΅Π½ΡΠΎΠ², ΠΎΠ±Π΅ΡΠΏΠ΅ΡΠΈΠ²Π°ΡΡΠΈΡ ΡΠΎΠ±Π»ΡΠ΄Π΅Π½ΠΈΠ΅ ΡΠ°Π½ΠΈΡΠ°ΡΠ½ΡΡ Π½ΠΎΡΠΌ ΠΏΠΎ Π²ΡΠ±ΡΠΎΡΠ°ΠΌ. ΠΡΠΎΠΏΠΈΡΠ΅Π»ΡΠ½ΡΠ΅ ΠΏΠ΅ΡΠΈ ΠΈΠ½Π΄ΠΈΠ²ΠΈΠ΄ΡΠ°Π»ΡΠ½ΡΡ Π΄ΠΎΠΌΠΎΠ² Π½Π΅ ΠΎΠ±Π΅ΡΠΏΠ΅ΡΠΈΠ²Π°ΡΡ ΡΠ°Π½ΠΈΡΠ°ΡΠ½ΡΡ Π½ΠΎΡΠΌ ΠΏΠΎ Π΄ΠΎΠΆΠΈΠ³Π°Π½ΠΈΡ ΡΠ»ΠΎΠΆΠ½ΡΡ ΡΠ³Π»Π΅Π²ΠΎΠ΄ΠΎΡΠΎΠ΄ΠΎΠ², Π½Π΅ ΡΠ»Π°Π²Π»ΠΈΠ²Π°ΡΡ ΡΠ°ΠΆΡ ΠΈ Π² ΡΠ΅Π·ΡΠ»ΡΡΠ°ΡΠ΅ ΡΡΡΠ³ΡΠ±Π»ΡΡΡ ΡΠΊΠΎΠ»ΠΎΠ³ΠΈΡΠ΅ΡΠΊΡΡ ΠΎΠ±ΡΡΠ°Π½ΠΎΠ²ΠΊΡ Π² Π³ΠΎΡΠΎΠ΄Π°Ρ .
Π Π½Π°ΡΡΠΎΡΡΠ΅Π΅ Π²ΡΠ΅ΠΌΡ ΡΠΈΡΠΌΠΎΠΉ Β«Firestone TyresΒ» Π² Π‘Π¨Π ΠΏΡΠΎΠ²Π΅Π΄Π΅Π½Ρ ΡΡΠΏΠ΅ΡΠ½ΡΠ΅ ΠΎΠΏΡΡΡ ΠΏΠΎ ΡΡΠ°Π½ΡΡΠΎΡΠΌΠΈΡΠΎΠ²Π°Π½ΠΈΡ ΡΠ΅Π·ΠΈΠ½Ρ Π² ΠΌΠ΅ΡΠ°Π½ΠΎΠ» Ρ ΠΏΠΎΠ»ΡΡΠ΅Π½ΠΈΠ΅ΠΌ ΠΏΡΠ»Π΅Π²ΠΈΠ΄Π½ΠΎΠΉ ΡΠ°ΠΆΠΈ, ΡΠΎΠΎΡΠ²Π΅ΡΡΡΠ²ΡΡΡΠ΅ΠΉ ΡΡΠ°Π½Π΄Π°ΡΡΡ Π΄Π»Ρ ΡΠ΅Π·ΠΈΠ½ΠΎΡΠ΅Ρ Π½ΠΈΡΠ΅ΡΠΊΠΎΠ³ΠΎ ΠΏΡΠΎΠΈΠ·Π²ΠΎΠ΄ΡΡΠ²Π°. ΠΠ΅ΡΠ²Π°Ρ ΡΡΡΠ°Π½ΠΎΠ²ΠΊΠ° ΠΈΠΌΠ΅Π΅Ρ ΠΏΡΠΎΠΈΠ·Π²ΠΎΠ΄ΠΈΡΠ΅Π»ΡΠ½ΠΎΡΡΡ ΠΏΠΎ ΠΌΠ΅ΡΠ°Π½ΠΎΠ»Ρ 300 Ρ/ΡΡΡΠΊΠΈ. Π£ΡΡΠ°Π½ΠΎΠ²ΠΊΠ° ΡΠ°ΡΡΡΠΈΡΠ°Π½Π° Π½Π° ΠΏΠ΅ΡΠ΅ΡΠ°Π±ΠΎΡΠΊΡ ΡΠΈΠ½ Π»Π΅Π³ΠΊΠΎΠ²ΡΡ Π°Π²ΡΠΎΠΌΠΎΠ±ΠΈΠ»Π΅ΠΉ Π΄ΠΈΠ°ΠΌΠ΅ΡΡΠΎΠΌ 50 ΡΠΌ. ΠΡΠ½ΠΎΠ²Π½ΡΠΌ ΠΏΡΠΎΡΠ΅ΡΡΠΎΠΌ Π΄Π΅ΡΡΡΡΠΊΡΠΈΠΈ ΡΠ΅Π·ΠΈΠ½Ρ Π΄Π»Ρ Π΄Π°Π»ΡΠ½Π΅ΠΉΡΠ΅Π³ΠΎ ΡΡΠ°Π½ΡΡΠΎΡΠΌΠΈΡΠΎΠ²Π°Π½ΠΈΡ ΠΏΡΠΎΠ΄ΡΠΊΡΠΎΠ² ΡΠ°Π·Π»ΠΎΠΆΠ΅Π½ΠΈΡ Π² ΠΌΠ΅ΡΠ°Π½ΠΎΠ» ΡΠ²Π»ΡΠ΅ΡΡΡ ΠΏΠΈΡΠΎΠ»ΠΈΠ· Π² ΠΎΠΊΠΈΡΠ»ΠΈΡΠ΅Π»ΡΠ½ΠΎΠΉ ΠΊΠ°ΠΌΠ΅ΡΠ΅ ΠΏΡΠΈ ΡΠ΅ΠΌΠΏΠ΅ΡΠ°ΡΡΡΠ΅ 1000 Β°Π‘. ΠΠ»Ρ ΠΏΠ΅ΡΠ΅ΡΠ°Π±ΠΎΡΠΊΠΈ ΡΠΈΠ½ Π½Π΅ΠΎΠ±Ρ ΠΎΠ΄ΠΈΠΌΠΎ ΠΈΡ ΡΠ°Π·ΡΠ΅Π·Π°ΡΡ Π½Π° ΡΠ°ΡΡΠΈ Ρ ΠΎΡΠ΄Π΅Π»Π΅Π½ΠΈΠ΅ΠΌ Π±ΠΎΡΡΠ°, ΠΊΠΎΡΠΎΡΡΠΉ ΠΈΡΠΏΠΎΠ»ΡΠ·ΡΠ΅ΡΡΡ ΠΊΠ°ΠΊ ΠΏΠΎΠ±ΠΎΡΠ½ΡΠΉ ΡΠΎΠ²Π°ΡΠ½ΡΠΉ ΠΏΡΠΎΠ΄ΡΠΊΡ.
ΠΠ΄Π½ΠΎ ΠΈΠ· ΠΏΡΠΎΠ³ΡΠ΅ΡΡΠΈΠ²Π½ΡΡ Π½Π°ΠΏΡΠ°Π²Π»Π΅Π½ΠΈΠΉ, Π½Π°ΠΈΠ±ΠΎΠ»Π΅Π΅ ΠΎΠΏΡΠΈΠΌΠ°Π»ΡΠ½ΠΎΠ΅ Ρ ΡΠ΅Ρ Π½ΠΈΡΠ΅ΡΠΊΠΎΠΉ ΡΠΎΡΠΊΠΈ Π·ΡΠ΅Π½ΠΈΡ ΠΏΡΠΈΠΌΠ΅Π½ΠΈΡΠ΅Π»ΡΠ½ΠΎ ΠΊ ΡΡΠ»ΠΎΠ²ΠΈΡΠΌ Π‘ΠΠ, – ΡΠΆΠΈΠ³Π°Π½ΠΈΠ΅ ΡΠΈΠ½, ΠΏΡΠΈΡΠ΅ΠΌ ΠΈΠ· Π²Π°ΡΠΈΠ°Π½ΡΠΎΠ² ΡΡΠΎΠ³ΠΎ Π½Π°ΠΏΡΠ°Π²Π»Π΅Π½ΠΈΡ ΠΏΡΠ΅Π΄ΠΏΠΎΡΡΠΈΡΠ΅Π»ΡΠ½Π΅Π΅ ΡΠΆΠΈΠ³Π°Π½ΠΈΠ΅ ΡΠΈΠ½ Π² ΡΠ΅Π»ΡΠ½ΠΎΠΌ Π²ΠΈΠ΄Π΅. ΠΠ° ΠΎΡΠ½ΠΎΠ²Π°Π½ΠΈΠΈ ΡΡΠΎΠ³ΠΎ Π±ΡΠ»Π° Π²ΡΠΏΠΎΠ»Π½Π΅Π½Π° ΠΏΡΠ΅Π΄ΠΏΡΠΎΠ΅ΠΊΡΠ½Π°Ρ ΠΏΡΠΎΡΠ°Π±ΠΎΡΠΊΠ° ΠΏΠ΅ΡΡΠΏΠ΅ΠΊΡΠΈΠ²Π½ΠΎΡΡΠΈ ΡΠΆΠΈΠ³Π°Π½ΠΈΡ ΡΠΈΠ½ Π² ΠΠ°Π·Π°Ρ ΡΡΠ°Π½Π΅.
Π ΡΠ΅ΡΠ΅Π½ΠΈΠΈ Π²ΠΎΠΏΡΠΎΡΠ° ΡΠΆΠΈΠ³Π°Π½ΠΈΡ ΡΠΈΠ½ ΠΌΠΎΠ³ΡΡ Π±ΡΡΡ Π΄Π²Π° Π²Π°ΡΠΈΠ°Π½ΡΠ°.
ΠΠ΅ΡΠ²ΡΠΉ – ΠΏΡΠΈΠΌΠ΅Π½Π΅Π½ΠΈΠ΅ ΠΎΡΡΠ°ΡΠΎΡΠ½ΠΎ ΠΊΡΡΠΏΠ½ΡΡ ΡΡΡΠ°Π½ΠΎΠ²ΠΎΠΊ Π΄Π»Ρ ΡΠΆΠΈΠ³Π°Π½ΠΈΡ. ΠΠΎ ΡΡΠΎΠΌΡ ΠΏΡΡΠΈ ΠΈΠ΄ΡΡ Π² Π‘Π¨Π, ΠΠ΅Π»ΠΈΠΊΠΎΠ±ΡΠΈΡΠ°Π½ΠΈΠΈ, ΠΡΠ°Π»ΠΈΠΈ. Π’Π°ΠΊ, Π΄Π²Π΅ ΡΡΡΠ°Π½ΠΎΠ²ΠΊΠΈ Π² ΠΠ΅Π»ΠΈΠΊΠΎΠ±ΡΠΈΡΠ°Π½ΠΈΠΈ (ΡΠΎΠΎΡΡΠΆΠ΅Π½ΠΈΠ΅ ΠΏΠ΅ΡΠ²ΠΎΠΉ ΠΈΠ· ΠΊΠΎΡΠΎΡΡΡ Π²Π΅Π΄Π΅ΡΡΡ Ρ ΡΡΠ°ΡΡΠΈΠ΅ΠΌ Π‘Π¨Π) ΠΌΠΎΠ³ΡΡ ΠΎΠ±Π΅ΡΠΏΠ΅ΡΠΈΡΡ ΡΡΠΈΠ»ΠΈΠ·Π°ΡΠΈΡ 50% ΡΠΈΠ½ Π² ΡΡΡΠ°Π½Π΅. Π‘ΠΎΠ·Π΄Π°Π½ΠΈΠ΅ ΠΊΡΡΠΏΠ½ΡΡ ΡΡΡΠ°Π½ΠΎΠ²ΠΎΠΊ ΡΠ΅Ρ Π½ΠΈΡΠ΅ΡΠΊΠΈ Π±ΠΎΠ»Π΅Π΅ ΡΠ΅Π»Π΅ΡΠΎΠΎΠ±ΡΠ°Π·Π½ΠΎ ΠΈ Π² Π½Π°ΡΠΈΡ ΡΡΠ»ΠΎΠ²ΠΈΡΡ . ΠΠ· ΠΎΡΠ²ΠΎΠ΅Π½Π½ΠΎΠ³ΠΎ ΠΏΡΠΎΠΌΡΡΠ»Π΅Π½Π½ΠΎΠ³ΠΎ ΠΎΠ±ΠΎΡΡΠ΄ΠΎΠ²Π°Π½ΠΈΡ ΠΌΠΎΠΆΠ½ΠΎ ΠΏΠΎΠ΄ΠΎΠ±ΡΠ°ΡΡ ΠΏΠ΅ΡΠΈ, ΠΊΠΎΡΠ»Ρ-ΡΡΠΈΠ»ΠΈΠ·Π°ΡΠΎΡΡ, Π³Π°Π·ΠΎΠ²ΡΠ΅ ΡΠΈΠ»ΡΡΡΡ. ΠΠΎ ΠΏΠΎΠ΄ΠΎΠ±Π½ΡΠΉ ΠΏΠΎΠ΄Ρ ΠΎΠ΄ ΡΡΠ΅Π±ΡΠ΅Ρ ΠΎΡΠ³Π°Π½ΠΈΠ·Π°ΡΠΈΠΈ ΡΠ±ΠΎΡΠ° ΠΈ Π΄ΠΎΡΡΠ°Π²ΠΊΠΈ ΡΠΈΠ½, Ρ.Π΅. Π΄ΠΎΠΏΠΎΠ»Π½ΠΈΡΠ΅Π»ΡΠ½ΠΎΠ³ΠΎ ΡΡΠ°Π½ΡΠΏΠΎΡΡΠ½ΠΎΠ³ΠΎ Π·Π²Π΅Π½Π° Π² ΡΠ΅Ρ Π½ΠΎΠ»ΠΎΠ³ΠΈΠΈ.
ΠΡΠΎΡΠΎΠΉ Π²Π°ΡΠΈΠ°Π½Ρ – ΡΠΎΠ·Π΄Π°Π½ΠΈΠ΅ Π½Π΅Π±ΠΎΠ»ΡΡΠΈΡ ΡΡΡΠ°Π½ΠΎΠ²ΠΎΠΊ, ΠΎΡΠ²Π΅ΡΠ°ΡΡΠΈΡ ΡΠΎΠ²ΡΠ΅ΠΌΠ΅Π½Π½ΡΠΌ ΡΠΊΠΎΠ»ΠΎΠ³ΠΈΡΠ΅ΡΠΊΠΈΠΌ ΡΡΠ΅Π±ΠΎΠ²Π°Π½ΠΈΡΠΌ. ΠΠ°Π»ΡΠ΅ ΡΡΡΠ°Π½ΠΎΠ²ΠΊΠΈ ΠΏΠΎ ΡΠΆΠΈΠ³Π°Π½ΠΈΡ ΡΠΈΠ½ ΠΌΠΎΠ³ΡΡ ΡΠΎΠΎΡΡΠΆΠ°ΡΡΡΡ Π² ΡΠΎΡΡΠ°Π²Π΅ Π°Π²ΡΠΎΡΡΠ°Π½ΡΠΏΠΎΡΡΠ½ΡΡ ΠΏΡΠ΅Π΄ΠΏΡΠΈΡΡΠΈΠΉ ΠΊΠ°ΠΊ Π½Π°Π΄ΡΡΡΠΎΠΉΠΊΠΈ ΠΊΠΎΡΠ΅Π»ΡΠ½ΡΡ , ΠΊΠΎΡΠΎΡΡΠ΅, ΠΊΠ°ΠΊ ΠΏΡΠ°Π²ΠΈΠ»ΠΎ, ΠΈΠΌΠ΅ΡΡΡΡ Π½Π° ΡΡΠΈΡ ΠΏΡΠ΅Π΄ΠΏΡΠΈΡΡΠΈΡΡ .
ΠΠ°Π±Π΅Π»ΡΠ½Π°Ρ Π°ΡΠΌΠ°ΡΡΡΠ°, ΠΠΎΡΠ΅Π»ΡΠ½Π°Ρ, ΠΠΎΡΠ½ΠΎΡΡΡ, Π’ΠΎΠΏΠ»ΠΈΠ²ΠΎ, ΠΠ»Π΅ΠΊΡΡΠΈΡΠ΅ΡΡΠ²ΠΎ , ΠΠ»Π΅ΠΊΡΡΠΎΡΠ½Π΅ΡΠ³ΠΈΡ , ΠΠ½Π΅ΡΠ³ΠΈΡ , ΠΡΠΎΠ²ΠΎΠ΄, ΠΠ»Π΅ΠΊΡΡΠΎΡΡΠ°Π½ΡΠΈΡ
www.eprussia.ru
ΠΏΠ΅ΡΠ΅ΡΠ°Π±ΠΎΡΠΊΠ° ΡΠΈΠ½ Π² Π΄ΠΎΠΌΠ°ΡΠ½ΠΈΡ ΡΡΠ»ΠΎΠ²ΠΈΡΡ Ρ ΠΏΠΎΠΌΠΎΡΡΡ Π΄ΡΠΎΠ±ΠΈΠ»ΠΊΠΈ, ΡΠ°ΠΌΠΎΡΡΠΎΡΡΠ΅Π»ΡΠ½Π°Ρ ΡΠ±ΠΎΡΠΊΠ° ΠΈΠ·ΠΌΠ΅Π»ΡΡΠΈΡΠ΅Π»Ρ Π΄Π»Ρ ΡΠ΅Π·ΠΈΠ½Ρ ΠΈ ΠΏΠΎΠΊΡΡΡΠ΅ΠΊ

ΠΠ°ΠΆΠ΄ΡΠΉ Π³ΠΎΠ΄ ΡΡΡΡΡΠΈ ΠΏΠΎΠΊΡΡΡΠ΅ΠΊ ΠΏΡΠΎΠΏΠ°Π΄Π°ΡΡ Π½Π° ΡΠ²Π°Π»ΠΊΠ°Ρ ΠΈ ΠΏΠΎΠ»ΠΈΠ³ΠΎΠ½Π°Ρ , Π½Π΅ΡΠΌΠΎΡΡΡ Π½Π° ΡΠΎ, ΡΡΠΎ Π΄Π»Ρ ΠΏΡΠ΅Π΄ΠΏΡΠΈΠΈΠΌΡΠΈΠ²ΠΎΠ³ΠΎ ΡΠ΅Π»ΠΎΠ²Π΅ΠΊΠ° ΠΎΠ½ΠΈ ΡΠ²Π»ΡΡΡΡΡ Π±Π΅ΡΠΏΠ»Π°ΡΠ½ΡΠΌ ΡΠ΅ΡΡΡΡΠΎΠΌ, ΠΈΠ· ΠΊΠΎΡΠΎΡΠΎΠ³ΠΎ ΠΌΠΎΠΆΠ½ΠΎ ΠΏΡΠΎΠΈΠ·Π²ΠΎΠ΄ΠΈΡΡ ΡΠ΅Π·ΠΈΠ½ΠΎΠ²ΡΡ ΠΊΡΠΎΡΠΊΡ.
ΠΡΠ»ΠΈ ΠΎΠ½Π° ΠΏΠΎΠ½Π°Π΄ΠΎΠ±ΠΈΠ»Π°ΡΡ Π»ΠΈΡΡ Π΅Π΄ΠΈΠ½ΠΎΠΆΠ΄Ρ, ΠΌΠΎΠΆΠ½ΠΎ ΠΊΡΠΏΠΈΡΡ Π΅Π΅ Π² Π½ΡΠΆΠ½ΠΎΠΌ ΠΊΠΎΠ»ΠΈΡΠ΅ΡΡΠ²Π΅ Ρ ΠΏΡΠΎΠΈΠ·Π²ΠΎΠ΄ΠΈΡΠ΅Π»Π΅ΠΉ.
ΠΠΎ Π³Π΄Π΅ Π²Π·ΡΡΡ ΡΠ΅Π·ΠΈΠ½ΠΎΠ²ΡΡ ΠΊΡΠΎΡΠΊΡ, Π΅ΡΠ»ΠΈ ΠΎΠ½Π° Π½ΡΠΆΠ½Π° Π½Π° ΠΏΠΎΡΡΠΎΡΠ½Π½ΠΎΠΉ ΠΎΡΠ½ΠΎΠ²Π΅ ΠΈ Π² Π±ΠΎΠ»ΡΡΠΈΡ ΠΊΠΎΠ»ΠΈΡΠ΅ΡΡΠ²Π°Ρ ?
Π‘ΡΠΎΠΈΡ Π·Π°Π΄ΡΠΌΠ°ΡΡΡΡ ΠΎ ΠΏΡΠΈΠΎΠ±ΡΠ΅ΡΠ΅Π½ΠΈΠΈ ΡΠΎΠ±ΡΡΠ²Π΅Π½Π½ΠΎΠ³ΠΎ ΠΎΠ±ΠΎΡΡΠ΄ΠΎΠ²Π°Π½ΠΈΡ Π΄Π»Ρ ΠΏΠ΅ΡΠ΅ΡΠ°Π±ΠΎΡΠΊΠΈ ΡΠΈΠ½.
ΠΠ΄Π½Π°ΠΊΠΎ ΠΏΠΎΠ»Π½ΠΎΡΠ΅Π½Π½Π°Ρ ΡΡΡΠ°Π½ΠΎΠ²ΠΊΠ° Π½Π΅ Π²ΡΠ΅ΠΌ ΠΏΠΎ ΠΊΠ°ΡΠΌΠ°Π½Ρ, ΠΈ Π½Π΅ Π΄Π»Ρ Π²ΡΠ΅Ρ ΠΎΠΊΠ°ΠΆΠ΅ΡΡΡ ΡΠ΅Π½ΡΠ°Π±Π΅Π»ΡΠ½ΡΠΌ ΡΠ°ΠΊΠΎΠ΅ Π²Π»ΠΎΠΆΠ΅Π½ΠΈΠ΅. ΠΡΡ ΠΎΠ΄ β ΡΠΎΠ·Π΄Π°ΡΡ ΠΎΠ±ΠΎΡΡΠ΄ΠΎΠ²Π°Π½ΠΈΠ΅ ΡΠ²ΠΎΠΈΠΌΠΈ ΡΡΠΊΠ°ΠΌΠΈ, ΠΈ Ρ Π΅Π³ΠΎ ΠΏΠΎΠΌΠΎΡΡΡ ΠΏΡΠΎΠΈΠ·Π²ΠΎΠ΄ΠΈΡΡ ΡΠ΅Π·ΠΈΠ½ΠΎΠ²ΡΡ ΠΊΡΠΎΡΠΊΡ ΠΈΠ· ΠΏΠΎΠΊΡΡΡΠ΅ΠΊ Π² Π΄ΠΎΠΌΠ°ΡΠ½ΠΈΡ ΡΡΠ»ΠΎΠ²ΠΈΡΡ .
ΠΠ΅ΡΠ΅ΡΠ°Π±ΠΎΡΠΊΠ° Π½Π΅Π±ΠΎΠ»ΡΡΠΎΠ³ΠΎ ΠΊΠΎΠ»ΠΈΡΠ΅ΡΡΠ²Π° ΡΠ΅Π·ΠΈΠ½Ρ Π² Π΄ΠΎΠΌΠ°ΡΠ½ΠΈΡ ΡΡΠ»ΠΎΠ²ΠΈΡΡ
ΠΡΠ»ΠΈ ΡΡΡΡΡ Π½ΡΠΆΠ½ΠΎ ΡΠΎΠ²ΡΠ΅ΠΌ ΠΌΠ°Π»ΠΎ, ΠΌΠΎΠΆΠ½ΠΎ ΠΎΠ±ΠΎΠΉΡΠΈΡΡ Π²ΠΎΠ²ΡΠ΅ Π±Π΅Π· ΠΎΠ±ΠΎΡΡΠ΄ΠΎΠ²Π°Π½ΠΈΡ.
ΠΠ»Ρ ΡΡΠΎΠ³ΠΎ ΠΏΠΎΡΡΠ΅Π±ΡΡΡΡΡ ΠΏΠΎΡΡΠ΅Π±ΡΡΡΡΡ ΡΠΎΠ»ΡΠΊΠΎΒ Π½ΠΎΠΆΠ½ΠΈΡΡ ΠΈ ΡΠ΅Π·Π°ΠΊ.
Π‘ ΠΏΠΎΠΊΡΡΡΠΊΠΈ Π²Π½Π°ΡΠ°Π»Π΅ ΡΠ±ΠΈΡΠ°ΡΡ ΠΌΠ΅ΡΠ°Π»Π»ΠΈΡΠ΅ΡΠΊΠΈΠΉ ΠΊΠΎΡΠ΄, Π·Π°ΡΠ΅ΠΌ ΡΠ°Π·Π΄Π΅Π»ΡΡΡ Π½Π° Π»Π΅Π½ΡΡ ΠΈ ΠΈΠ·ΠΌΠ΅Π»ΡΡΠ°ΡΡ ΠΈΡ Π½Π° Π±ΠΎΠ»Π΅Π΅ ΠΌΠ΅Π»ΠΊΠΈΠ΅ ΡΡΠ°ΠΊΡΠΈΠΈ Π΄ΠΎ Π½Π΅ΠΎΠ±Ρ ΠΎΠ΄ΠΈΠΌΠΎΠ³ΠΎ ΡΠ°Π·ΠΌΠ΅ΡΠ°.
ΠΠ° ΡΡΠΎΠΌ ΠΏΡΠΎΡΠ΅ΡΡ ΡΡΠΈΡΠ°Π΅ΡΡΡ Π·Π°ΠΊΠΎΠ½ΡΠ΅Π½Π½ΡΠΌ.
ΠΠ°ΡΠ΅ΡΠΈΠ°Π» Π΄Π»Ρ ΠΎΡΠΎΡΠΌΠ»Π΅Π½ΠΈΡ Π΄ΠΎΡΠΎΠΆΠ΅ΠΊ, ΠΊΠ»ΡΠΌΠ± ΠΈΠ»ΠΈ ΠΎΡΠ΄Π΅Π»ΡΠ½ΠΎΠΉ Π΄Π΅ΡΡΠΊΠΎΠΉ ΠΏΠ»ΠΎΡΠ°Π΄ΠΊΠΈ Π³ΠΎΡΠΎΠ² ΠΊ ΠΈΡΠΏΠΎΠ»ΡΠ·ΠΎΠ²Π°Π½ΠΈΡ.
ΠΠΎ ΡΡΠΎΠ±Ρ ΠΏΠΎΠ»ΡΡΠΈΡΡ Π±ΠΎΠ»ΡΡΠΈΠΉ ΠΎΠ±ΡΠ΅ΠΌ ΡΡΡΡΡ ΠΈΠ»ΠΈ ΠΈΠΌΠ΅ΡΡ Π΄ΠΎΡ ΠΎΠ΄ ΠΎΡ ΠΏΠ΅ΡΠ΅ΡΠ°Π±ΠΎΡΠΊΠΈ ΡΠΈΠ½ Π² Π΄ΠΎΠΌΠ°ΡΠ½ΠΈΡ ΡΡΠ»ΠΎΠ²ΠΈΡΡ , Π½ΡΠΆΠ½ΠΎ ΡΠΎΠΎΡΠ²Π΅ΡΡΡΠ²ΡΡΡΠ΅Π΅ ΠΎΠ±ΠΎΡΡΠ΄ΠΎΠ²Π°Π½ΠΈΠ΅.
Π‘ΠΎΠΎΡΡΠΆΠ΅Π½ΠΈΠ΅ Π΄ΡΠΎΠ±ΠΈΠ»ΠΊΠΈ Π΄Π»Ρ ΠΏΠ΅ΡΠ΅ΡΠ°Π±ΠΎΡΠΊΠΈ ΡΠΈΠ½
ΠΡΠΈΠΌΠ΅Π½ΡΡΡΡΡ ΡΡΠΈ ΠΎΡΠ½ΠΎΠ²Π½ΡΡ ΡΠΏΠΎΡΠΎΠ±Π° ΠΏΡΠΎΠΈΠ·Π²ΠΎΠ΄ΡΡΠ²Π° ΠΊΡΠΎΡΠΊΠΈ:
- ΠΡΠΎΠ±Π»Π΅Π½ΠΈΠ΅ ΡΠΈΠ½ ΠΏΠΎΡΠ»Π΅ ΠΈΡ ΠΎΡ Π»Π°ΠΆΠ΄Π΅Π½ΠΈΡ ΠΆΠΈΠ΄ΠΊΠΈΠΌ Π°Π·ΠΎΡΠΎΠΌ Π΄ΠΎ β190 Π³ΡΠ°Π΄ΡΡΠΎΠ².
- ΠΠΎΠ»ΡΡΠ΅Π½ΠΈΠ΅ ΠΊΡΠΎΡΠΊΠΈ Π½Π° ΠΏΡΠΎΠΌΡΡΠ»Π΅Π½Π½ΠΎΠΌ ΠΎΠ±ΠΎΡΡΠ΄ΠΎΠ²Π°Π½ΠΈΠΈ ΠΏΠΎΠ»Π½ΠΎΠ³ΠΎ ΡΠΈΠΊΠ»Π° Ρ ΡΠ΄Π°Π»Π΅Π½ΠΈΠ΅ΠΌ ΠΊΠΎΡΠ΄Π° ΠΈ ΠΏΠΎΡΠ»Π΅Π΄ΡΡΡΠΈΠΌ ΠΈΠ·ΠΌΠ΅Π»ΡΡΠ΅Π½ΠΈΠ΅ΠΌ ΡΠ΅Π·ΠΈΠ½Ρ.
- ΠΠ΅ΡΠ΅ΡΠ°Π±ΠΎΡΠΊΠ° Ρ ΠΈΡΠΏΠΎΠ»ΡΠ·ΠΎΠ²Π°Π½ΠΈΠ΅ΠΌ ΡΠ½ΠΈΠ²Π΅ΡΡΠ°Π»ΡΠ½ΡΡ Π΄ΡΠΎΠ±ΠΈΠ»ΠΎΠΊ, ΠΊΠΎΡΠΎΡΡΡ ΠΌΠΎΠΆΠ½ΠΎ ΠΎΡΡΡΠ΅ΡΡΠ²Π»ΡΡΡ Π² Π΄ΠΎΠΌΠ°ΡΠ½ΠΈΡ ΡΡΠ»ΠΎΠ²ΠΈΡΡ ΡΠ°ΠΌΠΎΠΌΡ.
ΠΠ΅ΡΠ²ΡΠ΅ Π΄Π²Π° ΡΠΏΠΎΡΠΎΠ±Π° ΡΡΠ΅Π±ΡΡΡ Π±ΠΎΠ»ΡΡΠΈΡ ΠΈΠ½Π²Π΅ΡΡΠΈΡΠΈΠΉ. Π’ΡΠ΅ΡΠΈΠΉ Π²Π°ΡΠΈΠ°Π½Ρ Π΄ΠΎΡΡΡΠΏΠ΅Π½ ΠΊΠ°ΠΆΠ΄ΠΎΠΌΡ, ΠΊΡΠΎ ΠΈΠΌΠ΅Π΅Ρ Π²ΠΎΠ·ΠΌΠΎΠΆΠ½ΠΎΡΡΡ ΠΈ ΠΆΠ΅Π»Π°Π½ΠΈΠ΅ ΠΈΠ·Π³ΠΎΡΠΎΠ²ΠΈΡΡ Π΄ΡΠΎΠ±ΠΈΠ»ΠΊΡ Π΄ΠΎΠΌΠ°.
ΠΠ΅ΠΎΠ±Ρ ΠΎΠ΄ΠΈΠΌΡΠ΅ Π°Π³ΡΠ΅Π³Π°ΡΡ ΠΌΠΎΠΆΠ½ΠΎ ΠΈΠ·Π³ΠΎΡΠΎΠ²ΠΈΡΡ ΡΠ°ΠΌΠΎΡΡΠΎΡΡΠ΅Π»ΡΠ½ΠΎ Π² ΠΌΠ°ΡΡΠ΅ΡΡΠΊΠΎΠΉ ΠΈΠ»ΠΈ Π½Π° ΠΏΡΠΎΠΈΠ·Π²ΠΎΠ΄ΡΡΠ²Π΅Π½Π½ΠΎΠΌ ΡΡΠ°ΡΡΠΊΠ΅ β ΡΠ°ΠΌ, Π³Π΄Π΅ Π΅ΡΡΡ ΠΌΠ΅ΡΠ°Π»Π»ΠΎΡΠ΅ΠΆΡΡΠΈΠ΅ ΡΡΠ°Π½ΠΊΠΈ (ΡΠΎΠΊΠ°ΡΠ½ΡΠ΅, ΡΡΠ΅Π·Π΅ΡΠ½ΡΠ΅) ΠΈ ΡΠ²Π°ΡΠΎΡΠ½ΡΠΉ Π°ΠΏΠΏΠ°ΡΠ°Ρ Π΄Π»Ρ ΠΈΠ·Π³ΠΎΡΠΎΠ²Π»Π΅Π½ΠΈΡ ΠΊΠΎΠΌΠΏΠ»Π΅ΠΊΡΡΡΡΠΈΡ Π΄Π΅ΡΠ°Π»Π΅ΠΉ.
ΠΡΠ»ΠΈ Π½Π΅Π»ΡΠ·Ρ ΡΠ°ΠΌΠΎΡΡΠΎΡΡΠ΅Π»ΡΠ½ΠΎ Π²ΡΠΏΠΎΠ»Π½ΠΈΡΡ ΠΌΠ΅Ρ Π°Π½ΠΈΡΠ΅ΡΠΊΡΡ ΠΎΠ±ΡΠ°Π±ΠΎΡΠΊΡ Π·Π°Π³ΠΎΡΠΎΠ²ΠΎΠΊ ΠΈ ΠΏΡΠΈΠ΄Π΅ΡΡΡ Π·Π°ΠΊΠ°Π·ΡΠ²Π°ΡΡ ΠΈΡ ΠΏΠΎ ΡΠ²ΠΎΠΈΠΌ ΡΠ΅ΡΡΠ΅ΠΆΠ°ΠΌ, Π²ΡΠ΅ ΡΠ°Π²Π½ΠΎ ΡΡΠΎΠΈΠΌΠΎΡΡΡ ΡΡΠ°Π½ΠΊΠΎΠ² ΠΏΠΎ ΠΏΠ΅ΡΠ΅ΡΠ°Π±ΠΎΡΠΊΠ΅ ΡΠΈΠ½ Π±ΡΠ΄Π΅Ρ Π² Π½Π΅ΡΠΊΠΎΠ»ΡΠΊΠΎ ΡΠ°Π· Π΄Π΅ΡΠ΅Π²Π»Π΅, ΡΠ΅ΠΌ Π°Π½Π°Π»ΠΎΠ³ΠΈΡΠ½ΡΡ ΠΏΠΎΠΊΡΠΏΠ½ΡΡ Π°Π³ΡΠ΅Π³Π°ΡΠΎΠ².
ΠΡΠ½ΠΎΠ²Π½ΡΠΌ ΠΊΠΎΠΌΠΏΠ»Π΅ΠΊΡΡΡΡΠΈΠΌ ΡΡΡΡΠΎΠΉΡΡΠ²ΠΎΠΌ Π½Π° Π»ΠΈΠ½ΠΈΠΈ ΠΏΠΎ ΠΏΠ΅ΡΠ΅Π΄Π΅Π»ΠΊΠ΅ ΠΏΠΎΠΊΡΡΡΠ΅ΠΊ ΡΠ²Π»ΡΠ΅ΡΡΡ ΡΡΠ΅Π΄Π΅Ρ (ΠΈΠ·ΠΌΠ΅Π»ΡΡΠΈΡΠ΅Π»Ρ Π΄Π»Ρ ΡΠ΅Π·ΠΈΠ½Ρ). Π Π°ΡΡΠΌΠΎΡΡΠΈΠΌ Π±ΠΎΠ»Π΅Π΅ ΠΏΠΎΠ΄ΡΠΎΠ±Π½ΠΎ ΠΈ Π½Π°Π·Π½Π°ΡΠ΅Π½ΠΈΠ΅ ΡΠ·Π»ΠΎΠ² Π΄Π°Π½Π½ΠΎΠ³ΠΎ ΡΡΠ°Π½ΠΊΠ°.
Π£ΡΡΡΠΎΠΉΡΡΠ²ΠΎ Π°Π³ΡΠ΅Π³Π°ΡΠ°
Π‘ΡΠ°Π½ΠΎΠΊ ΡΠΎΡΡΠΎΠΈΡ ΠΈΠ· ΡΠ»Π΅Π΄ΡΡΡΠΈΡ ΠΎΡΠ½ΠΎΠ²Π½ΡΡ ΡΠ·Π»ΠΎΠ²:
- ΡΠ»Π΅ΠΊΡΡΠΎΠ΄Π²ΠΈΠ³Π°ΡΠ΅Π»Ρ 5 ΠΊΠΡ β 2 ΡΡ;
- ΠΊΠΎΡΠΏΡΡ Ρ Π΄ΠΈΡΠΊΠΎΠ²ΡΠΌΠΈ Π²Π°Π»Π°ΠΌΠΈ;
- ΡΠ΅ΡΠ΅ΡΠΊΠ°;
- ΡΠ΅Π΄ΡΠΊΡΠΎΡ ΡΠ΅ΡΠ²ΡΡΠ½ΡΠΉ β 2 ΡΡ;
- ΠΊΠ°ΡΠΊΠ°Ρ ΡΡΠ΅Π΄Π΅ΡΠ°;
- Π·Π°Π³ΡΡΠ·ΠΎΡΠ½ΡΠΉ Π±ΡΠ½ΠΊΠ΅Ρ;
- Π½Π°ΠΏΡΠ°Π²Π»ΡΡΡΠΈΠΉ Π»ΠΎΡΠΎΠΊ;
- ΡΠΊΠ°Ρ ΡΠΏΡΠ°Π²Π»Π΅Π½ΠΈΡ.
ΠΠ΅ΡΠ°Π»ΠΈ ΡΡΡΠ°Π½ΠΎΠ²ΠΊΠΈ ΠΌΠΎΠ½ΡΠΈΡΡΡΡΡΡ Π½Π° ΠΌΠΎΡΠ½ΠΎΠΉ ΡΠ°ΠΌΠ΅, ΡΠ²Π°ΡΠ΅Π½Π½ΠΎΠΉ ΠΈΠ· ΡΠ²Π΅Π»Π»Π΅ΡΠΎΠ².
ΠΠΎΡΠΎΠ±ΠΊΠ° Ρ ΡΠ΅ΠΆΡΡΠΈΠΌΠΈ Π΄ΠΈΡΠΊΠ°ΠΌΠΈ
ΠΠ»Π°Π²Π½ΡΠΌ ΡΠ·Π»ΠΎΠΌ Π΄ΡΠΎΠ±ΠΈΠ»ΠΊΠΈ Π΄Π»Ρ ΡΠ΅Π·ΠΈΠ½Ρ ΡΠ²Π»ΡΠ΅ΡΡΡ ΠΊΠΎΡΠΏΡΡ Ρ ΡΡΠ΅Π·Π΅ΡΠ½ΡΠΌΠΈ Π²Π°Π»ΠΊΠ°ΠΌΠΈ.
ΠΡΠΈ ΡΡΠΎΠΌ ΡΠ΅ΠΆΡΡΠΈΠ΅ Π½ΠΎΠΆΠΈ Π²ΡΠΏΠΎΠ»Π½Π΅Π½Ρ ΠΈΠ· Π²ΡΡΠΎΠΊΠΎΠΏΡΠΎΡΠ½ΠΎΠΉ ΡΡΠ°Π»ΠΈ ΠΈ ΡΠ΅ΡΠΌΠΈΡΠ΅ΡΠΊΠΈ ΠΎΠ±ΡΠ°Π±ΠΎΡΠ°Π½Ρ, ΡΡΠΎ ΠΎΡΡΡΠΈΠΌΠΎ ΡΠ½ΠΈΠΆΠ°Π΅Ρ ΠΈΡ ΠΈΠ·Π½ΠΎΡ. ΠΠ½ΠΈΒ ΠΏΡΠ°ΠΊΡΠΈΡΠ΅ΡΠΊΠΈ Π½Π΅ ΡΡΠ΅Π±ΡΡΡ Π·Π°ΡΠΎΡΠΊΠΈ Π²ΠΎ Π²ΡΠ΅ΠΌΡ ΡΠΊΡΠΏΠ»ΡΠ°ΡΠ°ΡΠΈΠΈ.
Π Π°ΡΡΠ΅Ρ ΠΎΡΠ²Π΅ΡΡΡΠΈΠΉ ΠΊΠΎΡΠΎΠ±ΠΊΠΈ, Π²Π°Π»ΠΎΠ² ΠΈ ΡΠ΅ΠΆΡΡΠΈΡ ΡΠ»Π΅ΠΌΠ΅Π½ΡΠΎΠ² Π΄ΠΎΠ»ΠΆΠ΅Π½ Π±ΡΡΡ ΡΠΎΡΠ½ΡΠΉ, ΠΏΠΎΡΡΠΎΠΌΡ Π΅Π³ΠΎ Π½ΡΠΆΠ½ΠΎ ΠΏΡΠΎΠΈΠ·Π²ΠΎΠ΄ΠΈΡΡ ΡΠΏΠ΅ΡΠΈΠ°Π»ΠΈΡΡΡ Π² ΡΡΠΎΠΉ ΠΎΠ±Π»Π°ΡΡΠΈ (ΠΊΠΎΠ½ΡΡΡΡΠΊΡΠΎΡΡ).
Π Π΅ΡΠ΅ΡΠΊΠ° Π΄Π»Ρ ΠΊΠ°Π»ΠΈΠ±ΡΠΎΠ²ΠΊΠΈ ΠΊΡΠΎΡΠΊΠΈ
ΠΠ»Ρ ΡΠΎΠ³ΠΎ ΡΡΠΎΠ±Ρ ΠΏΠΎΠ»ΡΡΠΈΡΡ ΠΊΠ°Π»ΠΈΠ±ΡΠΎΠ²Π°Π½Π½ΡΡ ΡΡΠ°ΠΊΡΠΈΡ ΡΠΈΠ½Π½ΠΎΠ³ΠΎ ΡΡΡΡΡ, ΡΡΠ΅Π΄Π΅ΡΡ ΡΠ½Π°Π±ΠΆΠ°ΡΡΡΡ ΡΠΏΠ΅ΡΠΈΠ°Π»ΡΠ½ΠΎΠΉ ΡΠ΅ΡΠ΅ΡΠΊΠΎΠΉ, ΠΊΠΎΡΠΎΡΠ°Ρ ΡΡΡΠ°Π½Π°Π²Π»ΠΈΠ²Π°Π΅ΡΡΡ ΠΏΠΎΠ΄ Π²Π°Π»ΠΊΠ°ΠΌΠΈ.
Π Π΅Π΄ΡΠΊΡΠΎΡ ΡΠ΅ΡΠ²ΡΡΠ½ΡΠΉ
ΠΡΠ°ΡΠ΅Π½ΠΈΠ΅ Π²Π°Π»ΠΎΠ² Ρ Π΄ΠΈΡΠΊΠΎΠ²ΡΠΌΠΈ ΡΡΠ΅Π·Π°ΠΌΠΈ ΠΎΡΡΡΠ΅ΡΡΠ²Π»ΡΠ΅ΡΡΡ ΠΎΠ±ΠΎΡΠΎΠ±Π»Π΅Π½Π½ΠΎ, Π½Π΅ΠΏΠΎΡΡΠ΅Π΄ΡΡΠ²Π΅Π½Π½ΠΎ ΠΎΡ ΡΠ΅ΡΠ²ΡΡΠ½ΡΡ ΡΠ΅Π΄ΡΠΊΡΠΎΡΠΎΠ², ΡΠΎΠ΅Π΄ΠΈΠ½Π΅Π½Π½ΡΡ Ρ ΡΠ»Π΅ΠΊΡΡΠΎΠ΄Π²ΠΈΠ³Π°ΡΠ΅Π»ΡΠΌΠΈ ΡΠ΅ΡΠ΅Π· ΠΌΡΡΡΡ.
ΠΠ΅ΡΠ΅Π΄Π°ΡΠΎΡΠ½ΠΎΠ΅ ΠΎΡΠ½ΠΎΡΠ΅Π½ΠΈΠ΅ Π²ΡΠ±ΠΈΡΠ°Π΅ΡΡΡ ΠΎΡ 25 Π΄ΠΎ 35 ΡΠ°ΠΊΠΈΠΌ ΠΎΠ±ΡΠ°Π·ΠΎΠΌ, ΡΡΠΎΠ±Ρ ΡΠ΅Π·Π°Π½ΠΈΠ΅ Π±ΡΠ»ΠΎ Π±Π΅Π· Π·Π°Π΅Π΄Π°Π½ΠΈΡ ΠΈ Ρ Π΄ΠΎΡΡΠ°ΡΠΎΡΠ½ΠΎΠΉ ΡΠΊΠΎΡΠΎΡΡΡΡ.
Π Π°ΠΌΠ° Π°Π³ΡΠ΅Π³Π°ΡΠ°
ΠΠ°ΡΠΊΠ°Ρ ΡΠ²Π°ΡΠ΅Π½ ΠΈΠ· ΠΏΡΠΎΡΠΈΠ»ΡΠ½ΡΡ ΡΠ»Π΅ΠΌΠ΅Π½ΡΠΎΠ², ΠΎΠ±Π΅ΡΠΏΠ΅ΡΠΈΠ²Π°Π΅Ρ Π½Π°Π΄Π΅ΠΆΠ½ΠΎΡΡΡ ΠΈ ΡΡΡΠΎΠΉΡΠΈΠ²ΠΎΡΡΡ Π°Π³ΡΠ΅Π³Π°ΡΠ° Π²ΠΎ Π²ΡΠ΅ΠΌΡ ΡΠ°Π±ΠΎΡΡ, Π° ΡΠ°ΠΊΠΆΠ΅ ΠΏΠΎΠ³ΡΡΠ·ΠΎΡΠ½ΠΎ-ΡΠ°Π·Π³ΡΡΠ·ΠΎΡΠ½ΡΡ Π΄Π΅ΠΉΡΡΠ²ΠΈΠΉ.
ΠΠ°Π³ΡΡΠ·ΠΎΡΠ½ΡΠΉ Π±ΡΠ½ΠΊΠ΅Ρ
Π£ΡΡΠ°Π½ΠΎΠ²ΠΊΠ° Π΄Π»Ρ ΠΏΠ΅ΡΠ΅ΡΠ°Π±ΠΎΡΠΊΠΈ ΡΠΈΠ½ ΠΎΠ±ΠΎΡΡΠ΄ΡΠ΅ΡΡΡ Π±ΡΠ½ΠΊΠ΅ΡΠΎΠΌ Π·Π°Π³ΡΡΠ·ΠΊΠΈ ΠΏΠΎΠΊΡΡΡΠ΅ΠΊ ΠΈ Π»ΠΎΡΠΊΠΎΠΌ ΠΏΡΠΈ Π²ΡΠ΅ΠΌΠΊΠ΅ Π³ΠΎΡΠΎΠ²ΠΎΠΉ ΡΠ΅Π·ΠΈΠ½ΠΎΠ²ΠΎΠΉ ΠΊΡΠΎΡΠΊΠΈ.
ΠΠ»Π°Π³ΠΎΠ΄Π°ΡΡ ΡΠ²ΠΎΠ΅ΠΉ ΠΊΠΎΠ½ΡΡΡΡΠΊΡΠΈΠΈ Π±ΡΠ½ΠΊΠ΅Ρ ΠΈΡΠΊΠ»ΡΡΠ°Π΅Ρ ΠΎΠ±ΡΠ°Π·ΠΎΠ²Π°Π½ΠΈΠ΅ Π·Π°ΡΠΎΡΠΎΠ² ΠΈΠ· ΡΡΡΡΡ ΠΈ Π³Π°ΡΠ°Π½ΡΠΈΡΡΠ΅Ρ Π½Π°ΠΏΡΠ°Π²Π»Π΅Π½Π½ΠΎΠ΅ Π΄Π²ΠΈΠΆΠ΅Π½ΠΈΠ΅ ΠΌΠ°ΡΡΡ ΠΊ Π²ΡΠ°ΡΠ°ΡΡΠΈΠΌΡΡ Π²Π°Π»ΠΊΠ°ΠΌ.
ΠΡΠΈΡΠΏΠΎΡΠΎΠ±Π»Π΅Π½ΠΈΠ΅ Π΄Π»Ρ ΡΠ°Π·ΡΠ΅Π·Π°Π½ΠΈΡ ΠΏΠΎΠΊΡΡΡΠΊΠΈ
Π£ΡΡΠ°Π½ΠΎΠ²ΠΊΠ° Π΄Π»Ρ ΡΠ°Π·ΡΠ΅Π·Π°Π½ΠΈΡ ΡΠΈΠ½Ρ ΠΈ ΡΠ΄Π°Π»Π΅Π½ΠΈΡ ΠΊΠΎΡΠ΄Π°Β ΡΠΎΡΡΠΎΠΈΡ ΠΈΠ· Π½Π΅ΡΡΡΠ΅ΠΉ ΡΠ°ΠΌΡ ΠΈ ΡΡΠΎΠΉΠΊΠΈ.
ΠΠ° ΠΊΠ°ΡΠΊΠ°ΡΠ΅ Π½Π°Ρ ΠΎΠ΄ΠΈΡΡΡ Π·Π°ΠΆΠΈΠΌΠ½ΠΎΠΉ ΠΌΠ΅Ρ Π°Π½ΠΈΠ·ΠΌ ΡΠΈΠ½Ρ, Π²ΡΠ°ΡΠ°ΡΡΠΈΠΉΡΡ Π²ΠΌΠ΅ΡΡΠ΅ Ρ ΠΏΠΎΠΊΡΡΡΠΊΠΎΠΉ Π²ΠΎ Π²ΡΠ΅ΠΌΡ ΡΠ΅Π·Π°Π½ΠΈΡ. ΠΠ±ΠΎΡΠΎΡΡ Π΄Π²ΠΈΠ³Π°ΡΠ΅Π»Ρ ΡΠΌΠ΅Π½ΡΡΠ΅Π½Ρ Π·Π° ΡΡΠ΅Ρ ΡΠ°Π·Π½ΠΎΠ³ΠΎ Π΄ΠΈΠ°ΠΌΠ΅ΡΡΠ° ΡΠΊΠΈΠ²ΠΎΠ². ΠΠ° ΡΡΠΎΠΉΠΊΠ΅ ΡΠ°ΡΠΏΠΎΠ»ΠΎΠΆΠ΅Π½ Π²ΡΡΡΠΎΠ΅Π½Π½ΡΠΉ ΠΊΠ»ΠΈΠ½ΠΎΠ²ΠΈΠ΄Π½ΡΠΉ ΡΠ΅Π·Π°ΠΊ, ΠΊΠΎΡΠΎΡΡΠΉ Π½Π°ΡΡΡΠ°ΠΈΠ²Π°Π΅ΡΡΡ Π½Π° ΠΎΠΏΡΠ΅Π΄Π΅Π»Π΅Π½Π½ΡΠΉ ΡΠ°Π·ΠΌΠ΅Ρ Π·Π° ΡΡΠ΅Ρ ΠΏΠ΅ΡΠ΅ΠΌΠ΅ΡΠ΅Π½ΠΈΡ ΠΏΠΈΠ½ΠΎΠ»ΠΈ.
ΠΠ°ΠΊ ΠΈΠ·ΠΌΠ΅Π»ΡΡΠΈΡΡ ΠΏΠΎΠΊΡΡΡΠΊΠΈ?
Π’Π΅Ρ Π½ΠΎΠ»ΠΎΠ³ΠΈΡΠ½Π°Ρ ΡΠ΅ΠΏΠΎΡΠΊΠ° ΠΏΡΠ΅Π΄ΡΡΠ°Π²Π»ΡΠ΅Ρ ΡΠΎΠ±ΠΎΠΉ Π½Π΅ΡΠΊΠΎΠ»ΡΠΊΠΎ ΠΏΠΎΠ΄Π³ΠΎΡΠΎΠ²ΠΈΡΠ΅Π»ΡΠ½ΡΡ ΡΡΠ°ΠΏΠΎΠ², ΠΏΡΠ΅ΠΆΠ΄Π΅ ΡΠ΅ΠΌ ΠΏΠΎΠ»ΡΡΠΈΡΡΡ ΠΏΡΠΎΠ΄ΡΠΊΡΠΈΡ Π½Π΅ΠΎΠ±Ρ ΠΎΠ΄ΠΈΠΌΠΎΠΉ ΡΡΠ°ΠΊΡΠΈΠΈ.
ΠΡΠ° ΠΏΡΠΎΡΠ΅Π΄ΡΡΠ° Π²ΠΊΠ»ΡΡΠ°Π΅Ρ:
- ΠΡΠΌΠΎΡΡ ΠΈ ΡΠ΄Π°Π»Π΅Π½ΠΈΠ΅ ΠΏΠΎΡΡΠΎΡΠΎΠ½Π½ΠΈΡ ΠΏΡΠ΅Π΄ΠΌΠ΅ΡΠΎΠ² ΠΈΠ· ΠΏΠΎΠ»ΠΎΡΡΠΈ ΠΏΠΎΠΊΡΡΡΠΊΠΈ.
- ΠΡΡΠ΅Π·ΠΊΠ° ΠΊΠΎΡΠ΄Π°.
- ΠΠ°ΡΠ΅Π·ΠΊΠ° ΡΠΈΠ½Ρ Π½Π° Π»Π΅Π½ΡΡ ΡΠ°Π·ΠΌΠ΅ΡΠΎΠΌ 50-80 ΠΌΠΌ.
- ΠΠ·ΠΌΠ΅Π»ΡΡΠ΅Π½ΠΈΠ΅ ΡΡΡΡΡ ΠΏΠΎΡΡΠ΅Π΄ΡΡΠ²ΠΎΠΌ ΡΡΠ΅Π΄Π΅ΡΠ°.
- Π‘Π΅ΠΏΠ°ΡΠΈΡΠΎΠ²Π°Π½ΠΈΠ΅ ΠΈ ΠΎΡΠ΄Π΅Π»Π΅Π½ΠΈΠ΅ ΠΌΠ΅ΡΠ°Π»Π»ΠΈΡΠ΅ΡΠΊΠΈΡ ΠΎΡ ΡΠ΅ΠΊΡΡΠΈΠ»ΡΠ½ΡΡ ΡΠ°ΡΡΠ΅ΠΉ.
- ΠΠ°Π»ΠΈΠ±ΡΠΎΠ²Π°Π½ΠΈΠ΅ ΠΊΡΠΎΡΠΊΠΈ Π½Π° ΡΡΠ°ΠΊΡΠΈΠΈ Ρ ΠΏΠΎΠΌΠΎΡΡΡ Π²ΠΈΠ±ΡΠ°ΡΠΈΠΎΠ½Π½ΠΎΠ³ΠΎ ΡΠΈΡΠ°.
ΠΡΠΎΠΈΠ·Π²ΠΎΠ΄ΠΈΡΠ΅Π»ΡΠ½ΠΎΡΡΡ ΠΎΠ±ΠΎΡΡΠ΄ΠΎΠ²Π°Π½ΠΈΡ
Π Π°Π±ΠΎΡΠ° ΡΡΠΈΡ Π΄Π²ΡΡ ΠΎΡΠ½ΠΎΠ²Π½ΡΡ Π°Π³ΡΠ΅Π³Π°ΡΠΎΠ² ΠΏΡΠΈ ΠΏΠ΅ΡΠ΅ΡΠ°Π±ΠΎΡΠΊΠ΅ ΠΏΠΎΠΊΡΡΡΠ΅ΠΊ Π΄Π΅Π»Π°Π΅ΡΡΡ Π² ΠΏΠΎΠ»ΡΠ°Π²ΡΠΎΠΌΠ°ΡΠΈΡΠ΅ΡΠΊΠΎΠΌ ΡΠ΅ΠΆΠΈΠΌΠ΅.
ΠΠ»Ρ Π½ΠΎΡΠΌΠ°Π»ΡΠ½ΠΎΠΉ ΡΠ°Π±ΠΎΡΡ ΡΡΠΎΠΉ Π»ΠΈΠ½ΠΈΠΈ Π½Π΅ΠΎΠ±Ρ ΠΎΠ΄ΠΈΠΌΠΎ ΠΏΠΎΠΌΠ΅ΡΠ΅Π½ΠΈΠ΅ ΠΎΠΊΠΎΠ»ΠΎ 150-200 ΠΊΠ². ΠΌΠ΅ΡΡΠΎΠ². ΠΡΠΎ Π²ΡΠ·Π²Π°Π½ΠΎ ΡΠ΅ΠΌ, ΡΡΠΎ Π½ΡΠΆΠ½ΠΎ ΠΌΠ΅ΡΡΠΎ Π΄Π»Ρ ΡΠ°ΡΠΏΠΎΠ»ΠΎΠΆΠ΅Π½ΠΈΡ Π½Π΅ ΡΠΎΠ»ΡΠΊΠΎ ΠΎΠ±ΠΎΡΡΠ΄ΠΎΠ²Π°Π½ΠΈΡ, Π½ΠΎ ΠΈ Π΄Π»Ρ ΡΠΊΠ»Π°Π΄ΠΈΡΠΎΠ²Π°Π½ΠΈΡ ΠΈΠ·Π½ΠΎΡΠ΅Π½Π½ΡΡ ΠΏΠΎΠΊΡΡΡΠ΅ΠΊ, Π³ΠΎΡΠΎΠ²ΠΎΠΉ ΡΠΈΠ½Π½ΠΎΠΉ ΠΏΡΠΎΠ΄ΡΠΊΡΠΈΠΈ ΠΈ ΠΌΠ΅ΡΠ°Π»Π»ΠΈΡΠ΅ΡΠΊΠΈΡ ΠΎΡΡ ΠΎΠ΄ΠΎΠ².
ΠΡΠΏΡΡΠΊ ΡΠ΅Π·ΠΈΠ½ΠΎΠ²ΠΎΠΉ ΠΊΡΠΎΡΠΊΠΈ Π½Π° Π΄Π°Π½Π½ΠΎΠΌ ΠΎΠ±ΠΎΡΡΠ΄ΠΎΠ²Π°Π½ΠΈΠΈ Π·Π° ΡΠ°Ρ ΡΠΎΡΡΠ°Π²ΠΈΡ ΠΏΡΠΈΠΌΠ΅ΡΠ½ΠΎ 200-800 ΠΊΠ³ ΠΈ Π΄ΠΎ 100 ΠΊΠ³ ΠΌΠ΅ΡΠ°Π»Π»ΠΈΡΠ΅ΡΠΊΠΎΠ³ΠΎ Π»ΠΎΠΌΠ°, Π΄Π»Ρ ΠΎΠ±ΡΠ»ΡΠΆΠΈΠ²Π°Π½ΠΈΡ ΡΡΠ°Π½ΠΊΠΎΠ² ΠΏΠΎΠ½Π°Π΄ΠΎΠ±ΠΈΡΡΡ 2-3 ΡΠ°Π±ΠΎΡΠ½ΠΈΠΊΠ° Π±Π΅Π· ΠΊΠ²Π°Π»ΠΈΡΠΈΠΊΠ°ΡΠΈΠΈ.
ΠΡΠΎΠΌΠ΅ ΠΏΠΎΠΊΡΡΡΠ΅ΠΊ, Π½Π° ΡΡΠΎΠΌ ΠΎΠ±ΠΎΡΡΠ΄ΠΎΠ²Π°Π½ΠΈΠΈ ΠΌΠΎΠΆΠ½ΠΎ ΠΏΠ΅ΡΠ΅ΡΠ°Π±Π°ΡΡΠ²Π°ΡΡ Π΄ΡΡΠ³ΡΡ ΡΠ΅Π·ΠΈΠ½Ρ (ΡΡΠ°Π½ΡΠΏΠΎΡΡΠ΅ΡΠ½ΡΡ Π»Π΅Π½ΡΡ, ΠΊΠ°ΠΌΠ΅ΡΡ, ΠΏΡΠΎΡΠΈΠ²ΠΎΠ³Π°Π·Ρ). ΠΠ° Π²ΡΡ ΠΎΠ΄Π΅ ΠΏΠΎΠ»ΡΡΠ°Π΅ΡΡΡ ΠΊΡΠΎΡΠΊΠ° Ρ ΡΠ°Π·ΠΌΠ΅ΡΠ°ΠΌΠΈ ΠΎΡ 0,7 Π΄ΠΎ 4 ΠΌΠΌ, ΠΏΡΠΈ ΡΡΠΎΠΌ ΠΎΠ½Π° ΡΠΎΡΡΠ°Π²Π»ΡΠ΅Ρ 65-85% ΠΎΡ Π²ΡΠ΅ΠΉ ΠΌΠ°ΡΡΡ ΡΡΡΡΡ.
ΠΡΠ΄Π° ΠΏΡΠΈΠΌΠ΅Π½ΠΈΡΡ ΠΏΠΎΠ»ΡΡΠ΅Π½Π½ΠΎΠ΅ ΡΡΡΡΠ΅?
Π Π΅Π·ΠΈΠ½ΠΎΠ²ΡΡ ΠΊΡΠΎΡΠΊΡ ΠΌΠΎΠΆΠ½ΠΎ:
Π¦Π΅Π½Π° ΠΊΡΠΎΡΠΊΠΈ Π±ΡΠ΄Π΅Ρ Π·Π°Π²ΠΈΡΠ΅ΡΡ Π³Π»Π°Π²Π½ΡΠΌ ΠΎΠ±ΡΠ°Π·ΠΎΠΌ ΠΎΡ ΠΊΠ°ΡΠ΅ΡΡΠ²Π° ΡΡΡΡΡ, ΠΈ ΡΠΆΠ΅ Π²ΠΎ Π²ΡΠΎΡΡΡ ΠΎΡΠ΅ΡΠ΅Π΄Ρ β ΠΎΡ ΡΡΠ°ΠΊΡΠΈΠΈ.
ΠΠ°ΠΈΠ±ΠΎΠ»Π΅Π΅ ΠΏΠΎΠΏΡΠ»ΡΡΠ½ΠΎΠΉ ΡΠ²Π»ΡΠ΅ΡΡΡ ΠΊΡΠΎΡΠΊΠ°, ΡΡΠ°ΠΊΡΠΈΡ ΠΊΠΎΡΠΎΡΠΎΠΉ ΡΠΎΡΡΠ°Π²Π»ΡΠ΅Ρ 2-4 ΠΌΠΌ.
ΠΠ½Π° ΠΎΡΠ»ΠΈΡΠ½ΠΎ ΠΏΠΎΠ΄Ρ ΠΎΠ΄ΠΈΡ Π΄Π»Ρ ΡΠΎΠ·Π΄Π°Π½ΠΈΡ:
ΠΠΎΠΏΡΠ»ΡΡΠ½ΠΎΡΡΡ ΡΠ°ΠΊΠΎΠΉ ΠΊΡΠΎΡΠΊΠΈ Π²ΡΠ·Π²Π°Π½Π° ΡΠ΅ΠΌ, ΡΡΠΎ Π½Π° ΡΠΊΠ»Π΅ΠΈΠ²Π°Π½ΠΈΠ΅ Π΄Π°Π½Π½ΡΡ Π³ΡΠ°Π½ΡΠ» ΠΈΠ΄Π΅Ρ ΠΌΠΈΠ½ΠΈΠΌΠ°Π»ΡΠ½ΠΎΠ΅ ΠΊΠΎΠ»ΠΈΡΠ΅ΡΡΠ²ΠΎ ΠΊΠ»Π΅Ρ. Π ΠΏΠΎΠ»ΠΈΡΡΠ΅ΡΠ°Π½ΠΎΠ²ΠΎΠ΅ ΡΠ²ΡΠ·ΡΡΡΠ΅Π΅ Π²Π΅ΡΠ΅ΡΡΠ²ΠΎ ΠΈΠ½ΠΎΠ³Π΄Π° Π΄ΠΎΡΠΎΠΆΠ΅ ΠΊΡΠΎΡΠΊΠΈ Π² 5-8 ΡΠ°Π·.
ΠΠΈΠ΄Π΅ΠΎ ΠΏΠΎ ΡΠ΅ΠΌΠ΅
Π Π΄Π°Π½Π½ΠΎΠΌ Π²ΠΈΠ΄Π΅ΠΎ Π²Ρ ΠΌΠΎΠΆΠ΅ΡΠ΅ ΡΠ²ΠΈΠ΄Π΅ΡΡ, ΠΊΠ°ΠΊ ΠΈΠ·ΠΌΠ΅Π»ΡΡΠΈΡΡ ΡΠ΅Π·ΠΈΠ½Ρ ΠΈ ΡΠ΄Π΅Π»Π°ΡΡ ΠΊΡΠΎΡΠΊΡ Π² Π΄ΠΎΠΌΠ°ΡΠ½ΠΈΡ ΡΡΠ»ΠΎΠ²ΠΈΡΡ .
ΠΠ°ΠΊΠ»ΡΡΠ΅Π½ΠΈΠ΅
Π‘ΠΎΠ·Π΄Π°Π½ΠΈΠ΅ Π΄ΡΠΎΠ±ΠΈΠ»ΠΊΠΈ Π΄Π»Ρ ΡΠΈΠ½ ΡΠ²ΠΎΠΈΠΌΠΈ ΡΡΠΊΠ°ΠΌΠΈ β Ρ ΠΎΡΠΎΡΠ°Ρ ΠΈΠ΄Π΅Ρ Π΄Π»Ρ ΡΠ΅Ρ , ΠΊΡΠΎ Ρ ΠΎΡΠ΅Ρ ΡΠ΄Π΅Π»Π°ΡΡ ΡΠ΅Π·ΠΈΠ½ΠΎΠ²ΡΡ ΠΊΡΠΎΡΠΊΡ ΡΠ²ΠΎΠΈΠΌΠΈ ΡΡΠΊΠ°ΠΌΠΈ, Π½ΠΎ Π½Π΅ Π³ΠΎΡΠΎΠ² ΡΡΠ°ΡΠΈΡΡ Π΄Π΅ΡΡΡΠΊΠΈ ΡΡΡΡΡ Π΄ΠΎΠ»Π»Π°ΡΠΎΠ² Π½Π° ΠΎΠ±ΠΎΡΡΠ΄ΠΎΠ²Π°Π½ΠΈΠ΅.
Π‘ΠΎΠ·Π΄Π°ΡΡ ΠΈΠ·ΠΌΠ΅Π»ΡΡΠΈΡΠ΅Π»Ρ ΠΌΠΎΠΆΠ½ΠΎ ΠΏΡΠΈ Π½Π°Π»ΠΈΡΠΈΠΈ ΡΡΠΎΠ»ΡΡΠ½ΠΎΠΉ ΠΌΠ°ΡΡΠ΅ΡΡΠΊΠΎΠΉ, Π° ΡΠ°ΠΊΠΆΠ΅ ΠΎΠΏΡΠ΅Π΄Π΅Π»Π΅Π½Π½ΡΡ Π½Π°Π²ΡΠΊΠΎΠ² ΠΈ ΠΌΠ°ΡΠ΅ΡΠΈΠ°Π»ΠΎΠ², Π»ΠΈΠ±ΠΎ Π²ΠΎΡΠΏΠΎΠ»ΡΠ·ΠΎΠ²Π°ΡΡΡΡ ΡΡΠ»ΡΠ³Π°ΠΌΠΈ Π»ΡΠ΄Π΅ΠΉ, ΠΊΠΎΡΠΎΡΡΠ΅ Π½Π° ΡΡΠΎΠΌ ΡΠΏΠ΅ΡΠΈΠ°Π»ΠΈΠ·ΠΈΡΡΡΡΡΡ.
ΠΠΎΠ»ΡΡΠ΅Π½Π½ΡΡ Π² Π΄ΠΎΠΌΠ°ΡΠ½ΠΈΡ ΡΡΠ»ΠΎΠ²ΠΈΡΡ ΠΊΡΠΎΡΠΊΡ ΠΌΠΎΠΆΠ½ΠΎ ΠΈΡΠΏΠΎΠ»ΡΠ·ΠΎΠ²Π°ΡΡ Π΄Π»Ρ ΡΠ²ΠΎΠΈΡ Π½ΡΠΆΠ΄ ΠΈΠ»ΠΈ ΡΠ΅Π°Π»ΠΈΠ·ΠΎΠ²ΡΠ²Π°ΡΡ ΠΏΡΠ΅Π΄ΠΏΡΠΈΡΡΠΈΡΠΌ ΠΈ Π½Π°ΡΠ΅Π»Π΅Π½ΠΈΡ.
ΠΠΊΠΎΠ½ΡΠ°ΠΊΡΠ΅
Google+
ΠΠ΄Π½ΠΎΠΊΠ»Π°ΡΡΠ½ΠΈΠΊΠΈ
rcycle.net
Π£ΡΡΡΠΎΠΉΡΡΠ²ΠΎ Π΄Π»Ρ ΡΠΆΠΈΠ³Π°Π½ΠΈΡ ΡΠ²Π΅ΡΠ΄ΠΎΠ³ΠΎ ΡΠΎΠΏΠ»ΠΈΠ²Π° Π² ΠΏΡΠ»ΡΡΠΈΡΡΡΡΠ΅ΠΌ ΠΏΠΎΡΠΎΠΊΠ΅
ΠΠ·ΠΎΠ±ΡΠ΅ΡΠ΅Π½ΠΈΠ΅ ΠΎΡΠ½ΠΎΡΠΈΡΡΡ ΠΊ ΡΠ΅ΠΏΠ»ΠΎΡΠ½Π΅ΡΠ³Π΅ΡΠΈΠΊΠ΅ ΠΈ ΡΠΊΠΎΠ»ΠΎΠ³ΠΈΠΈ, Π² ΡΠ°ΡΡΠ½ΠΎΡΡΠΈ ΠΊ ΡΡΡΡΠΎΠΉΡΡΠ²Π°ΠΌ Π΄Π»Ρ ΡΠΆΠΈΠ³Π°Π½ΠΈΡ ΡΠ²Π΅ΡΠ΄ΡΡ ΠΌΠ°Π»ΠΎΡΠ΅Π°ΠΊΡΠΈΠΎΠ½Π½ΡΡ ΡΠΎΠΏΠ»ΠΈΠ², Π½Π°ΠΏΡΠΈΠΌΠ΅Ρ ΠΎΡΡΠ°Π±ΠΎΡΠ°Π½Π½ΡΡ ΡΠΈΠ½, ΠΈΠ»ΠΈ ΡΠ΅Π·ΠΈΠ½ΠΎΠ²ΡΡ ΠΎΡΡ ΠΎΠ΄ΠΎΠ² Ρ ΡΠ΅Π»ΡΡ ΡΡΠΈΠ»ΠΈΠ·Π°ΡΠΈΠΈ ΡΠ΅ΠΏΠ»Π°, ΠΏΡΠΈ ΡΠΎΠ΄Π΅ΡΠΆΠ°Π½ΠΈΠΈ Π² ΠΈΡ ΠΏΡΠΎΠ΄ΡΠΊΡΠ°Ρ ΡΠ³ΠΎΡΠ°Π½ΠΈΡ ΠΌΠ°Π»ΠΎΠΉ ΠΊΠΎΠ½ΡΠ΅Π½ΡΡΠ°ΡΠΈΠΈ ΠΊΠ°Π½ΡΠ΅ΡΠΎΠ³Π΅Π½Π½ΡΡ Π²Π΅ΡΠ΅ΡΡΠ².
ΠΠ·Π²Π΅ΡΡΠ½ΠΎ ΡΡΡΡΠΎΠΉΡΡΠ²ΠΎ Π΄Π»Ρ ΡΠΆΠΈΠ³Π°Π½ΠΈΡ ΡΠ΅Π·ΠΈΠ½ΠΎΡΠ΅Ρ Π½ΠΈΡΠ΅ΡΠΊΠΈΡ ΠΎΡΡ ΠΎΠ΄ΠΎΠ², ΡΠΎΠ΄Π΅ΡΠΆΠ°ΡΠ΅Π΅ ΡΠΈΠΊΠ»ΠΎΠ½, Π² ΠΊΠΎΡΠΎΡΠΎΠΌ ΠΊΡΡΠΏΠ½ΡΠ΅ ΡΠ°ΡΡΠΈΡΡ ΡΠΆΠΈΠ³Π°ΡΡΡΡ Π΄ΠΎ Π½Π΅ΠΊΠΎΡΠΎΡΠΎΠ³ΠΎ ΡΠ°Π·ΠΌΠ΅ΡΠ° ΠΈ Π²ΡΠ½ΠΎΡΡΡΡΡ ΠΏΠΎΡΠΎΠΊΠΎΠΌ, ΠΊΠ°ΠΌΠ΅ΡΡ Π²ΠΎΡΠΏΠ»Π°ΠΌΠ΅Π½Π΅Π½ΠΈΡ, ΡΠ΅Π·ΠΎΠ½Π°ΡΠΎΡΠ½ΡΡ ΡΡΡΠ±Ρ Π΄Π»Ρ Π΄ΠΎΠΆΠΈΠ³Π° Π½Π΅ΡΠ³ΠΎΡΠ΅Π²ΡΠΈΡ Π³ΠΎΡΡΡΠΈΡ ΡΠ»Π΅ΠΌΠ΅Π½ΡΠΎΠ² (Π‘Π±. ΠΠΈΠ±ΡΠ°ΡΠΈΠΎΠ½Π½ΠΎΠ΅ Π³ΠΎΡΠ΅Π½ΠΈΠ΅ Π² Π½Π΅ΠΊΠΎΡΠΎΡΡΡ ΠΌΠΎΠ΄Π΅Π»ΡΠ½ΡΡ ΡΡΡΡΠΎΠΉΡΡΠ²Π°Ρ . ΠΠ°Π·Π°Π½Ρ, ΠΈΠ·Π΄-Π²ΠΎ ΠΠΠ£, 1970, Ρ.148-149).
ΠΠ΅Π΄ΠΎΡΡΠ°ΡΠΊΠΎΠΌ Π²ΡΡΠ΅ΠΏΡΠΈΠ²Π΅Π΄Π΅Π½Π½ΠΎΠ³ΠΎ ΡΡΡΡΠΎΠΉΡΡΠ²Π° ΡΠ²Π»ΡΠ΅ΡΡΡ Π½Π΅ΠΎΠ±Ρ ΠΎΠ΄ΠΈΠΌΠΎΡΡΡ Π΄ΡΠΎΠ±Π»Π΅Π½ΠΈΡ ΡΠΈΠ½ Π½Π° ΠΊΡΡΠΊΠΈ, Π½Π΅ΡΡΡΠΎΠΉΡΠΈΠ²ΠΎΡΡΡ Π²ΠΈΠ±ΡΠ°ΡΠΈΠΎΠ½Π½ΠΎΠ³ΠΎ Π³ΠΎΡΠ΅Π½ΠΈΡ, ΡΠ²ΡΠ·Π°Π½Π½Π°Ρ Ρ Π½Π΅ΡΠ°Π²Π½ΠΎΠΌΠ΅ΡΠ½ΠΎΡΡΡΡ ΠΏΠΎΠ΄Π°ΡΠΈ ΡΠΎΠΏΠ»ΠΈΠ²Π° Π² ΠΊΠ°ΠΌΠ΅ΡΡ Π²ΠΎΡΠΏΠ»Π°ΠΌΠ΅Π½Π΅Π½ΠΈΡ, Π±ΠΎΠ»ΡΡΠΎΠΉ ΠΌΠ΅Ρ Π°Π½ΠΈΡΠ΅ΡΠΊΠΈΠΉ ΡΠ½ΠΎΡ Π²ΡΠ΅Π΄Π½ΡΡ ΠΏΡΠΎΠ΄ΡΠΊΡΠΎΠ² ΡΠ³ΠΎΡΠ°Π½ΠΈΡ ΠΈΠ· ΡΠ΅Π·ΠΎΠ½Π°ΡΠΎΡΠ½ΠΎΠΉ ΡΡΡΠ±Ρ Π² Π°ΡΠΌΠΎΡΡΠ΅ΡΡ.
ΠΠ·Π²Π΅ΡΡΠ½ΠΎ ΡΠ°ΠΊΠΆΠ΅ ΡΡΡΡΠΎΠΉΡΡΠ²ΠΎ, ΡΠΎΠ΄Π΅ΡΠΆΠ°ΡΠ΅Π΅ ΠΊΠ°ΠΌΠ΅ΡΡ Π²ΠΎΡΠΏΠ»Π°ΠΌΠ΅Π½Π΅Π½ΠΈΡ, ΠΏΡΠΈΠΌΡΠΊΠ°ΡΡΡΡ ΠΊ Π½Π΅ΠΉ ΡΠ΅Π·ΠΎΠ½Π°Π½ΡΠ½ΡΡ ΡΡΡΠ±Ρ, Π²ΠΎΠ·Π΄ΡΡ ΠΎΠ²ΠΎΠ΄Ρ, ΠΊΠ°ΠΌΠ΅ΡΡ ΠΏΡΠ΅Π΄Π²Π°ΡΠΈΡΠ΅Π»ΡΠ½ΠΎΠΉ ΡΠ΅ΠΏΠ»ΠΎΠ²ΠΎΠΉ ΠΏΠΎΠ΄Π³ΠΎΡΠΎΠ²ΠΊΠΈ ΡΠΎΠΏΠ»ΠΈΠ²Π° (ΠΠ‘ Π‘Π‘Π‘Π 237324, ΠΠΠ F23d 11/34, 1969, ΠΠ β8).
ΠΡΠΎ ΡΡΡΡΠΎΠΉΡΡΠ²ΠΎ ΠΈΠΌΠ΅Π΅Ρ ΡΠ°ΠΊΠΎΠΉ Π½Π΅Π΄ΠΎΡΡΠ°ΡΠΎΠΊ, ΠΊΠ°ΠΊ ΡΡΡΠ² Π²ΠΈΠ±ΡΠ°ΡΠΈΠΎΠ½Π½ΠΎΠ³ΠΎ Π³ΠΎΡΠ΅Π½ΠΈΡ, Π²ΠΎΠ·Π½ΠΈΠΊΠ°ΡΡΠΈΠΉ Π²ΡΠ»Π΅Π΄ΡΡΠ²ΠΈΠ΅ ΠΏΠ»ΠΎΡ ΠΎΠΉ ΡΠ΅ΡΠΌΠΈΡΠ΅ΡΠΊΠΎΠΉ ΠΎΠ±ΡΠ°Π±ΠΎΡΠΊΠΈ ΡΠΎΠΏΠ»ΠΈΠ²Π° Π² ΠΊΠ°ΠΌΠ΅ΡΠ΅, ΠΈΠ·-Π·Π° ΠΎΡΡΡΡΡΡΠ²ΠΈΡ Π²ΠΎΠ·ΠΌΠΎΠΆΠ½ΠΎΡΡΠΈ ΡΠ΅Π³ΡΠ»ΠΈΡΠΎΠ²Π°Π½ΠΈΡ ΠΏΠΎΠ΄Π°ΡΠΈ Π³ΠΎΡΡΡΠΈΡ ΡΠ»Π΅ΠΌΠ΅Π½ΡΠΎΠ² ΠΏΡΠΈ ΡΠΈΠ»ΡΠ½ΡΡ ΠΏΠΎΡΡΠ²Π°Ρ Π²Π΅ΡΡΠ°. ΠΡΠΈ ΡΡΡΠ²Π°Ρ ΠΏΡΠ»ΡΡΠ°ΡΠΈΠΉ ΠΏΠΎΡΠΎΠΊΠ° Π·ΠΎΠ½Π° Π²ΠΎΡΠΏΠ»Π°ΠΌΠ΅Π½Π΅Π½ΠΈΡ ΠΏΠ΅ΡΠ΅ΠΌΠ΅ΡΠ°Π΅ΡΡΡ Π² ΡΠ΅Π·ΠΎΠ½Π°Π½ΡΠ½ΡΡ ΡΡΡΠ±Ρ, Π° ΠΊΠΎΠ½ΡΡΡΡΠΊΡΠΈΡ ΡΡΡΡΠΎΠΉΡΡΠ²Π° Π½Π΅ ΠΏΠΎΠ·Π²ΠΎΠ»ΡΠ΅Ρ Π²Π΅ΡΠ½ΡΡΡ Π³ΠΎΡΠ΅Π½ΠΈΠ΅ Π² ΠΏΡΠ»ΡΡΠ°ΡΠΈΠΎΠ½Π½ΡΠΉ ΡΠ΅ΠΆΠΈΠΌ. ΠΡΠ»Π΅Π΄ΡΡΠ²ΠΈΠ΅ ΡΡΠΎΠ³ΠΎ ΡΠ΅Π·ΠΊΠΎ ΡΡ ΡΠ΄ΡΠ°ΡΡΡΡ ΡΠΊΠΎΠ»ΠΎΠ³ΠΈΡΠ΅ΡΠΊΠΈΠ΅ ΠΏΠ°ΡΠ°ΠΌΠ΅ΡΡΡ Π½Π° ΡΡΠ΅Π·Π΅ ΡΠ΅Π·ΠΎΠ½Π°Π½ΡΠ½ΠΎΠΉ ΡΡΡΠ±Ρ. ΠΠ°Π½Π½ΠΎΠ΅ ΡΡΡΡΠΎΠΉΡΡΠ²ΠΎ Π½Π΅ ΠΎΠ±Π΅ΡΠΏΠ΅ΡΠΈΠ²Π°Π΅Ρ Π²ΠΎΠ·ΠΌΠΎΠΆΠ½ΠΎΡΡΠΈ ΡΠ΄Π΅ΡΠΆΠΈΠ²Π°Π½ΠΈΡ ΠΌΠ΅Ρ Π°Π½ΠΈΡΠ΅ΡΠΊΠΈΡ ΠΏΡΠΈΠΌΠ΅ΡΠ΅ΠΉ, Π²ΡΠ½ΠΎΡΠΈΠΌΡΡ ΠΏΠΎΡΠΎΠΊΠΎΠΌ Π² ΠΎΠΊΡΡΠΆΠ°ΡΡΡΡ ΡΡΠ΅Π΄Ρ ΠΈ Π·Π°ΡΠΈΡΡ Π΅Π³ΠΎ ΠΎΡ ΡΠ΅ΠΏΠ»ΠΎΠ²ΠΎΠ³ΠΎ Π·Π°Π³ΡΡΠ·Π½Π΅Π½ΠΈΡ. ΠΠ°Π½Π½ΠΎΠ΅ ΡΡΡΡΠΎΠΉΡΡΠ²ΠΎ ΡΠ°ΠΊΠΆΠ΅ ΠΏΡΠ΅Π΄ΠΏΠΎΠ»Π°Π³Π°Π΅Ρ Π½Π΅ΠΎΠ±Ρ ΠΎΠ΄ΠΈΠΌΠΎΡΡΡ ΠΏΡΠ΅Π΄Π²Π°ΡΠΈΡΠ΅Π»ΡΠ½ΠΎΠΉ ΠΌΠ΅Ρ Π°Π½ΠΈΡΠ΅ΡΠΊΠΎΠΉ ΠΎΠ±ΡΠ°Π±ΠΎΡΠΊΠΈ ΡΠΎΠΏΠ»ΠΈΠ²Π° Ρ ΡΠ΅Π»ΡΡ Π΅Π³ΠΎ ΠΏΡΠ΅Π²ΡΠ°ΡΠ΅Π½ΠΈΡ Π² ΠΏΡΠ»Π΅Π²ΠΈΠ΄Π½ΡΡ ΡΠΎΡΠΌΡ, Π² ΡΠ΅Π·ΡΠ»ΡΡΠ°ΡΠ΅ ΡΠ΅Π³ΠΎ, Π΄Π°Π½Π½ΠΎΠ΅ ΡΡΡΡΠΎΠΉΡΡΠ²ΠΎ ΡΠ²Π»ΡΠ΅ΡΡΡ Π½Π΅ΡΡΡΠ΅ΠΊΡΠΈΠ²Π½ΡΠΌ ΠΈ ΠΏΡΠΈΠ²ΠΎΠ΄ΠΈΡ ΠΊ ΡΠ½ΠΈΠΆΠ΅Π½ΠΈΡ ΠΊΠΏΠ΄ Π°Π³ΡΠ΅Π³Π°ΡΠ°.
ΠΠ°ΠΈΠ±ΠΎΠ»Π΅Π΅ Π±Π»ΠΈΠ·ΠΊΠΈΠΌ, ΠΏΠΎ ΡΠ΅Ρ Π½ΠΈΡΠ΅ΡΠΊΠΎΠΉ ΡΡΡΠ½ΠΎΡΡΠΈ ΠΈ Π·Π°ΡΠ²Π»ΡΠ΅ΠΌΠΎΠΌΡ ΡΠ΅Ρ Π½ΠΈΡΠ΅ΡΠΊΠΎΠΌΡ ΡΠ΅ΡΠ΅Π½ΠΈΡ Π²ΡΠ±ΡΠ°Π½Π½ΠΎΠΌΡ Π² ΠΊΠ°ΡΠ΅ΡΡΠ²Π΅ ΠΏΡΠΎΡΠΎΡΠΈΠΏΠ°, ΡΠ²Π»ΡΠ΅ΡΡΡ Β«Π£ΡΡΡΠΎΠΉΡΡΠ²ΠΎ Π΄Π»Ρ ΡΠΆΠΈΠ³Π°Π½ΠΈΡ ΡΠΎΠΏΠ»ΠΈΠ² Π² ΠΏΡΠ»ΡΡΠΈΡΡΡΡΠ΅ΠΌ ΠΏΠΎΡΠΎΠΊΠ΅Β», ΡΠΎΠ΄Π΅ΡΠΆΠ°ΡΠ΅Π΅: ΠΊΠ°ΠΌΠ΅ΡΡ Π²ΠΎΡΠΏΠ»Π°ΠΌΠ΅Π½Π΅Π½ΠΈΡ, ΠΊΠ°ΠΌΠ΅ΡΡ ΠΏΡΠ΅Π΄Π²Π°ΡΠΈΡΠ΅Π»ΡΠ½ΠΎΠΉ ΡΠ΅ΠΏΠ»ΠΎΠ²ΠΎΠΉ ΠΏΠΎΠ΄Π³ΠΎΡΠΎΠ²ΠΊΠΈ ΡΠΎΠΏΠ»ΠΈΠ²Π° (Π±ΡΠ½ΠΊΠ΅Ρ), ΠΊΡΡΡΠΊΡ ΠΊΠ°ΠΌΠ΅ΡΡ ΠΏΡΠ΅Π΄Π²Π°ΡΠΈΡΠ΅Π»ΡΠ½ΠΎΠΉ ΡΠ΅ΠΏΠ»ΠΎΠ²ΠΎΠΉ ΠΏΠΎΠ΄Π³ΠΎΡΠΎΠ²ΠΊΠΈ ΡΠΎΠΏΠ»ΠΈΠ²Π°, Π²ΠΎΠ·Π΄ΡΡ ΠΎΠ²ΠΎΠ΄Ρ, ΡΠ΅Π·ΠΎΠ½Π°ΡΠΎΡΠ½ΡΡ ΡΡΡΠ±Ρ, ΡΠΎΡΡΠΎΡΡΡΡ ΠΈΠ· Π΄Π²ΡΡ ΡΠΎΡΡΠ°Π²Π½ΡΡ ΡΠ°ΡΡΠ΅ΠΉ, ΠΊΠΎΠ»ΠΎΡΠ½ΠΈΠΊ, ΡΡΡΠ±ΡΠ»ΠΈΠ·Π°ΡΠΎΡ, Π·ΠΎΠ»ΡΠ½ΠΈΠΊ, Π΄ΠΈΡΡΡΠ·ΠΈΠΎΠ½Π½ΡΡ Π³ΠΎΡΠ΅Π»ΠΊΡ (ΠΠ°ΡΠ΅Π½Ρ Π½Π° ΠΏΠΎΠ»Π΅Π·Π½ΡΡ ΠΌΠΎΠ΄Π΅Π»Ρ Π Π€ β11302, ΠΠΠ F23D 11/34, ΠΎΠΏΡΠ±Π»ΠΈΠΊΠΎΠ²Π°Π½ 16.09.1999).
ΠΠ΅Π΄ΠΎΡΡΠ°ΡΠΊΠ°ΠΌΠΈ Π΄Π°Π½Π½ΠΎΠ³ΠΎ ΡΠ΅Ρ Π½ΠΈΡΠ΅ΡΠΊΠΎΠ³ΠΎ ΡΠ΅ΡΠ΅Π½ΠΈΡ ΡΠ²Π»ΡΡΡΡΡ: 1) ΠΏΡΠΈ ΠΌΠ½ΠΎΠ³ΠΎΠΊΡΠ°ΡΠ½ΠΎΠΉ Π·Π°Π³ΡΡΠ·ΠΊΠ΅ ΡΡΡΠ°Π½ΠΎΠ²ΠΊΠΈ ΡΠ²Π΅ΡΠ΄ΡΠΌ ΡΠΎΠΏΠ»ΠΈΠ²ΠΎΠΌ ΠΈΠ·-Π·Π° ΡΠΈΠ·ΠΈΡΠ΅ΡΠΊΠΎΠ³ΠΎ ΡΠ²Π»Π΅Π½ΠΈΡ ΠΊΠΎΠ½Π΄Π΅Π½ΡΠ°ΡΠΈΠΈ Π½Π° Π²Π½ΡΡΡΠ΅Π½Π½Π΅ΠΉ ΡΡΠ΅Π½ΠΊΠ΅ ΠΊΠ°ΠΌΠ΅ΡΡ ΠΏΡΠ΅Π΄Π²Π°ΡΠΈΡΠ΅Π»ΡΠ½ΠΎΠΉ ΡΠ΅ΠΏΠ»ΠΎΠ²ΠΎΠΉ ΠΏΠΎΠ΄Π³ΠΎΡΠΎΠ²ΠΊΠΈ ΡΠΎΠΏΠ»ΠΈΠ²Π° ΠΏΡΠΎΠΈΡΡ ΠΎΠ΄ΠΈΡ ΠΎΡΠ°ΠΆΠ΄Π΅Π½ΠΈΠ΅ Π»Π΅ΡΡΡΠΈΡ ΠΊΠΎΠΌΠΏΠΎΠ½Π΅Π½ΡΠΎΠ² (ΡΠΌΠΎΠ»ΠΎΠΎΠ±ΡΠ°Π·Π½ΠΎΠΉ ΠΌΠ°ΡΡΡ). ΠΡΠ»Π΅Π΄ΡΡΠ²ΠΈΠ΅ ΡΡΠΎΠ³ΠΎ ΠΎΠ±ΡΠ΅ΠΌ ΠΊΠ°ΠΌΠ΅ΡΡ ΡΠΌΠ΅Π½ΡΡΠ°Π΅ΡΡΡ, ΡΡΠΎ ΠΏΡΠ΅ΠΏΡΡΡΡΠ²ΡΠ΅Ρ Π·Π°ΠΊΠ»Π°Π΄ΠΊΠ΅ ΠΎΡΠ΅ΡΠ΅Π΄Π½ΠΎΠΉ ΠΏΠ°ΡΡΠΈΠΈ ΡΠ²Π΅ΡΠ΄ΠΎΠ³ΠΎ ΡΠΎΠΏΠ»ΠΈΠ²Π°. ΠΡΠΎΠΌΠ΅ ΡΠΎΠ³ΠΎ, Π½Π΅ ΠΎΠ±Π΅ΡΠΏΠ΅ΡΠΈΠ²Π°Π΅ΡΡΡ ΠΏΠΎΠ»Π½Π°Ρ ΠΏΠΎΠΆΠ°ΡΠΎΠ±Π΅Π·ΠΎΠΏΠ°ΡΠ½ΠΎΡΡΡ, ΠΊΠΎΡΠΎΡΠ°Ρ ΡΠ²ΡΠ·Π°Π½Π° Ρ Π½Π°ΠΊΠΎΠΏΠ»Π΅Π½ΠΈΠ΅ΠΌ Π»Π΅Π³ΠΊΠΎΠ²ΠΎΡΠΏΠ»Π°ΠΌΠ΅Π½ΡΡΡΠΈΡ ΡΡ Π³ΠΎΡΡΡΠΈΡ (ΡΠΌΠΎΠ»ΠΎΠΎΠ±ΡΠ°Π·Π½ΡΡ ) Π²Π΅ΡΠ΅ΡΡΠ² Π½Π° Π²Π½ΡΡΡΠ΅Π½Π½ΠΈΡ ΡΡΠ΅Π½ΠΊΠ°Ρ ΠΊΠ°ΠΌΠ΅ΡΡ ΠΏΡΠ΅Π΄Π²Π°ΡΠΈΡΠ΅Π»ΡΠ½ΠΎΠΉ ΡΠ΅ΠΏΠ»ΠΎΠ²ΠΎΠΉ ΠΏΠΎΠ΄Π³ΠΎΡΠΎΠ²ΠΊΠΈ ΡΠΎΠΏΠ»ΠΈΠ²Π°; 2) ΠΈΠ·-Π·Π° ΠΊΠΎΠ½ΡΡΡΡΠΊΡΠΈΠ²Π½ΠΎΠΉ ΠΎΡΠΎΠ±Π΅Π½Π½ΠΎΡΡΠΈ ΡΡΡΠ°Π½ΠΎΠ²ΠΊΠΈ, Π½Π΅ ΠΎΠ±Π΅ΡΠΏΠ΅ΡΠΈΠ²Π°Π΅ΡΡΡ Π·Π°ΡΠΈΡΠ° ΠΎΠΊΡΡΠΆΠ°ΡΡΠ΅ΠΉ ΡΡΠ΅Π΄Ρ ΠΎΡ Π²ΡΠ΅Π΄Π½ΡΡ Π²ΡΠ±ΡΠΎΡΠΎΠ², ΡΠ°ΠΊ ΠΊΠ°ΠΊ ΠΏΡΠΈ Π²ΡΡΠΎΠΊΠΈΡ ΡΠ΅ΠΌΠΏΠ΅ΡΠ°ΡΡΡΠ°Ρ (Π±ΠΎΠ»Π΅Π΅ 450Β°Π‘) Π² ΠΊΠ°ΠΌΠ΅ΡΠ΅ ΠΏΡΠ΅Π΄Π²Π°ΡΠΈΡΠ΅Π»ΡΠ½ΠΎΠΉ ΡΠ΅ΠΏΠ»ΠΎΠ²ΠΎΠΉ ΠΏΠΎΠ΄Π³ΠΎΡΠΎΠ²ΠΊΠΈ ΡΠΎΠΏΠ»ΠΈΠ²Π° ΠΎΠ±ΡΠ°Π·ΡΡΡΡΡ ΡΠΎΠ΅Π΄ΠΈΠ½Π΅Π½ΠΈΡ ΡΠ΅ΡΡ, ΠΊΠΎΡΠΎΡΡΠ΅ Π²ΠΌΠ΅ΡΡΠ΅ Ρ Π²ΡΡ ΠΎΠ΄ΡΡΠΈΠΌΠΈ ΠΏΡΠΎΠ΄ΡΠΊΡΠ°ΠΌΠΈ ΡΠ³ΠΎΡΠ°Π½ΠΈΡ ΠΏΠΎΠΏΠ°Π΄Π°ΡΡ Π² Π°ΡΠΌΠΎΡΡΠ΅ΡΡ; 3) ΠΏΡΠΎΠ΄ΡΠΊΡΠΎΠΌ ΠΏΠ΅ΡΠ΅ΡΠ°Π±ΠΎΡΠΊΠΈ ΡΠΈΠ½ Π² ΡΡΡΡΠΎΠΉΡΡΠ²Π΅ Π΄Π»Ρ ΡΠΆΠΈΠ³Π°Π½ΠΈΡ ΡΠ²Π΅ΡΠ΄ΠΎΠ³ΠΎ ΡΠΎΠΏΠ»ΠΈΠ²Π° Π² ΠΏΡΠ»ΡΡΠΈΡΡΡΡΠ΅ΠΌ ΠΏΠΎΡΠΎΠΊΠ΅ ΡΠ²Π»ΡΠ΅ΡΡΡ ΡΠ²Π΅ΡΠ΄ΡΠΉ ΠΎΡΡΠ°ΡΠΎΠΊ Π² Π²ΠΈΠ΄Π΅ ΡΠΎΠΆΠΆΠ΅Π½Π½ΠΎΠΉ ΡΠ°ΠΆΠΈ, ΡΡΠΎ ΠΏΡΠΈΠ²ΠΎΠ΄ΠΈΡ ΠΊ ΠΏΠΎΡΠ΅ΡΠ΅ ΡΠ΅Π½Π½ΠΎΠ³ΠΎ ΠΌΠ°ΡΠ΅ΡΠΈΠ°Π»Π° Π² Π²ΠΈΠ΄Π΅ ΠΈΠ½Π΅ΡΡΠ½ΠΎΠ³ΠΎ ΠΏΠΎΡΠΎΡΠΊΠ°. ΠΡΠ΅ ΡΡΠΎ Π²Π΅Π΄Π΅Ρ ΠΊ ΡΠ½ΠΈΠΆΠ΅Π½ΠΈΡ ΡΠΊΠΎΠ»ΠΎΠ³ΠΈΡΠ½ΠΎΡΡΠΈ, Π±Π΅Π·ΠΎΠΏΠ°ΡΠ½ΠΎΡΡΠΈ, ΡΠΊΠΎΠ½ΠΎΠΌΠΈΡΠ½ΠΎΡΡΠΈ, ΠΈ Π² ΡΠ΅Π»ΠΎΠΌ – Π½Π΅ΡΡΡΠ΅ΠΊΡΠΈΠ²Π½ΠΎΡΡΠΈ ΡΡΡΠ°Π½ΠΎΠ²ΠΊΠΈ.
Π Π΅ΡΠ°Π΅ΠΌΠΎΠΉ Π·Π°Π΄Π°ΡΠ΅ΠΉ ΠΈΠ·ΠΎΠ±ΡΠ΅ΡΠ΅Π½ΠΈΡ ΡΠ²Π»ΡΠ΅ΡΡΡ ΡΠΎΠ·Π΄Π°Π½ΠΈΠ΅ Π²ΡΡΠΎΠΊΠΎΡΡΡΠ΅ΠΊΡΠΈΠ²Π½ΠΎΠΉ ΡΡΡΠ°Π½ΠΎΠ²ΠΊΠΈ, ΠΎΠ±Π΅ΡΠΏΠ΅ΡΠΈΠ²Π°ΡΡΠ΅ΠΉ ΠΏΠΎΠΆΠ°ΡΠΎΠ±Π΅Π·ΠΎΠΏΠ°ΡΠ½ΠΎΡΡΡ ΠΈ ΠΏΠΎΠ»Π½ΠΎΡΡ ΡΠ³ΠΎΡΠ°Π½ΠΈΡ ΠΏΡΠΎΡΠ΅ΡΡΠ° ΡΡΠΈΠ»ΠΈΠ·Π°ΡΠΈΠΈ, Ρ ΠΎΠ΄Π½ΠΎΠ²ΡΠ΅ΠΌΠ΅Π½Π½ΡΠΌ ΠΏΠΎΠ²ΡΡΠ΅Π½ΠΈΠ΅ΠΌ ΡΠΊΠΎΠ»ΠΎΠ³ΠΈΡΠ½ΠΎΡΡΠΈ ΠΈ ΡΠΊΠΎΠ½ΠΎΠΌΠΈΡΠ½ΠΎΡΡΠΈ.
Π’Π΅Ρ Π½ΠΈΡΠ΅ΡΠΊΠΈΠΌ ΡΠ΅Π·ΡΠ»ΡΡΠ°ΡΠΎΠΌ Π·Π°ΡΠ²Π»ΡΠ΅ΠΌΠΎΠ³ΠΎ ΡΠ΅Ρ Π½ΠΈΡΠ΅ΡΠΊΠΎΠ³ΠΎ ΡΠ΅ΡΠ΅Π½ΠΈΡ ΡΠ²Π»ΡΠ΅ΡΡΡ ΡΠΎΠ·Π΄Π°Π½ΠΈΠ΅ Π²ΡΡΠΎΠΊΠΎΡΡΡΠ΅ΠΊΡΠΈΠ²Π½ΠΎΠΉ ΡΠΊΠΎΠ½ΠΎΠΌΠΈΡΠ΅ΡΠΊΠΈ ΠΈ ΡΠΊΠΎΠ»ΠΎΠ³ΠΈΡΠ΅ΡΠΊΠΈ Π±Π΅Π·ΠΎΠΏΠ°ΡΠ½ΠΎΠΉ ΡΡΡΠ°Π½ΠΎΠ²ΠΊΠΈ Π΄Π»Ρ ΡΡΠΈΠ»ΠΈΠ·Π°ΡΠΈΠΈ ΡΠ²Π΅ΡΠ΄ΠΎΠ³ΠΎ ΡΠΎΠΏΠ»ΠΈΠ²Π°, Π² ΡΠ°ΡΡΠ½ΠΎΡΡΠΈ, ΠΈΠ·Π½ΠΎΡΠ΅Π½Π½ΡΡ ΡΠΈΠ½.
Π£ΠΊΠ°Π·Π°Π½Π½ΡΠΉ ΡΠ΅Ρ Π½ΠΈΡΠ΅ΡΠΊΠΈΠΉ ΡΠ΅Π·ΡΠ»ΡΡΠ°Ρ Π΄ΠΎΡΡΠΈΠ³Π°Π΅ΡΡΡ ΡΠ΅ΠΌ, ΡΡΠΎ ΡΡΡΡΠΎΠΉΡΡΠ²ΠΎ Π΄Π»Ρ ΡΠΆΠΈΠ³Π°Π½ΠΈΡ ΡΠ²Π΅ΡΠ΄ΠΎΠ³ΠΎ ΡΠΎΠΏΠ»ΠΈΠ²Π° Π² ΠΏΡΠ»ΡΡΠΈΡΡΡΡΠ΅ΠΌ ΠΏΠΎΡΠΎΠΊΠ΅, ΡΠΎΠ΄Π΅ΡΠΆΠ°ΡΠ΅Π΅ ΠΊΠ°ΠΌΠ΅ΡΡ Π²ΠΎΡΠΏΠ»Π°ΠΌΠ΅Π½Π΅Π½ΠΈΡ, ΠΊΠ°ΠΌΠ΅ΡΡ ΠΏΡΠ΅Π΄Π²Π°ΡΠΈΡΠ΅Π»ΡΠ½ΠΎΠΉ ΡΠ΅ΠΏΠ»ΠΎΠ²ΠΎΠΉ ΠΏΠΎΠ΄Π³ΠΎΡΠΎΠ²ΠΊΠΈ ΡΠΎΠΏΠ»ΠΈΠ²Π°, ΠΊΡΡΡΠΊΡ ΠΊΠ°ΠΌΠ΅ΡΡ ΠΏΡΠ΅Π΄Π²Π°ΡΠΈΡΠ΅Π»ΡΠ½ΠΎΠΉ ΡΠ΅ΠΏΠ»ΠΎΠ²ΠΎΠΉ ΠΏΠΎΠ΄Π³ΠΎΡΠΎΠ²ΠΊΠΈ ΡΠΎΠΏΠ»ΠΈΠ²Π°, Π²ΠΎΠ·Π΄ΡΡ ΠΎΠ²ΠΎΠ΄, ΡΠ΅Π·ΠΎΠ½Π°ΡΠΎΡΠ½ΡΡ ΡΡΡΠ±Ρ, ΡΠΎΡΡΠΎΡΡΡΡ ΠΈΠ· Π΄Π²ΡΡ ΡΠ°ΡΡΠ΅ΠΉ (Π²Π΅ΡΡ Π½Π΅ΠΉ ΠΈ Π½ΠΈΠΆΠ½Π΅ΠΉ) ΠΈ ΠΏΡΠΈΠΌΠΊΠ½ΡΡΡΡ ΠΊ ΠΊΠ°ΠΌΠ΅ΡΠ΅ Π²ΠΎΡΠΏΠ»Π°ΠΌΠ΅Π½Π΅Π½ΠΈΡ, ΠΎΠ±ΡΠ°Π·ΡΡ ΠΊΠΎΠ»ΡΡΠ΅Π²ΠΎΠΉ Π·Π°Π·ΠΎΡ ΠΌΠ΅ΠΆΠ΄Ρ Π΅Π΅ Π²Π΅ΡΡ Π½ΠΈΠΌ ΠΈ Π½ΠΈΠΆΠ½ΠΈΠΌ ΡΠ°ΡΡΡΠΌΠΈ, ΡΠ΅ΡΡΠ°ΡΡΠΉ ΡΡΡΠ±ΡΠ»ΠΈΠ·Π°ΡΠΎΡ, ΡΠΎΡΡΠΎΡΡΠΈΠΉ ΠΈΠ· Π½Π΅ΡΠΊΠΎΠ»ΡΠΊΠΈΡ ΡΠΎΡΡΠ°Π²Π½ΡΡ ΡΠ°ΡΡΠ΅ΠΉ, ΠΊΠΎΠ»ΠΎΡΠ½ΠΈΠΊ, ΠΌΠ½ΠΎΠ³ΠΎΡΠΎΠΏΠ»ΠΎΠ²ΡΡ Π΄ΠΈΡΡΡΠ·ΠΈΠΎΠ½Π½ΡΡ Π³ΠΎΡΠ΅Π»ΠΊΡ, ΡΠ±ΠΎΡΠ½ΠΈΠΊ ΡΠ²Π΅ΡΠ΄ΡΡ ΠΎΡΡ ΠΎΠ΄ΠΎΠ², ΡΠ±ΠΎΡΠ½ΠΈΠΊ ΠΈΠ½Π΅ΡΡΠ½ΠΎΠ³ΠΎ ΠΌΠ°ΡΠ΅ΡΠΈΠ°Π»Π°, ΡΠ½Π°Π±ΠΆΠ΅Π½ΠΎ Π³Π°Π·ΠΎΠΎΡΠ²ΠΎΠ΄ΡΡΠ΅ΠΉ ΡΡΡΠ±ΠΎΠΉ, Π²Π΅ΡΡ Π½ΠΈΠΉ ΡΡΠ΅Π· ΠΊΠΎΡΠΎΡΠΎΠΉ ΡΠ°ΡΠΏΠΎΠ»ΠΎΠΆΠ΅Π½ Π² ΠΊΠ°ΠΌΠ΅ΡΠ΅ ΠΏΡΠ΅Π΄Π²Π°ΡΠΈΡΠ΅Π»ΡΠ½ΠΎΠΉ ΡΠ΅ΠΏΠ»ΠΎΠ²ΠΎΠΉ ΠΏΠΎΠ΄Π³ΠΎΡΠΎΠ²ΠΊΠΈ ΡΠΎΠΏΠ»ΠΈΠ²Π° Π½Π° ΡΠ°ΡΡΡΠΎΡΠ½ΠΈΠΈ 2-3 Π΄ΠΈΠ°ΠΌΠ΅ΡΡΠ° ΡΡΠΎΠΉ ΡΡΡΠ±Ρ ΠΎΡ Π½ΠΈΠΆΠ½Π΅ΠΉ ΡΠ°ΡΡΠΈ ΠΊΡΡΡΠΊΠΈ ΠΊΠ°ΠΌΠ΅ΡΡ ΠΏΡΠ΅Π΄Π²Π°ΡΠΈΡΠ΅Π»ΡΠ½ΠΎΠΉ ΡΠ΅ΠΏΠ»ΠΎΠ²ΠΎΠΉ ΠΏΠΎΠ΄Π³ΠΎΡΠΎΠ²ΠΊΠΈ ΡΠΎΠΏΠ»ΠΈΠ²Π°, Π΄ΡΡΠ³ΠΎΠΉ ΠΊΠΎΠ½Π΅Ρ ΡΠ°ΡΠΏΠΎΠ»ΠΎΠΆΠ΅Π½ Π² Π½ΠΈΠΆΠ½Π΅ΠΉ ΡΠ°ΡΡΠΈ ΡΠ΅Π·ΠΎΠ½Π°ΡΠΎΡΠ½ΠΎΠΉ ΡΡΡΠ±Ρ ΠΈ Π²Π²Π΅Π΄Π΅Π½Π° Π°Π²ΡΠΎΠΌΠ°ΡΠΈΡΠ΅ΡΠΊΠ°Ρ ΡΠΈΡΡΠ΅ΠΌΠ° ΡΠ΅Π³ΡΠ»ΠΈΡΠΎΠ²Π°Π½ΠΈΡ ΡΠ΅ΠΌΠΏΠ΅ΡΠ°ΡΡΡΡ ΡΠ΅ΡΠΌΠΈΡΠ΅ΡΠΊΠΎΠ³ΠΎ ΡΠ°Π·Π»ΠΎΠΆΠ΅Π½ΠΈΡ ΡΠ΅Π·ΠΈΠ½Ρ, Ρ ΡΠ΅ΡΠΌΠΎΠ΄Π°ΡΡΠΈΠΊΠΎΠΌ ΡΠΈΡΡΠ΅ΠΌΡ ΡΠ΅Π³ΡΠ»ΠΈΡΠΎΠ²Π°Π½ΠΈΡ ΡΠ΅ΠΌΠΏΠ΅ΡΠ°ΡΡΡΡ, ΠΎΠ΄ΠΈΠ½ ΠΊΠΎΠ½Π΅Ρ ΠΊΠΎΡΠΎΡΠΎΠ³ΠΎ ΠΏΡΠΈΠΊΡΠ΅ΠΏΠ»Π΅Π½ ΠΊ ΠΊΠ°ΠΌΠ΅ΡΠ΅ Π²ΠΎΡΠΏΠ»Π°ΠΌΠ΅Π½Π΅Π½ΠΈΡ, Π° Π²ΡΠΎΡΠΎΠΉ ΠΊΠΎΠ½Π΅Ρ ΡΠ°ΡΠΏΠΎΠ»ΠΎΠΆΠ΅Π½ Π½Π°ΠΏΡΠΎΡΠΈΠ² Π²ΠΎΠ·Π΄ΡΡ ΠΎΠ²ΠΎΠ΄Π° Ρ Π²ΠΎΠ·ΠΌΠΎΠΆΠ½ΠΎΡΡΡΡ ΡΠΎΠ΅Π΄ΠΈΠ½Π΅Π½ΠΈΡ ΠΈ ΡΠ΅Π³ΡΠ»ΠΈΡΠΎΠ²Π°Π½ΠΈΡ Π΅Π³ΠΎ ΠΏΡΠΎΡ ΠΎΠ΄Π½ΠΎΠ³ΠΎ ΡΠ΅ΡΠ΅Π½ΠΈΡ, ΠΏΡΠΈΡΠ΅ΠΌ Π²ΠΎΠ·Π΄ΡΡ ΠΎΠ²ΠΎΠ΄ Π²ΡΠΏΠΎΠ»Π½Π΅Π½ Π² Π²ΠΈΠ΄Π΅ Π°ΡΡΠΎΠ΄ΠΈΠ½Π°ΠΌΠΈΡΠ΅ΡΠΊΠΎΠ³ΠΎ ΠΊΠ»Π°ΠΏΠ°Π½Π° Ρ ΠΈΠ·ΠΌΠ΅Π½ΡΠ΅ΠΌΡΠΌ ΠΏΡΠΎΡ ΠΎΠ΄Π½ΡΠΌ ΡΠ΅ΡΠ΅Π½ΠΈΠ΅ΠΌ, ΠΎΠ±Π΅ΡΠΏΠ΅ΡΠΈΠ²Π°ΡΡΠΈΠΌ ΠΏΠΎΠ΄Π΄Π΅ΡΠΆΠ°Π½ΠΈΠ΅ Π² ΠΊΠ°ΠΌΠ΅ΡΠ΅ Π²ΠΎΡΠΏΠ»Π°ΠΌΠ΅Π½Π΅Π½ΠΈΡ ΠΈ Π² ΠΊΠ°ΠΌΠ΅ΡΠ΅ ΠΏΡΠ΅Π΄Π²Π°ΡΠΈΡΠ΅Π»ΡΠ½ΠΎΠΉ ΡΠ΅ΠΏΠ»ΠΎΠ²ΠΎΠΉ ΠΏΠΎΠ΄Π³ΠΎΡΠΎΠ²ΠΊΠΈ ΡΠΎΠΏΠ»ΠΈΠ²Π° Π·Π°Π΄Π°Π½Π½ΠΎΠΉ ΡΠ΅ΠΌΠΏΠ΅ΡΠ°ΡΡΡΡ Π³Π°Π·ΠΎΠ² Π² Π°Π²ΡΠΎΠΌΠ°ΡΠΈΡΠ΅ΡΠΊΠΎΠΌ ΡΠ΅ΠΆΠΈΠΌΠ΅ ΠΈ ΡΠ΅ΡΠΌΠΈΡΠ΅ΡΠΊΠΎΠ΅ ΡΠ°Π·Π»ΠΎΠΆΠ΅Π½ΠΈΠ΅ ΠΎΡΡ ΠΎΠ΄ΠΎΠ² ΡΠ΅Π·ΠΈΠ½ΠΎΡΠ΅Ρ Π½ΠΈΡΠ΅ΡΠΊΠΈΡ ΠΈΠ·Π΄Π΅Π»ΠΈΠΉ Ρ Π²ΠΎΠ·ΠΌΠΎΠΆΠ½ΠΎΡΡΡΡ Π²ΡΠ΄Π΅Π»Π΅Π½ΠΈΡ Π»Π΅Π³ΠΊΠΈΡ ΡΡΠ°ΠΊΡΠΈΠΉ Π΄Π»Ρ Π΄Π°Π»ΡΠ½Π΅ΠΉΡΠ΅Π³ΠΎ ΡΠΆΠΈΠ³Π°Π½ΠΈΡ, ΠΏΡΠΈΡΠ΅ΠΌ Π² ΡΠ±ΠΎΡΠ½ΠΈΠΊΠ΅ ΠΈΠ½Π΅ΡΡΠ½ΠΎΠ³ΠΎ ΠΌΠ°ΡΠ΅ΡΠΈΠ°Π»Π° ΡΠ°Π·ΠΌΠ΅ΡΠ΅Π½Π° ΡΠΈΡΡΠ΅ΠΌΠ° ΡΠ½ΠΈΠΆΠ΅Π½ΠΈΡ ΡΠ΅ΠΌΠΏΠ΅ΡΠ°ΡΡΡΡ ΠΈΠ½Π΅ΡΡΠ½ΠΎΠ³ΠΎ ΠΌΠ°ΡΠ΅ΡΠΈΠ°Π»Π°, ΠΊΠΎΡΠΎΡΠ°Ρ Π²ΡΠΏΠΎΠ»Π½Π΅Π½Π° Π² Π²ΠΈΠ΄Π΅ Π³ΡΡΠΏΠΏΡ ΡΠΎΡΡΡΠ½ΠΎΠΊ, ΡΠ°ΡΠΏΠΎΠ»ΠΎΠΆΠ΅Π½Π½ΡΡ ΡΠΈΠΌΠΌΠ΅ΡΡΠΈΡΠ½ΠΎ ΠΏΠΎ Π΄ΠΈΠ°ΠΌΠ΅ΡΡΡ ΡΠ±ΠΎΡΠ½ΠΈΠΊΠ° ΠΈΠ½Π΅ΡΡΠ½ΠΎΠ³ΠΎ ΠΌΠ°ΡΠ΅ΡΠΈΠ°Π»Π°, Π° ΡΠΎΡΡΡΠ½ΠΊΠΈ ΡΡΡΠ°Π½ΠΎΠ²Π»Π΅Π½Ρ Π² ΠΊΠΎΠ»ΠΈΡΠ΅ΡΡΠ²Π΅, ΠΎΠΏΡΠ΅Π΄Π΅Π»ΡΠ΅ΠΌΠΎΠΌ ΠΎΠ±ΡΠ΅ΠΌΠΎΠΌ ΠΎΡ Π»Π°ΠΆΠ΄Π°Π΅ΠΌΠΎΠ³ΠΎ ΠΈΠ½Π΅ΡΡΠ½ΠΎΠ³ΠΎ ΠΌΠ°ΡΠ΅ΡΠΈΠ°Π»Π°.
ΠΠΎΠ²ΡΠΌ Π² ΡΡΡΡΠΎΠΉΡΡΠ²Π΅ ΡΠ²Π»ΡΠ΅ΡΡΡ:
ΠΡΠ΅Π΄Π»Π°Π³Π°Π΅ΠΌΠΎΠ΅ ΡΡΡΡΠΎΠΉΡΡΠ²ΠΎ ΠΏΠΎΠ·Π²ΠΎΠ»ΡΠ΅Ρ ΠΏΠΎΠ΄ΠΎΠ±ΡΠ°ΡΡ ΠΎΠΏΡΠΈΠΌΠ°Π»ΡΠ½ΡΠΉ, ΡΠΊΠΎΠ½ΠΎΠΌΠΈΡΠ΅ΡΠΊΠΈ Π²ΡΠ³ΠΎΠ΄Π½ΡΠΉ ΡΠ΅ΠΆΠΈΠΌ ΡΠ°Π±ΠΎΡΡ ΡΡΡΠ°Π½ΠΎΠ²ΠΊΠΈ Ρ ΡΠΈΠΊΠ»ΠΈΡΠ΅ΡΠΊΠΎΠΉ ΠΏΠΎΠ΄Π°ΡΠ΅ΠΉ ΡΠ²Π΅ΡΠ΄ΠΎΠ³ΠΎ ΡΠΎΠΏΠ»ΠΈΠ²Π° Π·Π° ΡΡΠ΅Ρ ΠΎΡΠ²ΠΎΠ΄Π° ΡΠ΅ΡΠ΅Π· Π³Π°Π·ΠΎΠΎΡΠ²ΠΎΠ΄ΡΡΡΡ ΡΡΡΠ±Ρ ΠΎΠ±ΡΠ°Π·ΡΡΡΠΈΡ ΡΡ Π² ΠΊΠ°ΠΌΠ΅ΡΠ΅ ΠΏΡΠ΅Π΄Π²Π°ΡΠΈΡΠ΅Π»ΡΠ½ΠΎΠΉ ΡΠ΅ΠΏΠ»ΠΎΠ²ΠΎΠΉ ΠΏΠΎΠ΄Π³ΠΎΡΠΎΠ²ΠΊΠΈ ΡΠΎΠΏΠ»ΠΈΠ²Π° ΠΏΡΠΎΠ΄ΡΠΊΡΠΎΠ² ΡΠ³ΠΎΡΠ°Π½ΠΈΡ ΡΠ²Π΅ΡΠ΄ΠΎΠ³ΠΎ ΡΠΎΠΏΠ»ΠΈΠ²Π°, ΠΊΠΎΡΠΎΡΡΠ΅ ΠΎΠ±ΡΠ°Π·ΡΡΡ Π½Π° Π΅Π΅ Π²Π½ΡΡΡΠ΅Π½Π½ΠΈΡ ΡΡΠ΅Π½ΠΊΠ°Ρ ΡΠΌΠΎΠ»ΠΎΠΎΠ±ΡΠ°Π·Π½ΡΡ ΠΌΠ°ΡΡΡ, ΡΠ΅ΠΌ ΡΠ°ΠΌΡΠΌ ΡΠΌΠ΅Π½ΡΡΠ°Ρ Π΅Π΅ ΠΎΠ±ΡΠ΅ΠΌ. Π’Π°ΠΊΠΆΠ΅, ΠΏΡΠΈ ΠΏΠ΅ΡΠ΅ΡΠ°Π±ΠΎΡΠΊΠ΅ ΡΠΈΠ½ Π² ΡΡΡΡΠΎΠΉΡΡΠ²Π΅ Π΄Π»Ρ ΡΠΆΠΈΠ³Π°Π½ΠΈΡ ΡΠ²Π΅ΡΠ΄ΡΡ ΡΠΎΠΏΠ»ΠΈΠ² Π² ΠΏΡΠ»ΡΡΠΈΡΡΡΡΠ΅ΠΌ ΠΏΠΎΡΠΎΠΊΠ΅ ΠΏΠΎΠ»ΡΡΠ°Π΅ΡΡΡ ΠΈΠ½Π΅ΡΡΠ½ΡΠΉ ΠΌΠ°ΡΠ΅ΡΠΈΠ°Π», ΡΠΎΡΡΠΎΡΡΠΈΠΉ ΠΈΠ· 75-85% ΡΠ°ΠΆΠΈ, 5-10% ΡΠ΅ΡΡ ΠΈ 10-20% ΠΌΠΈΠ½Π΅ΡΠ°Π»ΡΠ½ΡΡ Π²Π΅ΡΠ΅ΡΡΠ², ΠΊΠΎΡΠΎΡΡΠΉ ΡΠ²Π»ΡΠ΅ΡΡΡ Ρ ΠΎΡΠΎΡΠΈΠΌ ΡΡΡΡΠ΅ΠΌ ΠΏΡΠΈ ΠΏΡΠΎΠΈΠ·Π²ΠΎΠ΄ΡΡΠ²Π΅ ΡΠ΅Π·ΠΈΠ½ΠΎΠ²ΡΡ ΠΈΠ·Π΄Π΅Π»ΠΈΠΉ, ΡΡΡΠΎΠΈΡΠ΅Π»ΡΡΡΠ²Π΅ Π΄ΠΎΡΠΎΠ³. ΠΡΡ ΠΎΠ΄ Π³Π°Π·ΠΎΠΎΠ±ΡΠ°Π·Π½ΡΡ ΠΏΡΠΎΠ΄ΡΠΊΡΠΎΠ² ΡΠ³ΠΎΡΠ°Π½ΠΈΡ ΠΏΠΎΠ»ΡΡΠ°Π΅ΡΡΡ ΡΠΊΠΎΠ»ΠΎΠ³ΠΈΡΠ΅ΡΠΊΠΈ ΡΠΈΡΡΡΠΌ Π·Π° ΡΡΠ΅Ρ ΠΊΠΎΠ½ΡΡΡΡΠΊΡΠΈΠ²Π½ΠΎΠ³ΠΎ ΠΈΡΠΏΠΎΠ»Π½Π΅Π½ΠΈΡ ΡΡΡΡΠΎΠΉΡΡΠ²Π° Π΄Π»Ρ ΡΠΆΠΈΠ³Π°Π½ΠΈΡ ΡΠ²Π΅ΡΠ΄ΡΡ ΡΠΎΠΏΠ»ΠΈΠ² Π² ΠΏΡΠ»ΡΡΠΈΡΡΡΡΠ΅ΠΌ ΠΏΠΎΡΠΎΠΊΠ΅ ΠΈ ΠΈΠ·Π±Π΅Π³Π°Π½ΠΈΡ ΠΆΠΈΠ΄ΠΊΠΎΠΉ ΡΡΠ°ΠΊΡΠΈΠΈ Π² ΠΏΡΠΎΡΠ΅ΡΡΠ΅ ΠΏΠ΅ΡΠ΅ΡΠ°Π±ΠΎΡΠΊΠΈ ΡΠΈΠ½.
ΠΠ»Ρ ΠΏΠΎΡΡΠ½Π΅Π½ΠΈΡ ΡΠ΅Ρ Π½ΠΈΡΠ΅ΡΠΊΠΎΠΉ ΡΡΡΠ½ΠΎΡΡΠΈ ΠΈΠ·ΠΎΠ±ΡΠ΅ΡΠ΅Π½ΠΈΡ ΡΠ°ΡΡΠΌΠΎΡΡΠΈΠΌ ΡΠ΅ΡΡΠ΅ΠΆΠΈ: ΡΠΈΠ³.1 – ΠΏΡΠΈΠ½ΡΠΈΠΏΠΈΠ°Π»ΡΠ½Π°Ρ ΡΡ Π΅ΠΌΠ° (ΠΎΠ±ΡΠΈΠΉ Π²ΠΈΠ΄) Π·Π°ΡΠ²Π»Π΅Π½Π½ΠΎΠ³ΠΎ ΡΡΡΡΠΎΠΉΡΡΠ²Π°, ΡΠΈΠ³.2 – ΡΡΡΡΠΎΠΉΡΡΠ²ΠΎ Π΄Π»Ρ ΡΠΆΠΈΠ³Π°Π½ΠΈΡ ΡΠ²Π΅ΡΠ΄ΠΎΠ³ΠΎ ΡΠΎΠΏΠ»ΠΈΠ²Π° (ΠΏΡΠΈΠΌΠ΅Ρ ΠΊΠΎΠ½ΠΊΡΠ΅ΡΠ½ΠΎΠ³ΠΎ ΠΈΡΠΏΠΎΠ»Π½Π΅Π½ΠΈΡ), Π³Π΄Π΅:
1 – ΠΊΠ°ΠΌΠ΅ΡΠ° Π²ΠΎΡΠΏΠ»Π°ΠΌΠ΅Π½Π΅Π½ΠΈΡ,
2 – ΠΊΠΎΠ»ΠΎΡΠ½ΠΈΠΊ,
3 – ΡΠ΄Π°ΡΠ½ΡΠΉ ΠΌΠ΅Ρ Π°Π½ΠΈΠ·ΠΌ (Π²ΠΈΠ±ΡΠΎΡΠ΄Π°ΡΠ½ΠΈΠΊΠΈ),
4 – Π²Π΅ΡΡ Π½ΡΡ ΡΠ°ΡΡΡ ΡΠ΅Π·ΠΎΠ½Π°ΡΠΎΡΠ½ΠΎΠΉ ΡΡΡΠ±Ρ,
5 – Π½ΠΈΠΆΠ½ΡΡ ΡΠ°ΡΡΡ ΡΠ΅Π·ΠΎΠ½Π°ΡΠΎΡΠ½ΠΎΠΉ ΡΡΡΠ±Ρ,
6 – ΠΊΠΎΠ»ΡΡΠ΅Π²Π°Ρ Π³Π°Π·ΠΎΠ²Π°Ρ Π³ΠΎΡΠ΅Π»ΠΊΠ° Ρ ΡΠ»Π΅ΠΊΡΡΠΈΡΠ΅ΡΠΊΠΈΠΌ Π·Π°ΠΏΠ°Π»ΡΠ½ΠΈΠΊΠΎΠΌ,
7 – ΡΠΈΡΡΠ΅ΠΌΠ° ΡΠ½ΠΈΠΆΠ΅Π½ΠΈΡ ΡΠ΅ΠΌΠΏΠ΅ΡΠ°ΡΡΡΡ ΠΈΠ½Π΅ΡΡΠ½ΠΎΠ³ΠΎ ΠΌΠ°ΡΠ΅ΡΠΈΠ°Π»Π°,
8 – Π²ΠΎΠ·Π΄ΡΡ ΠΎΠ²ΠΎΠ΄,
9 – ΠΊΠ°ΠΌΠ΅ΡΠ° ΠΏΡΠ΅Π΄Π²Π°ΡΠΈΡΠ΅Π»ΡΠ½ΠΎΠΉ ΡΠ΅ΠΏΠ»ΠΎΠ²ΠΎΠΉ ΠΏΠΎΠ΄Π³ΠΎΡΠΎΠ²ΠΊΠΈ ΡΠΎΠΏΠ»ΠΈΠ²Π°,
10 – ΡΠ±ΠΎΡΠ½ΠΈΠΊ ΡΠ²Π΅ΡΠ΄ΡΡ ΠΎΡΡ ΠΎΠ΄ΠΎΠ²,
11 – ΠΊΡΡΡΠΊΠ° ΠΊΠ°ΠΌΠ΅ΡΡ ΠΏΡΠ΅Π΄Π²Π°ΡΠΈΡΠ΅Π»ΡΠ½ΠΎΠΉ ΡΠ΅ΠΏΠ»ΠΎΠ²ΠΎΠΉ ΠΏΠΎΠ΄Π³ΠΎΡΠΎΠ²ΠΊΠΈ ΡΠΎΠΏΠ»ΠΈΠ²Π°,
12 – ΡΡΡΠ°Π³ Ρ Π·Π°ΡΠ΅Π»ΠΊΠΎΠΉ,
13 – ΠΏΠ»ΠΈΡΠ°,
14 – ΡΡΠΎΡΠΈΠΊ,
15 – ΡΠ±ΠΎΡΠ½ΠΈΠΊ ΠΈΠ½Π΅ΡΡΠ½ΠΎΠ³ΠΎ ΠΌΠ°ΡΠ΅ΡΠΈΠ°Π»Π°,
16 – Π»ΡΠΊ ΡΠ±ΠΎΡΠ½ΠΈΠΊΠ° ΠΈΠ½Π΅ΡΡΠ½ΠΎΠ³ΠΎ ΠΌΠ°ΡΠ΅ΡΠΈΠ°Π»Π°,
17 – ΡΠΈΠ»ΠΈΠ½Π΄ΡΠΈΡΠ΅ΡΠΊΠΈΠΉ ΡΠ΅ΠΏΠ»ΠΎΠΎΠ±ΠΌΠ΅Π½Π½ΠΈΠΊ,
18 – Π²Ρ ΠΎΠ΄Π½ΠΎΠΉ ΡΡΡΡΠ΅Ρ,
19 – Π²ΡΡ ΠΎΠ΄Π½ΠΎΠΉ ΡΡΡΡΠ΅Ρ,
20 – ΠΌΠ½ΠΎΠ³ΠΎΡΠΎΠΏΠ»ΠΎΠ²Π°Ρ Π΄ΠΈΡΡΡΠ·ΠΈΠΎΠ½Π½Π°Ρ Π³ΠΎΡΠ΅Π»ΠΊΠ°,
21 – ΠΎΠΊΠ½ΠΎ Ρ Π·Π°Π³Π»ΡΡΠΊΠΎΠΉ,
22 – ΡΠ΅ΡΡΠ°ΡΡΠΉ ΡΡΡΠ±ΡΠ»ΠΈΠ·Π°ΡΠΎΡ,
23 – Π³Π°Π·ΠΎΠΎΡΠ²ΠΎΠ΄ΡΡΠ°Ρ ΡΡΡΠ±Π°,
24 – Π·ΠΎΠ»ΠΎΡΠ»ΠΎΠ²ΠΈΡΠ΅Π»Ρ,
25 – ΡΠ»Π΅ΠΊΡΡΠΎΠ΄Π²ΠΈΠ³Π°ΡΠ΅Π»Ρ Ρ ΡΠ΅Π΄ΡΠΊΡΠΎΡΠΎΠΌ,
26 – ΡΠ°ΠΌΠ½ΠΎΠ΅ ΠΎΡΠ½ΠΎΠ²Π°Π½ΠΈΠ΅, ΡΠ²Π°ΡΠ΅Π½Π½ΠΎΠ΅ ΠΈΠ· ΡΡΠ°Π»ΡΠ½ΡΡ ΡΠ³ΠΎΠ»ΠΊΠΎΠ²,
27 – ΠΈΠ·Π½ΠΎΡΠ΅Π½Π½ΡΠ΅ ΡΠΈΠ½Ρ,
28 – ΡΠ΅ΡΠΌΠΎΠ΄Π°ΡΡΠΈΠΊ ΡΠΈΡΡΠ΅ΠΌΡ ΡΠ΅Π³ΡΠ»ΠΈΡΠΎΠ²Π°Π½ΠΈΡ ΡΠ΅ΠΌΠΏΠ΅ΡΠ°ΡΡΡΡ,
29 – Π±Π»ΠΎΠΊ Π°Π²ΡΠΎΠΌΠ°ΡΠΈΡΠ΅ΡΠΊΠΎΠ³ΠΎ ΠΈΠ·ΠΌΠ΅Π½Π΅Π½ΠΈΡ ΡΠ΅ΠΌΠΏΠ΅ΡΠ°ΡΡΡΡ.
Π’Π΅ΡΠΌΠΎΡΠ΅Π°ΠΊΡΠΎΡ Π²ΡΠΏΠΎΠ»Π½Π΅Π½ Π² Π²ΠΈΠ΄Π΅ ΡΠΈΠ»ΠΈΠ½Π΄ΡΠ° ΠΈ ΡΠΎΡΡΠΎΠΈΡ ΠΈΠ· ΠΊΠ°ΠΌΠ΅ΡΡ Π²ΠΎΡΠΏΠ»Π°ΠΌΠ΅Π½Π΅Π½ΠΈΡ 1, ΠΊΠ°ΠΌΠ΅ΡΡ ΠΏΡΠ΅Π΄Π²Π°ΡΠΈΡΠ΅Π»ΡΠ½ΠΎΠΉ ΡΠ΅ΠΏΠ»ΠΎΠ²ΠΎΠΉ ΠΏΠΎΠ΄Π³ΠΎΡΠΎΠ²ΠΊΠΈ ΡΠΎΠΏΠ»ΠΈΠ²Π° 9, ΠΈ ΡΠ±ΠΎΡΠ½ΠΈΠΊΠ° ΡΠ²Π΅ΡΠ΄ΡΡ ΠΎΡΡ ΠΎΠ΄ΠΎΠ² 10. Π Π·Π°ΡΠ²Π»Π΅Π½Π½ΠΎΠΌ ΡΡΡΡΠΎΠΉΡΡΠ²Π΅ ΠΊΠ°ΠΌΠ΅ΡΠ° ΠΏΡΠ΅Π΄Π²Π°ΡΠΈΡΠ΅Π»ΡΠ½ΠΎΠΉ ΡΠ΅ΠΏΠ»ΠΎΠ²ΠΎΠΉ ΠΏΠΎΠ΄Π³ΠΎΡΠΎΠ²ΠΊΠΈ ΡΠΎΠΏΠ»ΠΈΠ²Π° 9 ΡΠΈΠ»ΠΈΠ½Π΄ΡΠΈΡΠ΅ΡΠΊΠΎΠΉ ΡΠΎΡΠΌΡ Ρ ΠΊΡΡΡΠΊΠΎΠΉ ΠΊΠ°ΠΌΠ΅ΡΡ ΠΏΡΠ΅Π΄Π²Π°ΡΠΈΡΠ΅Π»ΡΠ½ΠΎΠΉ ΡΠ΅ΠΏΠ»ΠΎΠ²ΠΎΠΉ ΠΏΠΎΠ΄Π³ΠΎΡΠΎΠ²ΠΊΠΈ ΡΠΎΠΏΠ»ΠΈΠ²Π° 11. ΠΠ»Ρ ΠΎΡΠΊΡΡΠ²Π°Π½ΠΈΡ ΠΈ Π·Π°ΠΊΡΡΠ²Π°Π½ΠΈΡ ΠΊΡΡΡΠΊΠΈ ΠΊΠ°ΠΌΠ΅ΡΡ ΠΏΡΠ΅Π΄Π²Π°ΡΠΈΡΠ΅Π»ΡΠ½ΠΎΠΉ ΡΠ΅ΠΏΠ»ΠΎΠ²ΠΎΠΉ ΠΏΠΎΠ΄Π³ΠΎΡΠΎΠ²ΠΊΠΈ ΡΠΎΠΏΠ»ΠΈΠ²Π° 11 ΠΏΡΠ΅Π΄ΡΡΠΌΠΎΡΡΠ΅Π½ ΡΡΡΠ°Π³ Ρ Π·Π°ΡΠ΅Π»ΠΊΠΎΠΉ 12. ΠΠ½ΡΡΡΠΈ ΠΊΠ°ΠΌΠ΅ΡΡ ΠΏΡΠ΅Π΄Π²Π°ΡΠΈΡΠ΅Π»ΡΠ½ΠΎΠΉ ΡΠ΅ΠΏΠ»ΠΎΠ²ΠΎΠΉ ΠΏΠΎΠ΄Π³ΠΎΡΠΎΠ²ΠΊΠΈ ΡΠΎΠΏΠ»ΠΈΠ²Π° 9 ΡΠ°Π·ΠΌΠ΅ΡΠ΅Π½Π° ΠΏΠ»ΠΈΡΠ° 13, ΠΊΠΎΡΠΎΡΠ°Ρ ΡΠ»ΡΠΆΠΈΡ Π΄Π»Ρ ΡΠΌΠ΅Π½ΡΡΠ΅Π½ΠΈΡ ΠΎΠ±ΡΠ΅ΠΌΠ° ΡΡΠΈΠ»ΠΈΠ·ΠΈΡΡΠ΅ΠΌΡΡ ΠΈΠ·Π½ΠΎΡΠ΅Π½Π½ΡΡ ΡΠΈΠ½ 27 ΠΏΠΎ ΠΌΠ΅ΡΠ΅ ΠΈΡ Π²ΡΠ³ΠΎΡΠ°Π½ΠΈΡ. ΠΠ»ΠΈΡΠ° 13 ΡΠ²ΡΠ·Π°Π½Π° Ρ ΠΊΡΡΡΠΊΠΎΠΉ ΠΊΠ°ΠΌΠ΅ΡΡ ΠΏΡΠ΅Π΄Π²Π°ΡΠΈΡΠ΅Π»ΡΠ½ΠΎΠΉ ΡΠ΅ΠΏΠ»ΠΎΠ²ΠΎΠΉ ΠΏΠΎΠ΄Π³ΠΎΡΠΎΠ²ΠΊΠΈ ΡΠΎΠΏΠ»ΠΈΠ²Π° 11 ΡΡΠΎΡΠΈΠΊΠΎΠΌ 14, ΠΏΡΠ΅Π΄Π½Π°Π·Π½Π°ΡΠ΅Π½Π½ΡΠΌ Π΄Π»Ρ ΠΏΠΎΠ΄ΡΠ΅ΠΌΠ° ΠΏΠ»ΠΈΡΡ 13, ΠΏΡΠΈ ΠΎΡΠΊΡΡΠ²Π°Π½ΠΈΠΈ ΠΊΡΡΡΠΊΠΈ ΠΊΠ°ΠΌΠ΅ΡΡ ΠΏΡΠ΅Π΄Π²Π°ΡΠΈΡΠ΅Π»ΡΠ½ΠΎΠΉ ΡΠ΅ΠΏΠ»ΠΎΠ²ΠΎΠΉ ΠΏΠΎΠ΄Π³ΠΎΡΠΎΠ²ΠΊΠΈ ΡΠΎΠΏΠ»ΠΈΠ²Π° 11. ΠΡΡΡΠΊΠ° ΠΊΠ°ΠΌΠ΅ΡΡ ΠΏΡΠ΅Π΄Π²Π°ΡΠΈΡΠ΅Π»ΡΠ½ΠΎΠΉ ΡΠ΅ΠΏΠ»ΠΎΠ²ΠΎΠΉ ΠΏΠΎΠ΄Π³ΠΎΡΠΎΠ²ΠΊΠΈ ΡΠΎΠΏΠ»ΠΈΠ²Π° 11 Π² ΠΎΡΠΊΡΡΡΠΎΠΌ ΠΏΠΎΠ»ΠΎΠΆΠ΅Π½ΠΈΠΈ ΡΠΈΠΊΡΠΈΡΡΠ΅ΡΡΡ Π·Π°ΡΠ΅Π»ΠΊΠΎΠΉ.
Π ΠΎΡΠ½ΠΎΠ²Π°Π½ΠΈΡ ΠΊΠ°ΠΌΠ΅ΡΡ ΠΏΡΠ΅Π΄Π²Π°ΡΠΈΡΠ΅Π»ΡΠ½ΠΎΠΉ ΡΠ΅ΠΏΠ»ΠΎΠ²ΠΎΠΉ ΠΏΠΎΠ΄Π³ΠΎΡΠΎΠ²ΠΊΠΈ ΡΠΎΠΏΠ»ΠΈΠ²Π° 9 ΠΏΡΠΈΡΠΎΠ΅Π΄ΠΈΠ½Π΅Π½ ΡΠ±ΠΎΡΠ½ΠΈΠΊ ΡΠ²Π΅ΡΠ΄ΡΡ ΠΎΡΡ ΠΎΠ΄ΠΎΠ² 10 ΡΠΎ ΡΠ±ΠΎΡΠ½ΠΈΠΊΠΎΠΌ ΠΈΠ½Π΅ΡΡΠ½ΠΎΠ³ΠΎ ΠΌΠ°ΡΠ΅ΡΠΈΠ°Π»Π° 15 Ρ Π»ΡΠΊΠΎΠΌ ΡΠ±ΠΎΡΠ½ΠΈΠΊΠ° ΠΈΠ½Π΅ΡΡΠ½ΠΎΠ³ΠΎ ΠΌΠ°ΡΠ΅ΡΠΈΠ°Π»Π° 16 Π΄Π»Ρ ΡΠ΄Π°Π»Π΅Π½ΠΈΡ ΠΈΠ½Π΅ΡΡΠ½ΠΎΠ³ΠΎ ΠΌΠ°ΡΠ΅ΡΠΈΠ°Π»Π° (ΠΎΡΡ ΠΎΠ΄ΠΎΠ²). Π ΡΠ±ΠΎΡΠ½ΠΈΠΊΡ ΡΠ²Π΅ΡΠ΄ΡΡ ΠΎΡΡ ΠΎΠ΄ΠΎΠ² 10 ΠΏΡΠΈΠΌΠΊΠ½ΡΡ Π²ΠΎΠ·Π΄ΡΡ ΠΎΠ²ΠΎΠ΄ 8. ΠΠΎΠ΄ ΠΊΠΎΠ»ΠΎΡΠ½ΠΈΠΊΠΎΠΌ 2 ΡΠ°Π·ΠΌΠ΅ΡΠ΅Π½Π° ΠΊΠΎΠ»ΡΡΠ΅Π²Π°Ρ Π³Π°Π·ΠΎΠ²Π°Ρ Π³ΠΎΡΠ΅Π»ΠΊΠ° Ρ ΡΠ»Π΅ΠΊΡΡΠΈΡΠ΅ΡΠΊΠΈΠΌ Π·Π°ΠΏΠ°Π»ΡΠ½ΠΈΠΊΠΎΠΌ 6. ΠΠ°ΠΌΠ΅ΡΠ° Π²ΠΎΡΠΏΠ»Π°ΠΌΠ΅Π½Π΅Π½ΠΈΡ 1 ΡΠΎΠ΅Π΄ΠΈΠ½Π΅Π½Π° Ρ ΡΠ΅Π·ΠΎΠ½Π°ΡΠΎΡΠ½ΠΎΠΉ ΡΡΡΠ±ΠΎΠΉ, ΡΠΎΡΡΠΎΡΡΠ΅ΠΉ ΠΈΠ· Π΄Π²ΡΡ ΡΠ°ΡΡΠ΅ΠΉ – Π²Π΅ΡΡ Π½Π΅ΠΉ 4 ΠΈ Π½ΠΈΠΆΠ½Π΅ΠΉ 5. ΠΠ° Π²Π΅ΡΡ Π½Π΅ΠΉ ΡΠ°ΡΡΠΈ ΡΠ΅Π·ΠΎΠ½Π°ΡΠΎΡΠ½ΠΎΠΉ ΡΡΡΠ±Ρ 4 ΡΠΌΠΎΠ½ΡΠΈΡΠΎΠ²Π°Π½ ΡΠΈΠ»ΠΈΠ½Π΄ΡΠΈΡΠ΅ΡΠΊΠΈΠΉ ΡΠ΅ΠΏΠ»ΠΎΠΎΠ±ΠΌΠ΅Π½Π½ΠΈΠΊ 17 Ρ Π²Ρ ΠΎΠ΄Π½ΡΠΌ ΠΈ Π²ΡΡ ΠΎΠ΄Π½ΡΠΌ ΡΡΡΡΠ΅ΡΠ°ΠΌΠΈ 18 ΠΈ 19 ΡΠΎΠΎΡΠ²Π΅ΡΡΡΠ²Π΅Π½Π½ΠΎ. Π ΠΎΡΠ½ΠΎΠ²Π°Π½ΠΈΡ Π²Π΅ΡΡ Π½Π΅ΠΉ ΡΠ°ΡΡΠΈ ΡΠ΅Π·ΠΎΠ½Π°ΡΠΎΡΠ½ΠΎΠΉ ΡΡΡΠ±Ρ 4 ΠΏΡΠΈΠΊΡΠ΅ΠΏΠ»Π΅Π½Π° ΠΌΠ½ΠΎΠ³ΠΎΡΠΎΠΏΠ»ΠΎΠ²Π°Ρ Π΄ΠΈΡΡΡΠ·ΠΈΠΎΠ½Π½Π°Ρ Π³ΠΎΡΠ΅Π»ΠΊΠ° 20. ΠΠ»Ρ ΠΏΠΎΠ΄ΠΆΠΈΠ³Π° Π³ΠΎΡΠ΅Π»ΠΊΠΈ Π½Π° Π±ΠΎΠΊΠΎΠ²ΠΎΠΉ ΠΏΠΎΠ²Π΅ΡΡ Π½ΠΎΡΡΠΈ ΠΊΠ°ΠΌΠ΅ΡΡ Π²ΠΎΡΠΏΠ»Π°ΠΌΠ΅Π½Π΅Π½ΠΈΡ 1 ΠΈΠΌΠ΅Π΅ΡΡΡ ΠΎΠΊΠ½ΠΎ Ρ Π·Π°Π³Π»ΡΡΠΊΠΎΠΉ 21. ΠΠ°Π΄ ΠΌΠ½ΠΎΠ³ΠΎΡΠΎΠΏΠ»ΠΎΠ²ΠΎΠΉ Π΄ΠΈΡΡΡΠ·ΠΈΠΎΠ½Π½ΠΎΠΉ Π³ΠΎΡΠ΅Π»ΠΊΠΎΠΉ 20 Π² ΡΠ΅Π·ΠΎΠ½Π°ΡΠΎΡΠ½ΠΎΠΉ ΡΡΡΠ±Π΅ ΡΠ°Π·ΠΌΠ΅ΡΠ΅Π½ ΡΠ΅ΡΡΠ°ΡΡΠΉ ΡΡΡΠ±ΡΠ»ΠΈΠ·Π°ΡΠΎΡ 22, ΡΠΎΡΡΠΎΡΡΠΈΠΉ ΠΈΠ· Π½Π΅ΡΠΊΠΎΠ»ΡΠΊΠΈΡ ΡΠΎΡΡΠ°Π²Π½ΡΡ ΡΠ°ΡΡΠ΅ΠΉ (ΠΏΠ»Π°ΡΡΠΈΠ½). ΠΡΠΈΡΠ΅ΠΌ Π·Π°Π·ΠΎΡ ΠΌΠ΅ΠΆΠ΄Ρ ΠΏΠ»Π°ΡΡΠΈΠ½Π°ΠΌΠΈ ΡΠ΅Π³ΡΠ»ΠΈΡΡΠ΅ΡΡΡ. ΠΠΈΠΆΠ½ΡΡ ΡΠ°ΡΡΡ ΡΠ΅Π·ΠΎΠ½Π°ΡΠΎΡΠ½ΠΎΠΉ ΡΡΡΠ±Ρ 5 ΠΏΡΠΈΠΌΠΊΠ½ΡΡΠ° ΠΊ ΠΊΠ°ΠΌΠ΅ΡΠ΅ Π²ΠΎΡΠΏΠ»Π°ΠΌΠ΅Π½Π΅Π½ΠΈΡ 1 ΠΏΡΠΈ ΠΏΠΎΠΌΠΎΡΠΈ ΠΏΠ°ΡΡΡΠ±ΠΊΠ°, Π² ΠΊΠΎΡΠΎΡΠΎΠΌ ΠΎΠ½Π° ΠΏΠ΅ΡΠ΅ΠΌΠ΅ΡΠ°Π΅ΡΡΡ ΡΠ²ΠΎΠ±ΠΎΠ΄Π½ΠΎ Π²Π΄ΠΎΠ»Ρ ΡΠ²ΠΎΠ΅ΠΉ ΠΎΡΠΈ. ΠΠ΅ΡΡ Π½ΠΈΠΉ ΡΡΠ΅Π· Π³Π°Π·ΠΎΠΎΡΠ²ΠΎΠ΄ΡΡΠ΅ΠΉ ΡΡΡΠ±Ρ 23 ΡΠ°ΡΠΏΠΎΠ»ΠΎΠΆΠ΅Π½ Π½Π° ΡΠ°ΡΡΡΠΎΡΠ½ΠΈΠΈ 2-3 Π΄ΠΈΠ°ΠΌΠ΅ΡΡΠ° ΡΡΠΎΠΉ ΡΡΡΠ±Ρ ΠΎΡ Π½ΠΈΠΆΠ½Π΅ΠΉ ΡΠ°ΡΡΠΈ ΠΊΡΡΡΠΊΠΈ ΠΊΠ°ΠΌΠ΅ΡΡ ΠΏΡΠ΅Π΄Π²Π°ΡΠΈΡΠ΅Π»ΡΠ½ΠΎΠΉ ΡΠ΅ΠΏΠ»ΠΎΠ²ΠΎΠΉ ΠΏΠΎΠ΄Π³ΠΎΡΠΎΠ²ΠΊΠΈ ΡΠΎΠΏΠ»ΠΈΠ²Π° 11, Π° Π½ΠΈΠΆΠ½ΠΈΠΉ – Π² Π½ΠΈΠΆΠ½Π΅ΠΉ ΡΠ°ΡΡΠΈ ΡΠ΅Π·ΠΎΠ½Π°ΡΠΎΡΠ½ΠΎΠΉ ΡΡΡΠ±Ρ 5.
Π£ΡΡΡΠΎΠΉΡΡΠ²ΠΎ Π΄Π»Ρ ΡΠΆΠΈΠ³Π°Π½ΠΈΡ ΡΠ²Π΅ΡΠ΄ΠΎΠ³ΠΎ ΡΠΎΠΏΠ»ΠΈΠ²Π° Π² ΠΏΡΠ»ΡΡΠΈΡΡΡΡΠ΅ΠΌ ΠΏΠΎΡΠΎΠΊΠ΅ ΡΠ°Π±ΠΎΡΠ°Π΅Ρ ΡΠ»Π΅Π΄ΡΡΡΠΈΠΌ ΠΎΠ±ΡΠ°Π·ΠΎΠΌ:
Π ΡΡΠ°Π³ΠΎΠΌ 12 ΠΎΡΠΊΡΡΠ²Π°Π΅ΡΡΡ ΠΊΡΡΡΠΊΠ° ΠΊΠ°ΠΌΠ΅ΡΡ ΠΏΡΠ΅Π΄Π²Π°ΡΠΈΡΠ΅Π»ΡΠ½ΠΎΠΉ ΡΠ΅ΠΏΠ»ΠΎΠ²ΠΎΠΉ ΠΏΠΎΠ΄Π³ΠΎΡΠΎΠ²ΠΊΠΈ ΡΠΎΠΏΠ»ΠΈΠ²Π° 11, ΠΊΠΎΡΠΎΡΠ°Ρ ΡΡΠΎΡΠΈΠΊΠΎΠΌ 14 ΡΡΠ½Π΅Ρ Π·Π° ΡΠΎΠ±ΠΎΠΉ ΠΏΠ»ΠΈΡΡ 13. Π ΠΎΡΠΊΡΡΡΠΎΠΌ ΠΏΠΎΠ»ΠΎΠΆΠ΅Π½ΠΈΠΈ ΠΊΡΡΡΠΊΠ° ΠΊΠ°ΠΌΠ΅ΡΡ ΠΏΡΠ΅Π΄Π²Π°ΡΠΈΡΠ΅Π»ΡΠ½ΠΎΠΉ ΡΠ΅ΠΏΠ»ΠΎΠ²ΠΎΠΉ ΠΏΠΎΠ΄Π³ΠΎΡΠΎΠ²ΠΊΠΈ ΡΠΎΠΏΠ»ΠΈΠ²Π° 11 ΡΠ΄Π΅ΡΠΆΠΈΠ²Π°Π΅ΡΡΡ Π·Π°ΡΠ΅Π»ΠΊΠΎΠΉ. Π ΠΊΠ°ΠΌΠ΅ΡΡ ΠΏΡΠ΅Π΄Π²Π°ΡΠΈΡΠ΅Π»ΡΠ½ΠΎΠΉ ΡΠ΅ΠΏΠ»ΠΎΠ²ΠΎΠΉ ΠΏΠΎΠ΄Π³ΠΎΡΠΎΠ²ΠΊΠΈ ΡΠΎΠΏΠ»ΠΈΠ²Π° 9 Π·Π°Π³ΡΡΠΆΠ°ΡΡΡΡ ΠΈΠ·Π½ΠΎΡΠ΅Π½Π½ΡΠ΅ ΡΠΈΠ½Ρ 27 (ΡΠΈΠ³.2). ΠΡΡΡΠΊΠ° ΠΊΠ°ΠΌΠ΅ΡΡ ΠΏΡΠ΅Π΄Π²Π°ΡΠΈΡΠ΅Π»ΡΠ½ΠΎΠΉ ΡΠ΅ΠΏΠ»ΠΎΠ²ΠΎΠΉ ΠΏΠΎΠ΄Π³ΠΎΡΠΎΠ²ΠΊΠΈ ΡΠΎΠΏΠ»ΠΈΠ²Π° 11 Π·Π°ΠΊΡΡΠ²Π°Π΅ΡΡΡ ΠΈ ΡΠΈΠΊΡΠΈΡΡΠ΅ΡΡΡ Π·Π°ΡΠ΅Π»ΠΊΠΎΠΉ. ΠΡΠΈ ΡΡΠΎΠΌ ΠΏΠ»ΠΈΡΠ° 13 ΠΏΠ»ΠΎΡΠ½ΠΎ ΠΏΡΠΈΠ»Π΅Π³Π°Π΅Ρ ΠΊ Π²Π΅ΡΡ Π½Π΅ΠΉ ΡΠΈΠ½Π΅. ΠΠ΅ΡΠΌΠ΅ΡΠΈΡΠ½ΠΎΠ΅ Π·Π°ΠΊΡΡΠ²Π°Π½ΠΈΠ΅ ΠΊΠ°ΠΌΠ΅ΡΡ ΠΏΡΠ΅Π΄Π²Π°ΡΠΈΡΠ΅Π»ΡΠ½ΠΎΠΉ ΡΠ΅ΠΏΠ»ΠΎΠ²ΠΎΠΉ ΠΏΠΎΠ΄Π³ΠΎΡΠΎΠ²ΠΊΠΈ ΡΠΎΠΏΠ»ΠΈΠ²Π° 9 ΠΎΠ±Π΅ΡΠΏΠ΅ΡΠΈΠ²Π°Π΅ΡΡΡ ΡΠΏΠ»ΠΎΡΠ½ΠΈΡΠ΅Π»ΡΠ½ΡΠΌ ΡΡΡΡΠΎΠΉΡΡΠ²ΠΎΠΌ ΠΌΠ΅ΠΆΠ΄Ρ ΠΊΠ°ΠΌΠ΅ΡΠΎΠΉ ΠΏΡΠ΅Π΄Π²Π°ΡΠΈΡΠ΅Π»ΡΠ½ΠΎΠΉ ΡΠ΅ΠΏΠ»ΠΎΠ²ΠΎΠΉ ΠΏΠΎΠ΄Π³ΠΎΡΠΎΠ²ΠΊΠΈ ΡΠΎΠΏΠ»ΠΈΠ²Π° 9 ΠΈ ΠΊΡΡΡΠΊΠΎΠΉ ΠΊΠ°ΠΌΠ΅ΡΡ ΠΏΡΠ΅Π΄Π²Π°ΡΠΈΡΠ΅Π»ΡΠ½ΠΎΠΉ ΡΠ΅ΠΏΠ»ΠΎΠ²ΠΎΠΉ ΠΏΠΎΠ΄Π³ΠΎΡΠΎΠ²ΠΊΠΈ ΡΠΎΠΏΠ»ΠΈΠ²Π° 11. ΠΠ»Π΅ΠΊΡΡΠΎΠ·Π°ΠΏΠ°Π»ΡΠ½ΠΈΠΊΠΎΠΌ ΠΏΠΎΠ΄ΠΆΠΈΠ³Π°Π΅ΡΡΡ Π³ΠΎΡΡΡΠΈΠΉ Π³Π°Π·, ΠΏΠΎΡΡΡΠΏΠ°ΡΡΠΈΠΉ Π² ΠΊΠΎΠ»ΡΡΠ΅Π²ΡΡ Π³Π°Π·ΠΎΠ²ΡΡ Π³ΠΎΡΠ΅Π»ΠΊΡ Ρ ΡΠ»Π΅ΠΊΡΡΠΈΡΠ΅ΡΠΊΠΈΠΌ Π·Π°ΠΏΠ°Π»ΡΠ½ΠΈΠΊΠΎΠΌ 6, ΠΊΠΎΡΠΎΡΡΠΉ Π²ΠΎΡΠΏΠ»Π°ΠΌΠ΅Π½ΡΠ΅Ρ ΠΈΠ·Π½ΠΎΡΠ΅Π½Π½ΡΠ΅ ΡΠΈΠ½Ρ 27. Π’Π΅ΠΌΠΏΠ΅ΡΠ°ΡΡΡΠ° Π² ΠΊΠ°ΠΌΠ΅ΡΠ΅ ΠΏΡΠ΅Π΄Π²Π°ΡΠΈΡΠ΅Π»ΡΠ½ΠΎΠΉ ΡΠ΅ΠΏΠ»ΠΎΠ²ΠΎΠΉ ΠΏΠΎΠ΄Π³ΠΎΡΠΎΠ²ΠΊΠΈ ΡΠΎΠΏΠ»ΠΈΠ²Π° 9 ΠΏΠΎΠ΄Π΄Π΅ΡΠΆΠΈΠ²Π°Π΅ΡΡΡ Π² Π΄ΠΈΠ°ΠΏΠ°Π·ΠΎΠ½Π΅ ΠΎΡ 350 Π΄ΠΎ 450Β°C. Π Π΅Π³ΡΠ»ΠΈΡΠΎΠ²ΠΊΠ° ΡΠ΅ΠΌΠΏΠ΅ΡΠ°ΡΡΡΡ ΠΎΡΡΡΠ΅ΡΡΠ²Π»ΡΠ΅ΡΡΡ ΠΏΠΎΠ΄ΠΌΠ΅ΡΠΈΠ²Π°Π½ΠΈΠ΅ΠΌ Π²ΠΎΠ·Π΄ΡΡ Π° Π² Π½Π°Π³ΡΠ΅ΡΡΠ΅ Π³Π°Π·Ρ, ΠΏΠΎΡΡΡΠΏΠ°ΡΡΠΈΠ΅ Π² ΠΊΠ°ΠΌΠ΅ΡΡ ΠΏΡΠ΅Π΄Π²Π°ΡΠΈΡΠ΅Π»ΡΠ½ΠΎΠΉ ΡΠ΅ΠΏΠ»ΠΎΠ²ΠΎΠΉ ΠΏΠΎΠ΄Π³ΠΎΡΠΎΠ²ΠΊΠΈ ΡΠΎΠΏΠ»ΠΈΠ²Π° 9 ΡΠ΅ΡΠ΅Π· Π²ΠΎΠ·Π΄ΡΡ ΠΎΠ²ΠΎΠ΄ 8, Π²ΡΠΏΠΎΠ»Π½ΡΡΡΠ΅Π³ΠΎ ΡΡΠ½ΠΊΡΠΈΡ Π°ΡΡΠΎΠ΄ΠΈΠ½Π°ΠΌΠΈΡΠ΅ΡΠΊΠΎΠ³ΠΎ ΠΊΠ»Π°ΠΏΠ°Π½Π°. Π‘ ΡΡΠΎΠΉ ΡΠ΅Π»ΡΡ Π² Π·Π°ΡΠ²Π»Π΅Π½Π½ΠΎΠΌ ΡΡΡΡΠΎΠΉΡΡΠ²Π΅ ΠΏΡΠ΅Π΄ΡΡΠΌΠΎΡΡΠ΅Π½Π° ΡΠΈΡΡΠ΅ΠΌΠ° ΡΠ΅Π³ΡΠ»ΠΈΡΠΎΠ²Π°Π½ΠΈΡ ΠΏΠΎΠ΄Π°ΡΠΈ Π²ΠΎΠ·Π΄ΡΡ Π° Π² ΠΊΠ°ΠΌΠ΅ΡΡ ΠΏΡΠ΅Π΄Π²Π°ΡΠΈΡΠ΅Π»ΡΠ½ΠΎΠΉ ΡΠ΅ΠΏΠ»ΠΎΠ²ΠΎΠΉ ΠΏΠΎΠ΄Π³ΠΎΡΠΎΠ²ΠΊΠΈ ΡΠΎΠΏΠ»ΠΈΠ²Π° 9, Π²ΠΊΠ»ΡΡΠ°ΡΡΠ°Ρ ΡΠ΅ΡΠΌΠΎΠ΄Π°ΡΡΠΈΠΊ ΡΠΈΡΡΠ΅ΠΌΡ ΡΠ΅Π³ΡΠ»ΠΈΡΠΎΠ²Π°Π½ΠΈΡ ΡΠ΅ΠΌΠΏΠ΅ΡΠ°ΡΡΡΡ 28 (ΡΠΈΠ³.2), Π±Π»ΠΎΠΊ Π°Π²ΡΠΎΠΌΠ°ΡΠΈΡΠ΅ΡΠΊΠΎΠ³ΠΎ ΠΈΠ·ΠΌΠ΅Π½Π΅Π½ΠΈΡ ΡΠ΅ΠΌΠΏΠ΅ΡΠ°ΡΡΡΡ 29 ΠΈ Π²ΠΎΠ·Π΄ΡΡ ΠΎΠ²ΠΎΠ΄ 8. ΠΡΠΈ ΠΏΠΎΠ²ΡΡΠ΅Π½ΠΈΠΈ ΡΠ΅ΠΌΠΏΠ΅ΡΠ°ΡΡΡΡ Π² ΠΊΠ°ΠΌΠ΅ΡΠ΅ ΠΏΡΠ΅Π΄Π²Π°ΡΠΈΡΠ΅Π»ΡΠ½ΠΎΠΉ ΡΠ΅ΠΏΠ»ΠΎΠ²ΠΎΠΉ ΠΏΠΎΠ΄Π³ΠΎΡΠΎΠ²ΠΊΠΈ ΡΠΎΠΏΠ»ΠΈΠ²Π° 9 Π²ΡΡΠ΅ 450Β°C ΡΠ΅ΡΠΌΠΎΠ΄Π°ΡΡΠΈΠΊ ΡΠΈΡΡΠ΅ΠΌΡ ΡΠ΅Π³ΡΠ»ΠΈΡΠΎΠ²Π°Π½ΠΈΡ ΡΠ΅ΠΌΠΏΠ΅ΡΠ°ΡΡΡΡ 28 ΡΠΈΠΊΡΠΈΡΡΠ΅Ρ ΡΠ΅ΠΌΠΏΠ΅ΡΠ°ΡΡΡΡ, Π±Π»ΠΎΠΊ Π°Π²ΡΠΎΠΌΠ°ΡΠΈΡΠ΅ΡΠΊΠΎΠ³ΠΎ ΠΈΠ·ΠΌΠ΅Π½Π΅Π½ΠΈΡ ΡΠ΅ΠΌΠΏΠ΅ΡΠ°ΡΡΡΡ 29 ΡΠΌΠ΅Π½ΡΡΠ°Π΅Ρ ΠΏΡΠΎΡ ΠΎΠ΄Π½ΠΎΠ΅ ΡΠ΅ΡΠ΅Π½ΠΈΠ΅ Π²ΠΎΠ·Π΄ΡΡ ΠΎΠ²ΠΎΠ΄Π° 8, Π²ΡΠΏΠΎΠ»Π½ΡΡΡΠ΅Π³ΠΎ ΡΡΠ½ΠΊΡΠΈΡ Π°ΡΡΠΎΠ΄ΠΈΠ½Π°ΠΌΠΈΡΠ΅ΡΠΊΠΎΠ³ΠΎ ΠΊΠ»Π°ΠΏΠ°Π½Π°, Π΄ΠΎΡΡΡΠΏ Π²ΠΎΠ·Π΄ΡΡ Π° Π² ΠΎΠ±Π»Π°ΡΡΡ Π³ΠΎΡΠ΅Π½ΠΈΡ ΡΠΌΠ΅Π½ΡΡΠ°Π΅ΡΡΡ, Π° ΠΏΡΠΈ ΡΠ΅ΠΌΠΏΠ΅ΡΠ°ΡΡΡΠ΅ Π½ΠΈΠΆΠ΅ 350Β°C ΡΠ²Π΅Π»ΠΈΡΠΈΠ²Π°Π΅ΡΡΡ. Π‘ΠΎΠΎΡΠ²Π΅ΡΡΡΠ²Π΅Π½Π½ΠΎ ΠΈΠ½ΡΠ΅Π½ΡΠΈΠ²Π½ΠΎΡΡΡ Π³ΠΎΡΠ΅Π½ΠΈΡ (ΡΠ΅ΡΠΌΠΈΡΠ΅ΡΠΊΠΎΠ³ΠΎ ΡΠ°Π·Π»ΠΎΠΆΠ΅Π½ΠΈΡ) ΠΏΠΎΠ½ΠΈΠΆΠ°Π΅ΡΡΡ ΠΈΠ»ΠΈ ΠΏΠΎΠ²ΡΡΠ°Π΅ΡΡΡ. ΠΡΠΈ ΡΠ°ΠΊΠΎΠΉ ΡΠ΅ΠΌΠΏΠ΅ΡΠ°ΡΡΡΠ΅ Π² ΠΊΠ°ΠΌΠ΅ΡΠ΅ ΠΏΡΠ΅Π΄Π²Π°ΡΠΈΡΠ΅Π»ΡΠ½ΠΎΠΉ ΡΠ΅ΠΏΠ»ΠΎΠ²ΠΎΠΉ ΠΏΠΎΠ΄Π³ΠΎΡΠΎΠ²ΠΊΠΈ ΡΠΎΠΏΠ»ΠΈΠ²Π° 9 ΠΈΠ· ΠΈΠ·Π½ΠΎΡΠ΅Π½Π½ΡΡ ΡΠΈΠ½ 27 Π²ΡΠ΄Π΅Π»ΡΡΡΡΡ Π»Π΅ΡΡΡΠΈΠ΅ ΡΠΎΡΡΠ°Π²Π»ΡΡΡΠΈΠ΅, ΡΠΎΠ΄Π΅ΡΠΆΠ°ΡΠΈΠ΅ Π³ΠΎΡΡΡΠΈΠ΅ ΡΠ»Π΅ΠΌΠ΅Π½ΡΡ, ΠΈ ΠΏΠΎΡΡΡΠΏΠ°ΡΡ Π² ΡΠ΅Π·ΠΎΠ½Π°ΡΠΎΡΠ½ΡΡ ΡΡΡΠ±Ρ 4, 5 Π΄Π»Ρ ΠΏΠΎΡΠ»Π΅Π΄ΡΡΡΠ΅Π³ΠΎ Π΄ΠΎΠΆΠΈΠ³Π°Π½ΠΈΡ. ΠΠΎ ΠΌΠ΅ΡΠ΅ Π²ΡΠ³ΠΎΡΠ°Π½ΠΈΡ ΠΈΠ·Π½ΠΎΡΠ΅Π½Π½ΡΡ ΡΠΈΠ½ 27 ΠΈΡΠΏΠΎΠ»ΡΠ·ΠΎΠ²Π°Π½ΠΈΠ΅ΠΌ ΡΠ΄Π°ΡΠ½ΠΎΠ³ΠΎ ΠΌΠ΅Ρ Π°Π½ΠΈΠ·ΠΌΠ° 3, ΡΠ°Π±ΠΎΡΠ°ΡΡΠ΅ΠΌ Π² ΡΠ°ΡΡΠΎΡΠ½ΠΎΠΌ Π΄ΠΈΠ°ΠΏΠ°Π·ΠΎΠ½Π΅ 1-10 ΠΡ Ρ ΠΏΠ΅ΡΠΈΠΎΠ΄ΠΈΡΠ½ΠΎΡΡΡΡ 3 ΡΠΈΠΊΠ»Π° Π² 1 ΡΠ°Ρ, ΠΏΡΠΎΠ΄ΠΎΠ»ΠΆΠΈΡΠ΅Π»ΡΠ½ΠΎΡΡΡΡ ΡΠΈΠΊΠ»Π° 5 ΠΌΠΈΠ½ΡΡ, ΠΎΡΠ΄Π΅Π»ΡΠ΅ΡΡΡ ΠΈΠ½Π΅ΡΡΠ½ΡΠΉ ΠΌΠ°ΡΠ΅ΡΠΈΠ°Π» ΠΎΡ ΠΌΠ΅ΡΠ°Π»Π»ΠΎΠΊΠΎΡΠ΄Π°. Π’Π΅ΠΌΠΏΠ΅ΡΠ°ΡΡΡΠ° ΡΠ²Π΅ΡΠ΄ΡΡ ΠΎΡΡ ΠΎΠ΄ΠΎΠ² ΠΈ ΠΈΠ½Π΅ΡΡΠ½ΠΎΠ³ΠΎ ΠΌΠ°ΡΠ΅ΡΠΈΠ°Π»Π° Π²ΡΡΠΎΠΊΠ°Ρ, ΠΏΠΎΡΡΠΎΠΌΡ ΠΏΡΠ΅Π΄ΡΡΠΌΠΎΡΡΠ΅Π½Π° ΡΠΈΡΡΠ΅ΠΌΠ° ΡΠ½ΠΈΠΆΠ΅Π½ΠΈΡ ΡΠ΅ΠΌΠΏΠ΅ΡΠ°ΡΡΡΡ ΠΈΠ½Π΅ΡΡΠ½ΠΎΠ³ΠΎ ΠΌΠ°ΡΠ΅ΡΠΈΠ°Π»Π° 7 Π² ΡΠ±ΠΎΡΠ½ΠΈΠΊΠ΅ ΠΈΠ½Π΅ΡΡΠ½ΠΎΠ³ΠΎ ΠΌΠ°ΡΠ΅ΡΠΈΠ°Π»Π° 15, ΠΏΡΠΈ ΡΡΠΎΠΌ Π²ΠΏΡΡΡΠΊ ΠΈΠ·Π²Π΅ΡΡΠΊΠΎΠ²ΠΎΠΉ Π²ΠΎΠ΄Ρ ΠΏΡΠΎΠΈΠ·Π²ΠΎΠ΄ΠΈΡΡΡ Π°Π²ΡΠΎΠΌΠ°ΡΠΈΡΠ΅ΡΠΊΠΈ ΠΏΡΠΈ ΡΠ°Π±ΠΎΡΠ΅ ΡΠ΄Π°ΡΠ½ΠΎΠ³ΠΎ ΠΌΠ΅Ρ Π°Π½ΠΈΠ·ΠΌΠ° 3, Π° ΡΠ°ΠΊΠΆΠ΅ Π² ΡΠ»ΡΡΠ°Π΅ ΠΏΡΠ΅Π²ΡΡΠ΅Π½ΠΈΡ ΡΠ΅ΠΌΠΏΠ΅ΡΠ°ΡΡΡΡ Π² ΡΠ±ΠΎΡΠ½ΠΈΠΊΠ΅ ΠΈΠ½Π΅ΡΡΠ½ΠΎΠ³ΠΎ ΠΌΠ°ΡΠ΅ΡΠΈΠ°Π»Π° 450Β°C. ΠΠΎΠ»ΠΈΡΠ΅ΡΡΠ²ΠΎ ΡΠΎΡΡΡΠ½ΠΎΠΊ, ΡΠ°ΡΠΏΡΠ»ΡΡΡΠΈΡ ΠΈΠ·Π²Π΅ΡΡΠΊΠΎΠ²ΡΡ Π²ΠΎΠ΄Ρ, ΡΠ°ΡΡΡΠΈΡΡΠ²Π°Π΅ΡΡΡ ΠΈΡΡ ΠΎΠ΄Ρ ΠΈΠ· ΠΎΠ±ΡΠ΅ΠΌΠ° ΡΠ±ΠΎΡΠ½ΠΈΠΊΠ° ΠΈΠ½Π΅ΡΡΠ½ΠΎΠ³ΠΎ ΠΌΠ°ΡΠ΅ΡΠΈΠ°Π»Π° 15 ΠΈ ΠΎΠ±ΡΠ΅ΠΌΠ° ΠΈΠ½Π΅ΡΡΠ½ΡΡ ΠΌΠ°ΡΠ΅ΡΠΈΠ°Π»ΠΎΠ², ΡΠ²Π»ΡΡΡΠΈΡ ΡΡ ΠΎΡ Π»Π°ΠΆΠ΄Π°Π΅ΠΌΡΠΌΠΈ ΠΎΡΡ ΠΎΠ΄Π°ΠΌΠΈ. ΠΠ°ΠΏΡΠΈΠΌΠ΅Ρ, ΠΏΡΠΈ ΠΎΠ±ΡΠ΅ΠΌ ΠΎΠ±ΡΠ΅ΠΌΠ΅ ΡΠ±ΠΎΡΠ½ΠΈΠΊΠ° ΠΈΠ½Π΅ΡΡΠ½ΡΡ ΠΌΠ°ΡΠ΅ΡΠΈΠ°Π»ΠΎΠ² ΡΠ°Π²Π½ΠΎΠΌ 4 ΠΌ3 Π½Π΅ΠΎΠ±Ρ ΠΎΠ΄ΠΈΠΌΠΎ ΠΈ Π΄ΠΎΡΡΠ°ΡΠΎΡΠ½ΠΎ 12 ΡΠΎΡΡΡΠ½ΠΎΠΊ Π΄ΠΈΠ°ΠΌΠ΅ΡΡΠΎΠΌ 10β¦12 ΠΌΠΌ, Π° ΠΏΡΠΈ ΠΎΠ±ΡΠ΅ΠΌΠ΅ Π½Π°ΠΏΡΠΈΠΌΠ΅Ρ, 2 ΠΌ3 – Π½Π΅ΠΎΠ±Ρ ΠΎΠ΄ΠΈΠΌΠΎ Π±ΡΠ΄Π΅Ρ 6 ΡΠΎΡΡΡΠ½ΠΎΠΊ, ΠΏΡΠΈ ΠΎΠ±ΡΠ΅ΠΌΠ΅, Π½Π°ΠΏΡΠΈΠΌΠ΅Ρ, 8 ΠΌ3 – Π½Π΅ΠΎΠ±Ρ ΠΎΠ΄ΠΈΠΌΠΎ 24 ΡΠΎΡΡΡΠ½ΠΊΠΈ, ΡΠ°ΡΠΏΠΎΠ»ΠΎΠΆΠ΅Π½Π½ΡΡ ΡΠΈΠΌΠΌΠ΅ΡΡΠΈΡΠ½ΠΎ ΠΏΠΎ Π΄ΠΈΠ°ΠΌΠ΅ΡΡΡ ΡΠ±ΠΎΡΠ½ΠΈΠΊΠ° ΠΈΠ½Π΅ΡΡΠ½ΡΡ ΠΌΠ°ΡΠ΅ΡΠΈΠ°Π»ΠΎΠ² (ΡΠ°ΡΡΠ΅Ρ ΠΊΠΎΠ»ΠΈΡΠ΅ΡΡΠ²Π° ΡΠΎΡΡΡΠ½ΠΎΠΊ ΡΠΌ. Π² ΡΠ°Π·Π΄Π΅Π»Π΅ ΠΎΠΏΠΈΡΠ°Π½ΠΈΡ Β«ΠΏΡΠΈΠΌΠ΅Ρ ΠΊΠΎΠ½ΠΊΡΠ΅ΡΠ½ΠΎΠ³ΠΎ ΠΈΡΠΏΠΎΠ»Π½Π΅Π½ΠΈΡΒ»). ΠΡΠΏΠΎΠ»ΡΠ·ΠΎΠ²Π°Π½ΠΈΠ΅ ΠΈΠ·Π²Π΅ΡΡΠΊΠΎΠ²ΠΎΠΉ Π²ΠΎΠ΄Ρ ΠΏΠΎΠ²ΡΡΠ°Π΅Ρ ΡΠΊΠΎΠ»ΠΎΠ³ΠΈΡΠ½ΠΎΡΡΡ ΡΡΡΡΠΎΠΉΡΡΠ²Π°, ΡΠ°ΠΊ ΠΊΠ°ΠΊ ΠΎΠ½Π° Π²ΡΡΡΠΏΠ°Π΅Ρ Π² ΡΠ΅Π°ΠΊΡΠΈΡ Ρ Π³Π°Π·ΠΎΠΎΠ±ΡΠ°Π·Π½ΡΠΌΠΈ Π·Π°Π³ΡΡΠ·Π½ΡΡΡΠΈΠΌΠΈ Π²Π΅ΡΠ΅ΡΡΠ²Π°ΠΌΠΈ, Π² ΡΠΎΠΌ ΡΠΈΡΠ»Π΅ ΠΎΠΊΠΈΡΠ»ΠΎΠΌ ΡΠ΅ΡΡ, ΠΊΠΎΡΠΎΡΡΠ΅ Π°Π΄ΡΠΎΡΠ±ΠΈΡΡΡΡΡΡ Ρ ΠΏΠΎΡΠ»Π΅Π΄ΡΡΡΠΈΠΌ ΠΎΡΠ΅Π΄Π°Π½ΠΈΠ΅ΠΌ Π² ΡΠ±ΠΎΡΠ½ΠΈΠΊΠ΅ ΠΈΠ½Π΅ΡΡΠ½ΠΎΠ³ΠΎ ΠΌΠ°ΡΠ΅ΡΠΈΠ°Π»Π° 15.
ΠΡΠΎΠ΄ΡΠΊΡΡ ΡΠ΅ΡΠΌΠΈΡΠ΅ΡΠΊΠΎΠ³ΠΎ ΡΠ°Π·Π»ΠΎΠΆΠ΅Π½ΠΈΡ ΠΈΠ·Π½ΠΎΡΠ΅Π½Π½ΡΡ ΡΠΈΠ½ 27 (Π»Π΅ΡΡΡΠΈΠ΅ ΡΠΎΡΡΠ°Π²Π»ΡΡΡΠΈΠ΅), ΡΠΎΠ΄Π΅ΡΠΆΠ°ΡΠΈΠ΅ Π±ΠΎΠ»ΡΡΠΎΠ΅ ΠΊΠΎΠ»ΠΈΡΠ΅ΡΡΠ²ΠΎ Π³ΠΎΡΡΡΠΈΡ ΡΠ»Π΅ΠΌΠ΅Π½ΡΠΎΠ², ΡΠ΅ΡΠ΅Π· ΠΊΠΎΠ»ΡΡΠ΅Π²ΠΎΠΉ Π·Π°Π·ΠΎΡ ΠΌΠ΅ΠΆΠ΄Ρ Π²Π΅ΡΡ Π½Π΅ΠΉ 4 ΠΈ Π½ΠΈΠΆΠ½Π΅ΠΉ 5 ΡΠ°ΡΡΡΠΌΠΈ ΡΠ΅Π·ΠΎΠ½Π°ΡΠΎΡΠ½ΠΎΠΉ ΡΡΡΠ±Ρ ΠΏΠΎΠΏΠ°Π΄Π°ΡΡ Π² ΡΠ΅ΡΡΠ°ΡΡΠΉ ΡΡΡΠ±ΡΠ»ΠΈΠ·Π°ΡΠΎΡ 22. ΠΡΠΈ Π²ΠΊΠ»ΡΡΠ΅Π½ΠΈΠΈ ΠΌΠ½ΠΎΠ³ΠΎΡΠΎΠΏΠ»ΠΎΠ²ΠΎΠΉ Π΄ΠΈΡΡΡΠ·ΠΈΠΎΠ½Π½ΠΎΠΉ Π³ΠΎΡΠ΅Π»ΠΊΠΈ 20, ΡΠ°Π±ΠΎΡΠ°ΡΡΠ΅ΠΉ Π½Π° Π³Π°Π·ΠΎΠ²ΠΎΠΌ ΠΈΠ»ΠΈ ΠΆΠΈΠ΄ΠΊΠΎΠΌ ΡΠΎΠΏΠ»ΠΈΠ²Π΅, ΠΏΡΠΎΠ΄ΡΠΊΡΡ ΡΠ΅ΡΠΌΠΈΡΠ΅ΡΠΊΠΎΠ³ΠΎ ΡΠ°Π·Π»ΠΎΠΆΠ΅Π½ΠΈΡ ΠΈΠ·Π½ΠΎΡΠ΅Π½Π½ΡΡ ΡΠΈΠ½ (Π³Π°Π·ΠΎΠ²ΡΠ΅ ΠΎΡΡ ΠΎΠ΄Ρ) ΡΡΡΠ±ΡΠ»ΠΈΠ·ΠΈΡΡΡΡΡΡ Π·Π° ΡΠ΅ΡΡΠ°ΡΡΠΌ ΡΡΡΠ±ΡΠ»ΠΈΠ·Π°ΡΠΎΡΠΎΠΌ 22 ΠΈ Π²ΠΎΡΠΏΠ»Π°ΠΌΠ΅Π½ΡΡΡΡΡ. ΠΠ±ΡΠ°Π·ΡΠ΅ΡΡΡ ΠΏΠ»ΠΎΡΠΊΠ°Ρ Π·ΠΎΠ½Π° Π³ΠΎΡΠ΅Π½ΠΈΡ, ΡΠ°ΡΠΏΠΎΠ»ΠΎΠΆΠ΅Π½Π½Π°Ρ Π½Π° Π²ΡΡΠΎΡΠ΅ ΠΎΠ΄Π½ΠΎΠΉ ΡΠ΅ΡΠ²Π΅ΡΡΠΈ ΠΎΠ±ΡΠ΅ΠΉ Π΄Π»ΠΈΠ½Ρ ΡΠ΅Π·ΠΎΠ½Π°ΡΠΎΡΠ½ΠΎΠΉ ΡΡΡΠ±Ρ, Π³Π΄Π΅ Π²ΠΎΠ·Π±ΡΠΆΠ΄Π°ΡΡΡΡ Π°ΠΊΡΡΡΠΈΡΠ΅ΡΠΊΠΈΠ΅ ΠΊΠΎΠ»Π΅Π±Π°Π½ΠΈΡ, ΡΠΏΠΎΡΠΎΠ±ΡΡΠ²ΡΡΡΠΈΠ΅ ΡΠ½Π΅ΡΠ³ΠΈΡΠ½ΠΎΠΌΡ ΠΏΠ΅ΡΠ΅ΠΌΠ΅ΡΠΈΠ²Π°Π½ΠΈΡ Π³Π°Π·ΠΎΠ²ΠΎΠ·Π΄ΡΡΠ½ΠΎΠΉ ΡΠΌΠ΅ΡΠΈ. ΠΠΎΠ·Π΄ΡΡ Π² Π·ΠΎΠ½Ρ Π³ΠΎΡΠ΅Π½ΠΈΡ ΠΏΠΎΠ΄Π²ΠΎΠ΄ΠΈΡΡΡ ΠΈΠ· Π½ΠΈΠΆΠ½Π΅ΠΉ ΡΠ°ΡΡΠΈ ΡΠ΅Π·ΠΎΠ½Π°ΡΠΎΡΠ½ΠΎΠΉ ΡΡΡΠ±Ρ 5. ΠΡΠΎΠ΄ΡΠΊΡΡ ΡΠ°Π·Π»ΠΎΠΆΠ΅Π½ΠΈΡ ΠΈΠ·Π½ΠΎΡΠ΅Π½Π½ΡΡ ΡΠΈΠ½ 27, ΡΠΊΠΎΠΏΠΈΠ²ΡΠΈΠ΅ΡΡ Π² ΠΊΠ°ΠΌΠ΅ΡΠ΅ ΠΏΡΠ΅Π΄Π²Π°ΡΠΈΡΠ΅Π»ΡΠ½ΠΎΠΉ ΡΠ΅ΠΏΠ»ΠΎΠ²ΠΎΠΉ ΠΏΠΎΠ΄Π³ΠΎΡΠΎΠ²ΠΊΠΈ 9, ΠΏΠΎ Π³Π°Π·ΠΎΠΎΡΠ²ΠΎΠ΄ΡΡΠ΅ΠΉ ΡΡΡΠ±Π΅ 23 Π·Π° ΡΡΠ΅Ρ ΡΡΡΠ΅ΠΊΡΠ° ΡΠΆΠ΅ΠΊΡΠΈΠΈ Π²ΡΠ°ΡΡΠ²Π°ΡΡΡΡ Π² Π½ΠΈΠΆΠ½ΡΡ ΡΠ°ΡΡΡ ΡΠ΅Π·ΠΎΠ½Π°ΡΠΎΡΠ½ΠΎΠΉ ΡΡΡΠ±Ρ. ΠΠ΅ΡΠ³ΠΎΡΠ΅Π²ΡΠΈΠ΅ ΡΠ»Π΅ΠΌΠ΅Π½ΡΡ, ΡΠΎΠ΄Π΅ΡΠΆΠ°ΡΠΈΠ΅ΡΡ Π² ΠΏΡΠΎΠ΄ΡΠΊΡΠ°Ρ ΡΠ³ΠΎΡΠ°Π½ΠΈΡ Π³ΠΎΡΡΡΠ΅ΠΉ ΡΠ΅Π·ΠΈΠ½Ρ, ΠΏΡΠΎΡ ΠΎΠ΄Ρ ΡΠ΅ΡΠ΅Π· Π²ΡΡΠΎΠΊΠΎΡΠ΅ΠΌΠΏΠ΅ΡΠ°ΡΡΡΠ½ΡΡ Π·ΠΎΠ½Ρ, ΠΏΠΎΠ»Π½ΠΎΡΡΡΡ Π΄ΠΎΠ³ΠΎΡΠ°ΡΡ, ΡΠ²Π΅Π»ΠΈΡΠΈΠ²Π°Ρ ΡΠ΅ΠΏΠ»ΠΎΠ½Π°ΠΏΡΡΠΆΠ΅Π½Π½ΠΎΡΡΡ ΡΡΠΎΠΉ Π·ΠΎΠ½Ρ.
ΠΠΎ ΠΌΠ΅ΡΠ΅ ΡΡΡΠ°Π½ΠΎΠ²Π»Π΅Π½ΠΈΡ Π΄ΠΎΡΡΠ°ΡΠΎΡΠ½ΠΎΠΉ ΡΠ΅ΠΌΠΏΠ΅ΡΠ°ΡΡΡΡ Π² ΠΊΠ°ΠΌΠ΅ΡΠ΅ ΠΏΡΠ΅Π΄Π²Π°ΡΠΈΡΠ΅Π»ΡΠ½ΠΎΠΉ ΡΠ΅ΠΏΠ»ΠΎΠ²ΠΎΠΉ ΠΏΠΎΠ΄Π³ΠΎΡΠΎΠ²ΠΊΠΈ ΡΠΎΠΏΠ»ΠΈΠ²Π° 9 Π³ΠΎΡΡΡΠΈΠΉ Π³Π°Π·, ΠΏΠΎΡΡΡΠΏΠ°ΡΡΠΈΠΉ Π² ΠΊΠΎΠ»ΡΡΠ΅Π²ΡΡ Π³Π°Π·ΠΎΠ²ΡΡ Π³ΠΎΡΠ΅Π»ΠΊΡ Ρ ΡΠ»Π΅ΠΊΡΡΠΈΡΠ΅ΡΠΊΠΈΠΌ Π·Π°ΠΏΠ°Π»ΡΠ½ΠΈΠΊΠΎΠΌ 6, ΠΎΡΠΊΠ»ΡΡΠ°Π΅ΡΡΡ. Π Π·ΠΎΠ½Π΅ Π³ΠΎΡΠ΅Π½ΠΈΡ ΠΏΠΎΠ΄Π΄Π΅ΡΠΆΠΈΠ²Π°Π΅ΡΡΡ ΡΠ΅ΠΌΠΏΠ΅ΡΠ°ΡΡΡΠ° Π² Π΄ΠΈΠ°ΠΏΠ°Π·ΠΎΠ½Π΅ 350Β°C-450Β°C, ΠΏΡΠΎΠΈΡΡ ΠΎΠ΄ΠΈΡ ΡΠ΅ΡΠΌΠΈΡΠ΅ΡΠΊΠΎΠ΅ ΡΠ°Π·Π»ΠΎΠΆΠ΅Π½ΠΈΠ΅ ΠΈΠ·Π½ΠΎΡΠ΅Π½Π½ΡΡ ΡΠΈΠ½ 27. ΠΡΠΈ ΠΏΡΠΎΡ ΠΎΠΆΠ΄Π΅Π½ΠΈΠΈ Π³ΠΎΡΡΡΠΈΡ Π³Π°Π·ΠΎΠ² (Π»Π΅ΡΡΡΠΈΠ΅ ΡΠΎΡΡΠ°Π²Π»ΡΡΡΠΈΠ΅) ΡΠ΅ΡΠ΅Π· ΡΠ΅ΡΡΠ°ΡΡΠΉ ΡΡΡΠ±ΡΠ»ΠΈΠ·Π°ΡΠΎΡ 22, ΠΏΡΠΎΠΈΡΡ ΠΎΠ΄ΠΈΡ ΠΈΡ ΡΠΌΠ΅ΡΠΈΠ²Π°Π½ΠΈΠ΅ Ρ Π²ΡΠΎΡΠΈΡΠ½ΡΠΌ Π²ΠΎΠ·Π΄ΡΡ ΠΎΠΌ ΠΈ Π°ΠΊΡΠΈΠ²Π½ΠΎΠ΅ Π΄ΠΎΠ³ΠΎΡΠ°Π½ΠΈΠ΅ Π³ΠΎΡΡΡΠΈΡ ΡΠ»Π΅ΠΌΠ΅Π½ΡΠΎΠ². ΠΡΠ»Π΅Π΄ΡΡΠ²ΠΈΠ΅ ΡΡΠΎΠ³ΠΎ ΡΠ΅ΠΏΠ»ΠΎΠ²Π°Ρ Π½Π°ΠΏΡΡΠΆΠ΅Π½Π½ΠΎΡΡΡ ΡΠ΅ΡΡΠ°ΡΠΎΠ³ΠΎ ΡΡΡΠ±ΡΠ»ΠΈΠ·Π°ΡΠΎΡΠ° 22 ΠΎΡΡΠ°Π΅ΡΡΡ Π΄ΠΎΡΡΠ°ΡΠΎΡΠ½ΠΎ Π²ΡΡΠΎΠΊΠΎΠΉ Π΄Π»Ρ ΠΏΠΎΠ΄Π΄Π΅ΡΠΆΠ°Π½ΠΈΡ Π°Π²ΡΠΎΠΊΠΎΠ»Π΅Π±Π°ΡΠ΅Π»ΡΠ½ΠΎΠ³ΠΎ ΠΏΡΠΎΡΠ΅ΡΡΠ°. Π ΡΠ΅Π·ΠΎΠ½Π°ΡΠΎΡΠ½ΠΎΠΉ ΡΡΡΠ±Π΅ ΠΏΡΠΎΠ΄ΡΠΊΡΡ ΡΠ³ΠΎΡΠ°Π½ΠΈΡ ΡΠΎΠ²Π΅ΡΡΠ°ΡΡ ΠΊΠΎΠ»Π΅Π±Π°ΡΠ΅Π»ΡΠ½ΠΎΠ΅ Π΄Π²ΠΈΠΆΠ΅Π½ΠΈΠ΅, ΠΊΠΎΡΠΎΡΠΎΠ΅ ΡΠ²Π΅Π»ΠΈΡΠΈΠ²Π°Π΅Ρ ΡΠ΅ΠΏΠ»ΠΎΠΎΡΠ΄Π°ΡΡ ΠΎΡ Π³Π°Π·Π° ΠΊ ΡΡΠ΅Π½ΠΊΠ΅ ΠΈ ΠΏΡΠ΅ΠΏΡΡΡΡΠ²ΡΠ΅Ρ ΡΠ»Π°ΠΊΠΎΠ²ΠΎΠΌΡ ΠΎΡΠ»ΠΎΠΆΠ΅Π½ΠΈΡ Π½Π° ΡΡΠ΅Π½ΠΊΠ°Ρ ΡΠ΅Π·ΠΎΠ½Π°ΡΠΎΡΠ½ΠΎΠΉ ΡΡΡΠ±Ρ 4, 5.
ΠΡΠΈΠΌΠ΅Ρ ΠΊΠΎΠ½ΠΊΡΠ΅ΡΠ½ΠΎΠ³ΠΎ ΠΈΡΠΏΠΎΠ»Π½Π΅Π½ΠΈΡ (ΡΠΈΠ³.2).
Π£ΡΡΡΠΎΠΉΡΡΠ²ΠΎ Π΄Π»Ρ ΡΠΆΠΈΠ³Π°Π½ΠΈΡ ΡΠ²Π΅ΡΠ΄ΠΎΠ³ΠΎ ΡΠΎΠΏΠ»ΠΈΠ²Π° Π² ΠΏΡΠ»ΡΡΠΈΡΡΡΡΠ΅ΠΌ ΠΏΠΎΡΠΎΠΊΠ΅ ΡΠ²Π»ΡΠ΅ΡΡΡ ΠΎΠ³Π½Π΅Π²ΡΠΌ Π°ΠΏΠΏΠ°ΡΠ°ΡΠΎΠΌ, ΡΠ°Π±ΠΎΡΠ°ΡΡΠΈΠΌ ΠΏΠΎ ΠΏΡΠΈΠ½ΡΠΈΠΏΡ ΠΏΡΠ»ΡΡΠΈΡΡΡΡΠ΅Π³ΠΎ Π³ΠΎΡΠ΅Π½ΠΈΡ. ΠΡΠΎΡΠ΅ΡΡ ΡΠΆΠΈΠ³Π°Π½ΠΈΡ ΠΎΡΡΡΠ΅ΡΡΠ²Π»ΡΠ΅ΡΡΡ Π² Π΄Π²Π΅ ΡΡΡΠΏΠ΅Π½ΠΈ: 1) Π³Π°Π·ΠΈΡΠΈΠΊΠ°ΡΠΈΡ ΡΠ΅Π·ΠΈΠ½ΠΎΡΠ΅Ρ Π½ΠΈΡΠ΅ΡΠΊΠΈΡ ΠΎΡΡ ΠΎΠ΄ΠΎΠ² Π² Π²ΠΎΡΡΡΠ°Π½ΠΎΠ²ΠΈΡΠ΅Π»ΡΠ½ΠΎΠΉ ΡΡΠ΅Π΄Π΅, 2) Π΄ΠΎΠΆΠΈΠ³Π°Π½ΠΈΠ΅ Π³Π°Π·ΠΎΠΎΠ±ΡΠ°Π·Π½ΡΡ ΠΏΡΠΎΠ΄ΡΠΊΡΠΎΠ² Π² ΡΠ΅ΠΆΠΈΠΌΠ΅ ΠΏΡΠ»ΡΡΠ°ΡΠΈΠΉ Π² ΡΠ΅Π·ΠΎΠ½Π°ΡΠΎΡΠ½ΠΎΠΉ ΡΡΡΠ±Π΅.
Π£ΡΡΡΠΎΠΉΡΡΠ²ΠΎ Π΄Π»Ρ ΡΠΆΠΈΠ³Π°Π½ΠΈΡ ΠΈΠ·Π½ΠΎΡΠ΅Π½Π½ΡΡ ΡΠΈΠ½ ΡΡΡΠ°Π½ΠΎΠ²Π»Π΅Π½ΠΎ Π½Π° ΡΠ°ΠΌΠ½ΠΎΠΌ ΠΎΡΠ½ΠΎΠ²Π°Π½ΠΈΠΈ 26, ΡΠ²Π°ΡΠ΅Π½Π½ΠΎΠΌ ΠΈΠ· ΡΡΠ°Π»ΡΠ½ΡΡ ΡΠ³ΠΎΠ»ΠΊΠΎΠ². Π Π²Π΅ΡΡ Π½Π΅ΠΉ ΡΠ°ΡΡΠΈ ΡΠ΅Π·ΠΎΠ½Π°ΡΠΎΡΠ½ΠΎΠΉ ΡΡΡΠ±Ρ 4 ΠΏΡΠΈΠΊΡΠ΅ΠΏΠ»Π΅Π½ Π·ΠΎΠ»ΠΎΡΠ»ΠΎΠ²ΠΈΡΠ΅Π»Ρ 24. ΠΠ·ΠΌΠ΅Π½Π΅Π½ΠΈΠ΅ ΠΏΠΎΠ»ΠΎΠΆΠ΅Π½ΠΈΡ Π½ΠΈΠΆΠ½Π΅ΠΉ ΡΠ°ΡΡΠΈ ΡΠ΅Π·ΠΎΠ½Π°ΡΠΎΡΠ½ΠΎΠΉ ΡΡΡΠ±Ρ 5 ΠΎΡΡΡΠ΅ΡΡΠ²Π»ΡΠ΅Ρ ΡΠ»Π΅ΠΊΡΡΠΎΠ΄Π²ΠΈΠ³Π°ΡΠ΅Π»Ρ Ρ ΡΠ΅Π΄ΡΠΊΡΠΎΡΠΎΠΌ 25.
Π‘ ΠΏΠΎΠΌΠΎΡΡΡ ΡΠ΅Π»ΡΡΠ΅ΡΠ° ΠΈΠ·Π½ΠΎΡΠ΅Π½Π½ΡΠ΅ ΡΠΈΠ½Ρ 27 Π·Π°Π³ΡΡΠΆΠ°ΡΡΡΡ Π² ΠΊΠ°ΠΌΠ΅ΡΡ ΠΏΡΠ΅Π΄Π²Π°ΡΠΈΡΠ΅Π»ΡΠ½ΠΎΠΉ ΡΠ΅ΠΏΠ»ΠΎΠ²ΠΎΠΉ ΠΏΠΎΠ΄Π³ΠΎΡΠΎΠ²ΠΊΠΈ ΡΠΎΠΏΠ»ΠΈΠ²Π° 9. Π Π΅Π·ΠΈΠ½ΠΎΠ²ΡΠ΅ ΠΎΡΡ ΠΎΠ΄Ρ ΠΏΠΎΠ΄ΠΆΠΈΠ³Π°ΡΡΡΡ Π±ΡΡΠΎΠ²ΡΠΌΠΈ Π³Π°Π·ΠΎΠ²ΡΠΌΠΈ Π³ΠΎΡΠ΅Π»ΠΊΠ°ΠΌΠΈ Β«ΠΠ»Π°ΠΌΡ-1Β», ΡΠ°Π±ΠΎΡΠ°ΡΡΠΈΠΌΠΈ Π½Π° Π±Π°Π»Π»ΠΎΠ½Π½ΠΎΠΌ Π³Π°Π·ΠΎΠ²ΠΎΠΌ Π³ΠΎΡΡΡΠ΅ΠΌ (ΠΏΡΠΎΠΏΠ°Π½Π΅ Π‘3Π8). ΠΠ΅ΠΎΠ±Ρ ΠΎΠ΄ΠΈΠΌΠΎΠ΅ Π΄Π»Ρ Π³ΠΎΡΠ΅Π½ΠΈΡ ΠΊΠΎΠ»ΠΈΡΠ΅ΡΡΠ²ΠΎ Π²ΠΎΠ·Π΄ΡΡ Π°, ΠΏΠΎΡΡΡΠΏΠ°Π΅Ρ ΡΠ΅ΡΠ΅Π· Π²ΠΎΠ·Π΄ΡΡ ΠΎΠ²ΠΎΠ΄ 8. ΠΠΎΡΠ»Π΅ Π²ΠΎΠ·Π³ΠΎΡΠ°Π½ΠΈΡ ΡΠ΅Π·ΠΈΠ½Ρ Π³Π°Π·ΠΎΠ²ΡΠ΅ Π³ΠΎΡΠ΅Π»ΠΊΠΈ Π²ΡΠΊΠ»ΡΡΠ°ΡΡΡΡ. ΠΡΠ΅ΠΌΡ Π²ΡΡ ΠΎΠ΄Π° Π½Π° ΡΠ°Π±ΠΎΡΠΈΠΉ ΡΠ΅ΠΆΠΈΠΌ ΡΠΎΡΡΠ°Π²Π»ΡΠ΅Ρ 18-20 ΠΌΠΈΠ½ΡΡ. Π Π΄Π°Π»ΡΠ½Π΅ΠΉΡΠ΅ΠΌ Π³ΠΎΡΠ΅Π½ΠΈΠ΅ ΡΠ΅Π·ΠΈΠ½Ρ Π² ΠΊΠ°ΠΌΠ΅ΡΠ΅ ΠΏΡΠ΅Π΄Π²Π°ΡΠΈΡΠ΅Π»ΡΠ½ΠΎΠΉ ΡΠ΅ΠΏΠ»ΠΎΠ²ΠΎΠΉ ΠΏΠΎΠ΄Π³ΠΎΡΠΎΠ²ΠΊΠΈ ΡΠΎΠΏΠ»ΠΈΠ²Π° 9 ΠΏΡΠΎΠΈΡΡ ΠΎΠ΄ΠΈΡ Π±Π΅Π· ΡΠΎΠΏΡΠΎΠ²ΠΎΠΆΠ΄Π΅Π½ΠΈΡ Π³ΠΎΡΡΡΠΈΠΌ Π³Π°Π·ΠΎΠΌ.
Π’Π΅ΠΌΠΏΠ΅ΡΠ°ΡΡΡΠ° Π² ΠΊΠ°ΠΌΠ΅ΡΠ΅ ΠΏΡΠ΅Π΄Π²Π°ΡΠΈΡΠ΅Π»ΡΠ½ΠΎΠΉ ΡΠ΅ΠΏΠ»ΠΎΠ²ΠΎΠΉ ΠΏΠΎΠ΄Π³ΠΎΡΠΎΠ²ΠΊΠΈ ΡΠΎΠΏΠ»ΠΈΠ²Π° 9 ΠΏΠΎΠ΄Π΄Π΅ΡΠΆΠΈΠ²Π°Π΅ΡΡΡ Π² Π΄ΠΈΠ°ΠΏΠ°Π·ΠΎΠ½Π΅ 350Β°-450Β°C. Π Π΅Π³ΡΠ»ΠΈΡΠΎΠ²ΠΊΠ° ΡΠ΅ΠΌΠΏΠ΅ΡΠ°ΡΡΡΡ ΠΎΡΡΡΠ΅ΡΡΠ²Π»ΡΠ΅ΡΡΡ ΠΏΠΎΠ΄ΠΌΠ΅ΡΠΈΠ²Π°Π½ΠΈΠ΅ΠΌ Π²ΠΎΠ·Π΄ΡΡ Π° Π² Π½Π°Π³ΡΠ΅ΡΡΠ΅ Π³Π°Π·Ρ, ΠΏΠΎΡΡΡΠΏΠ°ΡΡΠ΅Π³ΠΎ Π² ΠΊΠ°ΠΌΠ΅ΡΡ Π²ΠΎΡΠΏΠ»Π°ΠΌΠ΅Π½Π΅Π½ΠΈΡ 1. Π‘ ΡΡΠΎΠΉ ΡΠ΅Π»ΡΡ Π² Π·Π°ΡΠ²Π»Π΅Π½Π½ΠΎΠΌ ΡΡΡΡΠΎΠΉΡΡΠ²Π΅ ΠΏΡΠ΅Π΄ΡΡΠΌΠΎΡΡΠ΅Π½Π° ΡΠΈΡΡΠ΅ΠΌΠ° ΠΏΠΎΠ΄Π°ΡΠΈ Π²ΠΎΠ·Π΄ΡΡ Π° Π² ΠΊΠ°ΠΌΠ΅ΡΡ, Π²ΠΊΠ»ΡΡΠ°ΡΡΠ°Ρ ΡΠ΅ΡΠΌΠΎΠ΄Π°ΡΡΠΈΠΊ ΡΠΈΡΡΠ΅ΠΌΡ ΡΠ΅Π³ΡΠ»ΠΈΡΠΎΠ²Π°Π½ΠΈΡ ΡΠ΅ΠΌΠΏΠ΅ΡΠ°ΡΡΡΡ 28, Π±Π»ΠΎΠΊ Π°Π²ΡΠΎΠΌΠ°ΡΠΈΡΠ΅ΡΠΊΠΎΠ³ΠΎ ΠΈΠ·ΠΌΠ΅Π½Π΅Π½ΠΈΡ ΡΠ΅ΠΌΠΏΠ΅ΡΠ°ΡΡΡΡ 29 ΠΈ Π²ΠΎΠ·Π΄ΡΡ ΠΎΠ²ΠΎΠ΄ 8. ΠΡΠΈ ΠΏΠΎΠ²ΡΡΠ΅Π½ΠΈΠΈ ΡΠ΅ΠΌΠΏΠ΅ΡΠ°ΡΡΡΡ Π² ΠΊΠ°ΠΌΠ΅ΡΠ΅ Π²ΠΎΡΠΏΠ»Π°ΠΌΠ΅Π½Π΅Π½ΠΈΡ 1 ΠΈ Π² ΠΊΠ°ΠΌΠ΅ΡΠ΅ ΠΏΡΠ΅Π΄Π²Π°ΡΠΈΡΠ΅Π»ΡΠ½ΠΎΠΉ ΡΠ΅ΠΏΠ»ΠΎΠ²ΠΎΠΉ ΠΏΠΎΠ΄Π³ΠΎΡΠΎΠ²ΠΊΠΈ ΡΠΎΠΏΠ»ΠΈΠ²Π° 9 Π²ΡΡΠ΅ 450Β°C ΡΠ΅ΡΠΌΠΎΠ΄Π°ΡΡΠΈΠΊ ΡΠΈΡΡΠ΅ΠΌΡ ΡΠ΅Π³ΡΠ»ΠΈΡΠΎΠ²Π°Π½ΠΈΡ ΡΠ΅ΠΌΠΏΠ΅ΡΠ°ΡΡΡΡ 28 ΡΠΈΠΊΡΠΈΡΡΠ΅Ρ ΡΠ΅ΠΌΠΏΠ΅ΡΠ°ΡΡΡΡ, Π±Π»ΠΎΠΊ Π°Π²ΡΠΎΠΌΠ°ΡΠΈΡΠ΅ΡΠΊΠΎΠ³ΠΎ ΠΈΠ·ΠΌΠ΅Π½Π΅Π½ΠΈΡ ΡΠ΅ΠΌΠΏΠ΅ΡΠ°ΡΡΡΡ 29 ΡΠΌΠ΅Π½ΡΡΠ°Π΅Ρ ΠΏΡΠΎΡ ΠΎΠ΄Π½ΠΎΠ΅ ΡΠ΅ΡΠ΅Π½ΠΈΠ΅ Π²ΠΎΠ·Π΄ΡΡ ΠΎΠ²ΠΎΠ΄Π° 8, Π²ΡΠΏΠΎΠ»Π½ΡΡΡΠ΅Π³ΠΎ ΡΡΠ½ΠΊΡΠΈΡ Π°ΡΡΠΎΠ΄ΠΈΠ½Π°ΠΌΠΈΡΠ΅ΡΠΊΠΎΠ³ΠΎ ΠΊΠ»Π°ΠΏΠ°Π½Π°, Π΄ΠΎΡΡΡΠΏ Π²ΠΎΠ·Π΄ΡΡ Π° Π² ΠΎΠ±Π»Π°ΡΡΡ Π³ΠΎΡΠ΅Π½ΠΈΡ ΡΠΌΠ΅Π½ΡΡΠ°Π΅ΡΡΡ, Π° ΠΏΡΠΈ ΡΠ΅ΠΌΠΏΠ΅ΡΠ°ΡΡΡΠ΅ Π½ΠΈΠΆΠ΅ 350Β°C ΡΠ²Π΅Π»ΠΈΡΠΈΠ²Π°Π΅ΡΡΡ. Π‘ΠΎΠΎΡΠ²Π΅ΡΡΡΠ²Π΅Π½Π½ΠΎ ΠΈΠ½ΡΠ΅Π½ΡΠΈΠ²Π½ΠΎΡΡΡ Π³ΠΎΡΠ΅Π½ΠΈΡ ΠΏΠΎΠ½ΠΈΠΆΠ°Π΅ΡΡΡ ΠΈΠ»ΠΈ ΠΏΠΎΠ²ΡΡΠ°Π΅ΡΡΡ. ΠΡΠΈ ΡΠ°ΠΊΠΎΠΉ ΡΠ΅ΠΌΠΏΠ΅ΡΠ°ΡΡΡΠ΅ Π² ΠΊΠ°ΠΌΠ΅ΡΠ΅ ΠΏΡΠ΅Π΄Π²Π°ΡΠΈΡΠ΅Π»ΡΠ½ΠΎΠΉ ΠΏΠΎΠ΄Π³ΠΎΡΠΎΠ²ΠΊΠΈ ΡΠΎΠΏΠ»ΠΈΠ²Π° 9 Ρ ΠΈΠ·Π½ΠΎΡΠ΅Π½Π½ΡΡ ΡΠΈΠ½ 27 Π²ΡΠ΄Π΅Π»ΡΡΡΡΡ Π»Π΅ΡΡΡΠΈΠ΅ ΡΠΎΡΡΠ°Π²Π»ΡΡΡΠΈΠ΅, ΠΊΠΎΡΠΎΡΡΠ΅ ΠΏΠΎ Π³Π°Π·ΠΎΠΎΡΠ²ΠΎΠ΄ΡΡΠ΅ΠΉ ΡΡΡΠ±Π΅ 23, Π²Π΅ΡΡ Π½ΠΈΠΉ ΡΡΠ΅Π· ΠΊΠΎΡΠΎΡΠΎΠΉ Π½Π°Ρ ΠΎΠ΄ΠΈΡΡΡ ΠΎΡ Π½ΠΈΠΆΠ½Π΅ΠΉ ΡΠ°ΡΡΠΈ ΠΊΡΡΡΠΊΠΈ ΠΊΠ°ΠΌΠ΅ΡΡ ΠΏΡΠ΅Π΄Π²Π°ΡΠΈΡΠ΅Π»ΡΠ½ΠΎΠΉ ΡΠ΅ΠΏΠ»ΠΎΠ²ΠΎΠΉ ΠΏΠΎΠ΄Π³ΠΎΡΠΎΠ²ΠΊΠΈ ΡΠΎΠΏΠ»ΠΈΠ²Π° 11 Π½Π° ΡΠ°ΡΡΡΠΎΡΠ½ΠΈΠΈ 2-3 Π΄ΠΈΠ°ΠΌΠ΅ΡΡΠ° ΡΡΠΎΠΉ ΡΡΡΠ±Ρ (ΡΠ°ΡΡΡΠΎΡΠ½ΠΈΠ΅ ΠΎΡ Π²Π΅ΡΡ Π½Π΅Π³ΠΎ ΡΡΠ΅Π·Π° Π³Π°Π·ΠΎΠΎΡΠ²ΠΎΠ΄ΡΡΠ΅ΠΉ ΡΡΡΠ±Ρ Π΄ΠΎ Π½ΠΈΠΆΠ½Π΅ΠΉ ΡΠ°ΡΡΠΈ ΠΊΡΡΡΠΊΠΈ ΠΊΠ°ΠΌΠ΅ΡΡ ΠΏΡΠ΅Π΄Π²Π°ΡΠΈΡΠ΅Π»ΡΠ½ΠΎΠΉ ΡΠ΅ΠΏΠ»ΠΎΠ²ΠΎΠΉ ΠΏΠΎΠ΄Π³ΠΎΡΠΎΠ²ΠΊΠΈ ΡΠΎΠΏΠ»ΠΈΠ²Π° 11 ΡΠΎΡΡΠ°Π²Π»ΡΠ΅Ρ 2-3 Π΄ΠΈΠ°ΠΌΠ΅ΡΡΠ°, ΡΠ°ΠΊ ΠΊΠ°ΠΊ ΠΏΠΎΠ΄ Π΄Π΅ΠΉΡΡΠ²ΠΈΠ΅ΠΌ ΡΠΈΠ» ΠΡΡ ΠΈΠΌΠ΅Π΄Π° Π»Π΅ΡΡΡΠΈΠ΅ ΠΊΠΎΠΌΠΏΠΎΠ½Π΅Π½ΡΡ ΠΊΠΎΠ½ΡΠ΅Π½ΡΡΠΈΡΡΡΡΡΡ Π² Π²Π΅ΡΡ Π½Π΅ΠΉ ΡΠ°ΡΡΠΈ ΠΊΠ°ΠΌΠ΅ΡΡ ΠΏΡΠ΅Π΄Π²Π°ΡΠΈΡΠ΅Π»ΡΠ½ΠΎΠΉ ΡΠ΅ΠΏΠ»ΠΎΠ²ΠΎΠΉ ΠΏΠΎΠ΄Π³ΠΎΡΠΎΠ²ΠΊΠΈ ΡΠΎΠΏΠ»ΠΈΠ²Π° 9), ΠΏΠΎΡΡΡΠΏΠ°ΡΡ Π² ΡΠ΅Π·ΠΎΠ½Π°ΡΠΎΡΠ½ΡΡ ΡΡΡΠ±Ρ 4, 5 Π΄Π»Ρ ΠΏΠΎΡΠ»Π΅Π΄ΡΡΡΠ΅Π³ΠΎ Π΄ΠΎΠΆΠΈΠ³Π°Π½ΠΈΡ, ΠΈ, ΠΏΠΎΠ΄ΠΌΠ΅ΡΠΈΠ²Π°ΡΡΡ Ρ Π²ΡΠΎΡΠΈΡΠ½ΡΠΌ Π²ΠΎΠ·Π΄ΡΡ ΠΎΠΌ, ΡΠ³ΠΎΡΠ°ΡΡ Π² ΡΠ΅ΠΆΠΈΠΌΠ΅ ΠΏΡΠ»ΡΡΠ°ΡΠΈΠΉ. ΠΡΠΈ ΡΡΠ΅Π·ΠΌΠ΅ΡΠ½ΠΎΠΌ ΠΏΠΎΠ²ΡΡΠ΅Π½ΠΈΠΈ ΡΠΊΠΎΡΠΎΡΡΠΈ Π²ΠΎΠ·Π΄ΡΡΠ½ΠΎΠ³ΠΎ ΠΏΠΎΡΠΎΠΊΠ° (Π±ΠΎΠ»Π΅Π΅ 8 ΠΌ/Ρ) Π² ΡΠ΅Π·ΠΎΠ½Π°ΡΠΎΡΠ½ΠΎΠΉ ΡΡΡΠ±Π΅ Π°Π²ΡΠΎΠΊΠΎΠ»Π΅Π±Π°Π½ΠΈΡ ΠΈΡΡΠ΅Π·Π°ΡΡ, ΡΠ°ΠΊ ΠΊΠ°ΠΊ Π½Π΅ Π²ΡΠΏΠΎΠ»Π½ΡΠ΅ΡΡΡ ΠΊΡΠΈΡΠ΅ΡΠΈΠΉ Π Π΅Π»Π΅Ρ. ΠΠ»Ρ ΡΠΌΠ΅Π½ΡΡΠ΅Π½ΠΈΡ ΡΠΊΠΎΡΠΎΡΡΠΈ Π²ΠΎΠ·Π΄ΡΡΠ½ΠΎΠ³ΠΎ ΠΏΠΎΡΠΎΠΊΠ° ΡΠ°ΡΡΡΠΎΡΠ½ΠΈΠ΅ ΠΌΠ΅ΠΆΠ΄Ρ ΡΠ΅ΡΠ΅ΡΠΊΠ°ΠΌΠΈ ΡΠ΅ΡΡΠ°ΡΠΎΠ³ΠΎ ΡΡΡΠ±ΡΠ»ΠΈΠ·Π°ΡΠΎΡΠ° Π½Π΅ΠΎΠ±Ρ ΠΎΠ΄ΠΈΠΌΠΎ ΡΠΌΠ΅Π½ΡΡΠΈΡΡ. ΠΡΠΎ ΠΏΡΠΈΠ²ΠΎΠ΄ΠΈΡ ΠΊ ΡΠ²Π΅Π»ΠΈΡΠ΅Π½ΠΈΡ Π³ΠΈΠ΄ΡΠΎΠ΄ΠΈΠ½Π°ΠΌΠΈΡΠ΅ΡΠΊΠΎΠ³ΠΎ ΡΠΎΠΏΡΠΎΡΠΈΠ²Π»Π΅Π½ΠΈΡ – ΡΠΌΠ΅Π½ΡΡΠ΅Π½ΠΈΡ ΡΠΊΠΎΡΠΎΡΡΠΈ Π²ΠΎΠ·Π΄ΡΡΠ½ΠΎΠ³ΠΎ ΠΏΠΎΡΠΎΠΊΠ°. Π ΡΠ΅Π·ΠΎΠ½Π°ΡΠΎΡΠ½ΠΎΠΉ ΡΡΡΠ±Π΅ ΠΏΡΠΎΠ΄ΡΠΊΡΡ ΡΠ³ΠΎΡΠ°Π½ΠΈΡ ΡΠΎΠ²Π΅ΡΡΠ°ΡΡ ΠΊΠΎΠ»Π΅Π±Π°ΡΠ΅Π»ΡΠ½ΠΎΠ΅ Π΄Π²ΠΈΠΆΠ΅Π½ΠΈΠ΅, ΠΊΠΎΡΠΎΡΠΎΠ΅ ΡΠ²Π΅Π»ΠΈΡΠΈΠ²Π°Π΅Ρ ΡΠ΅ΠΏΠ»ΠΎΠΎΡΠ΄Π°ΡΡ ΠΎΡ Π³Π°Π·Π° ΠΊ ΡΡΠ΅Π½ΠΊΠ΅ ΠΈ ΠΏΡΠ΅ΠΏΡΡΡΡΠ²ΡΠ΅Ρ ΡΠ»Π°ΠΊΠΎΠ²ΠΎΠΌΡ ΠΎΡΠ»ΠΎΠΆΠ΅Π½ΠΈΡ Π½Π° ΡΡΠ΅Π½ΠΊΠ°Ρ ΡΡΡΠ±Ρ. ΠΠ΅ΡΠ°Π»Π»ΠΈΡΠ΅ΡΠΊΠΈΠΉ ΠΊΠΎΡΠ΄ ΠΈ ΡΠ°ΡΡΡ ΡΠ²Π΅ΡΠ΄ΠΎΠ³ΠΎ ΠΎΡΡΠ°ΡΠΊΠ° ΠΎΠΏΡΡΠΊΠ°ΡΡΡΡ Π² ΡΠ±ΠΎΡΠ½ΠΈΠΊ ΡΠ²Π΅ΡΠ΄ΡΡ ΠΎΡΡ ΠΎΠ΄ΠΎΠ² 10, Π° ΠΈΠ½Π΅ΡΡΠ½ΡΠΉ ΠΌΠ°ΡΠ΅ΡΠΈΠ°Π» ΠΎΠΏΡΡΠΊΠ°Π΅ΡΡΡ Π² ΡΠ±ΠΎΡΠ½ΠΈΠΊ ΠΈΠ½Π΅ΡΡΠ½ΠΎΠ³ΠΎ ΠΌΠ°ΡΠ΅ΡΠΈΠ°Π»Π° 15. ΠΡ Π»Π°ΠΆΠ΄Π΅Π½ΠΈΠ΅ ΠΈΠ½Π΅ΡΡΠ½ΠΎΠ³ΠΎ ΠΌΠ°ΡΠ΅ΡΠΈΠ°Π»Π° ΠΏΡΠΎΠΈΡΡ ΠΎΠ΄ΠΈΡ ΠΏΡΠΈ ΠΏΠΎΠΌΠΎΡΠΈ ΡΠΈΡΡΠ΅ΠΌΡ ΡΠ½ΠΈΠΆΠ΅Π½ΠΈΡ ΡΠ΅ΠΌΠΏΠ΅ΡΠ°ΡΡΡΡ ΠΈΠ½Π΅ΡΡΠ½ΠΎΠ³ΠΎ ΠΌΠ°ΡΠ΅ΡΠΈΠ°Π»Π°, Π΄Π»Ρ ΡΡΠΎΠ³ΠΎ ΡΠΎΡΡΡΠ½ΠΊΠΈ, ΡΠ°ΡΠΏΠΎΠ»ΠΎΠΆΠ΅Π½Π½ΡΠ΅ ΡΠΈΠΌΠΌΠ΅ΡΡΠΈΡΠ½ΠΎ ΠΏΠΎ Π΄ΠΈΠ°ΠΌΠ΅ΡΡΡ ΡΠ±ΠΎΡΠ½ΠΈΠΊΠ° ΠΈΠ½Π΅ΡΡΠ½ΠΎΠ³ΠΎ ΠΌΠ°ΡΠ΅ΡΠΈΠ°Π»Π° ΡΠ°ΡΠΏΡΠ»ΡΡΡ ΠΈΠ·Π²Π΅ΡΡΠΊΠΎΠ²ΡΡ Π²ΠΎΠ΄Ρ, ΠΊΠΎΡΠΎΡΠ°Ρ ΠΎΡ Π»Π°ΠΆΠ΄Π°Π΅Ρ ΠΈΠ½Π΅ΡΡΠ½ΡΠΉ ΠΌΠ°ΡΠ΅ΡΠΈΠ°Π». ΠΡΠΈ Π²ΡΡΠΎΡΠ΅ ΡΠ±ΠΎΡΠ½ΠΈΠΊΠ° ΠΈΠ½Π΅ΡΡΠ½ΠΎΠ³ΠΎ ΠΌΠ°ΡΠ΅ΡΠΈΠ°Π»Π° h=1,95 ΠΌ, ΡΠ°Π΄ΠΈΡΡΠ΅ R=1,4 ΠΌ, ΠΎΠ±ΡΠ΅ΠΌ ΡΠ±ΠΎΡΠ½ΠΈΠΊΠ° ΠΈΠ½Π΅ΡΡΠ½ΠΎΠ³ΠΎ ΠΌΠ°ΡΠ΅ΡΠΈΠ°Π»Π° ΡΠ°Π²Π΅Π½ VΡΠ±.ΠΈΠ½Π΅ΡΡ.ΠΌΠ°Ρ=4 ΠΌ3. ΠΠ»Ρ ΠΏΠΎΠ»Π½ΠΎΠ³ΠΎ ΡΠΌΠ°ΡΠΈΠ²Π°Π½ΠΈΡ ΠΈ ΠΎΡ Π»Π°ΠΆΠ΄Π΅Π½ΠΈΡ ΠΈΠ½Π΅ΡΡΠ½ΠΎΠ³ΠΎ ΠΌΠ°ΡΠ΅ΡΠΈΠ°Π»Π° Π½Π΅ΠΎΠ±Ρ ΠΎΠ΄ΠΈΠΌΠΎ VΡΠΌΠ°ΡΠΈΠ²=0,8 ΠΌ3 ΠΈΠ·Π²Π΅ΡΡΠΊΠΎΠ²ΠΎΠΉ Π²ΠΎΠ΄Ρ. Π‘ΠΈΠΌΠΌΠ΅ΡΡΠΈΡΠ½ΠΎ ΠΏΠΎ Π΄ΠΈΠ°ΠΌΠ΅ΡΡΡ ΡΠ±ΠΎΡΠ½ΠΈΠΊΠ° ΠΈΠ½Π΅ΡΡΠ½ΠΎΠ³ΠΎ ΠΌΠ°ΡΠ΅ΡΠΈΠ°Π»Π° ΡΡΡΠ°Π½Π°Π²Π»ΠΈΠ²Π°ΡΡΡΡ ΡΡΠ°Π½Π΄Π°ΡΡΠ½ΡΠ΅ ΡΠΎΡΡΡΠ½ΠΊΠΈ, Π΄ΠΈΠ°ΠΌΠ΅ΡΡΠΎΠΌ d=10β¦12 ΠΌΠΌ=0,01β¦0,012 ΠΌ. Π Π°ΡΡ ΠΎΠ΄ ΠΈΠ·Π²Π΅ΡΡΠΊΠΎΠ²ΠΎΠΉ Π²ΠΎΠ΄Ρ ΡΠ΅ΡΠ΅Π· ΠΎΠ΄Π½Ρ ΡΠΎΡΡΡΠ½ΠΊΡ Q=SΡΒ·Ο ), (Q – ΡΠ°ΡΡ ΠΎΠ΄ ΠΈΠ·Π²Π΅ΡΡΠΊΠΎΠ²ΠΎΠΉ Π²ΠΎΠ΄Ρ ΡΠ΅ΡΠ΅Π· 1 ΡΠΎΡΡΡΠ½ΠΊΡ, SΡ – ΠΏΠ»ΠΎΡΠ°Π΄Ρ ΠΏΠΎΠΏΠ΅ΡΠ΅ΡΠ½ΠΎΠ³ΠΎ ΡΠ΅ΡΠ΅Π½ΠΈΡ ΡΠΎΡΡΡΠ½ΠΊΠΈ, Ο – ΡΠΊΠΎΡΠΎΡΡΡ ΠΏΠΎΡΠΎΠΊΠ° ΠΈΠ·Π²Π΅ΡΡΠΊΠΎΠ²ΠΎΠΉ Π²ΠΎΠ΄Ρ) Q=SΡΒ·Ο =ΟΒ·r2Β·Ο =3,14Β·0,0062Β·10=0,001 ΠΌ3/Ρ (ΠΏΡΠΈ ΡΠΊΠΎΡΠΎΡΡΠΈ ΠΏΠΎΡΠΎΠΊΠ° ΠΈΠ·Π²Π΅ΡΡΠΊΠΎΠ²ΠΎΠΉ Π²ΠΎΠ΄Ρ 10 ΠΌ/Ρ). ΠΡΠ΅ΠΌΡ ΡΠ°ΡΠΏΡΠ»Π° t=1 ΠΌΠΈΠ½=60 Ρ. VΠ²ΠΎΠ΄Ρ ΡΠ΅ΡΠ΅Π· 1 ΡΠΎΡΡΡΠ½ΠΊΡ=QΒ·t=0,001Β·60=0,06 ΠΌ3. ΠΠ΅ΠΎΠ±Ρ ΠΎΠ΄ΠΈΠΌΠΎΠ΅ ΠΊΠΎΠ»ΠΈΡΠ΅ΡΡΠ²ΠΎ ΡΠΎΡΡΡΠ½ΠΎΠΊ n=VΡΠΌΠ°ΡΠΈΠ²/VΠ²ΠΎΠ΄Ρ ΡΠ΅ΡΠ΅Π· 1 ΡΠΎΡΡΡΠ½ΠΊΡ=0,8/0,06=12 ΡΠΎΡΡΡΠ½ΠΎΠΊ. ΠΠ°Π³ΡΡΠ·ΠΊΠ° ΡΠΈΠ½ ΠΎΡΡΡΠ΅ΡΡΠ²Π»ΡΠ΅ΡΡΡ ΡΠΈΠΊΠ»ΠΈΡΠ΅ΡΠΊΠΈ Π±Π΅Π· ΠΈΡ ΠΌΠ΅Ρ Π°Π½ΠΈΡΠ΅ΡΠΊΠΎΠ³ΠΎ Π΄ΡΠΎΠ±Π»Π΅Π½ΠΈΡ.
Π’Π°ΠΊΠΈΠΌ ΠΎΠ±ΡΠ°Π·ΠΎΠΌ, ΠΏΠΎ ΡΡΠ°Π²Π½Π΅Π½ΠΈΡ Ρ ΠΈΠ·Π²Π΅ΡΡΠ½ΡΠΌΠΈ Π°Π½Π°Π»ΠΎΠ³Π°ΠΌΠΈ ΠΏΡΠ΅ΠΈΠΌΡΡΠ΅ΡΡΠ²ΠΎΠΌ Π·Π°ΡΠ²Π»ΡΠ΅ΠΌΠΎΠ³ΠΎ ΡΠ΅Ρ Π½ΠΈΡΠ΅ΡΠΊΠΎΠ³ΠΎ ΡΠ΅ΡΠ΅Π½ΠΈΡ ΡΠ²Π»ΡΠ΅ΡΡΡ ΡΠΎΠ·Π΄Π°Π½ΠΈΠ΅ Π²ΡΡΠΎΠΊΠΎΡΡΡΠ΅ΠΊΡΠΈΠ²Π½ΠΎΠΉ ΡΡΡΠ°Π½ΠΎΠ²ΠΊΠΈ, ΠΏΠΎΠ·Π²ΠΎΠ»ΡΡΡΠ΅ΠΉ ΠΏΠΎΠ²ΡΡΠΈΡΡ ΠΏΠΎΠΆΠ°ΡΠΎΠ±Π΅Π·ΠΎΠΏΠ°ΡΠ½ΠΎΡΡΡ, Π·Π° ΡΡΠ΅Ρ ΠΊΠΎΠ½ΡΡΡΡΠΊΡΠΈΠ²Π½ΠΎΠΉ ΠΎΡΠΎΠ±Π΅Π½Π½ΠΎΡΡΠΈ – Π²Π²ΠΎΠ΄Π° Π³Π°Π·ΠΎΠΎΡΠ²ΠΎΠ΄ΡΡΠ΅ΠΉ ΡΡΡΠ±Ρ, ΡΠ°Π±ΠΎΡΠ°ΡΡΠ΅ΠΉ Π½Π° ΡΡΡΠ΅ΠΊΡΠ΅ ΡΠΆΠ΅ΠΊΡΠΈΠΈ, Π·Π° ΡΡΠ΅Ρ Π²Π²ΠΎΠ΄Π° ΡΠΈΡΡΠ΅ΠΌΡ ΡΠ΅Π³ΡΠ»ΠΈΡΠΎΠ²Π°Π½ΠΈΡ ΡΠ΅ΠΌΠΏΠ΅ΡΠ°ΡΡΡΡ, ΠΈ ΠΏΠΎΠ»Π½ΠΎΡΡ ΡΠ³ΠΎΡΠ°Π½ΠΈΡ ΠΏΡΠΎΡΠ΅ΡΡΠ° ΡΡΠΈΠ»ΠΈΠ·Π°ΡΠΈΠΈ, ΠΏΡΡΠ΅ΠΌ ΠΏΠΎΠ΄Π΄Π΅ΡΠΆΠ°Π½ΠΈΡ ΠΏΠΎΡΡΠΎΡΠ½Π½ΠΎΠ³ΠΎ ΠΎΠ±ΡΠ΅ΠΌΠ° ΠΊΠ°ΠΌΠ΅ΡΡ ΠΏΡΠ΅Π΄Π²Π°ΡΠΈΡΠ΅Π»ΡΠ½ΠΎΠΉ ΡΠ΅ΠΏΠ»ΠΎΠ²ΠΎΠΉ ΠΏΠΎΠ΄Π³ΠΎΡΠΎΠ²ΠΊΠΈ ΡΠΎΠΏΠ»ΠΈΠ²Π°, ΠΏΠΎΠ²ΡΡΠ°ΡΡΠ΅Π³ΠΎ ΡΠΊΠΎΠ»ΠΎΠ³ΠΈΡΠ½ΠΎΡΡΡ. Π ΡΠΊΠΎΠ½ΠΎΠΌΠΈΡΠ½ΠΎΡΡΡ ΠΏΠΎΠ²ΡΡΠ°Π΅ΡΡΡ Π±Π»Π°Π³ΠΎΠ΄Π°ΡΡ ΡΠΎΠΉ ΠΆΠ΅ ΠΊΠΎΠ½ΡΡΡΡΠΊΡΠΈΠ²Π½ΠΎΠΉ ΠΎΡΠΎΠ±Π΅Π½Π½ΠΎΡΡΠΈ, Π² ΡΠ΅Π·ΡΠ»ΡΡΠ°ΡΠ΅ ΡΠ΅Π³ΠΎ Π½Π΅ Π±ΡΠ΄Π΅Ρ ΠΎΡΠ»ΠΎΠΆΠ΅Π½ΠΈΠΉ ΡΠΌΠΎΠ»ΠΎΠΎΠ±ΡΠ°Π·Π½ΡΡ ΠΌΠ°ΡΡ Π½Π° Π²Π½ΡΡΡΠ΅Π½Π½ΠΈΡ ΡΡΠ΅Π½ΠΊΠ°Ρ ΠΊΠ°ΠΌΠ΅ΡΡ ΠΏΡΠ΅Π΄Π²Π°ΡΠΈΡΠ΅Π»ΡΠ½ΠΎΠΉ ΡΠ΅ΠΏΠ»ΠΎΠ²ΠΎΠΉ ΠΏΠΎΠ΄Π³ΠΎΡΠΎΠ²ΠΊΠΈ ΡΠΎΠΏΠ»ΠΈΠ²Π°, ΠΈ, ΡΠ»Π΅Π΄ΠΎΠ²Π°ΡΠ΅Π»ΡΠ½ΠΎ, ΠΈΡΠΊΠ»ΡΡΠ°Π΅ΡΡΡ Π½Π΅ΠΎΠ±Ρ ΠΎΠ΄ΠΈΠΌΠΎΡΡΡ Π΄ΠΎΠΏΠΎΠ»Π½ΠΈΡΠ΅Π»ΡΠ½ΡΡ Π·Π°ΡΡΠ°Ρ Π²ΡΠ΅ΠΌΠ΅Π½ΠΈ ΠΈ ΠΌΠ°ΡΠ΅ΡΠΈΠ°Π»ΡΠ½ΡΡ ΡΡΠ΅Π΄ΡΡΠ² Π½Π° ΠΎΡΠΈΡΡΠΊΡ Π²Π½ΡΡΡΠ΅Π½Π½ΠΈΡ ΡΡΠ΅Π½ΠΎΠΊ ΠΊΠ°ΠΌΠ΅ΡΡ.
Π£ΡΡΡΠΎΠΉΡΡΠ²ΠΎ Π΄Π»Ρ ΡΠΆΠΈΠ³Π°Π½ΠΈΡ ΡΠ²Π΅ΡΠ΄ΠΎΠ³ΠΎ ΡΠΎΠΏΠ»ΠΈΠ²Π° Π² ΠΏΡΠ»ΡΡΠΈΡΡΡΡΠ΅ΠΌ ΠΏΠΎΡΠΎΠΊΠ΅, ΡΠΎΠ΄Π΅ΡΠΆΠ°ΡΠ΅Π΅ ΠΊΠ°ΠΌΠ΅ΡΡ Π²ΠΎΡΠΏΠ»Π°ΠΌΠ΅Π½Π΅Π½ΠΈΡ, ΠΊΠ°ΠΌΠ΅ΡΡ ΠΏΡΠ΅Π΄Π²Π°ΡΠΈΡΠ΅Π»ΡΠ½ΠΎΠΉ ΡΠ΅ΠΏΠ»ΠΎΠ²ΠΎΠΉ ΠΏΠΎΠ΄Π³ΠΎΡΠΎΠ²ΠΊΠΈ ΡΠΎΠΏΠ»ΠΈΠ²Π°, ΠΊΡΡΡΠΊΡ ΠΊΠ°ΠΌΠ΅ΡΡ ΠΏΡΠ΅Π΄Π²Π°ΡΠΈΡΠ΅Π»ΡΠ½ΠΎΠΉ ΡΠ΅ΠΏΠ»ΠΎΠ²ΠΎΠΉ ΠΏΠΎΠ΄Π³ΠΎΡΠΎΠ²ΠΊΠΈ ΡΠΎΠΏΠ»ΠΈΠ²Π°, Π²ΠΎΠ·Π΄ΡΡ ΠΎΠ²ΠΎΠ΄, ΡΠ΅Π·ΠΎΠ½Π°ΡΠΎΡΠ½ΡΡ ΡΡΡΠ±Ρ, ΡΠΎΡΡΠΎΡΡΡΡ ΠΈΠ· Π΄Π²ΡΡ ΡΠ°ΡΡΠ΅ΠΉ (Π²Π΅ΡΡ Π½Π΅ΠΉ ΠΈ Π½ΠΈΠΆΠ½Π΅ΠΉ) ΠΈ ΠΏΡΠΈΠΌΠΊΠ½ΡΡΡΡ ΠΊ ΠΊΠ°ΠΌΠ΅ΡΠ΅ Π²ΠΎΡΠΏΠ»Π°ΠΌΠ΅Π½Π΅Π½ΠΈΡ, ΠΎΠ±ΡΠ°Π·ΡΡ ΠΊΠΎΠ»ΡΡΠ΅Π²ΠΎΠΉ Π·Π°Π·ΠΎΡ ΠΌΠ΅ΠΆΠ΄Ρ Π΅Π΅ Π²Π΅ΡΡ Π½Π΅ΠΉ ΠΈ Π½ΠΈΠΆΠ½Π΅ΠΉ ΡΠ°ΡΡΡΠΌΠΈ, ΡΠ΅ΡΡΠ°ΡΡΠΉ ΡΡΡΠ±ΡΠ»ΠΈΠ·Π°ΡΠΎΡ, ΡΠΎΡΡΠΎΡΡΠΈΠΉ ΠΈΠ· Π½Π΅ΡΠΊΠΎΠ»ΡΠΊΠΈΡ ΡΠΎΡΡΠ°Π²Π½ΡΡ ΡΠ°ΡΡΠ΅ΠΉ, ΠΊΠΎΠ»ΠΎΡΠ½ΠΈΠΊ, ΠΌΠ½ΠΎΠ³ΠΎΡΠΎΠΏΠ»ΠΎΠ²ΡΡ Π΄ΠΈΡΡΡΠ·ΠΈΠΎΠ½Π½ΡΡ Π³ΠΎΡΠ΅Π»ΠΊΡ, ΡΠ±ΠΎΡΠ½ΠΈΠΊ ΡΠ²Π΅ΡΠ΄ΡΡ ΠΎΡΡ ΠΎΠ΄ΠΎΠ², ΡΠ±ΠΎΡΠ½ΠΈΠΊ ΠΈΠ½Π΅ΡΡΠ½ΠΎΠ³ΠΎ ΠΌΠ°ΡΠ΅ΡΠΈΠ°Π»Π°,ΠΎΡΠ»ΠΈΡΠ°ΡΡΠ΅Π΅ΡΡ ΡΠ΅ΠΌ, ΡΡΠΎ ΠΎΠ½ΠΎ ΡΠ½Π°Π±ΠΆΠ΅Π½ΠΎ Π³Π°Π·ΠΎΠΎΡΠ²ΠΎΠ΄ΡΡΠ΅ΠΉ ΡΡΡΠ±ΠΎΠΉ, Π²Π΅ΡΡ Π½ΠΈΠΉ ΡΡΠ΅Π· ΠΊΠΎΡΠΎΡΠΎΠΉ ΡΠ°ΡΠΏΠΎΠ»ΠΎΠΆΠ΅Π½ Π² ΠΊΠ°ΠΌΠ΅ΡΠ΅ ΠΏΡΠ΅Π΄Π²Π°ΡΠΈΡΠ΅Π»ΡΠ½ΠΎΠΉ ΡΠ΅ΠΏΠ»ΠΎΠ²ΠΎΠΉ ΠΏΠΎΠ΄Π³ΠΎΡΠΎΠ²ΠΊΠΈ ΡΠΎΠΏΠ»ΠΈΠ²Π° Π½Π° ΡΠ°ΡΡΡΠΎΡΠ½ΠΈΠΈ 2-3 Π΄ΠΈΠ°ΠΌΠ΅ΡΡΠ° ΡΡΠΎΠΉ ΡΡΡΠ±Ρ ΠΎΡ Π½ΠΈΠΆΠ½Π΅ΠΉ ΡΠ°ΡΡΠΈ ΠΊΡΡΡΠΊΠΈ ΠΊΠ°ΠΌΠ΅ΡΡ ΠΏΡΠ΅Π΄Π²Π°ΡΠΈΡΠ΅Π»ΡΠ½ΠΎΠΉ ΡΠ΅ΠΏΠ»ΠΎΠ²ΠΎΠΉ ΠΏΠΎΠ΄Π³ΠΎΡΠΎΠ²ΠΊΠΈ ΡΠΎΠΏΠ»ΠΈΠ²Π°, Π΄ΡΡΠ³ΠΎΠΉ ΠΊΠΎΠ½Π΅Ρ ΡΠ°ΡΠΏΠΎΠ»ΠΎΠΆΠ΅Π½ Π² Π½ΠΈΠΆΠ½Π΅ΠΉ ΡΠ°ΡΡΠΈ ΡΠ΅Π·ΠΎΠ½Π°ΡΠΎΡΠ½ΠΎΠΉ ΡΡΡΠ±Ρ ΠΈ Π²Π²Π΅Π΄Π΅Π½Π° Π°Π²ΡΠΎΠΌΠ°ΡΠΈΡΠ΅ΡΠΊΠ°Ρ ΡΠΈΡΡΠ΅ΠΌΠ° ΡΠ΅Π³ΡΠ»ΠΈΡΠΎΠ²Π°Π½ΠΈΡ ΡΠ΅ΠΌΠΏΠ΅ΡΠ°ΡΡΡΡ ΡΠ΅ΡΠΌΠΈΡΠ΅ΡΠΊΠΎΠ³ΠΎ ΡΠ°Π·Π»ΠΎΠΆΠ΅Π½ΠΈΡ ΡΠ΅Π·ΠΈΠ½Ρ, Ρ ΡΠ΅ΡΠΌΠΎΠ΄Π°ΡΡΠΈΠΊΠΎΠΌ ΡΠΈΡΡΠ΅ΠΌΡ ΡΠ΅Π³ΡΠ»ΠΈΡΠΎΠ²Π°Π½ΠΈΡ ΡΠ΅ΠΌΠΏΠ΅ΡΠ°ΡΡΡΡ, ΠΎΠ΄ΠΈΠ½ ΠΊΠΎΠ½Π΅Ρ ΠΊΠΎΡΠΎΡΠΎΠ³ΠΎ ΠΏΡΠΈΠΊΡΠ΅ΠΏΠ»Π΅Π½ ΠΊ ΠΊΠ°ΠΌΠ΅ΡΠ΅ Π²ΠΎΡΠΏΠ»Π°ΠΌΠ΅Π½Π΅Π½ΠΈΡ, Π° Π²ΡΠΎΡΠΎΠΉ ΠΊΠΎΠ½Π΅Ρ ΡΠ°ΡΠΏΠΎΠ»ΠΎΠΆΠ΅Π½ Π½Π°ΠΏΡΠΎΡΠΈΠ² Π²ΠΎΠ·Π΄ΡΡ ΠΎΠ²ΠΎΠ΄Π° Ρ Π²ΠΎΠ·ΠΌΠΎΠΆΠ½ΠΎΡΡΡΡ ΡΠΎΠ΅Π΄ΠΈΠ½Π΅Π½ΠΈΡ ΠΈ ΡΠ΅Π³ΡΠ»ΠΈΡΠΎΠ²Π°Π½ΠΈΡ Π΅Π³ΠΎ ΠΏΡΠΎΡ ΠΎΠ΄Π½ΠΎΠ³ΠΎ ΡΠ΅ΡΠ΅Π½ΠΈΡ, ΠΏΡΠΈΡΠ΅ΠΌ Π²ΠΎΠ·Π΄ΡΡ ΠΎΠ²ΠΎΠ΄ Π²ΡΠΏΠΎΠ»Π½Π΅Π½ Π² Π²ΠΈΠ΄Π΅ Π°ΡΡΠΎΠ΄ΠΈΠ½Π°ΠΌΠΈΡΠ΅ΡΠΊΠΎΠ³ΠΎ ΠΊΠ»Π°ΠΏΠ°Π½Π° Ρ ΠΈΠ·ΠΌΠ΅Π½ΡΠ΅ΠΌΡΠΌ ΠΏΡΠΎΡ ΠΎΠ΄Π½ΡΠΌ ΡΠ΅ΡΠ΅Π½ΠΈΠ΅ΠΌ, ΠΎΠ±Π΅ΡΠΏΠ΅ΡΠΈΠ²Π°ΡΡΠΈΠΌ ΠΏΠΎΠ΄Π΄Π΅ΡΠΆΠ°Π½ΠΈΠ΅ Π² ΠΊΠ°ΠΌΠ΅ΡΠ΅ Π²ΠΎΡΠΏΠ»Π°ΠΌΠ΅Π½Π΅Π½ΠΈΡ ΠΈ Π² ΠΊΠ°ΠΌΠ΅ΡΠ΅ ΠΏΡΠ΅Π΄Π²Π°ΡΠΈΡΠ΅Π»ΡΠ½ΠΎΠΉ ΡΠ΅ΠΏΠ»ΠΎΠ²ΠΎΠΉ ΠΏΠΎΠ΄Π³ΠΎΡΠΎΠ²ΠΊΠΈ ΡΠΎΠΏΠ»ΠΈΠ²Π° Π·Π°Π΄Π°Π½Π½ΠΎΠΉ ΡΠ΅ΠΌΠΏΠ΅ΡΠ°ΡΡΡΡ Π³Π°Π·ΠΎΠ² Π² Π°Π²ΡΠΎΠΌΠ°ΡΠΈΡΠ΅ΡΠΊΠΎΠΌ ΡΠ΅ΠΆΠΈΠΌΠ΅ ΠΈ ΡΠ΅ΡΠΌΠΈΡΠ΅ΡΠΊΠΎΠ΅ ΡΠ°Π·Π»ΠΎΠΆΠ΅Π½ΠΈΠ΅ ΠΎΡΡ ΠΎΠ΄ΠΎΠ² ΡΠ΅Π·ΠΈΠ½ΠΎΡΠ΅Ρ Π½ΠΈΡΠ΅ΡΠΊΠΈΡ ΠΈΠ·Π΄Π΅Π»ΠΈΠΉ Ρ Π²ΠΎΠ·ΠΌΠΎΠΆΠ½ΠΎΡΡΡΡ Π²ΡΠ΄Π΅Π»Π΅Π½ΠΈΡ Π»Π΅Π³ΠΊΠΈΡ ΡΡΠ°ΠΊΡΠΈΠΉ Π΄Π»Ρ Π΄Π°Π»ΡΠ½Π΅ΠΉΡΠ΅Π³ΠΎ ΡΠΆΠΈΠ³Π°Π½ΠΈΡ, ΠΏΡΠΈΡΠ΅ΠΌ Π² ΡΠ±ΠΎΡΠ½ΠΈΠΊΠ΅ ΠΈΠ½Π΅ΡΡΠ½ΠΎΠ³ΠΎ ΠΌΠ°ΡΠ΅ΡΠΈΠ°Π»Π° ΡΠ°Π·ΠΌΠ΅ΡΠ΅Π½Π° ΡΠΈΡΡΠ΅ΠΌΠ° ΡΠ½ΠΈΠΆΠ΅Π½ΠΈΡ ΡΠ΅ΠΌΠΏΠ΅ΡΠ°ΡΡΡΡ ΠΈΠ½Π΅ΡΡΠ½ΠΎΠ³ΠΎ ΠΌΠ°ΡΠ΅ΡΠΈΠ°Π»Π°, ΠΊΠΎΡΠΎΡΠ°Ρ Π²ΡΠΏΠΎΠ»Π½Π΅Π½Π° Π² Π²ΠΈΠ΄Π΅ Π³ΡΡΠΏΠΏΡ ΡΠΎΡΡΡΠ½ΠΎΠΊ, ΡΠ°ΡΠΏΠΎΠ»ΠΎΠΆΠ΅Π½Π½ΡΡ ΡΠΈΠΌΠΌΠ΅ΡΡΠΈΡΠ½ΠΎ ΠΏΠΎ Π΄ΠΈΠ°ΠΌΠ΅ΡΡΡ ΡΠ±ΠΎΡΠ½ΠΈΠΊΠ° ΠΈΠ½Π΅ΡΡΠ½ΠΎΠ³ΠΎ ΠΌΠ°ΡΠ΅ΡΠΈΠ°Π»Π°, Π° ΡΠΎΡΡΡΠ½ΠΊΠΈ ΡΡΡΠ°Π½ΠΎΠ²Π»Π΅Π½Ρ Π² ΠΊΠΎΠ»ΠΈΡΠ΅ΡΡΠ²Π΅, ΠΎΠΏΡΠ΅Π΄Π΅Π»ΡΠ΅ΠΌΠΎΠΌ ΠΎΠ±ΡΠ΅ΠΌΠΎΠΌ ΠΎΡ Π»Π°ΠΆΠ΄Π°Π΅ΠΌΠΎΠ³ΠΎ ΠΈΠ½Π΅ΡΡΠ½ΠΎΠ³ΠΎ ΠΌΠ°ΡΠ΅ΡΠΈΠ°Π»Π°.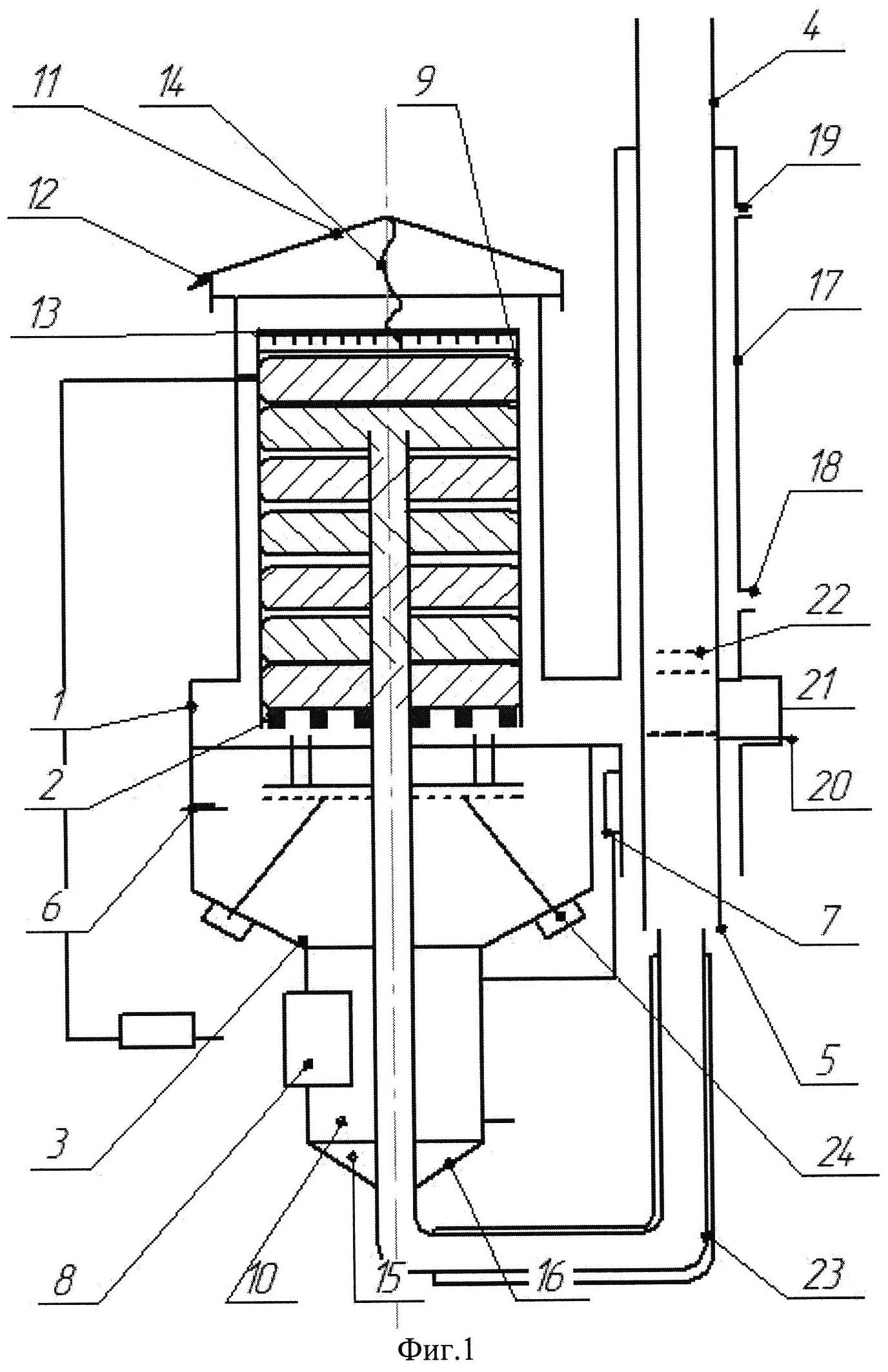
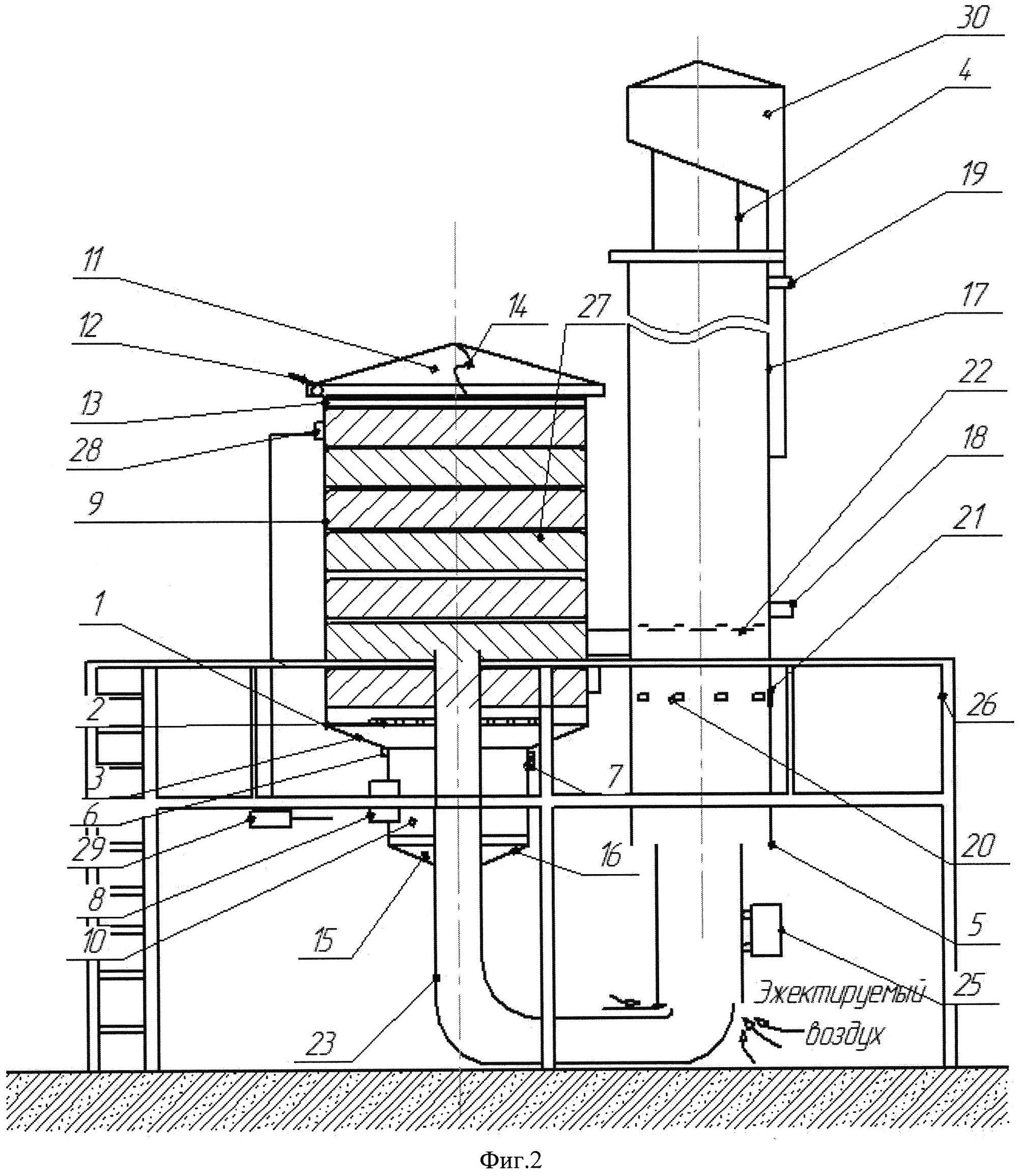
edrid.ru