Что такое направляющая для дрели, как сделать вертикальный держатель
Чтобы получить отверстие с минимумом заусенцев и строго вертикальными стенками, требуется качественный инструмент, но результат зависит не от одного его и навыков работника. Облегчить процесс вертикального сверления поможет направляющая для дрели, жестко фиксирующая инструмент и меняющая его позицию исключительно в заданном диапазоне. Держатель дрели для вертикального сверления заметно расширит функционал, причем сделать это приспособление для дрели совсем несложно своими руками. Размещение инструмента на стойке, которая может быть поворотной, позволит превратить обыкновенную дрель в сверлильный станок, на котором выполняется широкий круг технологических операций.
Конструкция
Приспособление состоит из частей, соединенных винтами. Нижняя часть играет роль опоры. На этой металлической платформе стабильно удерживается верхняя конструкция и сама дрель. С помощь винтов в опоре обеспечивается фиксация стойки на рабочем столе.
Основные характеристики
Главные параметра выбора стойки такие:
- Рабочая длина, по которой перемещается инструмент.
- Диаметр фиксирующего фланца.
Диаметр задает размеры длины дрели, которую можно зажать на стойке. Стандартный диапазон — 45−65 мм, но есть специализированные фланцы и адаптеры, которые позволяют расширить данный коридор. Крепежная оснастка чаще рассчитывается на работу с определенным инструментом.
Рабочая длина определяет ход перемещения. Если у приспособления большой диапазон перемещения, это позволяет сверлить крупные заготовки. Стандартный ход составляет 20−30 см, но у профессиональных стоек эта величина доходит до 50 см.
Как сделать стойку дома
Составными частями могут служить компоненты вышедших из строя станков, строительных монтажных профилей, сварочного оборудования. Первой изготавливается функциональная часть с полозьями для перемещения дрели. Использоваться может фурнитура мебели. Затем изготавливается платформа, которая делается из отрезка трубы, к примеру, на нее становится база с полозьями. Фиксировать рельсы можно на деревянную доску, которая затем прикручивается к трубе метизами или зажимается скобами.
К монтажному столу трубу желательно крепить «на века», так как разборная конструкция ненадежна. Фиксация на толстую металлическую пластину осуществляется с помощью саморезов или сварки. Вместо направляющего рычага самодельные стойки имеют, как правило, выдающуюся вверх ручку-толкатель, подающую платформу с закрепленным инструментом напрямую.
Достоинства и недостатки
Наиболее значимые плюсы самодельной стойки:
- Изготовление обходится гораздо дешевле покупки серийной модели.
- Материал изготовления — хлам, по сути.
- Легкость нахождения чертежей и обучающего видео.
- Возможность создания варианта конструкции с улучшенными характеристиками.
Недостатки такие:
- Для изготовления некоторых деталей стоек, нужны токарные станки, сварочное и прочее оборудование.
- По причине не идеально качественной подгонки конструктивных элементов часто возникает люфт, что плохо для точности обработки с помощью приспособления.
- Ограниченные функциональные возможности. С самодельной стойкой не удастся, например, сделать отверстия под углом.
Стойка из дерева
Понадобится:
- Доски минимум 20-миллиметровой толщины.
- Маленький ящик с мебельными направляющими.
- Стержень с резьбой для подвижной части.
- Пара десятков коротких и около трех десятков длинных шурупов.
- Столярный клей.
- Пила.
- Струбцина.
- Дрель.
- Отвертка.
- Наждачная бумага.
Стойка из металла
Основные конструктивные части:
- Несущая станина с прикрепленными к ней элементами станка.
- Стойки.
- Ручки.
- Дополнительные узлы, которые делают приставку для дрели функциональнее.
Самодельная стойка — устройство легкое в монтаже, и за счет его оснащения дополнительными узлами превращается в универсальное оборудование, при помощи которого выполняются разные технологические операции.
Станина
Этот элемент изготавливается из металлического 10-миллиметрового или из деревянного 20-миллиметрового листа. Массивность зависит от мощности дрели, а габариты — от специфики предполагаемых работ. Рекомендации по выбору габаритов будут следующими:
- Станки для вертикального сверления — 500×500 мм.
- Для разных технологических операций — 500×1000 мм.
Устойчивость стойки на станине обеспечивает подпорка. Фиксируются эти конструктивные элементы с помощью винтов.
Стойку, на которой будут направляющие, тоже можно сделать из деревянной или металлической плиты. Кроме направляющих в вертикальной плоскости на стойке монтируется зажим, с помощью которого инструмент фиксируется на ней.
Порядок сборки таков:
- На подставке-станине фиксируется подпорка.
- На основании винтовыми соединениями закрепляется стойка, которую соединяют затем с подпоркой.
- На стойке фиксируются направляющие, чью роль могут выполнять телескопические мебельные устройства.
- На подвижной части направляющих монтируется каретка, где размещается крепление для фиксации инструмента.
Подбирая направляющие, проверьте их на наличие поперечного люфта.
Длина каретки, также металлической или деревянной, зависит от размеров вашей дрели. Этот конструктивный узел, которым оснащается мобильная стойка, может выполняться в следующих двух вариантах:
- С закреплением дрели хомутами.
Используемые хомуты продеваются в отверстия, которые были предварительно просверлены в каретке. Зажим инструмента и надежная его фиксация на каретке обеспечивается благодаря затяжке хомутов.
- С использованием специальной колодки — кронштейна, где закрепляется дрель. Изготавливается он из деревянной плиты, крепящейся к каретке под 90 ° на металлических уголках. Для фиксации в колодке высверливается отверстие, чей диаметр на 0,5 мм меньше сечения инструмента, и делается прорезь, чтобы инструмент вошел в посадочное отверстие.
Отверстие в колодке для установки дрели выполняется по такому алгоритму:
- На поверхности колодки чертится круг, соответствующий диаметром устанавливаемой дрели.
- Во внутренней части окружности, по ограничивающей ее линии, высверливаются отверстия небольшого диаметра.
- Перегородки, образовавшиеся между просверленными отверстиями, прорезаются ножовкой или иным подходящим инструментом.
- Края отверстия обрабатываются напильником или надфилем полукруглой формы рабочей поверхности.
Механизм перемещения дрели вертикально
Конструктивные элементы узла:
- Рукоятка, с помощью которой каретка с закрепленной на ней дрелью подводится к поверхности обрабатываемой детали.
- Пружина, возвращающая каретку с инструментом в исходное положение.
Механизм можно сделать с использованием двух конструктивных схем:
- Пружину соединяется с ручкой станка.
- Пружины располагаются в пазах в нижней части каретки.
Первый вариант предполагает следующую схему выполнения:
- На стойке станка винтами фиксируются две металлические пластины, а между ними устанавливают ось, где и размещается ручка.
- На другой стороне стойки устанавливаются пластины и ось, на которой фиксируется один конец пружины, второй конец соединяется с рукояткой.
- Штифт, с помощью которого ручка соединяется с кареткой, располагается в продольном пазу каретки.
Если пружины расположены в нижней части возвратного механизма, рукоятка тоже фиксируется с помощью двух пластин и оси, которая обеспечивает ее движение.
Принцип работы сверлильного станка, где пружины расположены внизу каретки, довольно прост: опускаясь вниз при сверлении, каретка с закрепленным на ней инструментом давит на пружины и сжимает их; после прекращения этого механического воздействия пружины разжимаются и поднимают каретку с дрелью в исходное положение.
Дополнительное оснащение станка
Дополнительные приставки позволят использовать станок для сверления отверстий под углом и выполнять несложные токарные и фрезерные технологические операции.
Для выполнения на данном оборудовании фрезерных работ, нужно обеспечить горизонтальное перемещение обрабатываемой детали, для чего используется подвижный горизонтальный стол с тисками для фиксации обрабатываемой детали. Наилучшим приводом этого стола будет винтовая передача
, которая в движение приводится рукояткой.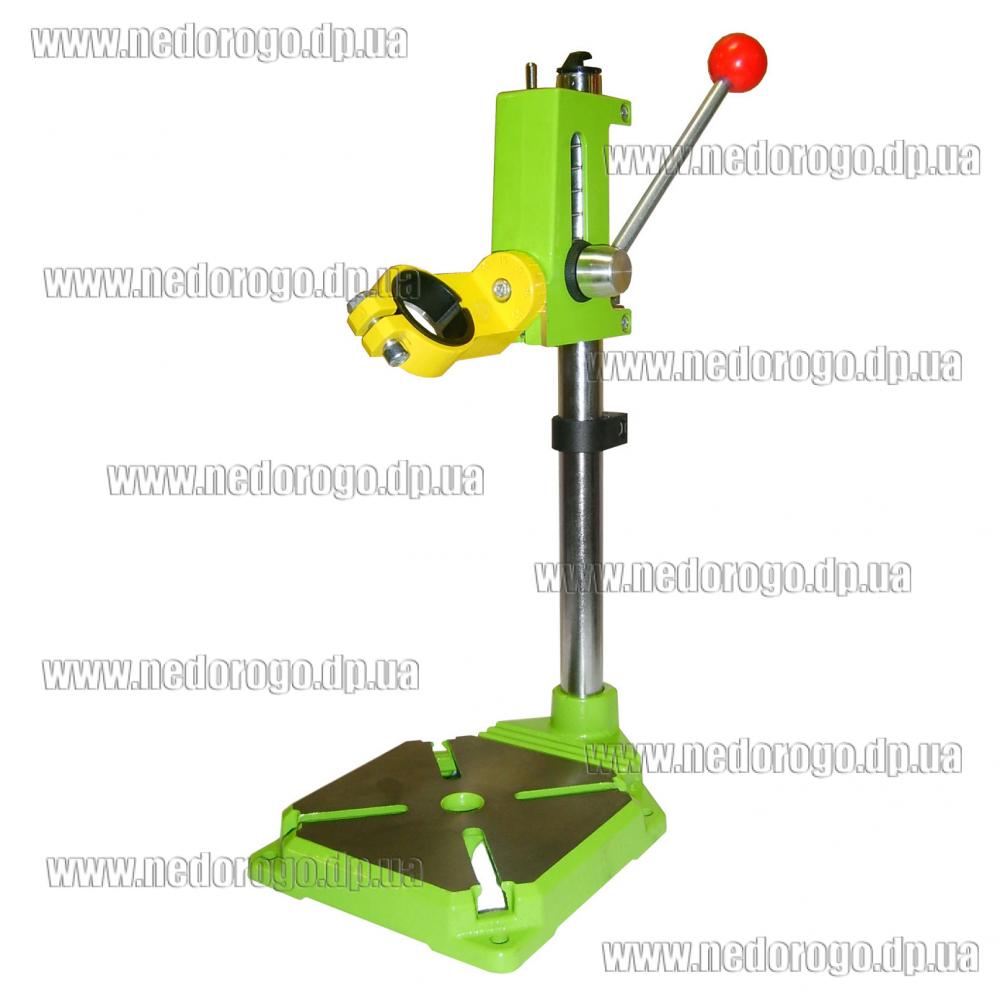
С помощью самодельного сверлильного станка, где роль рабочей головки выполняет ручная дрель, сверлятся отверстия под углом, если станок оснащен поворотной пластиной с отверстиями по дуге. На этой пластине, способной вращаться на оси, которая закреплена на стойке станка, расположена каретка и дрель. Отверстия на поворотной пластине выполнены под углами 30°, 45° и 60°. Порядок изготовления механизма:
- В стойке станка и поворотной пластине по центру высверливается отверстие для оси.
- С помощью транспортира на поворотной пластине намечаются оси отверстий, расположенных под самыми распространенными углами, и просверливаются отверстия.
- С использованием осевых отверстий на стойке и пластине совмещаются два этих элемента и фиксируются болтами.
- На стойке просверливаются три отверстия для фиксации поворотной пластины штифтами.
Поворотная пластина поворачивается на нужный угол с закрепленным на ней инструментом и фиксируется тремя штифтами, соединяющими неподвижную и поворотную часть стойки.
Станки с поворотной пластиной могут использовать и для выполнения нехитрых токарных работ. Для этих операций дрель с помощью поворотной пластины располагается горизонтально.
Подводя итоги
Учтите, что у полноценной станины надежное сопряжение функциональной и несущей части. Вертикальное приспособление контролируется оператором и не гарантирует само по себе точности сверления. Оно лишь позволяет свести к минимуму вибрации и устранить погрешности, допускаемые при ручном сверлении. Особенно важно контролировать самодельные стойки, в конструкции практически не обходится без больших люфтов и зазоров, которые влияют на точность подачи сверла.
Направляющая для дрели своими руками – подробная инструкция в википедии строительного инструмента
Чтобы сделать ровное отверстие на горизонтальной плоскости не нужно быть мастером. Можно воспользоваться направляющей для дрели. Это механический прибор фиксирующий инструмент перпендикулярно поверхности. Направляющая стойка для дрели зафиксирует инструмент и не даст ему смещаться во время работы.
Направляющая для дрели
Характеристики направляющей для дрели
Стойка для сверления дрелью обладает несколькими важными характеристиками:
- Ход по вертикали ( на какое расстояние можно двигать инструмент по вертикали).
- Диаметр фиксирующего фланца ( определяет инструмент какого размера можно зажать).
- Материал.
- Размер и массы прибора.
Стойки для сверления бывают мобильными и стационарными. Стационарные направляющие сильно напоминают небольшой сверлильный станок, они выглядят как штатив для дрели. Мобильные направляющие являются насадками для сверлильного инструмента. Их главное достоинство — это очень высокая мобильность.
Важным свойством стойки является способ крепления. Наиболее надёжным вариантом выступает магнитное крепление. Есть и вариант попроще — это вакуумное крепление.
Мобильные приборы спокойно фиксируется в руках и поглощает вибрацию при сверлении. Большинство людей выбирают именно мобильные направляющие. Всё благодаря их отличным характеристикам. Они очень надёжны, компактны и обладают низкой ценой.
Из чего состоит направляющая
Любая направляющая состоит из следующих элементов:
- Станина (опора, опорная плита, основание). Основание для всего механизма. Служит для придания устойчивости механизму. На станине расположены специальные зажимы для фиксации заготовок. Размеры и масса станины зависит от выполняемых на станке операций.
- Крепление для инструмента. Состоит их хомута, двух зажимов или колодки.
- Желоба для перемещения (механизм хода). Позволяют двигаться инструменту по вертикали.
- Ограничители перемещения.
Конструкционные особенности данного приспособления для дрели позволяют применять её для вертикального сверления
Как сделать направляющую самому
Сделать направляющую самостоятельно вполне реально. Однако использовать самодельные приборы для серьёзных целей не стоит. Лучше потратить деньги на качественный заводской прибор. Станина изготавливается из любой пластины. Желательно выбрать металлическую, но крепкое дерево или пластик тоже подойдут.
Достоинства и недостатки самодельной стойки
Выделяют следующие преимущества самодельных приборов:
- Самодельный станок очень дешевый.
- При конструировании прибора можно применять детали оставшиеся от старой техники.
- Найти все чертежи и подробные алгоритмы изготовления можно в свободном доступе.
- Можно сделать очень качественную и технологичную модель. У вас есть возможность изготовить действительно качественный прибор.
Однако существуют и недостатки:
- Для изготовления деталей потребуется специальное оборудование.
- Если направляющая будет плохого качества, то это сильно повлияет на точность сверления.
- Очень сложно сделать механизм превосходящий по качеству и функционалу заводской.
Станина направляющей
Станина — одна из самых главных частей станка для дрели. Она может сооружаться из металла или дерева. Толщина и размеры станины зависят от веса конструкции и инструмента. Размер станины также зависит от типа производимых на станке операций:
- Размеры 50 на 50 миллиметров используется для сверления.
- 100 на 50 для осуществления более сложных операций.
К станине крепиться стойка, которая может быть присоединена при помощи винтов, важно понимать что оно должно быть достаточно прочным.
Стойка направляющей
Стойка также может изготовлена из дерева или металла. Она состоит из направляющих (рельс для движения инструмента) и зажима для фиксации инструмента на одном уровне. Её изготовление происходит следующим образом:
- Зафиксировать стойку на станине.
- Прикрепление направляющий к стойке.
- Установите каретку, которая должна располагаться на направляющих.
Инструмент может крепиться на стойке при помощи хомутов или специальной колодки
Как сделать станок для дрели своими руками.
Для изготовления станка под дрель нам понадобятся следующие материалы:
- Пластиковая бутылка.
- Пластиковая крышка.
- Сверло.
- Канцелярский нож.
- Маркер или фломастер для разметки.
- Универсальный клей.
Стойка направляющей самодельного приспособления
Алгоритм изготовления прибора
Для начала необходимо измерить диаметр инструмента. Перед этим обязательно снимите гайку, которая удерживает сверло. Потом нанесите полученные данные на горлышко бутылки и вырезать окружность. Для безопасности и удобства можно также ошкурить края бутылки. Далее необходимо вставить в бутылку крышку до полного прилегания и приклеить при помощи клея. Этот прибор будет весьма примитивным и его конструкционные особенности не позволят сдвигать инструмент по вертикали. Зато он стоит очень дешево и очень прост в изготовлении.
Есть и способы посложнее. Для осуществления нам понадобиться гладкая деревянная доска, металлические стержни и пружины.
Первым делом также необходимо произвести измерения. Следующим этапом мы изготовим деревянные детали. Сделайте два закруглённых прямоугольника, и сделайте в них отверстия. Первое будет предназначено для самого инструмента.
А другие необходимо разместить в углах деревянного прямоугольника. В них мы ставим металлические стержни, они будут служить для перемещения дрели по вертикали. На стержни надеваем пружины и фиксируем механизм при помощи клея.
Данный прибор уже более функционален, ведь он позволяет смещать инструмент по вертикали.
Создание механизма для вертикального движения
Эта конструкция весьма простая. Она состоит из двух основных частей:
- Ручки которая подводит каретку к детали.
- Пружина, которая возвращает механизм в изначальное положение. При этом пружины могут располагаться как внизу конструкции, так и в специальных пазах.
Самодельный прибор высокого качества
Как сделать станок для дрели
Для начала берем небольшую часть металлической квадратной трубы и присвариваем по краям две втулки. Затем берём небольшое круглое кольцо( можно также сделать из части круглой трубы) и привариваем две гайки. В гайки вкручиваем болт. Из трёх металлический пластин делаем П образное основание. Дальше берём два металлических штыря и привариваем их к основанию. У нас получиться стойки с направляющими. На стойки нужно надеть пружины. Далее надеваем прямоугольную трубу со втулками на стержни с пружинами.
Также можете посмотреть видео по созданию металлических станков.
Как выбрать хорошую направляющую
В продаже имеется огромное количество вертикальное приспособление для дрели. Их можно разделить на несколько групп:
- Профессиональные и полупрофессиональные устройства.
- Самодельные направляющие для дрелей. Очень различаются по функционалу и конструкционным особенностям.
- Бюджетные заводские модели, служат для выполнения несложных сверлильных работ. Чаще всего используются в домашних условиях.
самодельный сверлильный станок для дрели
Рейтинг лучших моделей представляют следующие инструменты:
- “Tecmobit Wolfcraft”. Данная модель изготавливается из модифицированного чугуна. Благодаря этому срок службы прибора может составлять 15-20 лет. Высота станка составляет 298 мм, а вес около 1 килограмма. Есть возможно изменять угол наклона в пределах 45 градусов.
Tecmobit Wolfcraft
- “Калибр 96302“. Отличная бюджетная модель. Обладает хорошим качеством и низкой ценой. Приставка состоит из двух стержней из хромированного металла и пластикового основания. Также в приборе есть специальное приспособление для фиксации инструмента. Калибр показал себя как недорогой и надёжный инструмент.
Калибр 96302
- Китайская модель “KWB 7784“ уже давно занимает лидирующие места. Конструкция этого прибора схожа с российским Калибром.
Мнение потребителей на его счёт неоднозначное. Некоторые потребители отзываются о непродолжительном сроке службы прибора и о его поломках. Высота прибора небольшая, всего 213 мм. Обладает вертикальным ходом 160 мм и диаметром отверстия под инструмент равным 43 мм. Вес прибора немногим больше килограмма.
Продукция марки KWB
- Стойка ДИОЛД СМС-43. Она состоит из основания, колонны и зажима для крепления электродрели. В основании есть пазы для тисков. Имеет высоту 500 мм и диаметр отверстия под дрель 43 мм.
Обратите внимание на следующих производителей:
- Dremel – компания производит станки для дрелей. С их помощью можно сверлить под углом, полировать и шлифовать материалы.
- Sparta – Стационарные стойки. Важными достоинствами является высокое качество и плавность движения дрели.
- Skrab – Часто используется в домашних условиях и небольших мастерских. Отличный прибор за свою весьма скромную цену.
И это только самые основные вертикальные приспособления для дрели, кроме них существует ещё множество известных и не очень.
Важные практические советы при выборе товара
Для выбора хорошего инструмента на полках магазинов необходимо знать некоторые важные правила:
- Оцените качество товара, внимательно смотрите их каких материалов сделан товар и как он собран. На рынке большое количество некачественных китайских подделок. И этот совет поможет вам избежать их покупки.
- Оцените размеры станка. Не будет ли она занимать слишком много места. В особенности это касается стационарных прибор. Мобильные всегда можно убрать в шкаф или на полку.
- Смотрите можно ли регулировать диаметр посадочной шейки.
- Оцените ход по вертикали ( на какое расстояние можно сдвинуть инструмент по вертикальной оси).
- Обратите пристальное внимание на основание. Лучше всего если оно будет изготовлено из чугуна.
Обратите пристальное внимание на принцип работы перемещающего механизма. Направляющие для дрели должны быть оборудованы специальными пружинами, которые будут возвращать инструмент в исходное место.
Кондуктор для дрели
Кондуктор представляет из себя пластиковый корпус в котором есть отверстия для закрепления свёрл. Одной рукой необходимо удерживать кондуктор, а второй рукой держать дрель. Несмотря на свою простоту кондуктор широко применяется в мебельном производстве и строительстве.
Кондуктор для дрели
Заключение
Сверлить приходиться весьма часто и делать это под углом 90 градусов, пользуясь одной дрелью — это очень проблематично. Отверстие скорее всего получиться неровным. Облегчить работу помогут специальные направляющие. В этой статье мы описали устройство мобильных и стационарных направляющих. Вывели рейтинг самых лучших направляющих. И подробно рассказали о том как сделать направляющую своими руками.
Summary
Article Name
Направляющая для дрели своими руками – подробная инструкция
Description
✅Как сделать направляющую самому ➜– ✅Достоинства и недостатки самодельной стойки ➜–✅ Алгоритм изготовления прибора ➜–✅ Как сделать станок для дрели
Author
Сарычев Александр Викторович — судебный строительно-технический эксперт, кандидат технических наук
Publisher Name
Википедия строительного инструмента
Publisher Logo
Поделиться новостью в соцсетях
« Предыдущая запись Следующая запись »
варианты, материалы и технология изготовления
Для создания отверстий в стене обычно используется дрель.

Простейшая направляющая насадка для дрели своими руками
Рассматривая этот вариант насадки, следует принять во внимание тот факт, что на реализацию идеи не потребуется тратить какие-либо средства. Но вместе с тем не возникнет особых сложностей в изготовлении направляющей для дрели. Но при этом же, созданное приспособление сможет послужить достаточно недолго.Важно учесть то, что оно не должно рассматриваться в качестве полноценного дополнения для инструмента. В том случае, если заниматься созданием отверстия приходится на значительном расстоянии от мастерской и других альтернативных устройств не имеется, то именно с помощью подобной насадки и можно наиболее эффективно решить поставленную задачу. Вдобавок этому она принесет значительную пользу тем домашним мастерам, которые не так часто работают дрелью.
Материалы
Для изготовления направляющей необходимо подготовить следующие материалы и инструменты:
- пластиковая бутылка;
- пластиковая крышка;
- сверло;
- канцелярский нож;
- фломастер;
- универсальный клей;
- сверло кольцевое;
- бумага наждачная;
- дрель.
Процесс изготовления
Сперва необходимо выполнить определенные манипуляции со сверлильным инструментом. Для этого с дрели скручивают гайку и фиксирующую сверло После чего нужно отметить ее диаметр на пластиковой бутылке как можно ближе к горлышку. Затем перенести круг, соответствующий этому диаметру, используя фломастер. В конечном итоге должна получиться полная окружность.Этот шаблон, который необходимо в дальнейшем вырезать, следует отметить и на крышке бутылки, причем следует позаботиться о том, чтобы ее ширина была достаточной для этого.
На следующем этапе нужно обрезать бутыль или банку. К выбору обрезаемой конструкции следует подойти очень тщательно, поскольку это в дальнейшем повлияет на глубину создаваемых отверстий при помощи направляющей.
Следует уделить особое внимание безопасности работы. Для этого рекомендуется ошкурить края банки, чтобы сделать их ровными и гладкими.
Отверстия, которые были предварительно нанесены на бутылку и ее крышку, следует вырезать точно по намеченной линии, при помощи канцелярского ножа. Обработку следует провести с краями срезов, которые нужно основательно ошкурить. Затем берут крышку и лицевой стороной помещают ее в банку, воздействуя на нее физической силой, чтобы обеспечить максимально плотное прилегание. Именно на этом участке и выполняется ее приклеивание.
Добиться максимально прочного соединения можно, если после нанесения клея обеспечить сильное сжатие, которое должно сохраняться, пока клеящий состав не высохнет. Учитывая, что выполнение этой работы вручную сопряжено с определенными трудностями, полезно будет закрепить сверху несколько тонких резинок, благодаря которым можно поддерживать требуемое давление.
Дождавшись высыхания клея, насадка для дрели может быть использована по своему назначению. В нее просовывают сверло, после чего, используя пластиковую гайку, фиксируют на инструменте и начинают сверление отверстия. Хотя у нее не предусмотрена возможность выбора глубины, эту проблему можно решить путем изготовления нескольких подобных насадок и использования по мере необходимости наиболее подходящей.
Направляющая для получения прямых отверстий
В ситуации, когда приходится сверлить отверстие довольно массивной дрелью, возникают определенные трудности, связанные с необходимостью обеспечить отверстию угол 90 градусов и исключить его овальную форму. В случае если в арсенале мастера отсутствуют приспособления и инструменты, при помощи которых можно было сделать направляющую, эта проблема может быть решена за счет использования подручных материалов.Еще до создания отверстия необходимо позаботиться о наличии необходимых материалов: для этого можно взять брусок квадратного сечения, выполненный из дерева или иного материала.
Брусок нужно расположить к стене таким образом, чтобы он вплотную примыкал к отверстию, которое необходимо обработать. Причем край сверла должен касаться его, благодаря чему процесс сверления будет проходить ровно.
Для повышения удобства и точности сверления можно расположить под прямым углом два разных бруска, при этом сверло вставляют во внутренней угол между ними. Хорошей идеей представляется размещение брусков таким образом, чтобы они вместе образовали букву «Т». Благодаря этому появится возможность для придания ему необходимого положения и владелец сможет защитить свои руки от нанесения травмы.
Дрель, используемая в сочетании с направляющей, способна играть роль небольшого простейшего сверлильного станка, при помощи которого можно выполнять разные операции, к которым предъявляются требования по соблюдению точных размеров.
Важные нюансы
Решив создать подобное приспособление своими руками, нужно учесть такие важные моменты:
- подвижные элементы должны быть затянуты предельно плотно.
Для эффективной работы, созданной своими руками насадкой для дрели у нее должна быть предусмотрена возможность выбора подходящего вылета и величины хода. Причем, если направляющая стойка отличается довольно значительным весом, то это только упрощает процесс создания отверстий.
- В некоторых случаях стойка может применяться в сочетании с тисками, благодаря которым можно зафиксировать обрабатываемую деталь. В этом случае подобная конструкция легко превращается в полноценный станок для сверления. Причем необязательно приобретать подобные тиски, чтобы расширить функциональность оборудования. При наличии достаточного опыта можно сделать их также своими руками.
Заключение
Сверлильные работы относятся к числу наиболее часто выполняемых во время изготовления разнообразных конструкций. Причем домашний мастер чаще всего решает эту задачу при помощи бытовой дрели. Однако в большинстве своем, создаваемое отверстие не отличается точными размерами. А это может создать определенные трудности при использовании его по назначению.
Выйти из этого непростого положения можно при помощи направляющих для дрели, которые можно изготовить своими руками. Подобная идея представляется довольно привлекательной по той причине, что такую насадку может сделать любой владелец, учитывая, что для этого можно использовать любые подручные средства. Однако, осознав всю привлекательность направляющей, необходимо помнить о том, что она не сможет стать полноценным приспособлением для сверлильного инструмента, поэтому прибегать к помощи этой насадки следует лишь в экстренных ситуациях. В противном случае направляющая для дрели довольно скоро выйдет из строя.
Оцените статью: Поделитесь с друзьями!Сделать приспособление для вертикального сверления можно за день. Проверено.
Все, кто используют ручную дрель, знают, как трудно удержать руками строгую вертикаль. При сверлении заготовок большой толщины есть риск сломать сверло. Всякий раз возникает желание вести инструмент по направляющей, а такой возможности нет.
Вторая распространенная задача – насверлить множество однотипных отверстий в одной заготовке. Держа в руках дрель, делать такую работу долго и неудобно.
В слесарных мастерских издревле применяют сверлильные станки разной мощности. Но их стоимость для домашнего приобретения слишком велика.
К тому же домашний мастер не выполняет сверление в промышленных масштабах. Следовательно, такая покупка никогда не окупится.
Существуют фабричные приспособления для вертикального сверления, способные превратить ручную дрель в полноценный сверлильный станок. Многие из них снабжены координатными пластинами и подвижными тисками.
Стойка вертикальная для сверления отверстий дрелью
Это действительно удобное приобретение, но стоимость такого станка сопоставима со стоимостью дрели. Поэтому домашние мастера зачастую изготавливают самодельный сверлильный станок.
Главные преимущества конструкции – дешевизна и возможность создать приспособление, идеально совместимое с вашей ручной дрелью. При наличии в доме (сарае, гараже) ненужного фотоувеличителя, микроскопа или другого механизма с вертикальной подачей рабочего узла, задача упрощается.
Самодельная стойка из старого микроскопа
Остается лишь приспособить к изделию дрель. Если такого бонуса нет – подставка делается «с нуля».
Как сделать из дрели станок, используя подручные материалы
Из чего должна состоять направляющая подставка для ручной дрели?
Устойчивая станина
Желательно с возможностью установки тисков или другого приспособления, удерживающего заготовку. В домашних условиях изготавливается из толстого ДСП, фанеры, или текстолита. По центру оси устанавливаемой дрели, необходимо оставить отверстие диаметром пару сантиметров.
Описание необходимых частей сверлильного станка из дрели
Направляющая вертикальная стойка
Тут фантазия разработчиков неограниченна. Это может быть брусок, фанерная пластина, металлический профиль или труба.
Главный принцип при изготовлении – строгая вертикаль по отношению к опорной станине. В противном случае сверло будет отклоняться от прямолинейного движения, портить заготовку и ломаться.
Механизм хода
Может быть рычажного типа, или использовать пару шестерня-рейка. Принципиально не имеет значения, какую конструкцию выбрать. Важно соблюдать принцип доступности материалов, иначе может оказаться, что дешевле приобрести готовое изделие.
Механизм подъема и опускания сделан руками из досок | Второй пример подъемного механизма выполненный из металла |
Причем подаваться может не только дрель к заготовке. Иногда удобнее поднимать изделие к сверлу. Например – на компактных моделях.
Кронштейн для ручной дрели
Идеальное решение – использование посадочного места для ручки дрели с хомутовым захватом. Оно охватывает подшипник вала, и оптимально подходит для центровки всей конструкции.
На практике – не всегда ваша дрель имеет такое посадочное кольцо. В таком случае инструмент крепится хомутами за корпус. При таком способе, важно добиться хорошей центровки оси вращения, и, разумеется – идеальной ее вертикальности.
Самодельный вариант станка из монтажных пластин
ВАЖНО! Ось вращения дрели всегда вертикальна. Для сверления под углом – переориентируйте заготовку.
Существуют и более оригинальные конструкции крепления электроинструмента. Внешний вид не имеет значения. Главное – надежность и удобство применения.
Крепление дрели выполненное из фанеры
Выключатель дрели
Этот элемент конструкции важен, поскольку кроме удобства он обеспечивает безопасность работ. Если вы планируете навсегда оставить электроинструмент в станке – можно демонтировать кнопку и установить вместо нее стационарный включатель на корпусе станка.
Если же дрель будет периодически использоваться как ручной инструмент – оптимальным способом решения вопроса будет установка розетки и клавиши включения в удобном месте приспособления.
Лампа освещения рабочего места
Вариантов для творчества множество. Главное – она действительно необходима. Отдельно остановимся на способе крепления заготовки.
Станок с тисками, несомненно, более удобен, но обязательно надо предусмотреть возможность их демонтажа. При обработке крупногабаритных деталей поверхности станины должна быть ровной.
Рассмотрим удачные модели самодельных сверлильных станков
Эти варианты показывают полярные уровни технологии. От примитивного, собранного из отходов, до относительно технологичного, с использованием готовых узлов.
Конструкция, собранная буквально из подножных материалов
Чертежи для сборки не требуются, все детали подгоняются по ходу работ. Для изготовления станины используется лист ДСП 50х50 см. В качестве опоры для стойки применяем деревянный кругляк.
Он же придаст устойчивость конструкции, снижая центр тяжести. Механизм перемещения изготавливается из направляющей для мебельных ящиков. Разумеется, никакая из этих вещей не покупается в магазине, а извлекается из хлама в сарае или гараже.
Мебельную направляющую можно использовать для изготовления домашнего станка
Стойка из бруска прикручивается к кругляку, с противоположной стороны крепится направляющая.
Крепим направляющую к деревянной стойке
Кронштейн для дрели делается из небольшой дощечки, в которой коронкой высверливается подходящее отверстие. Единственная деталь, которая изготавливается с использованием сварки – это уголок с укосиной для жесткости, которым кронштейн крепится к направляющей.
Делаем крепление для дрели из куска доски или фанеры
Собираем механизм подъема и проверяем вертикальность хода и свободу перемещения. Рычаг подъема делается из подходящего тонкого бруска. На кругляк устанавливается металлический уголок, к нему крепится ось рычага.
Кронштейн с рычагом соединяется металлической тягой. При перемещении конструкции вверх-вниз никаких заклиниваний не происходит.
Крепим кронштейн для дрели к стойке и приделываем деревянный рычаг
Благодаря устойчивости кронштейна, никаких сложных креплений придумывать не нужно. Достаточно обычного затяжного хомута подходящего размера.
ВАЖНО! После первой затяжки хомута необходимо дождаться усадки, и повторно подтянуть винт.
Такое крепление достаточно прочно, при этом всегда можно демонтировать дрель и использовать ее в качестве ручного инструмента.
Крепление дрели хомутом проверяйте на затяжку
Крепим всю конструкцию на станину при помощи прочных металлических уголков. Именно на этот элемент будет приходиться половина усилия при сверлении. Так же, крепление кругляка должно выдерживать вес всего механизма и собственно ручной дрели.
Деревянный кругляк играет роль противовеса и служит основанием для крепления к нему стойки с болгаркой
Стойка для дрели обязательно оснащается возвратной пружиной. Ее мощность подбирается таким образом, чтобы кронштейн с дрелью плавно поднимался без усилия на рычаге, а процесс сверления не был утомительным для оператора.
Обязательно устанавливаем подставку для сверления, чтобы не портить станину. Качество не имеет значения, это фактически расходный материал. По мере образования большого количества дырок, подставка просто меняется на новую.
Ставим пружину на рычаг подъема | Для защиты основания кладем сменный подклад |
Сверлит станок уверенно, рычаг работает без усилий. Несмотря на простоту механизма – отверстие получается строго вертикальным, горизонтальных вибраций сверла не происходит.
Металлические заготовки так же легко сверлятся, дрель при этом не перегревается и сверла остаются целыми. В принципе – конструкцию можно признать удачной.
Сверлильный станок из рулевой рейки
Достаточно популярной среди отечественных кулибиных, является конструкция сверлильного станка из рулевой рейки. Этот элемент рулевого управления, после замены на новый по причине люфта, обладает достаточным запасом прочности для использования в качестве подъемного механизма сверлильного станка.
Если есть старая рулевая рейка от автомобиля, то своими руками можно смастерить сверлильный станок
Изготовление требует некоторой сноровки и применения более качественных материалов, нежели в предыдущем варианте. Размеры рулевой рейки подразумевают более массивную дрель, соответственно станина и стойка изготавливаются из металла.
На место крепления рулевой колонки приспосабливается маховик или другой поворотный механизм.
Осталось придумать чем будет осуществляться вращение привода рулевой рейки
На каретку для крепления рулевых тяг устанавливается кронштейн для дрели. Его так же следует изготовить из металла, поскольку вес ручного электроинструмента будет большим.
Каретку для крепления дрели делаем из металлической пластины
Возвратная пружина тоже выбирается помощнее, в соответствие с весом конструкции. По надежности и качеству исполнения такая конструкция приближается к заводским аналогам, а по стоимости составит не более 10% от покупной.
Поэтому такой вариант часто можно встретить в частных автомастерских или в арсенале слесарей-шабашников.
В этом видео направляющая для дрели изготавливается из обычных обрезков металла, которые не составит большого труда найти и сделать самому
В итоге получается отличная самодельная стойка, практически сверлильный станок, который по функционалу не уступает обычным промышленным образцам предназначенным для бытового использования. Но гораздо более экономичный в денежном эквиваленте.
Какую конструкцию выберет читатель? Главное – соблюсти баланс стоимости, необходимости и доступности материалов.
Сверлильный станок из дрели своими руками, видео уроки
Урок первый. Изготовление деталей для каркаса из фанеры
Урок второй. Сборка каркаса
Урок третий. Соединение всех узлов и первый пуск
About sposport
View all posts by sposport
как выбрать направляющие и станину для станка? Как сделать держатель для вертикального сверления?
Отвечая на вопрос о том, что такое стойка для дрели, перфоратора или шуруповерта, следует отметить, что речь идет о стационарном устройстве, к которому крепятся данные инструменты. Существуют различные виды таких приспособлений, существенно упрощающих сверление. Из-за достаточно широкого ассортимента устройств, представленного на рынке, к выбору конкретных моделей следует подходить с учетом целого ряда критериев.
Что это такое?
Сделать ровное отверстие в твердом и толстом материале непросто. Не меньше трудностей возникает при сверлении под углом, поскольку сверло или фреза могут соскальзывать, увеличивая диаметр отверстия. В подобных ситуациях самым рациональным выходом будет использование качественной стойки для дрели. Это приспособление в комплексе с самим сверлильным инструментом превращается в небольшой по размерам станок.
Сейчас на рынке представлена продукция многих производителей (на любой вкус и кошелек). Однако к выбору стоек, держателей и направляющих необходимо подходить с максимальным вниманием. Не стоит исключать также возможность изготовления устройств своими руками.
Стойки для сверлильной техники позволяют существенно расширить ее функционал. При этом одним из главных достоинств оборудования является его компактность и универсальность. Покупные модели могут иметь разную комплектацию (в зависимости от бренда и стоимости изделия). В частности – в комплект иногда входят тиски для жесткого крепления обрабатываемой заготовки и прочие дополнительные элементы.
Подавляющее большинство держателей являются компактными.
Исходя из этого, они могут успешно эксплуатироваться в небольших мастерских, гаражах и даже квартирах. Средние размеры станины составляют 15х20 см, а высота стойки – 50 см. При этом масса устройств варьируется в диапазоне 2-6 кг.
Преимущества и недостатки
Независимо от марки и ценовой категории, все стойки предназначены для упрощения процесса сверления, поэтому к их основным достоинствам относятся некоторые конкретные характеристики.
- Значительное расширение диапазона возможностей эксплуатируемого инструмента. Качественная стойка, к примеру, позволяет выполнять фрезерование поверхностей.
- Повышение точности выполняемых операций за счет позиционирования сверла и фрезы строго перпендикулярно или же под зафиксированным углом по отношению к обрабатываемому материалу.
- Возможность работы с твердыми материалами, при которой одним из важных моментов является исключение скольжения сверла по обрабатываемой поверхности на первоначальном этапе.
- Возможность сверлить отверстия не только перпендикулярно, но и под различными углами. Современные модели позволяют выполнять сверление под углом до 70 градусов.
Учитывая все перечисленное, можно сказать, что качественная стойка не только является эффективным дополнением для инструмента, но и позволяет превратить его в полноценный станок компактных размеров.
К сожалению, не обходится и без явных недостатков. Большинство минусов при этом обусловлено конкретными недоработками производителей.
Нередко даже дорогостоящие устройства не отвечают предъявляемым требованиям. Это относится как к качеству используемых материалов, так и к сборке. Многие пользователи в своих отзывах обращают внимание на отсутствие универсальных приспособлений для фиксации, которые позволяли бы использовать различные марки сверлильного инструмента. Однако унификация подобных элементов на практике невозможна.
Виды
Все представленные на рынке приспособления для сверления отличаются друг от друга, в первую очередь, конструктивными особенностями и функционалом. Помимо этого, они могут комплектоваться различным оборудованием, в перечень которого входят, например, тиски и пылесборники. Дополнительные элементы позволяют максимально упростить эксплуатацию инструментов.
По принципу использования можно выделить две категории устройств.
- Стационарные стойки, превращающие обычные дрель, перфоратор или шуруповерт в компактный аналог станка. Эти изделия за счет своего веса и жесткой конструкции обеспечивают высокую точность выполнения всех операций. К главным минусам относят отсутствие мобильности и высокую стоимость.
- Мобильные сверлильные приставки или направляющие, представляющие собой устройства, обеспечивающие приемлемую точность сверления при минимальных размерах.
Еще одним важным критерием является функциональность рассматриваемых приспособлений.
- Стойки для вертикального сверления, являющиеся универсальными держателями и характеризующиеся максимальной устойчивостью.
Они часто становятся незаменимым элементом мини-мастерских и помощниками домашних мастеров.
- Поворотные устройства, представляющие собой более сложное и функциональное оборудование. Помимо перемещения кронштейна с закрепленным сверлильным инструментом в вертикальной плоскости для установки требуемого расстояния от обрабатываемого материала до рабочего хода сверла, такие стойки позволяют устанавливать угол сверления. В итоге оборудование может использоваться также в качестве фрезерного или полировального.
Не менее важную роль играют особенности крепления самой стойки. Как показывает практика и свидетельствуют отзывы, максимально надежным вариантом являются магнитные модели. Большинство профессиональных приспособлений имеет именно такой способ крепления. Максимальная устойчивость в данном случае обеспечивается мощным электромагнитным полем. Магнитные стойки для сверления могут быть надежно зафиксированы в вертикальной, горизонтальной и наклонной плоскостях. Это позволяет выполнять работы в сложных эксплуатационных условиях. Как правило, подобное оборудование имеет ряд дополнительных опций. Например, включение инструмента невозможно, если от магнита не исходят импульсы.
Еще одним способом крепления является вакуумный. Он также доказал на практике свою надежность. Сравнивая такие стойки с магнитными, специалисты акцентируют внимание на более высокой стоимости последних.
Бренды
Описываемое оборудование является комфортным и полезным дополнением, обеспечивающим оперативную и надежную фиксацию сверлильных инструментов для выполнения стационарных работ с высокой точностью. С учетом спроса многие компании-производители наладили выпуск подобных приспособлений. Все представленные в этом сегменте рынка модели отличаются друг от друга конструкцией, функциями, комплектацией и стоимостью.
Одним из популярных брендов является «Энкор». Компания предлагает потребителю качественные устройства для работы с инструментами, имеющими различные характеристики (мощность, масса и диаметр шейки корпуса).
Не меньшим спросом пользуется продукция марки Sparky. В отзывах владельцы данной техники обращают внимание на повышенную устойчивость, обеспечиваемую наличием качественной плиты основания, отлитой из чугуна.
Также на сегодняшний день в рейтинге популярности присутствуют и другие модели стоек.
- «Калибр» – надежная и универсальная конструкция, трансформирующая ручной сверлильный инструмент в компактный, стационарный станок.
- Dremel – устройство, характеризующееся функциональностью, длительным сроком эксплуатации и доступной стоимостью. Данные модели позволяют осуществлять вертикальное сверление, сверлить отверстия под углом, полировать и шлифовать материалы в горизонтальной плоскости.
- Sparta – стойки, превращающие в стационарные устройства как дрели, так и шуруповерты. К основным плюсам относят наличие качественного механизма, отвечающего за плавность и равномерность подачи закрепленного инструмента.
- Skrab – поворотная модификация, ставшая рациональным вариантом для использования в небольших мастерских, гаражах и домашних условиях. Конструкция сочетает в себе прочность, долговечность доступную стоимость.
Помимо всего перечисленного, пользователи выделяют модели «Диолод» и Artu. Первые с одинаковой эффективностью эксплуатируются в бытовых и промышленных условиях. В зависимости от модификации варьируется диаметр шейки корпуса инструмента, который может быть закреплен в держателе.
Во втором случае речь идет о поворотных приспособлениях, выполняемых из алюминия. Наличие струбцины позволяет максимально оперативно установить конструкцию на любой столешнице.
Как выбрать?
Учитывая широкий ассортимент моделей, предлагаемых различными компаниями-производителями, к выбору наиболее подходящей модели следует подходить с соответствующим вниманием и ответственностью. В первую очередь, требуется внимательно осмотреть саму дрель на предмет наличия посадочной шейки, поскольку у некоторых образцов оборудования она может отсутствовать. Этот элемент представляет собой цилиндр длиной в несколько сантиметров. Большинство дрелей и шуроповертов имеют шейки стандартного диаметра – 4,3 см. Помимо конструктивных особенностей самого сверлильного инструмента, требуется уделить внимание и некоторым другим моментам.
- Параметры, материал изготовления и качество плиты основания. Как показывает практика, чугунные изделия являются более практичными и эффективными. Еще одной важной деталью будет наличие монтажных приспособлений и отверстий для крепления конструкции на столе и установки тисков.
- Расстояние между самой стойкой и осью сверла, определяющее максимальный размер обрабатываемых деталей.
- Особенности держателя, от которых зависит перечень моделей инструмента, подходящих для установки на стойке.
- Возможность регулировки глубины сверления. Данная опция актуальная в ситуациях, когда требуется сделать большое количество одинаковых отверстий.
- Принцип работы механизма перемещения.
Последний пункт заслуживает особого внимания. Некоторые модели держателей оборудованы специальными пружинами, за счет которых удается добиться плавного движения дрели. Еще одним преимуществом таких конструкций является автоматическое возвращение держателя в исходное положение при уменьшении давления на рычаг.
Необходимые детали
Любая стойка для дрели, независимо от ее габаритов и с учетом предназначения подобных приспособлений, имеет основные конструктивные элементы, каждый из которых выполняет свои функции и должен соответствовать определенным требованиям.
- Станина – одна из основных составляющих описываемого оборудования, являющаяся его основанием (подставкой) и обеспечивающая устойчивость всей конструкции. Помимо этого, на станине располагаются тиски для фиксации обрабатываемых заготовок. Вес и размеры данного элемента зависят от мощности используемого инструмента и перечня выполняемых задач.
- Направляющая стойка, которая располагается строго вертикально по отношению к основанию. Даже при незначительном отклонении может быть испорчена обрабатываемая заготовка и сломано сверло или фреза. В зависимости от конструктивных особенностей конкретной модели эта деталь может быть изготовлена из разных материалов.
- Механизм хода.
К устройству данного узла нет каких-либо строгих требований, не применяются шаблоны. Его главная задача – это обеспечение плавного перемещения, закрепленного с помощью кронштейнов или хомутов сверлильного инструмента вдоль штатива. Существует много вариаций таких механизмов.
- Держатель для оборудования (дрели, перфоратора, шуруповерта). В качестве эффективного крепления используются хомуты, колодки и прочие монтажные элементы.
Кроме перечисленных комплектующих, являющихся обязательными, сверлильное устройство для стационарных работ может оснащаться целым рядом второстепенных (вспомогательных) приспособлений. Они позволяют расширить функционал оборудования и упростить выполнение операций. Речь, в частности, идет о дополнительных упорах, различных приставках и осветительных приборах.
Как сделать своими руками?
Конечно же, самым простым способом расширить возможности имеющегося инструмента будет приобретение уже готовой конструкции. Однако многие интересуются возможностью изготовления сверлильных стоек ручной работы. Анализируя отзывы, можно сделать вывод, что это сравнительно несложный процесс. Однако для его реализации потребуются определенные знания, а также соответствующие практические навыки, материалы и инструменты.
С учетом особенностей конструкций, позволяющих обычную дрель превратить в сверлильный станок, изготовить их можно даже из фотоувеличителя, устройство которого изначально включает часть необходимых ключевых элементов. Существует несколько вариантов исполнения самодельной стойки. Перечень необходимых материалов, оборудования и инструментария будет зависеть от выбора в пользу деревянного или металлического приспособления.
Станину можно изготовить из пластины (металлической или деревянной), размеры которой определяются мощностью оборудования и габаритами заготовок. Еще одним определяющим фактором является функционал будущей конструкции. Если для сверлильного станка достаточно будет сделать станину с размерами в переделах 600х600 мм, то в случае с многофункциональным агрегатом данные показатели должны быть увеличены.
Непосредственно сама стойка и подпорки могут быть выполнены как из металлических труб, включая профильные, так и из деревянных брусков. Следует помнить, что стойка, выполняющая роль направляющей, должна быть максимально ровной. Не стоит забывать и о прочности.
Следующей важной составляющей является механизм перемещения дрели и другой техники вдоль направляющей. Основой данного узла будут ручка и пружины, а сам механизм может быть выполнен в нескольких вариациях.
- Возвратным и смонтированным непосредственно рядом с ручкой, которая при этом помещается между двумя пластинами, установленными на стойке. При движении рукоятки вниз происходит возврат пружины и самой каретки в исходное положение.
- В виде двух пружин, установленных в специальных пазах каретки под углом 90 градусов, к которым закрепляются штифт и боковые пластины. При нажатии на рычаг пружины сжимаются, а дрель – перемещается вниз. Как только воздействие на ручку прекратится, весь узел вернется в свое первоначальное положение.
Необходимо перечислить явные преимущества самодельных приспособлений:
- изготовление подобных конструкций своими руками обходится дешевле, чем приобретение готовых;
- отсутствие каких-либо ограничений позволяет использовать практические любые материалы и запчасти от вышедшего из строя или же устаревшего оборудования;
- чертежи приспособлений и подробные инструкции, включая соответствующие видеоматериалы, в большом количестве находятся в свободном доступе;
- каждый желающий при наличии необходимых знаний и навыков может создать стойку по своим чертежам и с учетом всех потребностей.
Говоря о наиболее значимых недостатках изготовления конструкций для сверления своими руками, следует обратить внимание то, что:
- на определенных этапах может потребоваться доступ к токарному станку, сварочному аппарату и другому профессиональному оборудованию;
- из-за ошибок, даже незначительных, появляются люфты, отрицательно отражающиеся на качестве сверления и других работ;
- чаще всего модели, созданные кустарно, имеют ограниченный функционал.
Однако при грамотном подходе и качественном изготовлении всех элементов самостоятельно можно собрать даже поворотную модель. Нередко самоделки не уступают (а по некоторым показателям превосходят) заводским моделям. Все зависит от правильного выбора материалов и качества сборки.
Установка
Любой компактный станок надо грамотно собрать и установить, надежно прикрепив к столу, верстаку или отдельной тумбе. В противном случае – качество выполняемых на нем работ и срок его эксплуатации существенно уменьшаться. Покупные модели монтируют в строгом соответствии с чертежной документацией и прилагаемыми инструкциями.
В ситуациях с самодельными конструкциями следует придерживаться общих правил и рекомендаций. Правильная установка станет залогом длительной работы и максимальной точности выполнения всех, предусмотренных функционалом стойки, работ. Сборка мини-станка осуществляется по следующему алгоритму:
- монтаж станины;
- установка направляющей и подпорок;
- монтаж ходового механизма;
- крепление непосредственно самого сверлильного инструмента (дрели, шуруповерта, перфоратора).
Важным моментом является проверка наличия люфтов и качества соединений на всех этапах сборки и установки конструкции. Помимо этого, требуется уделить особое внимание надежности крепления дрели.
Следует помнить, что сверло или фреза должны располагаться строго вертикально. В противном случае – понижается качество сверления и повышается риск поломки инструмента.
О том, как сделать самодельную стойку для дрели своими руками, смотрите в следующем видео.
Стойка для дрели своими руками: 3 варианта конструкции
Рассказываем, как в домашних условиях самостоятельно изготовить бюджетную сверлильную стойку для дрели. Предлагаем 3 разных варианта.
Это приспособление пригодится домашним мастерам, которые не могут позволить себе приобрести сверлильный станок.
В то же время в некоторых случаях стойка выигрывает за счет своей компактности и мобильности.
Если сделать стойку небольших размеров, которая не требует установки на рабочем столе, то ее можно будет без проблем транспортировать на машине (брать с собой на выездные работы).
В отличие от того же сверлильного станка, она позволит сверлить отверстия как в вертикальной, так и горизонтальной плоскости (например, если нужно просверлить отверстие в стене).
Чтобы сделать стойку для дрели своими руками, будем использовать недорогие и доступные материалы. Причем стойку можно использовать не только для дрели, но и для шуруповерта.
Назначение самодельной стойки такое же, как и у сверлильного станка — вертикальное сверление отверстий под углом 90 градусов относительно заготовки.
При помощи электродрели или шуруповерта не всегда получается просверлить идеально ровные отверстия. Самодельная стойка (даже самой простейшей конструкции) позволяет легко решить эту проблему.
Конечно, стойку для электродрели можно купить в строительном магазине или заказать через интернет. Но если ваша цель — сэкономить деньги, выгоднее будет изготовить ее своими руками.
Как сделать простую сверлильную стойку для электродрели
Первый вариант самодельной конструкции, несмотря на свою простоту, сочетает в себе сразу несколько плюсов: низкая себестоимость и функциональность.
Данная стойка больше напоминает настольный мини сверлильный станок.
Затраты на реализацию этой задумки минимальные. В любом случае такая самоделка обойдется дешевле покупки самой примитивной заводской модели.
Идея изготовления стойки под дрель своими руками принадлежит автору YouTube канала MakeTools. Основной материал для изготовления конструкции — профильная труба с толщиной стенки 1,5 мм.
Размер станины сверлильной стойки — 300х300 мм (однако можно сделать основание больше, если в этом есть такая необходимость).
Высота вертикальной стойки — 500 мм (опять же, можно изменить в большую или меньшую сторону, если надо).
Подвижная Т-образная часть, к которой крепится электродрель, состоит из двух деталей: вертикальной (длина — 150 мм) и горизонтальной (длина — 100 мм).
Дополнительно используются крепежные элементы в виде болтов и гаек разного размера: М10 — для соединения деталей, М8 — для крепления дверной пружины (возвратного механизма).
Приступаем к изготовлению стойки для дрели своими руками.
Первым делом необходимо будет изготовить станину (основание). Отрезаем четыре куска профтрубы с краями под углом 45 градусов, и свариваем их вместе.
После этого отрезаем еще четыре заготовки, и привариваем их внутри получившейся рамки.
Далее необходимо будет сделать регулируемые ножки. Для этого сверлим в станине четыре отверстия по краям, и привариваем гайки. В них вкручиваем болты (они и будут выполнять роль ножек).
На следующем этапе изготавливаем подвижную Т-образную часть. Торцевое отверстие в коротком отрезке (держателе для дрели) надо будет заглушить. Из листового металла отрезаем кусок квадратной пластины подходящего размера, вставляем в профильную трубу, и обвариваем.
После этого необходимо изготовить хомут для крепления дрели. Его можно сделать из куска металлической круглой трубы. Разрезаем, подгоняем его по размеру, и затем привариваем две гайки.
Отрезаем профильную трубу 25х25 мм (длиной 500 мм). Привариваем стойку к станине. Надеваем на нее подвижную часть. К держателю привариваем хомут.
Теперь нужно будет изготовить приводной рычаг, который будет опускать подвижную часть вместе с дрелью.
Отрезаем кусок профильной трубы 20х20 мм длиной 500 мм. Привариваем к рычагу удлиненную гайку, а к подвижной части надо будет приварить болт.
Далее необходимо изготовить еще один рычаг из профтрубы длиной 200 мм. С одной стороны профиля привариваем удлиненную гайку, с другой — болт. К длинному рычагу привариваем вторую удлиненную гайку.
Изготавливаем еще одну деталь. К шляпке болта привариваем удлиненную гайку, как показано на фото ниже.
В станине стойки сверлим отверстие, вставляем и фиксируем деталь. Крепим к ней короткий рычаг. А к нему уже крепим приводной рычаг.
На последнем этапе останется только установить дверную пружину, которая после сверления заготовки будет возвращать в исходное положение механизм для перемещения дрели. Фиксируется пружина при помощи двух удлиненных гаек и болтов.
Нижняя гайка приваривается к подвижной части, верхняя — крепится с помощью болтового соединения.
Для этого в стойке надо просверлить отверстие, в которое вставляется болт (изнутри профиля). На него накручивается удлиненная гайка. Зачищаем сварные швы и красим все элементы конструкции.
При помощи этого простого приспособления вы сможете просверлить вертикальные отверстия в заготовках из дерева, фанеры или металла, и не переживать, что что-то получится криво.
Пошаговый процесс изготовления основных деталей конструкции и сборки сверлильной стойки рекомендуем посмотреть в авторском видеоролике.
Вертикальная стойка для шуруповерта своими руками
Теперь давайте рассмотрим второй вариант самодельной стойки. В целом, конструкция очень простая, но самое главное — рабочая. Идея принадлежит автору YouTube канала Gökmen ALTUNTAŞ.
В данном случае она довольно компактная, поскольку рассчитана на использование в паре с шуруповертом.
Однако можно приспособить ее и для электродрели, немного увеличив в размерах. И получится тогда самодельная стойка для дрели.
Преимущество данной конструкции заключается в том, что для ее изготовления потребуется небольшое количество материалов. Многие детали даже покупать не придется — можно найти их в гараже.
Подставку сверлильной стойки изготовим из фанеры толщиной 20 мм. Можно также взять кусок доски.
Первым делом отпиливаем от фанеры заготовку нужного размера. Затем размечаем и сверлим в ней два отверстия. Используя эпоксидный клей, вклеиваем направляющие.
Острые углы основания закругляем на шлифовальном станке. Изготавливаем из дерева или фанеры подвижную площадку.
В подвижной части сверлим отверстия диаметром 19 мм под подшипники. Наружную часть подшипников смазываем эпоксидным клеем и вставляем подшипники в отверстия.
В сверлильный патрон вкручиваем переходник, на который надеваем круглую трубку. Ее нужно не просто надеть, а жестко зафиксировать при помощи эпоксидного клея.
В подвижной части сверлим посадочные места диаметром 29 мм под круглые подшипники.
Надеваем на трубку первый подшипник и запрессовываем его снизу площадки. Потом надеваем на трубу второй подшипник, и также запрессовываем его в посадочное место. Для надежности используем эпоксидный клей.
На направляющие надеваем пружины и шайбы. Потом устанавливаем подвижную площадку со сверлильным патроном.
На верхнюю часть направляющих необходимо будет напрессовать деревянные «заглушки» — для ограничения хода.
Хвостовик сверлильного патрона зажимаем в патроне шуруповерта, после чего при помощи коронки подходящего диаметра сверлим в основании отверстие.
На этом процесс изготовления самоделки можно считать завершенным. Потом останется только все покрасить или покрыть минеральным маслом. Из всех стоек данный вариант — самый простой и бюджетный.
Подробно о том, как сделать это приспособление, можно посмотреть в авторском видеоролике.
Направляющая для дрели своими руками
Предлагаем вашему вниманию третий бюджетный вариант самодельного устройства. Конструкция тоже довольно проста в изготовлении, но изготовлена из металла. Эта идея принадлежит автору YouTube канала Be Creative.
Материалы, которые потребуются для изготовления и сборки сверлильной стойки:
- профильная труба;
- металлические втулки;
- хомут для дрели;
- стальные пластины;
- направляющие;
- возвратные пружины.
В первую очередь необходимо изготовить подвижную часть стойки, к которой будет крепиться электродрель. В прошлом варианте она была деревянной, в этом — из профтрубы.
Отрезаем кусок квадратного профиля, и вырезаем на концах седловины. Потом к нему привариваем две втулки.
Посередине нужно приварить хомут для крепления электродрели. Изготовить его можно из куска круглой трубы, двух гаек и болта.
Далее отрезаем три куска стальной полосы, и свариваем из них основание стойки (опорную площадку).
Привариваем к основанию направляющие из гладкой арматуры. Надеваем на них пружины.
Фиксируем дрель с помощью хомута, и потом надеваем подвижную часть на направляющие.
Самодельная стойка для дрели готова. Да, она выглядит очень примитивно и хлипко, но зато изготовить ее можно очень быстро из обрезков металла.
Подробный процесс изготовления и сборки этой конструкции можно посмотреть на видео ниже.
Плюсы и минусы самодельных стоек
Самый главный и жирный плюс — экономия денег. В большинстве случаев изготовить сверлильную стойку (направляющую) для шуруповерта или дрели можно из подручных материалов.
Даже если каких-то комплектующих в гараже нет, их можно за копейки приобрести на металлоприемке (например, если надумаете делать направляющие для подвижной части из амортизаторов).
Для изготовления штатива (вертикальной стойки) обычно используется профильная труба — она у многих есть в наличии, да и купить ее не проблема.
Еще одно преимущество самодельной стойки в том, что конструкцию можно подогнать под себя — сделать нужного размера (например, если вы будете перевозить ее в машине).
При этом не нужно лазить по всему интернету, чтобы найти подходящие чертежи — стойку вы может сделать и без них.
Из минусов можно отметить только то, что самодельная сверлильная стойка не предназначена для выполнения высокоточных операция. И, конечно же, она во многом уступает сверлильному станку.
Как выбрать материал
Это зависит от того, какую цель вы преследуете. Если вам нужна стойка для разовых работ, смело используйте все, что найдете под рукой — обрезки металла, деревяшки, фанеру и т.д.
Если же вы хотите сделать настольный вариант сверлильного станка, то к выбору материалов нужно подойти ответственно.
Придется потратиться на покупку профтрубы и других комплектующих: в частности, потребуется приобрести хорошие направляющие и подшипники.
Мне нравится1Не нравитсяАндрей Васильев
Задать вопрос
Недорогая стойка для дрели своими руками с подробной инструкцией
Достоинства и недостатки самостоятельного изготовления стойки
Видео о том, как сделать стойку для дрели своими руками
Преимущество устройства заключаются в следующем:
- Дешевизна – стоит на порядок-два меньше промышленного (из магазина).
- Доступность деталей – в конструкции можно применять все, начиная от маленького бруска до частей от старых станков и автомобилей.
- Разнообразие конструкций в популярных изданиях и во всемирной паутине.
- Возможность творчества – создать свой надежный многофункциональный станок для дрели, который будет превосходить все опубликованные модели.
Недостатки устройств:
- При сборке многих опубликованных моделей необходимы детали, изготовленные на станках или узлы старых агрегатов (машин). Это повышает цену на изготовление.
- Люфт частей из-за неплотного монтажа и пригонки.
- Штатив для дрели не дает возможности выполнять ряд других работ (например, сверлить под углом и др.).
Универсальная стойка станка
Это устройство предназначено для выполнения разного рода сверлильных, токарных и других специализированных работ, которые осилит мотор и редуктор дрели. Если инструмент мощный, то ему под силу все виды работ.
Представляемое устройство, если оно предназначается только для сверления, выполняется (его основные части) из дерева. В случае изготовления универсальной стойки – сделайте ее из железных или стальных пластин. Устройство состоит из следующих главных узлов:
- Станина – служит главным опорным элементом всего станка.
- Стойка – предназначена для закрепления каретки с дрелью и позволяет перемещать ее с помощью ручки и дополнительных элементов.
- Ручка – служит для перемещения каретки по продольной оси стойки, чем обеспечивается подача вращающегося инструмента к детали.
- Дополнительные узлы – предназначены для расширения возможностей стойки и придания ей новых качеств.
Данный станок является, пожалуй, самым легким в монтаже и наладке, а дополнительные узлы позволяют превратить его в универсальное устройство, которое понравится многим умельцам-самодельщикам. Рассмотрим основные части станка.
Станина для дрели своими руками
Этот узел представляет плиту из 10 мм (и более) металла или 20 мм (и более)
дерева. Чем больше мощность инструмента (дрели), тем массивнее должно быть основание. Размеры станины зависят от выполняемых работ и могут варьироваться:
- для вертикального сверления – 500х500 мм;
- для остальных работ – 1000х500 мм.
Но эти габариты не окончательны и могут быть изменены под ваши запросы.
Самая дешевая и легкая для повторения станина вырезается из 20-40 мм куска дерева или выполняется из 10-20 мм стали. На ней закреплена основная стойка (выставлена вертикально) и подпорка из отрезков такой же толщины. Обе детали привинчены шурупами или винтами друг к другу и снизу (сквозь станину).
Совет: Для надежности следует соединить стойку и подпорку между собой с помощью уголков металлических.
Сверлильная стойка для дрели
Она выполнена из 20-40 мм доски или стальной 10-20 мм плиты. Ее длина составляет 50-75 см и зависит от размера применяемой дрели, а ширина – 20 см. На стойке укреплен механизм перемещения дрели по продольной оси с устройством для закрепления дрели.
Порядок сборки стойки таков:
- на станине укрепляется подпорка;
- к основанию прикручивают вертикальную стойку, которую затем привинчивают к подпорке;
- на вертикали укрепляют основания двух направляющих (телескопических мебельных), например от стола;
- далее, к подвижной части направляющих прикручивают каретку с устройством для закрепления дрели.
Совет: При выборе направляющих проверьте, чтобы не было поперечного люфта.
Длина каретки также зависит от габаритов дрели и составляет 50-100 см. Она выполнена из доски или плиты из стали той же толщины и ширины, как и стойка. Каретку можно выполнить в двух вариантах:
№ 1.Дрель закреплена хомутами.
На рисунке представлено крепление обычной эл. дрели. Доска просверливается, хомуты продеваются в отверстия. Затягивание хомутов ведется соответствующей отверткой.
№ 2.Дрель закреплена на специальной колодке.
Колодка представляет плиту, прикрученную перпендикулярно к оси каретки и укрепленную металлическими уголками. В колодке высверлено отверстие на 0,5 мм меньше диаметра «передка» дрели и сделана прорезь для надежной фиксации инструмента.
Отверстие высверливается специальной насадкой (цилиндрической) или следующим образом:
- измеряют диаметр инструмента и чертят круг;
- внутри окружности (ближе к линии) высверливают ряд отверстий;
- надфилем, ножом или пилкой прорезают оставшиеся перегородки;
- полукруглым или круглым напильником выравнивают окружность, доводя ее до необходимого калибра.
Механизм перемещения
Основные элементы этого узла:
- Ручка – служит для подачи дрели по направлению к обрабатываемой детали.
- Пружина – предназначена для возврата каретки в исходное состояние.
Механизм перемещения может быть выполнен в двух вариантах:
- Пружина находится непосредственно у ручки.
- Две пружины расположены внизу – в пазах направляющих каретки.
1Вариант 1.
- К основной стойке с одного края привинчены 2 металлические пластины, между которыми вставлена ось для ручки (можно применить винт М8-М12).
- На другом краю тоже привинчены пластины, между которыми установлена пружина. Для ограничения возможности ее соскока в сторону служат штифты, один из которых установлен на стойке, а второй на ручке, которая двигается между пластинами.
- В ручке сделан продольный паз для нормальной работы механизма.
- На каретке укреплен штифт или ось для обеспечения движения по вертикали.
2Вариант 2.
И в этом случае применяются боковые пластины и центральный штифт ручки, но пружины располагаются в пазах направляющих мебельных, которые немного дорабатываются. В пазы вставляются и завинчиваются обычные уголки металлические для невозможности проскока пружин вглубь направляющих.
Работа механизма проста. При нажатии на ручку (рычаг) каретка с дрелью перемещается вниз, обеспечивая сверление детали. Во время рабочего хода каретки пружины сжимаются, запасая энергию. При отпускании рычага энергия пружин направляется обратно, и каретка идет вертикально вверх.
Дополнительные узлы
Видео-урок: как создать стойку для дрели
Доработав стойку несложным узлом, вы сможете сверлить отверстия под углом и выполнять несложные токарные и фрезерные работы по дереву.
Фрезерные работы
Для выполнения мелких фрезерных работ необходимо, чтобы деталь перемещалась по горизонтали. Чтобы обеспечить подачу применяется вторая такая же стойка, которая укрепляется на станине горизонтально. Только вместо дрели на ней должны быть закреплены тиски.
Расстояние от края детали до вырезаемого паза ограничивается промежутком от дрели до вертикальных направляющих. Для горизонтальной подачи можно применить рычажную (с помощью ручки) систему, но во избежание трудностей найдите механизм подачи стола станка (винтовой).
Сверление отверстий под углом и токарные работы
Для выполнения этих операций необходимо дополнить стойку поворотным механизмом, который представляет добавочную пластину (ДП) с отверстиями, расположенными по дуге. Все детали механизма подачи и каретка располагают на этой дополнительной пластине, которая вращается на оси, закрепленной на основной стойке.
Основные углы наклонных отверстий – 30о, 45о, 60о. Поворотный механизм можно сделать так:
- сначала на стойке и в поворотной пластине высверливается отверстие для оси;
- далее, измеряя углы транспортиром или каким-либо другим измерителем, высверливают отверстия по кругу на ДП;
- затем совмещают осевые отверстия обеих пластин и закрепляют их винтом;
- после этого через ДП на стойке высверливают 3 отверстия, как показано на рисунке.
Добавочную пластину поворачивают на нужный угол и фиксируют с задней стороны стойки тремя штифтами или винтами с гайками (последнее предпочтительнее).
Токарные работы проводят, повернув дополнительную пластину горизонтально. Ввиду малого размера патрона дрели – детали большого калибра на ней не обработаешь.
Оцените статью: Поделитесь с друзьями!Обзор технологий вертикального и наклонно-направленного бурения для разведки и разработки глубоких залежей нефти
Разработка методов направленного бурения
Первое поколение методов наклонно-направленного бурения
Первое поколение методов наклонно-направленного бурения является результатом начального наклонно-направленного бурения. Существует два вида метода направленности (Inglis 1987; Short 1993; Chen 2011; Han 2011):
- 1.
Пассивно-направленное бурение: траектория скважины определяется законом естественного отклонения пластов, изгиб бурильной колонны и буровое долото также могут влиять на траекторию скважины, но траекторию скважины нельзя точно контролировать.
- 2.
Активное наклонно-направленное бурение: для активного управления траекторией скважины по ожидаемой траектории используются специальные устройства, инструменты и технологические мероприятия, суть активного наклонно-направленного бурения – изменение отклонения оси инструмента от оси скважины искусственным способом. В течение этого периода для бурения наклонно-направленных скважин использовались обычная компоновка низа бурильной колонны (КНБК) и клин-отклонитель.
- (я)
Обычная КНБК: обычная КНБК с мультистабилизатором может использоваться для управления углом отклонения ствола скважины на основе принципа рычага или маятникового эффекта, это начальный и активный метод направленности.
В соответствии с функцией КНБК может быть классифицирована как КНБК с наклоном, понижением угла, удержанием угла или жесткой КНБК.Этот метод полезен для очистки ствола скважины, уменьшения сопротивления бурильной колонны, уменьшения угла излома и экономии затрат на бурение. Но нет возможности контролировать азимут скважины.
- (ii)
Отклоняющий клин / отклоняющий клин: первым инструментом для отклонения скважины должен быть дефлектор, также называемый клином-отклонителем, это специализированный инструмент, который используется для отклонения бурового долота от оси скважины и направления в требуемом направлении.Таким образом, перед спуском в скважину выполняется направленный процесс. Для управления азимутом можно использовать клин-отклонитель, он преодолевает недостаток традиционной КНБК.
Однако у этого метода очень много недостатков: многократные и повторяющиеся отключения, отказ от отклонения, потеря времени и средств, сложные операции и низкая точность управления. При изменении азимута скважины грань инструмента фиксируется, что также называется режимом фиксированной грани инструмента. Чтобы продолжить изменение азимута скважины, торцовая поверхность инструмента должна регулироваться прерывисто, это означает, что новое отверстие и исходное отверстие существуют в сужающейся плоскости, поэтому это можно назвать режимом настройки азимута на сужающейся плоскости.В некоторых специализированных ситуациях этот метод по-прежнему работает эффективно, например, зарезка бокового ствола, зарезка бокового ствола – это процедура отклонения исходного ствола в точке над дном и бурение нового ствола в другом направлении, это может быть выполнено как в открытом, так и в обсаженном стволе. Обычно используется для обхода рыбы или бурения к другому объекту, расположенному вдали от исходного ствола скважины.
Кроме того, при бурении сверхглубокой скважины с высокой температурой, которая приводит к отказу ВЗД и не работает, этот метод может быть эффективным методом замены.
- (я)
Второе поколение направленных методов
Второе поколение направленных методов является результатом изобретения и развития инструментов. В этот период типичной особенностью является изобретение забойного двигателя и метода контроля.
- 1.
Забойный двигатель обычно включает поршневой двигатель (PDM), турбобур и электродрель (Short 1993; Chen 2011; Han 2011).ВДМ и турбобур используют давление и объем циркулирующего бурового раствора для вращения долота, а электродрель использует электрическую энергию для вращения долота. Это в сочетании с другими инструментами (гибочная штанга, гибочное соединение, эксцентриковое соединение или аналогичные инструменты) обеспечивает эффективный метод изменения направления ствола скважины.
- 2.
Метод мониторинга включает инклинометр с плавиковой кислотой и фотографический инклинометр (Short 1993; Chen 2011).Для достижения цели регулировки азимута ключом является фиксация всей бурильной колонны и позволяет забойному двигателю вращать долото, это означает, что поверхность инструмента фиксируется во время процесса регулировки, ее можно назвать фиксированной буровой головкой. струнный режим. Лицевую часть инструмента можно регулировать непрерывно, это означает, что новое отверстие и исходное отверстие существуют в плоскости сужения, поэтому этот режим также можно назвать режимом настройки азимута в плоскости сужения. Однако по сравнению с первым поколением траектория становится более плавной и точной.Между тем, буровые инструменты с ВЗД и турбо-бурильными инструментами также можно использовать как для скользящего, так и для вращательного бурения, вращательное бурение с ВЗД также называется композитным бурением, оно широко используется для повышения скорости проходки (ROP) как в направленном, так и в вертикальном направлении.
колодцы.
Кроме того, в этот период появляется еще один вид направленного метода, который называется струйным или подталкиванием. Это процедура отклонения ствола скважины без использования обычных направляющих узлов.Он наиболее эффективен в более мягких породах и для создания углов при низкой скорости наращивания. Это умеренно эффективный метод наклонно-направленного бурения при благоприятных условиях, но не имеет широкого применения. Максимальное нарастание угла составляет около 0,5–1,5 ° / 100 футов в скважинах с малыми углами сноса. Это дает длинный, гладкий, изогнутый участок с полунормальным сверлением. Процедура используется для постепенного отделения группы лунок друг от друга. Он также используется для перемещения точки зарезки в направлении цели и уменьшения угла, необходимого при более позднем наклонно-направленном бурении.
Третье поколение направленных методов
Третье поколение направленных методов является результатом передовых методов или инструментов мониторинга. В течение этого периода типичной особенностью является появление измерений во время бурения (MWD), которые улучшают измеряемую и контролируемую точность, направленные операции могут выполняться во время бурения (Chen 2011; Han 2011). Кроме того, из-за того, что изначально инструмент ВЗД был прямым, для повышения эффективности направленного бурения инструменты ВЗД были разработаны с изгибающимся корпусом, например, прямой ВЗД, ВЗД с одним изгибом, ВЗД с двойным изгибом и т. Д.Одной из популярных разновидностей двигателя является PDM с одним изгибом, изгиб которого расположен около нижнего конца. Этот метод относится к режиму фиксированной грани инструмента, грань инструмента можно регулировать непрерывно, это означает, что новое отверстие и исходное отверстие существуют в конической плоскости, поэтому этот режим также можно назвать режимом регулировки азимута на поверхности цилиндра. Благодаря усовершенствованию методов и инструментов мониторинга, работа с направлением значительно упростилась.
До сих пор третье поколение по-прежнему является основным методом наклонно-направленного и горизонтального бурения.
Четвертое поколение направленной техники
Четвертое поколение направленной техники является результатом автоматизации бурения, типичной особенностью является изобретение роторной управляемой буровой системы (RSDS) (Chen 2011; Han 2011). Из-за того, что забой инструмента необходимо регулировать искусственно, бурильную колонну необходимо фиксировать при наклонно-направленном бурении, то есть так называемом скользящем бурении. Поскольку сопротивление бурильной колонны всегда противоположно направлению движения, что приводит к увеличению сопротивления бурильной колонны и плохо влияет на эффективность бурения, очистку ствола, качество ствола и т. Д.Таким образом, для повышения эффективности бурения и контролируемой точности, а также уменьшения сопротивления бурильной колонны, RSDS была впервые разработана компанией Schlumberger в 1999 году. RSDS позволяет нам планировать стволы скважин сложной геометрии, включая наклонно-направленные, горизонтальные и скважины с большим отходом от вертикали. Это позволяет непрерывно вращать бурильную колонну при управлении скважиной и устранять неприятный режим скольжения обычных управляемых двигателей. В настоящее время отрасль классифицирует RSDS на две группы: более распространенные системы «контроля изгиба» и менее зрелые системы «контроля отклонений» (Даунтон и др.2000).
- 1.
Системы «контроля отклонения» разработаны на основе традиционной КНБК, стабилизатор переменного диаметра (DVS) используется для контроля отклонения скважины.
- 2.
Системы «контроля изгиба» также являются обычным RSDS, в отрасли системы «контроля изгиба» подразделяются на два типа: более распространенные системы «толкни бит», включая систему PowerDrive и систему AutoTrak, и менее развитые « наведи бит », включая систему Geo-Pilot и систему CDAL.
Развитие и особенности направленных методов можно резюмировать в таблице 2. Ясно обнаружено, что точность определения направления и качество ствола скважины улучшаются с развитием направленных методов.
Таблица 2 Развитие направленных методов (по Хань 2011 г.)Инструмент для направленного бурения
Большая часть скважинного оборудования для наклонно-направленного и горизонтального бурения обычно совпадает с вертикальным бурением, например бурильная труба, тяжелая труба, компрессионная труба, утяжеленная бурильная труба, спиральная бурильная труба с канавками, заменяющий переводник, сверло с короткой пони воротник, стабилизаторы и тд.Ясно, что без усовершенствованных инструментов для наклонно-направленного бурения может быть физически невозможно бурение данной скважины, скважина может быть пробурена в неоптимальном месте или может быть более дорогостоящим или рискованным. Развитие техники направленного действия обеспечивается передовыми инструментами направленного действия. Согласно истории развития методов направленного бурения, основные инструменты направленного действия можно резюмировать следующим образом: дефлектор, забойный двигатель, RSDS и система вертикального бурения.
Инструменты для отклонения
Инструменты для отклонения можно определить как клиновидный стальной инструмент, имеющий сужающуюся вогнутую канавку вниз с одной стороны для направления долота-отклонителя в стенку отверстия.Доступны два типа отклонителей (Inglis 1987; Short 1993; Chen 2011):
Съемный отклонитель
Съемный отклонитель может использоваться для инициирования отклонения в открытом стволе или выравнивания искривленных вертикальных скважин (Inglis 1987) . Как показано на рис. 4а, клин-отклонитель состоит из стального клина с долотом на дне для предотвращения движения после начала бурения. Коническая вогнутая часть имеет твердое покрытие для уменьшения износа. Вверху клина-отклонителя находится хомут, который используется для извлечения инструмента после того, как пробурена первая часть ствола скважины.К бурильной колонне клин-отклонитель крепится с помощью срезного пальца. Спустившись в скважину, бурильную колонну поворачивают до тех пор, пока режущая кромка клина-отклонителя не будет правильно установлена. Путем приложения веса с поверхности острие долота прочно устанавливается в пласт или цементную пробку. Стопорный штифт срезан, и можно начинать сверление. Пилотное отверстие малого диаметра пробурено на глубину примерно 15 футов ниже носка клина-отклонителя. После того, как это отверстие будет обследовано, долото и отклонитель отключаются.Затем запускают открывалку, чтобы развернуть отверстие до полного размера. После запуска отклоненного участка ствола скважины можно запустить роторную сборку здания для продолжения зарезки бокового ствола.
Принципиальная схема съемного и постоянного отклонителя. a Съемный отклонитель (Inglis 1987) и b Постоянный отклонитель (короткий 1993)
Постоянный клин-отклонитель
Постоянный клин-отклонитель в основном используется в обсаженном стволе для зарезки бокового ствола вокруг рыбы или обхода разрушенной обсадной колонны (Inglis 1987).Как показано на рис. 4b, обсадная колонна с заглушкой устанавливается в точке зарезки, чтобы обеспечить основу для клина-отклонителя. На клин-отклонитель работает фреза, которая прорезает «окно» в обсадной колонне. После установки клина-отклонителя в нужном направлении и срезания стопорного штифта начинается операция фрезерования. После того, как окно вырезано, мельница вынимается из отверстия и запускается пилотное долото малого диаметра. Впоследствии пилотное отверстие расширяется до полного размера. Следующим шагом является запуск ротационной сборки здания для продолжения зарезки бокового ствола.
Забойный двигатель
Наиболее распространенный в настоящее время метод отклонения скважины включает запуск забойного двигателя, включая ВЗД и турбобур, для приведения в движение долота без вращения всей бурильной колонны. Отклонение обеспечивается специальным переводником, размещенным над двигателем для создания боковой силы на долоте.
Инструменты PDM
Инструменты PDM чаще всего используются при наклонно-направленном и горизонтальном бурении. В 1940-х годах компания Smith создала первый PDM-инструмент. В 1950-х годах начали появляться коммерческие инструменты PDM, которые применялись в наклонно-направленном бурении.Благодаря успешному применению в наклонно-направленном и горизонтальном бурении, инструмент ВЗД находит все более широкое применение. В 1970-х годах PDM могли производить различные компании, такие как Dyna Drill, Navi Drill, Baker Drill, Christensen and Smith.
PDM состоит из нескольких компонентов, как показано на рис. 5, включая клапан сброса давления, моторную секцию, универсальный шарнир и подшипниковый узел. Клапан сброса устанавливается на верхнем конце двигателя, карданный вал установлен на нижнем конце двигателя, а подшипниковый узел подсоединяется к нижнему концу карданного шарнира. Основная функция клапана сброса давления – предотвращение вращения двигателя при спуске в скважину или выходе из нее. Секция двигателя состоит из статора и ротора: статор представляет собой формованную резиновую втулку, которая образует спиральный проход для размещения ротора, а резиновая втулка прикреплена к стальному корпусу двигателя; в то время как ротор представляет собой стальной вал, имеющий форму спирали или спирали (Inglis 1987). Когда ротор и статор собраны, геометрическая разница между ними образует серию полостей.Когда буровой раствор прокачивается через двигатель, он ищет путь между ротором и статором. При этом грязь смещает вал, заставляя его вращаться по часовой стрелке, пока грязь продолжает течь через проходы. Таким образом, функция моторной секции заключается в обеспечении мощности для вращения, а буровой раствор может быть газом или жидкостью. Универсальный шарнир соединен с ротором и вращается внутри подшипникового узла, который затем передается на долото. Подшипниковый узел, вероятно, является наиболее важным компонентом, поскольку срок службы PDM обычно определяется долговечностью подшипников.Подшипниковый узел выполняет две функции: передает осевые нагрузки на буровое долото и поддерживает центральное положение приводного вала для обеспечения плавного вращения (Inglis 1987; Short 1993).
Принципиальная схема типичного инструмента PDM
В настоящее время инструменты ВЗМ доступны в широком диапазоне диаметров около 2–11 дюймов, наиболее распространенный размер – 6–3 / 4 дюйма для ствола скважины 8–1 / 2 дюйма. Количество лепестков является очень важным аспектом двигателя, увеличение числа лепестков увеличивает скорость и снижает крутящий момент для данного размера, поэтому обычные двигатели используют один ротор и два лепестка для высокого крутящего момента.Инструменты PDM также имеют широкий диапазон скоростей около 100–800 об / мин, наиболее распространенные рабочие скорости варьируются в пределах 150–300 об / мин из-за наличия большого количества доступных сверл. Кроме того, материал статора также является критическим фактором для инструментов PDM, различные резиновые и эластомерные материалы были испытаны и испытаны. Но большинство эластомерных компонентов чувствительны к высоким температурам, и на них также влияют буровые растворы на масляной основе, которые вызывают набухание (Inglis 1987; Short 1993). Благодаря улучшенным эластомерным составам инструменты PDM могут выдерживать температуры примерно до 200 ° C.
Турбобуры
Турбобуры также могут использоваться как для вертикальных, так и для наклонно-направленных скважин. В 1873 году в Чикаго был запатентован одноступенчатый турбобур, но фактического использования не было. Вплоть до 1920-х годов исследования и разработки турбобура снова возродились в США и Советском Союзе. В 1940-х годах в Советском Союзе были произведены дальнейшие разработки турбобура, и большинство нефтяных и газовых скважин в СССР было пробурено с использованием турбобуров.
Турбобур состоит из ряда роторов и статоров, как показано на рис.6, роторы представляют собой лопасти, которые установлены на вертикальном валу, а статоры прикреплены к корпусу турбобура (Инглис, 1987 г.) ; Short 1993). Каждая пара ротор – статор называется «ступенью». Падение давления бурового раствора на каждой ступени должно быть постоянным. Каждая ступень также может вносить равную долю от общего крутящего момента и общей мощности. Количество ступеней зависит от требований и может варьироваться от 1 до 250 ступеней.Турбобуры обычно работают с более высокими частотами вращения, чем ВЗД в диапазоне 2000 об / мин, что делает выбор долота более ограниченным, чем ВЗД. Пропитанные биты более распространены из-за высокой скорости вращения. Турбосверла также доступны в различных размерах, но минимальный размер составляет около 2–7 / 8 ″ в диаметре, а максимальный – около 9 ″, поэтому их нельзя использовать в отверстиях малого диаметра из-за их сложной конструкции.
Рис.6Принципиальная схема типовой турбобура
Турбобуртакже может работать с конусным долотом и долотом PDC для бурения вертикальных, наклонно-направленных, горизонтальных скважин, скважин с большим отходом от вертикали и разветвлений.Для выполнения наклонно-направленного бурения турбобура должна работать с гнутым переводником или гнутым корпусом нового типа. К недостаткам относятся высокие скорости вращения, низкий крутящий момент, короткий срок службы подшипников, слишком много быстроизнашиваемых деталей и короткий срок службы долота. Чтобы преодолеть эти недостатки обычных турбо-сверл, было разработано множество специальных турбо-буров, таких как турбомотор с низкой скоростью и высоким крутящим моментом, турбо-бур с редуктором, турбо-бур со спиральным корпусом, и другие новые турбобуры.В настоящее время турбобур в основном применяется для бурения скважин с большим отходом от вертикали и повышения скорости проходки. Кроме того, из-за воздействия высокой температуры существует дефект для геотермального бурения с использованием инструментов PDM, полость с резиновым покрытием не может работать в условиях высоких температур. Возможно, для решения этой проблемы удастся использовать турбобур, ведь высокотемпературные рекорды турбобура достигли 260 ° C.
Ориентирующий переводник и изогнутый переводник
Ориентирующий переводник представляет собой короткую утяжеленную бурильную трубку длиной 2 фута, подковообразный башмак и ключ предназначены для помощи при исследовании ориентации изогнутого переводника.Изогнутый переводник также представляет собой короткую утяжеленную бурильную трубу длиной 2 фута, ось нижнего соединения немного отклонена от вертикали, угол смещения может варьироваться от 0,5 ° до 3 °. Изогнутый переводник заставляет долото и забойный двигатель бурить в заданном направлении, которое зависит от торца инструмента, в результате чего величина отклонения зависит от жесткости забойного двигателя, угла смещения изогнутого переводника и твердость образования.
Типичный отклоняющий узел показан на рис.7, изогнутый переводник устанавливается на верхнем конце забойного двигателя (PDM или турбобура), а ориентирующий переводник устанавливается на верхнем конце изогнутого переводника для измерения ориентации изогнутого переводника. Ключ «мулес» переводника ориентации совмещен с линией разметки, так что, когда геодезический инструмент установлен, он будет указывать направление торца инструмента (Inglis 1987). После спуска КНБК до дна ориентацию изогнутого переводника можно измерить с помощью геодезических инструментов в немагнитной манжете, установленной над изогнутым переводником.Для наклонно-направленного бурения без вращения бурильной колонны буровой раствор прокачивается через бурильную колонну для приведения в действие приводного двигателя и привода долота, что заставляет долото бурить в заданном направлении.
Рис.7Принципиальная схема изогнутого переводника и отклоняющего узла
Для некоторых особых причин, таких как отклонение через окно в обсадной колонне, улучшение управляемости, повышение эффективности работы и т. Д., Были разработаны забойные двигатели с изогнутым корпусом, что позволяет выполнять направленные операции без ориентации и изгиба. суб.Изогнутый корпус может быть установлен внутри самого двигателя, как показано на рис. 8. Изогнутый корпус – это специальное устройство, которое помещается между статором и подшипниковым узлом, чтобы обеспечить небольшой изгиб на 0–3 ° с примерно шестью приращениями в отклонение на градус изгиба, а изогнутый корпус может быть установлен как на верхнем, так и на нижнем конце забойного двигателя. Обычно изогнутый корпус устанавливается на нижнем конце забойного двигателя для достижения высокой отклоняющей способности. В реальной разработке наклонно-направленного бурения как ВЗД с изогнутым переводником, так и корпусом все еще чаще используются при наклонно-направленном и горизонтальном бурении.Существует также много типов ВЗД, как показано на рис. 8.
Рис. 8Принципиальная схема типов ВЗД с гнутым корпусом. a Обычный прямой PDM, b PDM с одним изогнутым корпусом, c Регулируемый вынос (AKO) PDM, d PDM с двойным отрывом (DKO), e с двойным наклоном универсальный (DTU) PDM и f сборка с фиксированным углом (FAB) PDM
Забойные двигатели также могут использоваться как при скользящем, так и при вращательном бурении, вращательное бурение с забойными двигателями также называется комбинированным бурением или вращательным бурением.Использование забойных двигателей во многом зависит от финансовой эффективности. При вертикальном бурении забойные двигатели могут использоваться исключительно для увеличения скорости проходки или для минимизации эрозии и износа бурильной колонны, поскольку бурильную колонну не нужно вращать с такой скоростью. В основном забойные двигатели используются в наклонно-направленных, включая наклонно-направленные скважины, горизонтальные скважины, скважины с большим отходом от вертикали, скважины с разветвлением. Хотя для направления долота в желаемую целевую зону также могут использоваться другие методы, они требуют больше времени, что увеличивает стоимость строительства скважины.Во время направленной работы применяется скользящий режим бурения, чтобы направлять долото в желаемом направлении; в то время как режим композитного бурения или роторного бурения может быть использован для решения проблем бурения, таких как высокий риск прихвата трубы, высокое сопротивление, плохая очистка ствола, низкая скорость проходки, высокая стоимость и т. д.
Роторная управляемая буровая система (RSDS )
Использование RSDS может помочь в оптимизации наклонно-направленного бурения. Поскольку полное вращение бурильной колонны может снизить сопротивление из-за скольжения бурильной колонны, повысить эффективность передачи нагрузки на долото (WOB), тем самым снизить риск прихвата, улучшить скорость проходки и достичь превосходной очистки ствола как показано на рис.9. Таким образом, RSDS позволяет использовать меньше времени для бурения до цели, улучшая управление траекторией в трех измерениях и пробурив более плавную траекторию скважины, что делает более сложные скважины также могут быть пробурены с использованием инструментов RSDS. Инструмент RSDS может быть установлен на поверхности и предварительно запрограммирован в соответствии с ожидаемой траекторией скважины. Когда команды необходимо изменить, последовательность импульсов в буровом растворе передает новые команды в забой скважины (Даунтон и др., 2000; Хелмс, 2008; Ву, 2012). Характеристики рулевого управления системы RSDS можно контролировать с помощью инструментов MWD, а также датчиков в блоке управления; эта информация передается на поверхность системой связи MWD (Даунтон и др.2000). Промышленность классифицирует RSDS на две группы: более распространенные системы «контроля изгиба» и менее зрелые системы «контроля отклонений». Мы представим три типичных типа RSDS, включая систему «push-the-bit», систему «point-the-bit» и гибридную систему.
Рис. 9Преимущества ОСБД (по Даунтону и др., 2000 г.)
Система «толкни долото»
Система «толкни долото» использует принцип приложения боковой силы к долоту, прижимая его к стенке ствола скважины для достижения желаемой траектории (Mitchell 2006).Типичные системы «толкни бит» включают систему Schlumberger PowerDrive и систему Baker Hughes AutoTrak, система PowerDrive рассматривается как типичный пример, объясняющий принцип работы систем «толкни бит». Как показано на рис. 10, система PowerDrive механически несложна и компактна, она состоит из блока смещения и блока управления, который увеличивает длину КНБК всего на 12–1 / 2 футов (Даунтон и др., 2000). Узел смещения, расположенный непосредственно за долотом, прикладывает усилие к долоту в контролируемом направлении, в то время как вся бурильная колонна вращается.Блок управления, который находится за блоком смещения, содержит электронику с автономным питанием, датчики и механизм управления для обеспечения средней величины и направления боковых нагрузок долота, необходимых для достижения желаемой траектории (Wu 2012). Узел смещения имеет три внешних шарнирных опоры, которые активируются регулируемым потоком бурового раствора через клапан; клапан использует разницу в давлении бурового раствора между внутренней и внешней частью устройства смещения (Al-Yami et al. 2008). Трехходовой поворотный дисковый клапан приводит в действие подушки, последовательно направляя грязь в поршневую камеру каждой подушки, когда она вращается, выравниваясь с желаемой точкой толкания – точкой, противоположной желаемой траектории – в скважине (Даунтон и др.2000).
Рис.10Система Schlumberger PowerDrive
Система «наведи бит»
В системе «наведи бит» используется тот же принцип, что и в системах двигателей с гнутым корпусом. В системах с «наведением на долото» изогнутый корпус содержится внутри муфты, поэтому его можно ориентировать в желаемом направлении во время вращения бурильной колонны (Mitchell 2006). Типичные системы «наведи бит» включают систему Halliburton Sperry-sun Geo-Pilot и систему Gyrodata CDAL, система Geo-Pilot рассматривается как типичный пример, объясняющий принцип работы систем «наведи бит». .Как показано на рис. 11, система Geo-Pilot в основном состоит из невращающегося внешнего корпуса, внутреннего вращающегося вала, двойных эксцентриковых колец. Одно эксцентриковое кольцо установлено другое внутреннее, двойные эксцентриковые кольца представляют собой своего рода управляемый эксцентриковый блок, внутреннее кольцо может настраивать внутренний вращающийся вал для отклонения, и, следовательно, изгиб достигается с помощью механических средств, поэтому бит наклоняется относительно остальных инструмента для достижения желаемой траектории (Wu 2012). Другими словами, системы «наведи на долото» изменяют траекторию скважины, изменяя угол забоя инструмента, траектория изменяется в направлении изгиба (Felczak et al.2011). Эта ориентация изгиба контролируется серводвигателем, который вращается с той же скоростью, что и бурильная колонна, но противодействует вращению бурильной колонны. Это позволяет ориентации торца инструмента оставаться геостационарной или невращающейся, в то время как муфта вращается (Al-Yami et al. 2008).
Рис.11Система Halliburton Sperry-sun Geo-Pilot
Гибридная система «нажми и наведи бит»
PowerDrive Archer RSDS – это настоящая гибридная система «нажми и наведи бит», разработанная Schlumberger (Bryan et al.2009; Wu 2012). Таким образом, система PowerDrive Archer обладает чертами системы «push-the-bit» и «point-the-bit». Как показано на Рис. 12, в отличие от систем «толкни долото», система PowerDrive Archer не полагается на внешние движущиеся подушки, которые толкают пласт. Вместо этого четыре исполнительных поршня внутри утяжеленной бурильной трубы прижимаются к внутренней части шарнирно-сочлененной цилиндрической рулевой втулки, которая поворачивается на универсальном шарнире, чтобы направить долото в желаемом направлении (Felczak et al. 2011).Кроме того, четыре стабилизирующих лопасти на внешней втулке над универсальным шарниром обеспечивают боковую силу буровому долоту, когда они контактируют со стенкой ствола скважины, позволяя этому RSDS работать как система «толкни долото». В настоящее время максимальная скорость наращивания составляет приблизительно 17 ° / 100 футов для инструмента PowerDrive Archer RSDS размером 8–1 / 2 дюйма. Это означает, что точное и точное управление позволяет RSDS направить траекторию скважины в зону наилучшего восприятия коллектора и расширить горизонтальную до общей глубины с более высокой скоростью наращивания, он начинает глубже и поддерживает вертикальность на больших глубинах (Felczak et al.2011).
Рис.12Система Schlumberger PowerDrive Archer
Кроме того, поскольку RSDS управляется на основе электронной системы управления, необходимо контролировать тепловые повреждения для защиты электронных плат инструмента. В настоящее время система PowerDrive, система AutoTrak и система Geo-Pilot почти могут работать при высокой температуре 200 ° C. При геотермальном бурении нижняя температура всегда выше, чем максимальная мощность RSDS, поэтому нам необходимо контролировать параметры бурения и дополнительную циркуляцию на забое, чтобы защитить электронные платы инструмента от тепловых повреждений.
Таблица 3 Сравнение трех типов методов передачиСистема вертикального бурения (VDS)
VDS – это еще один тип направленного инструмента, который используется для предотвращения отклонения и быстрого вертикального бурения, что в результате увеличивает скорость проходки для глубоких и сверхглубоких скважин. Это также очень важная техника для глубокого и сверхглубокого сверления из-за того, что на правку часто тратится слишком много времени. Хотя традиционные методы, такие как сборка эксцентриковой оси, эксцентриковая жестко-гибкая сборка, управляемая сборка, противомаятниковая сборка, динамика предварительного изгиба и т. Д., также можно использовать для выпрямления, но для замены бурового инструмента эти методы должны часто отключаться и заходить. VDS позволяет избежать частой выпрямления и автоматически удерживать ствол скважины в вертикальном положении.
В 1988 году первоначальный инструмент VDS использовался для бурения континентальных научных скважин по программе KTB в Германии, а первоначальный инструмент VDS был разработан Baker Hughes Inteq (Zhang 2005). В программе KTB максимальный угол наклона ствола успешно контролировался в диапазоне от 0 ° до 1 °.С тех пор буровые подрядчики начали разрабатывать инструменты VDS. В настоящее время существует четыре типа типичных инструментов VDS, включая систему Baker Hughes Verti-Trak, систему Schlumberger Power-V, систему Halliburton Sperry-sun V-Pilot и систему Smart Drilling Gmbh ZBE (Zhang 2005). На рисунке 13 показана система Baker Hughes Verti-Trak, она может автоматически удерживать ствол скважины в вертикальном положении без ущерба для критических параметров бурения – дебита, нагрузки на долото или скорости долота. Также можно поддерживать высокую скорость проходки и избежать длительных корректировок.VDS может свести к минимуму вероятность появления ключевых посадочных мест на кривой и уменьшить трение и износ на более поздних участках ствола скважины; Полученное в результате значительное улучшение качества ствола скважины и достигнутая точная траектория ствола скважины могут позволить использовать «профили тощей обсадной колонны», что снижает количество стали, цемента, бурового раствора и шлама (Reich et al. 2003). Последующие операции в скважине упрощены и более эффективны. Срок службы заканчивания увеличивается, а стоимость капитального ремонта снижается. Системы VDS также полезны для уменьшения расстояния между устьями скважин на поверхности.Системы VDS доступны для отверстий размером от 8–1 / 2 ″ до 9–7 / 8 ″ (инструмент 6–3 / 4 ″) и от 12–1 / 4 ″ до 28 ″ (9–1 / 2 ″). инструмент).
Рис.13Система VDS Baker Hughes Verti-Trak
Техника направленной съемки
Техника направленной съемки, ключевой аспект управления траекторией, измеряет наклон и направление на различных глубинах. Измерение торца инструмента требуется для определения направления отклонителя, изогнутого переводника или изогнутого корпуса.Таким образом, метод исследования также является ключом к наклонно-направленному бурению, которое подразделяется на две группы: более распространенные инструменты измерения во время бурения (MWD) и менее зрелые инструменты измерения после бурения (Short 1993; Chen 2011; Han 2011; Wu 2012). Магнитные однозарядные инструменты, магнитные многозарядные инструменты, электронные одноразовые инструменты и электронные многозадачные инструменты обычно используются для измерения траектории ствола скважины после бурения, но это неудобно и неэффективно для направленного бурения.Для решения этой проблемы были разработаны инструменты MWD для измерения траектории ствола скважины во время бурения. Ключевые методы MWD включают в себя метод съемки и метод передачи. Инструменты MWD применялись почти во всех наклонно-направленных скважинах по всему миру. Но в одно- и многозарядных приборах применяются вертикальные скважины. Мы сосредоточимся на методах MWD:
Методика измерения
Существует три вида скважинной информации, информация о направлении, информация о бурении и информация о пласте, которые необходимо измерять во время бурения (Wu 2012; Ma and Chen 2014; Ma et al.2015b). Информация о направлении может быть измерена с помощью обычных инструментов MWD. Измерение буровых работ было разработано на основе обычного метода MWD, в то время как измерение информации о пласте было разработано на основе традиционного метода каротажа и в основном использовалось для геонавигационного бурения для корректировки геологической цели в реальном времени.
Информация о направлении
Инструменты MWD, как правило, способны выполнять направленные исследования в реальном времени. Акселерометры и магнитометры используются для измерения наклона и азимута, а информация о наклоне и азимуте передается от места измерения на поверхность.Траекторию и местоположение ствола скважины можно рассчитать, используя данные разведки. Между тем, инструменты MWD также обычно способны обеспечивать измерения торца инструмента во время паузы в бурении, что позволяет использовать его при наклонно-направленном бурении с использованием клина-отклонителя, «забойного двигателя + изогнутого переводника», забойного двигателя с гнутым корпусом или инструмента RSDS. . Информация о направленности может помочь оператору наклонно-направленного бурения узнать, куда идет скважина и каковы последствия его усилий по рулевому управлению (Mitchell 2006; Chen 2011).
Инженерная информация по бурению
Для предотвращения аварий в стволе скважины и повышения эффективности бурения инструменты MWD также были разработаны для измерения инженерной информации по бурению, такой как забойное давление, нагрузка на долото, крутящий момент на долоте (TOB) , скорость вращения, вибрация, удар, температура, объем потока бурового раствора и т. д. (Ma and Chen 2015). Обычно инженерная информация измеряется с помощью специального отдельного вспомогательного инструмента и загружается с помощью инструментов MWD. На основе этой информации в режиме реального времени могут быть определены условия в забое скважины и рабочее состояние буровых инструментов, что делает операции бурения более эффективными, безопасными и экономичными.Кроме того, эта информация также ценна для геологов, ответственных за скважинную информацию о пробуренной формации (Mitchell 2006).
Информация о пласте
Обычные инструменты MWD, как сами по себе, так и в сочетании с отдельными переводниками / инструментами, обычно способны выполнять измерения свойств пласта в реальном времени, это так называемый каротаж во время бурения (LWD), который получил развитие от традиционных методов каротажа. Обычно доступна следующая информация о пласте, такая как естественное гамма-излучение, плотность, пористость, удельное сопротивление, акустический кавернометр, магнитный резонанс, пластовое давление и т. Д.Из-за влияния длины, включая забойные двигатели, вспомогательные инструменты и инструменты LWD, точка измерения информации о направлении должна перемещаться вверх, что снижает точность управления траекторией скважины. Таким образом, был разработан инструмент для измерения наклона около долота для измерения информации о направлении на буровом долоте. Измерения вблизи долота, такие как гамма-лучи, угол наклона и азимут, позволяют оператору внимательно следить за ходом бурения (Felczak et al. 2011). Обычный инструмент MWD позволяет передавать и оценивать эти измерения в реальном времени, что позволяет реализовать геоуправление.Геологическая цель также может быть скорректирована в соответствии с эволюцией свойств пласта, это так называемое георегулирующее бурение (Wu 2012). Измерения вблизи долота, такие как гамма-лучи, угол наклона и азимут, позволяют оператору внимательно следить за ходом бурения.
Техника передачи
В зависимости от среды передачи методы передачи скважинных данных можно разделить на три типа: гидроимпульсная телеметрия, электромагнитная телеметрия и проводная бурильная труба, их основные характеристики можно отсортировать в таблице 3.
Телеметрия гидроимпульсов
Телеметрия гидроимпульсов – это метод передачи скважинных данных (включая данные LWD и MWD) на поверхность с использованием импульсов давления бурового раствора внутри бурильной колонны (Chen 2011; Wu 2012 ). Для достижения цели передачи скважинных данных используется скважинный клапан для ограничения потока бурового раствора, который создает колебания давления и распространяется в буровом растворе к поверхности, где они поступают из стояка. датчики давления.Другими словами, информация представлена сигналами давления, которые поступают от датчиков давления в стояке. Полученные сигналы давления импортируются в компьютерную систему обработки и декодируются в измерения. Как правило, измерения кодируются в виде амплитудной или частотной модуляции импульсов бурового раствора (Chen 2011; Wu 2012). Телеметрия с гидроимпульсным сигналом является наиболее распространенным методом передачи данных, используемым инструментами MWD. В настоящее время гидроимпульсная телеметрия доступна в трех группах, включая положительный импульс, отрицательный импульс и непрерывную волну.
- а)
Инструменты MWD с положительным импульсом: как показано на рис. 14a, клапан на короткое время закрывается и открывается для создания импульсов давления. Когда клапан закрывается, давление в стояке увеличивается. Таким образом, этот метод называется положительно-импульсным. Это также наиболее распространенный метод, используемый инструментами MWD.
Рис. 14Три метода гидроимпульсной телеметрии. a положительный импульс, b отрицательный импульс и c непрерывный импульс
- (б)
Инструменты MWD с отрицательным импульсом: как показано на рис.14b клапан ненадолго открывается и закрывается для создания импульсов давления. Как только клапан открывается, давление в напорной трубе снижается. Таким образом, этот метод называется отрицательно-импульсным.
- (c)
Инструменты MWD с непрерывной волной: как показано на рис. 14b, значение упорядоченно закрывается и открывается для генерации синусоидальных импульсов давления во время вращения.Любая схема цифровой модуляции с непрерывной фазой может использоваться для наложения информации на сигнал несущей. Наиболее широко используются схемы модуляции с непрерывной фазовой модуляцией (Wu 2012).
Современные инструменты MWD с гидроимпульсным управлением в основном представляют собой положительные и отрицательные импульсы, хотя скорость передачи (0,5–3,0 бит / с) ниже, чем у инструментов MWD с непрерывной волной, их стабильность намного лучше и стоимость также ниже .Инструмент непрерывной волны MWD предлагает полосу пропускания до 18 бит / с. Скорость передачи падает с увеличением длины ствола скважины и обычно составляет 1,5–3,0 бит / с на глубине 10 000 м. Кроме того, при использовании аэрированного бурения на депрессии или аэрации бурового раствора сжимаемость бурового раствора увеличивается, что также снижает пропускную способность бурового раствора. В этом случае рекомендуется электромагнитная телеметрия MWD или проводная телеметрия бурильных труб.
Электромагнитная телеметрия
Электромагнитная телеметрия также называется EM-MWD.Для передачи скважинной информации инструменты EM-MWD включают излучающую субантенну в бурильную колонну, а другая принимаемая антенна устанавливается на поверхности, как показано на рис. 15. Инструмент EM-MWD генерирует электромагнитные волны с помощью излучающая субантенну, электромагнитные волны передают скважинную информацию через пласт на поверхность. На поверхности они принимаются наземной антенной, затем передаются в центр обработки поверхности и декодируются в измерения.Другими словами, инструмент EM-MWD передает электромагнитные волны через пласт вместо импульсов давления через столб жидкости. Таким образом, преимущества включают экономию времени за счет передачи данных разведки во время соединения, высокие скорости передачи данных и возможность работать в условиях, в которых не может работать гидроимпульсная телеметрия, таких как бурение с аэрацией на депрессии и бурение с использованием воздуха. Инструмент EM-MWD предлагает полосу пропускания до 400 бит / с. Однако при бурении исключительно глубоких скважин он обычно не работает, и сигнал может быстро терять силу при ослаблении пластов, эти зоны делают использование инструментов EM-MWD непрактичным.Чтобы преодолеть эту проблему, были изобретены некоторые усовершенствованные методы определения мощности и обнаружения сигнала EM-MWD, такие как повторители бурильной колонны, повторители обсадных труб, повторители проводов и т. Д. Эти методы обычно используются при бурении на депрессии и при аэрированном бурении на депрессии. воздушное бурение.
Рис.15Принципиальная схема электромагнитной телеметрии
Бурильная труба с проводом
Бурильная труба с проводом также называется электрической бурильной колонной или интеллектуальной бурильной колонной.Бурильная труба с проводкой была впервые изобретена в 1997 году при финансовой поддержке компании Новатэк и Министерства энергетики США. В 2001 году Национальная лаборатория энергетических технологий (NETL) начала предоставлять финансирование для проекта бурильных труб и дополнительного проекта передачи данных о бурильных трубах (Hernandez and Long 2010), результаты исследования включают сеть IntelliServ и Intellipipe. В 2006 году первая коммерческая бурильная труба с проводкой (продукт IntelliServ) была использована в Мьянме (Эдвардс и др.2013). В настоящее время IntelliServ, широкополосная сетевая система бурильной колонны, является продуктом National Oilwell Varco (NOV), который используется для передачи скважинной информации на поверхность во время бурения. Компоненты сети IntelliServ встроены в компоненты бурильной колонны (рис. 16), известные как IntelliPipe, которые передают геологические данные со скоростью 57 000 бит в секунду (Edwards et al. 2013). Кабельная бурильная труба обеспечивает высокоскоростной телеметрический канал от забоя к поверхности, а также позволяет передавать информацию на скважинные инструменты для управления с обратной связью.Кроме того, измерительные узлы также могут располагаться по всей длине бурильной колонны, что позволяет операторам собирать данные вдоль ствола скважины (рис. 16). Измерения могут включать в себя всю скважинную информацию, такую как информация о направлении, инженерная информация о бурении и информация о формации. На передачу данных больше не влияют свойства бурового раствора, свойства пласта и глубина. Однако бурильные трубы с проводкой по-прежнему слишком дороги, надежность все еще требует повышения из-за схемы тандемного соединения, бурильные трубы с проводкой не могут работать, даже если отсутствует только одно соединение.
Рис. 16Принципиальная схема бурильной трубы с проводкой (по Эдвардсу и др., 2013 г.)
Кроме того, из-за измерений инструментов MWD, основанных на электронных технологиях, необходимо контролировать тепловые повреждения для защиты электронных плат инструмента. В настоящее время большинство инструментов MWD могут работать при температуре 150 ° C, некоторые инструменты MWD могут работать при высоких температурах до 200 ° C. При геотермальном бурении нижняя температура всегда выше, чем максимальная производительность инструментов MWD, что делает инструменты MWD / LWD нестабильными, поэтому нам необходимо контролировать параметры бурения и дополнительную циркуляцию вне забоя, чтобы защитить электронные платы инструмента от тепловых повреждений.
Буровые долота
В нефтегазовой промышленности буровое долото – это инструмент, предназначенный для создания цилиндрической скважины (ствола скважины) в земной коре методом вращательного бурения. Размер ствола скважины, вызванный буровыми долотами, очень мал, от 3–1 / 2 ″ до 30 ″ (Centala et al. 2011; Bruton et al. 2014; Azar et al. 2015). Глубокие пласты разрушаются механически режущими элементами (называемыми зубами или резцами) долота путем соскабливания, шлифовки или локализованного сжатия трещин (Chen 2011).На основе режущего механизма промышленность классифицирует буровые коронки на две группы: шарошечные долота, долота с фиксированным резцом и гибридные долота.
Долота с роликовыми конусами
В долотах с роликовыми конусами обычно используются три конуса для удерживания зубьев, как показано на рис. 17, хотя иногда можно увидеть расположение с одним, двумя или четырьмя конусами. Долото с роликовым конусом состоит из корпуса, ножки, конуса, подшипника, уплотнения, зуба и сопла. Он бурит в основном за счет разрыва или дробления породы «зубцами» на конусах, которые катятся по забойной части ствола скважины при вращении долота.Роликовые конические коронки также можно разделить на два класса в зависимости от изготовления зубьев, например, фрезерованные зубчатые коронки и коронки из карбида вольфрама (TCI).
Рис.17Типичные шарошечные долота
- 1.
Долота с фрезерованными зубьями, также называемые долотами со стальными зубьями, имеют конусы с клиновидными зубьями, фрезерованными непосредственно в самой конической стали (Centala et al.2011).
- 2.
Биты TCI имеют формованные зубья из спеченного карбида вольфрама, запрессованные в просверленные отверстия в конусах, карбид вольфрама нанесен на поверхности зубьев для повышения долговечности благодаря его чрезвычайной твердости. Зуб TCI также применялся в некоторых типах фрезерованных зубчатых долот. Чтобы еще больше повысить долговечность буровых коронок, также должны быть разработаны некоторые современные материалы, такие как альвеолятный алмазный материал и карбид вольфрама с двойным цементированием.Конусы вращаются на подшипниках, которые обычно герметизированы вращающимся уплотнительным кольцом или металлическим торцевым уплотнением для защиты от среды бурового раствора в забое скважины. Долота с шарошечным конусом могут адаптироваться к инструментам с низкой, высокой, высокой температурой, высокой нагрузкой на долото и ВЗД; Области применения шарошечных долот включают высокоабразивные образования, мягкие абразивные образования, твердые образования. Для глубокого или геотермального бурения высокотемпературное шарошечное долото может быть специально разработано для работы в высокотемпературных условиях бурения, таких как геотермальные скважины, в течение продолжительных периодов времени.Долота с шарошечным конусом TCI, используемые для бурения твердых и абразивных пластов с целью доступа к пару или горячей породе в подземных пластах, подвергаются воздействию температур, превышающих 260 ° C.
Долота с фиксированными резцами
Долота с фиксированными резцами были первым типом сверл, которые использовались при роторном бурении, их режущие механизмы намного проще, чем у шарошечных долот, поскольку режущие элементы не перемещаются относительно долота.Долота с фиксированными режущими кромками можно разделить на четыре класса в зависимости от изготовления зубьев, такие как долота с поликристаллическим алмазом (PDC), долота из природного алмаза и долота с пропиткой (рис. 18).
Рис.18Типичные фиксированные фрезы
- 1.
Буровая коронка была первым типом бурового долота, который использовался при вращательном бурении, но его можно использовать только в мягких породах, поэтому в настоящее время оно редко используется в нефтяном бурении.
- 2.
Долото из PDC является наиболее распространенным буровым долотом, используемым сегодня, благодаря преимуществам высокой скорости проходки, долгому сроку службы и продолжительности бурения. Долото PDC состоит из корпуса, фрезы и насадки. Резец PDC (зуб) представляет собой цилиндр из спеченного карбида вольфрама с одной плоской поверхностью, покрытой синтетическим алмазным материалом. Резцы расположены на лопастях долота в шахматном порядке, при этом поверхность резца с алмазным покрытием обращена в направлении вращения долота, чтобы обеспечить полное покрытие забоя скважины (Bruton et al.2014; Азар и др. 2015). Долота PDC могут адаптироваться к низкой нагрузке на долото, высокой частоте вращения, высокой температуре, PDM, турбо-буровым станкам и даже RSDS; Применение долот PDC включает однородные пласты, пласты мягкой и средней твердости, но бурение твердых и абразивных межслоевых интервалов было непрактичным для долот PDC.
- 3.
Насадка из натурального алмаза и коронка с пропиткой похожи, самая большая разница – фрезы.В сверле из природного алмаза используются алмазные резцы из природного промышленного сорта, которые вставляются в матрицу корпуса долота, а в импрегнированном долоте используются термостойкие поликристаллические (TSP) алмазные резцы. Благодаря этому алмаз отличается наибольшей твердостью и высокой прочностью, что позволяет ему адаптироваться к твердым абразивным образованиям. Эти долота доступны в различных стилях как для моторного, так и для роторного бурения в твердых или абразивных породах. Хотя алмазы дороги, долговечность долот также достаточно высока, что делает их конкурентоспособными при бурении нефтяных скважин.Долота с природным алмазом получили широкое распространение в бурении RSDS, бурении турбобурами и колонковом бурении.
Кроме того, фрезы обычных фиксированных долот закреплены на корпусе долота, они легко изнашиваются и снижают срок службы долота. Чтобы решить эту проблему, СМИТ разработал режущий плоттер PDC, названный ONYX 360 (Bruton et al. 2014). Вращающийся резец PDC ONYX 360 значительно увеличивает долговечность долота PDC за счет поворота на 360 °, как показано на рис.19. Вся алмазная кромка PDC-резака ONYX 360, расположенного в зонах сильного износа режущей конструкции, используется для резки пласта. Вращающееся действие фрезы позволяет алмазной кромке фрезы оставаться острее дольше, продлевая срок службы фрезы ONYX 360 по сравнению с фиксированными фрезами премиум-класса. На основе данных, полученных при использовании 13-миллиметрового резака ONYX 360, был разработан резак 16 мм, обеспечивающий повышенную прочность и долговечность. По сравнению с долотами с фиксированными фрезами долота PDC, в состав которых входили вальцовые фрезы ONYX 360, продемонстрировали увеличение длины пробега до 57%, что привело к меньшему количеству спусков долота и снижению затрат на бурение.
Рис.19Сравнение фиксированного резака PDC и резака ONYX 360
Гибридные долота
С популяризацией и применением долот PDC и технологии резцов PDC для улучшения стационарных резцов буровые долота PDC в различных пластах постепенно заменяют конические долота. Но в твердых абразивных породах и при сложных операциях направленного бурения из-за производительности буровое долото PDC не может заменить коническое долото. Для решения этой проблемы в настоящее время также доступен гибридный тип долота, в котором сочетаются как накатная фреза, так и фиксированные режущие элементы (Pessier and Damschen 2011), как показано на рис.20. Существует две конструкции: одна представляет собой малоразмерное двустворчатое долото с двойным конусом, а другая – немного большее по размеру крыло Mito, трехконусное долото, основанное на этих сверлах с четырьмя ножами и шестью лопастями бурового долота PDC, лопасти тисков и короткие позиции были заменены на конус. Таким образом, центральное положение ствола скважины располагается на PDC-резце хирургического крыла для полного разрушения породы, а периферийная часть бурения скважины завершается резцами и лопастями, эффект разрушения породы зависит от конусов, лопастей и их сопряжения.Это гибридное сверло предназначено для сокращения времени бурения в самых сложных условиях. Благодаря прочности на раздавливание и стабильности конусов валков, а также превосходному резанию и непрерывному режущему действию алмазных коронок, эта технология позволяет выживать в сильно переслаивающихся пластах с стабильной производительностью и отличным контролем торца инструмента. В приложениях размером 12–1 / 4 дюйма в США операторы достигают увеличения скорости бурения до 62%; длина одиночного долота увеличивается более чем на 200%, сокращая количество выходных дней по сравнению со стандартным временем буровой установки.В Бразилии оператор пробурил на 90% быстрее и на 20% дальше, чем выносы. По сравнению с долотами с роликовым конусом вы можете увеличить скорость проходки и снизить нагрузку на долото с меньшим отскоком долота. По сравнению с PDC, наблюдается значительно повышенная долговечность в переслаивающихся пластах, меньшее прерывистое скольжение, более низкий и более стабильный крутящий момент при бурении, а также лучшая стабильность и управление направлением.
Фиг.20Кроме того, некоторые типы специальных долот разработаны с учетом требований к наклонно-направленному бурению, бурению с управляемым ротором, бурению с управляемым двигателем, воздушному бурению, тонкому стволу, колонковому бурению, бурению боковых стволов, пилотному бурению, расширению бурения, бурению на обсадных трубах и т.Таким образом, мы можем выбрать подходящие долота для проведения соответствующего бурения.
Буровые растворы
Термин буровой раствор (или раствор) охватывает все составы, используемые для содействия добыче и удалению выбуренной породы из скважины в земле (Дарли и Грей, 1988). Буровой раствор закачивается из буровых ям с помощью буровых насосов, прокачивается через наземный трубопровод, стояк, буровую вертлюг, бурильную колонну и разбрызгивается из сопел на буровое долото, затем очищается от обломков породы (или выбуренной породы) и охлаждается буровая установка. инструменты.Таким образом, шлам выносится на поверхность через раствор в затрубном пространстве. На поверхности шлам отфильтровывается с помощью сланцевого шейкера, а отфильтрованный ил возвращается в ямы. В этом процессе основные функции бурового раствора можно резюмировать следующим образом (Дарли и Грей, 1988; Канн и др., 2011; Чен, 2011): вынос шлама на поверхность, охлаждение и смазка долота и бурильных инструментов, очистка под долотом, уравновешивать пластовое давление, герметизировать проницаемые пласты, передавать гидравлическую энергию на скважинные инструменты и долото, поддерживать стабильность ствола скважины, контролировать коррозию инструментов и контролировать повреждение пласта.Существует много типов бурового раствора или бурового раствора, которые используются при бурении нефтяных скважин, они классифицируются в зависимости от их основы: буровой раствор на газовой основе (GBDF), буровой раствор на водной основе (WBM), буровой раствор на нефтяной основе (OBM).
- 1.
Буровой раствор на газовой основе (GBDF): GBDF означает, что непрерывная фаза бурового раствора представляет собой газ, включает воздух, азот, выхлоп дизельного двигателя, природный газ, буровой раствор в виде тумана и пену для бурового раствора (Chen 2011).Воздух, азот, выхлопные газы дизельных двигателей и природный газ в основном используются при газовом бурении или бурении на депрессии, шлам удаляется с помощью высокоскоростного воздушного потока. Однако из-за накопления воды при глубоком бурении шлам не может быть вынесен из забоя. Поэтому буровые растворы в виде тумана или пены обычно используются для решения проблем с добычей воды, возникающих при глубоком бурении. Иногда жидкий буровой раствор также используется для решения некоторых серьезных проблем с добычей воды. Кроме того, GBDF не может адаптировать все типы формаций, ее можно использовать только в стабильных формациях.Из-за давления колонны ГБДФ недостаточно для поддержания устойчивости ствола скважины.
- 2.
Буровой раствор на водной основе (WBM): вода является непрерывной фазой бурового раствора. Самым простым буровым раствором на водной основе может быть вода, что означает, что в раствор не добавлены какие-либо лечебные агенты или добавки. Однако вода не может приспособиться к подавляющему большинству глубоких пластов.Поэтому инженеры добавляют некоторые добавки, чтобы отрегулировать производительность в соответствии с требованиями глубокого бурения. WBM может содержать несколько растворенных веществ. К ним относятся щелочи, соли и поверхностно-активные вещества; органические полимеры в коллоидном растворе; капельки эмульгированного масла; и различные нерастворимые вещества (такие как барит, глина и стружка) в суспензии (Дарли и Грей, 1988). К наиболее распространенным нерастворимым веществам, используемым в WBM, относятся глина и барит. Глина используется для создания однородной смеси, что делает ее жидкой суспензией, в то время как барит обычно используется для регулировки плотности WBM.В процессе бурения из-за перемешивания бурового шлама, солей и поровой жидкости в WBM характеристики WBM не могут оставаться неизменными, щелочи, соли, поверхностно-активные вещества и полимеры, таким образом, добавляются в WBM. В общем, реологические свойства и характеристики строительства стены обезвоживания WBM являются ключевыми, и их трудно регулировать. Между тем, ингибирующая способность WBM также очень важна для бурения сланцевых пластов из-за влияния физико-химического эффекта между сланцами и буровым раствором.Таким образом, химические добавки обычно добавляют в систему WBM для достижения различных эффектов, включая контроль реологических свойств, удаление загрязнений, стабильность сланца, повышение скорости проходки при бурении, охлаждение и смазку оборудования. Для глубокого или геотермического бурения, из-за влияния глубины, высокой солености, высокого давления и высокой температуры, плотность бурового раствора должна быть улучшена с использованием барита и порошка железной руды, реологические свойства и характеристики строительства стены обезвоживания больше трудно контролировать, как показывает реология при низких и высоких температурах, трудно учесть, потери воды в HPHP большие, и глинистая корка толстая.Максимальная рабочая температура WBM составляет около 200 ° C. Итак, ключевая проблема заключается в том, как улучшить термостойкость WBM.
- 3.
Буровой раствор на масляной основе (OBM): буровой раствор на масляной основе – это буровой раствор, в котором базовой жидкостью является нефтепродукт, такой как дизельное топливо. Технология РУО продвинулась от использования только сырой нефти как средства повышения продуктивности до использования многофункциональных композиций, которые сыграли свою роль в многочисленных рекордных скважинах (Дарли и Грей, 1988).OBM используется по многим причинам, таким как повышенная смазывающая способность, улучшенное ингибирование сланца и улучшенные очищающие способности при меньшей вязкости. Кроме того, OBM также может выдерживать более высокие температуры, не ломаясь. Применения применялись в условиях экстремальных температур, высокого давления, водочувствительных сланцев, агрессивных газов и водорастворимых солей (Дарли и Грей, 1988; Каенн и др., 2011). Сведены к минимуму проблемы прихвата трубы, чрезмерного крутящего момента и сопротивления в наклонно-направленных скважинах, а также унос газа в буровой раствор.Однако использование РУО имеет особые соображения, включает в себя стоимость, экологические соображения, такие как размещение выбуренной породы в подходящем месте, и исследовательские недостатки использования бурового раствора на нефтяной основе. Следовательно, РУО может быть хорошим выбором для решения связанных проблем, вызванных высокой плотностью, соленостью, высоким давлением и высокой температурой. Максимальная рабочая температура OBM зафиксирована выше 220 ° C.
При вертикальном бурении глубоких скважин высокое давление / высокая температура (HP / HT) могут быть основными факторами, которые влияют на свойства буровых растворов.При горизонтальном бурении и бурении с большим отходом от вертикали главными факторами могут быть смазывающие свойства и несущая способность резания. Однако при геотермальном бурении из-за чрезвычайно высокого давления / высокой температуры (HP / HT), сложной системы давления в стволе скважины и множества источников загрязнения буровым раствором плотность, реологические свойства и характеристики обезвоживания бурового раствора являются более сложными поддерживать. В настоящее время OBM и WBM обычно используются при бурении глубоких скважин в мире, а максимальная рабочая температура бурового раствора близка к 220 ° C, максимальная плотность бурового раствора составляет около 2.4–2,7 г / см 3 .
7. Наклонно-направленное бурение и проходка туннелей | Технологии бурения и земляных работ будущего
Эдлунд, Пенсильвания, 1987, Применение недавно разработанной технологии горизонтального бурения средней кривизны в зоне Spraberry Trend: SPE 6170, Конференция по бурению SPE / IADC, Новый Орлеан, штат Луизиана, 15-18 марта, Ричардсон, Техас, SPE, стр. . 1057-1063.
Фульц, Дж. Д., и Питтард, Ф. Дж., 1990, Бурение открытого ствола с использованием гибких насосно-компрессорных труб и забойного двигателя прямого вытеснения: SPE 20459, 65 th Annual Technical Conference and Exhibition, New Orleans, La., 23–26 сентября, Ричардсон, Техас, SPE, стр. 551-559.
Фульц, Дж. Д., Питтард, Ф. Дж., Сойер, Ф. Д. и Фармер, Ф. Д., 1990, Бурение тонких отверстий в суровых условиях: IADC / SPE 19949, Конференция IADC / SPE по бурению, Хьюстон, Техас, 27 февраля – мар. 2, Ричардсон, Техас, SPE, стр. 333-340.
Гибсон, Дж., 1993, Роббинс Ко, Кент, Вашингтон, личное сообщение.
Глагола М. А., Вонг Л. Ф., 1986, Алюминиевая бурильная труба для наклонно-направленного бурения: SPE / IADC 14789, Конференция по бурению IADC / SPE, Даллас, Техас., 10–12 февраля, Ричардсон, Техас, SPE, стр. 553-560.
Хаас Р. К. и Стокли К. О., 1989, Бурение и заканчивание скважины в трещиноватом карбонате, World Oil, т. 204 (4), стр. 39-45.
Хаир, Дж. Д., 1989a, Технология перехода через реки: Трубопровод и газовый журнал, т. 215 (1), стр. 29-35.
Хэйр, Дж. Д., 1989b, Системы управляемого бурения малого диаметра: Pipeline and Gas Journal, v. 215 (4), p. 18-24.
Хаяси, М., и Мията, Ю., 1989, Окумура – метод туннелирования супер мини-щита Маркхэма: NO-Dig 89, Четвертая международная конференция и выставка по бестраншейному строительству для коммунальных предприятий, Лондон, ISTT, p.231-235.
Hourcard, M., и Bannerman, J., 1990, Остерегайтесь осыпающихся сланцев над горизонтальными скважинами: World Oil, т. 211 (1), стр. 101-105.
Джоши, С. Д., 1987a, Обзор технологии горизонтальных скважин и дренажных скважин: SPE 16868, Ежегодная техническая конференция и выставка SPE, Даллас, Техас, 27-30 сентября, Ричардсон, Техас, SPE, с. 339-354.
Джоши С. Д., 1987b, Обзор термической добычи нефти с использованием горизонтальных скважин: In situ, т. 11 (2/3), стр. 211-259.
Джоши, С. Д., 1988, Обзор технологии горизонтальных скважин и дренажных скважин: SPE 16868, Региональное собрание Скалистых гор, Каспер, Вайоминг, 11-13 мая, Ричардсон, Техас, SPE, стр. 89-108.
Кабак Д. С., Луни Б. Б., Кори Дж. К., Райт Л. М. и Стил Дж. Л., 1989, Горизонтальные скважины для восстановления грунтовых вод на месте
Выбор подходящего сверла – Руководства по закупке DirectIndustry
Сверлильный станок Knuth Machine ToolsСверлильные прессы в основном используются в мастерских.Это мощные прецизионные сверла , которые позволяют делать чистые отверстия в твердых материалах толщиной . Просверливают вертикальное отверстие. Самые мощные сверлильные станки позволяют сверлить отверстия диаметром до 30 мм.
Есть два типа сверлильных станков:
- Сверла, устанавливаемые на рабочий стол. Они позволят вам с высокой точностью сверлить небольшие кусочки дерева или металла.
- Стационарные сеялки размещаются на земле. Они внушительные, очень мощные и позволяют сверлить очень большие детали.
Перед тем, как выбрать модель сверлильного станка, необходимо знать, для чего он будет использоваться. Как и в случае с ручными дрелями, вам нужно будет обратить внимание на мощность вашей дрели. Вам также необходимо установить идеальное расстояние между столом и патроном , которое определяет размер деталей, с которыми вы можете работать. Кроме того, некоторые модели позволяют регулировать расстояние между пластиной и патроном, что обеспечивает большую гибкость в выборе размеров просверливаемых деталей.
Еще один фактор, который следует учитывать, – это удобство использования вашего сверлильного станка. Для удобства работы рекомендуем приобрести сверло с длинной ручкой , что упростит опускание патрона. Некоторые сверла даже оснащены маховиком , который делает опускание патрона более легким, плавным и точным.
Сверлильные станки оснащены однофазными или трехфазными двигателями. Трехфазный сверлильный станок может подвергаться большей нагрузке, чем однофазный.В результате он будет меньше нагреваться.
Наконец, вы должны подумать о вашей безопасности , в частности, о наличии аварийного выключателя и зажимных тисков для блокировки просверливаемых деталей. Зажимные тиски, необходимые для предотвращения несчастных случаев, можно приобрести отдельно.
Магнитный сверлильный станок– Что такое магнитный сверлильный станок?
Магнитный сверлильный станок – станок, оснащенный насадкой для режущего инструмента и электромагнитом, используется для сверления отверстий в металлах.Магнитный сверлильный станок прикреплен с режущими инструментами, называемыми корончатым сверлом, это корончатое сверло полое изнутри, но имеет режущие кромки на поверхности и на зубах.
Магнитный сверлильный станок также называется магнитным сверлильным станком, магнитным сверлильным станком, магнитным сверлильным станком, магнитным сверлильным станком, магнитным сверлом или магнитным сверлом.
Магнитный сверлильный станок также может выполнять такие операции, как нарезание резьбы (нарезание резьбы), спиральное сверление, развертывание и зенкование. Портативный магнитный сверлильный станок выполняет отверстия в металле с помощью специального режущего инструмента, называемого корончатым сверлом, кольцевым сверлом или кольцевым кольцевым сверлом.
Разница между обычным сверлильным станком и магнитным сверлильным станком:
Основное отличие состоит в том, что, в отличие от обычного сверлильного станка, станок для магнитного сверления является портативным и гибким, его можно перемещать с одного места на другое, его можно фиксировать горизонтально, вертикально, сбоку и т.д. никогда не достигается никаким другим сверлильным станком.
Еще одно отличие состоит в том, что станок для корончатого сверления выполняет резку только по периферии отверстия, а не по всей поверхности, поэтому он должен резать очень мало материала и, следовательно, быстрее и экономичнее.Вот почему в нормальных условиях магнитный сверлильный станок считается в три-четыре раза быстрее, чем традиционные сверлильные станки.
Описание магнитного сверлильного станка:
Портативный магнитный сверлильный станок – это машина новой технологии и более быстрая замена станкам для сверления отверстий в металле старой технологии, таким как сверлильный станок, сверлильный станок с зубчатой головкой, сверлильный станок с радиальным рычагом, фрезерное сверло и т. Д.
Портативный магнитный сверлильный станок – это машина с новой технологией и более быстрая замена устаревшим станкам для обработки отверстий в металле, таким как сверлильный станок, сверлильный станок с зубчатой головкой, сверлильный станок с радиальным рычагом, фрезерный сверло и т. Д.
Портативный магнитный сверлильный станок с корончатыми сверлами (кольцевыми фрезами) выполняет отверстия диаметром более 12 мм. Для отверстий диаметром менее 12 мм можно использовать спиральные сверла. Корончатые сверла, используемые для этих станков, обычно производятся из быстрорежущей стали (HSS) и наконечника из карбида вольфрама (TCT).
В зависимости от характера просверливаемого материала и диаметра отверстия пользователь решает использовать корончатые сверла HSS или TCT.
Магнитный сверлильный станок с кольцевыми фрезами дает точность 0.От 005 мм до 0,001 мм из стали, нержавеющей стали и т. Д.
Портативный магнитный сверлильный станок доступен в различных размерах, формах, конструкциях, электронике и оборудовании в зависимости от назначения станка. Он сочетает в себе универсальность сверлильного станка с сильной электромагнитной основой, позволяющей ему прилипать к поверхности из углеродистой стали (черного металла). Его можно расположить для бурения горизонтально, вертикально или даже вверх ногами (над головой).
Конструкция магнитного сверлильного станка:
Магнитный сверлильный станок состоит из четырех основных частей: магнитного основания, буровой стойки, двигателя и оправки.
Магнитное основание
Основание магнитного сверлильного станка оснащено мощным электромагнитом для легкого зажима (фиксации) станка на обрабатываемой детали. При подаче напряжения этот магнит прочно фиксируется на заготовке, фиксируя основание станка на металлической заготовке, что помогает оператору обеспечивать равномерную подачу на заготовку. Электромагнит играет очень важную роль в портативном магнитном сверлильном станке, поскольку он помогает машине оставаться устойчивой, не позволяет машине демонтироваться во время сверления, может работать с машиной над головой, в горизонтальном или вертикальном положении.Обычно магнитный сверлильный станок используется непосредственно для обработки черных металлов, но его также можно использовать для обработки любых черных металлов, таких как нержавеющая сталь, с помощью зажимных устройств.
Стойка для сверл
Стенд для сверления – это основной корпус магнитного сверлильного станка, на котором установлены электрические переключатели двигателя и магнита, установлен индикатор магнита, а также установлены печатные платы. Корпус магнитного сверлильного станка удерживает вместе двигатель и магнитное основание. Рукоятка подачи также прикреплена к корпусу.Корпус магнитного сверлильного станка помогает двигателю скользить по нему, обеспечивая подачу вверх и вниз. Корпус магнитного сверлильного станка также играет роль ручки для подъема и перемещения станка из одного места в другое. Материал, используемый для изготовления корпуса, обычно – чугун.
Двигатель
Двигатель является основным компонентом магнитного сверлильного станка. Это двигатель постоянного тока. Выходная мощность двигателя колеблется от 800 Вт до 2300 Вт в зависимости от мощности, необходимой для бурения.Отверстие большего диаметра потребует более мощного двигателя. Двигатель, используемый для сверлильных и резьбонарезных станков, также будет иметь возможность вращения по часовой и против часовой стрелки. Как правило, электроника для управления скоростью и крутящим моментом расположена на самом двигателе.
Беседка
К двигателю прикреплена оправка, также называемая держателем инструмента или патроном на магнитном сверлильном станке. Это тип зажима, который используется для крепления корончатых сверл. Для магнитного сверлильного станка доступны в основном два типа патронов, промышленные оправки (с ручной затяжкой) и быстросменные сверлильные патроны.Быстросменные сверлильные патроны – это простой и быстрый вариант установки корончатых сверл. Им не нужно затягивать винты / губки вручную. Втулка или патроны имеют различные типы держателей шпинделя (машинный конус), такие как конус Морзе MT 2, MT 3 и MT 4. Патрон позволяет вставлять в него различные типы валов корончатого сверла (хвостовиков).
Работа сверлильного станка с магнитным основанием:
Магнитный сверлильный станок предназначен в первую очередь для пользователей в области строительства, производства и тяжелого машиностроения.Эти машины идеально подходят для использования как на строительной площадке, так и в мастерских. Магнитные сверлильные станки предназначены не только для корончатого сверления, но также идеально подходят для спирального сверления, развертывания, зенкования и нарезания резьбы (нарезания резьбы). Если вы не делаете глухие отверстия или отверстия диаметром менее 12 мм, корончатое сверление заслуживает серьезного внимания, особенно если ваше приложение не находится в контролируемых производственных условиях.
Существует широкий выбор переносных сверл с магнитным креплением для сверления на месте отверстий для ремонта или строительства в конструкционной стали.Эти более новые, легкие машины также можно использовать в производственных цехах. Магнитные сверлильные станки, настраиваемые как в горизонтальном, так и в вертикальном положениях, также доступны с пневматическим или гидравлическим приводом для работы в подводных / опасных зонах.
Механизм и работа магнитного сверлильного станка:
Магнитный сверлильный станок работает так же, как и обычный сверлильный станок
, но преимущество состоит в том, что магнитный сверлильный станок можно поднести к заготовке.Это преимущество делает магнитный сверлильный станок очень портативным и полезным. Механизм электродвигателя магнитного сверлильного станка такой же, как и у электродвигателя постоянного тока с контролем скорости и крутящего момента. Работа магнитного сверлильного станка очень проста и легка и может быть объяснена в следующих шагах,
- Держите магнитный сверлильный станок на обрабатываемой детали.
- Прикрепите необходимое корончатое сверло (кольцевую фрезу) вместе с выталкивающим штифтом к оправке в соответствии с диаметром и глубиной резания создаваемого отверстия.
- Установите магнитный сверлильный станок в том месте, где нужно проделать отверстие.
- Отрегулируйте, чтобы получить центр отверстия.
- Подключите магнитный сверлильный станок к источнику питания (230 В или 110 В в зависимости от модели).
- Отрегулируйте скорость машины в соответствии со скоростью резания.
- Включить магнитный выключатель
- Включите двигатель.
- Включить кран для смазки.
- Подайте нисходящую подачу на станок для сверления.Это создает отверстие в заготовке.
- Пропустите всю кольцевую фрезу через заготовку, затем сделайте обратную подачу и приведите двигатель в исходное положение.
- Металлический стержень упадет, сделав в пластине идеальное отверстие.
НАЖМИТЕ ЗДЕСЬ, чтобы просмотреть подробную статью о том, как использовать магнитный сверлильный станок? Профессиональное руководство по использованию магнитных сверлильных станков
Типы магнитных пресов для сверл:
Существует множество магнитных сверлильных станков, использующих широкий спектр режущих инструментов, таких как кольцевые фрезы (корончатые сверла), спиральные сверла, метчики (инструменты для нарезания резьбы), развертки и зенковки.Магнитные сверлильные станки – чрезвычайно универсальные станки, которые могут просверливать отверстие диаметром до 130 мм и нарезать резьбу M42 в стали. Самый мощный станок для корончатого сверления диаметром до 130 мм под названием MAB 1300 произведен нашей компанией. Это самый мощный в мире магнитный сверлильный станок, который теперь также доступен в варианте с автоматической подачей под названием MAB 1300V.
Существует несколько типов или моделей магнитных сверлильных станков в зависимости от их использования, приводов, размера, подачи, работы и т. Д.Вот некоторые из популярных типов.
Легкая магнитная дрель:
Легкие типы магнитных сверлильных станков очень популярны для выполнения нескольких операций, в которых вес переносимой машины является большой проблемой, например, работа с электрическим столбом, мобильной вышкой, телебашней, мостами и т. Д. Наша легкая модель магнитной дрели называется МАБ 100К.
Магнитная дрель с автоматической и полуавтоматической подачей:
Магнитные сверлильные станки с полностью или полуавтоматической подачей сверла очень популярны в наши дни.Эти машины помогают сэкономить время и энергию, что приводит к увеличению производства. Наши полностью автоматические сверлильные станки – это AutoMAB 350 и AutoMAB 450, а проверенные автоматические магнитные сверлильные станки – MAB 825V / MAB 845V и MAB 1300V.
Пневматическая магнитная дрель:
Пневматические станки для корончатого сверления особенно используются там, где существует опасность возгорания из-за электричества. Эта модель используется в более безопасных целях. Двигатель приводится в движение пневматической средой, а магнит представляет собой постоянный магнит вместо электромагнита.Наша модель одевматического магнитного сверлильного станка – AirMAB 5000.
Станки для корончатого сверления рельсов:
Специально изготовленные станки для корончатого сверления рельсов – лучший вариант для сверления отверстий в железнодорожных путях. Эти станки оснащены специальными зажимными приспособлениями вместо магнита для зажима на рельсе. Модели для сверления рельсов доступны с электрическим приводом как RailMAB 915 и с бензиновым приводом как RailMAB 965.
Горизонтальная магнитная дрель:
Горизонтальные магнитные сверлильные станки с угловыми зубчатыми колесами специально используются для большинства стесненных условий бурения.Наш горизонтальный компактный магнитный сверлильный станок называется MAB 155.
Магнитный сверлильно-фрезерный станок:
Инновационный сверлильно-фрезерный станок с магнитным основанием также называется переносным фрезерным станком. Этот станок может выполнять легкое фрезерование, сверление, зенковку и развёртывание. Эта машина оснащена крестообразным основанием стола. Модель переносного фрезерного станка – МАБ 825 КТС.
Применение магнитного сверлильного станка:
Переносные сверлильные станки или магнитные сверлильные станки используются во многих областях,
- Строительство моста
- Быстровозводимое здание (ПЭБ)
- Предприятия тяжелого машиностроения
- Обрабатывающие производства
- Промышленное производство
- Котельное производство
- Рельс сверлильный
- Производство вагонов
- Производство ветряных турбин
- Автомобильная промышленность
- Башенно-опорная конструкция
Преимущества магнитного сверлильного станка перед обычным спиральным сверлильным станком:
Приводя станок к заготовке!
Существует широкий выбор переносных сверл с магнитным креплением для сверления на месте отверстий для ремонта или строительства в конструкционной стали.Эти более новые, легкие машины также можно использовать в производственных цехах. Магнитный сверлильный станок, настраиваемый как в горизонтальном, так и в вертикальном положениях, также доступен с пневматическим или гидравлическим приводом для работы в подводных / опасных зонах.
Магнитный сверлильный станок в 2-4 раза быстрее, чем обычный сверлильный станок для спирального сверления. Из-за того, что спиральные сверла имеют одноточечную режущую геометрию, для проделывания отверстий требуется машина с большей мощностью – чаще всего это громоздкая настольная машина, которая традиционно имеет вертикальную конфигурацию и менее портативна.Чем больше отверстие, тем больше времени и мощности требуется для эвакуации материала. Но благодаря многоточечной режущей геометрии корончатых сверл (кольцевых фрез) корончатое бурение на магнитном сверлильном станке может резать с более высокими скоростями подачи при меньшем потреблении мощности, что означает, что они могут работать на меньших станках и сверлить в 2-4 раза быстрее.
Еще одно преимущество корончатых сверл становится очевидным после завершения работы – очистка и переработка. При спиралевидном сверлении много острой стружки смешивается со смазкой.Разделение этих двух компонентов в целях защиты окружающей среды и утилизации является трудным, трудоемким и дорогостоящим процессом. Лом от кольцевых фрез состоит из минимального количества лома и твердой заготовки. Отделить цельный кусок металла проще, к тому же он принесет больше прибыли при обратной продаже лома.
- Обработка отверстий в два-четыре раза быстрее
- Экономит время
- Экономит деньги, поскольку сверла служат дольше
- Меньше съем материала при сверлении
- Переносные машины
- Привод станка к заготовке
- Возможно бурение в горизонтальном, вертикальном, поперечном и боковом направлениях
- Меньше шума
- Экологичный
- Легко транспортировать
- Экономичный
- Прочный
- Незначительное обслуживание
Определение горизонтальной скважины
Что такое горизонтальная скважина?
Горизонтальная скважина – это метод направленного бурения, при котором нефтяная или газовая скважина вырывается под углом не менее восьмидесяти градусов к вертикальному стволу скважины.В последние годы этот метод становится все более распространенным и продуктивным. Операторы используют его для извлечения нефти и природного газа в ситуациях, когда форма коллектора является аномальной или труднодоступной.
Ключевые выводы
- Горизонтальная скважина – это метод наклонно-направленного бурения.
- Операторы используют его для извлечения нефти и природного газа в ситуациях, когда форма коллектора является аномальной или труднодоступной.
- Позволяет получить доступ к подземным резервуарам, которые могут быть недоступны непосредственно сверху.
Как работает горизонтальная скважина
Горизонтальные скважины стали играть более заметную роль в добыче ископаемого топлива в 2010-х годах. По мере развития технологий горизонтальное бурение снизило затраты и повысило эффективность добычи нефти и природного газа, особенно в США.
Возникновению горизонтальных скважин способствовали два компонента бурового аппарата:
- Забойный двигатель – это насосный механизм, который просверливает землю и приводится в действие за счет подачи бурового раствора, известного как буровой раствор.Изменения конфигурации забойного двигателя позволяют ему направлять долото в невертикальных направлениях.
- Устройство измерения во время бурения (MWD), которое позволяет в режиме реального времени анализировать геологические условия и обеспечивает цель для горизонтального бурения.
Кроме того, современные методы бурения позволяют использовать буровые коронки, которые могут изгибаться. Этот изгиб, достигаемый за счет использования гидравлических форсунок, позволяет инженерам до некоторой степени регулировать направление бурения.
Горизонтальное бурение стало более популярной техникой, поскольку компьютерные технологии стали более распространенными.Угол используемого бурового долота может быть отрегулирован компьютером с использованием сигналов глобального позиционирования (GPS) для точного определения местоположения долота относительно нефтяного или газового месторождения.
Сравнение горизонтального бурения и вертикального бурения
Горизонтальное бурение стало ценным методом в последние годы из-за определенных преимуществ по сравнению с традиционным вертикальным бурением. Это позволяет получить доступ к подземным резервуарам, которые могут быть недоступны непосредственно сверху. Горизонтальное бурение также позволяет одной буровой площадке или начальной точке исследовать более обширную подземную область.
Горизонтальное бурение также можно использовать для перекрытия или снятия давления с неконтролируемой скважины путем бурения соседней разгрузочной скважины. Наконец, помимо добычи нефти, горизонтальное бурение может быть полезно при строительстве подземных трубопроводов или инженерных коммуникаций, которые должны проходить под рекой или существующим зданием.
Сравнение горизонтального бурения и ГРП
Горизонтальные скважины оказались особенно полезными в качестве компонента процесса гидроразрыва пласта.Фрекинг помогает добывать природный газ и нефть из огромных сланцевых пластов в США. Эти месторождения обычно недоступны для традиционного вертикального бурения из-за непроницаемости сланцевых пластов.
Вместо этого нефтегазовые компании бурят сланец горизонтально и закачивают в сланец смесь воды, химикатов и гуаровой камеди, также известной как грязь. Сила этих нагнетаний разрушает породу, создавая отверстия, через которые протекают нефть и природный газ.
Правила техники безопасности для сверлильного станка| LSU Машиностроение и промышленное строительство
- Запустите сверло с частотой вращения, соответствующей диаметру сверла и материалу.Спросите у персонала магазина для правильных оборотов.
- Всегда держите работу в тисках или зажиме на столе для сверления.
- Используйте правильно отшлифованное сверло для просверливаемого материала. Персонал магазина может помогите выбрать правильный бит.
- Используйте смазочно-охлаждающую жидкость, подходящую для сверляемого материала.Спросите у сотрудников магазина о жидкость, подходящую для обрабатываемого материала.
- Удаляйте стружку щеткой, а не вручную.
- Снизьте давление при бурении, поскольку сверло начинает пробивать нижнюю часть материал.
- Не используйте тупое сверло или сверло с трещинами. Осмотрите сверло перед использованием.
- Не сверлите с слишком большим давлением.
- Всегда старайтесь поддерживать деталь на параллелях или на опорной плите при сверлении сквозного материала.
- Никогда не размещайте инструменты с коническим хвостовиком, такие как сверла большого диаметра или расширители с коническим хвостовиком. в сверлильном патроне. Можно зажимать только инструменты с прямым хвостовиком, такие как стандартные сверла. в патронах.
- Всегда очищайте хвостовик сверла и / или гильзу сверла, а также отверстие шпинделя перед установкой.
- Снимите инструменты с коническим хвостовиком со шпинделя или втулки с помощью сверлильной выколотки и молотка.
- Никогда не пытайтесь ослабить сверлильный патрон при включенном питании.
- Опустите сверлильный шпиндель вплотную к столу при освобождении сверлильного патрона или конуса. сверло с хвостовиком, чтобы уменьшить вероятность их повреждения при падении на стол.
- Никогда не чистите машину во время движения !!
- Если сверло застревает в отверстии, остановите станок и вручную поверните шпиндель назад. освободить бит.
- При сверлении глубоких отверстий чаще извлекайте сверло для удаления стружки и смазки. бит.
- Всегда вынимайте шпонку патрона сверла, иначе сверло со шпинделя вылетает сразу. после его использования.
- Во время сверления используйте защитные очки.
- Позвольте шпинделю самостоятельно остановиться после выключения питания.Никогда не пытайся остановиться шпиндель рукой.
- Оргстекло и другие хрупкие пластмассы трудно сверлить. Спросите у мастера за советом по выбору сверла и СОЖ при сверлении этих материалов.
Безопасность выходит за рамки набора информации и правил, которые необходимо запомнить. Безопасность – это культура. Вы живете этим, изучая это, и узнаете это, живя этим… чтобы вы и другие могли продолжай жить. БЕЗОПАСНОСТЬ очень важна!
Как сверлить угловые отверстия в древесине
Сверление отверстий под углом – полезный навык, который пригодится во многих домашних проектах. Один знакомый пример – это когда вы хотите прибить 2×4 под углом 90 градусов к другому 2×4, чтобы создать каркас для стены, но у вас не так много места, чтобы размахивать молотком. Ногтей на ногах – это ответ на такие узкие места. Если вам трудно завести гвоздь, вам очень поможет короткое угловое направляющее отверстие, направляя гвоздь под правильным углом и уменьшая необходимое количество ударов молотком.
Другой пример, распространенный в проектах по деревообработке, – это сверление отверстий в карманах , когда два куска дерева необходимо соединить под углом и где вы хотите, чтобы головки винтов были утоплены под поверхностью заготовки.
Но сверление отверстий под углом в древесине сопряжено со своими уникальными проблемами. Возможно, самая неприятная проблема – это когда сверло начинает правильно растачиваться, а затем быстро скользит по дереву и смещается. Вот почему вам необходимо принять особые меры – либо путем покупки инструмента, который сделает эту работу за вас, либо путем применения техники с вашим сверлом, которая повышает вероятность получения отверстия с идеальным углом.
Нажмите “Играть”, чтобы узнать, как сверлить отверстия под углом
3 Методы сверления угловых отверстий
Существует три распространенных метода сверления отверстий под углом, но два из них больше подходят для опытных деревообработчиков, которые могут позволить себе инструменты.
Сверлильный станок: Сверлильный станок – лучший способ просверлить отверстие под углом. Однако сверлильный станок – это дорогой, громоздкий автономный инструмент, который позволяет работать только с небольшими кусками материала.Сверлильные станки плохо подходят для многих проектов по благоустройству дома, потому что их нельзя выносить из магазина.
Шаблон для отверстий в кармане: Хорошей альтернативой сверлильному станку является шаблон для отверстий в карманах. Карманные приспособления для отверстий, такие как Kreg R3 Jr., являются дешевыми и простыми приспособлениями, которые направляют сверло в материал под углом. Если вам нужно просверлить больше, чем несколько отверстий, возможно, стоит приобрести такой кондуктор. Однако приспособления для карманных отверстий не надежны. Им по-прежнему требуется время для практики, прежде чем перейти к собственно рабочему материалу.А хороший приспособление для карманных отверстий – довольно дорогой аксессуар, особенно если вы не используете его регулярно.
Ручной метод: Ручной метод не требует специальных инструментов. Наряду с утонченностью и терпением вам понадобится только дрель и набор хороших сверл. Одна коронка будет иметь размер предполагаемого отверстия, а другая – примерно половину размера предполагаемого отверстия. Однако у этого метода есть некоторые ограничения:
- Вы не сможете просверлить отверстия под любым углом ручным способом.Угол наклона до 45 градусов позволяет легко просверлить отверстие под углом. Между 45 и 15 градусами процесс становится более трудным, но не невозможным. Ниже 15 градусов сверло будет слишком много двигаться. Когда стартовый бит слишком много танцует, вы не можете создать четко определенное стартовое отверстие, чтобы завершить остальную часть отверстия.
- Более мягкая древесина работает лучше, чем более твёрдая. Хвойные породы древесины, в которую входят сосна, болиголов и древесина большинства пиломатериалов для обрамления, лучше всего подходят для ручного сверления под углом.Твердые породы дерева, такие как клен, орех и дуб, трудно сверлить вручную под углом.