
Навигация:
- Метод вакуумной формовки и особенности применения
- Вакуумная формовка пластиков. Области применения
- Вакуумно-пленочная формовка. Особенности применения
Вакуумной формовкой изготавливают изделия из пластиков, которые можно встретить повсюду. Вакуумно-пленочной формовкой изготавливают литейные формы, и она известна только специалистам литейного производства. Вакуумной формовкой получают:
- Торговое оборудование и оснастку для магазинов
- Продукцию рекламного характера и различные сувениры
- Объемные буквы и другие средства наружной рекламы магазинов и заведений
- Формы и оснастку для изготовления строительных элементов, дорожного ограждения и дорожных знаков
- Объемные контейнеры и блоки для упаковки пищевых продуктов
- Элементы украшения в сфере автомобильного тюнинга
- Емкости для упаковки различных товаров
- Емкости для оснащения зооуголков для растений и животных
- Контейнеры для вакуумной упаковки товаров
- Детские игрушки, товары для детей
Метод вакуумной формовки и особенности применения
В вакуумной формовке используют атмосферное давление воздуха для получения изделия необходимой формы. Главная особенность метода — создание равномерного газостатического давления величиной в 1 атмосферу на всей поверхности заготовки. Отметим универсальность метода. Вакуум является рабочим инструментом, деформирующим изделие при вакуумной формовке. В технологии вакуумно-пленочного формования вакуума формирует поверхность литейной формы из песка для последующей заливки расплавленного металла. В этом случае вакуум выполняет вспомогательную функцию.
Вакуумная формовка пластиков. Области применения
Вакуумным формованием получают детали пространственной формы из листовых термопластов. Разогретая листовая заготовка копирует форму полости в твердой матрице. При этом не требуется пуансон, что упрощает процесс изготовления формы и снижает издержки при производстве изделий. Эту технологию преимущественно применяют для масштабного производства объемных изделий. Иногда экономически целесообразно изготовление единичных изделий сложной формы или больших размеров.
Технологический процесс изготовления изделий из пластика методом вакуумной формовки включает несколько этапов. На первом этапе листовую заготовку нагревают в специальной камере и доводят до вязко-пластичного состояния. Затем разогретый материал помещают на матрицу и прижимают по контуру специальным прижимом. На следующем этапе воздух откачивают из под заготовки и создают вакуум. Атмосферное давление плотно прижимает заготовку к поверхности матрицы до полного затвердевания. Для получения высокого качества изделия полость матрицы должна быть полированной и иметь плавные сопряжения различных поверхностей. На следующем этапе готовое изделие выталкивают из полости матрицы, создавая давление воздуха. Следует отметить, что вместо отсоса воздуха иногда создают избыточное давление для заполнения пластиком полости матрицы. Такой технологический процесс называют пневматическим формованием.
Станок для вакуумной формовки пластика. Описание конструкции и технических характеристик некоторых моделей
Станки для вакуумной формовки просты по конструкции. Их разрабатывают и производят как специализированные фирмы, например, «ATSNGroup» «Flexplast», «Фолипласт», так и различные частные предприятия. В сети интернет-магазинов можно приобрести готовое оборудование и оснастку, а также заказать станок по спецзаказу.
Станок для формовки пластиков представляет собой бак определенных размеров. В комплекс входят рабочие органы и агрегат для создания вакуума, органы управления и энергообеспечения.
Размеры станков определяются габаритами получаемого изделия из листового термопласта. Компания «ATSNGroup» выпускает линейку станков с возможностью изготовления изделий в диапазоне от 400 х 400 до 5000 х 5000. Базовые модели ориентированы на размеры 600 х 600, 1000 х 100 и 2400 х 1400 мм с возможностью быстрой переналадки в сторону уменьшения размеров при необходимости выпуска соответствующей продукции. Станки оборудованы кварцевыми нагревателями мощностью 8; 19,5; 55 кВт и насосами производительностью 200, 750, 1000 литров/мин., соответственно типоразмерам моделей. Эти устройства обеспечивают быстрый нагрев заготовки и создание вакуума. Предусмотрена возможность локального разогрева. Станок с размерами стола 2400 х 1400 мм оборудован системой для предварительного выдува листа заготовки с последующим формованием готового изделия с требуемой точностью. Это позволяет существенно повысить производительность работы оборудования при изготовлении изделий больших размеров. Установки позволяют получать изделия из ПВХ, полистирола, полипропилена, полиэтилена и т.п.
Формы для вакуумной формовки. Материалы и особенности изготовления
Формы изготавливают из алюминия, эпоксидной смолы, МДФ, стеклопластика. На выбор материала влияют: масштабность производства, размеры изделия, температурный режим подготовки заготовки к процессу формования.
Формы из алюминиевых сплавов изготавливают литьем, а затем добиваются требуемой точности и качества с помощью фрезерования, шлифования и полирования. Формы из эпоксидной смолы получают путем заливки компаунда в мастер-форму, изготовленную по методу обратного копирования. Формы из МДФ и стеклопластика изготавливают горячим или теплым прессованием. В связи с различием физико-механических и химических свойств материалов, формы имеют различные эксплуатационные показатели. Главные из них: жесткость, химическая стойкость, долговечность и ремонтопригодность.
Вакуумно-пленочная формовка. Особенности применения
Технология вакуумно-пленочной формовки или V – процесс, относится к сфере литейного производства и имеет мало общего с вакуумной формовкой, применяемой в производстве изделий из листового пластика. Объединяет эти два направления только использование вакуума для создания атмосферного давления. При вакуумной формовке, вакуум является рабочим инструментом, обеспечивающим основной технологический процесс изготовления детали, т.е. воздействует непосредственно на поверхность изделия. В технологии вакуумно-пленочного формования вакуум воздействует на поверхность песка, подготавливая литейную форму к заливке расплавленным металлом. В этом случае вакуум исполняет вспомогательную роль в производстве отливки, т.е. непосредственно на поверхность изделия – отливки не действует.
В технологии вакуумно-пленочной формовки (ВПФ) используется тонкая синтетическая пленка и тонкодисперсный кварцевый песок без примеси глины. Поверхность литейной формы накрывают пленкой, разогревают и откачивают воздух через микроскопические отверстия в подмодельной плите. Затем заполняют опоку кварцевым песком и накрывают следующим слоем пленки. Откачивая воздух из промежутка между слоями пленки, создают твердый песчаный каркас, повторяющий форму модели. Откачка воздуха и поддержание вакуума продолжается в процессе заливки металла в форму вплоть до затвердевания готового изделия. В процессе заливки металла пленка газифицируется и газ проникает в песок, выполняя роль связующего.
Технология ВПФ создана в Японии и уже более 50 лет применяется в СССР и в странах постсоветского пространства, в том числе, в России для получения сложных отливок для различных сфер применения. Благодаря этой технологии удается значительно повысить точность и качество отливок и отказаться в ряде случаев от механической обработки. V — процесс пока не получил широкого распространения в нашей стране.
Преимущества технологии вакуумной формовки:
- Снижение издержек производства благодаря упрощению технологии изготовления литейных форм
- Увеличение ресурса работы всех элементов технологической оснастки
- Повышение точности и качества отливок
- Устранение операции обрубки и очистки поверхности отливок
- Повышение уровня экологической безопасности при проведении литейных операций
- Недостатки технологии:
- Необходимость поддержания вакуума в течение всего процесса изготовления отливки
- Усложнение оснастки и технологии ее изготовления
- Необходимость точного поддержания температуры пленки во избежание ее разрыва и образования брака литья
Вакуумной формовкой называется процесс производства серийных или единичных изделий из листовых полимерных материалов путем придания им формы матрицы под воздействием температуры и вакуума. В процессе производства изделия лист пластика нагревается до температуры размягчения и плотно облегает поверхность матрицы за счет создания отрицательного давления.
В серийном промышленном производстве для вакуумного формования изделий применяется современное высокотехнологичное оборудование, осуществляющее процессы разогрева сырья и откачки воздуха в режиме постоянно действующего конвейера.
В качестве сырьевых заготовок могут использоваться практически все полимеры, обладающие свойствами термопластов (полипропилен, полиэтилен, поливинилхлорид, поликарбонат и другие).
Методом вакуумной формовки выпускаются пластиковые изделия для всех направлений и сфер деятельности, в том числе:
- для авиационной, автомобильной и судостроительной отраслей промышленности;
- для производства упаковочной тары и емкостей всех видов;
- для нужд пищевого производства, химической промышленности, медицины;
- для производства бытовой техники, приборов и оборудования;
- для нужд строительства и дизайна.
Технология производства
Широкие возможности для применения автоматизированных производственных процессов позволяют наладить непрерывный цикл изготовления продукции самого различного назначения. Немаловажную роль играет и то, что для формовки используются готовые листовые материалы, не требующие глубокой переработки сырья.
Стандартный метод вакуумной формовки состоит из нескольких этапов, включающих в себя:
- фиксацию заготовки на матрице;
- нагрев полимерного листа;
- предварительное растяжение листа;
- откачку воздуха из матрицы и вдавливание заготовки;
- охлаждение материала;
- извлечение изделия из матрицы;
- окончательную доработку изделия.
Для того чтобы понять, что представляет собой вакуумная формовка пластика, необходимо подробно рассмотреть все стадии производственного процесса.
Фиксация заготовки
Листы полимера крепятся к матрице при помощи зажимной рамы. Фиксирующие элементы должны обеспечивать прижимное усилие, достаточное для удержания листов толщиною до 6 мм. При автоматизированной подаче заготовок на формовку работа подвижных элементов прижимной рамы должна исключать возможность повреждения готового изделия.
Нагрев заготовки
Главной особенностью этого этапа работ является обеспечение равномерного прогрева всего объема заготовки, так как в противном случае плотного прилегания материала к форме матрицы добиться не удастся. В технологии вакуумной формовки для нагрева заготовок применяются, как правило, инфракрасные излучатели и кварцевые лампы.
Общая площадь поверхности заготовки делится на несколько зон, каждая из которых нагревается отдельным элементом, а температура нагрева контролируется при помощи специальных пирометров. Данные о температуре обрабатываются компьютерной системой для своевременной корректировки разницы нагрева различных участков заготовки.
До окончания процесса нагрева лист полимера должен сохранять свое первоначальное положение. Провисание пластика фиксируется фотоэлектрическим сканером, после чего система дает команду, и в аппарат подается воздух для корректировки формы заготовки. Благодаря этому исключается возможность разрыва материала.
Предварительное растяжение листа
В некоторых случаях в процесс производства включают предварительное растяжение материала, называемое также раздувом. Растяжение выполняется после достижения пластиком рабочей температуры формовки и служит для выравнивания толщины заготовки. Процесс раздува необходим при формовании заготовок на глубоких матрицах со сложной геометрией поверхности.
Откачка воздуха и вдавливание заготовки
После предварительного нагрева и растяжения закрепленной заготовки из аппарата для формовки производится откачка воздуха вакуумным насосом. При снижении давления внутри аппарата полимерный материал, достигший состояния пластичности, начинает облегать форму матрицы.
В зависимости от требований, предъявляемых к конечному продукту, технология вакуумной формовки, может совмещаться с технологией штампования при помощи пуансона. В этом случае помимо откачки воздуха на заготовку сверху воздействует специальная конструкция, профиль которой повторяет поверхность матрицы.
Комбинацией этих методов можно добиться максимальной точности заданных форм деталей, а также обеспечить равномерное распределение полимерного материала по поверхности матрицы, полностью исключив образование складок и участков с различной толщиной.
Охлаждение изделия и извлечение из матрицы
Во избежание повреждения детали при извлечении из матрицы необходимо дождаться полного остывания материала. Если применяемое для процесса вакуумная формовка пластика оборудование оснащено системами воздушного охлаждения, время остывания изделий может быть сокращено на 20-30%.
Для изготовления наиболее ответственных деталей вакуумные матрицы оснащаются системами управления температурными процессами.
Наличие таких систем позволяет добиваться равномерного охлаждения изделия, что способствует повышению его эксплуатационных качеств. Извлечение остывшей детали из матрицы происходит под воздействием создаваемого внутри давления.
Окончательная обработка
Изделие, извлеченное из матрицы необходимо отделить по контуру от излишков полимерного материала. Сформованная деталь может являться полуфабрикатом для дальнейшего сборочного производства. Для этого изделие может разрезаться, в нем могут высверливаться отверстия для крепежных элементов и делаться пропилы для вставок.
Для окончательной обработки материала могут использоваться:
- механический обрезной пресс;
- ленточная пила вертикального или горизонтального типа;
- станок строгально-шлифовальный;
- фрезерный станок;
- сверлильный станок;
- ручной механический и электроинструмент.
Вакуумная формовка широко применяется в легкой и пищевой промышленности, а также в других отраслях деятельности с целью изготовления деталей объемных и сложных форм. Сама технология предполагает использование специальных станков, в которые устанавливают матрицы, а также заготовки из листового пластика, полиэтилена, ПВХ и других эластомеров. Лист термопластичного материала прогревается до нужной температуры, что придает ему эластичность, после чего сводится с матрицей, а из полости между ними откачивается воздух.
К чему такие сложности? На самом деле это значительно повышает качество изделий и упрощает процесс их изготовления. В отличие от термопластавтоматов, станки вакуумной формовки стоят значительно дешевле и не требуют сложного обслуживания. При этом они позволяют серийно штамповать сотни одинаковых изделий, что очень важно в массовом производстве.
Отрасли применения технологии вакуумной формовки
Итак, вот главные отрасли, в которых применяется метод вакуумного формования:
- Пищевая промышленность – изготовление тары и емкостей для хранения, складирования, ложементы;
- Машиностроение – изготовление различных пластиковых элементов кузова, салона, подкапотного пространства. Методом горячей вакуумной формовки производят кожухи, корпуса воздушных фильтров, различные элементы приборных панелей;
- Медицинская отрасль — пеленальные столики, ванночки, тележки для хранения и перевозки медикаментов и оборудования, раковины нестандартной формы, элементы мебели и многое другое;
- Приборостроение — корпуса приборов, декоративные элементы;
- Производство оборудования и готовой продукции — корпуса и элементы различных станков и готовых изделий;
- Изготовление сложного архитектурного декора и промежуточных форм для отливки гипса, бетона, металла;
- Производство рекламных конструкций.
Практически все изделия из пластика с толщиной до 10 мм изготавливаются методом горячей вакуумной формовки. Как это происходит?
Особенности процесса вакуумного формования
Чтобы получить готовую деталь, на станке с ЧПУ изготавливается рельефная 3D форма – матрица, которая предварительно разрабатывается дизайнером и проектировщиком. После ручной доводки ее устанавливают в станок для формования, в его рамке фиксируют заготовку – лист термопластичного материала, и прогревают ее. Когда она достигает оптимальной эластичности, ее сводят с матрицей, откачивая воздух из пространства между ними. В результате мягкий пластик покрывает всю поверхность матрицы, повторяя каждый изгиб даже самой сложной формы.
Затем происходит охлаждение изделия, отделение от матрицы, и на весь этот цикл уходит от 30 секунд до 15 минут. Затем все повторяется, а в промышленных условиях многие конвейерные линии работают в непрерывном режиме. Метод отличается экономической целесообразностью, что выгодным образом сказывается на стоимости готовой продукции для конечного потребителя.
Есть ли ограничения?
Метод горячей вакуумной формовки позволяет изготавливать детали любых форм. Существует также ограничение по толщине заготовки – в большинстве случаев она составляет максимально 10мм. В остальном все зависит только от таланта дизайнера и возможностей станка с ЧПУ, на котором будет изготавливаться форма. Именно такие неограниченные возможности стали причиной широкого распространения технологии вакуумной формовки пластика по всему миру.


Во время процесса формовки пластмассовый лист-заготовка нагревается до размягчённого состояния, а затем втягивается в матрицу. Благодаря вакууму лист принимает форму матрицы, и после остывания вынимается из неё.
На передовом производстве используется сложное пневматическое, гидравлическое и тепловое оборудование для вакуумной формовки, что позволяет получить более высокую скорость производства и более точное формование.
Практически все термопласты могут выпускаться в листовой форме и, следовательно, подвергаться процессу формования. Наиболее часто используемые материалы для вакуумной формовки:
В качестве примеров изделий вакуумной формовки можно назвать:
- ванны и поддоны для душа;
- стаканчики для йогурта;
- боксы для перевозки лыж;
- корпусы лодок;
- предохранители для оборудования;
- автомобильные внутренние панели;
- внутренние панели для холодильников;
- коробки для сэндвичей;
- детали для кабин транспортных средств;
- наружные вывески.
Особенности технологии
Метод вакуумной формовки имеет ряд преимуществ перед другими технологиями. Изделия изготавливаются под низким давлением, что позволяет использовать сравнительно недорогое оборудование.
Поскольку процесс производства происходит под низким давлением, пресс-формы для вакуумной формовки могут быть изготовлены из недорогих материалов, и время их изготовления может быть достаточно коротким. Благодаря этому экономичным становится и производство прототипов крупных или средних изделий, выпускаемых в ограниченном количестве.
Более сложные машины и пресс-формы используются для непрерывного автоматизированного производства большого количества предметов – например, стаканчиков для йогурта, одноразовой посуды и упаковок для сэндвичей.
В отличие от других технологий создания термопластов, где используются порошок или смола, вакуумная термоформовка подразумевает использование готовых пластиковых листов. Иногда после процесса формования требуется срезать излишки материала с торцов изделия, которые затем могут быть измельчены, переработаны и использованы повторно.
Видео: “Вакуумная формовка пластика”
Видео: “Технология вакуумной формовки АБС-пластика”
Процесс вакуумного формования пластика
Стандартно технология вакуумного формования пластика включает в себя следующие этапы: фиксацию, нагрев, предварительный раздув, откачку воздуха, вдавливание, охлаждение, извлечение и обработку.
Фиксация
Зажимная рама должна быть достаточно мощной, чтобы обеспечить надёжное закрепление заготовки в процессе формования. Зажим должен справляться с толстым материалом – до 6 мм для станков с одним нагревательным элементом и до 10 мм для оборудования с двойным нагревателем. В автоматизированном процессе работа движущихся частей должна быть защищена, чтобы избежать случайного повреждения изделия.
Нагрев
Нагреватели – это, как правило, инфракрасные элементы с отражающей пластиной из алюминия. Чтобы в процессе формовки получить наилучший результат – вне зависимости от того, какой материал используется, – лист нужно прогревать равномерно по всей поверхности и по всей его толщине. Для этого необходимо разделить площадь нагрева на несколько зон, которые бы контролировались при помощи регуляторов мощности. Керамические нагревательные элементы с этой точки зрения имеют некоторый недостаток – из-за своей высокой теплоемкости они медленно нагреваются (около 15 минут) и медленно реагируют на корректировку мощности.
Сейчас имеются более сложные – кварцевые – нагреватели, которые имеют меньшую теплоемкость и быстрее реагируют на изменение мощности. Пирометры позволяют точнее контролировать температуру нагрева, измеряя температуру плавления листа и взаимодействуя с системой контроля рабочего процесса. Точный контроль температуры также возможен с управляемой компьютером системой, работающей одновременно с пирометром(-ами). При формировке толстых листов рекомендуется использовать двойные нагреватели, так как они обеспечивают более равномерное проникновение тепла и сокращение времени цикла.
При формировке высокотемпературных материалов с критической температурой формования советуют использовать двойные кварцевые нагреватели. С пристальным контролем за интенсивностью теплового излучения можно полностью компенсировать теплопотери по краям, вызванные конвекционными воздушными потоками и поглощением областями, закреплёнными в зажимной раме.
Можно добиться также значительной экономии, если будут использоваться специальные кварцевые нагреватели: когда в процессе формования нагревательные элементы находятся с обратной стороны, можно регулировать падение мощности.
Контроль положения листа
На устройство обычно устанавливается фотоэлектрический датчик для сканирования пространства между нижним нагревателем и листом пластика. Если в процессе нагревания лист провисает и разрывает луч, в камеру вводится небольшое количество воздуха, поднимающего лист и останавливающего провисание.
Предварительный раздув листа (пузырь)
После того, как пластик достиг своей температуры формования или «пластичного» состояния, он может быть предварительно растянут – с тем, чтобы обеспечить будущему изделию равномерную толщину стенки. Предварительный раздув листового пластика для вакуумной формовки – полезная функция при глубокой вытяжке деталей с минимальным углом уклона и высокой поверхностью пресс-формы. Способ управления высотой «пузыря» должен быть таким, чтобы можно было получить постоянный результат.
Откачка воздуха
Как только материал предварительно растянут соответствующим образом, можно придавать листу форму при помощи вакуума. В больших станках резервуар используется в сочетании с мощным вакуумным насосом для формовки. Это позволяет создать двухступенчатую откачку воздуха, которая ускоряет формование нагретого листа.
Вдавливание
Эта часть процесса подразумевает использование пуансона – подвижной части пресс-формы, приводимой в движение пневматическим или гидравлическим цилиндром и расположенной над матрицей. Он используется для того, чтобы вдавливать материал в углубления в зоне формования. В сложном процессе глубокой вытяжки это позволяет производить изделия без складок и равномерно распределять толщину.
Идея заключается в том, чтобы до откачки воздуха подать столько материала, сколько необходимо для того, чтобы избежать истончения изделия. Пуансон, как правило, изготовлен из дерева или металла, его гладкая поверхность позволяет листу скользить во время растягивания.
Кожаная прокладка или прокладка из войлока гарантирует значительное снижение риска преждевременного охлаждения при контакте. Резиновый пуансон – хорошая альтернатива: будучи изолятором, резина не влияет на температуру листа.
Вдавливание – важный этап при формовании нескольких изделий из одного листа, поскольку пуансоны можно поместить рядом, не опасаясь возникновения складок между изделиями.
Охлаждение и извлечение
Прежде чем изделие можно будет извлечь после формовки, оно должно остыть. Если сделать это слишком рано, то можно деформировать изделие и получить брак. Для ускорения процесса остывания на оборудование для формовки устанавливаются вентиляторы системы охлаждения, которые включаются лишь после того, как изделие сформовано. Если в вентиляторы вмонтированы туманообразующие форсунки, на лист направляется мелкодисперсный туман. В общей сложности это может ускорить цикл охлаждения на 30%.
Также существуют блоки управления температурой пресс-формы, которые, регулируя температуру внутри неё, обеспечивают правильное равномерное охлаждение кристаллических и кристаллизующихся полимеров, таких как полипропилен, полиэтилен высокой плотности и полиэтилентерефталат.
После охлаждения изделие отсоединяется от пресс-формы под создаваемым системой давлением. Затем его вынимают и отправляют на обрезку.
Обрезка и отделка
После того как сформованное изделие остудили и извлекли из матрицы для вукуумной формовки, удаляются излишки материала. Затем в нём сверлят необходимые отверстия, щели и делают прорези. Также постобработка включает в себя отделку, печать, укрепление и сборку.
Для того чтобы отделить изделие от листа, используются различные способы обрезки. Выбор оборудования в значительной степени зависит от типа разреза, размера самого изделия, коэффициента вытяжки, толщины материала и объёмов производства. Также это факторы, которые следует учитывать при определении инвестиционной стоимости необходимого оборудования.
Тонкие части детали, как правило, обрезаются на механическом обрезном прессе, который ещё называют роллер-прессом. Тяжёлые изделия извлекаются из пресс-формы, помещаются в зажимы и обрабатываются при помощи специального оборудования: горизонтальной или вертикальной ленточной пилы, ручного строгально-шлифовального станка либо 3-х, 4-х или 5-ти осевого фрезерного станка.
Современная методика получения объемных 3D форм из листовых пластиков путем обработки материалов воздействием высоких температур в вакуумной среде. В ее основе лежит изменение физических свойств пластиков под воздействием нагрева.
Формование пластика (листовых материалов) на нашем производстве осуществляется на оборудовании термовакуумного формования со следующими рабочими полями:
Размеры рабочих полей оборудования термовакуумного формования листовых материалов, в миллиметрах | ||||
2000х3000 |
|
|
|
|
2000х2000 |
|
|
|
|
2000х1500 | 1500х1500 |
|
|
|
2000х1000 | 1500х1000 | 1000х1000 | 700х1000 |
|
|
|
1000х500 | 700х500 | 500х500 |
Глубина протяжки изделий до 750мм |
Технология активно применяется в различных сферах нашей жизни (автомобильная отрасль, промышленность, торговое оборудование и POS-продукция, выставочные стенды, наружная и интерьерная реклама, упаковка, макетирование), позволяя создавать объекты любых размеров с тиражированием от одной до десятков тысяч единиц.
Виды вакуумной формовки пластиков
- негативная – материал втягивается в прессформу,
- позитивная – материал натягивается на прессформу.
Процесс вакуумной формовки пластика
Этапы проведения термоформовки пластиков
- изготовление и подготовка матрицы (пресс-формы),
- устройство матрицы на подвижной платформе оборудования,
- установка листового пластика над пресс-формой,
- прогрев матриц и материалов до заданной температуры,
- подъем платформы к листу пластика,
- вакуумная формовка пластика – натяжение материала на матрицу под действием вакуума,
- охлаждение готового изделия.
- аппликация самоклеящейся пленкой по готовому изделия (уместна при малом тираже продукции),
- предварительная шелкография (чаще применяется при крупных тиражах).
У нас вы можете заказать изготовление продукции любой сложности. Используемое РПК «Телец» оборудование позволяет формовать пластиковые изделия любых размеров – от минимально возможных до объектов с габаритами 2000х3000мм, с глубиной протяжки до 750мм.
Наше оборудование
В 2014 году нашей компанией введено в эксплуатацию новейшее вакуумное термоформовочное оборудование и производится формовка листовых материалов толщиной от 1 до 10мм (ПММА (оргстекло / акриловое стекло), АБС, ПС (полистиролы), ПЭТ, ПВХ, ПВД, ПНД, САН, поликарбонат монолитный, декоративные пластики и покрытия, двухслойные пластики для гравировки, зеркальные пластики и с нанесением пленок 3М, другие).
Наше преимущество — уникальное оборудование, позволяющее формовать изделия от самых малых до огромных размеров (2000х3000мм) с глубиной протяжки до 800мм!
Наша стратегия – четкое выполнение как серийных, так и единичных заказов. Работаем с прессформами клиента, а также оперативно производим матрицы самостоятельно.
Цены на данные виды работ очень индивидуальны и могут быть просчитаны только после получения исходных данных (тираж, вид и толщина материала, наличие матрицы, необходимость постобработки, обрезки).
Станок ВФМ-2
![]() |
|
Параметры: |
|
|
Поле по оси X: | 2000мм | |
|
Поле по оси Y: | 3000мм | |
|
Высота по оси Z: | 800мм | |
|
Прогрев | односторонний |
Формы для формовки
Также, при сотрудничестве с нами вы можете предоставить как собственные формы для формовки, так и воспользоваться услугами нашей компании. Мы осуществляем:- разработку дизайна и изготовление пресс-форм,
- изготовление матриц по эскизам заказчика,
- доработку представленных матриц.
Изготовление и подготовка пресс-формы является самым трудоемким и затратным этапом термоформовки. В качестве основы для нее применяется МДФ, разновидности смол, алюминий. С учетом дизайна матрицы ее поверхность тщательно обрабатывается и подготавливается к дальнейшей работе.
Наиболее популярным методом изготовления матриц является 3D фрезерование на станке с ЧПУ, заказать которое вы можете в нашей компании.
Пожалуйста, заполните поля и мы вам перезвоним
Спасибо, за обращение в нашу компанию. В ближайшее время с вами свяжется менеджер

Формовка ABS пластика
Формовка ABS пластика
Формовка ABS пластика


Я понимаю, что не я первый и не я последний создаю свой вакуумно-формовочный станок, но все же хочу поделиться с вами статьей о нем.
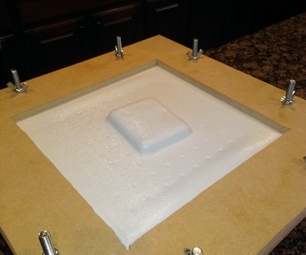
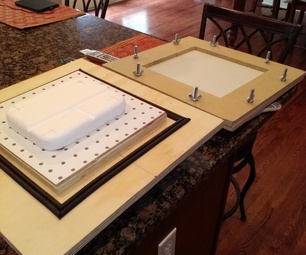
Конструкция для вакуумной формовки своими руками стандартная: деревянная рамка для фиксации материала, которому придается форма, и деревянный ящик с отверстиями в крышке сверху в качестве вакуумной камеры. Самый недорогой в исполнении вариант.
Шаг 1: Чертеж и материалы
Я хотел собрать простой и недорогой формовщик. Заранее зная, что листы материала для форм имеют размеры 30,5х30,5 см, при создании своей конструкции термовакуумной формовки пластика я отталкивался от этих размеров.
Дизайн вакуумного формовщика
Деревянное основание с отверстием для шланга обычного домашнего пылесоса. Деревянная рамка 28х28 см будет приклеена на это основание, затем швы нужно будет заполнить герметиком. На эту рамка сверху приклеиваем квадратную панель из перфорированного ДВП. Материал для формования зажимается между двумя одинаковыми рамками из ДВП с помощью болтов. По периметру рамка герметизируется резиновой клейкой лентой. Формовщик с зажатым в рамке материалом помещается в духовку, где пластик нагревается и размягчается.
Материалы:
- рейка 2,5х5 см 2,4 м
- белая перфориванная ДВП
- крылатые гайки 9,5 мм – 16 шт
- шестигранные болты 9,5ммХ2 – 12,7 мм (Х8)
- поролоновая уплотнительная лента
- лист ДВП 60х120 см толщиной 1,27 см
Инструменты:
Торцовочная пила, болгарка и дрель. Обязательно — столярный клей, по желанию – герметик (лучше с ним). Отверстие в рамке мне показалось удобно вырезать гравером, но тут как вам удобнее. Для проверки прямых углов используйте угольник.
Шаг 2: Выпиливаем деревянные детали
Вам нужно сделать детали следующих размеров:
- деревянную рейку 2,5х5 см разрежьте торцовочной пилой на 4 части, срезы под углом 45°, длинная сторона 28 см.
- из перфорированной ДВП вырежьте квадратную панель 28х28 см.
- из листа ДВП вырежьте 3 квадрата 45,7х45,7 см. Один будет основанием, из двух других сделаем рамки.
Ориентируйтесь на пояснения на фотографиях при работе.
Шаг 3: Собираем камеру
Собирать вакуумную камеру достаточно просто. Самым сложным здесь будет совмещение центров основания и рамки из реек. Можно отметить центр основания мелом или маркером, чтобы было легче устанавливать рамку и делать отверстие для шланга пылесоса.
Отметив границы, приклеиваем четыре рейки на место, пока клей сохнет сверлим отверстие для шланга (я решил вставить в отверстие кусок ПВХ-трубы). Отверстие можно прорезать кольцевой насадкой для дрели такого же диаметра, что и шланг. Заполните щели между куском трубы и основанием герметиком.
Пока герметик сохнет, нанесите столярный клей сверху по всему периметру рамки. Это поможет убрать ненужные воздушные зазоры, так как наносить герметик под перфорированной панелью будет очень трудно. Приклейте сверху перфорированную панель.
Шаг 4: Вырезаем две рамки
Возьмите два оставшихся квадрата из ДВП 45,7х45,7 см и вырежьте квадрат из середины, чтобы получились две рамки. Размер вырезаемой части примерно 28х28 см, но возможно чуть больше, так, чтобы рамка подходила к реечной на основании. Когда обе будут готовы, сложите их вместе и просверлите отверстия по периметру. Отверстия сверлите на расстоянии 2,5 см от внешнего края рамок и на расстоянии 12,5 см от внешнего края угла, ориентируйтесь на приложенный чертеж.
Шаг 5: Окончание сборки
Для простоты использования я сделал несколько усовершенствований простейшей конструкции вакуумного формовщика.
Во-первых, я вставил в отверстие ПВХ-колено, хотя можно просто вставлять в отверстие шланг пылесоса. Затем в это колено припаян кусок ПВХ-трубы, выходящий за пределы камеры, чтобы можно было легко подсоединить шланг пылесоса.
Во-вторых, я сделал стойки, чтобы приподнять камеру и трубу под ней. Стойки я просто приклеил к основанию.
И в-третьих, я наклеил уплотнитель по периметру реечной для дополнительной герметизации.
Шаг 6: Использование вакуумного формовщика
На фото показано изготовление в вакуум-формовочном станке пластикового корпуса для другого моего проекта. АБС-пластик я заказывал в интернет-магазине.
Зажмите лист пластика между двух ДВП-рамок. Проще всего расслабить все гайки и убрать два болта с одной стороны, и вставить в зазор лист пластика. Затяните все гайки. Поставьте вакуумную камеру поблизости от духовки и подсоедините пылесос. Поставьте форму для молдинга на перфорированную панель. Установите рамки с зажатым пластиковым листом в заранее разогретую духовку.
При разогреве духовки до температуры размягчения пластика и использовании материалов, не выделяющих ядовитые вещества в процессе нагревания, процесс формовки безопасен.
Я использовал АБС-пластик с температурой размягчения 162-176°С, температура духовки была 170°С. Через несколько минут (в зависимости от толщины пластика) вы увидите, как он провисает в рамке, это значит, что пластик готов к формовке. Включите пылесос и быстро достаньте форму с пластиком из духовки, сразу положив их на основание вакуумной камеры. Обязательно используйте прихватки, чтобы не обжечься. Пластик обтянет молдинг, дайте ему несколько минут30 секунд, чтобы застыть, и выключите пылесос.
Если пластиковая форма получилась не очень хорошо, возможно пластик был недостаточно нагрет, ил форма для молдинга была слишком высокой. Я получил нормальный результат после пары попыток. Советую почитать статьи в интернете об особенностях вакуумного формования, чтобы иметь представление об особенностях процесса.
Что такое вакуумное формование? | Formech
Термоформование – один из старейших методов обработки пластмасс. Вакуум-формованные изделия повсюду вокруг нас и играют важную роль в нашей повседневной жизни. Процесс включает в себя нагрев пластикового листа до мягкости и затем наложение его на форму. Вакуум применяется, всасывая лист в форму. Затем лист извлекается из формы.
1- Является ли вакуумное формование все еще важным процессом / технологией?
Вакуумная формовка берет свое начало с 1930-х годов, и все же она остается все более актуальной сегодня.
Ни один альтернативный процесс не может сравниться с низкой стоимостью, простотой инструментов, эффективностью и скоростью репликации для создания прототипов и небольших серий определенных форм. Одним из основных преимуществ вакуумного формования является скорость, с которой можно производить оснастку, а стоимость по сравнению с литьем под давлением значительно дешевле.
Сочетание вакуумного формования с новыми технологиями, такими как 3D-печать для дизайна инструмента, технология термоформования чернил и In-Mould Decoration, открывают новые возможности и преимущества для крупнейших мировых брендов и учреждений.Formech сотрудничает с Dupont, BASF, Кембриджским университетом и многими другими международными технологическими центрами для проведения исследований новых передовых композитных материалов, которые откроют новые возможности для вакуумного формования для высокотехнологичных отраслей. Ведущие мировые компании в области материаловедения продолжают вкладывать средства в разработку термоформованных пластиков, которые более эффективны в обработке и наносят вред окружающей среде. Инженерный сорт и композитные пластики, как правило, гораздо более требовательны к успешному формированию или требуют промышленного оборудования.В настоящее время Formech предлагает ряд высокопроизводительных и компактных машин, обеспечивающих возможности промышленной обработки в лабораторных условиях для эффективного тестирования и исследования новых материалов.
2- Вакуумная формовка, 3D-печать и литье под давлением
У каждого процесса есть веская причина, и обычно каждый процесс занимает свое собственное пространство в пределах всего производственного спектра. Вакуумная формовка является действительной альтернативой 3D-печати и литью под давлением, если смотреть на общую картину, принимая во внимание время и стоимость оснастки, сложность требуемой детали, отделку, количество и время доставки.Когда вы рассмотрите все эти важные аспекты, станет ясно, что вакуумная формовка, 3D-печать и литье под давлением играют свою роль.
Для одноразовых прототипов сложных форм 3D-печать дает определенные преимущества по сравнению с вакуумным формованием и большинством других процессов благодаря возможности создания законченного готового компонента без ограничений дизайна и требований к обрезке.
В Formech мы применяем 3D-печать как дополнительный процесс к вакуумному формованию для большинства задач дизайна.3D-печать дает новые возможности для творчества и универсальности в дизайне инструмента с экономичной и простой репликацией при использовании в сочетании с вакуумной формовкой. Большинство ведущих мировых дизайнерских лабораторий используют обе технологии вплотную.
3- Применение для вакуумной формовки
Не каждая конструкция или форма подходит для вакуумного формования, но она остается наиболее экономически эффективным и эффективным способом обработки самых разнообразных областей применения пластмасс.Вакуумно-формовочные машины Formech используются такими известными клиентами, как Apple, Google, Disney, Большой балет, Ford, Tesla, Ferrero Rocher, Nestle, Makita, Royal Air Force, Philips, Йельский университет, Dupont и многими другими в электронике, кино и кино. театр, автомобилестроение, авиакосмическая промышленность, кондитерские изделия, упаковка, образование и многое другое. Постоянно растущая популярность вакуумного формования среди этих ведущих компаний и учреждений демонстрирует, что этот процесс остается выбором номер один для самых разных областей применения.
4- Этическое использование пластмасс
Использование пластмасс в дизайне продукции, упаковке и в больших объемах остается чувствительной темой и часто вызывает споры. Любой выбор материала – от бумаги до пластика, металла, нетронутого или переработанного – оказывает воздействие на окружающую среду. Для определенных применений до сих пор нет подходящих альтернатив использованию термопластичных материалов, когда речь идет о стоимости, сроке службы и сохранности содержимого.Подобно источникам энергии, полученным из ядерного, ископаемого топлива, ветра и солнца, каждый метод имеет свои преимущества и недостатки, если учитывать все факты.
Formech стремится свести к минимуму воздействие обработки термопластичных материалов на окружающую среду, применяя кварцевый нагрев с эффективным управлением энергией на всех наших станках. Все машины Formech могут быть легко оснащены точными уменьшающими окнами, чтобы минимизировать использование пластика и отходов, где это возможно. Работая в тесном сотрудничестве с ведущими мировыми компаниями и учреждениями в области материаловедения, мы полностью поддерживаем разработку и использование материалов, которые снижают воздействие на окружающую среду.
Вакуумно-формовочные машины и машины Formechшироко представлены в учебных программах высшего образования для самых технически продвинутых колледжей и университетов во всем мире. Даже более 80 лет вакуумная формовка является постоянно развивающейся технологией, и мы рады быть в авангарде новых исследований и возможностей.
5- Характер использования и ограничения
Вакуумная формовка предлагает несколько технологических преимуществ по сравнению с другими процессами формования. Используется низкое давление формования, что обеспечивает сравнительно низкую стоимость инструментов.
Поскольку в процессе используются низкие давления, формы могут быть изготовлены из недорогих материалов, и время изготовления формы может быть достаточно коротким. Таким образом, требования к прототипам и небольшому количеству крупных деталей, а также средние размеры становятся экономичными. Более сложные машины и формы используются для непрерывного автоматизированного производства крупногабаритных изделий (банок для йогурта …).
В вакуумном формовании используется экструдированный пластиковый лист, и может потребоваться дополнительный процесс для обрезки формованного листа, чтобы получить готовую деталь.
6- Процесс вакуумного формования
Зажим
Рама зажима должна быть достаточно мощной, чтобы обеспечить надежную фиксацию пластикового листа в процессе формования. Он может обрабатывать самый толстый материал, который может быть сформирован на машине – до 6 мм с одним нагревателем и до 10 мм с двумя нагревателями. Если используется автоматизированный процесс, работа движущихся частей должна быть защищена и заблокирована, чтобы избежать случайного повреждения.Кроме того, должен быть предусмотрен защитный кожух для постоянной защиты оператора машины.
Отопление
Нагреватели– это, как правило, инфракрасные элементы, установленные внутри алюминиевой отражающей пластины. Чтобы получить наилучшие результаты вакуумного формования, используя любой материал, важно, чтобы лист нагревался равномерно по всей его площади поверхности и по всей его толщине. Для этого необходимо иметь ряд зон, которые контролируются регуляторами энергии.Керамика имеет некоторый недостаток в том, что ее высокая тепловая масса заставляет их медленно нагреваться (около 15 минут) и замедляет время отклика при выполнении настроек.
Доступны более совершенные кварцевые нагреватели, которые имеют меньшую тепловую массу, что обеспечивает более быстрое время отклика. Пирометры обеспечивают точный контроль температуры нагрева, измеряя температуру плавления листа и взаимодействуя с управлением процессом работы. Точное считывание температуры также доступно с системой, управляемой компьютером, работающей в унисон с пирометрами.Двойные нагреватели также рекомендуются при формировании более толстых материалов, поскольку они помогают обеспечить более равномерное проникновение тепла и более быстрое время цикла.
Двойные кварцевые нагревателирекомендуется использовать при формовании высокотемпературных материалов с критическими температурами формования. При строгом контроле областей интенсивности тепла потери тепла по краям, вызванные конвекционными воздушными потоками и поглощением из областей зажима, могут быть полностью компенсированы, и последовательные результаты достигаются на постоянной основе. Экономия также может быть значительной, если заданы кварцевые нагреватели, так как в процессе формования нагреватели имеют регулируемый процент снижения мощности, когда нагреватели находятся в заднем положении.
Уровень листа (автоуровень) – доступно не на всех машинах.
Фотоэлектрический луч активируется под листом пластика во время цикла нагрева. Если лист пластика провисает и ломает балку, то небольшое количество воздуха впрыскивается в нижнюю камеру под листом, таким образом поднимая лист, чтобы предотвратить его провисание, пока лист не очистит балку.
Предварительное растяжение (пузырьковый) – доступно не на всех машинах.
Как только пластик достиг температуры формования или состояния «пластика», его можно предварительно растянуть, чтобы обеспечить равномерную толщину стенки при применении вакуума.Метод контроля высоты пузырька должен состоять в том, чтобы были получены согласованные результаты. Вакуум, давление воздуха и дополнительные вспомогательные средства, такие как вспомогательная пробка, затем используются для облегчения формования нагретого, растянутого пластика.
Plug Assist – Доступно только для серий HD и TF.
Вакуумное формование с помощью пробки (литье) используется, когда прямое вакуумное формование не позволяет равномерно распределить термопластичный лист по всем участкам формы. Чтобы распределить лист более равномерно, используется устройство, известное как заглушка, для проталкивания листа в форму перед тем, как создается вакуум.Этот процесс позволяет большему количеству термопластичного материала достигать дна формы, и, таким образом, доступно больше материала для заполнения углов формы и ограничения утончения пластика.
Вакуум
Как только материал соответствующим образом нагрет, может быть применен вакуум, чтобы помочь в формировании листа. Вакуумный насос используется для подачи воздуха, захваченного между листом и формой. Вакуумные насосы варьируются от мембранных насосов до сухих и заполненных маслом роторных лопастных насосов.В больших машинах вакуумный резервуар используется в сочетании с вакуумным насосом большой емкости. Это позволяет применять двухступенчатый мгновенный вакуум, обеспечивающий быстрое формование нагретого листа (до того, как температура листа упадет ниже его идеальной температуры формования).
Охлаждение и выпуск – Доступно не на всех машинах
После того, как пластик сформирован, ему нужно дать остыть перед тем, как его выпустить. Если его освободить слишком рано, то деформация отливки приведет к отклонению детали.Чтобы ускорить цикл охлаждения с высокой скоростью, вентиляторы устанавливаются и включаются после формирования детали. Опция распыления тумана также доступна, посредством чего форсунки прикреплены к вентиляторам, и мелкий туман охлажденной воды направляется на лист. Это в сочетании с вентиляторами может ускорить цикл охлаждения до 30%, а также полезно для контроля усадки отформованных деталей.
Также доступны блоки контроля температуры, которые регулируют температуру внутри формы, обеспечивая точное и постоянное время охлаждения при охлаждении кристаллических и кристаллизующихся полимеров, таких как ПП, ПЭВП и ПЭТФ.
Отделка и отделка
После того, как формованная деталь остыла и вынута из машины, избыток материала удаляется. Затем в детали просверливаются отверстия, прорези и вырезы. Другие процессы постформинга включают в себя отделку, печать, укрепление, армирование и сборку.
Для обрезки изделия с листа используются различные методы обрезки. Тип оборудования, наиболее подходящего для использования, во многом зависит от типа резки, размера детали, коэффициента вытяжки, толщины материала и требуемого объема производства.Тонкостенные детали обычно обрезаются на механическом прессе – иначе известном как роликовый пресс.
Скачать Типичные области применения вакуумной формовки
Загрузить технический бюллетень 1 – Материалы для инструментов
Загрузить технический бюллетень 2 – Webbing
Скачать Технический бюллетень 3 – Популярные материалы и приложения
Загрузить технический бюллетень 4 – Способы обрезки
Скачать Технический бюллетень 5 – Литьевая смола для оснастки
Скачать Технический бюллетень 6 – Мужской и женский инструмент
Скачать Технический бюллетень 7 – Монтажные инструменты и пресс-формы
Скачать Технический бюллетень 8 – Уменьшение windows
Скачать Технический бюллетень 9 – Расстояние между инструментами и растяжение материала
,Услуги вакуум-формовочных компаний | IQS Directory
business Отраслевая информация
Вакуумная формовка
Вакуумная формовка – это упрощенная форма термоформования. Лист из пластика нагревают до температуры вакуумной формы и формуют в форму. Затем его натягивают на поверхность формы с помощью вакуума. Затем листу пластика дают остыть и выталкивают из формы, используя обратное давление. Это используется для превращения пластмасс в различные объекты.
Для облегчения удаления сформованного пластика из формы в конструкцию формы включены углы тяги. Механическое или пневматическое растяжение формуемых листов перед подачей вакуума позволяет соответствующим образом регулировать глубину формируемых деталей. Обычно подходящие материалы, используемые в вакуумном формовании, представляют собой термопластов .
Приложения
Основным назначением вакуумной формы является формирование различных предметов из пластмасс.Некоторые постоянные объекты, произведенные в этом процессе, являются защитными крышками и знаками магистрали. Процесс производит большое разнообразие продуктов, начиная от простых элементов упаковки и заканчивая экстремальными воздействиями на кабины самолетов.
Универсальность вакуумного формовщика способствует его широкому применению в различных отраслях промышленности. Многочисленные термопластичные материалы могут быть преобразованы в различные объекты и формы с помощью процесса вакуумной формы. Прозрачные материалы, такие как акрил, также подходят для вакуумного формования и широко используются в аэрокосмической промышленности в качестве окон пассажирских салонов.Это технология низкого уровня, которая обеспечивает легкий способ формовки.
![]() | ![]() | ![]() | ![]() |
Компонент Lexan с вакуумной формовкой – Engineered Plastic Products, Inc. | Пластмассы с вакуумной формовкой – Engineered Plastic Products, Inc. | Компонент вакуумной формовки пластикового корпуса – Conlet Plastics, Inc. | Вакуум-формованный пластиковый компонент – Conlet Plastics, Inc. |
Отрасли и продукты вакуумной формовки
В различных отраслях промышленности вакуумная форма используется для создания различных продуктов, как описано здесь.
Авиационные производители применяют вакуумную термоформу для производства панелей внутренней отделки, крышек и обтекателей. Внутренние секции космических челноков НАСА сделаны с помощью термоформовочной машины.
Широкий ассортимент продукции от сельскохозяйственных поставщиков изготавливается из пластмасс, которые подвергаются вакуумному формованию. Несколько примеров включают контейнеры для животных, части сельскохозяйственных машин, цветочные кадки, лотки с семенами и четко растущие купола.
С фармацевтическими производителями при изготовлении блистерных упаковок применяется вакуумная термоформа. Полости на блистерной упаковке изготовлены из листового пластика с помощью нагревательного элемента. Полости затем покрывают с помощью уплотнения из другой пластиковой или алюминиевой фольги для защиты и доставки единичных доз капсул, таблеток и пастилок.
В строительстве и строительстве используются вакуумные формы при изготовлении различных деталей, таких как дверные панели из ПВХ, пресс-формы для бетонного покрытия, элементы литого потолка, водосточные трубы, потолочные светильники и внутренние облицовки дверей. Камины, подъезды, а также другие детали используют вакуумные продукты.
Автомобилестроение и автомобилестроение в значительной степени полагаются на вакуумное формование многих деталей автомобилей, включая крышки ступиц колес, бамперы, брызговики, накладки, спинки сидений, стеллажи, лыжные боксы, внутреннюю отделку дверей, ветровые стекла, защитные панели, аккумуляторы и другие электронные корпуса.
Больницы и другие медицинские приложения зависят от вакуумной формы для изготовления протезов, масок под давлением, масок для радиотерапии, деталей инвалидных колясок и зубных отливок, изготовленных из вакуумной штамповки.
Существуют и другие отрасли, которые используют вакуумную формовку для производства различных элементов, включая мебель, упаковочные материалы, ванны, душевую кабину, сувениры, витрины в местах продаж, косметические футляры и столовые приборы.
История процесса вакуумной формовки
В 1860-х годах Джон Уэсли Хаятт открыл процесс изготовления целлулоида, первого искусственного пластика.Вместе с его братом они запатентовали этот пластик и обнаружили, что его можно нагревать в формах, образуя различные формы, такие как листы и стержни.
Однаковеками ранее римляне импортировали панцири черепах, содержащие кератин с Востока. Они использовали бы горячее масло, чтобы сформировать этот материал в различные кухонные принадлежности. Таким образом, можно утверждать, что именно римляне открыли термоформование, потому что они начали нагреваться.
В 20-м веке нагревание пластмасс и формование в форме превратилось в термоформование, как известно сегодня.В течение 1940-х и 1950-х годов пластмассы, отформованные в вакууме, были впервые задуманы как инструменты для демонстрации и маркетинга, разработанные на основе технологий вакуумного литья и формовки. В 1950 году была запатентована машина для изготовления изделий из тонкого листа пластика.
В 1964 году машина для вакуумного формования пластиковых листов была усовершенствована и запатентована. Эти вакуум-формовочные машины и термопласты использовали более старую концепцию, согласно которой для удаления избытка воздуха использовались вакуумы в различных формах литья и формования.К 1970-м годам технология развивалась и совершенствовалась по сравнению с методами, которые мы используем в настоящее время.
Типы и свойства материалов, используемых в процессе вакуумной формовки
В процессе вакуумной формовки используется широкий спектр материалов. Желательные свойства термопластичного материала для этого процесса включают низкие температуры формования, хорошую текучесть, термическую прочность, низкую усадку при охлаждении и высокую ударную вязкость.
Наиболее распространенные материалы, используемые для вакуумной формы, включают полиэстер (PET), поливинилхлорид (PVC), полиэтилен высокой плотности (HDPE), полиэтилен низкой плотности (LDPE), полипропилен (PP), полистирол (PS), поликарбонат, акрилонитрил-бутадиен стирол (ABS), акрил и Kydex, термопластик на основе ПВХ.
С полиэстером, вакуумная форма легко достигается при низких температурах. Характеризуется быстрыми циклами и отличными эксплуатационными характеристиками. Его основное использование в производстве упаковочных материалов, таких как контейнеры для пищевых продуктов, контейнеры для напитков и пакеты для переработанного мяса. С ПВХ производятся пищевые обертки, блистерная упаковка и бутылки с растительным маслом. ПВХ прочен, прочен, обладает хорошей прозрачностью и химической стойкостью.
Хотя полиэтилен высокой плотности (ПЭВП) может быть сложным в формовании, он имеет значительное применение в производстве бутылок для молока, вкладышей для хлопьев, пластиковых пакетов и пробирок с маргарином.Как и ПЭВП, полиэтилен низкой плотности (ПЭНП) также плохо образуется. После изготовления он подходит для производства пакетов для одежды, сжимаемых продуктов питания бутылок , пластиковых пакетов и термоусадочных пленок.
Полистирол является одним из наиболее часто используемых термопластов в вакуумной форме. Он легко образуется при значительно низких температурах, что позволяет сократить время цикла и не требует предварительной сушки. Ударопрочный полистирол жесткий и недорогой. Тем не менее, он имеет низкую стойкость к ультрафиолетовому излучению, поэтому не подходит для наружного использования.Его основное применение – производство лотков для фаст-фуда, одноразовых пластиковых изделий из серебра, коробок для яиц и оболочек для компакт-дисков.
Акрилонитрил-бутадиен-стирол (АБС) является твердым, жестким, устойчивым к атмосферным воздействиям материалом с удовлетворительной ударной вязкостью. Содержит немного резины, что повышает его ударопрочность. ABS применяется для багажа, транспортных средств, санитарных частей и электрических шкафов. Желаемыми характеристиками акрила являются его твердость, высокое качество термопласта и хорошая прозрачность.Некоторые вывески, ванны, сантехника и потолочные светильники выполнены с использованием акрила.
Этапы процесса вакуумной формовки
Процесс состоит из помещения пластикового листа в холодном состоянии в область зажима для формования. Нагревательный элемент используется здесь до желаемой температуры, так что пластмасса может быть сформирована. Форма поднимается снизу для формирования различных продуктов с горячим пластиком. Захваченный воздух удаляется с помощью вакуумной системы. Охлаждение следует с обратной подачей воздуха, активируемой для извлечения пластмассы из формы.Этот процесс включает в себя семь основных этапов: зажим, нагрев, выравнивание листа, предварительное растяжение, вакуум, помощь пробки, охлаждение и выпуск.
Зажим
Важно, чтобы используемая рама была достаточно мощной, чтобы надежно удерживать пластиковые листы во время процесса. Рама должна быть в состоянии обрабатывать самые толстые пластики, которые будут образовываться на вакуум-формовочной машине.
Отопление
Как правило, нагреватели, используемые в этом процессе, представляют собой инфракрасные элементы, помещенные в алюминиевую пластину.Независимо от используемых материалов, наилучшие результаты вакуумной формы получаются, пластиковый лист нагревается равномерно по всей его толщине и площади поверхности. Кварцевые обогреватели используются в более сложных процессах. Они имеют меньшую тепловую массу и, следовательно, позволяют быстрее реагировать.
В процессе нагрева используются пирометры, которые обеспечивают точный контроль температуры нагрева. Они чувствуют температуру плавления нагреваемых материалов и взаимодействуют с управлением рабочего процесса.Пирометры работают вместе с компьютеризированной системой, которая обеспечивает точные показания температуры.
Уровень листа
Это третий этап процесса вакуумной формы, хотя он встречается не во всех машинах. Он использует фотоэлектрический луч, который сканирует нижний нагреватель и нагреваемый пластиковый лист. Это используется, чтобы определить, опускается ли пластмасса, чтобы сломать луч. Если это произойдет, будет введен небольшой объем воздуха, чтобы поднять лист и остановить провисание.
Предварительно растянуть (пузырь)
Это четвертый шаг, который также недоступен на некоторых машинах. Предварительное растяжение выполняется, когда пластик достигает температуры вакуумной формы (пластическое состояние). Это обеспечивает равномерную толщину стенки после применения вакуума. Метод, используемый для контроля высоты пузырька, должен обеспечивать получение последовательных результатов.
Вакуум
Фактический вакуум применяется на этом этапе. После предварительного растяжения материалов создается вакуум, чтобы помочь в формировании листа.Воздух, захваченный между формой и пластиковым листом, удаляется вакуумным насосом. Используемые вакуумные насосы должны поддерживать перепад давления около 27 мм рт. В больших термоформовочных машинах вакуумные резервуары используются вместе с вакуумными насосами большого объема . Этот процесс допускает двухступенчатое применение вакуума, следовательно, быстрое формование нагретых материалов.
Вакуумная формовка с помощью штекера
Это этап, который следует за применением вакуума, особенно когда прямое вакуумное формование не распределяет пластиковый лист равномерно по форме.Это не доступно в некоторых машинах. Пробка вдавливает пластиковый лист в форму перед подачей вакуума, чтобы он распределялся более равномерно. Это позволяет материалам достигать дна формы, предотвращая их истончение.
Охлаждение и выпуск
Это последний шаг в процессе вакуумной формы. После формования пластику дают остыть, прежде чем он будет выпущен. Когда высвобождение сделано слишком рано, происходит деформация пресс-формы, что приводит к выбраковке продукта.Процесс охлаждения ускоряется благодаря установке и активации вентиляторов и распылителей тумана после образования продукта. Температуры охлаждения контролируются, чтобы обеспечить равномерное охлаждение и выпуск формованных деталей.
Наконец, выполняется отделка и отделка, посредством чего удаляются лишние материалы. Отделка также включает такие процессы, как сверление отверстий, вырезов и прорезей, а также отделка, печать, укрепление и сборка.
Дизайн и настройка
Процесс вакуумной пластиковой термоформовки похож на большинстве машин.Тем не менее, несколько настроек сделаны для удовлетворения конкретных требований. Например, форма, используемая для формирования деталей, может быть мужской (выступающая) или внутренней (утопленная). Формируемые детали и изделия определяют форму, которая будет использоваться.
Процесс формования под давлением очень похож на вакуумное формование, только в том, что для термоформования под давлением используется вакуумная среда вместе с дополнительным давлением воздуха, которое повышает герметичность пластикового листа на форме.Это используется при создании очень подробных вакуум-формованных пластиков .
Машины и Кастомизация
Специальный инструмент и оборудование используются в процессе вакуумной формовки. Они используются как для первичного производства деталей, так и для вторичной настройки, прежде чем они будут подготовлены для клиента. Используемые инструменты и оборудование зависят от типа продукта, размера, толщины и необходимого количества.
Триммеры, скальпели и ножи с подогревом используются для отделки и обрезки продукта в соответствии с желаемыми характеристиками.Другие машины, используемые для обрезки, включают в себя вертикальные и горизонтальные ленточные пилы, роликовые прессы, гильотины, перфораторы и ручные силовые маршрутизаторы. Производители станков с ЧПУ предлагают точные услуги по сверлению отверстий и созданию других функций индивидуальной настройки пластмасс 9109, отлитых под давлением.
Настройка выполняется путем тиснения и нанесения различных знаков и текстов в соответствии с требованиями заказчика.
Преимущества вакуумной формовки
Популярность вакуумной формы можно объяснить ее преимуществами.Продукты, полученные в процессе вакуумной формовки, соответствуют их проектным характеристикам. Один нагретый лист обеспечивает точность указанной конструкции, что является желательным признаком для изделий, предназначенных для соответствия друг другу.
Пластиковое вакуумное формование является экономически эффективным, поскольку используемые материалы являются недорогими, требуются низкие давления, а инструменты менее сложны. Некоторые изделия могут быть изготовлены из одного листа пластика, что снижает стоимость в количествах. Вторичная переработка уже использованного пластика также способствует снижению затрат.
Процесс вакуумной формы универсален и гибок, что позволяет создавать уникальные продукты и формы. Более быстрое время выполнения является привлекательным для бизнеса, потому что время может быть инвестировано в другое место для совершенствования операций и получения прибыли.
Выбор правильного производителя
В вакуумной формовочной промышленности есть много производителей. Можно найти любого хорошего производителя, но для покупателя важно найти правильного производителя. Правильный производитель гарантирует, что все потребности клиента будут удовлетворены.Когда нужен нестандартный пластик, правильный производитель сможет его доставить.
Типы вакуумной формовки
- Блистерные упаковки представляют собой прозрачную пластиковую неразделываемую упаковку, используемую для продуктов, которые могут быть подделаны.
- Раковины – это пластиковые пакеты, которые имеют петли, которые открываются и закрываются, как раковина моллюска.
- – это как защелка, кроме
что термопластичный лист вытянут к основанию формы.В обоих случаях использование воздуха для растягивания материала до вакуума
герметизация и нанесение на форму позволяет материалу равномерно утончаться.
- Пластиковые крышки представляют собой вакуумные пластики, предназначенные для защиты, удержания и защиты объектов от таких условий окружающей среды, как погода, освещение, пыль, вода или другой мусор.
- Пластмассовое формование – это группа производственных процессов, в которых термопласты используются для формования и формования в широкий спектр пластмассовых изделий для многочисленных промышленных, коммерческих и бытовых применений.
- Пластиковая упаковка включает в себя все устройства для хранения или хранения, произведенные путем манипулирования любым количеством полимерных смол.
- Пластиковые лотки представляют собой неглубокие платформы с выступающими краями, предназначенные для предотвращения скольжения или скатывания содержимого с поверхности.
- – это процедура термоформования с использованием вилки или штекера
пресс-форма для прессования нагретого термопластичного материала в пресс-форму
до применения вакуума.Этот метод помогает равномерно
раздать лист.
- Формирование давления – это процедура термоформования, которая включает приложение давления к
верхней части пластиковой пленки, в то время как сила вакуума тянет вниз. давление
формование осуществляется с помощью давления воздуха или механическими средствами, и обеспечивает
большая точность, потому что пластик способен достичь большего определения
формы в форме.
- – процесс предварительного растяжения листа
материал с вакуумной коробкой. Затем применяется частичный вакуум
до коробки, как раз для необходимого растяжения, и формы
является
толкнул
в материал, где коробка вентилируется до атмосферного давления
это опирается на вакуум.
- – вакуумное термоформование с использованием только женского пола
формы, которые производят распределение материала, противоположное
результатов
получено из мужских слепков.
- Термоформование включает нагревание и растяжение пластмасс.
- Термоформование с двумя листами – это технология пластической обработки, предусматривающая вакуумное формование двух отдельных пластиковых листов одновременно перед их сваркой, чтобы создать полую деталь или изделие.
- Пластмассы , отформованные в вакууме, создаются методом термоформования, в котором вакуум используется для всасывания пластикового листа в форму.
- Вакуумное литье – это метод производства, при котором термопласты обрабатываются и формуются в процессе формования в различные пластмассовые изделия.
- Вакуумная упаковка может относиться как к тем предметам, которые хранятся или выставляются в контейнерах с пониженным содержанием кислорода, так и ко всем без исключения упаковочным материалам, полученным вакуумным формованием.
Условия вакуумного формования
– темные частицы, которые появляются
в пластиковой пленке в процессе термоформования из-за загрязнения.
– Характеристика некоторых пластиков, теряющих свои цвета
при контакте с водой или определенными растворителями.Кроме того, это
нежелательное движение материалов на поверхность пластика или в
соседний материал.
– Термоформованные полужесткие пластиковые оболочки, обычно изготавливаемые
соответствовать форме упаковываемого продукта.
– Выступ на пластиковой части, который добавляет прочности, помогает
с выравниванием в сборке и допускает крепления.
– Части термоформованного пластика, где вакуум и
тепло создает отверстие в слабых или тонких точках.
– Изменение структуры пластика.
– отделение термоформованных деталей, таких как блистеры, от
друг друга для следующего этапа процедуры упаковки.
– Процесс снятия статического электричества с
пластик, чтобы меньше пыли цеплялось за него.
– Использование стального линейного штампа для резки готовых листов блистеров
или блистерные карточки для создания отдельных частей.
– Степень, до которой боковая стенка пузыря или
раскладушка имеет коническую форму, чтобы сгладить процесс снятия с термоформования
плесень и отложение пузыря.
– Техника, которая создает депрессии в конкретном
узор на пластиковую пленку и защитное покрытие.
– тенденция термоформованного пластика
растрескиваться под воздействием определенных химических веществ.
Внутренняя форма – Вогнутая форма, называемая негативной или полой формой.
– блистер карта, которая забита и вырублена, позволяя захватить блистер между двумя половинами карты.Это обеспечивает печать между двумя досками или между доской и блистерным фланцем, особенно полезно, когда блистер упаковка тяжелых предметов.
Gas-flush – Во время вакуумной упаковки камера продувается азотом, предотвращая плотное всасывание пластмассы хрупкими продуктами.
– Процесс соединения двух или более пластиков с применением тепла и давления.
наружная форма – выпуклая форма, называемая положительной или выступающей формой
– результат неадекватного контакта пластикового материала с поверхности формы из-за захваченного воздуха, влаги на поверхности формы или низкого давления в нерегулярных вмятинах на материале поверхность.
– модель по назначению часть. Прототипы показывают окончательный размер, а также дизайн.
– Термопластичный материал, полученный из промышленных пластиковый лом от другого процессора.
– Поток нагретого пластика
защитное покрытие в процессе термоформования, при котором провисают расплавленные пластиковые листы
до формирования. Расстояние провисания определяется электрическим глазком
и подходит для определения готовности материала к формованию.
– Процедура нагревания перед формированием термопластика
лист, который включает нагревание обеих сторон.
– любой пластик,
который не является частью продукта, который является результатом процедуры формования.
Этот материал обычно является ломом и может быть использован повторно.
– Конструкция, необходимая для создания пластиковой пленки,
состоит из экструдера, матрицы, полировочных валков, конвейера, вытяжных валков, резца
и укладчик.
– минутное изменение длины или объема
материал под воздействием тепла.
– Двойной блистер для капсулирования продукта
для видимости продукта с двух сторон.
– выемка или выступ, препятствующий удалению
из плесени.
Единичная доза Упаковка – лекарственная блистерная упаковка в единичных дозах для ясности.
Таблица вакуумных форм – Машина, которая производит вакуумные формованные детали и изделия.
Подробнее Вакуумная формовка
Вакуумно-формовочное информационное видео
,