Графитовый (угольный) электрод: виды, применение и строжка
В 1882 году российский ученый Н. Н. Бенардос впервые в мире соединил металлические детали с помощью электродуговой сварки. В своей установке он использовал неплавящиеся угольные электроды и раздельную подачу присадочного материала и флюса. Основываясь на этом методе, Бенардос также разработал сварку в защитном газе и электродуговую резку. Через шесть лет была изобретена сварочная технология с использованием плавящихся электродов, которые со временем практически полностью вытеснили угольные. В настоящее время последние ограничены в своем применении тремя основными направлениями: удаление излишков металла, дуговая резка и сварка отдельных материалов.
На просторах российского интернета в статьях о сварочных технологиях нередко можно встретить такое название, как «графитовый электрод». Не вдаваясь в подробности причин этого явления, следует отметить, что ГОСТ не предусмотрено изготовление сварочных электродов из графита. Государственным стандартом регламентированы только графитовые спектральные электроды, применяемые для лабораторных исследований. Производители могут выпускать угольные и графитовые стержни как фасонные изделия по ТУ 1915-086–00200851, но таким образом, как правило, изготавливают только толстые электроды для разделки лома и обработки отливок.
Кроме того, металлургические предприятия, на которых применяют графитированные электроды для электродуговых печей, самостоятельно производят нестандартные сварочные электроды из обломков этих крупногабаритных изделий, которые, по сути, тоже можно назвать графитовыми.
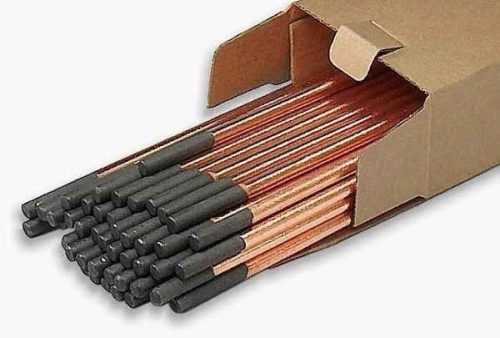
Рисунок 1 — Графитовый электрод
Назначение угольных электродов
Угольные электроды, в основном, используются для заделки дефектов в поковках, литых заготовках и металлопрокате, снятия излишков металла с поверхности сварочных швов и массивных заготовок, а также при сварке отдельных видов металлов и их сплавов. Обычно их применяют при таких видах работ, как:
- устранение приливов, раковин и прочих дефектов;
- строжка корней сварочных швов;
- срезание прихваток и старой сварки;
- прожигание отверстий;
- срезание заклепок;
- сварка металлических заготовок с тонкими краями;
- сваривание цветных металлов;
- сварочное соединение жил и шин при электротехнических работах.
При срезании лишнего металла обычно применяют метод строжки — выдувание кипящего металла из сварочной ванны узконаправленным потоком сжатого воздуха (см. далее). Таким способом вычищаются каверны в литых заготовках и поковках, а также снимается дефектный слой металла со сварных швов.
Применение этих изделий для сварки цветных металлов, в основном, ограничено чугуном, медью и ее сплавами (см. таблицу).
№ | Материал детали | Материал присадочных прутков | Флюс | Доп. условия |
---|---|---|---|---|
1 | Медь | Оловянно-фосфористая бронза, кремнистая латунь и медь (М1 или МСр1). | Бура с добавками древесного угля, гидрофосфата натрия и кремниевой кислоты. | – |
2 | Бронза | Тот же, что и основное изделие. | Для оловянистых бронз — бура, для алюминиевых бронз — хлориды и фториды. | Перед сваркой прогреть до 250÷350 °C. |
3 | Латунь | Тот же, что и основное изделие. | – | Погружение конца угольного стержня в расплавленный металл, чтобы дуга была полностью окружена парами цинка. |
4 | Чугун | Чугунные прутки марок А и Б. | На основе буры. | – |
Сварка угольными электродами листового проката обычно производится без использования присадочных прутков, путем расплавления металла кромок заготовки. При этом толщина свариваемых листов обычно составляет 1÷2 мм, а их края соединяются или встык с отбортовкой (подогнутыми кромками) или внахлест.
Устройство и характеристики
Угольные электроды — это стержни круглого или прямоугольного сечения, изготовленные из электротехнического угля, который представляет собой смесь углерода (в виде кокса или антрацита), сажи и связующих веществ (каменноугольная смола или жидкое стекло). Круглые изготавливают методом экструзии и поставляются потребителям в виде стержней диаметром от 4 до 18 мм и длиной 250÷700 мм, а прямоугольные — методом прессования в формах. Помимо типоразмеров ГОСТ также применяются специальные стержни увеличенной толщины (15х15, 20х20 и т. п.), изготовленные по ТУ.
Угольные электроды намного дешевле и прочнее графитовых. Но удельное сопротивление электротехнического угля в несколько раз выше, чем у графита. Поэтому для улучшения электротехнических характеристик угольных стержней их поверхность покрывают медью.
В качестве примера в таблице приведены основные параметры круглых омедненных угольных электродов марки ВДК длиной 305 мм.
Диаметр (мм) | Рабочий ток (А) | Удаление металла (г/см) | Канавка (ширина/глубина) (мм) | Толщина реза (мм) |
---|---|---|---|---|
4 | 150÷200 | 10 | 6÷8/3÷4 | 7 |
6 | 300÷350 | 18 | 9÷11/4÷6 | 9 |
8 | 400÷500 | 33 | 1÷13/6÷9 | 11 |
10 | 500÷550 | 49 | 13÷15/8÷12 | 13 |
Обязательное условие применения этих изделий — выполнение работ только на прямой полярности. При обратном включении дуга очень неустойчива, качество шва из-за науглероживания металла получается низким, рабочая температура угольного стержня гораздо выше, что увеличивает скорость его испарения.
Виды угольных электродов
Нормативной базой для производства отечественных угольных электродов является ГОСТ 10720-75, содержащий описание трех типов таких изделий: ВДК, ВДП, СК, — которые могут выпускаться как омедненными, так и без покрытия. ВДК (воздушно-дуговые круглые) должны изготавливаться длиной 300 мм и четырех типоразмеров по диаметру. СК (сварочные круглые) — длиной 250 мм и шести типоразмеров по диаметру. ВДП (воздушно-дуговые плоские) — длиной 350 мм и двух сечений. По запросу заказчика разрешается изготавливать изделия СК с линейным размером до 700 мм.
Кроме отечественных электродов на российском рынке представлена продукция известных международных сварочных брендов и производителей из Восточной Азии. Шведский концерн ESAB предлагает свыше двадцати видов омедненных угольных электродов. Кроме изделий, используемых для сварки на постоянном токе прямой полярности, в номенклатуре ESAB присутствуют четыре типоразмера для сварки на переменном токе. А известный немецкий производитель сварочных принадлежностей ABICOR BINZEL, рекламируя свою продукцию, акцентирует внимание на том, что она изготовлена из «синтетического графита» (т. е. графитированного углерода). Вполне вероятно, что эти изделия спрессованы из порошка, полученного из остатков и лома металлургических графитированных электродов.
Помимо этого, на рынке присутствуют прессованные электроды из электротехнического и графитированного углерода, которые изготавливаются на заказ производителями угольных и графитовых изделий по ТУ 1915-086–00200851.
Как правило, они представляют собой прямоугольные стержни толщиной 10, 20, 30 и более миллиметров и применяются для объемных работ на больших сварочных токах: разделке металлургического лома, устранении прибылей на отливках, сквозной резке толстого металла и пр.
Советы по сварке
При сварке медных проводников следует помнить, что в первую очередь нужно подготовить и очистить свариваемые поверхности, а затем надежно их зафиксировать. Сварка медных проводов и шин осуществляется только в положении сверху вниз, т. к. расплавленная медь обладает повышенной текучестью. При этом используется флюс «борный шлак». Еще одной особенностью данного типа электродов является то, что процесс плавления у них почти неразличим, т. к. практически сразу начинается испарение (электротехнический уголь плавится при температуре 3800 °C, а испаряется — при 4200 °C).
Рекомендуемый угол заточки торцов угольных стержней — 60÷70°, но для сварки цветных металлов их необходимо затачивать под углом 20÷40°. Листовую медь толщиной до 4 мм можно сваривать без использования присадочных прутков (но с обязательной отбортовкой кромок), а свыше 4 мм — встык с присадочным материалом и разделкой кромок под углом 45°. Технология сварки латуни требует разделки кромок под углом 60÷70° с притуплением торцов на 1÷2 мм. Сварка производится путем погружения конца стержня, который должен быть полностью окутан парами цинка.
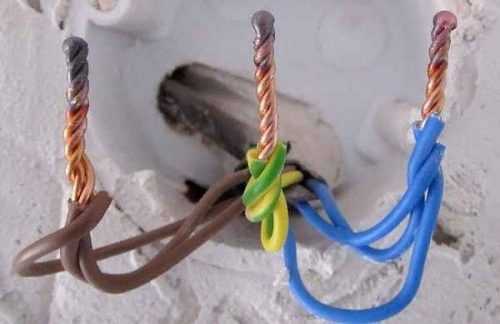
Рисунок 5 — Провода из латуни
Строжка угольным электродом
Строжка — это удаление узкого поверхностного слоя с использованием электродуговой сварки угольными электродами. Само слово ведет свое происхождение от глагола «строгать», т. к. этот процесс в чем-то аналогичен обработке пазов на строгальном станке. Технология строжки основана на разогреве металла электрической дугой до температуры кипения с последующим выдуванием его из сварочной ванны узконаправленным потоком воздуха. Строжка выполняется на глубины до десятков миллиметров, а ее производительность, зависящая от толщины угольного электрода и силы тока, измеряется в граммах удаленного металла на сантиметр канавки.
При выполнении строжки электрод под наклоном 30÷45° равномерно перемещают вперед, формируя канавку, которая на несколько миллиметров шире и глубже диаметра электрода. Строжка производится специальным воздушно-дуговым резаком, который имеет устоявшееся жаргонное название «строгач». Контактная пластина с соплами для подачи воздуха расположена на нижней губке строгача, поэтому поток воздуха направлен вдоль нижней части электрода в сторону сварочной ванны (см. рис. ниже). Подача воздуха должна прекращаться через несколько секунд после разрыва контакта электрода с металлом.
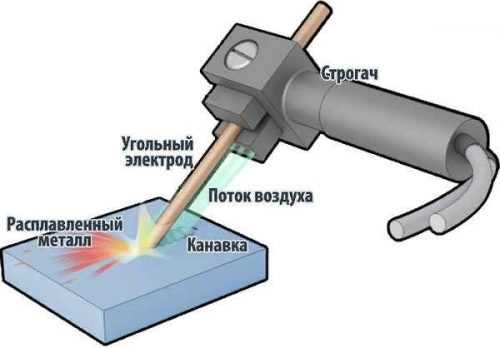
Рисунок 6 — Направление воздуха при сварке
Применение сварки угольными электродами для соединения электротехнических шин из меди и алюминия подробно регламентировано инструкцией «Росэлектромонтажа» И 1.08-08. Но там ничего не говорится о сварке проводов. Вместе с тем в интернете достаточно много фотографий, демонстрирующих использование такой сварки при монтаже электропроводки в обычных квартирах и офисных помещениях. Однако найти даже упоминание о нормативном документе, регламентирующем такую технологию, нам пока что не удалось. Если вам что-нибудь известно об этом, пожалуйста, напишите комментарий к этой статье.
wikimetall.ru
сварка графитированным электродом медных проводов
Выполнить соединение медных проводов можно разными способами, но именно сварка является наиболее эффективным, быстрым и надежным из них.
Созданные таким образом швы характеризуются высокой прочностью, отменным показателями электропроводимости, отвечают нормам и требованиям безопасности, служат долгие годы. Для сварки проводов мастера используют графитовые электроды, обладающие неоспоримыми достоинствами.
Достоинства и недостатки графита
Графитированные электроды способны проводить ток, не плавясь при этом, что случается с проволокой из иных материалов. В этом заключается главная отличительная особенность таких изделий. Электроды из графита выпускаются с наконечниками разных форм и длины, бывают обычными или омедненными.
Опишем наиболее выгодные характеристики электродов данного вида:
- доступная стоимость, широка распространенность;
- экономичный расход;
- материал, из которого создают стержень, не прилипает к соединяемым деталям;
- способность быстро разогреваться до температуры плавления металла;
- для разжигания дуги при работе инвертором потребуется ток в 5-10 А.
Также следует отметить, что сварной шов на медных проводах, изготовленный с применением графитовых электродов своими руками, получается стойким к коррозии, высоким температурам, но сама проволока при этом не склонна к образованию трещин при выполнении работы.
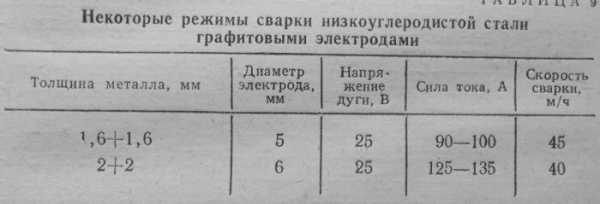
Таблица режимов сварки графитовыми электродами.
С их помощью можно сварить медностержень или алюминиевые провода, но у графитовых сварочных электродов существует несколько недостатков, чего не стоит забывать:
- соединение сваркой с применением графитовых стержней отличается сложностью, поскольку они имеют маленький диаметр ‒ 6 мм;
- эксплуатационные параметры соединяемых деталей могут ухудшиться в связи с повышенной концентрацией углерода в металле, которую провоцирует применение графитовых стержней;
- электроды из графита с определенным видом наконечника нужны для выполнения узкого списка операций, поэтому важно подбирать разные виды такой детали для стержней при выполнении разных видов работ;
Применение стержней и особенности работы с ними
Графитовый электрод нашел применение не только для выполнения сварных соединений проводов: его используют в гораздо более большом перечне операций.
Графитовые сварные стержни необходимы для предварительного обрабатывания металлических поверхностей перед сварочными работами, а также иными видами обработки, резки заготовок из металла, зачистки кромок металла и т.п. Не только металлургия активно использует электроды данного типа, но и судопроизводство.
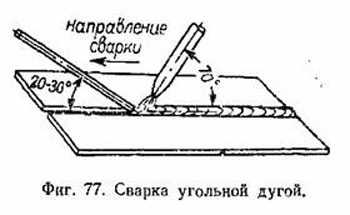
Сварка угольной дуги.
Электроды для сварки из графита позволяют оперативно и с высокой долей эффективности срезать заклепки, прошивать элементы из легированной, углеродистой стали.
Они также актуальны при плавлении стали и чугуна, а также некоторых сплавов в электротермических печах. А благодаря наличию ниппелей, такие стержни можно соединять между собой, что позволяет наладить непрерывную подачу расходного материала для сварки в печи.
На заметку! Практика показывает, что применение графитовых стержней для сварки медных проводов и для дуговой резки металла позволяет снизить количество брака и дефектов сварных швов. Главное, при работе графитом сварщику важно соблюдать технологию и придерживаться правил безопасности.
Графитовые стержни также актуальны для выполнения иных операций:
- сварные операции с изделиями из цветных металлов, элементов из тонкого металла;
- заварка дефектов, которые появились при нарушении технологии литья;
- наплавка твердосплавных деталей к металлической основе.
Часто графитовые электроды используются для сварки вместе с присадкой, подающейся в процессе выполнения операции или укладывающегося заранее в место расположения шва.
Стоит напомнить, что работа с графитом и сварочным аппаратом имеет свои особенности, которые непременно стоит учитывать для получения долговечных, максимально прочных и надежных сварных соединений:
- Для экономии расхода сварного стержня и поддержания дуги на стабильном уровне при длительной сварке следует использовать прямую полярность.
То есть, подавать минус нужно именно на электрод. - Сварные процессы важно осуществлять с учетом воздействия внешних факторов на стабильность дуги, это позволит добиться лучшего результата.
- При работе с графитовыми электродами значение КПД ниже, чем при работе с плавящимися электродами.
- Сварные соединения при сварке графитом характеризуются средними показателями пластичности.
По этим причинам сварку графитом должен выполнять квалифицированный мастер, а новичкам в данных вопросах стоит предварительно хорошенько потренироваться.
Чертеж сварочных работ с применением угольного электрода.
Существует два технологических приема, актуальных для работы с графитовыми стержнями:
- Материал подают прямо в пламя дуги.
При этом сварную проволоку размещают между элементом из металла и электродом под углом 30 градусов и подают несколько раньше, нежели сам электрод. Угол подачи стержня ‒ 70 градусов, что позволяет значительно ускорить процесс выполнения работы. - Мастер наплавляет валик основного металла с применением электрода, после чего в него подается присадка.
Основное отличие данной технологии заключается в том, что первым подается стержень и только после этого проволока.
Опасность применения данного технологического приема для неопытного сварщика состоит в большой вероятности прожога металла, хотя скорость работы при этом очень повышается. По этой причине он больше подходит для операций с металлическими деталями, имеющими толстые стеночки.
На заметку! Электролиз с использованием графита осуществляется исключительно при стабильном токе с прямым подключением.
При работе с электродами из графита важно помнить следующее: определяющий параметр при их использовании – плотность используемого тока. Если максимальное значение данного параметра превышается по каким-либо причинам, графит может испортиться.
Чтобы продлить эксплуатационный срок изделий, с обеих сторон можно вкрутить специальные ниппели для удлинения электрода. Такое решение позволит повысить надежность графитовых электродов и сэкономит денежные средства на приобретение новых стержней.
Регулирование силы тока
Регулировку тока для сварки проводов осуществляют в приделах 30-120 ампер, именно такой диапазон характерен для большинства инверторных сварочных агрегатов.
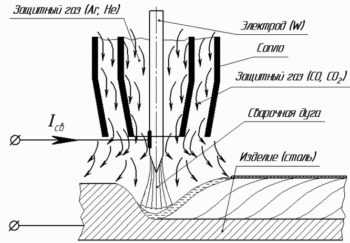
Схема сварки в среде защитного газа.
Точный ток сварки в любом варианте сварщику приходится определять опытным путем, в связи со следующими факторами:
- любая модель инвертора характеризуется определенными особенностями, поэтому крайне важно внимательно прочесть инструкцию к конкретному прибору;
- напряжение сети конкретного строения может не соответствовать 220 Вольтам;
- в медные жилы проводов входят разные по составу компоненты, если они изготовлены разными производителями;
- опыт мастера во многом определяет результаты сварной операции с использованием графитовых стержней.
Важно знать значения силы тока, при достижении которой можно производить эффективное соединение жил проводов с различным сечением при сварке графитовым электродом:
- при сваривании жил диаметром 1,5 мм2, инвертор настраивают на 70 ампер;
- три проводка с таким же сечением следует сваривать при токе 81-91 ампер;
- сила тока для соединения трех жил с диаметром 2,5 мм2 путем сварки должна достигать 81-101 ампер;
- четыре жилы 3 мм2 свариваются с силой тока в пределах 101-121 ампер.
Сварка алюминиевых проводов
Графитовым электродом осуществляют точечную сварку медных, а также алюминиевых проводов. Операции проводят под флюсом. Это специальный порошок внутри сварной проволоки, который расплавляется и продуцирует защитный газ.
Схема аргоно-дуговой сварки алюминия.
Последний предостерегает сварные кромки от контакта с кислородом и окисления вследствие этого.
Актуальное значение силы тока выставляют с помощью регулятора. Ток выпрямляют посредством применения диодного моста и фильтра пульсаций.
Хотя отметим, что опытные мастера могут соединить провода сваркой даже при переменном токе и без регулировки путем выжидания нужного времени удержания дуги. Но выполнение сварочных работ переменным током дает менее качественный результат.
Как правильно сделать и сварить скрутку?
Важно не допустить плавления изоляционного материала провода, для чего потребуется присоединить радиатор из металла к месту выхода скрутки из изоляции. Чаще остальных подбирают медный вариант, потому что этот металл характеризуется высокой теплопроводностью.
Большая площадь контакта улучшает процесс теплообмена и отводит тепло от скрутки.
Перед началом сварки жил проводов следует осуществить подготовительные работы. Очистите от изоляции и лакового покрытия, если оно присутствует. Скрутку делают максимально плотно, дабы витки тесно контактировали друг с другом.
Оптимальная длина скрутки ‒ 5-6 см. При этом концы проводов отрезают на одинаковом расстоянии, дабы они попали в зону действия сварки.
В месте фиксации радиатора к проводам потребуется присоединить зажим массы агрегата, а после ‒ поднести графитовый электрод к обрезанным краям. Контакт для сварки должен быть максимально кратковременным.
Оптимальное время – 1 секунда, по истечении которой на конце скрутки сформируется участок расплавленной меди в виде шара. Таким же образом поддают сварке с помощью графитовых электродов остальные скрутки жил проводов.
Требования техники безопасности при сварке графитом
Графитовый электрод позволяет создавать надежные соединения деталей разного рода металлоконструкций, но сварку крайне важно осуществлять с учетом норм безопасности.
Схема сварки меди с использованием графитового электрода.
Опишем их подробно:
- ток, подающийся к сварочным кабелям, обязательно следует отключить перед началом работы, дабы предостеречь себя от удара током;
- операции при помощи сварного аппарата нужно выполнять только в специальной одежде, обуви и с применением средств индивидуальной защиты, которые помогут уберечь глаза, руки и кожу тела от ожогов;
- место выполнения работ очищают от легко воспламеняющихся предметов, что позволит избежать риска возникновения пожара;
- после сваривания одной скрутки важно подождать, пока она остынет, и только тогда переходить к работе с последующей;
- чрезмерная спешка и нежелание выждать время, пока остынет первая скрутка, может привести к ожогу на теле сварщика;
- скрутки изолируют после сварки при помощи термоусадочной трубки, изолентой.
Если не придерживаться требований безопасности, описанных выше, при выполнении сварочных работ с графитовыми стержнями, можно получить ожог кожи, сетчатки глаз и т.п.
Подведем итоги
Графитированный электрод ‒ популярный расходный материал, применяемый для выполнения сварных соединений проводов из разных металлов: меди, алюминия, стали, чугуна и т.п.
Работать с графитовыми стержнями непросто, но при достаточном уровне мастерства сварные швы получаются долговечными, стойкими к коррозии, высоким температурам, иным негативным факторам извне.
tutsvarka.ru
Электроды ферросплавных печей
Назначение и характеристика электродов
Электроды служат для подвода электрического тока в рабочее пространство дуговой электропечи. Электроды должны иметь высокую электропроводность, достаточную механическую прочность, высокую термическую стойкость, а также низкую стоимость. Этим требованиям удовлетворяют электроды из углеродистых материалов.
Результаты рассмотрения основных свойств различных электродов (табл. 6) показывают, что наилучшими являются графитированные электроды, а качество самоспекающихся (самообжигающихся) электродов близко к качеству угольных электродов. В практике производства электростали графитированные электроды обычно называют графитовыми.
Преимущества графитированных электродов настолько существенны, что, несмотря на их высокую стоимость (в два раза выше стоимости угольных электродов), они используются на средних и крупных электросталеплавильных печах. Графитированные электроды выпускают диаметром от 75 до 555 мм со следующей допустимой плотностью тока (ГОСТ 4426—71):
В некоторых случаях производят электроды диаметром 610, 710 мм и более. На практике иногда допускается более высокая рабочая плотность тока на электродах (до 35 А/см2 для электродов диаметром 555 мм). Расход электродов при этом возрастает.
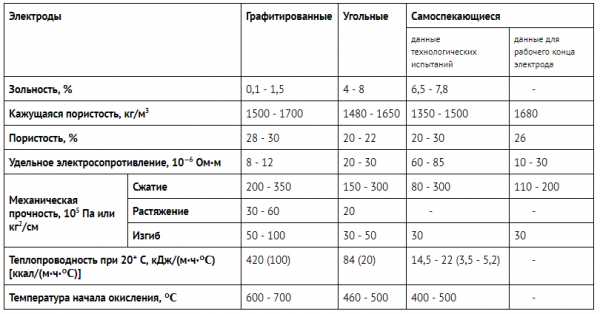
Электрод при плавке подвергается механическим воздействиям (обвал шихты, наклон печи и т. д,), часто направленным под углом к оси электрода, и поэтому он должен иметь достаточную механическую прочность. Повышенная пористость (пониженная плотность) электрода вызывает интенсивное его окисл.ение при высокой температуре. Угольные электроды по ГОСТ 4425—72 изготавливают диаметром от 100 до 750 мм, и рекомендуемая плотность трка на них составляет 7—12 А/см2.
В ферросплавной промышленности широкое применение получили самоспекающиеся электроды, заменяющие угольные и графитированные электроды там, где допускается некоторое науглероживание сплава и разбавление его железом. Угольные электроды применяют при выплавке кристаллического кремния, а графитированные при производстве безуглеродистого феррохрома, металлических хрома и марганца и т. п. Обычно используют. круглые самоспекающиеся электроды диаметром ≥2000 мм, реже (на прямоугольных печах) применяют плоские самоспекающиеся электроды размером до 3200×800 мм. Допустимая рабочая плотность в самоспекающемся электроде составляет 5—8,5 А/см2 (верхнее значение относится к малым электродам).
Изготовление графитированных электродов
Основными составляющими угольных электродов и электродной массы для самоспекающихся электродов являются антрацит и каменноугольный кокс. Для изготовления графитированных электродов применяют малозольные нефтяной, сланцевые и пековый коксы.
Для повышения эксплуатационных свойств электродов в шихту вводят искусственный и реже естественный графит, а также бой графитированных электродов. Для связывания твердых составляющих шихты электродных изделий применяют средне- и высокотемпературный каменноугольные пеки, а для производства электродной массы — среднетемпературный каменноугольный пек или смесь его с каменноугольной смолой.
При производстве электродной продукции сырые материалы дробят и прокаливают (за исключением графита и обожженного боя) в ретортных или трубчатых вращающихся печах, в результате чего увеличивается их плотность, удаляется основное количество летучих, повышается электропроводность и механическая прочность. Прокаленные материалы измельчают на дробилках и в мельницах различных типов с последующим рассевом материалов на барабанных ситах или вибрационных грохотах.
Подготовленные материалы точно дозируют по видам сырья и его гранулометрическому составу и затем подают в смесительные машины, куда задают и связующее, причем жидкие пек и смолу предварительно нагревают для удаления влаги и частично летучих веществ. В результате тщательного перемешивания при температуре ~150° С получается однородная смесь, называемая электродной массой, которую используют для последующей переработки на электроды, или выдается в качестве готовой продукции, применяемой для самоспекающихся электродов.
Электроды получают на гидравлических прессах методом выдавливания массы через мундштук при давлении (50—200) · 105 Па (50—200 кгс/см2) в зависимости от сечения изделия.
Спрессованные электроды охлаждают водой на специальных рольгангах и затем обжигают в многокамерных газовых печах непрерывного действия. В результате обжига связующее превращается в кокс, что обеспечивает резкое повышение механической прочности, электропроводности и термической стойкости электродов. Обжиг ведут при температурах 1200—1300° С под сводом печи в защитной засыпке из мелкого коксика, предохраняющей электроды от сгорания и деформации. Продолжительность обжига зависит от размеров и плотности изделий и обычно составляет 320—400 ч.
Для получения графитированных электродов обожженную заготовку подвергают графитизации в электрических печах сопротивления при 2500—3000° С в течение 50—60 ч, причем сопротивлением в этих печах служат сами электроды и пересыпка — коксик фракции 10—30 мм. Общая продолжительность графитизации, включая загрузку, графитизацию, остывание и разгрузку печи, составляет 7—10 сут. В результате графитизации повышается электропроводность, теплопроводность и химическая стойкость, уменьшается твердость электродов.
Обожженные угольные и графитированные электроды подвергают механической обработке: обточке цилиндрической поверхности, обработке торцов и нарезке ниппельных гнезд. Ниппельное соединение обеспечивается ниппелем с винтовой нарезкой, ввинчиваемым в ниппельные гнезда в торцах электродов. У угольных электродов иногда нарезают на одном конце электрода конический ниппель, а на другом конце —коническое гнездо. Для графитированных электродов применяют цилиндрические и конические ниппели (рис. 43). Ниппели вытачивают из специальных заготовок, обладающих высокой плотностью и механической прочностью, что обеспечивается дополнительной пропиткой обожженных заготовок пеком под давлением 5-106 Па (5 ат) при температуре 280—300° С.
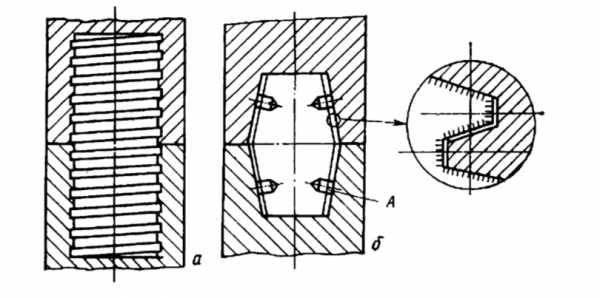
Для повышения эксплуатационных качеств графитированных электродов в ряде случаев на их поверхность наносят различные защитные покрытия, или их пропитывают различными солями, или вводят в массу при их изготовлении различные добавки, снижающие окисление электрода во время его службы. Это позволяет снизить расход электродов на 20—30%.
Самоспекающиеся электроды
Основными преимуществами самоспекающихся электродов при производстве ферросплавов являются возможность изготовления электродов большого диаметра и их низкая стоимость (они в три раза дешевле графитированных и в полтора раза дешевле угольных).
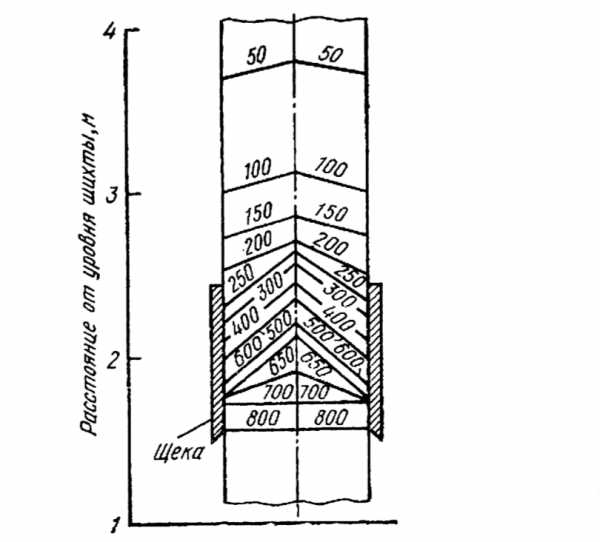
Самоспекающийся электрод представляет собой заполненный электродной массой металлический кожух с внутренними ребрами, выполненный из листового железа толщиной от 1,25 до 3 мм. Кожух, изготавливаемый из отдельных секций длиной 1,4—1,8 м, служит формой для электродной массы, предохраняет электрод от окисления воздухом, обеспечивает прохождение электрического тока от электрододержателя к обожженной части электрода, а также усиливает передачу тепла к верхней части электрода. Спекание и обжиг электродной массы протекают в печи.
На рис. 44 показано примерное распределение температуры в электроде в области электродного зажима. Первая стадия обжига массы на длине ~ 1 м состоит в нагреве ее с 25 до 65° С, в результате чего кусковая масса размягчается и сливается в блок (если масса загружалась в твердом виде без предварительного подогрева).
На втором участке длиной также ~ 1 м температуру массы повышают от 60 до 200° С у кожуха и до 350° С в центре электрода, образуя так называемый конус спекания. Под контактные щеки масса поступает еще пластичной. На последней стадии обжига, под щеками, на участке длиной ~ 1 м, температуру массы повышают до 800° С и из-под щек электрод выходит обожженным.
В зависимости, от особенностей технологического режима (уровень колошника печи, длина рабочего конца электрода, температура охлаждающего воздуха и т. п.) отмеченное распределение температуры может меняться. Нижний торец электрода, работающий в зоне высоких температур, подвергается графитизации.
Эксплуатация электродов
Электроды необходимо транспортировать и хранить, не допуская попадания влаги и оберегая их от механических повреждений. Для предотвращения саморазвинчивания в процессе эксплуатации ниппельные соединения графитированных электродов закрепляют, используя пробки из специальных паст, которые, расплавляясь и коксуясь при нагревании, обеспечивают надежное крепление. Перед установкой на печь электроды желательно просушивать, а ниппельное гнездо должно быть продуто сжатым воздухом.
Хорошее свинчивание электродов в свечу обеспечивается при проведении этой операции вне печи на специальном стенде при помощи устройства, состоящего из опорного хомута, стягивающего хомута и механизма для создания крутящего момента, который должен составлять для электродов диаметром 350—400 мм около 2,45 кДж (250 кгс·м) и для электродов диаметром 500— 555 мм—примерно 4—5 кДж (400—500 кгс·м).
На стойкость электрода влияют не только его физико-механические свойства, но и условия эксплуатации. На электрод, находящийся в рабочем пространстве, воздействует большое число факторов, которые снижают его стойкость и увеличивают расход. К числу таких факторов относятся термические напряжения, связанные с неравномерным распределением температуры по длине и сечению электрода.
Заметное разрушение электродов происходит вследствие попадания на его поверхность капель металла и шлака. Особенно этот процесс получает развитие при близком расположении электродов к поверхности ванны, что соответствует режиму при минимальном напряжении. И, конечно, недопустимо науглероживание металла путем опускания электродов в ванну.
Около 70% общего расхода электродов приходится на окисление. Поэтому большое значение для повышения стойкости электродов приобретает создание хорошего уплотнения между электродом и сводом. Излишнее использование кислорода, особенно при плохом усвоении его металлом, увеличивает расход электродов.
На расход электродов, кроме перечисленных факторов, влияют тип процесса, длительность плавления, сортамент выплавляемых сталей, емкость печи и т. д. Причиной облома электродов может быть плохая центровка электрододержателей, плохой контакт в ниппельном соединении, неправильная завалка шихты и ее обвалы и т. п.
Необходимо стремиться к снижению расхода электродов, так как их доля в общей стоимости передела составляет заметную величину. Расход электродов колеблется в пределах 4—9 кг на 1 т выплавляемой стали. Нижний предел характерен для крупных печей при выплавке углеродистых сталей.
В случае применения самоспекающихся электродов транспортирование и хранение электродной массы должно производиться в условиях, исключающих возможность ее загрязнения. Набивку кожухов электродной массой производят без отключения печи, причем масса загружается как в твердом, в виде кусков размером не более 200 мм, так и в жидком состоянии. Набивка должна производиться не реже одного раза в сутки. Электрод сверху должен быть закрыт крышкой во избежание попадания в кожух пыли, что может привести к облому электрода в дальнейшем.
metallurgy.zp.ua
Что такое графитовый электрод?
Во многих странах в мире есть заводы по переплавке металлов. Однако для того чтобы сталь хорошо плавилась нужны графитированные электроды. Они предназначены для ввода электроэнергии при плавлении ферросплавов и разных видов стали. Графитированные электроды используются в дуговых сталеплавильных или руднотермических электрических печах.
Что собой вообще представляет электрод? Сам по себе графитированный электрод это цилиндр, по краям которого есть гнезда с цилиндрической или конической резьбой. Эта резьба нужна для ввинчивания ниппеля. С помощью ниппеля электрод наращивается по мере расхода при плавлении стали.
Графитированные электроды являются более качественными, чем угольные. У них есть много тех качеств, которые не присущи угольным электродам: высокая чистота, повышенная стойкость к действию химических веществ, низкое сопротивление. Однако графитированные электроды дороже, чем угольные.
Графитированные электроды производятся из угольных. Угольные электроды нагревают до температуры 2500 градусов. Если электрод графитированный то его электросопротивление уменьшается в 5-6 раз, поэтому допустимый ток в 2-3 раза более плотен, нежели у угольных, а если подать одинаковый ток, то можно ставить графитированные электроды значительно меньшего сечения, чем угольные.
При нагревании графитированные электроды не трескаются. Несмотря на меньшую прочность графитированные электроды наиболее выносливы к термическим испытаниям. Они обладают большой упругостью и большой теплопроводностью.
Графитированные электроды более устойчивы к окислению на воздухе и легче поддаются обработке, чем угольные. Например, для угольных электродов температура окисления составляет 400-450 градусов, то для графитированных она составляет 600-650 градусов. Также они более устойчивы к химическим реагентам, в частности к соединениям хлора.
Графитированные электроды изготавливаются по ГОСТ 4426 – 62. Они выпускаются в цилиндрической форме с диаметром от 75 до 555 мм, длиной 1000 – 1700 мм., из уже готовыми ниппельными гнездами. Ниппели и электроды выпускаются с разными видами резьб. Самыми популярными являются трапециальные, цилиндрические и конические.
Также к преимуществам этих электродов можно отнести то, что они режутся намного легче угольных и при сварке именно они дают отличные результаты. Прежде всего, графитированные электроды являются проводником электрического тока, поэтому это самое важное свойство электрода. Если понижается удельное сопротивление, то соответственно уменьшается и диаметр. Следовательно, поверхность электрода, который находится в сталеплавильной, печи обеспечивает уменьшение расходов электрода.
Да, действительно у графитированных электродов много плюсов. Они намного превосходят своих предшественников – угольных электродов. Однако также стоит не забывать, что без угольного электрода не будет и графитированного.
welding-gear.ru
Графитовые электроды
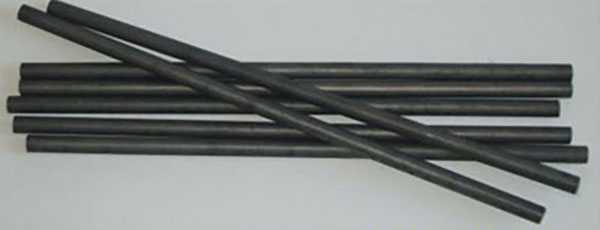
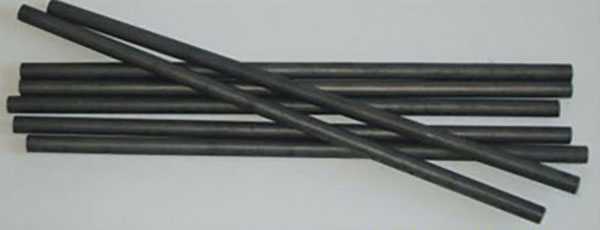
Используемые графитовые электроды, которые относятся к категории неплавких, нашли широкое распространение при выполнении сварочных работ. Изготавливаются такие графитовые стержни в широком ассортименте, что существенно расширяет их сферу использования. Распространение они получили в судостроении, и используются в тех случаях, когда требуется обеспечить максимальную прочность соединения металлических элементов. Графитовые электроды применяются для ликвидации конструктивных дефектов, появившихся после процедуры литья металлических элементов.
Благодаря своей температурной устойчивости такие графитовые электроды нашли свое применение для обработки металла и подготовки его к различным технологическим процессам. Графит сохраняет свою прочность даже при температурах, плавления металла, что позволяет использовать его для разрезания различных металлических изделий. Данный способ резки получил название воздушно-дуговой. Отдельные модификации инверторов позволяют с применением графитовых стержней выполнять так называемую строжку, при которой производится обработка кромок металла. С помощью таких элементов вы можете с легкостью срезать заклепки и выполнять прошивку изделий, изготовленных из углеродистых, низкоуглеродистых и легированных разновидностей стали.
В отличие от других металлов графит проводит электричество и не плавится, сохраняя все свои свойства и характеристики. В настоящее время изготавливаются разнообразные графитовые электроды, которые различаются своей формой наконечника и длиной. Также принято выделять обыкновенные и омедненные разновидности, которые имеют пятипроцентное медное покрытие для улучшения характеристик металлического сплава.
Преимущества
- Плотность и устойчивость материала к воздействию тока.
- Угольные графитовые электроды имеют доступную стоимость и отличаются простотой в изготовлении.
- Обладают отличной электропроводимостью, что уменьшает расход стержня во время работы.
- Материал не окисляется при высоких температурах, что позволяет продлить срок службы таких электродов.
- Во время сварки не требуется использовать специальные держатели.
Из имеющихся недостатков таких стержней из графита можно выделить следующее:
- Минимальный диаметр электрода составляет 6 миллиметров, что несколько усложняет использование таких стержней при необходимости выполнения тонкого соединения.
- Использование графитовых электродов для сварки может привести к увеличению количества содержания углерода в металле, что неизменно ухудшает начальные свойства соединяемых элементов.
Такие наконечники обладают узким спектром работы, при этом для сварки различных материалов следует использовать электроды со специальным наконечником.
Состав и свойства электродов из графита
Конструкция таких стержней состоит из двух рабочих частей, между которыми располагается прокладка, которая изолирует металлы друг от друга. В качестве прокладки может использоваться алюминий в виде порошка. Основные части электрода состоят из прессованного угля. Именно содержание угля и приводит в последующем к увеличению в металле содержания углерода.
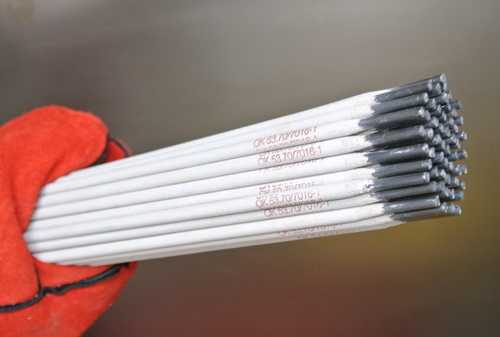
На технические характеристики напрямую оказывает влияние состав стержней. Из наиболее важных характеристик у электродов можно отметить размеры канавок, толщина срезаемого металлического сплава и диапазон рабочего тока. В каждом конкретном случае, такие характеристики будут существенно различаться, в зависимости от толщины стержней и материалов, из которых они изготовлены.
Популярные разновидности графитовых стержней
- ЭГ. Изготавливают графитированные электроды из кокса и пека. Это марка используется для работы с материалами, плотность которых не превышает 25 А/см. Это относительно простые в использовании электроды, которые могут применяться для сварки в бытовых условиях.
- ЭГС. Применяют электроды в плавильной сфере, где требуется обеспечить максимально качественные и прочные соединения элементов и устранить имеющиеся трещины в литых элементах.
- ЭГП. Эти пропитанные специальным графитом электроды предназначаются для резки металлических элементов. Они используются в плавильных печах, металлолитейной отрасли и с электродуговыми аппаратами.
- ЭГПС. Эта разновидность электродов изготавливается из кокса, который пропитан каменноугольным пеком. Применяются при сварке электродуговыми аппаратами и позволяют обеспечить качество выполненного соединения.
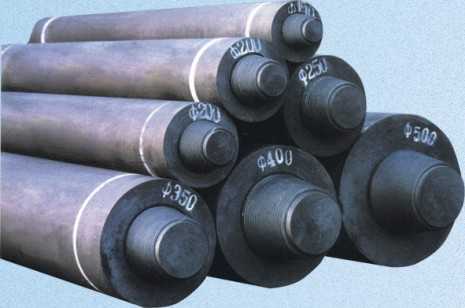
Маркировка и обозначение
Следует сказать, что определить назначение и тип конкретного электрода из графита можно по его маркировке. На сегодняшний день принята следующая маркировка стержней:
- Г – графитированный.
- Э — электрод.
- С – специальный.
- А – пропитанный.
Имеющиеся различия графитовых и угольных электродов
Необходимо сказать, что графитовые электроды отличаются практичностью и универсальностью при работе с проводами проводов. Они лучше угольных поддаются обработке, и позволяют с легкостью выполнять прочные гибкие соединения. В то же время угольные разновидности отличаются повышенной прочностью, но при этом они по причине высокого сопротивления уступают в электропроводимости. Для использования угольных электродов необходимо применять специальные держатели, что несколько усложняет сварку. Угольные электроды отличаются черным цветом, тогда как графитовые стержни имеют серый цвет.
Виды
При выборе таких изделий для резки и сварки необходимо в первую очередь ориентироваться на показатель мощность аппарата, который может работать с определенными диаметрами электродов. Обратите внимание на тот факт, что отдельные металлические сплавы неизменно потребуют использования стержней с различными видами наконечников. Также учитывайте тот факт, что необходимо выдерживать определенные режимы сварки при работе с теми или иными разновидностями графитовых электродов. Все это и станет гарантией качественно выполненной работы по сварке и резке металлов.
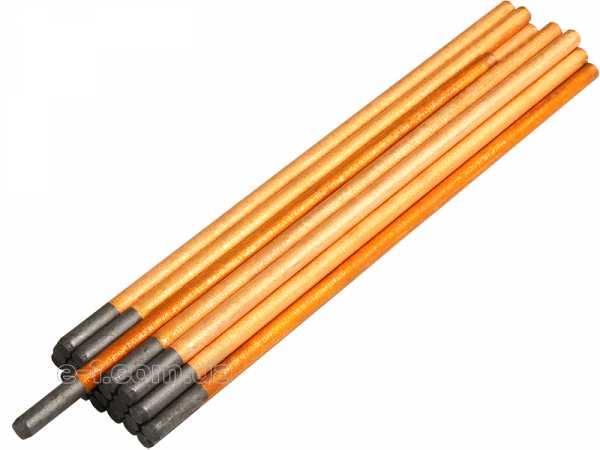
svarkagid.com
Графитированные электроды
Графитированные (графитовые) электроды и их применение
Графитированные (графитовые) электроды преимущественно находят применение при выплавке стали в дуговых электросталеплавильных печах и в процессах рафинирования стали при внепечной обработки в агрегатах печь-ковш. Графитированные электроды также используются и в других процессах плавки, например, плавки на штейн в руднотермических печах.
Дуговая электрическая печь при производстве стали обеспечивает большую эксплуатационную гибкость по сравнению с кислородным конвертером, так как может быть остановлена и перезапущена вновь относительно быстро, что дает возможность оперативно отвечать на запросы потребителей и динамику рынка. Именно поэтому дуговые печи широко применяются и небольшими сталелитейными заводами, и в литейном производстве. Соответственно, спрос на такой расходный материал, как графитированные электроды, неуклонно повышается.
Электрические дуговые печи работают с использованием либо переменного электрического тока или постоянного электрического тока. Подавляющее большинство электродуговых печей используют переменный ток. Каждая из этих печей, как правило, использует девять электродов (в трех колоннах по три электрода в каждой) за один раз. Остальные электродуговые печи, которые используют постоянный ток, как правило, используют одну колонну из трех электродов. В процессе плавки электроды постепенно потребляются, что требует добавление нового электрода. Графитированные электроды соединяются между собой посредством ниппельного соединения, для чего с обоих концов каждого электрода делается резьбовое ниппельное гнездо. Размер электродов варьируется в зависимости от размера печи, параметров трансформатора тока и планируемой производительности печи. Электроды могут быть как небольшие – 75 миллиметров в диаметре, так и довольно крупные – до 750 мм в диаметре и до 2800мм в длину. Соответственно, один графитированный электрод может весить в зависимости от размера от пяти килограмм и до двух тонн.
Особенности в сфере производства и реализации графитированных электродов
Электроды в настоящее время являются единственными доступными продуктами, которые обладают высоким уровнем электропроводности и способностью поддержания высокого уровня тепла в электрической дуговой печи в процессе производства стали. В настоящее время происходит активное развитие технологий производства графитированных электродов и постоянное повышение их качества для удовлетворения современных требований, поскольку любые изменения в металлургических, электрических и механических условиях эксплуатации могут оказать существенное влияние на поведение электродов. Новые технологии плавки в современных печах большого объема и повышенной мощности приводят к более быстрому прогреву электродов, чем в малых печах и требуют значительного повышения устойчивости электродов к термическим и механическим воздействиям. Повышение эффективности работы электродуговых печей приводит к снижению величины потребления графитированных электродов на тонну произведенной стали в электродуговых печах (удельного расхода).
Поставляемые ООО «Новые индустриальные технологии» графитированные электроды соответствуют условиям эксплуатации современных дуговых печей и обладают высокой механической прочностью, отличной теплопроводностью, низким электрическим сопротивлением, что имеет решающее значение для экономичного расхода.
Марки графитированных электродов
Графитированные электроды марки ЭГ (RP – regular power), а также ниппели производятся на основе каменноугольного пека и нефтяного кокса. Подходят для осуществления работы на плотностях тока до 25 А/см2 в дуговых сталеплавильных, рафинировочных ферросплавных, руднотермических печах и прочих электротермических устройствах.
Показатель | Диаметр, мм | RP |
Удельное электросопротивление, | ≤ 300 | 8,5 |
Предел прочности при изгибе, | ≤ 300 | 8,5 |
Плотность, | ≤ 300 | 1,53 |
Модуль Юнга, ГПа, не более | ≤ 300 | 9,3 |
Графитированные электроды марки ЭГП (HP – high power),а также ниппели производятся на основе каменноугольного пека и нефтяного кокса и имеют дополнительную пропитку пеком. Подходят для осуществления работы в дуговых сталеплавильных печах высокой мощности и установках печь-ковш.
Показатель | Диаметр, мм | HP |
Удельное электросопротивление, | ≤ 400 | 6,5 |
Предел прочности при изгибе, | ≤ 400 | 10,5 |
Плотность, | ≤ 400 | 1,62 |
Модуль Юнга, ГПа, не более | ≤ 400 | 12,0 |
Электроды графитированные марки ЭГСП (UHP – ultra high power), а также ниппели производятся на основе игольчатого кокса и каменноугольного пека и имеют дополнительную пропитку пеком.
Показатель | Диаметр, мм | UHP |
Удельное электросопротивление, | ≤ 400 | 5,5 |
Предел прочности при изгибе, | ≤ 400 | 11,0 |
Плотность, | ≤ 400 | 1,66 |
Модуль Юнга, ГПа, не более | ≤ 400 | 14,0 |
ООО “Новые индустриальные технологии” (Екатеринбург) является официальным поставщиком и дилером известных отечественных и зарубежных производителей графитированных электродов, что гарантирует высокое качество поставляемой продукции.
newindtech.ru
Электроды графитированные от производителя
Сделать запрос на электроды вы можете написав нам на почту info@aversgraphite.ru или позвонив по телефону +7(351)220-94-94
Описание изделияГрафитированные электроды применяются для плавки металлов в электродуговых рудотермических, сталеплавильных печах.
Актуальные цены на октябрь 2017г. : Уточняйте позвонив нам по телефону или отправив запрос на почту. Сроки изготовления и поставки :2-3 недели, у нас свое производство, электроды до 200-го диаметра мы производим сами, без посредников.
Материал изготовления:Подбор марки графита производится индивидуально под требования заказчика, доступные варианты:ЭГ(ЭГ-15, ЭГ-20, ЭГ-25) ЭГП, ЭГС, ЭГСП, а также их аналоги производства китай: RP(эг). HP(эгп), SHP(эгс), UHP(эгсп),
Размеры изделия:Доступные размеры графитированных электродов в диаметре от 75 до 200мм.
Условия доставки:Организовать отправку графитированных электродов мы можем как по России так и по странам СНГ а именно: Азербайджан, Армения, Белорусия, Казахстан, Киргизия, Молдавия, Таджикистан, Туркменистан, Узбекистан
Важно:
Для получения максимально низкой цены в коммерческом, указывайте предполагаемый годовой обьем закупа в заявке.
При отправке запроса на изготовление желательно также сразу указать марку материала, размеры требуемых электродов, если нужен счет или комерческое – то прикрепляйте карточку предприятия к письму.
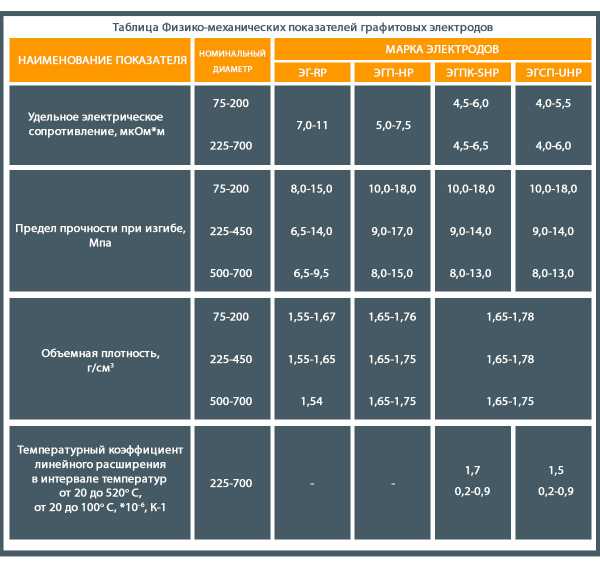
Электроды графитированные
Наша компания «НПП Аверс» осуществляет серийное производство и поставки обширной номенклатуры изделий из графита. Мы предлагаем электроды графитированные по умеренным ценам в количествах, необходимых заказчику. Изготавливаемая нашим предприятием продукция соответствует требованиям национального стандарта ГОСТ Р МЭК 60239-2014 и международного IEC 60239:2005.
Электроды графитированные ЭГ имеют цилиндрическую форму заданного диаметра и длины, и изготавливается методом обточки из стержней. Материалом для производства данных изделий является углерод, получаемый из кокса по классической технологии путем термического передела, обжига при определенной температуре и графитизации. В торцах изделий делаются гнезда с цилиндрической или метрической резьбой для объединения нескольких деталей при помощи ниппелей в сборку – колонну.
Назначение и области применения графитированных электродов
Данные элементы широко используются в металлургии для обеспечения процесса выплавки различных сортов чугуна и стали, в том числе и высоколегированных. Производимые нашей компанией электроды графитированные для электродуговых печей используются для создания дуги в сталеплавильной печи. При этом в рабочей зоне температура может достигать 1800C, что обеспечивает переход шихты из твердого состояния в жидкое. Полученный в результате данного процесса полупродукт проходит дополнительную обработку для получения расплава с требуемым химическим составом.
Графитированные электроды используются в дуговых сталеплавильных, ферросплавных, руднотермических и рафинировочных печах переменного и постоянного тока. Изделия вводятся в рабочую зону через отверстия в верхней части технологического оборудования. На них подается ток от мощного трансформатора, напряжение колеблется в пределах от 50 до 300 В, а в некоторых печах может достигать 1200 В. Токопроводящие элементы по мере использования выдвигаются вниз при помощи специальных механизмов.
В ходе выплавки металла происходит расход материала электрода со стороны электрической дуги. Для сохранения непрерывности процесса предусмотрена возможность наращивания электрода с другой стороны посредством соединения нескольких элементов в колонну с использованием конусообразных ниппелей. Существуют также моноэлектроды с одного конца, которого нарезана резьба, а с другого имеется соответствующее гнездо.
Номенклатура изделий
Наша компания осуществляет выпуск наиболее полного ассортимента изделий для металлургической промышленности. В частности мы производим следующие виды токоведущих элементов для дуговых сталеплавильных и других видов электрических печей:
Электроды графитированные ЭГ 25 с удельным сопротивлением от 7,0 до 8,0 мкОм*м в зависимости от диаметра.
Предел прочности детали на изгиб составляет от 6,4 до 7,8 МПа.
Электроды графитированные ЭГ150 с объемной плотностью в 1,61 г/см3 и содержанием зольных примесей не более 0,2-0,3%.
Модуль упругости изделия зависит от внешнего диаметра и колеблется в пределах от 7 до 9 ГПа.
Электроды графитированные ЭГ 200 с предельным значением плотности тока в процессе плавления до 200 А.
Описываемые изделия различаются по наружным размерам. Существует 18 разновидностей электродов графитированных с номинальным диаметром от 75 до 750 мм. Действующий ГОСТ допускает отклонение фактических параметров в пределах от 2 до 15 мм в соответствии со спецификацией.
Наша компания осуществляет выпуск нормальных и коротких электродов семи типоразмеров. Длина изделий составляет от 1000 до 2700 мм с предельным отклонением от 50 до 75 мм. Процентное соотношение коротких и нормальных изделий в каждой партии оговаривается с потребителем особо.
Преимущества и особенности электродов графитированных
Широкое применение данных изделий в металлургии обусловлено, прежде всего, невысокой стоимостью. Качественные электроды графитированные, цена которых в нашей компании значительно ниже среднерыночной, имеют ряд преимуществ перед аналогами:
Материал не окисляется при больших температурах.
Малое электрическое сопротивление значительно снижает потери тока во время плавки.
Простота изготовления.
Незначительный расход изделия в процессе работы.
Отсутствие склонности к растрескиванию, деформации и разрушению.
ООО «НПП Аверс» предлагает всем заинтересованным лицам и организациям электроды графитированные купить по умеренной цене. Наша компания готова выполнить разовые заявки от клиентов и наладить регулярные поставки продукции по согласованному графику. Оформить заявку можно непосредственно на сайте компании в соответствующем разделе или позвонив по контактному телефону. Наши специалисты проконсультируют вас по всем интересующим вопросам.
amasgroup.ru