Сварочные технологии: виды и способы сварки
Сварка — одно из важнейших ремесел для человека. С помощью сварочных технологий нам удается создавать по-настоящему удивительные вещи: от простейших бытовых приборов до космических ракет. В этой статье мы расскажем, как происходит сварка, какие существуют виды сварки и их краткая характеристика.


Содержание статьи
Общая информация
Что такое сварка? Каковы основы сварки? Эти вопросы задаю многие начинающие умельцы. По сути своей, сварка — это процесс соединения разных металлов. Соединение (его также называют швом) формируется на межатомном уровне с помощью нагрева или механической деформации.
Теория сварки металлов очень обширна и невозможно в рамках одной статьи описать все нюансы. Также как невозможно описать все способы сварки металлов, поскольку на данный момент способов около сотни. Но мы постараемся кратко классифицировать методы сварки, чтобы новички не запутались.
Итак, на данный момент возможна термическая, термомеханическая и полностью механическая сварка деталей из металла или других материалов (например, пластика или стекла). При выборе способа сварки учитывается каждый нюанс: толщина деталей, их состав, условия работы и прочее. От этого зависит технология сварки металла.


Термическая сварка — это процесс соединения деталей только с помощью высоких температур. Металл плавится, образуется надежное сварное соединение. К термическим методам относится, например, дуговая и газовая сварка (о них мы поговорим позже).
Термомеханическая сварка — это процесс соединения деталей с помощью высоких температур и механического воздействия, например, давления. К такому типу принадлежит контактная сварка. Деталь нагревается не так сильно, как в случае обычной термической сварки, а для формирования шва используется механическая нагрузка, а не плавление металла как такового.
Механическая сварка — процесс соединения деталей без применения высоких температур и вообще тепловой энергии. Здесь ключевой элемент — механическое воздействие. К такому типу относится холодная сварка, ультразвуковая сварка или соединение деталей трением.
Также существует классификация способов сварки по техническим признакам. Используя такую классификацию можно довольно кратко описать все имеющиеся типы сварки. Они делятся на:
- Сварку в защитной среде (для защиты может использоваться флюс, инертный газ, активный газ, вакуум, защита может быть комбинированной и состоять из нескольких материалов сразу).
- Сварку прерывистую и непрерывную.
- Сварку ручную, механизированную, полуавтоматическую, автоматическую, роботизированную.
Если вы ранее не сталкивались со сваркой и все перечисленное выше кажется чем-то запутанным и непонятным, то не беспокойтесь. Далее мы расскажем, какие самые популярные методы сварки используются в домашних и промышленных условиях.
Вам будем дана характеристика основных видов сварки и некоторые особенности, которые нужно учесть. Кстати, многим видам сварки мы посвящали отдельные статьи, которые вы можете прочесть, открыв рубрику «Виды и способы сварки» на нашем сайте.
Ручная дуговая сварка с применением неплавящихся электродов
Способ ручной дуговой сварки разных металлов с применением неплавящихся электродов — один из самых популярных методов как среди домашних умельцев, так и среди профессионалов своего дела. Ручная дуговая сварка — это вообще один из древнейших способов сварки. Благодаря большому выбору сварочных аппаратов для дуговой сварки такой метод стал доступен широкому кругу сварщиков.
Электрод — это стержень, выполняющий роль проводника тока. Он может быть изготовлен из различных материалов и иметь специальное покрытие.


Технология дуговой сварки неплавящимся электродом крайне проста: детали подгоняют друг к другу, затем электродом постукивают или чиркают о поверхность металла, зажигая сварочную дугу. В качестве основного оборудования используют сварочные инверторы.
Для сварки инвертором выбирают неплавящиеся электроды, сделанные из угля, вольфрама или графита. Во время сварки электрод нагревается до высокой температуры, плавя металл и образуя сварочную ванну, в которой как раз и формируется шов. Такой метод используют для сварки цветных металлов.
Ручная дуговая сварка с применением плавящихся электродов
Виды сварки плавлением металла не заканчиваются на применении неплавящихся стержней. Для работы также можно использовать плавящиеся электроды. Технология сварки металла с использованием плавящихся стержней такая же, что и при работе с неплавящимися материалами.


Отличие лишь в составе самого электрода: плавящиеся стержни обычно изготавливаются из легкоплавких металлов. Такие стержни также пригодны для сварки инвертором в домашних условиях. Здесь шов образуется не только за счет расплавленного металла детали, но и за счет расплавленного электрода.
Дуговая сварка с использованием защитного газа
Способ дуговой сварки разных металлов с использованием защитного газа выполняется с помощью плавящихся и неплавящихся электродов. Технология сварки такая же, как и при классической ручной дуговой сварке. Но здесь для дополнительной защиты сварочной ванны в зону сварки подается специальный защитный газ, поставляемый в баллонах.


Дело в том, что сварочная ванна легко подвержена негативному влиянию кислорода и под его воздействием шов может окислиться и получиться некачественным. Газ как раз и помогает избежать этих проблем. При его подаче в сварочную зону образуется плотное газовое облако, не дающее кислороду проникнуть в сварочную ванну.
Автоматическая и полуавтоматическая сварка с использованием флюса или газа
Автоматическая и полуавтоматическая сварка с применением флюса или газа — это уже более продвинутый способ соединения металлов. Здесь часть работ механизирована, например, подача электрода в сварочную зону. Это значит, что сварщик подает стержень не с помощью рук, а с помощью специального механизма.
Автоматическая сварка подразумевает механизированную подачу и дальнейшее движение электрода, а полуавтоматическая подразумевает только механизированную подачу. Дальнейшее движение электрода сварщик осуществляет вручную.


Здесь защита сварочной ванны от кислорода просто обязательна, поэтому используется газ (по аналогии с дуговой сваркой с применением газов) или специальный флюс. Флюс может быть жидким, пастообразным или кристаллическим. С помощью флюса можно значительно улучшить качество шва.
Прочие методы соединения металлов
Помимо традиционных способов сварки в современной промышленности применяются методы, позволяющие соединить уникальные металлы. Зачастую такие металлы обладают ярко выраженными химическими или тугоплавкими свойствами, отчего привычные способы сварки не подходят для их соединения. Конечно, такие металлы не используются в домашней сварке, но они широко применяются для создания ответственных деталей на крупном производстве.
Мы расскажем про виды сварки плавлением, когда суть сварки заключается в подаче большого количества тепла на маленький участок сварки. К таким методам относится лазерная сварка и плазменная сварка.
Лазерная сварка металлов выполняется с помощью автоматического и полуавтоматического оборудования. Такой процесс сварки может быть полностью роботизирован и не требует присутствия человека. Здесь деталь нагревается, а затем и плавится под воздействием тепла, исходящего от лазерного луча и направленного в определенную точку.
Тепло концентрируется строго в одной точке, позволяя сваривать очень мелкие детали размером менее одного миллиметра. Также с помощью призмы лазер можно расщепить и направиться в разные стороны, чтобы сварить несколько деталей сразу.
Плазменная сварка металлов выполняется с применением ионизированного газа, называемого плазмой. Газ струёй подается в сварочную зону, образовывая плазму. Она работает в связке с вольфрамовым электродом и газ нагревается за счет электрической дуги.
Сам ионизированный газ обладает свойством проводника тока, поэтому в случае плазменной сварки именно плазма является ключевым элементом в рабочем процессе. Также плазма активно защищает сварочную ванну от негативного влияния кислорода. Такой метод сварки используется при работе с металлами, толщиной до 9 миллиметров.
Технологический процесс сварки
Мало знать способы сварки, нужно еще понимать, какие необходимы документы на сварку и из каких этапов состоит сварочный процесс. Конечно, это справедливо только в отношении профессиональных сварщиков, выполняющих работу в цеху или на производстве. Вам это не нужно, если вы собираетесь варить забор на даче, но дополнительные знания тоже не помешают.
Итак, вот наше краткое описание технологического процесса сварки:
- Разработка чертежа
- Составление технологической карты
- Подготовка рабочего места сварщика и подготовка металла
- Непосредственно сварка
- Очистка металла
- Контроль качества
Сам по себе техпроцесс — это полное описание этапов сварки. Технический процесс разрабатывается после того, как будут готовы чертежи будущей металлоконструкции. Чертеж делают, опираясь на правила (ГОСТы, например), при этом во главу ставят качество будущей конструкции и разумную экономию.
Технологический процесс сварки оформляется на специально разработанных для этого бланках. Стандартный бланк для описания техпроцесса называется «технологическая карта». В технологической карте и описываются все этапы производства. Если производство серийное или крупномасштабное, то изложение может быть довольно подробным, с описанием каждого нюанса.


В технологическую карту заносят тип металла, из которого изготовлены детали, способы сварки металлов, используемые для соединения этих деталей, применяемое для этих целей сварочное или иное оборудование, типы присадочных материалов, электродов, газов или флюсов, используемых в работе. Также указывается последовательность формирования швов, их размеры и прочие характеристики.
Также в технологической карте указывают марку электродов, их диаметр, скорость их подачи, скорость сварки, количество слоев у шва, рекомендуемые настройки сварочного аппарата (параметр полярности и величины сварочного тока), указывают марку флюса. Перед самой сваркой детали тщательно подготавливают, очищая их от коррозии, загрязнений и масла. Поверхность металла обезжиривают с помощью растворителя. Если у детали есть значительные видимые дефекты (например, трещины), то она не допускается к сварке.
После сварки предстоит контроль сварочных швов. Этой теме мы посвятили отдельную статью, но здесь кратко расскажем об основных методах контроля. Прежде всего, применяется визуальный контроль, когда сварщик может сам определить наличие дефектов у сварочного соединения. Специалистами проводится дополнительный контроль с помощью специальных приборов (это может быть магнитный контроль, радиационный или ультразвуковой).
Конечно, не все дефекты считаются плохими. Для каждых сварочных работ составляется перечень с дефектами, которые допустимы и не сильно повлияют на качество готового изделия. Контролером может быть сварщик или отдельный специалист. Его имя обязательно указывается в документах, он является ответственным лицом на этапе контроля.
Вместо заключения
В этой статье мы рассказали самое основное. Конечно, мы не сможем перечислить и описать все виды сварочных работ в рамках одной этой статьи, но на нашем сайте вы можете найти материалы, где мы рассказываем все о сварке и объясняем основы сварки различных металлов.
Для любого мастера теория сварочных процессов имеет большое значения, но без практики она не работает. Так что не теряйте время и вслед за чтением статей применяйте знания на практике. Желаем удачи в работе!
[Всего голосов: 0 Средний: 0/5]svarkaed.ru
Виды сварки металла, обозначения ГОСТ и общая классификация

Если вы занимаетесь сварочными работами и считаете, что хорошо знаете все и ориентируетесь в новых технологиях, то вы, наверное, ошибаетесь. Сварочных способов очень много. В каждом плюсы, минусы, нюансы, которые нужно знать и понимать.
Для чего? – спросите вы. Для грамотного выбора самого оптимального способа «здесь и сейчас» – ответим мы. Читаем, разбираемся, принимаем решения. Поехали.
Физика, химия, немного лирики
Сварка – процесс неразрывного соединения разных конструкций нагреванием, деформированием или использованием того и другого.
Если коротко с точки зрения физики, в сварке используется либо тепло, либо давление, либо тепло с давлением вместе. Если коротко с химической точки зрения, в сварочном деле используется огромное количество разного рода порошковых лент, флюсов, газов и других комплектующих. Это зависит от материалов и условий. Благодаря химии мы имеем огромное число технических вариантов.
Важно! Мы не будет грузить вас полными списками видов сварки или всеми классификациями, какие существуют. Нам не хватит бумаги писать, вам не хватит терпения читать. Разобраться в логике группировки сварочных способов, чтобы потом легко находить информацию по каждому конкретному виду. В сети много сайтов, посвященных сварке: есть где найти все, что нужно.
Принципы классификаций, обзор

Классификация способов дуговой сварки.
Классификация видов сварки проводится по самым разным критериям, они аккуратно укладываются в смысловые рамки. Какие критерии самые важные? Пройдемся по некоторым, для начала лучше увидеть общую картинку.
Сколько видов сварки существует на сегодняшний день? Можно назвать цифру 150 со словом «около». Можно 250. Но цифры называть не советуем. Пока вы читаете эту статью, число видов может измениться – технологии на месте не стоят. А вот какая бывает сварка по материалам, физическим процессам, популярности, способам управления – говорить нужно, это как раз те самые принципы классификации, которые нам нужно понимать.
Пример простой понятной классификации по источнику энергии в сварке:
- электрический ток;
- электрическая дуга;
- трение;
- газовое пламя;
- лазерное излучение;
- электронный луч;
- ультразвук.
Еще один пример списка по типу сварочных швов. Их много, целые гроздья разных видов:
- стыковые, угловые швы – по соединению краев;
- по форме, длине – швы горизонтальные, вертикальные, кольцевые, прямолинейные, прерывистые, сплошные, длинные, короткие, средние;
- по виду используемого материала – швы для стали, цветных металлов, биметаллов, полиэтилена и др.;
- по объему наплавливаемого металла – усиленные, ослабленные, нормальные швы;
- по форме – продольные, поперечные швы;
- по количеству наложения слоев – сплошные, прерывистые, прихваточные, многослойные.
«Швейный» список можно продолжить, но нам важно понять общие принципы, поэтому заканчиваем с лирикой, двигаемся к главным способам.
Приварим намертво, недорого, звоните

Прихватка конструкций перед сваркой.
Основные способы сварки – частое, но неверное определение классификации в данном контексте. Правильнее будет «самые популярные».
Перед вами тройка заслуженных призеров:
- Ручная дуговая – золото.
- Газовая – серебро.
- – бронза.
Каждый призер относится к разным сварочным семействам, по идее их лучше описывать на своих законных местах вместе с близкими «родственниками». Но мы поступим неправильно – представим сварочных чемпионов в начале обзора.
Ручная дуговая сварка РД
Народная любимица №1, самый распространенный вид в быту и в промышленности. Три главных слова в РД – простота, дешевизна, транспортабельность. Физика процесса заключается в плавке специального покрытого электрода, который оставляет за собой след в виде варочного шва. Электроды применяются разные, в зависимости от металла. Дуга – это расстояние между электродом и поверхностью металла, который играет роль второго электрода.
По сути дуга представляет собой сильнейший разряд в газовом пространстве (воздухе). При РД плавятся три предмета: края двух соединяемых поверхностей с электродом. Чем лучше смешиваются продукты тройной плавки (для этого электрод двигают влево и вправо), тем качественнее шов.
Сварка РД имеет серьезные преимущества перед другими видами:
- способу РД легко научиться;
- варить можно в любых положениях в пространстве;
- варить можно самые разные металлы, в продаже есть электроды на любой вкус;
- доступное транспортабельное оборудование
Газовая сварка
Народная чемпионка №2, заслуженная серебряная медаль. Вот когда сварщики возят с собой газовые баллоны: им нужна смесь кислорода с каким-нибудь горючим газом – ацетиленом, пропаном или бутаном. Физика процесса – тоже плавление, но тепло подается не электродом, а газовой горелкой. Металл поверхностей плавится факелом горелки, процесс происходит плавно и довольно медленно. Чем толще слой металла, тем медленнее он плавится.
В чем газовая сварка лучше других способов:
- отлично варятся цветные металлы;
- оборудование проще, чем электрических методов;
- возможность контролировать смесь и пламя;
- не нужен мощный источник энергии, метод автономен.
Без минусов не обойтись, «газовые» недостатки следующие:
- очень медленный нагрев поверхностей;
- низкая концентрация тепла из-за рассеивания;
- высокая стоимость электричества.
По стоимости электричества дуговые способы могут поспорить с газовыми: при РД электричество тоже тратится нещадно. Но в итоге газовый метод из-за своей «тихоходности» обходится значительно дороже.
Важно! Там, где есть пара слов «горючий газ», обязательно присутствует вторая пара «техника безопасности». Правила по безопасности хорошо регламентированы, но выполнение требований несет дополнительные затраты денег и времени. Кстати, газовой сварке больше 100 лет – вот она, нержавеющая классика, аплодисменты.
Полуавтоматическая сварка

Классификация сварочной дуги.
Бронзовый чемпион, замыкает популярную тройку, но по своим перспективам легко обойдет первых призеров. По сути это вид знакомого нам дугового вида, прогрессивная эволюция РД. Отличается большим количеством технологических нюансов, вариантов, инструкций. Нам достаточно знать то, что «автоматическая часть» метода – это подача сварочной проволоки.
Ручная часть – сам процесс сварки с контролем подачи проволоки. Варить можно с газом (углекислым газом для новичков, аргоном для профессионалов), можно без газа, с подачей прямого тока. Вариант без газа любят в гаражах и на дачных участках, в этом случае нужна специальная порошковая или флюсовая проволока. Когда она горит, образуется газ с парами, которые защищают область горения.
Полуавтомат – безальтернативный метод на СТО: кузовные работы проводятся только с его помощью. В полуавтомате используются газ и специальная проволока вместо привычного электрода. Газ из горелки с проволокой подаются в сварочный рукав. В итоге процесс защищен от воздействия внешней среды. Режимы процесса определяет сварщик в зависимости от толщины металла.
У полуавтоматического метода серьезные преимущества перед другими видами:
- отличное качество шва;
- высокая скорость работы;
- удобство в работе;
- варятся как цветные и черные металлы;
- можно варить заржавевшие или оцинкованные металлы;
- широкий выбор материалов, скромные финансовые затраты.
Варим металлы
С народными любимцами разобрались, приступаем к «правильным» классификациям.
Начнем с настоящих тяжеловесов – типов сварки металлов, которые подразделяются на три группы по:
- Физическим признакам.
- Техническим признакам (механизация, непрерывность процесса, защита металла).
- Технологическим признакам (отдельные классификации для каждого способа – например, виды электродов).
По физическим признакам мы имеем три главных класса для всех видов сварки металлов:
Термический класс – сварочный процесс заключается в плавлении тепловой энергией:
- газовой;
- дуговой;
- лазерной;
- лучевой, термитной и т.д.
Важно! Основные виды сварки плавлением – самые распространенные в быту и в промышленности. Это самый густонаселенный класс, подавляющее большинство сварочных методов относится к нему.
Механический класс с использованием механической энергии:
- ;
- холодной;
- трением;
- взрывом и т.д.

Таблица сварки металлов.
Термомеханический класс, способы совместного действия тепловой энергии и давления:
- кузнечные;
- диффузионные;
- контактные и т.д.
В качестве примера варки металлов представляем МАДП – механизированную аргонодуговую сварку плавящимся электродом. Настоящий гибрид для электро-газового соединения металлов. Без него невозможная сварка цветных металлов или сложных сплавов.
Преимущества МАДП:
- соединение любых сплавов;
- устойчивость формы изделия из-за слабого нагрева;
- электроды нужно менять редко;
- широчайшая сфера использования;
Недостатки:
- сложно для новичков;
- невысокая скорость выполнения.
Варим полиэтилен

Области применения сварки пластмасс.
Что можно варить кроме металлов? Керамику. Стекло. Но на втором почетном месте стоят пластмассы или полимеры, прежде всего это полиэтиленовые трубы. С полиэтиленом можно работать терморезисторным, электромуфтовым методами, можно электросопротивлением: эти термины перечисляются в технической литературе. Не пугайтесь, все варианты можно называть коротко – сварка НЗ. НЗ – закладные нагреватели.
Суть процесса – расплавление полиэтилена в местах соединения с помощью металлических спиралей электрического нагревателя, который заложен в деталь. Способ чрезвычайно популярен, у него большие перспективы в промышленности: применяется в различных трубопроводах, замене старых металлических труб новыми полиэтиленовыми, установке и ремонте, развитии новых полимерных технологий.
В работе с пластмассами применяется еще один способ НИ или сварка нагретым инструментом. Самый простой вариант подвода тепла для нагрева полимерных поверхностей. Для работ с НИ существует множество вариантов сварочных инструментов – от простого электропаяльника для маленьких деталей до специальных сварочных аппаратов различной величины. Уважающие себя сантехники держат в своих рабочих чемоданах такого рода аппараты в обязательном порядке.
Кстати, способы сварки НЗ и НИ входят в том числе в список владения обязательными методами профессионального сварщика с подтвержденной квалификацией, например, аттестацией от НАКС – Национального Агентства Контроля Сварки.
Теперь классификация по типу механизации процесса:
- Автоматизированная
- Механизированная
- Ручная, начнем с нее.
Ручная сварка

Примеры сварных соединений.
Несмотря на быстрый рост новых автоматизированных способов, ручные методы незаменимы во многих случаях, этот вид сварки давно занимает законное важное место в современных технологиях.
Преимущества ручных способов:
- можно варить в труднодоступных местах;
- в разных положениях в пространстве;
- можно быстро переходить от одного материала, которые плавим, к другому;
- выбор электродов на любой вкус для любых видов стали;
- оборудование легко перевозить, просто обслуживать.
Кроме знакомого нам электрического дугового способа к этой группе относится ручной вариант аргонодуговой сварки с теми же принципами действия, как и механизированный вариант, о котором писалось выше.
К ручным видам относится точечная сварка своими руками, контактная метод, который возможен в домашних условиях в отличие от других контактных способов, применяемых только в промышленности.
Классическая газовая сварка также относится к ручным способам.
Автоматические способы
Классификация способов сварки с помощью автоматизации:
- Электродуговая технология.
- Газоэлектрическая, электрическая дуга защищена газом, чаще всего – инертным типа аргона или гелия.
- Электрошлаковая технология.

Сварка вольфрамом – схемы применения.
Электродуговой способ: близкая родственница ручной дуговой – автоматическая сварка под флюсом или АФ – разновидность дугового способа с великолепными показателями производительности. Здесь тоже используется плавящийся электрод, вся работа проводится под специальным защитным слоем флюса. В ручном дуговом способе серьезный риск горения в воздухе самой дуги, поэтому сила подаваемого тока ограничена.
При АФ защищена слоем флюса, риска горения нет. Сила сварочного тока никак не ограничена. Это делает возможным глубокое проплавление металла, в результате чего получается шов отличного качества. Слой флюса предотвращает разбрызгивание металла, его потери в процессе. Полная механизация метода позволяет допускать к АФ менее квалифицированных сварщиков. В итоге производительность способа АФ выше ручного дугового в 5 – 10 раз. Будем честными и представим недостатки АФ, их немного:
- флюсы стоят недешево;
- имеется вредное воздействие на оператора;
- работать можно только в ограниченном пространстве.
Электрошлаковая технология, «тяжелая артиллерия» на современном промышленном фронте. Это принципиально новый бездуговой способ плавления. Источником тепловой энергии выступает не дуга, а переменный ток, который проходит сквозь расплавленный шлак. Поверхности металла покрываются шлаком, который нагревается. Таким образом можно варить металлы практически любой толщины.
Преимущества бездуговой технологии:
- качественные плотные швы;
- швы сложной формы;
- отсутствие деформаций, особенно угловых;
- не нужно обрабатывать кромки;
- простота выполнения
- автоматизация труда, минимальное участие человека
Метод применяется в основном для крупногабаритных конструкций.
Дуговые способы
Выше мы разбирались с основными понятиями и физикой дуги (знаменитая РДС – ручная дуговая, абсолютный чемпион по популярности).
Но классификация способов сварки – дело строгое, поэтому представляем виды дуговой сварки отдельно взятым семейством:

Строение и свойства электрической дуги.
Ручные дуговые:
- РАД – ручная аргонодуговая неплавящимся электродом;
- РАДН – ручная аргонодуговая наплавка.
Автоматические способы дуговых:
- ААД, ААДН, АЛСН, АППГН и т.д. – обширная семья способов с применением либо электродов (плавящихся и неплавящихся), либо проволок, либо порошковых проволок. Варить можно с газом и без.
Дуговые под флюсом:
- знакомая нам АФ, автоматическая дуговая под флюсом;
- различные приварки, наплавки с ленточными или проволочными электродами;
- механизированная дуговая.
Дуговые с покрытыми электродами:
- вот где правильное место для народной чемпионки РДС;
- ручная дуговая наплавка;
Механизированные дуговые:
- МАДП, МПГН, МСОД и т.д. – многочисленная «механическая» семья.
Механический класс
Все виды, о которых говорилось выше, относятся к первому термическому классу. Главным героем в нем выступает тепловая энергия с плавлением. Следующий класс – механический. Главные «механические» слова в данном контексте – давление и пластическая деформация.
В нем также есть стройная классификация сварки:
- Холодная сварка (ковка)
- Сварка трением
- Ультразвуковая
Иногда механические методы объединяют под названием «сварка давлением», здесь есть логика, но речь идет об одном и том же.
Одна из перспективных механических технологий – сварка трением. Тепло в ней тоже присутствует, но образуется оно от силы трения. Поверхности, которые нужно сварить, вращаются, с силой сжимаются. Технология сварки трением особенно эффективна при работе с деталями круглого сечения – сверл, резцов, разверток.

Таблица видов сварки.
Виды сварки трением:
- Сварка трением с перемешиванием.
- Радиальная сварка трением.
- Штифтовая сварка трением.
- Линейная.
- Инерционная.
Рассмотрим эти типы сварки подробнее:
- Сварка трением с перемешиванием – довольно новый способ, в нем необходимо специальное оборудование для сварки трением – инструмент для вращения с двумя элементами – основанием (буртом) и наконечником (пином). Шов формируется с помощью двух процессов выдавливания и перемешивания.
- Радиальная сварка трением применяется в работах с трубами: в ней вращается кольцо между стыками, которое создает трение.
- Штифтовая сварка трением: просверливается отверстие, вводится штифт из того же металла, что детали. Штифт вращается, выделяет тепло, формирует соединение в виде металлических нитей. Великолепная технология сварки трением, когда «нужно заделать дырку».
- Линейный способ. Здесь вращения нет. Детали просто трут друг об друга до выделения тепла, повышения пластичности, затем увеличивают давление, вплоть до необратимого соединения. При этом способе образуется идеальная ровная поверхность, ни в каких других методах такой нет.
- Инерционная сварка. Движение поверхностей происходит за счет массивного вращающегося маховика, который разгоняется специальным двигателем.
Термомеханический класс
Третий класс с точки зрения физики: здесь используются оба вида воздействия на поверхности: тепло и давление. Представляем виды и способы сварки термомеханическим способом:
- Диффузионная. Поверхности сдавливают, затем нагревают в высоком вакууме, добиваясь взаимной диффузии атомов. Эффективен, когда металлы для сварки плохо совмещаются друг с другом или материалы разные по своей природе, например, металл с керамикой. Способ недешевый, применяется в основном в аэрокосмической сфере, других высокотехнологических отраслях.

Разновидности сварки давлением.
Все следующие пункты – виды контактной сварки
- электрическая. Здесь все просто: перед тем, как надавить, нужно хорошенько разогреть. Поверхности разогревают током в местах соединения, затем сдавливают или осаживают. Отличный высокопроизводительный способ, хорошо поддается автоматизации. Широко применяется в строительстве, машиностроении.
- Шовная контактная – разновидность контактной сварки: шов формируется электродами внахлестку.
- Точечная контактная. Между двумя электродами размещают поверхности. Ток включается после плотного сжимания, в результате чего образуется сварная точка с диаметром, равным диаметру поверхности электрода. Чрезвычайно интересна разновидность – рельефная сварка. Контакт электродов проводят по определенным заранее выступам – рельефам, которые в итоге деформируются, поверхность выравнивается.
- Точечная конденсаторная – «сварка с запасенной энергией в конденсаторах». Отличается малым потреблением мощности, применяется в работе с мелкими деталями и при использовании оптических приборов – часовых механизмов, авиационных приборов и т.д.
И на десерт
Особые виды сварки – понятие размытое, учитывая огромное число технических вариантов, групп, видов, подвидов. Каждый видит этот список по-своему.
В нашем списке классификация сварки определена по технологичности. Это уникальные способы, которые по праву относятся к технологиям высшего пилотажа.
Электронно-лучевая и плазменная сварка:
- Электронно-лучевая сварка. Здесь применяется электронная пушка и пучок ускоренных электронов из этой пушки. Работы проводятся в больших вакуумных камерах. Концентрация энергии и тепловая мощность – фантастические. получаются узкими, глубокими. Применяется для производства высокоточных деталей из специальных сплавов – удовольствие недешевое.
- Плазменная сварка. Один из самых высокотехнологичных видов – название говорит само за себя. Плазма – струя ионизированного газа (аргона, гелия, водорода) высочайшей температуры. Такая струя варит все – от самых тугоплавких металлов до неметаллических поверхностей. Великолепная производительность с фантастическим качеством швов и поверхностей.
Обобщаем и закольцовываем
Сваркой называется процесс формирования неразъединимых соединений поверхностей разных конструкций.
Сначала все виды и способы сварки делятся на три мощных класса с точки зрения физики:
- Термический (греем и плавим)
- Механический (трем, давим, толкаем и пр.)
- Термомеханический (греем и давим одновременно)

Аргонодуговая сварка алюминия.
Внутри этих классов методы можно группировать как угодно:
- с дугой или без дуги;
- с газом или без него, можно с дугой и газом вместе;
- ручные или автоматические. Или полуавтоматические;
- какие виды сварочных электродов используешь;
- все виды контактной сварки;
- виды сварок металла или наоборот, полимеров;
- и так далее, список вариантов длиннейший.
Главное – узнавать, пробовать, учиться и двигаться вперед к профессиональным вершинам. Не забывать читать обзоры, нужно быть в курсе. Нам на месте стоять нельзя. Желаем чистого металла, хороших заказов и рабочего настроения.
tutsvarka.ru
Сварка металла: виды и технология
Технологический процесс создания неразъемного соединения однородных материалов за счет образования атомных связей называется сваркой. При этом в месте контакта происходит плотное сплавление двух материалов в один. Несмотря на то что такое соединение используется уже длительное время, современная сварка металлов, виды и технология ее выполнения совершенствуются постоянно, что позволяет производить стыковку различных изделий с повышенной надежностью и качеством.
Особенности сваривания поверхностей
Весь процесс сварки металлов протекает в две стадии. Сначала поверхности материалов необходимо приблизить друг к другу на расстояние сил межатомного сцепления. При комнатной температуре стандартные металлы не способны соединиться даже при сжатии со значительным усилием. Виной этому служит их физическая твердость, поэтому контакт при сближении таких материалов происходит лишь в некоторых точках, независимо от качества обработки поверхностей. Именно загрязнение поверхности существенно влияет на возможность сцепления материалов, ведь пленки, окислы, а также слои примесных атомов всегда присутствуют в естественных условиях.
Поэтому создание контакта между кромками деталей может достигаться либо за счет пластических деформаций, которые возникают в результате приложенного давления, либо в случае расплавления материала.
На следующей стадии сварки металла осуществляется электронная диффузия между атомами соединяемых поверхностей. Поэтому поверхность раздела между кромками исчезает и получается или металлическая атомная связь, или ионная и ковалентная связи (в случае полупроводников или диэлектриков).
Классификация видов сварки
Технология проведения сварочных работ постоянно совершенствуется и становится разнообразнее. На сегодняшний день существует около 20 видов сварки металла, которые классифицируются на три группы:
- Сварка давлением осуществляется приложением механической энергии, когда связи между кристаллами получаются методом пластической деформации материала. В результате металл начинает течь, перемещаясь вдоль линии стыковки деталей, унося с собой слой загрязненных примесей. Процесс деформирования и соединения поверхностей без предварительного подогрева называется холодной сваркой для металла. В этом случае образуются межатомные связи, что приводит к плотной стыковке деталей.
- Сварка плавлением осуществляется путем соединения изделий без применения давления. Источниками тепла при такой сварке металла являются газовое пламя, электрическая дуга, энергия лучевого типа. При сваривании поверхности нагреваются и расплавляются, образуя межатомные связи между двумя металлами и электродом, объединяясь в общую сварочную ванну. После охлаждения и затвердевания состава образуется сплошной литой шов.
- Термомеханическая сварка металла осуществляется с использованием нагрева и давления. Место стыковки материала сначала разогревается, а затем прессуется. Подогрев детали придает ей необходимую пластичность, а механическое воздействие объединяет части изделия в монолитное соединение.
Сварка плавлением
Этот вид сварочных работ находит широкое применение, как в промышленных условиях, так и в быту. К соединению металлов плавлением относятся:
- Электродуговая сварка. Производится созданием между металлом и электродом высокотемпературной электрической дуги.
- При плазменном соединении источником тепла служит ионизированный газ, который проходит с высокой скоростью через электрическую дугу.
- Шлаковая сварка осуществляется благодаря нагреву расплавленного флюса (шлака) электрическим током.
- Лазерное соединение происходит благодаря обработке металлической поверхности лазерным лучом.
- При электронно-лучевой сварке нагревание места стыка осуществляется за счет кинетической энергии движущихся электронов в вакууме под воздействием электрического поля.
- Газовая сварка металлов основана на нагревании точки соединения потоком огня, который образуется при сгорании кислорода и газа.
Электродуговое сварочное соединение
Дуговая сварка предполагает использование источника тока с большим номинальным значением, при этом аппарат имеет небольшое напряжение. Подключение трансформатора происходит одновременно на металлическую заготовку и сварочный электрод.
В результате сварки металла электродом образуется электрическая дуга, за счет которой происходит расплавление кромок соединяемых заготовок. В зоне действия дуги создается температура около пяти тысяч градусов. Такого нагрева вполне достаточно для расплавления любых металлов.
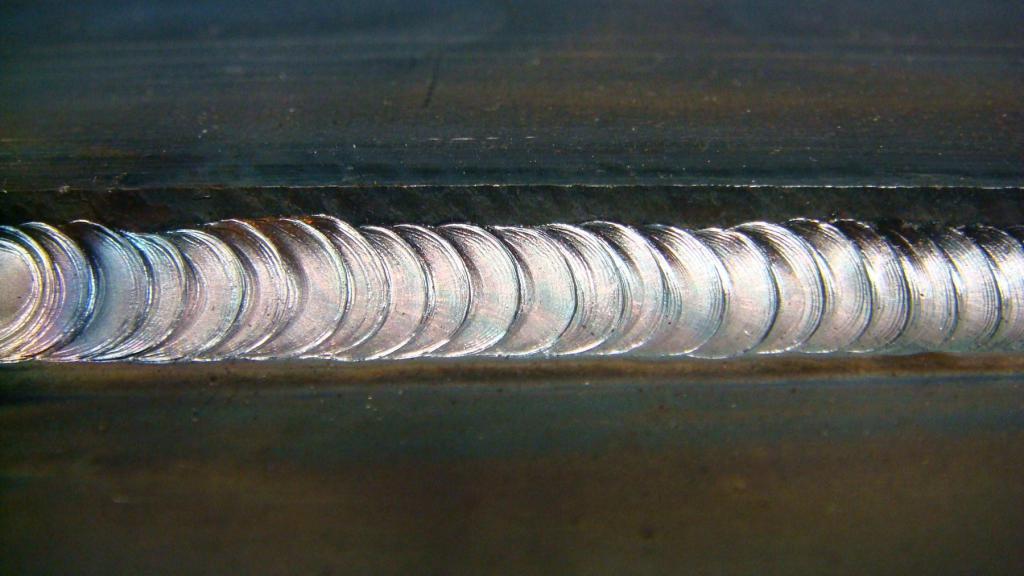
Во время плавления металла соединяемых деталей и электрода формируется сварочная ванна, в которой и происходят все процессы сцепления. Шлак поднимается на поверхность расплавленного состава и формирует специальную защитную пленку. В процессе дуговой сварки металла применяются электроды двух типов:
- неплавящиеся;
- плавящиеся.
При использовании неплавящегося электрода необходимо в зону действия электрической дуги вводить специальную проволоку. Плавящиеся электроды сварной шов формируют самостоятельно. В состав таких электродов добавляются специальные присадки, которые не позволяют дуге гаснуть и увеличивают ее устойчивость. Это могут быть элементы с высокой степенью ионизации (калий, натрий).
Способы соединения дугой
Электродуговая сварка осуществляется тремя способами:
- Ручным методом. В этом случае все этапы соединения выполняются вручную, с применением простой электродуговой сварки.
- Более производительной является сварка металла полуавтоматом. При таком способе сварной шов делается вручную, а присадочная проволока подается в автоматическом режиме.
- Автоматическая сварка производится под наблюдением оператора, а вся работа делается сварочным станком.
Технология газосварки
Этот вид сварочных работ позволяет соединять различные металлические конструкции не только на промышленных предприятиях, но и в бытовых условиях. Технология сварки металла не очень сложная, газовая смесь при горении расплавляет кромки поверхности, которые заполняются присадочной проволокой. При остывании шов кристаллизуется и создает прочное и надежное соединение материалов.
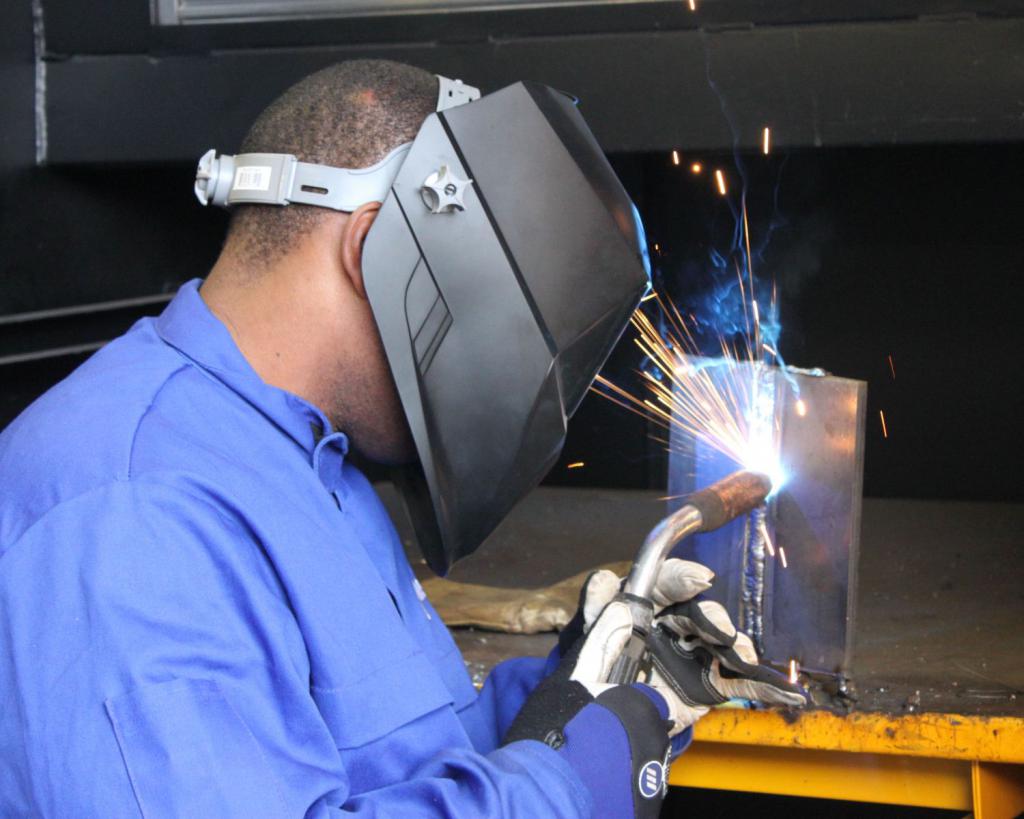
Газовая сварка имеет много положительных аспектов:
- Возможность соединять различные детали в автономном режиме. Причем для этой работы не требуется мощный источник энергии.
- Простое и надежное оборудование газосварки легко поддается транспортировке.
- Возможность осуществлять регулируемый процесс сварки, так как легко вручную изменять угол наклона огня и скорость нагрева поверхности.
Но есть и недостатки применения такого оборудования:
- Место нагрева имеет большую площадь, что отрицательно сказывается на соседних элементах детали.
- Отсутствие возможности автоматизировать процесс сварки.
- Необходимость строго соблюдать меры безопасности. Работа с газовой смесью имеет высокую степень взрывоопасности.
- Толщина металла для качественного соединения должна быть не более 5 мм.
Шлаковая сварка
Такой вид соединения считается принципиально новым способом получения сварного шва. Поверхности свариваемых деталей покрываются шлаком, который нагревается до температуры, превышающей плавление проволоки и основного металла.
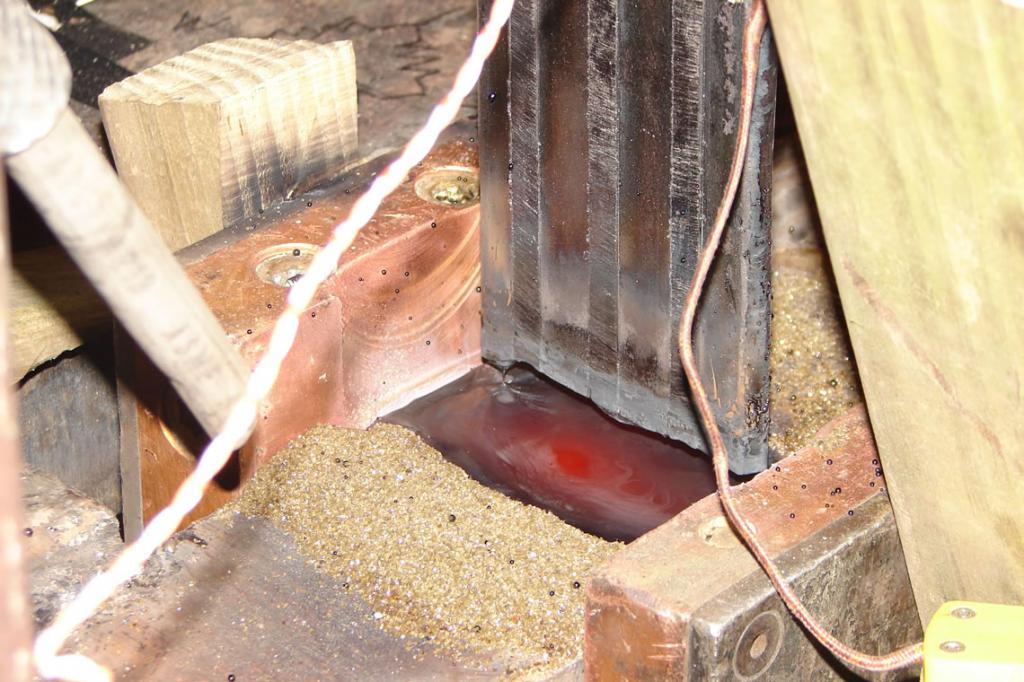
На начальной стадии сварка аналогична дуговому соединению под флюсом. Затем, после образования сварочной ванны из жидкого шлака, дуга прекращает свое горение. Дальнейшее расплавление кромок детали осуществляется за счет тепла, которое выделяется при протекании тока. Особенностью этого вида сварки металла является высокая производительность процесса и качество сварочного шва.
Сварочное соединение давлением
Соединение металлических поверхностей посредством механического деформирования чаще всего производится в условиях промышленного производства, так как для выполнения такой технологии требуется дорогостоящее оборудование.
К сварке давлением относятся:
- Ультразвуковая стыковка частей металла. Выполняется благодаря колебаниям ультразвуковой частоты.
- Холодная сварка. Осуществляется на основе межатомного соединения двух деталей путем создания большого давления.
- Кузнечно-горновой метод. Известен с давних времен. Материал нагревается в горне, а затем сваривается механической или ручной проковкой.
- Газовая с прессовкой сварка. Очень похожа на кузнечный метод, только для нагрева применяется газовое оборудование.
- Контактное электрическое соединение. Считается одним из самых популярных видов. При такой сварке нагрев металла осуществляется прохождением по нему электрического тока.
- При диффузионной сварке сила давления на металл невысокая, но зато необходима большая температура нагрева места соединения.
Точечная контактная сварка
Соединяемые поверхности при такой сварке находятся между двумя электродами. Под действием пресса электроды сжимают детали, после чего подается напряжение. Нагрев места сварки происходит за счет прохождения тока. От размера контактной площадки электрода полностью зависит диаметр места сварки.
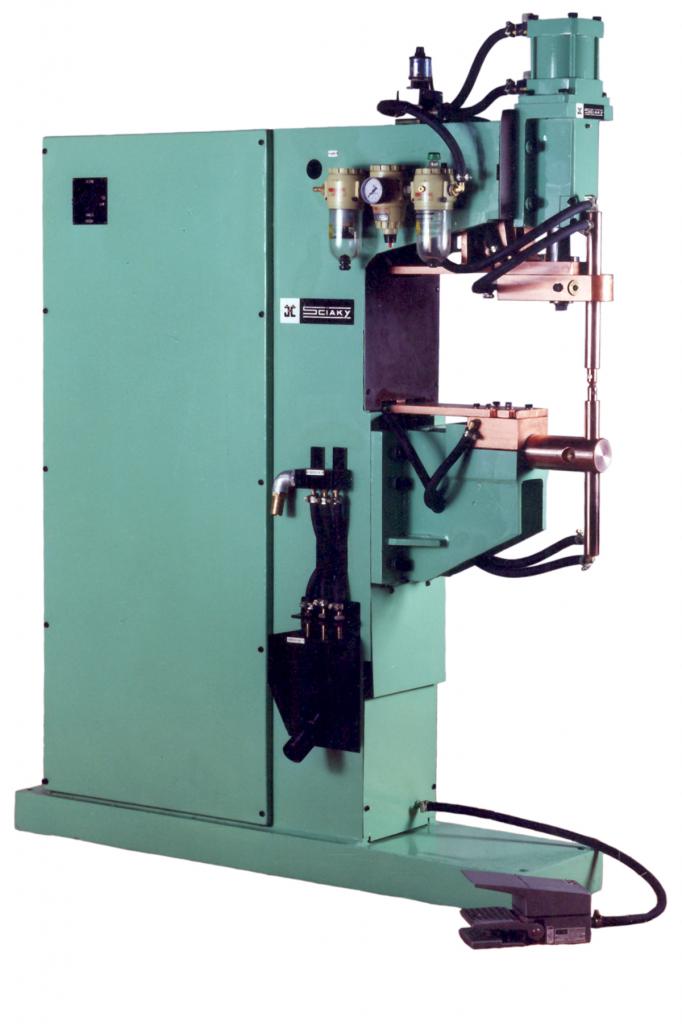
От того, как расположены электроды по отношению к соединяемым деталям, контактная сварка может быть односторонней или двусторонней.
Существует много видов контактной сварки, работающих по аналогичному принципу. К ним можно отнести: стыковую сварку, шовную, конденсаторную.
Техника безопасности
Работа со сварочным оборудованием сопряжена со многими опасными для здоровья оператора факторами. Высокая температура, взрывоопасная среда и вредные химические испарения требуют от человека строгого соблюдения мер безопасности:
- Все электрические агрегаты и устройства должны быть надежно заземлены и заизолированы.
- Работать необходимо в сухой спецодежде и рукавицах. Для защиты кожи лица и глаз обязательно нужно применять маску с темным стеклом.
- Обязательно должна находиться на рабочем месте сварщика аптечка и огнетушитель.
- Помещение, где проводятся сварочные работы, должно иметь хорошую вентиляцию.
- Работы запрещено проводить в непосредственной близости к легковоспламеняющимся предметам.
- Запрещено оставлять газовые баллоны без присмотра.
Существует большое количество видов сварки металла, какой из них выбрать решает сам сварщик, исходя из наличия оборудования и способности достичь требуемого результата работы. Сварщик должен знать устройство и принципы работы на определенном оборудовании.
fb.ru
Основные виды сварки / Полезная информация / Интернет-журнал сайта Кувалда.Ру
Сварка электротоком делится на 2 принципиальных класса: недуговая и дуговая.
Недуговую сварку чаще называют контактной. В контактной сварке электроды, подающие ток, прикладываются непосредственно к металлу, который сваривают. Сквозь метал, расположенный между поднесенными электродами, подается короткий, но очень мощный разряд тока (тысячи ампер). Сплавление при этом получается только между приложенными электродами. Если электроды расположены прямо друг против друга, то сварное соединение получается точечным. Хотя точечная сварка – не единственный вид контактной сварки, но зато самый распространенный. Поэтому понятия «точечной сварки» и «контактной сварки» часто используют в виде синонимов. Напряжение точечной сварки составляет считанные вольты. Поэтому контактная сварка применяется преимущественно для скрепления тонколистового металла. Например, в автомобилестроении.

В строительстве гораздо большее распространение получила сварка электродуговая. При электродуговой сварке между источником тока (электродом) и свариваемым металлом находится небольшой промежуток, заполняемый электрической дугой. Ошибочно предполагать, что это промежуток воздуха. Это промежуток ионизированного газа, проводящего ток. Дуговая сварка, как мы ее представляем сегодня, без газа невозможна. Просто газ может подаваться из отдельного баллона, а может образовываться в результате горения обмазки электрода.
Самыми распространенными в строительстве являются следующие технологии:
- ММА (в отечественной классификации – ручная дуговая сварка, или РДС)
- TIG (аргоно-дуговая)
- MIG-MAG (полуавтоматическая, проволокой).
ММА
Популярность данного вида сварки предопределена как раз отсутствием необходимости таскать с собой баллон с газом. Обмазка электрода – и есть «застывшее» газовое облако. Как только электрод коснется металла и полученный ток короткого замыкания расплавит металл электрода, расплавится и обмазка вокруг него. Образовавшееся облако газа обеспечит проводящую ионизированную среду для дуги и защиту расплавляемого металла от доступа кислорода.

Электроды подбираются по типу металла и диаметру. Тип металла важен, так как в процессе работы метал стержня электрода капля по капле перетекает в свариваемый метал и сплавляется с ним. Для крепкого соединения металл стержня электрода и свариваемый метал должны быть идентичны. На упаковке электродов всегда указывается, для каких металлов подходят данные электроды.

После того, как определились с типом электрода, необходимо определиться с его толщиной. Вопрос новичка: зачем нужны электроды разных диаметров? Все просто. Чем толще электрод, тем больше сила тока, которая его может расплавить. То же и с кромками свариваемого металла. Поэтому толщина электрода подбирается под толщину свариваемого металла. Для черных металлов рекомендуется:
Технология ММА позволяет работать с большинством распространенных металлов, за исключением алюминия и сплавов на его основе. Хотя теоретически и это возможно при наличии помощника, если добиться, чтобы зачищенные алюминиевые поверхности не успевали покрыться пленкой до расплавления. Но правильнее, конечно, просто использовать подходящие для этого сварочные технологии.
TIG
Потребители сварки TIG – сплошь профессионалы и продвинутые пользователи, причем почти поголовно не строительного направления. TIG обеспечивает более аккуратные швы, но сильно уступает ММА в производительности и простоте использования.

Например, многие «любители», отточив свое мастерство на аппаратах ММА, испытывают досаду от неудач при первом опыте с TIG. Оказывается, в отличие от ММА, зажечь дугу аппаратом TIG, если только он не оборудован таким устройством, как осциллятор, непросто. (А практически все аппараты «2 в 1» не оборудованы, конечно). Чиркает сварщик вольфрамовым электродом – искра есть, а дугу поднять не получается. Но вот бывалый сварщик подкладывает под электрод кусочек угля – и дуга пошла без проблем. Не случайно, что в продажах розничных магазинов специализированные аппараты TIG редко превышают долю в 1%.

Отдельного упоминания в сварке TIG заслуживают аппараты с возможностью переключения на режим переменного сварочного тока, т.н. AC/DC. Вот эти аппараты и являются основным оборудованием для сварки алюминия. Именно они преимущественно и составляют этот самый 1% TIG в розничных продажах сварочного оборудования.
MIG-MAG
Полуавтоматическая сварка проволокой применяется в основном для сварки листового металла. Поэтому традиционно ее основная сфера применения – кузовной ремонт, а также строительство конструкций из черного тонколистового металла. Использование проволоки вместо сменных электродов сильно повышает производительность. На бытовых аппаратах используются катушки емкостью 1 и 5 кг, а на профессиональных – 5 или 15 кг.

Проволока может использоваться как обычная (без обмазки), так и с обмазкой (т.н. флюсовая). В первом случае обязательно применение баллона с газом (режим GAS). Во втором баллон не требуется (NO GAS). Несмотря на то, что работать без баллона удобнее, в продажах с большим отрывом лидирует проволока без обмазки. Причина банальна: она гораздо дешевле флюсовой. Кроме того, многие профессионалы считают, что аккуратность швов в среде газа от баллона получается выше.

Несмотря на то, что данный вид сварки тоже относится к электродуговой, принцип устройства у MIG-MAG принципиально отличается от принципов MMA и TIG. В ММА и TIG важно поддерживать стабильность тока, несмотря на колебания электрода, в MIG-MAG важно поддерживать стабильность напряжения дуги. А сила сварочного тока в аппаратах MIG-MAG – показатель условный (хотя по привычке, выработанной в ММА, большинство ориентируется именно на него). Сила сварочного тока в MIG-MAG будет зависеть от выставленного напряжения, диаметра используемой проволоки, применяемого газа и скорости подачи проволоки. Так что сделать из аппарата ММА полуавтомат MIG-MAG путем приделывания блока подачи проволоки и горелки не получится.
Автор текста: Ю.Шкляревский
Если вы хотите чтобы ваши друзья тоже прочитали эту заметку, воспользуйтесь этими кнопочками:
www.kuvalda.ru
Сварка металла: оборудование, технологии, ошибки
Сварка металла позволяет соединять различные детали и создавать сложные конструкции. Ее применяют при строительстве мостов, зданий, прокладке трубопроводов, создании сложных деталей. Сваривать вместе детали можно не только на специальном предприятии, но и далеко от городов, линий электропередач.
Метод соединения деталей свариванием осваивают профессионалы, любители. В гаражах, сараях умельцы воплощают в жизнь свои задумки, ремонтируют различные механизмы, делают полезные в хозяйстве вещи.


Сварка металла
Как правильно варить
Со стороны сварочные работы не представляет сложности. Однако опытные сварщики по металлу рекомендуют сначала изучить теорию и попрактиковаться на ненужных вещах, а только потом приступать к работе.
Мало соединить вместе 2 железки. Такой шов лопнет при первом ударе. Важно научиться сваривать металл, чтобы он не терял своих характеристик. Только правильно разогретая ванна, смешанные вместе расплавы краев деталей способны образовать прочное, герметичное соединение.
Технология проведения работ
Различают около 100 видов сварки металла. Применяют в основном технологию электродуговой сварки электродами, проволокой, пластинами.
Технология сваривания заключается в нагреве металла до жидкого состояния и его дальнейшем смешивании. Для соединения разных деталей используют расплавленную проволоку или сам электрод.
Типы сварочных аппаратов
По производительности, мощности сварочные аппараты можно разделить на два типа: бытовые, промышленные. Первыми можно сваривать детали толщиной до 5–6 мм. Промышленное оборудование способно долго работать без остановки.
Сварка металлов происходит за счет нагрева до высоких температур. Расплавление достигается различными способами. Каждому из них соответствует свое оборудование. Оно делится на группы по принципу работы:
- трансформаторы;
- инверторы;
- выпрямители;
- TIG-аппараты;
- полуавтоматы;
- спотеры.
Кроме того, применяются аппараты для газовой обработки металлических заготовок, холодная сварка, создающая высокое давление и другие виды соединения деталей.


Сварочные аппараты
Трансформаторные
Классические сварочные аппараты были изобретены первыми. Они просто понижали напряжение тока, оставляя его переменным. Силовой трансформатор понижает напряжение сети до значений холостого хода — 50–60В. По настройке параметров работы различают следующие типы оборудования:
- тиристорные — фазовая регулировка;
- с магнитным рассеиванием;
- со стандартным рассеиванием.
Недостаток аппарата заключается в нестабильной дуге из-за переменного тока. Трансформаторы отличаются крупными габаритами и большим потреблением энергии.
Инверторы
Инверторы создают оптимальные условия для сварки металлов. Они выравнивают переменный ток и делают его высокомощным, регулируемым с большой точностью. Работают инверторы от потребительской сети 220V с частотой 50Грц, промышленной в 380 V.В процессе преобразования, ток проходит:
- сетевой выпрямитель;
- частотный преобразователь;
- высокочастотный трансформатор;
- силовой выпрямитель.
Инверторы настраиваются на работу с прямым, обратным током. Работают с электродами любого типа, варят высоколегированные черные, цветные металлы. Они имеют защиту от перепадов, скачков напряжения. Подходят для обучения новичков, поскольку имеют стабильную дугу.
Для работы с постоянным током используют и выпрямители, которые состоят из диодов и полупроводников. Они преобразуют переменный ток в постоянный, позволяют регулировать его величину. Тонкой настройки не имеют.
Все остальные виды сварочного оборудования представляют собой различные варианты трансформатора и инвертора.
Как выбрать сварочный инвертор для дома. Обзор от сварщика.
Watch this video on YouTube
Пошаговая инструкция по проведению сварочных работ
Перед началом сваривания необходимо проверить место проведения работ на соответствие технике безопасности. На участке не должно быть лишних предметов, особенно легковоспламеняющихся, луж с водой, разлитого масла.
Следует проверить на исправность и подключить оборудование. Плита должна быть заземлена. На деталь цепляется зажим с соответствующим значением тока. Заготовка подготовлена к сварке, если выполнены следующие действия:
- места соединений зачищены;
- заготовка установлена на сборочную плиту или стеллаж и закреплена;
- детали соединены между собой прихватами или зажаты в специальном устройстве.
Начинать варить следует после полной подготовки места, оборудования и инструмента.
Как же научиться варить металл. Советы новичкам, по просьбам подписчиков
Watch this video on YouTube
Инструменты и средства защиты
Кроме зажима для электродов у сварщика всегда должен быть с собой тонкий металлический молоток, чтобы отбивать шлак. Шов проверяется на наличие непроваров, подрезов, волчков. При необходимости режим работы можно изменить.
Сварка относится к числу вредных и опасных работ. Соблюдение техники безопасности особенно важно для начинающих работников, которые еще не имеют практических навыков. При проведении сварочных работ можно получить повреждения разного типа: поражение током, ожоги, поражение глаз, отравление парами при сгорании флюса.
Обязательные средствами защиты для сварщика при работе являются:
- маска;
- рукавицы или перчатки;
- штаны и куртка;
- рабочие ботинки;
- брезент.
Маска с темным стеклом защищает глаза от слепящего света, возникающего при сваривании. Рукавицы и костюм из негорючих материалов закрывают кожу от брызг металла и искр.
Средства защиты или чем пренебрегают профи во время сварки? Урок 7 + анонс 2-ой части видеокурса.
Watch this video on YouTube
При работе вне оборудованного сварочного поста рабочему может понадобиться брезент. Им он закрывает предметы, которые невозможно убрать. Например, стену и стоящую рядом мебель при сварке труб водопровода или отопления в доме.


Инструменты и средства защиты
Какие электроды использовать
Толщина металла и количество накладываемых швов определяют диаметр электрода. При сварке деталей большой толщины корневой шов прокладывается тонким электродом 2–3 мм. В дальнейшем используют четверку. При толщине листа более 20 возможно применение электрода диаметром 6 мм.
Для сваривания конструкций из низколегированных сталей, применяют электроды с обмазкой марок: УОНИ, ОЗС, АНО. Они широко используются в создании строительных конструкций, при прокладке трубопроводов и сварке других деталей, к которым предъявляются высокие требования в прочности соединений.
При сварке высоколегированных и углеродистых старей специалисты рекомендуют использовать хромоникелевые электроды марки ЭА 395.
Качественную сварку цветных металлов производят с помощью рутиловых электродов серии МР 3С. Вольфрамовые неплавящиеся марки WC 20 подходят для соединения деталей из сплавов цветных металлов.
Хромоникелевые и рутиловые электроды рекомендуют для обучения процессу сварки. Они легко зажигаются, хорошо держат дугу.
Электроды с рутиловым и другими специальными покрытиями считаются универсальными. Они могут работать на любом токе, шов ложится по горизонтали. Вертикаль только снизу-вверх. Разбрызгивание металла минимальное. После них переходить на УОНИ и другие марки тяжело, но только освоив классические электроды, можно стать сварщиком.
Подготовка
Перед началом работы следует провести подготовку металла под сварку. Поверхность заготовки должна быть очищена от грязи, масел, ржавчины. Пленки окислов удаляются химическим путем непосредственно перед сваркой.
Если толщина шва превышает 3–5 мм, следует разделать кромки на станке, сняв их под углом 45⁰.
Свариваемые детали соединяются прихватами. При массовом производстве могут использоваться специальные приспособления.


Зачистка места соединения
Подключение
Перед работой проверяется состояние оборудования и заземление. Затем к детали подключается 0 или минус, в зависимости от типа применяемого тока. Оборудование включается в сеть и производится настройка режимов. После этого вставляется электрод, включается сварочный аппарат.
Сварочный процесс
Перед тем как варить аппарат настраивается на нужный режим работы в соответствии с толщиной, материалом детали и рекомендованными для электродов токами. После этого можно приступить непосредственно к сварке.
- Зажечь дугу.
- Нагреть сварочную ванну.
- Электродом перемещать расплавленный металл вдоль шва, обеспечивая соединение кромок.
Во время проведения работ следует следить, чтобы флюс не оставался в шве, а расплавлялся и всплывал.
Какие могут быть ошибки
Неправильно выбранный ток — при его низком значении будет постоянно тухнуть дуга и прерываться шов. Высокое значение тока ведет к проплавлению, прожиганию насквозь тела сварных конструкций из металла.
Выход шлака регулируется углом наклона электрода и зависит от его типа. Если ванна перемещается быстро, остаются шлаковые включения в шве.
Высоколегированные стали перед обработкой нужно подогревать, в противном случае материал кромки не успеет расплавиться или образуется переходная зона.
Сварку цветных металлов необходимо проводить специальными электродами в среде защитного газа. Полярность тока должна быть прямой, чтобы плавился металл, покрытый окислами.
Что можно изготовить
Свариванием соединяют элементы изделий, выполненные с помощью холодной ковки. В результате получают ажурные заборы, неповторимую по красоте садовую мебель и другие поделки из металла. Умельцы превращают старые болты и гайки в очаровательных животных, морских монстров.
metalloy.ru
технология ручной дуговой сварки металлоизделий

– технология соединения деталей из металла различной степени сложности в единое целое при помощи специального оборудования.
Она может активно применяться в промышленном масштабе на крупных производствах опытными специалистами, а также для выполнения бытовых операций сварщиками-любителями. В любом варианте, соединения металлоконструкций характеризуется определенными особенностями, которые важно понимать при работе.
Требования к сварке металлических конструкций
Процесс сварки в технологическом плане должен обеспечить выполненным соединениям требуемые геометрические параметры, размеры и высокое качество. Конструкция должна получиться прочной и долговечной, а риск ее деформации – нулевым.

Сварка металлических конструкций.
Именно поэтому технология сварки металлоконструкций должна реализовываться с учетом некоторых требований, что во многом определит качество созданных :
- Если создаются простые соединения без применения кондуктора, а также при создании сложных швов перед включением данного инструмента важно оставить зазор между скрепляемыми деталями.
Тогда при смещении элементов шов не пострадает. Но размеры зазора должны соответствовать допустимой норме, иначе система не будет прочна и долговечна. - При выполнении сварки ответственных металлоконструкций сварщики проверяют строгое соответствие установленной детали своему местоположению, согласно карте.
При поступлении заготовки на стапель стоит подготовить каждую из них к завершающему этапу. - Все детали должны строго соответствовать по виду и размеру, указанным в проекте частям будущей конструкции.
Это позволит сохранить функциональные возможности изделия. - Корневые слои шва при ручном методе выполнения дуговой сварки важно накладывать электродами с диаметром, не превышающим 3-4 мм.
- Металлоконструкции при укреплении потребуется располагать так, дабы можно было накладывать швы преимущественно в нижнем положении.
Это необходимо для обеспечения сварщика безопасными условиями работы. - Важно взять под строгий контроль углы металлоконструкции, для чего стоит воспользоваться специальными инструментами и кондуктором.
Все углы между плоскостями должны быть прямыми, если это предусмотрено проектом. Иначе произойдет перекос деталей, что повлечет за собой нарушение целостности механизма, потере им своей функциональности. - Готовая конструкция должна иметь минимальные усадочные напряжения и деформации, для чего сварные работы нужно осуществлять в стабильном режиме с отклонениями от заданных значений величины тока и напряжения на дуге не более ±5 %.
Описанные рекомендации важно учитывать уже на этапе сборки деталей в целостную конструкцию, а не только перед непосредственным выполнением сварочных работ. Особенно, если выбран автоматический режим, при котором не выйдет откорректировать допущенные ошибки.
В целом же, именно этот вид сварных работ и считается наиболее приемлемым, так как при автоматизировании сварных процессов влияние человеческого фактора на качество выполненных швов сводится к нулю.
На заметку! Если при испытании образца на статическое растяжение предел прочности изготовленного шва оказался меньшим, чем предел прочности основного металла, то изделие браковано.
Также важно заварить технологическую пробу в условиях, которые полностью совпадают с условиями сварки конструкций на месте производства.
Если работать сварочным аппаратом придется при низкой температуре воздуха, стоит сварить стыковые образцы перед началом операций при отрицательном температурном режиме, предусмотренном технологическим процессом. Это позволит в дальнейшем провести их механические испытания.
Если нужно выполнить сварные работы с особо ответственными металлоконструкциями из новых марок сталей или с применением новых сварных расходников, мастеру потребуется изготовить контрольные образцы в таком же пространственном положении и с теми же материалами, оборудованием, что и при сварке монтируемых конструкций.
Это позволит сварщику оценить ситуацию со всех сторон перед началом работы и не допустить ошибок в процессе ее выполнения.
На заметку! Качество созданных соединений металлоконструкций во многом зависит не только от мастерства сварщика, но и от качества сварочного аппарата, примененного в работе. Лучше остановить свой выбор на модели известного бренда, качество которого проверено временем.
Классическая технология сварки конструкций из металла
– уникальный способ получения неразъемных металлических соединений, открывающих человеку широкие возможности по снижению трудоемкости создания и установки металлоконструкций.
Она позволяет использовать рациональные типы сечений в металлоконструкциях, что приводит к снижению показателей металлоемкости в несколько раз, по сравнению с применением иных технологий.
Сегодня сварные работы выполняются с помощью разных методов, но все они создавались на основе знаний о классической технологии. Она проста и может реализовываться, как для бытовых целей, так и в промышленных масштабах.

Углы сварки металлоконструкций.
Если изготавливать сварочные металлоконструкции по классической технологии, потребуется применить следующие источники энергии:
- электрическая дуга;
- газовое пламя.
Оба варианта предполагают три метода выполнения сварных швов:
Автоматический
Не подразумевает человеческое вмешательство в процесс выполнения сварных работ. Сварочный аппарат настраивается на актуальный режим функционирования с учетом конкретного вида выполняемой операции единственный раз перед началом работы.
Поэтому важно понимать основную цель приобретения сварного оборудования при выборе в магазине. Используя автоматический режим, можно применять контактную и электрошлаковую сварку.
Полуавтоматический
При использовании данного метода сварные швы формируются вручную, а электроды подаются в автоматическом режиме. Такое положение дел позволяет повысить производительность работы без ущерба для качества создаваемых металлоизделий.
можно применить газовый флюс, неплавкие электроды, сварочную проволоку.
Ручной
Все действия методом ручной дуговой сварки осуществляются сварщиком без применения автоматизированного оборудования: от контроля подачи электрода до формирования самого соединения.
Зачастую при ручном режиме применяют обыкновенную сварку под флюсом, электродуговую сварку или пайку газосварочным устройством. Данный метод рационально использовать в бытовых целях, а не на крупном производстве, потому что он чрезмерно затратный и характеризуется низкой производительностью.
На заметку! Полуавтоматический метод дуговой сварки металлических конструкций наиболее востребован на отечественном рынке. Он активно применяется в строительстве при монтаже железобетонных строений, в машиностроении при конструировании автомобилей, а также в быту.
Инновационные сварочные технологии
Со временем классический метод выполнения сварных работ совершенствовался, опытные специалисты разрабатывали инновационные способы соединения металлических деталей в единую конструкцию: сварка с применением лазерных установок, ультразвука, теплового эффекта и т. п.
Подобные новаторские идеи могут помочь сварщику в работе, облегчив выполнение некоторых задач и ускорив весь процесс сборки металлоконструкций в целом. По этой причине и сегодня в этой области не прекращаются научные разработки и исследования.

Способы сварки металлоконструкций.
Также применение инновационных технологий выполнения сварных работ позволяет сварщику получить ряд преимуществ:
- снизить показатели коробления металла;
- повысить скорость выполнения работы;
- сократить расходы зачистку сварного шва;
- снизить траты на закупку расходных материалов;
- выполнять соединения тонколистового металла.
Особенно интересны, с точки зрения продуктивности, качества полученных швов и экономичности, следующие технологии сварки:
- Электронно-лучевая сварка применяется при работе с глубокими соединениями – до 20 см, но только при условии определенного соотношения ширины шва и глубины погружения инструмента – 20:1.
Процесс формирования шва осуществляется в вакууме, поэтому использовать такую технологию в быту практически невозможно. Она применяется в сфере узкопрофильных производств. - Термитная сварка подразумевает нанесение особой смеси на контуры соединения деталей в процессе горения.
Технологию применяют для ответственных конструкций из металла в готовом виде, когда с помощью наплавки металла надо устранить имеющийся дефект в виде трещины или скола. - Плазменная сварка подразумевает применение ионизированного газа, проходящего сквозь электроды с высокими сварочно-техническими характеристиками и выполняющего функцию дуги.
Технология имеет более широкие возможности применения по сравнению с электронным типом, так как позволяет выполнить сварщику резку и сварку металлической конструкции с любой шириной металла. - Орбитальная аргонодуговая сварка с помощью вольфрамового применяется для работы со сложными деталями из металла.
Например, для неповоротных стыков труб с диаметром 20-1440 мм. В процессе работы активирующий флюс наносится 1 г/м шва. Это позволяет решить ряд важных технологических задач: уменьшить объем и вес сварной ванны за счет ведения операций пониженным током; благодаря давлению дуги на жидкий металл шов получается качественным в любом пространственном положении; сварку можно автоматизировать без разделки кромки. - Щадящие технологии сварки в смесях защитных газов Ar+CO2 и Ar+O2+CO2.
При использовании такого метода выполнения сварочных работ можно получить более качественные соединения при сравнении со сваркой в СО2. При этом актуальный объем расходных материалов сократиться на 20 % за счет резкого снижения набрызгивания электродного материала, а переход к свариваемым частям металлоконструкции станет плавным.
На заметку! Каждая из них имеет ряд недостатков, отличается своеобразными особенностями и принципами осуществления, которыми важно овладеть до начала применения на практике.
Современная наука многогранна и непредсказуема.
Она предоставляет человеку возможности применить на практике достоинства нано-технологий, поэтому ближайшее будущее сварочных операций представляется связанным с совершенствованием схем компьютерного управления сваркой, а также применением новых сварных материалов.
Заключение
Если соблюдать все требования к сварке металлоконструкций, можно получить высококачественные швы: долговечные, прочные и стойкие к воздействию. Использовать при этом можно как классический вид сварки, так и новые технологии.
Несмотря на то, что они в большей степени касаются профессионального уровня сварки, но при желании развивать свои навыки в этой сфере, ознакомиться с такой информацией будет не лишним и для новичка в подобных вопросах.
tutsvarka.ru
Сварка цветных металлов: виды основных сплавов


Содержание статьи
Особенности сварки цветных металлов
- Они легко окисляются.
- При плавлении этих металлов появляются тугоплавкие окислы, которые способны заполнить сварочный шов. Из-за этого повышается риск изготовления некачественного шва и возникновения трещин.
- Некоторые цветные металлы требуют применение более мощного источника энергии, так как их остывание происходит очень быстро. Работать в данном случае нужно оперативно.
- Существует вероятность испарения «лёгких» составляющих сплава, так как все они имеют разную температуру плавления.
- Цветные металлы, в отличие от черных, лучше взаимодействуют с газовой средой.
- При сварке на цветных металлах появляется оксидная пленка, которая мешает сварить качественный шов.
- Работы по сварке должны проходить в зоне с ограниченным объемом кислорода.


Встретить какой-то конкретный цветной металл в чистом виде почти невозможно. Обычно они используются в виде различных сплавов. Наиболее популярные составляющие сплавов: медь, никель, алюминий, титан, цинк.
Технология сварки цветных металлов: подготовка к работе
Любой сварочный процесс требует подготовки. Особенно, если речь идет о сварке цветных металлов. В первую очередь, детали требуют зачистки, чтобы удалить оксидную пленку. Жиры удаляются с помощью бензина или растворителя. Расположить детали нужно примерно в 2 мм друг от друга. Проводить работу рекомендуется в максимально нижнем положении, так как цветные сплавы отличаются повышенной текучестью.
Для того, чтобы защитить сварочную ванну от воздуха, сварку проводят в среде инертных газов. Чаще применяются азот, гелий или аргон. Электроды для сварки цветных металлов лучше использовать из угля, графита или вольфрама.
Сварка цветных металлов и их сплавов из алюминия
После железа алюминий считается самым популярным металлом. Он часто используется в чистом виде. Однако, его сплавы все равно используются чаще. Существует множество сплавов из алюминия. Алюминиевые сплавы используются в пищевой и химической промышленности, в строительстве и машиностроении. Если проводить классификацию по свойствам, то самыми часто применяемыми являются дуралюмин, силумин и авиель.
Перед началом работ алюминий зачищают от окисной пленки и обезжиривают. Затем детали, подлежащие сварке, одну-две минуты протравливают в водном растворе фтористого натра в соотношении 50/50. После этого их примерно на две минуты кладут в раствор азотной кислоты. Затем элементы нужно промыть горячей и холодной водой. С момента подготовительных работ до сварки не должно пройти более четырех часов. Аналогичные подготовительные работы должны производится и с проволокой для сварки. Запрещено зачищать кромки с помощью «наждачки». Элементы для сварки должны быть надежно зафиксированы.
Сборка элементов перед сваркой зависит от толщины свариваемых деталей. Если нужно, перед соединением элементов накладывают прихваточные швы. В таблице ниже указано примерное расстояние между ними.
Толщина свариваемого металла, мм | Растояние между прихватками, мм | Размеры прихваток, мм | |
Высота | Длинна | ||
До 1,5 | 20-30 | 1-1,5 | 2-4 |
1, 5-3 | 30-50 | 1,5-2,5 | 4-6 |
3-5 | 50-80 | 2,5-4 | 6-8 |
5-10 | 80-120 | 4-6 | 8-12 |
10-25 | 120-200 | 6-12 | 12-26 |
25-50 | 200-360 | 12-20 | 26-60 |
Никелевые и медные сплавы
Изделия из сплава никеля используются в устройствах с высокой рабочей температурой, около 700 – 1000 градусов (для деталей ракет, газовых турбин). Никелевые сплавы прочны, вязкие, пластичны, жаростойкие и очень чувствительны к газам. Последний фактор приводит к тому, что сварочный шов может получится пористым. Никель устойчив к коррозии. Для обезжиривания никелевого сплава не рекомендуется применять бензин. В основном, никелевые сплавы используются в химической и электрохимической промышленности. Для сварочных работ с никелем применяют электроды из металла, постоянный ток обратной полярности. Если используется аргонный сварочный аппарат – берут электроды из вольфрама.


Медные сплавы используются в машиностроении. Из них производят трубы, ёмкости различного предназначения, размеров и формы. Используются электроды из угля и графита при токе прямой полярности. Длина дуги примерно 35-40 мм. Если производится ручная дуговая сварка изделий из меди при температуре до 400 градусов, используется ток обратной полярности. Аргон и гелий используется для сварки в защитных газах, проволока из бронзы выступает в качестве присадочного материала. Подготовка к работе должна быть очень тщательной, кромки должны быть зачищены до металлического блеска. Сварка должна протекать быстро, без перерывов. Присадочным материалом может быть обычная медная проволока.
Соотношение толщин присадочной проволоки и свариваемой детали.
Толщина меди, мм | До 1,5 | 1,5-2,5 | 2,5-4 | 4-8 | 8-15 | Более 15 |
Диаметр присадочной проволоки, мм | 1,5 | 2 | 3 | 4-5 | 6 | 8 |
Защита сварочной ванны обеспечивается флюсами, перечень которых изложен в таблице ниже. Флюсы в сварочную ванну вводятся в порошкообразном или парообразном состоянии.
Компонент | Состав флюса, % | |||||||
№1 | №2 | №3 | №4 | №5 | №6 | №7 | №8 | |
Бура прокаленная | 100 | — | 50 | 75 | 50 | 50 | 70 | 56 |
Борная кислота | — | 100 | 50 | 25 | 35 | — | 10 | |
Поваренная соль | — | — | — | — | 20 | 22 | ||
Фосфорнокислый натрий | — | — | — | — | 15 | 15 | — | — |
Кварцевый песок | — | — | — | — | — | — | — | |
Древесный уголь | — | — | — | — | — | — | — | |
Углекислый калий (поташ) | — | — | — | — | — | — | — | 22 |
Флюсы для ацетилено-кислородной сварки.
Компонент | Состав флюса (по массе), % | |||
№1 | №2 | №3 | Марки БМ-1 | |
Бура прокаленная | 100 | 50 | 20 | — |
Борная кислота | — | 35 | 80 | — |
Фтористый натрий | — | 15 | — | — |
Метилборат | — | — | — | 75 |
Метиловый сирт | — | — | — | 25 |
Титановые сплавы. Работы с магнием.
Титан не являются широко распространенным металлом. Его используют в таких областях как самолетостроение, атомная энергетика, машиностроение. Особенности этого металла требуют и особенной работы с ним. Титановый сплав будет качественным, если содержание азота, водорода и кислорода в его составе свести к минимуму. Сварка аргоном должна производится только при использовании этого газа 1-го или высшего сорта. Используется постоянный ток прямой полярности.


Работа с магниевыми сплавами проходит с использованием гелия или аргона при переменном токе обратной полярности. При сварке кромки полностью расплавляют и кладут металлическую прокладку с низким уровнем теплопроводности.
Сварка цветных металлов и сплавов из свинца
Основная сложность при работе со свинцом заключается в том, что разница температуры плавления самого металла и его оксидов очень большая. Плавление свинца происходит при температуре примерно 327 градусов, а его оксиды расплавляются при температуре примерно 888 градусов. Свинец является жидкотекучим металлом. Подготовка к работе со свинцом аналогична подготовке к сварке алюминиевых сплавов. Защита сварочной ванночки происходит посредством использования флюса (стеарин, которым натирают кромки, либо смесь стеарина с канифолью).
Виды методов контроля
Качество – это объединение свойств изделия, которые характеризуют его способность удовлетворить потребности, отвечающие целям его создания. Для каждого вида продукции или изделия существуют свои требования по качеству. Качество сварного шва характеризуется прочностью, пластичностью, стойкостью к коррозии, структурой шва и зоны около шва, количеством исправлений и так далее.
Чтобы соединение было качественным, на различных этапах работы существуют разные методы контроля качества. Они позволяют выявить дефекты и предупредить их появление.
Существует два метода контроля в зависимости от способа воздействия на материал:
- Разрушающие
- Механические: изгиб, растяжение, сплющивание
- Металлографические
- Коррозийные
Разрушающие методы контроля обычно проводятся на образцах изделия, а не на самом изделии. Образец по составу должен быть аналогичен основному изделию.
- Неразрушающие. Подразделяются на акустические, магнитные, оптические, вихретоковые, радиационные, тепловые, электрические. Этот вид контроля проводят без образцов, на самих основных изделиях. При этом допускается незначительные нарушения целостности, изменения твердости.
Таким образом, сварка цветных металлов и сплавов требует многих знаний, навыков, опыта и профессионализма.
[Всего голосов: 0 Средний: 0/5]svarkaed.ru