Выбор режимов резания при фрезеровании плоскостей
Для обеспечения высокой производительности труда выгодно работать с возможно большим режимом резания. Однако его величина ограничивается главным образом режущими способностями фрезы и мощностью станка. Поэтому обычно выбирают не наибольший, а наивыгоднейший для данных условий режим резания, элементы которого рекомендуется назначать в определенной последовательности.
Вначале выбирают наибольшую возможную ширину фрезерования В и глубину резания t, затем — допустимые значения подачи на зуб Sz и скорости резания v. После этого по формулам (6) и (2) определяют требуемые частоту вращения n и минутную подачу Sм, которые принимают ближайшими меньшими из имеющихся на станке. Для наглядности этот порядок действий можно представить в следующем виде:
Ширину фрезерования устанавливают такой, чтобы обработку поверхности можно было бы провести за один проход. При работе торцовыми фрезами это условие осуществимо почти в любом случае, так как по действующим стандартам предусмотрен широкий диапазон диаметров таких фрез.

Для уменьшения времени обработки глубину резания также целесообразно принимать большей с целью сокращения количества проходов при фрезеровании поверхности. В связи с этим, если условия позволяют, весь припуск выгодно срезать за один проход, В иных случаях обработку выполняют за два или более проходов. При этом поверхности с малой шероховатостью (Rz20…Ra1,25) рекомендуется окончательно фрезеровать с малой глубиной резания 0,5…1,5 мм.
Подачу на зуб фрезы принимают в зависимости от вида обработки. При черновом фрезеровании она ограничивается жесткостью заготовки и фрезы, прочностью или твердостью обрабатываемого материала, мощностью станка; при чистовом фрезеровании — шероховатостью обрабатываемой поверхности. Причем с уменьшением подачи шероховатость поверхности также уменьшается.
Скорость резания оказывает наибольшее влияние на стойкость фрезы. С увеличением скорости резания выше допустимых значений резко ускоряется износ фрезы, требуется более частая ее замена, переточка. Поэтому скорость резания следует выбирать в допустимых пределах в зависимости от всех условий работы. Она может быть принята большей: при обработке менее твердых и прочных материалов с небольшой шириной фрезерования, глубиной резания и подачей, для фрез из более теплостойких материалов с малыми углами в плане, а также при применении смазывающе-охлаждающих жидкостей.
Подача и скорость резания обычно определяются из нормативных таблиц справочника. Однако для учебных целей в начальном периоде обучения при выборе элементов режима резания можно пользоваться их ориентировочными значениями, приведенными в табл.1.
Выбор режимов резания при фрезеровании чугуна и стали Таблицы с рекомендованными значеними подачи на зуб Фрезы концевые с напайными пластинами Высоколегированная Wal
Выбор режимов резания при фрезеровании чугуна и стали Таблицы с рекомендованными значеними подачи на зуб Фрезы концевые с напайными пластинами Высоколегированная Walter Prototyp В таблице указаны рекомендуемые значения подачи. В особых случаях необходима корректировка подачи. Техническая информация Фрезерование к Серый чугун Подача на зуб fz мм ae мм 0 16 мм 0 20 мм 0 25 мм 0 32 мм 0 40 мм 0 50 мм 0 63 мм 0 80 мм 0 100 мм 1,0 0,13 0,13 0,13 0,14 0,15 2,0 0,13 0,13 0,13 0,13 0,14 0,26 3,0 0,13 0,13 0,13 0,13 0,13 0,25 0,26 4,0 0,12 0,13 0,13 0,13 0,13 0,24 0,25 0,26 5,0 0,12 0,12 0,13 0,13 0,13 0,24 0,24 0,25 0,26 6,0 0,12 0,12 0,12 0,13 0,13 0,23 0,24 0,24 0,25 8,0 0,12 0,12 0,12 0,12 0,13 0,22 0,23 0,24 0,24 10,0 0,12 0,12 0,12 0,12 0,12 0,22 0,22 0,23 0,24 12,0 0,12 0,12 0,12 0,12 0,12 0,21 0,22 0,22 0,23 16,0 0,12 0,12 0,12 0,12 0,12 0,20 0,21 0,22 0,22 20,0 0,12 0,12 0,12 0,12 0,20 0,20 0,21 0,22 25,0 0,12 0,12 0,12 0,20 0,20 0,20 0,21 32,0 0,12 0,12 0,20 0,20 0,20 0,20 40,0 0,12 0,20 0,20 0,20 0,20 50,0 0,20 0,20 0,20 0,20 63,0 0,20 0,20 0,20 80,0 0,20 0,20 100,0 0,20 L Низколегированная сталь, высоколегированная сталь и высоколегированная инструментальная сталь Подача на зуб fz мм ae мм 0 16 мм 0 20 мм 0 25 мм 0 32 мм 0 40 мм 0 50 мм 0 63 мм 0 80 мм 0 100 мм 1,0 0,09 0,09 0,09 0,1 0,10 2,0 0,09 0,09 0,09 0,09 0,10 0,17 3,0 0,09 0,09 0,09 0,09 0,09 0,16 0,17 4,0 0,08 0,09 0,09 0,09 0,09 0,15 0,16 0,17 5,0 0,08 0,08 0,09 0,09 0,09 0,14 0,15 0,16 0,17 6,0 0,08 0,08 0,08 0,09 0,09 0,14 0,14 0,15 0,16 8,0 0,08 0,08 0,08 0,08 0,09 0,14 0,14 0,14 0,15 10,0 0,08 0,08 0,08 0,08 0,08 0,13 0,14 0,14 0,14 12,0 0,08 0,08 0,08 0,08 0,08 0,13 0,13 0,14 0,14 16,0 0,08 0,08 0,08 0,08 0,08 0,13 0,13 0,13 0,14 20,0 0,08 0,08 0,08 0,08 0,13 0,13 0,13 0,13 25,0 0,08 0,08 0,08 0,12 0,13 0,13 0,13 32,0 0,08 0,08 0,12 0,12 0,13 0,13 40,0 0,08 0,12 0,12 0,12 0,13 50,0 0,12 0,12 0,12 0,12 63,0 0,12 0,12 0,12 80,0 0,12 0,12 100,0 0,12 M Нержавеющая сталь (ISO P) Подача на зуб fz мм ae мм 0 16 мм 0 20 мм 0 25 мм 0 32 мм 0 40 мм 0 50 мм 0 63 мм 0 80 мм 0 100 мм 1,0 0,07 0,07 0,07 0,08 0,08 2,0 0,07 0,07 0,07 0,07 0,08 0,14 3,0 0,07 0,07 0,07 0,07 0,07 0,13 0,14 4,0 0,06 0,07 0,07 0,07 0,07 0,12 0,13 0,14 5,0 0,06 0,06 0,07 0,07 0,07 0,12 0,12 0,13 0,14 6,0 0,06 0,06 0,06 0,07 0,07 0,12 0,12 0,12 0,13 8,0 0,06 0,06 0,06 0,06 0,07 0,12 0,12 0,12 0,12 10,0 0,06 0,06 0,06 0,06 0,06 0,11 0,12 0,12 0,12 12,0 0,06 0,06 0,06 0,06 0,06 0,11 0,11 0,12 0,12 16,0 0,06 0,06 0,06 0,06 0,06 0,11 0,11 0,11 0,12 20,0 0,06 0,06 0,06 0,06 0,11 0,11 0,11 0,11 25,0 0,06 0,06 0,06 0,10 0,11 0,11 0,11 32,0 0,06 0,06 0,10 0,10 0,11 0,11 40,0 0,06 0,10 0,10 0,10 0,11 50,0 0,10 0,10 0,10 0,10 63,0 0,10 0,10 0,10 80,0 0,10 0,10 100,0 0,10 ширина резания в мм E-95
Выбор режима резания при фрезеровании
Режущий инструмент — это фрезы цилиндрические, торцовые, концевые, угловые, шпоночные, фасонные и пр.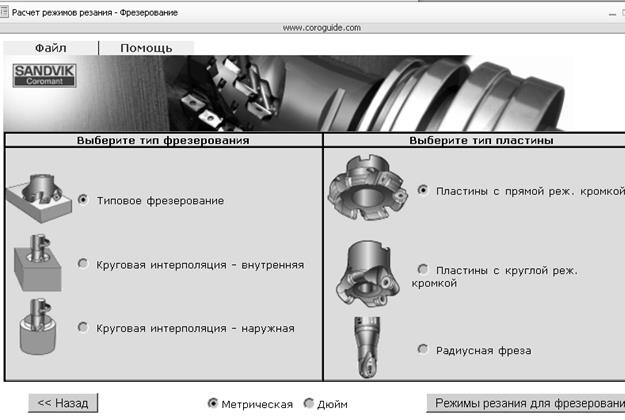
Выбор режимов резания при фрезеровании осуществляют главным образом для определения подачи на зуб фрезы и скорости резания, обеспечивающей требуемую стойкость, так как глубину резания и ширину фрезерования определяют видом фрезерования и припуском на обработку. [c.135]
Настройка станка на режим фрезерования. Выбор режима резания при фрезеровании плоскостей торцовыми фрезами производится по соответствующим таблицам, имеющимся в справочниках. [c.219]
Настройка станка на режим фрезерования. Выбор режима резания при фрезеровании уступов дисковыми быстрорежущими фрезами производим по табл. 181 Справочник молодого фрезеровщика .
Рассмотрим на конкретном примере порядок выбора режима резания при фрезеровании детали (бруска
[c. 71]
Настройка станка на режим фрезерования. Выбор режима резания при фрезеровании плоскостей торцовыми фрезами не отличается от выбора режима резания при фрезеровании цилиндрическими фрезами, но производится по таблицам, составленным специально для работы торцовыми фрезами. [c.121]
Настройка станка на режим фрезерования. Выбор режима резания при фрезеровании уступов дисковыми быстрорежущими фрезами производим по табл. 9. [c.159]
Настройка станка на режим фрезерования. Выбор режимов резания при фрезеровании пазов дисковыми фрезами производим по табл.. 10. Примем подачу на один зуб фрезы 0,03 мм. Тогда для фрезы 0 = 75 мм, при
[c.171]Глава ХХУП ВЫБОР РЕЖИМА РЕЗАНИЯ ПРИ ФРЕЗЕРОВАНИИ 78. УСЛОВИЯ, ОПРЕДЕЛЯЮЩИЕ ВЫБОР РЕЖИМА РЕЗАНИЯ [c.449]
Каков порядок выбора режимов резания при фрезеровании [c.147]
ВЫБОР РЕЖИМОВ РЕЗАНИЯ ПРИ ФРЕЗЕРОВАНИИ
[c. 349]
Выбор режимов резания при фрезеровании обычно производится по Общемашиностроительным нормативам режимов резания и времени для технического нормирования работ на фрезерных станках. Серийное производство (М., Машгиз, 1959) или по Общемашиностроительным нормативам режимов резания для технического нормирования работ на металлорежущих станках. Часть 1 (М., Машиностроение , 1967). [c.350]
Выбор режимов резания при фрезеровании [c.185]
Выбор режимов резания при фрезеровании, так же как и при других способах обработки, должен начинаться с определения глубины фрезерования. Как правило, при величине припуска больше 3—4 мм обработку следует вести в два прохода — черновой и чистовой. При припусках лоЗ мм к обработке под последующее шлифование или другой вид окончательной обработки следует ограничиваться одним полу-чистовым проходом. Определив глубину резания и зная ширину фрезерования, устанавливают типоразмер фрезы и соответственно виду обработки величину подачи на одни зуб 8 г-
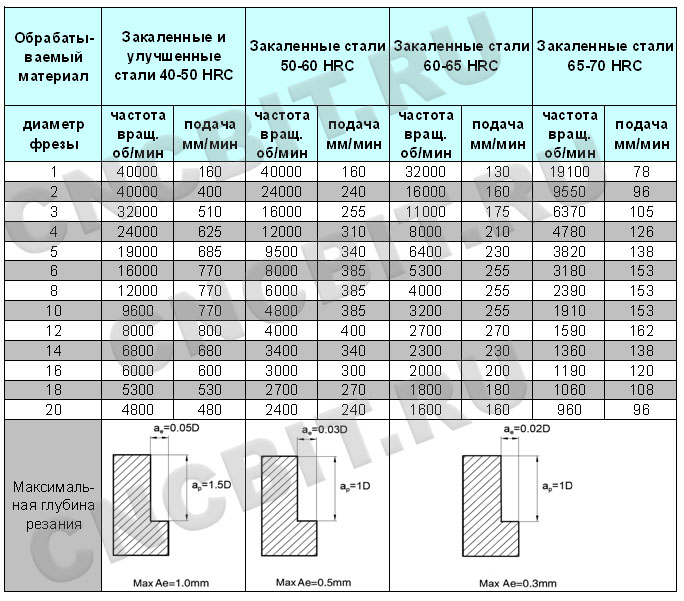
Повышение производительности труда при наименьшей затрате средств, труда и времени обеспечивается правильным выбором режимов резания при фрезеровании. [c.330]
Правильный выбор режимов резания при фрезеровании позволяет повысить производительность труда при наименьшей затрате средств, труда и времени.
[c.184]Выбор режимов резания при фрезеровании следует производить в следующей последовательности [c.220]
Выбор режима резания при фрезеровании пластмасс [17] [c.136]
Окончательный выбор режимов резания при цилиндрическом фрезеровании зависит от принятого критерия оптимизации и действующих ограничений. [c.221]
Основные положения выбора рациональных режимов резания при фрезеровании такие же, как и для других видов обработки нужно работать с максимально возможными глубиной и шириной резания, максимальной технологически допускаемой подачей и соответствующей скоростью резания.
[c.121]
Выбор варианта обработки. В примерах обработки, которые были последовательно разобраны в настоящей книге, мы в начале каждого примера обработки детали устанавливали порядок и метод ее (тип станка, операции, установки, переходы, проходы), намечали установочные базы, выбирали необходимые приспособления и инструменты и назначали режимы резания при фрезеровании, т. е. задавали технологический процесс. Назначение технологического процесса зависит от типа производства..
Какая последовательность выбора режимов резания при торцовом фрезеровании [c.77]
ВЫБОР РЕЖИМОВ РЕЗАНИЯ ПРИ ЧЕРНОВОМ И ЧИСТОВОМ ФРЕЗЕРОВАНИИ [c.185]
В Справочнике фрезеровщика главное место занимают описание устройства наиболее употребительных делительных головок и изложение правил их настройки при выполнении различных фрезерных работ. В нем также приведены необходимые указания и таблицы, относящиеся к часто выполняемым фрезерным работам — фрезерованию зубчатых колес, червяков и реек, различных кулачковых муфт и кулачков, шпоночных канавок, головок болтов, гаек и т. д. В Справочнике помещены основные сведения и рекомендации по общим вопросам фрезерной обработки процессу резания металла при фрезеровании,, точности и чистоте поверхностей, достигаемых фрезерованием, выбору режима резания при основных фрезерных работах и т. п.
[c.2]
Замечания, приведенные на стр. 390, относятся и к режимам резания при фрезеровании чугуна, за исключением рекомендаций по выбору охлаждающей жидкости. Фрезерование серого чугуна производится без охлаждения. [c.406]
Рекомендуемые обычно режимы резания при фрезеровании пластмасс характеризуются широким диапазоном скоростей резания и подач, а главное, отсутствием четких данных по их выбору в зависимости от условий обработки, обрабатываемого материала и материала инструмента, качества обрабатываемой поверхности, стойкости инструмента и т. д. Подобное разнообразие рекомендаций объясняется принципиально разными взглядами на вопрос обрабатываемости пластмасс резанием. Многие полагают, уто главным фактором, определяющим обрабатываемость, является не стойкость инструмента, а качество поверхности и точность обработки. Необходимо отметить, что скорости резания с точки зрения качества обработки и экономической стойкости инструмента не адекватно оптимальны, т. е. не совпадают, и это особенно четко проявляется при фрезеровании.
[c.39]
Приводятся практические рекомендации по выбору оптимальных параметров режущей части фрез и других элементов их конструкции, а также рациональных режимов резания при фрезеровании указан ных материалов. [c.2]
Выбор скорости резания. Скорость резания при фрезеровании зависит от материала режущей части фрезы, обрабатываемого. материала, геометрических пара.метров зуба фрезы, глубины фрезерования, подачи на один зуб, принятой стойкости фрезы и других факторов. Ее обычно назначают по нормативам режимов резания [5] и [6]. Рекомендуемые скорости резания при фрезеровании всеми видами фрез, изображенными на фиг. 1, наиболее применяемых материалов в зависимости от материала режущей части фрезы, глубины резания и подачи на один зуб приведены в табл. 38, 39, 40 и 41.
[c.305]
При фрезеровании стекло- и углепластиков фрезами, оснащенными вставками из СТМ марки АСБ, выбор режимов резания осуществляют по изложенной выше методике с помощью таблиц или формул. Стойкость фрез существенно выше, чем у твердосплавных качество поверхности удовлетворяет предъявляемым требованиям. [c.138]
От правильного выбора режима резания зависит в первую очередь производительность фрезерования, заданная точность и чистота поверхности. Отечественные ученые на основе науки о резании и опытной проверки результатов, полученных передовиками производства, разработали данные для выбора скоростей резания и подач при обработке инструментами из быстрорежущей стали, твердых оплавов и минералокерамики. [c.103]
Каждый из элементов геометрии зуба фрезы имеет свое значение в процессе резания, что подробно объясняется в курсе Фрезерное дело при изложении данного раздела имелось в виду, что читатель достаточно владеет основами теории резания при фрезеровании, и поэтому здесь приводятся только обобщающие сведения, позволяющие развивать их в направлении рационального применения при выборе режима резания.
[c.43]
Большое влияние на выбор режимов резания оказывает конфигурация обрабатываемой детали. Так при разрезке дисковой пилой, фрезеровании и шлифовании детал с плоскими поверх-ностями на выбор величины скорости перемещения стола оказывает большое влияние ширина обрабатываемой поверхности, поскольку она включается в формулу силы резания. Например, при фрезеровании приближенно можно считать, что сила резания Р пропорциональна ширине фрезерования [c.138]
Настройка станка на режим фрезерования. Выбор режимов резания при фрезеровании пазов дисковыми фрезами производим по табл. 182 Справочника молодого фрезеровщика . Примем подачу на один зуб фрезы 0,03 мм. Тогда для фрезы О = 75 мм, при 5 = 0,03 мм1зуб и глубине фрезерования t = 5 мм определяем скорость резания V = 42,2 м1мин, число оборотов п = 180 об/мин и подачу 5 = 97 мм1мин. Выбираем имеющееся ближайшее число оборотов шпинделя и ближайшую подачу и ставим лимб коробки скоростей на п = 190 об/мин, а лимб коробки подач на 5 = 95 мм/мин.
[c.251]
Расчет донусгимой скорости резания v по формулам (6.7) или выбор V 1ю картам режимов резания при фрезеровании. [c.122]
Кабальдин Ю. Г. Выбор оптимальной марки твердого сплава и режима резания при фрезеровании Информационный листок № 336-82. Хабаровск Хабаровский межотраслевой территориальный центр научно-технической информации и нропаганды, 1982. 180 с. [c.187]
Из формулы Q = В18ггп следует, что на объемную производительность фрезерования параметры В, 1, 8г, г и V оказывают одинаковое влияние, так как каждый из них входит в формулу в первой степени. Однако на стойкость инструмента эти параметры влияют по-разному. Поэтому с учетом стойкости инструмента выгоднее прежде всего выбирать максимально допустимые значения тех параметров, которые в меньшей степени влияют на стойкость инструмента, т. е. в такой последовательности глубина резания, подача на зуб и скорость резания. Следовательно, выбор этих параметров режима резания при фрезеровании на данном станке следует начинать в той же последовательности.
[c.141]
Выбор режима резания при обработке жаропрочной стали 1Х18Н9Т (ЭЯ1Т) можно производить по таблицам (стр. 425 и 426) скоростей и подач при фрезеровании кислотостойкой стали той же марки. [c.418]
Выбор режима резания при обработке окалиностойкой стали Х20Н80Т можно производить по таблицам скоростей резания и подач (стр. 417 и 418) при фрезеровании жаропрочной стали той же марки. [c.421]
Выбор режима резания при обработке нержавеющей стали 2X13 твердосплавными торцовыми фрезами можно производить по таблице скоростей резания и подач (стр. 415) при фрезеровании жаропрочной стали 4Х14Н14В2М. [c.423]
Режим резания при фрезеровании: расчет, определение, нормативы
Фрезерование – это далеко не самая простая операция по обработке металлов и других материалов, которая не всегда в деталях известна среднестатистическому человеку. Дело в том, что для этого процесса необходимо специальное устройство, которое называется фрезой – его можно найти на многих предприятиях, фабриках, заводах. Как происходит этот процесс? В данном случае в нем участвует режущий инструмент и заготовка. Режущим инструментом является сама фреза – она совершает вращательные движения, в отличие от самой заготовки, которая с помощью станка совершает поступательные движения по направлению к фрезе. В результате получается такой тип обработки, который сложно было бы повторить с помощью любого другого инструмента. Однако в данной статье не будет рассмотрена поверхностная информация – данный материал рассчитан на тех, кто уже более-менее знаком с процессом фрезерования. Главной и основной темой здесь будет режим резания, то есть здесь будет производится расчет и определение того, как именно должна функционировать фреза и какую насадку для нее использовать для конкретных видов металла разной твердости. Чтобы вам было легче разбираться в данных, которые будут предоставлены далее, вам сразу же стоит узнать, какие именно будут использоваться здесь понятия.
Все, что нужно знать
Итак, в каждом пункте будет указано, какой именно материал рассматривается, а также его твердость по методу Бриннеля – самому известному и распространенному из всех способов определения твердости тел. Измеряются они в HB, то есть единицах твердости Бриннеля. Далее будет определяться скорость резания, которая указывается в метрах в минуту (м/мин). Здесь вам стоит обратить особое внимание на то, что это не обороты фрезы, а именно абсолютно другой параметр. Данный параметр будет рассматриваться в нескольких примерах – если материал, который обрабатывается фрезой, не имеет никакого дополнительного покрытия, а также если фреза имеет разные типы покрытия TI-NAMITE. Ну и, конечно же, будет описан еще один очень важный параметр фрезерования – это подача на зуб. Для людей, далеких от этой сферы, данный параметр может показаться довольно необычным, но если внимательно изучить его детали, то все станет довольно просто. Итак, измеряется этот параметр в миллиметрах на зуб и определяет то, на сколько миллиметров перемещается заготовка, пока фреза поворачивается на один зуб. Из этой подачи можно высчитать и другие – например, оборотную и минутную, но именно подача на зуб является ключевым фактором.
И она также будет зависеть от диаметра используемого инструмента. Что ж, все основные данные вы получили – теперь пришло время узнать, какой режим резания при фрезеровании использовать в каком отдельно взятом случае.
Стали общего применения
Итак, первый материал, который рассматривается в данной статье – это стали общего применения. Какой режим резания использовать для такого материала? В первую очередь нужно определить твердость материала. Если твердость стали составляет менее 150 единиц Бриннеля, то необходимо выставлять скорость от 150 до 210 метров в минуту в зависимости от покрытия. 150, соответственно, при полном отсутствии покрытия, а 210 – при наличии наиболее эффективного покрытия TI-NAMITE-A. Что касается подачи на зуб, то здесь все зависит, как уже было сказано ранее, от диаметра инструмента. Если его диаметр менее трех миллиметров, то подача на зуб составит от 0,012 до 0,018 миллиметров, при росте диаметра до 5 мм, подача возрастает до 0,024 мм, если диаметр увеличивается до 9 мм, то и подача возрастает до 0. 050 мм, при диаметре до 14 мм подача может повыситься до 0.080 мм, ну а при максимальном диаметре в 25 миллиметров подача на зуб составит 0.18 мм. Эти данные и позволяют вам выбрать правильный режим резания. Но не забывайте, что есть и более твердые виды стали общего применения. При твердости менее 190 единиц Бриннеля скорость должна быть от 120 до 165 метров в минуту, а при твердости менее 240 единиц Бриннеля – от 90 до 125 метров в минуту. Естественно, меняется подача на зуб. Она становится меньше и в первом случае может быть от 0.01 до 0.1 миллиметра на зуб, в то время как во втором случае – от 0.008 до 0.08 миллиметра на зуб. Естественно, это не единственный материал, который используется при фрезеровании, так что стоит обратить внимание и на другие металлы.
Цементируемые стали
Режимы резания при обработке цементируемых сталей будут зависеть от твердости материала. Если она составляет менее 235 единиц Бриннеля, то и скорость резания будет соответствующей – от 100 до 140 метров в минуту. При твердости менее 285НВ показатель падает – от 80 до 110 метров в минуту. Но при этом не стоит забывать также и о подаче на зуб. В принципе, про нее можно много не говорить, потому что она не отличается от того, что вы уже видели в предыдущем пункте. В первом случае она будет иметь те же самые интервалы, что и при обработке стали общего применения твердостью менее 190НВ, а во втором – те же самые, что и при обработке стали общего применения твердостью менее 240НВ. Но при этом нельзя сказать, что подача на зуб будет идентичной, потому что к максимальному диаметру инструмента в первом случае подача составляет не 0.1, как в предыдущем примере, а 0.15. Именно поэтому расчет режимов резки и является такой сложной задачей, которую лучше всего выполнять по всем нормам и в соответствии со строгими предписаниями.
Азотируемые стали
Расчет режимов резания при обработке азотируемых сталей ничем не отличается от предыдущих случаев – только в данном случае материалы является немного более твердыми, чем прошлые, поэтому вам не стоит удивляться тому, что скорость резки здесь будет от 90 до 125 метров в минуту при менее твердой стали и от 70 до 95 метров в минуту при более твердом материале. Что касается подачи на зуб, то в первом случае здесь вполне стандартный разбег шага – от 0.008 до 0.08 миллиметров, но если металл будет обладать большим количеством единиц твердости Бриннеля, то это будет означать, что его подача снизится, причем заметно. При минимальном диаметре инструмента она составит 0.006 миллиметра, а при максимальном – 0.06 миллиметра. На данный момент это самая низкая подача на зуб, рассматриваемая в данной статье. Расчет режимов резания по данной информации проводится довольно обычно по стандартной формуле, о которой будет сказано в конце статьи.
Среднеуглеродистые стали
Среднеуглеродистые стали является очень распространенными, а самое главное – существует несколько различных уровней их твердости. И, естественно, у каждой из них будет своя скорость резки. Например, первые два типа стали имеют одинаковый показатель, если у фрезы нет покрытия – 80 метров в минуту. Но при максимальном покрытии у первого типа скорость возрастает до 110 метров в секунду, а у второго – только до 85 метров в секунду. Но при этом есть еще два типа, первый с твердостью менее 340НВ, а второй – менее 385НВ. Соответственно, у первого параметр резки будет от 50 до 70 м/мин, а у второго – от 35 до 50 м/мин. По сравнению с теми типами, что вы видели ранее, это довольно низкая скорость. Соответственно, у этих видов стали и подача на зуб не слишком высока – отдельно стоит выделить последнюю по твердости сталь, которая при минимальном диаметре инструмента имеет невероятно малую подачу, всего 0.005 миллиметра. Сразу стоит отметить, что здесь рассматривается фрезерование, а не режимы резания при точении. Как уже было сказано выше, для расчета используется формула, с которой вы ознакомитесь выше. Режимы резания при точении рассчитываются немного по иной формуле, поэтому вам не стоит пытаться применить один расчет ко всем видами работ.
Инструментальные стали
Инструментальные стали по твердости делятся на еще больше видов, чем среднеуглеродистые, поэтому режимы резания при фрезеровании инструментальной стали могут быть многочисленными. Если кратко рассказать именно об этой стали, то есть пять видов твердости: менее 230НВ, менее 285НВ, менее 340НВ, менее 395НВ и более 395НВ. Для каждого из них имеется своя скорость резки: от 90 до 125 м/мин, от 70 до 95 м/мин, от 60 до 85 м/мин, от 45 до 65 м/мин и от 30 до 40 м/мин соответственно. Собственно говоря, имя эти данные вы будете уже на полпути к восполнению всех недостающих пробелов в вычислении формулы, с помощью которой определяются режимы резания при фрезеровании. Чтобы в формуле все переменные заменились числами, вам нужно также знать диаметр инструмента (и полученные из него данные по подаче на зуб).
Как выбрать режим?
Выбор режимов резания производится довольно просто – на каждой фрезе имеется переключатель, который позволят вам контролировать скорость вращения режущего инструмента. С помощью этого маленького переключателя вы можете задать примерное значение оборотов в минуту, и тогда ваш станок будет работать именно на этом уровне. Собственно говоря, это и является режимом резания, но такой простой процесс имеет за собой большое количество расчетов, о которых речь пойдет далее. Дело в том, что определение скорость вращения режущего инструмента фрезы должно быть максимально точным, и редко когда у вас есть достаточно времени и материала, чтобы подбирать режимы резания металла наугад. Именно для этого и существует теория, которую необходимо использовать перед практическим применением.
Формула скорости резания
Очень важно соблюдать нормативы режимов резания, так как дело здесь не только в том, что вы потратите очень много времени, а что еще хуже – очень много материала на подбор нужного режима вслепую. Это также может быть небезопасно. Поэтому лучше всего руководствоваться теоретическими знаниями в первую очередь. Итак, сейчас вы узнаете формулу, по которой высчитывается режим для конкретного металла. То, как ее можно применять на практике, будет описано ниже. Сама формула предполагает, что скорость, выражаемая в метрах в минуту, умножается на переводной коэффициент 1000, а результат делится на произведение числа «пи», умноженного на диаметр фрезы. Это все необходимые вам элементы режима резания, чтобы высчитать скорость вращения фрезы.
Упрощенная формула
Нет смысла проводить два умножения, когда вы знаете, что число «пи» является цифрой без каких-либо переменных. Изначально принято сокращать 1000 и 3.14, чтобы получить 318. 318 умножается на скорость, а затем полученные результат делится на диаметр фрезы. Вот и все, эта формула уже гораздо проще, чем предыдущая, и именно с ее помощью чаще всего производится определение режима резания.
Расчет
В таком материале невозможно обойтись без примера. Что ж, для примера можно взять сталь общего применения с твердостью менее 150НВ и фрезу с покрытием TI-NAMITE и диаметром 10 миллиметров. Итак, сначала необходимо свериться с данными, которые были описаны в статье выше – при таких показателях скорость резания составит 175 м/мин, поэтому вам нужно умножить 318 на 175, получится 55650. Теперь это нужно разделить на диаметр фрезы, то есть 10 – получается 5565. Именно это и есть искомое значение. Теперь вам нужно выставить его на вашем станке, а если конкретно такое значение выставить невозможно, то рекомендуется взять немного меньшее.
Каталог иностранного инструмента
Если вы пользуетесь отечественной фрезой, то, вероятнее всего, вы сможете без труда отыскать необходимые данные по определению режима резания. Если же у вас имеется иностранный образец, то у вас могут возникнуть определенные проблемы. Именно поэтому при покупке иностранного фрезеровочного станка крайне необходимо попросить каталог со всеми необходимыми пояснениями, которые вы сможете затем использовать как теоретическую базу при работе со станком.
Специальные графики
Настоящим спасениям являются графики, которые составляются для более быстрого и удобного определения режима резания. Что представляет собой такой график? Это набор прямых линий разного цвета, которые находятся между двумя осями – одна из них показывает скорость, то есть величину, которая вам известна, так как вы знаете, какой материал вы обрабатываете, а вторая – количество оборотов в минуту, которое будет совершать ваша фреза, то есть, проще говоря, режим ее работы. Почему линии разного цвета? Если вы не забыли, то количество оборотов фрезы в минуту невозможно высчитать только по скорости резания – вам нужен еще и диаметр инструмента, и каждый цвет отвечает за свой диаметр.
Как пользоваться графиком
Все, что от вас требуется – это отыскать в таблице диаметр вашего инструмента и выбрать прямую нужного цвета на графике. Затем вам нужно определить скорость и провести прямую от оси y, то есть той оси, на которой указаны значения данного параметра. От места пересечения вашей линии с прямой выбранного вами цвета необходимо провести прямую к оси x, чтобы узнать уже точное количество оборотов в минуту.
3. Расчет наивыгоднейшего режима резания при фрезеровании. Назначение наивыгоднейших режимов резания и расчет машинного времени при различных видах обработки резанием
Похожие главы из других работ:
Гильза клапана Т500.45.021. Технологический процесс обработки детали
2.7 Расчет режима резания
Определить режимы резания и основное время на операцию 055 круглошлифовальную. Содержание операции: Шлифовать поверхность, выдерживая размер . Исходные данные: деталь – гильза клапана Т.500.45…
Методика расчётов режимов резания
Расчет режимов резания при фрезеровании
Материал заготовки сталь 40 Предел прочности материала заготовки 570МПа Ширина обрабатываемой поверхности В = 45мм Длинна обрабатываемой поверхности L = 30мм Требуемая шероховатость Ra = 6…
Назначение наивыгоднейших режимов резания и расчет машинного времени при различных видах обработки резанием
1. Табличный метод расчета наивыгоднейшего режима резания при точении
Задание: Определить наивыгоднейший режим резания при точении согласно рис. 1.1 и данных: 1) Обрабатываемый материал – ХН60ВТ; 2) ув=750 МПа; 3) Размеры заготовки: D=250 мм, t=5 мм, L=100 мм; 4) Класс шероховатости Ra=2…
Назначение наивыгоднейших режимов резания и расчет машинного времени при различных видах обработки резанием
2.

Задание. Определить наивыгоднейший режим резания при сверлении материала ХН60ВТ с охлаждением для заданной схемы (рис. 2.1) при D=10 мм; L=40 мм; l=40 мм; оборудование-2Н135. Рисунок 2…
Обработка металлов резанием на примере изготовления крышки
7.1 Режимы резания при фрезеровании
1) Глубина резания t, мм, зависит от припуска на обработку и требуемого класса шероховатости обрабатываемой поверхности. Если глубина резания t ? 5 мм, то обработку (фрезерование) ведут за один проход. В данном случае глубина резания t = 40…
Проект технологии восстановления ведомого вала редуктора ВОМ трактора Т150-К
2.4.3.2 Выбор режимов резания при фрезеровании
Глубину резания t (мм) выбирают в зависимости от припуска на обработку и требований чистоты поверхности. В большинстве случаев при черновом фрезеровании глубина резания составляет 2; 5; 8 мм, а при чистовом – 0,5…5 мм. ..
Проектирование привода главного движения металлорежущего станка
1.1 Расчет режимов резания при торцовом фрезеровании
Инструмент – торцовая фреза ГОСТ 22085-76. Марки инструментального материала: Т5К10 для чернового фрезерования, Т15К6 для чистового фрезерования. Скорость резания при фрезеровании: (1.1) – коэффициент…
Проектирование привода главного движения металлорежущего станка
1.2 Расчет режимов резания при цилиндрическом фрезеровании
Инструмент – торцовая фреза ГОСТ 3752-71. Марки инструментального материала: P6M5 Значения всех коэффициентов и показателей степени приведены в таблице 3…
Процесс точения заготовки
4.1 Исследование влияния параметров режима резания на силу резания и температуру резания с целью получения экспериментальных зависимостей (эмпирических формул), необходимых для расчёта параметров режима резания
Для получения экспериментальных зависимостей, необходимых для расчёта параметров режима резания при точении, исследуем влияние параметров режима резания на силу резания и температуру резания. ..
Разработка технологического процесса изготовления детали
2.2 Расчет режима резания при сверлении
L=75 Ds D=15 Сверлением называется образование отверстия в сплошном материале снятием стружки с помощью режущего инструмента – сверла. Сверлениеосуществляют при сочетании вращательного движения инструмента вокругоси – главного движения резания…
Разработка технологического процесса механической обработки шестерни ведущей
3.2.2 Режимы резания при фрезеровании (0,10; 0,30)
1.) Глубина фрезерования принимаем по чертежу. 2.) Подача . Принимаем согласно табличным данным. 3.) Скорость резания вычисляем по формуле: , 4.) Сила резания , H вычисляем по формуле: , 5.) Мощность резания N, кВт вычисляем по формуле: , 6…
Расчет режимов резания металла
Задание 1. Расчет режима резания при точении аналитическим способом
Исходные данные: – станок – токарно-винторезный 16К20 – деталь – вал; – операция – подрезка торца; – обрабатываемый материал – Сталь Ст3; ув = 600 МПа – вид заготовки – обработанная; – шероховатость обработанной поверхности Rа = 12. ..
Технологический процесс получения заготовок типа “вал-шестерня”
3.2 Проверка экономически наивыгоднейшего режима точения по мощности главного электродвигателя главного привода станка
Мощность, затрачиваемая на процесс резания: Мощность станка с учетом потерь: Nст=Nрез*з=1,22*0,82=1,5 кВт…
Технологический процесс получения литой заготовки в песчаной форме
2.3 Расчет режима резания при сверлении
Процесс резания при сверлении протекает в более сложных условиях, чем при точении. В процессе резания затруднены отвод стружки и подвод охлаждающей жидкости к режущим кромкам инструмента…
Технология машиностроения
3.2 Расчёт режима резания
Палец • Материал : Ст 18хг Ст 18хг – конструкционная качественная сталь содержащая хрома до 1% , марганца 1% и углерода 0,18% . • Определение глубины резания D=d+h=26+4,0=30, мм D=26+3,5=29,5=30, мм h=3,5,мм h – припуск i1=1,5 i2=0,5 – количество проходов, S=0. ..
Режимы резания при фрезеровании: таблица, элементы, выбор режимов
Скорость резания
Наиболее важным режимом при фрезеровании можно назвать скорость резания. Он определяет то, за какой период времени будет снят определенный слой материала с поверхности. На большинстве станков устанавливается постоянная скорость резания. При выборе подходящего показателя учитывается тип материала заготовки:
- При работе с нержавейкой скорость резания 45-95 м/мин. За счет добавления в состав различных химических элементов твердость и другие показатели меняются, снижается степень обрабатываемости.
- Бронза считается более мягким составом, поэтому подобный режим при фрезеровании может выбираться в диапазоне от 90-150 м/мин. Она применяется при изготовлении самых различных изделий.
- Довольно большое распространение получила латунь. Она применяется при изготовлении запорных элементов и различных клапанов. Мягкость сплава позволяет повысить скорость резания до 130-320 м/мин.
Латуни склонны к повышению пластичности при сильном нагреве.
- Алюминиевые сплавы сегодня весьма распространены. При этом встречается несколько вариантов исполнения, которые обладают различными эксплуатационными характеристиками. Именно поэтому режим фрезерования варьирует в пределе от 200 до 420 м/мин. Стоит учитывать, что алюминий относится к сплавам с низкой температурой плавления. Именно поэтому при высокой скорости обработки есть вероятность существенного повышения показателя пластичности.
Встречается довольно большое количество таблиц, которые применяются для определения основных режимов работы. Формула для определения оборотов скорости резания выглядит следующим образом: n=1000 V/D, где учитывается рекомендуемая скорость резания и диаметр применяемой фрезы. Подобная формула позволяет определить количество оборотов для всех видов обрабатываемых материалов.
Рассматриваемый режим фрезерования измеряется в метрах в минуту режущие части. Стоит учитывать, что специалисты не рекомендуют гонять шпиндель на максимальных оборотах, так как существенно повышается износ и есть вероятность повреждения инструмента. Поэтому полученный результат уменьшается примерно на 10-15%. С учетом этого параметра проводится выбор наиболее подходящего инструмента.
Скорость вращения инструмента определяет следующее:
- Качество получаемой поверхности. Для финишной технологической операции выбирается наибольший параметр. За счет осевого вращения с большим количеством оборотов стружка получается слишком мелкой. Для черновой технологической операции, наоборот, выбираются низкие значения, фреза вращается с меньшей скоростью, и размер стружки увеличивается. За счет быстрого вращения достигается низкий показатель шероховатости поверхности. Современные установки и оснастка позволяют получить поверхность зеркального типа.
- Производительность труда. При наладке производства уделяется внимание и тому, какова производительность применяемого оборудования. Примером можно назвать цех машиностроительного завода, где налаживается массовое производство. Существенное снижение показателя режимов обработки становится причиной уменьшения производительности.
Наиболее оптимальный показатель существенно повышает эффективность труда.
- Степень износа устанавливаемого инструмента. Не стоит забывать о том, что при трении режущей кромки об обрабатываемую поверхность происходит ее сильный износ. При сильном изнашивании происходит изменение показателей точности изделия, снижается эффективность труда. Как правило, износ связан с сильным нагревом поверхности. Именно поэтому на производственной линии с высокой производительностью применяется оборудование, способное подавать СОЖ в зону снятия материала.
При этом данный параметр выбирается с учетом других показателей, к примеру, глубины подачи. Поэтому технологическая карта составляется с одновременным выбором всех параметров.
Правила выбора режима резания при фрезеровании фрезами — таблицы и советы
На предприятиях, в составе которых есть подразделения, занимающиеся поверхностной обработкой заготовок, на основе нормативных документов составляются специальные карты, которыми руководствуется оператор при изготовлении той или иной детали. Хотя в некоторых случаях (к примеру, новое оборудование, инструмент) нюансы технологических операций фрезеровщику приходится определять самостоятельно. Если маломощный станок эксплуатируется в домашних условиях, тем более, никаких официальных подсказок под рукой, как правило, нет.
Эта статья поможет не только понять, на основе чего производится расчет режима резания при фрезеровании и выбор соответствующего инструмента, но и дает практические рекомендации, которые достаточны для обработки деталей на бытовом уровне.
Тем, кто по большей степени связан с металлами, для более детального ознакомления с нюансами фрезерования стоит обратиться к учебнику «Металлорежущие станки» – 2003 года, Черпаков Б.И., Альперович Т.А. Порядок расчета режимов резания также хорошо изложен в различных пособиях. Например, в методических рекомендациях от 2000 года (МГАУ – Колокатов А.М., Баграмов Л.Г.).
Особенность фрезерования в том, что режущие кромки вступают в прямой контакт с материалом лишь периодически. Как следствие – вибрации, ударные нагрузки и повышенный износ фрез. Наиболее эффективным режимом считается такой, при котором оптимально сочетаются следующие параметры – глубина, подача и скорость резания без ухудшения точности и качества обработки. Именно это позволяет существенно снизить стоимость технологической операции и повысить производительность.
Предусмотреть буквально все нюансы фрезерования невозможно. Заготовки, подлежащие обработке, отличаются структурой, габаритами и формой; режущие инструменты – своей геометрией, конструктивным исполнением, наличием/отсутствием защитного слоя и тому подобное. Все, что изложено по режимам резания далее, следует рассматривать всего лишь как некий ориентир. Для уточнения конкретных параметров фрезерования следует пользоваться специальными таблицами и справочными данными.
Выбор инструмента
Главным образом это относится к его диаметру. В чем особенность подбора фрезы (все виды описаны здесь) по этому параметру?
- Повышение диаметра автоматически приводит к увеличению стоимости инструмента.
- Взаимозависимость двух показателей – если подача возрастает, то скорость резания падает, так как она ограничивается структурой обрабатываемой детали (см. ниже).
Рекомендация
Оптимальным считается такой диаметр фрезы, при котором его величина соответствует (или немного больше) требуемой глубине резания. В некоторых случаях за 1 проход можно выбрать стружку и более толстую, но это относится лишь к материалам, характеризующимся невысокой плотностью. Например, пенопласт или некоторые породы древесины.
Скорость резания
В зависимости от материала образца можно ориентироваться на следующие показатели (м/мин):
- древесина, термопласты – 300 – 500;
- ПВХ – 100 – 250;
- нержавейка – 45 – 95;
- бронза – 90 – 150;
- латунь – 130 – 320;
- бакелит – 40 – 110;
- алюминий и его сплавы – 200 – 420.
Рекомендуется ориентироваться на среднее значение величины. Например, если материал – алюминий, за исходную взять скорость = 300. В процессе фрезерования заготовки станет ясно, уменьшить ее или увеличить.
Частота вращения фрезы
Простейшая формула выглядит так:
n (число оборотов) = 1000 Vc (желаемая скорость реза) / π D (диаметр фрезы).
Рекомендация
Гонять шпиндель на максимальных оборотах с точки зрения безопасности не следует. Значит, только за счет этого скорость резания уменьшится примерно на 10 – 15%. Частично компенсировать эту «потерю» можно установкой фрезы большего диаметра. Этим скорость несколько повышается. Если подходящей под рукой нет, придется решать – тратить деньги на новый инструмент или довольствоваться теми возможностями, которые имеются у фрезерного станка. Опять-таки, все это проверяется лишь практикой работы на конкретном оборудовании, но общий смысл рекомендации понятен.
Подача
На этот параметре фрезерования следует обратить пристальное внимание!
Долговечность фрезы и качество обработки заготовки зависят от того, какой толщины слой снимается за одну проходку, то есть при каждом обороте шпинделя. В этом случае говорят о подаче на 1 (2,3) зуба, в зависимости от разновидности инструмента (фреза одно- , двух- или трехзаходная).
Рекомендуемые значения подачи «на зуб» указываются производителем инструмента. Фрезеровщик по этому пункту режима резания сталкивается с трудностями, если работает с фрезами «made in China» или какого-то сомнительного (неизвестного) происхождения. В большинстве случаев можно ориентироваться на диапазон подачи (мм) 0,1 – 0,25. Такой режим подходит практически для всех распространенных материалов, подвергающихся обработке фрезерованием. В процессе реза станет понятно, достаточно или несколько «прибавить» (но не раньше, чем после 1-го захода). А вот менее 0,1 пробовать не стоит, разве только при выполнении ювелирной работы с помощью микрофрез.
Рекомендация
Начинать фрезерование следует с минимальной подачи – 0,1. В процессе станет понятно, насколько податлив обрабатываемый материал перед конкретной фрезой. Это исключит вероятность слома режущей кромки (зуба) и позволит поставить возможностям станка и инструмента точный «диагноз», особенно если это «чужое» оборудование.
Полезные советы
- Превышение значения оптимальной подачи чревато повышением температуры в рабочей области, образованием толстой стружки и быстрой поломкой фрезы. Для инструмента диаметром свыше 3 мм начинать следует с 0,15, не более
- Если скорость фрезерования детали повысить за счет оптимального использования возможностей оборудования не получается, можно попробовать установить фрезу двухзаходную.
- При выборе инструмента нужно учитывать, что увеличение длины режущей части приводит к снижению подачи и увеличению вибраций.
- Не следует стремиться повысить скорость обработки за счет замены фрезы на аналогичную, но с большим количеством зубьев. Стружка от такого инструмента отводится хуже, поэтому часто приводит к тому, что качество фрезерования резко снижается. В некоторых случаях, при полной забивке канавок, фреза начинает работать «вхолостую». Толку от такой замены никакого.
Вывод
Качественного фрезерования можно добиться только опытным путем. Конкретные станок + инструмент + практический опыт, навыки. Поэтому не стоит слепо доверять даже табличным данным. Например, в них не учитывается степень износа фрезы, с которой предстоит работать. Не нужно бояться экспериментировать, но начинать всегда следует с минимального значения параметров. Когда мастер «почувствует» и станок, и фрезу, и обрабатываемый материал, он сам определит, в каком режиме стоит работать.
Глубина резания
Другим наиболее важным параметром является глубина фрезерования. Она характеризуется следующими особенностями:
- Глубина врезания выбирается в зависимости от материала заготовки.
- При выборе уделяется внимание тому, проводится черновая или чистовая обработка. При черновой выбирается большая глубина врезания, так как устанавливается меньшая скорость. При чистовой снимается небольшой слой металла за счет установки большой скорости вращения инструмента.
- Ограничивается показатель также конструктивными особенностями инструмента.
Это связано с тем, что режущая часть может иметь различные размеры.
Глубина резания во многом определяет производительность оборудования. Кроме этого, подобный показатель в некоторых случаях выбирается в зависимости от того, какую нужно получить поверхность.
Мощность силы резания при фрезеровании зависит от типа применяемой фрезы и вида оборудования. Кроме этого, черновое фрезерование плоской поверхности проводится в несколько проходов в случае, когда нужно снять большой слой материала.
Особым технологическим процессом можно назвать работу по получению пазов. Это связано с тем, что их глубина может быть довольно большой, а образование подобных технологических выемок проводится исключительно после чистовой обработки поверхности. Фрезерование т-образных пазов проводится при применении специального инструмента.
Погружение и кромка реза
Фрезеровка должна выполняться буровым способом, схожим с осуществлением сверления. Если торец не задевает обрабатываемый материал, необходимо выполнить перенастройку. Из-за отличий между кантами прохода, качество обработки сторон отличается. Рекомендуется:
- выполнять фрезеровку внутренних контуров по часовой стрелке;
- осуществлять фрезеровку внешних контуров против часовой стрелки.
Благодаря фрезерованию по этой системе менее качественная сторона будет срезаться.
Важно! Чем глубже погружение, тем выше вероятность поломки. При высокой скорости фреза должна погружаться на минимальную глубину, а резание выполняться в несколько проходов.
Подача
Понятие подачи напоминает глубину врезания. Подача при фрезеровании, как и при проведении любой другой операции по механической обработке металлических заготовок, считается наиболее важным параметром. Долговечность применяемого инструмента во многом зависит от подачи. К особенностям этой характеристики можно отнести нижеприведенные моменты:
- Какой толщины материал снимается за один проход.
- Производительность применяемого оборудования.
- Возможность проведения черновой или чистовой обработки.
Довольно распространенным понятием можно назвать подачу на зуб. Этот показатель указывается производителем инструмента, зависит от глубины резания и конструктивных особенностей изделия.
Как ранее было отмечено, многие показатели режимом резания связаны между собой. Примером можно назвать скорость резания и подачу:
- При увеличении значения подачи скорость резания снижается. Это связано с тем, что при снятии большого количества металла за один проход существенно повышается осевая нагрузка. Если выбрать высокую скорость и подачу, то инструмент будет быстро изнашиваться или попросту поломается.
- За счет снижения показателя подачи повышается и допустимая скорость обработки. При быстром вращении фрезы возможно существенно повысить качество поверхности. На момент чистового фрезерования выбирается минимальное значение подачи и максимальная скорость, при применении определенного оборудования можно получить практически зеркальную поверхность.
Довольно распространенным значением подачи можно назвать 0,1-0,25. Его вполне достаточно для обработки самых распространенных материалов в различных отраслях промышленности.
Таблицы: скорость подачи
Материал | Скорость для 3-миллиметрового торцевого инструмента (в миллиметрах в минуту) | Скорость для 6-миллиметрового торцевого инструмента (в миллиметрах в минуту) |
Мягкие сорта дерева | от 1 до 1,5 тысячи | от 2 до 3 тысяч |
Твердое дерево | от 0,5 до 1 тысяч | от 1,5 до 2,5 тысячи |
Двухслойный пластик | 2 тысячи | отсутствует |
Акрил и разные виды полистирола | от 0,8 до 1 тысячи | от 1 до 1,3 тысячи |
ПВХ | от 1,5 до 2 тысяч | от 1,5 до 2 тысяч |
Алюминиевые сплавы | от 0,5 до 0,8 тысячи | от 0,8 до 1 тысячи |
Значения в таблице указывают минимальный и максимальный показатели, на которых фрезерные станки могут исправно резать без риска возникновения сбоев.
Ширина фрезерования
Еще одним параметром, который учитывается при механической обработки заготовок считается ширина фрезерования. Она может варьировать в достаточно большом диапазоне. Ширина выбирается при фрезеровке на станке Have или другом оборудовании. Среди особенностей отметим следующие моменты:
- Ширина фрезерования зависит от диаметра фрезы. Подобные параметры, которые зависят от геометрических особенностей режущей части, не могут регулироваться, учитываются при непосредственном выборе инструмента.
- Ширина фрезерования также оказывает влияние на выбор других параметров. Это связано с тем, что при увеличении значения также увеличивается количество материала, который снимается за один проход.
В некоторых случаях ширина фрезерования позволяет получить требуемую поверхность за один проход. Примером можно назвать случай получения неглубоких канавок. Если проводится резание плоской поверхности большой ширины, то число проходов может несколько отличаться, рассчитывается в зависимости от ширины фрезерования.
Как выбрать режим на практике?
Как ранее было отмечено, в большинстве случаев технологические карты разработаны специалистом и мастеру остается лишь выбрать подходящий инструмент и задать указанные параметры. Кроме этого, мастер должен учитывать то, в каком состоянии находится оборудование, так как предельные значения могут привести к возникновению поломок. При отсутствии технологической карты приходится проводить выбор режимов фрезерования самостоятельно. Расчет режимов резания при фрезеровании проводится с учетом следующих моментов:
- Типа применяемого оборудования. Примером можно назвать случай резания при фрезеровании на станках ЧПУ, когда могут выбираться более высокие параметры обработки по причине высоких технологических возможностей устройства. На старых станках, которые были введены в эксплуатацию несколько десятков лет назад, выбираются более низкие параметры. На момент определения подходящих параметров уделяется внимание и техническому состоянию оборудования.
- Следующий критерий выбора заключается в типе применяемого инструмента. При изготовлении фрезы могут применяться различные материалы. К примеру, вариант исполнения из быстрорежущей качественной стали подходит для обработки металла с высокой скоростью резания, фреза с тугоплавкими напайками предпочтительно выбирается в случае, когда нужно проводить фрезерование твердого сплава с высоким показателем подачи при фрезеровании. Имеет значение и угол заточки режущей кромки, а также диаметральные размер. К примеру, с увеличением диаметра режущего инструмента снижается подача и скорость резания.
- Тип обрабатываемого материала можно назвать одним из наиболее важных критериев, по которым проводится выбор режима резания. Все сплавы характеризуются определенной твердостью и степенью обрабатываемости. К примеру, при работе с мягкими цветными сплавами могут выбираться более высокие показатели скорости и подачи, в случае с каленной сталью или титаном все параметры снижаются. Немаловажным моментом назовем то, что фреза подбирается не только с учетом режимов резания, но и типа материала, из которого изготовлена заготовка.
- Режим резания выбирается в зависимости от поставленной задачи. Примером можно назвать черновое и чистовое резание. Для черного свойственна большая подача и небольшой показатель скорости обработки, для чистовой все наоборот. Для получения канавок и других технологических отверстий и вовсе показатели подбираются индивидуально.
Как показывает практика, глубина резания в большинстве случаев делится на несколько проходов при черновой обработке, при чистовой он только один. Для различных изделий может применяться таблица режимов, которая существенно упрощает поставленную задачу. Встречаются и специальные калькуляторы, проводящие вычисление требуемых значений в автоматическом режиме по введенным данным.
Примеры программ на сверление отверстий при помощи постоянных циклов
Постоянные циклы станка с ЧПУ
Пример № 1
Рис. 8.8. Необходимо просверлить 7 отверстий диаметром 3 мм и глубиной 6,5 мм
Код программы | Описание |
% O0001 N100 G21 N102 G0 G17 G40 G49 G80 G90 N104 T1 M6 N106 G54 X5.![]() | Номер программы Работа в метрической системе Строка безопасности Вызов сверла диаметром 3 мм Перемещение к отверстию № 1 Компенсация длины инструмента Ускоренное перемещение к Z10. Стандартный цикл сверления Сверление отверстия № 2 Сверление отверстия № 3 Сверление отверстия № 4 Сверление отверстия № 5 Сверление отверстия № 6 Сверление отверстия № 7 Отмена постоянного цикла Перемещение к Z100. Останов шпинделя Возврат в исходную позицию по Z Возврат в исходную позицию по X, Y Конец программы |
Пример № 2
Рис. 8.9. Необходимо просверлить 12 отверстий диаметром 5 мм и глубиной 40 мм, предварительно выполнить операцию центрования отверстий
№ отверстия | Координаты в прямоугольной системе координат (X; Y) |
1 | X21.![]() |
2 | X12.5 Y21.651 |
3 | X0. Y25. |
4 | X-12.5 Y21.651 |
5 | X-21.651 Y12.5 |
6 | X-25. Y0. |
7 | X-21.651 Y-12.5 |
8 | X-12.5 Y-21.651 |
9 | X0. Y-25. |
10 | X12.5 Y-21.651 |
11 | X21.651 Y-12.5 |
12 | X25. Y0. |
Код программы | Описание |
% O0002 (PROGRAM NAME – HOLES2 ) N100 G21 N102 G0 G17 G40 G49 G80 G90 ( CENTROVKA ) N104 T1 M6 N106 G54 X21.651 Y12.5 S1200 M3 N108 G43 h2 Z100. N110 Z2. N112 G99 G81 Z-.8 R2. F70. N114 X12.5 Y21.651 N116 X0. Y25. N118 X-12.5 Y21.651 N120 X-21.651 Y12.5 N122 X-25. Y0. N124 X-21.651 Y-12.5 N126 X-12.5 Y-21.651 N128 X0. Y-25. N130 X12.5 Y-21.651 N132 X21.651 Y-12.5 N134 X25. Y0. N136 G80 N138 Z100. N140 M5 N142 G91 G28 Z0. N144 G28 X0.![]() | Номер программы Название программы Работа в метрической системе Строка безопасности Комментарий Вызов центровки Перемещение к отверстию № 1 Компенсация длины инструмента Ускоренное перемещение к Z2. Стандартный цикл сверления Центрование отверстия № 2 Центрование отверстия № 3 Центрование отверстия № 4 Центрование отверстия № 5 Центрование отверстия № 6 Центрование отверстия № 7 Центрование отверстия № 8 Центрование отверстия № 9 Центрование отверстия № 10 Центрование отверстия № 11 Центрование отверстия № 12 Отмена постоянного цикла Перемещение к Z100. Останов шпинделя Возврат в исходную позицию по Z Возврат в исходную позицию по X, Y Временный останов Комментарий Вызов сверла диаметром 5 мм Перемещение к отверстию № 1 Компенсация длины инструмента Ускоренное перемещение к Z2.![]() |
Вперед >>
Выбор режима в зависимости от типа фрезы
Для получения одного и того же изделия могут применяться самые различные виды фрез. Выбор основных режимов фрезерования проводится в зависимости от конструктивных и других особенностей изделия. Режимы резания при фрезеровании дисковыми фрезами или другими вариантами исполнения выбираются в зависимости от нижеприведенных моментов:
- Жесткости применяемой системы. Примером можно назвать особенности станка и различной оснастки. Новое оборудование характеризуется повышенной жесткостью, за счет чего появляется возможность применения более высоких параметров обработки.
На старых станках жесткость применяемой системы снижается.
- Уделяется внимание и процессу охлаждения. Довольно большое количество оборудования предусматривает подачу СОЖ в зону обработки. За счет подобного вещества существенно снижается температура режущей кромки. СОЖ должна подаваться в зону снятия материала постоянно. При этом также удаляется и образующаяся стружка, что существенно повышает качество резания.
- Стратегия обработки также имеет значение. Примером можно назвать то, что получение одной и той же поверхности может проводится при чередовании различных технологических операций.
- Высота слоя, который может сниматься за один проход инструмента. Ограничение может зависеть от размера инструмента и многих других геометрических особенностей.
- Размер обрабатываемых заготовок. Для больших заготовок требуется инструмент с износостойкими свойствами, который при определенных режимах резания сможет не нагреваться.
Учет всех этих параметров позволяет подобрать наиболее подходящие параметры фрезерования. При этом учитывается распределение припуска при фрезеровании сферическими фрезами, а также особенности обработки концевой фрезой.
Классификация рассматриваемого инструмента проводится по достаточно большому количеству признаков. Основным можно назвать тип применяемого материала при изготовлении режущей кромки. К примеру, фреза ВК8 предназначена для работы с заготовками из твердых сплавов и закаленной стали. Рекомендуется применять подобный вариант исполнения при невысокой скорости резания и достаточной подаче. В тоже время скоростные фрезы могут применяться для обработки с высоким показателем резания.
Как правило, выбор проводится с учетом распространенных таблиц. Основными свойствами можно назвать:
- Скорость резания.
- Тип обрабатываемого материала.
- Тип фрезы.
- Частота оборотов.
- Подача.
- Тип проведенной работы.
- Рекомендуемая подача на зуб в зависимости от диаметра фрезы.
Использование нормативной документации позволяет подобрать наиболее подходящие режимы. Как ранее было отмечено, разрабатывать технологический процесс должен исключительно специалист. Допущенные ошибки могут привести к поломке инструмента, снижению качества поверхности заготовки и допущению погрешностей в инструментах, в некоторых случаях, поломке оборудования. Именно поэтому нужно уделять много внимания выбору наиболее подходящего режима резания.
Рекомендации при выборе режима
Идеально подобрать режим обработки практически невозможно, но есть ряд рекомендаций, которым желательно следовать:
- Диаметр инструмента должен соответствовать глубине обработки. Это позволяет провести обработку в один проход, но для слишком мягких материалов есть риск снятия стружки большей толщины, чем необходимо.
- По причине ударов и вибрации желательно начать с подачи порядка 0,15 мм на зуб и затем регулировать в большую или меньшую сторону.
- Не желательно использовать максимальное количество оборотов, это может привести к падению скорости реза. Повысить частоту можно при увеличении диаметра инструмента.
Определение режима реза производится не только с помощью таблиц. Большую роль играет знание особенностей станка и личный опыт фрезеровщика.
Выбор рациональных режимов фрезерования | ОБРАБОТКА МЕТАЛЛОВ
Назначение рациональных режимов резания предусматривает выбор для заданных условий обработки (обрабатываемый материал, размеры заготовки, припуск на обработку и др.) типа и размера фрезы, материала и марки режущей части, оптимальных геометрических параметров режущей части, условий охлаждения и др. После этого необходимо установить оптимальные значения следующих параметров режима резания: В, t, sz . v, n, Nn, Т.Зависимость производительности фрезерования от объема снятого слоя металла выражена формулой
см. формулу (2).
Подставляя вместо п его выражение, получим
Следовательно, при постоянном диаметре фрезы на производительность фрезерования параметры В, t, s z и v оказывают одинаковое влияние, так как каждый из них влияет в первой степени.

Задача выбора рационального режима резания состоит в выборе наиболее выгодного для заданных условий режима резания. С учетом стойкости инструмента выгоднее прежде всего выбирать максимально допустимые значения тех параметров, которые в меньшей степени влияют на стойкость инструмента, т. е. в порядке, обратном их влиянию на стойкость фрезы. Так как скорость резания оказывает самое большое влияние на стойкость, то ее выбирают исходя из принятой для данного инструмента нормы стойкости.
Выбор режимов резания при фрезеровании следует производить в следующей последовательности:
1. Определить максимально допустимую глубину резания исходя из припуска на обработку. Припуск на обработку желательно снять за один проход.
2. Найти максимально допустимую по условиям обработки подачу на зуб sz. При черновом фрезеровании она ограничивается прочностью зуба фрезы, прочностью фрезы (концевые фрезы, фрезы малых диаметров и др.
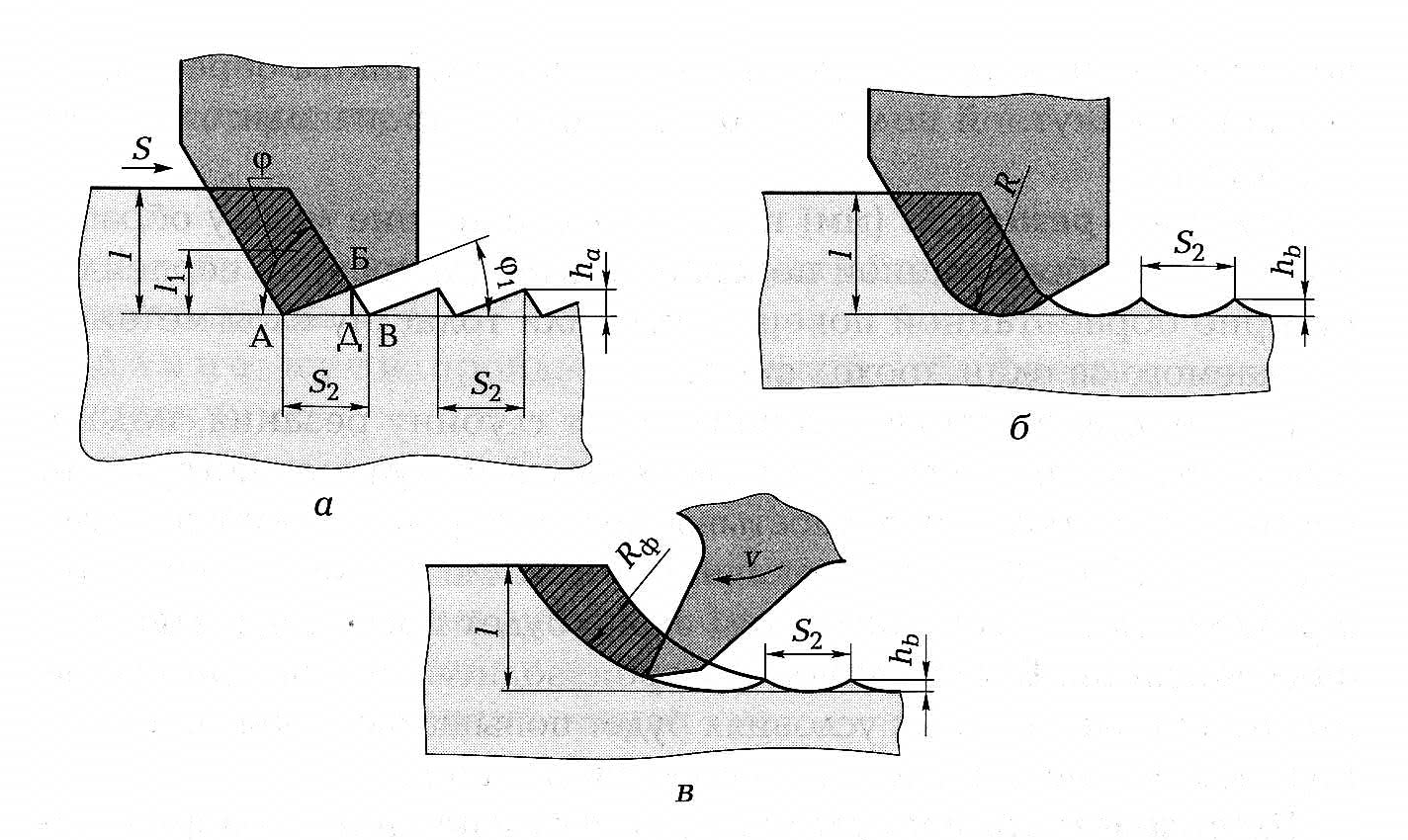
3. По выбранной глубине резания и подаче на зуб (и заданной ширине фрезерования) определяют по таблицам нормативов режимов фрезерования скорость резания v.
4. Определяют эффективную мощность резания Ne. Выбранный режим может быть осуществлен, если Ne
Если окажется, что Ne >NCT. то необходимо прежде всего снизить скорость резания пропорционально недостатку мощности по формуле
где vN — скорость резания по станку, м/мин;
vT — скорость резания по нормативам режима резания, м/мин;
NCT — эффективная мощность станка, квт:
N3 — эффективная мощность резания, квт.
5. В зависимости от принятой скорости резания vT или VN определяют ближайшую ступень чисел оборотов шпинделя станка из числа имеющихся на данном станке по формуле (2) или по графику (см. рис. 48).
6. Определяют минутную подачу по формуле или по графику (см. рис. 49) и выбирают ближайшую из имеющихся на данном станке.
7. Определяют машинное время.
Автор – nastia19071991
Влияние условий резания при токарной обработке
Влияние условий резания при токарной обработке
ВЛИЯНИЕ УСЛОВИЙ РЕЗКИ
Идеальные условия для резки – короткое время резания, длительный срок службы инструмента и высокая точность резания. Для достижения этих условий необходим выбор эффективных режимов резания и инструментов в зависимости от рабочего материала, твердости, формы и характеристик станка.
Скорость резания сильно влияет на срок службы инструмента.Увеличение скорости резания увеличивает температуру резания и приводит к сокращению срока службы инструмента. Скорость резания зависит от типа и твердости обрабатываемого материала. Необходимо выбрать сплав, подходящий для скорости резания.
Влияние скорости резания
1. Увеличение скорости резания на 20% снижает стойкость инструмента на 50%. Увеличение скорости резания на 50% снижает стойкость инструмента на 80%.
2. Резка на низкой скорости резания (20–40 м / мин) может вызвать вибрацию.Таким образом сокращается срок службы инструмента.
При резке обычным держателем подача – это расстояние, на которое держатель перемещается за оборот заготовки. При фрезеровании подача – это расстояние, на которое стол станка перемещается за оборот фрезы, деленное на количество пластин. Таким образом, это указывается как подача на зуб. Подача относится к шероховатости готовой поверхности.
Влияние подачи
1. Уменьшение подачи приводит к износу по задней поверхности и сокращению срока службы инструмента.
2. Увеличение скорости подачи увеличивает температуру резания и износ по задней поверхности. Однако влияние на стойкость инструмента минимально по сравнению со скоростью резания.
3. Увеличение скорости подачи повышает эффективность обработки.
Глубина резания определяется в зависимости от требуемого съема материала, формы заготовки, мощности и жесткости станка и жесткости инструмента.
Влияние глубины резания
1. Изменение глубины резания не сильно влияет на стойкость инструмента.
2. Малая глубина резания приводит к трению при резке закаленного слоя заготовки. Таким образом сокращается срок службы инструмента.
3. При резке неразрезанных поверхностей или поверхностей из чугуна, глубина резания должна быть увеличена настолько, насколько позволяет мощность станка, чтобы избежать резания загрязненных твердых слоев острием режущей кромки, чтобы предотвратить выкрашивание и ненормальный износ.
Условия резания и износ инструмента при обработке древесных материалов :: BioResources
Хладил, Дж., Седлак, Й., Рыбаржова, Э. Р., Кучера, М., и Дадо, М. (2019).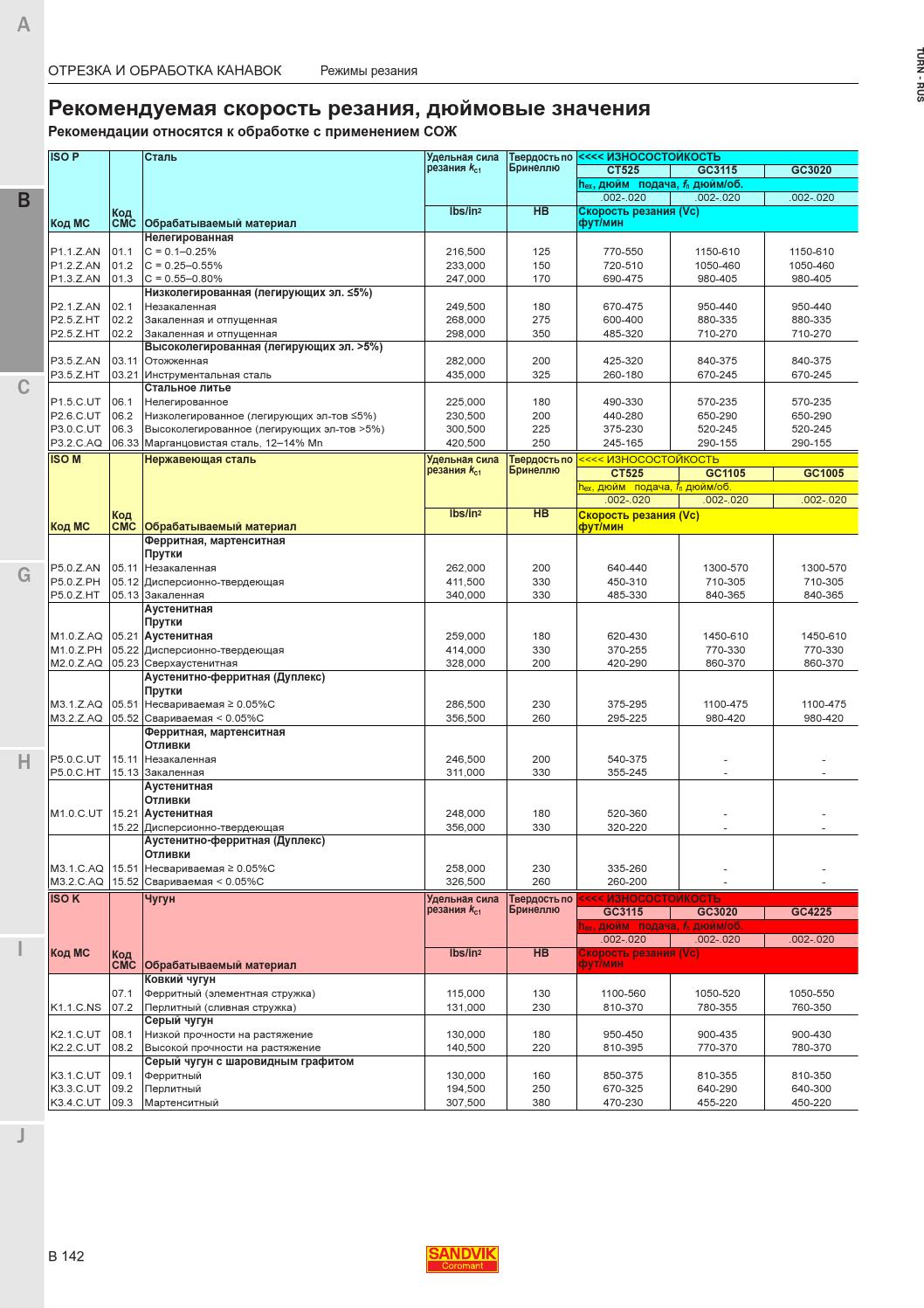
Реферат
В статье рассмотрены данные в процессе резки древесных материалов. Процесс резки влияет на форму и размеры режущей кромки. Эксперименты были сосредоточены на мониторинге изменения режущей кромки при обработке ДСП и влияния скорости резания на износ инструмента.Испытания на резание проводились во время фрезерования при скоростях резания в диапазоне от 7,95 до 17,9 м / с (от 477 до 1074 м / мин), глубине резания 9,5 мм и подаче на зуб 0,05 мм. Процесс износа режущего клина при фрезеровании ДСП характеризуется уменьшением режущей кромки режущих пластин. Сравнительный цифровой индикатор часового типа использовался для измерения рецессии режущего клина. Процесс изнашивания древесных материалов в графическом представлении имел сходство с резанием абразивным материалом.Полученную зависимость можно использовать для выбора наиболее подходящих условий резания в соответствии с требованиями оператора.
Скачать PDF
Полная статья
Условия резания и износ инструмента при обработке древесных материалов
Josef Chladil, a * Josef Sedlák, a Eva Rybářová Šebelová, b Marián Kučera, c и Мирослав Дадо c
В статье рассмотрены данные в процессе раскроя древесных материалов.Процесс резки влияет на форму и размеры режущей кромки. Эксперименты были сосредоточены на мониторинге изменения режущей кромки при обработке ДСП и влияния скорости резания на износ инструмента. Испытания на резание проводились во время фрезерования при скоростях резания в диапазоне от 7,95 до 17,9 м / с (от 477 до 1074 м / мин), глубине резания 9,5 мм и подаче на зуб 0,05 мм. Процесс износа режущего клина при фрезеровании ДСП характеризуется уменьшением режущей кромки режущих пластин.Сравнительный цифровой индикатор часового типа использовался для измерения рецессии режущего клина. Процесс изнашивания древесных материалов в графическом представлении имел сходство с резанием абразивным материалом. Полученную зависимость можно использовать для выбора наиболее подходящих условий резания в соответствии с требованиями оператора.
Ключевые слова: Механическая обработка; Древесина; Орудие труда; Носить; Тусклый; Условия резания
Контактная информация: a: Технологический институт, факультет машиностроения и технологии, Технологический университет Брно, Technická 2, 61600 Брно, Чешская Республика, b: The Display Company CZ s.r.o., Londýnské náměstí 4, 63900 Брно, Чешская Республика, c: Кафедра производственных технологий и менеджмента качества, Факультет экологических и производственных технологий, Технический университет в Зволене; * Автор, ответственный за переписку: jo.chla@seznam.cz
ВВЕДЕНИЕ
Древесина – это пористая и волокнистая структурная ткань, встречающаяся в стеблях и корнях деревьев и других древесных растений. Это органический материал, натуральный композит из целлюлозных волокон, обладающих прочностью при растяжении и погруженных в матрицу лигнина, сопротивляющуюся сжатию. Дерево – один из немногих возобновляемых материалов (Kučerová et al. 2016). К сожалению, древесина является относительно малопрочным материалом и требует особого ухода для обеспечения длительного срока службы. По этой причине также широко используются модифицированные древесные материалы или материалы с поверхностным покрытием. В определенной степени такие древесные материалы сохраняют хорошие свойства древесины и смягчают некоторые из ее неблагоприятных свойств (Квиеткова, и др., 2015a, b, c; Gaff et al. 2016; Седлецки и Сарвашова Кветкова 2017).
Механические и физические свойства являются важными факторами при обработке древесины. Агломерированные материалы изготавливаются из древесины или других лигноцеллюлозных частиц.
ДСП – это термин, обозначающий материал, состоящий из древесных частиц, которые производятся различных форм и размеров. Стружку склеивают синтетическим клеем под высоким давлением и повышенной температурой. Для внутреннего использования эти материалы часто необходимо облицовывать, ламинировать или складывать, чтобы улучшить их внешний вид. Этот материал является наиболее широко используемым и наиболее производимым агломерированным материалом в деревообрабатывающей промышленности (Thoemen et al. 2010).
Во время процесса фрезерования режущие пластины во вращающемся инструменте отделяют материал заготовки в виде стружки. Скорость подачи ограничена размером и типом режущего инструмента, перпендикулярного обрабатываемой детали. Процесс резания прерывистый, и зубья резца попеременно срезают стружку разной толщины. Древесные материалы фрезеруются во всех направлениях, но чаще всего по направлению древесных волокон.Направление вращения обычно выбирают обычным, , то есть против направления подачи. Что касается положения оси вращения и поверхностей, созданных режущими кромками, фрезерование делится на два типа: либо ось цилиндрического инструмента параллельна поверхности заготовки, либо передняя ось инструмента перпендикулярна. к поверхности заготовки.
Процесс фрезерования контролируется сроком службы инструмента. Срок службы инструмента – это период, в течение которого лезвие находится в рабочем состоянии в процессе обработки.Это время, когда инструмент работает, от заточки до затупления. При обработке металла абразивный износ наблюдается на задней поверхности режущей кромки и называется износом по задней поверхности VB. На рис. 1 этот процесс показан на кривой износа. К отдельным фазам относятся: I – начальный быстрый износ, II – линейный износ и III – окончательное нестабильное течение. При практическом измерении износа используется значение критического износа VB в линейной фазе II; этот выбор обусловлен точностью считываемого значения (Shaw 2005; Csanády and Magoss 2012).
Рис. 1. Графическое изображение зависимости VB или KR = fn ( T ) при резке металла
Режущая кромка образована пересечением двух поверхностей – торцевой плоскости (передний угол γ ) и задней плоскости (задний угол α). Дармаван и др. (2001, 2012) изучал процесс износа на задней поверхности под влиянием различных древесных материалов и материалов кромки режущего инструмента. Во время обработки древесных материалов без абразивов отслеживается износ рецессии режущей кромки инструмента в зависимости от времени (Šebelová and Chladil 2013).Этот тип износа называется износом носа (Shaw 2005; Mazan et al ,2017), и его размер соответствует радиальному износу KR (см. Рис. 2).
Рис. 2. Тип износа носика инструмента
В этом исследовании материал на основе древесины – ламинированная древесно-стружечная плита – использовался для экспериментального изучения влияния условий резания на износ инструмента. Цилиндрическое фрезерование использовалось для проверки свойств материала инструмента в процессе резания, и применялась правая фреза с двумя зубьями.Процесс затупления инструмента контролировался, поскольку это влияет на срок службы режущего инструмента и, следовательно, на эффективность обработки. Время Тейлора против . Для оценки использовалась формула скорости резания (Shaw 2005).
ЭКСПЕРИМЕНТАЛЬНАЯ ИНФОРМАЦИЯ
Материал заготовки
Ламинированная ДСП использовалась как представитель древесных материалов, ламинированных буком. Поставщиком ЛДСП (бук 045 BS Westfalen толщиной 18 мм) выступила компания INTEREXPO Brno Ltd, Чехия.Объемный вес плиты составлял от 600 до 750 кг. М -3 , а влажность 14,2%, определенная в соответствии с EN 323 (1993).
Режущий инструмент
Для экспериментов использовалась двухзубая фреза по часовой стрелке FRSTHW 19x30x12z2 (Aparathea Ltd., Брно, Чехия) диаметром D 19 мм. На фрезу использовались режущие пластины из спеченного карбида К10, HW 29,5x12x1,5 4S T04F (рис. 3). Геометрия режущего инструмента: передний угол γ 15 ° и задний угол α 20 °.
Рис. 3. Фреза HW 19 x 30
Пластины из спеченного карбида (SC) были зажаты во фрезу и закреплены болтом. Твердосплавные пластины были обозначены буквой с соответствующей буквой-символом, чтобы различать их использование при обработке отдельных образцов и уникальность отдельных измерений. Номер, обозначающий конкретную режущую пластину, имел нижний регистр a / b для обозначения стороны лезвия. Режущие пластины с маркировкой от U1 до U4 Рис.4 были использованы для резки ЛДСП.
Рис. 4. Режущие пластины SC HW 29,5x12x1,5 4S T04F
Станок
Выбранные материалы обрабатывались на трехосном фрезерном станке с ЧПУ SCM Tech 99 (Римини, Италия) со следующими параметрами: рабочие размеры X, 3119 мм, Y, 1012 мм, Z, 100 мм; мощность двигателя 6,6 кВт, максимальная частота вращения 1800 об / мин. Фреза с двумя зубьями по часовой стрелке зажималась на фрезерном станке с ЧПУ.
Методы
Условия резания
Для обработки выбрано подъемное фрезерование. Диапазон минимальных 4000 об / мин и максимальных 18000 об / мин был определен для постоянной подачи на зуб ( f z = 0,05 мм) и постоянной ширины пропила a p = 18 мм (толщина материала). . Значения скорости резания и подачи основаны на соотношении между значением подачи на зуб, скоростью резания, скоростью инструмента и диаметром фрезы. Все переменные определены в таблице 1. Скорость резания ( v c ) была определена уравнениями. 1 и 2.
(1)
(2)
Скорость подачи v f была рассчитана по формуле. 3.
(3)
Таблица 1. Условия процесса резки для экспериментов
На стойкость режущей кромки больше всего влияет скорость резания v c . Экспериментальное определение зависимости стойкости инструмента от скорости резания, i.e ., T = fn ( v c ), было выполнено с использованием нескольких скоростей резания. Необходимо было обеспечить постоянство других условий труда. Износ инструмента был представлен кривыми износа для отдельных скоростей резания на диаграмме KR = fn ( T ) для радиального износа. Измерение износа по задней поверхности VB, которое в основном используется при резке металла, не могло быть использовано из-за сложности измерения каких-либо изменений во время экспериментов. Износ инструмента
Для измерения радиального износа инструмента KR, который определяется зависимостью KR = fn ( T ), необходимо было рассчитать время по следующему уравнению:
(4)
, где T – время резания (мин), L = 700 – длина заготовки (мм), а v f – скорость подачи (мм ∙ мин -1 ).Критерий износа инструмента был определен как KR = 10 мкм.
Рис. 5. Измеритель сравнения
Измерительное оборудование
Для измерения износа инструмента цифровой индикатор часового типа (KINEX 0-12,7 / 0,001, Прага, Чехия) был закреплен на измерительном приспособлении, разработанном для экспериментов (см. Рис. 5). Инструмент измеряет отклонения от заданного размера. Во-первых, необходимо было откалибровать инструмент в соответствии с новыми вставками.Используемое устройство имело точность измерения 1 мкм и максимальный ход касания 12,7 мм.
Оценка измеренных значений
Статистическое программное обеспечение Minitab® 15 (State College, PA, USA) использовалось для оценки измеренных значений в экспериментах.
РЕЗУЛЬТАТЫ И ОБСУЖДЕНИЕ
Радиальный износ и . Время
Радиальный износ режущего инструмента KR зависит от времени.
Фиг.6. Износ режущей пластины (красная отметка)
Через интервалы времени, указанные во время резки, было выполнено измерение износа KR. Результаты представлены в виде графиков зависимости от времени. Износ режущих пластин показан красной меткой на рис. 6.
Полученные зависимости износа инструмента KR = fn ( T ), взятые из линейного износа детали, которые выделены серым в таблицах, приложены к таблицам измерений на рис.С 7 по 10.
Таблица 2. Измерение износа инструмента и . Время, пластины U1a / U2a, скорость v c1 = 477 м / мин
Таблица 3. Измерение износа инструмента и . Время, пластины U1b / U2b, скорость v c2 = 716 м / мин.
Рис. 7. Регрессия линейного износа для v c1 = 477 м / мин, KR [мкм] и T [мин]
Фиг.8. Регрессия линейного износа для v c2 = 716 м / мин, KR [мкм] и T [мин]
Таблица 4. Измерение износа инструмента и . Время, пластины U3a / U4a, скорость v c3 = 895 м / мин
Рис. 9. Регрессия линейного износа для v c3 = 895 м / мин, KR [мкм] и T [мин]
Таблица 5. Измерение износа инструмента и .Время, пластины U3b / U4b, скорость v c4 = 1074 м / мин
Рис. 10. Регрессия линейного износа для v c4 = 1074 м / мин, KR [мкм] и T [мин]
Связь между стойкостью инструмента T и скоростью резания v c выглядит следующим образом:
т. v c м = конст. (5)
Здесь уравнение Тейлора заменяет показатель степени m = 1 / n .Скорость износа 10 мкм от первоначального значения режущей кромки была определена как критерий для определения стойкости инструмента для этой скорости. Для определения зависимости стойкости инструмента от скорости резания значения T и v c для критерия износа инструмента были использованы в графическом представлении log ( T ) = fn (log v c ) (см. Таблицу 6). Затем для решения применялся статистический метод линейной регрессии. Были обработаны графики доверительных интервалов (95%) измеренных данных T = fn ( v c ) для материалов из ЛДСП.Результаты показаны на рис. 11.
Таблица 6. Скорости резания и соответствующий срок службы инструмента T1-T4 для KR = 10 мкм
Рис. 11. Регрессия T = fn ( v c ) с доверительным интервалом 95%
Уравнение 5, соответствующее функции из графического представления на рис. 11, затем находится в окончательной формуле (уравнение 6).
T v c 2,082 = 252.35 x 10 5 или v c T 0,48 = 3590,7 (6)
ВЫВОДЫ
- Механизм износа ДСП отличается от механизма износа абразивными частицами, которые характерны для металлов с абразивными частицами. Дармаван и др. (2001, 2012) использовали измерение износа поверхности зазора.
- В статье сравнительный цифровой датчик использовал измерение радиального износа KR, которое соответствует вылету режущего инструмента, которое использовалось во время экспериментов.Процесс износа древесных материалов демонстрировал сходство графического изображения с резанием абразивного материала.
- Была определена окончательная зависимость T = fn ( v c ) для механической обработки ламинированного ДСП для выбора правильной скорости резания для заданного срока службы инструмента.
Окончательное уравнение можно использовать для расчета скорости резания / стойкости инструмента в соответствии с требованиями оператора.
- Критерий определения стойкости инструмента был выбран в линейной части кривой износа для получения правильных и точных результатов с использованием линейной регрессии
- Эксперименты оценивали с помощью регрессионного анализа.
БЛАГОДАРНОСТИ
Авторы выражают признательность за финансовую поддержку, предоставленную The Science Fund 2016, Технологический университет Брно, факультет машиностроения FV 16-28 и грант « Исследование современных производственных технологий для конкретных приложений», рег. нет. FSI-S-16-3717 и проект VEGA 1/0642/18: «Анализ воздействия конструктивных элементов лесных механизмов на лесную среду с точки зрения энергетических и экологических требований.”
ССЫЛКИ
Чанади Э. и Магосс Э. (2012). «Механика обработки древесины» (2 nd Ed. ), Springer , New York, NY.
Дармаван В., Танака К., Усуки Х. и Отани Т. (2001). «Характеристики твердосплавных инструментов с покрытием при токарной обработке древесных материалов: влияние скорости резания и материалов покрытия на характеристики износа твердосплавных инструментов с покрытием при токарной обработке древесно-стружечных плит», Wood Science 47 (5), 342-349.
Дармаван В., Рахаю И., Нандика Д. и Марчал Р. (2012). «Важность экстрактивных веществ и абразивов в древесных материалах при износе режущих инструментов по дереву», BioResources 7 (4), 4715-4729. DOI: 10.15376 / biores.11.4.4715-4729
Гафф, М., Сарвашова-Квиеткова, М., Гашпарик, М., и Славик, М. (2016). «Зависимость изменения шероховатости и образования трещин от параметров тиснения поверхности древесины» Wood Research 61 (1), 163-174.
Кучерова, В., Lagaňa, R., Výbohová, E., and Hýrošová, T. (2016). «Влияние химических изменений во время термической обработки на цвет и механические свойства древесины ели», BioResources 11 (4), 9079-9094. DOI: 10.15376 / biores.11.4. 9079-9094
Квиеткова М., Гафф М. и Гашпарик М. (2015a). «Влияние термической обработки на качество поверхности древесины бука после строгания», BioResources 10 (3), 4226-4238. DOI: 10.15376 / biores.10.3. 4226-4238
Квиеткова, М., Гафф, М., Гашпарик, М., Каплан, Л., и Барчик, Ш. (2015b). «Качество поверхности фрезерованной древесины березы после термической обработки при различных температурах», BioResources 10 (4), 6512-6521. DOI: 10.15376 / biores.10.4. 6512-6521
Квиеткова М., Гафф М., Гашпарик М., Кминиак Р. и Крис А. (2015c). «Влияние количества зубьев пильного полотна на уровень шума и износ кромок полотна при распиловке древесины», BioResources 10 (1), 1657-1666. DOI: 10.15376 / biores.10.1.1657-1666
Мазань, А., Ванко, М., и Барчик, С. (2017). «Влияние технологических параметров на стойкость инструмента при обработке молодой древесины», BioResources 12 (2), 2367-2378. DOI: 10. 15376 / biores.12.2. 2367-2378
Šebelová, E. and Chladil, J. (2013). « Износ инструмента и обрабатываемость древесных материалов в процессе обработки, » Технологии производства 13 (2), 231-236.
Седлецки М. и Сарвашова Квиеткова М. (2017). «Волнистость поверхности древесноволокнистых плит средней плотности (МДФ) и клееных панелей EGP после фрезерования», Wood Research, 62 (3), 459-470.
Шоу, М. К. (2005). «Принципы резки металла» (2 nd Ed.), Oxford University Press, , Оксфорд, Великобритания.
Томен, Х., Ирле, М., Сернек, М. (2010). Деревянные панели – Введение для специалистов, Brunel University Press, Лондон.
Поступило: 12 декабря 2018 г .; Рецензирование завершено: 17 февраля 2019 г .; Исправленная версия получена и принята; 5 марта 2019 г .; Опубликовано: 8 марта 2019 г.
DOI: 10.15376 / biores.14.2.3495-3505
Оптимизация условий резания для минимальной шероховатости поверхности при торцевом фрезеровании высокопрочной стали с использованием твердосплавных пластин
Метод полного факторного проектирования используется для исследования влияния параметров обработки, а именно скорости шпинделя, глубины резания и скорости подачи стола на полученные шероховатость поверхности (и) при торцевом фрезеровании высокопрочной стали. Модель регрессии второго порядка была построена с использованием метода наименьших квадратов в зависимости от результатов факторного проектирования для аппроксимации математической зависимости между шероховатостью поверхности и параметрами исследуемого процесса.Был проведен дисперсионный анализ для оценки значимости каждого фактора и взаимодействия в отношении шероховатости поверхности. Результаты показывают, что скорость шпинделя, глубина резания и скорость подачи стола оказывают значительное влияние на шероховатость поверхности как в линейном, так и в квадратичном выражении. Также существует взаимосвязь между глубиной резания и скоростью подачи. Также кажется, что скорость подачи имеет наибольшее влияние на изменение данных, за которым следует глубина резания. Для, результаты показывают, что скорость подачи стола является наиболее эффективным фактором, за которым следует глубина резания, в то время как скорость шпинделя имела незначительное влияние только в квадратичном члене.Условия минимума и определяются с помощью оптимизации по методу наименьших квадратов.
Кроме того, проводится многокритериальная оптимизация для минимизации и максимизации скорости съема металла, и представлены результаты.
1. Введение
Повышение качества продукции, сроков поставки и производительности обрабатываемых деталей – основные задачи металлургической промышленности. Растет интерес к оптимизации условий обработки для удовлетворения производственных требований, в том числе самого важного – чистоты поверхности.Качество поверхности считается одним из важнейших критериев в технологии производства. Характеристики и качество продукта напрямую связаны с целостностью поверхности, достигаемой при окончательной механической обработке, что отражается в небольшом допуске и минимальной шероховатости поверхности. Высокая производительность и пропускная способность напрямую связаны с высокоскоростной обработкой, которая может быть достигнута с помощью технологии фрезерования с числовым программным управлением (ЧПУ). Для этой цели используются автоматизированные и гибкие производственные системы, а также станки с ЧПУ, которые способны обеспечивать высокую точность при очень коротком времени обработки. Шероховатость поверхности является ключевым фактором качества поверхности, поскольку она оказывает существенное влияние на износостойкость, пластичность, растяжение и усталостную прочность обрабатываемых деталей.
Raju et al. [1] смоделировал и оптимизировал шероховатость поверхности в зависимости от параметров резания для алюминиевого сплава 6061, обработанного концевым фрезерованием быстрорежущей сталью (HSS) и твердосплавными инструментами в сухих и влажных условиях. Был проведен множественный регрессионный анализ с использованием дисперсионного анализа и предложена математическая модель второго порядка параметров резания.Прогнозируемая шероховатость поверхности модели сравнивается со значениями, измеренными экспериментально. В этом исследовании сообщается, что скорость подачи является доминирующим параметром, а шероховатость поверхности быстро увеличивается с увеличением скорости подачи и уменьшается с увеличением скорости шпинделя, тогда как влияние глубины резания не является регулярным.
Пименов [2] исследовал влияние подачи, скорости резания и износа твердосплавного инструмента Т5К10 на шероховатость плоских поверхностей, полученных торцевым фрезерованием, из стали 45.В работе проанализирован характер изменения микропрофиля обработанных поверхностей в зависимости от увеличения поверхности износа на боковой поверхности зуба. Он показал, что шероховатость увеличивалась с 15 до 30% для выбранных режимов резания при увеличении износа по задней поверхности от 0 до 3,1–4 мм. Увеличение подачи при постоянной скорости резания привело к увеличению шероховатости; однако увеличение скорости резания при постоянной подаче привело к уменьшению шероховатости. Показано, что с увеличением износа задней поверхности по задней поверхности снижалась частота выступов и впадин на профилограммах микропрофиля обработанной поверхности.
Pusavec et al. [3] изучали альтернативные условия охлаждения / смазки по сравнению с традиционной обработкой Inconel 718 и их связь с разрушаемостью стружки. Генетические алгоритмы (GA) использовались для оценки и оптимизации процесса обработки с точки зрения стойкости инструмента, качества обработанной поверхности, ломкости стружки, производительности и энергопотребления.
Фелхо и Кундрак [4] представили новый метод расчета профильных (2D) и поверхностных (3D) параметров теоретической шероховатости при торцевом фрезеровании плоских поверхностей.Этот новый метод был основан на целесообразно разработанной модели САПР и использовал профессиональную программу для оценки шероховатости. Эксперименты по резке были выполнены на образцах 42CrMo4 для проверки точности модели. Результаты показали, что этот метод позволяет предсказывать шероховатость поверхности с хорошей точностью.
Rawangwong et al. [5] провели исследование шероховатости поверхности полутвердого материала AA 7075, обработанного торцевым фрезерованием на фрезерном станке с ЧПУ с мелкозернистым твердосплавным инструментом диаметром 63 мм с двойной режущей кромкой.Факторами процесса были скорость, скорость подачи и глубина резания. Результаты показали, что фактором, влияющим на шероховатость поверхности, было отношение скорости подачи к скорости резания, в то время как глубина резания не влияла.
Кивак [6] использовал дисперсионный анализ (ANOVA), метод Тагучи и регрессионный анализ для исследования влияния параметров обработки на шероховатость поверхности и износ по задней поверхности при фрезеровании стали Гадфилда с PVD TiAlN и CVD TiCN / Al 2 O 3 Твердосплавные пластины с покрытием в условиях сухого фрезерования.Было проведено несколько экспериментов с использованием полного факторного проектирования со смешанным ортогональным массивом на вертикальном обрабатывающем центре с ЧПУ. Переменными процесса были режущий инструмент, скорость резания и скорость подачи. Был сделан вывод, что скорость подачи была доминирующим фактором, влияющим на шероховатость поверхности, в то время как скорость резания была доминирующим фактором, влияющим на износ по задней поверхности.
Rawangwong et al. [7] исследовали влияние основных факторов обработки на шероховатость поверхности чугуна с шаровидным графитом FCD 400, фрезерованного твердосплавными инструментами.Эксперименты по травлению проводились на полуавтоматической фрезерной машине Obraeci Strojie марки FGV 32 модели. Изучаемыми факторами были скорость, скорость подачи и глубина резания. Эксперименты показали, что факторами, влияющими на шероховатость поверхности, были скорость подачи и скорость резания с тенденцией к снижению значений шероховатости при более низкой скорости подачи и большей скорости резания.
Аббас [8] представил сравнительный анализ характеристик, включающий критерии шероховатости поверхности (,, и) во время токарной обработки высокопрочной стали между обычными пластинами и пластинами Wiper.Основными параметрами, рассматриваемыми в этом исследовании, были скорость резания, скорость подачи и глубина резания. Результаты показали важность глубины резания и скорости подачи для уменьшения шероховатости поверхности. Сообщалось, что качество поверхности, полученной с помощью пластины из карбида Wiper, значительно улучшилось по сравнению с обычной пластиной из карбида. Максимальное улучшение в 3,5 раза между пластиной Wiper и обычной пластиной было достигнуто при скорости резания 75 м / мин.
Текущая работа направлена на обеспечение всестороннего исследования влияния параметров процесса обработки, а именно, хода подачи, скорости резания и глубины резания, на шероховатость поверхности с помощью полного факторного проектирования DOE для торцевого фрезерования высокопрочной стали. с помощью твердосплавных инструментов. Исследуются четыре уровня для каждого параметра процесса. Дисперсионный анализ (ANOVA) будет использован для определения влияния параметров обработки на шероховатость поверхности и для разработки математической модели посредством регрессионного анализа, которая наилучшим образом описывает вариации в экспериментальных данных.
2. Материалы и методы
Это исследование направлено на изучение влияния основных факторов на шероховатость поверхности высокопрочной стали в процессе торцевого фрезерования с использованием фрезерного станка с ЧПУ и твердосплавных пластин. Использовался вертикальный фрезерный станок с ЧПУ Emco Mill Concept 45, оснащенный Sinumeric 840-D с техническими характеристиками, включая диапазон скоростей 50–10 000 об / мин и скорость подачи 0–10 м / мин. Образцы заготовок представляют собой высокопрочные стали с химическим составом, указанным в таблице 1.Термическая обработка материала включала аустенизацию при 900 ° C в течение 5 часов с последующим охлаждением на воздухе, нагреванием при 880 ° C в течение 5 часов, закалкой в масле, отпуском при 590–600 ° C в течение 8 часов и затем охлаждением на воздухе. . Достигнутая в результате твердость составила HRC 41–43. Площадь поверхности каждого образца составляет мм, а высота – 60 мм. Использовался режущий инструмент с твердосплавными пластинами модели торцевой фрезы с державкой Sandvik R245-063Q22-12M и твердосплавными пластинами Sandvik с покрытием R245-12 T3M-PM4240. Диаметр фрезы 63 мм с 5 лезвиями.Этот тип фрезы был разработан для получения высокого съема металла и получения зеркальной поверхности.
Он разработан с увеличенными углами, чтобы уменьшить образование заусенцев и рассыпание детали. Этот тип фрезы подходит для торцевого фрезерования всех типов материалов, таких как сталь, нержавеющая сталь, чугун, алюминий, жаропрочные и титановые сплавы. Испытательный стенд для обработки деталей показан на рисунке 1. Устройство для измерения шероховатости поверхности для оценки рельефа поверхности представляет собой модель TESA Rugosurf 90-G и показано на рисунке 2.
905 96 Cu P
|
План испытаний был выполнен на 64 образцах, группа (A), и повторен для получения дубликатов в группе (B). Каждая группа была разделена на 16 групп. Каждые четыре группы подвергаются одной общей скорости обрабатывающего шпинделя. Группы 1–4, 5–8, 9–12 и 13–16 обрабатывались со скоростью вращения шпинделя 500 об / мин, 750 об / мин, 1000 об / мин и 1250 об / мин, соответственно.Каждая группа была обработана с использованием четырех уровней глубины резания (0,25, 0,50, 0,75 и 1,0 мм), и каждая глубина была обработана с использованием четырех уровней скорости подачи стола (50, 75, 100 и 125 мм / мин). Для выполнения вышеуказанных условий использовался фрезерный станок с ЧПУ, оснащенный Sinumeric 840-D. Тестер шероховатости поверхности TESA использовался для измерения параметров шероховатости поверхности, где – среднее арифметическое отклонение оцененного профиля, а – максимальная высота профиля. Обработанные поверхности дублировались для каждого набора режимов резания.На каждой поверхности были измерены три показания шероховатости поверхности, и среднее значение было записано в Приложении для групп (A) и (B).
3. Экспериментальный план
Полный факторный план – это комплексный метод, который требует большого количества экспериментов и дает подробное описание всех системных отношений и взаимодействий. В этом исследовании был использован полный факторный план для построения эксперимента с тремя независимыми переменными (факторами) и четырьмя уровнями для каждой. В таблице 2 приведены переменные и их уровни.Дисперсионный анализ (ANOVA) был проведен для проверки значимости факторов и их взаимодействия с уровнем достоверности 95%. Метод наименьших квадратов использовался для построения моделей множественной регрессии второго порядка. Minitab 17 использовали для проведения анализа DOE.
и Обсуждение
На рисунках 3 (a) и 3 (b) показано влияние скорости подачи стола на разную глубину резания при скорости шпинделя 500 об / мин (a) и 1000 об / мин (b). Предварительное наблюдение этих кривых показывает, что значения шероховатости поверхности () увеличиваются с увеличением скорости подачи стола для обеих скоростей вращения.Сравнение влияния скорости вращения для двух значений глубины резания, 1,0 и 0,25 мм, можно увидеть на рисунке 4. Для глубины резания 1,0 мм значение шероховатости поверхности () при скорости вращения шпинделя 1000 об / мин выше. по сравнению с 500 об / мин. Противоположный вывод можно сделать для глубины резания 0,25 мм, где значение выше при частоте вращения шпинделя 500 об / мин по сравнению с 1000 об / мин. Это ведет к возможности существования седловой (минимаксной) точки среди различных испытанных условий обработки.Это будет ясно проверено на графиках поверхности, представленных в следующем разделе. Более подробный анализ будет проведен путем анализа отклонений в следующем разделе.
4.1. Результаты дисперсионного анализа для
Используя опцию множественной регрессии Minitab 17, данные были подогнаны к кубической модели. Однако результаты показали высокий уровень мультиколлинеарности между кубическими членами (члены третьего порядка) и линейными членами, даже с закодированными данными. Чтобы избежать этой проблемы, кубические члены были удалены из модели.Адекватность подгонки модели, измеряемая коэффициентом детерминации (скорректированный квадрат), была снижена с 82% до 79% за счет удаления кубических членов.
Результаты дисперсионного анализа модели представлены в таблице 3. Значения менее 0,05 указывают на значимый член. Незначительные члены затем удалялись из модели один за другим, начиная с членов, имеющих наибольшее значение, если только они не являются частью термина или взаимодействия более высокого уровня (Zhang and Chou [9], Fydrych and Rogalski [10], и Ding et al. .[11]). Результаты дисперсионного анализа сокращенной модели приведены в таблице 4. Столбец процентного вклада рассчитывается для каждого члена как процент скорректированной суммы квадратов члена к общей скорректированной сумме квадратов. Он дает грубую, но эффективную оценку относительной важности каждого члена модели (Монтгомери [12]).
скорость вращения шпинделя
|
11 9096 9096 09095
| Настр.![]() | Настр. MS | -значение | значение | % вклад | |||||||||||||||||||||||||||||||||||||||||||||||||||||||||||||||||||||||||||||||||||||||||||||||||||||||||||||
Регрессия | 7 | 0.473893 | 0,067699 | 68,2 | 0 | |||||||||||||||||||||||||||||||||||||||||||||||||||||||||||||||||||||||||||||||||||||||||||||||||||||||||||||
1 | 0,005935 | 0,005935 | 5,98 | 0,016 | 05 05 05 05 05 05 | 0 | 17,2 | |||||||||||||||||||||||||||||||||||||||||||||||||||||||||||||||||||||||||||||||||||||||||||||||||||||||||||
1 | 0,317063 | 0,317063 | 319,42 | 0 | 53,5 | |||||||||||||||||||||||||||||||||||||||||||||||||||||||||||||||||||||||||||||||||||||||||||||||||||||||||||||
1 | 01274 | 0,01274 | 12,83 | 0 | 2,1 | |||||||||||||||||||||||||||||||||||||||||||||||||||||||||||||||||||||||||||||||||||||||||||||||||||||||||||||
1 | 0,017414 | 0,017414 | 17,54 | 60 0 | 0,01 | 0 | 0 | 11,81 | 0,001 | 2,0 | ||||||||||||||||||||||||||||||||||||||||||||||||||||||||||||||||||||||||||||||||||||||||||||||||||||||||
1 | 0,00683 | 0,00683 | 6,88 | 0,01 | 1,2 | |||||||||||||||||||||||||||||||||||||||||||||||||||||||||||||||||||||||||||||||||||||||||||||||||||||||||||||
Ошибка | 0,000993 | |||||||||||||||||||||||||||||||||||||||||||||||||||||||||||||||||||||||||||||||||||||||||||||||||||||||||||||||||
Неподходящий | 56 | 0,118994 | 0,002125 | 1138,02 | 60 0 | |||||||||||||||||||||||||||||||||||||||||||||||||||||||||||||||||||||||||||||||||||||||||||||||||||||||||||||
Всего | 127 | 0,5 | ||||||||||||||||||||||||||||||||||||||||||||||||||||||||||||||||||||||||||||||||||||||||||||||||||||||||||||||||
605 | ||||||||||||||||||||||||||||||||||||||||||||||||||||||||||||||||||||||||||||||||||||||||||||||||||||||||||||||||||
-кв.![]() | ||||||||||||||||||||||||||||||||||||||||||||||||||||||||||||||||||||||||||||||||||||||||||||||||||||||||||||||||||
Результаты показывают, что скорость шпинделя, глубина резания и скорость подачи стола значительны. от шероховатости поверхности () как в линейном, так и в квадратичном выражении. Также существует взаимосвязь между глубиной резания и скоростью подачи. Однако, глядя на столбец процентного вклада, кажется, что фактор (скорость подачи таблицы) имеет наибольшее влияние на разброс данных, за которым следует фактор (глубина резания).
На рисунке 5 показаны графики остатков для ответа. По-видимому, остатки не показывают закономерности и распределяются случайным образом в соответствии с подобранными значениями и порядком наблюдения. График нормальной вероятности и гистограмма показывают нормальность остатков. Нормальность была проверена с помощью теста нормальности Андерсона-Дарлинга, и результаты показали, что остатки нормально распределены со значением AD = 0,545 и значением = 0,158 (значение <0,05 показывает ненормальность), как показано на рисунке 6.
Адекватность модели меры, отраженные в значениях коэффициентов детерминации (-квадрат, скорректированный -квадрат и предсказанный -квадрат), показывают разумные уровни адекватности модели.Что касается скорректированного квадрата, модель объясняет около 80% вариации данных. Значение 77% от прогнозируемого квадрата очень близко к скорректированному квадрату, что доказывает, что модель не переобучена и имеет хорошую предсказуемость.
Уравнение (1) – это уравнение регрессии, заданное сокращенной моделью. Оптимум (минимум) определяется значениями об / мин, мм и мм / мин. На рис. 7 показана оптимизация для рис. 8–10, показаны графики поверхности двух параметров обработки при фиксации третьего параметра на его среднем значении.На рисунках показан умеренный кривизный характер взаимосвязи между исследуемыми факторами.
4.2. Результаты ANOVA для
Выполнение анализа, как описано в разделе 4. 1, Таблица 5 показывает окончательные результаты ANOVA модели для. Однако модель не могла быть сокращена из-за наличия значимого третьего уровня взаимодействия ABC. Результаты показывают, что скорость подачи стола является наиболее эффективным фактором, за которым следует глубина резания, в то время как скорость шпинделя имела незначительное влияние только в квадратичном члене.Кроме того, существует взаимосвязь между скоростью подачи и глубиной резания, как и в случае с.
чистая ошибка0002
|
На рисунке 11 показаны остаточные графики для ответа.По-видимому, остатки не показывают закономерности и распределяются случайным образом в соответствии с подобранными значениями и порядком наблюдения. График нормальной вероятности и гистограмма показывают нормальность остатков. Нормальность была проверена с использованием теста нормальности Андерсона-Дарлинга, и результаты показали, что остатки нормально распределены со значением AD = 0,425 и значением = 0,311, как показано на рисунке 12.
Коэффициенты определения значений сопоставимы с этим и, следовательно, верны те же выводы.Уравнение (2) представляет собой взаимосвязь между изучаемыми факторами: оптимальные (минимальные) значения следующие: об / мин, мм и мм / мин. Замечено, что только значение скорости подачи является общим между минимальным и минимальным.
4.3. Оптимизация для нескольких целей и скорости съема металла
Хотя уменьшение скорости подачи и глубины резания улучшает шероховатость поверхности, оно также снижает скорость съема металла, которая является показателем производительности во время процесса обработки.Максимизация должна быть целью с экономической точки зрения. В этом анализе была проведена многокритериальная оптимизация для одновременного минимизации и максимизации. Скорость съема металла рассчитывалась исходя из того, что рабочее зацепление во всех тестовых экспериментах составляет 35 мм.
Была поставлена цель минимизировать и максимизировать сохранение от 0,15 до 0,2 мкм м (из промышленного опыта тонкого фрезерования) с более высоким приоритетом оптимизации. В результате оптимизации частота вращения шпинделя = 1250 об / мин, глубина резания = 1.0 мм, и скорость подачи стола = 67 мм / мин при желательности композита 0,83. Составная желательность измеряет качество оптимизации и находится в диапазоне от нуля до единицы, где единица является идеальным случаем, а ноль означает, что по крайней мере один из членов выходит за пределы. Ожидаемые и были рассчитаны равными 0,15 мкм м и 2333 мм 3 / мин, соответственно. На рисунке 13 показан график многокритериальной оптимизации.
Высокопрочная сталь имеет относительно высокую твердость, которая хорошо коррелирует с хорошим качеством поверхности.Это связано с тем, что более твердый материал обладает низкой способностью к пластической текучести, что приводит к лучшей отделке поверхности. Это объясняется хрупким характером взаимодействия между режущим инструментом и поверхностью заготовки для твердых материалов, что приводит к разделению материалов, а не к пластическому течению, которое может привести к неровностям поверхности. Было обнаружено, что шероховатость поверхности увеличивается с увеличением скорости подачи и глубины резания, что приводит к увеличению площади реза, что, следовательно, связано с более высокими силами резания и повышенным трением, что приводит к плохой чистоте поверхности.По профилю шероховатости поверхности было замечено, что высокие скорости подачи связаны с большим расстоянием между отметками шероховатости по горизонтали. Кроме того, при большей глубине вырезов расстояние по вертикали между выступами и впадинами неровностей поверхности было больше. Таким образом, более высокие скорости подачи и глубина резания привели к более высокой шероховатости поверхности.
На рисунке 14 представлена оптическая микроскопия обработанной поверхности при скорости вращения шпинделя 1250 об / мин, глубине резания 0,5 мм и скорости подачи стола 50 мм / мин, а на рисунке 15 представлена оптическая микроскопия для следующих условий резания: шпиндель скорость 1250 об / мин, глубина резания 0. 5 мм, и скорость подачи стола 125 мм / мин. Влияние скорости подачи очевидно, в том смысле, что низкая скорость подачи дает относительно тонкие отметки шероховатости поверхности, которые расположены близко друг к другу, тогда как высокая скорость подачи дает относительно толстые отметки шероховатости, расположенные на большом расстоянии. 5. Заключение. , скорость подачи стола, глубина резания и скорость шпинделя.Два показателя шероховатости поверхности, а именно и, были экспериментально измерены с помощью серии из 64 экспериментов и их повторений. Записанные значения шероховатости представляют собой среднее значение четырех измерений на каждой поверхности. Результаты показывают, что скорость, глубина резания и скорость подачи стола оказывают значительное влияние на шероховатость поверхности как в линейном, так и в квадратичном выражении. Также существует взаимосвязь между глубиной резания и скоростью подачи. Также кажется, что скорость подачи имеет наибольшее влияние на изменение данных, за которым следует глубина резания.
Минимум был достигнут при следующих условиях обработки: частота вращения шпинделя = 1250 об / мин, глубина резания = 0,447 мм, скорость подачи стола = 50 мм / мин. Для, результаты показывают, что скорость подачи является наиболее эффективным фактором, за которым следует глубина резания, в то время как скорость имела незначительное влияние только в квадратичном члене. Кроме того, существует взаимосвязь между скоростью подачи и глубиной резания, как и в случае с. Минимум был достигнут при следующих условиях: частота вращения шпинделя = 500 об / мин, глубина резания = 0.29 мм, а скорость подачи стола = 50 мм / мин. Замечено, что только значение скорости подачи является общим между минимальным и минимальным. Кроме того, была проведена многокритериальная оптимизация с целью минимизировать и максимизировать скорость съема металла. Оптимизация привела к скорости шпинделя 1250 об / мин, глубине резания 1,0 мм и скорости подачи стола 67 мм / мин при желательности композита 0,83, чтобы получить значения 0,15 и 2333 мм 3 / мин, соответственно.
Приложение
См. Таблицы 6 и 7.
17 9205 A4205 9205 A420100 905 905 905 905 967 A205 905 901 9206 920509 905 905 A331205 905 90519605 9601 9601 7 9605 905 519096.![]()
|
1 | ||||||||||||||||||||||||||||||||||||||||||||||||||||||||||||||||||||||||||||||||||||||||||||||||||||||||||||||||||||||||||||||||||||||||||||||||||||||||||||||||||||||||||||||||||||||||||||||||||||||||||||||||||||||||||||||||||||||||||||||||||||||||||||||||||||||||||||||||||||||||||||||||||||||||||||||||||||||||||||||||||||||||||||||||||||||||||||||||||||
111111 |
Глубина резания | Подача стола | Обработка поверхности ( µ м) | |||||||||
номер | # | (об / мин) | (мм) | (мм / мин) | |||||||
B1 | B1 | 500 | 0.25 | 50 | 0,044 | 0,298 | |||||
B2 | 75 | 0,122 | 1.042 | ||||||||
B3 | 100 | 0,1605 | 1,417 | ||||||||
B5 | B2 | 500 | 0,5 | 50 | 0,056 | 0,338 | |||||
B6 | 75 | 0.![]() | 0,948 | ||||||||
B7 | 100 | 0,173 | 1,257 | ||||||||
B8 | 125 | 0,211 | 1,368 | 0,211 | 1,368 | ||||||
0,075 | 0,854 | ||||||||||
B10 | 75 | 0,166 | 1,133 | ||||||||
B11 | 100 | 0,196 | 1,371 | ||||||||
1,428 | |||||||||||
B13 | B4 | 500 | 1,00 | 50 | 0,087 | 0,928 | |||||
B14 | 75 | B14 | 75 | 75 | 0,242 | 1,401 | |||||
B16 | 125 | 0,256 | 1,598 | ||||||||
B17 | B5 | 750 | 0,25 | 50.![]() | 0,605 | ||||||
B18 | 75 | 0,186 | 1,223 | ||||||||
B19 | 100 | 0,209 | 1,738 | 1,738 | B6 | 750 | 0,5 | 50 | 0,088 | 0,872 | |
B22 | 75 | 0.106 | 1.067 | ||||||||
117 | 1,150 | ||||||||||
B24 | 125 | 0,146 | 1,179 | ||||||||
B25 | B7 | 750 | 0,71 | 50 | 0,09 905 905 | 0,09 | 0,121 | 1,102 | |||
B27 | 100 | 0,138 | 1,318 | ||||||||
B28 | 125 | 0,169 | 1,549 | 9205 9205 0 | 0 | 50 | 0,110 | 1,002 | |||
B30 | 75 | 0,200 | 1,990 | ||||||||
B31 | 100 | 100 | 2,261 | ||||||||
B33 | B9 | 1000 | 0,25 | 50 | 0,049 | 0,338 | |||||
B34 | 75 | 0.![]() | 0,896 | ||||||||
B35 | 100 | 0,120 | 1,007 | ||||||||
B36 | 125 | 0,140 | 1,176 | ||||||||
9601 | 0,096 | 0,605 | |||||||||
B38 | 75 | 0,118 | 0,952 | ||||||||
B39 | 100 | 0,136 | 1,112 | 905 905 | 1,722 | ||||||
B41 | B11 | 1000 | 0,75 | 50 | 0,110 | 0,746 | |||||
B42 | 7521 | 7521 905 905 96 | 0,240 | 1,677 | |||||||
B44 | 125 | 0,262 | 1,857 | ||||||||
B45 | B12 | 1000 | 1,00 | 5096.118 | 0,856 | ||||||
B46 | 75 | 0,242 | 1,600 | ||||||||
B47 | 100 | 0,268 | 1,917 | 5 | B13 | 1250 | 0,25 | 50 | 0,060 | 0,861 | |
B50 | 75 | 0,110 | 1,084 | 1,084 | 1,113 | ||||||
B52 | 125 | 0,165 | 1,437 | ||||||||
B53 | B14 | 1250 | 0,5 | 1 | 50 | 0,122 | 0,899 | ||||
B55 | 100 | 0,138 | 0,908 | ||||||||
B56 | 125 | 0,166 | 1.![]() | 50 | 0,068 | 0,323 | |||||
B58 | 75 | 0,129 | 1,235 | ||||||||
B59 | 100 | 0,175 | 0,175 | 2,189 | |||||||
B61 | B16 | 1250 | 1,00 | 50 | 0,075 | 0,412 | |||||
B62 | 75 | 0.165 | 1,516 | ||||||||
B63 | 100 | 0,192 | 1,715 | ||||||||
B64 | 125 | 0,225 | 1,822 | ||||||||
605 | Глубина резания, мм | ||||||||||
: | Рабочее зацепление, мм | ||||||||||
: | Скорость шпинделя, об / мин | ||||||||||
: | Скорость резания, м / мин | ||||||||||
: | Общее количество зубьев фрезы | ||||||||||
: | Скорость съема металла, мм 3 / мин.![]() |
Конкурирующие интересы
Авторы заявляют, что у них нет конкурирующих интересов.
Выражение признательности
Этот проект поддержан Университетом Короля Сауда, деканатом научных исследований, Центр инженерных исследований колледжа.
1.3: Блок 2: Скорость, подача и нарезание
ОбъективПосле завершения этого модуля вы должны уметь:
- Определять и выбирать настройки и операции вертикального фрезерного станка для различных задач обработки.
- Выберите подходящую скорость резания для различных типов материалов.
- Расчет скорости резания и подачи для концевого фрезерования.
- Объясните, как правильно настроить нарезку резьбы с механической подачей.
Скорость резания определяется как скорость на внешней кромке инструмента во время резания. Это также известно как поверхностная скорость. Скорость движения на поверхности, съемка на поверхности и площадь поверхности – все это напрямую связано. Если два инструмента разных размеров вращаются с одинаковыми оборотами в минуту (об / мин), у большего инструмента будет более высокая скорость резания.Скорость на поверхности измеряется в поверхностных футах в минуту (SFM). Все режущие инструменты работают по принципу метража поверхности. Скорость резания в первую очередь зависит от типа материала, который вы режете, и от типа режущего инструмента, который вы используете. Твердость обрабатываемого материала во многом зависит от рекомендуемой скорости резания. Чем тверже обрабатываемый материал, тем меньше скорость резания. Чем мягче обрабатываемый материал, тем выше рекомендуемая скорость резания (см. Рисунок 1).
Сталь Чугун Алюминий Свинец
Рисунок 1: Увеличение скорости резания в зависимости от твердости рабочего материала
Твердость материала режущего инструмента также во многом зависит от рекомендуемой скорости резания. Чем тверже сверло, тем выше скорость резания. Чем мягче сверло, тем ниже рекомендуемая скорость резания (см. Рисунок 2).
Углеродистая сталь Карбид быстрорежущей стали
Рисунок 2: Увеличение скорости резания в зависимости от твердости режущего инструмента
Таблица 1: Скорости резания для типов материаловТип материала | Скорость резания (SFM) | ||||
---|---|---|---|---|---|
Низкоуглеродистая сталь | 40-140 | ||||
Среднеуглеродистая сталь | 70-120 | ||||
905 Высокоуглеродистая сталь 9060 100 | |||||
Свободная обработка Сталь | 100-150 | ||||
Нержавеющая сталь, C1 302, 304 | 60 | ||||
Нержавеющая сталь, C1 310, 316 | 70 | ||||
Нержавеющая сталь, C1 410 | 100 | ||||
Нержавеющая сталь, C1 416 | 140 | ||||
Нержавеющая сталь, C1 17-4, pH | 50 | ||||
Легированная сталь, SAE 4130, 4140 | 70 | Легированная сталь, SAE 4030 | 90 | ||
Инструментальная сталь | 40-70 | ||||
Чугун – обычный | 80-120 | ||||
Чугун – твердый | 5-30 | ||||
Серый чугун | 50-80 | ||||
Алюминиевые сплавы | 300-400 | ||||
Никелевый сплав, Монель 400 | 402 | ||||
Никелевый сплав, монель K500 | 30-60 | ||||
Никелевый сплав, инконель | 5-10 | ||||
Сплавы на основе кобальта | 5-10 | ||||
Титановый сплав 20602 | |||||
Нелегированный титан | 35-55 | ||||
Медь | 100-500 | ||||
Бронза – обычная | 90-150 | ||||
Бронза – Твердая | 30-95 70-90 | ||||
Латунь и алюминий | 200-350 | ||||
Неметаллические соединения без кремния | 100-300 | ||||
Кремнийсодержащие неметаллические вещества | 30-70 |
После определения SFM для данного материала и инструмента можно рассчитать шпиндель, поскольку это значение зависит от скорости резания и диаметра инструмента.
Где:
- об / мин = число оборотов в минуту.
- CS = Скорость резания в SFM.
- D = Диаметр инструмента в дюймах.
Подача (подача фрезерного станка) может быть определена как расстояние в дюймах в минуту, на которое деталь перемещается в фрезу.
На фрезерных станках LBCC подача не зависит от скорости шпинделя.Это хорошее расположение, позволяющее ускорить подачу больших, медленно вращающихся фрез.
Скорость подачи на фрезерном станке зависит от следующих факторов:
- Глубина и ширина резания.
- Тип фрезы.
- Резкость фрезы.
- Материал заготовки.
- Прочность и однородность заготовки.
- Требуемая отделка.
- Требуемая точность.
- Мощность и жесткость станка, удерживающего устройства и оснастки.
Подача на зуб
Подача на зуб – это количество материала, которое должно быть удалено каждым зубом фрезы при ее вращении и продвижении к работе.
По мере того, как деталь продвигается к фрезу, каждый зуб фрезы продвигается в работу на равное количество, образуя стружку одинаковой толщины.
Эта толщина стружки или подача на зуб, а также количество зубьев фрезы формируют основу для определения скорости подачи.
Идеальная скорость подачи для фрезерования измеряется в дюймах в минуту (IPM) и рассчитывается по следующей формуле:
IPM = F x N x RPMГде:
- IPM = скорость подачи в дюймах в минуту
- F = подача на зуб
- N = количество зубьев
- об / мин = оборотов в минуту
Например:
Подачи концевых фрез, используемых в вертикальных фрезерных станках, варьируются от.Подача от 001 до 0,002 дюйма на зуб для фрез очень малого диаметра по стальному материалу до подачи 0,010 дюйма на зуб для больших фрез по алюминиевым заготовкам. Поскольку скорость резания для низкоуглеродистой стали составляет 90, частота вращения 3/8 ”высокоскоростной концевой фрезы с двумя канавками составляет
об / мин = CS x 4 / D = 90 x 4 / (3/8) = 360/375 = 960 об / минДля расчета скорости подачи выберем 0,002 дюйма на зуб
IPM = F x N x об / мин = 0,002 x 2 x 960 = 3.
Машинная подача
Движение станка, которое заставляет режущий инструмент врезаться в или вдоль поверхности заготовки, называется подачей.
Количество подачи обычно измеряется в тысячных долях дюйма при резке металла.
Каналы выражаются немного по-разному на разных типах машин.
Сверлильные станки с механической подачей предназначены для продвижения сверла на заданную величину за каждый оборот шпинделя.Если мы настроим машину на подачу на 0,006 дюйма, машина будет подавать на 0,006 дюйма за каждый оборот шпинделя. Это выражается в (IPR) дюймах на оборот
Процедуры нарезания резьбы
Передовой опыт:
Использование направляющих для метчиков
Направляющие для метчиков являются неотъемлемой частью удобной и прямой резьбы. При использовании токарного или фрезерного станка метчик уже ровный и отцентрованный. При выравнивании метчика вручную будьте осторожны, так как направление метчика на 90 ° намного точнее, чем человеческий глаз.
Использование масла
При сверлении и нарезании резьбы критически важно использовать масло. Он предохраняет сверла от визга, делает рез более гладким, удаляет стружку и предохраняет сверло и инструмент от перегрева.
Клевка
Pecking помогает предотвратить перегрев и поломку сверл при использовании их для сверления или нарезания резьбы. Клевое сверление включает в себя просверливание части детали с последующим ее втягиванием для удаления стружки, одновременно позволяя детали остыть.Поворот ручки на полный оборот, а затем на пол-оборота назад – обычная практика. Каждый раз, когда сверло или метчик откручивается, удалите как можно больше стружки и добавьте масло на поверхность между сверлом или метчиком и заготовкой.
Процедура нарезания резьбы вручную
- Выберите размер сверла из таблицы.
При выборе размера крана в первую очередь следует обратить внимание на эту таблицу.
- При необходимости добавьте фаску к отверстию перед нарезанием резьбы.
Фаски и зенковки – это дополнительные функции, которые иногда требуются для винтов. Для достижения наилучших результатов частота вращения шпинделя должна быть от 150 до 250 об / мин. - Получите направляющую для крана.
Отверстие готово для нарезания резьбы. Для этого используйте метчики и направляющие блоки возле ручных фрез. В направляющих блоках будет несколько отверстий для метчиков разного размера. Выберите тот, который ближе всего к размеру используемого метчика, и поместите его над просверленным отверстием. - Постучите по резьбе.
Подбейте метчик с помощью гаечных ключей. Слегка надавите, поворачивая ключ до упора, а затем на пол-оборота. Клевать метчик на нужную глубину. - Заполните кран.
Если кран не идет дальше или желаемая глубина достигнута, ослабьте давление на кран; он, вероятно, достиг дна. Выньте кран из отверстия. Если приложить дополнительное давление, кран может сломаться.Чем меньше размер крана, тем больше вероятность его поломки.
Процедура нарезания резьбы с механической подачей (вертикальная фреза)
- Нарезание резьбы с механической подачей аналогично ручному нарезанию резьбы.Однако вместо нарезания резьбы вручную используйте вертикальную фрезу для нарезания резьбы по заготовке.
- Перед запуском машины переключите фрезу на низшую передачу.
- Отпустите фиксатор пера и переместите перо как можно ниже. Это гарантирует, что будет достаточно места для установки на желаемую глубину.
- Включите шпиндель ВПЕРЕД и установите скорость вращения шпинделя на 60 об / мин.
- Протяните кран вниз. Когда метчик захватывает приклад, он автоматически входит в отверстие.
- Когда желаемая глубина будет достигнута, быстро переведите переключатель направления шпинделя из прямого в обратное. Это изменит направление крана и вытащит его из отверстия. Изменение направления одним плавным движением предотвратит повреждение резьбового отверстия и крана.
- Выключите машину.
- Очистите резьбовое отверстие, метчик и механический подающий механизм перед тем, как уйти.
- Объясните скорость резания более твердых и мягких материалов.
- Какова скорость резания инструментальной стали и алюминия?
- Рассчитайте число оборотов в минуту для концевой фрезы из быстрорежущей стали диаметром ½ дюйма для обработки алюминия.
- Рассчитайте подачу для инструмента с тремя зубьями. Используйте RPM из вопроса 3.
- Рассчитайте число оборотов в минуту для концевой фрезы из быстрорежущей стали диаметром ¾ дюйма для обработки бронзы.
- Рассчитайте скорость подачи твердосплавной концевой фрезы с двумя канавками диаметром ½ дюйма для обработки низкоуглеродистой стали.
- Какова цель клевания при использовании их для сверления или метчика?
- Выберите подходящий размер сверла для метчиков 5/16 – 24.
- Почему используются смазочно-охлаждающие жидкости?
- Опишите разницу между нарезанием резьбы вручную и с механической подачей.
Walter Tools »Engineering Kompetenz
Используемый вами браузер устарел и больше не поддерживается. Пожалуйста, обновитесь до более новой версии.
Оптимальный подбор рабочих параметров при концевом фрезеровании рабочих материалов Al-6061 с использованием многоцелевого подхода | Механика современных материалов и современных процессов
Экспериментальные работы проводятся на фрезерном центре с ЧПУ (MAXMILL-make MTAB), использующем определяемые пользователем скорости шпинделя, глубину резания и движения подачи. Инструмент из быстрорежущей стали диаметром 12 мм с четырьмя режущими канавками с вылетом 50 мм и скоростью вращения шпинделя 4000 об / мин использовался во всех экспериментах. Концевые фрезерные работы выполняются с полным процентом радиального погружения заготовок из Al6061. Химический состав этого сплава: 0,3% Cu, 0,04% Mn, 0,85% Mg, 0,04% Ti, 0,5% Si, 0,2% Cr, 0,5% Fe, 0,25% Zn, остальное – алюминий. Все образцы были взяты в виде блоков размером 100 × 80 × 10 мм. При указанных скоростях шпинделя и глубине резания амплитуды вибрации регистрируются следующими приборами: акселерометром (PG 109 M0, диапазон частот от 1 до 10 000 Гц), 4-канальным цифровым осциллографом (модель DPO 43034) с усилителем заряда. (Модель: CA 201 A0).Акселерометр помещается в корпус шпинделя, и соответствующие данные записываются в осциллограф. На рисунке 1 показана экспериментальная установка, используемая в настоящей работе на обрабатывающем центре.
Экспериментальная установка, используемая для измерения вибрации на месте
Шероховатость поверхности является важным критерием оценки качества продукта. Это сильно влияет на производительность механических деталей, а также на стоимость производства.Правильный выбор параметров резки обеспечивает хорошее качество поверхности. Шероховатость обработанных поверхностей исследовали с помощью прибора Talysurf, как показано на рис. 2.
Используемый прибор Talysurf для определения шероховатости поверхности
Дизайн Бокса-Бенкена (BBD) методологии поверхности отклика (RSM) используется для проведения пятнадцати наборов экспериментов с математической моделью. Этот метод обычно требует меньше экспериментов по сравнению с вращающейся центральной композитной конструкцией (RCCD) RSM.Выбираются три параметра обработки для изучения подачи (мм / мин), скорости (об / мин) и осевой глубины резания (b). Эти три параметра обработки выбираются на основе предварительных пробных испытаний. В таблице 1 показаны параметры обработки и их уровни.
Таблица 1 Параметры обработки и их уровни Обычно этого достаточно, чтобы соответствовать квадратичной модели, и он содержит линейные члены, квадраты членов и произведения факторов. В таблице 2 показаны экспериментальные результаты параметров входного отклика.
Моделирование поверхности отклика
RSM – это набор статистических и математических методов для моделирования и оптимизации технических задач. Этот метод используется для установления связи между входными параметрами и рабочими характеристиками. Во время моделирования производственных процессов с использованием RSM собирается достаточный объем данных посредством планирования эксперимента. В общем, регрессионная модель второго порядка в основном разрабатывается, потому что модели первого порядка часто дают некоторую несогласованность.Предполагается, что все входные параметры процесса являются измеряемой величиной во время моделирования, и соответствующие отклики могут быть выражены следующим образом:
$$ y = f \ left ({x} _1, {x} _2, ……, {x} _p \ right) $$
(1)
где x 1 , x 2 , x 3 ,…, x p – входные параметры процесса, а y – ответ. Во время экспериментов предполагается, что все входные параметры управляемы и имеют незначительные ошибки.2} + {\ displaystyle \ sum_i {\ displaystyle \ sum_j {b} _ {i j}}} {x} _i {x} _j $$
(2)
где b 0 постоянна и b и , б II , б ij ……, – коэффициенты регрессии, определенные методом наименьших квадратов.2-0,00003 \ times f \ times N + 0,07750 \ times f \ times b + 0,00083 \ times N \ times b \ Big) \\ {} \ kern6em \ end {array} $$
(4)
Коэффициенты в приведенных выше выражениях обозначают значения весовых коэффициентов для выходных откликов. Положительный и отрицательный знаки коэффициентов отражают соответствующую пропорциональность.
Многоцелевая оптимизация
Чтобы получить оптимальные решения для различных задач проектирования с различными наборами входных данных, крайне необходимы методы оптимизации.В единственной задаче оптимизации есть только один критерий выхода, и такая работа изучалась на протяжении последних 50 лет. Когда существует более одной цели, требуется другой подход. Многоцелевые проблемы возникают в сложных отраслях реального мира, таких как машиностроение, проектирование, транспорт и т. Д. Видно, что все важные практические проблемы реального мира, включающие несколько критериев с несколькими ограничениями, привлекают большое внимание к многоцелевой оптимизации.Эти проблемы могут быть эффективно решены с меньшими вычислительными затратами и высокой точностью. В многоцелевых задачах оптимизации подход с использованием генетических алгоритмов является лучшим методом по сравнению с другими методами и получил значительное внимание исследователей. GA основан на принципе выживания для сильнейшего. В этом методе изначально случайным образом выбирается совокупность строк. Они кодируются двоичными цифрами и традиционно используются для обозначения хромосом с помощью нулей и единиц.Далее вычисляется значение пригодности (задачи максимизации или минимизации). Далее для создания новой популяции последовательно применялись такие операции, как размножение, скрещивание и мутация. После создания новой популяции ее дополнительно оценивают и тестируют на соответствие.
Целью данного исследования является минимизация амплитуды вибраций и в то же время минимизация шероховатости поверхности (R a ). Здесь параметры отклика (A и R a ) являются нелинейными функциями скорости подачи (f), скорости шпинделя (N) и осевой глубины резания (b).Целевая функция определяется следующим образом:
$$ Minimize \; \ left \ {f (X), g (X) \ right \} $$
(5)
Подлежит ограничению переменных
$$ 1800 \ le N \ le 3000 $$
(6)
$$ 0,2 \ le b \ le 0,8 $$
(8)
При X = [N, f, b ] T и N, f и b представляют скорость, подачу и осевую глубину резания. Функция f (X) и g (X) представляет собой амплитуду вибрации и шероховатость поверхности, которые неизвестны и должны соответствовать экспериментальным данным.
После успешного применения всех операторов генетического алгоритма будет создан новый набор популяции. Далее они декодируются и рассчитываются соответствующие значения целевой функции. Все эти операции завершат одно поколение генетического алгоритма. Итерации будут продолжаться до тех пор, пока не будет получено необходимое условие завершения.Поток концепций генетических алгоритмов показан на рис. 3.
Рис. 3Блок-схема генетических алгоритмов
скоростей и подача 101 – в лупе
Общие сведения о скоростях и нормах подачи
ПРИМЕЧАНИЕ: В этой статье рассматриваются скорости и скорости подачи для фрезерных инструментов, в отличие от инструментов , токарных и инструментов.
Перед использованием режущего инструмента необходимо понять скорость резания инструмента и скорость подачи, которую чаще называют «скорости и подачи». «Скорости и подачи – это переменные резания, используемые при каждой операции фрезерования, и они различаются для каждого инструмента в зависимости от диаметра фрезы, операции, материала и т. Д. Понимание правильных скоростей и подач для вашего инструмента и операции перед началом обработки имеет решающее значение.
Сначала необходимо определить каждый из этих факторов. Скорость резания, также называемая поверхностной скоростью, – это разница в скорости между инструментом и заготовкой, выраженная в единицах расстояния с течением времени, известная как SFM (поверхностные футы в минуту).SFM основан на различных свойствах данного материала. Скорость, называемая числом оборотов в минуту (об / мин), зависит от SFM и диаметра режущего инструмента.
Хотя скорость и подача являются общими терминами, используемыми при программировании фрезы, на идеальные рабочие параметры также влияют другие переменные. Скорость фрезы используется при расчете скорости подачи фрезы, измеряемой в дюймах в минуту (IPM). Другая часть уравнения – это загрузка микросхемы. Важно отметить, что нагрузка стружки на зуб и нагрузка стружки на инструмент различаются:
- Нагрузка стружки на зуб – это соответствующее количество материала, которое одна режущая кромка инструмента должна удалить за один оборот.Это измеряется в дюймах на зуб (IPT).
- Нагрузка стружки на инструмент – это соответствующее количество материала, снимаемого всеми режущими кромками инструмента за один оборот. Это измеряется в дюймах на оборот (IPR).
Слишком большая нагрузка стружки может скапливать стружку в фрезу, вызывая плохой отвод стружки и, в конечном итоге, поломку. Слишком малая стружка может вызвать трение, вибрацию, прогиб и плохое общее резание.
Скорость съема материала
Коэффициент съема материала (MRR), хотя и не входит в программу режущего инструмента, является полезным способом расчета эффективности инструмента.MRR учитывает два очень важных параметра движения: осевая глубина резания (ADOC) или расстояние, на котором инструмент входит в зацепление с заготовкой по ее средней линии, и радиальную глубину резания (RDOC), или расстояние, на которое инструмент входит в заготовку. .
Глубину резания инструмента и скорость его резания можно использовать для расчета, сколько кубических дюймов в минуту (в 3 / мин) удаляется с заготовки. Это уравнение чрезвычайно полезно для сравнения режущих инструментов и изучения того, как можно уменьшить время цикла.
Скорости и подачи на практике
Хотя многие параметры резания определяются материалом инструмента и заготовки, принимаемая глубина резания также влияет на скорость подачи инструмента. Глубина резания определяется выполняемой операцией – она часто подразделяется на прорезание пазов, черновую обработку и чистовую обработку, хотя существует множество других более конкретных типов операций.
Многие производители инструментов предоставляют таблицы полезных скоростей и подач, рассчитанные специально для их продуктов.Например, Harvey Tool предоставляет следующую таблицу для концевой фрезы диаметром 1/8 дюйма, инструмент № 50308. Заказчик может найти SFM для материала слева, в данном случае из нержавеющей стали 304. Нагрузку на стружку (на зуб) можно определить путем пересечения диаметра инструмента сверху с материалом и операциями (на основе осевой и радиальной глубины резания), выделенными на изображении ниже.
В следующей таблице вычислены скорости и подачи для этого инструмента и материала для каждой операции на основе приведенной выше таблицы:
Прочие важные соображения
Для каждой операции рекомендуется уникальная нагрузка стружки в зависимости от глубины резания.Это приводит к различным скоростям подачи в зависимости от операции. Поскольку SFM зависит от материала, он остается постоянным для каждой операции.
Получите немедленное повышение эффективности магазина: загрузите руководство по HEM сегодняОграничение скорости шпинделя
Как показано выше, скорость фрезы (об / мин) определяется SFM (в зависимости от материала) и диаметром фрезы. При использовании миниатюрных инструментов и / или определенных материалов расчет скорости иногда дает нереалистичную скорость шпинделя. Например, резак 0,047 дюйма из алюминия 6061 (SFM 1000) обеспечит скорость ~ 81 000 об / мин. Поскольку эта скорость достижима только с высокоскоростными воздушными шпинделями, полный SFM в 1000 может быть недостижим. В таком случае рекомендуется, чтобы инструмент работал на максимальной скорости станка (которая удобна для машиниста) и чтобы поддерживалась соответствующая нагрузка стружки для диаметра. Это обеспечивает оптимальные параметры в зависимости от максимальной скорости машины.
Эффективный диаметр фрезы
Для угловых инструментов диаметр фрезы изменяется по LOC.Например, спиральный инструмент № 07001, фреза для снятия фаски с плоским концом и спиральными канавками, имеет диаметр вершины 0,060 дюйма и основной диаметр стержня 0,250 дюйма. В сценарии, когда он использовался для создания излома кромки 60 °, фактическое режущее действие происходило бы где-то между кончиком и большим диаметром / хвостовиком. Для компенсации приведенное ниже уравнение можно использовать для определения среднего диаметра по фаске.
Используя этот расчет, эффективный диаметр фрезы составляет 0,155 дюйма, который будет использоваться для всех расчетов скорости и подачи.
Нелинейный путь
Подача предполагает линейное перемещение. Однако бывают случаи, когда траектория проходит по дуге, например, в углу кармана или круговой интерполяции. Так же, как увеличение DOC увеличивает угол зацепления инструмента, выбор нелинейной траектории тоже увеличивается. Для внутреннего угла задействуется больше инструмента, а для внешнего угла – меньше. Скорость подачи должна быть соответствующим образом компенсирована для увеличения или уменьшения зацепления инструмента.
Эта корректировка еще более важна для круговой интерполяции.Возьмем, к примеру, приложение для нарезания резьбы, в котором резец совершает круговое движение вокруг предварительно просверленного отверстия или выступа. Для внутренней регулировки скорость подачи необходимо уменьшить, чтобы учесть дополнительное зацепление. Для внешней регулировки скорость подачи должна быть увеличена из-за меньшего зацепления инструмента.
Возьмем этот пример, в котором резьбовая фреза Harvey Tool № 70094 с диаметром фрезы 0,370 дюйма обрабатывает внутреннюю резьбу 9 / 16-18 в нержавеющей стали 17-4. Расчетная скорость составляет 2064 об / мин, а линейная подача – 8.3 IPM. Диаметр резьбы 9/16 составляет 0,562 дюйма, который используется для внутреннего и внешнего диаметра в обеих регулировках. После добавления этих значений в приведенные ниже уравнения скорректированная внутренняя подача станет 2,8 IMP, а внешняя подача станет 13,8 IPM.
Щелкните здесь, чтобы увидеть полный пример.
Заключение
Эти расчеты являются полезными рекомендациями для оптимальной работы режущего инструмента в различных областях применения и различных материалах. Тем не менее, параметры, рекомендуемые производителем инструмента, – это лучшая отправная точка для определения исходных значений.После этого глаза, уши и опыт машиниста помогут определить наилучшие рабочие параметры, которые будут зависеть от настройки, инструмента, станка и материала.