Ремонт радиатора своими руками: паять или менять?
Car.ruиещё 1
Каждая деталь автомобиля имеет свой собственный ресурс, а работа без поломок на протяжении длительного времени невозможна ни для одного устройства.
© Car.ruЭто относится и к радиатору автомобиля, рассматриваемого как наиболее слабая часть мотора. Его соты со временем будут забиты грязью, попадающей в них из рубашки охлаждения двигателя. И самое главное, что в него на постоянной основе прилетают камни и разного рода мусор, вылетающие из-под колес других автомобилей. В зимнее время года на него оказывают сильное влияние химические вещества, находящиеся в составе смеси для посыпки дорог. Результатом этого может стать протечка радиатора.
Видео дня
Действия при протекании радиатора. После того, как была обнаружена течь радиатора, перед владельцем автомобиля встает вопрос – заменить неисправный радиатор или же попробовать его отремонтировать? Естественно, что приобретение новой детали позволит предотвратить возникновение проблем еще на протяжении нескольких лет. Касательно же ремонтных работ, то современные средства для пайки дают возможность практически полного восстановления вышедшей из строя детали, потратив не это даже меньше третьей части ее общей стоимости.
Еще одним положительным моментом от выполнения ремонта становится то, что если ваш автомобиль зарубежного производства, то заказ запчастей для него может выполняться только за границей, и их доставка может занимать длительное время. Проведение же ремонтных работ может быть завершено за один день.
Но без наличия практических навыков, за это лучше не браться. Попытка устранения проблемы «народными методами» может не только не помочь, но и привести к тому, что его дальнейшее использование будет невозможно. Одним из вариантов может быть закрытие герметиком места течи, но при этом велика вероятность, что им забьются и рабочие соты.
Помимо этого, при попадании частиц герметика в систему охлаждения, они могут забить каналы, ведущие к отопителю и патрубкам, что может вызвать нарушение системы циркуляции воды или другой жидкости для охлаждения. Это намного увеличит стоимость ремонта, так как придется выполнять полную чистку системы и замену охлаждающей жидкости. Но пайка радиатора только отсрочит его замену на некоторое время, в то же время снижая его функции.
Самостоятельный ремонт. После принятия решения о попытке самостоятельного ремонта, необходимо в первую очередь снять радиатор с автомобиля и полностью слить из него всю жидкость. Это сделает ремонт намного более удобным, так как можно будет подобраться ко всем местам, требующим ремонта, и заливка припоя будет производиться равномерно. Для выявления всех поврежденных мест радиатора стоит закрыть его отверстия полиэтиленом и погрузить в воду. Поврежденные места проявят себя выходящими пузырьками.
После того, как они будут обнаружены, радиатор необходимо отмыть от грязи, и до блеска зачистить те места, где планируется проведение работ. Делается это при помощи щетки по металлу, наждачной бумаги и мелкого надфиля. Именно от качества этой работы и будет зависеть успешность соединения припоя и металла, потому очистка должна быть выполнена очень тщательно. По ее окончании зачищенные места обезжириваются ацетоном.
Проще всего производить пайку медных радиаторов, немного более трудоемкими окажутся алюминиевые.
Итог. Пайка получившего повреждения радиатора – дело несложное. Цена такого варианта будет намного меньше, чем при покупке нового. Но его эффективность будет уже не настолько большой, и в полной мере полагаться на его нормальную работу уже не стоит.
Другое
Car.ru: главные новостиАвтоВАЗ будет оснащать Lada Niva моторами от Lada Vesta
В Сети представлен Mustang, построенный на базе KIA Spectra
Как правильно использовать АКПП в летнюю жару
Производство радиаторов FENOX!
В продолжение знакомства с радиаторами представляем Вам видео с их производства!Совсем недавно мы уже писали обширный материал по радиаторам FENOX. Сегодня мы готовы предоставить немножко больше и показать Вам видео поэтапного производства. И по традиции, без лишних слов и музыкальных вставок покажем этапы производства данной товарной группы, в формате #NOCOMMENTS. В ассортименте компании FENOX представлены как радиаторы, произведенные по классической технологии, где при сборке радиатора донья и трубки уплотняются посредством резиновых колец (сборные), так и с использованием более совершенной технологии – пайки.
Чтобы отследить все этапы и разобраться в технологиях, давайте проведем подробный обзор видео.
Итак, в ассортименте компании FENOX представлены радиаторы, произведенные по двум принципиально разным технологиям:
- Механическая сборка – сборный алюминиевый радиатор
- Пайка – паяный радиатор
Обычный современный радиатор состоит из 5 компонентов: гофрированная алюминиевая лента, алюминиевые трубки, боковые коллекторы – доньи, бачки и ребра жесткости.
Сборный же алюминиевый радиатор представляет собой пакет гофрированной алюминиевой фольги (ленты), сквозь который вставляются алюминиевые трубки.
Полученный пакет поджимается, следом устанавливаются боковые коллекторы (доньи). Трубки дорнуются (увеличивают наружный диаметр на концах).
Затем на коллекторы монтируются бачки из армированного пластика.
На финальном участке сборки монтируются ребра жесткости.
Данная технология производства сборных радиаторов отличается более низкой стоимостью, а также уменьшает вес конечного продукта. Но стоит также заметить, что из-за конструктивных особенностей у сборных радиаторов есть свои недостатки. Во-первых, ограниченная теплоотдача (из-за отсутствия жесткой связи между трубкой и ребрами охлаждения). Во-вторых, такие радиаторы выдерживают меньшее давление. В основном сборные радиаторы используются в двигателях малой кубатуры.
Паяный алюминиевый радиатор FENOX состоит из алюминиевых трубок овального сечения и гофрированной алюминиевой ленты*. Все алюминиевые части радиатора соединяются между собой пайкой – такая технология исключает появление зазоров меду трубкой и ребрами системы охлаждения. В свою очередь, благодаря отсутствию зазоров увеличивается площадь теплоотдачи и значительно повышается вибростойкость всей конструкции радиатора FENOX. Стоит также отметить, что в настоящее время практически все автопроизводители на своих конвейерах устанавливают в автомобили именно паяные алюминиевые радиаторы.
*Изготовление гофрированной ленты для рёбер системы охлаждения производится на формовочной машине.В машину подается алюминиевый лист толщиной 0,2 мм.
На специальном стенде происходит сборка адиатора. Сначала устанавливаются коллекторы и рёбра жесткости, после происходит установка плоскоовальных трубок охлаждения, затем монтаж гофрированной ленты охлаждения между трубками. Далее конструкция обжимается и переходи на следующий этап – пайка.
Предварительно, в специальной установке происходит подготовительная очистка радиаторов.
После очистки в специальной камере происходит нанесения флюса для пайки (технология NOKOLOK).
После нанесения флюса, радиаторы направляются в специальную печь. В печи происходит термохимическая реакция: флюс и нанесенный ранее припой расплавляются. Фактически, конструкция радиатора представляет собой единое целое.
На финальной стадии сборки происходит монтаж бачков на готовую продукцию и дальнейшее ее тестирование.
Что касается контроля качества на производстве, все радиаторы FENOX проходят проверку на герметичность – на специальном стенде радиатор опускается в ванну с водой. При подаче воздуха под давлением,оператор визуально производит контроль,чтобы не было утечки (пузырьки воздуха).
Стоит также напомнить, что около года назад компания FENOX сменила упаковку на более практичную, стильную и более узнаваемую. В данном случае наша новая упаковка радиаторов обеспечивает лучшую сохранность при перевозке.
Полный список артикулов радиаторов FENOX в Excel
Внимание! Указанная в таблице информация не гарантирует точного подбора запчасти, а также не является основанием для обращения по гарантии в случае несоответствия применяемости.
С полным каталогом запчастей FENOX можно ознакомиться здесь, а выбрать ближайшую розничную торговую точку/СТО или дистрибьютера в Вашем регионе можно по этой ссылке.
Предоставляемая гарантия сроком 2 года на всю продукцию подтверждает высокий стандарт качества FENOX.
Вы можете обратиться в FENOX Global Service с любым вопросом, комментарием или предложением, воспользовавшись онлайн-сервисами на сайте, которые расположены в правом нижнем углу сайта fenox.com, а также в социальных сетях Vkontakte, Facebook, Instagram
, Viber и на портале Drive2.ru.Медно-латунные радиаторы CuproBraze® в производстве
Применение меди в автомобилестроении
Конрад Дж. А. Кундиг, доктор философии.
Сочетание легкого веса, высокой прочности и непревзойденной теплопередачи возвращает медь на важный автомобильный рынок
Автомобильные радиаторы претерпели многочисленные технологические изменения за последние 100 лет, хотя ни одно из этих изменений не является более очевидным, чем металлы, из которых изготовлен радиатор. В медно-латунном радиаторе ребра радиатора сделаны из почти чистой меди, а трубки и напорные баки – из латуни. В алюминиевом радиаторе все компоненты изготовлены из алюминиевого сплава.
Когда-то медь/латунь доминировали на рынке легковых и грузовых автомобилей; сегодня алюминий используется для радиаторов в большинстве новых автомобилей, в то время как медь/латунь сохраняет сильные позиции в радиаторах грузовиков и вторичном рынке для автомобилей всех типов. Вот краткая хронология произошедших изменений:
1900–1970 годы: медь/латунь 100 %, алюминий Zero
Радиаторы появились, когда автомобили и грузовики впервые были оснащены двигателями с водяным охлаждением. Радиаторы были необходимы для предотвращения перегрева воды или охлаждающей жидкости в двигателе. Для оригинальных радиаторов использовалась медь из-за отличной теплопроводности металла. Это физическое свойство определяет скорость, с которой радиатор может передавать тепло: более высокая проводимость = более быстрое охлаждение = более высокая эффективность и т. д. Среди других свойств меди, которые сделали ее естественным выбором для радиаторов, являются высокая естественная коррозионная стойкость металла и легкость, с которой он можно изготовить и отремонтировать. Кроме того, медно-латунные радиаторы можно снять со списанных автомобилей и переработать для получения других медных сплавов, таких как латунь и бронза.
До начала 1970-х медно-латунные радиаторы устанавливались во всех новых легковых и грузовых автомобилях по всему миру. Не было веской причины использовать что-то еще, потому что ничто другое не могло конкурировать со многими преимуществами меди/латуни.
1970–1990-е годы: алюминий растет, но медь/латунь по-прежнему лидирует на рынке
Среда радиаторов изменилась в 1970-х годах, когда Volkswagen решил переоборудовать свои автомобили с двигателя с воздушным охлаждением на легкую силовую установку с водяным охлаждением. После мирового нефтяного кризиса и настоятельных призывов к сокращению потребления топлива крупные производители автомобилей в Европе и США начали производить легковые и грузовые автомобили из более легких материалов.
Для радиаторов и других теплообменников (радиаторы отопителей, масляные радиаторы, кондиционеры) был выбран более легкий материал — алюминий. Алюминий имеет только одну треть теплопроводности меди, но также только одну треть плотности меди/латуни. В необработанном виде алюминий также дешевле меди. (Этот факт применим к слиткам, производимым алюминиевыми заводами. Однако это не обязательно верно, когда металл находится в форме полосы радиатора.) Эти качества, наряду с мрачными, хотя и нереализованными прогнозами товарных дефицит в 1980-е — вызвали волну увлечения чем-то «новым».
В результате алюминий постепенно заменил медь/латунь в качестве металла для радиаторов в новых автомобилях. Медь/латунь продолжали удерживать большую часть общего рынка радиаторов, поскольку они доминируют в секторе грузовых автомобилей и удерживают более 80% рынка замены. Эта ситуация сохраняется и в новом столетии.
1990: Начало разработки новой технологии меди/латуни
По мере того, как алюминий становился все популярнее среди автопроизводителей, производители меди и латуни начали искать способы улучшить свой когда-то доминирующий продукт. Продажа медной и латунной полосы производителям радиаторов, в конце концов, представляет собой важный рынок, на который приходится около 200 000 метрических тонн меди ежегодно.
Очевидно, что в традиционном изделии из меди/латуни есть место для усовершенствования. Помимо того, что радиаторы были слишком тяжелыми для современных автомобильных конструкций, радиаторы имели тенденцию выходить из строя в самых слабых местах их изготовления, где свинцово-оловянный припой соединяет различные компоненты. Сам свинцово-оловянный припой считался экологическим недостатком, хотя он был полностью переработан вместе с остальной частью радиатора.
После того, как алюминиевые радиаторы прослужили несколько лет, однако, у них стал проявляться ряд недостатков.
Кроме того, алюминиевый сплав, используемый для полосы радиатора, слабее и менее устойчив к нагрузкам, вызванным вибрацией, чем латунь. В результате на многих алюминиевых радиаторах появились трещины, особенно вызванные усталостью металла, в местах крепления радиаторов к раме автомобиля. Кроме того, было обнаружено, что алюминиевые радиаторы особенно подвержены точечной коррозии со стороны охлаждающей жидкости. Когда это происходит, радиатор не подлежит ремонту. Промышленное «исправление» этого досадного недостатка заключалось в использовании сложных охлаждающих жидкостей (урожденная антифриз ), содержащий ингибиторы коррозии. Медь / латунь не требует таких ингибиторов в хладагенте, что является одной из причин, по которой радиаторы из меди / латуни остаются практичным выбором в тропических или развивающихся странах, где наиболее доступным «хладагентом» по-прежнему является обычная вода.
Наконец, в то время как алюминиевые радиаторы могут быть переработаны, алюминиевый сплав в них не может быть переработан для производства новой полосы радиатора или других продуктов, в которых требуется высокая формуемость. В результате было выброшено 9 алюминиевых радиаторов.0037 переработал для менее требовательных применений, таких как литье. Таким образом, алюминиевые и медно-латунные радиаторы одинаково пригодны для вторичной переработки в одном смысле, хотя переработка медно-латунных радиаторов, дающая ценные латуни и бронзы, имеет явные экономические преимущества.
Проблемы выполнены, введите
Cu proBraze Промышленные эксперты признали, что новый медно-латунный радиатор должен иметь такой же вес, как алюминий, и при этом избегать недостатков (слабые паяные соединения, припой, содержащий свинец) традиционных конструкций. Еще одна проблема заключалась в том, что большая часть производственных мощностей по производству радиаторов для новых автомобилей была переведена на печи, предназначенные для алюминиевых радиаторов. Необходимо было найти способ использовать эти печи для производства медно-латунных радиаторов и таким образом избежать естественного нежелания промышленности инвестировать в новое оборудование.
Эта задача была возложена на Международную ассоциацию меди, ООО (ICA), а в более ранние годы на предшественницу ICA, Международную ассоциацию исследований меди, Ltd., INCRA.) К началу 1990-х годов инженеры определили новую технологию, которая сделать возможным производство более легкого, прочного и долговечного медно-латунного радиатора. Ключом к успеху стала новая технология пайки под названием Cu proBraze.
Радиатор CuproBraze® можно сделать меньше и компактнее, чем алюминиевые модели с аналогичными характеристиками. Как следует из названия, процесс Cu proBraze использует пайку твердым припоем вместо традиционной пайки для соединения медных и латунных компонентов радиатора. При пайке используются сплавы, которые значительно прочнее обычных свинцово-оловянных припоев.
Поскольку паяные соединения прочнее пайки, появилась возможность сделать сам металл тоньше, чем тот, который используется для обычных медно-латунных радиаторов. Это усовершенствование привело к дальнейшему преимуществу, заключающемуся в том, что тонкие поперечные сечения приводили к еще более высокой теплопередаче. Всего Cu Радиаторы proBraze могут быть:
- Сильнее
- Зажигалка
- Более устойчивый к коррозии
- Более эффективный и, следовательно, потенциально меньший
, чем их алюминиевые аналоги, в зависимости от приоритета, присвоенного различным свойствам. Дополнительные преимущества для OEM-производителей автомобилей включают более низкий перепад давления на стороне воздуха, меньшие паразитные потери двигателя (и, следовательно, лучшую экономию топлива), а также более низкие затраты на модуль охлаждения.
Преимущества процесса
Cu proBraze® по сравнению с процессом Nocolok®Процесс Cu proBraze сам по себе предлагает производителям значительные преимущества по стоимости. Эти преимущества очевидны, если сравнить процесс Cu proBraze с процессом Nocolok, который обычно используется для изготовления алюминиевых радиаторов:
- Время пайки, необходимое для процесса Cu proBraze, примерно вдвое меньше, чем для процесса Nocolok, несмотря на то, что оба процесса работают при температуре около 600°C (1112°F). Это возможно благодаря тому, что разница между температурой пайки медно-латунных радиаторов и температурой плавления латуни составляет более 300°С (540°F), а соответствующая разница для алюминиевых радиаторных сплавов составляет всего 30°С-40°С. (54-72°F). Поэтому температуру пайки алюминиевых радиаторов следует повышать медленно и осторожно, чтобы не допустить превышения температуры плавления в любой части радиаторов.
Эта предосторожность не требуется для медно-латунных радиаторов, потому что отклонение на несколько десятков градусов не вызовет проблем ни в меди, ни в латуни. Удвоенная часовая производительность Cu Процесс proBraze, являющийся результатом этого технического преимущества, означает для производителя экономию капитала и рабочей силы. Технология CuproBraze идеально подходит для теплообменных устройств, таких как радиаторы ( справа ), масляные радиаторы, нагреватели, охладители наддувочного воздуха и конденсаторы.
- Опыт показал, что процент брака в процессе Cu proBraze значительно ниже, чем при использовании Nocolok. Опять же, это преимущество является результатом большего запаса температуры, который возможен при использовании меди/латуни.
- Любые утечки в недавно изготовленных радиаторах Cu proBraze можно просто и эффективно отремонтировать, добавив дополнительное количество паяльной пасты и пропустив устройство через печь для пайки.
Утечки в установленных радиаторах также легко устраняются. Алюминиевые радиаторы нельзя легко отремонтировать, если вообще возможно, таким способом.
- Потребление энергии в процессе Cu proBraze значительно ниже, чем в Nocolok, поскольку удельная теплоемкость меди составляет всего 40% от удельной теплоемкости алюминия.
- Медь и латунь легче формовать и изготавливать, чем алюминиевую полосу радиатора. Это свойство снижает износ инструмента и затраты на техническое обслуживание при производстве сырья.
- Стоимость изготовления радиаторов по технологии Cu proBraze полностью конкурентоспособна по сравнению со стоимостью изготовления радиаторов по технологии Nocolok.
И, наконец,
- Процесс Cu proBraze может осуществляться в печах Nocolok, что устраняет необходимость в дополнительных капиталовложениях.
Universal Auto Radiator Manufacturing Company (UAR), Питтсбург, производит первые коммерческие радиаторы Cu proBraze в конфигурациях, которые подходят для более чем 90 моделей американских, европейских и японских легковых и грузовых автомобилей.
Автомобильная промышленность, похоже, довольна новыми изделиями из меди и латуни. Радиаторы Cu proBraze, срок службы которых в три-четыре раза превышает срок службы спаянных моделей, успешно прошли более 140 000 миль в ходе дорожных испытаний. «У нас нет сообщений о сбоях», — говорит президент UAR Питер Россин. «Эта технология впечатляет своей силой».
Большая тройка Детройта уже давно ищет радиатор, способный прослужить 100 000 миль. Теперь Cu proBraze позволяет достичь этой цели, причем не только для радиаторов.
«Мы видим большой потенциал для других применений теплопередачи», — говорит г-н Россин. «Маслоохладители, сердечники нагревателей, охладители наддувочного воздуха, конденсаторы и другие устройства — все это возможности для Cu proBraze».
Во всем мире в настоящее время реализуется более 80 независимых проектов с использованием технологии CuproBraze. Продукция изначально предлагается (и в настоящее время доступна) на вторичном рынке радиаторов, где медь/латунь сохраняет сильные позиции. Кроме того, Cu Охладители наддувочного воздуха proBraze были допущены к производству одним крупным производителем дизельных двигателей. Тестирование производителями автомобилей продолжается, и вскоре медно-латунные радиаторы снова можно будет найти в автомобилях оригинальной комплектации.
Для получения дополнительной информации обращайтесь в International Copper Association, Ltd. по адресу Энтони Ли.
Также в этом выпуске:
- Honda Insight полагается на медь
- Медно-латунные радиаторы CuproBraze® в производстве
- Все, что блестит, в основном медь — Часть 2
- Все, что блестит, в основном медь — Часть 1
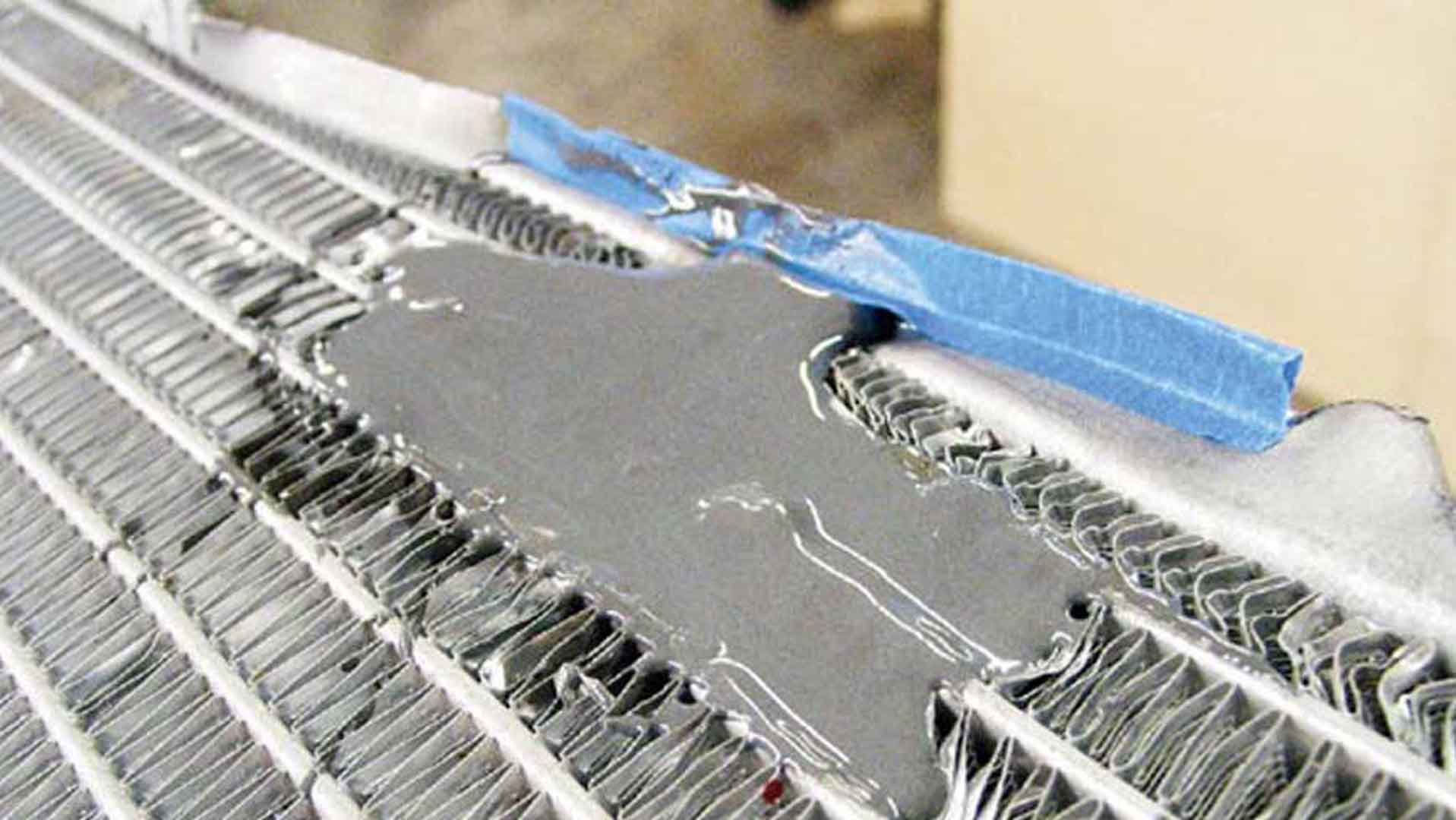
Паяные алюминиевые радиаторы радиаторов — алюминиевые радиаторы DeWitts™ Direct Fit®
Любой может изготовить алюминиевые радиаторы. Все, что вам нужно, это ножницы, чтобы разрезать материал, тормоз, чтобы согнуть материал в коробку, и сварочный аппарат, чтобы прикрепить резервуары коробки к сердечнику. Благодаря популярности алюминиевых радиаторов и минимальным вложениям в оборудование, показанное ниже, десятки людей начали производить радиаторы и продавать их через Интернет.
У большинства этих парней действительно впечатляющие веб-сайты или аукционные магазины, и трудно отличить реальный бизнес от человека, работающего в своем гараже. Некоторые дилеры могут вообще не производить радиаторы, а вместо этого покупать их за границей, что обычно означает в Китае. Многие китайские компании производят полностью алюминиевые радиаторы, но они также продают сердцевины радиаторов.
Термин «сердечник» обычно неправильно используется в отношении рядов труб, используемых в сердечнике. На самом деле не существует такого понятия, как 4 ядра, это просто то, что передавалось из поколения в поколение и всегда будет использоваться неправильно.
«Ядро» на самом деле представляет собой сумму группы частей. Это включает в себя коллекторы, которые представляют собой пластину с несколькими прорезями, в которую припаяны все концы труб. Набор трубок, ребер и боковых каналов составляет оставшуюся часть сердечника. Сердцевина и только сердцевина определяет эффективность излучателя, в котором она используется.
Алюминиевые сердцевины радиаторов спаиваются в печи для соединения труб, ребер и коллекторов. Этот процесс пайки обычно называют CAB (пайка в контролируемой атмосфере) или Nocolok® по названию флюса, используемого в процессе.
Типичная печь CAB состоит из нескольких секций, соединенных болтами в большую единую систему. Эта сборка может иметь длину 75-150 футов и стоить до одного миллиона долларов.
Перед пайкой сердечников их необходимо очистить и офлюсовать. Самый распространенный способ нанесения флюса — смешать флюс с водой и распылить его на сердечник. Флюсовая машина обычно имеет несколько зон, включая зону нанесения распылением, зону нагнетания воздуха и секцию сушки. Флюсовая машина должна быть изготовлена из нержавеющей стали, чтобы предотвратить ржавчину. Механизм конвейерной ленты используется для перемещения детали через три зоны в печь для обезвоживания. Отдельный резервуар с двигателем перемешивания используется для перемешивания суспензии воды и флюса. Для перекачки смеси используются специальные мембранные насосы.
В одних областях ядра требуется больше флюса, чем в других, но большинство компаний просто применяют одинаковое количество везде, потому что это проще. Мы выбираем трудный путь, потому что конечный результат явно лучше. На фотографии (справа) показано, как смесь 15% флюса и воды распыляется на активную зону, заливая трубу и секцию ребра. Это гарантирует, что 100% внутренних компонентов покрыты флюсом, но в меньшем процентном соотношении, чтобы свести к минимуму накопление избыточного флюса и засорение ребер.
После машинного флюсования сердцевины удаляются, а на область трубы и коллектора наносится второй слой флюса. Это наиболее критическая область активной зоны, и здесь используется более высокая (30%) концентрация флюса/спирта.
Пайка алюминия требует огромных инвестиций, а стоимость эксплуатации этого оборудования очень высока. Единственный способ для производителей радиаторов получить сердечники — это купить их у кого-то, у кого есть такая возможность. Реальность такова, что пайка CAB довольно редка и обычно предоставляется крупным поставщикам автомобилей. Есть дилеры, которые продают сердечники, но почти все эти блоки импортные и качество неизвестно. Нет контроля качества, спецификаций или стандартов, которым нужно соответствовать. В большинстве случаев утечка не обнаруживается до тех пор, пока радиатор не будет завершен, а испытание под давлением не выявит утечку в сердцевине, которую можно устранить только с помощью эпоксидной смолы.
Дефекты сердцевины можно практически устранить с помощью CAB, если соблюдаются все процессы и осуществляется контроль качества. Все алюминиевые детали должны быть очищены от всех штамповочных масел перед флюсованием и пайкой. Концентрация флюса должна быть правильной и регулярно регулироваться. Профиль пайки в печи (температурные настройки и скорость ленты) должен соответствовать заданной массе, а атмосфера не должна содержать кислорода. Если все эти пункты будут соблюдены в точности, процесс CAB позволит получить сердцевины без утечек и превосходное соединение ребер. И наоборот, если какой-либо из этих пунктов не будет выполнен правильно, возникнут дефекты. Эти дефекты могут быть чем-то очевидным, например, незакрепленное ребро или зазоры в соединениях трубы и коллектора. Темные пятна или обесцвеченные участки могут указывать на плохую промывку или наличие загрязнения и, следовательно, на слабую пайку.
К сожалению, визуальные осмотры являются лишь частью процесса оценки, и необходимо провести разрушающие испытания, чтобы определить процент соединения ребер по всей глубине сердечника. После создания профиля пайки и пайки множества сердечников сердечник разрезают, чтобы проверить соединение внутренних ребер. Вышеприведенная фотография является примером плохого нанесения флюса, и соединение ребер было установлено только на внешних краях сердцевины. В результате это ядро эффективно только на 50%, и это невозможно обнаружить при визуальном осмотре.
Ваш поставщик радиаторов может рекламировать себя как лучшего в своем деле по качеству сварных швов или превосходным технологиям изготовления, но сердцевина может быть низкого качества, и они даже не подозревают об этом. Радиатор с самыми красивыми сварными швами и полированными баками может выглядеть как произведение искусства, но может работать не так хорошо, как должен. Радиатор DeWitts является единственной компанией по производству радиаторов вторичного рынка, которая владеет и управляет печью CAB. Мы контролируем весь процесс в доме, гарантируя качество изготовленного ядра. Мы сами скручиваем плавник, штампуем коллекторы и собираем сердечники в современных стержнегенераторах.
Каждая часть ядра важна, но качество заголовков абсолютно необходимо. Прорези для трубок должны быть пробиты с максимальным зазором 0,002 дюйма для хорошей посадки трубки. В то время как другие используют материал с односторонней оболочкой, DeWitts использует двустороннюю оболочку для всех коллекторов. Это обеспечивает угловое соединение вокруг трубы с обеих сторон коллектора, удваивая прочность соединения.
Лучшее и сильное ядро просто невозможно построить. Использование материала с двойной оболочкой .080 и экструдированных боковых каналов обеспечивает сердечник, достаточно прочный, чтобы выдерживать более миллиона циклов давления без разрушения соединения трубы с коллектором.
Стандартные боковые каналы радиатора имеют U-образную форму. Эти каналы очень слабые и имеют тенденцию сгибать и ломать плавник с очень небольшим усилием. В сердцевинах радиаторов DeWitts используются экструдированные конструкционные трубки для всех боковых каналов. Процесс экструзии не только позволяет создавать несколько форм, но и создает сердцевину, которая в три раза прочнее, чем изготовленный лист.
Доступны открытые U-образные, прямоугольные и шляповидные каналы типа GM.
Профили пайки создаются для каждого сердечника на основе общей массы. Температура печи и скорость ленты регулируются на основе обратной связи с регистратором данных. Регистратор хранится в специальном «горячем ящике» из нержавеющей стали, а термопары прикреплены непосредственно к сердечнику, чтобы гарантировать, что материал достигает оптимальной температуры пайки для текучести оболочки. Затем результаты загружаются в компьютер для анализа и при необходимости вносятся коррективы.
Эти дополнительные этапы и мероприятия по контролю качества выполняются задолго до процесса создания радиатора. Мы начали изготавливать сердечники самостоятельно, потому что это был единственный способ убедиться, что все сделано правильно и дефекты устранены. Теперь, когда у нас есть качественная сердцевина, мы можем приступить к изготовлению радиатора.
Сердечники перемещаются в наш производственный отдел, где будут приварены концевые резервуары и установлены входные и выходные трубы.
Компания DeWitts вложила средства в специальные пресс-формы для производства баков со свободным концом. В отличие от стандартных резервуаров коробчатой формы, для которых требуется несколько угловых сварных швов и областей напряжения, наши резервуары представляют собой цельную деталь. Они часто имеют ребра для усиления бака и придания оригинального вида.
Термин «Direct Fit» для нас не просто прилагательное , это наша торговая марка. Каждый производимый нами радиатор подойдет для вашего классического автомобиля без каких-либо модификаций.