Пайка алюминия в домашних условиях паяльником, газовой горелкой
Пайка алюминия в домашних условиях можно считать сложным занятием. Но при правильном подходе и соблюдении соответствующей технологии, выполнить ее вполне реально даже неопытному мастеру.
Пайка алюминия в домашних условияхПроблемы часто возникают при использовании неподходящего флюса, например, для пайки стали или меди. Очень важно использовать специальный вещество для пайки алюминия, а также подходящий припой. В случае их применения, пайка алюминия не вызовет особых трудностей.
Особенности пайки алюминия
Пайка алюминия в домашних условиях может сопровождаться некоторыми трудностями, которые связаны с особыми характеристиками этого металла. В частности с тем, что поверхность алюминиевых деталей покрыта оксидной пленкой. Она препятствует процессу выполнению соединений из-за высокой температуры плавления, превышающей свойства чистого алюминия. Также оксидная пленка устойчива к воздействию агрессивной среды и активным химическим веществам. Из-за этого пленка препятствует соединению алюминиевых деталей и припоя.
Чтоб избежать подобных трудностей, стоит очищать поверхность изделий от пленки, что можно сделать с помощью абразивных материалов или применения флюса. Флюс состоит из сильнодействующих веществ, которые способны разрушить оксид.
Температура плавления алюминия, в отличие от оксида, намного ниже, примерно 660 градусов, что часто становится причиной осложнений. При перегреве алюминий может значительно потерять в прочности, деформироваться или полностью стать непригодным.
Температура плавления алюминия и его окисной пленки
Следует избегать использования припоев, которые имеют в составе такие компоненты. Они плохо соединяются с алюминием, что становиться причиной создания некачественного соединения.
Лучше всего с алюминием взаимодействует цинк, который обладает хорошим свойством растворимости.
Методы пайки в домашних условиях
Существует несколько способов пайки, наиболее популярными являются методы с использованием паяльника и пайка алюминия газовой горелкой. Можно выделить три способа пайки деталей:
- Пайка с канифолью применяется для соединения небольших алюминиевых деталей, проводов и кабелей. Для этого нужно зачистить рабочую область и покрыть канифолью. Затем прижать нагретым паяльником несколько раз. Для этих целей нужно использовать канифольный раствор в диэтиловом эфире.
Процесс пайки алюминия
Пайка выполняется без отрывания от рабочей области с последующим добавлением канифоли. Рекомендуется использовать паяльник с мощностью 50 Вт. Если толщина деталей и проволоки превышает 1 мм, следует увеличить мощность до 100 Вт, а более толстые предметы лучше заблаговременно прогревать.
Данный способ наиболее широко применяется в электротехнических работах и пайке автомобильных деталей. Перед выполнением работ детали нужно залужить. Это позволяет соединять детали с другими сплавами и металлами. В данном случае происходит пайка алюминия оловом или припоем с содержанием цинка и кадмия. Это позволяет выполнять соединения при температуре 400 градусов, что не влияет на физические свойства алюминия.
- Припой необходим при использовании практически всех методов пайки, будь то использование паяльника или горелки.
- Электрохимический метод предусматривает создание гальванического покрытия, которое выполняется с помощью специальной установки или ручным способом. Для этого нужно на зачищенную поверхность нанести раствор медного купороса. После этой процедуры на детали воздействуют отрицательным электрическим полюсом.
Материалы и инструменты
Для выполнения пайки алюминия следует иметь различные материалы и инструменты, к которым относят нагревательные инструменты, припои и флюсы.
Необходимые материалы и инструменты
Наиболее часто в качестве нагревательного инструмента используют электропаяльник. Его можно считать универсальным инструментом, который легко использовать в домашних условиях. Но с его помощью можно проводить ремонт предметов только небольших размеров, обычно трубок небольшого диаметра, проволоки и кабелей, а также небольших электроприборов. Его можно использовать в дома в проветриваемом помещении, так ка он не требует особых условий и много пространства.
Большие предметы следует паять с помощью газовой горелки, работающий на аргоне, пропане или бутане. В домашних условиях можно также использовать паяльную лампу.
При использовании горелок стоит строго контролировать подачу пламени, которое должно характеризоваться сохранением баланса газа и кислорода. При проведении работ, пламя должно быть ярко-синим. Любые изменения цвета могут свидетельствовать об излишнем количестве кислорода.
Припои для пайки алюминия
Пайка алюминия припоем очень сложное занятие. Поэтому выбор припоя важен для создания качественного шва и прочного соединения. При использовании обычного паяльника нужно подбирать припой из металла, имеющего низкую температуру плавления. Наиболее распространенные сплавы это:
- цинково-оловянный;
- висмутово-оловянный;
- медно-оловянный.
Эти виды очень часто называют радиолюбительскими. Они имеют низкую температуру плавления, что очень важно для сохранения алюминия в первоначальном состоянии без изменения структуры и физических свойств. Стоимость таких припоев низкая, поэтому их приобретение становиться доступным для домашних мастеров.
Припои для алюминия
Но их использование имеет ряд минусов и ограниченную сферу применения. Так, соединение предметов с помощью таких припоем не отличается высокой прочностью и надежностью. Поэтому они применяются практически исключительно при ремонте электрооборудования, в том числе соединения проводов и кабелей.
При ремонте крупногабаритным алюминиевых предметов с помощью таких припоев соединение быстро потеряет прочность и разрушиться. В таких случаях лучше использовать тугоплавкий припой, в состав которого входит цинк и олово.
Но для создания прочных соединений следует применять тугоплавкие припои, имеющие в составе алюминий, медь и кремний. Благодаря наличию алюминия в составе, припой хорошо растворяется в структуре ремонтированного предмета.
Использовать такого припоя при работе с паяльником невозможно, так как их температура плавления составляет порядка 600 градусов. Поэтому для работы с ними нужно иметь газовую горелку.
Следует отметить, что при пайке с помощью газовой горелки металл заготовки не расплавляется, произйдет плавление только припоя.
Флюсы для пайки алюминия
При пайке алюминия нужно использовать специальные флюсы, так как не каждый флюс активен по отношению к алюминию. Наиболее подходящими считаются вещества на основе фторборатора аммония и триэтаноламина. Большинство специальных флюсов помечены специальной маркировкой, которая указывает на возможность их применения при пайке алюминия.
Флюсы для пайки алюминия
В случае необходимости работы при высоких температурах следует обратить внимание на смеси, содержащие хлористый калий, который составляет половину; хлорида калия; фторита натрия и хлористого цинка. Подобный состав позволяет создать наиболее оптимальные условия при высокотемпературных работах.
Пошаговая инструкция
Технология пайки зависит от способа выполнения работ. Но подготовительный этап практически идентичен во всех случаях. Начинать работу следует со следующих операций:
- обезжиривание поверхности заготовки с помощью растворителя, например, бензина или ацетона;
- зачистка оксидной пленки, которую можно выполнить с помощью металлической щетки, наждачной бумаги или другого абразивного материала.
Затем следует подогреть место паяльных работ. В зависимости от размеров предмета можно сделать это с помощью паяльника или горелки. При этом следует соблюдать несколько рекомендаций:
- Не рекомендуется перегревать поверхность — это может привести к расплавлению алюминия.
Контроль нагрева можно проводить с помощью припоя, если он при касании к заготовке начинает плавиться, то это значит, что температура нагрева оптимальна и последующий нагрев стоит прекратить.
- Не нужно использовать дополнительное насыщение кислородом, что может привести к химической реакции с алюминием и созданию оксидной пленки.
Выполнение паяльных работ стоит проводить в зависимости от типа нагревательного предмета. При использовании газовой горелки нужно приложить припой с флюсом к рабочей поверхности с последующим его нагревом.
Очень важно полностью расплавить припой, но не перегреть заготовку. С паяльником сделать это проще, но выполнить большой объем работ в таком случае затруднительно.
Посредством контроля скорости движения припоя и температуры воздействия можно создавать шов, желаемый толщины и структуры. Для повышения качества работы рекомендуется предварительное лужение места обработки и обработка антикоррозийным средством.
Способы пайки алюминия своими руками (припои и флюсы)
Алюминий – довольно специфический материал, требующий специальных методов обработки. Если возникла необходимость соединить между собой детали из этого металла, использование технологий, хорошо зарекомендовавших себя при работе с медью или латунью неоправданно. И всё же, паять алюминий можно! Главное, правильно выбрать материалы и инструменты.
Содержание страницы
Точная информация
Сначала следует, если есть такая возможность, точно определиться, из какого сплава изготовлены соединяемые детали. Ведь в чистом виде алюминий используется в электронике и технике крайне редко. От того, с какими химическими элементами и в каком количестве он смешан, будет зависеть многое.
- Критическая температура плавления. Некоторые добавки существенно увеличивают этот предел, который для чистого металла составляет 658 – 660 градусов Цельсия.
- Механические свойства. В зависимости от своего состава, некоторые сплавы становятся более пластичными, иные демонстрируют возросшую прочность.
- Взаимодействие с другими химическими элементами.
Заранее зная, с каким материалом предстоит работать, мастер сильно упрощает свою задачу.
Зачем нужен флюс
Основным препятствием при пайке алюминия является его оксидная плёнка. Утверждение о том, что её можно удалить механическим путём, несостоятельно, поскольку новая плёнка появляется практически мгновенно. Именно поэтому выполнение работы без использования активных флюсов, за редким исключением, невозможно. Задача этих флюсов – разрушение барьера Al2O3, чтобы металл мог беспрепятственно соединиться с материалами, входящими в состав припоя.
При желании можно изготовить флюс для пайки алюминия своими руками. Но дело это – довольно сложное, а потому проще приобрести уже готовый состав. Тем более что промышленность выпускает их в достаточном количестве.
- Ф-64. Он способен разрушать прочную оксидную плёнку значительной толщины, а потому хорошо подходит для пайки даже деталей большой массы. При этом он подходит для работы не только с алюминием, но и с оцинкованным железом, медью, бериллиевой бронзой и т. п.
- Ф-34А. Такой состав успешно используется с тугоплавкими припоями, содержащими значительное количество химических добавок.
- Ф-61. Его можно рекомендовать для низкотемпературной пайки или лужения изделий из алюминиевых сплавов.
- Castolin Alutin 51 L.Этот состав лучше всего оправдывает себя при использовании припоев того же производителя.
Окончательный выбор марки флюса зависит от многих факторов. Прежде чем принимать решение о непригодности состава, стоит убедиться в том, что соблюдены все важные технологические требования.
Выбор припоя
После того как оксидная плёнка разрушена, вступает в дело припой. Как и в случае с флюсом, его составу следует уделить самое тщательное внимание. Работающие при разной температуре, эти материалы должны выполнять основную задачу – соединяться с обрабатываемыми металлами. Применение низкотемпературных составов себя не оправдывает, поскольку они могут разрушаться при нагреве в процессе эксплуатации. Наибольшее распространение получили смеси со средней и высокой температурой плавления. Но окончательный выбор будет зависеть от многих факторов.
Неплохо зарекомендовали отечественные припои ЦОП-40, содержащий олово и цинк в процентном соотношении 60 на 40, и 34А, применение которого оправданно при использовании газопламенного нагрева. Тем не менее, при определённых условиях, конкуренцию им вполне способны составить припои Германиевый-1 и Германиевый-2, В-62, П550А, П575А и другие. Многие из них изготавливаются в смеси с флюсами, что упрощает их использование.
Следует знать, что содержащие большое количество кремния составы после своего застывания существенно отличаются по цвету от самого алюминия. Там, где цветовое несовпадение недопустимо, их применение нежелательно.
Принято считать, что чем больше цинка входит в состав припоя, тем прочнее будет получившееся соединение.
Подготовка к работе
Прежде чем приступать к пайке, зону соединения придётся тщательно очистить, удалив с металла краску, если таковая имеется, и обычные загрязнения. Полностью избавиться от оксидной плёнки не удастся, но зато можно сделать её как можно тоньше, обработав детали металлической щёткой или специальной насадкой. В отдельных случаях можно использовать абразивные круги, наждачную бумагу или простой напильник. После этого обрабатываемую поверхность придётся хорошенько обезжирить. Лучше всего для этого подойдёт чистый спирт.
Если речь идёт о пайке алюминиевых проводов или деталей электросхем, достаточно будет вооружиться паяльником. Но с увеличением массы деталей этого будет уже недостаточно. Обладающий высокой теплопроводностью металл будет быстро остывать, не позволяя создать качественное соединение. Улучшить ситуацию позволит постоянный нагрев зоны, где производиться пайка. Для этого можно использовать газовую горелку или даже паяльную лампу. Тут важно соблюсти два важных условия.
- Пламя горелки и паяльной лампы должно быть тщательно отрегулировано. В противном случае образующиеся частицы копоти загрязнят металл и не позволять выполнить работу качественно.
- Коридор между критическим значением плавления алюминия и температурой плавления припоя узок. Тем не менее, его придётся выдерживать. Это умение приходит с опытом. До того как начинать работать с ответственными деталями, стоит потренироваться на чём-нибудь попроще.
Прежде, чем приступать к тренировкам, а тем более работе, рекомендуется посмотреть, как выполняется пайка алюминия на видео.
Пайка
Когда пламя горелки хорошо отрегулировано, а детали прогреты до оптимальной температуры, можно приступать к следующему этапу работ – собственно пайке.
- Прежде всего, следует нанести на поверхность деталей флюс. Проще всего это сделать кисточкой. Многие производители включают её в конструкцию флаконов с составом. Если нет, придётся приобрести её отдельно. Поскольку флюсы обладают высокой химической активностью, необходимо следить, чтобы они не попадали на посторонние предметы, а тем более на кожу, глаза или слизистую оболочку.
- Вооружившись паяльником, распределить по месту соединения припой. Хороший результат дают паяльники, жало которых имеет специальные зазубрины, разрушающие оксидную плёнку непосредственно в момент нанесения припоя. Однако использование подобного инструмента требует дополнительных навыков.
- Когда работа закончена и детали остыли, следует самым тщательным образом удалить остатки флюса. В противном случае они будут способствовать возникновению очага коррозии. Рекомендуется последовательная промывка изделия в воде различной температуры, затем – обработка слабым раствором каустической соды и снова промывка в воде.
Только когда все эти условия соблюдены, изделие готово к эксплуатации.
Подход к технологии выполнения работ может быть различен. Как правило, это связано с размерами соединяемых деталей. Если они относительно малы, то вполне может быть произведена пайка алюминия паяльником. Но когда размеры возрастают, более оправданной становится пайка алюминия газовой горелкой, разогревающей достаточное по размеру металлическое жало. Здесь уж, как говорится, дело техники.
Область применения
В различных источниках встречаются утверждения, что пайка алюминия получила широкое распространение в самых разных областях техники и производства. Особенно рекомендуют её при выполнении ремонта повреждённых автомобильных деталей, таких как лопнувшие блоки цилиндров и головки блоков, пробитые поддоны картеров или потёкшие радиаторы.
Предел прочности
Детали, подверженные высоким механическим или температурным нагрузкам, не прослужат долго, как бы хорошо они ни были они спаяны. Ведь прочностные характеристики припоев всё же ниже, чем у алюминия и его сплавов. Следует понимать, что качественное сварное соединение всё же предпочтительнее. Использовать технологию пайки имеет смысл в тех случаях, когда сварочное оборудование по каким-то причинам недоступно или хуже подходит для выполнения задачи. Как вариант – для пайки автомобильных радиаторов и алюминиевых трубок.
Нежелательный контакт
С большой осторожностью следует подходить к пайке или лужению ёмкостей, вступающих в контакт с пищевыми продуктами. Ведь в состав припоев и флюсов могут входить откровенно ядовитые химические добавки, избавиться от которых не помогут дополнительные промывки и обработка.
Подходящий выбор
По-настоящему высокую эффективность технология демонстрирует при изготовлении электрических и электронных приборов. Доля деталей из алюминия в их конструкции велика, а использование электросварки часто недопустимо. Ведь размер изделий бывает крайне мал, а скачки напряжения способны вывести из строя чувствительные электронные компоненты.
Одно из основных достоинств пайки алюминием – отсутствие в необходимости приобретения сложного и дорогостоящего оборудования. Благодаря этой особенности пайка алюминия в домашних условиях становится хорошей альтернативой технологически более сложным способам создания соединительных швов. Но окончательно определиться с выбором удастся, лишь чётко очертив круг задач и взвесив все за и против.
Простой способ пайки алюминия
Это невероятно простой способ пайки алюминия который только можно представить. С помощью него любой желающий, дома или в гараже сможет без проблем чинить и восстанавливать любые изделия из алюминия, без всякой аргоновой сварки.

Теперь, чтобы запаять радиатор или раму велосипеда из алюминия не обязательно ехать в мастерскую и отдавать огромные деньги, все можно спаять дома.
При грамотном подходе пайка получается не хуже сварного соединения, но уж точно надежней любой холодной сварки, которую обычно применяют как альтернативу.
Понадобится
Газовая горелка не обязательно должна быть профессиональная. Достаточно обычной насадки-горелки на газовый баллон, или подойдет любая другая.
Поподробней я расскажу о специализированном припое который нужно будет приобрести. Это трубчатый порошковый припой специально предназначенный для пайки алюминия (почему порошковый? – порошок внутри трубки). Он состоит из двух компонентов: оболочки и порошковой основы внутри. Не будем вдаваться в подробности о химическом составе, это ни к чему.
Его можно приобрести в специализированных магазинах, его используют в мастерских по ремонту автомобилей.
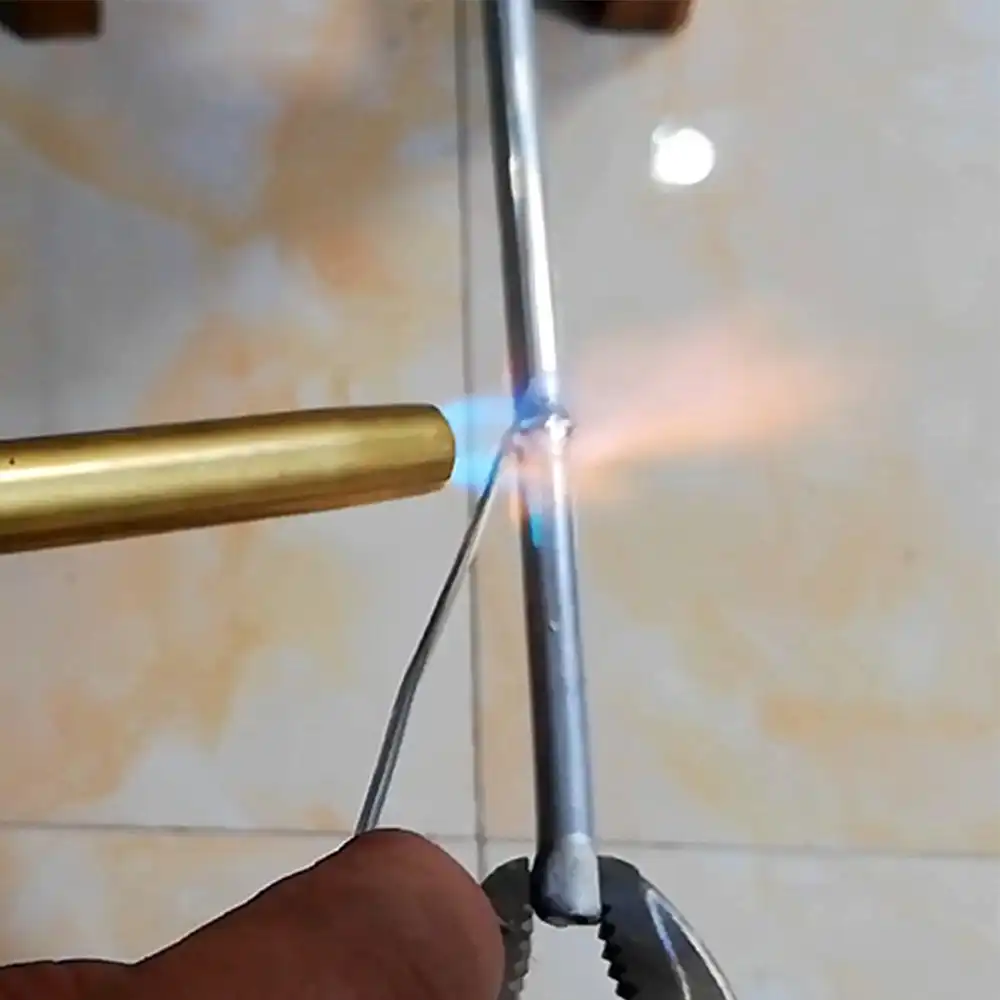
Стоит недорого, советую брать сразу упаковку – в жизни точно пригодится.
Пайка алюминия газовой горелкой
Берем профиль или детали которые нужно сварить.
Зачищаем поверхность щеткой по металлу. Как вариант можно взять наждачную бумагу с крупным зерном. Чем шероховатость поверхности для пайки будет больше, тем лучше будет связь с припоем.
Струбциной или другим приспособлением фиксируем соединение. Включаем газовую горелку и нагреваем стык.
Подносим трубчатый припой. Он расплавляется и растекается по шву.
Весь процесс происходит примерно при температуре 450 градусов Цельсия.
Припой имеет невероятную текучесть и сам затекает в любые, даже самые мелкие щели в металле.
После распределения припоя прогреваем соединение ещё чуть-чуть, чтобы он распределился и расплылся в стыках узла максимально.
Подведем итоги
Лично я, когда узнал о таком простом и доступном способе пайки был невероятно удивлен.
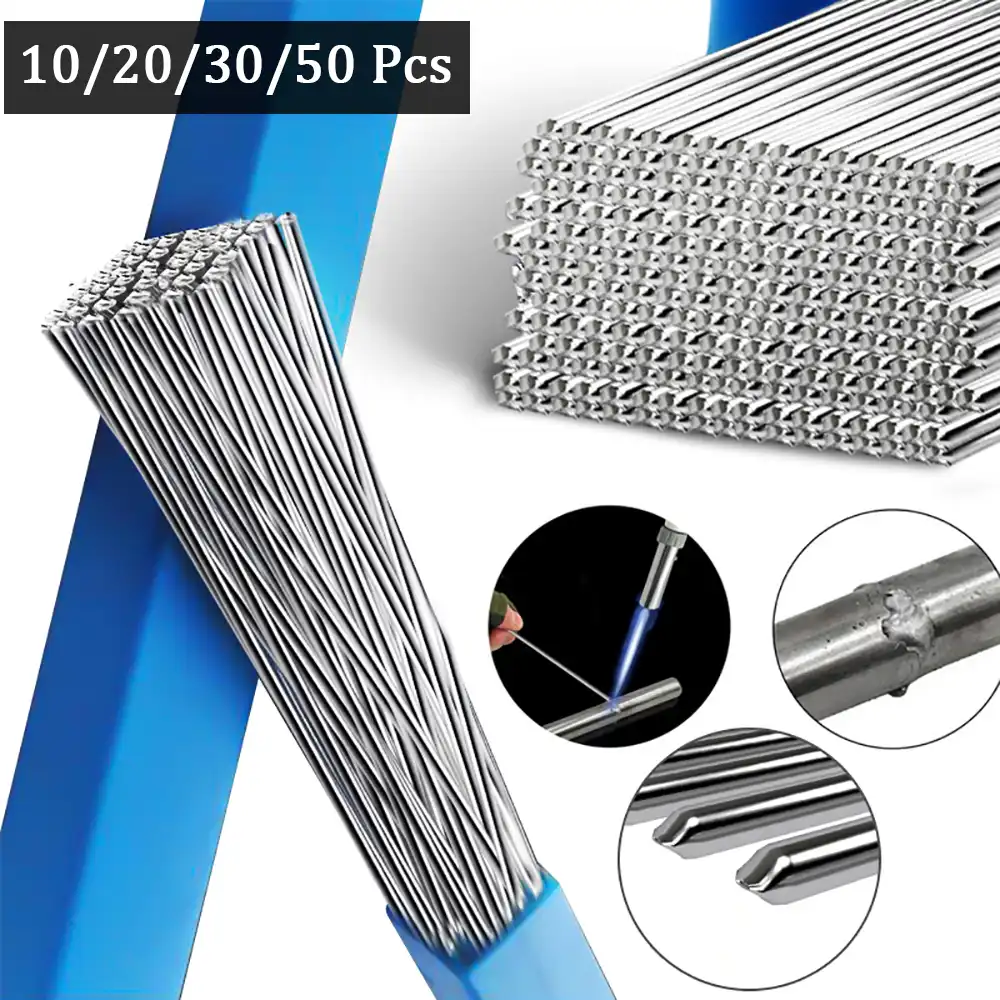
Пару слов о надежности. Конечно сварка выигрывает, так как идет объединение и перемешивание структур, но данный метод ненамного уступает. При условии изгиба соединения, гнется сама деталь. Соединение пайки крайне надежно и вполне способно выдержать почти любые нагрузки, как будто соединение литое.
Единственное, если получилась не совсем качественная пайка – это скорей всего не достаточный прогрев горелкой. В остальных случаях держится все намертво.
Теперь запаять дырку в алюминиевой кастрюле, сделать бачек из листового металла, сделать стеллаж из профиля для вас не составит труда.
Берите способ на вооружение и пользуйтесь друзья! До новых встреч!
Смотрите видео
Пайка алюминия: методы, особенности, рекомендации
Так же, как и остальные виды пайки, пайка алюминия, позволяет соединять компоненты, состоящие из паяемых сплавов и припоя.
При осуществлении пайки изделий из алюминия специалисты сталкиваются с рядом проблем, без решения которых очень трудно обеспечить желаемый результат. Рассмотрим факторы, мешающие обеспечить высокое качество пайки.
Алюминий является материалом с высокой способностью к окислению. На поверхности изделий образуется слой оксида алюминия (А120 ). Данное химическое соединение появляется за счет контакта материала детали, алюминия, с газовой смесью, содержащей кислород, например, с воздухом. Отличительная особенность оксида алюминия – высокая твердость. Расплавленный материал припоя, контактируя со слоем оксида, не вступает в контакт с материалом обрабатываемого изделия. Процесс пайки изделий происходит не в полной мере, что ведет к образованию брака. Поэтому очень важно устранить данный слой перед проведением пайки и предотвратить его формирование перед завершением плавки и повторным затвердением присадочного материала. Удаление слоя оксида производят, используя коррозийно-активный флюс, кислоту или магний. Подготовку поверхности можно провести и с помощью механического воздействия, например, методом пескоструйной очистки.
При производстве пайки изделий из алюминия необходимо очень точно регулировать и отслеживать температуру нагрева. Ведь интервал температур плавления основного и присадочного металла очень невелик. Специалисту необходимо точно подобрать температуру процесса и гарантировать равномерное распределение тепла по деталям садки.
Температура перехода алюминиевых сплавов из жидкого в твердое состояние определяет, могут ли они подвергаться пайке. Эта температура должна быть выше минимальной температуры пайки припоя.
Таким образом, температура солидуса материала обрабатываемого изделия должна быть выше 600°С. Поэтому многие сплавы алюминия с температурой солидуса около 570СС не могут подвергаться операции пайки. Также необходимо учитывать содержание магния в сплаве, подвергаемом пайке. Если содержание магния в сплаве более 2%, образующийся на поверхности детали оксид становится слишком твердым, и потому пайку данного изделия производить крайне не рекомендуется.
К материалам, которые рекомендуется обрабатывать, относят следующие сппавы алюминия:
•Алюминий технический с содержанием AI > 99% (марки типа АО, А5, А6, А8, А85, А995, А999 и им подобные). Механические свойства данных сплавов могут быть невозвратно ухудшены при осуществлении пайки
•Силумин, сплавы Al-Mn, Al-Mg, Al-Si-Mg (марки типа АЛ4, АЛ9, АК9, АК8М, АК12, АМ4,5, АМ5, АМгЮ и им подобные)
•Дюралюминий, сплавы Al-Cu, Al-Zn-Mg (марки типа АЛ11, АЛЗ, АЛ5, АЛ6, Д16, Д18, АДЗЗ, АД31Е, АД35 и им подобные)
При осуществлении пайки силумина или дюралюминия рекомендуется обеспечить высокую скорость охлаждения по завершении процесса с последующим натуральным или искусственным старением.
Высокое содержание магния в сппавах понижает температуру плавления, но уменьшает склонность сплава к пайке. Данные марки наиболее часто используются в вакуумной пайке без флюса.
На данный момент в промышленности используется около 4000 марок припоев. Их основными отличиями друг от друга являются температуры плавления и интервал температур ликвидус-солидус. При выборе припоя для пайки алюминия и его сплавов руководствуются близостью к эвтектике алюминий-кремний (табл. 1). Это позволяет понять точку плавления материала припоя.
Табл. 1. Соотношение влияния кремния в материале припоя на точку солидус-ликвидус
Содержание Si, % | Солидус-ликвидус, °С |
7,5 | 575 – 615°С |
10 | 575 – 590°С |
12 | 575 – 585°С |
Альтернативой данному методу пайки служит метод пайки изделий в среде защитного газа с использованием флюса, основным назначением которого является подготовка поверхностей обрабатываемых изделий.

Процесс пайки данным методом осуществятся по следующему принципу:
-На контактную поверхность изделия, которая будет паяться, наносят тонким слоем флюс – фторалюминат калия
-Между обработанными флюсом поверхностями помещают припой
-Изделия нагревают в среде защитного газа до температуры 565- 572°С, флюс расплавляется и вступает во взаимодействие с поверхностью обрабатываемой детали. По отношению к материалу припоя флюс абсолютно нейтрален. Происходит подготовка поверхности изделия с материалом припоя, и при достижении необходимой температуры происходит пайка изделий
Данный метод является более прогрессивным, чем описанный выше, но имеет ряд особенностей, без соблюдения которых невозможно обеспечить требуемое качество пайки:
•Обязательна тщательная подготовка поверхности обрабатываемых изделий. Необходимо удалить слой оксида алюминия. В противном случае, оксид вступит в реакцию с флюсом, что приведет, в конечном итоге, к получению низкого качества пайки
•В рабочем пространстве оборудования во время проведения пайки необходимо обеспечить полное отсутствие воздуха или соединений кислорода. Иначе,произойдет коррозия материала обрабатываемого изделия и самого припоя
•В качестве защитного газа необходимо использовать только азот. Газ должен быть сухим и иметь чистоту содержания основного элемента не менее 99,99% от объема
Следующим методом пайки явпяется пайка изделий в условиях вакуума. Например, с использованием вакуумной печи серии ВА производства французской фирмы Fours Industriels B.M.I, (рис. 1).
При осуществлении технологического процесса пайки на данном оборудовании также используется флюс.
Технология пайки состоит из четырех последовательных фаз:
I фаза: подготовка поверхности обрабатываемых изделий флюсом, размещение припоя и сборка изделия; достижение необходимого уровня вакуума и нагрев изделия до температуры 400°С. На данном этапе процесса необходимо обеспечить высокую степень точности и необходимую скорость нагрева. За счет этого происходит частичное разрушение слоя оксида алюминия. Это происходит потому, что оксид алюминия и сплав алюминия имеют несколько разную степень термического расширения
2 фаза: при достижении температуры 560°С материал изделия, припоя и флюса остаются в твердом состоянии
3 фаза: флюс, нагретый до температуры 565°С начинает плавиться и вступать во взаимодействие с материалом обрабатываемого изделия. -600°С расплавляется и вступает в реакцию с материалом обрабатываемых изделий. По завершению выдержки производится охлаждение обработанных деталей и их выгрузка
Представленное Вашему вниманию оборудование для обработки изделий в условиях вакуума отвечает самым высоким технологическим требованиям и позволяет вести четкий учет параметров процесса, точно регулировать температуру нагрева. Обработка в условиях вакуума обеспечивает чистоту обработанной поверхности обработанного изделия.
Мы рассмотрели три метода пайки изделий, изготовленных из алюминия. Суммируем недостатки и преимущества каждого из методов.
1. Метод пайки алюминия в условиях окислительной атмосферы: – необходимость проведения дополнительной подготовки поверхности обрабатываемых изделий; – присутствие в рабочем пространстве воздуха создает условия для восстановления слоя оксида за счет контакта газовой смеси с материалом обрабатываемого изделия. Из-за этого очень трудно обеспечить достойный уровень качества пайки; – негативным фактором является также процентное соотношение содержания кремния и магния как во флюсе, так и в припое – они вступают в реакцию и образуют соединения с кислородом. Отсутствие кремния повышает стойкость оксида алюминия и препятствует улучшению качества пайки. Магний предотвращает образование оксида алюминия. При его отсутствии ничего не мешает образованию слоя и его увеличению; – низкая степень повторяемости результатов пайки
2. Метод пайки алюминия в условиях защитной атмосферы: – по сравнению с методом пайки в среде окислительной атмосферы – сокращение степени воздействия кислорода на материал изделий, флюса и припоя; – не требуется подготовка поверхности обрабатываемых изделий; – необходима дополнительная термическая обработка; – необходимость и сложность обеспечения высокой скорости охлаждения обрабатываемых изделий; – средняя степень повторяемости результатов пайки; – невозможность использования конвективного нагрева за счет наличия в рабочем пространстве печи остаточного кислорода
3. Метод пайки алюминия в условиях вакуума: – полное отсутствие воздействия кислорода на материал изделия, флюса и припоя; – не требуется подготовка поверхности обрабатываемых изделий; – «использование метода конвективного нагрева; – высокая точность нагрева изделий; – сохранение и использование кремния и магния в полной мере; – высокая степень повторяемости результатов пайки; – полная готовность изделия. Таким образом, пайка в вакууме является самым передовым, обеспечивая высокое качество обрабатываемых изделий
Источник: “Индустрия” №3/2014
Как паять алюминий оловом своими руками
Чем паять алюминий в домашних условиях
Пайка соединений проводов с припоем считается самым надежным методом соединения проводов и жил кабелей. Хорошо, если нужно паять только медные провода, которые легко облуживаются припоем. Не зря в электронике все вывода элементов медные, луженые.
Пайка алюминия в домашних условиях
После того как цельные провода и многожильные жилы кабелей облудят, их довольно легко соединять пайкой. А как паять алюминий оловом, если припой отторгается окисью алюминия. Как известно алюминий покрыт тонким слоем окиси, которая мгновенно образуется на алюминии при контакте с кислородом. Чтобы припой хорошо держался на алюминиевом проводе нужно снять окись алюминия, а затем лудить.
Для этой цели в качестве флюса существуют: паяльная кислота, специальные флюсы для алюминия, смесь канифоли с ацетоном. Все эти плюсы разрушают или затрудняют образование пленки окиси на алюминии. После применения данного типа флюса процесс лужение алюминия упрощается.
Необходимые инструменты для пайки алюминия оловом являются: электрический паяльник, острый нож, плоскогубцы для скрутки проводов, мелкий напильник для подготовки жала паяльника. Из материалов потребуется: припой ПОС 61 или ПОС 50, флюс для пайки алюминия Ф-64 или аналогичный, губка.
Пайка алюминия оловом и флюсом Ф 64
Флюс Ф 64 предназначен для пайки алюминия. Методика пайки не сложна. В первую очередь нужно снять изоляцию с проводов на 5 см. Изоляция снимается острым ножом под углом к проводу, чтобы не надрезать его. Надрезанный алюминий легко обламывается.
Инструменты и материалы для пайки алюминиевого провода
Далее нужно хорошо зачистить провод мелкой наждачной бумагой или острым ножом. Зачистив провод, его смачивают кисточкой с плюсом и острым ножом продолжают зачищать провод, но уже под флюсом. Таким образом снимают пленку окиси алюминиевого провода, не давая вновь окисляться на воздухе. Далее разогретым паяльником с припоем начинают лужение провода с его конца.
Если начать облуживать провод около изоляции, тогда можно ее подпалить. В этом случае потеряются изоляционные свойства провода. Провод облуживают паяльником, движениями вперед-назад, одновременно снимается окисная пленка с алюминия. Облудить провод ровно сразу не получится. Поэтому на не облуженные участки провода снова наносят флюс и горячим паяльником с припоем и движениями вперед-назад снимают участки оставшейся окисной пленки и обслуживают.
Таким образом покрывают припоем алюминиевый провод полностью. После лужения алюминиевый провод окунают в раствор соды (5 ст. л. на 200 гр. воды) и зубной щеткой смывают остатки флюса. В состав флюса входят активные кислоты, которые не только разъедают пленку, но и сам провод. Поэтому остатки флюса нужно смыть. Смыть его полностью не получится, так как он частично остаётся под припоем и въедается в провод.
Но хоть частично его нужно смывать. Медный провод не обслуживают флюсом Ф 64, лучше использовать раствор канифоли и спирта (50% на 50%). Кисточкой наносят жидкую канифоль на медный провод (предварительно зачистив его) и горячим паяльником обслуживают провод, начиная с конца. Жало паяльника должно быть ровным и чистым. Раковины на конце жала паяльника убирают мелким напильником.
А остатки сгоревшего припоя (шлака) вытирают губкой или тряпкой. Как только алюминиевый и медный провода облуженны, их скручивают пассатижами, кисточкой наносят жидкую канифоль и спаивают соединение, начиная также с конца. Если соединить алюминий без лужения припоем, то это соединение может нарушиться со временем. Соединение алюминия с медью представляет собой гальваническую пару, и при прохождении через него тока нагревает и разрушает соединение.
Таблица температурных режимов марок припояВ результате место скрутки сильно нагревается и обугливается, что повышает пожароопасность. Оловянный припой нейтрален к алюминию, поэтому алюминиевые провода перед соединением с медью нужно лудить. Для пайки алюминиевых проводов хорошо подходят припой ПОС 61 и ПОС 50 с низкой температурой плавления 190 – 210С.
Пайка алюминия с медью оловом и канифолью
Пайка электрических проводов с помощью паяльной кислоты запрещена в ПУЭ. Это связано с тем, что эта кислота полностью не сгорает при пайке. В результате место соединения проводов со временем разъедается кислотой, образуются окиси, которые нагреваются при прохождении тока и могут вызвать возгорание изоляции. К таким кислотно содержащим флюсам относятся специальные флюсы для пайки алюминия, в том числе и Ф 64.
Так как же паять алюминий с медью, чтобы соединение было качественным и долговечным. По сложности метод лужения алюминия оловом и канифолью даже легче, чем лужение алюминия флюсом Ф 64. Но качество и надежность при лужении в канифоли будет высоким. При лужении алюминия в канифоли нужно сделать или подобрать низкую ванночку для жидкой канифоли (канифоль 60% и спирт 40%).
Флюсы для пайки алюминияЗаполняют ванночку жидкой канифолью так, чтобы провод утопал в ней с изоляцией на 5-10 мм. Очищенный от изоляции провод кладут в канифоль и острым ножом (удобно скальпелем) снимают плёнку окиси с алюминиевого провода, не вынимая его из ванночки. То есть под канифолью защищают провод по всей его длине со всех сторон. Под канифолью пленка на очищенных местах алюминиевого провода не образуется, так как нет соприкосновении с кислородом.
Теперь берут разогретой паяльник с припоем мощностью не менее 60 Вт и опустив его на оголенный и очищенный от окиси провод, у самой поверхности канифоли, понемногу прокручивают и вытаскивают уже облуженные участки провода. Суть метода заключается в том, чтобы провод облуживался у самой поверхности жидкой канифоли. Чтобы зачищенные участки провода от окиси не могли соприкасаться с воздухом.
Паяльник может быть временами погружен на 2-3 мм в канифоль. Немного облудив провод поднимите паяльник, чтобы он вновь нагрелся. Да в начале, будет много дыма, поэтому лучше учиться паять на улице или в помещении с хорошей вентиляцией. После нескольких попыток у вас выработается своя техника лужения и появится небольшой опыт.
Вы определитесь с положением паяльника, скорость лужения провода увеличится, то есть появится навык, и уменьшится количество дыма. Зато провод будет облужен идеально. Далее, как обычно, скручивают провода и так же паяют их небольшим количеством припоя.
Остатки канифоли на пропаянной скрутке проводов смывают кисточкой со спиртом. Недостаток такого метода – это невозможность пайки в труднодоступных местах. Для таких случаев, лучше использовать другие методы безопасных соединений алюминия с медью.
Пайка алюминия.
ПАЙКА АЛЮМИНИЯ
г. Рига, Ю. БИТЕ
Для пайки алюминия обычными оловянно-свинцовыми припоями ПОС может быть рекомендован метод, предложенный зарубежными радиолюбителями и проверенный автором этой заметки, заключающийся в следующем.
На
алюминий в мосте пайки наносится жидкое минеральное масло и поверхность
алюминия под слоем масла зачищается скребком или лезвием ножа для
удаления имеющейся пленки окиси. Припой наносится хорошо нагретым
паяльником. Для пайки тонкого алюминия достаточна мощность паяльника 50
вт, для алюминия толщиной 1 мм и более желательно применение паяльника
мощностью 90 вт. Если припой не пристал к металлу, процесс облуживания
необходимо повторить.
Лучшие результаты получаются в случае применения щелочного масла для чистки оружия после стрельбы, хорошее и удовлетворительное качество пайки обеспечивают минеральное масло для швейных машин и точных механизмов, вазелиновое масло и масло “Универсал”.
Припой должен содержать не менее 50% олова, наиболее удобным для работы является легкоплавкий припой ПОС-61. Припой ПОС-30 не обеспечивает хорошего качества пайки.
При пайке алюминия толщиной 2 мм место пайки перед нанесением масла желательно предварительно прогреть паяльником.
Данный
метод можно применять для припаивания монтажных проводов к корпусам
электролитических конденсаторов, не нарушая их работоспособности.
Радио N 8 1966 г.с.35
Пайка алюминия припоями ПОС.
Пайка оловянно-свинцовыми припоями алюминиевых изделий затруднительна, но все же возможна, если оловянно-свинцовый припой содержит не менее 50% олова (ПОС50, ПОС61, ПОС90).
В качестве флюса применяют минеральное
масло. Лучшие результаты получаются при использовании щелочного масла
(для чистки оружия после стрельбы). Удовлетворительное качество пайки
обеспечивет минеральное масло для швейных машин и точных механизмов.
На место пайки наносят флюс и
поверхность алюминия под слоем масла зачищают скребком или лезвием
ножа, чтобы удавить имеющуюся всегда на поверхности алюминия оксидную
пленку. Паяют хорошо нагретым паяльником. Для пайки тонкого алюминия
достаточна мощность паяльника 50 Вт, для алюминия толщиной 1мм и более
желательна мощность 90 Вт. При пайке алюминия толщиной более 2 мм место
пайки нужно предварительно прогреть паяльником и только после этого
наносить флюс
ПАЙКА АЛЮМИНИЯ
Те, кому приходилось хотя бы раз иметь дело
с алюминием, знает, насколько трудно он поддается лужению и пайке.
В обычных условиях поверхность алюминиевых деталей покрыта тонкой и
прочной оксидной пленкой. Разрушенная пленка сразу же восстанавливается
благодаря кислороду воздуха.
И все соединять алюминиевые детали можно. И не только с медными и
железными, но и с алюминиевыми же. Делается это так. Место стыка хорошо
прогреваем и покрываем слоем канифоли. Затем набираем на жало паяльника
немного оловянно-свинцового припоя, смешанного с железными опилками, и
круговыми движениями жала залуживаем разогретое место. Опилки разрушают
окисную пленку, и алюминий, защищенный канифолью и потому не успевающий
снова окислиться, прочно связывается с припоем. Необходимо только
следить за тем, чтобы паяльник не перегревался и не сжигал канифоль.
Пайка алюминия припоем П250А.
Припой содержит 80% олова и 20% цинка.
Коррозионная стойкость паяных швов, выполненных припоем П250А,
несколько ниже, чем выполненных оловынно-свинцовыми припоями.
Флюс представляет собой смесь олеиновой
кислоты и йодида лития. Йодид лития (2-3гр) помещают в пробирку или
колбу и добавляют 20 мл (около 20гр) олеиновой кислоты (в состав флюса
может входит от 5 до 17% йодида лития). Смесь слегка подогревают до
полного растворения соли. Готовый флюс сливают в чистую стеклянную
посуду и охлаждают. Если используется водная соль лития, то при ее
растворении на дно пробирки опускается слой водной смеси, а флюс
всплывает, и его осторожно сливают.
Перед
пайкой жало хорошо прогретого паяльника (температура жала должна быть
около 350 °С) зачищают и лудят припоем П250А, пользуясь чистой
канифолью. Соединяемые поверхности деталей смачивают флюсом, лудят и
паяют. После охлаждения остатки флюса удаляют тампоном из ткани,
смоченным в спирте, и покрывают шов защитным лаком.
Флюс в процессе пайки не выделяет
токсичных или обладающих резким запахом веществ. С ткани и кожи рук он
легко смывается водой с мылом.
ПАЙКА АЛЮМИНИЯ И ЕГО СПЛАВОВ
К известным методам пайки алюминий я предлагаю добавить еще
один, очень простой. Зачищенное и обезжиренное место пайки покрывают с
помощью паяльника тонким слоем канифоли, а затем сразу же натирают
таблеткой анальгина (бенальгина). После этого облуживают поверхность
припоем ПОС-50 (или близким к нему), прижимая к ней с небольшим усилием
жало слегка перегретого паяльника. С облуженного места ацетоном смывают
остатки флюса, еще раз осторожно прогревают и снова смывают флюс.
Спаивание деталей производят обычным образом.
А. ГЛОТОВ с. Галиевка Воронежской обл
На главную страницу.
Пруток для пайки алюминия в домашних условиях / Инструменты / iXBT Live
Всем привет! Многие знают, что алюминий паяют в основном в аргоновой среде специальным сварочным аппаратом, но есть еще вариант для работы с газовой горелкой, да даже турбозажигалкой в небольших масштабах можно пользоваться.
Вообще это не первое мое знакомство с данной проволокой, но опыт покупок не очень хороший, так что поделюсь не только результатом тестирования, но и проверенными местами для покупки, чтобы не получить образец №2, но начнем по порядку.
Характеристики
Диаметр: 2,0 мм
Длина: 500 мм
Мягкий припой ISO 3677: ~B-Zn98Al 381-400
Примерный состав (вес %): 2,4 Al – остальное Zn
Температура плавления ºС: 360
Прочность на разрыв (МПа): До 100 (Al)
Плотность (г/cм3): 7,0
Распаковка и внешний вид
Последним и самым выгодным приобретением был образец №3 из banggood.
Пришел в небольшом сером пакете
Пруток дополнительно упакован в прозрачный зип-пакет.
5 метров обошлись мне в $8 с поинтами, то есть $1.6 за метр — перейти в магазин
В центре виден белый порошковый флюс, пруток в меру жесткий, выглядит как алюминий без окисления
Сравнение
Первым был куплен крайний левый образец №1 в али. Он абсолютно идентичен по свойствам с образцом №3, но 3 метра обошлись мне в $12, то есть $4 за метр, что почти втрое дороже. проверить текущую цену
В центре образец №2. Он стоит $5 за 3 метра или $1.7 за метр, как и образец №3
Но как только берешь пакет в руку, понимаешь, что это ПОС с не очень густым флюсом внутри.
не покупать тут
Еще два образца по $8 за 3 метра так и не были доставлены, вероятно их даже не отправили.
Тестирование
Алюминий со временем покрывается оксидной пленкой, из-за которой поверхность становится матовой, так вот, перед спаиванием поверхности обязательно нужно зачищать до блеска, иначе припой просто будет шариками скатываться по поверхности независимо от степени ее нагрева. Образец №1
Вообще правильно нагреть деталь до температуры около 400 градусов, а затем просто водить прутком, который будет плавиться и заполнять собой щели, но у меня мало опыта, поэтому чтобы не перегреть поверхность, я периодически вношу пруток в пламя горелки. Если температура низкая, припой скатится по поверхности шариком, если достаточная — залудит ее.
Проверка на излом показывает хороший результат — разрыв происходит не по шву
Образец №2. Плавится очень хорошо, выделяет много дыма, воняет горелым «аспирином». К алюминию липнет, но если перегреть, довольно быстро выгорает.
Работать неудобно из-за вони и необходимости контролировать температуру.
Образец №3. Решил спаять трубки внешними стенками
Пробуем разорвать шов. После того как трубка выскочила из тисков, я зажал ее выше, выведя из фокуса и заметил это только на стадии создания гифок
Но есть фото результата на котором видно, что шов не пострадал.
Ну и напоследок срастим алюминиевую трубку с куском «дюральки»
Тест на разрыв так же прошел успешно
Итоги
Занятная проволока — алюминий паяет отлично, заполняя собой даже мелкие щели, главное чтобы стыки не были загрязнены. К меди тоже липнет хорошо, но опытные люди говорят, что для работы с ней лучше использовать другие сплавы, хотя для экстренного полевого ремонта вполне сгодится и этот пруток.
Температура плавления алюминия около 660ºС, казалось бы, можно использовать прутки и на 450-500 градусов, но можно столкнуться с двумя проблемами:
1. Массивную деталь до 500 градусов нужно еще чем-то прогреть
2. Можно перегреть место пайки и испортить деталь
Самым оптимальным мне показался образец №3. Соответствует заявленным характеристикам и стоит дешевле остальных минимум вдвое. Так же на выбор есть лоты разной длины:
1 метр — $2.89
2 метра — $4.39
3 метра — $6.39
5 метров — $9.89
перейти в магазин
Вопрос по пайке алюминия – Металлообработка, пайка и металлическая арматура
Есть несколько идей, которые вы можете адаптировать к технологии сварки полноразмерных труб:
1. Сварка с муфтой. В этом методе труба меньшего диаметра вставляется в фитинг большего диаметра, при этом соединение фиксируется угловым сварным швом между трубой и фитингом.
2. Опорное кольцо – при выполнении стыкового соединения между двумя трубами одинакового диаметра меньшее кольцо с наружным диаметром перекрывает зазор между двумя трубами и действует как перемычка для поддержки жидкого сварочного металла, скрепляющего два конца трубы вместе.
3. Предварительно наплавленный металл сварного шва. Здесь между двумя соединяемыми концами трубы помещается кольцо из металла шва. Затем кольцо плавится, и поверх него можно наплавить металл, чтобы завершить соединение.
Алюминий при нагревании легко образует оксидную пленку, которая предотвращает прилипание наплавленного металла шва. По этой причине его обычно сваривают горелкой, защищенной инертным газом. Поэтому попробовать спаять его обычной пропановой или бутановой горелкой не получится.Он также должен быть чистым. Есть старая история о сварке первых алюминиевых лодок. Когда сварные швы продолжали разрушаться, два куска очищенной пластины устанавливали в чистой комнате, и за сварщиком наблюдали через окно. Он взял сварочную горелку, откинул капюшон и по давней привычке провел рукой в перчатке по канавке для подготовки к сварке, чтобы удалить посторонний материал, тем самым загрязнив стык!
Алюминий плавится при температуре около 1200 ° F, поэтому любой припой должен плавиться при температуре ниже этой.
Я бы механически очистил соединение, чтобы удалить анодированную и оксидную пленку, обезжирить ацетоном и, предполагая, что правильный алюминиевый паяльный материал припаял с помощью электрического утюга. Также казалось бы важным как-то предотвратить окисление материала после чистки и перед пайкой.
Более многообещающим методом может быть использование описанной выше техники сварки опорного кольца / раструба и эпоксидной смолы, поскольку алюминиевые трубки небольшого диаметра доступны в телескопических размерах.Отрежьте короткий кусок меньшей мелодии, вставьте ее в большую, чтобы она выступала на короткое расстояние, закрепите каплей эпоксидной смолы и наденьте конец другой части, которую нужно соединить, на выступ, закрепив эпоксидной смолой. Для «сварного шва» просверлите отверстие, равное диаметру меньшей трубки на стороне участка, вставьте выступающий конец меньшей трубки на конце ответвления и закрепите эпоксидной смолой. Я считаю, что вы сможете легко найти эпоксидную смолу с алюминиевым наполнителем. На ум приходит бренд JB weld.
Роджер
Как паять алюминиевый лист
Научиться паять алюминиевый металлический лист – отличный навык, который можно добавить в свой набор инструментов для рукоделия. Пайка – это процесс, при котором два или более металлических предмета соединяются вместе путем плавления присадочного металла в стыке. Хотя пайка, как правило, проста, при работе с определенными материалами становится все труднее.Одним из наиболее сложных для пайки материалов является алюминиевый лист, потому что пленка оксида алюминия на алюминиевом листе настолько устойчива, что ее очень трудно удалить, даже используя тепло от паяльника. Следовательно, очень сложно паять и создавать прочные соединения двух алюминиевых листов.
Это причина, по которой многие энтузиасты DIY избегают работы с алюминиевым листом. Однако вот несколько хитростей, как правильно припаять алюминиевый металлический лист.
Шаг 1. Очистите алюминиевый металлический лист
Используйте чистую тряпку, чтобы протереть алюминиевый лист от любой грязи, и нанесите растворитель или средство для удаления жира, чтобы удалить масло или жир. Этот шаг необходим, потому что, когда вы работаете с алюминием, очень сложно его правильно припаять, поэтому вам нужно удалить все препятствия с металлического листа, чтобы облегчить процесс пайки.
Шаг 2 – Установите алюминиевый лист вместе
Установите алюминиевый лист вместе и попросите друга крепко удерживать оба листа на месте, или вы можете использовать зажимы, чтобы скрепить алюминиевые листы вместе.Прежде чем переходить к следующему шагу, убедитесь, что вы носите необходимое снаряжение, например рабочие перчатки, защитные очки и рабочую рубашку с длинными рукавами, чтобы защитить себя от искр.
Шаг 3 – Нанесите флюс на область, подлежащую пайке
Подобрать дешевый флюс на Amazon
Следующим шагом является нанесение флюса на области, где вам нужно припаять. Флюс – это химическое чистящее средство, которое облегчает процесс пайки за счет удаления окисления с материала, с которым вы работаете.Флюс чрезвычайно важен при сплавлении сложного алюминиевого листового металла с другим материалом.
Шаг 4 – Нагрейте флюс и металл с помощью горелки
Нагрейте область, где вам нужно паять, с помощью горелки. Убедитесь, что металлический припой или наполнитель плавятся мгновенно. Не прикладывайте тепло непосредственно к наполнителю припоя, чтобы предотвратить выгорание металла припоя. Вы узнаете, что алюминиевый лист был правильно припаян с использованием флюса и припоя, если расплавленный наполнитель течет по алюминию и просачивается внутрь соединения, но если он просто скатывается, вам нужно попробовать другой флюс и припой металла и повторить продолжайте до тех пор, пока не увидите просачивание металла в алюминиевый стык.
Когда вы совершаете покупки по ссылкам на нашем сайте, мы можем получать комиссионные бесплатно для вас.
Как паять алюминий – Обсуждение ювелирных изделий
Как поступает алюминий в продаже? Работает нормально? Уилл Сильвер Припой работать?
Лаура,
Алюминий – это металл, сильно отличающийся от серебра. Одно из ключевых отличий
заключается в том, что он имеет чрезвычайное сродство к кислороду. Любая открытая поверхность алюминия
мгновенно образует непроницаемый оксидный слой, который затем предотвращает попадание кислорода
на поверхность, и поэтому металл
сохраняет свою металлическую природу.Но этот оксидный слой препятствует нормальной пайке
. Серебряные или золотые припои вообще не подойдут. Фактически,
многие из них плавятся при более высокой температуре, чем сам алюминий, что не принесет вам особой пользы от
.
, однако, есть припои, предназначенные для алюминия. Обычно это
комбинация довольно твердого припоя и специально разработанного флюса
. При использовании вы «протираете» припой на стыке
, который механически помогает флюсу вытеснить этот очень прочный оксидный слой
, достаточный для прилипания припоя.Припои гораздо больше похожи на припои на основе олова
, которые ювелиры называют «мягкими» или «свинцовыми» припоями. Но они
работают. Тем не менее, эти вещи обычно предназначены для ремонта перил крыльца
, а не для изготовления ювелирных изделий. Если вы думаете, что
аккуратно поместите маленькие пайетки из алюминиевого припоя вокруг алюминиевой рамки
, пока вы припаиваете ее к алюминиевому кольцу, то
вам не повезло. Вы, вероятно, не добьетесь того, чтобы это работало … Обратите внимание, что
, как правило, эти припои предназначены для соединения алюминия с алюминием.
Не алюминий по отношению к другим металлам.
Алюминий обычно крепится с использованием так называемого «холодного склеивания»
, такого как ривиты, винты, механически сформированные соединения и т. п. Одним из методов плавления металлов является сварка плавлением
, для которой требуется специальный аппарат. Обычно это используется для
вещей, таких как серьги или аналогичные детали, прикрепляемые к алюминию
. Они сделаны специально для этого использования, с крошечным «наконечником» из металла
, выступающим вниз из области, предназначенной для приклеивания к алюминию
.Машина помещает электрический заряд между находкой
и деталью, к которой нужно прикрепить, и хлопает их вместе. Когда это маленькое перо
касается другого куска металла, оно вызывает искру.
Искра обращается с этим маленьким наконечником, как с предохранителем, перегорая его. По сути,
делает то же самое, что и отвертка, которой вы случайно однажды коснулись
провода под напряжением. Воспоминание? испарил половину наконечника отвертки
, когда он образовал дугу? Будет, это контролируется, но
маленьких «перьев» металла испаряются так же, как
сближаются две большие поверхности.Это создает очень горячую плазму на мгновение
между металлами, которая не только вытесняет весь атмосферный газ,
включая кислород, но также расплавляет поверхности достаточно, чтобы они могли смешиваться
и связываться при контакте друг с другом.
Сварка плавлением, как я уже отмечал, обычно используется для установки штифтов сережек и
других деталей. но его можно использовать как более универсальную технику склеивания
, если учесть, что хорошо приклеенный штырь серьги
также можно рассматривать как заклепку, готовую к вставке через отверстие в другом куске металла
и зачищенной поверх … идеи?
Машины, начиная с маленьких «игристых» сварочных аппаратов, проданных за
около 400 баксов…
И если у вас есть доступ к обычному оборудованию для электродуговой сварки,
также предлагает методы сварки, предназначенные для алюминия.Обычно они
требуют какой-то газовой защиты зоны сварки, например, при сварке TIG
или MIG. Опять же, это обычно не ювелирная шкала, но кто знает
…
Надеюсь, это поможет.
Питер Роу
Использование алюминиевой пайки для ремонта двигателей – Журнал «Газовый двигатель»
Персоналом
1/9
Фото 1. Возьмите шило и проткните дно банки.
2/9
Фото 4 – Сторона картера газового двигателя, через которую был пробит шатун.
3/9
Фото 2. «Лужа» тонким слоем поперек дыры.
4/9
Фото 3. Возьмите две алюминиевые банки и спаяйте их вместе.
5/9
Фото 5 – Чтобы отремонтировать бобышку, которая вырвалась из крышки клапана Honda, основную металлическую трещину следует «выпилить» шлифованием. Затем основной металл нагревается, и припой плавится в V-образной канавке до тех пор, пока он не заполняет канавку.Опять же, отшлифуйте стык заподлицо, и никто не узнает.
6/9
Фото 7. На новой металлической накладке нет пористости, поэтому винт теперь можно балансировать и красить.
7/9
Фото 6 – Обратите внимание, что часть коллектора также была припаяна к коллектору.
8/9
Дисплей ремонта алюминия.
9/9
Облицовка фары от антикварного авто, отремонтированная алюминиевым припоем.
❮ ❯На нескольких выставках старинных тракторов и двигателей в этом районе есть мужчина в небольшом трейлере, который демонстрирует использование алюминиевого паяльного стержня, который он продает.По рекомендации других моделистов и реставраторов двигателей, которые использовали продукт, я наблюдал и слушал его демонстрацию. Затем он позволил мне припаять немного алюминия прямо на его дисплее. Затем я купил некоторые из алюминиевых паяльных стержней, которые он продает, и взял их домой, чтобы поэкспериментировать. Из всего этого я узнал, что алюминиевый припой ДЕЙСТВИТЕЛЬНО РАБОТАЕТ и может быть очень ценным в нашем хобби.
Давайте начнем с описания некоторых вещей, которые можно сделать с помощью алюминиевого припоя, а затем обсудим методы.Картер картера небольшого бензинового двигателя, у которого была выломана сторона из-за того, что сломанный шатун прошел через картер, был залатан алюминиевым припоем. Крышка клапана мотоцикла, у которой была сломана резьбовая втулка, была припаяна на место. Крышка коробки передач, через которую протерлась незакрепленная цепь, была отремонтирована алюминиевым припоем. Резьба крепления карбюратора на впускном коллекторе двигателя была снята. Для вставки места не было, но деталь спасла алюминиевый припой.С помощью изделия отремонтированы двигатели авиамоделей. Детали отделки антикварных автомобилей, изготовленные из литого под давлением «горшечного металла», были отремонтированы и заделаны припоем. Алюминиевый гребной винт лодки (настоящий гребной винт, а не модель), у которого был сломан кусок, был отремонтирован этим алюминиевым припоем.
Это улучшенная версия алюминиевого припоя. Более ранний припой работал так же хорошо, но требовал большей подготовки поверхности, а именно, зачистки стыка щеткой из нержавеющей стали (никогда не используйте стальную щетку) в горячем состоянии.Новый припой не требует этой подготовки, хотя старая литература все еще отправляется вместе с новым припоем.
Процесс довольно простой. Сначала очистите поверхность паяемого металла. Припой не прилипает к грязному или окисленному алюминию. Запомните этот факт, потому что он нам пригодится позже. Металл можно очистить наждачной бумагой, наждачным кругом, фрезой в инструменте Dremel и т. Д. Никогда не используйте наждачную бумагу, потому что некоторые наждачные полотна содержат масло, которое может загрязнить поверхность.Вам нужно будет заделать некоторые трещины, чтобы освободить место для припоя. Опыт приведет вас сюда. Во-вторых, нагрейте основной металл пропановой горелкой до температуры выше 732 градусов плавления припоя. Основной металл должен быть горячим, потому что тепло открывает поры металла. Расплавленный припой заполняет эти поры, заставляя его прилипать к основному металлу. Основной металл должен быть достаточно горячим, чтобы расплавить стержень. Расплавьте припой, царапая его по поверхности основного металла, в то время как горелка направлена на точку соприкосновения стержня припоя с основным металлом.Припой будет «растекаться» и течь туда, куда вы хотите. Дайте металлу остыть и отшлифуйте стык или залатайте, если хотите. Вот и все.
Единственный способ научиться пользоваться алюминиевым припоем – это попробовать и попрактиковаться. Хорошее место для начала – алюминиевая банка из-под газировки. Это также покажет прочность припоя. Возьмите шило и проткните дно банки. (ФОТО 1) Слегка отшлифуйте поверхность и заполните отверстие припоем. Припой имеет тенденцию покрывать корку и заполнять отверстия, поэтому все, что вам нужно сделать, – это нанести тонкий слой на отверстие.(ФОТО 2) После того, как банка остынет, попробуйте проткнуть шилом отверстие в припое. Вы не сможете. Припой намного прочнее и тверже основного металла. Это метод заполнения небольших отверстий. Теперь возьмите две алюминиевые банки и спаяйте их вместе. (ФОТО 3)
Для более крупных отверстий, таких как сторона картера газового двигателя, через которую был пробит шатун, существует другой метод. (ФОТО 4) Помните, что припой не прилипает к окисленному алюминию.Сначала зачистите область вокруг разрыва наждачной бумагой. Возьмите кусок алюминия, который подходит к отверстию за отверстием, и установите его на место. Не чистите этот кусок. Теперь нагрейте основной металл и начните плавить алюминий с одной стороны, работая расплавленным металлом через отверстие. Подложка предотвращает вытекание расплавленного металла. Необязательно, чтобы он идеально подходил, потому что металл быстро затвердевает, создавая основу для большего количества расплавленного металла. Когда закончите, дайте ему остыть и снимите подложку.Подложка может быть плоской или круглой, например трубкой, в зависимости от того, что будет соответствовать внутреннему контуру. Если хотите, отшлифуйте заплатку заподлицо, и никто никогда не узнает, что картер был залатан.
Чтобы отремонтировать бобышку, которая вырвалась из крышки клапана Honda, основную металлическую трещину следует «выпилить» шлифованием. Затем основной металл нагревается, и припой плавится в V-образной канавке до тех пор, пока он не заполняет канавку. Опять же, отшлифуйте стык заподлицо, и никто не узнает. (ФОТО 5)
Для ремонта резьбы, которая была снята с коллектора, на котором установлен карбюратор, был использован действительно новый метод.Сначала просверлите отверстие большего диаметра, чем диаметр резьбы. Вставьте болт в отверстие и как-нибудь удерживайте его на месте. Теперь нагрейте основной металл и расплавьте припой в отверстие вокруг болта. Припой будет прилипать к открытым порам алюминия, но не прилипнет к неочищенному стальному болту. Когда остынет, открутите болт и у вас будет новая резьба. Если это звучит слишком хорошо, чтобы быть правдой, я видел, как это было сделано! (ФОТО 6) Обратите внимание на фото, что часть коллектора также была припаяна к коллектору.
Ремонт деталей, отлитых под давлением, может производиться таким же образом, так как припой прилипает к отливкам под давлением, а также к «металлическому корпусу». Был произведен ремонт игрушечного колеса со спицами «металлический горшок», у которого отсутствовала спица, путем изготовления новой спицы из расплавленного алюминия. Спица была «отлита» на месте и доведена до окончательной формы. Таким образом была восстановлена старинная игрушка. Металл также можно расплавить и отлить в форму.
В алюминиевом гребном винте лодки был выломан кусок. Сломанный край обработали щеткой из нержавеющей стали для удаления краски и оксидов.К плоскому краю гребного винта приставили кусок окисленной меди. Алюминиевый припой использовался для формирования нового участка от скошенной кромки гребного винта. Сделайте ремонт немного больше оригинального металла. После остывания винт стачивался до исходного контура. Новый металлический патч не имеет пористости, поэтому винт теперь можно балансировать и красить. (ФОТО 7)
А как это соотносится с нашим хобби? Алюминиевые детали, которые пришлось бы выбросить, можно сэкономить, если нет замены.Изношенные поверхности можно наращивать и повторно обрабатывать. Отливки с дефектами можно отремонтировать. Вы можете изготовить практически любую форму, спаяв секции вместе. Используйте свое воображение, и вы сможете найти еще больше применений для этого продукта. Когда паяльный стержень становится слишком коротким, не выбрасывайте его, а приварите к новому стержню.
СТАТЬИ ПО ТЕМЕ
Узнайте о высоковольтной системе зажигания и о том, почему существует конденсатор, чтобы вернуть искру в двигатель Клинтона 1952 года.
Следуйте за Рональдом Макклелланом через создание карбюратора и замену воздухозаборника для восстановления его газового двигателя Франклина.
Повторная сборка начинается со сложной фазы восстановления и заканчивается магнето, топливной системой и стартером, часть 3 из 3.
Произошла ошибка при настройке пользовательского файла cookie
Этот сайт использует файлы cookie для повышения производительности. Если ваш браузер не принимает файлы cookie, вы не можете просматривать этот сайт.
Настройка вашего браузера для приема файлов cookie
Существует множество причин, по которым cookie не может быть установлен правильно.Ниже приведены наиболее частые причины:
- В вашем браузере отключены файлы cookie. Вам необходимо сбросить настройки своего браузера, чтобы он принимал файлы cookie, или чтобы спросить вас, хотите ли вы принимать файлы cookie.
- Ваш браузер спрашивает вас, хотите ли вы принимать файлы cookie, и вы отказались. Чтобы принять файлы cookie с этого сайта, нажмите кнопку «Назад» и примите файлы cookie.
- Ваш браузер не поддерживает файлы cookie. Если вы подозреваете это, попробуйте другой браузер.
- Дата на вашем компьютере в прошлом.Если часы вашего компьютера показывают дату до 1 января 1970 г., браузер автоматически забудет файл cookie. Чтобы исправить это, установите правильное время и дату на своем компьютере.
- Вы установили приложение, которое отслеживает или блокирует установку файлов cookie. Вы должны отключить приложение при входе в систему или проконсультироваться с системным администратором.
Почему этому сайту требуются файлы cookie?
Этот сайт использует файлы cookie для повышения производительности, запоминая, что вы вошли в систему, когда переходите со страницы на страницу.Чтобы предоставить доступ без файлов cookie потребует, чтобы сайт создавал новый сеанс для каждой посещаемой страницы, что замедляет работу системы до неприемлемого уровня.
Что сохраняется в файле cookie?
Этот сайт не хранит ничего, кроме автоматически сгенерированного идентификатора сеанса в cookie; никакая другая информация не фиксируется.
Как правило, в файлах cookie может храниться только информация, которую вы предоставляете, или выбор, который вы делаете при посещении веб-сайта.Например, сайт не может определить ваше имя электронной почты, пока вы не введете его. Разрешение веб-сайту создавать файлы cookie не дает этому или любому другому сайту доступа к остальной части вашего компьютера, и только сайт, который создал файл cookie, может его прочитать.
Пайка алюминиевого сплава 7075 с использованием электроосажденных прослоек Ni-P и Cu-Cr
Реферат
Прямая пайка алюминиевого сплава 7075 очень трудна или даже невозможна. Для этого были разработаны гальванические покрытия и методики их нанесения на поверхности сплавов.В статье представлены структура и механические свойства паяных соединений из сплава 7075, выполненных косвенным способом с использованием покрытий Ni-P и Cu-Cr, нанесенных электролитически. Описано нанесение недавно разработанных покрытий Ni-P и Cu-Cr на основные поверхности из сплава 7075. Представлены результаты исследования смачиваемости припоя S-Sn97Cu3 в капельном тесте и при нанесении на покрытия, нанесенные на подложки 7075. Угол смачивания обоих покрытий был менее 30 °.Приведены результаты металлографических исследований с использованием световой и электронной микроскопии. Было показано, что адгезия металлических покрытий к алюминиевому сплаву хорошая, превышающая прочность на сдвиг припоя S-Sn97Cu3. Прочность паяного соединения на сдвиг составляла 35 ± 3 МПа. Измеренная твердость прослойки Ni-P достигла высокого значения 471 HV 0,025.
Ключевые слова: алюминиевый сплав 7075, пайка, электроосаждение, прослойка: Ni-P, Cu-Cr
1. Введение
Алюминиевые сплавы серии 7xxx относятся к группе материалов с ограниченной связывающей способностью, особенно при использовании традиционные методы пайки / пайки и дуговая сварка [1,2,3].Благодаря своим очень хорошим механическим свойствам, высокой прочности на разрыв (более 500 МПа) и твердости (более 150 HV) [4,5,6] при низком удельном весе они все чаще используются в качестве строительных материалов во многих отраслях промышленности. Этому также способствует широкий спектр термических процедур и быстрое естественное старение [7,8]. Наибольшие области применения этих сплавов – авиастроение и автомобилестроение [9,10], а также космическая, военная и машиностроительная промышленность [5].
Большинство сплавов серии 7ххх имеют самую высокую прочность среди всех коммерческих алюминиевых сплавов [3].Растворимость цинка и магния в алюминии в твердом состоянии непостоянна, а их добавки делают сплавы склонными к дисперсионному твердению [3,11]. Кроме того, добавка от 1 до 2 мас.% Меди улучшает механические свойства сплавов [3]. Их можно подвергать термообработке рекристаллизационным отжигом при 390–430 ° C или дисперсионным упрочнением, состоящим из пересыщения при 465–480 ° C с последующим искусственным старением при 120–150 ° C [11]. Неблагоприятной особенностью этих сплавов является их относительно низкая стойкость к коррозии (особенно коррозии под напряжением) и к повышенным температурам, что изменяет их структуру и отрицательно сказывается на их механических свойствах [11].
При склеивании сплавов серии 7ххх возникают значительные металлургические трудности [12]. В частности, ограничены традиционные методы сварки (сварка плавлением), когда соединение получается в результате плавления и смешивания легирующих компонентов основных материалов и присадочного металла [13,14]. Смешивание легирующих элементов часто инициирует образование твердых и хрупких интерметаллических фаз, которые отрицательно сказываются на механических свойствах соединений и, в случае ограниченной взаимной растворимости легирующих элементов, также может приводить к горячим трещинам в соединениях и / или тепловым трещинам. зона поражения (ЗТВ) [13].По этой причине традиционные методы сварки заменяются методами сварки трением с перемешиванием (FSW), дуговой сваркой пайкой, чаще всего сваркой в среде инертного газа (MIG, TIG) плавящимися электродами и лазерной сваркой пайкой, чаще всего многолучевой (трифокальной). лазерная сварка [13,14]. Кроме того, все более популярными становятся низкоэнергетические методы сварки и пайки, например, сварка с переносом металла (CMT) [15,16].
Широкий диапазон температур ликвидуса – солидуса от 477 до 635 ° C для сплава 7075 [5] исключает его пайку с использованием традиционных припоев на основе Al-Si.При использовании силуминовых припоев процесс пайки должен выполняться при температуре ок. 600 ° С [17,18]. Также невозможно соединить сплавы серии 7ххх непосредственной пайкой из-за нехватки присадочных металлов и, в первую очередь, флюсов, обеспечивающих хорошую смачиваемость () и, как следствие, создание качественных паяных соединений.
Отсутствие смачиваемости присадочного металла S-Sn97Cu3 на подложке из алюминиевого сплава 7075: общий вид ( a ) и сечение ( b ).
На практике пайка несмачиваемых припоями тугоплавких сплавов часто осуществляется косвенным путем.Он заключается в создании промежуточных слоев (покрытий), в основном металлических и хорошо смачиваемых припоями, на поверхностях соединяемых материалов. Таким способом, например, припаиваются алюминий с медью [19], графит с медью [20] или алюминием [21] и керамика с металлами [22]. Покрытия могут наноситься на поверхности основных материалов различными способами, начиная от гальванических методов, с помощью методов химического (CVD) и физического осаждения из паровой фазы (PVD), до методов термического плазменного напыления или холодного газа низкого и высокого давления. опрыскивание.
В рамках исследования были проведены испытания по пайке алюминиевого сплава 7075 с использованием недавно разработанных авторами покрытий Ni-P и Cu-Cr с электролитическим осаждением [23,24]. Что касается широкого диапазона ликвидуса – солидуса сплава 7075, то для пайки использовался припой на основе олова. Это ограничивает потенциальную область применения соединениями, не несущими высоких эксплуатационных нагрузок, но сохраняющими металлическую целостность и обеспечивающими хорошую электрическую или теплопроводность.
2.Материалы и методика
В рамках исследования образцы сплава 7075-Т6 были соединены непрямым способом с использованием слоев Ni-P и Cu-Cr. Алюминиевый сплав 7075 отличается высокой механической прочностью (предел прочности при растяжении 480–540 МПа), но при этом имеет относительно низкую стойкость к коррозии, особенно к коррозии под напряжением. Из-за высокой чувствительности к высоким температурам, при низких температурах предпочтительнее склеивать, используя технологию пайки. По этой причине были применены технологии печной и газовой пайки.В качестве припоя использовался сплав S-Sn97Cu3 с температурой плавления от 232 до 290 ° C [25]. Также использовался флюс на основе хлорида цинка и хлорида аммония, рекомендованный для пайки меди, медных сплавов и никеля с использованием припоев на основе олова. Флюс остается активным до 316 ° C [25]. Химический состав основного металла и присадочного металла согласно [26,27], а также результаты проведенного спектрального анализа приведены в.
Таблица 1
Химический состав основного металла и присадочного металла.
Химический состав, мас.% | ||||||||||||||||||||||||||||||||||||||||||||||||||||||||||||||||||||||||||||||
---|---|---|---|---|---|---|---|---|---|---|---|---|---|---|---|---|---|---|---|---|---|---|---|---|---|---|---|---|---|---|---|---|---|---|---|---|---|---|---|---|---|---|---|---|---|---|---|---|---|---|---|---|---|---|---|---|---|---|---|---|---|---|---|---|---|---|---|---|---|---|---|---|---|---|---|---|---|---|
Элемент | Si | Fe | Cu | Mn | Mg | Cr | Zn | Ti Al 7075 сплав | Макс. 0,40 | Макс. 0,50 | 1,20–2,00 | Макс. 0,30 | 2,10–2,90 | 0,18–0,28 | 5,10–6,10 | Макс. 0.20 | Рем. | Анализ SP * | 0,12 | 0,07 | 1,80 | 0,09 | 2,88 | 0,19 | 6,04 | 0,06 | Ост. | Элемент | Cu | Fe | In | Bi | Pb | Ag | Ni | Прочие | Sn | Sn322 | S-323 Max. 0,02 | Макс. 0,10 | Макс.0,07 | Макс. 0,10 | Макс. 0,10 | Макс. 0,01 | Макс. 0,186 | Рем. | Анализ SP * | 2,65 | 0,01 | 0,08 | 0,04 | 0,05 | 0,09 | 0,01 | 0,18 | Ост. | |
Для исследования смачиваемости припоя капельным методом и методом растекания использовались образцы из сплава 7075 толщиной 30 × 30 мм и 3 мм.Для паяных соединений внахлест использовались образцы толщиной 25 × 80 мм и 3 мм.
После механического шлифования и химической очистки на образцы были нанесены металлические покрытия электролитическим способом. Электролиз проводили в двух различных недавно разработанных гальванических ваннах с параметрами, выбранными для получения покрытий Ni-P и Cu-Cr толщиной около 12 мм. Такая толщина покрытий должна предотвращать их хрупкость, но обеспечивать их герметичность и долговечность при пайке. Толщину и химический состав нанесенных покрытий измеряли с помощью рентгенофлуоресцентного анализатора FischerScope XRAY XDL-B type X-ray от FISCHER GmbH (Ахерн, Бадения-Виртембергия, Германия).
После нанесения покрытий их смачиваемость оценивалась путем измерения свободной поверхностной энергии (SFE), ее полярных и дисперсионных компонентов с использованием анализатора Krüss DSA HT 1200 (Krüss GmbH, Гамбург, Германия), интегрированного с компьютерной программой DSA3. . В качестве эталонных жидкостей использовались дистиллированная вода, дииодметан и этиленгликоль с известной поверхностной энергией и известными полярными и дисперсными компонентами, см. [28]. Отдельные капельки каждой жидкости помещали на должным образом подготовленные поверхности исследуемых образцов, и угол смачивания θ считывался из программы с точностью до 0.1 °. Все значения θ были определены методом Оуэнса – Вендта – Рабеля – Кельбла (OWRK) [29]. В этом методе смачиваемость и адгезия зависят от влияния дисперсного и полярного взаимодействий измерительной жидкости. Используя метод OWRK, можно определить и оптимизировать влияние различных методов обработки (например, плазменной обработки или нанесения покрытия) на величину адгезионных взаимодействий в таких процессах, как склеивание, покраска, гидрофобные покрытия и т. Д., Используя эффект изменение поляризации при контакте поверхностей разной полярности [28,29].
Таблица 2
Свойства выбранных измерительных жидкостей.
Жидкость | Поверхностная свободная энергия (SFE), γ w [мДж / м 2 ] | Дисперсная составляющая, γ wD [мДж / м8 2 2 2 2 2 [мДж / м 2 ] | Полярный компонент, γ wP [мДж / м 2 ] | |||||||||||||||||||||||||||||||||||||||||||||||||||||||||||||||||||||||||||||||||||||||||||||||||||||||||||||||||||||||||||||||||||||||||||||
---|---|---|---|---|---|---|---|---|---|---|---|---|---|---|---|---|---|---|---|---|---|---|---|---|---|---|---|---|---|---|---|---|---|---|---|---|---|---|---|---|---|---|---|---|---|---|---|---|---|---|---|---|---|---|---|---|---|---|---|---|---|---|---|---|---|---|---|---|---|---|---|---|---|---|---|---|---|---|---|---|---|---|---|---|---|---|---|---|---|---|---|---|---|---|---|---|---|---|---|---|---|---|---|---|---|---|---|---|---|---|---|---|---|---|---|---|---|---|---|---|---|---|---|---|---|---|---|---|---|---|---|---|---|---|---|---|---|---|---|---|---|---|---|---|
Дистиллированная вода | 72,8 | 21.8 | 51,0 | |||||||||||||||||||||||||||||||||||||||||||||||||||||||||||||||||||||||||||||||||||||||||||||||||||||||||||||||||||||||||||||||||||||||||||||
Диодметан | 50,8 | 48,5 | 2,3 | |||||||||||||||||||||||||||||||||||||||||||||||||||||||||||||||||||||||||||||||||||||||||||||||||||||||||||||||||||||||||||||||||||||||||||||
Этиленгликоль | 48,0 | 29,0 | 19,0 | -выход путем нанесения припоя S-Sn97Cu3 на подложки 7075 с нанесенными покрытиями. На образцы наносили навески припоя по 0,1 г с вдвое меньшей массой флюса.Далее образцы (по 5 в каждой серии) помещали на керамическую подставку и вместе помещали в печь, нагретую до 300 ° C. Электропечь Czylok FCF 7SM 2,6 кВт (Czylok, Jastrzębie-Zdrój, ląsk, Польша) с рабочей температурой до 1100 ° C. Из-за относительно высокой тепловой инерции образцов флюс активировался, и припой начал плавиться через 120 с. С этого момента образцы выдерживались в печи еще 30 с. Вынутые из печи образцы были очищены от остатков шлака и подвергнуты дальнейшим исследованиям. Соединения для металлографических исследований и механических испытаний, т. Е. Для испытания на статический сдвиг при растяжении и измерения твердости по Виккерсу, были приготовлены методом газовой пайки. Из-за низкой температуры процесса использовалось нагревание пропановоздушным пламенем. Для получения повторяемых результатов использовались дистанционные элементы в виде стальной проволоки диаметром 0,2 мм, обеспечивающие постоянную ширину пайки. Ширина нахлеста составляла 10 мм. С момента плавления припоя швы нагревали еще 5 с, а затем охлаждали на воздухе.Соединения для металлографических исследований разрезали пополам, закрепляли в смоле, шлифовали и полировали для получения микроскопических образцов. Предел прочности при растяжении на сдвиг определяли на универсальной механической испытательной машине Zwick / Roell ZMARTPRO (Zwick-Roell GmbH, Бадения-Виртембергия, Ульм, Германия). Измерения твердости по Виккерсу проводились на поперечных сечениях паяных соединений с использованием низкой нагрузки на индентор 25 Г. Твердость измеряли с использованием испытательной машины Sinowon PMT3 (Sinowon, DongGuan, Guangdong, China). 3. Результаты и обсуждение3.1. Электроосаждение покрытий Ni-P и Cu-CrУсловия нанесения покрытия определяли с помощью диаграммы Пурбе [30]. Из диаграммы следует, что сплав 7075 показывает значительно ограниченную область коррозионной стойкости в диапазоне возможных гальванических ванн. Таким образом, даже если сплав 7075 можно было бы покрыть в сильно кислых ваннах, это практически невозможно из-за положения алюминия в гальванической серии.Поэтому покрытие сплава производилось с использованием промежуточных слоев, прочно сцепленных с подложкой. Для нанесения гальванических покрытий была построена лабораторная станция, состоящая из источника питания (Elektro-Tech типа ETZ 10/10, Elektrotech, Kryniczno, Dolny ląsk, Польша) с плавно регулируемой силой тока от 0 до 10 А и напряжением. от 0 до 10 В, магнитная мешалка (IKA тип ETS 06, IKA Sp. z oo, Варшава, Мазовецкое воеводство, Польша) с плавно регулируемой скоростью вращения и системой нагрева с контролем температуры.На мешалку помещали стакан объемом 1 дм 3 , содержащий электролитическую ванну и анод размером 50 × 120 × 5 мм. Анод, используемый для нанесения покрытия Cu-Cr, был изготовлен из титана с родиевым покрытием, а для нанесения покрытия Ni-P – из катодного никеля. Процессу наплавки предшествовала надлежащая подготовка поверхности подложки. На первом этапе образцы шлифовали абразивными бумагами № 150 и 280, а затем промывали в 5% растворе SurTec 131 (Surtec Poland Sp.z o.o., Яниково, Великопольское воеводство, Польша) при 40 ° C в течение 5 мин. Затем образцы промывали под водопроводной водой и удаляли колпачки в 5% растворе SurTec 495L (Surtec Poland Sp. Z o.o., Яниково, Великопольское воеводство, Польша) при 30 ° C в течение 3 минут. Перед нанесением необходимых покрытий наносились промежуточные слои. Этому процессу предшествовала обработка низкотемпературной аргоновой плазмой в течение 30 с для увеличения сцепления покрытий с алюминиевой подложкой. Благоприятное влияние низкотемпературной плазменной обработки на адгезию медного покрытия к подложке из графитового композита указано в [31].Предварительные исследования также показали, что обработка низкотемпературной плазмой привела к увеличению силы, необходимой для царапания Cu-Cr-покрытия, нанесенного на алюминиевую подложку, более чем на 40%. Сначала образцы были подвергнуты химическому цинкованию в ванне SurTec 652Q Surtec Poland Sp. z o.o., Яниково, Великая Польша, Польша при температуре от 15 до 40 ° C в течение 1 мин. Далее предварительное электролитическое меднение в ванне SurTec 864 Surtec Poland Sp. z o.o., Яниково, Великая Польша, Польша, с pH 9,5, проводили при 55 ° C в течение 2 мин.Плотность катодного тока составляла 0,5 А / дм 2 , а анод был изготовлен из бескислородной меди (OFHC). На подготовленные таким образом подложки наносились покрытия, предназначенные для пайки. С этой целью были разработаны две ванны:
Сплав Cu-Cr может использоваться в качестве покрытия с повышенной стойкостью к истиранию. В соответствующих ссылках не упоминаются гальванические ванны для нанесения покрытий из сплава Cu-Cr, но можно найти информацию о получении этих покрытий в металлургических процессах, в основном применяемых в энергетике. Состав ванны и параметры процесса нанесения покрытия Cu-Cr следующие:
Сплав Ni-P применяется, в частности, при производстве присадочных металлов, используемых для безфлюсовой пайки. Может использоваться в гальванике в качестве декоративного никелевого покрытия с повышенной коррозионной стойкостью (альтернатива хромированию). Покрытия Ni-P, наносимые химическим путем, используются в качестве технических покрытий с высокой коррозионной стойкостью, зависящей от концентрации фосфора. Химическое покрытие никелем также применяется в пластмассовой промышленности. В литературе можно найти публикации, касающиеся разработанных ванн для электрохимического осаждения покрытия Ni-P. Ванны для нанесения такого покрытия, содержащего 18 мас.% P, как альтернативу хромовому покрытию, разработаны немецкими и итальянскими компаниями [32].В этих ваннах ионы фосфора доставляются с помощью натриевой соли фосфорной кислоты III, добавленной в количестве 5–7 мас.%. Покрытия применяются в качестве декоративных покрытий при производстве арматуры, деталей бытовой техники и в автомобильной промышленности. Состав ванны и технологические параметры нанесения разработанного покрытия Ni-P следующие:
3.2. Оценка нанесенных покрытийЭлектролитически нанесенные покрытия были подвергнуты предварительному анализу. Их толщина и химический состав измеряли с помощью рентгенофлуоресцентного анализатора FISCHERSCOPE X-RAY XDL-B производства Fischer GmbH (Ахерн, Бадения-Виртембергия, Германия).Концентрация Cr (мас.%) Была измерена для покрытия Cu-Cr, концентрация P (мас.%) Была измерена для покрытия Ni-P, и остатки были соответственно содержаниями Cu и Ni. Приложения для измерения покрытия Ni-P являются коммерческими продуктами, но приложение для измерения покрытия Cu-Cr было разработано компанией Helmut Fischer GmbH Achern, Бадения-Виртембергия, Германия для нужд этого исследования. Измерения толщины и химический состав покрытий, нанесенных на подложки 7075, показаны на. Таблица 3Толщина и состав нанесенных покрытий.
Проверка адгезии покрытий проводилась в соответствии с EN ISO 2819: 2018 [33]. Предварительные измерения были выполнены методом «теплового удара», и после положительного результата адгезия была определена методом царапания с использованием Micro-Combi-Tester производства CSM Instruments (Needham Heights, MA, США). Тестер определяет профиль поверхности как основы, так и покрытия. Во время процесса отслаивания регистрируется сила и акустический сигнал.Кроме того, регистрируется профилограмма поверхности, а также глубина проникновения в покрытие и в основу. После электролиза все образцы хранили в электрической печи при 200 ° C в течение ок. 30 мин, а затем уронили в емкость с водой комнатной температуры. Через 1 мин отслаивание покрытия оценивали визуально. Все образцы положительно прошли испытание на тепловой удар без видимого отслаивания. Тестирование адгезии с помощью Micro-Combi-Tester было начато с измерения силы царапания непокрытой основы, а затем было измерено усилие, необходимое для отслаивания покрытия от покрытой основы.Испытание проводилось на расстоянии 5 мм при силе давления 29 Н. Покрытие отслаивалось одновременно в двух местах и приводилось среднее значение приложенных усилий. Испытание на адгезию проводили следующим образом. Головка для отслаивания, нагруженная вышеупомянутой силой, начала отслаивание покрытия, и компьютер записал все события, сопровождающие процесс (например, разрыв покрытия). После проникновения в материал подложки были сделаны микроскопические фотографии во всех точках, где непрерывность измерения была нарушена, и, наконец, была сфотографирована вся царапина.После испытания получают распечатку, содержащую профилограмму поверхности, величину усилия, необходимого для отслаивания покрытия, величины сил, возникающих в возмущениях, и полную фотодокументацию. Величины сил, необходимых для царапания подложки без покрытия и подложек с электролитическим нанесением покрытий, показаны на рис. Результаты представляют собой средние значения 10 измерений. Результаты скретч-теста. Смачиваемость подложки 7075 и нанесенных покрытий Cu-Cr и Ni-P была предварительно определена капельным тестом, как описано выше.Примерная смачиваемость поверхности 7075 и покрытий дистиллированной водой показана на рис. Видно, что смачиваемость покрытий значительно лучше, чем у основного металла. Смачиваемость основания и покрытий дистиллированной водой. Средние значения углов смачивания для различных эталонных жидкостей приведены в. Дополнительно представлены значения поверхностной свободной энергии, ее дисперсионной и полярной составляющих. Поверхностная энергия нанесенных покрытий выше, чем у подложки.Более высокая поверхностная энергия связана с более низким поверхностным натяжением и, следовательно, лучшей смачиваемостью (меньшие углы смачивания с отдельными контрольными жидкостями). Таблица 4Свободная энергия поверхности и смачиваемость электроосажденных покрытий и подложек из алюминиевого сплава 7075.
3,3. Испытание на смачиваемостьКак было упомянуто выше и показано в, подложка из сплава 7075 не смачивается мягкими припоями.В результате невозможно выполнить пайку напрямую. Пригодность нанесенных покрытий Cu-Cr и Ni-P для пайки определялась путем измерения смачиваемости их поверхностей припоем на основе олова. Образцы были изготовлены описанным выше способом. Согласно критериям смачиваемости, чем меньше угол смачивания и чем больше площадь поверхности растекающихся капель, тем лучше паяльные свойства подложки. Считается, что хорошая смачиваемость достигается, когда угол смачивания ниже 30 ° и стремится к 0 ° [34,35,36]. Средний размер плоских поверхностей на этой 0,1 г припоя составлял 74 мм 2 ( σ = 7,2 мм 2 ) для покрытия Cu-Cr и 59 мм 2 ( σ = 8,1 мм 2 ) для покрытия Ni-P. Примерные площади растекаемости припоев и поперечные сечения капель припоя на подложках, используемых для определения углов смачиваемости, показаны на рис. Средние значения угла смачивания составили 28 ° ( σ = 7,3 °) для покрытия Cu-Cr и 17 ° ( σ = 4.8 °) для покрытия Ni-P. Согласно критериям оценки [34,35,36], такие значения угла смачивания указывают на хорошую смачиваемость покрытий и должны обеспечивать хорошие условия для выполнения качественных паяных соединений. В случае покрытия Cu-Cr изменение цвета можно увидеть в зоне воздействия флюса (c), но сплошность покрытия не нарушилась. Растекаемость и смачиваемость припоя S-Sn97Cu3 на покрытиях Ni-P ( a , b ) и Cu-Cr ( c , d ). 3.4. Металлографическая оценка паяных соединенийКак упоминалось ранее, соединения внахлест с длиной нахлеста 10 мм и постоянной шириной пайки фиксируются с помощью дистанционных элементов диам. 0,2 мм были подготовлены к металлографическим исследованиям и механическим испытаниям. Стыки выполнялись пламенной пайкой с использованием пропановоздушной горелки. За исключением очень мелких газовых пор и остатков флюса, никаких других дефектов пайки обнаружено не было. После пайки покрытия все еще оставались сплошными и хорошо сцеплялись с подложкой из сплава 7075.Соединение, выполненное с промежуточным слоем Cu-Cr толщиной 12 мкм, показано на рис. а, б показаны разные участки паяных соединений. Обе микроструктуры очень похожи, но на b видны следы очень мелких газовых пор. На основании равновесной системы Cu-Sn [37] и анализа EDS (Energy Dispersive Spectroscopy) микроструктура слоя припоя состоит из эвтектической смеси Sn + Cu 6 Sn 5 с серыми первичными кристаллами твердого раствора. Cu 6 Sn 5 .Покрытие Cu-Cr хорошо сцепляется с алюминиевой подложкой 7075. Отсутствуют видимые несовместимости припоев, снижающие качество паяного соединения, за исключением очень маленьких газовых пор или остатков флюса. Микроструктура паяного соединения, выполненного через прослойку Cu-Cr, две разные части стыка ( a , b ): 1 – подложка (алюминий 7075), 2 – прослойка Cu-Cr, 3 – припой. Для анализируемой системы характерно линейное распределение элементов в стыке (). Покрытие (2) состоит из меди (98.99 мас.% Cu) и хрома (1,01 мас.% Cr), что соответствует техническим характеристикам ванны для гальваники. Припой (3) состоит из олова (96,7 мас.% Sn) и меди (3,3 мас.% Cu). Из-за низкой температуры пайки в стыке не видно диффузионных зон. В процессе пайки элементы покрытия не переходят в припой и не возвращаются от припоя к покрытию. BSE (Back Scattered Electrons) изображение переходной зоны ( a ) и линейный EDS-анализ паяного соединения, выполненного через прослойку Cu-Cr ( b ): 1 – подложка (алюминий 7075), 2 – прослойка Cu-Cr , 3 – припой. В соединении, припаянном через прослойку Ni-P, также не было обнаружено значительных дефектов микроструктуры пайки. Покрытие хорошо прилегает к подложке 7075 по всей длине стыка (а). Покрытие Ni-P хорошо заполняет поверхностные дефекты подложки (б), создавая прочные точки механического крепления. Как и прежде, микроструктура слоя припоя состоит из эвтектической смеси Sn + Cu 6 Sn 5 с серыми первичными кристаллами твердого раствора Cu 6 Sn 5 . Микроструктура паяного соединения, выполненного через прослойку Ni-P ( а ), заполненные дефекты поверхности подложки ( b ): 1 – подложка (алюминий 7075), 2 – прослойка Ni-P, 3 – припой. Морфология обоих припоев в паяных соединениях, выполненных с использованием промежуточного слоя Cu-Cr () и Ni-P (), очень похожа. Форма серых первичных кристаллов твердого раствора Cu 6 Sn 5 в обоих паяных соединениях аналогична, но больше кристаллов находится в соединении, выполненном с Ni-P.Скорее всего, разница может быть результатом разницы во времени пайки обоих соединений. Стыки были выполнены ручной пайкой в пламени, когда точный контроль времени пайки затруднен. Место, выбранное в совместной структуре для анализа EDS, показано в a. На b – f вертикальными линиями отмечено покрытие Ni-P и линейное распределение элементов в отдельных зонах стыка. В этом соединении также не было обнаружено диффузионных зон или элементов, движущихся от припоя к покрытию или обратно от покрытия к припою.Покрытие Ni-P (2) состоит из никеля (87,7 мас.% Ni) и фосфора (12,3 мас.% P), что соответствует техническим характеристикам ванны для гальваники. Концентрация фосфора в покрытии увеличивается с расстоянием от алюминиевой подложки 7075 (f) с 11,5 до 13,2 мас.%. Это закономерность в результате курса электролиза. Припой (3) состоит из олова (96,9 мас.% Sn) и меди (3,1 мас.% Cu). Механизмы диффузии не обнаружены из-за низкой температуры процесса пайки. BSE (Back Scattered Electrons) изображение переходной зоны паяного соединения, выполненного через прослойку Ni-P ( a ) и линейного содержания элементов ( b – f ): 1 – подложка (алюминий 7075), 2 – прослойка Ni-P, 3 – припой. В отличие от покрытий, нанесенных методом холодного напыления при низком давлении (LPCS), покрытия, нанесенные электролитическим способом, не являются пористыми, что благоприятно сказывается на их применении при пайке. Это связано с тем, что пористость покрытий, нанесенных методом термического напыления, способствует образованию газовых пор в паяном соединении [38]. 3.5. Испытания механических свойств паяных соединенийИспытания на сдвиг при растяжении соединений, выполненных с использованием прослоек Cu-Cr и Ni-P, проводились на универсальной испытательной машине Zwick / Roell Zmart-PRO (Zwick-Roell GmbH, Бадения. -Виртембергия, Ульм, Германия). Паяные соединения помещались в зажимы станка с использованием подходящих дистанционных вставок и затем растягивались со скоростью 2 мм / мин. Для каждого покрытия было приготовлено пять комплектов паяных соединений. Перед испытанием на сдвиг с обеих сторон соединения были механически удалены пятна припоя.Результаты испытания паяных соединений на статическое растяжение и сдвиг представлены на рис. Таблица 5Прочность на сдвиг паяных соединений, выполненных через прослойки Cu-Cr и Ni-P.
Прочность паяных соединений на сдвиг в обоих случаях была примерно одинаковой, примерно 35 МПа. Механизм разрушения обоих соединений носил когезионный характер и происходил в слое припоя (). Что важно, покрытия Cu-Cr и Ni-P сохранили сцепление с подложкой. Таким образом, можно предположить, что соединения могут выдерживать более высокие нагрузки, если механические свойства используемого припоя выше.Прочность соединений с электролитически нанесенными покрытиями более чем на 40% выше, чем у соединений с покрытиями, нанесенными методом LPCS [38], где в результате разрушения покрытий происходило их разрушение в результате их декогезии. Как сообщается в [38], причиной может быть высокая пористость напыляемых покрытий LPCS. Когезионные трещины в припое после испытания на прочность на сдвиг: соединения, спаянные с прослойкой Cu-Cr ( a ) и Ni-P ( b ). Твердость по Виккерсу измеряли также в отдельных зонах паяных соединений [39].Из-за малой толщины электролитических слоев нагрузка пенетратора составляла 25 Г. Распределение твердости в соединениях показано на рис. Представленные точки являются средними значениями 10 измерений. Распределение твердости HV 0,025 в паяных соединениях, выполненных через прослойки Ni-P ( a ) и Cu-Cr ( b ). Твердость покрытия Ni-P, составляющая в среднем 471 HV 0,025 ( σ = 14,4 HV 0,025), намного выше, чем у металла подложки.Как сообщается в [40], твердость электролитически осажденных покрытий Ni-P, содержащих 16 мас.% P, составляет ок. 600 HV. Покрытия с более высокой твердостью более 700 HV могут быть получены добавлением керамических частиц SiC или B 4 C [40]. Твердость покрытия Cu-Cr практически такая же, как у металлической подложки, и составляет в среднем 121 HV 0,025 ( σ = 8,7 HV 0,025). В [41] указано, что твердость покрытия Cu, нанесенного электролитическим способом на слой Cr, ранее нанесенный на подложку из углеродистой стали, составляет от 42 до 84 HV и зависит от напряжения, используемого во время электроосаждения.Наименьшую твердость в паяных соединениях показывает S-Sn97Cu3, в среднем 18,9 HV 0,025 ( σ = 3,6 HV 0,025). 6 способов пайки алюминиевых деталей с помощью электрического паяльника – Yantai Baodi Copper & Aluminium Co., LtdПри обслуживании радио и бытовой техники иногда необходимо паять небольшие алюминиевые детали, потому что поверхность алюминиевого устройства легко окисляется, что новичкам сложно паять прочно. Автор ссылается на информацию о сварке алюминиевых деталей и прошла успешную проверку.В этой статье для справки представлены эти практические методы пайки алюминия. Сначала на место пайки алюминиевой детали наносится припой, а затем горячий паяльник пропитывается и помещается в место пайки для предварительного нагрева. Когда температура повышается, припой уплотняется, а затем добавляется немного припоя и припоя, чтобы припой содержал жало паяльника, а затем используйте жало паяльника, чтобы протереть переднюю и заднюю часть паяльной станции. Расстояние трения не должно быть слишком большим.Обычно пленка из алюминиевого сплава на поверхности алюминиевого компонента разрезается на жало паяльника на 3–5 мм. Паяное соединение не может образовывать новую оксидную пленку из-за включения расплавленного олова и воздуха, и олово может быть нанесено на алюминиевый элемент оксидной пленки, который только что был удален. Изотермическое олово изменяется с сферической формы на плоскую, что указывает на то, что алюминиевый элемент прочно соединен с оловом. В это время трение прекращается, а оставшийся флюс стирается, а затем припаивается к подводящему проводу или другим компонентам олова.Это очень удобно. Во-вторых, сначала капните несколько капель разбавленной соляной кислоты в паяное соединение алюминиевого компонента, чтобы удалить поверхностную оксидную пленку, подождите некоторое время, затем добавьте несколько капель концентрированного раствора сульфата меди и подождите, пока сварной шов покроется медью. , смойте водой. Затем избыток раствора сульфата меди и раствора соляной кислоты можно сварить паяльником мощностью 45-75 Вт, который работает хорошо. В-третьих, поместите кусок алюминия в тигель для нагрева и расплавления, затем добавьте 2–5 раз олова, чтобы расплавить, и затем используйте, и тогда удобно сваривать обычным способом.В-четвертых, при обработке чистой алюминиевой поверхности, покрытой раствором нитрата ртути, съешьте больше олова с помощью жала паяльника мощностью 100 Вт и используйте жало паяльника, чтобы втереть раствор нитрата ртути в сварочную поверхность. Это можно надежно сварить. Но обратите внимание: ртуть токсична, ее следует сваривать в проветриваемом месте и не использовать высокотоксичный хлорид ртути. 5. Алюминиевые детали свариваются методом заземления. Белый порошок стеклопластиковой плиты готовится заранее, помещается на поверхность свариваемой поверхности и натирается паяльником мощностью 75 Вт на поверхность сваривания до тех пор, пока слой олова не будет прикреплен к алюминиевой поверхности, а затем ткань используется.Смесь белого порошка и канифоли удаляется, а затем ее можно сварить обычным способом. Практика проста, а сварочный эффект удовлетворительный. Также можно смешать канифоль и железные опилки, затем отполировать алюминиевую поверхность наждачной бумагой, нанести канифоль и железный порошок на полированную поверхность паяльной поверхности, несколько раз протереть алюминиевую поверхность паяльником, а затем нажать обычным способом. |